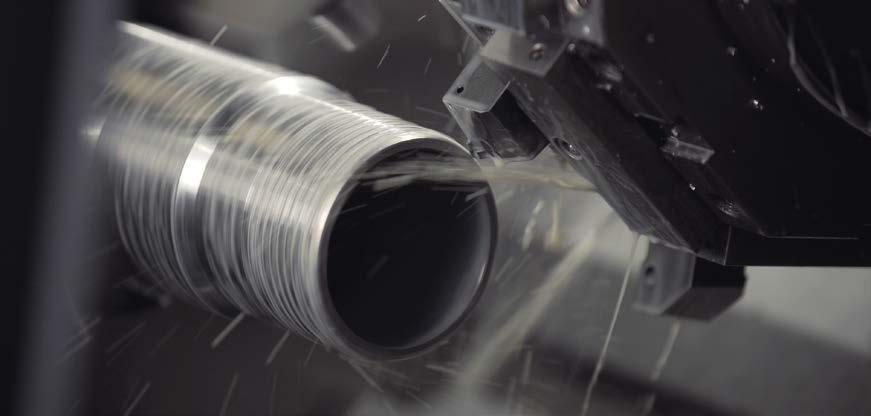
7 minute read
Danobat Hembrug specialisti nelle lavorazioni in hard turning
@Studer
TORNITURA:
L’EVOLUZIONE DI UNA LAVORAZIONE ANTICA
ANCHE SE NEL TEMPO IL TORNIO HA SUBITO NUMEROSE EVOLUZIONI, IL CONCETTO SU CUI SI BASA IL FUNZIONAMENTO DI QUESTA MACCHINA UTENSILE È SEMPRE DATO DALLA COMBINAZIONE DI DUE MOTI RELATIVI FONDAMENTALI, TRA UTENSILE E PEZZO: IL MOTO DI TAGLIO, ROTATORIO UNIFORME, CHE È IMPRESSO AL PEZZO, E IL MOTO D’AVANZAMENTO, PERLOPIÙ RETTILINEO, IMPRESSO ALL’UTENSILE
SSi tratta quindi di un processo che asporta il residuo noto come truciolo. Nel corso dei secoli, a partire dal 1453, quando fece la sua apparizione in Francia il tornio idraulico, il precursore dei moderni torni, lo sviluppo scientifico e tecnologico, nonché gli studi della scienza dei materiali, hanno portato a sviluppare macchine in grado di soddisfare ogni esigenza di tornitura, dalle più semplici, che non richiedono torni particolarmente complessi, alle più impegnative, che richiedono macchine sofisticate, spesso corredate da sistemi di automazione spinta. La tornitura dei metalli è una lavorazione che comporta due passaggi, la sgrossatura, con la quale si rimuove il grosso del sovrametallo tramite utensili in grado di resistere a forti sollecitazioni e la finitura, nella quale il pezzo viene lavorato al fine di ottenere una superficie finale con dimensioni, tolleranze e rugosità previste. Questo tipo di lavorazione viene impiegato per generare pezzi ascrivibili a solidi di rivoluzione che possono presentare, ad esempio, fori, filetti, scanalature, vari gradini di diametro, conicità e superfici sagomate.
Il tornio
Il tornio è una delle macchine utensili più antiche che sembra risalire addirittura al Neolitico, quando strumenti, una sorta di torni rudimentali, venivano utilizzati per la realizzazione del vasellame. Basta pensare all’importanza che ha avuto nella storia il tornio del vasaio, un precursore del tornio verticale utilizzato per modellare l’argilla. Ma solamente verso la metà del XVIII secolo nasce il tornio per la lavorazione dei metalli, in una versione concettualmente molto simile a quello attuale. Per quanto concerne la lavorazione dei metalli vengono impiegati torni di varie tipologie: torni orizzontali, torni verticali, torni a controllo numerico, centri di lavoro, torni plurimandrino ecc. In tutte queste macchine, il pezzo da lavorare viene fissato ad un mandrino autocentrante, posto in rotazione da un motore elettrico ed è installata la torretta portautensili che può montare vari tipi di utensili di tornitura quali sgrossatori, finitori, troncatori o filettatori. A seconda della superficie che si desidera ottenere, si può impiegare una tornitura piana, conica, cilindrica, elicoidale oppure una profilatura per una figura complessa. Le operazioni eseguibile tramite tornitura possono classificarsi in interne od esterne a seconda che l’utensile lavori la superficie del pezzo o lo scavi assialmente. Nella tornitura esterna l’asse del macchinario è posto parallelamente al moto di avanzamento dell’utensile mentre, in quella interna, che riguarda un pezzo cavo, sia l’avanzamento che l’asse dell’utensile sono in parallelo a quello di rotazione. In sostanza nella tornitura le parti in eccesso del pezzo, cioè il sovrametallo, sono staccate dal tagliente che penetra nel materiale e forma il truciolo. Questa lavorazione viene impiegata su metalli, legno e pietra.
Operazioni eseguibili mediante il tornio
Nella tornitura esterna, l’utensile da tornitura si muove assialmente e radialmente lungo il pezzo in lavorazione, formando coni, smussi o “gradini”. Tipicamente viene applicata una piccola profondità di taglio radiale e vengono effettuate passate multiple.
Tra le operazioni esterne rientrano la sfacciatura, in cui l’utensile si sposta radialmente lungo l’estremità del pezzo rimuovendo un sottile strato di materiale al fine di ottenere una superficie liscia e piana; la scanalatura, in cui l’utensile si sposta radialmente sul lato del pezzo incidendo i solchi della scanalatura e per la quale possono essere utilizzate passate multiple per realizzare solchi di diverse geometrie o scanalature più profonde; la troncatura, in cui l’utensile da taglio pur spostandosi radialmente, analogamente a quanto accade per la scanalatura, raggiunge il centro del pezzo e lo taglia separandone una sezione; la filettatura, in cui l’utensile filettatore si muove sulla superficie del pezzo, filettando il pezzo in rotazione. Le operazioni interne consistono nella foratura, in cui la punta penetra nel pezzo in lavorazione producendo un foro (contrariamente alla foratura tradizionale effettuata mediante il trapano, nella foratura assiale sul tornio la punta resta ferma, il moto rotatorio viene invece impresso al pezzo in lavorazione); alesatura e barenatura, in cui, a differenza dei metodi tradizionali dove vengono impiegate macchine utensili quali il trapano o la fresatrice, quando eseguite sul tornio il moto rotatorio è impresso al pezzo da alesare/barenare mentre l’utensile resta fermo (tramite la tornitura è possibile eseguire anche operazioni di rifinitura di fori); la maschiatura, in cui il maschio entra assialmente nel pezzo in lavorazione tramite un foro preesistente asportando il materiale necessario per realizzare la filettatura interna.
Principali parametri di tornitura
Nella tornitura i parametri variano in funzione del metallo da lavorare, del materiale e della dimensione dell’utensile impiegato ecc. Acciaio dolce o duro, ghisa, ottone e alluminio hanno diverse durezze che richiedono differenti velocità di taglio. Per impostare la tornitura desiderata, occorrono considerare la velocità di taglio, cioè la velocità della superficie del pezzo in relazione al bordo dello strumento da taglio in fase di lavorazione, quella di rotazione del mandrino (misurata in giri al minuto), la velocità di avanzamento rispetto al pezzo (la distanza che l’utensile copre rispetto al pezzo in lavorazione durante un giro di mandrino), la profondità di taglio assiale, ovvero la profondità dell’utensile lungo l’asse del pezzo in lavorazione durante l’esecuzione di un taglio. Grandi profondità di taglio richiedono basse velocità di avanzamento; in caso contrario è possibile compiere la lavorazione in più passaggi.
Tipologie di lavorazione
Le tipologie sono molte e comprendono la tornitura verticale, in cui il tornio è ruotato di 90° e si sviluppa in modo tale da orientare il mandrino verticalmente, che consente di realizzare componenti di grandi dimensioni che possono trovare impiego ad esempio nel settore navale o ferroviario; la tornitura CNC (Computer Numerical Control) con la quale, essendo il processo è interamente automatizzato e controllato da un computer e la lavorazione costantemente monitorata da sensori, sono possibili tolleranze di centesimi o anche millesimi di millimetro e si raggiungono precisione e ripetibilità del processo che lo rendono ideale per le lavorazioni di precisione o per le produzioni di serie; la tornitura plurimandrino in cui la testa, generalmente ad asse orizzontale, alloggia più mandrini portapezzo (fino a 12) che possono ruotare anche a velocità diverse permettendo la lavorazione contemporanea di più pezzi incidendo significativamente sulla velocità di lavorazione. La tornitura plurimandrino permette infatti di utilizzare il medesimo utensile tagliente su più prodotti, prima di cambiarlo per passare ad una successiva fase di lavorazione, in tal modo i fermi macchina dovuti al cambio utensile vengono sostanzialmente ridotti.
Le richieste del mercato
Il trend di mercato è l’equipaggiamento di macchine in grado di fare sgrossatura e finiture molto precise, accorpando il più possibile tutte le lavorazioni in un’unica soluzione per minimizzare i costi legati alla logistica, ottimizzare i tempi di lavorazione e avere un beneficio in termini di consegna rapida del prodotto finito al cliente. Questo si traduce in un risparmio nei costi di produzione e in una maggiore competitività sul mercato. Tutto ciò orienta la produzione verso macchine flessibili, customizzate su richiesta del cliente, in grado di realizzare il componente finito, partendo dalla trasformazione della materia prima, ovvero dal forgiato, passando dalla sgrossatura pesante, fino alla realizzazione di finiture molto precise. Oggi le macchine non sono più semplici macchine di tornitura, in grado solo di sgrossare e finire il pezzo, ma sempre più spesso sconfinano nel campo della rettifica e vengono equipaggiate con degli accessori o parti di macchina dedicate per eseguire questa lavorazione sui componenti dopo il trattamento termico. Particolarmente conveniente si è dimostrata la lavorazione di precisione di pezzi a sbalzo di piccole dimensioni, mediante processo combinato di “tornitura e rettifica in una sola macchina”. Oggi parlare di macchine multitasking è d’obbligo, ad esempio, per i torni verticali di grandi dimensione. Inoltre, la continua evoluzione degli inserti, ad esempio quelli in CBN (nitruro di boro cubico) che garantiscono una lavorazione stabile, e dei rivestimenti applicabili, ha reso possibile la tornitura di acciai temprati, ottenendo elevato rendimento in termini produttivi. Quando la tipologia del pezzo lo consente, è proficuo pensare alla “Tornitura sul duro” (Hard Turning) al posto della rettifica. Grazie a macchine specifiche, con possibilità di operare fino a 12.000 giri/min., si possono affrontare lavorazioni complesse ottenendo rugosità superficiali Ra< 0,1 ed errori di rotondità contenuti entro 1 micron.
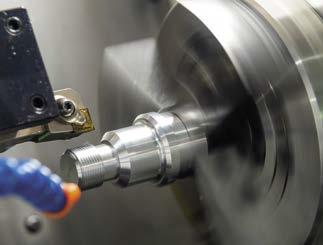