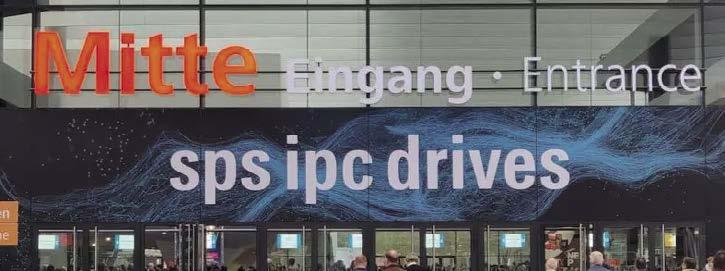
79 minute read
Prodotti
L’AUTOMAZIONE VI ASPETTA A SPS NORIMBERGA
Dall’8 al 10/11/2022 saranno presentati a Norimberga i prodotti e le soluzioni più innovative nonché le tecnologie avveniristiche per l›automazione industriale
Lo scorso 12 luglio a Milano i è tenuta la conferenza stampa di presentazione della 31 edizione di SPS Norimberga. Alla manifestazione di quest’anno sono attesi circa 1.100 espositori provenienti da tutto il mondo, per una superficie complessiva di 100.000 mq. Anche quest’anno sarà attiva la piattaforma digitale integrativa “SPS on air” per una visione completa del mercato. La piattaforma infatti farà da presentazione di SPS con una serie di eventi preparatori; durante la manifestazione permetterà una miglior organizzazione di appuntamenti e incontri e, non ultimo continuerà a fornire anche dopo la conclusione dell’evento l’accesso a contenuti e collegamenti in rete.
Un vasto programma di conferenze SPS fornirà informazioni su argomenti attuali provenienti dal settore dell’automazione. Tale programma si svolgerà al forum comune delle associazioni VDMA e ZVEI in fiera nel padiglione 3 nonché nel Live Studio a Norimberga attraverso l’integrazione digitale “SPS on air”. Quest’anno gli argomenti principali delle tavole rotonde, delle presentazioni di prodotti o delle conferenze saranno: • Trasformazione digitale/Industria 4.0 • Comunicazioni industriali • Sicurezza e protezione • Nuovi metodi logistici e integrazione di robot • Modelli di controllo e visualizzazione intelligenti e
basati sui dati • Sensori intelligenti • Drives • Casi di utilizzo dell’intelligenza artificiale • Sostenibilità nell’automazione Nel padiglione 6 lo stand collettivo ”Automation meets IT” con circa 16 espositori offrirà ai visitatori la possibilità di informarsi approfonditamente su temi specifici e di ricevere una consulenza individuale da parte dei fornitori. Le tematiche trattate allo stand collettivo saranno le seguenti: • Gestione del patrimonio • Servizi basati su cloud • Servizi incentrati sui dati • Manutenzione preventiva • OPC Unified Architecture Punto di fondamentale importanza resta la tutela della salute degli espositori, dei visitatori, dei Service Partner e dei collaboratori, che per l’organizzatore ha la massima priorità. Allo stato attuale la fiera si potrà svolgere senza l’applicazione di misure anti-Covid. Qualora in autunno venissero applicate nuove norme di igiene o misure di contrasto alla diffusione del coronavirus, ovviamente saranno rispettate. Informazioni più dettagliate sul programma della fiera, sull’acquisto dei biglietti, sulla manifestazione ibrida e sulle offerte speciali di viaggio nonché suggerimenti per la preparazione, sono disponibili sul sito web sps-messe. de.
CMASIC DI WIBU-SYSTEMS
Sinergie tra la tecnologia CodeMeter per la protezione e la distribuzione sicura dei beni digitali e il mondo embedded
Wibu-Systems, l’azienda creatrice di CodeMeter, la famosa soluzione per la protezione e la concessione in licenza di software, firmware e dati sensibili, è al servizio di utenti di ogni settore, dai normali editori di software agli ingegneri dell’automazione industriale o agli sviluppatori di elettronica. CmASIC, il piccolo ma potente elemento hardware sicuro, apporta tutte le funzionalità di protezione e gestione licenze tipiche della tecnologia CodeMeter al mondo embedded e alla scena IoT, rendendolo un concorrente favorito per l’edizione 2023 del GIT Security Award. Con un chip smart card, incapsulato in un packaging dalle dimensioni estremamente ridotte, i CmASIC presentano il minimo ingombro tra le soluzioni hardware della linea CodeMeter. Caratterizzati da basso consumo, intervallo di temperatura operativa esteso, certificazione CC EAL5+, includono due interfacce per una connettività flessibile: USB o SPI. Il modulo è stato concepito per facilitarne l›inserimento su circuiti stampati o all›interno di altri sistemi o dispositivi embedded, in alternativa a soluzioni esterne rappresentate da dongle USB (CmStick) o carte di memoria (CmCard). I CmASIC sono pienamente compatibili con l’intera gamma di contenitori licenze CodeMeter, siano essi hardware (CmDongle), software (CmActLicense) o cloud (CmCloudContainers). Ciò include anche l›intera selezione di funzionalità offerte da CodeMeter, compresa la pluripremiata metodologia crittografica Blurry Box di Wibu-Systems e l’integrazione con tutti gli ulteriori moduli CodeMeter per la gestione licenze. A corredo dei CmASIC, il software CodeMeter è disponibile anche sotto la denominazione CodeMeter Embedded in configurazioni più snelle e personalizzabili per una moltitudine di sistemi operativi e architetture tipiche dei sistemi embedded Scelta popolare per soluzioni IoT e di embedded computing, i CmASIC stanno diventando un pilastro per la gestione licenze e la protezione dei beni digitali nel panorama dell’automazione industriale. In questo settore si sta prestando sempre più attenzione alle questioni relative all›affidabilità e alle identità digitali sicure e verificabili. I mezzi, per identificare e autenticare dispositivi, attori e dati in un sistema industriale connesso, si rivelano pertanto preziosi per mantenere la sicurezza e l›integrità operativa. I CmASICs possono inoltre fungere da fattore abilitante per i moderni modelli di business adibiti alla servitizzazione, come il manufacturing-as-a- service, che dipendono da un flusso affidabile e completamente tracciabile di dati attraverso marketplace, sistemi contabili e di elaborazione ordini nel back office e macchine nelle fabbriche. Con Wibu-Systems, che ha aperto la strada a nuovi concetti per modelli di business sicuri e basati sulla commercializzazione di dati in numerosi progetti di ricerca nazionali e internazionali e implementazioni di propri clienti sul campo, i CmASIC stanno dimostrando il loro valore come parte integrante di progetti, ad ampio respiro, basati su CodeMeter. I CmASIC supportano tutte le normali caratteristiche di CodeMeter e, applicando funzionalità avanzate come CodeMoving, raddoppiano la sicurezza. Questo metodo trasferisce parti di codice particolarmente sensibili nell’ambiente protetto di un elemento hardware sicuro per l’esecuzione. Con i CmASIC, non è solo il codice a essere trasferito in un luogo concettualmente irraggiungibile, ma è l’elemento hardware stesso ad essere incorporato in un circuito stampato e inserito all’interno di una macchina. Il premio annuale GIT Security Award viene assegnato ogni anno ai creatori di prodotti e innovazioni di punta, che propong soluzioni di sicurezza fisica e logica più efficaci – un›ovvia corrispondenza con la visione e la missione di Wibu-Systems. I numerosi vantaggi di CmASIC rendono l’hardware un vero e proprio concorrente per il GIT Security Award, dopo il riconoscimento ottenuto da WibuSystems lo scorso anno con AxProtector Python. Oliver Winzenried, AD e fondatore di Wibu-Systems, ritiene che sia giunto il momento giusto di dare risalto ai CmASIC con una vittoria: “L’industria di oggi è incentrata su identità sicure, certificati digitali e sistemi affidabili. Il nostro CmASIC, unitamente alla tecnologia CodeMeter, è il dispositivo che può fornire tutto questo ai sistemi industriali embedded. Per i nostri clienti è già una tecnologia vincente».

innovazioneInnovazione

digitalizzazione, automazione: DKC a SPS Italia
A SPS Italia abbiamo incontrato Luca Minetto e Mauro Zanni, rispettivamente Direttore Marketing e Direttore Commerciale di DKC Group, player di riferimento nel settore della progettazione e della realizzazione di soluzioni per il settore elettrico e dell’automazione industriale. Con loro abbiamo fatto il punto sui temi più sfidanti dell’industria di domani
DDopo due anni di forzata assenza, a maggio di quest’anno ha riaperto i battenti SPS Italia, la più grande fiera dell’Automazione e del Digitale per l’Industria che, mediante i 3 padiglioni del percorso District 4.0, ha affrontato le tematiche del Digital & Software, della Robotica e Meccatronica, dell’Additive Manufacturing e dell’Automazione Avanzata. È un appuntamento cruciale per il settore e tanto atteso dai decision maker del comparto manifatturiero, in un contesto di grande innovazione tecnologica. Tra i principali protagonisti di SPS Italia abbiamo incontrato DKC Group, portavoce di un prezioso know how made in Italy che la contraddistingue per la versatilità e la competitività di un’offerta produttiva che spazia dal settore elettrico a quello dell’automazione industriale.
Come tutti sappiamo, sono stati due anni particolarmente intensi. Quali sfide avete dovuto affrontare e come le avete risolte?
Mauro Zanni: “Gli ultimi due anni sono stati molto impegnativi, impossibili da prevedere; ma, nonostante la pandemia, siamo riusciti a mantenere gli stabilimenti operativi, a garantire le consegne e a organizzare in maniera ottimale i flussi lavorativi degli uffici mediante lo smart working. Abbiamo migliorato anche i risultati aziendali, riuscendo a governare con successo sia la parte di realizzazione prodotti che del recupero delle materie prime. Un problema, quest’ultimo, legato anche agli inevitabili aumenti imposti dal mercato. Rispetto ad alcuni nostri competitor, siamo riusciti a non avere mai mancanza di materia prima nei nostri stabilimenti produttivi e a rispettare al 90% le “promise” fatte. Anzi, abbiamo anche registrato
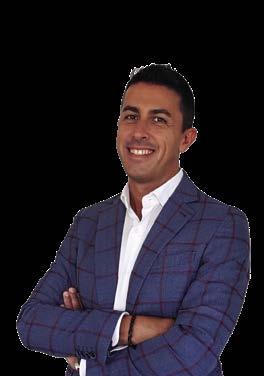
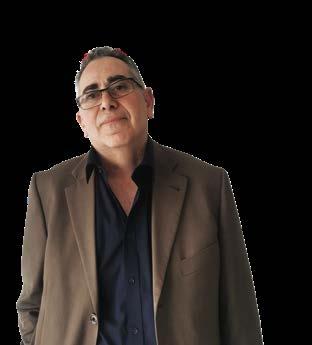
un incremento del carico di lavoro proprio perché molte aziende si sono rivolte a noi per sopperire alla mancanza di consegne di alcuni competitor”.
DKC torna in fiera dopo due anni di stop fiere. Con quali premesse e aspettative vi siete presentati a SPS e che cosa è cambiato per voi dall’ultima edizione, sia dal punto di vista tecnologico che di relazioni con i clienti e partner?
Luca Minetto: “Dopo due anni di stop forzato, siamo stati entusiasti di riprendere questo tipo di attività. Le fiere per il Gruppo DKC sono sempre state vitali perché offrono la possibilità di esporre i prodotti, le principali novità, e anche perché consentono di migliorare la qualità delle relazioni sia con i clienti che con i nostri partner e distributori. In questi due anni, dunque, nonostante le difficoltà sociosanitarie generate dalla pandemia e le conseguenti complessità gestionali, DKC non si è mai fermata, sia nella produzione che nella Ricerca&Sviluppo. Merito di una vision aziendale lungimirante e di un gruppo affiatato e appassionato del proprio lavoro. Elementi fondamentali che ci hanno permesso di tornare a SPS Italia con una gamma di soluzioni ancora più ampia e innovativa, sia per quanto riguarda le canalizzazioni che per la carpenteria, gli armadi per l’automazione, i sistemi metallici e plastici per la protezione dei cavi della linea Cosmec, come ad esempio la nuova serie di cassette di derivazione elettrica JBOX. Anche l’offerta di prodotti attivi, quali i gruppi statici di continuità UPS e il nostro Compact Data Center, è stata ampliata. Le novità riguardano anche i servizi e i supporti che siamo in grado di offrire al cliente attraverso strumenti che migliorano e riducono le tempistiche di assemblaggio e di realizzazione impianti, avendo accelerato in questi due anni un processo che era già in atto in DKC. Durante la pandemia, infatti, abbiamo incrementato la produzione di materiale digitale con video di assemblaggio e istruzioni di montaggio, configuratori e supporti cartacei per l’inquadramento normativo e l’utilizzo dei nostri prodotti. Ci siamo presentati anche con due nuove importanti acquisizioni: la prima, nel 2019, di RGM Spa, azienda di Genova specializzata nel settore dell’elettronica di potenza nelle sue numerose ed eterogenee applicazioni. Un’acquisizione che guarda al futuro del Gruppo DKC in relazione al tema sfidante della transizione energetica; l’altra è quella di SATI Italia Spa, leader nella canalizzazione metallica, che ci pone come il primo produttore italiano del settore e ci consente di stringere importanti sinergie, sia logistiche che industriali, e di aumentare le potenzialità e i rapporti con il mondo della distribuzione elettrica, nostro primo obiettivo”.
Quali sono gli obiettivi futuri del Gruppo DKC?
Mauro Zanni: “Gli obiettivi del Gruppo DKC per il futuro non cambiano rispetto alla mission che ci siamo dati, ovvero lavorare sempre di più con la distribuzione e diventare uno dei primi dieci player del mercato elettrotecnico italiano, per il settore della distribuzione, automazione e dell’installazione. Tra l’altro, con le ultime due acquisizioni, siamo riusciti ad aumentare la nostra presenza presso i distributori già forte grazie a brand come Conchiglia e Cosmec, e oggi ulteriormente potenziata con Sati. Quello a cui puntiamo è dunque una strategia di cross selling che spinga sempre di più ogni distributore a creare sinergia con tutti i brand del Gruppo DKC, gestendo al meglio gli equilibri del mercato. Questi sono gli obiettivi per quanto riguarda il mercato italiano”.
Abbiamo visto che avete lanciato la nuova piattaforma di Innovation Hub. In cosa consiste?
Luca Minetto: “Innovation Hub va proprio nella direzione di cui stavamo parlando: evoluzione, digitalizzazione e sostenibilità. Lo scorso anno abbiamo realizzato un evento in streaming, “Battito”, in cui abbiamo raccontato la storia di DKC, lanciando dei messaggi chiari sul futuro del Gruppo, su ciò che rappresenta la transizione energetica e su come questa evoluzione cambierà anche il mercato elettrotecnico. Con Innovation Hub abbiamo voluto dare continuità a questo messaggio e, attraverso una piattaforma digitale, mettere a disposizione uno spazio web con tutta una serie di contenuti gratuitamente fruibili per i lettori, non necessariamente nostri clienti e utilizzatori, interessati ad Luca Minetto approfondire alcuni temi che saranno sempre più importanti non solo per il futuro ma anche per il presente. Con il supporto di nostri esperti, insieme al dipartimento di R&D e di divulgatori scientifici, come Maurizio Melis, presidenti e responsabili Mauro Zanni di enti di ricerca, abbiamo realizzato approfondimenti, articoli, video interviste e selezionato una serie di normative specifiche per il settore, per spiegare in modo semplice e chiaro a progettisti e installatori, ma anche a chi non è esperto, il futuro del mondo elettrico ed energetico e le novità del mondo DKC, tecniche, di prodotto, di supporto e di servizio”.
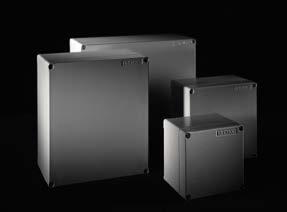

La produzione di auto elettriche richiede disponibilità a gestire la varietà e la complessità. Le tecnologie digitali e l’automazione avanzata abilitano le aziende a trovare la necessaria flessibilità e a rispondere adeguatamente alle richieste di un mercato in crescita
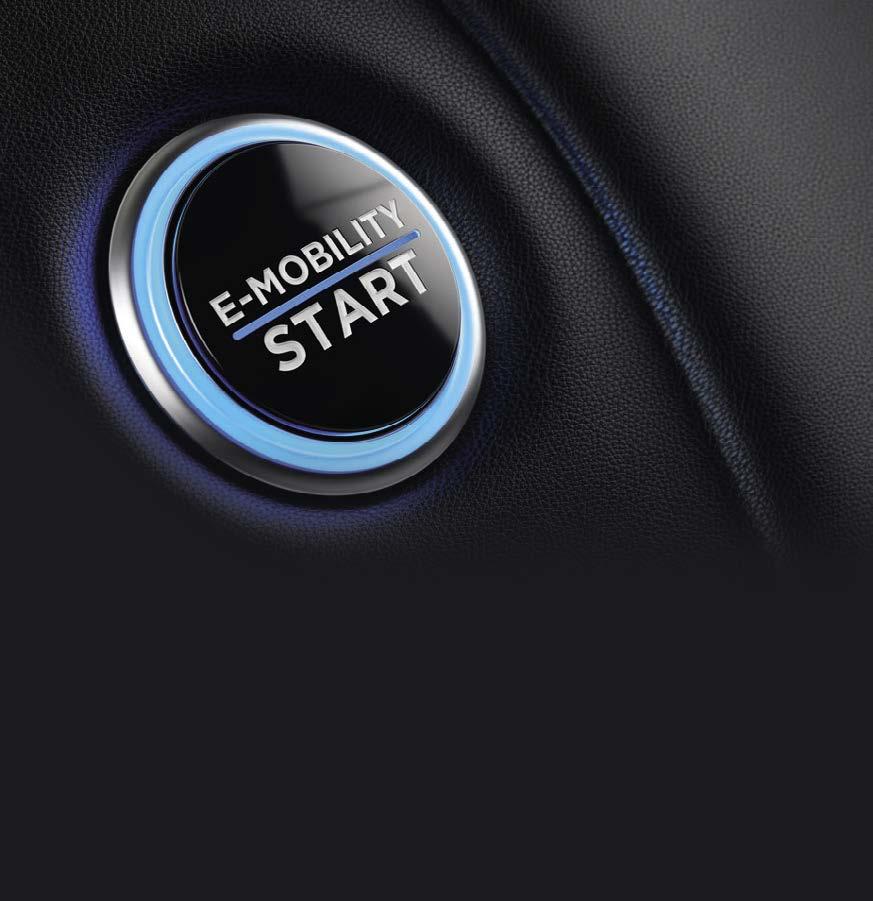
UUn rapido sguardo al mondo dell’automotive consente di affermare che gli EPV (Electrified Powertrain Vehicles, cioè le auto a powertrain elettrificato) sono usciti da una fase introduttiva e che sono ormai entrati nella fase di pieno sviluppo, presentandosi di fatto come una alternativa alla pari con i powertrain tradizionali. Quando si parla di EPV ci si riferisce a un insieme di tipologie di motorizzazione degli autoveicoli che comprende le auto elettriche pure (BEV, Battery Electric Vehicles), le auto ibride non ricaricabili (HEV, Hybrid Electric Vehicles), le auto ibride ricaricabili (PHEV, Plug-in Hybrid Electric Vehicles) e anche le vetture alimentate a idrogeno (FCV, Fuel Cell Vehicles). Da alcuni anni si registra in Europa una crescita significativa degli EPV anche se non in modo uniforme tra i vari Paesi e tra i diversi tipi di powertrain; lo segnalano gli Osservatori sulla componentistica automotive italiana realizzati da ANFIA, Associazione Nazionale Filiera Industria Automobilistica, notando inoltre come alla maggiore diffusione degli EPV in Europa e in Italia faccia riscontro un crescente coinvolgimento della filiera automotive nazionale in questo tipo di tecnologia: già l’Osservatorio 2020 riportava che quasi il 30% delle aziende intervistate dichiarava che la propria attività era principalmente posizionata su powertrain elettrificati. Ancor più significativo è quanto indicato nel Rapporto 2021: “Gli effetti della pandemia sul mercato europeo, l’evoluzione di alcuni fattori strutturali, uniti a una pioggia di incentivi che per intensità e diffusione non ha precedenti, hanno spinto le auto elettriche ed ibride a quote di mercato record: oltre un terzo delle autovetture immatricolate nel primo semestre del 2021 in Europa1 era un EPV. Ancor più significativo è il fatto che in un mercato europeo che nell’anno della pandemia è calato del 24%, le vendite di auto elettrificate siano cresciute dell’85% (più 122% nel primo semestre 2021 rispetto allo stesso periodo dell’anno precedente)”.
Gestire la varietà
A fronte di questi trend, si deve peraltro osservare che le tecnologie di prodotto (del powertrain, ma non solo) sono ancora in una fase di relativa fluidità e vale la pena approfondire gli scenari tecnologici nei quali si inquadra questo sviluppo della mobilità elettrica per poi tratteggiare il nuovo volto dell’industria automotive e capire quali possono essere le tecnologie abilitanti che determineranno la produzione del futuro. Può essere utile a tal fine seguire l’analisi e le indicazioni contenute nel Rapporto Flexing for the Future - Global vehicle production forecast by powertrain to 2035, realizzato in collaborazione tra Automotive Manufacturing Solutions (AMS) e ABB Robotics & Discrete Automation. La citata varietà nel mix dei powertrain e quella delle tariffe nell’elettrificazione hanno forti implicazioni nei sistemi e nella gestione della produzione, portando verso livelli più elevati di flessibilità, controllo qualità e collaborazione. Anche se le piattaforme per i veicoli puramente elettrici in genere richiedono meno componenti e consentono una maggiore standardizzazione, i maggiori volumi di produzione nei prossimi anni richiederanno adeguate piattaforme per ospitare le produzioni di EPV. L’elettrificazione comporta anche nuovi parametri per materiali, per le custodie delle batterie e per l’elettronica. “In molti casi gli stessi OEM produrranno più motorizzazioni sulla stessa linea di produzione, aumentando la complessità nei tempi di fornitura, programmazione e ciclo; per gestire tale complessità, OEM e fornitori stanno accelerando l’implementazione della digitalizzazione, dell’automazione e della connettività tra le fabbriche. Si stanno orientando, in particolare, verso tecnologie di automazione più flessibili, come i robot autonomi (AMR) e collaborativi (Cobot): ciò offre l’opportunità di spostare i processi di assemblaggio dalla produzione lineare a una più modulare, combinando anche un mix di compiti umani e robotici”. Alta velocità, connettività Internet e Edge Computing - in particolare attraverso reti 5G – saranno essenziale per l’attuazione di processi più autonomi nella produzione e la logistica. I produttori stanno anche aumentando la connettività tra strutture e apparecchiature nel cloud, sfruttando i Data Analytics, il Machine Learning e i Digital Twins per ridurre i tempi di fermo macchina e fare manutenzione predittiva. L’aumento della variabilità della produzione e la sua gestione saranno quindi un fattore chiave per gli investimenti in automazione e per determinare modifiche dei processi produttivi, con ruoli sempre più centrali per tecnologia e i partner di robotica.
Tecnologie abilitanti per produzioni flessibili
La produzione di motori elettrici richiede tecnologie e processi diversi rispetto a quella dei tradizionali propulsori a combustione interna. Gli OEM hanno investito, ad esempio, nella produzione di batterie elettriche, anche attraverso accordi con produttori di batterie o con acquisizioni e operazioni di integrazione verticale negli impianti di produzione esistenti. Una delle tecnologie più significative per supportare la necessaria flessibilità è quella che consente una autonomia nella logistica e nella movimentazione dei materiali negli stabilimenti. Molti OEM stanno integrando i già menzio-
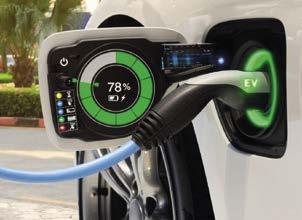
nati AMR che permettono di spostare i materiali in modo flessibile. Nel Rapporto ABB, Joerg Reger di ABB Robotics osserva che questo sviluppo ha poco a che fare specificamente con i veicoli elettrici ma supporta un più personalizzato approccio alla produzione dei veicoli stessi. “Come consumatori stiamo arrivando al punto in cui possiamo specificare e ordinare un prodotto da casa: fai clic e il tuo ordine viene eseguito in una fabbrica altamente flessibile che è in grado di fabbricare prodotti in lotti di dimensioni molto ridotte. Riteniamo che gli AMR e la logistica intelligente faranno da super driver per la fabbrica automotive del futuro”. Secondo ABB, i cobot sono progettati in modo che i clienti non debbano ricorrere a specialisti di programmazione interni e che quindi anche organizzazioni che hanno storicamente bassi livelli di automazione saranno in grado di far funzionare il loro cobot in pochi minuti dall’installazione; l’obiettivo è rendere i robot più facili da usare, non solo per i grandi OEM ma anche per fornitori più piccoli. “Il punto critico per produttori e specialisti dell’automazione è che questo non potrà essere un cambiamento semplicemente sulla robotica ma dipenderà molto dalla disponibilità di soluzioni di automazione complete, concepite considerando il processo di fabbricazione nella sua globalità. Solo con questo approccio olistico gli OEM ei fornitori saranno in grado di sviluppare quella produzione che offre la flessibilità di cui i clienti hanno bisogno”. Un’altra condizione essenziale per abilitare la produzione flessibile è la connettività di rete unitamente all’Internet ad alta velocità. Produttori come Volkswagen, BMW e Ford stanno sperimentando in locale reti 5G per abilitare, ad esempio, l’high data Edge Computing; la connettività sarà essenziale anche per aumentare l’uso di AMR e per la robotica intelligente, come pure per tracciare apparecchiature e processi in aree quali il controllo qualità. È noto che i componenti dei veicoli elettrici non possono essere rilavorati come gli equivalenti tradizionali e quindi gli OEM si affidano ai dati in tempo reale per monitorare i cambiamenti. Allo stesso modo con i pacchi batteria, i produttori devono verificare l’integrità delle connessioni e dei fissaggi, l’installazione dei materiali per la gestione termica, i sistemi di controllo e monitoraggio e la sigillatura del vano batteria. Il tracciamento dei processi di produzione con questo livello di analisi non è un compito semplice: richiede di poter raccogliere dati da ogni azione e da ogni sensore sulla linea di produzione, e anche di considerare i fattori ambientali. Risulta perciò fondamentale la tecnologia dei Big Data, che le grandi aziende tendono ad introdurre gradualmente, iniziando da progetti pilota relativamente limitati: come ha fatto Volkswagen con lo stabilimento Transparent Factory di Dresda, il primo a produrre solo veicoli elettrici; o anche Ford col progetto E:Prime per il quale ha costruito una struttura pilota presso il suo campus di ricerca e sviluppo a Dunton, fuori Londra, che produce statori, rotori e array di batterie.
Il ruolo del software
Proprio come i veicoli, anche lo sviluppo futuro della fabbrica sarà definito dal software. La pandemia ha illustrato l’importanza vitale della visibilità delle operazioni di produzione per quanto riguarda le carenze di forniture e le possibili interruzioni. La capacità dei produttori di visualizzare i sistemi di produzione e identificare i potenziali problemi in anticipo sarà una questione di sopravvivenza aziendale. Un “gemello digitale” delle operazioni dell’impianto, ad esempio, consente ad OEM e fornitori di esaminare gli effetti di qualsiasi cambiamento nello spazio virtuale, prima che venga implementato, aiutandoli a ottimizzare i prodotti e ad accelerare lo sviluppo dei processi, il che può ridurre drasticamente il time-to-market per un nuovo prodotto. Con i progressi nella connettività, nelle comunicazioni 5G, nella gestione dati, nei Data Analytics e nell’Artificial Intelligence, diventa possibile un approccio più predittivo alla produzione, utilizzando il Machine Learning e la manutenzione predittiva per prevenire potenziali interruzioni. Nelle linee di assemblaggio definita dal software, i produttori sfrutteranno il potenziale di raccolta e analisi dei dati, anche da microservizi e applicazioni. Tali App devono integrarsi nel software esistente, nei sistemi legacy e di altri fornitori, il che può risultare problematico senza standard comuni o anche quando le App si aggiornano su scale temporali diverse. In risposta, i produttori stanno sviluppando piattaforme più aperte, come con i fornitori di servizi cloud che i fornitori possono utilizzare con standard comuni aperti. “Tuttavia, è necessario trovare un equilibrio. Da un lato, qualsiasi piattaforma comune deve essere personalizzabile per soddisfare le esigenze specifiche di un particolare impianto; dall’altro, deve essere abbastanza generica per consentire a nuove App e sistemi di integrarsi rapidamente e senza soluzione di continuità”.
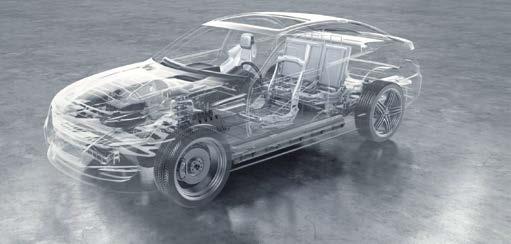
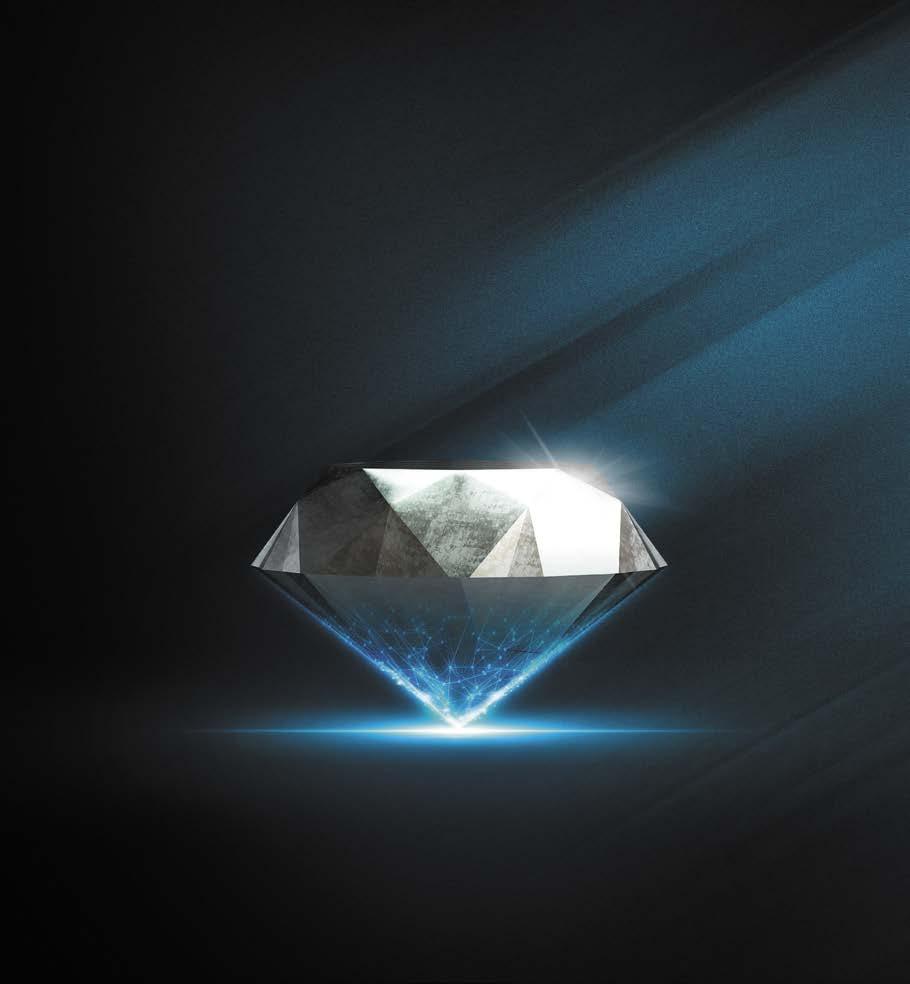
Il robot IRB5500 dipinge l’opera d’arte “Zebra Utopia” di Advait Kolarkar
Con la tecnologia PixelPaint
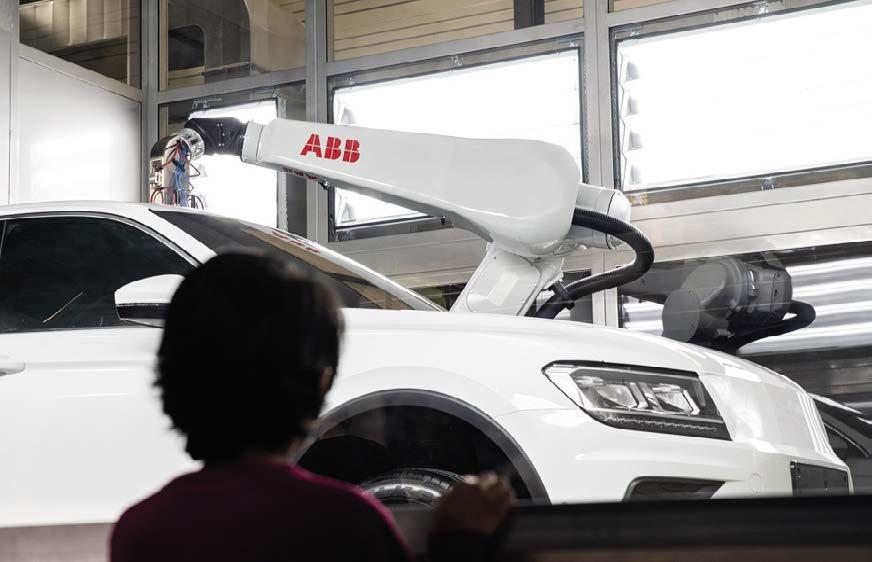
la prima “art car” al mondo ART CARABB ha realizzato la prima automobile al mondo aerografata da un robot creata in soli 30 minuti

AABB Robotics ha collaborato con due artisti di fama mondiale, Advait Kolarkar, bimbo prodigio indiano di soli otto anni, e Illusorr, collettivo di design digitale con sede a Dubai, per realizzare il primo esemplare al mondo di auto aerografata da un robot. Advait realizza opere d’arte acclamate in tutto il mondo, creazioni caleidoscopiche e astratte, utilizzando diverse forme, disegni intricati, schizzi e spruzzi di linee intrecciate. Il team di creativi di Illusorr proviene dall’avanguardia dell’architettura e del design. I disegni digitali traggono ispirazione da una combinazione di natura e fantascienza. La premiata tecnologia PixelPaint di ABB, senza alcun intervento umano, ha riprodotto perfettamente le immagini vorticose monocromatiche di Advait e i motivi geometrici tricromatici di Illusorr. Grazie alla testa di stampa con mille ugelli, i robot per verniciature IRB 5500 di ABB sono riusciti a realizzare le complesse opere d’arte in meno di 30 minuti. La tecnologia PixelPaint vanta livelli di precisione e velocità senza precedenti, consentendo di ottenere dettagli intricati ed elaborati che sarebbero impossibili da realizzare manualmente. Sami Atiya, Presidente della business area Robotics & Discrete Automation di ABB, ha commentato: “La tecnologia PixelPaint di ABB non è una semplice evoluzione, ma una vera e propria rivoluzione. È un esempio scintillante di come l’automazione robotica e il nostro software RobotStudio® possano non solo aprire la strada a una manifattura più sostenibile, ma anche riprodurre perfettamente sofisticate opere d’arte che celebrano l’originalità e la bellezza dello spirito umano. In un momento in cui i consumatori chiedono prodotti più personalizzati, PixelPaint cambia le regole del gioco consentendo di riprodurre qualsiasi disegno in modo sia sostenibile sia economico”.
ABB è all’avanguardia nello sviluppo di principi e tecnologie di smart manufacturing a supporto dell’industria automobilistica mondiale, che sta vivendo una delle fasi di trasformazione più rilevanti della sua storia recente. Questa transizione porterà a un utilizzo più diffuso dei robot insieme ad altre tecnologie, fra cui i robot mobili autonomi (AMR). Le aziende del settore clienti di ABB potranno così ottimizzare la distribuzione di componenti all’interno dei propri stabilimenti e collegare celle di produzione modulari, integrate e scalabili come PixelPaint, assicurandosi la flessibilità necessaria
ABB Robotics PixelPaint Art Car - Illusorr design
Advait Kolarkar osserva il robot in azione
per soddisfare diversi tipi di domanda. Sami Atiya ha aggiunto: “Siamo nel pieno di un decennio importante nella storia dell’industria automobilistica e all’alba di una nuova era. Le case automobilistiche devono valutare nuove modalità di lavoro per assecondare la transizione ai veicoli elettrici. Noi stiamo lavorando per supportare il settore in questa transizione e sono fiducioso che, grazie all’automazione flessibile, il trasporto sostenibile diventerà presto realtà”.
La tecnologia PixelPaint
La rivoluzionaria tecnologia PixelPaint di ABB reinventa il processo di applicazione della vernice e risponde alla crescente richiesta di personalizzazione sostenibile da parte dell’industria automobilistica, soprattutto per la livrea degli autoveicoli. Dipingere le auto con colori elaborati è da sempre un processo laborioso e costoso, che richiede numerosi passaggi di mascheratura, mentre la tecnologia di ABB consente di riprodurre qualsiasi motivo con qualsiasi colorazione, in modo dettagliato e accurato. Grazie all’elevata precisione, la vernice può essere applicata velocemente con un unico passaggio. Questa svolta nell’automazione del processo di verniciatura apre le porte alla creazione di decorazioni speciali e personalizzate nel mercato automobilistico. Ian Callum, l’influente designer di auto che ha realizzato l’estetica della Aston Martin Vanquish e, più recentemente, dell’innovativa Jaguar I-Pace, ha dichiarato: “Un’auto ha qualcosa di molto speciale: le persone si affezionano ad essa e la personalizzazione diventa quindi sempre più importante. Infatti sto lavorando con molti clienti che chiedono di decorare le loro auto in modo esclusivo. In questo contesto, questa tecnologia di verniciatura, che consente di realizzare qualsiasi tipo di design, è incredibile”. La tecnologia PixelPaint migliora anche la sostenibilità in produzione, eliminando l’uso di materiali per mascherare la carrozzeria e sistemi di aspirazione aggiuntivi, con una conseguente riduzione delle emissioni e dei consumi di acqua ed energia. Guidata dal software RobotStudio di ABB, la testa di verniciatura si muove molto vicino alla scocca del veicolo per garantire che il 100% della vernice venga applicato sulla carrozzeria, senza dispersioni nebulizzate (overspray). Diversi colori vengono così applicati velocemente ed è sufficiente un solo passaggio dell’auto nel reparto di verniciatura. Questo sistema consente alle case automobilistiche di dimezzare i tempi di produzione e ridurre i costi del 60%. Per realizzare l’auto decorata, ABB ha recuperato un SUV Volkswagen danneggiato nelle catastrofiche inondazioni che colpirono la Germania nell’estate del 2021. Il riciclo dell’auto ribadisce l’impegno di ABB alla sostenibilità su tutti i fronti.

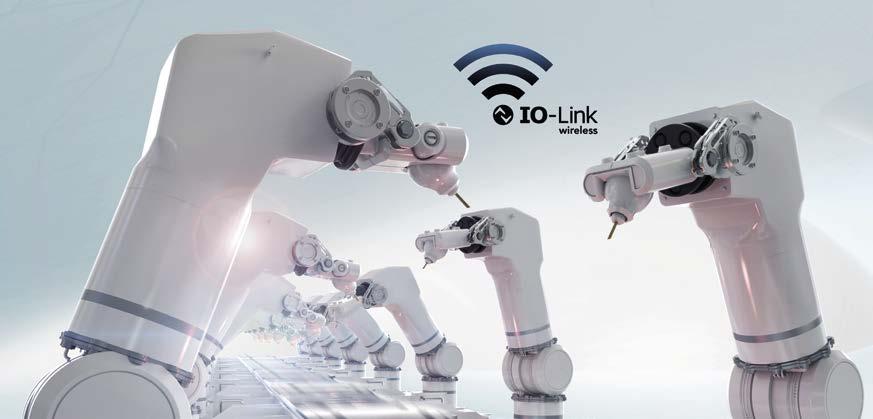
IO-Link Wireless:
intelligenteintelligente, comunicativo, senza fili La comunicazione dei sensori ad un nuovo livello per la fabbrica del futuro
AAttualmente, ci vuole molto cablaggio per comunicare, sia a livello della macchina che a livello di produzione nel suo insieme. I sensori e gli attuatori, così come i dispositivi binari e/o analogici, sono stati fino a oggi integrati mediante cavi. Tuttavia, in alcune aree, specialmente per una varietà di soluzioni di controllo del movimento, la comunicazione via cavo non è la migliore opzione. La combinazione intelligente di reti industriali e standard di comunicazione IO-Link di Balluff costituisce un elemento essenziale per la fabbrica del futuro. IO-Link Wireless è un nuovo promettente standard per la comunicazione senza fili nell’automazione di processo e di fabbrica. IO-Link Wireless, infatti, non è una sostituzione delle soluzioni cablate, ma un’estensione che permette di beneficiare di tutti i vantaggi delle soluzioni IO-Link cablate ora anche in modalità wireless. Con IO-Link Wireless, si ottiene la piena flessibilità e mobilità necessarie per molte soluzioni di automazione. Permette il controllo e il monitoraggio nell’azienda in tempo reale e con una connessione di qualità, senza l’uso di cavi.
La fabbrica del futuro
IO-Link Wireless è estremamente affidabile, anche molte volte di più delle reti wireless tradizionali come W-LAN o Bluetooth. È anche molto robusto e resistente alle interferenze quando si trova in prossimità di altri sistemi o altre

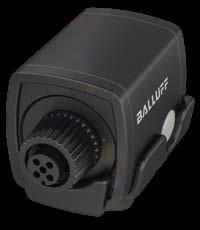
fonti di interferenze wireless ed elettromagnetiche. Anche condizioni industriali estreme non impediscono ad IO-Link Wireless di funzionare senza problemi. Con una grande scalabilità e adattabilità, la tecnologia si adatta perfettamente a qualsiasi impianto o macchina. Possono essere collegati all’IO-Link Wireless Master fino a 40 dispositivi, con cinque tracce. Questo sistema, inoltre, può essere collegato e integrato in macchine e sistemi esistenti, consentendo la modernizzazione senza fili con la più recente tecnologia dei sensori. IO-Link Wireless rende possibile l’utilizzo di IO-Link in aree della macchina dove prima non era possibile, facendo compiere un passo in avanti alla fabbrica comunicativa, connessa e intelligente del futuro, nella quale le tecnologie cablate non devono più essere lo standard puro.
Nessun cavo, molti vantaggi
Il sistema wireless Balluff è composto da un master, un hub e un bridge. Contrariamente a quanto accade di solito, il master wireless non riceve i dati del sensore via cavo, ma tramite un bridge o un hub via radio. Ciò comporta vantaggi significativi rispetto a un sistema cablato, tra cui progettazione e installazione più facili, grazie alla possibilità di integrare fino a 40 dispositivi IO-Link, una maggiore flessibilità nel design e nella mobilità, grazie a una velocità di trasmissione di 1 byte/5ms, e nessuna usura di connettori o cavi.
Retrofitting dei sistemi esistenti
IO-Link Wireless rende più agevole anche il retrofit dei sistemi esistenti, laddove non era ancora possibile o economicamente fattibile a causa di requisiti più complessi causati dalla posa di cavi altrimenti necessari. Il sistema Wireless costituisce l’aggiunta ideale al sistema IO-Link già esistente su macchine e sistemi perché non c’è bisogno di intervenire sull’intera architettura dell’impianto. Le soluzioni Balluff sono facili da integrare e non interferiscono con l’architettura esistente delle macchine e dei sistemi. La configurazione collaudata rimane invariata. Nessun sensore deve essere sostituito, nessun attuatore deve essere rinnovato, non ci sono incompatibilità. In breve, la comunicazione intelligente attraverso la variante wireless IO-Link permette un’integrazione ancora più flessibile di sensori e attuatori con la comprovata affidabilità e prestazioni dello standard IO-Link cablato, attraverso un tasso massimo di errore di dati a pacchetto di 10⁻⁹. Ad esempio, nei sistemi di trasporto altamente dinamici, l’IO-Link wireless consente di installare sensori compatibili direttamente sul carrello, monitorandone con maggiore precisione movimenti e posizionamento. Con la tecnologia wireless IO-Link, è possibile portare senza sforzo un sistema collaudato a un nuovo livello e sbloccare potenziale aggiuntivo per il futuro. L’estensione IO-Link Wireless rende lo standard di comunicazione IOLink adatto a nuove sfide e crea possibilità completamente nuove per il monitoraggio e il controllo delle macchine e dei sistemi.
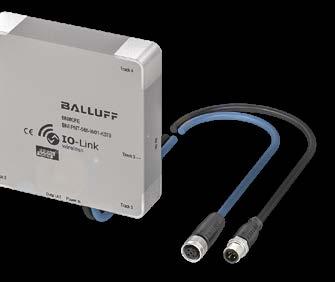
Tecnologia dei sensori wireless per la robotica e i sistemi di trasporto
IO-Link Wireless facilita il funzionamento di applicazioni dinamiche, mobili e difficili da raggiungere. Tra le possibili aree di applicazione che possono beneficiare della nuova tecnologia IO-Link Wireless ci sono la robotica e i sistemi di trasporto, che trovano notevole applicazione anche nel settore automotive. Le sequenze di movimento dinamico su tre assi, come quelle utilizzate nella robotica, rendono difficile il cablaggio, che diventa molto complesso e costoso. Inoltre, il cablaggio fisso di sensori e attuatori è associato ad una serie di svantaggi derivanti da cavi e contatti soggetti a forti sollecitazioni, fatica o rottura a causa delle forze di flessione e torsione. Questo può portare a un aumento dei tempi di fermo macchina non pianificati. Per robot, bracci robotici e sistemi di trasporto, invece, la trasmissione dei dati senza contatto permette nuove applicazioni che prima non erano fattibili. In combinazione con gli accoppiatori induttivi (BIC) per l’alimentazione senza contatto di Balluff, in futuro saranno possibili casi d’uso completamente nuovi. Questa soluzione è basata sullo standard internazionale IO-Link wireless. Il risparmio di tempo si traduce in una messa in produzione ancora più rapida, offrendo così un vantaggio in mercati altamente competitivi proprio come l’industria dell’automotive e dei relativi fornitori di componenti e ricambi. Facilità, velocità, efficienza: la soluzione IO-Link Wireless di Balluff soddisfa i requisiti specifici di un settore altamente competitivo come quello dell’automotive comunicando i dati in modo digitale e quindi scambiando, in modo trasparente, valori di processo, nonché informazioni di configurazione e dati diagnostici.

Innovative
soluzioni di automazione per l’industria automobilisticaautomobilistica Grazie alla struttura scalabile e aperta della piattaforma PC Beckhoff, è possibile sviluppare soluzioni di controllo efficienti e competitive. Quello automobilistico è uno dei set-G Un passo decisivo con la tecnologia di controllo PC-based ed EtherCAT! accompagna un progresso tecnologico che pone i costruttori e i fornitori di automobili di fronte a un’elevata pressione sui costi e a crescenti esigenze di produttività e qualità. La tecnologia di automazione basata su PC ed EtherCAT di Beckhoff offre all’industria automobilistica soluzioni tori industriali più importanti. Dopo per ottimizzare tutti i processi produttivi. L’integrazione di anni di internazionalizzazione e boom globale, l’industria tutte le funzioni di controllo su una piattaforma PC centrale continua ad affrontare nuove sfide. La crescente consapevo- garantisce un’interazione efficiente tra tutti i componenti e la lezza nei confronti dell’ambiente e le richieste di maggiore massima produttività. Si evitano le inefficienze o i tempi di sostenibilità richiedono un cambiamento di mentalità, che si latenza che si verificano quando sistemi diversi comunicano riflette, tra l’altro, nei concetti di mobilità intelligente. A ciò si tra loro. Allo stesso tempo, il controllo PC-based consente di
beneficiare di vantaggi in termini di costi, eliminando l’hardware e riducendo i lavori di installazione e manutenzione. Un’ampia gamma di interfacce e il supporto per tutti i più comuni sistemi di bus di campo e protocolli software garantiscono una comunicazione orizzontale e verticale coerente, a partire dal collegamento in rete delle singole macchine sul campo fino al networking a livello IT e al cloud. L’elevato livello di compatibilità di EtherCAT garantisce la semplice integrazione di molti dispositivi diversi, anche di fornitori terzi, nel sistema di controllo. Ciò consente di ottenere la massima flessibilità nella progettazione delle macchine.
Integrato ed efficace: il controllo PC-based per la produzione di autoveicoli
La tecnologia di controllo PC-based di Beckhoff è ideale per l’automazione completa di molti processi complessi nella produzione di autoveicoli: dal controllo delle presse e della saldatura nella produzione di carrozzerie alla produzione di batterie e motori per veicoli elettrici. I tempi di ciclo rapidi e l’elevato grado di scalabilità garantiscono l’ideale predisposizione per la rivoluzione dei veicoli elettrici con il controllo da PC. La flessibilità e l’apertura, sia nel software che nell’hardware, facilitano le estensioni funzionali, le modifiche e i retrofit: vantaggi importanti in considerazione della riduzione dei cicli di vita dei prodotti e della maggiore varietà di varianti.
Soluzioni di controllo intelligenti ottimizzano la produzione di batterie
Il controllo basato su PC consente l’automazione end-to-end di tutti i processi di produzione delle batterie: dalla produzione degli elettrodi all’assemblaggio delle celle fino alla loro finitura. Tempi di ciclo rapidi e sincronizzazione ottimale delle funzioni di controllo nel software TwinCAT garantiscono la massima efficienza del processo.
Progettare macchine e impianti senza quadro elettrico per la produzione automobilistica
Soluzioni di automazione che riducono l’ingombro della macchina, requisiti di cablaggio e manutenzione stanno diventando sempre più importanti nella produzione automobilistica. Offriamo diverse tecnologie e prodotti che supportano l’implementazione di concetti di macchine e impianti privi di quadro elettrico: il Sistema MX: questo rivoluzionario sistema modulare con grado di protezione IP67 racchiude in sè tutte le innovazioni tecnologiche dell’automazione. Essendo possibile montarlo direttamente sulla macchina, i quadri elettrici possono essere ridotti al minimo o addirittura eliminati, grazie all’approccio olistico, modulare e plug-in. EtherCAT P: l’automazione One Cable per il livello di campo combina la comunicazione e l’alimentazione su un unico cavo Ethernet standard, riducendo così i costi di cablaggio e installazione. Servoazionamenti: i servomotori delle serie AMP8000 e
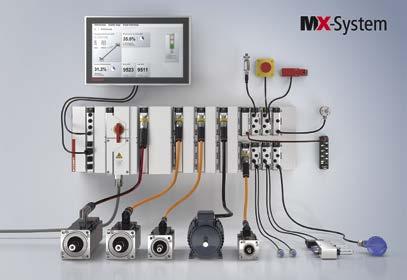
Il sistema MX migliora significativamente l’efficienza rispetto alla tecnologia convenzionale degli quadri elettrici durante l’intero ciclo di vita di una macchina. Picture credits/ Copyright: Beckhoff Automation GmbH & Co. KG
AMI8100 consentono di realizzare concetti di macchine modulari. L’integrazione diretta del servoamplificatore nel motore consente di risparmiare spazio nel quadro elettrico e di ottenere la massima flessibilità nella progettazione della macchina.One Cable Display Link: la soluzione CP-Link 4 con un unico cavo combina comunicazione e alimentazione per il collegamento di pannelli e Panel PC su distanze fino a 100 m.
Scalabile e modulare: l’automazione personalizzata di Beckhoff
Un’automobile in media è composta da circa 10.000 pezzi singoli. Di conseguenza, nella produzione di automobili sono coinvolte numerose fasi di produzione e molte macchine, che comportano compiti di controllo diversi e complessi. Allo stesso tempo, cicli di vita dei prodotti ancora più brevi richiedono una maggiore flessibilità di produzione. È proprio in questo ambito che la tecnologia di controllo PC-based di Beckhoff offre un vantaggio competitivo decisivo: soluzioni scalabili e flessibili con prestazioni elevate e alta precisione. Con la gamma di prodotti Beckhoff è possibile configurare soluzioni di controllo individuali per un’ampia gamma di applicazioni e requisiti. PC industriali ad alte prestazioni, pannelli multi-touch, componenti I/O molto veloci, EtherCAT come bus di campo aperto e in tempo reale, tecnologia di servoazionamento versatile e dinamica e il software di automazione TwinCAT costituiscono la base per il controllo sequenziale, la visualizzazione, il controllo del movimento, la sicurezza e la tecnologia di misura e monitoraggio delle condizioni. Tutti i componenti sono scalabili individualmente in termini di prestazioni e design, in modo che la piattaforma di controllo possa essere adattata con precisione alla rispettiva applicazione. L’utilizzo di standard industriali e informatici e di componenti per la comunicazione cloud e i big data rendono la piattaforma di controllo PC-based ideale per il networking end-to-end e per l’implementazione dei concetti di Industriea4.0.
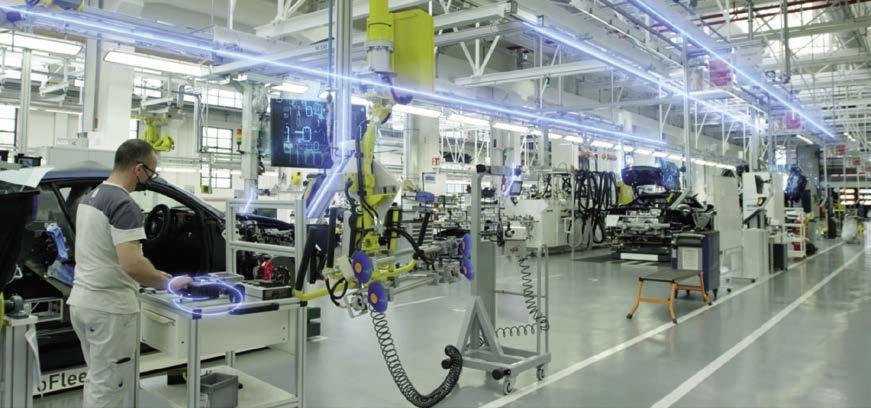
L’innovazione del Gruppo Bosch nei processi produttivi di Maserati MC20 maserati La supercar MC20 è la prima vettura al mondo con il 100% delle viti monitorate elettronicamente grazie ai sistemi Bosch Rexroth
BBosch Rexroth, società del Gruppo Bosch e leader nelle tecnologie di automazione per il mondo industriale, è partner di Maserati nello sviluppo della linea di produzione Industry 4.0 della MC20 presso la storica sede della Casa del Tridente a Modena. La linea di produzione della MC20 è un esempio di industria connessa, ovvero i dati generati in linea nelle varie stazioni di lavorazione e dalle diverse operazioni vengono raccolti, conservati e analizzati. Le postazioni operatore Bosch Rexroth equipaggiate con gli avvitatori wireless NEXO hanno risposto a questa esigenza di connettività e trasparenza di produzione, risolvendo importanti sfide qualitative e tecniche. Sulla linea Maserati MC20 sono state installate in totale 63 postazioni con avvitatori NEXO, 8 nella linea motore e 55 nella linea di montaggio, tutte perfettamente integrate nel software di produzione. Questo significa che è possibile visualizzare processi e stati delle macchine in qualsiasi momento, ovvero meno errori e meno omissioni durante il processo produttivo. Anche il sistema di condotta guidata riduce la quantità di rilavorazione, previene i ritardi e minimizza eventuali difetti di assemblaggio, migliorando la qualità dell’output. “L’area montaggio motori trasmette esattamente il senso della nostra partnership con Bosch Rexroth – commenta Jonata Azzali, Responsabile Engine Lab Maserati –. Per esempio, grazie al sistema di avvitatura Bosch Rexroth totalmente integrato al software di produzione (MES), siamo in grado di riconfigurare le performance di ogni singolo avvitatore in base all’esigenza produttiva specifica”.
Linea Maserati 4.0: configurabile e flessibile grazie agli avvitatori Rexroth
NEXO di Bosch Rexroth è un avvitatore a batteria wireless dotato di controller integrato attraverso il quale è possibile verificare le operazioni di avvitatura durante tutto il processo produttivo. In ottica Industry 4.0, può immagazzinare e inviare tutti i dati e le curve di serraggio tramite la connessione wireless. NEXO offre sicurezza nei serraggi e semplicità di installazione oltre ad una elevata flessibilità nelle attività produttive. Può infatti essere utilizzato a multilivello, ad esempio in modalità manuale attraverso cui l’operatore può scegliere il programma o l’attività da eseguire mediante tastierino o lettore codice a barre integrati. In modalità automatica, invece, è il controllore di stazione che trasmette all’avvitatore il programma o l’attività da eseguire. L’intuitiva programmazione di NEXO richiede solo una formazione di base e permette di ridurre tempi e possibili errori. La postazione di montaggio, equipaggiata con NEXO, è dotata di un sistema software di guida per l’operatore. Questa soluzione fornisce una rappresentazione visiva step-by-step delle istruzioni di assemblaggio, aiutando così gli operatori nelle varie sequenze e prevenendo eventuali errori e difetti. Il sistema di condotta guidata fornisce istruzioni dettagliate per selezionare il componente giusto: i bulloni necessari, la bussola o l’inserto corretto, l’esatta posizione di serraggio, la coppia a disegno, lo strumento di serraggio, il programma e la sequenza di lavoro corretti. Nel caso in cui la vista dell’operatore sul monitor fosse ostruita, come nei lavori all’interno della carrozzeria, il display può supportare l’attività mostrando direttamente le informazioni necessarie sull’avvitatore. “In un partner noi cerchiamo tre caratteristiche speciali che sono: flessibilità, configurazioni speciali e garanzia della qualità – spiega Salvatore Cinquegrana, team Leader MC20 Assembly di Maserati – caratteristiche che Bosch Rexroth ha pienamente dimostrato di possedere. La flessibilità è importante per avere la possibilità di customizzare il 100% delle vetture. Le soluzioni speciali in linea servono a rendere speciale la produzione della MC20”, continua Cinquegrana. Continuità produttiva e completa connettività grazie ai serraggi controllati elettronicamente La garanzia di una produttività efficiente è stata ottenuta anche grazie all’estrema adattabilità delle soluzioni software Bosch Rexroth che hanno mantenuto la sartorialità della produzione industriale Maserati. Flessibilità che si traduce in una personalizzazione di ogni singola vettura prodotta e della conseguente riconfigurazione della linea, senza eccessivi sforzi ingegneristici o stress per gli stessi operatori. “Una parola d’ordine ci ha guidato in questo percorso tecnologico: sartorialità produttiva – commenta Alessandro de Franceschi, EU Sales Engineer di Bosch Rexroth –. Abbiamo ottenuto il massimo in termini di produttività e flessibilità all’interno delle linee grazie all’elevato grado tecnologico dei nostri sistemi di avvitatura NEXO. Questo ha garantito a Maserati di sposare sulle proprie linee l’animo sportivo di MC20 con la classe luxury che le compete. Su questi presupposti abbiamo potuto applicare il controllo totale della qualità su tutta la vettura: requisito fondamentale per una supercar di questo calibro”.
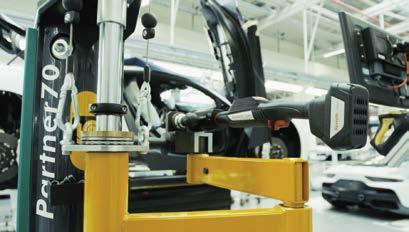
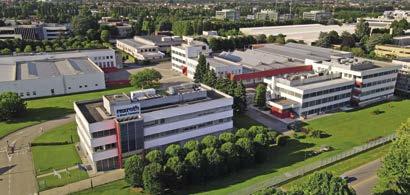
Tecnologie Bosch a bordo di Maserati MC20
La collaborazione tra Bosch e Maserati va oltre i processi produttivi e continua a bordo vettura. Bosch fornisce, infatti, centralina elettronica controllo motore (ECU), servosterzo elettrico con trasmissione a cinghia (EPSapa) e sensori a ultrasuoni. In particolare, il motore V6 da 3 litri a bordo della vettura è equipaggiato con una centralina elettronica controllo motore di Bosch che garantisce massime prestazioni. Inoltre, la centralina consente alla Maserati MC20 di contenere i consumi, limitando di conseguenza le emissioni. Il servosterzo elettrico Bosch con trasmissione a cinghia, invece, controlla e supporta lo sterzo del veicolo, garantendo un’eccellente sensazione di sterzata e di precisione nella scelta delle traiettorie. Inoltre, contribuisce a una maggiore sicurezza in caso di anomalie, garantendo una riduzione delle emissioni e dei consumi rispetto a un servosterzo idraulico tradizionale. Infine, gli 8 sensori a ultrasuoni posizionati sul paraurti anteriore e posteriore del veicolo supportano il guidatore durante le manovre di parcheggio. Grazie alla tecnologia a ultrasuoni Park Pilot, il sistema rileva gli ostacoli presenti durante la manovra e, in caso di avvicinamento, avverte il guidatore con un segnale acustico.
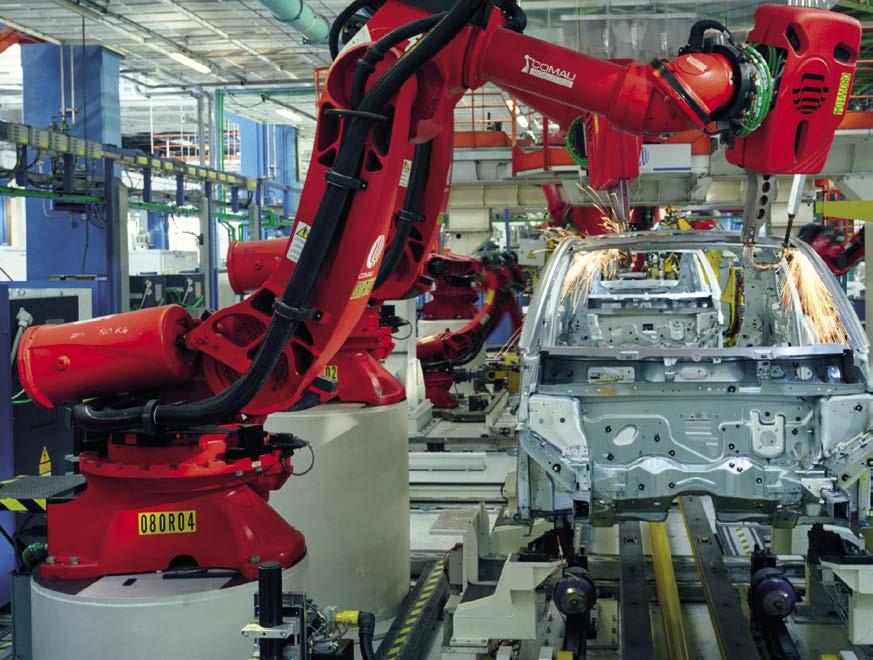
Progetti e soluzioni per progetti l’e-Mobility
Sistemi su misura, concreti e sostenibili, per i settori dell’elettrificazione e dell’automazione industriale auto
CComau, azienda leader nello sviluppo di soluzioni e prodotti innovativi per l’automazione industriale, è uno dei protagonisti nel settore dell’elettrificazione, con progetti in tutto il mondo. L’azienda è specializzata nella risoluzione di problemi complessi grazie all’uso di tecnologie innovative, che possono essere standardizzate e replicate per consentire e automatizzare la fornitura, lo stoccaggio e la consegna di energia. Grazie ad una significativa percentuale degli investimenti in Ricerca e Sviluppo destinata alla realizzazione di sistemi per la produzione e l’assemblaggio di celle, moduli e pacchi batterie per qualunque settore industriale, nel campo dell’e-Mobility Comau vanta numerosi progetti – in particolare in Asia, Europa e Stati Uniti - per la produzione e l’assemblaggio di moduli batterie di qualunque tipologia, sia a livello prototipale che per la produzione su larga scala. Nelle medesime aree territoriali sopra citate, l’azienda è impegnata anche nella progettazione e nella realizzazione di sistemi di assemblaggio per pacchi batteria e nella fornitura di impianti per la costruzione di celle, lavorando in stretta collaborazione con alcuni tra i principali costruttori mondiali. Cercando di anticipare le tendenze tecnologiche che andranno a orientare il futuro dell’elettrificazione - grazie a una forte propensione all’innovazione e alla sperimentazione di soluzioni all’avanguardia - Comau sta collaborando direttamente con produttori di batterie, con sviluppatori di tecnologie e con centri di ricerca internazionali per l’industrializzazione dei processi di produzione di celle di nuova generazione, come le batterie allo stato solido. Inoltre, a livello internazionale, l’azienda è impegnata anche in numerosi progetti nel campo dello sviluppo di sistemi di trasmissione per le vetture elettriche e ibride. Attualmente, Comau è in grado di coprire tutte le fasi del ciclo di produzione delle batterie - prismatiche, cilindriche e pouch - passando dai pacchi completi - come, ad esempio, il gruppo batteria che viene posizionato nell’auto - ai singoli elementi, compresi moduli e celle.
Progetti per l’e-Mobility
Nel settore della produzione di batterie, Comau UK e Ilika, pioniere nella tecnologia ASSB per i veicoli elettrici, stanno collaborando a un progetto finanziato dall’Advanced Propulsion Center (APC), della durata di 12 mesi, per potenziare la capacità produttiva ottenuta in laboratorio da Ilika. L’obiettivo è quello di aumentare la produzione delle celle allo stato solido di Ilika, da 1kWh alla settimana a 10kWh alla settimana, presso la sua struttura pilota. Un secondo obiettivo del progetto in corso sarà quello di passare a 2 MWh all’anno entro la fine del 2023. Comau condurrà inoltre uno studio di fattibilità del processo tecnologico per la produzione delle batterie allo stato solido Goliath, e svilupperà una strategia

scalabile e conveniente per aiutare Ilika a raggiungere livelli di produzione in serie. Per quanto riguarda i sistemi di trasmissione per vetture elettriche, sono diversi i progetti che hanno vista coinvolta l’azienda. Comau ha ampliato le linee di produzione della carrozzeria in uno dei più moderni stabilimenti di produzione auto nello stato brasiliano di Pernambuco per produrre il nuovo SUV Jeep Commander a 7 posti. Inoltre, ha potenziato 14 linee di produzione complesse per incrementare la capacità produttiva ad alta velocità di Jeep, passando da 3 a 4 modelli. Presso lo stabilimento AMEC a Tunica, nello stato del Mississippi, Stati Uniti, Comau e Mullen Automotive stanno sviluppando un impianto di lastratura all’avanguardia. Mentre, in collaborazione con Geely Automobile Holdings, Comau ha progettato e implementato una linea di assemblaggio automatizzata per e-drive, integrata nello stabilimento dell’azienda a Ningbo, in Cina. La linea si basa su un sistema automatizzato e flessibile che consente di assemblare rotori a magneti permanenti, cambi e trasmissioni elettroniche, gestendo anche il controllo qualità e i test automatizzati sul prodotto finale. A questa collaborazione, si aggiungono numerosi progetti, attualmente in essere, con aziende presenti in tutto il mondo, per la progettazione, la costruzione e l’installazione di linee di produzione per motori elettrici e per le trasmissioni, oltre che per sistemi di assemblaggio per statori - che vanno dalla piccola serie alla produzione di massa.
Soluzioni produttive per il settore dell’e-Mobility
Nel settore automotive, Comau collabora con i principali costruttori automobilistici mondiali e con i new comer, affiancandoli nella progettazione e nella realizzazione di processi produttivi innovativi, con l’obiettivo di contribuire allo sviluppo della mobilità elettrica del futuro. Inoltre supporta le aziende con la fornitura di soluzioni innovative, integrando sistemi robotizzati all’avanguardia e impianti per la saldatura laser con tecnologie abilitanti. Un approccio che consente a Comau di rendere più efficaci e flessibili i processi manifatturieri dei clienti, massimizzando i risultati. L’azienda ha progettato e implementato le linee di produzione dedicate alle parti strutturali della prima Fiat 500 completamente elettrica. Comau ha lavorato con Fiat nella riprogettazione della carrozzeria adatta a ospitare la batteria e la trasmissione dell’iconico veicolo. Per costruire la Nuova 500 sono stati utilizzati un totale di 187 robot Comau di nuova generazione. I robot erano dotati di sistemi di movimentazione, progettati su misura per il veicolo elettrico, tra cui una speciale pinza stampata in 3D. Negli Stati Uniti, Comau collabora con Mullen Automotive, produttore emergente di veicoli elettrici, per la realizzazione di un impianto di lastratura all’avanguardia presso lo stabilimento di Tunica, nello stato del Mississippi. La linea ha l’obiettivo di migliorare l’intero ciclo di produzione del nuovo crossover Mullen FIVE EV, garantendo all’azienda significativi vantaggi in termini di efficienza e qualità per la lavorazione della scocca.
Centri di competenza e di innovazione per l’elettrificazione
Forte della sua esperienza nel campo dell’elettrificazione per numerosi settori industriali, Comau ha sviluppato laboratori e centri di competenza dedicati e ad alta specializzazione. In questo modo è in grado di aiutare le aziende ad aumentare la capacità, la velocità e il valore della propria produzione nel settore dell’elettrificazione. Nel suo headquarter di Grugliasco (Torino), l’azienda ha realizzato un innovativo Laser Lab per supportare le aziende nella progettazione, nell’implementazione e nell’ottimizzazione di processi laser per applicazioni di assemblaggio delle batterie elettriche. Ad oggi, sono stati assemblati al suo interno più di 200 prototipi di batterie elettriche. Inoltre, Comau mira ad aumentare l’efficienza, la velocità e il valore della produzione delle aziende, consentendo loro di offrire soluzioni operative altamente competitive nel campo dell’elettrificazione, attraverso i test di prototipi di linee per batterie elettriche e l’utilizzo delle tecnologie più innovative, dall’Intelligenza Artificiale al Digital Twin. Nella sede centrale di Comau è presente anche il Battery Cell Global Competence Center, destinato allo studio e allo sviluppo di innovativi sistemi e tecnologie per la produzione in serie di celle e nel quale viene fornito supporto diretto ai clienti per la definizione e l’ottimizzazione del processo di lavoro. Comau ospita anche un e-Motors Competence Center e un Battery Competence Center (per pacchi e moduli batterie), che oggi consentono all’azienda di coprire con team specifici e dedicati tutta la catena produttiva di una vettura elettrica. Fin dall’avvio del progetto, Comau ha affiancato Stellantis nella realizzazione del Mirafiori Battery Lab, partecipando alle attività di co-design e fornendo sistemi di produzione per lo stabilimento.

La stampa 3D di Formlabs per componenti e attrezzature per l’automotiveautomotiveMateriali e soluzioni per le auto del futuro
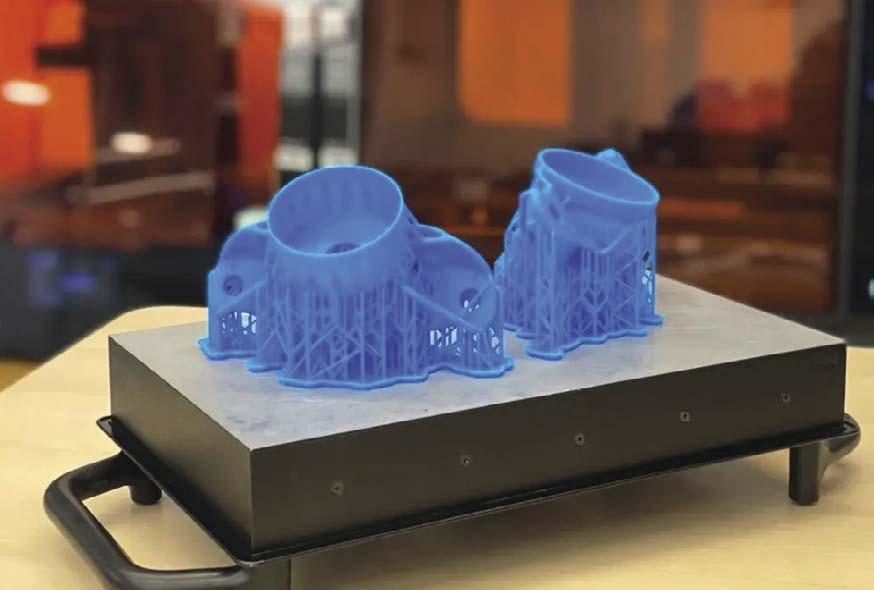
FFormlabs sta ampliando l’accesso alla fabbricazione digitale, per rendere la stampa 3D alla portata di tutti. Con sede a Somerville, Massachusetts, e uffici in Germania, Giappone, Cina, Singapore, Ungheria e Carolina del Nord, Francia e Ohio, Formlabs è il fornitore di stampanti 3D professionali scelto da ingegneri, designer, produttori e dirigenti di tutto il mondo. Grazie ai prodotti e alle soluzioni Formlabs, diverse aziende leader nello sviluppo di prodotti automobilistici leggeri in plastica e materiali compositi e famosi studi di design per auto, sviluppano prodotti per la realizzazione di prototipi funzionali, dalla fase di progettazione concettuale per la verifica delle geometrie, fino alla fase di progettazione dettagliata e creano le concept car di domani. Come nel caso di IGESTEK, un’azienda spagnola con sede a Bilbao, e di Vital Auto, uno studio di design industriale situato nel cuore del settore automobilistico del Regno Unito con una notevole esperienza nel design di auto che annovera fra i suoi clienti alcuni dei più importanti produttori di automobili, come Volvo, Nissan, Lotus, McLaren, Geely, TATA.
Iterazioni di un componente automobilistico progettato con il metodo generativo sulla Form 3L
Il team di IGESTEK sviluppa tecniche di lavorazione ibride e le integra tra loro per produrre componenti in materiali compositi, che vengono successivamente implementate da fornitori di primo livello del settore automobilistico e produttori di parti originali per realizzare parti per auto e moto di alta gamma. L’azienda utilizza la stampa 3D dall’inizio alla fine del processo di sviluppo dei prodotti, dalla fase di progettazione concettuale per la verifica delle geometrie, fino alla fase di progettazione dettagliata per la realizzazione di prototipi funzionali. Inoltre, la stampa 3D viene impiegata per la creazione rapida di attrezzature, come inserti per stampi a iniezione in plastica o attrezzature per la termoformatura di materiali compositi. Uno dei progetti più innovativi di IGESTEK è un supporto per ammortizzatori (Top Mount). Questi componenti fanno parte del sistema di sospensione di un’automobile e aiutano a ridurre le vibrazioni prodotte dal movimento del veicolo per migliorare il comfort dei passeggeri. Il supporto per ammortizzatori è stato sviluppato con il software di design generativo Fusion 360 di Autodesk, che ha fornito varie soluzioni in base a una serie limitata di requisiti. Successivamente, il team ha stampato in-house i design più promettenti usando la stampante 3D stereolitografica (SLA) Form 3L, convalidando così la geometria e sfruttando il grande volume di stampa per realizzare fino a tre diverse iterazioni contemporaneamente. La stampa 3D SLA ha permesso di realizzare le geometrie complesse ottenute attraverso il design generativo e di convalidare i processi cinematici e di assemblaggio utilizzando prototipi funzionali, senza dover investire in attrezzature costose. Il processo di ricerca e sviluppo ha portato all’elaborazione di un’architettura realizzata in diversi materiali, che combina la stampa 3D in metallo, basata su geometrie generative, con materiali compositi più leggeri, per offrire le migliori prestazioni possibili a fronte di una riduzione del peso pari al 40% rispetto alle soluzioni attualmente sul mercato.
Utilizzo di diversi materiali di stampa 3D SLA per creare uno strumento per la termoformatura
Oltre che per la prototipazione, il team di IGESTEK, utilizza la stampa 3D anche per la creazione rapida di attrezzature destinate alla produzione di parti in materiali compositi, come la termoformatura della fibra di carbonio attraverso laminatura pre-preg. Nerea Romero, responsabile dell’innovazione di IGESTEK ha dichiarato: “Le resine di Formlabs, come la Rigid 10K Resin e la High Temp Resin, sono davvero utili nel settore ingegneristico. Solitamente impieghiamo tecnologie che riguardano la termoformatura a compressione di materiali compositi. Gli strumenti che verranno inseriti nelle presse devono essere rigidi e resistenti al calore, perché saranno soggetti a pressione [per formare le parti in materiali compositi] e ad alte temperature, di solito intorno ai 180-200 gradi”. Un esempio recente è uno strumento sviluppato dal team per produrre tubi in materiale composito. La Rigid 10K Resin è stata impiegata per produrre i pilastri di supporto del componente, che richiedevano un’elevata rigidità, la High Temp Resin per produrre i morsetti, che richiedevano resistenza alle alte temperature e alla pressione dell’aria, e la Draft Resin per produrre in modo rapido i tappi terminali dello strumento. “[Senza la stampa 3D], avremmo dovuto utilizzare il metallo e avremmo impiegato molto più tempo e denaro per la produzione”, ha affermato Romero.
Produzione di design complessi con diversi materiali con la Form 3L
Lo studio Vital Auto crea prototipi estremamente fedeli e concept car, eseguendo rapidamente diverse iterazioni utilizzando una serie di strumenti avanzati, tra cui una vasta flotta di stampanti Formlabs Form 3L e Fuse 1. Il team Vital sviluppa le auto partendo da un foglio bianco, progetta il telaio, tutti gli elementi interni ed esterni, aperture e chiusure, e le parti interattive. Un progetto può durare da tre a dodici mesi, impegnando da cinque a trenta persone per un singolo concept. In questo lasso di tempo, un’auto da esposizione viene sottoposta a una dozzina di iterazioni del design di base e, all’interno di queste, si susseguono ulteriori iterazioni di
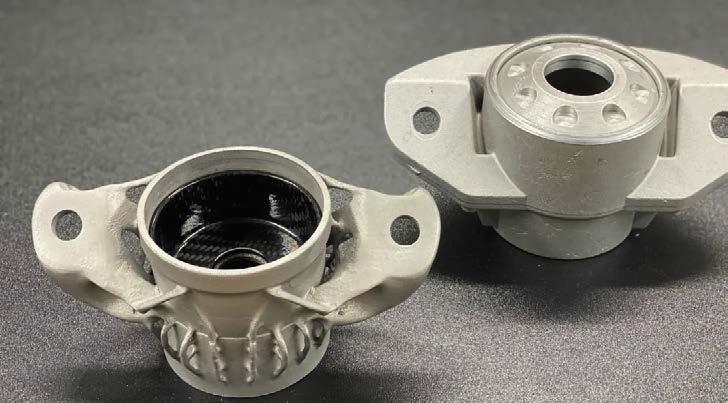
I prodotti Formlabs
I prodotti Formlabs includono le stampanti Form 3+, Form 3B+, Form 3L e Form 3BL, basate sulla stampa 3D Low Force Stereolithography (LFS)™, le soluzioni di post-elaborazione Form Wash, Form Cure, Form Wash le stampanti 3D SLS Fuse 1 e Fuse 1+ 30W e il sistema per il recupero della polvere Fuse Sift. Inoltre, Formlabs sviluppa una gamma di materiali ad alte prestazioni, che consentono di continuare a superare i limiti della stampa 3D, nonché software all’avanguardia per la stampa 3D, come il PreForm.
componenti più piccoli, fino a quando il design non soddisfa pienamente le aspettative del cliente. Per produrre parti personalizzate necessarie per concept una tantum, Vital Auto ha introdotto nel suo processo di produzione la stampa 3D, non solo per ridurne i costi, ma anche per offrire ai clienti maggiore diversità per i loro design e le loro idee. Col tempo hanno predisposto un intero reparto per la stampa 3D, che comprende dieci stampanti FDM di grande formato, tre stampanti SLA Form 3L di Formlabs, sempre di grande formato, e cinque stampanti SLS Fuse 1. Tutte le stampanti hanno funzionato al 100%, 24 ore su 24, 7 giorni su 7, praticamente dal primo giorno e vengono utilizzate per tutte le aree dei concept e design. In particolare, le Fuse 1 vengono generalmente usate per le parti che si basano sulla produzione e le Form 3L per le parti basate sul concept. “Utilizziamo le Form 3L per tutte le finiture superficiali di classe A, come ad esempio, in un contesto automobilistico, un interno in cui siano presenti parti che non vengono rifinite con pelle o Alcantara o, in generale, con un tessuto. I materiali di Formlabs producono una finitura bella e liscia con cui possono lavorare i verniciatori. In questo modo, possiamo usare le parti appena stampate direttamente su un veicolo”, ha detto Anthony Barnicott, ingegnere di progettazione, responsabile della produzione additiva, aggiungendo “Quello che mi interessa maggiormente degli apparecchi Form 3L è la loro versatilità, la capacità di fare un cambio di materiale in meno di cinque minuti. La variabilità dei materiali, da quelli morbidi e flessibili a quelli rigidi, per noi non ha prezzo”. Il team usa le Form 3L con molteplici materiali per una vasta gamma di applicazioni, come ad esempio, pacchetti di interruttori e guarnizioni per le portiere; mentre utilizza le Fuse 1 soprattutto per le parti meccaniche, come le cerniere, gli interni delle maniglie e gli interni delle portiere, e per le applicazioni strutturali. Le parti si possono utilizzare da subito, sin dopo la stampa, con rifiniture minime.
Concept interattivo per una supercar
La stampa 3D ha inoltre consentito al team Vital Auto di combinare i materiali SLA con quelli SLS per realizzare diverse iterazioni di design in un progetto specifico. Questo metodo consente di produrre rapidamente più iterazioni, associando entrambi i processi, utilizzandoli per le loro proprietà specifiche, per ottenere un design finale. Può trattarsi di qualsiasi cosa, dalle parti meccaniche a quelle trasparenti, per verificarne la qualità ottica e la resa. La stampa 3D non solo aiuta il team a creare prodotti migliori più velocemente, ma anche ad aumentare gli ordini. Molti dei clienti si rivolgono a loro perché vogliono avere accesso alle ultime tecnologie e vogliono che i loro componenti vengano realizzati con materiali all’avanguardia.
Integrando le soluzioni di automazione di Mitsubishi Electric, l’azienda piemontese Nord Engineering ha sviluppato un innovativo sistema di sollevamento polivalente bilaterale per la raccolta dei rifiuti
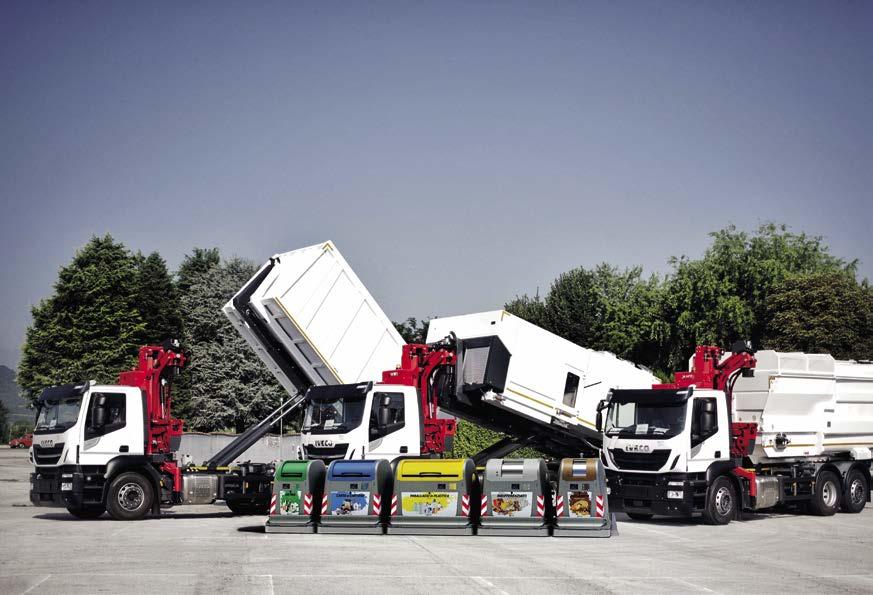
NNata venticinque anni fa a Caraglio, in provincia di Cuneo, Nord Engineering è oggi è una realtà dello smart waste management riconosciuta a livello internazionale, che progetta soluzioni altamente tecnologiche, sostenibili ed efficienti. Con l’obiettivo di superare i limiti dei tradizionali sistemi di raccolta dei rifiuti, Nord Engineering ha sviluppato l’esclusivo sistema Easy, un’attrezzatura automatica mono operatore bilaterale capace di raccogliere diverse tipologie di contenitori. Easy è costituito da un braccio robotico che, grazie ad un apposito dispositivo di aggancio brevettato situato al centro del contenitore, raccoglie il cassonetto dei rifiuti, lo solleva e lo porta sopra il compattatore per poi svuotarlo all’interno del mezzo. Come spiega Andrea Fissore, responsabile marketing dell’azienda, “Easy è un sistema integrato che include sia il robot che i contenitori, che sono in grado di interagire perfettamente tra loro. Si tratta di una macchina monooperatore perché, grazie ad apposite videocamere, l’operatore è in grado di agganciare i contenitori, manovrarli e svuotarli senza mai scendere dal mezzo”. Oltre all’allestimento del mezzo, Nord Engineering si occupa anche della realizzazione di varie tipologie di contenitori per la raccolta differenziata, sia fuori terra che interrati e seminterrati, anche di grandi dimensioni per utilizzi commerciali e industriali. Gli automezzi utilizzati dall’azienda cuneese permettono di realizzare tre soluzioni in una: su un unico mezzo è infatti possibile adattare il compattatore, il cassone a cielo aperto e il lavacontenitori. L’innovativo sistema Easy di Nord Engineering viene oggi utilizzato in quasi tutte le regioni italiane, grazie ad accordi con numerosi Comuni, multiutility e Consorzi, ma ha anche varcato i confini nazionali essendo esportato in oltre 20 Paesi. “Per noi è un orgoglio che un prodotto made in Italy venga utilizzato in tutto il mondo. Solo per citare qualche esempio, abbiamo realizzato sistemi di raccolta dei rifiuti con la nostra soluzione in Florida, a Buenos Aires e a Dubai”, dichiara con grande soddisfazione Andrea Fissore.
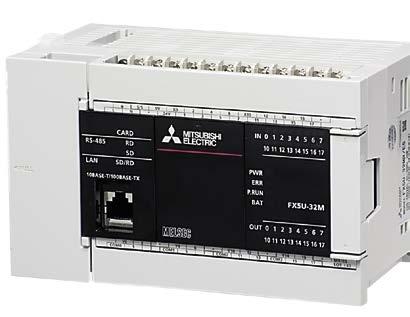
Green e Smart
Particolarmente sensibile ai temi della sostenibilità ambientale e dell’economia circolare, Nord Engineering realizza esclusivamente contenitori per la raccolta dei rifiuti in acciaio 100% riciclato e riciclabile. Inoltre, tra i veicoli utilizzati per effettuare la raccolta differenziata l’azienda cuneese ha scelto di inserire anche una linea di mezzi elettrici non inquinanti. Oltre ad essere eco-sostenibili, i contenitori di Nord Engineering sono anche “intelligenti”, grazie all’integra-
PLC compatto FX5U di Mitsubishi Electric
zione di componenti elettronici in grado di comunicare sia tra di loro che con il cloud. L’utente che conferisce i rifiuti deve identificarsi, attraverso un’apposita card o uno smartphone, per permettere alla bocca di conferimento di aprirsi per l’inserimento dei rifiuti. Il contenitore memorizza quello che viene conferito al suo interno e, in un’ottica di “smart city”, è in grado di comunicare con una centrale in cloud e, quindi, con il mezzo di raccolta: all’interno del contenitore è inserito, infatti, un sensore volumetrico di riempimento che invia alla centrale un segnale al raggiungimento di una soglia preimpostata e questo permette di ottimizzare tutto il processo di raccolta. Inoltre, in caso di anomalie nel conferimento, il contenitore è in grado di inviare degli alert per far sì che in brevissimo tempo il sistema possa essere ripristinato.
Una partnership consolidata
Il sistema Easy monta le soluzioni di automazione di Mitsubishi Electric. La partnership tra Nord Engineering e Mitsubishi Electric risale al 2005 e ha consentito a Easy di evolversi negli anni contemporaneamente al miglioramento tecnologico delle soluzioni della multinazionale giapponese. “Il rapporto quasi ventennale con Mitsubishi Electric ci ha permesso di evolverci insieme, integrando nella soluzione Easy un sistema elettronico che include PLC, HMI e tutta la componentistica necessaria”, spiega Fissore. “Mitsubishi Electric si è fin da subito allineata al nostro progetto, fornendoci un prodotto customizzato e assistendoci in tutte le fasi della realizzazione del sistema Easy, dalla progettazione alla messa in opera, inclusi i successivi aggiornamenti che hanno permesso la continua evoluzione tecnologica della nostra soluzione fino ad oggi. Il supporto di Mitsubishi
Piattaforma di automazione scalabile
La piattaforma di automazione MELSEC iQ-F di Mitsubishi Electric offre un bus ad alta velocità evoluto, funzioni integrate avanzate e un supporto SSCNETIII/H d’avanguardia. MELSEC iQ-F è in grado di comunicare con tutti i tipi di bus, inclusi quelli automotive. Per la programmazione e parametrizzazione viene utilizzato il software di sviluppo GXWorks 3. Il PLC compatto FX5U della piattaforma iQ-F offre un enorme incremento delle prestazioni rispetto ai modelli precedenti della serie FX, garantendo grande velocità di elaborazione, espandibilità, funzioni integrate, oltre a funzioni di posizionamento e motion. Grazie alla sua scalabilità, MELSEC iQ-F è espandibile verso la piattaforma di automazione MELSEC iQ-R, che offre funzioni avanzate per il Process Control e la Safety integrata, totalmente supportate dall’ambiente di sviluppo iQ Works per realizzare architetture PAC semplici o ridondate. Le prestazioni del nuovo controllore iQ-R sono impressionanti: bus scambio dati 40x più veloce, sincronizzazione tra moduli CPU, Motion e reti di comunicazione, sicurezza incrementata con protezione Security Key, data logging integrato per interfacciamento diretto con MES / ERP. Questa piattaforma di controllo flessibile e potente permette alle aziende un accesso strategico ad automazione e controllo, poiché consente la piena integrazione del livello di fabbrica nel livello di gestione risorse dell’azienda.
Electric è stato costante e sempre improntato alla massima collaborazione: anche in presenza di eventuali problematiche abbiamo lavorato insieme per arrivare a una soluzione condivisa”. “I nostri prodotti di automazione montati sulla soluzione Easy hanno accompagnato nel tempo l’evoluzione tecnologica di Nord Engineering”, conferma Gianmichele Piciocco, Marketing Manager South EMEA Mitsubishi Electric Factory Automation. “Siamo partititi da un PLC compatto molto piccolo, il modello iQ-F, che comandava degli ingressi e delle uscite remote, poi abbiamo integrato i primi pannelli operatore per permettere al personale di lavorare restando sempre a bordo del camion”. Recentemente Nord Engineering ha compiuto un ulteriore passo tecnologico, rendendo “smart” sia i cassonetti che l’automezzo utilizzato per la raccolta. “C’era la necessità di realizzare un collegamento con la centralina del camion, per cui il PLC di Mitsubishi Electric doveva connettersi con un bus proprietario, doveva sapere cosa succedeva all’autoveicolo, incorporare delle telecamere e dare un’esperienza di touch-screen che permettesse di movimentare correttamente il braccio robotizzato”, spiega Gianmichele Piciocco. “Il risultato raggiunto va ben oltre quelle che erano le nostre aspettative iniziali: Nord Engineering è riuscita ad usare una tecnologia general purpose come un PLC per farla diventare un prodotto custom di alto livello. Adesso stanno valutando l’integrazione della nostra piattaforma avanzata di automazione MELSEC iQ-R, passando così da un PLC compatto ad uno modulare per aumentare le velocità e le prestazioni nella lettura dei sensori integrati nel sistema Easy”.

Sicurezza, velocità e ottimizzazione del processo
Anche per quanto riguarda la visualizzazione, il sistema Easy oggi utilizza una soluzione tecnologicamente avanzata: un computer industriale touch screen con a bordo uno Scada che permette una visualizzazione tridimensionale. “Quella realizzata con Nord Engineering è una soluzione che è cresciuta moltissimo negli anni, partendo da un concetto base di automazione fino a raggiungere un livello di avanguardia tecnologica”, aggiunge Gianmichele Piciocco. “L’esigenza da cui è nato questo sistema altamente tecnologico era quella di migliorare la raccolta dei rifiuti, realizzando una soluzione automatizzata che superasse i sistemi tradizionali per ottenere una maggiore sicurezza e velocità delle operazioni di raccolta, ma anche un’ottimizzazione generale del processo. In tutte le città dove abbiamo lavorato e stiamo lavorando è aumentata la percentuale di raccolta differenziata, a conferma del fatto che il nostro sistema, grazie anche alla tecnologia di Mitsubishi Electric, permette effettivamente di migliorare l’intero sistema di raccolta dei rifiuti”, conclude Andrea Fissore.
Organizzato da
Pannello operatore GOT2000 di Mitsubishi Electric

Sfide e soluzioni per la tracciabilità nella produzione automobilistica oggi e cosa prendono in considerazione decision maker ed esperti
CCi sono diversi motivi per cui i produttori devono tenere registri accurati delle parti che compongono una nuova vettura. Dal punto di vista della qualità, ad esempio, il tracciamento dei codici a barre aiuta a garantire che vengano assemblate insieme le parti giuste. Ancora più importante, tuttavia, è la capacità di risalire fino al fornitore originale per ciascuna parte. In caso di richiamo o di identificazione di un componente difettoso, i produttori devono essere in grado di individuare in modo rapido e completo la provenienza di ciascun componente. Con l’espansione globale del settore automobilistico, la produzione di veicoli leggeri dovrebbe raggiungere circa 96 milioni di unità entro il 2023. Ciò significa che anche una singola parte difettosa può avere un impatto enorme e pertanto si tratta di una circostanza che deve essere evitata a tutti i costi. Inoltre, la tracciabilità riduce al minimo la contraffazione poiché le parti originali possono essere tracciate fino a identificare la loro provenienza.
Lettori di codici e RFID: la garanzia di lettura del codice al 100%
Negli ultimi 30 anni, OMRON ha acquisito una vasta conoscenza nel campo della lettura dei codici. L’esperienza e l’innovazione vanno di pari passo con OMRON in un’ampia gamma di prodotti RFID e per la lettura dei codici per fornire la soluzione di acquisizione dei dati corretta per qualsiasi sfida di tracciabilità. Grazie all’algoritmo di decodifica X-Mode e alle funzionalità di messa a fuoco automatica, anche le più complesse marcature dirette dei pezzi potranno
essere lette in modo affidabile, senza necessità di configurazione. I controlli integrati monitorano la qualità del codice durante la lettura e, per eventuali problemi, funzionano come un sistema di allarme tempestivo. Ciò garantisce che nessun codice illeggibile esca dalla fabbrica. “Un altro vantaggio dell’identificazione diretta delle parti, delle etichette o delle etichette RFID – dichiara Nico Hooiveld, Business Development Manager presso OMRON Europe - è rappresentato dalla semplificazione del processo di produzione, infatti i sistemi di tracciabilità in tempo reale trasmettono le informazioni sui processi a tutti i livelli del processo di produzione, consentendo l’ottimizzazione della supply chain e riducendo i tempi di consegna”. I codici a barre garantiscono che ogni parte abbia con sé un identificativo univoco ovunque si trovi. In genere si tratta di un Direct Part Marking, inciso o stampato direttamente sulla parte stessa. “Tra i dati chiave codificati per scopi di tracciabilità nel settore automobilistico vi sono informazioni quali numero del componente, di serie, di lotto o di modello. Altre informazioni che potrebbero essere codificate nei codici a barre sono il produttore, il luogo di origine, la data e l’ora di produzione, la data di scadenza, lo stabilimento di produzione o assemblaggio, i componenti utilizzati nell’assemblaggio e/o nella versione software”, afferma Hooiveld. Ogni volta che un codice viene letto nel reparto produzione, il sistema di tracciabilità trasmette questi dati a un Manufacturing Execution System o a un software di Enterprise Resource Planning, contribuendo ad assemblare correttamente le parti e a controllare altri elementi della linea di produzione in base ai dati. La sfida consiste nel realizzare una raccolta di dati affidabile con costi di implementazione limitati. La tracciabilità viene utilizzata per etichettare i componenti della trasmissione con dimensioni specifiche per garantire un adattamento perfetto. L’automazione dei processi riduce significativamente la probabilità di errori in questo contesto. “Ciò non è sempre semplice – continua Hooiveld - poiché i lettori di codici a barre o RFID devono essere integrati nei macchinari delle linee di assemblaggio con spazi limitati. Pertanto è opportuno utilizzare lettori di codici a barre particolarmente compatti. Dei lettori potenti, inoltre, dovrebbero essere in grado di leggere un’ampia gamma di codici senza dover installare software complessi, anche se il codice è distorto, sbiadito o danneggiato”. Per garantire che ogni parte riporti i dati richiesti, alcuni codici a barre devono essere particolarmente piccoli. Come per i codici danneggiati, i codici di piccole dimensioni richiedono lettori ad alte prestazioni in grado di leggere i dati con la velocità e la precisione richieste. Poiché sempre più marcature vengono applicate nelle prime fasi del processo di produzione, è sempre più probabile che vengano danneggiate nelle condizioni difficili di produzione. Per questo motivo è importante che i codici a barre abbiano il massimo livello di leggibilità fin dall’inizio. OMRON offre un’ampia gamma di soluzioni per la verifica del codice che misurano la qualità del codice in base agli standard ISO e GS1 pertinenti e che aiutano i produttori a controllare la qualità di stampa.
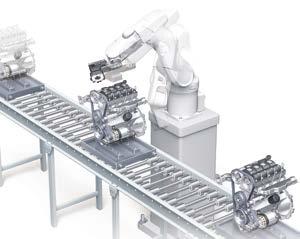

Raccolta dati affidabile
I sistemi di tracciabilità offrono un modo per contestualizzare le modifiche ai processi e analizzare gli effetti che hanno sulla qualità del prodotto risultante. Aiutano a identificare i rischi, a ridurne l’impatto e, in generale, a mantenere uno stato di costante vigilanza. Più un sistema di tracciabilità è automatizzato con un monitoraggio delle decisioni in tempo reale, migliore è l’analisi del processo di produzione e l’individuazione delle fasi problematiche. Sebbene la tracciabilità possa sembrare complessa, la struttura di fondo è relativamente semplice. Grazie all’applicazione di codici a barre univoci in fase di lavorazione e alla scansione di questi codici durante l’intero processo di assemblaggio, i produttori possono raccogliere e memorizzare quantità significative di dati sulla posizione e la cronologia di ciascun articolo in ogni momento. I controller di tracciabilità OMRON, combinati con i dispositivi di acquisizione dati OMRON, offrono un basso costo di implementazione riducendo notevolmente il tempo necessario per lo sviluppo e la messa in servizio. I pannelli HMI, i gruppi di continuità (UPS) e i sensori necessari per completare la soluzione di tracciabilità sono immediatamente disponibili nell’ampio portafoglio di prodotti OMRON per l’automazione.
Un sistema pionieristico con 6 robot Stäubli serie TX2-60L, 13 sistemi visione e controllo della qualità in linea, garantisce una produzione con flessibilità massima
Robot compatti e dinamici per soluzioni personalizzate di automazione e assemblaggioassemblaggioL’ L’elettromobilità rappresenta una delle più grandi sfide per il pianeta. La e-mobility è il futuro: si stima che entro il 2032, la metà dei veicoli venduti a livello globale saranno elettrici. Stiamo quindi assistendo ad una vera e propria ondata storica di innovazione, in un mondo che cambia ad dell’assemblaggio di PCB e produzione di connettori, è stata recentemente convocata da una multinazionale messicana, produttrice di componenti per l’automotive, allo scopo di ideare e realizzare una linea di assemblaggio per connettori ad alta tensione. Il sistema doveva essere in grado di eseguire non solo il lavoro di assemblaggio effettivo, ma anche l’ispezione visiva in ogni singola fase, il test di ogni connettore per l’impermeabilizzaaltissime velocità. Infatti, il commer- zione e, infine, l’imballaggio dei prodotti. cio dei veicoli con azionamenti elettrici sta guadagnando “Le speciali caratteristiche del progetto includevano il target costantemente quote di mercato in tutto il mondo. Questa di un output di 5 milioni di unità all’anno, un tempo ciclo tendenza stimola anche la domanda di soluzioni per l’assem- serrato non superiore a tre secondi per connettore e un design blaggio dei componenti elettrici. del sistema a prova di qualsiasi possibile variante di futuro Eberhard AG, azienda fondata nel 1964 a Schlierbach vicino connettore. Con queste specifiche, l’unica soluzione possia Stoccarda (Germania) con un’ampia esperienza nel campo bile era includere dei robot, un sistema di elaborazione delle
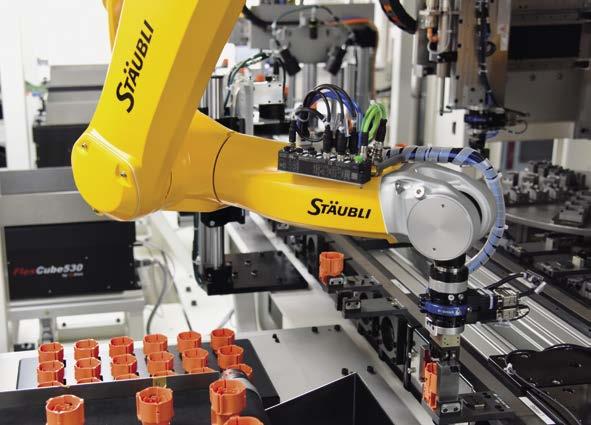
immagini e un sistema di alimentazione estremamente flessibile”, commenta Abdullah Kotan, Project Planning and Application Team Leader di Eberhard. Le soluzioni personalizzate di automazione e assemblaggio sono tra le competenze chiave dell’azienda, per cui la direzione era fermamente convinta che, in collaborazione con i giusti partner, avrebbe potuto portare a termine il progetto con successo. Grazie ai robot Stäubli, il team di progettazione è riuscito a realizzare una linea di montaggio destinata al Messico flessibile, compatta ed efficiente, raggiungendo, così, l’obiettivo prefissato.
Un capolavoro di automazione compatta
Il progetto richiedeva l’inserimento, su una linea di produzione, dallo spazio ridotto, di 13 stazioni con 6 robot e 13 sistemi di visione. L’ottimizzazione degli spazi è stata la chiave vincente per la riuscita del progetto. Per ottimizzare l’area di lavoro e ridurre gli spazi occupati, i progettisti hanno quindi deciso di sospendere i robot a sei assi sopra le stazioni. I sei robot Stäubli appartengono alla serie TX2-60L, sono dotati di sei assi superveloci e sono estremamente precisi in ogni condizione. In particolare, questi robot sono in grado di operare con una ripetibilità di ± 0,03 mm e un raggio d’azione di 920mm. “Abbiamo scelto questi robot non solo per la loro dinamica, ma anche per il loro design compatto, le interfacce con gli alimentatori e le telecamere e, non da ultimo, per la loro riconosciuta affidabilità”, afferma Kotan. “Dobbiamo garantire ai nostri clienti una disponibilità totale del sistema superiore al 95% e possiamo quindi utilizzare solo componenti di prima classe”. I sistemi di alimentazione ultra-flessibili sono una delle caratteristiche delle linee di assemblaggio progettate e costruite da Eberhard, in quanto assicurano l’assenza di regolazioni meccaniche quando si passa da una variante all’altra. In caso di una nuova variante, infatti, il sistema la riconosce e la memorizza semplicemente tramite elaborazione dell’immagine.
Assemblaggio e test all’unisono
L’assemblaggio dei connettori segue uno schema preciso e ogni fase di lavoro include un controllo di qualità. Prendiamo ad esempio la stazione 1: il primo robot TX2-60L dotato di tracking preleva un alloggiamento del connettore da un nastro di alimentazione, costantemente in funzione, e lo posiziona in un portapezzi, dove vi rimane attraversando tutte le stazioni del sistema. Alla stazione 2 viene effettuato un controllo di qualità ottico, durante il quale vengono memorizzati codice e colore. Lo stesso schema si applica alle due stazioni successive. La seconda macchina a sei assi Stäubli preleva da una tavola vibrante il blocco connettore, tramite identificazione della posizione del pezzo grazie al sistema di visione, montandolo nell’alloggiamento. Anche in questo caso, Eberhard applica il QA istantaneo, con il processore di immagini che si concentra sul duplice criterio di rilevamento dei difetti e sulla posizione di assemblaggio. Lo stesso schema viene applicato quando l’alloggiamento del connettore passa attraverso tutte le successive stazioni. A questo punto ci sono altri tre passaggi durante i quali le macchine ultraveloci Stäubli a sei assi montano una guarnizione, un telaio e l’interno completo del connettore. A valle, i consueti controlli di qualità in linea vengono effettuati dopo ogni stazione. Prima che il connettore ad alta tensione completamente assemblato venga trasferito dall’ultimo dei sei robot Stäubli al sistema di pallettizzazione Eberhard PTS 64, viene testato contro eventuali perdite. Infine, allo scopo di mantenere il tempo ciclo ed evitare colli di bottiglia, Eberhard ha installato una tavola rotante di indicizzazione con quattro stazioni e un dispositivo quadruplo di test.
Riattrezzaggio in 10 minuti esatti
Attualmente, il sistema gestisce solamente tre varianti, con cambi programmati una o due volte al giorno. Questo numero dovrebbe aumentare significativamente a breve e il design estremamente flessibile della linea di montaggio eviterà al cliente qualsiasi problema. “Il nostro cliente produce in piccoli lotti e quindi il passaggio deve essere completato nel più breve tempo possibile. Dall’ultima unità di un lotto alla prima del lotto successivo, il riattrezzaggio viene completato entro massimo soli 10 minuti”, spiega Kotan.
Target tempo ciclo superato
Già durante la fase di collaudo della linea di montaggio, il target tempo ciclo di tre secondi è stato raggiunto con ampio margine. L’attuale tempo ciclo del sistema tocca i 2.7 secondi per connettore ad alta tensione, che corrisponde esattamente alla simulazione fatta in fase di ideazione del sistema in collaborazione con Stäubli Robotics. Il fatto che la simulazione fosse così vicina alla realtà sottolinea la validità del metodo utilizzato, sempre a condizione che vengano implementati i giusti strumenti. “Siamo sicuri che saremo in grado di ottimizzare ulteriormente alcuni passaggi quando il sistema sarà installato nello stabilimento di produzione del cliente in Messico, aumentando la produzione di alcuni punti percentuali. Se riuscissimo, ad esempio, a ridurre il tempo ciclo dal 12% al 14%, sarebbe davvero un risultato notevole nel contesto di un volume di produzione annuale di cinque milioni di connettori”, conclude Abdullah Kotan.
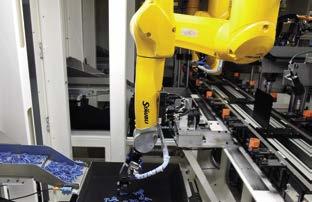
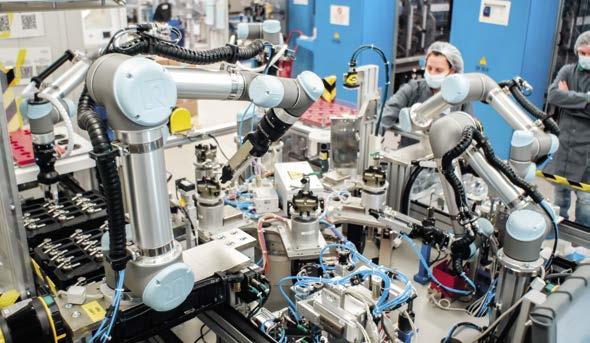
I cobot sono flessibili e possono automatizzare con successo numerosi processi all’interno di un’industria che tradizionalmente ha scelto la robotica tradizionale. I cobot UR sono applicati in decine di stabilimenti sia di grandi marchi che nella subfornitura. Ecco alcuni esempi applicativi e vantaggi
Automotive, l’alternativa alternativa di automazione è collaborativa
PPer molto tempo l’unica forma di automazione creduta compatibile con un settore ad alta cadenza come l’automotive è stata quella di tipo tradizionale. La gestione di pesi e di aree di lavoro ampie rendeva la robotica antropomorfa l’unica realmente applicabile al settore automobilistico. In realtà, come in molti altri settori “pesanti” vi sono miriadi di attività che possono essere adeguatamente automatizzate con altre forme di robotica, ad esempio quella di tipo collaborativo. In ogni processo vi sono porzioni di task che possono avvalersi della robotica collaborativa con evidenti vantaggi. Tutte quelle porzioni – ad esempio - in cui l’intervento umano è ancora preponderante. Spesso gli operatori di linea vengono applicati su attività caratterizzate da un valore aggiunto piuttosto basso, scarsa ergonomia, rischi potenziali per la salute. È il caso, ad esempio, di tutte quelle attività di assemblaggio e avvitatura sulle linee di ferratura, che espongono gli operatori a un duplice rischio: lesioni dovute alla lamiera tagliente, contraccolpi articolari dati dagli strumenti di avvitatura. In questi task la robotica collaborativa è un valido aiuto e consente di ottimizzare i processi con valori di qualità e rendimento più elevati.
La gamma Universal Robots
La gamma cobot UR comprende 5 modelli, caratterizzati da payload e sbraccio progressivi e dalle medesime safety native (17 completamente personalizzabili) in PLD. Cat. 3. UR3e (3kg di portata e 500 mm di raggio d’azione), pensato come tool evoluto da banco e per piccoli assemblaggi (resi possibili anche dalla rotazione infinita al polso). UR5e (5kg di payload e 750 mm di reach) flessibile e sufficientemente potente per il machine tending di piccoli componenti e per assemblaggi minuti. UR10e (10 kg di capacità di carico e 1300 mm di raggio d’azione) pensato per l’automa-
zione di attività pesanti e su un’ampia area di lavoro. UR16e, dotato di una capacità di carico di 16 kg e di 900 mm di reach. Infine UR20, il cobot più potente della gamma, con payload di 20 kg e un raggio utile di 1750 mm: la soluzione per la pallettizzazione, il welding e il carico e scarico macchine con componenti di peso elevato. UR5e e UR10e sono al momento i cobot più utilizzati dall’industria automobilistica.
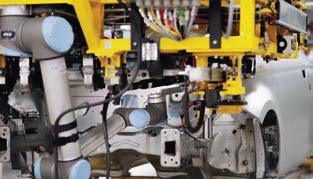
I cobot per l’automotive: applicazioni e vantaggi
I cobot Universal Robots vengono applicati con successo nel settore automotive in molti grandi marchi e nella subfornitura. Ne sono un esempio le applicazioni in Nissan, Continental, Stellantis, PSA, Vitesco…Aziende che hanno tratto dai cobot diversi vantaggi. Di ordine economico, andando a migliorare produttività e qualità e coerenza dei processi, di ordine ergonomico (sollevando gli operatori da attività faticose e usuranti o supportando una popolazione particolarmente anziana nello svolgere mansioni quotidiane). Infine, i cobot sono anche il veicolo con cui inserire competenze nuove in azienda, creando processi di reskilling della popolazione aziendale. Vediamo alcuni esempi concreti. Stellantis, una delle maggiori realtà dell’automotive al mondo, ha implementato 11 cobot Universal Robots lungo la dorsale di produzione della nuova 500 elettrica. I cobot sono applicati in diverse attività: assemblaggio e avvitatura, controllo qualità, dispensing. La popolazione aziendale dello stabilimento di Mirafiori, storico centro produttivo del marchio, era particolarmente anziana. Dopo un’accurata analisi ergonomica dei processi, i cobot sono stati applicati laddove era più impellente migliorare la qualità del lavoro degli operatori. Ecco quindi che i cobot sono stati integrati nella linea di rullatura delle portiere, dove – con un rullino dinamometrico integrato al polso – procedono alla sigillatura del telino paracqua all’interno delle portiere (sollevando quindi gli operatori dall’eseguire un’azione particolarmente usurante per l’articolazione del polso). Oppure sono stati inseriti nella linea di ferratura, dove svolgono assemblaggi del cofano, dei parafanghi, del portello posteriore della versione a 3 porte della 500. In tutte queste applicazioni il vantaggio per gli operatori è duplice: minori rischi di lesioni e ferite contro i bordi taglienti della lamiera, minori lesioni articolari date dagli strumenti di avvitatura. Inoltre, molte delle operazioni di avvitatura e assemblaggio dovevano avvenire con cofani e parafanghi in posizione vettura, cioè chiusi. Questa configurazione pone non poche sfide all’operatore che deve avvitare (con coppia costante) in luoghi non facilmente raggiungibili e con scarsa o nulla visibilità. L’ergonomia così raggiunta per gli operatori, si sposa però anche con un miglioramento della qualità dei processi: le avvitature e gli assemblaggi vengono infatti eseguiti con coerenza e coppia costanti. Un altro esempio di come i cobot abbiamo migliorato i parametri di ergonomia e produttività è quello fornito da Vitesco Technologies Italy. L’azienda – fra i leader mondiali nella produzione di valvole e iniettori per motori endotermici – ha integrato nei propri stabilimenti di San Piero a Grado e Fauglia in provincia di Pisa 24 cobot Universal Robots. Vitesco, che ha sempre investito in automazione e che da anni si avvale dei processi di lean manufacturing per progettare le sue linee, è partita dall’analisi delle attività a minor valore per progettare alternative automatizzate al lavoro manuale. I cobot UR sono stati così integrati nell’assemblaggio dei DDU (sistemi per la rigenerazione dei filtri antiparticolato) oppure nella linea di produzione delle RDU (valvole per il dosaggio dei gas in camera di scoppio). Oppure ancora nel carico/scarico macchine e nella pallettizzazione di componenti metallici all’interno di tray. I cobot hanno dovuto superare diverse sfide per assicurare un’automazione di successo. L’assemblaggio delle RDU prevede infatti l’inserimento di guaine gommose su componenti tubolari di diversa forma e angolazione e con tolleranze diversificate. Soltanto un’automazione flessibile, con un evoluto controllo di forza integrato al polso, avrebbe potuto eseguire il compito assicurando la qualità dell’esecuzione. PSA, gigante francese che raccoglie i marchi Peugeot, Citroen e altri, ha integrato i cobot danesi all’interno del proprio stabilimento di Sochaux. Due cobot UR10 sono stati implementati nello stabilimento in applicazioni di avvitatura su linee di assemblaggio body-in-white per aumentare le prestazioni e ridurre i costi di produzione in fabbrica. I risultati ottenuti dall’applicazione includono risparmi sui costi, una migliore tolleranza geometrica e migliori condizioni di lavoro ergonomiche per gli operatori. Nella fattispecie i cobot UR sono stati inseriti all’interno di una struttura a gabbia che si cala sulla scocca della vettura in transito sulla linea. La gabbia assicura la geometria del veicolo. Una volta acquisita quest’ultima i cobot eseguono 2 coppie di avvitature nella parte posteriore e inferiore della scocca, posizioni poco ergonomiche per gli operatori, che oltretutto non avrebbero potuto garantire avvitature corrette operando quasi alla cieca nel sottoscocca.
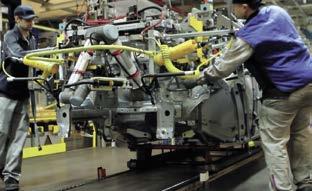
di Andrea Mazzoleni – AFIL; Annalisa Giavarini, Angelo Iapichino – Consorzio Intellimech, Fabio Sana – Brembo S.p.A. Tecnologie
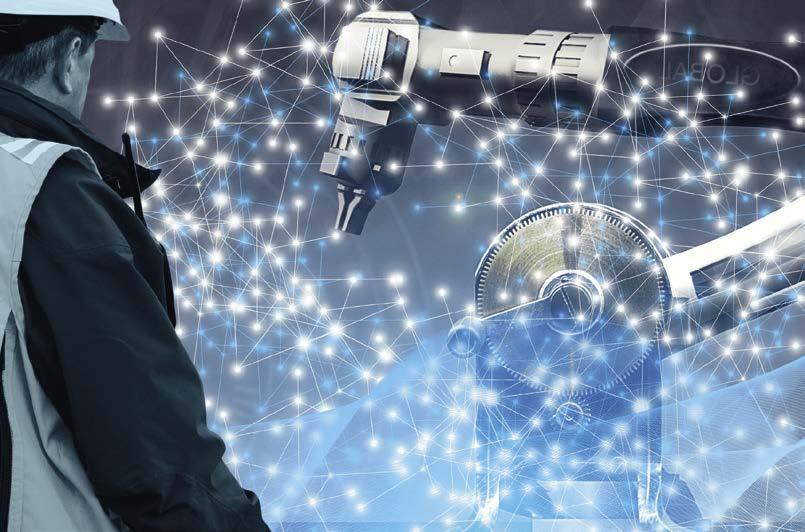
L’HUB LOMBARDO PER L’INTELLIGENZA ARTIFICIALE
La visione del progetto Watchman e il dimostratore Brembo
È
È opinione consolidata che i sistemi di visione artificiale e gli algoritimi di computer vision ad essi legati possano contribuire a risolvere diverse sfide e problematiche in ambito industriale contribuendo in maniera significativa alla competitività delle imprese. Tramite essi è infatti possibile acquisire un’ immagine e tradurla in dati utili per supportare le decisioni aziendali, contribuendo, ad esempio, alla riduzione delle difettosità nei prodotti, all’incremento dell’efficienza complessiva dei processi produttivi nonché al miglioramento della sicurezza e dell’ergonomia complessiva delle mansioni lavorative. Si stima infatti che nel 2027 il valore di mercato globale dei sistemi di visione e dei relativi algoritmi, come i modelli di deep learning, possa raggiungere 74,9 miliardi di dollari di fatturato cifra che testimonia le ampie opportunità applicative ed essi connesse. Da un punto di vista generale, inoltre, il mercato mondiale dell’intelligenza artificiale, a cui gli algoritimi di sistemi di visione appartengono, varrà, al 2030, 15,1 triliardi di dollari, dei quali 2,5 in Europa (fonte: PwC’s Global Artificial Intelligence Study: Exploiting the AI Revolution) . In aggiunta a queste stime, i recenti documenti pro-


grammatici emanati sia a livello comunitario che nazionale, come ad esempio il Coordinated Plan on Artificial Intelligence della Commissione Europea e il Piano Nazionale per l’Intelligenza Artificiale del Ministero dell’Università e della Ricerca, del Ministero dello Sviluppo Economico e del Ministro per l’Innovazione Tecnologica, evidenziano l’importanza di diffondere l’uso dell’intelligenza artificiale nei settori produttivi, in particolare tra le PMI. Infatti, a causa di complessità, costi ancora elevati, necessità di competenze specifiche e consolidate, aspetti regolatori ed etici, queste tecnologie risultano ancora non ampiamente utilizzate. È in linea con queste considerazioni che si colloca il progetto Watchman. Coordinato dal Consorzio Intellimech, l’obiettivo è realizzare un hub di competenze e di sperimentazione sull’applicazione dell’intelligenza artificiale nella visione artificiale in Lombardia per generare conoscenza, impatti tecnologici e ricadute sociali per la competitività del sistema industriale regionale. Co-finanziato da Regione Lombardia nell’ambito della Call Hub Ricerca e Innovazione, il progetto, generato nell’ambito della Strategic Community Digital Transformation del Cluster AFIL, vede coinvolte otto realtà rappresentative di imprese, università e centri di ricerca: i fornitori di tecnologie hardware e software Smart Robots, Sorint.TEK, Vision e Fincons, gli utenti finali Brembo e S.A.L.F. Laboratorio Farmacologico, l’Università degli Studi di Bergamo e il Consorzio Intellimech. Il tratto distintivo dell’approccio è la sinergia tra le diverse specializzazioni presenti nel consorzio, che spaziano dalla visione artificiale sino allo sviluppo di algoritmi, gestione dei dati e robotica collaborativa. Facendo leva sulle singole competenze, le soluzioni tecnologiche sono sviluppate con una logica modulare e riconfigurabile. L’intento è realizzare sistemi di visione che possano essere utilizzati sia in maniera indipendente sia interconnessa in una logica flessibile e replicabile in diversi contesti produttivi, favorendo così la diffusione ad altre realtà che potranno beneficiare dei risultati generati. L’integrazione dei diversi moduli è implementata attraverso due casi industriali. Il primo è realizzato da S.A.L.F Laboratorio Farmacologico e si focalizza sul settore farmaceutico mentre il secondo da Brembo e riguarda l’automotive. La finalità è dimostrare l’impatto della visione artificiale per risolvere questioni legate al monitoraggio della qualità dei prodotti e per aumentare l’efficienza complessiva del lavoro. Il primo aspetto riguarda la rilevazione delle difettosità, attività ad oggi ancora legata alla soggettività e all’esperienza dell’operatore, mentre il secondo intende diffondere approcci che migliorino e valorizzano la qualità del lavoro svolto dagli operatori. Infatti, le mansioni di controllo qualità sono ripetitive e richiedono precisione ed elevati livelli di concentrazione con conseguente aumento del livello di stress per l’operatore. In linea con ciò, la presenza di un robot collaborativo che possa automatizzare i processi
Tecnologie

ed affiancare l’operatore può contribuire a ridurre lo stress psico-fisico del lavoratore abilitando attività a maggiore valore aggiunto. In ambito automotive, il dimostratore Brembo si prefigge di realizzare una stazione prototipale per rilevare i difetti superficiali o di verniciatura delle pinze freno tenendo conto di fattori come l’alta variabilità geometrica e dimensionale, le diversità di colorazione, le molteplici tipologie di difettosità che possono emergere e il riconoscimento di falsi scarti che emergono a causa di riflessi di luce, sporco, impronte digitali e impurità. In aggiunta, la stazione prototipale intende contribuire al miglioramento dell’ergonomia complessiva dell’operatore sia da un punto di vista posturale, riducendo l’impegno sia a livello dell’apparato muscoloscheletrico, che cognitivo andando a migliorare gli aspetti inerenti alla gestione dello stress, la sicurezza e l’interazione tra uomo e robot all’interno dell’area di lavoro. La soluzione integra moduli di visione per l’acquisizione e l’elaborazione delle immagini, algoritimi di deep learning per l’addestramento del sistema, il riconoscimento e la classificazione dei difetti e un robot collaborativo per la movimentazione e il posizionamento del sistema di visione. Coerentemente con l’obiettivo descritto, il robot si occupa della rilevazione delle anomalie mentre l’operatore è coinvolto nel suo addestramento e nella gestione degli algoritmi di deep learning. Nel dettaglio, la probabilità di fault detection è comunicata dal sistema all’operatore che, in caso di anomalie nella valutazione, interviene classificando quanto rilevato. Dal punto di vista dell’ergonomia, le tecnologie di visione sono utilizzate per riconoscere le operazioni manuali svolte all’interno delle postazioni di lavoro. In tal modo, è possibile acquisire informazioni per ridurre i casi di infortunio e migliorare la percezione cognitiva dell’operatore permettendo così di conseguire maggiori livelli di qualità ed efficienza complessiva. Watchman è nella fase conclusiva ma diverse sono le prospettive che possono essere perseguite dai partner capitalizzando i risultati ottenuti sia all’interno dei dimostratori realizzati da Brembo e S.A.L.F Laboratorio Farmacologico che a livello di impatto sul territorio. Nello specifico, all’interno del caso Brembo, una possibile traiettoria di sviluppo riguarda la realizzazione di un sistema che permetta di istruire il robot nel posizionamento corretto del punto di ispezione della pinza freno nonché nell’individuazione di efficienti modalità per la gestione dei tempi di archiviazione della mole di dati acquisiti al fine di rendere sempre più oggettivi i processi di controllo qualità supportando l’uomo in un’attività il cui risultato è direttamente visibile dal cliente finale. Da un punto di vista di sistema, il progetto Watchman, mediante i suoi dimostratori e la riconfigurabilità dei singoli moduli, ha posto le basi per una maggiore diffusione delle tecnologie di visioni artificiale all’interno delle imprese, le quali potranno beneficiare della conoscenza generata a beneficio della competitività del sistema manifatturiero lombardo nella sua totalità.
Per maggiori informazioni sul progetto Watchman: https://www.watchman-hub.it/
1 https://www.ilsole24ore.com/art/visione-artificiale-orapionieri-lavorano-la-manifattura-AEHA3r9
2PwC’s Global Artificial Intelligence Study: Sizing the prize

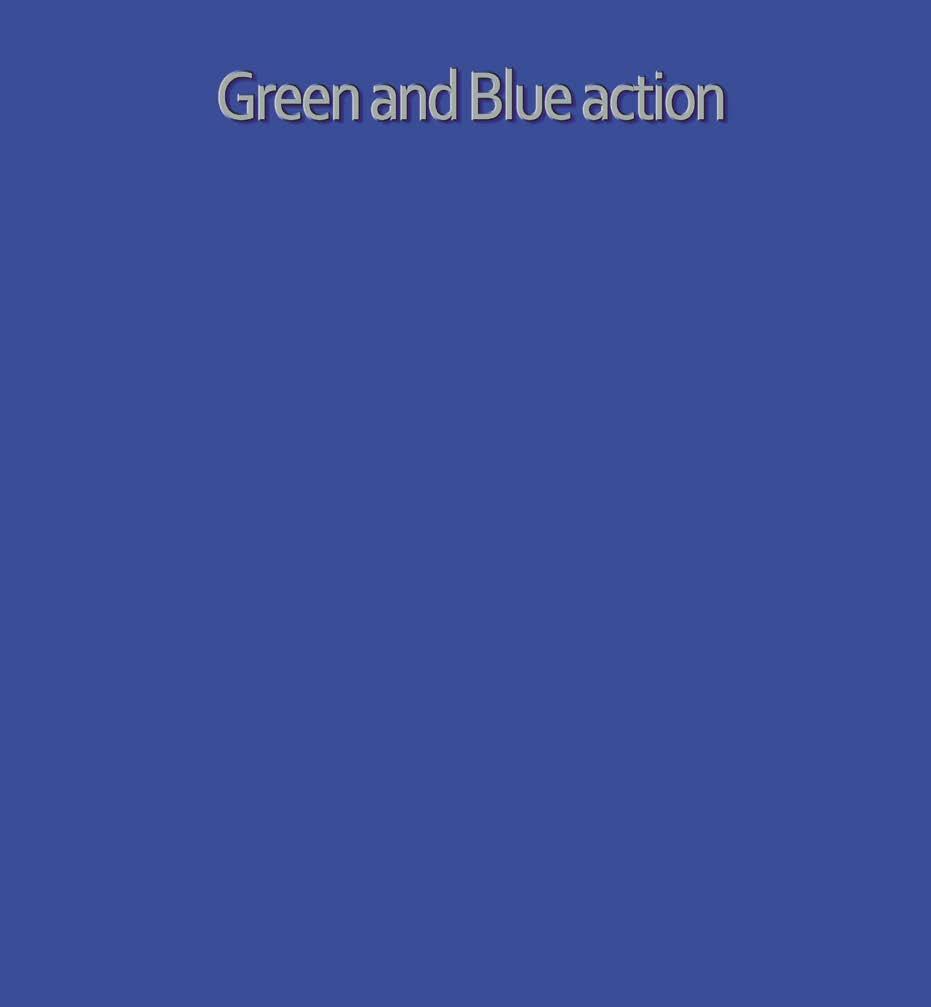

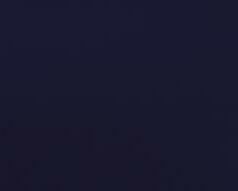
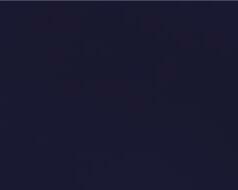
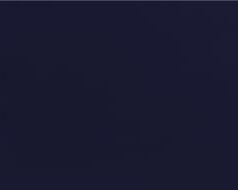
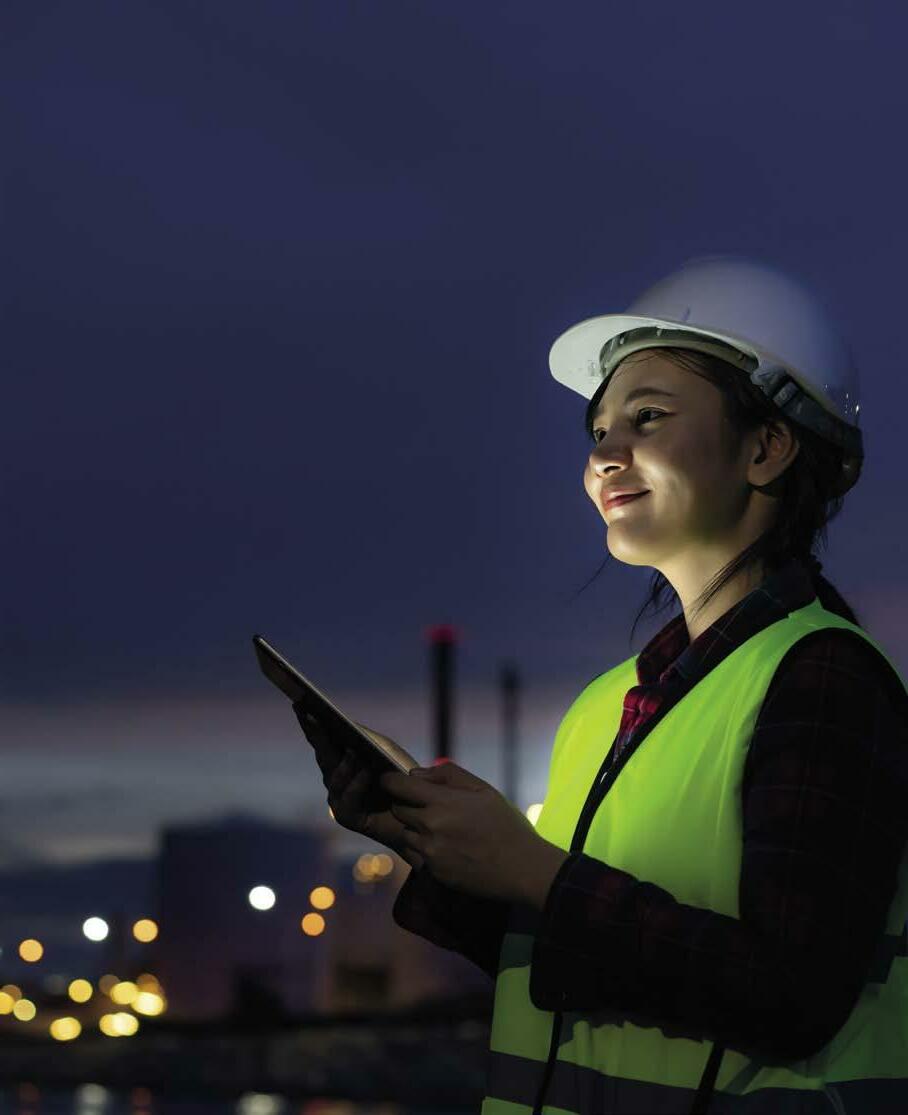

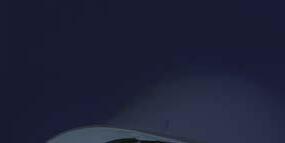
INGE
Engineering & Manufacturing Technical Recruiters
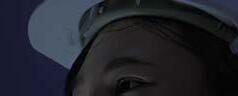
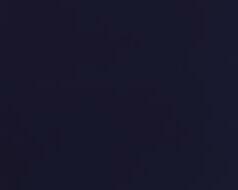




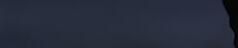