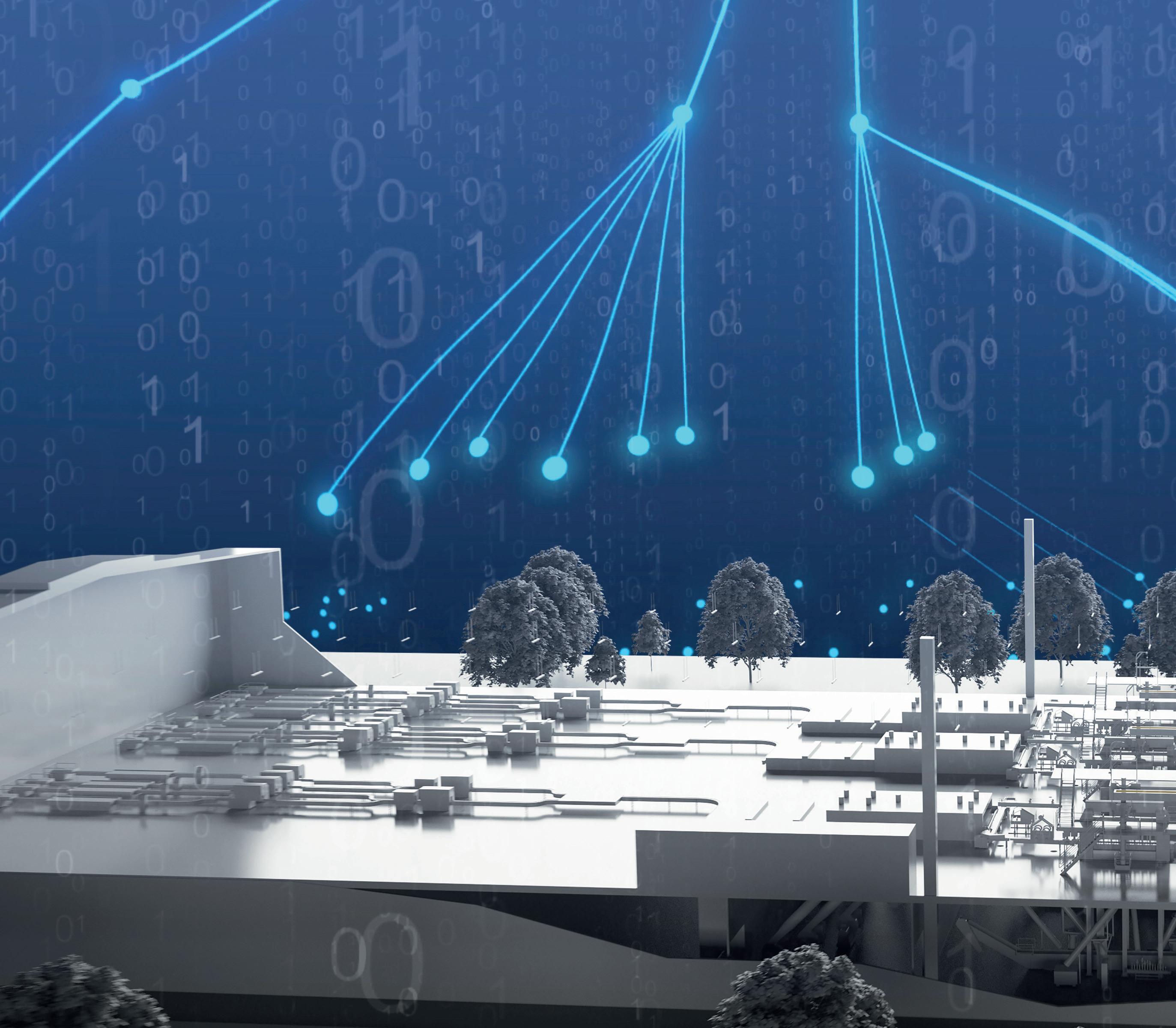
12 minute read
Fabricación de vidrio digital
Todo preparado para un futuro digital
� Planta inteligente.
El Dr. Michael Kellner analiza la digitalización, las emisiones y la inteligencia artificial en la fabricación del vidrio.
El Dr. Michael Kellner, oriundo de Jena, ya había entrado en contacto con el vidrio en sus días de estudiante a través de una pasantía en Schott Glas.
«Vidrio, eso es exactamente lo que debería ser», comenta mirando hacia el pasado, tras haber estudiado en Weimar materiales de la construcción e ingeniería de procesos con especialización en vidrio.
En 1986, colaboró con las primeras cámaras de procesamiento de imágenes y cómo utilizarlas para controlar el vidrio.
«La teoría estaba ahí, pero la tecnología aún no era lo suficientemente potente para la industria del vidrio», afirma.
El Dr. Kellner comenzó a trabajar en Schott Glas mientras estudiaba su doctorado en automatización y tecnología del procesamiento de imágenes en la fabricación de vidrio.
Tras el doctorado, empezó como aprendiz en la antigua empresa Heye-Glas, una empresa mediana innovadora. Al principio, fue el nexo entre la producción y el desarrollo para incorporar soluciones de automatización a la fabricación de vidrio. En 1992, fue responsable de probar en Heye las primeras aplicaciones de procesamiento de imágenes basadas en procesadores de imágenes, y poco después comenzó a desarrollar soluciones de procesamiento computarizado de imágenes. «Los expertos de la época pensaban que el procesamiento de imágenes nunca podría funcionar en un PC», comenta Kellner. «¡Cuán equivocados estaban!». El «ingeniero de procesos» con un doctorado deja la empresa en el año 2000, pero regresa a Heye en 2006 como jefe de desarrollo.
Desde 2019 ha sido responsable del desarrollo de sistemas digitales, un campo en el que Heye ha venido participando desde los años 90. Heye introdujo un sistema de temporización electrónico, parametrizable por PC, para controlar las máquinas IS (siglas en inglés para «de secciones individuales») y el sistema de descarte con «hot-end», además de la evaluación del empuje de los recipientes de vidrio desde la placa de enfriamiento hasta la cinta transportadora de la máquina por medio de empujadores.
El proceso completo con «hot-end» fue convertido a la tecnología servo, por ej., desde la formación de la gota hasta la manipulación de la mercancía.
«Esto supuso un gran paso hacia el futuro, ya que ahora las secuencias de movimiento se ajustaban y se seguían por los generadores de feedback de acuerdo con las curvas de movimiento dadas», afirma Kellner.
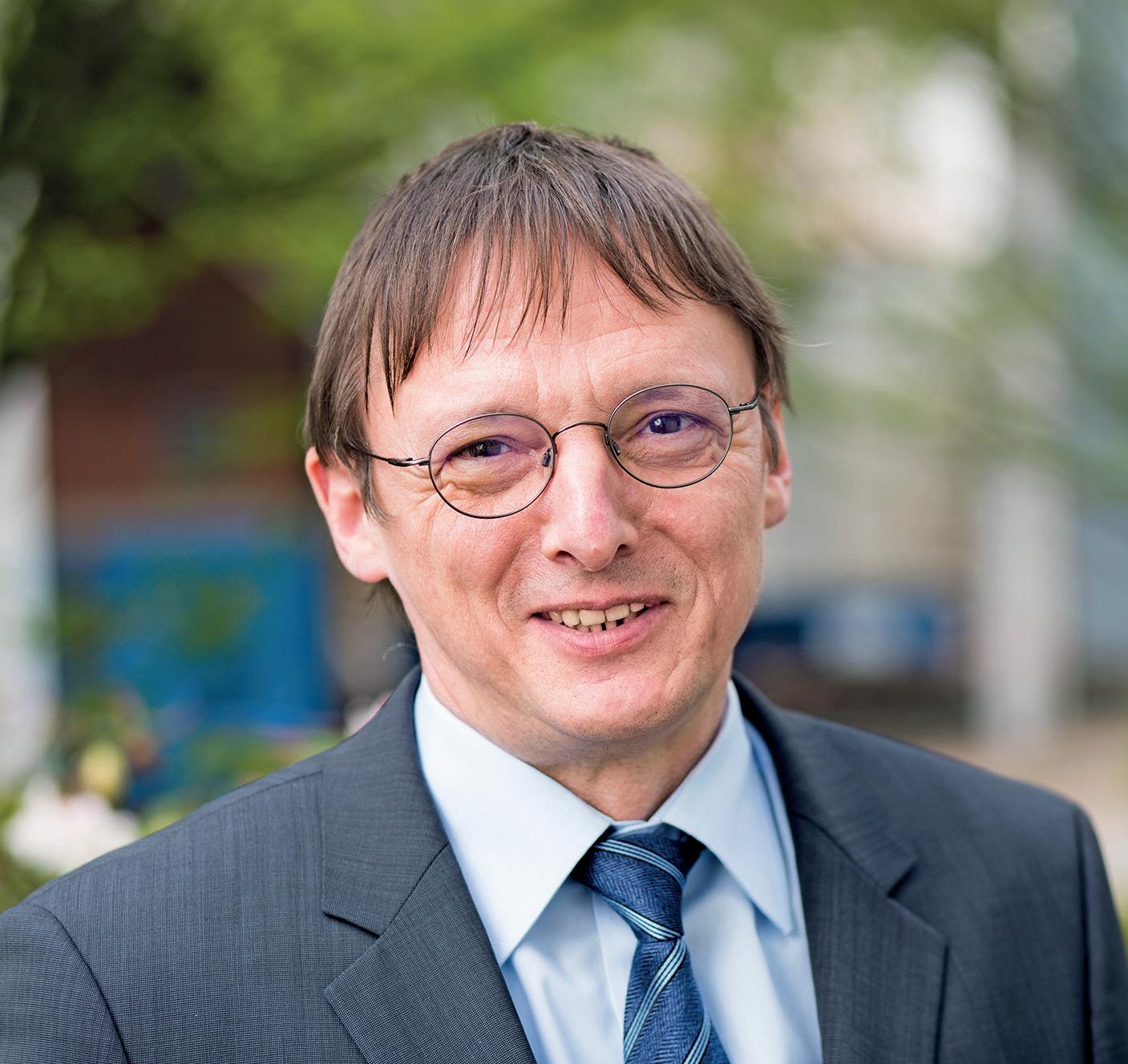
� Dr. Michael Kellner.

Poco después, también se utilizaron los primeros servomotores en la máquina IS para hacer que las secuencias críticas del proceso fuesen reproducibles y así evitar defectos en los envases.
La introducción del Control de procesos de Heye es sin duda un importante componente en la producción de vidrio ligero, ya que registra y visualiza el proceso de prensado mediante el registro de las posiciones del émbolo.
Cámara de gotas con «hot-end»
En 1998, Heye trabajó en una cámara de gotas con «hot-end» para registrar el corte de las gotas.
Pero la resolución de las cámaras y el rendimiento de los ordenadores no eran suficientes.
La experiencia adquirida fue importante para desarrollar los conocimientos necesarios para los años siguientes. Cuando estuvieron disponibles los primeros digitalizadores grabber o tarjetas de captura de imágenes, se compraron los nuevos ordenadores Terra y se desarrollaron un lector de números de molde con cámara y un verificador de superficies de sellado con cámara.
La empresa ha transformado plataformas de máquinas completas porque el mercado ha ido triplicando y cuadruplicando las operaciones de las gotas.
«En consecuencia, hemos logrado que todos los equipos con «hot-end» sean «aptos para el futuro». Hoy ofrecemos la plataforma tecnológica completa para todas las aplicaciones. El continuo desarrollo de sensores y actuadores ha creado nuevas oportunidades. Desde la introducción de la industria 4.0, estamos poniendo el listón cada vez más alto».
Por ejemplo, la nueva máquina IS, a la que llamamos Heye SpeedLine, es la primera máquina enteramente apta para bus.
El siguiente objetivo de desarrollo fue crear zonas en la máquina IS en las que se pudieran instalar los sensores, los actuadores, los cables necesarios y la tecnología del procesador de manera segura y fiable. Seguridad y fiabilidad significan, en este contexto, protección contra el calor, los aceites, vapores de aceite, el agua, el vapor de agua, la suciedad y el vidrio.
«Hemos tenido éxito con la SpeedLine porque hemos concebido el diseño de manera diferente. En primer lugar, se diseñó el trazado de los cables y se probó dónde debían ubicarse los sensores y cómo podíamos protegerlos desde el punto de vista técnico para garantizar su estabilidad a largo plazo.
«Hacer funcionar los sensores sin fallos en un ambiente caluroso de 1000 °C no es tan sencillo. Gracias al sistema bus, todos los sistemas en la máquina están conectados en red y se puede gestionar un gran número de sensores.
«Naturalmente, esto trae nuevas posibilidades y productos, por ejemplo,

� Máquina de inspección «cold-end» Smartline 2.
el control inteligente de los intervalos de lubricación, la Lubricación centralizada multicircuito de Heye, que ahorra aceite y aumenta la vida útil de los componentes. También cabe mencionar la medición en línea de las presiones y temperaturas de los equipos.
«Con esta máquina hemos dado un paso gigante hacia la digitalización. Ahora hay una "torre de comunicación" que combina todos los componentes de la red, los ordenadores y los servidores en un solo gabinete.
«Los componentes están interconectados y se comunican entre sí. SpeedLine es una tecnología de plataforma en la que los componentes tales como robots o los sistemas de control y medición se pueden integrar fácilmente».
A través de la Torre de comunicación existe también una puerta de acceso al exterior, es decir, al cliente.
La Interfaz de programación de aplicaciones SmartLink de Heye le brinda al cliente los datos del proceso de fabricación para el análisis individual de datos.
«Nosotros desarrollamos la mayor parte del software, especialmente en las áreas técnicas clave.
«La industria del vidrio hueco es un segmento de mercado relativamente pequeño y especial. Es difícil explicar los procesos a empresas externas. Hay algunos componentes que compramos, como, por ejemplo, los sensores. Sin embargo, los proveedores trabajan para la industria del vidrio a largo plazo y, por lo tanto, conocen los requisitos».
Descarbonización
El tema de mayor interés en este momento es la huella de CO2 o descarbonización. Si se considera el consumo de energía y se dejan a un lado los modelos de compensación, entonces se trata básicamente de utilizar la energía de manera sensata y evitar el desperdicio energético.
«Para nosotros como fabricantes de máquinas, existen dos direcciones diferentes que son relevantes en cuanto a las emisiones.
«Por un lado, es cuestión de minimizar las pérdidas, lo que significa producir hasta el 100 % de las botellas de vidrio posiblemente sin defectos. De este modo no se desechan las botellas de vidrio, no se desperdicia la energía necesaria para fabricarlas, y se obtiene una mejor huella de CO2.
«Por otro lado, el enfoque está en la disponibilidad del equipo. Es mejor que la máquina funcione las 24 horas del día, los 7 días de la semana, y que fabrique botellas de vidrio sin ningún defecto. Esto también incluye la reducción de los tiempos de cambio de trabajo.
«Para evitar las emisiones, es importante encontrar y eliminar los errores lo antes posible. Por eso es importante reducir la brecha entre la recolección de información del «cold-end» y el procesamiento de la información del «hot-end». Para aumentar la eficiencia, utilizamos el sistema de información PlantPilot, que registra la situación de la eficiencia y envía mensajes sobre las desviaciones a los puntos en los que se deben hacer correcciones».
Esto se traduce en una mejora de la disponibilidad de los equipos y un aumento en el rendimiento al reducir las pérdidas en transporte y calidad. Por lo tanto, el aumento de la eficiencia y la reducción del CO2 están muy relacionados.
Entonces, lo ideal sería que las mediciones se realizaran en el «hot-end».
«Sin embargo, esto no es fácil, ya que muchas de estas mediciones son de contacto. Y si toco una botella caliente con una herramienta de medición, la primera se deforma y se vuelve inservible.
«Todavía no tenemos una solución para que se pueda girar una botella caliente y, por ejemplo, medir el espesor de la pared. No es factible por el momento. Hoy en día, queremos medir directamente los parámetros del proceso de formación y mantenerlos constantes dentro de unos límites reducidos.
«Utilizamos cámaras infrarrojas en el "hot-end" para identificar rápidamente las desviaciones en el proceso y, sobre todo, para no sobrepasar los límites o quedar por debajo de ellos, y tomar medidas paliativas inmediatamente».
Esta tecnología se denomina Bucle cerrado del «hot-end». Lo ideal es que los sensores sin contacto controlen y regulen el proceso.
Bucles de control
También se utilizan diferentes sensores en distintos sitios para las diferentes secciones del proceso. Así, se los utiliza para influir en los parámetros de la gota, el párison o la botella.
Si se empieza con la formación de la gota, se utiliza una cámara de gotas para regular y controlar el peso y la forma de la gota. Además, se pueden medir las temperaturas de la gota para influir en la temperatura de la cubeta en el alimentador. En el lado de la pieza en bruto, se puede detectar y regular el suministro de la gota en el molde preliminar. También se pueden medir y controlar las temperaturas de las herramientas en el lado de la pieza en bruto (molde preliminar, anillo-collar y émbolo). Las cámaras infrarrojas sobre la cinta transportadora de la máquina se utilizan con frecuencia hoy en día para medir la distribución del grosor de la pared y detectar errores globales. Está previsto instalar cámaras ópticas en la cinta transportadora de la máquina para
medir y controlar la geometría del envase y para detectar los defectos del vidrio.
El proceso de fabricación finaliza cuando el envase de vidrio pasa por el túnel de recocido. El «cold-end» no se encarga de controlar el proceso.
No obstante, lo que sí hay que mencionar es la comprobación automática del ajuste correcto de las máquinas de inspección mediante el uso de envases de muestra.
Sin embargo, también se pueden controlar y medir los procesos posteriores, tales como la impresión o los tratamientos de la superficie para incrementar la fuerza.
Peso y forma
En los años 90, se desató una guerra de precios en los envases desechables. Para ahorrar en costes de materia prima, energía y transporte, y también para reducir las cargas del sistema dual para los productos a granel desechables, se pusieron en marcha proyectos para reducir el peso de los envases de vidrio, es decir, para fabricarlos con paredes más delgadas.
Heye cuenta con la ventaja de su experiencia en la tecnología H1-2 y pudo transferirla a la tecnología de las máquinas IS. Una reliquia de estos tiempos es la famosa botella de cerveza Paderborner.
Se demostró que la forma tiene una inmensa influencia en el peso del envase mientras mantiene su resistencia. Actualmente, se procura conciliar la forma individual de la botella, su volumen y peso con la suficiente resistencia.
«Si queremos ser más ecológicos, tendremos que sacrificar la forma individual de la botella en favor del peso del envase», afirma Kellner.
Muchos de los componentes de las máquinas y los productos HI, que ya fueron desarrollados en su momento para la tecnología del vidrio ligero, son ahora estándar en la industria. Desde el control de procesos hasta la refrigeración axial y el transporte «hot-end», todos constituyen componentes que pueden ser utilizados con conocimientos para la fabricación de envases ligeros.
Los retos del vidrio ligero

La característica del vidrio ligero simple es que se rompe rápidamente. Se puede solucionar este problema con un tratamiento térmico o químico posterior, pero esto aumentará el coste por unidad. Probablemente nadie haría un depósito de varios euros por una botella de leche hecha de «Gorilla Glass».
Para el futuro, debemos desarrollar una tecnología que se base en la fabricación actual de vidrio hueco y que sea eficiente.
«Quien consiga aumentar y mantener la resistencia de la superficie del vidrio en la fabricación de vidrio ligero estará a la cabeza en el futuro.
«Veo el gran ahorro de emisiones en la industria del vidrio a nivel mundial en el reciclaje del calcín del mercado (recolección y tratamiento de residuos de vidrio), porque para fabricar botellas de vidrio a partir del calcín se necesita mucha menos energía que para hacerlo a partir de materias primas.
«El ahorro de energía a través de la recuperación de calor en los procesos de formación y en el túnel de recocido tienen más potencial. El enfoque ecológico le sigue el enfoque económico: Si ahorras energía, también ahorras dinero. Esto es un fuerte incentivo. El mayor factor de coste en la fabricación del vidrio es la energía».
Mantenimiento a distancia
Para el acceso a distancia a través de Internet, es esencial tener en cuenta la seguridad. Los ciberdelincuentes están al acecho en todas partes, y como consecuencia, las empresas se aíslan cada vez más. Esto implica que los proveedores de servicios no pueden entrar en las redes de la empresa para conectarse a la máquina y prestar asistencia desde allí sin un esfuerzo considerable. Hay que encontrar soluciones en conjunto con los departamentos de informática de los clientes.
Inteligencia artificial
«La IA ocupa actualmente un lugar destacado en la agenda. Ahora me encuentro en la tercera ola: La primera fue en los años 80, la segunda en los 90, y la tercera está empezando ahora. Sin duda se pueden hacer muchas cosas con la inteligencia artificial.
«Pero hay que tener en cuenta los límites: La inteligencia artificial se determina a partir de la información aprendida en el pasado.
«Para aprender una red neuronal correspondiente se necesita un gran número de objetos que actúen de ejemplos buenos y malos: hablamos de entre 500 y 5000 datos de información. Conseguir y aprender estos ejemplos supone un gran esfuerzo. Y cuando aparecen nuevos objetos, la red neuronal no puede empezar con ellos».
Existen aplicaciones de IA, y la decisión ya funciona muy bien. En la industria del vidrio, en cambio, solo funciona para aplicaciones sencillas, tales como la lectura de los números de los moldes en el código de siete segmentos. Por otro lado, los defectos del vidrio se vuelven más difíciles porque siempre lucen diferente.
Si se añade nueva información que el sistema entrenado no conoce, la IA no llegará más lejos. Básicamente no hay dos comprobaciones exactamente iguales.
Quizá una combinación de procesos de imágenes y redes neuronales pueda ayudar, pero eso es todavía un sueño para el futuro». �
* Ingeniero de desarrollo, Heye International, Obernkirchen, Alemania www.heye-international.com
Máquina IS SpeedLine de Heye

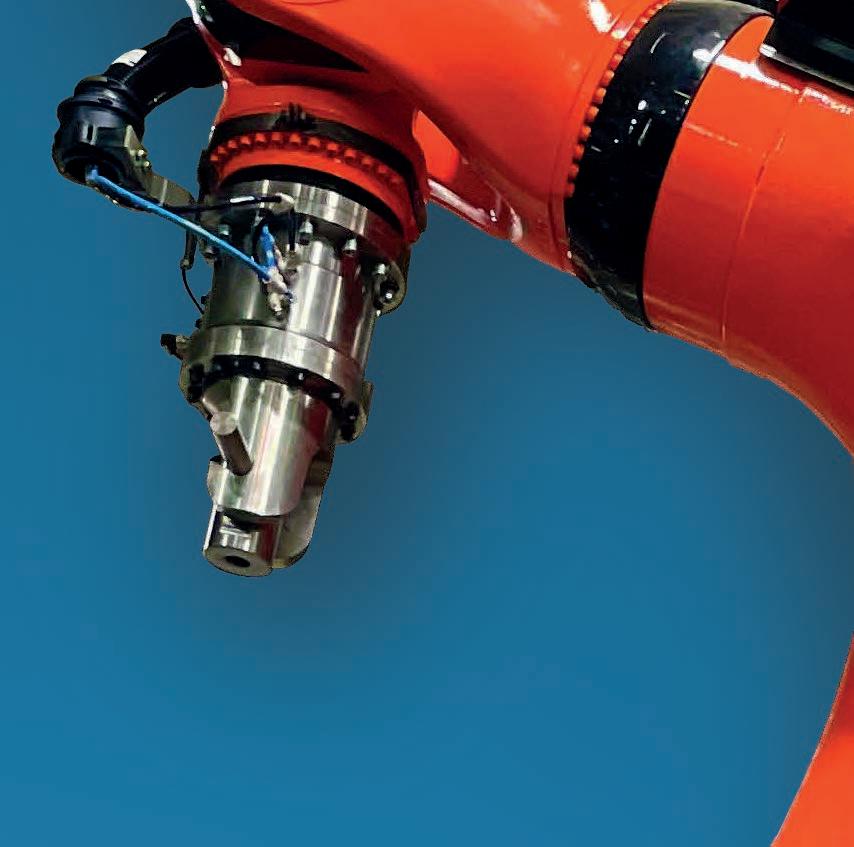
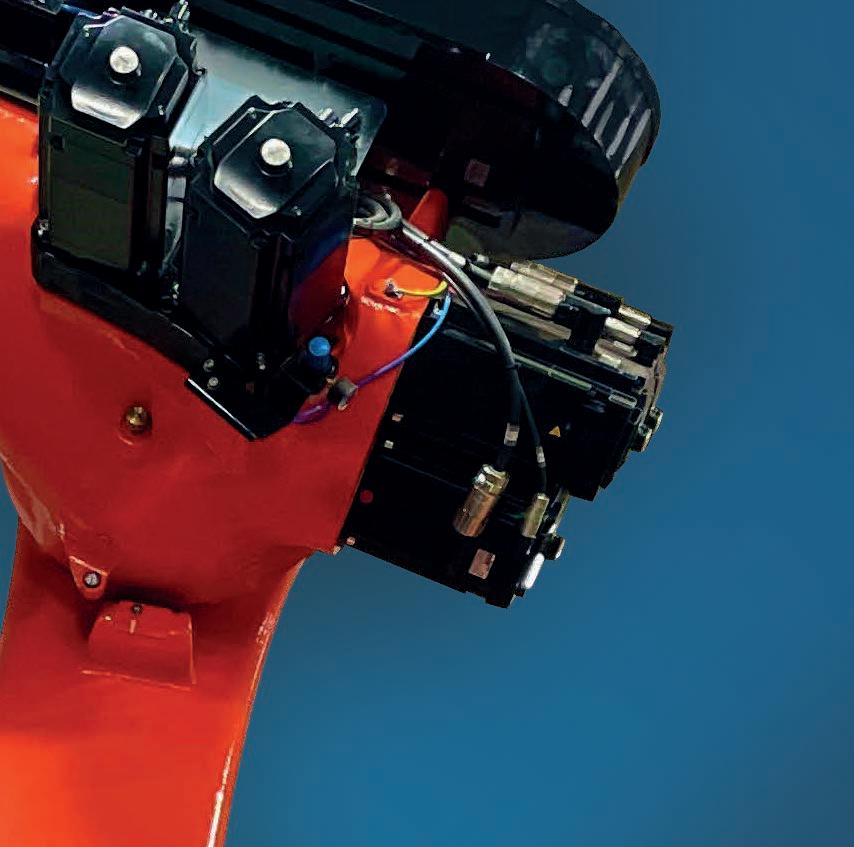


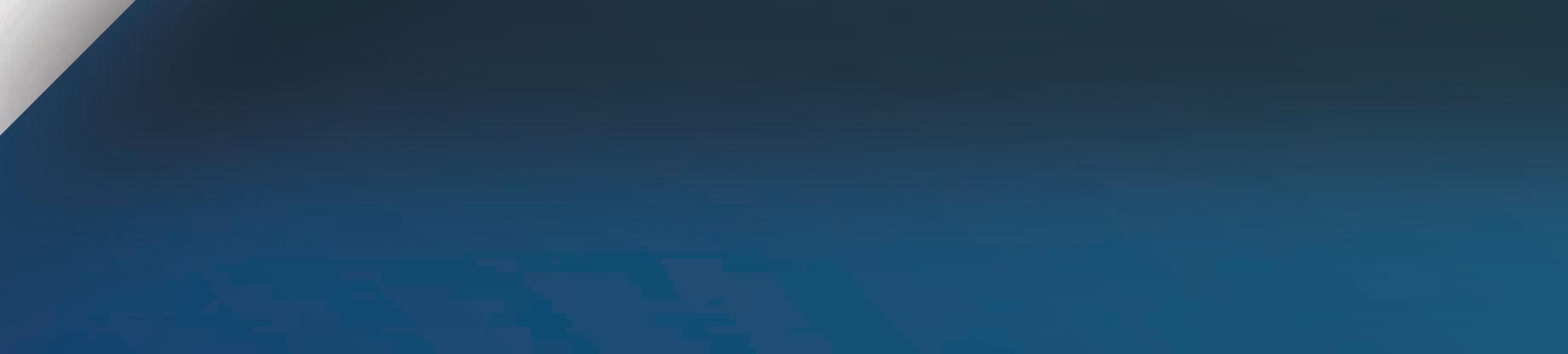
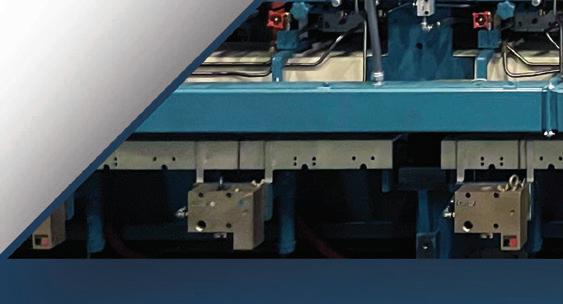