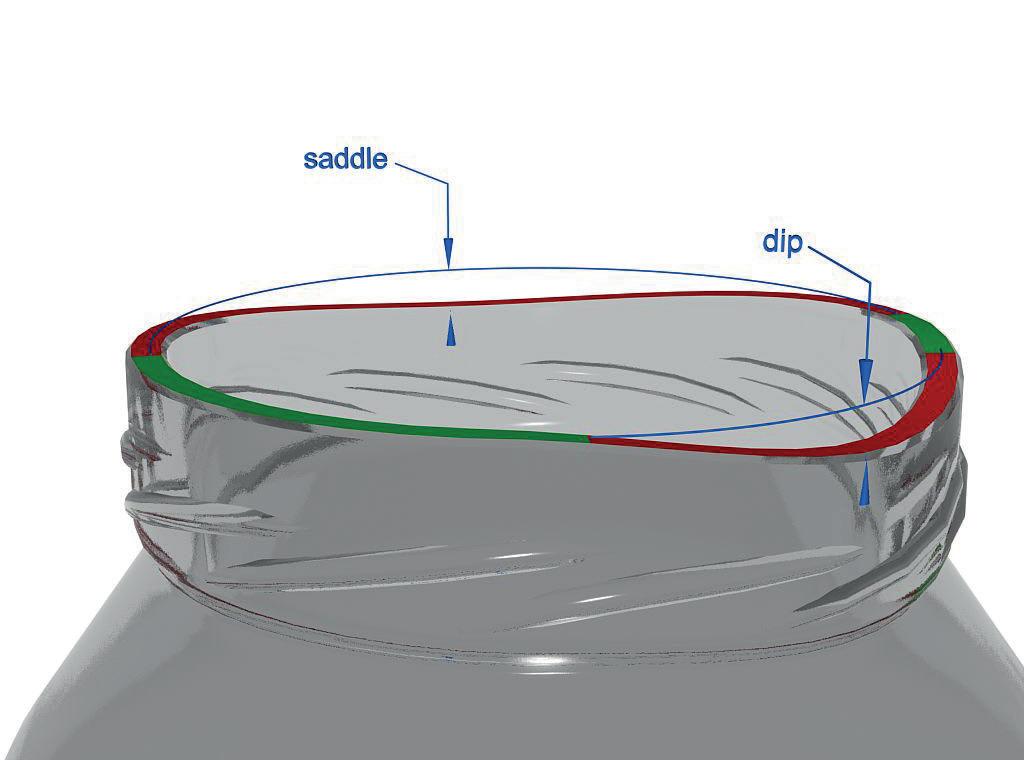
4 minute read
Inspection: Dr Gunther
A marketplace of inspection solutions
As container inspection technology progresses towards fully automated glass plants, the replacement of mechanical solutions is imperative. During glasstec’s exhibition, Dr Guenther Inspections will present a number of flexible camera inspection solutions for new cold end lines or re-engineering existing lines.
Cracks in the finish, an unfilled or overpressed finish and a wire edge are among the most critical defects. Camera-based check detection becomes a good alternative to sensors for check detection in star-wheel inspection machines.
For many container types, the check detection can be transferred to the camera sidewall inspection machine (CSWI) and the bottom/mouth inspection machine (BMF), which the Günther team is presenting during the glasstec exhibition.
With new features, booth machine types cover a wide range of the inspection needs of a modern glass plant. The combination of both machines and the unique camera/light source design allows several images from different positions, but all with the same optical conditions. This paves the way for the detection of defects in the mouth, body and bottom of the container.
Two-camera inspection for planity and finish breakouts
When inspecting for planity (flatness) and tightness, the wider the mouth, the greater the challenge. Dr Günther offers an improved solution integrated into the standard camera sidewall inspection machine (CSWI) or as stand-alone solution.
Two cameras survey the mouth rim. Even smallest deviations (±20 microns) can be found and as a result, dip or saddle deviations or breakouts are detected.
Any containers with a critical tightness defect are eliminated by these two camera solutions. The machine’s footprint is just 550mm x 650mm and it can be installed on existing conveyor belts with ease. The machine can be moved from one line to another; it is also available with wheels for easier re-positioning (Fig 1).
Detecting wire edge and overpress
container production are overpress and wire edge, particularly for narrow neck press and blow (NNPB) producers.
An overpress is located on the inner rim of the sealing surface, like a fin of glass extending above the sealing surface. Wire edge is also a fin of glass but it is located under the inner ring of the sealing surface.
The reasons for both defects lie in a toohigh gob weight or in problems related to the plunger movement. Dr Friedrich Günther, founder of the company, is proud to have been among the first to offer a technology solution for these critical defects in high-speed NNPB productions (Figs 2 and 3).
Fig 1. Dip and saddle detection.�
Camera for bore diameter
Detection of the inner bore diameter has been done with mechanical solutions in the past, causing high costs for tooling and maintenance.
Dr Günther Inspections (DGI) has developed a solution that can be used as stand-alone retrofit machine, or integrated into a standard bottom/ mouth camera inspection machine (BMF type).
The inspection unit consists of a camera above the bottle and a light source, mounted below the bottle. In addition to the inner bore diameter, spikes and also ovality problems are detected as well. Optional for the stand-alone unit is a second camera, allowing inspection of the outer diameter and checks in the mouth rim (Fig 4).
Multi-image inspection for high class cosmetics
Recognition of the logo and engraving is essential today. Tilo Günther, R&D director of Dr Günther optical inspections, describes the complete solution package offered for this sector.
“Smart lighting is a key component. For this reason, specific R&D investments have been made by the team. A special image processing module in the software makes even the smallest cosmetic defects visible. Checking washboards and folds of flacons is just as easy as checking for symmetry of the overall shape and the inner bottom contour.”
Data management
Innovative and user-friendly data management is crucial today. In
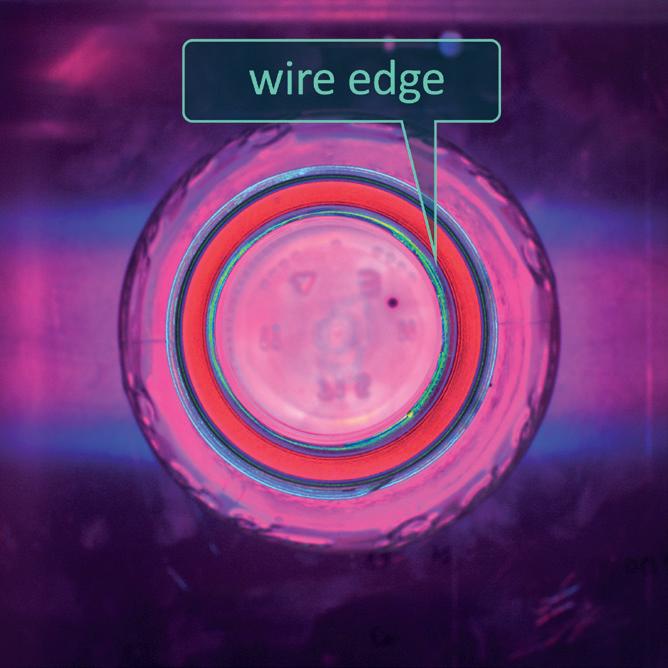
� Fig 2. Wire edge. � Fig 3. Overpressed.
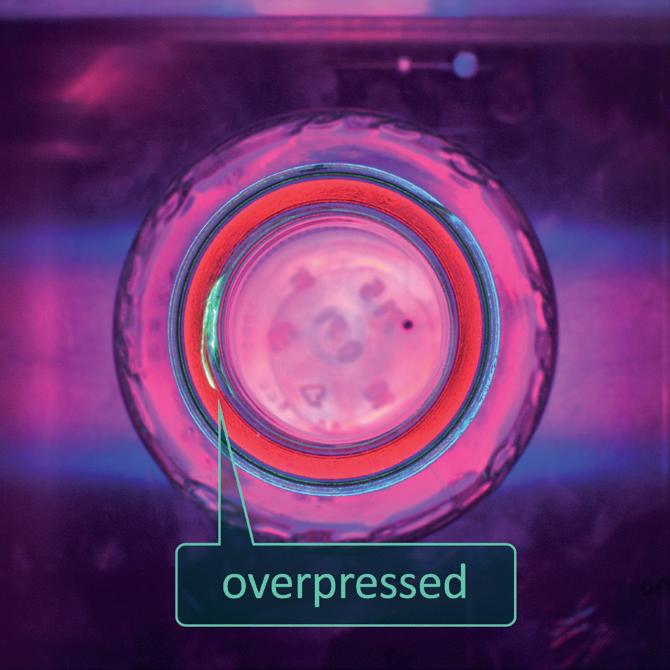
addition to machine- and line-specific analysis tools, a central data and quality management tool is available.
Among the latest developments is a user-interface with detailed, articlespecific reporting and data storage possibilities.
“With our new software module, the quality manager is able to improve the plant performance and to create customer-specific reports”, says Tilo. “Potential customers can have a look at our solution on the booth in Duesseldorf. “In summary, we see a big need for new, higher precise inspection systems. The extreme rise in energy costs force higher precision in inspection technology, to increase the pack-to-melt ratio while avoiding risks in the quality standard”, states Linda Günther, Commercial Director of the company. “We are happy to show all visitors our latest solutions

Fig 4. Bore diameter.�
during this year’s glasstec exhibition.” �
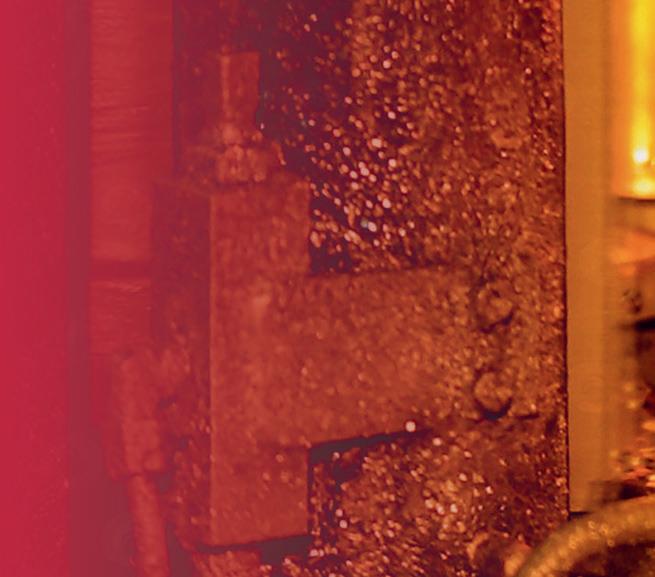
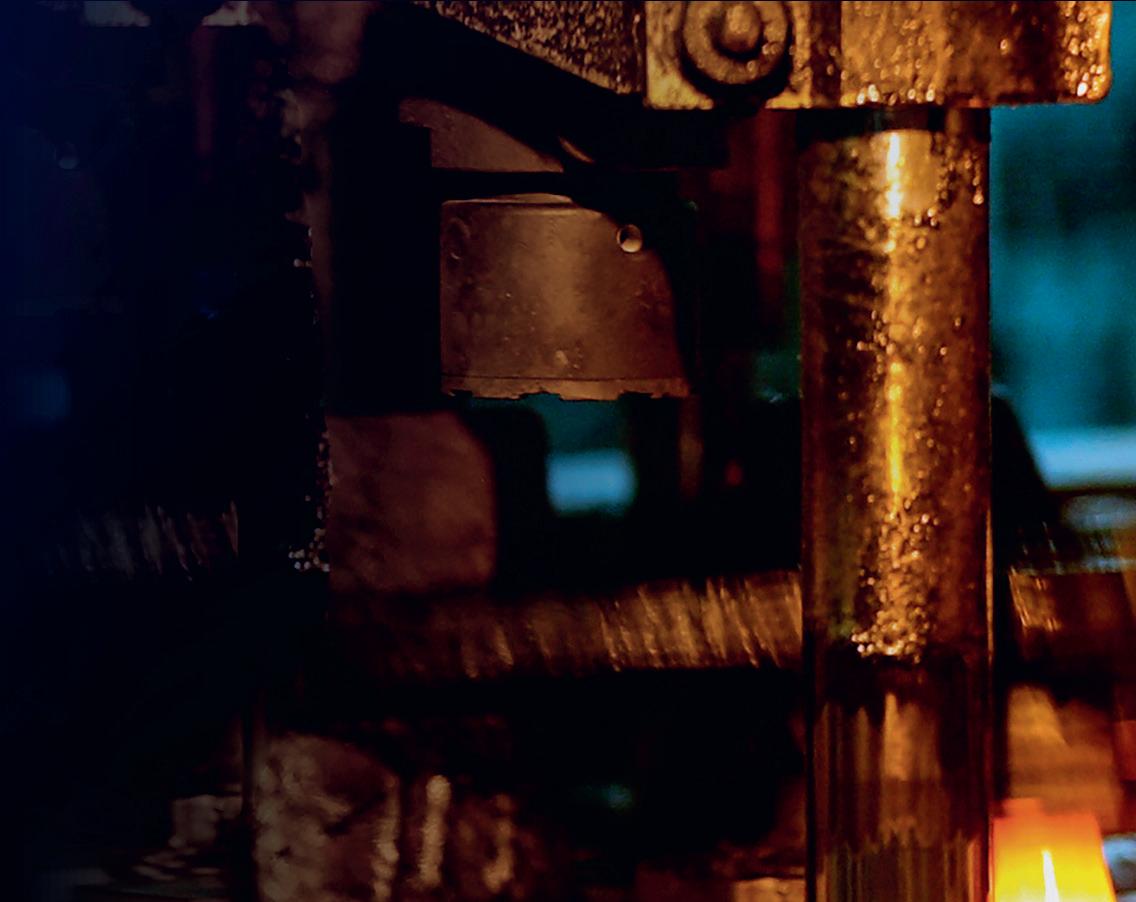
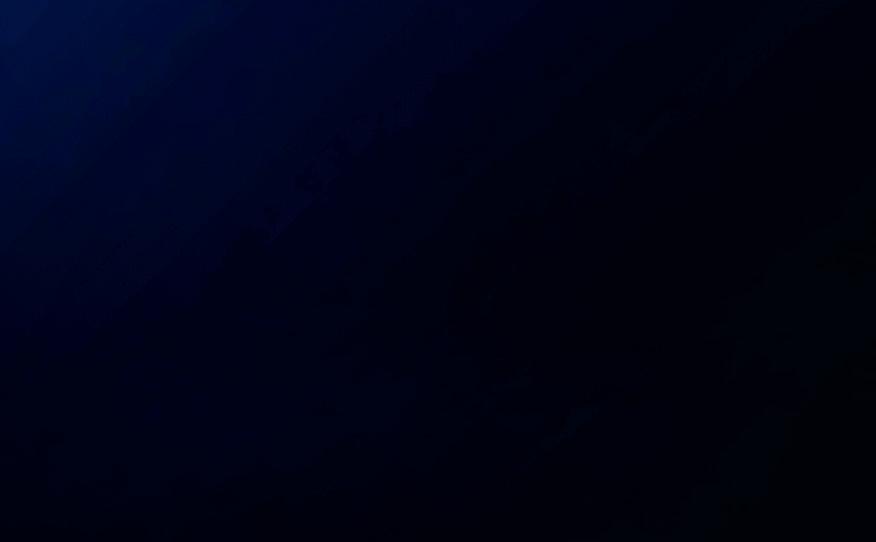

Vacuum Control System VCS
Zero defect quality in the vacuum process

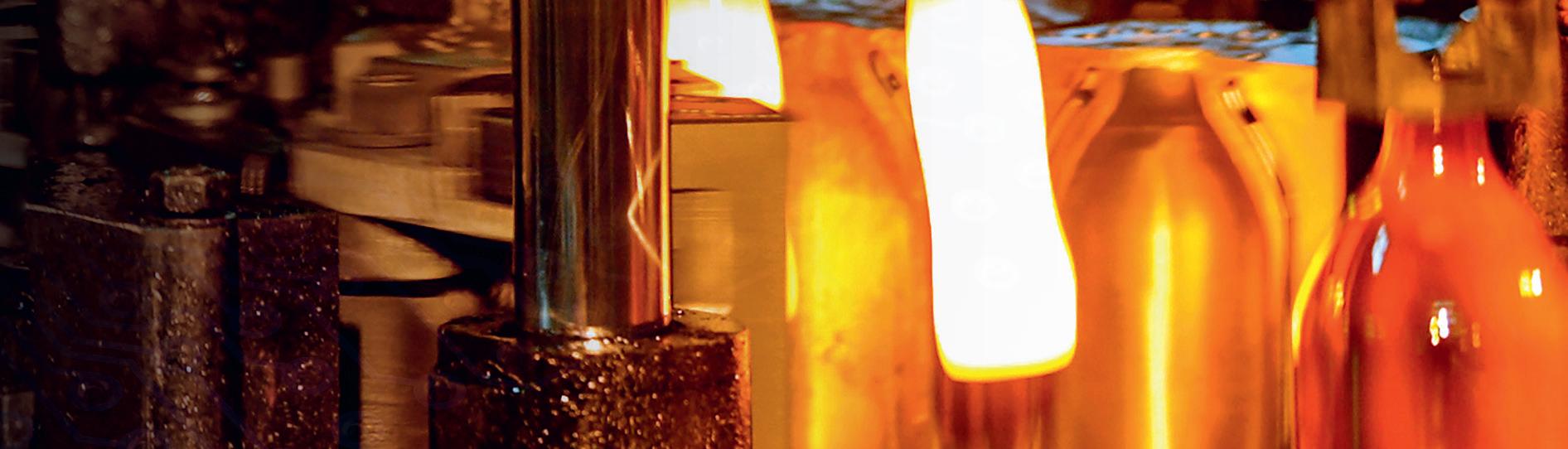
Inexpensive reject system Early detection of manufacturing and system problems Reduced error rate Signifi cantly improved quality of products and production
