Better times ahead for North American Infrastructure. Will steelworkers be the swing vote in 2024?
DECARBONIZATION
The blast furnace is not dead yet, says Rutger Gyllenram.
If EV demand rises, can we reduce the impact of mining?
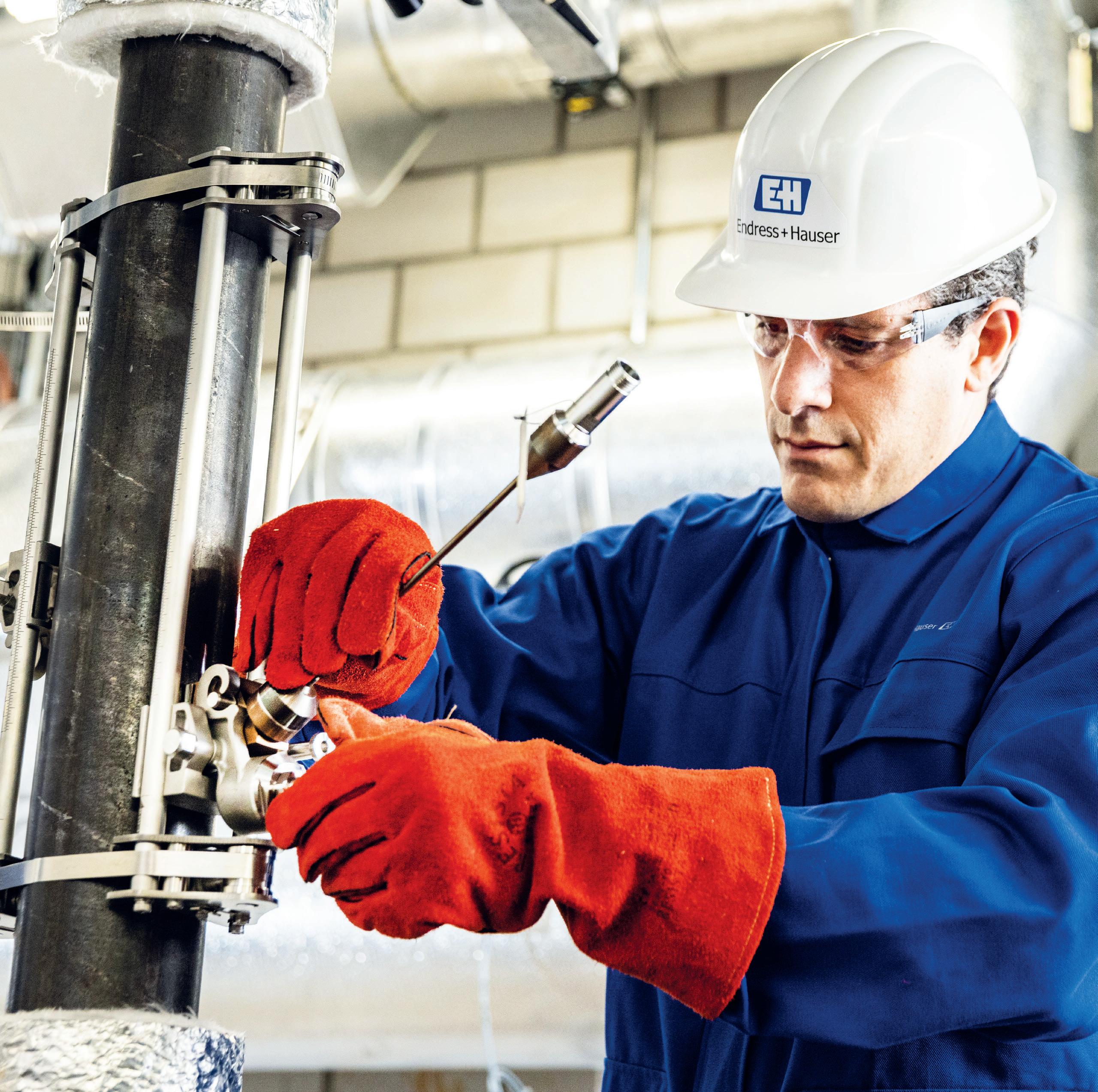
Better times ahead for North American Infrastructure. Will steelworkers be the swing vote in 2024?
The blast furnace is not dead yet, says Rutger Gyllenram.
If EV demand rises, can we reduce the impact of mining?
Metals offers the entire steel value chain an exceptional opportunity for curbing their CO2 emissions.
The unique combination of its historic and recently developed product portfolio, make John Cockerill one of the industry’s most relevant suppliers of equipment for both the hot and cold phase of the steelmaking and processing industry.
Our three distinct business segments are addressing todays and tomorrow’s challenges supporting sustainable and green steel production:
Our new upstream offering related to DRI (Direct Reduced Iron), EAF (Electric Arc Furnaces) technologies and the use of hydrogen in steelmaking. Next to offering indirect electrification (DRI-EAF&H2-DRI-EAF),John Cockerill is also working on Volteron®: A first-of-a-kind iron reduction and steel processing route via direct cold electrolysis. This CO2 free steelmaking process, has been co-developed with the world’s leading steelmaker ArcelorMittal.
Regrouping our historical downstream product portfolio, this segment also includes:
¡ the Jet Vapor Deposition (JVD®) technology set to replace today’s hot-dip or electro galvanizing processes. This novel high-productivity vacuum coating technology provides previously unknown coating flexibility and possibilities, all while offering lower CAPEX and OPEX.
¡ our E-Si® equipment & processing lines specifically designed to produce high-quality Non-Grain Oriented (NGO) steel in response to the need for electrical steel meeting precise metallurgical properties, essential to support the shift towards green mobility.
This segment not only embraces all services and after-sales activities but will be strongly focusing on downstream furnace electrification (reheating and processing line furnaces), as well as hydrogen combustion, and the optimization of plant operations, including energy audits and the modernization of steel production equipment and installations.
EDITORIAL
Editor
Matthew Moggridge
Tel: +44 (0) 1737 855151
matthewmoggridge@quartzltd.com
Assistant Editor
Catherine Hill
Tel:+44 (0) 1737855021
Consultant Editor
Dr. Tim Smith PhD, CEng, MIM
Production Editor Annie Baker
Advertisement Production Carol Baird
SALES
International Sales Manager
Paul Rossage
paulrossage@quartzltd.com
Tel: +44 (0) 1737 855116
Sales Director
Ken Clark
kenclark@quartzltd.com
Tel: +44 (0) 1737 855117
Managing Director
Tony Crinion
tonycrinion@quartzltd.com / Tel: +44 (0) 1737 855164
Chief Executive Officer
Steve Diprose
SUBSCRIPTION
Jack Homewood
Tel +44 (0) 1737 855028 / Fax +44 (0) 1737 855034 Email subscriptions@quartzltd.com
Steel Times International is published eight times a year and is available on
Annual subscription: UK £226.00 Other countries: £299.00 2 years subscription: UK £407.00 Other countries: £536.00 3 years subscription: UK £453.00 Other countries: £625.00 Single copy (inc postage): £50.00 Email: steel@quartzltd.com Digital subscription: (8 times a year) - 1 year: £215.00 - 2 years: £344.00 3 years: £442.00. Singe issue: £34.00
Published by: Quartz Business Media Ltd, Quartz House, 20 Clarendon Road, Redhill, Surrey, RH1 1QX, England. Tel: +44 (0)1737 855000 Fax: +44 (0)1737 855034 www.steeltimesint.com
Steel Times International (USPS No: 020-958)
Moggridge.
Mark Bulla Arise, the pellet king!
Reports of the end of blast furnaces are greatly exaggerated.
Minimizing mineral demand and mining impacts in the transition to
Steel, trade and the 2024 US presidential election.
Clean steel helps student racing team gear up for success.
toward the future.
Mono and composite tubes for green energy technologies.
The future of steel processing.
Sights set on optimization.
The growth of iron and steelmaking at Port Talbot – Part 2.
Matthew Moggridge Editor
matthewmoggridge@quartzltd.com
There’s nothing like being offered the chance to moderate a discussion panel on hydrogen steelmaking to exercise the mind. And just as soon as I close our October edition (after completing this leader) I’ll be taking a closer look at a subject that is relatively new in the greater scheme of things, even if it seems to have been around for some time.
Over the past few weeks, and prior to my invitation to moderate, I have been collecting notes on the subject of hydrogen steelmaking and there are, of course, many aspects to the process that will need to be looked at in Linz, Austria, at the end of this month; and I must say I’m looking forward to it, especially considering the cutting edge panel of experts involved.
When people talk about decarbonizing the steelmaking process, a lot of the experts in the field of steel production technologies claim that to successfully decarbonize the steel industry will only become a reality if multiple technologies are employed. In other words, it’s not all about hydrogen; and of course we all know that. There are many different technologies under development designed to help steelmakers reduce their emissions
and we all know that while there seems to be a perception that, one day soon, the industry will press a button and everybody will be making steel using hydrogen and EAFs, the reality is completely different. For a start, to make zero carbon steel requires renewable energy, and it is argued that there simply isn’t enough of it ‘to support the aspirational demand for green hydrogen’.
Steel made from hydrogen is widely regarded as the ‘gold standard’ and it will be produced – initially at any rate –by a select few, including SSAB, with its pioneering HYBRIT initiative and, of course, H2 Green Steel (recently renamed Stegra). There are others, like BLASTR Green Steel (see exclusive interview with CEO Mark Bula on page 20) and there will be more, but as Rutger Gyllenram of Kobolde & Partners says in this issue, ‘new process ideas are nothing more than ideas until proven in full-scale’. In the meantime, he says, ‘we must do what we can with what we have – and produce low-emission sponge iron with natural gas using CCS in both EAFs and BFs.’ So don’t think you’ve heard the last of the traditional blast furnace...you haven’t.
To meet strong demand from China for green iron, mining company Fortescue is planning to build a pilot plant that will produce the product using renewable energy in 2025. Fortescue will use green electricity from solar farms at its Christmas Creek iron ore operation in Western Australia to produce 1.5kt of high-purity green iron per year. The company will allocate A$50 million for the project and expects to start production in 2025. Fortescue is testing several methods to produce green iron, and it is expected that renewable energy steelmaking will not be commercialized until the next decade.
Source: Yieh Corp Steel News, 2 September 2024.
Ukrainian steel and mining group Metinvest is considering the possibility of building or acquiring new
Arabian Gulf Steel Industries (AGSI), a company based in Abu Dhabi specialising in
More than 2,000 workers have applied for voluntary redundancy at Tata Steel’s south Wales sites, according to reports. The majority are based in Port Talbot. Tata Steel has already decommissioned one of the two blast furnaces at Port Talbot, the largest steel plant in the UK, as part of its strategy to transition to greener production methods.
The restructuring, which is expected to lead to approximately 2,800 job losses, aims to curb daily losses exceeding £1 million, according to the steelmaker.
Source: Manufacturing Management, 2 September 2024.
The Argentinian steelmaker Tenaris has launched its new electric arc furnace, based on Consteel technology, at the Campana Industrial Center Steelworks. The company said in a statement that the objective of this new furnace, which cost an investment of $100 million and involved the participation of more than 700 workers, is to improve the energy efficiency of the steel production process, increase operational safety and productivity, and reduce CO2 emissions.
Source: Yieh Corp Steel News, 2 September 2024.
facilities for the production of green steel outside Ukraine, which would then be powered by Ukrainian raw materials. One of these plants is planned to be built in Italy. In addition, the group is open to other opportunities, including the acquisition of assets in neighbouring countries.
Source: GMK Center, 4 September 2024.
manufacturing sustainable steel, has announced the achievement of net zero
US vice president Kamala Harris has said that US Steel should remain domestically owned, saying during a campaign stop in Pittsburgh that it is ‘vital for our nation to maintain strong American steel companies.’ Harris’ comments marked the first time she lent her voice to the dispute over the proposed sale of US Steel to Nippon Steel, Japan’s biggest steelmaker. “The president mentioned it: US Steel is a historic American company, and it is vital for our nation to maintain strong American steel companies,” Harris said at the Labour Day event after being introduced by Joe Biden. “US Steel should remain American-owned and American-operated.”
Source: CNN, 2 September 2024.
carbon emissions within its steelmaking operations. The company claims to be the first steel plant in the world to achieve carbon neutrality (accredited by a leading global auditor). AGSI is the largest steel recycler in the UAE, with a facility producing
Miami-based investor Atlas Renewable Energy has inked a joint venture with the Brazilian arm of steel manufacturing giant ArcelorMittal – through which the two companies will promote sustainable steel production in Brazil. As part of this partnership, Atlas will invest in the construction of a 315 MWp solar photovoltaic plant within the Luiz Carlos Solar Photovoltaic Complex in Paracatu, Minas Gerais. This new facility will provide renewable energy to power ArcelorMittal’s steel plants in South and Southeastern Brazil.’
Source: Latin Lawyer, 3 September 2024.
600kt of steel products annually from 100% locally sourced steel raw material.
Source: Gulf News, 4 September 2024.
Emirates Steel Arkan, the UAE’s largest publicly listed steel and building materials company, has rebranded as EMSTEEL, as part of a broader strategy to ‘accelerate its operational transformation and extend its global presence.’ The new brand identity and operating model were officially launched at an event in Abu Dhabi attended by customers, partners and employees. The new brand identity represents the merger of Emirates Steel and Arkan Building Materials, completed in late 2021.
Source: ZAWYA, 5 September 2024.
Wales-based adventure company Zip World has announced its takeover of the ArcelorMittal Orbit sculpture at the Queen Elizabeth Olympic Park in Stratford, London.
The ArcelorMittal Orbit sculpture and observation tower designed by Anish Kapoor and Cecil Balmond will be Zip World’s ninth location and its first in the south-east of England. Zip World plans to invest £2.6 million into the visitor attraction, which stands at 114.5 metres tall and offers the world’s tallest and longest tunnel slide.
Source: Blooloop, 5 September 2024.
Brazil’s state-owned energy company Petróleo Brasileiro (Petrobras) has signed a memorandum of
India’s Ministry of Steel has set the target of achieving 500Mt of steel production by 2034, urging the industry to find new ways towards low emission processes, high productivity, and the use of AI. The country’s crude steel production shot up by over 35Mt in the last four years, from 109.14Mt in 2019-20 to 144.30Mt in 2023-24, as per the latest government data from August.
Source: Ommcom News, 5 September 2024.
understanding with Gerdau S/A to explore commercial opportunities and potential partnerships aligned with their diversification and decarbonization strategies.
"In a strategic move to face the environmental challenges of the 21st century, Petrobras and Gerdau have announced an agreement to explore and develop sustainable solutions within the scope of lowcarbon businesses”, Maurício Tolmasquim, Petrobras' director of energy transition and sustainability, said.
Source: RigZone, 13 September 2024.
Handling equipment supplier
Kalmar has signed an agreement to supply Finnish steel producer Outokumpu with three light electric forklift trucks and one medium electric forklift truck. The machines will be deployed at Outokumpu’s integrated stainless steel plant in Tornio, Finland. The order, which includes a preventive maintenance agreement, was booked in Kalmar’s Q3 2024 order intake. The light electric forklift trucks will be delivered during Q1 of 2025, while the medium electric forklift truck is scheduled for delivery during Q4 of 2025.
Source: StreetInsider.com, 6 September 2024.
An Italian appeals court has scrapped the convictions of the former owners of one of Europe's largest steelworks for failing to curb toxic emissions, ordering a retrial, lawyers told media. Brothers Fabio and Nicola Riva were sentenced to 20 and 22 years, respectively, in 2021 by a court in the southern city of Taranto after years of the plant's non-compliance with environmental controls.
To support Indonesia’s green transition, the International Finance Corp has issued a $60 million loan to steel manufacturer PT Gunung Raja Paksi, known as GRP, to expand low-carbon steel production using electric arc furnace technology. EAFs, which use electricity rather than coal as an energy source, can reduce the carbon intensity of steel production by up to 80% or 90%, depending on the source of the electricity. GRP is looking to halve the carbon intensity of its steel production and increase its metal recycling capacity.
Source: Impact Alpha, 9 September 2024.
But the Rivas' legal team appealed, arguing there was a conflict of interest in trying the case in Taranto, where judges may feel directly affected by the plant, which is located nearby the city. The objection was accepted by an appeals court, which ordered a retrial in Potenza.
Source: Barrons, 13 September 2024.
Plans to build the UK's first deep coal mine in more than 30 years have been quashed. Two campaign groups had brought legal action over the previous government's decision to grant planning permission for the site near Whitehaven in Cumbria. At the High Court, judge Justice Holgate said the assumption the mine would not increase greenhouse gas emissions was ‘legally flawed’.
Source: BBC, 13 September 2024.
Russian steelmaker Severstal is building an pellet plant at its Cherepovets site, the company has announced. "Work is underway to build roasting, pelletizing and crushing facilities, control and desulphurization facilities," said the company. It previously said in late 2023 that it planned to develop its own pellet production in Cherepovets. It signed a special investment contract to build a plant with a capacity of 10Mt/yr in June. The plant will cost 97 billion rubles, it has been reported. Source: Interfax, 24 September 2024.
A Chinese company is investing $1 billion to build a steel plant in the Sarangani province of the Philippines. It is the single biggest foreign direct investment so far under the Marcos administration, according to Secretary Frederick Go, the special assistant to the president for investment and economic affairs. Go said the venture of Panhua Integrated Steel Inc. was among those approved by various investment promotion agencies of the government, such as the Board of Investments and the Philippine Economic Zone Authority, in Mindanao.
Source: Inquirer.net 14 September 2024.
US Steel has announced that it is the first steel company in
A plaque has been unveiled in memory of two firefighters who died following an explosion at a steel plant in Sheffield, UK. Bob Smith, 47, and Paul Parkin, 27, died from injuries sustained in the blast at British Steel Corporation’s Tinsley Plant on 25 February 1974. Their story was a ‘vital part of local history and the history of the fire service’, the Fire Brigades Union said. The tribute was unveiled at Parkway Fire Station in Sheffield in a ceremony attended by serving and retired firefighters and family members.
Source: BBC, 14 September 2024.
the world to qualify to sell its products as ResponsibleSteel Certified Steel at its Big River facility in Osceola, Arkansas. Big River received the first ResponsibleSteel Site Certification in North America in 2022 and has now achieved certification for sustainably sourced and manufactured steel. “ResponsibleSteel
A worker at ArcelorMittal Dofasco died after being pinned between two large vehicles at the company’s plant in Hamilton, Ontario. The incident, which occurred on 20 September, is now under investigation by Ontario's ministry of labour, immigration, training, and skills development. “It was reported a worker was pinned between two vehicles, resulting in fatal injuries,” a ministry spokesperson said in a statement to Canadian Occupational Safety. Two inspectors were dispatched to the site, as part of the ongoing probe.
Source: Canadian Occupational Safety, 25 September 2024.
Jindal Steel (JSPL) and Jindal Renewables (JRPL) have signed a Memorandum of Understanding (MOU) to implement India's biggest investment in green hydrogen by any Indian steelmaker to date. The MOU outlines JSPL's plan to integrate green hydrogen into its DRI units in Angul, Odisha. In the first phase, JRPL will develop a green hydrogen generation capacity of up to 4.5kt/yr set to commence by December 2025.
Source: Business Standard, 16 September 2024.
employs a comprehensive approach to its certification standards, and that is evident in the work we do here at Big River Steel,” said Dan Brown, senior vice president of advanced technology steelmaking at US Steel and COO of Big River Steel Works. Source: US Steel, 24 September 2024
Tata Steel Nederland has launched a new decoiling line and an automated sheet packaging line at its Feijen steel service centre in Maastricht. Feijen's collaboration with Tata Steel IJmuiden targets customers worldwide in Europe and other regions, primarily in the agricultural and earthmoving machinery, trailer, crane, and shipbuilding industries. Tata Steel Nederland comprises of two business units: Tata Steel IJmuiden (TSIJ) and Tata Steel Downstream Europe (TSDE). The Maastricht service centre is part of TSDE and includes the Multisteel and Feijen plants.
Source: Yieh Corp Steel News, 26 September 2024.
Hydnum Steel, the first green steel plant on the Iberian Peninsula, has entered into a Memorandum of Understanding (MOU) with Knauf Interfer, a European steel processing and distribution company. This partnership is designed to expand the availability of emission-free green steel across Europe and reinforce the commitment
International steel and technology group voestalpine has successfully issued its first green corporate bonds for €500 million, the company said in a statement. The bonds have a five-year maturity and a coupon of 3.75%, which reportedly meets high investor demand. All proceeds from the issue will be used to finance or refinance voestalpine’s sustainability projects, such as greentec steel.
Source: GMK Center, 26 September 2024.
to sustainability within the steel industry. Through the collaboration, Hydnum Steel will supply Knauf Interfer with green steel, worth approximately €80 million, annually.
Source: Chem Analyst, 2 October 2024.
French train manufacturer Alstom has signed a partnership agreement with Swedish steel firm SSAB for the supply of fossil-free steel for use in its new Traxx Shunter locomotives.
“We are very glad to sign this partnership agreement with SSAB,” said Christophe Gourlay, Alstom chief procurement officer. “By supplying steel with low carbon emission footprint for our Traxx Shunter™ locomotive, SSAB will contribute in the delivery of Alstom’s sustainable procurement strategy, which includes the reduction of the carbon emissions of purchased goods and services by 30% by 2030.”
Source: Hydrogen Insight, 27 September 2024.
India’s Ministry of Steel is pushing for a doubling of the basic customs duty on steel imports, suggesting an increase from the current rate of 7.5% to 15%. This is reportedly due to a substantial rise in steel imports from China, which now makes up around one-third of all steel imports in India, according to internal government assessments. Source: Swarajya, 3 October 2024.
Mining company Vale and renewable energy company Green Energy Park have announced a partnership to offer decarbonization solutions for the global steel sector. The companies will develop feasibility studies for the set-up of a green hydrogen production unit in Brazil to supply a future ‘mega-hub’, an industrial complex which will produce low-carbon steel products.
Source: Steel Orbis, 1 October 2024.
BZI®, a Utah-based group of steel construction and engineering companies, has announced it is now utilizing virtual reality technology to enhance customer experiences and products. The group is one of the first in the steel industry to adopt the technology as part of the systems and services offered, it claims. BZI is also integrating VR-simulation training into the safety, quality control and skills instruction provided at its training centre, SteelTech Academy.
Source: Business Wire, 3 October 2024.
We understand how it is important to efficiently extract and process precious metals and minerals.
You save valuable resources while keeping your employees and the environment safe.
Improve your processes with our comprehensive portfolio of measuring instruments, solutions and services:
Liquiline CM44 and CPS11E: Versatile transmitter and Memosens pH sensors ensure reliable measurement and safe calibration in the lab.
FieldPort SWA50: Intelligent Bluetooth or WirelessHART adapter for the easy connection of all HART field devices to the Netilion Cloud via Edge Devices.
Cerabar PMC71B: Absolute and gauge pressure transmitter combining measurement accuracy with IIoT functionalities.
Precision sensor manufacturer Micro-Epsilon has extended its surfaceCONTROL range of 3D snapshot measurement sensors for automated, inline measurement of geometry, shape and surface quality of objects. The surfaceCONTROL SC3xx0-30 offers a smaller measuring field of 30mm x 18 mm with a z-axis range of 12mm. The sensor delivers the measurement results at a z-axis distance of between 124 and 136mm.
With high repeatability of < 0.25 µm and a data processing speed of up to 2.2 million 3D points per second, the sensor sets a new benchmark in high precision 3D measurement technology, claims Micro–Epsilon.
The new 30mm measuring range is available in all classes and models of the surfaceCONTROL SC3xx0 series, i.e. the surfaceCONTROL 3D 3200 and surfaceCONTROL 3D 3500 ranges, with each offering a different measuring area. Both models are fully integrated industrial sensors that are protected to IP67 with passive cooling
(active cooling is available for higher operating temperatures).
The surfaceCONTROL SC35xx-30 is suitable for a wide range of flatness measurement, coplanarity measurement, and surface defect detection applications, including flatness inspection of circuit boards; planarity inspection of unpopulated PCB substrates; completeness check of electronic components on fitted PCBs; 3D measurement of high precision mechanical parts; width, tilt angle, and position measurement of rivets; detection and evaluation of breaks on clutch discs; 3D text recognition of embossments that cannot be solved using 2D image processing due to lack of contrast; inspection of height and thickness of adhesive beading on smartphone shells; and determination of shape deviation defects on injection moulded parts.
All surfaceCONTROL 3D systems support the very latest GigE Vision and GenICam standards for easy integration into third-party image
processing software. A comprehensive software development kit that allows customers to develop their own analysis software is also provided. Included in the scope of supply is Micro-Epsilon’s 3D Inspect software, which offers a convenient user interface for surfaceCONTROL sensors. The software allows for the commissioning and evaluation of the sensor, set up and optimisation of parameters, and ensures the correct positioning of the measuring object.
For further information, log on to www.micro-epsilon.co.uk
Swedish premium fastener manufacturer BUMAX AB has appointed Star Stainless Screw Company as its new master distribution partner in the US. The announcement, says the company, marks a step forward in the BUMAX route to market in the US and is part of BUMAX’s ongoing development strategy for the North America region.
“We at Star Stainless Screw Company are so excited to be partnering with BUMAX. We feel the quality of product from BUMAX, partnered with the reputation Star has for offering the highest of quality of product and service, will be a perfect fit. We look forward to our partner-
ship and thank BUMAX for their trust in Star’s excellence in distribution,” said Tim Roberto, president, Star Stainless Screw Co.
Star Stainless will be responsible for stocking and supplying the BUMAX range of high-strength stainless steel products to fastener distributors and industrial product suppliers throughout the US. This partnership will significantly improve the availability, accessibility and speed of supply of BUMAX products to customers in the US, says BUMAX.
“After a long road, I am happy to see our agreement finalized. A key challenge in the US
has always been the geographic size and diversity of the market. Bringing together the expertise of both companies, we can now begin the important work of raising awareness of the advantages of BUMAX high-strength stainless steel fasteners in the US market and making our products more readily available throughout the region,”said Jacob Bergström, BUMAX segment manager, distribution.
For further information, log on to https://www.bumax-fasteners.com/
The goal of Henkel Adhesive Technologies’ latest product innovation was to achieve more sustainability and greater process efficiency in colour coating processes. With Bonderite M CR 1405, the surface treatment experts have developed a RoHS-compliant (restriction of the use of certain hazardous substances) agent that, the company claims, provides coils with passivation and pre-treatment properties as well as corrosion resistance in a single pre-treatment step.
The classic treatment of metal surfaces uses two different lines: one for pre-treatment and one for passivation. With the conventional process, the parts go either directly to the user or on to the painting line. The rust preventive (RP) oil used before painting must be removed in the subsequent cleaning and rinsing stage. If a passivation coat is applied, a single rinse prior to the subsequent application of paint is sufficient.
Henkel’s new development aims to enable users to substantially shorten their process. Bonderite M CR 1405 can be used as a passivation for bare substrates and pretreatment for painted substrate. After passivation, the coils are either sent directly to the end user or on for painting. Bonderite M CR 1405 has good recoatability, and coils passivated with this product can be used on
the colour coating line without a cleaning step and can only be rinsed with hot water to remove any contamination. This results in savings with respect to energy and water usage, since the cleaner that has now been eliminated is typically used in large tanks at temperatures between 60-70°C. The absence of chemical cleaning agents also means that wastewater pollution is significantly lower, says Henkel.
This combination is made possible by a newly developed product: Bonderite M CR 1405, a chromium III-based passivation pre-treatment. “Normally, when paint is applied to a passivated coil without subsequent treatments, insufficient paint adhesion and corrosion resistance is achieved. Conversely, pre-treatment used as passivation usually fails within one day,” said Gerko Odink, senior manager, PD Metals EU, at Henkel Adhesive Technologies. “We have an agent here that combines the best of both worlds and is compatible with both chromium-based and chromium-free primers.”
As this is a chromium III-based product, it meets users’ performance expectations for high corrosion protection while also being RoHS-compliant. This directive prohibits the use of hexavalent chromium in Europe. “We are closing
the gap between legislation and performance by using a bridging technology that meets the requirements for architectural applications, for example,” added Odink. Testing on galvanized and Galvalume substrate shows blank corrosion resistance of more than 96 hours. The salt spray test shows resistance of 800 hours with a chromium primer and 500 hours with a chromium-free primer.
By reducing the number of process steps and the associated energy and water consumption, the new product is in line with Henkel’s long-standing commitment to sustainability. “Enabling safer, cleaner and more efficient processes is at the heart of our business,” says Volker Mansfeld, vice president, industry, EIMEA region, at Henkel Adhesive Technologies. “Together with our customers, we strive to rethink design and processes to identify opportunities for sustainable innovation and defossilization of the industry while delivering the highest performance.”
For further information, log on to https://www.henkel-adhesives.com/uk/ en.html
Sinosteel Engineering & Technology Co., Ltd. (Sinosteel E&T), an industrial technology and engineering service provider offering low-carbon metallurgy full lifecycle solutions, and Tenova, a developer and provider of sustainable solutions for the metals industry, have recently completed the performance test for Baosteel Zhanjiang Iron & Steel Co., Ltd.’s new hydrogen-based 1Mt/yr ENERGIRON Direct Reduction (DR) plant.
The plant, designed by Tenova using ENERGIRON, the DRI technology jointly developed by Tenova and Danieli, and completed with engineering by Sinosteel, is located in the Zhanjiang Economic and Technological Zone, Guangdong Province. During the performance test, the plant achieved a milestone production of a total of 21.62kt of direct reduced iron, after 168 hours of continuous full-load production, with a metalliza-
tion rate of more than 94% and using a 70% hydrogen-based reducing gas.
The ENERGIRON solution is the most flexible DR technology for virgin metallic unit production in terms of make-up gas utilization, and the most sustainable as it is designed to maximize reduction of CO2 emissions, Tenova claims. The plant installed at Baosteel, a Baowu Group company, has the flexibility to use different reducing gases, like Hydrogen (H2), Natural Gas (NG), and Coke Oven Gas (COG), in any combination or proportion, using the same ENERGIRON Zero Reformer (ZR) scheme.
“The successful operation of the Baosteel Zhanjiang 1Mt hydrogen-based shaft furnace stands as a pivotal initiative in Baowu’s efforts to promote low-carbon production. Thanks to this project, Baosteel is proceeding towards its path
of reducing carbon emissions, paving a new way for green steel production,” stated Liang Lisheng, assistant general manager of Baosteel Zhanjiang Iron & Steel Co., Ltd., and director of the ironmaking plant.
“We are really satisfied with this project which confirms the great collaboration among all parties that participated in this achievement. Thanks to our ENERGIRON technology, we have provided Baosteel with the first direct reduction iron production line integrating hydrogen, natural gas, and coke oven gas for industrial production”, added Stefano Maggiolino, president and CEO at Tenova HYL.
For further information, log on to www.tenova.com
Calderys has reached a significant milestone in its global growth strategy with the commencement earlier this year of a project in the state of Odisha, India. This project will be the world’s largest single-site greenfield plant dedicated to refractories and steel casting fluxes, the company says. It represents a strategic move from Calderys to expand its product range with acidic and basic bricks, and overall production capacity in line with the evolving needs of the Indian refractory market, particularly in the eastern and southern regions.
When finished, the 40-acre plant will include five production lines for acidic and basic bricks and monolithics, ready-shaped products, and steel casting fluxes, as well as quality testing facilities. Construction began five months ago, and
several manufacturing lines will be progressively commissioned starting from late 2025.
During its construction, and when it is fully operational, the new plant will benefit from the latest safety management standards and technical innovations, says Calderys, to ensure the project complies with safety protocols and Indian regulations, at every stage of its life cycle.
Michel Cornelissen, president and CEO of Calderys, said: ‘‘This project is the largest single site investment in the history of Calderys. It demonstrates our commitment to India and is an important step in Calderys’ global production strategy. It is further evidence of the group’s solid growth and potential, and we are grateful to the Odisha state for its trust in Calderys.’’
Ish Mohan Garg, senior vice president and
managing director of the Asia Pacific region of the group, stated: ‘‘This landmark project is a strategic move towards broadening our product portfolio to meet the evolving and unprecedented demand of the Indian refractory market. It reaffirms our commitment to giving the best products and possible service to our customers. We would like to express our deepest gratitude to the government and people of Odisha for their valuable support. Our collaboration will accelerate Calderys’ growth but, vitally, it will also make a huge contribution to the economic and industrial advancement of the city and the region.’’
For further information, log on to www.calderys.com
As the election campaign heats up, political opposition to the Nippon-US Steel merger rises, with Cleveland-Cliffs applauding US president Biden’s decision to block the deal. By Manik Mehta*
THE controversy over the US Steel takeover bid by Nippon Steel threatens to become a major issue for politicians eager to gain support both from the domestic industry and the powerful steelworkers’ union in the ongoing presidential election campaigning. The Biden administration keeps harping that the acquisition would be harmful not just for the overall steel industry’s interests but would also collide with the principles of fair competition, giving monopolistic advantages to Nippon and resulting in job losses. But the question also being asked is to what extent the Biden administration would go against Japan, a staunch US ally. US politicians and steel industry experts are ‘deeply concerned’ over the acquisition’s impact on steel supply for infrastructure projects requiring large quantities of steel. Cleveland-Cliffs Inc., North America’s largest flat-rolled steel company and a leading supplier of automotive-grade steel, strongly opposes the deal. The company, which had made an unsuccessful $7.3 billion bid to purchase US Steel, applauded President Biden’s warning to block the deal. In a statement, Cleveland-Cliffs’ chairman/ CEO, Lourenco Goncalves commended president Biden for his decision, and said that the industry was ‘best served by American companies that are committed to the long-term prosperity of domestic manufacturing, supported by good paying
union jobs, under American ownership’. Goncalves also said that it was ‘no surprise’ that the United Steelworkers (USW) union opposed any transaction involving Nippon Steel, ‘a company with an extensive track record of injurious trade practices’. He described US Steel’s threat of shutting down integrated steelmaking production, firing union workers, and moving their headquarters from Pittsburgh if the deal did not close, as ‘a pathetic blackmail attempt on the United States government and the Commonwealth of Pennsylvania. By taking immediate action, our government is showing that this type of shameless behaviour will never be tolerated’.
He reiterated Cleveland-Cliffs’ interest in buying unionized mills that US Steel is threatening to close, should its takeover by Japan’s Nippon Steel get blocked by President Biden.
‘Hot-button
Indeed, the deal has become what experts describe as a ‘hot-button issue’ in the ongoing election campaigning, with neither Republicans nor Democrats showing any softening on the ‘sensitive issue of the nation’s steel sovereignty’. There are also deep underlying security concerns over the deal.
Senators in the Midwest’s steel-producing
*US correspondent, Steel Times International.
states point to Nippon’s partnership with Baoshan Iron & Steel, a state-owned firm linked to the Chinese Communist Party, even though Nippon withdrew from the partnership arrangement with Baoshan in August 2024. Senator Sherrod Brown (D-OH), facing a tight re-election race, was among the first lawmakers to publicly oppose the deal.
Nippon’s $14.9 billion takeover bid was also criticized by vice president and Democrat presidential nominee, Kamala Harris who, while addressing union leaders in Pittsburgh, ‘the heart of the steel industry’, on Labour Day (3 September), in President Biden’s company, announced that US Steel should remain domestically owned. She described the company as a ‘historic American company … and it is vital for our country to maintain strong American steel companies’.
A letter sent by the Committee on Foreign Investment in the US (CFIUS) to Nippon Steel and US Steel, maintained that Nippon’s decisions could create a reduction in domestic steel production capacity. The CFIUS said that the takeover would harm national security, particularly transportation, infrastructure, construction and agriculture.
Nippon Steel reaction
In a letter to the CFIUS, Nippon Steel said that it would invest billions of dollars to
maintain and boost US Steel facilities that otherwise would have been idled. Nippon added that the deal ‘indisputably will maintain and potentially increase domestic steelmaking capacity in the United States.’
According to CFIUS, a continued loss of visible commercial production capabilities and jobs would jeopardize the US steel industry’s ability to meet the ‘full spectrum of national security requirements’.
Nippon assured that it would not transfer any US Steel production capacity or jobs outside the US, nor would it interfere in US Steel’s decisions on trade issues. Indeed, Nippon even proposed a detailed draft agreement to address CFIUS’ concerns.
In a recent statement, the Washingtonbased Japan-US Business Council said that the group was ‘very alarmed’ by attempts to politicize the CFIUS review process which should be conducted objectively based on fair rules and processes.
Japanese politicians have generally maintained a stoic silence, but Taro Kono, a prime ministerial candidate, said governments should not intervene in deals
in an arbitrary manner, when asked by Japanese journalists about US attempts to block the Nippon Steel-US Steel deal. Washington cannot fully ignore the sensitivities involved, since Japan is a close US ally; Japan is also the biggest foreign investor in the US.
US Steel, on its part, has warned that it may have to move its headquarters from Pittsburgh and thousands of unionized jobs could be at risk if the Nippon takeover deal collapsed. US Steel said that its own employees would rally in support of the sale at its Pittsburgh headquarters.
US Steel’s CEO, David Burritt, who had remarked at the Global Steel Dynamics Forum in June in New York that the deal would pass in the end, noted in his latest comment that the workers’ rally was to demonstrate support for the Nippon deal. “We want elected leaders and other key decision makers to recognize the benefits of the deal as well as the unavoidable consequences if the deal fails,” Burritt said in a press release. The company would then ‘largely pivot away’ from its blast furnace
facilities, risking thousands of jobs.
On another note, Midrex Technologies Inc., a company specializing in direct reduction ironmaking technology and aftermarket solutions for the steel industry, signed a technical co-operation agreement with iron-ore mining company Vale to further collaborate over the use of ironore briquettes in direct reduction plants. The companies said that initial test results have shown promising results in using iron-ore briquettes in the direct reduction process. Both partners plan to evaluate the creation of a joint venture to provide briquette technology to the market as most direct reduction plants use iron ore pellets as a feedstock. Vale’s briquette production process represents an alternative to the pelletizing process with reportedly lower production costs, lower investment intensity, and approximately 80% less emissions. According to both companies, the technology would vastly help in decarbonizing the global steel industry. �
to
For 135 years, steel producers and steel service centers have counted on Butech Bliss to deliver the design, engineering and technological advantages necessary to help them succeed. From entry to exit end we build it all. Our product lines include roller and stretch leveling technology, a full line of shears, material handling equipment and complete coil processing lines. We are more than a scrap chopper manufacturer. Learn more about our world-renowned coil processing technology call +1 (330) 337-0000, visit ButechBliss.com or email sales@butech.com. If our name is on the machine, it’s built better.
Volatile economic conditions have forced Chilean steelmaker Compañía Siderúrgica Huachipato into decline, impacting thousands of workers, as well as the financial stability of the region. By Germano Mendes de Paula*
EARLIER this year, Compañía Siderúrgica Huachipato (CSH), a subsidiary of Compañía de Acero del Pacífico (also known by its acronym CAP Group) briefly outmanoeuvred Chinese steelmakers (STI Digital, June 2024, pp. 18-19) as Chile’s Anti-Price Distortion Commission imposed provisional antidumping duties (AD) of 33.5% on steel grinding balls and 24.9% on steel bars imported from China. The measure was in force from April-September 2024.
In response, the Chinese ambassador to Chile, Niu Qingbao, issued a strongly worded statement, which was notable given his diplomatic position. He argued: a) the Chinese steel companies do not receive government subsidies and their products are not sold at prices below normal or unfair value, thus the AD were unjust; b) the competitive edge of Chinese steelmakers stems from their high efficiency; c) the Chilean steel mills’ difficulties and operating losses are mainly due to their technological obsolescence and poor management, leading to a loss of competitive advantage over the years. The ambassador claimed that blaming China for issues within Chilean companies lacks evidence and does not aid in resolving these internal challenges. He also mentioned China’s intent to contest
the imposed duties.
The ambassador emphasized that the AD were detrimental to the bilateral relationship, recalling Chilean president Gabriel Boric’s visit to Xi Jinping in October 2023. He expressed concern that these duties could harm the friendly ties between Chile and China. It is worth noting that, in 2023, Chile exported $37.45 billion to China and imported $19.83 billion, resulting in a significant trade surplus. The Chile-China free trade agreement was signed in November 2005.
The virulent attack from China’s ambassador could be considered an overreaction as the country’s steel exports to Chile, impacted by the AD, were modest. However, his response is further contextualised by two factors. Firstly, in a strategic deal, Chinese lithium miner Tianqi, which owns about a fifth of Sociedad Quimica y Minera de Chile (SQM), has appealed a ruling by a Chilean financial regulator, which proposes that shareholder approval is not needed to proceed with a major tie-up set to boost state control over the country’s lithium sector, regarding a planned partnership between state miner Codelco and SQM. Secondly, Qingbao’s statement can be understood as a proactive
attempt to discourage the imposition of AD from countries with significant trade surpluses with China.
Chilean steelmaker lost the war In August 2024, CSH announced it would indefinitely cease steel operations by September, citing over $500 million in losses over two years due to an increase in imports from China. This decision was influenced by several factors: a) the inability to pass on the price hikes recommended by the Anti-Price Distortion Commission, as they could not reach a sales and pricing agreement with local steel ball manufacturer Molycop, a key steel customer; b) intensified Chinese dumping; c) long-standing financial difficulties.
Chile’s government, led by the minister of economy, Nicolás Grau, expressed dissatisfaction with CSH and Molycop for failing to develop a sustainable business strategy despite interventions like the AD duties. On its side, CSH justified that the temporary AD alone would not sufficiently transform the market to secure the steel business’s financial viability. From 2019 through Q1 2024, when Chinese exports surged, CSH incurred losses exceeding $700 million, with a deficit of $386 million in
* Professor in Economics, Federal University of Uberlândia, Brazil. E-mail: germano@ufu.br
2023 and an additional $42 million in Q1 2024, a trend that continued in subsequent months.
CSH will maintain other activities in the Bío Bío Region, including port and logistics services, limestone extraction and sales, rare earth extraction, and a green steel pilot project. However, the specifics of its engagement in the latter, following the closure of their steel operations, remain unclear. Though the project may herald innovative steel production, its associated risks are likely elevated.
In early September, the Anti-Price Distortion Commission announced that it had unanimously decided to end early the AD investigation into imports of Chinese steel grinding balls. This decision was preceded by the announcement of the indefinite suspension of operations at the CSH, the main driver of the analysis of the commercial defence measure for this type of product.
The shutdown of CSH, the country’s only coke-integrated mill, is expected to conclude by late 2024, affecting
approximately 20,200 direct and indirect jobs in the Bío Bío region. This region has a population of 1.5 million inhabitants, and is divided into three provinces: Arauco, Bío Bío, and Concepción (where CSH is located). The company plans to offer a comprehensive exit strategy, including financial compensation, and support for retraining and new job placements.
CSH and the trade union have finalised the details of the agreement reached in the context of the indefinite suspension of the plant’s operations. In addition to the benefits stipulated in the law, the workers
will receive ‘special compensation’, from $4k to $17.5k based on the working years in the company: a) less than one year: $4k; b) one to four years: $9.4k; c) four to six years: $13.5k; d) six or more years: $17.5k. Those aged 50 or older will be compensated directly with the $17.5k
The Bío Bío region has witnessed a long history of deindustrialisation. A similar crisis occurred with the collapse of sugar-producing companies (mid1970s), coal mining (early 1990s), and wood textiles (early 2010s). CSH’s closure poses additional significant threats to economic stability in the region, prompting calls for immediate revitalisation efforts and potential fiscal incentives to attract alternative activities and sustain employment. Regional leaders stress the urgency of strategic planning to combat rising unemployment and uphold economic vitality. Thus, while CSH has lost its battle against Chinese steel, the region faces the daunting challenge of transforming an economy heavily reliant on the steel industry. �
Already facing several headwinds, a new challenge has emerged for Indian steel mills in the form of a new mining cess imposed by some states, following a recent judgement by the Supreme Court of India (SCI). This development is poised to compress
primary and secondary producers.
By Dilip Kumar Jha*
across the steel
IN August, India’s Supreme Court confirmed that the authority of states would impose taxes on mineral rights and mineral-bearing land, allowing them to claim refunds of royalties dating back to 1 April 2005. This implies that mineral-rich states may charge a mining cess for the extraction of minerals with retrospective effect from April 2005. Odisha, which accounts for 46% of the value of minerals, plays a key role in the levy of the mining cess. The recent Supreme Court ruling has brought renewed focus on the Orissa Rural Infrastructure and SocioEconomic Development Act, 2004 (ORISED), which allows for approximately 15% cess on iron ore and coal.
If fully enforced, this could result in around an 11% increase in the landed costs of iron ore, directly affecting the cost competitiveness of domestic steel companies. The new mining cess is bound to raise the procurement cost of minerals such as iron ore and chrome ore, which will eventually lead to higher steel production costs, thereby lowering India’s competitiveness in the global market. In a related move, the Jharkhand government
Source: Ministry of Mines: Annual Report (Financial Year 2023-24).
recently imposed a modest cess increase of INR 100/tonne on iron ore and coal, setting a precedent for other states to follow. This increase is expected to have a minimal impact on steel companies’ operating margins, reducing them by around 30-40 basis points (bps).
It is worth noting that India’s steel
industry has been struggling to cope with a slowdown in demand during April-June 2024 due to the Parliamentary elections and the resulting slowdown in infrastructure development. While new infrastructure project sanctions were deferred, work on existing sites was delayed during the June quarter. As a result, India’s
steel demand remained stable throughout this time period.
According to T V Narendran, managing director at Tata Steel, “Levying cess on minerals has a huge impact across industries, as it will ultimately raise questions about a company’s profitability and investment capabilities. The effective tax rates on minerals in India are the highest in the world. If the tax is too high at an early stage, it will affect the motivation for production.”
As a preventive measure, Tata Steel has already set aside INR 177.34 billion for mining taxes following the SCI order. Tata Steel reported an 18% decline in net profit at INR 33.29 billion in the April-June 2024 quarter, down from INR 40.50 billion in the previous sequential quarter. During this time period, subdued steel demand across most regions weighed on global steel prices. In India, steel demand remained broadly stable despite some impact from the Parliamentary elections and heat waves.
Credit rating agency ICRA estimates that
primary steel producers’ margins could shrink by approximately 60-180 basis points, while secondary producers, with already lower profitability, may face a more severe impact, with margin declines ranging from 80 to 250 basis points, depending on various scenarios where cess rates could vary between 5% and 15%. The power sector, which heavily depends on coal, may see a rise in supply costs by 0.6% to 1.5%, potentially leading to higher retail tariffs.
Girishkumar Kadam, senior vice-president and group head of corporate sector ratings at ICRA Ltd, said, “The enforcement of the new mining cess by key mineral-rich states could heighten cost pressures for the steel industry. While most states haven’t set the rates yet, any substantial cess could adversely impact margins, especially for secondary steel producers, as merchant miners are expected to pass on the increased costs. Consequently, the strategies adopted by various state governments will be crucial in shaping the competitive landscape of the steel industry”.
A Fitch Ratings report added, “Steel mills could face increased risks from a sustained weakening of their profit margins because of mining cess levies. Given limited ability to pass on the potential increase in operating costs, metal and mining companies are likely to be more affected by the SCI’s ruling compared to power and cement companies.”
Experts have warned that the SCI’s ruling on mining royalties, with retrospective effect from April 2005, could deal a substantial blow to the Indian mining sector, with potential financial repercussions amounting to INR 1.5-2 trillion. The premier industry body, the Federation of Indian Mining Industries (FIMI), believes that the Indian mining sector is already burdened with the highest taxation in the world. The Supreme Court’s judgement has granted unchecked powers to impose various taxes and levies, which will severely impact not only the mining sector but also the entire value chain, leading to significant inflationary pressures on end products. �
GLAMA Maschinenbau GmbH
Hornstr. 19, 45964 Gladbeck, Germany fon: +49 2043 9738 0 fax: +49 2043 9738 50
GLAMA Maschinenbau GmbH
email: info@glama.de
Hornstr. 19, 45964 Gladbeck, Germany
GLAMA USA Inc.
fon: +49 2043 9738 0 fax: +49 2043 9738 50 email: info@glama.de
60 Helwig St., Berea, Ohio 44017 fon: +1 877 452 62 66 email: sales@glama-us.com
“STEEL follows population growth,” said Mark Bula. He believes that the future of steel usage will be in the MENA region so when he took a surprise call from a member of the Jindal family asking if he would be interested in a CEO role at Vulcan Green Steel in Oman, he jumped at the chance.
Vulcan was looking at developing something akin to H2 Green Steel (H2GS), where, at the time, Mark was chief commercial officer.
“I’d promised H2 that I would see through developing a go-to-market strategy, getting a certain level of offtake agreements that would get them financed and I felt comfortable that I had accomplished that,” Mark said.
He liked the idea of Oman as a place to live and work and agreed an amicable exit deal with H2GS. “They were gracious enough to come up with an agreement that made sense for us to exit from each other and so I moved to Muscat.”
He described his time in Oman as a wonderful experience where he gained valuable insights into what it was like to be a CEO.
“In the Middle East, there’s a lot of cheap, natural gas and they have a very good solar profile, but Oman brought a wind profile that was very attractive,” said Mark. “Probably one of the best wind profiles in the world,” he added.
Mark didn’t stay long at Vulcan Green Steel. His plan had been to inject a more global management style into the business. “And in the end that wasn’t as easy as I thought and maybe I wasn’t the right guy to make it happen,” he said, explaining how, since his departure, other Western managers (from US Steel and Nucor Corporation) had been and gone too.
Mark then received a call from Norwegian start-up BLASTR Green Steel asking if he’d be interested in a consultancy role at the company. He was looking to move out of Oman and one thing led to another. “They called when they thought I was still employed and said ‘would you consider making a change?’ I said, as luck would have it, I’m probably making a change and that’s how it really happened.”
He had considered taking time off, recharging his batteries and finding the right opportunity that would suit him best – and not necessarily in the steel industry. He’d thought about returning to the United
Mark Bula is very familiar with the phrase ‘cutting edge’. He was chief commercial officer at US-based Big River Steel, which offered the steel industry its first ever ‘learning mill’, he took on a similar role at H2 Green Steel in Sweden, a leading player in the race towards the realization of hydrogen steelmaking, and now he is CEO of Norwegian start-up BLASTR Green Steel, a company with a ‘mine-to-gate’ business model and a strong vision of decarbonizing the steel value chain. Matthew Moggridge* meets Mark Bula**
States, but realized he enjoyed working overseas and that he was a steel man to the core. He views himself as more of a steel guy than a company guy.
According to BLASTR’s website, the company was established in 2021 ‘to leverage Nordic advantages and become an integrated low CO2 steel producer, based on a vision of decarbonizing the steel value chain’.
“When I look at the European steel industry, I wonder why it has not transitioned away from blast furnace steelmaking,” he said. “Nobody can give me a straight answer. Some say it’s because they don’t think that the EAF and scrap make good steel. But we know in the United States that EAF steelmaking has been extremely successful.”
He cited the stock valuations of Nucor and Steel Dynamics Inc and said that stateside EAF steelmaking had flipped in the last 20-30 years from being the minority of
the volume to most of the volume. “There’s a new steel mill built in the United States every five to seven years. Three of them are under construction right now. When was the last real mill, integrated mill, built in Europe? 1967? 1971?”
Mark, an American through and through, has an absolute right to big up the US steel industry and big it up he did, citing a report by the Steel Manufacturers Association showing that the US industry has one of the lowest CO2 footprints on the planet and leads the world in terms of being a green steelmaker. “The bottom line is the US steel industry has transformed itself from blast furnace steelmaking to EAF steelmaking and leads in steel recycling. I think the automotive recycling rate in the United States is higher than in Europe and this is when I look at Europe and say there’s an opportunity here,” Mark said.
He believes in the entrepreneurial spirit; he likes interesting projects and is happy
*Editor, Steel Times International, **CEO, BLASTR Green Steel
to put in the long hours, thriving on the adrenaline rush and the anxiety, everything that comes with trying to raise money and build a business from scratch.
The opportunity at BLASTR revolves around the company’s ‘really good mineto-gate value proposition’ and it is this, said Mark, that sets the company apart.
We were sitting in the London headquarters of Cargill on a sunny day in the City of London and it was no accident. “Our partnership with Cargill brings a lot of credibility and ability to the project,” explained Mark. “They also bring with them marketing rights to mines around the world, particularly in the Nordics, and they’re building this out. So, in essence, we’re able to de-risk our project because we’re sourcing iron ore from Cargill that has multiple sources around the world and some of those are exclusive agreements,” he added.
The Cargill link drew Mark in because he saw the competitive advantage it afforded BLASTR. “It’s not only being able to control
your iron ore and your raw materials sourcing, but it also allows us to go back and track all the way to the mines,” he said, explaining how, going forward, BLASTR may have an even more symbiotic relationship with mining companies that would make the business stratospherically more attractive to investors and steel buyers. So, let’s talk pelletising.
“We see ourselves as having three business units: pelletising; green iron; and low emissions steel. Decarbonization really happens at the ironmaking stage, that’s where the magic happens,” he said, explaining how it’s the most important and key component of the process and why BLASTR’s focus has been on how to solve that part of the value chain. It’s all about changing the model a little bit and asking the question: ‘do we have to be in the hydrogen business?’
BLASTR’s focus, then, is on iron. “Let’s focus on the pelletising, that’s a mine-togate value proposition that is unique in the industry and I think it’s something we
can sell on the marketplace,” said Mark, explaining how buyers of steel ‘will see us owning the mine-to-gate process and that will give the company the necessary leverage to get agreements in place. It means somebody wanting to build a hydrogen plant adjacent to BLASTR’s steel plant [in Finland] would have the confidence to do so, he said, “Because we’ll be the off-take for it, we’ll be the green ironmaking company – and that’s the difference of thinking.”
At this stage in BLASTR’s development, it’s all about attracting investors and Mark believes that a strong sense of entrepreneurialism will give greater credence to the project.
“Why have US minimills been so successful? It’s man hours per ton, or it’s tons per employee,” he said, referencing the very real aspirations of big US minimill operators who, claims Mark, produce in the region of 3,500 to 4,000 tons of steel per employee. “If you look at the man hours per ton in Europe, I guarantee you it’s probably well under 1,000 tons per employee,” he added. It is Mark’s belief, therefore, that the European steel industry needs to create a more efficient and fastmoving business model powered by an entrepreneurial spirit.
BLASTR aspires to being the lowest-cost producer of green steel in Europe, making it a more attractive proposition for investors. “We believe we are going to be at the lower cost percentile of green steelmaking,” he said. Whether other companies in the green steel sphere are following similar models is anybody’s guess, but Mark believes iron ore sourcing is where the challenge lies. “But you also have to source the pellets and if you’re sourcing from different parts of the world there’s also transportation costs,” he said.
Cargill moves 50Mt of iron ore annually, most of which comes out of blast furnaces. “But the point is, they know the flows of iron ore around the world, and they have a logistics business that owns vessels that move iron ore, it’s a huge advantage,” he said.
BLASTR will need high purity iron ore pellets for its EAF. Cargill has been establishing relationships with mines that produce higher purity iron ore, but some of them don’t have pelletising facilities. “Which is why we’re going to build a pelletiser,” said Mark. “Most pelletising is owned by the mine, we’re going to be a
steel mill that owns it.”
The pelletising plant will be located in the UK, on Teesside, because BLASTR’s steel plant, which is to be located in Inkoo, Finland – where BLASTR can exploit affordable energy on-site – can only handle Panamax vessels even if the port there is expanded.
The Teesside facility (an old British Steel plant) incorporates a terminal owned by Red Bulk Terminals, which can accommodate larger Cape size vessels, allowing BLASTR to leverage Nordic iron ore – which Mark thinks the company can secure – but also ore from Canada and potentially Brazil and Australia. The plan is to sell 50% of the ore shipped into the UK and converted by BLASTR to DR pellets to other steelmakers globally.
“The Teesside location is really central when you think about North America and the Nordics,” said Mark, explaining how the UK port’s ability to handle large vessels is a ‘big deal’. The Inkoo facility – ‘for the most part’ – does not need high-end ice class vessels which are limited in number and fuelled by fossil energy. “We’ve tried to eliminate all the disadvantages of being in an iced port six months of the year,” he added.
In essence, phase one of the project is the pellet plant and phase two is DRI and the steel plant. “Hydrogen will come from the natural development of the Inkoo facility,” said Mark, adding that it will be developed either in conjunction with a third party or a third party will use BLASTR as the offtake and develop the hydrogen plant themselves. “I’d be comfortable with that,” said Mark. BLASTR has signed a Memorandum of Understanding (MoU) with Austrian production technology company Primetals Technologies to provide the Inkoo electric arc furnace, the hot mill and all the
“When I look at the European steel industry, I wonder why it has not transitioned away from blast furnace steelmaking. Nobody can give me a straight answer. Some say it’s because they don’t think that the EAF and scrap make good steel. But we know in the United States that EAF steelmaking has been extremely successful.”
ultimately produce 2.5Mt of ultra-low CO2 steel based on ‘gross embodied emissions’, which means the total greenhouse gases emitted during a product’s production –“I’m a purist in this way,” said Mark, adding that BLASTR aims to reduce emissions by 90% ‘from what is traditional steelmaking’. It all recalls the big question: what is ‘green’ steel? Mark says the green steel industry is still evolving, as is the terminology, and everybody will have a different opinion. “All that should really matter in the end is what are you willing to pay for a gross embodied emission of a number that means something to you as a customer,” he said. With a plan to be producing 2.5Mt of green steel by 2029 – and with predictions of global demand for low CO2 flat steel of 30-40Mt by 2030 (and 100Mt by 2050) – the question of expansion entered the conversation. “We’re already looking at other sites to build either more pelletising capacity and/or pelletising and DRI capacity, again, to serve other steelmakers,” he said.
While all businesses exist primarily to turn a profit, BLASTR wants to be seen as a company that helped to decarbonize the steel industry. “We think the best way to do that is to have green ironmaking, and to have that you’ve got to have iron ore; so it’s been our focus, but I think there’s an opportunity to sell hot-rolled coil as a semifinished product for those unable to make hot-roll affordably – or in a culture where we think we can make it,” and by that he means producing 3,500 tons per employee. “It’ll be a multi-faceted business and the whole of it goes towards making the steel industry greener,” he said.
Asked if everything was going to plan, Mark commented, “Let’s be honest, things never go to plan.”
automation surrounding it. “We’ve signed an MoU with Midrex to be the DRI provider but have not yet announced the technology provider for the pellet plant in the UK.
The Inkoo facility, says Mark, will
BLASTR was first introduced to the market over two years ago. Since then, there has been a leadership change with Mark now in charge. The company has successfully raised the first round of funding. “We’re going to be capital-hungry for a very long time,” he said, adding that every day since he started, he’s felt as if he was taking a step forward and improving the business model along the way. “It’s all about solidifying and connecting the dots on the mine-to-gate value chain and involving Cargill more,” he said, but it’s also about building a USstyle minimill culture in Europe based on a tons per employee scenario with a view to creating a more sustainable business over a longer period of time.
Mark recognizes the differences between European and North American trade policies, arguing that the former is more protectionist of the consumer than the latter. In other words, he believes, “EU trade policy by favouring the consumer, discourages risk taking by the existing industrial companies”. And that creates a different scenario here in Europe and you have to navigate it, it’s part of the challenge, because there are great things that I’ve learned from how to build steel companies and entrepreneurial thinking in the United States that may not work in Europe,” he said.
“Right now, in Europe there’s been a push-by policy; I think there will be a pull-by demand [for green steel] and that’s when things are really going to take off,” Mark explained.
Since 2021, when the likes of H2Green Steel first arrived on the scene, the capital markets have changed, thanks to Russia’s invasion of Ukraine, rising interest rates and the energy crisis. For BLASTR, therefore, it’s no longer sufficient just to have a good story, it needs data to support what it is claiming is a viable proposition.
While there is plenty of talk about dramatically changing supply chains because of the ongoing ‘green steel transition’ Mark wants to see DRI, green ironmaking and hot-rolled coils made somewhere in Europe. That, he said, is BLASTR’s plan. “We don’t want to add finishing capacity, there’s plenty of that already,” he said. “So, let’s not add more, let’s build an efficient operation that’s focused on cost sensitivity that allows us to be on the lower quartile of the cost curve,” he said.
While BLASTR is busy building up its team, Mark admits it could have been faster conveying the key facets of its business model to investors. “If we had done that, we’d probably have attracted more financing by now and ultimately, the judge of success is can you get the project funded and start the company?”
And can you?
“I reckon we can.” �
For more information on BLASTR Green Steel, visit: https://www.blastr.no
and QSP–DUE are the winning Danieli direct-rolling technologies for the most competitive production of long and flat green-steel products.
They are the result of the research and continuous improvement profused over 20 years, along with multi-million dollars of investment.
Their unmatched performances have fueled their success worldwide, thanks to lower resource consumption and carbon emissions, unbeaten OpEx, and outstanding product quality.
So, top technology becomes copied technology, the shortest route for competitors that, abandoning their solutions, now try to imitate MIDA–QLP and QSP–DUE
Equipment and layout may be copied, but experts know that details make the difference. Automation and process solutions are not easy to copy, and this will be the experience of anyone trusting in those imitations.
The competitive advantage for our customers, obtained by field results, is the best defense for our technology – more than court rulings protecting our patents.
Danieli offers the best guarantees for speedy learning curves, steady performances, and now Digital Plants with no men on the floor. Buy the Original.
GIANPIETRO BENEDETTI CHAIRMAN OF THE BOARD OF DIRECTORS
There seems to be a consensus today that renewable energy and hydrogen are the means by which the steel industry shall be decarbonized. Billions are put into research projects for new processes and yet very little so far has happened. European integrated plants struggle with reinvestment plans in technology that they know will never be profitable or just give up and convert to scrap-based production. In the meantime, new blast furnace plants are being built around the world and nothing indicates that the process will lose its dominant position in the period until 2050 or even this century. To paraphrase the American writer Samuel Langhorne Clemens, better known as Mark Twain: ‘The reports of the death [of the blast furnace] are greatly exaggerated.’ By Rutger Gyllenram*
IN principle there are three energy sources for low-emission ironmaking:
1) fossil reductants coal and natural gas combined with CCS.
2) low emission electricity from wind, solar, and nuclear power.
3) biomass.
The products are either a liquid hot metal with or without carbon or a solid sponge iron also with or without carbon. Without pretence of being exhaustive, some of the possible process alternatives are shown in figure 1. Low-emission hydrogen can be made from natural gas with CCS (blue H2),
electrolysis of water using low-emission electricity or from biomass (both considered green H2). Future process development will tell whether it is preferable to have a mix of carbon monoxide and hydrogen as reductants or if pure hydrogen is more efficient. Reduction mechanisms are complex, and it is doubtful whether one can draw far-reaching conclusions from calculations, simple lab experiments, or even pilot plant tests.
Fossil reductants and CCS
To the left in Fig 1 we have the processes
that use fossil coal and natural gas which all face the challenge of abating the upstream emissions of methane from coal mining and gas extraction that can be as important as capturing and storing the inherent carbon dioxide emissions. The blast furnace (BF) whether it is using a blast of oxygen enriched air, or as in the oxygen blast furnace with top gas recycling (O2BF TGR), pure oxygen, needs a minimum amount of coke to ensure a permeable bed, often said to be around 280-300 kg/ton hot metal. When that is satisfied, alternative non-fossil reductants or sponge iron with a
*Founder of Kobolde & Partners AB, co-founder of FerroSilva AB (email: rutger.gyllenram@kobolde.com)
low-carbon footprint can be used to reduce the emissions and avoid another 200 kg of coke. HIsarna has the advantage of not needing agglomerated raw materials but is dependent upon carbon capture and storage to decrease emissions if fossil coal is used. All alternatives have been tried in pilot plant tests but have not yet had a commercial breakthrough.
MIDREX, which is the dominant sponge iron process patented by the eponymous company, has announced a variant where the ironmaker starts with natural gas and then increases the hydrogen level when hydrogen is available. Until then, the carbon dioxide has to be captured from a diluted flue gas. Energiron, a process jointly developed by Tenova and Danieli, uses natural gas as a reductant but the companies claim that they can increase the hydrogen level to close to 100%. On the other hand, the process today uses carbon capture as an inherent part of the process in order to recycle carbon monoxide into the shaft and, therefore, a process enhancement capturing most of the carbon dioxide would be possible with only minor adjustments to the layout.
Low emission electricity as energy source
Molten Oxide Electrolysis (MOE) is a process that is currently developed for the reduction of both iron and ferroalloys. An MOE plant is designed to run multiple cells in parallel with oxygen as an off gas and the production of a carbon-free liquid metal with a high temperature. Siderwin is another electrolysis process that produces iron cathodes at a low temperature. MOE and Siderwin are both at an early stage of
development and the outline with many small cells makes the competitiveness with shaft furnaces something of a challenge for a low-cost material like iron, despite an expected low energy use.
Hybrit can serve as the first example of producing an initially carbon-free sponge iron with hydrogen made from the electrolysis of water. Pilot plant tests have concluded and a demonstration project is planned with a production rate of 1.3 Mt/ yr, with construction due to begin in 2025. A challenge identified by the Hybrit team is the efficiency and stability of electrolysers for production of the large volumes of hydrogen needed in a commercial plant. Circored, Hymet and Hyrex are fluidised bed processes intended to produce coalfree sponge from fines. They all have a
background in reduction with reformed natural gas or gasified coal but have now been redesigned for hydrogen.
Carbon dioxide emissions from biogenic sources are considered to be non-existent in most carbon accounting systems, except when captured and stored (or used to replace fossil carbon), when they are then given a negative value as a carbon sink. A smelter process is suggested as a way to do the smelting, final reduction, and carburisation of sponge iron before a converter step. Today most smelters use electrodes from fossil carbon which in the future must be produced from biogenic carbon to produce low emission iron. In the Tecnored process, charcoal is used to reduce iron ore in the form of cold-bound briquettes producing a hot metal similar to that from a blast furnace. Tecnored can be considered an alternative to charcoal blast furnaces. By gasifying biomass like forest residuals, as well as other biogenic materials, a syngas can be produced with the same composition as the reformed natural gas used in the MIDREX process. The FerroSilva process uses biogenic syngas to produce sponge iron with a normal carbon content while capturing the biogenic carbon dioxide for offtake. The project is in the early stages of development, with the first production of 50kt/yr planned for 2028.
MIDREX and Energiron can of course use green hydrogen, and Hybrit in the same
way uses blue hydrogen, and to conclude, the fluidised beds may use any reducing gas. However, the way they are developed and marketed today indicates the most likely alternative.
Producing low-emission iron and steel
Paramount to low-emission iron and steelmaking are the availabilities of coal and natural gas with low upstream emissions, CCS capacity, low-emission electricity, and biomass. These will vary with location, time and available means of transportation. Technology readiness is an issue, although it does not seem to be recognised today. In my mind: new process ideas are nothing more than ideas until proven in full-scale and only then can they be put into any trustworthy pathway and the improvement of existing and functioning processes may be put aside to give room for new inventions.
The role of low-emission sponge iron
When more and more blast furnaces close and switch to electric arc furnaces, the need for sponge iron increases to ensure a high steel quality. If the admixture is in the order of 20%, the gangue content is
of less importance, even if a low content is preferable. Replacing blast furnace production with sponge iron melted in an electric arc furnace is only possible to a certain degree since it demands sponge from iron ore with a low gangue content and that constitutes a limited resource. However, the process that is available today to take care of ore or sponge iron with a high gangue content is the blast furnace. A maximum mixing of sponge iron in blast furnaces globally is, therefore, both a way to reduce carbon dioxide emissions and to use this type of ore economically.
The cost to reduce iron ore to sponge iron, also called DRI, Direct Reduced Iron, with low emissions is shown in Fig 2. In the figure, the carbon dioxide from natural gas is captured and stored and the carbon dioxide from biogenic syngas is captured for offtake giving a premium. Of course, a calculation like this is only indicative and shows the reductant cost ceteris paribus which means that the ore cost and distance to the market is the same.
One conclusion that we can draw from
Fig 2 is that if we are looking for a place where we can reduce iron ore to low emission sponge iron as a means to reduce the emissions from the global steel industry, we must, for the foreseeable future, look for countries with low-cost natural gas. Another conclusion is that in order to produce sponge iron with hydrogen, you must have advantages such as closeness to iron ore. Merely being close to a steelmaking site may, as I see it, not be enough.
Meeting climate challenges with limited resources
Meeting the goals of the Paris agreement is a task for the entirety of society, and not just the steel industry, although it seems that exactly that is the narrative today. Having available low-emission electricity is key to decarbonizing all sectors, and the first question must be how to optimise the global impact. Is the use of renewable electricity to produce hydrogen optimal if the rest of the grid is powered with coal? Is replacing functioning blast furnaces with electric arc furnaces with a scrap burden reasonable when it results in new blast furnaces being built elsewhere when competition for scrap intensifies?
To anyone following the development in ironmaking it is obvious that the main ironmaking process still is the blast furnace in countries without natural gas and will stay so until we have a breakthrough in fossil-free energy production drastically decreasing the electricity cost. In the long run, we will have fossil-free new processes like in Fig 1, but it will take time before they are ready and can play a major role in the world market.
The availability of low-emission electricity and biomass will set limits and decide competitiveness and what markets in which they will thrive.
In the meantime, we must do what we can with what we have – and the easiest and most economical way to decrease the emissions in the global steel industry is to produce low-emission sponge iron with natural gas, using CCS to use in both electric arc furnaces and blast furnaces. �
Let us end with another classic Mark Twain quote: “The secret of getting ahead is getting started. The secret of getting started
is breaking your complex overwhelming tasks into small manageable tasks, and starting on the first one.”
Earlier this year, the Financial Times published an article that asked what has become a key question in the run-up to the US presidential election: Will steelworkers be the swing vote in 2024? To fully examine that question, one must understand how trade policies and voter opinions in the US have evolved since 2016. While there are stark differences between the Trump and Biden administrations, they have more common ground on steel trade and tariffs than many would think. This article will examine how steel trade policy evolved in recent elections and government legislation since 2016, and will identify trends that can be expected when the next president is sworn into office in January 2025.
By Matthew Groch*
ACROSS the globe, as countries grapple with the threat of climate change, the challenges of transitioning to low-carbon steel, and China’s trade practices, the 2024 US election will set the tone for global discourse as the Intergovernmental Panel on Climate Change’s (IPCC) 2030 goals loom. As noted by Financial Times reporter Rana Forrohar: ‘‘I’ll just summarise the big takeaway, which is that this isn’t just another old-line battle about steel. It will impact the 2024 election cycle, as well as global economic and security relations … It will also set some new precedents for how business operates in the post-neoliberal era in the US, as unions become far more strategic about their labour actions and demands.’’
Beyond the international impacts of steel on this election cycle, the steel vote in the US can swing key states in the election to Trump or Harris. This can be seen in the critical state of Pennsylvania, the thirdlargest producer of raw steel in the US.
According to a 2023 economic study by the Pennsylvania Economy League, there are over 123,000 full- and part-time jobs in the state’s steel sector, with more than 30,000 of these directly in iron and steel mills, and ferroalloy manufacturing. In 2016, Donald Trump beat Hillary Clinton in Pennsylvania 48.18% to 47.46%, a difference of fewer than 45,000 votes. In the 2020 election, Biden beat Trump by just over 80,000 votes, 50.01% to 48.84%. According to reporting from Axios, the Trump and Harris 2024 campaigns are set to spend more than double on advertising in Pennsylvania than in any of the other six swing states.
A similar story can be told about the swing state of Michigan, which ranks #6 out of US states in steel production and is home to 60,000 United Steel Worker (USW) members. In 2016, Trump narrowly beat Clinton 47.50% to 47.27%, a margin of just over 10,000 votes. In 2020, Michigan flipped to Biden, who beat Trump 50.62% to 47.84%, a margin of over 150,000 votes.
*Senior director, Mighty Earth.
Both Pennsylvania and Michigan are critical battleground states for both Trump and Harris, to secure enough electoral votes to win the White House in November.
According to the Bureau of Labour Statistics, there are over 14 million union workers in the United States, and 1 in 6 people reported having a union member in their household. Studies show that number jumps to 1 in 4 households in states like Michigan. While the USW reports over 850,000 members nationwide, many of which are in critical swing states like Pennsylvania and Michigan, the story of the past two elections can be measured by how candidates over-performed or underperformed with all union voters.
In 2008, Barack Obama secured 59% of union households, compared to only 39% secured by John McCain, and in 2012, he received 58% to Mitt Romney’s 40%. However, in 2016, Donald Trump was able to win 42% of union households, compared to Clinton’s 51%. By cutting the
Elevate your steel production with improved yields, superior quality, and reduced downstream costs.
Our high-resolution thermal imaging camera ensures a seamless transition between steel and slag, delivering real-time data to empower operators. Experience quick termination of taps after triggering alarms to prevent ladle issues.
Say goodbye to excessive slag and hello to enhanced productivity!
gap with union voters, Trump was able to break through the Democrats’ ‘blue wall,’ and win swing states like Michigan and Pennsylvania. According to American statistician and writer Nate Silver, that swing in union votes may have been enough to account for Clinton’s losses in Pennsylvania, Wisconsin, and Michigan. In 2020, Biden was able to win back much of the gains lost to Trump with union households, winning 56% to Trump’s 40%. Exit polling from Michigan in 2016 and 2020 demonstrates how vital these votes are in critical swing states. In 2016, Clinton lost Michigan, despite carrying union households 53% to Trump’s 40%. However, in 2020, Michigan flipped back to the Democrats, with Biden receiving 62% of the union households, compared to Trump’s 37%. According to polling from NBC News, prior to his dropping out of the race, Biden’s lead had dropped to just 9% among union households.
Over the last two administrations, it has become clear that US policy on steel tariffs has become the norm. The most relevant example during the Trump administration is the 25% tariff on steel imports, based on Section 232 of the Trade Expansion Act of 1962, aiming to protect US national security and revive the domestic steel industry. Trump also enacted a series of tariffs targeting China after initiating an investigation under Section 301 of the Trade Act of 1974. The Trump administration argued that the tariffs targeted global overcapacity and Chinese trade practices, including subsidies and dumping. The move was supported by the United Steelworkers and some Democratic lawmakers, and it became a focal point of
Trump’s 2020 re-election campaign.
In contrast, Joe Biden’s administration has continued many of these tariffs while seeking alternative approaches. In April 2022, Biden reached agreements with the EU, UK, and Japan to replace simple tariffs with tariff-rate quotas, reducing trade tensions, and avoiding retaliatory tariffs. Biden also maintained a tough stance on Chinese steel, raising Section 301 tariffs on steel, and addressing the mislabelling of steel from China as Mexican-made. In May, the Biden Administration proposed raising 301 tariffs on Chinese steel from 7.5% to 25%, and in July 2024, he imposed a 25% tariff on Mexican steel unless there is documentation of the steel being melted and poured in Mexico, in order to prevent Chinese evasion of tariffs.
Both Trump’s and Biden’s approaches to trade and tariffs are a major departure from the free trade tendencies of the Republican and Democratic policies of the past. However, the shift in policy closely mirrors the swing in America’s views of international trade. According to 2016 presidential election exit polls, only 39% of Americans said trade ‘creates US jobs,’ compared to 42% who said trade ‘takes away US jobs.’ According to a Pew Research poll from April 2024, 59% of Americans say that the US has ‘lost more than it gained’ from the increase in foreign trade, compared to only 37% who feel the US has ‘gained more than it has lost.’
According to international trade expert and director of ReThink Trade, Lori Wallach, the changes in US trade policy by Trump and Biden reflect America’s shift away from failed free trade policies: “The United States, like so many countries around the world, has come to a transpartisan consensus about the old theories of how trade could
work, and should work, and believes that it did not play out according to the promises. Now, people accept there’s a much more practical approach as a matter of trade policy to deal with fundamental security, supply chain, and infrastructure needs. The politics of trade in the US has gone back to what it was for a very long time in support of having a robust manufacturing capacity that provides national security, employment, innovation, and skills development. I don’t see that changing, whoever is elected next.”
According to a February 2024 survey of US adults by YouGov on tariffs, the new status quo seems to be the consensus of most US voters as well. The survey showed that 24% of US adults would like tariffs increased, 27% would like them kept the same, and only 20% would like tariffs decreased. The same survey found that 45% believe tariffs help domestic industries, compared to only 18% who said it hurts them. Additionally, the survey also found that 61% of US adults would support increasing tariffs on foreign goods, even if it leads to higher prices for American consumers. Regarding China, 33% of respondents said the US has a fair trade policy with China, compared to 23% who said it is unfair, with 44% not sure.
What should we expect from the 47th US president on steel tariffs?
With the bipartisan consensus on the need to protect domestic industries and national security, steel trade and tariff policies are unlikely to change significantly, regardless of who becomes the next president. As noted by Kevin Dempsey, president and CEO of the American Iron and Steel Institute (AISI) at the CRU Steel Market Update Atlanta Summit in August: “I believe there will be continuity on trade issues in the administration’s agenda, no
matter the outcome. There has thus far been continuity on the issues impacting steel from the Trump administration through the Biden-Harris administration–which has been driven by the problems that these policies are designed to address. For example, the problem of global steel overcapacity actually came to the forefront for steel under the Obama administration and it continued to be highlighted by the Trump administration. Trump added some new tools with the Section 232 national security steel tariffs and Biden maintained those tariffs. He made some adjustments, but he kept the tariffs. And I think it’s very likely we are going to see the same continuity on the Section 232 tariffs to address the global overcapacity problem, regardless of who is elected.”
On US trade policy with China, Dempsey also remarked: “The same is true with the administration’s approach
administration has continued, and which I think will continue. Following the lead of the United States, Canada also just announced some actions earlier this week in terms of higher tariffs on steel and electric vehicles to respond to trade-distorting
Reflecting the shift in national sentiment, both the Trump and Biden administrations have implemented tariffs to protect the US steel industry, a shift away from free trade toward an approach focused on securing American manufacturing and addressing global trade imbalances. As noted by the Coalition for a Prosperous America senior vice president, Nick Lacovella, “On economic policy and trade issues, you have both major parties moving in the same direction… it’s still going to be a tariffs administration, and an industrial policy one.”
US public opinion strongly supports maintaining or increasing tariffs to safeguard domestic jobs, and ongoing concerns about supply chain vulnerabilities and international competition imply that future administrations are likely to continue these policies. While Harris and Trump exchange barbs over tariff rates on the campaign trail, with the electoral and strategic importance of the steel industry, and the prevailing economic attitudes among Americans, steel tariff policy will continue, if not increase, under the next administration. �
In-Line Profile Measurement Systems for Hot / Cold Steel Applications with increased sampling rate up to 2 kHz.
Benefits:
Best measuring accuracy thanks to temperature-stabilized measuring systems
New algorithms for surface inspection and defect detection
Defect detection based on multiple maps and surface properties (reflectivity and intensity)
Detects process problems at an early stage
Quick maintenance and easy cleaning
Profile measuring solutions with global references
New research commissioned by Earthworks from the Institute for Sustainable Futures at the University of Technology Sydney, outlines five principles to minimize mineral demand and mining impacts associated with the transition to EVs. Minimizing Mining Impacts on the Road to Zero Emissions shows that solutions are available to allow a shift to zero emissions transportation without a rapid increase in mining and its associated social and environmental costs. By
AS industry leaders and policymakers scramble to meet mineral demands in the global transition to electric vehicles, public outcry should give them pause. From the American West to Serbia and Indonesia, residents are rejecting the highly exploitative practices of the past and demanding greater protections for the environment, their families, and mine workers.
Governments and companies, rushing to figure out how to decarbonize economies and curb heavy reliance on fossil fuels, have been quick to push the expansion of mines for minerals like lithium, copper, nickel and steel as part of the transition to renewable energy. While these are crucial material inputs for low carbon technologies like EVs, mining comes with its own sizeable carbon footprint to consider.
According to recent data from the UN Environment Programme, metal and mineral extraction and processing is responsible for 17% of global greenhouse gas emissions. As stated by the International Energy Agency, “The direct CO2 intensity of crude steel production has decreased slightly in the past few years, but efforts need to be accelerated to get on track with the pathway in the Net Zero Emissions by 2050 Scenario.”
Paulina Personius*
At the same time, people around the world, often in the Global South and often indigenous, are facing new and expanded mining operations with no regard for past
impacts, affected communities, or fragile ecosystems. A study in the scientific journal Nature Sustainability found that 54% of transition minerals projects are located
on or near indigenous peoples’ territories, resulting in disproportionate harm to indigenous communities.
Mining can have disastrous consequences for water reserves and quality, especially when not properly managed. The process of removing minerals from the Earth generates huge quantities of tailings, that is, toxic waste that has to be mitigated in perpetuity. Mineral extraction is often implemented in a way that ignores the right of frontline communities to have a healthy environment and the right of indigenous peoples to exercise sovereignty over their lands and territories.
However, there are pathways forward for transitioning from fossil fuels while avoiding the expansion of mining. Many of these shifts can take place along various points in the mineral supply chain, not just at the point of extraction.
Societies can expand public and active transit options so that we are not as dependent on personal vehicles, build the infrastructure to reuse, refurbish and recycle EV batteries, and build strong mandatory protections for the rights of frontline communities, workers, and indigenous peoples along the entire supply chain.
Our report shows that we can reduce mineral demand while working towards zero emissions road transport. The first step is to reduce car dependence, redesigning our cities to encourage public transport, walking and biking.
Bogota, Colombia, launched the TransMilenio Bus Rapid Transit System in 2000, opening 110km of new bus routes. This resulted in reduced passenger travel time of 30%, a 92% reduction in roadrelated deaths, decreased car use, and a 40% reduction in air pollutants.
Electric vehicles are one of the principal drivers of mineral demand in the renewable energy sector. Adding more public and active transport infrastructure and options makes transit in cities more accessible, can reduce noise and air pollution from traffic, and help make cities safer for pedestrians and cyclists.
Shift to smaller and more efficient vehicles and EV batteries
Another step to reduce mineral demand is to shift to smaller and more efficient vehicle batteries. Global modeling of a shift towards smaller vehicles found that this could reduce cumulative material demand for batteries until 2050 by up to 25%.
This would also help vehicle size match vehicle use patterns, meaning that the size of cars would be better aligned with how the vehicle is used. In the US, there is a trend towards larger vehicle sizes despite the fact that car trips have an average of 1.5 passengers. Together, reducing car use and smaller vehicle batteries are the most impactful and fastest way to reduce mineral demand.
Close the loop on battery materials
Closing the loop on lithium and other minerals involved in EV production can reduce mining demands just as steel recycling has for iron ore extraction. Steel production from recycling, for example, also takes up to 10 times less energy than
from iron ore. Policymakers should focus on advanced recycling and recovery, such as by improving recovery rates and ensuring recycling meets rigorous environmental and labour standards.
Use vehicles and batteries more intensively over their lifespan
Along with manufacturing smaller batteries, automakers, battery designers and recyclers can commit to remanufacturing and repurposing EV batteries at end-of-life. Reusing them in this way helps extend a battery’s overall lifespan, and combined with recycling to recover battery minerals, it can reduce overall mineral demand for EVs.
minerals responsibly
Lastly, for mining that does take place, governments, regulators and mining companies must implement the most stringent protections for frontline communities, workers, indigenous peoples and the environment. Considering that indigenous peoples are disproportionately impacted by mining, their right to free, prior and informed consent must be upheld in recognition of their sovereignty. These strategies can help build an energy transition that results in more equitable access to the benefits of a renewable energy economy, a greater overall decrease in greenhouse gas emissions and mineral demand, and an energy transition that is more just, equitable, and clean. As the report highlights, these are solutions that are already being implemented at varying scales in regions around the world. Replicating the patterns from a dying fossil fuel era will not protect those most at risk from the impacts of industrial extraction and climate change.
Solutions that reduce our consumption of these finite resources are, ultimately, what will have the greatest impact. Shifting from internal combustion engines to electric vehicles alone is not enough to limit the adverse impacts of global climate change. Reducing the use of private vehicles is the most cost-effective way to achieve a just energy transition and mitigate climate change. Solutions to recycle minerals and regulate mining, while important, can only get us so far. Experts and case studies in cities around the world show us that we can achieve zero emissions road transport without building more risky mines if we have the support of policymakers and actors along the entire mineral supply chain. �
Christoph Gallo*, explains how a switch to clean steel helped the BRS Motorsport racing team boost the transmission performance on its Formula Student car to take the checkered flag in the Engineering Design category.
FORMULA Student (FS) is Europe’s leading educational engineering competition. It celebrated its 25th anniversary in 2023. With the backing of industry and highprofile engineers, the competition aims to develop enterprising and innovative young engineers and encourage more of them to take up a career in engineering, with over 100 university teams taking part every year.
The project usually forms part of a degree-level project and is viewed by the motorsport industry as the standard for engineering graduates, transitioning them from university to the workplace. During the championship, student teams design, construct and build small formula race cars to compete in international competitions. The competition is divided into static and dynamic disciplines. The winner of the competition is the team which wins the most points across both.
Germany’s BRS team https:// brsmotorsport.de/en/, from Hochschule Bonn-Rhein-Sieg, is a seasoned competitor. For its attempt on the 2023 title, it fielded a new design – the G23 ‘Moni’.
One of the G23’s key refinements was an uprated transmission system that would improve chassis dynamics by
allowing the motors to be moved further into the wheels. At the same time the 1.5-stage planetary gearbox was replaced by a 1-stage design, increasing the gear ratio from 13.6 to 14.3. This boosted performance within a more compact package, and at the same weight. The previous 1.5 stage set-up was also complex to manufacture and demanding to maintain, as well as requiring special tools.
The challenge for the BRS team was that it recognized that the steel it had been using for the planetary and sun gears, 18CrNiMo7-6 (a case hardening steel with high toughness), would be pushed close to its safety margins by the new design. This was due to the higher loadings imposed by the 1-stage gearbox.
Specialist software plots the route to improved fatigue performance
Fatigue strength is a limiting factor in the life of many powertrain components. However, all steels are not created equally. While they all contain microscopic nonmetallic particles called inclusions, the number and size of these is limited in clean steel grades.
Inclusions are important to fatigue
*Technical customer support, Germany, Ovako.
strength. The larger the inclusions, the greater the risk of failure. Inclusions cause tiny imperfections that act as stress-raisers and can develop as cracks that propagate through cyclic loading – and eventually cause fatigue failure.
Clean steel is produced under careful conditions by specialist steel mills to have significantly smaller inclusions and, therefore, higher fatigue strength. Therefore, it’s no surprise that many original equipment manufacturers use clean steel to reach higher performance levels in terms of increased loads and longer service life.
However, the adoption of clean steel has been limited due to the traditional approach to powertrain design. Engineers are usually guided by company specifications and lists of approved materials. These include tried and trusted grades of steel with performance parameters that the designer knows and understands. Some procedures even draw on allowable stress levels that were established in the 1930s.
To help designers like the BRS team benefit from the fatigue properties of clean steel, the engineering software provider GWJ Technology has incorporated two of Ovako’s ultra-clean steels into its gear
For more information, visit our website at www.guildint.com or call +1.440.232.5887
design software packages, eAssistant, TBK and GearEngineer.
This step provides mechanical design engineers with straightforward access to high-performance clean steel. As a result, they can increase the power density of their designs.
The software packages are designed to support engineers as they develop designs for mechanical transmission and power train systems. They cover various types of gears, bearings and shafts, and are scalable – so a designer can make a calculation for a single gear or an entire gearbox. They can help design any size from small gears in medical devices to the large systems in wind turbines. In addition, the software can interface with a 3D Computer Aided Design (CAD) package so that an engineer can generate the code for machining.
GWJ developed the packages using knowledge of different types of gears, materials science, mechanics, CAD and machining, as well as the relevant international standards and design guidelines. As a result, the packages help engineers to evaluate and optimize the design of transmission components quickly and efficiently. This compares with the traditional approach, where the designer needs to take many iterative steps between design calculations and drawing components. With the software, the designer can input details such as gear ratios, gear type and loading. They can then choose from 30 materials ranging from polymers to different steel alloys.
The software is pre-configured with the properties of the materials, including the contact fatigue strength and the bending fatigue strength. These are the two properties where clean steels are differentiated from conventional grades of steel.
The software combines the properties of the materials with engineering equations to help engineers size transmission
components and develop designs.
GWJ has integrated two grades of Ovako’s ultra clean steel: 159X and 159Q. Both contain the same quantities of alloying elements as 18CrNiMo7-6. However, they are produced under carefully controlled process conditions to have smaller inclusions and, therefore, higher contact and bending fatigue strength.
As a bearing quality (BQ) steel, 159X provides improved fatigue properties to give engineers a first step in improving the design life or increasing the torque handling capability of an existing design.
The next step in performance is 159Q, an isotropic quality steel (lQ-Steel®) that is produced with strict control over inclusions so that they are small and spherical. The spherical shape means that the material provides the same consistently high fatigue strength to ensure uniform and excellent properties in all loading directions.
Clean steel makes the difference
After consulting the GWJ software, the BRS students found the answer to their materials performance challenges in the form of 159Q.
The next step was for the team to engage with Ovako. Together with my colleague Elias Lothman, senior research and development engineer at Hofors, we were happy to provide help, advice and sample materials. We were able to confirm that 159Q achieves its exceptional properties as an isotropic quality steel (lQ-Steel®).
Building in an increased safety factor
The innovative G23 gearbox, unique in the Formula Student series, features a sun gear and six planetary gears, all manufactured from 159Q. They rotate within a ring gear manufactured from 255G, which is Ovako’s BQ-Steel® (bearing quality) version of 18NiCrMo14-6, a case hardening steel with high toughness used for bearing and transmission components.
The switch to 159Q enabled the safety factor on the gear tooth flank to be increased from the marginal level of 1.037 with the standard steel to 1.373, providing a higher reliability in racing conditions. The new design delivers increased performance within the same weight package as the old design, which was a crucial element as total weight is often a limiting and decisive factor when designing a racing car.
The BRS team fielded the G23, proudly bearing an Ovako logo, at two Formula Student events during 2023, in Italy and the Czech Republic. It was at the second outing where the team enjoyed its greatest success, with second place in the Cost and Manufacturing category followed by first place in Engineering Design, which was the team’s third acknowledgement in this category, following previous triumphs in Italy in 2016 and Spain in 2021.
At Ovako, we love working with student teams like BRS, because it enables us to capture the minds of the students at the start of their career and educate them on the performance benefits of clean steels. This is important as many of these students will go on to have careers in the automotive industry. And, of course, their experiences provide us with useful case studies.
Furthermore, both Elias and I as the primary contacts for the student teams have gained a lot of insights by participating in the technical discussions about their drivetrain concepts.
We find that they experience the same basic challenges as the major automotive OEMs – just on a smaller scale. Hence, our dream scenario is to be able to transfer these small case studies in racing into substantial industrial applications. �
The lack of momentum currently witnessed in the North American infrastructure sector, is not necessarily a marker of decline, but of better times ahead. By Myra Pinkham*
WHILE US infrastructure construction activity has been stronger than that for private construction, at least at this point, it hasn’t been picking up quite as rapidly as many had anticipated. This comes as recently passed federal legislation that is seen as being supportive of the infrastructure sector has not kicked in as quickly as expected.
Associated General Contractors of America (AGC) noted, pointing out that certain types of non-residential buildings construction, such as of data centres, manufacturing plants, power plants, solar/alternative energy projects, overall infrastructure, and other public works construction, has been faring better than private non-residential construction.
(including rail, truck and mass transit) up 3% year-over-year, sewage and waste construction spending up 6%, water supply construction spending up 10%, and conservation and development construction spending up 5% year-over-year.
Once it does, it is also expected to be very supportive of the kinds of steel products used in infrastructure construction projects, including such steel long products as steel reinforcing bar (or rebar), structural steel, merchant bar and wire rod, as well as steel plate.
“The overall US non-residential construction market has slowed somewhat this year much as we expected it would do,” given the inflationary environment and high interest rates, Philip Gibbs, a senior equity research analyst at KeyBanc Capital Markets said.
That, however, has varied by sector, Ken Simonson, chief economist for the
And while he said that, broadly, US construction contractors working on infrastructure projects are busy, there has been some variation in the year-on-year infrastructure construction spending. This, Simonson said, has been tapering off in recent months, even though it has been three years since the passage of the Infrastructure Investment & Jobs Act (IIJA) bipartisan infrastructure bill, which is expected to eventually bolster US infrastructure construction spending.
He noted that, based upon data from the US Census Bureau, highway and street construction spending in June was up 6% year-over-year, transportation infrastructure
*North America correspondent, Steel Times International.
While the actual construction for much of the above examples has yet not begun, Scott Hazelton, a consulting director for S&P Global Market Intelligence’s steel service, said that mostly because of the phasing in of the IIJA, the number of new US infrastructure construction projects are forecast to grow by 7.8% this year, which is a somewhat slower rate than the 11.2% growth rate in 2023. He said that this growth rate is expected to slow further to about 4.7% next year, and that there could even be declines in the number of infrastructure projects in 2026-28 as some big projects currently in the works get finished.
Hazelton noted that the IIJA is expected to inject about $200 billion a year into the US economy over the next five years.
Marisa Geldert-Murphey, president of the American Society of Civil Engineers (ASCE) agreed that there has already been a sizeable uptick in project letting by the US Department of Transportation (DOT), noting that as of July, there was already about $461 billion in IIJA funding in the works for more than 60,000 projects. But she pointed out that it would take another year or so for that to have an impact upon steel demand as they need to undergo planning, designing, permitting, land acquisition and other work before they can actually be constructed.
She pointed out that this comes after infrastructure construction funding has been very austere for decades and that there is a need to create a system to supply, manufacture and build what is needed now that recent legislation is expected to immensely increase demand. But that isn’t easy to do given certain challenges, including the shortage of engineers and construction workers, as well as the labour issues at material suppliers and the DOTs.
While some infrastructure construction projects have been started, Alexandra
Anderson, a CRU senior steel analyst, said that there hasn’t been a big wave in demand as many people had expected to see by this time.
AGC’s Simonson said that there have been a number of factors contributing to this slow rollout, including such provisions in the bill as the Build America, Buy America and apprenticeship requirements. Also, there is some risk that, depending upon the outcome of the upcoming presidential and congressional elections, some projects may need to be scaled back. Philip Bell, president of the Steel Manufacturers Association (SMA) agreed, noting the impact of who will be in the White House and the makeup of Congress upon future regulations and fiscal policies.
On the other hand, Simonson pointed out that as opposed to private developerfinanced construction projects, the impact of interest rates, high financing costs and tight lending standards have been less pronounced for infrastructure projects.
That isn’t to say that it hasn’t been a factor, Gibbs said, noting that states have been very careful about how they are letting funds, watching their budgets, waiting for financing rates to go down. And it is still too early to say what the impact will be following the US Federal Reserve’s first interest rate cut last month.
Anderson said that most of the current infrastructure construction activity has actually been from projects that had been on the books before recently passed legislation. Also, she said that as far as the impact of recently passed legislation is concerned, the most immediate response has come from the CHIPS & Science Act from infrastructure related to the building of semiconductor manufacturing plants. Meanwhile, she said, “Because of all of the bureaucratic red tape to get the funding through the IIJA, the Infrastructure Reduction Act (IRA) has taken longer than expected to have an impact.”
She, however, said that while funding from the IIJA officially ends in 2026, due to the delay in many actual project start-ups, the increase in infrastructure construction activity could continue through late 2027 or even beyond that.
There is clearly a need for additional infrastructure construction, which is evidenced by the ASCE’s latest Report Card for America’s Infrastructure. Released in 2021 (with the next one slated for March 2025), the grades ranged from ‘B’ to ‘D-’,
including a ‘D’ for road, a ‘C’ for bridges and 11 categories in the ‘D’ range.
Also, Geldert-Murphey noted that ASCE’s recent Bridging the Gap: Failure to Act report indicates that even with the IIJA and IRA, there will still be less funding over the next 10 years than is needed to get US infrastructure up to what the association considers to be a ‘B’ grade, or to be in good condition.
Similarly, early in September the American Road & Transportation Builders Association (ARTBA) said that, based on data from the Federal Highway Administration’s National Bridge Inventory, nearly 221,800 US bridges need major repair or replacement with about 42,000 of them classified as structurally deficient.
SMA’s Bell pointed out that in July the US DOT had released about $5 billion to repair or replace about 13 bridges across the US, which is only a small part of the $1.2 trillion available. “While directionally that is good, much more is needed,” he said.
And it is believed that more is coming. Dan Snyder, vice president of construction at the American Iron and Steel Institute (AISI) noted that about $40 billion of IIJA funds will be used to repair or replace as many as 15,000 bridges with states being required to use at least 15% of that new money to build ‘off system’ or short-span bridges. He pointed out that short-span bridges account for almost half of the National Bridge Inventory.
The recent stabilization of prices in raw materials like steel is good news for infrastructure construction activity, said Geldert-Murphey, given that project planning tends to be based upon past costs. “Previously we had been seeing some project costs increasing by as much as 30%, but this year’s costs have been less volatile and more predictable.”
KeyBanc’s Gibbs said that it is hoped that the expected new infrastructure construction projects will fill some of the gaps left by softness in certain private construction sectors. “But it remains to be seen if it will be strong enough to do that,” he said, “Because the private side is historically the bigger portion of the construction market.’’
The expected increase in infrastructure projects is expected to be very positive for steel demand. In fact, Citigroup has estimated that with every $20 billion invested in infrastructure, steel demand increases by about 1 million short tons.
SMA’s Bell said that this could result in about 45Mt of incremental steel demand over the next six years.
“There are many well-known benefits to using steel in public works construction projects, including its durability, long service life, design versatility, ease of quality of installation and high performance,” AISI’s Snyder said, noting that it not only plays a vital role in the construction of such transportation projects as bridges, roadways and guardrails, but it is also crucial in advancing the energy grid, supporting energy development and transmission, reinforcing water infrastructure and ensuring public safety.
The impact, however, is expected to vary among the various steel products used in infrastructure construction projects, with the most widely used products being long products such as rebar, structural steel, wire rod and merchant bar as well as steel plate and hollow structural sections (HSS) – which in the US are almost exclusively produced by electric arc furnace steelmakers.
While structural steel demand has been getting a boost from current and expected non-residential construction activity, John Anton, director of S&P Global Market Intelligence’s steel service, said that much of that isn’t related to infrastructure construction but rather for the building of data centres, new and expanding manufacturing facilities and to some extent warehouses for online retailers. And he noted that many of the warehouses have already been built and demand from that sector could start to taper off.
On the other hand, SMA’s Bell called rebar the unsung hero of the major steel products used in infrastructure construction given that anything with a concrete foundation, therefore most infrastructure projects, require rebar. And he said that
rebar demand has been largely steady and that its price movements haven’t been as volatile or as deep as that for flat roll and certain other steel products.
But even though there has been some pick-up in demand for rebar, Anton said that, at least at this point, it hasn’t been the kind of surge you would expect given the level of spending. On the positive side, he said that it has helped rebar prices to remain higher than sheet prices, which, he said, is something that doesn’t normally happen.
And even with expectation of increased infrastructure construction activity, CRU’s Anderson said the market isn’t concerned about the availability of rebar and the other steel products for those projects. “No one wants to make big purchases when prices could potentially fall further,” she said. Also, Anton noted that given the public records of what projects have been awarded, the domestic steel mills have done a good job matching their steel production to demand.
In addition, the availability of steel products used in infrastructure construction will continue to be bolstered by recent and future investments in production capacity. For example, Anderson said, it is
expected that another 2Mt of annual rebar production capacity is expected to come online over the next three to four years.
Gibbs noted that even though there isn’t currently a shortage of rebar capacity, CMC is not only currently ramping up its new Arizona rebar/merchant bar micro-mill, but is planning to build another micro-mill in West Virginia. Nucor (which is also in the process of ramping up its new Brandenburg plate mill) plans to build a rebar micro-mill in the Pacific Northwest. Also, Hybar is building a rebar mill in Arkansas and Gibbs said that there are also other potential mill projects for rebar and other steel products that may or may not come to fruition. For example, he said that Zekelman has been talking about adding more HSS capacity.
This, SMA’s Bell said, has also been supported by the Buy America requirements that are part of the recent federal legislation, which are also supportive of environmental concerns given the sustainability of US-produced steels, which he said are cleaner than those produced elsewhere. “We are helping the federal government to shape their procurement policies to meet the Administration’s goal for lowering carbon emissions. This, AISI’s Snyder said, is consistent with the longstanding application of the existing statutory requirements of the DOT and other federal agencies.
While the rate has been somewhat disappointing this year, AGC’s Simonson, said that US infrastructure construction activity still showed modest growth and that next year, as more project contracts are awarded, it should be a stronger year. Also, the end of the election season and further lowering of interest rates should not only make 2025 a more positive year for their construction, Gibbs said, but also for the steels used for infrastructure projects. �
A Reducing & Sizing Block for long products keeping its promises. Achieve your goals with KOCKS RSB®
finishing size in round or hexagonal dimensions up to 160mm
increase in production up to 20%
up to 10% energy savings in the mill line
The demand for renewable energy is growing fast, and the share of global power generation is expected to grow substantially. The shift from fossil fuels to renewable energy sources requires new technologies and solutions for energy production, system enablers, and infrastructure. Many of these new technologies will be exposed to material challenges and require materials and constructions that will need to be lighter, stronger and able to withstand higher temperatures and more corrosive atmospheres.
By Angela Philipp*
WHEN considering the most appropriate tubes for a green energy facility – from biomass-to-energy boilers, waste-toenergy boilers, concentrated solar power (CSP) receiver tubes, CSP thermal storage, supercritical water, supercritical CO2 or gasification – fabricators and asset owners must ensure they select both the right materials and the right tubing design –either mono or composite tubes.
Choosing the most appropriate materials and tubing type to deal with corrosion, strength, high pressures, and temperatures can increase efficiency and safety while reducing unplanned standstills. Making the wrong choices can increase the risk of unplanned standstills, impact production targets and, when leaks or explosions happen, have very serious consequences. This article examines the suitable material options for tubing in a range of green
energy plants and processes, and the best applications for mono or composite tubes.
Making the right choices
There are several key factors to consider in selecting the right material for boiler tubing in green energy production. These include: Fuel – the complexity of the fuel being burned. Some fuels are more corrosive than others.
Temperature and pressure – what impact will high steam temperatures and pressures have on the tubing material? What is the composition of the flue gas and how corrosive is it?
*Technical marketing specialist, Alleima Tube EMEA.
Standstill costs – how much will an unexpected standstill affect the plant’s production and profits? Will the tubes be easy and quick to replace?
unexpected standstill affect the plant’s and
Operating hours – what is the expected lifetime of the boiler and the tubing?
Engineering fabricators and boiler designers must consider all these factors when choosing the best material for their facility.
Mono tube materials for supercritical water applications
Esshete1250 (UNS S21500)
Esshete1250 (UNS S21500) has been used for tubing in pulverized coal-fired boiler superheaters and reheaters in the UK since the 1960s and more recently has successfully transitioned as a boiler tube material in biomass-to-energy applications.
Creep test data of various materials at 100,000 hours. For many biomass-to-energy boilers, tubes made from UNS S21500 remain outside creep temperatures.
Nominal creep strengths values – VDTÜV/PED. UNS S31035 shows the highest creep strength up to 700ºC compared to other austenitic stainless steels for boiler tubes. Nickel alloys perform better above 700ºC.
Steam pressures and temperatures experienced by components made from UNS S21500 used in a biomass plant. Comparisons with components in coal-fired operations found no reduction in performance.
UNS S21500 is an austenitic chromiumnickel-manganese steel. It has excellent high-temperature strength (up to about 650°C), a high cross-over temperature (approx. 620°C), and good fireside corrosion and steam oxidation resistance. The high cross-over temperature means that the tubes remain outside the creep temperature range at operating temperatures up to 620°C. Therefore, the inner and outer protecting oxides are less prone to spalling off the metal surface than in cases where the material is operated in the creep range.
The fine grain size of UNS S21500 (10 -11 ASTM E112) compared to materials like
347HFG (7 – 10 ASTM E112), which are used in biomass power vessels, contributes to good corrosion resistance by increasing the paths of chromium diffusion through the grain boundaries. And, although the grain size is fine, the creep strength for UNS S21500 is still very good compared to materials such as TP347H (1.4912), TP316N (1.4910) and 347 HFG, particularly when considering its crossover temperature (147 MPa at 620ºC), which is below the required operating temperatures for many boilers.
Different fuels: same quality performance
Two-year tests of boiler superheater
tubes, made from UNS S21500, at a UK power plant converted from coal-firing to 100% biomass-firing showed corrosion performances and a life expectancy of nine to 12 years, consistent with the plant’s previous coal-fired operations. Reassuringly for the operator, despite changing the fuel, using UNS S21500 for the tube material did not reduce the tube performance. (Table 1)
Sanicro® 25 (UNS03135) mono tubes for supercritical water and gasification applications
In the early 1990s, to increase the operating efficiency of coal-fired boilers, industry targets for next-generation power plants were to achieve higher pressures with final steam temperatures of about 700ºC. It was estimated that this would increase efficiency to around 50%-55% and create a reduction in CO2 emissions. An EUfunded project called AD700 was launched to develop a new type of coal-fired power plant with higher steam pressures and temperatures.
The operating conditions in these advanced ultra-supercritical (A-USC) coalfired boilers would require new, more heatresistant materials than those available at the time. The requirements were improved high-temperature strength, enhanced creep properties, and high-temperature
Combining an outer layer of UNS NO8028 (Sanicro® 28) with an inner layer of carbon steel (such as 4L7) delivers effective thermal conductivity and expansion HT7 (ASME SA-213 T91/EN 1.4903), HT8 (ASME SA-213 T22/EN 1.7380).
corrosion resistance compared with the materials used in contemporary boilers, which operated at a maximum temperature around 650°C.
One of the initiatives of the AD700 project was to develop a range of new advanced materials that could permit the raising of main and reheat steam temperatures in boilers up to 700°C (1292°F) and beyond. This led to the development of the austenitic stainless steel grade Sanicro® 25 (UNS S31035) by Alleima in conjunction with several different industrial partners in the AD700 project.
UNS S31035 bridges the gap between other stainless steel grades operating up to 650°C and expensive nickel alloys for performance above 700°C. It has excellent high-temperature strength, creep properties, and corrosion resistance at material temperatures up to about 700°C. It also has the highest creep strength (around 100MPa at 700°C for 100,000 hours) among commercial heat-resistant austenitic stainless steels for boiler tubes. These properties make it a good candidate for use in superheaters and reheaters in A-USC boilers at material temperatures up to 700°C.
The high creep strength also makes UNS S31035 an interesting option for use in high-pressure superheaters instead of alternative materials that would result in too heavy wall thicknesses.
The alloy has excellent steam oxidation resistance, good hot corrosion resistance, and very good fabrication and weldability properties, making it a cost-efficient option in high-efficiency and super critical applications operating at metal temperatures up to 700°C. For temperatures beyond 700°C the only option is to use more costly nickel-based materials.
However, the industry’s shift in focus away from high-temperature coal-fired power plants at the turn of the century created new opportunities for the deployment of UNS S31035 in other hightemperature, high-pressure applications. These include concentrated solar power receiver tubing and thermal storage units, supercritical water and CO2, and gasification.
It can also be used in lower-temperature supercritical water conditions for the gasification of, for example, biomass into synthetic gases such as methane and hydrogen.
Composite tubes can be a suitable alternative where process conditions require properties and cost evaluations that cannot be met by one material alone. They combine the best features of low-alloyed steel (pressure, stress corrosion cracking resistance, and thermal conductivity and expansion) with the advantages of stainless steel or nickel alloys (flue gas corrosion resistance). Applications in the green energy sector include tubing for biomass-to-energy boilers, and waste-to-energy. (Fig 4)
A typical composite tube consists of an outer corrosion-resistant component and a load-bearing inner component, made of carbon steel. A second version can be produced, with a corrosion-resistant layer inside the tube.
In the early 1970s, the first composite tubes for black liquor recovery boilers were introduced and consisted of a corrosionresistant outer component in UNS S30400. At the beginning of the 1980s, several cases of cracking were observed in composite
tubes in the most vulnerable positions in the boiler, such as floors, smelt spouts, and airport openings. This cracking is mainly caused by thermal fatigue and stress corrosion cracking (SCC). A new composite tube with a high alloyed NiCrFe-alloy UNS N08825 (alloy 825) on the outside was developed to increase the corrosion resistance and decrease the susceptibility to cracking. The new composite tube showed resistance against stress corrosion cracking (SCC) and thermal fatigue that was superior to the previous composite tubes based on UNS S30400.
Severe conditions
Today, a popular material for use in composite tubes for boilers is Sanicro® 28 (UNS N08028) – a high-alloy multi-purpose austenitic stainless steel designed for service in highly aggressive and corrosive environments.
These tubes are frequently used as superheater tubes in black liquor recovery, biomass, or waste-to-energy boilers. UNS N08028 has excellent corrosion resistance due to its high chromium and molybdenum content. It also shows good resistance to chloride-induced pitting corrosion.
While the thermal conductivity of UNS N08028 is lower than for carbon steels such as 4L7(ASME SA-210 Gr. A1/EN 1.0425), the thermal expansion of the austenitic stainless steel is much higher. The co-extrusion of the two components at high temperatures and pressures forms the metallurgical bond and creates tubing that provides an effective balance between thermal conductivity and expansion.
Production method and testing
The carbon steel inner component and the austenitic stainless steel outer
component are joined together to form an extrusion billet. Hot co-extrusion at 1200ºC establishes the critically important metallurgical bond. It is only when this is achieved that the benefits of thermal conductivity and expansion and the corrosion properties of the tube can be achieved. A sound metallurgical bond will allow only very limited diffusion of the alloying elements.
Cold pilgering is an important step in the Alleima production process for boiler tubing because it delivers a smooth surface with tighter tolerances compared to hot-finished tubes. The smoother surface reduces the amount of ash built up from the fuel on the tubes and means the tubes can be more easily cleaned. It also reduces metal loss.
Alleima composite tubes undergo 100% non-destructive ultrasonic testing. This verifies the metallurgical bond, identifies any defects on the inner and outer surfaces, and allows the measurement of the thickness tolerances of the corrosion-protective layer. By contrast, composite tubes made using the overlay welding process produce a ‘waved’ or less smooth surface than cold pilgered tubes. The surfaces of overlay welded tubes do not allow effective ultrasonic testing. This raises the risk of unbonding between the two material layers going unnoticed.
Case story: UNS N08028 increases superheater tube lifetime in waste-toenergy plant
A waste-to-energy plant in Europe required frequent superheater tube replacements due to corrosion, leading to unplanned standstills. The existing 16Mo3 grade tube was suffering from severe metal loss due to flue gas corrosion. The asset operator’s target was to increase the lifetime of the superheater tube and, as a result, operating stability.
A composite tube made from UNS N08028 with a HT8 inner layer (10CrMo901) was tested over a two-year period. The tests found that the 16Mo3 grade corroded by 2mm per year while UNS N08028 corroded by only 0.25mm per year. As a result, the plant operator selected a replacement composite tube made from UNS N0828 with an anticipated lifetime increase from two to six years.
Case story: UNS N08028 composite tubes deliver over 18 years lifetime
Composite superheater tubes made of UNS N08028 and HT8 were installed in a recycled demolition wood-to-energy plant with a steam temperature of 475ºC and a steam pressure of 67 bar. To date, the composite tubes have been operational for more than 18 years.
Summary of applications for mono tubes and composite tubes
For mono tubes, UNS S21500 is a proven and appropriate choice for biomass to energy boiler tubing in material temperatures up to 650ºC. However, for higher temperatures, pressures and more corrosive environments, UNS S31035, which performs best in the 650ºC – 700ºC temperature range, is most appropriate. At supercritical conditions for biomass gasification Sanicro25 should also be investigated. The target applications for
composite tubes are biomass-to-energy and waste-to-energy – conditions requiring properties that cannot be met by only one material.
A progressive partner
For green energy boiler tubing fabricators and asset owners, understanding and selecting the most appropriate materials and the right tubing design – either mono or composite – can save millions of dollars through increased tube efficiency, extended service life, reduced unplanned standstills and enhance on-site safety. In contrast, making the wrong choices can increase the risk of costly unplanned standstills.
In making these decisions, fabricators and asset owners must have the confidence to trust their selected materials manufacturer to deliver not only the absolute best in advanced materials quality, but also the most appropriate advice, so the optimal choice of tubing can be made for the required application. �
SPEAK: Join industry leaders like Blastr Green Steel’s CEO Mark Bula in Bilbao at the 2025 Future Steel Forum. Apply now and contact Matt Moggridge to secure your spot!
matthewmoggridge@quartzltd.com
+44 (0)1737 855151
SPONSOR OR EXHIBIT: For any exhibition or sponsorship opportunities, contact Paul Rossage paulrossage@quartzltd.com
+44 (0)1737 855116
WHAT THIS YEAR’S ATTENDEES HAD TO SAY…
“Very well organized event with a good line of speakers focused on digitalization and decarbonization.”
“Great immersive atmosphere and excellent platform to learn and network.”
“Unique blend of upcoming technologies, challenges and the latest innovation in digital transformation for the iron and steel industries.”
“A good mixture of high-level presentations, panels and networking opportunities at an excellent location.”
Steel processors are increasingly turning to advanced analytical technologies that promise to refine and streamline their operations. These technologies are vital in navigating the complex steel production process, which spans from mining iron ore and sintering to steelmaking. As each stage of production presents its own challenges, achieving higher efficiency and superior product quality hinges on the ability to precisely analyze and control various parameters throughout the steelmaking process.
By Kevin Gordon* and Raphael Yerly**
STEEL has been a driving force behind modern innovation, serving as the backbone of industries ranging from automotive engineering to infrastructure development. With an escalating global demand for clean steel, which is projected to increase by more than a third through to 2050, the industry faces pressure to evolve.
The intricacies of steel processing underscore the necessity for technological advancements. From the beginning of the development lifecycle, understanding the composition of raw materials is crucial for optimizing downstream production, as it allows for better control over the sintering process and ultimately results in higherquality iron. Consistency in sinter feed composition plays a critical role in efficient sintering and iron making, while meticulous quality control of the final steel products
ensures they meet and exceed stringent industry standards.
Innovative solutions such as X-ray fluorescence (XRF) analyzers for raw material analysis, prompt gamma neutron activation analysis (PGNAA) for real-time elemental monitoring, and X-ray diffraction (XRD) for accurate identification and quantification of materials are reshaping the landscape of steel production. These technologies not only enhance operational efficiency and product quality but also align with the industry’s growing focus on sustainability by reducing waste and optimizing resource use.
Driving process control with raw material analysis
The journey towards higher-quality steel begins with a thorough analysis of raw
materials, where maintaining consistency in process control is essential. XRF analyzers play a crucial role in achieving this precision. XRF spectroscopy, a nondestructive analytical technique, determines the elemental composition of materials by measuring the fluorescent X-rays emitted from a sample when it is excited by a primary X-ray source. Each element in the sample produces a unique set of fluorescent X-rays, similar to a fingerprint, which are distinct for each element. This specificity allows for accurate and detailed quantitative and qualitative measurements of material composition; analyzers have become essential tools in steel manufacturing due to their ability to deliver lab-quality data efficiently and effectively. These sophisticated instruments offer rapid and precise analysis of raw materials,
*Senior manager, applications, process analytics, Thermo Fisher Scientific.
**Product manager, x-ray division, Thermo Fisher Scientific.
slags, and alloys, streamlining the process of quality control and material verification. By enabling real-time analysis, XRF technology provides steel manufacturers with immediate insights into material composition, which is crucial for optimizing production processes. This real-time capability allows manufacturers to quickly detect and address any compositional deviations or inconsistencies, ensuring that the final product meets stringent quality standards.
Beyond their immediate analytical benefits, advanced XRF technologies contribute significantly to the broader efficiency of steel production. The ability to conduct detailed elemental analysis in various environments – from desktops to inline field locations – adds a level of flexibility and robustness to the quality control process. These technologies not only enhance the accuracy of material analysis but also support more informed decision-making and process optimization.
By providing actionable insights, XRF analyzers help manufacturers reduce waste, minimize operational costs, and improve overall productivity. The integration of such advanced tools into the steel production workflow not only elevates material quality but also aligns with the industry’s goals of efficiency and sustainability.
Overcoming process challenges with sinter feed control
Moving further down the production lifecycle, the efficiency of the sintering and ironmaking processes is critically dependent on the quality of the sinter feed material. Basicity, a key parameter, significantly influences furnace performance and output. To achieve optimal results and maintain stable production rates, it is essential to ensure consistent sinter chemistry. However, steel processors face numerous challenges that threaten this consistency – including variability in sinter quality, declining iron ore grades, and raw material contamination –all of which complicate the maintenance of desired chemical consistency.
Addressing these challenges requires advanced technological solutions to enhance process control and efficiency. Online analyzers using PGNAA or Pulsed Fast Thermal Neutron Activation (PFTNA) are among the most effective tools. These non-contact, non-destructive techniques are ideal for determining the elemental composition of bulk raw materials. PGNAA and PFTNA work by bombarding materials with neutrons, which penetrate dense substances like rock and interact with their elements. This interaction causes the materials to emit secondary gamma rays, which are then measured to identify their elemental composition. PGNAA analyzers, in particular, have increased penetration depth compared to XRF. Positioned directly on the conveyor belt, PGNAA devices can scan the entire cross-section of the material stream, providing continuous, uniform measurements rather than just analyzing sub-samples.
In contrast, surface analysis technologies such as XRF and X-ray diffraction (XRD) measure only limited depths and surface areas, which might not represent the entire material on the belt. PGNAA reduces sample errors and provides frequent analysis, minimizing variations in material quality and improving overall measurement accuracy.
PGNAA technology specifically measures
these gamma rays, which are emitted when a thermal or low-energy neutron (with an energy level less than 0.025 eV) interacts with an atom’s nucleus. The energy released as the nucleus returns to its stable state, and corresponds to the specific element from which it originated, providing a unique identifying signature for each element. This allows for precise identification and quantification of material composition. The real-time data provided by PGNAA enables continuous monitoring and adjustment of sinter feed chemistry, helping to reduce feedback loops, mitigate the impact of raw material variability, and enhance overall process efficiency.
Further, the capability of PGNAA to analyze the entire volume of materials –rather than just the surface – improves process control and reduces operational costs. Its applicability extends beyond steel manufacturing to various industries, offering valuable insights and supporting better decision-making throughout the production cycle. As such, PGNAA and PFTNA play crucial roles in optimizing material processes, ensuring consistent quality, and advancing efficiency across a range of processing industries.
As demand for cleaner steel intensifies, the steel industry faces a crucial opportunity to advance more sustainable practices. To meet evolving market demands, steel manufacturers must embrace more robust analytical technologies and methodologies that enhance the entire steel production process. Embracing innovative solutions – such as real-time monitoring systems, energy-efficient processes, and advanced waste reduction techniques – can significantly improve steel quality while streamlining workflows and boosting productivity.
These advancements not only enhance operational efficiency but facilitate compliance with stringent environmental regulations by significantly reducing carbon footprints and lowering energy consumption. The impact extends well beyond profitability, driving broader economic and social benefits such as job creation and improved public health. Steel processors, integral to modern infrastructure, must integrate advanced analytical technologies throughout the production cycle to align with global
sustainability goals and meet consumer demand for eco-friendly products.
This commitment to innovation is evident in the steel industry’s progress: today, producing a lot of steel in the US requires less than half the energy compared to 40 years ago, resulting in a 50% reduction in greenhouse gas emissions.
This achievement underscores the industry’s active adoption of new technologies and sustainable practices, reflecting a continued dedication to reducing the environmental impact of steel manufacturing globally and advancing steadily toward a cleaner, safer, and more sustainable future.
The steel industry is at a transformative crossroads, where embracing advanced analytical technologies is key to meeting the growing demand for cleaner, higherquality steel. From real-time monitoring of elemental composition to the precise control of sinter feed material, these technologies – including PGNAA, and advanced process control systems – are revolutionizing steel production as they address critical challenges such as raw material variability and declining ore grades, while enhancing process efficiency and product quality.
Beyond operational improvements, these innovations align with global sustainability goals by reducing environmental impact, lowering carbon footprints, and conserving resources. As the industry evolves, integrating these cutting-edge solutions not only drives profitability and efficiency but also supports broader economic and social benefits, including job creation and public health enhancements.
By advancing towards a more sustainable production model, the steel industry can continue to play a pivotal role in modern infrastructure while contributing to a cleaner, safer, and more sustainable future for all. �
The Thermo Scientific™ ARL iSpark™ Plus Series OES Metal Analyzer uses single-spark acquisition to provide rapid elemental analysis—up to 15% faster than previous models. The increased speed and reliability minimize tap to tap times, save energy, reduce carbon footprints, and realize a faster return on investment.
Capable of providing ultra-fast, on-line analysis of nonmetallic inclusions, the ARL iSpark Plus adds to the versatility, dependability, and productivity of metal processing operations.
Passionate about delivering high performing solutions for the steel industry, GelSight is constantly working to improve its offering to make its users’ experiences smoother and more reliable, says Thierry Mantel*
1. How are things going at GelSight? Is the steel industry keeping you busy?
GelSight is doing well and has established itself as a valuable, high-performing solution for quality control and predictive maintenance in the steel industry. The tactile intelligence capabilities of both our hardware and software product offerings have received strong interest from customers in cold rolling and extrusion. By providing them with the ability to measure and monitor the surface characteristics of their final products, as well as the tools used in the manufacturing process, we are opening new doors for the quality control and predictive maintenance of metal sheets and extruded profiles manufacturing.
2. In which sector of the steel industry does GelSight mostly conduct its business?
Cold rolling and extrusion are two areas of the steel industry where GelSight’s technology offers a unique solution to the demanding surface finish quality control requirements. Since the end products of these processes are often used as structural profiles for cars or panels for aerostructures, manufacturers need a reliable way to measure key characteristics such as surface roughness or to quantify defects on the metal sheets before they can be used. GelSight’s surface inspection capabilities can also help control the quality of extrusion molds to meet necessary standards and ultimately ensure the surface properties of the final product are consistent across the board and meet the customer requirements.
3. Where in the world are you busiest at present?
Today, most of GelSight’s sales in the steel industry are to customers in North America and Europe. We believe there is also potential in the Asia-Pacific region
and we are looking to leverage those opportunities going forward. To do so, we are working to establish a strong network of representatives and partners who have a deep knowledge and understanding of the steel market to help build our presence in the region.
4. Can you discuss any major steel contracts you are currently working on?
GelSight currently works with some of the global leaders in the steel industry. For confidentiality reasons, we cannot disclose any technical or commercial details of these contracts.
5. Where does GelSight stand on the aluminium versus steel argument? Since our technology can measure the surface characteristics of any material, in any place, with the same level of accuracy and simplicity, GelSight does not have a stance in the steel versus aluminium debate. The use of either steel or aluminium purely depends on the market segment and application for the part. For example, in the aerospace industry, aluminium and titanium
are well suited for its needs, while steel is traditionally a better fit in the appliance and automotive industries.
6. What are your views on Industry 4.0 and steelmaking?
Similar to other sectors, Industry 4.0 represents an opportunity for the steel industry to revisit its processes and industrial organization. New technologies and sensors like GelSight’s can be fully integrated into a production line to enable real time monitoring of process parameters through both hardware and software. Integrating these new technologies and leveraging Application Programming Interface (API) modules allows users to control processes remotely, helps digitize valuable information, and allows them to transfer this data to a remote database to be combined with other types of information and ultimately make more data-driven analysis decisions.
7. In your dealings with steel producers, are you finding that they are looking to companies like GelSight to offer them solutions in terms of energy efficiency and sustainability? If so, what can you offer them?
Yes, we have heard this. Solutions like GelSight’s directly help steel producers increase their productivity, improve the efficiency of their predictive maintenance processes, and reduce the number of parts scrapped due to quality issues. These combined factors also help to optimize energy consumption in the steel industry and makes the overall production process more sustainable.
8. Where does GelSight lead the field in terms of steel production technology?
GelSight is a leader in tactile intelligence and digitizing surface inspection processes, offering innovative solutions that help
*Vice-president of global distribution and key accounts, GelSight.
streamline quality control and predictive maintenance in the steel industry. Our tactile sensing technology can be integrated into a manufacturing environment to gather new insights on surface characteristics of the final product and better monitor the parameters of the tools used in the manufacturing process.
9. How do you view GelSight’s development over the short-tomedium term in relation to the global steel industry?
We’ve seen a strong demand for our tactile sensing technology to be integrated into IoT environments in the steel industry and beyond. As a result, we are working to develop deeper integration for our sensors into automated industrial environments. We’re also investing in our technology to offer new solutions for quality control in the steel industry that will offer even better productivity benefits.
10. How optimistic are you for the global steel industry going forward and what challenges face global producers in the short-to-medium term?
From our discussions with customers and prospects in the steel industry, we’ve heard the challenges of the complex, continuous production process which requires large infrastructure, costly equipment, and huge amounts of energy. Each stop on the production line for quality control and maintenance operations typically requires significant time and financial investment to produce steel plates that meet the quality expectations of customers in demanding industries such as automotive, aerospace, appliance, and more.
However, I am optimistic about the future of the steel industry and solving these challenges through the implementation of new technologies that digitize traditionally manual quality control processes and efficiently provide precise and reliable information for predictive maintenance programmes.
11. What exhibitions and conferences will GelSight be attending in over the next six months?
In September, GelSight will attend the International Manufacturing Technology Show (IMTS) in Chicago. IMTS is one of the largest manufacturing technology exhibitions in the world. If you will be in
attendance, please drop by our booth.
12. Apart from strong coffee, what keeps you awake at night?
At GelSight, we are passionate about arming metrologists, engineers, inspectors, manufacturers and other users with the data-driven insights they need to deeply analyse surface characteristics, while also streamlining and simplifying their processes. We’re constantly working to improve our hardware and software solutions to make our users’ experience smoother and more reliable.
13. If you possessed a superpower, how would you use it to improve the global steel industry?
If I could have one superpower to help improve the steel industry, it would be superhuman vision to simplify surface inspection and quality control. While this may never be possible, GelSight’s solutions do offer superhuman touch sensors with micron-level resolution, which can provide steel producers and inspectors with datadriven insights on surface characteristics that allow them to make more informed quality control decisions. �
Following the closure of blast furnace ironmaking at the Port Talbot works in South Wales last month, this article continues the history of the works from 1950 following the replacement of open hearth (OH) steelmaking; first by the use bottom-blown oxygen converters, to the present set-up of a basic oxygen steelmaking plant. By Dr Tim Smith*
IN 1947, The Steel Company of Wales was formed by the amalgamation of The British Iron & Steel Co (consisting of Baldwins and Guest Keen), Richard Thomas & Baldwins (RTB), John Lysaght Newport works (a subsidiary of GKN) and Llanelli Associated Tinplate. This was in recognition of a need to modernise the sheet and tinplate industries of South Wales.
Due to congestion in the Margam site, it was decided that a location south to the works should be expanded, which was an area of marshy ground. The new site was called Abbey works, the name being chosen in recognition of remains being found of the Cistercian Margam Abbey during construction. The works was to have an initial capacity of 1Mt/yr, later increasing to 2Mt/yr.
After much argument between the joint owners, it was agreed the works was to have a continuous wide hot strip mill, the third to be installed in the UK after Richard Thomas & Co’s Ebbw Vale’s 54”
(1.37m) wide continuous hot strip mill in South Wales built by United Engineering, and John Summers & Sons, 56” (1.42m) wide hot strip mill at Shotton on Deeside, NW England, constructed by Mesta. Both companies had installed this US technology in the 1930s. At this time, in Europe, there were only two other continuous hot strip mills, one at Dinslaken in Germany, and the other at Zaporozhstal in the then Soviet Union, now within Ukraine. Post-war, the Dinslaken mill was shipped to Kuibyshev Metallurgical Works at Nizhne Tagil in the Urals as war reparations.
Abbey works
Abbey works was built in an area of rough coastal pasture and wetlands. The elevation of the ground, was just 6 to 12’ (1.83.6m) above the spring high-water mark, protected from the sea by a bund. It was, therefore, decided to increase the elevation of the land to 21’ (6.4m) which required the transport of some 5Mt of earth and
*Consulting editor, Steel Times International.
spoil. This increase in height also brought the area closer to the 24’ (7.3m) elevation of the adjacent Margam works thereby facilitating rail connections between the two sites. Approval of the 500-acre (202 hectares) site had been granted in 1945 and groundwork started in 1947 but work did not commence on equipping the new steelworks until 1950 with completion some three years later.
A high-lift slabbing mill was installed in 1950 by United Engineering & Foundry Co of USA. This had 45”(1143mm) diameter work rolls each driven by a 4600HP DC electric motors. Edging rolls were driven by 800HP synchronous motors. It could handle ingot weighing up to 20 tons. Slab with a maximum width of 60” (11684mm) up to 18’ (5.48m) long and 5.5” (140mm) thick for strip, or 8.5” (148.6mm) thick for tinplate was produced in this reversing mill. Cold slab, after inspection and scarfing if necessary, was charged to one of three reheating furnaces fuelled by coke oven
gas for hot rolling in the wide continuous strip mill. Much argument had taken place as to the width of this mill, 80” (2m) being eventually agreed to meet the needs of the motor industry as well as tinplate demand, whereas a narrower mill would have sufficed for tinplate at a significant saving in cost of construction. Fred Cartwright, a charismatic and determined leader, was the driving force for the adoption of the 80” mill. He went on to become works manager of Port Talbot and deputy-chairman of the British Steel Corporation.
A slab squeezer was also installed at the entry end to reduce slab width prior to rolling if required.
The mill consisted of a scale breaker, followed by three 2-high roughing stands and six 2-high finishing stands and a delay table between the roughers and finishers to ensure the correct finishing temperature. There was a rotary shear to remove hot band ends prior to the finishing stands. The mill was constructed during 1950-51. Supplied by United Engineering of USA, it was part-funded by the post-WWII Marshall Plan. Each roughing stand was powered by a 4500HP synchronous motor, and the first three finishing stands were driven by DC motors of similar 4500HP while stands F4 & F5 had 5000HP DC motors, and stand F6 had a 4000HP DC. The choice of DC motors for the finishing train was to enable greater speed control to assure each subsequent stand could match the accelerating speed of the thinning hot band as it passed through each finishing stand as
a continuous strip.
Output from the mill could be cut to plate with a weekly capacity of 2.5kt, or supplied as hot coil with a 3.5kt capacity. Plate of up to 50’ (15.2m) length could be processed on a hot leveller and trimmer after cooling.
Coil handling was equipped with a skin pass mill, a slitting line, cut-up line, and batch pickler. In 1951, a continuous pickle line was installed for coil.
Coil for cold reduction passed to a threestand 4-high mill with roll lubricant. This was built by Davy-United of Sheffield under an agreement with United Engineering of USA.
Following reduction, coiled strip was either cut to sheet for batch annealing in
one of four furnaces, each with 12 bases, or batch annealed as coil in a further four dedicated coil furnaces also with 12 bases. A further four furnaces could be converted from sheet to coil annealing. Inert NX gas produced from cracked COG was used during annealing to prevent oxidation.
For temper rolling, three separate single stand mills were installed, one for piece material, one for sheet or coil and one for coil only.
Commencing in 1951, eight 200-ton open hearth (OH) furnaces were built and fed with a 50:50 mix of scrap and hot metal from the Margam blast furnaces, the metal being held in one of two 800-ton mixers for distribution to the OH furnaces. Firing of the OHs was by oil. Weekly output was 20kt. Space was left for a further four furnaces. Scrap was brought in by rail, each train carrying 600 tons. Ingots weighing up to 20 tons were top-teemed from crane-carried ladles into cast iron moulds, stripped and placed in bottom-fired soaking pits, of which there were 20 in pairs giving a capacity of 25kt/week. OH steel was thus now produced at all three sites, Port Talbot, Margam, and Abbey. OH steelmaking continued at these sites until 1961, 1963, and 1970 respectively.
The steelmaking plant at Abbey was increased to 12 100-ton OH furnaces, eight 200-ton furnaces and four 230-ton furnaces. The original slabbing mill could no longer cope with this increased output and was replaced in 1958 by a universal mill to increase capacity by 12kt, more than the OH steelmaking shops could produce. The Abbey melting shop survived until November 1970 when it was replaced by a
basic oxygen steelmaking (BOS) plant.
In 1949, The Steel Company of Wales was one of a number of steelmakers nationalised by the Labour government. Existing names and structures were maintained. This made it relatively easy for the following Conservative government to re-privatise the industry on coming to power in 1951.
By 1950, with the advent of tonnage oxygen developed as a rocket fuel in WWII becoming available, oxygen was used both to accelerate the OH process but, more significantly, it was also used in the bottom-blown Basic Bessemer converter, and, from the early 1950s, in top-blown converters in a process developed by the Austrian steelmaker Voestalpine, the origin of today’s BOS process. These converter systems produced a steel of lower nitrogen content than could be produced by the open-hearth method.
The Port Talbot complex initially decided against adopting the BOS process and in 1959, a bottom-blown converter shop blown with oxygen and steam, the latter as a coolant for the tuyeres, was built by Demag. This was known as the ‘Very Low Nitrogen Plant’ (VLN or Violin) and will be the subject of a later History article. Three such converters were initially installed and a fourth added in 1962. Nitrogen levels were typically 0.001%. In 1966, this plant was replaced by the more widely adopted top-blown basic oxygen converter, two 330-tonne converters being installed in 1966 to replace the VLN and Abbey OH melt shops which closed in July 1969 and November 1970 respectively. It took a further two years for the BOS plant to reach the output of the combined Abbey and VLN plants to provide a steelmaking capacity of 3.25Mt/yr. A continuous slab caster was also introduced, by then an established technology, but one not easily adopted for open hearth steelmaking that required several hours of processing time in contrast to 30-40 minutes for converter methods. A vertical continuous caster had been introduced for the VLN plant to produce continuously cast rimming steel, but with limited success.
The hot strip mill was rebuilt between 1983 and 1986 to a semi-continuous form with the replacement of the three roughing stands by a single large reversing mill with
edgers and a Stelco Coil Box which allows for a short delay table. The Coil Box retains the heat of the breakdown strip which is coiled in the box and reverses the direction for rolling into the finishing stands so that the colder end of the strip is now rolled first. The original finishing stands have been retained and an additional finishing stand F7 added. The electric motors were replaced for all stands. Capacity is 3Mt/yr. A second walking beam reheat furnace was commissioned in 1987.
Improvements in control technology and plant design enabled the present two blast furnaces to produce close to 2.5Mt of iron a year from two 10.8m hearth diameter furnaces. This contrasts with as many as five blast furnaces between 1959 to 1978, the largest of which had a hearth diameter of 6.5m. Indeed, Port Talbot was a leader in on-line computer control in the steel industry. The complete computer installation on the hot strip mill was supplied by GE of America in 1965 and a copy of this pioneering computer control was also installed at the nearby wide hot strip mill in Llanwern. The cold mill was computerised by 1971 by a joint team drawn from the electrical company AEI, Imperial College London, and the Steel Company of Wales itself. Such was the confidence in computer control that a joke going around at the time was that you just
needed a man and a dog in the control pulpit – why a dog? To stop the man touching anything!
In 1967, the Steel Company of Wales, along with all major British steelworks, was again nationalised under a Labour Government and renamed British Steel Corporation. In 1988, it was privatised again as British Steel Plc and in 1999 merged with the Dutch steelmaker, Koninklijke Hoogovens to form the Corus Group. The company is presently owned by Tata Steel who took over control of the works in 2007 from the Corus Group.
The Port Talbot complex employed 13,000 people in 1980. By 2013, the number had dropped to 5,000. �
This article relies partly on information published in the PhD Thesis ‘History of the Steel Industry in the Port Talbot Area 1900-1988’ by Stephen Parry, University of Leeds School of History, December 2011. Further information is from ‘A Technical Survey of the Abbey, Margam, Trostre & Newport Plants of the Steel Company of Wales Ltd’ published as a Special Issue of the Iron & Coal Trades Review circa 1950s. Information on the VLN plant is from the Historical Metallurgy Journal, Vol 33 No1 1999 p43, and my thanks to Jonathan Aylen for his comments on the script and the supply of archive photographs.
Solar Turbines is your total solutions provider and can offer you the latest power plant technology tailored to your specific requirements. Generating power with our highly flexible gas turbine packages contributes to sustainable development, enabling you to meet your growing needs for great power, efficiency and availability − all while helping to protect the environment. Solar ® gas turbines will provide your business with a competitive edge. There has never been a better time to review your energy strategy. Contact us today.
Visit us at www.solarturbines.com , call +1-619-544-5352 or email infocorp@solarturbines.com