www.meccanica-automazione.com
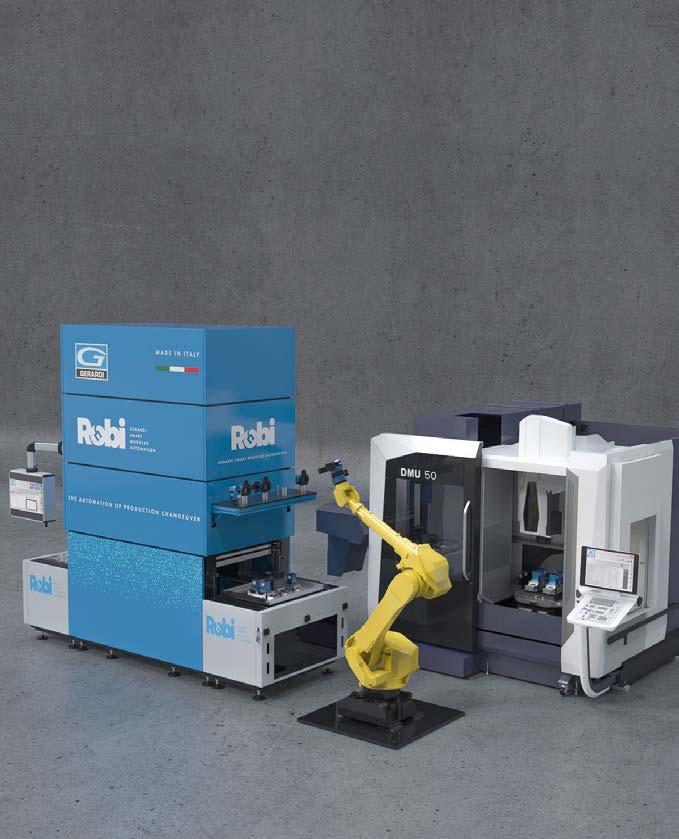
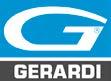
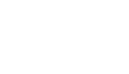
www.meccanica-automazione.com
Scopri come i panni per la pulizia Tork exelCLEAN® possono aiutare la tua impresa a risparmiare tempo riducendo i tempi di lavoro del 35% rispetto agli stracci.*
Igiene migliore per una maggiore produttività www.tork.it/riduzionedeirifiuti
GARANT TURNTABLE
Carico di morse e pallet in centri di fresatura a 3 o 5 assi
GARANT BASIC
Carico e scarico di pezzi in centri di tornitura e/o fresatura a 3 o 5 assi
di Chiara Tagliaferri
VVi propongo un esperimento. Fate un sondaggio per capire quale sia la consapevolezza relativa all’uso delle tecnologie più conosciute di questa ultima rivoluzione industriale. La domanda sembra semplice: che sentimento suscita in voi l’utilizzo dell’intelligenza artificiale o della realtà estesa o della robotica? Provate a porre la stessa domanda in una classe di scuola, in ufficio o durante una cena tra amici. Non dovreste stupirvi se la separazione di vedute sarà profonda ed evidente. Sono argomenti molto discussi e divisori.
Ho recentemente partecipato a un incontro informativo sull’intelligenza artificiale per le scuole di alcune province lombarde. Prima degli interventi è stato condotto un sondaggio per capire quale sentimento suscitasse questa tecnologia. Ci si potrebbe aspettare approvazione, eccitazione, curiosità o energia, invece, il 67% degli intervistati ha espresso paura, timore, diffidenza e persino ostilità! Da adulti, ci si aspetterebbe una risposta di positiva predisposizione ad utilizzare, comprendere e fare propria questa tecnologia. E invece, non è così. Non si tratta di una reazione opposta, ma di un significativo sconcerto. Siete sicuri che un test simile nei vostri reparti o uffici, oggi, genererebbe risultati diversi?
Personalmente credo che la differenza la farebbe il grado di conoscenza, competenza e approfondimento individuale almeno quanto la condivisione dello scopo dell’introduzione della tecnologia e del suo utilizzo. La paura, la diffidenza nascono dall’ignoraranza, da ciò che non si conosce,
dalle ombre che si intravedono nel buio di una caverna. Platone diceva che, conoscere le sole ombre, ovvero le opinioni, ci rende prigionieri. Acquisire la conoscenza vera vuol dire uscire dalla prigione dell’ignoranza, per conoscere e comprendere la realtà e governarla. Il timore e l’ostilità potrebbero essere anche colpa di una comunicazione che punta troppo spesso più sul sensazionalismo che alla verità oggettivita o forse è veramente tutto troppo rapido, ed è il solito timore del progresso a far tremare le giovani generazioni. Ad ogni modo ritengo che la comunicazione tecnico scientifica abbia un ruolo cruciale nell’indirizzare le percezioni del pubblico riguardo le tecnologie emergenti. Errori comunicativi allontanano le persone da certe tecnologie almeno quanto le ingannano rispetto il loro utilizzo. Occorre bilanciare attentamente la propria narrazione, non minimizzare ma neanche spaventare. Dare chiarezza di messaggi e certezza scientifica delle fonti. Sarebbe bello riuscire a parlare delle tecnologie facendosi guidare dall’ideale aristotelico dell’equilibrio che evita gli estremi. “La virtù sta nel mezzo” ovvero nel giusto bilanciamento degli estremi.
L’accettazione delle nuove tecnologie dalle maggioranze non può essere tutta una questione di razionalità e valuzioni oggettive ma, magari, sarebbe bene indagare il “sentimento” solo dopo aver fornito notizie chiare, utili, trasparenti e verificate.
chiara.tagliaferri@cnr.it
5 La verità nel mezzo
12 Focus sulla sostenibilità
14 Il futuro della visione artificiale
16 Massimizzare l’efficienza
18 SEPEM Industries 2024
20 Una nuova pietra miliare nel mercato
26 Grand Opening all’insegna della machining transformation
30 Un polo tecnologico per la transizione 5.0
34 Ottimizzare produzione e stoccaggio ci pensa “ROBI”
38 Espansione dei cobot nelle aziende italiane
40 Controllo qualità al grammo con il cobot LBR iisy
44 TS Welde Mate saldatura compatta e trasportabile
46 Innovazione e collaborazione la proposta Yaskawa
48 Robotica integrata: il motore dell’industria manifatturiera del futuro
RICERCA E INNOVAZIONE
66 Collaborazione Uomo-Macchina: le sfide della Robotica Collaborativa nel JOiiNT LAB
70 Corrente continua la chiave per la transizione energetica verso un’industria 5.0
RASSEGNA 34 BI-MU
72 Successo di partecipazione e innovazione, appuntamento al 2026 per i 70 anni di BI-MU
74 Intervista a Cristian Bosi verso una nuova smart factory
78 Da specialisti di prodotto a solutions provider
82 Soluzioni che portano la sostenibilità della macchina
84 Il partner di software, prodotti e servizi tecnologici per il mondo dell’industria
PRISMA
86 Prodotti
RayScan + Quicksurface per il reverse engineering
Rayscan B11
Laser Scanner 3D portable 24 linee (tra incrociate e fisse), velocità di 1.360.000 punti/sec. Area di lavoro di 320 × 250 mm, precisione di 0,02 mm, risoluzione di 0,05 mm
QUICKSURFACE
una soluzione di reverse engineering completa in grado di esportare dati mesh STL o nuvole di punti PTX. QUICKSURFACE fornisce tutti i necessari strumenti per convertire le mesh in modelli CAD modificabili.
PROMOZIONE
18.000 Euro
Rayscan B11 + QUICKSURFACE + corso uso (1 gg) + set marker magnetici
Secondo il sondaggio diffuso da Anima Confindustria alle aziende associate, nel secondo semestre 2024 circa il 40% delle imprese prevede una contrazione del fatturato. Crollano gli ordini per un’impresa su due Lieve calo del fatturato e portafoglio ordini in peggioramento. È il quadro di un’industria meccanica in sofferenza quello che emerge dal sondaggio periodico diffuso da Anima Confindustria tra le mille aziende associate. In linea con la tendenza gia evidenziata prima dell’estate, per il secondo semestre del 2024 l’andamento negativo della manifattura sembra non dare segni di miglioramento, con il 37,5% delle aziende associate ad Anima che vede una diminuzione delle vendite. Per un’azienda su cinque, il calo del fatturato superera il 5% rispetto al secondo semestre dello scorso anno. Meno di un’impresa su tre riesce a crescere nella seconda metà dell’anno. Uno scenario che si riflette nei dati relativi al portafoglio ordini. Secondo il sondaggio, nel corso del secondo semestre 2024 meno di un terzo delle aziende prevede ordinativi in crescita, mentre il 45% delle imprese meccaniche registra una contrazione degli ordinativi rispetto al secondo semestre 2023. «A pesare sull’attivita delle imprese è il generale rallentamento che ormai da tempo sta interessando l’economia globale,
soprattutto nei termini della forte incertezza che blocca gli investimenti» commenta il presidente di Anima, Pietro Almici. «Ma incidono anche le criticita dovute ai conflitti internazionali e alla frenata di economie importanti per il mercato italiano, come la Germania. Una stagnazione, alimentata dai conflitti in corso, che sta dando ripercussioni sui mercati di molti paesi europei, e che desta preoccupazione quando a rallentare è un settore fondamentale per l’economia italiana come l’industria meccanica rappresentata da Anima, che nel nostro paese dà lavoro a 222.000 persone. Ci sono poi fattori di criticita endogeni – prosegue Almici – come la carenza di piani strutturali a livello nazionale a sostegno delle imprese, che lamentano anche una diffusa difficoltà nel reperire manodopera specializzata. La meccanica oggi necessita di un rafforzamento delle politiche industriali volte a sostenere le imprese, soprattutto quelle medio-piccole che costituiscono la gran parte del comparto. Per questo il nostro impegno ora è finalizzato ad accompagnare le imprese per sfruttare appieno le potenzialita del Piano Transizione 5.0 che, malgrado la complessita delle procedure e la ristretta tempistica, è la misura che puo rinnovare la fiducia negli investimenti e aiutare le aziende a rafforzare la propria competitivita e riprendere il trend di crescita».
Nel terzo trimestre 2024, il fatturato di Henkel a livello di Gruppo ha raggiunto i 5,5 miliardi di euro, con una crescita organica del 3,3% legata sia all’andamento favorevole dei prezzi, sia all’incremento dei volumi. In termini nominali, il fatturato è aumentato dell’1,0% rispetto allo stesso trimestre dell’anno scorso.
“Abbiamo continuato a crescere nel terzo trimestre, accelerando lo sviluppo di Henkel grazie al contributo di entrambe le divisioni. Abbiamo mantenuto una buona marginalità e questo ci consente di aumentare gli investimenti nel business e nei nostri marchi. Anche il margine EBIT depurato ha visto una crescita significativa. Ciò dimostra che siamo sulla strada giusta nell’implementazione della nostra agenda di crescita”, ha affermato Carsten Knobel, CEO di Henkel (nella foto). “Siamo convinti che il 2024 sarà un altro anno di successo per Henkel, raggiungeremo gli obiettivi di fatturato e profittabilità già rivisti al rialzo nei mesi scorsi. Oggi possiamo confermare le stime e, sulla base dei solidi risultati attuali, abbiamo buone probabilità di centrare questi obiettivi nella loro fascia alta”.
La divisione Adhesive Technologies ha avuto uno sviluppo molto soddisfacente nel terzo trimestre, supportata da tutti i segmenti di mercato. Il fatturato organico di Consumer Brands è cresciuto soprattutto grazie al contributo del business Hair. Nel terzo trimestre 2024, il fatturato di Henkel a livello di Gruppo è cresciuto in termini nominali dell’1,0% a 5.492 milioni di euro. Acquisizioni e disinvestimenti hanno incrementato le vendite dell’1,2%, mentre gli effetti dei cambi valutari hanno pesato negativamente sul risultato per il 3,6%. In termini organici, ovvero depurati dagli effetti dei cambi valutari e delle operazioni straordinarie, il fatturato è cresciuto del 3,3% in ragione dell’andamento favorevole dei prezzi e dell’incremento complessivo dei volumi.
Nei primi nove mesi del 2024, il fatturato
ha raggiunto i 16.305 milioni di euro, con un calo nominale pari allo 0,4% e una crescita organica del 3,0%.
La crescita organica del fatturato nel terzo trimestre è stata più significativa in Europa,
regione IMEA, Asia-Pacific e America Latina. Il Nord America ha registrato un
andamento negativo per entrambe le divisioni. In modo analogo, la crescita organica del fatturato nei primi nove mesi dell’anno è stata sostenuta da tutte le regioni ad eccezione del Nord America.
La versione integrale di questa nota trimestrale è disponibile in inglese sul sito Henkel.com
Dopo poco meno di due mesi dall’acquisizione di ipTest nel Regno Unito, il Gruppo Microtest, leader italiano nella realizzazione di sistemi di test e nel testing di microchip su package e su wafer di silicio, ottiene l’autorizzazione da parte del governo statunitense a procedere con l’acquisizione di Focused Test, azienda specializzata in testing di microchip in carburo di silicio (SiC) e nitruro di gallio (GaN), con sedi a Boulder (US) e Cabuyao (Filippine). Focused Test vanta un’esperienza sul mercato americano da più di 25 anni, conta un fatturato di 3 milioni di dollari nel 2023 e un organico di 15 risorse.
Il Gruppo Microtest, quindi, raggiunge un fatturato aggregato di oltre 80 milioni di euro e supera le 400 persone in organico, consolidando la propria posizione di principale operatore del settore delle macchine per il test (ATE) e dei servizi di testing dei microchip in Italia e di partner privilegiato dei leader mondiali nella produzione di microchip e semiconduttori.
Questa operazione, la quinta acquisizione per il Gruppo in poco più di un anno – dopo quella della britannica ipTEST a luglio e di quelle realizzate nel 2023 dall’olandese Test Inspire, alla tedesca RoodMicrotec e dell’italiana GEDEC – s’inserisce nella strategia di crescita dimensionale e di sviluppo internazionale avviata nel 2022 con il supporto di Xenon Private Equity, che mira a rendere Microtest l’unica società in Europa in grado di gestire tutto il flusso di sviluppo microelettronico a partire dal design del chip, con particolare accento nella produzione di ATE e nei servizi correlati.
degli inverter la cui crescita attesa nei prossimi 5 anni è di oltre il 30% l’anno grazie alla transizione energetica ormai avviata. Con questa nuova acquisizione sarà possibile servire i produttori di microchip di potenza e inserirsi nel mercato di Nord e Centro America.
In seguito all’operazione, Microtest è ora presente in 13 sedi operative tra Europa, Stati Uniti e Far East: dall’head quarter di Altopascio (Lucca) a quella di Malacca in Malesia e i due uffici commerciali a Singapore e Tokio, dalle sedi GEDEC a Genova e Torino, a quella di Test Inspire a Welsum in Olanda, e ancora dalle sedi RoodMicrotec a Nördlingen e Stoccarda in Germania,
di Microtest. L’ingresso nel mercato statunitense consentirà infatti un salto ulteriore per il Gruppo, che continua a crescere e affermare la propria leadership nel settore della microelettronica in Europa e nel mondo» ha commentato Franco Prestigiacomo, CEO di Xenon e Presidente di Microtest.
alle nuove di ipTEST a Guildford, in Regno Unito, e Ipoh, in Malesia, e alle new entry di Focused Test, in Boulder in Colorado e Cabuyao nelle Filippine.
Nei laboratori all’avanguardia di Microtest vengono testati quotidianamente enormi quantità di prodotti dalle molteplici applicazioni nella vita quotidiana: dall’automotive alle tecnologie 5G, dai dispositivi medici all’aerospazio.
«Grazie al supporto di Xenon, stiamo raggiungendo traguardi importanti in un mercato complesso come quello dei semiconduttori, dove dimensioni e presenza globale sono essenziali per la crescita. Diamo il benvenuto a Focused Test, azienda con un importante know-how tecnologico, con cui siamo certi lavoreremo in grande sintonia. La nostra ambizione rimane quella di poter continuare a sviluppare soluzioni di test innovative che permettano ai nostri clienti di avere un vantaggio competitivo sul mercato, soluzioni efficienti e a basso impatto ambientale per diventare punto di riferimento a livello globale nei sistemi di test e nel testing di microchip. Focused Test ci permetterà di espandere il nostro mercato negli Stati Uniti, di vitale importanza nella nostra strategia di crescita globale. La nuova sede in Colorado ci permetterà di promuove in maniera più efficace la vendita di tutti i nostri servizi/sistemi negli Stati Uniti» ha commentato Moreno Lupi, Managing Director di Microtest.
Dal punto di vista industriale, l’ingresso di Focused Test porterà al gruppo Microtest un’importante expertise nella realizzazione di dispositivi innovativi per il test semiconduttori in carburo di silicio e nitruro di gallio, i semiconduttori di frontiera per la gestione delle batterie, dei motori elettrici e
«Quando abbiamo deciso di investire in Microtest, ci siamo interfacciati con una realtà del tutto votata all’innovazione tecnologica e guidata da imprenditori dalla forte visione strategica, in linea con l’approccio industriale di Xenon. Con orgoglio annunciamo l’acquisizione di Focused Test, e con essa il raggiungimento di un ulteriore traguardo internazionale che apre quindi a un nuovo capitolo della storia
«Siamo entusiasti di entrare a far parte del Gruppo Microtest, realtà con cui condividiamo gli obiettivi e l’approccio innovativo. Con Microtest potremo continuare a dare forma ai nostri progetti, lavorando in un contesto solido e in crescita. La nostra cultura aziendale è analoga a quella di Microtest, e siamo entusiasti di lavorare con tutto il team per portare nuove competenze a bordo ed offrire al Gruppo un punto d’ingresso privilegiato al mercato US» ha dichiarato Peter Hancock, Presidente di Focused Test.
Deloitte ha supportato Microtest nelle due diligences finanziaria e fiscale, Pavia e Ansaldo negli aspetti legali.
NUOVI MERCATI
Qingdao Fervi International Trading Co. Ltd è la nuova società di FERVI GROUP con sede nell’omonima città portuale, un punto strategico per migliorare logistica e go-to-market puntando sull’internazionalizzazione del Gruppo.
FERVI Group amplia la propria rete internazionale inaugurando una nuova sede a Qingdao, una delle città portuali economicamente più rilevanti della Cina, snodo logistico internazionale strategico a cui anche le altre aziende del Gruppo (Rivit, Vogel Germany, Riflex Abrasives, Sitges SL) possono fare riferimento per sviluppare e accelerare le attività quotidiane con tutti i partner del sud-est asiatico.
L’apertura di una società in Cina – controllata al 100% dalla capogruppo Fervi SpA – consolida dunque il processo di internazionalizzazione del Gruppo, aggiungendo una sede cinese ai due uffici esteri di Rivit in India e Marocco, alla sede centrale di Vogel in Germania e alla sede centrale spagnola di Sitges SL, offrendo un punto di riferimento di rilevanza strategica a tutte le attività delle aziende del Gruppo, soprattutto per quanto riguarda la logistica, il controllo qualità, le certificazioni e gli adeguamenti normativi e burocratici prima che i prodotti arrivino sul mercato, migliorando in questo modo tutta la gestione della filiera, dalla progettazione allo scouting fino ad arrivare all’introduzione sul mercato.
“L’apertura della Qingdao Fervi International Trading Co. Ltd è per noi un passo necessario e fondamentale che consolida la dimensione internazionale di un Gruppo come il nostro che opera in oltre 50 Paesi. L’apertura in Cina risulta infatti strategica per velocizzare e facilitare le operazioni di controllo delle merci che partono da questa area, semplificando tutte le procedure doganali e di relazione con il nostro network di partner internazionali. In questo modo avremo la possibilità di alzare ulteriormente i nostri standard di servizio e qualità della nostra offerta, rendendo ancora più fluido il go-tomarket di tutti i prodotti dei nostri marchi, a beneficio della catena commerciale e degli utenti finali” ha commentato Guido Greco, Amministratore Delegato FERVI GROUP.
Il nuovo portautensile ad espansione idraulica per foratura e alesatura dall‘ottimo rapporto qualità prezzo.
schunk.com/tendosilver
Il fornitore di servizi tessili Mewa offre alle aziende soluzioni sostenibili ed efficienti per la pulizia industriale. L’utilizzo di panni, zerbini e tappeti assorbiolio consente di mantenere pulito l’ambiente di lavoro e di ridurre al contempo la quantità di rifiuti. I prodotti tessili vengono periodicamente ritirati e riconsegnati puliti: in questo modo si risparmiano risorse e si garantisce la loro costante disponibilità. Inoltre, per la pulizia dei componenti Mewa offre anche lavapezzi a pennello e lavapezzi ad alta pressione: non utilizzano sostanze chimiche dannose per la salute e per l’ambiente e vengono proposte con un servizio a 360°, riparazione e manutenzione incluse. Il liquido detergente a base acquosa delle lavapezzi è certificato in conformità alle linee guida per la produzione di alimenti (NSF Nonfood). Per mantenere pulite la fabbrica e i macchinari rispettando l’ambiente, sono disponibili le seguenti soluzioni, offerte con un servizio che include anche l’assunzione e l’adempimento scrupoloso di tutti gli obblighi ambientali: Macchine e impianti impeccabili grazie ai panni riutilizzabili
Per assorbire rapidamente solventi, lubrificanti o sporcizia, Mewa offre quattro diversi tipi di panni. I robusti panni in cotone “Mewatex” e
“Mewatex Plus” rimuovono anche lo sporco più ostinato e i trucioli di metallo, mentre “Mewatex Ultra” è adatto alla lucidatura ed è praticamente privo di pelucchi. Il panno in microfibra “Mewa Protex” è infine ideale per la pulizia di superfici delicate.
Con gli zerbini lo sporco rimane fuori
Per ridurre la quantità di sporco proveniente dall’esterno, Mewa offre zerbini resistenti dotati di uno speciale rivestimento contro il rischio di scivolamento. Sono disponibili diversi tipi di zerbini per ambienti interni ed esterni che aiutano a mantenere il pavimento pulito nell’area reception, nei locali destinati alle vendite o nelle officine.
Protezione sicura contro le perdite: tappeti as-
sorbiolio riutilizzabili
I tappeti assorbiolio Mewa Multitex di Mewa proteggono il pavimento dell’officina dalle perdite, per es. di olio e di refrigeranti, pericolose per l’ambiente. Disponibili in varie dimensioni, questi tappeti sono in grado di assorbire fino a otto litri di liquido e vengono forniti con un servizio a 360°: in questo modo contribuiscono a mantenere pulito il luogo di lavoro ed evitano l’impiego e lo smaltimento di granuli assorbenti usa e getta.
Lavapezzi con servizio a 360°: sempre pronte per l’uso
Per la pulizia dei componenti, le lavapezzi Mewa sono una soluzione affidabile e priva di sostanze nocive per l’ambiente. Vengono offerte con un servizio completo che comprende la manutenzione regolare, la sostituzione del liquido detergente e la riparazione. I detergenti a base acquosa, conformi agli standard NSF, rimuovono efficacemente grasso, olio e altri tipi di sporcizia, anche in presenza di componenti con superfici molto irregolari.
Tutte queste soluzioni vengono offerte esclusivamente con un servizio a 360° che comprende il ritiro, il lavaggio, il controllo della qualità e la riconsegna. In questo modo Mewa aiuta le aziende a mantenere gli ambienti di lavoro puliti in modo sostenibile ed efficiente.
Non si dovrebbero accettare compromessi quando si tratta di fresatura di spallamenti.
Che voi diate la priorità a una lavorazione sicura e priva di problemi, a un'elevata produttività o a una maggiore efficienza costi, la nuova soluzione per la fresatura di spallamenti CoroMill® MS20 è ciò che fa per voi.
Accuratamente sviluppata per le operazioni che vanno dalla sgrossatura alla finitura in acciaio inossidabile e superleghe resistenti al calore, CoroMill® MS20 offre eccellenza su tutta la linea.
IL TERZO “ITALIAN MACHINE VISION FORUM” HA VISTO LA PARTECIPAZIONE DI 270 PERSONE, UN GRANDE SUCCESSO PER UN EVENTO DEDICATO AI SISTEMI DI VISIONE INDUSTRIALE, ORGANIZZATO DA ANIE AUTOMAZIONE IN COLLABORAZIONE CON MESSE FRANKFURT ITALIA.
L’EVENTO SI È SVOLTO IN PROVINCIA DI BERGAMO, UNA ZONA RINOMATA PER L’ECCELLENZA
NELLA MANIFATTURA INTELLIGENTE di Cristina Gualdoni
Il forum rappresenta un’occasione preziosa per il mondo dell’industria italiana, in cui la tecnologia diventa un alleato per migliorare i processi produttivi. Grazie all’innovazione, le macchine infatti stanno diventando sempre più capaci di “vedere”, raccogliere ed elaborare dati in modo autonomo, rendendo la produzione più efficiente.
Aldo Peretti, Presidente del Comitato Scientifico di IMVF, ha sottolineato come il livello dell’evento sia cresciuto di edizione in edizione, sia per quanto riguarda i relatori, sia per il pubblico, che include grandi aziende, costruttori, enti di ricerca, università e istituti scientifici. Tra i temi discussi c’è stato anche l’impatto delle nuove tecnologie sull’industria, come il deep learning, la compressione dei modelli, lenti liquide e iperspettrali, e le nuove opportunità offerte dall’intelligenza artificiale. Peretti ha però evidenziato anche alcune sfide: i ritardi negli investimenti e nel piano Industria 5.0, nonché le future problematiche energetiche derivanti dall’espansio-
ne dell’intelligenza artificiale. La vera sfida sarà pianificare con cura l’evoluzione tecnologica in modo strategico e sostenibile, valorizzando al massimo le opportunità disponibili.
Nicola Lo Russo, Presidente del Gruppo Sistemi di Visione di ANIE Automazione, ha espresso grande soddisfazione per la riuscita dell’evento, che ha registrato una notevole partecipazione, dimostrando il crescente interesse verso i sistemi di visione industriale. Questi sistemi sono fondamentali per l’innovazione tecnologica e stanno diventando sempre più
importanti per lo sviluppo delle fabbriche del futuro, orientate alla digitalizzazione e alla sostenibilità. Durante l’evento, si è discusso anche del ruolo dei sistemi di visione nell’Industry 5.0, in cui l’interazione uomo-macchina e la creazione di nuove opportunità di lavoro giocano un ruolo centrale per migliorare la competitività e l’efficienza delle aziende. Donald Wich, Amministratore Delegato di Messe Frankfurt Italia, ha espresso soddisfazione per l’interesse costante verso il forum, sottolineando come le imprese presenti abbiano avuto accesso a contenuti utili per aumentare la loro competitività sia a livello nazionale che internazionale. Durante l’evento è stato anche assegnato l’Italian Machine Vision Award, vinto da Beckhoff Automation con una presentazione intitolata “Vision, Machine Learning e Automazione”. Sono state inoltre conferite menzioni speciali ai contributi di Basler Italy e Opto Engineering.
Per chi desidera approfondire, gli atti del convegno sono disponibili sul sito ufficiale dell’evento: machinevisionforum.it.
BLUE ORIGIN HA AFFIDATO A SORALUCE LO SVILUPPO DI NOVE UNITÀ MULTITASKING PER LA LAVORAZIONE DEGLI INVOLUCRI DEI MOTORI A RAZZO, CON L’OBIETTIVO DI MIGLIORARE LA PRODUTTIVITÀ E RIDURRE I COSTI. QUESTA COLLABORAZIONE SOTTOLINEA LA QUALITÀ DI SORALUCE NEI PROGETTI AEROSPAZIALI di E.S.
Forte dei suoi 60 anni di esperienza e ispirato dall’innovazione, il produttore di macchine utensili Soraluce continua a far progredire il settore delle macchine utensili con soluzioni ingegneristiche innovative e pionieristiche. La chiave del suo successo risiede nello sviluppo di soluzioni all’avanguardia impegnate nel progresso tecnologico dei suoi clienti, affrontando le sfide più impegnative dei macchinari in modo efficiente, con alti livelli di produttività.
La sua capacità tecnologica di personalizzare ogni prodotto in base alle esigenze di ogni cliente e una visione completamente internazionale ne hanno fatto un vero e proprio punto di riferimento settoriale in mercati strategici come la Germania e l’Italia in Europa, ma anche in Cina e negli Stati Uniti, spingendo l’export al 95%.
Soraluce ha completato con successo la progettazione e la produzione di nove nuove unità di fresatura-tornitura multitasking per la lavorazione degli involucri
dei motori a razzo di Blue Origin. Situate strategicamente in Alabama, queste unità all’avanguardia rappresentano una pietra miliare significativa nella produzione aerospaziale.
Oier Elguezabal, Global Business Development Director, sottolinea l’impatto di questo risultato, affermando: “Questa soluzione consente all’azienda aerospaziale di migliorare la propria capacità produttiva, garantire una precisione superiore nella lavorazione, migliorare la qualità complessiva dei pezzi e contem-
poraneamente ridurre i costi relativi all’usura degli utensili e ai tempi di lavorazione”.
La decisione di Blue Origin di affidare a Soraluce un progetto così importante sottolinea la fiducia reciproca e l’impegno per l’eccellenza condiviso tra le due aziende. Questa collaborazione segna un notevole risultato nel progresso della tecnologia aerospaziale e sottolinea la reputazione di Soraluce come leader nelle soluzioni di produzione innovative.
Tecnologia automatizzata multitasking all’avanguardia
Il progetto, avviato a dicembre 2021 e completato nell’agosto 2023, è la più grande commessa di sempre di Soraluce e presenta una serie di tecnologie brevettate da Soraluce come i sistemi intelligenti DAS ® per eliminare le vibrazioni, il Chip Breaker , per garantire la continuità della produzione rompendo i trucioli lunghi durante il processo di tornitura, e il sistema AccuraHeads per garantire un migliore posizionamento della testa. In questa occasione, tutte
queste tecnologie sono al servizio del settore aerospaziale. Lo sviluppo di Soraluce è una soluzione di fresaturatornitura polivalente per la lavorazione di pezzi rivestiti con Inconel, un materiale in nichel-cromo in grado di resistere alle alte temperature, per gli involucri dei motori aerospaziali.
«Uno dei principali vantaggi di queste macchine è la produzione automatica dei pezzi: dispongono di un sistema di pallettizzazione automatica non presidiato per il carico e lo scarico dei pezzi, riducendo al minimo i tempi di preparazione e massimizzando l’efficienza, insieme a un’elevata produttività”, aggiunge Elguezabal.Inoltre, queste macchine vantano la capacità di eliminare le vibrazioni dai processi di lavorazione dei pezzi, garantendo una maggiore precisione nella lavorazione e una qualità complessiva dei pezzi. Delle nove macchine progettate da Soraluce, una sarà di stanza presso l’impianto di prototipazione di Blue Origin in Alabama. Questa distribuzione strategica riflette l’impegno di Blue Origin
a sfruttare tecnologie all’avanguardia in tutte le sue operazioni, consolidando ulteriormente il ruolo della partnership nel far progredire gli standard di produzione aerospaziale.
Solida crescita basata sull’innovazione
Con la costante motivazione dell’innovazione, negli ultimi cinque anni Soraluce ha investito circa 18 milioni di euro nello sviluppo e nell’implementazione di una serie di tecnologie e soluzioni R+S+i, contribuendo a rafforzare la sua presenza in mercati strategici come Italia, Stati Uniti, Germania e Cina, e anche ad ampliare la sua gamma di prodotti, con un’ampia varietà di fresatrici, alesatrici, torni verticali, soluzioni multitasking e linee e sistemi automatizzati. La crescita a vari livelli e i numerosi sviluppi tecnologici interni di prodotti, applicazioni, sistemi tecnologici e software nel settore delle macchine utensili hanno incrementato il fatturato del 30% nell’ultimo decennio e l’hanno introdotta nel nuovo territorio dell’aerospace.
IL SALONE CHE SI TERRÀ MARTEDÌ 3 E MERCOLEDÌ 4 DICEMBRE PRESSO IL LINGOTTO FIERE TORINO, IN VIA NIZZA 294, RIUNIRÀ TUTTI GLI ATTORI DELL’INDUSTRIA MANIFATTURIERA DEL NORD-OVEST PER RIFLETTERE SU TEMI COME LA SOSTENIBILITÀ E LA SICUREZZA SUL LAVORO E PROPORRE SOLUZIONI CONCRETE AI PROBLEMI QUOTIDIANI
A cura della redazione
Il conto alla rovescia per SEPEM Industries 2024 è ufficialmente iniziato: il 3 e il 4 dicembre Lingotto Fiere Torino diventerà un vero e proprio punto d’incontro per le istituzioni e le imprese manifatturiere del territorio piemontese, e non solo.
Organizzata da GL Events
Exhibitions Industrie, con il patrocinio di Regione Piemonte, Città di Torino, Camera di Commercio Torino, API Torino, CNA Piemonte e Unione Industriali Torino, la due giorni rappresenterà un’occasione imperdibile
per i manager, i tecnici e gli specialisti di settore che desiderano aggiornarsi e confrontarsi sui servizi e soluzioni destinati all’industria manifatturiera. Considerata la complessa situazione del mercato industriale italiano in questo periodo storico, se da una parte le imprese hanno bisogno di investire nell’innovazione, dall’altra devono trovare le migliori soluzioni possibili per risolvere i problemi del quotidiano, restare al passo con la concorrenza e gestire i propri flussi in modo veloce, sicuro e funzionale.
Sepem, la fiera delle soluzioni concrete
SEPEM Industries 2024 promette di essere molto più di una semplice esposizione: con oltre 90 espositori e marchi presentati, il Salone offrirà un’esperienza immersiva nel mondo dei servizi per l’efficienza, la sicurezza e la sostenibilità degli stabilimenti produttivi. Per l’occasione, Lingotto Fiere accoglierà realtà consolidate e nuove promesse del settore, che esporranno soluzioni per rispondere alle esigenze, anche quotidiane, di un’industria in continua evoluzione. “L’innovazione e le tematiche legate
all’industria 4.0. sono sicuramente aspetti importanti per lo sviluppo di un’azienda, ma è fondamentale non trascurare le esigenze quotidiane che le industrie necessitano, al fine di restare competitive in un mercato in continua evoluzione” afferma Giacomo Bottaro –Head of Marketing & Communication, GL Events Exhibitions Italia. “Nato in Francia oltre 15 anni fa, il Salone è cresciuto per rispondere a una necessità reale e oggettiva: avvicinarsi agli specifici bisogno dei territori, per generare innovazione e progresso a livello locale. La scelta di Torino non è casuale; questa città, con la sua lunga tradizione industriale e un tessuto produttivo forte, è il fulcro della manifattura del Nord-Ovest in specifici comparti produttivi, un crocevia di competenze e tecnologie”.
Conferenze e tavole rotonde
Nel corso delle due giornate, il Salone ospiterà un programma ricco di conferenze e workshop.
I temi al centro del dibattito? Sostenibilità, sicurezza sul lavoro ed efficienza.
Tra gli eventi in programma:
• Momenti di approfondimento sulle normative e sulle best practices per
la gestione sostenibile e sicura degli stabilimenti, con un focus sull’ ESGEnvironmental, Social, e Governance, le tre dimensioni fondamentali per verificare, misurare, controllare e sostenere l’impegno in termini di sostenibilità di una impresa o di una organizzazione.
• Workshop interattivi sulla digitalizzazione dei processi produttivi, sessioni che illustreranno come l’integrazione di tecnologie smart possa ottimizzare i processi e abbattere i costi.
• Tavole rotonde per riflettere sulle sfide del mercato, opportunità per discutere con le imprese sui cambiamenti in atto nel settore e confrontarsi sulle soluzioni
da adottare per affrontare le sfide e complessità del nuovo anno.
Un evento per l’intero ecosistema industriale
Il Salone, ispirato alle edizioni francesi, accoglierà responsabili di produzione, addetti alla logistica, specialisti della sicurezza, oltre a imprenditori e startupper che ambiscono a posizionarsi in un mercato sempre più competitivo e attento ai temi della sostenibilità.
“Questa prima edizione italiana di SEPEM offre alle aziende del Piemonte e non solo una piattaforma di confronto e soluzioni: qui si potranno scoprire risposte concrete alle esigenze di sostenibilità, di sicurezza sul lavoro e di miglioramento continuo delle linee produttive e della manutenzione. Con un’area dedicata al mondo del lavoro, sviluppata in collaborazione con il partner UMANA, fra le principali Agenzie per il Lavoro in Italia, SEPEM intende inoltre creare connessioni tra domanda e offerta, aiutando a costruire il capitale umano che guiderà l’industria del domani. Siamo convinti”, conclude Giacomo Bottaro “che SEPEM possa diventare un appuntamento irrinunciabile per chiunque lavori nel mondo manifatturiero. Vogliamo che Torino rappresenti anche negli anni a venire il cuore pulsante di un evento che fa della prossimità e della concretezza il suo punto di forza, capace di ispirare crescita, innovazione e una vera collaborazione tra imprese, enti e lavoratori”.
SEPEM Industries 2024 sarà una piattaforma unica di scambio e ispirazione, dove ogni partecipante avrà la possibilità di connettersi con fornitori, distributori e potenziali clienti per creare sinergie e opportunità concrete di crescita.
Maggiori informazioni su turin.sepemindustries.com.
La partecipazione di Salvagnini a EuroBLECH 2024 rappresenta un importante traguardo nel settore della lavorazione della lamiera.
L’azienda, sempre focalizzata sull’innovazione, svela la nuova Generazione 4 (G4) che interesserà tutta la sua gamma tecnologica. L’intento è quello di offrire una nuova visione per superare le sfide della manifattura, affrontando problemi come la mancanza di manodopera e la necessità di soluzioni sempre più efficienti per aumentare la produttività, ridurre errori e consumi, e garantire una qualità superiore del prodotto.
Con la nuova Generazione 4, Salvagnini propone soluzioni all’avanguardia per semplificare l’uso e migliorare la ripetibilità dei processi, eliminare attività poco valore aggiunto, ridurre i tempi di produzione e ottimizzare i flussi lavorativi, tutto ciò per mantenere i costi per prodotto competitivi e aumentare l’efficienza in fabbrica.
Per perseguire questi obiettivi, Salvagnini presenta a EuroBLECH l’intera gamma delle sue soluzioni, rendendo visibili, grazie a sistemi di automazione multilivello, due diverse configurazioni produttive. Queste saranno in grado di operare in modalità lineare, con lavorazioni
Le numerose soluzioni di automazione multilivello Salvagnini intervengono sia sulla singola fase produttiva sia sull’eliminazione delle attività a basso valore aggiunto e dei colli di bottiglia:
la combinata punzonatrice-cesoia è dotata di testa multi-pressa con utensili sempre disponibili; azzera gli allestimenti, garantendo alta qualità nelle lavorazioni e tempi ciclo ridotti;
la pannellatrice è dotata di utensili di piega universali che si adattano automaticamente alle dimensioni e alla geometria del pezzo da produrre, in ciclo, senza fermi macchina; non richiede riattrezzaggi e processa tutto il range di spessori e materiali lavorabili;
il laser, con testa di taglio a ottica unica per processare tutti gli spessori e i materiali lavorabili, non richiede aggiustaggi e accelera i cambi di produzione.
P-Robot, con il nuovo sistema di visione artificiale, massimizza l’autonomia della cella senza ridurne la flessibilità; la serie di presse piegatrici, con i dispositivi ATA, ATA.L, MVM e AU-TO, si adatta automaticamente nell’attrezzaggio e nella gestione degli utensili in funzione di ciò che deve produrre, estendendo la propria flessibilità e autonomia.
P-Robot è l’applicazione Salvagnini che combina una pannellatrice e un robot antropomorfo per produrre kit, lotti e pezzi singoli. È la risposta dell’azienda a un contesto industriale caratterizzato da alto indice di rotazione dei codici, lead-time compressi e costante carenza di personale. Automazione e robotizzazione estendono la produzione oltre i tradizionali turni di lavoro presidiati, mentre gli operatori posso dedicarsi ad attività ad alto valore aggiunto.
P-Robot è una soluzione smart, molto più semplice di quelle disponibili sul mercato: è facile da programmare, da utilizzare e capace di elevare a potenza la flessibilità e la produttività della pannellatrice.
La configurazione di P-Robot può essere personalizzata: Salvagnini propone flussi produttivi semplici, di solo asservimento carico/ scarico, e sistemi più complessi che prevedono, per esempio, movimentazioni automatiche di pallet o integrazioni di terza parte come stazioni di formatura degli angoli, etichettatura, marcatura laser, rivettatura, saldatura.
L’organo di presa ribaltabile si adatta automaticamente alle dimensioni della parte da movimentare. È dotato di ventose su entrambi i lati che consentono di prelevare il pezzo finito dal tavolo di lavoro della pannellatrice e, in tempo mascherato, sostituirlo con una nuova parte da piegare. Il tutto a vantaggio di un’ottimizzazione dei tempi di carico/scarico della lamiera, un miglioramento della cadenza produttiva e una sostantiva riduzione dei tempi di attesa.
P-Robot permette di scegliere la strategia più adatta a esigenze produttive contingenti. In turni non presidiati, o in contesti produttivi in cui un singolo operatore controlla numerosi sistemi, P-Robot lavora naturalmente in modalità R2R (robot to robot) occupandosi di carico, scarico ed eventuale impilamento delle parti. Ma non si tratta di una strategia esclusiva: la stessa P-Robot può, senza soluzione di continuità e senza riattrezzaggi, lavorare in modalità differenti. In modalità R2H (robot to human) si occupa solamente del carico dello sviluppato assegnando all’operatore lo scarico del pannello. Si tratta di una strategia vantaggiosa se l’operatore deve completare la lavorazione del pannello in una stazione di lavoro differente – ad esempio con una pressa piegatrice o una saldatrice. In modalità H2R (human to robot) è l’operatore a caricare lo sviluppato sul campo di lavoro, il robot scarica il pannello a fine ciclo: una strategia utile per gestire produzioni a lotto unitario estremamente diversificate. Senza dimenticare che la pannellatrice rimane comunque disponibile per eventuali lavorazioni completamente gestite dall’operatore.
autonome, o attraverso tecnologie singole che, se necessario, possono collaborare in modo sinergico.
Automazione: proposta ampia e modulare
In contesti produttivi caratterizzati da bassi volumi e rapidi cambi di produzione, asservire dispositivi di carico/ scarico automatici ai propri sistemi permette di recuperare efficienza. Laser, punzonatrici e pannellatrici sono sistemi estremamente rapidi, mentre le fasi di carico e scarico sempre più spesso rischiano di trasformarsi in pericolosi colli di bottiglia.
La proposta di automazione Salvagnini,
estremamente ampia e modulare, si è naturalmente evoluta negli anni per configurare ogni sistema in modi diversi, a seconda delle esigenze produttive, e comprende: dispositivi automatici di carico/scarico e sorting che riducono i tempi di attesa per l’approvvigionamento della lamiera e i rischi di errore o danneggiamento del materiale durante l’impilamento; dispositivi automatici di carico che azzerano i tempi di attesa della lamiera in ingresso assicurando la cadenza produttiva; dispositivi robotizzati di scarico che assicurano la disponibilità immediata della macchina per la lavorazione successiva e che rendono subito disponibile il
pezzo per le lavorazioni a valle, anche su stazioni non Salvagnini dispositivi di automazione intermedi – trasferitori, ribaltatori, ecc. – che bilanciano i tempi di trasferimento del materiale da una stazione di lavoro alla successiva; un’ampia gamma di soluzioni software semplici e intuitive che facilitano il processo produttivo riducendo errori e tempi di intervento degli operatori.
Flexible Smart Job Shop: competitività garantita per lavorazioni fuori linea
L’altro protagonista allo stand Salvagnini è un Flexible Smart Job Shop. Si tratta
della combinazione di tre diversi impianti stand-alone capaci, in caso di necessità, di collaborare per gestire produzioni convergenti. La connessione tra i diversi impianti è garantita dal software, ma anche da trasferitori e AMR. Flexible Smart Job Shop può prevedere anche l’integrazione di un magazzino intermedio o di altre stazioni di lavoro a monte e a valle.
A comporre questo FSJ troviamo: il nuovo laser L3.G4 in configurazione completamente automatizzata, con magazzino LTWS, dispositivo di sorting MCU e trasferitore a nastro; le sue applicazioni di visione artificiale basate su reti
neurali sono distintive; P-Robot, applicazione che combina una pannellatrice P2-2120.G4 e un robot antropomorfo a 6 assi; in anteprima mondiale, propone l’innovativo sistema di visione artificiale RVS: P-Robot riconosce le parti in arrivo e, a prescindere dal loro posizionamento, ne gestisce il carico senza intervento da parte dell’operatore e senza centraggio; la pressa piegatrice B3 con dispositivi ATA per l’allestimento degli utensili di piega superiori e inferiori, ideale per lavorazioni in kit, dotata della nuova programmazione parametrica. Una nuova architettura che combina alta
La P-Robot sotto i riflettori ad Hannover presenta anche una novità significativa, l’opzione RVS (Robot Vision System). RVS sfrutta un sistema di visione artificiale, unico sul mercato, per semplificare ulteriormente l’utilizzo della tecnologia, ottimizzare i flussi produttivi accelerando le fasi intermedie di riconoscimento, movimentazione e programmazione – e per massimizzare il valore del pezzo finito grazie al sistema di controllo qualità delle parti prodotte.
Con l’integrazione di RVS P-Robot riconosce e processa le parti in modo del tutto autonomo. Il dispositivo di visione artificiale acquisisce, con telecamera e sensori, un’immagine dell’ambiente circostante e la interpreta grazie all’intelligenza artificiale. RVS riconosce le parti, distingue i singoli fogli di lamiera, individua senza riferimenti la posizione di pallet e pile. Tutte queste informazioni sono condivise in tempo reale con pannellatrice e robot, che si adattano autonomamente per garantire che la lamiera sia manipolata e posizionata in modo preciso.
accessibilità ed elevata rigidezza, una sorgente 8kW ad alta densità di potenza ad alto rendimento che riduce i consumi e raggiunge prestazioni tipiche di sorgenti a 10kW: sono solo due delle caratteristiche distintive di L3.G4, il nuovo sistema di taglio laser in fibra Salvagnini, presentato in anteprima mondiale a EuroBLECH.
Nella configurazione proposta ad Hannover, L3.G4 è alimentato da un magazzino a torre LTWS a 10 vassoi, dotato di automazione di carico/scarico.
Il dispositivo di sorting automatico MCU completa il layout e consente di impilare agilmente parti con geometrie, dimensioni e pesi differenti. Ma il sistema di taglio che Salvagnini propone al proprio pubblico è dotato anche di un ampio ventaglio di soluzioni avanzate per il controllo e l’efficienza di processo, che migliorano ulteriormente le prestazioni e ne fanno un laser produttivo e versatile, con consumi ridotti e costi di esercizio competitivi. Tagliare non è mai stato così semplice. L3.G4 cambia il paradigma architetturale dei sistemi laser Salvagnini con una innovativa soluzione a gantry ad alta accessibilità. Questa soluzione presenta delle caratteristiche uniche e innovative di design che garantiscono la massima l’accessibilità al campo di lavoro, elevata rigidezza e precisione nelle lavorazioni a tutto vantaggio delle prestazioni su spessori medi e sottili, superiori del 15% rispetto al passato.
La sorgente da 8kW ad alta densità di potenza ad alto rendimento, distintiva
dei laser Salvagnini, garantisce velocità di taglio superiori a qualsiasi altra sorgente a 8kW tradizionale, e per spessori fino a 6 mm raggiunge velocità di taglio addirittura superiori a quelle di sorgenti a 10 kW. La sua efficienza energetica superiore al 50% la rende estremamente vantaggiosa anche per la sostenibilità economica: ridurre la potenza mantenendo elevate velocità di taglio significa, a parità di prestazione, ridurre i consumi di energia e di gas. L3.G4 è dotato di un ampio ventaglio di soluzioni avanzate per il controllo e l’efficienza di processo, che migliorano le prestazioni e ne fanno un laser facile da usare, produttivo e versatile, con consumi ridotti e costi di esercizio competitivi. L’opzione ACUT consente a L3.G4 di tagliare con aria compressa opportunamente trattata. In base alla potenza della sorgente, ACUT permette di tagliare lamiere fino a 20mm di spessore, con produttività simile a quella del taglio in azoto ma a costi decisamente contenuti. Il taglio in aria compressa è infatti più economico di quello in azoto, e questo è tanto più vero all’aumentare del costo al m3 dell’azoto: maggiore è il costo dell’azoto, maggiore è la convenienza del taglio in aria compressa lasciando invariata la qualità e la precisione di taglio. Alla sostenibilità di ACUT contribuisce anche APM2, il nuovo dispositivo compatto e chiavi in mano che si collega direttamente alla rete pneumatica e che assicura i valori di pressione necessari al processo di taglio. Per
semplificare ulteriormente alcune attività che possono richiedere tempo, generare errori o scarti – e quindi ridurre l’efficienza complessiva del sistema – L3.G4 è dotato anche di alcune applicazioni di visione artificiale basate su reti neurali. Sono soluzioni semplici, che accrescono la flessibilità del sistema e ne estendono i campi di applicazione. NVS verifica il centraggio del fascio laser e, grazie agli algoritmi di machine learning, monitora lo stato dell’ugello per ridurre gli scarti. SVS permette di recuperare spezzoni di lamiera per rispondere alle urgenze o per sostituire eventuali scarti nelle lavorazioni a valle. Con la nuova funzionalità multisheet, SVS può organizzare una lista di produzione posizionando sul campo di lavoro più di un formato di lamiera, e associarvi i differenti programmi da produrre con un semplice drag&drop. Tutti i programmi e i nest di L3.G4 sono realizzati con STREAMLASER, il software Salvagnini dedicato al mondo laser, che fa parte della suite di programmazione software STREAM. STREAMLASER migliora l’efficienza del materiale e riduce i costi grazie ad alcune caratteristiche distintive. L’algoritmo di nesting OPTI ottimizza l’utilizzo della lamiera riducendo al minimo lo sfrido. SAFE GRID ottimizza automaticamente il posizionamento delle parti rispetto alle griglie riducendone l’usura e i costi di manutenzione, migliorando la qualità delle lavorazioni e l’affidabilità del laser.
B3 è la pressa piegatrice Salvagnini ideale per produzioni dinamiche, coniuga perfettamente produttività e flessibilità. Progettata combinando caratteristiche e benefici delle soluzioni elettriche e idrauliche disponibili sul mercato con le approfondite competenze aziendali di automazione, software, meccanica ed elettronica, B3 è disponibile in 19 modelli, da 2 a 6 metri di lunghezza, da 80 a 400 tonnellate.
La pressa piegatrice B3 che Salvagnini presenta a EuroBLECH per completare il proprio Flexible Smart Job Shop ha lunghezza 3 metri e 135 tonnellate di forza. Dotata di dispositivi ATA e ATA.L, B3 regola automaticamente la lunghezza degli utensili di piega superiori e inferiori recuperando tempi ed efficienza produttiva. Il cambio, veloce, avviene in pochi secondi e la programmazione è semplice e intuitiva. ATA è un dispositivo brevettato ed esclusivo, che garantisce totale flessibilità anche da un punto di vista degli utensili permettendo di integrare manualmente sulla linea di piega utensili standard WILA o utensili speciali, come ad esempio gli utensili schiacciatori.
A rendere particolarmente interessante la pressa piegatrice Salvagnini B3 sono anche le soluzioni tecniche adottate, come Direct Drive e KERS, che consentono di rispettare l’uomo e l’ambiente senza ridurre la produttività. Grazie alla tecnologia Direct Drive i movimenti del pestone sono comandati da una coppia di motori brushless a funzionamento indipendente e a trasmissione diretta che consentono di raggiungere rapidi movimenti in veloce (sia in discesa che in risalita) e raggiungere velocità fino a 250 mm/s. Il sistema di recupero dell’energia, KERS, invece, consente di recuperare l’energia normalmente sprecata e riutilizzarla nelle fasi successive per ottenere, a parità di consumo, accelerazioni e velocità superiori. Tutte le presse piegatrici B3 sono dotate di MAC3.0 – un insieme di tecnologie adattative integrate che rendono il sistema intelligente e azzerano scarti e correzioni. S-Crowning è il sistema di centinatura intelligente che garantisce pieghe ad angolo costante su tutta la lunghezza di piega: al variare dei parametri – materiale, spessore, lunghezza e quindi forza di piegatura necessaria – l’effettiva curvatura della tavola inferiore viene rilevata e compensata in tempo reale, senza alcun intervento dell’operatore. TFC2.0, il Total Frame Control, previene deviazioni nell’angolo di piega grazie a un algoritmo ricavato dallo studio FEM di ogni singolo modello, TFC2.0 permette di compensare eventuali deformazioni in ciclo della struttura della pressa piegatrice al variare delle caratteristiche del particolare in lavorazione. AMS è il sistema laser di misurazione dell’angolo, che rileva e corregge le variazioni dell’angolo di piega dovute al ritorno elastico della lamiera. A prescindere dalla lunghezza della piegatrice e d el pezzo in lavorazione, la misura dell’angolo è sempre rilevata in un solo punto: un approccio che permette di ridurre il tempo ciclo senza rinunciare alla precisione.
B3 si può programmare a bordo macchina, ma è la programmazione in ufficio a massimizzarne l’efficienza: il software
STREAMFORMER crea automaticamente le sequenze di piega, gli allestimenti e le stazioni di piegatura, integrandosi perfettamente con i dispositivi ATA, esaltandone le prestazioni. Programmare in ufficio consente di essere più produttivi, perché mentre in ufficio un addetto si occupa dei programmi l’operatore può continuare a piegare. STREAM massimizza le performance della pressa piegatrice mettendola in comunicazione anche con gli altri sistemi componenti il Flexible Smart Job Shop.
LA STRATEGIA (MX) MACHINING TRANSFORMATION, CON I SUOI QUATTRO PILASTRI DI INTEGRAZIONE DEI PROCESSI, AUTOMAZIONE, TRASFORMAZIONE DIGITALE E TRASFORMAZIONE VERDE PROTAGONISTI DURANTE L’INAUGURAZIONE DEL TECHNOLOGY
CENTER DMG MORI A MILANO di Luca Vieri
L’inaugurazione del Technology Center di Milano, ha permesso a DMG MORI di offrire un’opportunità unica per vivere appieno la strategia Machining Transformation (MX), che si fonda su quattro pilastri: integrazione dei processi, automazione, trasformazione digitale (DX) e sostenibilità ambientale (GX). Questo evento, che si è svolto in contemporanea con BIMU 2024, oltre ai temi strategici dell’MX, ha illustrato le macchine di DMG MORI dedicate alla lavorazione integrata. Nella sezione dedicata a fresatura e tornitura, erano esposti
il centro di lavoro orizzontale INH 63 e il centro di fresatura/tornitura DMC 80 FD duoBLOCK, mentre nel comparto Turn & Mill si sono potuti ammirare i modelli CTX Beta 450 TC e NTX 500. Maggiore produttività e precisione con le soluzioni di automazione integrate Il pilastro dell’automazione nella strategia Machining Transformation (MX) include un’ampia varietà di soluzioni di automazione integrate e flessibili di DMG MORI, che i clienti possono adottare per garantire una produzione sostenibile nel futuro. Queste soluzioni non solo aumentano la produttività in officina, massimizzando l’uso
delle macchine anche durante i turni non presidiati, ma garantiscono anche una qualità costante dei pezzi attraverso la produzione automatizzata. Inoltre, il personale beneficia di un significativo risparmio di tempo, potendo concentrarsi su attività più complesse, come la programmazione o il controllo qualità. Infine, le moderne soluzioni di automazione, come il PH Cell 800 e l’AMR 2000, offrono agli utenti la massima flessibilità.
Vantaggi competitivi grazie alla Digital Transformation (DX)
La digitalizzazione intelligente, al pari dell’hardware, è una componente
La Machining Transformation (MX) si propone ai clienti di DMG MORI come un modello innovativo per il futuro della produzione. Grazie all’integrazione dei processi, all’automazione, alla trasformazione digitale (DX) e alla sostenibilità ambientale (GX), DMG MORI sta creando un contesto ideale per il successo aziendale. La visione di una produzione efficiente, con processi automatizzati e reti digitali, è supportata da un approccio ecologico che rappresenta anche un contributo sociale. La Machining Transformation (MX) si basa su un ciclo continuo di apprendimento, scambio e sviluppo, coinvolgendo attivamente la forza lavoro e consentendo una formazione ottimale dei talenti.
I nuovi centri di lavoro orizzontali INH 63 e INH 80 di DMG MORI stabiliscono nuovi standard nella lavorazione orizzontale. In combinazione con la Machining Transformation (MX) di DMG MORI, i due modelli supportano i clienti nel loro percorso verso un futuro sostenibile, efficiente e competitivo della produzione CNC. Questi centri di lavoro orizzontali sono progettati per componenti d’alta complessità impiegati nella costruzione di stampi e utensili, nonché nel settore dell’energia e del greentech, compresa, ad esempio, la tecnologia di azionamento per l’elettromobilità. L’attenzione è rivolta anche ai componenti complessi per il settore aerospace. L’INH 63 è pensata per la lavorazione di pallet da 630 mm, mentre l’INH 80 per pallet da 800 mm. Grazie alla loro stabilità, precisione e versatilità di lavorazione – sono disponibili in versione a 5 assi – queste due macchine rappresentano la base perfetta per la Machining Transformation a tutti i livelli. E non è tutto: l’INH 63 e l’INH 80 consentono un elevato grado di integrazione dei processi, possono essere automatizzate con la massima flessibilità e sono predisposte in modo ottimale per la trasformazione digitale. La struttura simmetrica ottimizzata FEM, le doppie viti a ricircolo di sfere sugli assi X, Y e Z e la slitta X sfalsata nel montante del telaio conferiscono all’INH 63 e all’INH 80 un’elevata stabilità e una lavorazione dinamica. La precisione necessaria è garantita dai sistemi di misura twin di MAGNESCALE, nonché dall’affidabile sistema di raffreddamento delle viti a ricircolo di sfere e di altre fonti di calore. Grazie a queste soluzioni, si riducono al minimo le derive termiche e possibili modifiche alla struttura della macchina. Entrambi i centri di lavoro orizzontali si distinguono anche per l’ampio raggio d’azione degli assi, che garantisce un’efficiente rimozione dei trucioli. L’INH 63 e INH 80 convincono la clientela in tutte le applicazioni: dalla lavorazione leggera fino alla truciolatura pesante. La dotazione di serie offre un mandrino powerMASTER con una velocità di rotazione di 12.000 giri/min e una coppia di 808 Nm, mentre sono disponibili in opzione mandrini con velocità fino a 16.000 giri/min o con coppia di 1.414 Nm (8.000 giri/min). In tutti e tre i casi, si applica una lunga garanzia di 36 mesi senza limiti di ore di esercizio.
L’INH 63 e INH 80 sono un buon esempio della forte attenzione
fondamentale della Machining Transformation (MX). Temi come intelligenza artificiale, Internet of Things, Big Data e Digital Twin giocano un ruolo centrale e influenzano profondamente la catena dei processi produttivi. Attraverso il networking e l’interazione end-to-end di macchine utensili intelligenti insieme a prodotti e servizi digitali, DMG MORI sta promuovendo una straordinaria trasparenza dei dati all’interno dell’officina, nell’ambito della Machining Transformation (MX).
che DMG MORI dedica al progresso sostenibile sotto forma di Machining Transformation (MX). L’integrazione dei processi, l’automazione, la trasformazione digitale (DX) e la trasformazione verde (GX) ne sono i pilastri principali. La loro crescente interazione dimostra chiaramente che la sostenibilità e l’eccellenza operativa non sono affatto obiettivi contrapposti, ma possono assolutamente andare di pari passo. L’integrazione di diversi processi produttivi in un’unica macchina – tornitura, fresatura e altri processi come la misurazione o la dentatura – accorcia la catena di processo. I tempi di attrezzaggio si riducono, mentre la qualità aumenta e nel complesso migliora l’efficienza nell’uso delle risorse, contribuendo alla sostenibilità. Se collegate a celle e sistemi di produzione flessibili, l’INH 63 e INH 80 possono lavorare anche per tre turni in modalità non presidiata. La gestione automatizzata di utensili e pallet e il computer master intelligente CELL CONTROLER LPS 4 incrementano le ore produttive del mandrino da 2.000 a oltre 6.000 all’anno rispetto all’installazione della singola macchina. La dotazione di tecnologie digitali consente inoltre l’integrazione in sistemi di produzione olistici. E non è tutto: il GREENMODE ha anche un impatto diretto sulla trasformazione verde (GX), riducendo il consumo energetico delle macchine di oltre il 30% e ottimizzando, allo stesso tempo, l’uso delle risorse.
Questo approccio crea le condizioni per decisioni informate e consente alle aziende di agire in modo proattivo, sviluppando nuovi modelli di business e garantendo vantaggi competitivi sostenibili nel tempo.
La Green Transformation (GX) promuove gli obiettivi di sostenibilità
La Green Transformation (GX) deriva in larga misura dalle misure di aumento dell’efficienza previste nei primi tre pilastri. Si tratta di un percorso che consente di raggiungere gli obiettivi di
protezione del clima e compensazione dell’aumento dei prezzi dell’energia. Il principio guida della cosiddetta Green Economy di DMG MORI persegue un approccio olistico, che comprende macchine high-tech prodotte impatto climatico pari a zero (Greenmachine), una modalità di produzione efficiente dal punto di vista energetico (Greenmode) e partnership tecnologiche con gli OEM per la produzione sostenibile di beni e merci di ogni tipo (Greentech).
La lavorazione completa su 6 lati dei centri di tornitura/ fresatura della serie CTX beta TC è tradizione in DMG MORI ormai da parecchi anni. Il nuovo CTX beta 450 TC continua a scrivere questa storia di successo. Il comfort operativo, l’efficienza, l’integrazione di tecnologie e processi e le opzioni di automazione sono valsi come criteri fondamentali per lo sviluppo di questo modello. Ed è così che il nuovo centro di tornitura/fresatura è diventato un perfetto esempio di trasformazione della lavorazione (Machining Transformation / MX) e dei suoi quattro pilastri: integrazione dei processi, automazione, trasformazione digitale (Digital Transformation / DX) e trasformazione verde (Green Transformation / GX). Questo è l’approccio con cui DMG MORI ridisegna il futuro della produzione. La fresatura simultanea a 5 assi, la lavorazione
completa su 6 lati con mandrino principale e contromandrino, nonché l’integrazione di rettifica, dentatura e misurazione garantiscono la massima produttività e tecnologia sul pezzo. Con un ingombro di soli 10 m², il CTX beta 450 TC è la nuova soluzione entry level nella gamma di centri di tornitura/fresatura high-tech di DMG MORI. La zona lavoro offre spazio per pezzi con diametro fino a ø 500 mm e lunghezza fino a 1.100 mm. Il passaggio barra del mandrino principale è di ø 76 mm o, in opzione, di ø 102 mm. Il cuore del nuovo modello è ancora una volta il mandrino di tornitura/fresatura compactMASTER con una velocità di rotazione di 15.000 giri/min di serie e 20.000 giri/min in opzione. I mandrini principali e i contromandrini offrono un numero di giri massimo di 5.000 giri/min o una coppia fino a 720 Nm.
L’ultima generazione di centri di tornitura CTX convince per il design compatto e la zona lavoro più ampia pur con un ingombro ridotto, che nel caso del nuovo modello CTX 350 4A arriva appena a 7 m². Il CTX 350 4A dispone di due torrette VDI30 per un totale di 28 posizioni utensile. Gli utensili motorizzati raggiungono velocità di rotazione massime di 12.000 giri/min e valori di coppia fino a 14 Nm. Sono, inoltre, disponibili un mandrino sinistro (ISM 65), che vanta una velocità di rotazione fino a 5.500 giri/min e una coppia di 171 Nm, ed un mandrino destro (ISM 50), che raggiunge i 6.000 giri/min e i 93 Nm di coppia. Entrambe le torrette possono essere utilizzate separatamente sui due mandrini o contemporaneamente su un solo mandrino. L’elevata versatilità
del CTX 350 4A consente, quindi, una lavorazione completa su 6 lati altamente produttiva di pezzi di dimensioni fino a ø 230 x 100 mm con una corsa di +/- 50 mm sull’asse Y. Il passaggio barra misura ø 65 mm e la predisposizione per un caricatore di barre è già inclusa nella configurazione standard della macchina. La rimozione dei trucioli ad alta efficienza e i componenti all’avanguardia, che assicurano prestazioni rapide, precise e affidabili, fanno del CTX 350 4A un valido aiuto in qualsiasi impianto di produzione orientato al futuro. Il pannello di controllo da 24” dotato di CELOS X su Siemens offre alla macchina un elevato livello di connettività per la produzione digitalizzata. In alternativa, il CTX 350 4A è disponibile con sistema di controllo FANUC.
SCHNEIDER ELECTRIC ANNUNCIA LA TRASFORMAZIONE DELL’INNOVATION HUB A CASALECCHIO DI RENO: IL CENTRO CHE DAL 2018 SUPPORTA L’INDUSTRIA 4.0, ORA SI RINNOVA CON FOCUS SULLA TRANSIZIONE 5.0. CON L’OCCASIONE ABBIAMO APPROFONDITO QUESTO TEMA CON CLAUDIO GIULIANETTI, VICE PRESIDENT INDUSTRIAL AUTOMATION, SCHNEIDER ELECTRIC di Cristina Gualdoni
Il concetto di Transizione 5.0 rappresenta un’evoluzione nell’industria, che punta a combinare digitalizzazione avanzata e sostenibilità energetica, promuovendo soluzioni per l’efficienza operativa ed energetica. Il rinnovato Innovation Hub accoglie ora nuove tecnologie di automazione, intelligenza artificiale e sistemi software, che aiutano le aziende, in particolare i costruttori di macchine industriali, a restare competitive in un mercato globale sempre più digitalizzato. L’Innovation Hub di Casalecchio, parte della rete Schneider in Italia con hub anche a Bergamo, Napoli e Pieve d’Alpago, rappresenta un polo di formazione e scoperta tecnologica. I visitatori possono
sperimentare tecnologie di automazione avanzate e macchine digitali, esplorare ambienti di simulazione tramite gemelli digitali e realtà aumentata, e operare da remoto per monitorare e ottimizzare macchinari installati in tutto il mondo.
L’hub è inoltre un centro di consulenza per i clienti, fornendo risorse, supporto tecnico, e collaborazioni con partner per favorire il percorso di innovazione richiesto dalle attuali normative.
La sede di Casalecchio, attiva da quasi cinquant’anni, è anche un centro di eccellenza nel settore del packaging, con un team di circa 100 professionisti che supportano le aziende clienti dalla progettazione all’implementazione di macchinari indu-
striali. Schneider Electric, inoltre, collabora attivamente con istituzioni scolastiche e università locali, come l’Università di Bologna e Ferrara, e con enti di formazione come l’ITS Fondazione Aldini e Valeriani, proponendo corsi di formazione nell’ambito dell’Industria 4.0 e dell’efficienza energetica. Questa rete educativa si estende anche a iniziative con Confindustria Emilia e il centro di competenza BIREX dell’EmiliaRomagna, e a collaborazioni con la Bologna Business School, con un particolare impegno verso la sostenibilità.
Per inaugurare il nuovo hub, Schneider Electric ha organizzato un evento intitolato “IMPACT – OEM protagonisti della transizione digitale”, rivolto ai costruttori
di macchine industriali, dove ha presentato le proprie strategie tecnologiche e discusso con esperti di finanza e innovazione sul futuro del settore. L’azienda, leader mondiale nella gestione digitale dell’energia e dell’automazione, con oltre 168.000 dipendenti, conferma così il proprio impegno per un futuro industriale più sostenibile, digitalizzato e connesso. Ne parliamo con Claudio Giulianetti, Vice President Industrial Automation, Schneider Electric.
Nel corso dei decenni la tecnologia ha fatto enormi passi avanti ma mai come negli ultimi dieci anni, con la dirompente irruzione della digitalizzazione, si è visto un radicale cambiamento dei paradigmi produttivi. Come state vivendo la transizione 4.0 e come vi preparate a quella 5.0?
L’avvento dell’Industria 4.0 ci ha visti puntare con decisione sul ruolo della digitalizzazione a supporto delle industrie del nostro paese. La roadmap della nostra offerta si stava già orientando sulla proposta di soluzioni connesse, sui tre livelli dei componenti, dei sistemi di controllo e delle applicazioni e servizi; siamo quindi stati al fianco di moltissimi clienti che hanno adottato, anche nel quadro degli incentivi disponibili dal
2017 in poi, questo nuovo approccio alla produzione e alla gestione dei processi; ci siamo posti a servizio dell’innovazione dei clienti come consulenti, non solo come fornitori, unendo le nostre profonde conoscenze di dominio con l’esperienza e la competenza specifica delle diverse imprese. E’ con questo stesso approccio che stiamo ora affrontando la cosiddetta “transizione 5.0”, forti di una proposta completa su tutti gli assi del nuovo scenario – dalla sostenibilità, all’efficienza energetica e produttiva fino arrivare al software – e di un continuo lavoro di integrazione delle nuove tecnologie emergenti, come l’Intelligenza
Artificiale, per aiutare la competitività e la crescita di costruttori di macchine e aziende manifatturiere. Tutto questo con una convinzione, che non si possa affrontare questa sfida da soli: pertanto ci stiamo circondando di una rete di partner per poter creare una filiera di valore capace di rispondere a tutti i bisogni della Transizione 5.0, per esempio gli aspetti progettuali e fiscali.
In questo nuovo contesto produttivo, quali sono i parametri sui quali si gioca la competitività sul mercato?
L’ingrediente di questa ricetta ha un solo nome: INNOVAZIONE. Ovviamente su questo asse si può lavorare in diverse direzioni, noi ne individuiamo due distintive. Un parametro fondamentale per la competitività oggi è proprio la sostenibilità. Se guardiamo per esempio ai costruttori di macchinari automatici, gli OEM sono inseriti in filiere nelle quali è sempre più diffusa la richiesta di rispettare requisiti specifici, di contribuire come fornitori al raggiungimento di obiettivi che coinvolgono la supply chain e di supportare l’adeguamento alle normative. Non basta più costruire macchine sempre più compatte, veloci, prestazionali: bisogna costruire macchine
che garantiscono prestazioni ottimali con un impatto inferiore in termini di consumi ed emissioni, essere in grado di certificare questi aspetti in tutto il ciclo di vita della macchina, creare soluzioni che aiutano l’impresa a migliorare e a controllare la sua produzione anche da questo punto di vista. Riteniamo che su questo aspetto si giochi un elemento fondamentale della competitività di queste aziende che potranno sfruttare la leva della sostenibilità per differenziarsi rispetto ai competitor dei paesi emergenti. L’altro tema importante sono le competenze: allinearle all’evoluzione sempre più vorticosa delle tecnologie, sia in ottica di digitale sia in ottica di sostenibilità, è cruciale. Mai come oggi è importante formare, trattenere e valorizzare personale con le qualifiche giuste, così come capire su quali scenari puntare per restare sempre aggiornati anche in futuro.
Come è cambiato il vostro approccio al cliente e quali cambiamenti organizzativi ci sono stati in azienda negli ultimi anni?
Innanzitutto, Schneider Electric negli ultimi anni ha investito molto per portare al suo interno nuove competenze, e per portare le competenze sul mercato, verso i clienti. Per raggiungere in modo capillare le imprese italiane alle prese con la transizione 4.0 abbiamo creato dei team di professionisti, presenti in tutte le nostre aree commerciali, dedicati ad accompagnare le imprese nel loro percorso digitale e di decarbonizzazione per creare insieme a loro, con il supporto dei nostri partner sul territorio, progetti innovativi. Siamo oggi in grado di supportare i clienti in progetti di Trasformazione Digitale e di Elettrificazione e Efficientamento
dei processi atti a ridurre le emissioni di CO2 grazie ad un approccio consulenziale che parte dalla definizione di una strategia dedicata, seguita da un planning operativo, che dà evidenza dei ritorni dell’investimento.
Siamo cresciuti con l’offerta di sistemi, componenti, piattaforme cloud per creare strumenti agili ed efficaci di innovazione a disposizione di imprese di ogni dimensione; la nostra offerta di servizi si è parallelamente evoluta per abbracciare con più facilità le diverse esigenze. Come azienda, abbiamo acquisito nuove forze e allargato la nostra piattaforma anche attraverso un percorso di acquisizioni in particolare nell’ambito software e in settori specifici, per ampliare il nostro ecosistema; questo è avvenuto a livello globale a servizio delle nostre attività nei vari paesi, inclusa l’Italia.
Quali sono gli obiettivi che la vostra azienda si è fissata nel medio lungo termine?
Gli obiettivi di medio/lungo termine che ci siamo posti si sposano con una visione strategica incentrata sull’obiettivo di diventare un leader dell’Industrial Tech: un’azienda che fa leva su una expertise unica, a livello mondiale, negli ambiti dell’elettrificazione, dell’automazione e della digitalizzazione per abilitare una innovazione sostenibile in tutti i settori in cui operiamo – dall’industria alle infrastrutture, ai data center ed edifici. L’industria del futuro che vogliamo costruire insieme ai nostri partner, con i nostri clienti e per i nostri clienti, ha bisogno sempre più di software, servizi, di integrare le tecnologie emergenti come l’AI
per abilitare la crescita, e per consentire di continuare a incrementare l’efficienza operativa ed energetica, che va di pari passo con la ricerca di sostenibilità.
Nel campo della sostenibilità, efficientamento energetico e produttivo possiamo mettere a disposizione dei nostri Partner le competenze e le soluzioni che abbiamo implementato all’interno della nostra azienda negli ulti 15 anni e che ci ha permesso di essere riconosciuti come riferimento da molte voci autorevoli, come recentemente avvenuto con il primo posto tra le aziende più sostenibili al mondo ottenuto nella classifica di Time- Statista.
Mettere a terra in concreto queste strategie, oggi e in futuro, richiede da parte nostra di continuare ad essere quello che siamo sempre stati: un trusted advisor, un’azienda che non si limita a fornire tecnologie, una presenza costante che ascolta, che aiuta l’ecosistema a maturare, innovare e a costruire nuove strade per la competitività.
In prospettiva, come valuta l’introduzione dell’IA nel contesto manufatturiero? Pensate di implementarla?
Schneider Electric ha preso molto sul serio l’avvento dell’Intelligenza Artificiale. Il nostro approccio è concreto e ci vede da un lato studiare come l’IA può supportare le nostre attività e processi interni, dall’altro come applicare l’IA generativa e il machine learning nelle soluzioni che offriamo. L’azienda ha creato un AI Hub composto al momento da tre poli che operano a livello globale: una struttura che oggi conta oltre 300 specialisti dedicati a questo e che si nutre anche della collaborazione con i partner chiave di questo settore, come Open AI, Microsoft e NVIDIA. Abbiamo iniziato a lavorare su alcune aree rendendo disponibili ad esempio un copilot per aiutare la scrittura di codice di programmazione industriale e introducendo strumenti di raccomandazione e di analisi intelligente dei dati. L’AI ha un potenziale trasformativo enorme, che riconosciamo e che crediamo vada compreso e gestito. Il nostro impegno sarà supportare anche in questo i nostri clienti e assicurare il rispetto di rigorosi principi di sicurezza, etica e responsabilità.
GERARDI
ROBI: I PUNTI DI FORZA IN SINTESI
Cambio ciclo, particolari, attrezzature e grippers
Carico Continuo senza
Interruzioni
Tutto gestito da un software intuitivo con supervisore integrato
Gestione automatizzata dei Carichi di Lavoro
Asservimento fino a tre macchine
Grande Capacità di Stoccaggio
Monitoraggio in tempo reale
Monitoraggio isola non presidiata
Teleassistenza
Connessione remota
GERARDI HA PRESENTATO IL RIVOLUZIONARIO SISTEMA MODULARE DI PRODUZIONE COMPLETAMENTE AUTOMATIZZATO, IDEATO PER OTTIMIZZARE LE ATTIVITÀ DI PRODUZIONE E STOCCAGGIO
di Fabio Chiavieri
LLe aziende manifatturiere oggi affrontano sfide significative nell’era della mass customization, un approccio che combina l’efficienza della produzione di massa con la personalizzazione del prodotto. Questa trasformazione comporta diverse problematiche quali la richiesta di prodotti personalizzati che aumenta la varietà e la complessità dei processi produttivi, la gestione delle risorse che richiede estrema flessibilità operativa, la necessità di investire ingenti cifre in tecnologie, digitalizzazione e automazione. Inoltre, i clienti sono abituati a scelte illimitate e a tempi di risposta rapidi. Passando da un prodotto all’altro, è necessa-
rio fermare la linea produttiva per riconfigurare le macchine, ma la variabilità dei prodotti e dei lotti rende difficile pianificare in modo accurato la produzione, portando a ritardi nelle consegne, sovrapproduzione o carenze di magazzino. Per aiutare le imprese ad affrontare queste problematiche, Gerardi S.p.A. di Lonate Pozzolo (VA) ha progettato e realizzato “Robi” un rivoluzionario sistema modulare di produzione completamente automatizzato, creato per ottimizzare le attività di produzione e stoccaggio: integra magazzino attrezzature e macchine utensili, incrementando i processi produttivi. Robi rappresenta un’innovativa soluzione che
integra quattro aree chiave:
1. magazzino verticale con due baie indipendenti;
2. robot Robot Antropomorfo;
3. attrezzature necessarie alla movimentazione e alla presa pezzo (grippers, morse e zero point);
4. software innovativo.
Il tutto per ottenere un vero e proprio cambio automatico della produzione, dai particolari da lavorare, ai grippers di presa pezzo, alle attrezzature, ai cicli di lavoro.
Un software unico
Dopo più di due anni di sviluppo, il sof-
tware supervisore è in grado ora di gestire automaticamente la cella produttiva, assegnando priorità e ottimizzando i carichi di lavoro, eliminando la necessità di intervento manuale. Una funzionalità che nessun altro sistema di automazione offre. E non è necessaria alcuna esperienza o programma con i robot.
Con una normale macchina difficilmente si raggiungono le 14001500 h/anno, ma ipotizzando di usare Robi per un minimo di 8 ore per 200 giorni avremmo i seguenti risultati: 8h x 200gg x1 macchina - 1600h / anno Ovviamente il calcolo è minimalista e considera solo 8 ore giornaliere, tuttavia, l’impiego di ROBI consente di sfruttare un potenziale produttivo significativamente maggiore, operando 24 ore su 7 giorni.
Ipotizzando di lavorare ad un costo orario di 50 euro/h, si raggiungerebbe un fatturato di 240.000 € , anzichè 75.000 € Inoltre, la possibilità di asservire due o addirittura tre macchine utensili indipendenti permette di ottimizzare ed incrementare ulteriormente la produzione, eseguendo lavorazioni ed anche particolari diversi in contemporanea, aumentando nel contempo l’efficienza complessiva del sistema
È il software con supervisore a fare la vera differenza : con questo sistema, gli operatori non devono più eseguire manualmente i punti sul pannello del robot all’inizio della produzione. Questo è un grande vantaggio perché gli operatori delle macchine utensili generalmente non sono esperti nella gestione dei robot, un compito che richiederebbe un corso specifico. Grazie a Robi, però, tutto diventa più semplice: ogni operatore può lavorare in autonomia , inserendo i dati (dimensione dei grezzi) il software determina autonomamente dove e cosa deve fare il robot e di conseguenza propone la macchina libera.
Estrema flessibilità di stoccaggio
Robi, con 56 vassoi e una capacità di carico fino a 250 kg ciascuno offre una grande flessibilità nello stoccaggio di diversi materiali. I vassoi standard 600x800 semplificano il trasporto e lo spostamento. In più è dotato di due baie:
• per l’operatore per il carico e scarico del particolare e delle attrezzature;
• per il Robot e per la gestione dei particolari da essere lavorati e l’installazione delle • attrezzature.
La scelta del robot è caduta su un Fanuc M710iC/70, un modello a 6 assi adatto a varie applicazioni e combina una capacità utile di 70 kg con velocità degli assi estremamente elevate e una ripetibilità di ± 0,04 mm, garantendo straordinaria ripetibilità, facile manipolazione di lastre di grandi dimensioni e velocità e prestazioni di movimento eccellenti e un’affidabilità senza pari.
Focus sulla produzione
Robi migliora la pianificazione della produzione combinando i tre ingredienti indispensabili per evitare le complicazioni più comuni durante l’inizio di una produzione, semplifi-
candone i processi e fornendo la possibilità di pianificarli e automatizzarli:
1. vertical warehouse: magazzino verticale di particolari e attrezzature;
2. grippers & robot: presa & movimentazione dal magazzino alle macchine;
3. zero point e morse automatiche: posizionamento e serraggio sulla macchina utensile.
Integrando Robi insieme alle attrezzature Gerardi, è possibile ottenere processi semplificati, una gestione dello stoccaggio ottimizzata e una significativa crescita della produttività. Un ulteriore vantaggio di Robi è l’adattabilità alle macchine utensili già esistenti in officina, permettendo di ottimizzare lo spazio e aumentare la produttività senza dover acquistare nuove attrezzature.
L’importanza della modularità
Robi è un sistema modulare che permette l’aggiunta di magazzini e macchine. È possibile configurare il layout in base alle proprie esigenze produttive. Inoltre, si può modificare la disposizione delle macchine per adattare il layout allo spazio e ottimizzare il flusso di lavoro.
L’IMPIEGO DEI COBOT NELLE AZIENDE ITALIANE SI STA DIFFONDENDO SEMPRE PIÙ. LA
ROBOTICA COLLABORATIVA STA RIVOLUZIONANDO IL MODO DI INTENDERE L’AUTOMAZIONE ALL’INTERNO DI FABBRICHE, LABORATORI E PERSINO UFFICI. RAPPRESENTA UNA VALIDA SOLUZIONE IN MOLTEPLICI CONDIZIONI PRODUTTIVE, AFFIANCANDOSI AI TRADIZIONALI ROBOT INDUSTRIALI PER RISPONDERE ALLE NUOVE ESIGENZE DI MERCATO
Lotti ridotti, maggiore flessibilità, semplicità di programmazione e sicurezza operativa sono caratteristiche che li rendono ideali in un numero sempre crescente di applicazioni.
I cobot uniscono due distinte qualità: l’automazione flessibile tipica dei robot e la possibilità di essere utilizzati ovunque, data la loro natura “collaborativa”. Possono essere utilizzati anche al di fuori di contesti industriali, anche se tendenzialmente è lì che offrono il massimo dei vantaggi. Un esempio classico è l’asservimento di una macchina automatizzata, come un tornio, una pressa o marcatrice laser. Le applicazioni realizzate con robot industriali tradizionali sono le più idonee dove le produzioni richieste sono elevate. Viceversa, i cobot
danno maggiori vantaggi nei contesti in cui si ha necessità di riprogrammare spesso le mansioni da svolgere, ridurre gli spazi utilizzati e nei casi in cui sia necessario che un operatore interagisca durante il ciclo di lavoro col robot. Il fatto di essere compatti e facilmente adattabili agli ambienti lavorativi li rende inoltre facilmente spostabili all’interno di uno stabilimento o di un laboratorio senza particolari vincoli. Ed ecco che è più semplice ricollocare un cobot al fianco di un’altra macchina per automatizzarla, oltretutto in una manciata di minuti. Una prerogativa che permette di aggiungere flessibilità (operativa) a flessibilità (di utilizzo).
Quella del robot industriale è una soluzione operativa da decenni in
numerosi settori applicativi
Tra i principali utilizzatori c’è il mondo automotive, ma molti vengono impiegati anche nel settore del “bianco” per la produzione di elettrodomestici, nell’elettronica e nella chimica e farmaceutica. Per sua natura, invece, il cobot si presta a eseguire compiti più “leggeri”, come la pallettizzazione, l’asservimento, l’avvitatura o l’assemblaggio di piccoli oggetti. Se pensiamo al tessuto imprenditoriale italiano, ricco di PMI che fanno della flessibilità uno dei propri punti di forza, risulta evidente come un cobot possa offrire quella spinta in più per risultare ancora più competitivi sui mercati. ABB ha pensato perciò a una serie di opzioni capaci di rispondere alle specifiche esigenze delle imprese, che possono così trovare soluzioni concrete e convenienti.
Spesso l’ostacolo più difficile da superare non è tecnico, ma psicologico. Per chi si affaccia per la prima volta al mondo della robotica, in alcuni casi vi può essere il timore iniziale circa la reale capacità di utilizzare a pieno il cobot; in altri, il cobot sarebbe ideale ma i volumi bassi di produzione o ancora cicli di stagionalità o domanda variabile, lo rendono una scelta poco appetibile. Per questo ABB ha pensato a un programma capace di fare breccia anche nelle realtà più diffidenti sfruttando un meccanismo già apprezzato in molti altri ambiti: il noleggio operativo. Usando una terminologia più attuale, proponiamo il servizio Robot as a Service che prevede il pagamento delle sole ore di utilizzo del cobot, svincolando così il cliente dal costo di acquisto e dai possibili imprevisti che talvolta lo frenano. Come già avviene con le auto, le fotocopiatrici, i telefoni e molti altri dispositivi, una PMI può scegliere di noleggiare un cobot con un contratto studiato apposta sulle singole esigenze. Ciò consente di gestire meglio anche eventuali picchi di lavoro, potendo contare su una automazione intelligente e flessibile direttamente in azienda.
ABB Cobot Expert
Sempre in ottica di offerta il più possibile personalizzata, ABB ha anche pensato di creare un network di professionisti o system
integrator in grado di rispondere a esigenze più complesse.
Per questo è nato ABB Cobot Expert, un servizio pensato per mettere in comunicazione due figure altrimenti distanti tra loro. Da un lato le PMI che cercano un supporto snello, capace di offrire risposte rapide e, se possibile, geograficamente vicino. Dall’altro integratori o programmatori, che altrimenti non avrebbero modo di mettersi in contatto con questi potenziali clienti. Dal canto suo, ABB offre un piano formativo che include tutti i principali step necessari per sviluppare una soluzione pienamente operativa: dalla progettazione alla programmazione sul campo, il tutto integrato con eventuali ecosistemi di terze parti. Chiude il cerchio
il corso dedicato alla certificazione delle isole collaborative.
Un altro fattore che ostacola l’introduzione di un robot all’interno di una piccola o media impresa è il timore di saper programmare e utilizzare il robot al meglio. Anche in questo caso, il cobot vanta una marcia in più poiché offre differenti modalità di programmazione semplificata. Attraverso RobotStudio di ABB è possibile sfruttare un software dedicato, denominato Wizard Easy Programming, un vero e proprio “aiutante” che, sulla base di pochi e semplici passaggi, traduce le esigenze pratiche in linguaggio macchina. Questo software si basa sull’utilizzo di blocchi dedicati a specifiche attività che possono essere selezionati e trascinati all’interno del programma. Pertanto, senza dover essere esperto di robotica, è sufficiente avere una conoscenza di base della logica della applicazione e la programmazione è fatta. La proposta di ABB è iniziata nel 2015 con Yumi, un cobot a doppio braccio, seguito dalla versione a braccio singolo, entrambi integrabili facilmente in diversi contesti applicativi. Successivamente, ABB ha introdotto GoFa, un cobot con capacità di carico maggiore e una velocità operativa più elevata, adatto a molteplici compiti in officine e laboratori. SWIFTI rappresenta invece un ponte tra i robot industriali e quelli collaborativi, operando in sicurezza accanto agli operatori grazie a funzionalità avanzate di rilevamento e sicurezza. L’offerta di ABB nel campo della robotica collaborativa è diversificata e in grado di soddisfare le diverse esigenze delle aziende, promuovendo una maggiore flessibilità e competitività nel mercato.
NEL MONDO DELL’AUTOMAZIONE INDUSTRIALE, L’USO DI ROBOT COLLABORATIVI, O “COBOT”, STA RIVOLUZIONANDO I PROCESSI PRODUTTIVI OFFRENDO SOLUZIONI FLESSIBILI E ALTAMENTE EFFICIENTI. LA TS WELD MATE, UNA CELLA DI SALDATURA COMPATTA E TRASPORTABILE DOTATA DEL ROBOT COLLABORATIVO CL110N DELLA KAWASAKI ROBOTICS, È UNA SOLUZIONE PENSATA PER LE AZIENDE CHE CERCANO SEMPLICITÀ, PRODUTTIVITÀ E SICUREZZA
Una delle caratteristiche distintive della TS Weld Mate è la sua dimensione compatta, con un ingombro di 1650 x 2400 mm, incluse le stazioni di lavoro da 800 x 550 mm ciascuna.
Grazie a queste dimensioni ridotte, la cella può essere facilmente integrata anche in spazi produttivi limitati. La TS Weld Mate è inoltre progettata per essere completamente trasportabile: grazie alla cabina autonoma e all’integrazione di tutti i componenti essenziali, può essere spostata agevolmente all’interno del capannone o in altri siti produttivi, offrendo una straordinaria flessibilità operativa. Questa versatilità si rivela particolarmente utile per realtà produttive
che devono adattare le linee a diverse esigenze o operare su più stabilimenti. Progettata per la General Industry e per chi ha la necessità di saldare piccoli lotti, la TS Weld Mate è l’alternativa ideale alla saldatura manuale. Anziché dedicare risorse umane alle operazioni manuali e ripetitive, le imprese possono affidare il lavoro alla cella robotizzata, ottenendo maggiore precisione e migliorando la qualità delle operazioni.
Al cuore della TS Weld Mate c’è il robot collaborativo CL110N, progettato per offrire un’esperienza d’uso intuitiva ed accessibile. Con un carico massimo di 10 kg e uno sbraccio di 1000 mm, questo cobot è progettato per affrontare con efficienza operazioni di saldatura collaborativa, manipolazione e pallettizzazione.
A differenza dei tradizionali robot industriali, che possono richiedere competenze tecniche avanzate e una programmazione più o meno complessa, questo modello si distingue per l’estrema semplicità di programmazione. Il CL110N utilizza infatti un sistema di programmazione a blocchi, che consente di creare percorsi e comandi con la funzionalità drag&drop, sfruttando macro predefinite e riutilizzando parti di programmi già creati. Questa soluzione accelera notevolmente il processo di configurazione e riduce il rischio di errori. Una volta configurato, il percorso del robot può essere simulato all’interno di un ambiente virtuale, dove è possibile verificare e ottimizzare i movimenti, le traiettorie e le operazioni prima di passare alla produzione vera e propria, riducendo
costi e tempi legati ad eventuali modifiche durante la fase operativa. Anche chi ha poca esperienza con l›automazione può dunque imparare a gestirlo in tempi rapidi. Questa caratteristica riduce la necessità di operatori altamente specializzati, rendendo l’automazione accessibile a una più ampia gamma di realtà produttive.
Il CL110N fa parte della Serie CL, lanciata da Kawasaki Robotics nel 2023, che comprende quattro modelli progettati per adattarsi a una vasta gamma di applicazioni. Si caratterizza per il montaggio con orientamento libero e la protezione IP66, che gli garantisce resistenza a polveri e liquidi. Come tutti i robot della Kawasaki Robotics, anche i cobot della serie CL integrano soluzioni che migliorano la gestione e la sicurezza dei cavi. Tutti i cavi di dati e di alimentazione passano attraverso il braccio del robot, garantendo un design pulito e sicuro, facilitando le operazioni di manutenzione e pulizia. Dal punto di vista delle prestazioni, il
CL110N è estremamente efficiente: con una velocità leader del settore pari a 200°/s e una ripetibilità di ± 0,02 mm, garantisce precisione e rapidità in ogni operazione. Questi risultati sono possibili grazie ai componenti di alta qualità integrati, come gli encoder a 24 bit, che offrono una delle risoluzioni più elevate disponibili sul mercato, e a una struttura leggera ma robusta, tipica dei robot industriali di Kawasaki Robotics. L’introduzione della TS Weld Mate offre, in sintesi, una serie di vantaggi tangibili. Grazie alla doppia stazione di lavoro su tavola rotante manuale, gli operatori possono preparare un pezzo mentre il robot lavora sull’altro,
riducendo al minimo i tempi morti e aumentando la produttività complessiva. L›automazione del processo di saldatura consente anche una significativa riduzione dei costi operativi, poiché diminuisce il bisogno di manodopera manuale, riducendo al contempo errori e scarti di produzione. Il robot CL110N garantisce una qualità costante, offrendo saldature precise e uniformi, riducendo la variabilità tipica delle operazioni manuali e migliorando la qualità del prodotto finito. Infine, con il robot che si occupa delle saldature, si riduce drasticamente il rischio di infortuni per gli operatori, migliorando così la sicurezza generale e le condizioni di lavoro in azienda.
55.000 passaggi di macinatura e pesatura: il cobot LBR iisy di KUKA ha supportato gli ingegneri progettisti di Gronbach nel controllo qualità di un nuovo macinacaffè
MACINARE LA QUANTITÀ DI CAFFÈ CON PRECISIONE AL GRAMMO: CON QUESTA FUNZIONE, CHE IN PRECEDENZA ERA RISERVATA ALLE COSTOSE MACCHINE DA CAFFÈ PER LA RISTORAZIONE, IL NUOVO MARCHIO LIGRE STA CONQUISTANDO IL SETTORE CONSUMER. GLI INGEGNERI PROGETTISTI DI GRONBACH SI SONO AFFIDATI AL SUPPORTO DEL COBOT LBR IISY DI KUKA, SVILUPPANDO UNA CONFIGURAZIONE DI PROVA PER UN CONTROLLO DI QUALITÀ APPROFONDITO DEL NUOVO MACINACAFFÈ, SIA IN TERMINI DI DURATA CHE DI PRECISIONE DEL PESO PRESTABILITO DEL CAFFÈ
Il gruppo Gronbach è stato fondato nel 1964 come produttore di cerniere. Lo sviluppo commerciale è stato rapidissimo: oggi l›azienda gestisce cinque siti produttivi in Europa, ha un ufficio vendite negli Stati Uniti e impiega circa 1.200 persone. In qualità di OEM, la Gronbach è specializzata nello sviluppo e nella produzione di gruppi tecnici, ovvero di prodotti completi,
che vengono forniti a livello internazionale a oltre 500 clienti diversi, dalle Xgrandi aziende alle start-up, principalmente del settore degli elettrodomestici , ad esempio macchine da caffè, piani cottura a induzione, vaporiere e molto altro. La base clienti comprende anche i settori ristorazione, medico, automotive e beni di consumo. Alla qualità viene data la massima importanza. Nel sito di Niederndorf in Tirolo, dedicato alla produzione e alla ricerca e allo sviluppo, lavorano circa 200 dipendenti. Il sito riveste grande importanza per il Gruppo Gronbach nell’ambito dello sviluppo complessivo di soluzioni di prodotto, infatti qui convergono ambiti diversi, come la meccanica, l’elettrotecnica, l’elettronica, il software ecc. Un team dedicato di esperti è impegnato nella ricerca e nello sviluppo su misura di apparecchi e gruppi costruttivi.
Tutti i prodotti hanno un elevato standard di qualità in termini di tecnologia, sostenibilità ed efficienza energetica. Per il controllo approfondito della qualità di un nuovo macinacaffè, gli ingegneri progettisti si sono affidati al supporto del cobot LBR iisy di KUKA, con l’obiettivo di migliorare i processi in una configurazione di prova. In qualità di OEM premium, Gronbach ha un’ampia esperienza nella produzione, con un know-how completo nell’area della ricerca e dello sviluppo. Il patrimonio di esperienza maturato in centinaia di progetti specifici e riusciti confluisce ora nel proprio marchio LIGRE: con questo nome, l’azienda sta entrando nel mercato come produttore di macchine high end per la preparazione del caffè. Oltre alla macchina espresso, uno dei primi prodotti lanciati sul mercato è il macinacaffè LIGRE siji. Una funzione completamente nuova per un macinacaffè nel segmento consumer è la possibilità di preimpostare al grammo esatto la quantità di caffè da macinare. Per garantire che la qualità premium non rimanga solo uno slogan, gli esperti di ricerca e sviluppo di Gronbach hanno deciso di sottoporre questo nuovo prodotto ad un approfondito controllo qualità, utilizzando una serie di test. Il punto di partenza era la previsione che il macinacaffè avrebbe macinato o lavorato circa 500 kg di caffè nel
corso di circa dieci anni. Per poter pesare nel lungo periodo circa mezza tonnellata di caffè con un risultato di pesatura preciso in varie condizioni operative, era necessario utilizzare un metodo che non solo consentisse una forte accelerazione del processo, ma che garantisse anche un’enorme precisione di ripetibilità. Inoltre, i risultati
ottenuti dovevano essere affidabili e le conoscenze acquisite dovevano poter essere integrate negli sviluppi e nei miglioramenti futuri.
La convenienza del controllo qualità Attraverso una configurazione di prova, gli esperti di ricerca e sviluppo di Gronbach hanno convenuto che un controllo qualità conveniente fosse possibile solo attraverso l’automazione mediante robot. La scelta è caduta subito su KUKA, anche perché vari robot industriali erano già in uso presso la sede di Niederndorf, vicino a Kufstein. Per fortuna KUKA ha in programma un robot, il cobot LBR iisy, perfetto per processi come questi.
Con il suo carico utile massimo di 3 kg, questo agile cobot non viene sollecitato al massimo nel caso specifico, ma “siamo contenti che ci sia margine per eventuali altre applicazioni e processi”, afferma Alexander Fahringer. Quest’ultimo si dice convinto che il progetto iniziale dimostrerà che i robot collaborativi, in particolare, in futuro avranno un posto permanente nei reparti di sviluppo, come in quello della gestione della qualità. Ovviamente, anche i carichi più grandi non rappresentano un problema: infatti, KUKA propone anche i cobot LBR iisy, con un carico utile massimo fino a 15
kg e un raggio d’azione compreso tra 760 e 1.300 mm.
Gestione della qualità: test in sei fasi
Per testare il controllo qualità vero e proprio è stato previsto un periodo di due mesi, durante il quale il cobot LBR iisy è stato incaricato di eseguire 55.000 processi di macinatura e pesatura del caffè completamente automatizzati. Ogni processo è stato eseguito in sei fasi identiche: taratura del portafiltro sulla bilancia di precisione, presa del portafiltro e traslazione fino al macinacaffè, sgancio del portafiltro e attesa della fine del processo di macinatura, presa del portafiltro pieno e traslazione fino alla bilancia, sgancio e memorizzazione del valore della bilancia nel database, presa del portafiltro, svuotamento e riposizionamento sulla bilancia. Il cobot LBR iisy si distingue soprattutto per la semplicità di programmazione attraverso la collaborazione uomo-robot, grazie al pulsante Teach:“È possibile guidare il robot collaborativo a mano e insegnargli i compiti desiderati, come i movimenti e i tempi di attesa ecc. semplicemente premendo un pulsante”, Michael Reindl, Account Manager di KUKA, sottolinea l’alto livello di facilità d’uso del
robot. Grazie alla gestione intuitiva, il cobot LBR iisy permette una grande flessibilità applicativa e può essere messo in funzione e utilizzato in modo rapido e sicuro sia dagli esperti di automazione che dai principianti della robotica. Naturalmente, il robot soddisfa tutti i requisiti di sicurezza per il funzionamento collaborativo.
Diversi milioni di cicli
“I piccoli cobot LBR iisy, nella versione con un carico utile fino a 3 kg, sono predestinati per lo svolgimento di compiti di movimentazione piuttosto semplici, monotoni e spesso ripetitivi con la massima sicurezza, nelle immediate vicinanze dei dipendenti”, afferma Michael. Le versioni da 11 e 15 kg sono anche resistenti alla polvere e agli spruzzi (classe di protezione IP 54).
La semplicità di funzionamento e l’elevata flessibilità distinguono i cobot dai robot industriali convenzionali.
In questo modo si evitano fasi di lavoro poco gradite o anche pericolose, con il valore aggiunto tangibile della precisione, dell’accuratezza della ripetibilità e della semplicità di utilizzo. Questo vale anche nel caso concreto della gestione della qualità. Ogni singola fase, sia la macinazione che la pesatura, è stata eseguita e registrata in modo assolutamente affidabile in un processo continuo, in modo da poter riconoscere rapidamente eventuali scostamenti e garantire la massima qualità. Reindl: “In questa applicazione, il controllo robot fungeva da master per tutti gli altri componenti”. Ciò è possibile grazie alla capacità di interfacciarsi con svariati sistemi. Ecco l’ottimo risultato del test: “Il macinino ha funzionato benissimo e per una durata di vita simulata di oltre dieci anni, non mostrando praticamente alcun segno di usura, il che significa che durerà molto più a lungo”, dice Fahringer. E non è tutto: per il cobot, svolgere le 55.000 macinature di prova è stato un gioco da ragazzi. “È a malapena un rodaggio”, dice Reindl con ironia, alludendo agli svariati milioni di cicli che i robot KUKA sono in grado di svolgere normalmente.
Un avvio facile
Il team di ricerca e sviluppo dell’azienda è convinto che il cobot LBR iisy utilizzato nell’ambito di questo progetto presso la Gronbach non sarà l’ultimo. “In quanto tecnici dell’automazione, stiamo già pensando ad ulteriori modi in cui il cobot può affiancarci per altri controlli qualitativi e processi”, dice Fahringer. A ciò ha contribuito naturalmente anche l’eccellente collaborazione con KUKA. Infatti, gli specialisti della robotica rendono molto facile l’adozione dei robot: “È con piacere che mettiamo a disposizione dei clienti i nostri agili robot collaborativi, come il cobot LBR iisy, da provare e testare direttamente in azienda senza troppe formalità”, afferma Reindl. Dopotutto, il trasporto non è assolutamente un problema: infatti, il compatto robot trova posto in qualsiasi bagagliaio.
NEGLI ULTIMI ANNI, IL MERCATO DELLA ROBOTICA HA ASSISTITO A UN’EVOLUZIONE SIGNIFICATIVA, SPINTA DA ESIGENZE SEMPRE PIÙ COMPLESSE IN AMBITO PRODUTTIVO. LE AZIENDE STANNO CERCANDO DI INTEGRARE SOLUZIONI AUTOMATIZZATE PER OTTIMIZZARE I PROPRI PROCESSI, MIGLIORARE L’EFFICIENZA E RIDURRE I COSTI OPERATIVI. IN QUESTO CONTESTO, LA ROBOTICA COLLABORATIVA STA EMERGENDO COME UNA RISPOSTA EFFICACE A TALI NECESSITÀ
La sinergia tra uomo e macchina non solo ottimizza i processi produttivi, ma promuove anche un ambiente di lavoro più sicuro e collaborativo. L’adozione di robot collaborativi rappresenta pertanto una chiave di volta per affrontare le sfide moderne, aprendo la strada a un’era di innovazione e successo nelle operazioni industriali. I robot collaborativi, o cobot, sono progettati per lavorare a fianco degli operatori, migliorando l’efficienza e la sicurezza in ambienti di lavoro condivisi. Tuttavia, l’utilizzo di un
robot collaborativo non è sufficiente per rendere un’applicazione sicura: affinché un’applicazione si qualifichi veramente come collaborativa e sicura, infatti, è necessario considerare l’intero sistema e l’applicazione robotica. Ciò include il robot, il pezzo in lavorazione, l’area di lavoro del robot e anche l’utensile a fine braccio (EOAT). Se una qualsiasi di queste aree critiche non soddisfa gli standard di sicurezza specificati durante una valutazione del rischio, l’applicazione non può essere considerata collaborativa - a meno che il rischio identificato non venga
adeguatamente mitigato.
Assistente cobot
La sempre più crescente attenzione verso l’automazione collaborativa è particolarmente evidente in settori quali ad esempio l’assemblaggio, l’imballaggio, la movimentazione di materiali e la saldatura. Grazie alla loro capacità di adattarsi a diverse applicazioni e ambienti, i cobot rappresentano una risorsa strategica per le aziende moderne. In questo contesto, Yaskawa si distingue come attore di primo piano, rispondendo a queste esigenze
con una gamma di soluzioni innovative che si integrano perfettamente all’interno di un mercato in continua evoluzione: la serie HC, che rappresenta una nuova generazione di robot capace, conveniente, versatile, semplice da usare e costruito con la resilienza industriale per cui i prodotti Yaskawa sono noti. La loro progettazione ergonomica consente la collaborazione in sicurezza con gli operatori umani, senza necessità di recinzioni, grazie ai sensori avanzati che rilevano la presenza di persone nelle vicinanze. Questo non solo aumenta l’efficienza operativa, ma favorisce anche un flusso di lavoro più dinamico e reattivo. Inoltre, sono facili da programmare, rendendo l’integrazione nei processi produttivi rapida e intuitiva, anche per personale non specializzato. Inoltre, i cobot Yaskawa sono progettati per essere economicamente vantaggiosi, contribuendo a ridurre i costi di produzione e migliorando la competitività aziendale. Non da ultimo, i robot della serie HC sono robot ibridi, ossia capaci di alternare il proprio funzionamento da collaborativi e da industriali puri e di offrire dunque ottimi tempi di ciclo.
Vantaggi e Applicazioni dei cobot Yaskawa
I cobot Yaskawa trovano applicazione in
molteplici settori industriali, ognuno con le proprie esigenze specifiche. La loro flessibilità infatti consente loro di adattarsi a vari compiti, contribuendo a migliorare la produttività e la qualità del lavoro. La semplicità di utilizzo è uno dei punti di forza di questi robot, che possono essere facilmente programmati anche da personale non specializzato. Nel settore dell’assemblaggio, i cobot possono gestire compiti ripetitivi e delicati, migliorando la qualità e riducendo il rischio di errori. La loro flessibilità consente di adattarsi rapidamente a cambiamenti nella produzione, rendendo più agevole la gestione di linee produttive dinamiche. Nel campo dell’imballaggio e della pallettizzazione, i robot Yaskawa ottimizzano i processi, riducendo i tempi di ciclo e aumentando la produttività. Questi robot possono essere configurati per gestire diversi tipi di prodotti, garantendo che le linee di produzione possano adattarsi alle esigenze del mercato senza lunghe interruzioni. Un’ulteriore applicazione è rappresentata dalla movimentazione di materiali. In ambienti industriali dove il sollevamento e lo spostamento di oggetti pesanti sono all’ordine del giorno, i cobot di Yaskawa alleviano il carico fisico degli operatori, contribuendo a migliorare la sicurezza sul posto di lavoro. Questo approccio non solo aumenta l’efficienza, ma riduce anche il rischio di infortuni, un fattore cruciale in qualsiasi ambiente produttivo.
La qualità del prodotto è un altro aspetto fondamentale. I robot Yaskawa possono essere dotati di sistemi di visione artificiale dello Yaskawa Ecosystem, permettendo loro di eseguire ispezioni di qualità in tempo reale. Questo non solo garantisce che i prodotti finiti soddisfino gli standard richiesti, ma
consente anche di identificare e correggere eventuali difetti nel processo di produzione.
Saldatura Collaborativa con Yaskawa
Una delle soluzioni più significative offerte da Yaskawa è Weld4Me per la saldatura MIG / MAG. Utilizzabile in alternativa o in aggiunta alle soluzioni manuali con attrezzatura di saldatura raffreddata ad aria, Weld4Me rappresenta una valida soluzione per ottenere la qualità costante della saldatura robotizzata anche in impianti destinati prevalentemente a lavorazioni di piccole o medie dimensioni. Oltre ad avere un ingombro estremamente ridotto risulta comoda e facile da spostare anche solo con l’ausilio di transpallet. L’indiscussa qualità Yaskawa nella saldatura robotizzata e nei processi di produzione è espressa in questa cella compatta dotata di robot collaborativo HC10DT IP67 con funzione di Easy Teaching.
Parte integrante dello Yaskawa ECOSYSTEM
I cobot Yaskawa sono parte integrante dello Yaskawa Ecosystem, una rete innovativa che offre una vasta gamma di soluzioni per l’automazione industriale. Questo ecosistema, in linea con la filosofia Plug&Play, include non solo i robot collaborativi, ma anche accessori, servoazionamenti, assi lineari e pacchetti software, permettendo agli utenti di configurare sistemi altamente personalizzati. Con oltre 110 prodotti già disponibili e in continua espansione, lo Yaskawa Ecosystem è progettato per soddisfare le esigenze sia dei neofiti della robotica sia degli esperti del settore. La semplicità di installazione, la programmazione intuitiva e il facile funzionamento sono alcuni dei principali vantaggi offerti. Inoltre, l’ecosistema consente ai robot Yaskawa di adattarsi rapidamente alle mutevoli esigenze produttive grazie a un’ampia gamma di pinze, periferiche e accessori. La programmazione può essere eseguita tramite l’innovativo Smart Pendant, dotato della funzione brevettata Smart Frame, o attraverso il tradizionale Pendant di programmazione. In questo modo, Yaskawa non solo facilita l’integrazione dei cobot nei processi produttivi, ma potenzia anche la loro versatilità e capacità di adattamento, contribuendo a una maggiore efficienza e innovazione nelle operazioni industriali.
COME L’INTEGRAZIONE DELLA ROBOTICA AVANZATA GUIDA
L’INNOVAZIONE E TRASFORMA LE FABBRICHE MANIFATTURIERE VERSO NUOVI STANDARD
Di Patrizia Ricci
NNel contesto della crescente trasformazione digitale delle aziende manifatturiere, l’integrazione dei robot all’interno di sistemi produttivi e operativi aziendali, in modo che possano lavorare in sinergia con altri macchinari, software e, in molti casi, operatori umani è ormai un fattore chiave per incrementare efficienza, flessibilità e capacità produttiva. Soluzioni innovative come la robotica mobile, l’intelligenza artificiale (AI) e il deep learning, insieme a sofisticati sistemi di visione e sensoristica avanzata, stanno rivoluzionando i processi produttivi. Questi sistemi, accompagnati da software intuitivi e integrati come la Robotic Process Automation (RPA) e altri applicativi di collaborazione uomo-macchina, consentono una sinergia mai vista prima tra risorse umane e automazione.
Nelle moderne aziende manifatturiere, infatti, i robot possono assumere ruoli vari, dal montaggio alla movimentazione di materiali, fino al controllo qualità. L’integrazione implica la programmazione dei robot per eseguire specifiche attività in linea con le esigenze della produzione e del flusso di lavoro dell’azienda, spesso tramite l’uso di sensori, intelligenza artificiale e sistemi di controllo avanzati. L’obiettivo è migliorare l’efficienza, ridurre i tempi di inattività e ottimizzare le operazioni per mantenere standard di qualità elevati e ridurre i costi operativi.
In combinazione con l’intelligenza artificiale, i robot diventano strumenti flessibili e adattabili, capaci di eseguire operazioni complesse, analizzare dati e prendere decisioni autonome in tempo reale. L’integrazione robotica va quindi oltre la semplice automazione: crea un ecosistema tecnologico e produttivo dinamico e flessibile, in cui la produzione può essere ottimizzata e adattata rapidamente ai cambiamenti del mercato e alle esigenze di personalizzazione dei prodotti, aprendo la strada all’industria manifatturiera del futuro.
Intelligenza Artificiale e Deep Learning: automazione intelligente AI e deep learning, componenti centrali dell’automazione avanzata, permettono ai robot di imparare
dai dati e dalle esperienze, diventando capaci di prendere decisioni autonome e adattarsi a nuovi compiti senza interventi manuali. Nell’ambito della produzione, l’intelligenza artificiale migliora i processi di manutenzione predittiva, individuando possibili anomalie prima che diventino problematiche. Applicato ai sistemi di visione, il deep learning consente ai robot di identificare oggetti complessi, rilevare difetti e persino eseguire controlli qualità in modo autonomo e altamente accurato.
Sistemi di visione e sensoristica: il “tatto” della robotica I sistemi di visione e i sensori costituiscono gli “occhi” e il “tatto” della robotica moderna. Spesso arricchiti da algoritmi di AI, i sistemi di visione permettono ai robot di analizzare e comprendere l’ambiente circostante, facilitando compiti come il posizionamento di precisione e la selezione degli oggetti. I sensori di prossimità, pressione, temperatura e vibrazione, integrati nei robot, consentono un’interazione più raffinata con l’ambiente e sono cruciali per l’automazione nelle industrie ad alto rischio. Questi dispositivi forniscono una mole continua di dati che il robot utilizza per perfezionare i movimenti e ottimizzare la sicurezza, garantendo un ambiente collaborativo e sicuro.
Software di integrazione per periferiche: flessibilità e personalizzazione
Un aspetto fondamentale dell’automazione è la capacità dei robot di adattarsi a diverse esigenze, gestendo periferiche come pinze, sistemi di visione e altre funzionalità. I software di integrazione semplificano questa operazione, permettendo di configurare facilmente le periferiche e gestire la comunicazione tra diversi dispositivi. La possibilità di aggiungere e rimuovere periferiche rende il sistema di automazione estremamente flessibile, adattabile alle variazioni nella produzione e altamente personalizzabile in base alle esigenze specifiche del settore.
Robotic Process Automation (RPA): l’automazione del lavoro digitale
La RPA, ovvero l’automazione dei processi robotizzati, ha un impatto trasformativo sul lavoro amministrativo e di back-office, automatizzando attività ripetitive come la gestione dei dati, l’elaborazione dei documenti e il controllo dei flussi. Integrata con i sistemi produttivi, l’RPA consente ai robot di operare in sinergia con le piattaforme digitali aziendali, riducendo il margine di errore e velocizzando il flusso di lavoro. Con l’adozione di applicativi RPA, le aziende possono garantire continuità e ridurre i tempi di fermo, migliorando efficienza e ottimizzando i costi.
Collaborazione uomo-macchina e integrazione macchina-macchina Tecnologie avanzate come la realtà aumentata e la realtà virtuale, che forniscono agli operatori strumenti di supporto e istruzioni in tempo reale, stanno giocando un ruolo chiave nel migliorare la cooperazione tra uomini e robot, creando un ambiente di lavoro più collaborativo e favorendo un’interazione più armoniosa e produttiva tra lavoratori e automazione e un’esperienza lavorativa più sicura e appagante, proprie dell’Industria 5.0. La Human-Robot Collaboration (HRC) permette agli operatori di lavorare fianco a fianco con i robot, delegando a questi ultimi le operazioni ripetitive e a basso valore aggiunto, mentre l’operatore può concentrarsi su attività di supervisione e controllo di qualità. Al contempo, l’integrazione macchina-macchina (M2M) consente ai dispositivi robotici di comunicare tra loro e prendere decisioni collaborative, ottimizzando la catena produttiva e aumentando la velocità e l’accuratezza dei processi.
In conclusione, l’integrazione tra robotica e automazione, facilitata da tecnologie come la robotica mobile, l’intelligenza artificiale, i sistemi di visione e la sensoristica avanzata, sta trasformando radicalmente il panorama produttivo, portando maggiore flessibilità, sicurezza e precisione. I software per la facile integrazione delle periferiche, uniti alla RPA, rendono i processi produttivi più agili e resilienti, creando un ecosistema in cui uomo e macchina lavorano in simbiosi. In un’epoca di continua innovazione, l’adozione di queste tecnologie consente alle aziende di rispondere prontamente alle esigenze del mercato, garantendo una produzione sostenibile e competitiva.
a scoprire di più su mewa.it/servizio-a-360
BOSCH REXROTH
La robotica collaborativa vive una fase di espansione, trainata dagli ambiti industriali nei quali è in grado di esprimere un maggiore influsso: la manifattura leggera (assemblaggio e montaggio di piccoli componenti), l’industria metalmeccanica classica, con riferimento all’asservimento macchine (operazioni di finishing, di handling e di levigatura), l’automotive, la logistica e, in chiave più generale, il fine linea dei processi produttivi, vedi pallettizzazione ed etichettatura. Senza dimenticare un comparto con forte potenziale di mercato: la produzione di beni di largo consumo, specialmente per ciò che riguarda il confezionamento.
L’acquisizione di Kassow Robots, avvenuta poco più di due anni fa, ha consentito a Bosch Rexroth di rivestire in breve tempo un ruolo da protagonista nel campo della robotica collaborativa. I vantaggi offerti dalla gamma Kassow Robots sono molti. In primis, il settimo asse, che consente al robot di possedere la destrezza di un braccio umano, peculiarità che assicura sicurezza, precisione, flessibilità dei movimenti e facile
integrazione con una macchina in condizioni di spazio minime. Da un punto di vista software, il mercato apprezza l’apertura del sistema, e di conseguenza la possibilità di procedere a configurazioni personalizzate. Un fattore non secondario che depone a favore dei Kassow Robots è il rapporto tra qualità e prezzo, agevolato dalla presenza nel catalogo Bosch Rexroth di prodotti con “taglie” particolari: contrariamente allo standard della robotica collaborativa, secondo cui la potenza dei motori debba andare di pari passo con l’ampiezza dello sbraccio, Bosch Rexroth offre soluzioni con sbraccio molto elevato ma con payload ridotto, utili quando il peso da supportare, a dispetto dell’ampiezza di movimento, è minimo. Ciò consente un cospicuo risparmio sui costi di acquisto. Il catalogo Kassow Robots dispone al momento di cinque “taglie”, destinate a breve a diventare sette, ed è imminente la presentazione di modelli disponibili sia a 220 Volt, sia a 48 Volt. I secondi avranno il controller nella base del robot e saranno ottimizzati per il montaggio su veicoli a guida autonoma. È un’integrazione, attualmente non disponibile sul mercato, che andrà a servire il mondo della logistica e molte delle applicazioni legate alla robotica mobile. A breve Bosch Rexroth proporrà anche modelli con sensori di forza integrati, e sta lavorando fianco a fianco con partner appartenenti al suo ecosistema, fornitori
di soluzioni plug and play di sistemi di visione, di pinze intelligenti e di tutta una serie di componenti, così da arricchire ulteriormente la propria proposta. Un esempio di questo approccio è la collaborazione con Vision System, società che si occupa di sistemi di visione speciali ad altissimo valore aggiunto basati sull’utilizzo delle tecnologie più moderne a livello di immagini 2D, 3D, multispettrali ed iperspettrali. Una partnership favorita dal fatto che Bosch Rexroth dispone di ctrlX AUTOMATION, piattaforma per l’automazione concepita per rendere semplice l’implementazione di nuove funzionalità. L’applicazione sviluppata per rendere i sistemi di visione intelligenti, lavora a bordo di un robot collaborativo, in un sistema decentralizzato, in cui l’elaborazione delle immagini avviene su un controllo esterno, ovvero ctrlX AUTOMATION permettendo una maggiore interazione, ad esempio, con i sistemi di controllo delle macchine industriali, riducendo al minimo i tempi di comunicazione tra ambiti diversi. I campi di applicazione della soluzione creata da Vision System e da Bosch Rexroth, un sistema di visione basato sull’intelligenza artificiale, sono i più svariati, poiché la soluzione è totalmente aperta all’inserimento di diverse tipologie di rete e di algoritmi di processing, caricabili attraverso un’interfaccia di upload e tali da rendere la scelta dell’algoritmo da utilizzare semplicissima. Gli ambiti più comuni in cui utilizzarla riguardano il sorting (classificazione di pezzi in ambito logistico e di packaging secondario-filling con modelli ibridi) e il controllo della qualità, in questo caso per identificare vizi superficiali di produzione o difetti di stampa.
Elettromeccanica Pantanetti realizza un sistema di presa per le Cartiere Fabriano per prelevare scatole, pallet e interfalde, grazie alla nuova valvola proporzionale VPPI Festo applicata al braccio robotico.
Elettromeccanica Pantanetti è una realtà marchigiana fondata nel 1958, anche se le sue origini risalgono ad anni precedenti. “Tutto è iniziato per mano di mio nonno materno che era sarto”, racconta l’ingegnere Franco Pantanetti proprietario dell’azienda insieme al fratello Sauro Pantanetti, “raggiunse un parente a Milano che gli disse che era meglio puntare all’elettricità, che quello sarebbe stato il futuro. Così è nata l’allora Elettromeccanica Pasqualini, azienda ereditata da mio padre e poi passata a me e mio fratello, e che oggi porta il nostro cognome”. Una storia di famiglia fatta di passione per l’automazione che ha portato Elettromeccanica Pantanetti a crescere negli anni, fino a produrre PLC. “Installare il primo PLC a Francoforte ci ha portati a lavorare sempre di più con questa tipologia di apparecchiature che hanno trasformato il mondo dell’automazione”, continua Pantanetti. “Per noi è sempre stato importante partecipare attivamente all’evoluzione tecnologica ed essere presenti con soluzioni innovative. Questo è l’approccio con cui viviamo il nostro lavoro, un aspetto che cerchiamo anche nei nostri collaboratori come Festo”.
La collaborazione con Festo: dall’automazione elettrica alla pneumatica
“Ci siamo avvicinati a Festo per la proposta di assi elettrici e abbiamo continuato con la parte pneumatica”, spiega Pantanetti. “Abbiamo ricevuto servizio e supporto costanti, e nel tempo abbiamo consolidato il rapporto. Per noi è stato come allargare la famiglia: abbiamo trovato grande disponibilità, soprattutto nei tecnici specializzati come l’ingegnere Erik Messori”. “Il rapporto non è solo quello tra cliente e fornitore. Aziende storiche che si uniscono per dare importanza al rapporto umano prima di ogni cosa”, continua Erik Messori, Application Sales Engineer Festo. “Ci siamo sentiti tutti coinvolti sin dal primo momento. Quando un cliente ti spiega la sua applicazione così a fondo possiamo dare una consulenza personalizzata e ottenere dei risultati eccellenti”. Sono proprio la capacità di evolversi e la collaborazione tra le persone i punti di forza di Elettromeccanica Pantanetti: “il nostro approccio è quello di metterci a disposizione del cliente con il nostro know-how, a partire dalla fase progettuale”, spiega Matteo Pantanetti, Tecnico del dipartimento progettuale e programmazione. “Dal piccolo al grande progetto, vogliamo instaurare un rapporto limpido mettendo tutte le carte in tavola. Il nostro obiettivo è sempre quello di accontentare il cliente, e questo ci porta ad affrontare nuove strade e sperimentare nuove applicazioni. Proprio come nel caso dei componenti Festo, dai motori passo-passo agli assi meccanici”.
Cartiere Fabriano: sistema di pinza flessibile
L’ultima applicazione realizzata da Elettromeccanica Pantanetti è un sistema di presa flessibile che sfrutta la pneumatica Festo. “Con le Cartiere Fabriano abbiamo un rapporto di lavoro solido. Grazie a loro siamo cresciuti e abbiamo avuto l’occasione di realizzare apparecchiature legate alla carta moneta, sia per gli stati europei sia per la Cina. Arrivando a realizzare anche interi stabilimenti”, racconta Francesco Pantanetti. “Con l’ultima commissione avevamo l’esigenza di prelevare scatole, pallet e interfalde, tre oggetti con caratteristiche molto diverse”.
“Di solito per prendere una scatola si usa una pinza capace di afferrare e stringere, e che poi si sposti velocemente. Questo può generare problemi di deformazione nella scatola”, continua l’ingegnere Daniele Cardelli, progettista software. “Avevamo quindi bisogno di una pinza precisa e capace di prelevare la scatola dal lato inferiore, così da farla scivolare sulle forche. Per evitare che la scatola scivoli durante il movimento, abbiamo inserito due cilindri Festo che permettono di bloccare la scatola stessa. Mentre la presa dei pallet è gestita da un ulteriore pistone”.
Valvola proporzionale VPPI applicata al braccio robotico
“Per l’interfalda, invece, l’esigenza era quella di un sistema di presa con il vuoto regolabile. La soluzione applicata al braccio robotico è stata la nuova valvola proporzionale VPPI disponibile anche nella versione in grado di regolare pressioni negative”, spiega Messori.
“Con la VPPI si riesce a regolare il vuoto in maniera molto precisa.
Grazie a questa soluzione la pressione negativa applicata all’interfalda varia all’interno del ciclo, più bassa quando preleviamo il foglio (per evitare di prenderne più di uno) e più elevata quando lo spostiamo orizzontalmente”.
“Integrare la tecnologia Festo alla robotica ci ha permesso di portare avanti il nostro processo di crescita”, spiega l’ing Daniele Pantanetti, progettista meccanico nell’azienda di famiglia. “Il vantaggio principale di questa soluzione è la flessibilità data dal sistema di presa pneumatico che consente tre operazioni distinte”. L’intera applicazione è stata realizzata con il supporto a distanza a causa della pandemia in atto. Come racconta Francesco Pantanetti, “la cartiera ha deciso di sfruttare un momento in cui la produzione fosse ferma a causa del primo lockdown, per investire sul potenziamento del proprio parco macchine e tutto questo è avvenuto in un momento molto particolare. All’inizio si faticava a capire come muoversi e come altre aziende italiane, abbiamo curato le regole sin dal primo momento, sfruttando al meglio la tecnologia per lavorare a distanza”.
HEIDENHAIN
I robot stanno conquistando settori di attività sempre più complessi: vengono impiegati, ad esempio, per lavorazioni ultra precise su componenti di grandi dimensioni, come le fusoliere, oppure si muovono come cobot nella collaborazione diretta uomo-robot. In entrambi i casi, la precisione di movimento del braccio del robot è un requisito essenziale.
HEIDENHAIN ha messo a punto i trasduttori rotativi induttivi KCI 1300 (monogiro) e KBI 1300 (multigiro) studiati appositamente per motori compatti di robot e altre applicazioni. Sono composti da un’unità di scansione e un disco graduato con fissaggio a vite o in alternativa un disco graduato con mozzo da applicare a pressione sull’albero motore. Con albero cavo del diametro di 25 mm, design compatto e peso ridotto sono
anche insensibili alle contaminazioni e ai campi magnetici. Il montaggio è molto semplice grazie alle ampie tolleranze con collegamento meccanico sicuro e all’interfaccia EnDat 2.2 con Functional Safety per la trasmissione dati. L’affidabilità operativa è assicurata dal sensore di temperatura esterno che protegge contro il sovraccarico.
Sono inoltre disponibili anche le versioni KCI 1318 FOT e KBI 1335 FOT. Grazie alla fan-out-technololgy (FOT), HEIDENHAIN è riuscita ad applicare i componenti elettronici e le tracce conduttive direttamente su un supporto in metallo con duplice utilizzo da coperchio terminale del motore. Si riduce così non solo il numero di componenti e lo spazio necessario ma, tramite il supporto in metallo, è anche possibile dissipare il calore
direttamente all’esterno. Il disco graduato con mozzo viene montato a pressione sull’albero.
I trasduttori rotativi compatti KCI 120 e KBI 136 per alberi cavi di grandi dimensioni con diametri di 30 mm o 40 mm completano la gamma degli encoder rotativi induttivi HEIDENHAIN specificatamente concepiti per applicazioni nella robotica. Vantano i punti di forza della serie più piccola 1300 ma per motori di robot essenzialmente più robusti e potenti. Molto interessante è anche il dual encoder KCI 120 Dplus HEIDENHAIN che fornisce motor feedback e misurazione di posizione in un unico trasduttore rotativo. Per la sua doppia funzionalità, dispone di un’unità di scansione centrale e due dischi graduati separati, sottoposti a scansione secondo il principio di misura induttivo. Con la misurazione di posizione a valle del riduttore di velocità, compensa le imprecisioni strutturali di robot altamente mobili e dinamici.
KCI 120 Dplus è disponibile in tre versioni per poter impiegare il dual encoder nel maggior numero possibile di applicazioni. L’unità di scansione centrale e i due dischi graduati separati con mozzo sono quindi adatti per alberi cavi di diverso diametro e differenti dimensioni di montaggio.
KCI 120 Dplus HEIDENHAIN di facile integrazione offre sempre la stessa funzionalità nonostante le dimensioni compatte.
Tutte le versioni di KCI 120 Dplus ampliano il ventaglio di applicazioni dei robot a funzioni di lavorazione di elevata precisione. L’interfaccia EnDat 2.2 puramente seriale con Functional Safety consente inoltre l’impiego in applicazioni sicure, come i cobot per la collaborazione uomo-robot.
In Losma, da 50 anni, ci impegniamo nella ricerca di nuove soluzioni che aiutino le aziende a preservare l’ambiente che le circonda e le persone che lo vivono.
I sistemi di asservimento automatizzato di Hoffmann Group hanno aperto la corsa all’automazione anche alle piccole e medie officine meccaniche che vogliono aumentare la produttività e crescere in un mercato sempre più competitivo
La scarsità di manodopera specializzata, insieme a un mercato sempre più instabile, incerto e competitivo che impone alle aziende di reagire rapidamente alle sue esigenze, nonché la crisi di settori industriali trainanti, come quello dell’automotive, ha reso essenziale per molte imprese del settore metalmeccanico ottimizzare processi, costi e risorse coinvolte nella produzione.
Tra le diverse soluzioni adottate, l’automazione sembra già portare i primi risultati in termini di aumento della produttività. Resta però da chiedersi se questa sia una strategia praticabile anche per le numerose piccole e medie officine meccaniche presenti in Italia. La risposta è sicuramente positiva. Le tecnologie che fino a poco tempo fa erano riservate alle grandi industrie sono ora state adattate anche alle PMI, rendendo per loro i sistemi di automazione una scelta possibile, anzi auspicabile.
Cosa è necessario affinché le PMI possano abbracciare l’automazione?
Le officine meccaniche richiedono principalmente due condizioni: che i sistemi di automazione siano semplici da usare e che si integrino facilmente nell’ambiente esistente. Questo significa che devono occupare poco spazio e, soprattutto, essere in grado di automatizzare macchine utensili datate già in uso, senza richiedere ulteriori investimenti da parte dell’azienda.
Sistemi di asservimento automatizzato di questo tipo sono già disponibili sul mercato. Oggi, le piccole e
medie officine meccaniche hanno la straordinaria opportunità di automatizzare semplici attività e così di ridurre il carico di lavoro dei propri operatori, destinandoli a mansioni a più alto valore aggiunto come la pianificazione e il controllo qualità, e di sfruttare appieno il potenziale delle proprie macchine utensili.
Ad esempio, Hoffmann Group ha lanciato una linea di soluzioni di automazioni sviluppate proprio per le PMI che, in pochissimo tempo, ha già riscosso grande successo tra le aziende che hanno deciso di accelerare il passo verso l’innovazione.
GARANT Automation Basic è stato il primo prodotto presentato sul mercato: un sistema di asservimento automatizzato progettato per centri di tornitura e/o fresatura a 3 o 5 assi che carica e scarica i prezzi grazie a un telaio solido e a un preciso braccio robotico. Senza necessità di un’interfaccia di automazione, di una porta automatica e di competenze di programmazione, rappresenta una soluzione efficace, ammortizzabile in pochi mesi, per aggiornare macchine datate in officine che producono piccoli lotti. Ad oggi, le numerose aziende che hanno scelto questo sistema, si dicono estremamente soddisfatte poiché sono riuscite a farlo andare a regime in pochi mesi, hanno aumentato la loro produttività e senza impattare troppo sull’operatività e sulla struttura dell’officina.
“Ho visto GARANT Basic e mi sono detto «proviamo» e da lì è cambiato tutto, mi si è aperto un mondo che non conoscevo. Abbiamo imparato a usare questo sistema in breve tempo
e la sua semplicità ci ha permesso di partire dopo solo un mese e mezzo raggiungendo numeri importanti”, afferma Alessandro Boeris, titolare di MECAB, azienda di Luserna San Giovanni, specializzata in lavorazioni meccaniche a controllo numerico per la produzione di attrezzature, prototipi e lotti di piccola e media entità. Sulla scia dei riscontri positivi ottenuti, Hoffmann Group ha presentato di recente anche GARANT Turntable, un sistema di carico per la movimentazione di dispositivi di serraggio, come morse, torri, attrezzature o pallet, in centri di fresatura a 3 o 5 assi. Questo sistema, composto da un piano di carico girevole e un braccio telescopico inseriti in una struttura compatta con un’impronta a terra di appena 2,5 mq, alimenta la macchina attraverso una finestra di carico laterale o frontalmente tramite la porta della macchina e può alloggiare fino a 18 dispositivi di serraggio con un peso complessivo fino a 25 kg l’uno oppure 24 con un peso massimo di 20 kg l’uno. GARANT Turntable si distingue per la facilità d’uso, grazie al sistema meccanico di Start/Stop a perno, e per la possibilità di automatizzare anche le fresatrici e i centri di lavoro CNC meno recenti poiché non necessita di un’interfaccia di automazione o di particolari predisposizioni.
Come avviene per la maggior parte delle soluzioni di automazione, anche nell’ambito della robotica è fondamentale, per la progettazione e realizzazione, adottare un approccio modulare in modo tale che possa essere espandibile, scalare e allo stesso tempo offrire la massima flessibilità. La filosofia costruttiva di Keba applicata alla robotica attribuisce una particolare attenzione a quella che è la massima razionalizzazione di software e hardware. Ad esempio, una piattaforma base modulare è un ottimo punto di partenza per sviluppare diverse tipologie di robot mobili. Questi, in base a requisiti specifici, possono essere dotati di vari sistemi di navigazione come anche di svariati tipi di moduli superiori. Inoltre, l’intelligenza artificiale (AI), tanto per fare un esempio, è ora perfettamente in grado di supportare il processo di distinzione e riconoscimento degli oggetti, il calcolo dei punti di presa come anche il calcolo ottimale dei percorsi di movimentazione. L’AI viene oramai integrata largamente in campo industriale, ad esempio nei processi di controllo per rilevare riconoscere e tracciare oggetti in tempo reale. I concetti contenuti nell’applicazione di pose estimation (estrema semplicità, modularità e scalabilità) sono stati ripresi e sviluppati da Keba in un pacchetto dedicato allo sviluppo di applicazioni più complesse e articolate che prevedono l’uso dell’AI. A questo proposito, Keba ha sviluppato l’AI Development Kit (AI DevKit), un kit completo, dedicato all’intelligenza artificiale che consente di sviluppare varie applicazioni, anche in campo robotico. Il DevKit è costituito da un’unità di controllo C5, soluzione collaudata e all’avanguardia, basata sul sistema operativo Linux. Con la filosofia di modularità, si aggiungono all’unità C5 una scheda di I/O e un modulo di espansione per AI. Quest’ultimo è stato espressamente sviluppato per le applicazioni nei contesti industriali, in pieno rispetto di tutte le norme vigenti. Nel modulo AI vi è inoltre la toolchain, che comprende tutti gli strumenti fondamentali per l’addestramento delle reti neurali, oltre alla disponibilità di blocchi
funzionali che consentono l’esecuzione di modelli direttamente nel codice del PLC. L’esempio dimostrativo concreto che riassume le tecnologie Keba di azionamento, controllo e AI (presentato in occasione di SPS Italia 2024) riguarda un robot mobile dotato di modulo superiore costituito da un braccio antropomorfo munito di web cam per il riconoscimento visivo e la distinzione degli oggetti in tempo reale. Questo sistema è stato concepito per determinare i punti di presa corretti dei vari oggetti. La particolarità del robot mobile è quella di essere in grado di acquisire i dati di percorso tramite QR Code. Questo robot è l’esempio di come Motion Control, PLC, Navigazione, Robotica e AI sono state perfettamente integrate nell’ecosistema KemroX, che tra gli altri vantaggi, richiede solo un’unica CPU per poter funzionare in modo coordinato. Il risultato è perfettamente in linea con la mission di Keba ossia semplificare le applicazioni rendendole il più snelle possibile e in grado di girare su di un’unica CPU, quindi meno componenti, meno peso, meno energia, più flessibilità.
La Serie 3D VGR di KEYENCE Italia
è progettata appositamente per risolvere ogni applicazione di bin picking e per automatizzare le fasi di assemblaggio, depallettizzazione, carico e asservimento di macchinari.
L’innovativo hardware integrato, composto da 4 telecamere ed un unico proiettore a luce strutturata, acquisisce fino a 136 immagini in soli 0,5 secondi per creare immagini 3D coerenti e senza punti ciechi. I pattern a strisce multiple vengono proiettati ad alta velocità. La luce riflessa dai target è analizzata in tempo reale da un sensore CMOS ad alta densità di punti, alta precisione e bassa rumorosità che fornisce prestazioni di rilevamento ineguagliabili e da un processore ad alta velocità di recente introduzione che esegue calcoli 3D ultra veloci per generare un’immagine 3D. Il sistema proietta ed analizza la luce strutturata con angolazioni di 90 gradi, riducendo l’impatto dei riflessi provenienti da superfici lucide. Dotato di algoritmi di ricerca di nuova concezione, rileva in modo stabile e veloce tutti i pezzi anche se disposti alla rinfusa, riducendo nettamente il takt time. Queste caratteristiche risolvono i problemi legati ai metodi tradizionali, migliorando l’efficienza della produzione. Il sistema è in grado di rilevare svariate tipologie di prodotti di materiali diversi, poiché le impostazioni ideali dell’immagine vengono selezionate automaticamente per eliminare i punti
ciechi e tenere conto delle differenze di colore, di materiale e di forma del prodotto. Inoltre, il sistema è progettato per funzionare in modo continuo e il rilevamento efficace consente alla strumentazione di funzionare 24 ore al giorno.
La Serie RB si distingue per la facilità d’uso e per la capacità di abbattere i costi ed ottimizzare il tempo ciclo. Grazie alle funzioni di simulazione e di pianificazione automatica della traiettoria robot, il sistema rileva potenziali collisioni, anomalie e problemi già in fase progettuale, eliminando laboriose programmazioni manuali.
L’utente non è tenuto a creare complicati programmi per i robot, poiché lo strumento di pianificazione del percorso calcolerà il movimento necessario per prelevare ogni parte evitando collisioni e anomalie del robot.
Nel prelievo robotizzato, vi sono alcune situazioni in cui il movimento lineare (CP) è ideale, ad esempio quando si passa dalla posizione di avvicinamento alla posizione di presa per consentire alle pinze di allinearsi correttamente al target. Tuttavia, quando si utilizza il movimento lineare, esiste il rischio che il robot si arresti inaspettatamente a causa di un’anomalia. Il movimento articolato (PTP) impedisce eventuali anomalie, ma può causare altre collisioni del robot o del target prelevato con il contenitore o le aree circostanti. Lo strumento di pianificazione del percorso è l’unica soluzione per evitare tali collisioni del robot poiché è in grado di generare automaticamente un nuovo percorso di movimento per ogni target. Ecco perché KEYENCE ha sviluppato questo strumento, in modo da evitare collisioni e anomalie senza complicate programmazioni lato robot. I programmi robot forniti da KEYENCE acquisiscono questi percorsi generati direttamente dal sistema di visione. Calcolando un percorso univoco per ogni target prelevato, il sistema consente di
evitare interruzioni di funzionamento causate da collisioni o anomalie del robot, permettendo al robot di prelevare target in precedenza irraggiungibili. Il simulatore di prelievo può identificare i problemi connessi al design dello strumento di presa o al layout della cella di lavoro prima di qualsiasi implementazione e realizzazione fisica dell’isola robotizzata, fornendo così importanti dettagli relativi al prelievo dei pezzi dal contenitore. Tutte le impostazioni dei programmi possono essere sviluppate nel software del simulatore e poi testate istantaneamente su qualsiasi numero di pezzi simulati dentro il cassone, in modo da permettere all’utente di familiarizzare con il programma e verificarne il funzionamento prima ancora di caricarlo sul sistema reale. Il sistema è semplice da configurare: basta caricare i dati CAD oppure acquisire l’oggetto reale per eseguire ricerche ad alta precisione in 3D. È sufficiente un clic del mouse per definire la posizione della presa per l’oggetto target, rendendo molto più rapido il completamento della configurazione rispetto ai metodi di apprendimento tradizionali. La connessione diretta con le principali marche di robot e la funzione di autocalibrazione permettono un funzionamento agevole senza scrivere una riga di codice. Nello specifico, la calibrazione automatica della velocità dell’otturatore per adattarsi alla condizione del target crea le condizioni ideali per la misurazione 3D, evitando i problemi connessi con la calibrazione manuale, più difficoltosa e dispendiosa in termini di tempo, nella quale il grado di precisione varia a seconda dell’operatore.
Con prestazioni di rilevamento e fruibilità senza pari, i sistemi di visione KEYENCE stabiliscono il nuovo standard per il bin picking.
Maggiori informazioni ed esempi pratici sono disponibili su www.keyence.it/RBpress.
Attraverso l‘applicazione del rilevamento dei pallet e il superamento degli ostacoli basati sull‘intelligenza artificiale, il MiR1200 Transpallet stabilisce nuovi standard per la logistica automatizzata dei pallet e risolve molte delle problematiche per l’automatizzazione della movimentazione dei materiali in ambienti dinamici e complessi.
Lo scorso marzo, Mobile Industrial Robots (MiR) ha annunciato il lancio del MiR1200 Transpallet. Grazie al rilevamento avanzato dei pallet tramite intelligenza artificiale (AI), basato su NVIDIA Jetson AGX OrinNVIDIA, il MiR1200 Transpallet utilizza la visione 3D per identificare pallet e altri oggetti e può prelevare e consegnare pallet con un livello di precisione senza precedenti. “Il MiR1200 Transpallet è il risultato dei nostri più recenti sforzi per superare i limiti della movimentazione autonoma dei materiali. Riteniamo che i sistemi di percezione AI integrati rappresentino un miglioramento significativo rispetto ai metodi di rilevamento convenzionali. Il nostro approccio ridurrà i tempi dei cicli di pick-and-place, offrirà il più elevato livello di precisione di prelievo sul mercato e consentirà di offrire costantemente ai nostri clienti funzionalità e valore aggiunti basati sull‘intelligenza artificiale”, ha dichiarato Mads Paulin, Vice President R&D di MiR.
MiR1200 Transpallet funziona perfettamente con gli altri robot mobili autonomi e con il software MiR
Progettato per integrarsi perfettamente nelle flotte di robot mobili autonomi (AMR) MiR esistenti e per interagire con la piattaforma MiR per il carico degli AMR, il MiR 1200 Transpallet rappresenta la soluzione ideale per le imprese di grandi dimensioni, che in genere gestiscono flussi di lavoro più complessi con flotte più grandi e sedi multiple. Queste aziende possono ora rivolgersi a MiR come unico interlocutore per la movimentazione dei materiali.
“L‘ultimo nato della vasta gamma di AMR MiR, il MiR 1200 Transpallet, aggiunge un nuovo segmento applicativo alle nostre soluzioni esistenti per il trasporto di carichi leggeri e pesanti, il trasporto di pallet e molto altro. Tutti i robot possono essere perfettamente gestiti e integrati tramite il nostro tool di gestione delle flotte, MiR Fleet, e monitorati e ottimizzati tramite MiR Insights”, afferma Jean-Pierre Hathout, Presidente di MiR.
Adatto a navigare in ambienti complessi
Grazie alle sue capacità di visione 3D, il MiR 1200 Transpallet risolve le problematiche che molte aziende devono affrontare nella movimentazione dei materiali ad alta intensità di risorse, dove gli ambienti complessi rendono difficile l‘automazione, che tuttavia è necessaria a causa della crescente carenza di manodopera. Il MiR 1200 Transpallet è in grado di modificare dinamicamente il suo percorso per evitare ostacoli, come ad esempio oggetti presenti sul pavimento o cavi sospesi. È in grado di gestire in tempo reale un gran numero di
telecamere e dati lidar, accelerando l‘intero stack sulla GPU e su diversi altri processori integrati nel modulo NVIDIA Jetson AGX Orin. La sua capacità di muoversi senza problemi in spazi ristretti senza necessità di infrastrutture aggiuntive lo rende perfetto per ottimizzare l‘efficienza logistica e garantire la consegna puntuale dei pallet. “Con il MiR 1200 Transpallet abbiamo sviluppato un robusto transpallet AMR in grado di funzionare in strutture già esistenti che presentano sfide ambientali uniche per l‘automazione. Durante la progettazione di questo robot, abbiamo sfruttato la nostra esperienza maturata nel software e gli AMR ad alta capacità di carico, frutto della fusione di MiR con AutoGuide, un‘altra società di Teradyne, acquisita nel 2022. Inoltre, il robusto sistema di trazione a tre ruote del MiR1200 Transpallet è stato sviluppato grazie alla collaborazione con Logitrans, partner di MiR, che vanta oltre 80 anni di esperienza nella movimentazione dei materiali”, afferma Hathout.
La sicurezza prima di tutto Il MiR 1200 Transpallet non significa solo velocità ed efficienza. Il fattore sicurezza rimane sempre la priorità assoluta, come sottolinea Hathout: “la sicurezza è nel DNA di ogni prodotto MiR. Il MiR 1200 Transpallet è stato progettato per essere conforme ai più recenti standard di sicurezza, tra cui l‘ISO3691-4. La fusione di più piattaforme di sensori e di funzioni di sicurezza di alto livello offre un‘alternativa molto più sicura ai carrelli elevatori, ai transpallet elettrici e manuali”.
Le caratteristiche principali del MiR 1200 Transpallet:
• Percezione basata sull’intelligenza artificiale e potenziata da NVIDIA: addestrata su oltre 1,2 milioni di immagini reali e sintetiche, questa soluzione consente un rilevamento rapido e preciso di pallet e ostacoli.
• Elevata capacità della batteria e ricarica rapida: grazie a un rapporto di ricarica di 1:14 e alla possibilità di effettuare ricarica parziale, il MiR 1200 Transpallet è l’ideale per flussi di lavoro intensi, 24 ore su 24, 7 giorni su 7.
• Conformità agli standard di sicurezza ISO: progettato per essere conforme alla norma ISO3691-4, garantisce un funzionamento sicuro in vari ambienti.
• Sensoristica 3D per il rilevamento degli ostacoli: il MiR1200 Transpallet combina un sensore LIDAR e la visione 3D per un rilevamento preciso degli ostacoli su pavimento, in altezza e nell’ambiente garantendo un posizionamento preciso e sicuro dei pallet.
• Mobilità robusta: il grado di protezione IP52 e le robuste ruote consentono una mobilità perfetta su diverse superfici, anche quelle difficili.
L’integrazione tra robotica e automazione sta ridefinendo i confini dell’efficienza operativa, inaugurando una nuova era in cui la collaborazione tra uomo e macchina diventa fondamentale. Non si tratta più solo di avanzamenti tecnologici, ma di una sinergia in cui robot collaborativi, intelligenza artificiale e deep learning convergono per trasformare radicalmente i processi produttivi, segnando un passo avanti verso una produttività più adattiva e resiliente, capace di rispondere in tempo reale a variabili e sfide operative. Questo approccio apre nuove prospettive per l’industria, creando un ambiente in cui la robotica diventa un vero alleato dell’operatore, garantendo interazioni naturali e sicure.
Da oltre 30 anni, RS Italia si distingue come partner tecnologico per le aziende che desiderano implementare queste innovazioni. Con un portafoglio ampio e mirato, offre soluzioni per automatizzare e ottimizzare ogni aspetto del processo produttivo. La gamma di prodotti di RS Italia si basa su una doppia proposta: da un lato, collaborazioni con i principali marchi del settore, con un’attenzione particolare al mercato italiano, dall’altro, le soluzioni RS PRO, marchio di proprietà del Gruppo RS.
All’interno della gamma RS PRO, sono disponibili componenti di alta qualità progettati per supportare l’integrazione con sistemi robotici e applicazioni industriali avanzate. Oltre ai componenti meccanici e di controllo, RS offre soluzioni di connettività e accessori robotici -come pinze e attuatori- ottimizzati per un contesto produttivo sempre più automatizzato. La gamma include anche dispositivi per il monitoraggio e la gestione energetica, soluzioni per la trasmissione dati e sistemi di sicurezza integrati, pensati per aumentare l’efficienza e ridurre i costi di manutenzione.
Parallelamente, RS Italia propone una vasta gamma di soluzioni per la robotica mobile (AGV), sviluppate per affrontare le esigenze produttive moderne. Il concetto di AGV si basa sull’idea di un’automazione flessibile, capace di adattarsi ad ambienti produttivi dinamici. Grazie ai progressi nell’intelligenza artificiale e nel deep learning, i robot mobili possono operare senza necessità di infrastrutture fisse, interpretando l’ambiente circostante attraverso avanzati sistemi di visione.
I dispositivi di RS Italia sono progettati per essere compatibili con una varietà di piattaforme di automazione e software di controllo, rendendo l’integrazione semplice e modulare. I sistemi di visione per robot, a marchio RS PRO, ad esempio, sono equipaggiati con sensori ad alta definizione e algoritmi integrati per l’analisi delle immagini, assicurando una lettura accurata delle informazioni visive e migliorando sia il processo decisionale che la sicurezza. Questa tipologia di robotica mobile non solo rende le operazioni più sicure e scalabili, ma rappresenta anche un passo significativo verso una gestione autonoma delle linee di produzione
Un altro pilastro fondamentale per la modernizzazione dell’industria è il controllo di processo, che permette alle aziende di monitorare in modo preciso e in tempo reale le operazioni. L’integrazione di software di automazione robotica (RPA) con prodotti di controllo di processo consente di sviluppare processi collaborativi, in cui i robot lavorano a fianco degli operatori umani, garantendo maggiore sicurezza e riduzione dei tempi di fermo macchina.
In questo contesto, RS Italia offre una gamma di strumenti per il controllo di processo, tra cui sensori, attuatori e sistemi di interfaccia utente avanzati. Questi dispositivi permettono il monitoraggio continuo
delle variabili operative -come temperatura, pressione e umidità- assicurando che i parametri rimangano entro limiti ottimali e prevenendo eventuali malfunzionamenti o inefficienze. I dispositivi di controllo proposti da RS Italia sono ideali per realizzare una gestione intelligente e ottimizzata della produzione, in cui le operazioni possono essere regolate e personalizzate in tempo reale in base alle condizioni variabili del processo produttivo.
Con la sua vasta gamma di soluzioni per l’integrazione robotica e il controllo di processo, RS Italia si pone come partner fondamentale per le imprese che aspirano a trasformare i propri impianti secondo i principi dell’Industria 4.0. I prodotti e i sistemi offerti permettono un alto grado di personalizzazione e sono pensati per adattarsi a contesti produttivi in evoluzione, consentendo alle aziende di ridurre i tempi di inattività, aumentare la produttività e migliorare la sicurezza.
L’adozione dei servizi specializzati di RS Italia non solo aiuta le aziende a rispondere alle sfide del mercato, ma fornisce anche le basi per una crescita sostenibile e scalabile, in cui l’innovazione tecnologica rappresenta un vantaggio competitivo reale. Integrando AI, RPA e sistemi IoT, RS Italia consente infatti di realizzare un ecosistema produttivo interconnesso, capace di rispondere rapidamente alle mutevoli condizioni di mercato e alle nuove opportunità offerte dalla digitalizzazione e dall’automazione intelligente.
Le aziende manifatturiere oggi affrontano una sfida comune: mantenere o espandere la produzione a fronte di una crescente carenza di personale. Per rispondere a questa necessità, molte realtà puntano sull’automazione di molte fasi di produzione, concentrandosi, soprattutto, sulle attività fisicamente impegnative o monotone, per cui è sempre più difficile trovare dipendenti. I recenti progressi in robotica, intelligenza artificiale e sistemi di presa hanno permesso lo sviluppo di soluzioni automatizzate economicamente vantaggiose, ma l’installazione e gestione di questi sistemi sta diventando complessa, soprattutto per le piccole e medie imprese. In particolare, la gestione dei componenti con i robot richiede sistemi avanzati, come quelli basati su telecamere per il posizionamento preciso per la presa. Di conseguenza, molte aziende devono ricorrere a fornitori esterni, con un aumento dei costi e dei tempi di implementazione, rendendo più difficile l’automazione a lungo termine.
Iniziare con l’automazione è facile SCHUNK ha presentato il 2D Grasping kit, un kit applicativo che consente di implementare rapidamente, in maniera semplice ed economica processi di pick & place automatizzati grazie all’AI. Il kit è composto da una telecamera con obiettivo, un PC industriale, il software SCHUNK AI e i cavi necessari. Tutti i componenti sono coordinati tra loro e, grazie a un’interfaccia TCP/ IP aperta, possono essere combinati con qualsiasi robot o anche con un controller di livello superiore (come, ad esempio, un PLC Siemens). Consente di gestire e smistare vari componenti disposti in modo casuale su un piano. Finalmente una soluzione per quei compiti complessi da automatizzare, monotoni e poco attrattivi per i lavoratori, come, ad esempio, lo smistamento a mano all’interno dei cassoni dei pezzi torniti in uscita da una macchina in un’officina meccanica conto terzi e il loro corretto posizionamento su vassoi per l’automazione delle fasi di lavorazione successive.
SCHUNK utilizza il 2D Grasping kit nei propri stabilimenti produttivi in Germania. I clienti hanno l’opportunità di testare le proprie applicazioni nel centro applicativo di robotica e automazione, il CoLab, e di scoprire come il sistema può migliorare la loro produzione in modo facile e intuitivo.
Un compito complesso reso semplice: lo smistamento dei componenti in sacchetti trasparenti
Se il sistema fosse strutturato meccanicamente, un utente medio avrebbe bisogno di meno di mezza giornata per imparare i (nuovi) componenti del sistema. L’interfaccia web del software del 2D Grasping kit, invece, guida l’utente passo dopo passo verso il risultato.
Step 1: Il sistema di visione dei componenti
La telecamera osserva dall’alto un nastro trasportatore, un vassoio o un piano di stoccaggio. Il software di intelligenza artificiale riconosce e differenzia i componenti sulla base di immagini precedentemente apprese e fornisce la posizione di presa ottimale. Ad esempio, se il compito del robot è quello di afferrare i componenti insieme a un imballaggio trasparente (come viti e dadi in un sacchetto di plastica) per l’evasione dell’ordine, l’operatore scatta semplicemente diverse foto dei componenti in varie posizioni. Il 2D Grasping kit non richiede una fonte di illuminazione dedicata e, grazie al software AI-powered, è molto più resistente alla luce ambientale rispetto ai sistemi di visione convenzionali. La telecamera è progettata per gestire condizioni di illuminazione variabili, compresi i cambiamenti di luce diurna in base alla posizione del sole, ed è anche in grado di adattarsi a sfondi diversi. Anche il colore e la riflettività della superficie hanno un impatto minimo. Il sistema rileva in modo affidabile i componenti metallici anche su sfondi luminosi.
Step 2: individuazione dell’oggetto e dei punti di presa
In questa fase, l’operatore deve semplicemente contrassegnare e denominare i componenti. Il software AI di SCHUNK rileva automaticamente il contorno dell’oggetto dallo sfondo, lo isola e calcola le variazioni per gli angoli di visuale, l’esposizione alla luce e altri parametri. Dopo solo 10-20 immagini, il software dispone già di una serie sufficiente di dati sugli oggetti da rilevare.
Step 3: Istruisci l’AI e dai il via al processo!
Una volta completate le prime due fasi, l’intelligenza artificiale si addestra completamente offline. Il cliente ha il pieno controllo dei dati in ogni momento, poiché questi rimangono interamente all’interno della sua rete aziendale. L’addestramento richiede solo una o due ore. Il 2D Grasping kit è quindi pronto per l’uso. La telecamera assistita dall’intelligenza artificiale riconosce ora i componenti dei sacchetti in base a forma, dimensioni e colore. L’intelligenza artificiale regola e compensa le variazioni che possono verificarsi, come i riflessi o le deformazioni dei sacchetti. Il software di elaborazione delle immagini comunica quindi con il robot, dicendogli quali componenti riconosce, dove sono posizionati, quanto deve essere aperto il sistema di presa (nel caso di pinze parallele) e con quale angolo di rotazione può afferrare al meglio i componenti. Il robot sposta quindi la sua pinza verso il componente, lo preleva e lo colloca nella posizione corretta in un punto predefinito. Durante il processo di presa e spostamento, la telecamera rileva contemporaneamente l’oggetto successivo e ne calcola il tipo e il punto di presa. Questa operazione richiede circa due secondi, consentendo al robot di afferrare immediatamente il secondo oggetto dopo aver posato il primo. Se lo si desidera, l’utente può memorizzare manualmente più punti di presa con estrema facilità. In questo esempio, il 2D Grasping kit funziona con la pinza universale EGK. In futuro, il kit funzionerà anche con pinze parallele pneumatiche e meccatroniche, nonché con pinze magnetiche, a vuoto e adesive.
Come l’integrazione di AMR e smart sensor riduce i rischi per il personale e migliora la produttività nei settori produttivo e logistico.
La necessità di ridurre i tempi di produzionea fronte di lotti di maggiore qualità e quantità, imposta dall’esigenza di essere sempre al passo con le richieste del mercato, determina una maggiore efficienza operativa che può mettere a rischio la sicurezza dei dipendenti. Per affrontare questa sfida e proteggere i propri lavoratori, oggi le aziende si affidano agli AMR (Autonomous Mobile Robot) che, grazie all’integrazione con sensori di sicurezza, si configurano come una delle tecnologie più efficaci e affidabili per l’industria 4.0. Nel settore della logistica, ad esempio, è ormai diventato importante adattarsi e reagire in modo rapido e flessibile, tanto quanto in quello della produzione. Gli AMR rappresentano una valida alternativa ai carrelli elevatori poiché riescono, in completa autonomia, a prelevare, trasportare e consegnare pallet attraverso ambienti dinamici, sollevando gli esseri umani da compiti a più alto rischio. I sensori di sicurezza intelligenti di cui sono muniti permettono loro di navigare autonomamente, muovendosi nell’ambiente circostante senza la necessità di essere supervisionati da un operatore o di seguire un percorso fisso e prestabilito, potendo gestire le numerose sfide che si trovano ad affrontare. Per i robot mobili, infatti, “movimento” significa “sfida”, perché i requisiti loro richiesti sono molto complessi.
Sensori di sicurezza per la navigazione nell’ambiente lavorativo Le piattaforme mobili e gli AMR si spostano in modo automatico e autonomo tra diversi punti dell’ambiente produttivo o logistico. Gli smart sensor supportano i robot mobili nella localizzazione, mappatura e navigazione, nonché durante le fasi di coordinamento e le manovre di aggancio, consentendo flessibilità e libertà di posizionamento. Ma il movimento nello spazio libero richiede molto di più. Sensori di sicurezza specifici, infatti,
sono necessari per adattare i veicoli in base alla situazione di marcia, in curva, deviazione di ostacoli, sotto la pioggia o sotto la neve, ed evitare collisioni che rappresentano una delle sfide più impegnative per gli AMR. Ogni collisione di veicoli comporta costi aggiuntivi dovuti a guasti e tempi di fermo. La gamma di soluzioni di sensori di sicurezza per gli AMR è molto ampia, scalabile e modulare: dalle applicazioni più semplici a quelle high-end, basate su LiDAR, encoder, sensori di visione, dispositivi di scrittura e lettura RFID o ultrasuoni. Ciascuna soluzione è concepita individualmente sulla base delle esigenze del singolo cliente per garantire che localizzazione, posizionamento o movimentazione dei carichi possano svolgersi in modo affidabile.
Sensori di sicurezza per il rilevamento ambientale: la cooperazione uomorobot
Quando le persone e le piattaforme mobili condividono gli stessi ambienti di lavoro, la cooperazione tra uomo e robot deve avvenire senza pericoli e in sicurezza. I robot mobili devono evitare oggetti sia statici che in movimento ed essere sempre in grado di rilevare l’ambiente che li circonda. I sensori di sicurezza consentono l’individuazione degli umani o degli ostacoli che i robot incontrano sul percorso, permettendo di navigare in modo sicuro intorno a loro, con la possibilità di interrompere le attività nel caso gli ostacoli si facciano troppo vicini. Per il rilevamento ambientale, soluzioni basate su sensori di sicurezza, quali barriere fotoelettriche e laser scanner di sicurezza per una lettura dei dati affidabile anche in condizioni ambientali difficili, encoder e sensori 2D e 3D assicurano sicurezza funzionale, meccanica, elettrica e in movimento, permettono la protezione di zone, accessi e punti pericolosi e consentono di evitare potenziali collisioni tra oggetti ed operatori o tra sistemi di movimentazione automatica. Oltre a ridurre il rischio di collisioni, i robot mobili autonomi contribuiscono anche a mantenere il personale in sicurezza,
assumendo quei compiti ripetitivi e rischiosi, sostituendosi agli stessi negli ambienti meno salubri e più pericolosi, consentendo loro di svolgere funzioni a maggiore valore aggiunto e in condizioni di maggiore sicurezza.
Sensori di sicurezza per l’Industry 4.0 “Safety first” deve essere il claim per l’azienda del futuro. In uno scenario in cui il futuro degli impianti produttivi sarà sempre più caratterizzato dalla Human Robot Collaboration (HRC), cioè dalla condivisione delle aree di lavoro tra operatori, robot e sistemi di guida autonoma, l’adozione di adeguati strumenti di sicurezza è fondamentale. I sensori di sicurezza sono indispensabili per la riduzione del rischio, permettendo di raggiungere i Required Performance Level (PLr), in movimento, velocità e rotazione, nel pieno rispetto delle norme vigenti per le applicazioni di robotica mobile. I Perfomance Level vanno da PLa (basso) a PLe (alto) e sono definiti dalla norma ISO 13849-1.
I sensori di sicurezza realizzati per applicazioni mobili come piattaforme, AGV e AMR, supportano queste applicazioni nella localizzazione e nell’impedimento delle collisioni. Per rilevare in modo affidabile gli oggetti e le persone, questi sensori di sicurezza devono essere molto resistenti rispetto all’incidenza della luce solare o ambientale, allo sporco, alla polvere. Grazie all’uso di tecnologie di scansione e soluzioni innovative, i sensori di sicurezza sono in grado di effettuare rilevazioni di posizione e distanza anche in condizioni ambientali difficili. Adottando misure basate su sensori di sicurezza adeguati, si riduce il rischio complessivo sia per i dipendenti che per le macchine, creando un ambiente sicuro e affidabile, in grado di mantenere elevato il grado di produttività.
Quando noi esseri umani afferriamo un oggetto, agiamo intuitivamente e senza pensare consapevolmente. I calcoli complessi, invece, richiedono un pensiero consapevole. Per un’intelligenza artificiale, è il contrario: una formula matematica è facilmente calcolabile. Se le regole sono note in anticipo, anche strategie complesse di presa, supportate da sensori di visione, possono essere valutate automaticamente. Nel caso della presa di oggetti non conosciuti, le regole dovrebbero essere suddivise in molte istruzioni e soprattutto, differenti per ogni tipologia di oggetto.
Lavoro monotono e costoso
Prendendo il caso delle operazioni di picking e kitting nel settore e-Commerce e logistica distributiva, è utile sapere che queste sono svolte principalmente da operatori umani. Soprattutto nei magazzini di beni di consumo, la capacità di manipolare vari oggetti tra le scatole è ancora indispensabile. Gli oggetti, le forme, le dimensioni e gli imballaggi cambiano costantemente. Nell’ultimo decennio, circa il 15% dei magazzini è stato semplicemente meccanizzato, mentre solo il 5% di essi utilizza sistemi di automazione avanzati. L’E-Commerce, quindi, aumenta la complessità delle operazioni di magazzino ed oltre il 90% di tutte le attività di picking nei magazzini sono ancora eseguite manualmente, portando dal 30% al 55% dei costi totali di magazzino attribuibile a queste operazioni fondamentali. In ultimo, l’aumento globale della carenza di manodopera, insieme alla crescente domanda dei consumatori, porta a un dilemma critico per le aziende.
Il picking autonomo
internazionale e che ora può finalmente essere messa a disposizione di tutti gli esperti di automazione, democratizzando l’utilizzo congiunto di robotica, visione e intelligenza artificiale.
Elevata disponibilità in tempi sorprendenti
Simatic Robot Pick AI è un algoritmo pre-addestrato e non richiede un ulteriore addestramento da parte dell’utente, che può concentrarsi invece sulla parte operativa dell’impianto. Il sistema è talmente robusto che la messa in servizio di una stazione di picking, già attrezzata da robot e visore 3D, può impiegare meno di 30 minuti per prelevare qualsiasi prodotto di consumo da una cesta. Rendere l’accesso a questa tecnologia il più semplice e rapido possibile, è stato fin da subito un obiettivo primario per i progettisti di Simatic Robot Pick AI. Aver integrato la messa in servizio guidata e intuitiva direttamente nell’interfaccia uomo-macchina, ha eliminato il gap culturale dei tipici sistemi di automazione, sorprendendo le aspettative degli utilizzatori.
Integrazione nel TIA Portal e simulazione
Per i casi d’uso complessi che troviamo nell’e-commerce, dove gli oggetti non sono prevedibili e in cui le regole fisse fallirebbero, l’Intelligenza Artificiale (IA) sviluppata da Siemens, una combinazione di deep learning ed elaborazione di immagini 3D, offre finalmente una soluzione affidabile. Simatic Robot Pick AI, questo è il nome della soluzione, è un sistema aperto, modulare e soprattutto adatto agli esperti di automazione che possono integrarlo anche senza avere conoscenze approfondite di AI. Siemens punta su moduli software pre-addestrati e facili da implementare, la cui scalabilità parte dalla presa di oggetti stoccati dalle ceste, al prelievo di oggetti su nastri, fino ad arrivare alla depallettizzazione e a modalità di deposito regolate, attraverso la versione Simatic Robot Pick AI Pro. La soluzione di Siemens analizza le immagini nelle tre misure fondamentali: altezza, larghezza e profondità. Così facendo, in pochi millisecondi, fornisce il punto di presa (pick point) che risulta più affidabile per garantire un prelievo senza errori. Questo è il risultato di anni di ricerca, che ha coinvolto diversi gruppi di lavoro a livello
Si possono già immaginare i molteplici benefici di questa soluzione e soffermandoci sugli sviluppatori, è possibile facilitare il loro lavoro attraverso integrazione in TIA Portal e gli strumenti di simulazione. Grazie alla Simatic Robot Library infatti, è possibile programmare le sequenze del robot attraverso un set di Function Block PLC open-like standardizzati, mantenendo le stesse performance che si avrebbero utilizzando solamente il robot controller. E se si volesse anticipare le fasi di programmazione? Simatic Robot Simulator è uno strumento avanzato per la simulazione e la programmazione di robot industriali, anch’esso integrato in TIA Portal e compatibile con la Robot Library. Consente di creare, testare e ottimizzare i movimenti dei robot in un ambiente virtuale, riducendo i tempi di messa in servizio e migliorando l’efficienza operativa. Le funzionalità includono la programmazione offline, la verifica delle traiettorie, l’analisi delle collisioni e l’ottimizzazione dei cicli di lavoro. Un altro uso è quello della formazione del personale, offrendo un ambiente sicuro per l’apprendimento e la sperimentazione senza rischi per le attrezzature reali. Ideale per ottimizzare i processi produttivi e migliorare la qualità delle operazioni industriali. In conclusione, Simatic Robot Pick AI rivoluziona il picking con l’IA, offrendo soluzioni scalabili e intuitive. Democratizza l’automazione, riducendo i costi e migliorando l’efficienza operativa in tempi record. Grazie all’integrazione con TIA Portal e strumenti di simulazione avanzati, facilita il lavoro degli sviluppatori e ottimizza i processi produttivi. Ideale per l’e-commerce, dove la flessibilità e l’efficienza sono cruciali.
Fondata nel 2022 da Michael Zandri, MZ Robotics è una realtà piccola nelle dimensioni, giovane nei collaboratori, ma grande nelle competenze e nelle ambizioni, con un particolare focus sulla progettazione e costruzione di soluzioni automatizzate per l’industria, basate su una delle tecnologie più innovative e ad elevato potenziale: la visione artificiale applicata alla robotica, in particolare quella collaborativa.
Robotica collaborativa, ma anche tradizionale
Grazie all’ottimo rapporto esistente con Schmalz, importante realtà che si occupa di soluzioni di presa con vuoto per l’automazione e per la movimentazione, MZ Robotics ha potuto fin da subito contare sulla fiducia di un partner di rilievo che le ha permesso di sperimentare nuove soluzioni tuffandosi nel mondo della robotica industriale e collaborativa. Quando vi sono task da eseguire con flessibilità, precisione e qualità, la parola chiave usata dall’industria spesso e volentieri è una sola: ‘robot’. Ma non sempre basta. “Ai clienti oggi non basta disporre di un ‘semplice’ tool di presa: ciò che serve è fornire loro una soluzione, una cella completa, già configurata per eseguire uno specifico compito. Ecco dove MZ Robotics poteva fare la differenza! Ed ecco perché abbiamo deciso di specializzarci nella robotica collaborativa, una tecnologia il cui trend nei prossimi anni continuerà a segnare l’evoluzione del mondo industriale”, afferma Michael Zandri. Oggi MZ Robotics è integratore certificato Universal Robot. Tuttavia, per molte applicazioni, MZ integra anche robot industriali di tipo tradizionale, operando con marchi primari come, ad esempio, ABB.
Con la visione è meglio
Per incrementare la flessibilità di un robot, l’ideale è integrarlo con un sistema di visione in grado di guidarlo opportunamente in funzione delle operazioni che esso deve svolgere. Ed è qui che MZ Robotics ha incrociato la propria strada con quella di wenglor. “La conoscenza di wenglor risale ad alcuni anni fa, ma è stato recentemente, con la nascita di MZ Robotics, che il rapporto si è ampliato e intensificato”, sottolinea Zandri. “Devo ammettere che inizialmente le mie conoscenze in ambito di visione artificiale erano piuttosto limitate: l’occasione di acquistare con una offerta lancio una delle nuove smart camera B60 di wenglor con attacco C-mount mi ha permesso di avvicinarmi a questa tecnologia e di prenderne quasi immediatamente confidenza. Merito di uno strumento che è semplice e potente, in quanto dispone di un software, uniVision, che ne semplifica l’utilizzo e fornisce una base eccezionale per lo sviluppo di un gran numero di applicazioni”. La B60 si distingue da soluzioni simili presenti sul mercato per le elevate performance assicurate dall’hardware e dal software uniVision 3, integrabile con le librerie HALCON. Ciò rende possibile ottenere con un solo dispositivo dei risultati che un tempo erano raggiungibili solamente con sistemi di visione basati su controllori dedicati e soluzioni software personalizzate.
Il valore aggiunto del software
Con la smart camera B60 è possibile gestire un’ampia gamma di
applicazioni: misurazioni, calcolo della posizione, pattern matching, riconoscimento oggetti, lettura di codici ecc. Oltre alla semplicità di configurazione e alla praticità di installazione, dovuta alle dimensioni molto compatte, la Smart Camera B60 dispone di un giroscopio integrato, che ne consente il rapido riposizionamento in caso di spostamento accidentale: un led integrato segnala l’anomalia, permettendo all’operatore di ripristinare le condizioni ottimali di utilizzo. “Un esempio delle potenzialità delle Smart Camera B60 di wenglor è stato mostrato in occasione della scorsa edizione di Mecspe, a Bologna, dove abbiamo approntato una demo particolarmente impegnativa. Avevamo posizionato all’interno di un contenitore un insieme di cubetti e palline colorate in materiale semitrasparente: il programma doveva riconoscerle e pilotare di conseguenza un robot collaborativo UR per prelevarle e posizionarle correttamente su una superficie di appoggio. Nonostante le problematiche che potevano crearsi in funzione della sovrapposizione degli oggetti e delle interferenze luminose, la telecamera le ha sempre riconosciute correttamente, sia per forma che per colore, così da consentire al robot di prelevarle e disporle senza errori”. Nello sviluppo di questa applicazione un ruolo decisivo lo ha giocato il software: innanzitutto URCap, una app sviluppata da wenglor appositamente per i cobot UR, che permette l’invio diretto al robot delle quote rilevate dalla smart camera. Questa soluzione riduce la complessità del sistema, in quanto l’interfaccia di comunicazione è integrata e lo scambio dati tra camera e robot è diretto. Quindi uniVision 3, un ambiente di sviluppo completo che semplifica l’approccio ai sistemi di visione e velocizza le attività di programmazione grazie a una modalità di configurazione guidata step by step.
L’importanza del service
wenglor mette a disposizione degli integratori come MZ Robotics un comodo servizio di rental, che consente di avvalersi di dispositivi e attrezzature per un periodo di prova al fine di valutare la fattibilità tecnica dell’applicazione. Identificata la migliore soluzione, l’attrezzatura può quindi essere restituita, ordinando ciò che serve e, di conseguenza, avendo la certezza del risultato voluto in fase di sviluppo definitivo dell’applicazione. “L’esperienza che i tecnici wenglor hanno messo a nostra disposizione è impagabile”, afferma Zandri. “Indipendentemente dal tipo di problematica che ho sottoposto loro, ho sempre avuto una risposta risolutiva in una manciata di minuti”. Non solo. Oltre ai sistemi di visione, in particolare le smart camera B60, MZ Robotics si avvale di altri prodotti wenglor: sensori che utilizza a bordo delle stazioni robotizzate che progetta, realizza e installa direttamente presso il cliente. “L’ampiezza del catalogo, la perfetta conoscenza del prodotto e la competenza in ambito applicativo sono qualità da non dare per scontate. Per noi non è solo la Smart Camera B60 ad essere un’ottima alleata nell’affrontare le sfide che il cliente ci richiede, ma lo è l’intero pacchetto di hardware, software e servizi che, insieme al know-how, wenglor mette a disposizione di aziende come la nostra”, conclude Zandri.
Quando si verifica uno strappo tra gli anelli della catena hi-tech, il più delle volte il responsabile è un microchip. Senza di lui niente sembra più funzionare. Il fatto che la sua produzione sia a pieno regime anche in Germania è reso possibile da alcune aziende hidden champion – con i centri di lavorazione automatizzati di HERMLE. www.hermle.de
NEL CONTESTO INDUSTRIALE ATTUALE, L’INTELLIGENZA ARTIFICIALE SI DISTINGUE COME UNA DELLE TECNOLOGIE PIÙ AVANZATE E RIVOLUZIONARIE, IN GRADO DI TRASFORMARE PROFONDAMENTE I PROCESSI PRODUTTIVI E IL NOSTRO RAPPORTO CON LE MACCHINE. IN TALE CONTESTO, LABORATORI DI RICERCA COME IL JOiiNT LAB DIVENTANO CENTRI DI ECCELLENZA FONDAMENTALI PER TRASFORMARE SCOPERTE SCIENTIFICHE IN SOLUZIONI INDUSTRIALI PRATICHE
di Stefano Ierace, Annalisa Giavarini – Consorzio Intellimech; Martina Imarisio Neviani - AFIL
NNel panorama dell’industria moderna, tra le tecnologie abilitanti dell’industria 4.0, un ruolo importante è rivestito dall’Intelligenza Artificiale e dalla robotica collaborativa. Queste tecnologie sono in grado di ridisegnare i paradigmi di produzione in diversi settori e di modificare il rapporto tra macchina e uomo così come è stato inteso tradizionalmente.
Il laboratorio di ricerca JOiiNT LAB, situato a Bergamo, nasce proprio dall’esigenza di creare maggiore consapevolezza sulle tematiche di robotica collaborativa e
di effettuare il trasferimento tecnologico nel mondo manifatturiero. Esso si propone come punto di riferimento per lo sviluppo di tecnologie avanzate ed è frutto della collaborazione tra Istituto Italiano di Tecnologia (IIT) ed alcuni attori centrali dell’ecosistema bergamasco, che hanno in comune anche l’associatura al Cluster AFIL (Associazione Fabbrica Intelligente Lombardia), ovvero Consorzio Intellimech, Confindustria Bergamo, Kilometro Rosso Innovation District ed Università degli Studi di Bergamo.
JOiiNT LAB non è solo un laboratorio,
ma un vero e proprio hub dove la tecnologia di base incontra le esigenze pratiche dell’industria. L’obiettivo principale è trasformare le idee e le scoperte scientifiche in soluzioni concrete, capaci di migliorare i processi industriali, aumentare la produttività e garantire maggiore sicurezza sul lavoro. Nell’ecosistema di JOiiNT LAB, infatti, convivono sia enti di ricerca che aziende manifatturiere, le quali aderiscono direttamente predisponendo un dipendente per essere formato in laboratorio affinché apprenda e trasferisca il know how in azienda.
Il laboratorio di ricerca bergamasco affronta la complessità della robotica collaborativa attraverso quattro principali macroaree di ricerca, ognuna delle quali rappresenta una sfida strategica e tecnologica.
La prima sfida individuata riguarda la flessibilità dei robot, fondamentale per supportare le aziende in processi produttivi in costante evoluzione. L’obiettivo è sviluppare robot che possano essere facilmente riprogrammati, rendendoli strumenti intuitivi e accessibili anche a operatori non esperti. Questo approccio permette di ottimizzare la personalizzazione della produzione, una necessità crescente soprattutto per le Piccole e Medie Imprese (PMI) che devono spesso adattarsi rapidamente alle richieste di mercato. Occorre rendere queste tecnologie accessibili e user-friendly promuovendo un approccio pratico alla digitalizzazione industriale, similmente a quanto accaduto con gli smartphone, che di fatto sono piccoli computer e sono utilizzati in maniera intuitiva da tutti.
2. Automazione di task ripetitivi
In linea con la prima sfida, la seconda si concentra sull’automazione delle attività ripetitive e a basso valore aggiunto. Molti contesti produttivi presentano vincoli logistici che rendono il lavoro umano scomodo e poco efficiente. Qui, i robot possono intervenire per eliminare compiti gravosi e non appaganti, liberando i lavoratori per attività più qualificate. Si tratta di una questione non solo di produttività, ma anche di benessere e sicurezza sul lavoro. L’introduzione di robot agili e adattabili, capaci di operare in
spazi non strutturati e in situazioni difficili, potrebbe rappresentare una svolta significativa per molte industrie.
3. Interazione fisica uomo-macchina
La terza sfida vede un cambiamento di paradigma: non più una semplice coesistenza tra uomo e robot, ma una collaborazione fisica. Perché ciò sia possibile, è necessario sviluppare sistemi di programmazione intuitivi con robot che percepiscano l’essere umano adattandosi ad esso e supportandolo durante le fasi produttive. Questo tipo di interazione è particolarmente utile in settori come l’assemblaggio e le lavorazioni meccaniche, dove le competenze umane sono indispensabili, ma dove i robot possono supportare in compiti fisicamente impegnativi o pericolosi. Al contempo, è possibile monitorare in tempo reale l’ergonomia dell’operatore, con l’obiettivo di migliorare le prestazioni, tutelare il benessere e la sicurezza sul lavoro.
Casi di Studio: soluzioni concrete per il settore industriale
4. Robot Avatar: estensione del corpo umano
La quarta sfida introduce il concetto di “robot avatar”, una tecnologia futuristica che mira a risolvere problemi concreti e attuali. La pandemia ha reso evidente la necessità di remotizzare molte operazioni fisiche, soprattutto in situazioni di rischio. I robot avatar, dotati di interfacce di Realtà Virtuale (VR), permettono a un operatore di controllare a distanza un robot, replicando i suoi movimenti e rendendolo un’estensione del corpo umano. Questo tipo di robotica collaborativa è particolarmente utile in contesti legati alla sicurezza, come le operazioni in ambienti pericolosi o isolati, ma trova applicazioni anche nell’assistenza clienti, ispezione di infrastrutture e in altri settori dove è preferibile limitare la presenza fisica.
L’applicazione delle tecnologie all’interno del JOiiNT LAB non si limita alla teoria, ma si concretizza in progetti pratici che coinvolgono aziende del territorio. Un esempio emblematico è la collaborazione con le aziende champion Elettrocablaggi, specializzata nella produzione di pannelli di controllo per macchine utensili, e ABB, azienda specializzata nelle tecnologie per l’energia e l’automazione, nonché con la start-up innovativa Exsensia. Grazie all’integrazione di robot collaborativi, telecamere 3D e basi mobili, l’azienda ha potuto esplorare l’automatizzazione del carico e scarico del magazzino verticale. Ciò che rende questo progetto particolarmente innovativo è l’uso dell’Intelligenza Artificiale, che permette la programmazione intuitiva dei sistemi robotici attraverso metodi basati sul “learning from demonstration”. Questi metodi, ispirati all’apprendimento umano, consentono ai robot di apprendere i task attraverso l’osservazione e l’emulazione, permettendo agli operatori di linea, anche senza esperienza in robotica o informatica, di programmare autonomamente l’intero sistema.
Un secondo esempio significativo è la collaborazione con Cosberg, un’azienda champion che progetta e assembla linee di produzione personalizzate e modulari. Essa ha sviluppato un sistema di digitalizzazione capillare all’interno delle sue macchine, integrato con intelligenze artificiali per monitorare e migliorare continuamente le prestazioni produttive. Grazie al supporto del JOiiNT LAB, Cosberg sta esplorando l’uso di robot semi-antropomorfi, capaci di intervenire autonomamente sulle macchine o di essere controllati da operatori in remoto per fornire assistenza ai clienti.
Un altro caso emblematico è quello di Fassi, azienda champion specializzata nella produzione di gru. Grazie alla collaborazione con l’Istituto Italiano di Tecnologia, Fassi sta trasformando le sue gru in veri e propri “robot intelligenti” per la manipolazione dei carichi. Le nuove gru saranno dotate di interfacce di controllo intuitive,
sistemi di programmazione intelligenti e capacità di operare da remoto, diventando così una sorta di “avatar” dell’operatore. Questo tipo di innovazione rappresenta un passo avanti significativo nel settore della movimentazione dei carichi, con applicazioni che vanno ben oltre l’uso tradizionale delle gru.
La contaminazione tecnologica come chiave di successo
L’adozione della robotica collaborativa non riguarda solo l’efficienza dei processi produttivi, ma può anche portare alla creazione di nuovi modelli di business. Per esempio, l’integrazione tra robotica e Intelligenza Artificiale consente alle PMI di fornire servizi a livello globale, senza la necessità di una presenza fisica capillare. Questo modello è particolarmente vantaggioso in settori dove la manutenzione e l’assistenza tecnica richiedono competenze specifiche difficilmente reperibili in loco. Grazie alla tele-presenza e alla manipolazione remota, le aziende possono intervenire sui propri macchinari da qualsiasi parte del mondo, offrendo un servizio tempestivo e di qualità ai clienti.
A valle di queste considerazioni, si può affermare che uno dei punti di forza di JOiiNT LAB risieda nella capacità di creare un terreno comune tra mondo della ricerca e industria, promuovendo una contaminazione tecnologica continua, che favorisce lo scambio di competenze tra aziende e ricercatori, attraverso la creazione di un ambiente di crescita reciproca. Collaborare con aziende di settori diversi permette di affrontare le sfide da prospettive multiple, facilitando l’innovazione e il trasferimento tecnologico. Tale approccio ha permesso di sviluppare un “framework trasversale” che integra componenti hardware e software, consentendo la prototipazione rapida di sistemi robotici adattabili a diverse esigenze aziendali. Le tecnologie sviluppate all’interno del laboratorio non solo migliorano l’efficienza produttiva, ma offrono anche nuove opportunità di business e innovazione di prodotto. Le sfide affrontate dal laboratorio sono destinate a plasmare il futuro dell’industria, ponendo l’essere umano al centro di un processo di innovazione tecnologica inclusiva e sostenibile.
AFIL (Associazione Fabbrica Intelligente Lombardia) è il Cluster Tecnologico per il Manifatturiero Avanzato ufficialmente riconosciuto da Regione Lombardia. Attraverso le Strategic Communities, ovvero gruppi di lavoro formati da grandi imprese, PMI, start-up, associazioni, università e centri di ricerca che lavorano su tematiche strategiche per il manifatturiero lombardo, AFIL accompagna i propri associati in un percorso collaborativo di crescita attraverso incontri tematici, workshop, webinar, matchmaking e missioni internazionali, facilitando così lo sviluppo di progettualità comuni e promuovendo la R&I anche a livello interregionale. Ad oggi, le Strategic Communities di AFIL sono 7: Machinery, De- and Remanufacturing for Circular Economy, Advanced Polymers, Additive Manufacturing, Secure and Sustainable Food Manufacturing, Smart Components, Digital Transformation. Per maggiori informazioni in merito alle attività di AFIL e per le modalità di adesione al Cluster, si invita a visitare il sito www.afil.it oppure a scrivere all’indirizzo comunicazione@afil.it.
E I BENEFICI
PER L’AMBIENTE
DELL’ADOZIONE
DELLA DC LAPP
di E.S.
IInsieme a quella della digitalizzazione, il settore industriale si trova oggi ad affrontare la sfida della transizione energetica verso modelli più efficienti e sostenibili. Un tema di portata globale, particolarmente sentito nel nostro Paese, le cui aziende si trovano a sostenere prezzi per l’approvvigionamento energetico tra i più alti in Europa, fra il 40% e il 50% in più, in media, rispetto alle concorrenti europee, secondo Confindustria.
In questo contesto, una transizione alla corrente continua si delinea per l’industria come una delle soluzioni più promettenti, rispondendo alle esigenze di sostenibilità ed efficienza, offrendo al tempo stesso vantaggi economici e operSrente continua in uno stabilimento produttivo può idealmente portare ad una riduzione delle perdite di energia del 15%, un risparmio del 30% su risorse e componenti e del 20%
nella gestione energetica complessiva.
“Il potenziale della corrente continua negli impianti produttivi è ancora poco noto. Una transizione alla corrente continua assicurerebbe, infatti, una maggiore efficienza energetica e costi minori per la componentistica”, sottolinea Gaetano Grasso, Direttore marketing di LAPP Italia.
La corrente continua porterebbe con sé diversi altri vantaggi per applicazioni che già oggi si basano su “circuiti intermedi” in DC, nonché una più facile integrazione con impianti fotovoltaici e accumulatori, per impianti industriali più green e resilienti.
Un’energia più verde e resiliente, un’opportunità per Il Piano Transizione 5.0
In un impianto alimentato tramite DC grid, infatti, l’energia prodotta può essere utilizzata direttamente e accumulata. Que-
sta capacità di autoconsumo e stoccaggio locale riduce la dipendenza dalla rete pubblica e protegge gli impianti dai blackout, garantendo continuità operativa. Alla luce di queste considerazioni, il Piano Transizione 5.0, che nasce nel contesto del Green Deal e del PNRR, e ha un focus particolare sull’efficienza energetica, rappresenta un’ottima opportunità per l’adozione della DC.
Grazie ai fondi stanziati, che sommati a quelli del Piano 4.0 sono pari a circa 13 miliardi di euro nel biennio 2024-2025, le imprese italiane possono accedere a incentivi significativi per finanziare un intervento di efficientamento energetico che utilizzi la DC, abbinato all’autoconsumo da fonti rinnovabili come il fotovoltaico. La corrente continua si inserisce perfettamente in questo contesto. Le aziende che migliorano l’efficienza energetica possono benefi-
ciare di aliquote più elevate. Un intervento di efficientamento energetico che utilizzi la DC, abbinato all’autoconsumo da fonti rinnovabili come il fotovoltaico, potrebbe infatti far crescere l’aliquota fino al 60%. Non a caso l’interesse per la corrente continua comincia a farsi largo nel settore industriale, come emerge da una recente survey condotta da LAPP: il 60% degli intervistati dimostra un atteggiamento positivo nei
confronti della DC, uno su due sta considerando investimenti in questo senso, mentre un 10% li ha già fatti.
“Investire nella corrente continua non significa solo migliorare l’efficienza operativa, ma rappresenta una scelta strategica in termini di sostenibilità e competitività economica. Inoltre, permette di beneficiare indirettamente degli incentivi del Piano Transizione 5.0. L’adozione della DC diventa quindi un’op-
portunità concreta per le imprese italiane di guidare la transizione energetica e digitale. LAPP è pronta ad affiancare le aziende in questa evoluzione”, commenta Francesco Basile, Product Marketing Manager di LAPP Italia. LAPP pronta per il futuro
Come pioniere nel campo, oltre a impegnarsi nel promuovere i vantaggi della corrente continua in ambito industriale e la necessaria standardizzazione internazionale, LAPP è stato il primo produttore di cavi a presentare un portfolio prodotti dedicati.
Questi includono, ad esempio:
- Il cavo ÖLFLEX® DC GRID 100 per l’approvvigionamento energetico di impianti in reti con corrente continua negli edifici e per il collegamento negli impianti industriali),
- Il cavo ÖLFLEX® DC 100, per applicazioni DC in ambito industriale,
- il cavo ÖLFLEX® DC SERVO 700 DC per servomotori per posa fissa o impiego con movimento occasionale per il collegamento alla rete DC,
- il cavo ÖLFLEX® DC CHAIN 800 per applicazioni in catene portacavi in condizioni gravose,
- il primo cavo DC per robot ÖLFLEX® DC ROBOT 900, studiato per resistere a sollecitazioni a torsione e flessione in condizioni gravose,
- il cavo ÖLFLEX® DC ESS SC, privo di alogeni e autoestinguente, ideale per applicazioni DC fino a 1,5 kV per l’utilizzo in sistemi di accumulo di energia.
- il cavo ÖLFLEX® SOLAR, destinato al collegamento dei pannelli fotovoltaici, dal design ottimizzato e dall’elevata resistenza al volume anche dopo lunghi periodi in acqua.
Rivedi il recente webinar organizzato da LAPP e ANIE e scopri di più sui vantaggi della corrente continua, anche in relazione al nuovo Piano Transizione 5.0 QR CODE
L’EVENTO, CONCLUSOSI LO SCORSO 12 OTTOBRE, HA VISTO LA PARTECIPAZIONE DI OLTRE 750 IMPRESE, L’85% IN PIÙ RISPETTO AL 2022, SU 65.000 METRI QUADRATI DI SPAZIO ESPOSITIVO, CON IL 37% DELLE AZIENDE PROVENIENTI DALL’ESTERO
di Giaime Lotti
LLa 34ª edizione di BI-MU, fiera internazionale biennale dedicata all’industria delle macchine utensili, robot, automazione, digital manufacturing e additive manufacturing, si è conclusa il 12 ottobre 2024 a Fieramilano Rho. L’evento, organizzato da EFIM (Ente Fiere Italiane Macchine) e promosso da UCIMU-Sistemi per Produrre, ha avuto una partecipazione significativa con oltre 750 aziende espositrici, un incremento dell’85% rispetto all’edizione precedente. Le imprese hanno occupato una superficie totale di 65.000 metri quadrati, e il 37% di queste proveniva dall’estero, rappresentando paesi come Germania, Giappone, Stati Uniti, Cina, Corea del Sud, Regno Unito e molti altri. Durante i quattro giorni di fiera, sono stati registrati circa 35.000 visitatori professionali, di cui il 5% provenienti dall’estero, rappresentando 62 nazionalità diverse. Le presenze straniere più significative includevano operatori da Germania, Svizzera, Francia, Spagna, Stati Uniti, Brasile, Cina, Giappone, Corea del Sud e Taiwan. Nell’ambito di una missione organizzata da UCIMU in collaborazione con ICE-Agenzia e il Ministero degli Affari Esteri, sono stati invitati circa 80 operatori e giornalisti da 16 paesi, tra cui Cina, Brasile, Egitto e Vietnam. Un’importante novità di questa edizione è stata la forte partecipazione dei giovani.
la partecipazione di otto team scolastici che si sono sfidati in una finale svoltasi il 12 ottobre.
La fiera ha ospitato più di 80 eventi organizzati sia dagli espositori che dall’organizzazione stessa, molti dei quali si sono svolti nell’Arena BI-MUpiù.
Oltre 4.000 studenti hanno visitato la fiera, accompagnati da 55 tutor provenienti da istituti tecnici superiori (ITS). Per la prima volta, l’evento ha aperto le porte anche agli studenti delle scuole medie, incoraggiando il dialogo tra scuola e industria attraverso il progetto “Education & Job” e l’area ROBOTGAMES. Un concorso speciale di automazione e robotica, il “ROBOTGAMES”, ha visto
Qui, durante la cerimonia inaugurale, il fisico Federico Faggin, inventore del microprocessore, è stato intervistato da Simone Spetia di Radio 24. I numerosi interventi, tra cui 60 speech, hanno coinvolto oltre 1.400 partecipanti dal vivo e circa 5.000 online, grazie al servizio di live streaming. Di particolare rilievo è stata la “Giornata della Robotica”, con la partecipazione di organizzazioni chiave come IFR, SIRI, I-RIM e AIxIA, che hanno discusso le potenzialità delle nuove tecnologie nei mercati globali. L’IFR ha inoltre scelto BI-MU per ospitare la propria assemblea annuale. L’impegno della manifestazione per la sostenibilità ha portato al conseguimento della certificazione ISO 20121:2013, attestando la sua organizzazione secondo criteri di sostenibilità ambientale, economica e sociale. Anche l’attività online di BI-MU è stata significativa: il sito ufficiale ha visto un aumento dell’8% di visitatori unici rispetto al 2022, mentre sui social media la community è cresciuta notevolmente. LinkedIn ha registrato il maggior numero di interazioni, con un incremento di circa 1.000 follower solo nel mese precedente alla manifestazione, arrivando a 4.017 utenti, il doppio rispetto alla precedente edizione.
Il prossimo appuntamento con la 35ª edizione di BI-MU è fissato per ottobre 2026, in cui la manifestazione celebrerà i suoi 70 anni di attività, continuando a essere un punto di riferimento per il settore delle macchine utensili e dell’automazione
La visione di Fanuc sulla nuova fabbrica intelligente ed efficiente. Ne parliamo con Cristian Bosi nuovo Managing Director della filiale italiana di Fabio Chiavieri
La presenza a una manifestazione fieristica come BIMU rappresenta un momento dove, oggi più che mai, le aziende, oltre a presentare il meglio della loro produzione, colgono l’occasione per trasmettere al mercato il concept e le strategie che stanno indirizzando lo sviluppo tecnologico. Fanuc ha offerto un doppio appuntamento per esplorare le tecnologie e le strategie della nuova fabbrica intelligente ed efficiente, presentando soluzioni innovative, tra cui l’anteprima del nuovo controllo numerico FS500i-A, il controllore R-50iA per robot e il centro di lavoro ROBODRILL Mixtype.
In ottica Transizione 5.0 ha inoltre introdotto un sistema di certificazione dei consumi, fondamentale per accedere ai crediti d’imposta del piano. A Industria 5.0 è stato anche dedicato il Technova-
tion Forum 2024, un evento dedicato al mondo industriale italiano. Al netto dell’innovazione tecnologica, rimane da capire quali sono le strategie che si celano dietro un gruppo così importante che punta a mantenere la propria leadership sul mercato. In occasione di BIMU abbiamo così incontrato il nuovo Managing Director di Fanuc Italia Cristian Bosi.
Ing. Bosi, alla luce del contesto economico e geopolitico che stiamo vivendo quale sarà l’andamento dei prossimi anni?
Gli anni post Covid sono stati molto altalenanti per tutti i settori industriali. Il 2023 è stato sicuramente un anno importante, mentre l’anno in corso lo vedo più di transizione. Sul prossimo triennio,
a parte il primo trimestre 2025 di difficile interpretazione, secondo molti indici economici si può essere cautamente positivi.
La robotica ha passato anni di forte crescita, oggi in alcuni paesi si nota un certo rallentamento. Quale sarà il ruolo della robotica nei prossimi anni?
L’automazione in generale, e la robotica in particolare, sono visti come elementi essenziali di guadagno di produttività e competitività per le imprese, in un’epoca in cui il passaggio generazionale marca una carenza di forza lavoro specializzata. Per quanto riguarda i Cobot, penso che siano in una fase iniziale di diffusione, essendo presenti molte opportunità per comunicare i vantaggi che i collaborativi
possono offrire. Ancora siamo in presenza di un problema culturale che all’interno delle singole imprese, soprattutto di medio e piccole dimensioni, ostacola il reale percepimento delle opportunità e delle applicazioni possibili. Il ruolo di Fanuc è anche quello di diffondere la cultura in questo settore.
Al vostro stand si possono apprezzare vere e proprie soluzioni applicative piuttosto che il singolo prodotto, quanto è importante questo approccio al cliente?
Direi che è fondamentale. Il cliente ha bisogno di una soluzione completa ed è evidente che bisogna proseguire in sinergia con integratori e programmatori. A tale scopo organizzeremo degli eventi basati su incontri tecnici con l’obiettivo di offrire questi servizi al cliente finale. Questo è solo un elemento della nostra strategia sul mercato che si fonda su innovazione tecnologica, digitalizzazione e sostenibilità. Quest’ultima diverrà ancora più preponderante in ottica transizione 5.0, sebbene Fanuc porti avanti già da decenni questi paradigmi come filosofia propria. Oggi, c’è sicuramente da parti di tutti una sensibilità maggiore all’utilizzo delle risorse e alla diminuzione degli sprechi.
C’è un altro elemento che oggi sta diventando sempre più dirompente ed è l’Intelligenza Artificiale. Qual è la vostra visione?
È un tema molto delicato che va regolato in termini etici, sociali e politici. Rimanendo nell’ambito manifatturiero, quindi di automazione industriale, penso che sia portatrice di benefici nell’IoT delle imprese, dove peraltro Fanuc si propone come unico player mondiale in grado di fornire e costruire al proprio interno tutti i componenti. In questo contesto, se saremo in grado attraverso la digitalizzazione di far dialogare i singoli componenti per essere più efficienti, migliorare i cicli di lavoro, sprecare meno energia e materiale, possiamo capire che l’IA è una tecnologia da abbracciare.
Qual è la fotografia del mercato ita-
liano dal vostro punto di vista?
In Italia, la robotica vive di una maggiore diversificazione settoriale per cui, avendo anche alle spalle un macrotrend positivo, sta andando molto bene, tenendo conto che il 2023 è stato per Fanuc un anno eccellente e il 2024 è di tenuta. Come ho già detto pensiamo che nel triennio a venire assisteremo nuovamente a una crescita sostenuta.
In Europa c’è un grosso problema nel settore Auto legato al cambiamento in atto che punta ai motori elettrici con tutto ciò che ne consegue. Oltre a ciò, ogni giorno si mescola una voce che rimette in gioco i motori endotermici. Questa mancanza di chiarezza sta penalizzando gli investimenti?
La penalizzazione è molto forte perché, senza entrare nel merito della valutazione, c’è un indirizzo ormai molto chiaro che non trova riscontro né sul mercato, né nella parte infrastrutturale pronto ad accoglierlo. Questo ha comportato dei carichi enormi sui costruttori automobilistici dal punto di vista economico e stanno condizionando gli investimenti. L’Italia attraverso la Transizione 5.0 cerca di rinvigorire gli investimenti con incentivi importanti che impatteranno positivamente sul mercato già a partire dal prossimo anno.
La digitalizzazione, l’automazione spinta, l’IA sono tecnologie che richiedono nuove competenze, e qui entra in gioco la formazione. Cosa fa Fanuc in questo ambito?
Tra le strategie di Fanuc, oltre a quelle che sono citate nella domanda, è inclusa una parte considerata molto importante che è il mondo Education. Fanuc è impegnata ad avvicinare la scuola a questo nostro settore e ad aiutare gli studenti a essere certificati e acquisire una competenza spendibile sul mercato. Siamo attivi in più di 300 Istituti scolastici, inoltre, Fanuc è sponsor ufficiale a livello internazionale della categoria Sistemi robotici integrati nelle WorldSkills, le cosiddette olimpiadi dei mestieri. Nell’ultima edizione, tenutasi a Lione, Fanuc ha seguito due ragazzi italiani che si sono misurati con altri loro coetanei provenienti da altri paesi. Durante l’anno, poi, ospitiamo studenti delle scuole fornendo loro una formazione avanzata presso la nostra sede di Lainate.
Le principali proposte Fanuc alla BIMU
Sono numerose le novità per l’automazione intelligente dei processi produttivi che Fanuc ha introdotto nel corso della kermesse milanese, a partire da una preview assoluta per l’Italia: la nuova serie di controlli numerici FS500i-A, anteprima dell’evoluzione futura della serie di CNC Plus, progettati specificatamente per supportare le aziende nella transizione a Industria 5.0. Un concetto progettuale che spinge nella direzione della semplicità di utilizzo, anche da parte degli operatori meno esperti, grazie all’interfaccia basata su web. Le prestazioni sono potenziate dalla CPU più veloce, architettura dual engine e da tempi di elaborazione 2,7 volte superiori alla serie Plus precedente. Massima attenzione anche al risparmio energetico, con miglioramenti che abilitano una produzione assai più sostenibile e l’implementazione di componenti ottimizzati per la rigenerazione rapida dell’energia, come i nuovi servomotori iD/iB; amplificatori e motori sono più piccoli, più potenti e più efficienti, e il design rigenerativo dei componenti di automazione contribuisce a ridurre i consumi di energia fino al 10% in meno rispetto ai consumi tradizionali
Anteprima italiana anche per il nuovo controller R-50iA per robot industriali e collaborativi, caratterizzato da cybersecurity integrata, nuove funzioni intelligenti e consumi energetici ridotti. Le ventole a bassa potenza e i servo amplificatori ad alto rendimento riducono significativamente il consumo di energia, contribuendo a diminuire l’impatto ambientale delle attività produttive.
La modalità di funzionamento Eco, inoltre, ottimizza ulteriormente i consumi energetici, garantendo al contempo movimenti fluidi e traiettorie precise. Il supporto degli standard IEC 62443-4-1
e IEC 62443-4-2 garantisce una protezione solida e certificata contro attacchi informatici e intrusioni non autorizzate. Le funzioni di sicurezza integrate, come SFTP, HTTPS e firewall, unite all’autenticazione utente corporate con password, offrono un livello di protezione senza precedenti.
Il Digital Twin è una tecnologia sempre più protagonista dei processi produttivi del manifatturiero. Questa replica virtuale permette di ottimizzare la produzione, ridurre i costi, migliorare la qualità e prendere decisioni più informate grazie alla simulazione e all’analisi dei dati in tempo
reale. Le proposte di FANUC per il Digital Twin comprendono software sia per la replica digitale dei robot che delle macchine utensili. Si tratta di una prospettiva unica nel mondo dell’automazione, perché FANUC è l’unico fornitore di soluzioni di automazione che produce sia robot che controlli numerici e macchine utensili, oltre a software IoT. Il software ROBOGUIDE per la programmazione e la simulazione in ambiente 3D dei robot consente di replicare con precisione i movimenti dei robot e dei dispositivi esterni all’interno di una cella di lavoro. Il tool CNC Guide 2 risulta particolarmente utile per individuare alcune impostazioni del controllo assi migliorative senza dover effettuare continui test su macchine già in ramp-up di produzione.
L’applicazione CNC Reflection Studio rappresenta l’intera macchina in un ambiente virtuale 3D, inclusa la verifica di eventuali collisioni prima della produzione effettiva del pezzo, semplificando il virtual commissioning e offrendo una replica digitale accattivante della macchina CNC per visualizzarne il comportamento, così come quello dei pezzi, delle attrezzature e delle configurazioni degli utensili.
La flessibilità produttiva è oramai un imperativo in ambito manifatturiero, unitamente alla compattezza e alla richiesta di soddisfare requisiti stringenti. Ecco, quindi, la new entry nella gamma di centri di lavoro Fanuc Robodrill: si tratta del nuovo centro di lavoro Fanuc Robodrill α-DiB5 ADV Y500 “Mixtype” per effettuare lavorazioni di fresatura e tornitura, caratterizzato da cambio utensile superveloce di 0,7 secondi, magazzino potenziato fino a 28 utensili, corsa dell’asse Y estesa a 500 mm, tavola più grande e accelerazione dell’asse Z incrementata per una traslazione più rapida. Progettata per coprire una gamma più ampia di lavorazioni che coinvolgono pezzi di grandi dimensioni, come le parti EV, la nuova ROBODRILL dispone di un controllo ottimale di accelerazione e decelerazione per una maggiore efficienza.
17 - 18 - 19 GIUGNO 2025
Un appuntamento dedicato ai progettisti di impianti, macchine, processi e software per dare luce ai nuovi trend tecnologici dei principali settori industriali.
www.progettistapiu.it
info@progettistapiu.it
“Design, Make, Inspect”: Hexagon presenta il concetto di innovazione integrata in ogni fase del ciclo di vita del prodotto di Fabio Chiavieri
La partecipazione di Manufacturing Intelligence di Hexagon alla scorsa edizione di BI-MU è stata caratterizzata da un chiaro file rouge: “Design, Make, Inspect”, rappresenta un approccio integrato che abbraccia ogni fase del ciclo di vita del prodotto con soluzioni integrate che migliorano l’efficienza, la qualità e l’innovazione nel processo di sviluppo e produzione. Partendo da questo presupposto, i visitatori hanno “toccato con mano” applicazioni CAD/ CAE per la progettazione, software
CAM e tecnologie di automazione per la produzione così come strumenti di metrologia e ispezione laser per il controllo qualità, accompagnati da analisi dei dati e soluzioni di intelligenza artificiale per ottimizzare i processi produttivi.
In particolare, sono stati presentati, per la prima volta a un evento pubblico italiano, i nuovi scanner manuali Atlascan Max e MarvelScan che consentono a ingegneri e personale di produzione di scansionare con
facilità ciò che serve in molteplici ambienti di ispezione, per tutti i settori industriali, tra cui automotive, ferroviario, delle apparecchiature industriali e del manufacturing.
Inoltre, allo stand erano esposti una macchina di misura a coordinate della serie Global progettata per effettuare misurazioni precise e dettagliate di oggetti tridimensionali, un braccio articolato di misura della gamma Absolute Arm con scanner laser ad altissima definizione per la misurazione e l’ispezione tridimensionale di oggetti e un laser tracker della linea Leica Absolute Tracker, strumento avanzato di misurazione 3D utilizzato per misurare pezzi di grandi dimensioni come l’elica di una petroliera o la sezione della pala di una turbina eolica, e per pianificare il loro allineamento e assemblaggio.
Chiaramente non sono mancate le offerte software CAE per la progettazione e la simulazione che consentono di analizzare e ottimizzare le prestazioni dei modelli 3D in fase di sviluppo, compresa la progettazione meccatronica e l’ottimizzazione di azionamenti per motori e sistemi robotici, software di produzione virtuale per la manifattura additiva, processi di lavorazione della lamiera, saldatura assemblaggio nonché le offerte software CAM per la programmazione di macchine utensili e l’ottimizzazione dei percorsi utensile, per migliorare l’efficienza e la precisione nella produzione.
“La partecipazione a questa nuova edizione di BI-MU – ha spiegato Luca Ruggiero Managing Director Sales di Hexagon Manufacturing Intelligence incontrato in fiera – è per noi l’occasione per consentire ai nostri clienti di ammirare tutte le nostre tecnologie sebbene in pochi metri quadrati. L’approccio verso di loro sta cambiando passando dall’essere specialisti di prodotto a solutions provider, quindi, anche al nostro interno, stiamo cercando di concatenare tutte le tecnologie per aiutare i nostri clienti a realizzare la Digital Transformation, attraverso un concept che si chiama “Design, Make, Inspect”. Questi tre termini identificano altrettanti aspetti del
La divisione Manufacturing Intelligence di Hexagon ha presentato una nuova tecnologia che permette di ridurre i tempi delle operazioni di controllo della qualità dimensionale nella produzione di grandi componenti. Grazie alla combinazione delle funzionalità di laser tracking e di laser radar è possibile effettuare misurazioni precise e dettagliate da decine di metri di distanza, rispettando ristrette tolleranze di assemblaggio. Il Leica Absolute Tracker
ATS800, realizzato con una consolidata tecnologia di misura e posizionamento, consente di migliorare significativamente la produttività nella produzione di parti di grandi dimensioni e nelle attività di assemblaggio, misurando in modo affidabile e veloce gli elementi critici e riducendo al minimo i comuni colli di bottiglia della produzione. Inoltre, questo nuovo sistema permette di misurare con precisione bordi ed elementi sottili su grandi componenti, garantendo un’elevata produttività del processo di misurazione da una distanza di sicurezza. Sia che si tratti di ispezionare grandi strutture aerospaziali o automobilistiche, sezioni di navi o componenti di turbine eoliche, non è necessario che gli operatori o i robot siano in prossimità del pezzo da misurare. In questo modo si evitano misure imprecise e problemi di sicurezza, il tutto con un notevole risparmio di tempo.
processo produttivo: progettazione, produzione efficiente e ispezione. Siamo tra i pochi a poter offrire sia tecnologie software relativamente alla parte di progettazione, sia tecnologie inerenti alla qualità che sono più afferenti all’hardware. Inoltre, impieghiamo tecniche di machine learning e Intelligenza Artificiale grazie alle quali è possibile modificare in modo autonomo una serie di parametri di processo in maniera da ottimizzare il risultato finale. Questo nuovo approccio è il frutto di una
strategia aziendale che negli ultimi 25 anni ha puntato su un certo numero di acquisizioni. In una prima fase si è puntato soprattutto sull’hardware, mentre nell’ultimo decennio si è concentrato tutto sul software. L’obiettivo ultimo è quello di riposizionare Hexagon come solutions provider.”
Qual è l’impatto che hanno e che avranno in futuro il machine learning e l’IA?
Certamente un impatto considerevole sia per quanto riguarda il mercato sia per
Hexagon. Tutto ciò che sta accadendo negli ultimi tempi è indirizzato alla ricerca di ottimizzazione dei processi e sostenibilità. Tuttavia, non è possibile analizzare in modo dettagliato se la strada percorsa è quella corretta senza avere dei dati da verificare. Per questo stiamo costruendo una piattaforma che si chiama Nexus, che sarà un collettore di tutte le nostre tecnologie e centralizzerà la raccolta dei dati analizzandoli in maniera esperienziale grazie all’impiego di un kernel di prodotti basato sul machine learning e intelligenza artificiale. Da tutte le parti – e torno al concept Design, Make, Inspect” – vengono prodotti dati che giocoforza dovranno essere analizzati per ottimizzare i processi che li generano. Oggi siamo in una fase cruciale dove queste tecnologie stanno facendo i primi velocissimi passi di penetrazione sul mercato ed Hexagon è pronta a investire molto per non farsi trovare impreparata. Industria 4.0 è stata il primo step che ha imposto alle aziende di acquisire tecnologie che
La divisione Manufacturing Intelligence di Hexagon ha annunciato una nuova tecnologia di scansione 3D portatile che va ad integrarsi nell’ampia gamma di dispositivi di controllo della produzione dell’azienda, offrendo funzionalità di misura flessibile senza precedenti. I nuovi dispositivi manuali di scansione 3D, unici nel loro genere, consentono a ingegneri e personale di produzione di scansionare con facilità ciò che serve in molteplici ambienti, sia all’interno che all’esterno della fabbrica.
I nuovi dispositivi manuali Atlascan Max e Marvelscan sono ideali per la misura in molteplici ambienti di ispezione in cui la metrologia non è tradizionalmente impiegata, tra cui il settore automotive, ferroviario, delle apparecchiature industriali e del manufacturing in generale, nonché in progetti di conservazione e restauro al di fuori della produzione. I nuovi scanner 3D, estremamente portatili, sono ideali per applicazioni di controllo della qualità manuale e automatizzato e per molteplici esigenze di reverse engineering.
consentono di monitorare in dettaglio i dati generati. Con Industria 5.0 entra in gioco il concetto di sostenibilità che sta diventando un’esigenza diffusa tra i nostri clienti di tutto il mondo; anche Hexagon sta implementando al proprio interno tutte le tecnologie per essere
sempre più sostenibile.
Qual è il vostro trend di mercato a fronte di un rallentamento del comparto macchine utensili? Offrendo soluzioni di processo, Hexagon segue trend di mercato che sono in crescita. Il calo generalizzato del consumo di macchine utensili non è stato inaspettato vista la fine del grosso degli incentivi legati alla Transizione 4.0, ma anche per le note vicende che hanno portato a un aumento dei tassi di interesse con la conseguente diminuzione degli investimenti. Anche per noi la divisione hardware è stabile mentre è in crescita tutta la divisione software per cui ci riteniamo soddisfatti considerando ciò che sta accadendo nel mondo e la frenata di alcuni mercati abitualmente trainanti come Germania e Cina.
Cosa presentate di nuovo in BIMU?
Oltre alla visione di “Design, Make, Inspect” ben chiara all’interno dello stand con la volontà di mettere in evidenza la bontà della soluzione e non del singolo prodotto, presentiamo in fiera alcune grosse innovazioni quali il Leica Absolute Tracker ATS800 e due nuovi scanner 3D manuali.
Dossier di approfondimento tematico
Tutorial di aggiornamento professionale
Case history selezionate dal comitato
Progettisti d’impianti, società di
* diffusione che verrà assoggettata a certificazione
Versione cartacea
Si amplia l’appuntamento con l’inserimento dei nuovi lemmi della meccatronica alla guida multilingue dei termini della meccanica che raggruppa circa 3.000 termini tecnici, già tradotti in ben 9 lingue. Un fascicolo personalizzabile nelle copertine, nella foliazione (con l’inserimento di quartino) e disponibile anche per piccole tirature.
Versione web
www.terminidellameccanica.com, guida online gratuita, consultata quotidianamente da tutti gli attori del mondo della meccanica, permette la sponsorizzazione di una serie di termini, collegando la selezione ai dati aziendali o di prodotto, immediatamente visibili durante la consultazione.
HEIDENHAIN alla 34.BI-MU:
soluzioni sostenibili per utilizzatori e costruttori di macchine utensili riducono carbon footprint e TCO
HEIDENHAIN
A che punto sono gli utilizzatori e i costruttori di macchine utensili nel percorso verso la maggiore sostenibilità? Quali misure potrebbero adottare con l’obiettivo di ridurre il footprint CO2 e il costo totale di gestione (TCO)? “Stairway to Sustainability – Maggiore produttività fin dal primo pezzo” è lo slogan con cui HEIDENHAIN si è presentata alla 34.BI-MU
Tre nuove versioni hardware con monitor da 24“, 19“ e 16“ e due diverse tastiere ampliano la flessibilità applicativa del controllo numerico intuitivo TNC7 HEIDENHAIN. Alla 34.BI-MU i riflettori sono puntati su TNC7 basic, la variante con monitor da 16“. Completa la gamma TNC7 verso il basso in termini di dimensioni e offre tutti i vantaggi tipici di TNC7 per macchine a 3+2 assi. Anche per l‘evoluzione del controllo numerico TNC 620 sono disponibili gli highlight di TNC7: monitor con risoluzione Full HD e ampio pacchetto di opzioni con
funzioni quali setup grafico 6D MAS, Controllo anticollisione dinamico DCM oppure cicli di fresatura trocoidale OCM, che migliorano ulteriormente facilità d‘uso, efficienza e affidabilità della nuova generazione di controlli numerici HEIDENHAIN.
Soluzioni software innovative per la Fabbrica Digitale: l’ultima versione del software StateMonitor con monitoraggio energetico e collegamento ERP
Il software MDA StateMonitor della
Fabbrica Digitale HEIDENHAIN consente di consultare in tempo reale lo stato di produzione delle macchine CNC in officina. StateMonitor rileva i dati macchina quali operatività, dati utensile, tempi di esecuzione dei programmi NC oppure segnali PLC, li analizza e li visualizza. Nell‘ultima versione software gli operatori possono perfettamente analizzare anche i dati dettagliati dei consumi effettivi di energia elettrica, aria compressa e acqua di processo permettendo di individuare le potenziali ottimizzazioni
sulla base delle informazioni acquisite. Il nuovo collegamento ERP consente inoltre di condividere automaticamente i dati con i sistemi ERP e MES per processi altamente efficienti nella Fabbrica Digitale. StateMonitor HEIDENHAIN assicura così una trasparenza ancora maggiore in officina.
3 funzioni in 1 sistema per la verifica completa degli utensili: telecamera VT 122 con software intelligente VTC La nuova telecamera di misura VT 122 con il software VTC di HEIDENHAIN svolge tre funzioni in un unico sistema: dispositivo di presetting, microscopio e ispezione visiva degli utensili. Invece di portare gli utensili ai laboratori metrologici, le immagini riprese direttamente nell‘area di lavoro della macchina consentono di ispezionare in modo dettagliato i taglienti fornendo informazioni per la valutazione globale degli utensili. Le caratteristiche intelligenti e combinate di telecamera VT 122 e software VTC consentono una misurazione automatizzata di lunghezza e diametro. Le immagini acquisite consentono di misurare manualmente la larghezza di usura e di ispezionare gli utensili fin nei minimi dettagli. I vantaggi per gli utilizzatori consistono in un sensibile incremento della produttività, una documentazione automatizzata, riproducibile in ogni momento, dello stato dell‘utensile e dello sviluppo dell‘usura come pure notevoli risparmi di tempo riducendo il TCO per le
Risparmio di 6 secondi a ogni controllo di rottura: il sensore di rottura utensile TD 110 HEIDENHAIN verifica anche microutensili direttamente nell’area di lavoro della macchina e in rapido
prove di durata utile.
Tempi produttivi più lunghi e sicurezza di processo più elevata: il sensore di rottura utensile TD 110
HEIDENHAIN
Verifica della rottura di utensili nell‘area di lavoro della macchina completamente integrata in processi automatizzati: il sensore di rottura utensile TD 110
HEIDENHAIN garantisce notevoli vantaggi in termini di tempo per gli utilizzatori minimizzando al contempo gli scarti, due aspetti cruciali per una produzione sostenibile. TD 110 risparmia fino a 6 secondi per
l‘ispezione della rottura utensile, e anche a ogni cambio utensile. Questo perché identifica un utensile rotto nel passaggio dal magazzino utensili all‘area di lavoro della macchina o viceversa. Il sensore di rottura utensili TD 110, compatto e robusto, può essere installato nell‘area di lavoro di quasi tutte le macchine utensili nelle immediate vicinanze della tavola.
Lettura perfetta della riga graduata senza pressurizzazione: i sistemi di misura HEIDENHAIN con tecnologia innovativa True Image riducono il footprint CO2 del 99% L‘uso di lubrorefrigeranti durante la lavorazione determina contaminazioni liquide e formazione di condensa nella macchina utensile. I sistemi di misura lineari HEIDENHAIN delle serie LC e LB e i sistemi di misura angolari delle serie RCN ed ECA offrono tuttavia una lettura chiara della riga graduata nonostante le contaminazioni. La tecnologia innovativa True Image è così affidabile che le apparecchiature possono essere impiegate in molti casi senza aria compressa, semplificando il sistema di pressurizzazione. I vantaggi del rilevamento di posizione nel Closed Loop possono essere sfruttati con footprint CO2 ridotto fino al 99% e costi di sistema molto più bassi.
PRODOTTI E SERVIZI TECNOLOGICI PER IL MONDO
Hilti Italia ha partecipato alla Bi-Mu in qualità di partner per l’innovazione con uno stand che ha ospitato numerosi visitatori interessati alle ultime soluzioni tecnologiche per il settore Machinery & Automation che evidenziano il contributo dell’IoT e della digitalizzazione nel migliorare la produttività. Inoltre, il 10 ottobre presso l’arena BI-MUpiù, Hilti ha tenuto uno speech per presentare le potenzialità del software Fieldwire per la gestione digitalizzata dei cantieri industriali
Tra le novità di Hilti, sono stati presentati gli attrezzi cordless Nuron ideali per l’uso in aree di produzione e non, il software di field management Fieldwire e i servizi di ingegneria per progettare e verificare ancoraggi per macchinari e robot nel pieno rispetto delle normative vigenti. La gamma di soluzioni Hilti per le aree di produzione e manutenzione considera la velocità di montaggio e di installazione come punti di riferimento. Tra le soluzioni di punta, si distingue la piattaforma Nuron che conta oltre 70 attrezzi cordless come trapani, avvitatori, avvitatori a impulsi e smerigliatrici angolari, 4 tipologie di batterie ad alte prestazioni, una interfaccia e servizi IoT. Questi attrezzi sono dotati di funzioni di sicurezza come la regolazione attiva della coppia e i sistemi di controllo della polvere, che aiutano a proteggere in sicurezza le squadre durante i lavori di assemblaggio e manutenzione. Inoltre, la connettività delle batterie e degli elettroutensili Nuron di Hilti offre vantaggi pratici sul campo. Sono infatti in grado di raccogliere i dati relativi ai singoli strumenti e trasmetterli alla piattaforma cloud, connettendo così cantieri e imprese, assicurando maggiore produttività e riducendo i costi di esercizio.
Il software di Field Management all-inone Fieldwire Nel corso dello speech di Michele Nicoletti, Sales Development Manager Fieldwire, presso l’arena BI-MUPIù, è emerso come il software di Hilti sia una soluzione chiave per aumentare la produttività e ridurre i ritardi nei cantieri industriali. Creato nel 2013 da un ex sviluppatore di videogiochi e acquisito da Hilti nel 2021, facilita la comunicazione tra tutte le figure coinvolte e la committenza, integrando IoT e tecnologia cloud per una gestione ottimizzata. Fieldwire ha un’interfaccia semplice e intuitiva e mira a rendere la gestione dei cantieri industriali facile e divertente. Fieldwire digitalizza infatti i documenti di cantiere in modo che le squadre possano compilare moduli sul campo e inviarli direttamente al Project Manager, migliorando la comunicazione. Questi moduli digitali possono essere firmati anche dai clienti e salvati in ordine cronologico, nel rispetto delle normative, come la ISO 9001.
Le Soluzioni per la connessione e il supporto modulare per impianti meccanici di Hilti
La connessione di macchinari o altre attrezzature che richiedono fissaggio su
acciaio o calcestruzzo può essere realizzata mediante sistemi di ancoraggio o fissaggio diretto Hilti. Ciascuna soluzione è qualificata e idonea ad applicazioni o ambienti specifici. I supporti impiantistici modulari, per tubazioni o canaline portacavi, sono progettati per rendere l’installazione più produttiva, sicura e semplice.
Le soluzioni di Hilti per progetti Industry Dal segmento manufatturiero, oil&gas, minerario, fino alle costruzioni navali, le soluzioni di progetto complete firmate Hilti integrano software, hardware e servizi tramite la digitalizzazione ed il project management, con l’obiettivo di ottimizzare e ridurre i costi durante l’intero ciclo di vita.I sistemi di ancoraggio e i supporti impiantistici modulari Hilti presentati alla Fiera BI-MU hanno mostrato come la tecnologia avanzata e la sostenibilità possano andare di pari passo, migliorando la produttività e la sicurezza delle installazioni. Queste caratteristiche permettono una totale flessibilità operativa ed una riduzione dei tempi di inattività, spesso causati da interruzioni della produzione per le manutenzioni. Inoltre, gli esperti di Hilti offrono un’assistenza completa e continua, che supporta nell’ottenimento delle autorizzazioni necessarie e nella riduzione dei costi.
25 - 26 - 27 - 28
Un appuntamento dedicato ai professionisti del settore, per approfondire insieme i temi dominanti del mondo delle costruzioni
www.costruirepiu.it 4 GIORNATE 20 SESSIONI
info@costruirepiu.it
DKC rinnova la gamma dei suoi convertitori di tensione e di frequenza della Linea RamBatt. Lo fa nel solco di una tradizione consolidata che vede nella versatilità, nell’efficienza e nella sicurezza i perché del successo che da sempre i suoi sistemi di conversione dell’energia riscuotono. Questi i punti di forza, oggi resi ancora più solidi, non solo di questi specifici prodotti, ma dell’intero catalogo che DKC propone, ricco di soluzioni interamente ideate e sviluppate in Italia e concepite per essere tra loro facilmente integrabili, così da assicurare ai professionisti di diversi comparti un’offerta davvero coordinata. Nel contesto di questa visione si inserisce l’aggiornamento della famiglia di convertitori di tensione e di frequenza della Linea RamBatt, destinati a tutte quelle aziende che ambiscono a rendere i propri prodotti adeguati ad un uso in contesti internazionali, senza per questo dover intervenire con modifiche progettuali della parte elettrica delle apparecchiature e ad una riscrittura del software che le governa. I nuovi convertitori della Linea RamBatt di DKC trovano la loro primaria applicazione nei laboratori dove vengono eseguiti test riproducendo gli scenari più diversi, contesti dove le simulazioni necessitano di fornire energia con potenze e frequenze differenti.
I nuovi convertitori si presentano al mercato in due macro versioni: monofase e trifase.
La prima, monofase UNIVAR, è stata concepita per fornire strumenti per l’adattamento e la prova di apparecchiature in differenti contesti operativi, garantendo flessibilità ed efficienza. Sono disponibili con una potenza nominale compresa in un range tra i 3kVA e i 12 kVA, possono essere forniti in configurazione rack o tower, essere alimentati con tensioni da 96V monofase ed erogare da 25V a 270V monofase, con frequenza regolabile da 45 a 400 Hz. Ideali per una loro integrazione con macchinari industriali perché evitano dispendiosi interventi per il loro adeguamento a reti elettriche con tensioni e frequenze tra loro diverse, risultano altresì eccellenti se utilizzati in laboratori di prova, ambienti dove la loro compattezza ne facilita l’alloggiamento e l’uso.
La seconda, trifase TRIVAR, si articola in tre tipologie diverse di convertitori:
TRIVARTT: (da 8kVA a 20kVA, ideali per applicazioni di bassa potenza, compatti, facilmente trasportabili, offrono una grande versatilità e la capacità di gestire tensioni da 45V a 460V e frequen-
ze in uscita comprese tra 45 Hz e 400 Hz);
TRIVARXT: (da 15kVA a 50kVA, adatti ad alimentare macchinari di dimensioni medie, erogano corrente da 40A a 72A e frequenze in uscita da 45 Hz a 400Hz);
TRIVARXTG: (da 30kVA a 50kVA, realizzati in carpenterie industriali robuste e dotati di trasformatore interno, sono in grado di fornire tutta la potenza disponibile anche a tensioni più basse). Di assoluta rilevanza il fatto che la nuova gamma di convertitori della Linea RamBatt di DKC offre, allo scopo di garantirne un controllo efficiente e flessibile, funzionalità avanzate di monitoraggio e di gestione remota secondo caratteristiche e modalità differenziate in base al modello.
Nel caso di UNIVAR e di TRIVARTT il controllo da remoto avviene tramite porta DB15 per la selezione della tensione (variabile entro il range desiderato mediante un segnale esterno 0-10V) e della frequenza di uscita, nonché per l’accensione e lo spegnimento del dispositivo. Da evidenziare che la gestione dei parametri di uscita con software avviene attraverso la porta RS232. Per ciò che invece riguarda TRIVARXT e TRIVARXTG, l’impostazione diretta dei valori di tensione e di frequenza in uscita è resa possibile utilizzando una varietà di ingressi analogico-digitali, mentre opzioni avanzate di gestione remota sono consentite attraverso connessione USB con protocollo proprietario, garantendo in questo modo una flessibilità superiore.
La nuova gamma di convertitori della Linea RamBatt di DKC può essere personalizzata con una selezione di accessori opzionali, disponibili su richiesta al momento dell’ordine, pensati per soddisfare specifiche esigenze operative. Tra essi ruote, utili per facilitare la movimentazione, switch USB, per consentire il collegamento da remoto di più dispositivi, facilitato con l’accesso tramite un unico
punto di controllo e trasformatori, che tutti i convertitori possono integrare per adattarsi perfettamente alle diverse esigenze di installazione. Infine, DKC offre l’opportunità di “tropicalizzare” i convertitori, cioè di fornirli con schede elettroniche trattate con una lacca speciale che forma uno strato protettivo superficiale, in maniera tale da garantirne un corretto funzionamento anche in ambienti ad alta umidità e/o con elevata concentrazione salina nell’aria o in presenza di olii o trucioli ferrosi. DKC, secondo una logica che vede il puntuale supporto tecnico come la condizione indispensabile per assicurare la massima soddisfazione dei clienti, dispensa informative aggiuntive per un utilizzo ideale dei suoi convertitori di tensione e di frequenza della Linea RamBatt. L’azienda consiglia, per stabilire un loro adeguato dimensionamento e per assicurarne un uso in totale sicurezza e a lunghissimo termine, una puntuale analisi a monte dei fattori legati al carico da alimentare. Tra gli elementi su cui porre attenzione ci sono i motori (possono generare significativi
Il Gruppo DKC è una realtà storica italiana riconosciuta per la sua comprovata esperienza maturata nel campo della progettazione e della realizzazione di soluzioni per il settore elettrotecnico e dell’automazione industriale.
Il suo raggio d’azione spazia dai sistemi portacavi ai dispositivi di ricarica auto, dalla canalizzazione metallica ai gruppi di continuità, estendendosi fino alle soluzioni destinate all’ambito BT e alla distribuzione dell’energia.
Fin dalla sua fondazione, risalente agli anni Novanta, il Gruppo DKC ha perseguito una massiccia politica di acquisizione di solide e importanti aziende presenti sul territorio nazionale, strategia che ha permesso di arricchire
picchi di corrente all’avviamento e per questo può essere necessario equipaggiarli con un dispositivo soft starter) e le correnti di ritorno (nei casi in cui i motori delle macchine alimentate le inducano durante la fase di frenata queste possono provocare lo spegnimento improvviso del convertitore).
In tema di assistenza dedicata ai convertitori della Linea RamBatt, DKC mette a disposizione dei propri clienti il reparto DKC Service, dedicato al supporto tecnico e strutturato per garantire un servizio di eccellenza e la massima soddisfazione. DKC Service ne accompagna la messa in servizio con personale qualificato che si occupa della configurazione e dell’avviamento dei dispositivi, assicurando la loro piena operatività presso il sito di installazione e assicura forme di manutenzione preventiva attraverso controlli periodici effettuati sul posto finalizzati a monitorare lo stato delle apparecchiature e a sostituire parti soggette a usura, in maniera tale da prevenirne malfunzionamenti e prolungarne la vita.
progressivamente la sua offerta, allargando così senza sosta gli orizzonti del proprio business e sviluppando in più direzioni know-how e competenze tecniche specifiche.
Grazie ad una proposta di sistemi coordinati e tecnologicamente evoluti capaci di assicurare all’utente valore aggiunto e sostenibilità, frutto dell’impegno di un avanzato Reparto di Ricerca e Sviluppo, il Gruppo si è reso protagonista di una crescita rapida e incessante, garantita da un’alta professionalità e da una logistica in grado di assicurare alla clientela un livello di servizio efficace ed efficiente.
Oggi il Gruppo DKC vanta 40 tra stabilimenti produttivi (dislocati su un’area complessiva di 200 mila mq) e magazzini
(115 mila mq) sparsi nel mondo, dei quali 12 ubicati in Italia, dispone di 26 sedi in 7 Nazioni e di un organico composto da oltre 4.000 risorse.
In virtù dell’esperienza acquisita, del bagaglio di conoscenze accumulato, di uno spirito aziendale che ha la sua primaria ragione d’essere nell’affrontare con entusiasmo le sfide che il futuro riserva, nonché di una vicinanza ai clienti puntuale e fattiva, il Gruppo DKC rappresenta un alleato prezioso per installatori e progettisti e costituisce il partner ideale per l’ideazione, la progettazione e la realizzazione di soluzioni tailor-made.
Per ulteriori informazioni visita il sito https://www.dkceurope.com/it
Il nuovo tool online per moduli rotanti permette di risparmiare fino a tre settimane sui tempi di progettazione e di costruzione
Grazie al nuovo configuratore online, ingegneri e progettisti possono mettere a punto e ordinare in pochi istanti sistemi di alimentazione per applicazioni rotanti. Questo innovativo strumento permette di risparmiare settimane di lavoro di coordinamento in fase iniziale, riducendo notevolmente i tempi di progettazione complessivi. Inoltre, il risparmio ottenuto si riflette direttamente sul prezzo della soluzione configurata, offrendo agli utenti anche un interessante vantaggio economico.
“La messa a punto di soluzioni personalizzate spesso necessita di un notevole impegno nelle attività di coordinamento che possono richiedere anche diverse settimane di lavoro”, spiega Marcello Mandelli Country Manager di igus Italia e responsabile della divisione e-chain. Proprio per ottimizzare tempi e processi, igus ha sviluppato un nuovo configuratore online per i moduli rotatori. Grazie a questo strumento, ingegneri e progettisti possono ordinare in modo semplice e veloce un sistema di alimentazione personalizzato per le loro applicazioni rotanti. Ovviamente, il fatto di poter semplificare e velocizzare la progettazione assicura ai clienti anche vantaggi economici”, afferma Mandelli.
“Vogliamo aiutare i nostri clienti a risparmiare quanto più tempo e denaro possibile” Il configuratore online è stato sviluppato per offrire una user experience molto intuitiva. L’utente deve soltanto specificare il diametro esterno del sistema e decidere la serie e la larghezza della catena portacavi. Attraverso la funzione di anteprima è possibile visualizzare sul configuratore le dimensioni del sistema di alimentazione in millimetri: il diametro interno minimo, la lunghezza della catena portacavi compreso l’attacco, l’angolo di rotazione massimo e l’altezza del sistema. Se tutti i parametri soddisfano le esigenze, l’utente può passare allo step successivo visualizzando direttamente online il prezzo e i tempi di consegna del suo sistema per poi inoltrare la richiesta d’ordine con un semplice clic. Il tool consente anche di scaricare un PDF che riporta tutti i parametri dell’applicazione e di ottenere un modello CAD in formato STEP. Mandelli continua: “Dalla configurazione iniziale fino all’offerta e all’integrazione del sistema, vogliamo aiutare i nostri clienti a risparmiare quanto più tempo e denaro possibile. Ora stiamo lavorando ad uno shop online, in modo che in futuro sia possibile anche ordinare il sistema configurato in base alle esigenze specifiche”.
Secondo i dati dell’International Energy Agency (IEA) e dell’International Renewable Energy Agency (IRENA), l’energia eolica si posiziona al secondo posto per capacità installata tra le fonti rinnovabili, dietro all’energia idroelettrica e seguita dall’energia solare fotovoltaica. La rapidità della crescita dell’energia eolica è seconda solo a quella del solare fotovoltaico: la capacità degli impianti eolici secondo il Global Wind Energy Council è arrivata a superare i 900 GW nel 2023, con un tasso di crescita del 9% rispetto al 2022. La continua espansione è dovuta sia all’aumento di efficienza degli impianti e della conseguente riduzione dei costi di generazione, sia al supporto che governi e comunità tendono ad accordare a questa forma di energia nella maggior parte dei Paesi industrializzati.
Le turbine eoliche, una volta installate, non emettono gas serra durante il loro funzionamento e utilizzano una risorsa inesauribile come il vento; inoltre, hanno anche un impatto ambientale relativamente basso, se installate in siti dove non interferiscano in modo irreparabile con ecosistemi e habitat naturali, utilizzando componenti e tecnologie innovative che riducano l’impatto visivo e acustico e attuando piani di manutenzione efficiente per garantire la longevità degli impianti. Sempre secondo il Global Wind Report 2023 del Global Wind Energy Council (GWEC), l’energia eolica ha rappresentato circa l’8% della produzione globale di energia elettrica nel 2023, con un aumento rispetto al 7,3% dell’anno precedente. Inoltre, il World Energy Outlook 2023 dell’International Energy Agency (IEA) conferma che le politiche di supporto all’energia pulita stanno accelerando il ritmo di cambiamento in molti mercati chiave, contribuendo alla crescita della quota di energia eolica nel mix energetico globale. Per quanto riguarda l’Italia, secondo i dati di Terna, la società che gestisce la rete elettrica nazionale, l’energia eolica ha coperto circa il 7% del fabbisogno energetico italiano nel 2023. In quest’anno, gli impianti eolici in Italia hanno prodotto circa 20.000 GWh di energia elettrica, una quantità di energia sufficiente a soddisfare il fabbisogno annuo di una città come Los Angeles, con circa 4 milioni di abitanti. Le previsioni per il 2024 indicano un ulteriore aumento della quota di energia eolica sia a livello globale che in Italia. Il GWEC prevede che il 2024 sarà il primo anno in cui la nuova capacità eolica installata supererà i 100 GW, con una crescita del 15% rispetto al 2023. In Italia, si prevede che la capacità installata continuerà a crescere grazie agli incentivi governativi e agli investimenti nel settore delle energie rinnovabili, aumentando ulteriormente la percentuale di energia eolica nel mix energetico nazionale. Questi dati evidenziano l’importanza crescente dell’energia eolica nel panorama energetico globale e nazionale, e sottolineano come le politiche di supporto e gli investimenti tecnologici stiano contribuendo a una transizione energetica sostenibile.
Gli impianti in Italia
Attualmente, sono presenti circa 6.000 impianti eolici attivi sul territorio italiano, con una tendenza verso
l’incremento delle installazioni, soprattutto nelle regioni meridionali e nelle isole dove condizioni geofisiche e climatiche rendono più facile installarli mantenendo un equilibrio fra elevata efficienza e ridotto impatto ambientale. Esistono alcuni produttori di impianti totalmente italiani, specializzati soprattutto nella progettazione e realizzazione di turbine di piccole e medie dimensioni, che si distinguono per la semplicità di installazione. La maggior parte delle attività pertinenti al settore eolico in Italia si concentra però sulla gestione e manutenzione degli impianti, assemblati utilizzando componenti prodotti all’estero, mentre la produzione delle turbine di maggiori dimensioni è generalmente affidata a grandi multinazionali del settore. Anche in questo settore non manca però un certo successo del Made in Italy: le piccole e medie turbine hanno un mercato nell’Est europeo, mentre diverse nostre aziende esportano componenti e conoscenze tecniche.
Funzionamento dell’impianto eolico
Gli impianti eolici trasformano l’energia cinetica del vento in energia meccanica, che viene poi convertita in energia elettrica. Questo processo avviene attraverso diversi passaggi e componenti cruciali.
Le pale del rotore utilizzano la loro forma aerodinamica per convertire l’energia del vento in movimento rotatorio; questo viene trasmesso, tramite il mozzo e l’albero principale, alla scatola degli ingranaggi, se presente, o (nelle turbine a trasmissione diretta) direttamente al generatore. Nel generatore, l’energia meccanica viene convertita in energia elettrica tramite il principio dell’induzione elettromagnetica. Infine, un convertitore adatta l’energia prodotta in modo da consentirne l’immissione immediata in rete o l’immagazzinamento in batterie o altre forme di accumulo.Oltre ai componenti di base, le turbine comprendono altri elementi come il sistema di controllo e di raffreddamento, il regolatore di direzione che mantiene le pale allineate con la direzione del vento, la torre che eleva il rotore a un’altezza dove il vento è più forte e stabile, nonché la navicella, struttura che contiene albero, generatore ed eventuale scatola degli ingranaggi, proteggendo questi componenti dagli agenti atmosferici e facilitando l’accesso per le operazioni di manutenzione.
Limitatori di coppia nelle turbine eoliche
Le turbine eoliche sono progettate per funzionare in un intervallo specifico di velocità del vento: generalmente iniziano a funzionare con una velocità del vento compresa tra 3 e 4 metri al secondo (velocità di avvio), raggiungono la produttività massima trai 12 e i 15 metri al secondo (velocità nominale) e continuano a funzionare finché il vento raggiunge velocità intorno ai 25 metri al secondo (90 Km/h). Se questa velocità viene superata per un intervallo di tempo significativo è opportuno che la turbina si fermi automaticamente; in caso contrario potrebbero verificarsi danni strutturali anche gravi, dalla deformazione o rottura delle pale, ai danni alla scatola degli ingranaggi, fino al surriscaldamento e danneggiamento del generatore. Proprio nella navicella, fra
l’albero principale e la scatola degli ingranaggi (o, nel caso di turbine a trasmissione diretta, fra l’albero e il generatore) trova collocazione il limitatore di coppia a frizione. Questo componente, fondamentale per garantire la sicurezza e la longevità della turbina, previene i sovraccarichi che potrebbero danneggiare i componenti meccanici.Per essere adeguati all’utilizzo in un impianto eolico, i limitatori di coppia a frizione devono avere specifiche caratteristiche. Le condizioni estreme che possono crearsi in caso di forti raffiche impongono componenti di grande robustezza e affidabilità, in grado di resistere ai cicli di carico variabili e intensi. I limitatori di coppia devono inoltre avere necessità di manutenzione minima per ridurre i costi operativi. Infine, è fondamentale che siano precisi, per garantire la prevenzione dei danni, intervenendo al superamento della coppia preimpostata, senza però interrompere la produzione di energia al di sotto della soglia critica.
Funzionamento dei limitatori di coppia a frizione I limitatori di coppia a frizione sono dispositivi meccanici che controllano la quantità di coppia trasmessa dall’albero principale alla scatola degli ingranaggi e/o al generatore. Una velocità eccessiva del vento, una direzione diversa da quella prevista o una turbolenza eccessiva, a seconda delle caratteristiche progettuali della turbina, può far attivare il limitatore. In questo caso, il meccanismo di frizione inizia a slittare, limitando la trasmissione della coppia e proteggendo gli altri componenti della turbina. Il limitatore di coppia naturalmente non può ridurre la velocità del vento, però può prevenire che questo causi un eccessivo aumento di velocità del rotore garantendo che continui a funzionare in sicurezza. Riducendo i picchi di carico, previene danni alla scatola degli ingranaggi, al rotore e ad altri componenti meccanici.
Vantaggi dei limitatori di coppia a frizione per l’eolico
Il funzionamento dei limitatori di coppia a frizione è studiato in modo tale da permettere di dissipare gradualmente l’energia in eccesso tramite slittamento controllato, mantenendo la connessione meccanica mentre viene ridotta la coppia trasmessa.
Queste caratteristiche li rendono ideali nelle applicazioni in cui è preferibile evitare interruzioni improvvise e dove una gestione graduale del sovraccarico può prevenire danni senza fermare l’intero sistema. Gestendo i sovraccarichi con maggior gradualità, un limitatore di coppia a frizione può ridurre i costi di manutenzione e i malfunzionamenti improvvisi.
Per questo motivo i limitatori di copia a frizione sono utilizzati spesso in impianti che richiedono continuità operativa nonostante i sovraccarichi temporanei, come appunto nelle centrali eoliche.
I limitatori di coppia a frizione ROBA
I limitatori di coppia a frizione ROBA (ROBA-slip hub) prodotti da Mayr hanno aspetti progettuali e costruttivi che li rendono perfettamente idonei all’utilizzo di impianti eolici e si distinguono per diverse caratteristiche specifiche che offrono notevoli vantaggi.
Anche in applicazioni ad alta intensità, questi limitatori offrono una precisione elevata e costante nel tempo, senza che siano necessarie regolazioni frequenti per mantenerla. ROBA-slip hub si caratterizza
infatti per un’elevata precisione di disconnessione e una ripetibilità accurata, garantendo che il sistema si disinnesti sempre al valore di coppia predefinito. Questa precisione è cruciale per proteggere componenti costosi e delicati nelle turbine eoliche. I limitatori di coppia a frizione ROBA sono estremamente affidabili, con una costruzione robusta ideale per condizioni operative difficili e variabili. Sono inoltre ampiamente configurabili, il che consente un’accurata personalizzazione per esigenze specifiche, come la gestione di differenti intervalli di coppia e velocità operative. ROBA-slip hub è facile da installare e ha esigenze di manutenzione molto ridotte. La regolazione continua della coppia permette una calibrazione fine senza necessità di strumenti complessi. Rispetto ad altri limitatori di coppia a frizione, la precisione di ROBAslip hub è maggiore e la manutenzione meno frequente, grazie alle superfici di frizione particolarmente resistenti all’usura. Anche il confronto con i limitatori di coppia a sfera evidenzia i vantaggi di ROBA-slip hub, che non richiede un reset manuale dopo ogni disinnesto, aumentando l’efficienza anche in applicazioni ad alta frequenza di sovraccarico. Infine, rispetto ai limitatori con la rottura della spina a taglio, ROBAslip hub presenta il vantaggio di non dover essere sostituito quando si verifica il sovraccarico, il che nelle turbine eoliche implicherebbe una manutenzione laboriosa e costosa.
I limitatori di coppia a frizione svolgono un ruolo vitale nella protezione delle turbine eoliche, permettendo di operare in sicurezza anche in condizioni di vento avverso. Essi assicurano che la produzione di energia rimanga stabile e che i componenti meccanici non subiscano danni, prolungando la vita utile della turbina e garantendo un funzionamento efficiente e sicuro. Utilizzando i limitatori di coppia a frizione ROBA, i costruttori di impianti eolici possono beneficiare di tempi di fermo ridotti, maggior efficienza e allungamento della vita utile delle turbine.
La gamma Mayr per l’eolico
Oltre ai limitatori di coppia a frizione ROBA, Mayr mette a disposizione di progettisti e produttori di generatori eolici anche le sue competenze e la sua esperienza pluridecennale nel settore fornendo un’ampia gamma di freni di sicurezza, in grado di garantire tempi di fermo minimi e caratterizzati da elevata flessibilità del design costruttivo. I freni Mayr per le applicazioni offshore sono disponibili anche in versioni per climi freddi, certificate per applicazioni fino a -40°C dal Germanic Lloyd (GL).Fra i modelli di freno più apprezzati nel settore si può ricordare ROBA-stop-M Servo-pitch, progettato per installazione all’estremità libera dell’albero e perfetto per i servomotori dell’asse pitch dei generatori eolici, che pongono requisiti molto elevati in termini di densità di prestazioni e temperature. Questi freni garantiscono una tenuta affidabile e possono decelerare carichi o masse in movimento. In caso di interruzione dell’alimentazione, guasto o malfunzionamento del servofreno nel motore di azionamento, i freni ROBA-stop-M mantengono l’asse in qualsiasi posizione, proteggendo gli organi di trasmissione e il sistema da eventuali danni.
Non va dimenticato inoltre il modulo di controllo per sistemi frenanti ROBA-brake checker, progettato per monitorare i freni senza l’impiego di sensori esterni, in grado di rilevare possibili guasti prima che si verifichino e facilitando la manutenzione predittiva.
SANDVIK COROMANT
Sandvik Coromant è orgogliosa di presentare CoroMill® MS20, una soluzione per la fresatura di spallamenti a 90 gradi effettivi. Studiata nei minimi dettagli per operazioni che vanno dalla sgrossatura alla finitura su acciaio inossidabile e superleghe resistenti al calore, questa soluzione è in grado di garantire una sicurezza, una versatilità e una produttività senza compromessi. “CoroMill® MS20 è la nostra nuova soluzione prioritaria monolaterale a due taglienti per applicazioni di fresatura di spallamenti a 90 gradi effettivi su materiali ISO M e ISO S, particolarmente adatta al settore aerospaziale, petrolifero e del gas”, spiega Sangram Dash, Global Product Application Specialist per utensili di fresatura multitaglienti presso Sandvik Coromant. “Grazie alla sua versatilità, CoroMill® MS20 è perfetta per fresatura di spallamenti ripetuta, spianatura, lavorazioni in rampa lineare ed elicoidale, esecuzione di cave dal pieno e applicazioni di lavorazione a tuffo”. Una delle principali caratteristiche di CoroMill® MS20 risiede nelle sue geometrie ottimizzate, pensate su misura per diversi materiali ISO, in modo da garantire una sicurezza superiore del filo tagliente. “Gli utilizzatori non potranno fare a meno di apprezzare l›affidabilità degli inserti CoroMill® MS20, dotati di un modello di usura prevedibile e graduale sul tagliente, anche nelle applicazioni più impegnative”, commenta Dash. “In sintesi, si tratta di una soluzione che offre la massima sicurezza e che consente una maggiore produttività”.
Assortimento di qualità per risultati di qualità
La combinazione tra corpi fresa e inserti di alta qualità garantisce finiture superficiali impeccabili e un’ottima qualità delle pareti (senza gradini) nelle applicazioni di fresatura di spallamenti ripetuta. Il robusto corpo fresa offre prestazioni straordinarie in termini di controllo delle dimensioni, adattandosi perfettamente al diametro nominale con tolleranze più strette
sul runout assiale e radiale. Ciò determina una migliore qualità del componente, meno scarti e una durata estesa del tagliente. Prodotti ricorrendo a una nuova tecnologia di pressatura, gli inserti offrono una maggiore precisione dimensionale, aumentando ulteriormente la qualità dei componenti e la durata tagliente dell’inserto. L’elevata precisione degli inserti CoroMill® MS20 a pressatura diretta permette loro di sostituire le geometrie rettificate dell›inserto periferico con prestazioni analoghe.
“Non si dovrebbero mai accettare compromessi quando si tratta di fresatura di spallamenti”, conclude Dash. “Che diate la priorità a una lavorazione sicura e priva di problemi, a un’elevata produttività o a una maggiore efficienza costi, la nuova soluzione per la fresatura di spallamenti CoroMill® MS20 è ciò che fa per voi”.
L’assortimento include corpi fresa nella gamma di misure 15,8–84 mm (con frese in misure imperiali equivalenti), oltre a inserti dotati di geometrie ottimizzate per l’acciaio inossidabile e le applicazioni HRSA.
Controlriv GEN3 è il nuovo sistema di controllo di processo, messo a punto da Rivit per garantire l’eccellenza e la verifica della qualità di fissaggio, 100% made in Italy. Grazie a costanti attività di R&D, questo sistema integra le versioni precedenti di nuove e potenziate funzionalità.
Dall’esperienza di Rivit nei sistemi di fissaggio, nasce Controlriv GEN3, il dispositivo elettronico industriale made in Italy che verifica in tempo reale il corretto sistema di fissaggio, pensato per ambiti industriali quale automotive, carpenteria pesante, automazione industriale, assemblaggi vari e sistemi di movimentazione handling. Grazie alle sue caratteristiche, Controlriv GEN3 si colloca in una posizione molto competitiva sul mercato: un unico modello permette infatti di verificare il corretto fissaggio del rivetto/inserto/ bullone a strappo attraverso il controllo di ogni tool Rivit a cui è collegato. In questo modo, è possibile segnalare tempestivamente eventuali errori, risparmiando tempo e costi dovuti a un fissaggio errato. Grazie alla sua versatilità, il nuovo Controlriv GEN3 può essere utilizzato in due modalità: stand-alone o cluster (una rete di dispositivi collegati tra di loro).
Tra le caratteristiche principali che rendono il nuovo Controlriv GEN3 il nuovo riferimento del mercato si sottolinea:
• una meccanica robusta e compatta;
• la separazione fisica tra parte pneumatica ed elettronica per un’installazione facile e veloce e una manutenzione più agevole;
• la misurazione in tempo reale della pressione di aria compressa fornita al tool, con range di tolleranza programmabile e segnalazione di errore in caso di fuori range;
• il monitoraggio in tempo reale del processo di fissaggio con un sistema di alert tramite notifiche e codice colori;
• la raccolta dati e la memorizzazione degli stessi, e la configurabilità da controllo remoto;
• L’interfacciamento al Controlriv GEN3 può essere effettuato in due modalità: via Ethernet/Profinet oppure tramite WiFi/Bluetooth.
Il nuovo sistema di controllo pensato da Rivit prevede, inoltre, un pratico frontalino dotato di display grafico, pulsante di accensione/ spegnimento illuminato, 6 tasti per le principali funzioni e 1 porta USB. Sul lato posteriore della macchina invece è presente un pannello con 1 porta USB, ingresso/uscita dell’aria compressa, 4 input/3 output opto-isolati e alimentazione, tutti collegabili tramite morsettiera.
Per maggiori informazioni www.rivit.it
Con Automation Studio Code, B&R introduce un’esperienza di progettazione completamente nuova. Incorpora una serie di funzioni di editing avanzate, attingendo alle ultime novità dell’industria del software. Con un accesso flessibile locale o basato su cloud, supporta la progettazione collaborativa senza soluzione di continuità. Completamente integrato in questo nuovo ambiente è Automation Studio Copilot, un assistente di programmazione IA generativo sviluppato in collaborazione con Microsoft. Tra i numerosi aggiornamenti della nuova versione, queste importanti aggiunte promettono un impatto notevole sull’esperienza di sviluppo del software per i costruttori di macchine e gli integratori di sistemi. Nella versione 6 del software di progettazione di B&R, Automation Studio Code aggiunge nuove potenti funzionalità di progettazione, offrendo al contempo la piena flessibilità di aprire gli stessi progetti nel nuovo ambiente o nella familiare interfaccia standard di Automation Studio. Tra le nuove funzionalità vi sono una ricca evidenziazione della sintassi, che facilita la lettura del codice, e la programmazione orientata agli oggetti in Structured Text, che aiuta gli ingegneri a organizzare il codice in modo più logico e a lavorare in modo più efficiente. Il rilevamento degli errori in tempo reale elimina poi i cicli ripetitivi di compilazione e correzione, mentre la possibilità di adattare il tema alla modalità dark aiuta a prevenire l’affaticamento visivo dello sviluppatore. Uno dei contributi più significativi all’accelerazione dello sviluppo delle macchine è rappresentato da Automation Studio Copilot, il compagno di intelligenza artificiale integrato nel nuovo ambiente di programmazione. Copilot consente agli sviluppatori di generare codice macchina
eseguibile semplicemente inserendo richieste in linguaggio naturale. Inoltre, aiuta a ottimizzare e commentare il codice esistente, rendendolo più facile da condividere e riutilizzare. Le applicazioni complesse possono essere riassunte rapidamente per facilitare le discussioni con gli stakeholder non tecnici.
Sviluppo semplificato con ingegneria basata su cloud
Una soluzione di progettazione basata sul cloud elimina la necessità di installare l’ambiente di sviluppo in locale. In questo modo si evita che i problemi di gestione delle versioni e delle dipendenze diventino dei colli di bottiglia per l’efficienza del gruppo. I team di sviluppo devono spesso affrontare lunghi cicli di vita dell’hardware e più versioni di strumenti su macchine diverse, aggiungendo complessità ai loro processi. Inoltre, le restrizioni IT sulla gestione locale del software possono ostacolare ulteriormente la produttività, richiedendo macchine virtuali o configurazioni di sviluppo specializzate per supportare diverse versioni dell’ambiente. L’ingegneria basata sul cloud elimina questi ostacoli, semplificando la configurazione e la manutenzione.
Con una dashboard che offre una chiara panoramica dei loro progetti in un unico posto, gli ingegneri possono facilmente vedere cosa è in corso e cosa ha bisogno di attenzione. “Si perde meno tempo a cercare i file o a ricordare dove si era rimasti, e si ha a disposizione più tempo per sviluppare e perfezionare il codice”, spiega Sanchez-Marchan. I progetti possono essere condivisi inviando un link, che un collega o un cliente può aprire direttamente nel proprio browser senza dover installare alcun software aggiuntivo.
Eaton introduce due nuove funzionalità per il suo relè di controllo easyE4: la connessione integrata alla piattaforma cloud Amazon Web Services (AWS) e un web editor integrato per una più semplice progettazione e visualizzazione su dispositivi connessi. Queste nuove caratteristiche migliorano ulteriormente le capacità di easyE4, un controllore compatto e versatile che può essere utilizzato in varie applicazioni come l’automazione degli edifici, il controllo delle macchine o i sistemi di illuminazione.
Con l’ultimo aggiornamento, easyE4 può ora connettersi direttamente ad AWS, uno dei principali fornitori di servizi cloud sul mercato. La connessione avviene tramite MQTT, il protocollo di messaggistica leggero compatibile un’ampia varietà di sensori e dispositivi mobili. Trasferendo in modo sicuro i dati nel cloud, gli utenti possono sfruttare i servizi AWS come archiviazione, analisi e visualizzazione dei dati. Questo consente l’implementazione di soluzioni Internet of Things (IoT), dal monitoraggio da remoto al machine learning. Eaton è anche partner AWS, con la registrazione dei dispositivi per la linea di prodotti easyE4, che semplifica il processo di installazione e configurazione.
Grazie al server web crittografato di easyE4, è possibile accedere rapidamente e facilmente ai dati e ai parametri anche su qualsiasi dispositivo mobile come smartphone o tablet. Inoltre, il nuovo web editor
integrato consente agli utenti di creare semplici visualizzazioni sui dispositivi dotati di browser web, inclusi grafici ed elementi operativi personalizzati. Il web editor fa parte del software easySoft di Eaton e consente un’integrazione perfetta tra l’interfaccia utente grafica e la programmazione di easyE4. Una volta creata la visualizzazione utilizzando il web editor, il contenuto viene caricato in modo sicuro sul server web easyE4.
Nella generazione precedente di easyE4 questo server web era un sito web fisso, dove determinate informazioni venivano visualizzate in modo permanente e solo alcune impostazioni potevano essere modificate. Nella nuova versione, gli utenti potranno scegliere tra contenuti già esistenti e visualizzazione web più avanzata.
“Con queste nuove caratteristiche, stiamo migliorando la funzionalità e l’utilizzo di easyE4, rendendo più semplice per i nostri clienti connettersi al cloud e accedere ai propri dati da qualsiasi dispositivo” commenta Daniel Jansen, Product Manager, easyE4 di Eaton. “easyE4 è un relè di controllo potente e flessibile che soddisfa le esigenze di diverse applicazioni e settori. Aggiungendo connettività cloud e funzionalità di visualizzazione web, stiamo consentendo ai nostri clienti di abbracciare l’IoT e sfruttare i vantaggi della digitalizzazione”.
Per maggiori informazioni su easyE4 www.eaton.com
n.7 Ottobre/Novembre 2024 www.meccanica-automazione.com
Redazione Direttore Responsabile
Giorgio Albonetti
Coordinamento Editoriale Area Industry
Marco Tenaglia –marco.tenaglia@quine.it – cel. 3298490024
Direttore tecnico
Chiara Tagliaferri
Segreteria di Redazione
Cristina Gualdoni cristina.gualdoni@quine.it – cel. 3477623887
Hanno collaborato a questo numero
Mattia Barattolo, Fabio Chiavieri, Annalisa Giavarini, Stefano Ierace, Giaime Lotti, Patrizia Ricci, Eleonora Segafredo
Pubblicità Costantino Cialfi | Direttore Commerciale c.cialfi@lswr.it - tel. +39 3466705086
Elena Genitoni | Ufficio Traffico e.genitoni@lswr.it – tel. 0289293962
Servizio abbonamenti abbonamenti.quine@lswr.it
Abbonamento annuale € 49,99
Costo copia singola € 7,07 (presso l’editore)
Produzione Antonio Iovene | Procurement Specialist a.iovene@lswr.it | Cell. 349.1811231
Grafica e Fotolito: Fabio Castiglioni Stampa: New Press Edizioni srl Via Della Traversa 22 - 22074 Lomazzo (CO)
Registrazione del Tribunale di Milano n. 653 del 21.09.2005.
Iscrizione al R.O.C. n. 12191 del 29/10/2005 Tutti gli articoli pubblicati su m&a meccanica &automazione sono redatti sotto la responsabilità degli Autori. La pubblicazione o la ristampa degli articoli deve essere autorizzata per iscritto dall’Editore. Ai sensi dell’art. 13 del D.Lgs. 196/03, dati di tutti i lettori saranno trattati sia manualmente sia con strumenti informatici e saranno utilizzati per l’invio di questa e di altre pubblicazioni e di materiale informativo e promozionale. Le modalità di trattamento saranno conformi a quanto previsto dall’art. 11 D.Lgs. 196/03. I dati potrebbero essere comunicati a soggetti con i quali Quine S.r.l. intrattiene rapporti contrattuali necessari per l’invio delle copie della rivista. Il titolare del trattamento dei dati è Quine S.r.l. - via Spadolini, 7 - 20141 Milano Tel +39 02 864105 Fax +39 02 72016740, al quale il lettore si potrà rivolgere per chiedere l’aggiornamento, l’integrazione, la cancellazione e ogni altra operazione di cui all’art. 7 D.Lgs. 196/03.
Ai sensi dell’art. 13 Regolamento Europeo per la Protezione dei Dati Personali 679/2016 di seguito GDPR, i dati di tutti lettori saranno trattati sia manualmente, sia con strumenti informatici e saranno utilizzati per l’invio di questa e di altre pubblicazioni e di materiale informativo e promozionale. Le modalità di trattamento saranno conformi a quanto previsto dagli art. 5-6-7 del GDPR. I dati potranno essere comunicati a soggetti con i quali Edra S.p.A. intrattiene rapporti contrattuali necessari per l’invio delle copie della rivista. Il titolare del trattamento dei dati è Edra S.p.A., Via G. Spadolini 7 - 20141 Milano, al quale il lettore si potrà rivolgere per chiedere l’aggiornamento, l’integrazione, la cancellazione e ogni altra operazione di cui agli articoli 15-21 del GDPR.
Testata associata
turin.sepem-industries.com
La fiera delle soluzioni a tutte le tue necessità produttive: servizi, sicurezza, processi, manutenzione.
◦ Workshop, conferenze e tavole rotonde.
◦ Un’offerta dedicata al comparto manifatturiero.
◦ Rafforzare il rapporto professionale con il mercato locale.
Con il patrocinio di:
ora il tuo accredito gratuito:
IL
• Interconnessione
• Gestione dei processi
• Sistemi CAD CAM
• Preventivazione
• Gestione commesse
• Pianificazione dei carichi di lavoro
• ERP di produzione
• Analisi dei dati
• Software per la simulazione
Vero Project è il partner affidabile ed esperto nella digitalizzazione e l’organizzazione dei processi aziendali nel settore degli stampi e della meccanica di precisione, offre soluzioni personalizzate per migliorare l’efficienza e la produttività aziendale.
Scopri la soluzione più adatta alle tue esigenze visitando il sito www.veroproject.it
SEDI OPERATIVE: Brescia Milano Treviso Parma
tel: +39 0308910006 - www.veroproject.it info@veroproject.it - workplan@veroproject.it