Insights for the green steel transformation. Coal microlithotypes.
Betting on clean steel.
Nucor’s journey to energy leadership.

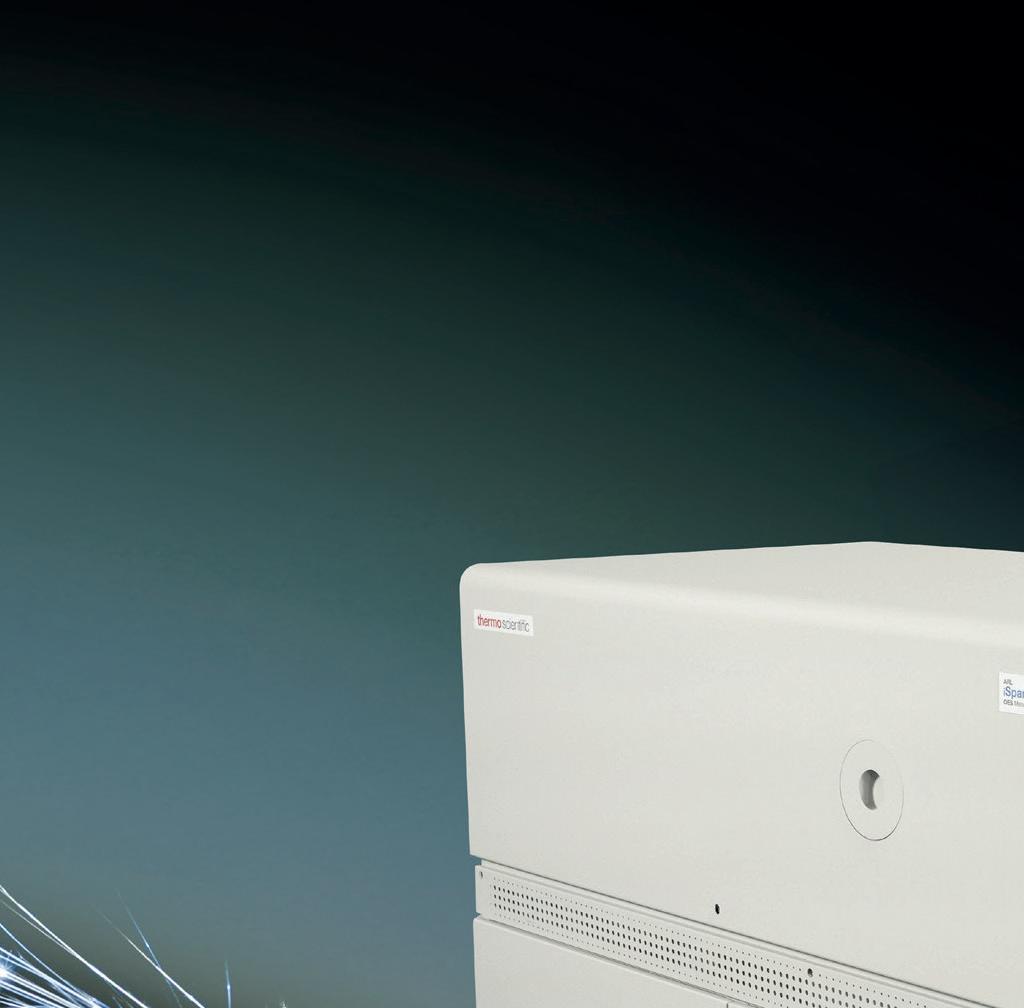

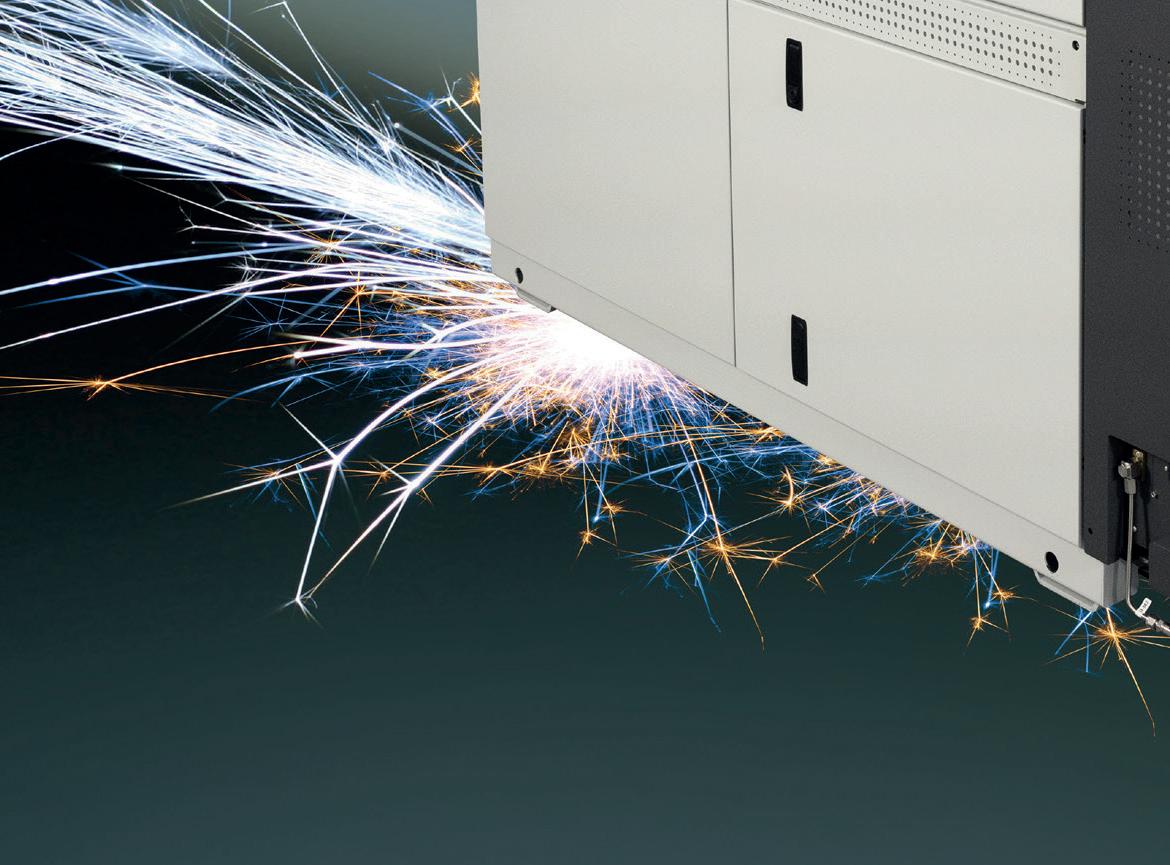
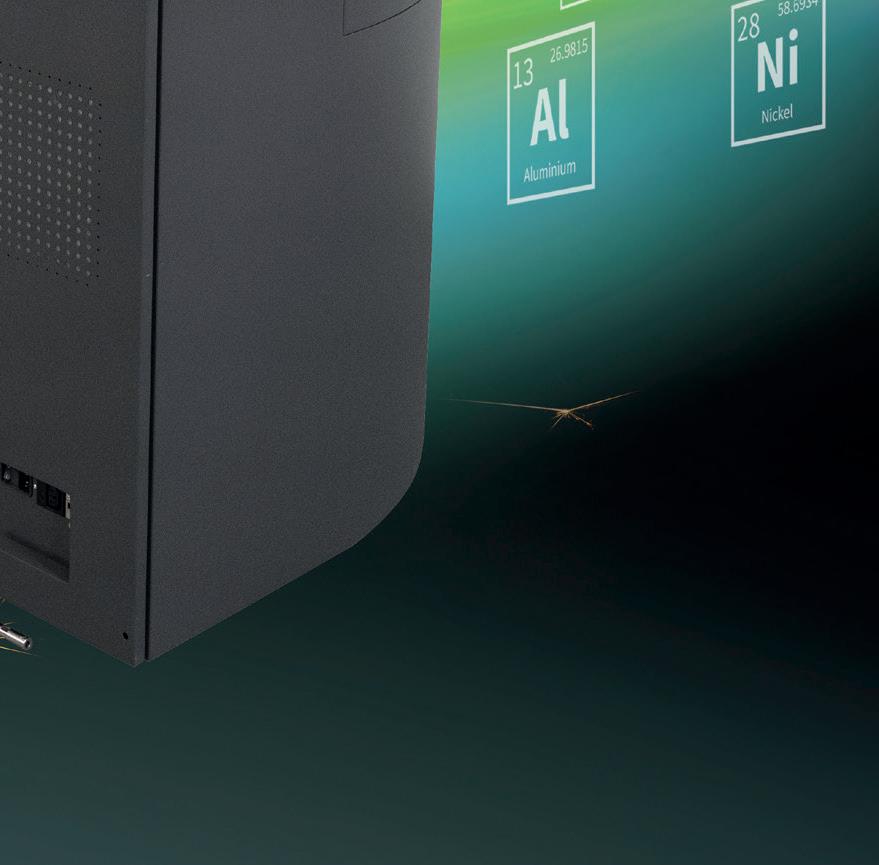
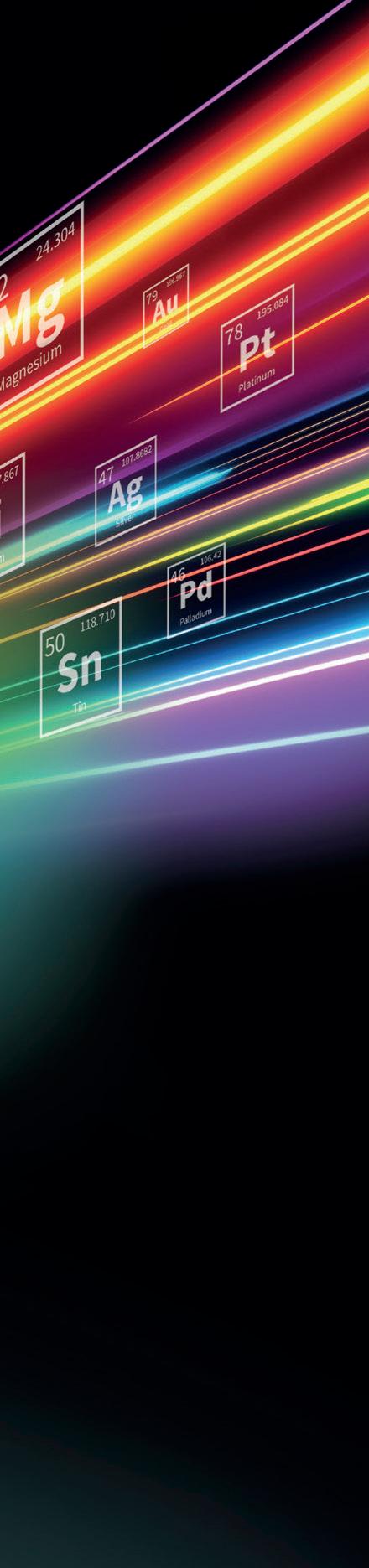
Insights for the green steel transformation. Coal microlithotypes.
Betting on clean steel.
Nucor’s journey to energy leadership.
The Thermo Scientific™ ARL iSpark™ Plus Series OES Metal Analyzer uses single-spark acquisition to provide rapid elemental analysis—up to 15% faster than previous models. The increased speed and reliability minimize tap to tap times, save energy, reduce carbon footprints, and realize a faster return on investment.
Capable of providing ultra-fast, on-line analysis of nonmetallic inclusions, the ARL iSpark Plus adds to the versatility, dependability, and productivity of metal processing operations.
EDITORIAL
Editor Matthew Moggridge
Tel: +44 (0) 1737 855151
matthewmoggridge@quartzltd.com
Assistant Editor
Catherine Hill
Tel:+44 (0) 1737855021
Consultant Editor
Dr. Tim Smith PhD, CEng, MIM
Production Editor
Annie Baker
Advertisement Production
Carol Baird
SALES
International Sales Manager
Paul Rossage
paulrossage@quartzltd.com
Tel: +44 (0) 1737 855116
Sales Director
Ken Clark
kenclark@quartzltd.com
Tel: +44 (0) 1737 855117
Managing Director
Tony Crinion
tonycrinion@quartzltd.com
Tel: +44 (0) 1737 855164
Chief Executive Officer
Steve Diprose
SUBSCRIPTION
Jack Homewood
subscriptions@quartzltd.com
Tel +44 (0) 1737 855028
Fax +44 (0) 1737 855034
Front cover photo courtesy of Kocks.
Advanced 4D EAGLE S by KOCKS & LAP allows combined profile measurement and surface inspection in the rolling mill of Saarstahl AG.
Four
20
India update
Import delays slow investment.
Decarbonization
24 Pressure on Russia to be greener.
30 Forging pathways: insights for the green steel transformation.
New
Nucor’s journey to energy leadership.
Biden
Betting on clean steel.
Coal petrography and coke quality.
Perspectives Q&A: OMP Innovation: the foundation of industry.
According to Bill Brown’s Thing Theory, an object ‘becomes a thing when it can no longer serve its common function’, that is to say, we begin to confront the ‘thingness of objects when they stop working for us’; when the laptop breaks, when the car stalls, when the shoes wear through. What the theory fails the address, however, are the lost objects–absences that ‘stand before us with which we must contend’; the difference between a set of keys, and the same set being missing. The object in material terms remains, but the negative space of its absence negotiates a new understanding. Not quite a thing, but not quite an object either. It is in this space in which the modern steel furnace now functions; with the blast furnace facing multiple trajectories of relining, closure, demolition, and replacement. It remains a point of contention for governments and industry experts alike; how to modify without compromise; how to rebuild without destruction.
In recently attended events, metallurgists and CEOs have claimed that the blast furnace is here to stay, while environmentalists continue to
urge its timely conclusion. The truth perhaps, lies in a statement found in the feature ‘Forging pathways: insights for the green steel transformation’ from The Australasian Centre for Corporate Responsibility (p.30). ‘‘Steel does not have a ‘climate problem’, it has a coal problem’’; in other words, to decarbonize steelmaking is to decarbonize ironmaking. The two are irrevocably connected, with the potential to enable us in reaching climate targets, or drag us further toward environmental catastrophe. The furnace, once again, lies within this statement; either as an object that performs the task required, or a ‘thing’ that fails to relinquish its carbon-rich history. There are ways in which to negotiate the movement from one to another, with some less costly than others, but it is the urgency that must be prioritised; rather than the argument of what must remain. History is significant in its nature of having been passed; the steel industry must align on a future that offers tangible solutions to maintain its production, and prevent the ideological slippage from objectual action, to malfunctioning disrepair.
For 135 years, steel producers and steel service centers have counted on Butech Bliss to deliver the design, engineering and technological advantages necessary to help them succeed. From entry to exit end we build it all. Our product lines include roller and stretch leveling technology, a full line of shears, material handling equipment and complete coil processing lines. We are more than a scrap chopper manufacturer. Learn more about our world-renowned coil processing technology call +1 (330) 337-0000, visit ButechBliss.com or email sales@butech.com. If our name is on the machine, it’s built better.
Q-ONE reduces EAF overall OPEX with a shorter power-on time and very low network disturbances. It is a scalable system that can be implemented on new or existing AC EAFs, and it can be directly powered by renewable energy sources.
Singapore-based steelmaker Meranti Green Steel has formally reserved a site in the IRPC Industrial park in Rayong, Thailand, for its new green steel plant. The DRI facility will have an annual production capacity of 2.5Mt, and is scheduled to be commissioned in 2027. The plant will be developed with Danieli, and will use renewable energy.
Source: Steel Orbis, 9 May 2024.
The first minister of Wales, Vaughan Gething, has said that he held a ‘candid meeting’ with Tata Steel on the issue of expected job losses at the company's Port Talbot plant in South Wales. The first minister, who was on a visit to India as part of a trade mission, also expressed hope that the Indian steel major, which has a ‘positive reputation’, would take the same approach for the workers at the Welsh plant.
Source: The Economic Times, 10 May 2024.
The German Embassy in Hanoi, Vietnam, hosted an inaugural panel discussion seeking solutions on decarbonizing Vietnam’s steel industry.‘‘In Vietnam, the steelmaking industry, which ranks number one in Southeast Asia, remains one of the main contributors to the country’s carbon emissions," said Dr. Guido Hildner, ambassador of the Federal Republic of Germany, at the panel. "We all know that the green transition of heavy industries is a global challenge. Therefore, Germany launched the Climate Club during last year’s COP28…to offer support for developing and emerging economies…to leapfrog into climate-friendly industrial development’’.
Source: Vietnam News, 10 May 2024.
Liberty Steel has been strongly criticised by the Czech government for its alleged handling of Liberty Ostrava’s financial issues. Czech minister of labour Marian Jurecka said that Liberty Ostrava has outstanding social security tax payments, while Minister of Finance Zbynek Stanjura said the British-based steel group's restructuring plans were ‘not realistic’. “It would be a different attitude and different search of possible solutions and forms of co-operation if there was an owner here who submits plans that are realistic,” Jurecka stated.
Source: BNE IntelliNews, 10 May 2024.
Three steelworkers from Jindal Steel in Karnataka, Southwest India, drowned when water was suddenly released in a tunnel where they were conducting an inspection of a faulty pipeline, local police have stated. According to police, the incident took place following a disruption in the power supply which had halted the flow of water through the tunnel. The water tunnels, integral to the steel manufacturing process, serve as conduits for cooling hot iron rods, with excess water stored in various tanks within the facility. Source: The Hindustan Times, 11 May 2024.
The US Department of Energy’s Argonne National Laboratory will be receiving $3 million over three years for a project that aims to decarbonize iron production. Alongside partners including the University of Illinois at Urbana-Champaign, Purdue University Northwest, Starfire Industries and ArcelorMittal, the project involves the research and production of a microwave-powered hydrogen plasma in a rotary kiln furnace. The hydrogen plasma allows reduction to take place at much lower temperatures, under 1,400 deg F, according to the parties involved. Typically used in cement production, the rotary kiln furnace eliminates the need for heating the iron ore and forming pellets, also lowering the energy requirement. The culmination of these advances aims to achieve a 50% reduction in energy consumption compared with conventional blast furnaces. Source: Green Car Congress, 12 May 2024.
ArcelorMittal has started the construction of an EAF for long products in Gijón, Spain, with the facility expected to begin ramping up in the first quarter of 2026. The nearly $230 million investment will be the first major EAF project to be implemented within the company’s decarbonization programme in Europe and ‘will constitute the first step toward low-carbon emissions steelmaking’ in the Asturias region of Spain.
Source: Recycling Today, 12 May 2024.
The former minister of health of Victoria, Australia, Daniel Andrews, has teamed up with Andrew Forrest – Australia's ‘wealthiest man’ – to sell 'green' iron to China. Andrews’ consultancy firm, Forty Eight and Partners, is partnering with Andrew Forrest's company Fortescue, the Sydney Morning Herald reported. The two firms have pledged to deliver 100Mt of 'green' iron to China after having recently met at the Boao Forum for Asia in Hainan Province in March. It marks the first high-profile gig Andrews has participated in since stepping down as health minister last year.
Source: Mail Online, 13 May 2024.
British Steel has secured a multi-million-pound contract to supply rail for a new high-speed electric railway in Turkey. The company will provide tens of thousands of tonnes of track for the project from its Scunthorpe steel works, which will connect Mersin with the cities of Adana, Osmaniye and Gaziantep in southern Turkey. The project is expected to help establish a lower-emission transport link between Turkey's secondlargest container port and inland cities more than 150 miles away, potentially reducing CO2 emissions by more than 150kt annually. Source: Grimsby Live, 15 May 2024.
Mining company Anglo American has laid out plans for a potential breakup of the group via a demerger or sale of its steelmaking, coal, nickel, diamonds and platinum businesses, as it attempts to ‘fend off a takeover bid’ from BHP Group, according to media reports. The Londonlisted miner previously rejected a raised $43 billion offer from BHP, saying it continued to significantly undervalue the company and was ‘highly unattractive’ for its shareholders.
Source: Nikkei Asia, 14 May 2024.
Eastern Cape detectives are investigating an incident at a steel plant in the Coega Special Economic Zone, South Africa, where two workers died in a furnace and two others sustained burn wounds. According to a police spokesperson, at approximately 1300hrs on 14 May, police and other emergency services responded to a distress call at a steel plant in Coega where two males aged 39 and 48 had lost their lives. "Two other coworkers aged 38 and 49 years old sustained burn wounds and were taken to hospital for treatment," stated the spokesperson.
Source: PE Express, 15 May 2024
US president Joe Biden has instructed the US Trade Representative to increase tariffs under Section 301 of the Trade Act of 1974 on $18 billion worth of imports from China. This step includes an increase in the tariff rate on certain steel and aluminium products of Chinese origin from 0.0-7.5% to 25% in 2024. The American Iron and Steel Institute (AISI) has welcomed Biden’s decision, noting that ‘China continues widespread unfair trade practices that harm American steel producers’.
Source: GMK Center, 15 May 2024.
Austrian steelmaker voestalpine is embarking on a flagship initiative aimed at showcasing the technical viability of circular economy endeavours within the premium segment. This project, as part of a partnership with Mercedes-Benz and TSR Recycling, entails recycling post-consumer scrap into high-quality scrap, subsequently processing it within the steel-producing industry to yield high-grade steel, which will then be utilized in the automotive sector.
Source: chem analyst, 16 May 2024.
Offshore foundations
manufacturer Sif has reached agreements with German steelmaker Dillinger for the supply of lower-emission steel for offshore wind foundations and to progress monopile recycling efforts. The addendum signing to the companies’ long-term steel plate supply framework agreement aims to achieve full circularity of monopiles. This MOU marks the finalisation of a joint-research project executed by Sif, KCI and Dillinger to produce a detailed design for a monopile recycling factory.
Source: renews Biz, 16 May 2024.
Liberty Steel’s Hungarian subsidiary, Liberty Dunaújváros, formerly known as Dunaferr, has signed a contract to complete a full feasibility study for the installation of a modern electric arc furnace (EAF) with China’s CISDI Engineering. The development of the feasibility study follows a comprehensive technical analysis and engineering study conducted by NPT, a Swiss engineering services company. The contract includes the installation of a new EAF, as well as the modernization of secondary metallurgy and the hot strip mill.
Source: GMK Center, 17 May 2024.
Quinbrook Infrastructure Partners has announced plans to invest in an ongoing project to convert Queensland magnetite ore into green iron, using the state’s wind and solar resources, touted as one of the biggest renewable hydrogen projects under development in Australia. The $3.5 billion Gladstone Green Iron project centres on a ‘world class’ magnetite ore deposit and its ready access to what Quinbrook describes as the ‘exact fundamentals’ to produce and export green iron, including existing port and transmission infrastructure and abundant renewables.
Source: Renew Economy, 20 May 2024.
India's JSW Steel will buy a coking coal company in Mozambique to secure supply of key steelmaking raw material and shield against any price volatility. The company's board of directors approved the acquisition of coal mining firm Minas de Revuboe (MDR) for about $74 million. The purchase of a 92% stake in MDR gives JSW access to more than 800Mt of premium hard coking coal reserves in Mozambique, the steel producer said on 17 May. MDR's mine is not yet operational but the company aims to start developing it between 2024-25.
Source: Argus Media, 20 May 2024.
Tata Steel has signed an agreement with National Grid ESO to build the power infrastructure required to switch its Port Talbot site to a low-carbon plant. The deal will see the British grid operator build the new electrical framework capable of powering the Indian company’s 3.2Mt EAF by the end of 2027. “This will help us replace our ageing and carbon-intensive blast furnaces with a state-of-the-art electric arc furnace capable of producing our customers’ most demanding steel products,” said Rajesh Nair, chief executive of Tata Steel UK, in a website statement.
Source: Bloomberg News, 20 May 2024.
PyroGenesis Canada Inc., a company that designs, develops, manufactures and commercializes advanced plasma processes and sustainable solutions geared to reduce greenhouse gases (GHG), has announced that its subsidiary, Pyro Green-Gas Inc., has signed contracts totalling $1.3 million with a global steel company based in India, for the development and supply of technology to desulphurize and clean the gas that is released during the creation of metallurgical coke from coal.
Source: Canadian Manufacturing, 24 May 2024.
Algerian steelmaker Tosyali Algeria, a subsidiary of Turkey’s Tosyal Holding, has commissioned a new flat-rolled steel plant based on an electric arc furnace with an annual capacity of 2.2Mt. The company has started producing slabs and will soon open a hot strip mill and a new direct reduction module. The current project is part of a phase four expansion of Tosyali Algeria’s steel complex. The 800kt/yr cold rolling mill and 400kt/yr galvanizing line are expected to be commissioned in 2025. Source: GMK Center, 28 May 2024.
ArcelorMittal Liberia has unveiled plans to build an iron ore concentration plant at its Yekepa facility in Nimba County. Valued at approximately $1.7 billion, this project will become one of Africa's largest iron ore concentration plants. The first phase is expected to be completed by December this year. CEO Josephus Cohen revealed that the plant will create local employment opportunities for over 500 young Liberians currently training as mechanical engineers for future management roles.
Source: Yieh Corp Steel News, 28 May 2024.
CHAR Technologies has announced the ‘imminent commencement’ of a production run of 500 tonnes of pelletised biocarbon. The pelletised biocarbon is destined for use at various heavy industrial facilities, including ArcelorMittal sites, to fulfill a portion of the company’s previously announced biocarbon offtake agreement. The production run is an important milestone in the ongoing commercial upgrades at CHAR Tech’s state-of-the-art Thorold facility, according to the organisation.
Source: Bioenergy Insight, 30 May 2024.
American steel giant Cleveland-Cliffs is in talks to acquire the assets of Russia’s largest steelmaker Novolipetsk Steel in the United States, according to news report from Bloomberg, citing confidential sources familiar with the matter. NLMK’s assets –steelmaking facilities in Indiana and Pennsylvania – could be valued at more than $500 million if sold. If the negotiations are successful, it will be Cliffs’ first step towards such a deal after an unsuccessful attempt to acquire US Steel.
Source: GMK Center, 29 May 2024.
A research group at the University of Cambridge, UK, has developed a process that recycles cement from waste demolition concrete – which comprises cement, sand, aggregates and water – by using it as a lime supplement to remove impurities in steel recycling. One of the results of this is that cement is re-clinkered in the process, enabling it to be reused in new concrete, while less lime is needed to recycle steel. The process, argues the project team, could potentially slash carbon emissions for both the cement and steel industries.
Source: Chemistry World, 31 May 2024.
The Commercial Chamber of the Strasbourg Court of Justice has granted Italian steel company Marcegaglia permission to acquire the Ascometal steel plant in Fos-sur-Mer, France, which is currently undergoing rehabilitation. The modernization project envisages increasing the capacity of the EAF to 1-1.2Mt/yr of steel, building a new continuous caster, and a modern hot strip mill. Total production capacity will be 1.6-2Mt/yr of steel.
Source: GMK Center, 3 June 2024.
Rio Tinto, Australia’s biggest iron ore producer, will bankroll a $215 million research facility in the heart of Rockingham’s industrial area in Western Australia, in a bid to drastically decarbonize the steelmaking process. The facility will trial using raw biomass and microwave energy, instead of coal, to convert Pilbara iron ore to metallic iron. The mining giant claims it has the capacity to reduce the process’ carbon emissions by up to 95%. Source: WA Today, 4 June 2024.
Production at ArcelorMittal Mexico's principal steel mill in Lazaro Cardenas, Michoacan, was halted by a blockade at its entrance by members of the miners union, a company source said on 31 May. "There is no production, and this situation hampered both markets: flat and long steel; however we had enough inventories to deliver May orders without problems," the source stated at the time.
Source: SP Global, 31 May 2024.
AIC has been awarded an order by a major Italian steel producer for a robot guidance system for the drawing line.
The system operates after the load of the coil is delivered by forklift onto the reel in a horizontal position. The application handles stainless steel products from 11 to 40 mm diameter and rotates the reel so that the retaining wire of the coil can be identified using an artificial intelligence-based vision system. With this technology, AIC claims that it can detect any type of alloy regardless of the light present and the brightness of the surface. Once the image acquisition is complete, the robot proceeds to remove the bands. Afterwards, the search for the start of the coil is made and once this is reached, the robot proceeds with the clamping.
Once the material has been clamped, the combined movement of the reel and the translation of the robot allows the reel to be placed in its working position (vertical position), thus enabling the robot to unroll the coil for its introduction into the pre-bending machine and consequently into the drawing line.
The robot is equipped with a vision system with an hydraulic clamp and a de-strapping system. The robotic island consists of a 600 kg KUKA KR robot with a slide to allow the robot to move along the axis of the drawing line. The cycle time is three minutes from the loading of the reel from the forklift to the introduction of the tip into the pre-conveyor, while the slide/seventh axis has a run of eight metres.
AIC was also responsible for securing the plant,
supplying perimeter guards, destrapper and safety devices that allow the line to be CE certified.
The main objectives of the job were to increase safety and reduce the heavy workload for operators. Future developments of the project may include the loading of the coil with AGV autonomous driving systems.
The AIC machine is the first of its kind to make the process fully automated using mechanical manipulators and avoiding human intervention.
The installation of the system was carried out alongside modernization activities without interrupting the production activities, claims AIC.
For further information, log on to www.aic.it
Ma’anshan Iron & Steel (Masteel), part of Baowu Group, chose Fives, an international engineering group, to supply an annealing furnace equipped with the latest technologies to expand the steelmaker’s capabilities to produce coils for the automotive industry.
The project includes the design and supply of Stein Digiflex®, an annealing furnace with an annual capacity of 450kt, and for a new continuous galvanizing line dedicated to Advanced HighStrength Steel (AHSS).
“We look forward to launching this new CGL NO6 to further enhance our product quality and market competitiveness. We plan to build this new production line as a benchmark project in the steel industry together with Fives Group, which has rich experience in steel making technology and in which we have great confidence,” said Yuxiang Jiang, chairman of Masteel Group.
The new furnace will be equipped with the latest generation AdvanTek® combustion system, pre-oxidation control and FlashCooling®, a tech-
nology with high hydrogen content. The furnace will be supported by VirtuoTM-L, a thermal optimization solution to achieve the desired mechanical properties.
Masteel already operates four strip processing lines dedicated to automotive steel grades, all equipped with Stein Digiflex® furnaces.
For further information, log on to www.fives.com
Chinese steel producer Baosteel Zhanjiang has awarded Primetals Technologies a contract for the engineering, supply, and start-up of a bowtype 2-strand continuous caster for the production of thick slabs. The caster will be implemented at Baosteels’s plant in Zhanjiang, Guangdong province. It will produce slabs measuring up to 2,700 mm, with a width of 450 mm.
Primetals Technologies is responsible for the engineering and implementation as well as the supply of mechanical equipment and a comprehensive Level 2 automation package. With
an annual capacity of 3.5Mt of slabs, the new equipment will enable Baosteel to produce plates for heavy-gauge sectors like the shipbuilding and wind turbine industries.
Baosteel’s caster will be equipped with unique Single Roll DynaGap (SRD) segments from Primetals Technologies. When changing parameters that influence production, like steel grade, cooling practice, and casting speed, the process models of the Level 2 automation package dynamically determine the best casting gap, allowing for the SRD segments to optimally
adjust individual roll gaps and forces. The caster’s SRD segments can handle capacities of 5,000 kN per roll, enabling large thickness reductions in the casting process. This, says Primetals, leads to superior internal quality of the cast slabs, and, in turn, results in the production of defect-free ultra-thick plates of high quality.
For further information, log on to www.primetals.com
Metals offers the entire steel value chain an exceptional opportunity for curbing their CO2 emissions.
The unique combination of its historic and recently developed product portfolio, make John Cockerill one of the industry’s most relevant suppliers of equipment for both the hot and cold phase of the steelmaking and processing industry.
Our three distinct business segments are addressing todays and tomorrow’s challenges supporting sustainable and green steel production:
Our new upstream offering related to DRI (Direct Reduced Iron), EAF (Electric Arc Furnaces) technologies and the use of hydrogen in steelmaking. Next to offering indirect electrification (DRI-EAF&H2-DRI-EAF),John Cockerill is also working on Volteron®: A first-of-a-kind iron reduction and steel processing route via direct cold electrolysis. This CO2 free steelmaking process, has been co-developed with the world’s leading steelmaker ArcelorMittal.
Regrouping our historical downstream product portfolio, this segment also includes:
¡ the Jet Vapor Deposition (JVD®) technology set to replace today’s hot-dip or electro galvanizing processes. This novel high-productivity vacuum coating technology provides previously unknown coating flexibility and possibilities, all while offering lower CAPEX and OPEX.
¡ our E-Si® equipment & processing lines specifically designed to produce high-quality Non-Grain Oriented (NGO) steel in response to the need for electrical steel meeting precise metallurgical properties, essential to support the shift towards green mobility.
This segment not only embraces all services and after-sales activities but will be strongly focusing on downstream furnace electrification (reheating and processing line furnaces), as well as hydrogen combustion, and the optimization of plant operations, including energy audits and the modernization of steel production equipment and installations.
Tata Steel Nederland, one of the largest steel producers in Europe, has selected Tenova, a company specializing in sustainable solutions for the metals and mining industries, to develop a new steel production line at its IJmuiden facility in the Netherlands.
In 2023, Tata Steel Nederland launched its current Green Steel Plan, an ambitious initiative to transform the production of liquid steel to dramatically reduce the environmental impact of the IJmuiden site. The project is based on the installation of a Direct Reduction Plant (DRP) and a new steelmaking line that will replace the largest blast furnace on the site (BF7) and one of the coke-making plants (KGF2).
The overall contract will include engineering, supply, and advisory services for a 3Mt EAF equipped with Consteel® and Consteerrer®, the electromagnetic stirrer developed through an exclusive global partnership with ABB. It will also comprise secondary metallurgy facilities (ladle
furnaces and RH vacuum degassers) required to refine the liquid metal from the EAF to the quality needed to meet current operational specifications (high-quality steel for the automotive sector).
The production equipment will also include a range of technologies aimed at minimizing the environmental impact of the new plant, including a fumes treatment plant, a waste energy recovery system, and a dry slag granulation unit.
ENERGIRON®, jointly developed by Tenova and Danieli, was already selected last year as the technology for the facility’s Direct Reduction Plant.
“Tenova’s strategy of focusing on cost-effective and environmentally friendly technologies is paying off with customers like Tata Steel Nederland who are aligned with our priorities. From the outset of negotiations, our teams have worked with mutual esteem, resulting in a smooth co-operation and full agreement on technical and contractual aspects. We are honoured to be part
of Tata Steel Nederland’s investment plan and to accelerate its path to decarbonization”, said Paolo Argenta, executive vice president for the Tenova upstream business unit.
“The demand for steel continues to grow, with an increasing need for recycled and sustainably produced steel,” said Hans van den Berg, CEO of Tata Steel Nederland. “Due to our location on the North Sea, we are in one of the best locations to make the transition to a more responsible steel production – clean, green, and more circular. And we are working hard to realize that ambition.
“At the same time, we recognize the call to further minimize the impact of our company on the immediate living environment at an accelerated pace.”
For further information, log on to www.tenova.com
The PROFILEMASTER® SPS is a light section measuring device for measuring contours and dimensions on profiles of all kinds in cold and hot steel applications.
Benefits:
Maximum measuring accuracy thanks to temperature-stabilized measuring systems
Shape fault detection (SFD) thanks to high sampling rate
High-precision measurements
Detects process problems at an early stage
Fast maintenance and easy cleaning
KOCKS and LAP presented their jointly developed 4D EAGLE S measuring system for precise profile measurement and surface inspection at Wire & Tube 2024 in Dusseldorf. As part of a strategic alliance, the two companies offer steel producers advanced measuring systems for various applications in the future.
In December last year, KOCKS Measure + Inspect GmbH & Co.KG and LAP Measurement Technology GmbH went public on a long-term
development and sales co-operation initiative. This collaboration has now resulted in the 4D EAGLE S measuring system.
The system uses laser light section technology to capture the complete profile of long products and precisely detect and classify various rolling defects. According to KOCKS, users can access SMART CORE X, a modern software application, for a detailed analysis of acquired data, claims the company. 4D EAGLE S can also be integrated
into higher-level quality assurance systems using OPC-UA.
Two systems had already been successfully installed and put into operation at a well-known German steel producer before their official premiere at the global trade fair.
For further information, log on to www.kocks.de
US president Joe Biden continues to drive policies that aim to protect the national steel industry from Chinese overcapacity. By Manik Mehta*
THE US steel industry has welcomed the 30 April announcement by the administration of president Joe Biden, who faces a tough election in November this year, that it had recommended to the US trade representative to treble the duties against Chinese steel and aluminium shipments to the US market.
A White House statement; a so-called ‘fact sheet’, dated 17 April, a copy of which was sent to this correspondent, suggests that president Biden – as someone who ‘knows that steel is the backbone of the American economy, and a bedrock of our national security’ – is keen to preserve American jobs by preventing cheap, heavily subsidized steel and others products from entering the US market.
Indeed, the statement notes that president Biden’s strategic trade and
investment agenda was to protect workers, consumers, and businesses from unfair competition.
American workers in the steel and aluminium industries face a ‘significant challenge from Chinese exports of steel and aluminium which are among the most emissions-intensive products in the world’.
“China’s overcapacity and non-market investments in the steel and aluminium industries mean high-quality US products have to compete with artificially low-priced alternatives produced with higher carbon emissions,” the statement maintained.
The Biden administration is facing pressure in an election year to crack down on what is widely described as ‘unfair Chinese trade practices, including flooding the market with below-market-cost steel’.
A separate petition outlining such concerns
* US correspondent, Steel Times International
was made to the US Trade Representative (USTR) by five labour unions calling for an investigation into Chinese acts, policies and practices.
Indeed, president Biden has asked the USTR to consider trebling the existing section 301 tariff rate on Chinese steel and aluminium; the current average tariff on certain steel and aluminium products is 7.5% under section 30. American workers continue to face unfair competition from Chinese imports of steel and aluminium products which, according to the Biden administration and environmental experts, are among the world’s most emissionsintensive.
The administration underscores the fact that since president Biden took office, the Department of Commerce has imposed over 30 anti-dumping and countervailing
duties on steel-related products. These are, essentially, tariffs on steel imports ‘that are priced below the fair and competitive value’. The Department of Commerce has also conducted some 27 investigations into anti-competitive actions by Chinese exporters and efforts by countries like China to evade trade rules.
The Biden administration is making what it calls ‘historic investments’ in American steel and manufacturing; while maintaining that the previous (Donald Trump) administration failed to deliver an infrastructure bill, and stating that president Biden’s Bipartisan Infrastructure Law, CHIPS and Science Act, and inflation Reduction Act were ‘spurring hundreds of billions of dollars’ in privatesector manufacturing and clean energy investments. Construction of new factories had more than doubled, ‘after falling under the previous administration even before the pandemic’, while creating a record high of nearly 800,000 manufacturing jobs. The administration said that the US trade deficit with China was the lowest in over a decade – lower than any year under the previous administration.
American workers in the steel and aluminium industries face a significant challenge from Chinese exports of steel and aluminium; China’s over-capacity and non-market investments in the steel and aluminium industries mean high-quality US products have to compete with artificially low-priced alternatives produced with higher carbon emissions, the administration said.
Steel is a critical input for the US domestic shipbuilding industry – from the commercial shipping vessels that carry American products, to the US naval vessels that keep global seas safe. Commercial shipyards provide industrial capacity for
maintaining the US Navy’s dominance and support thousands of suppliers and jobs.
The administration said that it recognizes growing concerns that unfair Chinese trade practices, including flooding the market with below-market-cost steel, are distorting the global shipbuilding market and eroding competition. These concerns were also outlined in the petition to the USTR from five labour unions requesting an investigation into Chinese acts, policies, and practices.
AISI applauds Biden’s China tariff hike announcement
The American Iron and Steel Institute (AISI), which calls itself the ‘voice’ of the US steel industry, applauded the administration’s call on the USTR to treble the existing Section 301 tariff on Chinese steel. Kevin Dempsey, AISI’s president, said that the AISI was ‘very concerned about the recent significant increase in Chinese steel exports to world markets and welcomes president Biden’s actions to strengthen the US tariffs on steel from China and to take other actions to address the threats from China’s unfair trade practices’.
“As the largest contributor to the global steel overcapacity problem, China continues to engage in widespread unfair trade practices that harm American steel producers,” Dempsey said, citing OECD figures to the effect that Chinese steel exports grew from 68Mt in 2022 to 95Mt in 2023, a 40% increase in just one year.
“While we have not yet seen a similar surge in direct Chinese steel shipments to the United States, Chinese steel exports to third country markets are often further processed into other steel or downstream manufactured products that are then exported to the US market,” he said.
According to a company statement, ArcelorMittal Calvert, wholly owned by ArcelorMittal, is planning to set up an advanced manufacturing facility in Calvert, Alabama that could deliver 150kt of domestic production capacity of non-grainoriented electrical steel (NOES) annually. The US Department of Energy (DOE) describes electrical steel as a critical material for energy as part of its 2023 Critical Materials Assessment.
In support of this clean energy project, ArcelorMittal Calvert was awarded $280.5 million in investment tax credits from the US Internal Revenue Service (IRS) as part of the Qualifying Advanced Energy Project Credit (48C) programme, funded by the Inflation Reduction Act of 2022 (IRA). The 48C program, which provides a tax credit of up to 30% for investments in advanced energy projects, is designed to support secure and resilient domestic clean energy supply chains.
“We know that around the world, demand is increasing for clean products, produced with less pollution, built to last. And we want all those products stamped Made in America,” energy secretary Jennifer Granholm said during a visit to ClevelandCliffs’ Butler facility in Pennsylvania.
The Butler facility produces grain-oriented electrical steels (GOES). The plant and its GOES product were at risk under originally proposed efficiency standards for power transformers set forth by the Energy Department.
The standards were later amended to include the GOES product to protect American steel manufacturing and American jobs. �
and QSP–DUE are the winning Danieli direct-rolling technologies for the most competitive production of long and flat green-steel products.
They are the result of the research and continuous improvement profused over 20 years, along with multi-million dollars of investment.
Their unmatched performances have fueled their success worldwide, thanks to lower resource consumption and carbon emissions, unbeaten OpEx, and outstanding product quality.
So, top technology becomes copied technology, the shortest route for competitors that, abandoning their solutions, now try to imitate MIDA–QLP and QSP–DUE
Equipment and layout may be copied, but experts know that details make the difference. Automation and process solutions are not easy to copy, and this will be the experience of anyone trusting in those imitations.
The competitive advantage for our customers, obtained by field results, is the best defense for our technology – more than court rulings protecting our patents.
Danieli offers the best guarantees for speedy learning curves, steady performances, and now Digital Plants with no men on the floor. Buy the Original.
GIANPIETRO BENEDETTI CHAIRMAN OF THE BOARD OF DIRECTORSChinese steel continues its assault on the Chilean steel market, with steelmakers demanding long-term legislative action to prevent dumping. By Germano Mendes de Paula*
ACCORDING to the Chilean Steel Institute (ICHA), the national apparent consumption of steel reached 2.34Mt in 2022, showing a 4.4% y-o-y improvement. However, this growth was still not enough to recover to the levels recorded prior to the pandemic.
ICHA highlights that since 2016, the domestic players have been experiencing a gradual loss of market share, even though in 2023, imports fell from 69% in 2022 to 67%. In addition, concerning the origin of imported steel, 65% of it came from China, which is the highest figure recorded since 2016.
The apparent consumption of long steel products was equivalent to 1.04Mt in 2023, reflecting a drop of 3.9% compared to 2022. This was the lowest value between 2019-2023. It is worth mentioning that since 2016, around 80% of long steel
imports has come from just six countries, of which China and Turkey are the nations that ship the largest volumes each year, approximately 75% of total long steel imports.
The apparent consumption of flat steel products totalled 1.31Mt in 2023, which represented a 12.3% jump in relation to the previous year. Imports of flat steel are mainly of Chinese origin, followed by Brazil and Japan. It is important to highlight that Compañía Siderúrgica Huachipato (CSH), a subsidiary of Compañía de Acero del Pacífico (also known by its acronym CAP Group), which is the only coke-integrated mill in the country, paused the production of flat steel products in 2013. Since then, Chile has been totally dependent on imported flat steels.
ICHA estimates that the country’s apparent steel consumption will experience a 1.5% retraction in 2023 y-o-y and a 1.6% recovery in 2024 y-o-y. In this sense, the expected performance can be described as quite a stable trajectory.
CSH’s fight for surviving
In October 2023, CSH asked Chile’s AntiPrice Distortion Commission (CNDP), an independent body that advises the country’s presidency, to initiate an investigation into unfair competition from Chinese steel at prices that were below market costs. The request was accepted and the process began in December.
In March 2024, the Commission stated that there was ‘evidence of dumping’ and recommended applying restrictions on the
* Professor in Economics, Federal University of Uberlândia, Brazil. E-mail: germano@ufu.br
import of steel grinding balls (mainly consumed by the mining industry) and steel bars from China, a country with which Chile has had a free trade treaty since 2006. The same body specifically recommended applying surcharges of 9.2%, 14.2% and 22.5% (average of 15.3%) to three Chinese companies that represent more than 85% of steel grinding ball imports; and additional tariffs of 10.3%, 10.4%, 19.8% and 19.8% (average of 15.1%) to four Chinese companies that account for 100% of steel bar imports.
Located in the southern city of Talcahuano, 500km from the country’s capital, CSH decided, one day after the Commission’s recommendation, to indefinitely suspend its operations. The company claimed that the additional duty was insufficient to resolve the market imbalance that Chinese steel has been producing, which is 40% cheaper than Chilean steel, based on its calculations. The closing of CSH would create serious problems for Talcahuano, as the steel mill has been key to its economy for more than 70 years, and plays an important social role. CSH also claimed to be the largest steel producer for mining in Latin America, in particular serving the Chilean and Peruvian copper miners.
The political reaction to CSH’s decision was quite strong, due to the elimination of direct and indirect jobs. Parliamentarians of different political colours from the Biobío Region, where the steelmill is located, announced a proposal of constitutional reform to establish temporary 50% anti-dumping duties against Chinese steel during a three-year period. The minister of finance, nevertheless, said this practice would be totally incompatible with international trade rules, besides the fact that China is a priority commercial partner.
CSH has appealed to the Anti-Price Distortion Commission, which decided to enlarge the temporary anti-dumping duties. According to the published decree, Chinese steel grinding balls and steel bars will be subjected to anti-dumping duties of 33.5% and 24.9%, respectively. The measures are applicable from April 2024 for a six-month period. Consequently, CSH withdrew its previous plan to cease steel operations.
CSH, however, defended that the provisional measure should be converted into a definitive one. Moreover, the company, which is a coke integrated mill, will continue to study the feasibility of developing projects for the future production of green steel from a pilot plant based on direct reduction using green hydrogen. In this sense, it can be argued that CSH has won a battle, but it is still far from winning the war.
CSH’s experience shows the difficulties faced by the Chilean steel industry due to the massive volume of imports. CSH was created to serve as an instrument to foster industrialisation. The construction of the steel plant began in early 1947 and it was officially inaugurated in late 1950. It was privatised in 1987. In 2011, even before pausing its flat steel production, iron ore mining was already responsible for 94% of CAP’s EBITDA generation, against zero for steel production (STI, July/August 2012, p. 12). In 2023, CAP’s EBITDA was equivalent to $842M, of which mining contributed with $907M, steel production with -$156M, infrastructure with $58M, and steel processing with $42M (Graph 1). Furthermore, CSH’s net losses increased from $122M in 2022 to $386M in 2023. CSH’s fight against Chinese imports is difficult, especially when large forthcoming investments that will be required to decarbonize its steel operations are taken into consideration. �
INDIAN steelmakers slowed investment in greenfield and brownfield expansions in the financial year 2023-24 (April-March) due to delays in importing machinery from China, following a diplomatic row between New Delhi and Beijing. New approvals for the export of plant and machinery from China faced an unprecedented delay from Chinese officials, with India retaliating by holding up visa issuances for Chinese experts for project installations at the production sites in India. Consequently, Indian investors extended the project deadline for the
recommencement of steel production. India has emerged as the world’s second-largest crude steel producer since 2018 and the second-biggest consumer of finished steel since 2019.
The Indian government launched a production-linked incentive (PLI) scheme to encourage steelmakers to increase fund allocations in fresh capacity additions either through brownfield or greenfield routes. The PLI scheme was confined only to the specialized steel sector, to which India continued to be a net importer.
*India correspondent, Steel Times International
Under this PLI scheme, 27 leading Indian steelmakers, including Tata Steel Ltd, JSW Steel Ltd, ArcelorMittal Nippon Steel Ltd, among others, signed 57 agreements with the government and proposed a cumulative investment of $3.54 billion (INR 295.30 billion) for five years beginning in the financial year 2023-24, to create new value-added steel production capacity of 24.7Mt. In the first year of this period, the government proposed to create 1Mt of speciality steel production capacity and accelerate gradually later.
Indian steelmakers’ investments in new projects have slipped below target due to delays in machinery imports.
By Dilip Kumar Jha*Of the total investment, a sum of $2.52 billion (INR 210 billion) was allocated for the financial year 2023-24. However, Indian steel mills managed to invest only $1.8 billion (INR 150 billion), falling 40% short of the target. The slowdown in investment has yielded a proportionate decline in capacity expansions despite Indian steel demand remaining strong in the current financial year and expected to continue double-digit growth in the short term. India’s valueadded steelmaking capacity was recorded at 18Mt/yr in the financial year 2020-21, which is estimated to have increased to 23 Mt/yr against the consumption of
25-26Mt/yr as of today. Therefore, the PLI scheme was aimed at plugging the import loopholes. India’s high-value special steel production was estimated at 7.5Mt.
An Indian steel ministry official, stated, “Steel companies have been facing challenges in importing machinery from China due to diplomatic rows between the two Asian neighbours. The unresolved border issues came into the limelight with the Galwan Valley clash in June 2020 that killed soldiers from both sides, followed by claims of illegal territory occupation, and thus strained bilateral relations. Indian steelmakers who managed to import plant
and machinery on time failed to commence commercial production due to the inordinate delay in visa approval for Chinese experts.”
The government of India outlined the border infrastructure plan, encouraging steelmakers to ramp up investment and boost capacity. In the financial year 202324, the Indian steel industry demonstrated unprecedented performance, achieving its highest levels of production and consumption compared to analogous periods in previous years.
#itsmorethanjustamachine
A Reducing & Sizing Block for long products keeping its promises. Achieve your goals with KOCKS RSB®
finishing size in round or hexagonal dimensions up to 160mm
increase in production up to 20% up to 10% energy savings in the mill line
Source: Ministry of Steel, Indian government
The production of crude steel was recorded at 143.6Mt, indicating a growth of 12.9% from the previous year. Similarly, India’s finished steel production increased by 12.4% to 138.5Mt, and its consumption grew by a staggering 13.4% to 135.9Mt in the financial year 2023-24. The substantial increase in India’s finished steel consumption was supported by increased demand from the automotive and infrastructure sectors, comprising approximately 40% of overall demand.
The construction sector, which consists of approximately 40% of consumption, also recorded stellar growth in the past few years. Total steel consumption in India was recorded at 119.17Mt in the preceding financial year.
Demand from the automotive industry improved in the financial year 2023-24, with an increasing focus towards electric vehicles. The infrastructure and construction
sectors showed resilience with investments, mostly supported by government-funded development projects, including the modernization of existing projects and the construction of new ones. T V Narendran, managing director of Tata Steel, estimates a 10% growth in India’s steel consumption in the financial year 2024-25 due to increasing fresh investments in infrastructure projects. Once these newly invested projects come on stream, India will be able to bridge the import-centric gap. �
Russia’s large steel industry is dominated by emissions-intensive, coal-based blast furnace-basic oxygen furnace (BF-BOF) steelmaking technology. However, the opportunity to switch to low-emissions electric arc furnace (EAF) steel production is growing in response to pressure from international decarbonization initiatives, including carbon tariffs and corporate climate disclosures. Caitlin Swalec*, Hanna Fralikhina**, Zhanaiym Kozybay***
DESPITE this opportunity, Russia continues to cling to dirty steelmaking technologies by refurbishing blast furnaces through relinings, rather than investing in new, low-emissions direct reduced iron (DRI) production (Fig 1).
In 2022, Russia was the fifth-largest producer of steel, with a total annual production of 71.5 million tonnes. Nearly two-thirds of Russia’s steel industry uses the coal-based BF-BOF steelmaking route (Table 1). The country also has smaller amounts of less carbon-intensive steelmaking processes, including scrapbased EAF and DRI-fed EAFs.
The most promising technology for decarbonizing the steel industry is hydrogen-based DRI-EAF production, which can fully replace BF-BOF steelmaking. Currently, Russia’s DRI units operate using fossil fuels, but they could be modified or replaced with hydrogen-based units. (Table 2)
will continue trade with the EU, thus becoming subject to CBAM.
In addition, corporate sustainability reporting is now mandatory in the EU under the Corporate Sustainability Reporting Directive and is set to become mandatory in the United States next year under the Securities and Exchange Commission’s Climate Rule. While these rules mainly target the EU and US-based companies, respectively, they will also affect tens of thousands of companies globally, including exporters from Russia.
capacity represents total nominal capacity. It’s unclear
While Russia’s national plan for decarbonization has been deemed critically insufficient, international pressures from carbon tariffs and corporate climate disclosures mean that the country’s exportheavy iron and steel industry will need to act.
One such pressure, the EU Carbon Border Adjustment Mechanism (CBAM), entered into force in October 2023 and will be in full effect starting in 2026. Unless Russian industry cleans up its production routes, Russian exports to the EU are expected to become more difficult and expensive due to
carbon pricing.
Although Russian steel companies were impacted by EU sanctions applied in response to Russia’s invasion of Ukraine, extended grace periods have enabled Russia to maintain the EU as a main customer of iron and steel product exports.
For example, the latest EU sanctions package extended the grace period for Russian steel slab imports through 2028, rather than the original plan to stop imports in 2024. While the EU market has gradually decreased Russian iron and steel imports, the lack of consistency in restrictions leaves steel trade experts predicting that Russia
Despite the mounting pressures of international decarbonization efforts, numerous reconstruction and modernization works keep Russian coalbased blast furnaces online. While Russia has operated many blast furnaces for decades, regular reconstruction works have renewed the lifecycle of units, positioning the Russian blast furnace fleet to continue operating for many years to come unless there is a change in current operations (Fig 2).
Russian steel companies have investment plans to build new and refurbish old blast furnaces and associated infrastructure, including new units equipped with carbon capture and storage projects (Table 3).
Carbon capture and storage (CCS) has not yet been proven at scale in the iron and steel industry, and even if top capture rates are achieved, CCS is limited in its ability to decarbonize the BF-BOF process. Instead, these investments could be redirected to a transition away from BF-BOF processes and towards hydrogen-based DRI-EAF
steelmaking, creating domestic demand for hydrogen, which the country currently lacks.
Russia’s hydrogen production strategy Russia has a plan to produce 550,000 tonnes of hydrogen per annum (ttpa), but it currently faces major challenges with limited options for export and few incentives to encourage domestic consumption. Russia’s hydrogen strategy initially focused on exports to the EU, but, in the face of energy export sanctions, has pivoted to hydrogen production intended for domestic consumption. Russia’s main hydrogen goal is to become a prominent producer globally.
In the absence of ready customers abroad, Russia now needs to foster domestic demand and has identified the transportation sector as a possible target. But its steel industry also presents a promising opportunity to absorb some of the hydrogen supply.
If Russia reallocated future investments from building new blast furnace units and relining old units to building out more hydrogen-based DRI units, Russia could stimulate its domestic hydrogen demand, while also aligning itself with an increasingly decarbonized global market.
The average emissions intensity for hydrogen-based DRI-EAF steelmaking is less than a third that of coal-based BF-BOF steelmaking (at 0.7 tonnes CO2 per tonne of crude steel, compared to 2.2 tonnes
CO2 per tonne for BF-BOF steelmaking) and approximately half that of fossil gas-based DRI-EAF (1.4 tonnes CO2 per tonne of crude steel).
Russia faces challenges in building its planned DRI-EAF units – a few of them have been postponed (Table 3) due to the exit of Midrex, Danieli, and Primetals from the Russian market, three of the world’s top iron and steel furnace suppliers.
Additionally, Russia’s hydrogen strategy is vague about which type of hydrogen production the country will pursue, meaning it’s unclear exactly how big the emissions savings will be by switching to hydrogen-based DRI.
Grey hydrogen is produced using fossil gas without capturing the greenhouse gas emissions, while blue hydrogen is produced in a similar manner but includes the use of carbon capture and storage technologies (CCS). Green hydrogen is produced via electrolysis with renewable energy sources providing electricity for this process, producing hydrogen with near zero emissions.
Regardless of hydrogen type, the hydrogen-based DRI process still produces steel at a lower emissions intensity than BFBOF or gas-based DRI-EAF steelmaking.
Russian steel giants need to awaken to decarbonization
A few Russian steel giants like Metalloinvest and NLMK experience particularly strong outside pressure to switch to low-carbon
production to accommodate the EU CBAM and increasingly more stringent corporate sustainability reporting requirements.
NLMK accounted for 80% of Russian slab imports by the EU in 2022. NLMK’s process is dominated by coal-based BF-BOF steelmaking. With the grace period for the import of slabs extended from 2024 to 2028, NLMK’s products will be subject to EU CBAM pricing starting in 2026, significantly raising the costs for NLMK if the company does not transition away from BF-BOF production.
Metalloinvest operates both BF-BOF and gas-based DRI-EAF steelmaking plants. In 2021, Metalloinvest accounted for 60% of all EU imports of DRI and, in 2022, DRI imports increased to 1.65 million tonnes. But with the new sanctions package, Metalloinvest can now export only 1.14 million tonnes and 652kt of DRI in 2024 and 2025, respectively.
With diminishing markets, Metalloinvest has an added incentive to transition from fossil gas-based DRI to the cleaner hydrogen-based DRI sooner, since it would face additional profit loss from carbon pricing in the future. The company plans to switch its BF ironmaking to DRI production between 2026 and 2036, while also beginning to implement green hydrogen, though Metalloinvest remains vague about how it will use green hydrogen in its production processes. The company currently uses fossil gas as a reductant to produce DRI, but it can switch to 30%
hydrogen in existing units today. In the short term, the company plans to focus on CCS instead, which is risky given the unproven success of CCS in the steel industry thus far.
Other Russian steel companies impacted by the sanctions, such as Magnitogorsk Iron & Steel Works and Severstal, seem to focus on domestic demand, exports to the Commonwealth of Independent States (CIS) countries, as well as new markets in Asia and North Africa. Nonetheless, the growing global need or decarbonization of steel made its way to their agenda, visible in their decarbonization and GHG reduction
initiatives (Evraz, Severstal, OMK).
Russia’s nascent hydrogen economy could play a key role in decarbonizing its steel industry
The growing need to decarbonize steel, coupled with domestic hydrogen production goals, creates an opportunity for Russia to transition away from emissionsintensive steelmaking toward cleaner production technologies. Switching from blast furnace steelmaking to low-carbon hydrogen-based DRI would create domestic demand for hydrogen, with the added benefit of decarbonizing the country’s
steel industry, thus aligning Russian steel producers with the requirements of CBAM and other international emissions standards.
To realize these goals, further development of DRI technology in Russia is necessary. The Russian government intends to develop its own domestic technology and equipment in hydrogen production, storage, and transportation. As for the proposed new EAF and DRI units, the dissolution of partnerships with Western suppliers and lack of domestic technology to produce the necessary equipment has halted projects. Russian steel companies are
searching for new partners, yet the progress is unknown.
While the cost of hydrogen and switching to hydrogen-based DRI production may represent a significant challenge for Russian
steelmakers, reallocations of the millions of dollars of investments planned for blast furnace relinings and government support and financing of the projects could narrow this gap. Given Russia’s efforts to keep up
with the growth of the global hydrogen market, strategic government support could help to transition the ailing steel industry and build the nascent hydrogen market. (Fig 3) �
BACKGROUND ON GLOBAL ENERGY MONITOR
Global Energy Monitor (GEM) develops and shares information in support of the worldwide movement for clean energy. Follow us at www.globalenergymonitor.org and on Twitter/X @ GlobalEnergyMon.
NOTE:
Global Energy Monitor’s report, ‘Shifting decarbonization to high gear’, published in the April issue of Steel Times International, contained some potentially outdated figures, due to publication delays within the issue. For updated reports and information, please visit www.globalenergymonitor.org
The decarbonization of the steel sector is underway, yet nearterm decisions by investors, companies and policy makers will determine if emissions from steel drop significantly or stay stubbornly high, according to a new report from the Australasian Centre for Corporate Responsibility (ACCR).*
While the steel industry is actively committing to long-term decarbonization, with nearly all the analysed companies setting ambitious net-zero targets by 2050 alongside quantifiable medium-term reduction goals, short-term commitments are scarce – suggesting the steel industry is deferring the majority of its decarbonization efforts to after 2030, raising concerns about its ability to meet net-zero emissions targets and achieve Paris alignment.
According to the report, not all technologies labelled ‘green’ offer the same potential for decarbonization, and steel makers and iron ore companies are distributing investments across technological solutions that vary in their potential to reduce emissions. Investors and companies need to reallocate capital towards genuine green steel processes in the next six years to prevent the lock-in of carbon-intensive steelmaking methods.
Green steel’s moment is here, but there is a critical investment window.
Between now and 2030, 71% of the world’s steelmaking assets will reach the end of their operating lives, necessitating significant investment in relining coaldependent blast furnaces. Reallocation of capital to genuine green steel processes is urgently required to prevent locking-in coalbased methods for the next 20 years – the typical lifespan of a blast furnace.
There is evidence of an appetite to move away from conventional, coal-based production. This includes:
• a surge in market demand for greenproduced steel
• significant investments and advancements in green steel technology
• industry-wide commitments to reduce
Scope 1, 2, and 3 emissions across the value chain
• rapid growth in green steel partnerships, new supportive initiatives, and a rise in green steel procurement policies boosting industry-wide transformation
Eliminating steel’s coal problem
Steel does not have a ‘climate problem’, it has a coal problem. Around 90% of the emissions from steel production are due to the use of metallurgical coal in conventional blast furnaces to produce iron. Eliminating coal-dependent processes from ironmaking is key to steel decarbonization.
To achieve zero emissions steel production, the most energy-intensive part of the steel value chain – ironmaking – is
best undertaken near plentiful renewable energy resources to produce high-value green iron. This strategy would involve a shift where the ironmaking and steelmaking process is decoupled, with green iron production occurring where there is significant renewable energy potential, either close to iron ore mines or within a reasonable distance for transport. The resulting green iron, preferably transported as hot briquetted iron (HBI), can then be moved to locations where green steel is manufactured in EAFs powered by renewable energy or basic oxygen furnaces (BOFs).
Using renewable energy to produce green iron, either closer to iron ore mines or within a reasonable distance, would:
*The full report can be found via this link: https://www.accr.org.au/research/forging-pathways-insights-for-the-green-steel-transformation/
• capitalise on the availability of renewable resources in or accessible to ironrich regions
• create logistical and economic efficiencies to help facilitate green iron offtake agreements
• situate green hydrogen production at the point of iron reduction, circumventing the complexities associated with shipping hydrogen.
Capital allocation toward innovative, green iron technologies in regions with abundant renewable energy resources is imperative to realising this shift.
Differing decarbonization potential
Advancements in technology and production innovation are enabling steelmaking to become less carbon-
intensive during every stage of the steelmaking process. Yet the emissions reduction potential of each process differs significantly.
• Green hydrogen-based processes, supported by renewable energy, are the most promising for emissions reductions.
• Gas-based direct reduced iron and other lower-emission technologies offer some emissions reductions in the near term, yet to avoid reinforcing fossil fuel reliance, these should not be adopted as permanent solutions.
• Carbon capture utilisation and storage or offsets are looking less cost-effective, with significant uncertainty around viability and effectiveness.
Terminology including ‘net-zero’, ‘carbonfree’, ‘green’ and ‘low-emissions’ are all
used interchangeably, which can lead to confusion and misinterpretation. Without clear definitions, it becomes challenging to measure and compare the environmental impact of different steel production methods accurately.
The global iron and steel market is valued (by revenue) at approximately $167 trillion, and is expected to reach a market size of $2.25 trillion by 2030, with a compound annual growth rate (CAGR) of 3.7%.
Fairfield Market Research expects the market size for green steel to increase, projecting a CAGR of over 122% from 2023-2030. In this context, the shift towards green steel production and the potential for higher prices in green steel sales presents a major opportunity for companies and their investors.
As EAF technology becomes more prevalent, the demand for high-quality steel, particularly advanced high-strength steel used in automotive applications, is expected to triple by 2030. In the USA, 71% of steel is now produced using EAFs, utilising scrap steel as the primary input. China anticipates it will grow its scrapbased EAF production share from 12% in 2022 to 34% by 2030.
Customers are demonstrating a willingness to bear higher prices to ensure low-emissions steel:
• Swedish steelmaker H2 Green Steel has a 25% premium on its steel.
• SSAB, also a Swedish steelmaker, estimates the gross premium on steels with almost zero CO2 emissions will be around EUR 300/tonne ($325) by 2026, in line with the full implementation of the EU’s Carbon Border Adjustment Mechanism (CBAM).
• Japan’s JFE Steel Corporation currently charges a 40% premium on its mass balance approach, which allocates emissions reductions to its specific steel product, “JGreeX”.
Given the limitations of mass balance’s material impact on emissions reduction, it would be optimal for any revenue made to be reinvested into authentic green steel production.
Government policies are also shifting to drive green steel demand, with many nation states, including almost all OECD countries, enacting green public procurement (GPP) programmes and other policies.
Green steel off-take agreements
Off-take agreements have become crucial mechanisms for locking in green steel demand and ensuring a stable supply chain.
Various sectors, including transportation, automakers, and construction, have shown significant interest in procuring green steel using these agreements, demonstrating the depth and breadth of consumer demand.
• Mercedes-Benz has partnered with H2 Green Steel (H2GS) to secure around 50kt of green steel per year for its manufacturing plants in Europe and North America.
• Automakers like Volvo and BMW have entered agreements with H2GS, SSAB and HBIS to obtain green steel and lowemissions steel.
• Cargill has signed a multi-year offtake agreement with H2GS. This agreement not only secures a supply for Cargill but expands the availability of green steel to markets beyond the European Union.
• IKEA’s agreement with H2GS for the delivery of green steel to be used in warehouse racking from 2026 onwards highlights the demand from the retail and logistics sectors.
The prevalence of green steel offtake agreements within European companies highlights the region’s proactive stance on decarbonisation, supported by robust financial structures and policy settings. It also highlights the need for wealthier nations, especially those with historic contributions to carbon emissions, to take the lead and invest in technologies with green potential.
ACCR reviewed 16 steelmaking companies, collectively representing 27% of global steel production (521 Mt) and 23% of global steel sector emissions.
Of these 16 companies, 94% have ambitious net-zero-by-2050 targets, alongside quantifiable mediumterm reduction goals, but short-term commitments are scarce. While this shows that steel decarbonization is a real industry concern, it also suggests there is a challenging path ahead to deliver the rapid and substantial emissions reductions the companies’ targets require.
• 50% of the projects steelmakers have invested in have significant emissions reduction potential, while 40% of the projects still focus on solutions with limited
potential to reduce emissions.
• Less than 20% of companies have net-zero emissions targets that explicitly encompass Scope 3 emissions, raising concerns about the industry’s alignment with the Paris Agreement and global decarbonization goals.
• None currently verify whether their decarbonization targets are in alignment with the Science Based Target Initiative’s (SBTi) Steel Science-Based Target-Setting Guidance, and at the time of the report’s publication, only two plan to do so in the future.
ACCR reviewed four iron ore companies – Rio Tinto, Fortescue, BHP and Vale –representing 41% (1.1 Gt) of global iron ore production. The collective Scope 3 emissions of these four companies represent 54% of the global steel sector’s emissions.
These scope 3 emissions, predominantly from steelmaking, also account for more than 95% of the four miners’ total emissions footprint, and pose a unique emissions reduction challenge that is both separate to and enmeshed with the challenges steelmakers are facing.
Like the steel companies ACCR reviewed, the four miners are showing a mix of caution and ambition in their climate targets and decarbonization investments, collectively pursuing 64 steel decarbonization projects that span an array of technologies with varying degrees of emissions reduction potential.
Furthermore:
• All are directing substantial capital expenditure towards operational decarbonization by 2030. However, all need to improve disclosure of their expenditure, which should include detailed breakdowns of capital allocations toward steel decarbonisation projects, including forward-looking allocations for the next three years.
• Market certainty would be enhanced if all four companies commit more specific funding towards steel decarbonization –the largest portion of the miners’ respective emissions profiles. This would help provide clear signals to shape policy and guide investments.
While Europe is currently at the forefront of technological and product innovation, the majority of steelmaking capacity development occurs in Asia, particularly in
China. Despite a noticeable shift towards EAF production in China, the overall pace of decarbonization in Asia is inconsistent with global decarbonization goals.
For example, India’s expansion of coal-based blast furnace capacity would potentially quadruple the country’s steel emissions between 2021 and 2050 –jeopardising its 2070 carbon neutrality target.
Japan and South Korea, with limited natural resources, rely heavily on imports of raw materials, complicating their green steel transition. Their challenges are exacerbated by ageing infrastructure, high energy costs, and reliance on thermal power, hindering renewable energy integration for steel production.
On the other hand, the EU and USA, leveraging their industrial legacies, lead in steel innovation and sustainability. The EU’s stringent regulations – including its Carbon Border Adjustment Mechanism (CBAM) and renewable resources drive its green practices, while the USA’s abundant scrap supply and the Inflation Reduction Act (IRA) are catalysing a shift towards technologies with low-carbon potential.
Policymakers can hasten green steel’s trajectory
While policy initiatives like the CBAM and IRA, alongside green public procurement policies and international agreements like the Paris Agreement, set solid frameworks for incentivising clean energy use and penalising carbon-intensive production, they address only a portion of the global equation.
There is an immediate need for policy initiatives that help facilitate access to renewable energy and quality green iron for EAF-based production globally, especially in emerging markets, where gaps in policy and regulatory settings are creating distinctive challenges for the steel industry as a whole. The absence of comprehensive carbon pricing mechanisms outside of the EU and parts of North America is one such gap. Although China has announced its emissions trading scheme, its impact and breadth in driving significant steel decarbonization is yet to be fully seen. This disparity in carbon pricing creates unequal pressures for steel producers worldwide, and can lead to ’carbon leakage’, where production moves to regions with less stringent regulations, undermining global decarbonization efforts.
Furthermore, the financial incentives and support for transitioning to green steel technologies, like those offered by the IRA, are lacking in many steel-producing nations. This deficiency impedes the adoption of EAF technology and the development of infrastructure for renewable energy and green hydrogen production, particularly in countries that could most benefit from these solutions.
International collaboration and funding mechanisms intended to address these gaps are still in their infancy. For example, while the Industrial Deep Decarbonisation Initiative (IDDI) aims to stimulate global demand for low-carbon steel, the effective implementation of supportive policies and investments in necessary infrastructure across major steel-producing regions remain inconsistent.
The way forward Investors have five key levers available to them that can help ensure that a decarbonized steel sector is a reality by 2050.
1. Reallocate capital away from coaldependent blast furnaces and towards processes with high decarbonization potential.
• Engage with companies, using escalation where necessary, to ask for disclosures of transition pathways to lowemissions iron/steelmaking, along with a detailed outline of the capital allocation for the transition.
• Direct investments towards regions lagging in green steel production capability, specifically to accelerate decarbonization efforts.
• Engage with policymakers directly and indirectly to encourage positive policy settings for steel decarbonisation.
2. Increase renewable energy capacity
to enable the green electricity and green hydrogen required for low-emissions steelmaking.
• Fund renewable energy projects, particularly in developing countries with steelmaking operations.
3. Work towards standardised, comprehensive, and robust emissions disclosure across the industry.
• Engage with companies to ask for transparent disclosures.
• Integrate emissions data and trends into investment analysis, so shareholders can invest in companies that demonstrate transparency, lower carbon intensities and a strong commitment to reducing absolute emissions.
• Update financial risk assessment models to accurately incorporate the physical impacts of climate change, ensuring investment strategies adequately address climate risk.
4. Catalyse immediate action towards decarbonization with short-term climate commitments that are ambitious and science-based.
• Engage with companies, using escalation where necessary, to ask for the disclosure of short-term climate targets and alignment with the Science-Based Targets initiative (SBTi).
5. Ensure that the transition of iron and steelmaking to green processes is just and equitable, supporting communities and workers.
• Hold companies to account on providing a just transition timeline, clear framework, and outcomes for impacted workers.
• Incorporate just transition metrics and information into investment analysis and decision-making.
• Advocate for policies promoting a just transition �
IN early March, I found myself onstage at SXSW – a culture-moving conference that, in the organizers’ words, “proves that the most unexpected discoveries happen when diverse topics and people come together”.
My mission was in line with that. As a steel industry executive, I was asked to moderate a panel featuring Sachin Desai, general counsel of nuclear fusion startup Helion Energy, April Salas, director of global sustainability policy at Microsoft, and Dr. Kathryn Huff, assistant secretary for nuclear energy at the US Department of Energy.
Clean energy is an issue of ‘urgent concern’ for Nucor, as well as the wider steel industry, says Tabitha Stine*, who in this feature covers the four major topics of a recent SXSW panel focused on the future of clean energy.
How did I wind up in that kind of company?
The answer says something about the direction the steel industry needs to take –why innovation is essential – and the paths that will take us where we need to go.
Focus on energy
The title of the panel was, ‘Powering the Future of Clean Energy.’ That is an issue of urgent concern to Nucor, as it should be for the steel industry as a whole. Why the focus on energy? Anyone
* General manager of energy solutions services, Nucor
involved in the industry is already familiar with the issues, and with the stakes. Traditionally manufactured steel – that is, steel made via extractive processes – has a massive carbon footprint. According to the World Steel Association, each ton of steel produced by extraction produces, on average, 2.33 tons of CO2. That is – if you’ll pardon the double meaning – not sustainable. It underscores the reasoning behind Nucor’s longstanding commitment to circular steel. By relying on recycled versus extracted steel, and by replacing the
blast furnace with an electric arc furnace, we have been able to reduce the CO2 output per ton of steel to 0.76 tons – one third the global average for extractive steel.
We are now extending the approach to include other forms of metal recovery – our advanced metal recovery plant in Bushnell, Florida makes us effective in capturing metals such as aluminium, copper, and stainless steel as we work to be, not only America’s largest recycler, but a leader in enhancing circularity for all metallics.
We firmly believe that these efforts – our circular steel process, related metal recovery processes, and their positive GHG impact
– are essential in a world where we are a significant component of customers’ Scope 3 emissions, and where they are striving just as we are to achieve the Science-Based Targets initiative’s (SBTi) 2030 global average temperature targets and 2050 netzero goals.
But like every innovation, ours raises new challenges. Energy is among the most significant. All roads lead to energy. Our circular steel process is superior to extractive steelmaking in terms of its carbon footprint as well as its avoidance of the negative environmental impacts of extraction itself. But circular steel demands large-
scale electric power. Nucor is the largest electricity customer in nearly every state in which we operate. Data sourced from the World Steel Association establishes that producing steel in an electric arc furnace, as we do, requires approximately 400 kiloWatt hours per ton. Nucor is planning steel production facilities that will require 500 megaWatts of electricity – enough to power 400,000 homes.
The need to provide for energy demand through clean power comes into even clearer focus when we consider the steel requirements – and the potential related carbon impact – of renewables themselves.
Simply on a materials level, solar arrays and wind turbines require large quantities of steel. It’s been noted that building enough wind turbines to meet 2050 net-zero targets will require 1.7 billion tons of steel – enough to build the Golden Gate Bridge 22,000 times over. Add to that the steel that will be needed for green buildings, EV charging facilities and 21st century transportation systems, and the need is clear – carbon-free electricity, at industrial scale and at industrial levels of reliability – is essential to our mission and our planet’s future. We must drive down the carbon content for these projects. Or, as we put it –the green economy will be built with steel, and the steel it’s built with matters.
Finally, our commitment to achieving net zero in Scope 1, 2 and 3 emissions means that our energy challenges must be met through collaboration with our supply chain partners and our customers.
For all those reasons, Nucor is laserfocused on energy. The future of our industry and the future of our planet depends on it.
Nucor’s energy priorities have sparked new partnerships
sufficient to power one of our new plants. Our $35 million investment in Helion is one of several we have made in order, first of all, to solve our own power needs – investments that include solar power as well. Thanks to these partnerships, we are on our way to helping decarbonize the industrial sector.
Microsoft represents the demand side of our partnerships – a logical next step as we work to meet our own energy needs, and then look beyond to find new applications. Microsoft and Google are major offtakers – that is, consumers of power. Each relies on data centres that consume massive
All of which explains how I found myself onstage with representatives of a fusion pioneer, a global organization that consumes dramatically increasing levels of power for its data centres, and a major government organization that supports the energy transition.
All three are central to our mission and to our net zero commitments.
The fact that Microsoft and Helion are Nucor’s partners underscores the centrality of energy to both our operations and our planning.
Helion is one of Nucor’s major energy partners – we are collaborating with them on a project to meet our clean energy needs by developing a 500 MW fusion reactor –
amounts of power – enough to strain the capacity of the US power grid. The boom in AI – in which both are major players – will only intensify the demand. In 2023, the US Federal Energy Regulatory Commission predicted that demand on the grid would grow 81% in the next five years – double the previous year’s forecast. Microsoft and Google are natural collaborators on the power solutions we are developing – new nuclear, next-generation geothermal, clean hydrogen, long-duration energy storage and more. Without that added clean energy capacity, their enterprise value is at risk. Beyond the conversation at SXSW, Nucor
is working with these partners to develop new business models and aggregate their demand for advanced clean electricity technologies. Pooling demand will enable other large energy buyers to access larger volumes of carbon-free electricity from multiple power plants, creating efficiencies and reducing risk.
The good news is that all of these can potentially be developed in off-grid, site-specific applications, shortening transmission distances, enhancing reliability, and reducing cost. Helion’s fusion reactor is one such off-grid, on-site solution. Here, the value of Nucor’s energy projects to major offtakers becomes clear. The clean power solutions we develop to drive circular steel production can naturally be applied to other off-grid applications such as data centres.
Dr. Huff represents the necessary support that government must provide – as in fact it is. Funding and research support can greatly accelerate the development of nextgeneration solutions such as small-scale fusion reactors and their rapid evolution to industrial scale.
At SXSW, a wide-ranging discussion of energy issues
Our discussion was far ranging. We covered four major themes – the role of the public sector in accelerating climate transition and achieving Paris targets, the role of the private sector in achieving the same goals, the role of clean energy in a net zero future, and how clean energy should happen.
Among the highlights of the discussion:
• The need for industrial-scale, always-on power. “We tend to think of energy in terms of the ‘duck curve,’ with peak demand in the morning and the evening,” said Microsoft’s April Salas. “But our loads are not like that – they are consistent [throughout the day],” she said. That explains Nucor’s interest in small-scale nuclear power, which unlike wind or solar, is not subject to variation because of peak wind or sun times.
• The scale of the need. “Helion will build a 500MW fusion reactor for Nucor at the turn of the decade,” said Desai. “It will be about 30,000 square feet – a few football fields – and capable of powering about 400,000 homes. But you can look at that the other way – the power needs of 400,000 homes are equal to one Nucor steel mill. And that’s a fraction of what will
be needed for data centres. That’s the scale of the need.”
• Accelerating the transition. “It’s the government’s job to do a lot of things,” said Huff, “to take on risks industry can’t, take on capabilities that industry can’t or shouldn’t, and cost-share with companies for technology development and maturation together with the national laboratories. There are reactors available for testing at the national labs… we are also there to help partner universities on high-risk projects – some will fail – that industry can then commercialize.” The Biden-Harris administration has supported clean energy through policy, but more is needed, she said – including plans for the mass regulation of fusion reactors.”
• Taking advantage of existing infrastructure. “The administration pursues economic justice in the energy transition,” said Huff. “That drives policy goals, including seeing the opportunity in the transition from coal communities to nuclear communities. Some coal plants are destined to close; many are recently retired. How many are suitable for nuclear sites? It’s about 80% of coal plants, which [if converted to nuclear] would be in the 250GW range.” Converting coal plants to nuclear would create jobs, many of them for coal plant workers with skills in boiler making, welding and steam systems that are directly transferrable, Huff said. “By taking this approach we can make building a nuclear power plant 35% cheaper – that’s how we make it more equitable, by locating it in coal communities that are most suited to nuclear energy.
• The scope of the opportunity. “All communities have an energy problem,” said Salas. “The goal is to bring cheap abundant energy to America. Industry wants to build but it’s capped by energy. If you can overcome that, then you can eliminate the barrier. America can win – not just Silicon Valley.”
Even this brief summary of the issues we’re exploring should make it clear Nucor today is focused on energy with the same intensity that we bring to bear on circular steel.
I’ve described the reasoning that brought us to this stage – the ‘why’. But what about the ‘how’?
The realization – that a focus on energy
solutions could create massive value for a new array of partners and address a pressing global need – was the natural outcome of our culture.
Culture is our innovation driver. It is grounded in two things – relentless customer focus and a consultative approach.
In the context of steelmaking, one of the best examples that comes to mind is our work with a major auto manufacturer on an EV manufacturing project – one that we supported with a premium lightweight steel that saved 20% in vehicle weight, contributing directly to range and performance.
We assigned a dedicated gigafactory to support the project. But challenged by the manufacturer’s rapidly escalating schedule, we then chose to draw on the capacity of another plant – one that we had scheduled for a planned outage. We changed the outage schedule – making the plant’s capacity and the labour of an additional 1,000 of our people available to meet the timeline. Which they did.
Our ongoing support for that customer includes thousands of tons of sustainable steel for autos, tens of thousands more for battery facilities, and the Scope 3 benefits of our circular steel process to their carbon targets.
Seen in this light, our commitment to energy is clearly the logical next step in our consultative, customer-driven culture.
As we invest in our own energy solutions, it is only natural that we would make them available to our current customers – and to a new array of partners. Microsoft and Google are cases in point.
So far, I’ve talked about our company. But what does all this mean for the steel industry as a whole? What lessons do we have to offer?
The fundamental lesson is the industry must change with the times and find new ways to add value.
The days are past when the steel industry could get by delivering a commodity – or escape commoditization simply by focusing only on the quality of the delivered material. Solutions must be the new focus.
In a challenged world, steel is essential. It must also be part of the solution. And what is true of steel is also true of the steelmaker.
That is the approach that put Nucor onstage at SXSW – and that can take other steelmakers, and the industry, into the future. �
With pushes from buyers, consumers, government policies, and international treaties, the North American steel sector is driving momentum in its bid for a decarbonized steel industry.By Myra Pinkham*
GIVEN the universal desire for lower emissions and greater sustainability, American steelmakers, as well as steelmakers throughout the world, continue to invest in their operations to find ways to make their products ‘greener’ or lowcarbon.
And while they are generally making these moves in the name of being more environmentally friendly with lower greenhouse gas (GHG) emissions, Philip Gibbs, an equity research analyst with KeyBank Capital Markets, said that he believes that their motivation goes beyond that, stating, “While sustainability is a nice theme, it typically goes hand-in-hand with lowering their costs and being more globally competitive,” as well as giving them the ability to get financing from companies that have stated environmental, sustainability and governance (ESG) goals.
Philip Bell, president of the Steel Manufacturers Association (SMA) agreed. “Most companies realize that their overall
financial performance will be better if they embrace a circular economy approach to steel production, where they are reusing and recycling steel and producing steel with lower emissions,” he said. “Investors are happy, their customers are happy and the public is happy when they do.”
While ‘green steel’ is clearly an increasingly used buzzword, Kevin Dempsey, president and chief executive officer of the American Iron and Steel Institute (AISI), pointed out that it doesn’t have a clear definition, with different meanings to different stakeholders, different companies and different countries and governments.
Because of that, Adina Renee Adler, executive of the Global Steel Climate Council (GSCC), whose steel climate certification standard was written to be a straightforward, transparent and sciencebased approach to get this steel into the market, said that it is better to refer to it as either low-carbon, or lower-carbon, steel.
Adam Rauwerwdink, senior vice president*North America correspondent, Steel Times International
of business development with Boston Metal, a company that is focused upon developing technologies to transform how steel and other metals are produced, said that the US steel industry has been moving quickly to make lower-carbon steels with virtually all steelmakers having announced sustainability targets.
He said that with certain net-zero (or nearly net-zero) targets being pursued universally, and to varying degrees globally, steelmakers have already been pursuing an assortment of solutions to at least get to their 2030 targets, although he said it remains to be seen how they will achieve their 2050 goals.
Dempsey pointed out that with the investments that steelmakers have already made – and continue to make – in their operations, the US has the lowest carbon dioxide emissions per ton of steel produced compared to other major steel-producing countries, with the average global steel emissions being about double that as per
which is in the process of acquiring US Steel, is replacing some of its blast furnaces in Japan with EAFs. But he said that some other countries, such as China and India, have been slower in making these kinds of changes.
opportunities than challenges to making lower-carbon steels, and that is where the industry is headed, GSCC’s Adler said, explaining; “We have to do that. The effects of climate change are everywhere and are high in the consciousness of the global community. And because the technologies are there to make this happen – many of which are at commercial scale with others still in development – demand is growing.
One big push is coming from all the recent investments in electric arc furnace (EAF) flat roll mills, Bell said, given that EAF steelmaking is seen as an existing, proven, highly commercialized way to make lower emissions steel.
Gibbs said that at the same time, many integrated sheet and plate steelmakers have been migrating bit-by-bit from blast furnaces to EAFs. This has not just been the case in the US, but also elsewhere in the world. In fact, he noted that Nippon Steel,
AISI’s Dempsey pointed out that US steelmakers have also been making significant investments to increase their use of direct reduced iron (DRI) and hot briquetted iron (HBI), which can lower emissions for both integrated blast furnacebasic oxygen furnace steel mills and EAF steel mills. Also, he noted that a number of new iron and steel facilities are being designed, with some recently built, with a goal to be hydrogen-ready once clean hydrogen is available at scale.
While still in a very nascent stage, SMA’s Bell noted that many hydrogenrelated investments are being aided by grants from the US Department of Energy (DOE) to help build a number of hydrogen hubs around the US. He explained that, given that hydrogen is a very volatile substance, before it can be used to produce lower carbon iron or steel there needs to be a distribution network in place that is strategically located near to the steel mills that will be using it.
Recognizing this, some companies, including ArcelorMittal North America, have been looking to produce line pipe that meets the American Petroleum Institute’s requirements to transport hydrogen. Reportedly much of the pipe currently in operation isn’t wide enough to facilitate large-scale hydrogen transportation.
“Additional innovative technologies are also continuing to be developed,” Dempsey said, noting that this is in part through investments by American steel producers in partnership with the DOE’s Industrial Demonstration Program, which is funded in part by the bipartisan IIJA infrastructure bill and the Inflation Reduction Act (IRA). This, he noted, includes projects involving the development of clean hydrogen
technologies and other breakthrough steelmaking processes, as well as for clean electricity projects, including those related to nuclear technologies, carbon capture and power utilization and storage.
For example, Cleveland-Cliffs will potentially get grants from the DOE totalling up to $575 million for two projects that it is undertaking. That would include $500 million to help defray the cost of its $1.3 billion project to replace the blast furnaces at its Middletown Works, with a hydrogen-ready DRI plant, as well as two electric melting furnaces (EMFs), giving it the ability to feed the hot DRI directly into the EMR, creating a pig iron equivalent that could be fed into its existing basic oxygen furnaces to be processed further.
Lourenco Goncalves, Cliffs’ chairman, president, and chief executive officer, told investors during its first quarter earnings conference call that once this project is full operation in 2029, Middletown will be the lowest cost steel producing facility in the US. He said that it is uncertain if it will need in the short term to use natural gas, but by the early 2030s it will be 100% hydrogenpowered.
Cliffs is also expecting to be awarded $75 million from the DOE to replace two of its existing natural gas-fired hightemperature slab reheat furnaces at its Butler Works with four electric induction reheat furnaces, which Goncalves said will reduce the carbon emissions there, improve its productivity, and enhance its production of grain-oriented electrical steel (GOES), which he said was at risk under the initial draft proposal of the DOE’s new emissions standard.
Bell noted that several other steelmakers are also being considered for grants under this DOE programme, including SSAB, which he described as a pioneer and leader in fossil-free steelmaking. The steelmaker has been selected to receive up to $500 million from the DOE programme to be used to fund both the potential construction of a HYBRIT® manufacturing facility capable of producing fossil-free iron by using green hydrogen instead of fossil fuels as well as the potential to expand the capacity and capabilities of SSAB’s steel manufacturing operations in Montpelier, Iowa, including increased use of renewable energy.
Chuck Schmitt, president of SSAB Americas, said this initiative would enable the company to both expand its sustainable
Steel Times International is the key publication for the steel market, reporting on iron and steel making issues from all corners of the globe.
The Steel Times International Directory is the essential guide to steel manufacturers, producers, suppliers of plant equipment and services to the steel industry. Order your print or digital copy priced from £105 or subscribers.
Packed with information on the steel industry and continually updated with news for steel professionals, www.steeltimesint.com features special articles and interviews with leading industry gures.
A round-up of the top news stories is sent to more than 7,000 industry professionals each week. You can register online to receive the weekly newsletter and keep up-to-date with the latest news from across the steel manufacturing industry. www.steeltimesint.com/e-newsletter
domestic steel product supply chain and to advance its US renewable energy transition objectives.
Boston Metal is being considered for a $50 million grant for its project to build a new chromium metal facility in Weirton, West Virginia. Rauwerwdink said that the chromium metal produced there will be used for the anodes that it uses in its new molten oxide electrolysis process. The company is currently looking to license this to steelmakers and other metals producers to produce lower carbon products.
Boston Metal already has a plant that it owns itself under construction in Brazil that will be using technology to make metals such as tin, niobium and tantalum, while licensing the technology (a brand-new high temperature metallurgical furnace that uses iron ore as its input) to steelmakers.
“When deployed at blast furnace scale, this could help to fully decarbonize the steel industry,” Rauwerwdink said, as this electrolysis process would replace the integrated steelmakers’ blast furnace and basic oxygen furnace with a high temperature furnace. “It involves having iron ore going in and high purity liquid iron going out,” while everything downstream will stay the same, but there will be no embodied emissions from the production process as long as clean electricity is used as the power source.
He said that another advantage with this new technology is that there is flexibility as to the grade of iron ore used. Unlike with DRI, which needs premium iron ore, the steelmaker could use the low grade ore that they are currently using in their blast furnaces.
There have been a number of other steelmakers that are benefiting from federal monies, which Gibbs said is resulting in them announcing some projects that might not otherwise be considered because they are too expensive. “However, some other companies have been able to pay for some of their projects out of their own pockets – partly because of the benefits they have gotten from things like tariff monies.”
There have also been some co-operative
agreements. For example, US Steel recently signed a definitive agreement with CarbonFree to use that company’s SkyCycle technology to capture as much as 50kt/yr of carbon emissions (the equivalent of the emissions produced by 12,000 passenger cars) at US Steel’s Gary Works plant in Indiana. The SkyCycle plant is expected to be up and running by 2026.
Another thing some steelmakers have pursued is the development of new lowcarbon steel grades. One example of that
is SSAB Fossil-free® steel which is produced through its HYBRIT™ technology and emits water instead of carbon dioxide. Another is Nucor’s Econiq™-RE, which Leon Topalian, the company’s president and chief executive officer, said is made with 100% renewable energy and has a GHG intensity that is half that of steels produced via blast furnaces. He noted that in March Nucor signed an agreement with Mercedes Benz to supply this steel to the automaker for vehicles produced at its Tuscaloosa, AL, manufacturing plant.
SMA’s Bell pointed out that steelmakers are also using more renewable energy, whether wind, solar, hydropower or even nuclear power. “For example, one of the largest solar arrays in the country was built by Evraz North America in Pueblo, Colorado. Also, Commercial Metals is using solar at its new facility in Arizona and Nucor’s Sedalia, Missouri, facility uses wind turbines.” He noted that Nucor is also pursuing small modular nuclear reactor technology.
This is a two-way street, Dempsey said, maintaining that steel is the only material that is essential to all these clean energy technologies.
“The North American Market has already accomplished a lot in its push to be greener with about 70% of its steel already being low carbon,” GSCC’s Adler declared. “We now have to see that same kind of success in the rest of the world,” she said. “While Europe has been improving, Asia still has a long way to go, but with us having the technology and with new technologies coming onboard, everyone is hopeful that we will get there.” �
Furnaces International is an English language journal dedicated to the production of rnaces. Circulated each quarter in March, June, September and December.
The Furnaces International Buyers’ Guide is the essential guide to rnace manufacturers and suppliers of rnace equipment and services to the industrial heating/process industry. Providing comprehensive company listings, product information and key contact details, the guide is published in December each year.
Packed with information on the rnaces industry and continually updated with news for professionals, rnaces-international.com also features special articles and interviews with leading industry gures.
A round-up of the top news stories is sent to more than 44,000 industry professionals every month. You can register online to receive the weekly newsletter and keep up-to-date with the latest news from across the rnaces manufacturing industry. Sign up at rnaces-international.com
Aluminium International Today (AIT) is the leading bi-monthly English language journal dedicated to all sectors and regions of the international aluminium manufacturing and processing industry. Subscribe to the free weekly newsletter at aluminiumtoday.com
Glass International o ers readers the latest news from across the hollow, container, flat, and speciality glassmaking industry and is the o cial media partner for Glassman events. Subscribe to the free weekly newsletter at glass-international.com
Steel Times International is the key publication for the steel market, reporting on iron and steel making issues from all corners of the globe. Subscribe to the free weekly newsletter at steeltimesint.com
Coal petrography has become a useful technique to establish the formulation of a blend of coals to predict the quality of the resultant coke. B Ghosh1*, B K Sahoo1, B Chakraborty1 & A K Varma2
THE coking behaviour of coal is a significant factor in the selection of coal for metallurgical use and in other industries. The carbonization behaviour mainly depends on the properties of coal rank (i.e. coal type from peat to anthracite), petrography, composition, ultimate composition and rheology. It is generally established that a blend containing optimal reactive components produces a coke of maximum strength. The coking properties of coal not only depend on the composition of the macerals (analogous to the use of the term ‘mineral’ in rock) but also on the way in which these are distributed to form preferential associations of microlithotypes (the microscopic distribution of macerals).
In this article, the distribution of microlithotype macerals in coal samples is analysed and correlated with the coal properties and coke quality. The distribution of bi-maceral and tri-maceral microlithotypes (vitrinertite, duroclarite and clarodurite) in coal samples play an important role in coke quality. The inter-growth of vitrinite and inertinite as vitrinertite microlithotypes indicates a significant role in coke quality. Therefore, maceral and microlithotype distribution analyses are important in determining the caking property for coke quality.
The relationship between the plastic range of coal with the proposed petrographic caking index, (PCI) has been studied. The distribution of mono, bi and tri-maceralic in coal has been found to influence the coke cold strength (M40 and M10 indices) as well as hot strength properties (CRI and CSR). The microlithotype coke strength index (MCSI) relationship has been linked to the Coke Reactivity Index (CRI) and separately, Coke Strength after Reaction (CSR).
Coal is formed by decomposing plants
consisting mainly of carbon, hydrogen, oxygen, nitrogen, and sulphur. This vegetable matter is transformed into peat, lignite, sub-bituminous, bituminous coal, semi-anthracite and anthracite of increasing rank or maturity at different biochemical and geochemical coalification stages.
In this study, representative indigenous coal samples from India, and imported coking coal have been investigated. The indigenous coking coal was beneficiated by wet media density separation to differing coal fractions to reduce the ash content to that of imported coking coal. Four different sets were selected based on the mean of the maximum vitrinite reflectance of the sample. The details of coal characterization, including microlithotype distribution, were carried out. Experimental coke was produced as a 10kg charge in an electrically heated pilot coke oven at RDCIS SAIL Ranchi. The coke characterization, including cold strength property (M10, M40) and hot strength property (CRI and CSR), were determined. The correlations between microlithotype distribution and maceral composition with the caking property of coal and coke quality were observed. A review of the literature indicated that this was a topic with few published papers.
The coking behaviour of coal is an essential factor in selecting coal for metallurgical use. The carbonisation behaviour of coal mainly depends on its rank (ranging from peat to anthracite) and petrographic composition (Rentel et al 1987). The ultimate composition for coking coals in respect of carbon, hydrogen, oxygen, nitrogen, and organic sulphur have previously been published (Jasienko et al 1978). Vitrinite and liptinite macerals (the organic component analogous to the use of the term ‘mineral’ in rocks) are reactive and part of the coking process (Hacquebard
et al 1958; Alpern et al. 1966; Stach et al 1982). The associated macerals control the behaviour of liptinite (finely-ground and softened remains). The vitrinite macerals become fused by the product generated on the decomposition of associated liptinite. The products generated on the decomposition of the alkanes, sporinite and cutinite within liptinite does not affect inertinite (partially oxidised organics) (Stachet et al. 1982). It is assumed that inertinite macerals are largely infusible (Stach et al. 1982). The behaviour and reactivity of inertinites has interested many scientists (Ammosov et al 1957; Schapiro et al 1961; Okuyama et al 1970; Nandi and Montgomery 1975; Mackowsky et al 1977; Diesel et al 1983; Varma et al 1991; Varma et al 1996a, b; Varma et al 1997, Varma, 2002). Thermogravimetric analysis was probably applied for the first time as a tool for predicting coal’s coking and caking behaviour (Varma. 2002). During carbonization, two physio-chemical changes of coal, such as thermal decomposition and secondary de-gasification, were observed. In this feature, the authors intend to characterize various types of coal, their blends, and resulting cokes to develop an optimal coke-making model.
The quality of coke affects the performance of the blast furnace. In turn, coke quality depends on coal properties, coal charge granulometry, and carbonization conditions. Coal properties include the petrographic properties such as maceral composition and rank; the rheology properties such as maximum plasticity, temperature range of plasticity, contraction, dilatation, free swelling, and the Roga index; the chemical properties such as moisture, ash yield, volatile and sulphur content and the size analysis of coal.
The coke properties comprise of size
1 Coal Carbonization Group, Research & Development Centre for Iron & Steel, SAIL, Ranchi, Jharkhand, Pin-834002, India
2 Coal Geology and Organic Petrology Laboratory, Department of Applied Geology, IIT, Indian School of Mines (ISM), Dhanbad 826004, India
*Corresponding author: B Ghosh: bablu.ghosh@sail.in
analysis, cold strength (M40, M10), and hot strength (Coke Reactivity after Index: CRI, Coke Strength after Reaction: CSR) as well as structural properties such as coke structure and texture. Structural properties consist of the porosity, pore-cell wall, and pore sizes, while texture includes the carbon forms in the coke. The degree of heterogeneity in a microlithotype is also important in its technological behaviour, particularly in carbonization. The microstructures formed by individual coal grains are directly related to their microlithotypes. The behaviour of microlithotypes during carbonization is the behaviour of macerals of which they are composed, especially when the microlithotypes consist mainly or wholly of one maceral. In those which contain two or more macerals, some interaction between macerals occurs and hence the coke from such a mixture of macerals differs.
In the present work, an attempt has been made to study the washability characteristics of different Indian coals by carrying out a float-and-sink analysis. A total of five coal samples were collected from different coalfields using the channel sampling procedure. The coal ash yield was more than 25%.
An analysis of the microlithotype
Table 1. Washability study of indigenous coal measured by the mean max vitrinite reflectance.
distribution of coal samples was conducted. For this, 12 samples were prepared, five of indigenous coals, six of imported coking coals, and one blend of indigenous and imported, selected from four differing ranks.
The indigenous coal samples were beneficiated in the laboratory by the
‘Float and Sink’ method selecting specific gravities of 1.30, 1.35, and 1.40 to achieve below 10% ash yield content. Tetrachloro-ethylene and toluene were used to prepare each density media. Washability of the indigenous coals was difficult due to the presence of the mineral origins and distribution within the coals. The yield of coal achieved after washing was 20%-25%. The mean max vitrinite reflectance (MMR) of the washed coals was measured (Table 1).
Detailed characterization of the coal samples was conducted. The individual coals constituting each blend were weighed and mixed thoroughly to produce the specified blend composition shown in Table 2. 10kg blends were then carbonized in a mini pilot coke oven. (Fig 1).
Each individual coal sample was screened and crushed in a hammer mill. The crushing index of each coal was maintained at 81±1% of < 3.2mm size fraction. Homogenization and air-drying was carried out wherever necessary. A representative master sample of each coal was then drawn by coning and quartering the samples prepared for the following laboratory characterization tests:
• Proximate analysis
• Gieseler Fluidity
• Crucible Swelling Number (CSN)
• LTGK Coke Type
• Petrographic analysis
• Maceral Composition
• V-Type Distribution
• Reflectance of Vitrinite (RoR/MMR)
• Microlithotype distribution
The samples selected for coking were sized from plus 25mm fraction to minus 25mm. The coals constituting each blend were weighed and mixed thoroughly, and placed in an open box for coking for 3.45 hours at 850°C. The coke formed is illustrated in Fig 2
Analysis of chemical and coking properties
Proximate Analysis (IS 1350 Part-1): The thermogravimetric analyser performs a proximate analysis, which shows the percentages by weight of fixed carbon, volatiles, ash yield, and moisture content in coal. The amount of fixed carbon and combustible material directly affects how efficient coal is as a heat source. During combustion, fixed carbon serves as the primary heat producer. Products produced with a high proportion of volatile matter will burn more easily. The coal blending procedure depends on the ash yield content.
CHNS (Elemental) analysis: Analysis of carbon, hydrogen, nitrogen and sulphur in each coal blend was performed using an elemental analyser.
Coal petrography analysis (ISO 7404 (Part3 to 5): Coal petrography is the optical measurement of the maceral composition, the reflectance of vitrinite macerals, V-type distribution, and association of different macerals (microlithotype distribution).
Free Swelling Index/Crucible Swelling Number (FSI/CSN) (ISO 501): Some types of coal, during and after the release of volatile matter, become soft and pasty and form agglomerates. These types are called caking coal. Due to this, the coal does not burn completely, yielding low combustion efficiency. The coal that does not agglomerate is called free-burning coal. The qualitative evaluation method of determining the extent of caking is called the swelling index. Free-burning coal has a very high value in the swelling index.
For pulverized coal burners the swelling property of coal is less important.
Low-Temperature Gray-King carbonization assay (IS 1353): This test requires the heating of 20gm of coal in a special horizontal retort tube at a rate of 5°C/ minute from 300°C to 600°C. The coke pencil produced is classified according to set standards. The residue is visually compared with standard profiles, and a letter A to G or G1 to G9 is assigned, representing LTGK Coke Type. Letter ‘A’ represents non-coking. Letters B to G9 indicate increasing order of caking and swelling capacity. If the coal has>17% ash yield, the sample must be washed before testing.
Gieseler Fluidity Test (ASTM D 2639):
Coking coals can, when heated in the absence of air, soften, swell, and then resolidify to form a coherent, porous, hard coke structure. The Gieseler plastometer test is used to evaluate the rheological or plastic properties of a coal or coal blend.
Coke Testing (IS 1354)
Four tests for quality of the coke produced from each blend were carried out to the IS 1354 standard. The tests were: 1) Shatter test, 2) Size analysis, 3) Micum test, and 4) CSR and CRI
Sample preparation for coal petrography
About 10g of minus 1.18mm (particle size BS 18) size, representative of the coal sample was mixed thoroughly with a combination of epoxy resin and hardener in the ratio 6:1. This was compressed in a heated cylindrical mold to 28 to 35 MP for three to five seconds and released. This
was repeated about 15 times, and then the pressure held for five minutes with the jacket heater on and the temperature set between 60 to 80°C. The pressure was released, and the mounted pellet was ejected, marked, and allowed to cure overnight. One of the flat surfaces of the pellet was prepared for microscopic examination.
Microlithotype determination provides the distribution of the various maceralmicrolithotype and coal inorganic matter (carbo-minerites) in the coal samples (ICCP, 1963). ISO 7404/4 describes the analysis method. The investigation methodology for microlithotype distribution and maceral study is conducted in a comparable way. In the case of microlithotype examination, a suitable 20-point reticule is placed in one of the oculars of the microscope as a replacement for the micrometre or crosshairs. Two important observations are required (ICCP, 2001): (1) the smallest width of bands, the association to be calculated should be 50 microns, and (2) macerals present in amounts less than 5% should not be counted (the 5% rule). Each experimental value is regarded as one point on a 20-intersection reticule in the analysis, and each intersection on the reticule corresponds to 5% of the total number of intersections. At least 500 points should be measured for a complete microlithotype analysis, and the outcome should be reported as a volume percentage. Microlithotype analysis is more accurate than maceral analysis. The estimation for repeatability and reproducibility is made in a similar method as for maceral analysis as defined by the International Organization for Standardization. Microlithotype analysis of the 12 coal samples was carried out, and is shown in Table 3
Geiseler Fluidity analysis: This test measures the rheology of the coal and is important for assessing coking properties. From this test, the initial softening temperature, maximum fluidity, plastic range, and maximum fluidity of each coal are determined. Plasticity is an important aspect of coal carbonization for coke making. The maximum fluidity and plastic range vary from 8ddpm, (dial divisions per minute), to 1582 ddpm, for temperatures of 48°C to
93°C, respectively. The maximum fluidity is the time-bound test. The fluidity of coal depends on the effect of weathering. Weathered coal has a lower fluidity than a fresh sample. The compatibility of the coal blending process depends upon the coal fluidity of each coal sample. The highest maximum fluidity was seen in imported (Hard) No.2 coking coal which has a plastic range of 78°C, and the lowest maximum fluidity was observed in imported (Hard) No.3 with a plastic range of 55°C. It has been noticed that the plastic range and the fluidity is governed by different factors to the coking property.
Coal microlithotype analysis: Coal microlithotypes analysis was carried out using the DP4500P reflected light coal petrography microscope. The distribution of microlithotypes is playing an important role in the coal carbonization process and, hence, coke making. The role of maceral compositions and distribution in a coal blend is well appreciated, but the microlithotype distribution in the blend and its effect on coke quality is a new concept. The analyses was carried out on all 12 coal samples, both from indigenous and imported coking coal (Table 3). The brief microlithotypes analysis of each sample is given below:
• Imported (Hard) -1: The coal is comprised of 48.0% mono-maceralic
(41.0% vitrite), 42.0% bi-maceralic (41.8% vitrinertite) and 3.4% tri-maceralic (3.2% duroclarite).
• Imported (Hard)-2: The coal is comprised of 40.6% mono-maceralic (36.8% vitrite), 35.2% bi-maceralic (28.4% vitrinertite) and 16.0% tri-maceralic (10.0% duroclarite and 4.8% clarodurite).
• Imported (Soft): The coal is comprised of 27.0% mono-maceralic (14.6% inertite), 53.0% bi-maceralic (47.2% vitrinertite) and 11.2% tri-maceralic (6.4% duroclarite, 4.4 clarodurite).
• Imported (Hard)-3: It is comprised of 35.6% mono-maceralic (18.8% vitrite), 51.6% bi-maceralic (48.6% vitrinertite) and 7.0% tri-maceralic (5.4% duroclarite).
• Imported (Hard)-4: It is comprised of 54.4% mono-maceralic (18.8% vitrite), 38.2% bi-maceralic (48.6% vitrinertite) and 2.0% tri-maceralic (5.4% duroclarite).
• Imported (Hard)-5: The coal has 85.6% mono-maceralic (83.8% vitrite), 9.2% bi-maceralic (5.8% vitrinertite) and 1.8% tri-maceralic (1.0% duroclarite).
• Indigenous-1: The coal has 39.0% mono-maceralic (26.0% vitrite, 13.0% inertite), 45.6% bi-maceralic (41.8% vitrinertite) and 5.4% tri-maceralic (2.4% vitrinertoliptite).
• Indigenous-2: The coal has 10.0% mono-maceralic (8.0% vitrite), 55.4% bi-maceralic (30.4% vitrinertite, 23.6% durite) and 26.0% tri-maceralic (12.0%
duroclarite).
• Indigenous-3: The coal has 32.8% mono-maceralic (26.2% vitrite), 46.6% bi-maceralic (38.4% vitrinertite) and 17.0% tri-maceralic (6.4% duroclarite, 5.8% vitrinertoliptite, 4.8% clarodurite).
• Indigenous-4: The coal has 42.0% mono-maceralic (35.0% vitrite), 42.6% bi-maceralic (34.6% vitrinertite) and 5.5% tri-maceralic (2.6% duroclarite).
• Indigenous-5: The coal has 32.4% mono-maceralic (20.4% vitrite, 11.2 inertite), 40.2% bi-maceralic (38.6% vitrinertite) and 15.0% tri-maceralic (10.4% duroclarite, 3.4% clarodurite).
Blend of Indian and imported
• Blend coal: Blend coal has 72.0% mono-maceralic (60.0% vitrite), 15.0% bi-maceralic (12.2% vitrinertite) and 5.4% tri-maceralic (2.6 duroclarite).
The highest vitrite content of 83.8% was found in imported (Hard)-4 coal samples corresponding to 5.8% vitrinertite. The highest vitrinerite content was found in coal Indigenous-1, corresponding to 26.0% vitrite. Indigenous coal 3 has a maximum of 5.8% of vitrinertoliptite, and PCC while Coal No 3 has the highest content of duroclarite at 10.4%. Sample indigenous-2 shows a maximum of 23.6% of the non-reactive microlithotype, durite at 23.6%.
Maceral distribution of caking property: Coke of a specified quality is required to produce, at optimum cost, smooth blast
furnace operation (Hu et al. 2021). During the coal carbonization process, the coal undergoes a thermoplastic phase at a particular temperature and forms a plastic mass or metaplast, which helps to produce a porous hard coke (Taylor et al. 1998; Normura and Arima et al. 2000, 2001; Varma et al.2002; Xiang et al. 2016; Lee et al. 2018; Hu et al. 2019, 2021).
Fig 3 shows the total coal characterization report for the 12 coal samples. The relationship between (Fig 4), the plastic range of coal, and the ratio of hydrogen to carbon (vitrinite+ 1.3 liptinite + 0.50 inertinite)* H/C shows significantly
correlation. The relationship between the plastic range of coal with the proposed petrographic caking index, (PCI) is evident. This relationship is polynomial, and the hydrogen content is attributed to the plastic range of coal. There is a strong correlation between the coal rank and plastic phase. High-rank coal has more aromatic carbon than lower-rank coal. Medium rank coal exhibits a branched aliphatic carbon chain with a rich hydrogen content which gives greater fluidity and a higher plastic range (Takanohashyieldi et al. 2005).
Controls on coke quality
The MCSI (Microlithotype coke strength index) shows a relationship with the Coke Reactivity Index (CRI) and, separately, Coke Strength after Reaction (CSR).
The relationship between different combinations of microlithotype distribution with coke strength is presented in Figs 5 & 6. It is observed that vitrinertite microlithotype and vitrinertoliptite do not fully participate in the carbonisation process; only 90% actively participate in the plastic phase. The relationship shows a positive impact on CRI (Coke Reactivity Index) for the inertinite group of maceral inert, except for some of the Australian bituminous coking coal during the carbonisation process (Diessel et al. 1983). The vitrinite and liptinite groups of coking coals behave as reactive macerals during the coking process (Hacquebard et al. 1958; Alpern et al. 1966; Stach et al. 1982).
Evaluation of caking property by regression analysis
Regression analysis of the relationship between the plastic range and composition of macerals with the atomic H/C ratio is expressed as: PPR1 = 249 - 1.94 Vt - 0.76 L - 2.47 I + 3.52*H/C............Eq (1) R2 = 80.7% R2adj = 69.7%
(key: Vt : Vitrinite, L: Liptinite and I: Inertinite combination with atomic proportion ratio to Hydrogen/Carbon, PPR: Petrographic Plastic Range).
The authors have developed the PPR
Fig 5. Relationship between proposed MCSI index (Vitrinite+Clarite+0.9* Vitrinertite +0.9 *Vitrinertoliptite) with CSI. (Key: CRI: Coke reactivity index, VI: Vitrinite, CL: Clarite: VI: Vitrinertite, VL: Vitrinertoliptite, MSCI: microlithotype coke oven strength index).
(Petrographic plastic range) relationship between macerals composition of vitrinite, liptinite, and inertinite along with the atomic proportion ratio of H/C. The R2 value shows a 0.87 fit. The hydrogen ratio is attributed to enhancing the plastic property of coal. In medium rank coal the presence of a branched aliphatic carbon chain of rich hydrogen content gives greater fluidity and a higher plastic range (Takanohashyieldi et al. 2005). Equation 1 shows the highest corelation between macerals composition and atomic proportion of the H/C ratio to predict the plastic range of coal samples.
Regression analysis between CRI and Microlithotype Composition (Vitrite, Clarite, Vitrinertite, Vitroinertoliptite, atomic proportion ratio H/C):
MCRI1 = -0.59 VT+ 1.63 CL -0.59 VI1.49 VL+0.16 H/C + 69.09..... Eq (2) R2 = 0.70, R2adj = 0.46
(key) MCRI: Microlithotype coke reactivity index, VT: Vitrite, CL: Clarite, VI: Vitrinertite, VL: Vitroinertoliptite, atomic proportion ratio H/C).
This equation for MCRI (Microlithotype coke reactivity index) is represented between the microlithotype composition ratio and the atomic ratio H/C. R2 is 0.70. It is observed that vitrinertite microlithotype and vitrinertoliptite do not fully participate in the carbonisation process; only 90% actively participate in the plastic phase. The relationship shows a positive impact on CRI (Coke Reactivity Index). The
inertinite group of maceral act inert except, as stated previously, in some of the Australian bituminous coking coal during carbonisation. (Diessel et al. 1983).
Regression analysis in between CSR and PCR (Varma., 2002) with atomic Proportion ratio N/H and H/C ratio. Equation 3 is:
MCSR1 = -0.33 PCR – 22.52 H/C + 0.03 (PCR×H/C) + 1226.792 N/H+78.40.
Eq…..(3)
R2 = 0.96, R2adj = 0.95
(key) MCSR: Microlithotype coke strength ratio, PCR: Petrographic coking ratio, atomic proportion ratio H/C, organic nitrogen may influence caking behaviour (Tsubouchi et al. 2014)
The hydrogen ratio H/C is attributed to enhancing the plastic property of coal. Whereas in medium rank coal the presence of branched aliphatic carbon chain rich in hydrogen gives greater fluidity and a higher plastic range (Takanohashyieldi et al 2005)).
In equation 3 - MCSR (Microlithotype coke strength ratio) is a representation between the atomic ratio of H/C and the N/H ratio. The R2 value at 0.96 indicates strong correlation to determine coke quality from the microlithotype distribution.
The properties of India’s indigenous coking coal, such as the Crucible Swelling Number (CSN), and vitrinite content can be improved by washing using wet media of a specific gravity from 1.40 to 1.30. The resultant ash content falls from 1.40 to 1.30 density, but the coal yield is reduced. The proximate analysis data of the coal shows that the yield of volatile matter varies from 20.4% to 30.8%, fixed carbon from 52.2% to 68.8%, and fuel ratio from 2.16 to 3.28. It is concluded that the washed coal sample has fallen into the category of bituminous to super bituminous coal.
Fig 6. Relationship between proposed MCSI index (Vitrite + Clarite+0.9* Vitrinertite + 0.9 *Vitrinertoliptite) with CSR. (Key: CSR: Coke strength after reaction, VI: Vitrite, CL: Clarite: VI:Vitrinertite, VL: Vitrinertoliptite, MCSI: microlithotype coke strength index).
The relationship between the plastic range of coal with the development of the petrographic caking index, PCI (vitrinite+ 1.3 liptinite + 0.50 inertinite)* H/C is significant with an R2 value of 0.90. The relationship is polynomial, and here the hydrogen content is attributed to the plastic range of coal. The relationships between the microlithotype coke strength index, MCSI (Vitrite + Clarite+0.9* Vitrinertite +0.9 *Vitrinertoliptite) and CSR, CRI, carbon content and R0max, O/C ratio and H/C ratio, O/S ratio and the plastic
Acknowledgements
The authors are very much thankful to the management of RDCIS, SAIL, Ranchi for their financial grant to carry out this research.
Bibliography
[1] Alpern, W.M., Charles, A.G. and Friedman, E.A., 1966. Amniocentesis in the management of Rh-sensitized pregnancies: Technique, accuracy of results, and complications. American Journal of Obstetrics and Gynecology, 95(8), pp.11231128.
[2] Ammosov, I.I., Eremin, I. V., Sukhenko, F and Oshurkova LS., 1957. Calculation of coking changes on basis of petrographic characteristics of coals. Coke Chem. U.S.S.R. 2:pp. 9-12.
[3] ASTM D2639/D2639M: Standard Test Method for Plastic Properties of Coal by the Constant-Torque Gieseler Plastometer [4] Diessel, C.F., 1983. Carbonization reactions of inertinite macerals in Australian coals. Fuel, 62(8), pp.883-892
[5] Hacquebard, P.A., 1958. The value of a quantitative separation of the maceral vitrinite into its constituents telinite and collinite for the petrography of coking coals. Proc. Third Int. Congr. Coal Petrology, Heerlen, pp.131-138
[6] Hu, W. J., Wang, Q., Zhao, X.f., Yang, S., Wu, H., Zhang, S., and Sun, J., 2021. Relevance between various phenomena during coking coal carbonization. Part 3: understanding the properties of the plastic layer during coal carbonization. Fuel, (292), 120371.
[7] International Committee for Coal and Organic Petrology (ICCP). 2001. The new vitrinite classification (ICCP Systems 1994). Fuel,(80), pp. 459-471.
[8] IS 1350 ( Part 1 ) : 1984 Methods Of Test for Coal and Coke Part 1 Proximate
Analysis
[9] IS 1354: Method of Test for CokeSpecial Test
[10] ISO 501: Hard Coal-Determination of the crucible swelling number.
[11] ISO 7404 Part 3: Method of determining maceral group composition
[12] ISO 7404 Part 4: Method of determining microlithotype, carbominerite and minerite composition.
[13] ISO 7404 Part 5: Method of determining microscopically the reflectance of vitrinite
[14] Jasienko, S., 1978. The nature of coking coals. Fuel, 57(3), pp.131-146
[15] Lee, S., Yu, J., Mahoney, M., Tremain, P., Moghtaderi, B. and Tahmasebi, A., 2018. A study on the structural transition in the plastic layer during coking of Australian coking coals using Synchrotron micro-CT and ATR-FTIR. Fuel, 233, pp.877-884.
[16] Mackowsky, M.T., Teichmuller, M., Taylor, G.H., Chandra, D., Teichmuller, R., Bwnfraeger, G., Berlin, S., Cloth, D.M., Hacquebard, P.A. and Darfmoufh, N.S., 1997. Stach’s textbook of coal petrology. Gebruder borntraeger microscopically the reflectance of vitrinite. Geneva, 4 pp.
[17] Nandi, B.N. and Montgomery, D.S., 1975. Nature and thermal behaviour of semi-fusinite in Cretaceous coal from western Canada. Fuel, 54(3), pp.193-196.
[18] Nomura, S., Arima, T. and Kato, K., 2004. Coal blending theory for dry coal charging process. Fuel, 83(13), pp.17711776.
[19] Okuyama, Y., Miyazu, T., Sugimura, H. and Kumagai, M., 1970. Prediction of the coking property of coal by microscopic analysis. J. Fuel Soc. Jpn, 49(522), pp.736743.
[20] Rentel, K., 1987. The combined maceral-microlithotype analysis for the characterization of reactive inertinites.
range and O/S ratio and CRI have a good correlation. The MCSR (microlithtype coke strength ratio) and MCRI (microlithotype coke reactivity index) relationship provides good correlations with the Coke Reactivity Index (CRI) and with Coke Strength after Reaction (CSR). �
Thermogravimetric – Analyser uses for proximate analysis of coal and coke samples.
International journal of coal geology, 9(1), pp.77-86.
[21] Schapiro, N., Gray, R.J. and Eusner, G.R., 1961. Recent developments in coal petrography. In Proc. Blast Furnace, Coke Oven Raw Materials Conf., Am. Inst. Min. Metall (Vol. 2, p. 89).
[22] Stach, E., Mackowsky, M.T., Teichmüller, M., Taylor, G.H., Chandra, D. and Teichmüller, R., 1982. Stach’s Textbook of Coal Petrology: Berlin (Gebrüder Borntraeger).
[23] Takanohashi, T., Yoshida, T., Iino, M., Kato, K. and Kumagai, H., 2005. Structural changes of coal macromolecules during softening. Structure and thermoplasticity of coal.
[24] Tsubouchi, N., Mochizuki, Y., Ono, Y., Uebo, K., Takanohashi, T. and Sakimoto, N., 2014. Sulfur and nitrogen distributions during coal carbonization and the influences of these elements on coal fluidity and coke strength. ISIJ International, 54(11), pp.2439-2445.
[25] Varma, A.K., 1996. Facies control on the petrographic composition of inertitic coals. International journal of coal geology, 30(4), pp.327-335.
[26] Varma, A.K., 1996. Influence of petrographical composition on coking behavior of inertinite-rich coals. International journal of coal geology, 30(4), pp.337-347.
[27] Varma, A.K., 2002. Thermogravimetric investigations in prediction of coking behaviour and coke properties derived from inertinite rich coals. Fuel, 81(10), pp.13211334.
[28] Xiang, L.I., QIN, Z.H., BU, L.H., Zhuang, Y.A.N.G. and SHEN, C.Y., 2016. Structural analysis of functional group and mechanism investigation of caking property of coking coal. Journal of Fuel Chemistry and Technology, 44(4), pp.385-393.
Michael Walter* discusses how OMP, a company delivering advanced supply chain solutions, helps the world’s largest companies face their planning challenges with the company’s flagship Unison Planning™ solution – all through the lens of the global steel industry.
1. How are things going at OMP? Is the steel industry keeping you busy?
There are a lot of challenges in the industry, but OMP takes a strategic approach. Amid the post-Covid-19 recovery, the war in Ukraine, and the current impact of the mix of high interest rates and low margins in a low-demand market environment –OMP’s blend of strategic planning and optimization is increasingly seen as a musthave.
2. What is your view on the current state of the global steel industry?
I see various trends going on at the same time. In the US, local market protections are actively supporting the steel industry, so strategic investment is continuing. European markets are having to navigate a landscape of rising energy prices and decarbonization. India is aiming to become the second-largest steel producer in the world with a lot of growth-driven activity, while China is transitioning towards greater efficiency and decarbonization. All this is happening while the market is still digesting the impact of Covid-19.
3. In which sector of the steel industry does OMP mostly conduct its business?
We’re supporting all kinds of metal businesses – carbon steel, stainless, tool steel, special alloys, aluminium, and copper. At the same time, the OMP solution is performing well in a whole range of industries, from chemicals and consumer goods, to life science, paper, plastic film, and packaging. Trusted customers like Aperam and P&G are proof of our expertise and the value of our approach.
4. Where in the world are you busiest at present?
OMP’s activities are strong everywhere but with different focuses. We’re based in
Europe, but we also have teams in Brazil, US and India. So we are ready to expand and extend to most continents.
5. Can you discuss any major steel contracts you are currently working on?
I can share with you our latest success – our collaboration with Outokumpu in Finland. By implementing Unison Planning™, our enhanced planning solution, we unlocked the ability to approach operations more tactically at the company’s two European business lines – Advanced Materials and Stainless Europe – so that they can respond more rapidly to changing customer demands.
6. Where does OMP stand on the aluminium versus steel argument? From a planning perspective, they both present similar challenges and face similar operational constraints. But their levers for decarbonization are different and, compared to aluminium, steel has a clear advantage in getting greener faster.
*Senior commercial manager, OMP.
7. What are your views on Industry 4.0 and steelmaking?
The steel industry is gradually embracing automation and digitalization, but at a slower pace than other industries due to its inherently complex processes and infrastructure. The industry’s evolution is hindered by the dominance of brownfield strategies, which makes seamless digital progress challenging. There’s some focus on automation, but AI in steelmaking is mainly applied to just particular tasks rather than overall digital enterprise design.
8. In your dealings with steel producers, are you finding that they are looking to companies like OMP to offer them solutions in terms of energy efficiency and sustainability? If so, what can you offer them?
Energy efficiency has been part of OMP’s planning since the company was formed in 1985. And our digital supply chain planning solution encompasses a whole range of sustainability parameters including CO2 impact, hot charging, reducing work-inprogress, higher material yields, and making transportation more efficient. We’re seeing that sustainability is more top-of-mind for our European customers, where we get more questions about energy efficiency, compared to customers in India or the US. But the details of our offering and the way we approach these demands depend on customers’ business decisions.
9. How quickly has the steel industry responded to ‘green politics’ in terms of making the production process more environmentally friendly and are they succeeding or fighting a losing battle?
‘Green politics’ strategies have been in place for years, but they’ve only recently gained focus and a sense of urgency. The steel industry will not lose this battle because
innovation has always been, and still is, the foundation of this industry, especially when it comes to machinery and equipment directly involved in steel production. But the availability of green energy is not entirely in the industry’s hands. From a geopolitical angle, depending on the region, there are bound to be winners and losers.
10. Where does OMP lead the field in terms of steel production technology?
OMP leads in tactical planning with S&OP, and demand planning as well in operational planning including master scheduling and detailed scheduling.Our focus lies in powerful optimization, supported by AI-based solver strategies, with a keen focus on scenario-based constrained planning. This means extended statistical forecasting, optimizing blends for the melt shop, optimizing downstream cuts, and allocating equipment and resources over the full production chain. A good example of this is the OMP for Detailed Scheduling functionality for precise machine load planning, with targeted optimization techniques and seamless integration with operational planning.
11. How do you view OMP’s development over the short-tomedium term in relation to the global steel industry?
They directly correspond. OMP for Metals is growing just as the steel industry is.
12. China dominates global crude steel production. How should the industry react to this situation?
Personally, I believe that in the years to come, decarbonization will have a bigger impact on the steel industry than the
Chinese domination. With a five-year strategy already announced, the Chinese steel industry will need to shift their focus internally to introduce the necessary radical change to achieve greater efficiency and higher quality.
While decarbonization means a global reset for the entire steel industry, factors such as the availability of raw materials, affordable sources of energy, and demographic change are just the start, and China does not have the advantage.
13. Where do you see most innovation in terms of production technologies – primary, secondary or more downstream? Definitely primary, because it impacts decarbonization the most.
14. How optimistic are you for the global steel industry going forward and what challenges face global producers in the short-to-medium term?
Relatively optimistic. Steel is an essential industry. We are deliberate and forwardthinking because we know that any potential mis-step could have a severe impact. I believe that, in the next 10 years, we‘ll see competition between different technologies. And then, in the 10 years that follow, we’ll know what the dominant force is. It will be standardized in the market and transform global distribution.
15. What exhibitions and conferences will OMP be attending in over the next six months?
This June, OMP is at the Future Steel Forum in Stockholm, and we’ll be at ABM Week in São Paulo in September. I’m also presenting
at both SMR Conferences. So, plenty of opportunities for networking, hearing about OMP’s innovations and sharing perspectives on the challenges and future of the steel industry.
16. OMP is headquartered in Belgium; what’s happening steel-wise in the area?
Our Belgian location gives us easy access to the entire European market, from north to south, supported by local offices in France and Germany. And we cherish OMP’s close collaborations with ArcelorMittal, Aperam, and Bekaert, among other great local companies. But beyond that, at the headquarters, we are doing what every global company does – innovating to solve new supply chain challenges and stay ahead of the competition.
17. Apart from strong coffee, what keeps you awake at night?
Working with OMP colleagues all around the world! No matter where we’re based and what the time difference is, it gives us a global presence for every OMP customer.
18. If you possessed a superpower, how would you use it to improve the global steel industry?
I would like two steel superpowers. First, I’d make sure steelworkers were as strong as steel itself, and not get injured during production. The other, related to decarbonization, would be to give everyone in the industry infinite access to a clean source of energy.
We’re undergoing a much-needed transformation, and I’m glad to be involved in the digitalization progress that makes it easier. �