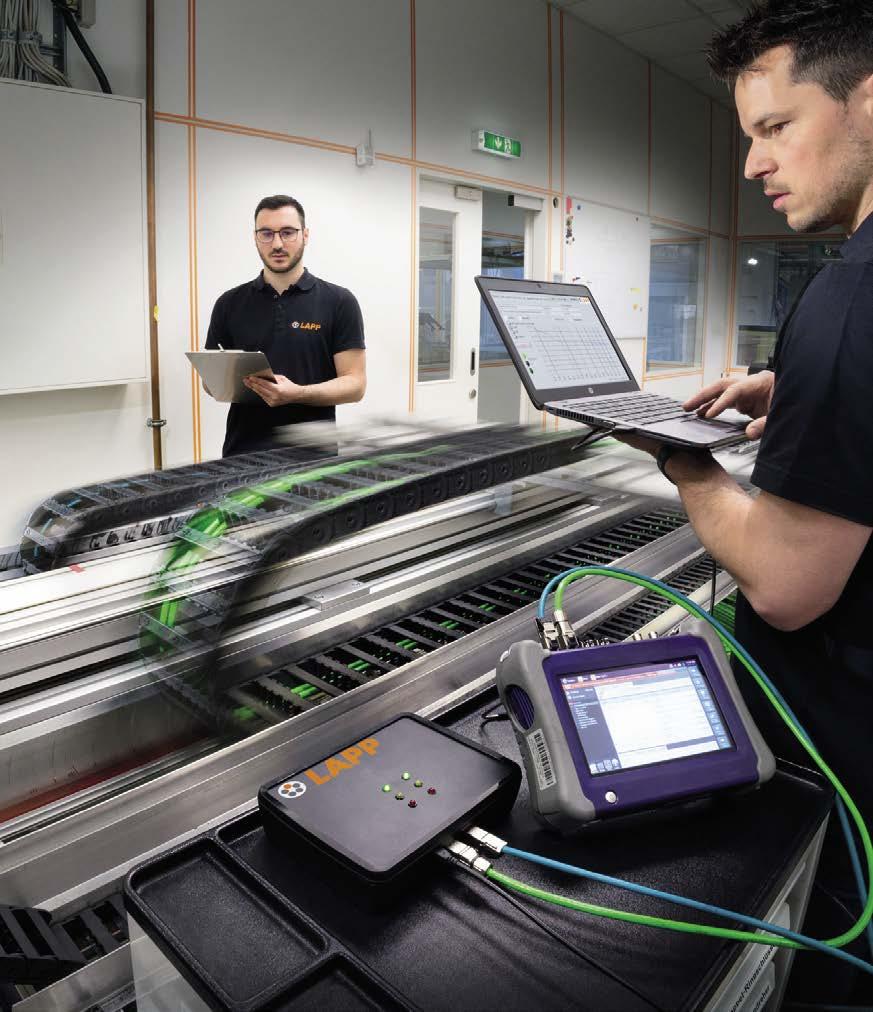
25 minute read
Sistemi di I-IoT: applicazioni e affidabilità
Sistemi di I-IoT:
APPLICAZIONI E AFFIDABILITÀ
L’INDUSTRIAL IOT È PROTAGONISTA DEI PROCESSI DELL’INNOVAZIONE DIGITALE, SOPRATTUTTO NEL CONTESTO DI QUELLI PRODUTTIVI, GRAZIE AL PARADIGMA DELL’INDUSTRIA 4.0, E IL SUO PERCORSO EVOLUTIVO È DI CONTINUA CRESCITA. PROPRIO QUESTO ASPETTO RENDE TALI SISTEMI PIÙ ESPOSTI AI RISCHI PER LA SICUREZZA
Di Patrizia Ricci
Secondo quanto emerge da un sondaggio condotto dall’Osservatorio Internet of Things del Politecnico di Milano su un campione di 102 grandi aziende e 295 PMI italiane, prosegue la crescita dell’Industrial IoT e si riduce il divario fra grandi aziende e PMI in termini di consapevolezza e propensione a innovare in ottica 4.0. In base al Report 2021 dell’Osservatorio, il 94% delle grandi aziende conosce le soluzioni IoT per l’industria 4.0 e il 68% ha avviato almeno un progetto, mentre fra le PMI solo il 41% ne ha sentito parlare e appena il 29% ha attivato iniziative. Tuttavia, nel 2020 il gap è diminuito del 5% in termini di conoscenza e del 6% per quanto riguarda la presenza di progetti. Le applicazioni più diffuse sono legate alla gestione della fabbrica (Smart Factory, 66% dei casi), soprattutto per il controllo in tempo reale della produzione e dei consumi energetici, poi quelle di supporto alla logistica (Smart Logistics 27%), guidate dalla tracciabilità dei beni nel magazzino o lungo la filiera, e lo Smart Lifecycle (7%), con progetti per migliorare lo sviluppo di nuovi modelli e l’aggiornamento dei prodotti. L’emergenza ha portato le imprese a rivedere le proprie priorità in termini di avvio di progetti e di investimenti. Nel 2020 solo il 15% delle PMI e il 12% delle grandi aziende ritiene prioritario attivare iniziative di I-IoT, contro rispettivamente il 25% e il 16% che le mettono in secondo piano. Il 22% delle grandi imprese ha aumentato il budget dedicato ai progetti IoT per l’Industria 4.0 (il 14% lo ha ridotto), contro solo l’11% delle PMI (il 12% lo ha diminuito), mentre un quarto delle grandi imprese e un terzo delle PMI rimandano la decisione ai prossimi mesi. “L’emergenza ha portato incertezza fra le imprese ma non ha arrestato la crescita dell’Industria IoT – afferma Giovanni Miragliotta, Responsabile scientifico dell’Osservatorio Internet of Things -. Il mercato si sta progressivamente spostando dalla vendita del solo hardware alla vendita di servizi aggiuntivi, con tre aziende su quattro che hanno avviato progetti di questo tipo, fra cui spiccano i servizi di tipo informativo (84%, come le notifiche push in caso di evento avverso), e quelli per l’energy management (45%). La possibilità di attivare questi servizi passa dalla capacità di analizzare, gestire e valorizzare i dati raccolti da impianti e macchinari connessi, che però è ancora scarsa sia nelle grandi aziende (solo il 38% usa i dati) sia nelle PMI (39%), a causa di scarse competenze e risorse finanziarie e della difficoltà di integrazione tecnologica” (fonte: “L’Internet of Things alla prova dei fatti: il valore c’è, e si vede!” dell’Osservatorio Internet of Things del Politecnico di Milano, aprile 2021).
Cos’è l’Industrial IOT
L’Industrial Internet of Things (I-IoT) altro non è se non l’applicazione dell’Internet of Things (IoT) nel mondo industriale con l’obiettivo di rendere i processi industriali più efficienti e sicuri. Il sito osservatori.net del Politecnico di Milano ne dà la seguente definizione: “per Industrial Internet of Things si intende quel percorso evolutivo della rete Internet attraverso la quale ogni oggetto fisico acquisisce una sua contropartita nel mondo digitale. Alla base dell’IoT (e quindi dell’I-IoT) vi sono oggetti intelligenti (capaci cioè di identificazione, localizzazione, diagnosi di stato, acquisizione di dati, elaborazione, attuazione e comunicazione) e reti intelligenti (aperte, standard e multifunzionali)”. In pratica è una tecnologia chiave nell’industria 4.0, che abbraccia le tecnologie smart, i dati, l’automazione, l’interconnettività, l’Intelligenza Artificiale e numerose altre tecnologie e funzionalità, con soluzioni che spaziano dalla sensoristica ai cobot, dai digital twin all’AI per offrire benefici tangibili alle aziende di ogni dimensione. Fanno parte del segmento industriale dell’IoT macchine, computer e persone che consentono operazioni industriali smart, ovvero strutture e sistemi che operano in modo semi-indipendente o con un intervento umano minimo in grado non solo di rispondere in modo intelligente alle informazioni ricevute ma, eventualmente, persino di cambiare il loro corso d’azione. Queste applicazioni sono anche note con l’espressione “Industrial Internet” o,
con una accezione più ampia e recente, ricomprese sotto il paradigma dei “Cyber-Physical Systems”, in quanto comprendono smart object in rete, beni cyberfisici, tecnologie informatiche generiche associate e piattaforme cloud o di edge computing, finalizzate all’accesso, la raccolta, l’analisi, le comunicazioni e lo scambio in tempo reale, intelligente e autonomo, di informazioni su processi, prodotti e/o servizi in ambiente industriale, che consentano l’ottimizzazione della produzione. Attraverso questi sistemi e servizi si riesce a migliorare la consegna del prodotto o del servizio, aumentare la produttività, ridurre il costo del lavoro, il consumo di energia e il ciclo build-to-order.
Differenze tra IoT e I-IoT
Viene spontaneo chiedersi quali siano le differenze tra IoT e I-IoT, dato che alla base di entrambi ci sono gli “smart object”, cioè “oggetti intelligenti” capaci di identificazione, localizzazione, diagnosi di stato, acquisizione di dati, elaborazione, attuazione e comunicazione, e reti intelligenti, ovvero aperte, standard e multifunzionali. Tali oggetti, dotati spesso di dispositivi e sensori grazie ai quali si realizza la connettività di rete per la raccolta di dati a distanza, analisi e capacità di gestione, richiedono un intervento umano minimo per generare, scambiare e consumare dati. Ebbene una sostanziale differenza va ricercata nel fatto che l’IIoT – Industrial Internet of Things - connette macchine e sensori critici nei settori industriali considerati a rischio più o meno elevato quali l’aerospaziale, la difesa e l’energia, per i quali è richiesto un indice di sicurezza adeguato, dato che le possibili conseguenze potrebbero mettere a repentaglio vite umane, oltre che compromettere l’azienda. Mentre l’IoT è destinato a mercati con un più basso impatto di rischio. In base alla tipologia di macchine che è chiamato a gestire, l’I-IoT necessita di sensori più sensibili e precisi nell’impianto e tecnologie, controlli e analisi più sofisticate e avanzate per questo motivo, si prevede che IoT crescerà di più con un prezzo meno costoso dell’I-IoT, considerando il volume di produzione e le capacità tecnologiche.
Ambiti d’impiego dell’Industrial IoT
L’Industrial Internet of Things rappresenta una delle sei tecnologie alla base dell’Industria 4.0. Le tecnologie digitali in grado di aumentare l’efficienza e il valore della produzione stimolando interconnessione e cooperazione tra tutte le risorse, interne e dentro l’impresa, sarebbero infatti i dispositivi IoT, la sensoristica, il cloud, il machine learning, la robotica collaborativa e la stampa 3D. Gli ambiti d’impiego dell’Industrial IoT possono essere riassunti in: • Smart Factory: controllo avanzamento produzione, sicurezza sul lavoro, manutenzione, movimentazione materiali, controllo qualità, gestione rifiuti; • Smart Logistics: tracciabilità / monitoraggio della filiera tramite tag RFId (Radio-Frequency Identification) e sensoristica, monitoraggio della catena del freddo, gestione della sicurezza in poli logistici complessi, gestione delle flotte (es. tramite GPS /
GPRS); • Smart Lifecycle: miglioramento del processo di sviluppo nuovi prodotti (es. tramite dati provenienti da versioni precedenti dei prodotti connessi), end of life management, gestione fornitori nella fase di sviluppo nuovi prodotti. La gestione automatizzata delle attrezzature permette a un sistema centralizzato di gestire e controllare da remoto, tramite macchine e software digitali, tutti i processi aziendali. Questo offre alle aziende la possibilità di sorvegliare, costantemente e in qualsiasi località geografica, i progressi della propria produzione in tempo reale. Un’altra ragione per implementare un sistema di acquisizione, analisi e gestione dei dati è la manutenzione predittiva, ovvero la possibilità di rilevare la necessità di manutenzione di una macchina prima che si verifichi una crisi e che la produzione debba essere fermata con urgenza. Questa è una delle applicazioni Industrial IoT più efficaci. Anche la gestione automatizzata dell’inventario consentita dai sistemi di I-IoT è essenziale per mantenere un flusso di lavoro costante ed efficiente. Mentre il controllo qualità, cioè la possibilità di monitorare la qualità dei prodotti fabbricati in qualsiasi fase, dalle materie prime utilizzate fino alle reazioni del cliente finale una volta ricevuto il prodotto, è ormai imprescindibile per un’azienda ai fini dell’ottimizzazione dei processi e del rilevamento dei problemi nella catena di produzione. Da ultimo, non meno importante, un altro vantaggio delle applicazioni di I-IoT riguarda l’ottimizzazione della supply chain così come il miglioramento della sicurezza degli impianti.
Garantire la cybersecurity
La maggiore dipendenza dai nuovi trend tecnologici, come Industrial Internet of Things (I-IoT) insieme a wireless e 5G, obbliga i leader in ambito OT (Operational Technologies) a prestare maggiore attenzione al tema della cybersecurity e all’affidabilità dei sistemi I-IoT. In base alla definizione di ENISA (European Union Agency For Network And Information Security) nel “Baseline Security Recommendations for IoT in the context of Critical Information Infrastructures”, del novembre 2017, l’Internet of Things è “a cyberphysical ecosystem of interconnected sensors and actuators, which enable decision making”, ovvero “un ecosistema cyber-fisico di sensori e attuatori interconnessi, che consentono un processo decisionale intelligente”. Essendo dunque i sistemi IoT dei mini sistemi cyber fisici (CPS, cyber-physical system), in quanto tali, appartengono al dominio della cosiddetta Operational Technology (OT). Tali sistemi
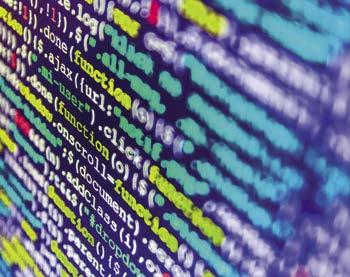
sono composti da elementi fisici dotati di capacità computazionale e contemplano strettamente le cosiddette tre “C”: Capacità computazionale, Comunicazione e Capacità di controllo. Una maggiore circolazione di dati porta a maggiori occasioni di perderne il controllo e li rende suscettibili di attacchi: da qui la necessità di proteggerli. Il mondo industriale è caratterizzato da un numero elevato di sistemi vulnerabili direttamente connessi ad internet privi di aggiornamenti e non aggiornati, tutto questo diventa terreno fertile per i criminali informatici. Possiamo considerare gli anni duemila come il momento d’inizio di questi attacchi, quando con la standardizzazione della connettività dei sistemi industriali (SCADA, PLC, ecc.) attraverso i protocolli TCP/IP si è realizzata la convergenza dell’IT con l’OT (Operational Technology). Nello scenario dell’ I-IoT occorre per prima cosa instaurare un dialogo tra il responsabile IT e il responsabile di produzione al fine di formulare una strategia comune di sicurezza che rispetti le esigenze di entrambi. Troppo spesso, infatti, vengono sfruttate vulnerabilità dovute all’assenza di un processo di Vulnerability Management, alla presenza di software obsoleti, alla mancanza di patch o a comuni errori di configurazione o configurazioni di default. La progressiva apertura e integrazione del mondo OT con il resto dei processi informatici ha reso i due domini sempre più interconnessi. Tuttavia, ancora oggi IT ed OT hanno priorità differenti, cosa che rende difficile l’interconnessione. Infatti, in ambito IT ha la massima priorità la confidenzialità del dato, che non deve essere rubato (Confidentiality), mentre in ambito produttivo (OT), è la disponibilità del dato l’aspetto più importante, perché se il dato non è più disponibile (Availability), o viene alterato (Integrity) la produzione rischia di bloccarsi. Al giorno d’oggi, gli attacchi informatici ai sistemi IT sono sempre più frequenti. Sono particolarmente diffusi i ransomware, che criptano i file, bloccando l’operatività delle aziende. Per questo, ancor più con la diffusione di Industry 4.0, i sistemi OT vanno protetti con la massima attenzione in quanto hanno la necessità di essere collegati. Questi collegamenti alla rete IT dovranno essere presidiati e controllati con sistemi di protezione e con grande attenzione, segregando la rete industriale in sottoreti protette, mediate le quali comunicano con i sistemi IT dell’azienda. Si parla dunque di IDMZ (Industrial Demilitarized Zone), ovvero una zona demilitarizzata industriale che si trova tra i sistemi aziendali (IT) e l’area OT industriale, che consente di collegare in modo sicuro reti con diverse esigenze di sicurezza (IT e OT). Impedendo la comunicazione diretta tra i sistemi IT e OT, si aggiunge un ulteriore livello di separazione nell’architettura complessiva della rete aziendale e si rendono i sistemi nei livelli industriali non direttamente esposti ad attacchi. Questa architettura segregata con IDMZ serve proprio ad impedire quello che si configura come il rischio più frequente: un attacco ai sistemi OT che arriva attraverso la rete IT, tipicamente più esposta. Molti dei più famosi e gravi cyber attacchi ai sistemi industriali sono arrivati proprio attraverso la rete IT e in molti casi hanno sfruttano l’errore umano. Vediamo ora alcune soluzioni di I-IoT che si basano su tecnologie digitali in grado di aumentare l’efficienza e il valore della produzione, operando nell’ambito della interconnessione e cooperazione tra tutte le risorse, fuori e dentro l’impresa.
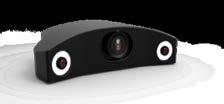
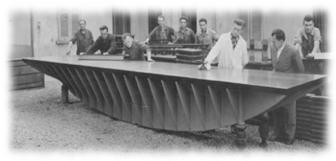

Semplicemente Custom Dal 1943 investiamo nelle risorse e nella ricerca e sviluppo al fine di poter offrire ai nostri clienti le migliori soluzioni con le migliori tecnologie disponibili. Dal 1943 guardiamo avanti grazie ad un solido passato. WWW.ROTONDI.IT Fratelli Rotondi S.r.l. - Via Fratelli Bandiera 36 - 20025 Legnano(MI)
SOLUZIONI DALLE AZIENDE
BALLUFF SMART REORDERING SYSTEM
In molte aziende, la produzione si basa su un principio pull. Pertanto, è importante avere sempre abbastanza materiale in magazzino per poter evadere gli ordini. Spesso, i livelli di scorte sono gestiti manualmente tramite schede Kanban o con soluzioni di codici a barre, con intervalli di tempo fissi che regolano la catena di approvvigionamento del materiale. Questo rende il flusso di materiale poco flessibile; oltretutto sono presenti innumerevoli processi manuali che rendono impossibile una gestione fluida delle scorte e quindi una produzione dinamica. Tutto ciò porta a una gestione inefficiente dell’inventario e a scorte di magazzino esagerate che richiedono spazio e vincolano il capitale nella logistica di produzione. Lo Smart Reordering System (SRS) vi permette di monitorare digitalmente il vostro flusso di materiale. Inoltre, elimina tutti gli svantaggi della gestione manuale delle scorte, come alti livelli di stock, costi di inventario non necessari e spazio sprecato. Semplice, economico e di facile installazione
Sensore wireless alimentato a batteria
• Semplice installazione e configurazione tramite software basato su cloud • Gateway con scheda SIM (ideale per installazioni pilota) • L’applicazione cloud non richiede software aggiuntivo
Ridurre lo sforzo manuale
• Monitoraggio automatico dei livelli tramite un sensore ottico • Notifica diretta della domanda quando i livelli critici di inventario non vengono raggiunti
Ottimizzare i livelli di stock e i processi di riordino
• Le funzioni di analisi permettono di ridurre il livello delle scorte • La notifica tempestiva riduce le scorte di sicurezza • Le notifiche di fabbisogno permettono di ottimizzare i cicli di approvvigionamento
Garantire la disponibilità
• Monitoraggio continuo e automatico dei livelli di materiale • La notifica tempestiva previene i colli di bottiglia
Automatizzare i processi di ordinazione
• Può essere collegato ai sistemi ERP e di gestione dei materiali tramite API • Possibilità di connessione di fornitori esterni via mail o accesso diretto
Che si tratti di zone di consegna o di ritiro, di stazioni di assemblaggio, di scaffali kanban o di aree di stoccaggio di pallet, lo Smart Reordering System monitora in modo affidabile i vostri livelli di stock e vi fa sapere in modo tempestivo quando è necessario un rifornimento. Lo Smart Reordering System è facile da installare e intuitivo da usare. Tutto ciò che serve sono tre componenti: sensore, gateway e l’applicazione cloud. Passo 1: Sensori I sensori SRS sono alimentati a batteria e possono essere montati senza cablaggio nei punti di consegna, nelle postazioni pallet, nelle postazioni di assemblaggio e negli scaffali Kanban. Passo 2: Gateway La connessione tra il gateway e i sensori può essere stabilita tramite LTE o Ethernet sulla rete domestica. Il gateway invia quindi i dati di inventario criptati al database e all’applicazione cloud. Passo 3: Applicazione cloud Puoi facilmente raggiungere il tuo terminale personale con l’accesso all’applicazione cloud via web browser. Lì puoi richiamare, analizzare e ottimizzare i dati dell’inventario corrente in qualsiasi momento e da qualsiasi luogo.
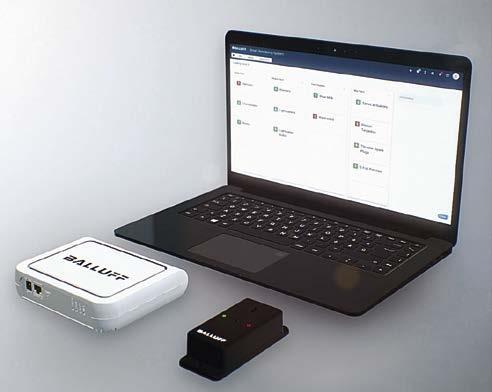
FANUC LA FABBRICA INTELLIGENTE SI COSTRUISCE A PARTIRE DAI DATI
Non solo fornitore di tecnologie intelligenti per l’automazione di fabbrica: con lo sviluppo della piattaforma FIELD System, FANUC si propone come abilitatore di soluzioni IIoT, dimostrando di poter offrire agli utilizzatori un unico interlocutore affidabile per la trasformazione tecnologica e digitale delle attività produttive. Il passaggio all’IIoT sottintende un’elevata complessità tecnologica; è impensabile che le aziende, soprattutto le PMI, possano farsi carico di tutte le competenze necessarie per abilitare la trasformazione digitale in ottica 4.0, implementare soluzioni di automazione nei propri stabilimenti produttivi e risolvere criticità legate alla sicurezza e all’interoperabilità dei protocolli. FIELD (FANUC Intelligent Edge Link & Drive) System è una piattaforma IIoT innovativa sotto diversi aspetti; basata su un ecosistema di applicazioni, FIELD consente di raccogliere e analizzare con il supporto dell’Intelligenza Artificiale i dati lungo l’intera catena di processo, con l’obiettivo di creare previsioni accurate e veloci per la manutenzione predittiva e incrementare l’OEE delle fabbriche. Perché FIELD è diverso dalle altre piattaforme IIoT? Innanzitutto è un sistema aperto. Basandosi su OPC UA, raccoglie dati da tutte le macchine e i dispositivi, anche quelli di produttori diversi da FANUC, anche quelli di generazioni precedenti (basta installare un convertitore). Inoltre, le applicazioni che girano nel sistema sono sviluppate sia da FANUC che dai suoi partner tecnologici, e sono facilmente personalizzabili dagli sviluppatori che possono così adattarle alle esigenze della propria azienda di riferimento, e renderle disponibili alla community di utilizzatori di FIELD. FIELD è un sistema sicuro, perché elabora i dati alla sorgente, vicino a dove vengono prodotti, secondo la modalità on edge. Significa che i dati sensibili relativi ai processi produttivi non escono dalla fabbrica, e che l’analisi dei dati ha luogo in maniera più rapida ed efficiente, praticamente in tempo reale, con vantaggi sia funzionali che dal punto di vista della cybersecurity e della riduzione dei costi operativi. È sempre possibile inviare i dati più importanti al cloud per archivio, oppure procedere con la loro analisi nel cloud. Questo punto evidenzia un nodo cruciale: sono gli utilizzatori i padroni dei dati, che decidono cosa farne e come utilizzarli. Terzo, essendo basato su applicazioni ognuna con una sua funzione specifica, FIELD è un sistema altamente flessibile e scalabile: non è necessario sovradimensionare la piattaforma con funzioni che resteranno inutilizzate, basterà installare e utilizzare solo quelle che davvero servono. Inoltre, FIELD è predisposto per l’interfacciamento con i sistemi superiori quali ERP (Enterprise Resource Planning), SCM (Supply Chain Management) e MES (Manufacturing Execution Systems), mettendo in comunicazione i reparti OT e IT in modo trasparente. L’ecosistema FANUC FIELD si basa su app. Quelle sviluppate direttamente dal gruppo giapponese rispondono ad esigenze generiche di manutenzione predittiva, o semplificazione delle procedure di programmazione e utilizzo delle soluzioni FANUC. Vi sono poi le app sviluppate dai partner tecnologici di FANUC, che sfruttano tecnologie abilitanti come la realtà aumentata, l’elaborazione del linguaggio naturale (NLP) e l’AI per migliorare le prestazioni e ottimizzare l’efficienza operativa. La piattaforma IIoT FANUC FIELD è stata progettata per essere alla portata di tutti, delle grandi imprese così come delle PMI: il concentratore FIELD Base Pro permette infatti di collegare e monitorare fino a 30 dispositivi (per esigenze di controllo maggiore sono disponibili unità di collegamento fino a 150 macchine). Questo concetto è importante, perché permette anche alle aziende di dimensioni più piccole di approfittare dei vantaggi dell’Intelligenza Artificiale nella digitalizzazione della filiera produttiva nel monitoraggio e gestione da remoto delle attività.

LAPP MANUTENZIONE PREDITTIVA DELLE RETI PER SMART FACTORY: NASCE ETHERLINE® GUARD, LA PREDICTIVE MAINTENANCE BOX DI LAPP
LAPP, leader nello sviluppo e produzione di soluzioni integrate nella tecnologia di connessione e cablaggio, annuncia il lancio sul mercato di ETHERLINE® Guard, un innovativo dispositivo in grado di analizzare le condizioni dei componenti hardware della rete e prevederne la fine del ciclo di vita. La Predictive Maintenance Box farà il suo debutto ufficiale in occasione della fiera SPS Norimberga, in programma dal 23 al 25 novembre 2021. “La manutenzione predittiva è tra i principali vantaggi dei processi produttivi basati sull’industria 4.0. Tuttavia, è un aspetto ancora molto sottovalutato quando si tratta dei sistemi di connessione” dichiara Marco Artoli, Project Manager Industrial Communication & Product Marketing Manager di LAPP che continua: “Cavi e connettori, infatti, benché progettati per resistere diversi anni, sono soggetti a possibili stress sia meccanici, che ambientali. In circostanze di questo genere, possono verificarsi una serie di anomalie che portano alla rottura del cavo e ad un conseguente fermo macchina. In tal senso, gli operatori hanno a disposizione due possibilità: sostituire il cavo prima del guasto, quando ancora funzionante, oppure agire a posteriori, una volta verificatosi il fermo macchina non pianificato, come tipicamente avviene nella manutenzione reattiva. Grazie ad ETHERLINE® Guard, introduciamo una terza opzione, con l’obiettivo di assicurare ai nostri Clienti i massimi livelli di efficienza”.
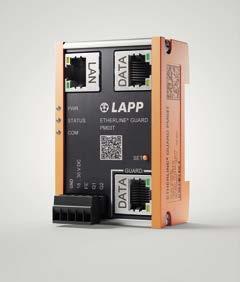
In dettaglio, ETHERLINE® Guard consente di monitorare in tempo reale lo stato di efficienza di cavi Ethernet installati in applicazioni sottoposte ad elevato stress meccanico, come nelle catene portacavi o nel braccio di un robot. Attraverso la lettura e l’analisi di diversi parametri, confrontati con curve di riferimento, lo strumento identifica lo stato di usura del cavo e invia un alert al sistema di supervisione mediante, ad esempio, il protocollo MQTT. La funzione di diagnostica è basata su un apposito algoritmo, il LAPP Predictive Indicator (LPI), in grado di calcolare la vita residua delle linee, attingendo ai valori di milioni di set di dati, raccolti ed esaminati in diversi anni nel centro Prove di LAPP. ETHERLINE® Guard è dotato di due porte Ethernet e si collega semplicemente al cavo da monitorare, rendendo superfluo l’utilizzo di cosiddetti “cavi sacrificali” aggiuntivi. In altri termini, il sistema si adatta facilmente alle macchine esistenti, senza ulteriori oneri di installazione. Inoltre, poiché i pacchetti dati vengono trasferiti in modo trasparente da una porta Ethernet all’altra in modalità “cut through”, la Predictive Maintenance Box risulta invisibile al PLC collegato: questo significa che non sono richieste modifiche al software e non viene esercitata alcuna influenza sulla trasmissione dati della macchina. In aggiunta, ETHERLINE® Guard è ideale per progetti di retrofit su tutti i sistemi basati su Ethernet, in quanto assicura una totale compatibilità con la struttura del cavo, che non necessita di una costruzione speciale. Infine, i valori soglia del sistema sono regolabili direttamente dall’operatore della macchina ed è reso disponibile un Log file dettagliato su SD card. “Il principale vantaggio nell’utilizzo della Predictive Maintenance Box risiede in una Overall Equipment Effectiveness (OEE) migliorata, in virtù di misure di manutenzione programmabili, che consentono di evitare fermi macchina imprevisti dovuti al danneggiamento di un cavo dati” conclude Marco Artoli. Infine, ETHERLINE® Guard si inserisce in un’offerta più ampia di servizi che LAPP propone ai Clienti, come l’analisi on site e il collaudo di reti Industrial Ethernet, a cura degli IC Experts di LAPP, accreditati anche Profinet Certified Engineers.
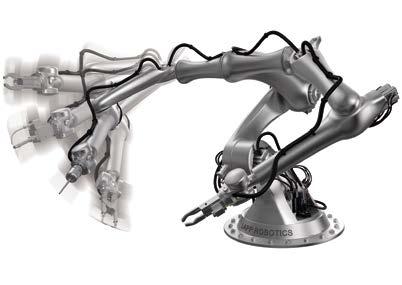
MITSUBISHI ELECTRIC SOLUZIONI INDUSTRIAL IOT COMPLETE E SICURE
Per supportare il processo di digitalizzazione della smart factory in ottica Industria 4.0 e Industrial IoT, Mitsubishi Electric offre una serie di soluzioni di interconnessione tra i dispositivi di fabbrica e Internet, che consentono una semplice integrazione dei diversi componenti a livello OT, come PLC, CNC, Servo, Robot, con le strutture a livello IT in cloud.
Software IIoT
Tra le soluzioni per l’IIoT che Mitsubishi Electric propone per facilitare il percorso di trasformazione digitale delle aziende che operano nel settore della meccanica e dell’automazione c’è il tool di connettività IoTWorX™ di Iconics, azienda statunitense recentemente acquisita dalla multinazionale giapponese. Con IoTWorX™ Mitsubishi Electric è in grado di offrire una soluzione software IoT completa, a partire dal gateway di raccolta dati fino al cloud. IoTWorX™ è anzitutto una soluzione Edge che, installata su PC o altro hardware minimo, oltre a raccogliere i dati può fornire anche una visualizzazione e una pre-analisi per poi trasferire i dati al cloud. IoTWorX™ è di fatto un gateway IoT con funzioni già fruibili localmente senza dipendere dalla rete e dalla connessione, che permette di avere un’interfaccia locale dei dati (dashboard, grafici, trend, allarmi) su un tablet o uno smartphone o su un altro PC, tramite un semplice collegamento Wi-Fi. Oltre alla visualizzazione locale, IoTWorX™ garantisce anche un primo livello di estrazione di informazioni sullo storico dei dati e invia poi i dati ricavati verso il cloud, per abilitare funzioni di monitoraggio remoto e manutenzione predittiva. La sicurezza nel trasferimento dei dati da IoTWorX™ al cloud è garantita dall’utilizzo di appositi protocolli come MQTT o AMQP o HTTPS, adatti per l’apertura di canali di scambio dati protetti, grazie alle tecnologie di cybersecurity disponibili nel mondo Internet basate sui certificati e sulla criptazione dei dati. Mitsubishi Electric può fornire quindi alle aziende una soluzione IoT completa end-to-end, che include il software IoTWorX™ di Iconics e l’utilizzo della piattaforma Azure di Microsoft. Sulla piattaforma cloud si possono infatti attivare lo SCADA di Iconics Genesis 64, o il database Hyper Historian per la storicizzazione dei dati, oppure altri Big Data Analytics (AnalytiX BI).
Modulo integrato nella piattaforma iQ-R
Un’altra soluzione proposta da Mitsubishi Electric per applicazioni IIoT è il C Intelligent Function Module, un modulo integrato nella piattaforma di controllo MELSEC iQ-R e utilizzabile in chiave IoT per realizzare un gateway di tipo flessibile. Il C Intelligent Function Module è un coprocessore che, nella sua versione più recente, integra il sistema operativo Debian Linux su cui sono disponibili numerosi applicativi open source per realizzare dei trasferimenti dati su Internet. Questo modulo embedded nella piattaforma iQ-R apre, quindi, un ponte verso un collegamento IoT, permettendo ad esempio di realizzare un’applicazione di monitoraggio remoto e di manutenzione preventiva su un robot, o su un altro dispositivo di fabbrica collegato al controllore iQ-R. Anche in questo caso la sicurezza dei dati è assicurata, grazie all’utilizzo dei protocolli OPC UA e MQTT nativi delle tecnologie di cybersecurity.
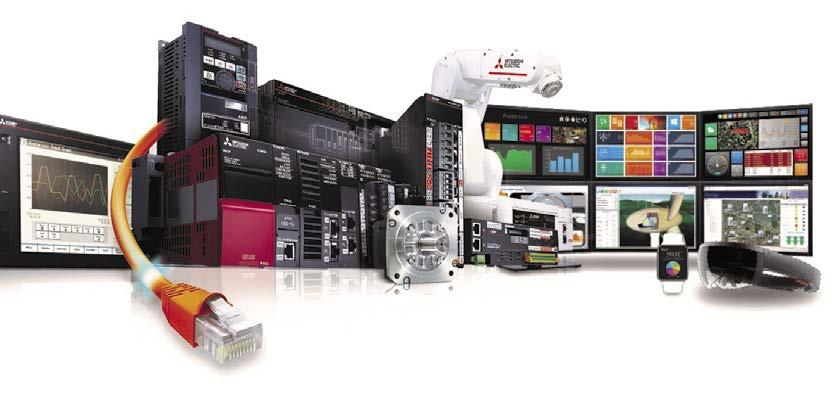
SCHNEIDER ELECTRIC ECOSTRUXURE MACHINE ADVISOR – SCHNEIDER ELECTRIC
EcoStruxure Machine Advisor è una piattaforma di servizi digitali basata sul cloud che consente ai costruttori di macchine di fornire ai clienti soluzioni innovative per la gestione e la manutenzione della base installata, in qualunque sede produttiva e in ogni parte del mondo. La piattaforma infatti offre funzionalità dedicate per il tracciamento, il monitoraggio e la manutenzione. Con EcoStruxure Machine Advisor gli OEM possono avere un controllo completo sulle macchine per l’intero ciclo di vita, sfruttando il potenziale della connettività. Possono creare servizi che consentono agli operatori di macchina di interagire in qualsiasi luogo e momento con le apparecchiature, cogliendo i vantaggi della mobilità; possono usare i dati raccolti per realizzare analisi evolute, estrarre informazioni utili a fini decisionali e di innovazione; infine, dispongono di una piattaforma che permette di operare a livello globale, elemento particolarmente rilevante quando – come avviene per moltissimi OEM italiani – si opera su mercati geografici molto ampi. Le tre aree di funzionalità disponibili nella piattaforma sono le seguenti • Track: permette di tenere sempre sotto controllo il parco macchine installato (elenco dei materiali documenti, architettura), di registrare tutte le attività svolte sulle macchine, di semplificare la realizzazione di architetture di automazione accedendo a cataloghi di modelli/dispositivi di proprietà o pubblici • Monitor: con gli strumenti di monitoraggio l’OEM può raccogliere e visualizzare i dati della macchina, rilevarne le anomalie tramite tool di analisi per intervenire tempestivamente -aumentando quindi la disponibilità – ricevendo apposite notifiche; ha la possibilità inoltre di creare e gestire dashboard, aggiungere e configurare nuovi widget per monitorare i KPI chiave (dall’OEE alle prestazioni) • Fix: consente di utilizzare il software as a service, via cloud, per risolvere i problemi delle macchine riportati dai clienti , attraverso un collegamento con il builder della realtà aumentata , ( Augmented Operator Advisor ) e mette a disposizione un tool per migliorare l’efficienza e lo sviluppo dei codici applicativi delle macchine denominato Machine advisor Cloud Code Analysis. I costruttori di macchine possono adottare queste evolute soluzioni disponibili in cloud con la massima tranquillità, contando sul cloud Schneider Electric che è sviluppato e gestito in modo sicuro; questo si aggiunge all’integrazione dei necessari elementi di sicurezza informatica, in conformità con certificazioni quali Achilles Level II, che caratterizzano i componenti di connettività e controllo per le macchine proposti dall’azienda.

Il settore manifatturiero sta fronteggiando nuove sfide per rispondere alla complessità crescente del mercato: innovarsi può essere complicato ma le tecnologie digitali vanno in aiuto alle aziende per una trasformazione digitale. Ma come? Creando relazioni tra i player del mercato ed entrando a far parte di un ecosistema IoT industriale in un’ottica di condivisione di know-how, competenze e collaborazione. È questo il nuovo modo di fare innovazione. Per questo sempre più aziende decidono di entrare a far parte della famiglia di utilizzatori di MindSphere: un ecosistema di aziende che mettono insieme le loro conoscenze per accelerare la trasformazione digitale dell’industria tramite l’adozione di tecnologie basate su cloud computing. La community ruota intorno alla piattaforma aperta MindSphere di Siemens, la soluzione leader di IIoT as-a-Service. Grazie alla facile e rapida integrazione, MindSphere consente l’analisi con rapidità ed efficienza di enormi volumi di dati generati dagli impianti per migliorare le prestazioni, l’ottimizzazione dei processi, la riduzione dei tempi di fermo impianto, la creazione di nuovi flussi di guadagno, il potenziamento della redditività aziendale e l’ampliamento dei vantaggi competitivi sul mercato. MindSphere, inoltre, consente di collegare facilmente le proprie macchine e infrastrutture fisiche al mondo digitale, supportando nativamente la maggior parte dei protocolli industriali di comunicazione. A rinforzare questa architettura di Industrial IoT c’è l’edge computing. Industrial Edge è la soluzione proposta da Siemens per portare la digitalizzazione direttamente nei sistemi di produzione e automazione. Tale piattaforma consente l’analisi dei dati direttamente in prossimità delle macchine, supportando di conseguenza il cloud nel processare e pre-elaborare dati ad alta frequenza e applicare soluzioni di intelligenza artificiale in realtime. MindSphere è inoltre integrato alla soluzione di sviluppo software low-code Mendix, che mette a disposizione degli utenti gli strumenti necessari per sviluppare applicazioni personalizzate, anche senza conoscenze approfondite di programmazione. Mendix e MindSphere di Siemens, assieme alle app realizzate da terzi, sono a disposizione dei clienti grazie a un app store dedicato. Forte del suo ruolo di partner tecnologico, Siemens fornisce alle imprese manifatturiere una vera e propria soluzione “chiavi in mano”, con applicazioni e servizi digitali pronti all’uso, semplificando le sfide di connettività e offrendo ad ogni azienda la possibilità di diventare un’impresa digitale e raggiungere i propri obiettivi di digitalizzazione.
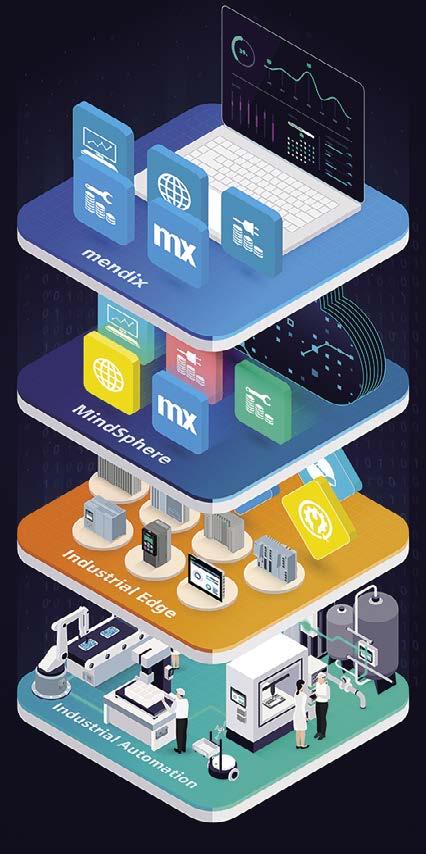