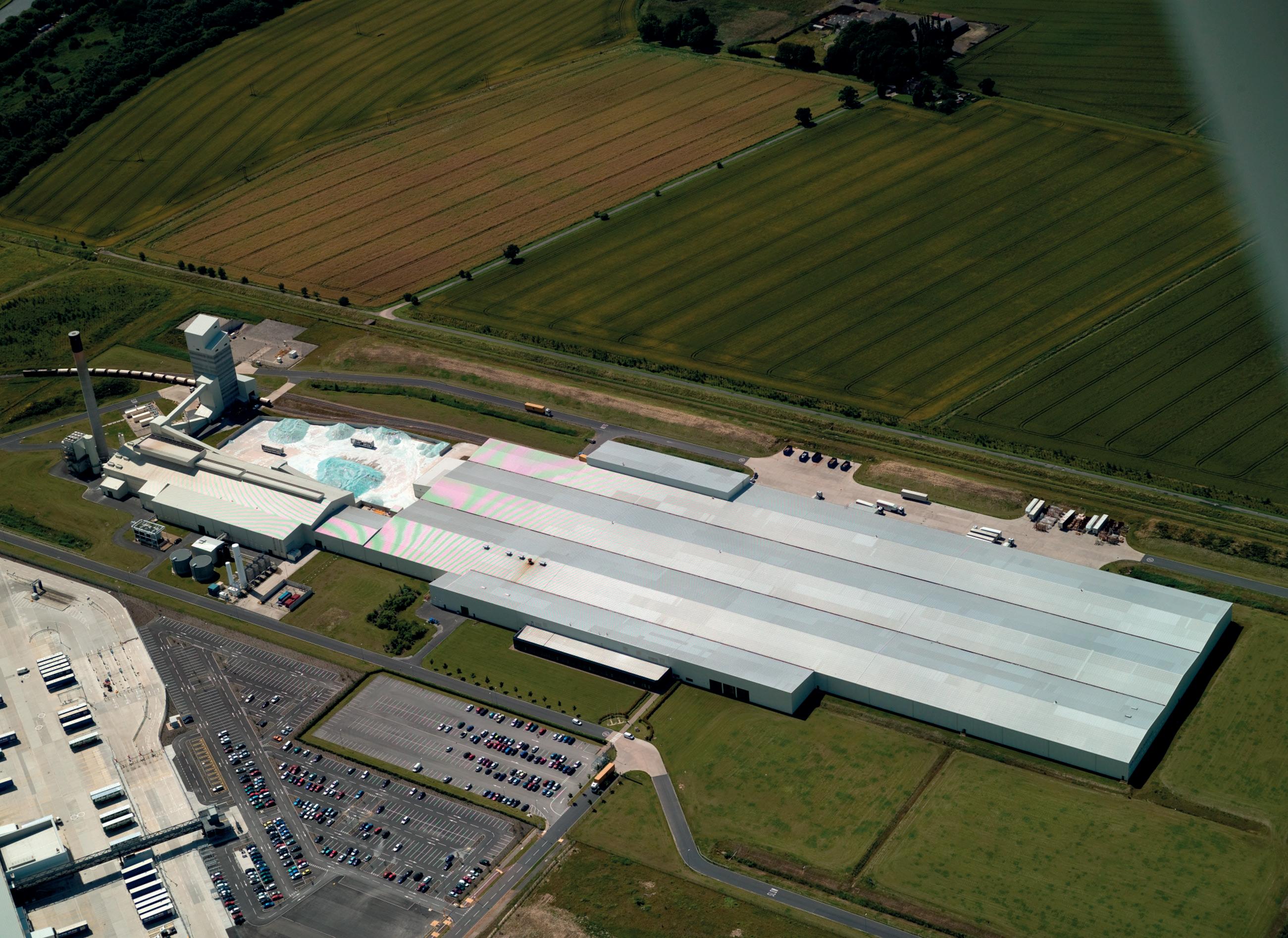
5 minute read
Company profi le: Guardian Glass
Demand for flat glass prompts Guardian’s Goole furnace investment
The furnace was recently installed at its Goole, UK facility.�
Guardian Glass recently completed a furnace investment at its Goole, UK production facility. Greg Morris spoke to Guus Boekhoudt* about the flat glass manufacturer’s plans
Guardian Glass’ recent furnace investment in its Goole site resulted in a 20% increase in its melting capacity to 825 tonnes a day.
The investment, completed in October, was made for a variety of reasons; while the facility’s previous furnace, which had started operations in 2003, was reaching the end of its campaign life there was also a compelling case to increase capacity.
Continuing growth in glass demand from Guardian’s UK and Ireland customers, as well as the opportunity to improve the plant’s energy efficiency, were further incentives to invest.
Guus Boekhoudt, the company’s Executive Vice President, said market analysis had indicated demand for flat glass across Europe is expected to continue until at least mid-2022.
The company expects UK demand to also continue to increase. A 2.5% growth is expected in new construction while a 4% rise is anticipated in the renovation/refurbishment sector.
Mr Boekhoudt said: “Guardian is rapidly becoming one of the largest glass producers in the UK – where close to 95% of the solar control glass produced in Goole serves the UK market.
“This means less carbon impact in terms of bringing glass in from continental Europe.”
It is the latest in a number of investments at the facility. The group installed a vacuum coater at the Goole site in 2012 and a laminating line in 2008.
Despite the positive market outlook, there are a few issues to consider. The group is concerned by the disruption caused by supply issues across the construction industry, as well as on-going supply chain problems and inflation pressure. The muchpublicised energy inflation, which has impacted much of industry, has also led to price increases.
“In this volatile environment, business transformation is more important than ever. We are very focused on minimising waste across the organisation, and on driving transformation across all aspects of our business.”
Environment
The company said the new furnace will be the largest in the UK and, based on the company’s own insights, is expected to have the highest energy and direct carbon emission efficiency.
Mr Boekhoudt said: “While we prefer to not quote specific numbers, the carbon efficiency of the furnace is also expected to improve by a range in the double digits percentage versus the previous one.”
The furnace’s footprint was enlarged to increase its production capacity, and its design was based on combustion engineering first principles – as opposed to retrospective add-ons to old technology.
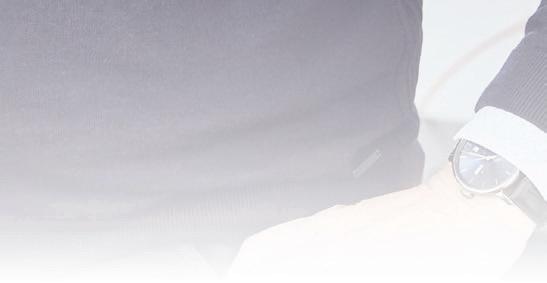
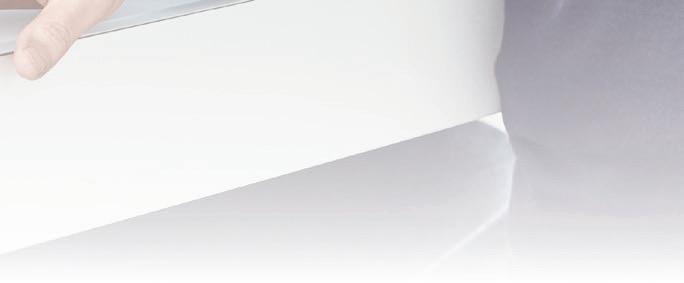
Mr Boekhoudt declared: “This has meant a larger investment and longer engineering time, but, in the long run, it will mean a more consistent operation and better energy performance.”
About 400 Guardian staff were involved in the project, which included all of the Goole plant team as well as support from its sister plants and the global Guardian team. At its peak, there were 600 contractors on site.
Technology partners contracted to the project were Zippe, Sorg, Horn, Grenzebach, STG Combustion Control, HFT, Tucheng, Termeca Choquenet, Compagnie Thermique Europeenne (CTE) and UAS Messtechnik.
The furnace installation was just the latest in a line on investments focused on the environment at the facility.
There is an on-going initiative to recycle more cullet. Increasing the cullet ratio in products cuts energy consumption, reduces raw materials and reduces waste. Cullet melts at a much lower temperature than sand, so it reduces the plant’s overall energy needs. For every 10% of cullet used in its processes, the facility’s energy demand is reduced by up to 3%, which in turn reduces its greenhouse gas missions.
Several follow up sustainability investments are also planned at the site. This includes integrating enhanced control systems to drive its process energy use down. It will also upgrade several pieces of its mobile plant equipment with the latest battery technology and, fi nally, work will begin on planting the grounds to create a more positive impact on the wildlife in the area.
Digitisation
The company took the opportunity to boost its digital manufacturing footprint at Goole.
Its digital investments across all its production facilities aim to integrate digital and physical systems. These will acquire and use data from connected equipment to improve operational visibility and therefore drive operational improvements.
This has included investment in the areas of digital performance management with the adoption of the Industrial Internet of Things (IIoT), the automation of warehouse logistics and the use of advanced analytics for its operations.
It will connect different type of sensors that measure vibration, temperature and humidity to capture data from certain critical assets to make the process more effi cient, predictable and reliable.
This data will also enable the group to move from preventive maintenance strategies to predictive maintenance – machine learning algorithms that can predict errors and rectify them before they occur.
Mr Boekhoudt said the company’s Tudela and Llodio plants in Spain have already undergone transformations to maximise their operational effi ciencies.
� Guus Boekhoudt.
This has included the implementation of automation solutions in its manufacturing areas and warehouses as well as the adoption of digital and data-driven technologies to run its processes.
“Digitisation initiatives will help our teams to make better, on-time decisions thanks to access to real time data.
“Its outcome will be a more effective and effi cient use of time and resources, optimising the use of material and energy and enhancing operational effi ciency with improved processes and waste reduction.”
Outside of operations, the company recently launched a Guardian Glass website and plans to launch an e-commerce and service portal in 2022.
With the portal, customers will be able to fi nd all the information they require in one place - request a quote, place an order, check on shipping, submit claims and more.
“We are very excited about this development because it will enable our customers to reach out to us whenever will be best for them,” stated Mr Boekhoudt.
Development
A key focus within Guardian Glass is employee development. Its Market-Based Management culture is the belief that each person brings different perspectives, aptitudes, skills, knowledge, experiences and backgrounds to the organisation that determines how and where they can contribute to the most.
“We treat each person as a unique individual and strive to create an open, inclusive, and empowering environment so every employee can make the greatest contribution.
“Our supervisors constantly support our employees on that journey; providing coaching and agile feedback is critical for team members growth.” �
*Executive Vice President, Guardian Glass, Goole, UK www.guardian.com www.glass-international.com
PSR CORD DISPERSAL SYSTEM
Proven and guaranteed.
