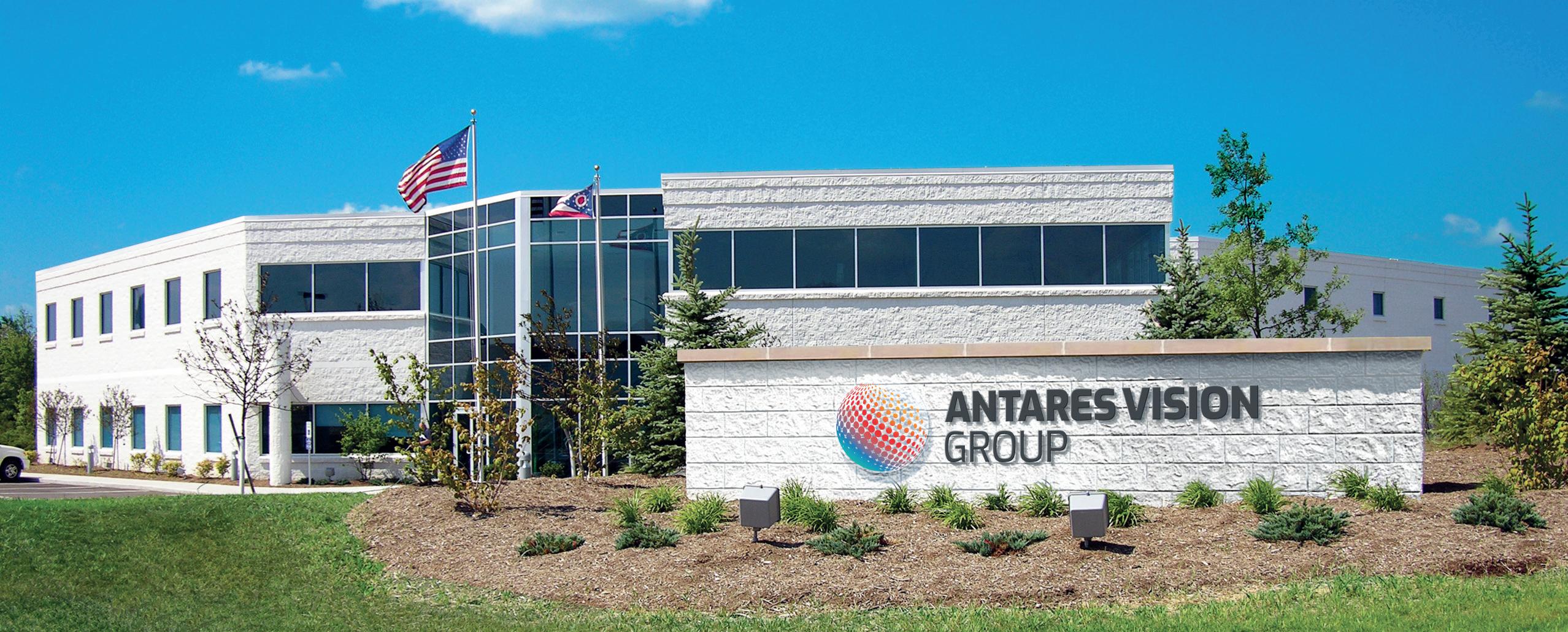
12 minute read
Inspection: Antares Vision Group
Antares Vision Group – Rigid
� Containers is the new name for Applied Vision, owned by Antares Vision Group.
Glassmakers stand to improve product quality, brand protection, business growth, customer experience and sustainability with one reference partner.
Applied Vision Corporation will begin operating under a new goto-market name – Antares Vision Group – Rigid Containers – as part of Antares Vision Group.
It is a global provider of machine vision inspection systems, track and trace solutions and smart data management possibilities.
With the acquisition of Applied Vision in December 2020, Antares Vision Group expanded its technological leadership to encompass a wider spectrum of inspection competencies and services in the food and beverage sector.
Antares Vision Group – Rigid Containers is also benefiting from the purchase that strengthens its own can and bottle inspection capabilities.
The company now combines Applied Vision technology with digital solutions for product and supply chain visibility that enable efficiency improvements from sourcing and production to distribution.
By leveraging team knowledge and digitisation tools across the Antares Vision Group enterprise, Antares Vision Group – Rigid Containers aims to help its customers build a clearer picture of their operations end-to-end.
Innovation
founded in 1997 and operating as Applied Vision Corporation until the fall of 2022, has developed vision systems for nearly 25 years based on patented optical, lighting and electronic image capture techniques combined with digital processing and AI algorithms that allow machines to adapt to normal process variation challenges. Jeff Hartung, V.P. of Sales and Customer Service for Antares Vision Group – Rigid Containers explains, this proven technology is now more accessible to customers.
“Our name is different, but our purpose of enabling quality inspections remains the same. We continue to build the tools that enable glass makers to increase their yields by accurately detecting and identifying defects,” Hartung said.
“As part of Antares Vision Group, we are dedicated to ensuring customers receive the excellent performance in quality products and services they deserve and making use of more world-class resources now available to us to accomplish our mission.”
Creating Excellence
Antares Vision Group – Rigid Containers is now benefiting from the synergy and collaboration between Antares Vision Group business areas that drive R&D and commercial advantages – everything from reducing the development time for new inspection solutions to expanding the options available to glass container manufacturers to applying serialisation on empty bottles.
Centers of Excellence spread across the Antares Vision Group enterprise help to spur innovation that only happens when people, process and technology come together to discover what’s possible. Knowledge sharing between engineering and manufacturing disciplines – coupled with operational best practices within the group – means more mindshare is concentrated on solving for emerging needs. Often the inspection cameras, lighting and AI logic used by one manufacturer can address the challenges faced by another.
Capturing Data
Hartung went on to say that moving forward, the company will serve as both a reference partner for quality inspections and for achieving high-quality standards across product and supply chains.
As bottle makers continue to prioritise efforts around quality and safety, brand protection, and efficiency and sustainability, a partner that combines an ecosystem of relevant technologies into
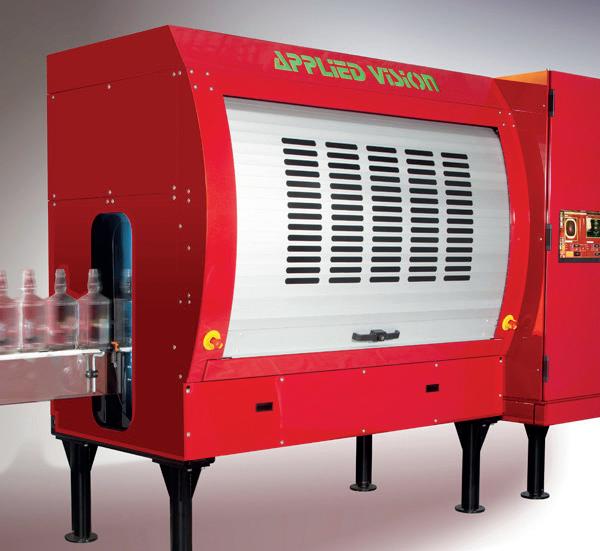
Volcano systems �� using Applied Vision technology can provide mold-correlated statistics as well as image maps of defect locations without rotating glass containers.
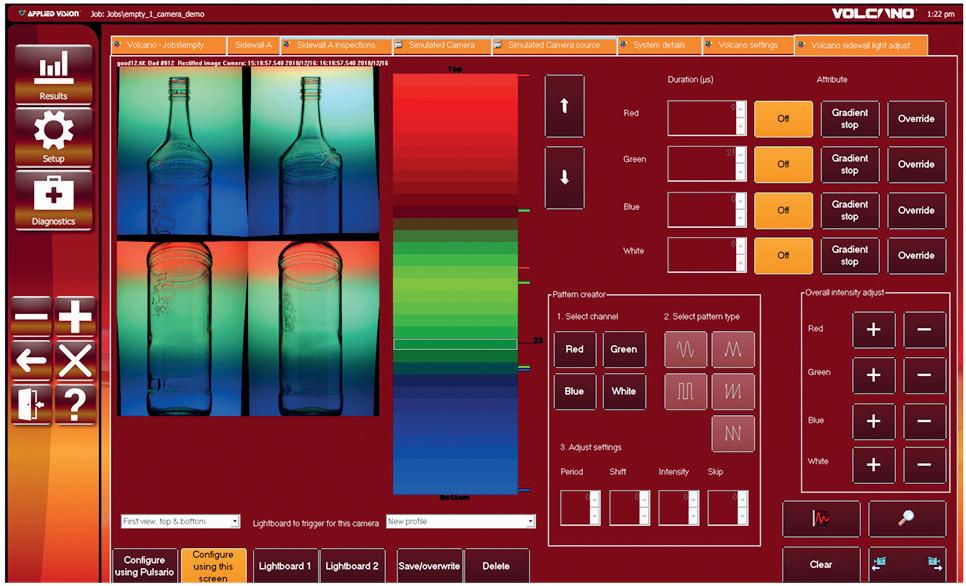
one convenient offering can accelerate enterprise digitalisation and innovation goals.
“If you want to pinpoint the cause of dimensional flaws for lean, height or finish E&T for example, or you’re having trouble identifying the most problematic checks, we can offer a solution.
“Other times it’s knowing that the treatments performed on line three are producing a great result, and how can I apply this to lines or machines in other plants?” Hartung said. “As part of Antares Vision Group, we can leverage more resources and expertise to help customers replicate the best results throughout their facilities, minimize waste from discarded bottles, improve recycling and take confident steps to fortify their operations against market uncertainties or the threat of a voluntary recall.”
“Maybe you want eyes on goods and materials from the source to the shelf, or your concern is improving returnable container management or recycling, and we can support those activities with supply chain transparency that brings your physical and digital worlds together.”
Same Inside
Inspection systems from the company will incorporate the same Applied Vision technology that has always powered the company’s machines. Proprietary imaging techniques at the base of Applied Vision solutions, together with deeprooted technological know-how, allow Antares Vision Group – Rigid Containers to stand out in the marketplace according to Hartung.
“We remain a US-based multinational leader that sets a high standard for quality inspection of glass containers,” he said. “Our complete Volcano line includes Sealing Surface and Base, Sidewall and new Check vision systems for performing comprehensive inspections.
“These systems can be electronically coupled to give plants a broader view of the container being inspected and a better idea of where problems may exist in the production process.”
Volcano systems using Applied Vision technology can provide mouldcorrelated statistics as well as image maps of defect locations without rotating glass containers. Simple setup and operation also support the efficient implementation of virtually any inspection sequence a plant requires.
Growing Globally
Thanks to Antares Vision Group’s considerable global footprint, Antares Vision Group – Rigid Containers has also expanded its customer service footprint in Europe, the Middle East, South America and across the Asia-Pacific region.
Hartung points to excellent aftersale service as a key contributing factor to the company’s past success. Antares Vision Group – Rigid Containers has traditionally hosted a service center within its US headquarters building to help customers get ahead of the curve with classroom training and hands-on instruction.
“Sharing the knowledge that helps bottle makers eliminate error from their inspections is at the heart of what we do, and now we can offer our expertise to more customers as a member of the Antares Vision Group,” said Hartung.
“From installation and troubleshooting assistance to getting parts to where they’re needed, we are localising our services in more places to provide an instant response.”
Recently, Antares Vision Group – Rigid Containers opened a new service centre in Italy leveraging the group’s Beverage Business Area main office that provides inspection and control devices for bottling and packaging lines.
This co-location initiative expands its presence in Europe and supports customers in the Middle East. The company is also moving forward to open a third service location to benefit South American customers. Based in Brazil, the centre will operate from the group’s local branch office that specialises in the inspection of life science and pharmaceutical applications while also delivering track and trace and smart data management solutions to a variety of industries.
One Shared Vision
Strategic acquisitions have made Antares Vision Group a technology partner for food and beverage, life science and cosmetics supply chains. By aggregating high-growth organisations of excellence that have demonstrated technologies at a global level, the group is striving to represent a technological hub of excellence that helps container manufacturers ensure the safety of product, profit, people and the planet.
“We help ensure optimal inspection effectiveness on the fastest, most advanced production lines in the world, regardless of container complexity,” said Hartung.
“For those who already know us, it’s business as usual but now there’s more to see. Let’s also talk about transforming your plant into a digital factory to better understand your product’s journey. Others will find there’s no one more qualified to improve their quality and production efficiencies through accuracy, reliability and speed.” �
Antares Vision Group-Rigid Containers, Ohio, USA www.appliedvision.com.
TECHGLASS celebrates commissioning of 480tpd furnace
TECHGLASS has been designing and supplying completely equipped furnaces, working ends and forehearths for over 30 years. In July 2022 a 480tpd furnace was commissioned - the Stoelzle Group’s largest and one of the largest end port furnaces in Europe.
Cooperation between TECHGLASS and Stoelzle Czestochowa dates back to the establishment of the Polish branch of this Austrian company, which took place in 2001.
To date, TECHGLASS has delivered there the furnace, working end and forehearths three times, and has completed more than 150 smaller orders.
In 2020, the decision was made to implement a furnace with a pull of 480 tons per day with 5 forehearths, in a hall designed for a furnace with a 40% smaller melting area, the most ambitious option among those considered. The six-month tender process was completed in February 2021 with the victory of TECHGLASS. Forehearths, working end and furnace

In house business model
The execution of the project took place during the Covid pandemic and the war in Ukraine. Lead times for some components have been extended several times over. It has become common practice for suppliers to provide offers that are not binding in terms of neither prices nor deadlines.
However, the TECHGLASS business model based on designing and manufacturing almost all of the systems in-house has helped address these challenges.
The status of each of thousands of orders Massive regenerator was monitored in real time, allowing a quick response in case of any problems. This would not have been possible if production had been carried out by subcontractors.
Share of electric energy in melting up to 40%
The furnace is designed to melt of up to 192tpd out of 480tpd by electric current.
This allows the melting process to be optimized according to cost and availability of energy sources.
It also offers the potential for dramatically greater reductions in CO2 emissions than standard solutions with electricity at an estimated 20%.
The furnace was equipped with a combustion system with automatic individual burner control.
This makes it easier to operate the system and, most importantly, reduces nitrogen oxide emissions and has a positive impact on energy consumption.
Alternative fuels
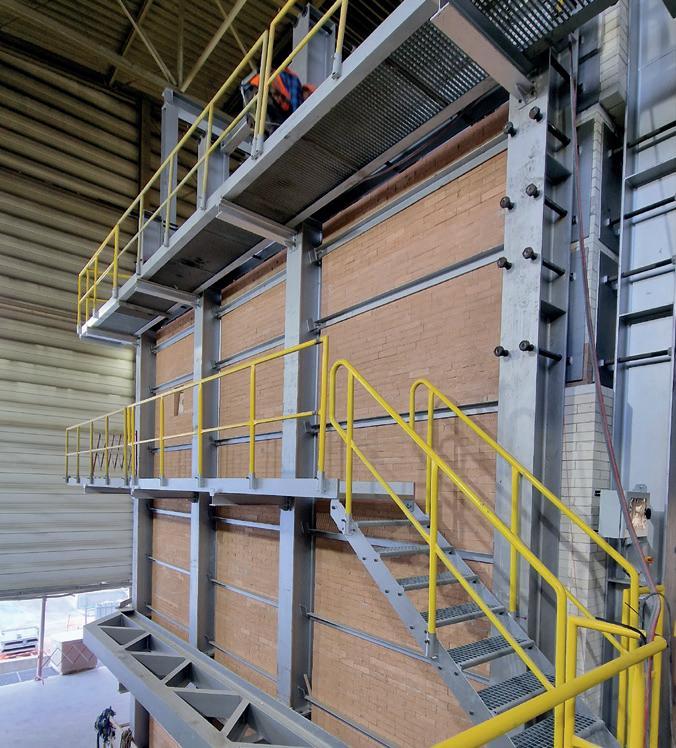
Short glass to glass time
It took only 67 days from the glass drainage from the previous furnace to the start of the heat-up of the new one - three days less than originally anticipated.
It is difficult to interpret this result without knowing the extent of the necessary demolition, construction and installation works.
However, anyone who witnessed the situation before the drainage and then before the heat-up must consider this result to be record-breaking.
The determination and dedication of TECHGLASS employees have been recognised by the management of Stoelzle Czestochowa. The combustion system is designed for easy extension of LPG or oil supply.
The furnace control system ensures the stability of the combustion process, regardless of the amount of each fuel fed, reducing the impact on the production process to a minimum.
This functionality becomes of vital importance in the current situation of uncertain natural gas availability and unpredictability of its price.
Machine Learning
It has been repeatedly confirmed that good learning algorithms achieve better results than experts. TECHGLASS is implementing a programme to introduce Machine Learning modules into control systems.
In the first stage, ML is planned to be used to minimize glass level disturbance after changing the combustion side. TECHGLASS engineers are also working on applications of ML in other areas, such as optimising forehearths operation during assortment changes.
Obtaining even a small amount of energy savings from these measures is worth the effort put into them.
TECHGLASS offers solutions for production of all types of glass
Recently a TECHGLASS furnace of pull of over 300tpd for melting sodium silicate has been commissioned.
The furnace is part of a project executed for CIECH Vitrosilicon S.A. which also covered engineering and supply of batch house and three modern production lines
CIECH Vitrosilicon is the biggest supplier of sodium silicates in Europe. It has two production plants in Poland. The company belongs to CIECH Group – an international, expanding group operating in chemical industry with strong global presence.
TECHGLASS’ innovation
The standard is to transfer solutions for soda-lime glass, mainly container glass, to sodium silicate production. The innovative TECHGLASS furnace was designed from the ground up for melting this glass.
This allowed the production of high-quality sodium silicate with energy efficiency unattainable with standard approaches and with very low NOX emission. The furnace can be operated without investing in and maintaining any secondary methods of reducing nitrogen oxides.
Low energy demand
The furnace supplied by TECHGLASS has exceptionally low energy demand, which is especially important with today’s rising gas prices and carbon dioxide emission costs.
To meet the customer’s very stringent requirements in this area, TECHGLASS has made a number of improvements.
A very efficient transfer of energy to the melt from the furnace’s combustion space was achieved by equipping the furnace with two “extra wide” dog houses and four oscillatory batch chargers for excellent batch distribution.
The furnace combustion system for CIECH Vitrosilicon was equipped, as in the case of Stoelzle Czestochowa, with automatic individual burner control. It is also designed for easy extension with LPG or oil supply.
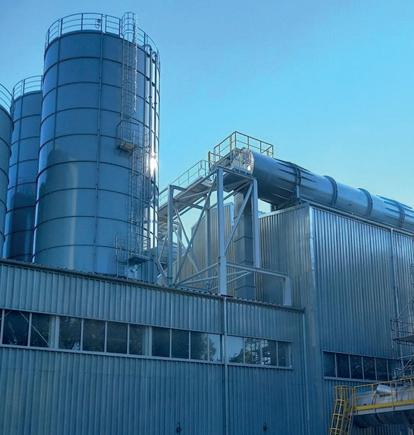

Left: Production hall. Right: Glass cubes production From left to right: Andrzej Skowiniak - President of TECHGLASS, Robert Janeczko - Chairman of the Board, CIECH Vitrosilicon. Hubert Domaradzki - Member of the Board, CIECH Vitrosilicon

Reduced module
An important feature of the furnace design is to reduce the time between the production of products with different specifications, the so-called module. As a result, the amount of unwanted transient product is significantly reduced, which translates into savings and reduced environmental impact.
Scope of supply
As part of the project, TECHGLASS also designed and supplied a batch house and three complete lines for producing frit in the shape of almost any size of cubes.
Each of the three frit production lines is equipped with forming machines, conveyors, a cooling water system, all auxiliary systems, and a control system integrated with the furnace control system.
The execution of the project was such a success, that soon after its completion CIECH Vitrosilicon ordered a rebuild of the existing furnace with TECHGLASS. The rebuild was based on a significant modification of the furnace’s design.