SteelWatch on the future that lies ahead. We report from the Global Steel Dynamics Forum.
Pinkham on the US stainless steel market.
How Coolbrook decarbonizes high-temperature processes.
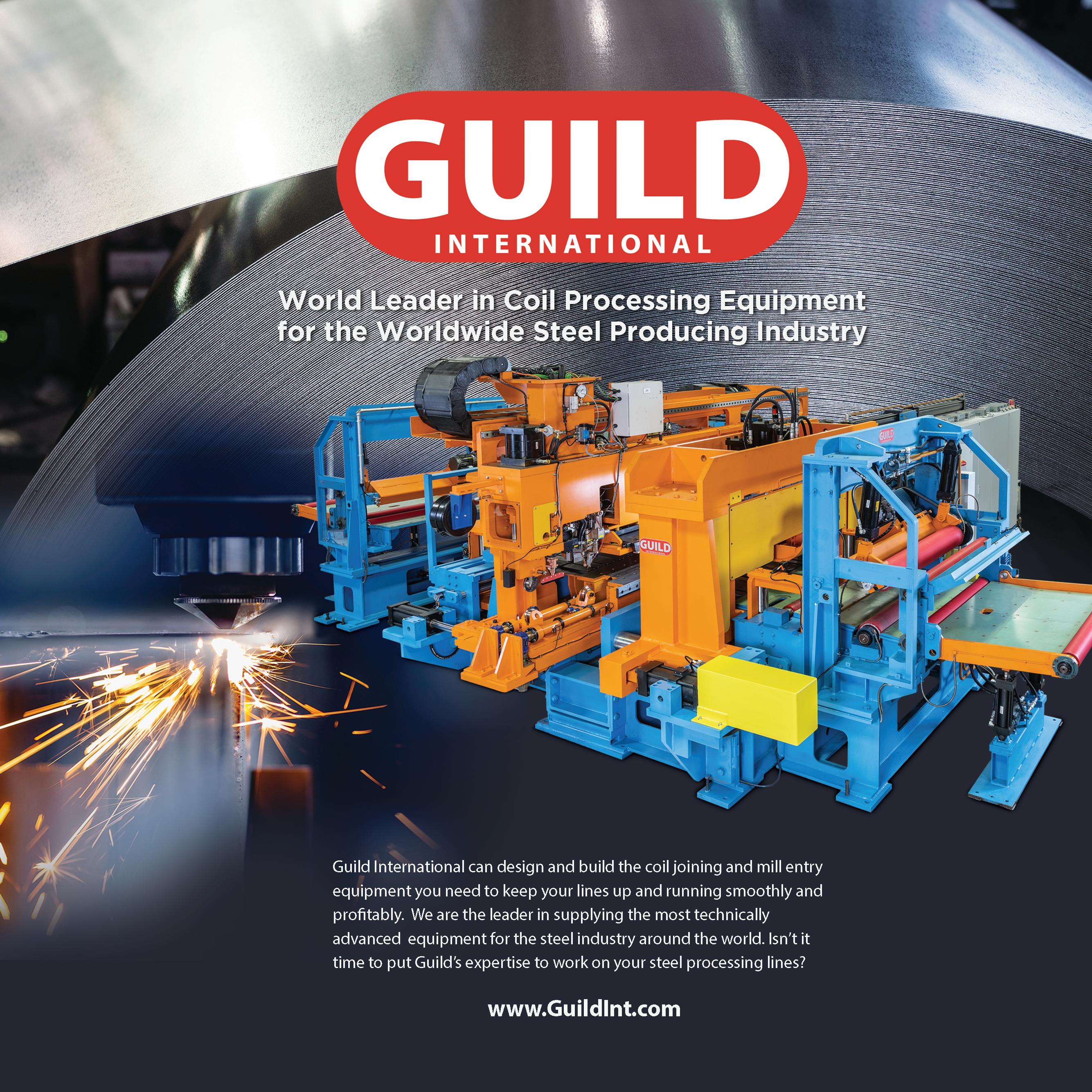
SteelWatch on the future that lies ahead. We report from the Global Steel Dynamics Forum.
Pinkham on the US stainless steel market.
How Coolbrook decarbonizes high-temperature processes.
Metals offers the entire steel value chain an exceptional opportunity for curbing their CO2 emissions.
The unique combination of its historic and recently developed product portfolio, make John Cockerill one of the industry’s most relevant suppliers of equipment for both the hot and cold phase of the steelmaking and processing industry.
Our three distinct business segments are addressing todays and tomorrow’s challenges supporting sustainable and green steel production:
Our new upstream offering related to DRI (Direct Reduced Iron), EAF (Electric Arc Furnaces) technologies and the use of hydrogen in steelmaking. Next to offering indirect electrification (DRI-EAF&H2-DRI-EAF),John Cockerill is also working on Volteron®: A first-of-a-kind iron reduction and steel processing route via direct cold electrolysis. This CO2 free steelmaking process, has been co-developed with the world’s leading steelmaker ArcelorMittal.
Regrouping our historical downstream product portfolio, this segment also includes:
¡ the Jet Vapor Deposition (JVD®) technology set to replace today’s hot-dip or electro galvanizing processes. This novel high-productivity vacuum coating technology provides previously unknown coating flexibility and possibilities, all while offering lower CAPEX and OPEX.
¡ our E-Si® equipment & processing lines specifically designed to produce high-quality Non-Grain Oriented (NGO) steel in response to the need for electrical steel meeting precise metallurgical properties, essential to support the shift towards green mobility.
This segment not only embraces all services and after-sales activities but will be strongly focusing on downstream furnace electrification (reheating and processing line furnaces), as well as hydrogen combustion, and the optimization of plant operations, including energy audits and the modernization of steel production equipment and installations.
photo courtesy of
EDITORIAL
Editor
Matthew Moggridge
Tel: +44 (0) 1737 855151
matthewmoggridge@quartzltd.com
Assistant Editor
Catherine Hill
Tel:+44 (0) 1737855021
Consultant Editor
Dr. Tim Smith PhD, CEng, MIM
Production Editor Annie Baker
Advertisement Production Carol Baird
SALES
International Sales Manager
Paul Rossage
paulrossage@quartzltd.com
Tel: +44 (0) 1737 855116
Sales Director
Ken Clark
kenclark@quartzltd.com
Tel: +44 (0) 1737 855117
Managing Director
Tony Crinion
tonycrinion@quartzltd.com
Tel: +44 (0) 1737 855164
Chief Executive Officer Steve Diprose
SUBSCRIPTION
Jack Homewood
Tel +44 (0) 1737 855028
Fax +44 (0) 1737 855034 Email subscriptions@quartzltd.com
International Guild International has been an industry leader in the development of coil processing equipment used around the world in the steel processing, tube producing, and stamping industries since 1958. Guild has led these industries in innovative design and manufacturing processes to build cutting-edge equipment to aid companies improve production, reduce scrap, and become more efficient and profitable.
Matthew Moggridge.
The latest global steel news.
Published by: Quartz Business Media Ltd, Quartz House, 20 Clarendon Road, Redhill, Surrey, RH1 1QX, England. Tel: +44 (0)1737 855000 Fax: +44 (0)1737 855034 www.steeltimesint.com
Steel Times International (USPS No: 020-958) is published monthly except Feb, May, July, Dec by Quartz Business Media Ltd and distributed in the US by DSW, 75 Aberdeen Road, Emigsville, PA 17318-0437. Periodicals postage paid at Emigsville, PA. POSTMASTER send address changes to Steel Times International c/o PO Box 437, Emigsville, PA 17318-0437. Printed in England by: Stephens and George Ltd • Goat Mill Road • Dowlais • Merthyr Tydfil • CF48 3TD. Tel: +44 (0)1685 352063 Web: www.stephensandgeorge.co.uk ©Quartz Business Media Ltd 2024
The latest products and contracts.
Innovations special
Harnessing RotoDynamicTM technology. 18
Latin America update POSCO and Tsingshan’s Argentine adventure.
20 India update Budget cheers for Indian steel producers. 22
African steel industry
Africa’s steel industry: plans and strategies.
Global Steel Dynamics Forum 2024
Big players, big issues.
Climate action
Just how different will future steel be?
Green steel
Groundbreaking success for sustainable mobility.
Special & stainless steels
Demand recovery ahead!
Digitalization
Pathways to green steel excellence. 50
Perspectives: Schaeffler
Shaping the transformation. 52 History
Dr. Tim Smith looks back at the history of Tata Steel’s Port Talbot plant in South Wales, United Kingdom.
Matthew Moggridge Editor
matthewmoggridge@quartzltd.com
AUTOMATION & MECHATRONIC SOLUTIONS
Over the weekend I had two moments where I sat back and thought long and hard. The first was after returning from a trip to the supermarket where I spied an elderly lady working on the check-out. I think she’s great and for two reasons: one, she’s very friendly and nice, and two, she looks like the sort of woman who would make a really good roast dinner, somebody who probably makes her own gravy and might offer home-made apple pie and custard. I’ll never know, of course, because I don’t possess the cheek to ask her whether I could pop round of a Sunday and enjoy the fruits of her labour, it simply won’t happen and besides, I’m pretty good at making roast dinners myself although I doubt whether anybody would deduce this fact from my appearance, and perhaps I’m not the wizard I think I am at roast chicken, roast potatoes, greens and gravy followed by a traditional dessert.
The second moment of deep thought came when I was told that somebody close to one of my family members believes that in the not-too-distant future we will all be underwater, meaning that the world will be flooded as a direct result of climate change, or rather the adverse effects of
climate change. At the moment, a lot of people joke about it, saying things like they’d welcome tropical summers in the UK as they wouldn’t have to go abroad for their holidays. Fair point, but I was taking the doom-laden view of global flooding, having read JG Ballard’s Drowned World, a book I highly recommend to anybody looking for something decent to read. Anyway, I was thinking along the lines of buying a boat instead of an electric car or perhaps ‘going direct to Mayfair without passing go’ and getting a houseboat on the Thames; that way, I could ready myself for when the floods begin: I’d just sail off into the sunset, possibly ride a few tsunamis, but by and large I would get away with it. I would probably try to find the woman from Waitrose, the one who I believe would make a good roast dinner, just in case I can’t, and invite her along for the voyage because life would be unbearable if I couldn’t enjoy such a meal as I headed towards the inevitable oblivion awaiting me and the rest of humanity. The message here is simple: we need to look after the environment and address the pressing case of climate change before it’s too late. See page 34 for more.
AIC has 50 years of experience in steel automation.
AIC offers state-of-the-art systems and technological solutions designed for meltshops, casters, long and flat rolling and processing lines.
We take care of every step from Power Control, PLC, HMI and level 2 systems, we also handle robotic applications, automatic tying machines for bundles and stacks, and manage every phase from design to after sales services
At SMS group, we have made it our mission to create a carbon-neutral and sustainable metals industry. We supply the technology to produce and recycle all major metals. This gives us a key role in the transformation towards a green metals industry.
DR. KEITH WALKER, 1963-2024
Dr. Keith D Walker, who recently passed away, adored working in the steel industry. Having been born in Skipton, Yorkshire, he grew up near Sheffield and studied metallurgy at Leeds University, eventually leaving in
1987 having completed a PhD concerning continuous casting.
He went to work for British Steel in Scunthorpe and stayed with the company through its various name changes, staying on the technical side and eventually becoming head of technology with Corus and finally group director of R&D Programmes, before setting up his consultancy Steelfolk. He served as secretary of the Lincolnshire Iron and Steel Institute between 1992-93, and as director from 2003 to 2014, eventually becoming president.
Keith loved the beauty and excitement of steelmaking and found it disappointing how so many people (including at government level) simply didn't understand steel's complexity, versatility and importance. He was often frustrated by incorrect portrayals of steel in film and on television, and metallurgical inaccuracies in many documentaries.
Away from work he played piano and enjoyed walking, tai chi, nature – birds and wild flowers in particular, good food and wine, music of all kinds (especially Pink Floyd) and following Test cricket.
Keith very kindly wrote a number of informative and accessible articles on metallurgy for Steel Times International
UK-based Cocoon, a climate technology company, which ‘enables steel and concrete to decarbonize in tandem’, has announced it has raised $5.4 million in pre-seed funding from Wireframe Ventures, Celsius Industries, Gigascale Capital and SOSV. The company will use the funding to scale its engineering and science teams, accelerate commercialization efforts, and build an industrial lab and demonstrator plant in the UK.
Source: Reuters, 8 August 2024.
Chile’s largest steel mill has said it will shut down in the face of competition from cheap Chinese imports, in a blow to the country’s government, which had imposed tariffs on China earlier this year in a bid to save it. Chilean steelmaker CAP, which runs the Huachipato mill in Chile’s central BiobÍo region, said that it would shutter its steel operations ‘indefinitely’ by September, blaming an influx of imports from China for more than $500 million in losses over the past two years.
Source: The Financial Times, 7 August 2024.
An investigation has unveiled that officials from Northwestern Liberia directed the illegal removal of scrap assets belonging to ArcelorMittal Liberia. The scrap was gathered as a result of ongoing work on the railway, involving the repair of a damaged bridge and replacing old wooden ties with new steel sleepers as part of the company’s phase two expansion project to increase the rail’s capacity. ArcelorMittal intends to donate the now recovered scrap to local communities, with 30% of sales going to the county authority, and 70% going to local people.
Source: Front Page Africa, 9 August 2024.
The board members of Turkish steel producer Tosyali Holding have stated that the company will continue to invest in increasing its annual spiral pipe capacity. At the beginning of the year, the company acquired Spanish steel pipe manufacturer Baika Steel Tubular System (STS) to ‘strengthen its position in Europe’ and increase its annual global pipe production capacity.
Source: Steel Orbis, 8 August 2024.
Steelmaker Rudra Global Infra Products has said the company will invest around Rs 190 crore to set up a 30-megawatt captive solar project in Gujarat. The solar plant is scheduled to commence operations by January 2025, the company said in a statement. "The first phase of the project entails a capital expenditure of Rs 190 crore, with 80% of the funding secured through financial institutions over a five-year tenure. The remaining 20% will be invested by the company," the statement said. The clean power generated will be primarily utilised to meet the energy requirements of the company's existing billet and TMT bar manufacturing operations.
Source: Business Standard, 9 August 2024.
Miner and steelmaker
EVRAZ has confirmed that there has been a fatality at its Pueblo steelmaking facility. A spokesperson from the company stated: “We are saddened to confirm there was a fatality at our steelmaking facility in Pueblo. Our deepest condolences go out to the family, friends, and coworkers of our deceased team member. We will work with all relevant agencies, including OSHA and the United Steelworkers, to ensure a full investigation. As the investigation is ongoing, it would not be appropriate to provide further comment at this time.”
Source: KOA NEWS5, 9 August 2024.
Kazakhstan's Qarmet steel company, formerly ArcelorMittal Temirtau, plans a further $1.5 billion investment in coal and iron ore mining, the Kazakh president's press office said. During his working visit to the Karaganda Region, president KassymJomart Tokayev toured the Qarmet metallurgical plant
Thyssenkrupp's steel division requires around $1.4 billion in additional funds beyond what its parent is prepared to pay in a planned separation process, the division's supervisory board chairman has said.
Sigmar Gabriel, who spoke after a supervisory board meeting of Thyssenkrupp Steel Europe (TKSE), said an external audit would now be carried out to determine the unit's restructuring and funding needs, adding that this could happen before yearend.
Source: Mint, 10 August 2024.
in Temirtau, where he was briefed on plans to expand the plant's capacity and make additional investments. Qarmet's new investor and board chairman, Andrei Lavrentiyev, and CEO Vadim
The UK Trade Remedies Authority (TRA) has proposed to increase the import quota for hot-rolled flat products due to a reduction in domestic production. The proposal is driven by the recent closure of a blast furnace at Tata Steel UK’s Port Talbot plant as part of the transition to an electric arc furnace. Changing market conditions have affected domestic flat steel production in the country. According to the TRA, this led to an increase in imports, which consistently exhausted part of the quota for hot-rolled steel for four consecutive quarters, which, in turn, led to an increase in the cost of these products on the British market.
Source: GMK Center, 12 August 2024.
Basin said ongoing and upcoming projects total over $3.5 billion. "Additional investments include $500 million for the coal department and $978 million for the iron ore department," the president's press service stated. Source: Interfax, 14 August 2024.
Polish steelmaker Liberty Czestochowa, a subsidiary of global steelmaker Liberty Steel, has filed an appeal against a Czestochowa court decision to initiate bankruptcy proceedings. Liberty intends to restart an electric arc furnace with a capacity of 700kt of steel per year and a rolling mill (1.2Mt/yr). The company believes that it has demonstrated strong support from its largest creditor and has the prerequisites to maintain a €100 million working capital loan from a reputable financial institution. Source: GMK Center,14 August 2024.
China’s steel industry is facing a crisis more serious than the downturns of 2008 and 2015, Hu Wangming, chairperson of China Baowu Steel Group warned at the company’s half year meeting, highlighting a need to preserve cash and likening conditions to a ‘severe winter.’ The crisis will likely be ‘longer, colder and more difficult to endure than we expected,’ Wangming added.
Source: Engineering News, 14 August 2024.
South African coal exporter Thungela Resources is searching for new mines to buy and may consider acquiring coking coal assets if it finds a good fit, CEO July Ndlovu has said. The thermal coal producer bought Ensham mine in Australia last year to diversify from South Africa where shipments are hobbled by lack of sufficient rail capacity – although Ndlovu said that situation was set to improve. The performance and returns from the Australian mine so far justify Thungela’s strategy of growing through acquisitions, Ndlovu told Reuters in an interview. “We’re always looking for opportunities and coal in general, including coking coal, is of interest to us,” Ndlovu said.
Source: Mining.com, 19 August 2024.
AM/NS India, the country’s fourth-largest steel producer and a joint venture between ArcelorMittal and Nippon Steel, has introduced a new colour-coated steel brand, a patented product originally developed by ArcelorMittal. This move comes as India’s annual consumption of coated steel reaches around 3.2Mt, with demand in this valueadded segment growing faster than the broader steel market. The newly launched product, branded as ‘Optigal,’ will be produced at a volume of 700kt/yr, with plans to increase production to 1Mt over time. The initial manufacturing will take place at AM/NS India’s facility in Pune, with further expansion to other locations planned.
Source: Machine Maker, 20 August 2024.
British steel foundry Furniss & White, which specialises in high integrity stainless steel castings, fabrications and precision machining, has signed a long-term agreement to produce its castings using ‘high-performance alloys’ from the N’GENIUS Series under license. The Sheffieldbased firm has successfully completed a range of Manufacturing Procedure Qualification Tests at its facilities in various grades from the N’GENIUS Series and will be providing castings for engineering products made using these advanced materials to its customers.
Source: Manufacturing Management, 21 August 2024.
Global steelmaker
ArcelorMittal, in co-operation with energy company
ENVERIO, is implementing a project to build a solar power plant with a capacity of 4.1 million kWh per year to meet the needs of the ArcelorMittal
Auto Processing Deutschland service centre in Neuwied, Germany. The solar power
Atlas Renewable Energy and ArcelorMittal will form a joint venture to build a solar plant in Minas Gerais state in Brazil, the companies said on 21 August. The aim is to supply power to the steelmaker's operations in Southern and Southeastern Brazil. The joint project in the city of Paracatu will have an installed capacity of 264.6 megaWatts alternating current (MWac) and an associated energy transmission system.
Source: yahoo! Finance, 21 August 2024.
plant will be built on the roof of the production facilities and will cover more than 50% of the company’s annual demand.
Source: GMK Center, 22 August 2024.
Japanese steelmakers Nippon Steel Corporation and JFE Steel have collectively bought 30% of Whitehaven Coal’s Blackwater metallurgical coal mine in Queensland, Australia. Whitehaven Coal is seeking to extend the life of the Blackwater mine by an additional 60 years, pushing the mine’s life out to 2085, as part of its Blackwater North Extension Project. Commenting on the announcement, Fiona Deutsch, lead analyst at the Australasian Centre for Corporate Responsibility said: “The recent strong support for three climate-related shareholder proposals at Nippon Steel’s annual general meeting suggests investors see a delay in decarbonization as a risk to corporate value, and this investment will raise questions about the company’s commitment to decarbonization and meeting investor expectations.’’
Source: ACCR, 22 August 2024.
Tata Steel Utilities and Infrastructure Services has outlined its plan to convert all food waste produced in Jamshedpur, India, into biogas by March 2026. Managing director of Tata Steel UISL, Ritu Raj Sinha, announced the initiative during a press conference, in which he emphasised the potential of biogas production. According to Sinha, biogas production could ‘transform the city's waste management’ and, if all goes to plan, Jamshedpur will be the first city to utilise its entire food waste for biogas production. The city currently generates around 260 tonnes of waste each day, with 40% of the total estimated to be food waste.
Source: Bioenergy Insight, 22 August 2024.
thyssenkrupp Steel Europe (Duisburg, Germany) is scaling up its research activities in the field of lowcarbon steel production to include a co-operation with BlueScope Steel. The focus of this co-operation is on the smelting units, which form a core component of the first step in the transformation towards carbon-neutral steel production, namely the replacement of the first blast furnace by a direct reduction (DR) plant with downstream smelters.
Source: Chemical Engineering, 22 August 2024.
Liberty Ostrava has started issuing layoff notices to around 1,600 employees. The affected workers have been offered two-month notice periods or the option to leave by mutual agreement. The plant, which had about 4,000 employees, has been inactive since December due to halted energy supplies. Earlier this year, the company announced plans to close its coke plant and reduce its workforce by 2,600 employees by autumn.
NLMK Indiana recently restarted a 118-ton-capacity EAF after it was shut down for six weeks to undergo the installation process, and a single-point roof lift system and an integrated gantry, both provided by Primetals, were added. “With this solution, operator safety is improved when replacing small roofs or lifting the roof, as direct contact with the roof is no longer required when disconnecting the chain,” Primetals says. “Within four days [after restart], the furnace reached an astonishing 21 heats per day and has maintained a steady performance since then, now exceeding the 5,000 heat mark.”
Source: Recycling Today, 23 August 2024.
Many workers have already left voluntarily, with over 600 resigning in July alone.
Source: Radio Prague International, 23 August 2024.
India-based NMDC Steel (NSL) has hit the milestone of 1Mt of hot rolled coil output, four days ahead of the first anniversary of hot-rolled coil production. This achievement, claims the steelmaker, underscores its position as one of the fastest and most efficient plants in the industry and builds on the company having produced 1.5Mt of hot metal from its blast furnace on 21 July. Source: The Hindu, 23 August 2024.
Swedish energy company
Vattenfall and newly formed industry collaboration Industrikraft will work together to research the conditions for joint investments in new, green electricity production in Sweden. Industrikraft currently consists of Alfa Laval, Boliden, SKF, Stora Enso and the Volvo Group, which will work towards meeting Sweden’s increasing power demand in a way that ensures its industrial competitiveness.
ArcelorMittal Nippon Steel India (AM/NS India) – a joint venture between ArcelorMittal and Nippon Steel, has announced the launch of Optigal® – a colour coated steel brand with a Zinc-Aluminium-Magnesium (ZAM) metallic coating. The brand is currently available only in global markets but now it is being produced and distributed in India for the first time by AM/NS India. AM/ NS India has stated that the new offering ‘reinforces the company’s pioneering efforts to introduce internationally benchmarked quality products’ to meet the growing need for colour coated steel. Source: Realty Plus, 23 August 2024.
The collaboration with Vattenfall aims to address issues such as a framework for co-investment, identification of projects and assessment of feasibility in terms of permits, grid connections and profitability. Source: Power Engineering International, 23 August 2024.
Local British council leader Rob Waltham is set to lead a small delegation to China to meet British Steel’s owner in an attempt to protect the future of steelmaking in Scunthorpe. British Steel’s owner, Jingye, has previously announced a £1.25bn development plan to create new green steel making facilities in Scunthorpe. North Lincolnshire Council has pledged to develop 300 acres at the site to create new, green engineering and energy jobs, creating more opportunities for residents to access sustainable, high-paid jobs.
Source: NorthLincs.gov.uk, 23 August 2024.
For more information, visit our website at www.guildint.com or call +1.440.232.5887
Motion technology company Schaeffler has announced that more than 5,000 additional charging points for electric vehicles are to be constructed worldwide by 2030. These include 3,000 charging points at European locations alone. The locations at Herzogenaurach and Schweinfurt in Germany are acting as pilot projects for the technology and the operator model. Following the successful completion of the test phase, the project will be gradually rolled out in all other regions of the Schaeffler Group.
“Schaeffler stands for sustainability and is committed to e-mobility,” said Andreas Schick, chief operating officer of Schaeffler AG. “We are pursuing the higher-level objective of reducing our CO2 emissions on a continuous basis. This includes the carbon footprint for individual mobility. Through this project, we will increase Schaeffler’s attractiveness as a sustainable em-
ployer and further motivate our workforce to act in an environmentally conscious manner.”
As part of the redevelopment of a parking lot in Herzogenaurach, 40 charging points have been installed, which are initially available for employees without charge. These charging stations are the standard model used at all Schaeffler locations. They provide up to 22 kiloWatts of charging capacity per station and are to be operated and maintained by an external partner in the future. The expansion plan for the Herzogenaurach location allows for the construction of a further 245 charging points for employees, company cars and visitors in 2025. In Schweinfurt, the electrical infrastructure will first be expanded to allow the construction of a further 122 charging points. Initial operation is planned for 2025. In the UK, the Schaeffler production plant in Sheffield and the Vehicle Lifetime Solu-
tions distribution centre in Hereford have already installed charging points for electric vehicles.
For further information, log on to www.schaeffler.com
A British steel foundry has become the first company in the world to manufacture castings using an new series of high-strength austenitic stainless steels.
Furniss & White, which specialises in high integrity stainless steel castings, fabrications and precision machining, signed a long-term agreement to produce its castings using high-performance alloys from the N’GENIUS Series under license.
The Sheffield-based firm has successfully completed a range of Manufacturing Procedure Qualification Tests at its facilities in various grades from the N’GENIUS Series and will be providing castings for engineering products made using these advanced materials to its customers.
The N’GENIUS Series, which is patent protected in 30 countries, represents the total reinvention of conventional austenitic stainless steels – commonly known as the 300 Series.
Dr Ces Roscoe, CEO of N’GENIUS Materials Technology and inventor of the N’GENIUS Series, said: “Furniss & White is a company that shares our own passion and drive for innovation and we are absolutely delighted to be collaborating with them on what is destined to be an industry changing technology. With a long history of steelmaking, Sheffield is widely regarded as the birthplace of stainless steel and it seems befitting that it will essentially be ‘reborn’ in the same city more than a century later.”
Sam Scholes, managing director of Furniss & White, said: “For more than 44 years we have built a strong reputation as a high-quality British
manufacturer of high integrity castings made in our modern foundry in the UK. Now, as an approved licensed N’GENIUS manufacturer, we are writing an exciting new chapter in our history and to be the first foundry in the world to have this capability makes us extremely proud. We expect these game-changing N’GENIUS materials
will be extremely popular with our existing customers and help open up new opportunities in other markets including the US and Canada and in clean energy industries such as hydrogen.”
For further information, log on to www.ngeniusmaterials.com
Steel Dynamics Inc. (SDI) and ArcelorMittal/Nippon Steel (AM/NS) have chosen Sarclad’s latest electro discharge texturing technology (EDT) featuring the company’s ‘MultiServo Array’ (MSA) system for their flagship plant expansions.
The AM/NS installation is the second such system to be delivered and is the first to be specified in the full 72-electrode configuration, for the
company’s Cold Mill No.2 expansion in Hazira, India. This ‘EDT-MSA’ machine features two texture heads, each with 36 individually controlled electrodes.
The texturing efficiency generated by MSA technology, enables unrivalled accuracy, speed and consistency of surface texture on the roll and ultimately on the strip, claims Sarclad.
Plant supplier Fives recently installed a new Taylor-Wilson hydrostatic tester for one of its clients. The hydrostatic tester, claims Fives, has the highest bench load capacity in its size range category which ensures greater productivity, flexibility, and
better product requirements.
The customer needed a reliable solution in order to adapt to challenging market requirements and increased capacity. As a result, Fives designed, supplied, and installed a new Taylor-Wil-
Steel Dynamics Inc. (SDI) has selected Sarclad’s Rolltex MSA 36 for its mill investment in Sinton, Texas. The system features a single-sided texture head, which could be expanded to a 72-electrode capacity by adding a second texture station.
For further information, log on to www.sarclad.com
son hydrostatic tester for tubes and pipes in the oil and gas sector. The supplied hydrotester can test pressures of up to 21,700 PSI.
“This project is a great achievement for us. Not only does it mark the highest bench load capacity in its size range category, which is a major milestone in Fives Bronx history, but we were also able to commission, start-up, and fine tune the machine in rapid time. I am proud of our team for their efforts to make the project successful,” said Gary Lisitsa, director of operations at Fives Bronx, Inc., a subsidiary specializing in finishing equipment.
For further information, log on to www.fives.com
ZUMBACH Electronics has developed the PROFILEMASTER® SPS product family with high-speed versions. The latest generation of high-speed cameras acquires full product contours at a rate of 2000Hz. This, claims the company, allows it to achieve six times more contours within a certain length, which enables classification of the defects instead of only detection.
The maps are created from multiple ‘unfolded’ contour images. Depending on the user’s preferences, the surface faults are also shown as single contours or as a 3D model (partial or full view of
the profile).
The new set-up design aims to improve the performance of the optical path of the cameras, optics and lasers by a factor of eight, which eliminates the limitation of camera exposure times. The new high-speed set-up enables the PROFILEMASTER® SPS product family to work even under harsh light absorbing the surface conditions of hot steel products, says ZUMBACH.
For further information, log on to www.zumbach.com
Primetals Technologies has recently received the final acceptance certificate (FAC) for a plate finishing mill at Kobe Steel’s plant in Kakogawa, Japan. This rolling mill was ordered in 2021 as Kobe Steel wanted to improve product quality and further enhance its delivery times. Primetals Technologies was responsible for the supply of core mechanical equipment, auxiliary and ancillary technologies, as well as on-site supervision for construction work and implementation.
The plate finishing mill at Kobe Steel’s Kakogawa Works had been in operation since 1972.
The new finishing mill processes plates with thicknesses from 4.5 to 360 millimetres at widths of 1,000 to 4,500 millimetres. The plate finishing
mill enables Kobe Steel to enhance mill performance both in terms of product quality and delivery times while increasing its competitiveness within the steel plate industry, stated Primetals Technologies.
Kobe Steel is a global company operating worldwide under the unified group brand of ‘KOBELCO’. The company’s proprietary portfolio of steel plate products includes Ecoview Plus, a steel plate for the bridge sector, and EX-Facter, a fatigue-resistant steel plate.
For further information, log on to www.primetals.com
Konecranes has introduced a heavy-duty version of its flagship E-VER electric forklift for lifting capacities of 18-25 tons. With growing industry demand for low-carbon solutions, this new range of lift trucks is part of the company’s commitment to electrify its entire lift truck fleet by the end of 2026.
“Higher capacity on the E-VER is the next step on the road to zero tailpipe emissions across all of our lift trucks portfolio. As the global market transitions to carbon neutrality, an even broader environmental responsibility is clear. We have a product road map to deliver the right products at the right time, paving the way to a decarbonized and circular world by eliminating emissions in the entire value chain from production to usage and eventually enabling repurposing and efficient recycling,” said Jeffrey Stokes, director, product and technology management, lift trucks, Konecranes.
“Konecranes has received a Gold rating from EcoVadis three years in a row which shows that
we are a leader in sustainability. Focusing on electrifying the offering is an enabling factor. Major industry awards like this help spark customer enthusiasm as we bring them the latest developments in our technology. Soon our customers will be able to enjoy the benefits of electrification and power up for the future through every one of our lift truck models,” added Andreas Falk, senior vice president, lift trucks, Konecranes.
The new 18-to-25-ton Konecranes E-VER is intended for heavy-duty industrial applications with low energy consumption and zero tailpipe emissions. Manufactured with clean energy, a lithium-ion (Li-ion) battery pack fuels the truck’s electric motors. A combination of high voltage and low current reduces energy consumption and losses, claims Konecranes, allowing the truck to use up to 90% of available energy. When no longer able to hold enough charge to run the motors, the battery can be repurposed as a power reserve at charging stations, or a back-up power supply if regular sources fail.
The truck is equipped with safety features, including a battery management system (BMS) that monitors battery condition, a thermal management system (TMS) that controls the battery, and a protective frame around the battery to prevent physical damage in the event of a collision. Redundant sensors throughout the machine provide data for faster analysis and safer functioning.
The Konecranes E-VER is a Smart Connected Lift Truck, using TRUCONNECT® to collect real-time data on a range of variables, including battery charge monitoring and estimated truck autonomy; energy consumption per lift, distance or load; the amount of energy recovered from braking; and alarms, alerts and other diagnostics. All this data transmits to the yourKONECRANES customer portal to monitor and control the truck’s operational efficiency, productivity, safety and environmental impact.
For further information, log on to www.konecranes.com
and QSP–DUE are the winning Danieli direct-rolling technologies for the most competitive production of long and flat green-steel products.
They are the result of the research and continuous improvement profused over 20 years, along with multi-million dollars of investment.
Their unmatched performances have fueled their success worldwide, thanks to lower resource consumption and carbon emissions, unbeaten OpEx, and outstanding product quality.
So, top technology becomes copied technology, the shortest route for competitors that, abandoning their solutions, now try to imitate MIDA–QLP and QSP–DUE
Equipment and layout may be copied, but experts know that details make the difference. Automation and process solutions are not easy to copy, and this will be the experience of anyone trusting in those imitations.
The competitive advantage for our customers, obtained by field results, is the best defense for our technology – more than court rulings protecting our patents.
Danieli offers the best guarantees for speedy learning curves, steady performances, and now Digital Plants with no men on the floor. Buy the Original.
GIANPIETRO BENEDETTI CHAIRMAN OF THE BOARD OF DIRECTORS
This article explores the intricacies of decarbonizing high-temperature processes within the steel industry using electrification. By Joonas Rauramo*
STEEL is a fundamental building block within virtually every sector in the global economy, valued for its high durability, ease of mass manufacturing, and 100% recyclability. However, as it stands, the steel industry is the largest emitting manufacturing sector, accounting for 7% of all man-made emissions worldwide, and requires urgent transformation if it is going to meet the goal of net zero emissions by 2050. This becomes even more of a priority as global demand for steel continues to rise, from 1.8 billion tons in 2020 to an estimated 2.0 billion tons by 2030. Steel is primarily made up of iron, which is bonded with a low percentage of carbon to give it its unique properties. In the first stage of primary steel production, mined iron ore is taken and reduced to metal using carbon and simultaneously smelted into pig iron in a blast furnace – a process that requires a considerable amount of energy – and then, in the second stage, the molten pig iron is converted into steel in a converter or blast oxygen furnace (BOF) and alloyed to the desired composition. This process is known as the BF-BOF process. Secondary steelmaking involves taking recycled iron and smelting it in an electric arc furnace (EAF) to remove impurities and add carbon and other alloying elements. Both processes require temperatures of over 1,600°C to bring iron to its melting point and
purify and alloy the steel.
In addition to smelting, steel also goes through additional processes including casting, hot rolling, often also cold rolling, annealing and tempering to optimise its qualities – requiring temperatures of up to 1,200°C. Around 85% of total energy consumption in steel manufacturing primarily arises from the burning of fossil fuels. In primary steelmaking, the production of hot metal iron in a blast furnace requires coke made from coal as a raw material. The production of coke itself requires additional energy and, therefore, releases further CO2 emissions.
Now, cutting-edge electrification technologies are ushering in a new era for the steel industry, paving the way for steel manufacturers to make significant progress towards net zero emissions. Coolbrook’s RotoDynamic HeaterTM (RDHTM), a patented heating technology powered completely by renewable electricity, is on track to generate temperatures up to 1,700°C. On the point about a system being ‘powered completely by renewable electricity’, Joonas Rauramo responded to the fact that not everywhere in the world has access to renewable energy by saying: “While it’s true that not all parts of the world currently have widespread access to renewable energy, there are a few important factors to consider.
*CEO at Coolbrook
Firstly, renewable electricity can be accessed directly in many regions or through Power Purchase Agreements (PPAs), where companies can source green energy even if it’s not locally available. This is a key strategy for global decarbonization, as the demand for green electricity drives further investment in renewable infrastructure.
“Moreover, transitioning to renewable energy often happens in phases. Even in regions where green electricity isn’t yet fully established, investing in technologies like RDH helps accelerate the shift by increasing demand. Many of our customers are also investing directly in renewable projects to secure their supply.
“It’s also important to note that CO2-free power sources, such as nuclear energy, play a significant role in some regions. For example, in Europe in 2023, the electricity mix included 22.8% from nuclear and 44.7% from renewables, meaning that over 67% of the electricity was completely CO2-free. This highlights the ongoing shift towards cleaner energy and shows that a substantial portion of electricity in some areas is already sourced from carbon-free technologies.
“So, even if renewable energy isn’t yet universally accessible, adopting technologies powered by it is a crucial step in the global transition to sustainable energy.”
This novel technology can replace fossil fuel combustion as the heat source throughout the steel manufacturing process, eliminating 600Mt of global CO2 emissions annually in the steel industry alone. The RotoDynamic HeaterTM is a product of two decades of research and development by Coolbrook, and partnering with notable academic institutions such as the universities of Oxford and Cambridge in the United Kingdom.
A better way to reach steelmaking temperatures
In mere milliseconds, the RotoDynamic HeaterTM can generate the temperatures required for steel production, boasting an impressive 95% conversion rate of electrical energy to thermal energy, without relying on the combustion of fossil fuels. This feat is accomplished through a cyclical sequence of steps.
Initially, powerful electric motors, optimised for industrial use, set rotor blades in motion, propelling gas molecules – such as air, nitrogen, steam, CO2, or hydrogen – at supersonic speeds. Subsequently, these swiftly moving gas molecules undergo rapid deceleration upon encountering a diffuser, transitioning to subsonic velocities. This abrupt change in speed triggers turbulence and shockwaves, effectively converting the kinetic energy of the gas into thermal energy, thereby generating heat. This process iterates through multiple stages, each seamlessly transitioning to the next within milliseconds, progressively elevat-
ing temperatures up to a remarkable 1,700°C. By directly heating the gas efficiently within itself, this method eliminates the necessity for bulky resistive heating components. Consequently, the RotoDynamic HeaterTM boasts a compact footprint of just a few metres for capacities of dozens of megaWatts while achieving the desired temperatures with unparalleled efficiency and speed.
Another key advantage of the RotoDynamic HeaterTM lies in its seamless integration potential into existing steel manufacturing plants without imposing complexities on current infrastructure. Due to very high energy intensity and compact equipment size the RotoDynamic Heater can be installed directly at the location where heat is needed thus enabling efficient energy integration also in brownfield sites. This straightforward application facilitates swift adoption of the technology by steel manufacturers, sidestepping additional complications, laborious tasks, or infrastructure investments. Utilisation of the RotoDynamic Heater also enables capture of waste heat streams which can significantly improve the overall energy efficiency of the process.
Other decarbonizing technologies for steelmaking are aiming to facilitate the reduction of iron ore into metallic iron using hydrogen gas, instead of the conventional natural gas. However, the reaction between hydrogen and iron oxide still requires temperatures up to 1,000°C, and the process itself has to be constantly heated as it consumes thermal energy. The RotoDynamic Heater can be integrated into hydrogen-based iron oxide reduction plants to provide the high temperatures and constant heating needed for the reaction and process without fossil fuels or emissions.
Moreover, RDH technology can be used to improve efficiency and reduce emissions in recycling of steel. For instance pre-heating of scrap metal can be used to remove impurities and reduce the energy input required in electric arc furnaces improving plant throughput in addition to a lower carbon footprint per ton of steel.
As a result, the RotoDynamic Heater can decrease fossil fuel usage per tonne of steel, decarbonizing processes ranging from the preheating of air to blast furnaces, provisioning of heat for hydrogen-based reduction processes, casting, hot rolling, annealing, coking, tempering lime
production for use in removing impurities from steel, reheating furnaces, and other supporting processes. In electric arc furnaces, the RotoDynamic Heater can be used in scrap preheating to shorten the smelting sequence.
By reducing fossil fuel usage per tonne of steel throughout the manufacturing process, the RotoDynamic Heater significantly brings down the cost to decarbonize each tonne of steel produced, allowing manufacturers to improve the overall return on investment of their decarbonization efforts and more efficiently advance towards a prosperous net zero future.
The technical feasibility of the RotoDynamic Heater has been proven at Coolbrook’s largescale pilot facility, inaugurated in December 2022 at the Brightlands Chemelot Campus in Geleen, the Netherlands. There, its capability to attain the required temperatures for heavy-duty industrial operations was successfully showcased. The initial phase of pilot testing concluded in September 2023, surpassing the 1,000°C threshold and validating the RotoDynamic Heater’s suitability for industrial-scale high-temperature process heating; underscoring its potential to annually reduce global industrial CO2 emissions by 30%. Furthermore, this breakthrough not only unlocks a significant portion of the €1 trillion global industrial heating market for RotoDynamic TechnologyTM but also paves the way for its deployment in large-scale projects at customer sites.
The steel industry holds great decarbonization potential
In the pursuit of net zero emissions within the steel industry, the integration of complementary decarbonization technologies is paramount. For instance, the lime used in steelmaking is obtained through the decomposition reaction of calcium carbonate, which releases CO2 as a natural byproduct.
While clean heating technologies such as the RotoDynamic Heater can provide the heat required for this reaction, the CO2 byproduct must also be removed to achieve total decarbonization, which can be achieved using carbon capture and storage processes. Combustion-free heating technologies such as the RotoDynamic Heater can enable a more efficient, streamlined carbon capture process by producing a much higher concentration of CO2 gas from the decomposition reaction, eliminating the nitrogen and argon from the exhaust gases.
A clean, new industrial era for all
At the forefront of catalysing full decarbonization in the steel industry, the RotoDynamic Heater boasts a compact footprint, delivering the extreme temperatures required for steel manufacturing, with an excellent 95% energy efficiency, without reliance on fossil fuels. Manufacturers that invest in existing and developing decarbonization technologies now can have a competitive advantage moving forward by operating at the cutting edge of steel manufacturing and contributing to the widespread implementation of steel decarbonization worldwide — leading a clean, new industrial era for all.
Solar Turbines is your total solutions provider and can offer you the latest power plant technology tailored to your specific requirements. Generating power with our highly flexible gas turbine packages contributes to sustainable development, enabling you to meet your growing needs for great power, efficiency and availability − all while helping to protect the environment. Solar ® gas turbines will provide your business with a competitive edge. There has never been a better time to review your energy strategy. Contact us today.
Visit us at www.solarturbines.com , call +1-619-544-5352 or email infocorp@solarturbines.com
Argentina, Bolivia, and Chile are known as South America’s ‘lithium triangle’, with approximately 55% of the world’s reserves, writes Germano Mendes de Paula*
ACCORDING to JP Morgan, Chilean share of global lithium production is projected to be 23% in 2024, while Argentina is expected to contribute 7%, and other Latin American countries are set to provide 8%. In comparison, Australia will lead with a 33% production share, followed by China at 21%. Africa will have a 5% participation in global lithium output.
This year marks the commencement of operations for two lithium projects in Argentina, supported by investments from two of the world’s largest steelmakers: Posco Holdings from South Korea (ranked 7th in worldsteel’s ranking for crude steel production in 2023) and Tsingshan Holding from China (ranked 23rd in terms of crude steel, but the world’s largest producer of stainless steel and nickel).
In 2018, Posco ventured into Argentina’s lithium sector by acquiring a brine lithium project from Galaxy Resources, an Australian mining company, for approximately $280M. Brine lithium is extracted from high-concentration saltwater solutions typically found in salt flats, known as salars. The project is situated in the Hombre Muerto salt flat, which is located in the Provinces of Salta and Catamarca. By April 2024, Posco completed the construction’s first stage of a
commercialization plant adjacent to the lake for the production of lithium hydroxide. As of December 2023, this project was estimated to cost $1bn, of which $169M was the projected remaining cost of completion. The second phase, scheduled to start-up in June 2025, is projected to require $962M. Upon conclusion of both stages, the commercialization plant is expected to have a production capacity of 25kt/yr of lithium hydroxide and 23kt/yr of lithium carbonate, essential materials for cathode fabrication.
Posco’s lithium initiatives extend beyond Argentina globally, reflecting its broader ambition to secure critical materials for the expanding electric vehicle (EV) and energy storage markets, providing an input essential for lithium-ion batteries. For instance, it made inaugural shipments of hard rock lithium from its 43kt/yr capacity Gwangyang plant in Korea in April 2024. This project, which has capex of $848M, is an 82:18 joint venture between Posco and Pilbara Minerals. Additionally, in 2018, Posco acquired a 2.74% stake in Pilbara Minerals and secured off-taking of the mineral spodumene from the Pilgangoora Project, which is located 120km from Port Hedland, Western Australia.
JP Morgan reported that the Gwangyang plant’s operating utilisation has already achieved 70%-80% in Q2. The Argentine
plant, with a capacity of 25kt/yr, is expected to reach 50% utilization by Q3. Upon full ramp-up in 2025, the company anticipates a double-digit EBITDA margin. However, this margin is likely to be lower than under a $30k/t lithium price environment. JP Morgan assumed a mid-term lithium price of $17k/t compared to the spot lithium price range of $12-14k/t in late July 2024. Moreover, JP Morgan’s Sum-Of-The-Parts (SOTP) analysis in July 2024 indicated that the steel business is equivalent to 46.5% of the valuation, stakes in affiliated companies to 32%, and lithium business for 21.5%. This is an impressive breakdown considering that the lithium projects are still in the ramping-up phase.
In July 2024, Salar de Centenario-Ratones Project Phase 1, situated in the Province of Salta, was inaugurated. It is operated as a joint venture owned by Eramet (50.1%) and Tsingshan (49.9%). The venture plays a critical role for Tsingshan’s strategy to secure a reliable lithium supply for its downstream battery manufacturing operations. Production is scheduled to begin in November 2024, with ramp-up expected to be achieved by mid-2025. Once operating at full capacity, the plant is projected to produce 24kt/yr battery-grade lithium carbonate equivalent (LCE), meeting
* Professor in Economics, Federal University of Uberlândia, Brazil. E-mail: germano@ufu.br
the needs for 600k EVs annually.
Nonetheless, production in 2024 is anticipated to be limited. The plant is designed to extract lithium from the salar brine as well. During the construction phase, the project has contributed to job creation, resulting in over 2,500 direct jobs. The Centenario Phase 1 plant is expected to employ approximately 350 individuals.
The total investment initially planned for Centenario Phase 1 was $735 M, but was later increased to $800M (of which $480m funded by Tsingshan) reflecting the impact of local inflation. Previously, Eramet had invested more than $30M in research to develop in-house a Direct Lithium Extraction (DLE) technology and additional $15M in external costs for development studies. At full capacity, the cash cost for Phase 1 is expected to be positioned in the first quartile of the industry cost curve, estimated at around $4.5k to $5k/t of LCE. The annual EBITDA is projected to range between $210M and $315M, based on a long-term price assumption of $15k-$20k/t of LCE.
In addition, in March 2023, Tsingshan
announced that it will invest $120M to install a 100kt/yr hydrogen chloride and 35kt/yr sodium hydroxide manufacturing plant in the Perico industrial park, Province
of Jujuy, Argentina, to produce lithium carbonate. Construction work is expected to last 18 months and employ more than 1,000 people for the construction period, and some two thousand workers during its
operational stage.
In October 2023, Chilean President Gabriel Boric revealed that Tsingshan intends to make a $233M investment in lithium-related projects in the country. According to the government, the plant is planned to produce 120kt/yr of lithium iron phosphate.
Located in northern Chile and projected to commence operations in May 2025, the plant is expected to generate 668 jobs when operating at full capacity.
The Chilean economic development agency Corfo has stated that Yongqing Technology, which is owned by Tsingshan, will have access to 11kt of battery grade lithium carbonate from Chilean lithium miner Sociedad Química y Minera de Chile (SQM) at a preferential price until 2030. Furthermore, the project will involve importing lithium carbonate from Tsingshan’s joint lithium venture with Eramet in Argentina.
In summary, Argentina has become an essential hub for the diversification strategies of both Posco and Tsingshan towards the lithium industry. �
We are your premium partner for refractory solutions for the heat treatment of steel
We offer solutions of the highest performance to meet your most demanding requirements. With RATH you can count on:
• A comprehensive range of premium refractories
• Engineering, production, on-site supervision
• Solutions to reduce your carbon footprint and to save energy
• No compromise on quality, here we remain as tough as steel
www.rath-group.com/metals
India’s infrastructure-centric Union Budget 2024-25 has brought good news for domestic steel producers with an 18-month extension of the customs duty exemption on ferrous scrap and a reduction in the import duty on ferronickel from 2.5% to ‘nil’. The current financial year’s Union Budget proposes to extend the ‘nil’ customs duty regime on ferrous scrap until March 2026, extending it from the earlier deadline of September 2024. By
Dilip Kumar Jha*
THIS decision bodes well for Indian steel producers, especially given the robust production growth expected in the near future. The government’s increased focus on infrastructure has led steel producers to augment production capacity through both greenfield and brownfield projects to meet the growing demand. In addition to large steel mills that use ferrous scrap for blending with sponge and pig iron, as well as separately melting the waste in foundries, India’s micro, small, and medium enterprises (MSMEs) will also benefit from this proposal. India’s MSMEs have been struggling to cope with higher interest rates, a lack of working capital, and outdated plant and machinery, which makes it difficult for them to compete with large steel mills.
While the government has already introduced several schemes for their revival, these MSMEs were hesitant to invest due to fears of the re-imposition of the ferrous scrap customs duty levy. However, the 18-month extension of the duty exemption will help them plan their businesses for long-term sustainability. The government considers MSMEs as the backbone of the Indian economy, especially in terms of employment generation and regional reach.
Source: Directorate General of Commerce,
India’s steel industry has been enjoying ‘nil’ import duty on ferrous scrap since 2021, following the announcement by Union Finance Minister Nirmala Sitharaman in the Union Budget 2021-22. The duty exemption was introduced after steel producers, particularly MSMEs, were severely impacted by the Covid-19 pandemic and the resulting periodic lockdowns worldwide. In the 2021-22 Budget, the Finance Minister also revoked the anti-dumping duty (ADD) and
correspondent, Steel Times International.
countervailing duty (CVD) on certain steel products, while reducing customs duty uniformly to 7.5% on semis, flat, and long products of non-alloy, alloy, and stainless steel, down from the previous 10-12.5%.
The customs duty on ferrous scrap was reduced to ‘nil’ to support user industries that were hit hard by the sharp increase in steel prices. Initially, this duty cut was announced for one year, which was later extended by another year in the Budget 2022-23, and further extended until
September 2024. It was expected that the duty exemption on ferrous scrap would provide MSMEs with a new ‘lease on life’, but the erosion of their working capital and the prolonged period of elevated interest rates failed to protect them from bankruptcy
Additionally, the lower import duty was expected to help MSME user industries bring in end products at competitive prices from overseas, allowing them to compete with prevailing prices in India. It was also intended to provide a check on domestic metal producers to prevent prices from rising to abnormally high levels. Unfortunately, India’s steel MSMEs failed to fully benefit from the duty exemption, primarily due to market volatility, despite phenomenal demand growth. Now, the government hopes that the continued duty exemption will help bring them back to business.
Import reliance
India’s ferrous scrap demand was estimated to have reached a record 28Mt in FY 2022-23 (April-March), but it declined
by 7% to 26Mt the following year due to unavailability from domestic sources. During the financial year 2024-25 (AprilMarch), India’s steel scrap consumption is likely to set another record of 31Mt due to rising steel production capacity, and a proportionate increase in raw materials demand. If this trend continues, India’s ferrous scrap consumption may rise to a record 55Mt by the end of 2030.
Interestingly, the country showed an increased appetite for imported scrap. Data revealed that India’s ferrous scrap imports reached 11.03Mt in FY 2023-24, a 13% increase from the previous year. The sharp spurt in imports can be attributed to decreased demand from other consuming countries such as Turkey, Pakistan, and Bangladesh. Industry sources noted that shipments meant for these destinations were redirected to India, resulting in a dramatic increase in imports. Thus, India met up to 45% of its ferrous scrap demand through imports.
The volume of ferrous scrap imports has tripled in the last three years, primarily due to rising domestic demand and the
growing importance of scrap usage in steel manufacturing. India’s steel production through electric arc furnaces – using ferrous scrap and sponge iron – rose by 15% to 82Mt in FY2023-24 (April-March). Surprisingly, India’s ferrous scrap generation is likely to rise substantially – by 70% – to 45Mt by 2030.
T V Narendran, managing director and CEO of Tata Steel, said, “The increased provision for capital expenditure of approximately INR 110,000 billion is a major boost for building and improving infrastructure and would have a strong effect on the economy. As a key component of all infrastructure development, steel will see an increased demand going forward.”
Echoing a similar statement, Amarendu Prakash, chairman of Steel Authority of India Ltd (SAIL), commented, “Focus on urban housing, enhancement of rural infrastructure, further improvement in road connectivity and development of various corridors is expected to boost domestic steel consumption.” �
The African steel industry plays a crucial role in the continent’s economic development, however, it faces multiple challenges that must be overcome in order to achieve sustainable growth.
By Joseph X
F Ribeiro1, Umaru Musa 2,3, Faiz Iqbal4, Aliyu Aliyu4
THE steel sector significantly contributes to global economic development, providing over six million direct and indirect jobs (Vögele et al., 2020). As one of the most valuable metals globally (Pal et al., 2014), steel production and consumption increased from about 1,450Mt in 2010 to approximately 1,900Mt in 2023 and is projected to reach 2,030Mt by 2030 (World Steel Association, 2022). Steel is essential for numerous manufacturing industries (Muslemani et al., 2021), with the global steel market valued at around $1 trillion and expected to grow. With ongoing urban development, steel remains crucial for the infrastructure, transport, energy, and technology sectors, as well as for renewable energy deployment in wind turbines, solar panels, and electric vehicles (The Commonwealth, 2023). The steel industry in Africa has evolved significantly since
the colonial era, driven by technological advancements, globalisation, and changing market dynamics amidst political transitions and conflicts. Initially reliant on imports from Europe, the USA, and the Far East, African countries now produce steel from small-scale to large integrated plants, serving various sectors like construction, automotive, machinery, and energy (UN Comtrade). Steel production involves primary conversion from raw ore and secondary recycling via basic oxygen furnaces (BOF) and electric arc furnaces (EAF). Raw material availability varies across the region, with some countries like South Africa and Egypt having selfsufficient deposits, while others rely on imports (CABARO Group, 2024). As Africa pursues sustainable development goals, the steel industry faces unique challenges and opportunities, highlighting the importance
of effective policy frameworks and market mechanisms for growth, sustainability, and decarbonization.
As of 2023, African steel production reached approximately 39.49Mt and is projected to grow at a CAGR of 3.10% from 2024 to 2032, reaching 51.86Mt by 2032 (African Steel Market Report, 2024). This growth is driven by increasing infrastructure projects across the continent, including roads, bridges, and power plants, which boost steel demand (African Steel Market Report, 2024). Governments are promoting the use of locally produced steel to stimulate domestic industrial activity, job creation, and economic development (African Steel Market Report, 2024). Table 1
The industry is also attracting investments from public and private
1. Department of Petroleum Engineering, Kumasi Technical University, Ghana
2. Faculty of Engineering, University of Nottingham, Triumph Road, Nottingham NG7 2TU, United Kingdom
3. Department of Chemical Engineering, Federal University of Technology Minna, PMB 65, Minna, Nigeria
4. School of Engineering, University of Lincoln, Brayford Pool, LN6 7TS, United Kingdom
(Source: The World Steel Association, 2024a, b)
sectors, leading to capacity expansion. Despite these advancements, Africa’s global steel production contribution remains relatively low. Key countries driving steel production include Egypt, South Africa, Algeria, Morocco, Libya, Nigeria, Kenya, Ghana, Angola, and Tunisia, as depicted in production figures from these top 10 African nations (The World Steel Association, 2024). To unlock its full potential, experts emphasise the importance of adopting sustainable practices, fostering innovation, and enhancing collaboration within the African steel industry (Expert Market Research, 2024). Egypt, South Africa, and Algeria, ranked 20th, 34th, and 39th in the 2022 global rankings, respectively, appear to occupy the top three positions in steel production within Africa. In the Eastern African region, the Abyssinia Group of Industries (AGI) has grown to become one of the largest steel producers, with an annual capacity close to 1Mt throughout the group, with manufacturing and mining operations spread in East Africa, namely Kenya, Uganda, Ethiopia, and Rwanda. Fig 1
Major current investments and expansion plans
Africa’s steel production success is driven by increasing public and private investments supported by infrastructure development, government policies, and rising demand (Expert Market Research, 2024). Significant private sector investments in Egypt, South Africa, Morocco, Nigeria, and Kenya have led to the establishment of modern steel mills, reducing reliance on imports and meeting local demand (SAISI, 2022; CABARO Group, 2024). For instance, Libya’s LISCO partnered with Danieli to construct a direct reduction plant, while Kenya’s Devki Steel Mills invested in a large plant in Kwale, creating jobs and boosting the local industry (Expert Market Research, 2024). Liberia produced 5Mt of iron ore valued at
$346.9 million in 2021 (International Trade Administration, 2024), and Zimbabwe is set to become a major steel producer with Tsingshan’s $1.5 billion Dinson Iron and Steel project (The Herald, 2024). In Nigeria, the ANRML’s iron ore processing plant in Kaduna represents a significant FDI, expected to enhance the country’s steel production and create thousands of jobs (African Industries, 2024). Kenya also plans substantial investments in new iron and steel plants over the next five years (Nation, 2024).
Several African countries, including Algeria and Libya, are investing heavily in steel production infrastructure to reduce import dependency and enhance economic self-sufficiency. West African nations like Liberia are attracting significant investments from companies like ArcelorMittal and Fortescue to expand iron ore production capacity (Forbes, 2023). South Africa, Nigeria, Algeria, and Morocco have announced plans to expand their iron and steel production capacities (Steel Radar, 2024). Governments across the continent are implementing strategies to promote local steel consumption and discourage imports through tariffs. For instance,
Egypt has supported its steel industry since the late 1990s, including imposing tariffs and establishing local production facilities (ZAWYA, 2023; Selim, 2006). In South Africa, a master plan for the steel industry aims to revitalise the sector and boost production (The DTIC, 2021). Nigeria has also focused on revitalizing its steel industry, refurbishing the Ajaokuta Steel Company and developing comprehensive plans for sector revival and attracting foreign investments (Udofia, 2024; Nigerian Steel, 2024). The African steel market is expected to grow significantly due to a rise in construction projects across the continent. Increased investments from both public and private sectors, supported by government initiatives, are set to boost the construction industry and drive demand for steel. Governments are promoting the use of locally produced steel to stimulate economic development and employment, leading to greater adoption of local steel in construction projects throughout Africa (Africa Steel Market Report, 2024).
Innovation, technology, and local content
Traditionally, steel production in Africa has employed basic oxygen furnaces. Gradually, innovations including electric arc furnace (EAF) technology, capable of recycling scrap metal into high quality steel products, has become prevalent. The reduced energy requirements, coupled with its flexibility makes it a suitable alternative for regions with limited access to natural resources such as coking coal (CABARO Group, 2024). Numerous green steel projects are underway in Mauritania. Société Nationale Industrielle et Miniere
(SNIM) and ArcelorMittal signed an MoU in 2022 to develop a 2.5Mt green iron ore pelletizing and direct reduced iron plant. A €300 billion European Union Global Gateway grant will facilitate a new road network and high-power transmission line to support green hydrogen plant development. Mauritania aims to capture 1% of the global green steel market by 2050 (Energy Capital and Power, 2024). In South Africa, the Leadership Group for Industry Transition and Trade & Industrial Policy Strategies workshop in 2023 highlighted green hydrogen direct reduced iron (GH-DRI) technology as transformative for green iron ore production, leading to a national plan to decarbonize the steel industry (Stockholm Environment Institute, 2023). In Kenya, Abyssinia Steel and Spenomatic partnered with Empower New Energy to solarise the Awasi steel factory with a 2.5MWp solar project, generating 4.8 GWh of clean electricity annually, saving 2,500 metric tons of carbon emissions, and reducing electricity costs (AFSIA, 2023). African production systems are increasingly embracing digitalisation and automation. Industrial Internet of Things (IIOT) platforms enable real-time monitoring, predictive maintenance, and optimised production flows. Advanced materials handling systems and CNC machinery facilitate precision shaping and
cutting of steel products. Companies are also integrating innovations to reduce CO2 emissions and water consumption, meeting sustainability targets (CABARO Group, 2024). Heavy investment in advanced technologies by South African companies has led to efficient production processes, making them leading suppliers domestically and competitive exporters in Africa. Similar investments in Egypt’s steel industry have increased its market share and made it a significant player in the MENA region.
Africa’s steel sector holds significant opportunities fuelled by abundant natural resources and increasing demand from the construction sector. Expanding the steel industry could create jobs and drive industrial development. Regional collaborations, particularly through initiatives like the African Continental Free Trade Area (AfCFTA), offer prospects for unified markets and streamlined trade in raw materials and steel products across borders (CABARO Group, 2024). Adoption of advanced technologies such as AI, IoT, and automation presents opportunities to enhance productivity, efficiency, and global competitiveness in steel manufacturing in Africa (Fig 2).
Promoting sustainable practices and green steel production also offers a
significant opportunity for African steel producers. By investing in renewable energy and eco-friendly production methods, they can align with global sustainability goals and enhance their competitiveness in markets that prioritise environmentally friendly products. Mauritania, Africa’s second-largest producer of iron, exported 13Mt of raw iron in 2022 and aims to reach 39Mt by 2030. Despite this, the country has not fully capitalised on manufacturing and exporting steel due to high production costs and energy poverty. However, renewed interest in renewable energy, such as green hydrogen, could enhance domestic green steel production, boost local industry growth, generate revenue, and facilitate steel exports to Europe (Energy Capital and Power, 2024). In Uganda, Muko town has 150Mt of highquality hematite iron ore deposits. Meeting the Ugandan market’s demand requires at least 800kt of iron ore annually, while 4Mt/ yr are needed to satisfy the East African region (Kenya, Tanzania, Uganda) (Regional Investment Agency, 2024).
Despite Africa’s strides in steel production, several challenges hinder further growth. Access to capital remains a significant barrier, limiting modernisation and expansion efforts in the industry.
Infrastructure deficiencies, including inadequate railways and ports, also impede efficient transportation of raw materials and finished steel products. The high cost and unreliability of energy sources further exacerbate challenges, impacting production costs and efficiency in the energy-intensive steel manufacturing process (CABARO Group, 2024). The steel industry in Nigeria, for instance, faces significant challenges due to unreliable power and transportation infrastructure. Corruption further exacerbates the situation, potentially deterring the foreign direct investment necessary for the industry’s development (Nigerian Steel, 2024). This issue is common across many African countries. In Sierra Leone, the Chinese company Shandong Iron and Steel Group plans to invest $700 million in an iron ore processing plant at its Tonkolili mine. However, currently, Shandong exports all the unprocessed ore produced at this mine to the Port of Qingdao in China (African Business, 2016).
Raw materials, critical to steel production,
BIGGER.
Superior Machine has joined the Woodings’ group creating the most capable hot metal equipment supplier group in North America. Offering the combined knowledge, engineering, manufacturing, and construction expertise for all your equipment needs.
Wherever hot metal is produced, you will find equipment from Woodings, Superior Machine, and
Munroe operating at the highest level in the most demanding conditions. Our products and professional installation services reduce downtime and extend campaign cycles.
We are better together. Let us show you. woodings.com
We can provide you with more value than ever before from concept to installation, service to replacement, our size, scope, and experience gives us a unique ability to help you increase productivity and solve problems.
are also not uniformly available and well distributed across the continent. For instance, countries like Egypt and South Africa are well endowed with iron ore and coking coal, making their industries self-sufficient. Others rely on imported materials, which present economic and logistical challenges (CABARO Group, 2024). The Nigerian steel industry, exemplified by the Ajaokuta plant, relies heavily on imported raw materials and machinery despite having ample iron ore at the Itakpe mine (Essien, 1997). In Eastern Africa, countries like Tanzania, Kenya, and Uganda import around 4 metric tons of steel products annually, with expected annual growth of 5%. Uganda’s steel imports alone are valued at $350 million (Regional Investment Agency, 2024).
African steel production varies widely, with facilities ranging from small to
References
Africa Steel Market Report (2024). Online at: https://tinyurl.com/4mwh6b49. Accessed on 09.06.24.
African Industries (2024). Nigeria to start steel production, https://tinyurl.com/mwbp5s34. Accessed on 09.06.24.
African Business (2016). Sierra Leone: Chinese steel firm to invest in $700m iron ore processing plant. https://tinyurl.com/299dj2cr. Accessed on 10.06.2024.
AFSIA (2023). African Solar Industry Association. https://tinyurl.com/3299hp7f. Accessed on 19.06.2024.
CABARO Group, Steel Production in Africa: Opportunities and Challenges, https://tinyurl. com/2hdy85jh. Accessed on 17.05.24.
Niccolo Conte. (2021, June 2). Visualizing 50 Years of Global Steel Production. Visual Capitalist, https://tinyurl.com/j2a2f3cw. Energy Capital and Power (2024). Mauritania’s Steel Industry Fueled by Green Hydrogen. https:// energycapitalpower.com/mauritania-steelindustry-fueled-by-green-hydrogen, accessed on 09.06.24.
Expert Market Research, 2024, Africa Steel Market Size, Share, Growth, Analysis 2024 –2032.
Forbes, 2023, Africa’s Heavy Industrial Revival: A Future Hub of Industrial Goods
International Trade Administration (2024). Liberia- Country Commercial Guide. https:// tinyurl.com/7e6v2hsj, accessed on 10.06.2024.
Muslemani, H., Liang, X., Kaesehage, K., Ascui, F., & Wilson, J. (2021). Opportunities and challenges for decarbonizing steel production
large integrated plants. The industry’s technological sophistication and modernity of equipment are critical, with some countries still using outdated machinery, which hampers both quality and quantity of production (CABARO Group, 2024). Market competitiveness is a major challenge, as cheaper imported steel, especially from China, forces local producers to incur high costs, reducing profit margins and market share. Additionally, inconsistent trade policies, high tariffs, and bureaucratic red tape further complicate operations and inhibit industry growth. Stricter environmental regulations are being enforced to reduce pollution and carbon emissions, necessitating investments in green technologies that may lack funding. Additional challenges include infrastructure deficits, energy supply constraints, skilled labour shortages, competition from
by creating markets for ‘green steel’ products. Journal of Cleaner Production, 315, 128127. Nation (2024). State takes on steel tycoons with new Sh220bn plants. https://tinyurl. com/29t2v7fj. Accessed 19/06/2024.
Pal, P., Gupta, H., & Kapur, D. (2016). Carbon mitigation potential of Indian steel industry. Mitigation and adaptation strategies for global change, 21, 391-402.
Regional Investment Agency (2024). Muko Iron and Steel Project. https://tinyurl.com/ msht8shp. Accessed 19/06/2023.
Francisca Oluyole. (2017). Ajaokuta: How Nigeria’s largest industrial project failed. Premium Times Nigeria. https://tinyurl.com/5c94w22s.
SAISI, 2022, A South African Steel Industry Report, Reflecting on 2021 and an Outlook for 2022, https://tinyurl.com/3s4mfyur. Accessed on the 19.05.24.
Selim T. H., 2006, Monopoly: The Case of Egyptian Steel, Journal of Business Case Studies, third quarter, 2(3).
Steel Radar, 2024, Iron and Steel Markets, Investments in the iron and steel industry are increasing in Africa, https://tinyurl. com/2p88nb27. Accessed on 19.05.24.
Stockholm Environment Institute (2023). The green steel production in South Africa: insights from decarbonization workshop. https://www. sei.org/features/the-green-steel-transition-southafrica/, Accessed on 10.06.2024.
The Department of Trade, Industry and Competition (The DTIC), 2021, The South African Steel and Metal Fabrication Master Plan 1.0: Support for the Steel Value Chain, https://tinyurl. com/5n8pen5x. Accessed on 16.05.24.
imported steel, and environmental concerns (CABARO Group, 2024).
Concluding remarks
The African steel industry plays a crucial role in the continent’s economic development, supported by infrastructure growth, government policies, and rising demand. However, it faces challenges such as limited access to capital, inadequate infrastructure, energy supply constraints, uneven raw material distribution, outdated technology, and competition from cheaper imports. Overcoming these challenges through strategic investments, technological advancements, and regional co-operation, including initiatives like the African Continental Free Trade Area (AfCFTA), is essential to unlocking Africa’s steel sector potential and achieving sustainable growth.
The World Steel Association, 2024a, December 2023 Crude Steel and 2023 Global Crude Steel Totals, https://tinyurl.com/yv4hdfbe. Accessed on 15.05.24.
The World Steel Association, 2024b, Crude Steel Production, (https://worldsteel.org/data/ steel-data-viewer/), accessed on 01.06.24.
The World Steel Association, 2022. World Steel in Figures 2022 (https://worldsteel.org/steeltopics/statistics/world-steel-in-figures-2022/ The Herald, (2024). Brick by brick, steel by steel: Zim- China Collaboration builds Industrial Giants. https://tinyurl.com/5n6z86v8. Accessed on 09.06.24.
Udofia E., 2024, Steel Rising: Harnessing Nigeria’s Potential for Global Competitiveness in the Steel Industry, Payne Institute Student Commentary Series, The Payne Institute for Public Policy, https://tinyurl.com/mspxnfcr. Accessed on 18.05.24.
UN Comtrade. (2024). UN Comtrade Database (Free Access to Detailed Global Trade Data). UN.ORG, https://comtradeplus.un.org/ Vögele, S., Grajewski, M., Govorukha, K., & Rübbelke, D. (2020). Challenges for the European steel industry: Analysis, possible consequences and impacts on sustainable development. Applied energy, 264, 114633.
Wårell, L. (2014). Trends and developments in long-term steel demand–The intensity-of-use hypothesis revisited. Resources Policy, 39, 134143. Accessed on 11.10.2022.
ZAWYA, 2024, Egypt’s Steel: A Flourishing Industry with Future Potential, https://tinyurl. com/muprxzc7. Accessed on 16.05.24.
Our Manipulators for cleaning, clearing and sandfilling at the EBT Functions.
Clearing of the EBT tap hole from debris and bulky items after tapping
Cleaning of EBT tap hole with an oxygen blowing function
Automated & fully controlled filling of the EBT taphole
Camera Inspection to check the filling process
Safe operation from the pulpit
Process standardization leads to higher efficiency
Optimized positioning & filling process
Clearly defined position above the EBT taphole
Precise Dosing of filling sand
SOME of the dominant issues discussed at great length at the recently-held Global Steel Dynamics Forum (GSDF) 2024 in New York included decarbonization, steel imports into the US market and the USMCA trade route used by some suppliers to ship steel into North America.
In an election year, steel producers, trade unions and politicians have been fiercely debating the economic prudence of further allowing imports of heavily-subsidized steel – ‘dumping’, to use a common term – into the US market through third countries.
Ron Ashburn, executive director of the Association for Iron and Steel Technology (AIST) which had jointly organized the GSDF event with World Steel Dynamics, emphasized in his opening remarks that while steel has an ‘unbeatable value proposition’ manifested in its properties of
being strong, durable, easily formed and machined, ‘steel struggles in the court of public opinion which has the perception that it is obsolete material, that it involves the use of outdated technology, and that it is bad for the environment and unsafe’.
“We have to overcome the energy problem. Steel production consumes a lot of energy. Most of the carbon-generated steel comes from China. We need to engage in diplomacy, not just energy debate.” He said that the green energy economy is vital for the steel industry.
Linde plc CEO Sanjiv Lamba underscored the global steel industry’s commitment to adaptation and innovation.
“You constantly innovate. Efficiency is right on top of your agenda. All great steel companies demonstrate that commitment,” he noted in his remarks at the GSDF.
*USA correspondent.
Lamba alluded to the industry’s futuristic outlook, with billions of dollars invested in new process technologies, new sustainability practices that are being introduced and responsive adaptation to shifting market demands, for instance, for greener steels; but he emphasized that successful decarbonization in the industry would materialize by deploying multiple technologies that would include, but not limited to, hydrogen. But he admitted there was not enough renewable energy in the world to support the aspirational demand for green hydrogen.
Francois David Martino, executive president of John Cockerill, which offers technological solutions to its customers, told Steel Times International: “We also help in processing steel, providing value-added properties to the unfinished
The Global Steel Dynamics Forum 2024 attracted the big guns of US and global steelmaking and tackled the big issues, such as decarbonization, the US Steel-Nippon takeover and the USMCA.
By Manik Mehta*
products. We have been collaborating with ArcelorMittal in developing technology,”
Martino said, adding that his company’s responsibility included marketing technology. The company signed an agreement with ArcelorMittal in January this year and ‘five months later we already have our first client in a Swedish steel plant with which a multi-million dollar agreement has been signed’.
John Cockerill also has its eye on the strong-growth markets of Asia, particularly India and China. He was encouraged by the fact that India’s government and private
sector were opening up.
Goncalves on decarbonization, USMCA and US Steel
Lourenco Goncalves, chairman, president and CEO of Cleveland Cliffs – his company recently announced that it was planning to purchase all issued and outstanding shares of Canadian integrated steelmaker Stelco for C$3.4 billion (US$ 2.5 billion) – recalled during his on-stage conversation with Philipp Englin, the WSD’s chief executive, that the Covid pandemic had affected supply chains, adding that some companies
were dependent on supply chains.
“Our (carbon) emissions are very low and we deserve some reward,” he said.
Goncalves also expressed his disappointment over the USMCA trade pact and predicted that the “M” in the agreement’s acronym would disappear because Mexico had become a ‘dumping route’ for certain countries. “This (Mexico’s expulsion) could happen in 2026. Mexico is being used as a shipment route for low-cost and polluted steel to the US and Canada,” he said, referring to China which has increased its presence in Mexico to use
“We also help in processing steel, providing value-added properties to the unfinished products. We have been collaborating with ArcelorMittal in developing technology” Francois David Martino, executive president of John Cockerill.
it as a production/assembly site and for shipments to the US and Canada.
Later, in a press conference, Goncalves told this correspondent that Mexico, which is on the ‘wrong side’, should not be a party to the USMCA negotiation. It should be excluded from the USMCA.
Goncalves, who had also been critical of US Steel’s decision to allow Nippon Steel to buy it out, was reserved in his comments at the GSDF. While reiterating previous skepticism over the deal, he said that Cleveland-Cliffs’ offer ‘doesn’t exist anymore.’ His company was focusing its attention on other matters, such as recasting its Middletown, Ohio, mill as a leading example of how to decarbonize an integrated plant and launching a new downstream electrical transformer manufacturing venture.
Cleveland-Cliffs had also made an unsuccessful bid to buy out US Steel; Japan’s Nippon Steel Corp. has been negotiating with US Steel which seems inclined to the takeover overtures by the Japanese steel giant for US$14.9 billion.
In the backdrop of the decarbonization debate, Korean steelmaker POSCO Holdings’ chairman Chang In-Hwa, speaking through an interpreter, argued that consumers have demonstrated a willingness to pay for higher-priced sustainable goods. “Consumers are already practicing sustainable consumption. Because they are concerned about the environment as well as their health, they’re already purchasing organic foods and electric vehicles, so this is already sustainable consumer practice,” the POSCO chairman said, adding “A green premium is a must for a sustainable future,” he said.
Amid the growing environmental consciousness among Europeans, Steel Dynamics Inc. CEO Mark Millett suggested that European steelmakers might be in danger of pricing themselves out of the market.
Millett said energy costs are already high in Europe, and, in addition, billions of dollars in investment are being made there now to move the continent’s steelmakers to where their US counterparts already are in terms of CO2 intensity.
“Someone has to pay for that,” he said. “We all can hope there is going to be a green premium…”
Patrick Bolduc, sales manager of mining group Rio Tinto in Canada, said in an interview with Steel Times International that
Rio Tinto maintained a ‘major industrial footprint, given its two iron-ore mines, several smelters, one bauxite refinery and one diamond mine’.
“We produce high-grade iron-ore and make pellets as well. Our iron-ore mine is
“Our (carbon) emissions are very low and we deserve some reward.”
Lourenco Goncalves, chairman, president and CEO of Cleveland Cliffs.
a joint venture with a Japanese company and the First Nation (Canadian) Co. The joint venture is called Iron Ore Co. (IOC) of Canada,” Bolduc said, adding that China was a major buyer of iron ore with a total requirement of about one billion tons. “After all, some 50% of the world’s steel capacity is in China.” Asked if ironore demand had declined because of the industry’s emphasis on de-carbonization and the use of steel scrap in steel production, he said that iron ore will still be needed, including in the decarbonization process.
The GSDF was attended not only by steelmakers but also by service providers and others such as ports dealing with steel cargo shipments. The Port of Brownsville
(PoB) has been a regular participant at the GSDF meeting.
PoB’s deputy port director, Arturo Gomez, told Steel Times International that the port, located in the southernmost tip of Texas and the only deep-water port at the US/Mexico border, had seen sound growth in steel shipments over the past five years. PoB handled some 5.5Mt of steel imports, mostly from Brazil, destined for Mexico. Along with Nippon Steel and Companhia Siderurgica Nacional, the steel group Ternium SA, which manufactures flat and long-steel products and has plants in Argentina, Brazil, Mexico, Guatemala, Colombia and the US, owns Usiminas of Brazil.
Steel exports to Mexico are estimated to have increased to 5.5Mt in 2023, thanks to the development and expansion of Ternium’s industrial centre located in Pesquería Mexico. The company is utilizing the Port of Brownsville for receiving, staging, and shipping all the steel slab processed at its plant, one of the most modern industrial complexes in the world supporting the automotive, construction and white appliances industries in Mexico.
According to Gomez, PoB’s total cargo traffic, currently at 17.8Mt, is expected to surge to some 27Mt of cargo, once the port’s infrastructure to accommodate the growing LNG trade, is completed. “We hope to complete this by 2029,” he said.
Regional development agencies highlight opportunities for steel State agencies charged with regional development were also present at the conference. Mike Culbertson, president/ CEO of Corpus Christi Regional Economic Development Corporation (CCREDC), said that the agency’s primary task is to promote the region’s development by providing support to local industries such as steel, petrochemicals, oil and gas exploration, manufacturing/automation and aerospace. With the establishment of both a steel pipe factory and an iron-ore plant, the region is creating conditions for establishing a steel-making cluster. The region provides access to rail and a deep water port, with adequate skilled workers for the steel sector. The availability of high quality briquettes is an added advantage for production facilities in this area.
Culbertson said that his agency worked with Steel Dynamics. “We were instrumental in bringing Steel Dynamics
Elevate your steel production with improved yields, superior quality, and reduced downstream costs.
Our high-resolution thermal imaging camera ensures a seamless transition between steel and slag, delivering real-time data to empower operators. Experience quick termination of taps after triggering alarms to prevent ladle issues.
Say goodbye to excessive slag and hello to enhanced productivity!
“China is exporting steel via Mexico. We have been busy with the (Presidential) elections … this has slowed down our discussions which will follow. This is crucial for the US, which will work towards finding a viable solution to China’s shipments through Mexico, once the elections are over in the US.”
Kevin Dempsey, AISI president
to Corpus Christi,” he said. “We also help corporations find suitable corporate partners… the investment flow to Corpus Christi in the past decade amounted to some $57.4 billion,” he said.
William Cork, the executive director of the Mississippi Economic Development Corp. (MEDC), another regional development agency, highlighted the investment opportunities for steel companies and others in his state; he told this correspondent that Mississippi offered ‘superior logistics facilities’ that appealed to steelmakers.
“We are surrounded by waterways facilitating shipments and also have excellent rail services. We have abundant low-cost power supply, including hydroelectric and nuclear power plants. Most of the steel produced in Mississippi is for the domestic market. Europe’s metal industry has shown interest in the state because of the power supply. Mississippi is also a favourite site of Mid-West companies because of availability of iron-ore, bauxite, low power and labour costs, etc.” he said. Mississippi also has plants of international
carmakers Toyota and Nissan.
Cork also said that Mississippi provides an individual benefits package for each company setting up an operation in the state. “However, Mississippi does not have a standard set of benefits depending on a number of factors related to the operation being set up.”
Kevin Dempsey on decarbonization, tariffs and the USMCA
The American Iron and Steel Institute (AISI) was represented by its president, Kevin Dempsey. He said in an interview with Steel Times International that ‘more steel in the US needs to be decarbonized’.
Dempsey welcomed President Joe Biden’s suggestion of trebling Section 201 tariffs, a decision that was ‘well within his powers’.
“Demand in the steel industry is a bit soft right now but things are improving because of the government policy, including the CHIPS and Science Act, the Infrastructure Investment and Science Act, etc.,” Dempsey said.
“Allocations are slower but the money for infrastructure is still coming,” he said,
adding that the government was providing tax credits for 10 years; and that there would be emphasis on green energy through wind and solar power.
Dempsey also touched on China’s use of the USMCA to push its steel through Mexico. “China is exporting steel via Mexico. We have been busy with the (Presidential) elections … this has slowed down our discussions which will follow. This is crucial for the US, which will work towards finding a viable solution to China’s shipments through Mexico, once the elections are over in the US,” he said.
Though the Federal Government did not give any direct incentives to foreign investors, Dempsey described the US as ‘a great place to make steel’.
The GSDF’s most interesting – and muchanticipated – discussion, perhaps, was about US Steel’s takeover by Nippon Steel Corp. for US$14.9 billion. The takeover bid by a foreign steel group of an iconic and unionized US steelmaker has not been uncontroversial.
David Burritt, US Steel’s CEO, in an on-stage conversation with Philipp Englin, World Steel Dynamics’ CEO, defended the merger and was confident that it would come to fruition. Describing Nippon as the ‘right choice’, Burritt was confident that ‘we are going to be able to close this deal this year’, adding that it would be a ‘win’ for all stakeholders and that all employees, particularly the union employees, would benefit as Nippon Steel had committed to honour the basic labour agreement and forego any layoffs.
“Moreover, the company will invest US$1.4 billion in US Steel facilities.” A combined US Steel-Nippon company would benefit the customers because of the enhanced competition as a result of a combined company in the North American market.
“Customers love (this deal),” Burritt claimed. They had sent letters to the Department of Justice saying the deal would strengthen competition, not diminish it. The country would also benefit from the technological achievements of Nippon Steel which has 30,000 patents and long-standing expertise in integrated steelmaking. The company has a US$500 million R&D budget which was “more than the steel companies in the US combined in a year”. �
Benefits:
Maximum measuring accuracy thanks to temperaturestabilized measuring systems
The PROFILEMASTER® SPS is a light section measuring device for measuring contours and dimensions on profiles of all kinds in cold and hot steel applications. 4 - 8
Shape fault detection (SFD) thanks to high sampling rate
High-precision measurements
Detects process problems at an early stage
Fast maintenance and easy cleaning
Zumbach Electronic AG | Hauptstrasse 93 | 2552 Orpund | Schweiz Telefon: +41 (0)32 356 04 00 | sales@zumbach.ch | www.zumbach.com
The challenge of the climate crisis, says Caroline Ashley*, requires everyone to wake up to change, and make it fast and fair.
THERE is no question that huge change will happen in the next two decades as the planet warms, and we finally pivot to a zero-emissions economy. From the point of view of SteelWatch, the only questions that really matter are:
• How fast? Will we change quickly enough to avoid the most catastrophic impacts on the planet and society?
• And how fair? Does the journey to a decarbonized economy also take us to a thriving society, a world where we can all flourish?
Of course, there is another question for companies in the sector: Will our company create and ride the wave of change, or will it simply get left behind as first-movers and disruptors get ahead of the game? We believe that companies that resist change are not only bad for the planet but jeopardise their business competitiveness.
Let’s start with a few things that we already know about the change that is coming:
First, climate change is already having major impacts. We have all witnessed headlines – or the direct trauma – of people in Africa, the Americas, Asia, Australia, Europe and the Middle East dealing with fires, floods or famine. My own work in recent years has focused on rural women who are already walking longer to fetch water in arid areas and farmers finding they are planting crops at what should be harvest time. The health impacts of heat stress are evident even in developing foetuses, and extreme environmental changes are believed to alter our brains.
There will be no new ‘normal.’ There will be widening unpredictability and tangled chains of change across societies. In the industrial sector, mines, production plants, supply chains, stock markets and business
models will not escape these shocks.
Before the Paris Agreement was signed, global emissions had us on track to suffer 4 degrees of global warming. With improvements since then, we are now on course for just under 3 degrees of climate change. Policy change works.
We know that unimaginable transformative change is possible in just decades. Look at the Space X programme – from initial founding in 2002 to commercialisation, a new sector and paradigm emerged in just a couple of decades. We are not just victims of change. We have the power to shape change, too.
This much we know. What more do we think or predict?
The biggest impacts of climate change will be ones we have not even begun to think about yet. Think how many apps and
actions have been unleashed by the iPhone, so many of which were inconceivable at the time when Apple launched a new device called a ‘phone’ in 2007 – as if making ‘phone calls’ was the essence of it.
In the world of climate, we now see rising ocean temperatures going literally off the graph [Fig 1]. The only thing we know is that we do not know enough about the impacts of this. But they will not be negligible. Horror and dismay hardly do justice to the scientists’ reactions.
As impacts hit, policies will tighten further, and litigation escalates on those that pollute. Politicians will have no option to finally tighten the pace of transition. As it’s called from the business investment point of view, this’ transition risk’ has been recognised for some time.
The more recent trend is litigation: legal action against polluters for the harm they have caused. This is new, but it is taking off: from state-versus-state action in the Inter-American Court of Human Rights to over 30 actions against oil companies for their contribution to climate change, to the recent success of 2,000 Swiss women taking their own government to court. The trend is clear: polluters will be held responsible for their harm, eventually.
Source: Posted by Professor Eliot Jacobson at https://x.com/EliotJacobson/status/1803830894236422150
Further updates continue to be posted on Professor Jacobson’s timeline.
So, what does this mean for steel companies?
It means that the transition to near-zero steel is inevitable, and while companies today are clinging to the ‘hard-to-abate’ label and reasons to go slow, the transition may well hit a speed that leaves some behind.
The shifts to near-zero emissions steel cannot be achieved by tinkering, such as capping blast furnaces with carbon capture or injecting some hydrogen into the blast furnace. It does indeed require a transformation, shifting the energy system entirely. Transformations can seem unimaginable – until they happen.
A host of changes will ripple out, going beyond what many realise today.
The geography of production will be repatterned. Production will follow demand, new investments flowing first to emerging economies and thence to Africa. There is a risk of companies exploiting lower regulatory standards but a responsibility and an opportunity for technological leapfrogging to the best available technology.
Greater change – and opportunity – lies in decoupling iron and steel production. Without other technological breakthroughs, green hydrogen is essential for green steel. Shipping hydrogen is a bad idea. However, shipping embodied green hydrogen in the form of clean hot briquetted iron looks like the logical way to square the circle of decarbonising the global steel economy. So, iron production will no longer be driven by the location of steel production or the operations of the integrated steel plant. Future-facing iron production investments will be driven by the availability of abundant renewable energy combined with access to iron ore.
Some other fundamental ways of thinking will change. The basics of steel invariably start with the distinction between primary and secondary production. The term ‘EAF’ is still so often assumed to mean ‘scrap-based production’, in contrast to primary production with BF-BOF. But the dichotomy will wither in the world of direct reduced iron, higher-quality scrap, and the shift to EAFs. DRI and scrap will be balanced as feedstocks for the EAF, depending on the supply and quality demanded. The textbooks will need to be rewritten.
Steel producers’ business models could transform. EAFs will offer more flexibility
“SteelWatch’s vision is transformation to a steel sector that is fully decarbonized and supports a thriving net zero economy and fair society. This goal will take decades – it’s a marathon, not a sprint. ”
than current integrated plants: they may be smaller in size, producing steel closer to customers and in volumes that allow for more customised batches; running hours will be optimised to take advantage of variable electricity prices connected with a smarter, renewable-powered grid; and iron feedstock flexibility will increase as collected scrap volumes increase.
‘Steel as a service’
Will ‘steel producer’ even hold the central role? Some of today’s steelmakers started as scrap collectors and moved up the value chain. With the flexibility offered by EAFs it might be that tomorrow, steel users will do the same and produce themselves very specific alloys for their own needs (maybe with the help of AI, as biotech and pharma companies do today to test proteins) and collect them back at the end of products’ lifetime in closed-loop systems. Something similar is emerging in the battery and auto industries. For these companies of the future, the key metrics will not be production or sales of crude steel. Steel will just be one of the materials to choose from in their catalogue to deliver a specific product or service. ‘Steel as a service’ in action.
For other businesses, steel might be a byproduct of the new hydrogen economy. We hear so much at present about the limits of green hydrogen capacity compared to
what is needed for decarbonised steel. But the day will come when renewable energy is the only energy source, and there will be times of huge surplus, with near-zero marginal cost of energy. In that world, not so far away, green hydrogen is a good way of using surplus energy; green iron is a good way of capturing and transporting that green hydrogen, and green steel becomes one way of capitalising on the low marginal cost of hydrogen.
SteelWatch’s vision is transformation to a fully decarbonised steel sector and supports a thriving net zero economy and fair society. This goal will take decades – it’s a marathon, not a sprint. But the work has to start now, today because every investment decision matters, and every extra tonne of CO2 creates more harm. We suspect that it’s a downhill run, picking up speed. There will be many debates on the details of change. But we start by urging companies to embrace the opportunity for change.
Defending the status quo and protecting the current business model simply prolongs pollution, delays adaptation, and risks competitiveness.
The pace of change may feel slow day-byday and week-by-week. But the change that happens in a year or decade can be beyond what many anticipate today. The challenge of the climate crisis requires everyone to wake up to change, and make it fast and fair. �
With over 50 years in the Steel Industry, we have a wide variety of solutions to keep your mill rolling.
allow for quick and accurate pass changes
· Honours existing mill attachment points and guide base, no machining on your stands required
· Made from stainless steel and speci cally tailored to your mill ensuring perfect t, operation and longevity
Our roller entry guides keep your product on the pass
· Single point, centralized adjustment during operation
· 2, 3 and 4 roller con gurations
· Rigid, stainless steel construction
· Broad size range
Maximize your mill speed while meeting your quenching requirements on all bar sizes. Not just controlled cooling, but correct cooling
· Fewer surface defects and better scale control
· Available in Box, Trough and Restbar-mounted con gurations
Rail transport is already considered climate-friendly. However, green rails produced from low-CO2 steel by Saarstahl Rail, a subsidiary of Saarstahl Group, are claimed to enable rail network operators to drastically reduce their carbon emissions even further.
THE French subsidiaries of the Saarstahl Group – Saarstahl Rail and Saarstahl Ascoval – are currently the only providers throughout Europe to have scrutinized conventional processes and production methods, and then develop decarbonized rails. In close alliance with the state-owned railroad operator in France (SNCF – Société Nationale des Chemins de Fer Français), Saarstahl Rail claims it has been successfully implementing the green rail concept in
practice since 2019, working to a circular economy model. In the meantime, further railroad network operators such as Belgian company Infrabel or infrastructure firms, such as the Société du Grand Paris, have awarded Saarstahl Rail contracts for green rails worth millions of Euros.
The sustainable production method and the use of almost 100% recycled steel scrap are the keys to success for the decarbonized rails. Guaranteeing the necessary supply
reliability of environmentally friendly rails for rail network operators requires a sufficient stock of industrial scrap and – depending on the desired steel specifications – up to 70% used rails as well as other steel components from rail networks. Saarstahl Rail, therefore, purchases used rails and steel scrap from rail network operators in order to recycle these at Saarstahl Ascoval. In Saint-Saulve near Lille, Saarstahl Ascoval melts down the mix of raw materials in
an electric arc furnace (EAF) and casts the rail steel produced into blooms. These are then transported by train to the Saarstahl Rail production facility in Hayange to the north of Metz, where they are rolled to create green rails. The comprehensive final testing, using laser, ultrasound, and visual inspections, is also performed in Hayange. The checks performed here include compliance with the stipulated Euronorm flatness tolerance of < 0.3mm per three metres of rail in order to guarantee optimum tracking stability and passenger comfort for the high-speed trains, which reach speeds in excess of 300 kph (185 mph). Compared with conventional rail steel, which is produced in a blast furnace with an oxygen converter using iron ore and
1. Saarstahl Ascoval melts the steel scrap in an electric arc furnace.
2. Dominique Chiesura, commercial director, Saarstahl Rail.
3. Blooms are reheated in the furnace at Saarstahl Rail in Hayange ahead of the rolling process.
4. Ready-to-install green rails are transported to customers by train.
5. Rail steel is casted into blooms.
coal as raw materials, the new production method reduces carbon emissions by up to 70%. Whereas 2.61 tons of CO2 are generally emitted per ton of steel, this figure is reduced to just 0.77 tons per ton of steel with the new process.
The manufacturer specializes in all types of rail networks worldwide. Its portfolio comprises over 100 different rail profiles and 25 steel grades in lengths of up to 108 metres with metallurgical and mechanical properties in conformity with customers’ specifications – all offered from a single source, regardless of whether they are produced from green or conventional steel. SNCF, one of Saarstahl Rail’s most 1 2 3 5 4
1 2
3 4
important customers, was the first rail network operator to seek a solution for decarbonization of rails. It found the right development partner in the supplier that has demonstrated expertise and reliability over many years. According to Cyrille Blard (in charge of sustainable economy at SNCF) there were two key reasons behind the decision to place greater emphasis on development of sustainable products in its procurement policy. By procuring materials through a regional circular economy, the aim was to secure independence from geopolitical influences, such as those encountered during the COVID-19 pandemic or due to the war in Ukraine. “This allows us to produce brand new materials from used custom materials, which represents a win for both sides of the lifecycle.” The fact that the French government has issued a target to reduce carbon emissions by 25% by 2030 was the
other key factor in increasing the focus on sustainable products. “SNCF Réseau already greatly exceeded this target in 2022 with a reduction of 34%,” comments Cyrille Blard with pride, adding: “The green rails made a significant contribution to this!”
Saarstahl Rail produced its first green rails in the summer of 2020. SNCF Réseau, the owner of the French rail network, tested the product that same year. With test rails having already successfully passed both the test and official approval process in Rennes and Cannes at the start of December, Saarstahl Rail supplied SNCF with almost 1,000 more tons of green rails that same month. Since 2020, all major rail renewal projects in the French rail network have been implemented with green rails. As part of a seven-year contract, SNCF Réseau is ordering around 130kt/yr of rails (more
than 1,000 kilometres of railroad line) from Saarstahl Rail. In 2023, some 90% (125kt) of these were already green rails. This helped the railroad network operator save around 200kt of CO2 equivalents. The annual requirement for rails as per SNCF’s multi-year track renewal plan remains constant up to 2030. Saarstahl Rail delivers the desired batches to a production unit of SNCF in Saulon-la-Chapelle by train. The 108-metre-long rails are then welded together to produce segments of up to 432 metres in length. On a project-by-project basis, used rails are cut into 1.5-metrelong segments directly on the construction site or at the SNCF facility in Saulon-laChapelle, or transported once a month by train in segments measuring no more than 18 metres in length to the steelworks in Saint-Saulve, where they are cut and then melted down. This process of returning and recycling 50kt of used rails per year (status
as at 2023) is contractually agreed with Saarstahl Rail and is of critical importance for SNCF in securing the specific chemical composition and mechanical properties of the rails.
Cyrille Blard emphasizes the commitment of both parties to make every effort to use old, unusable rails for reprocessing as green rails. However, the actual figure is currently lower due to a lack of availability of used rails. The SNCF manager links this objective to the vision of finding a new way of pricing steel in the long term, whereby SNCF is the process-independent owner of the steel material and the rail manufacturer is a contractor that converts used rails into new green rails. “This would require the rail supplier and SNCF to work together even more closely in future.”
Saarstahl Rail and SNCF have already been co-operating for many years. Besides supplying rails, this cooperation encompasses joint research and development. “We engage in a very wide range of activities and hold regular meetings to discuss both technical and logistical questions,” comments Dominique Chiesura, commercial director of Saarstahl Rail. Cyrille Blard adds: “This is a genuine partnership, which is precisely what we need for the new rails. Saarstahl Ascoval requires used rails as raw material, while SNCF requires new green rails from Saarstahl Rail.” The success already enjoyed shows that he is right: “At first, only very few people believed that the new green rails were really as good as the ones currently in use.” The key was, therefore, to do a lot of convincing, both internally and externally, but: “We demonstrated that the recycled material in the green rails offers the same consistently high quality as new material.” For him, this proves that things have changed, together with the mindset and the way in which the network is operated. For example, his team also demonstrated that recycled and reprocessed gravel can be even better than new ballast from the quarry. “We’re also working on using our old rails from a high-speed line for a less busy route with lower speeds before they actually reach the end of their useful life and are then sent off to Saarstahl Ascoval.” A renegotiation of the multi-year contract with Saarstahl Rail is scheduled for the coming year. “Obviously, we hope that we can continue working with Saarstahl
Rail and Saarstahl Ascoval in the future, but since we’re talking about one of the largest economic markets for rails, a public tender process is stipulated,” comments Cyrille Blard. This tender process will also include an evolution clause for CO2 reduction through green rails, as well as the return of used rails.
For Saarstahl Rail, the chances of winning a follow-up order from SNCF Réseau look pretty good, as underlined by various other tender processes that the company has successfully won recently. For example, the company has to date supplied all rails for the Grand Paris Express megaproject (four new metro lines), involving some 20kt of green rails. Among other uses, these were laid along the first low-carbon Metro line in Paris – the new line 16, which connects the north of the French capital with the east in a 26-kilometre loop. In total, the ring railroad that is currently under construction for the greater Paris area will cover 220
kilometres, which will double the scope of the existing Metro network. The Société du Grand Paris, the company responsible for construction of the network infrastructure, is keen to reduce carbon emissions by 25% along the entire route, which would mean a total saving of 1Mt of CO2. This represents a steep challenge for Dominique Chiesura: “We need to make sure that 100% of the new routes included in Europe’s largest infrastructure project run on green rails!” Belgian railroad network operator Infrabel is also investing in the environmentally friendly rails. Some 2,800 kilometres of green rails have been ordered. A total of 20kt of these rails from Saarstahl Rail are now planned to be used for reconstruction of the destroyed rail network in Western Ukraine.
Green Steel from Saarstahl is also used in other railway components such as fastenings and pre-stressed steel for concrete sleepers.
For the Saarstahl Group, which operates out of Völklingen, Germany, the rapidly growing development of the business with
1.
2. Rails are formed to their final shape and dimensions at Hayange in a multi-stage rolling process.
3. Rails cool down slowly after rolling.
4. Rails are prepared for finishing.
5.
green rails is seen as the spearhead for decarbonization in the Group. The Group, which specializes in the manufacture of thermomechanically rolled spring and bar steel, as well as semi-finished and forged products for the automotive, construction, and aerospace industries, is helping drive the transition to more eco-friendly modes of transport with green steel. �
SPEAK: Join industry leaders like Blastr Green Steel’s CEO Mark Bula in Bilbao at the 2025 Future Steel Forum. Apply now and contact Matt Moggridge to secure your spot!
matthewmoggridge@quartzltd.com
+44 (0)1737 855151
SPONSOR OR EXHIBIT: For any exhibition or sponsorship opportunities, contact Paul Rossage
paulrossage@quartzltd.com
+44 (0)1737 855116
WHAT THIS YEAR’S ATTENDEES HAD TO SAY…
“Very well organized event with a good line of speakers focused on digitalization and decarbonization.”
“Great immersive atmosphere and excellent platform to learn and network.”
“Unique blend of upcoming technologies, challenges and the latest innovation in digital transformation for the iron and steel industries.”
“A good mixture of high-level presentations, panels and networking opportunities at an excellent location.”
While down slightly from a year ago, it appears that the North American stainless steel market has bottomed out and is on a path of gradual improvement. This is supported by a number of factors, most notably expectations that the US Federal Reserve is about to reduce interest rates, which will have a positive impact in a number of stainless steel consuming markets. By Myra Pinkham* interest rate- and consumer-sensitive, and
“LAST year’s cocktail of inflation and rising interest rates created a lot of uncertainty,” which, negatively impacted consumer confidence and the willingness for companies to make capital investments, Markus Moll, Steel & Metals Market Research (SMR)’s managing director and senior market research analyst, pointed out, noting that because of that North American real stainless steel demand declined about 5% last year.
“US stainless steel demand hasn’t been that great this year – flattish year-to-date through July,” Amanda Eglinton, associate director of S&P Global Market Intelligence, said, noting that higher costs, higher interest rates and certain lingering supply chain bottlenecks have been weighing on demand.
“But now we are starting to see some signs of higher investment activity,” Moll said, noting that while this year it is nowhere as strong as it had been in 2022, he believes that the market has now troughed and that things will gradually improve.
Recent speculation that the Federal Reserve is almost certain to start lowering US interest rates in September, and to potentially follow that with more cuts later this year and into next year, is supportive of increased demand, according to Philip Gibbs, a senior equity analyst for KeyBanc Capital Markets.
He noted that while it varies somewhat by end-use market, at this point overall US stainless steel demand continues to be flat to modestly down given that generally the
bill, the Inflation Reduction Act (IRA) and Myra Pinkham*
US stainless steel market tends to be very interest rate- and consumer-sensitive, and in general consumer buying, especially of durable goods, has been slowing over the past couple of years.
But even though the Institute for Supply Management’s manufacturing purchasing managers index slipped further into negative territory and the University of Michigan’s Consumer Sentiment Index dropped to an eight-month low in July, Gibbs said that the expected interest rate cuts could stimulate growth given that it will make it more affordable for consumers to finance purchases.
Eventually certain recently passed legislation like the Infrastructure Investment and Jobs Act (IIJA) bipartisan infrastructure
Brett Reed, a CRU steel analyst, said that is isn’t having much of an impact yet with much of funding for projects still being delayed.
“Overall, I am somewhat bullish about the future of the US (and global) stainless steel market,” Dennis Oates, chairman of Specialty Steel Industry of North America (SSINA) and executive chairman of Universal Stainless & Alloy Products, declared, predicting that there is potential for longterm growth due to such factors as a greater understanding of stainless steel’s lifecycle advantages, increases in consumer spending and some of the innovations by the industry. Because of this he said that he believes that real consumption could increase by a 3-5% annual rate over the next four-to-five years.
“In general, the market is now very similar to how it had been prior to the pandemic, before the market had major supply disruptions and domestic mill allocations,”
Eric Kellaway, Combined Metals’ stainless steel commercial director, said, maintaining that, with the exception of products used for the aerospace market, which is on an upward super cycle, stainless steel supply chains have largely stabilized with availability and end-user demand getting back to more typical, easier-to-sustain, levels.
While the market could still see some year-on-year growth this year, Oates said that on average the rate of growth will be about 3-5%, which is much lower than
the sequential jump that it experienced between the fourth quarter of 2023 and the first quarter of 2024. But that could vary by the type of stainless steel product – and their end-use applications with both the demand and prices of stainless steel long products faring better than that for flat products.
Eglinton said that another factor influencing this is import competition, noting that with domestic prices being significantly higher than those in the rest of the of the world, US imports of cold-rolled flat products were up about 41% year-todate through May.
While still up year-on-year, the US International Trade Administration reports that overall US stainless steel imports were down about 17% month-on-month in June. This, Oates said, comes as US stainless steel long product imports are down slightly this year from their 2023 levels.
Eglinton noted that while US cold-rolled stainless premium versus European import prices has come down considerably to about a 20% gap, US domestic prices remain about double that for Asian imports. This, she said, comes with a significant amount of new production capacity added in Asia at the same time as its domestic demand had also slowed.
“For commodity stainless grades, either US prices need to fall further, Asian prices would need to rise and/or there would need to be a significant slowdown in demand to stem the tide of rising imports,” Eglinton said. However, CRU’s Reed said that stainless steel imports from Asia to the US West Coast have been very competitive. That, he said, is why domestic mills have generally been pricing their products differently east and west of the Rocky Mountains.
In addition to the pricing differential, recent moves to monitor and influence the melting and pouring origins of the steel related to Section 301 and Section 232 tariffs are likely to have some impact upon stainless steel imports, Kellaway said, especially with some speculation of circumvention, that some imports from Mexico – a major importer – were actually melted and poured in China or another country that doesn’t have a trade agreement in place with the US.
S&P Global noted that, for example, one such move by the Biden administration has been for only the Mexican steel and aluminium imports with raw materials
melted and poured in North America will continue to be exempt from Section 232 tariffs.
Oates, however pointed out that there has also been some speculation of India potentially circumventing US trade laws.
Meanwhile there has been a lot of variation in recent end-use market dynamics. But while some leading indicators for durable goods, including the Institute for Supply Management’s manufacturing purchasing managers index, have been softening over the past 18 months or so, KeyBanc’s Gibbs said it appears as though they are bottoming out, which could mean improved stainless steel demand next year.
Moll agreed, noting that there are already signs that the US housing market could
for replacements than being related to housing starts.
Also, after a negative year in 2023, Moll said he expects about 9% growth in the architecture, building and construction and infrastructure sector this year, which will be supportive of stainless steel ornamental and structural tubes. “I also expect to see some improvement in the use of stainless steel rebar for bridges,” Moll said, although he admitted that stainless steel currently accounts for less than 1% of the rebar market.
Automotive-related stainless steel demand is somewhat uncertain. Gibbs noted that over the past few years the auto sector, which traditionally has been a big consumer of ferritic stainless steels, has
be starting to recover, which might be supportive of such demand for not only home appliances, which is a big consumer of stainless steel, but ornamental tubes and water pipes, as well as HVAC systems. This comes with US mortgage rates recently dropping to a 15-month low of 6.47%.
Over the past year, there has been a cooling off of stainless steel demand for home appliances, which Oates said isn’t surprising given the high interest rates and all the appliance purchases that were made during the pandemic and the long lead times for getting appliances delivered. CRU’s Reed maintained that at this point most of the new appliance orders are more
been somewhat choppy over the past few years given the pandemic-related supply chain issues and the short-term impact of the United Autoworkers’ strike and other factors.
Oates observed that North American light vehicle output is expected to continue to move upwards this year, to about 15.8 to 16.0 million autos from 15.4 million in 2023 and a low of 13.8 million in 2019.
But the question is what types of vehicles will be produced given that, according to Moll, electric vehicles use about 80% less stainless steel than internal combustion engine (ICE) vehicles. But he said that could change if, as some hope, some EV battery
casings could be converted from aluminium to stainless, which could provide safety advantages in event of an accident resulting in the explosion of the battery.
Another question is how the vehicle mix will change. Moll said that even though EV demand hasn’t grown as fast as some had predicted, he believes that the majority of North American autos produced after 2030 will be EVs.
The aerospace and defense markets are a bright spot for stainless demand, said Tony Amabile, director of marketing at TW Metals.
Industry observers said this is even the case with Boeing not building as many commercial aircraft as they thought they would in 2024, noting that commercial plane build rates are still way higher than they had been and are forecast to be even stronger next year when Boeing fixes its issues and increases its build rates, which they said Boeing needs to do given that Airbus is largely sold out.
Amabile said that at the same time defense demand – for both aircraft and weapons – is seeing double digit growth and the business jet and space sectors are also extremely strong.
While US distributors are continuing to work down their stainless steel inventories, as they have been doing since they peaked in mid-2022, Gibbs said that they are no longer being overly cautious about their stainless steel purchases given that with 3.2 to 3.4 months of supply on hand, inventories are now at much more normal levels relative to demand.
Oates agreed, noting that even inventories used for certain ‘red hot’ applications such as aerospace have recently come down somewhat, noting, “While they are still solid, they aren’t as high as they had been.”
Eglinton noted that the two dominant US flat-rolled stainless steel producers – North American Stainless (NAS) and Outokumpu – have been focusing on controlling their production to keep it in line with demand. “Currently domestic mill lead times are about as short as they can be,” she said, noting that it is possible that the domestic mills could possibly consider cutting back their production and take some of their capacity offline if necessary.
Gibbs pointed out that these shorter lead times have allowed buyers to keep inventories lean without fears of shortages, adding that with nickel prices
recently moving downwards it is unlikely that companies will be increasing their inventories, particularly of austenitic grades of stainless steel.
While early this year US stainless steel base prices (other than for aerospace grades, which have been rising and continue to do so on tight supply) came down a little, CRU’s Reed said they have been flat for much of this year, although there have been some early signs that, with supply outpacing demand, some austenitic grades could inch down. That, Amabile noted, is at a fairly high pricing level.
But Eglinton said it is possible that some stainless steel grades, such as cold-rolled stainless, could slip into more of a surplus situation if imports continue to come in as domestic demand slows. If that happens, she said, base prices would slip either later this year or early next year.
Meanwhile, stainless steel surcharges, particularly nickel surcharges, have been volatile this year. Moll pointed out that nickel prices went up in late May on supply concerns, but have since declined given
indications that less nickel than expected is needed for EV batteries.
At the same time, Eglington noted that after surging in the second quarter due to investor speculation on the LME nickel contract through late May, they collapsed back to their February lows amid a growing oversupply of nickel in Asia that has accumulated in LME warehouses over the first half of the year. She said that the drop in nickel prices in June and July will drive austenitic surcharges lower in August and September.
Currently it remains uncertain what will replace the European benchmark in figuring out chrome surcharges going forward. Moll said that while NAS has already announced its solution – one based upon a European pricing index and a Chinese import index –which it believes better represents the real cost of chrome – it is still uncertain what Outokumpu and Cleveland-Cliffs will do. Reed said that CRU is looking to offer an alternative that will reset monthly instead of quarterly.
Movement in the surcharges for ferritic stainless steels will depend largely on chrome and iron pricing movements. John Anton, director of S&P Global Market Intelligence’s pricing and purchasing service, noted that while ferrous scrap prices have been down considerably over the past few years, it is expected to be relatively flat in the near term even with the new US electric arc furnace capacity coming online.
“Overall, 2024 has been a fairly normal year for the US stainless steel market,” TW Metals’ Amabile said, even though it has softened somewhat from 2023. “But I am optimistic that we will see some demand recovery next year, particularly from the aerospace, medical and energy sectors, but from other end-use markets as well.
Gibbs agreed that anyone who isn’t currently servicing the aerospace market is currently experiencing weaker demand and pricing. “But overall, the US stainless steel market is in a bottoming out phase right now and things should improve next year. But that will depend upon certain still unknown factors, Combined Metals’ Kellaway said, including whether the federal reserve lowers interest rates, as is anticipated, as well as the outcome of the US presidential election and how that will impact the US economy and consumer confidence. �
As steelmakers make tracks to change the way they make steel and focus more on reducing the industry’s carbon footprint, many of them are examining how automation and digital manufacturing can lead to greener steel.
By Mo Ahmed* and Geoffrey Scaringella**
WITHIN the iron and steel sectors, responsible for up to 9% of worldwide CO2 emissions, a pressing demand to decarbonise operations has emerged. This is driven by governmental regulations, public expectations, and the insistence of major clients. Prominent manufacturers in the automotive and construction industries now require their steel suppliers to furnish them with green steel – a type of steel produced without reliance on fossil fuels. This shift aims to reduce the carbon footprint of constructing automobiles and trucks, potentially influencing consumer choices.
Advancements in technology, particularly the adoption of electrification and hydrogen production, have paved the way for a shift in the steel industry. It is now possible to substantially replace coal with cleaner energy sources, facilitating the production of green steel on a larger scale. A recent report by the NGO Global Energy Monitor revealed that electric arc furnaces currently contribute to 31% of the existing steelmaking capacity, illustrating a significant stride towards sustainable and environmentally conscious steel manufacturing.
In line with regulations, the production of green steel is now subject to a stringent certification process that requires the precise measurement and reporting of CO2 emissions. This regulatory framework imposes taxation on manufacturers that surpass the designated CO2 emissions thresholds, creating a financial incentive to stick to environmentally responsible
practices in the production of green steel. Marketplace trends are radically transforming the way steel companies conduct their business. For example, leading organisations such as Liberty Steel and ArcelorMittal are converting to electric arc furnaces to reduce carbon emissions by 60 to 70%. They are positioning themselves for long-term growth in the growing green steel market.
Consider the journey of European steel producer Liberty Ostrava, which is in the process of transitioning its operations to expand green steel production by:
• Planning to invest hundreds of millions of dollars over the next eight years to achieve carbon neutrality by 2030.
• Replacing their four traditional coalfired blast furnaces with two hybrid electric arc furnaces.
• Installing an updated power infrastructure will accommodate hydrogen production and enable the use of a higher volume of steel scrap and a more extensive
range of charge materials.
These strategies will reduce the company’s reliance on imported coal and significantly reduce carbon emissions. However, upgrading furnaces and electrical infrastructure is only part of the steel decarbonisation story. The company is also modernising its automation software in preparation for its roll-out of electric arc furnaces (EAF) and direct reduced iron (DRI) process capabilities. The continued deployment of the AVEVA PI System digital platform will allow the steel plant stakeholders to:
• Perform detailed operational analysis.
• Optimise both existing legacy and new systems.
• Implement a real-time, conditionbased programme for maintenance, process, environmental emissions and energy consumption.
Cloud-based automation platform
Condition-based maintenance aims to identify emerging issues and apply fixes
before any major downtime occurs. This is accomplished by collecting and analysing historical and real-time operational data with conditions that reliability engineers already know.
When anomalies are identified, operators are notified and can take preventative measures to avoid downtime. Besides improving efficiencies in combustion and conversion processes, the monitoring system also helps operators optimise raw material usage and energy consumption.
The AVEVA PI System enhances operational efficiency and profitability, empowering operators to make precise decisions. Liberty Ostrava, using the system for one year, achieved a 10% reduction in production losses and a 15% increase in quality, resulting in substantial monthly savings. These savings are poised for exponential growth with the implementation of new EAF and DRI technologies.
The company has strategically implemented AVEVA digital twin solutions a cloud-based virtual model enabling
engineers to test control logic and streamline start-up or shutdown processes in a virtual commissioning scenario. This digital twin provides a visual representation of the steel mill’s process and automation aspects, including a deep dive into the blast furnace operation. Engineers can use these tools to optimise set points and monitor parameters like natural gas input or chemical reactions, resulting in reduced carbon emissions, enhanced process stability, and significant energy savings.
Integrating sensor and equipment data into the AVEVA PI System enables realtime advanced process monitoring and analysis. This consolidation supports the implementation of efficient maintenance strategies like predictive and prescriptive maintenance, ensuring proactive issues resolution and optimising maintenance schedules for sustained operational reliability. �
The rst continuous monitor of strip cleanliness providing real-time data with unprecedented precision that distinguishes between oil and iron nes contamination.
The only system to differentiate between Oil and Iron Fines
Real-time cleanliness monitor for strip processing lines
Utilising Laser Induced Breakdown Spectroscopy (LIBS)
sales@sarclad.com
sales@sarcladna.com
sarclad.com
sales.china@sarclad.com
sarclad.india@sarclad.com
Non-contact sampling 20Hz sample rate
Eliminates need for ‘tape test’
Having established a co-operation with Swedish green steelmaker H2 Green Steel, Schaeffler claims it is actively ‘shaping the transformation’ of the steel industry. With hot and cold rolling mills as key customers for its rolling bearings and service solutions, Manfred Henneck* says the company is very busy in Europe and in the Asia Pacific region and is working on several tenders with steel plant operators and OEMs in Turkey, India and China.
1. How are things going at Schaeffler? Is the steel industry keeping you busy?
Yes. We have several inquiries with the key steel machinery OEMs worldwide. Steel producers are trying to optimise and the extend operating times of their machinery and equipment.
2. What is your view on the current state of the global steel industry?
Steel commodity markets are currently under pressure, especially in China. However, overall, there are still high activity levels with OEMs and steel operators for upgrades. In the medium term, crude steel production will show robust growth as a result of global economic development and infrastructure investments.
3. In which sector of the steel industry does Schaeffler mostly conduct its business?
Schaeffler supplies rolling bearings and service solutions for the entire steel production process. From a value perspective, hot and cold rolling mills provide the largest demand. We supply the critical bearings, particularly in the core applications, but we can also serve all ancillary applications in a steel plant.
4. Where in the world are you busiest at present? Europe and Asia Pacific.
5. Can you discuss any major steel contracts you are currently working on?
We are working on several tenders with steel plant operators and OEMs, e.g. for rolling mill projects in Turkey, India and China. In Europe, we see a clear direction to CO2-reduced steel with a pipeline project,
for example, in Scandinavia.
6. Where does Schaeffler stand on the aluminium versus steel argument? We have no ‘argument’ towards either material. Steel overall has a higher relative business relevance for us.
7. What are your views on Industry 4.0 and steelmaking and how, if at all, is the company reliant upon digitalization?
We anticipate that increased insight into bearing field data will play a key role in controlling bearing lifetime and optimising future bearing design. By using, for example, bearing condition monitoring, unplanned shutdowns can be avoided. In the future, bearing life can also be predetermined and thus intelligent maintenance can be planned.
8. What is your view on hydrogen steelmaking?
Schaeffler is actively shaping the transformation of the steel industry and has
*Head of raw materials business unit, Schaeffler
established a co-operation with the Swedish start-up H2 Green Steel on multiple levels: equity holding, offtake agreement for green steel and technology partnership.
9. In your dealings with steel producers, are you finding that they are looking to companies like yours to offer solutions in terms of energy efficiency and sustainability? If so, what can you offer them?
Yes. Customers expect from us, for example, high performance rolling mill bearings which provide longer operating lifetimes, reduced friction and optimised lubrication. Furthermore, we are optimising our upstream CO2 emissions by using proprietary steel materials (such as Schaeffler Mancrodur) in our bearings.
10. How quickly has the steel industry responded to ‘green politics’ in terms of making the production process more environmentally friendly and are they succeeding or fighting a losing battle?
It will take time and require large amounts of capital. Recently there has been lots of momentum in the market and projects were announced, supported by governments.
11. Where does Schaeffler lead the field in terms of steel production technology?
We are a premium bearing supplier and are able to equip the entire steel plant with high performance bearings. Furthermore, we have built up a holistic service portfolio including wired and wireless condition monitoring and automatic lubrication solutions called “Schaeffler Lifetime Solutions” which safeguard steel plant availability and performance. Schaeffler has also set up a strategic business field for
hydrogen which is engaged in electrolyzer components and sub-systems.
12. How do you view Schaeffler’s development over the short-tomedium term in relation to the global steel industry?
We are a truly global player, with strong relationships to all major industry participants in all regions and thereby are well prepared to contribute to the steel industry transformation.
13. China dominates global crude steel production. How should the industry react to this situation? China is and will remain important for the global steel industry. Still, local steel production is key in all regions to secure robust supply chains.
14. What is Schaeffler’s experience of the Chinese steel industry?
Schaeffler has operated production facilities in China for many years now. China is both a large steel source for our own production and an important customer base for our bearings and service solutions.
15. Where do you see most innovation in terms of production technologies – primary, secondary or more down-stream?
We see a lot of dynamics in the metallurgical part of the value chain, especially with regards to the direct reduction of iron ore. Further growth will be the smelting of steel scrap, which means the circular economy will come into greater focus.
16. How optimistic are you for the global steel industry going forward and what challenges face global producers in the short-to-medium term?
The necessary decarbonisation of the steel industry will provide lots of opportunities,
but will also require lots of capital to make it happen. This requires support from all stakeholders involved in the transformation.
17. What exhibitions and conferences will Schaeffler be attending over the next six months?
We currently focus on bilateral ‘tech days’ and roadshows with our key customers.
18. Schaeffler is headquartered in Germany; what’s happening steel-wise in the country?
Major steel manufacturers in Germany are rebuilding their production and moving from blast furnace to direct reduction. A major success factor will be the hydrogen infrastructure and competitive energy prices.
19. Apart from strong coffee, what keeps you awake at night?
Securing Germany’s strong position as an industrial powerhouse.
20. If you possessed a superpower, how would you use it to improve the global steel industry?
More speed with regards to the hydrogen energy chain. �
As Tata Steel’s UK steelworks at Port Talbot in South Wales undergoes a major transformation, we look at the plant’s lengthy back story.
By Tim Smith*
THE UK’s largest steelworks (at Port Talbot in South Wales) is closing its two blast furnaces as a means of reducing emissions, and is to replace them with an electric arc furnace. Blast furnace No5 closed in July 2024 and blast furnace No4 will close at the end of September. The two BFs had a combined capacity of 5Mt/yr. The EAF will be in place in 2027. The UK government offered £500 million towards its construction.
Closure of the BFs will result in closure of the coke ovens and the oxygen steelmaking shop with a loss of 3000 jobs. This has an impacted on the town of Port Talbot which is dominated by the present steel plant. The plant is the sole national producer of flat products, making sheet and strip for the car and white goods industries, as well as tinplate. Rolling continue with slab brought in from elsewhere.
The origins of the present-day steelworks can be traced back to 1901 with the building of the Port Talbot Iron & Steel Co., followed by the Margam blast furnace and steelworks in 1923 and the Abbey Steelworks in 1951.
Port Talbot works
Sandwiched between the coast and the South Wales highlands, in an area congested by the Great Western Railway main line and branch lines to a then small, but deep-water dock, the building of a steelworks in the town of Port Talbot would seem unlikely. However, by the start of the 20th century, such was the demand for tinplate bar to supply over 400 South Wales tinplate manufacturers, and, in 1899, a 50% jump in the price for tinplate, land was found south of the present-day railway station to build a steelworks that was to grow in three stages into the present-day plant with a capacity in excess of 5Mt/yr. The area offered all raw materials needed, except good quality low phosphorus ore. Coking coal, limestone, dolomite, silica bricks and a consistent water supply were
all available, while the railway transported in domestic ore and raw materials. The port could bring in higher quality European ore, but its limited size prevented access to large bulk carriers from further afield.
The original Port Talbot Iron & Steel Co., established in 1901, was shortlived, running out of capital to continue operations in 1903. It had built three cupola furnaces to supply remelted, bought-in, pig iron to two 60-ton basic open-hearth furnaces (OHF) operated on a continuous basis, one to initially part remove P and the second to complete refinement. Target output was 650-700 tons per week. A third OHF was added, and a 3-stand bar mill – the first in UK to have all auxiliaries electrically driven.
The works was reopened as the Port Talbot Steel Co. in 1906 by Baldwins Ltd in a joint 50/50 ownership with a railway
carriage builder, the latter joining to ensure a supply of plate steel. The OHFs were rebuilt for cold charging, one acid and one basic, each of 50-ton capacity, and the cupolas removed. Steel was first rolled again in August 1907 and two more 50-ton basic OHFs were added in 1908, as well as a light plate mill. In January 1912 a 3-high section mill was commissioned, soon to be modified to produce light rail. In May 1914, a second melt shop was constructed with four 60-ton basic OHFs and a 42” (1066mm) reversing heavy plate mill to produce ship plate. Shipbuilders took a stake in the company to ensure supplies.
On the outbreak of war in August 1914 the Ministry of Munitions demanded greater output from British mills and partially funded the addition of blast furnaces. The construction of three furnaces was started on an adjacent site following the agreement of the Great Western Railway Company to re-route some of its lines. The new site was the start of the Margam iron and steel works, named after the nearby village.
In 1916, Baldwins Ltd became sole owners of the works. Port Talbot works continued to expand, reaching a capacity of 364kt/yr from 11 OHFs. It also added a heavy and light bar mill and a plate mill. With the building of steelmaking shops at Margam, the elder of two melting shops at the Port Talbot works was closed in 1920. The second shop survived until 1961.
The building of blast furnaces at Margam was to secure a source of pig iron for steelmaking. However, the rapid expansion in demand for steel during the war had led to over-capacity in peace time, as well as a surplus of scrap from war-damaged infrastructure resulting in a five-year delay before iron was first produced at Margam in 1922.
The works was solely owned by Baldwins Ltd. The foundations for three blast furnaces were laid down in 1917, but only two furnaces were completed, and these only after hostilities had ended in 1919. The hearth diameter of each was 12’ 6” (3.8m). The first furnace was not blown in until 1922 when five 70-ton OHFs were erected that year on the Margam site. The second furnace started up in 1923. Nominal output was 2000-ton/week from each furnace.
Already, in 1920, a three stand side-byside reversing mill, consisting of cogging, roughing and finishing stands had been installed to produce billet, bar, sections and rail from steel ingot.
The Margam works was refurbished in 1930. In 1938, half of the coke ovens were demolished and replaced with a battery of 54 ovens. A third blast furnace of 16’ (4.87m) hearth diameter was built and No 2-furnace rebuilt to 16’ (4.87m) hearth diameter. An additional blower of
46,000cfm was installed. The blast was pre-heated to 1000°F (540°C) by means of stoves, with three per furnace. The gas cleaning plant was replaced and the water supply enhanced. The additional gas available enabled the OHFs to be fired with
a mixture of coke oven gas (COG) and BF gas. As demand for pig iron for the OHFs grew, a fourth blast furnace of 21.5’ (6.5m) hearth diameter was built to replace BF No 1, which by then had a 14’ (4.26m) hearth diameter. In 1946, this furnace was blown in, and had a nominal output of 5,000 tons/week, achieving a record 5,420 in August 1948. A fifth BF was added in 1959, this number remaining until 1978 when it was reduced to four and eventually to two.
The OHFs were enlarged one-by-one, each to 100-ton capacity and converted back to oil firing. A 6-ton EAF had previously been added to the melt shop to make special steels. Open-hearth steelmaking at Margam survived until 1963 by which time an oxygen steelmaking process, known as VLN (Very Low Nitrogen) had been introduced.
Part 2 of this article ‘From OH to BOS’ will follow in a future issue. �
Automatic Yard means no human on the floor, nor on the cranes. Q3-DYMS represents a breakthrough technology to automate semifinished and finished product logistic operations, simplifying the complex management of a yard during production in fully automatic mode. Its features make it part of a plant digitalization strategy.