
6 minute read
L3, il laser secondo Salvagnini
SALVAGNINI
L3 È LA SOLUZIONE PRODUTTIVA E VERSATILE, A CONSUMI RIDOTTI E COSTI DI ESERCIZIO COMPETITIVI, CHE RISPETTA L’AMBIENTE, L’UOMO E IL SUO LAVORO
Testa bevel cy-laser soluzione a 5 assi con cianfrinatura variabile
LL3 di Salvagnini è un laser fibra produttivo e versatile, con consumi ridotti e costi di esercizio competitivi, destinato ad un utilizzo trasversale, indipendente da applicazioni, materiali e spessori perché è equipaggiato con una testa di taglio unica che consente di tagliare tutti gli spessori e i materiali lavorabili.
“L3 è un laser agile,” spiega Pierandrea Bello, Product Manager Salvagnini per le tecnologie laser. “Le sue numerose funzioni proprietarie, l’interfaccia uomo-macchina FACE e i sistemi di visione artificiale consentono all’operatore di risolvere senza sforzo i problemi che quotidianamente incontra nel proprio lavoro. E risponde perfettamente alle tendenze di mercato che hanno contribuito negli ultimi anni a ridefinire lo scenario del taglio laser: il recupero di autonomia ed efficienza da una parte, la riduzione dei costi operativi dall’altra.”
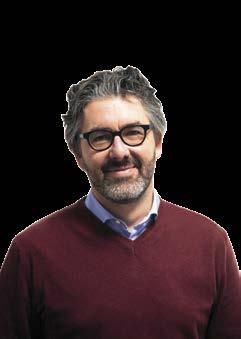
Recuperare efficienza con automazione e visione artificiale
“Per parlare di recupero di autonomia e efficienza dobbiamo parlare di automazione e di applicazioni di visione artificiale,” riprende Bello. “La gamma di automazioni laser Salvagnini è ampia e modulare: magazzini a torre o a vassoi, diverse soluzioni di carico/carico, dispositivi di sorting automatico o manuale. A fiera Lamiera presentiamo ufficialmente anche ADC, una nuova automazione compatta per carico e scarico della lamiera che estende ulteriormente la nostra gamma con una soluzione a ingombro ridotto. I suoi punti di forza sono proprio la compattezza, il tempo ciclo rapido e l’installazione veloce. Anche ADC, come tutte le nostre automazioni, utilizza per le attività di carico/scarico pettini dotati di cinghioli, che depositano la lamiera facendola scivolare piano piano: un’accortezza che sostanzialmente azzera il rischio di danneggiare il materiale o le parti tagliate.”
Per semplificare ulteriormente alcune attività che possono richiedere tempo, generare errori o scarti – e quindi ridurre l’efficienza complessiva del sistema – i laser Salvagnini possono essere dotati anche di alcune applicazioni di visione artificiale. Sono soluzioni semplici, che accrescono la flessibilità del sistema e ne estendono i campi di applicazione. AVS trasforma il taglio laser in una stazione di lavoro a valle rispetto a precedenti attività di punzonatura, garantendo massima precisione delle parti tagliate. NVS verifica il centraggio del fascio laser e, grazie agli algoritmi di machine learning, monitora lo stato dell’ugello per ridurre gli scarti. SVS permette di recuperare sfrido e spezzoni di lamiera per rispondere alle urgenze o per sostituire eventuali scarti nelle lavorazioni a valle. “E un’altra interessante novità che presenteremo a Milano riguarda proprio SVS,” aggiunge Bello. “Abbiamo dotato SVS di un’ulteriore funzionalità, quella dell’allineamento foglio, in alternativa al sensore capacitivo o ad AVS. Nell’allineamento con sensore capacitivo la testa di taglio deve posizionarsi nei classici 3 punti ed eseguire il rilievo. Il rilievo con AVS è più rapido perché i punti sono solo 2, mentre con questa nuova versione di SVS possiamo completamente eliminare i rilievi perché l’allineamento avviene subito dopo il cambio pallet attraverso le telecamere di SVS e senza richiedere spostamenti della testa. La lamiera viene caricata in macchina, le telecamere di SVS identificano il formato di partenza con la stessa precisione del rilievo con sensore capacitivo. Non è una nuova opzione, ma un aggiornamento di un’opzione già a catalogo che oggi può fare qualcosa in più: non permette soltanto di recuperare sfridi e spezzoni, ma anche di ridurre il tempo ciclo eliminando la fase di allineamento senza rinunciare alla precisione.”
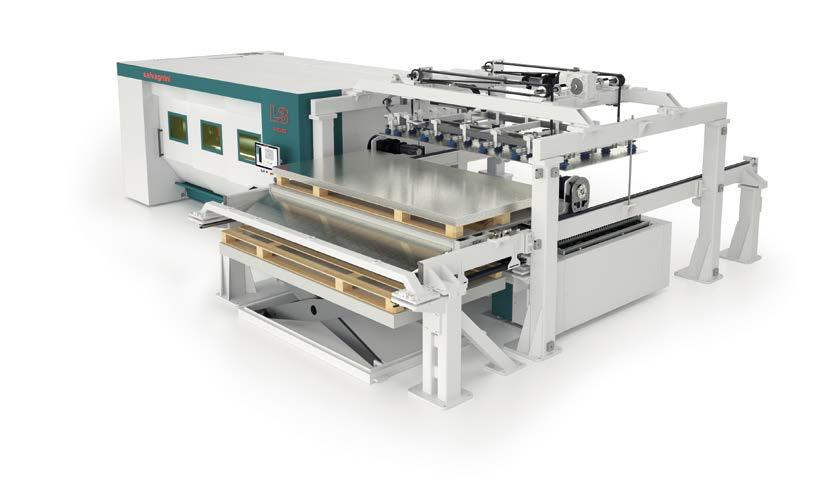
Ridurre i costi operativi: taglio in aria compressa e software
Per quanto riguarda la riduzione dei costi operativi, la progressiva affermazione delle sorgenti in fibra ha stravolto il costo orario dei sistemi laser. La loro elevata efficienza ha notevolmente ridotto i consumi energetici, mentre le loro caratteristiche intrinseche hanno permesso di ridurre i costi di manutenzione ordinaria e straordinaria. L’aumento delle velocità di taglio ha permesso di ridurre anche i tempi di lavorazione, e di conseguenza il costo pezzo.
“Il costo del gas era una delle poche voci a restare invariate,” dice ancora Bello. “L3 è nativamente predisposta per il taglio in azoto e in ossigeno, ma proprio per ridurre i costi operativi abbiamo introdotto l’opzione ACUT, che consente ai nostri laser di tagliare con aria compressa opportunamente trattata. Il taglio in aria compressa è più economico di quello in azoto, e questo è tanto più vero all’aumentare del costo al m3 dell’azoto: maggiore è il costo dell’azoto, maggiore è la convenienza del taglio in aria compressa. La produttività è molto simile, mentre la qualità dipende dall’applicazione: i riscontri che abbiamo dal mercato indicano che il taglio in aria sia sempre più accettato. L’evoluzione di ACUT è stata rapida: oggi, in base alla potenza della sorgente, permette di tagliare in aria compressa spessori fino a 20mm. La scelta di introdurre una sorgente da 10 kW si spiega anche così, per tagliare alti spessori pur riducendo la dipendenza dall’azoto. Ma a questo risultato ha contributo anche la testa di taglio di terza generazione, progettata da Salvagnini, ideale per le alte potenze.”
È una testa di taglio unica, che consente di tagliare tutti gli spessori e i materiali lavorabili e che contribuisce a migliorare l’efficienza del laser grazie alla sensoristica evoluta di cui è dotata. Il sistema brevettato DRY-COOLING esegue il controllo attivo della temperatura delle ottiche, mentre i sensori di processo di cui è provvista controllano e adattano in tempo reale le fasi di sfondamento e permettono il monitoraggio di eventuali perdite di taglio, arrestando il processo e riavviandolo con parametri opportunamente corretti. La funzione TRADJUST, integrata nel controllo proprietario, consente la modulazione automatica dei parametri in funzione delle traiettorie per rendere il sistema più semplice da usare. “Parlando di taglio in aria compressa, credo sia davvero impossibile non citare anche l’opzione APM,” spiega ancora Bello. “Si tratta di un sistema compatto e chiavi in mano, che si collega direttamente alla rete pneumatica aziendale o a un compressore a monte del sistema. APM normalizza i valori di pressione, filtraggio ed essicazione dell’aria compressa ottimizzandoli per il taglio in aria, e evita spese in compressori dedicati. Considerati i costi attuali dei gas, il ritorno dell’investimento per le opzioni ACUT e APM è inferiore ad 1 anno. Superato questo periodo il risparmio è notevole.”
E l’impatto positivo si percepisce anche nel lavoro quotidiano, perché ridurre il consumo di gas significa ridurre il numero degli approvvigionamenti: questo significa ridurre i costi di trasporto e i costi fissi, ma anche ridurre l’entropia dell’officina.
“Anche il software può dare un contributo alla riduzione dei costi operativi. Il nostro software dedicato ai programmi di taglio si chiama STREAMLASER, e fa parte della nostra suite di programmazione STREAM. Oltre a funzioni che consideriamo standard, come la definizione automatica di attacchi, sequenze di taglio e nesting su cui il programmatore può poi intervenire in modo interattivo, ha due caratteristiche distintive orientate proprio a migliorare l’efficienza del materiale, e quindi a ridurre i costi. La prima è SAFE GRID, che ottimizza automaticamente il posizionamento delle parti rispetto alle griglie evitando la sovrapposizione di sfondamenti, attacchi e tagli sull’asse Y. SAFE GRID riduce l’usura delle griglie, i costi di manutenzione, ma migliora anche la qualità delle lavorazioni e l’affidabilità del laser. La seconda è OPTI, l’algoritmo di nesting, che ottimizza l’utilizzo del foglio di lamiera riducendo al minimo lo sfrido. Un bel vantaggio, pensando a quanto sia aumentato il costo della lamiera negli ultimi mesi,” conclude Bello.
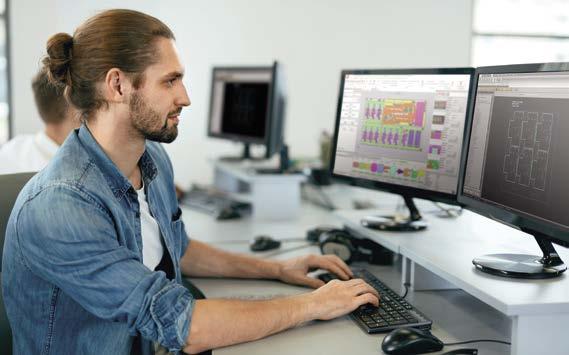