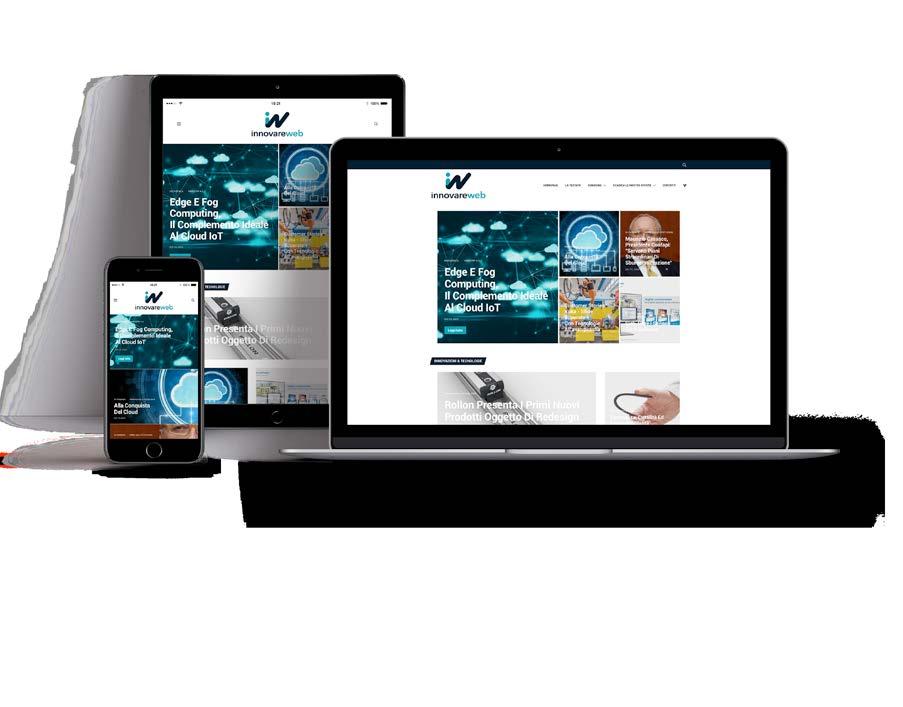
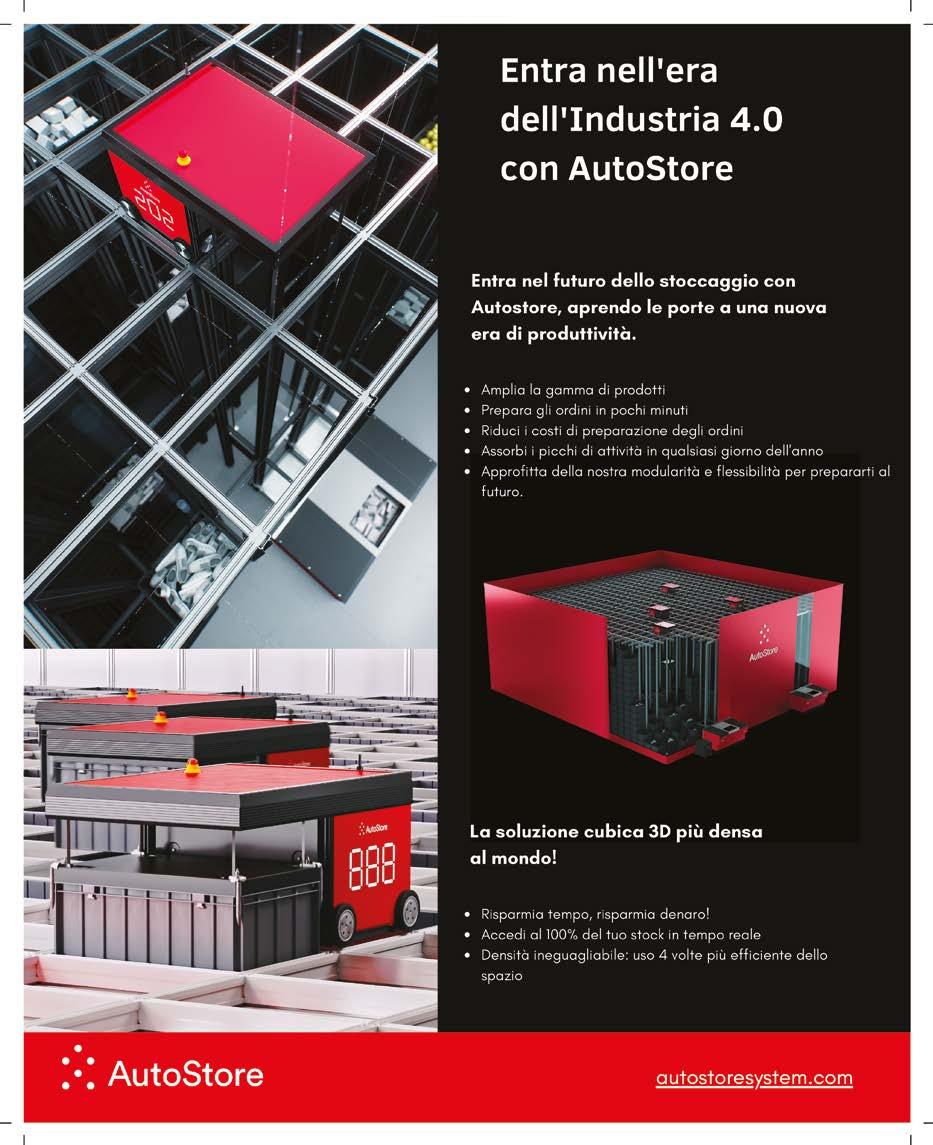


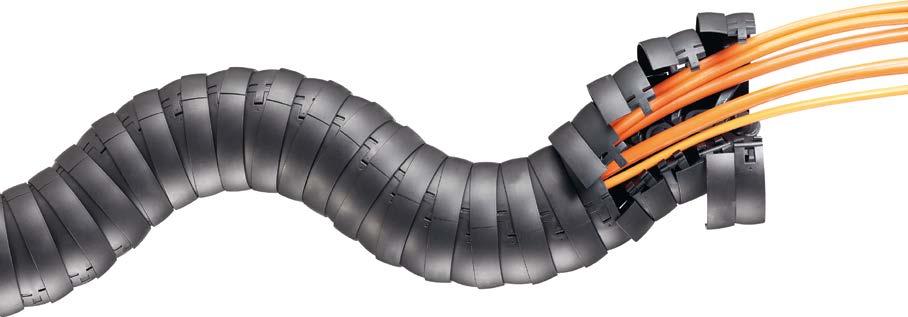
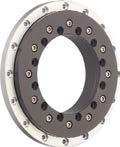

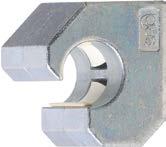
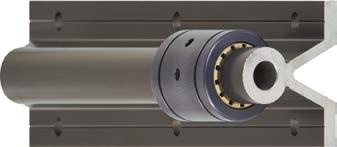

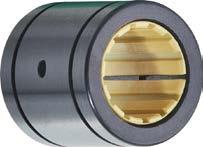
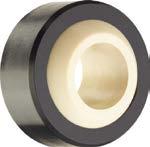
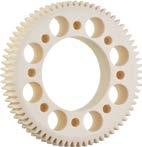
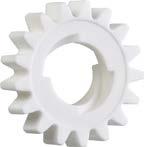
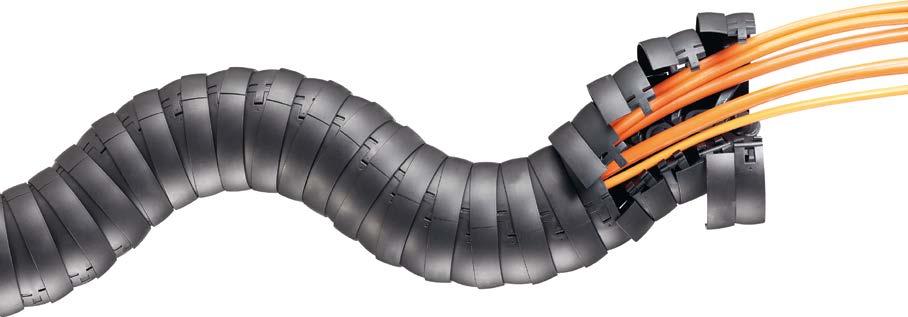

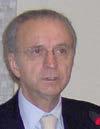
www.linkedin.com/in/carlomarchisio/
www.linkedin.com/in/carlomarchisio/
LLa direttiva (atto legislativo dell’Unione europea che prevede un recepimento da parte degli Stati membri) viene quindi trasformata in un regolamento. Il nuovo regolamento macchine si applicherà a partire dal 14 gennaio 2027, ovvero 42 mesi dopo la data di entrata in vigore, e in pari data verrà abrogata l’attuale direttiva 2006/42/CE. La direttiva macchine si applica alle macchine nuove e non ha mai considerato gli interventi di modifica, regolamentati finora solamente dalle legislazioni nazionali, differenti tra una nazione e l’altra. Possiamo identificare la modifica di una macchina o di un prodotto correlato: mediante mezzi fisici o digitali dopo che tale macchina o prodotto correlato è stato immesso sul mercato o messo in servizio; che non è prevista né pianificata dal fabbricante; che incide sulla sicurezza della macchina o del prodotto correlato creando un nuovo pericolo o aumentando un rischio esistente. Quest’ultimo punto richiede ripari o dispositivi di protezione aggiuntivi, il cui controllo modifica il sistema di comando legato alla sicurezza esistente e l’adozione di misure di protezione supplementari per garantire la stabilità o la resistenza meccanica di tale macchina o prodotto correlato. Nell’elenco dei “componenti di sicurezza” del nuovo regolamento macchine sono stati inseriti anche: software che garantisce funzioni di sicurezza e componenti di sicurezza dotati di un
comportamento integralmente o parzialmente autoevolutivo che utilizzano approcci di apprendimento automatico che garantiscono funzioni di sicurezza. Un software che svolge funzioni di sicurezza immesso sul mercato separatamente dovrà quindi essere marcato CE ai sensi del regolamento macchine ed essere accompagnato da una dichiarazione di conformità UE e da istruzioni per l’uso. Sono state immesse sul mercato macchine più avanzate, meno dipendenti dagli operatori umani. Tali macchine lavorano a compiti definiti e in ambienti strutturati, tuttavia, possono imparare a svolgere azioni nuove in tale contesto e diventare più autonome. Tra gli ulteriori perfezionamenti alle macchine, già realizzati o attesi, figurano l’elaborazione in tempo reale di informazioni, la risoluzione di problemi, la mobilità, i sistemi di sensori, l’apprendimento, l’adattabilità e la capacità di funzionare in ambienti non strutturati. Il nuovo regolamento
macchine dovrebbe disciplinare i rischi di sicurezza derivanti da nuove tecnologie digitali. La valutazione dei rischi dovrà tenere conto dell’evoluzione del comportamento delle macchine progettate per funzionare con diversi livelli di autonomia, anche durante la fase di apprendimento. Nell’ambito della collaborazione uomo-macchina in cui è prevista la condivisione di uno spazio di lavoro, come avviene nelle applicazioni con i robot (collaborative robot), è stato modificato il R.E.S.S. 1.3.7 Rischi dovuti a elementi mobili. In particolare, è stata aggiunta la seguente parte: la prevenzione di rischi derivanti da contatto che determinano situazioni di pericolo e le tensioni psichiche che possono essere causate dall’interazione con la macchina deve essere adeguata in relazione coesistenza uomo-macchina in uno spazio condiviso in assenza di collaborazione diretta e interazione uomo-macchina. Deve essere garantita la protezione dei dati di macchine e prodotti correlati in caso di connessione da remoto. A tal proposito è stato modificato il R.E.S.S. 1.2.1 Sicurezza ed affidabilità dei sistemi di comando ed introdotto ex-novo R.E.S.S. 1.1.9 Protezione dall’alterazione.
SETTEMBRE 2023/NUMERO #3
5 Nuovo regolamento (UE) 2023/1230 relativo alle macchine NEWS
8 Un secolo di eccellenza
10 UR Academy superata la soglia dei 200.000 iscritti
11 Nuovo servizio CNC super fast
12 Manifatturiero vivo e dinamico
14 Burn-out come evitarlo?
16 igus investe nella start up Cirplus
18 Nuovo regolamento macchine novità in arrivo per smart factory sempre più sicure
IIOT
20 L’internet delle macchine trasforma la fabbrica
24 Sicurezza e produttività grazie alla tecnologia IO-Link smart di Gefran
26 Quattro scenari per l’utilizzo dei master IO-Link Pepperl+Fuchs
28 Profilometri Wenglor, saldatura di precisione al millimetro!
30 Sicurezza interrotta dal sensore/
attuatore al controllore
34 Snap Signal l’IIoT reso semplice!
ROBOTICA
36 Integrare l’automazione nei processi: l’impatto sul mondo del lavoro
LOGISTICA E INTELLIGENZA
ARTIFICIALE
40 Un binomio in continua espansione
INTERVISTA
46 Digitale umano integrato
TECNOLOGIE PULITE
50 Il futuro dell’energia, le cleantech e la sostenibilità
APPLICAZIONI
54 Limitatori di coppia per l’industria alimentare
58
n. 3 Settembre 2023
www.innovareweb.it
Redazione Direttore Responsabile
Giorgio Albonetti
Coordinamento Editoriale Area Industry
Marco Tenaglia –marco.tenaglia@quine.it – cel. 3298490024
Direttore tecnico
Carlo Marchisio
Segreteria di Redazione
Cristina Gualdoni
cristina.gualdoni@quine.it – cel. 3477623887
Hanno collaborato a questo numero
Mario Gargantini, Patrizia Ricci, Chiara Tagliaferri
Pubblicità Ufficio Traffico
Elena Genitoni e.genitoni@lswr.it – tel. 0289293962
Servizio abbonamenti abbonamenti.quine@lswr.it
Abbonamento annuale € 25
Costo copia singola € 7,07 (presso l’editore)
Produzione Antonio Iovene | Procurement Specialist a.iovene@lswr.it | Cell. 349.1811231
Grafica e Fotolito Fabio Castiglioni
Stampa Aziende Grafiche Printing Srl Peschiera Borromeo (MI)
Iscrizione al R.O.C. n. 12191 del 29/10/2005 Tutti gli articoli pubblicati su Industry 4.0 Design magazine sono redatti sotto la responsabilità degli Autori. La pubblicazione o la ristampa degli articoli deve essere autorizzata per iscritto dall’Editore. Ai sensi dell’art. 13 del D.Lgs. 196/03, i dati di tutti i lettori saranno trattati sia manualmente sia con strumenti informatici e saranno utilizzati per l’invio di questa e di altre pubblicazioni e di materiale informativo e promozionale. Le modalità di trattamento saranno conformi a quanto previsto dall’art. 11 D.Lgs. 196/03. I dati potrebbero essere comunicati a soggetti con i quali Quine S.r.l. intrattiene rapporti contrattuali necessari per l’invio delle copie della rivista. Il titolare del trattamento dei dati è Quine S.r.l. - via Spadolini, 7 - 20141 Milano Tel +39 02 864105 Fax +39 02 72016740, al quale il lettore si potrà rivolgere per chiedere l’aggiornamento, l’integrazione, la cancellazione e ogni altra operazione di cui all’art. 7 D.Lgs. 196/03.
Ai sensi dell'art. 13 Regolamento Europeo per la Protezione dei Dati Personali 679/2016 di seguito GDPR, i dati di tutti i lettori saranno trattati sia manualmente, sia con strumenti informatici e saranno utilizzati per l’invio di questa e di altre pubblicazioni e di materiale informativo e promozionale. Le modalità di trattamento saranno conformi a quanto previsto dagli art. 5-6-7 del GDPR. I dati potranno essere comunicati a soggetti con i quali Edra S.p.A. intrattiene rapporti contrattuali necessari per l’invio delle copie della rivista. Il titolare del trattamento dei dati è Edra S.p.A., Via G. Spadolini 7 - 20141 Milano, al quale il lettore si potrà rivolgere per chiedere l’aggiornamento, l’integrazione, la cancellazione e ogni altra operazione di cui agli articoli 15-21 del GDPR.
Testata associata
Nel 2023 l’azienda giapponese Yamawa festeggia un traguardo unico: il centesimo anno dalla sua fondazione. Ma come nasce un successo lungo un secolo? Ecco la sintesi di una lunga storia di dedizione ed eccellenza, iniziata nel 1923, che si è sviluppata negli anni a seguire e, ancora oggi, guarda al futuro con la stessa fiducia del primo giorno
Tutto ebbe inizio a Tokyo nel 1923. La filettatura è un passaggio fondamentale nella lavorazione di molti prodotti e all’inizio del secolo il Giappone importava tutti gli utensili per filettare. Il fondatore di Yamawa, Mr. Jokichi Watanabe, era fermamente convinto che la produzione interna di maschi fosse la chiave di svolta per lo sviluppo dell’industria manifatturiera giapponese. È con questa convinzione che il 10 ottobre 1923 fonda la società privata YAMAWA MFG. Co., Ltd. e inizia la ricerca verso la standardizzazione dei maschi e dei metodi per la produzione di massa di utensili di elevata qualità.
Yamawa opera con la volontà di contribuire allo sviluppo tecnico dell’industria e della società attraverso il costante impegno a fornire prodotti per la filettatura di alta qualità e alte prestazioni. È il concetto di Qualità Totale che guida la produzione, che si distingue per l’attenzione posta a ogni dettaglio del processo e per l’eccellenza del suo controllo qualità, basato su un protocollo ben definito che prevede:
-Triplice controllo della qualità sul 100% della produzione;
-Controlli regolari sulla calibratura delle macchine;
-Garanzia totale di adesione agli standard Yamawa per ogni utensile prodotto
Yamawa si differenzia per l’attenzione estrema dedicate alla qualità delle materie prime, al processo di progettazione, al processo produttivo, e alla qualità dei suoi prodotti. Particolare attenzione è posta su prestazioni e precisione dei maschi, per una maggiore affidabilità delle filettature interne e stabilità dei processi.
È stata la prima azienda giapponese produttrice di maschi ad ottenere le certificazioni ISO9001 (Quality
management system) e ISO14001 (Environment management system) e continua a mantenere l’impegno a seguire la propria vocazione nel perseguire la più alta qualità nella progettazione e realizzazione del proprio prodotto, con una speciale attenzione ai temi ambientali. Negli anni successivi alla fondazione viene consolidato lo statuto della società. Con lo scoppiare della Seconda guerra mondiale la produzione venne trasferita a Yonezawa, attualmente il più grande dei quattro siti produttivi dell’azienda, dove è ubicato – tra l’altro – un Centro di Test equipaggiato con la strumentazione più moderna. Dopo la guerra, Yamawa contribuì attivamente alla definizione dello standard giapponese JIS per i maschi e, in qualità di produttore specializzato in utensili per filettatura, si sviluppò in parallelo all’industria manifatturiera giapponese concretizzando appieno il sogno di Watanabe.
In giapponese, YA-MA-WA significa Grande prosperità, più unione. In queste parole risuona ancora oggi il desiderio di Watanabe: più l’impresa è florida, più si rafforza l’armonia tra i collaboratori.
2023
Nel corso degli anni la presenza di Yamawa si è diffusa a livello mondiale. Oggi, nel mondo, l’attività è portata avanti da tre società:
-YAMAWA MFG. Co., Ltd., che produce maschi e altre soluzioni per filettatura e foratura
-Yamawa Engineering Service Co., Ltd., la cui attività è centrata sulle vendite nel mercato interno e fornisce supporto tecnico per i prodotti Yamawa
-Yamawa International Co., Ltd., che segue i mercati esteri e fornisce supporto tecnico alle filiali di distribuzione in Asia, America e infine a Yamawa Europe, fondata nel 2016 e con sede in Italia a Mestre-Venezia
I siti produttivi sono tutti ubicati in Giappone. Lo stabilimento principale è a Yonezawa, che comprende anche un Centro di Test equipaggiato con la più moderna strumentazione. Lo stabilimento di Fukushima produce
maschi per asportazione e ospita il Centro di Ricerca e Sviluppo per l’intero gruppo Yamawa, oltre ad un’unità dove vengono progettate e realizzate le affilatrici usate nelle linee produttive. Lo stabilimento è equipaggiato con un sistema centralizzato di gestione dell’olio da taglio e le più moderne macchine per trattamenti termici.
Aizu è un punto di riferimento per l’elevata automazione dei suoi processi. Progettato per la produzione di massa e dotato dei macchinari più avanzati, produce maschi, maschi in metallo duro e punte a centrare. Infine, Tsutsumi, il sito produttivo più recente, che fornisce semilavorati a tutte le altre unità produttive del Gruppo.
Uno sguardo ai prossimi cento anni
Come gruppo, con il motto Reliable Screw Threads, Yamawa mantiene il suo impegno nella produzione di utensili per assicurare filettature di precisione. La società investe molto in ricerca e sviluppo e nel sistema di controllo qualità della produzione, sempre prestando attenzione alle problematiche legate alla sostenibilità ambientale nell’intento di supportare l’industria manifatturiera con utensili ad alta affidabilità. Tra le novità di prodotto degli ultimi anni, la serie dei rivoluzionari maschi Z-PRO che definisce nuovi standard nella maschiatura ad alte prestazioni. Introdotta sul mercato nel 2019 e rappresentata dai maschi a macchina VU per fori ciechi e per fori passanti, Yamawa sta ampliando la serie Z-PRO anche ad altre tipologie.
Attualmente, sono parte della famiglia:
-VU, maschi di ultima generazione per alte prestazioni nei moderni centri di lavoro
-AUSP, maschi per filettatura gas
-HVSP, maschi per fori di grandi dimensioni
-MH, maschi per acciai al carbonio di media durezza
-GG, maschi per materiali abrasivi
Esterno del magazzino Yamawa – MHSL - miniNuovi corsi e nuovi centri di formazione locali, la UR Academy cresce e offre una formazione sempre più efficace
Dal 2016 Universal Robots, l’azienda leader mondiale nella produzione di robot collaborativi (cobots), ha offerto formazione sulla robotica ai propri clienti e ad altri soggetti interessati ai robot collaborativi. E ora, dopo essere diventata sempre più popolare negli anni passati e con oltre 120 centri di formazione locali in tutto il mondo, ha superato la soglia di 200.000 operatori formati attraverso i corsi erogati dalla propria Academy.
«È incredibile vedere che così tanti appassionati di robotica da tutto il mondo si siano uniti a noi per migliorare le proprie competenze in ambito robotico e trarre vantaggio dalla formazione che offriamo», afferma Mikkel Vahl, Responsabile Globale dell’Accademy e del settore Istruzione. «Siamo un’azienda con una missione: l’automazione per chiunque, ovunque. Una parte
• 2016, anno di creazione
• +205.000 utenti registrati ad agosto 2023
• 130 nazionalità diverse
• 119 Centri di Formazione Certificati in tutto il mondo, con l’apertura di altri centri imminente
fondamentale di ciò è fornire ai nostri clienti e agli appassionati di robotica una formazione di alta qualità che fornisca loro le competenze necessarie per sfruttare appieno il potenziale dei loro cobot».
Con clienti che vanno dalle grandi aziende globali alle piccole imprese a conduzione familiare, Universal Robots aiuta ad automatizzare qualsiasi cosa, dalla raccolta di pezzi alla palettizzazione di carichi pesanti e alla saldatura in ambito navale. Questa varietà di applicazioni, settori e dimensioni industriali, si riflette nell’Accademy UR che offre una vasta gamma di corsi, dall’e-learning virtuale gratuito alla formazione in aula approfondita condotta in piccoli gruppi da trainer esperti.
«I nostri corsi vanno dal livello base fino ai più specifici approfondimenti sul mondo della robotica, quindi, indipendentemente dal compito o dalle dimensioni della tua azienda, puoi trovare una formazione rilevante che ti aiuti a diventare ancora più efficace con la tua automazione. E l’efficacia di questo approccio è chiara: i clienti che si formano con noi sperimentano un successo produttivo maggiore e godono di maggiore sicurezza nei confronti del mercato», afferma Mikkel Vahl.
Le ragioni di questa connessione sono semplici, aggiunge: «Rispetto ad altri robot industriali, i cobot sono più semplici da programmare e utilizzare. Ma che tu sia un ingegnere applicativo, un esperto di robotica o un neofita, potrai beneficiare della formazione guidata da istruttori esperti».
Nuove offerte formative in arrivo
Gli utenti della UR Academy provengono da più di 130 paesi diversi e hanno tutti seguito alcuni dei corsi online gratuiti o partecipato alla formazione sulla robotica, sia virtuale che in classe, guidata da specialisti altamente qualificati provenienti sia da Universal Robots che da un Partner di Formazione Autorizzati.
La UR Academy, che aggiorna costantemente la propria offerta formativa, ha diverse interessanti novità in programma per la fine di quest’anno e per il 2024. Queste includono il nuovo modulo e-learning su UR20, che insegna ai clienti come configurare e programmare il nuovo cobot di Universal Robots. Nuovi percorsi formativi sulla valutazione del rischio, un percorso di apprendimento per la palettizzazione e un nuovo e migliorato simulatore sono tra le prossime nuove offerte dell’Accademy UR.
Per ulteriori informazioni: www.universal-robots.com/it
Weerg lancia un nuovo e innovativo servizio CNC caratterizzato da una rapidità e una precisione senza precedenti. Grazie all’implementazione di tecnologie avanzate, Weerg è il primo service online di manifattura in Europa in grado di offrire ai progettisti tempi di consegna ancora più brevi, garantendo al contempo gli alti standard qualitativi che da sempre la contraddistinguono.
A caratterizzare il nuovo servizio è l’utilizzo di macchinari a 5 assi, che rispetto alla tradizionale lavorazione a 3 assi offre molte più opportunità e meno vincoli progettuali.
Grazie a questa tecnologia è infatti possibile lavorare su pezzi complessi riducendo così il tempo di lavoro del macchinista, aumentando il tasso di produzione e permettendo di ottenere pezzi più precisi e meglio rifiniti.
Grazie alla riduzione dei tempi di lavorazione l’azienda è ora in grado di garantire tempi di consegna super rapidi: solamente 48 ore per ricevere il prodotto finito
in Italia, e 72 in Europa. Questa tempestività è resa possibile oltre che dall’efficienza dei processi produttivi anche dall’impiego di un team altamente qualificato e dedicato. Per offrire un supporto ancora più personalizzato e mirato ai clienti business, Weerg introduce il servizio di consulenza one-to-one, inserendo tre nuove figure altamente qualificate che si occuperanno di supportare i clienti business in tutte le fasi della customer experience.
“La nostra consulenza personalizzata è pensata per comprendere appieno le esigenze specifiche di ogni cliente e guidarlo nella scelta delle migliori soluzioni di lavorazione CNC e stampa 3D” - commenta Matteo Rigamonti, Presidente e Fondatore di Weerg, “Per garantire il massimo livello di dedizione e competenza abbiamo formato il personale esistente e introdotto nuove figure specializzate che andranno a supportare i nostri clienti in modo mirato in tutte le fasi del processo d’acquisto”
Il settore della manifattura online è in continua evoluzione e Weerg continua ad essere una pioniera in questa trasformazione. Con il lancio di questo nuovo servizio CNC, l’azienda veneta ridefinisce gli standard di efficienza, qualità e soddisfazione del cliente, dimostrando ancora una volta il suo impegno nell’offrire soluzioni all’avanguardia.
Nei prossimi due anni il 73% delle aziende pronte ad avviare un percorso di crescita e un quarto sta valutando operazioni di acquisizioni e fusioni
L’industria manifatturiera ha un effetto positivo, diretto e indiretto, sul tessuto socioeconomico italiano, oltre ad avere un impatto importante nella vita delle persone. Automotive, alimentare, energia, aerospaziale e così via, non c’è settore dove le imprese manifatturiere negli
ultimi anni non abbiano portato valore e innovazione. Per questo è importante valutare lo stato di salute del settore, non solo dal punto di vista economico, ma anche verificando la propensione degli imprenditori alla “crescita”. E su questo, i capitani d’azienda italiani
MECSPE torna a Bari (23-25 novembre) e con uno speciale appuntamento alla Milano Digital Week (6 ottobre) insieme a MADE – Competence Center Industria 4.0, per approfondire i temi della sostenibilità e delle tecnologie abilitanti per l’industria 5.0.
hanno un’idea molto chiara: secondo l’ultimo Osservatorio MECSPE quasi tre su quattro hanno in programma un percorso di crescita entro i prossimi due anni. In particolare, un terzo ha intenzione di farlo dimensionalmente, un quarto ampliando la produzione in nuovi settori e il 15% puntando sull’internazionalizzazione. Non solo, tanti imprenditori (ben il 26%), sempre nei prossimi due anni, guardano con interesse alle operazioni straordinarie come fusioni e acquisizioni (M&A). Per quanto riguarda le modalità per reperire le risorse economiche, sebbene la maggior parte attingerà dal capitale già a disposizione (53%), sono in aumento le aziende che valuteranno la partecipazione a bandi pubblici (31%) e l’ingresso di nuovi soci (12%). I dati mostrano quindi un comparto, quello manifatturiero, vivo e dinamico, ma che ha bisogno di una guida che aiuti le imprese a comprendere il mercato in tutti i suoi aspetti. Ed è proprio questo il ruolo di MECSPE, che ritorna a Bari con tante iniziative ed eventi per facilitare le imprese in questa fase di sviluppo puntando su temi essenziali per tutta l’industria manifatturiera: innovazione, sostenibilità e formazione.
Cosa può spingere gli imprenditori a investire per rendere le imprese più digitali, green e con competenze adeguate? Sicuramente gli aiuti economici hanno un ruolo fondamentale ma su questo ci sono luci (molte) e ombre: il 55% delle imprese ha infatti già usufruito degli incentivi statali Industria 4.0 e quattro su dieci hanno investito oltre 500mila euro, con il 13% che ha superato i 3mln di euro. Eppure, secondo gli imprenditori, le misure adottate non bastano, ma non si tratta di una bocciatura completa: quasi la metà giudica i provvedimenti insufficienti ma comunque importanti per l’innovazione, mentre solo per il 12% sono totalmente inadeguati.
Guardando agli incentivi che le imprese richiederanno nel 2023, il più gettonato è il credito d’imposta beni strumentali per la trasformazione digitale (47%), seguito da quello formazione 4.0 (37%) e dagli incentivi per l’innovazione area ricerca e sviluppo (27%).
In questo scenario, MECSPE può realmente fare la differenza grazie alla sua piattaforma fieristica, quest’anno aggiungendo una tappa a Bari dal 23 al 25 novembre alla Nuova Fiera del Levante, Fin dall’inizio la manifestazione ha offerto agli imprenditori occasioni di scambio e apprendimento seguendo proprio i tre temi focali per tutta l’industria manifatturiera. Macro argomenti che si svilupperanno partendo dal nuovo Cuore Mostra “Transizione energetica & sostenibilità nell’industria manifatturiera: dai trasporti alle imprese”, area centrale della manifestazione in cui esperti di
tecnologia e mercato illustreranno le nuove sfide del comparto con focus su mobilità, industria manifatturiera e filiera dell’idrogeno. Inoltre, quest’anno c’è una novità: il 6 ottobre MECSPE, insieme a MADE –Competence Center Industria 4.0, sarà tra i protagonisti della Milano Digital Week con l’evento “Il nuovo volto dell’industria manifatturiera capace di unire benessere, sostenibilità ambientale ed economicità dell’impresa”. Aziende ed esperti del settore esploreranno i temi della sostenibilità e delle nuove tecnologie digitali abilitanti applicate all’industria manifatturiera, essenziali acceleratori verso un nuovo modo virtuoso di fare impresa sempre più 5.0 e che risponde alle esigenze dei giovani e dell’ambiente.
“Per supportare il processo di digitalizzazione delle aziende italiane, i competence center istituiti dal Ministero delle Imprese e del Made in Italy, oggi hanno un ruolo importante – afferma Federico Ravasio, Responsabile comunicazione di MADE Competence Center – Le imprese, attraverso MADE 4.0, possono accedere a due importanti strumenti di finanziamento a fondo perduto. Il primo riguarda i servizi standard come corsi di formazione, consulenza su innovazione tecnologica di prodotto e processo, proprietà intellettuale, accesso al credito, etc. Il secondo è un bando per progetti di innovazione di ricerca industriale, studio di fattibilità e sviluppo sperimentale. Gli imprenditori avranno così a disposizione 14 mln di euro di risorse e potranno trovare tutti gli strumenti e le competenze idonee per attuare i propri progetti di transizione digitale sostenibile.”
"Le imprese italiane hanno una straordinaria capacità di adattamento e i numeri dell’ultima edizione di MECSPE testimoniano quanto queste realtà abbiano compreso la necessità di evolversi - afferma Maruska Sabato, Project Manager di MECSPE- Il nostro impegno è quello di proporre una manifestazione dinamica e completa, in cui le aziende possano scoprire e abbracciare le tecnologie più innovative per raggiungere gli obiettivi in termini di crescita e di digitalizzazione. Siamo convinti che, guidando le imprese verso l'adozione di pratiche virtuose e promuovendo la coesione e il networking, possiamo trasformare le sfide in opportunità e aprire nuove strade verso un’industria che guarda al futuro."
1 L’indagine è stata condotta da GRS Ricerca e Strategia su un campione di 749 aziende manifatturiere italiane, utilizzando il metodo CAWI (Computer Assisted Web Interviewing). L’indagine è relativa al I quadrimestre 2023.
La pressione ad innovare è più forte che mai. Questo è quanto è emerso da uno studio condotto sul settore manifatturiero e promosso dal produttore digitale Protolabs
Lo studio, intitolato “The Balancing Act: Unlocking Innovation in Manufacturing”, è stato condotto in collaborazione con FT Longitude e rivela che i dirigenti più innovativi eccellono nel riconoscere le aree aziendali che richiedono un’attenzione urgente, come il mantenimento dei talenti, la promozione della creatività e la prevenzione del burn-out.
L’indagine rivela che le aziende produttrici non hanno mai sentito così tanta pressione per innovare come oggi. Infatti, solo il 22% dei 450 professionisti del settore manifatturiero intervistati ritiene che non sia così. La richiesta di nuove idee, senza precedenti, è determinata dalla necessità di creare nuovi prodotti e servizi più velocemente e di operare in modo più efficiente e sostenibile.
Lo studio ha identificato un gruppo di “leader”, separando le risposte di coloro che ritengono di superare le aspettative in termini di innovazione, per capire come i loro atteggiamenti riescono a fare la differenza. È emerso che i leader hanno una mentalità più attenta all’urgenza e alle opportunità emergenti. Il gruppo dei “leader” ha identificato le sfide principali nella necessità di trattenere i talenti più brillanti, evitare il burn-out e sostenere l’ingegno umano nel boom dell’IA.
Gli intervistati sono stati ulteriormente interpellati in
merito alla cultura del lavoro, ai processi e alla tecnologia, facendo emergere i loro atteggiamenti e approcci nei confronti della strategia della supply chain, delle modalità di lavoro dei dipendenti e delle iniziative tecnologiche su cui si stanno concentrando. Altri intervistati riconoscono che le loro aziende non hanno abbracciato il modello di “fallire velocemente”, ovvero capire in brevissimo tempo se un progetto può essere un successo o no, di lanciare e scalare nuovi prodotti o servizi o di lavorare in modo più collaborativo con terzi per realizzare più rapidamente nuove idee.
Bjoern Klaas, vicepresidente e amministratore delegato di Protolabs Europe, ha dichiarato: “Le aziende con cui siamo entrati in contatto capiscono che l’innovazione è più importante che mai per migliorare l’efficienza, creare crescita e promuovere la sostenibilità. I professionisti sentono la pressione della propria azienda, dei clienti, dei concorrenti e del settore nel suo complesso. La decisione di innovare è significativa, poiché comporta delle sfide e le nuove strategie che richiede possono portare a degli sconvolgimenti nell’azienda. Un numero maggiore di organizzazioni deve abituarsi al rischio, abbracciando l’approccio “fail-fast” e di anticipare le iterazioni del prodotto”.
Lo studio ha rilevato che:
• Quasi due terzi (65%) dei leader ritengono che le loro aziende abbiano urgentemente bisogno di aggiornare il loro approccio all’innovazione e stanno cercando attivamente dei modi per farlo.
• Quasi tre quarti (73%) dei leader affermano di essere preoccupati su come trattenere i propri dipendenti più innovativi
• Due terzi (66%) dei dirigenti ritengono che la creatività umana sia trascurata dall’entusiasmo per le nuove tecnologie
• Un quarto (25%) di tutti gli intervistati afferma che la propria azienda non sono in grado di capire in tempi brevi il grado di successo di un progetto.
È possibile scaricare una copia del rapporto completo dal sito di protolabs o inquadrando il qr-code
Peter Richards, Vice-President Marketing e Sales EMEA di Protolabs Europe, ha dichiarato: “Nel compilare lo studio, abbiamo isolato i professionisti che sono in prima linea quando si tratta di innovazione, per darci una visione di ciò che funziona per i team di innovazione leader di oggi. Inoltre, ci ha dato una prospettiva su dove gli altri potrebbero essere in difetto”. Il support alla creatività viene talvolta trascurato nell’entusiasmo per le nuove tecnologie come l’intelligenza artificiale. L’adozione di un maggiore senso di urgenza è stata considerata la chiave del successo, ma i leader sono consapevoli che ciò comporta dei rischi, come il burn-out, che porta alla perdita dei migliori talenti”.
Obiettivo: avviare una rivoluzione nel commercio dei materiali riciclati derivanti da termoplastiche, anche tecniche
“In qualità di produttori di materie plastiche, riteniamo di avere un obbligo nei confronti dell’ambiente e un dovere nella conservazione delle risorse”, afferma Michael Blass, CEO della divisione catene portacavi di igus GmbH. A questo scopo il nostro gruppo, specializzato nei tecnopolimeri, sta promuovendo da tempo diverse attività concrete come il ritiro di vecchie catene portacavi in plastica (indipendentemente dal produttore), l’utilizzo di materiali rigranulati e riciclati e il continuo sviluppo di nuovi prodotti ottenuti esclusivamente da rifiuti post-consumo. Risale al 2019 il lancio del progetto Chainge che permette di riciclare una varietà sempre più ampia di plastiche tecniche e di acquistare plastica riciclata con standard di qualità garantiti. Per estendere il programma a più aziende possibili, lo scorso anno igus ha messo a disposizione del mercato la piattaforma online del programma Chainge.
Dare forma al futuro della plastica riciclata grazie alle tecnologie digitali Oggi, per accelerare ulteriormente il progresso dell’economia circolare digitale, igus annuncia l’investimento in cirplus, start-up con sede ad Amburgo (Germania) specializzata in circolarità. “Con cirplus condividiamo la volontà di iniziare una vera rivoluzione nel commercio di materiali riciclati da termoplastiche tecniche e non”, aggiunge Michael Blass.
L’obiettivo comune di agevolare l’accesso e l’utilizzo delle materie plastiche rigenerate è quindi alla base della collaborazione tra igus e cirplus. Le due realtà, infatti, sono complementari: da un lato, igus ha già ottenuto importanti risultati nel riciclo delle plastiche tecniche; dall’altro, cirplus opera con successo nei mercati delle materie termoplastiche standard, offrendo alle aziende di smaltimento, ai centri di riciclaggio e ai
vari produttori un marketplace digitale che permette di acquistare in tutto il mondo materiali riciclati standard in modo affidabile, tracciabile e conveniente. Cirplus è stata responsabile, inoltre, dello sviluppo delle norme DIN SPEC 91446 e DIN SPEC 91481, le prime al mondo riguardanti il riciclo delle materie plastiche di alta qualità. L’intento era di individuare e certificare catene di approvvigionamento affidabili e trasparenti per i riciclati di plastica, grazie alla combinazione di digitalizzazione e standardizzazione. Grazie a questa nuova collaborazione, igus e cirplus lavoreranno congiuntamente alla creazione di un’intera rete incentrata sulle materie plastiche e il loro riciclo.
Il programma Chainge permette già ai clienti igus di attuare in modo rapido e semplice il riciclo delle materie plastiche tecniche. Con cirplus, igus può contare su un partner di rilievo nel settore del commercio digitale di materiali riciclati standard. In futuro, gli utenti potranno attingere ad una rete integrata per il commercio delle materie termoplastiche riciclate tecniche o standard, con la possibilità di acquistare qualsiasi materiale in modo semplice e trasparente da un’unica fonte. In 60 anni di attività nella produzione e nella vendita
di tecnopolimeri, igus ha sviluppato una rete globale che gli ha consentito di consolidare flussi di materiali ottimizzati. Aggiungendo l’expertise di cirplus in ambito software, il percorso verso il commercio digitale avanzato di materiali riciclati è ben tracciato. Le due aziende guardano con interesse al potenziale di una collaborazione strategica che presenta tutti i presupposti per la creazione della più importante piattaforma al mondo per l’economia circolare delle materie plastiche. “I nostri sforzi per moltiplicare e ampliare le nostre attività e renderle accessibili a tutti ci hanno portato a unire le forze con cirplus”, spiega Michael Blass. Con questo investimento vogliamo creare una rete che permetta alla gente di cambiare concretamente le cose”. Christian Schiller, CEO di cirplus, aggiunge: “In igus abbiamo trovato un partner che condivide i nostri valori e con cui collaborare per far progredire la digitalizzazione nel settore del riciclo delle materie plastiche. L’esperienza di igus nel settore delle materie plastiche tecniche, unita alla nostra competenza nel settore della digitalizzazione e delle materie termoplastiche standard, rappresenta il punto di partenza ideale per la realizzazione di un’economia circolare chiusa, in tutti i settori industriali”.
In uno scenario caratterizzato da una crescente complessità delle reti di fabbrica, sia a livello di architetture che di topologie, a causa dell’elevato numero di dispositivi, della sempre maggiore interconnessione delle macchine e dello scambio di grandi quantità di dati, le aziende sono sempre più esposte a nuovi potenziali rischi di attacco alla sicurezza
Secondo quanto evidenzia il Rapporto CLUSIT 2023, i cyber attacchi sono aumentati esponenzialmente negli ultimi 5 anni. In Italia, dal 2018 al 2022, la crescita del numero di attacchi è stata del 60%, passando da 1554 a 2489, raddoppiando in ambito Manufacturing. In tal senso, in presenza di macchinari sempre più smart, dotati di sistemi sofisticati e in continuo aggiornamento è diventato imprescindibile adeguare l’attuale Direttiva Macchine con un nuovo Regolamento Macchine, che entrerà in vigore a partire da Gennaio 2027. Al fine di rendere gli impianti conformi al Regolamento Macchine UE 2023/1230, LAPP offre una gamma di servizi a valore aggiunto come la valutazione del livello
di sicurezza dei macchinari e l’analisi e il collaudo di network industriali. Promuovere un’adeguata informazione e formazione in merito alle opportune misure da adottare per garantire reti connesse e sicure è di fondamentale importanza, affinché i clienti possano trarre vantaggio dall’affidarsi a esperti del settore per proteggere le proprie infrastrutture. Recentemente pubblicato in data 29 giugno 2023, a garanzia di una superiore sicurezza per le Smart Factory, il Regolamento abroga la direttiva 2006/42/CE ed è stato redatto in conformità con le indicazioni del nuovo quadro legislativo e si integra con altre direttive applicabili alle macchine, quali bassa tensione e compatibilità elettromagnetica. Le no-
vità riguardano l’applicazione sia ai macchinari nuovi che quelli che abbiano subito “modifiche sostanziali”, ovvero qualsiasi alterazione che vada ad influenzarne la sicurezza, creando potenziali nuovi pericoli o aumentando il rischio di quelli già esistenti. Inoltre, il Regolamento si esprime anche in merito alla cyber security e introduce la necessità di progettare sistemi che svolgano funzioni di sicurezza, al fine di evitare attacchi malevoli alle reti dati. Infine, include per la prima volta anche i componenti digitali, tra cui il software, che dovrà essere marcato CE e accompagnato da una dichiarazione di conformità UE e da istruzioni per l’uso.
LAPP crede nell’importanza della Cyber Security, anche in ambito OT, per limitare la perdita di dati, di know-how e i fermi produzione, con conseguenti ricadute negative in termini di reputazione. In dettaglio, l’Azienda propone ai suoi Clienti un assessment secondo IEC 62443, che definisce le linee guida per la sicurezza delle reti OT. La valutazione del Security Level (SL) della macchina o impianto e delle eventuali implementazioni necessarie per raggiungere il SL target si svolge in tre fasi: collezione e analisi documentale, valutazione in campo, stesura del report e identificazione del SL e di eventuali azioni correttive. Un approccio ideale per supportare i costruttori dei singoli componenti di rete, gli utilizzatori finali, i costruttori di macchine e i system integrator.
Analisi e collaudo di reti industriali, a prova di futuro
Servizio premium proposto da LAPP, è l’analisi e collaudo di reti industriali condotto dai LAPP Expert mediante uno strumento di diagnostica in grado di fornire un chiaro e immediato riscontro sullo stato di salute delle reti a cui le macchine sono connesse. Grazie alla loro
consolidata competenza, i tecnici LAPP sono in grado di condurre valutazioni dettagliate del traffico dati sulla rete e di elaborare una scansione completa di quest’ultima, al fine di ricavare informazioni sui dispositivi, la topologia ed effettuare analisi diagnostiche. LAPP ha strutturato il processo in diverse fasi per valutare la stabilità della trasmissione dati, in real time. In tal modo, è possibile rilevare eventuali anomalie, quali fermi macchina, sovraccarichi ed errori di rete, dispositivi non raggiungibili, instabilità della connessione tra il cavo e il connettore, danneggiamento della guaina o dell’isolamento e rottura del cavo. Al termine di tale attività, LAPP rilascia report completi dei dati diagnostici estrapolati, a cui si aggiunge un rendiconto di collaudo contenente le informazioni sulla comunicazione e la configurazione di rete.
“In tal senso, l’expertise nel condividere linee guida utili alla progettazione di una rete a regola d’arte rende LAPP un partner strategico sul mercato, grazie anche alla sua consolidata e pluriennale esperienza capitalizzata direttamente sul campo.” conclude Roberto Pomari, Managing Director & Head of Industrial Communication Center of Competence LAPP Italia.
Mario GargantiniIl settore manifatturiero sta sperimentando i vantaggi della digitalizzazione. Progressivamente tutte le apparecchiature, le macchine, la strumentazione, gli impianti vengono connessi in rete implementando un sistema di Industrial Internet of Things. Perché ciò avvenga efficacemente bisogna riempire le fabbriche di sensori intelligenti, garantire una solida infrastruttura di comunicazione, migliorare gli strumenti di analisi dei dati
LLa nuova stagione di Internet si chiama IoT, Internet of Things, e non c’è ambito industriale, civile, sociale che non se ne stia accorgendo. Internet delle cose significa estendere agli oggetti la interconnessione che ormai indissolubilmente collega in tutto il mondo tutti i soggetti, singoli e collettivi; significa quindi associare ai diversi oggetti un indirizzo IP e consentire loro di scambiare dati con qua-
lunque altro oggetto o soggetto connesso alla grande rete. Se ne sta accorgendo da tempo il mondo dell’industria, dove IoT diventa IIot, Industrial Internet of Things, e in particolare il settore metalmeccanico, dove si parla ormai di Internet delle macchine. Tra i vari oggetti collegabili alla rete ci sono infatti le macchine, secondo l’accezione più ampia del termine: si va da un semplice congegno che raccorda altri componenti, a sistemi che manipolano e movimentano vari materiali, alle più versatili macchine utensili, fino ai componenti di complessi impianti e linee
di produzione.
È un momento particolarmente ricco di sviluppi, progetti, applicazioni in questa direzione che va di pari passo con gli altri aspetti della digitalizzazione e sfrutta la trasversalità di queste tecnologie consentendo di rendere più utilizzabili ed efficaci altre tecnologie disruptive, come i digital twin o la predictive maintenance che mostrano tutto il loro potenziale se applicate a macchine e oggetti già connessi e pronti a ricevere e trasmettere dati e informazioni.
Sensori ovunque
Le principali domande che ora si pongono molte aziende, soprattutto nell’ambito delle Pmi sono del tipo: come avviene l’introduzione dell’Internet delle macchine in un’industria? Che cosa è necessario predisporre o attivare perché l’IIoT rappresenti un effettivo vantaggio e porti a un miglioramento del processo produttivo? In generale, quali i vantaggi ottenibili in tempi non troppo lunghi?
Iniziamo dalle condizioni più generali. Anzitutto bisogna che le macchine, e le apparecchiature in genere, abbiamo occhi e orecchi, cioè che siano in grado di poter intercettare tutti i segnali che fluiscono ininterrottamente lungo la catena produttiva. Parliamo quindi della sensoristica e in particolare di sensori smart, meglio se wireless.
I sensori IIoT sono progettati per raccogliere dati direttamente dal campo. Sono in grado di rilevare e acquisire dati in qualsiasi situazione e hanno ormai trovato applicazione in vari settori dell’industria manifatturiera. Possono essere utilizzati per misurare diversi parametri di uscita delle apparecchiature come, tra gli altri, temperatura, pressione, umidità e vibrazioni; trovano quindi la loro applicazione in quasi tutti i tipi di industrie di processo, siano esse petrolifera, mineraria, cementizia, chimica, farmaceutica; ma possono anche essere utilizzati per misurare i parametri fisici delle macchine come portata, velocità o coppia; come pure nel settore edilizio, logistico e delle infrastrutture civili. Alcuni dei settori che stanno iniziando a utilizzare i sensori IoT industriali includono metalli, estrazione mineraria, edilizia, produzione, petrolio e gas, servizi pubblici, centrali nucleari, trasporti, logistica, strutture sanitarie ecc. I sensori IoT wireless sono in grado di monitorare macchine e set di apparecchiature da qualsiasi parte del mondo, senza bisogno di accesso fisico; sono dotati di un minuscolo trasmettitore e ricevitore radio integrato, tramite il quale possono comunicare tra loro senza essere cablati insieme: ciò consente loro di allontanarsi ulteriormente da una fonte di alimentazione e trasmettere informazioni più preziose, come i dati complessi della macchina. Sono inoltre in grado di immagazzinare la propria energia, il che significa che possono essere installati facilmente anche in luoghi remoti e difficili da raggiungere; non richiedendo una fonte di alimentazione esterna. hanno la capacità di trasmettere dati su lunghe distanze e non necessitano di monitoraggio o manutenzione costanti.
Gli smart sensor offrono la flessibilità di connettere le macchine in pochi minuti: sono facili da installare e possono raccogliere dati automaticamente; essendo wireless, viene garantita un’implementazione rapida senza il fastidio di complessi cablaggi.
Rendono possibile monitorare macchine, set di attrezzature o qualsiasi altra risorsa da qualsiasi parte del mondo senza dover accedere manualmente alla macchina o all’ambiente. I dati possono anche essere trasmessi direttamente dal sensore a un cruscotto analitico per l’analisi e per una facile rappresentazione visiva. Possono anche essere raccolti più dati rispetto ai tradizionali sensori cablati in quanto non vi è alcuna restrizione sulla frequenza di ricezione e di ritrasmissione: ciò facilita il monitoraggio in tempo reale dello stato delle risorse critiche, per consentire una migliore supervisione operativa della produzione. Inoltre, le funzionalità edge di questi sensori consentono loro di raccogliere, elaborare e archiviare i dati in loco.
Una solida infrastruttura di comunicazione è essenziale per
trasmettere i dati della macchina per l’analisi. Uno dei maggiori colli di bottiglia della tecnologia IoT nella produzione è la larghezza di banda. Più dati possono essere comunicati contemporaneamente, più veloci ed efficienti saranno questi sistemi. La velocità della rete è essenziale per il successo delle applicazioni in tempo reale e per l’edge computing; tuttavia, se i dati non devono essere comunicati il più velocemente possibile, potrebbe non essere necessaria una larghezza di banda molto elevata. È necessario ogni volta valutare le specifiche esigenze e scegliere le opzioni migliori.
Per le soluzioni più coerenti e veloci, le connessioni cablate di più dispositivi IoT insieme in una rete sono le migliori opzioni; si possono utilizzare efficacemente i protocolli EtherCAT, Ethernet/IP e Profinet. Le connessioni Usb sono limitate in termini di velocità e portata; sulle grandi distanze, per collegare impianti industriali a chilometri di distanza uno dall’altro, possono essere utilizzati i cavi in fibra ottica.
Essendo una tecnologia più matura, le soluzioni cablate offrono comprovata affidabilità e immunità al rumore. Il loro principale svantaggio è la componente fisica: il cablaggio può occupare spazio, avere limitazioni ambientali e richiedere più tempo per la configurazione; oltre a un problema di costi.
Per versatilità e facilità di configurazione, le connessioni wireless sono molto più efficaci. Sebbene le connessioni wireless siano intrinsecamente vulnerabili, per ogni situazione si può trovare una soluzione più adeguata per i sistemi IIoT.
Il Wi-Fi è molto più adatto per i sensori delle macchine
nelle fabbriche: con punti di accesso a 5 GHz, si possono fornire connessioni ad alta velocità a dispositivi fino a circa 60 m, offrendo la massima copertura con punti distribuiti in tutta la fabbrica.
Zigbee è un tipo di connessione alternativo che funziona meglio con i sensori a batteria con un basso throughput di dati. Si basa su nodi che interconnettono più percorsi; è comunque necessario un hub centrale di coordinamento, il che aumenta la complessità del sistema.
Bluetooth Low Energy è una tecnologia più efficiente di Wi-Fi e Zigbee. Può rappresentare un’ottima scelta per i dispositivi portatili e alimentati a batteria. Tuttavia, è possibile trasferire meno dati contemporaneamente a causa delle restrizioni energetiche; è inoltre soggetto a interferenze nella gamma di 2,4 GHz, utilizzati da molti sistemi, che influenzare il funzionamento dei dispositivi. C’è poi il problema della sicurezza informatica: con l’espansione di più dispositivi wireless negli impianti di produzione, il numero di potenziali minacce aumenta. Oggi esistono numerose strategie per affrontare le minacce informatiche ma il tema deve essere ben presente anche quando si imposta un sistema Iiot.
Software per analisi dati
Un terzo aspetto riguarda l’analisi dei dati raccolti e ci porta quindi a parlare delle risorse software necessarie per implementare un efficace sistema IIoT.
L’adozione dell’IoT è in aumento e il numero di dispositivi connessi continua a crescere mentre le organizzazioni faticano a gestire le enormi quantità di dati generati poiché i dati raccolti dall’IoT sono meno strutturati e i set di dati
sono più complessi. Servono quindi strumenti di analisi efficaci e affidabili, concepiti e organizzati per l’analisi IoT ma in grado di inserirsi negli ecosistemi digitali presenti e di integrarsi facilmente con gli strumenti di analisi esistenti. Servono strumenti che sappiano raccogliere i dati nei punti più significativi, eseguire analisi rapide e fornire approfondimenti rilevanti per prodotti e servizi.
Alcune funzionalità chiave che l’analisi IoT dovrebbe fornire riguardano: la piena integrazione con piattaforme IoT e stack aziendali e la gestione di più tipi di dati; diverse opzioni di distribuzione per un’ampia gamma di ambienti (installazione on-premise, l’hosting nel cloud, compatibilità con ecosistemi ibridi complessi); la possibilità per i dipendenti di accedere ed esplorare facilmente i dati, oltre a creare dashboard personalizzati; la collaborazione nella gestione dei dati e la condivisione delle analisi tra i flussi di lavoro.
L’IoT industriale offre una quantità di vantaggi agli operatori del settore manifatturiero, quali:
- una completa visibilità operativa;
- una maggiore efficienza operative;
- l’ottimizzazione delle risorse;
- la riduzione dei tempi di inattività non pianificati;
- una migliore produttività;
- una maggiore sicurezza sul lavoro;
- una gestione degli impianti di produzione senza intoppi e a costi inferiori.
Tra i vantaggi più immediatamente verificabili c’è la possibilità di attuare la manutenzione predittiva, quella cioè che consente ai produttori di identificare tempestivamente potenziali problemi, programmare i tempi di inattività quando opportuno, garantire che le parti e il personale siano preparati e mantenere le operazioni in esecuzione come pianificato.
Grazie alle informazioni ricavate dai dati e alle metriche delle prestazioni, le aziende possono adottare un approccio proattivo alla manutenzione delle apparecchiature. I guasti alle apparecchiature possono causare tempi di inattività e perdita di produttività, con un impatto negativo sull’efficienza e sulla qualità della produzione, in particolare per le imprese del settore manifatturiero.
Con l’IoT, le organizzazioni sono in grado di controllare e tracciare i propri sistemi da remoto con il monitoraggio automatizzato della garanzia della qualità.
É possibile anche applicare tecnologie innovative per sviluppare capacità di ispezione visiva automatizzate. Queste funzionalità utilizzano I sensori IoT di cui abbiamo detto,le moderne fotocamere e I sistemi di Intelligenza Artificiale per rilevare anomalie ed estrarle dalle linee di produzione. In tal modo, le aziende possono garantire la massima qualità nelle loro operazioni e in tutto il ciclo produttivo.
Un altro importante risultato ottenuto con l’applicazione dell’IIoT fa riferimento alla questione energetica. É possibile migliorare la gestione dell’energia in un sito produttivo proprio tramite l’implementazione dell’IIoT. Si tratta di strutturare la rete di smart sensor in modo da poter tracciare e gestire l’utilizzo di energia degli impianti e delle macchine, andando a identificare dove è possibile ridurre i consumi. Utilizzando i sensori IIoT di ottimizzazione dell’energia per monitorare lo stato elettrico e l’utilizzo di dispositivi e macchine in una fabbrica, gli operatori possono mettere a punto il processo e ottimizzare automaticamente l’utilizzo di energia da parte di vari dispositivi. È possibile pertanto:
- identificare picchi o cali nell’uso dell’energia che possono indicare un’anomalia da controllare;
- comprendere meglio come le singole macchine e i processi contribuiscano al consumo energetico complessivo e utilizzare questi dati per migliorare le previsioni;
- migliorare la sostenibilità ambientale generale.
Il protocollo IO-Link, in forte crescita nell’automazione industriale, abilita la comunicazione dal livello di campo a quelli superiori e permette lo scambio di molteplici dati, utili per funzioni avanzate di diagnostica e di ottimizzazione di processi produttivi
GGefran - multinazionale italiana specializzata nella progettazione e produzione di sensori, strumentazione per il controllo di processi industriali e sistemi per l’automazione – offre una gamma, unica per ampiezza, di dispositivi intelligenti con architetture basate su IO-Link, che include sia sensori che attuatori smart, ideali per ogni esigenza in ottica Industry 4.0 e in ogni ambito operativo, come negli impianti di estrusione. Tra i prodotti IO-Link, spiccano la serie di trasduttori di posizione con tecnologia magnetostrittiva WPL, con interfaccia Io-Link 1.1, che assicura un’integrazione e una comunicazione ottimizzata con le nuove architetture 4.0, i trasduttori di misura della pressione industriale KS-I, che soddisfano i più elevati standard in termini di performance e affidabilità, TWIIST, l’innovativo trasduttore multivariabile per il rilevamento della posizione senza contatto e la gamma di power controller
GRM-H, per il controllo dei carichi resistivi nel riscaldamento industriale.
In virtù di una connettività potenziata, gli smart sensor WPL si distinguono per la capacità di raccogliere una maggior quantità di dati di processo e per la loro trasmissione rapida e sicura in modalità digitale, con bit di errore e byte di controllo di coerenza (checksum). L’accurata interpretazione di un numero superiore di informazioni si traduce in un vantaggio concreto per i Clienti, in termini di manutenzione preventiva e predittiva sia del sensore che dell’impianto, a favore di un efficientamento dell’intero processo. Inoltre, la sostituzione del trasduttore risulta particolarmente veloce, in quanto il master IO-Link riconfigura i parametri, rendendoli idonei al nuovo sensore. I trasduttori della famiglia KS, grazie all’elemento sensibile realizzato tramite tecnologia proprietaria a film spesso su acciaio, garantiscono una notevole resistenza a shock meccanici e vibrazioni e sono immuni a disturbi elettromagnetici. Inol-
tre, il grado di protezione IP67 rende l’intera gamma particolarmente idonea per numerose applicazioni idrauliche e pneumatiche. Tra le principali novità dei modelli KS-I, figura la capacità di misurare sia pressione che temperatura, con una frequenza di campionamento pari a 1.000 volte al secondo. Le sonde KS-I sono in grado di comunicare con il Master IO-Link alla velocità COM3, pari a 230.4 Kbaud, la più elevata disponibile. La connettività potenziata permette la registrazione di numerose informazioni acicliche, tra cui i valori massimi di pressione e temperatura, i picchi raggiunti e il numero di ore di lavoro fondamentali per la manutenzione predittiva, in ottica Industry 4.0.
Una gamma in continua evoluzione
Tra le soluzioni presentate più di recente sul mercato figura TWIIST, il trasduttore multivariabile in grado di misurare contemporaneamente posizione, accelerazioni lineari, velocità angolari e temperatura del sensore. Implementa inoltre sensori virtuali di velocità e di inclinazione. Lo smart sensor supporta lo sviluppo di algoritmi proprietari specializzati per applicazione, che aprono orizzonti completamente nuovi nel mondo della sensoristica. Grazie alle uscite digitali IO-Link e CANopen, le misure relative alle variabili di processo, come posizione e velocità oppure l’angolo di inclinazione, vengono trasmesse fino a 1.000 volte al secondo. Ulteriore novità è la possibilità di aggiornare il firmware tramite bus, grazie alla presenza di un Boot Loader, che consente di effettuare l’update direttamente in campo: per i clienti, questa funzione si traduce in un sensore sempre up-to-date, in grado di arricchirsi di nuove funzionalità nel tempo.
In testa alle novità spiccano i nuovi controllori di potenza
GRM-H con diagnostica integrata, basati sulla piattaforma scalabile GRx, dedicati al controllo dei carichi resistivi nel riscaldamento industriale. Un’innovativa serie che integra le caratteristihce tipiche di un power controller all’interno delle dimensioni di un relè a stato solido (SSR). Un elemento particolarmente distintivo della serie GRM-H, oltre al loro design ultracompatto, è la connettività IOLink. Sono infatti i primi controllori di potenza al mondo a adottare questo protocollo che abilita una comunicazione digitale dal livello di campo a quella di livello superiore di fabbrica. E’ possibile quindi registrare, oltre a informazioni di processo cicliche, anche variabili acicliche come le ore di lavoro, i picchi di temperatura, l’energia e la temperatura interna, a favore di un’efficiente manutenzione predittiva della macchina. Infine, le sonde di MELT con uscita IO-Link misurano, oltre alla pressione, anche la temperatura del materiale estruso, registrandone in ambedue i contesti i picchi massimi, così come le ore di funzionamento con pressione di esercizio maggiore di 2 bar. Tali parametri sono essenziali per lo sviluppo di algoritmi di manutenzione predittiva, a favore di una riduzione dei fermi macchina imprevisti. La famiglia completa, certificata PLd e SIL2, si declina in quattro gamme: ILI, caratterizzata dall’assenza di fluido di trasmissione; ILK, con una miscela di Sodio + Potassio (NaK) quale fluido di trasmissione; ILW, che può essere utilizzata nei processi di estrusione in ambito alimentare grazie all’uso di un olio certificato FDA e, infine, ILM con riempimento a mercurio, impiegata nei casi consentiti dalla Direttiva Europea 2011/65/UE – RoHS II. Quattro sono anche i design disponibili: stelo rigido, guaina flessibile, flessibile con termocoppia e a capillare esposto.
Collegare in rete sistemi di produttori diversi - tutti caratterizzati da interfacce, profili e meccanismi di comunicazione differenti - questa è la sfida dell’Industria 4.0 e dell’Industrial Internet of Things (IIoT). È qui che entra in gioco OPC UA. Crea una base uniforme per lo scambio continuo di informazioni dal campo al cloud
OOPC UA, acronimo di Open Platform Communication Unified Architecture, consente una collaborazione indipendente dalla piattaforma, interoperabile e trasversale tra i vari fornitori di macchine in produzione. Rende possibile la comunicazione tra macchine e sistemi, sia in reti chiuse che via Internet. Ma OPC UA non è solo un protocollo di comunicazione: L’architettura comprende anche modelli di dati e concetti di interazione. La scalabilità è un altro grande vantaggio dello standard. A seconda del profilo dei requisiti e della portata dell’applicazione, l’attenzione può essere rivolta alle prestazioni o alla sicurezza, ad esempio l’autorizzazione, la crittografia, la certificazione o l’autenticazione. Vediamo, di seguito, quali applicazioni sono possibili con lo standard di scambio dati aperto.
OPC UA può essere utilizzato in parallelo con i sistemi di controllo macchine industriali standard, consentendo il trasferimento di dati a valore aggiunto al cloud. Grazie alla tecnologia MultiLinkTM sviluppata da Pepperl+Fuchs Comtrol, il master IO-Link è in grado di trasferire i dati dei sensori sia al PLC che al cloud attraverso diversi protocolli. Il gateway edge intermedio BTC12 stabilisce la comunicazione con il master IO-Link, si adatta all’interfaccia del cloud e garantisce
una trasmissione sicura dei dati. In questo modo è possibile implementare diverse applicazioni IoT, come la manutenzione predittiva.
Scenario 2. Retrofit
OPC UA può essere utilizzato anche in soluzioni di retrofit Se è già in uso un master IO-link convenzionale, è possibile sostituirlo con un master IO-link delle serie ICE2 (EtherNet/IP) e ICE3 (PROFINET) dotato di interfaccia OPC UA. Con l’aiuto della funzione MultiLinkTM integrata, è possibile fornire dati a diversi sistemi, come ad esempio a più cloud, simultaneamente e in tempo reale. Oltre al trasferimento dei dati a più cloud, un server OPC UA integrato consente anche la comunicazione parallela con un PLC di livello superiore tramite PROFINET.
Scenario 3. Applicazione senza un ambiente
PLC tradizionale
In future applicazioni, gli utenti dovranno affrontare la sfida di non disporre né di un PLC tradizionale né di un PLC con prestazioni sufficienti.
Un esempio di questo tipo di applicazione è la gestione degli
asset e il track and trace dei componenti con connessione diretta all’ERP o al MES tramite OPC UA. Ma anche in altre aree applicative, come quella dei veicoli a guida automatica, non è necessario utilizzare PLC ad alte prestazioni. Grazie all’ingombro scalabile, i client OPC UA possono invece essere portati su microcontrollori relativamente economici. Tuttavia, ci sono anche applicazioni in cui le nuove funzionalità non possono essere mappate tramite il PLC e si utilizzano invece sistemi di controllo basati su PC.
L’interfaccia OPC UA integrata nel master IO-Link stabilisce una connessione diretta a questi sistemi, ad esempio a un gateway edge come il thin client box BTC12 di Pepperl+Fuchs. In questo modo è possibile implementare applicazioni senza un ambiente PLC tradizionale.
Le celle di saldatura sono un tipico esempio di utilizzo di più PLC. All’interno di una cella di saldatura complessa, sono presenti diversi PLC, robot con relativo controllo, una stazione di misura basata su PC, controlli ottici di qualità basati su PC e un’alimentazione di acqua di raffreddamento. Un PLC di livello superiore controlla tutti i processi del sistema tramite PROFINET. I sistemi basati su PC sono dotati di una scheda di rete Ethernet TCP/IP e la stazione di raffreddamento dell’acqua e il controller del robot funzionano ciascuno tramite un protocollo proprietario.
Caso 1: OPC UA consente la comunicazione e lo scambio diretto di dati tra i sistemi nonostante i diversi protocolli fieldbus. Ad esempio, consente al robot di comunicare con altri sistemi all’interno dell’impianto direttamente o tramite il cloud.
Caso 2: i valori di scarico dell’acqua di raffreddamento (compresi altri parametri di processo come il tempo di ciclo e i valori di temperatura) vengono registrati e valutati per la manutenzione preventiva. Tramite OPC UA, i valori determinati vengono trasferiti a sistemi di livello superiore o direttamente al cloud, dove i servizi digitali e altri possono accedervi. Questi ultimi analizzano le registrazioni per identificare le irregolarità sulla base di possibili deviazioni, al fine di prevenire errori e danni conseguenti.
Caso 3: la stazione di misura fornisce i dati di misura a un database e, in parallelo, a un sistema di controllo. Utilizzando OPC UA, i dati di misura possono essere facilmente trasmessi attraverso due canali diversi.
Si chiama TPS, ovvero Tube & Profile System, il rivoluzionario sistema di IPG Photonics per la produzione di tubi saldati al laser, che monta i profilometri 2D/3D MLSL di wenglor, grazie ai quali è possibile rilevare l’allineamento dei lembi da saldare con una precisione fino a 5 centesimi di millimetro
PParte di un gruppo multinazionale quotato al Nasdaq, con stabilimenti di produzione situati, oltre che in Italia, negli Stati Uniti, in Germania e in Russia e uffici regionali di vendita in Giappone, Corea, India e Regno Unito, IPG Photonics di Cerro Maggiore (MI) è nata nel 1990 come produttore di amplificatori per il settore telecom. Alla fine degli anni ’90, l’azienda è entrata nel settore dei laser fibra ad alta potenza, divenendo ben presto un punto di riferimento in ambito di lavorazioni laser specialistiche.
Negli ultimi anni, la sede produttiva di Cerro Maggiore, già deputata alla vendita dei laser e all’assistenza sul territorio oltre che alla produzione di amplificatori in fibra ottica per telecomunicazioni, ha avviato la produzione e la progettazione di sistemi basati sui laser fibra di realizzazione del gruppo IPG.
Le sorgenti in fibra hanno rivoluzionato la tecnologia laser degli ultimi anni, sia nel taglio, nella saldatura, marcatura o apporto di materiale. Tra i tanti benefici, il più evidente è l’elevata velocità di lavoro, seguito dai bassi costi operativi e dalla semplicità costruttiva degli impianti.
All’importante cambio generazionale rappresentato dal passaggio dalla tradizionale tecnologia optomeccanica al laser fibra, che ha preso piede sostanzialmente durante la crisi economica del 2009, quando molte aziende, soprattutto nel settore del taglio metalli, hanno cominciato a investire in nuove tecnologie, si deve la rapida crescita di IPG Photonics Italia, società con più di 80 dipendenti, ancora oggi in forte espansione, che fattura circa 70 milioni di euro e produce in toto
alcuni dei sistemi commercializzati dalla corporate. Uno dei fiori all’occhiello prodotti presso gli stabilimenti di Cerro è il cosiddetto TPS (Tube & Profile System), un sistema di saldatura al laser espressamente progettato per la realizzazione di tubi e profili.
Il Tube & Profile System (TPS) è una soluzione completa e integrata per la produzione in continuo, provvista di una sorgente laser, un refrigeratore, un pannello di controllo e un armadio elettrico per la gestione di tutto il sistema. A questi elementi si aggiungono un posizionatore a 3 assi e, tra le opzioni, un sensore per il rilevamento di precisione dell’allineamento dei lembi da saldare.
“È un sistema di saldatura per la produzione di tubi e profili, che combina una testa di saldatura e un’unità di tracciamento dei giunti con una piattaforma di movimentazione di precisione”, spiega Cassarini, responsabile della Divisione Sistemi presso IPG Photonics di Cerro Maggiore.
Il TPS permette di effettuare saldature in continuo ad alta integrità - ovvero prive di ossidazione - dei lembi aperti dei tubi che vengono fatti scorrere sotto la sua testa. I tubi, precedentemente formati mediante operazione di calandratura, possono avere varie lunghezze, anche di alcuni metri, e spessori della parete tipicamente compresi tra 0,7 e 4 mm, ma il sistema permette oggi la produzione anche di profili fino a 12 mm. L’assenza di specchi ha consentito di realizzare un sistema dal design molto compatto, mentre, grazie all’utilizzo dei laser ad alta efficienza e senza manutenzione di IPG Photonics, i costi operativi e dei materiali di consumo sono in genere inferiori del 25% rispetto alle alternative di saldatura tradizionali a CO2.
Grazie alle sue caratteristiche - alta qualità, inerte al suo interno ed estremamente stabile rispetto alle saldature ad alta
frequenza - il tubo saldato al laser viene utilizzato soprattutto per applicazioni di gamma elevata, dove non sono ammesse imperfezioni o la presenza di residui, come ad esempio, nel settore farmaceutico e alimentare.
Tutto sotto il controllo vigile dell’elettronica
Il sistema TPS è totalmente elettronico. Oltre al controllo di tutte le parti di cui si compone la macchina, assi, laser, gas di copertura ecc., il TPS consente alla macchina di memorizzazione le ricette di produzione, impostazione che ne favorisce l’integrazione nella linea di fabbricazione del cliente e nella rete di fabbrica, in ottica Industria 4.0.
“Un aspetto estremamente critico della saldatura è costituita dall’allineamento dei lembi che devono passare sotto il laser. Se prima della saldatura i lembi non sono perfettamente allineati, il tubo presenterà un difetto”, afferma Cassarini. “Per correggere il cordone è possibile fondere localmente il tubo al suo interno, ma spazzolandolo esternamente se ne ridurrebbe lo spessore. Su alcune tipologie di tubi particolarmente sottili questo non è accettabile, in ottica di compliance non solo geometrica, ma anche funzionale, poiché il tubo potrebbe non reggere i carichi previsti”. Può inoltre accadere che la saldatura sia instabile, a causa del movimento dei lembi durante le operazioni di manipolazione precedenti la saldatura stessa. Nel caso del tradizionale controllo manuale di allineamento dei lembi, questo costringerebbe a fermare la linea, determinando anche un concreto rischio di scarti, con sprechi potenzialmente anche molto elevati nella lavorazione di tubi di particolare valore. Come assicurare il massimo della qualità agli utilizzatori del sistema?
Una soluzione unica, grazie ai profilometri 2D/3D wenglor
“Grazie al supporto diretto fornito dall’azienda, optare per i profilometri 2D/3D wenglor per la misurazione dei lembi è stato naturale, dal momento che conoscevamo già wenglor, con cui avevamo precedentemente fatto alcune positive esperienze. Oggi, le nostre macchine più performanti, che forniscono all’utilizzatore la garanzia di una qualità pressoché assoluta delle lavorazioni, montano i sensori wenglor”, afferma Cassarini.
Il principio base che è stato adottato è del tutto diverso da quello che viene solitamente impiegato: IPG Photonics ha infatti scelto di misurare il profilo del tubo immediatamente dopo la saldatura – e non prima – ovvero quando ormai il prodotto non può più essere soggetto a modifiche. Eseguendo la misurazione anche pochi centimetri prima della saldatura, come fanno altre aziende, non si ha infatti la garanzia che i lembi risulteranno allineati anche
in fase di saldatura. D’altra parte, eseguire la misura sul punto di saldatura è molto difficile, perché un sistema meccanico si troverebbe in presenza di altissime temperature e un sistema ottico verrebbe inevitabilmente abbagliato. La misura deve tuttavia essere presa prima della successiva fase di lavorazione del tubo, costituita dal suo ricalco mediante una coppia di rulli: si tratta di un’operazione meccanica di pressatura dei lembi che, poiché provoca una deformazione, non rende più possibile fruire di una chiara indicazione. Occorre quindi concentrare la misurazione nello spazio, molto ridotto, fra la saldatura e la rullatura del cordone. Per le applicazioni dove il diametro dei tubi è relativamente grande, il disallineamento dei lembi viene misurato con un’accuratezza tipica di un decimo di millimetro. Tuttavia, in funzione del diametro e dello spessore del tubo, la precisione della misura - e quindi dell’allineamento dei lembi - può spingersi fino ad un massimo di 5 centesimi di millimetro. Benché i sensori di profilo wenglor siano caratterizzati da prestazioni di gran lunga superiori, queste risulterebbero inutili per via delle precisioni tipiche dei sistemi meccanici.
Non solo hardware, anche software
Il sensore scelto, dalla serie MLSL, ha ingombri molto contenuti, ma è decisamente performante. Ciò ha consentito di risolvere egregiamente le problematiche degli spazi limitati in cui doveva essere installato, assicurando precisione e ripetibilità eccezionali. wenglor ha fornito un supporto non solo nella fase di individuazione del sensore ottimale, ma anche in quella dello sviluppo software.
“Un aspetto molto significativo, che ha reso wenglor un vero e proprio partner di IPG Photonics nello sviluppo di questo nuovo sistema, è stata la disponibilità a fornire il massimo supporto nello sviluppo del software”, sottolinea Cassarini. Gran parte dello sviluppo è stato eseguito con il codice che wenglor ha messo direttamente a disposizione e che gli sviluppatori di IPG Photonics hanno integrato nel supervisore di macchina, offrendo così all’utilizzatore la possibilità di selezionare agevolmente i parametri insieme alle ricette di lavorazione in un unico ambiente integrato e user friendly. Dall’HMI di macchina, tra le pagine di cui si compone il supervisore vi sono anche quelle di analisi dell’allineamento dei lembi, il che consente di utilizzare il sistema avvalendosi di un’unica interfaccia. “Il sensore dispone di comunicazione con protocollo TCP/IP e invia al supervisore i dati dimensionali che, successivamente, vengono elaborati per essere presentati e analizzati qualitativamente”, aggiunge Cassarini. “Al supervisore vengono trasmesse quote in millimetri e non sottoforma di punti fra cui calcolare le distanze, poiché il sensore è uno strumento di misura già calibrato e in grado di comunicare le dimensioni in unità di misura reali”.
Tutto il sistema software di controllo, non solo della macchina ma anche del rilevamento dei profili, è integrato all’interno del supervisore di macchina. L’utente deve semplicemente impostare i parametri e le ricette per il tipo di produzione richiesto. Questo risultato è stato reso possibile dall’apertura e modularità del sistema wenglor, ovvero dalla disponibilità di una interfaccia di comunicazione a bordo sensore e alla possibilità che gli sviluppatori di IPG hanno avuto di integrare il codice sorgente. Questo aspetto è estremamente importante in ottica di ulteriore sviluppo del sistema TPS, in quanto, anche grazie ai suggerimenti e ai feedback forniti dai clienti, sarà possibile ampliarlo con nuove funzionalità senza dover ricorrere a soluzioni di terze parti.
IIl numero annuale di dispositivi IO-Link installati ammonta a 6,3 milioni di nodi nel 2021, portando il numero complessivo fino ad oggi installato a oltre 27 milioni. Per i numerosi utenti, la IO-Link Tecnology si sta rivelando una componente essenziale del concetto di macchinario e di impianto. In quanto fattore abilitante della digitalizzazione, IO-Link garantisce un aumento significativo del contenuto informativo dei sensori e degli attuatori installati in macchinari ed impianti.
“La tecnologia punto-punto offre diversi vantaggi, ad esempio il cavo di collegamento standardizzato o la semplice parametrizzazione tramite una descrizione del dispositivo IO-Link (IODD IO-Link Device De-
A partire dal suo ingresso sul mercato oltre dieci anni fa, la tecnologia punto-punto IO-Link si è affermata nella costruzione di macchinari ed impianti, affermazione confermata dai dati recentemente pubblicati dalla comunità IO-Link
scription), tuttavia non è esente da difetti. Ad esempio, IO-Link ha spesso posto agli utenti una serie di sfide nel contesto della sicurezza funzionale nell’utilizzo dei relativi dispositivi nell’installazione sul campo. Questo perché non era disponibile sul mercato una soluzione paragonabile allo standard IO-Link per integrare sensori e attuatori sicuri nel sistema di automazione”, afferma Marcel Franzke, Strategic Product Marketing – Safety Automation Infrastructure, Phoenix Contact. Nel concetto di macchinario ed impianto, i diversi sensori e attuatori sicuri dovevano essere collegati in modo classico, con diversi cavi di collegamento, al sistema di valutazione associato, ad esempio un sistema di controllo sicuro. “Con la pubblicazione dell’estensione del sistema di sicurezza IO-Link Safety V1.1.3 nel marzo 2022, è
ora disponibile uno standard con cui l’utente può realizzare un concetto di soluzione integrata. L’estensione del sistema descrive l’uso di IO-Link Safety basato su IO-Link, che consente l’utilizzo di master e dispositivi IO-Link Safety”, precisa Franzke.
Utilizzo indipendente dal produttore dei dispositivi IO-Link Safety
Dal 2016, nel campo dell’automazione sono disponibili diverse soluzioni Safety over IO-Link. Si tratta di approcci specifici del produttore che non soddisfano il concetto su cui si basa IO-Link. I dispositivi Profisafe over IO-Link possono essere utilizzati solo con il master IOLink appropriato e solo nel sistema Profisafe. I dispositivi non sono fondamentalmente dispositivi IO-Link Safety, piuttosto un elemento del sistema Profisafe. A tale scopo, il telegramma Profisafe viene trasmesso tramite tunnel IO-Link, per cui IO-Link funge solo da percorso di trasmissione. Il necessario master IO-Link inoltra le informazioni tunnelate tramite Profinet al controllore di sicurezza richiesto (figura 1).
IO-Link Safety, invece, offre tutti i vantaggi di IO-Link apprezzati dagli utenti, come l’indipendenza dalla rete dei sensori e degli attuatori, una tecnica di connessione standardizzata, l’uso di un IODD per la parametrizza zione o la semplice sostituzione dei dispositivi. Inoltre, i dispositivi IO-Link Safety sviluppati secondo le specifi che sono utilizzabili indipendentemente dal produttore del master IO-Link Safety. L’utente può quindi sceglie re sul mercato il dispositivo più adatto per la propria applicazione.
IO-Link Safety anche per IO-Link standard Oltre a gestire una soluzione IO-Link Safety, anche il master IO-Link Safety funziona nella modalità operativa IO-Link classica, offrendo all’utente la massima flessibilità in un unico dispositivo. Grazie al nuovo standard, si può ipotizzare che in futuro ci sarà un solo dispositivo IO-Link/IO-Link Safety che coprirà tutte le funzioni richieste, trasferendo le informazioni al sistema di controllo tramite il master IO-Link Safety. Inoltre, anche le barriere fotoelettriche, gli scanner laser o gli hub di sicurezza IO-Link Safety si baseranno su questi vantaggi.
Varie opzioni di configurazione per le porte IO-Link Safety
Un ulteriore aspetto che depone a favore dell’utilizzo dell’estensione del sistema di sicurezza IO-Link Safety è l’ampia gamma di opzioni di configurazione per le singole porte di sicurezza IO-Link Safety. “A questo scopo sono stati creati diversi “livelli di funzionalità” nell’espansione del sistema. Attraverso le modalità operative IOLink, IO-Link Safety e la modalità mista di entrambi i concetti, è possibile configurare segnali digitali sicuri e segnali digitali non sicuri, aumentando ulteriormente la flessibilità del master di sicurezza IO-Link Safety”, spiega Franzke. Sarebbe ad esempio possibile parametrizzare una porta di sicurezza IO-Link Safety di classe A che supporta il livello di funzionalità c con le seguenti fun-
ingresso digitale sicuro a due canali (FS-DI) (figura 2). L’espansione del sistema affronta anche il tema della porta di classe B, che in futuro potrà alimentare i dispositivi IO-Link con un fabbisogno energetico più elevato. Grazie alle funzioni estese, il nuovo standard consente una facile migrazione della soluzione di sicurezza esistente sul campo. Inoltre, l’utente ottiene un concetto a prova di futuro per l’attuazione della sua strategia di digitalizzazione.
Una caratteristica particolare degli standard IO-Link e IO-Link Safety è la facilità di configurazione dei parametri con IODD e la sostituzione dei dispositivi resa possibile da IO-Link, supportata anche dalla tecnologia IO-Link Safety. È sempre più evidente che quasi tutti i vantaggi della tecnologia IO-Link si stanno diffondendo nel mondo della sicurezza funzionale.
Per la costruzione di macchinari, IO-Link Safety si sta rivelando un elemento importante per realizzare un collegamento ininterrotto di sensori e attuatori al livello di controllo. I primi master di sicurezza IO-Link Safety e i primi dispositivi di sicurezza IO-Link Safety sono stati introdotti da diversi fornitori nel 2023. In definitiva, lo standard crea per gli utenti un percorso indipendente dal produttore per la digitalizzazione di macchinari e sistemi.
La PLCnext Technology collega i mondi IT e OT
La progettazione precisa del sistema di automazione
aperto è altrettanto importante quanto l’ampliamento flessibile e modulare. La digitalizzazione e la globalizzazione pongono nuove sfide per l’automazione industriale. PLCnext Technology è l’ecosistema per l’automazione industriale composto da hardware aperto, software di progettazione modulare, community globale e mercato di software digitale, ideale per rendere ogni applicazione adatta all’IIoT e all’Industry 4.0. Oltre alla programmazione standard dei sistemi PLC secondo IEC 61131-3, con PLCnext Control è possibile anche la programmazione in parallelo e la combinazione di linguaggi di programmazione come C/C++, C# o MATLAB® Simulink® in tempo reale.
La revisione completa della direttiva macchine 2006/42/ CE ed il conseguente passaggio al regolamento macchine comportano conseguenze di vasta portata per tutti gli operatori del mercato. In particolare, si raccomanda ai produttori di macchinari e componenti di sicurezza di allinearsi tempestivamente ai cambiamenti previsti, in particolare per quanto riguarda la sicurezza informatica. Anche gli operatori di macchinari ed impianti saranno chiamati ad agire: alla luce degli attuali scenari di minaccia, devono emergere nuovi concetti di automazione che devono essere implementati congiuntamente dal produttore e dall’utilizzatore. Con la propria vasta esperienza in termini di soluzioni, Phoenix Contact fornisce un valido supporto lungo questo percorso.
La
Signal di Turck Banner riduce le barriere per l’entrata nel mondo dell’IIoT, con un nuovo modo per accedere ai preziosi «machine data»
TTurck Banner Italia, tra i principali fornitori di sensoristica, illuminatori e segnalatori industriali, sistemi bus e sicurezza presenta Snap Signal, un portafoglio completo e facilmente implementabile di hardware e software IIoT modulare che fornisce dati macchina utilizzabili in tutta la fabbrica. Più che un altro esempio di cosa si possa fare con l’IIoT (Industrial IoT), Snap Signal è una vera e propria rete di sovrapposizione (overlay network) in grado di acquisire segnali di dati da qualsiasi fonte, convertendoli in un unico protocollo standard di settore, per poi distribuirli per un rapido e semplice utilizzo. La famiglia di prodotti Snap Signal di Turck Banner offre flessibilità nel monitoraggio delle apparecchiature più importanti all’interno di un’area o in quello di un’intera struttura. Vediamo come la famiglia di prodotti Snap Signal consente un’integrazione perfetta tra dispositivi e protocolli rappresenti un modo semplice per aggiungere funzionalità IIoT al proprio impianto.
Fa parte dell’offerta Snap Signal il DXMR90, controllore
industriale abilitato all’IIoT che trasmette informazioni da più fonti simultaneamente in un protocollo unificato per l’analisi e il consumo in tempo reale. Il DXMR90 di Turck Banner opera anche in edge processing attraverso la logica e la gestione dei dati.
Questo controllore industriale è dotato di un processore che riceve segnali da sensori e altri dispositivi collegati, attraverso quattro porte Modbus dedicate. Il DXMR90 accoppia tutti questi segnali in un flusso unificato di dati, che può essere esportato attraverso i protocolli Ethernet industriali.
Snap Signal di Turck Banner significa anche Master IO-Link. I master IO-Link consentono agli operatori di raccogliere più dati in tempo reale da un numero maggiore di dispositivi. I master IO-Link della famiglia Snap Signal sono disponibili nei modelli a due (R45) o quattro porte (R90). Ognuno di essi funge da gateway per il collegamento dei dispositivi IO-Link ai più comuni sistemi di controllo presenti sul mercato. I master IO-Link trasmettono dati macchina, parametri di processo e informazioni diagnostiche tramite Modbus RTU, Ethernet IP o Modbus TCP (a seconda del modello). Questa configurazione consente di inviare dati IO-Link a PLC,
HMI, SCADA e piattaforme cloud. I vantaggi chiave dei Master IO-Link risiedono nella sua forma compatta e nel Design espandibile per adeguarsi a una produzione in crescita. I master IO-Link di Turck Banner possono gestire la raccolta di segnali IO-Link per l’implementazione IIoT su larga scala e offrono anche una soluzione conveniente per chi dispone solamente di un piccolo numero di dispositivi IO-Link. Questo approccio offre agli utenti una grande flessibilità per iniziare da una scala più piccola e decidere in seguite se aggiungere più dispositivi man mano che l’attività si espande nel tempo.
Se i dispositivi collegati al master IO-Link devono essere sostituiti a causa di danni o per qualsiasi altra ragione, possono essere sostituiti con pezzi identici; il master IO-Link riconoscerà automaticamente e configurerà rapidamente il nuovo sensore impostandolo correttamente per l’applicazione. Poiché i sensori IO-Link non richiedono alcun cablaggio speciale o complicato, possono essere collegati ai nuovi master IO-Link utilizzando convenienti cavi M12 non schermati a tre conduttori standard di settore.
Anche l’Hub IO-Link fa parte della famiglia Snap Signal. L’hub IO-Link converte e consolida i
segnali discreti in un flusso di dati IO-Link compatibile con altri dispositivi, compreso i nuovi master IO-Link R45 e R90. Può essere utilizzato anche nei sistemi IOLink tradizionali per la trasmissione del segnale di un gran numero di ingressi/uscite discrete a sistemi di controllo di livello superiore.
L’hub IO-Link dispone di quattro porte di ingresso con due canali discreti ciascuna (PNP o NPN). Questi ingressi sono indirizzati a una singola porta di interfaccia IO-Link. Oltre a portare segnali discreti, gli operatori hanno anche la possibilità di pilotare un’uscita NPN o PNP da ciascuna delle quattro porte.
Completano la gamma della famiglia Snap Signal di Turck Banner i convertitori S15C e R45C che accettano vari tipi di segnali, tra cui quelli discreti, analogici e altri, e li trasformano in protocolli industriali come IO-Link o Modbus e l’R70SR Serial Data Radio, un dispositivo di comunicazione wireless compatto e a basso consumo, utilizzato per estendere la portata delle reti di comunicazione seriale.
Dispositivi radio per dati seriali
I dispositivi radio per dati seriali R70SR sono unità di comunicazione wireless a bassa potenza e compatta utilizzate per estendere la portata di una rete di comunicazione seriale. Il dispositivo è dotato di una base con connettore M12 per una rapida installazione.
IIn questo articolo Alessandro Delucchi, Area Sales Manager di Mobile Industrial Robots affronta un argomento abbastanza delicato, poiché non si parla soltanto di prodotto, robotica e di sistemi per ottimizzare l’intralogistica, ma si prendono in esame aspetti estremamente importanti che coinvolgono l’uomo e le implicazioni generate dal cambiamento industriale.
L’automazione, un processo già vissuto
È innegabile che quando parliamo di automazione siamo portati a immaginare aziende, siti produttivi come anche sportelli informativi, popolati da robot e dove l’uomo non rappresenta più colui che fornisce un servizio ma ne usufruisce. Il timore di vedersi sostituiti nel lavoro può essere paragonato al sentimento generatosi durante le prime rivoluzioni industriali e successivamente con l’avvento dei primi sistemi di automazione. Cambiano i tempi e le innovazioni ma i timori in questo senso, sebbene non proprio uguali, restano. In effetti l’automazione non è un concetto nato dieci o venti anni fa, ma ben più antico, poiché fin dall’avvento dell’industria l’uomo ha sentito l’esigenza di automatizzare alcuni processi.
Per meglio comprendere questo concetto, possiamo fare l’esempio delle lamiere destinate alla carrozzeria dei primi veicoli; un tempo sagomate a mano e nemmeno molti anni dopo stampate attraverso l’uso delle presse. Ciò che è successo è che la figura del battilastra è andata scomparendo nel tempo a favore dell’addetto alla pressa prima, e del robot posizionatore dopo. Se consideriamo i fattori come carico di lavoro, capacità produttiva e sicurezza, si può dire che il battilastra aveva una produttività bassa (un parafango, una portiera, dovevano essere realizzati uno alla volta) con un carico di lavoro relativamente alto (ai tempi le autovetture non erano ancora alla portata di tutti) e un livello di sicurezza scarso (tagli e schiacciamenti agli arti erano frequenti). L’addetto alla pressa aveva una produttività senza dubbio molto più elevata in relazione ad un alto carico di lavoro, ma con un livello di sicurezza che presentava grossi rischi. I robot posizionatori non prevedono la presenza umana per svolgere il lavoro, pertanto si è raggiunta una produttività elevata con grandi carichi di lavoro e la totale sicurezza per l’uomo. Qual è la differenza che si evince da queste tre figure? È il netto cambiamento del ruolo ricoperto dall’uomo; da mero esecutore ad assistente alla macchina è arrivato a ricoprire un ruolo da supervisore. Questo esempio è utile a comprendere che, nonostante l’avvento dell’automazione
Nell’odierno panorama industriale è un dato di fatto che molte attività vengano svolte da macchine e robot. Dalla produzione alla movimentazione dei materiali, l’automazione riveste un ruolo sempre più importante ed è destinata a crescere esponenzialmente durante i prossimi anni, forte del fatto che la maggior parte dei paradigmi siano stati consolidati e collaudati positivamente. Tuttavia, se è vero che l’automazione è necessaria per le aziende per aumentare la produttività e contenere i costi, non sempre questo cambiamento è accettato facilmente dai collaboratori
sempre più evoluta, l’uomo ha sempre trovato una dimensione all’interno dei processi creando nuove mansioni e di conseguenza nuove figure. L’uomo infatti in questo processo non è del tutto scomparso ma ha acquisito competenze di livello superiore per svolgere incarichi più qualificati. Allo stesso modo è possibile la trasposizione di questo concetto laddove sono in atto trasformazioni che si avvalgono dell’automazione di processi intralogistici e di produzione moderni. È già stato ampiamente dimostrato che l’automazione può essere un ottimo strumento per le aziende perché consente ai collaboratori di affrancarsi da compiti pericolosi, alienanti e sporchi, oltre ad aumentare la propria efficacia e creatività. Questo percorso però presenta tuttora alcuni ostacoli da eliminare, come ad esempio quello di riuscire a comunicare e far comprendere in modo efficace i vantaggi dell’automazione e dimostrare ai propri collaboratori come può contribuire a migliorare il futuro del loro lavoro. Vi sono alcuni aspetti che devono essere presi in considerazione durante questo non facile percorso e che comprendono la comunicazione, il coinvolgimento, l’ascolto, la formazione e il giusto approccio del personale.
Il processo di automazione può riguardare soltanto una parte dell’azienda o l’intera struttura. Nel momento in cui un’azienda è decisa a compiere il passo verso l’automazione dei processi, oltre agli aspetti tecnici è molto importante stabilire una comunicazione trasparente, puntuale e sincera
sul percorso. Infatti è importante spiegare con chiarezza quali saranno i cambiamenti che dovranno affrontare i collaboratori. Qualsiasi informazione in merito, se tralasciata, può generare un sentimento di incertezza, pertanto, è necessario rispondere a tutte le domande e ai dubbi creando un crescente interesse. La massima chiarezza non lascerà spazio a timori, sentimenti contrastanti, idee sbagliate, poiché ogni figura coinvolta nel cambiamento sarà perfettamente al corrente di ogni dettaglio.
Coinvolgere i collaboratori rendendoli partecipi del processo, ha il duplice vantaggio di far sentire ogni figura parte integrante di un progetto nuovo che sta per essere portato a compimento e ad avere elementi utili per plasmare il percorso adattandolo alla filosofia e al metodo operativo di ogni azienda. Infatti, dare spazio a proposte e idee durante le fasi di automatizzazione contribuisce a identificare meglio i punti di interesse all’interno degli spazi e gettare le basi per poter interagire quotidianamente con successo con i sistemi di automazione. È importante ricordare che tutte le informazioni raccolte dai collaboratori rappresentano uno strumento eccellente per poter utilizzare l’automazione nel modo più efficace, rendendo il processo piacevole per i dipendenti.
La formazione come percorso parallelo Unitamente alla condivisione e al coinvolgimento dei dipendenti anche la formazione è un elemento imprescindibile, poiché nessun sistema di automazione può essere efficiente e redditizio se fatto funzionare
MiR sviluppa e produce una delle gamme più avanzate di robot mobili autonomi (AMR) del settore, in grado di automatizzare in modo rapido, semplice ed economico la logistica interna e di ottimizzare la movimentazione dei materiali. MiR offre una delle flotte più innovative di robot mobili che vengono utilizzate sia da grandi imprese che da clienti di piccole e medie dimensioni in diversi settori, dalla produzione alla logistica e alla sanità. Fondata in Danimarca nel 2013, l’azienda è cresciuta fino a diventare un leader globale con quasi 220 distributori e integratori di sistema certificati in 60 paesi. MiR è stata acquisita da Teradyne nel 2018, la quale nel 2022 ha fatto confluire AutoGuide Mobile Robots a MiR in un’unica realtà per offrire un’ampia linea di prodotti AMR con un range di carico utile, da leggero a pesante. Per ulteriori informazioni mobileindustrial-robots.com
da solo. Anche questa fase del percorso è importante poiché, una perfetta comprensione del funzionamento dei sistemi da parte degli utilizzatori, si traduce in un rendimento ottimale. La formazione è anche l’occasione per far acquisire ai collaboratori nuove competenze che permetteranno un nuovo inquadramento all’interno dei processi. L’automazione, infatti, non viene implementata per rilevare il lavoro dei collaboratori bensì rappresenta uno strumento con cui raggiungere nuovi obiettivi, più performanti, e per rendere tutto questo efficace occorre farlo conoscere. Il futuro del lavoro non sarà rappresentato soltanto dall’automazione e dai robot ma dall’insieme coordinato e collaborativo di uomo e macchina, che oltre ad aumentare l’efficienza garantirà nuovi e sempre più elevati standard di sicurezza, che si ripercuote in qualità migliore negli ambienti di lavoro. All’interno delle aziende la formazione non è solo una fase ma un binario parallelo al percorso di automazione, anche quando il progetto è al
termine, poiché sono necessari continui aggiornamenti per stare al passo con le tecnologie e restare sul mercato.
In base all’esperienza di MiR sul campo, possiamo fare alcune considerazioni in base a quanto vissuto fianco a fianco ai nostri clienti. Ciò che abbiamo visto e che accomuna tutte le aziende è l’iniziale timore verso l’automazione dell’intralogistica. Nonostante casi di successo e best practice siano alla portata di tutti, l’aspetto di “come muoversi” inizialmente non è del tutto scontato. Qui entra in azione il produttore o anche il system integrator il quale ha il compito di sfatare i falsi miti e le convinzioni errate che i robot mobili inevitabilmente suscitano. È proprio il giusto approccio costituito da un rapporto di reciproca fiducia e di fattiva collaborazione che rappresenta il primo passo. Una volta gettate queste fondamenta può avere inizio il processo di ascolto e analisi dei flussi che andranno ad essere ottimizzati e che effettivamente andranno a generare beneficio.
Su questo punto, è bene ricordarlo, automatizzare non significa soltanto ricevere gli incentivi messi a disposizione dal Governo, bensì creare le basi per sviluppare il proprio futuro. Una volta completata l’implementazione di un processo automatizzato superare timori e diffidenze iniziali è una naturale conseguenza positiva. Altro aspetto importante è che spesso si ritiene più che sufficiente illustrare il progetto al proprio organico e iniziare con l’implementazione mentre si tende a tralasciare la percezione dell’automazione dei processi come innovazione all’interno dell’organizzazione volta a semplificare il lavoro anche sotto l’aspetto ergonomico.
Per supportare i propri clienti, MiR punta alla promozione di eventi incentrati sui robot dove le aziende, e in particolar modo il personale, possano realmente sentirsi parte del processo di integrazione, con il risultato di far percepire i robot come un collega a tutti gli effetti, anziché una minaccia.
Sebbene le applicazioni dell’IA sono ancora in fase di sviluppo embrionale e il numero delle imprese, che decidono di utilizzare sistemi basati su IA, è ancora minimo, la logistica rappresenta il campo di applicazione in cui l’IA ha riscosso maggior successo
Nel processo evolutivo della logistica è possibile individuare tre principali passaggi che hanno portato allo sviluppo della catena di distribuzione, più comunemente conosciuta come “Supply Chain”:
• logistica tradizionale;
• logistica integrata;
• Supply chain management.
Negli anni ’60, secondo la concezione della “logistica tradizionale”, le attività logistiche all’interno dell’azienda erano gestite da diverse aree funzionali, le quali erano scarsamente coordinate fra loro. Ne risultò un sistema inefficiente e incapace di rispondere alle variazioni di esigenze da parte del cliente, dal momento che l’obiettivo principale era esclusivamente l’organizzazione dei magazzini e dei trasporti ai fini della distribuzione fisica del prodotto all’utente finale.
A partire dagli anni ’80 si registrò un cambiamento del trend logistico con incidenza maggiore su approvvigionamento, supporto alla produzione e distribuzione. Ciò si traduce in un unico termine: “logistica integrata” (in inglese Integrated Logistics), la quale ha lo scopo di ottimizzare il trade-off tra efficienza ed efficacia, ovvero minimizzare il costo totale delle attività logistiche a fronte di un livello di servizio da garantire. Per estensione, ne derivò un “sistema logistico integrato”, ossia un sistema unico e interfunzionale che coniuga in maniera strategica tutte le attività fisiche, gestionali e organizzative dell’azienda. Questo nuovo concetto di logistica implicò l’organizzazione del ciclo produttivo non più basato sulla ricerca dell’efficienza della singola operazione, come accadeva nella logistica tradizionale, ma su una visione sistemica incentrata sull’ottimizzazione dei flussi sia fisici che informativi.
Inoltre, ha portato il superamento della “logica stock” con una conseguente adozione della “logica flow” e una maggiore enfasi sulla “customer satisfaction” e sulla creazione di valore aggiunto. Secondo la “logica stock” o “dello stock control”, denominata anche “logica push”, viene predisposto un livello di scorta reintegrato o quando il livello dello stock è al di sotto di una certa soglia rispetto al fabbisogno previsto o secondo scadenze costanti nel tempo, che coincidono con la data di ordinazione per il ripristino della giacenza. Mentre secondo la “logica flow” o “del flow control”, denominata anche “logica pull”, l’attenzione si sposta dal controllo dello stock al controllo del flusso dei materiali15.
È sulla base di quest’ultima logica che operano il “Material Requirements Planning” (MRP), che si basa sul concetto di far coincidere le scorte con i fabbisogni di breve periodo in modo da ridurre al minimo l’accumulo di giacenze, e il “Justin-Time” (JIT), il sistema produttivo che mira a eliminare tutti gli sprechi e i difetti, considerando la giacenza stessa uno spreco.
A partire dagli anni ’90 con l’avvento delle nuove tecnologie e con l’aumentare delle informazioni immesse nella filiera logistica è nata l’esigenza di introdurre un nuovo concet-
to di logistica per rispondere alle mutate esigenze espresse dai mercati. In questo contesto, si è sviluppata la cosiddetta “Supply Chain”, tradotta letteralmente come “catena di distribuzione”, il cui obiettivo principale era quello di governare tutte le fasi del processo produttivo, anche esterne all’azienda, seconda una visione sistemica.
Per “supply chain” si intende «un sistema di organizzazioni, persone, attività, informazioni e risorse necessarie per trasferire un prodotto o un servizio dal fornitore al clienti»16. Tecnicamente, la “supply chain” include una serie di attori, quali produttori, fornitori, trasportatori, magazzini, rivenditori e clienti, che operano in tutti gli stadi coinvolti nella rete in base al proprio ruolo. Pertanto, i termini più appropriati per descrivere tale rete sono “supply network” e “supply web”17.
All’interno dell’azienda, la “supply chain” comprende tutte le funzioni, come sviluppo del prodotto, marketing, distribuzione, finanza e servizio al cliente, necessarie per soddisfare le richieste di quest’ultimo. Dunque, il cliente rappresenta una parte integrante dell’intera catena di distribuzione. L’obiettivo principale della “Supply Chain” è massimizzare la creazione di valore, ossia la differenza tra ciò che è la percezione del prodotto finito da parte del cliente e quanto realmente la supply chain spende per soddisfare le richieste del cliente. Tale valore è legato alla redditività della “Supply Chain”, cioè la differenza tra il guadagno generato dalla vendita al cliente e i costi complessivi lungo la supply chain.
Nell’ultimo decennio l’Intelligenza Artificiale ha raggiunto importanti traguardi in numerosi ambiti applicativi. Le principali applicazioni dell’IA si possono osservare nei campi della logistica, della robotica e della medicina. La maturità e la disponibilità delle soluzioni tecnologiche ha portato la potenzialità dell’IA in molti segmenti, tra i quali spiccano:
• il settore delle vendite: impiega sistemi esperti adatti per la configurazione commerciale di proposte particolarmente complesse a causa della natura stessa dei prodotti in vendita (es. impianti o macchinari che devono operare in particolari condizioni climatiche o ambienti industriali critici) e/o delle variabili che incidono sul risultato finale, in particolare sulla sua realizzazione e sul suo prezzo (es. numero elevato di componenti, utilizzo di materiali particolari). I configuratori di prodotto “esperti e intelligenti” sono capaci di guidare i clienti nella scelta del prodotto da acquistare, senza ricorrere all’intervento di un esperto.
• marketing;
• customer service;
• IT sicurezza, cybersecurity;
• Operations;
• HR.
Per far fronte alla crescente complessità della domanda da parte di un mercato sempre più esigente, sono state introdotte alcune tecnologie di IA a supporto dei diversi stadi che compongono una supply chain con conseguenti van-
taggi in termini di efficienza e di competitività. Le aree, in cui le soluzioni di IA possono portare benefici e miglioramenti, sono:
• la gestione dei fornitori;
• la gestione delle scorte;
• la gestione dei trasporti.
Attraverso l’implementazione di modelli di previsione della domanda, in queste aree della catena di distribuzione, è possibile ottenere informazioni più accurate riguardo la domanda dei consumatori e le esigenze dei fornitori e dell’azienda stessa.
Facendo riferimento alle aree qui sopra elencate, i modelli predittivi alimentati da tecnologie di IA consentono di:
- migliorare la pianificazione della produzione e delle consegne dei prodotti, monitorando i dati di stock del cliente ed evitando inutili sovrapproduzioni (cioè una maggiore sincronizzazione tra azienda e fornitori);
- individuare le adeguate quantità di merce da mantenere a stock, riducendo da un lato le scorte di sicurezza e limitando dall’altro le mancate vendite dovute all’assenza dei prodotti in magazzino. Si stima che gli errori previsionali possano diminuire dal 20 al 50%, portando a una riduzione delle mancate vendite fino a una percentuale pari al 65%.
- Ottimizzare le modalità di spedizione e i tempi di consegna con sistemi di movimentazione automatizzati di tipo “self-driving”.
Inoltre, essi possono essere impiegati per automatizzare il processo di manutenzione dei macchinari e degli impianti, attraverso un confronto tra i dati relativi allo stato di salute di tutta l’attrezzatura e lo storico degli interventi manutentivi. In questo modo, permettono di individuare il momento migliore in cui effettuare gli interventi, in modo da minimizzare i fermi di produzione. Pertanto, il beneficio apportato nei processi di manutenzione è duplice: da un lato si può assistere a un aumento del 20% in termini di produttività, dall’altro a una riduzione del 10% in termini di costi di manutenzione con un conseguente aumento di sicurezza all’interno dell’ambiente di lavoro. 27
Secondo il parere degli esperti, l’Intelligenza Artificiale sarà la base della futura automazione industriale, all’interno della quale la gestione dell’intero ciclo produttivo sarà affidata completamente ai sistemi dotati di IA capaci di recepire e
ottimizzare il 99% di tutte le informazioni possedute. Si giungerà quindi ad una stretta collaborazione tra il settore dell’industria e quello informatico in direzione della creazione di un nuovo concetto noto come “Industry 4.0”. Sebbene le applicazioni dell’IA sono ancora in fase di sviluppo embrionale e il numero delle imprese, che decidono di utilizzare sistemi basati su IA, è ancora minimo, la logistica rappresenta il campo di applicazione in cui l’IA ha riscosso maggior successo. Ciò è riscontrabile non solo su scala globale, ma anche su scala nazionale.
Prendendo in considerazione il territorio italiano, le aree di specializzazione maggiormente interessate sono: IoT, manifattura e robotica. In generale, l’Italia presenta una forte specializzazione nella combinazione dell’IA con sistemi fisici, detti “embedded”, i quali includono sensori, oggetti intelligenti, robot e impianti di automazione. A questo proposito si parla di “embedded AI”, il quale rappresenta un fattore distintivo del know-how italiano in ambito di IA.
Secondo il rapporto stilato dal gruppo di ricerca del Ministero dello sviluppo economico (MISE), l’Italia è ai vertici europei nel settore della manifattura e dell’automazione industriale, dove si evince un netto miglioramento grazie all’introduzione di robot di nuova generazione. Quest’ultimi, infatti, sono in grado di fornire livelli superiori di garanzia e qualità, riducendo i costi operativi e migliorando la produzione.
Secondo il Council of Supply Chain Management Professionals (CSCMP), il “Supply Chain Management” (in italiano “Gestione della catena di distribuzione”) «abbraccia la pianificazione e la gestione di tutte le attività inerenti alle risorse e agli approvvigionamenti, alla conversione di esse e a tutte le attività di gestione logistica. Essa include anche, in maniera preponderante, la coordinazione e la collaborazione con i partner di canale, che siano fornitori, intermediari, terzi fornitori di servizi o clienti. In sostanza, il Supply Chain Management integra la gestione della fornitura e della domanda all’interno e attraverso le imprese.» Inoltre, ne definisce anche i limiti e le relazioni: “Il Supply Chain Management è una funzione integratrice con responsabilità primarie nel connettere le principali funzioni e processi aziendali all’interno e attraverso le aziende in un modello di business coesivo e altamente performante. Esso include tutte le attività di gestione logistica sopra menzionate, come le operazioni di produzione portando all’integrazione dei processi e delle attività all’interno e attraverso le funzioni di marketing, vendite, progettazione del prodotto, finanza e IT (Information technology).
Tuttavia, è opportuno non confondere il termine “Logistica” con “Supply Chain Management”, dal momento che non rappresentano il medesimo concetto. Mentre il primo riguarda esclusivamente la movimentazione dei prodotti dal magazzino del produttore a quello del consumatore, il secondo termine riguarda la gestione di tutta la catena di
distribuzione, con particolare riferimento alla logistica e al rapporto con i fornitori. All’atto pratico, la logistica può essere considerata un sottoinsieme della supply chain. Nello specifico, il Supply Chain Management (SCM) è il processo di supervisione dei materiali, delle informazioni e dei flussi finanziari che si spostano dal fornitore al produttore, dal grossista al rivenditore e al consumatore, in modo da massimizzare la redditività totale della supply chain. Esso si compone di nove attività secondo un ordine ben preciso:
• marketing;
• rapporto con i fornitori;
• approvvigionamenti;
• gestione e stoccaggio delle materie prime;
• produzione;
• gestione e stoccaggio dei prodotti finiti;
• gestione degli ordini di acquisto;
• gestione delle consegne;
• logistica di restituzione dei resi.
Il punto sulla smart factory e la logistica 4.0
La Smart Factory rappresenta la concretizzazione dei principi dell’Industry 4.0. Si tratta di un approccio totalmente nuovo di organizzazione dei processi produttivi all’interno delle imprese industriali e manifatturiere. Tutte le singole risorse interne alla fabbrica intelligente, ovvero impianti, macchine e persone, sono interconnesse e cooperano al fine di adattare le proprie produzioni alle specifiche e sempre più mutevoli esigenze dei clienti (l’azienda diventa più “agile”), migliorando l’efficienza nella gestione delle risorse e riducendo i tempi di produzione e di arrivo sul mercato di prodotti altamente personalizzati.
Secondo quanto stilato dal Ministero dello Sviluppo Economico (MISE) nel piano nazionale Industria 4.0., i benefici che la Smart Factory apporta all’ecosistema produttivo sono molteplici:
• Maggiore flessibilità attraverso la produzione di piccoli lotti ai costi della grande scala;
• Maggiore velocità dal prototipo alla produzione in serie attraverso tecnologie innovative;
• Maggiore produttività attraverso minori tempi di set-up, riduzione errori e fermi macchina;
• Migliore qualità e minori scarti mediante sensori che monitorano la produzione in tempo reale;
• Maggiore competitività del prodotto grazie a maggiori funzionalità derivanti dall’Internet delle cose
Le imprese, che già hanno introdotto tecnologie abilitanti all’interno di un impianto, stimano una crescita di efficienza produttiva pari al 30-50%.
La Logistica 4.0 è l’applicazione al mondo della supply chain dei paradigmi dell’Industry 4.059, evidenziati nel paragrafo precedente. Essa si traduce in nuovi sistemi di stoccaggio, movimentazione e trasporto caratterizzati da un livello di sviluppo variabile lungo tre assi: a) Automazione fisica, b) Connessione e c) Processo decisionale.
a) Il primo asse indica il grado di “Automazione fisica” del sistema: le soluzioni di Logistica 4.0 non includono soltanto macchine completamente automatiche, ma anche sistemi, in cui le attività vengono svolte, parzialmente o totalmente, in modo manuale grazie all’intervento dell’uomo. Sulla base delle soluzioni impiegate è possibile attuare un’automazione full, ibrida o assente, corrispondente ai tre diversi valori dell’asse.
b) Il secondo asse (Connessione) fa riferimento alla capacità di un oggetto o di una macchina di raccogliere e trasmettere dati: si passa da sistemi con oggetti non connessi, in cui i dati vengono acquisiti in modo manuale o con lettura barcode, a soluzioni in cui oggetti smart sono in grado di rilevare e memorizzare i dati in maniera autonoma mediante dispositivi specifici, quali sensori o tag RFId60 (acronimo del termine inglese “Radio Frequency Identification” per indicare le etichette elettroniche con tecnologia a “Identificazione a radiofrequenza”), fino ad arrivare a contesti in cui sistemi di movimentazione, stoccaggio e trasporto possono anche inviare e ricevere informazioni strutturate, stabilendo una comunicazione tra risorse
c) Il terzo asse (Processo decisionale) misura il grado di autonomia decisionale delle macchine, il cui aumento risulta possibile dalla disponibilità di informazioni a livello decentralizzato: se tradizionalmente le decisioni vengono prese in modo centralizzato, talvolta con l’ausilio di sistemi software quali WMS (dall’inglese “Warehouse Management System”) o MES (dall’inglese “Manufacturing Execution System”), le soluzioni 4.0 possono portare ad un processo decisionale parzialmente decentralizzato, in cui le macchine si auto-configurano, soprattutto in situazioni standard, senza l’intervento di agenti esterni, o ad un processo completamente decentralizzato, in cui le macchine hanno ampia autonomia decisionale, in quanto sono in grado di interpretare il contesto e decidere azioni appropriate. La rivoluzione Industry 4.0 ha costituito un processo di trasformazione graduale per l’ottimizzazione della catena di distribuzione di una Digital Supply Chain. Dopo una prima fase, in cui l’adozione delle nuove tecnologie 4.0 era rivolta a processi aziendali interni, in particolare, all’ottimizzazione dei singoli processi di produzione, negli ultimi anni, questa trasformazione si è estesa, interessando anche le aree del magazzino e dei trasporti.
Digitalizzazione della Supply Chain
Grazie all’interconnessione delle nuove soluzioni 4.0 nelle differenti aree aziendali e alla creazione di un flusso di materiali e informazioni visibile e controllato, risulta possibile creare un ecosistema completamente integrato di processi e attori, capace di armonizzare e migliorare la pianificazione e la gestione delle attività di produzione, ricevimento merci e stoccaggio e delle attività di allestimento ordini e spedizioni: si tratta dell’obiettivo della “Digital Supply chain”.
La digitalizzazione dell’intera catena logistica richiede come prerequisito fondamentale l’informatizzazione delle attività di business. È necessario, dunque, che le aziende abbiano completato il proprio percorso di informatizzazione (siano già 3.0) per potersi dedicare alla trasformazione digitale dei propri processi. In termini pratici, esse devono aver acquisito la capacità di ricevere, organizzare e interpretare i dati, provenienti da fonti e formati eterogenei, per scoprire ciò di cui hanno bisogno, per prevedere rischi futuri e migliorare i processi aziendali in chiave più fluida e collaborativa, in modo da risultare sempre più competitive sui mercati internazionali.
La “digital trasformation” porta con sé il concetto di “innovazione”. Essa rappresenta un profondo cambiamento che spinge le imprese a sfidare sé stesse, a sperimentare nuove frontiere, a superare le resistenze culturali, ridimensionando e migliorando il proprio modello di business.
La definizione di “The Agile Elephant” fornisce una visione precisa in merito: “La trasformazione digitale comporta un cambiamento di leadership, un diverso modo di pensare, l’incoraggiamento all’innovazione e la spinta verso nuovi modelli di business, incorporando la digitalizzazione delle risorse e un maggiore uso della tecnologia per migliorare l’esperienza dei dipendenti, dei clienti, dei fornitori, dei partner e delle parti interessate della propria organizzazione.”
Pertanto, quando si parla di “digital trasformation” non si fa riferimento soltanto alla semplice adozione delle nuove tecnologie all’interno di un’azienda, ma è un concetto che va ben oltre questa visione strategica. Questo cambiamento coinvolge tutto il capitale umano di un’organizzazione e necessita delle giuste competenze. In questo scenario è necessario investire sullo sviluppo di nuove figure professionali e ripianificare le tradizionali soft skills in chiave digitale.
Esaminando le soluzioni di Logistica 4.0 per il magazzino, è possibile individuare tre gruppi di sistemi in cui esse vengono implementate e per i quali l’Osservatorio del Politecnico di Milano ha classificato e analizzato in dettaglio le singole soluzioni:
1) sistemi di movimentazione:
• Carrelli trilaterali semi-automatici: carrelli trilaterali ad automazione ibrida che sono in grado di raggiungere in modo automatico la posizione di picking all’interno del corridoio;
• Carrelli con sistema di guida ibrido: carrelli ad automazione ibrida, guidati da un operatore (per operazioni non standard e nelle aree del magazzino in cui sono presenti persone) oppure a guida autonoma (per operazioni ripetitive nelle aree del magazzino libere da persone). Tuttavia, tali carrelli non dispongono di sensoristica sufficientemente avanzata per interagire con il personale e con altri carrelli.
• Carrelli a guida autonoma: carelli completamente automatici, con sistemi di navigazione sempre meno vincolati. In particolare, i sistemi più recenti si basano su guida inerziale o navigazione naturale. Nel primo caso, il carrello rivela la posizione leggendo marker magnetici o digitali (QR code) posti sul pavimento ed è in grado di spostarsi in modo autonomo tra un marker e l’altro. Nel secondo caso, in fase di installazione il carrello effettua automaticamente una scansione laser del magazzino e crea un profilo 2D dell’ambiente; successivamente il carrello è in grado di rivelare la propria posizione senza l’ausilio di riflettori o altri dispositivi esterni.
• Lettori RFId: sistema in cui la Connessione è basata su “comunicazione da oggetti”, con utilizzo di lettori RFId posti a bordo di carrelli manuali o automatici (ad esempio sulle forche) per la lettura automatica dei pallet/colli prelevati o della postazione di stoccaggio o prelievo.
• Sensoristica- Fleet management: sistema in cui la Connessione è basata su
“comunicazione da oggetti”, tramite sensori installati a bordo di carrelli manuali o automatici che rivelano dati e li inviano al sistema informatico tramite una connessione di rete o bluetooth. I dati possono essere relativi a: stato di funzionamento del carrello, velocità, carica della batteria o consumo energetico, posizione del carrello all’interno del magazzino. Tale sensoristica può essere integrata con soluzioni di augmented reality per guidare le missioni degli operatori.
• Sensoristica-Safety: sistema in cui la Connessione può basarsi sia su “comunicazione da oggetti” sia su “comunicazione tra risorse”. Nel primo caso, avviene mediante sensori di movimento o telecamere, installati sui carrelli, sulle scaffalature o sulle pareti del magazzino in corrispondenza di angoli ciechi, e collegati a sistemi che emettono suoni, luci o vibrazioni per segnalare la presenza di altri carrelli o persone lungo il percorso, al fine di prevenire incidenti. Nel secondo caso, avviene mediante dispositivi, installati a bordo dei carrelli e indossati dagli operatori, che, comunicando tramite onde radio, sono capaci di rilevare automaticamente l’avvicinamento dei carrelli alle persone ed emettono vibrazioni o suoni per segnalarlo ai carrellisti e agli operatori a terra.
• Sistema di frenata automatica: sistema con Connessione basata su “comunicazione tra risorse” e Processo Decisionale parzialmente decentralizzato, formato da dispositivi montati su carrelli manuali che rilevano ostacoli tramite sensori o transponder63 ed azionano automaticamente il sistema frenante per evitare collisioni.
• Interazione tra macchinari e carrelli a guida autonoma: sistema con Automazione full, Connessione basata su “comunicazione tra risorse” e Processo decisionale parzialmente decentralizzato. Rulliere e macchine utensili comunicano direttamente con gli AGV (Automated Guided Vehicle), i quali,
in alcuni casi, sono in grado di evadere gli ordini e definire le priorità in modo autonomo senza l’intervento dell’uomo o di un software centralizzato.
• Autonomous Intelligent Vehicle: sistema con Automazione full, Connessione basata su “comunicazione tra risorse” e Processo decisionale decentralizzato, con carrelli o shuttle che si muovono in modo autonomo all’interno del magazzino (navigazione naturale), sono in grado di rilevare ed aggirare ostacoli, e comunicano tra loro per gestire le precedenze ed assegnare gli ordini. Tali carrelli movimentano sia piccoli contenitori che unità di carico pallettizzate.
2) sistemi di allestimento ordini:
• Postazioni ergonomiche (goods to man): stazioni di pallettizzazione ergonomiche, caratterizzate da Automazione fisica ibrida e Connessione basata su “comunicazione tra risorse”, che modificano automaticamente l’altezza del pallet. Dopo il completamento di ciascuno strato, le stazioni riportano il pallet all’altezza dell’operatore. Tali stazioni sono servite da un sistema automatico operante in una logica “materiale verso operatore”.
• COBOT: sistema con Automazione full o ibrida, Connessione basata su “comunicazione tra risorse” e Processo decisionale parzialmente decentralizzato. Il COBOT (COllaborative RoBOT) è definito “collaborativo” perché può lavorare senza barriere di sicurezza anche in aree in cui sono presenti operatori. Ciò consente di aumentare l’efficienza di alcune operazioni grazie alla cooperazione tra uomo e robot.
3) sistemi di stoccaggio:
• Smart Pallet: sistema in cui la Connessione è basata su “comunicazione da oggetti”, con beacon64 dotati di batterie a lunga durata (fino a 10 anni) che, integrati nei pallet, pos-
sono rilevare alcuni parametri, quali ad esempio posizione, urti, umidità e temperatura.
• Smart warehouse: sistema con Automazione full e Connessione basata su “comunicazione tra risorse”, costituiti da magazzini automatizzati che uniscono alla funzione di stoccaggio soluzioni di movimentazione e rivelamento peso-volume, con sensoristica che rivela i dati in real time e li invia al sistema informatico. Inizialmente queste tecnologie sono state introdotte nel mondo della logistica distributiva per supportare un singolo processo, senza considerare possibili sinergie derivanti dalla connessione con altri sistemi. Successivamente, è stato scoperto come l’interconnessione tra diverse soluzioni di logistica 4.0 abiliti l’integrazione tra i diversi nodi della supply chain, non solo all’interno delle aree del magazzino, ma lungo l’intera filiera. Ciò consente di migliorare la pianificazione e la gestione delle attività di ricevimento merci e di stoccaggio, grazie all’integrazione tra fabbriche e magazzini, e delle attività di allestimento ordini e spedizioni, mediante l’interconnessione tra magazzini centrali, periferici e mezzi di trasporto.
A supporto delle attività di trasporto e di magazzino della logistica 4.0, intervengono, inoltre, moderne soluzioni software e hardware. È possibile identificare cinque tipologie per ciascuna soluzione:
Soluzioni software:
• Fleet Management: software cloud per la gestione (e ottimizzazione delle prestazioni) della flotta in ambito locale o internazionale.
• Supply Chain Visibility: soluzioni specifiche per il tracking di mezzi e spedizioni in real time con segnalazione automatica di eventuali ritardi e/o imprevisti nella consegna.
• Advanced TMS (acronimo dell’inglese “Transportation Management System”): software che permette ai committenti di integrare flussi informativi relativi a spedizioni effettuate da diversi vettori. Inoltre, ha anche la possibilità di sviluppare meccanismi di cross-selling65 e gestire le etichette per le spedizioni internazionali.
• Data Analytics: algoritmi di Big Data Analytics e Machine Learning, applicati alla pianificazione dinamica delle attività logistiche. Le funzionalità spaziano dal calcolo di KPI alla previsione della domanda o di altri parametri come l’ETA.
• Inventory & Order Management: soluzioni software per la gestione delle scorte rivolti a rivenditori eCommerce, che abilitano la gestione integrata delle disponibilità di prodotti su diversi market place attraverso un’unica piattaforma.
Soluzioni hardware:
• Warehouse Robotics: sistemi automatizzati a supporto delle attività di prelievo e movimentazione in magazzino. Le soluzioni più interessanti riguardano shuttle altamente flessibili, capaci di muoversi sia all’interno che all’esterno del magazzino, e convogliatori, capaci di movimentare colli ad alta velocità o elevate pendenze, grazie alle forze elettrostatiche.
• Smart Vehicle: droni a decollo verticale (“Unmanned Aerial Vehicle”- UAV), robot per la consegna nelle aree urbane e veicoli con sistemi di alimentazione alternativa (es. veicoli elettrici a guida autonoma);
• Smart Mailbox: cassette postali “connesse” e appositamente progettate per la consegna eCommerce, alle quali si ha accesso digitando il codice associato alla spedizione o, in alternativa, leggendo un QR code.
• Wearable Device: dispositivi indossabili dagli operatori, utilizzabili all’interno dei magazzini per facilitare alcune attività, come la lettura dei codici a barre e il picking.
Articolo tratto dalla tesi di laurea dal titolo “Impiego dell’intelligenza artificiale per la gestione della supply chain”di Francesco Capobianco, relatore prof. Maurizio Bevilacqua – Università Politecnica delle Marche, Facoltà di Ingegneria
Cresce sempre di più la neccessità di trovare partner affidabili in grado di offrire soluzioni rapide e customizzate. Protolabs è in grado di fornire queste soluzioni grazie all’impiego di innovativi processi di stampa 3D, lavorazione con macchine CNC e stampaggio a iniezione. Ne abbiamo parlato con Matteo Carola, Country Manager per l’Italia di Protolabs
L’azienda fu fondata nel 1999 da Larry Lukis, imprenditore di successo e genio dell’informatica con l’intento di ridurre drasticamente i tempi di realizzazione di pezzi per prototipi in plastica stampati a iniezione.
La soluzione ideata da Lukis fu quella di automatizzare il tradizionale processo di produzione sviluppando un software complesso in grado di comunicare con una rete di frese e presse. Grazie a questo fu quindi possibile produrre pezzi in plastica e metallo in un tempo decisamente minore rispetto a quello richiesto sino ad allora. Durante il decennio successivo, l’aziena è cresciuta ampliando l’offerta di processi di stampaggio a iniezione introducendo la lavorazione rapida con macchine CNC e inaugurando sedi globali in Europa. Nel 2014, sono stati lanciati i servizi di stampa 3D di tipo industriale per passare dalle prime fasi della prototipazione alla produzione in volumi ridotti. Oggi, Protolabs è il fornitore più rapido al mondo di prototipi su misura e pezzi di produ zione su richiesta con stabilimenti operativi in otto paesi.
Sig. Carola che cosa fa Protolabs in Italia?
Protolabs è tra i maggiori Digital Manufacturing Con tractor sul mercato italiano. Protolabs in Italia offre un servizio end to end che, partendo dalla piattaforma digitale accessibile su protolabs.it, permette ai partners di otte nere il meglio dai tool di preventivazione disponibili ma soprattutto di ottenere il massimo dell’expertise del team tec nico per un risultato che si concretizza in velocità e tranquillità sulla sicurezza del risultato finale. Tutti gli aspetti pro duttivi sono in carico a Protolabs che, anche grazie all’acquisizione di Hubs, è in grado di supportare il cliente lungo tutto il ciclo di vita del prodotto, incluse le produzioni di massa. La proposta di valore di Protolabs trova un grado di adozione crescente anno dopo anno in Italia, anche grazie al valore consulenziale insito nella nostra offerta, che è un elemento di spicco e di diffe renziazione rispetto ai concor renti. Sempre più i nostri clienti non ci chiedono semplicemente di realizzare un oggetto, ma di con sigliarli sulla migliore tecnologia di
realizzazione e sui materiali da impiegare in base alle caratteristiche che dovrà avere il pezzo finale.
Ha notato dei cambiamenti dal lato della domanda negli ultimi due anni?
Sempre più clienti diventano consapevoli delle potenzialità del digitale perché ne apprezzano la trasparenza e la rapidità, così come la capacità di avere accesso ad un’ampia gamma di materiali e processi produttivi. La possibilità di verificare insieme ai nostri Account Manager e Application Engineers i dettagli dei progetti direziona la collaborazione su un punto cardine: quale è la tecnologia più adatta per il progetto in questione, e come si può lavorare insieme per rispondere alle richieste specifiche del progetto? La piattaforma di Protolabs si potrebbe definire come una piattaforma di MaaS (manufacturing as a service) dove più utenti possono lavorare in contemporanea sullo stesso progetto, in una sorta di progettazione collaborativa dove ognuno può, attraverso le proprie competenze specifiche, contribuire alla bontà del progetto. La possibilità di condividere il “carrello” semplifica ulteriormente il lavoro del progettista e dell’ufficio acquisti, eliminando i possibili errori.
Quali sono state le principali novità che avete presentato per aiutare i clienti a supportarli nei loro progetti?
Una caratteristica di Protolabs riconosciuta da tutti è l’approccio che si potrebbe porre su due layer imprescindibili: quello umano e quello digitale.
Lato digitale, i nostri clienti possono fruire – per Injection Molding, 3D Printing e CNC – di una Design For Manufacturability analysis che in tempi rapidissimi sgombera i dubbi su alcune domande cruciali:
Il particolare disegnato è producibile?
Le tempistiche proposte rispettano il time to market?
La parte economica è in linea con l’investimento pre-
Lo step successivo apre le porte a una discussione approfondita con un team dedicato di Account Manager / Application Engineer per approfondire gli output dell’analisi DFM.
Abbiamo ulteriormente arricchito il supporto a 360 gradi al cliente offrendo il servizio CDS: consulenza progettuale su misura del cliente, incentrato sull’ottimizzazione dei file CAD dei componenti caricati nel portale dai nostri clienti. Grazie al supporto dei nostri esperti in ingegneria, i clienti possono ottenere file CAD ottimizzati per la produzione,
tenendo conto di vari aspetti quali i materiali, il processo produttivo, le specifiche tecniche. Possiamo sicuramente affermare che i nostri clienti ci chiedono sempre più quali siano le migliori soluzioni tecniche per fare un oggetto, che sia esso in plastica o in metallo, non siamo più solo un service.
Nel vostro sito internet si trovano dei designer che sono vostri partner? Che cosa fanno?
I designer rivestono un ruolo fondamentale per i clienti che ci approcciano e necessitano di un supporto fondamentale per percorrere il primo step “dal concept al primo file CAD 3D”. In diversi casi i nostri clienti non hanno questo tipo di risorse interne, o preferiscono avere un supporto e un punto di vista esterno. La pagina dei designer nasce proprio allo scopo di colmare questo gap. Abbiamo recentemente concluso la nostra partecipazione presso gli Envisioning Design Days, seconda edizione di un evento organizzata dal NABA di Milano per informare e formare tramite delle Masterclass su nuovi tool e tecnologie a disposizione dei designer. La presentazione è stata molto stimolante e ha ulteriormente confermato la nostra offerta di valore anche per designers e free-lancers.
Come si sta integrando l’offerta di Hubs all’interno dei servizi offerti da Protolabs?
L’offerta di Hubs si è inserita in maniera complementare
a quanto proposto ai nostri clienti. Poter rispondere alle necessità offrendo nuove tecnologie (quali lo sheet metal o l’FDM nel campo del 3D printing) o usufruendo di una rete di partner manufatturieri pronti a supportare la produzione di massa, rispettando le stringenti certificazioni molto spesso richieste per produzione in serie, è per noi un’ottima leva per qualificarci come interlocutore unico end to end.
Per le tante piccole e medie imprese italiane, non dimenticando le start-up, che servizio dedicato offre Protolabs?
La piccola e media impresa italiana del settore manifatturiero ha bisogno di tecnologie avanzate e soluzioni di produzione personalizzate per rimanere competitiva. Deve essere in grado di gestire i propri processi produttivi in modo efficiente, riducendo i tempi e i costi di produzione. Inoltre, deve essere in grado di adattarsi rapidamente alle esigenze dei clienti, fornendo prodotti personalizzati e servizi di alta qualità. Infine, è importante per le PMI italiane del settore manifatturiero essere consapevoli dei principali trend tecnologici, produzione digitale in primis, per poter innovare e rimanere al passo con la concorrenza.
Collaborare con Protolabs significa affrontare insieme queste sfide.
Quali sono, secondo lei, gli aspetti del service che non
sono ancora completamente assodati?
(i.e. standard qualitativi costanti, tracciabilità, rifiniture, prezzo, ecc.)
Un aspetto non sempre chiaro è il contributo umano rispetto al digitale, che si declina nelle fasi di pre e post sale support e rimane un contributo imprescindibile per progetti complessi. Non a caso abbiamo recentemente inserito la funzione nella nostra piattaforma tramite la quale è possibile verificare la disponibilità del nostro application engineer ad una call via Teams dedicata alla discussione del progetto caricato sul nostro portale e alla risoluzione di ogni dubbio. Altro aspetto fondamentale è legato alla continuità sul progetto che un Partner come Protolabs può dare: ciò è visibile negli elevati standard qualitativi anche legati alla ripetibilità del progetto (rior-
dini) o alla documentazione a corollario delle nostre produzioni (report dimensionali, certificazioni, etc)
Quali settori sono maggiormente interessati ai servizi di Protolabs in Italia?
I principali settori che usufruiscono di Protolabs in Italia sono quelli tradizionalmente legati al manifatturiero: automotive, medicale, tempo libero e aerospaziale. A questi si aggiungono le tantissime aziende che sviluppano prodotti e componenti per i più diversi settori, come il settore del lusso, del design e dei mobili. I servizi di produzione e post-produzione di Protolabs, affiancati alla consulenza sulla progettazione e ai servizi di finitura, rendono Protolabs il partner ideale per una miriade di aziende.
Per oltre vent’anni, scienziati e climatologi hanno messo in guardia sugli effetti del riscaldamento globale e sul legame con le emissioni di gas a effetto serra (GreenHouse Gas – GHG), ma ora l’attenzione si è rivolta all’azione e al modo in cui noi, come società globale, possiamo affrontare sia le cause che gli effetti del cambiamento climatico. I semiconduttori sono il cervello dei dispositivi moderni, dei veicoli elettrici (EV), degli smartphone, dei robot e non solo, e potrebbero essere la chiave per risolvere la crisi della sostenibilità attraverso l’innovazione mirata e l’intelligenza periferica (edge intelligence) adattativa
LLa disponibilità di energia è stata alla base della crescita sociale ed economica fin dagli albori della rivoluzione industriale, quando tecnologie come quella del motore a combustione interna, del motore a vapore e dei motori elettrici hanno portato a una dipendenza mondiale dalla produzione energetica accessibile e centralizzata. Negli ultimi due secoli, tale
energia è stata fornita attraverso la combustione di fonti basate sugli idrocarburi. Se da un lato ciò ha consentito una grande crescita economica, dall’altro questa crescita ha avuto un costo elevato. Dal 1820, le emissioni di gas serra sono cresciute di 686 volte,1 portando a un riscaldamento globale medio di circa 1,1 °C2 e a una serie di significative conseguenze ecologiche, economiche e sociali. Questi effetti vanno da 166 milioni di persone che hanno richiesto aiuti alimentari a causa di crisi cli-
matiche nel 2015-20193 a 3 trilioni di dollari in perdite economiche legate a disastri nel periodo 2000-2019.4
Mantenendo le tendenze attuali, entro il 2050, per sostenere la traiettoria di sviluppo globale prevista, il mondo avrà bisogno del doppio dell’energia che consuma oggi. In assenza di modifiche alle nostre fonti di energia e di strategie di efficienza energetica complessiva, si prevede che la nostra attuale traiettoria di emissioni porterà a un aumento della temperatura di 1,9-2,9 °C entro il 2050 (rispetto ai livelli preindustriali). Secondo gli esperti, le conseguenze associate potrebbero anche causare la migrazione del 33% della popolazione mondiale,5 una riduzione dell’11-18% del PIL globale6 e fino a 23 trilioni di dollari di perdite annuali dovute a disastri climatici.7
Elettrificazione ed efficienza energetica
cazioni. Un esempio lampante, già in atto, è l’eliminazione graduale dei veicoli con motore a combustione interna a favore dei veicoli elettrici”, ha dichiarato Greg Henderson, Senior Vice President of Automotive and Energy, Communications and Aerospace Group. “Man mano che un maggior numero di prodotti viene progettato per essere alimentato dall’elettricità, entra in gioco un ampio ecosistema che comprende la generazione, la distribuzione e lo stoccaggio dell’energia. A livello globale, abbiamo bisogno di un sistema energetico flessibile, resiliente, efficiente e sicuro.”
differenziazione competitiva", ha dichiarato Martin Cotter, Senior Vice President Industrial Multimarkets Group. "Investire negli obiettivi di sostenibilità e promuovere la redditività non escludono a vicenda: investendo nell'efficienza industriale, abbiamo la possibilità di ridurre consumo di energia ma anche di aumentare la competitività. Il mondo ha bisogno di fabbriche nuove che riadattate, e le fabbriche digitali connesse e adattive sono progettate per risparmiare energia e quindi ridurre le emissioni."
cerca di affrontare problemi urgenti, come quello della povertà globale, l'energia fondamentale per garantire l'accesso universale a servizi essenziali come l'elettricità e il cibo Tuttavia, per evitare i peggiori effetti del cambiamento climatico, il mondo deve emissioni-nette-zero entro il 2050 e limitare il riscaldamento globale a 1,5 °C. La chiave questi obiettivi è la crescita energetica e la decarbonizzazione rapida.
Mentre la società cerca di affrontare problemi urgenti, come quello della povertà globale, l’energia sarà fondamentale per garantire l’accesso universale a servizi essenziali come l’elettricità e il cibo nutriente. Tuttavia, per evitare i peggiori effetti del cambiamento climatico, il mondo deve raggiungere emissioni-nette-zero entro il 2050 e limitare il riscaldamento globale a 1,5 °C. La chiave per raggiungere questi obiettivi è la crescita energetica e la decarbonizzazione rapida.
DOBBIAMO AGIRE ORA
Elettrificazione ed efficienza
Foto 2
e ridurre le nostre emissioni dell’81%
“Esiste un’opportunità senza precedenti di promuovere la transizione verso l’energia pulita, eliminando le tecnologie che generano gas a effetto serra attraverso l’elettrificazione a energia rinnovabile delle varie appli-
DOBBIAMO AGIRE ORA e ridurre le nostre emissioni dell'81%
“Contemporaneamente alla riprogettazione della rete energetica per le fonti rinnovabili, è necessario concentrarsi sulla promozione dell’efficienza energetica in tutte le applicazioni. Nel contesto delle emissioni totali, circa il 50% dell’energia globale è consumata dall’industria.9 Attraverso l’implementazione di tecnologie digitali per la fabbrica connessa, possiamo migliorare il controllo delle attività industriali all’interno delle fabbriche dismesse esistenti e, così facendo, incrementare la produttività che porta benefici all’intera catena del valore e consente una differenziazione competitiva”, ha dichiarato Martin Cotter, Senior Vice President Industrial and Multimarkets Group. “Investire negli obiettivi di sostenibilità e promuovere la redditività non si escludono a vicenda: investendo nell’efficienza industriale, abbiamo la possibilità di ridurre il consumo di energia ma anche di aumentare la competitività. Il mondo ha bisogno di fabbriche, sia nuove che riadattate, e le fabbriche digitali connesse e adattive sono progettate per risparmiare energia e quindi ridurre le emissioni.”
Si prospetta all'orizzonte una crescita enorme della spesa per bassa emissione8
Da oggi al 2035, McKinsey stima un aumento di 4,5 trilioni di dollari nella spesa annuale per beni materiali
La crescita energetica e la decarbonizzazione rapida richiedono la sostituzione massiccia dei combustibili fossili con le energie rinnovabili (cioè una crescita della domanda pari a 9 volte da oggi al 2050) e un netto miglioramento dell’efficienza energetica globale (cioè un aumento pari a 2 volte da oggi al 2050).8
energetica e la decarbonizzazione rapida richiedono la sostituzione massiccia dei fossili con le energie rinnovabili (cioè una crescita della domanda pari a 9 volte da un netto miglioramento dell'efficienza energetica globale (cioè un aumento pari a 2 2050).8
un'opportunità
senza precedenti di promuovere la transizione verso l'energia pulita ,
Da oggi al 2035, McKinsey stima un aumento di 4,5 trilioni di dollari nella spesa annuale per materiali a sostegno della transizione verso le basse emissioni, per un totale di 78,4 trilioni di spesa cumulativa in questi anni8 In tutti i mercati serviti da ADI, ci aspettiamo di vedere investimenti a livello mondiale per l'efficienza industriale e la riqualificazione degli edifici, per il continuo sostegno alla diffusione degli EV e delle relative infrastrutture, alla generazione
Foto 3
per eliminare e ridurre le emissioni
a sostegno della transizione verso le basse emissioni, per un totale di 78,4 trilioni di dollari di spesa cumulativa in questi anni8. In tutti i mercati serviti da ADI, ci aspettiamo di vedere investimenti a livello mondiale per l’efficienza industriale e la riqualificazione degli edifici, oltre che per il continuo sostegno alla diffusione degli EV e delle relative infrastrutture, alla generazione di energia verde e alla modernizzazione della rete elettrica.
ADI confida nella portata e nella probabilità di questa maggiore spesa di capitale, grazie a una confluenza di tendenze secolari. Tra queste, l’aumento della regolamentazione, l’incremento degli sforzi pubblici e privati, la crescita degli investimenti privati, la maturazione dei mercati del carbonio e la diminuzione dei costi complessivi di gestione per applicazioni come i pannelli solari.
Cosa succederebbe se questi beni a basse emissioni fossero adottati su larga scala?
La spesa prevista per i beni a basse emissioni offre l’opportunità di considerare uno scenario in cui le soluzioni più ecologiche vengano pienamente adottate e scalate. Per ridurre le emissioni globali di gas serra dall’attuale livello di 51 miliardi di tonnellate (o 51 Gt) all’anno a zero, è necessaria più di una soluzione.
Se le applicazioni, rese possibili in parte da tecnologie come quelle di ADI, venissero scalate pienamente, potrebbe essere eliminata o ridotta circa la metà delle
“Ci siamo impegnati a comprendere l’entità della decarbonizzazione che soluzioni come quelle di ADI potrebbero potenzialmente consentire, se queste applicazioni fossero adottate e diffuse pienamente. Come è emerso, è circa la metà”, ha dichiarato Tony Montalvo, Vice President of Tecnology e ADI Fellow. “Abbiamo cercato di collegare l’impatto abilitante del nostro più ampio portafoglio di soluzioni, concentrandoci su quelle applicazioni in cui la nostra tecnologia è un fattore abilitante critico.”
scuna cella, bilanciando le celle all’interno del pacco e garantendo che la batteria non venga mai sotto o sovra-caricata. La gestione della batteria, tecnologia in cui ADI è leader di mercato, è quindi una tecnologia abilitante per i veicoli elettrici. Immaginando un mondo in cui la piena adozione dei veicoli elettrici sia una realtà, riconosciamo che i progressi nell’hardware e negli algoritmi di gestione della batteria si affiancheranno ai progressi su altri fronti tecnologici, tra cui la chimica di batteria e i gruppi di trasmissione efficienti, economici e affidabili.
La nostra valutazione ha portato a due categorie principali di soluzioni: quelle tecnologie tradizionali che generano GHG o quelle che rendono la tecnologia di vista energetico. Tra gli esempi di tecnologie sostitutive vi sono i veicoli elettrici, energetica e gli elettrolizzatori alimentati da energie rinnovabili. Esempi di prodotti efficienti dal punto di vista energetico sono i motori industriali, le comunicazioni sistemi HVAC connessi.
La nostra valutazione ha portato a due categorie principali di soluzioni: quelle che sostituiscono le tecnologie tradizionali che generano GHG o quelle che rendono la tecnologia più efficiente dal punto di vista energetico. Tra gli esempi di tecnologie sostitutive vi sono i veicoli elettrici, la transizione energetica e gli elettrolizzatori alimentati da energie rinnovabili. Esempi di prodotti finali più efficienti dal punto di vista energetico sono i motori industriali, le comunicazioni wireless 5G e i sistemi HVAC connessi.
Riconosciamo che le tecnologie di ADI non rappresentano i prodotti finali stessi. In molti casi, tuttavia, senza di esse l’applicazione finale non sarebbe realizzabile. Un esempio è rappresentato dagli EV, che si basano su batterie agli ioni di litio e non sarebbero utilizzabili senza una tecnologia di gestione della batteria che valuti costantemente lo stato di salute di cia -
Un altro esempio di come le soluzioni ADI stiano potenzialmente contribuendo a ridurre le emissioni di CO 2 è rappresentato dall’impiego di azionamenti a frequenza variabile che utilizzano la tecnologia di controllo di precisione di ADI. Questi vengono utilizzati in combinazione con sistemi di motori il cui carico o la cui velocità variano. La tecnologia ADI consente di regolare con precisione la velocità e la coppia del motore in base al carico da gestire. In questo modo si risparmia energia, adeguando la capacità del motore all’attività da svolgere. L’installazione degli azionamenti elettronici su tutti i motori potrebbe far risparmiare, ipoteticamente, il 10% delle emissioni globali.
Riconosciamo che le tecnologie di ADI non rappresentano i prodotti finali stessi. tuttavia, senza di esse l'applicazione finale non sarebbe realizzabile. Un esempio dagli EV, che si basano su batterie agli ioni di litio e non sarebbero utilizzabili gestione della batteria che valuti costantemente lo stato di salute di ciascuna celle all'interno del pacco e garantendo che la ba tteria non venga mai sotto o gestione della batteria, tecnologia in cui ADI è leader di mercato, è quindi una per i veicoli elettrici. Immaginando un mondo in cui la piena adozione dei veicoli realtà, riconosciamo che i progressi nell'hardware e negli algoritmi di gestione affiancheranno ai progressi su altri fronti tecnologici, tra cui la chimica d i batteri trasmissione efficienti, economici e affidabili.
Se le applicazioni (come gli EV o gli azionamenti a frequenza variabile) abilitate in parte dalla tecnologia di ADI dovessero essere scalate e adottate universalmente, la società potrebbe realizzare un risparmio di circa 26 Gt di GHG.10 Questa rivelazione sottolinea il nostro desiderio di sfruttare la nostra leadership unica sui mercati finali per contribuire alla decarbonizzazione di molteplici settori.
Un altro esempio di come le soluzioni ADI stiano potenzialmente contribuendo di CO2 è rappresentato dall'impiego di azionamenti a frequenza variabile che di controllo di precisione di ADI. Questi vengono utilizzat i in combinazione con
Foto 4:
Variazione del ghiaccio marino e dell'assorbimento solare nei mesi estivi nell'Artico
2014. Il blu indica i punti in cui il ghiaccio marino è diminuito e il rosso quelli in cui della radiazione solare è aumentato.
La realtà del cambiamento climatico è che ne stiamo vedendo le prove ovunque: lo scioglimento del ghiaccio marino artico a un ritmo di quasi il 13% per decennio,11 la perdita di ossigeno negli oceani che ha un impatto sulle barriere coralline tropicali,12 l’aumento dei livelli di CO2 e il declino della biodiversità in regioni di tutto il mondo.13 Per ridurre drasticamente le emissioni di gas serra entro il 2050, sono necessari tecnologia, infrastrutture e i giusti impegni.
di collaborare con i nostri clienti per sviluppare soluzioni complete ai loro problemi – e a quelli del mondo – tra i più difficili. Non c’è momento migliore di questo per sfruttare tali competenze e progettare insieme ai nostri partner le soluzioni necessarie per la transizione a emissioni-nette-zero.
La realtà del cambiamento climatico è che ne stiamo vedendo le prove ovunque: lo
Riferimenti
Esiste tuttora un notevole potenziale non sfruttato e i prossimi anni saranno fondamentali per sviluppare le soluzioni esistenti su larga scala e investire in innovazioni rivoluzionarie. ADI non è estranea alle rivoluzioni tecnologiche. La nostra storia (e il nostro futuro) come catalizzatore di progressi rivoluzionari si basa sulla nostra ricca esperienza nel settore e sulla nostra capacità
ghiaccio marino artico a un ritmo di quasi il 13% per decennio,11 la perdita di ossigeno che ha un impatto sulle barriere coralline tropicali, 12 l'aumento dei livelli di CO2 e il declino biodiversità in regioni di tutto il mondo.13 Per ridurre drasticamente le emissioni di gas 2050, sono necessari tecnologia, infrastrutture e i giusti impegni. Esiste tuttora un notevole potenziale non sfruttato e i prossimi anni saranno fondamentali per sviluppare le soluzi su larga scala e investire in innovazioni rivoluzionarie.
1Hannah Ritchie, Max Roser and Pablo Rosado (2020) - “CO₂ and Greenhouse Gas Emissions”. 2 NASA Earth Observatory – “World of Change: Global Temperatures”.3 Patrick Galey, Marlowe Hood and Kelly MacNamara (2021) - “UN draft climate report: Impacts on people”.4 Gabriel Gordon-Harper (2020) - “UNDRR Report Calls for Improved Governance to Address ‘Systemic Risk’”.5 Harry Gray Calvo and Gayle Markovitz (2022) - «Global Public Braces for ‹Severe› Effects of Climate Change by 2032, New Survey Finds”.6 Swiss Re (2021) - «World economy set to lose up to 18% GDP from climate change if no action taken, reveals Swiss Re Institute›s stress-test analysis”.7 Tom Kompas, Van Ha Pham, Tuong Nhu Che (2018) - “ The Effects of Climate Change on GDP by Country and the Global Economic Gains From Complying With the Paris Climate Accord”.8 ADI analysis based on figures from “The economic transformation: What would we change in the net-zero transition.” McKinsey & Company. 24 Gennaio 2022.9 Paul Waide and Conrad U. Brunner. “Energy-Efficiency Policy Opportunities for Electric MotorDriven Systems.” International Energy Agency, 2011.10 ADI analysis based on internal calculations assuming sustainable end applications are fully adopted and scaled. Additional study is needed to account for end products’ full life cycle. Source of 51GT is from Bill Gates’ book, How to Avoid a Climate Disaster.11 World Wildlife Fund - “Six ways loss of Arctic ice impacts everyone”.12 “Ocean Deoxygenation: A Driver Of Coral Reef Demise,” Reefcause Conservation, 25 Settembre 2021 13 “Biodiversity - our strongest natural defense against climate change,” United Nations, 2022
ADI non è estranea alle rivoluzioni tecnologiche. La nostra storia (e il nostro futuro) come catalizzatore di progressi rivoluzionari si basa sulla nostra ricca esperienza nel settor capacità di collaborare con i nostri clienti per sviluppare soluzioni complete ai loro problemi . Non c'è momento migliore di questo per sfruttare competenze e progettare insieme ai nostri partner le soluzioni necessarie per la transizione
Riferimenti
Non c’è dubbio che l’industria alimentare italiana sia uno dei settori economici più importanti del paese. E Mayr® l’assiste con tecnologie all’avanguardia che rendono la produzione non solo più efficiente, ma molto più sicura
II numeri parlano da soli: “179 miliardi di euro di fatturato annuo, 60 mila imprese, 464 mila addetti e oltre 50 miliardi di export in valore in un anno. Nelle graduatorie dei settori manifatturieri italiani è al primo posto per fatturato, al secondo posto per numero di imprese, per addetti e anche per l’export in valore. In dieci anni il suo fatturato ha registrato un incremento del 24,7% in termini reali, il numero di addetti del 12,2% e il valore delle esportazioni in termini reali del 60,3%” (fonte: RAPPORTO FEDERALIMENTARE –
L’Italia è famosa in tutto il mondo per la sua cucina, la varietà dei suoi prodotti alimentari e la qualità dei suoi ingredienti. La produttività e l’eccellenza dell’industria alimentare italiana rappresentano dunque un solido pilastro per il paese e per il mondo.
Basti pensare che l’Italia è uno dei principali esportatori globali di prodotti alimentari. Formaggi, salumi, pasta, olio d’oliva, vino, dolci, caffè e molto altro, sono richiesti per la loro qualità e autenticità, grazie anche al fatto che ogni regione italiana ha le sue specialità culinarie e prodotti tradizionali unici al mondo. Questo facilita la proliferazione
di piccole e medie imprese, molte delle quali a conduzione familiare e specializzate nella produzione di prodotti tradizionali e regionali.
L’importanza vitale di questo settore a livello nazionale e internazionale ha portato l’Italia a creare varie certificazioni di qualità per i prodotti alimentari. Ad esempio, il marchio DOP (Denominazione di Origine Protetta) e il marchio IGP (Indicazione Geografica Protetta) garantiscono l’origine geografica e la qualità anche in vista dell’esportazione verso gli Stati Uniti, la Germania, la Francia, il Regno Unito, il Canada e la Cina, di cui l’Italia è uno di principali fornitori di prodotti alimentari.
Ad incrementare ulteriormente la notorietà dell’industria alimentare partecipa anche l’agricoltura biologica. L’Italia è uno dei principali produttori di alimenti biologici in Europa e grazie alla loro crescente popolarità, la produzione e la domanda sono aumentate considerevolmente.
Per assicurare questo successo, l’industria alimentare italiana non solo ha saputo puntare sulla qualità dei prodotti ma anche adottare tecnologie sempre più innovative per migliorare la propria produttività e garantire sicurezza, conservazione e distribuzione anche tenendo in mente la sostenibilità; un tema sempre più importante che sta spingendo il settore a ridurre l’impatto ambientale della propria produzione e promuovere pratiche sostenibili, come l’uso di imballaggi ecologici.
Ed è proprio in questo contesto di grande attenzione ai processi produttivi che Mayr® offre soluzioni come ROBA-contitorque, un eccellente limitatore di coppia ad
isteresi magnetica con mantenimento costante della coppia, e ROBA-capping head, teste di tappatura per impianti di riempimento, preziosi alleati della sicurezza ed efficienza dei macchinari per l’industria alimentare italiana.
Limitatori di coppia per eccellere in ogni processo
Molti macchinari utilizzati nell’industria alimentare eseguono lavorazioni particolarmente delicate o possono subire variazioni di carico durante il loro funzionamento. In tali casi ROBA-contitorque, un limitatore di coppia ad isteresi magnetica, può rivelarsi di estremo aiuto.
Limitando la coppia, il freno evita i sovraccarichi che potrebbero accadere anche durante il processo di separazione degli ingredienti nel caso di blocchi accidentali del materiale lungo la linea di produzione. Anche nel caso dei processi di taglio, separazione e confezionamento della carne, dove sono impiegati robot, un limitatore di coppia ad isteresi magnetica come ROBA-contitorque aiuta a mantenere la coppia costante e previene danni.
In particolare, le macchine per il confezionamento, come le sigillatrici o le etichettatrici possono trarre grande vantaggio da un limitatore di coppia, che può aiutare a prevenire danni alle etichette o al materiale di confezionamento nonché ridurre il rischio di blocchi o danni al macchinario.
Più in generale, tutti i macchinari utilizzati nell’industria alimentare che richiedono una lavorazione delicata, una velocità o una coppia costante e che possono essere soggetti a variazioni di carico durante il funzionamento possono trarre vantaggio dall’utilizzo di un limitatore di coppia ad isteresi magnetica con mantenimento costante della coppia come quello offerto da ROBA-contitorque. Questo tipo di dispositivo aiuta a garantire la sicurezza, la stabilità e la qualità del processo di produzione alimentare.
contatto tramite forze magnetiche, generate da magneti permanenti, che magnetizzano il materiale ad isteresi. ROBA-contitorque trasmette in maniera sincrona la coppia impostata da un albero di ingresso a un elemento di uscita. ROBA-contitorque è caratterizzato da una rapida e facile regolazione della coppia. In caso di sovraccarico se la coppia operativa supera la coppia limite impostata, i componenti di ingresso e uscita ruotano tra loro con una velocità relativa nota come velocità di slittamento. Il materiale ad isteresi viene costantemente magnetizzato e demagnetizzato e la coppia limite continua ad essere trasmessa con estrema uniformità. Dopo la rimozione del sovraccarico, la velocità relativa torna a zero e la coppia trasmessa tra i componenti di ingresso e uscita è quella operativa.
ROBA-contitorque fa uso di un’innovativa tecnologia a vite, che permette la regolazione continua della coppia, particolarmente adatta all’uso nell’industria alimentare ed è completamente esente da manutenzione.
Ma quali sono i principi di funzionamento e caratteristiche di tale dispositivo?
Un freno limitatore di coppia che fa la differenza
Il freno limitatore di coppia ROBA-contitorque è un prodotto innovativo che garantisce una frenatura affidabile e precisa ed è basato sul principio di funzionamento ad isteresi magnetica.
I freni di questo tipo sfruttano le proprietà dei materiali ferromagnetici per creare una coppia frenante sull’asse di rotazione dell’albero. Nel caso specifico di ROBAcontitorque, che può essere utilizzato sia come limitatore di coppia sia come freno, la coppia viene trasmessa senza
Per applicazioni speciali, un prodotto unico Nel settore dell’industria alimentare, il segmento del “beverage” rappresenta un’attività di primaria importanza. In questo settore, specializzato nella produzione e confezionamento di bevande, l’applicazione di tappi in plastica su bottiglie in PET è diventata predominante. Questo ha fatto emergere nuove esigenze produttive, come la richiesta di maggiore precisione e quindi requisiti più stringenti per l’avvitamento dei tappi, inclusa la necessità di una coppia di serraggio costante su tutti i tappi.
Mayr® ha risposto prontamente a questa sfida industriale proponendo ROBA-capping head. Si tratta di una testa di avvitamento ad isteresi con particolari caratteristiche e vantaggi d’uso. Il prodotto offre infatti un’avvitatura perfetta per bottiglie in PET e bottiglie in vetro senza reso. Si tratta di una soluzione a prova di corrosione, al contempo
compatta e a ingombro ridotto.
Al contrario dei giunti a magneti permanenti, le soluzioni ad isteresi garantiscono una coppia di serraggio estremamente costante e omogenea. Questo rende i giunti ad isteresi come ROBA-capping head più adatti per il serraggio dei tappi rispetto ai giunti a magneti permanenti con l’addizionale, e non secondario, vantaggio di offrire una durata di servizio considerevolmente maggiore.
In particolare, ROBA-capping head offre massima precisione di ripetitività della coppia di serraggio e un ottimo comportamento in presenza di sporco e di sostanze grazie alla resistenza alla corrosione e alla costruzione chiusa. La durata di ROBA-capping head è garantita dall’assenza di coppie di picco e alla tecnologia priva di vibrazioni, ma offre anche molti altri vantaggi. Tra essi emergono i coni di avvitatura ispezionabili disponibili per tutti i tappi standard, la semplice regolazione della spinta della testa nonché la sostituzione veloce della teste di avvitatura e delle parti superiori alla testa.
Queste caratteristiche rendono ROBA-capping head ideale per l’uso ovunque alta efficienza, precisione e qualità siano desiderati.
Il partner perfetto per l’industria alimentare Mayr® rappresenta un partner perfetto per l’industria alimentare grazie alla vasta selezione di prodotti offerti di cui ROBA-contitorque e ROBA-capping head rappresentano solo un esempio. Altri prodotti progettati e costruiti da Mayr® e perfetti per l’industria alimentare sono i giunti di sicurezza EAS-compact, EAS-compact F, EASsmartic, EAS-HTL e i giunti di trasmissione ROBA-DS (servo, acciaio), smartflex e ROBA-ES.
Con una gamma così ampia di opzioni disponibili, scegliere quella ottimale potrebbe rivelarsi complesso, ma May r® ha pensato anche a questo grazie al suo team di tecnici esperti in grado di fornire supporto nella selezione e ottimizzazione dei prodotti utili ad ogni applicazione.
La nuova tecnologia di movimento ad altissima scorrevolezza sviluppata da NSK per le guide lineari Serie NH/NS è la prima al mondo nel suo genere. Grazie all’uso di corpi volventi elastici, questa tecnologia brevettata raggiunge un profilo di attrito dinamico estremamente omogeneo ideale per apparecchiature di misura e controllo ad alta precisione. Le caratteristiche di basso attrito e fluidità di scorrimento delle guide lineari ne fanno un componente prezioso
per tutti i tipi di sistemi che richiedono un controllo di movimento ad alte prestazioni. Per questo motivo, le guide lineari NH/NS hanno un’ampia gamma di applicazioni, dagli impianti per la produzione di semiconduttori e schermi LCD agli impianti per l’industria automobilistica, dai robot trasportatori alle apparecchiature di ispezione e misura, fino alle macchine utensili. Oggi le apparecchiature utilizzate in queste applicazioni raggiungono livelli di sofisticatezza sempre più elevati. In particolare, le apparecchiature di ispezione e controllo più recenti richiedono movimenti ancora più fluidi e precisi, che pongono requisiti elevati alle guide lineari. Partendo da queste considerazioni, NSK si è dedicata allo sviluppo di una tecnologia di movimento ad altissima fluidità di scorrimento, ottimizzando la forma del percorso di ricircolazione delle sfere e utilizzando corpi volventi elastici per sopprimere i fenomeni di “micro-balbettii” (brevi sobbalzi durante il movimento causati da fluttuazioni localizzate dovute ad attrito). Questi accorgimenti riducono l’effetto della collisione fra le sfere nei tratti curvi del percorso di ricircolazione, aiutando a prevenire l’incremento dell’attrito e, di conseguenza, assicurando un movimento molto fluido. Oltre alle apparecchiature di ispezione e misura, le guide lineari di NSK con tecnologia di movimento ad altissima scorrevolezza portano benefici alle applicazioni con posizioni di esercizio verticali e altre posizioni di montaggio nelle quali le caratteristiche operative tendono a deteriorarsi. Inoltre, queste guide lineari innovative hanno dimensioni intercambiabili con le Serie NH/NS standard di NSK, agevolando la sostituzione di componenti attualmente installati senza alcuna modifica progettuale. La nuova tecnologia ad altissima scorrevolezza di NSK è disponibile per le guide lineari Serie NH 15, 20 e 25 e NS 15, 20, 25 e 30. Complessivamente, NSK può fornire 28 varianti con diverse lunghezze e tipologie di carrelli. Le unità sono compatibili con un’ampia gamma di optional, fra cui l’unità di lubrificazione NSK K1-L, configurazioni in acciaio inox e trattamenti speciali di superficie.
L’illustrazione mostra il meccanismo che sta alla base della tecnologia di movimento ad altissima scorrevolezza di NSK. A sinistra sono evidenziati il carrello, la rotaia, il percorso di ricircolazione delle sfere e i copri volventi elastici. A destra, il percorso ottimizzato di ricircolazione delle sfere e i corpi volventi elastici aggiunti.
“FACTORY OF THE FUTURE”
In settori quali l’edilizia, l’agricoltura e l’industria, è fondamentale che le macchine di movimentazione di materiali e sollevamento di persone siano caratterizzate da un elevato grado di affidabilità, nel rispetto delle normative più stringenti. Nel caso delle soluzioni con braccio telescopico, ad esempio, le norme della serie EN 1459, aggiornate nel 2020, determinano nel dettaglio i requisiti di sicurezza, con particolare riguardo all’avviamento, ai dispositivi di stabilizzazione e ai sistemi di sollevamento. Contare su un parco sensori di prim’ordine rappresenta, pertanto, un must per gli operatori del settore. In tal senso, Manitou Italia - azienda parte del Gruppo Manitou, multinazionale specializzata nella produzione di soluzioni per la movimentazione dei materiali e il sollevamento delle persone – si affida ai sensori Gefran - multinazionale italiana specializzata nella progettazione e produzione di sensori, strumentazione per il controllo di processi industriali e sistemi per l’automazione – per soddisfare ogni esigenza applicativa, anche la più complessa.
In oltre 60 anni di attività, Manitou Italia si è affermata come Azienda di riferimento per il mercato, con una gamma ampia, modulare e versatile: dai sollevatori telescopici ai carrelli elevatori, dalle piattaforme aeree ai
carrellli imbarcati, fino alle attrezzature per il magazzinaggio. In virtù del suo consolidato know-how, Manitou Italia propone numerosi accessori, come pinze, benne e argani, che completano l’offerta in funzione della destinazione d’uso. A ciò si aggiungono i progetti custom, per soddisfare specifiche istanze da parte dei Clienti in ambito ad esempio aeronautica, difesa e attività estrattive. Il Gruppo, quotato alla borsa di Parigi, ha capitalizzato nel 2022 oltre 2,4 miliardi di euro in 140 paesi e impiega attualmente 5.000 dipendenti.
“Manitou è da sempre sinonimo di eccellenti prestazioni delle macchine, comfort dell’utente, un ridotto Total Cost of Ownership e impatto ambientale delle macchine.” dichiara Alessandro Tonini, Manager Purchasing di Manitou, che prosegue “Nel nostro settore, i fattori chiave sono la versatilità e la sicurezza degli operatori. Quest’ultimo aspetto si traduce nella necessità di avvalersi di sensori tecnologicamente avanzati ed estremamente precisi, come quelli di Gefran, affinché le macchine siano in grado di auto-spegnersi o fermarsi in caso di pericolo durante la movimentazione”.
In particolare, i trasduttori di posizione lineari a filo GSH, senza contatto, sono impiegati per il rilevamento
dell’estensione del braccio di gru o piattaforme aeree, oltre che nei bracci di estensione dei piedi di stabilizzazione veicolo, grazie alle dimensioni estremamente compatte (64 mm). Alle sonde KH, dotate di elettronica SMD di ultima generazione e certificate SiL2, viene affidato il compito di misurare la pressione dei circuiti idraulici. Infine, gli inclinometri GIB, con grado di protezione IP67 e tecnologia MEMS, rilevano l’inclinazione della cabina di guida, al fine di prevenire il ribaltamento del mezzo.
“Le motivazioni alla base della pluriennale partnership sono strettamente correlate a tre fattori essenziali. In primo luogo, Gefran è per noi un One Stop Supplier: oltre a offrire tutti i sensori di cui abbiamo bisogno ovvero dai sensori filo-stabilizzatori, di pressione o posizione, fino agli inclinometri, rispetta le tempistiche concordate e semplifica le operation delle nostre linee di assemblaggio. In secondo luogo, Gefran si distingue per la sua expertise tecnologica, alla base della sinergia tra i nostri rispettivi Uffici Tecnici, grazie a cui co-progettiamo soluzioni innovative in tempi decisamente rapidi ” afferma Alessandro Tonini, che conclude “Ne è una dimostrazione concreta l’avviamento di progetti inediti, in un’ottica di miglioramento continuo. Fattore, quest’ultimo, che non può che aumentare la nostra soddisfazione nel collaborare con un partner di qualità come Gefran”.
“Gefran e Manitou Italia, due Aziende unite da una visione comune: da una parte, l’attenzione al Cliente, sempre al
centro e, dall’altra, il focus sull’innovazione.” commenta Renzo Privitera, Direttore Vendite Italia Sensori e Componenti di Gefran, che prosegue “Manitou Italia trova in Gefran un’offerta ampia e performante, un’elevata affidabilità delle forniture e un’assistenza di primo livello. In virtù dei traguardi raggiunti con Manitou Italia, Gefran sta attivando ulteriori collaborazioni con i siti produttivi di Manitou nel mondo”.
La documentazione della Linea Hercules si rifà il look: i cataloghi della gamma Lightech e Distritech offrono ai professionisti del settore una veste grafica più attuale e aggiornata, oltre a nuovi e interessanti prodotti. Stiamo parlando di una gamma di soluzioni da subito impostasi sul mercato, perché l’utilizzo di energia sicura nei settori industriali e commerciali richiede sicurezza, affidabilità e anche design. La Linea Hercules di DKC, con i suoi condotti sbarre, racchiude proprio questi canoni e si differenzia dai competitor per la sua versatilità, adattandosi alla perfezione in contesti di grande, media e piccola potenza richiesta. Delle tre serie che caratterizzano la gamma Hercules, il catalogo della linea Lightech – dedicata a condotti sbarre con corrente nominale da 25A e da 40A per le piccole utenze – è quello dal restyling più d’impatto. La grafica è raffinata e minimale, definendo con chiarezza i tratti essenziali della gamma e del Gruppo e allineandosi ai più moderni strumenti di marketing di DKC con una comunicazione visual contemporanea. All’interno, una chiara divisione dei prodotti, tutti corredati da testi bilingue che inquadrano ogni differente soluzione e ne definiscono le caratteristiche tecniche.
Il risultato è un vero e proprio progetto, che consente ai
professionisti di settore di essere guidati nella scelta e nell’applicazione con completezza e preparazione.
Di tipo contenutistico è invece l’intervento riservato alla serie Distritech, specifica per i condotti sbarre con conduttori in alluminio per il supporto di correnti nominali da 160A a 800A. La gamma, infatti, si è arricchita delle cassette di derivazione in plastica disponibili in quattro modelli – vuota, con base portafusibili, predisposta per interruttori modulari e prese industriali – con portata da 32A fino a 160A. Ciascuno dei cataloghi è stato poi fornito della codifica Metel, un formato completo e relativamente complesso per i fornitori di materiale elettrico con la finalità di utilizzo per l’interscambio dei dati.
Con questi upgrade, DKC conferma la centralità che ripone da sempre verso i propri clienti: sono loro, infatti, la principale guida per un costante miglioramento delle tecnologie così come degli strumenti destinati ad affiancarli. Attraverso la sinergia tra team tecnici e forza vendita, DKC assicura l’ottimizzazione delle proprie Linee anche attraverso un servizio di consulenza e assistenza che vede nei cataloghi e nelle diverse declinazioni del marketing il punto di partenza per un rapporto costante di fiducia e crescita competitiva.
Gli impianti di filtrazione centralizzati (ZFA) di Vomat sono costituiti da moduli separati configurabili in molteplici modi. Vomat assembla i componenti necessari in base ai requisiti di sistema dell’utente. Se variano le esigenze o le capacità produttive, è possibile ampliare il sistema con un’apposita pianificazione preventiva.
Per garantire un’affilatura di utensili conveniente, sicura e di alta qualità è indispensabile disporre di oli di rettifica estremamente puliti. Per questo, oltre agli impianti di filtrazione singoli e compatti della serie FA, l’azienda Vomat, con sede nella cittadina tedesca di Treuen, offre anche impianti di filtrazione centralizzati (ZFA) estremamente flessibili che si possono collegare a più affilatrici. Il grande vantaggio di questi impianti consiste nella struttura a moduli separati abbinabili in molteplici modi. Vomat mette a disposizione i componenti necessari in funzione delle esigenze del sistema. Se variano le esigenze o il volume di produzione, è possibile ampliare il sistema con un’apposita pianificazione. In questo modo si ottiene il massimo delle prestazioni nelle diverse fasi produttive e di sviluppo dell’azienda, sempre perfettamente in linea con le esigenze specifiche dell’utente.
Vomat è una nota azienda specializzata nella microfiltrazione dei lubrorefrigeranti nell’industria della lavorazione dei metalli. La sua ampia gamma di prodotti comprende soluzioni per impianti singoli, impianti centralizzati e configurazioni speciali su misura con funzioni centralizzate e decentralizzate. Steffen Strobel, responsabile vendite di Vomat, afferma: “I nostri impianti centralizzati sono ideali per la rimozione del particolato che si accumula negli oli durante i processi di rettifica, levigatura, lappatura, erosione e altri processi analoghi. Anziché utilizzare complicati processi di bypass, durante il controlavaggio le nostre macchine lavorano con una filtrazione a flusso pieno precisa e adeguata alle necessità. Il ciclo automatico si adatta pertanto al grado di sporcizia. Ciò significa che l’olio esausto viene separato da quello pulito al 100%. Inoltre, grazie ai nostri innovativi filtri prestrato lavabili ad alte prestazioni, non è più necessario l’uso di costosi coadiuvanti di filtrazione.”
Sistema modulare flessibile
Gli impianti di filtrazione centralizzati ZFA Vomat sono composti da moduli separati. Il loro vantaggio risiede nella versatilità. I moduli vengono assemblati in base ai requisiti di sistema dell’utente. Il modello base degli impianti di filtrazione centralizzati Vomat è lo ZFA 1200, la cui unità filtrante presenta dimensioni compatte di 1200 x 1200 x 2200 mm (lungh. x largh. x alt.). Il grado di efficienza filtrante è di 3-5 µm. Stef-
fen Strobel spiega: “Grazie alle speciali caratteristiche di progettazione, anche durante il controlavaggio è disponibile in modo costante anche olio pulito di qualità NAS 7.
L’unità di raffreddamento a controllo PLC è dimensionata in base alle esigenze del processo di produzione. La precisione di regolazione arriva fino a +/- 0,2 K. La dispersione del calore è ottenuta tramite un condensatore esterno. A richiesta, Vomat offre anche un sistema di raffreddamento ad acqua.
Vomat fornisce pompe di alimentazione a consumo energetico ottimizzato in base alla potenza delle macchine. La configurazione degli impianti su misura per il cliente assicura la riduzione al minimo del volume di smaltimento e perdite di trascinamento trascurabili. Lo smaltimento dei materiali avviene in maniera del tutto automatica, tramite un sedimentatore, direttamente nei contenitori di trasporto delle aziende addette al riciclaggio.
Il comando centralizzato si occupa del collegamento dei
moduli e della gestione dei componenti esterni, come le pompe di alimentazione delle macchine. Inoltre, la funzione di controllo remoto consente di svolgere le attività di sorveglianza e manutenzione a distanza. Steffen Strobel aggiunge: “Vomat offre grandi impianti di filtrazione centralizzati su misura per ogni tipo di produzione e scalabili a passi di 1200 litri. L’ampia varietà dell’offerta di moduli e accessori opzionali assicura la massima flessibilità. Grazie ai nostri impianti di microfiltrazione di nuova generazione, i lubrorefrigeranti con un grado di pulizia elevato possono rimanere nel sistema per periodi di tempo molto più lunghi rispetto ai sistemi di filtrazione tradizionali. In questo modo aumenta anche la durata delle mole affilatrici. Nel complesso, il lavoro di manutenzione e il consumo energetico si riducono nettamente, mentre la riduzione dei tempi di fermo delle macchine abbassa ulteriormente i costi di produzione. Nel complesso, è possibile ottenere una microfiltrazione dei lubrorefrigeranti più redditizia e a basso consumo di risorse.”
Il volume di smaltimento viene ridotto al minimo con perdite di trascinamento trascurabili. I materiali da smaltire vengono scaricati in maniera del tutto automatica nei contenitori di trasporto delle aziende addette al riciclaggio tramite un sedimentatore.
Editore: Quine srl, via Spadolini, 7 - 20141 Milano - tel. +39 02.86.41.05 - E-mail: abbonamenti@quine.it
Attivazione immediata
Invia questo modulo compilato a: abbonamenti@quine.it abbinando copia della ricevuta di pagamento
Sì desidero abbonarmi a
1 anno (4 numeri ) Euro 25,00 (Italia)
Assegno non trasferibile intestato a Quine srl - via Spadolini, 7 - 20141 Milano
Bonifico a favore di Quine srl - Credito Valtellinese, ag.1 di Milano - IBAN: IT88U052160163000000000855 (ALLEGARE COPIA)
CREDIT CARD N.
TITOLARE
*Ii CVV è il codice di tre cifre posizionato sul retro della carta di credito dopo i numeri che identificano la carta stessa per il circuito Visa