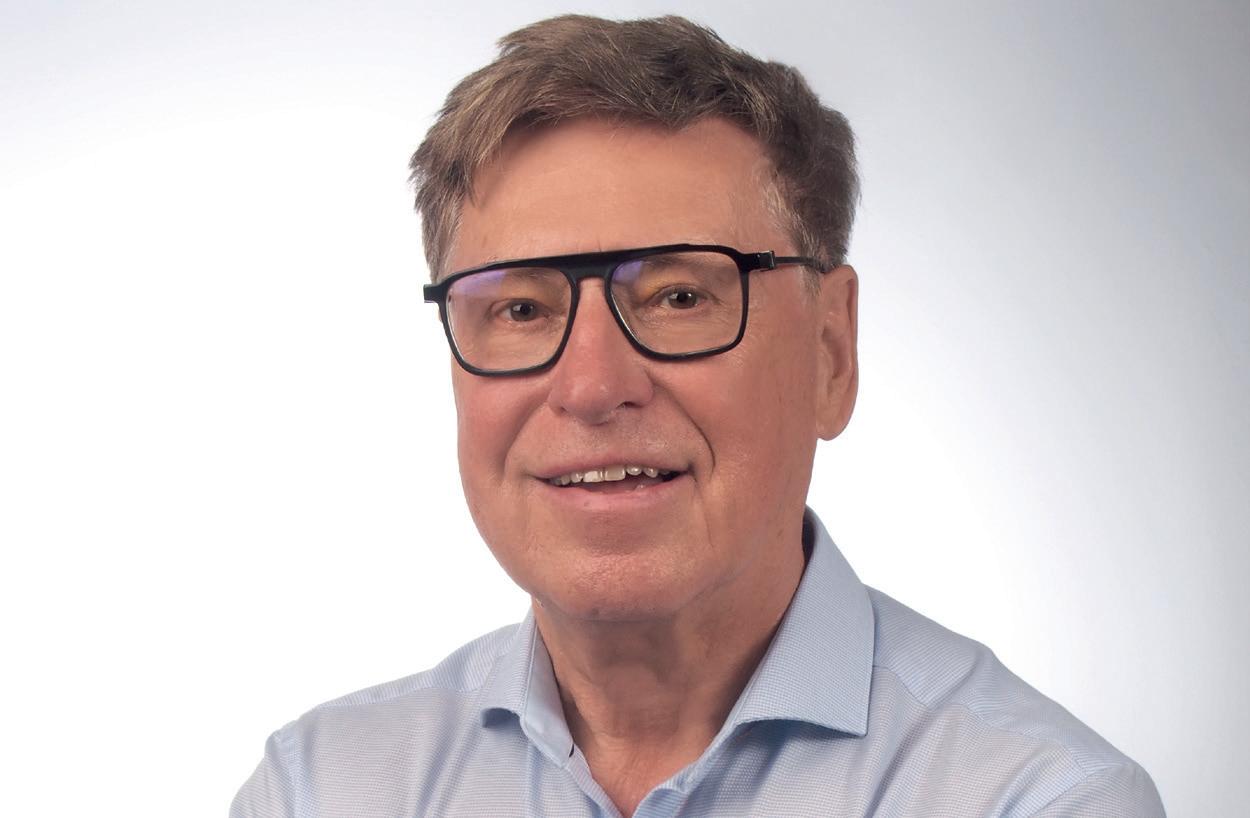
7 minute read
Company profi le: Techglass
An all round furnace provider
c Fresh from installing its largest ever furnace at Stoelzle Czestochowa, Techglass President Andrzej Skowiniak describes the installation process of the energy efficient oven as well as the future prospects for the furnace industry in general.
1 Congratulations of the recent furnace installation at Stoelzle. Can you describe the feeling of when the last brick has been put in place and you have completed the job? Thank you. Completing every big project is very satisfying, but this one was especially so as a combination of factors made it more challenging than any other we’ve executed before.
At the pull of 480tpd the furnace is the biggest in our history, the biggest in Stoelzle Group and one of the largest end-port regenerative furnaces.
Throughout the entire manufacturing process we had to manage unprecedented supply chain disruption. Some of our suppliers refrained from providing binding offers altogether!
At times it was tough, but we’ve managed to solve every single problem that we encountered and here we are today – happy, satisfied and with a feeling of relief.
Techglass President � Andrzej Skowiniak
2 How long have you been working on this project for? When did discussions start with Stoelzle about the furnace, for example? Stoelzle started analysing possible variants of the new furnace a couple of years ago. That gave them plenty of time to meticulously check all possibilities. They settled on the most ambitious option and then the tender process took roughly five months. The project was awarded to Techglass in February 2021. The works on site started on May 9 with glass drainage from the existing furnace. The commissioning of the new furnace took place on July 27.
c 3 Have you worked with Stoelzle Czestochowa before? If so does that previous working relationship help when you start on a new project such as this?
cYes, we’ve been working with Stoelzle Czestochowa since 2001, that is since this Polish branch of the Austrian company was established. To date we’ve supplied three complete furnaces with working ends and forehearths and executed numerous smaller orders. We also supplied a furnace with working end and forehearths to Stoelzle’s Knottingley, UK plant. Naturally, the long-term business relationship helped us in being awarded this recent project. There is no way to predict the future, but the next best thing is to draw conclusions from experience. Based on the trust we gained over the last 20 plus years of working together, the decision makers in Stoelzle could be confident that we were able to execute this challenging project. And they were not mistaken. 4 What type of furnace was chosen for this job and why this particular furnace? What are its characteristics? The furnace is an end-port regenerative, with the maximum pull of 480 tpd, working end and five forehearths. The combined length of all channels – working end and forehearths – is an impressive 85 metres. The production hall, in which the furnace has been installed, had been designed for a furnace smaller by 40%. It was virtually the biggest furnace that fit there without any major modifications of the foundation plate.
5 Stoelzle states the furnace will reduce the amount of energy used in melting. Can you tell us about the furnace’s environmental/ energy efficiency capabilities, as well as the improved e-boosting? The new furnace is designed to be more energy efficient than the previous one - also supplied by Techglass. It was no easy feat as the technology of regenerative furnaces is mature and the progress in terms of energy efficiency is limited. The furnace can melt up to 40% of maximum pull by electric current, which is a lot, considering the industry standard at roughly half of that. This feature offers potential to dramatically reduce CO2 emissions, of course only if the electric current is generated from renewable sources.
6 Construction was completed in less than 70 days. What were the challenges and how did you overcome them? It took 67 days from the start of drainage to the start of heat-up. If someone says that it is not record-breaking, they surely either haven’t seen the situation before or after the works or both. The types of problems encountered on site are always the same, only this time it was all more difficult due to the complexity of the project. There is certainly no secret formula for overcoming the challenges. What makes this possible instead, is a team of skilled and hardworking employees who are all solutionoriented and solve problems one by one as effectively as possible.
7 Tell us more about Techglass? Is Poland your main market or do you supply furnaces outside Poland? What are the company’s strengths? Techglass was founded in 1990. We supply furnaces, working ends and forehearths: all works and all supplies required. First, our engineers do all necessary designs, from refractory materials through steel structure to systems and equipment. Most of the projects in the glass industry are rebuilds with modification and therefore it is crucial to offer tailored solutions as we do, because the off-the-shelf ones do not account for the existing situations, different in each case. When all engineering is done, manufacturing starts. In Techglass the vast majority of systems and equipment is manufactured in-house. This helps overcome challenges of disrupted supply chains as it makes quick reactions for problems possible: the status of every order out of thousands is monitored in real time. When all deliveries are ready, we execute all works on site: drainage, demolition, installation, heat-up and start-up. We also provide a range of services for furnaces, working ends and forehearths. We are basically capable of doing everything but the ceramic welding. 8 Is the container glass industry the only one you operate in? The majority of our clients are container glass producers but we provide solutions for producers of all types of glass. Recently we supplied a batch house, a furnace of pull of over 300tpd and three frit production lines – that is a complete solution from raw materials to product - for the biggest producer of sodium silicate in Europe, CIECH Vitrosilicon. We were able to achieve very good operational parameters of the system, such as low energy demand and low NOx emissions, thanks to our engineering focused on the specific requirements of sodium silicate glass. The project was so successful, that soon after it had been completed, we were awarded another rebuild with modification project at the same customer.
9 Hot topics in the industry Currently, in September of 2022, the hottest topic among our customers is alternative fuels. There is a lot of uncertainty regarding the availability and prices of the natural gas in the months to come, especially in Europe. The good news is natural gas can be partially or fully replaced by LPG or oil for combustion in furnaces. We supply all engineering and systems required for this purpose. The other interesting topic is Machine Learning. Good algorithms fed by a lot of samples may yield results better and faster than even the best experts are capable of. There is a potential to improve many processes in the operation of furnaces, working ends and forehearths by ML. We invest in integrating ML-based solutions in our control systems and expect to see first successful applications next year.
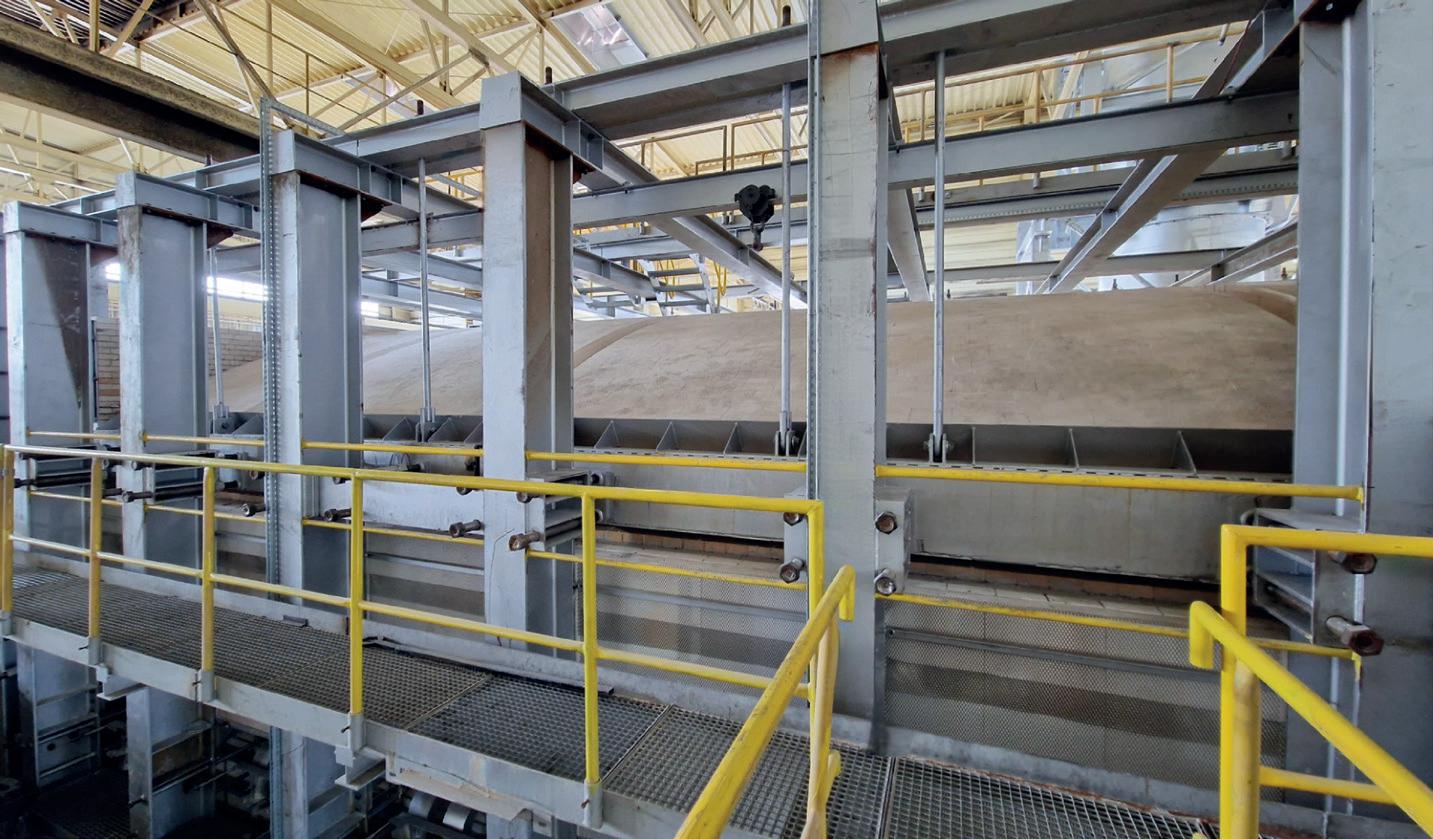
10 Finally, and more generally, there is a lot of talk about climate change and what the glass industry can do to improve on emissions in the melting process. Many ideas are indeed being discussed regarding decreasing the negative impact of the glass industry on climate change: from relatively easy to implement, through very demanding to straight bizarre. The fact of the matter is that the more reduction in CO2 emissions a concept promises, the more expensive and demanding it is to implement. We believe that a radical decrease of the CO2 emissions is possible through transformation to all-electric furnaces. This would, by all means, be a massive undertaking, but since the required technology is there, it should in our opinion be considered as the most realistic way forward. Of course, it is not the role of the glass industry but rather the governments to create conditions to make the change possible. A step in this direction is to use electric power to melt 40-50% of total pull, just like in the furnace we designed for Stoelzle Czestochowa. It goes without saying that the electric power should be generated by renewable sources and should be at the very least no more expensive than other available fuels. At the end of the day, the glass producers need to make a profit.
c