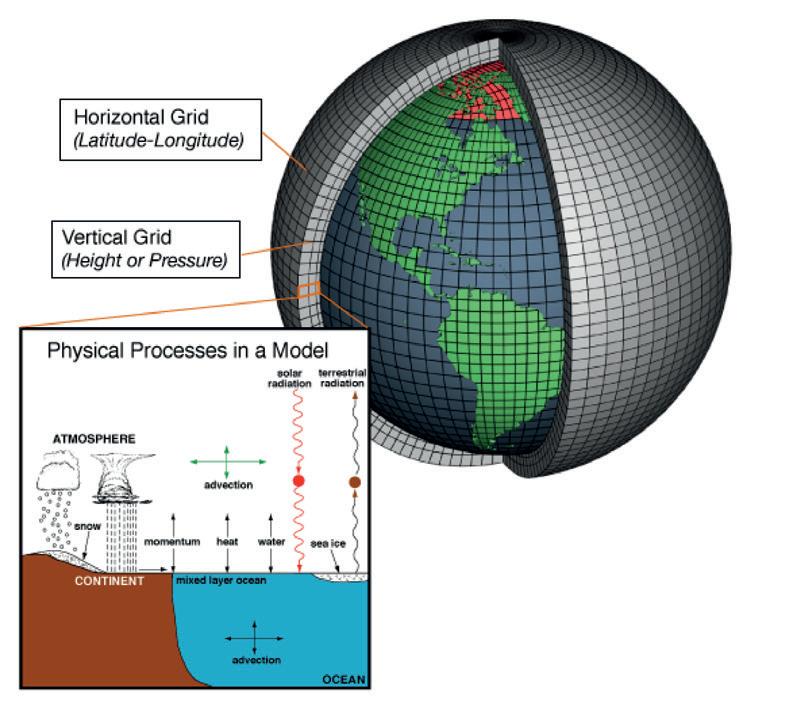
7 minute read
Furnaces: Celsian
Furnace simulations to assist in daily operation
CelSian has developed a simulation software, GMT-X, for glass furnaces. Andries Habraken* outlines how the software’s dedicated models allow it to accurately describe the inside of a glass furnace.
Computer simulation started its development in the previous century. The initial goal was to have a tool that could help understand and predict heat and mass transfer, fluid flow, chemical reactions, and other related processes that occur in engineering equipment, in the natural environment, and in living organisms. The processes of heat transfer and fluid flow pervade many aspects of our life.
Like in real life, the best approach to solve a complex problem is to divide it into smaller pieces and try to solve it piece by piece. One of the first simulation methods described was based on this principle and worked as follows: a process is cut into many small boxes, and for each box, the laws of physics are calculated.[1] For the complete process, there is information exchange between the boxes. This is the principle of computational simulation tools as we know them today (Fig 1).
The weather forecast is a well-known example of a simulation tool that is used to predict wind, rain, and temperatures. Fig 2 shows an example of a climate model.[2] The Earth’s atmosphere is cut into a finite number of connecting blocks, and in each block, equations are solved to describe the local situation. The model includes all the basic components of the climate factors (atmosphere, ocean, land, and sea ice). The boundaries of this model lie in the energy coming from the sun and the heat losses toward the surrounding space.
Weather forecast models are incorporated into our daily life. We use them to schedule activities or decide how to commute to the office for instance.
Glass furnace simulation
CelSian developed simulation software for glass furnaces. This simulation software, named GTM-X, is similar to the software used for the weather forecast or the one used in the automotive and airplane industries, but it is equipped with dedicated models that allow it to accurately describe the phenomena inside a glass furnace.
Data from laboratory experiments and many years of field experience is used to define and validate dedicated models like the model for the batch blanket[3] and the model to calculate the dissolution of sand grains.[4] CelSian’s laboratory is supporting the modelling of cold top furnaces, as the request for full electric furnace technology is rapidly increasing (Fig 3).
This simulation software is used inhouse by CelSian’s engineers to support process improvement projects, as well as by the engineering teams of several glass producers and furnace designers. Continuous developments are driven by feedback from the industry, like the implementation of a special radiation model needed for low iron glass melts.[6]
Nearly all furnace designs are validated by mathematical furnace simulations. GTM-X is widely accepted simulation software and CelSian is proud that most furnace designers use GTM-X to improve current furnaces performances and work on new designs. The questions that
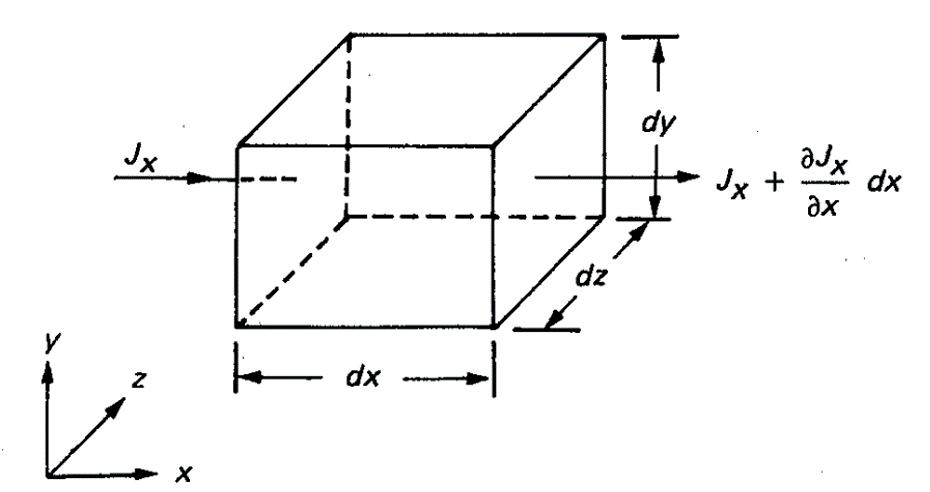
� Fig 1. Example of an energy flow balance over a control volume (Patankar). � Fig 2. US NOAA, a model based on the ocean and atmosphere interactions.
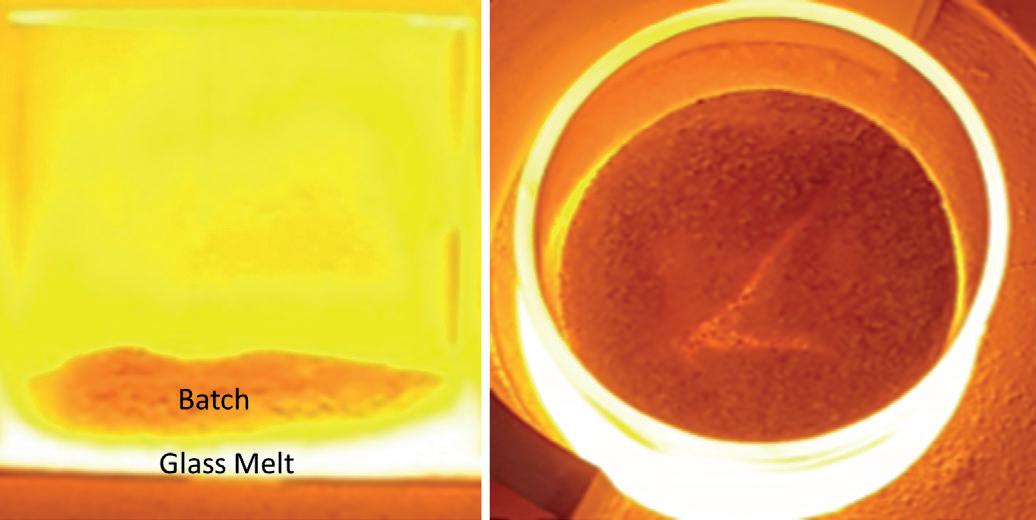
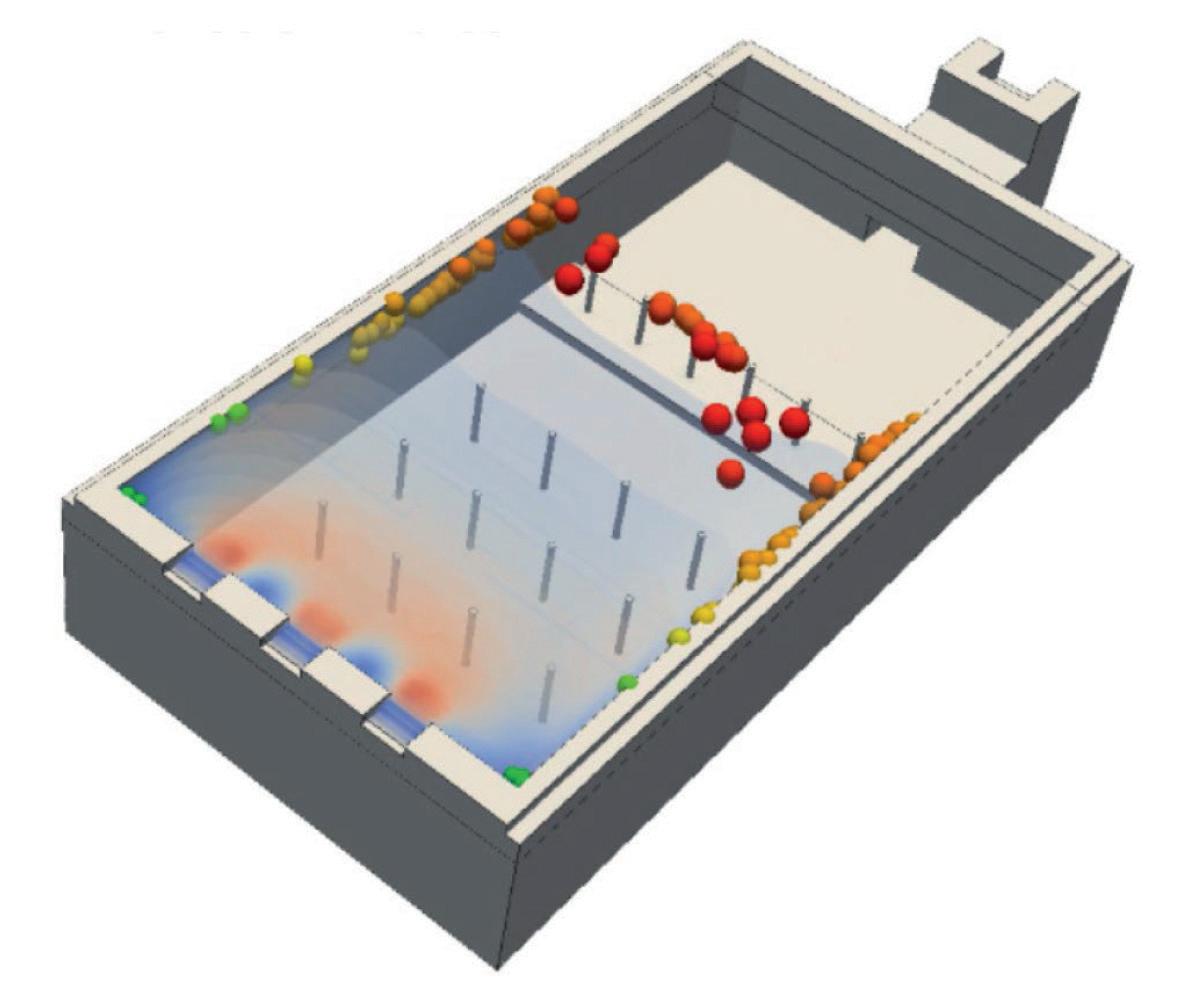
Fig 3. The cold top
� furnace experiment in CelSian’s laboratory.
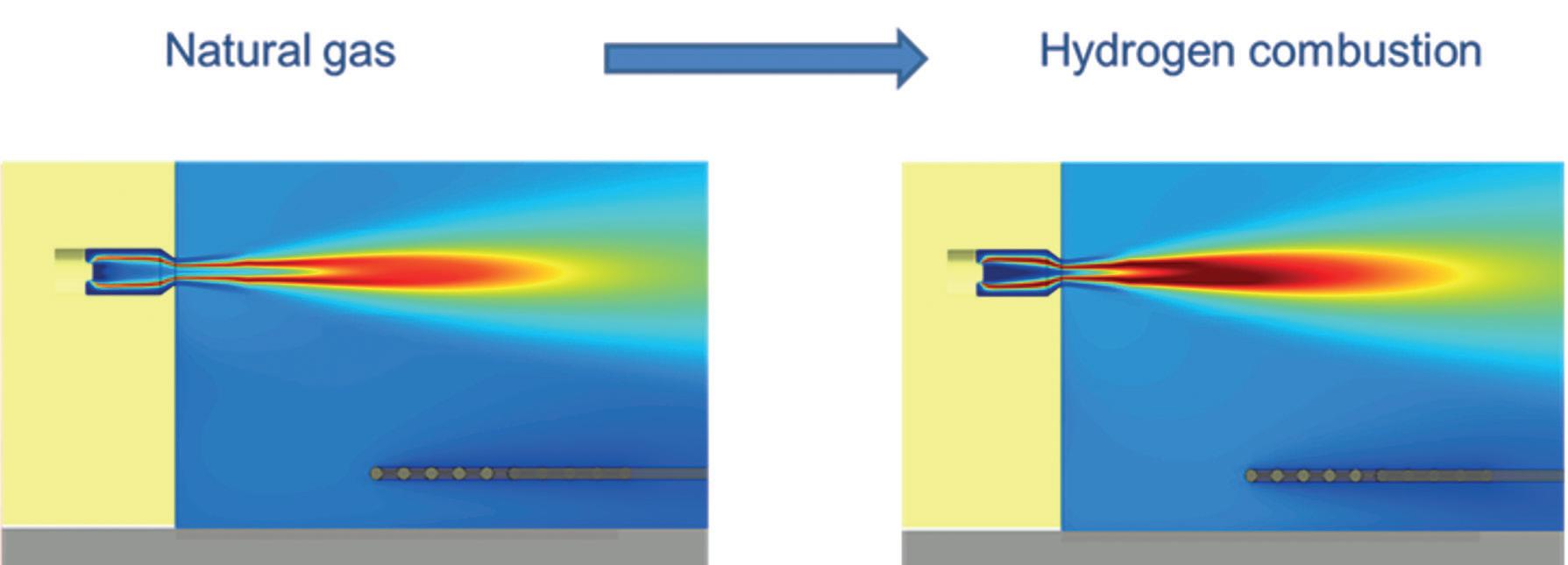
� Fig 5. Modelling and validation of hydrogen combustion.
GTM-X answers are related to low energy use, good product quality, low emissions, and a long furnace lifetime.
Future-proof furnaces
Reducing carbon footprints is one of the largest challenges that new furnace designs will need to tackle. Current initiatives focus on reducing energy use and investigating alternative energy sources like biofuel, electrical energy, and hydrogen. Although the best choice will most likely be driven by availability, technical challenges can be solved by computer modelling.
Increasing the amount of electrical boosting energy in a conventional furnace should not be done without carefully checking the impact on product quality. The flow of the glass melt is driven by temperature differences, and the wrong location of the electrodes can lead to production issues (Fig 4).
Using an alternative energy source like hydrogen leads to questions like burner design, the impact on product quality, and the consequence on the furnace’s lifetime. Fig 5 shows the result of a project in which modelling is combined with lab-scale testing to look at the impact of hydrogen combustion on heat transfer.
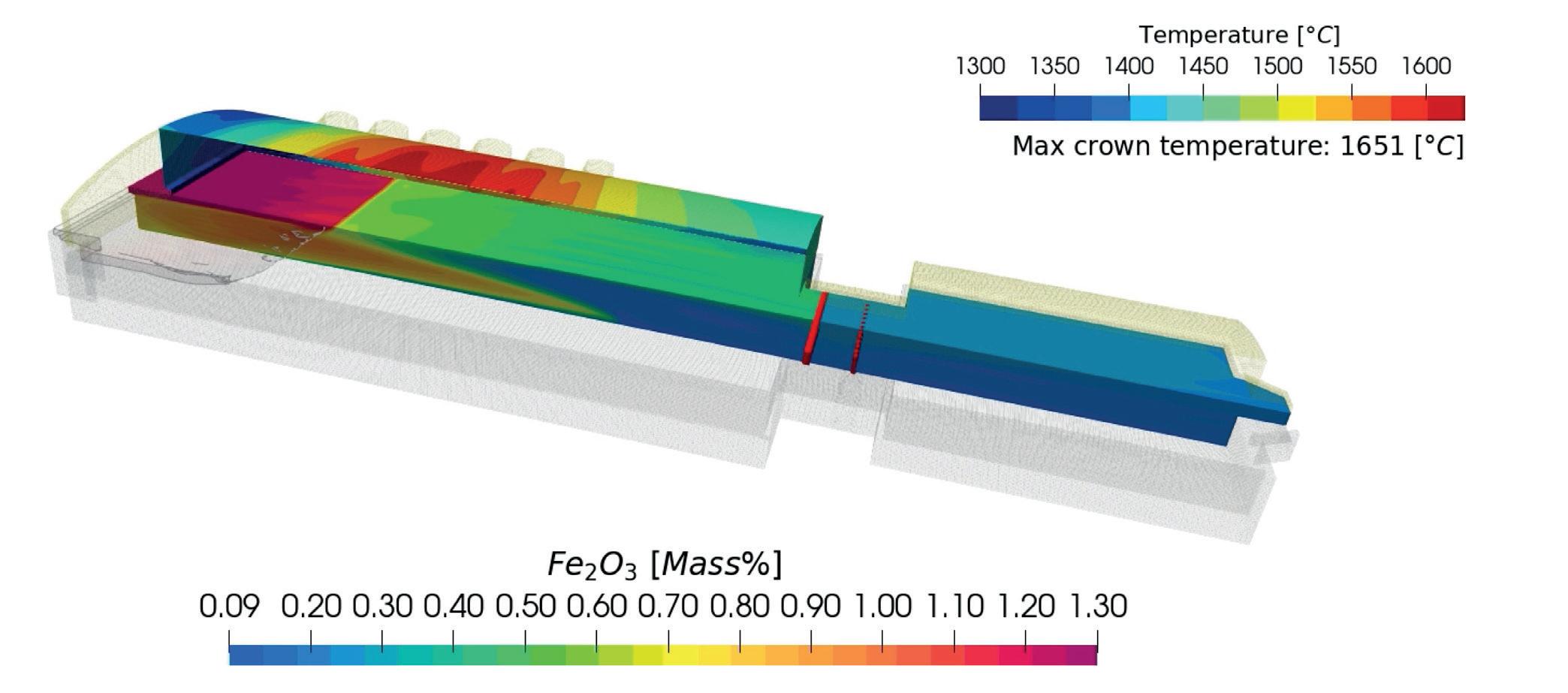
Support daily production
Solid inclusions, bubbles, and blisters are investigated in a laboratory, and their source of origin can be traced via computer modelling. Once the cause of a defect is known, possible solutions are safely tested in the computer model, leading to the safest and most promising solution to be applied in the real furnace. This approach has been proven in hundreds of projects.
For furnaces in which the product colour changes, it is profitable to reduce the time at which the product is out of the spec. Fig 6 shows a model of a float furnace that is in the process of a colour change. The simulation reveals the change in iron oxide in the glass melt, which affects the product colour but also the radiative properties of the glass smelt. These properties are important to consider as they have an impact on the crown temperatures in the furnace. The simulation shows how the energy needs to be corrected to prevent overheating the crown.
� Fig 6. Time transient modelling of a colour change and the impact on temperatures. � Fig 4. Example of a hybrid furnace design (courtesy of Fives Stein).
Furnace control
Having a time changing computer model opens the road to other applications. The model predicts how and when changes occur as a result of a change in the process. As the response of a glass furnace is very slow, it is difficult for a furnace operator to understand how the furnace responds. The dynamic computer model is a very helpful tool to support the operator. It is a digital twin of the real furnace, providing many virtual sensors beneath the melt surface.
The simulation as described above is almost as fast as in real-time, but still too slow to steer the glass furnace directly. For direct control of the furnace, a much faster model is created from the CFD model, by performing a series of step tests on the digital twin. This method is safe
Continued>>
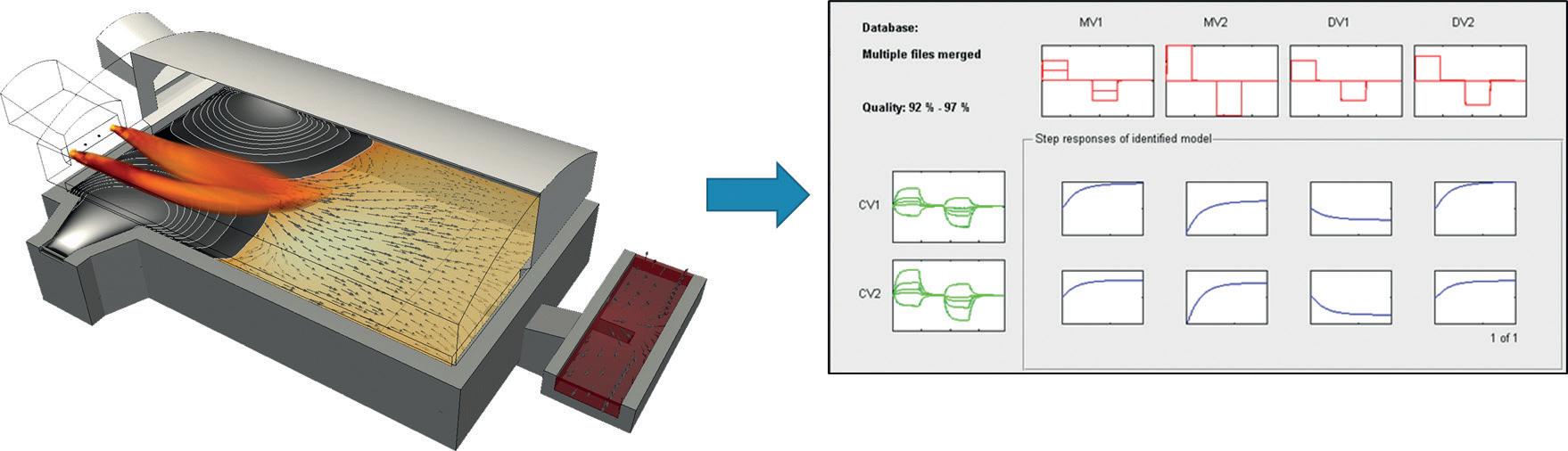
� Fig 7. Using a detailed furnace simulation to generate a fast and accurate control model.
for the furnace, does not impact product quality, and results in a control model without information from unknown disturbances.
The reduced model can be used directly in an MPC to estimate glass melt temperatures in the furnace, and change the setpoints to keep these temperatures stable and within the allowed bounds. [7] By using this technique, it has been proven that the standard deviation for average glass melt temperatures reduced from 1° C to 0.25 °C.
By using the controller, temperature stability is achieved and the unstable period after a large process change, like a job change, is reduced to a minimum.
If you are interested in the services and software CelSian offers, please contact us and we will find the best solution together. �
*Segment Leader of Process Optimisation, CelSian, Eindhoven, Netherlands www.celsian.nl
References
1) Numerical heat transfer and fluid flow, Suhas V. Patankar, 1980, McGrawHill Book Company 2) National Ocean Service, a model based on ocean and atmosphere interactions, January 21, 2021. 3) A.J. Faber, R.G.C. Beerkens, H. de Waal: Thermal behaviour of glass batch on batch heating, Glastech. Ber. 65(7), 177–185 (1992) 4) R.G.C. Beerkens, H.P.H. Muijsenberg, T. van der Heijden: Modelling of sand grain dissolution in industrial glass melting tanks, Glastech. Ber. 67, 179–188 (1994) 5) R.G.C. Beerkens: Analysis of elementary process steps in industrial glass melting tanks – Some ideas on innovations in industrial glass melting, Ceram. Silik. 52(4), 206–217 (2008) 6) A.M. Lankhorst, L. Thielen, P.J.P.M. Simons, A.F.J.A. Habraken: Proper modeling of radiative heat transfer in clear glass melts. In: 73rd Conference on Glass Problems, ed. by S.K. Sundaram (Wiley, Chichester 2013) pp. 249–258 7) L. Huisman: Control of Glass Melting Processes Based on Reduced CFD Models, PhD Thesis (Technical University TU Eindhoven, Eindhoven 2005)
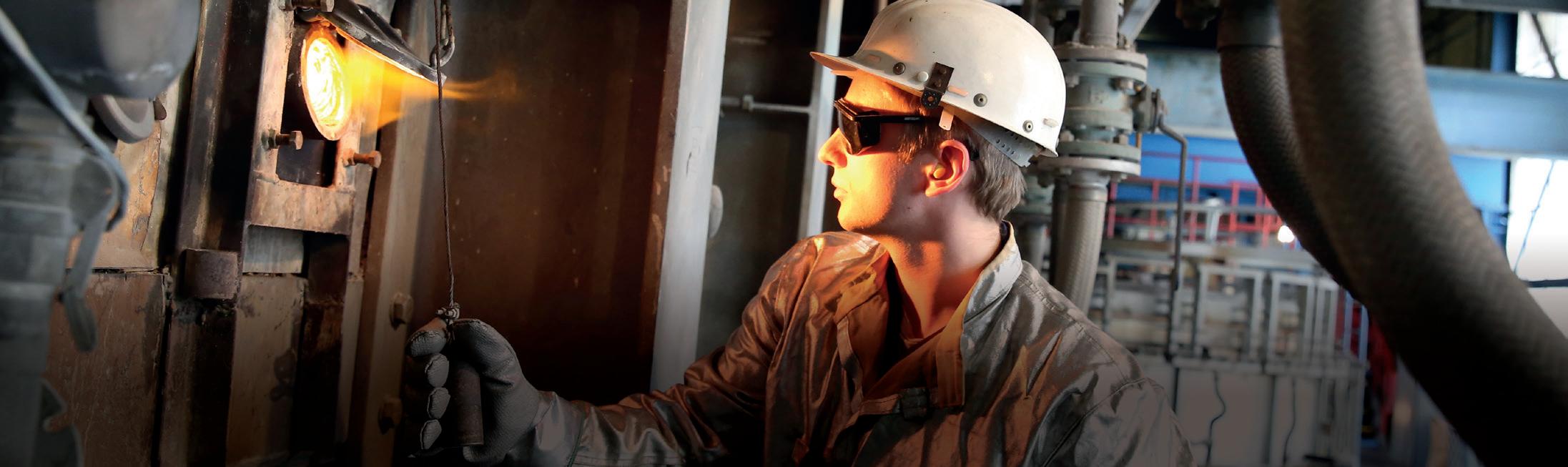
Glass experts
Furnace support Process optimization Training and R&D
Celsian’s aim is to minimize the cost of making glass for end users and the environment. We have an agile team of glass experts using proven methods like furnace modelling, laboratory measurements and practical furnace health checks to optimize glass melting processes. We also train operators and glass technologists through our standard course, dedicated programs and various e-learning modules. We strive to be the best partner for optimization of glass production worldwide.