in
September
Carbon Border Adjustment Mechanisms the US and Europe.
ENVIRONMENT
Articles from Danieli and Primetals Technologies on the subject of rolling.
INNOVATIONS
ROLLING
Strengthening demand for climate-friendly steels.
www.steeltimesint.com 2022 - Vol.46
No6Vol.46–2022September–INTERNATIONALTIMESSTEEL CHANGING THE WAY STEEL IS MADE Since 1866
GREEN STEELMAKING
No6
The latest global contracts and new products news for the steel industry.

Via Bonaldo Stringher, 4 33042 Buttrio (UD) Italy
Phone +39 0432 518 111 www.dca.itwww.digi-met.com
INDIGITALQ3-PREMIUMTRANSFORMATIONQUALITYCONTROL
Danieli Automation’s innovative digital solution to support smart quality control and management for high-end metals production, a software tool for plant-wide quality assurance and management.

Follow us on Linkedin

Steel Times International is published eight times a year and is available on subscription. Annual subscription: UK £215.00 Other countries: £284.00 2 years subscription: UK £387.00 Other countries: £510.00 3 years subscription: UK £431.00 Other countries: £595.00 Single copy (inc postage): £47.00 Email: steel@quartzltd.com Published by: Quartz Business Media Ltd, Quartz House, 20 Clarendon Road, Redhill, Surrey, RH1 1QX, England. Tel: +44 (0)1737 855000 Fax: +44 (0)1737 855034 www.steeltimesint.com Steel Times International (USPS No: 020-958) is published monthly except Feb, May, July, Dec by Quartz Business Media Ltd and distributed in the US by DSW, 75 Aberdeen Road, Emigsville, PA 17318-0437. Periodicals postage paid at Emigsville, PA. POSTMASTER send address changes to Steel Times International c/o PO Box 437, Emigsville, PA 17318-0437.PrintedinEngland by: Pensord, Tram Road, Pontlanfraith, Blackwood, Gwent NP12 2YA, UK ©Quartz Business Media Ltd 2022 ISSN0143-7798 Cover courtesy of BSW. September 2022 Vol.46 No6 ENVIRONMENT INNOVATIONS ROLLINGGREEN STEELMAKING Carbon Border Adjustment The latest global contracts and new Strengthening demand for CHANGING THE WAY STEEL IS MADE 1866 CONTENTS – SEPTEMBER 1
Rolling
Officer
India23 update
Overall sentiment remains upbeat.
InternationalSALES Sales Manager
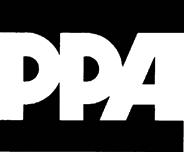
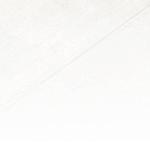
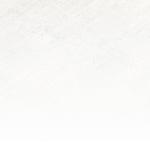
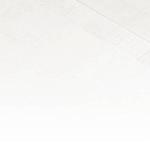
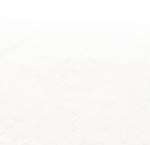
Fax +44 (0) 1737 855034
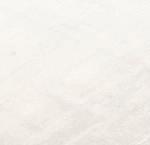
Innovations12
Protectionism turns ‘green’ –here’s how.
Tel:paulrossage@quartzltd.comRossage+44(0)1737855116
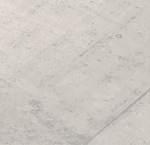
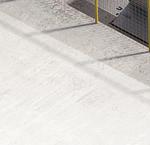
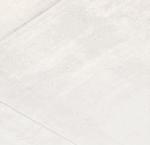
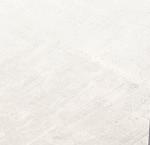
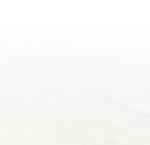
EditorEDITORIAL
Sales Director
Tel: +44 (0) 1737 matthewmoggridge@quartzltd.com855151
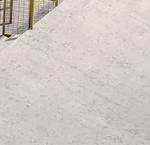
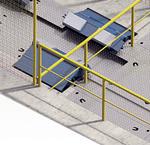
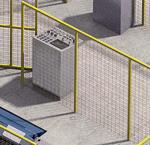
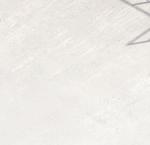

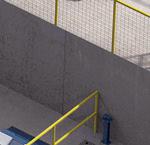
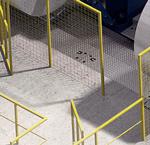

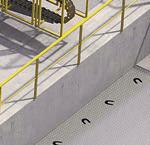
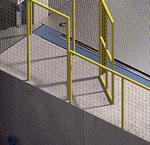
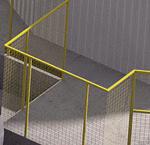
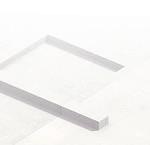

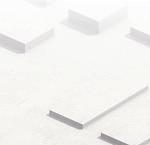
Tel:+44 (0) 1737855021
Dr. Tim Smith PhD, CEng, MIM
Ken Tel:kenclark@quartzltd.comClark+44(0)1737855117
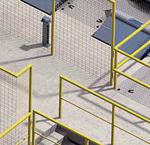
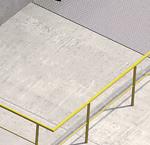
Managing Director
www.steeltimesint.com
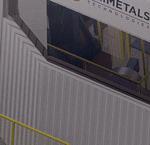
Editorial assistant
Catherine Hill
Chief Executive
USA17 update
Consultant Editor
Environment27
How green steel finds its way into products

30 Meeting demand for electrical 34steels.Maximum quality and production flexibility.
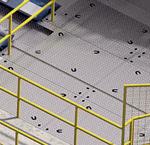
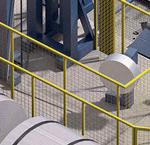


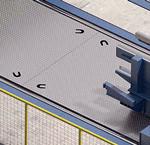
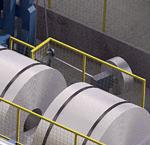
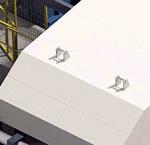
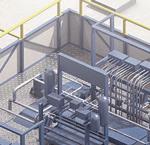
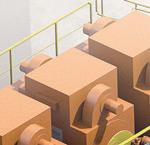
Matthew Moggridge
Betting on a winning horse.
Martin Lawrence
Advertisement Production
Tony Tel:tonycrinion@quartzltd.comCrinion+44(0)1737855164
New products and contracts.
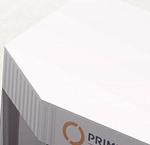
The latest global steel news.
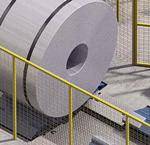
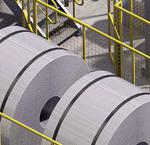
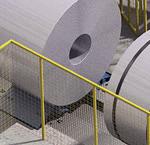
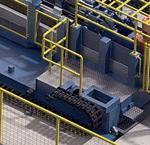

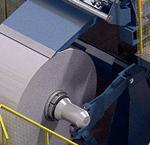
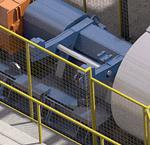
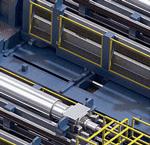
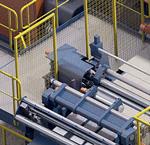
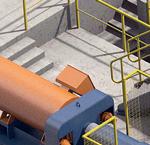
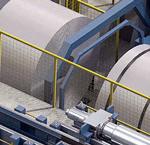

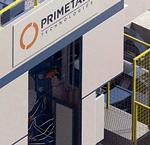
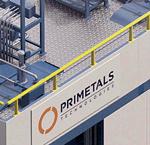

Perspectives45
Employee safety and comfort.
Perspectives46
Production Editor
Steve Diprose
History48
The early days of ironmaking at Scunthorpe Part 1. 1864-1912. 30
3D38 printing
Environment41
Annie Baker
3D printing a hot commodity.
Jack Homewood
Email subscriptions@quartzltd.com
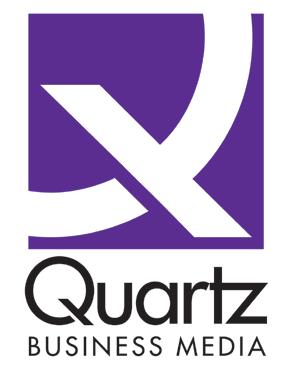
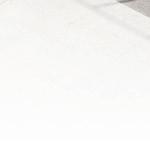
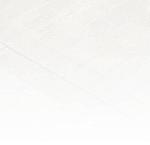

SUBSCRIPTION
2 Leader By Matthew Moggridge.
Q&A: Dassault Systèmes Employee safety and comfort.
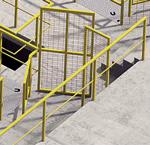
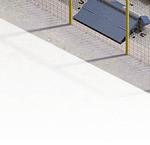
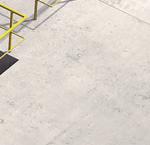

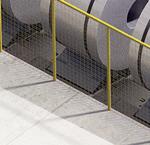
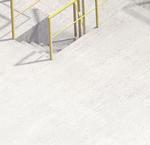
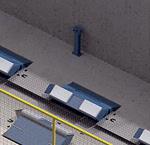

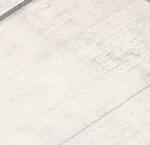



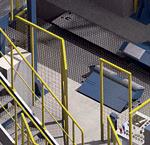
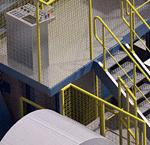
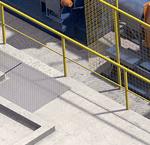
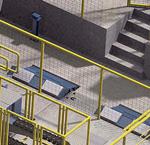
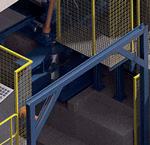

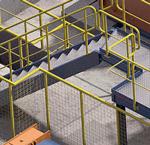


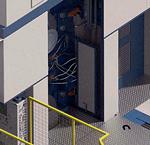
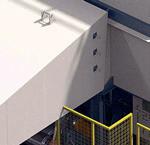
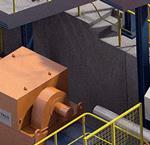
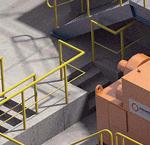
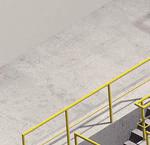
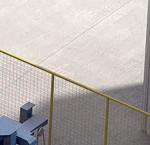
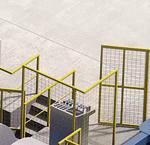

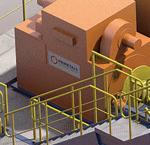
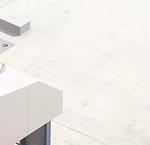
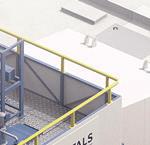
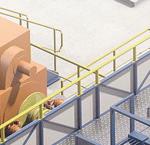
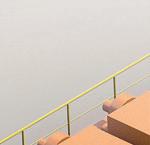
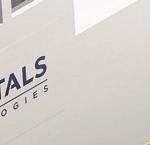
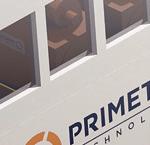
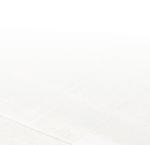
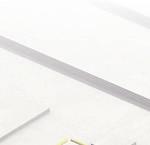

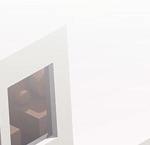
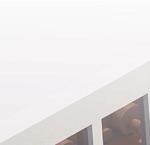
Environment25
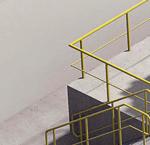
Tel +44 (0) 1737 855028
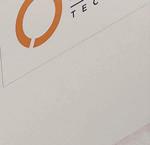
News4 round-up
America surfs the green wave.
Paul
Latin20 America update Votorantim’s steel strategy.
Q&A: Big Ass fans
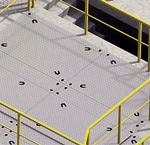
2 LEADER
Axel Eggert, director-general of EUROFER (the European Steel Association), says that current gas and electricity prices threaten


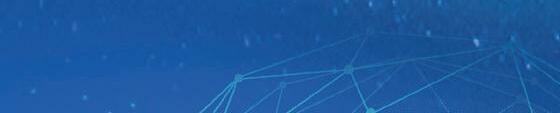


Eggert says that urgent measures by EU policymakers are needed if the destruction of Europe’s industrial base is to be avoided. He speaks of third countries who haven’t followed Europe’s example against Russian aggression or who are not subject to the same constraints of European steelmakers taking advantage of the situation and ‘exporting massively into Europe at distorted prices’.
ArcelorMittal Germany’s CEO Reiner Blaschek – like MAKE UK and EUROFER –wants urgent political action to get energy prices under control. In essence, a perfect storm is brewing and steelmakers in the UK, Europe and around the world, must brace themselves for the storm to come and realise that their survival is uncertain.
For MAKE UK, the British Government should be treating the whole situation with the same urgency it attached to the pandemic and bring forward a package of measures to deal with the crisis. In fact, it is argued that the energy crisis might be a bigger threat to global manufacturers than the pandemic.
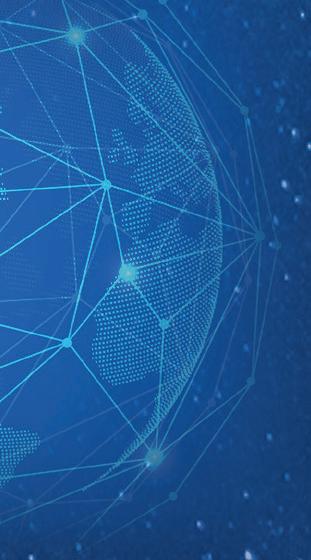
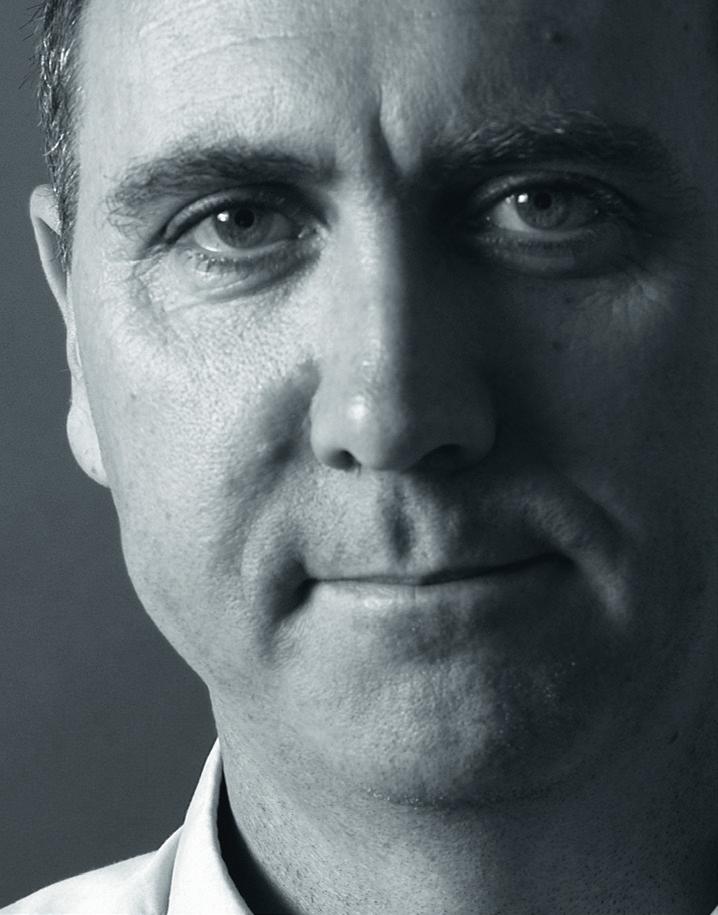
In a perfect storm, your survival is uncertain...
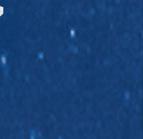


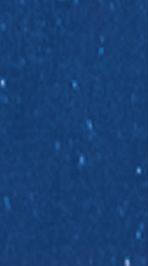
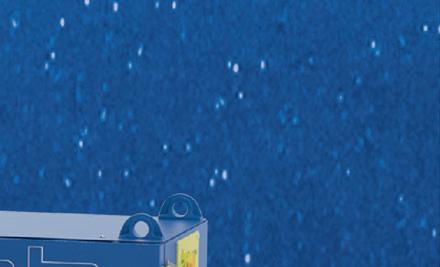


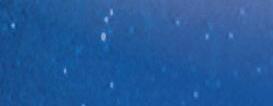
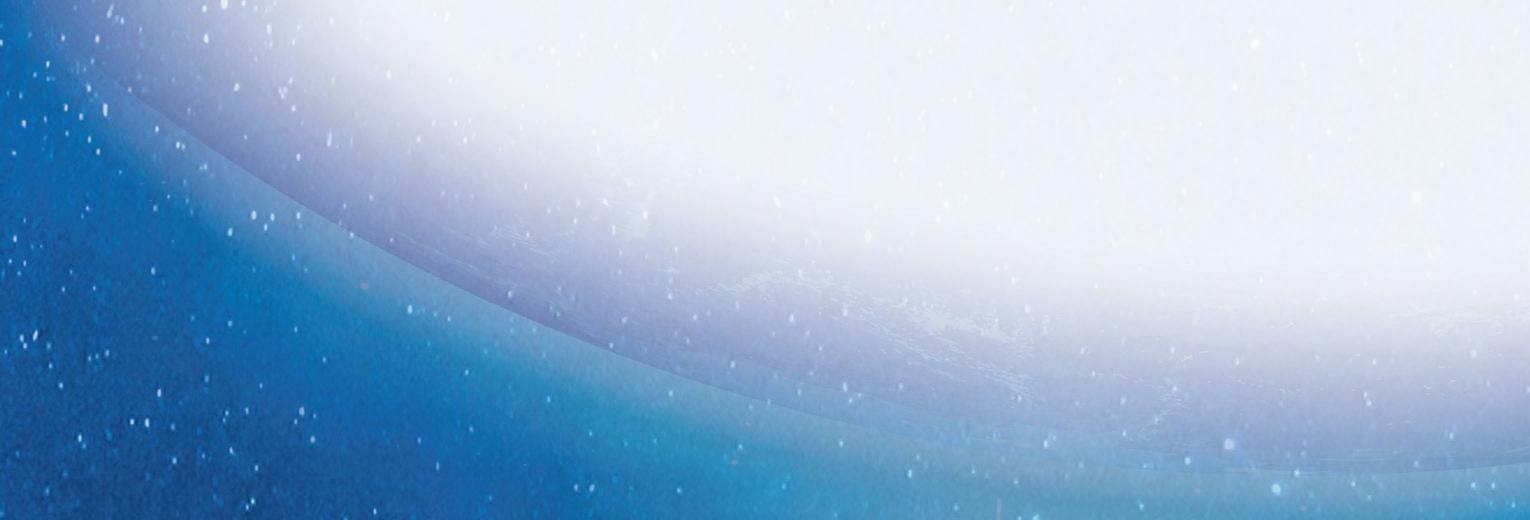
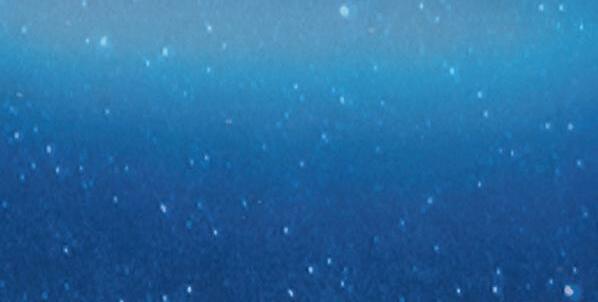
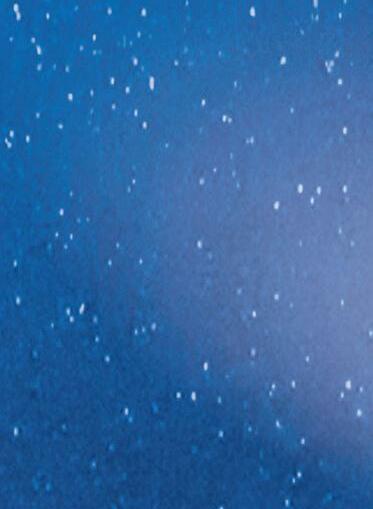
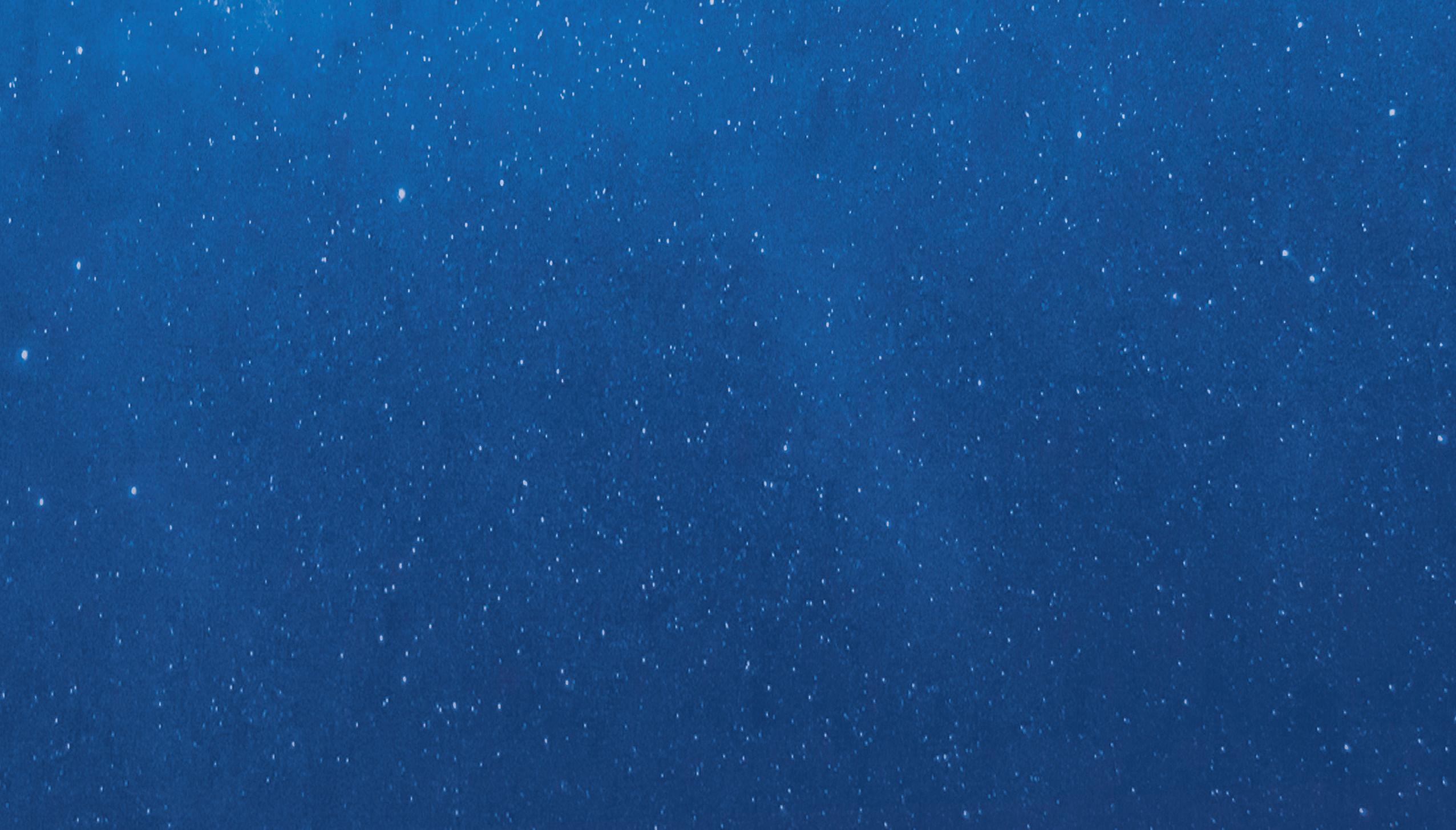
Matthew matthewmoggridge@quartzltd.comEditorMoggridge
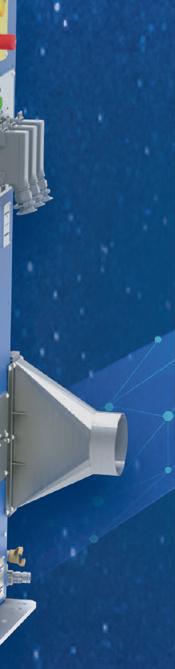

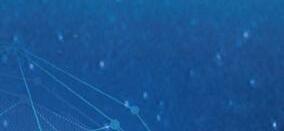

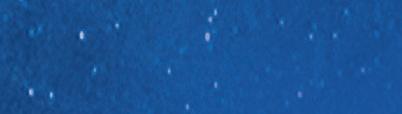
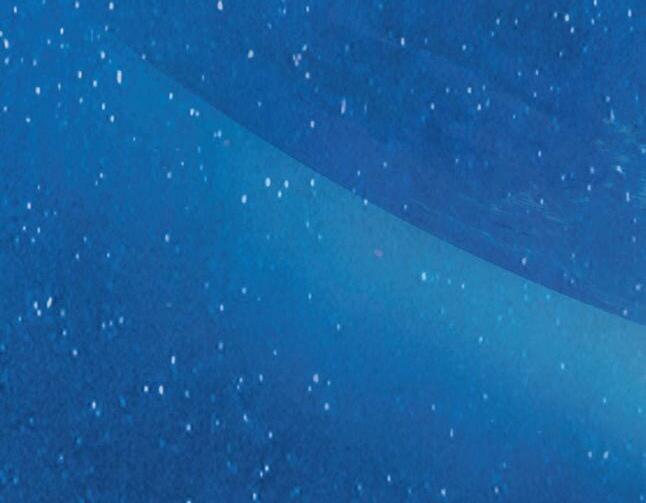
In Europe it’s a similar story. The European Steel industry’s key trade body, EUROFER, is calling on EU policymakers to provide immediate relief against high energy prices and costs for Europe’s energy-intensive industries exposed to international competition.
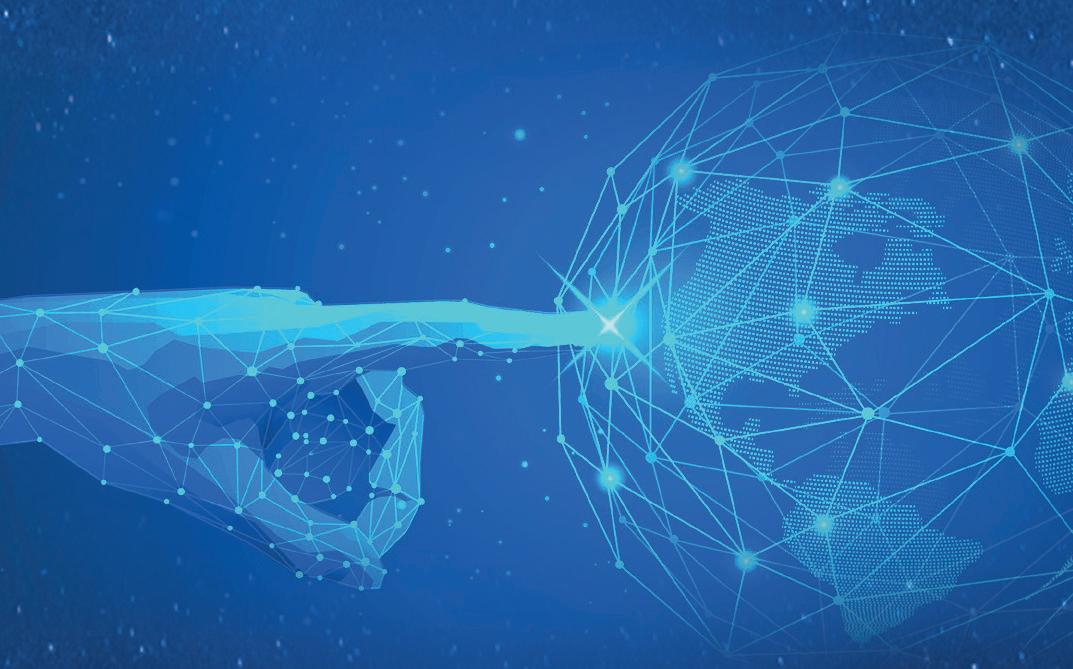
the viability of steelmaking in Europe and, once again, we find ourselves discussing the need for a ‘level playing field’ and realising that’s it’s not level at all...and probably never will be.
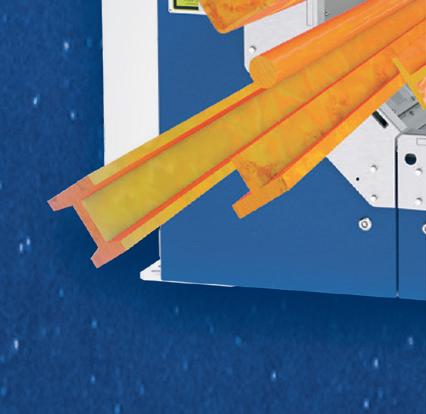
You don’t need me to tell you that a major energy crisis is looming and that if action isn’t taken soon there will be big trouble for energy-intensive industrial sectors like the steel industry. Already, alarm bells are ringing. In the UK, a recent survey by MAKE UK suggests that rising energy costs are causing major disruption for half of those surveyed and that one in five companies believe that energy costs will be a huge issue for the next two years.
But perhaps it’s already too late. From mid-September, ArcelorMittal plans to switch off one of two furnaces at its steelworks in Bremen, Germany, citing soaring gas prices, weak market demand and a negative economic outlook.
InlinePrecisionProfile Measurement•Fullprofilemeasurement•Surfacefaultdetection•3Dimageanalysis Family owned since 1957, Zumbach is a global leader in the industry. Driven by innovation and experience. We are here for you and ready to build the future together. www.zumbach.com • sales@zumbach.ch


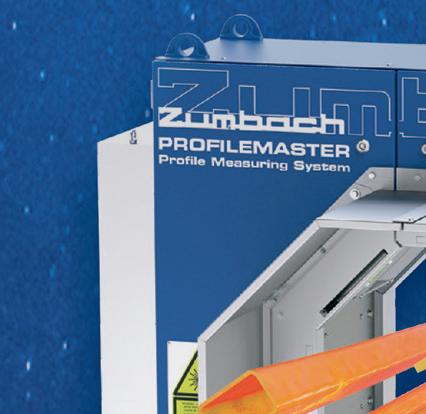
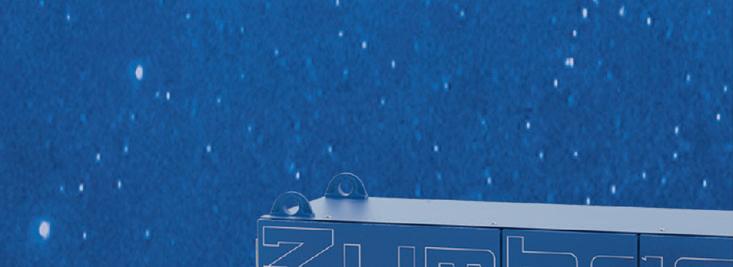
We understand how it is important to efficiently extract and process precious metals and minerals. PROCESS + PROTECT You save valuable resources while keeping your employees and the environment safe. Do you want to learn more? Improvewww.de.endress.com/primaries-metalyourprocesseswithour

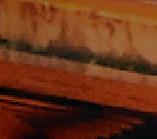
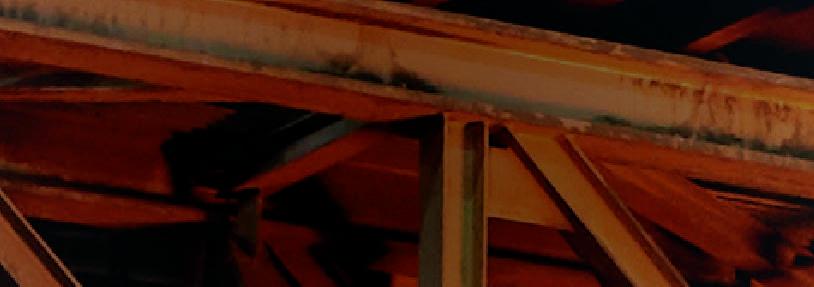
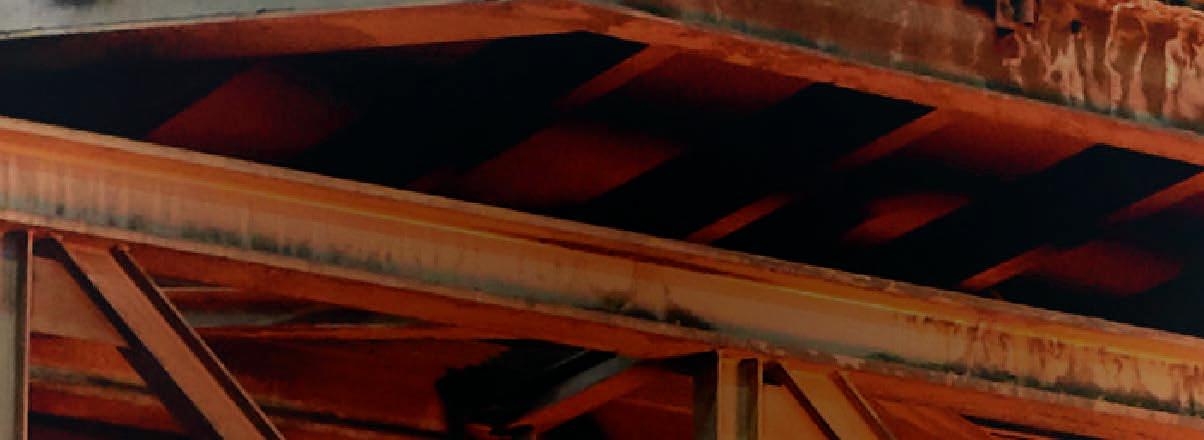
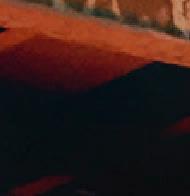
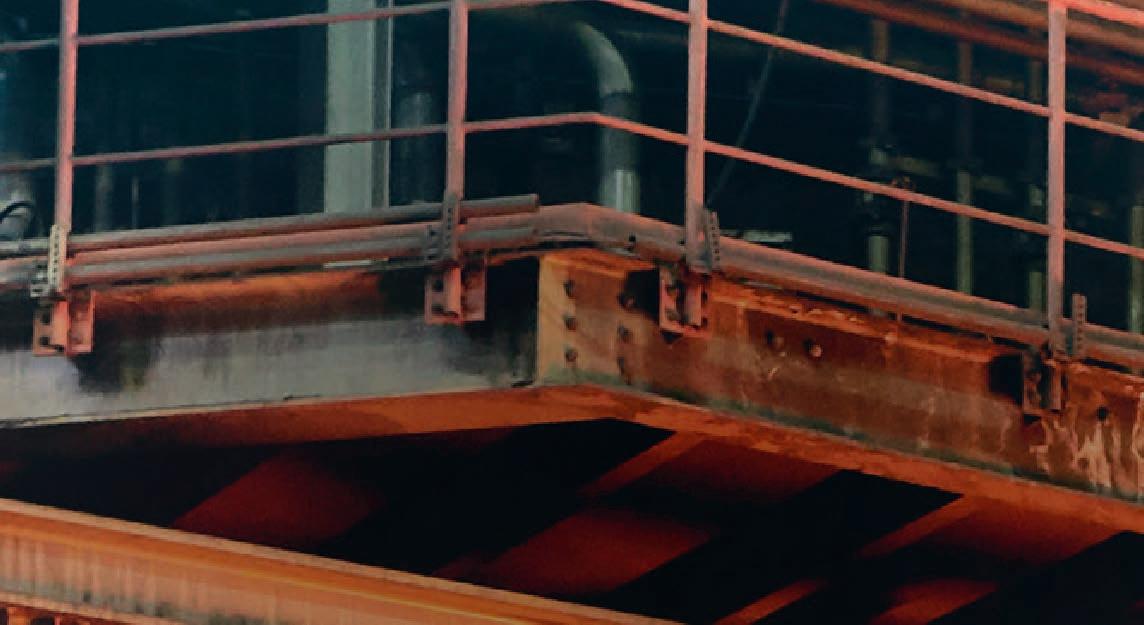
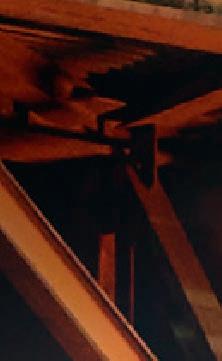
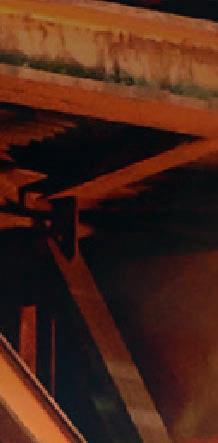
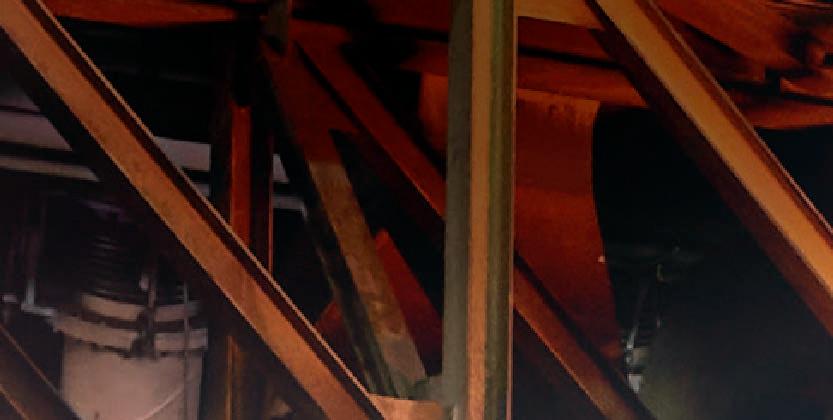

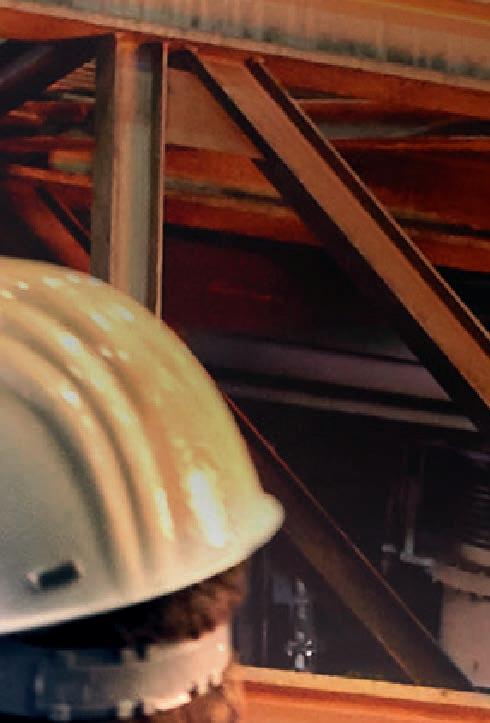
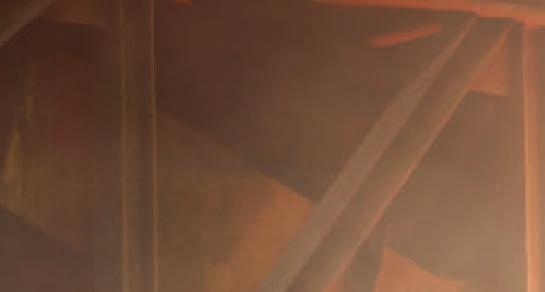

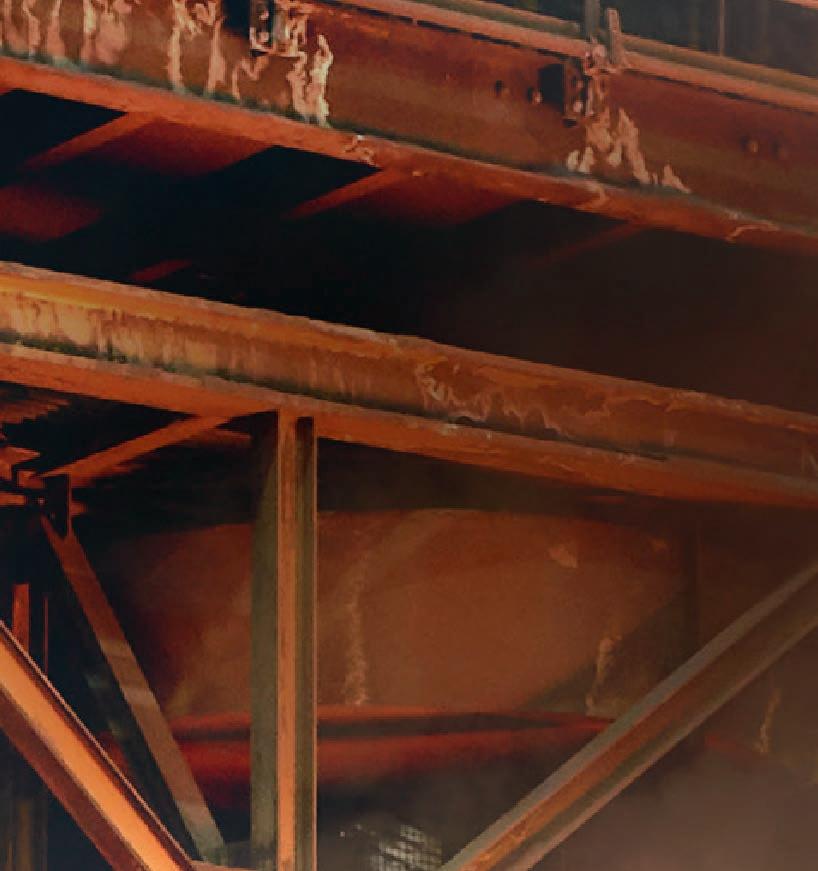
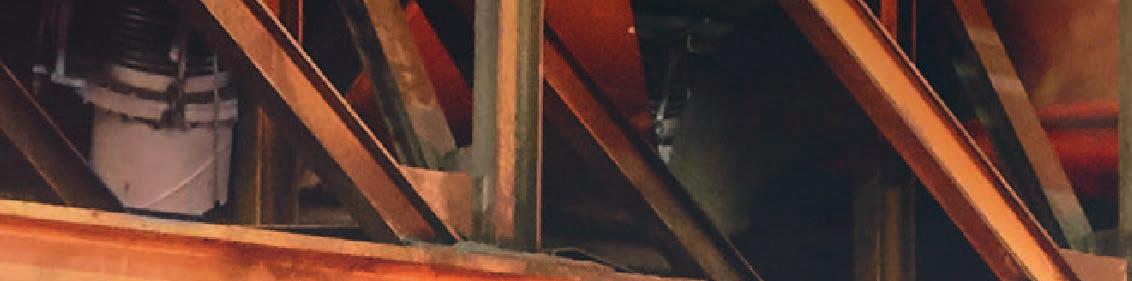
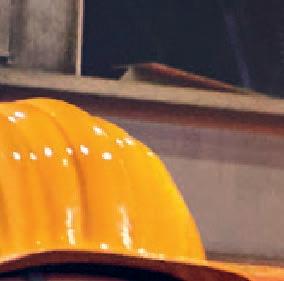
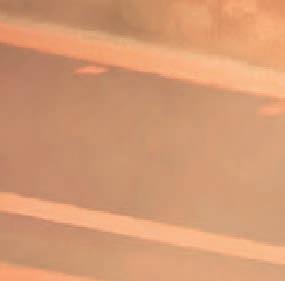
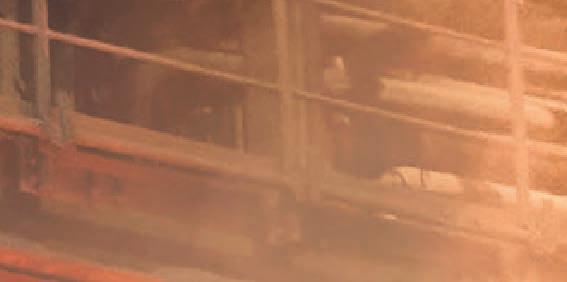
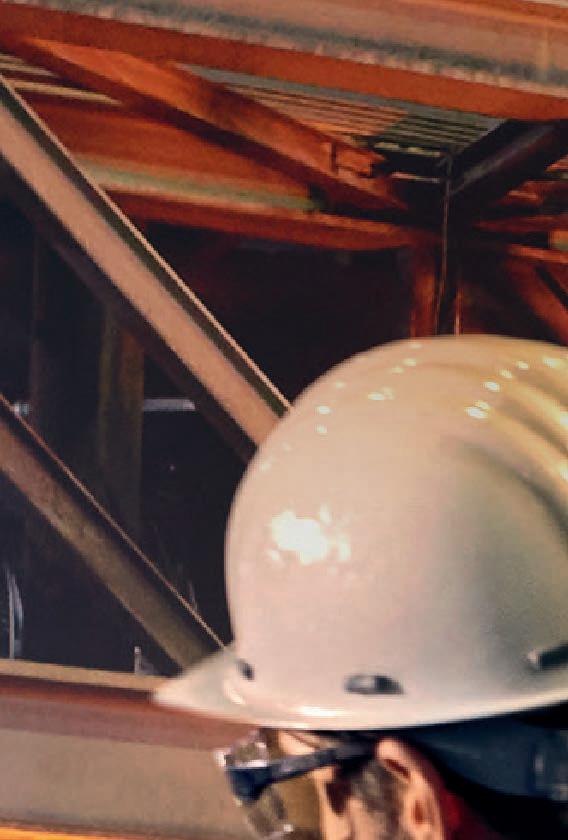


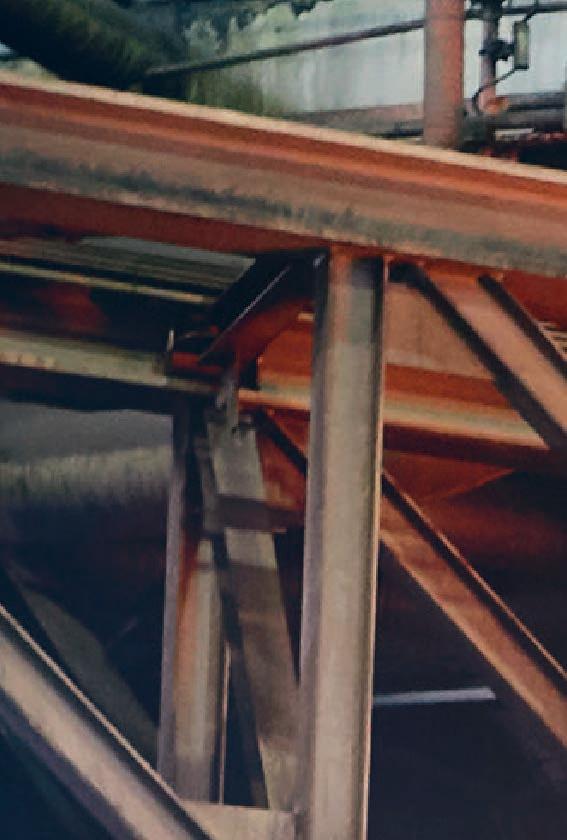
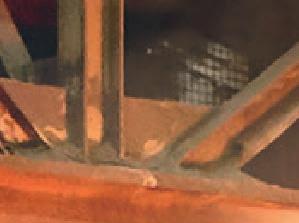
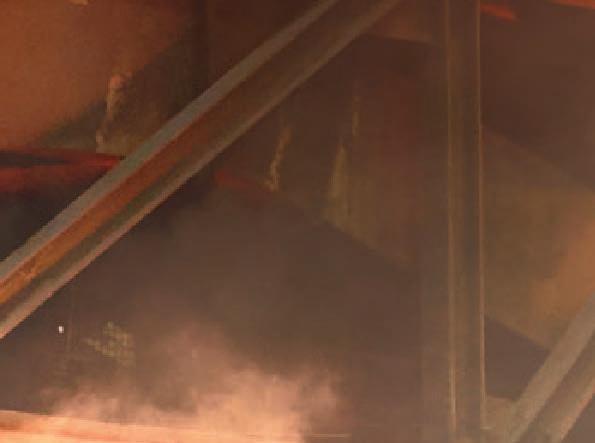

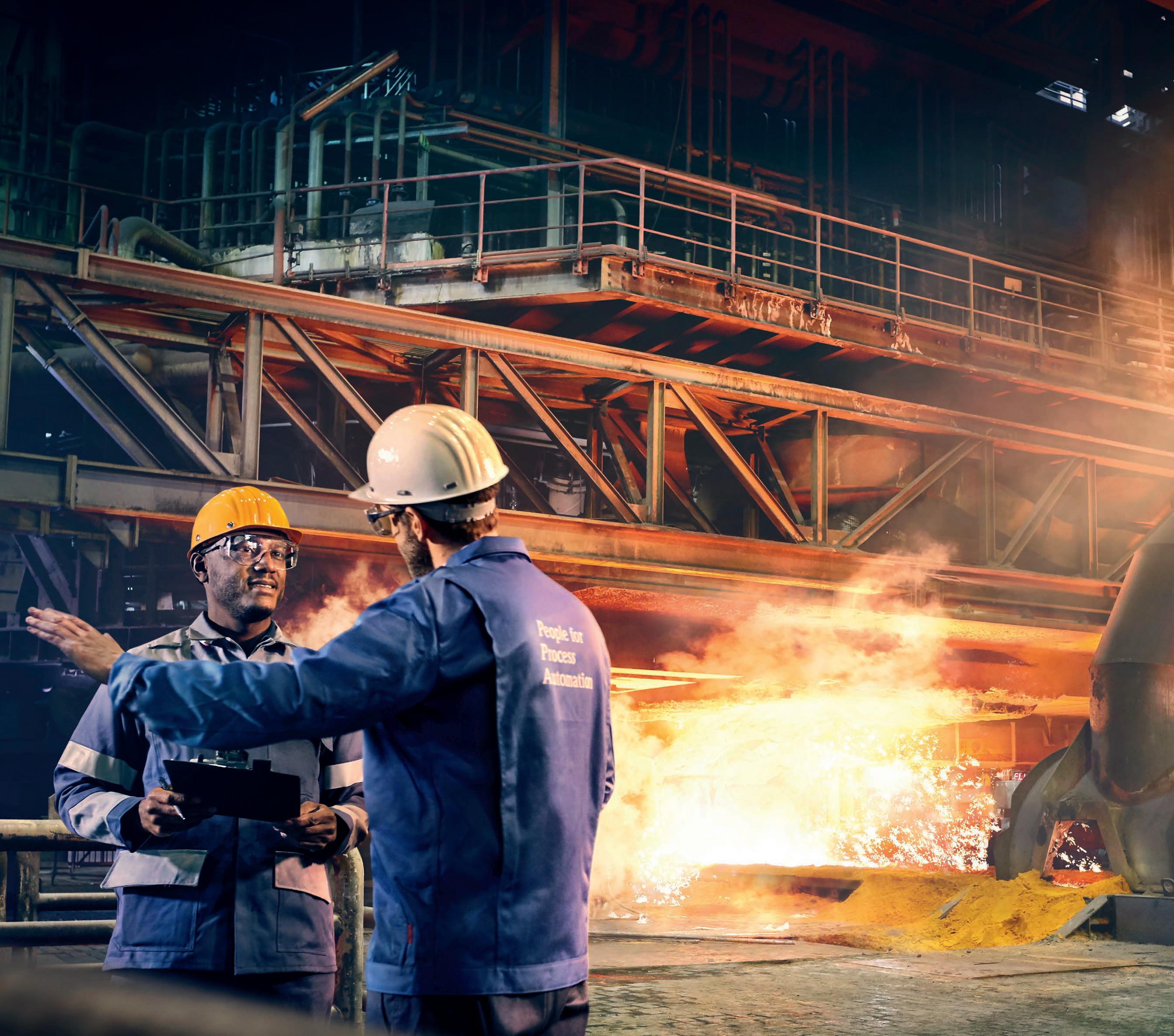
measuring instruments: Liquiline CM44 and CPS11D: Versatile transmitter and Memosens pH sensors ensure reliable measurement and safe calibration in the lab. FieldPort SWA50: Intelligent Bluetooth or WirelessHART adapter for the easy connection of all HART field devices to the Netilion Cloud via Edge Devices. Cerabar AbsolutePMC51B:andgauge pressure transmitter combining measurement accuracy with IIoT functionalities.

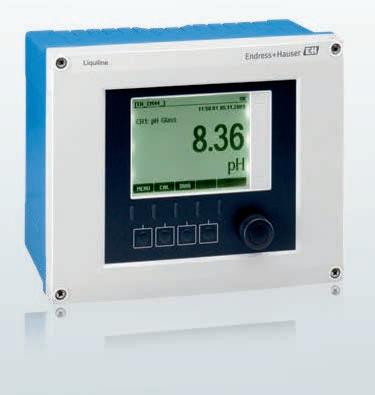
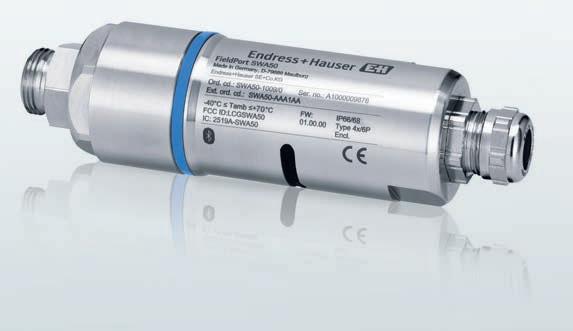
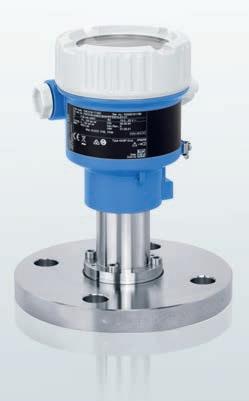
comprehensive portfolio of
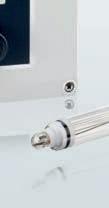
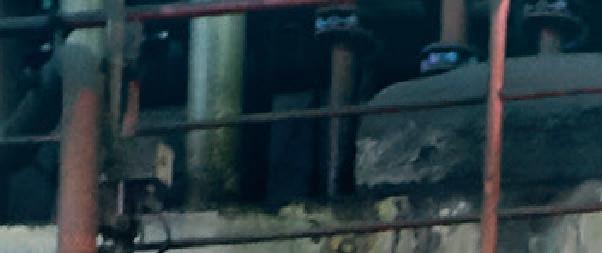

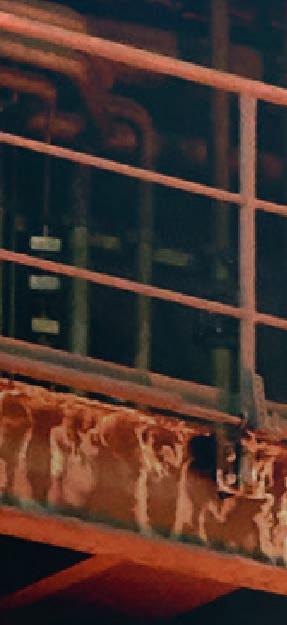
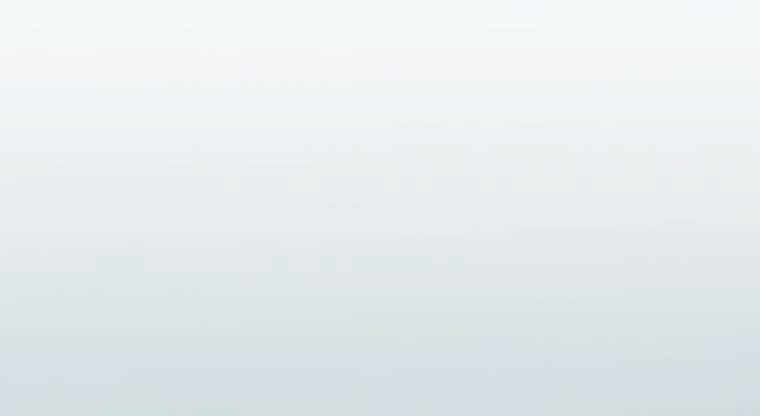
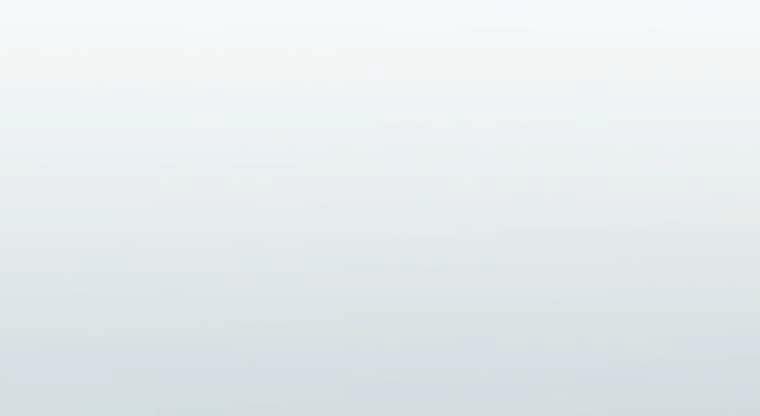
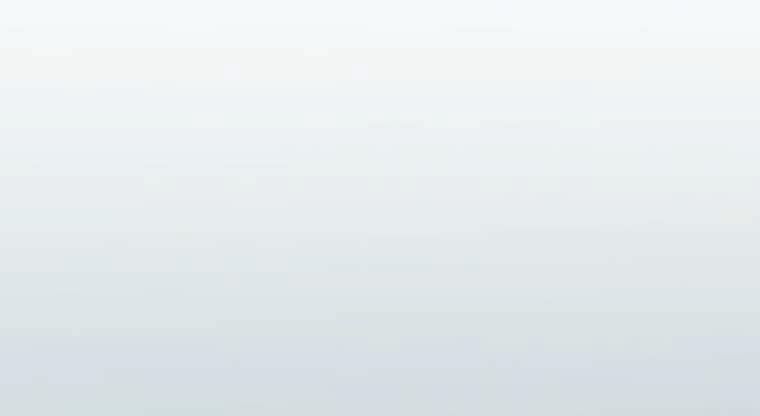
South Korean steelmaker POSCO, Indonesian state-owned PT Krakatau Steel, and the Indonesian government have signed an agreement to invest $3.5bn in expanding their local steel production capacity over the next five years, according to a memorandum of understanding signed on 28 July. “We are delighted with the government’s support in realising the expansion of PT Krakatau-Posco. PT Krakatau-Posco will be the largest integrated steel company in Southeast Asia,” said Krakatau Steel CEO Silmy Karim in a company statement.
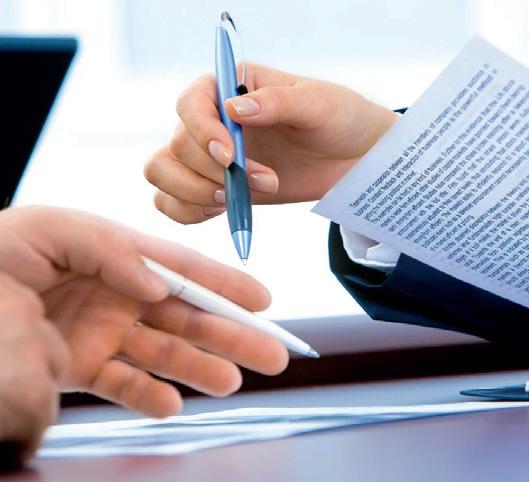
Source: FDI Intelligence, 9 August 2022
4 August 2022
Ron Blake, a historian hailing from Liberty County, Texas, USA, has ensured that two steel medallions, marking the installation dates of two bridges, were kept from being scrapped. The medallions – one on the 1919 bridge on the west side of the Trinity River and one on the 1904 bridge on the east side of the river – and two vertical sections will one day be used to anchor historical signage in a public place, preferably next to the Trinity

Ray Horsburgh, Liberty Steel Group non-executive director and InfraBuild acting chairman, has passed away, the company has announced. Mr Horsburgh suffered a fall while on business in Romania. He had vast experience in the steel industry and was a former chairman of Toll Holdings. He has served as CEO of Smorgon Steel Group and has held various directorships. He was acting chairman of Sanjeev Gupta’s Infrabuild business. Gupta paid his respects to Horsburgh and his family, describing him as a Monthly,Source:manufacturing.’steeladvocate‘passionateoftheAustralianindustryandAustralianManufacturers’9August2022
BMW Group and HBIS Group (HBIS), a state-owned Chinese iron and steel manufacturing conglomerate, signed a memorandum of understanding (MOU) to co-build a green and lowcarbon automotive steel supply chain, the German auto giant announced via its WeChat account. Under the MOU, BMW will use HBIS' low-carbon steel on massproduced vehicle models manufactured at its Shenyang production factory starting
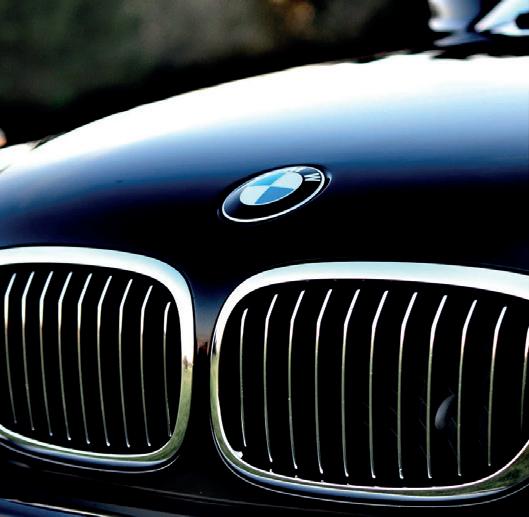
Italy4Source:mid-2023.Gasgoo,August2022planstoinject
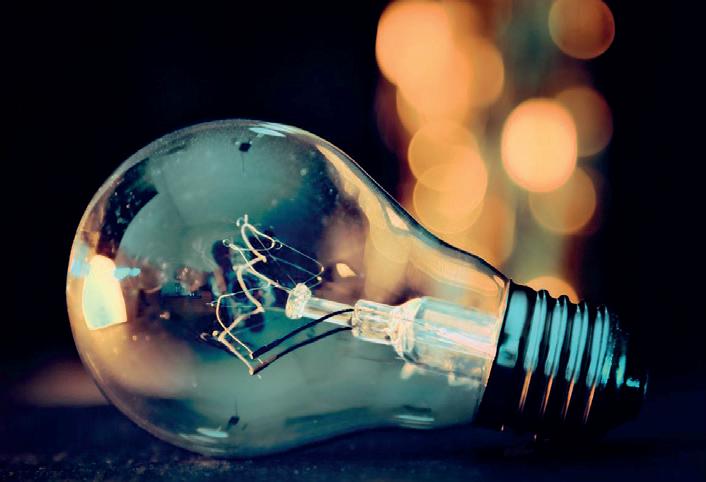
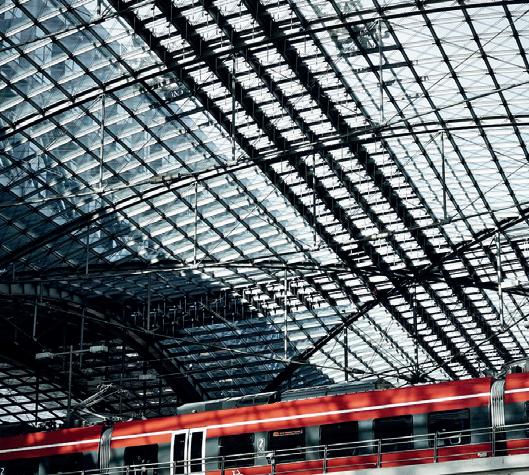
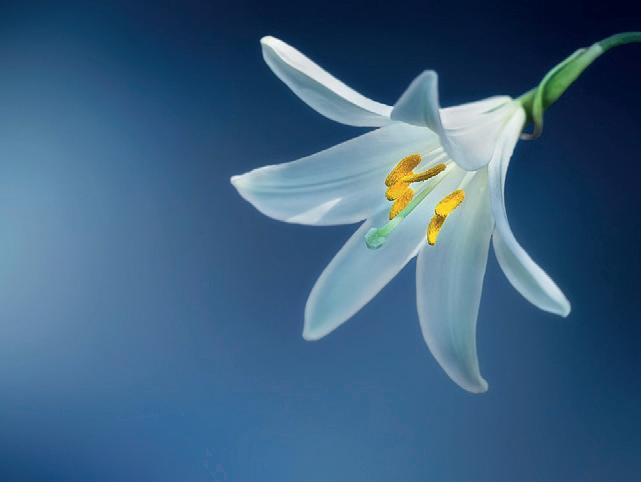
up to $1.02 billion into one of the largest steel plants in Europe to help it cope with soaring energy prices, a draft government decree has stated. Geopolitical tensions stemming from Russia’s invasion of Ukraine have propelled gas prices to historic highs, adding to supply-chain issues and environmental problems for plant owners Acciaierie d’Italia, formerly known as Ilva. The group, whose main plant is in the southern Italian city of Taranto, is 38% controlled by state-owned agency Invitalia and 62% by ArcelorMittal, the world’s second largest Source:steelmaker.Financial Post,
4 NEWS ROUND-UP www.steeltimesint.com
A new sculpture has been erected at Workington railway station in the UK as the town celebrated its contribution to the steel industry. It features the Bessemer Converter and a 7ft interpretation of Bessemer himself. Workington was the home of Henry Bessemer, who invented the Bessemer Converter in 1856 – a new way of making steel that revolutionised the industry. The project has seen the railway station become an exhibition centre to celebrate the time when the town was a world leader in rail Source:technology.Cumbria Crack,
6 August
As part of its efforts to contribute to richness of biodiversity, Tata Steel Mining Limited (TSML) in India, in association with its corporate social service responsibility wing, Tata Steel Foundation (TSF), has come forward to conserve Sukinda Ecorace, an indigenous silkworm breed located in the Jajpur district of Odisha. Senior members of the Central Silk Board (CSB), TSML, TSF and other experts deliberated in a workshop organised at the Sukinda Chromite Mine of TSML, alongside scientists and farmers, and prepared a road map for the conservation of the Source:silkworm.Orissa Diary, 7 August 2022
Source:River. Bluebonnet News, 8 August 2022
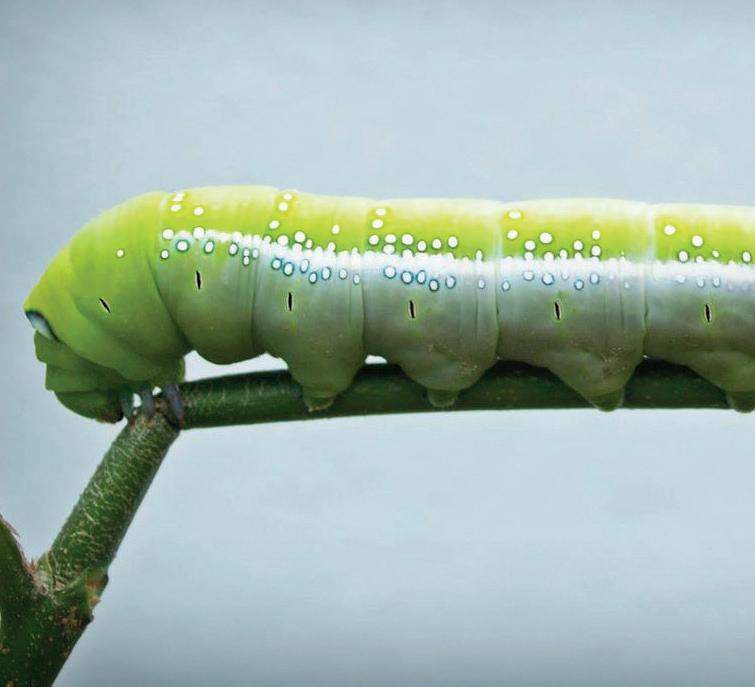
Multinational steel company
Gerdau Metaldom carried out an inventory of greenhouse gases for the period 2019 to 2021, which showed a 30% reduction in the intensity of its direct and indirect controlled emissions, which the company says translates into the manufacture of steel products with a smaller environmental footprint and higher
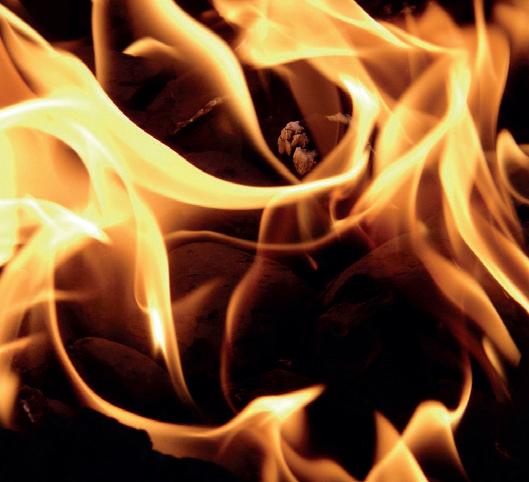
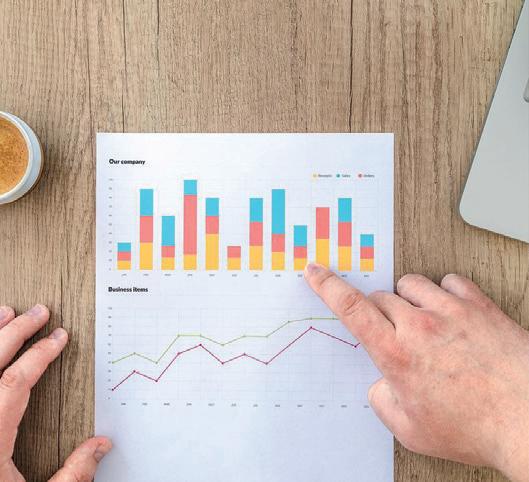
South Korea’s steel conglomerate SeAH Group has set up a joint venture with Saudi Arabian energy giant Aramco to produce special steel pipes. SeAH Changwon Integrated Special Steel Corp, the group’s special steel division, said the joint venture –to be known as SeAH Gulf Special Steel Industries (SGSI) – will accelerate the expansion of the group in the Middle East. The project will be established in King Salman Energy Park (SPARK), a new megaproject under construction and located between Damman and Al-Ahsa in Saudi Arabia’s Eastern Province,

Source: Zawya, 10 August 2022
Evraz plc, a Russian steelmaker, has officially started soliciting proposals for the acquisition of its north American subsidiaries, which includes Evraz Steel in Regina, Canada. In a press release, the company said the sale would allow it to ‘unlock the stand-alone value of the North America business.’ Currently, Evraz North America (ENA) operates two EAF-based steel facilities, four rolling mills and eight tubular mills along with 17 scrap recycling facilities.
Source: Global News, 11 August 2022
Source: yahoo!finance, 9 August 2022
September 2022 NEWS ROUND-UP 5 www.steeltimesint.com
10Source:productivity.DominicanToday,August2022
Nigeria's Minister of Mines and Steel Development, Arc Olamilekan Adegbite, has expressed optimism that the reconstituted National Steel Council raised hope of the country becoming selfsufficient in steel production. “This decision is a step in the right direction, which brings us closer to our goal of achieving self-sufficiency in steel production. Indeed, the importance of achieving such a feat cannot be over-emphasized as the steel industry remains the backbone of modern society’’, said

Algoma Steel Group has announced that a fire occurred on 7 August 2022, on one of its coal conveyors that supplies coal to two of its three coke batteries. According to the company, no one was injured. Iron and steelmaking operations are expected to continue as normal while the damage is repaired. The company can continue to produce coke at a reduced rate, and believes it has sufficient coke inventory and supply contracts for purchased coke to support steelmaking operations.
Source: The Statesman, 11 August 2022
9Source:Adegbite.Vanguard,August2022
Source:retirement.Gazette & Herald, 10 August 2022
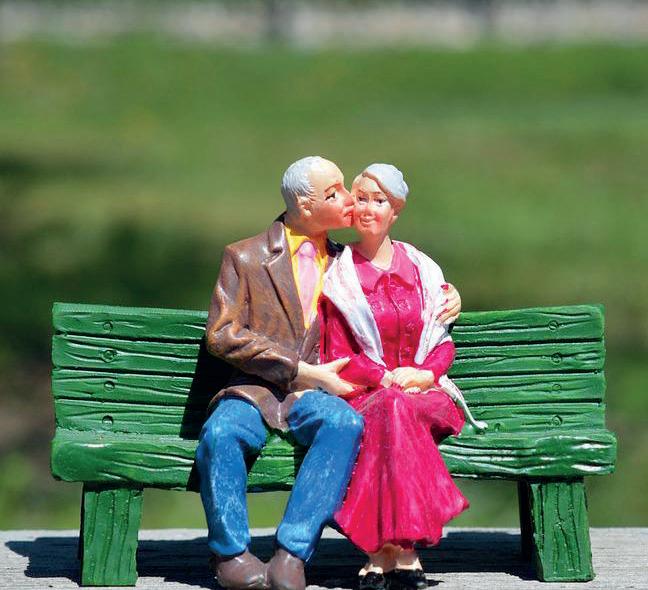
The fourth edition of Tata Steel Chess has been announced, with the introduction of a women's section within the tournament. This is the first time a separate women’s section has been added with the prize money equivalent to that of the Open section. More female players are likely to play in the women’s category than in the Open, as the chances of winning the prize money are higher in the former, an official stated.
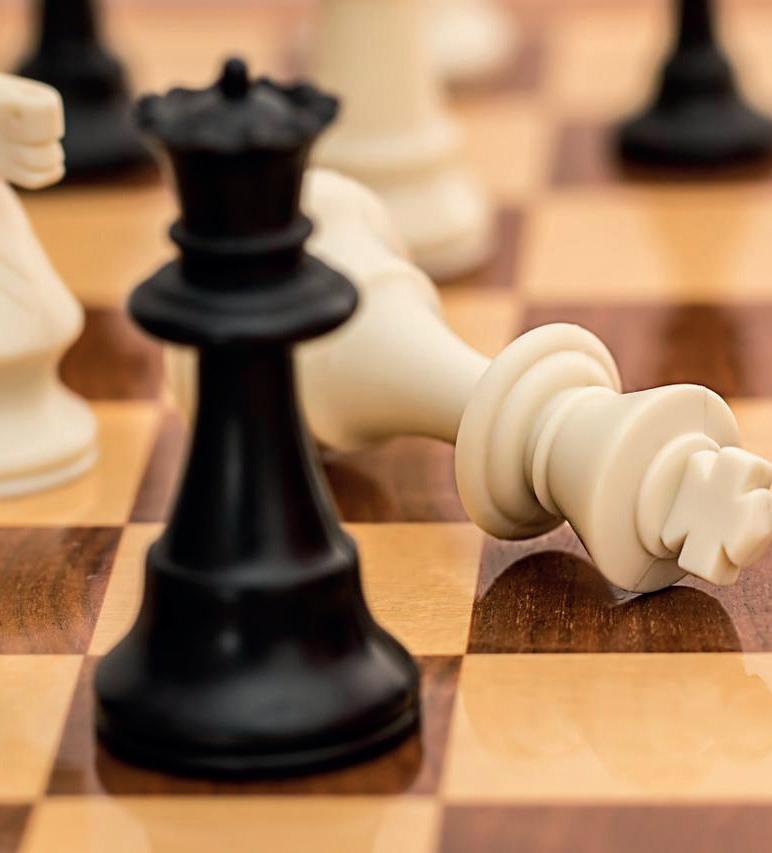
A steel buyer from Norton, UK, has retired after 50 years of service. David Paterson, 67, started working at Bright Steel in 1972. The family-run business is based in Norton and is one of the largest producers of bright drawn steel flat and square bars in England, and among the largest in Europe. David worked his way up through the company from his initial junior position to assistant steel buyer. He was then made steel buyer in 1992 and held the role until his

Vedanta-Iron and Steel has partnered with IIT, Bombay for a research and development project to develop cost-effective technology for producing green-steel using hydrogen, thereby targeting significant carbon footprint reduction in iron and steel space. Sauvick Mazumdar, CEO, iron and steel sector, Vedanta said: “At Vedanta, we are fully committed towards our ESG goal of achieving ‘carbon neutrality’ by 2050 or before, and this engagement with IIT-B is a massive step forward in our endeavour to adopt ‘Green Technologies’ to significantly reduce the carbon
Tata Steel’s Shotton Works is trialling the use of a special type of bio-based diesel alternative in its on-site vehicles to reduce the site’s carbon footprint as part of its sustainability commitment. The Hydrotreated Vegetable Oil (HVO) fuel is a low-carbon, low-emission, fossil-free and sustainable alternative to conventional diesel, made from 100% renewable raw materials. Works manager Bill Duckworth explained: “Switching to HVO is straightforward, as it can be used in conventional diesel engines. The bio-based liquid fuel comes from many kinds of vegetable oils such as rapeseed, sunflower and soybean, and offers a fossil-free alternative to conventional diesel.
Liberty Steel UK has said that 45 redundancies have taken effect at Liberty Performance Steels in Albion Road, West Bromwich. It had announced consultation over the job losses as part of a wider restructuring and transformation plan in April. The steel group, part of GFG Alliance, is getting rid of 207 jobs across the country. Liberty said that the consultation had been longer than the statutory period and many of the redundancies at West Bromwich had been voluntary and had already taken place.
Source: ReNews, 17 August 2022
Source:emissions.Port News, 18 August 2022
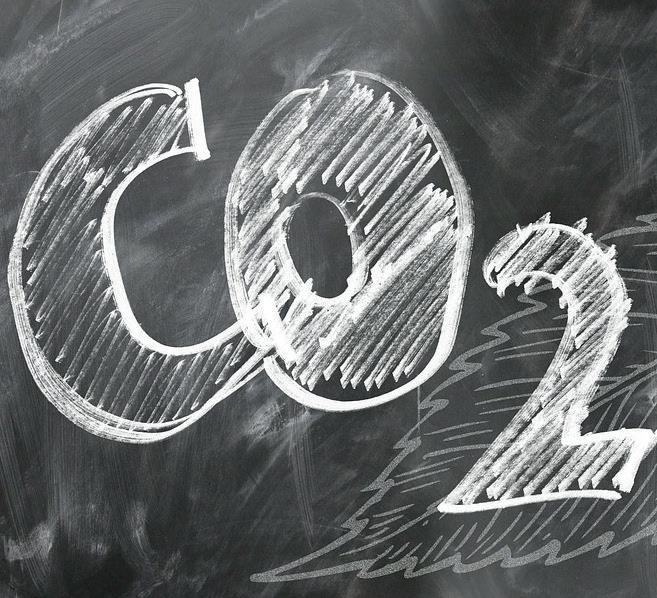
6 NEWS ROUND-UP www.steeltimesint.com
India's Jindal Stainless has announced that it will build a green hydrogen steel plant to reduce carbon dioxide emissions by nearly 2.7kt per year. The company said that it has reached an agreement with Hygenco India Private Limited to build a green hydrogen steel plant and become the first stainless steel manufacturer in India to use green hydrogen to meet its energy requirements.
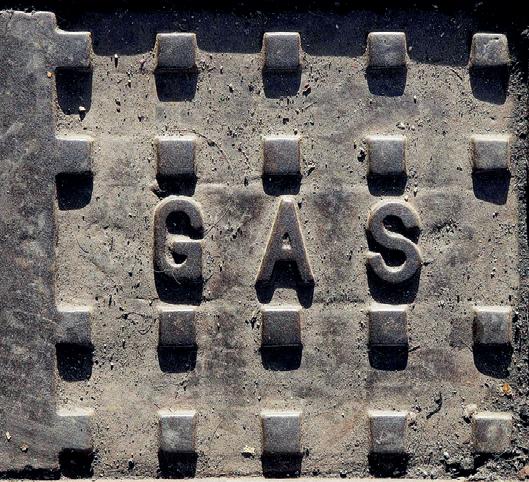
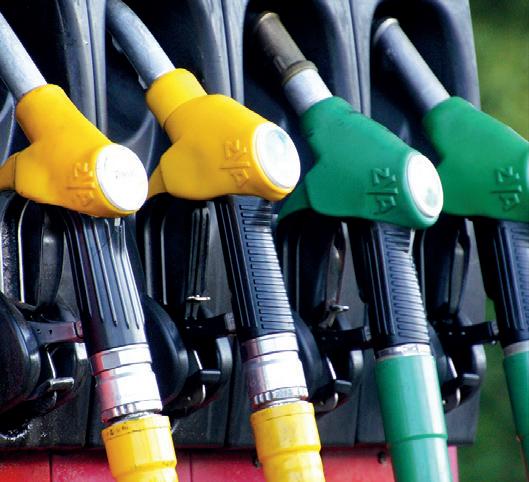
Fluxys,2022
Shell is scaling back its involvement in an electrolyser pilot project in Australia located at BlueScope Steel’s Port Kembla Steelworks in the Illawarra, New South Wales. In its latest annual report, published on 15 August, BlueScope Steel confirmed it continues to progress its assessment of a hydrogen electrolyser and a hydrogen hub in the Illawarra region. “BlueScope is continuing to work with a range of industry and research organisations on our plans, noting that Shell will now pursue its involvement in this project as a supporting partner rather than lead partner,” the steel manufacturer stated.
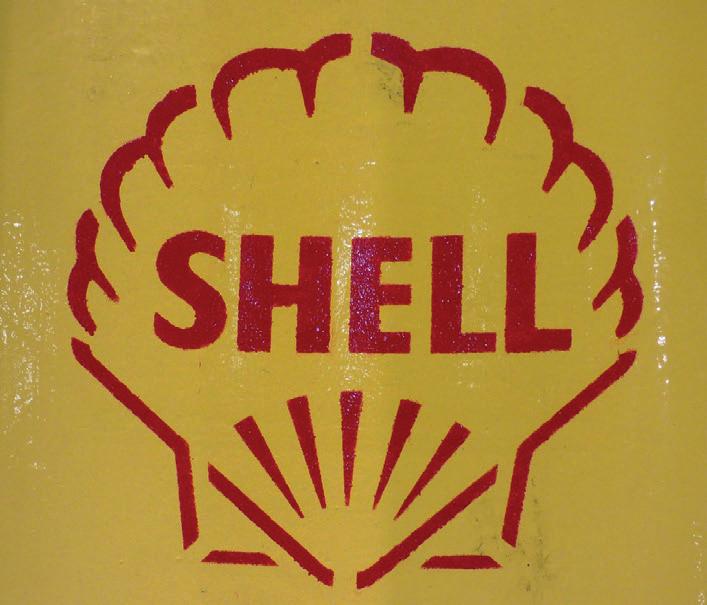
A landmark steel factory in Teesside, UK, has been demolished in a controlled explosion. The Sinter Plant formed part of the former steelworks site in Redcar. The area has a rich history of iron and steelmaking, which began in 1850 when iron ore was discovered in the Cleveland Hills near Eston. Around 8.5kt of steel were brought down in the demolition on 11 August. Only the nearby waste gas stack and two supporting structures now remain in the area.
Source: ITV, 12 August 2022
Source: Yieh Corp, 15 August 2022
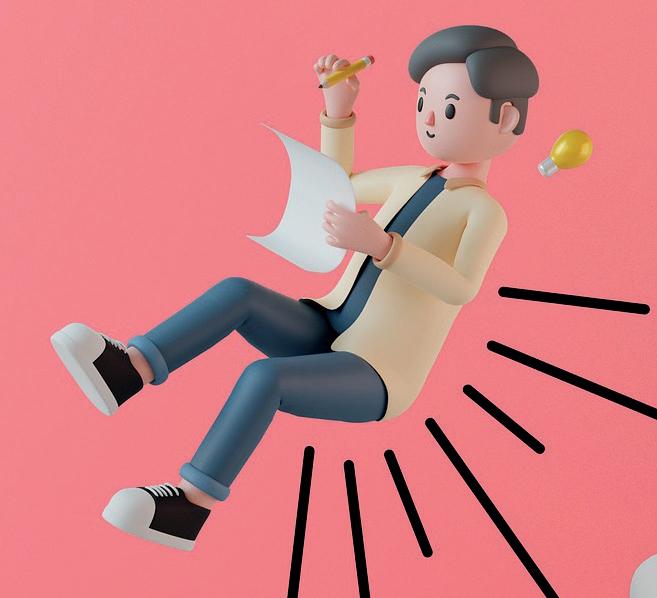
Source: Express & Star, 18 August
Source:footprints.’’Construction Week, 12 August 2022

Source: Deeside.com, 12 August 2022
a natural gas transmission system operator, ArcelorMittal Belgium, and the North Sea Port have started a feasibility study for the Ghent Carbon Hub project, an open-access CO2 storage and liquefaction hub in the Ghent part of the North Sea Port. Besides the use of carbon-neutral energy, carbon capture, utilisation and storage (CCUS) is essential for CO2 intensive industries to achieve net zero emissions, especially in hard-to-abate sectors with processes inherently generating CO2
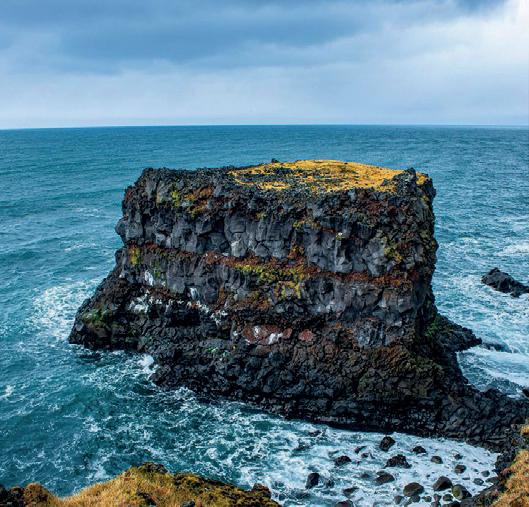
Source: Outlook India, 22 August 2022
Province Government Public Institute of Health and Environment, the key beneficiary, will carry out a study on the effectiveness of utilizing used coffee grounds in reducing odour in livestock farms. Out of 150kt of coffee beans imported annually, Hyundai Steel said, only 0.2% actually goes into the coffee we drink, while the remaining 99.8% is discarded as waste.
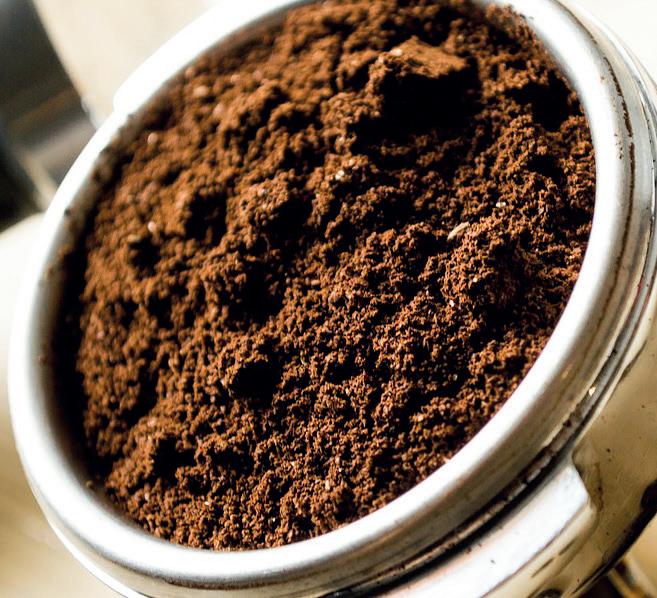
A 17-year-old male leopard died after water flooded Tata Steel Zoological Park due to high water levels in Jamshedpur city, India. The water entered the low-lying areas of the zoo, causing the tragic incident, Tata Steel said in a press statement. The leopard, named Mithun, was born in 2005 and was brought to the zoological park in 2007.
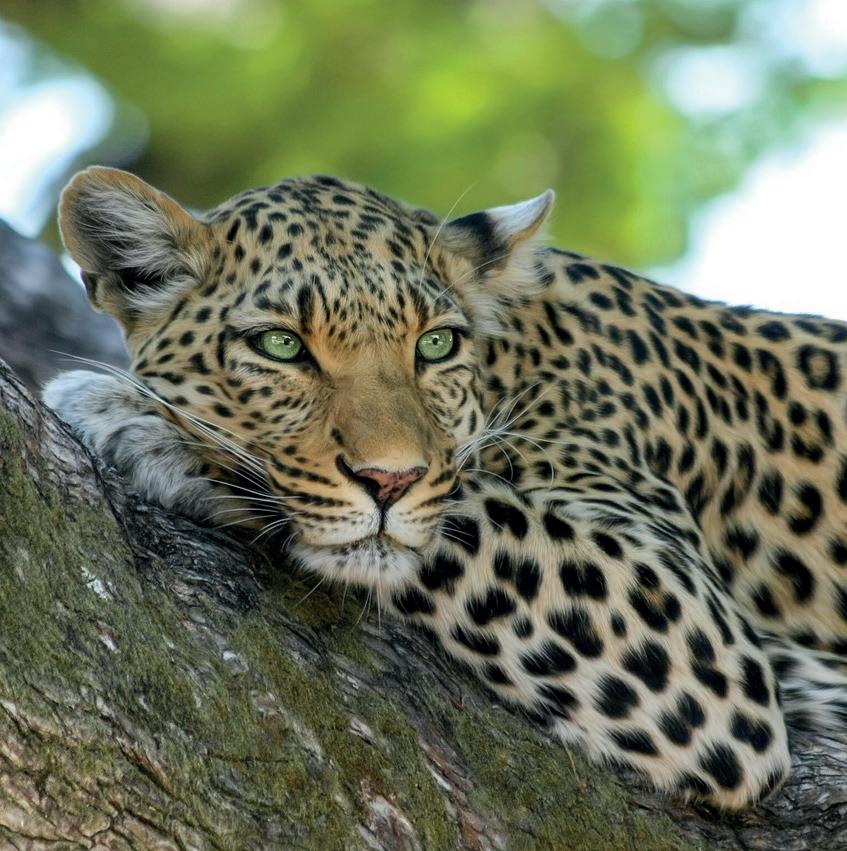
Source: The Korea Herald, 21 August 2022
Source: Institute for Energy Economics and Financial Analysis, 22 August 2022
Steel
September 2022 NEWS ROUND-UP 7
19Source:withinfurnacetheinyrthecompaniesininvestmentagreementaandGroupTEDAChinese19Source:themthatandalsodemonstratenowannually.350ktandNextThemadealternativeproductionpartArcelorMittalmanufacturerisswitchingofitscoalusedforsteeltobiocoal,antocoalthatisfromwoodresidues.DutchcompanyPerpetualmakesthebiocoalwilleventuallysupplytoArcelorMittalPerpetualNextisworkingonresearchtothatbiocoalissuitableforthecementchemicalindustries,soitcanbegintosupplytoo.InnovationOrigins,August2022companiesTianjinInvestmentHoldingandDelongSteelGroupNewTianjinSteelsignedstrategicco-operationtoattractinsteelprojectsSaudiArabia.Thetwowillco-operateondevelopmentofa10Mt/steelmakingindustrialparkSaudiArabia.Aspartofagreement,anelectricarcwillbeconstructedthepark.GMKCentre,August2022
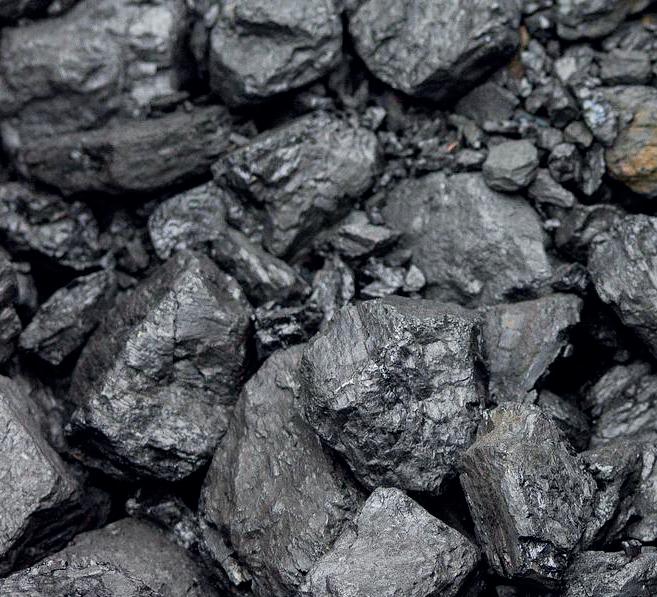
A £63m superyacht owned by a Russian steel magnate will become the first to go under the hammer since powerful Russians were sanctioned as a result of the country’s invasion of Ukraine. The 72.5 metre Axioma, which was owned by Dmitrievich Pumpyansky, was seized after docking in Gibraltar earlier this year. The Axioma can sleep 12 people in six luxury cabins, has space for 20 crew, and boasts a gym, swimming pool, jacuzzi, spa and 3D cinema. Forbes estimated that Pumpyansky, 58, the owner and chairman of steel pipe manufacturer OAO TMK, was worth £1.7bn last year.
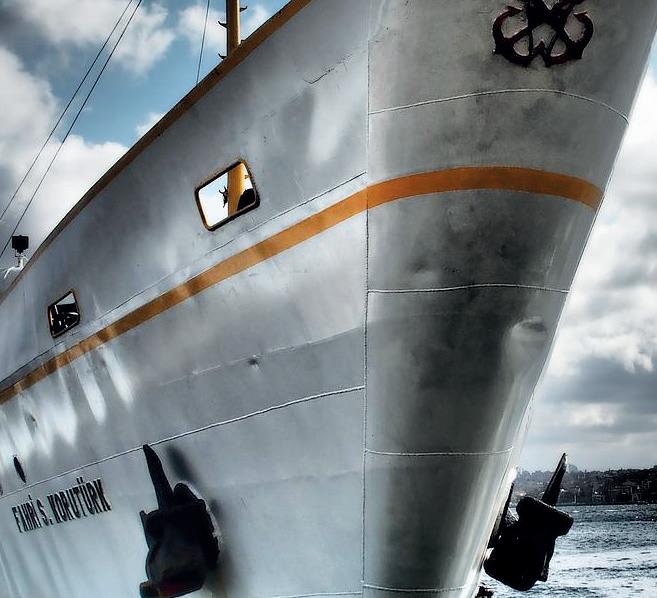

Source:metres.Offshore
Energy, 22 August 2022
Kenyan steel and cement company, Devki Group, has unveiled plans to develop a wind power plant in the country to cut power costs. The firm said in a disclosure to the National Environment Management Authority that it plans to develop a 60 MW plant in Samburu, Kwale County, Kinango Sub County. The power generated will be used for Devki Group's own consumption in the Samburu plant in Kwale County.
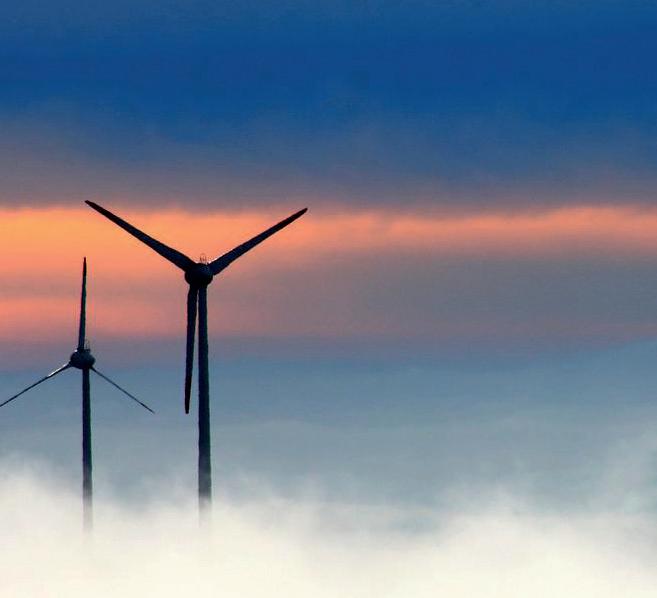
Source: i News, 20 August 2022
China’s Jiangnan Shipbuilding hosted a steel cutting ceremony on 19 August for the first 7,600 CEU LNG dual-fuel pure car and truck carrier (PCTC) being built for SAIC Anji Logistics, a subsidiary of China’s automobile manufacturer SAIC Motor. Two vessels were ordered in January 2022. Described as the world’s largest dual-fuel PCTC, the vessels will span 199.9 metres in length, a width of 38 metres, and a structural draft of 10.2
Hyundai Steel, the Korean steelmaker, has recycled used coffee grounds as part of its social contribution activities. The North Gyeongsang

Emirates Steel Arkan’s Group CEO, Saeed Ghumran Al Remeithi, said the group is considering expanding into new markets in Asia and Africa, which will enhance its international competitiveness. In an interview with the Emirates News Agency, Al Remeithi said the group would explore new markets and increase its production and efficiency. The group increased the number of its export markets to 60 by the end of H2 2022, compared with 56 markets at the start of the year. Source: Construction Week, 28 August 2022
Canadian steelmaker Stelco renewed five-year collective bargaining agreements with its employees represented by three United Steelworkers local chapters, thus averting a strike and andprovideandstabilityagreementshascurtailments,potentialthecompanyannounced."Thesewillprovideforouremployeestheirfamiliesandourcustomersshareholderswith
Source: BBC, 23 August 2022
JFE Steel, Japan's second largest steelmaker, will switch one of its blast furnaces to an electric arc furnace around 2028 as it aims to go greener, according to a company release. This, says the report, will be the first time that any of Japan's top three steel companies have aimed to make their blast furnaces electric. According to people familiar with the matter, JFE will switch the No. 2 blast furnace at the Kurashiki Area of the West Japan Works, Kurashiki City, Okayama Prefecture, that needs to be replaced in the next five to six years to an electric arc furnace. Source: Nikkei Asia, 26 August 2022
A fabrication yard in the Isle of Lewis, Scotland, has secured its largest contract since its takeover by Harland and Wolff last year. Arnish, located near Stornoway, is to manufacture steel components for a mine in Greenland. Work on the project is to start at the yard in September, with the final delivery expected next April. The value of the contract has not been disclosed. Some of the components are to be used for a mooring system for barges at the mine at a site known as White Mountain.
25Source:beandcompanyaroundyearcompanyMassachusetts-basedsigneda30-agreementtooccupyhalfofthespace.Thewillmanufacturecellgenetherapiesthatcanshippedworldwide.90.5WESA,August2022
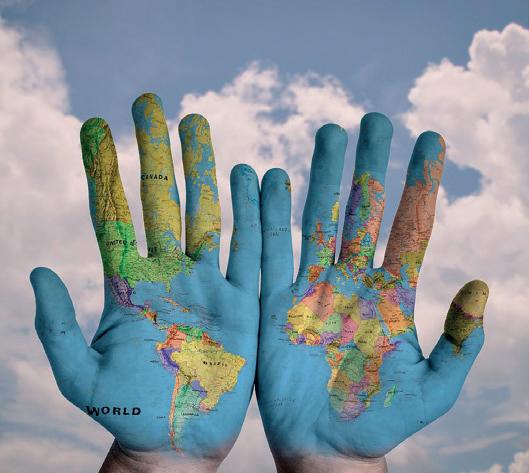
A former steelworks in Pittsburgh, Pennsylvania is to be transformed into a gene therapies facility. The University of Pittsburgh has announced that ElevateBio would be the ‘anchor tenant’ for a planned $250 million facility in Hazelwood Green. The
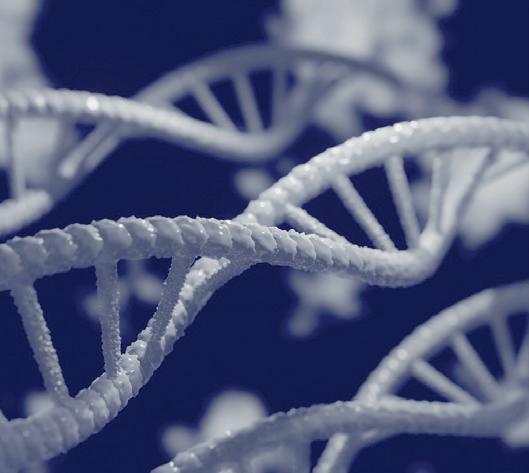
Orders for eight new Danieli Zerobucket electric arc furnaces have been placed by five Chinese steelmakers over the last six months. Qiananshi Jiujiang, Hebei Puyang, Tangshan Zhongshou, Changshu Longteng and Zhejiang Yuxin relied on Danieli electric steelmaking Zerobucket technology for their investments in new melting units. All of them selected the original Danieli horizontal, continuous scrapcharge system. The ordered furnaces will have capacities from 210 to 330 t/ph, and are expected to start operation between the end of 2022 and the beginning of 2023.
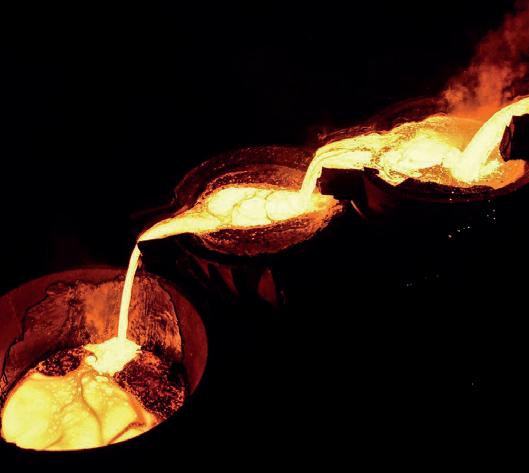
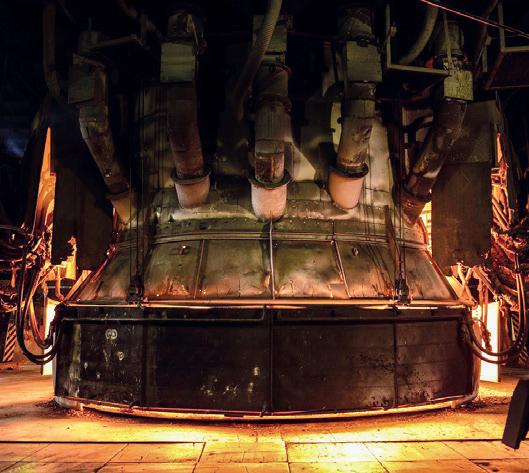
Source: Market Screener, 25 August 2022
confidence in Stelco's ability to continue to deliver on its commitments," Stelco CEO Alan Kestenbaum said in a Source:statement.SP Global, 22 August 2022
ArcelorMittal Nippon Steel India Ltd will acquire certain infrastructure assets from Essar Group for $2.4 billion, the steel manufacturer has said, in a deal that will strengthen its steelmaking business in the country. The purchase of steelmaking business assets, including power, ports and other logistics and infrastructure operations, will be funded by the Indian unit of the joint venture between ArcelorMittal and Nippon Steel Corp, the company said. Source: Reuters, 26 August 2022
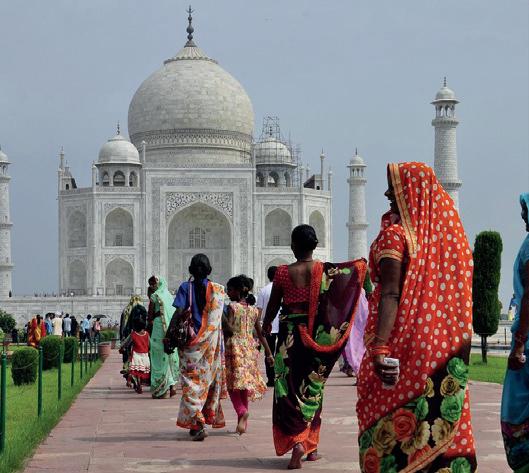
www.steeltimesint.com 8 NEWS ROUND-UP

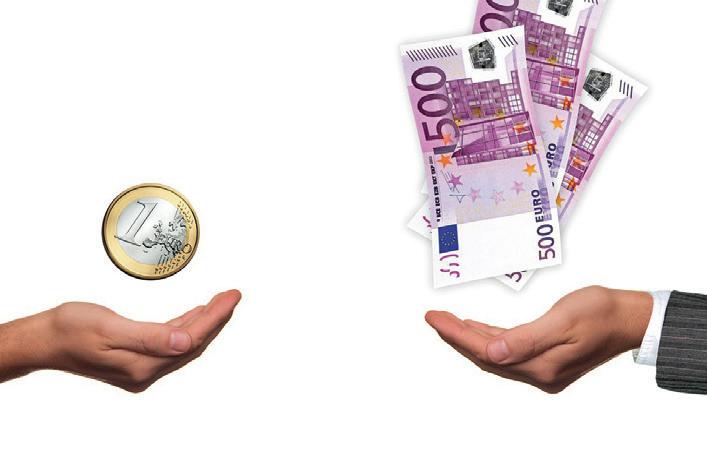
Saudi Steel Pipe Co. has won a contract worth $24 million from Uruguay-based Tenaris, a global steel tube supplier. Under the contract, the Saudi company will provide oil and gas pipes to Tenaris, according to a company filing. The financial impact of the contract is likely to take effect toward the end of the year and the beginning of 2023, it said. In 2019, Tenaris acquired 47.8% of Saudi Steel Pipe.

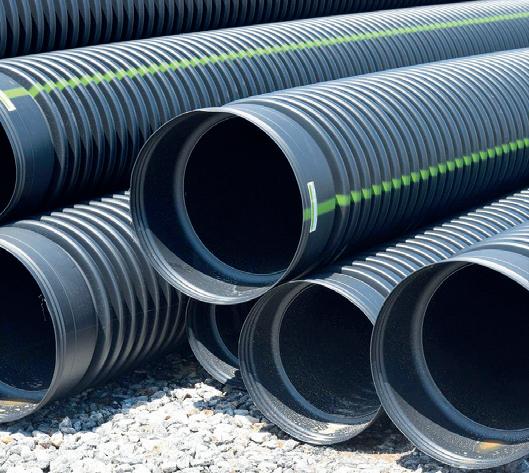
The UK government has approved extending measures to prevent dumped imports of cold rolled flat steel from China and Russia until 2026.
Tata Steel Nederland has signed contracts with three companies for the further technical preparations of hydrogen-based steel production at Ijmuiden in the Netherlands. The first development will cost more than $65m and will result in an engineering package that forms the basis for a final permitting and project planning. The three companies involved
Metalbook, a digital supply chain platform for the metals industry, has raised $5 million in seed funding led by Axilor Ventures. The round also saw participation from Foundamental, RTP Global, Stride Ventures and others. The Delhi-based start-up has received its exports licence and has plans to scale to 12 other locations with the newly secured funding. It also plans to use the capital to strengthen its global network of processing centres, build the team, and enhance its cloud factory platform.
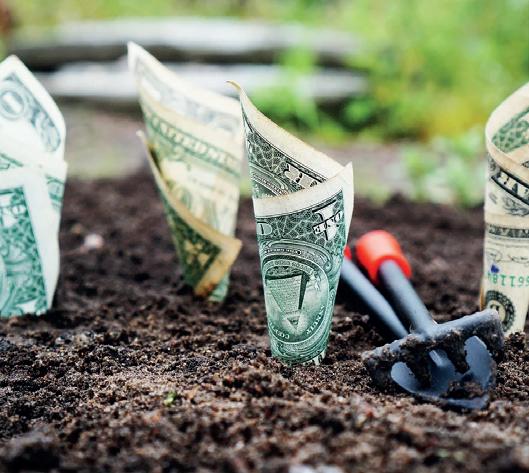

are McDermott, Danieli and Hatch. The overall project is led by the Tata Steel internal project and sustainability team, with close support from the main delivery partners.
Source: BBC, 30 August 2022
The decision came following a review by the Trade Remedies Authority (TRA), which said that cold rolled flat steel from China and Russia would likely be dumped in Britain if the measure were to be removed, affecting domestic producers which produce 40-50% of the local 30Source:market.Reuters,August2022

Source: Reuters, 29 August 2022
Mineral Resources, a West-Australian mining resources company, has pulled the trigger on a $3 billion iron ore project with the backing of China’s biggest steelmaker, state-owned Baowu, in a sign Beijing is still willing to invest in Australian mining despite tensions with Canberra. The decision to press ahead with the Onslow Iron Project, through joint venture vehicle Red Hill, will open up a major new iron ore province and associated port in WA’s West Pilbara, on the doorstep of Australia’s iron ore giants Rio Tinto, BHP and Fortescue Metals Group. Source: AFR, 29 August 2022
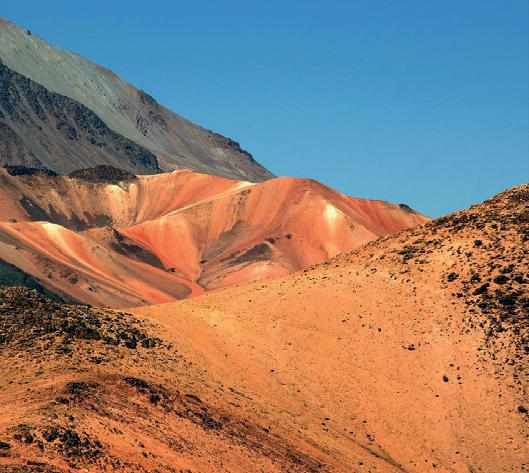
Swedish steel venture H2 Green Steel has announced that it has raised €190 million from a group of investors for building a fossil fuel-free steel plant in the north of Sweden that would start production in 2024. H2 Green Steel plans to have an annual production capacity of 5Mt of green steel by 2030. The new round was co-led by investors including AMF, GIC, Schaeffler and Altor. Swedbank Robur Alternative also participated in the equity raise.
Source: Business Today, 31 August 2022
Source: Arab News, 29 August 2022
The company behind the tin used in Heinz baked beans cans is celebrating its 70th anniversary. Tata Steel's Trostre Tinplate Works first opened its doors in Llanelli, Carmarthenshire, Wales, in 1952. And with orders piling in, one manager said the firm could be around for another 70 years. Some of its 600 workers are the third generation to have worked at the plant in the town, once nicknamed Tinopolis. The Carmarthenshire site has been working full throttle after a surge in demand for canned goods driven by Brexit and Covid stockpiling, one boss said.
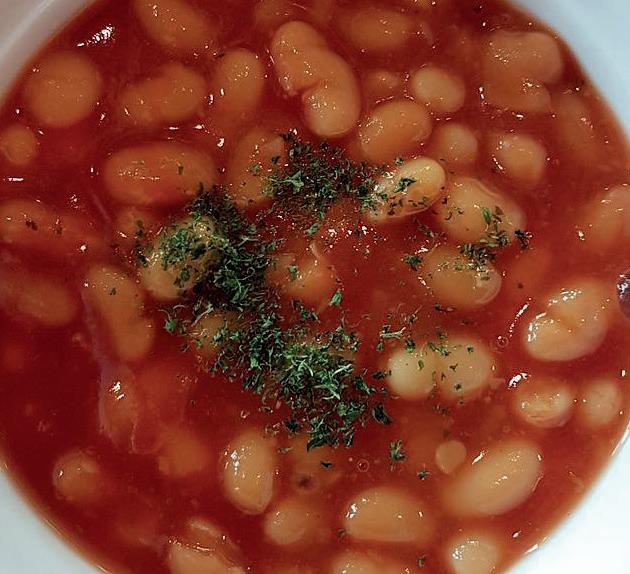
Source: YourStory, 29 August 2022
9NEWS ROUND-UP www.steeltimesint.com
The last Norwegian coal mine on the Svalbard archipelago will produce coal for another two years to help bolster industrial production in Europe. Mine 7 will continue production of bituminous coal, used primarily in the steel industry, until July 2025, the Norwegian government has said. The mine, which was due to close in 2023, delivers about 80kt of coal to the metallurgical and chemical industry in Europe.
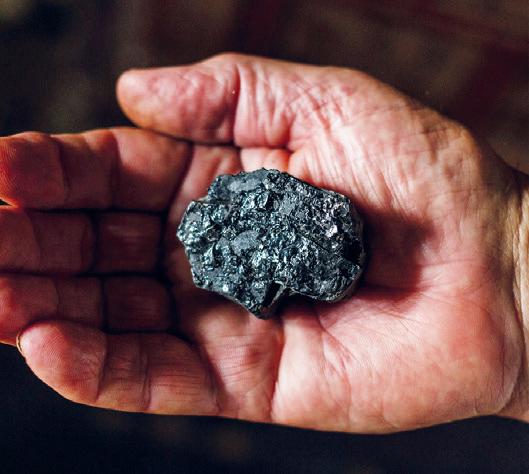
twin technologies into injection molding machines. The agreement ensures energy and carbon reduction throughout the entire industry by incorporating energy efficiency from the very start of the production process. Through this agreement, the three parties are aiming to launch Taiwan to the forefront of a global manufacturingsustainablepush.
TaiwanKing Steel Machinery Co. and German multinational conglomerate Siemens have joined forces, in collaboration with industrial equipment supplier Ruhyih Automation, to begin integrating digital
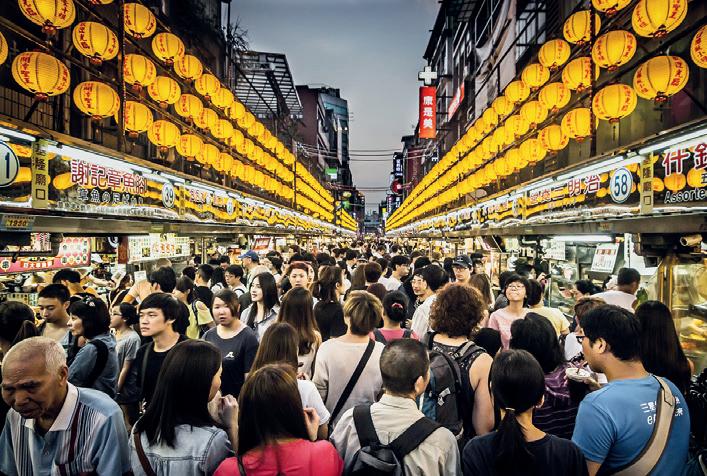
Brazilian steelmaker Gerdau, and heavy vehicle parts manufacturer Randon have announced that they have agreed to form a strategic partnership to provide truck and semi-trailer rental services. The companies will share the same equity interest in the new venture, with total initial investments seen reaching $47.70 million, they said in separate securities
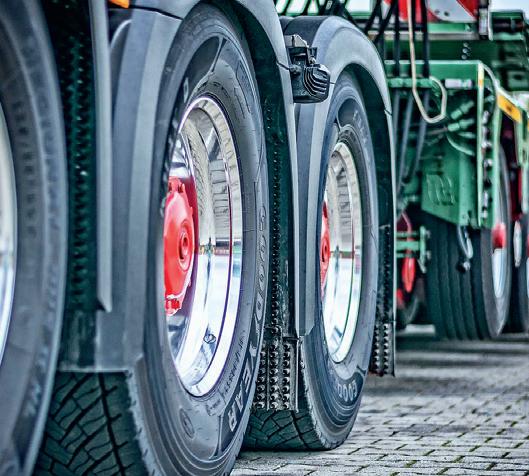
Swiss steel mill Stahl Gerlafingen has gained regulatory approval to put staff on shorter working hours to contend with soaring energy bills that will cost in a month what they normally cost in a year, the NZZ am Sonntag paper reported. “High energy prices threaten our existence,” the paper quoted chief executive Alain Creteur as saying in regard to the mill, owned by Italy’s Beltrame
Source: BBC, 5 September 2022
JFE Steel Corporation has agreed with Itochu Corporation and Emirates Steel Arkan, the largest steel company in the United Arab Emirates (UAE), to jointly conduct detailed feasibility studies on the establishment of a supply chain of a ‘Ferrous Raw Material for Green Ironmaking with Low-carbon Emission’, at a project site in Abu Dhabi. Production of the material is expected to begin in the second half of 2025 at a joint venture to be established in the UAE. The supply of the material to users in the Asian market, including JFE Steel, is to begin thereafter.
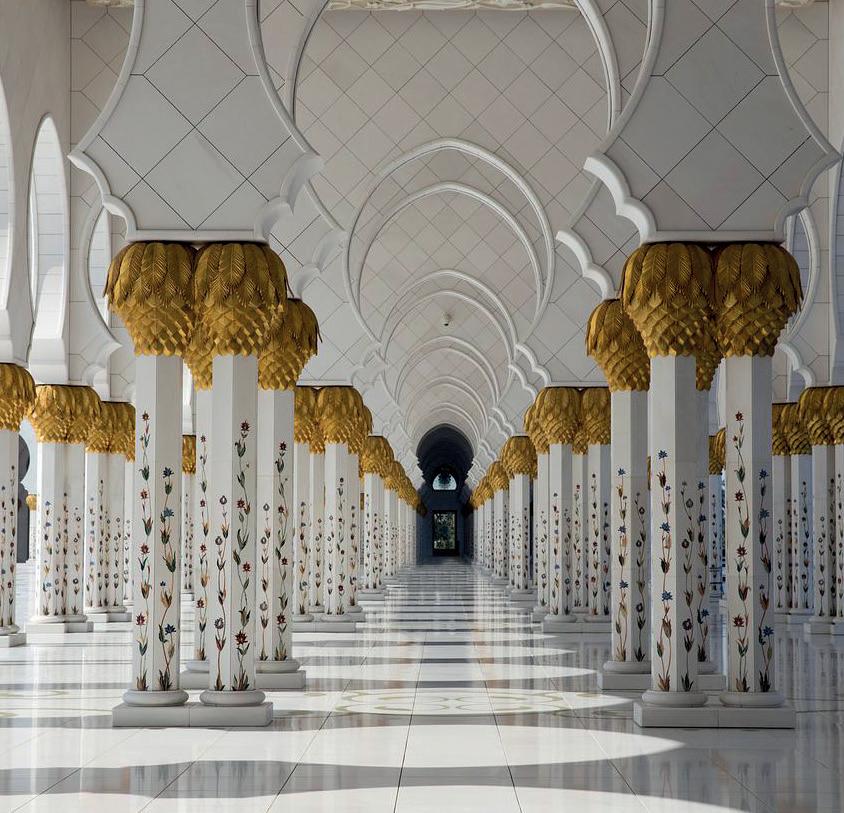
Source: Odissa Diary, 3 September 2022

Source: Bloomberg News, 2 September 2022
Source:filings. Nasdaq, 2 September 2022
10 NEWS ROUND-UP
million in brownfield and greenfield projects to expand its production capacity. According to the company, North India has huge growth potential for the steel sector, and Shyam Steel aims to be a leader in the primary TMT bar segment across the region.
Source: yahoo!finance, 5 September 2022
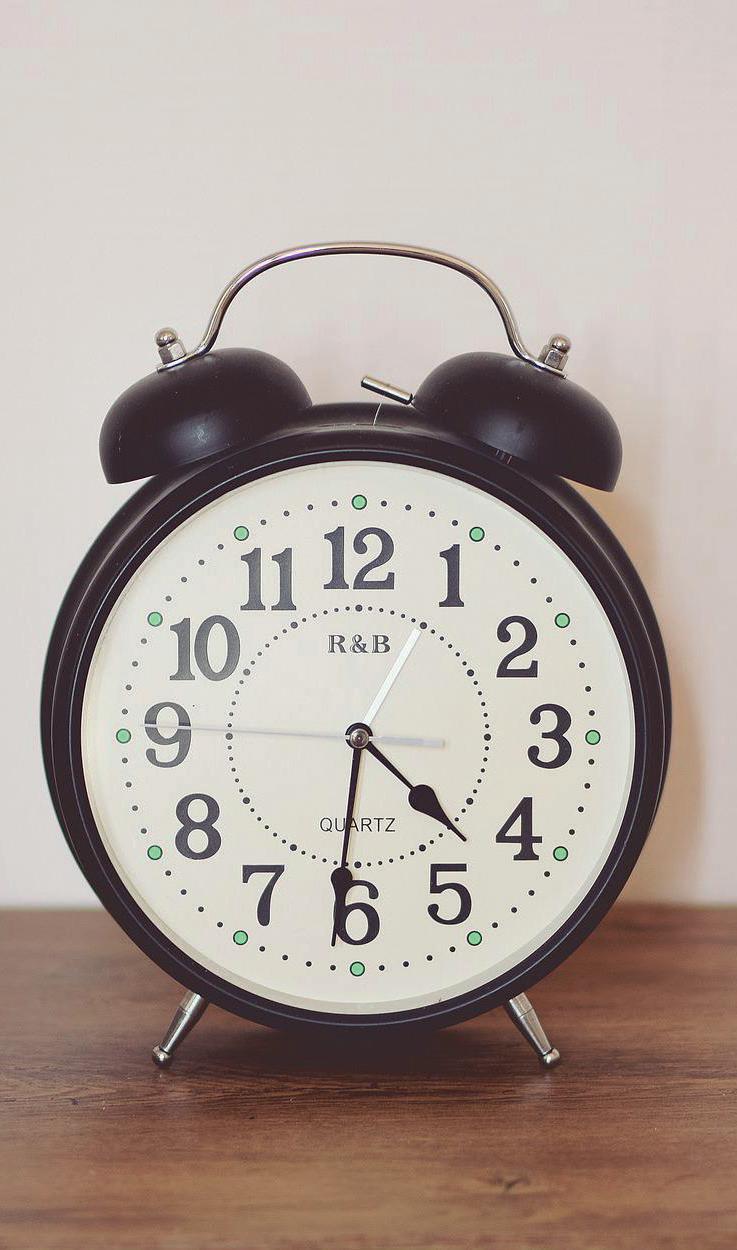
Cyrus Mistry, the former chairman of Tata, India’s largest conglomerate, died on 4 September in a road accident while travelling to Mumbai. One other person was killed and two more passengers were injured, police in India's western Maharastra state said. Mistry, who was 54, was ousted as Tata’s chairman in 2016, following criticism of his performance. He was replaced by Ratan Tata – the man who Mistry had himself replaced just four years earlier.
Source:Group. Reuters, 4 September 2022
Shyam Steel, one of the leading producers and manufacturers of investmentscompanyPradesh,Jammuofwhichoperationsplans(TMT)thermomechanicallyprimarytreatedbars,hasannouncedtoexpanditsretailacrossNorthIndia,willincludethestatesDelhi,Punjab,Haryana,&Kashmir,HimachalandRajasthan.Theplanstoundertakeofover$313
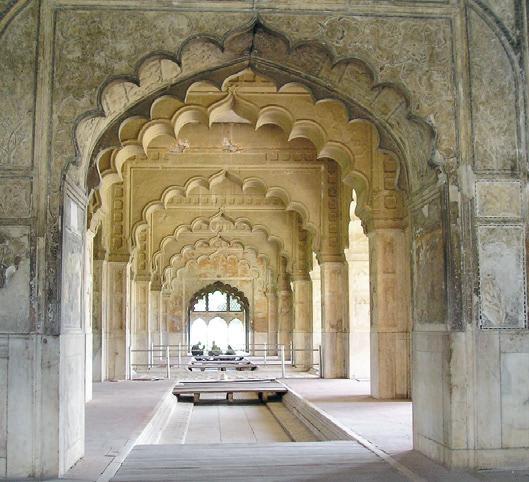
Source: Hydrogen Central, 5 September 2022
www.steeltimesint.com
For more information, visit our website at www.guildint.com or call +1.440.232.5887 World Leader in Coil Processing Equipment for the Steel Processing, Tube Producing and Stamping Industries Since 1958 The most technically advanced coil joining equipmentPeriod.available. Guild International can design and build the welding machinery you need to keep your coil processing lines up and running smoothly and profitably. We are the world leader in supplying highly-engineered coil processing equipment known for reliability and performance. Contact us today to begin designing the perfect coil joining equipment for your processing lines.
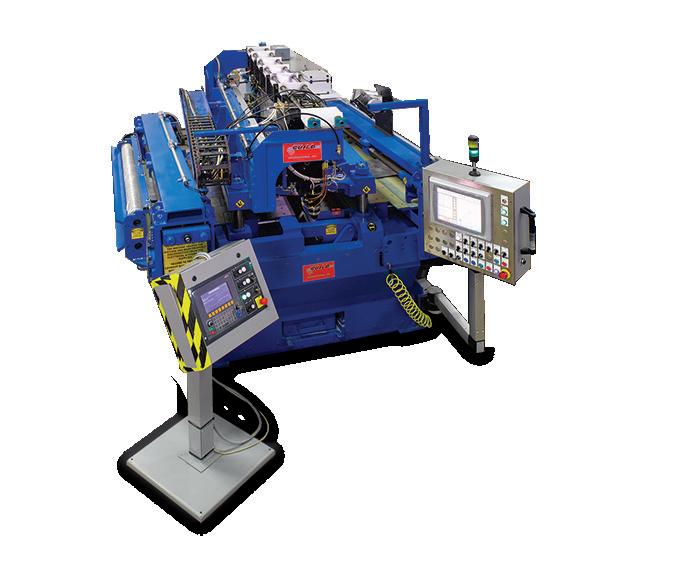
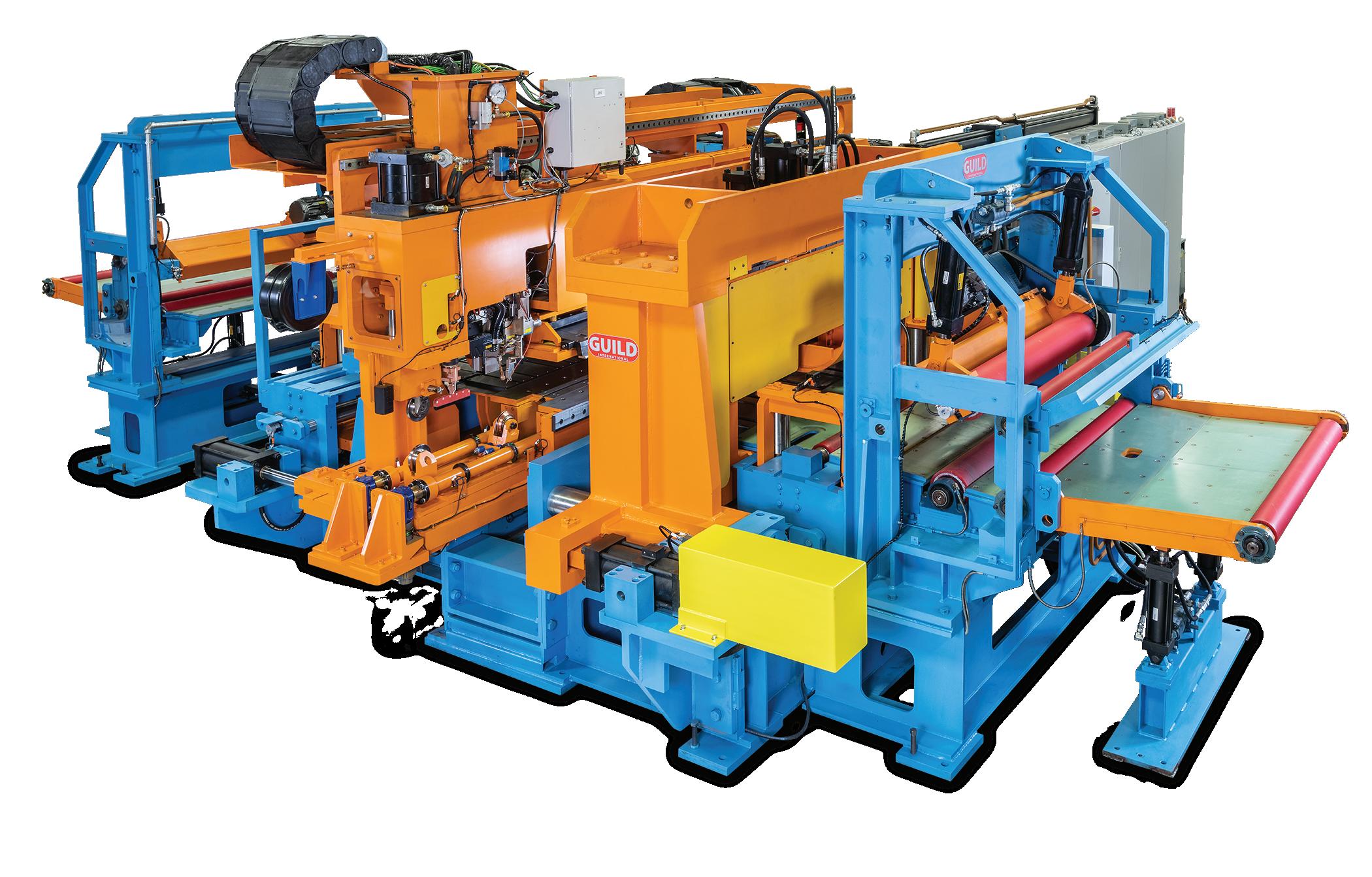
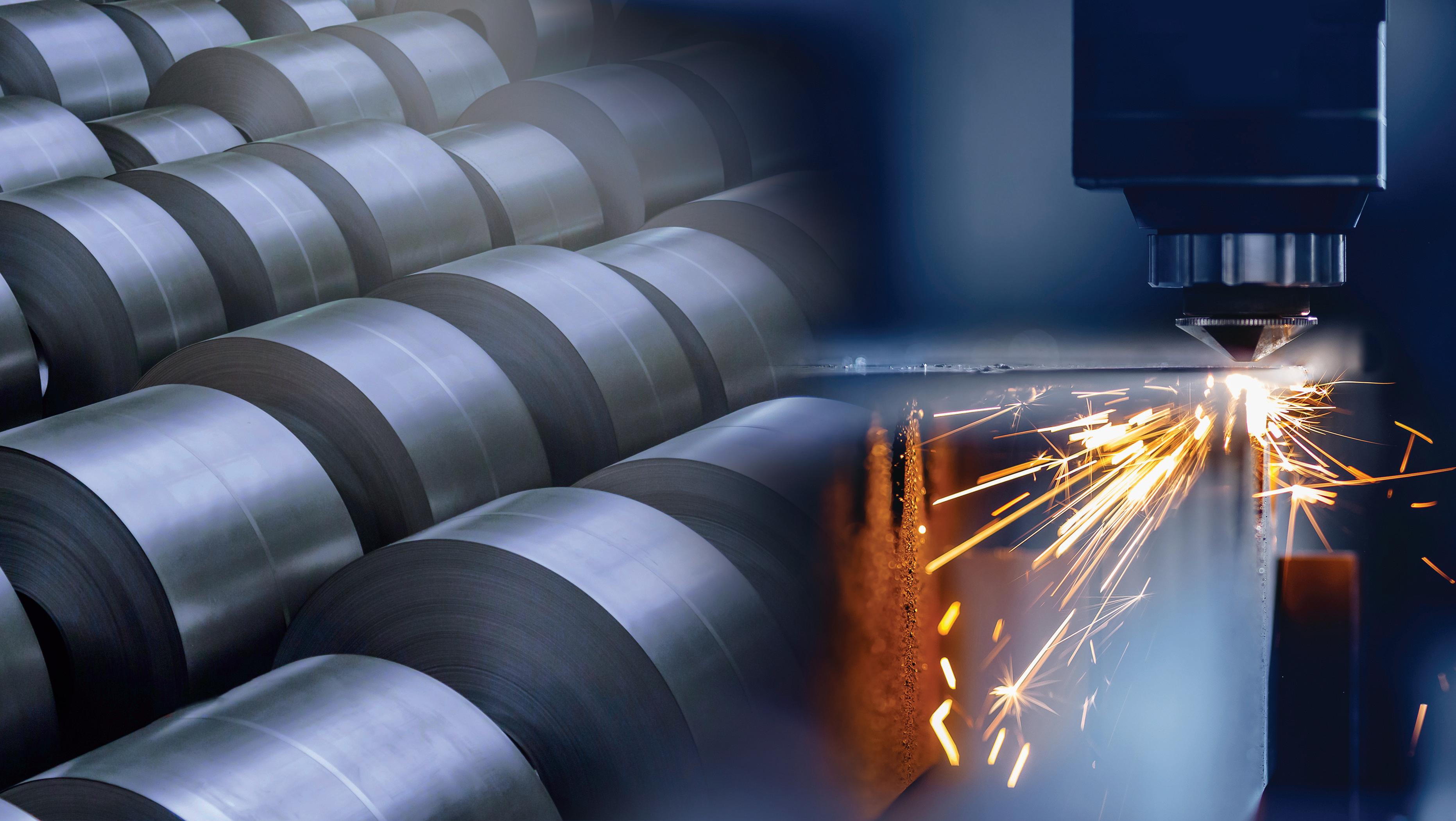
Kennametal2022 introduces new ceramic grade
According to Dinkle, the resulting assembly provides the advantage of compactly combining all signal connections for sensors and actuators requiring two-wire, three-wire, and four-wire installation, while saving up to 75% of panel space over traditional multi-terminal installations.
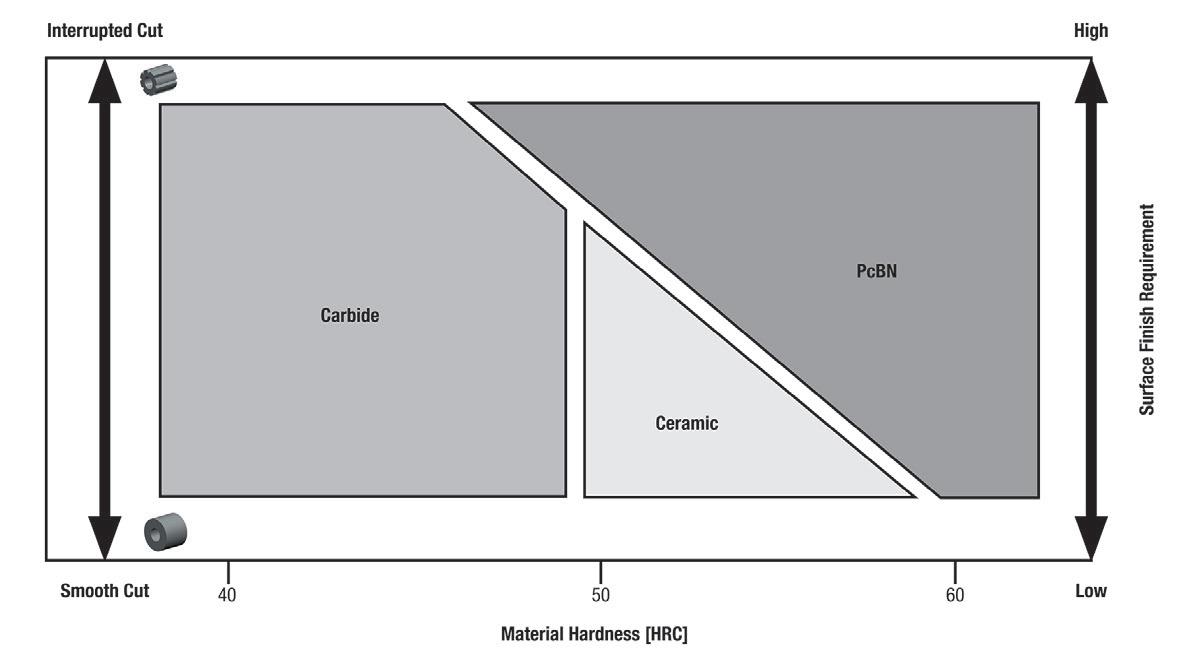
60% of the wiring time compared to screw-based methods.Thesignal terminal blocks carry a UL rating of 600V and 20A, accepting wires ranging from 26 to 12AWG; power distribution terminal blocks are rated for 300V and 10A, with wires ranging from 26 to 14AWG.
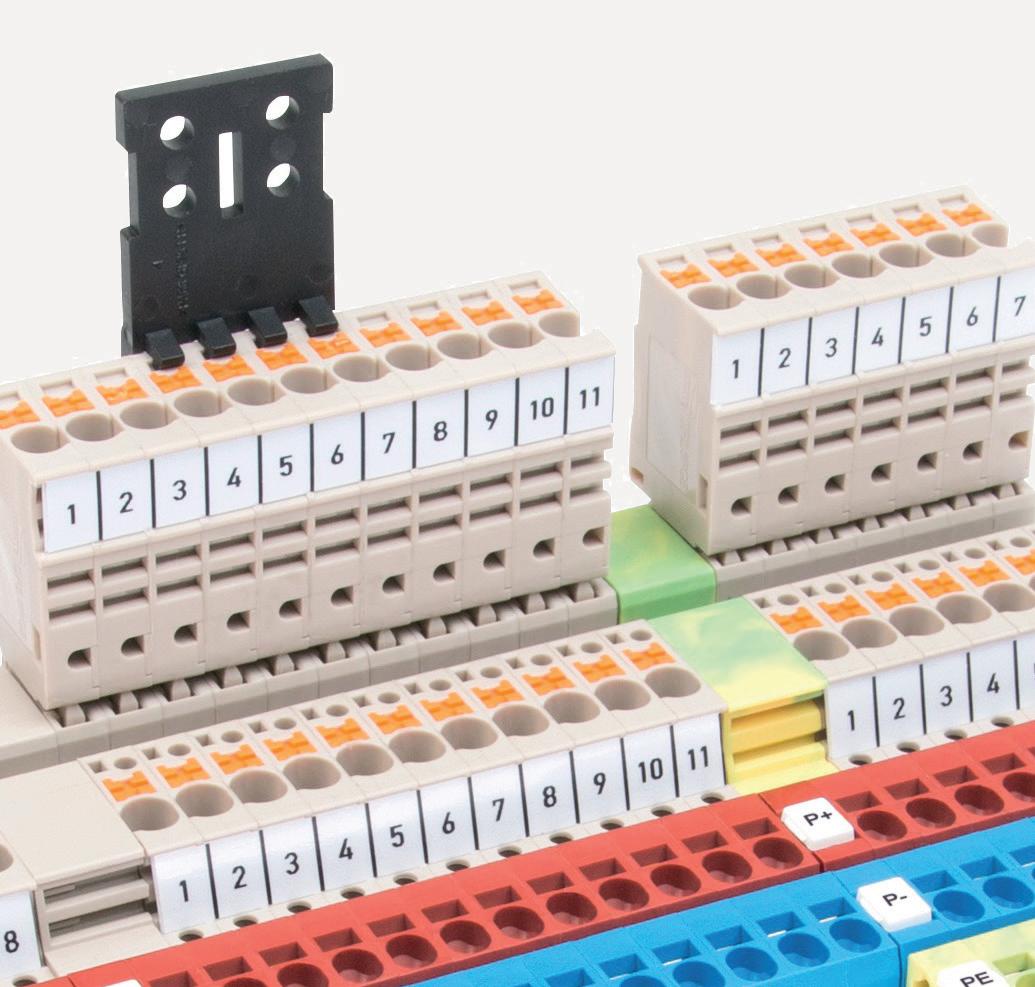
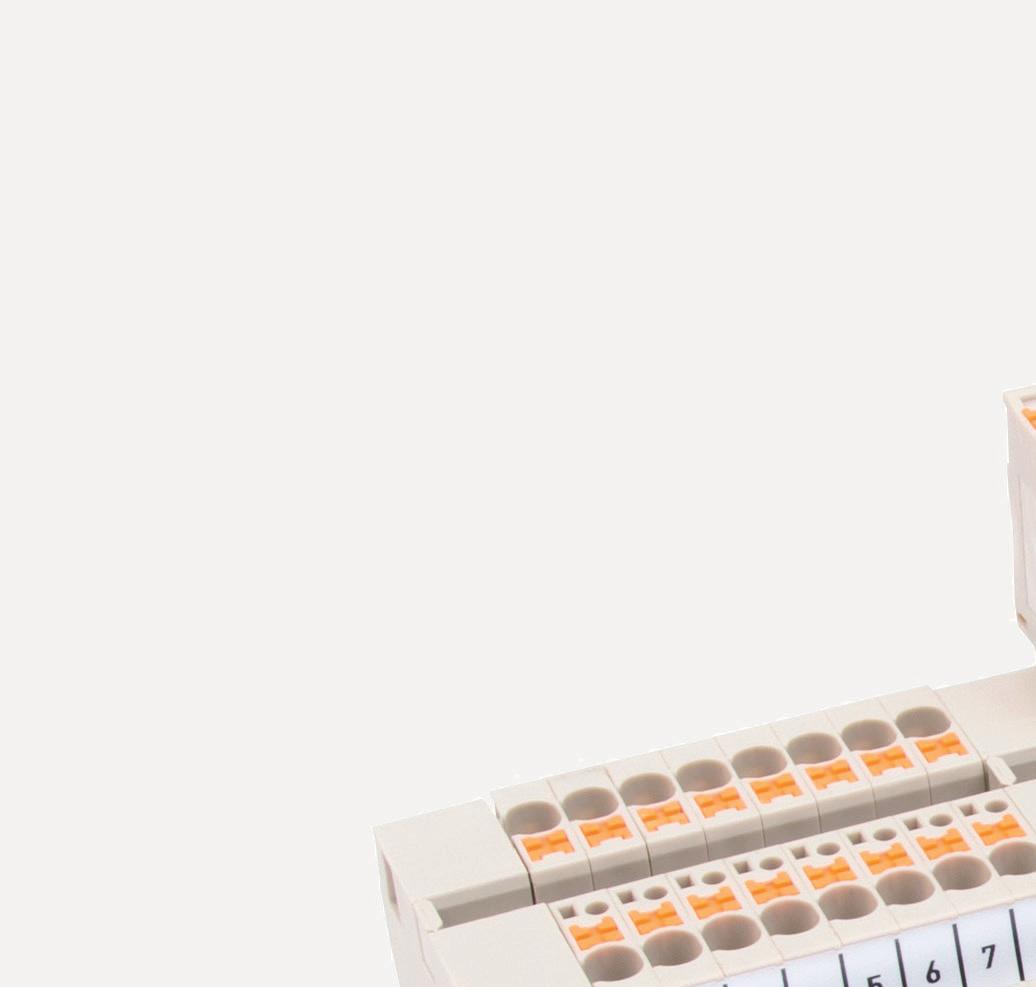
“KYHK15B provides excellent edge stability, high chipping resistance, and a PVD gold coating makes wear progression identification very easy. From smooth and varying depths of cut to heavy depths of cut, KYHK15B can be an economic alternative to PcBN inserts,” said Robert Keilmann, product manager, Kennametal.
Depending on the surface requirement and the type of cut, the ceramic grade KYHK15B can be an economic alternative to PcBN inserts when machining hard materials >48 HRC. KYHK15B builds on an existing line of high-performance ceramic turning grades, providing manufacturers
Contact materials are tin-plated copper alloy, using push-in design (PID) for wire terminations over an operating temperature range of -40 to +115O C. Exclusive PID connectivity enables tool-free insertion of solid wires, stranded wires, or ferrules, saving up to
INNOVATIONS12 www.steeltimesint.comSeptember
Dinkle International releases new terminal block family
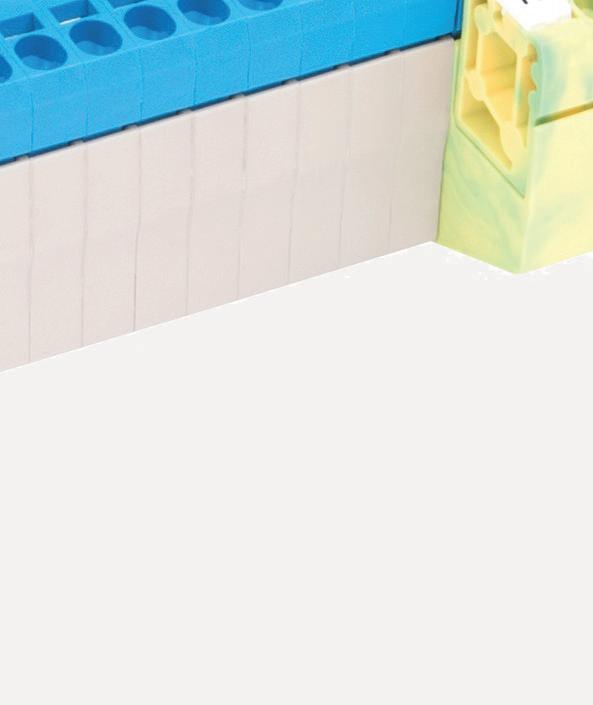
Kennametal has introduced its latest ceramic turning grade, KYHK15B™, designed to deliverincreased productivity and lower cost per edge in hard turning operations. According to the company, the new grade provides greater depth of cut capabilities than PcBN inserts when machining hardened steel, high temperature alloys, and cast iron, as well as maximum tool life and wear resistance for the most demanding turning applications.Abroadrange of styles, sizes, and edge preparations are available. These include the most popular styles of double-sided roughing and finishing inserts for predictable machining.
A modular design based around DP2.5SG terminal blocks – single-level pass-through type mountable on a standard DIN rail – provides flexible installation options for a variety of applications, says the company. Additional components are available to add colour-coded distribution of positive (red) and negative (blue) power, and ground earth potential (green/yellow) connections as needed. An optional pluggable terminal block is available for even more convenient factory-to-field wiring installation.
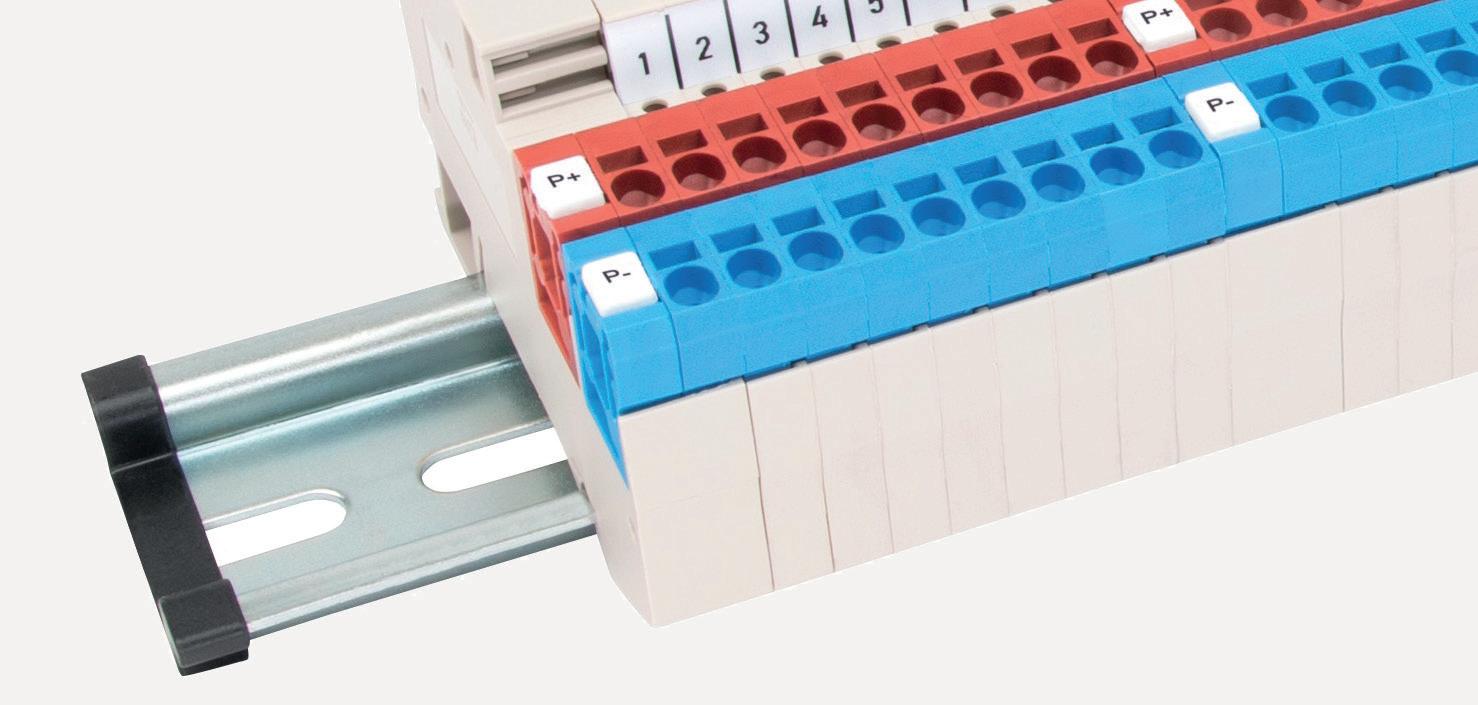
Dinkle International, the largest terminal block manufacturer in Asia, has announced the release of the DP2.5SG sensor/actuator terminal block family, providing cable connectivity options for a variety of automation needs.
For further information, log on to www.kennametal.com
with a productive solution for hard turning applications even in varying or heavy depths of cut.
The new KOCKS reducing and sizing block works reliably, and, says KOCKS, where rolling products are concerned, achieves great overall results.

13 www.steeltimesint.com September 2022 INNOVATIONS
Now available nationwide, the new KBE 32 magnetic core drill includes a 1200-Watt high-power motor reliable for drilling holes up to 32 mm. It is also, claims FEIN, the first tool on the market to combine a weight of 10.8 kg with 1200-Watts, offering a power-to-weight ratio with a high magnetic holding force, which, the company claims, ensures optimum control accessibility for those working in tight spaces.
The KBE 32 has been developed with a real focus on accessibility from a size, weight and controls standpoint. This was a key priority throughout the entire research and development process.Withover 150 years’ experience in manufacturing power tools, FEIN has a rich history of innovation, providing application-based solutions for end-users in the metalworking and construction“Heresectors.atFEIN, we pride ourselves on our application-based approach and providing trusted expertise to our customers, which ultimately
FEIN launches magnetic core drill
Fujian Sangang Minguang Group (Sanming) has issued the Final Acceptance Certificate (FAC) for its new KOCKS RSB® 370++/4 in 5.0 design. Sanming produces bar in coil within a dimension of Ø 16 to 48 mm and straight bars of Ø 20 to 90 mm in an 800 kt/yr mill line.
For further information, log on to www.kocks.de
“The KBE 32 has been designed with this philosophy in mind. Its entire development has focused on accessibility, from the size, weight and controls, each of which were key priorities throughout the entire R&D (research and development) process. To add to this, it has been built to stand the test of time, while its mechanical components have been designed for up to 70,000 drill holes,” Mills concluded.
FEIN, a leading power tools and accessories manufacturer, has released a new magnetic core drill, the KBE 32, to the UK’s metalworking market.
enables them to source the best solution for each job they undertake.

For further information, log on to www.fein.com/en_uk/.
For further information, log on to https://www.dinkle.com/en/
Just four weeks after the first bar rolled from the new block, the Chinese producer of SBQ products and Friedrich KOCKS GmbH & Co KG signed the official documents.
All Dinkle connector products support the Industry 4.0 trend by helping users create solutions for connecting power, networking, and communications to support increasingly complex equipment and automation solutions in all types of environments.

“We’re expecting the KBE 32 to rapidly become a market leader, thanks to its ground-breaking power-to-weight ratio and ergonomic design. Equipped with innovative FEIN technology, the tool is the first of its kind in terms of weight and functionality.
Each terminal block is 5.08mm wide, available individually or in pre-installed kits of 4, 8, 14, 18, and 24 poles. The components are UL recognized, ROHS and REACH compliant, and carry the CE marking.

“Easy to use, robust and extremely lightweight, the KBE 32 will make the perfect aid for the steel industry,” commented Andy Mills, managing director, FEIN UK.
According to KOCKS, due to the pandemic and current global situation, the project was demanding but ultimately successful. The modernized SBQ mill of the steel producer in the Fujian province on the southeastern coast of China has now gone into regular operation.
KOCKS receives FAC for new RSB® 370++/4
demonstrate that SIRF pellets work particularly well as a substitute to coal, including coking coal, pet coke and industrial coal, in cement kilns, coal-fired power stations and steel manufacturing. As a substitute for natural gas, for example in brickmaking, there are also significant benefits.
The research was commissioned by wasteto-pellet company WKE, which turns materials such as wood, paper, card and non-chlorinated plastics that are destined for landfill into alternative fuel for power plants, cement kilns and steel manufacturers. According to the findings, there are substantial benefits to using SIRF pellets, including that they perform two times better on CO2 emissions than natural gas, and three and a half times better than coal.
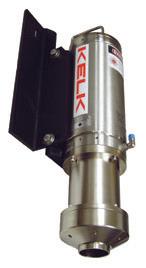

Jones continued: “We’ve seen a significant spike in interest in our SIRF pellets recently, as people wake up to the issues surrounding energy security and look to boost their green credentials. Another key benefit of our SIRF pellets is that they’re cheaper than coal and gas, as well as
Solid improved recovered fuel (SIRF) pellets perform significantly better than coal and natural gas on carbon emissions, according to a new report by management consultant and waste specialist Monksleigh.
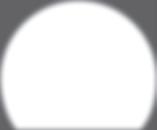
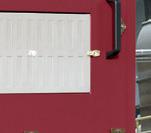
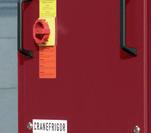
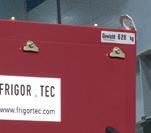
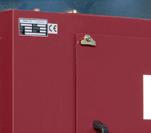
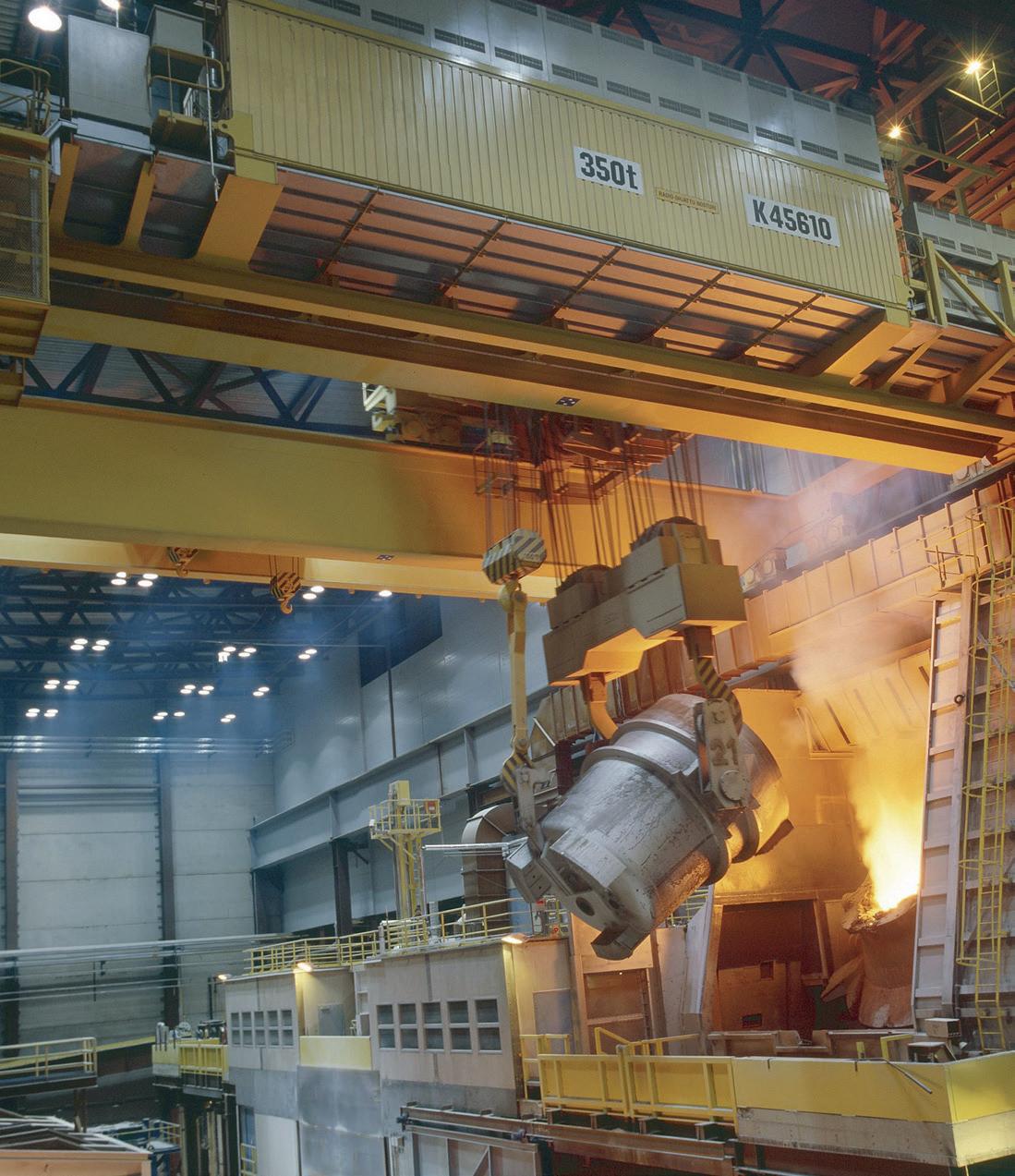
WKE commissions report on pellets

kelk.comBesthead and tail imaging (ACCUBAND) “+” Best transfer bar tracking (ACCUSPEED) “+” Best crop shear control (ACCUCROP) “=” Best overall crop shearing accuracy Very quick return on investment (ROI) Scan for details or reach out directly +1-416-445-5850 | kelk.sales@vpgsensors.com © 2022 VPG - All Rights Reserved 12973-EN_May22 ACCUBAND Crop Optimization System + +ACCUBAND ACCUCROPACCUSPEED FrigorTec GmbH • info@frigortec.de • www.frigortec.com CRANEFRIGOR ™ –AC-unit for severe duty conditions works. Since more than 50 years! AZ_S+T_CRANEFRIGOR_87x128_Steel-Times_Int_EN.indd 1 05.04.19 10:16

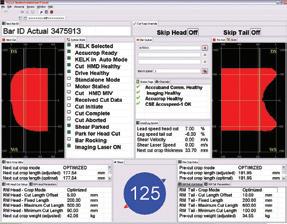
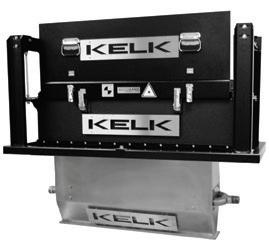
being cleaner and greener.”
For further information, log on https://www.wasteknot-energy.com/to

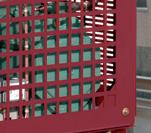
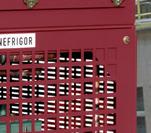
Ian Jones, CEO at WKE, said: “The results
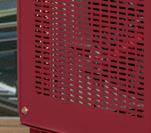
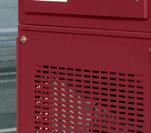
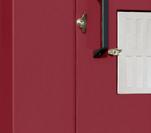

“The report also shows that the carbon emissions produced in the manufacture of our pellets are considerably lower than sending waste directly to landfill.”
Currently the UK exports around 2.75 Mt of refuse derived fuel (RDF) and solid recovered fuel (SRF) from England to European and Nordic countries – something that Jones would like to change.“AtWKE, we fully support the RDF and SRF industries but believe that, rather than exporting waste, it should be repurposed in this country and used to build UK fuel security. We’re a long way from self-sufficiency and need to look at all our options if we’re to reduce our reliance on expensive fossil fuels.”
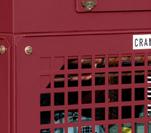
INNOVATIONS14 www.steeltimesint.comSeptember 2022

The company operates six manufacturing plants across the country, located in Bulacan, Batangas, Cebu, Davao, and Misamis Oriental. It is expected to open its seventh plant this year, located in Compostela, Cebu, and increase its output from 2 Mt of steel annually to 3 Mt.
want our technology to be at par with global standards in efficiency and environmental sus tainability,” said Benjamin O. Yao, president and CEO of SteelAsia. “Thanks to our partnership with Tenova, we can increase our steel productivity to support nation-building while ensuring that we also take care of the environment.”
Tenova and Steel Asia partner for green-tech project

“We are greatly honoured by Baowu’s choice which opens another page in our long-stand ing partnership of more than 30 years. This is a key moment of our strategic collaboration with Baowu, who will continue to lead the steel industry in terms of quality, productivity and new product developments,” said Guillaume Mehl man, president of steel and glass division at Fives.
For further information, log on to www. fivesgroup.com
“This project is a significant step in our collab oration, with a perfect combination of Baowu’s manufacturing experience and Fives’ know-how in cold rolling mill engineering,” commented
and maintenance practices. The split housing mill allows for a larger gap between upper and lower work rolls during maintenance and changeover, while the monobloc mill provides better mechani cal stability and dimensional properties.
For further information, log on to www.tenova.com
portfolio of different technolo gies, Fives is able to offer tailored cold rolling mill solutions to both the Baoshan and Wuhan pro duction sites according to their specific operation
15 www.steeltimesint.com INNOVATIONS
Gabriel Poullet, CEO of Fives DMS, a subsidiary of Fives and a specialist in cold rolling mill design and supply. “RollBotTMtechnology, recently de signed by our engineers, is able to automatically replace any type of rolls and avoid any safety risk. We are confident that our technologies will bring a great success to this important project.”
China’s Baowu Group, the world’s largest steel producer, entrusted Fives, a global industrial engineering group, with the design and supply of two reversible cold rolling mills with automatic roll change for production of electric steel at its Baoshan and Wuhan production sites.
The cold rolling mill is key to achieve the de manded electric steel properties. Fives will supply two DMS 20Hi EcoMills – a split housing mill for the Baoshan site and a monobloc mill for the Wuhan site – for grain-oriented (GO) with high permeability (HiB) and non-grain oriented (NGO) electric
The project also includes a proprietary break through RollBotTMtechnology for both mills. Roll BotTM is a fully automatic roll change system that according to Fives, performs fast, precise and safe roll change with no manual intervention, ensur ing optimal safety and product quality.
Fives supplies two cold rolling mills
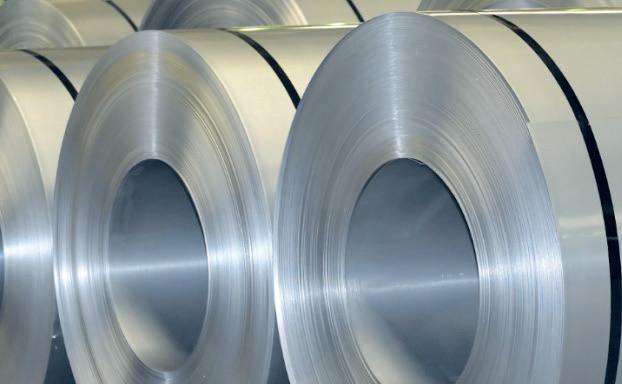
Tenova, a leading developer and provider of sustainable solutions for the green transition of the metals industry, and SteelAsia Manufacturing Corporation, the flagship steel manufacturing company in the Philippines, recently inked a part nership for Consteel® Evolution, a state-of-the-art low-impact technology for steel manufacturing. It will be the first of its kind in the country and will be employed in SteelAsia’s new melt shop in Lemery, Batangas, in 2024.
The new Consteel® Evolution melt shop will recycle local scrap metal to produce high-grade billets for steel sections. The advanced Lemery facility will also be one of the cleanest steel plants in the world, says Tenova, as it will generate the lowest carbon emissions, providing Filipinos with top-quality steel sections produced with the most environmentally friendly technology.
According to Tenova, the Consteel® Evolution technology saves energy, decarbonizes steel production, and reduces environmental impacts through efficient energy recovery and pollution control innovations. Scrap metal is a vital national resource used in steel production with low car bon emission, and SteelAsia aims to increase its output by maximizing the use of scrap metal. Across many countries, there has been a shift
“Our company’s long-term vision is to develop the Philippine steel industry because this is the backbone of industrialization. We have seen our neighbouring Asian countries grow faster because they can manufacture their steel. The Philippines needs to catch up. As we do so, we
“Thanks to Tenova’s continuous efforts to enable a more sustainable metals production, SteelAsia found in our portfolio the most suitable technologies to produce high-quality steel from recycled scrap. We are honoured to support SteelAsia in the green industrial development of the Philippines,” commented Paolo Stagno li, commercial director – electric arc and ladle furnaces at Tenova.
In order to guarantee the seamless opera tion of the entire line, Tenova’s scope of work includes the EAF (Electric Arc Furnace) Consteel® Evolution, the secondary metallurgy station, the billet caster, the Fume Treatment Plant (FTP) and the material handling systems, along with all engineering services for the civil works and the balance of plant.
Baowu has a diversified product portfolio, dominating China’s steel market, especially in auto sheet and electrical steel. The production of the latter is a top priority for the domestic market for hybrid electric vehicles and ultra-high voltage power transmission.
from ore-based to scrap recycling-based steel production due to the global industry’s grow ing desire to reduce emissions and dependence on coal. SteelAsia’s partnership with Tenova to further pursue its decarbonization efforts aims to make steel production more sustainable without compromising its output and financial returns.
Thankssteel.toits
We are Steelmakers! Badische Stahl-Engineering GmbH Robert-Koch-Straße 13 D-77694 Kehl/Germany Phone (+49) 7851/877-0 Fax (+49) 7851/877-133 eMail info@bse-kehl.de www.bse-kehl.de www.harald-wehrle.deThe Future is Manless Technology ProtectingSTEELSAFEPeople ® SAFEEBT FlapBalconyEBT MonitoringEBT fillingSandEBT THM Tap ManipulatorHoleTHM MultiROB SLD Smart LeakageDetectorDetector Leakage TSM/LM2TechnologyTechnologySpray SandMan
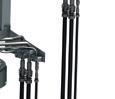
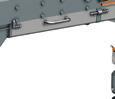


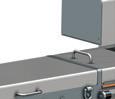


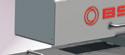





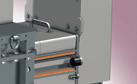

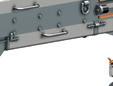


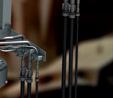
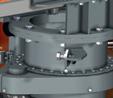


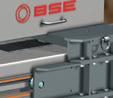
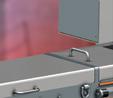



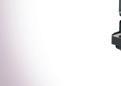
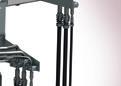





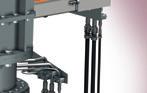
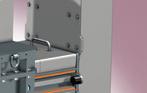
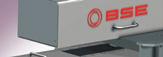


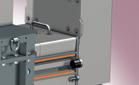


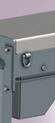

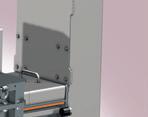
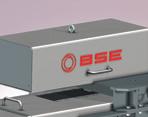

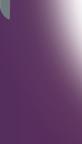

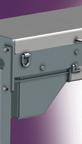
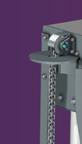

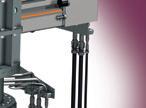
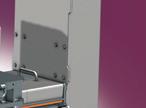
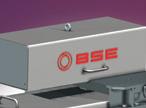



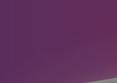


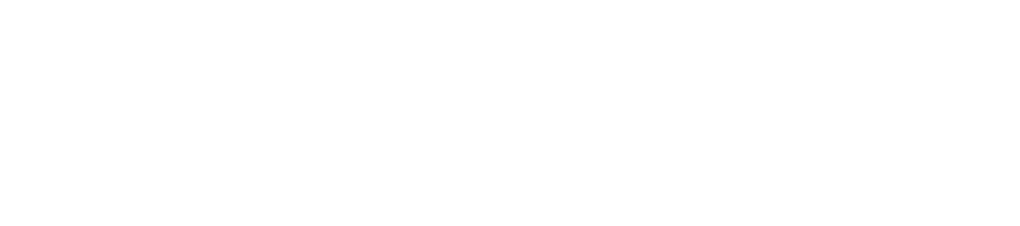
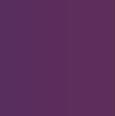
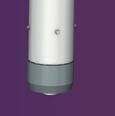
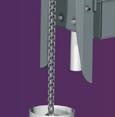
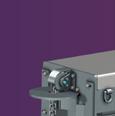
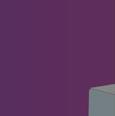
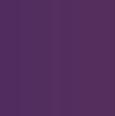


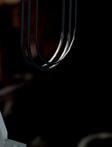
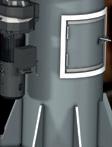
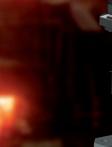
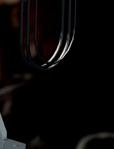
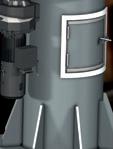
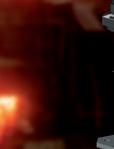


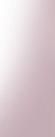

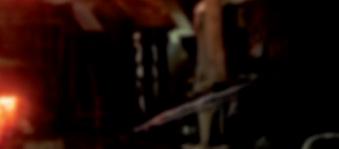

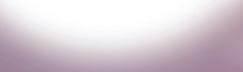



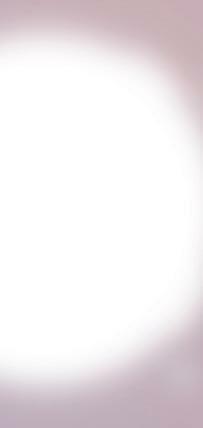


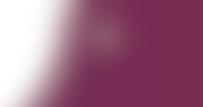
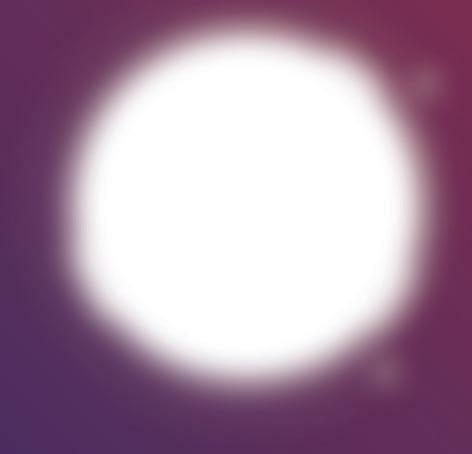


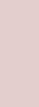



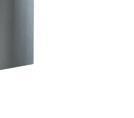
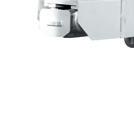
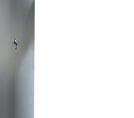
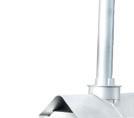
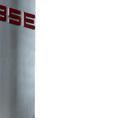


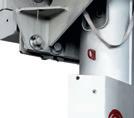

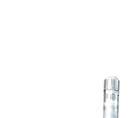
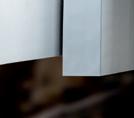
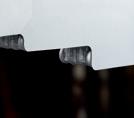
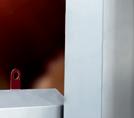
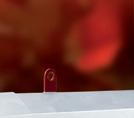

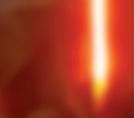
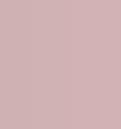
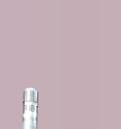

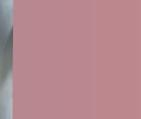
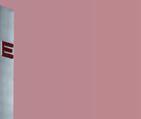
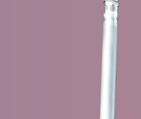
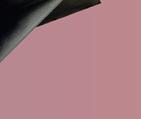
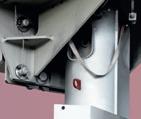



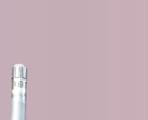

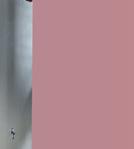
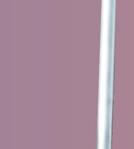

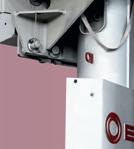
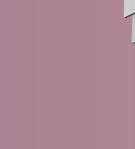



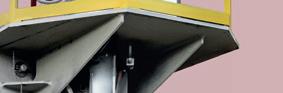

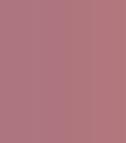
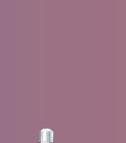
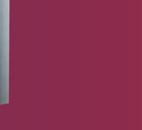
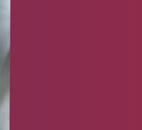
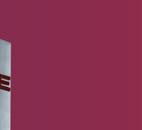
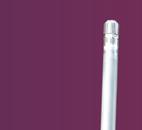

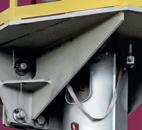


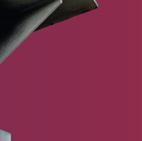
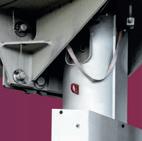
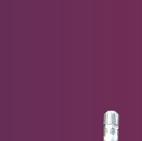
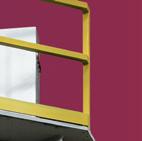
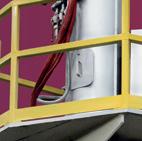
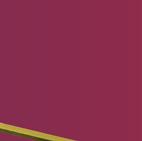
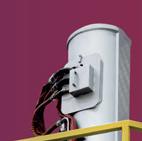
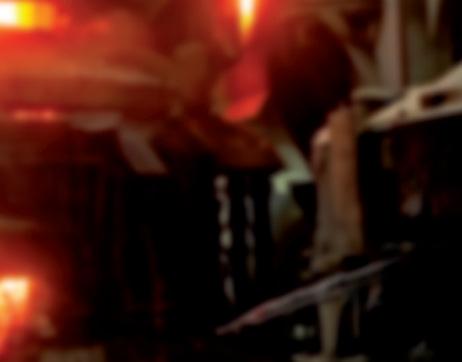








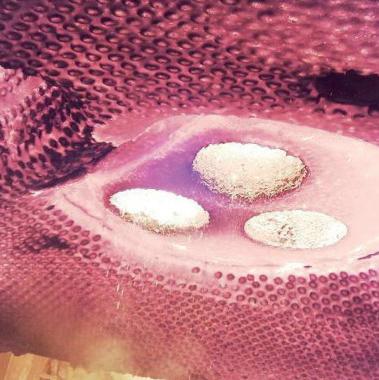
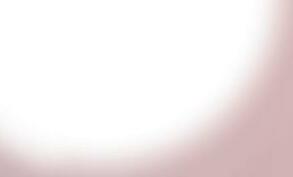
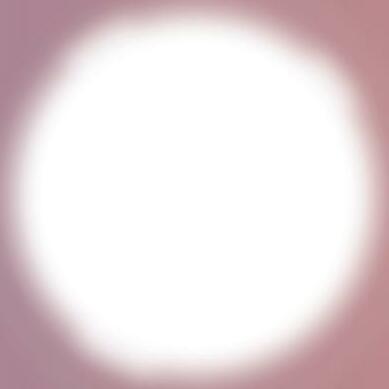
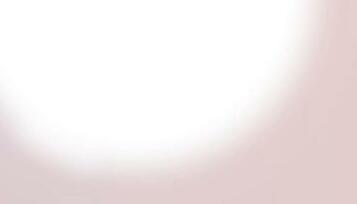
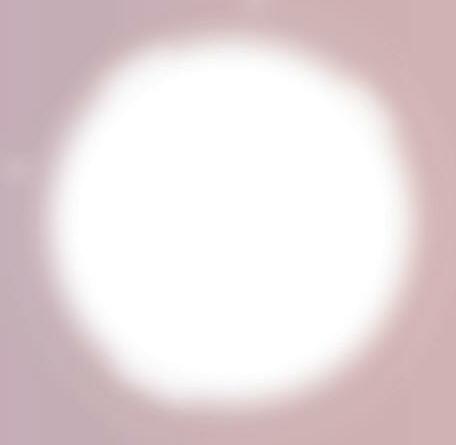
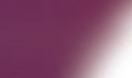


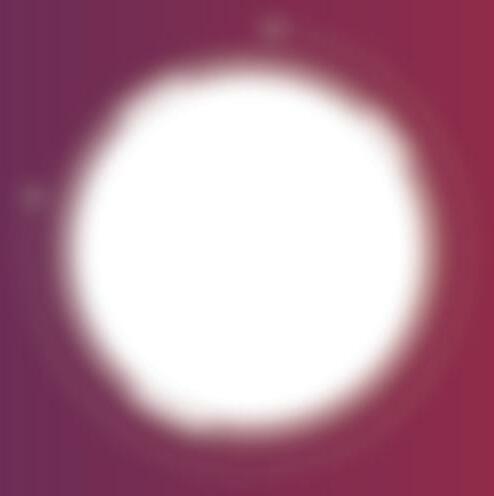









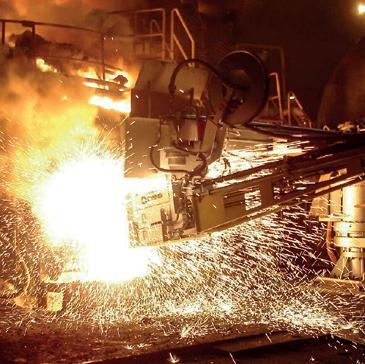
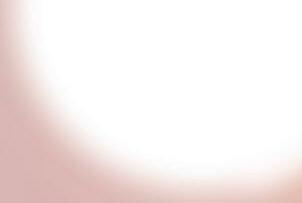
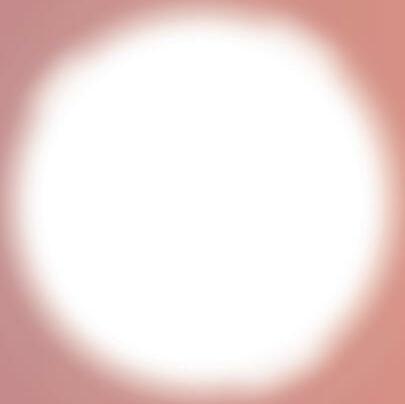
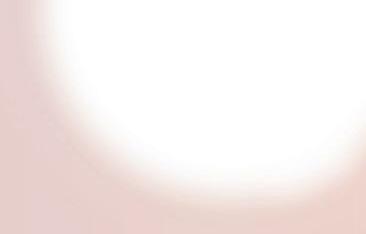

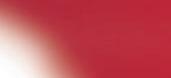





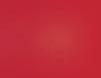






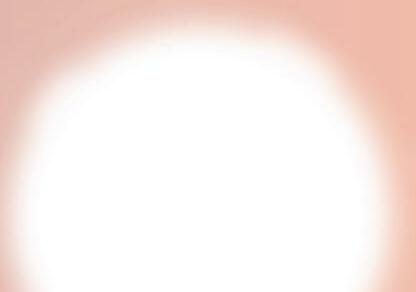

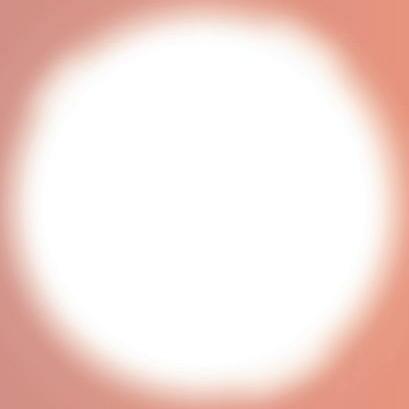
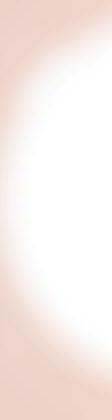
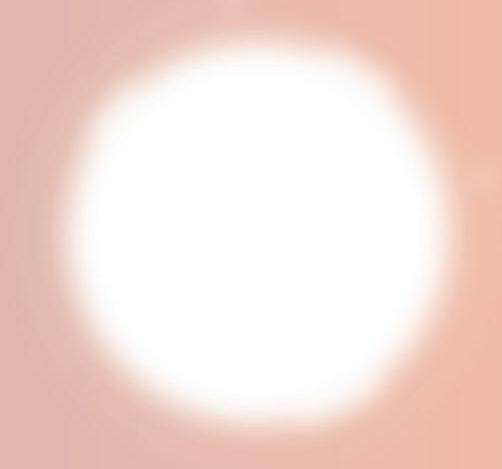
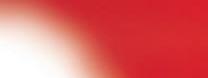


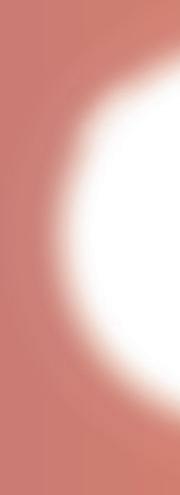

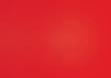

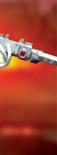
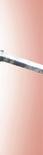


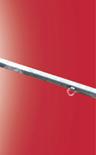
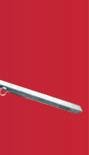


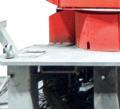
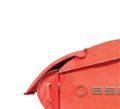
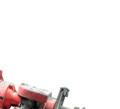

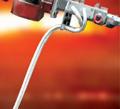
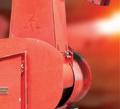
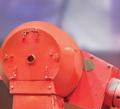






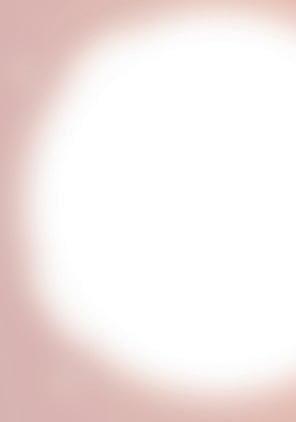



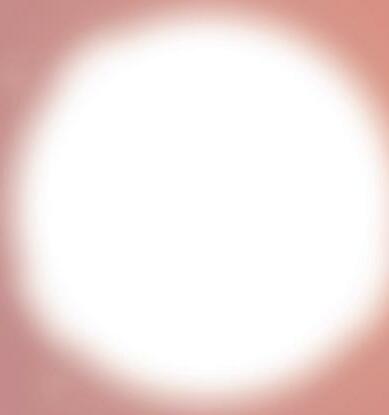

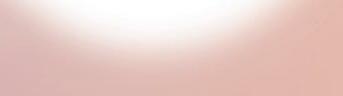
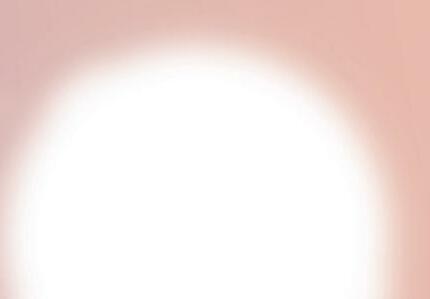




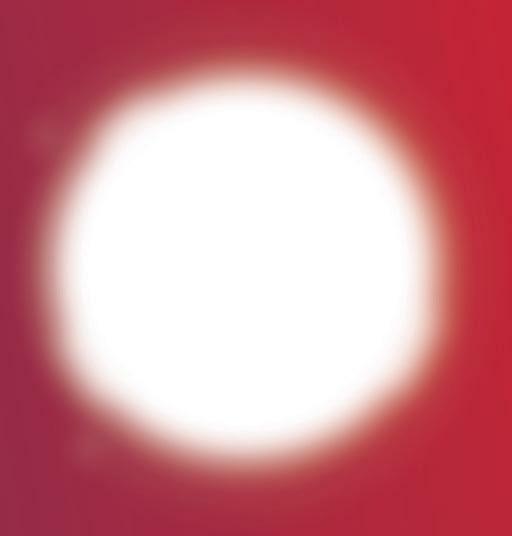
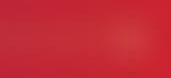
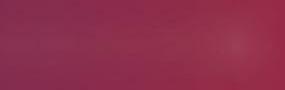




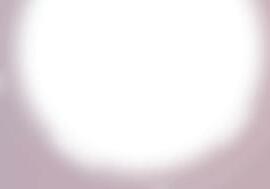
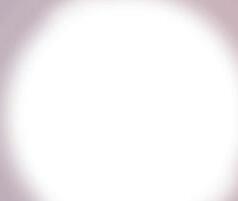
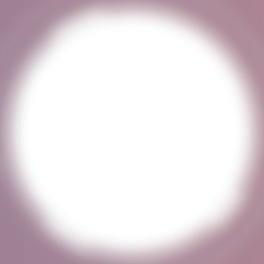
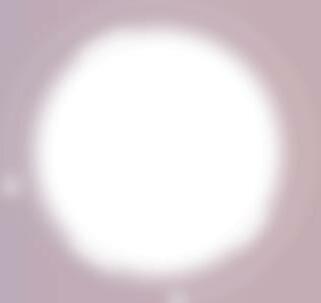
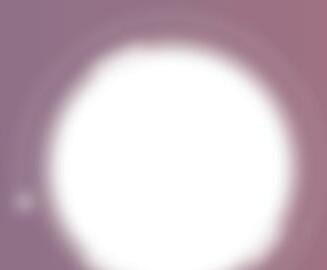







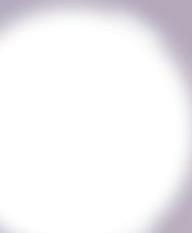

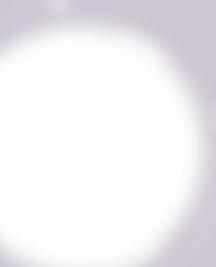








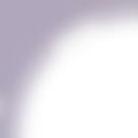
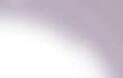
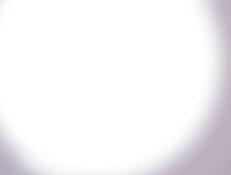
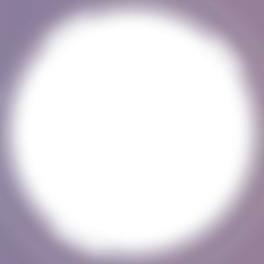
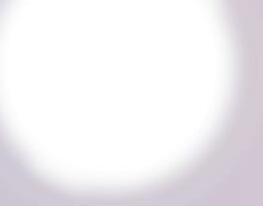

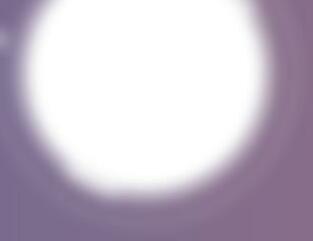

But watching how others react to issues such as decarbonization – Americans
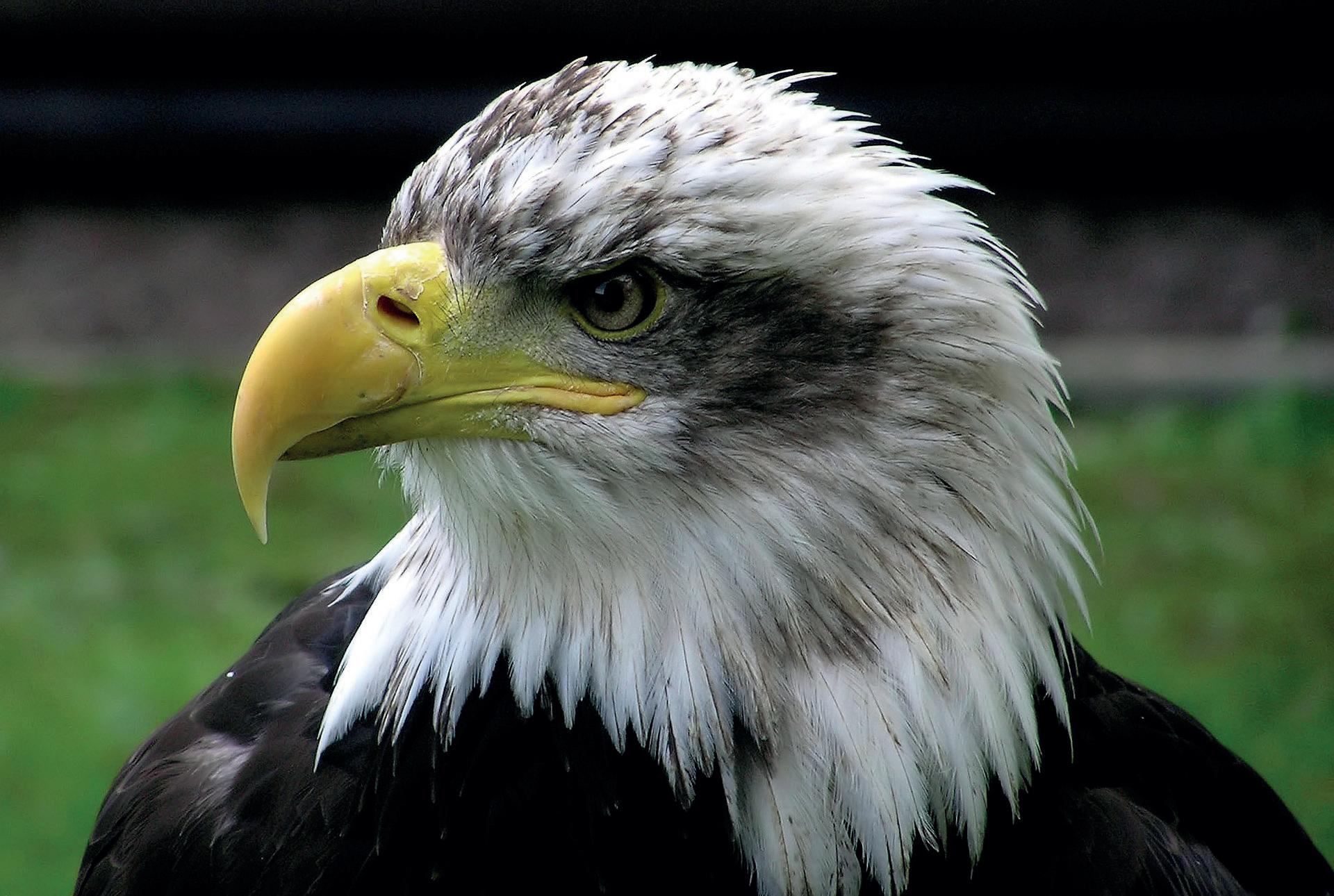
USA UPDATE
US Steel announced in mid-August that it would co-operate with two energy companies on creating a clean energy hub in the Ohio, West Virginia and Pennsylvania region.USSteel revealed that under a newlysigned non-exclusive co-operation agreement with Equinor US Holdings Inc. and Shell US Gas & Power, it would cooperate in some capacity with companies to help build up a regional hub focused on carbon capture utilization and storage as well as hydrogen production and utilization.
agreement would address BMW Group’s upstream scope 3 emissions and include recycling and other measures aimed at decarbonization. The agreement includes technical co-operation between the two companies to address BMW Group’s science-based targets and contributing to meeting its CO2 reduction timeline.
The regional CCUS (Carbon Capture Utilization and Storage) and hydrogen hub aligns with the ambitions of both the United States and its project partners to realize net-zero carbon emissions by 2050.
In the USA electric steelmaking rules the roost, making North America a far greener place to make steel than other parts of the world where the integrated steel mill is king. US-based steelmakers are bullish about their green credentials and are shifting up a gear as the greening process gets underway.
By Manik Mehta*
But, as the US steel industry’s greening gets underway, developments taking place even outside America have caught the attention of US analysts who closely monitor any moves made by both steel producers and steel-consuming industries. The automotive industry has been resorting, for instance, to the use of light metal in car production. One analyst, preferring not to be named, described it as ‘very interesting’ that H2 Green Steel, a Swedish steel company, and the BMW Group have recently finalized an agreement on the supply of CO2 reduced steel.
Henrik Henriksson, H2 Green Steel’s chief executive, said in a statement that his company was ‘on a mission to decarbonize’ the steel industry, and that working with progressive companies like BMW Group had pushed ‘us to be better both in our own operations and our value chain’.
Equinox and Shell plan to jointly apply
THE ‘green wave’, a term in vogue in the steel industry while referring to the growing consciousness about producing steel with as minimum carbon as possible, is spreading across America, with many steel companies announcing measures to cut down CO2 emissions in their plants.
The BMW Group will take some of H2 Green Steel’s CO2 reduced steel. The Swedish company has said that the
17 www.steeltimesint.com September 2022 * US correspondent, New York
US steel pundits say that recycling scrap will constitute a key element of the equations which further ensures circularity. Both companies have agreed that 40% of pre-consumer steel scrap volumes will be returned to H2 Green Steel’s electric arc furnaces for recycling.
often use the term ‘clean energy’ – can be enlightening and even inspiring for some US steel producers. Some American steel companies have also made progress on the path towards decarbonization.
America surfs the green wave
It may be that the steel industry’s environmental consciousness was aroused not only by environmentalists and others with a deep concern for the environment, but also by the World Steel Association’s report which describes steel as ‘a vital industrial metal, widely used in energy, construction, transportation, infrastructure, packaging and machinery’. “But producers need to get a lot greener if this world is to deliver on its ambitious net zero targets,” it admonished. The Biden administration, with its focus on climate change, accelerated the steel industry’s sway towards decarbonization.
Amid such attempts by individual steel companies to reduce decarbonization, steel production in the United States decreased to 6.9kt in June from 7.2kt in May of 2022.
�
“With an abundance of low carbon gas, a robust industrial sector, and a skilled workforce, the tri-state region boasts the optimal location for a potential hub. Equinor and Shell are uniquely positioned to help develop a clean energy hub in the region with each having several operational projects around the world. US Steel has made strides in achieving energy efficient production of steel.
Steel accounts for about one-third of supply-chain emissions for cars and buildings, and around half for white goods, or larger electrical devices such as refrigerators and washing machines, and renewable energy equipment. “But decarbonising the sector is far from easy, given the lack of commercially viable alternatives to coal,” the report acknowledges.“Butthereis a real urgency to act, given the industry’s long lead times for development,” the report said. “Blast furnaces tend to have an average life of around 40 years but need significant upgrades after 25. Decisions need to be taken now if companies want to meet their 2050 emissions targets.”
with the US Department of Energy for funding to create a regional clean-energy hub, according to US Steel which, however, added that it was examining what role it could play in the creation of the hub –whether as a potential holding participant, customer, supplier or partner.
‘Best for all’ strategy
During the company’s second quarter earnings call on 29 July, US Steel’s Burritt spoke about sustainability. “The United States remains the leader in sustainable steelmaking as many in our industry have embraced the electrification of the steelmaking process, which is the most sustainable way to make steel,” he had said, going by the transcript of the call.
“We’re proud of the collaboration with Equinor and US Steel,” said Lee Stockwell, GM US Carbon Capture and Storage for Shell. “Together, we’ll continue to leverage our deep technical experience, existing networks, and seek to build the partnership with our customers and other partners.”
www.steeltimesint.comSeptemberUSA2022 UPDATE18
phenomenon known today as climate change, the steel industry in the present century is confronted with the challenge of reducing its carbon footprint.
sustainable jobs that will support families for many years to come,” says Grete Tveit, SVP Equinor Low Carbon Solutions. “For 14 years we have been engaged and investing in this region, and our significant equity gas production in the Appalachia region has proved to be an important low carbon asset in our portfolio. In collaboration with partners and the local community, we’re proud to advance this initiative and America’s net zero future.
A leader in sustainable steelmaking
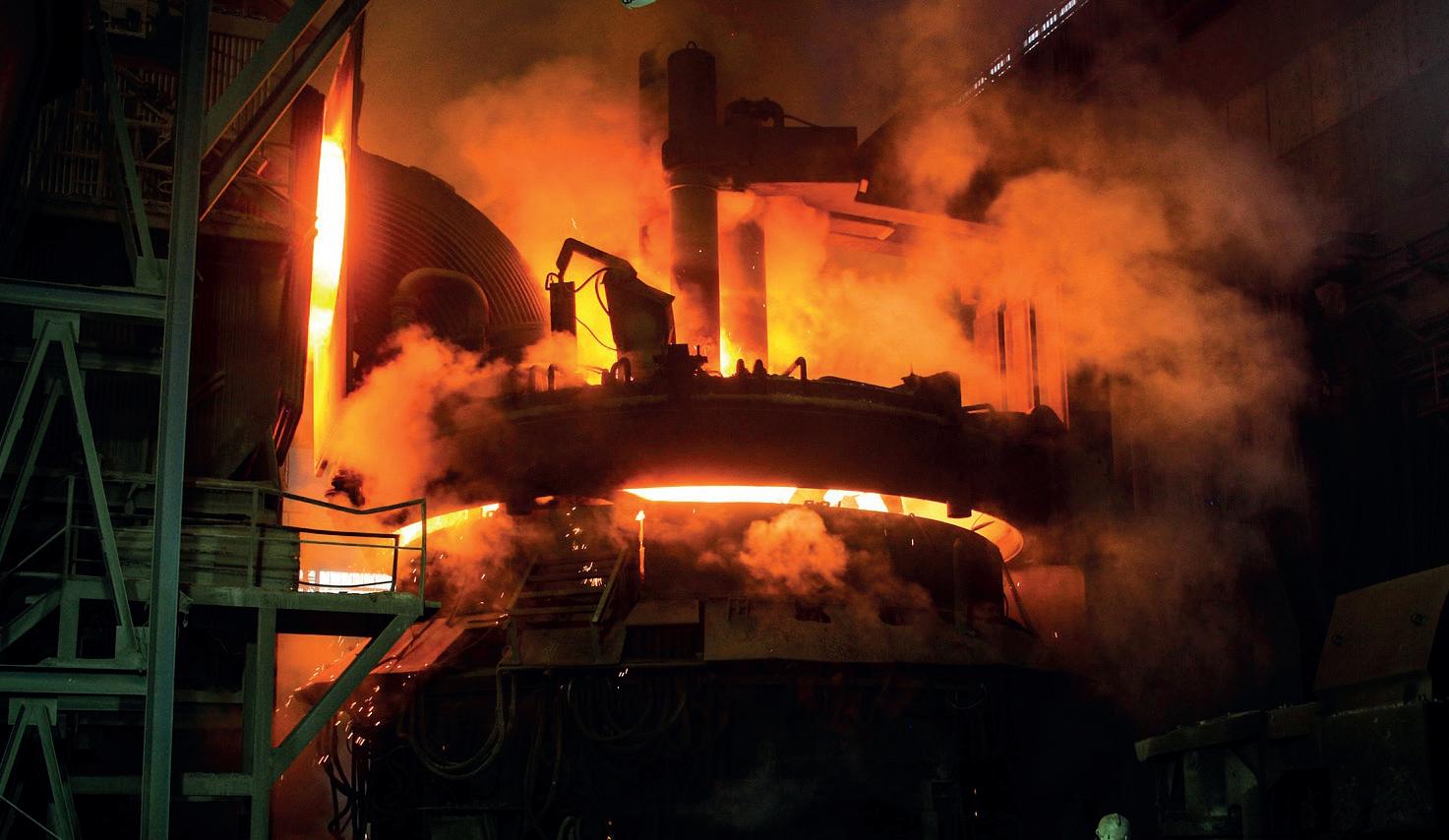
Burritt said the company’s greenhouse gas emissions intensity had been steadily reduced by 16% since 2018; indeed, he added, US Steel was well positioned to reach its 2030 target of 20% reduction in GHG emissions intensity.
US Steel had announced on 21 April, 2021 that it would become carbon neutral by 2050. David Burritt, the company’s president/CEO, had described climate change as the ‘challenge of this generation’. “Climate change is a global crisis that requires a global response,” he had said in a statement. “With our 120-year history of innovating to solve any challenge, US Steel intends to be a part of the climate solution.”Whilein the past century, people did not realize or even understand the
“We cannot – and will not – stand still, and this agreement is another effort to advance profitable, sustainable steel solutions for people and the planet,” he emphasized.
Richard L. Fruehaut, chief strategy and sustainability officer at US Steel, said that the company was ‘investing significant resources to achieve the sustainability goals in our Best for All strategy, and we know we cannot do it all alone. Successfully addressing the climate crisis requires public and private collaborations’.
Meanwhile, EVRAZ said that it was inviting proposals for acquisition of its North American subsidiaries. The process of soliciting proposals is conducted by the Office of Financial Sanctions Implementation (OFSI) and would be subject to regulatory and corporate approvals and applicable sanctions laws, and will require approval from relevant sanctions authorities, including the OFSI.
US steel maintained that the development of the hub and the requisite infrastructure, would generate new, sustainable jobs, stimulate economic growth, and help achieve significant reductions in carbon emissions.“Establishing a low carbon hub in this region could have a profound impact on both the climate and the economy, creating


Up until the year 2000, Votorantim was only operating in Brazil, but in 2001 the company began to expand its interests and developed an internationalisation strategy, including the acquisition of cement and concrete plants in Canada and the USA. In part two of a series of articles Germano Mendes de Paula* examines the company’s activities in Columbia and Argentina.
AS mentioned in the first part of this article, published in last month’s issue, Votorantim started its activities as a textile producer in the late 1910s. Afterwards, it engaged in a comprehensive industrial diversification strategy, but was restricted to operate only in Brazil until 2000. Nonetheless, in the following year, it began its internationalisation strategy, by acquiring cement and concrete plants in Canada and the USA, followed by further US cement assets. Regarding the mining sector, it purchased Cajamarquilla (a zinc smelter) in 2003 and a minority stake in Milpo (a zinc concentrate producer) in 2005, both in Peru. It entered into the Colombian and Argentinian steel business in 2007. Votorantim has opted to reduce its number of operational industrial sectors (lowering its level of diversification) and instead amplifying the number of countries in which it operates (a higher degree of internationalisation). It is was in this context that the acquisitions of Acerías Paz del Rio (APR), in Colombia, and Aceros Bragado (Acerbrag), in Argentina, should be analysed.
Columbia
winner. Primarily, it is quite important to highlight that the transaction took place during the commodities boom, which goes some way to explaining part of the substantial price paid.
Indeed, 52% of the capital of APR was offered, for an initial value of $192M. Votorantim acquired that majority control for a consideration of $489M. Consequently, the premium paid was over 150%. Out of the total stocks on sale, 65.16% belonged to the company’s workers and pensioners, the Colombian government had 17.57% and another 17.27% was controlled by private investors. That Votorantim purchased 52% of APR for $489M implies a $1.04bn total value, including some $100M debt. It was quite a substantial amount of money, equivalent to 13 times the EBITDA generated in 2006. However, according to the Brazilian business newspaper Valor Econômico, Votorantim expected a strong turnaround at APR, aiming to improve EBITDA from $70-80M to approximately $200M in 2008. If the company achieved this goal, the multiple would be reduced to 5x EBITDA (see Steel Times Intl, May-June 2007).
Fig 1. Steel as a proportion of Votorantim’s net revenues and EBITDA, 2015-2021(21%)
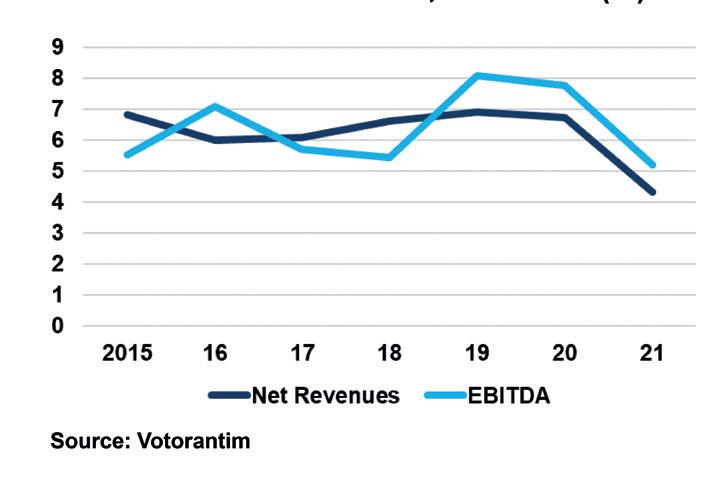
www.steeltimesint.comSeptemberLATIN2022 AMERICA UPDATE20
Votorantim’s steel strategy
In March 2007, APR was sold at auction. Several large enterprises, such as ArcelorMittal, Gerdau, Companhia Siderúrgica Nacional (CSN), and Votorantim were in contention – the latter was the


* Professor in Economics, Federal University of Uberlândia, Brazil. E-mail: germano@ufu.br
APR’s mineral resources (iron ore, coal, and lime) are among the main competitive advantages that attracted Votorantim, as it usually operates with a high degree of vertical integration. APR was focused on the common long-rolled products segment, although 20% of the capacity was related to common flat rolled products. It was decided, however, to shut down its flat carbon line (an 80kt/yr Steckel mill), because it was a relatively small and
Fig 1 shows the steel business as a proportion of Votorantim’s net revenues and EBITDA over the period 2016-2021. In the first year of this series, contemplating Brazilian, Colombian and Argentinean operations jointly, steel was equivalent to 6.8% of net revenues and 5.5% of EBITDA. Last year, considering only the Argentinian business, the respective figures were 4.3% and 5.2%. Thus – not surprisingly – the conglomerate has maintained operations with higher financial performances, lined up with an active portfolio management.
21 www.steeltimesint.com September 2022 LATIN AMERICA UPDATE
� +1.914.968.8400 www.GRAPHALLOY.com Yonkers, NY USA Handle ConditionsTemperaturesHighandHarshOperatingwithEase. • Survives when others fail • Run hot, cold, wet or dry • Corrosion resistant • Self-lubricating • Low maintenance • -400˚F to 1000˚F (-240˚C to 535˚C) • Ovens, furnaces, conveyors, mixers, dampers GRAPHALLOY®Bearings...WeGotoExtremes HeatAd_60mmx270mm.qxp_Layout 1 11/9/20 11:55 A

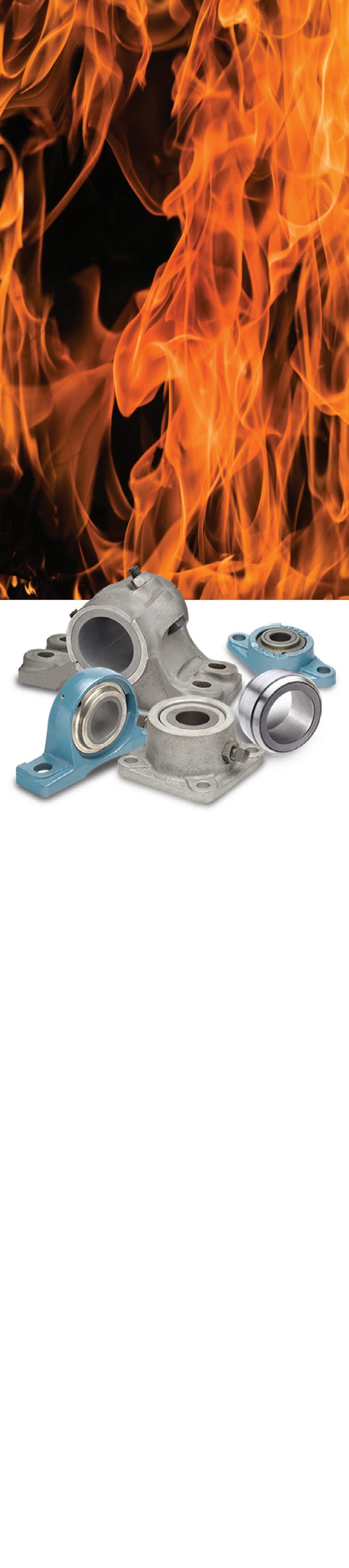
uncompetitive business. Votorantim’s initial intention was to expand APR’s volume from 315kt in 2006 to 430kt in 2010 and even to 700kt in the medium-term period. Valor Econômico was informed that Votorantim had invested $100M to amplify its voting stake in APR from 52% to 82%. The sales transaction was announced in November 2021 and involved two Columbian funds – Trinity Capital and Structure. The deal was concluded in April 2022, for a consideration of $19.2M, which was a small fraction of the initial and subsequent investments. APR’s installed capacity is still equivalent to 450kt/yr of crude steel, with rolling capacity of around 165kt/yr of rebar and 225kt/yr of wire rod. It reported EBITDA of $85M and an EBITDA margin of 24% in 2021.
Argentina
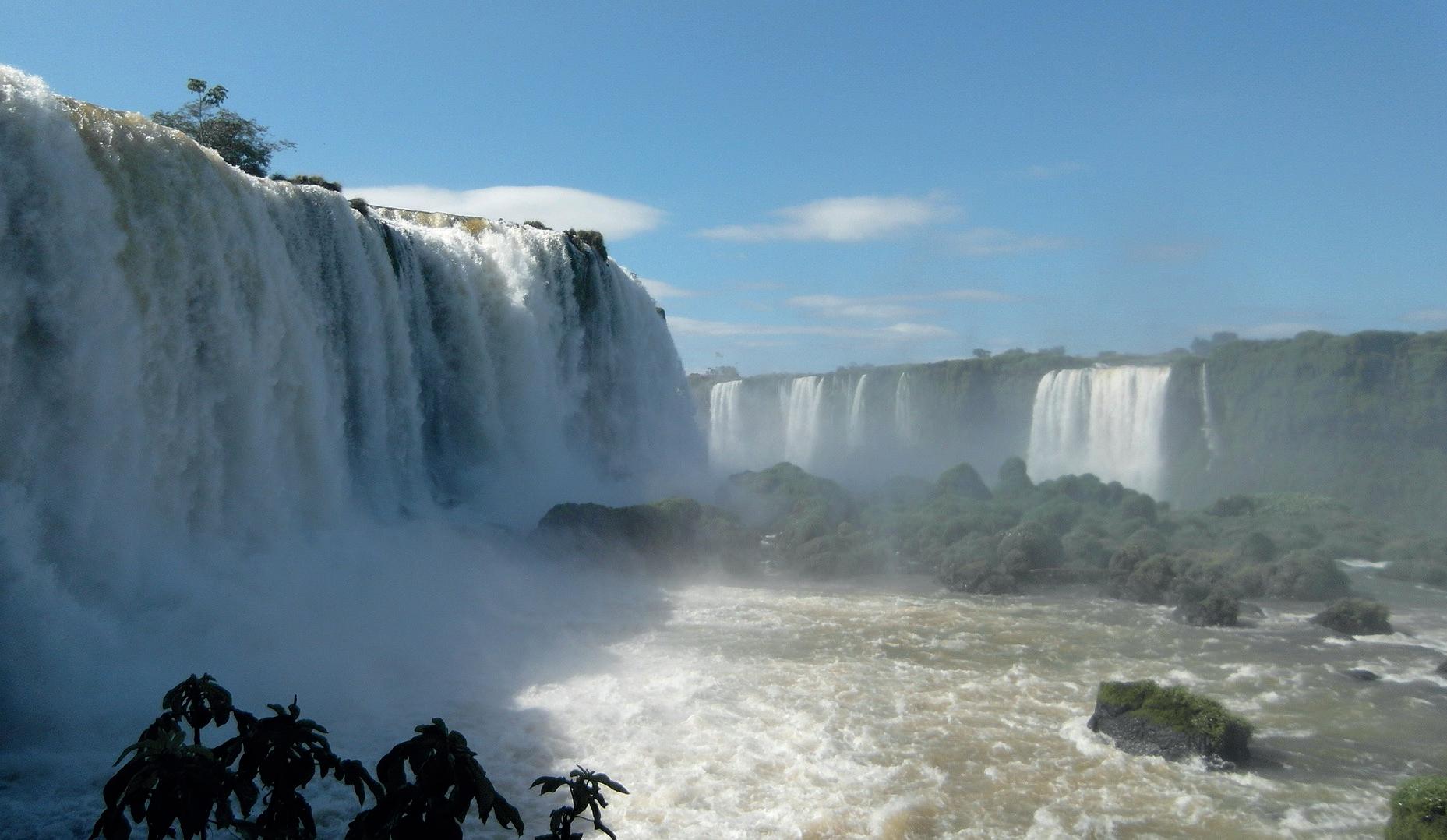
Acerbrag is a typical 400kt/yr crude steel minimill, focused on common long steel products. It produces wire, wire rod, bar, rebar and mesh, and resells profiles and nails. It is the third largest player in the country’s long steel market, after ArcelorMittal and Gerdau, both of whom have extensive operations in Latin America in general and particularly in Brazil. Shortly after achieving full control of Acerbrag, in February 2011, Votorantim explained that it was operating at 70% of its nominal capacity due to energy supply problems. Since then, it seems that the company was able to circumvent the problem and invest in optimising the business.
Votorantim purchased a 27.2% stake of Acerbrag in December 2007 for an undisclosed sum. In addition, in June 2008, it made a capital contribution, which allowed it to expand its participation to 53%. The Lupier family, who had bought Acerbrag in 1997, had other industrial investments – such as petrochemicals – and became a minority shareholder. In January 2008 – before Votorantim became the largest shareholder – it started to operate the mill. The Lupier family’s role turned out to be restricted to institutional issues (as a local partner) and to follow major operational and financial performance indicators. Votorantim took full control of Acerbrag at the end of 2010.
Acerbrag is facing a challenging macroeconomic scenario in Argentina. Last year, inflation reached 51% and the domestic currency experienced a 23% devaluation. Nevertheless, this situation has been underpinned by civil construction activities; Argentinean investors regard real estate as a way to mitigate the impacts of currency devaluation. It is important to highlight that the country’s real estate market is strongly dollarised.Acerbrag produced 324kt of billets in 2021, which was an all-time record for the company. Moreover, it obtained the best financial performance of its history: net income of some $380M, EBITDA of $107M and an EBITDA margin of 28%. After Votorantim Siderurgia merged its Brazilian operations with ArcelorMittal Longos (and retained a 15% stake of the resulting company) and sold its controlling stake in APR, it is only natural to wonder if the Brazilian conglomerate wants to dispose Acerbrag – or not. Votorantim has not been very vocal about it and it is understood to be quite satisfied with its Argentinean subsidiary’s performance.
APPLICATIONSFORSOLUTIONSPOSITIONLINEARSTEEL ABSOLUTE POSITION SENSORS WITH DETACHEDINDEPENDENTELECTRONICS Highest performance with Industry 4.0 and 85 ºC (185 ºF) Higher temperatures up to +105 °C (+221 °F) temposonics.com | info.us@temposonics.com | 800 633 7609 MTS Systems Corporation, Sensors Division • 3001 Sheldon Drive Cary, NC www.mtssensors.com/industrial Temposonics® Magnetostrictive Linear Position Sensors SOLUTIONS FOR HIGH TEMPERATURE APPLICATIONS Absolute Position Sensors with Independent Detached Electronics Accurate Measurement | Varied Operating Temperatures up to +105 °C (+221 °F) Contact applications support at 1-800-633-7609 / sensorsinfo@mts.com Model RD4 Model GBSModel ET V


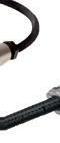

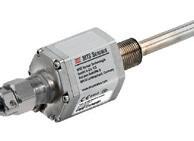




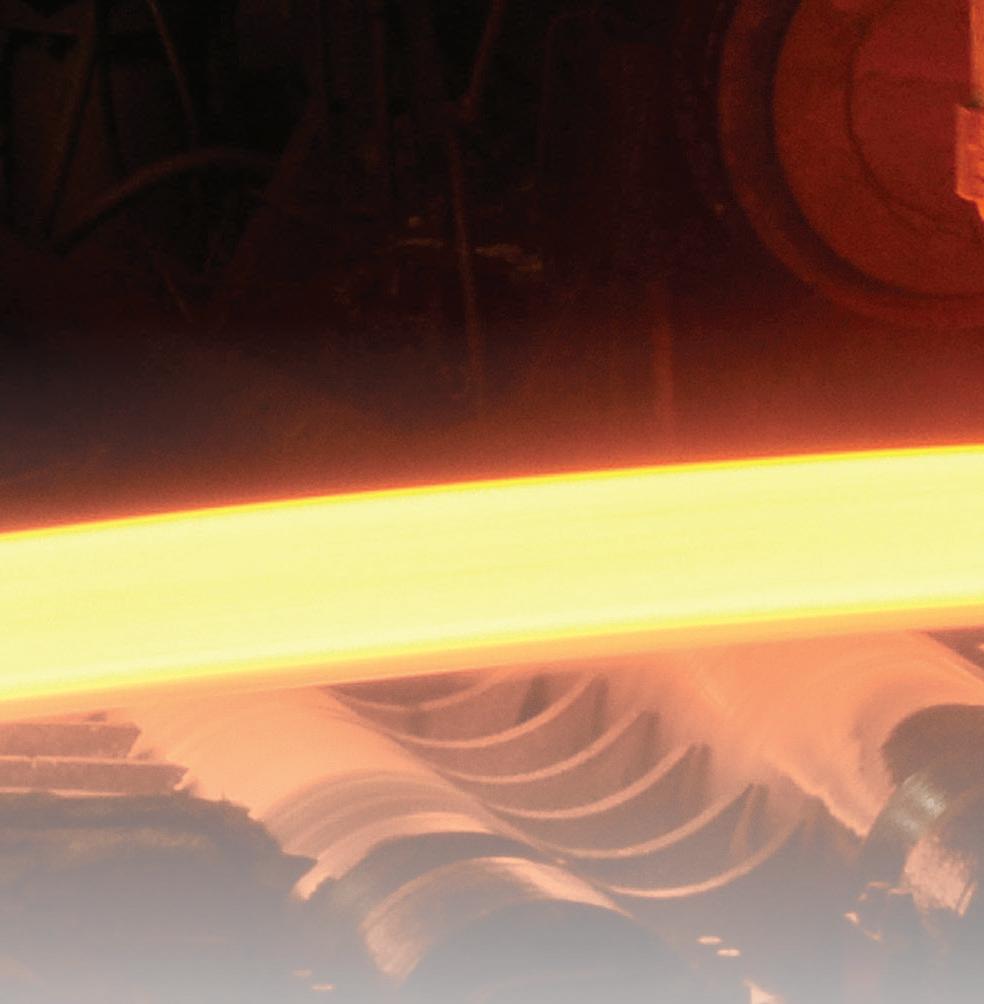
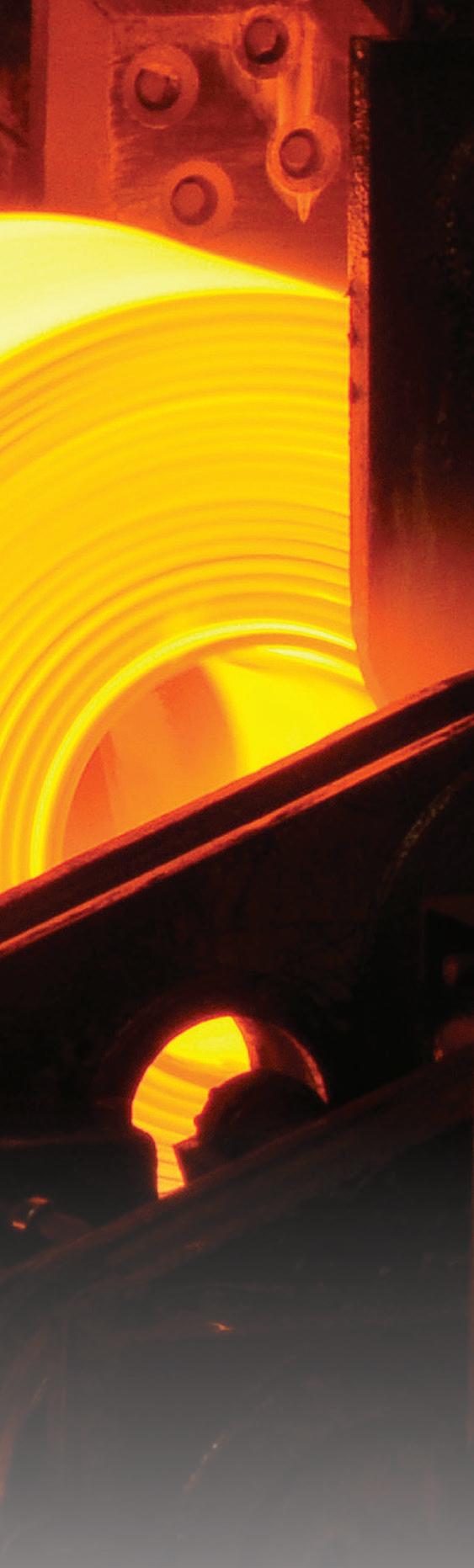
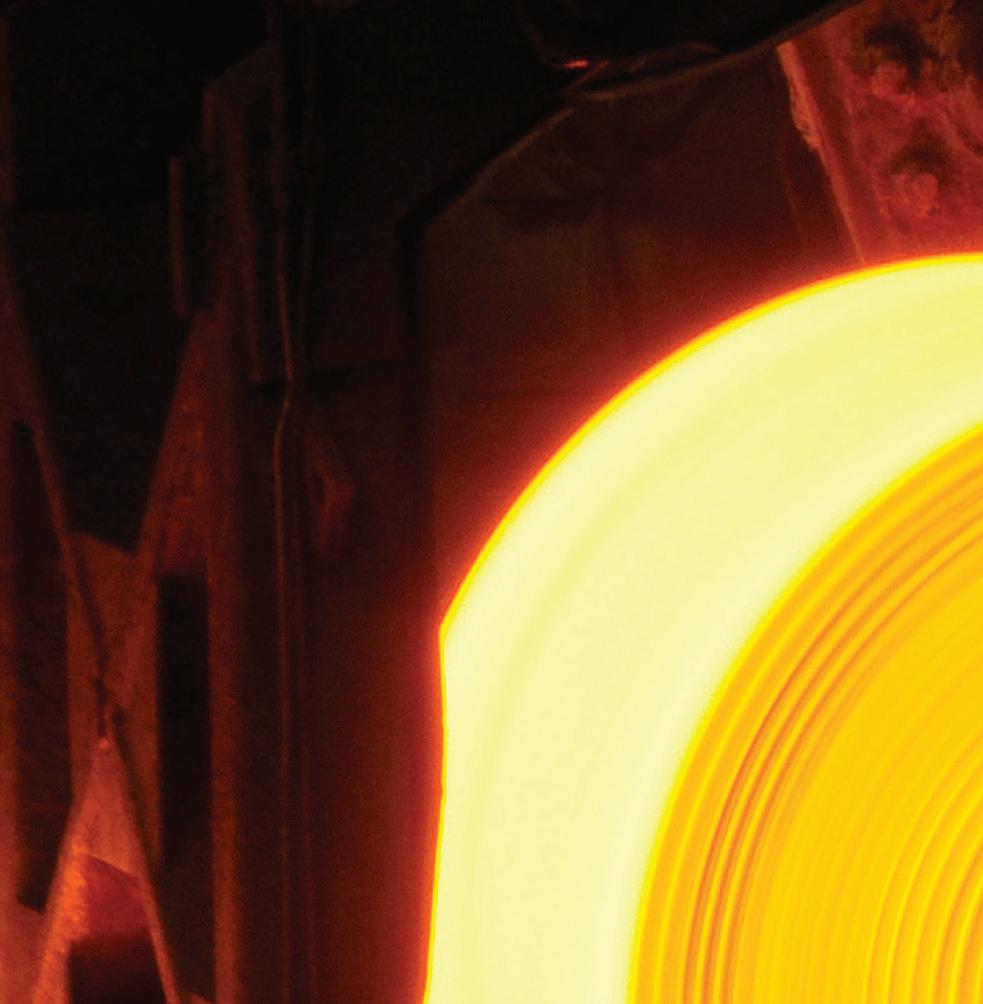

2019-20 100.17 6.77 93.40 6.8 93.2 2020-21 94.89 4.75 90.14 5.0 95.0 2021-22 105.75 4.67 101.08 4.4 95.6 2022-23(April-June) 27.69 1.17 26.52 4.2 95.8
partners, but both primary and secondary producers’ stockpiles continued to swell as they continued steel production unabated. Experts attribute the slowdown in steel demand during the peak construction season to high inflation which cast a shadow on the Indian economy.
RISING WITH TIME
Volatile demand
GROWTH IN LINE
Year Consumption in million tonnes In consumption Total Import Domestic Share of import Share of domestic production (%) production (%)
Source: Joint Plant Committee, Ministry of Steel
INDIA UPDATE
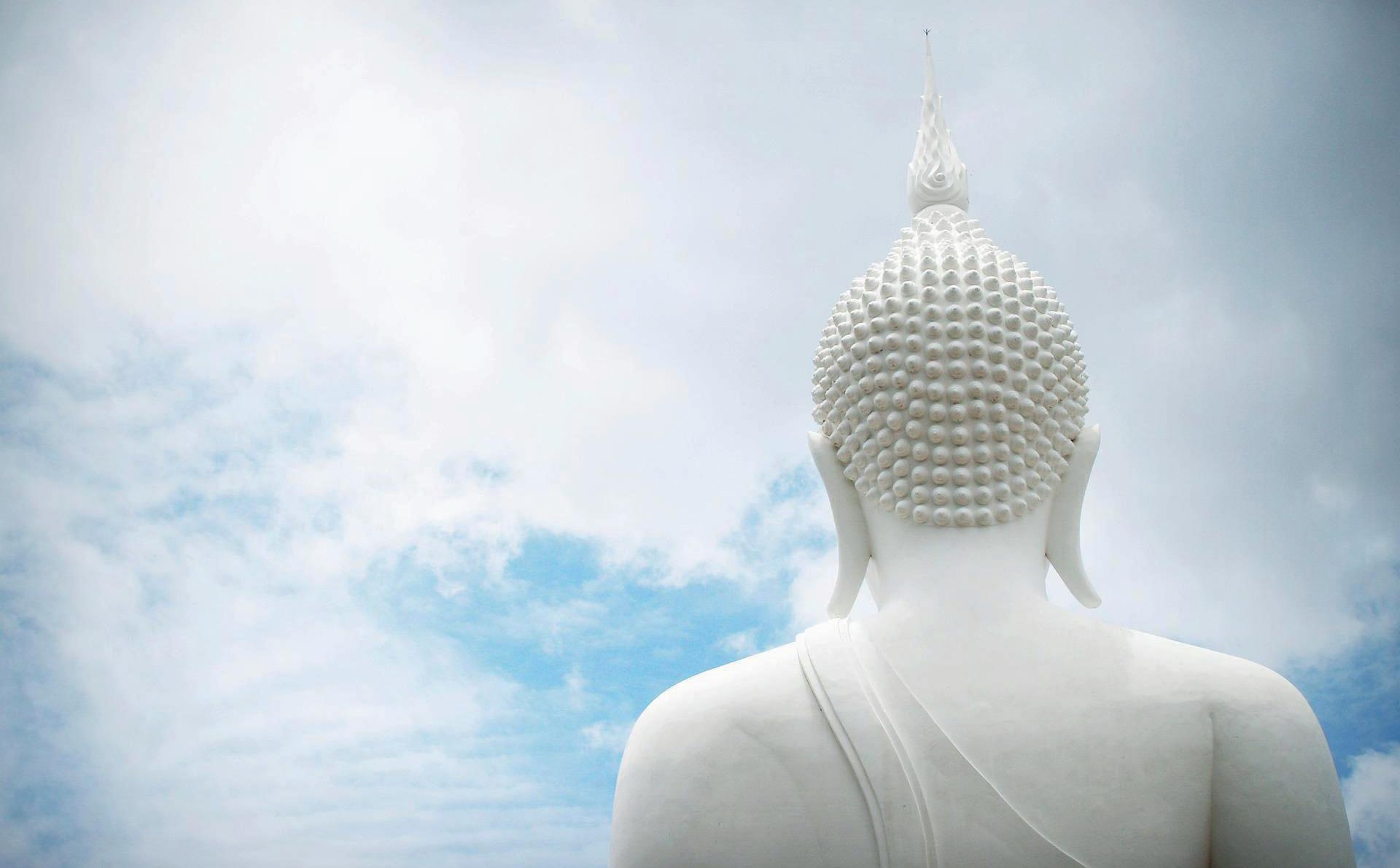
Source: Ministry of Steel, Government of India
Despite geopolitical strife, a 15% export levy and other pressures, Indian steelmakers are hopeful that demand will remain healthy. By Dilip Kumar Jha*
Overall sentiment remains upbeat
India’s crude steel production and plant utilisation (million tonnes) Financial year (April-March) Capacity Production Capacity utilisation (%)
While India’s apparent steel consumption may have been contracted during this volatile period, overall sentiment around the consumer industries continues
Suddenly, steel demand recovered after the second half of June, but not across all segments. According to Sheshagiri Rao, joint managing director and chief financial officer of JSW Steel, India’s long steel demand recovered in July with sporadic orders coming in from channel partners as an overall sluggishness continued
Share of domestic production versus import in India’s finished steel consumption
After a sharp post-Covid improvement at the beginning of 2022, India’s steel industry has faced a drawdown in demand during the peak construction season of May and June. Dealers, stockists and retailers normally stockpile a large quantity of steel ahead of the peak demand season to meet consumer demand in the early summer period. Against these expectations, activities around the manufacturing, infrastructure and housing sectors during this season remained subdued until the second half of June primarily due to high prices and record high consumer inflation. The weakness across these sectors reflected the proportionate slump in steel demand. All channel partners across the value chain preferred to use their existing stocks and thus avoid fresh stockpiling amid expectations of a price decline. This kept the pipeline inventory low with channel
23 www.steeltimesint.com September 2022 * India correspondent
in construction activities around the consumers’ level.
“Demand for flat steel products is yet to catch up. On a cumulative basis, demand for structural steel in the real estate sector had done really well until recently due to the government’s enhanced focus on road construction and a boost on the ‘Housing for All’ policy. But, private sector consumption needs to catch up, which is sluggish at this moment,” said Rao.
THE steel industry in India has been facing sharp fluctuations in demand since the beginning of the year due to a rapid change in the geopolitical and economic landscape in domestic and international markets. Russia’s prolonged military action in Ukraine coupled with escalating tensions between the USA and China over Taiwan, has pushed the global economy in a broadbased uncertainty. The Indian economy in general and the steel industry in particular is not immune to global geopolitical and economic unpredictability.
2017-18 137.97 103.13 75 2018-19 142.24 110.92 78 2019-20 142.30 109.14 77 2020-21 143.91 103.54 72 2021-22 154.06 120.29 78
to remain upbeat. With a recovery in demand expected to gain momentum, India’s overall annual steel consumption is forecast to remain flat at around 105Mt in the financial year 2022-23 (April to March). Of India’s total steel consumption, flat products contribute nearly 47%, long products share around 43%, and structural steel takes the rest at 10%.
Amit Harlalka, deputy director, ArcelorMittal Nippon Steel India, believes that weakening overall demand across various consumer sectors has created a margin pressure for Indian steel mills at least for the current year, which was reflected on the financial performance of primary producers. JSW Steel, for example, reported a massive 86% decline in its consolidated net profit at INR 8,380 million during the April-June quarter of 2022 versus INR 59,040 million posted in the same period last year. The company’s topline, however, jumped by 30.89% on high steel prices to Rs 37,500 million for the April-June 2022 quarter against INR 28,430 million for the same period the previous year. JSW Steel’s profit margins were also hurt by a sharp reduction in export volumes on account of an export levy and a fall in apparent consumption due to destocking at the users’ level.
www.steeltimesint.com INDIA UPDATE24
Manage your steel more safely and more productively using less space with Combilift’s materials handling solutions
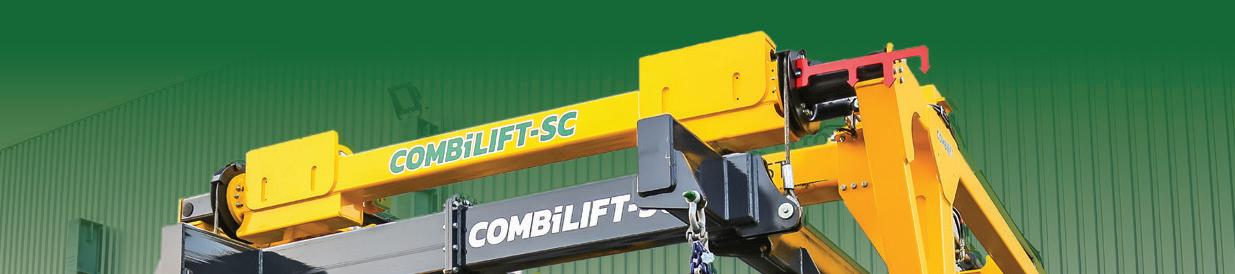

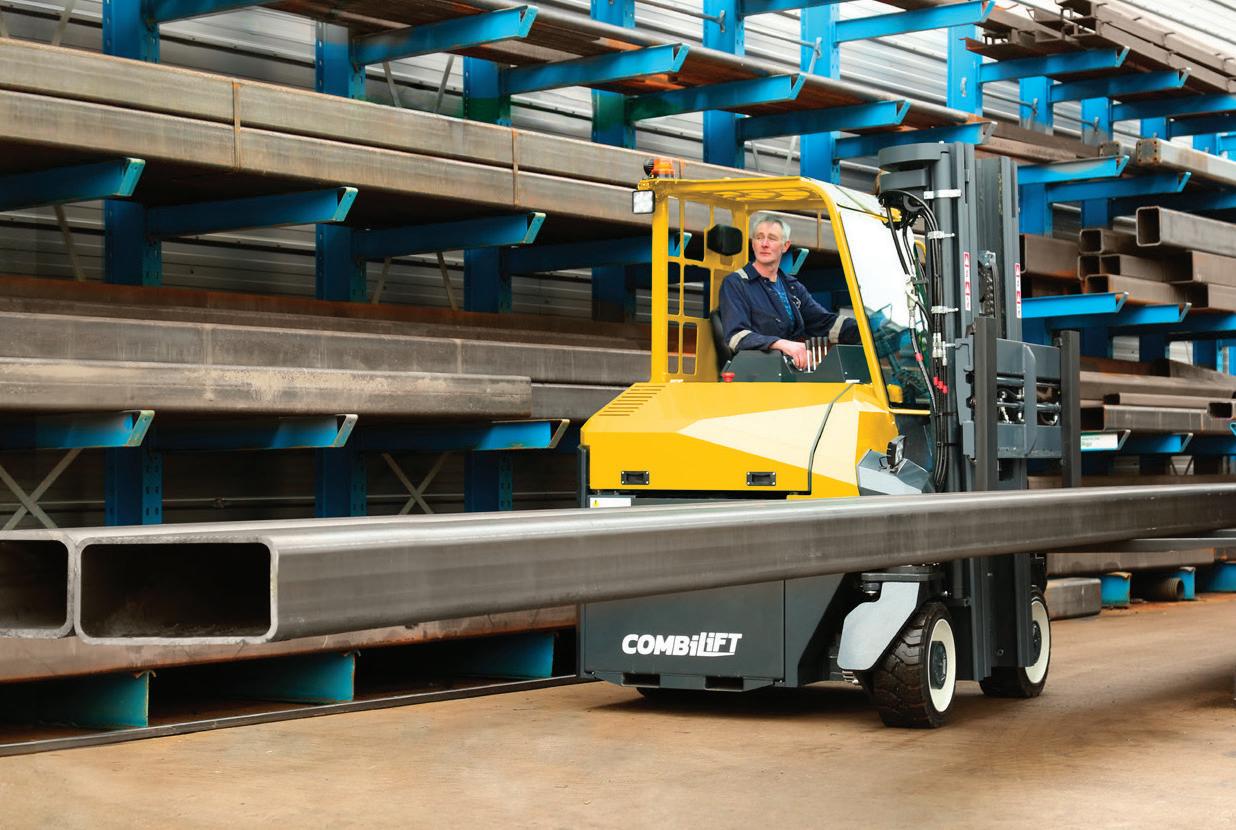
Safety Storage Efficiency
Steel contributes nearly 2% of India’s gross domestic product (GDP) and hence, is an important industrial segment for the Indian economy. The sector employs around 600,000 workers directly and two million indirectly. According to Rajiv Guja, an industry veteran, the steel industry is cyclical in nature. “The cycle used to be longer earlier and has become shorter now, primarily because of frequent change in government policies either in the steel or allied sector. Policy changes in leading consumption sectors like white goods, housing, railways and highway constructions have a direct bearing on steel demand,” Guha added.
Additionally, Indian steel producers have urged the government to either exempt steel products from the recently levied 15% export levy or slash it at least by a half to 7% for exporters to take advantage of the Russian supply disruptions to global markets.
Revival forecast in the second half Soma Mondal, chairman of the government-owned Steel Authority of India Ltd (SAIL) hopes India’s steel demand will remain healthy in the second half of the current financial year beginning October 2022, with sustained domestic consumption coming from the infrastructure, manufacturing, packaging, and automotive sectors as indicated from the present consumption cycle and future trends.
combilift.com

The government of India is understandably considering the proposal which will be a bonus for Indian steel makers in terms of a resurgence in the overall sentiment in coming months. �
Private sector steel behemoth Tata Steel reported a 12.8% decline in its net profit at Rs INR 74,650 million in the April-June 2022 quarter versus INR 89,070 million in the corresponding quarter last year. “This has been a challenging quarter for the global and the Indian economy with rising interest rates, supply chain constraints, and a slowdown in China due to Covid. Despite these multiple headwinds, we delivered a strong performance. High raw material costs increased operating costs. Additionally, the aforementioned export duty levy choked up the company’s shipments to overseas consumers which hurt overall sales volume,” said T V Narendran, chief operating officer and managing director, Tata Steel.
Margins under pressure
*Analyst with GMK Center, Ukraine
The Carbon Border Adjustment Mechanism (CBAM) was just the beginning of a new trend, says Dr. Andrii Glushchenko*
ENVIRONMENT
THE Carbon Border Adjustment Mechanism (CBAM) story started four years ago, when the European Union launched its first discussions on the issue. Industry players thought that the current carbon leakage mechanism was insufficient and that new restrictions were needed. European officials supported the idea and included CBAM in the European Green Deal. While preparing the regulatory framework, it became clear that the reality would differ from the expectations of industrialists.
The introduction of a CBAM in the EU requires changes to the EU ETS, as it forms the CO2 prices. The ideology of the EU ETS was to create conditions for reducing CO2 quotas and later increasing their prices. The EU ETS mechanism includes measures against excessive increases of CO2 prices, specifically free quotas. These quotas had to ensure the competitiveness of European producers compared to their foreign counterparts, who do not operate under the conditions of strict European environmental directives.
A2032.variety
of opinions led to the withdrawal of draft laws on CBAM and the EU ETS on 8 June with the requirement to send them (the draft laws) to the European Parliament’s committees for review. The decision was initiated by the Social Democrats and the Greens, who believed that the proposed bills did not contribute
It is difficult to talk about the prospects of adopting this bill. The very debate about CBAM in the United States is important. There is some support for the introduction of a CBAM in industrial circles. In particular, Kevin Dempsey, president of the American Iron and Steel Institute (AISI), said at a conference recently that he supported its introduction, stating that the American steel industry had already reached one of the lowest levels of CO2 emissions per ton of steel in the world, so it is wise to use a new tool (CBAM) to protect it from carbonintensiveTechnically,imports.the American CBAM, if adopted, will be unlike the European version. The United States has neither a carbon tax nor a greenhouse gas emissions trading system. Therefore, the question of setting a CO2 price, which will be calculated by a CBAM, is open. The registered bill sets a starting price of $55/t with further
The European Commission has proposed abolishing free quotas by 2035, while the European Parliament’s environmental committee called for a complete abolition of free quotas by 2030. The European Parliament’s Industrial Committee has supported the abolition of free quotas by 2034, and the Social Democrat faction considered it possible to abolish free quotas by
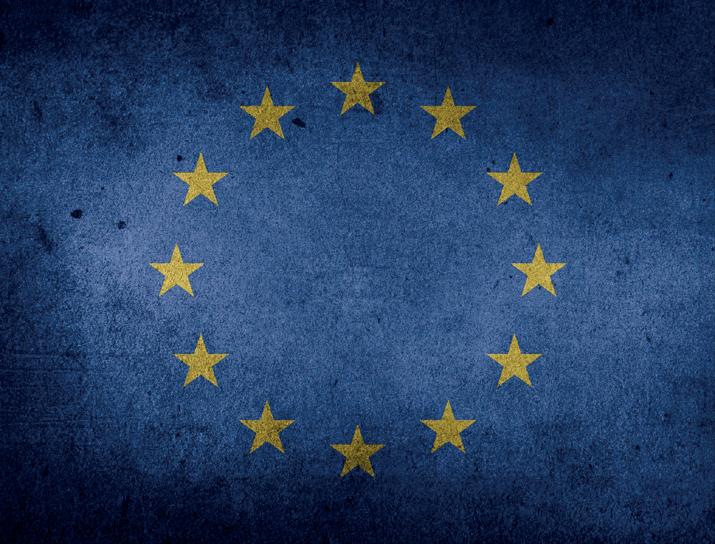
Protectionism turns ‘green’: here is how
quotas reducing annually until they reach zero. Some discussions on the timing of abolishing free quotas have already started.
25 www.steeltimesint.com September 2022
enough to the EU’s ambitious goals of decarbonization.Itisobviousthat a compromise will be found, and that all parties will have to give up some of their interests. Some media outlets expect new bills to appear by the end of the summer. However, amid the bureaucratic process, the work on the introduction of a CBAM in the United States intensified. The very possibility was discussed a year ago, but on 7 June, a relevant bill was registered in Congress.
The European Commission considered a CBAM as an alternative to free quotas, as both mechanisms counter carbon leakage (relocating production to countries with less stringent environmental regulations). Therefore, with the introduction of a CBAM, the abolition of free quotas was on the agenda. Everyone understands that this process should be gradual, with free
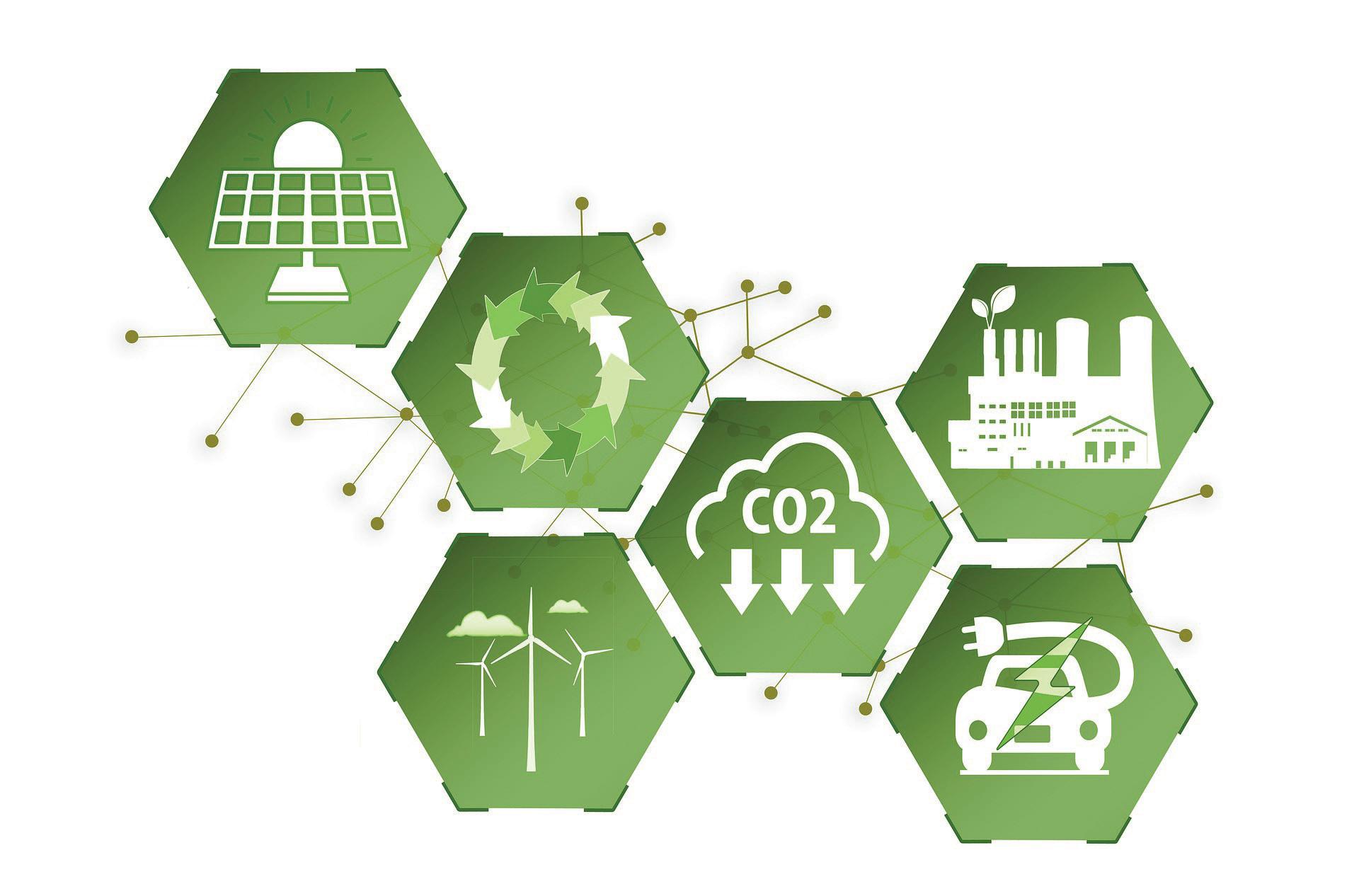
One option is exports compensations (subsidies). Probably to support not all exporters, but only those that produce the most environmentally friendly products (with the lowest CO2 emissions). There are fears that the World Trade Organisation (WTO) will not approve such a measure. However, as some previous cases of trade restrictions have shown, the WTO is not strong enough to act as an effective arbiter of global trade. Environmental protectionism is already changing the global trade system. These changes are far from ending. We can still influence them, as the process is at an early stage. This is particularly important for Ukraine, as the war significantly damages the country’s economic development and deprives it of opportunities for a ‘green transition’. Post-war reconstruction of Ukraine will be impossible without access by Ukrainian enterprises to foreign markets. Some diplomatic talks with international partners are needed so that CBAMs and other new protectionism measures will not delay Ukraine’s post-war development. �
Another interesting aspect is who will fall under a CBAM in the United States? The bill proposes that its payers be both domestic consumers and importers. Local industrialists will clearly not like this idea, because, for domestic producers, a CBAM will become a carbon tax. The AISI’s Dempsey said the United States did not need a carbon tax or a greenhouse gas emissions trading system. These instruments are seen as a punishment for businesses that have already significantly reduced CO2Theemissions.debateon a CBAM in the US will be no less interesting than in the EU. In the future, other countries may choose the path of introducing their own CBAMs. In each case, CBAM will be different, as the conditions for its implementation will be different. This may be a new trend in the evolution of protectionism. We see traditional trade restrictions gradually erode as bilateral political arrangements to ease them increase. There is a demand for new tools of protectionism, including CBAMs.
Delivering Innovative Solutions. Your Success Is Our Goal. Cut-To-Length Lines Crop RotaryShearsShears Stretcher Levelers Hydraulic Roller Levelers Scrap Choppers When it comes to building equipment to process ferrous and non-ferrous metals, nobody does it better than Butech Bliss. We Build Things. Better. Salem, Ohio USA For 135 years, steel producers and steel service centers have counted on Butech Bliss to deliver the design, engineering and technological advantages necessary to help them succeed. From entry to exit end we build it all. Our product lines include roller and stretch leveling technology, a full line of shears, material handling equipment and complete coil processing lines. We are more than a scrap chopper manufacturer. Learn more about our world-renowned coil processing technology call +1 (330) 337-0000, visit ButechBliss.com or email sales@butech.com. If our name is on the machine, it’s built better.
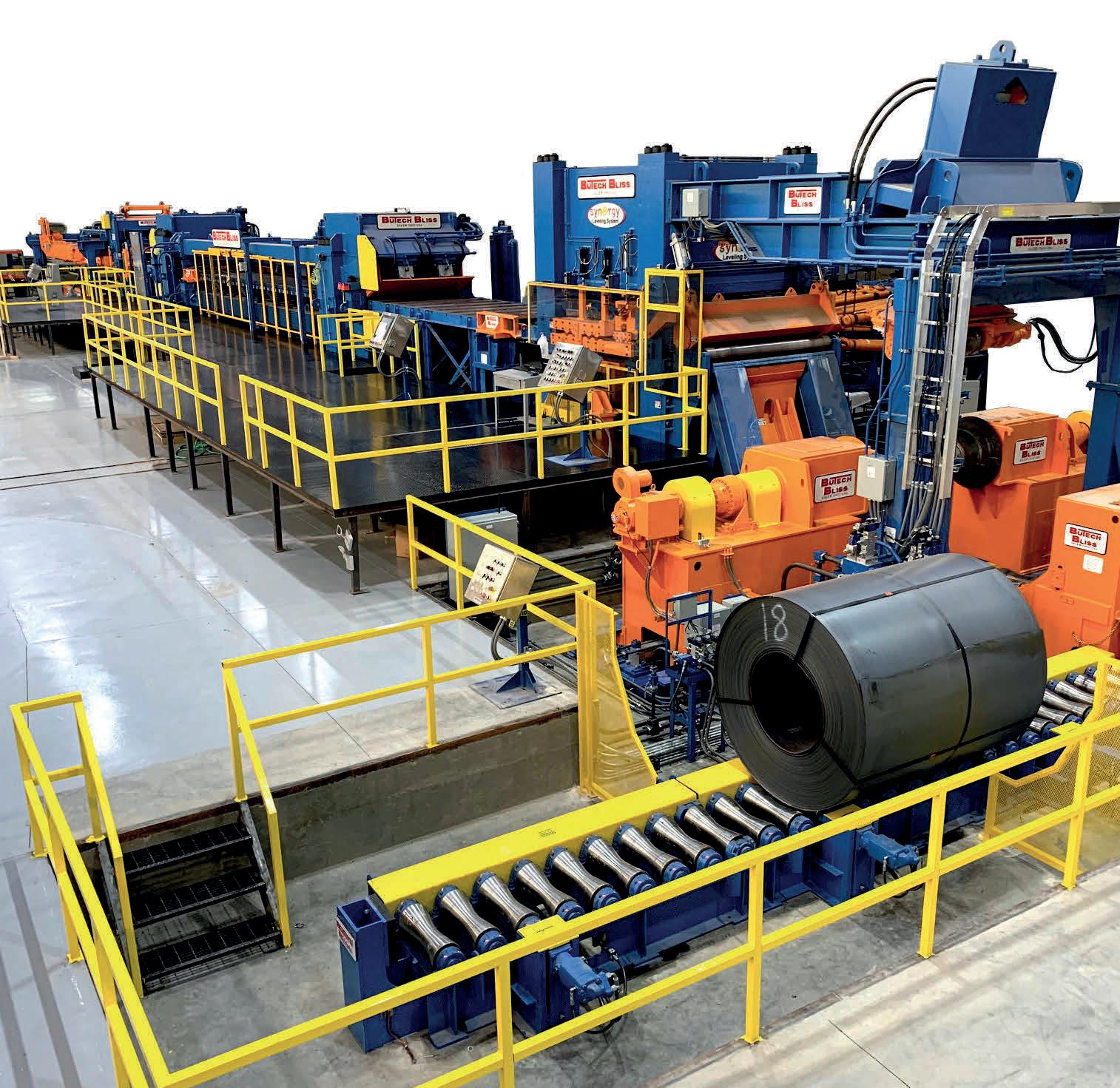
indexation to inflation + 5%.
It is unlikely that CBAMs will remain the only instrument of environmental protectionism. The EU is discussing the need to protect exports after the introduction of a CBAM. European industrialists rightly argue that free greenhouse quotas have supported the competitiveness of enterprises both in the
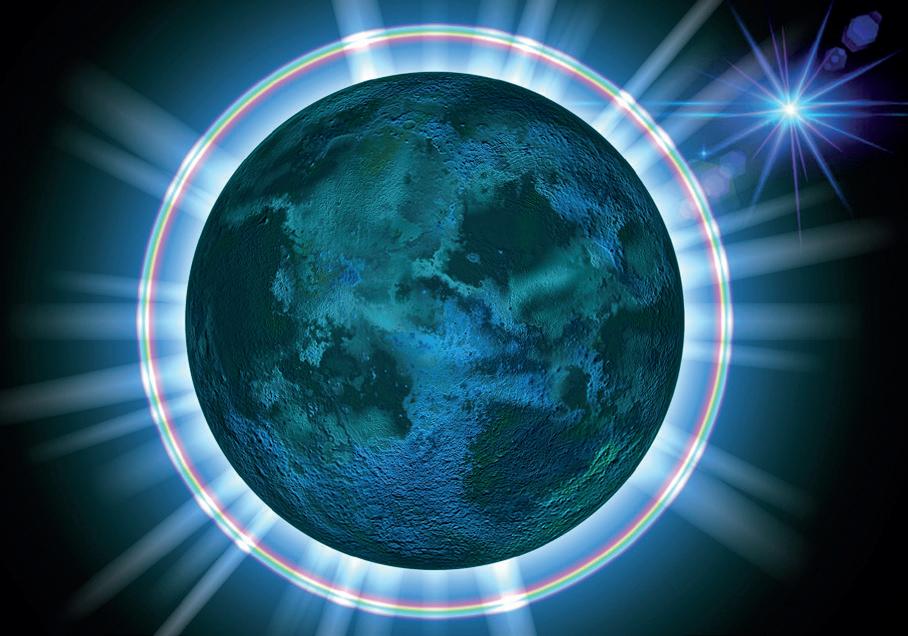
domestic market and in exports, while a CBAM protects only the domestic market from carbon-intensive imports. Therefore, with the abolition of free quotas, other tools to support exports will be needed.

ENVIRONMENT26 www.steeltimesint.comSeptember 2022
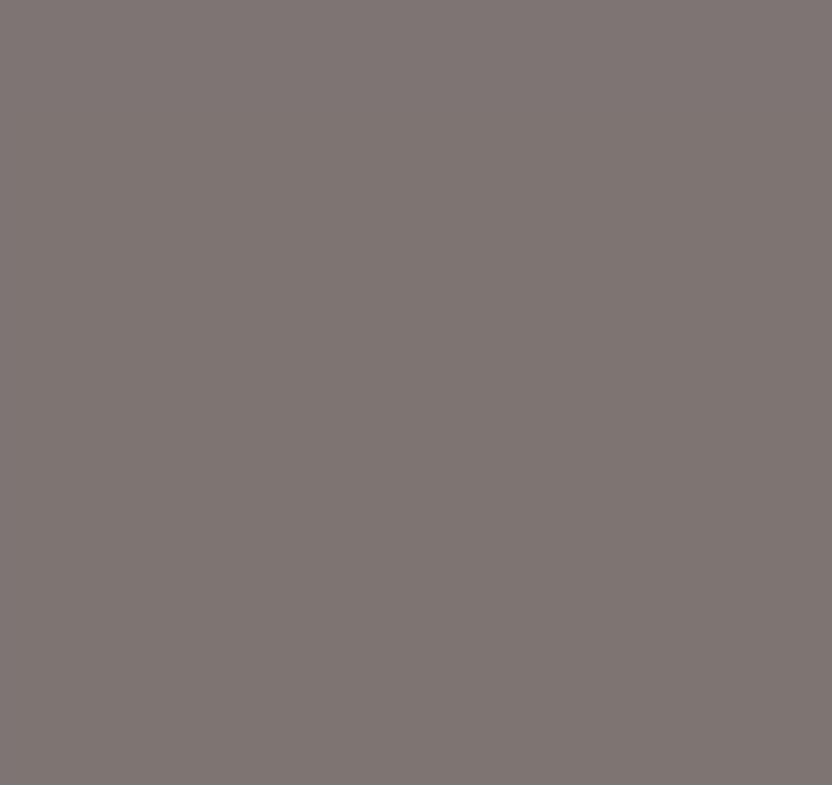
The effect of green steel on user industries is large, but the costs in relation to the end product are small. For example, in the case of an electric car 16% of total production-related emissions can be reduced through the use of climateneutral steel alone – and this with a cost increase for end consumers of significantly less than 1%. The financing of green steel via the market is, therefore, economically imperative. The appropriate framework must now be created for this.
ENVIRONMENT 27 www.steeltimesint.com September 2022
This is where ‘green lead markets’ comes into play. The aim is to strengthen the demand for climate-friendly steel with the help of regulatory measures or to establish sales markets where a so-called green premium can be achieved. This, in turn, can offset the additional costs of switching to climate-friendly processes. The state compensation payments agreed in climate protection contracts would be reduced accordingly.Suitablelead markets for green steel are, for example, public procurement and those customer segments in which there is already high pressure to reduce upstream emissions. Those lead markets represent a bridge until climate neutral materials have become fully established. This requires binding incentives for users and buyers,
How green steel finds its way into products
Green steel greens value chains
Green lead markets: a clear definition and categorisation of green steel is key Markets for climate-friendly products can only develop if they are based on clear definitions. It is central that it must
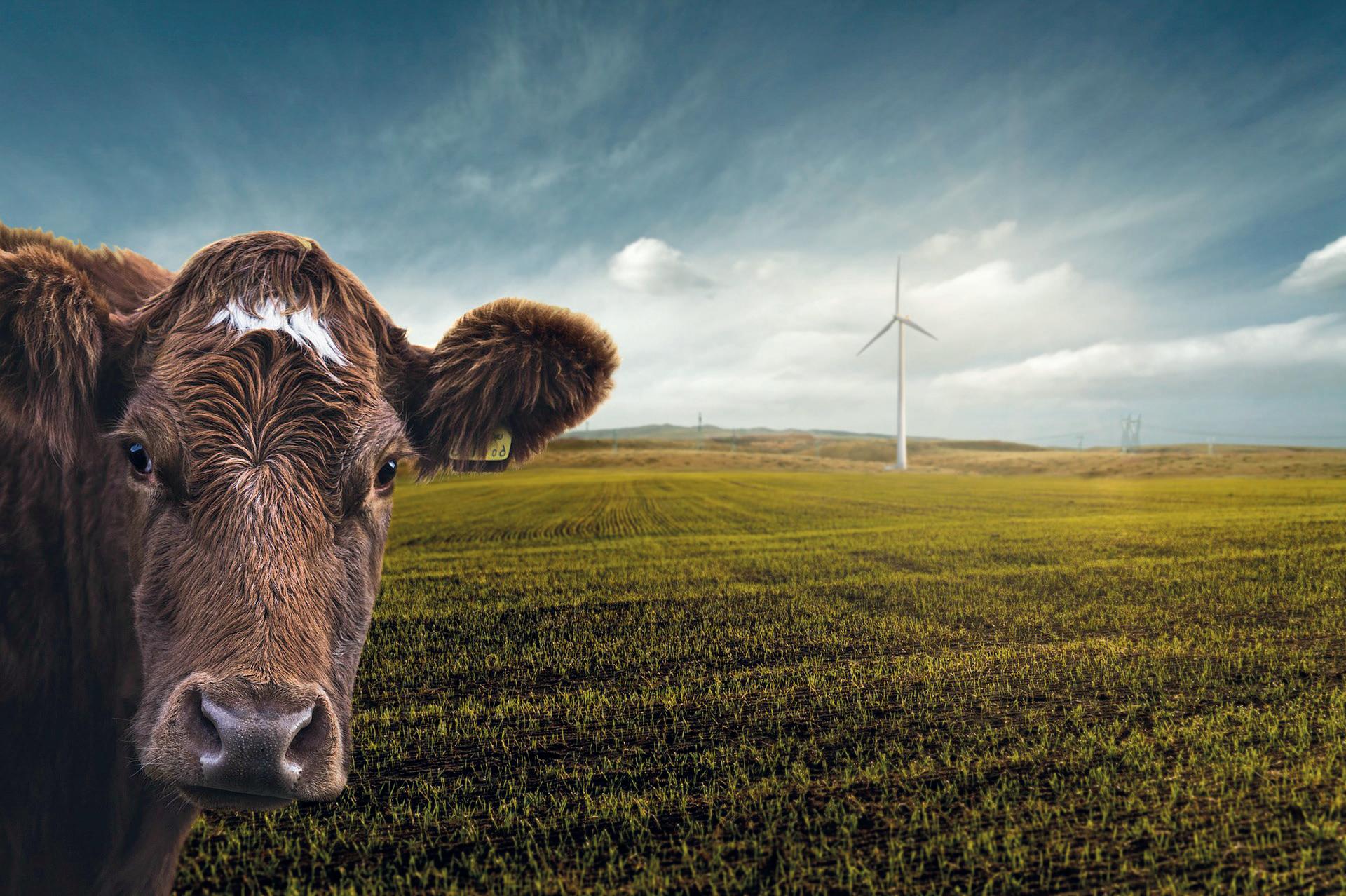
be it in the form of minimum standards, premium models or targeted credit options.
How can the steel industry ensure that green steel finds its way into use? The answer is to develop green lead markets and thereby strengthen demand for climate-friendly steel with the help of regulatory measures or to establish sales markets where a so-called green premium can be achieved, says Dr Martin Theuringer*
*Managing director of Wirtschaftsvereinigung Stahl (German Steel Federation)
THE steel industry in Germany is on its way towards climate neutrality. By converting processes with high CO2 emissions and with the help of an efficient circular economy, the industry can, wants to, and must produce almost emission-free by the middle of the century. The technological challenges are immense, but achievable. On the other hand, there is the question of how to ensure that green steel, which is likely to be much more expensive to produce, finds its way into use. Government support, especially in the form of so-called climate protection treaties currently under discussion, is therefore indispensable. However, this can only be start-up funding. To ensure that public funding is minimised and completely replaced in the long term, further political instruments are needed to support the transformation.
Further reading: “Green lead markets and key building blocks of a green steel definition”
�
Label level A is reserved for green steel produced in an almost climate-neutral manner. Intermediate levels are defined in a technology-open manner and are so ambitious that considerable effort is required to reach the next one up.
(A Position Paper by German Steel Federation).
The German Steel Federation has proposed a five-stage system for this: to keep it manageable, the system does not extend beyond hot rolled steel. The first ambition level is label D, which is oriented towards state-of-the-art technology.
Such a system would be a good basis for steering lead markets in practice. For example, specifications could be made that insist that a certain amount of category C steel would have to be used in public construction products from a certain date. Over time, with the increasing ramp-up of hydrogen and the advancing energy transition, the lead market requirements for the category to be achieved will become more stringent, thus creating incentives for further transformative steps. The labelling system can also be used to define interim targets with which the success of the transformation and the ramp-up process can accordingly be tracked and controlled. When designing the system, it is

To map the different forms of climate-friendly steel produced over

be recognisable for every buyer what CO2 emissions were given off in the manufacture of a finished steel product. If such transparency existed, this information could be used in procurement strategies to reduce Scope 3 emissions, i.e., indirect emissions in the supply chain. Products with low CO2 content thus gain competitive advantages over those with high emission intensity. It is important that the CO2 footprints include the emissions along the entire value chain, that the accounting area is clearly defined, and that the emissions are calculated according to the same rules. However, a uniform rule book necessary for this is not yet available.
important to ensure that the use of steel scrap is also considered: this is because its availability is limited worldwide and, if available, it is used in its entirety. By substituting scrap for pig iron, a steel producer can reduce his individual carbon footprint. However, the CO2 emissions in the overall system remain unaffected. Therefore, only ‘real’ transformative steps that also lead to CO2 emission reductions in the overall system should be rewarded in the labelling system. In other words, incentives must also be created for the transformation of primary steel. At the same time, it must be ensured that manufacturers who already use almost 100% scrap, and thus already produce in a climate-friendly way, do not suffer any disadvantages.Proposalsto implement this were recently put forward by the International Energy Agency (IEA) and taken up by the G7 countries as part of their Industrial Decarbonisation Agenda (IDA). The task now is to develop these further. Germany, with its strong industrial value chains in which steel plays a decisive role, should play a decisive role in shaping the framework’s conditions.ThenGermany as an industrial and steel location can become a leading lead market for green steel, in which the steel companies in Germany will also be strongly positioned.
time, a categorisation system would be appropriate, as is used in other areas such as household appliances, in the form of an energy label. The primary goal here, however, is the direct link to the lead market concept: companies that take substantial transformative steps can be rewarded if they thereby achieve a classification in a category that qualifies them for lead markets in which green premiums can be obtained.
For the control and implementation of green lead markets, however, the consideration of a footprint is not sufficient to specifically stimulate the process of decarbonising steel production. In addition, the industry’s stepwise transformation process must be taken into account: pure green steel will not be physically available until sufficient quantities of green hydrogen are available. Initially, natural gas will play a crucial role as a bridge in the operation of the first reduction plants, with a growing proportion of H2 as the hydrogen economy ramps up. Early on, sites will also only be partially transformed. In the area of secondary steel, which is already produced in a climate-friendly way, further CO2 reductions depend crucially on the availability of green electricity, the use of which is also associated with additional costs. For further processing, hydrogen and green electricity are equally crucial.
ENVIRONMENT28 www.steeltimesint.comSeptember 2022
ww w.magnesitasnavarras.es MAGNA North America Minneapolis, USA +1 (612) 638 2160 MAGNA Magnesitas Navarras Navarra, Spain +34 948 421 644 MAGNA Refractarios México Monterrey, Mexico + 52 (81) 83367196 From the mine to the steel mill
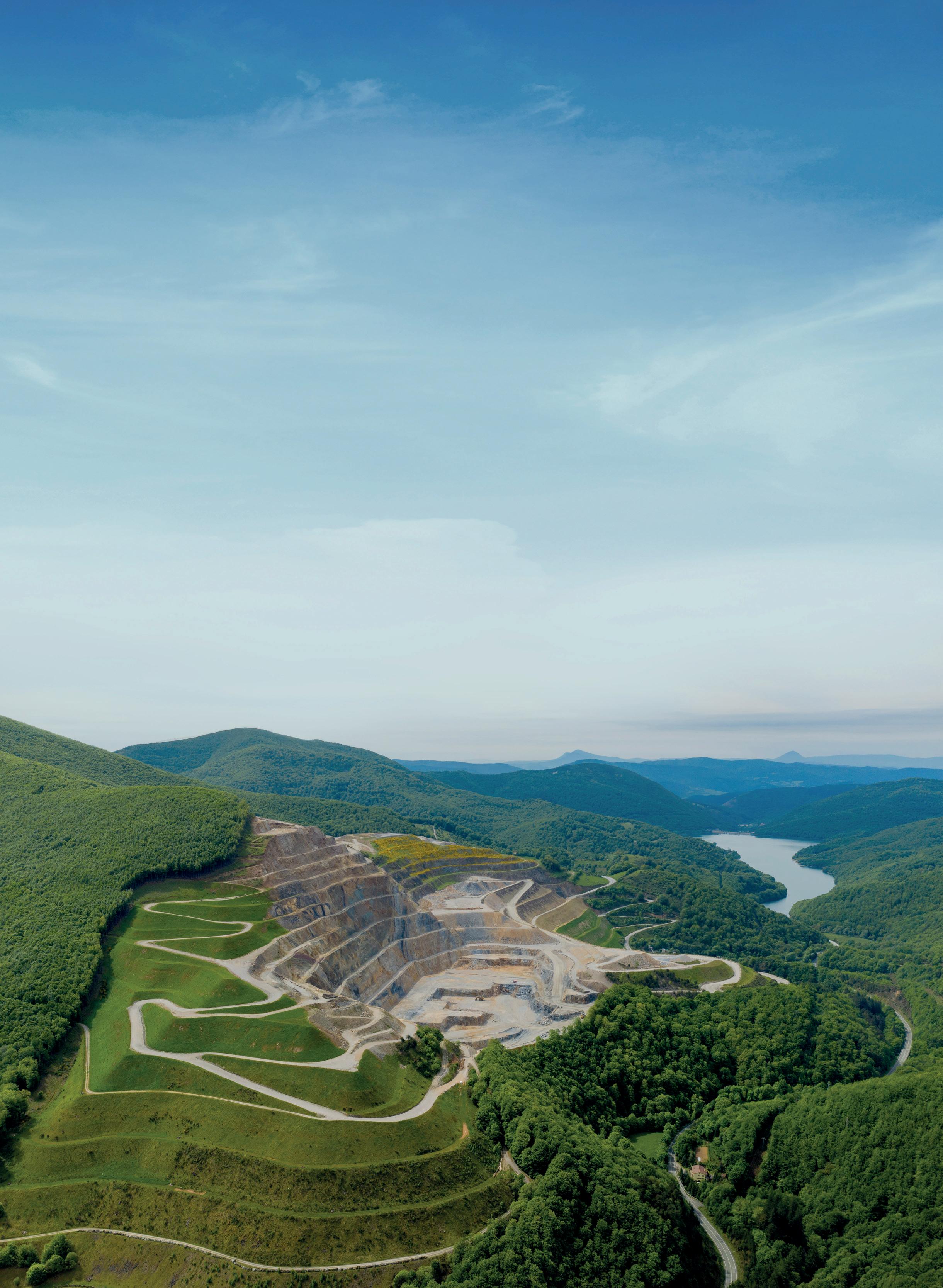
WITH all eyes on decarbonization activities, sustainable and effective actions against climate change are in demand. One solution from the automotive industry is a transformation toward e-mobility or electric vehicles to reduce their environmental impact. With a lightweight design and reduced greenhouse gas emissions, electrified vehicles will certainly positively impact the vehicle’s carbon footprint over its entire lifecycle. However, these changes in the automotive industry place a direct demand on the steel industry to produce thin-gauge, high-permeability, grain-oriented, and non-grain-oriented electric steel grades. In application, these steel grades will improve energy efficiency in electric motors, transformers, and high-performance generators. But steel producers must increase volume and maintain stable operating conditions to ensure high-quality end products that meet the growing demand for highstrength materials with excellent magnetic properties.
Meeting demand for electrical steels

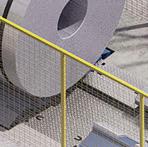
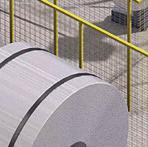
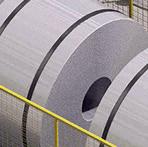
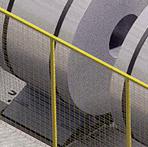
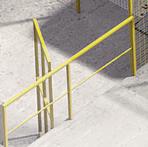




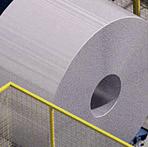

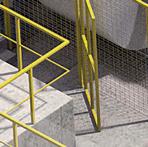

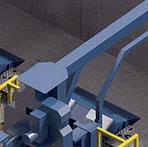
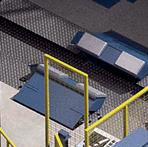
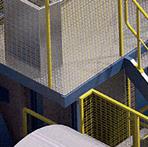
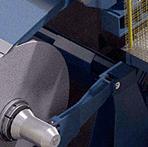
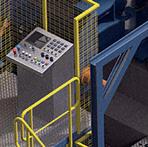
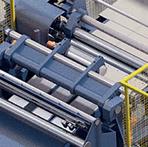
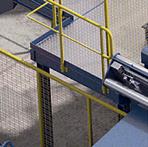
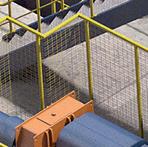
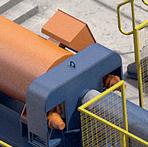
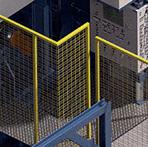
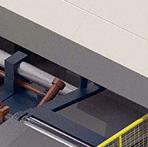

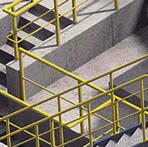
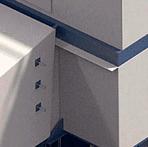
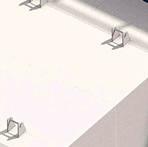
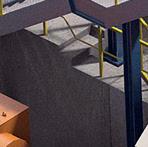
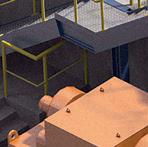
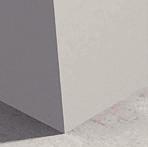

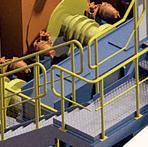
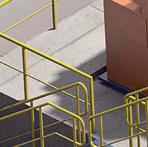

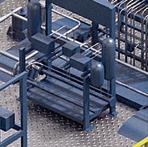

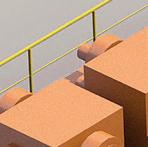
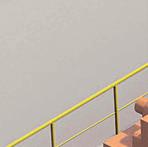
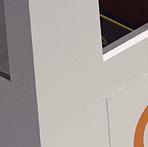
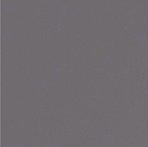
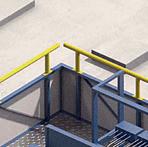


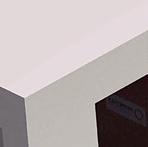

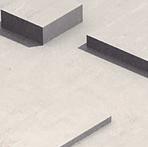
The conventional combustion engine car contains approximately 25 to 30kg of silicon steel. Today, automobile manufacturers are developing and producing electrified vehicles with light steel body structure designs that reduce the overall mass of a vehicle and greenhouse gas emissions. By replacing the combustion engine with a highly efficient electric motor, car manufacturers achieve a lightweight design but effectively double the amount of silicon steel per car to anywhere from 60 to As70kg.demand for silicon steel increases in the automotive industry, the use of more silicon steel in electrical appliances has also increased. Moreover, there are
demands to develop ultra-thin electrical steels in a thickness range of 0.25mm and below. While current production of silicon steel represents only 1% of global steel production, the market for electrical steel is expected to grow by 7.5% in the coming
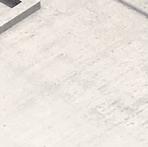
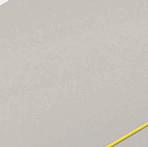
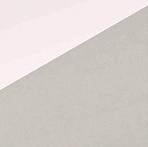
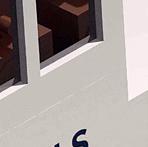
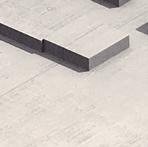

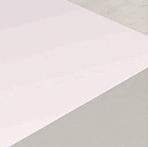
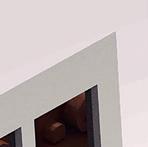
with exceptionally thin gauges is a nonissue, the current equipment cannot quickly increase product yield. Thus, producers look toward re-engineering existing equipment to transform their operations. Introducing a Universal Crown Control Mill (UC-Mill) is one step among many to improve quality. Beyond this, introducing a Tandem Cold Mill (TCM) to reduce thickness rapidly
Electrical steel for expanding markets
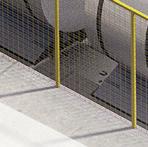

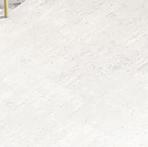
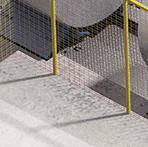
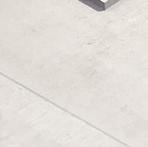

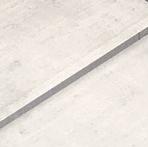
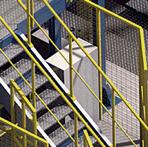
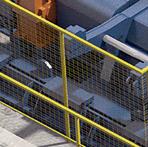
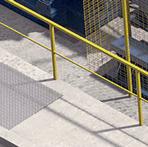
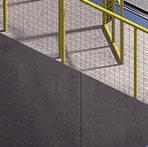
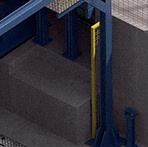
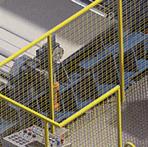
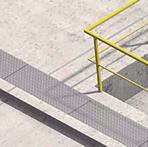
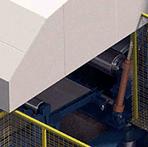

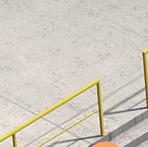

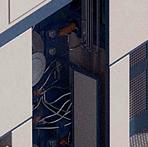


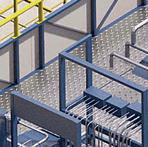


ROLLING30 www.steeltimesint.comSeptember 2022
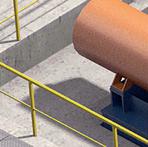
years.The anticipation of increased demand for electric steel grades is good news for speciality steel producers. However, meeting these growing demands for improved quality and strength while increasing capacity presents several challenges.Asdemand for high-quality electric steel grades increases, current speciality steel producers will struggle to keep up. Although processing high-strength steels
*.Primetalsnew Technologies Austria GmbH. ** Primetals Technologies Japan Ltd.
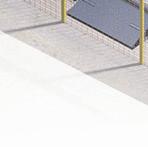
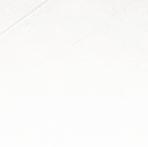

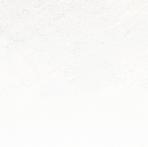
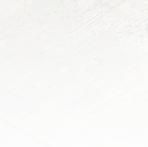


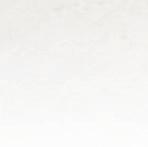

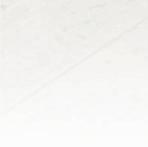
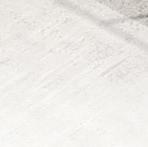
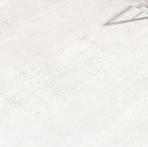
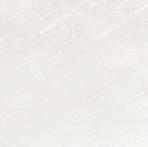
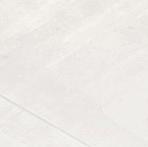
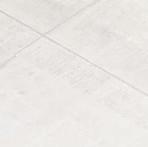

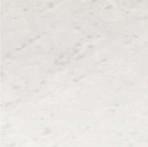

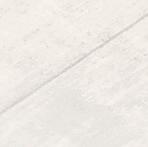
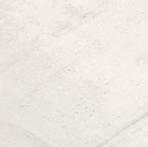
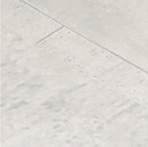

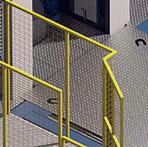
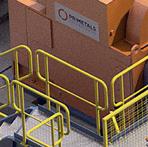
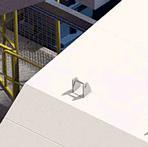
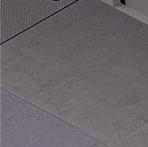

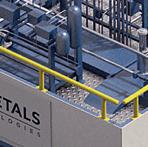

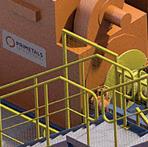

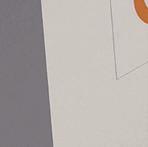
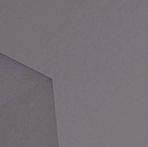


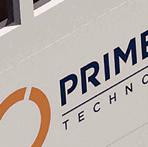
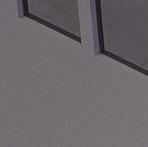
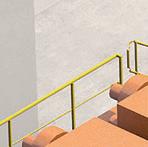
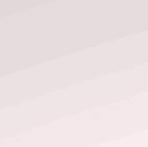
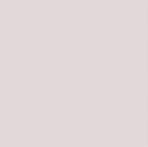
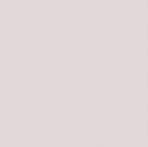
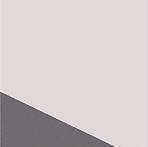
Electrical steel grades, from grain-oriented to non-grain-oriented, from thin to ultra-thin, will aid industries with exceptionally strong, lightweight materials made using cutting-edge cold rolling solutions by Primetals Technologies. By Konrad Krimpelstätter * and Ichiro Maeno**

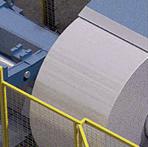
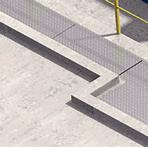
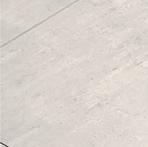
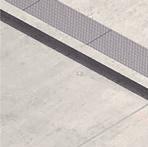

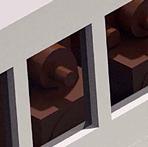

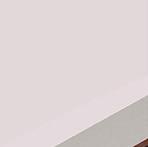
producers when cold-rolling hard and fragile electrical steel grades. Thankfully, the latest cold-rolling innovations provide technologies to navigate these challenges and produce high-quality electrical steels in terms of thickness, flatness, and surface quality.
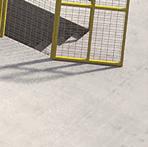
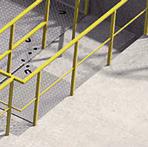
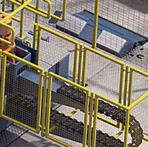

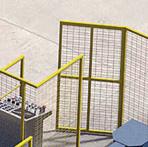

To effectively produce electrical steels, consideration of the status quo of the work roll diameters in conventional cold rolling mills is essential. By increasing the force to produce thinner products, the pressure inadvertently causes elastic deformation of the work rolls themselves. However, reducing the work roll diameter
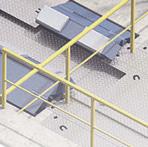
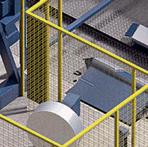
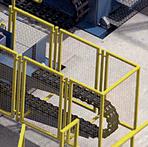
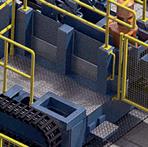
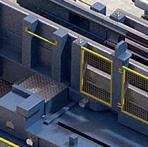
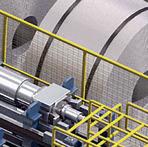
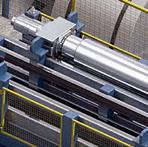
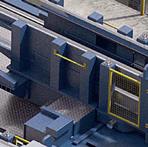
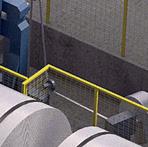

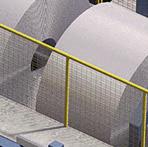
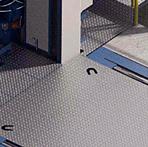
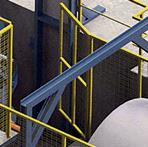
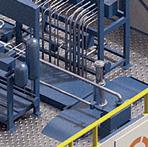
As UC-Mills have become industry standard for thin gauges, a Hyper UCMill, with smaller work roll diameters and increased torque, has a typical work roll diameter to maximum strip width ratio of about 20% compared to 25% for a UC-Mill. A 20% ratio and a work roll drive are ideal for rolling high-silicon electrical steels, such as high-permeability non-grain-oriented electrical steels and even advanced highstrength steels.
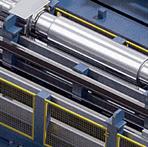
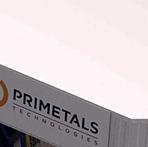
Fig 1. 2-stand Hyper UC-Mill for the production of non-grain oriented electrical steel and advanced high-strength steel

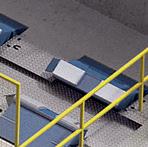

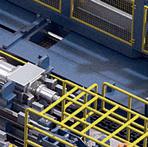
Fig 2. Typical configuration of a tandem cold mill for electrical steel sheet

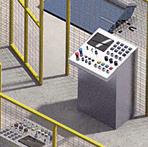
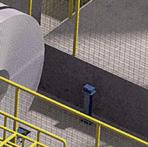
Yet, a focus on increased capacity goes hand-in-hand with the reality of increased risks and challenges for high-silicon electrical steel. High-silicon electrical steel involves high brittleness, meaning edge cracks can emerge and grow, leading to strip breakage, damaged equipment, and production delays. Moreover, increasing demands on quality target thicknesses of 0.2mm put additional pressure on
Tackling thinner steel
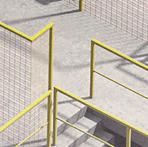
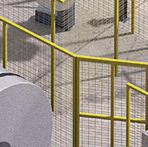
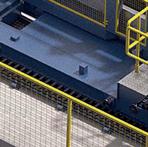
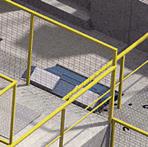
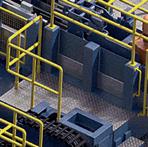
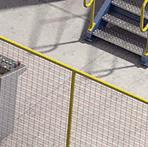
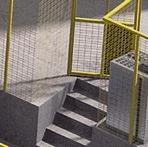
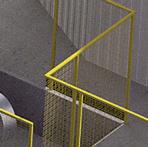
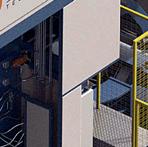
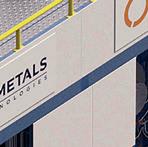
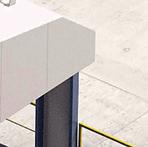

Precise edge control
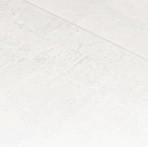
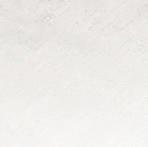
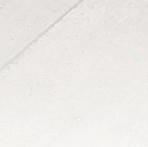
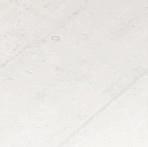
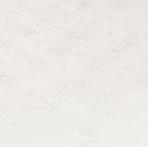
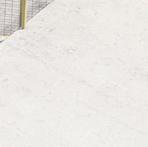

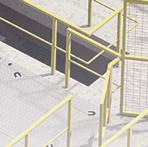
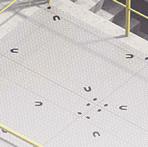

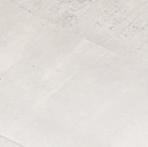

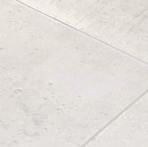
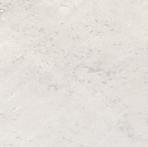


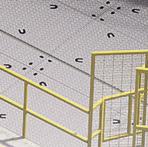
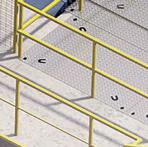
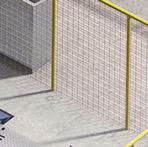
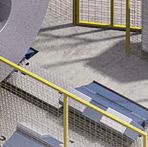
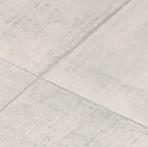
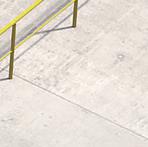
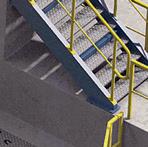
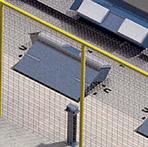
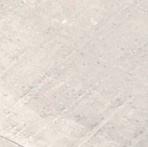
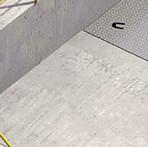
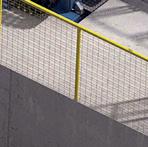

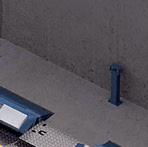


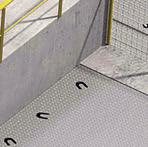
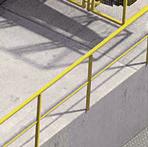
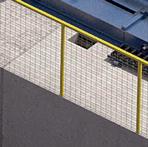
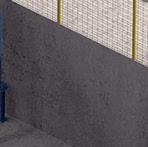
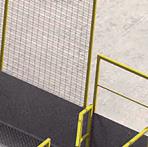

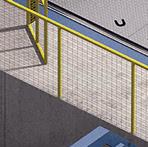
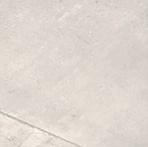
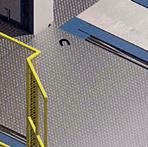
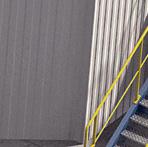

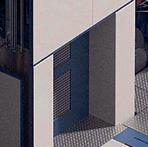
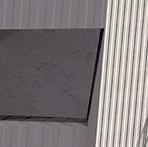
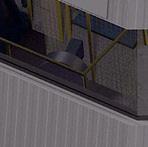

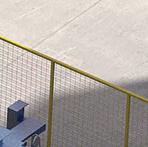
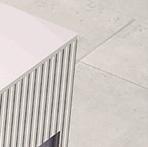
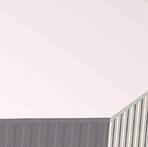
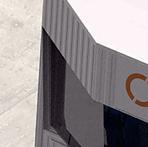
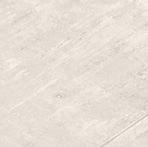
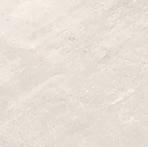
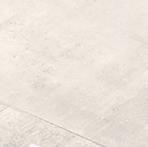
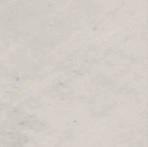
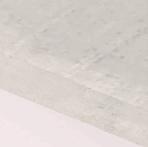
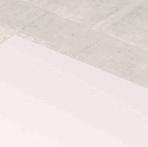

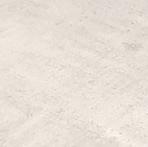
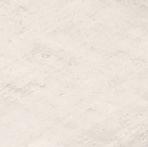
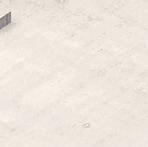


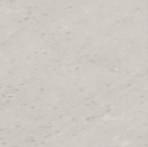
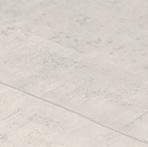

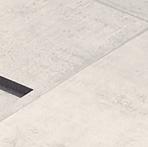
increases production times.
The Hyper UC-Mill is a six-high Universal Crown Control Mill with reduced work roll diameters and work roll drive, and high torque transmission capabilities. At the core of the Hyper UC-Mill design is the work roll diameters. After studying the current reduction capacities of a conventional mill, the research found that a Hyper UC-Mill can achieve higher reduction ratios using work rolls approximately 20 to 40% smaller in diameter. The ideal diameter for reduction capacities for a 4-feet Hyper UC-Mill is 230 to 290mm compared to a standard UC-Mill with a range from 385 to 425mm. Finally, to compensate for the smaller diameter work rolls, an ‘MH-Spindle’ provides 2.7 times the torque of a conventional Universal Joint (UJ)-type spindle.
ROLLING 31 www.steeltimesint.com September 2022
decreases the amount of rolling force to achieve specific thicknesses. Obtaining the approved thickness with less force is vital as demand grows for thinner steels with a higher silicon content. For this reason, many producers turn to a UC-Mill to produce thinner gauges. However, to deliver even thinner gauges with higher silicon content, Primetals Technologies developed the Hyper UC-Mill.
Another challenge when rolling hard electrical steels is the decrease in the thickness profile at the edge of the strip, a phenomenon called edge drop. Edge drop occurs due to roll bending and work

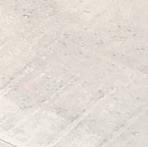
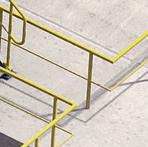

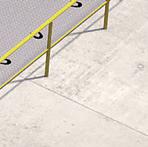
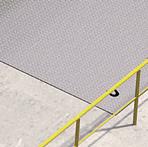

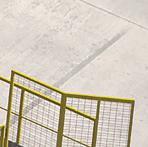

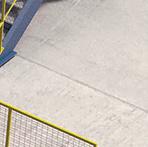
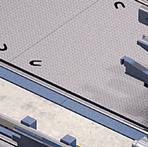
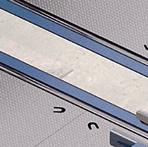
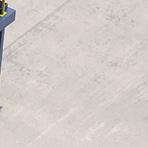
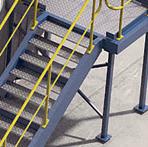
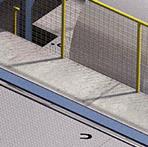
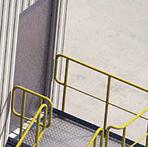
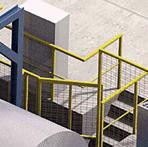
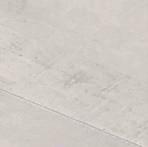
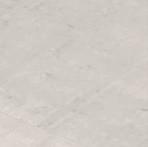
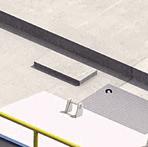
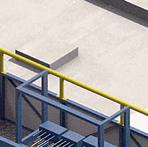
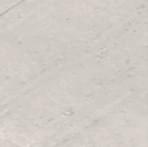
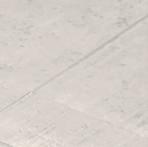
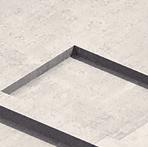
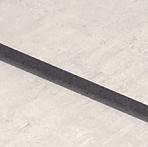

ROLLING32 www.steeltimesint.comSeptember 2022
distribution, and induction heating. By using an advanced strip temperature model, these various factors can advise the best course of action for the optimal deformation behaviour of high-silicon electrical steels.

Above all, emulsion lubrication can be detrimental to energy efficiency, particularly after strip heating to reach ‘warm rolling’ conditions. Minimum Quantity Lubrication (MQL) was developed by Primetals Technologies in order to maintain the temperature using atomized rolling oil sprayed directly onto the surface of the work rolls. MQL creates an oil layer on the work roll surface to improve friction conditions. A consistent and thin oil layer ensures that roll-gap lubrication will not affect strip temperature, which can drop significantly with typical lubrication strategies. A state-of-the-art lubrication and temperature control system increases efficiency, reduces costs, and, most importantly, improves the consistency of the end product.
Adding heat to cold rolling
Typically, cold rolling involves room temperature steel – eg, 20 to 30°C – with high silicon and aluminium content and this can lead to reduced flexibility and formability during cold rolling. To lower the brittleness of steel with a high silicon content, an induction heating device can be installed to increase the temperature to anywhere from 60 to 160°C, creating the conditions for ‘warm rolling’ in the first tandem mill stand or the first pass of a reversing mill. Producers can increase mill speeds or deformation rates by reducing the risk of strip breaks through ‘warm rolling’, meaning improved productivity and production rates for high-silicon electrical steel.
Fig Rolling capability of different mill technologies
3.
While a Hyper UC-Mill provides immediate benefits to producing high-quality electrical steels, using a tandem cold mill with multiple stands in series provides a straightforward means for improved yield. Yet, while Hyper UC-Mill technology offers immediate solutions for revamped and greenfield tandem and reversing cold mills, a different approach is required to reduce harder materials, such as grain-oriented or high-grade non-grain-oriented electrical
With its approach to tandem cold mill configurations – eg, a six-stand tandem cold mill featuring all Hyper UC-Mills – the company has the cutting-edge solutions to increase yield without diminishing product quality. Finally, as electrical steel will undoubtedly become more than a niche commodity with the expansion of electric vehicles, solutions that increase production capacity will help producers keep pace with growing
steels.Aspreviously mentioned, high-silicon electrical steel – i.e., Si ≥ 2.5% – also suffers from an increased risk of strip breaks due to its brittleness at normal cold rolling temperatures. Increased rolling loads – ie, strip tension, contact pressure, and shear stresses in the roll bite – can increase edge cracks, slowing production. One means of reducing such brittleness is reintroducing heat before cold rolling.
Moreover,demands.withquality and thickness requirements becoming ever-more stringent, the company is further developing mills for ultra-thin materials. For example, the 20Hi HZ-Mill, or advanced split housing ZR-Mill, uses exceptionally small work roll diameters for ultra-thin hard materials like grain-oriented electrical steels. In conclusion, Primetals Technologies has raised the bar and set the standard for the production of grain-oriented and non-grain-oriented electrical steels and has developed innovations to meet increasing demands in the years to come. �
roll flattening. Controlling it is crucial because less edge drop allows for high lamination factors and low core losses in electric motors. Edge drop control is commonly applied on tapered work rolls. It uses hydraulic cylinders to shift the rolls accordingly and apply uniform pressure, known as a UC-Mill featuring work roll shifting or UCMW.
The Hyper UC-Mill combines work roll shifting, intermediate roll shifting, work roll bending, and intermediate roll bending to achieve precision edge drop control and flatness control to maintain highly effective reduction ratios and consistency. In summary, using hydraulic shifts on the work rolls and intermediate rolls, the Hyper UC-Mill effectively compensates for edge drop and unflat strip, ensuring consistent product quality. The Hyper UC-Mill can be applied to single or twin-stand reversing cold mills for smaller production capacities and continuous tandem mills for maximum production capacities to meet the most stringent electrical requirements.
Keeping the temperature just right Strip temperature guidance is crucial to further regulate the processed strip’s temperature. If the strip is too cool, edge cracks and strip breaks may occur, and if the strip is too hot, heat streaks or surface defects can emerge. Strip temperature is maintained using strip cooling, work roll cooling, strip speed, rolling pass
Advancing production
To meet growing demand for high-grade electrical steel, grain-oriented and nongrain-oriented, exceptional control of specifically designed rolling mills is crucial. While raising the bar with the Hyper UC-Mill, Primetals was able to improve strip thickness reduction and quality.
Coal blend optimization
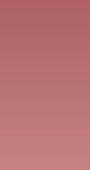
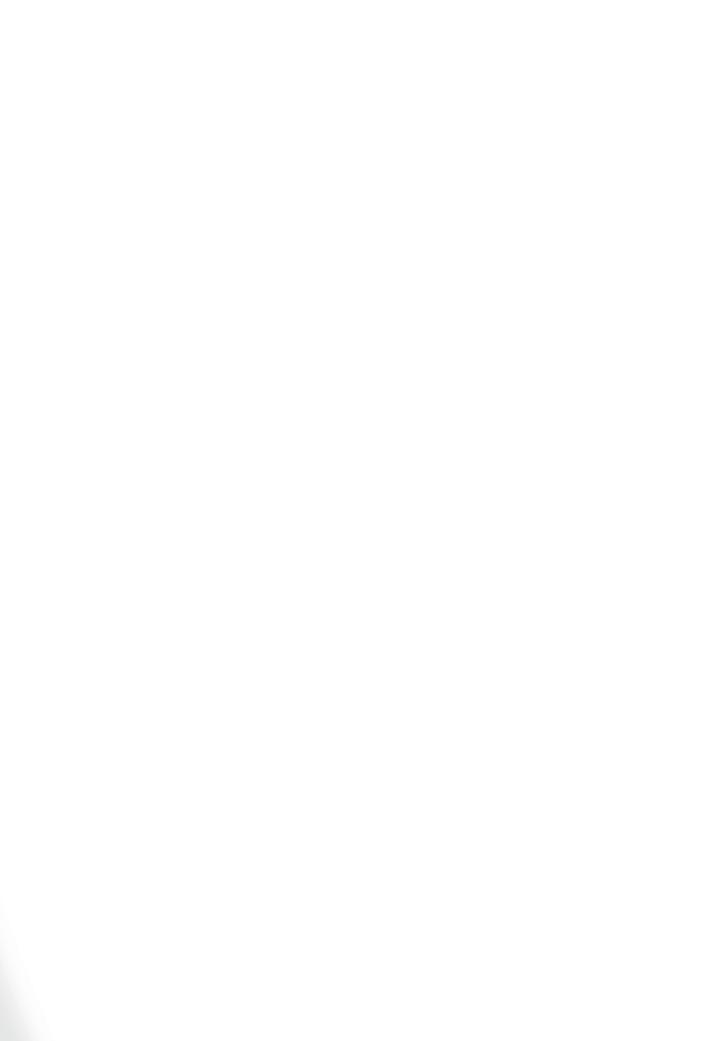
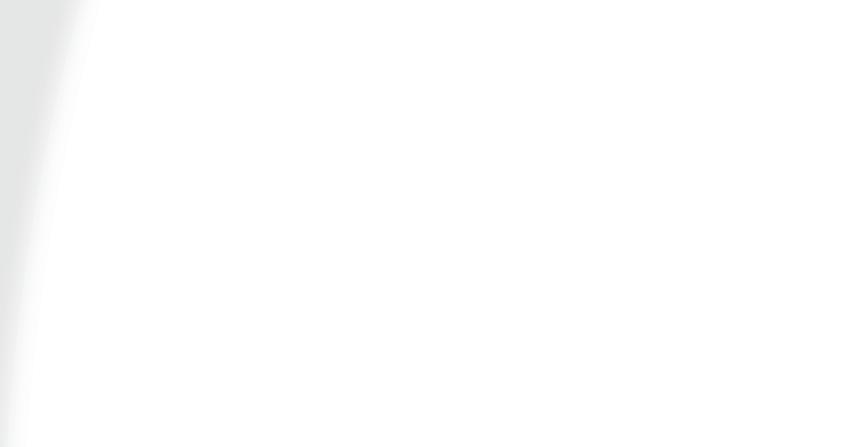
We are indeed proud to look back upon more than sixty years of research and development in the field of cokemaking. DMT providing state-of-the-art investigation methods for stamp and top charging supportedPilot-scaleby testing in a 10kg-retort Semi-industrial movable coke oven 60-year experience of coal blending Generation of coal blends with coals from different origin to perform reference tests
Earth. Insight. Values.
http://www.dmt-group.com/en/services/consulting/coke-making-services.html Raw DR-EAFassessmentmaterialfortheroute
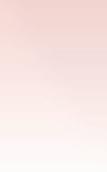
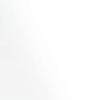
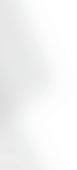
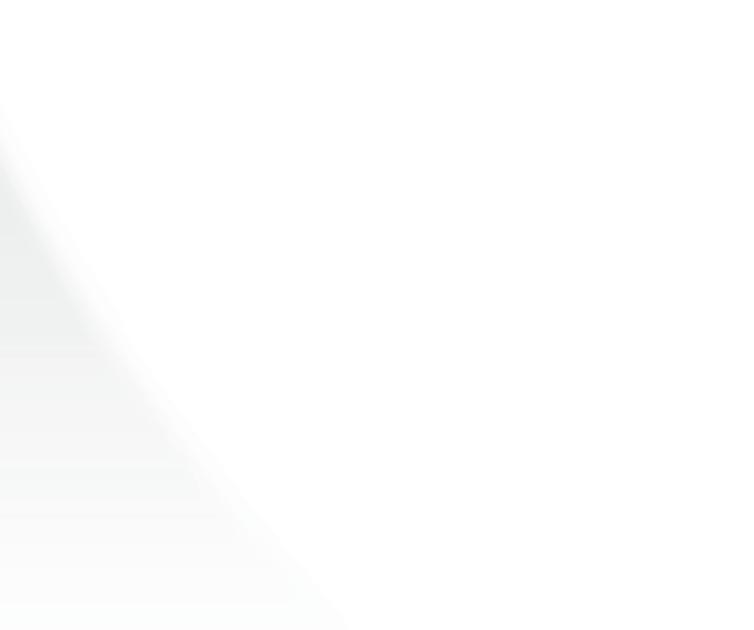

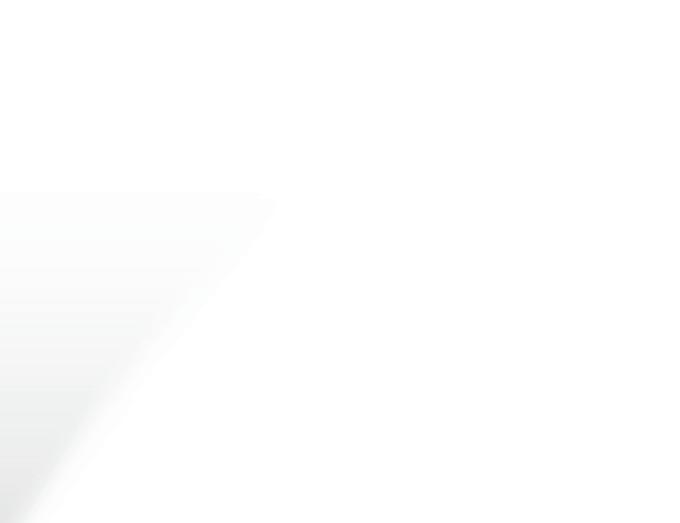
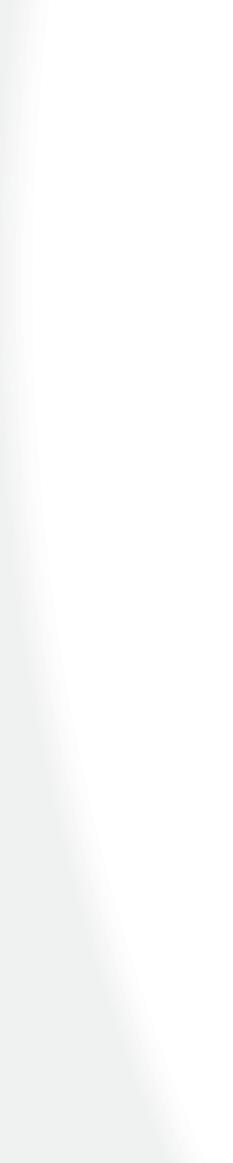
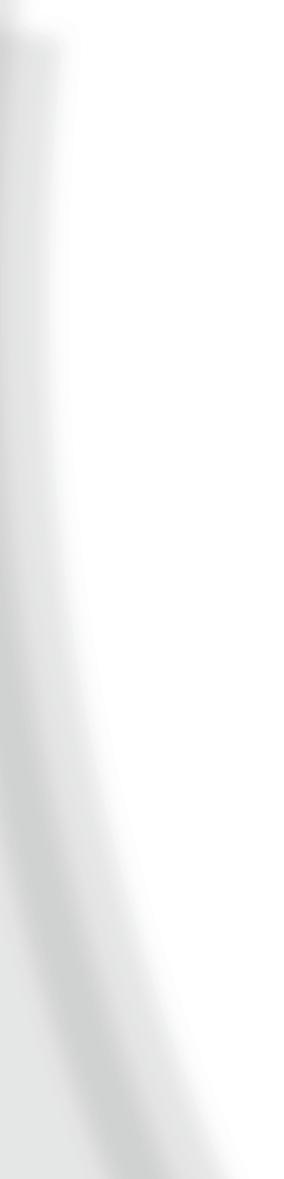
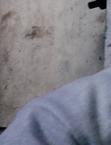
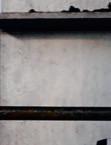

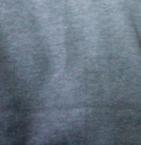

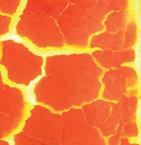
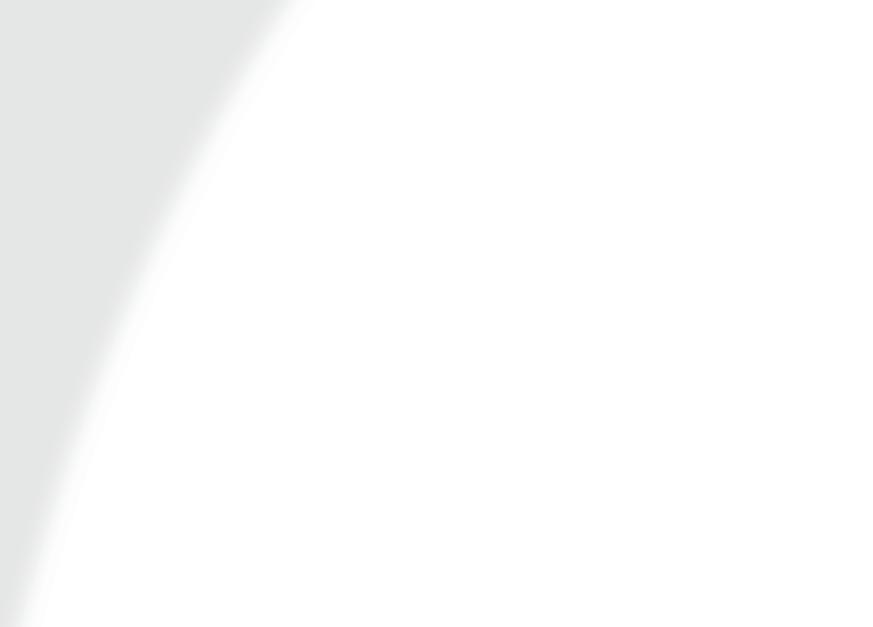
DMT supports coke plants in their continuous quality control of the used coal and the produced coke
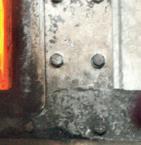

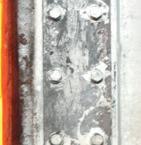
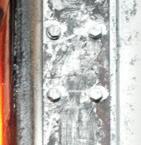

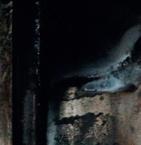
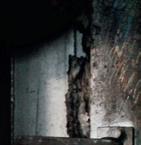
• Value in use considering productivity, environment and resource efficiency • Scrap chemical analysis and uncertainty • Benchmarking recipe cost against theoretical optimum Contact rutger.gyllenram@kobolde.com / www.kobolde.com

DMT use international standards to determine coal properties and coke qualities
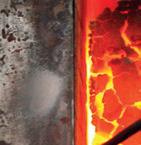
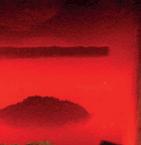
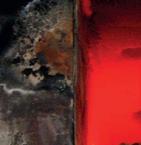
www.dmt-group.comCokemaking

Services
Coal & Coke quality
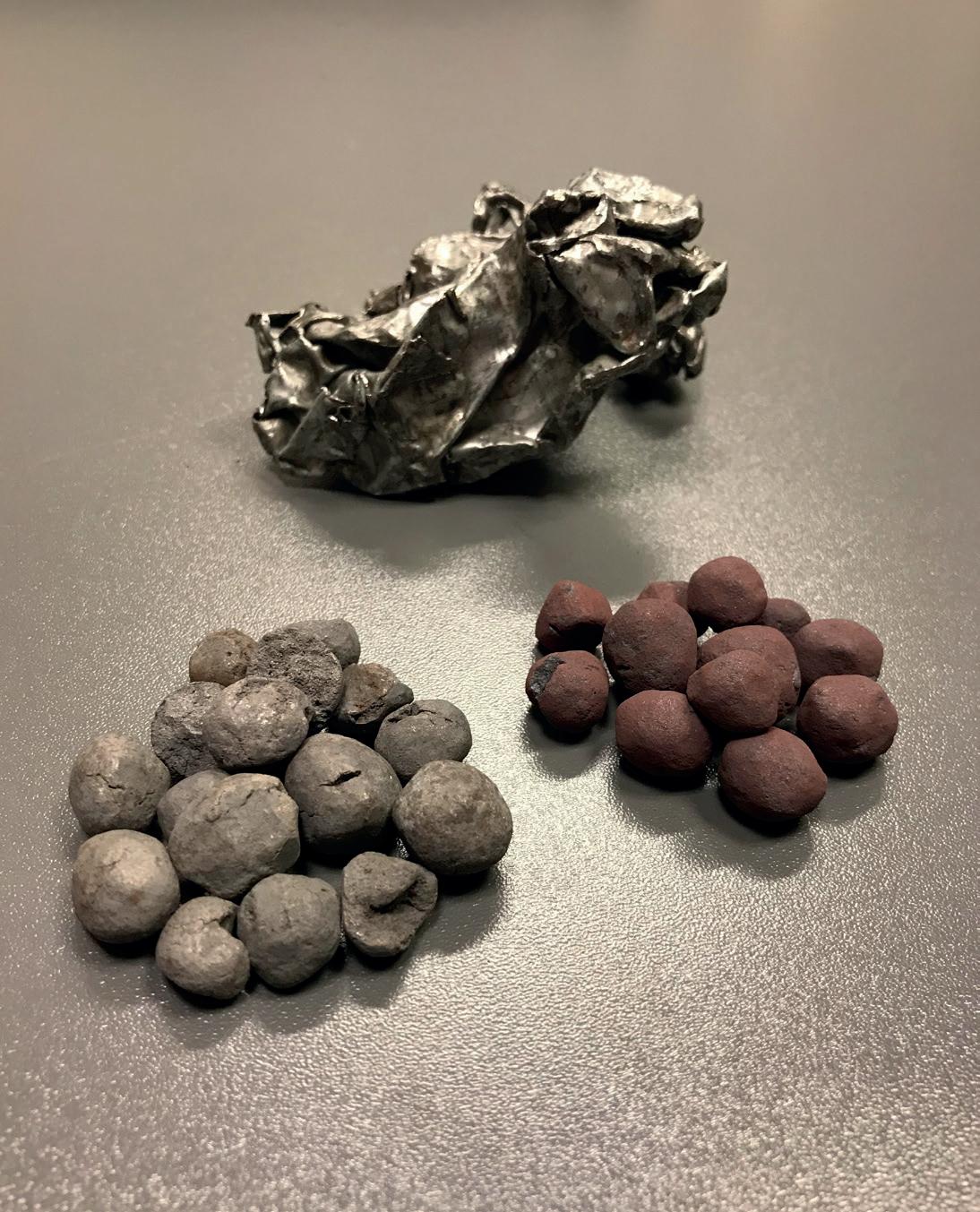
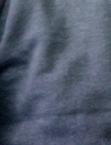
Value in Use considering Productivity, Environment and Resource Efficiency.

DMT assists coal merchants and assess their product for the marketing
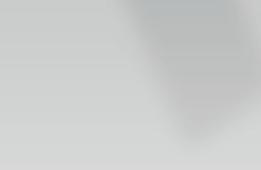
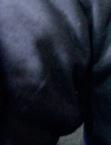

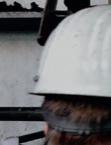
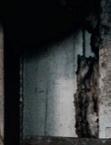
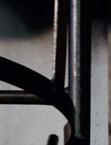

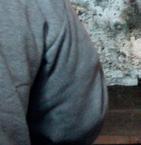
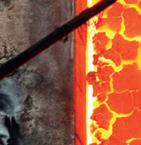
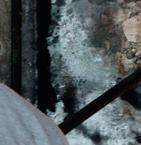


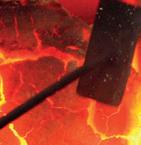

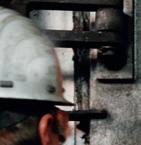
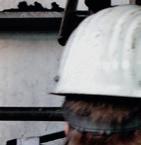
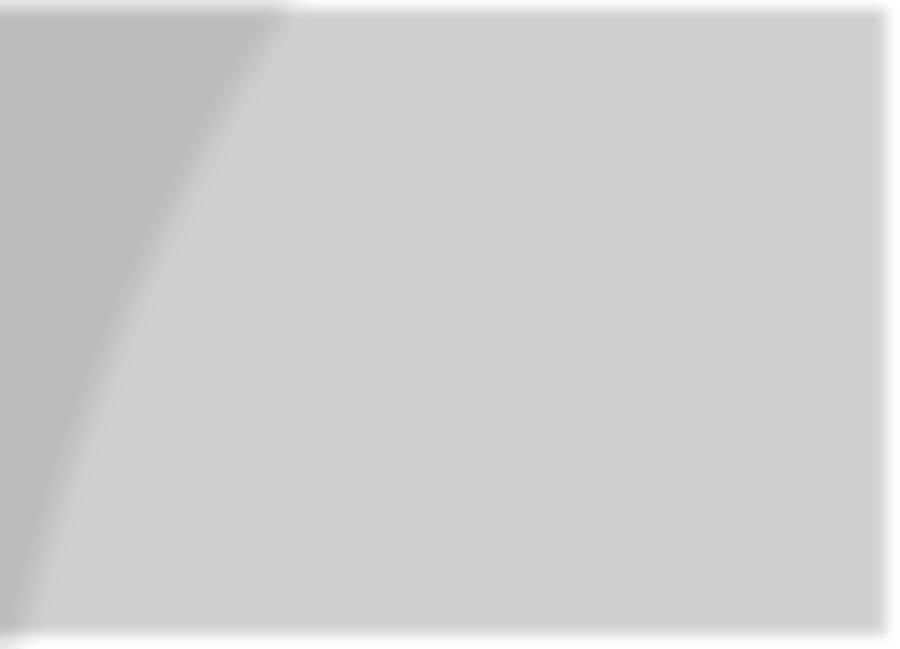
Maximum quality and production flexibility
A combination of high plant productivity, efficiency, superior-quality finished products and plant flexibility are the keys to success in the wirerod market. These requirements, in addition to Danieli’s latest research efforts and industrial set-up activities, point the way to environmental sustainability, true green-steel production and the adoption of a circular economy model, as seen in the tangible results achieved by the ABS QWR 4.0 project, which rolled its first billet on 27 November 2020, and now is considered a world leader and benchmark among wirerod suppliers.
ABS QWR plant layout
The plant layout was developed following the principle by which the entire rolling mill production area is intended more as a mechanical workshop, like those used for numerical control machines, rather than a conventional rolling mill. The building structure is a clear expression of this concept: a low roof height with a shortspan shed, with individual machines used only when needed, optimizing spaces, process flexibility and equipment readiness. The workshop area is located behind the shutter doors, and all installed equipment can be automatically moved there to be prepared or changed due to wear.
Material production flow characterizes the equipment that makes up the plant, proving that ultra-productivity, reliability and efficiency are key ingredients that contribute to the success of the facility. The first scale-free (with 0.32% scale formation), energy-saving Danieli Centro Combustion walking-beam furnace is designed to minimize oxidation phenomena through a combination of highly accurate combustion control in sub-stoichiometric conditions and a tightly sealed furnace chamber.Thepatent-pending furnace chamber has been separated into several ‘microchambers’ using walls, noses and diaphragms to control individual volumes with a different air-gas ratio. By controlling such parameters, it is possible to actively intervene on oxidation kinetics to inhibit scaleEnhancedformation.combustion control was developed through higher pressuredrop flow transmitters for gas, and flow straighteners for air. Furthermore, postcombustion air injected into the furnace by
Sisak (HR) facilities.
With a 190-million-euro investment, the plant in Cargnacco (Udine) produces 500 kt/yr of special steel and automotive application wirerod, from 5.0 to 25 mm diameter at finishing speeds of 430 km/h. The final product is equally shared between the Italian and European markets.
ROLLING34 www.steeltimesint.comSeptember 2022
Italian plant builder Danieli’s inspiring ABS QWR 4.0 project is regarded by the company as a ‘milestone installation’ that redefines rolling mills with an original approach for enhanced operational performance, sustainability, operator safety and product quality. By Maicol Cimolino*
Key technological equipment
High plant productivity and flexibility are guaranteed not only by the up-to-130 tonnes/hr capacity but by the 170 to 230mm round blooms and the 150 to180mm square billets, to be used as starting material, which come only from ABS (IT) or
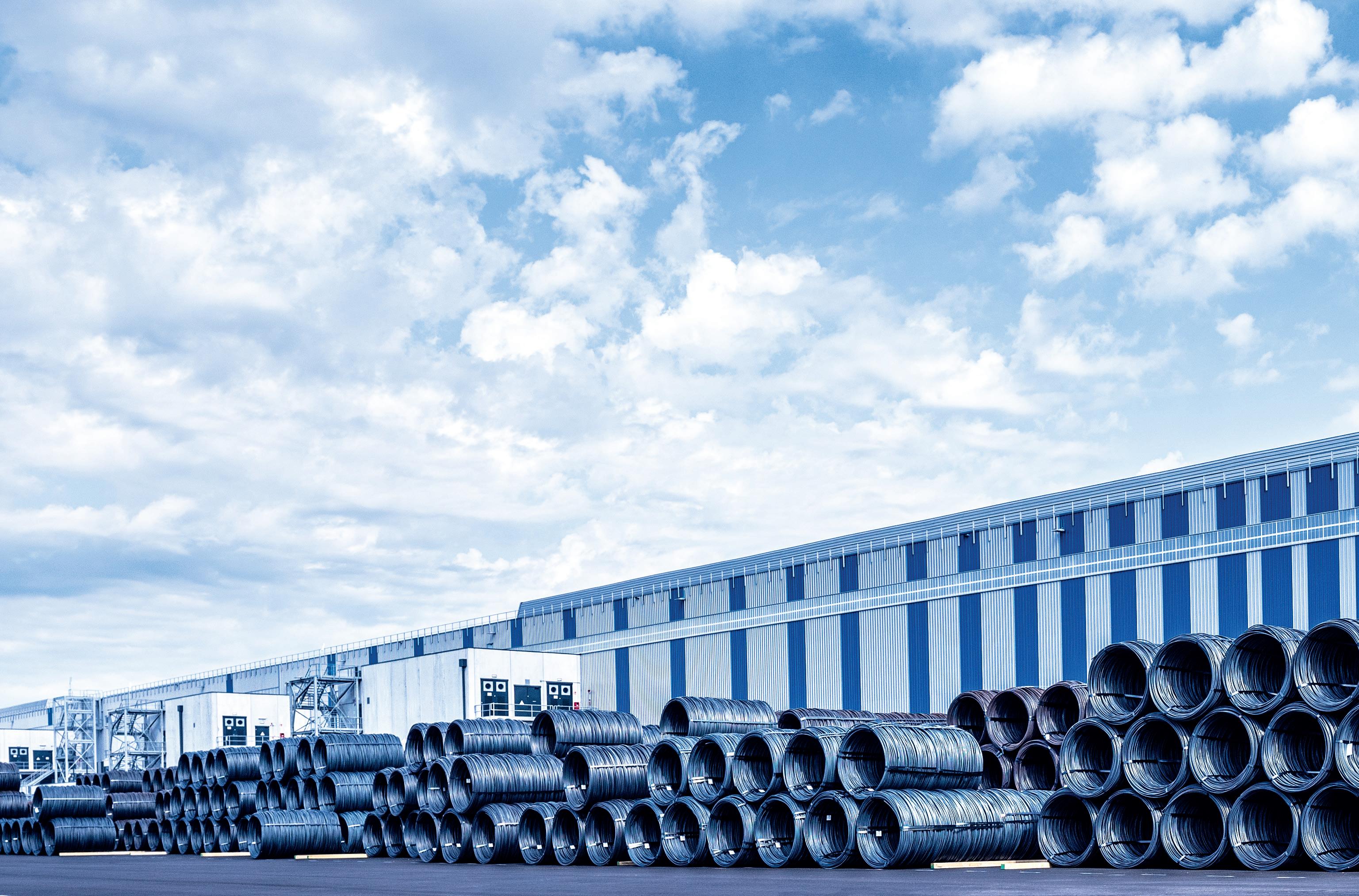
This integrated approach embraces the design of long-life, easily refurbished equipment, with resources and energy consumption optimization favouring renewable sources. The 10 kt of Ecogravel® (EAF slag recovery) used for paving is a good (and virtuous) example of environmental care, but also a profitable investment.
*Process technology manager, rolling mills, Danieli Morgårdshammar
ROLLING 35 www.steeltimesint.com September 2022
SHS 4.0 housingless stands are fully electrified to comply with the ‘green mill’ concept. Replacing hydraulic controls with electrical ones ensures multiple advantages, from eliminating oil and oil leaks to cutting off the central hydraulic unit’s electrical consumption, as well as savings in civil works and erection time.
high accuracy and repeatability at 430 Km/h and beyond, synchronizing the laying head to ensure proper coil laying on the cooling conveyor. One additional benefit from this equipment is that it increases operator safety in the area.
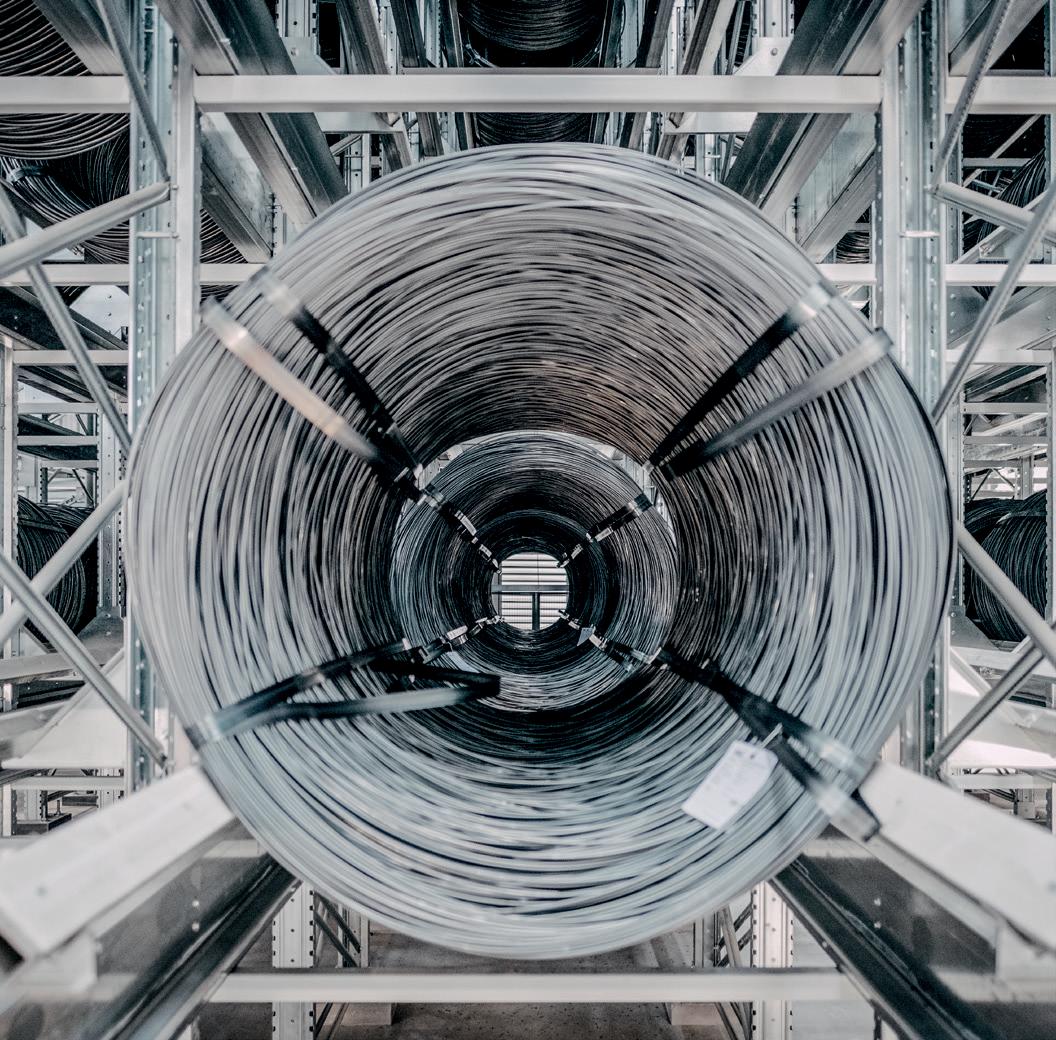
coldThedrawability.mostrecent

The aforementioned automation system includes a high-speed shear, which avoids manual operation head and tail trimming and, therefore, the need for a dedicated workforce. It can trim rolled material with
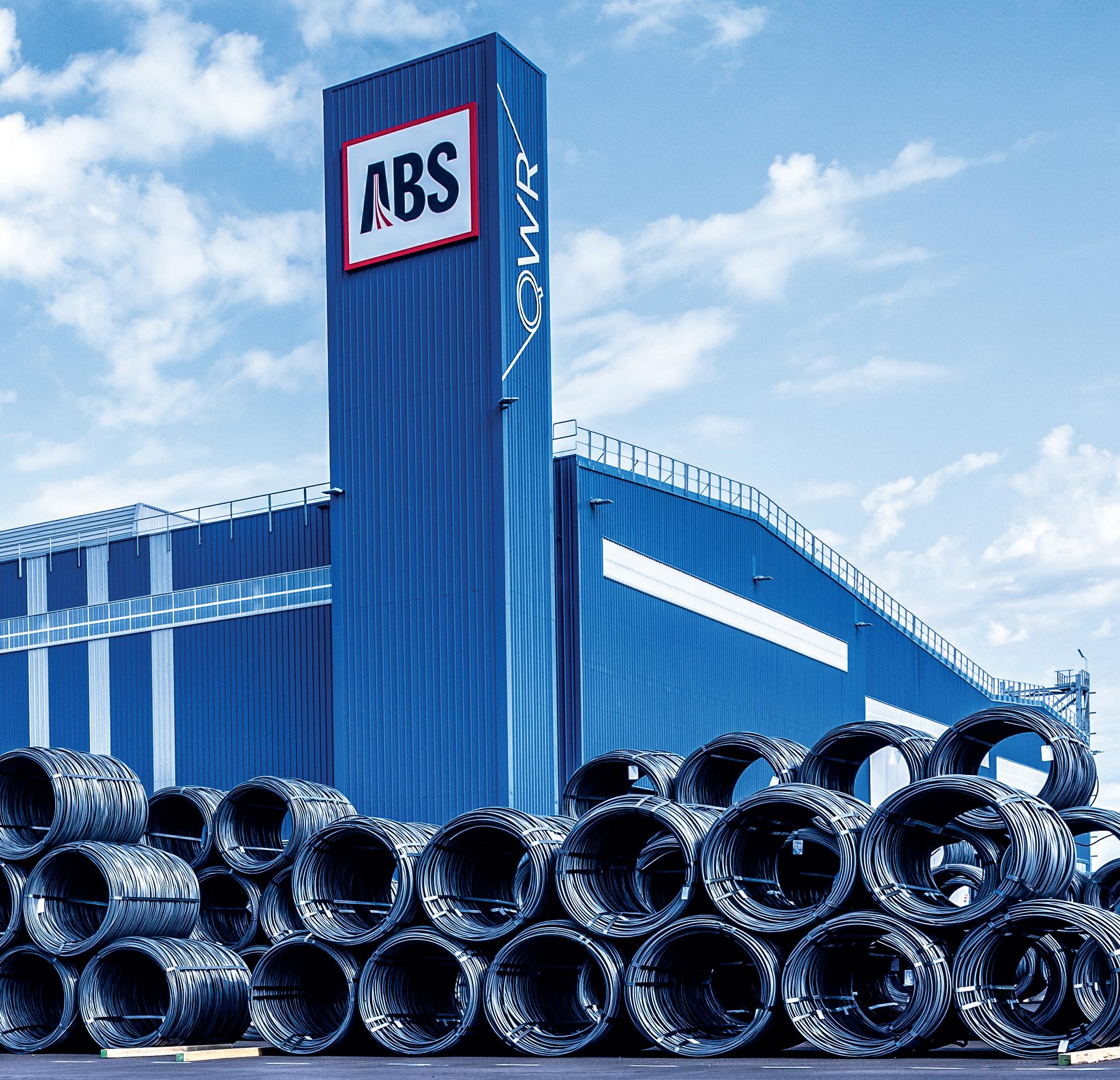
Several pyrometers and thermal imaging cameras are placed along the entire line and continuously monitor and record material temperature, while fine-adjustments to the reheating furnace, on-line induction heating system and all in-line water box treatment status are made possible thanks to sophisticated automation systems.
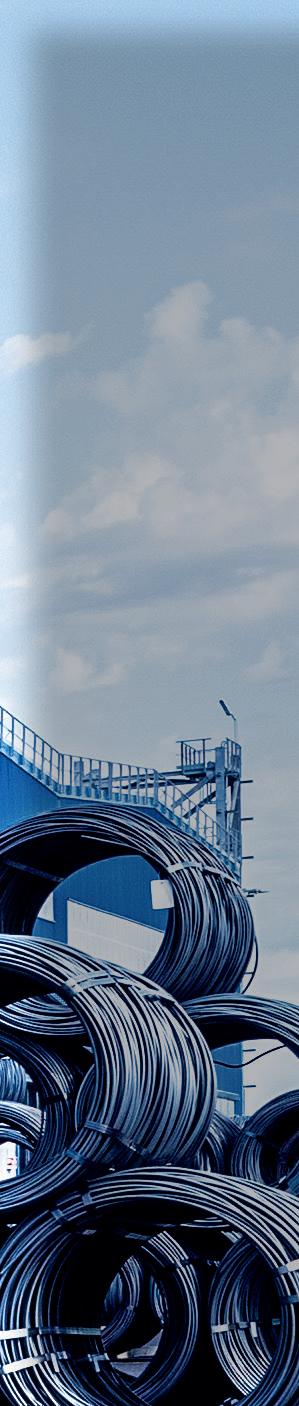
nozzles arranged on the roof and side walls compensate for the reducing atmosphere generated in the hottest zones. A laser spectrometer continuously detects the percentage of oxygen in the recuperative zone before waste gases leave the furnace; this parameter is inserted in a safety control loop that acts on post-combustion air in order to have the desired oxygen at fumes
An Easy Drawing Continuous system – EDC for short – can be applied as an alternative to traditional cooling fans to achieve in-line-patenting of high-carbon grades using boiling water. For maximum flexibility, the system has been designed to shift sideways from in- to off-line position in order to treat suitable steel grades and dimensions through a process water tank. Compared to other methods, the EDC process provides a sorbitic microstructure, which brings uniformity and controls grain growth and scale formation, enhancing
A 3-MW Danieli Automation induction heating system is installed between the free roughing stands and the continuous mill and represents an environmentally friendly solution for reheating steel and reducing scale formation. The environmental advantages include reduced consumption when efficiently transferring energy to the material, and no gas emissions, while required electrical energy comes from renewable sources via green energy production systems.

Additionally, Hi-Section (eddy-current mass flow meters) and Hi-Profile (laserbased measurement instrumentation)
iteration of automatic, motorized smart guides is installed in both the stands and the wirerod blocks and will receive real-time feedback from each billet, adjusting the guide force acting on the bars as well as on the position of the rollers position, and monitoring bearing status.
exit.All
On 17 September 2021, equipment reliability and process toughness enabled the mill to set a rolling speed record of 132.4 m/s, equal to 476.6 Km/h rolling 5.5-mm-dia wirerod. This record remains unbeaten by other special steel producers.
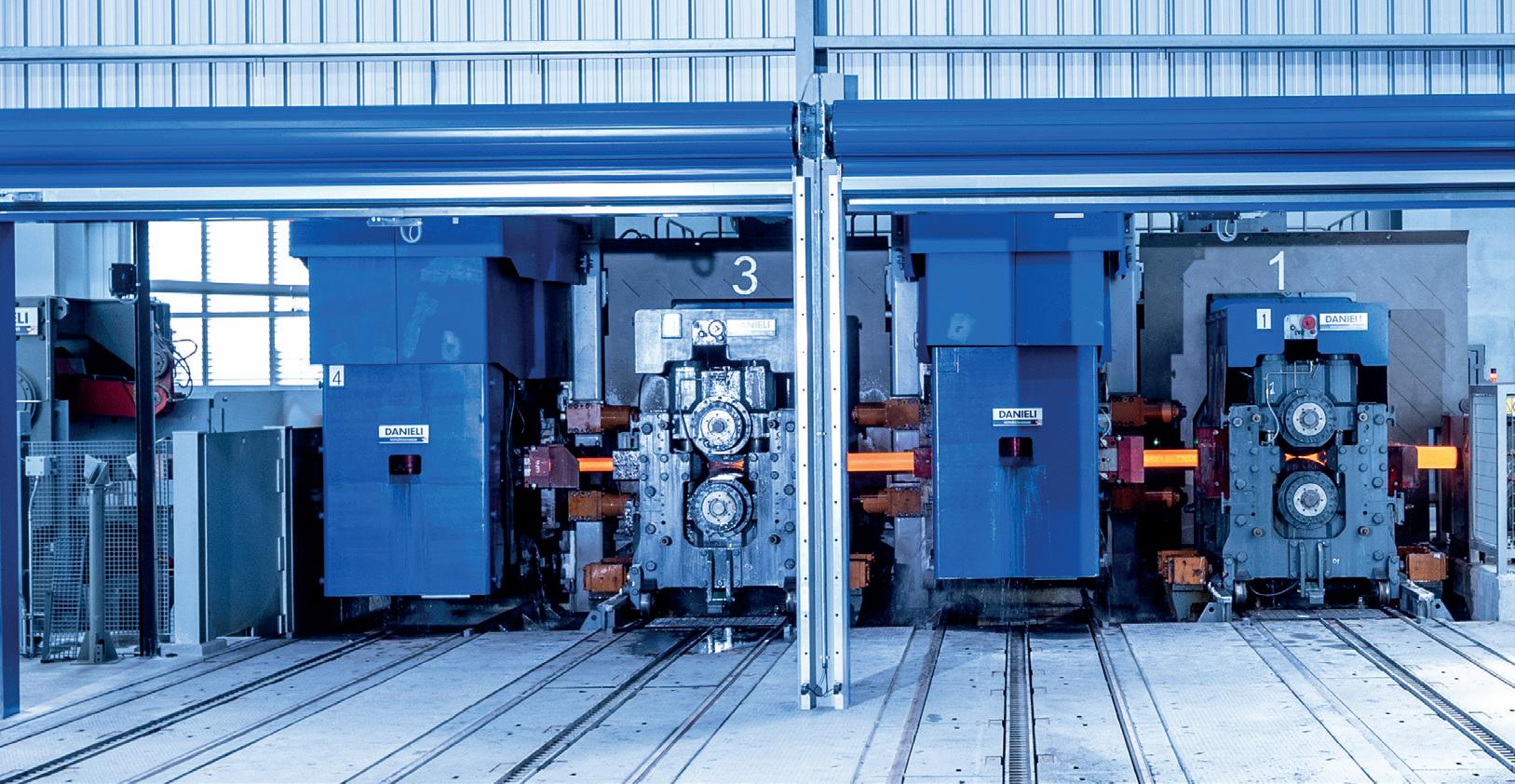
are worthy of mention, thanks to their ability to control steel by applying thermomechanical rolling, ensuring appropriate final wirerod metallurgical and mechanical properties to improve steel strength, toughness and ductility. That is why grain refinement may be considered the mosteffective way to deal with these demands without increasing alloying elements, thanks to several controlled cooling stages along the mill and roller conveyor. The thermo-mechanical rolling process is characterized by deformation in the non-recrystallization region of austenite, usually ranging from 750 °C to 850 °C, where it may be carried up to a specific area of reduction to obtain the desired grain refinement and microstructure modification.Formedium-carbon, micro-alloyed
An additional advantage of the pulpit is that all mill functions and process
parameters are supervised by only two operators – one for the mill process itself and the other for on-line heat treatments – who monitor the main plant KPIs and process parameters.
Process efficiency is directly related to the ability to manage the process: that is why the rolling line is controlled via a monitoring system with more than 2,000 data acquisition sensors, and over 15,000 continuously recorded parameters. Sensors provide continuous real-time process and plant data, whether directly measuring physical values or applying process models. Digitalization helps the operators to avoid mistakes, increasing workplace safety and, as an added benefit, product quality.
steels for cold forming, the reduced prioraustenite grain size (PAGS) achieved by means of thermomechanically controlled processes, avoids hardness hot spots that would have required annealing treatments before cold forming. Also, improvements in cold drawability can be achieved by controlling the scale layer, which is thinner and uniformly distributed.
Quality performance from the start
Product traceability and quality control Danieli believes maintenance is paramount to ensure high plant availability and reliability. That is why all key equipment includes an ID tag with a barcode to identify device information, such as storage operations and remaining tons/ hours before refurbishment. Many devices, such as cartridges, cylinders and guides, are equipped with radiofrequency identification tags. A workshop management system supervises equipment preparation and organization, checking and providing continuous grooves and guides status updates. An advanced, integrated laboratory located next to the coil finishing facilities is used for instant feedback on the rolled products’ final mechanical and metallurgical properties; additionally, it allows final product certification before shipping, with real-time product traceability, closing the circle on a fundamental requirement for a modern plant, tracking the product from melting to customer delivery.
The Danieli original process solution
solutions continuously control material dimension, offering live feedback to automatically regulate workflow, ensuring bar optimization in terms of size tolerance, cobble reduction and rolling guide wear. Special cameras installed between the stands check material tension for a looperless mill layout.
Finally, coils are stored in a fully automated warehouse designed to safeguard the products’ surface quality while ensuring a high degree of process flexibility with short lead-times on orders. It can hold more than 11kt of wirerod coils. After being automatically tagged and stored, the material can be organized in relation to incoming orders and production requirements.Anew-generation pulpit with 3Q technologies is fundamental to support advanced technologies such as artificial intelligence, augmented and mixed reality, empowering the operators’ perception and helping them to both identify and predict anomalous process behaviours.
ROLLING36 www.steeltimesint.comSeptember 2022
The mechanical strength of high-carbon steel is related to interlamellar pearlite spacing and can be enhanced through control of continuous cooling on a roller conveyor; thanks to this, variation in the mechanical properties along the coil and ring can be reduced. Benefits can also be achieved for the bearing grades where deformation at a non-recrystallization region of austenite may permit enhanced carbide distribution and dimension.
The QWR approach is to have the operator supervise and control all changes and mill preparation activities with limited-to-null manual intervention, enhancing equipment robotization, extensively using on-line instruments and sensors for quality and product check-up in a closed-loop control, and multi-route layout for different steel grades and product dimensions. The automatic set-up for heat treatments is an example of this, where the process control system automatically loads the proper setup table from the database and sends it to the equipment control, without manual intervention.Theequipment has been changed from traditional maintenance management and condition-monitoring systems to real-time
The facility’s in-line heat treatments
Events (Points of Interest) are identified and stored in the system, allowing the
support and diagnostics.
The benefits of such an approach are manifold: it preserves operator safety and significantly improves working conditions; only 14 highly qualified operators are required per shift, compared with a traditionally-operated rolling mill with a similar product portfolio, thanks to a strong emphasis on automation control.
the material (air cooling, slow cooling under the hoods, fast cooling with fans or by the EDC), and there is the possibility to collect the material in two different positions, using the hot or cold pit.
Points of interest then are used for ex-post analysis, identifying possible malfunctions and quality issues, allowing for discovery of trends and improvements. The resulting data builds up a data lake (numeric, visual, audio and other information) to support artificial intelligence models, which will automatically improve plant performances.
The process has been developed so that models and monitoring are widely deployed to manage all parameters along the mill and, consequently, optimize final product quality and mill performance. Additionally, predictability is now possible, to understand a phenomenon before it manifests. The implementation of the ‘Danieli Intelligent Plant’ philosophy is a revolution for plant management and post-processing analysis.
ROLLING 37 www.steeltimesint.com September 2022
Flexibility in configuration, speed in set-up changes, no-trial billets, and first coil produced in full quality (both for dimensions and metallurgical characteristics) cannot be achieved by overwhelming operators or by stressing the equipment. In recent years the production of quality wirerod grades has boosted research into new and more efficient technologies in response to increasing demand for high-value-added wirerod to be used in hardware factories for many applications, such as cold heading wire for bolts, and high strength cables, galvanized wire for suspension bridges and roadways, railroad switches, spring wire, reinforcement strands, rods for the reinforcement of prestressed concrete structures, bearing steel, piano wire, welding wire and so on. The large number of steel producers and the continuously progressing technology make the long product market steadily more competitive and selective.
Today, exploiting the IIOT platform and advanced technologies, an entire plant can be controlled from a single pulpit, which no longer needs to be in the production area, just like at ABS new quality wirerod mill plant in operation in Italy.
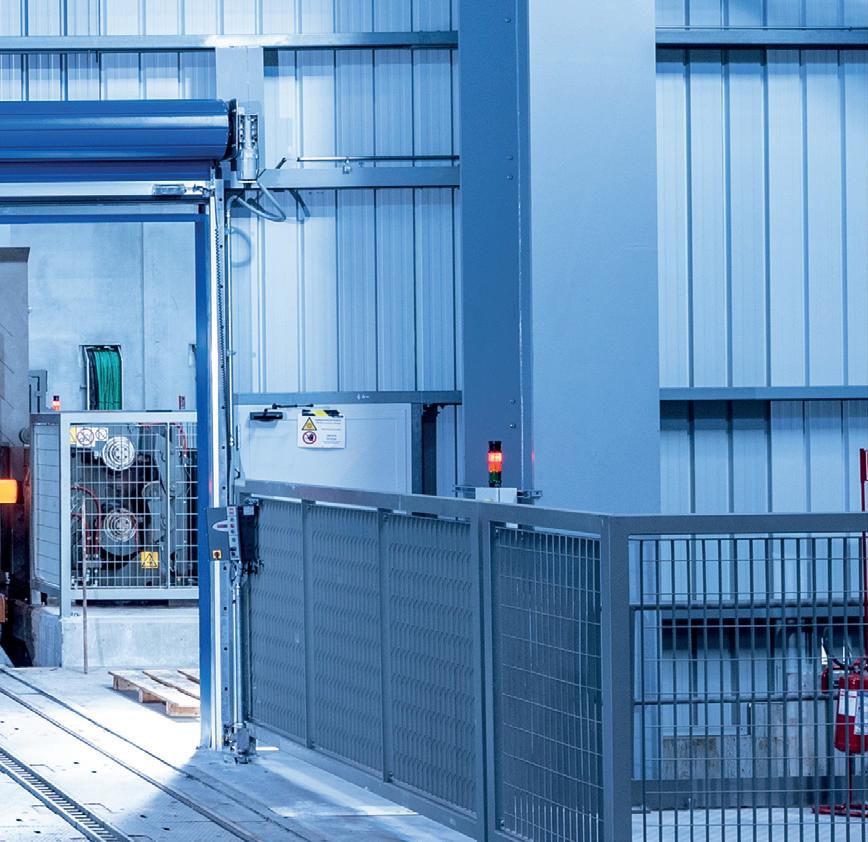
Maximum production flexibility
Zero-man-on-the-floor concept
The QWR approach is to adopt an automation with a human-centric approach, actively contributing to the growth of the operatormanaged plants, while surrounding technologies are designed to achieve easier target identification and an immediate product quality.
All mill activities are performed automatically thanks to strong automation control. There are no operators in the field.
“time machine” to track all anomalies or specific situations, based on automatic and manual triggering, including voice control.
The plant makes 35 automatic changes on rolling stands, blocks, water boxes, high-speed shears, HiProfile devices, looplaying head and Hi-Profile guide channels. Everything that is required to change a section is fully automatic and automated. Only eight minutes are required to change the entire mill – and, generally, no more than 15 minutes in particular circumstances – to which should be added three minutes between one billet’s end and the beginning of a new Advancedsection.automation plays a fundamental role throughout the plant, especially with the ‘first coil in quality’ concept (i.e. without trial losses), which is achieved thanks to on-line sensors and measuring instruments working in a closedloop control and managing metallurgical, dimensional, and quality aspects.
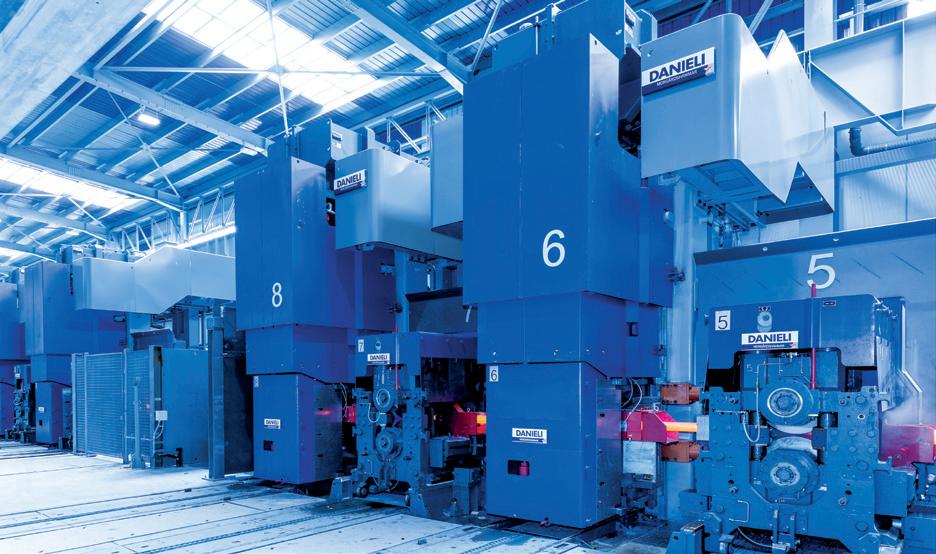
the “any size, any grade, at any time” motto, this concept optimizes process flexibility in terms of steel grades to be produced, rolling strategies to be applied, and quick size changes.
Conclusion
ABS QWR 4.0 is the latest wirerod mill exclusive reference for Danieli and features the most advanced technical solutions. The plant is the realization today of the rolling mill of tomorrow in terms of technological innovation, digitalization, safety and a green steel approach. �
and machine utilization and availability. The straight roll pass-line is adopted for 5.0 to 11.5-mm final diameters; the second one allows bypassing the eight-pass, semi-multidrive Fast Finishing Block, and is adopted for 12.0–23.0-mm final dimensions. The third line is used for final sizes ranging from 23.5 to 25 mm and also permits bypassing the six-pass, multi-drive Pre-Finishing Block, guiding the feeder material into the sizing Twin Module Block, operated by a multidriveRespectingsystem.
To further confirm the flexibility of the plant, it also is possible to adopt different routes on the roller conveyor to cool down
ABS QWR 4.0 is the only wirerod mill in the world today where mill management is remotely controlled, based on the zero-man-on-the-floor approach during production and size changes.
To maximize the product size change, Danieli custom-designed three routes for specific dimensions and steel grades – ABS has more than 1,000 steel grades in its portfolio – which play a fundamental role in the changing sequences. Three specific rolling lines are installed to optimize process
DIP – Danieli Intelligent Plant
Application of QWR special steel products
The system proactively interacts with the operator, focusing his attention just on what is needed at that precise moment, not only for the controls on the HMI page or on the Operator Assistant, replacing obsolete pushbuttons, but also in the LED walls displaying images from the plant.
Molybdenum metal is indispensable to several industries because of its strength at high temperatures. But some applications require complex and not so-easily-fabricated shapes. 3D printing is one approach to overcoming production issues with complicated parts, however, when produced in molybdenum metal, such parts often suffer from defects. A new process, alloying it with titanium carbide, may indicate a turning point. By Karlee Williston*
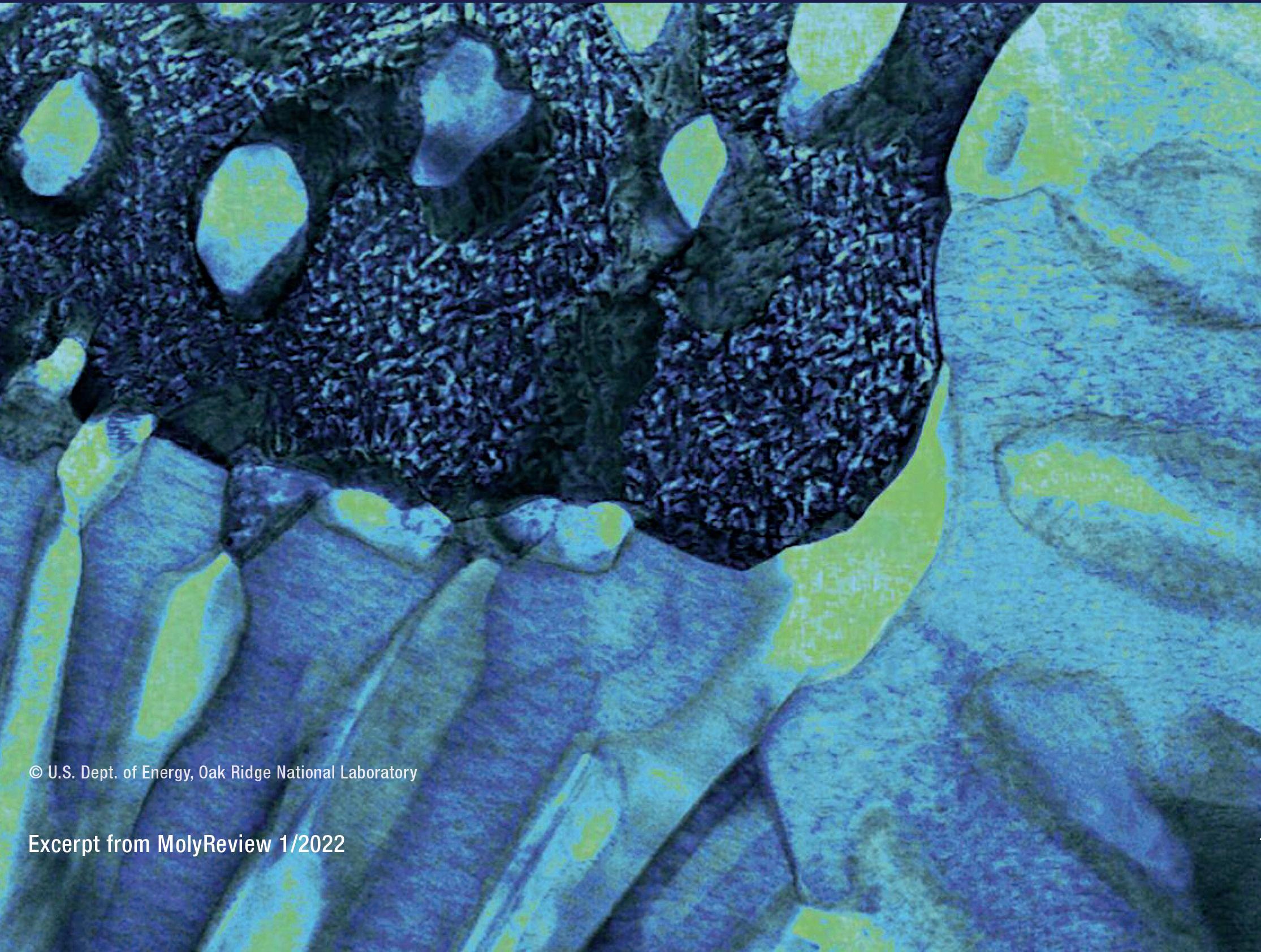
3D PRINTING38 www.steeltimesint.comSeptember 2022 * Editor, MolyReview
3D printing a hot commodity
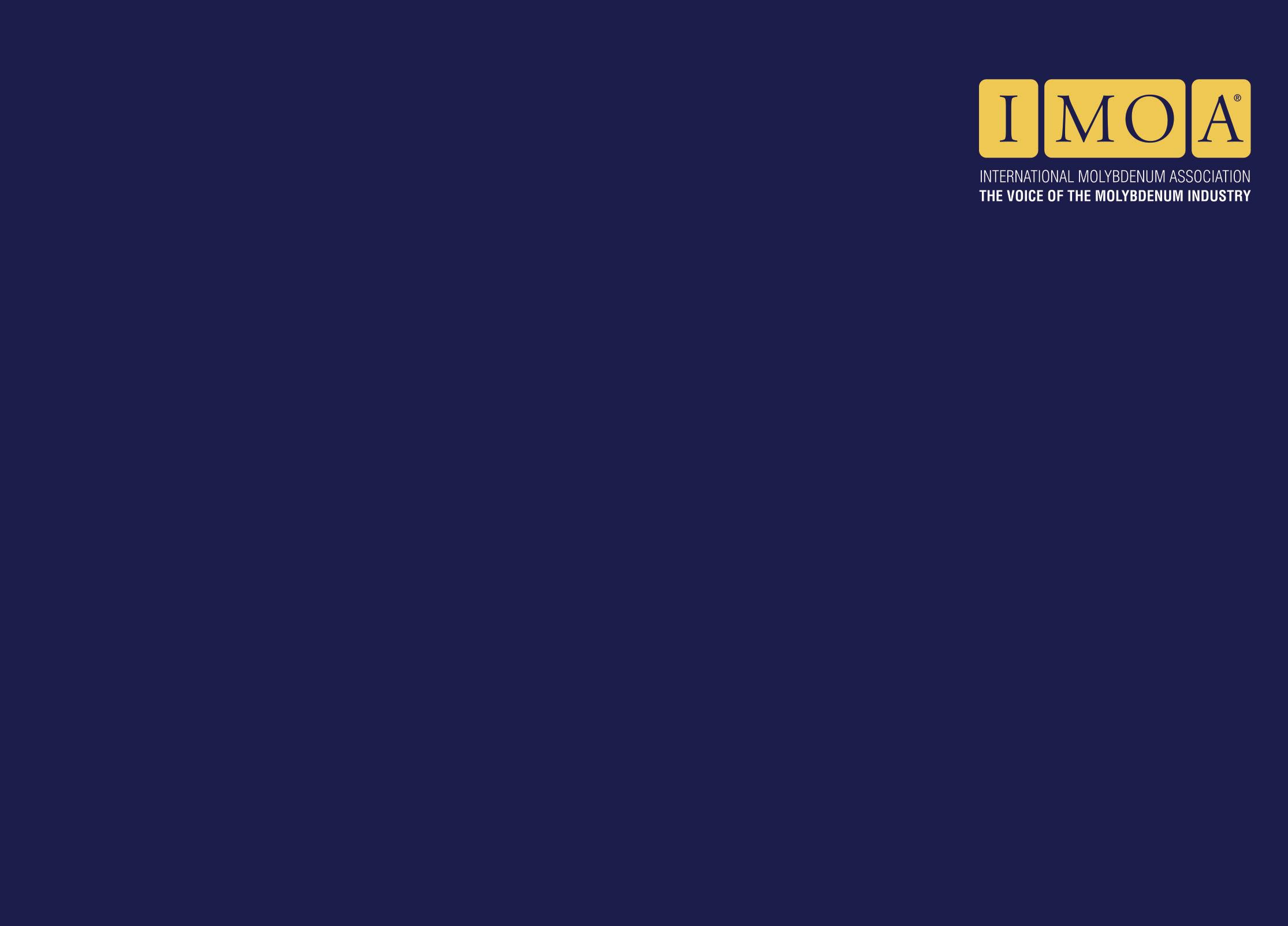
IN 30 years, the world is projected to need double the electricity it currently uses. But expanded energy production must coincide with emissions decreasing below current levels to avoid the worst effects of climate change. The solution to increasing the power supply without increasing emissions will be multi-faceted, but it’s likely to involve raising the operating temperature inside power conversion plants to increase their efficiency. For example, upping the temperature inside nuclear reactors from 900 to 1000°C would raise productivity by 10%.Although this offers major opportunities to reduce emissions as well as costs, turning up the heat in these sectors is a materials science conundrum. Only a few materials are potential candidates for such infernos. Mo-metal and Mo-metal alloys can tolerate temperatures that warp or liquify others. This is because molybdenum has one of the highest melting points of any element in existence (2622°C). Most importantly, it retains its shape and strength at high
3D printing allows complex shapes to be printed which cannot be fabricated in any other way. These are prototype parts for highly efficient Mo-TiC heat exchangers.
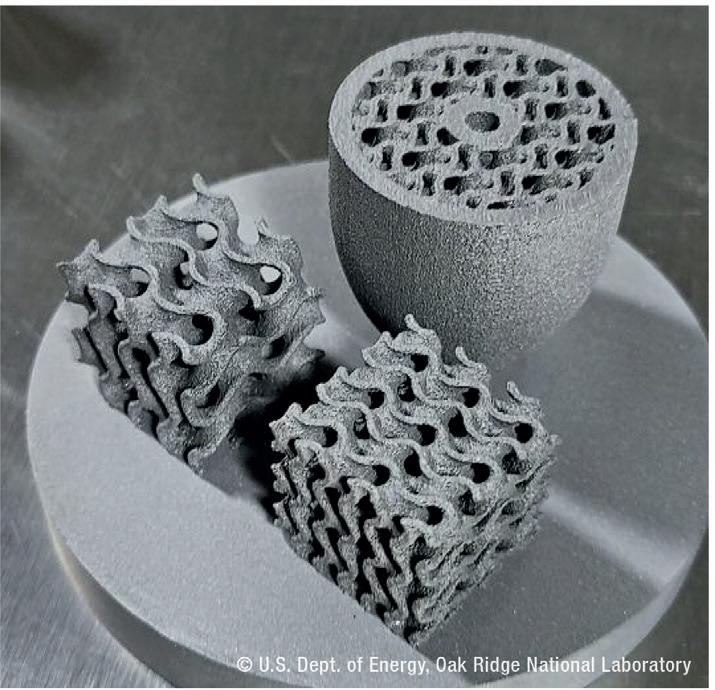
heats. Other metals that tolerate extreme temperatures well, like rhenium and niobium, are naturally less abundant than molybdenum and can be expensive or confer supply risks. Mo-metal is sometimes used in tandem with carbon-composites, which offer even greater stability at high heats. However, carbon-composites are wildly expensive and time consuming both to design and to manufacture. Thus, the scientific community continues to consider Mo-metal as a solution – but it also presents challenges.
Printing a paradigm-shift
Parts for highly-specialized industries are increasingly produced through additive manufacturing (AM), also known as 3D printing. AM originated in the mid-1980s to accelerate the development of product prototypes. The process is characterized by fusing layers of material together, often at the microscopic level. The “printer” references a computerized 3D model, producing an exact replica layer by layer.
Unlike the “subtractive” methods of traditional milling, cutting, drilling and grinding – successful AM produces virtually no waste. It is often more cost-effective to add complexity to a part with AM because the design can be simply altered on the computer. Some designs that are difficult or even impossible to make with traditional manufacturing, such as parts with hollow portions that lack a connection to the external part surface, can be realized with 3DTheprinting.ability to 3D print Mo-metal in the complex shapes required by the aerospace, defense and energy conversion sectors could result in increased thermal efficiency, which ultimately means more power generated with fewer resources. The challenge, however, is that 3D printed Mo-metal can suffer a loss of mechanical properties and stability that can render it unusable. This is because the 3D printing of Mo-metal and Mo-alloys is prone to the formation of defects such as porosity and cracks under improper print conditions.
Schematic of the customized electron beam PBF build chamber and secondary feeder (A) and a Mo-Mo + TiC-Mo sandwich sample (B). Source: US Dept. of Energy, Oak Ridge National Laboratory

Molybdenum powder (A), TiC particles (B) and the 60% molybdenum/40% TiC powder created by mechanically alloying the two feedstock powders. © US Dept. of Energy, Oak Ridge National Laboratory
3D PRINTING 39 www.steeltimesint.com September 2022

No more slipping through the cracks

In addition to Mo-metal, the researchers successfully printed composite matrix Moalloy titanium carbide material. In materials science terminology these are known as cermets. To create the cermet, researchers mechanically alloyed feedstock powders of 60% molybdenum powder and 40% titanium-carbide and printed them. After printing, there were no defects detected. Such materials offer the potential to enable advancements in energy systems requiring materials to operate in extreme environments such as super critical CO2
Raising the efficiency of thermal powerplants – like nuclear reactors –depends on the developments of better materials, particularly those with high temperature strength. Molybdenum is arguably the best candidate for the job. The ability to 3D print the material in the shapes required by industry could have major implications for generating more power with fewer resources. �
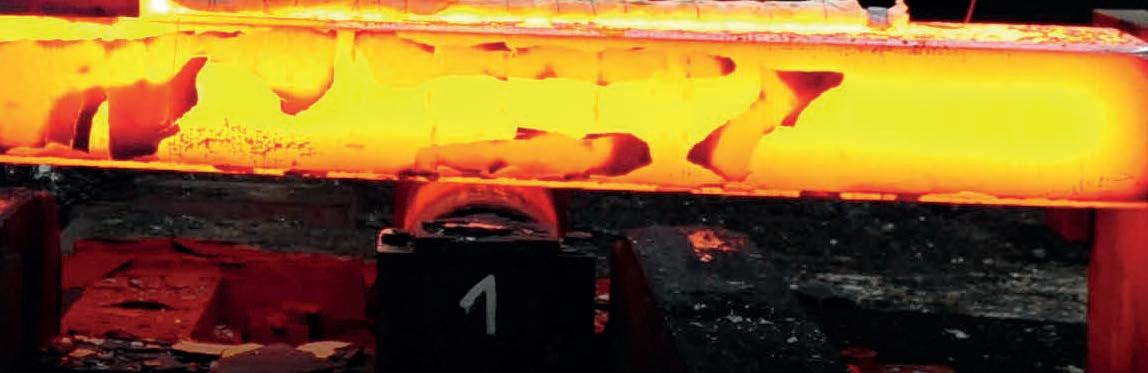
to print high-quality Mo-metal with unique grain structures not achievable through traditional Mo-metal manufacturing routes. These PBF processing advancements have enabled Mo-metal to be successfully printed into structural parts used in nuclear thermal propulsion systems.
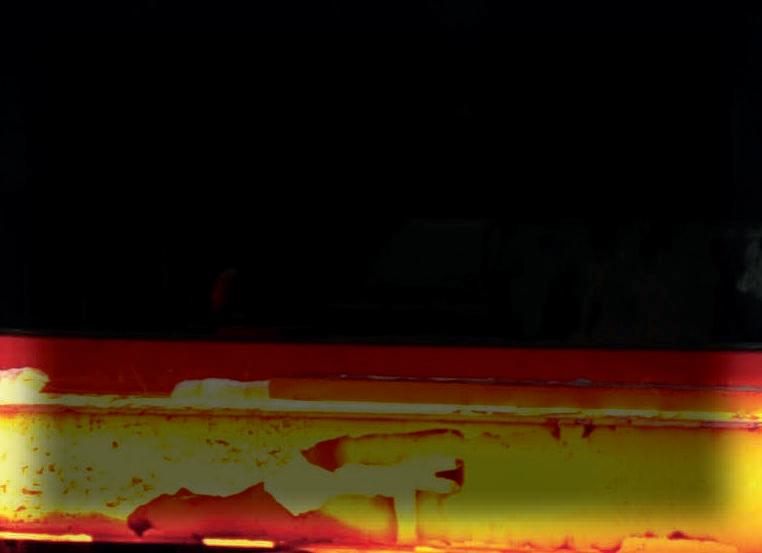
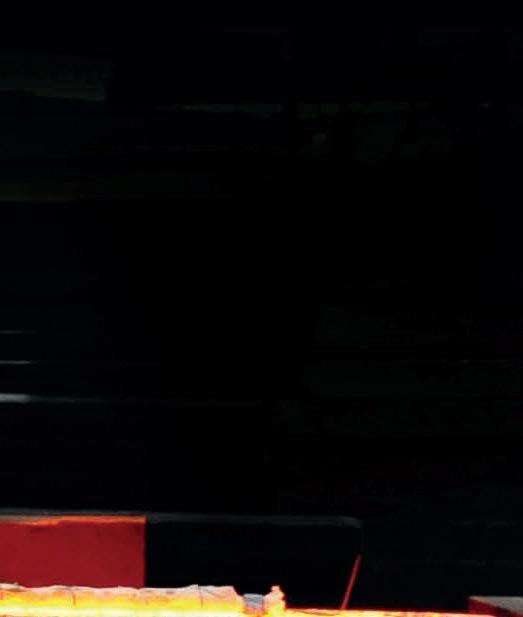

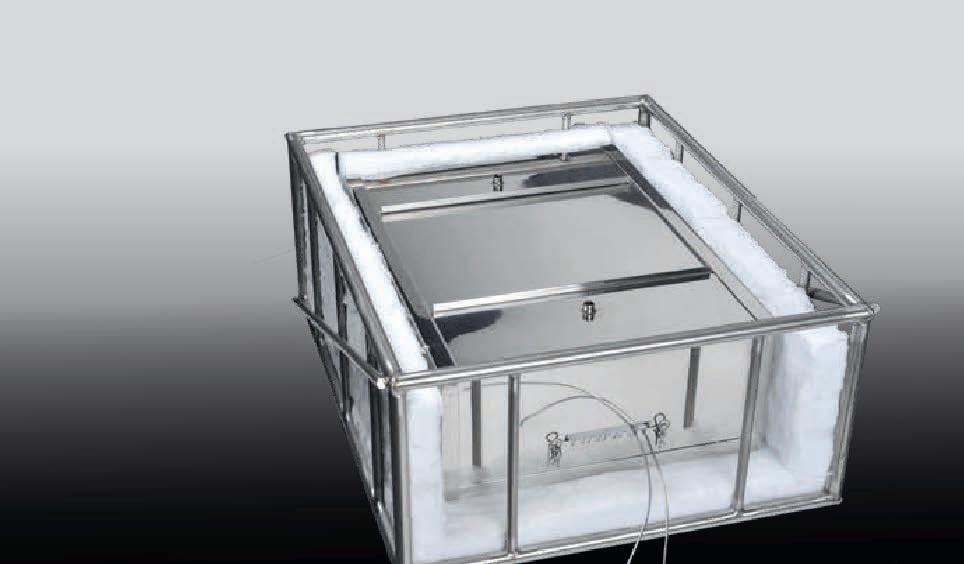

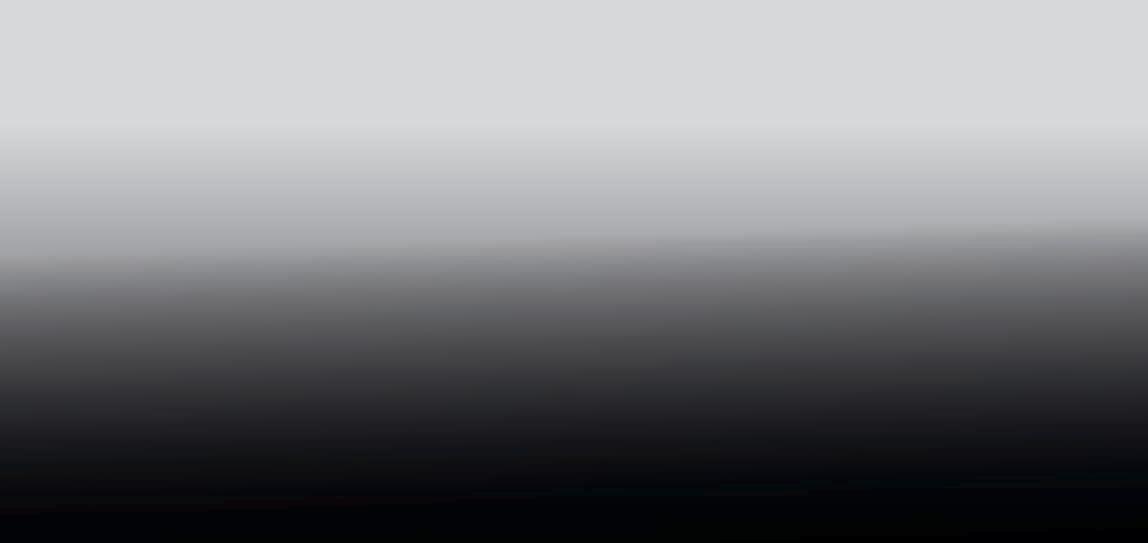
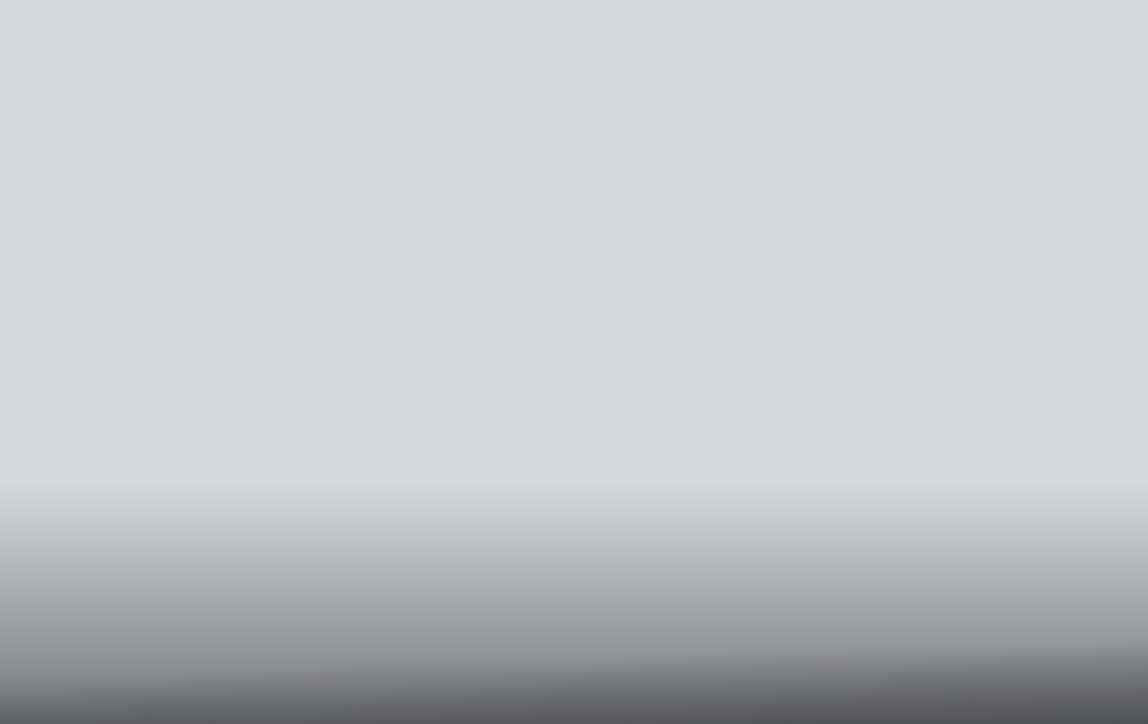
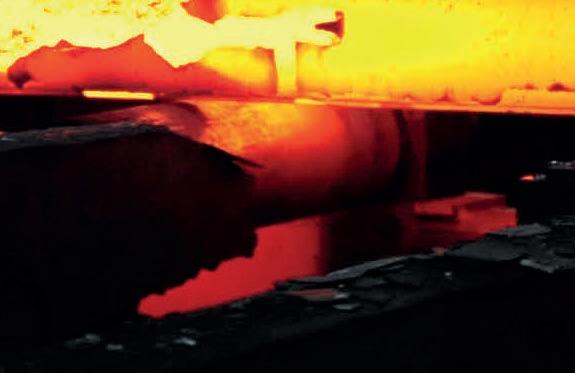
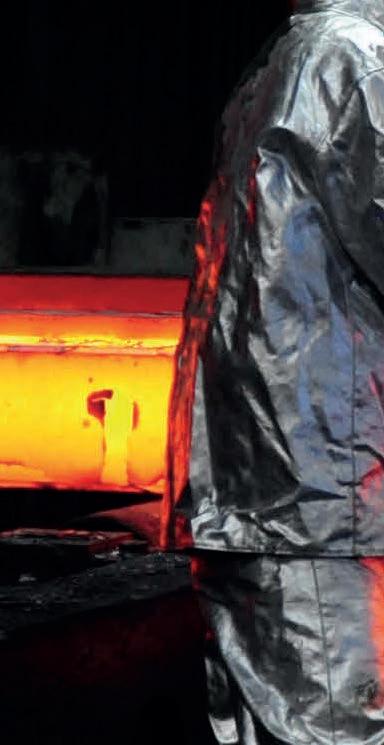
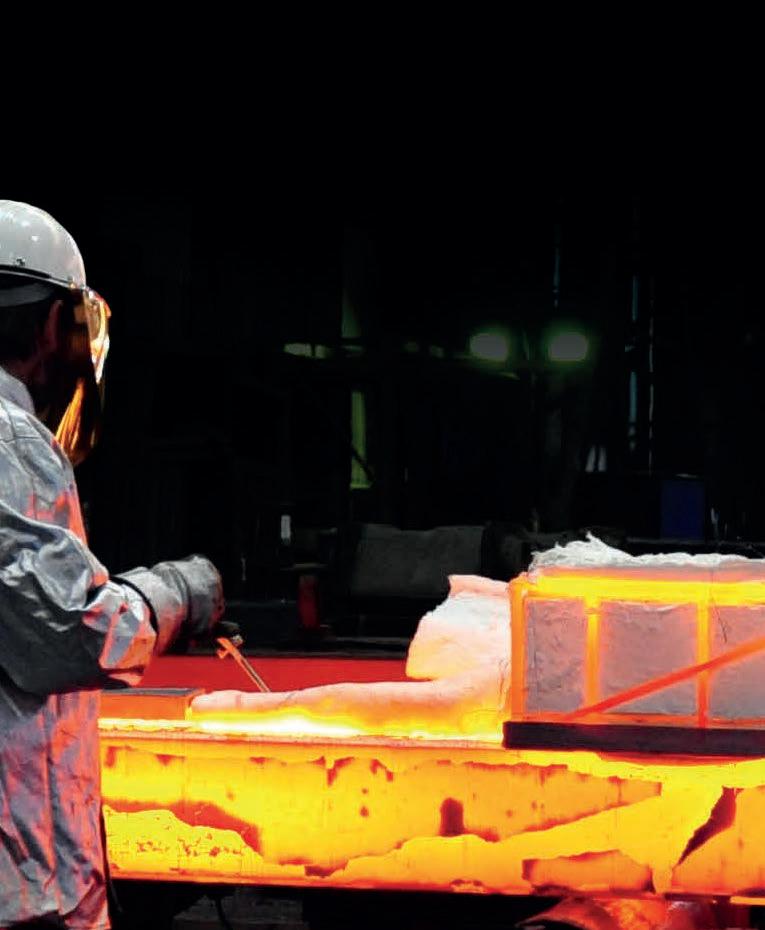
3D PRINTING40 www.steeltimesint.comSeptember 2022
However, through carefully controlling the 3D print process, Mo-metal and Mo-alloys such as titanium carbide Mo-matrix alloys can result in high quality crack-free parts with consistent properties. Scientists at the Oak Ridge National Laboratory (ORNL) in the southeastern United States are now partnering with external stakeholders to trial Mo-metal and Mo-alloy objects at scale.
This manufacturing process uses an AM method called “powder bed fusion” (PBF) to melt the powdered feed material into a solid. PBF requires either a laser or an electron beam to melt and fuse the powdered constituent. The researchers used the latter method, citing better control over temperature variation during printing. PBF with Mo-metal has yet to be successful at commercial scale due to the defect-prone nature of these materials during processing, but recent findings suggest that soon may change.Theresearchers demonstrated the ability
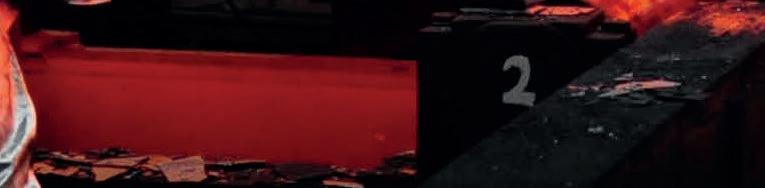
Cermets

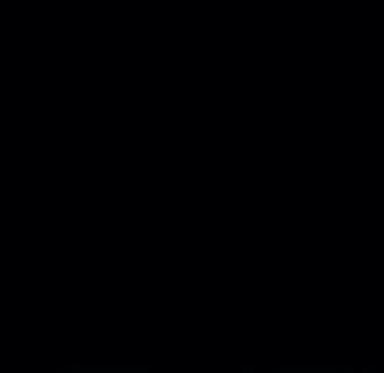
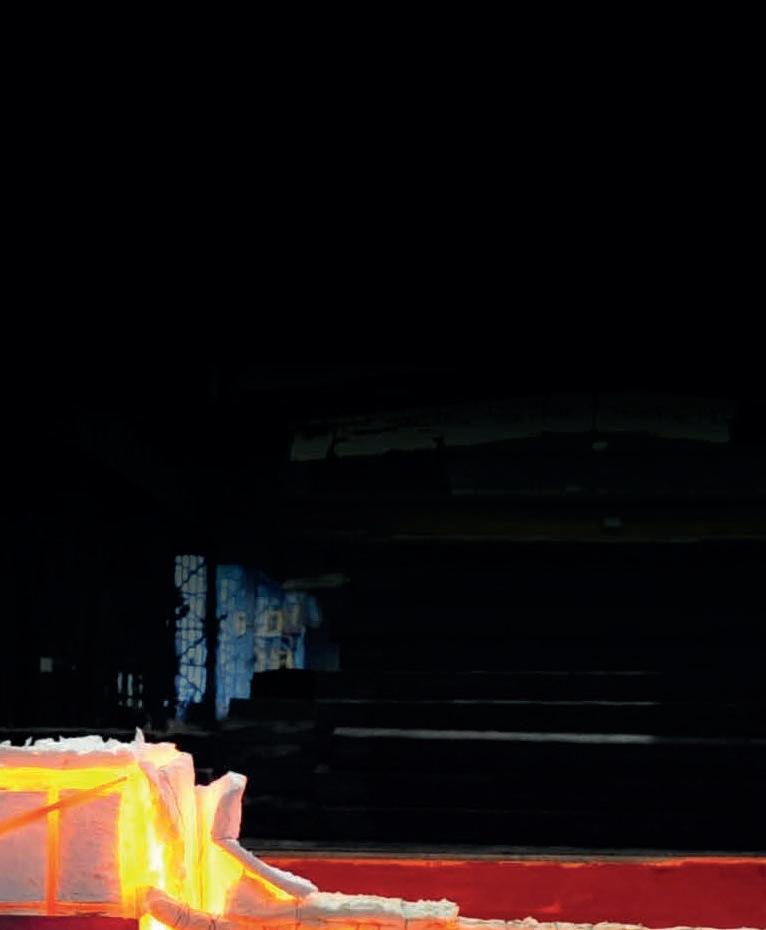

Other research teams have also yielded promising results. In 2019, the Beijing Institute of Technology developed 3D printed Mo-metal components for ion thrusters in the aerospace industry. The
Temperature Profiling Solutions In the Steel Reheat Industry •Comprehensive Passes through furnace with Slab • Get an accurate Slab temperature profile • Measurement at up to 20 points • Live 2 way radio communications •SafeSafe system installation without production delays • Reliable protection of data logger up to 1300°C •EasyOptimise your process accurately • Validate your furnace mathematical PhoenixTMmodel.GmbH Germany info@phoenixtm.de PhoenixTM Ltd UK sales@phoenixtm.com PhoenixTM LLC USA info@phoenixtm.com Benefits • Optimise furnace programs • Save energy and increase production • Obtain optimal drop out temperatures • Minimise scale build up • Prevent hot roller wear & tear Where experience counts ! www.phoenixtm.com
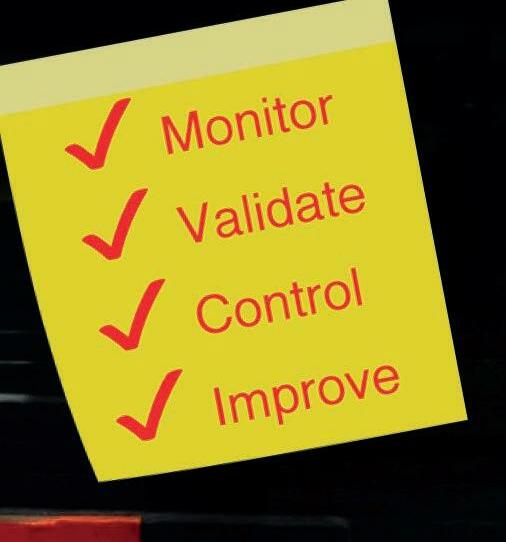
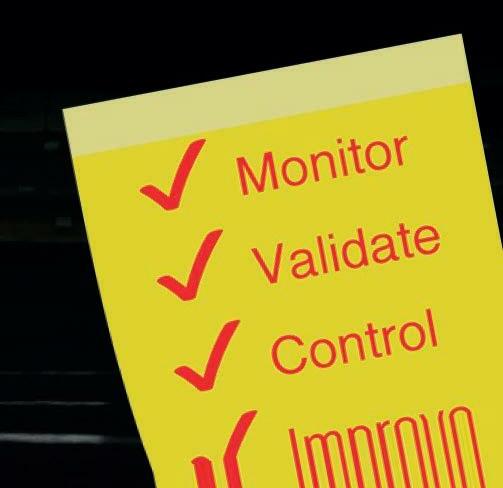
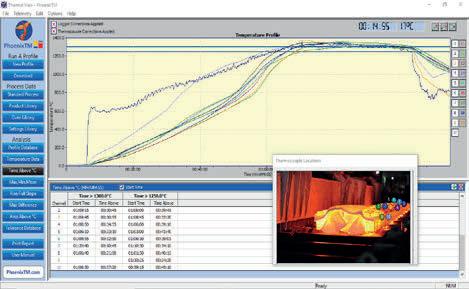
research group also combined Mo-metal powder with a titanium carbide powder to form a stable, oxidation-resistant composite product. The composite approach seems to yield positive results, not only with pure Mo-metal but also with other Mo-containing alloys. A research team in Singapore mixed titanium diboride nanoparticles with the molybdenum-loaded nickel base alloy Inconel 625, also resulting in better printability. These developments further attest to the future viability of vastly improved 3D printed Mo-metal and Mocontaining alloy components. Such projects demonstrate the unique properties of molybdenum and their increasing value in a decarbonizing world.
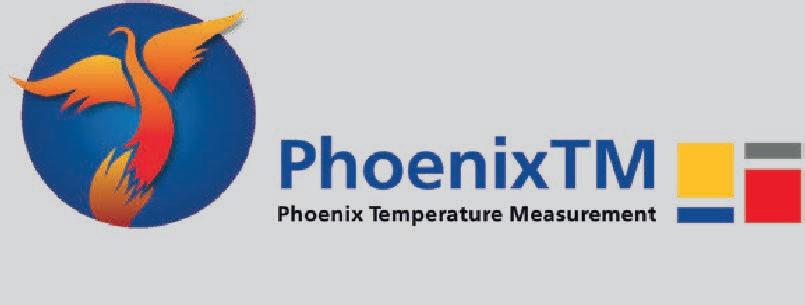
WHO WILL MAKE THE PELLETS AND DRI IN THE FUTURE?
Rutger Gyllenram. Photo by Pelle Berglund, Znapshot.
Betting on a winning horse
ENVIRONMENT 41 www.steeltimesint.com September 2022
“OUR industry has changed very quickly in the past.” The words are from Professor Chris Pistorius from Carnegie Mellon University, the venue was AISTech 2022 in Pittsburgh, USA and the context was the Brimacombe memorial lecture that, at the end, addressed decarbonisation in the steel industry. I guess we all agree when Pistorius states that it is encouraging to see how the steel industry embraces new technology, noting examples of how the Bessemer process took over from the puddling process in little more than 10 years around 1865, the BOF process taking over from open hearth and continuous casting replacing most of the ingot casting in just a number of decades after the second world war.Itis, however, fair to note that it took several years after Sir Henry Bessemer presented his invention before the first Bessemer charge succeeded. Furthermore, both using oxygen instead of air in the converter process, as in the BOF, and designs for continuous casting, were suggested by Bessemer but could not be realized in his time for technical reasons. The three technologies all increased the productivity and decreased the costs so the driving force for change was immense. The impact on society of the transition was also remarkable with smaller plants and whole communities closing and bigger plants growing.
*CEO,
In Fig 1 production steps are shown from the mine to the end of life of a steel product followed by recycling. Necessary actions to achieve a fossil free steel production like fossil free electricity production, producing fossil free reductants, electrification, improving resource efficiency, all central to Kobolde
Finally, we may ask if the changing iron and steelmaking map opens for more forward and backward integration in the industry. One of the main challenges for the mining industry in supplying the steel industry with pellets is to balance supply with demand with various quality premiums fluctuating. The dilemma of having one industry taking the cost and the other the benefit of ore beneficiation and pelletising is illustrated in Fig 3 taking iron yield as an example. DRI as a product has more potential customers and might offer a more stable demand and stable prices. So will mining companies start to make DRI, DRI producers beneficiate and pelletise ore or will things stay the same?
The winds of change are blowing in the steel industry and we are now offered long lists of new processes that are being developed to save the planet. It’s like betting on horses. Who will win and can the steel industry change? By Rutger Gyllenram*

And now it is time to change again in a multitude of ways. A roadmap for the global steel industry to reduce emissions of carbon dioxide (CO2) and other greenhouse gases includes multiple steps
Fossil free steel or fossil CO2-emission free steel
along the steel life cycle. The development of Life Cycle Assessment, LCA, has made emission data transparent upstream and downstream from a producer together with the producers’ own emissions making it possible for anyone in the supply chain to make informed decisions.
decarbonisation, are pointed out. The main questions that we need to ask ourselves are found at the bottom: do we need more stakeholder incentives, research, public information or regulations to make this happen?Foramining company the emissions from mining, beneficiation, agglomeration and transportation are important areas for abatement of CO2. Much can be done with electrification but using hydrogen, biofuels or other measures are necessary for some operations. The public discussion today is to a large extent focused on fossil-free reductants which will dominate discussions
& Partners AB
• What kind of immediate actions and long-term roadmaps can investors demand from steelmakers?
to decrease greenhouse gas emissions from steelmaking by either replacing or modifying the blast furnace process, three questions spring to mind:
The transition of the entire steel industry to production without using fossil coal or natural gas will most certainly take the best part of this century and be limited by a number of critical factors. It will have to take place in several steps with intermediary solutions. One is Carbon Capture Utilisation and Storage (CCUS) where CO2 is either used for products or liquified and stored, sequestrated in geological formations. Sequestrating fossil CO2 will abate the fossil emissions. Sequestrating biogenic CO2 will create carbon sinks. Both are probably necessary to reach the climate goals set for 2050. Whether we shall call steel produced from fossil reductants followed by CCUS ‘fossil free’ steel or ‘fossil CO2-emission free steel’ or something else we may leave to academia?Today,when we look for solutions
and development in the coming decades. The yield issue is to a large extent related to the amount of gangue from ore that is processed in the furnaces which is discussed later.Finally, the steel with the lowest CO2 emission comes from recycling but although the amount of available scrap is expected to increase in the decades to come, it will always be a limiting factor, determined by the amount of steel that goes into the use phase, the life time of the products and the collection rate. Therefore, closing blast furnaces to migrate to scrapbased production may do well for a single company, but can only work as a global solution in a rate to match an increased availability of scrap. Although scrap comes as a raw material almost free of burdens, a lot can be done to lower the total emissions for steel by utilising alloys in scrap and avoiding tramp elements like copper.
ENVIRONMENT42 www.steeltimesint.comSeptember 2022
• Will we see the same rapid conversion to new processes and technical solutions to meet the climate challenge as in the introductory examples? Indeed, a lot is going on but when will they reach the market?•Where will new ironmaking capacity be built? Will the availability of energy, the scale-up status of new ironmaking processes and availability of CCUS infrastructure draw a new iron and steelmaking map?
Fig 1. Decarbonisation in the steel lifecycle, from Worldsteel RAMCO meeting, Nov 18 2021. © Rutger Gyllenram Kobolde & Partners AB 2021

© Rutger Gyllenram Kobolde & Partners AB 2021.
The last time we had this enormous interest in new iron and steelmaking technology was after the energy crisis of the 1970s. A big number of processes challenged the blast furnace by not demanding agglomeration of ore and/ or coal. In economic evaluations the new process suggestions all outperformed the blast furnace process but at the end only a few survived to serve in niche applications. In hindsight one might conclude that the time and effort needed to develop a completely new process was underestimated and the projects ran out of funding or underperformed mainly due to low productivity, high refractory wear and difficulties in process control. On the other hand, the suppliers of blast furnace technology showed a great ability to improve, modify and scale up the process. Without questioning the good will of the
Fig 2. Implementing technologies for decarbonisation in the BF-route (Medium-High Si ore). From Worldsteel RAMCO meeting Nov 18 2021.
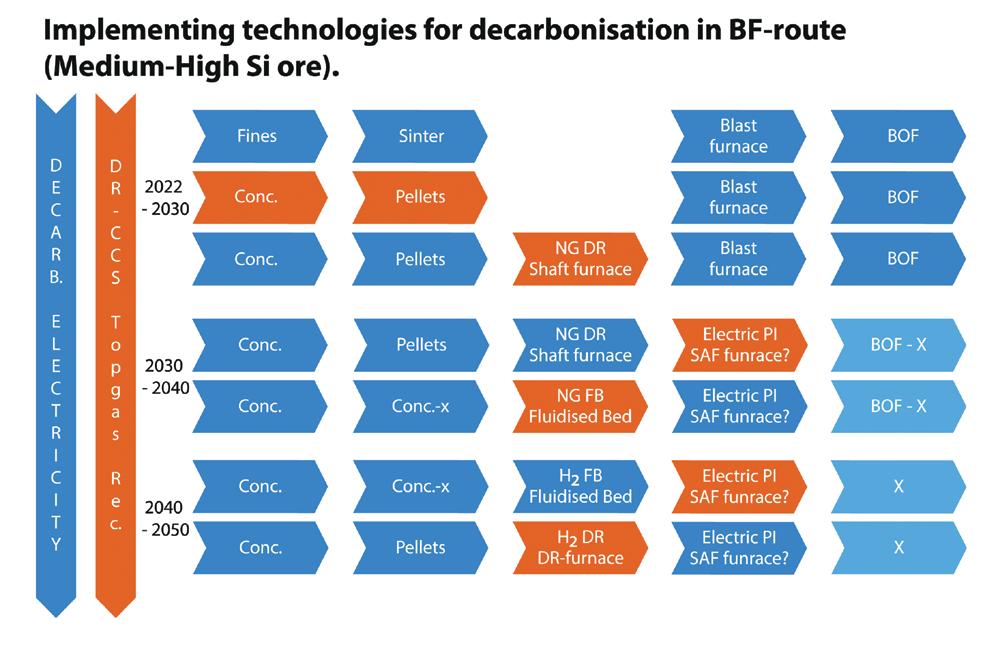
2. Technology that needs to be scaled up and given the right economic conditions.3.Development projects where function and profitability still need to be proven.
Processes and technical solutions
The A group includes lowering slag volumes in furnaces, replacing air with oxygen in combustion and replacing coal and coke with other reductants in the blast furnace and applying CCUS wherever possible. In group 2. we have, for example, top gas recycling, hydrogen and biogenic syngas reduction to avoid carbon, electric pig iron furnaces to melt high gangue DRI and fluidised bed reduction technology to avoid agglomeration. All very promising, but yet to be proved. In group 3. we have, for example, electrolysis projects that probably have a long way to go to the market so we will leave them out of the discussion for now.
Probably we can divide technology candidates to abate emissions into three categories:1.Established, ready-to-implement, technologies profitable from the start.
steelmakers, one may conclude that the only thing that has changed is that this time, the cost of emitting greenhouse gases has been added to the equation. Is it a game changer for alternative ironmaking processes or will the blast furnace adapt? The chief objective of the EU-financed ULCOS project is to decarbonize ironmaking and it came along with other things, such as blast furnace top gas recycling which was implemented at the LKAB experimental blast furnace in Luleå, Sweden. After almost a decade of silence, it seems that the ULCOS ideas are again on the table.

Immediate actions and long-term roadmaps
Chile and Australia will become hubs for hydrogen-reduced DRI while the MENA region may supply DRI from natural gas withWhatCCUS.will happen to existing integrated plants with blast furnaces and basic oxygen furnaces? Eventually they will surely be equipped with electric arc furnaces when the availability of scrap and low gangue DRI allows for that. Until then they might continue production reinventing the blast furnace process with top gas recycling, CCUS and other measures or outsource the reduction and replace the blast furnaces with electric pig iron furnaces.
Fig 3. Cost benefit of decarbonisation thru ore beneficiation. After “How to Satisfy Steelmakers – What’s in it for the Miners?” Fastmarkets Global Iron Ore 2021, © Rutger Gyllenram Kobolde & Partners AB 2021. Available at https://vimeo.com/526605624/6b72216f40.
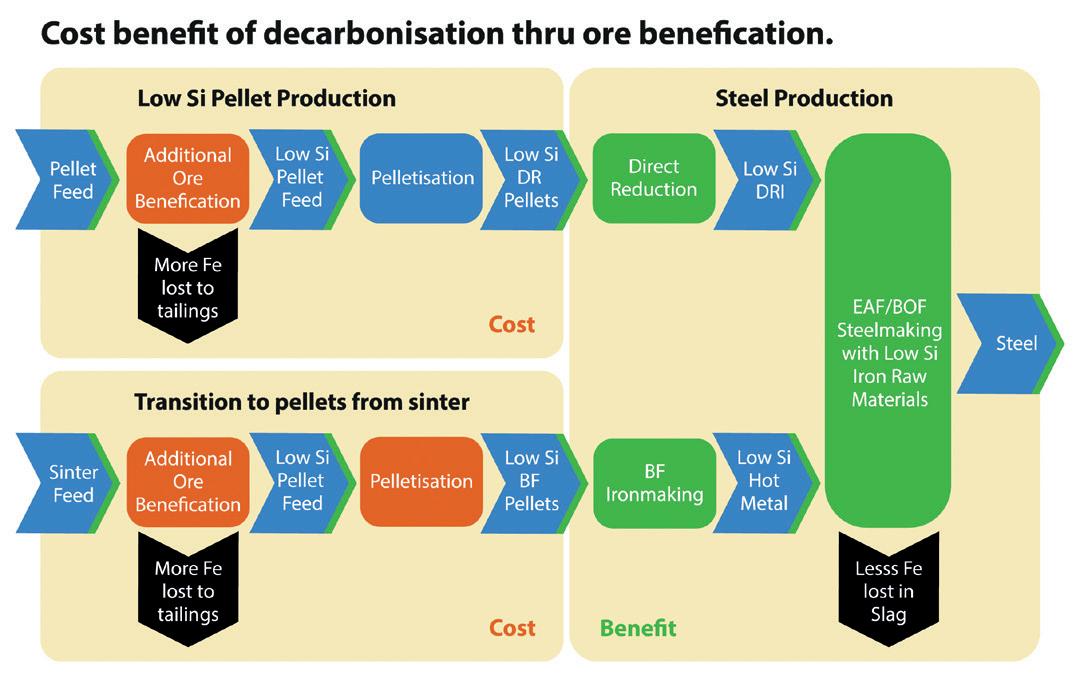
A possible timeline for material and process development to decarbonise steelmaking using medium-to-high silica iron ore is shown in Fig 2. The first row shows the situation today where sinter with a high silica content is reduced in the BF and decarburised in the BOF. In the second row the ore is beneficiated to a lower silica content and agglomerated to pellets. This will normally decrease the slag volume in the BF and lower the coke consumption and CO2 emissions. In the third row, pellets are reduced to DRI to reduce coke consumption and CO2 emissions in the BF. Even if natural gas is used it will decrease the emissions. If CCUS in the DRI production step is applied, the reduction will be even higher. This might be how far we get this decade, and what happens the next we can only guess. Maybe we can replace blast furnaces with electric pig iron furnaces and DR-shafts with fluidised beds, and use hydrogen made without emitting CO2 but we do not know.
The debate has already started and regions with constant wind, sun and CCUS capacity are mapped. We will probably not see liquid natural gas or hydrogen shipped for iron ore reduction purposes due to liquefaction and transportation costs other than to bridge over-supply or technology gaps. The commodities transported long distances will be iron ore, DRI and steel. It has been suggested that countries like
Aut Caesar, aut Nihil! Caesar or nothing, the famous proverb of Cesare Borgia often interpreted as all or nothing, comes to mind in today´s discussions when incremental improvements of existing technology are viewed as ‘less green’ and, therefore, less attractive than new processes solving all our problems in an unknown future. Since we do not know when the shift will come, we have to muddle through with what we know and can do today to make whatever small steps that are possible. At the same time, we have to work hard to make the game changers ready to enter the market. It might be sooner or later. When they are ready the shift might be fast.
of gangue melted in any process should be given the highest priority in order to decrease energy use and improve yield.
A new iron and steelmaking map
For mining companies with ores that cannot be beneficiated to DR-quality it is essential that either the blast furnace is adapted to new demands on CO2 mitigation or that projects on electric pig iron furnaces with the same slag chemistry as the blast furnace succeed.
ENVIRONMENT44 www.steeltimesint.comSeptember 2022
Bearing in mind that the possibility of beneficiating a certain ore depends on mineralogy and that getting permissions to build tailing dams has become increasingly difficult for some mining companies, it must be noted that decreasing the amount
Ore products are either intended for the blast furnace – basic oxygen furnace route, BF-BOF; or direct reduction via the electric arc furnace route, DR-EAF. Although both routes benefit from a low gangue content in the ore, the blast furnace is less sensitive since it operates with a basicity (CaO/SiO2) around 1 whereas the EAF operates with a basicity of around 4.
Most fossil-free projects, planned for implementation this decade, are aimed at DRI production based on DR-pellets followed by an electric arc furnace. When talking about replacing the impacts from blast furnaces on a larger scale we must, therefore, look at what to do with the majority of ores which are of medium-tohigh gangue content.
Which horse to bet on? Probably a herd of horses that moves fast and saves as much CO2 as possible already today with existing technology and has prospects of achieving ambitious goals in the future. �
A century ago, steelmaking plants were generally co-located with energy resources, close to a stream and a forest. Ores were by far the resources easiest to transport, easier than, for example, charcoal that is more voluminous. Coking coal and steam coal were denser and were more suitable for locations with blast furnaces producing close to 4Mt/yr of pig iron. Gas-based DR plants emerged more than 70 years ago and have now reached module sizes of more than 2Mt/yr of DRI often found in coastal locations where sea bound DRpellets and local natural gas are the main resources.Forthenew process installations that we discuss today we might, at least initially, be restricted by the availability of key resources. Regarding reductants, hydrogen production needs electricity, limited by available production and grid capacity, biogenic syngas needs a supply of biomass which is voluminous and finally, CCUS infrastructure may be limiting for processes emitting fossil or biogenic CO2. These locations may, however, be excellent incubators and profit centres for new processes that are limited in module size depending on how far they have come in scaling up.
Like any industry, wherever there is a need for airflow, we’re there. It’s hard to pinpoint one area as we serve people working in every facility in the form of condensation mitigation to prevent the formation of rust.
45
Big Ass Fans operates across multiple industries where the key concern is looking after the workers. During the summer, the company gets busy as the weather warms up and the key concern is to keep employees cool in what can be an oppressive working environment, says Scott Fehrenbach*
No matter the state of any industry, we typically see the same focus on employee safety and comfort. Even truer now with the current labour market and a lack of applicants and trained staff to perform manufacturing jobs. Once a company makes that investment in attracting a new employee, it’s better to invest in retaining that same employee and to do so by providing the best possible environment is paramount. Whether it is the steel industry or another industrial segment, it has never been more important than now to invest in employee safety and comfort.
* Senior key account manager, Big Ass Fans
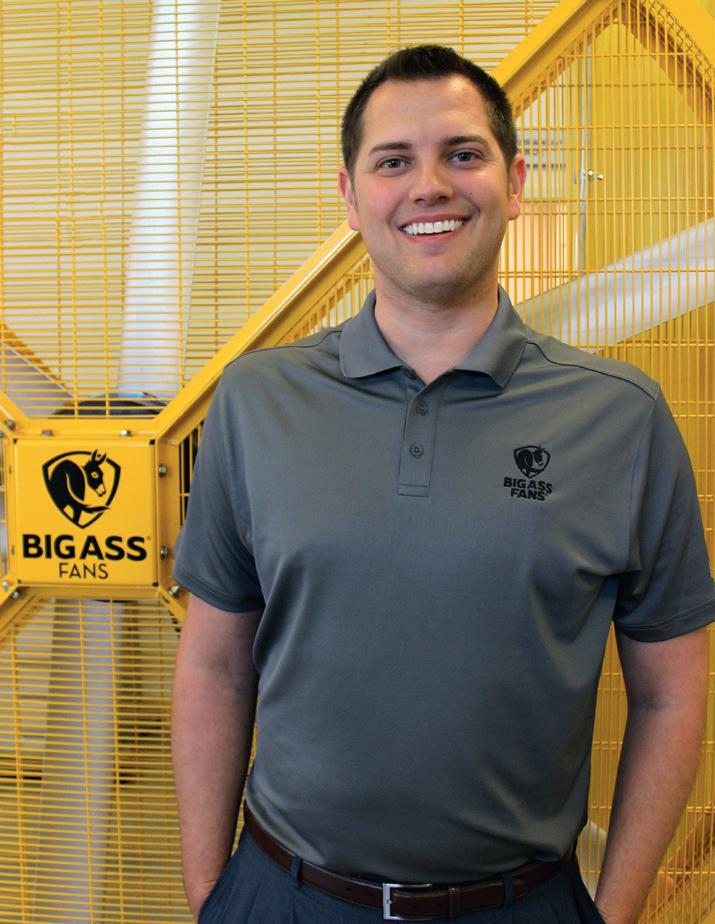
2. What is your view on the current state of the global steel industry?
6. In your dealings with steel producers, are you finding that they are looking to companies like BIG ASS FANS to offer them solutions in terms of energy efficiency and sustainability? If so, what can you offer them? Yes. Many of our customers are looking to provide a sustainable means of comfort that reliably delivers a safer environment for those working diligently and tirelessly to provide the materials we need around the world to create infrastructure and drive growth. It’s not possible to condition every industrial space in the world, so what can
A large focus in every industrial segment is on attracting and retaining workers. That’s where we come in and deliver big results.
Not sure this one directly relates to our business as adding even the most efficient product to create a safer, more comfortable facility for employees would still be drawing some power, but it’s still dramatically less than the alternative.
PERSPECTIVES Q&A: BIG ASS FANS
3. In which sector of the steel industry does BIG ASS FANS mostly conduct its business?
8. What exhibitions and conferences will BIG ASS FANS be attending over the next six months?
Employee safety and comfort
www.steeltimesint.com
Every May we really start seeing the upswing in phone calls and outreach as potential customers begin to feel the heat. Our steel customers in the Southeast (US) really begin to focus on their employees’ comfort, safety, and wellbeing in the warmer months. We’re coming off our best May in the company’s history and look to continue the trend as we wrap up June.
The majority of our business is conducted in the warmer months, so right now we see that in North America, but our Australian office picks up in the later months of the year as well.
be done to ensure employees remain safe while performing difficult work? That’s our entire mission. To provide a safer, healthier, more productive world for all and do it all sustainably and efficiently.
7. How quickly has the steel industry responded to ‘green politics’ in terms of making the production process more environmentally friendly and are they succeeding or fighting a losing battle?
4. Where in the world are you busiest at present?
From Reliance Steel to Nucor, Sabel Steel to O’Neal Flat Rolled Metals, our attention towards the NASA and SMU Steel Summits of the past few years, we’re about as visible as any other vendor or supplier in the industry and typically one of the more interesting as we’re both a buyer and then seller of the finished goods back to the industry we purchased from.
1. How are things going at BIG ASS FANS? Is the steel industry keeping you busy?
5. Can you discuss any major steel contracts you are currently working on?
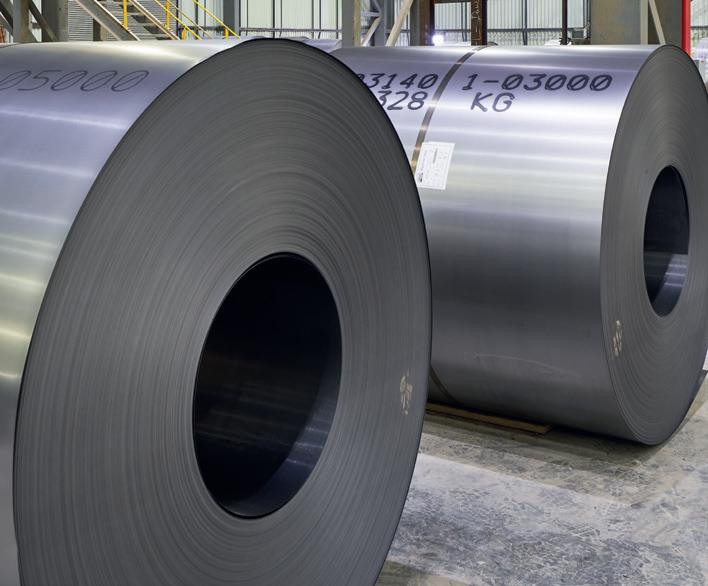
9. BIG ASS FANS is headquartered in the USA, but what’s happening steelwise in the country?
As a global manufacturer of fans and airflow solutions, we’ll be attending IMTS, SEMA, Fabtech, and some other smaller shows.
10. Apart from strong coffee, what keeps you awake at night? We’re an energetic bunch so we like to stay as active as possible for our customers. Getting them the solutions they need to help them do what they do a little more comfortably is our mission! �
7. What are your views on Industry 4.0 and steelmaking and how, if at all, is DASSAULT SYSTÈMES using it?
Industry 4.0 has been crucial in the development of the manufacturing industry, and when it comes to steel and future operations, it will continue to push innovation. From traceability to data management, our solutions track and manage production throughout the product life cycle. Unified solutions allow organisations to share a common source of operational information. For example, simplified and more sustainable production in automotive manufacturing can be achieved when car makers and steel makers work from the same data source.
‘Digitalisation is happening, but there is still a lot of room for transformation,’ says Dassault Systèmes’ Corinne Bulota*. The company is busy throughout the world and expects ‘significant growth’ in North America, Europe and Japan where its customers include US Steel, ArcelorMittal and Nippon Steel.

The industry faces a variety of challenges, from inflation to customer expectations and calls for more sustainable practice. It has been slow to evolve from ancient practices, manual processes, and legacy technology, creating a difficult environment for operations to keep pace with demand. Digitalisation is happening, but there is still a lot of room for transformation – especially when it comes to improving sustainability.
Corinne Bulota
it anything from use to recyclability – is reflected in the different markets each are concerned with. And each have specific applications: aluminium is often used in the likes of packaging and aerospace while steel is used for reinforcement in vehicles or infrastructure. Yet, despite their differences, we have the same strategy offer for aluminium and steel so our virtual experiences can help manufacturers find the best, sustainable solutions to meet their needs.
A great example in the steel industry space would be our work with SIJ Acroni. The company produces flat-rolled steel products and is one of the largest producers of stainless and speciality steels in Europe. The company wanted to improve production planning while keeping a high level of quality. As a partner, we provide our expertise in steel production planning to equip the organisation with end-toend visibility of its operations – from steelmaking to slitting to packaging. We needed to provide a robust system to meet SIJ Acroni’s most stringent requirements, while also flexibly adapting to their unique production operations. The improved production cycle now generates an increase of more than 12% in on-time in full delivery rates.
3. In which sector of the steel industry does DASSAULT SYSTÈMES mostly conduct its business?
4. Where in the world are you busiest at present?
PERSPECTIVES Q&A: DASSAULT SYSTÈMES46 www.steeltimesint.comSeptember 2022
Creating a single source of truth
Hydrogen steelmaking is certainly a big step towards decarbonisation in this industry. The challenge will be to be able to produce enough hydrogen – green hydrogen – to meet demand, but we are not there yet.
2. What is your view on the current state of the global steel industry?
Dassault Systèmes has a wide portfolio to offer to the steel industry. We enable many of our customers in every sector of the steel industry to imagine sustainable operations, using, just as an example, simulation to automatise manufacturing lines or using material sciences solutions to accelerate the development of new recipes to make steel.
The steel industry is in a transition phase where the techniques that are being developed – meaning new technologies to turn iron ore into steel with lower CO2 emissions – have yet to come into full force.
The steel industry is keeping us very busy. The modernisation of steel manufacturing is a challenge in itself. Due to the reliance on age-old metallurgy practices, manual processes, legacy planning tools and systems, the industry has been struggling to keep up with the pace of innovation.
The world is keeping us busy everywhere, but our focus goes towards North America, Europe and Japan with references like US Steel, ArcelorMittal and Nippon Steel. We expect significant growth in our activities in these geographical areas, with also interesting opportunities in the APAC and LATAM areas.
1. How are things going at DASSAULT SYSTÈMES? Is the steel industry keeping you busy?
9. In your dealings with steel producers, are you finding that
8. Hydrogen steelmaking appears to be the next big thing. What’s your view?
* Vice-president, infrastructure, energy and materials
The difference between the products – be
5. Can you discuss any major steel contracts you are working on?
6. Where does DASSAULT SYSTÈMES stand on the aluminium versus steel argument?
13. China dominates global crude steel production and is accountable for almost half of global production. How should the industry react to this situation?
To support carbon neutral targets set out by the UN and strive towards a sustainable environment, steel companies need to innovate and find solutions to change the manufacturing process in this direction. Speed is critical if we are to make real, lasting change that reduces the impact of climate change. Success is not there yet, but partnerships within the industry to support the innovation to cut carbon emissions will be key to accelerate these emissions reductions now.
11. Where does DASSAULT SYSTÈMES lead the field in terms of steel production technology?
Even though we are based in France, we are a global company and consider the steel market globally. While demand for steel differs from region to region, its usage, consumption and lifecycle affects the whole planet. So, for us at Dassault Systèmes, we view steel as an international market and approach operations and support at this level.
Despite Covid disruptions, China’s steel production is expected to continue to increase. We are following this trend and, in China, like everywhere in the world, help transform the steel industry towards sustainability and digitalisation.
As organisations continue to explore more sustainable solutions to current practice, our mission is to facilitate these conversations and ensure our platform supports companies to innovate sustainably. When it comes to the global steel industry, we will continue to develop our virtual twin experiences to ensure organisations can take the necessary steps towards their own sustainable manufacturing environments.
www.steeltimesint.com September 2022
15. Where do you see most innovation in terms of production technologies – primary, secondary or more downstream?
Most innovation takes place at the primary stages of production, Future direct reduction reactors with green hydrogen will be an essential breakthrough, with an interesting transition period over the next years. But innovation happens at every step of the production chain, especially with the creation of new products like third generation steel grades.
17. What exhibitions and conferences will DASSAULT SYSTÈMES be attending over the next six months?
47
19. Apart from strong coffee, what keeps you awake at night?
The decarbonisation of steel will require a level of green hydrogen production that is not reachable today. If I possessed a superpower, I would probably use it to increase green hydrogen production, as this is going to be a twin challenge of the steel industry over the next years. �
PERSPECTIVES Q&A: DASSAULT SYSTÈMES
The industry must work on their production costs to remain competitive in terms of price. Going forward, steel manufacturers must re-evaluate their technological infrastructures and reimagine more economically viable ways to reduce their carbon footprint, and we accompany them on this path.
happening fast. There is a lot of drive and energy behind initiatives which are moving towards effective change. With the help of governments and funding which will fuel the steel market to reach its goals in terms of sustainability, I am looking forward to what is in store and the massive potential there is for future development.
20. If you possessed a superpower, how would you use it to improve the global steel industry?
short-to-medium term in relation to the global steel industry?
16. How optimistic are you for the global steel industry going forward and what challenges face global producers in the short-to-medium term?
12. How do you view DASSAULT SYSTÈMES’ development over the
The exhibitions and conferences season for steel is behind us for 2022, with already a lot of fruitful exchanges in the industry, but we are looking forward to go back to several events in 2023 such as the Future Steel Forum and AISTech.
18. DASSAULT SYSTÈMES is headquartered in France, but what’s happening steel-wise in the country?
14. What is DASSAULT SYSTÈMES’ experience of the Chinese steel industry?
they are looking to companies like DASSAULT SYSTÈMES to offer them solutions in terms of energy efficiency and sustainability? If so, what can you offer them?
I am optimistic that the industry will meet any challenges ahead – even if current digitalisation levels are low, change is
10. How quickly has the steel industry responded to ‘green politics’ in terms of making the production process more environmentally friendly and are they succeeding or fighting a losing battle?
I am very concerned about the future of our planet. So ‘apart from strong coffee’, this is what gives me energy every day, the opportunity to push for a more sustainable world, and it goes through a transformation for steel. I would like to quote Bill Gates on this: “Whenever I hear an idea for what we can do to keep global warming in check, I always ask this question: “What’s your plan for steel?” I know it sounds like an odd thing to say, but it opens the door to a very important subject.” Not so odd, actually.
Our mission is to support organisations to push the boundaries of innovation, learning and production, to achieve more sustainable operations. We enable our customers to lead the field in any area of steel production with collaborative 3D virtual environments that allow them to imagine sustainable innovations, which can become a reality. Our belief: virtual worlds extend and improve the real world. Our goal: deliver transformative solutions to push the limits of the possible.
For many steel producers – and manufacturers across the board – deploying energy efficient and sustainable processes is a priority. We recently launched a virtual twin solution that enables organisations to compute the environmental impact of an asset, from its construction to use during operations, using data from our partner the ecoinvent Association. Here, it’s not just about CO2 – our solution computes the use of utilities of water, energy consumption, etc. This enables decisions to be made early in the design phase about the impact of an asset – a critical element if manufacturers are to make real progress towards sustainable operations.
Trent Iron Works
North Lincolnshire Iron Company
Today, Scunthorpe steelworks is one of two integrated ironworks in the British Isles, with its four ‘Queens’ blast furnace capable of producing in excess of 2.5Mt/yr.
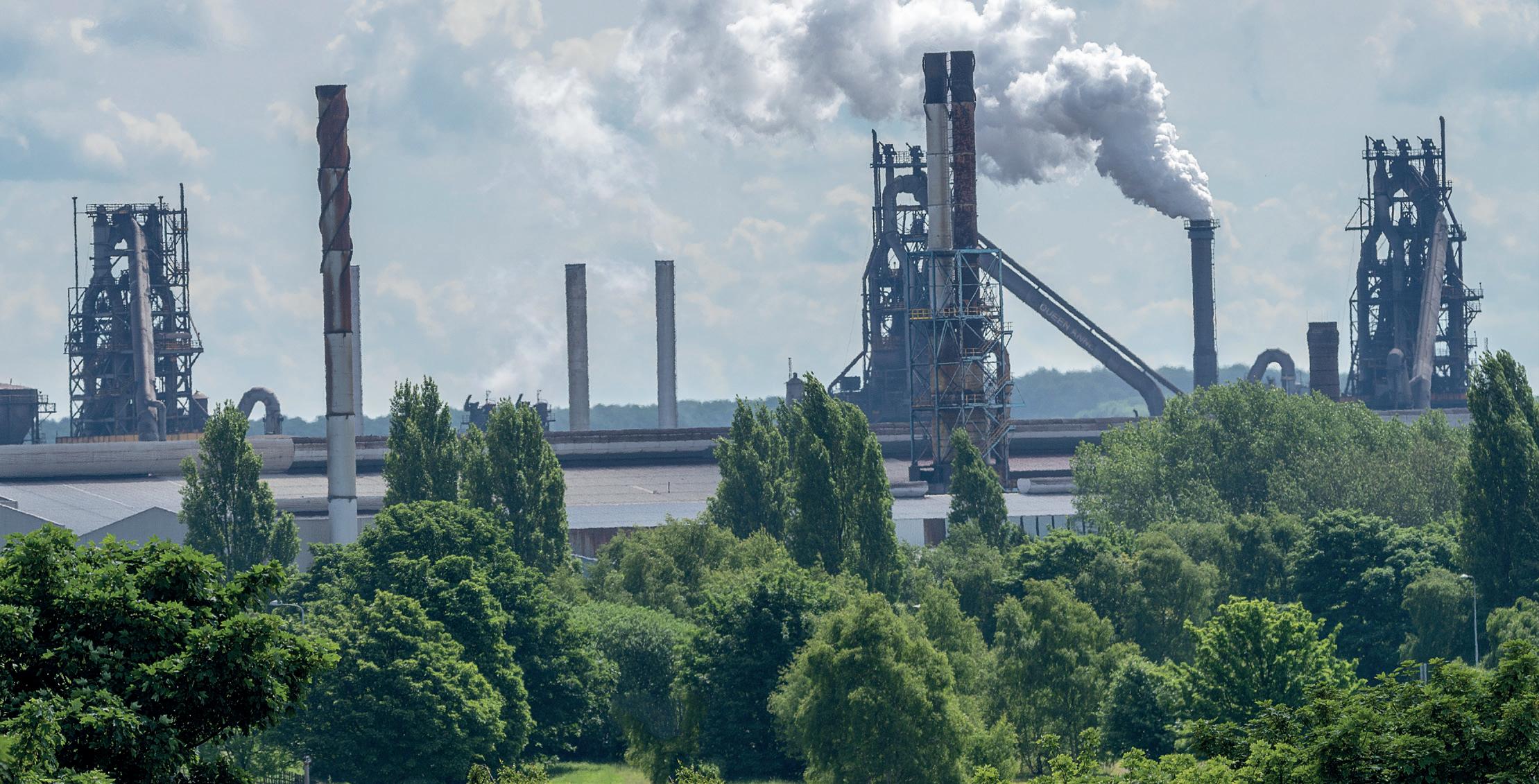
Located in Lincolnshire in the north east of England, the building of the first ironworks in the area commenced in January 1860 followed by a further five works during the second half of that century. Despite evidence of ironworking in Roman times, Lincolnshire was late in setting up ironworks, nearby Yorkshire having established coke blast furnaces by 1788 and Shropshire and South Wales were the main UK producers by this date. What attracted ironworks to the area was 2.25Mt of local ironstone, some close to the surface available to open-cast mining, others deep seams not mined underground until 1931.
of 20 tons a day. 100% coke was used in the charge. Difficulties arose with the ore and the first furnace was blown out after just five months. In August 1865, the top of the furnace fitted with the bell charger was blown off in an explosion. Despite removing the bell to operate open-topped, the works suffered from several explosions as a result of charging uncalcined ore with high lime and moisture content. However, attempts to calcine the ore in clamps prior to charging failed due to weathering of the clamps disintegrating the ore to powder. In 1871, two larger iron-cased furnaces were built to replace the earlier two brick-built ones. These were 63’ (19m) high with bosh diameters of 18’ (5.5m).
In 1865, a champion of the Manchester Ship Canal, Daniel Adamson, was granted a lease to build three furnaces to the SE of the Trent ironworks. Standing 70’ (21m) high and 20’ (6m) in diameter at the bosh, with closed tops, these were the largest furnaces so far. However, it was not until 1872 that the second furnace was completed. The company was named the North Lincolnshire Iron Company. Again, difficulties were experienced with the ore and on 1 September 1866 the top 20’ (6m) of No 1 furnace were destroyed in an explosion halting production for the next two months. As experienced by the other works, the high quantity of moisture and lime in the ore was the problem. Unrecognised at the time, this required blending with silica. Indeed, initially,
In1864 the first ironworks was completed east of Scunthorpe, adjoining a new railway line, by W H Dawes who had been the first to take a mining lease in 1859. Named the Trent Iron Works, the furnaces were small at 40’ (12m) high and worked badly, the first having to be blown-out after just 10 months. Trent No 3 started in October 1864, but No 2 did not start until 1867. The furnaces were operated with hot blast, initially charging coal but later a 50:50 mix of coal and coke. No processing of the pig iron was performed, this being sent elsewhere via the River Trent on barges. Additional furnaces were added and, in 1875, two larger furnaces each 60’ (18m) high and 18’ (5.5m) in diameter at the bosh, bringing the total to seven of which three were in blast. Like the earlier furnaces, these were iron-cased and open topped.
The second ironworks started production in 1864. Owned by Joseph Cliff, a brickmaker from Leeds, and his brotherin-law, William Hirst, it was built in the village of Frodingham, from where it took its name, the Frodingham Iron Company. The two furnaces were built of brick with iron bands to reinforce the stacks. At 65’ (19.8m) high they were taller than Trent’s first furnaces and measured 18’ (5.5m) at the bosh. One of the furnaces was fitted with a charging bell, the gas collected being used within the works. The other was open-topped. Daily output rose from five tons, to 12 with an expected production
Over the next two issues, we will examine the early days of ironmaking in Scunthorpe. By Tim Smith*
The early days of ironmaking at Scunthorpe Part 1. 1864-1912
Frodingham Iron Company
*Consulting editor, Steel Times International and a member of the Historical Metallurgy Society
Despite the adverse chemistry, such was the growing demand for iron that the deposits attracted experienced ironmasters and inexperienced entrepreneurs to set up ironworks around Scunthorpe, with varying degrees of success.
Landowner Rowan Winn first worked the Frodingham ore fields in 1858-9 after locating ore stretching 10 miles west of the river Humber, nearly to Scunthorpe. At its greatest thickness, seams were 32 feet (9.7m) deep. An analysis showed it to be far from ideal for ironmaking, rich in lime – too rich for ease of blast furnace operations, high in sulphur and moisture and low in iron. Despite this, such was the demand for ore from nearby Yorkshire, Winn was able to lease out areas of the ore fields for mining to serve Yorkshire furnaces.
HISTORY48 www.steeltimesint.comSeptember 2022
*Output from 1883 includes Holwell Iron & Co, Leicester
Lincolnshire Iron Smelting Co Ltd
To support and facilitate the transition towards cleaner manufacturing in the USA, Sustainable Industrial Manufacturing will be staged in Cleveland, Ohio in December 2022.


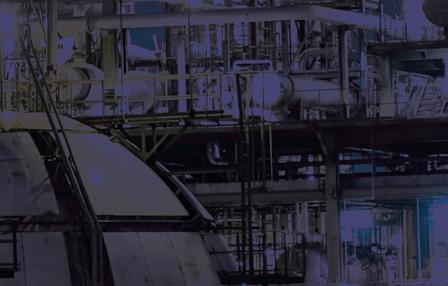
49 www.steeltimesint.com September 2022 HISTORY
Sustainable Industrial Manufacturing (SIM) is a global series of regional exhibitions and conferences supporting and facilitating the transition towards cleaner manufacturing around the world.

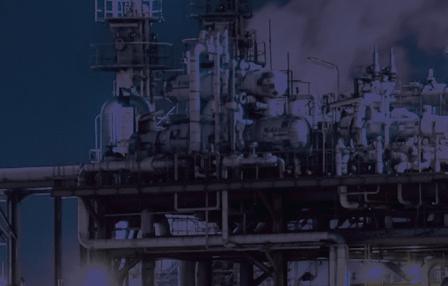
President Biden’s goal of a carbon-neutral economy by 2050 is dependent on the decarbonization of heavy industry. The Inflation Reduction Act of 2022 (IRA) passed by the United States Congress and signed into law by President Joe Biden this August, will raise $737 billion and authorise $369 billion in spending on energy and climate change. The law represents the largest investment into addressing climate change in United States history.
1905 443.4 9608 5 1910 512.3 10012 5
Year kilo tons UK Output kt % UK share
Source: British Blast Furnace Statistics 1790-1980
Hosting leaders from industry, innovation, science, government and investment, SIM USA will bring together those responsible for driving sustainability across hard-to-abate sectors.
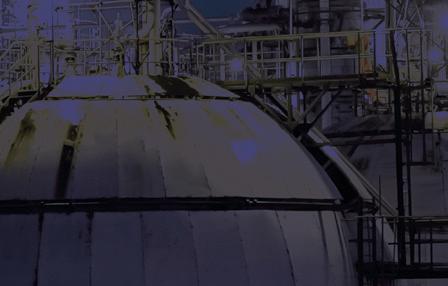
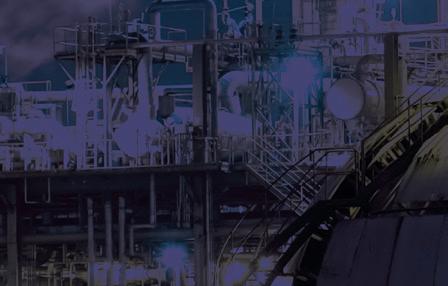
In 1872, Winn agreed a lease for the building of two furnaces between Scunthorpe and the Trent Works at present day Dawes Lane. Called the Lincolnshire Iron Smelting Co Ltd, the furnaces were 70’ (21m) high with bosh diameters of 20’ (6m). At first they were open-top but later one was fitted with bell charging. Output from both furnaces commenced in 1875 but the company ceased output in 1881 and entered voluntary liquidation in 1882.
Redbourn Hill Iron & Coal Co Ltd
Part 2 will look at developments post 1919.
1885* 235.4 7416 3
Appleby Iron Co Ltd
1880 207.7 7749 3
1895 349.2 7703 5
1875 111.7 6366 2
1870 31.7 5964 1
Co. Named Redbourn Hill Iron & Coal Co Ltd, two furnaces were erected each 75’ (22.8m) high with 20’ (6m) boshes. Both were closed top, and output commenced in 1875. In 1883, Redbourn took over the Lincolnshire Iron Smelting Co Ltd. The works was renamed North Lindsey Works.
Pig iron output Lincolnshire 1866 – 1910 (ktons)
The sixth company of the area was also established by Scottish businessmen led by Blair and Gilmour of Kilmarnock. The firm was granted 15 acres in Appleby parish by
1890 268.4 7904 3
Winn in 1874, initially for two furnaces with not more than a 23’ (7m) bosh diameter with two more furnaces to be built within the following four years. The company was named Appleby Iron Co Ltd, but was generally referred to as ‘Scotch Company’. The first furnace was lit in December 1876 and the second the following year. The furnaces were 62’ (18.9m) high with bosh diameters of 18’ (5.5m), small compared with others in the area. A third furnace was built in 1884, but the fourth not until 1898. Only Frodingham and Redbourn survived well into the 20th century. The Appleby company was taken over by Redbourn in 1912 and the North Lincoln works was sold to Stewarts and Lloyds, which in turn sold it to the United Steel Companies Ltd in 1931, the parent company of Appleby Frodingham. The Lindsey works were closed by the end of 1899 and the Trent passed to Firth Brown and John Lysaght and then to Appleby Frodingham Steel Co, who demolished the plant. �
SCAN ME TO JOIN THE MAILING LIST REGISTER TODAY www.SustainableIndustrialManufacturing.com EARLY BIRD TICKETS NOW AVAILABLE Organised by: Part of: SITEEVENTSNETWORKINGDEBATESROUNDTABLECONFERENCEEXHIBITIONTOURS Untitled-1 1 13/09/2022 11:50
LIGHTENING THE IMPACT OF HEAVY INDUSTRY
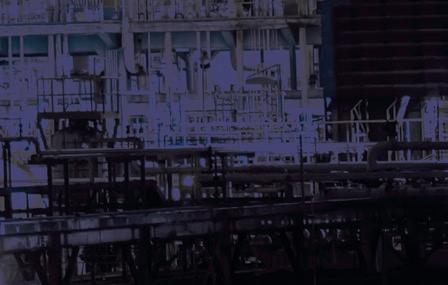
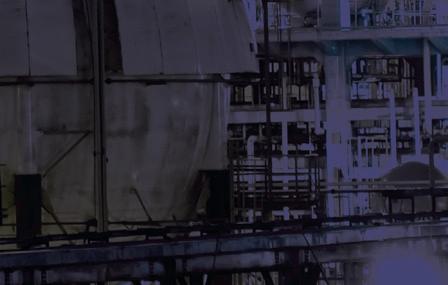
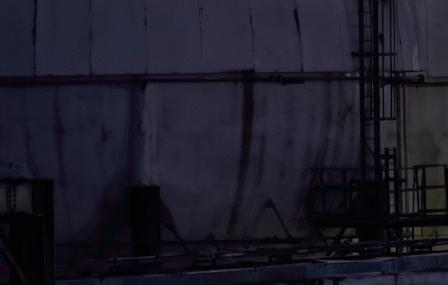
1900 388.7 8960 4
1866 13.8 4524 1
additional quantities of lime were added to the charge, exasperating the situation. When the need for silica to counteract the lime was appreciated, siliceous bearing ore from Northamptonshire was first brought in until deposits of similar siliceous ores were located south of Lincoln in 1873. Coke ovens were established to provide the fuel/ reductant.
In June 1872, Winn negotiated with Scottish businessmen to set up an ironworks to the east of the North Lincoln
IT‘S MORE THAN JUST A MACHINE. WE MAKE YOUR PRODUCT GOLD focused R ELIABILITY unique S PECIALISTS ingenious B KOCKSELIEF rolled ® Do you want more?
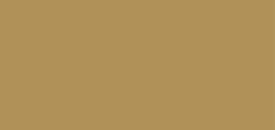
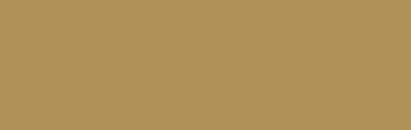
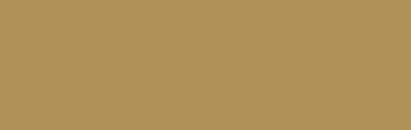
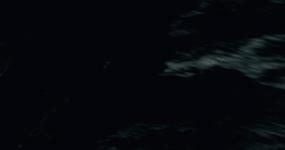

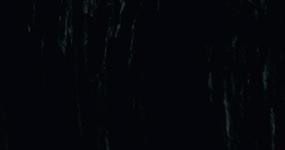
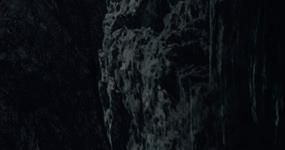
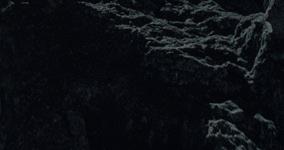

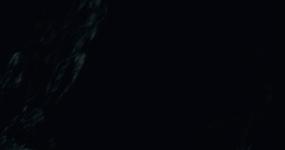


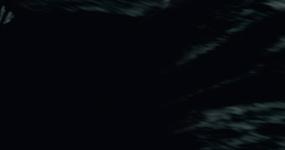

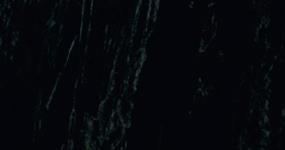
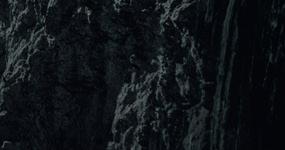
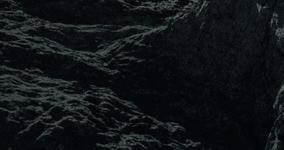
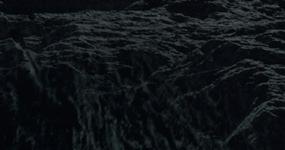

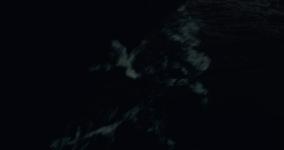
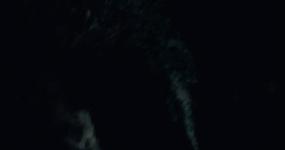
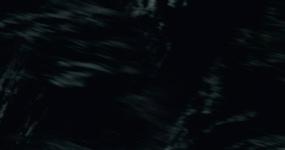

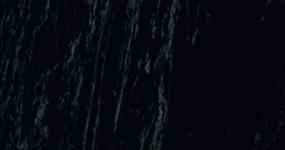
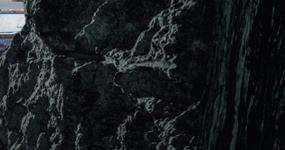


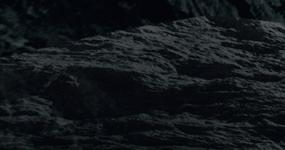
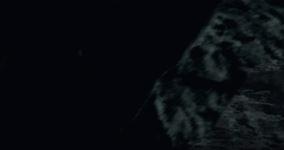
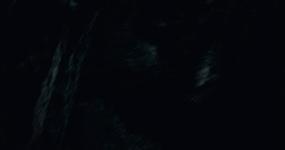
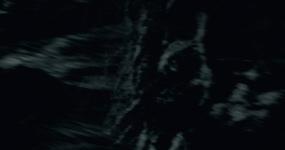
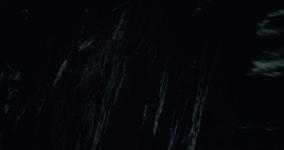
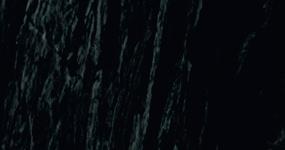

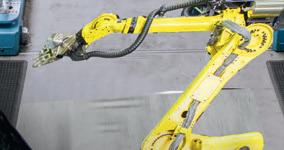

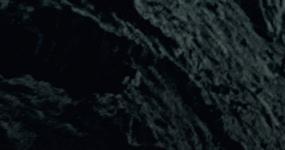
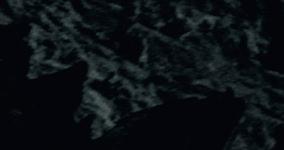
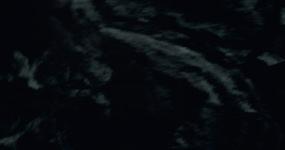

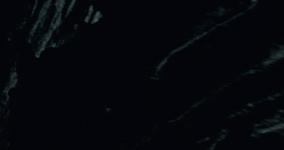
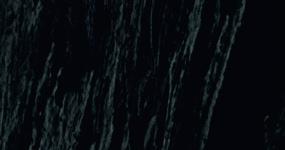

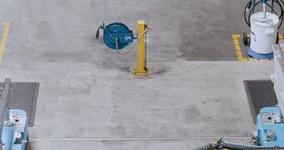
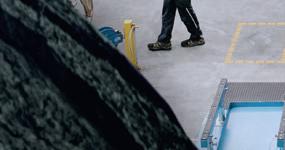

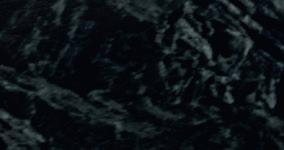
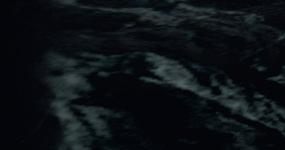
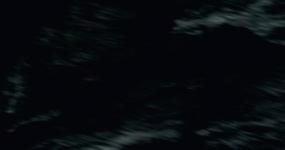

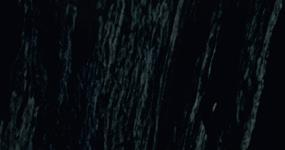

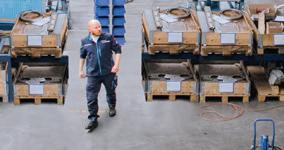

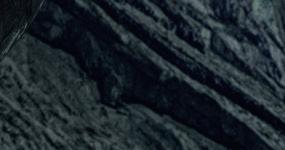
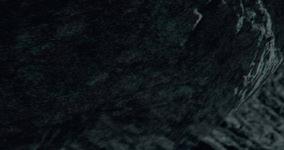

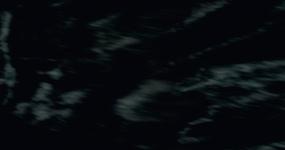



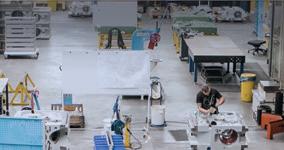
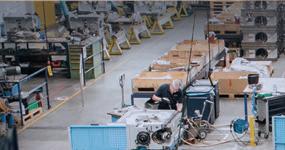
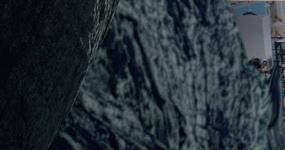
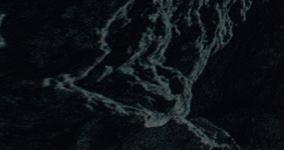
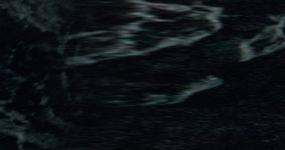
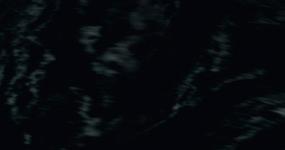

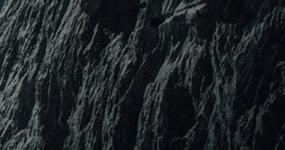
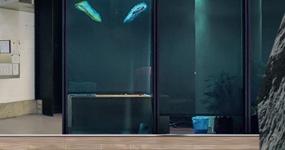

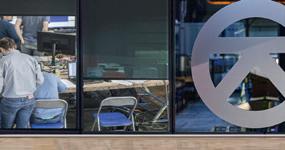
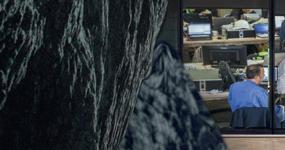


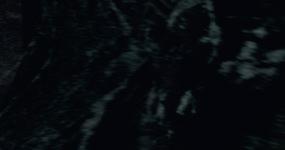
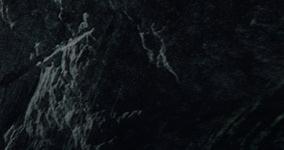
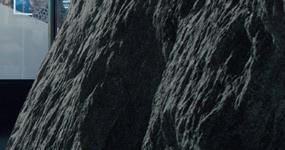
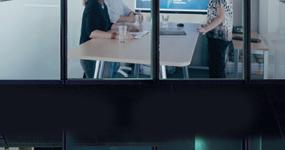
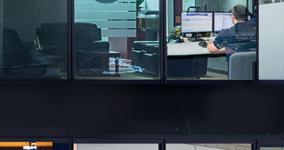
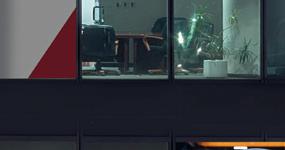
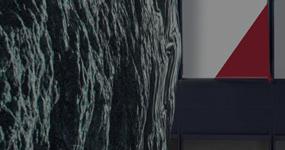

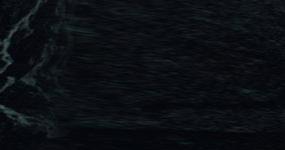

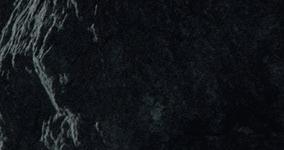
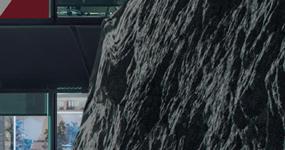
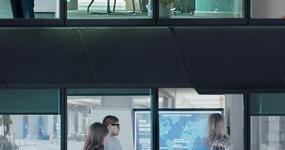
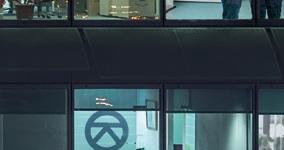
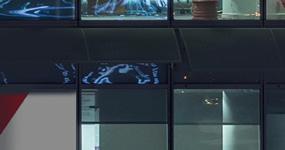

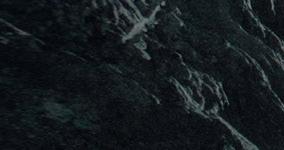
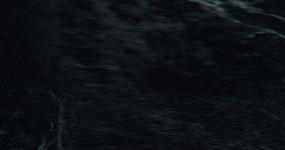

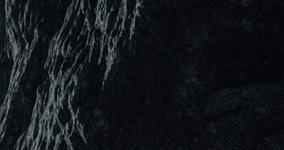


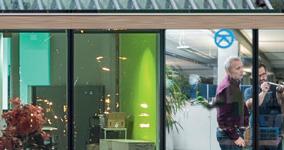
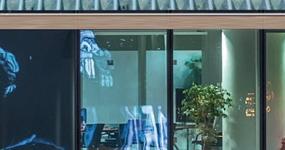
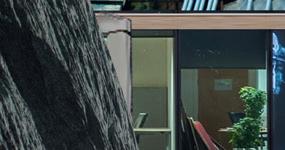
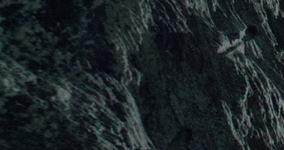
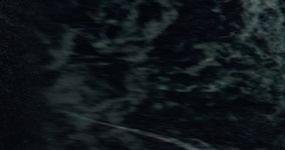

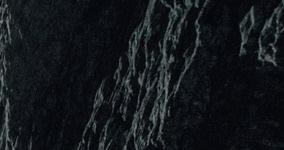
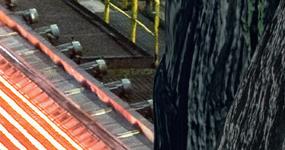
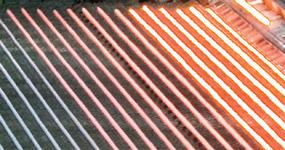

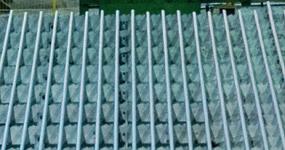
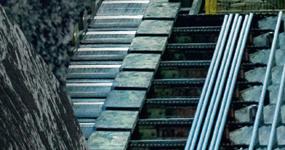
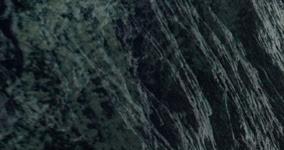
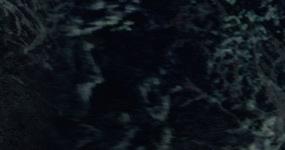
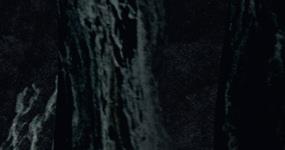
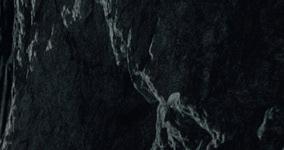
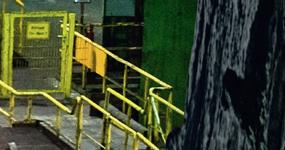
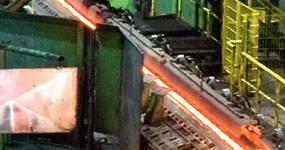
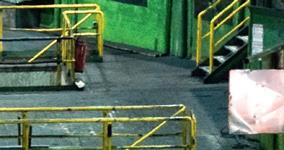
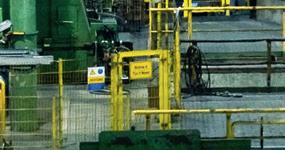
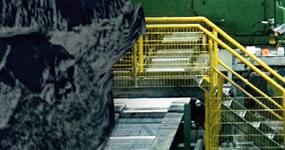
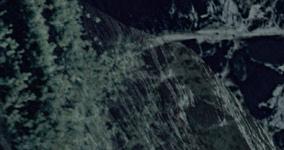
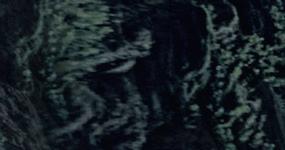
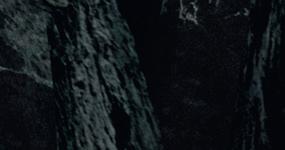
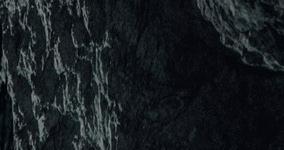
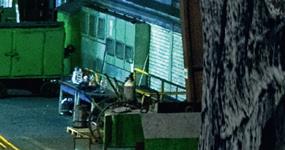
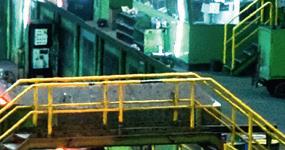
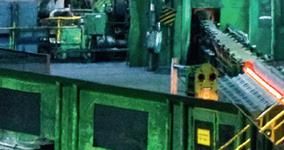
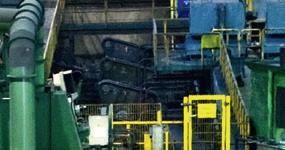
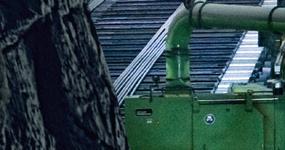
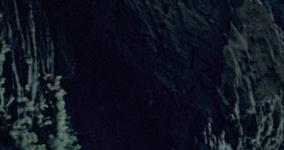
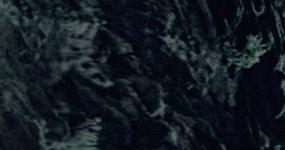
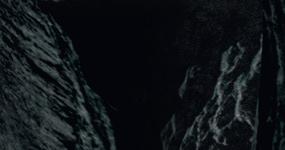

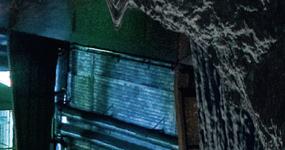
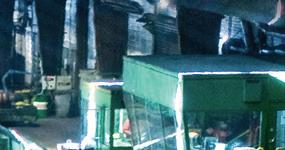

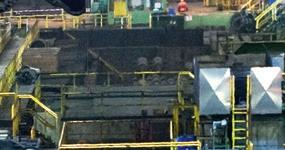
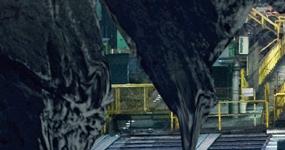



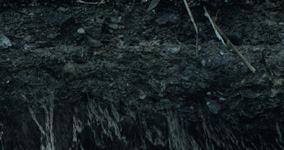



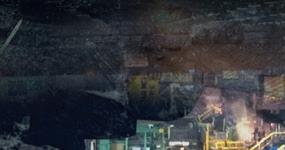
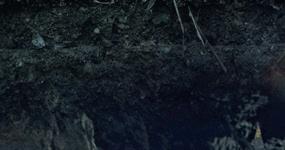
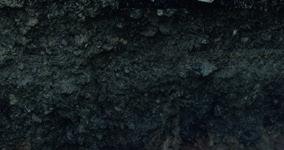
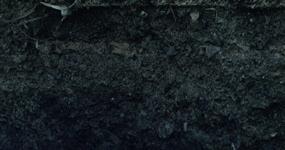
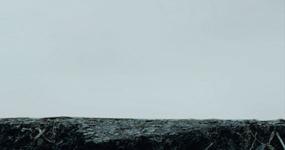


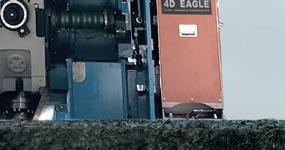
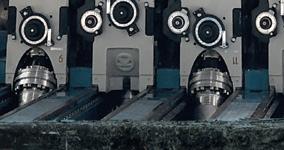
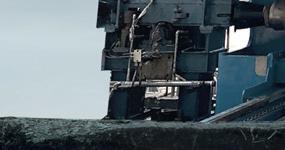
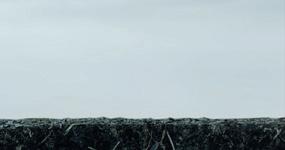
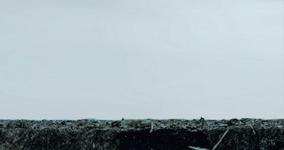


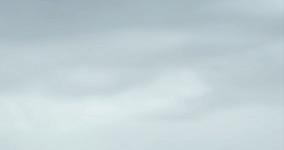
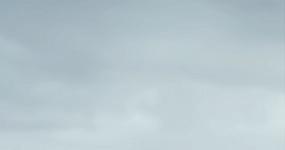
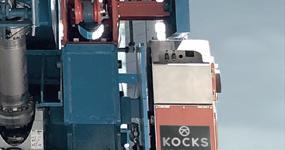

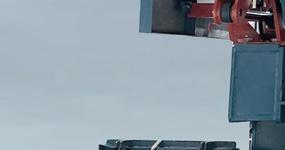
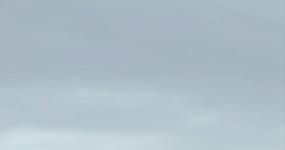
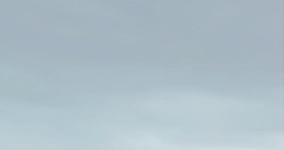


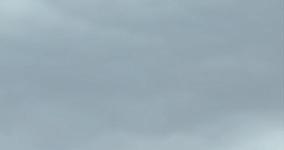

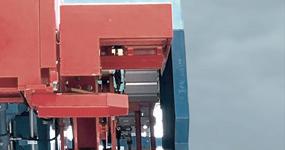

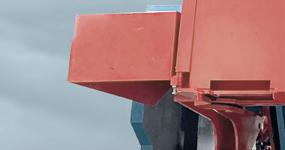
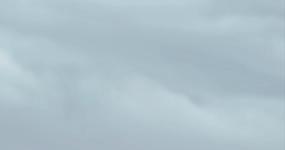
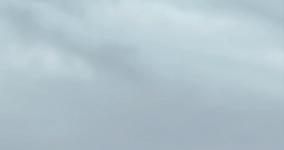

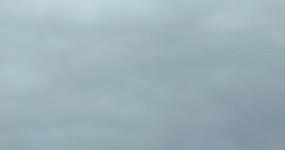
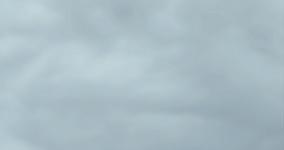
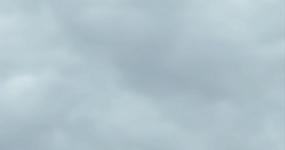
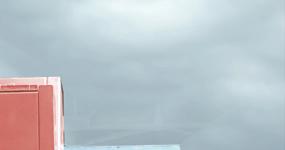
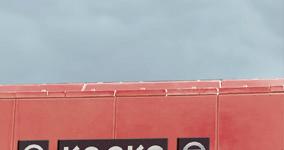

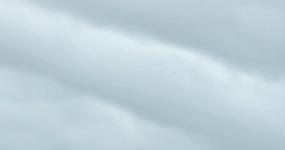



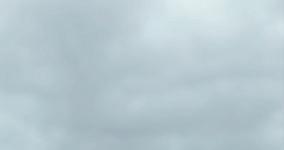
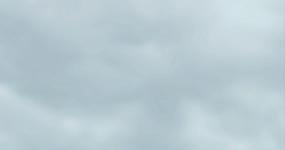
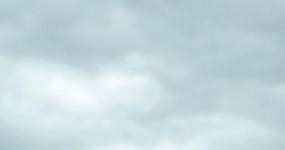

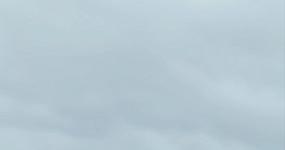
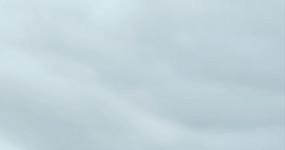
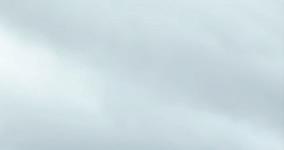
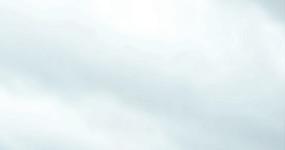
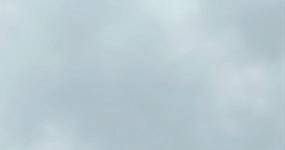
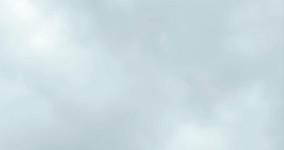
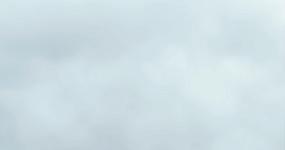

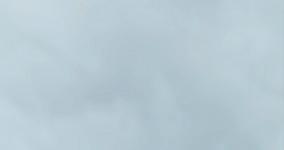
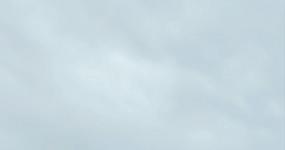
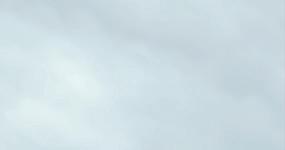

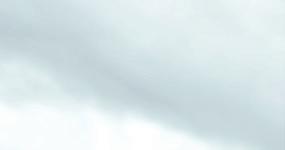
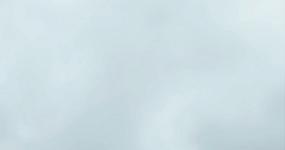

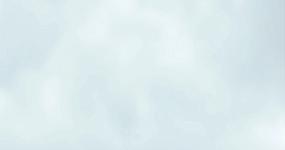

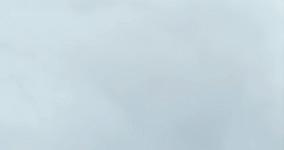
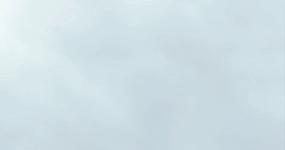

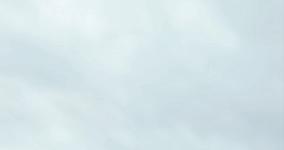

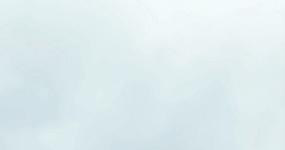
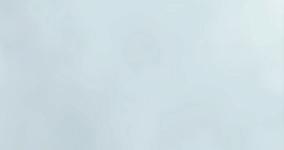
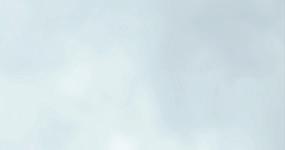
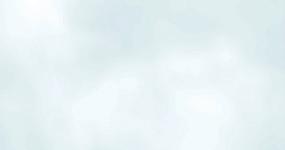
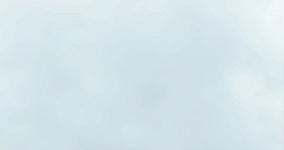
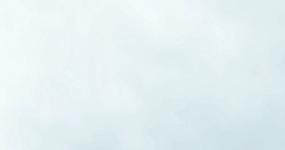

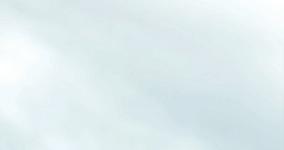
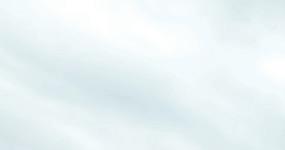