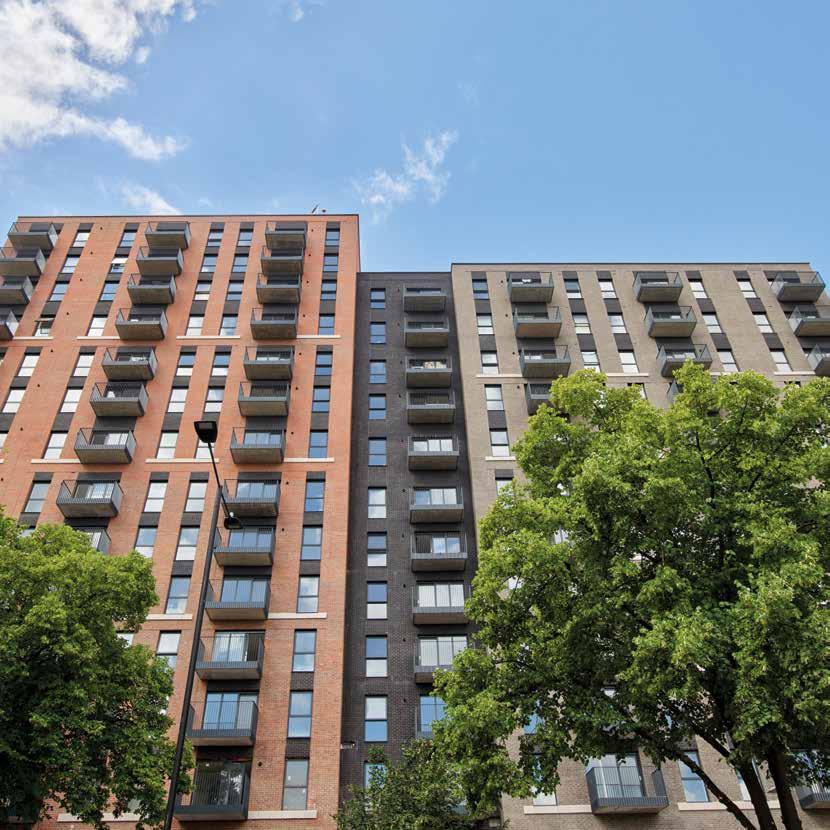
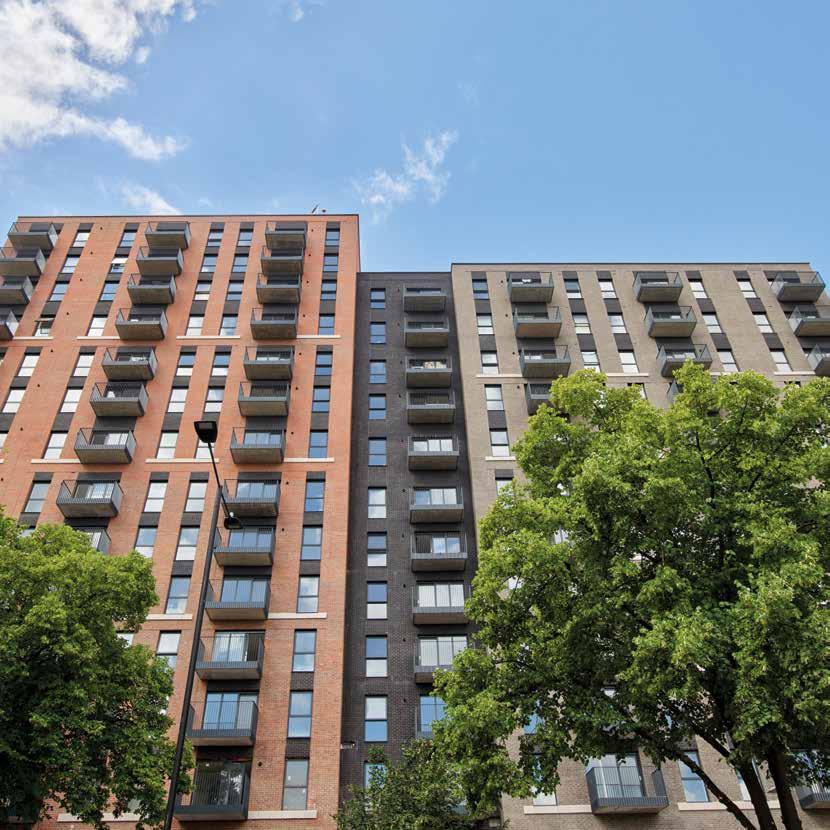
How to Choose the Right Howick Framing System



Standard Howick Framing Systems. The quickfire guide to finding the right Howick machine
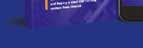



































From the workhorses FRAMATM 3200 and 5600 – great for all standard framing needs – to specialised machines like the X-TENDATM 3600 (extendable frames for infill spaces) and the FRAMATM 6800 (floor joist system) that are highly optimised to produce specific components, you will find we have a system available that meets most framing component manufacturing needs.
If you are thinking of something out of the ordinary, we also provide a range of customised options for our standard machines; we have even designed and manufactured new innovations to help solve specific challenges. Just talk to us about what you are trying to do.








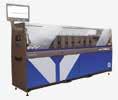
Want a great compact workhorse system that will produce most standard framing requirements for housing and low-rise? You do not need to look any further than the FRAMA™ 3200.

You want a workhorse capable of making heavier load-bearing framing for large build projects, low-rise and commercial with greater capacity and increased flexibility? The FRAMA™ 5600 is the right horse to jump on.
You want a dedicated truss system that is highly efficient and produces in volume? Step up to the FRAMA™ 4200 and try that for size. It is the system you can truss. (See what we did there?)






You want a dedicated flooring system that manufactures more efficiently than assembling lattice flooring? The FRAMA™ 6800 pops out floor joist cassettes with gusto. Plus, you will find them much more efficient to install.


You want a convertible frame and truss system with high output capacity that can be adjusted to handle 5 different profiles in the one machine? Welcome to the ultimate flexibility of the FRAMA™ 7600. It offers 5 different profiles and can be configured for floor joist production, framing production, or customised for both frame and joist tooling.
You want a convertible system that can handle heavier gauge than the FRAMA™ 7600? The FRAMATM 7800 is the big brother of all the rest, it offers everything the FRAMATM 7600 does, and it can handle thickness of up to 2.5mm / 13 gauge.
You want the fastest way to build retrofit and infill framing for interior spaces? The X-TENDATM 3600 makes telescopic framing that is extendable in any direction to fill any space fast. It is the latest innovation in infill framing technology.


You want to improve the efficiency of your framing plant by 5%? Just add the option of a Howick dedicated coil-loading system. Over a 7-hour shift, you will improve efficiency by 5%.







To find out more about setting up construction manufacturing with light gauge steel framing automation, simply scan the QR code to download our Machine Buyer Guide.
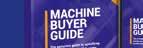
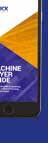

PUBLISHING
FRONT COVER British Offsite
PRINTED ON:
FSC Mix paper by Buxton Press
PUBLISHER:
Offsite Magazine is produced and published by Radar Communications:

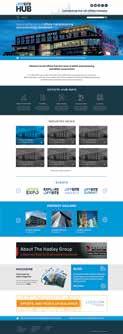
©Radar Communications Ltd.
Radar Communications Ltd, 101 Longden Road, Shrewsbury, Shropshire, SY3 9PS
T: 01743 290001
www.radar-communications.co.uk
SUBSCRIBE TO RECEIVE OFFSITE:
This magazine is a bimonthly publication and the annual subscription fee for UK postage is £29.70 plus VAT for all six issues (£4.95 per copy). Visit www.offsitemagazine.co.uk
ADVERTISING ENQUIRIES PLEASE CONTACT:
Julie Williams // T: 01743 290001
E: julie.williams@offsitemagazine.co.uk
SEND US YOUR NEWS:
Gary Ramsay // T: 01743 290001
E: gary.ramsay@offsitemagazine.co.uk
BACK ISSUES VISIT: www.offsitemagazine.co.uk
FOR OFFSITE ENQUIRIES PLEASE CONTACT:
E: info@offsitemagazine.co.uk
DISCLAIMER: The content of Offsite Magazine does not necessarily reflect the views of the editor or publishers and are the views of its contributors and advertisers. The digital edition may include hyperlinks to third-party content, advertising, or websites, provided for the sake of convenience and interest. The publishers accept no legal responsibility for loss arising from information in this publication and do not endorse any advertising or products available from external sources. The publisher does not accept any liability of any loss arising from the late appearance or non-publication of any advertisement. Content including images and illustrations supplied by third parties are accepted in good faith and the publishers expect third parties to have obtained appropriate permissions, consents, licences or otherwise. The publisher does not accept any liability or any loss arising in the absence of these permissions for material used in both physical and digital editions. No part of this publication may be reproduced or stored in a retrieval system without the written consent of the publishers. All rights reserved.
KEEP IN TOUCH:
THE STAKES ARE ALWAYS HIGH
Greetings and welcome to the latest edition of Offsite Magazine. The magazine continues to grow to cover the burgeoning world of offsite manufacture and MMC, the term that seems to have now become the favoured catch-all way to describe factory-led manufacture.
Our world of offsite manufacture is in a constant state-of-flux, arguably busier and more dynamic than ever before historically. But whilst exciting opportunities for growth and successful business are plentiful, so are the pitfalls. As we went to press, news filtered through that L&G Modular Homes had called a halt to production of new modules at its facility in Sherburn-inElmet.
Sadly, for many industry insiders this came as no real surprise, but the threat of redundancies for the 450+ staff is a miserable development. Running up cumulative losses of £176million since it was established in 2016, the dissection of its demise will no doubt continue. Time will tell if the business can be reformed or re-energised in some fashion. But after beginning with high hopes and mega-investment, L&G Modular Homes never seemed to give any confidence that it was going to deliver the transformational change
to the housebuilding industry on the scale that everyone was anticipating. Blame has been laid at the door of long planning delays, COVID-19 and the lack of pipeline to make the ‘current model’ work, but the feeling is that there was much more to it than those factors, that affected every other business in the industry.

For all of that, the enthusiasm for offsite methods shows no sign of slowing down. Not least in healthcare. David Clowe, recently appointed Director and Head of MMC at Turner & Townsend, tells us how new hospitals are helping galvanise the use of offsite construction where pressures on capital budgets and the net zero ambitions have put ‘the use of MMC front and centre for enablers.’
Loads more inside. Including a special focus on precast concrete and some real insight into social value and ESG goals from Akerlof and the Supply Chain Sustainability School – concepts that are hugely important aspects of offsite and MMC, even if you don’t actually realise it.
Thanks to all our contributors, advertisers and supporters for their help and guidance this issue.
Gary Ramsay Consultant Editor
Email: gary.ramsay@offsitemagazine.co.uk
•
• Online Newsroom
•
• Podcasts & Webinars
• Suppliers Directory
• Awards & Events
• Project Profiles
• Offsite Blog
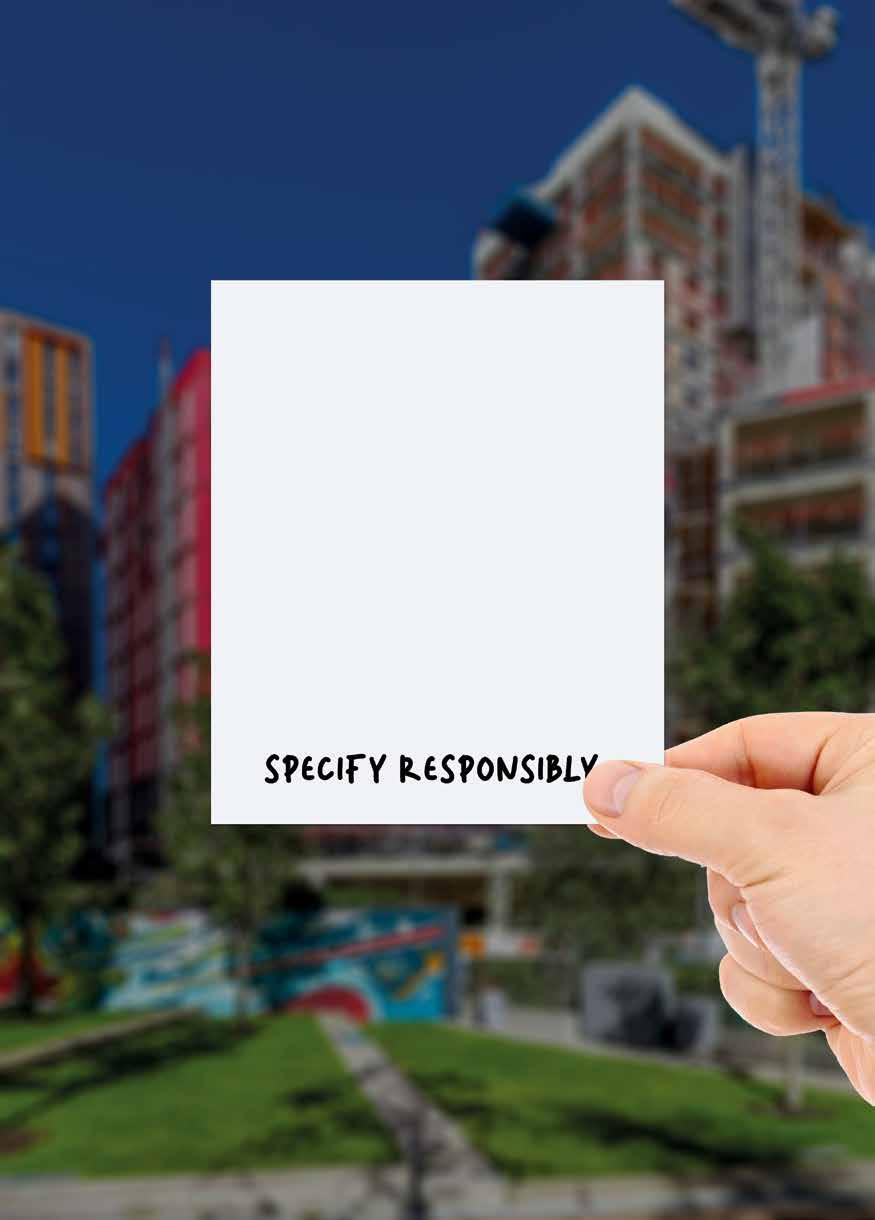
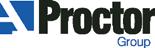
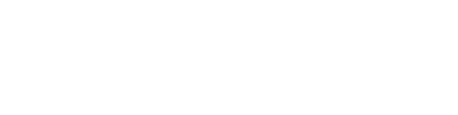
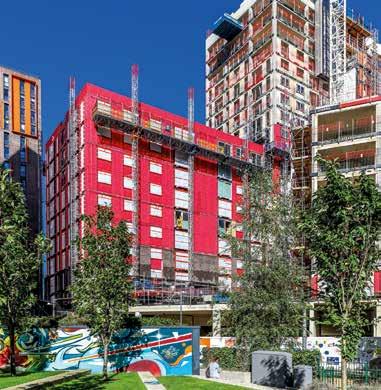


COVER STORIES
British Offsite offers a range of solutions to the complexities of modern housebuilding by utilising ‘best in class’ modern methods of construction (MMC) alongside traditional construction techniques. They also employ a factoryled ‘Fabric First’ approach to energy efficient construction.
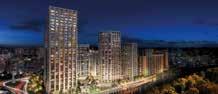
The healthcare sector offers huge potential for offsite methods to provide modern, cutting-edge facilities. We spoke to David Hartley, Managing Director of MTX on how they are providing award-winning fast-track healthcare solutions.

CONTENTS
34 | Insight Impact & Influence
As Make UK Modular releases its year one impact report, Director Steve Cole outlines the huge progress made so far and what lies ahead for the modular housing sector.
38 | Setting the Future Homes Standard
Trevor Richards, Operations Director at VOLUMETRICTM, discusses how they are ‘ahead of the game’ in terms of designing modular homes.
40 | Strengthening Market Position
More investment into volumetric modular provider TopHat signals a new era for housebuilding, with FTSE-100 housebuilder Persimmon injecting cash into precisionengineered homes.
50 | Superior Performance Benefits
Mike Fairey, Managing Director of Fusion Steel Framing, outlines why FusionTRAX – a new non-load-bearing infill walling system –is set to boost the offsite marketplace.

52 | Universal Standards
David Johnson, UK Preconstruction Director at Volumetric Building Companies, believes the future of UK offsite construction is in need of urgent change.
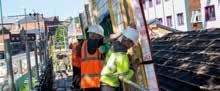
What does Environmental, Social and Governance (ESG) responsibilities offer the offsite sector and what more can you do to apply these principles to your business?
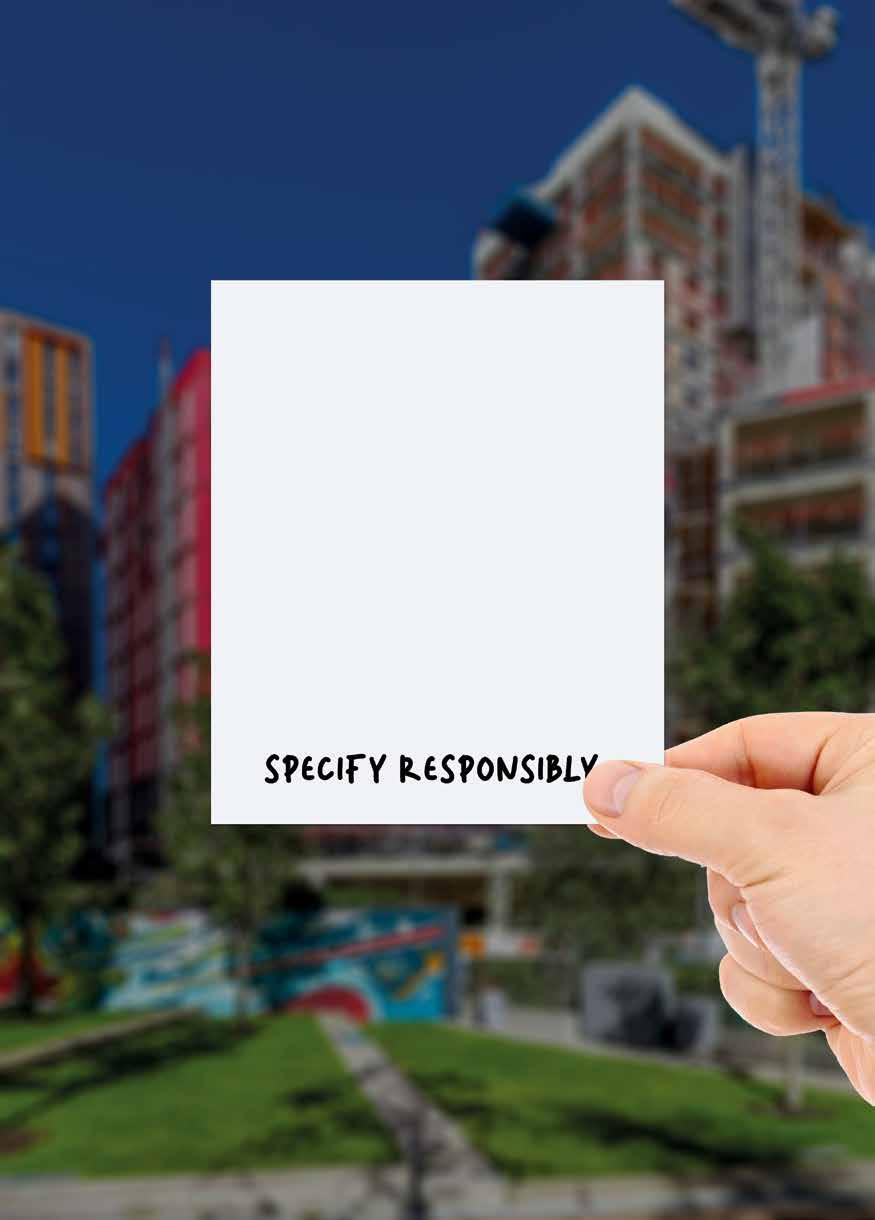
David Emery, Consultant at the Supply Chain Sustainability School (SCSS) lets us know.
08 | Industry News
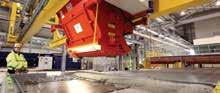
News and developments from across the UK offsite industry and wider construction arena including: Legal & General stops new production at its Sherburn-in-Elmet modular facility, Timber Development UK launches a Structural Timber Price Index, offsite recruiter ARV Solutions gets investors in people platinum accreditation and DLUHC embarks on a MMC Standardisation Research and Kit of Parts’ project.
A special section dedicated to one of the mainstay materials of the offsite world, with a range of case studies including: FP McCann, PCE, Carlow Concrete and Everton FC’s new stadium, plus a pioneering development in Finland that sees concrete and timber combining in a hybrid approach.
FEATURES
26 | Building In Better Health
As the construction industry accelerates towards more efficient, sustainable and resilient strategies, MMC is becoming pivotal to the success and sustainability of both public and private sectors across the UK. David Clowe, Director and Head of MMC at Turner & Townsend explains more.
70 | Designing With Data in Mind
Simon Reid, Managing Director at Lungfish Architects, explains how their data-rich approach to design has led to success in delivering multiple projects across the education sector.
72 | Aligning Offsite with Social Value
Social value is much more than a buzzword. It is central to offsite manufacture’s wider development. Penny Anderson, Head of Social Impact at Akerlof, tells us more.
82 | A ‘Perfect Storm’?
Andrew Pryke, Managing Director at BAM Design, gives us a quick reminder about why offsite methods are so relevant and why the industry is perfectly positioned to succeed.
CREATIVE CONTROL
British Offsite offers a range of solutions to the complexities of modern housebuilding by utilising best in class modern methods of construction (MMC) alongside traditional construction techniques.
Borough of Barking & Dagenham where 13 residential blocks range from 7 to 29-storeys in height. The six-acre, 1,000 homes scheme will be delivered over the next five-years. Given the scale of the development, the project team opted for a hybrid solution using British Offsite’s UNisystem, the most advanced light gauge steel panel system in the marketplace. UNisystem incorporates a highly flexible set of products capable of meeting every architectural need with precision.
High density, urban brownfield development presents some of the most challenging projects in the residential arena. The pressure to deliver units at scale and within clearly defined design parameters means many projects default to a more traditional approach to construction. This leaves them vulnerable to supply chain delays, labour shortages, storage and delivery issues – all of which can result in increased costs and a slower return on investment. These time and budgetary pressures, alongside commitments to environmental/ sustainability and health and safety targets, make running a site a complex task.
By bringing critical processes offsite, project teams can eliminate risk and take total control over their final design solutions. This, alongside traditional on-site volume housebuilding methods, results in a hybrid solution that eases the pressure of delivering world-class architecture and design. This results in development projects that benefit from:
• Acceleration of overall delivery/ completion
• Reduced site waste
• A reduction in on-site inventory (i.e. less breakage/wastage)
• No more labour/skills shortages
• Better cash-flow management
• Improved health & safety issues
• Reduced noise pollution & disruption.
British Offsite’s approach also helps it deal with the skills shortages facing the industry. British Offsite Managing Director Shaun Weston says: “The skills shortage in the construction industry was widely reported before Brexit, and now we’re in a post-Brexit environment where the pandemic has further reduced access to skills. With the work of up to five trades consolidated into our panels, our customers are more protected from the skills shortage and construction can continue unhindered.”
A good example of how this works is at Abbey Quay, Barking, a new urban riverside development in the London
For the superstructure, the project team at Abbey Quay utilised UNipanel, a light gauge steel (LGS) closed panel system. This LGS system comes pre-fitted with insulation, doors, windows, vent apertures, fire stopping and façade fixing systems. This is complemented by the use of UNiwall, an internal LGS compartmentalisation closed panel pre-fitted with insulation, doorways, MEP and service void battens.
Manufactured offsite, these systems offer benefits including the rapid delivery of dry envelopes, reducing weather-induced delays, improving health and safety, streamlining fitout and accelerating handovers. All homes provide contemporary open plan living with designer kitchens, luxury bathrooms, smart technology incorporating a range of British Offsite fitted modules including bathroom vanity units, quartz worktops and bespoke storage solutions. Its MMC approach cuts down the time between a site’s ground-breaking and first handovers by up to 20%.
As champions of precision, the consistent quality of each panel produced is guaranteed by the technical design process, state-of-theart machinery, robotics capabilities and quality control systems. British Offsite is equally exact about construction sequencing and have a
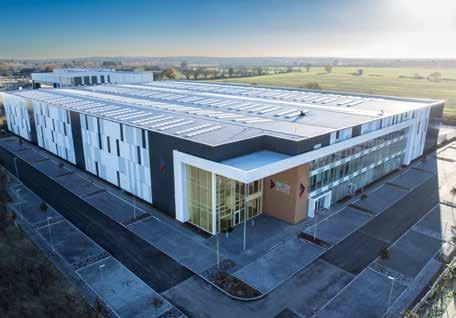
full set of accreditations to meet the requirements of technical managers.
The future is exciting for British Offsite – the second British Offsite factory – the new 180,000sq ft Horizon factory in Braintree is now complete. The new factory will be operational from July 2023. The company estimates the new factory will deliver 4,000 homes per year. The new steel panel factory will include a £6million production line, being delivered by Swedish manufacturer Randek AB. Shaun Weston is overseeing a workforce of around 130 people, ensuring those Randek’s robots, programmed by British Offsite’s design and software experts, toe the line.
The robots – mesmerising giants that have multi-jointed mobile ‘arms’ with claws and magnets – are guided in part by sensors and can transport, grab, cut, drill, nail, screw, weld, glue, fill, spraypaint and much, much more. Randek’s systems, developed specifically for the building industry and tailored for each client, have no-nonsense names like AutoWall, AutoFloor, AutoEye and even ZeroLabor, and their customers hold world record speed records for making and assembling basic building components, such as walls, floors and roofs.
Shaun Weston is a robot convert because he’s a passionate homebuilder: “You are actually going to get a home which is more perfectly tailored for you then you could perhaps ever imagine, and infinitely better made,” he says. Choice of fittings and surfaces is multiplied through more efficient sourcing, buying, delivery and storage systems. The specifications and overall quality are checked at every turn.
Hyper-accurate machinery ensures precision cutting and assembly for every component, which will be delivered to site flawlessly finished and carefully packages. This helps to eliminate mistakes through human error. Because the company is not building outside there is no mess or waste and little chance of damage from bad weather or inexpert handling. The robots – or more precisely the designers and technicians who programmed them – know what they want.
Costs are radically reduced which means higher quality for less money.

“We even have the technology and the budget to build-in sophisticated extras like our digital showers and our hot water kitchen taps,” adds Shaun. Wait times are substantially cut. The robots minimise waste, too, and even manage their own recycling. There is an acknowledged skill shortage throughout the building industry and British Offsite’s robots are filling the gap, though some traditional trades are still used on-site for finishing touches.
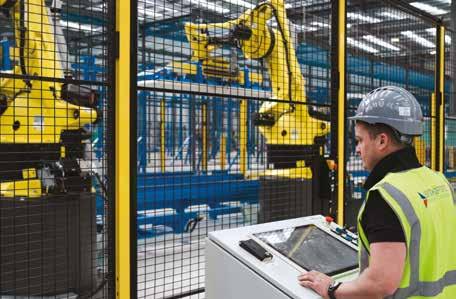
British Offsite’s factories are part of its innovative ‘Fabric First’ approach to homebuilding. In simple terms, this makes the basic structure of a building the priority. Reducing heat loss is done at source using smart building materials and construction methods. Cutting heat loss in turn cuts energy use and carbon emissions – the golden goal of modern life. It’s good for the planet and good for the homebuyer.
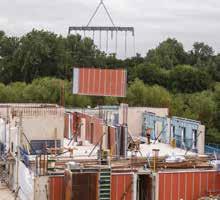
For more information visit: britishoffsite.com
Images:
01. The Horizon factory
02. Randek robots inside the Horizon factory
UK INDUSTRY NEWS
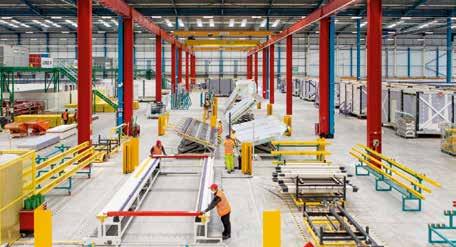
L&G Modular Homes Halts New Production
As has been widely reported in the trade press and across the mainstream media, Legal & General has stopped new production at its modular housing factory at Sherburn-in-Elmet, near Leeds with over 450 redundancies expected. The troubled provider blamed ‘long planning delays and weak demand’ for the problems.
Strategic options for the factory include a sale, merger, fundraising from third parties or eventual closure. The company will begin a consultation with employees about redundancies, retaining a number to build modular homes for existing projects in Bristol, Selby and Broadstairs in Kent. L&G’s modular housing business has made slower progress than expected, running up cumulative losses of £176million since it was established in 2016.
The L&G statement read: “Legal & General has announced today that it is proposing to reduce business activity and cease new modular production at its modular housing factory in Selby, Yorkshire, whilst reviewing and assessing potential strategic options for the business. As a start-up business with a significant fixed cost base, a strong and predictable site pipeline is required to make L&G Modular Homes a successful sustainable business.
Construction Commences at Moderna Innovation & Technology Centre
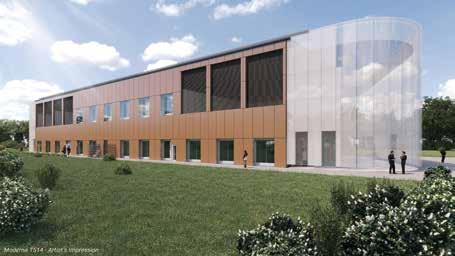
Moderna, Inc. (Nasdaq: MRNA), a biotechnology company pioneering messenger RNA (mRNA) therapeutics and vaccines, has commenced construction of its Moderna Innovation and Technology Centre (MITC) in Harwell, Oxfordshire. The MITC will encompass research, development and a manufacturing facility, which aims to provide the UK public with access to mRNA vaccines for a wide range of respiratory diseases, pending independent regulatory assessment and licensure.
The Moderna investment will create hundreds of jobs during construction and operation. The MITC will include a clinical biomarker laboratory that will be constructed by the offsite construction and engineering specialist Merit. The Drug Substance and Manufacturing facility will be fitted out by Birmingham-based engineering firm IPS and is expected to become operational in 2025.
Darius Hughes, UK General Manager at Moderna, said: “We are delighted to celebrate this important milestone today alongside our partners from the UK Government and Harwell. We look forward to continuing our collaboration throughout construction of the Moderna Innovation and Technology Centre,
“However, a number of factors, including long planning delays and the impact of recent macro events such as Covid, have meant the business has not been able to secure the necessary scale of pipeline to make the current model work. Without this pipeline, it has not proved possible to build a business that can sustain the significant running costs of the large factory in Selby. As a result, Legal & General is also commencing consultation with all employees around the proposal to make the majority of modular homes roles redundant. The business will be doing all that it can to support employees during this difficult time and will be actively exploring opportunities for redeployment.”
Bill Hughes, Chair of the L&G Modular Homes board added: “Legal & General is proud of what we have achieved in bringing forward a new approach to construction through our factory. However, without the necessary scale of pipeline it is not sustainable to continue producing more modules. We are therefore reluctantly proposing to reduce business activity and cease production of new modules at the factory. We recognise this will be a challenging and uncertain period for staff and we will be actively exploring redeployment opportunities.”
Source: www.legalandgeneral.com
and beyond, to bring innovative vaccines to the UK public to help protect against emerging respiratory health threats.”
A groundbreaking ceremony was attended by Health Minister Maria Caulfield, CEO of the UK Health Security Agency Dame Jenny Harries, local community leaders and representatives from the UK’s health resilience and life sciences community.
Health Minister Maria Caulfield, said: “Thanks to this partnership between the government and Moderna, NHS patients across the country will have access to cutting edge mRNA vaccines to fight future Covid
variants and other respiratory viruses, so it’s great to see construction starting on this new centre.”
Professor Dame Jenny Harries, chief executive of the UK Health Security Agency, said: “This facility will significantly strengthen the UK’s vaccine development and research capabilities, helping shore up our defences against future health threats, including pandemics. Once built, it will be capable of producing millions of vaccines against respiratory diseases and other illnesses, placing the UK at the global forefront of health science and innovation.
Source: www.merit.co.uk
Our UK-made net carbon negative sheet materials are the number one choice in the construction, furniture and DIY sectors.
uk.westfraser.com
M-AR’s Growth Recognised in Yorkshire Fastest 50 Awards
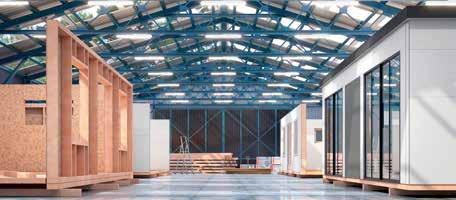
Specialist offsite contractor M-AR has been named as one of the 50 fastest growing companies in Yorkshire. The prestigious Ward Hadaway Yorkshire Fastest 50 Awards, in association with The Yorkshire Post, celebrate growth, innovation and the commercial achievements of Yorkshire businesses.
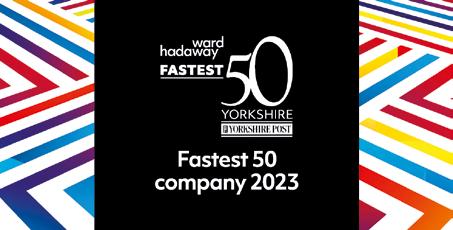
Based on financial data filed with Companies House, the list ranks the fifty best performing independent companies which have consistently increased turnover over the past three financial years, whilst remaining profitable. M-AR was ranked third as a result of its continued and strategic growth which has seen it not just increase turnover but also successfully scale up operations by investing back into its manufacturing facilities. As a result, the company is successfully undertaking projects of larger scope including a recently completed 33 apartment development built in London for the UK’s leading youth homelessness charity, Centrepoint.
Emma Digby, who is Executive Partner at Ward Hadaway's Leeds Office, said, "I’d like to take this opportunity to congratulate M-AR alongside all the companies in the Ward Hadaway Yorkshire Fastest 50 list for 2023 for their outstanding achievements. The companies in the Fastest 50 demonstrate that real, genuine growth is happening.
“Yorkshire businesses are thriving because they’ve not been afraid to go against the grain, take risks or follow their instincts at a time when uncertainty
New MMC Moves by Government
The Department for Levelling Up, Housing and Communities (DLUHC) has embarked on a ‘Modern Methods of Construction (MMC) Standardisation Research and Kit of Parts’ project to develop an open-source kit of parts that will encourage the uptake of MMC.
Following through on commitments set out within the Transforming Infrastructure Performance Roadmap to 2030 and Construction Playbook, the project represents a key step by government to translate policy into practice. Akerlof, a specialist MMC consultancy, has been appointed by DLUHC through competitive tender to lead a consortium of partners, including Buro Happold, HLM Architects and Limberger Associates, that will collectively undertake research and engagement to help shape a strategy that uses standard parts.
The focus of the project will be on MMC Categories 2 (2D primary structural systems) and 5 (nonstructural assemblies and sub-assemblies). Extensive
is the norm. They’ve been brave, they’ve been bold and, as a result, rewarded through continued growth. This year’s Fastest 50 list, as always, boasts many management teams with an unwavering passion to succeed who have created high growth, profitable businesses. It’s this spirit, and the business success that it creates, that we are delighted to celebrate."
Ryan Geldard, Director at M-AR added: “It’s a real honour to be named as one of the fastest growing businesses in Yorkshire this year alongside 49 other incredible Yorkshire companies. We set ourselves a mission just a few short years ago to increase the size of our operations here at M-AR so that we could take on larger projects, but more importantly to carve out a place for ourselves so that we could continue to champion the benefits of offsite construction to the wider industry. I think this award recognises the fact that we’re well on our way to achieving our goal and with our passionate and dedicated team at the helm there is more to come from M-AR so watch this space!”
M-AR recently strengthened its core leadership team with a trio of new department heads appointed to co-ordinate both the offsite manufacture and on-site construction elements of projects for greater efficiency.
In the last six months, Ryan Guest, Steve Tate and Keith Hill have been appointed as Head of Commercial, Head of Manufacturing, and Head of Construction respectively. Together they also form part of M-AR’s newly created Senior Leadership Team where they’ll work alongside John Leitch (Preconstruction), Dan Lowther (Procurement), Robert Cousins (Design) and Charlotte Smith (Finance) to engage in open multi-departmental conversations intended to drive innovation and foster a mindset of collaboration and a ‘one team’ culture.
Source: www.m-ar.co.uk
consultation with the wider industry and supply chain will ensure the solutions reflect the requirements of the sector and unlock growth within the MMC market. Commenting on the project, Housing Minister, Rachel Maclean MP, said: “Delivering more, better quality and greener homes is central to our levelling up mission. I encourage all industry partners to engage in this research which will harness the benefits of modern methods of construction, drive up productivity in the sector and help deliver the high-quality homes this country needs.”
Jamie Hillier, Partner at Akerlof added: “Akerlof is delighted to be working with the Department for Levelling Up, Housing and Communities, our consortium partners and the wider industry on this exciting project which will accelerate the move towards MMC within the housing sector. As a business we are committed to driving transformation that leads to a better built environment. We hope that this project will demonstrate the benefits of using common parts to create greater choice across housing and set the direction of travel for the sector.”
Source: www.akerlof.co.uk
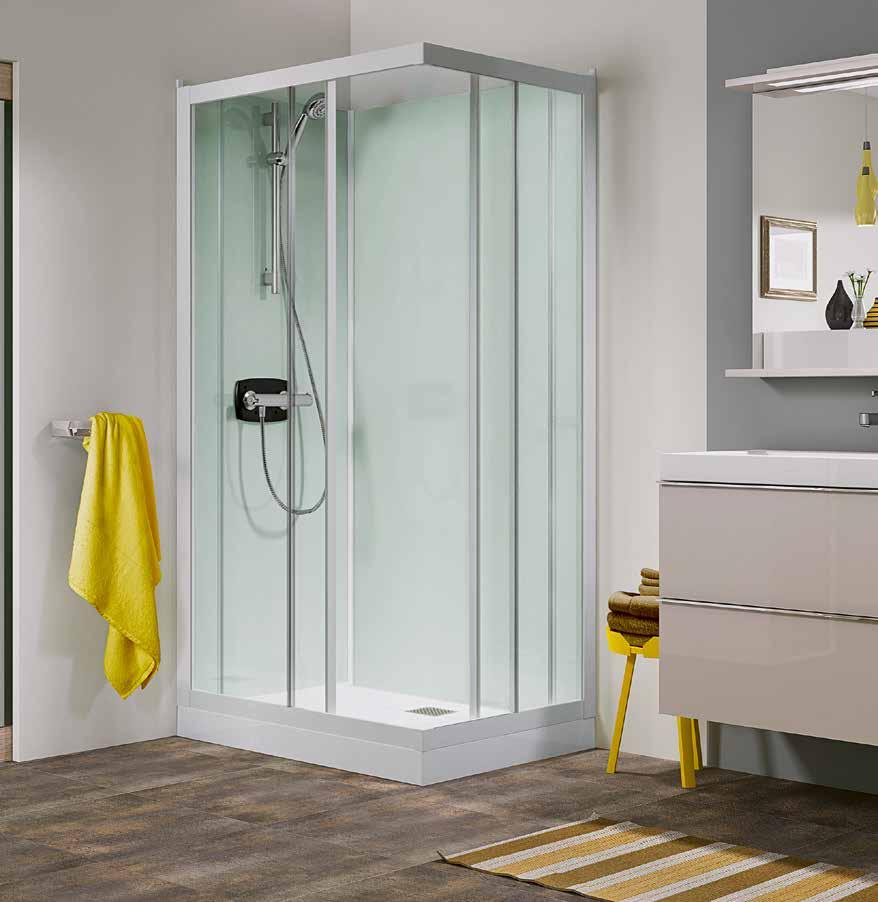
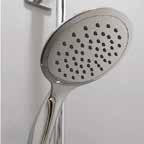
Mulberry Homes Goes MMC
Mulberry Homes has made its first foray into the world of modern methods of construction (MMC) with a hybrid approach that combines an offsite roofing solution with traditional brick-and-mortar builds. A collaboration with Roofspace Solutions will see 37 i-Roof™️ units installed at a new residential development in Rugby – Mulberry Homes at Houlton – which will comprise two, three, four and five-bedroom homes.
Mulberry Homes’ ambition to modernise and increase the efficiencies of its build program led them to approach Roofspace Solutions, which has been pioneering MMC housebuilding systems as part of the Saint-Gobain Off-Site Solutions division. The i-Roof is a room-in-roof solution for 2.5-storey homes and was selected to be the first solution trialled across the Houlton site thanks to its ability to save time, minimise waste, reduce reliance on on-site labour and provide cost certainty.
Manufactured at Roofspace Solutions’ specialist manufacturing site in Alcester, the i-Roof system helps accelerate construction by reducing the roof element to a one-day install and providing the developer with
enhanced preliminary savings. When built traditionally, the roof element can often take up to seven weeks –a timeline which can slip further with labour shortages or bad weather.
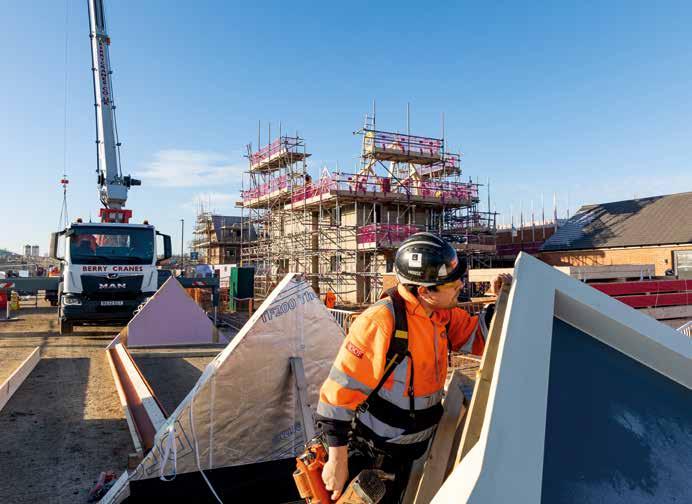
With most of the build taking place in a controlled factory setting, this reduces risk to workers on-site. For example, the danger of unsupported blockwork and gables collapsing in adverse weather conditions is replaced with a secure timber-engineered solution which works alongside traditional build methods. The factory environment also adds a layer of additional quality control, with inspections and audits ensuring that the MMC components are compliant with all regulations and standards.
Further time savings are achieved during installation as the system is delivered to the site ready for assembly. This also improves the development’s sustainability credentials, as it negates the need for multiple deliveries and minimises on-site waste.
Simon Yates, Business Development Manager at Roofspace Solutions, said: “i-Roof is an ideal MMC solution for property developers as it accelerates the
room in the roof construction considerably, allowing the developers to deliver quality homes faster. Our goal is to make life better on-site by taking things off-site, and that includes managing the process from factory to installation. Doing it this way reduces carbon emissions and waste, while also increasing the speed of the project and the standards of on-site health and safety.”
David Morris, Associate Commercial Director at Mulberry Homes, said: “We’re working to strengthen our vision for the future of housebuilding. Working with the Roofspace Solutions team was a pleasure. They’ve shown us how MMC brings consistency to the build pattern and the manufacturing methods. It is also clear that they put health and safety first. The UK has a desperate shortage of housing, so anything that speeds up delivery is important. We saw how i-Roof could increase the quality of our homes and help us to build them faster, we knew we wanted to work together. I’m confident that MMC will become a common sight on Mulberry Homes’ developments in the future.”
Source: www.roofspacesolutions.co.uk
NG Bailey Appoints New Leader Role
NG Bailey has appointed Jonathan Stockton to the newly created role of Chief Operating Officer (COO). Clare Salmon, previously Group Financial Controller, has been promoted to Group Finance Director.
As COO, Jonathan will oversee and optimise the Group’s operational capabilities and administration, alongside developing and implementing key business strategies. Jonathan will also continue as a Group Board Director.
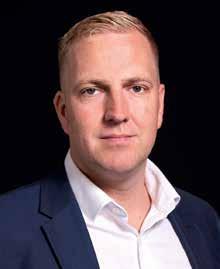
Jonathan has played a key role alongside Chief Executive David Hurcomb and the NG Bailey Board in driving the Group’s growth agenda, which included several successful acquisitions within the services business. The NG Bailey Group, which has operated for over 100 years, is supported by a positive balance sheet, strong order book, diversified business plan and solid market positions.

David Hurcomb, CEO at NG Bailey, said: “It is pleasing to see Jonathan move up into this newly created and strategic role. He has been an important part of the senior team since joining in 2016 and has contributed much to ensure the continued success of the business. As a business, we are committed to recognising and rewarding our own talent and Clare’s promotion is testament to that. It also shows our
succession plans are working and that colleagues can thrive and succeed in their careers with us.


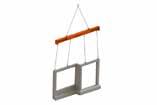
“Moving forward we have exciting plans across the Group, including a continued commitment to the net zero agenda and making a positive impact in everything we do. Both Jonathan and Clare’s wealth of experience across the business will ensure we remain at the forefront of the industry.”
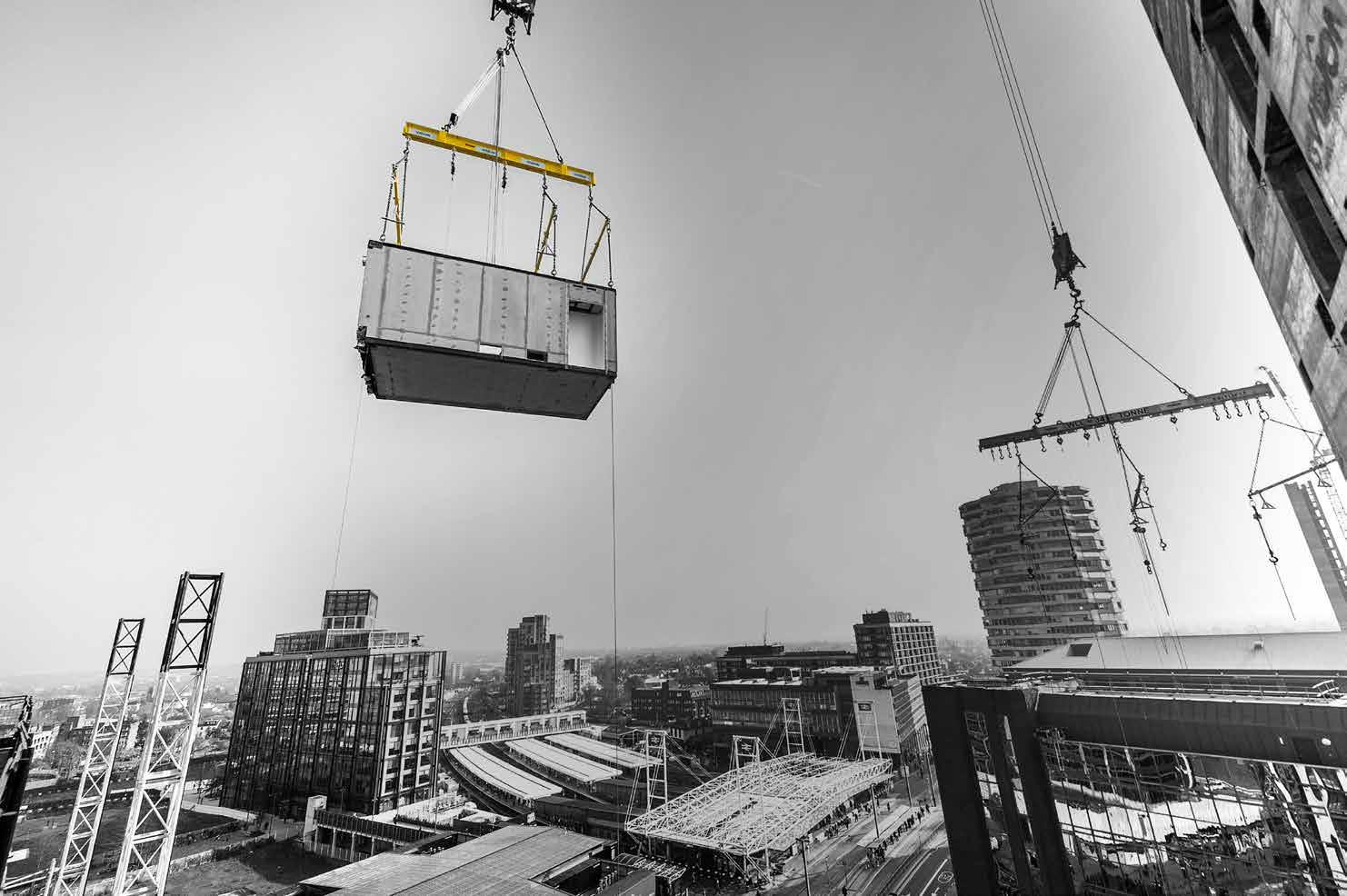
Speaking about his new role, Jonathan said: “NG Bailey continues to be a leader within its field, and I am excited about the opportunity this role presents to deliver important work that further enhances our
market leading position and supports our people – the lifeblood of the business. I look forward to developing further in this new role and making a positive contribution to our ongoing success.”
In her new role Clare joins the Group Operating Executive. Clare will manage the financial integrity and day-to-day performance of the business to support and build on the company’s solid financial position.
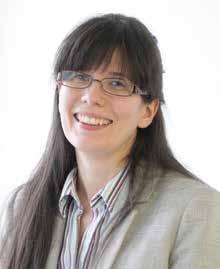
(L-R) Clare Salmon, Group Finance Director and Jonathan Stockton, Chief Operating Officer (COO).
Source: www.ngbailey.co.uk


IDMH Rebrand as Lighthouse
One of the UK’s leading modular housebuilders –IDMH Limited – has rebranded to Lighthouse. The rebranding marks the start of a new era for the business which has undergone major changes since a restructuring in 2020 that saw Tom White appointed as CEO and the nurturing of a talented team.
“The past two years have been about laying the foundations for the business and providing a strong operational platform that enables us to invest in our people and processes to create an innovative and scalable business,” says Tom. “We have built a best-in-class team and continue to hire top talent for key roles. We have also developed a strong culture for excellence, hard work and transparency. We are working with a wide range of clients on some highprofile projects across the UK.
“The rebrand signals that we are entering a new chapter. One where our focus on quality, speed and sustainability reflects the important role of modular construction in building more homes in the UK at the pace the nation needs, whilst driving significant environmental benefits in the construction sector.”
The new name, Lighthouse, represents the business’s focus on robust quality, an emphasis on homes that are well designed with respect to light and space and
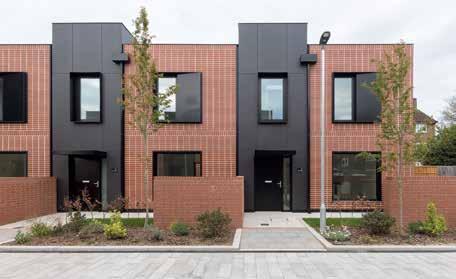
the company’s pioneering spirit. Supporting the new company name is a new website. The company’s legal entity and legal name (IDMH Limited) remain unchanged.
Using proprietary software, rigorous processes and sustainable materials at its factory in Tinsley, Sheffield, Lighthouse manufactures high quality modular buildings that can be delivered at speed. Current projects include delivering modular solutions for the Fair Isle Bird Observatory Trust, The Royal Borough
of Greenwich, nHouse in Cirencester, Youngman Lovell at Bicester Village and apartments in Worthing for BoKlok, a partnership between Skanska and IKEA. Lighthouse employs over 100 people at its manufacturing facility in Sheffield and its regional office at The Innovation Centre, Sci-Tech Daresbury in Warrington.
Source: www.lighthouse.co.uk
Commercial Timber Guidebook Available
New
To foster cross-sector industry alignment on solutions to ensure the widespread adoption of large-scale mass timber offices, the Built by Nature Fund has awarded a €200,000 grant to a diverse UK consortium focused on unlocking the barriers to structural timber through the development of a technical Commercial Timber Guidebook.

The project lead is engineering consultancy Elliott Wood, joined by implementing partners Waugh Thistleton Architects, fire engineers OFR Consultants and insurance specialists Lignum Risk Partners –technical and design experts in the built environment known for their advocacy of structural timber. The development of the Commercial Timber Guidebook has additional backing and input from some of the largest investors, developers and asset owners in the UK including Stanhope PLC, Related Argent, Lendlease, British Land, Derwent London, Landsec, MUSE, Berkeley Estate Asset Management (BEAM) and Hines.
The involvement of developers is significant, as the Guidebook seeks to show that a wide-ranging coalition of the biggest industry stakeholders in the UK can reach consensus on how to mitigate risks of large and complex timber developments, while demonstrating the industry’s technical competency to insurers and developers.
The Guidebook will establish common ground and a realistic route for the wider adoption of structural timber in commercial buildings through consensus on defined design principles, mass timber building typologies and technical design measures. With agreed guidelines and clear framework in place as to how risk can be quantified and mitigated, the Guidebook can address the challenges and costs around insuring timber structures, the single largest barrier to mass timber construction in the UK.
The project will also complement existing projects targeting insurance barriers through direct engagement and leverage recognised industry networks such as the UK Green Building Council, Better Buildings Partnership and the Institution of Structural Engineers for dissemination of the Guidebook.
Built by Nature CEO Amanda Sturgeon: “This is an exciting, important project given the scope of its cross-sector collaboration and the involvement of major UK developers. The Guidebook can be a milestone on the roadmap to wider acceptance of timber by creating a clear, peer-reviewed framework for overcoming the insurance barriers. And by securing the endorsements from major developers, asset owners and designers in the UK, we can create better policy conditions for mass timber offices and bring the market significantly closer to large-scale insurability.”
According to James Souter, Structural Engineering Director at Elliott Wood, “There is a clear need for a collective voice on the subject to agree consensus on good practice and to educate the industry, to unlock the barriers to adopting structural timber. The scale of the opportunity we’re addressing is huge, and we need to bring all the right people together to address the different facets collectively. Gaining the backing of Built by Nature is a major step forward in making the guide a reality, we’re over the moon to be taking this project forward.”
Source: www.builtbn.org
FIRST-CLASS
Delivering more light steel residential structures than any other European producer
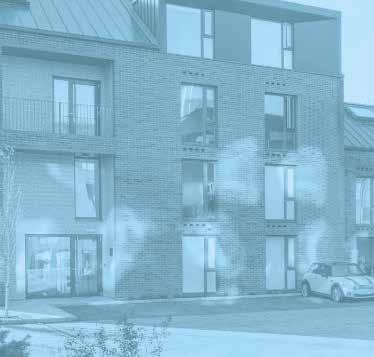
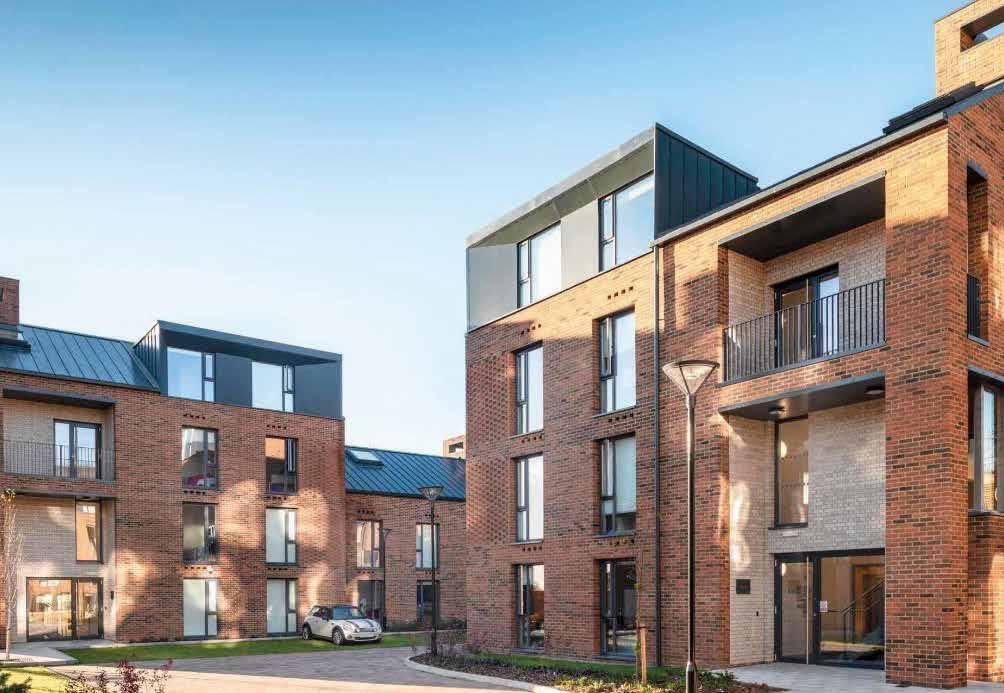
At Fusion, we are leaders in light steel framing solutions, a modern method of construction that brings huge benefits to our clients. Our light steel solutions and accompanying products offer outstanding precision, efficiency, adaptability, sustainability and performance. Using digitally enabled processes, we work closely with our clients across a range of schemes to help them achieve exceptional results.
Whatever your project, speak to us today to find out how we can assist you.
Setanta Construction Launch 'SoLow' Homes
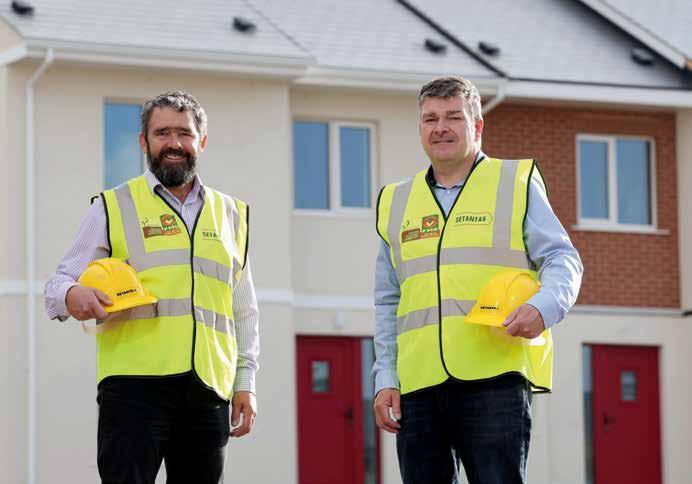
Mid-Ulster based Setanta Construction, is looking towards revolutionising the housing market through the development of low energy, volumetric, Passive certified homes.
The company recently unveiled the construction of its 'SoLow' pilot housing project at its site in Magherafelt to a group of international delegates attending the 'Building a Sustainable Future' conference in Northern Ireland and detailed their ambitious plans for growth within the energy efficient housing market.
Mark Gribbin, Director at Setanta Construction says: "Our newly launched 'SoLow' volumetric house aims to put energy performance at the heart of the housing market, delivering significant cost, time, health and environmental benefits for all. We’ve worked alongside industry experts in the design process including The Electric Storage Company to ensure outstanding functional performance throughout. Key components include 4kW of photo voltaic panels installed with an 11kw electric storage battery with heating and hot water provided by an integrated heat pump and ventilation system.
“We want to maintain our lead position in the energy efficient housing market, and we’re committed to
continuously refining and perfecting the production, processes and rollout of our bespoke offsite building concepts. The advantage of working with Setanta means that our housing components are built here at our factory before they are delivered and assembled to sites.
“Currently it takes just two weeks to construct our 'SoLow' passive house in the factory and it can be assembled onsite in just a few hours. In time we intend to scale up with plans for a new 30,000sq ft factory underway, which will enable us to increase productivity to one fully-completed house every day.”
Research into the overall benefits and potential cost savings of Passive built homes are far-reaching and its widely accepted that they have the potential to use 80 - 90% less energy than a typical home, not only helping the environment but helping homeowners save money too.
Setanta have enlisted the support of Ulster University’s Centre for Sustainable Technologies team to conduct a detailed study into the actual performance and overall energy efficient benefits of Passive Home living, specifically Setanta’s ‘SoLow’ pilot housing project.
Niall Gribbin, Director at Setanta: “We’re fully convinced of the advantages of building offsite Passive Homes with low embedded carbon, but to fulfill our assurances to potential homeowners and industry professionals we’ve committed to undertake a detailed study to examine the full benefits in comparison to conventional builds and further explore what works well for the ultimate occupants and the environment we live in.”
Trevor Hyde of Ulster University’s Centre for Sustainable Technologies adds: “It’s widely accepted that the Passive House concept is a smart longterm investment, which leads to lower energy consumption, reduced maintenance, and expense with improved occupant comfort. We're excited to team up with Setanta Construction to investigate this concept further and undertake a detailed study, analysing factors such as air quality, temperature fluctuations and energy usage on a yearly basis. We look forward to the findings of the study and the potential impact this work can have as we transition towards net zero.”
(L-R) Mark Gribbin and Niall Gribbin
Source: www.setantaconstruction.com
Beattie Passive Achieves ISO Boost
Passivhaus pioneer Beattie Passive, a major offsite manufacturer of modular housing and the first company in the UK to be certified for a complete build system by the Passivhaus Institut in Germany, announced that it has achieved UKAS ISO 9001, ISO 14001 and ISO 45001 certification. These certifications reaffirm its commitment to quality management, environmental responsibility and occupational health and safety.
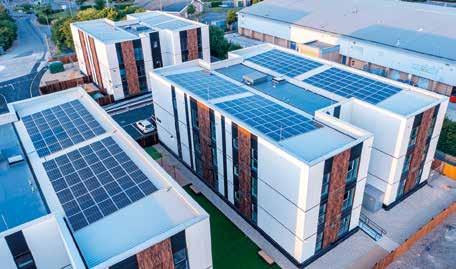
ISO 9001 is a standard that sets out the requirements for a Quality Management System (QMS). By achieving this certification, Beattie Passive has demonstrated that it can consistently provide products and services that meet customer and regulatory requirements, while also enhancing customer satisfaction. ISO 14001 is a standard for environmental management, which provides a framework for identifying and controlling an organisation's environmental impact. ISO 45001 is a standard for occupational health and safety management, which provides a framework for identifying and controlling risks related to the health and safety of employees and stakeholders. By achieving this certification.
“We’re incredibly proud to have achieved these certifications because they demonstrate our
commitment to quality, sustainability and safety,” says Ron Beattie, Managing Director of Beattie Passive. “We always strive to provide the highest standards of quality to our customers, while minimising our environmental impact and safeguarding the health and safety of our employees."
Jack Randall, Chief Commercial Officer at Beattie Passive, added: “These certifications will enable us to work with organisations that demand ISO standards from their partners. We’re also BOPAS approved, and we’re named on Crown Commercial Service’s offsite construction framework and the Offsite Homes Alliance’s modular construction framework.
“Our aim is to increase awareness of Passivhaus and make it more accessible to public sector organisations that want to tackle fuel poverty, raise living standards and achieve their net zero ambitions. Our patented, Passivhaus-certified build system combines all the energy efficiency, comfort and carbon-saving benefits of the Passivhaus standard with the speed and versatility of volumetric modular construction. It’s a very compelling solution to many of the challenges facing the housing sector and the construction industry.”
Source: www.beattiepassive.com
Setting the standards for timber fastening
BeA your partner for timber frame and offsite construction manufacturing
Across Europe and worldwide, BeA’s fastening technology, tools and consumables are the trusted choice for some of the biggest and best known names in timber frame and offsite construction.
BeA manufacture an extensive range of market leading fasteners, nails, staples and tools. We offer customers:
• An unrivalled range of manual and semi-automatic fastening solutions combined with a fully automated range in Autotec.
• I ndustry leading quality controls, BeA meet or exceed standards such as Eurocode 5.
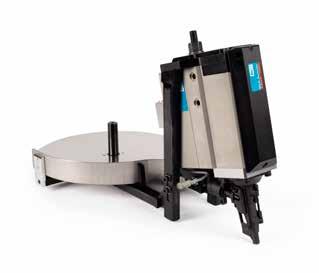
Reliable products, competitive prices and the kind of service and delivery you can depend on from BeA.
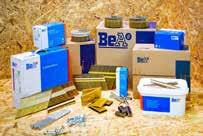
01482 889 911 sales@uk.bea-group.com visit our website www.bea-group.uk
THE POWER OF FASTENING

ARV Solutions Gain Investors In People Platinum Accreditation
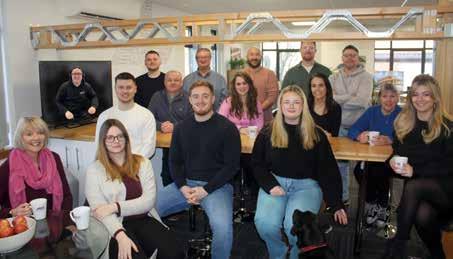
Platinum is the highest level of the standard possible to achieve on the We Invest in People accreditation. ARV Solutions first achieved IIP Gold accreditation in 2016 at the first assessment and has maintained this since. They have also been finalists for Gold Employer of the Year in 2020, the best pivot during COVID-19 in 2021 and the best Reward and Recognition in 2022. Their Managing Director was awarded Manager of the Year by Investors In People in 2017.
Investors In People means policies and practices around supporting people are embedded in every corner of ARV Solutions. Key measures cover leadership and support, structuring work for high performance, and really delivering on continuous improvement. In a platinum company, everyone –from the Managing Director to a trainee – knows they have a part to play in the company doing well and is always looking for ways to improve.
Paul Devoy, CEO of Investors in People, said: “We’d like to congratulate ARV Solutions. Platinum accreditation on We Invest in People is a remarkable effort for any organisation, and places ARV Solutions in fine company with a host of organisations that understand the value of people.”
ARV Solutions are the market-leading recruitment agency in the offsite construction sector. Their expert team is supported with the most advanced and innovative technology, which they have further developed to create high levels of success for both their clients and candidates across the UK and worldwide.
Commenting on the award, Jim Roach, Managing Director added: “This is a massive achievement for our business – Investors In People is ‘THE’ benchmarking standard for a people-oriented business such as ours so we are over the moon to have achieved their highest accreditation. I should say
detailed and accurate design, plans and material pricing of developments from the first day. From start to finish, the process can be completed in under an hour, saving weeks of work.
Baxi has supplied over 160 tried-and-tested configurations using its specialist heating range so that WholeHouse users can select the most suitable, fully compliant low carbon heating solution for their properties. By including Baxi Assure’s ASHP, the platform is futureproofed to comply with the Future Homes Standard set to come into effect from 2025. For projects built before 2025 that are more suited to a gas boiler, units are available with the latest and most efficient Baxi Assure combi boilers. Controls and accessories are also available to ensure optimal efficiency in line with latest Standard Assessment Procedure (SAP) regulations.
we worked hard to achieve it – but more importantly for me, we worked hard to build a great business. It also happens to meet the highest standards for this accreditation. We are mid-way through our ambitious three-year growth and development plan and our journey is as exciting now as it’s ever been in our 20-year history. We’re looking forward to continuing to grow with many more clients in offsite, as well as related and new sectors.”
Source: www.arvsolutions.co.uk
Baxi has supplied a new range of prefabricated understairs heating solutions to Travis Perkins’ WholeHouse®, an industry-first platform that allows smaller regional housebuilders and developers across the UK to plan and design a complete, bespoke digital model of a house before beginning construction. Based on the BIM process, the new platform ensures

The prefabricated understairs unit provides a quick and easy way to install the system into each property that improves its carbon footprint by reducing waste. WholeHouse platform users can also access Baxi’s design and engineering expertise throughout the project, from initial installation training to final commissioning, to help ensure best performance from the appropriate system.
Nick Platt, Commercial and Marketing Director at Baxi, said: “The WholeHouse platform is a powerful tool for small to medium sized housebuilders, who are
under mounting pressure to build new homes quickly while adhering to sustainability requirements. Regional developers using the platform will get access to the very best in efficient heating technologies, and expert support to give them the confidence that their chosen design is fully optimised for the new home.”
Lee Jackson, Director of WholeHouse® said: “We are delighted to be working with Baxi and take great pride in supporting our customers with new value-added services that help them to navigate an increasingly complex construction landscape with new legislation and decarbonisation targets. WholeHouse will do just that, and help SME housebuilders, who are the lifeblood of regional property markets, to build better, more sustainable homes quickly and safely, whilst retaining control over the creative design elements and saving time and money.”
The first two homes built through WholeHouse and using Baxi’s air source heat pumps and prefabricated understairs units will be ready by September. Baxi is part of the €2.2billion-turnover BDR Thermea Group, one of the three largest producers of heating appliances worldwide.
Source: www.baxi.co.uk
From interim housing for the homeless to on-the-spot overnight accommodation for keyworkers...
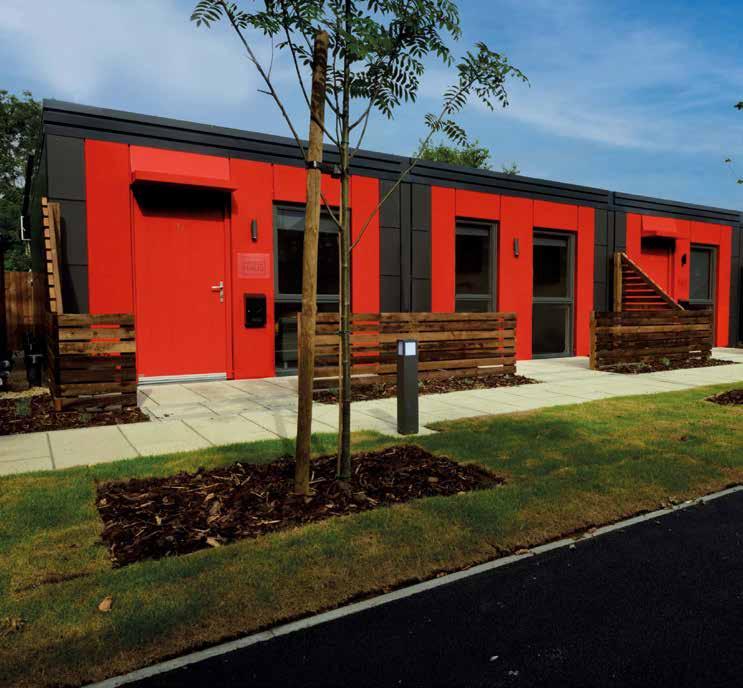
MODULHAUS™ provides award-winning, energy efficient and secure accommodation
...rigorously tested to ensure outstanding performance and quality




Tide Construction Gets Go-Ahead For ‘The Castle’ Co-Living Scheme
Tide Construction has been granted full planning permission to develop a 462-home co-living scheme, known as The Castle, in Ealing, West London. Located in the Old Oak and Park Royal Opportunity Area, The Castle will create a co-living community across two towers and 32 storeys. Created to increase the supply of high-quality homes, co-living combines intelligently designed studio apartments with an exceptional amenity offer.
Tide is both the developer and the contractor for this exemplar co-living scheme, a residential typology that is emerging in the UK. The Castle has been designed in collaboration with architects HTA Design. The scheme will provide unparalleled shared amenities for residents, featuring over 16,000 sq ft of communal spaces across four floors. It will include lounge areas, private dining and co-working spaces, a library, a bespoke gym, cinema and games rooms, cycle parking spaces and a cycle hiring scheme available for residents.
Regeneration is a key focus of the project, as well as creating 462 new homes on this brownfield site, it will create a new home for The Castle public house, revitalising a social hub that dates to the 1930s but has remained vacant since 2020. The new pub will
have a renewed street presence, with a sculptural elevation that pays homage to the historic architecture of everyday London pubs. It will also include dedicated space for community use.
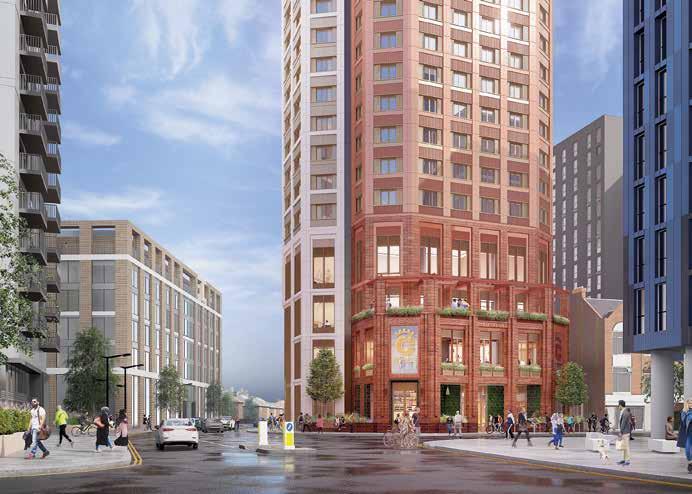
The two towers will also act as a gateway to the cluster of surrounding developments and provide convenient access to North Acton underground station, enabling access to central London in 30 minutes. As with all its volumetric schemes, Tide will work with its sister company, Vision, to deliver The Castle. Offering smoother logistics and minimal disruption, Tide’s volumetric approach cuts construction time by up to 50%. As a result, The Castle is expected to have an 18-month construction programme, including an extensive two-level basement under the 32-storey building. In addition to delivering high-quality homes efficiently and at pace, Tide’s volumetric technology enables greener methods of construction.
Christy Hayes, Chief Executive of Tide Construction, said: “The Castle’s 462 homes further strengthen Tide’s pipeline of homes and our sustained year-onyear growth. The Castle is another step forward for Tide in demonstrating how volumetric construction can deliver the housing London needs in a safe, sustainable, and efficient way.”
Helen McManus, Planning Manager for Tide Construction, said: “This ambitious scheme will play a significant role in the regeneration of the Old Oak and Park Royal Opportunity area. The Castle will not only bring much needed revitalisation and quality new homes to this part of Ealing, but it will do so while cutting construction time by approximately 50% compared to traditional methods of construction, enabling the project to be delivered swiftly and with minimal disruption to the local community.”
Simon Toplis, Partner at HTA Design, added: “The Castle is our tenth project with Tide Construction, and will build on our joint track record of delivering high quality homes that demonstrate the incredible potential of volumetric modular. The design flexibility afforded by Vision’s volumetric system enables us to create bespoke and highly crafted schemes that respond to the neighbourhood context and character, time and time again. The Castle is particularly exciting in this respect, combining the delivery of innovative co-living with the rare opportunity to reimagine a classic London pub for the 21st Century.”
Source: www.tideconstruction.co.uk
www.visionmodular.com
www.hta.co.uk
ilke Homes Secures
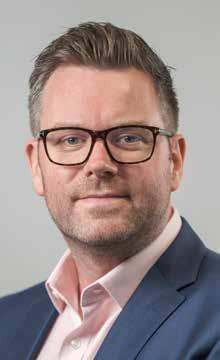
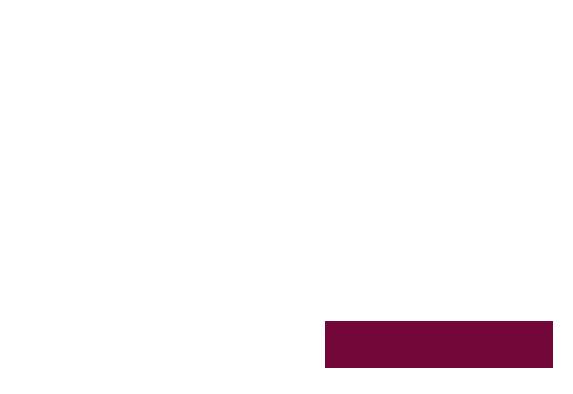
Milton
Keynes Site for Energy Efficient Homes

ilke Homes has purchased a seven-acre site in Milton Keynes where the company plans to deliver up to 140 highly energy-efficient homes for the local community. Subject to Reserved Matters planning approval from Milton Keynes City Council, ilke Homes plans to deliver a mix of houses and apartments ranging from one to four bedrooms – the majority of which will be manufactured offsite at the company’s 250,000sq ft factory in Knaresborough, North Yorkshire. Not less than 30% of the homes are expected to be made available for affordable tenures.
The site will form part of the 4,330-home Whitehouse masterplan, which is being delivered by L&Q Estates, one of the UK’s largest strategic land developers, and their development partner Milton Keynes City Council. L&Q Estates is the master planner behind the development at Whitehouse which is expected to create hundreds of jobs, 4,300 homes, a secondary school, three primary schools, a health facility, indoor sports and other leisure facilities, and play areas.
ilke Homes is already in conversation with several organisations with appetite to acquire and forward fund ilke’s exemplar modular homes at Whitehouse. They will be submitting a Reserved Matters planning application to Milton Keynes Council in April and subject to planning, anticipate starting work on site by the end of 2023. The first homes are expected to be installed from Summer 2024.
Tom Heathcote (pictured) Executive Director of Development at ilke Homes, said: “ilke Homes continues to expand across the South East, with today’s announcement marking our first site acquisition in Buckinghamshire. Our teams are excited to be working alongside L&Q Estates and some of the UK’s most well-known housebuilders as part of this fantastic consortium, which promises to deliver a well-designed community with placemaking at its heart. Since launching in 2020, our land-led, turnkey offering has seen exponential growth, demonstrating the strength of our vertically-integrated approach to development.”
Adrian Clack, Managing Director of L&Q Estates, added: “L&Q Estates and Milton Keynes City Council have been involved in the development of this site for over 20 years, facilitating the delivery of muchneeded homes, social infrastructure and facilities for the community in Whitehouse. Modular housing is a really exciting advancement in building energyefficient properties at a much faster rate and it will be fantastic to see these high-quality properties lowered into place for families to move into and start creating their dream homes. These will be the first modular homes in Whitehouse and we look forward to the first families moving into them next year.”
Source: www.ilkehomes.co.uk
Verified PMV for DTS Timber Frame
Donaldson Timber Systems (DTS), has become the first timber frame manufacturer to offer a verified pre-manufactured value (PMV) score of 55% or more. Following a six-month material and labour cost analysis completed by specialist construction consultancy, Cast Consultancy, the DTS Sigma® II build system has been verified to achieve a minimum of 55% PMV, increasing to 58% for a detached home.
In conjunction with the Stewart Milne Group, the DTS timber system was tested on a live project, on a range of building typologies, including a two-bedroom mid terrace, a three-bedroom end-terrace and a four-bedroom detached home. In these tests, the DTS Sigma® II build system achieved a verified PMV of 55.7%, 55.8% and 58.4% respectively.
PMV is a way of calculating the proportion of a building’s construction that takes place offsite or nearsite using any of the seven categories of MMC. It can be achieved through a combination of offsite, near site and on-site manufacturing techniques, as well as through materials innovation and site-based process improvement and technology.
The PMV value of Sigma® II is achieved by a combination of offsite elements of the build, including: traditional strip footings and in-situ suspended floor
slabs, conventional brickwork external cladding, external doors installed on-site, conventional felt, batten and tiled roof installed on-site, services and internal linings to walls and ceilings installed on-site, sanitaryware and kitchens installed on-site and prefabricated doorsets and stair flight with handrail components installed on-site.
The Affordable Homes Programme from Homes England, launched in 2021, requires all projects it funds to have at least 25% of the units delivered through MMC and a calculated PMV of 55%.

The verification by Cast confirms that DTS can achieve this target PMV value through the build system alone, when using the award-winning, BOPAS and BBA-approved, closed panel Sigma® II Build System. While the system can be used in conjunction with other offsite technologies to further improve PMV, Sigma® II achieves the target levels of PMV without reliance on any other offsite technologies.
Cast Consultancy has published a PMV Technical Manual explaining how the calculations are carried out. The baseline for the calculator, building a ‘traditional’ house without any additional MMC elements, provides a PMV of just 39.74%. While adding a basic structural framing system, such as timber frame (MMC Category 2a), raises it up to
44.74%, it still falls short of the required 55%. Setting the target of 55% is pushing the industry to innovate and to drive more offsite construction.
There are numerous benefits of increasing PMV, including increased quality and performance, improved productivity, minimal waste, faster on-site delivery and reduced health and safety risk.
John Smith, Technical Director at Donaldson Timber Systems, explains: “We were confident that our Sigma® II Build System would deliver the required level of PMV, but it’s fantastic to be able to prove it. This is of particular interest to our clients who are building affordable homes, as this certification will make their lives easier when applying for funding through the Affordable Homes Programme because the use of Sigma® II alone achieves the minimum target required to unlock funding and secure land from Homes England. We have long championed the use of offsite timber frame construction as the best way to achieve efficiencies and sustainable building practices, and we have developed our timber systems to ensure they are market-leading in every way. Our award-winning, third-party certified Sigma® II Build System is a robust and effective solution to achieving high levels of fabric performance.”
Source: www.donaldsontimbersystems.com
First Modules Arrive at Imjin Barracks
A £13million construction project to improve living conditions for soldiers at Imjin Barracks has reached a key milestone, following the arrival on-site of the first modules for new Single Living Accommodation (SLA).
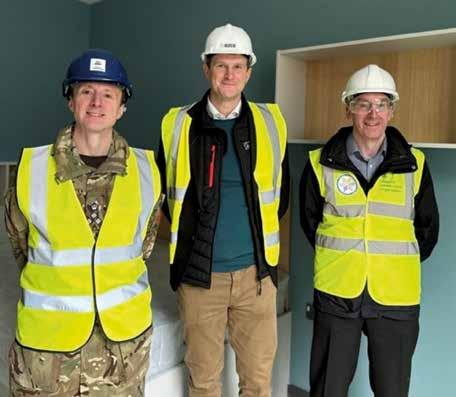
The major infrastructure works at the Gloucestershire barracks are due for completion this summer and will provide 69 new single ensuite bedspaces, along with communal living and kitchen/diner facilities. The project is being delivered by the Defence Infrastructure Organisation (DIO) on behalf of the British Army, using offsite construction specialist Reds10 and Design and Engineering consultants Arcadis.
Brigadier Richard Brown, Army’s Head of Infrastructure Plans said: “This is a significant milestone in building new Single Living Accommodation at Imjin Barracks – the first of over a hundred new SLA blocks due to be delivered across the Army estate. It’s great to see the progress being made here which will enhance the communal living experience for our people.
The new modular SLA block is manufactured offsite and features a high-spec interior fit-out, central break-out spaces and increased natural daylight into rooms. The building will use SMART building technology to react to external and internal elements to reduce energy consumption. It has achieved an ‘Excellent’ rating under the Defence Related Environmental Assessment Methodology (DREAM).
Warren Webster, Defence Infrastructure Organisation, MPP Programme Director – Army added: “I am extremely proud of the team. It not only demonstrates DIO’s commitment to providing quality accommodation to Service personnel, but also shows
Key Appointment for NHBC Housing Association Team
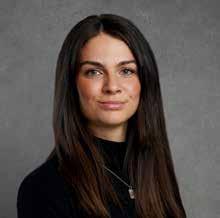
the significant benefits of permanent module offsite construction both in terms of speed of delivery and ability to meet demanding carbon net zero targets. This is the first of a number of projects that will follow this proven delivery model.”
Paul Ruddick, Reds10 Chairman, said: “The SLA at Imjin Barracks is real, tangible proof of concept for modern methods of construction (MMC). It shows, in practical terms, how MMC can deliver a high quality, fit for purpose product at speed. We are extremely proud to be working with the British Army, DIO, Arcadis, HLM Architects and everyone else involved in this project, it’s a true team effort.
Imjin Barracks is the first site to benefit under the Army’s Single Living Accommodation Programme, which is investing £1.2billion and delivering 8,500 SLA bedspaces over 10 years. In addition to this, 8,000 SLA bedspaces are being delivered by the Defence Estate Optimisation (DEO) Army Programme through new build SLA blocks and refurbishing works, bringing the combined total of SLA bedspaces being delivered over 10 years to 16,500.
(L-R) Brigadier Richard Brown Head 0f Infrastructure Plans (Army), Paul Ruddick Chairman, Reds 10 Warren Webster MPP Programme Director (Army) Defence Infrastructure Organisation.
Source: www.reds10.com
NHBC announced that Charlie Ash has been appointed Sector Lead for Housing Associations. Charlie, who previously worked in the team as Customer Relationship Executive, will now manage relationships and partnerships with housing associations, their contractors and other sector stakeholders, with a focus on building it right first time.
Charlie’s priorities will centre on early-stage client engagement across housing association and contractor development pipelines and will champion NHBC’s partnership approach in her new role. Charlie commented: “I’m excited to step up into this new role and look forward to meeting the challenges the current market presents. NHBC’s affordable housing products and services are a key part of our partnership offering and I’ll be growing this part of our business, promoting our great credentials and track record.”
Tim Reid, Customer Relationship Director at NHBC added: “The housing association sector is facing
more challenges than ever before and NHBC offers a wealth of expertise and experience to help guide and assist clients all the way through the design and build process. Charlie’s appointment will help our housing association clients navigate the market and protect their homes and residents, with Charlie acting as a valuable key single point contact for UK housing associations.”
NHBC takes a partnership approach, working with customers from the earliest stages of land acquisition through design, construction and ultimately handover.
As the UK’s leading independent provider of warranty and insurance for new homes, NHBC offers unrivalled expertise, supporting clients across a range of sectors beyond volume housebuilding, including affordable and social housing, Build to Rent, integrated retirement communities and strategic land.
www.nhbc.co.uk
Cala Acquires Taylor Lane Timber Frame
Cala Group, a major UK homebuilder has announced the 100% acquisition of Taylor Lane Timber Frame Ltd, one of the UK’s leading timber frame construction specialists. The investment will help drive Cala’s progress towards their sustainability targets and support delivery of the group’s ambitious growth plans in the South of England.

Cala’s carbon reduction strategy sets out their transition to timber frame across all the homes they build in England, where possible. The investment in Taylor Lane will help Cala to increase the use of timber frame in England to c.1,500 new homes per annum, over the next five years. In Scotland, Cala has been using timber frame construction for over 40 years, and around 80% of Cala’s homes there are built using this method.
With factories in Hereford and Wales, Taylor Lane will supply Cala’s five English businesses in the Cotswolds and South of England, while continuing to service existing customers and grow their presence in the wider market. The investment illustrates Cala’s confidence in Taylor Lane’s potential and provides a strong platform for continued growth, while ensuring both consistency and stability for Taylor Lane’s employees, customers and operations.
Kevin Whitaker, CEO at Cala Group, said: “Today’s announcement is a hugely positive step forward for
Structural Timber Price Index Tool Offers Powerful Market Analysis
Timber Development UK (TDUK) is launching a powerful new tool, the Structural Timber Price Index, to help the construction industry assess changes in the UK timber market. The Structural Price Index displays the monthly price of structural timber stretching back to 2018, giving users the ability to compare today’s timber prices to those seen five years ago. The figures seen in 2018 were pre-Brexit, pre-COVID-19 and pre-war in Ukraine, making them arguably the most recent ‘normal’ year we have experienced and therefore a sensible point for comparison.
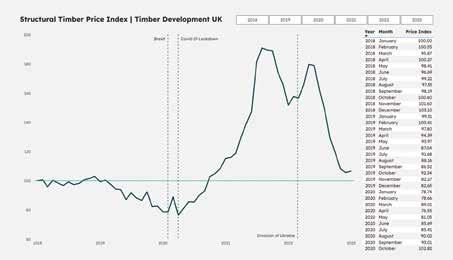
TDUK Head of Technical and Trade Policy, Nick Boulton, explains: “The TDUK Structural Timber Price Index is a powerful new tool for the construction industry to understand the state of the timber market in the UK. As you can see from this first iteration, now online for public use, the price of structural timber has been on a rollercoaster journey over the past three years – in between major events like Brexit, COVID-19, and the invasion of Ukraine.
both Taylor Lane and Cala. Taylor Lane is a successful business with an experienced management team and talented workforce. For Cala, this also demonstrates our clear commitment to delivering our climate targets. The investment in Taylor Lane sets out our path to transitioning to timber frame across our English developments, a key element of our sustainability strategy. The positive arguments for timber frame construction have never been more compelling.”
Jonathan Lane, Managing Director at Taylor Lane, added: “This marks the start of an exciting new chapter for Taylor Lane and is a fantastic endorsement of our potential from a highly respected UK homebuilder. We are delighted to being moving forward with Cala as our new owners. Over the past
40 years we have successfully grown Taylor Lane to a £30million turnover business delivering around 2,000 timber frame units per year, to a wide variety of sectors. This is testament to the vision of our cofounders, Colin Taylor and Barrie Lane, and the hard work and commitment of our employees alongside the quality of our product and our approach to customer service. We are all incredibly proud of Taylor Lane’s achievements to date.”
Pictured L-R Brian Johnson, Group Development Director, Cala Group & Jonathan Lane, Managing Director, Taylor Lane
Source: www.cala.co.uk www.taylor-lane.co.uk
“Timber is a globally traded commodity, and the UK is a major importer of structural timbers, so large geopolitical events can ripple across the trade. The abnormal structural timber prices we have seen over the past three years reflect the abnormal market we have all lived through. However, the three most recent months shown on the index – from November 2022 to January 2023 – are among the most stable price periods we’ve seen since 2019 – which likely reflects the balance between supply, demand, and price. While no one can predict the future, the commodity market for structural timbers has historically been a steady, and dependable one. We will be watching
the market carefully to see whether this trend will be re-established.”
This latest tool is part of TDUK’s ongoing mission to provide comprehensive market data to help the timber supply chain navigate the changing economic climate. This includes monthly timber import statistics, quarterly reports on UK timber demand and supply, and weekly economic and construction updates from the Construction Products Association.
Source: https://timberdevelopment.uk/ supply/market-data

BUILDING IN BETTER HEALTH
David Clowe, Director and Head of MMC at Turner & Townsend tells us how new hospitals are helping galvanise the wider adoption of offsite construction.
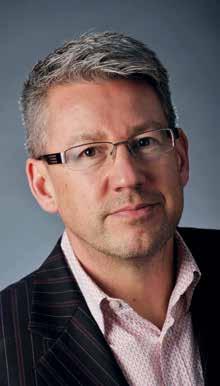
Our current economic climate sees us in a period of ‘stagnation’ rather than recession. With material prices rapidly increasing, inflation high and the labour pool tight, construction is finding that it needs to be innovative to do more with less. As our industry also accelerates towards more efficient, sustainable and resilient strategies, modern methods of construction (MMC) are becoming pivotal to the success and sustainability of both public and private sectors across the UK.
This is particularly true of the healthcare sector, where increasing pressure on capital budgets and the net zero promise has put the use of MMC front and centre for enablers. Like many other industries, the UK health service faces pressure to economise and deliver improved services simultaneously. Bolstered
by the government’s presumption in favour of MMC, we are seeing firsthand how many MMC techniques can deliver these goals.
To realise this potential, however, we must look at how we invest in building MMC capabilities and nurturing its supply chain.
Rising to the challenge in healthcare
The government’s New Hospitals Programme (NHP) exemplifies its aspirations to reboot the UK’s healthcare provision. This is an essential project of huge scale but in order to meet its demands the Department of Health and Social Care (DHSC) has recognised the need for new ways of working.

MMC is ideal because it’s allowing buildings to progress quickly and precisely. We’ve seen delivery
schedules cut by half and the merits of being able to operate in tight, live city centre environments with relative ease.
The recognised environmental benefits of MMC are also a major draw as healthcare construction looks to keep its net zero promises. From the reduction in embodied carbon inherent in the use of recycled and low carbon products, to the improved airtightness and thermal properties resulting from MMC’s greater construction precision – these factors are no longer nice-to-haves and are now central to MMC’s appeal to programmes like NHP.
Our own ongoing work with the Northumberland Healthcare Trust is helping deliver 650 pre-assembled modules (PAMs) and 17 prepacked MEP POD’s, using a Design for Manufacture & Assembly (DfMA)
approach to Berwick Hospital –providing a quick and crucial upgrade to the local community. At a time where pressures on skilled workforces are high, MMC’s factory set-up provides greater resilience to the unpredictability of labour costs and other supply chain risks.
Hospitals, and particularly wards and ancillary areas, are designed in such a way that they can be easily repeatable at a high volume, which is ideal for modular construction work. The consistency of pre-fabrication as well as its quality and precision are well suited to the stringent demands of clinical space. Its repeatability also leads to a reduction in the design time and sign-off period, with aggregated demand of the premanufacture of repeatable components at scale reducing costs and providing predictability.
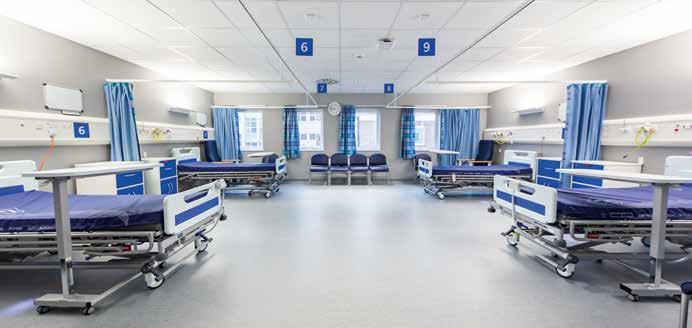
Building momentum in new sectors
The integration of a Platform design approach to construction within the government’s NHP is an encouraging sign for MMC. It shakes off the image that it is a novel concept and has potential to help propel the sector in the mainstream. To fulfil that ambition, however, more work still needs to be done to build confidence in the sector so that it can invest in the skills and scale-up needed to be truly transformational.
A critical step is to champion and showcase how the sector has changed and matured – playing on the lessons
of healthcare. This needs to happen right from the outset of programme and project planning, helping clients understand MMC as an option in the first decision and design stages and setting out the efficiency and value.
To do this, the industry needs to position itself in the context of a wider trend towards digitalisation. Projects comfortable with being digital from first principles, and which use the full range of digital tools, will be a more natural fit for an MMC approach. Options and variations can be assessed using BIM and digital twins to consider best fit MMC solutions which standardise the design.
At the most advanced end, technology like virtual reality and augmented reality can be used to help clients visualise plans and designs and significantly reduce detailing and interface risk. By optimising the design of the product, it is possible to manufacture and assemble structures in ways that are simpler, safer and at a lower cost, while also reducing waste and improving quality. Factories and large sites can become assembly hubs of components and sub-assemblies rather than traditional construction sites.
The key to successful implementation for clients is establishing their MMC strategy as early as possible and finding the right solution for the project or programme. From there, clients need to be given informed decisions to achieve maximum
value within the project constraints – identifying the most viable MMC solution.
As clients aspire to deliver faster, greener and smarter large-scale portfolios a shift towards the industrialisation of the construction industry is afoot. This demand, buoyed by a guaranteed pipeline of work to secure inward investment and change, will need the support of a supply chain that can reliably deliver high quality component and products at pace.
In our work, we are seeing this balance already start to shift, with government, major clients and contractors increasingly placing their confidence in MMC, and the results across healthcare demonstrating the approaches’ transformative potential. It’s our responsibility as a sector to now go further – educating the market on the opportunity to embed modern and digital methods across projects and set out the benefits of MMC to clients at the earliest stages. We’re on the cusp of a bright technological future, and it will help the construction industry as a whole better deliver on the needs of the country.
For more information visit: www.turnerandtownsend.com
NEW FIRE TESTS FILL THE GAP
voestalpine Metsec’s offsite product, Metframe uses Light Gauge Steel Framing systems (LGSF) sections bolted together in a 2D panel format to create complete loadbearing structures up to 15 storeys.
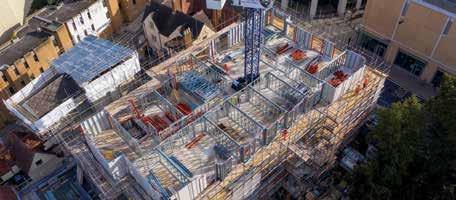
Whilst efficiency, versatility and sustainability are desirable attributes for any building system, they count for little without certified proof of the system’s ability to meet the required technical performance standards in the areas of acoustics, thermal efficiency, loadbearing and, most importantly, fire protection.
With LGSF, fire performance in accordance with Part B of the Building Regulations and thermal efficiency in accordance with Part L are achieved through the combination of materials that are used in conjunction with LGSF to construct the wall. For external wall constructions, from inside to out, this would typically consist of plasterboard dry lining, LGSF, insulation within the stud zone, sheathing board and insulation.
A more assured approach
Since Grenfell, there has been increasing recognition for the need to undertake fire testing of the entire wall construction under laboratorycontrolled conditions rather than arriving at a theoretical figure through calculation. This testing provides a true ‘through-wall’ performance which gives designers and contractors added assurance of a solution’s performance capabilities, in accordance with BS EN 1364-1 (non-loadbearing covering Infill, Continuous Walling and High Bay Walling applications)
and BS EN 1365-1 and 2 (covering Loadbearing LGSF structure walls and floors).
The reason for the ‘through-wall’ concept is that, with so many exterior façade materials available, it wouldn’t be impossible to test every possible wall construction. The ‘through wall’ approach to performance allows manufacturers to test a meaningful number of material combinations. The tested solutions will either be from the dry lining through to the sheathing board or from the dry lining to external insulation – all using non-combustible Class A1 or A2 materials.
Freedom and choice
This approach provides the design team with the freedom to choose the desired external façade, provided, of course, that the necessary performance requirements are met, including compliance with the 2022 update of Approved Document B 2022 which means that all materials in façades over 11m are to be noncombustible too.
Independent testing
In order to achieve ‘through-wall’ fire performance data, voestalpine Metsec constructs different complete wall build-ups for testing at UKASaccredited laboratories. The buildups measure 3m x 3m and comprise various combinations of boards and
insulation materials applied to the LGSF. Each build-up is tested using a large-scale, high temperature test (reaching up to 600 degrees Centigrade in 5 minutes), which measures the performance of the entire wall by simulating fire trying to break through a solid wall. Tests are conducted to British Standards EN 1364-1 and BS 476-22 (for nonloadbearing walls) to achieve the 120-minute, 60-minute and 30-minute fire ratings typically required by building regulations. This vast suite of testing enables voestalpine Metsec to provide a 30-year though-wall warranty to support the system performance.
A positive step
Whatever the circumstances, throughwall fire testing and the performance data it returns for the combinations of materials used in wall constructions is a positive step forward. The benefit this brings to the client is having choice of the various manufacturers of plasterboard, sheathing board and insulation, all at various thicknesses, which provides flexibility in supply and availability, commercial aspects and supply chain preferences.
Being able to determine if a particular thickness of plasterboard and number of layers the LGSF wall is being lined with has the capacity to achieve particular fire and acoustic performance is a key benefit to simplifying not only the specification but also the site installation to benefit logistics and programme. At voestalpine Metsec, we currently offer a choice of more than 400 configurations.
For more information visit: www.voestalpine.com
Images:
01. The final wall construction can vary according to the external façade that might be selected to achieve the desired exterior finish and/or budget
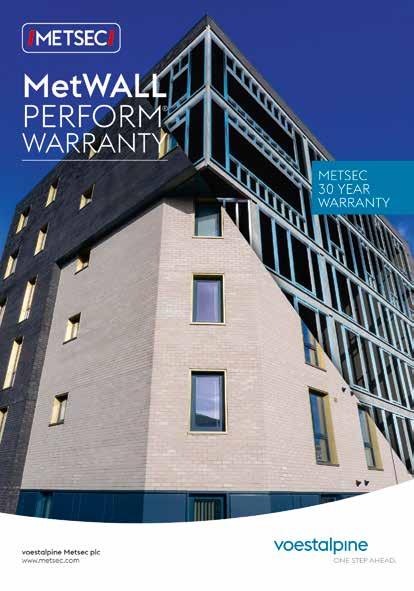
OPERATING WITH OFFSITE
The healthcare sector offers huge potential for offsite methods to provide modern, cutting-edge facilities. We spoke to David Hartley, Managing Director of MTX on how they are providing award-winning fast-track healthcare solutions.
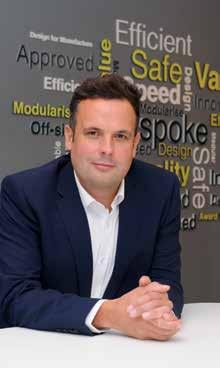
Q: MTX has decades of experience in healthcare facilities. For those unfamiliar with what MTX does, when did you start on the journey with modular manufacture and providing offsite solutions to the sector’s needs?

David Hartley (DH): MTX has been doing business for four decades but the company in its current form emerged in 2002, focused on extending, refurbishing and remodelling facilities for hospitals across the UK using traditional building and fit-out techniques. Operating theatres was a big focus for that work, and there was an increasing demand for modular operating theatres. We already had the project management skills and contractor know-how and developed a more flexible approach to modular theatres that was not driven by the demands of a factory.
We formed strategic partnerships with specialist steel fabricators who build the structures offsite to our precise specification for transport and assembly on site, quite literally constructing the building around the needs of the healthcare provider for bespoke solutions. Our first modular theatre project in Aberdeen and was a huge success, and we built up the business from there, evolving to take on board the latest developments.
Q: The DfMA concept is central to successful offsite construction – how has MTX embedded this into its manufacturing approach and overall construction design mindset?
DH: We have strategic partnerships with a small number of specialist steel fabricators who build the structures offsite to our precise design and specification for transport and
assembly on-site. They manufacture to our highly flexible and adaptable solutions dependent on layout and site configuration. Cladding is manufactured off the critical path to minimise the activity on the busy operational site and we ensure a seamless external finish by installing in situ, in the same way you would on a traditional build. Our projects make extensive use of prefabricated MEP modules from partners who also embrace MMC. Modules incorporate main mechanical services such as LPHW pipework, medical gases, and ductwork delivered to be assembled on-site in line with the Government’s Public Sector Playbook. Our unique approach is to ‘modularise’ the building around architects’ and design teams’ internal footprints which ensure there is no compromise in our final solution.
Q: From your experience, is the public sector – certainly healthcare – better at understanding what procuring an offsite solution brings e.g. better quality facilities, quicker and more sustainably, or is there still a knowledge gap?
DH: There is still a knowledge gap and more education is needed. Every business case for investment in new medical facilities has to embrace MMC to succeed. That is the driver to change building techniques and move forward. There is increasing recognition that the new operating theatres, ward accommodation and other facilities we create for health trusts across the UK are delivered more quickly with reduced waste and less disruption than conventional build projects. But offsite sceptics need to understand that there are no cutting corners or compromising qualitybecause MMC must meet the same standards and is subject to the same building regulations as a conventional build. Our technology represents a high quality and economically viable proposition where our design and project delivery teams meet individual client requirements while ensuring all of the advantages of offsite construction are realised without compromise.
Q: MTX’s appointment to the new Crown Commercial Services framework has put the business in a great position and provides opportunities to showcase your modular expertise. Is the appointment more than just ensuring maximum pre-manufactured value?
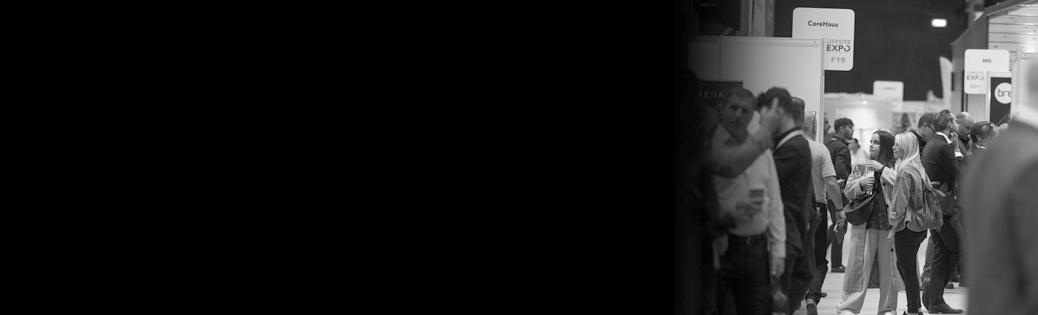
DH: It is hugely encouraging to see the UK Government driving acceptance of MMC and DfMA through the new CCS framework and the Public Sector
Playbook. Offsite construction is a prerequisite in virtually every outline business plan for new development on hospital sites, and quite frankly if it is not in that plan, then the development is unlikely to happen. That commitment to offsite construction not only makes sense in terms of build efficiency and economy, but it also builds confidence in the process as people are forced to consider it as a viable alternative to traditional construction methods. Our appointment to the framework is another step in legitimising offsite construction and MMC for those who
doubt its value, and it also reinforces our position as an approved provider of new facilities for the NHS.
Q: The award-winning project for the Oxford Critical Care facility grabbed a lot of headlines – what were the key take-away learning points from this for MTX?

DH: The Oxford project clearly demonstrated that early engagement is vital and the importance of having a good working relationship with a very proactive partner. It also showed that
OFFSITE EXPO has a range of exhibition packages available to suit any marketing aims, resources and budget.
www.offsite-expo.co.uk/exhibit
MAXIMISE THE OFFSITE OPPORTUNITY
our implementation of MMC and DfMA can be flexible and nimble – because the design changed substantially during build process to accommodate the Oxford University Hospitals NHS Foundation Trust’s requirements. The Oxford Critical Care unit employed a ‘hybrid’ MMC construction method and rapid design and planning process. The five-storey structure used 148 offsite-manufactured steel structural units craned into position floor by floor, before fit-out on site with concrete flooring, offsite manufactured walling units and glazing, and extensive modularised M&E services. MTX added critical value to the initial concept by linking to the adjacent and
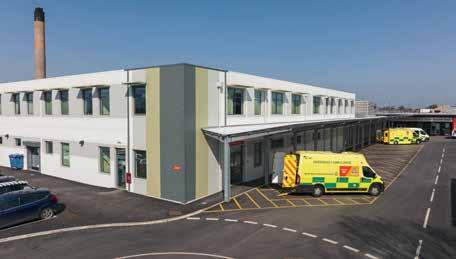
recently refurbished Trauma building on four of the five levels to deliver fire safety and evacuation standards that enabled both the new building and the Trauma centre to meet modern benchmarks.
Q: MTX is active in several other sectors including education – how easy is it to reconfigure/transfer the prefabrication process from cleanroom to classroom for example?
DH: We are a specialist supplier to the healthcare sector for on-site hospital facilities such as operating theatres and ICUs and scanning facilities, and also the new Community
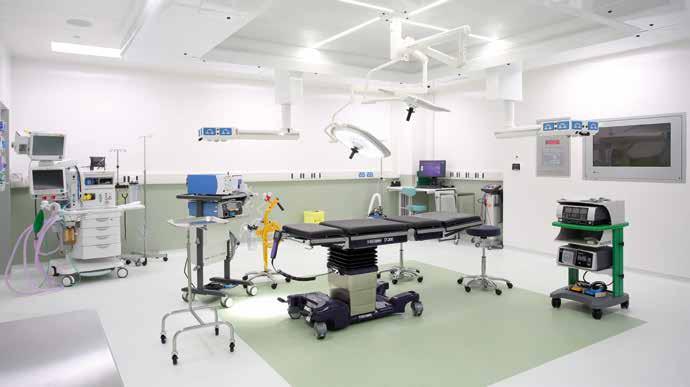
Diagnostic Units. We provide very high-performance buildings for the healthcare market that are designed to meet the requirements of hospitals and health trusts – such as concrete structural floors constructed to meet the necessary response factors of operating theatres, or ultra-clean air handling systems. The level of sophistication and advanced specification that goes into these structures is not suitable for classrooms and is far more advanced than the normal requirements for a building to be used in a school or college location. MTX is, of course, capable of creating classrooms and has done so in the past, but currently our primary focus is on healthcare and meeting the specific requirements of that market.
Q: The use of technology and digital tools within factory environments is critical to offsite manufacture with toolkits, platform approaches and repeatable components – how is MTX embracing the ‘Industry 4.0/Smart Factory approach?
DH: We work with key partners who embrace those principles and are driven by continuous improvement both within MTX and through our construction partners. We have evolved to optimise our processes –and constantly review those processes to do things better. Manufacturing
and tooling techniques continue to improve, and we work with our partners to ensure they upskill and that MTX stays at the forefront of the MMC and DfMA revolution. Not having our own factory has proved to be an advantage. Modular building providers are often factory-led and sell a ‘product line’, but our business model has enabled us to be much more flexible in the solutions we provide. MTX is a main contractor with core engineering design and project managing skills and we pull in the resources we need for our turnkey solutions. By partnering with advanced manufacturers, we can provide our clients with optimised programmes and proven best value.
Q: How do you see the offsite and volumetric modular sector developing over the next 18 months and what ideally do you want to see from an MTX perspective?
DH: MMC and offsite construction will be more widely used and MTX wants more health trusts to embrace the concept as they strive to implement the Government’s ambitious plans to build 40 new hospitals by 2030. That objective cannot be achieved without employing the principles of MMC and DfMA. It is generally accepted that the plans for new UK hospitals will also include substantial upgrades and refurbishments to existing NHS estates. Brand new hospital developments on greenfield sites will continue to use offsite construction, but MMC is particularly important for creating new
facilities within existing hospital sites where limited space and the need to reduce on-site disruption are vital elements. The new operating theatres, ward accommodation and other facilities we are creating for health trusts across the UK are delivered more quickly with reduced waste and less disruption than conventional build projects, and that is exactly what health trusts require.
For more information visit: www.mtxcontracts.co.uk
Images:
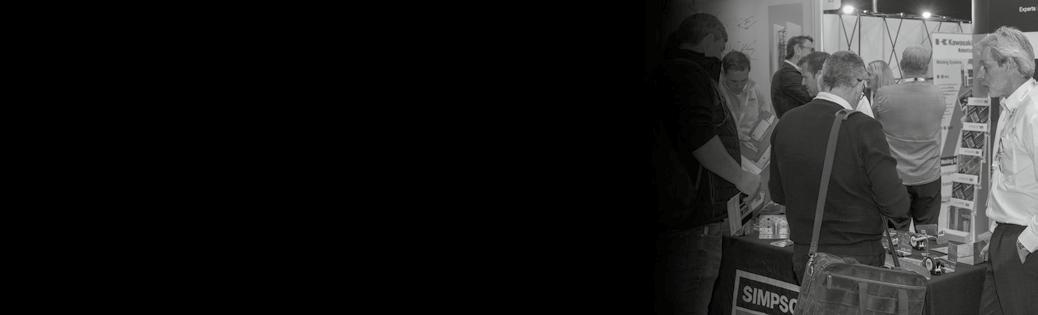
01. David Hartley, Managing Director, MTX
02-03. John Radcliffe Hospital, Oxford
04. Operating theatres can be delivered quickly and to exceptional standards using offsite methods. Kent & Canterbury Hospital
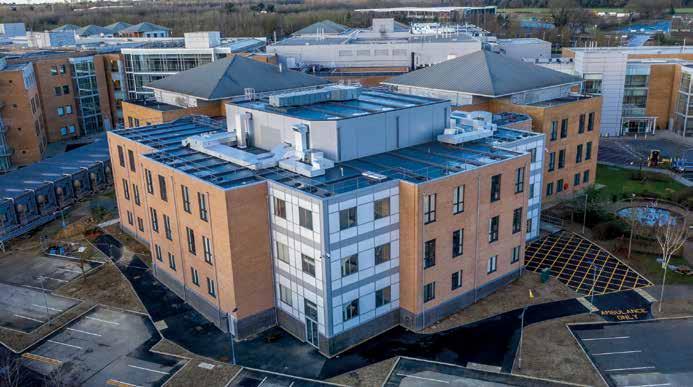
05. Leighton Hospital extension, Crewe
06. Norfolk & Norwich University Hospital
...at the UK’s biggest showcase of offsite manufactured construction technology and solutions.
www.offsite-expo.co.uk/exhibit
ALIGN YOUR PRODUCTS AND SERVICES WITH THIS INCREASINGLY IMPORTANT SECTOR
MAKE UK MODULAR INSIGHT IMPACT & INFLUENCE

desire to really make an impact on the housing crisis. Of course, we can’t simply rest on our laurels.
With all the understandable noise about the short-term prospects of the housing market it’s easy to lose sight of the medium and long-term. Of course, this is a true in Government as it is in business. Over the next 12 months we’re likely to see political parties commit to new (most likely vague) targets around the total number of homes built, increasing home ownership, increasing affordable housing, and greening our old, cold housing stock.
However, as our recent report ‘Who will be the builders? Modular’s role in solving the housing labour crisis’ shows, there is a whopping great elephant in the room. Labour shortages. No Government can come close to its 300,000 new homes a year target by 2025 or even by 2030 without dramatic change in way we build houses the construction workforce is simply too small. Let alone can they deliver the net zero and building safety retrofit our housing stock so badly needs.
To say that politics has been volatile since Make UK Modular launched in December 2021 is an understatement. But, as politicians begin to turn their thoughts towards a general election, one thing is clear – housing has slowly, inexorably, and perhaps inevitably returned to frontline politics.
For the team at Make UK Modular this means redoubling our efforts. In our year one impact report ‘Insight, Impact & Influence 2022’ we made strong initial progress in a number of areas. Our priority for year one was to establish ourselves as the voice of the modular housing sector by:
• Establishing a strong working relationship with Government, the opposition, MPs, and the Civil Service
• Building a robust and credible evidence base about the benefits and potential of modular housing
• Establishing and delivering against policy priorities
• Delivering a consistent, positive media and public affairs presence
• Growing our membership.
I’m proud that we made significant progress on all of these areas so quickly. It’s a testimony to the can-do attitude of our members and their
Even if all planning rules were abolished and housebuilding had all the cash ministers could throw at it, the sector could still build no more homes as they don’t have the specialist workforce to make them. A big part of the solution, is, of course, driving up the number of housebuilding apprentices which delivered only 11,000 completed apprenticeships for the entire construction industry last year.
We also need to look at how we build, and how we bring people from different backgrounds into housebuilding. Modular homes can be a mainstay of this because these factory-made houses target a different pool of
As Make UK Modular releases its year one impact report, Director Steve Cole outlines the huge progress made so far and what lies ahead for the modular housing sector.
WHAT NEEDS TO CHANGE?
As outlined in the report ‘Who will be the builders? Modular’s role in solving the housing labour crisis’, if we are to have any chance of delivering 300,000 homes a year by 2030 modular housing must be scaled up and put at the forefront of any Government’s housebuilding strategy. The following policy changes would require no additional spending by government but would help to grow modular so that it can drive up housing supply and lead much-needed market transformation in housebuilding, delivering greener, better homes faster.
1. Sustainability: Enhance housebuilding sustainability by introducing a more robust commitment to and targets for net zero
• Bring forward requirements for all new homes to perform at EPC A
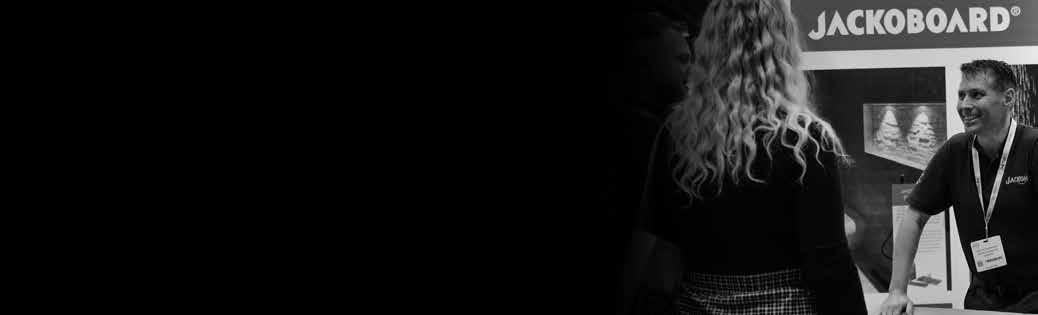
• Adjust stamp duty rates based on energy efficiency and net-zero performance.
• Require all for sale and to let homes to provide accurate data on energy bills.
• Introduce a carbon trading scheme for new build housing.
2. Scale: Dedicate at least 40% of the Affordable Homes Programme to MMC, and at least 50% of this to modular
• Dedicate at least 40% of the Affordable Housing Programme (AHP) to modern methods of construction
• Dedicate at least 50% of this share to modular (Category 1)
• Switch public Value for Money assessments from focusing on upfront costs to considering value across the whole life of a house.
3. Capacity and Supply Chain: Decrease barriers to market for modular manufacturers
• Remove the unintended double levy charge on modular manufacturers by exempting them from the scope of the CITB levy (because few modular manufacturers benefit from a scheme delivering traditional construction skills, but they still have to pay into it).
• Repurpose the £10million allocated to the MMC Taskforce to support a supply chain improvement programme like those government have supported in aerospace, civil nuclear and offshore wind.
4. Planning and Land: Government to provide a fast-track planning route for modular or low-carbon homes and require a minimum percentage of its land bank to be allocated for modular homes
Currently, modular has to navigate a planning system designed for traditional builders. It can be slow and add significant delays for modular manufacturers, reducing the time-saving benefits that modular can bring. Government can reduce these barriers to modular, while also helping to provide modular manufacturers with a steady supply of land for housing. We would like:
• Government to provide a fast-track planning route for all net zero housing schemes; these should be prioritised for accelerated planning permission.
• Government to ensure modular homes are given parity with traditional build in all local plans.
• Government to require a minimum percentile of its land bank to be allocated to modular housing (Category 1) and/or EPC A rated or low-carbon housing – or give priority or discounts to land used for low-carbon housing. This percentile of land should be subject to a ratchet mechanism increasing year on year.
• Government frameworks should mirror this ratchet with increased weighting towards modular housing in their scoring criteria.
5. Levelling Up: Create a modular capacity strategy linking new factory location, high housing demand areas, and levelling up priority regions
MAKE UK MODULAR OFFSITE EXPO EXHIBITOR EXCLUSIVE
• Government to create a modular capacity strategy working with combined authorities, freeports, transport hubs and other government agencies to ensure new factories are optimally located to maximise the associated employment and housing delivery benefits. This has already been done in the automotive and renewables industries.
OFFSITE CONNECT BUYERS AND SPECIFIERS FORUM - facilitating meetings with those seeking the latest offsite innovation.
www.offsite-expo.co.uk/exhibit
MAKE UK MODULAR
the 34,000 needed to replace retirees) with a far greater proportion in scarcely available construction trades.
Like any nascent sector, in order to deliver, the sector needs government’s backing as it scales up. Of course, we like the whole of the housebuilding sector would also like to see progress on the permacrisis facing planning and we are working closely with other leading trade bodies on this. There are also a number of specific policy levers to grow modular specifically. Therefore, we are calling on Government to:
• Remove the accidental double government levy charge on modular manufacturers by exempting them from the scope of the CITB levy.
• Build supply chain capacity by repurposing the £10million allocated for the MMC Taskforce and use it to support a match-funded supply chain transformation programme based on those government has successfully delivered in aerospace, offshore wind, and nuclear.
• Solve the housing crisis faster by dedicating 40% of the Affordable Homes Programme to modern methods of construction.
4
workers with the skills to work in precision manufacturing. Only 10% of modular workers are in construction roles. Instead, they are in manufacturing. The skills needed are easy to learn on the job with inhouse training, and efficient assembly line processes mean modular house builders use 50% fewer workers to construct the same number of homes. This builds additionality in supply while also delivering productivity gains of up to 40%.
This isn’t about replacing traditional labour or skills or putting people out of work. It’s about creating additionality in the market, meaning more homes,
more jobs, more taxes paid into the Treasury, and more economic activity and growth. Traditional building can and must keep building, but modular can supplement what it does without cannibalising an already overstretched workforce.
The UK needs to build nearly 92,000 extra houses annually to reach the 300,000 homes target. Hypothetically, modular could deliver this with as few as 46,000 extra workers, of which only 5,000 to 10,000 may need to be in skilled construction trades. In contrast, building these extra homes traditionally would likely require 103,000 additional workers (on top of
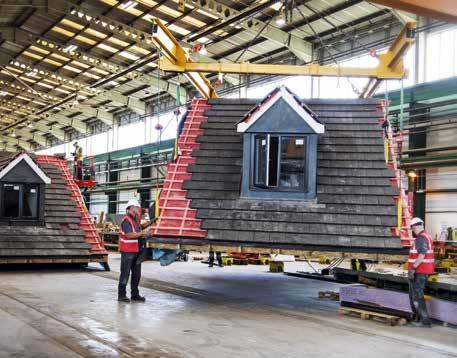
It seems that these messages are starting to land with a recent series of parliamentary questions from Shadow Ministers to the Government following the publication of the report combined with increased interest from the civil service and national press. With a general election next year, the window is closing for whoever forms the next government to set out their plans to finally deliver a housing market which works for all. For the entire housebuilding sector, it is crucial that modular is part of those plans.
For more information and to download the reports ‘Insight, Impact & Influence 2022’ and ‘Who will be the builders? Modular’s role in solving the housing labour crisis’ visit:
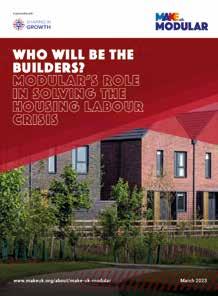
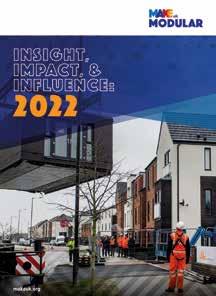
www.makeuk.org/about/make-uk-modular
Images:
01. Steve Cole, Director, Make UK Modular and Chair, ilke Homes’ Dave Sheridan
02-03. New Make UK Modular reports have shed light on where the many pressure points are within the modular housing market 04. The integration of offsite manufacture is key to increase the amounts of homes the UK requires
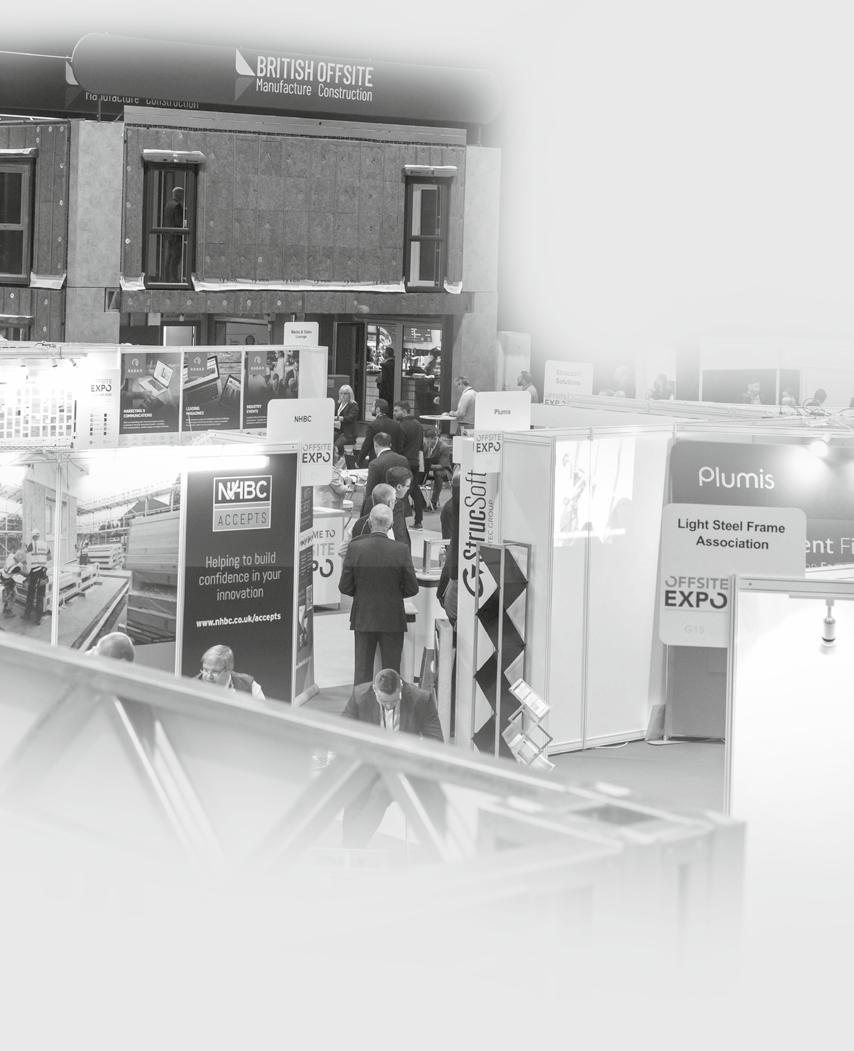

VOLUMETRIC MODULAR SETTING THE FUTURE HOMES STANDARD
Arguably one of the first innovations in the UK to surpass the Future Homes Standard, back in 2021 MODULHAUS TM was crowned ‘Winner of Winners’ at the Offsite Awards. Trevor Richards, Operations Director at VOLUMETRICTM – the company behind this achievement, discusses how they were ‘ahead of the game’ in terms of designing modular homes.

In January 2021 when the government published the outcome of the Future Homes Standard consultation, the first MODULHAUSTM units had been designed and manufactured to incredible energy efficiency standards. Right from the initial concept stage, the decision was reached to develop a modular solution that would exceed the Future Homes Standard to relieve the burden on Local Authorities of ongoing expenses associated with traditional interim accommodation and negate fuel poverty.
The Devil is in the Detailing There was a lot more to achieving the Future Homes Standard than we initially thought. Getting the balance right was challenging. Sometimes the benefits of one solution counter-acted the benefits of another, it seemed like it was one step forward, and one back. Not willing to compromise on expected performance, our team modelled and re-modelled our designs, with countless materials and technologies assessed and evaluated to ensure we achieved our optimum position.
We were on a mission and had an end goal in sight. Our aim was to create the ultimate modular solution for developer Hill Group to support their Foundation200 initiative – a charity established by Hill to gift 200 single person interim homes for rough sleepers to mark the company’s 20th anniversary.
The pioneering MODULHAUSTM system is now the technology behind a range of award-winning interim homes – all exceeding the Future Homes Standard. SOLOHAUSTM, the initial
single person home for rough sleepers is an outstanding success story, with 200 now manufactured and allocated under the Foundation200 initiative to homeless charities and councils across the UK. This was quickly followed by the double occupancy DUOHAUSTM and finally FAMILYHAUSTM was launched last year maximising space and comfort, with two and three bedroom options for a safe, familyfriendly home offering an alternative solution to low quality, high-cost interim housing.
SOLOHAUSTM, DUOHAUSTM and FAMILYHAUSTM are all now commercially available and have been used for a range of interim requirements from providing onsite accommodation for healthcare keyworkers, to housing refugees and those who find themselves homeless.
The Future Homes Standard outlines changes to Building Regulations
Part L (conservation of fuel and power) and Part F (ventilation). These regulations will ultimately come into effect in 2025 to ensure that all new homes in England are futureproofed with low-carbon heating systems and high levels of energy efficiency. These standards should ensure that all new homes will produce 75-80% less carbon emissions than houses delivered under current Building Regulations.
The first interim uplift, surrounding changes to Part L came into force last year to ensure new homes built from 2022 will produce 31% less carbon emissions. Full technical specification for the Future Homes Standard will be consulted later this year, with the necessary legislation introduced ahead of implementation in 2025. So, change is happening and happening at pace.
Net Zero Living
The futureproof energy strategy for our MODULHAUSTM range is designed to exceed the Future Homes Standard with Environment B and A rating and emissions as low as 229.5KG CO2/year.
Modules are factory fitted with sustainable technologies, low energy lighting and white goods together with controlled flow shower mixers and dual flush cisterns to minimise energy and water consumption.
Our revolutionary Energy Centre, developed by VOLUMETRICTM – meets the energy requirements of up to six modules. Containing an Air Source Heat Pump (ASHP), Mechanical Ventilation and Heat Recovery (MVHR) systems, solar panels and a battery storage unit, this intelligent technology is digitally connected to each module – instantly responding to demands for hot water, heating and energy requirements.
Although modules have mains connections, the Energy Centre can meet demand at most times of the year as energy generated during the day can be stored in battery cells until required. Surplus energy goes back into the grid, carbon offsetting – creating ‘free’ energy and net zero living.
COST EFFICIENT CRISIS ACCOMMODATION
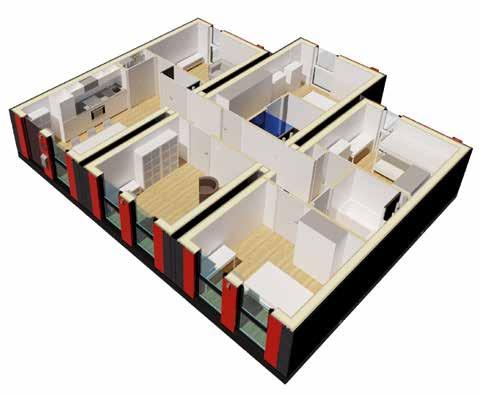
MODULHAUSTM is also fully relocatable and can be moved to meet future demands with all aspects of the dwelling fully recoverable, including screw-pile foundations and service umbilical pipe work, along with the Energy Centre, meaning that over 95% of a project can be re-used in another part of the country at any point in the future.
This has been a massive learning curve and reaching the Future Homes Standard is simply not just a case of adding more insulation. It is far more complex than that. With 2025 on the horizon and as a trailblazer in reaching these challenging standards, I would say it is better to take time now and get your design and testing protocols right, than taking a risk and failing to meet the complexities involved.
Images: 01-02. The futureproof energy strategy for the MODULHAUSTM range is designed to exceed the Future Homes Standard. FAMILYHAUSTM is the latest addition to the range.
Dramatically reducing ongoing energy costs, the MODULHAUSTM range provides greater dignity and independence to the most vulnerable members of society whilst also relieving the burden on Local Authorities of ongoing expenses associated with traditional temporary accommodation.
For more information visit: www.volumetric.co.uk
STRENGTHENING MARKET POSITION
Another tranche of investment into volumetric modular provider TopHat signals a new era for housebuilding, with FTSE-100 housebuilder Persimmon and institutional investor Aviva injecting cash into factory-built precision-engineered homes.
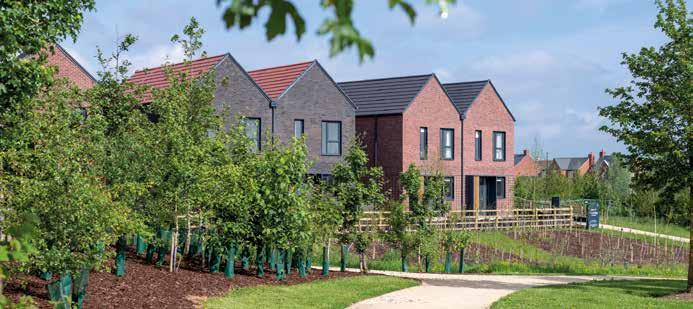
TopHat recently raised £70million from new and existing shareholders as the company draws closer to opening Europe’s largest modular housing factory, from which it will manufacture up to 4,000 ultra low-carbon homes a year. In a major show of confidence in TopHat and the UK’s fast-growing modular housing sector, Persimmon and institutional investor Aviva, through its Aviva Capital Partners unit, have each made a substantial investment in the Company.
Existing shareholders Goldman Sachs Asset Management also subscribed to TopHat’s latest fundraising round. Homes England, which has funded TopHat’s development at Kitchener Barracks in Chatham, continues to explore the potential for additional support as part of its ongoing commitment to the sector.
Persimmon aims to embrace the innovative manufacturing techniques used by TopHat to complement its existing Space4 timber frame product,
drive further build efficiencies while expanding its product offering to customers and support moves to meet the Future Homes Standard. “Persimmon is delighted to announce this partnership,” said Dean Finch, Group Chief Executive at Persimmon. “Combining the country’s most innovative modular manufacturer with the most cost-effective volume housebuilder. This investment provides Persimmon with guaranteed access to very energy-efficient volumetric modular units as well as TopHat’s innovative brick façade to use with our Space4 timber frame products.
“This will provide further build efficiencies, manage the growing challenge of labour shortages in key trades and expand our product range for customers. Combining our complementary industry-leading capabilities alongside other significant new investment makes me excited for the opportunities ahead.”
Aviva Capital Partners, Aviva plc’s newly launched in-house capital unit which originates infrastructure assets using Aviva group capital, has invested to bolster its sustainable community strategy. Thanks to the quality of TopHat’s manufactured homes, outstanding energy performance helps to reduce long-term operating costs for both investors and households, as well as protecting consumers from rising bills.
John Cummins, CEO, Aviva Capital Partners, said: “Aviva is using its financial strength to invest in the sustainable infrastructure and real estate which are central to the UK’s net zero transition. TopHat is a pioneer of low-carbon homes, and this investment will make sustainable housing more widely available, making a difference to communities and providing a retirement income for our customers.” Homes England’s active support during this process was critical to this successful outcome and it remains committed to helping to catalyse this
still-nascent sector in order to improve the supply-side economics and sustainability of housebuilding.
Jordan Rosenhaus, CEO and Founder at TopHat, said: “Today’s announcement is testament to the innovative approach that TopHat continues to take to house building and marks a step-change for the future of housing. It has been clear for some time that designing and building green, beautiful homes in factories is a critical part of solving the housing crisis – and today’s announcement will enable TopHat to reach the scale where the new generation of modular homes can be made available to everyone.”
Ramping up the delivery of homes will be vital to address chronic housing shortages across the UK, where there is a shortfall of 4.3 million homes according to some estimates. A recent report from the House of Lords’ Built Environment Committee suggested modular housing will be instrumental in speeding up development and improving the quality of newbuild homes.
This successful fundraise will help to cement TopHat’s leadership of the modular homebuilding sector. In addition to its current output of up to 800 homes a year from its first factory in Derby, it will begin production from its cutting-edge 650,000 square feet manufacturing facility in Corby, Northampton in 2024. The new factory will employ 1,000 people, many of whom will be apprentices or employees entering the sector for the first time, working alongside the most advanced house building robots operating at scale in the UK.
Every home that is manufactured along TopHat’s production lines is capable of being zero-carbon, meaning no operational emissions are produced from heating and utilities. This is achieved through exceptional building fabric and the incorporation of low-carbon technologies such as solar panels and battery storage. When combined, these efficiencies will help to drastically reduce a home’s carbon footprint while helping to cut energy bills, which have reached record-highs over the last year.
“Modern Methods of Construction have the potential to revolutionise the housing sector, driving greater efficiency and productivity, reducing carbon emissions, decreasing disruption caused by construction and increasing consumer choice, added Harry Swales, Chief Investment Officer at Homes England. “As the Government’s housing and regeneration agency, we’re committed to increasing the use of MMC, and supporting our partners in the sector
to invest in it. This investment from TopHat, Persimmon and Aviva Capital is not only an important step forward for TopHat, but really encouraging for the wider sector.”
Reducing the UK housing stock’s operational emissions is deemed vital if the UK is to meet its legally binding net zero targets. Energy use in homes currently makes up 23% of the UK’s greenhouse gas emissions – more than double the amount from agriculture, and nearly as much as all transport emissions. TopHat is already working with some of the UK’s biggest developers and investors, including BoKlok, Man Group and Urban & Civic.
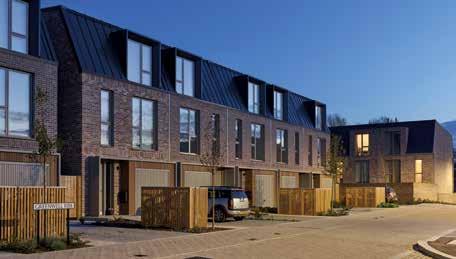
For more information visit: www.tophat.io
Images: 01-04. The new manufacturing facility at 650,000sq ft will be the size of 11 football pitches and will be able to produce 16 houses a day at the rate of about one house per hour. The new facility will be built to BREEAM ‘Excellent’ standard
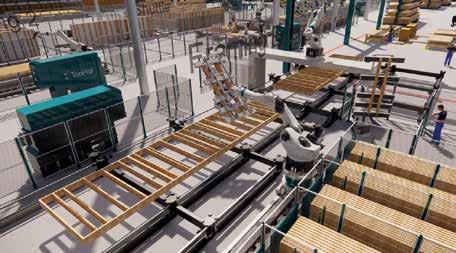
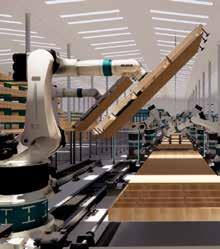
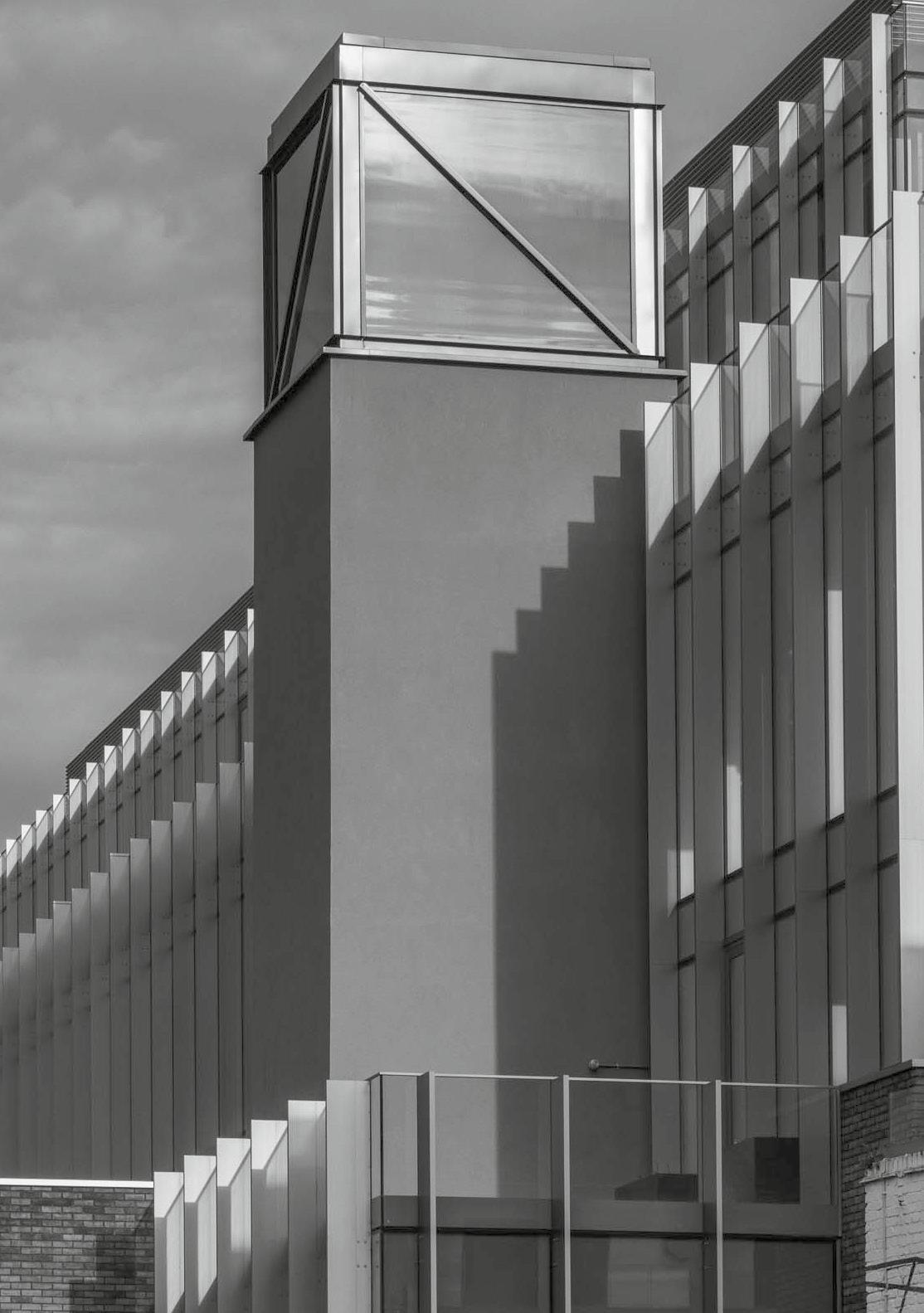
MEET THE JUDGES...
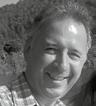
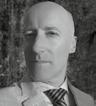


LIMITED SPONSORSHIP PACKAGES REMAINING

The 2023 marketing campaign is ramping up and many of the sponsorship packages have already been snapped up by savvy companies wanting to gain the full exposure in the coming months leading up to the event.

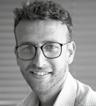
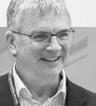
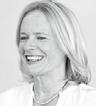
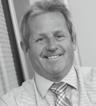
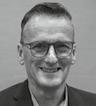
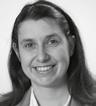
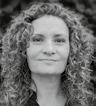
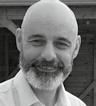
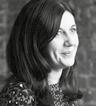
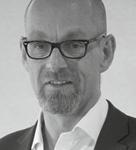
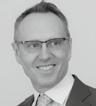

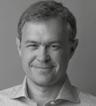
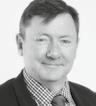
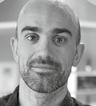
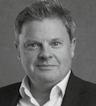
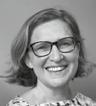
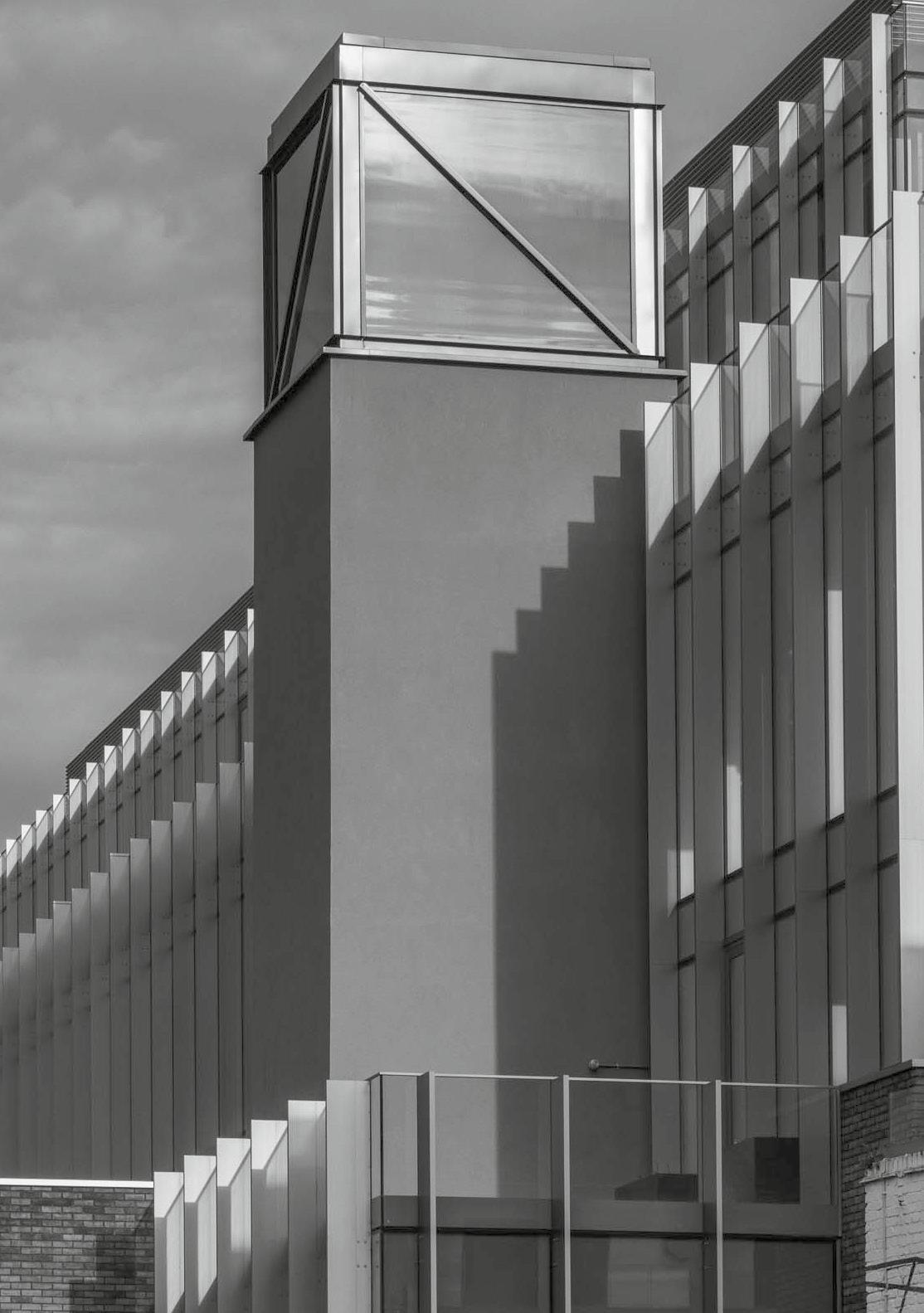
To discuss the sponsorship packages and bespoke advertising opportunities available please contact Julie Williams on 01743 290042 or email julie.williams@radar-communications.co.uk

GETTING AHEAD IN THE SUSTAINABILITY STAKES
EOS Framing aims to inspire housebuilders to develop homes that are safe and sustainable and, in the last decade, has transitioned from a component supplier to a panelised light steel systems manufacturer that can also incorporate factory fitted insulation and windows.
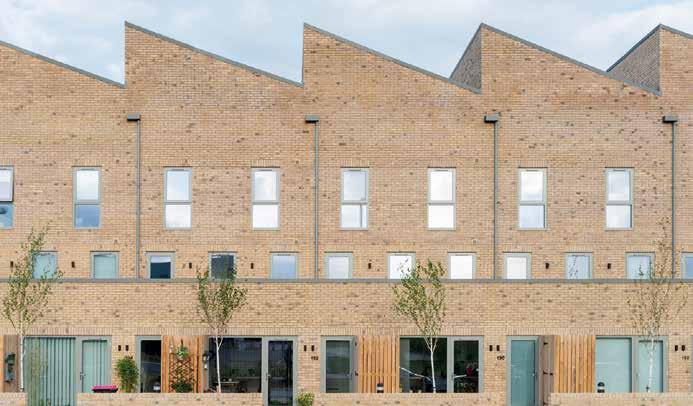
1
At a time when energy prices are at an all-time high and the cost-of-living crisis continues to have an impact, developing highly airtight homes is both good for the environment and helps hard pressed families to reduce ongoing energy bills.
By taking the construction of the building structure offsite, on-site waste is virtually eliminated compared to industry norms in excess of 10%. Using Design for Manufacture and Assembly (DfMA) protocols integrated with Building Information Modelling (BIM), light steel frame systems are digitally designed and tested to optimise material use and create highly airtight structures.
Findings from studies such as the Post Occupancy Review of Buildings and their Engineering (PROBE) reveal that energy consumption in buildings is often as much as twice that predicted at the design stage. Performance data reveals EOS’ panelised light steel systems create highly airtight structures, reducing in-use energy requirements and carbon emissions for the lifetime of the building.
Offering the best strength-to-weight ratio improves efficiencies. EOS’ systems provide a lightweight but robust response to complex buildings where additional structural integrity may be required. Lighter structures not only reduce material consumption but
also concrete in the ground. As well as reducing environmental impact, this means that foundation loads and sizes can be reduced by over 70% relative to concrete and block-work construction.
To demonstrate EOS take their responsibility towards the environment seriously, the light steel specialist has been awarded an Environmental Product Declaration (EPD). The scope of this EPD is cradle-to-gate which includes a comprehensive lifecycle assessment. This assessment considers the extraction of raw materials, the manufacturing process, distribution and its end-of-life value. The systems designed and manufactured by EOS currently use steel that is made from
59% recycled content and are 100% recyclable. This EPD is an important validation tool which provides transparent data and helps residential developers make informed decisions to achieve net zero goals.
Looking for Inspiration?
For architects looking to discover more about the design capabilities of light steel framing systems, the new EOS Case Study Compendium provides a rich vein of information and inspiration. With embedded videos featuring case studies and charting the light steel journey from factory to site, together with a site study tour and client testimonials – this compendium is a
EOS FRAMING
must for those wanting to explore the possibilities of light steel frame.
The Compendium presents a snapshot of EOS’ work and achievements, but a comprehensive index of case studies, colour coded by sector – help navigate to specific points of interest. As experts in advanced light steel framing technologies, the team at EOS have a mandate to challenge the norm and take the construction industry forward by pioneering a new certified systems approach. This is just another step on that journey to help construction professionals appreciate the versatility of light steel and the safety, sustainability and performance advantages it brings.
By working closely with residential developers, EOS are now able to provide scalable light steel frame solutions – delivering precisionengineered homes that meet building safety regulations and can be produced at scale better than, faster than and more cost-efficiently than other market offerings.
Images:
01-03. Using EOS Thrubuild® light steel system, Sky Houses set the standard for 21st Century living

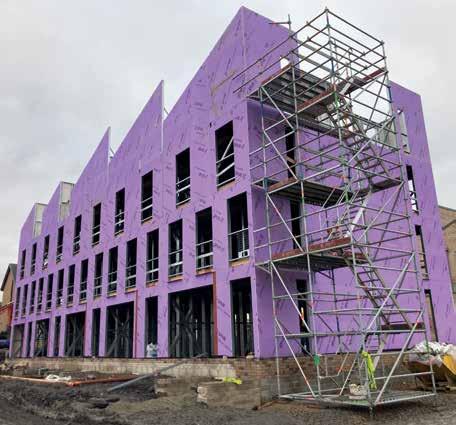
04. The EOS Case Study Compendium provides a rich vein of information and inspiration

Delivering confidence and certainty in the construction process, EOS empower construction professionals to be technical forerunners in the offsite sector. In-house highly skilled technical teams work collaboratively with clients to ensure specifications are accurately designed, manufactured, and fit first time. EOS are committed to technical competence and as part of Etex, have some of the best fire protection experts in the UK on their team. Technical support is available throughout the lifecycle of the project, from concept to completion – in person, online or by phone.
You can view the EOS Case Study Compendium at: https://indd.adobe.com/view/00b9498a-d7e8-4879-a927-e31ab8b15295
For more information visit: www.eosframing.co.uk
100% RECYCLABLE INFINITELY REUSABLE
Large scale use of raw materials is standard in construction, but as Mike Fairey, Chair of the Light Steel Frame Association (LSFA) says
economy credentials both as a material which is strong and durable and as a structural framing system which is lightweight, adaptable and reusable. The qualities of strength, longevity, recyclability, availability, versatility and affordability make light steel frame unique.
Circular Construction Principles
Design optimisation is crucial in a circular construction approach and a lot of thinking has to be done up front. Once the architectural priority was form and function but now there are a raft of considerations coming to the fore such as design for longevity, flexibility, adaptability and the offsite mantra of – design for manufacture and assembly (DfMA). But that is not all, it is imperative to plan for a building’s ‘end’ right at the beginning of the design stage to enhance the sustainability value chain through design for disassembly and recoverability protocols.
Long Lasting Asset
The offsite industry can play a vital role in achieving a circular economy and reducing the burden on nature by ensuring resources remain in use as long as possible.
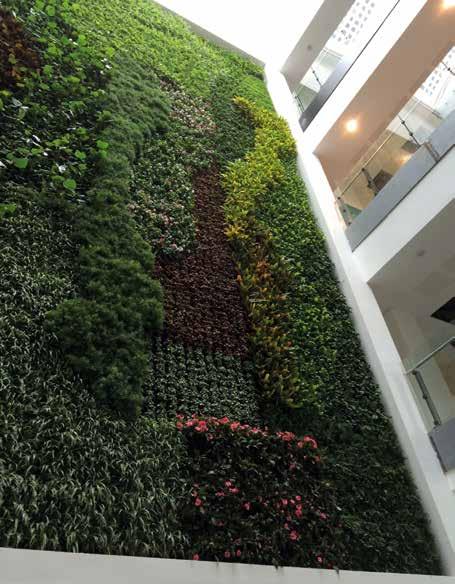
At its simplest, the circular economy prioritises the reuse of materials, preventing the over extraction of natural resources and the amount of usable construction components that
end up in landfill. There is growing pressure on the construction industry to reduce waste and to achieve this we have to move towards resource efficiency.
But first we have to address the commercial realities associated with making this practically happen by ensuring information is readily available. Steel has excellent circular
Manufactured from the most abundant component on earth, steel can be recycled or reused endlessly without detriment to its properties. This unique characteristic gives steel a high value at all stages of its lifecycle. The recovery infrastructure for steel recycling is highly developed and extremely efficient and has been in place for decades. Current recovery rates from demolition sites in the UK are 99% for structural steelwork and 96% for all steel construction products – figures that far exceed those for any other construction material.
Research carried out by the LSFA’s technical partner, the Steel Construction Institute (SCI) has estimated that there are around 100 million tonnes of steel in buildings and infrastructure in the UK. This ‘stock’ of steel is an important and valuable material asset that means we
– there must be a better way.
are largely self-sufficient in steel and can virtually produce all the steel we need through recycling or reusing our latent stock to satisfy market demand. The LSFA is on a mission to champion steel’s sustainability benefits and its role in the circular economy. Many of our members use light steel framing systems which contain over 50% of recycled stock.
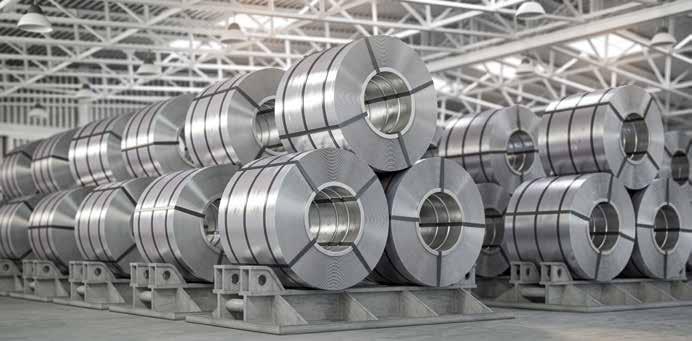
Recycling is often seen as the ultimate goal although reuse for its original or similar purpose without vastly altering the physical form, is equally if not more important but it rarely gets a mention. But how many construction components can be reused with little or virtually no reprocessing? I can only think of one. Reuse offers even greater environmental advantages than recycling since there is no, or few environmental impacts associated in reprocessing.
Material Efficiency
Light steel frame is often used for complex buildings where additional structural integrity is necessary and provides the answer to complex questions where a lightweight response is required. Low weight equates to improved efficiencies – you get a lot of structure for relatively little weight which reduces embodied carbon. This is where steel cannot be beaten. Lighter structures not only reduce material consumption but also concrete in the ground with foundation loads and sizes reduced by over 70% relative to block-work construction.
World Leading
The UK leads the world in steel construction commercially, technically and in terms of quality. The industry has made dramatic improvements in technology, productivity and efficiency. According to research carried out by independent consultants Construction Markets – steel continues to be overwhelmingly the structural framing material of choice with their survey showing that steel now has a 72.5% share of the multi-storey office market and a 60.9% share in the ‘other multistorey buildings’ which includes retail, education, leisure and healthcare sectors.
Sustainability Guide
With an objective to support specification through developing a better understanding of the benefits, the LSFA has launched an informative Sustainability Guide to verify the
environmental credentials of light steel framing technology.
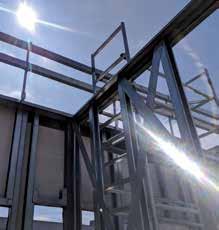
Areas covered in the guide include sustainability in light steel frame construction, key environmental benefits and ways of reducing embodied carbon now and in the future. There are also references for further reading which covers the subject of sustainability in more detail. For more information and to download the Sustainability Guide visit: www.lsf-association.co.uk
Images:
01. David Attenborough Building, Conservation Campus Cambridge – light steel system supplied by EOS Framing
02-04. Strong, lightweight, recyclable and reusable, light steel frame has excellent circular economy credentials
TEKLA GETS PERFORMANCE UPGRADE
Trimble has announced the introduction of the latest versions of its Tekla® software for constructible Building Information Modelling (BIM), structural engineering and steel fabrication management.
Tekla Structures 2023, Tekla Structural Designer 2023, Tekla Tedds 2023 and Tekla PowerFab 2023 all offer significant improvements in construction productivity, efficiency and quality. This latest Tekla software raises the bar for automated and connected workflows across project phases and stakeholders.
These latest Tekla versions include significant performance enhancements, enabling smoother information delivery on projects that are typically growing in both size and intricacy. Robust software performance is key to enabling multiple stakeholders to consult, use and feed data into the models in connected workflows. The Tekla software provides a truly connected construction environment with an integrated suite of solutions, centralised data, streamlined workflows and comprehensive visibility throughout the course of a project.
Connected construction enables precision production and reducing rework through constructible design. It forms the basis for green construction strategies to optimise the use of resources, minimise waste and enable full asset lifecycle maintenance. With the use of open standards, Trimble’s Tekla software products have an active partner community, developing on the Tekla API complementary applications and integrations for specialised
industry sectors such as scaffolding design, industrial projects and detailing for modular construction such as light metal framing.
Tekla
Structures 2023
The structural BIM software continues to improve the user experience of both new and more experienced users by making it easier to learn and adopt time-saving functionalities faster. Apart from several improvements in software performance, the upgraded drawing editing user experience makes the software easier to learn and use. Tekla Structures raises advanced detailing for fabrication workflows and project communication to a new level. In rebar detailing, complex bar shape designs are easier to share with procurement, manufacturing and the construction site. Customers in steel fabrication benefit from greater flexibility by being able to cover more detailing options related to bolts and holes for specialised industries. The software also features updated outputs and exports in the field of detailing for fabrication of multiple types of projects and materials.
Tekla
Structural Designer 2023
The design and analysis software introduces a rigorous analytical approach to footfall analysis that can bring substantial cost benefits as well as a reduction in risk through accurate quantification of performance. The engineer can run multiple footfall scenarios in a single model effortlessly.
Tekla
Tedds 2023
The structural design software now offers seamless integration of structural design information and documentation with Tekla Structures, to improve collaborative design-to-
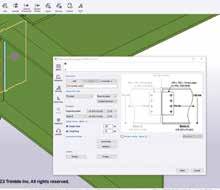
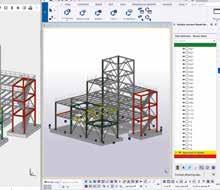
detailing workflows. Particularly for steel connection design, the improved integration with Tekla Structures now enables linking Tedds calculations to Tekla Structures components. With this added functionality, Tekla software now provides a seamless workflow for endto-end connection checking between the engineer and steel detailers. In addition, the Tekla Tedds calculations help support multi-material design in Tekla Structural Designer with a specific focus on timber/wood design. The latest version also includes new and updated calculations for faster, more reliable structural element design.
Tekla PowerFab 2023
The steel fabrication management software suite offers new functionalities that help fabricators manage changes in their projects efficiently to minimise errors. In the latest version of Tekla PowerFab, subscribers can gain quick and easy access to the visual production dashboards and a shipping calendar. The mobile tool Tekla PowerFab Go provides new time-saving functionalities. To support sustainable material sourcing, Tekla PowerFab now features improvements for tracking the origin of raw materials.
Michael Evans, Senior Product Director of Trimble Structures, says: “Our product development focuses on delivering solutions that make building information more easily available, constructible and shareable to stakeholders across the industry, to optimise the use of resources. Through continuous enhancements, in-product intelligence and expanded support for sustainable construction, we provide our customers with one of the most advanced BIM technology platforms on the market today.” All Tekla products are certified to be fully compliant with ISO27001, the leading global standard for information security management.
For more information visit: https://support.tekla.com/tekla-2023
Images:
01. Model reviews using Trimble Connect - an easy way of communicating from Trimble Connect to a Tekla Structures model, streamlining collaboration between users
02. Tekla Structures 2023 improves workflow for simple steel connection design using Tekla Tedds
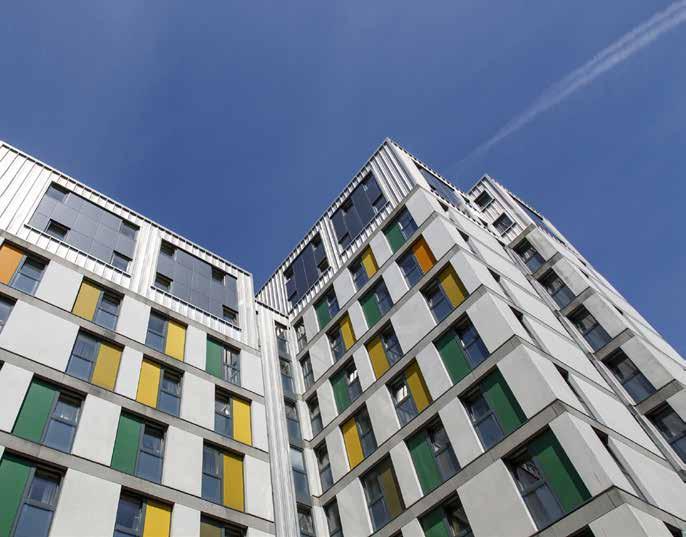






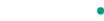






STEEL SUPERIOR PERFORMANCE BENEFITS
Mike Fairey, Managing Director of Fusion Steel Framing, outlines why FusionTRAX TM – a new non-load-bearing infill walling system – is set to boost the offsite marketplace.
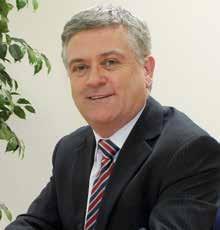
Fusion Steel Framing has a clear mission to improve the entire building process through more efficient supply chain solutions that integrate highquality offsite manufacturing with onsite processes. Products like FusionXTM, our load-bearing external walling system, continue to help reshape the construction process for a range of our developer and contractor clients.
The past month has seen the roll-out of another product which we believe will bring significant programme and performance benefits to the construction industry. FusionTRAXTM is a non-load-bearing infill walling system designed for concrete or steel mainframes, and capable of supporting a wide range of cladding systems.
One of the key advantages of FusionTRAXTM is that it can be custom-designed to fit any project specification. We have a team of experienced designers who work closely with the client to ensure that the FusionTRAXTM system meets their specific requirements. Once the design is finalised, we rollform the steel components in our own factory using advanced CAD/CAM technology to ensure a high level of precision and consistency.
We then deliver and install the FusionTRAXTM system on-site, taking full responsibility for the project. By serving as a ‘one-stop-shop’ for our clients in this regard, we can simplify the construction process and vastly reduce the risk of errors and delays. This can rapidly accelerate construction projects while de-risking the process of installing an infill system, which is so often a crucial element of any new development.
In terms of its application, the FusionTRAXTM system is designed for use in residential buildings such as apartments, hotels, and student accommodations. It can also be used for care buildings like hospitals, care homes, extra care facilities, and retirement living, as well as educational buildings like schools, colleges, and universities. Installation of FusionTRAXTM is straightforward and the product can be assembled on-site by our experienced team.
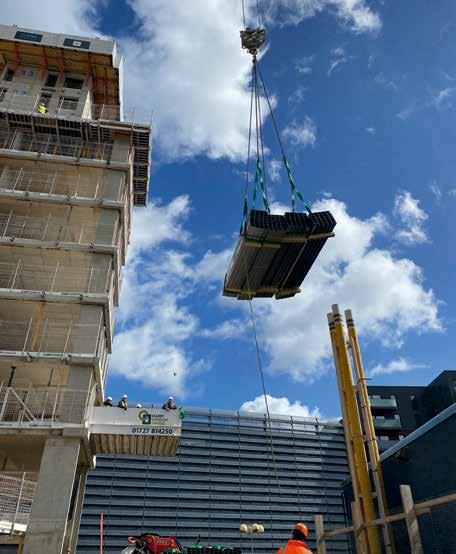
The FusionTRAXTM system consists of lipped ‘C’ shaped studs and plain ‘U’ shaped channels as base tracks, head tracks, and intermediate noggins, all designed to resist the projectspecific loads required. FusionTRAXTM is typically supported at the edge of the concrete floor slab or on top of the perimeter Hot Rolled Steel (HRS) beams. We use a deflection head detail at the top of each panel/ stud and secure it to the underside of the floor slab or HRS beam above, allowing for vertical movement (deflection) to the floor above, without impacting the finishes applied to the external façade.
Beyond simplifying the construction process, another major advantage of FusionTRAXTM is its ability to provide a high level of thermal and acoustic insulation. The system is designed to minimize thermal bridging, ensuring that projects are well-insulated and energy efficient. Using FusionTRAXTM can also help our clients achieve their sustainability targets as the steel framing is 100% recyclable and can be repurposed at the end of its lifespan, reducing the amount of waste that ends up in landfills.
Additionally, because FusionTRAXTM is fabricated offsite, it reduces the amount of on-site waste generated during the construction process. FusionTRAXTM is also a highly durable and long-lasting system. The steel is resistant to corrosion and manufactured to the highest standard of building regulations, ensuring that a completed project retains low maintenance costs and maintains its value over time. In providing a complete service, we can also provide FusionTRAXTM on a supply-only or supply-and-install basis, making it a flexible option for developers, contractors, sub-contractors, or any other parties seeking a reliable Steel Framing System (SFS).
A forthcoming project where we are excited to see the benefits of FusionTRAXTM in action is Kew Bridge Rise, the redevelopment of the former Citroen garage in Brentford by The Hill Group and L&Q. Fusion Steel Framing has been working closely with the production team on opportunities to improve performance with our offsite solutions.
At Kew Bridge Rise, we will use over 10,000 sqm of FusionTRAXTM across
the whole project. The development will have a concrete frame structure and FusionTRAXTM will be used for the infill between floors, sitting on the floor slab up to the ceiling. In addition, we will create the window apertures, install EDPMs, breather membranes, external insulation, and wall tie channels thus providing a complete solution for the project. The scheme is an extensive regeneration project for West London, delivering 441 new homes, and so it promises to be a great example of the capabilities of delivering prefabricated SFS at scale.
Working with The Hill Group has brought us far closer to the development process and increased our understanding of customer needs, as well as the role that Fusion can play in improving construction programmes and delivery. The FusionTRAXTM product is a great example of how we can help our clients improve their processes. It is custom designed, fabricated offsite, and installed entirely by Fusion as a single provider, simplifying the construction supply chain and reducing the risk of errors and delays.
We aim to be the partner of choice for developers and contractors seeking to benefit from light steel framing solutions. Our expert team is always happy to engage with new clients,
project teams and interested parties who want to learn more about our innovative product range. With the roll out of FusionTRAXTM, now is the ideal time to speak to us about the solutions we can offer.
Offsite manufacturing has come a long way in recent years, and I am proud that Fusion remains at the forefront of this exciting sector. Since 2000 we have delivered more light steel residential structures than any other European producer, and we have worked alongside a host of prestigious developers and contractors. Our approach is one of collaboration, working closely with our clients to find efficiencies that will simplify their construction projects. This outlook has led to Fusion advising a range of government and industry bodies, and our doors are always open to new conversations with clients, developers, contractors, and industry professionals.
For more information visit:
www.fusionsteelframing.co.uk
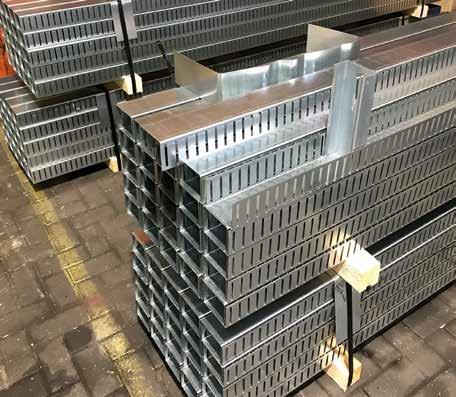
Images:
01. Mike Fairey, Managing Director, Fusion Steel Framing
02. Fusion TRAX system being loaded at Kew Bridge Rise
03. Fusion TRAX is fabricated offsite and reduces the amount of on-site waste dramatically
PLATFORM DESIGN
UNIVERSAL STANDARDS
Can a single modular solution create a platform? David Johnson, UK Preconstruction Director at Volumetric Building Companies, believes the future of UK offsite construction is in need of urgent change.
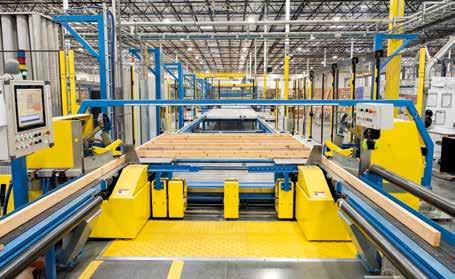

The UK Government has made no secret of the need for faster, higher quality, and more predictable construction solutions in every sector –from schools and hospitals to housing. And there is a considerable drive for a unified platform design and a greater level of standardisation across the modular industry.
In recent years, there have been multiple attempts to drive standards in offsite construction with the use of specialist MMC procurement frameworks developed by the Department for Education, Ministry of Defence and Ministry of Justice. Whilst these client-led attempts to introduce standardisation have been very welcome, they just haven’t gone far enough. Too many requirements have been left open to interpretation, leading to the introduction of a host of similar but different types of building solutions.
To exacerbate the problem, as each scheme percolates through the various stages of procurement, the sustained
tinkering by building designers, cost consultants and local authority planners and building control, combine to completely erode the strategic ambition for an increased level of standardisation to improve the efficiency and quality of project delivery. Traditional in-situ methods of construction have to adhere to standardisation through compliance with Building Regulations. This gives clients the vital confidence that the contractor will deliver the project to the required standard – and if not, that it will be rectified.
The offsite sector absolutely must come together to agree a truly universal standard against which compliance can be measured and assured. Many modular manufacturers are simply selling their own ‘platform solutions’ in an attempt to ‘capture the zeitgeist’, when in fact they are promoting their own system completely independently and calling it a platform. A genuine platform solution has to embrace and represent the whole MMC sector.
How to foster greater confidence in modular technology
With the unfortunate demise of some big industry names in recent months, the time for pride and individual business trailblazing has passed. We need to come together as an industry and provide a unified solution that will foster a much great level of confidence in modular technology and in the built solutions.
And if we don’t achieve this? The UK Government will lose faith and volumetric MMC as a viable building solution will be set back 20 years. Let’s be honest, what we do is not rocket science. We do not use space age materials or really cutting-edge technology. What we do is apply well-managed processes and robust control systems to the historically chaotic and continually bespoke world of construction.
There are many other intrinsic benefits of modular solutions that provide really persuasive arguments for its use over traditional in-situ building methods
– from reduced material waste, improved safety on-site, consistent delivery on time and budget, shorter build programmes to less disruption and enhanced thermal performance. However, none of these advantages are dependent on the need to protect new or innovative technology.
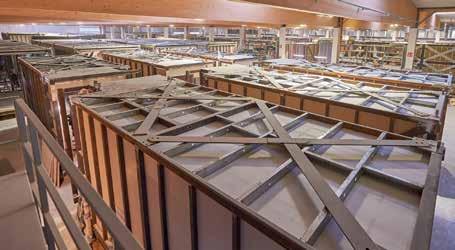
Beyond the box, it really doesn’t matter what happens inside. Does the colour of the seat fabric or the quality of an in-car entertainment system affect the legal compliance or reliability of
PLATFORM DESIGN
a new car? Is it really worth the effort of protecting a particular modular solution that is only a slight variation on a theme? Our industry has to pool its expertise and collaboratively develop a regulatory compliant genuine ‘white box’ standard that we can all support, promote and take to Government as a truly game changing platform design solution. Without that, we risk remaining a niche specialism rather than a universally adopted construction standard.
VBC AWARDED £10MILLION MODULAR CONTRACT FOR HOLIDAY HOTEL
VBC has secured a contract worth more than £10million for the construction of a 500-bedroom hotel for the Tropical Islands resort near Berlin, one of the world’s largest waterparks. Worldwide leisure park operator Parques Reunidos is investing £22million in the new hotel, which will expand the resort’s facilities by 500 beds and create its largest hotel on the Tropical Islands site.

VBC’s contract is for the modular manufacture, furniture production, offsite fitting out and installation of five storeys of guest room accommodation.
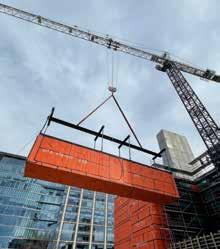
For more information visit: www.vbc.co/uk
Images:
01. David Johnson, Preconstruction Director, Volumetric Building Companies
02-04. Offsite manufacturing has enormous benefits but still risks being seen as a niche method of delivery
05. Tropical Islands Resort will benefit from a 500 bedroom modular hotel
There will be a range of guest room types, including two- and four-bedroom family suites – double, accessible, and 36sq m deluxe rooms. These will be installed by VBC on to a concrete podium which accommodates the public areas and guest amenities. In addition to the manufacture of 155 steel-framed hotel modules, VBC’s contract includes production of a full range of bespoke, contemporary furniture for the guest rooms at its factory in Poland – from beds and sofa beds to shelving, bathroom vanity units, and wood and glass partitions between the main bedrooms and bathrooms.
Commenting on the project, Wouter Dekkers, Corporate Development Director at Parques Reunidos, said: “The use of an offsite manufacturing solution for the guest rooms will significantly reduce disruption to our existing operations and guests during the build phase. The hotel’s modular construction will also have much less environmental impact – fewer vehicle movements through the park, less material waste, and the reduced carbon footprint of the steel structure.”
The attractions at the Tropical Islands Resort include an indoor rainforest which is home to 50,000 plants and 600 species, a beach and 1,200sqm swimming lagoon, spa and saunas spanning 10,000sqm, and the world’s longest double water slide. The park welcomes around 1.2m visitors each year, making it one of the most popular leisure destinations in Germany.
The guest room modules will arrive on-site in Summer this year and will be installed in just two months. The hotel is due to open early 2024.
ENTRY DEADLINE 23.06.2023

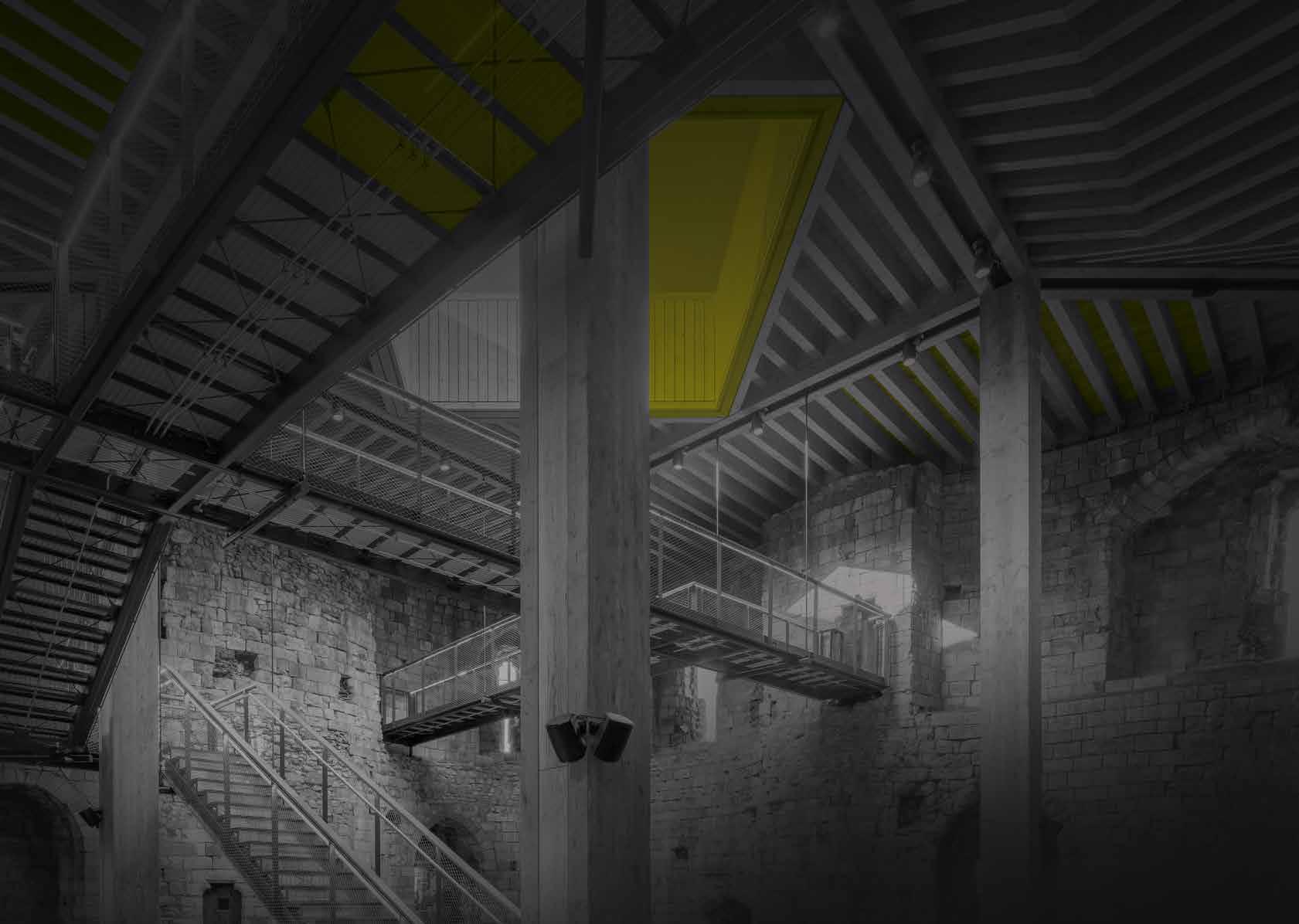
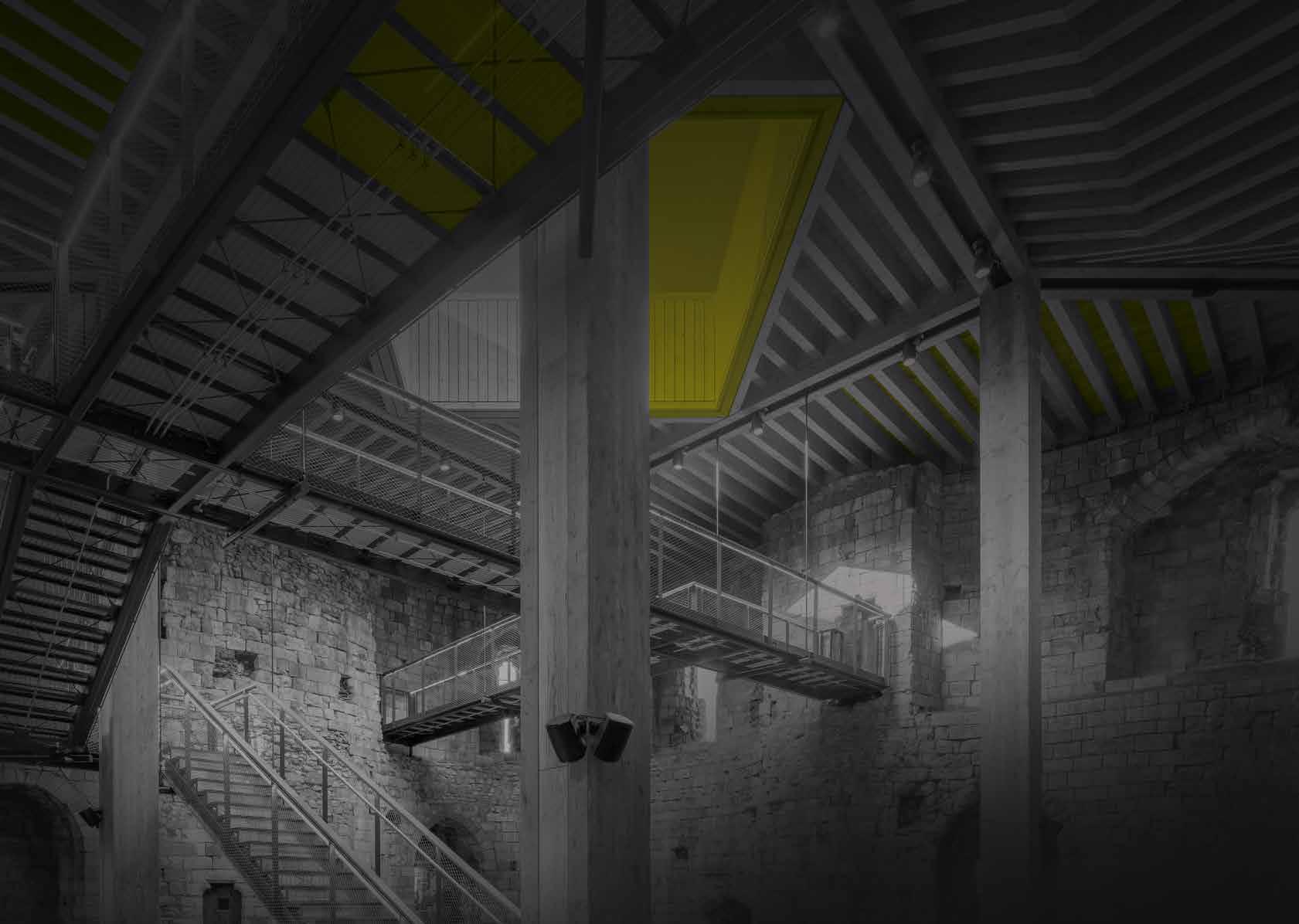
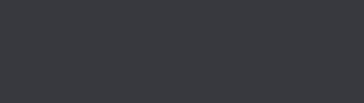

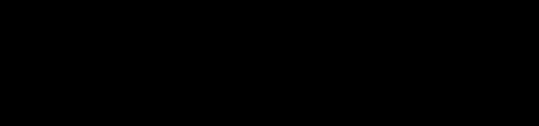
TIMBER FOR MIND & BODY BUILDING
Timber plays many roles in a learning environment with structural solutions only one of them. Mila Duncheva, Business Development Manager UK & Ireland, at Stora Enso Building Solutions outlines it contributions to lifelong learning.
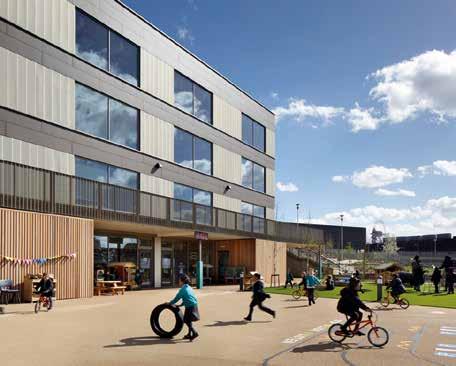
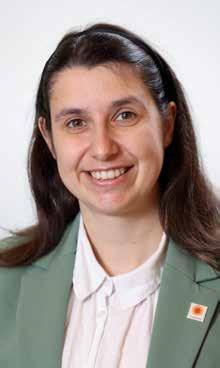
A study by Cornell University found that subpar learning environments led to low test scores, absenteeism and poor academic achievement in schools. And that trend continues into the workplace, where the opposite is true. In fact, a more considered and cultivated working space, with plants and biophilic elements, improves selfreported wellbeing 15% and overall workforce productivity by 31%.
Setting the workforce up for commercial success should be seen as no different to setting future generations up for academic success. This is done by creating environments for their formative years in education, particularly when examination grades play such a crucial role in determining a student’s future and so there’s no reason why we shouldn’t at least be thinking of building greener, healthier school environments for pupils.
Against the backdrop of a £2.4billion cash crunch and teacher strikes over low-pay, local authorities and school management still mistakenly believe that traditional construction materials, such as concrete and steel might seem initially like the most obvious option for slashing construction costs. Instead, our recent cost study showed that by using cross laminated timber (CLT) elements, it is possible to cut the overall construction costs by more than a third. There are many reasons to believe that greener buildings not only can be possible within this financial context but must be in the wider one.
Build now and build well In the face of tight school budgets why should school administrators be thinking about constructing new buildings at all? Over the past four years, England has seen an influx of additional students enter the primary
and secondary school system, to fill the equivalent of over 12,000 classrooms. In response to this and the vast number of schools in need of refurbishment, the UK Government launched its school rebuilding programme in 2020. In some years, 50 schools are chosen, in others, 200. But even 200 schools are not enough, particularly when many projects are in need of refurbishments to make them safe, not necessarily increasing capacity or building anew.
As such, this still leaves a concerning gap between classroom availability and demand. Overall, growing class sizes and governmental focus on preventing collapse instead of creating new classrooms, means that creating quality spaces for young minds must be top of school administrators’ own agendas when factoring in costs for the year.
Solving this with speed
Speed is an important factor for schools to consider and when it comes to speeding up construction, there’s a few ways that this can be done – but we can’t afford to let speed impede quality. One of these is doing as much as possible with modern methods of construction (MMC) – a favourable solution when schools only have a few months when children are away on holiday. Constructing the superstructure in a factory environment means finding a suitable material, like CLT elements that are precisionengineered in a factory, ready to slot together on-site when the time comes.
Many examples exist in the form of timber in the UK already, for example: Sherborne Girls School Arts Centre (B&K Structures, Dorset, 2018), and in higher education the New Model Institute for Technology and Engineering (Hybrid Structures, between Birmingham and Wales, 2021). Once assembled, these easy to build kits provide schools with the tools to minimise disruption and accelerate construction once on-site. This also allows for fewer deliveries to be made and less time spent on construction sites. In turn, this reduces labour costs and could very well eliminate the need to rent temporary classrooms (which tend to become permanent over the decades they remain on school grounds) whilst newer ones are being built.
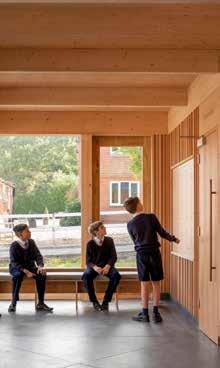
Lightweight enough to be transported to site in prefabricated parts, timber is an impressive candidate when it comes to constructing with innovative materials. When building with timber, there are some cost reductions per square metre, which make CLT a considerably attractive option for school buildings. If we’re grading materials, timber also has impressive sustainability scores. In fact, each cubic metre of CLT is estimated to remove one tonne of climate damaging CO2 and store that in the building. With a prefabricated school kit, like Sylva™ by Stora Enso, it is possible to reduce emissions by up to 70% compared to a steel and concrete framed building.
Timber: better for mind and better for body

Timber also provides us with the opportunity to build more modern buildings, fully equipped for classes (and minds) of the 21st century. And unlike the schools of old, engineered wood is a safe building material without the risks of COSHH and RAAC. In an era where there is knowledge about these issues, choosing a safer material is a no brainer. And while some may fear the fire risk as a safety concern, evidence points to the fact that engineered timber, such as CLT, is designed to withstand fires up to 120 mins for safe evacuation and meets the same fire regulations as steel and concrete.
Moreover, studies on the effect of working in a timber environment have found that buildings with a biophilic design can lower stress levels, increase productivity and enhance creativity. These wellbeing benefits cannot be underestimated, especially as children catch up on education missed during COVID-19 lockdowns. Whilst schools might think that building high quality, modern buildings to foster imagination and boost wellbeing is not a priority, this investment is set to pay dividends in classroom creativity and academic outcomes later down the line.
Budgets will always be an issue that school administrations have to contend with – with or without governmental funding. With the ball now in their court, schools have the opportunity to undertake projects which will not only save time and money, but also make a tangible difference to wellbeing and the environment.
For more information visit: www.storaenso.com/en
Images:
01. Mila Duncheva, Business Development Manager UK & Ireland, at Stora Enso Building Solutions
02. Mossbourne Riverside Academy, London
03. David Brownlow Theatre, Newtown
04. CLT is produced in a precision factory environment
YB Fixings Ltd was established as a private limited company in 1979 and became part of the Indutrade family in 2017.


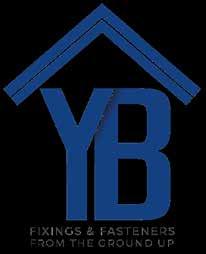
Our head office is in Swindon, Wiltshire and we have a National Sales Team that covers the UK and Ireland.

We distribute many types of fixings, fasteners and high-quality tooling for all applications from top to bottom of the industrial, construction and modular industries.
RB441
RB441T is a 7th generation of MAX REBAR-TIER products, the most advanced cordless rebar tying
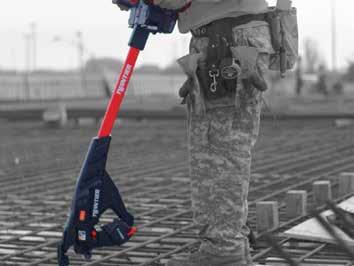

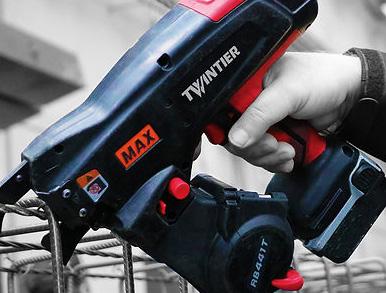
RB401-T
Tie while standing up with the RB401T-E. The extended frame allows you to stand up and tie rebar for concrete slabs. Being up to 88% less effort while having 48% less compression on lumbar joints, the RB401T-E is the perfect solution for slab work.
RB611
RB611T is a 7th generation of MAX rebar tying products for larger rebar combinations between D16xD16 and D29xD32, the most advanced cordless rebar tying machine.
REBAR CUTTER
The PJRC160 is a professional grade cordless brushless re-bar cutter with a 360 degree rotatable head. Cutting up to 176 times per charge and with its brushless electric motor offering higher efficiency and a longer lifetime, cutting rebar has just got a whole lot easier.
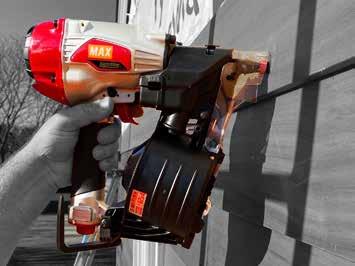
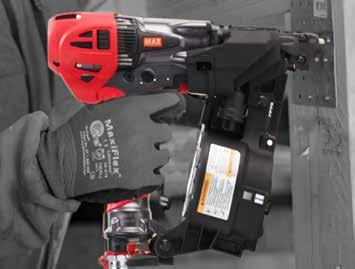
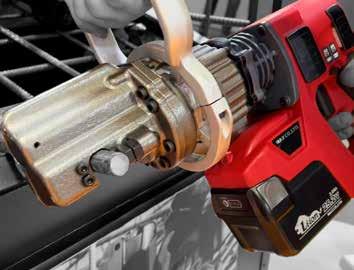
PNEUMATIC 8-BAR

YB Fixings supply the highest quality MAX, Montana and Fasco tooling and fasteners used within all sectors from factory manufacturing to construction sites.


HIGH PRESSURE
PowerLite tools are extremely powerful yet their size is 40% smaller and tool weight is 30% lighter than conventional regular pneumatic tools with a wide variety of fasteners.
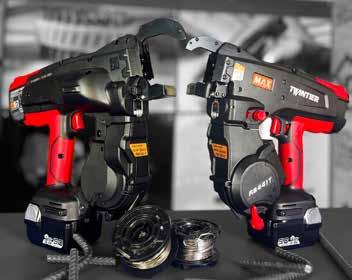
ARCHITECTURE OF SUFFICIENCY
Opening in January 2023, the Black & White Building has become the latest in a series of landmark structures showcasing the best in timber technology and sustainable architecture.
Mass timber developments
TOG and Waugh Thistleton set out to create a building that minimised carbon in both its construction and, once complete, its operations. The architects proposed a structure built from the ground up using cross laminated timber (CLT) and laminated veneer lumber (LVL). “The principal message of The Black & White Building is sustainability, says Andrew. “This is a mainstream, grade-A central London office building, built entirely from timber. It clearly demonstrates that mass timber is a viable replacement for concrete and steel in the mainstream office market, saving thousands of tonnes of CO2. We’re trying to change the way we build, to transform the industry.”
Design-led workspace specialist The Office Group (TOG) has come together with Waugh Thistleton Architects to explore a new approach to workplace design. In The Black & White Building, they have explored an ‘architecture of sufficiency’– where every element serves a purpose, nothing is superfluous, and all materials and processes are as efficient and sustainable as possible.
The new seven-storey mass timber building in the heart of Shoreditch sets out to demonstrate that timber is not just a viable alternative to the conventional concrete and steel used to build offices, when it comes to performance and sustainability, it is the preferable option. Standing 17.8m above the Shoreditch streetscape, it can serve as a model for the office architecture of the future.
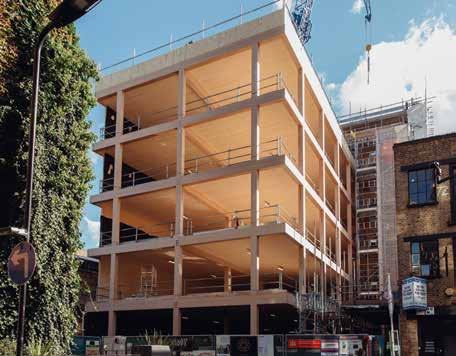
The previous building on the site – a 11,000sq ft structure painted black and
white – was incapable of meeting the area’s growing workspace demand but also unviable for extension, so TOG co-founders and co-CEOs Olly Olsen and Charlie Green were determined to create the most sustainable building that they possibly could. Their research led them to Waugh Thistleton Architects – a firm responsible for pioneering timber designs for over a decade, including landmark residential blocks such as Dalston Works and Murray Grove, as well as Vitsoe’s Leamington Spa HQ.
“When I heard that TOG were thinking about a new sustainable office building, it's like I was standing in the queue for a nightclub and they put my favourite song on,” says Andrew Waugh, Waugh Thistleton Architects.
“I admire the fact they had the commitment and the courage to do this in the first place. They flew in the face of naysayers, and they took the lead. It was very bold of them.”
The CLT frame was chosen for its perfect balance of sustainability, lightness and strength. Glulam is used for the curtain walling, and the columns and beams are made out of beech LVL.
The structure comprises a combination of timbers from 227 beech and 1,547 pine and spruce trees harvested from PEFC-certified forests in Austria and Germany. For a sustainable forest to regenerate the quantity of wood used in the construction of The Black & White Building would take approximately 137 minutes – meaning that it’s possible to grow enough timber to construct a six-storey, sevenfloor building in less time than it takes to bake a loaf of bread.
CLT is significantly lighter and easier to transport than conventional building materials such as concrete and steel, which means that fewer deliveries are required to bring the necessary quantities to the construction site. This not only represents a carbon-reduction in terms of logistics, it also makes building in dense urban areas a more efficient process that is less disruptive for neighbours and other road users.
Because the timber components are prefabricated, and precisionengineered to be slotted together, the ‘screwed not glued’ building not only requires a smaller workforce to construct, it also has a part to play in the circular economy. At the end of its life, the building can be easily disassembled rather than demolished, and the materials can be recovered and reused. Overall, The Black & White Building creates 37% less embodied carbon than a comparable concrete structure, and serves as a long-term carbon store for 1,014.7 tonnes of CO2 equivalent (55% of the building’s total) sequestered in the timber structure. The team expects to achieve a BREEAM Excellent rating once the building is complete.
“The Black & White Building represents a major step forward for us,” says Charlie Green, co-founder, TOG. “And – I hope – the wider industry too. It’s a statement of who we are and how we will approach sustainability – we don’t need to build the traditional way with concrete and steel anymore. We always retrofit when we can, and when we build new buildings in future, TOG is committed to constructing them from timber and other sustainable materials.”
Sustainable inside and out
The Black & White Building is powered by 100% renewable energy sources
– including 80 solar panels on the rooftop. No element of The Black & White Building is purely decorative – everything has a purpose. Notably, the exterior is clad in timber louvres that run from street level to the roof. These provide natural shade, reducing solar gain on the façade and boosting the natural light reaching the interior. The louvres change in depth as they ascend the building in order to optimise energy efficiency.
The entire building is, as Waugh Thistleton has described it, ‘visibly sustainable’. The sensory impact of the space is significant. “I love that kind of ‘whoosh’ sensation you get when you first come in,” adds Andrew. “The beauty, excitement and aroma. When you walk through the front door and discover the contemporary-cathedral quality to the space, you just feel that there's a sense of overwhelming optimism about the building.”
A benchmark for building sustainably
For both TOG and Waugh Thistleton Architects, The Black & White Building represents a proof of concept that they hope will inspire and encourage the wider architectural community to
adopt carbon-minimal construction methods and engineered timber materials. In the short term, the building will provide a Shoreditch home for creative businesses determined to make a credible sustainability statement. In the long term, it is a call to kickstart a new era of architecture, founded on low-carbon construction, circular thinking, and natural materials.
For more information visit:
www.theofficegroup.com/uk/theblackand-white-building
www.waughthistleton.com
Images: 01-03. The Black & White Building is another example of timber providing a low carbon solution to commercial construction. Courtesy TOG/Waugh Thistleton

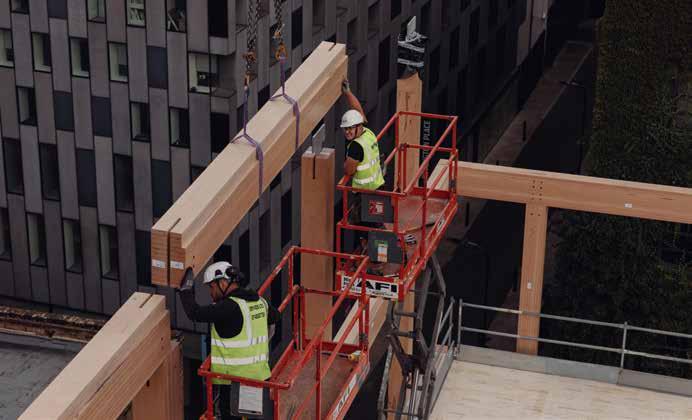
SAFE & SECURE ACCOMMODATION
while we press ahead with the biggest expansion of prisons in over a century – building six new jails and creating thousands of additional cells by renovating and expanding existing sites. The first rapid cells at HMP Norwich are already boosting capacity while our multi-million-pound renovation of the Elizabeth Fry wing will create long-term places to protect the public.”
multiple locations. The temporary accommodation we have already supplied to the Ministry of Justice was to a very high standard, which we will continue with these longer-term structures.”
Wave 1 of the CCS framework (current framework RM6014) involves the supply of 396 units across several locations including at HMP Norwich in Norfolk. Wave 2a is valued at £11.9million and requires the supply of 215 units across further locations. The Rapid Deployment Cells Project requires Algeco to provide ‘safe and decent accommodation’.
Algeco’s Cannock facility will manufacture the cells utilising Design for Manufacture and Assembly (DfMA) and Lean Manufacturing techniques. The company will install and commission a variety of units including sleeper accommodation, accessible accommodation and ancillary units at multiple locations around the country.
MoJ has secured funding to design and build 1,000 additional temporary prison places, the majority of these will be delivered in 2023. The Rapid Deployment Cells Project was initiated to create a new design that can be quickly deployed to a variety of sites to help meet the short term demands of the prison estate.
Minister for Prisons and Probation
Damian Hinds said: “Prison cells protect the public by making sure we have enough space to put dangerous offenders behind bars – that’s why we’re investing £4billion to deliver 20,000 extra places. We’re rolling out a thousand Rapid Deployment Cells to create extra spaces quickly

James Withey, Managing Director at Algeco Offsite, said: “Utilising DFMA and Lean Manufacturing, along with our platform-based approach, will deliver high quality units across these
ALGECO UNVEILS NEW WIGAN SUSTAINABLE SITE
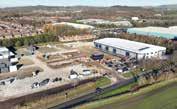
The Crown Commercial Service’s (CCS) £10billion Offsite Construction Solutions Framework aims to promote modular design in a drive to cut costs and help providers meet carbon net zero targets.
Images:
01. The Framework contract (Wave 1) totals £21.9million to supply secure units to the MoJ 02. Algeco’s new Wigan site
Algeco has a new site in Wigan to serve the North-West region with its wide range of temporary buildings and associated products for hire. The official opening took place on 20 April, supported by Councillor Marie Morgan, Wigan Mayor, Diane Elbert Morgan, Director at Greater Manchester Chamber of Commerce and Jackie Maginnis, CEO of the Modular and Portable Building Association (MPBA).
Sustainability is a central theme of the Wigan site. Photo-voltaic panels help power the on-site workshops and no fewer than eight EV chargers provide plentiful recharge points for customers, visitors and colleagues. All of the mechanical handling equipment on-site is electric-powered to minimise emissions – a considerable investment by the company.
Hiring buildings contributes to the circular economy by re-using modules when they are no longer required by the first customer. The Algeco Wigan site refurbishes and re-uses portable and modular buildings for use as temporary offices, welfare facilities, toilets, anti-vandal units, secure storage units, site accommodation and gatehouses, amongst many others.
Richard Dey, Area Director, North at Algeco, said: “We’re pleased to announce our new site in Wigan as we look to strengthen our brand presence across the country. It offers customers from a wide range of sectors easy access to the huge range of Algeco temporary building solutions for hire. By adding this new site to our network, we have been able to raise the bar on our sustainability, which now provides a blueprint for future Algeco sites.”
For more information visit: https://www.algeco.co.uk/permanent
Algeco has been awarded a Framework contract (Wave 1) totalling £21.9million to supply secure units to the Ministry of Justice (MoJ), with the option to order further units.
Together, we build sustainable futures
Whether you need to hire a storage unit for a month or create a permanent multi-storey, inspirational building, Algeco has everything you need.
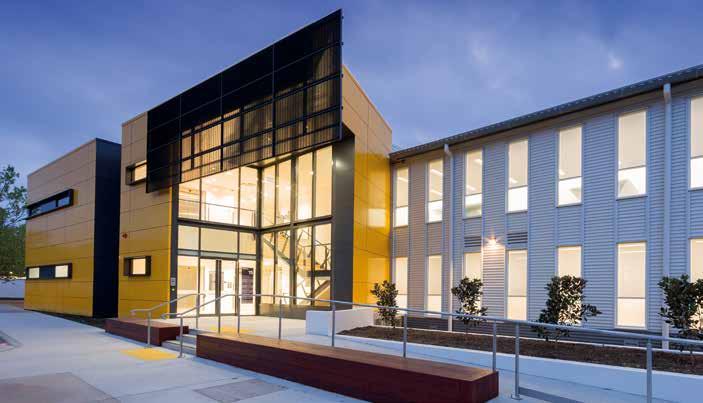
Our turnkey services - whether you hire or buy – deliver the complete solution. All made and installed to leading Health & Safety practices for total peace of mind.
are the perfect fit with your own environmental priorities.

IRELAND: FOCUSING ON BETTER BUILDING
Speakers and panellists include:
Pat Barry, CEO -
Irish Green Building Council
Graham Couchman, CEOSteel Construction Institute
Charlotte Garrett, DfMA Lead - KOPE
Michael Hough, Director -
MJH Structural Engineers
As organisers of the Explore Offsite Events, Offsite Expo and the Offsite Awards, Radar Communications are working in partnership with MMC Ireland to deliver the first annual MMC Ireland National Conference. Presenting an insight into the future of construction, this event represents a great opportunity to gain industry intelligence and network with those who are at the forefront of offsite construction both in Ireland and internationally.
Last year saw the launch of MMC Ireland, an industry collective established to represent companies involved in the delivery of offsite and other modern methods of construction (MMC) in Ireland. As in the UK, construction in Ireland is seeking innovative, cost-effective and sustainable ways to build. The Irish Government has strongly committed to enabling a more efficient and sustainable approach to building design, construction and operation.
More than three years in the making, MMC Ireland is a collaboration of industry talent and experience and is focused on seven categories of MMC: volumetric modular, structural panellised, offsite components, additive manufacture, non-structural assemblies and sub-assemblies, offsite building material improvements and on-site process improvement.
As many MMC Ireland members operate in markets other than Ireland, there is a sense that the Irish industry needs to upskill beyond current standards and technologies and regain the global leadership position that it held two decades ago. The genesis of this organisation can be traced back to a gathering in 2019 where the Chairman of both Tide Construction & Vision Modular Systems, John Fleming, inspired the industry with a vision of ‘Rebuilding Ireland through Modular Construction’.
Members are already working to gather insights and to identify common challenges or obstacles to MMC adoption. For 2023, the MMC Ireland team will continue to work closely with stakeholders from the public sector, the private sector and from academia to ensure those insights feed into relevant policymaking for the successful growth of offsite and MMC in Ireland.
Whether you are involved in the planning, design, procurement or delivery of offsite and MMC in Ireland, or seeking to work with world class experts, MMC Ireland is the central resource and connection point, and you will be able to hear about a wide range of technologies and market developments during the conference. The Confex will also host interactive and dynamic panel discussions focused on: ‘The Use of Volumetric Modular in Providing Housing Solutions for Ukrainian Refugees' and 'Digital Platforms Leading the way in MMC’.
Declan Hughes, Assistant Secretary
General, Innovation and Investment Division - Department of Business, Enterprise and Innovation
Craig Johnson, Business Development
Manager Detailing & Manufacturing Structures Division - Trimble
Pat Kirwan, Director, Head of MMC
Delivery - C+W O'Brien Architects
Dave Lomax, Associate Director –Waugh Thistleton
Ian Lydon, Managing DirectorHines Ireland
Sarah-Jane Pisciotti, Head of DesignSisk Group
Darren Richards, Managing DirectorCogent Consulting
Daniel Shea, Senior Technical Innovation Co-ordinatorBarratt Homes
Declan Wallace, CEOEvolusion Innovation
Eoin Waldron, General ManagerCastle Group
Expectations
and excitement
are high for this event and the supporting Exhibition & Sponsorship opportunities are SOLD OUT, with leading companies all booked to take part, including: A Proctor Group, Benx, C+W O’Brien Architects, CarlowBuild, Castle Group, Creagh Concrete, Framecad, Greenspan, Horizon Offsite, Howick, James Latham, Mac Zero Modular Buildings, Modular Building Automation, O’Dwyer Steel, Petruf Consulting Structural Engineers, Rothoblaas, Saint Gobain Construction Products, Sapphire Balconies, Tenmat and Vision Built.
For more information or to book your place visit: www.offsitehub.co.uk For more information and to enquire about membership of MMC Ireland visit: www.mmcireland.ie
Coming soon and new for 2023 - the MMC Ireland National Conference will take place on 6 June at Croke Park, Dublin and will showcase the Irish offsite sector and the many opportunities ahead for development.

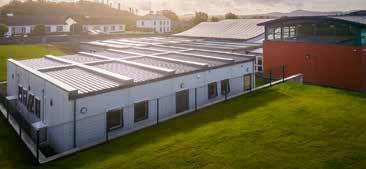
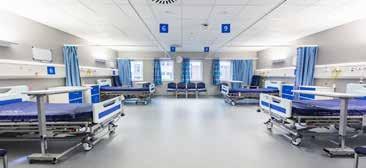

KEEPING UP WITH EVOLVING DEMANDS
Mark Rooney, Rental Divisional Director at Premier Modular, discusses healthcare challenges, and how temporary modular units can help NHS Trusts meet and balance huge demands on services.
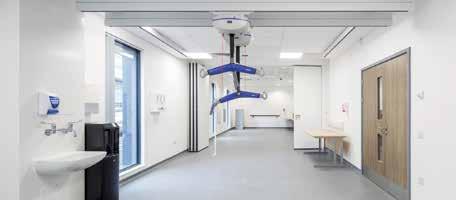
Capacity
The continual cycle of unpredictable spikes in service demand, including outpatient and social care, pushes the need for additional space. Once installed, a modular building can be reconfigured – widened, enlarged and stacked – to adapt to use changes or numbers of patients. To relieve healthcare service pressure and capacity, Trusts can rent modular units for as long or as little as needed –expanding and altering them to meet current demands and facility needs.
NHS healthcare services are continuing to be at the forefront of dealing with the country’s unpredictable evolving needs – facing high spikes of demand due to winter pressures, on top of pandemic backlogs and social care incidents – which strain capacity. Additional spaces – including ambulance units, medical discharge lounges, decant facilities and bed spaces – are required at pace to keep up with these ever-changing demands. As healthcare requirements constantly evolve, many NHS Trusts are uncertain of what they may need, even in the near future.
The healthcare demand cycle
Once winter pressures have been reduced, healthcare trusts need to move on to dealing with the next set of demands. All this limits how well the NHS can provide elective medical needs. As soon as the NHS has recovered from last winter’s bottlenecks, they’re then into summer and focus is on preparation for winter again.
Year after year, the NHS is put through a continuous cycle of various healthcare demands – with some being more urgent than others. This endless swerving from crisis to crisis restricts the NHS’ ability to plan, leading to Trusts struggling with issues – including outpatient capacity – to support
intense seasonal needs. Some spikes in healthcare demands are endless, such as flu cases. However, the NHS can’t reliably forecast how well it will cope with a particular interruption because government input, as well as other factors, vary so frantically over the years.
Efficiency
All healthcare services are interlinked, so it’s essential to relieve each part of the health service to avoid it blocking another stage – for example, care homes being filled up, so hospitals are unable to discharge those patients in need of care. The speed at which relief arrives is just as important as the shape the relief takes, because it allows the NHS to stay one step ahead.
Plans to ease the load on the NHS tend to be last-minute and balanced between competing demands and stakeholders with fixed income targets, so Trusts need their building projects to be installed and delivered quickly.
Offsite modular units can provide space at pace. Built in half the time it would take using traditional bricks and mortar, a modular building operates just as effectively and can accommodate substantial patient numbers within a few weeks rather than months.
Flexibility
To account for the needs and pressures that Trusts are facing, bespoke solutions that offer full adaptability can be essential to solving these demands. If you need a turnkey solution, this can cover: designing, planning, foundations and internal layouts, connecting the modular unit with existing buildings, and ensuring the building is compliant with all NHS standards and healthcare regulations, including clinical sign off.
By collaboratively working with key healthcare stakeholders who are looking to put together specific business cases, processes can be adjusted to deliver bespoke, futureproofed solutions, removing any obstacles that may be present.
By actively working with knowledgeable modular providers to forecast where bottlenecks may occur, a proactive approach can be taken for emergency response – meeting budgets, as well as capacity needs and, most importantly, caring for patients effectively.
For more information visit: www.premiermodular.co.uk
Get creative with space & light
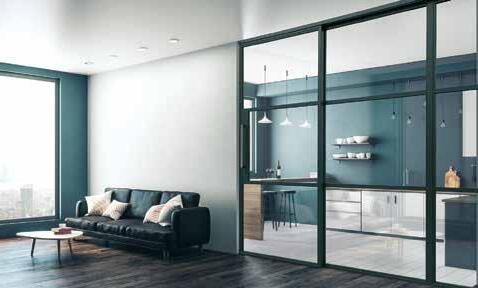
Our AluSpace Interior Screening System is designed to divide or delineate both residential and commercial spaces, while at the same time providing an effective acoustic barrier. Choose from hinged single, double doors, pivot or sliding doors to accompany our stylish fixed glazed screen. This flexible and versatile system provides almost limitless design options whilst requiring minimal maintenance. AluSpace will provide many years of assured, reliable and robust performance.
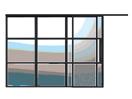

For more information visit smartsystems.co.uk/aluspace
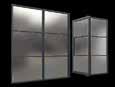
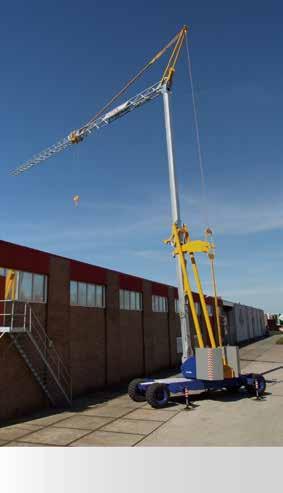

E sales@smartsystems.co.uk
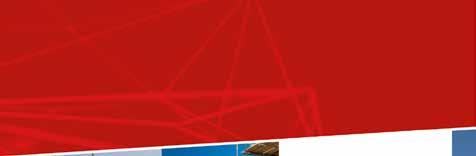

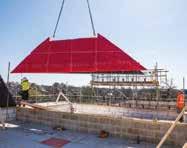
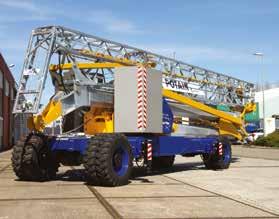
ENSURING TRANSPARENCY AND ACCOUNTABILITY
is now referenced in ADB as the only recognised method of making these extensions or assessments. It requires following a process of ‘test, extend and classify’.
This involves testing to the appropriate EN fire testing standard. Next, test data can be extended to similar applications, but only by qualified and approved third-party bodies using the test standard or EXAP – and critically only where the standards explicitly allow it. Finally, this evidence must be validated and summarised in an official third-party classification report.
the provision of a Golden Thread of performance data.
By producing a Golden Thread of information and ensuring it is available throughout the lifecycle of a building, industry professionals can prove that buildings meet regulations and that testing standards have been met. In fact, this is expected to become embedded in law within the next few years and will not only impact future projects but will also have a major retrospective impact on existing buildings, too.
Many questions have been raised since the tragedy of Grenfell Tower. Who was to blame? Did construction professionals cut corners? Why weren’t more stringent rules and regulations in place? Ever since the tragedy, the government has been trying to overcome ambiguity by tightening up the fire safety guidance. But what can we as a construction industry do to ensure we are building safely and to the most robust safety standards?
While the government is looking at ways to tighten up regulations, as an industry, we need to take ownership and be proactive in ensuring fire safety, if we are serious are about improving the standards of our buildings. One of the most important ways we can do this is by specifying materials that meet the most robust standards and ensuring that we have adequate testing and classification data, before we even consider using them in a project.
For systems used for fire safety, this means following the guidance in ADB and shifting from testing to BS, or even EN, and moving towards extended field of application (EXAP). EXAP is the standard used to extend a fire test’s results to other similar systems and it
EXAP is more onerous and demands the extensive additional testing, extension and classification of a manufacturer’s entire portfolio of systems. This is a laborious and expensive task and, therefore, required a transitionary period following its initial introduction in 2019. But years down the line, projects that require EXAP should not be proceeding without adequate fire safety data. It is all of our responsibility to check whether a project requires EXAP and ensure that the materials specified have been through the appropriate testing.
We must all hold ourselves accountable. This means that while manufacturers should be providing EXAP reports as standard, specifiers, architects and main contractors must engage with manufacturers early on in the project to confirm whether the project requires EXAP, and if so, request third-party reports. By ensuring a project adheres to the correct standards early on, we can ensure that standards are met, which is the simplest way of ensuring we are building safely.
Another way that we can increase transparency and accountability within the construction industry is through
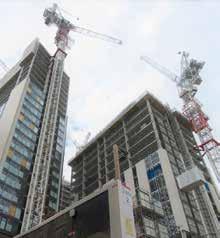
If we do not hold ourselves accountable, someone else will. Regulation 38 states that not only organisations can be held responsible, but individuals can be prosecuted too. In fact, any person responsible for inadequate fire safety can be held liable retrospectively for up to 30 years since a build, and 15 years prospectively. On top of this, under the new legislation, residents and homeowners will now have 15 years to claim compensation for substandard work – a significant increase on the previous threshold of six years.
Ultimately, the inclusion of third-party EXAP reports within a building’s Golden Thread will provide vital evidence that those involved in a project have worked to the most robust standards. This, in turn, helps to mitigate liability issues, increase transparency and, most importantly, prevents further tragedies from ever happening again.
For more information visit: www.siniat.co.uk/en-gb/uk/exap
Images:
01. Responsibility and accountability for building safety has never been so important
Can EXAP and the Golden Thread help the construction industry increase transparency and accountability to secure better building safety? Robert Cridford, Technical Manager for Siniat explains how.
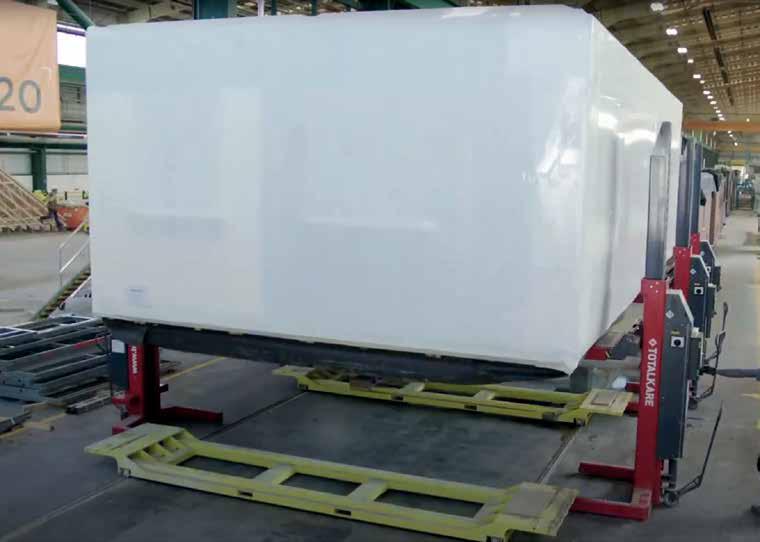

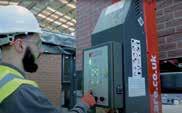
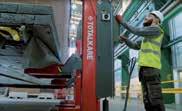


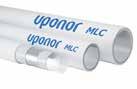
EDUCATION DESIGNING WITH DATA IN MIND
Simon Reid, Managing Director at Lungfish Architects, explains how their data-rich approach to design has led to success in delivering multiple projects across the education sector.
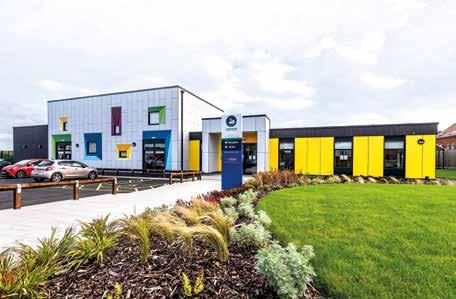

The role of data is a fundamental important topic in the modular construction industry – how we collect it, what we do with it, and how we can use it to improve building performance. But, in an industry laden with facts and figures, are we seeing where the opportunities lie? Are we doing enough to utilise the tools and resources available to improve the way we design and build?
There is a lot of talk surrounding data usage in the modular construction and educational sectors, not just within the industries but also from external sources such as educational governing bodies and community groups. After attending the Modular Matters event in February, where I participated in the Designing for the Future panel debate, it is clear there are many questions about what more we can do to use the huge amounts of information available to us when delivering a project. How can we make the design process quicker, more efficient and offer certainty for clients?
On an individual project basis, the industry is very good at ensuring that there is plenty of data available once a project is complete, for example: we can provide a trouble-shooting guide explaining how the finished building works. But the industry isn’t at a place yet where it can truly show clients how valuable that data is.
In many cases, we can attribute this to the fact that data is often assessed at the end stages of the project. We need to create a culture where we can look for opportunities to gather information from the start of a project. As an industry, we need to be more data-driven early on, capturing details with more surety. By doing this, we can give the client a better understanding of what they want to achieve and what we can deliver for them.
In our experience, projects are more successful when everyone has the chance to get around the table from the outset – early engagement is crucial – and set expectations not only for the client but for all those involved in the planning stages, procurement and property management.
Lungfish Architects recently delivered more than £30million worth of educational facilities in Derby, whereby timesaving was a huge factor for our clients Derby City Council and Derbyshire County Council –particularly as rising energy prices and cost of materials have led to delays across the board. Data needs to prove how these delays can be minimised. We work with our clients to understand the benefits of modular design and the speed with which we can get a project planned, designed, and costed because we have that mine of data available.
From our perspective as designers and architects, we know there are external pressures – for example, housing developers building in the local community creates an increased need for accessible school places. We understand the objectives and what affects this bigger local picture. Having that knowledge and project data at our fingertips from the outset, means we can design accordingly. We can get one of our schools through the planning process in the minimum
turnaround time of 12 weeks, but this level of speed and performance can often only be achieved with modular design.
One of our most successful projects, Ravensdale Infant & Nursery saw the design and delivery of a brand-new school, replacing an outdated building damaged by fire during the pandemic. The existing structure needed complete demolition and replacement. The wealth of data available from the initial stages allowed us to understand not only the restrictions of the budget
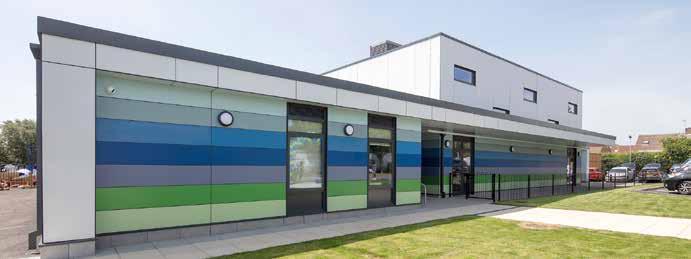
but the requirements for the pupils, staff and local community. Already having a strategically built family of schools available nearby meant students could be accommodated elsewhere in other schools while the work took place.
For us, we have seen how the early use of data can really elevate a project. There’s no denying data is highly valuable to use once a project is complete, but having a data-rich approach from the start allows us to not only see what we have created
once the project is ready to hand over to the client, but to better understand how we got there in the first place.
For more information visit: www.lungfish-architects.co.uk
Images:
01. Simon Reid, Managing Director, Lungfish Architects
02. Highfield Spencer Academy
03. Ravensdale Infant and Nursery School
DIGITAL MARKETING PACKAGES AVAILABLE
The Offsite Hub receives over 5,000 unique visitors per month, complemented by 42,300 newsletter subscribers, making these digital opportunities an attractive proposition for marketers planning future activity.
Prices start from just £150
Suppliers Directory
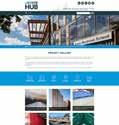

Monthly Newsletters
Video Features
Weekly Blog
Project Gallery Insert
Web Banner

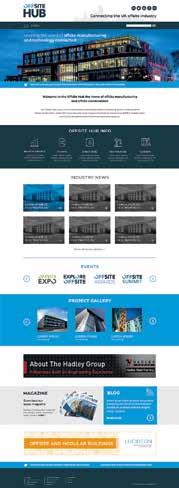
Training & CPD Listing
Podcasts & Webinars
ALIGNING OFFSITE WITH SOCIAL VALUE
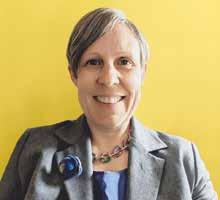
It can be as simple as starting with your own team – looking at your employees, where they come from, and what areas you are employing new people in. Understanding and measuring things like social mobility, educational routes, and diversity provides genuine benefits to organisations increasing its understanding of its own social landscape.
What exactly is social value? We hear a lot about terms such as corporate social responsibility (CSR), environmental, social, and governance (ESG) with business and individual commitments to these areas increasingly important, but how do we define what we mean by these?
“Social impact is talked about in many ways,” says Penny. “But all these things essentially encompass the same ideas. It is about looking at what we create and how it impacts lives and communities socially, economically, and environmentally. How can we ensure that we add value, not just from a profit perspective, but in terms of enriching our people and the planet?
“In the offsite sector, we need a better understanding of how our buildings affect our communities. We are gaining momentum and making headway in collating and recording environmental data and the rules and regulations around capturing data related to energy use, carbon emissions is clear. As for social data? We are still very much at the beginning of that journey.”
The increased focus on social impact is a clear call to action for all construction companies. Gathering social value data does not have to be complex.
“The Construction Playbook details explicit expectations from the government regarding social outcomes of building projects,” adds Penny. “The use of offsite methods aligns with many of the social value requirements that are becoming increasingly important to clients. A solid strategy and approach to measuring social impact is a good way to start delivering on those expectations.
“This is a great opportunity for manufacturers and offsite companies. By understanding this bigger picture, we can create better working environments and attract new talent to the industry. The offsite model allows for a lot of flexibility – we can think about local job creation, looking at areas of economic need and how we can develop and engage with those communities.
“This is an exciting sector to be a part of, and getting the message out about what we’re doing, what the opportunities are, and how much we can offer to our communities is vital. There are a lot of opportunities to capitalise on – looking at alternative routes for entering training to attract fresh talent, improving employee retention, and diversifying our skillsets. Offsite is making strides in creating better working environments more conducive to a healthier work life.”
Clients and developers have become more aware of the demand for added social value to their operations. Being able to offer clear evidence of offsite’s abilities to deliver will put companies in an advantageous position when it comes to winning work. Projects that identify and meet the needs of the housing shortage, homelessness and fuel poverty can really become a truly long tern sustainable solution. But what are the next steps?
“One of the next steps is redefining what we mean by ‘space’ and I think this will be a key topic in the modular industry over the next few years,” says Penny “How do we measure the impact of a safe, secure, and permanent space? We know modular construction offers incredible benefits – faster installation speeds, improved energy efficiency and cost efficiencies. But speaking to people who have moved from temporary to settled accommodation for example, I hear people talk about the importance of ‘space’ as somewhere to find stability. Having your own space can mean being in a better position to find employment, enter training or education, or get your kids settled into school – these are powerful things.”
Being clear about what social value means to an organisation is also a key next step – breaking through the jargon and range of definitions and settling on a strategy which is right for your organisation is crucial. Only when you know what social value means to your organisation can you start to talk with confidence about how you will deliver it and how you will collaborate with others to maximise impact.
For more information visit:
www.akerlof.co.uk
www.supplychainschool.co.uk
‘Social value’ is much more than a buzzword. It is central to offsite manufacture’s wider development as a better way to build on all sorts of different levels. We sat down with Penny Anderson, Head of Social Impact at Akerlof, to find out more.


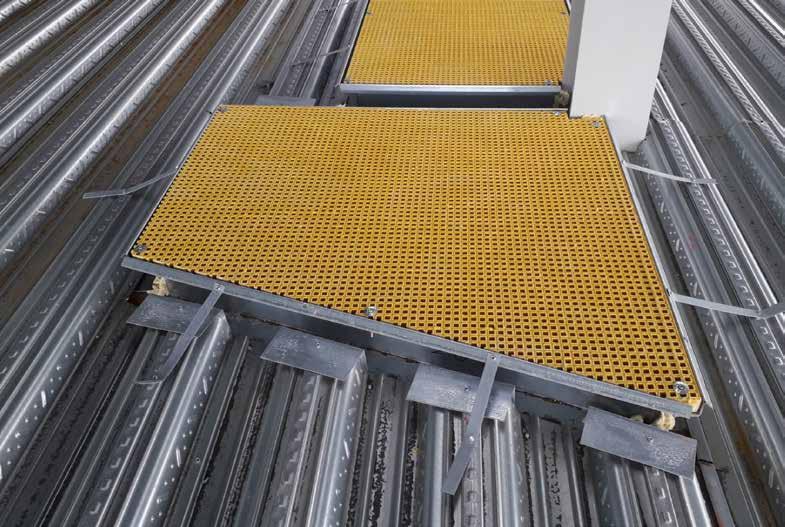
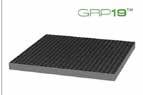
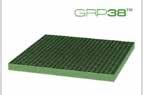
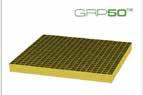
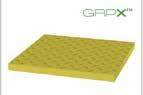
MEANINGFUL CONSTRUCTION CHANGE 1 2
There have been many critiques of the construction industry, which collectively paint a picture of an inefficient and wasteful industry that, at its worst, is harmful to its workforce, its neighbours and the environment. Readers of this magazine will no doubt have their own ideas about the numerous benefits offsite solutions can offer, but might offsite be able to improve the industry’s Environmental, Social and Governance responsibilities (ESG)?
ESG refers to the: “principles of environmental, social, and governance responsibility as they relate to the firm’s society relationships.” So Environmental governance might include policies aimed at protecting the environment from damage caused by firms’ activities. Social governance might refer to the means of improving relations with stakeholders. Corporate governance could be thought of as creating trust among stakeholders, such as employees, consumers, suppliers, and communities near where the construction activities are to take place. In short, companies’ ESG
policies demonstrate the opportunities they’ve created to address the climate crisis and enhance the environment we all live in, whilst at the same time improving working and living conditions.
The drivers for establishing ESG policies are numerous, but perhaps one of the most significant is the availability of finance – a strong ESG profile can help attract investment since two-thirds of investors take ESG into account when making an investment decision.
The SCSS has produced two reports in the last year, both authored by my colleague Naomi Pratt, and both of which are relevant to ESG policies; the first is entitled ‘Delivering Social Value Through Offsite Construction’ and the second ‘Whole Life Carbon Guidance for Offsite Construction’.
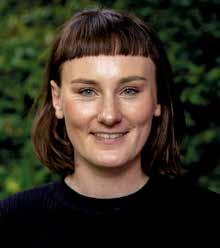
The first report explores the tension between trying to deliver social value locally, whilst simultaneously taking work away from the locale in which the construction site is located to
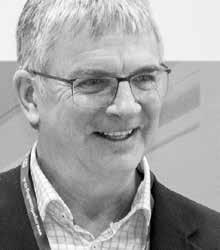
remote factories. This tension arises from client requirements stipulating social value outcomes to be within a set proximity of the site and it cannot be ignored: for example, in the public sector PPN06/20 requires a mandatory 10% weighting on the social value accruing from the award of a contract. Therefore, the challenge for offsite construction, where the pre-manufactured value (PMV) of components and modules is much higher, is that the traditional benefits of local job creation and local spend may be harder to achieve.
Of course, offsite creates significant local value in the areas where factories are located, but these are likely to be remote from the construction site. The report recognises, however, that significant benefits nevertheless still can be achieved locally to the site, for example through improved workplace wellbeing and air quality, and reduced carbon, nuisance and waste.
Also, offsite does not wholly negate the need for traditional trades. For example, during the ‘Enabling Housing Innovation for Inclusive Growth’ programme, SNUG Homes found suitable roles for trainees, residents, local subcontractors and the core team through trialling and refining allocation of construction tasks. Furthermore, depending on the design, jobs requiring less formal training can still be created local to the site, helping to empower community builds or bringing new entrants into the sector.
Meanwhile, the opportunities that arise in factories include benefits such as long-term engagements with education providers, creating opportunities for work experience and apprenticeships, not to mention
What does Environmental, Social and Governance (ESG) responsibilities offer the offsite sector and what more can you do to apply these principles to your business? David Emery, Consultant at the Supply Chain Sustainability School (SCSS) lets us know.
improved work conditions, the potential for shift work (which can attract a more diverse workforce) and improved Health and Safety. All these elements can improve a firm’s talent pipeline and recruitment opportunities, and through enhancing a firm’s reputation and brand, it can support bid winning.
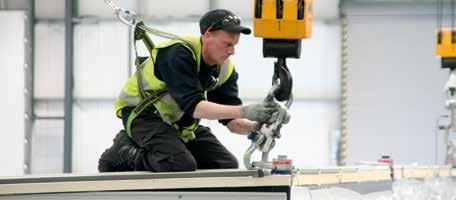
The second report, ‘Whole Life Carbon Guidance for Offsite Construction’ (see box out) acknowledges that the buildings and infrastructure that we build and operate are significant contributors to the climate emergency, with direct control over 25% and influence over 42% of the total carbon footprint of the UK. It identifies significant opportunities by which the offsite sector can help drive decarbonisation in construction projects, both new build and in the retrofitting of existing assets.
Significantly, though, the report highlights some specific features of offsite projects which may result in increases in embodied carbon.
For example, some elements may contain superfluous material mass for their specific use due to a standardised rather than tailored approach – also, in volumetric modular construction there are examples of additional structural elements being incorporated to enable the transporting and lifting of units, neither of which would be necessary in traditional construction solutions. The report recommends that project teams should consider these and work to offset these drawbacks by finding savings elsewhere.
On a more positive note, there are numerous ways in which the whole delivery team can drive out waste and reduce carbon. These include designing out waste, improving processes (made possible once work is moved to factories), decarbonising factories and using innovative low-carbon materials. During the construction stage, offsite can deliver shorter contract periods, which reduces energy consumption on-site, as well as reduced vehicle movements. Also, by considering the maintenance
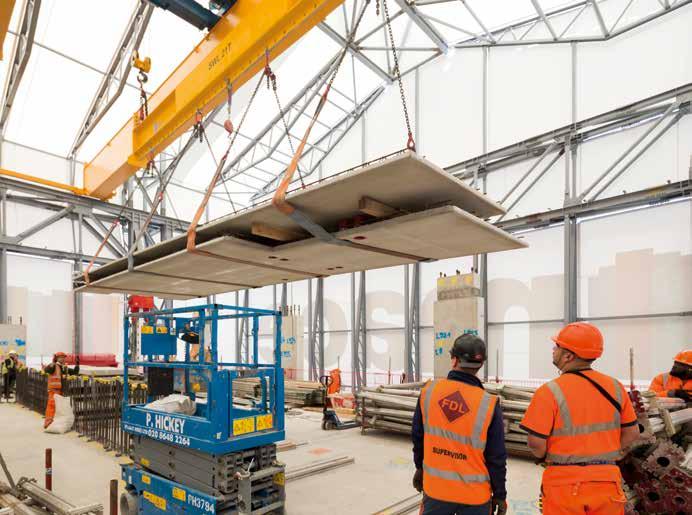
and any re-use opportunities at the outset, we maximise the asset lifespan and the higher quality manufacturing processes – compared to traditional construction – should result in better in-use energy performance.
Images:
01. David Emery, Consultant, Supply Chain Sustainability School
02. Naomi Pratt, lead author of the report ‘Whole Life Carbon Guidance for Offsite Construction’
03-05. The new report highlights opportunities and challenges for carbon management and reduction for the offsite sector
NINE WAYS TO DRIVE DOWN CARBON
A new report, published by the Supply Chain Sustainability School, reveals that nine significant opportunities exist for offsite manufacturers to help their clients in their drive for low carbon construction projects, both newbuild and in the retrofitting of existing buildings.
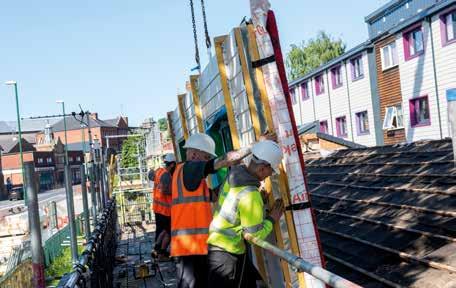
Drawing on the experience of more than 40 organisations working across homes, commercial, public and infrastructure, the new report, ‘Whole Life Carbon Guidance for Offsite Construction’ highlights opportunities and challenges for carbon management and reduction for the offsite sector.
The built environment industry needs to rapidly decarbonise existing and new buildings, as well as reduce embodied carbon produced in production of building materials and elements, construction, and maintenance of assets. The ability of offsite construction processes to reduce whole life carbon is often expressed, but evidence of this has been patchy.
This includes common benefits around the material and resource efficiency of premanufacture, reduced fuel and energy use in logistics and on-site, as well as greater confidence in operational energy performance with standardised designs. Some of the strongest evidence for carbon reductions exist in energy and fuel use for transport and construction processes, with studies finding savings of 30-40%, even when factory energy use is included. However, most of the embodied carbon within construction projects comes from materials and manufacturing: the product stage.
The report proposes that there is a big opportunity for Design for Manufacture and Assembly (DfMA) to drive emissions savings in this stage, sharing evidence for this across homes, schools, and commercial projects. It recommends early collaboration between manufacturers and design teams in order to fully realise low carbon design options. This collaboration will also aid robust whole life carbon estimates, which are likely to become mandatory in the coming years. The report also encourages manufacturers and contractors to embed processes for the collection and communication of activity data.
Andrew Shepherd, Managing Director at TopHat Communities, said: “We all know carbon is a problem, but without knowing how much of a problem, it is very difficult for us to start addressing some of the key problem areas. This report provides guidance on how to start assessing whole life carbon and understanding the impact each stage of the development cycle has on the environment about us.”
Naomi Pratt, lead author of the report and Consultant at Action Sustainability, said: “It’s been really encouraging to see projects cutting embodied carbon through offsite techniques. What these have in common is a design approach driven by material and carbon efficiency. What we need to see now is more organisations adopting this focus and sharing data.”
Ian Heptonstall, Director of Supply Chain Sustainability School, added: “The good news from this report is that yes, offsite and MMC can help us tackle the climate emergency. However, as the evidence suggests, we are currently missing many opportunities and it’s clear as an industry we need to think and act differently. My challenge to those not at the forefront of tackling carbon is: will you act now and make a difference, or be left behind whilst your customers transition to a low carbon economy?”
The examples of best practice highlighted in the report are crucial for whole life carbon reduction and the journey to net zero. The authors encourage organisations working within the sector to show leadership, take advantage of the opportunities, and share data and experiences.
For more information and to download the report visit: www.supplychainschool.co.uk
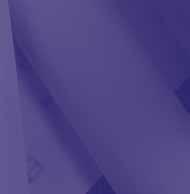


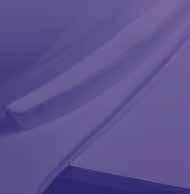
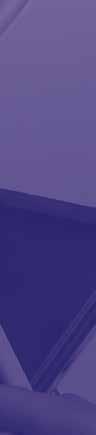
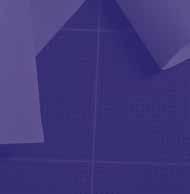
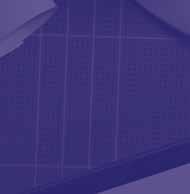



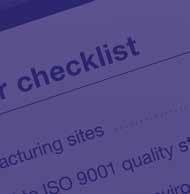
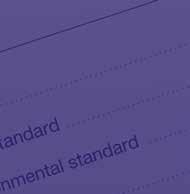
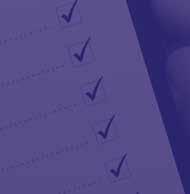
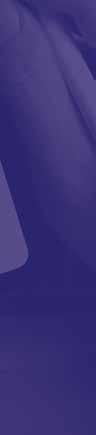
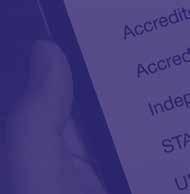
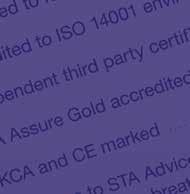
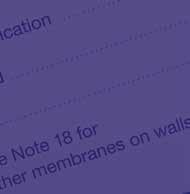
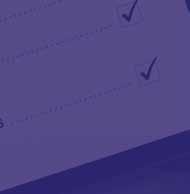
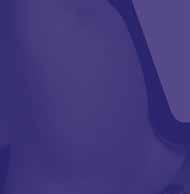
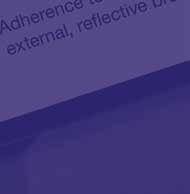


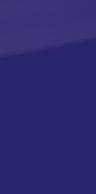
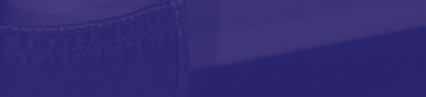
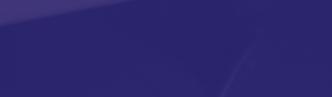
EDUCATION EVERYDAY NET ZERO OPTIONS
support for 3-16 year-old pupils with special educational needs (SEN). Treetops’ building solution comprised of a hybrid, structural timber panel system with a highly insulated envelope. The NZP ‘kit-of-parts’ system included floors, external and internal walls, the primary frame for the Hall and the panelised roof solution to the entire building.
Net Zero Panels has launched as a new division of the Premier Modular Group and is set to minimise construction’s embodied carbon through offsite components and panelised solutions.
Joining the Premier Group alongside Net Zero Buildings (NZB) – which focuses on delivering buildings that are net zero in operation – Net Zero Panels (NZP) enables a holistic approach to sustainability, helping clients to ensure compliance, reduce embodied carbon. NZP will support several sectors –particularly education – as it continues to help clients gain traction towards optimal use of offsite components via a ‘kit-of-parts’.
Panelised construction can be either structural – a whole building comprising of internal and external load-bearing walls, floor cassettes and a number of structural roof options – or a wrap, where external walls and a roof ‘wrap’ around a concrete or steelframed building.
“NZP is designed to strike a balance between compliance and carbon reduction,” explains Dan Allison, Director, NZP. “Compliance is at the heart of the approach, and we ensure extensive acoustic and structural fire testing is built into every system – along with carbon assessments – so we’re best placed to advise on the best materials for your project and their embodied carbon impact. Using a Design for Manufacture and Assembly (DfMA) approach, with NZP, buildings can be configured from a pre-defined kit-of-parts – offering the simplicity of structured panels with all the advantages of flat-packed, volumetric building.”
Designing for purpose
“NZP is an integrator and distributor, which innovated X-Guard panels,” adds David Harris, Managing Director of Premier Modular Group. “X-Guard panels are made of either timber or light-gauge steel structural elements, but we also use other materials in our kit of parts, such as glulam, hot rolled steel, modified gypsum fibreboard and precast concrete. It’s a question of what’s fit for purpose for your individual building, and it can be provided in one package.
“The business has taken off so well that it’s worthy of its own division as an integral part of our group. NZP has all the agility of a start-up with all the financial stability, capacity and ESG credentials you’d expect from a longestablished company.”
The Department for Education (DfE) and other public procurement frameworks help schools prioritise the use modern methods of construction for new buildings, which is increasing their prevalence. NZP is taking advantage of this and has already delivered the kit of parts for DfE’s first carbon pathfinder scheme at Treetops Free School in Grays in Essex.
Treetops Free School – the UK’s first net zero carbon pathfinder
The DfE commissioned the 3,293m2 extension to Treetops School as the government’s first zero carbon pathfinder project, which completed in August 2022. Zero carbon pathfinder projects follow a ten-point plan to achieve net zero carbon in operational energy and dramatically reduce embodied energy in their construction.
NZP delivered the structural solution for Treetops, which provides full-time education and therapeutic behavioural

“This was all made possible by our design, engineering, production, manufacturing and installation capabilities, as well as the transparent ways we collaborate with the school, main contractor and our supply chain,” says Dan Allison. Treetops shows how green the schools of the future will be because of its net zero considerations, and it can be reconfigured as needs change.”
Lawrence Sheriff School in Rugby, Warwickshire – less school more panels
A long-established school – Lawrence Sheriff in Rugby, Warwickshire –needed a new facility to expand teaching capacity. It required new science classrooms and a studio, as well as a modern dining room. Completed in December 2021, the 346m2 extension needed to complement and integrate seamlessly with the heritage building and adhere to best practice in net zero construction.
In this project, the main contractor built a primary hot-rolled steel frame, and NZP wrapped the structure with its highly insulated timber panel system. NZP provided a structural, closed-panel system with a factoryfitted drylined service zone and clad with cedar and airtight brick facades on-site. This provided high thermal and air permeability performance to maximise energy efficiency throughout the project and improve the building’s environmental impact.
For more information visit: www.netzerobuildings.co.uk
Images:
01. Cedar-clad and airtight brick façade for the 346m2 extension at Lawrence Sheriff School, Rugby, Warwickshire
02. Treetops School was the DfE’s first zero carbon pathfinder project
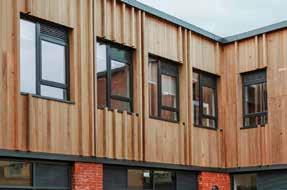
Innovative products. Dedicated service. Concrete results.
Thermomass Connectors from Leviat are one of the most tested sandwich panel connector systems in the world suitable for use in factorymanufactured precast concrete and site-cast projects.


The range comprises innovative fibre-composite connectors which, when installed with rigid thermal insulation, create a thermally-broken building envelope.


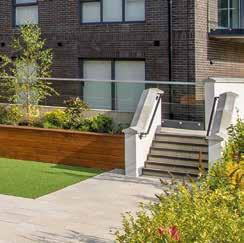

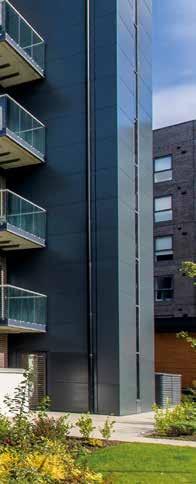
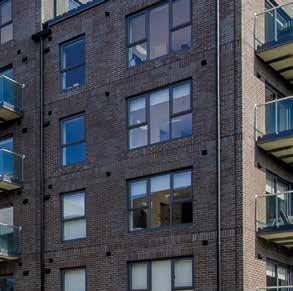
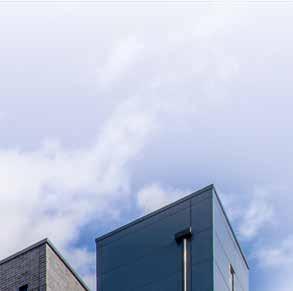

Leviat’s trusted range includes Ancon, Halfen, Isedio and Thermomass products which are synonymous with high performance, quality and reliability.

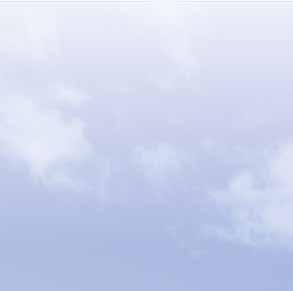
Leviat Tel: 01582 470300
thermomass.uk@leviat.com
Leviat.com/thermomass-uk

THE LARSEN KIT OF PARTS
Building regulations, environmental impact and rising fuel prices are driving demand for a genuine fabric first approach to low energy buildings. In response, Timber Innovations has launched a new innovative, systemised proposition – The Larsen 'Kit of Parts'.
This technical manual will assist anybody engaged in the design or procurement of low energy buildings and is available as an e-book. Timber Innovations, part of the market leading WB Group of companies with over 100 years of timber engineering experience, originally developed their low energy ‘Larsen System’ for relatively niche clients building Passivhaus certified houses but over the last couple of years the market for such has rapidly evolved.
David Himmons, Managing Director of Timber Innovations comments: “Clients have a greater understanding and need for buildings to perform. The spectrum of market sectors now demanding and understanding efficient building envelopes is such that it really is the new norm.”
A flagship project for the Larsen System is the new innovative Museum of Land Speed, opening to the public in May on Pendine Seafront. Together with the Caban, an affordable 14-room hotel which was also built using the Larsen System, they are part of the brand-new Tourism Attractor facility at Pendine Seafront, Carmarthenshire. The Museum of Land Speed tells the story of Pendine and the speed records set on the seven miles of fine, white sand.
The Larsen system has a unique twin stud design to virtually eliminate cold bridging through the envelope and is flexible to achieve almost any
NEW FIRE-RATED BREATHER MEMBRANES
Partel, a leading manufacturer of airtight and windtight membranes, has developed two new fire-rated breather membranes that exceed current fire-safety regulation levels for high-rise and high-risk buildings: EXOPERM DURO A1 and EXOPERM MONO DURO A2. The high-performance membranes are designed to achieve the highest levels of fire-performance while also protecting the building structure by allowing vapour to diffuse from within the structure towards the exterior, preventing ‘thermal bypass’ of external air through the insulation, and performing the secondary task of weather protection.
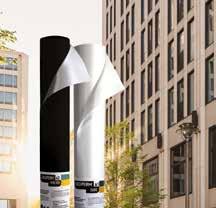
Suited to offsite and on-site construction, residential or commercial projects,
EXOPERM DURO A1 and EXOPERM MONO DURO A2 are fully independently certified and tested in accordance with EN13501-1. The membranes are compliant with Document B Fire Safety and are suitable for use in a range of external wall types, especially in high-rise buildings or those that pose a greater risk of fire safety.
EXOPERM DURO A1 is noncombustible and suitable for use on closed joint facades. Alongside fire performance, EXOPERM DURO A1’s technical attributes ensure long-term protection of the assembly, with a highly vapour open Sd value of 0.03 m, along with resistance to water penetration and dimensional stability.
EXOPERM MONO DURO A2 is an innovative airtight yet vapour permeable façade membrane, based on Monolithic Technology. This is

required U-value with a wide choice of insulation materials. “What we’ve done is harness all of our experience from many years of low energy and Passiv projects to develop a systemised approach for our clients so they can eliminate common pitfalls and build with confidence,” says Gareth Lloyd, Technical Director.
Many commercial applications demand an A1 non-combustible insulation and fire test data to prove compliance. “Last year we successfully tested and achieved a 100-minute result which further demonstrates the capabilities of the Larsen system,” adds David Coleman, Business Development Director.
The Larsen Kit of Parts can be found at: https://online.fliphtml5.com/ywlrr/ maws/#p=1
Class A2-s1,d0, guaranteeing limitedcombustibility, absent or very limited smoke emissions, and no burning droplets. It is suitable for use on open or closed joint facades and balances airtightness, moisture management and secondary weather protection with fire performance.
For more information visit: www.partel.co.uk
Images:
01. The new membranes are designed to achieve the highest levels of fire-performance
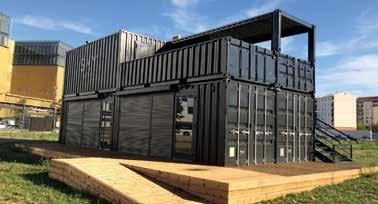
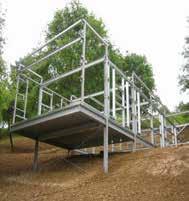
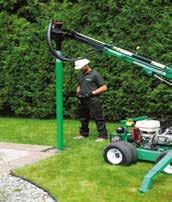
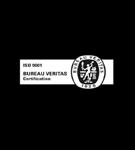


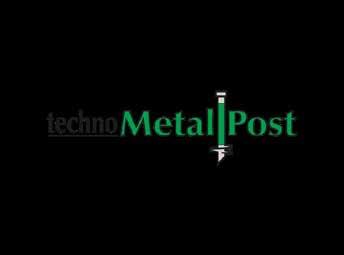

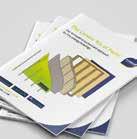
A ‘PERFECT STORM’?
• The United Nations/ IPCC (Intergovernmental Panel for Climate Change) has highlighted that we need to address sustainability immediately otherwise the earth’s temperature will rise above the 1.5 degrees with dire consequences for the planet
• Inflation is at its highest level for over 40 years
• Materials shortages, triggered by the COVID-19 pandemic, has left us with major availability and delivery issues
• The ‘skills gap’ has left us without the knowledge, capability and workforce to build
• Digital is in everyone’s everyday lives, but the construction industry is still slow to adopt it.
quality benefits. This approach is being driven forward by initiatives such as the UK Government financed Construction Innovation Hub, which is working with industry partners, such as BAM Design who are lead designer, to create a Platform DfMA enabler project, for use by all UK Government departments.
Bill Gates reportedly said that a lot of his success was down to being at the ‘right place at the right time’. Like Bill, others were in the same place, but the difference was that he acted while others waited. Today the use of Microsoft software is ‘business as usual’ for billions of people around the globe, but what has this got to do with modular and offsite construction?
Offsite is not new, examples can be found throughout history. From the Greeks and Romans with their ‘classical’ style to the Georgian kit of parts and pattern book. More recently we have had architectural exemplars such as the Habitat 67 flats in Montreal and the Nakagin Capsule Tower in Tokyo (1972). Apart from the Residential Sector, our industry has been slow to adopt offsite and a manufacturing process for delivering buildings, but changes are on the way. This change can be summarised as a ‘Perfect Storm’ or like Bill Gates being in ‘the right place at the right time’:
Offsite gives us the opportunity to address and harness that ‘perfect storm’. New net zero targets and whole life procurement requirements are also forcing us to think differently. As Mark Farmer said in his 2016 report, we are now in a situation where we need to ‘Modernise or Die’.
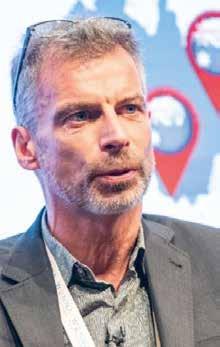
Our clients are also pushing us towards change. In the public sector many new frameworks tenders are requesting offsite solutions and the Government’s Construction Playbook asks for ‘Faster, Greener, Better’. At the same time, private clients are looking for ‘industry partners’ to help them. They want also to want faster and more efficient delivery, coupled with solutions that allow them to address climate change and develop their businesses and brand.
The ‘Platform Approach’, which creates a focused digital ‘operating system’, could be one solution. It combines whole life data, standardised designs and components, within a digital kit of parts, allowing us to measure and improve our product over time to achieve even greater cost, time and
Working across the construction industry and with four universities, the Hub has developed a digital prototype modular building that contains elements that can be used in many sectors including a residential studio, educational classroom or a hospital waiting room. Showcased at the Modular Matters event earlier this year, it provides guidance and processes for the industry, to give organisations the confidence to take their first step into modular. The platform also addresses the biggest challenge related to modular – creating enough volume of similar modules/parts for manufacturers to make a profit.
Construction has a long way to go but is learning fast and gaining knowledge from other industries. After several stop/start attempts, it looks like modular methods and offsite are finally gaining traction and on the way to becoming the ‘new norm’. The industry is in the ‘right place” and like Bill Gates, it is now taking action to realise the opportunity at the ‘right time’.
For more information visit: www.bam.co.uk
Images:
Andrew Pryke, Managing Director at BAM Design, gives us a quick reminder about why offsite methods are so relevant and why the industry is perfectly positioned to succeed.
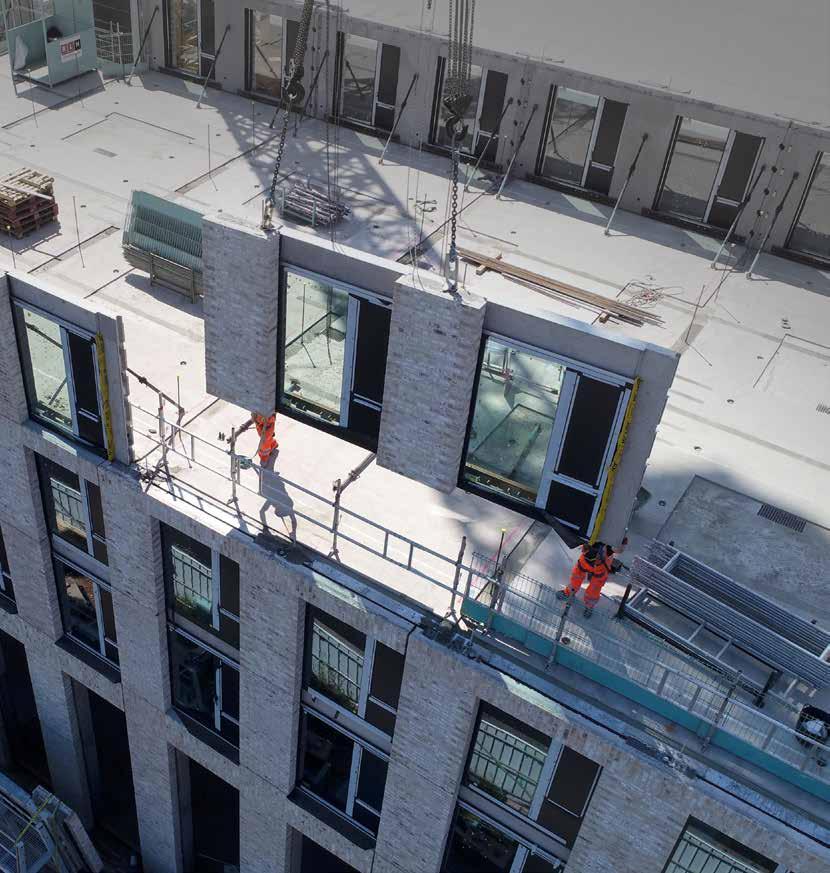
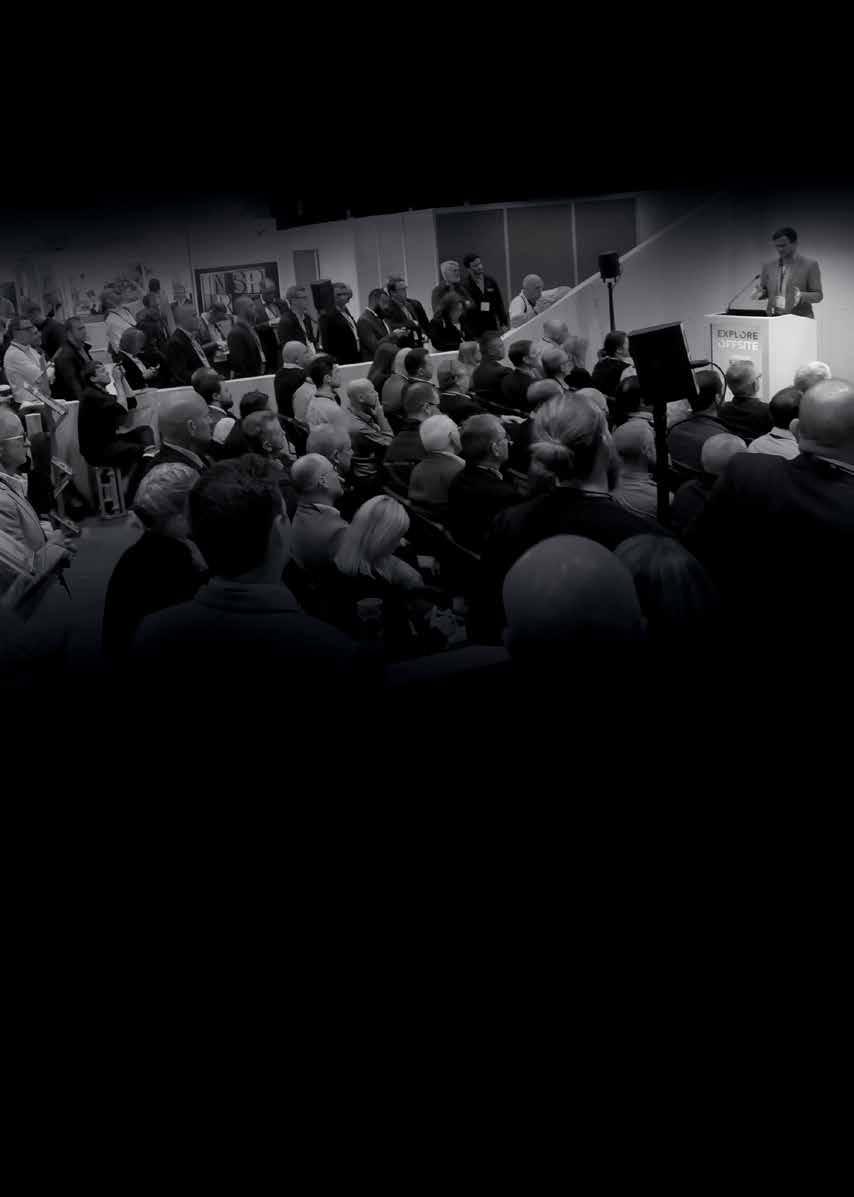
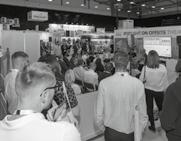
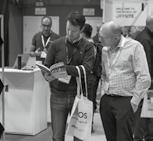

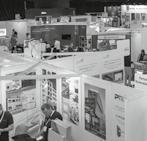


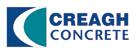


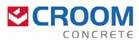

MASS APPEAL
Precast concrete is well understood for its structural strengths, solid reliable mass and its ability to suit a variety of applications and sectors – this is perhaps a central reason for its success. Precast concrete is not limited to a particular sector such as student accommodation or hotels but stands ready to provide stable solutions across the whole construction and infrastructure world.
Of course, sustainability and low carbon design is of paramount importance in any construction programme and the concrete industry is working hard to reduce its embodied carbon levels and has embarked on a detailed decarbonisation programme led by companies such as Forterra and PCE – some of which you will see over the next few pages.
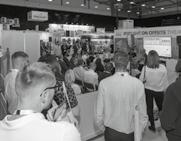
As Elaine Toogood, Director, Architecture & Sustainable Design at MPA The Concrete Centre said recently: “The construction industry is developing a much greater understanding of carbon impacts across the entire lifecycle of buildings and materials, from embodied carbon at construction, to operational energy efficiency, to what happens at endof-life. Offsite concrete benefits
particularly from low factory wastage thanks to reusable forms and volumes of batched concrete matched to need. In addition, its robustness and resilience mean less packaging is needed with large panels simply lifted straight off the delivery vehicle, ready for assembly on-site.”
What can Precast Concrete Offer?
Acoustically Versatile
As precast can be moulded to any shape, size and texture it can be used to deflect or absorb noise. This makes it a good acoustic host for music but also an effective sound barrier alongside busy roads. Privacy and effective sound reduction are ensured, which makes precast an ideal choice for residential buildings.
Architectural
Precast concrete has the potential to be made in any shape. Moulds can be designed to be customised, replicate patterns, shapes or other materials. There are also many different aggregates and additions that can be incorporated into precast which gives designers considerable scope to produce subtle or contrasting colourways.
Durable
The factory-controlled production process means that cover to rebar is consistent and correct, as are strength and concrete quality. Hence the inherent durability of the delivered product is assured.
Fireproof
Precast protects against the spread of fire between rooms or buildings and it cannot catch fire, burn or drip molten particles. In test, concrete performs consistently well in fire, often requiring only minor repairs.
Strong
Precast concrete goes on increasing its strength for hundreds of years after it is cast. What's more, during that time it won't shrink, warp, move or creep excessively so can be relied upon to perform consistently year after year.
Sustainable
All the materials that go into precast concrete products come from natural and recycled sources. This means they are subject to minimal processing or chemical treatments to render them suitable for use, which results in concrete having a relatively low embodied energy value.
Thermally Efficient
The versatility of precast can be seen in its application as a carrying medium for heating or cooling. As concrete can be dense or lightweight, precast concrete can act as a thermal sink or as an insulator and in some buildings, you can see precast doing both.
Weather-proof
Precast concrete is resistant to rain penetration and wind-blown debris. It can also withstand many winters of freeze-thaw cycles.
The next few pages feature a range of case studies including: FP McCann, PCE, Carlow Concrete and Everton FC’s new stadium, plus a pioneering development in Finland that sees concrete and timber combining in a hybrid approach.
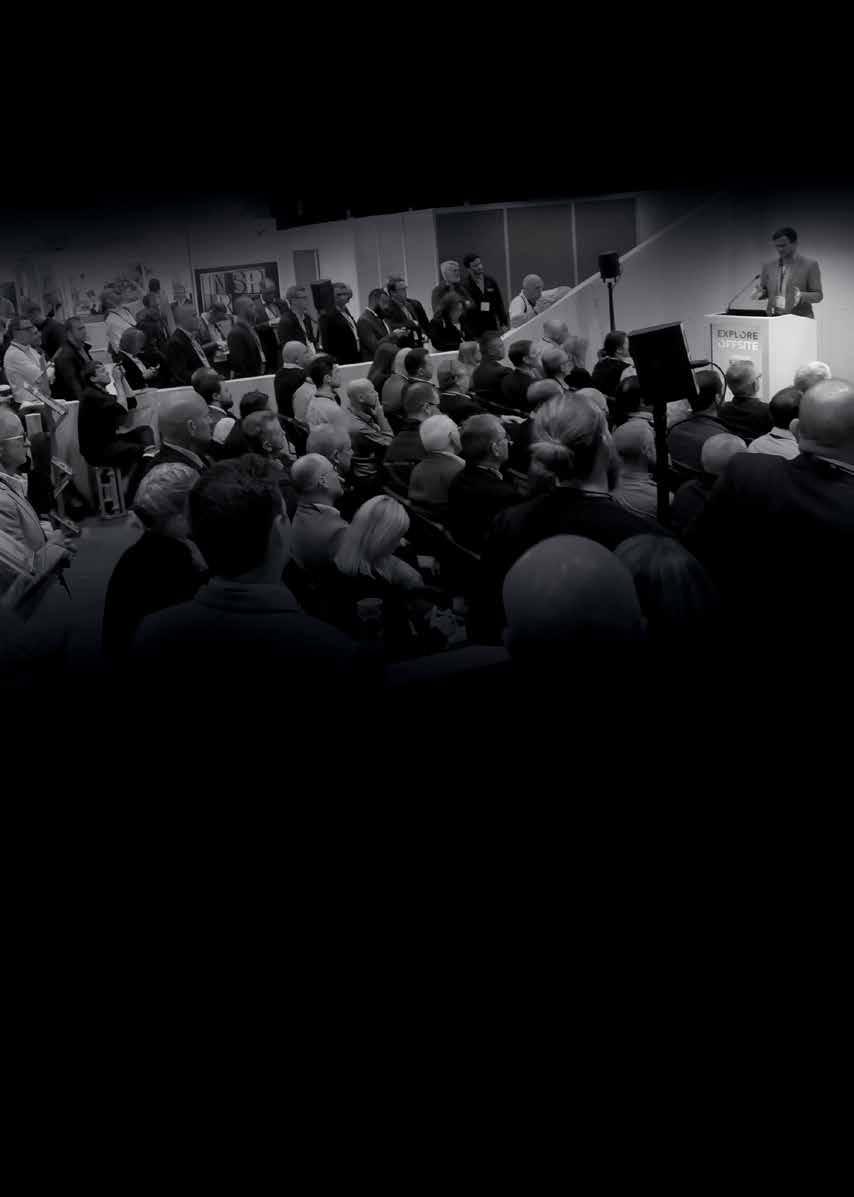
For more information visit: www.mpaprecast.org
Images:
01. Precast concrete panels are craned into position to make construction quicker and safer. Courtesy Creagh Concrete
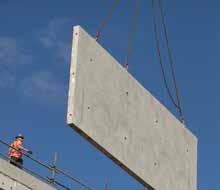
Familiar to all in the construction world and a mainstay of the offsite sector, precast concrete is at the centre of many landmark projects. This special section of the magazine highlights some of the awardwinning schemes where precast concrete has been used.
PRECAST CONCRETE
PRECAST TRANSFORMATIONS
Precast concrete specialists FP McCann have delivered many projects successfully including two landmark education schemes for York and Leicester Universities.
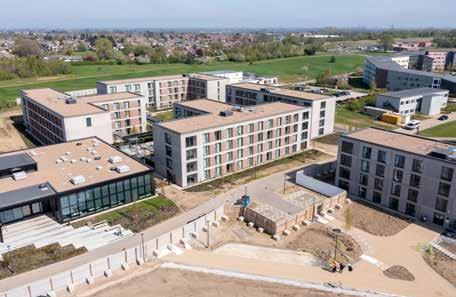
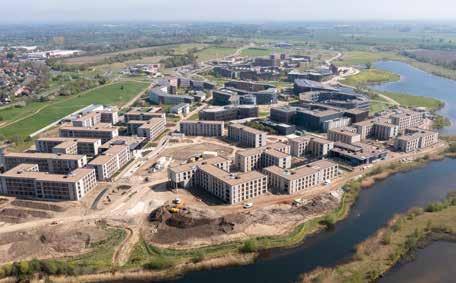
The strong, simple forms of the precast concrete modular blocks, characterised by striking architectural finishes, have been designed to be a modern interpretation of the character of the university’s original 1960s campus.
1 2
FP McCann's Precast Off-Site Building Products Division has worked in close partnership with national construction group Graham on the construction of a 1,480 bed student accommodation project – part of York University’s ‘Campus for the Future' masterplan. The £130million flagship scheme to help transform the Heslington
East Campus commenced in 2019 and completed ahead of the 2022 academic year. Architect on the project Sheppard Robson, designed the residential development in a natural waterside setting which has been broken down into 18 blocks that step down from four to three storeys in height as they get closer to the waterfront.
Working closely alongside Sheppard Robson and main contractor Graham, FP McCann were able to satisfy the requirement for the design and build project to fully embrace Modern Methods of Construction (MMC). The key elements of MMC include prefabricated insulated sandwich panels with integrated external brick faced, acid-etched and stencilled finishes, factory fitted windows, first fix services and factory finished internal walls and ceilings.
Sub-contractor to FP McCann, Ulster based precast concrete installation specialist McVey Stone, has constructed the 18-block precast modular buildings in just 58 weeks. The offsite manufactured precast concrete crosswall/insulated sandwich panel system was specified on the build to enhance quality, safety and sustainability. Construction times were reduced by up to 60% and significant other benefits associated with MMC such as reduced wastage and allweather working were achieved.
FP McCann has manufactured and delivered a total of 7,177 individual precast concrete units for the internal structural frames and the cladding envelopes, including walls, floor slabs and external architectural sandwich panels. Additionally, and included in the supply contract, are precast stairs and landings, precast concrete columns and architectural cladding to support steels on all overhang areas.
The internal crosswall sections are 160mm, 180mm and 200mm thick and
the external sandwich facade panels are 465mm thick. The inner leaf of the sandwich panel is typically a 150mm thick structural concrete skin designed to carry its own dead loading and that of the external skin. Insulation between the concrete faces is 200mm thick and the outer concrete/brick façade 115mm. The facade skin of the sandwich panels is a combination of half brick and projecting full solid bricks, acid-etched smooth concrete finish and an acid-etched architectural stencilled design, created using the Reckli rubber formliner system. The precast units were manufactured at FP McCann’s Byley, Littleport and Grantham manufacturing facilities and delivered on a just-in-time basis.
Commenting on the build Special Projects Director for Graham, Neil McFarlane says: “We adopted the FP McCann offsite modular precast concrete building system for our construction programme, as we recognise it is a well tried and tested methodology that brings enhanced quality and delivery confidence to such ambitious residential development schemes. The consortium of companies has delivered innovative, energy efficient and sustainable living to support student and University growth at York.”
Leicester University
FP McCann also worked in collaboration with regeneration and facilities management company Equans on the £200million contract to build student accommodation at the Freeman’s Common Student Village, part of Leicester University. The flagship scheme includes seven residential blocks, a 550-space multistorey car park and the creation of a new 9,000sq m teaching and learning centre.
Architect on the project Sheppard Robson designed the residential development that was completed in 2022. The regeneration of the site which includes refurbishment of the historic Grade 2 listed Freeman’s Cottages creates a new gateway link through to the city centre.
Working closely alongside Sheppard Robson and managing build partner/ client Equans, FP McCann’s engineers and supply/install teams were able to satisfy the requirement for the design and build of two of the
seven residential blocks whilst fully embracing MMC. The key elements of MMC on the project include prefabricated insulated sandwich panels with integrated external brick faced and acid-etched finishes, factoryfitted windows, first fix services and factory finished internal walls and ceilings.
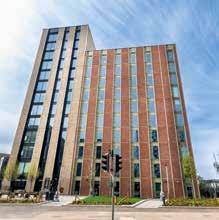
The offsite manufactured precast concrete crosswall/insulated sandwich panel system was specified on the build to enhance quality, safety and sustainability. Construction times were reduced by up to 60% and significant other benefits associated with MMC such as reduced wastage and allweather working were achieved.
FP McCann has manufactured, delivered and installed around 6,000 individual precast concrete units for the internal structural frames and the cladding envelopes, including walls, floor slabs and external architectural sandwich panels. Additionally, and included in the supply contract, were precast stairs and landings.
The internal crosswall sections are 160mm & 200mm thick and the external sandwich facade panels are 535mm thick (including a 100mm architectural fin detail). The inner leaf of the sandwich panel is typically a 150mm thick structural concrete skin designed to carry its own dead loading and that of the external skin. Insulation between the concrete faces is 150mm thick and the outer concrete/brick façade 135mm. The facade skin of the sandwich panels is a combination of half brick and acid-etched smooth concrete finish. The precast units
were manufactured at FP McCann’s Grantham manufacturing facility and delivered on a just-in-time basis.
Commenting on the build, Jake Fellows, Development Director (Places and Communities) for Equans said: “We adopted the FP McCann offsite modular precast concrete building system for our construction programme, as we recognise it is a well tried and tested methodology that brings enhanced quality and delivery confidence to such ambitious residential development schemes. The consortium of companies and designers has delivered innovative, energy efficient and sustainable living to support student and University growth at Leicester.”
For more information visit: www.fpmccann.co.uk
Images: 01-02. York University, Heslington East Campus 03-04. Leicester University, Freeman’s Common Student Village
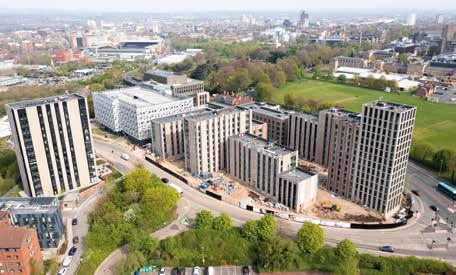
PRECAST CONCRETE RE-ENERGISING PRISON ESTATES
Precast concrete has a huge role to play in the construction of new prisons and revitalising the UK’s custodial estate. One project at HMP Millsike, York will also see the development of the UK’s first ‘all-electric’ prison.
The new prison – opening in 2025 – will hold nearly 1,500 prisoners with the site set to be the first prison in the UK to run solely on electricity, with solar panels and heat pump technology meaning it will use 78% less energy than HMP Wormwood Scrubs – a traditional Victorian prison – cutting energy costs to taxpayers by over £1.1million a year. HMP Millsike –situated on land opposite the existing HMP Full Sutton – has been named after Millsike Beck, a local river that runs adjacent to the new jail. The building project is also set to boost jobs in East Yorkshire, with a quarter of those working on the build and 40% of the construction spend falling within 50 miles.
PCE Ltd has been appointed by Kier as its superstructure and façade delivery partner, with the Ministry of Justice project having an overall contract value of £400million. This once again sees PCE’s award winning HybriDfMA Secure Prison System being used following the successful completion of HMP Five Wells, at Wellingborough and HMP Fosse Way, Glen Parva.
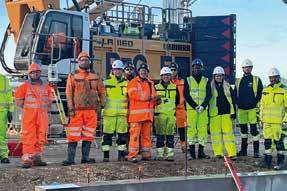
The plan is for HMP Millsike to operate as zero-carbon in the future, with an all-electric design, solar panels, heat pumps and more efficient lighting systems to reduce energy demand significantly. The new buildings will sit adjacent to the existing HMP Full Sutton and is part of the Government’s plan to create thousands of new prison places.
Through applying the findings of the government-sponsored Decarbonisation of Precast Concrete study, PCE have established and implemented carbon-reduction solutions on HMP Millsike – currently in construction – achieving a 12% reduction in embodied carbon when compared with HMP Fosse Way, constructed in 2021.
Working with multiple manufacturers across the supply chain, PCE collaboratively reviewed, innovated and tested mix designs, ensuring the revised mix design would continue to deliver structural integrity and other required performance properties, whilst simultaneously achieving a reduction in carbon content. The 12% reduction achieved translates to a saving of over 1,200 tonnes of CO2 with an actual average of 443kg e/m³ against the HMP Fosse Way project of 501kg CO2/m³. In other words, the new prison at Full Sutton has seen a reduction of over 753kg CO2 per prison place.
When scaled up across the Government’s entire new prison programme, these savings alone would result in a saving of over 15,000 tonnes of CO2. By transferring this knowledge across the other PCE systems and other sectors, the impact can truly and fundamentally help revolutionise the construction industry.
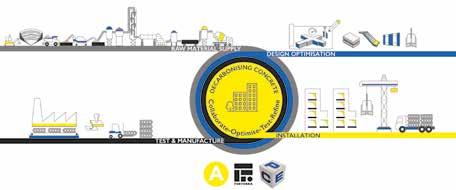
The research project based on PCE’s solutions for both the HMP Five Wells and HMP Foss Way prisons, developed an optimised structural design and concrete mix technical specification improving material efficiency and delivering a net reduction of up to 40% in the structural precast concrete’s embodied carbon emissions, when benchmarked against the ICE’s database.
“Through leveraging Hybrid DfMA and an offsite ‘kit of parts’ philosophy, we do not just embrace modern methods of construction, but revolutionise it,” said Simon Harold, Business Development Director at PCE. “This coupled with our shared commitment for continuous improvement with our partners, will help facilitate continued practical progress in a more environmentally friendly, structurally robust and commercially sound approach to design and build.”
Liam Cummins, Group Managing Director of Kier Construction, said: “We will deliver this new prison as a cutting-edge facility, built on engineering excellence that we have utilised on other projects, and using innovative sustainable methods which will achieve net zero in operation. Alongside this, we’ll create hundreds of jobs throughout the lifecycle of the project, supporting local people and the supply chain, as well as providing opportunities for prisoners on release.” The new site will set a gold-standard for energy efficiency – set to use 68% less energy from the national grid than even the newly-built HMP Five Wells in Wellingborough and draw 18 GWh less energy from the electricity and gas networks every year than HMP Belmarsh – which is equivalent to powering 1,200 homes for a year.
For more information visit: www.pceltd.co.uk
www.kier.co.uk
Images:
01. PCE team on-site at HMP Millsike. Courtesy PCE Ltd
02. Decarbonisation is hugely important to the concrete sector. Courtesy Akerlof
MANCHESTER AESTHETICS
Manchester Goods Yard is the fulcrum for Enterprise City, a new digital media technology hub in Manchester city centre that has used precast concrete to provide stunning new work and leisure facilities.
Architects Chapman Taylor paid attention to detail and reflected Manchester’s industrial vernacular as key factors in ensuring this scheme's context. They were able to define the design, assembly, logistics and quality at a very early stage which also included the installation of the windows in the factory, in factory conditions to create a complete modular assembly ready for hanging on the building.
The ultra-modern, flexible workspaces will be supplemented by a mix of café bars, restaurants and leisure facilities, with the aim of creating a vibrant neighbourhood in which to live, work, shop and relax. Manchester Goods Yard (MGY) is a significant new office scheme at the heart of the St. John’s regeneration development, a new city centre neighbourhood underpinned by enterprise, culture and living.
Techrete precast panels were used that are 100% recyclable at the end-oflife stage fulfilling the futureproofing and circular economy approach. Techrete also promotes the use of partial cement replacement in their mixture to minimise embodied carbon impact. The collaborative offsite approach between the façade suppliers meant that the overall embodied carbon implication from transport was significantly reduced. Each panel provides a deep concrete reveal – vital in emphasising the industrial aesthetic. The 400mm thick precast concrete panels with 200mm mineral wool insulation behind them
provides a betterment against current Part L U-values. Offsite manufacture enabled cost certainty, as materials are quantifiable, and less wastage occurred due to the production process.
A mix of construction techniques were used for the building superstructure. The two satellite cores were constructed with twin-wall precast concrete panels and the main core was cast in-situ. This hybrid approach allowed areas of the building to be accelerated to improve commercial viability, and to improve programme by allowing different disciplines to safely work on elements at different phases and stages of the building.
The façade subcontractors, Lindner Prater and Techrete worked collaboratively to facilitate the installation of the curtain wall systems into the precast concrete panels at the Techrete’s factory before being transported to the construction site. This benefitted offsite manufacturing processes – e.g. waste mitigation and controlled quality, and importantly lessened the number of lifts that were required by combining two separate components.
The level of automation, factory consistency and quality provided by the offsite manufacturing process of
the precast panels ensured consistency in the appearance, performance, and finish. The precast panels have increased lifecycle capability with minimal maintenance required due to their durability. No applied finishes were added to the exposed concrete, reducing maintenance requirements whilst evoking an industrial feel in a contemporary environment. The precast concrete donut panels have been designed to interlock into one another for both ease of assembly and future disassembly.
MGY is rated BREEAM Excellent and used offsite manufacture and assembly to maximise opportunities to reduce waste, improve quality and minimise its carbon footprint. This innovative approach to designing new office space has provided c.31,000m² of shell and core commercial space across 10 floors, two levels of basement parking and cycle facilities.
For more information visit: www.chapmantaylor.com www.techcrete.com
Images: 01-03. Precast concrete has given a contemporary feel to Manchester’s latest multi-purpose commercial project
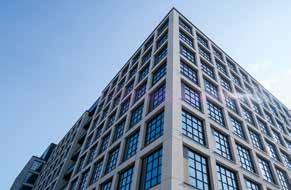
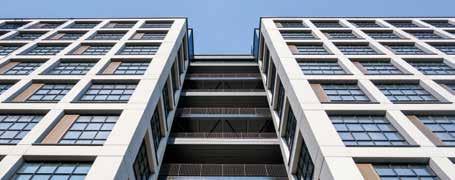
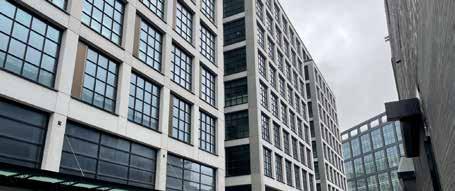
TRIED & TRUSTED PRECAST SOLUTIONS
Carlow Concrete are the market leader in water retaining precast concrete structures in both the United Kingdom & Ireland – what do they provide?
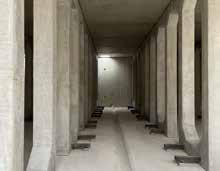
• Modular precast attenuation/ detention tank which satisfies clients mandatory Sustainable Urban Drainage (SUDS) requirements
• Most cost effective storm water attenuation solution on the market
• Watertight to BS8007 or Eurocode 2
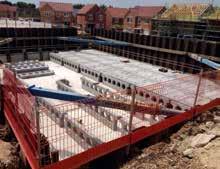
• Fully section 104 adoptable
• CESWI & Sewers for adoption compliant
• 100 Year + Design Life
The flagship product of Carlow Concrete is the Carlow Tank. Recognised by both water companies and councils, our stormwater attenuation system satisfies mandatory SUDs requirements and is fully S104 adoption compliant.
In terms of stormwater attenuation, the Carlow Tank offers clients the most efficiently and economically designed solution in its class. This attenuation powerhouse promises the most robust solution on the market and may be located in highly trafficked areas such as roads and carparks.
Design, innovation, accreditations and approvals
Carlow Concrete prides itself on continuous design innovation and improvement. At design stage each project undergoes rigorous structural design using cutting edge analysis software and the option of 3D building information modelling (BIM) modelling at both approval and construction stages. The extensive design service is implemented by a highly qualified design department which consists of civil, structural, environmental and process design engineers. Our design department also maintain our innovation centre in terms of research and development which are very important to the group. Carlow Concrete are the only precast supplier to design out flotation issues and fully comply with BS8007 and Eurocode II.
Production and experience
As part of the Burren Precast Concrete Group, Carlow Concrete has the resources and infrastructure to meet the high demands of their customers in relation to quality of service and product. The organisation benefits from a team with combined expertise of over 100 years in the precast industry. Carlow Concrete has technical expertise, flexibility in production methods and the resources to interpret, design, manufacture and assemble to the highest standards in meeting the requirements of every project, bringing modern methods of construction (MMC) through the benefits of offsite construction, BIM and highly experienced installation teams.
Why Carlow Concrete stormwater attenuation tanks?
At Carlow Concrete a key ingredient of quality production are our technicians and in-house concrete testing lab. To back this up in delivering the best possible stormwater attenuation solution an ID tag provides each element of an installation with its own unique reference number so it is fully traceable from production to final location. Here are some of the features and benefits of the Carlow Tank.
• Available in depths from 0.8M to 7.0M in 100mm increments
• Configured to exactly suit client requirements including irregular shapes
• No need expensive imported fill or waterproofing, simply backfill as dug material
• Rapid installation times from highly trained, experienced crews
• Reduction in labour and plant requirements during install
• Deep burial and heavy duty loading applications
• Superior quality finish and zero maintenance
• Multifunctional applications
• Trusted by top companies across the construction industry.
Design, manufacture, deliver and install – your turnkey solution
Carlow offer a range of flexible models to our clients, the most popular being that of a Procurement Framework Agreement. Many clients have taken full advantage of this approach when ordering the same service over an extended period of time on multiple projects and across several regions. This supply framework is an ideal platform where the client has a real focus with us to develop a strategic long term relationship which ultimately offers a sustainable, best value supply chain for precast concrete attenuation/ flood alleviation products.
For more information visit: www.carlowconcrete.com
Images: 01-02. Precast concrete offers a premium solution to the design and delivery of stormwater attenuation systems
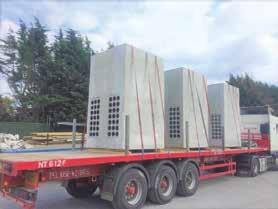
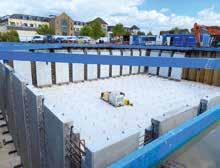
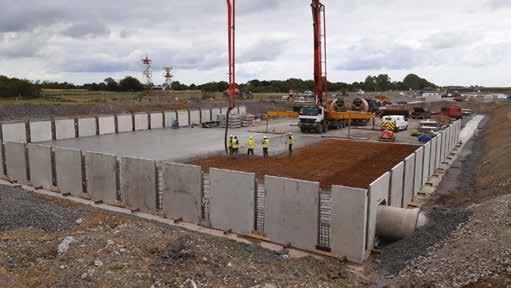

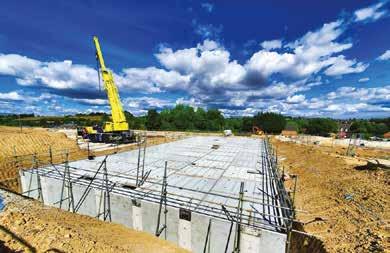
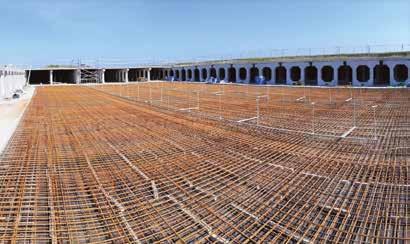

PRECAST CONCRETE
DECARBONISATION FOR BETTER BUSINESS
THE CIRCULAR CEMENT VALUE CHAIN
A circular economy of concrete and cement could produce €110billion in net value and avoid or mitigate two billion tons of CO2 emissions by 2050, according to a new McKinsey & Company report. As the new report spells out, cement and concrete are the ‘linchpins of the built environment’ with its global demand having nearly tripled over the past 20 years. With circular economy principles driving much sustainable thinking, what decarbonisation principles are at stake?
The ‘Circular cement value chain: Sustainable and profitable report’ projects that adoption of circular technologies could also decarbonise 80% of all cement and concrete emissions by 2050. This will be driven by capture, storage and usage of CO2 from cement and concrete production, re-use of energy from waste material and recirculation of materials and minerals across the built environment.
Adoption of circular economy principles is estimated to offset more than half of the losses to the cement industry from rising costs and reduced demand. And adoption of circular technologies could be further accelerated by rising CO2 prices, landfill costs and decarbonization subsidies. The report reveals that recycling and re-using construction materials and minerals alone will add nearly €80billion of annual EBITDA while reusing concrete modules and structures will drive an estimated €24billion of net value by 2050. Regions with high landfill costs and construction and demolition waste will also reap major benefits from the use of alternative fuels from waste material with the global average share of alternative fuels reaching 43% by 2050.
Sebastian Reiter, Partner at McKinsey's Global Energy & Materials adds: “Cement and other industry players should engage in circular business building and use circular technologies to react to evolving financial risks. The total value at risk from rising CO2 prices and landfill costs could reach approximately €210billion by 2050 and this will significantly accelerate uptake of circular technologies. For example, our research shows that technologies utilising CO2 such as curing ready-mix or precast concrete can create positive economic value at carbon prices of approximately €80% of CO2 while using construction waste as aggregates for concrete production avoids landfill costs.”
Central to all future behaviour is increasing customer centricity will likely create new opportunities across the built environment. New business models for all players in the built environment—not only cement and concrete manufacturers—are expected to evolve from actions that facilitate circularity along the value chain as well as actions that deliver the value of circularity to consumers.
For more information visit: www.mckinsey.com
Ibstock and Earth Friendly Concrete form partnership to support ESG ambitions
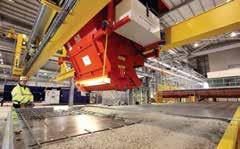
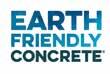
Ibstock, a UK leading manufacturer of clay and concrete building products, and Earth Friendly Concrete (EFC) have entered into a new partnership to create ultra-low carbon concrete products.
This exciting partnership supports Ibstock’s ambitious ESG targets. Having recently launched its ESG Strategy to 2030, Ibstock is committed to ‘Manufacture Materials for Life’ and improving the environmental performance of its products. Its milestone 2030 target is to achieve 20% of sales turnover revenue from new and sustainable products.
With the built environment accounting for 25% of the UK’s carbon emissions, Ibstock is proactively seeking to develop new solutions with improved environmental performance. EFC is more sustainable than traditional concrete, with around 70% less embodied CO2 saving 250kg of CO2 per cubic metre poured. It is made from a binder consisting of industrial waste products, ground granulated blast furnace slag and pulverised fly ash with no Portland Cement.
The partnership will see EFC’s ultra-low carbon, zero
In some quarters, concrete comes in for much criticism for its lack of sustainability credentials compared to competing materials, but there are many innovative moves being made by industry with low carbon and circularity in mind.
PRECAST CONCRETE
cement technology integrated into Ibstock’s diverse portfolio of highperformance building products for the construction industry, including its range of products for the rail, infrastructure and UK housing markets. The technology has performance advantages over Ordinary Portland Cement-based products including improved durability, lower shrinkage, higher flexural tensile strength and increased fire resistance and is the only zero-cement concrete technology that has been proven at scale on real life commercial projects across the world.
Darren Waters, Chief Operating Officer at Ibstock, said: “As a business at the heart of building, our ambition is to be the most sustainable manufacturer of concrete products in the UK. Collaborating with EFC marks a significant step in achieving this goal as we collaborate and innovate to manufacture materials for life. More than ever, customers are looking for products which offer great functionality but also have robust sustainability credentials. In 2020, the Ibstock concrete division invested in a new concrete laboratory at its site in Anstone, Sheffield, to facilitate the development of sustainable concrete that features reduced embodied carbon and therefore has a lower environmental impact. At this advanced facility, we are already developing and testing innovative new concrete mixes that incorporate EFC to ensure we achieve our own sustainability goals, as well as contribute to those of the wider sector, without compromising on quality or performance.”
EFC UK Regional Manager Andy Izod said: “We are delighted to strengthen our presence in the UK through this partnership with Ibstock. We will not only focus on introducing Earth Friendly Concrete into the wider construction market across a range of projects, regions, applications and supply chains but will also share our ground-breaking technology with partners like Ibstock, which will help them to achieve ultra-low carbon outcomes for their business.” Since it was launched in 2020, EFC has saved around 2,000 tonnes of CO2 across construction projects. It has been used in several high-profile projects including High Speed 2 (HS2) and Silvertown Tunnel.
For more information visit: www.ibstockplc.co.uk www.earthfriendlyconcrete.com
LOW CARBON CONCRETE NOW STANDARD ON LAING O’ROURKE UK PROJECTS
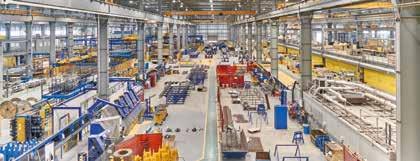
Laing O’Rourke has announced it is mandating the switch to low carbon concrete on all of its new UK projects. The exclusive use of low carbon concrete from 1 April this year will accelerate the company’s progress towards its net zero targets. The change will be introduced with immediate effect and applies to all new projects that begin main construction on or after 1 April 2023. It will result in a significant reduction in the company’s scope 3 carbon emissions.
Following a long-term research programme co-funded by Laing O’Rourke and Innovate UK, and in collaboration with the University of Cambridge and Sheffield University’s Advanced Manufacturing Research Centre (AMRC), the business has proven that a range of low carbon concrete options can be successfully deployed on projects as a like-for-like substitute for traditional concrete. The overall carbon reduction will be 28% when compared with the company’s concrete usage in 2022. This equates to a saving of 14.4 million kgCO2e, which is the same as planting 120,000 trees or 94 hectares of forest.
Cathal O’Rourke, Laing O’Rourke’s newly appointed Chief Operating Officer, said: “We’ve committed to being a net zero company before 2050 and we are looking at every possible measure to accelerate our progress. In construction, the greatest challenge is reducing scope 3 emissions – the embodied carbon in purchased materials. Reducing all carbon emissions is a priority for our business. The built environment makes a significant contribution to global warming and constructors must work with clients and design partners to deploy new technologies and innovations that make modern methods the norm and enable us to build in less carbon intensive ways.”
Rossella Nicolin, Laing O’Rourke’s Head of Sustainability for Europe, said that the expertise of the specialist businesses that make up the company’s internal supply chain had helped introduce the policy so rapidly across all new projects. “The expertise of our in-house concrete technologists, the experts who operate our advanced manufacturing facility in Nottinghamshire (the Laing O’Rourke Centre of Excellence for Modern Construction, CEMC), and our supply chain partners, have all contributed to this significant step forward. Last year, 43% of the concrete products we manufactured for our live projects were low carbon. It’s exciting to think this will rise to 100% this year, and that very soon all our new projects will only use low carbon concrete. I want to thank the team whose hard work has made it possible.”
Laing O’Rourke’s low carbon concrete uses lower carbon alternatives to Portland cement. These include GGBS (Ground Granulated Blast-furnace Slag) and PFA (Pulverised Fly Ash), both of which are industrial by-products with a much lower carbon footprint. The company recognises that this is the first step in a longer journey to decarbonisation. Its ongoing research programme focuses on wider scale deployment of cement-free options, which are ultra-low carbon, and it expects to introduce more of these materials going forward. The company became a founding member of ConcreteZero in 2022 and is already decarbonising beyond the programme’s near-term objectives.
For more information visit: www.laingorourke.com
PRECAST CONCRETE MASTERING WHISKEY STORE CONSTRUCTION
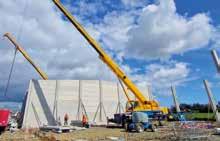
Constructing a whiskey store is a delicate affair. As O'Reilly Precast appreciate, the significance of selecting the right materials is essential and precast concrete has proven to be a superior option, offering a wealth of benefits for whiskey store projects.
Precast concrete has consistently demonstrated its value in constructing whiskey stores that withstand the test of time. Discover the key advantages of using precast concrete in whiskey store construction:
Temperature and Humidity Control: precast concrete ensures excellent insulation, maintaining consistent conditions crucial for top-notch whiskey maturation.
Fire Resistance: with flammable materials in whiskey stores, precast concrete’s fire-resistant properties offer added safety and reassurance.
Durability and Strength: precast concrete guarantees a long-lasting structure, capable of bearing the weight of whiskey barrels.
Pest and Rodent Resistance: unlike other materials prone to infestations, precast concrete safeguards hygiene and quality.
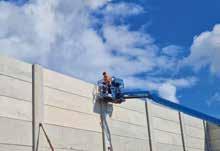
Design Flexibility: customised to meet specific requirements, precast concrete is the ideal choice for bespoke whiskey maturation facilities.
Speed of Construction: offsite manufacturing allows for efficient construction, reducing costs and minimising disruptions to ongoing operations.
Ready to enhance your whiskey store construction with the precast concrete advantage? Contact our team of experts at O'Reilly Precast to discuss your project needs. Phone: 0121 630 3472, email: sales@oreillyprecast.co.uk, or visit: www.oreillyprecast.co.uk
IMPACT Precast Software
• Increase productivity by up to 20% by optimising your production planning.
• Track your precast elements through all stages of the process (from anywhere and on any device).
• Save your money with your transport and handling.
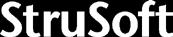
• Easy to use 3D planning software linking with your Tekla®, Revit & CAD models.


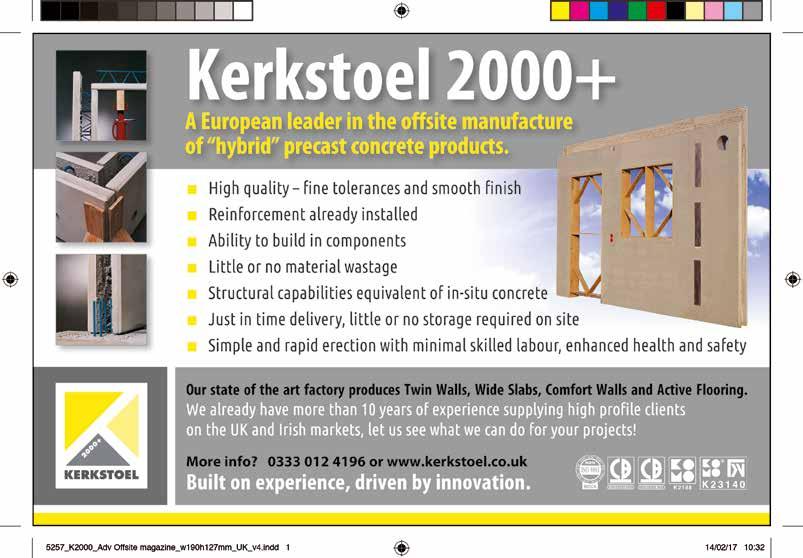
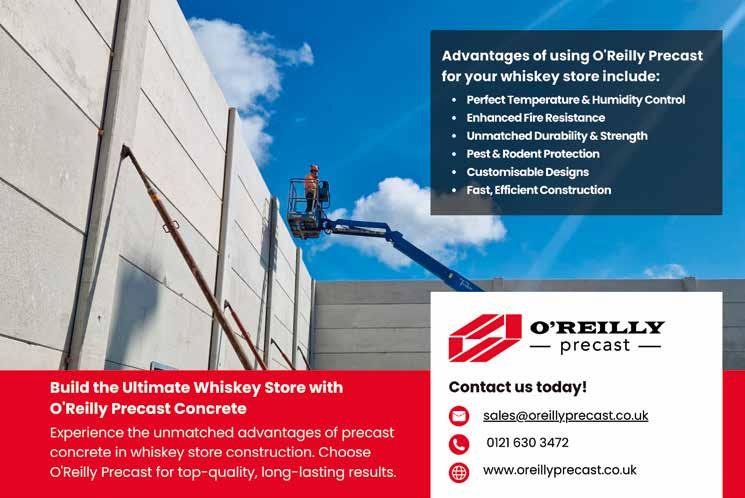
PRECAST CONCRETE

A WINNING COMBINATION
Finland's leading precast concrete element manufacturer Consolis Parma, housebuilder Arkta Rakennus and Metsä Wood – one of Europe’s leading manufacturers of engineered wood products – have launched a research project on hybrid construction that promotes low-carbon construction. The aim is to develop a completely new kind of construction concept mainly for the needs of residential multi-storey construction, which will reduce the environmental impacts of construction by utilising hybrid structures.
The sustainable development of the construction industry focuses on energy and material efficiency, as well as low-carbon construction and the circular economy. “Radically cutting the climate impact is a common concern for the entire construction industry,” says Juha Rämö, Technology
Director at Consolis Parma. “In line with our strategy, we have put climate issues at the centre of our development work, and our goal is to reduce our emissions by 5% annually and halve them by 2035.
“In terms of the climate impacts of the built environment, the transition from fossil fuels to renewable energy means that the influence of the actual construction phase in the building's lifecycle emissions will increase. As a result, structural solutions and the material choices in construction will play an increasingly crucial role in reducing the climate impact of the construction phase in the future.
“We have launched a whole product family of low-emission concrete products that can significantly reduce material-based emissions from construction. In this research project,
we are looking for new ways to reduce even more material emissions by utilising new hybrid structures and the best properties of different materials.”
The aim of the partnership between Parma, Arkta and Metsä is to create a material-efficient and low-emission hybrid construction concept. In this context, hybrid construction refers to combining the best features of timber and concrete both in a building frame and façade solutions to make the building low-carbon, energy-saving, long-lasting and cost-effective.
"Hybrid construction enables increasing the share of renewable material in multi-storey construction without compromising building process efficiency or the performance of solution,” says Jussi Björman,
Director, Business Development Constructionat Metsä Wood. “Metsä Wood's lightweight, material-
Although competing materials on many levels, concrete and timber can combine to provide sustainable hybrid building solutions that will be evidenced by some pioneering developments in Finland.
efficient and carbon-storing Kerto® LVL engineered wood product is well suited for hybrid construction applications. In co-operation with our partners, we have the best prerequisites for finding the most effective overall solutions.”
The structural solutions being developed as part of the research project will be tested in an apartment building project in Finland.
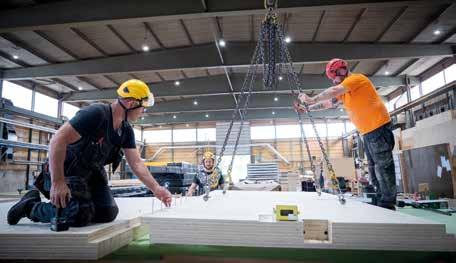
“We are an expert in both concrete and wood construction and we know very well how these two different building materials behave. By utilising this know-how, our goal is to together develop solutions that combine the best properties of wood and concrete with the new hybrid construction system," says Marko Nikander, Technical Director at Arkta Rakennus. “We act as an expert of the construction site and installation process. We want to ensure the development of functional hybrid solutions using the best expertise of the project parties. The end goal of the research project is to produce costeffective and easily replicable lowcarbon hybrid element structures that create a brand new way of building both in Finland and around the world.”
For more information visit: www.metsagroup.com
Images:
01-02. Concrete and timber will combine to provide a long-term hybrid panel product.
03. Kerto LVL are part of the hybrid sandwich timber elements
04. Thanks to their special design and structure, DURAForm formwork panels allow for considerably leaner and resource-saving formwork structures and easy handling on-site
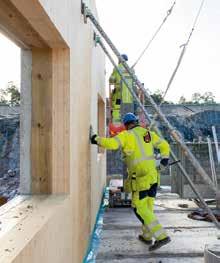

MORE CONCRETE & TIMBER SOLUTIONS
Formwork systems give precast concrete its ‘form’ allowing for quick project delivery. As an aid Metsä Wood has expanded its range of formwork panels with DURAForm. The DURAForm formwork panel line features high stability and reduced deformation, despite its reduced weight. The long-lasting maintenancefree birch plywood panels are very easy to work with and provide an especially smooth concrete finish thanks to their special surface.
Produced from high-strength birch plywood, the material offers minimal deflection, even with wide spans. Despite its low weight, DURAForm demonstrates especially high strength. Thanks to the special design and structure, the panels allow for considerably leaner and resource-saving formwork structures and easy handling on-site.
Concrete formwork is heavily stressed during use at construction sites. In this context, the hard scratch-resistant composite surface of the Metsä Wood DURAForm elements makes cleaning and later reuse of the panels easy. The improved crack resistance and reduced chipping, even when fastening using nails, contribute to a consistently high surface quality. Since they can be reused up to 200 times, the DURAForm panels have proven to be particularly resource-friendly beyond their lifecycle in line with the principles of a sustainable circular economy.
LOOK OUT FOR NEW MINERAL TRENDS
The Mineral Products Association (MPA) has published a new regional construction and mineral products markets report, giving a detailed assessment of historic, current and future trends across every region of Great Britain.
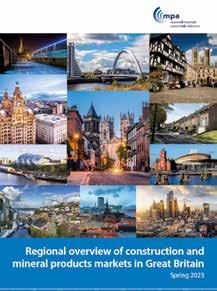
Primarily prepared to help inform and support the local mineral planning system, the annual report compiles a range of industry data and broader context to paint a clear picture of the main drivers of activity in heavy-side construction materials and industrial minerals – it’s an essential tool for producers and planners alike.
The report includes summaries for all regions and devolved administrations in Great Britain, illustrating the recent performance of construction and mineral products markets, with critical insight on the sectors that are expected to drive growth in mineral products demand over the next five years (2023-27).
While London is often regarded as the key hub of new construction projects and infrastructure, representing 21% of the total value of construction output in 2022, the report highlights that the East of England and Yorkshire and the Humber are both expected to see the fastest rate of growth (2.2%) over the next five years, led by energy-related projects.
Data on mineral products sales volumes is collected through a rigorous survey process among MPA producer members, who make up the vast majority of the total mineral products markets, including 90% of total GB market sales for primary aggregates and asphalt, for example, and 75% for ready-mixed concrete. The report reveals that construction demand for mineral products in 2022 recorded a gradual loss in momentum as the year progressed on the back of a worsening macroeconomic environment and slowing activity in key segments of construction. Tonnages of primary aggregates sales fell by 8.2% on an annual basis compared to 2021, asphalt by 6.5%, and ready-mixed concrete by 3.8%.
The East Midlands was the biggest market for asphalt and crushed rock in 2022, accounting for 15% and 29% respectively of total sales in Great Britain. It is also the region that emerged as the most resilient to the downturn last year, recording the smallest falls in demand. Meanwhile, London was the biggest centre of demand for ready-mixed concrete, accounting for 19% of total sales volumes from fixed plants. Demand in London last year remained broadly flat, in contrast to the 5.5% decline recorded at national level.
Luke George, Economist at MPA and author of the report, said: “This new report provides a valuable insight to the contrasting dynamics in construction and mineral products markets across the various regional and devolved administrations of Great Britain. Our aim is to provide a unique, easy-to-use point of reference to support MPA members, planning professionals and other industry experts in their decision-making processes. This report cuts through the overwhelming quantity of industry data that’s available and revised almost daily.
“Minerals, and the wide range of construction products that are derived from them, are key elements to the successful delivery of many of Government’s ambitious policy objectives, such as on housing and infrastructure, including achieving the energy transition and delivering net zero. The success of the UK economy to deliver on these objectives will depend on local mineral planning authorities and mineral producers having robust evidence around future market needs, given delivery is heavily reliant on the availability and supply of essential mineral products.”
The report ‘Regional overview and forecasts of construction and mineral products markets in Great BritainSpring 2023’ can be downloaded at: www.mineralproducts.org
Images:
01. The new report outlines what can be expected across the concrete, masonry and mineral sectors
02. Precast concrete is a staple product of countless drainage and infrastructure projects

With over twenty five years of experience in the construction industry, Euro Accessories Ltd are the UK's largest Independent supplier of Lifting & Fixing Systems for the Precast Concrete Industry. In addition to free technical support, we offer a comprehensive technical manuals on our Lifting and Fixing Sockets, Pin Anchor System and Spread Anchor System.
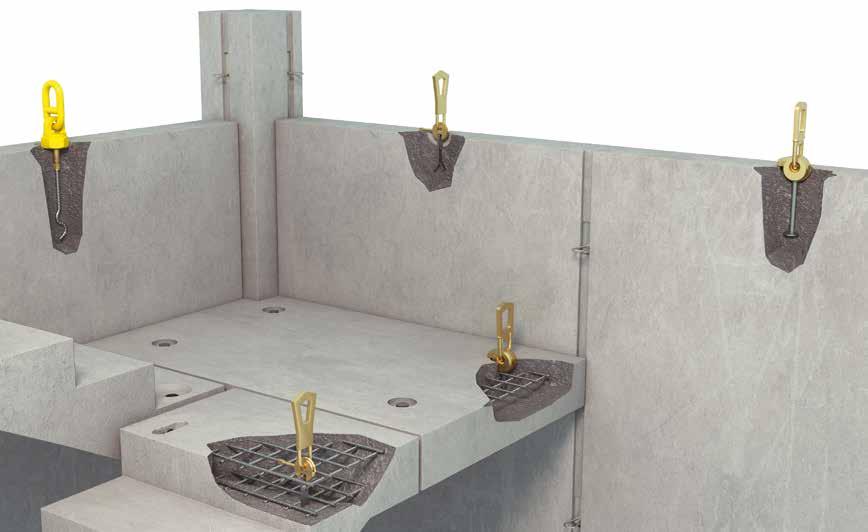
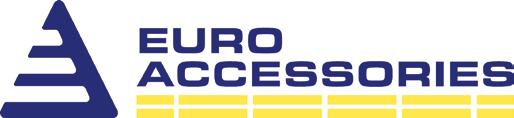
All our Lifting and Fixing components are fully certified in accordance to the Machine Directive 2006/42/EC.
We also operate a quality assurance program in accordance with ISO9001.
North Units 1-3
Shannon Industrial Estate Lodge Road
Sandbach
Cheshire CW11 3HP
t. +44 (0) 1270 90 20 20
e. sales@euroacc.co.uk
South Unit 3
Stewart Road
Kingsland Business Centre
Basingstoke
Hampshire RG24 8NF
t. +44 (0) 118 981
t. +44 (0) 28 3755 1397
e. armagh@euroacc.co.uk
STADIUM DESIGN
PRECAST: THE HEART OF MODERN STADIUM DESIGN
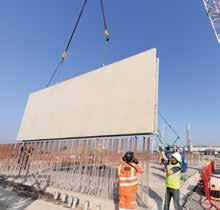
Almost every football and rugby ground, athletics stadium and indoor arena features some form of precast component, as does much of the associated infrastructure. “Of particular concern in stadium design is the effect of resonant frequency, when a structure moves due to the dynamics of crowd movement,” explains Elaine Toogood, Director, Architecture & Sustainable Design with The Concrete Centre. “The use of concrete is widely understood to limit this.”
This was why precast sections were a safe choice for the terraces on iconic venues like the London Olympic Stadium. In all, 9,250m³ of reinforced precast concrete was used within the Olympic Stadium bowl and more than 12,000 precast elements were required for the seating steps alone. Besides terrace units, other precast components typically used on stadia include raking beams, staircases and step blocks, vomitory walls, hollowcore slabs, flooring and cladding panels. Modern Methods of Construction (MMC) in the precast concrete sector are now enabling the next generation of stadia.
Everton Stadium Takes Shape

Currently rising up from the banks of the river Mersey, Everton Football Club’s new 52,888-seater stadium
has already won numerous accolades with its eye-catching design, brilliantly blending the modern with the traditional. Nothing exemplifies this better than the precast concrete structure and terraces, a solution used in stadium design for decades but now deployed with all the benefits of MMC.
The stadium is scheduled for completion in 2024, but the primary concrete structure in all four stands is now complete. Precast concrete elements were produced offsite ready to slot together to form the floors, walls and supporting pillars of the stands. Each component was created in a specialist factory and brought to site using the modern digitally enabled process known as Design for Manufacturing and Assembly (DfMA). It is precast concrete which will also put bums on seats with 1,217 terracing units, forming the internal bowl lining. The bespoke, double-stepped terracing units manufactured by Banagher Precast Concrete in Ireland and delivered by boat to Liverpool docks, were lifted and bolted into place by the construction team from Laing O’Rourke.
Laing O’Rourke have stated that upon completion Everton Stadium will have a real ‘wow’ factor having already created a virtual model of the
stadium. Using Building Information Modelling (BIM), the digital version of the stadium has been mapped out in intricate detail. The model includes everything from the precast concrete walls, through to precise positioning of wiring, plumbing, light switches and plug sockets.
This digital approach allows for efficiency gains, risk reduction and leads to programme and cost benefits. It also provides a digital reference throughout the lifecycle of the build allowing for easier design of extensions or repairs. Concrete MMC also enables the linking of a model to the construction programme, the construction team can visualise the construction sequence and assess potential risks or clashes in the programme. This programme optimisation can then feed into just-intime delivery and a faster build overall.
For information on how precast concrete is shaping the UK construction sector visit: www.mpaprecast.org
Images: 01-03. The use of precast concrete is widespread across sporting arenas everywhere including the new stadium on the banks of the River Mersey for Everton football club. Courtesy Everton F.C
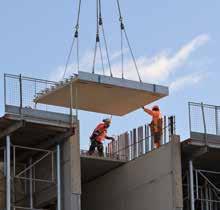
Precast concrete has been a star player in the construction of sporting venues around the UK. One, perhaps obvious appeal, is precast concrete’s robustness and durability.
Sophisticated manufacturing and quality control procedures mean concrete MMC techniques deliver a high quality, robust and reliable product every time.
Modern digital construction practices are repeatable, reliable and traceable throughout the asset life-cycle.
Significant time savings can be achieved by using concrete MMC solutions, from just-in-time delivery through to faster build programmes.
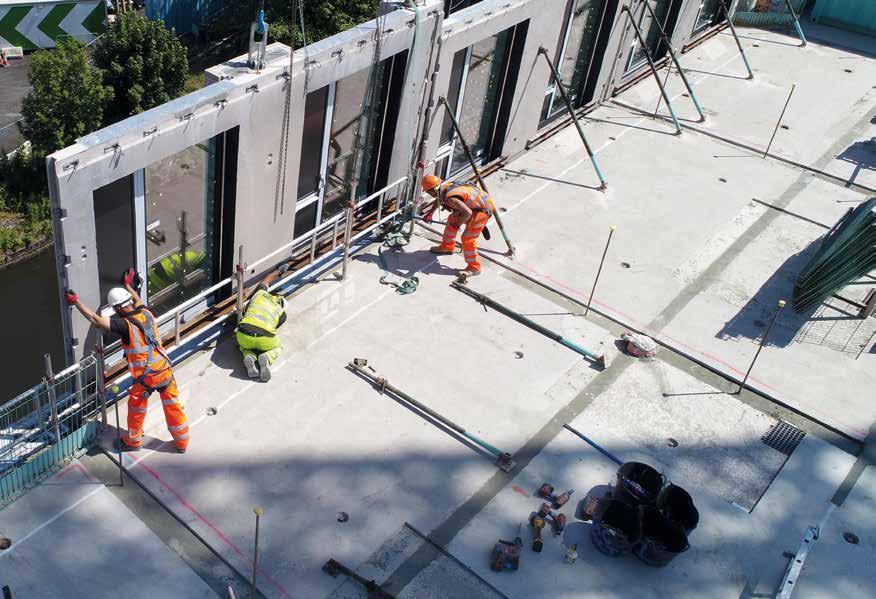
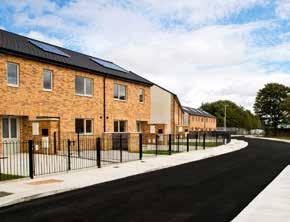


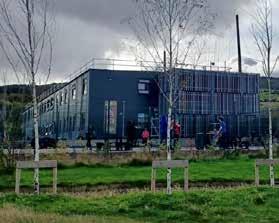

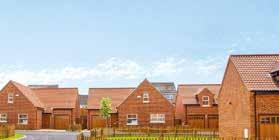
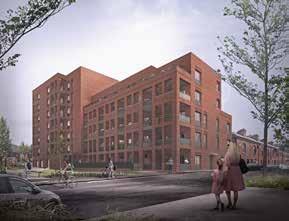
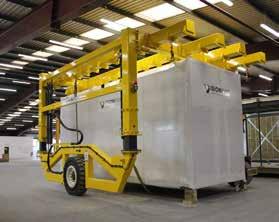
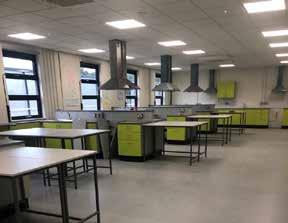