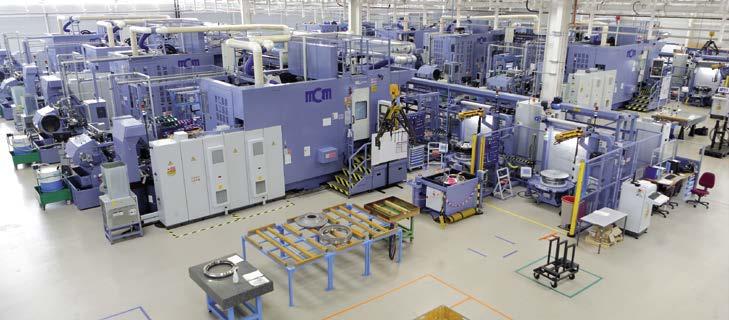
5 minute read
Applicazioni speciali su richiesta del cliente
riconosciuto il ruolo delle tecnologie dell’informazione quale elemento di distinzione della propria offerta, consapevole dei vantaggi garantiti dall’integrazione sinergica tra impianti di produzione e software di supervisione. L’architettura del software di controllo e supervisione jFMX è strutturata per livelli, ovvero in grado di gestire crescenti complessità impiantistiche e informative. A livello base è possibile l’integrazione con il CN di macchine stand alone per il miglioramento della gestione e dell’operatività delle stesse. Ad un grado superiore vi è la possibilità di coordinare l’automazione di sistemi FMS con più macchine integrate (prevalentemente impianti MCM). Crescendo di livello vi è poi la gestione di sistemi complessi, con macchine operanti con diverse tecnologie, fino a un possibile coordinamento e la gestione centralizzata di un’intera officina. Il software può automatizzare i flussi informativi relativi ai dati tecnici, integrando i CNC con gli uffici di ingegneria di processo e gli strumenti CAD/CAM, quelli relativi ai dati di produzione al fine di gestire tutte le risorse (macchine, utensili, pallet, attrezzature) in modo integrato con il sistema ERP aziendale. Inoltre, jFMX abilita l’integrazione dei flussi d’informazione verso la tool room, i sistemi aziendali di controllo qualità e di gestione delle manutenzioni. Pianificazione della produzione, monitoraggio avanzato delle risorse produttive, gestione integrata delle informazioni associate al processo e al controllo della qualità, sono i servizi disponibili e che offrono una dimensione strategica al controllo e alla gestione integrata degli impianti.
Dischi turbina in superlega di Nichel
Per la produzione di dischi turbina del moderno motore aeronautico ‘LEAP’, MCM ha fornito, al più importante equipementier aeronautico francese, 12 centri di lavoro Tank 1600 Multitasking organizzati in 3 linee FMS, ottimizzando la distribuzione delle macchine sul layout del sito di produzione, riducendo il numero delle fasi di lavorazione ed il flusso di semilavorati in transito. Tutti aspetti fondamentali per la riduzione del tempo ciclo e dei costi di produzione.
La struttura Tank 1600 offre elevata rigidezza rendendo la macchina estremamente robusta per sostenere sia le elevate forze di taglio che le inerzie legate alla notevole dinamicità. Caratteristica peculiare delle macchine installate è la presenza di un sistema cosiddetto “divisore”, solidale alla tavola rotante e in grado di posizionare il gruppo pezzo-pallet con asse di rotazione orizzontale, ottimizzando le operazioni di tornitura e permettendo la facile evacuazione del truciolo. Questo anche grazie alla presenza, integrata nel “divisore” stesso, di un mandrino usato per la tornitura e capace, in questo caso, di raggiungere 500 RPM.
Questa soluzione ha comportato l’adozione di un esclusivo sistema di cambio pallet inclinato di 45°, in grado di prelevare il pallet dalla navetta dell’FMS (dove si muove in piano orizzontale) e posizionarlo sul divisore con piano verticale e, quindi, asse di rotazione orizzontale.
L’elettromandrino di fresatura offre una potenza di 60 kW con 8000 RPM di velocità massima e coppia massima di 487 Nm. Il sistema di attacco utensile è capto C8.
Di fondamentale importanza per la regolarità della frammentazione del truciolo è la disponibilità di un sistema di alta pressione del fluido lubrorefrigerante che, nelle fasi di tornitura, raggiunge i 250 bar. Tale pressione ha sia la funzione di rompere il truciolo che quella di assicurare l’ottimale raffreddamento delle operazioni di taglio, accrescendo la resistenza all’usura degli inserti e minimizzando l’impatto degli stessi sui costi complessivi.
A testimonianza dell’affidabilità della soluzione MCM, per lo stesso stabilimento, il cliente ha recentemente ordinato un ulteriore impianto, attualmente in corso di costruzione in MCM, composto da due centri di lavoro TANK 1600 Multitasking con performance aggiornate alle richieste odierne (pezzi di diametro fino a 1350 mm) ed anche un sistema “Supertool” per la gestione centralizzata e la disponibilità condivisa degli utensili.
APPLICAZIONI SPECIALI
SU RICHIESTA DEL CLIENTE
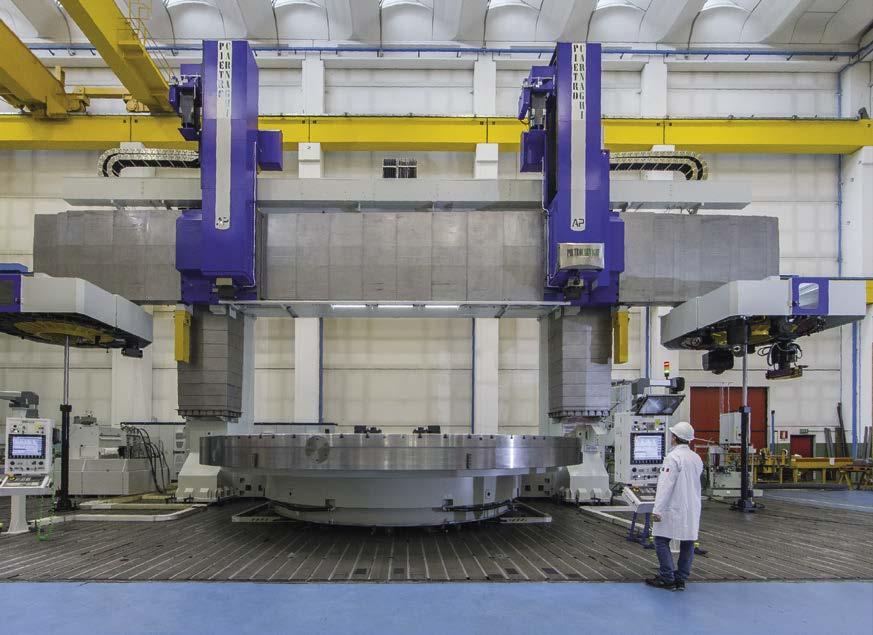
LEADER MONDIALE NELLA PRODUZIONE DI TORNI VERTICALI DI GROSSE DIMENSIONI, PIETRO CARNAGHI OFFRE, OLTRE AI MACCHINARI, ANCHE LE SOFISTICATE TECNOLOGIE DI LAVORAZIONE CHE CONTRIBUISCONO NELLA RISOLUZIONE DI TUTTI I PROBLEMI PRODUTTIVI DEL CLIENTE
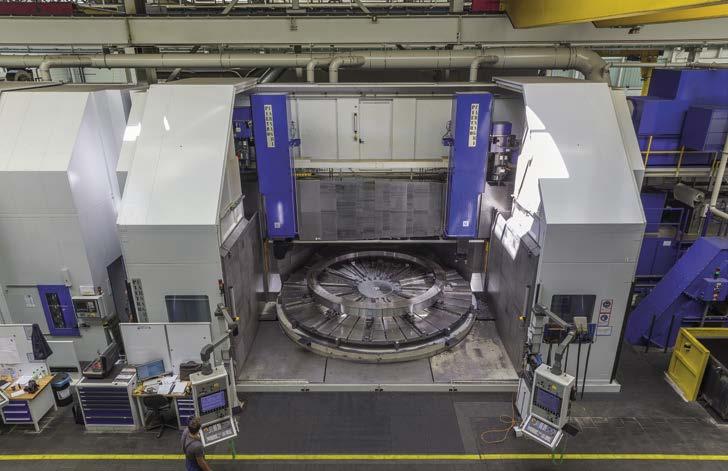
FFondata nel 1922 da Pietro Carnaghi, l’azienda è oggi un importante punto di riferimento nel panorama internazionale dei produttori di macchine utensili dalle alte prestazioni e qualità, grazie al continuo e costante sviluppo delle tecnologie e delle idee, supportate da quasi 100 anni di esperienza diretta sul campo. Proprio il prossimo anno l’azienda festeggia infatti 100 anni di attività nella produzione di torni verticali di tornitura e fresatura, fresatrici a portale mobile di tipo Gantry e celle flessibili di produzione (FMS). Da sempre, punto di forza dell’azienda è quello di offrire una gamma di prodotti fortemente personalizzati in funzione delle esigenze del cliente in termini di lavorazioni, flessibilità e produttività del processo richiesto. Ne parliamo con Davide Lavazza, Direttore commerciale di Pietro Carnaghi.
Macchine su misura
“Attualmente le maggiori richieste del mercato sono legate al settore energia, – spiega Davide Lavazza - uno dei principali settori di utilizzo delle realizzazioni PIETRO CARNAGHI insieme all’aeronautica con i motori aerei, all’aerospazio, le macchine movimento terra e i cuscinetti. Gli operatori del settore richiedono macchinari sempre più flessibili e ottimizzati per realizzare il componente finito, partendo dalla trasformazione della materia prima, ovvero dal forgiato, passando dalla sgrossatura, fino alla realizzazione del componente finito. Oggi si tende ad accorciare sempre di più la catena di passaggi tra conto terzisti che intercorrono tra la sgrossatura e la finitura. Il trend di mercato è l’equipaggiamento di macchine in grado di fare sgrossatura e finiture molto precise, accorpando il più possibile tutte le lavorazioni in un’unica soluzione per minimizzare i costi legati alla logistica, ottimizzare i tempi di lavorazione e avere un beneficio in termini di consegna rapida del prodotto finito al cliente. Questo si traduce infatti in un risparmio nei costi di produzione, che significa riuscire ad essere più competitivi sul mercato quando si quota la lavorazione meccanica”. In risposta a questa esigenza, PIETRO CARNAGHI da sempre produce macchine flessibili customizzate su richiesta del cliente, in grado di eseguire sgrossatura pesante e realizzare finiture molto precise.
“Nelle macchine per il settore dei cuscinetti, ad esempio, in cui viene richiesta la capacità di eseguire lavorazione di tornitura con oltre 15 mm di asportazione, spesso equipaggiate anche con due RAM con capacità di sgrossare fino a 300 KW di potenza, la richiesta del cliente è quella di eseguire sulla stessa macchina operazioni di finitura sul componente prima e dopo il trattamento termico”, precisa Lavazza. “Le macchine vengono quindi dimensionate e concepite per eseguire entrambe queste lavorazioni. Oggi le macchine non sono più semplici macchine di tornitura, in grado solo di sgrossare e finire il pezzo, ma sempre più spesso sconfinano nel campo della rettifica e vengono equipaggiate con degli accessori o parti di macchina dedicate per eseguire questa lavorazione sui componenti dopo il trattamento termico. Questo rende la realizzazione della macchina ancora più complessa e orienta la richiesta del cliente sempre più spesso in termini di esperienza, dato che non è più sufficiente la realizzazione del prototipo. È necessario avere