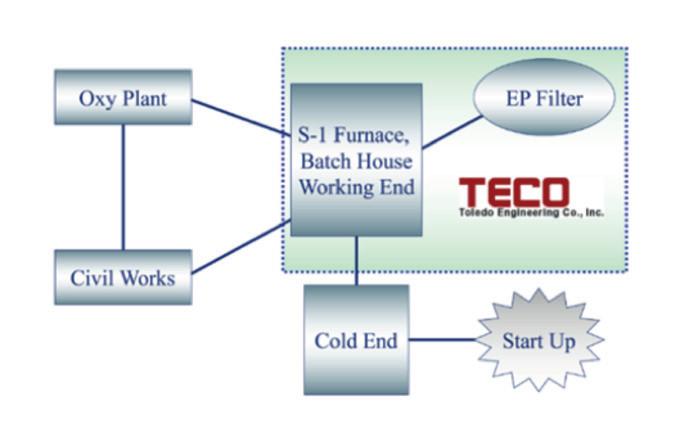
9 minute read
Teco
Vida y tiempos prolongados de un horno de oxicombustible
La colaboración entre empresas conduce al éxito de los proyectos. Uno de tales proyectos entre TECO y un cliente había llevado a que un horno de oxicombustible funcionara con éxito durante 17 años, informa Brian Naveken*.
� Img. 1. Vista general de los elementos principales del proyecto.
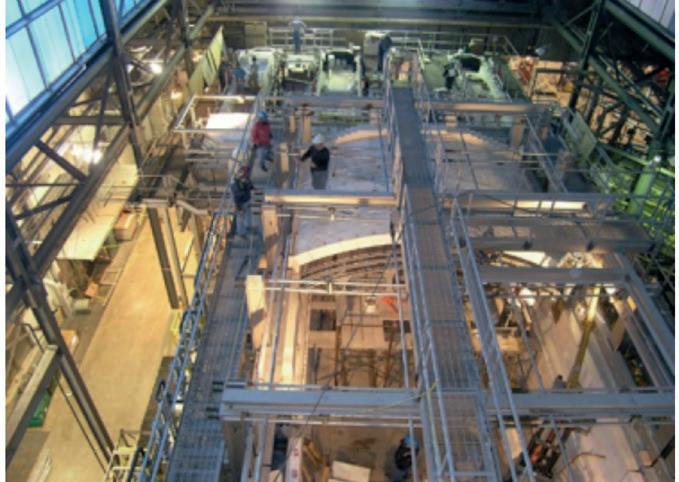
� Img. 4. Horno de oxicombustible casi terminado. � Img. 2. Cronología del proyecto.
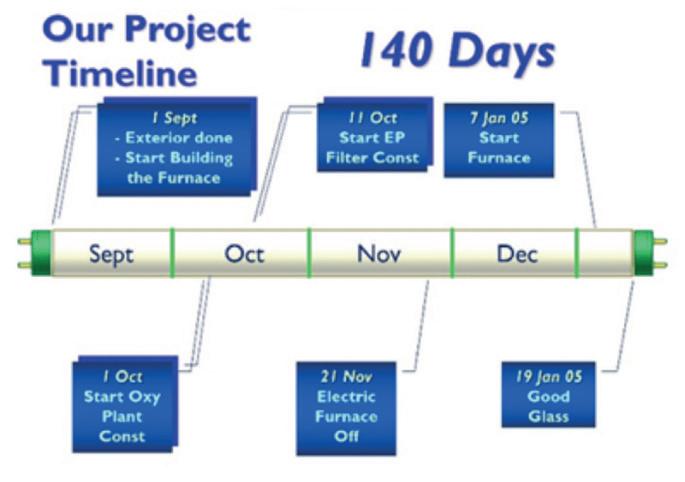
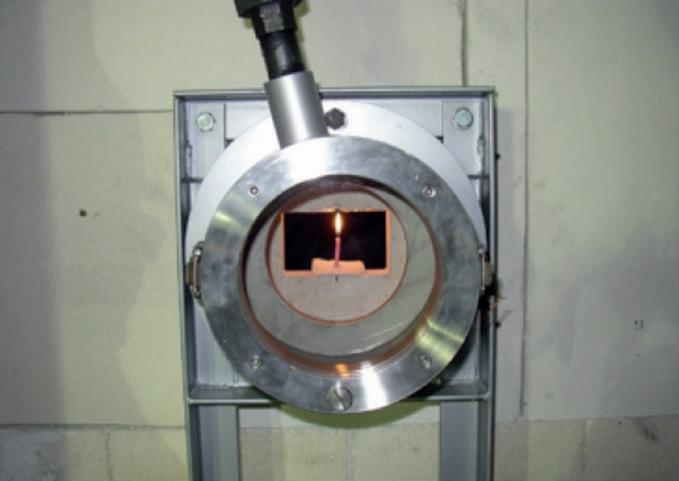
� Img. 5. “Cumpleaños” del horno.
La colaboración es sinónimo de liderazgo y trabajo en equipo sobresalientes. Las empresas que trabajan en colaboración se benefician de un mayor acceso a los recursos, de comunicación y de confianza. También es la clave para la innovación y las prácticas innovadoras y es la piedra angular de los proyectos de diseño y construcción. La conclusión es que las empresas que trabajan juntas en estrecha colaboración, tanto durante el proyecto y la campaña del horno, tienen más éxito. Uno de esos proyectos es un horno de oxicombustible para la producción de tubos de vidrio que actualmente está operando en su decimoséptimo año de funcionamiento continuado. La siguiente es una cronología o un diario del ciclo de vida de este horno.
Diseño basado en el coste total de propiedad - 2003
Un proyecto define las relaciones, roles y responsabilidades del equipo de diseño, ingeniería y construcción necesarios para proporcionar la realización de un horno de vidrio desde su concepción hasta su clausura. Originalmente, uno de nuestros clientes operaba un fusor totalmente eléctrico de doble escuadra TECO para producir tubos de vidrio. El cliente se puso en contacto con TECO antes de su siguiente reconstrucción, programada para 2004-2005. Las conversaciones sobre la reconstrucción se centraron en si se reconstruía el fusor eléctrico existente o se construía un nuevo horno de oxicombustible 200 USTPD con tres nuevos alimentadores Zedtec. La reconstrucción también incluiría la conversión del método de conformación, de un proceso Danner a un proceso Vello, para aumentar la productividad de la fabricación de tubos, lo que requería un aumento en la elevación de la línea de vidrio. Un nuevo horno de oxicombustible implicaría modificaciones en la planta de material, modificaciones en la construcción, un sistema de emisiones y una granja de oxígeno. Considerando todos estos cambios, la mayor calidad, el objetivo de un mayor rendimiento y una vida útil de 10 años frente a una de cuatro años, se seleccionó un horno de oxicombustible para lograr el Coste Total de Propiedad más bajo.
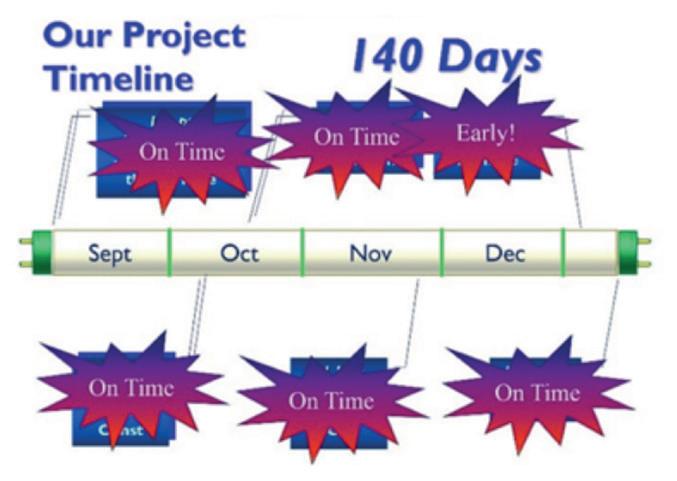
� Img. 3. Cronología del cumplimiento del proyecto con el calendario.
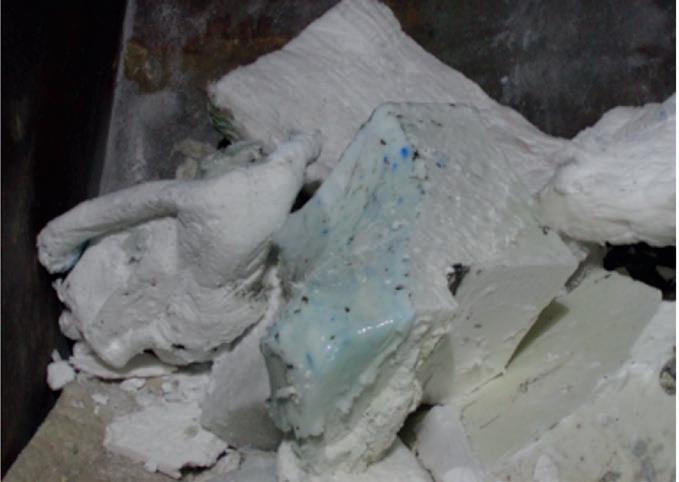
� Img. 6. Degradación del material de espinela en el fundidor debido al arrastre.
Comienza la construcción –1 de septiembre de 2004
La construcción del horno y los alimentadores comenzó el 1 de septiembre de 2004 y se completó en 140 días, dentro del presupuesto y el calendario,
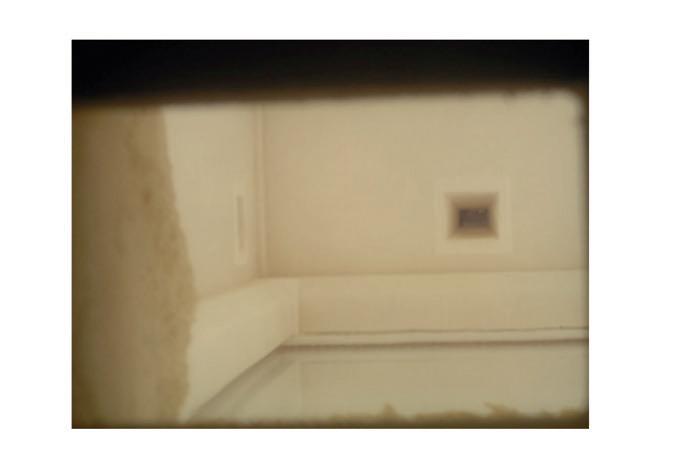
� Img. 7. Material de espinela no afectado en refinador.
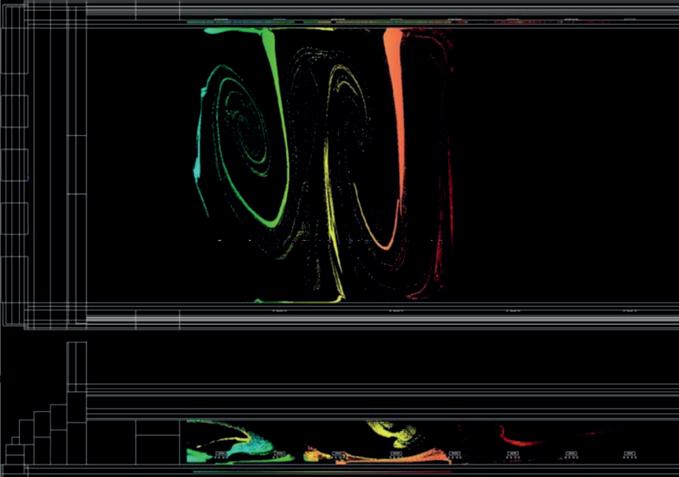
� Img. 10. Validación de Modelo.
utilizando el método de entrega de proyecto Diseño-Construcción. El horno eléctrico TECO existente se desmanteló el 21 de noviembre de 2004.
Año de campaña 1 – enero de 2005
El 7 de enero se inició la puesta en servicio y calentamiento del horno y los alimentadores. El 19 de enero, se producen tubos de vidrio empaquetados con el objetivo inicial de 176 USTPD. En mayo, la tasa de producción se incrementa a 191,1 USTPD. La primera auditoría del horno TECO se programa para seis meses después de su encendido y dos veces al año a partir de entonces.
Año de campaña 2 – 2006
La pared lateral en la sección de fusión del horno experimenta una degradación severa debido al uso de dolomita decrepitante en el material. Durante la fase de diseño del proyecto, el cliente quería utilizar un material de espinela como material de cara caliente en la superestructura completa del horno, incluida la corona. Debido a la falta de experiencia probada de producción con este material y su uso en áreas críticas, específicamente la corona, el material de espinela solo se usó en las paredes laterales y la pared frontal. La corona se construyó con AZS moldeado fundido y Alfa Beta Alúmina. El material de espinela resulta ser un gran material para este tipo de vidrio, excepto en las áreas que experimentan un ataque al material vítreo debido a la dolomita que se está utilizando (Img. 6). Como resultado, el fusor (el refinador no se vio afectado; ver Img. 7) las paredes laterales y los ladrillos de calaje se tuvieron que reemplazar, y se realizó una reparación en caliente. El material de espinela se reemplazó con un AZS unido.
TECO realiza una serie de modelos CFD. Los resultados del rastreo de partículas de polvo del material vítreo, Img. 10, validan el impacto del material en la pared del pecho.
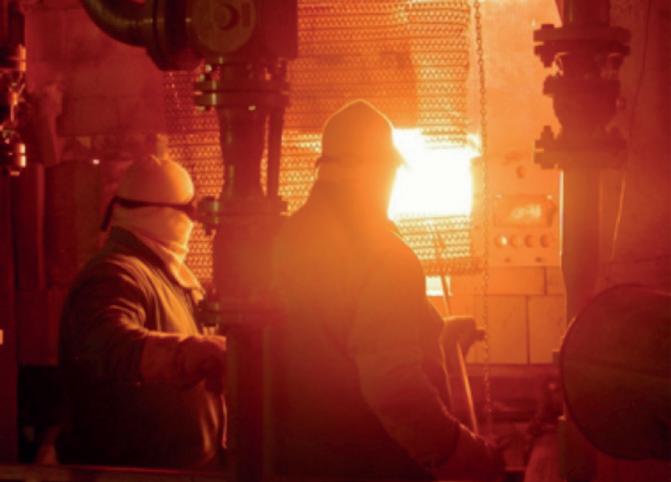
� Img. 8. Reparación en caliente de la pared lateral.
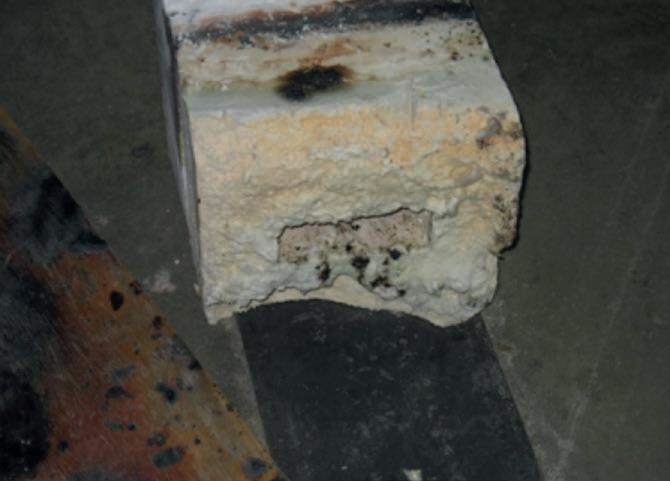
� Img. 11. Extremos de los ladrillos de calaje rotos.
Año de campaña 6 – 2010
Dreicor lleva a cabo el primer revestimiento del horno.
Durante este tiempo, los puntos calientes se identifican en varios lugares de las paredes del tanque. Después de aplicar los materiales de recubrimiento, se agrega un enfriador de agua a todas las ubicaciones de los puntos calientes y también se agregan enfriadores de agua de la línea de fundente.
La producción del horno aumenta cuando se agrega un cuarto alimentador ZEDTEC para la producción de tubos de menor diámetro, lo que aumenta la producción máxima hasta 215 USTPD. El horno diseñado por TECO puede lograr un rendimiento superior al diseño nominal de 200 USTPD.
Se lleva a cabo una segunda reparación con ladrillos de calaje en la sección del fusor debido a que las puntas de los ladrillos de calaje se caen (Img. 11 y 12) después de la reparación en caliente, que expone partes del acero de la placa del manto.
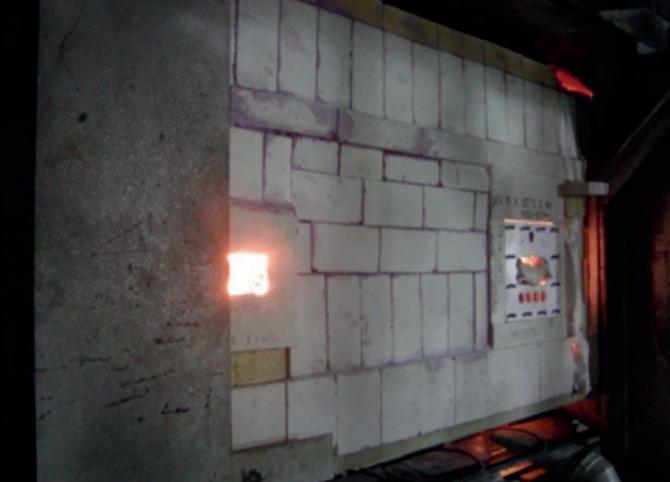
� Img. 9. Reparación completa de la pared lateral.
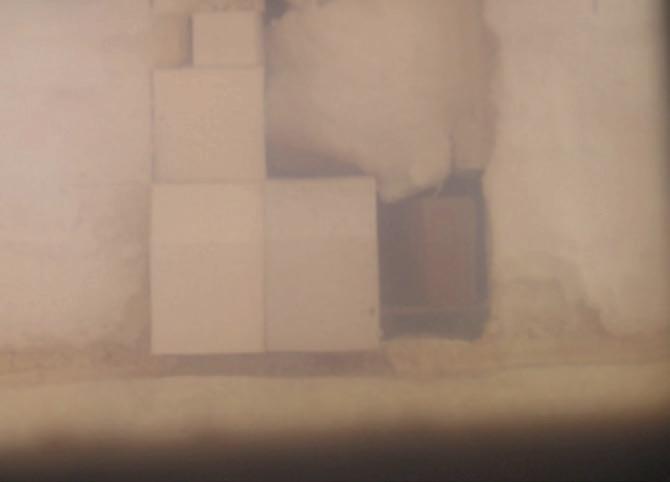
� Img. 12. Reemplazo de los ladrillos de calaje rotos.
Año de campaña 7 – 2011
Dreicor recubre la garganta con un material cromado. Las bajantes de ambos lados han comenzado a mostrar desgaste, resultando en cierta inestabilidad. Se agregan refuerzos y rejillas al tercio superior del tubo de bajada.
Año de campaña 11 – 2015
El horno alcanza su tiempo normal de reconstrucción y aún funciona excepcionalmente bien sin necesidad de reparaciones importantes. Como resultado de la edad del horno, el cliente está aumentando las auditorías del horno TECO de dos veces al año a tres veces.
Año de campaña 13 – 2017
Dreicor recubre el horno por segunda y última vez. No será posible aplicar una tercera capa, ya que expondría demasiado acero de la placa del manto. Nota: Utilizando la filosofía de mejora continua, el diseño de TECO 2003 ahora se ha cambiado para permitir tres capas.
Se recubrió la pared objetivo del puerto de escape derecho (Img. 13).
Año de campaña 14 – 2018
La conexión entre el tubo de bajada
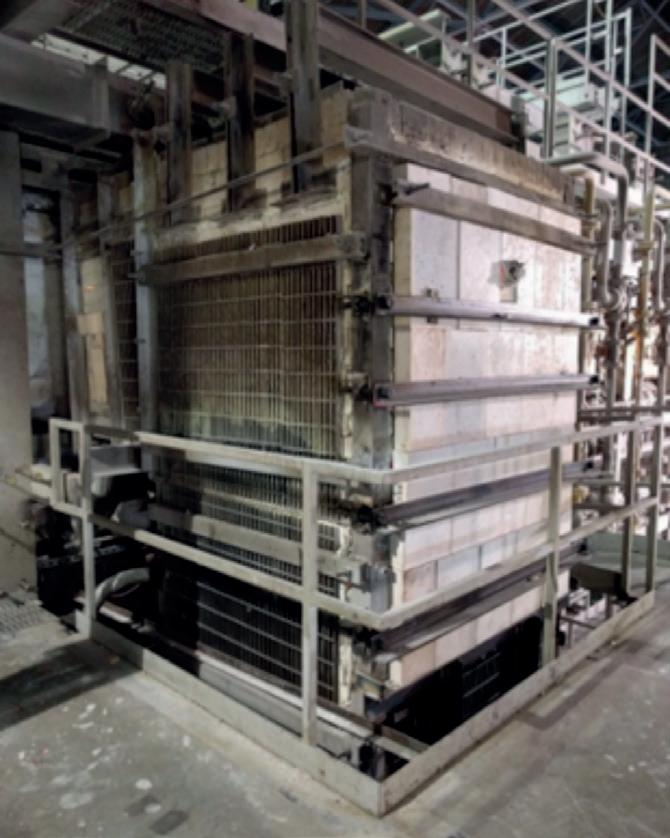
� Img. 13. Sobrecapa en la pared objetivo del tubo de
escape.
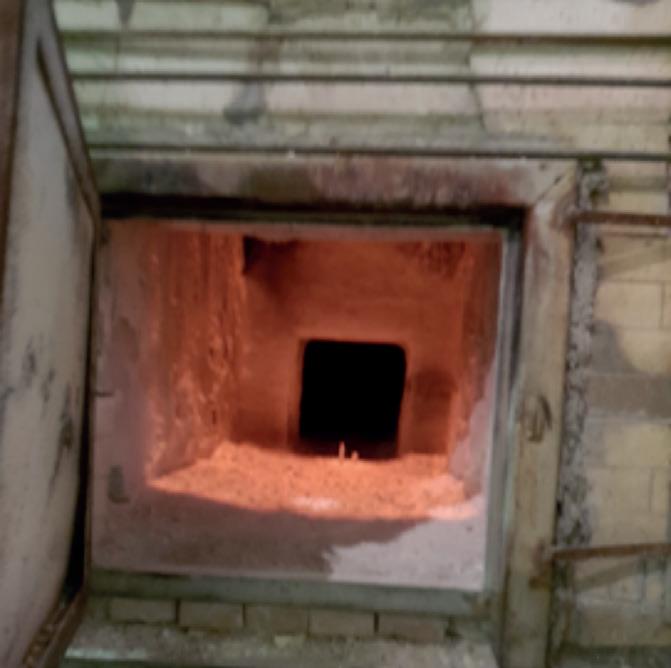
y el conducto de humos se ha visto comprometida en el arco del dintel (Imgs. 14-16). La reparación se realiza desde el interior. La presión y el funcionamiento del horno se ajustan para gestionar la apertura del conducto de humos reducida.
El alimentador 1 se apaga y se cierra debido a la reducción de la demanda de tubos de mayor diámetro. La tasa de producción del horno se reduce correspondientemente.
Año de campaña 15 – 2019
La placa del manto comienza a quedar expuesta debido al desgaste y la degradación de los bloques de las paredes laterales en la línea de flujo (Img. 17). Como precaución, se reduce el nivel del vidrio para evitar posibles fugas de vidrio.
Año de campaña 17 – 2021
En el momento de escribir estas líneas, el horno todavía está operativo.
Conclusiones
Es notable que un horno de oxicombustible haya alcanzado una vida útil de 17 años, considerando el problema del material vítreo con la superestructura dentro de los primeros dos años de operación. El mérito de este logro es doble. Uno es el excelente trabajo en equipo entre el personal de administración, ingeniería y operaciones y su diligente compromiso con el mantenimiento preventivo y de rutina, que permite al cliente alcanzar sus metas de producción.
En segundo lugar, está la colaboración entre el cliente y TECO durante la vida útil de este horno en estos puntos clave: � El cliente fue proactivo. Ellos mismos monitorizaron y mantuvieron las áreas identificadas por las auditorías de TECO, ocupándose de cualquier inconveniente antes de que se convirtiera en un problema. � Mejora continua – el cliente empleó prácticas operativas Six Sigma y mejoras operativas asesoradas por TECO. � El cliente le pidió a TECO que completara las auditorías del horno dos veces al año, comenzando en el año uno de su campaña, y luego tres veces al año después de que el horno alcanzara su vida útil normal por diseño. No se puede exagerar el valor de adherirse a las recomendaciones del informe de auditoría por parte de TECO, que fueron seguidas fielmente por la planta. � El cliente realizó programas de mantenimiento preventivo y de rutina para quemadores y bloques de quemadores, resellado de línea de flujo y línea oblicua, soldadura y parcheo de cerámica, y agregando rejilla de soporte y enfriamiento según estaba justificado. � El cliente colaboró con TECO en la planificación de todos los futuros
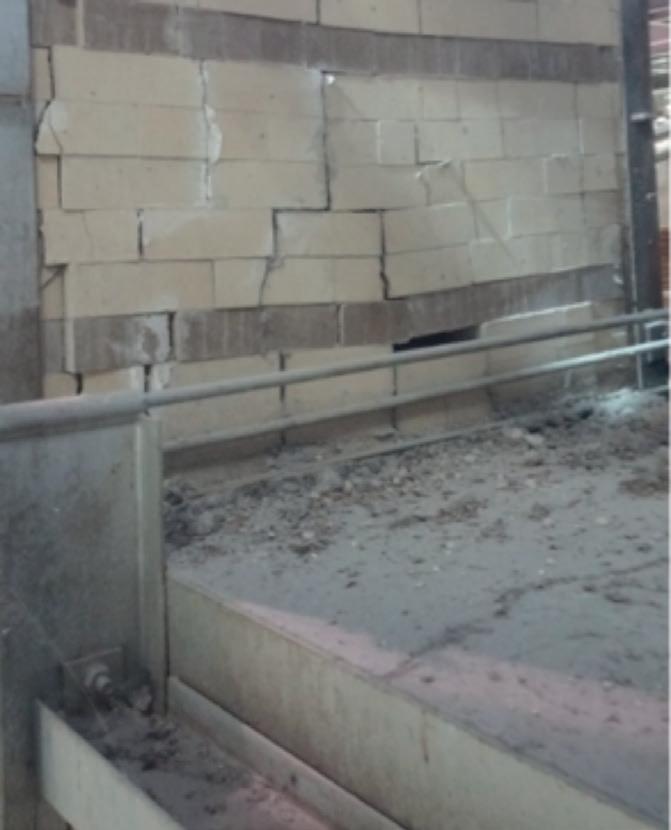
� Img. 14. Fallo del arco del escape de humos del dintel (exterior).
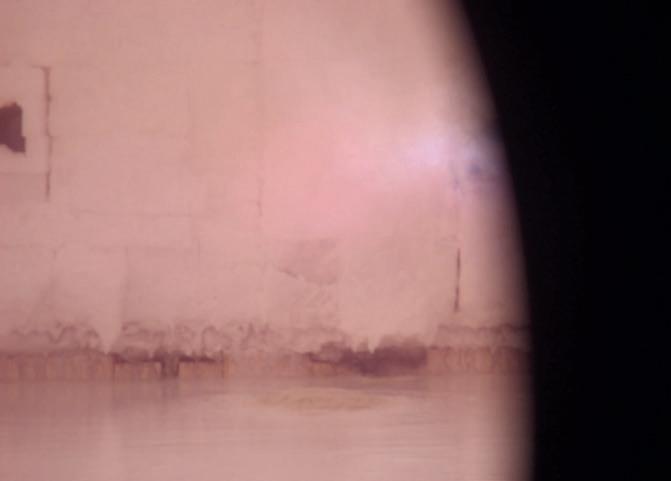
� Img. 17. Acero de la placa de manto expuesto.
� Img. 16. Reparación del dintel del arco. � Img. 15. Fallo del arco del escape de humos del dintel (interior).
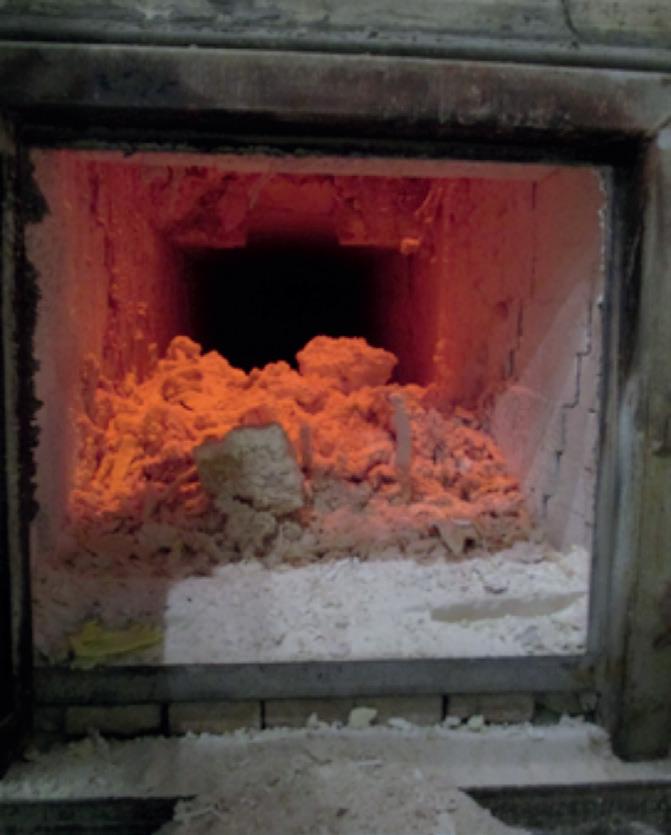

� Img. 18. Imagen actual de la pared de la pared lateral del fusor y del refinador.
trabajos y reparaciones, como agregar un alimentador adicional, agregar enfriadores de agua, realizar soldaduras de cerámica y llevar un control de la duración de todos los recubrimientos. Un contratista de diseño y construcción como TECO es un miembro del equipo durante toda la campaña del horno y parte del éxito de este equipo en general.
Como parte del Grupo TECO, Toledo Engineering, Tecoglas y KTG Systems ofrecen capacidades completas en hornos de vidrio de todo tipo, con KTG Engineering apoyando esta instalación como fabricantes de equipos para plantas de vidrio. Zedtec son los especialistas del Grupo TECO en tecnología de hornos de alimentación y partes operativas. EAE Tech proporciona servicios de ingeniería de automatización industrial de alta calidad y sistemas de control personalizados. Dreicor es un contratistaproveedor único que se especializa en adquisiciones, fabricación, instalación y construcción de procesos para la industria de fabricación de vidrio.
El Grupo TECO ha estado diseñando, construyendo y modernizando para la principal industria de la fabricación de vidrio del mundo desde 1927. �
*Gerente de Ventas Técnicas, TECO, Toledo, EE.UU. www.teco.com