Walking robots improve worker safety.
Open-box models: revolutionizing production.
Enhancing efficiency through AI-based predictions.
Government considers import restrictions to fight dumping.
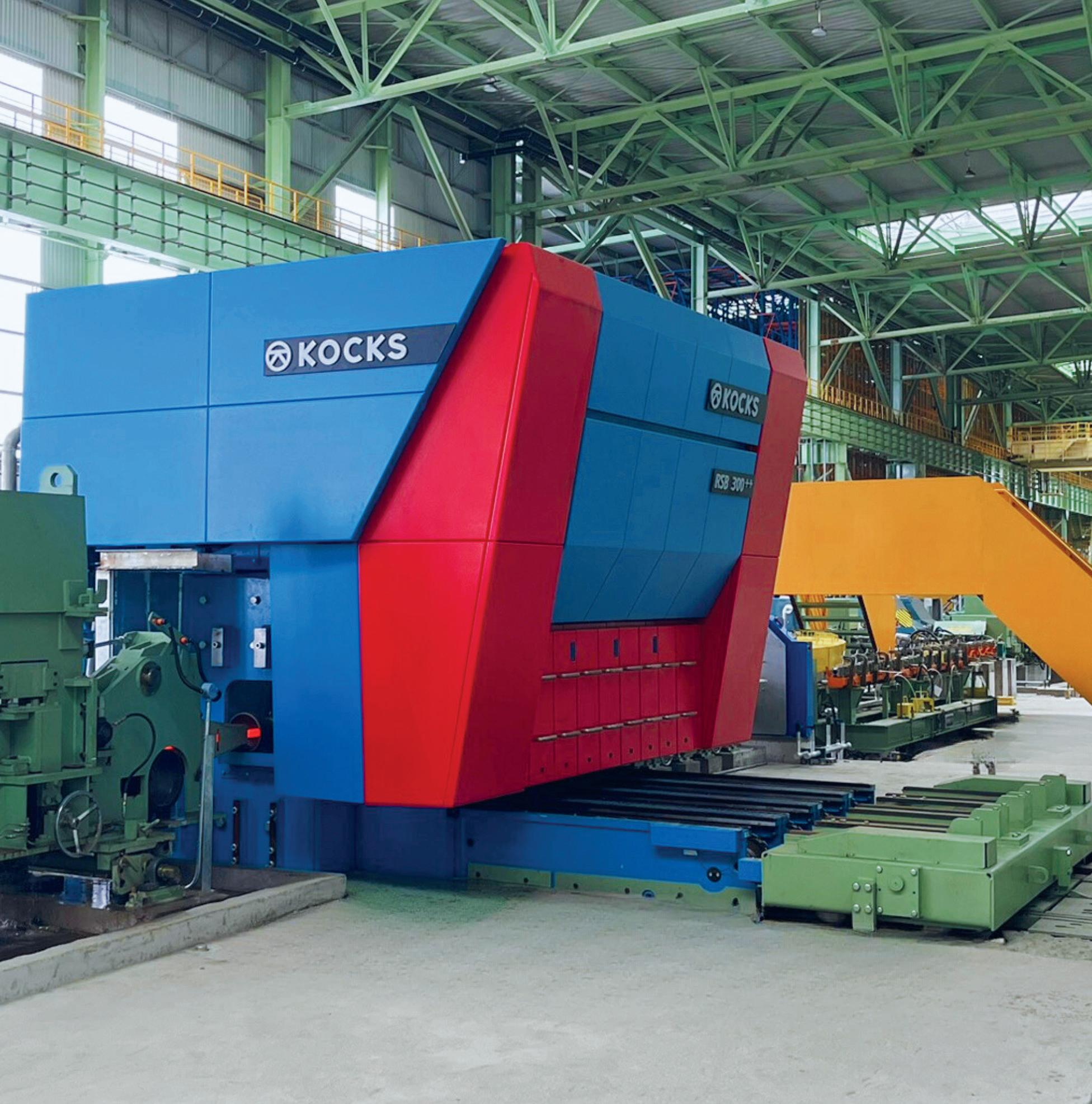
Walking robots improve worker safety.
Open-box models: revolutionizing production.
Enhancing efficiency through AI-based predictions.
Government considers import restrictions to fight dumping.
HiPROFILE
EDITORIAL
Editor Matthew Moggridge
Tel: +44 (0) 1737 855151
matthewmoggridge@quartzltd.com
Assistant Editor
Catherine Hill
Tel:+44 (0) 1737855021
Consultant Editor
Dr. Tim Smith PhD, CEng, MIM
Production Editor
Annie Baker
Advertisement Production Carol Baird
SALES
International Sales Manager
Paul Rossage
paulrossage@quartzltd.com
Tel: +44 (0) 1737 855116
Sales Director
Ken Clark
kenclark@quartzltd.com
Tel: +44 (0) 1737 855117
Managing Director
Tony Crinion
tonycrinion@quartzltd.com
Tel: +44 (0) 1737 855164
Chief Executive Officer
Steve Diprose
SUBSCRIPTION
Jack Homewood
subscriptions@quartzltd.com
Tel +44 (0) 1737 855028
Fax +44 (0) 1737 855034
Front cover photo courtesy of Kocks.
KOCKS RSB® 300/4 in further advanced design at a Chinese SBQ rolling mill.
KOCKS | T. Säuberlich
Open-box models: enabling guided automation.
Catherine Hill Assistant editor catherinehill@quartzltd.com
A few months ago in the UK, disaster struck; major IT outages across several prominent supermarket chains meant shoppers were unable to apply their e-coupons, use contactless payment, and scan their shopping as they went. A man stood in front of me, on this darkest of dark days, and muttered laconically under his breath: ‘This is how the world will end’.
Surveying the room, it didn’t seem too close to the irremediable apocalypse he appeared to be referring to, a couple was arguing over the size of a loaf of bread, a toddler screamed as his parents wrestled a lego set out of his sticky grip. All seemed as normal, but perhaps on a wider scale, the man’s aphorism held some truth.
Patterns only emerged later, as banks faced hacking incidents, and flights were grounded, even the billboards in Times Square went blank. Our reliance on technology makes us deeply vulnerable to its failure; as industries increasingly drive toward digitalized processes, the complex balances between worker and machine become critical to assess.
Companies like stainless steelmaker Outokumpu, which claims to be first
in the steel industry to use robotics for safety management (p24), and software specialist Tvarit, with its hybrid AI-based prediction advancements (p30), epitomize the potential for technology, as a tool that works alongside, rather than replaces.
As artificial intelligence evolves apace, territories for its exploitation pervade more widely, and with the huge deposits of private information; email addresses, passwords, phone numbers increasing day-by-day, boundaries between what is shared and what is hidden become urgent, if not crucial to uphold.
Data is now charged with political tension, as we fight over who can hold what information, and for what length of time. As these questions drift over us with rising potency, all aspects of our relationship with the digital must be addressed.
It is only through the interrogation of each transformation, as we enter this automated era, that the threshold of its risk can be understood. There’s a lot of talk about ‘harnessing’ data, and the digital; but this can only apply if it’s us holding the reins.
The Thermo Scientific™ ARL iSpark™ Plus Series OES Metal Analyzer uses single-spark acquisition to provide rapid elemental analysis—up to 15% faster than previous models. The increased speed and reliability minimize tap to tap times, save energy, reduce carbon footprints, and realize a faster return on investment.
Capable of providing ultra-fast, on-line analysis of nonmetallic inclusions, the ARL iSpark Plus adds to the versatility, dependability, and productivity of metal processing operations.
Emirates Steel Arkan, based in Abu Dhabi, is considering the installation of an electrical Process Gas Heater (e-PGH) at its DRI plant, which would use renewable energy. A memorandum of understanding was recently signed by Saeed Alghafri, CEO of Emirates Steel Arkan, and Rolando Paolone, CEO and CTO of Danieli, with a view to collaborating on low-carbon steelmaking projects.
Source: Yieh Corp Steel News, 1 July 2024.
Spain-based Celsa Group, which has a recycled-content EAF steel mill in Wales, has started operating a new shredding plant. A social media post from the company stated, “This cutting-edge shredder with advanced magnetic separation technology is now operational. Capable of processing up to 300kt annually, it significantly boosts our recycling capabilities and operational efficiency.” The plant is being equipped with a 3-megaWatt motor that allows for an input capacity of 130 metric tons per hour.
Source: Recycling Today, 8 July 2024.
ArcelorMittal's South African division has decided against shutting its rolled bars steel plant and is now working on a plan to make the business viable, more than six months after it announced plans to close the plant. “The board and management have decided the longs business will continue to operate to allow an opportunity for the short, medium and longerterm initiatives aimed at securing its sustainability to be fully explored,” ArcelorMittal South Africa said. Source: The Times Live, 2 July 2024.
Mining firm Anglo American has suspended production at its Grosvenor mine in the Bowen basin region of Australia's Queensland due to an underground methane gas ignition. The company was instructed by independent regulator Resources Safety and Health Queensland on 29 June to suspend all operations and activities underground. According to media reports, the closure is expected to last for several months, depending on ongoing evaluations.
Source: Argus Media, 5 July 2024.
ArcelorMittal Gent is hosting the first industrial trial of climate tech company D-CRBN’s new technology, using a carbon capture unit
manufactured by Mitsubishi Heavy Industries. It provides high-purity carbon dioxide (CO2) for the D-CRBN unit, which converts the CO2
Trade body UK Steel is calling on the new government to take action to rectify the disparity of energy pricing, with UK wholesale prices averaging £66 per MegaWatt hour (MWh) over the past three months. This compares with France’s £27/MWh and Spain’s £28/MWh. “The steel industry is the foundation of the UK’s manufacturing and economic strengths,” said Frank Aaskov, UK Steel's energy and climate change policy manager. According to UK Steel, the comparatively high price of electricity will hamper the industry’s green transition, as more steelmakers move to EAFs for production.
Source: The Engineer, 8 July 2024.
captured at ArcelorMittal’s plant into carbon monoxide for use in steel and chemical production. This is the first industrial testing of D-CRBN’s plasma technology, making ArcelorMittal Gent the first steel plant to trial the process. Source: EUReporter, 8 July 2024.
Steel made with green hydrogen and electric arc furnaces, or produced from scrap, can reduce the CO2 emissions of producing cars in Europe by 6.9Mt in 2030, a report by Transport & Environment (T&E), based on a new study by consultancy Ricardo, has shown. Switching to 40% green steel would add just €57 to the sticker price of an electric vehicle in 2030, according to the analysis. Switching to 100% green steel by 2040 will cost only €8 – compared to using conventional steel – due to CO2 pricing as well as the falling costs of green steel production. Source: Transport & Environment, 10 July 2024.
Roland Junck, former managing director of ArcelorMittal and Liberty Steel’s Europe CEO, will become president of Ascometal when it is taken over by British buyout firm Greybull Capital. The company has a factory and a research centre in Hagondange, and three other French machining and finishing sites. French officials offered Greybull a €45 million loan this year and further public support of €40 million to take over the operations, the Economy Ministry said.
Source: Luxembourg Times, 9 July 2024
Tata Steel UK has partnered with WWT Llanelli, a wetland centre based in Wales, with the refurbishment of the popular ‘Heron’s Wing’ footbridge. The steelmaker is contributing funding to the restoration of the footbridge, having maintained a longstanding relationship with the wetlands charity
Jindal Steel and Power (JSP) will set up the world’s largest steel plant in Angul by 2030, chairman Naveen Jindal has said. “JSP is working on the expansion of its Angul steelmaking facility and will achieve 12Mt/yr capacity from the current capacity of 6Mt/yr by next year. We will build the world’s largest steel plant in Angul in the next six years,” Jindal told reporters, after a meeting with Mohan Charan Majhi, chief minister of Odisha. During the meeting, Jindal discussed Odisha’s leading role in the Indian steel industry due to its ‘rich mineral resources and strategic geographical location.’ He also emphasised the importance of green energy and sustainable practices in the steel sector.
Source: The New Indian Express, 10 July 2024.
since the Llanelli Wetlands was opened in 1991 by Sir David Attenborough. Since its construction in 1998, exposure to the elements and general wear and tear took its toll on the structure, necessitating its refurbishment.
Source: Herald Wales, 11 July 2024.
Swedish bearing manufacturer SKF, and voestalpine Wire Technology, a subsidiary of steel and technology group voestalpine, have successfully produced the first prototype bearing made from steel that contains hydrogen direct reduced iron (H-DRI). This, says the companies, represents a breakthrough in the efforts to decarbonize bearing production as H-DRI is a low-emission alternative to conventional iron ore-based steelmaking.
Source: MSN, 10 July 2024
China didn’t seek permits for any coal-based steelmaking projects in the first half of the year for the first time since announcing its major climate neutrality goals in 2020, according to a report released on 25 July. All 7.1Mt/ yr of steelmaking capacity approved by provincial governments in the first half of the year used electric arc furnaces, a cleaner process that runs on recycled scrap and electricity, said the Centre for Research on Energy and Clean Air (CREA) in its report.
A deal between steel producer ArcelorMittal and Mexico’s miners’ union was rejected by workers, Mexico’s labour ministry said a statement, adding that the deal had been ‘favourable.’ The deal would have put an end to a work stoppage at ArcelorMittal’s western Mexico site that started at the end of May. Industry analysts have stated that the shutdown is likely to have a significant impact on the North American division, as the plant represents almost half of the division’s capacity. Source: Kitco, 11 July 2024.
The US has announced new rules targeting firms from China and other countries that are routing shipments of steel and aluminium through Mexico in order to evade tariffs. The White House said firms shipping via Mexico must now prove the origins of their products if they want to avoid border taxes. The measures expand protections for US steel and aluminiummakers that were launched under former president Donald Trump in 2018 in the name of national security.
Source: BBC, 10 July 2024
The move to stop permitting coal-based projects could be a turning point in China’s steel decarbonization progress, CREA stated.
Source: yahoo!finance, 11 July 2024.
Liberty Steel’s Whyalla Steelworks is back to normal operations, with the rolling mill having returned to production in late July.
Managing director Tony Swiercizuk said the final piece of the process had run smoothly with the very first trial bar processed, measured within tolerance, and cleared as product. “This is a fantastic final milestone in what has been a long and often frustrating recovery journey since the planned maintenance shutdown of the blast furnace which began in March,” Swiercizuk said.
Source: GFG Alliance, 12 July 2024.
A decision to grant planning permission for a new coal mine in the UK ‘smacked of hypocrisy’, the High Court has been told. Friends of the Earth (FoE) and South Lakes Action on Climate Change (SLACC)
British Steel’s Teesside beam mill has successfully completed its £1.4 million summer maintenance and improvement programme. More than 300 colleagues took part, with David Hogg, plant manager, commenting: “The team have performed superbly and I’d like to thank them for their significant efforts over the last two weeks. “Rolling has resumed and we’re now focused on delivering the high-quality constructional steel our customers require.”
Source: British Steel, 12 July 2024.
are bringing legal action over a government decision in 2022 to grant planning permission for the site near Whitehaven in Cumbria. The government had been due to defend the claim, but on 11 July 2024, FoE said it had withdrawn its defence. The mine would produce metallurgical coal, also called coking coal, for use by the steel industry.
Source: BBC, 16 July 2024.
Westfalen Group has signed a deal to supply an electrolyser to ArcelorMittal’s steelwork site in Florange, France, in support of hydrogen-based steelmaking. In a recent announcement, the energy company said it hopes to have the electrolyser in operation
by 2026. The electrolyser will be built directly on the site of the steel processing facility. The supply contract between Westfalen and ArcelorMittal is expected to run until the 2040s.
Source: GasWorld, 15 July 2024.
Cleveland-Cliffs has announced that it will acquire Canadian steelmaker Stelco. The acquisition increases Cliffs’ steelmaking footprint and doubles its exposure to the flat-rolled spot market, with cost advantages in raw materials, energy, health care, and currency. Stelco has two operational sites, both in the province of Ontario, including Lake Erie Works, the newest and lowest-cost integrated steelmaking facility in North America. Stelco ships approximately 2.6Mt of flat-rolled steel annually. Upon closing the transaction, Stelco is expected to continue operations as a whollyowned subsidiary, preserving the name and legacy of the business.
Source: Upper Michigan Source, 15 July 2024.
ArcelorMittal Poland (AMP) has decided to close the remaining coke oven at its Krakow plant after the hoped-for rebound in steel demand did not materialise. The firm idled the coke oven last November due mainly to weak demand, but also the ‘narrowed differential between coke and coking coal prices’. The hot idling allowed for the oven to be restarted once market conditions improve, but ‘unfortunately, that didn’t happen’, said AMP chief executive Wojciech Koszuta. Source: Kallanish, 19 July 2024.
Rabat - Riva Industries, a Moroccan steel manufacturer, has opened an integrated industrial complex in Jorf Lasfar, backed by a substantial investment of approximately $290 million. The complex will include facilities that aim to produce a diverse range of metallurgical products to meet the demands of both domestic and international markets, such as reinforcing steel bars, wire rods, large-diameter coils, steel ingots, and special steels. The investment is expected to create 3,000 jobs. Source: Morocco World News, 20 July 2024.
Steelmaker Ternium expects to complete a new slab steel mill that it is building in Nuevo León state, Mexico, by mid-2026. “The new 2.6Mt steel slab mill in Pesquería continues to advance, with completion expected by
South Korean steelmaker
Hyundai Steel is expanding its low-carbon plate sales base in international markets such as Europe and the Americas in response to global demand for carbon neutrality and the European Cross-Border Carbon Adjustment Mechanism (CBAM). The company recently signed memorandums of understanding with Czech auto parts manufacturer Tawesco and Italian automotive sheet processing company Eusider to supply reduced carbon steel plates. These companies supply materials to major European automakers such as Volkswagen and Stellantis.
Source: GMK Center, 21 July 2024.
mid-2026. This project will enhance our capabilities in the USMCA region and position us as a leader in low-emission steelmaking. This is the largest expansion project in our history, and we are thrilled about its progress,” Ternium CEO Maximo Vedoya said during the firm's Q2 earnings call.
Source: BN Americas, 1 August 2024.
China's biggest listed steelmaker, Baoshan Iron and Steel Co (Baosteel) has said that it will more than double its investment in a steel plate joint venture in Saudi Arabia to $1 billion from around $437.5 million previously.
Baosteel, a subsidiary of the world's largest steelmaker China Baowu Steel Group, signed agreements in May with Saudi Aramco and the Saudi Public Investment Fund (PIF) to build a steel plate manufacturing joint venture. Baosteel holds 50% in the joint venture, while Saudi Aramco and PIF will each take a 25% stake.
Source: Reuters, 25 July 2024.
ArcelorMittal SA says that exports from China have left the steel market in an unsustainable position, as the steelmaker reported a fall
North American steelmaker Nucor is looking to bring a number of major capital projects across the finish line over the next two years. “The next two years will likely be our most capitalintensive with several active construction projects occurring simultaneously,” Nucor chief executive Leon Topalian said during the company’s secondquarter earnings call in late July. Topalian said Nucor expects to begin ramping up its Lexington, N.C., rebar micromill in the first quarter of 2025. Following that will be the start of two highly automated utility tower manufacturing plants serving the electrical transmission and telecommunications markets.
Source: yahoo!finance, 29 July 2024.
in Q2 profit. “Current market conditions are unsustainable,” ArcelorMittal said. “China’s excess production relative to demand is resulting in very low domestic steel spreads and aggressive exports; steel prices in Europe and the US are below the marginal cost,” the company added.
Source: AJOT, 1 August 2024.
India has begun forming a consortium to develop green steel technology. The initiative involves labs, steelmakers, and equipment manufacturers. In addition, the government is developing a decarbonization roadmap to reduce the steel sector’s carbon footprint, which accounts for 12% of India’s total emissions. The plan includes increased use of hydrogen and carbon capture technologies in steel production. India aims to reduce the carbon intensity in steel production by about 20% from the current 2.5 tonnes of carbon per tonne of steel.
Source: Manufacturing Today, 2 August 2024.
and QSP–DUE are the winning Danieli direct-rolling technologies for the most competitive production of long and flat green-steel products.
They are the result of the research and continuous improvement profused over 20 years, along with multi-million dollars of investment.
Their unmatched performances have fueled their success worldwide, thanks to lower resource consumption and carbon emissions, unbeaten OpEx, and outstanding product quality.
So, top technology becomes copied technology, the shortest route for competitors that, abandoning their solutions, now try to imitate MIDA–QLP and QSP–DUE
Equipment and layout may be copied, but experts know that details make the difference. Automation and process solutions are not easy to copy, and this will be the experience of anyone trusting in those imitations.
The competitive advantage for our customers, obtained by field results, is the best defense for our technology – more than court rulings protecting our patents.
Danieli offers the best guarantees for speedy learning curves, steady performances, and now Digital Plants with no men on the floor. Buy the Original.
GIANPIETRO BENEDETTI CHAIRMAN OF THE BOARD OF DIRECTORS
KOCKS’ Reducing & Sizing Blocks (RSB®) have been awarded the internationally renowned iF Design Award, which the company states ‘demonstrates its commitment to innovation in the steel production sector’.
KOCKS Reducing & Sizing Blocks are an integral part of special steel production, says the company, enabling precise rolling processes.
The jury awarded KOCKS’ RSB® product family an award in the category ‘Industry Product’. This recognition honours the ‘outstanding achievement’ of the team of engineers and designers.
“The iF Design Award is also a valuable recognition of our pursuit of excellence in rolling mill technology,” said Günther Schnell, managing director, sales and marketing at KOCKS. The award-winning design extends across the entire RSB® sizing family. The rolling blocks now form a consistent visual unit that clearly stands out in the mill line,” he explained.
Three RSB®’s in the award-winning design have already been put into operation by Chinese steel producers. Additional blocks in various configurations are already under construction or in the planning stages and will be put into operation in rolling mills worldwide in the near future.
For further information, log on to www.kocks.de
GLAMA Maschinenbau GmbH
Headquarters:
Hornstraße 19 D-45964 Gladbeck / Germany
Fon: +49 (0) 2043 9738 0
Fax: +49 (0) 2043 9738 50
Italian steel producer Acciaieria Arvedi has recently tasked Primetals Technologies with an upgrade of its two vacuum degassers (VD) at its steel plant in Cremona, Italy. The project is scheduled to be completed in the second half of 2025.
Arvedi has plans to expand its product portfolio to encompass both electrical and ULC/IF steel grades. Traditionally, these types of steel grades are manufactured through the LD converter (BOF) – ladle furnace (LF) – RH-degasser route. Arvedi plans to pioneer the production of electrical steels with the electric arc furnace (EAF) – LF –VD-OB route.
Arvedi will upgrade its VD plants to vacuum
oxygen decarburization (VOD) systems capable of handling the vacuum degassing and oxygen blowing process under vacuum conditions for the manufacture of silicon steel. Primetals Technologies will supply key mechanical components, including water-cooled copper-plated ladle covers, oxygen lance systems, gas coolers, vacuum control systems, and waste-gas burners. Experts from Primetals Technologies will also support Arvedi in the development and fine-tuning of the vacuum degassing process steps.
The VOD plants, which are tank degassing units equipped with oxygen blowing lances, are designed for handling extra-low-carbon steel
grades together with the addition of aluminium and/or silicon during the process. Arvedi’s new equipment will feature copper-cladded, water-cooled ladle covers from Primetals Technologies, designed to avoid skull formation. These kind of ladle covers will also reduce the need for maintenance-related work and, in addition, enhance occupational safety at the plant, says Primetals.
For further information, log on to www.primetals.com
Zolo Carbon Smartech, Inc. (ZoloCS) has purchased ZoloSCAN and ZoloSCAN2, which are technologies that support the monitoring and minimizing of high-temperature emissions in industrial applications. This purchase includes aftermarket parts and service, for all existing ZoloSCAN customers, which the company claims underscores its commitment to environmental sustainability.
“We aim to support the existing ZoloSCAN systems installed worldwide, instilling confidence in our customers that this technology is not only enduring but evolving to maintain its position as a market leader,” Fernando Martínez, chairman of the board at ZoloCS, stated.
ZoloSCAN Technologies delivers laser-based combustion monitoring and diagnostic capabilities for harsh environments to optimize the yield,
efficiency, and safety of combustion applications. ZoloSCAN monitoring and sustainability solutions provide real-time, in-furnace measurements of temperature, O2, H2O, and CO, enabling the maintenance of target combustion profiles.
Martínez added; “Zolo Carbon Smartech was founded to harness the proven ZoloSCAN technology, installed in harsh environments globally.
“Our commitment is to lead innovative solutions
Pomini Tenova and Sinosteel E&T (Sinosteel Engineering & Technology Co., Ltd.,) have formalized their collaboration with a signing ceremony for an order of new roll grinders, marking a milestone in their ongoing partnership. Paolo Gaboardi, executive vice president of Pomini Tenova, and Lu Pengcheng, chairman of Sinosteel E&T, convened in Beijing for the ceremony, where they discussed cold rolling projects, green low-carbon development, and the industry’s digital transformation.
“Tenova is a valuable partner of Sinosteel E&T, and Mr. Gaboardi is an old friend of mine.
28 years ago, we collaborated to bring Pomini’s advanced equipment to China, contributing to the rapid development of China’s steel industry. Our friendship with Tenova continues to grow, “ said Pengcheng.
Gaboardi highlighted Tenova’s role in supplying advanced equipment for Sinosteel E&T’s pivotal overseas cold rolling project.
“Being chosen to provide advanced equipment for Sinosteel E&T’s Cold Rolling project for Tosyali Algeria signifies trust in Tenova’s technology and services and deepens our partnership,” he added.
For further information, log on to www.tenova.com
with AI-driven innovation that strengthens ESG initiatives. Our vision is to develop and introduce advanced hardware and software sensors, driven by AI. These advancements will enable seamless monitoring and regulation of combustion processes, optimi zing performance, productivity, and reducing costs and emissions.”
For further information, log on to www.zolotech.io
THE steel industry, which continues to take centrestage in the nation’s economy, will play a crucial role in the manufacturing of essential materials for automobiles, appliances and infrastructure. The sector has demonstrated resilience and sustenance power despite the influences of what pundits describe as the ‘many economic ups and downs’, the technological changes brought about by innovations, challenges facing the industry and trade in the form of China and environmental pressures. Nevertheless, demand for steel and steel-based products is expected to rise in 2024, as some industry soothsayers have suggested.
Although tariffs were imposed by the Trump administration to check imports of cheap and heavily subsidized steel, produced with a high level of pollution, tariffs should not be construed as a solution for all the economic ills and an end in itself. While tariffs were imposed to check imports, their effectiveness in this respect should be seen in its economic entirety. Imposed under Section 301, tariffs have also affected US steel-consuming industries that have been plagued by rising prices; indeed, the tariff leverage over China to reduce trade deficits has not made much difference to America’s import profile.
“Large companies still rely on China for supplies, with many passing on the higher costs resulting from tariffs to their customers … in the end the consumers have to pay higher prices. The US-China trade war has trapped both sides and it will not be easy to extricate from it,” predicts John Warwick, a New York-based analyst.
But the US also needs to address the problem of structural imbalances and sharpen export competitiveness, as well as maintaining a competitive exchange rate and review, besides negotiating trade agreements and taxing capital inflows.
While infrastructure expansion is expected to boost steel demand in 2024, analysts see a marginal weakening in the steel market, caused by a slowdown in the construction sector, or by an oversupply of steel. This is said to have prompted Nucor, the largest North American steel producer, to once again adjust its Consumer Spot Price (CSP) for hot-rolled coil, a key steel product. Effective 1 July, Nucor announced a CSP base price of $670/ton for most of its producing mills, marking a further decrease of $10/ton, compared to the previous week’s price of $680/ton. This downward slide in Nucor’s CSP started in early June, recording a decline of $100/ton during the last five weeks.
However, the construction sector is just one steel-consuming industry that can influence steel prices; other major steelconsuming industries are automotive manufacturing, and appliance production. Steel prices can also be influenced by other factors such as trade policies, the global economy, and geopolitical developments/
While Nucor has so far been publicizing its weekly price developments, other steel producers have maintained a lowkey posture on pricing, possibly resorting to reviewing and adjusting their pricing internally without public announcements.
With the 2024 elections around the corner, American steel producers know they can vent their frustration with China’s surreptitious steel shipments by using third countries – Mexico and Vietnam, for example – to evade US tariffs; the steel producers know that American politicians, keen to mollify their constituencies and also the workers, will be open to looking into their grievances.
A number of industry organizations representing steel have urged the Biden administration to do more to counter China’s continued defiance of US trade laws by resorting to third-country shipments to the US. Last May, the Biden administration had announced plans to impose new
With the country facing elections in November, domestic politics will keep many industries, including the steel industry, busy vying for the attention of politicians. By Manik Mehta*
tariffs on imports from China, including those produced by strategically important industries like steel, aluminium, EVs, solar panels and other items.
American customs officials and other experts have said that Mexico, in particular, was being used by China to circumvent US trade action; Mexico is the top exporter to the US, but a large part of the goods are either made by Chinese companies operating inside Mexico or are simply shipped in from China using Mexico as the route to the US market. As a member of the USMCA trade pact, Mexico enjoys access to the US market. Although the US auto industry has raised the alarm several times, the steel and aluminium industries have also complained that China’s unfair trade practices were hurting their business interests; they have called on the US Trade Representative (USTR) to act against Mexico and other countries that facilitate such unfair trade practices.
Kevin Dempsey, president of the American Iron and Steel Institute (AISI) has told this correspondent on a number of occasions that he supports the increase of tariffs on Chinese steel announced by the Biden administration in May. The AISI chief has, in fact, called for imposing tariffs on all steel products made of the original raw steel melted and poured in China, regardless of the subsequent countries where the final processing was done.
Mexico – gateway to the USA! As can be expected, the clandestine dumping of Chinese steel, using Mexico as a gateway to the US market, is gradually
raising temperatures in US-Mexico relations. Indeed, there have increasingly been calls from steel executives to make Mexico stop China’s flow of cheap and polluted steel into the US, or force Mexico to exit from the USMCA free trade pact. Senator Sherrod Brown, a Democrat from Ohio, urged the Biden administration to pressurize Mexico to stop the ‘unsustainable surge of Mexican steel imports into the US, contravening the 2019 Joint Agreement on Steel and Aluminium’.
He pointed out that the matter continued to harm the interests of US steel workers. Referring to the recent election of a new president in Mexico, Brown asked the Biden administration to address this issue with president-elect Claudia Sheinbaum’s cabinet. Brown had played a key role in imposing a 25% tariff on US imports of steel from Mexico.
Mexico’s iron and steel agency Canacero countered the allegation with its own statement, saying that the ‘reality is … that the Mexican steel surge is simply not happening’, and the US steel industry has steadily maintained a significant trade surplus in finished products with Mexico in excess of $3 billion in 2023 alone. Leading US steel experts believe that the issue of China will take centrestage with the new administrations in Mexico and the US.
US imports of finished steel products in May 2024, at 2.23Mt, recorded a 6.6% increase over April, the AISI reported.
The total May imports amounted to 2.85Mt of steel in May 2024 (including 2.23Mt of finished steel – up 1.7% and 6.6% respectively over April 2024). �
•
•
•
•
•
Brazil’s steel imports have surged in the last few years, which has been predominantly driven by China boosting its export volume. By Germano Mendes de Paula*
BRAZIL’S steel imports jumped from 3.4Mt in 2022 to 5.0Mt in 2023. This significant increase was largely driven by China, which boosted its export volume to Brazil from 1.8Mt to 2.9Mt over the same period. Consequently, China’s share of Brazilian steel imports rose from 53% to 58%.
Given the exponential growth in steel imports, and considering that many countries (including the USA, the European Union, and Mexico) have implemented import tariffs besides the ongoing trade
defence measures, Brazilian steel companies have requested similar actions. Indeed, the country’s steel and tube manufacturers have demanded a rise in import tariffs to 25% for 31 items out of 273 steel products within the Mercosur Tariff Schedule.
Although the tariff increase was not intended to target Chinese steel products specifically, China will be affected due to the significant share it holds in Brazilian steel imports.
In April 2024, the Brazilian government
decided to introduce a tariff quota measure, allowing a limited quantity of specific products to be imported at standard tariff rates. Initially, 11 steel products were included in this temporary tariff quota regime: eight flat steel products (heavy plate in coils, HRC, CRC, HDG, and aluminium zinc sheets), one long steel product (wire rod), and two types of tubes (welded line pipes, seamless casing, and other pipes for the oil and gas industry). Of these product categories, nine refer to items
* Professor in Economics, Federal University of Uberlândia, Brazil. E-mail: germano@ufu.br
produced by companies associated with the Brazil Steel Institute, which accounted for 43.1% of the country’s imports of steel products in 2023. The Ministry of Development, Industry, Commerce, and Services (MDIC) will monitor market conditions to evaluate whether the measure is efficient to keep the market balanced.
Under this new tax scheme, a quota equivalent to 130% of the average import volume from 2020-2022 is set for the mentioned 11 steel products. The system started in June 2024 and will last one year, divided into three four-month periods: 1 June to 30 September; 1 October to 31 January; and 1 February to 31 May. Any quota balance remaining at the end of a four-month period cannot be carried over to the next period.
Quotas are distributed as follows: a) 80% for companies that imported 3% or more of the total volume of the respective product in the last year (priority group), with specific allocations based on past import volumes; b) 20% for smaller importers, assigned on a first-come, first-served basis for import licenses. For HDG and aluminium zinc sheets, allocations are different: 60% to the priority group and 40% based on import license requests.
The 25% import tariff rate for those 11 items became effective immediately as of
1 June. However, for the companies that apply for the quota and obtain the import license, the standard rate can be applied (ranging from 9% to 12.6%).
Before the implementation of the measure,
Brazil’s steel imports for the first five months of 2024 jumped to 2.3Mt, showing a 26% increase compared with the same period of the previous year. Meanwhile, the imports from China grew 35% to 1.6Mt as well.
With the introduction of such mechanisms, as shown in Table 1, quotas for some steel products are rapidly being filled. Since the import modality via import licenses is released by order of requisition, there is an initial rush in issuing orders. For instance, the quota for smaller importers was fully utilised for HDG and CRC and reached 98% for aluminium zinc sheets as of 1 July 2024. For the larger importers, the utilisation rates were 75%, 23% and 70%, respectively. This means that a 25% import tariff would likely apply to additional volumes in the coming weeks.
Considering the combined quotas in the first month of application, the utilisation rates were as follows: HDG (85%), aluminium zinc sheets (81%), wire rod (44%), HRC (42%), CRC (38%), heavy plate in coils (17%), and tubes (4%). This variation indicates that the impacts of the tariff quota regime on supply-demand dynamics differ significantly among the 11 steel products. �
The tools you need for high productivity and reliability in today’s demanding market.
When it comes to building equipment to process ferrous or non-ferrous metals, nobody does it better than Butech Bliss. Butech Bliss is an industry leading equipment builder offering a comprehensive suite of shape correcting technologies and coil processing equipment. From Cut-To-Length Lines, Slitting Lines, Multi-Blanking Lines, Pickling Lines and Continuous Process Lines – or stand alone equipment – our customers know they are getting the absolute best in coil processing advancements with the highest productivity available in the industry
+1 (330) 337-0000 ButechBliss.com sales@butech.com
India turned into a net steel importer in the financial year FY2023-24 (April-March), with the country’s finished steel imports rising to 8.32Mt, surpassing exports of 7.49Mt registered in the recently ended fiscal year. These figures show India’s imports surpassing the volume of exports for the first time in FY2023-24, with imports rising to the highest level in six years. Surprisingly, the country’s finished steel exports almost halved to 7.49Mt in FY2023-24 from the record volume of 13.49Mt reported in FY2021-22.
The Joint Plant Committee (JPC), under the Ministry of Steel, reported a similar trend continuing during April-May 2024, with imports rising to 1.14Mt, a 20% increase from 0.95Mt in the corresponding period of the previous year. In May 2024 alone, India’s finished steel imports surged by over 12% to 0.55Mt from 0.49Mt reported in the same month last year. Notably, China overtook Korea to become the largest exporter of finished steel to India in FY2023-24. Data collated by the Joint Plant Committee (JPC), under the Ministry of Steel, registered China’s share at 32.4% (2.7Mt) of India’s overall finished steel imports of 8.32Mt in FY2023-24,
Source: Joint Plant Committee, Indian government
Source: Joint Plant Committee, Indian government; FY = Financial Year (April-March)
pushing Korea’s share to 32% (2.6Mt). In FY2022-23, China and Korea accounted for 23.4%, and 37% of India’s finished steel imports of 6.02Mt, respectively. Japan continued to the third place in India’s finished steel import market share at 14% and 15.3% in FY2022-23 and FY2023-24, respectively. Vietnam’s share in India’s
finished steel imports jumped to 9% in FY2023-24 from 5.3% in the previous year. The remaining market share was distributed among Taiwan, Nepal, and Indonesia, among others.
“India has become a net steel importer since FY2016-17, recording an overall steel trade deficit of 0.83Mt in FY2023-24. This
In order to combat the dumping of cheap finished steel from Asian steel producers, India’s steel sector has demanded the government considers import restrictions to protect the country’s production.
By Dilip Kumar Jha*
development highlights a dynamic change in India’s steel trade landscape, primarily triggered by surging domestic demand and increased imports from major steel-producing nations. Additionally, China’s aggressive export strategy has been a key factor negatively impacting India’s steel exports. Known for its overcapacity, China has increasingly targeted international markets, including India’s, as its key export destinations with competitive pricing,” said a report from the credit rating agency Crisil.
During FY2023-24, the Indian steel sector demonstrated unprecedented performance, achieving its highest levels of production and consumption compared to analogous periods in previous financial years. The production of crude and finished steel stood at 143.6Mt and 138.5Mt, registering a growth of 12.9%, and 12.4%, respectively. Similarly, the country’s finished steel consumption reached 135.9Mt during FY2023-24, indicating a growth of 13.4% over FY2022-23.
Backed by strong capex allocated for the infrastructure sector, India’s steel consumption has been rising steeply. Increasing domestic demand is a positive indicator for the steel industry, underscoring the robust economic activities and government-led infrastructure projects that are driving steel consumption.
Conclusion
The Indian government has so far received multiple complaints requesting quick action against increasing finished steel imports from China. However, a curb on Chinese steel imports may contribute to price increases and have a ripple effect on already high retail inflation, which may not be advisable at this point. �
The deployment of autonomous robots has enabled global steelmaker Outokumpu to improve worker safety, while boosting productivity. By Thorsten Piniek*
THE steel industry is characterized by harsh conditions and stringent safety requirements. Heat, dust and chemicals put people and machinery to the test every day. At Outokumpu, we are breaking new ground to improve occupational safety, and at the same time increase efficiency. By deploying autonomous robots, dangerous and monotonous activities can be automated and the workload on employees reduced. Our project with the walking robot ANYmal shows how co-operation between people and machines can succeed – and what challenges companies face in doing so. It’s a window into the future of industrial work.
Steel mill operators make a tremendous effort to ensure no one on-site is harmed by using the correct personal protective equipment (PPE) and following robust procedures. But to create a truly ‘zero incident’ environment, the next logical step is to significantly reduce personnel exposure to hazardous conditions. So, what if you were to automate some parts of the inspection process? At Outokumpu, we now have three new robots operating at our sites in Germany, Sweden and Finland that do just that.
The technology is being used primarily to reduce employees’ exposure to the mills’ hazardous environment. But the robots also optimise production through preventative maintenance, decrease environmental impacts, and collect data.
Swiss robots company ANYbotics supplies the robots we’ve named Rosie, Angie and Jokkeri. They all perform multiple daily tasks at each of their respective sites. At our Avesta site in Sweden, Angie works to reduce the time workers must spend on inspections in areas where we use acids. A typical routine for Angie is to inspect 90 points per shift, 270 per day, and 1,890 per week. Meanwhile, at our Krefeld site in Germany, Rosie currently performs tasks similar to the robot in Sweden, but we aim to expand its capabilities to inspect both the furnace and the insulation areas in the near future.
The most recent addition to the Outokumpu robotic family is Jokkeri who now operates at the Tornio site in Finland. Here, the robot focuses on reducing personnel exposure to noise, dust and vibration when measuring temperatures from different bearings and gearboxes in the sites’ Ferrochrome plant. The robot also
* Vice president of health and safety, Outokumpu
checks that conveyor belts are operating correctly.
Tackling harsh environments
All three of Outokumpu’s steel mills where the robots operate come with their own challenges. We intentionally chose these three particular sites because they have different lines and production facilities.
For example, the Tornio site houses Outokumpu’s only Ferrochrome plant while Avesta is home to our press plate facility and hot and cold rolling mills.
Significant variations in temperatures in the surrounding environment are one of the biggest challenges. The Torino site sits far north of Finland, which means much colder temperatures compared to those in Sweden and in Germany. Ice on sites also create an additional hazard.
Meanwhile at the Tornio site, the crushing of ferrochrome, which contains asbestos, creates dust. In addition to the environmental conditions, these sites have multiple levels and stairs often made of steel grates. Workers must navigate these areas with extra care.
With all this in mind, the robots we have deployed must adapt to the obstacles they
may face on the job. This adaptation, in turn, will reduce downtime and allow for smoother operations. For instance, the robots must be able to climb stairs without toppling over, while their batteries must be able to endure the extreme hot and cold temperatures.
Advanced capabilities
Outokumpu’s robotics journey started in spring 2023 when we started our partnership with ANYbotics. We found that they were the most ideal partners as they built robots specifically designed for the industrial environment rather than for a wide range of applications.
The ANYmal robot mimics the physical characteristics of a dog. Its four-legged locomotion, based on reinforcement learning models, enables robust manoeuvring in multi-floor facilities. It can safely climb up and down open grated stairs as well as move in and out of cramped spaces. The robot can also navigate through wet and bumpy terrain and can work for around two hours.
ANYmal’s use of Pharos, ANYbotics’ 3D software for simultaneous localisation and mapping (SLAM), helps the robot perform its defined inspection missions without human intervention. A fusion of LiDAR, 360° vision and near-field perception helps the robot achieve centimetre-accurate mapping. Its autonomous capabilities help the robot find the most optimal and fastest route around the facility. It can also autonomously plan alternate routes in the event of an obstacle being in its way.
Furthermore, ANYmal is able to detect overheating machine parts on predefined inspection points and alert the operators before parts get hot enough to cause a breakdown, or in the worst case a fire.
Outokumpu places a key focus on improving health and safety at our sites. From 2016 to 2023, we have improved our performance by 83%, reducing our TRIFR (total recordable injury frequency) from 8.7 to 1.5. But we didn’t achieve these successes through a single measure. Instead, we focus on consistency and continuous improvement in several areas. However, our main objective is to achieve the lowest accident frequency rate in the industry by 2025. ANYmal’s robots help support this vision.
It’s important to note that these robots
will not replace the human workforce but instead automate some parts of the inspection work. We estimate that by transferring certain inspection tasks to the robots, employees’ exposure time to hazardous substances present throughout the mills can be reduced by more than 80%. Furthermore, possibly the need to undertake maintenance in hazardous areas could be reduced by 20%.
Enhancing safety is not the only purpose of the robots. They are also used to drive efficiency and fully optimise the production process. Indeed, by having the robots handle certain tasks, it frees up skilled people to focus on more complex, valueadded activities that leverage their expertise and problem-solving abilities. This can lead to increased productivity and better utilisation of human skills and knowledge on-site.
Additionally, as the robots take over the more mundane and routine tasks, our skilled workers can be retrained and upskilled to take on higher-level roles. This involves programming, maintenance, and supervision of robotic systems, as well as other specialised tasks that require their expertise. Better interactions with the robots can pave the way for the scaling up of autonomous operations so that they cover more areas within the facilities.
Currently, the robots read data from a range of tools like manometers, LCD displays, and valves. In addition, ANYmal detects leaks on steam and pressured air pipes, for example, through its camera or its ultrasonic sensor. This could lead to significant savings in energy by avoiding unnecessary CO2 emissions. We plan to introduce additional AI-powered capabilities that can, for example, track incremental
changes that are hard for a person to see by eye, to these systems. This has the potential to improve maintenance operations across our sites.
The robots already come with AI capabilities and generate large volumes of data during operations. Manually interpreting this data would be inefficient and time-consuming. To address this, we are collaborating internally with our own AI team led by Matti Aksela, head of AI and digital platforms at Outokumpu. The goal is to develop AI powered systems that automatically analyse and interpret the robot’s data. This will allow us to gain insights and make data-driven decisions much more efficiently, without manually processing vast amounts of data.
Deploying Rosie, Angie and Jokkeri is just the beginning of our journey. Our initial focus is to achieve as close to 100% utilisation of the robots as possible, maximising their radius of operation. This knowledge will be crucial for us to calculate our exact needs to enhance safety and operations.
But our success does not solely depend on the robots themselves. We work in a cross-functional team that involves a range of expertise – from maintenance to IT to health and safety. Aligning the needs and priorities across these different functions is essential. We initially had doubts about using the robots, but it became an interesting learning curve. We constantly communicated with our unions and shopfloor representatives to ensure our workers were content with the decision to use these robots across our operations. In fact, we asked our employees to vote on the name of the first robot, “Rosie”.
We anticipate expanding our robotic capacity, deploying five to 10 times more robots across our major sites in Europe, the US and Mexico, in the coming years. This, however, will be an incremental process. And we are taking a step-by-step approach to develop and scale-up our robotic operations.
In the future, besides the walking robots, we plan to use drones, driverless transport systems, and collaborative robots (Cobots) to improve safety and productivity at our sites. Our long-term strategy aims to invest in new technologies and create intelligent plants where people and machines work seamlessly together. �
The steel industry is continuing to implement digital technology into its processes, as producers cite advantages such as improved efficiency, lowered costs, and predictive maintenance.
By Myra Pinkham*
*North America correspondent, Steel Times International
WHILE the steel industry hasn’t made as many inroads into digital manufacturing as some other industries, it has recently made some progress – and steelmakers are expected to continue to incorporate more digital technologies into their operations.
However, while steelmakers are continuing to make some pretty aggressive automation investments, Philip Gibbs, a senior equity analyst with KeyBanc Capital Markets said he doesn’t believe there has been a tectonic shift as far as the steel industry’s use of digital technologies is concerned.
Stefan Koch, global metals lead for SAP, said the same could be said for digital manufacturing technologies in general. He said that while digital devices are getting more intelligent, that isn’t anything new, but rather an ongoing, evolutionary shift, in line with the evolution of Cloud offerings –even in the manufacturing space.
But at the same time, Koch noted that the steel industry’s move towards increased sustainability and ‘green’ products, and the legal and compliance issues related to that, has propelled the industry’s digitalization efforts, particularly given the steelmaker’s need to track data about where their steel is coming from and its sustainability rating. “This has resulted in a big push to digitalize manufacturing processes,” Koch said, given that steel companies have to not only report such data to regulatory authorities, but also to their customers.
considerably, much as it has done with its use in people’s daily lives with generative AI applications such as Chat GPT.
Andrew Callaghan, principal of Crowe’s metals group, observed that there has also been a lot of interest by steel companies to leverage the use of generative AI, whether in the drafting of communications, as part of electronic data interchange applications, or to summarize data.
Muthusami said that for companies that are just starting to venture into digital manufacturing, they are largely just investing in systems to collect more data, while for companies that have already been collecting data, it is more about how they can leverage that data to improve their efficiency and to make better decisions.
Karthick Valluru, Boston Consulting Group’s managing director and global sector leader for materials and process industries, said that steel and other metals companies, while progressing, aren’t as advanced in their digital manufacturing journey as some other industrial sectors, such as high tech companies.
Also, what digital technologies the steel industry is embracing varies company by company, Rivers Cornelson, a consulting manager for Crowe LLP maintained, adding that the closer they are to the mill itself the more likely they are going to employ digital twins, smart factories, artificial intelligence, machine learning and robotics. However, he said, further downstream (and at distributors) such innovative technologies are not quite as needed.
But it goes beyond that. According to Venkatesh Muthusami, principal machine learning data scientist for Canvass AI, the early adopters were the companies that had enough money to do research and to try new things to see what value they would have, while it was only once those companies proved they that they could achieve beneficial cost saving and efficiency improvements that it encouraged other companies to follow.
Kurt Herzog, vice president of Industry 4.0 at Primetals Technologies, noted that in the past there were great expectations about the future of digital manufacturing driven by what he described as ‘fantastic promises’. But, he said that a certain amount of that hype has now eased, with people realizing that while digitalization can help, it is hard work.
“We used to think that one aspect of artificial intelligence could solve all of the companies’ problems,” Herzog noted, “But now we realize that there are different solutions and that we have to select the right tool out of the AI toolbox.” Also, he said that companies have come to realize that it isn’t sufficient just to store data, that they also have to prepare or refine the data in a way that it is fit for future use.
However, Koch noted that this varies for different steel segments, given that there is a need to first attempt to use digital technologies in easier, less complex applications, such as processing and fabrication, rather than to do so in core operations like rolling and casting. as
Gibbs agreed, noting that several years ago Big River Steel – now a subsidiary of US Steel – was one of the first US steelmakers to use AI-centred technology to improve the quality of its rolling mill products.
But that depends upon how you define digital manufacturing, which Michael Peintinger, managing director – Americas for Smart Steel Technologies, describes as a rather broad buzzword for the technologies that have been following in the footsteps of Industry 4.0, including those that involve big data and artificial intelligence (AI) models, which he said the steel industry has been using to some extent over the past decade or so.
However, while Nucor has also been using artificial intelligence for some time, Gibbs said that their motivation has been different to Big River’s. Rather, he said, they have been looking to use data they have collected to troubleshoot problem areas in their operations rather than to use it to make day-to-day steelmaking decisions.
In fact, Peintinger said he believes that virtually all steel companies have ongoing projects that use artificial intelligence, although many of those projects were at first experimental in nature, with companies, through trial and error, figuring out what works and what the benefits are. But, he said that industry’s understanding of what AI can do and how it could be helpful – particularly within the context of machine learning – has now matured
“A lot of digital technologies could be seen as different sides of the same coin,” Crowe’s Cornelson pointed out, although he said the lines could be blurry. For example, he said that artificial intelligence and machine learning could be thought of as overlapping concepts with machine learning sitting inside of the bigger circle of AI.
He explained that when companies use machine learning they are teaching the computer the patterns that had existed in their historical data, so they can produce a reasonable forecast following the same patterns in the future.
“This doesn’t necessarily relate to a specific machine,” Cornelson said, noting that companies are more likely to benefit from utilizing AI and machine learning from the data that has been collected from one of its digital twins or smart factories.
Boston Consulting’s Valluru said there
#itsmorethanjustamachine
A Reducing & Sizing Block for long products keeping its promises. Achieve your goals with KOCKS RSB®
finishing size in round or hexagonal dimensions up to 160mm
increase in production up to 20% up to 10% energy savings in the mill line
are essentially three steps to the digital manufacturing journey – putting sensors on their equipment to collect data; using advanced analytics and other computing models such as digital twins to conduct business planning; and using that information to find ways that the machines and human workers can interconnect to provide greater business value.
Primetals’ Herzog said that in an effort to increase the consistency of the decisions being made, one potential goal is to get people away from making decisions that could be made by a computer. He explained that by using data to analyze their process and having computer models to extract information, steelmakers can gain insights into how to make better decisions. However, he said that at least in the near term, he doesn’t see rules for decision making being generated automatically by artificial intelligence without humans checking them.
“I don’t know if steelmakers are currently more or less willing to invest in digital technologies,” SAP’s Koch said, “But they are looking to leverage the technologies that are available.” For example, they are improving their sensor capabilities, including finding better ways to use visual data by investing in more cameras and in the ability to better interpret visual data.
Canvass AI’s Muthusami pointed out that computer vision offers steel companies many opportunities to better monitor their production processes. For example, it could be used to flag certain problems, including surface defects. Meanwhile, it could also be used to promote greater safety – ensuring that workers aren’t going into less safe parts of the steelmaking plant – and could also be used for training purposes.
“I don’t believe that automation could be used throughout the steelmaking process given the capital intensity of doing so,” KeyBanc’s Gibbs said. But it is particularly helpful when used in the pulpits of large steel mills to give a lot more information to their operators. He explained that by having more information at their disposal, it allows the operators to make quicker decisions that reduce steelmaking costs, downtime and defects and increase the mills’ productivity.
Also, Herzog said that one very important area for digitalization is in material development, with steelmakers using data to develop digital models, helping them to vary chemistries or production processes
to develop steel grades that have more desirable mechanical properties.
Valluru noted that there are also a lot of predictive maintenance technologies that are available so steelmakers can improve their operations and maintenance technologies by getting advanced indications of potential failures.
As far as how to incorporate the new, emerging digital technologies, this is being done both in new and recently built steelmaking facilities and in older, existing plants.
“The newer plants are being embedded with a number of these technologies,” Valluru pointed out, noting that, for example, they might have more of the sensors needed to capture data that could be applied to things like machine learning or have the needed abilities to create digital twins. “But they still need to make further investments in how to use the data they have collected and to incorporate it into their manufacturing processes.
Muthusami noted that steelmakers have been building those new mills with digitalization in mind and trying to do their best to have the hardware and tools they need to support that.
But while on paper digital manufacturing is more easily incorporated into a new mill, Crowe’s Cornelson said that steelmakers shouldn’t just look toward their greenfield sites to drive all their innovation. “They also need to focus on upgrading their existing operations.”
Herzog, however, said that this could be challenging given that steelmakers’ current automation systems often come from a variety of suppliers and because there is a lack of standardization in the steel industry. “Therefore, the process parameters could vary between two different machines at the same plant and with every steelmaker having their own standards the industry can’t agree which is the best standard.”
But Koch said that going forward there
will likely be more standardization of certain production processes, with digitalization helping steelmakers to make changes to their production lines. That, he said, will allow steel companies to more directly connect production, sales and purchasing and to offer different product qualities.
“Digital manufacturing is a trend that has being going on for a while,” Peintinger declared, “And I think that it will continue to be very promising going forward.”
Gibbs agreed, saying that this is the case even if steel is an industry that doesn’t tend to lend itself to quick technological changes. “But some steelmakers have been using artificial intelligence-based technology for a while,” albeit more for trouble shooting that the actual running of their mills.
“But now it is less experimental as there is better understanding by the industry about what technologies they can use and when they should do so,” Peintinger said. “With continued advancements in artificial intelligence, machine learning and predictive maintenance, I think that we are on a good path to further these innovations.”
He said that the use of digital twin technology as a representation of the steelmaking process and steel products is also helping as it facilitates the industry’s ability to use more sophisticated automation tools. “And that will drive the industry to be more data-driven and more reactive to what is going on in the mill.”
“Overall, this is an exciting time for digitalization,” Koch said. “Companies will continue to be more connected and there will be more data sets,” he observed, noting that while there might be some concerns about what is needed and what the cost will be, ‘generally deploying technology and innovation will provide more connectivity, more harmonization of standards, and the ability to be more competitive [against] other materials. ‘ �
Blast furnaces are pivotal to the iron and steel industry, producing approximately 70% of the world’s steel. Recent advancements in artificial intelligence (AI) and data analytics present new avenues to optimize processes and reduce energy consumption. By Vikas Goel*, Kamal Galrani**, and Vishal Marje*** from Tvarit.
IN BLAST furnaces, iron ore, coke, and sinter products are transformed into pig iron, the primary component of steel. The process involves alternately charging coke and iron ore from the furnace top and blowing a hot blast in, which reduces iron ore via the carbon in the coke, producing molten pig iron. This molten pig iron is further processed to remove impurities like sulphur and phosphorus. Further refinement reduces carbon using a steel converter. The resultant molten steel is then cast into blooms, billets, and slabs, and subsequently processed into various steel products.
The intricate interaction of material properties and furnace dynamics necessitates precise control for efficient and safe blast furnace operation. One of the critical challenges is channelling, a phenomenon marked by uneven gas flow through the burden material. This disruption affects heat transfer and reduction reactions, leading to reduced productivity, localized overheating, compromised furnace integrity, and increased coke consumption.
Channelling originates from the inherent complexity of the blast furnace charge. The burden material’s non-uniformity in size, shape, density, and distribution creates varying permeability across the furnace cross-section, fostering preferential pathways for ascending blast gases. These ‘channelled’ flows bypass dense regions rich in fines, disrupting preheating and reduction processes, resulting in unstable
production, and decreased furnace productivity.
Traditional methods of predicting channelling rely on indirect indicators like gas flow, pressure changes, and temperature variations. These methods often lack accuracy and provide limited advance warning, hindering timely intervention. Despite some success, they remain imprecise and fail to predict channelling well in advance, emphasizing the need for a more reliable and proactive approach to channelling prediction.
Inaccurate and untimely predictions can result in significant production and energy losses.
The technology proposed here utilizes advanced data analytics and machine learning to predict channelling events in blast furnaces. Real-time data from sensors, including pressure gauges, temperature probes, and gas analysers, are fed into a machine-learning model trained to identify patterns and anomalies associated with impending channelling. The model generates a prediction score indicating the probability of channelling within a specific timeframe.
Hybrid AI framework
The approach integrates real-time data
collection through sensors, ensuring continuous information flow on crucial parameters. This real-time data is the foundation for subsequent analytical processes.
a. Data preprocessing: The collected data undergoes rigorous preprocessing to ensure integrity and reliability, involving cleaning to eliminate outliers or inconsistencies and normalizing to a standardized format. This step is crucial for maintaining analysis and modelling accuracy.
b. Feature engineering: First principles-based modelling is applied to engineer new features, leveraging fundamental principles of blast furnace operations to extract additional insights from the data. Incorporating domain knowledge enhances the model’s predictive capabilities.
“This AI-driven technology uses real-time data analytics and machine learning to predict channelling events.”
c. Machine learning algorithm selection: Various algorithms were evaluated, leading to the selection of a treebased algorithm trained on the engineered features using a curated dataset.
d. Model evaluation: The trained model’s performance was assessed using a held-out test set, ensuring it generalizes well to new, unseen data. This phase provided insights into accuracy, precision, and recall, establishing reliability in detecting channelling anomalies.
e. Deployment: The model is deployed in production environments, operating in real- time to continuously
monitor furnace data, promptly detecting and alerting operators to channelling anomalies. This proactive approach enables swift intervention, minimizing channelling impact on furnace efficiency and production.
Identification of key process indicators to estimate channelling condition
To assess channelling potential, key process indicators (KPIs) play a crucial role. Accurately detecting blast furnace channelling requires recognizing KPIs that subtly indicate gas flow imbalances.
a. CO/CO2 ratio: Indicative of
Integrating insights from these KPIs allows operators to proactively address channelling issues and maintain optimal furnace performance.
combustion efficiency, a low ratio suggests incomplete combustion due to channelling, while a high ratio hints at excessive coke combustion, indicating potential instability from direct air paths.
b. Top gas temperature: Linked to heat distribution, it serves as an early warning for channelling. Channelling causes localized hot zones, leading to uneven temperature distribution.
c. Differential pressure: Measuring pressure differences across furnace zones, it is influenced by channelling. A lowerthan-expected pressure drop suggests air bypassing the burden, while severe
channelling can increase the pressure drop if the channel becomes blocked.
d. Wind volume: Channelling may initially allow increased wind volume due to lower resistance from the burden, but the presence of channels over time can disrupt flow and distribution, resulting in decreased overall wind volume or fluctuations.
e. Coke fines: Excessive fines accumulation in the channel hinders proper burden descent and gas flow distribution, providing additional clues for channelling identification.
The research employs a first principlebased modelling approach to engineer innovative features for predicting blast furnace channelling. This methodology integrates fundamental principles of furnace operations, focusing on crucial parameters like hot blast pressure and temperature across different furnace zones.
Key process variables such as hot blast pressure, gas composition, wind volume, and temperature directly influence gas flow and permeability within the furnace bed. A pressure-temperature index, developed during feature engineering, captures the interplay between pressure and thermal expansion, providing a clearer understanding of burden behaviour. This index serves as the foundation for deriving a ‘permeability index,’ quantifying gas flow ease through the burden. These engineered features form the basis for constructing a sophisticated channel prediction model.
Efforts were made to identify the time lag between KPI changes and actual channelling formation for proactive control. Correlations were established across different time lags affecting channelling, leveraging operational practice knowledge. Ensemble learning algorithms were explored for predicting channelling phenomena. Compared to single-model approaches, ensemble methods leverage diverse algorithms’ strengths, mitigating individual weaknesses and yielding robust predictions. Specific ensemble algorithms like Random Forests and Gradient Boosting were particularly adept at capturing complex non-linear relationships within furnace data.
The model was trained on historical data with temporal annotations, predicting channelling events based on current and
past furnace behaviour. This capability empowers operators to take proactive measures before channelling significantly impacts performance. The model generates a prediction score indicating the probability of channelling, presented as an odometer to indicate the threat level as ‘low,’ ‘medium,’ or ‘high.’
The technology development has progressed through several stages, with the initial research and development phase completed. Currently, it is undergoing testing and validation in a simulated blast furnace environment.
This technology offers several advantages over existing channelling prediction methods:
a. Early and accurate predictions: Enabling timely preventive measures to avoid significant losses.
b. Seamless integration: This can be integrated into existing control systems, offering real-time insights into furnace operations.
c. Data integration and management: Ensuring data accuracy and consistency for accurate predictions.
d. Algorithm development and refinement: Continuous improvement enhances prediction accuracy and adapts to changing conditions.
e. Human-machine interaction: Intuitive interfaces help operators effectively interpret predictions and take appropriate actions.
f. Standardization and
deployment: Establishing industry-wide standards and facilitating technology adoption across different plants for broader impact.
The successful implementation of this technology can significantly impact the iron-making process:
a. Early detection: Predicting channelling well in advance allows ample time for corrective measures.
b. Enhanced efficiency: Proactive prevention optimizes furnace operation, increasing productivity and reducing energy consumption.
c. Improved accuracy: Machine learning algorithms provide more accurate predictions compared to traditional empirical methods.
d. Reduced costs: Minimizing channelling occurrence reduces associated costs, including furnace damage and lost production.
e. Reduced production losses: Early detection minimizes disruptions and maximizes output.
f. Enhanced safety: Predicting and preventing channelling reduces furnace damage risks and associated safety hazards.
7. Additional considerations
Data quality and availability
Prediction accuracy relies heavily on the quality and availability of real-time data from furnace sensors, necessitating continuous monitoring and maintenance.
Model training and maintenance
The machine learning model needs constant updates with new data and refinement to adapt to changing operating conditions.
Seamless integration with existing control systems is essential for efficient and effective technology utilization.
Conclusion
This research introduces a technology employing advanced analytics and machine learning to predict blast furnace channelling. As the steel industry transitions towards sustainability, this transformative approach offers a proactive solution to longstanding operational challenges, promising increased efficiency and reduced costs of blast furnace operations. �
SPEAK:
SPONSOR
WHAT THIS YEAR’S ATTENDEES HAD TO SAY…
“Very well organized event with a good line of speakers focused on digitalization and decarbonization.”
“Great immersive atmosphere and excellent platform to learn and network.”
“Unique blend of upcoming technologies, challenges and the latest innovation in digital transformation for the iron and steel industries.”
“A good mixture of high-level presentations, panels and networking opportunities at an excellent location.”
The integration of digital manufacturing techniques is revolutionizing the steel industry by enhancing efficiency and productivity. This article examines the shift from mid-term to reactive short-term production scheduling, highlighting the inadequacies of manual scheduling and the constraints of full automation.
By Michael Peintinger, PhD*
AS the steel industry continues to evolve, the integration of digital manufacturing techniques becomes essential to address challenges like managing its highly interconnected production processes, responding to dynamic market demands, reducing equipment downtime, maintaining high-quality standards, and achieving energy efficiency. While the key value drivers, as discussed later, are different for integrated steel production (Fig 1) and thin slab casting setups (Fig 2), better planning and production scheduling can drastically increase efficiency by optimizing resource utilization, minimizing disruptions, and enhancing overall productivity for both scenarios.
Fully integrated steel production is critical in addressing global demand for high
quality steel products. In such mills, slabs or bars can be stored in hot or cold storage between casting and hot rolling. This flexibility allows for a wide range of steel grades to be produced, catering to diverse industrial needs. However, it also adds complexity to the scheduling process due to the need to co-ordinate multiple stages and manage inventory effectively. One of the key value drivers is to increase the average furnace charging temperature.
Modern steel production technology enables minimills to quickly switch from one grade to another. This leads to grade transitions, when production switches from one steel grade to another with different chemistry. The losses can be significant, especially when producing expensive steel grades and if transitions affect multiple coils. Better scheduling can help reduce the average number of transitions dramatically.
The overall goal in both scenarios is to increase the number of prime coils per order, e.g. by reducing jumps in the rolling schedule and avoiding large width adjustments while casting and, therefore, improving casting and rolling processes.
Mid-term planning defines the coarse parameters for short-term scheduling
Mid-term planning in steel production is essential for managing long-lead activities and aligning them with production capabilities and order commitments. Unlike short-term scheduling, which deals with the specifics of daily operations, mid-term planning provides a broader overview necessary for making strategic decisions. This includes purchasing scrap or external slabs, accepting and committing to large or complex orders, and scheduling significant maintenance activities.
*Managing director, Americas, Smart Steel Technologies Inc
Given the expected order book, one can anticipate future bottlenecks and future scarcities and suggest a mid-term plan to minimize or avoid them altogether. These activities require a rough but realistic plan that considers the plant’s capacity and order book, ensuring that critical constraints are accounted for. Such plans typically sum up capacities and compare them with the order book, aiming for a balance that will later be refined in shortterm scheduling. Although these plans are often rudimentary, they form the backbone for more detailed and precise short-term scheduling, ensuring that strategic decisions are feasible and align with production capabilities.
Traditional production scheduling in steel mills often relies on manual methods, such as simple pen-and-paper techniques or Excel spreadsheets. These approaches, while familiar and straightforward, are labour-intensive and prone to human error. Manual scheduling requires schedulers to consider numerous variables and constraints, including equipment availability, material flow, and production priorities. This complexity makes it diffcult
to optimize schedules efficiently. Manual scheduling also struggles with process disruptions. Equipment breakdowns or safety-related events necessitate the creation of an instant schedule, often resulting in suboptimal production sequences and increased costs. This highlights the limitations of manual methods and points towards the need for automation and, therefore, more sophisticated scheduling solutions.
The idea of fully automating production scheduling, possibly through advanced algorithms or artificial intelligence, seems like a promising solution. However, full automation faces significant challenges. Automation of schedules usually requires strictly defined objective functions with exact dollar value trade-offs between objectives. In reality, production environments are dynamic, with economic conditions and stakeholder demands frequently changing.
Experienced schedulers often state, ‘I know it when I see it,’ indicating that what constitutes a ‘good’ schedule can vary and is diffcult to parameterize. Stakeholders’ daily scheduling requests, often not transmitted via computer systems but verbally communicated in phone calls, are diverse and challenging to generalize,
requiring flexibility that fully automated systems struggle to provide.
Given the limitations of both manual scheduling and fully automated systems, a hybrid approach that combines automation with user guidance is necessary. Open-box models offer a solution by allowing users to understand and adjust the scheduling process. Unlike black-box AI models, which are opaque and often require retraining with new data sets to tweak, open-box models provide transparency and flexibility.
A more suitable approach for guided automation is Mixed Integer Linear Programming (MILP). MILP models the scheduling problem as a linear programme with integer variables representing discrete decision-making elements. MILP solvers can incorporate a wide range of constraints and objectives, enabling the generation of schedules that minimize costs and maximize efficiency.
In MILP models, constraints are implemented as a set of rules based on mill capability and the vast experience of operators and schedulers. These rules are formulated into linear equations or inequalities that define the boundaries
within which the scheduling algorithm must operate. This allows the system to leverage practical knowledge and operational realities to create feasible and optimized schedules.
MILP models are open-box, meaning they can be understood and tweaked by the user. This transparency allows users to impose specific priorities and constraints, guiding the algorithm to meet their needs. For example, a user might instruct the system to produce a particular order, even at the cost of suboptimal schedules and late orders, as long as hard constraints are not violated. Alternatively, during periods of resource scarcity, users can direct the system to allocate materials, focusing on the most critical orders.
Our approach to automatic scheduling involves combining MILP with user guidance. This approach ensures that broad control, which is impossible with black-box algorithms, is maintained. Users must understand how the algorithm behaves to steer it in the desired direction, necessitating a user-friendly interface that allows for concise input and adjustments.
Smart Steel Technologies’ SST Scheduling can be guided by users by order selection filters, adjustment of constraints, and cost functions. The systems can rapidly process
large volumes of data, continuously update schedules in response to real-time changes, and provide optimized solutions that account for complex interdependencies between different stages of production. By adding AI models as additional optimized or predictive cost functions, the systems can forecast potential quality deviations and initiate proactive rescheduling.
Guided automatic scheduling offers numerous benefits. It minimizes grade transitions, reducing losses when switching between steel grades. Slab yard logistics are optimized, ensuring efficient material storage and retrieval, while higher furnace charging temperatures lead to significant energy savings and reduced CO2 emissions. The life of the planning group becomes easier as they are relieved from labourintensive tasks, allowing them to focus on strategic decisions. Automated systems respond better during mill events, quickly generating new schedules that account for disruptions. They also optimize the calculation of order to products, increasing yield and enhancing material utilization. AI-supported cost functions improve cost forecasting and management, maintaining production quality while controlling expenses. Additionally, guided
scheduling maximizes the number of fly tundish changes by planning programmes in sequence, maximizes and minimizes tundish wear depending on the type, reduces slab stock production, increases roll change wear, and lessens diameter changes in rebar mills. However, these benefits often compete, making savings difficult to evaluate. For instance, similar plants may have different hardware, leading to varied bottlenecks and KPIs, and even a single plant’s KPIs can change over time. Therefore, a flexible scheduling system incorporating user input is essential to navigate these complexities effectively.
Manual scheduling is the current statusquo due to its familiarity and simplicity, but it cannot optimize complex production processes effectively. Full automation is also not feasible due to the need for dynamic adjustments and stakeholder inputs. The ideal solution lies in user-guided automation using open-box models like MILP, which combine the best of both worlds: the efficiency and optimization of automated systems with the flexibility and insight of human guidance. This approach not only enhances productivity but also ensures that the scheduling process can adapt to the ever-changing demands of the steel production environment. �
In the rapidly evolving landscape of the steel industry, companies like Chemcoaters are staying ahead of the game through investment in development, all while keeping the customer at the forefront of the conversation. By
Connor McMenamin*
1. How are things going at Chemcoaters? Is the steel industry keeping you busy?
Like many – things are ‘OK’ at the moment in most of our market segments. We’d all like a bit more business, but anything is better than 2020.
2. What is your view on the current state of the global steel industry?
The last few years have been a roller coaster – price and demand soared up, then plummeted just as quickly. Rinse and repeat. We’ve seen more stability in 2024 – but there are potential economic stress points on the horizon. Locally, it has been encouraging to see American steel companies invest aggressively in new capacity and capabilities.
3. In which sector of the steel industry does Chemcoaters mostly conduct its business?
Chemcoaters’ book of business is divided into three roughly equal segments based on purpose/need; corrosion-inhibiting coatings, advanced lubricants, and cleaning /retreatment. Looking at end-use, we estimate >50% going into the construction sector. Other prominent end-use segments include appliance and heavy transport (truck/bus).
4. Where in the world are you busiest at present?
99% of Chemcoaters’ business is related to supply chains in the USA. Occasionally our work makes it to Canada. In 2021 we started working in Mexico – which has been challenging, yet extremely exciting!
5. Can you discuss any major steel contracts you are currently working on?
We see increased activity in the heavy transport segment in 2024 – the use of salt to keep roads drivable in the winter
months here forces creative thinking where galvanized steel is used. In general, OEMs seem to be very interested in RoHScompliant pre-treatments that further delay rust formation and promote good adhesion as part of a paint system. This happens to be an area where we are strong.
6. Where does Chemcoaters stand on the aluminium versus steel argument?
Most of our technology/R&D budget is dedicated towards products for carbon steel – but we process both ferrous and non-ferrous alike. OEMs will ultimately need to rely on a suite of raw material options (including steel and aluminium). If a customer needs a coil cleaned or coated, and we can run it on our line – we’re taking the order. In that sense we’re somewhat neutral.
7. What are your views on Industry 4.0 and steelmaking?
Industry 4.0 becomes increasingly relevant as all parties in the supply chain fight to
*President, Chemcoaters
improve material yields, and as mills are asked to produce more advanced products over time. A customer order for a few truckloads worth of steel might sound small but involves a lot of cash! The pressure to ‘get it right the first time’ is immense. Further downstream – robots will be tasked with more complicated welding/painting / processing schedules, across a wider range of materials. We need serious computing power and data management – no question.
8. In your dealings with steel producers, are you finding that they are looking to companies like Chemcoaters to offer them solutions in terms of energy efficiency and sustainability? If so, what can you offer them?
We do occasionally receive questions related to CO2 emissions and expect that frequency to increase as time progresses. Our initial work suggests that application of our flagship technology (InterCoat® ChemGuard) at a galvanizing line does indeed present potential CO2 reductions on galvanized steel.
On the chemical side, Chemcoaters only works with low-solvent/low-VOC, water-borne product. In that sense, we are relatively environmentally friendly as a coilcoater. InterCoat® ChemGuard also now features trivalent chromium (Cr+3)-based technology, whereas we initially worked with hexavalent chromium (Cr+6) tech (the product family was born 14 years ago).
Our R&D team is also developing a robust chrome-free corrosion inhibitor, which we hope to bring to trial and market before year-end. They’re getting close!
9. Where does Chemcoaters lead the field in terms of steel production technology?
Chemcoaters is unique in that we are (1) a coil-coating company, and (2) develop our
own coating technology for applications. Generally, we focus on applications that run in-house, but we also service other coaters. Chemcoaters is the market leader in noncross-linking dry-film lubricants for extradeep draws and other complicated forming operations. Our InterCoat® ChemGuard family is very tough on rust (white AND red rust) and features the only post-applied cold-reducible coating – as best we know.
10. How do you view Chemcoaters’ development over the short-tomedium term in relation to the global steel industry?
Chemcoaters will continue to focus on what it does well: formability, corrosioninhibition, and cleaning. We expect to see more opportunity in renewables (solar) and spend more time supporting external partners apply our technologies in-plant. Product development timeframes often range from two to five years – so we spend a long time in the planning phase, and then ‘voila’ – the ramp-up is very quick. Chemcoaters tends to grow in spurts.
11. China dominates global crude steel production. How should the industry react to this situation? It’s hard for Chemcoaters to advise on macro-trends like this – as we occupy niches in the North American Steel market. That said, steel mills and processing equipment represent major capital investments – so we would expect overcapacity in China to remain for the medium/long-term.
12. Where do you see most innovation in terms of production technologies – primary, secondary or more downstream?
Evolving needs of major OEMs (particularly in automotive) are pushing innovation into their supply chains at break-neck speed (at least, for the metals industry). New steels (TWIP, Multi-Phases, Gen 3 Advanced High Strength) combine properties you couldn’t previously find in a single specification – helping OEMs combine parts, remove processes, reduce scrap, etc. The mills and processors aligned to these supply chains then need to invest in more capable equipment to handle steel with tensile strengths at 1000-2000 MPa. Similar changes are occurring in heavy transport/ mining industries – thicker coils, higher abrasion resistance, specialty quench and tempered products.
13. How optimistic are you for the global steel industry going forward and what challenges face global producers in the short-to-medium term?
The primary challenge facing major steel producers will continue to be overcapacity elsewhere – creating knock-on effects in their home markets. Producers will have to secure competitive energy sources and reduce carbon emissions. The entire industry needs to focus on recruiting the next generation and passing on tribal knowledge – though we have improved in the last decade. You see a lot of new faces these days at industry events. The
steel industry is a critical one – we aren’t going anywhere – but we’ll always be under pressure to adapt, and more rapidly than before.
14. What exhibitions and conferences will Chemcoaters be attending over the next six months?
We regularly rotate our appearances at conferences based on where we find more customer interest or interaction with peers in our chosen market segments. Chemcoaters will have a presence at the SMU Steel Summit in August (everyone is there!), RE+ in California mid-September, and then Metalcon in Atlanta end-October. Similarly, our R&D team usually attends the National Coil Coating Association fall meet.
15. Apart from strong coffee, what keeps you awake at night?
Chemcoaters is essentially a pure tollprocessor; we don’t buy steel. We do not control the flow of steel/aluminium, upon which we depend. It is paramount that we understand our customer base – the way they think, their forecasts, and their problems. The customer will always be our obsession here – and necessarily so.
16. If you possessed a superpower, how would you use it to improve the global steel industry?
Carbon emission reduction will remain a major theme for the foreseeable future. I would invent the technology to help us produce greener steel even faster – time is of the essence. �
Furnaces International is an English language journal dedicated to the production of rnaces. Circulated each quarter in March, June, September and December.
The Furnaces International Buyers’ Guide is the essential guide to rnace manufacturers and suppliers of rnace equipment and services to the industrial heating/process industry. Providing comprehensive company listings, product information and key contact details, the guide is published in December each year.
Packed with information on the rnaces industry and continually updated with news for professionals, rnaces-international.com also features special articles and interviews with leading industry gures.
A round-up of the top news stories is sent to more than 44,000 industry professionals every month. You can register online to receive the weekly newsletter and keep up-to-date with the latest news from across the rnaces manufacturing industry. Sign up at rnaces-international.com
Aluminium International Today (AIT) is the leading bi-monthly English language journal dedicated to all sectors and regions of the international aluminium manufacturing and processing industry. Subscribe to the free weekly newsletter at aluminiumtoday.com
Glass International o ers readers the latest news from across the hollow, container, flat, and speciality glassmaking industry and is the o cial media partner for Glassman events. Subscribe to the free weekly newsletter at glass-international.com
Steel Times International is the key publication for the steel market, reporting on iron and steel making issues from all corners of the globe. Subscribe to the free weekly newsletter at steeltimesint.com
Steel Times International is the key publication for the steel market, reporting on iron and steel making issues from all
The Steel Times International Directory is the essential guide to steel manufacturers, producers, suppliers of plant equipment and services to the steel industry. Order your print or digital copy priced from £105 or FREE for paid subscribers.
Packed with information and continually updated with news for steel professionals, www.steeltimesint.com also features special articles and interviews with leading industry gures.
A round-up of the top news stories is sent to more than 7,000 industry professionals each week. You can register online to receive the weekly newsletter and keep up-to-date with the latest news from across the steel manufacturing industry. www.steeltimesint.com/e-newsletter
Steel Times hosts regular webinars and virtual events. Head to www.steeltimesint.com to see what’s coming up.
Tintagel Castle, a place inextricably linked with the legend of King Arthur, has since 2019 been home to a 70m long footbridge allowing visitors to access the most isolated part of the castle.
By Tim Smith*
TINTAGEL Castle, on the Cornish northwest Atlantic coast, is attributed as the place where the legendary King Arthur was conceived by the deceit of Uther Pendragon, King of Britain, who used ‘magical’ powers to seduce Queen Igerna, wife of the Duke of Cornwall. Arthur, as a boy, is famed as having drawn the sword ‘Excalibur’ from a rock, a feat no man could accomplish. This legend, dating from the 5th century (or the ‘Dark Ages’) declares drawing the sword could only be achieved by a true king of the British Isles. There may indeed be a modicum of truth in this myth in that those with the skill to smelt iron were much esteemed for their ‘magical’ ability to produce iron from stone.
Today’s remains of Tintagel castle were built in the 13th century by Richard, Earl of Cornwall on a rocky headland using a site that had been occupied for at least 300 years. The approach to the castle was
on the mainland with the castle proper located effectively on an island linked to the mainland by a narrow land bridge. This link was washed away sometime between the 14th and 17th centuries leaving the castle separated by a deep chasm that had to be negotiated to access the castle.
Geoffrey of Monmouth in his ‘Historia regum Britanniae’ written between 1135 and 1139, first brought Arthur to European fame.
In the 15th century, Sir Thomas Malory created the concept of Camelot in his poem ‘Le Morte d’Arthur’, based on French romance poems – possibly reflecting the similarity of the Cornish with the Bretons, whose languages and lifestyles may have common origin.
The Arthurian legend was revived in the 19th century, in particular by Alfred Lord Tennyson, who wrote a sequence of 12 poems between 1859 and 1885 based on
*Consulting editor, Steel Times International
Malory’s work. This inspired visitors to arrive in numbers to see the castle. But, to access the ruins, the chasm had to be negotiated. It took 41 years, commencing in 1851, to cut steps into the rock to enable visitors to access the isolated part of the castle, but climbing the 148 steps was challenging for all but the most dedicated visitor. By 1930, the lower part of the route had become even more difficult so a short low-level footbridge was built. This was rebuilt in the 1970s. As visitor numbers increased, congestion became a major problem on the narrow pathway and footbridge.
By now, the castle was under the care of English Heritage, who recognized the need for a high-level bridge across the chasm. In June 2015, they launched a competition for the design of a bridge which would blend in with the rugged surroundings and natural beauty of the area. Civil Engineering firm, Ney & Partners, and architects William
Matthews Associates were announced as the winners of the competition and work began on assembling the bridge in June 2018.
The 70m long footbridge is 57m above sea level, with cantilevers out in two parts from either side of the chasm; the two parts meeting, but not actually touching, leaving an expansion gap of four centimetres.
A steel fabricating company, Underhill Engineering in Plymouth, made the 18 steel sections to be assembled on-site. These were first assembled in the workshop to ensure everything fitted correctly, and then dismantled to be taken to Tintagel. The total weight of steel was 47.5 tonnes, and along with this, 140m of oak were used. A temporary cable crane running across the chasm, was installed to transfer materials to the far side, and a helicopter was used to carry parts to the most inaccessible areas. The sections were assembled by a team who abseiled to insert the connecting links to each of the 18 sections.
The deck way consists of 40,000 Cornish slates, quarried from nearby Pengelly quarry. These are set on edge, supported beneath by a steel structure. Stainless steel balustrades are attached to both sides, their design being so slender that if viewed from a distance against the sky they disappear.
The bridge opened in August 2019, just one year after work started on construction.
A 10-minute video on the building of the bridge is available on YouTube at https://www.youtube.com/watch?v=YCHjpbyuuLw