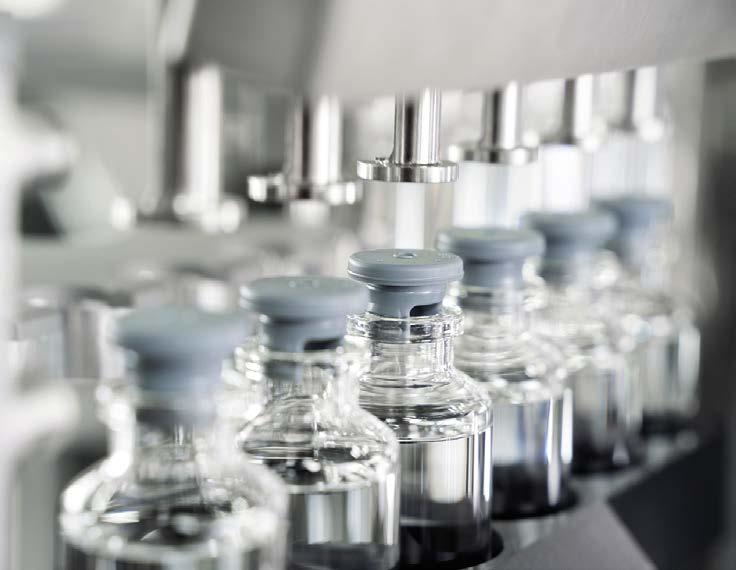
6 minute read
Injecta di IMA Life: flessibilità e tecnologia
FOCUS ON
Di Maria Rossi
“INJECTA” DI IMA LIFE: FLESSIBILITÀ E TECNOLOGIA

AL SERVIZIO DELL’INDUSTRIA FARMACEUTICA
L’INNOVATIVA SOLUZIONE PER RIEMPIRE SIRINGHE E FLACONI STERILIZZATI IN AMBIENTE ASETTICO SI AVVALE DEI ROBOT KAWASAKI DI MANIPOLAZIONE FORNITI DALLA TIESSE ROBOT
La richiesta di maggiore flessibilità, velocità, precisione e qualità nel processo di riempimento e chiusura (fillfinish) di prodotti iniettabili in contenitori Ready-To-Use quali flaconi, siringhe e carpule, è costante che da sempre caratterizza il comparto del medicale. Una tendenza accelerata, negli ultimi anni, dai nuovi prodotti farmaceutici e dalla crescente pressione degli enti regolatori. Per stare al passo, le aziende farmaceutiche ed i Contract Development Manufacturing Organizations (CDMOs) devono essere in grado di gestire un’ampia varietà di tipi di container e formati di confezionamento. L’utilizzo della robotica in impianti operator-less o glove-less, che possono escludere la presenza dell’operatore in attività critiche come l’introduzione di materiale sterile o la manipolazione di tools mediante guanti, è fondamentale ed è stato fortemente sollecitato dalle authority internazionali per evitare i rischi di contaminazione connessi all’intervento umano, la possibilità di commettere errori ed il mancato rispetto delle procedure operative.
IMA e la soluzione INJECTA
La serie INJECTA di IMA Spa Life Division di Bologna è il risultato di sei anni di progettazione e sviluppo condotti da un team di esperti aziendali, il primo costruito attorno ad un concetto completamente robotizzato. I tentativi convenzionali di
utilizzare i robot sono in genere limitati ad una sola fase produttiva, come spostare flaconi o siringhe da una stazione all’altra oppure rimuovere il tyvek da un tub o tray. INJECTA, invece, sfrutta tutto il potenziale dei suoi robot. Grazie alla tecnologia robotica integrata, offre innumerevoli vantaggi: in primis la riduzione del footprint di impianto, grazie alla configurabilità del sistema che permette di usare un’unica macchina per affrontare diverse tipologie di riempimento, formati e processi. Quindi differenti soluzioni per alimentare i container pre-sterilizzati inseriti in Tub/ Tray (flaconi, siringhe, carpule) attraverso metodi “no-touch” oppure, nel caso di flaconi, in Bulk tramite collegamento con tunnel depirogenanti. Altri benefit sono la compressione dei tempi di changeover, in quanto l’elevata flessibilità per la manipolazione multi-prodotto e multiformato consente il passaggio rapido tra i diversi prodotti farmaceutici ed il confezionamento primario del prodotto; la possibilità di decontaminazione automatica con perossido di idrogeno vaporizzato a inizio produzione e di procedure automatizzate di lavaggio e de-attivazione a fine campagna, in caso di prodotti tossici o biologicamente attivi. Si riducono chiaramente al minimo le operazioni manuali, evitando di contaminare la camera sterile ed attivando un perfetto controllo delle traiettorie, che minimizza il rischio di passaggio su zone critiche. Abbiamo anche una configurabilità di tutte le fasi di processo di fill-finish, attraverso ricette selezionabili via pannello di controllo, con un minimo apporto di regolazioni di tipo meccanico. Infine, la possibilità di un controllo accurato della movimentazione nelle fasi critiche, come il posizionamento dei contenitori su bilance per l’IPC di processo o durante le fasi di filling. Le soluzioni integrate con INJECTA sono costituite da diversi moduli, ognuno dotato di uno o più robot Kawasaki in grado di automatizzare l’intero processo produttivo e che possono essere configurati per creare layout a seconda delle esigenze produttive e
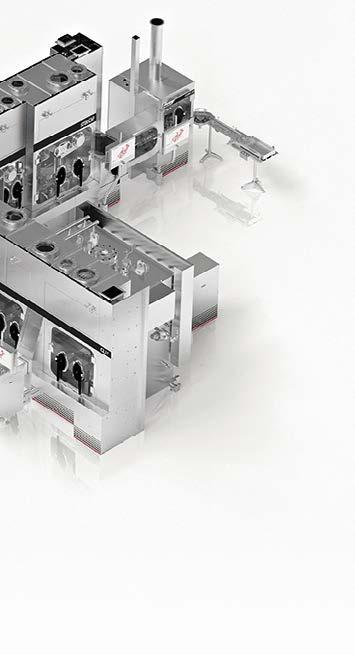
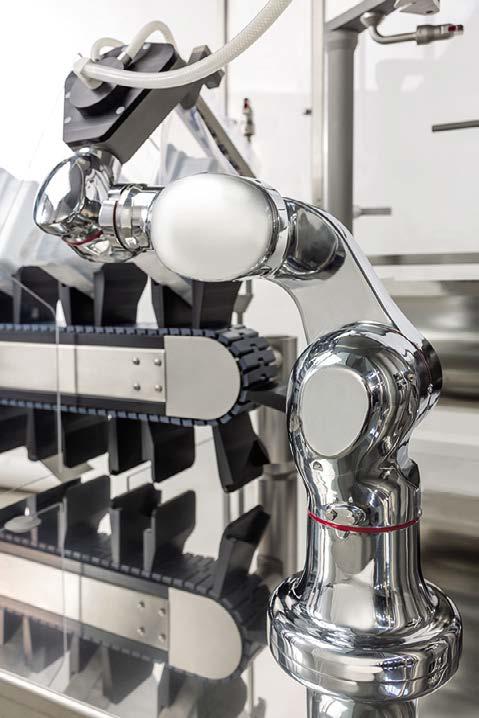
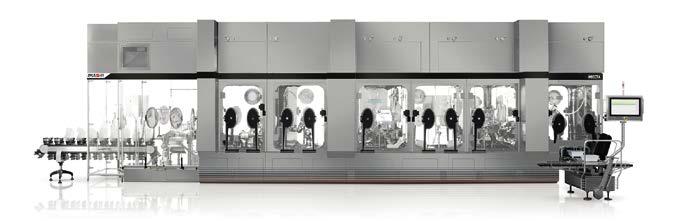
del protocollo richiesto. Il modulo iniziale di apertura busta è il punto di ingresso per tub o tray imbustati, ricevuti dal nastro caricato dall’operatore in cleanroom. Il braccio robotico preleva il package attraverso una pinza afferrante i lembi della busta; un cutter automatico la apre sul bordo, mentre la pinza robot la mantiene chiusa preservando l’interno sterile dalla contaminazione. Il robot Kawasaki porta quindi la busta alla camera successiva, in un sistema “docking station” che esegue il passaggio del tub/tray con approccio “no-touch-transfer” o NTT, senza ricorrere a processi di decontamina o compromettere il contenitore interno e la classificazione dell’area. Il modulo di apertura busta viene integrato all’interno di un Open RABS (Restricted Access Barrier System) che limita la contaminazione particellare e microbiologica e, a seconda del package (singola o doppia busta), spinge il tub/tray nella camera successiva. A valle, nella prima camera in condizione asettica, quindi isolata e decontaminata in modo da raggiungere un Grade A farmaceutico, viene aperto il tub/tray, rimuovendo il tyvek superiore ed il lid interni. L’operazione è eseguita da un braccio robotizzato Kawasaki dotato di pinze e ventose, che sfrutta specifiche traiettorie evitando il passaggio sopra alla zona esposta e massimizzando il lavaggio dei contenitori con il flusso laminare nell’isolatore. Infine, il sistema procede al modulo di de-nesting dove verranno estratti i contenitori per il riempimento e tappatura (fill-finish), controllato al 100% tramite bilance posizionate sotto al punto di ripartizione del prodotto in ogni flacone o siringa. INJECTA può eseguire un riempimento “in nest”, quindi senza togliere i contenitori dal nest di trasporto, e de-nesting, cioè con estrazione del contenitore singolo dal nest/ tray. La successiva operazione prevede la tappatura del flacone o l’inserimento del plug all’interno della siringa/carpula. In caso di prodotti liofilizzati, la linea è collegata a sistemi di carico/scarico per/dai liofilizzatori; viceversa, i flaconi procedono verso la zona di ghieratura dove verrà applicata la ghiera in alluminio e sigillato definitivamente il contenitore.
Il robot Kawasaki MC004-V
INJECTA è stata sviluppata con un approccio integrato fra tre componenti fondamentali: macchina, isolatore e robot. Per l’impiego dei robot, IMA Life ha identificato un partner strategico in grado di seguire tutte le fasi di sviluppo proponendo soluzioni innovative per il settore farmaceutico. I robot Kawasaki MC004-V sono stati forniti da Tiesse Robot di Visano (Bs), leader nell’automazione industriale e storico partner di Kawasaki Robotics. Il modello è dotato di 6 gradi di libertà, coating VPHP resistant, payload di 4 kg, grado IP65, polso cavo con cavi e tubazioni completamente integrati. Gli esperti del team IMA Life-Kawasaki hanno scelto il Fraunhofer Ipa per eseguire tutti i test di laboratorio volti a validare l’uso del robot Kawasaki MC004-V in area asettica, dall’hygienic design della meccanica e dei componenti esterni alla valutazione dell’efficacia di lavaggi manuali ed automatizzati con metodi basati su residui di liquidi di contrasto visibili con UV (riboflavina), mentre per gli aspetti di decontamina è stata testata la resistenza a perossido di idrogeno vaporizzato ed anche l’impatto sulla riduzione logaritmica della carica microbiologica nel tempo (D-value). Per quanto riguarda il profilo del robot dal punto di vista aerodinamico, sono stati eseguiti degli smoke test sotto flusso laminare. Una delle principali difficoltà nello sviluppo della macchina INJECTA è stata quella di identificare un partner affidabile come Tiesse Robot e Kawasaki, disposto a seguire IMA Life nello sviluppo di un robot con caratteristiche e finiture adeguate all’ambiente asettico, vincolato alle stringenti norme per la produzione di iniettabili. A livello europeo, la principale linea guida di riferimento è la cGMP Annex 1-Manufacture Of Sterile Medicinal Products, che ha il proprio corrispettivo in ambito nord americano nella FDA. Avere robot adeguati ad essere integrati in Grade A area, dove sono presenti processi farmaceutici critici, come il riempimento e la tappatura, impone requisiti che spesso impattano in modo radicale sul design meccanico e sulle performance del sistema antropomorfo. Flessibilità e semplicità nel controllo e nella programmazione non sono poi un aspetto secondario, poiché bisogna realizzare traiettorie parametrizzate tali da raggiungere gli obiettivi di tempo ciclo, accuratezza e ripetibilità. È importante poter interfacciare il robot con diverse tipologie di pinze, ventose e tool intercambiabili. Per evitare la presenza di tubi e cavi scoperti in area asettica, si è cercata una soluzione che ne preveda il passaggio all’interno del corpo del robot. Il ricorso a manipolazioni robotizzate avanzate durante tutte le operazioni di produzione, dall’apertura della busta esterna/interna alla stazione di tappatura, ha consentito un processo di produzione molto fluido, riducendo drasticamente i rischi di cross-contamination.
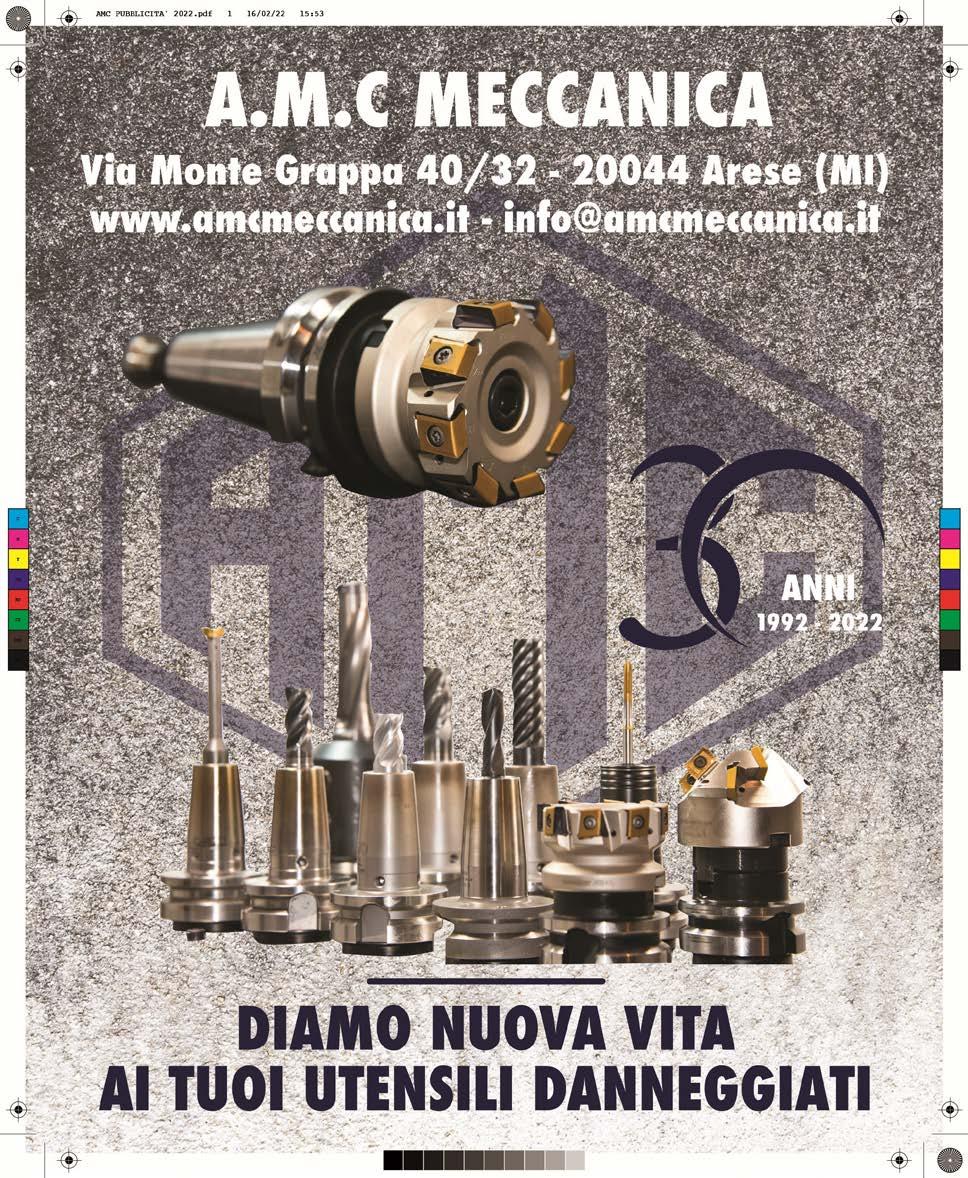
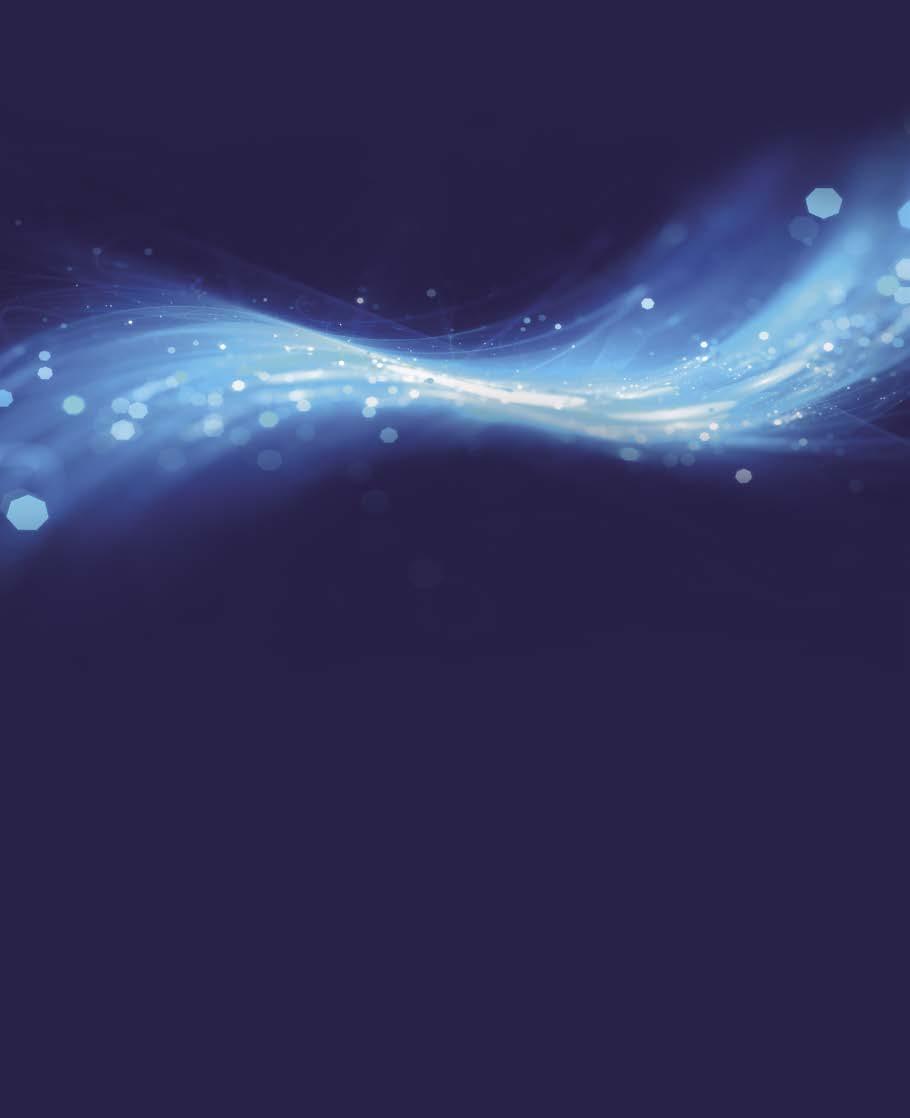