
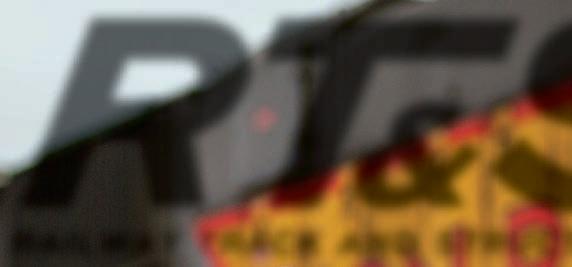
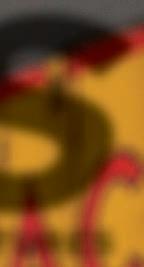

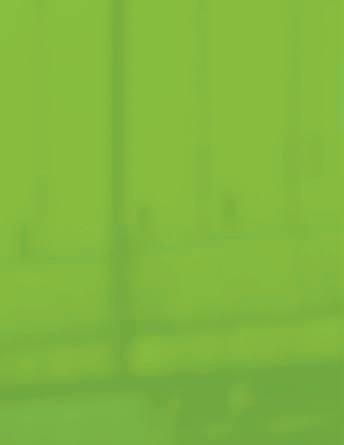
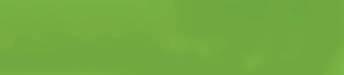
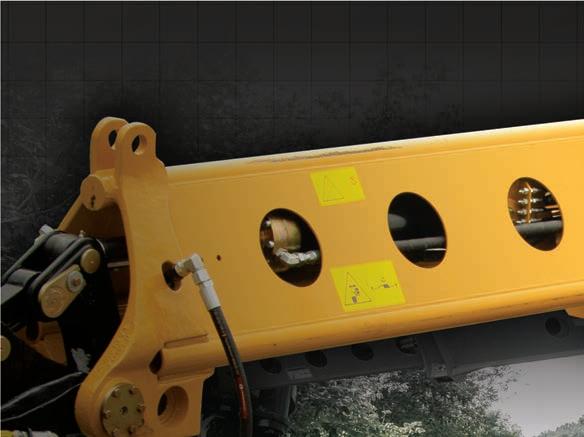
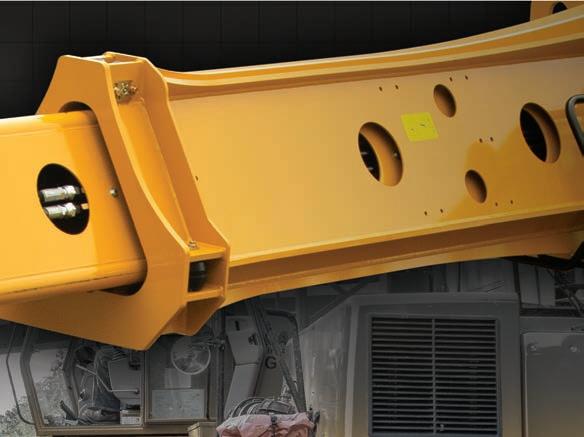
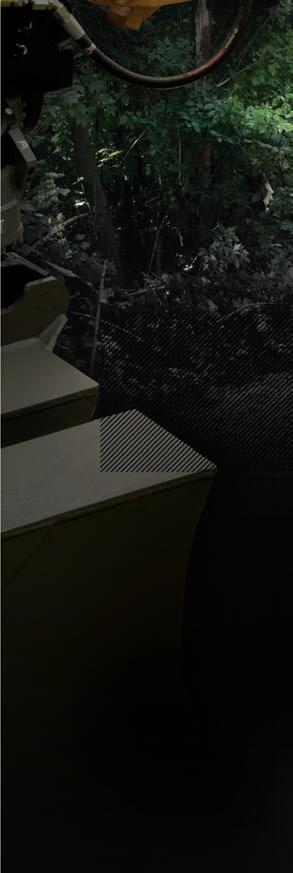

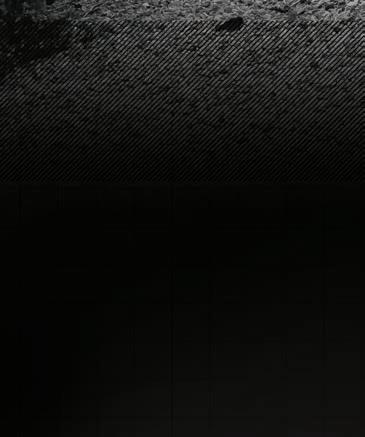
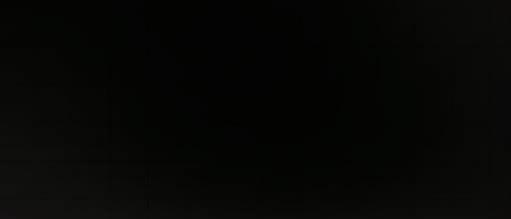
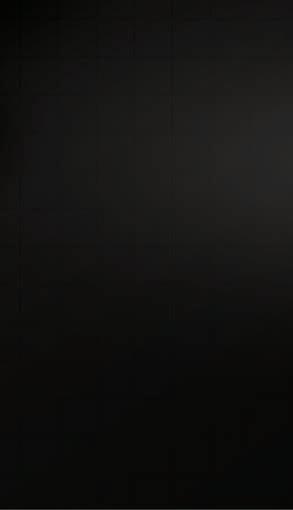

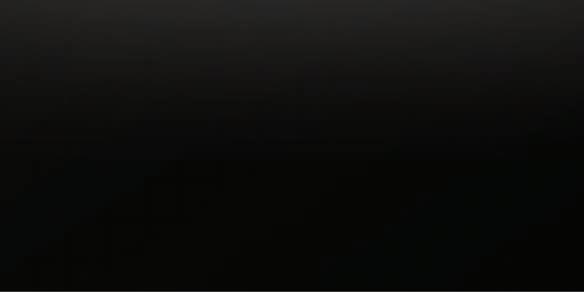
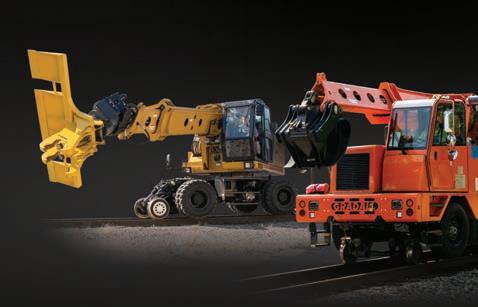
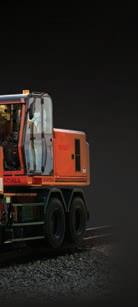
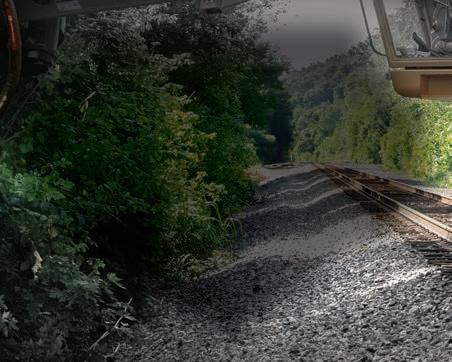








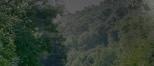
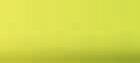

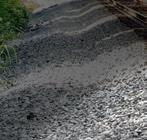


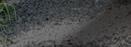




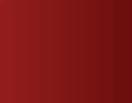
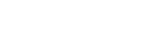





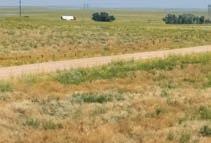
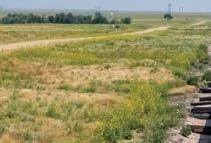
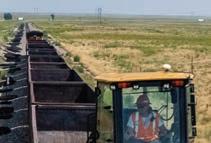
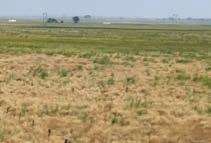
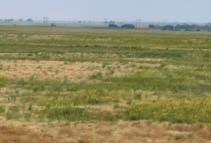
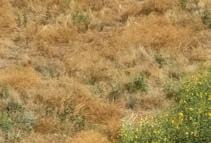
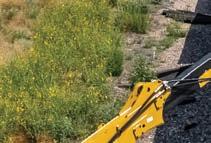
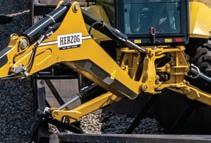
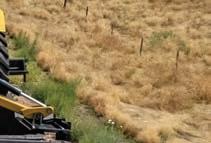


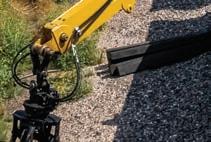

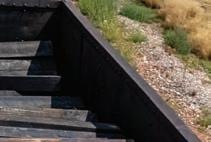
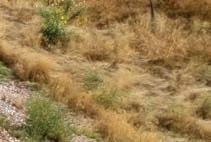
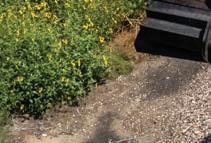
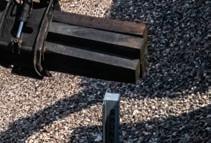
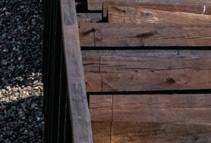
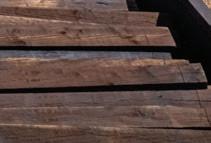
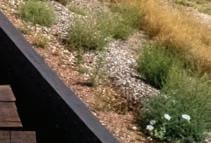
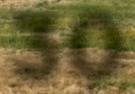
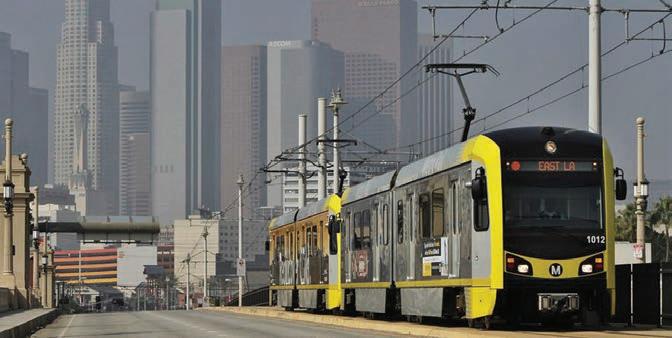
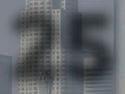

Vol. 119, No. 4
Print ISSN # 0033-9016, Digital ISSN # 2160-2514
EDITORIAL OFFICES
1025 Rose Creek Drive Suite 620-121
Woodstock, GA 30189 Telephone (470) 865-0933
Website www.rtands.com
DAVID C. LESTER
Editor-in-Chief dlester@sbpub.com
KYRA SENESE Managing Editor ksenese@sbpub.com
CORPORATE OFFICES
1809 Capitol Avenue Omaha, NE 68102
Telephone (212) 620-7200
Fax (212) 633-1165
ARTHUR J. MCGINNIS, JR. President and Chairman
JONATHAN CHALON Publisher
MARY CONYERS
Production Director
NICOLE D’ANTONA Art Director
HILLARY COLEMAN
Graphic Designer
JO ANN BINZ Circulation Director
MICHELLE ZOLKOS Conference Director
CUSTOMER SERVICE: 402-346-4740
Reprints: PARS International Corp.
253 West 35th Street 7th Floor
New York, NY 10001
212-221-9595; fax 212-221-9195
curt.ciesinski@parsintl.com
The railroad industry has taken signi cant hits in the national press over the past several months. e situation reached the point where relatively minor derailments that would not ordinarily attract national attention were seized upon like vultures on an animal carcass. I believe the railroad industry has handled a tough situation about as well as it could.
Nevertheless, our hearts go out to the residents of East Palestine whose lives were upended by the derailment and any others who have had to deal with potential hazardous material exposure due to an accident.
While some in the national press have tried to focus on factual reporting, much of the work has been inaccurate and overly dramatic. For example, I heard one national reporter express surprise on more than one occasion that he was “shocked” that there were “only” two (actually, three) crew members in the cab at the time of the East Palestine derailment. He was obviously not aware of today’s debate over crew size. How many people does he want in the cab? Ten? irty? Obviously, this reporter had failed to do his research nor was he properly briefed by his sta .
However, a major focus of the industry over the past ve years has been on using
arti cial intelligence, machine learning, and predictive data analytics to improve its view of what’s happening with the trains, all in the name of identifying equipment issues before they become accidents – i.e., improving safety.
Moreover, even though Positive Train Control (PTC) was apparently not a factor at East Palestine, I did not read or hear anything about the herculean, unfunded work done by the rail industry to create this safety system from scratch. Not that it should have been brought up, but with all of the accusations of corporate greed and lack of care about safety, you would think someone would have mentioned that the industry has made some signi cant safety strides at tremendous cost, even if PTC was mandated by the government.
I believe it’s unfair to say that the rail industry has been lax about safety. Could it do a better job around safety? Sure. Yet, who cannot nd ways to improve what they’re doing in life? e truth is that all people and entities can improve their performance, and the railroads are no di erent. We’ve seen the number of derailments drop like a rock since the industry was relieved of lots of onerous economic regulation in 1980. at’s because, a er deregulation, the roads could nally a ord to make signi cant investments in physical plant and improve safety.
ere is more work to do, but it’s not the goal of this column to detail that work. Should Congress pass legislation requiring more e orts for safety improvements included in the current Senate and House bills? I don’t know – maybe. Should we see some proposed rulemaking from the Federal Railroad Administration (FRA) or other agencies? Perhaps. Whatever happens, though, we will have the best outcomes if clear, level-headed thinking is applied by all stakeholders in railroad safety.
DAVID C. LESTER Editor-in-ChiefSignificant differences exist between the rail grinding procedure used on open track and the procedure used in the vicinity of turnouts. Typically, rail grinding on open track is a highly automated process done with large production grinders. During this process, a laser-based measurement system captures the existing worn rail profile, and a software algorithm aligns this profile with a grinding template before positioning the grinding stones in a pattern that minimizes the differences between the grinding template and the post-ground profile.
Near turnouts, a production grinder lifts its grinding stones about 50 feet ahead of the point of switch (POS) and resumes grinding about 50 feet past the frog to avoid damage to special trackwork. The track within a turnout is ground with a smaller specialty grinder capable of grinding within several feet of
the POS and the frog without damaging the special trackwork. Grinding without damaging the trackwork is accomplished by independently lifting and lowering various carts containing the grinding motors and stones at different locations throughout the turnout.
Under the Association of American Railroad’s Strategic Research Initiatives program, MxV Rail investigated the effects of using tangent grinding templates versus high-rail and low-rail grinding templates on vehicle performance and rail wear in an American Railway Engineering and Maintenance-of-Way Association (AREMA) Number 20 turnout.
Until recently, specialty grinding in turnouts was a relatively manual process, requiring a track worker to estimate the crown radius of the worn rail and select an appropriate grinding pattern. The specialty grinder would then make grinding passes until the rail crown reached the target shape. As specialty rail grinders incorporate new technology to automate the grinding process and better control the resulting rail profile, questions regarding the optimal target grinding templates in turnouts have arisen.
A series of simulations was conducted using MxV Rail’s multi-body dynamic simulation software, NUCARS® , to simulate a freight car negotiating an AREMA Number 20 turnout. The simulated
turnout geometry included a nominal switch entry angle, 1/4-inch switch point risers, and closure curve. Alignment and surface deviations were not modeled.
For the main route, the following three rail profile conditions were simulated:
1. New conditions: Represented by a series of rail profiles measured on a newly installed turnout.
2. Service-worn conditions: Represented by rail pro les measured on a mainline turnout with over a decade of service.
3. Freshly ground conditions: Simulated by applying a tangent rail grinding template to the service-worn profiles using a previously developed MATLAB® script. (1) The same tangent template was applied on the open track before the POS. Near the POS, truncated grinding templates were used to simulate rail grinding between 10- and 45-degree contact angles on the gage side only. This corresponded to a specialty grinder raising and lowering different carts with the grinding motors and stones at different locations within the turnout. Divergent route simulations included new conditions, service-worn conditions, and two different freshly ground conditions. One freshly ground condition applied a tangent template on both rails. The other condition applied a low-rail template to the inside rail of the diverging
curve and to the stock rail on the open side, as well as a high-rail template to the curved closure rail and closed switch rail/ stock rail.
Rail profile changes throughout the frog were not modeled.
For the purposes of analysis, the turnout used for the simulation was divided into ve di erent zones as shown in Table 1 and Figure 1. Zone 1 represents the open track before the POS. Zones 2, 3, and 4 demonstrate the di erent grinding template applications in the transition area between the POS and the heel blocks. Zone 5 includes the rails past the heel blocks.
The vehicle, an older hopper car with standard three-piece trucks, was selected to represent vehicle performance at or below the expected performance for the North American freight car fleet. Both empty and loaded conditions with 63,000pound and 263,000-pound gross rail loads, respectively, were simulated. The simulated wheel profile cases included a new condition with AAR-2A profile; a moderately worn profile condition with 0.5 mm hollow wear; and a heavily worn profile condition with 4 mm hollow wear.
The simulation matrix consisted of 1,260 total cases, including the vehicle, wheel profile, and rail profile cases described above simulated in both directions (facing point and trailing point moves) at multiple speeds (40-60 mph for main route, 35–45 mph for diverging route), and under different wheel-rail friction conditions (dry, gage face lubrication, and gage face lubrication plus topof-rail friction modifier).
The results of the dynamic simulations were evaluated using dynamic criteria of minimum vertical wheel load ratio and maximum lateral-to-vertical (L/V) wheel force ratio, as well as average rail wear.
The minimum vertical wheel load ratio and L/V ratios are used to evaluate the safety against derailment. (2) Higher minimum vertical wheel load ratios and lower maximum L/V ratios indicate greater safety margins.
In all simulated cases, the minimum vertical wheel loads remained above 50 percent of the static wheel load; thus, these loads were of little interest for additional investigation. Figure 2 illustrates the other dynamic metric, L/V ratio. On the main route, simulations predicted moderate hunting at higher speeds for the unground rail pro les due to
the higher e ective conicity of the wheelsets on these rail pro les. Rail grinding reduced the propensity for hunting and signi cantly decreased the maximum L/V ratios throughout the main route. In contrast, rail grinding to either tangent or high/low rail templates had relatively little e ect on the L/V values in the diverging route where L/V ratios were dictated by ange contact due to curving rather than hunting. e e ect of grinding on predicted rail wear was evaluated using a metric known as Tγ, which is calculated as a multiplication
of creepage and creep force at the wheel/ rail contact patch. (3,4) Higher Tγ values correspond to higher rail wear. Figures 3 and 4 show these values for each of the ve analysis zones from Table 1 and Figure 1.
On the main route, unground worn rail pro les showed higher predicted wear than new rail pro les (Figure 3). Rail grinding reduced the predicted rail wear and brought it closer to new rail conditions. Moreover, in Zone 2, near the POS, rail grinding reduced rail wear on the closed side rail compared to either new or worn
rail conditions. Although only the open side stock rail was ground in this zone, this grinding indirectly improved wheel/rail contact conditions on the closed side rail.
As expected, predicted rail wear was substantially higher on the diverging route (Figure 4) than on the main route due to higher creepages during curving. In
Zones 2 and 3, rail grinding to the tangent template reduced predicted rail wear, but, counterintuitively, rail grinding to curve templates has not reduced rail wear for the following reasons:
1. At the transition between Zones 1 and 2, the rail profile changed from a tangent template grind to a lowrail template grind, which caused the wheelset to steer abruptly towards the closed side and create heavy flange contact. In an actual grinding operation, this transition in rail profiles would occur less abruptly and would be expected to have less of an effect on the results.
2. In Zones 2 and 3, severe two-point contact occurred between heavily worn wheels and the rail on the closed side of the turnout. e atter low rail template on the open side of the turnout contacted the wheels closer to the ange compared to the tangent rail template. is contact restricted the bene cial rolling radius di erential between mated wheels, leading to higher wheel forces and higher rail wear.
Simulations show bene cial results from rail grinding in terms of reducing vehicle hunting on the main route and reducing rail wear rates in the critical areas of the main and diverging routes of the turnout. Using high-rail and low-rail templates on the diverging route may provide some bene t to rail wear rates on the closure rails, but tangent grinding templates appear to produce more desirable results in the switch rail/stock rail area of the turnout.
Additional information can be found in MxV Rail’s Technology Digest TD21019.5
1. Keylin, A. and S. Cummings. 2016. “Comparison of Rail Grinding Template Alignment Methods.” Technology Digest TD16-053, TTCI/AAR.
2. “Service-Worthiness Tests and Analyses for New Freight Cars.” 2015. AAR Manual of Standards and Recommended Practices, M-1001. Washington, DC.
3. Bevan, A., P. Molyneux-Berry, B. Eickho , and M. Burstow. 2013. “Development and
validation of a wheel wear and rolling contact fatigue damage model.” Wear 307, pp. 100–111.
4. NUCARS® Manual, 2020. Transportation
Technology Center, Inc., Pueblo, CO.
5. Cummings, S. and A. Keylin, “Simulations of Rail Grinding in Turnouts.” 2021. Technology Digest TD21-019, TTCI/AAR.
WITH ALL THE RECENT COVERAGE surrounding railroad safety and labor disputes, the major announcement that the Canadian Pacific and Kansas City Southern merger was approved by the Surface Transportation Board (STB) may not have received the attention it’s due. As this is a story that we will continue to follow, it’s appropriate for NewsWatch.
This is the first major change in the North American Class I railroad landscape since the Consolidated Rail Corporation (Conrail) was divided between Norfolk Southern and CSX in 1999. Since then, there have been seven Class I roads: Norfolk Southern, BNSF, Union Pacific, Canadian National, Canadian Pacific, CSX and Kansas City Southern.
With the merger of CP and KCS (named CPKC), tentatively scheduled to begin operation as a consolidated company sometime in April, North America will be left with six Class I railroads. While there has been debate over the years around whether, in the United States, at least, there should be two transcontinental to provide coast-to-coast single-line service (e.g., UP+CSX or NS+BNSF) there are arguments for and against such a move,
and we will likely see these four railroads remain independent for many years, if not forever. While the arguments for single-line service from east to west is appealing, many believe that smoother interchanges between these roads can be achieved with improved and streamlined processes, without having to go through the major disruptions previous mergers have brought about.
Will we see in CPKC, as in previous mergers, tremendous growing pains? Computers that will not talk to each other, major terminal backups that ruin service quality, lost shipments, and cars rolling around the country because the railroad cannot determine where they should be sent? Well, let’s hope not, but merging the operations of two railroads is a major, complex task.
One of the great benefits, as well as a significant challenge, is that CPKC is our first transnational railroad, providing singleline service between Canada, through the United States, and on to Mexico. This combination will provide significant support to the USMCA agreement. Of course, this agreement, which is essentially the NAFTA agreement renegotiated by the Trump
Administration is still taking hold, and it will be interesting to see if any issues arise with the CPKC regarding this agreement.
One of the best reports we’ve seen on the CPKC merger was penned by colleague William C. Vantuono, Editor-in-Chief of Railway Age. Here is an abridged version of his report.
“As widely expected, the Surface Transportation Board has approved, with certain conditions, Canadian Pacific’s acquisition of Kansas City Southern to form Canadian Pacific Kansas City, North America’s first transnational railroad.
“The Board approved the merger, first proposed on March 21, 2021, by a 4-1 vote. Member Robert Primus was the only dissenter. The decision authorizes CP to exercise control of KCS as early as April 14, 2023, a date that CP and KCS have now set to combine to create the new CPKC. CP also announced the CPKC executive leadership team.
“CP completed its US$31 billion acquisition of KCS on Dec. 14, 2021. Immediately upon the closing of that acquisition, shares
of KCS were placed into a voting trust with Dave Starling, former KCS President and CEO, appointed as the trustee. Upon Starling’s death, Ronald L. Batory was appointed as successor trustee with the STB’s approval.The Voting Trust “has ensured that KCS operates independently of CP during the regulatory review process, and until CP exercises control pursuant to the STB decision, CP and KCS will continue to operate independently,” CP noted.
“Headquartered in Calgary, Alta., Canada, CPKC would remain the smallest of six U.S. Class I railroads by revenue, and have a much larger and more competitive network, operating approximately 20,000 miles of rail, employing close to 20,000 people. Once combined, full integration of CP and KCS is expected to happen over the next three years, ‘unlocking the benefits of the combination.’”
STB Summary – Here are the first two paragraphs of the STB decision. To read the complete decision, please go to https://www.rtands.com/ regulatory/cpkc-merger-approved/ “The Board expects that this new single-line
service will foster the growth of rail traffic, shifting approximately 64,000 truckloads annually from North America’s roads to rail, and will support investment in infrastructure, service, quality, and safety. The transaction is also expected to drive employment growth across the CPKC system, adding more than 800 new union represented operating positions in the United States,” STB said in its 212-page decision. “Of additional importance, the merger will foster new Amtrak passenger rail opportunities, as applicants have committed to support Amtrak’s existing plans for expanded service on the new railroads lines. These commitments, along with CP’s strong record as an Amtrak host railroad, have won Amtrak’s endorsement of the merger. “This transaction is ‘end-to-end,’ meaning that there are little to no track redundancies or overlapping routes. If consummated, it will reduce travel time for traffic moving over the single line service; that should result in increased incentives for investment; and it will eliminate the need for the two nowseparate CP and KCS systems to interchange traffic moving from one
system to the other. This will enhance efficiency, which in turn will enable the new CPKC system to better compete for traffic with the other larger class one carriers. It is not surprising that there is substantial (though not unanimous) shipper support for this transaction — the Board has received more than 450 support letters. It is also not surprising that the other Class I railroads seek conditions, and other remedies that appear aimed at protecting their own traffic from competition with CPKC and at limiting the ability of the combined CPKC to meet its potential. Consistent with the Board’s policy to protect competition and not competitors, the Board is denying those requests while also ensuring that existing competitive gateway options are preserved.”
As students of rail history know, the North American system was formed through hundreds of mergers since the 1800s. There were major mergers in the 1980s. This merger is another major milestone in U.S. railroad history, and will likely set the North American rail landscape for years, if not decades to come.
RT&S recently talked with Pettibone, one of the stalwart producers of railroad cranes and other equipment, about the latest revision of its Speed Swing 445F, the Speed Swing 445F2. Pettibone calls the Speed Swing “the industry’s original do-it-all rail crane.” The 445F2 accepts more than a dozen attachments for laying rails, setting ties, and other maintenanceof-way tasks.
Mitch Fedie, the project manager for Pettibone, told RT&S that the original 445F was introduced in 2015, and the main driver for the new model was to achieve Tier 4 emissions standards. “Ever since 2015, we’ve been making upgrades, but the 445F2 sports the greatest changes of our previous upgrades,” Fedie added. e rail industry uses the Speed Swing for threading and replacing rail, and a lot are sold with magnet packages to clean up old metal scrap (e.g., tie plates and spikes). “ e machine can also pick up 11 yards of 90 lb. rail when a road is upgrading rail on a branch line and is especially useful for short lines in this regard. e machine is also used for snow removal, handling railroad ties, and palletized loads,” Fedie said.
The 445F2 sports a 163-hp Cummins QSB4.5 Tier 4 diesel engine and offers a 49-gallon fuel tank, a 28% increase in fuel capacity over the previous model. The added fuel capacity allows for extended working intervals, primarily when covering longer stretches of rail maintenance or relocating to a remote job site.
The new model also offers a maximum front load capacity of 10,000 lbs. and a maximum side load capacity of 8,000 lbs. The boom provides 180-degree rotation. In addition to threading out old rail and threading in new rail, as mentioned above, the 445F2 can also tow rail carts, move rail cars, and supply air for hydraulics or hand tools.
Fedie told RT&S the air system also powers train line braking and can pull up to three fully-loaded rail cars if they need to be relocated so the track gang can access the work site. “The Speed Swing is not a rail car mover, but it’s nice to have that versatility when you need it, and a regular car mover is not available.”
One of the interesting things Pettibone did when testing the new engine in the 445F2 was to modify the torque converter to provide a 16% increase in tractive e ort. While testing the new, smaller, but Tier 4 compliant engine, the company learned that the new version of the Speed Swing could not pull a given load as quickly as the old engine, nor was it able to pick up items o the ground as e ectively. erefore, Pettibone decided to change the torque converter type in the new model, which increased tractive e ort and power. With this change, the 445F2 was more energy e cient and emissions rated at Tier 4, but the new model’s power was greater than the old one. e 445F2 can travel up to 25 m.p.h. on a hi-rail and up to 20 m.p.h. with all-terrain rubber tires. e tires and four-wheel drive with a rear wheel disconnect provide greater maneuverability o the rails.
JosephCarter
PennStateAltoona CanadianNationalRailway CompanyScholarship
MichaelJ.Copley UniversityofIllinoisUrbanaChampaign
AREMAEducational FoundationScholarship
NickFrost ClarksonUniversity
NewYorkCentralRailroad MemorialScholarship
OliviaN.Hansen IllinoisInstituteof Technology
AREMAEducational FoundationScholarship
AlexanderLehnert MichiganTechnological University
NorfolkSouthernFoundation Scholarship
MatthewMcIlhinney
NorthCarolinaStateUniversity NorthCarolinaRailroad CompanyScholarship
JustinMicillo
MichiganTechnological University
AREMAEducational FoundationScholarship
VenkataSaiShashank Muddana University ofIllinoisUrbanaChampaign
AREMAEducational FoundationScholarship
DanielMueller UniversityofIllinoisUrbanaChampaign
AREMAEducational Foundation Scholarship
MatthewM.Parkes UniversityofIllinoisUrbanaChampaign
AREMAEducational Foundation Scholarship
GeordieRoscoe
UniversityofTexasatAustin
AREMAEducational FoundationScholarship
LoganA.Sava
PennsylvaniaStateUniversity
AREMAEducational Foundation Scholarship
KenzaSoufiane
UniversityofDelaware
CSXScholarship
ThomasJ.Stogin
UniversityofIllinoisUrbanaChampaign
UnionPacificWilliamE. WimmerScholarship
NoahStruck
UniversityofMinnesota-Twin Cities
AREMAEducational FoundationScholarship
NicholasSwoboda
KansasStateUniversity
AREMAEducational FoundationScholarship
JiaxiZhao
UniversityofTexasatAustin
WilliamE.andBarbaraI.Van
TrumpScholarship
FormoreinformationabouttheAREMAEducational Foundationorthescholarshipprogram,visit www.aremafoundation.org.
With nearly 50 nominees, choosing the top ten young railroad engineering practitioners for this year’s 10 UNDER 40 honors was no easy task. Although the nominees practice different types of engineering and their careers have taken very different paths, all were strong candidates
for inclusion in the top ten. These individuals handle tasks that would make most of us quiver with anxiety. Derailments, bridge problems, track and roadbed problems, and others that seem insurmountable, are all in a day’s work for these folks. We would like you to meet this year’s 10 honorees, along with three runners up.
engineering leadership is critical for the railroad industry
For the past four years, Matt has served on the project management team for Brightline’s $2.7B Orlando extension project that will connect South Florida to Central Florida with high-speed intercity passenger rail. Specifically, Matt has served as a leader on Brightline’s East/ West rail infrastructure, a 35-mile corridor along SR 528 between Orlando International Airport and Cocoa. Brightline’s East/West corridor will ultimately be the location where Brightline travels at its maximum speed (125mph) and will be the fastest rail corridor in the Southeast. Matt’s work has consisted of managing rail construction including the supporting civil infrastructure of ten bridges, including bridges over Interstate 95 and the St. Johns River, two tunnels, including the innovative arch structure at I-95 and SR 528 and the second boxjacking project on the extension project as well as three miles of state highway. In the past 12 months, Matt has facilitated the placement of 95,000 tons of ballast, 44,000 concrete ties and over 14 miles of rail through Brevard County.
CARROLL HAS SERVED AS A LEADER ON BRIGHTLINE’S EAST/WEST RAIL INFRASTRUCTURE, A 35 MILE-LONG CORRIDOR ALONG SR 528 BETWEEN ORLANDO INTERNATIONAL AIPORT AND COCOA.
As a recognized Canadian Paci c leader, De Blois’s work is critical in bringing the railroad to the forefront of safety. She has introduced and supported novel technology innovations for the rail industry. e Remote Safety Inspection (RSI) and Cold Wheel Technology (CWT) processes have raised the performance of freight car safety and air brake inspections. De Blois developed the Remote Safety Inspection process with technology to ensure every aspect of the inspection process is followed. She also supported the installation of Cold Wheel Technology systems at the base of mountain grades where the air brakes require application when descending, resulting in a 32% increase in repairs versus manual inspection. De Blois also led the installation of a Train Inspection Portal System (TIPS) using over 30 cameras to take 72 images of each freight car within the train. RSI enables the train to be inspected while in-train forces are acting on the components providing a holistic and better inspection versus the manual inspection identifying 85% more defects. With a future of automation, this step lays the groundwork for the advancement of remote inspection technologies.
AS A RECOGNIZED CANADIAN PACIFIC LEADER, DE BLOIS’S WORK IS CRITICAL IN BRINGING THE RAILROAD TO THE FOREFRONT OF SAFETY. SHE HAS INTRODUCED AND SUPPORTED NOVEL TECHNOLOGY INNOVATIONS FOR THE RAIL INDUSTRY.
Amtrak
Chad has held various positions at Amtrak, but most recently has led the agency’s Undercutter team. Chad has used his experience with the railroad as well as his education to implement a data-driven approach to Amtrak’s Undercutting program, using GPR data to target locations that require undercutting and drainage improvements, build out more accurate schedules with the understanding of the track conditions, and save costs when certain locations can be skipped. Chad has also been involved with Amtrak’s System Track o ce to develop a new approach to transitioning between ballast and open deck bridges, improving the ride quality for Amtrak passengers. Chad has been very involved in Amtrak’s recent major equipment acquisition, ensuring new equipment (undercutters, material distribution cars, tilt cars) meet Amtrak’s requirements, and working with the manufacturers to better their product for the rail industry. Amtrak has also been testing out new technology to supplement our roadway worker protection. Chad’s teams have been involved in the testing of this technology and provided valuable feedback to improve this technology for the future use of Amtrak and other railroads.
CHAD HAS BEEN INVOLVED WITH AMTRAK’S SYSTEM TRACK OFFICE TO DEVELOP A NEW APPROACH TO TRANSITIONING BETWEEN BALLAST AND OPEN DECK BRIDGES, IMPROVING THE RIDE QUALITY FOR AMTRAK PASSENGERS.BEN HABIG Regional Director of Bridges and Structures, Western Region Genesee & Wyoming
With a level of professionalism unmatched in his peer group across Genesee &Wyoming, Ben’s work has made G&W railroads safer and more reliable. He is responsible for 2,744 structures totaling more than 50 miles in length. During his tenure in his current position, Ben has led the recovery efforts for at least two major bridge fires per year that have resulted in a total structural loss. The largest was Bridge 1178.16 on Arizona Eastern Railway’s main line in 2021. All of the timber elements of this 667’ bridge over the Gila River near Calva, Ariz., were lost to a wildfire that swept through the Gila River Valley. Upon warnings of the approaching fire, Ben coordinated pushing the brush line well back from the bridge, but the winds and heat from the fuel load in the valley was too intense. In just 15 days, Ben restored service by designing cost-efficient and effective repairs that accounted for available materials and contractor resources.
HABIG IS RESPONSIBLE FOR 2,744 STRUCTURES TOTALING MORE THAN 50 MILES IN LENGTH DURING HIS TENURE IN HIS CURRENT POSITION, HABIG HAS LED THE RECOVERY EFFORTS FOR AT LEAST TWO MAJOR BRIDGE FIRES PER YEAR THAT HAVE RESULTED IN TOTAL STRUCTURAL LOSS.
Klaumann has provided major contributions to the industry as part of several signi cant assignments. Early in his career, while at a Class I railroad, Klaumann served as a Manager of Bridge Maintenance in Denver, with responsibility for all structures across a 2,100-mile territory comprising some of that railroad’s most heavily tra cked subdivisions. Subsequently, as a consultant, he continues to use his practical experience to inform designs and recommendations for his clients, including several Class Is, short lines, industries, and agencies. Klaumann has been an active participant in AREMA Committee 16 (Economics of Railway Engineering and Operations) and the AREMA Conference Operating Committee, which assists in the planning and execution of the AREMA Annual Meeting. He also published and presented two papers at AREMA’s Annual Meeting–“Modernizing Infrastructure at Federal Facilities” (2022) and “Consideration of Alternative Transportation of a Rail Corridor: A Team E ort (2019). e Iowa Highway Research Board also published a paper he contributed to “Develop an Improved Selection Methodology for Safety Improvements at Public Highway-Railroad Grade Crossings.”
We want to congratulate Stephen Ng, Construction Manager, on being an RT&S “2023 10 under 40” honoree. Stephen is an experienced track and structures designer, track and construction expert, and project manager. He is passionate about including up-and-coming technologies such as electrification and Net Zero in rail projects. Thanks for being part of Team RailPros, Stephen!
The rail industry is striving to improve safety and as a core bearing supplier to the rail industry, so is Timken. To consistently deliver on time, high quality new and reconditioned bearings to the company’s wide customer base, it first must work safely. The company’s goal is to develop a culture where safety is a core value vs. just another metric. Since Timken’s journey began 4 years ago at its flagship plant in Mascot, TN, it has averaged a 54% reduction in OSHA recordable rate compared to the four years average prior to that. Timken has also set a new plant record for days without a LTA at 1,628 days. The Mascot team does both physically and mentally tough work every day, and an accident can happen in a heartbeat. Under Koesters’ leadership, workers have been buying in to the change, participating in work area safety teams, coming up with excellent ideas, implementing effective permanent solutions, sharing best practices, and most importantly helping take care of each other day in and day out.
Congratulations to Ben Habig, Director of Bridges and Structures, for securing a spot in this year’s “10 Under 40” feature!
Ben’s unwavering commitment to the integrity of our structures and to continuously enhancing our maintenance procedures is a direct contribution to our safety and service culture.
Stephen is an experienced track and structures designer, track and construction inspector and project manager. He has worked with numerous rail transit projects in California over the last 14 years. Some of his recent projects include serving as the project manager for the on-call operations project for the POLB. He is also involved with the Alameda Street Widening Design Project, acting as project manager for the At-Grade Railroad crossings upgrade design, adjacent to the project. Ng was given design projects early on as a deputy project manager and with his knowledge of heavy rail, he had to pivot to research and learn about electrified light rail design and apply his field site visits and knowledge gained into the new design. The limited amount of space given, and the client’s constraints required thinking outside of the box to maximize the space provided and place mechanical and operational equipment in new areas.
As an experienced Project Manager, Frank Spinozza managed two of RCC’s largest, multi-million-dollar, designbuild projects for Long Island Rail Road. Each project contributed to the improvement of MTA’s infrastructure: the Hicksville Station and North Track Siding Improvement and the New Mid-Su olk Electric Yard. Frank is currently managing RCC’s Joint Venture with Michels Corporation (Railroad-Michels Joint Venture, LLC) MTA Construction and Development CH058B East Bound Re-Route Construction for the East Side Access Project, within Harold Interlocking, the largest railroad junction in New York City and the busiest in the United States. Once complete, the improvements will re-route track carrying Metro-North, LIRR and Amtrak trains, improving daily travels of thousands of commuters and providing congestion relief for trains traveling along the Northeast Corridor. Frank is a member of the Moles, an organization for the heavy construction industry, the most prestigious organization of its kind in the world. Moles members are leaders in their profession who are dedicated to promoting the industry and supporting their colleagues through outreach program and networking opportunities.
Nicely done, Agi.
Congratulations to
Programs Agi Van Wetering for being named one of RT&S’ 2023 “10 Under 40.”AGI SEBASTIAN VAN WETERING Director, Track Programs Union Pacific Railroad
A leader in one of our country’s longest standing industries, Agi is not afraid to ask “why?” He challenges status quo and thoughtfully questions well-established practices. Agi understands that past decisions, although once appropriate, may not be applicable to today’s operation. This tenacity led him to challenge Union Pacific’s approach to rail joints. Assigned a terminal territory with thousands of joints, Agi quickly became intimately familiar with joint-induced challenges. Eliminating joints with the centermost holes drilled required maintenance employees to change the rail and shoot two welds – a costly and time intensive process. Determined to reduce the risk entirely, he researched and proposed center-drilled track joints for field and flash butt welding in yards and other appropriate locations (a practice historically prohibited). Agi’s research proved the team could successfully repurpose the existing rail and eliminate the joint via one weld, significantly reducing cost while producing a higher quality product.
Jaclyn worked in Bridge Design as a consultant for 8 years before joining Conrail. She led the Project Management team for the Point-noPoint bridge replacement project, modernized department ling and operation procedures, and is a member of AREMA committees 10 and 15.
She is focused on continuing her development in the rail industry to meet the expectations of rail customers and the general public. Jaclyn quickly rose through the ranks at Jacobs Engineering, then AECOM before joining Conrail in 2021.
Card currently serves as Vice President and Group Manager for Benesch’s Railroad Division overseeing thousands of active public projects in the western United States. He has a national practice and had been involved in railroad projects in over 30 states, providing a wide breadth of experience in railroad engineering and project management for the rail industry. His current practice includes representation of Class I railroads on major public infrastructure projects across the country in project management, structural review, owner representation, construction managment, utility coordination, real estate contracts and database development/management. Over the course of his career at Benesch, Card has handled various positions of increased responsibility
SHANE STIFFLER
Supervisory Railroad Track Safety Specialist
Federal Railroad Administration
Shane Sti er is the most tenured Supervisory Railroad Track Safety Specialists at the FRA. Sti er is always leading at least one special committee or project, and he is the rst to volunteer. ese projects have positively in uenced and impacted railroad safety across his six-state, mid-Atlantic territory, as well as the nation. Sti er has served as an active member in federal rule-making proceedings in the Railroad Safety Advisory Committee (RSAC), providing technical expertise to the committee in support of the Track Safety Standards Working Group on track geometry and track inspection. Sti er also developed the monitoring procedures used for the industry’s recent Automated Track Inspection Test Pilot Programs.
Karlene has addressed hazards for all departments and in all aspects of railroad operations. She has performed tabletop reviews of new timetables and schedules, reviewed onboard employees’ working tasks and potential hazards, and development of a Fatigue Potential Analysis Tool. Ms. Mayerhofer interfaces with unions and regulators alike to assure a safe and healthy environment for LIRR employees, customers and the general public. Her work with the Track Department has involved exposure assessments and risk-based hazard analyses for ballast and silica, for continuous welded rail and metal exposures, and for ergonomics and electric hazards associated with temporary platform installations. Mayerhofer has shown the drive and desire to rise as a leader in Safety for LIRR employees, customers and the general public. She never shies from a challenge and accepts all responsibilities given her. Her peers and mentors expect to see her running a railroad safety organization in the not-too-distant future.
Subparts A-F
TrackSafetyStandards, containstheTrackSafety Standards,SubpartsA-F,forClassesoftrack1-5.The standardscovergeneralinformation,Roadbed,Track Geometry,TrackStructure,TrackAppliancesand Track-RelatedDevices,andInspection.IncludesDefectCodes. Updated January6,2023.
BKTSSAF TrackSafetyStandards,SubpartsA-F $11.95 Only$10.75forordersof50ormore!
FRAPart237establishesFederalsafetyrequirements forrailroadbridges.Thisrulerequirestrackownersto implementbridgemanagementprograms,whichinclude annualinspectionsofrailroadbridges,andtoauditthe programs. Part237 alsorequirestrackownerstoknow thesafeloadcapacityofbridgesandtoconductspecialinspectionsif theweatherorotherconditionswarrantsuchinspections. Updated January6,2023.
BKBRIDGE BridgeSafetyStandards $8.95
Only$8.00forordersof50ormore!
ThisreprintincludestheFRA's RailroadWorkplaceSafety Standards addressingroadwayworkersandtheirwork environments.Theselawscoversuchthingsas:personal protectiveequipment,fallprotection,andscaffoldingfor bridgeworkers;andtrainingissues.Alsoincludessafetystandardsfor on-trackroadwayvehicles. UpdatedJanuary6,2023.
BKWRK RailroadWorkplaceSafety $11.50 Only$10.35forordersof50ormore!
The TrackSafetyStandardsCalculator isamustfor anyonewhoworksontrack.Thisslideruletype calculatorcontainsmanyofthedetailsforClassesof track1-5.Deviationfromuniformprofileandfromzero crosslevel.Differenceincrosslevel.Compliantwithpart213.
BKTCAL TrackCalculator $11.50 Only$10.75forordersof50ormore!
UpdatesfromtheFederalRegistermaybesuppliedin supplementform.
Building any new railroad line, whether freight, passenger, commuter, or light rail, is complex and demanding. While each comes with unique challenges, building a light rail system in a moderately or densely populated urban area can be incredibly challenging because the line is close to many neighbors.
RT&S recently spoke with Wyman Jones, Senior Director – Rail Operations & Maintenance Engineering with LA Metro. A key focus for Jones is the operation and maintenance of LA Metro’s four light rail lines–the Blue, Green, Gold, and Expo (Turquoise) lines. LA Metro also has the Regional Connector in the heart of downtown that serves as a junction for four lines. Construction on the Regional Connector began four years ago and should finish later this year. A line
also under construction is the Crenshaw Line, which is mainly done, except for the interface to the people mover at the Los Angeles airport. And an extension for the Gold Line, which represents the line’s fourth extension stage, is scheduled to open sometime in 2024. The Gold Line has been in service since 1996.
Construction of the Regional Connector comes with special challenges because it is underground, below downtown. Building the tunnels and track required special care because of the number of music studios and production facilities overhead. The owners of these facilities are concerned about vibration and noise. Jones points out, “We have mitigated noise and vibration with conformal wheels and frogs and special grinding of the rails to match the profile of our
custom wheelsets. We have also installed sound attenuation in the tunnels to help reduce noise.”
LA Metro owns its grinding equipment and does maintenance grinding on its own. Jones told RT&S, “we used contractors to do the initial profile grinding, then LA Metro takes over.”
The ventilation systems in the Regional Connector are complex. There is a system for general ventilation, but there are also special fans and requirements for the fire department, which require regular maintenance. The system also handles gas mitigation, which requires testing and is routinely maintained. Indeed, Jones says that “all of this maintenance and monitoring maintains the reliability of the Connector, which helps our teams get track time for all types of maintenance.”
Jones also said that digging tunnels for the Connector can be delayed by
discovering artifacts. “These must be evaluated to ensure that we’re not going to dig up and destroy something of historical significance.” Jones adds that building foundations must be considered, and occasionally they must dig deeper than called for by the original plans. “Sometimes, this requires equipping a station with high-speed elevators to get people in and out, whether passengers or emergency crews.”
Because the Connector is not a junction in the traditional sense, the track forms a wye on which trains turn. “We have train service going back and forth to feed the lines, and we have to turn our trains, so a special train control system was required to allow trains to be moved back out to yards without interfering with normal train traffic,” Jones adds. Getting track time for crews is a real challenge, as a system that runs 24 hours leaves little time for maintenance windows. However, Jones says, “We have to work out a plan to get the necessary track time to maintain the system.”
The Gold Line extension is an at-grade project extending east into the foothills and is adjacent to a Metrolink commuter
anyone trespassing on the freight line from getting to the Gold Line.” When construction on the Gold Line extension began, the freight railroad had to be aligned to enable everyone (Metrolink, LA Metro, and freight) to run together with proper clearances.
rail corridor to Pomona. Jones said, “We also have a freight railroad beside us, and we have to make sure adequate separation and fencing are present to help prevent
In addition, the freight railroads have customers to serve, sometimes requiring them to cross over the Gold Line. And as railroaders know, some customer pickups and deliveries require multiple moves. LA Metro controls the freight movements across their line. The agency, on occasion, has overpasses built for their line to eliminate a crossing. Jones said, “All of the rail crossings are built to a higher standard to support the weight of freight trains and prevent damage to the light rail line. So, our employees have to be FRA certified to maintain light rail switches and freight line switches. That way, we’re able to repair both without delay.” LA Metro also has four gates at each road crossing to prevent people from getting around the gate to beat a
DIGGING TUNNELS FOR THE REGIONAL CONNECTOR CAN BE DELAYED BY DISCOVERING ARTIFACTS, WHICH MUST BE EVALUATED FOR HISTORICAL SIGNIFICANCE.
freight train only to be hit by a light rail or commuter train.
“In fact,” Jones said, “the length of the Gold Line extension is also a challenge because the line is long and crosses streets and bodies of water.” When it rains heavily, provision for drainage runoff is required and is often a retention pond that the railroad must cross over, requiring a bridge or overpass. And these structures must be substantial to deal with the runoff. Jones added, “We’ve had to build many bridges and overpasses, which has taken a good bit of time. Not only planning and construction but environmental impact studies for these structures.”
On several occasions, the agency has had to share an existing bridge with other carriers. Instead of building its bridge, LA Metro sometimes had to arrange for existing bridges to be extended or widened. Jones said, “The bridges already carry freight and commuter trains, and there are different owners and ownership responsibilities for inspections and
repairs. If possible, we’d prefer to build our bridge.”
Locating stations is also a challenge for the Gold Line extension. “Parking can
determine how to provide parking space for our passengers. Moreover, we must locate parking facilities so passengers do not have to cross railroad tracks.”
Another challenge for the Gold Line extension is that some of the light rail fencings must have detectors installed such that if there is a freight derailment and a load has breached the line, we must know about it so we can take immediate action. The same situation exists where the light rail line runs in the middle of a freeway. If there’s an accident on the highway, the potential exists for debris to land on the LA Metro right-of-way, which requires immediate attention.
be a problem at some of the places we’re locating stations,” Jones said. “We either must build our parking lots or combine with Metrolink or another agency to
All rail projects–freight, passenger, commuter, and light rail–have a variety of challenges. Intuitively, it may seem that light rail projects are the easiest of all because of the lighter rails and equipment used. However, Wyman Jones has shown us that this is not necessarily the case, as most light rail projects are in urban areas where space is a premium and it’s not easy to move around.
INTUITIVELY, IT MAY SEEM THAT LIGHT RAIL PROJECTS ARE THE EASIEST OF ALL BECAUSE OF THE LIGHTER EQUIPMENT USED. WYMAN JONES HAS SHOWN US THIS IS NOT THE THE CASE.
exacerbated corrugation.
ese systems have taken steps over time to remediate and manage corrugation, but corrugation is persistent. “Even if corrugation is addressed via design and maintenance, we should expect it to reappear,” Magel said. e reason for this is the fundamental mechanisms involved; the vehicle and track system itself combines many mechanical components, each with its own mass, sti ness, dampening, and their resultant resonances. On top of that, the wheel/ rail interface sees a wide range of operating conditions, including:
•new and worn pro les
• lubricated and non-lubricated rail
•dry and wet seasons
•up-grade and down-grade running
•braking and accelerating
e wheel/rail system is constantly experiencing at least one of three damage mechanisms: rolling contact fatigue (RCF), plastic ow, and wear.
Railroads around the world, despite their di erences, encounter and contend with many of the same wear and damage mechanisms and the maintenance di culties they cause. Rail corrugation is one such universal problem. But as railroads have begun to collect and leverage more data on their systems, the approaches to corrugation mitigation have become more sophisticated. Rail corrugation appears on freight lines, commuter lines, and transit systems. “If there is a system in the world without corrugation, I haven’t seen it,” said Eric Magel, Principal Engineer at the National Research Council of Canada, currently Manager of R&D for Ensco/Transportation Test Center. Corrugation is associated with noise, vibration, and fatigue damage to rail and vehicle components. “It’s pervasive and persistent, but the question we all want answered is: is it preventable?,” Magel asked the assembled at the annual Wheel/ Rail Interaction conference.
Although corrugation is ubiquitous, its form and concurrent symptoms can vary across systems. On San Francisco’s Bay Area Rapid Transit system (BART), the corrugation ranges from subtle to very pronounced,
occurring in 1-inch to 4-inch wavelengths, which indicates multiple di erent mechanisms at work, he said. Seattle’s Sound Transit experiences corrugations ranging from 20 mm to 3 inches. Additionally, the corrugations on Sound Transit are heavily associated with squat development.
Ongoing investigations at Sound Transit have also shown that there appears to be a relationship, which may be coincidental, between the wavelength of corrugation and the grinding signature le behind —particularly with coarse-grade grinding stones, he said.
Vancouver Skytrain is another system with signi cant corrugation. “Skytrain is an interesting case in that the system was designed in many ways to allay these kinds of issues,” Magel said. To that end, it uses a linear induction propulsion system, automatic train control, small wheels, aggressive wheel pro les, and steered bogies – and yet, signi cant corrugation arose very soon a er the system opened. A er multiple investigations and interventions, it turned out that some of the design features, including dampening corrugation development, had the opposite e ect. For example, he said the consistent train speeds, acceleration, and braking a orded by automatic train control
“When all these systems and their resonances are brought together, an inevitable feedback loop is created,” Magel said. e rate at which damage occurs increases and reinforces the wavelength- xing mechanism. ere is always a damage mechanism (o en multiple) and always a dominant resonance, and while neither of these can be eliminated, they can be treated. “ at’s why it’s important to grind preventively; grinding arrests that feedback loop at an early state,” he said.
An investigation into severe corrugation and gauge-corner collapse on a transit system in South America highlights the complex interaction of all these systems. Magel said that the rail showed no evidence of RCF or plastic ow, indicating that the damage mechanism was strictly wear. To pinpoint the cause of the corrugation, the investigators took measurements to identify the corrugation wavelength- xing mechanism in the system. In this case, it turned out to be a torsional bending of the sleeper that caused the rail to vibrate vertically as the trains passed. “ e culprit being sleeper resonance was completely unexpected,” Magel said. Since replacing all of the sleepers would have been prohibitively expensive,
the transit system instead focused on the wear mechanism. is took the form of an extensive grinding program to remove the corrugation and the introduction of multiple rail pro les to improve the wear pattern of the wheels and steering in curves.
“Rail corrugation is a natural phenomenon that will always assert itself, so as a matter of course, there should be a maintenance plan to address it,” he said. e challenge then is developing more e cient and cost-e ective methods of corrugation remediation, which begins with good data.
Accurate and detailed data is necessary to guide and optimize complex maintenance strategies around complex phenomena like corrugation. Without good data, systems o en resort to “ re ghting” or heavilycorrective maintenance methods — moving from one critical issue to another, never getting ahead of the root problems.
Vancouver’s SkyTrain presents an enlightening case study as an example of how data can be leveraged to get ahead of a problem like corrugation. SkyTrain, which is maintained and operated by British Columbia Rapid Transit Company (BCRTC) as part of TransLink, Metro Vancouver’s transportation authority, has historically dealt with several issues related to corrugation — particularly in the period between 2010 and 2015, “we became a bit of a household name in terms of corrugation,” said Peeter Vesik, BCRTC’s Asset Integration Project Manager. He added that many of these issues stemmed from signi cantly increased service levels related to the 2010 Olympics that were not ultimately aligned with maintenance practices at the time. With a growing corrugation problem and falling behind on corrective grinding, SkyTrain contracted the National Research Council of Canada (NRC) to assess the system and provide a roadmap for remediation. e general takeaway from that assessment was that signi cant re-railing would be required unless changes were made to maintenance practices.
Following the assessment, SkyTrain brought in Advanced Rail Management (now part of Global Rail Group) to implement an aggressive corrective grinding and repro ling program and to perform a wheel/rail pro le compatibility analysis. To avoid repeating this large-scale corrective grinding later, SkyTrain worked with ARM to develop a regular grinding program to move the system from a corrective to a transitional and nally to a preventive-grinding state.
e foundation of an e ective grinding program is good data; this is especially true of preventive grinding, which must balance metal removal, pro le compliance, defect removal, and surface condition to maximize rail life and optimize vehicle performance and ride comfort.
SkyTrain uses several datasets to inform its maintenance and grinding programs.
ese include track geometry data, ultrasonic defect detection, rail and wheel pro le data, surface roughness, and noise and vibration data. “Maintenance is never the same from year to year because the conditions are always changing and always being monitored,” Vesik said. Additionally, the data ensures a more cost-e ective grinding strategy — some track sections require grinding every three months. In contrast, others on the system are ground every two years, and he added that there is no value in over- or under-grinding rail.
e surface nish or roughness le postgrind, in conjunction with rail hardness, also signi cantly a ects the rate at which corrugation returns (see Figure 1). “We noticed that if you “polished” or acoustically-ground harder rail steels, it tended to stave o corrugation development for longer.” On the other hand, SkyTrain’s Expo Line, which has so er steels (in the 260 Brinell range), saw corrugation development soon a er grinding, regardless of the surface nish.
Another dataset that SkyTrain has found helpful to fold into their maintenance planning is data on grinding e ciency. Due in part to the system’s very short maintenance windows and complicated logistics, rail grinding presents a few unique challenges.
Since 2016, SkyTrain has kept data on spark minutes per shi and spark minutes per track minute. ey have realized tremendous bene ts by improving planning and grinding support logistics over the
years. In 2016, rail grinding averaged 30% spark time per shi ; by 2022, it averaged just over 50% (see Figure 3). ese gains are primarily the result of improving staging and decreasing grinder travel time, singletracking, and performing stone changes and refueling during o hours. And because SkyTrain, like any system, has a xed grinding budget, these e ciency gains ultimately translate into more ground rail and improved system health.
Looking forward, SkyTrain has two track expansions slated for the 2025 – 2030 period and a eet expansion in the same window.
is means that the existing track will have heavier usage in addition to more track miles to maintain. Given this signi cant expansion, Vesik noted that it’s essential that a maintenance budget is commensurate with the demands of the system and that having good quantitative data is critical to making that nancial case. “ e key to developing an e ective maintenance strategy,” he said, “is robust data that enables constant input, feedback, and adjustment, in pursuit of a quantitative optimum.”
While there is no perfect remedy for corrugation, railroads and transit systems are nding great success in expanding both their data collection and utilization – developing increasingly sophisticated strategies for arresting corrugation growth and preventing its formation in the rst place. For many systems, the data required for these programs already exist and must be put to work.
Je Tuzik is the Managing Editor of Interface: The Journal of Wheel/Rail Interaction.
Information for this article previously appeared in Interface Journal and was derived from the 2022 Wheel/Rail Interaction Conference.
Regarding track construction and maintenance, there are many moving parts to manage. Contractors must have access to the necessary equipment to complete tasks from routine maintenance to emergency response situations. While material handling equipment can be specialized or multi-purpose, suppliers say all these moving parts are critical to getting the job done.
As spring gets underway, suppliers are observing a rebound in demand and have noted customers taking on deferred maintenance projects in recent years. With more work slated to get done in 2023, vendors highlight their o erings that aim to reduce daily operating costs and manage work time on-site as e ciently as possible.
Suppliers highlight e cient loading and unloading capabilities.
Omaha Track has continued e orts
to innovate its material handling solutions with the latest introduction of its car moving solutions. Omaha Track said there had been an increasing need for more e cient ways of handling materials in condensed work windows. e new carmoving solutions have increased e ciency and reduced handling and stockpiling of materials.
Omaha Track’s heavy-duty car mover trucks have excavators that can pull atcars and gondolas of all railroad materials.
is new spin on long-standing material handling concepts has helped increase rail industry productivity, the company said.
In addition to the car mover trucks, Omaha Track now o ers road-to-rail power by the day for maintenance of way, bridge rehab, and construction projects.
e company owns and operates Brandt Power Units for short-term car pulling and spotting needs. e OT Power Program package includes one Power Unit with up
to 60,000 lbs. tractive e ort and one qualied Power Plan Operator 10 hours per day, seven days per week.
Omaha Track says its car moving solutions and road-to-rail power options o er a range of bene ts. e car mover trucks o er increased e ciency and productivity, reducing the time and e ort required to handle materials. e company said its road-to-rail power options provide a convenient and cost-e ective way to transport materials from one location to another, reducing the need for expensive transportation options. Additionally, the rental and purchasing options for Omaha Track Equipment allow customers to choose the equipment that best suits their requirements.
Omaha Track Equipment has a stock of hi-rail grapple trucks, section trucks, rotary dump trucks, pickups, and rail and tie carts available for sale and rent. e company o ers exible rental and purchasing options
to meet the speci c needs of its customers.
Overall, Omaha Track said its material handling solutions aim to provide customers with the tools they need to increase productivity and e ciency within their operations. e company said it is committed to innovation and customer satisfaction and notes its new car-moving solutions and road-to-rail power options underscore its commitment to design with the speci c needs of the rail industry in mind.
Loram o ers a complete line of material handling services to support delivering product where and when customers need it. Loram said the 2023 forecast is positive for material handling services, with customers planning and executing work postponed in previous years.
e Loram eet continues to experience strong demand from customers that utilize the exibility of DumpTrain®, SlotMachine®, and MHC Series Material Handling Cars to support almost any material handling needs.
In 2023, Loram Technologies, Inc. is experiencing growing demand for its new Tie Set Out Services (TSO). Utilizing Aurora tie inspection data as well as the railroad’s tie replacement logic to identify precisely which ties need replacement, the TSO system can then optimize the plan for tie distribution, allowing customers to know exactly where to set out ties and eliminate the need for someone to walk the track and physically mark where to set out ties ahead of the tie distribution team.
e so ware lets users know where to set out ties and how many are required for each drop as they travel along the track. Loram said that ties are placed much closer to their installation location, allowing for increased productivity for tie replacement teams as they will spend less time moving ties around to the appropriate spot.
For decades, Herzog has provided versatile material handling solutions that have altered maintenance-of-way work. By using specialized equipment like the CarTopper® and Multi-Purpose Machine®, railroads can optimize their e ciency during designated work windows, resulting in increased productivity and safety on the railroad. Herzog developed and built the rst CarTopper® a er identifying a need for a more e cient and safer method of loading and unloading crossties from railcars.
is modi ed backhoe can mount and
dismount itself on a railcar in less than 10 minutes and requires only one operator, reducing the need for ground personnel. It can also easily move between cars of varying heights as its grapple loads and unloads ties onto the right-of-way. While the train travels, the CarTopper® can lower into the cars for e cient storage and transportation to the next job site.
The Multi-Purpose Machine® is another Herzog offering that the company said has changed the game for MOW tasks and accelerated the speed of loading and unloading high volumes of material with increased versatility and safety. The MPM performs numerous material handling tasks along the ROW for routine maintenance or emergency response situations.
The MPM can travel at track speed in either direction under its power and is compatible with multi-track environments because of its ability not to foul adjacent track. The company said that a zero-turn radius track hoe travels atop the well car gantry system in both directions and requires just one operator. With standard attachments like the bucket, magnet, tie grapple, and basket grapples, as well as increased versatility attachments like the auger, brushcutter, rail shear, and tree shear, Herzog said the MPM is capable of handling any material handling task.
Herzog o ers a complete line of material handling equipment and operators to handle any situation, including rail distribution and pickup, aggregate hauling and distribution, tie distribution and pickup, ditching, PTC infrastructure installation, and OTM distribution and retrieval.
Whether customers pick up ties from the captain’s chair of a material handler or maintain the catenary on their light-rail system from the raised platform on the back of a truck, it is vital to have a dependable rail gear system that provides safe and smooth operation, says Diversi ed Metal Fabricators.
e DMF RW-2300HS is a front-mounted hydrostatic creep drive system designed to operate independently of the vehicle transmission. With a 33,000lb GAWR, the front hydrostatic system can be mounted forward of the front tandems and, in special applications, behind the cab.
Complete wireless control operates the Neotec motorized front axle without integrating it into the vehicle. e system will operate up to 7mph in creep mode and disengage for up to 25mph in freewheel mode using vehicle propulsion. Rated for 88k# at a 2% incline and up to 200k# on level track, the company said this system can meet various customer needs.
Additionally, the system allows the user to operate the vehicle equipment without disengaging the PTO to advance the truck
RailwayGeotechnics coverstrack,tracksubstructure,load environment,materials,mechanics,design,construction, measurements,andmanagement.Itiswrittenprimarilyfor professionalsandgraduatestudents.
down the track, saving time and money. Since the RW-2300HS is independent of the transmission, the vehicle can be moved o track if any issues arise, unlike some current split sha systems. e system includes the Neotec axle, DMF integration package, and the DMF RW-1630 or RW-1650 rear axle assembly with auto mechanical locks.
Customers rely on multi-purpose and custom-engineered equipment Industry-Railway Suppliers , founded in 1966, is the distribution representative of Swingmaster and a North American distributor of AREMA track tools, battery tools, abrasives, heavy railroad equipment, work equipment wear parts, and car shop tools.
Swingmaster has provided the rail industry with specialized and custom-engineered material handling products since 1985. e company produces mobile hi-rail Swingloaders, a ermarket solutions, and machine upgrades—all manufactured in the U.S.
e Swingmaster Tie Manager is
Railgrindingsavesmillionsofdollarseveryyear!TheArt andScienceofRailGrindingisthefirstbookdedicated exclusivelytothesubject.
YourGuidetoRailwaySignals isanexcellentguidefor trainingsignalpersonnelespeciallyrailwaycross-function managers,supervisors,andsupportpersonnel.High-quality graphicsanddiagramshavebeenusedthroughout. Complieswithallstandardsandcommonlyusedpractices.
Reprintedbypopulardemand,thisbookisavaluablereference forroadmasters,tracksupervisors,trackforeman,surveyors andothersinvolvedintheplanningandexecution oftrackmaintenanceandconstructionwork.
Fold-outdiagrams.Softcover.301pages.
Themostcomprehensivecollectionofdefinitionsrelatingto track.Over1500termsfromantiquatedforgottenslangto today'sjargon.Clearlyillustratedlineartenhancesthetext.
TheRailroad:WhatItIs,WhatitDoes is evenmorevaluablethanbefore.Insideyou’llfinda comprehensivelookathowtoday’srailroadsfunction—from equipmenttoproceduresandmarketingtomaintenance.
the company’s latest material handling machine. Swingmaster said that the STM is a state-of-the-art tie crane equipped with a non-DEF, Tier 4 nal Cummins power unit, resulting in lower daily operating cost. It has a strategically o set telescopic jib boom for improved operator visibility, an enhanced reach diagram, and maximized operator e ciency for tie-to-tie tasks—the Tie Manager sports proportional failsafe spring-applied, hydraulic-release brakes.
e STM provides the operator with unmatched machine control and system customization via a 12-inch touch display and ergonomic joysticks. New to Swingmaster, the new control system o ers full pointto-point machine diagnostics, aiding in troubleshooting and maximizing machine uptime. e company said a 360-degree camera system and display provides the operator with complete awareness of the immediate machine surroundings.
operator comfort, visibility, ergonom ics, and ingress/egress. It includes ducted heating, cooling, defrosting, and abundant
storage. e machine-centered operator station keeps the operator’s focus straightforward to reduce fatigue, and the integrated stairwells and handrails improve the ingress and egress of the cab.
Mitchell Rail Gear’s solution for material handling is Hydraulic Excavators, both Rubber Tired Hydraulic Excavators, and Track Driven Hydraulic Excavators. Mitchell equips all brand rubber-tired and track excavators to give customers various choices depending on their needs. e company said that various work tools can attach to both excavators to enhance material handling and allow the machines to be multi-purpose.
Tilt Rotators attach various work tools to rotate 360 degrees and tilt to position the tool for optimum e ciency. Rubber- tired
ties to improve stability when working over the side of the machine.
Mini, small, and medium size track excavators can be equipped with Mitchell’s hydraulic drive system to travel on rail at higher speeds to self-propel to the job site over long distances. Excavator material handling tools include magnets, buckets, grapples, and hoists.
Multi-purpose work tools include undercutters, blowers, tie-inserters, tampers, and ballast regulators. e company said customers are looking for various solutions to handle materials o track with multipurpose machines.
“One brand or one type of machine cannot satisfy the vast number of di erent applications,” Mitchell Rail Gear said. “Customers are looking for solutions for machine brands they are familiar with and have local service to keep their machines running. ey cannot always do this with
ment, making dual-purpose converted equipment for material handling an
(president and son of founder James J. Hill), created the “See America First” promotional campaign. In 1910 he hired John Fery to paint scenes from Glacier National Park that would be placed in GN train stations and ticket agencies across the U.S. e campaign was designed to not only promote rail travel but also to ll the railway’s hotels in the National Parks. Fery is the most heavily collected artist in the BNSF collection with more than 60 pieces. Over his lifetime he created more than 300 large format paintings.
It has been typical that the President’s message discusses some aspect of AREMA or a relevant engineering topic. is month I am going to step out of that box and discuss a piece of railroad heritage that may not be well known to the younger generations. I have always been impressed by BNSF Railway’s ne art collection. John Fery’s large format oil-on-canvas paintings have always caught my eye. e combination of the painting style and the scenic presentations of Glacier and other US National Parks are striking images that portray these spectacular places well.
BNSF has over 1,000 works of art, including paintings, photos, and sculptures, most of which are displayed at the campus. ey depict the land and people of the Northwest and Southwest regions of the U.S. Dating from the early 1900’s, they come from three predecessor railroads – Great Northern Railway, Northern Paci c Railway, and Santa Fe Railway. ey were commissioned by the railroads to entice the public to board a passenger train to see these beautiful destinations. It is interesting to note that only a handful of these works depict a train. Today, BNSF o ce employees in Fort Worth and other locations work in buildings graced by paintings that vividly depict how railroads encouraged westward development. A walk through the headquarters campus takes employees and visitors on a journey into canyons, deserts, pueblos, forests and mountain ranges. BNSF believes in its privilege and duty to maintain and protect this one-of-a-kind art collection , not only to preserve the railroad’s history but more importantly—our American history.
At Great Northern (GN), Louis W. Hill
John Fery was born Johann Nepomuk Anton Levy in Austria in 1859. It is unknown why he changed his name. It may have resulted from anti-Semitic reactions to his birth name. He came from a privileged family and was introduced to ne art at an early age. He was an enthusiastic outdoorsman who enjoyed hunting, hiking and being in open wild spaces. In 1881 he enrolled at the Vienna Academy of Art and also studied painting in Germany. In 1883 he joined the American Panorama Company, based in Milwaukee, Wisconsin where he worked on large scale panorama or cyclorama paintings for a while before returning to Europe. A er marrying and starting a family, he returned to the U.S. in 1886. He started traveling to the west where he saw the Yellowstone and Grand Teton regions for the rst time. is is when he became enamored with the rugged wilderness of the western U.S. A er an unsuccessful attempt at a hunting expedition business for wealthy Europeans, his painting allowed him to eke out a living.
e o er Hill made was a perfect match for Fery. He was o ered studios in Glacier
Park and St. Paul, supplies, a modest annual salary, and all expenses covered to spend the summers in Glacier Park to prepare sketches that would become paintings. In about 3-years’ time Fery had completed 267 paintings. By the fall of 1913 Fery had completed 347 paintings which were on display in 25 states, Canada, and Germany. By late 1915 the deal with Hill had ended and Fery moved back to Milwaukee. GN extended a second o er in 1925 that matched the rst, but without a studio and salary when not in Glacier Park. Painting for Fery was never about the money, so he accepted a second chance to live his dream painting wilderness scenes. In 1929 Fery moved with his wife to Ocas Island, Washington to live with one of their daughters and her family. A studio was built so that he could continue his painting, but tragedy struck when it burned down and destroyed a life’s worth of sketches and a year’s worth of nished painting for GN. Fery’s services for the railroad ended a er 1930.
John Fery died in 1934 at the age of 75 in Everett, Washington. rough his artistic talent, he helped to create public awareness of the National Parks and the importance of preserving them for future generations. And of course, he generated passenger travel on the GN Railway. Fery’s Glacier Park oil painting “Grinnell Mountain – McDermott Falls” is shown below (40” x 60.5”) and demonstrates the quick “wet on wet” paint layering technique he used with wide, active stokes.
Enjoy your journey until next month.
TRENT M. HUDAK AREMA President 2022-2023Registration opens April 18th for the AREMA 2023 Annual Conference in conjunction with Railway Interchange. Back after four years at the Indiana Convention Center, October 1-4. For the latest information about Keynote Speakers, Technical Presentations, Sponsorship, and more, visit www. conference.arema.org.
Did you know we have a wide variety of On Demand education for learning on your time? Browse our most popular webinars, seminars, and Annual Conferences to earn your PDH credits on the go. Visit www.arema.org to start your On Demand learning today.
Is your Library up to date? Order the NEW 2023 Communications & Signals Manual today. With over 35 new, revised, reaffirmed, or extended Manual Parts, including over 500 pages of
updates, it’s the perfect time to get your copy of the 2023 Manual. Order online now at www.arema.org.
Don’t miss out on the conversation happening in AREMA’s Member Forum. The Member Forum connects you with other Members allowing you to send messages, start conversations, and more. See what everyone is talking about today: https://community.arema. org/home.
If you’re looking for a podcast to binge, listen to AREMA’s Platform Chats. It features guests from every aspect of the railway industry. Come ‘roll with AREMA’ available on all of your favorite listening services.
Order the NEW, 2022 edition of the Portfolio of Trackwork Plans. This edition features new plans and
specifications that relate to the design, details, materials and workmanship for switches, frogs, turnouts & crossovers, crossings, rails and other special trackwork. Order online now at www. arema.org or contact publications@ arema.org for more details.
Leverage the power of your trusted association’s Railway Careers Network to tap into a talent pool of job candidates with the training and education needed for long-term success. Visit www.arema.org/careers to post your job today.
NOT AN AREMA MEMBER?
JOIN TODAY AT WWW.AREMA.ORG
CONNECT WITH AREMA ON SOCIAL MEDIA:
MAY 2-3
Committee 37Signal Systems Germantown, WI
MAY 15-17
Committee 5 - Track Dallas, TX
MAY 2-4
Committee 13Environmental Welaka, FL
MAY 16-17
Committee 15Steel Structures Pueblo, CO
MAY 3-4
Committee 36 - HighwayRail Grade Crossing Warning Systems
Germantown, WI
JUNE 15-16
Committee 8 - Concrete Structures & Foundations
Washington, DC
Joining a technical committee is the starting point for involvement in the Association and an opportunity for lifelong growth in the industry. AREMA has 30 technical committees covering a broad spectrum of railway engineering specialties. Build your network of contacts, sharpen your leadership skills, learn from other members and maximize your membership investment. If you’re interested in joining a technical committee or sitting in on a meeting as a guest, please contact Alayne Bell at abell@arema.org.
For a complete list of all committee meetings, visit www.arema.org.
The second iteration of the Tracks to the Future program is looking for students interested in rail transportation and engineering to join for a week-long summer program.
The 2022 edition was a resounding success! 66 total students from 17 different states participated in the program that featured a hybrid option for the first time, with two days of virtual activities at student’s home locations, followed by
a travel day and two days of hands-on activities and field trips at one of three universities, Michigan Tech, Penn State Altoona, or University of Illinois, UrbanaChampaign. Our students all received both hands-on instruction and valuable field trip experiences. Both students and parents commented favorably about the experience and parents were particularly impressed how the virtual portion of the program held their students’ interest and
kept them engaged in the process.
2023 will be even better! We are offering the hybrid program twice and have expanded it to six universities, adding University of South Carolina, University of New Mexico, and California State University - Fresno (Fresno State) as the new hosts. We have room for a total of 120 students (20 students at each site) and they all receive full scholarships! We will again feature the hybrid format that uses
extensive interactive learning during the virtual portion, making use of Kahoot, breakout rooms, tabletop activities and other learning tools organized in Canvas learning system to keep students engaged. The on-campus sessions focus on a day of hands-on activities that include (among others) building track, moving trains and intermodal containers, and testing students’ skills as locomotive engineers (in a simulator). The second campus day
will feature field visits to local rail industry sites.
More information about the program and available sessions is available at Michigan Tech Rail Program Web site. Students and families can also access the Registration page directly.
We are all excited to see the new group of students exploring the rail transportation and engineering field…so join us and ride on Tracks to the Future!!!
GET PDHS AT YOUR OWN PACE WITH AREMA’S ON DEMAND EDUCATION
Access to important professional development content is just a few clicks away with AREMA Education. Our On Demand content spans many disciplines of PDH accredited courses that allow you to get your PDHs by learning from experts online without leaving your office.
BENEFITS OF LEARNING ONLINE
1. LEARN MORE
Studies show that participants learn more while taking On Demand courses as you can skim through the material you understand and take more time in the more challenging areas.
2. GET INSTANT ACCESS With AREMA On Demand courses, you don’t have to wait to learn and get your PDH’s as they’re available instantly after purchase.
3. CONVENIENT AND FLEXIBLE
Above all things, On Demand education is meant to take at your own pace and on your time. Study from anywhere in the world, whether from your office or the convenience of your sofa.
4. COURSE VARIETY AREMA On Demand education offers a wide variety of topics for all studies of the railway engineering community.
Register and Start Learning today at www.arema.org.
BECOME A MEMBER AND SAVE
Not an AREMA member? Join today at www.arema.org and get discounts on all AREMA Educational Offerings, from Virtual Conferences to our Webinars.
“ WE ARE ALL EXCITED TO SEE THE NEW GROUP OF STUDENTS EXPLORING THE RAIL TRANSPORTATION AND ENGINEERING FIELD . . .SO JOIN US AND RIDE ON TRACKS TO THE FUTURE!Students at Penn State-Altoona, 2022
MAIN OFFICE
JONATHAN CHALON Publisher (212) 620-7224 jchalon@sbpub.com
AL, KY, TN, CHINA
JONATHAN CHALON (212) 620-7224 jchalon@sbpub.com
CT, DE, DC, FL, GA, ME,MD, MA, NH, NJ, NY, NC, OH, PA,RI, SC, VT, VA, WV, CANADA: QUEBEC AND EAST, ONTARIO
JEROME MARULLO (212) 620-7260 jmarullo@sbpub.com
AR, AK, AZ, CA, CO, IA, ID, IL, IN, KS, LA, MI, MN, MO, MS, MT, NE, NM, ND, NV, OK, OR, SD, TX, UT, WA, WI, WY, CANADA: ALBERTA, BRITISH COLUMBIA, MANITOBA, SASKATCHEWAN HEATHER DISABATO (CHICAGO OFFICE) (312) 683-5026 hdisabato@sbpub.com
AMERICAS, EUROPE, ASIA, AFRICA, AUSTRAL ASIA NORTH AMERICA - CT, DE, DC, FL, GA, ME, MD, MA, NH, NJ, NY, NC, OH, PA, RI, SC, VT, VA, WV, AND EASTERN CANADA. EUROPE EXCEPT GERMANY, AUSTRIA, GERMAN SPEAKING SWITZERLAND, EASTERN EUROPE, ITALY, AND ITALIAN-SPEAKING SWITZERLAND. ASIA EXCEPT JAPAN AND CHINA. JEROME MARULLO (212) 620-7260 jmarullo@sbpub.com
GERMANY, AUSTRIA, GERMAN-SPEAKING SWITZERLAND, LATVIA, LITHUANIA, ESTONIA, POLAND, CZECH REPUBLIC, SLOVAKIA, HUNGARY, SLOVENIA, CROATIA AND SERBIA SIMONE AND SIMON FAHR Breitenbergstr. 17
Füssen 87629
Germany
Tel: +49 8362 5074996 sfahr@railjournal.com
ITALY, ITALIAN-SPEAKING SWITZERLAND
DR. FABIO POTESTA
Media Point & Communications SRL
Corte Lambruschini
Corso Buenos Aires 8 V Piano, Genoa, Italy 16129 +39-10-570-4948
Fax: +39-10-553-0088 info@mediapointsrl.it
JAPAN
KATSUHIRO ISHII
Ace Media Service, Inc. 12-6 4-Chome, Nishiiko, Adachi-Ku Tokyo 121-0824
Japan
+81-3-5691-3335
Fax: +81-3-5691-3336 amkatsu@dream.com
IRJ PRO AND CLASSIFIED ADVERTISING SALES
JEROME MARULLO (212) 620-7260 jmarullo@sbpub.com
This section has been created solely for the convenience of our readers to facilitate immediate contact with the RAILWAY TRACK & STRUCTURES advertisers in this issue. The Advertisers Index is an editorial feature maintained for the convenience of readers. It is not part of the advertiser contract and RTS assumes no responsibility for the correctness.
On several occasions, we have reported on the impact of the “work from home” (WFH) phenomenon on our nation’s transit and commuter rail service. On March 24, Managing Editor Kyra Senese penned a story about ridership concerns among BART leadership: she writes, “One of the country’s largest infrastructure projects, carrying Bay Area Rapid Transit trains through downtown San Jose, is taking shape. Nevertheless, the number of passengers who will use the extension—and its future as a key component for regional transport—is becoming increasingly uncertain.” e link to her story is https:// www.rtands.com/news/bart-ridership-forecast-could-rede ne-south-bay-transit/.
is month, we’re taking a deeper dive into WFH. e U.S. is in a conundrum around people working from home vs. coming to the o ce daily. is was born from the pandemic, when employers told anyone who could work from home to do so. However, many people who make our society function could not WFH. Whether in construction, public transit, law enforcement, re- ghting, or bedside healthcare, to name a few, people’s presence in the workplace was essential, and all they could do was take as many precautions as they could.
Now that the pandemic has been o cially declared “over,” most people have returned to a normal lifestyle, except in the workplace. I believe the development of so ware tools during the pandemic that facilitate WFH, along with some surprise among employers that teams could e ectively WFH and not see a drop in productivity, has kept a lot of life in the idea of WFH.
e situation with commuting is complex. For example, when WFH started, several leaders of tech companies said that their employees could work from home forever. Now, these same companies are laying o tens of thousands of workers, partly because they expected a boom in the business of WFH tools and hired lots of people. While many still work from home, the boom tech companies were looking for has not occurred. Yet, as we’ve reported, public transit ridership has not returned to anywhere near pre-pandemic levels. e diminished o ce population has negatively impacted others selling goods and
services in downtown areas, such as restaurants, grocery stores, drug stores, and drycleaning establishments.
Moreover, there have been recent reports that this trend is beginning to hit the value of commercial real estate. Companies are hesitant to renew leases for premium and expensive urban real estate if those buildings may sit for years only partially occupied. Moreover, the owners of these buildings do not want to pay high utility bills and taxes only to see the value of their investments drop.
While the economics of WFH is signicant, the social implications are, too, especially for children and young adults beginning their careers. Part of growing up is meaningful socialization, which most kids can only get in a school setting. Learning to play and work with other children is essential
said, “If I have to come into the o ce more than three days a week, I’m not interested.” How much longer are folks going to be able to take such a cavalier attitude? Especially when so many layo s are occurring?
Some respond by saying that many young people have seen their parents not treated well at or laid o from work that they’re not buying into corporate life. ere is some truth to this. Yet, our corporate and national leaders must carefully evaluate the long-term impact of such a major cultural shi in concert with employees and eliminate practices such as bullying, gaslighting, mobbing, and other ills of the workplace or any social group.
A ip side to all this is that policy makers must consider is the tremendous waste of resources resulting from the daily journey to work. Clogged freeways with vehicles standing still, belching exhaust fumes in the atmosphere, and wasting gallons of fuel, to say nothing of the impact on personal productivity, is sickeningly wasteful. e air quality in U.S. urban areas was measurably higher with the major reduction of auto tra c during the pandemic.
to their development. Similarly, young people starting careers a er high school or college need precious development experiences to help them be productive workers and learn their trades, cra s, and professions. Graduating from school or college only to take a job where you WFH for years can, in my view, only have long-term adverse e ects. e person’s professional growth is signi cantly slower, and seeing colleagues for only a day or two each week does not allow them to get to know others. Of course, our society has always had people, especially stay-at-home moms or dads and folks in professional jobs, for who WFH was the norm. You’ll have those types of roles in any society.
e expectations of young people starting their careers who receive job o ers have grown over the years. For example, a friend recently told me of a person just out of college he was trying to hire for a professional job
One must also account for the cost of car and engine repairs. Between repair, maintenance, and the cost of fuel, owning an automobile is high for the individual and the environment. And I haven’t even raised the subject of the cost of injuries and deaths that occur on our highways.
So, what is the solution to all of this? I don’t know. However, one thing that occurs to me is that many in this nation have longed for a four-day workweek. Could this be the solution to the complex situation we nd ourselves in now? Four nine-to-tenhour workdays and a three-day weekend? If leaders can nd a way to get commuters out of their cars with clean and safe buses, light rail, heavy rail, and commuter trains, this would help tremendously. Transit ridership would return to pre-pandemic levels, workers would occupy downtown buildings, boosting the commercial real estate sector, and store owners and shopkeepers who depend on those who commute to the o ce daily would ourish. Practical questions need answers, and some will likely think it’s too big to accomplish, which is balderdash.
IF I HAVE TO COME INTO THE OFFICE MORE THAN THREE DAYS PER WEEK, I’M NOT INTERESTED
TheAREMA2023AnnualConferenceinconjunctionwith RailwayInterchangeisbackafterfouryears.Joinusto network,expandyourknowledgefromthenearly80Technical Presentations,findsolutionsintheExhibitHallfeaturingover 700companies,andmuchmore.