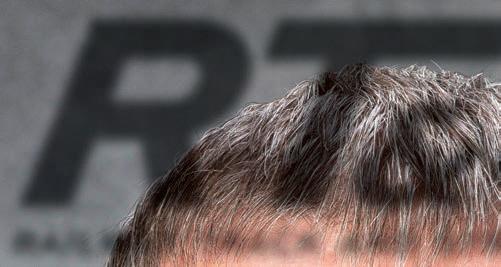
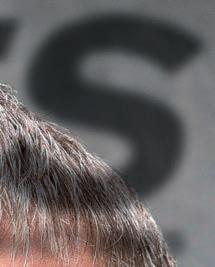
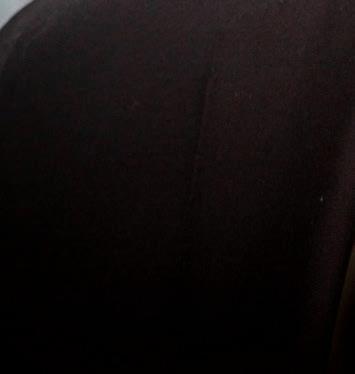
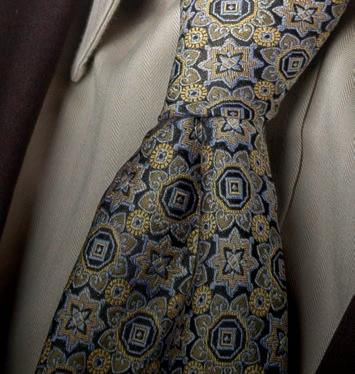
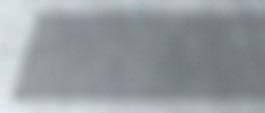

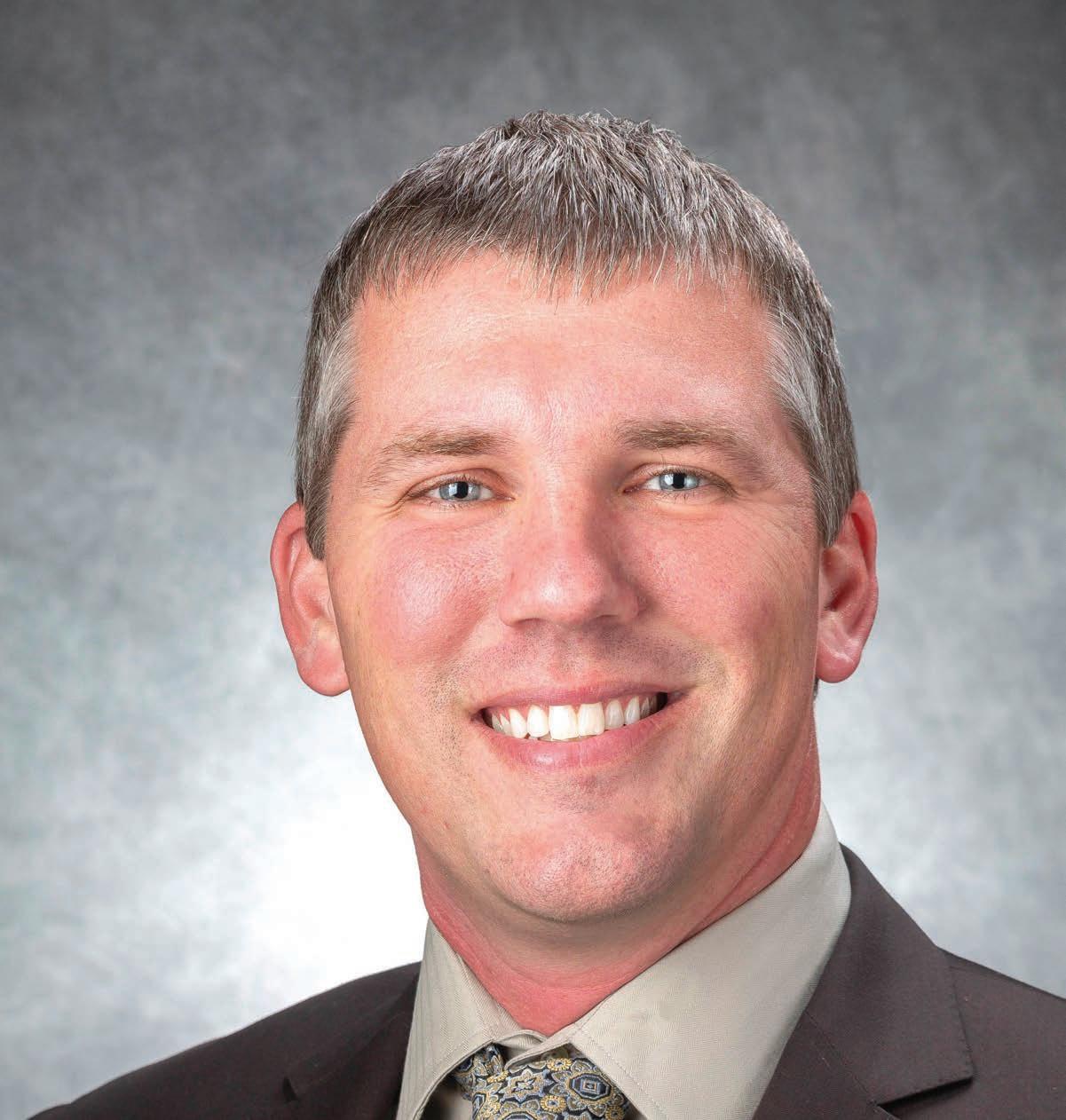
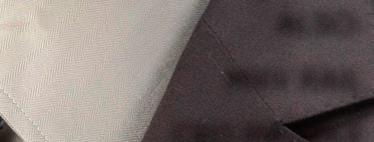
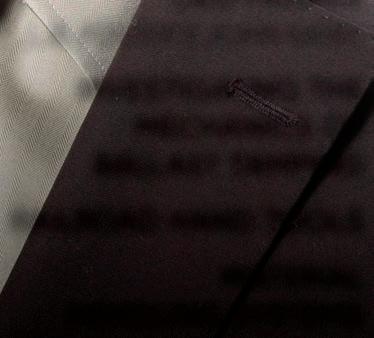
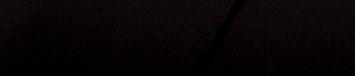
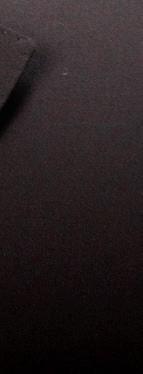
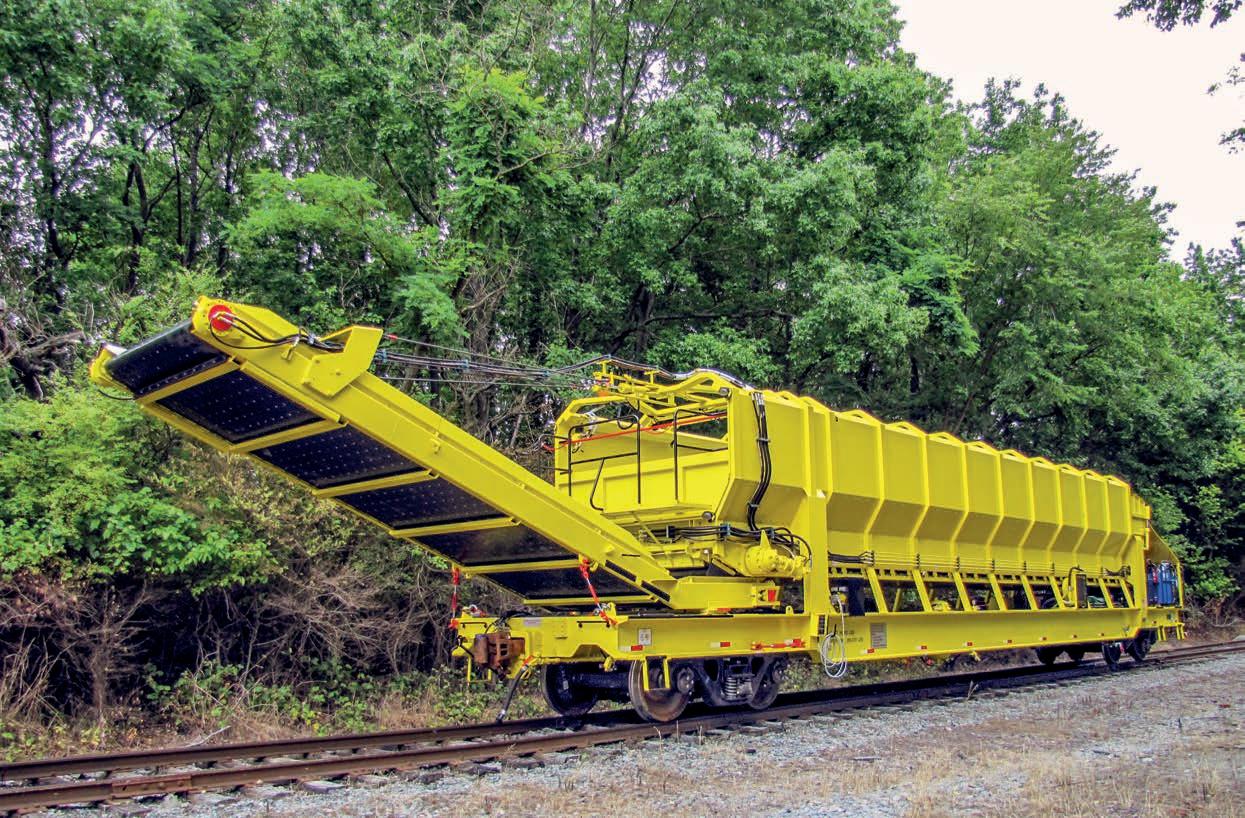
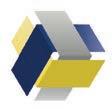
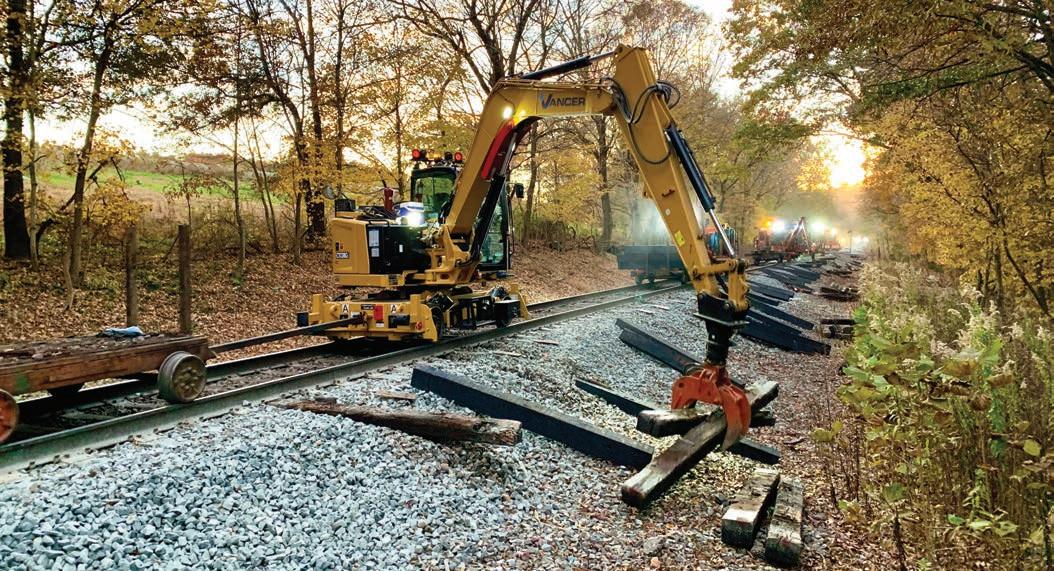



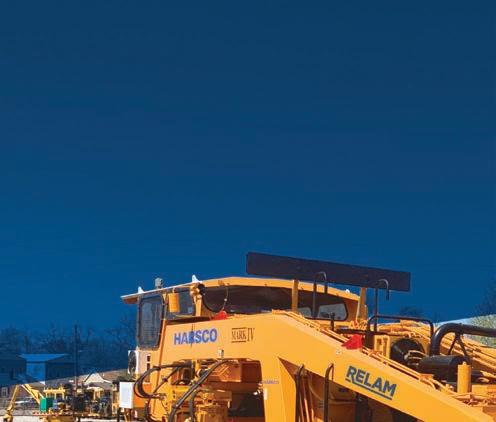
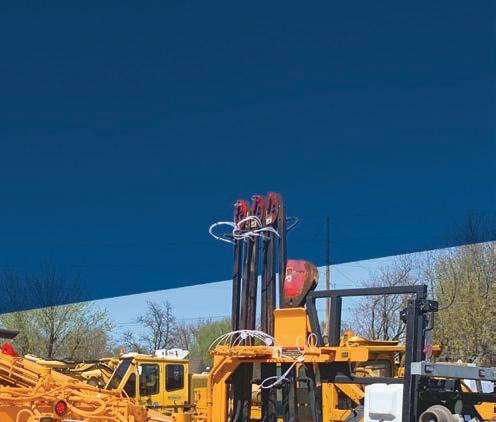



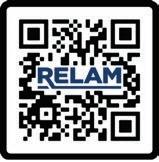









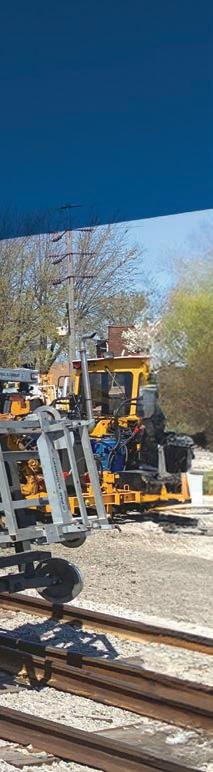

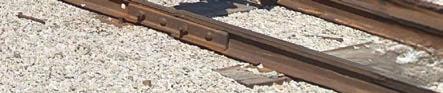
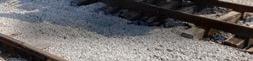
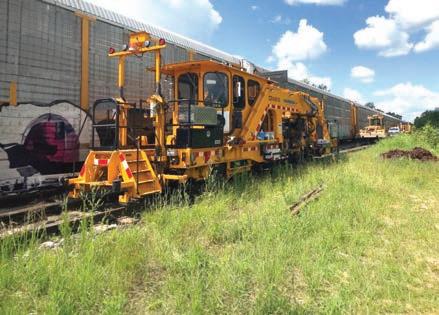
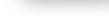

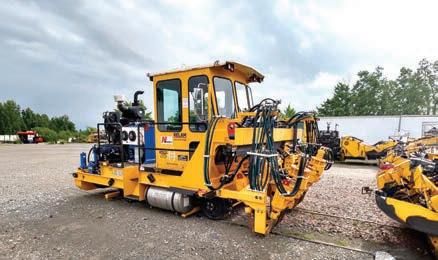
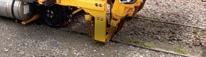
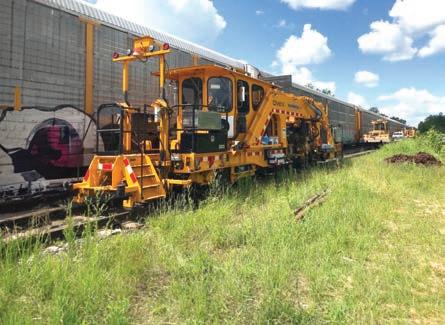

In an industry as mature as railroading, it’s not o en that truly historic events occur. Nevertheless, we have one coming up in April –– the transnational journey of a special CPKC train pulled by Canadian Paci c 4-6-4 Hudson 2816. (Sorry, but given the engine’s heritage, it’s hard for me to refer to it as CPKC 2816).
While this locomotive was built in 1930, it was part of a group of 2800s that were built between 1929 and 1930. e renowned David P. Morgan, longtime editor of Trains magazine and editor of the book Canadian Steam! (Kalmbach Publishing Company, 1961) said this about the rst group of Hudsons: “ e original 2800s of 1929-1930 were handsome, almost rakish creatures with boiler-tube pilots, visible feedwater heaters, obvious domes.”
Morgan goes on to share the story of the next series of these locomotives, known as Royal Hudsons (so named with the “permission of the British Government to commemorate eir Majesties 1939 visit)” which pulled the Royal visitors on a tour of Canada. Morgan adds that the Royal Hudsons were “identically dimensioned 4-6-4s but semi-streamlined with recessed headlights, contoured pilots and running board skirts, and domeless boilers. Each series doubtless had its supporters, but the point is that CP refrained from modifying the appearance of the rst 2800s to conform with that of the newest.”
While this upcoming event is historic because of the steam power on the train, the
most important reason is that it’s celebrating the rst anniversary of the driving the “ nal spike” ceremony that took place last year in Kansas City, Mo., marking the completion of the merger of Canadian Paci c and Kansas City Southern. Indeed, the trip has been named the Final Spike Anniversary Steam Tour and will depart April 24 from the company’s headquarters in Calgary, Alberta and arrive in Mexico City on June 4.
In my view, this trip will celebrate three major things: rst, the creation of a transnational railroad that will provide single-line service within and between the countries of North America; second, promoting trade and economic development in each country and contributing to the economic strength of North America as a whole; and, nally, the operation of a classic steam locomotive over a longer distance and being exposed to more people than any steam operation in the twenty- rst century.
Keith Creel, President and CEO of CPKC said this about the upcoming trip: “Our combination on April 14, 2023, brought together two railroads with long and proud histories that together created the rst and only railroad network connecting North America. “ is special cross-continental journey of the 2816 steam locomotive serves as a reminder of our past and a celebration of our future. We are excited to share this extraordinary experience with communities across our network as we mark the one-year anniversary of our CPKC journey. e Final Spike Anniversary Steam Tour will be the rst ever steam-powered passenger train in North America to traverse Canada, the U.S. and Mexico in a single trip.”
CPKC has published a schedule for the trip which is available on their website. If you have the opportunity, I encourage you to see this train at one of its stops along the route. Who knows if anything close to this will happen anytime soon.
Optimal management of rolling contact fatigue (RCF) in rails requires reliable, e ective, and e cient non-destructive evaluation (NDE) technologies for detecting and characterizing surface damages. MxV Rail worked in conjunction with Canada-based Athena Industrial Services, Ltd. (Athena) to introduce in-motion electromagnetic eld imaging (EMFI) technology as a means of detecting and characterizing rolling contact fatigue (RCF) in rails. A technology originally developed for mapping corrosion and determining stress corrosion cracking in pipelines for the oil and gas industry, EMFI has been repurposed for RCF detection and characterization under the Association of American Railroads’ (AAR) Strategic Research Initiatives (SRI) program.
As a non-contact NDE method, EMFI uses an exciter core and coil to generate a focused electromagnetic eld (EMF) in the rail head. A total energy sensor is used to measure the exact strength of the eld emitted by the
exciter coil assembly. e sensor also uses a series of antennas (receivers) precisely placed around the periphery of the excitation eld to create a full three-dimensional (3D) map of the EMF shape changes. e changes in the local magnetic eld strength of the back EMF generated by the surface eddy currents are measured by these antennas. In turn, the antenna coils produce a sine wave-like signal that is proportional to the position of the average magnetic eld passing through each sensor element. e change in signal level is proportional to the depth of the encountered cracks, i.e., the deeper the crack, the larger the shi or deviation from the undisturbed eld, thereby allowing the depth of the crack to be quanti ed. Outside literature describes the details of the technology.
is project allowed MxV Rail to help facilitate the development and evaluate the technology readiness level (TRL) of Athena’s EMFI technology for future commercial deployment or implementation in revenue-service.
e AAR/SRI program provides the “bridge”
that facilitates the development of innovative technologies for railway applications with the potential goal of revenue service implementation. Figure 1 illustrates the various phases/ TRL of the EMFI development project. Several tests were designed between project phases at Athena and MxV Rail to bring this technology to the railroads. Phase I corresponds to TRL 3 (proof of concept), and Phase V corresponds to TRL 7 ( eld testing). During the life cycle of this project, several iterations of hardware and soware were made. Each iteration further re ned the technology for determining the RCF crack depths to further the grinding initiatives of a eld deployable EMFI system.
ere were signi cant design modi cations between the earlier generation sensor array (Phases I-III) and the fourth-generation sensor array (Phase IV). e development of the fourth-generation sensor, named “RAGA” by the manufacturer, focused on meeting the in-service inspection requirements (e.g., the ability to inspect through switches, frogs, crossings, joint bars, guard rails, and vertically
o set rails). e EMFI sensor (both prior and current) operates in the “shadow” of a railcar or trolley wheel. By selecting this location for the EMFI sensor, researchers/developers were able to use the wheel as a guard for the sensor so that the sensor can travel a path identical to that of the railcar wheel.
Field testing was performed on a test track segment with replaceable rail retrieved from a heavily used curve. e rail installed as the outside rail was 52 feet long, and the rail installed as the inside rail was 66 feet long. ere were nine measurement locations on the outside rail and 10 measurement locations on the inside rail, each speci ed by tie number. ese test rails were also characterized by taking both MiniProf rail pro le and liquid dye penetrant (PT) measurements at each speci ed location. e EMFI test runs, made at crawling speeds and at 5, 10, and 15 mph, were repeated ve times at each speed. A target grind depth was determined based on the aggregate data, and the rails were ground accordingly. Instead of removing the RCF cracks entirely, the grinding was intended to leave the cracks behind to allow the destructive analysis to compare and validate the post-grind EMFI measurements. A er grinding, the EMFI, Miniprof, and PT measurements were repeated. e rails were removed for destructive testing, which involved sectioning the rails and examining the cracks at each measurement location.
A correlation study was rst conducted to test the repeatability of the EMFI system. Overall, many of the correlation results between di erent speeds and runs showed a Pearson’s correlation coe cient (PCC) of 0.80 or above (Figure 2). e low correlations that occurred between the crawling and 5-mph run on the low rail were expected due to issues in exact signal alignment (starting and stopping distances) and di erences in the encoding steps used for di erent speeds.
e EMFI RAGA sensor has several antennas positioned to measure and map EMF responses along the rail head (from gage corner to the eld corner). is positioning of the antennas allows the mapping of RCF crack depth in di erent locations within the rail head. ree zones (Zone 1-Gage, Zone 2-Center, and Zone 3-Field) were selected to represent di erent sections of the rail head, and the maximum value from each channel located in the three zones was selected for RCF crack depth analysis. Similarly, the maximum grind depth was determined by calculating the vertical distance di erences
(W1) value between pre- and post-grind MiniProf measurements. Figure 3 shows the pre- and post-grind EMFI maximum RCF crack depths for three zones in the low rail along with the maximum grind depths and PT measurements for low rail tie location 273. A er the post-grind measurements were taken, the test rails were removed and dissected at all measurement locations for destructive microscopy analysis. is analysis was performed to determine the remaining crack depth values. e maximum crack depth value measured was 427 µm with an average crack depth value of 117 µm and a standard deviation of 90 µm. Figure 4(a) shows a comparison of the EMFI and microscopy ndings for Zone 3 of the postgrind low rail. e EMFI system provides reasonable quantitative measurements, but crack depths in the range of 0 to 0.5 mm are insigni cant at the li -o where the sensor is currently being operated. ese crack depths can be a ected by grinding marks and are within the error band of the EMFI sensor. Based on the di erent measurement methods employed, it is extremely di cult to correlate EMFI readings with the precise crack depths because the EMFI system reports cracks within a volume of rail, and the microscopy is focused on a particular cross section.
e revised electronics and the EMFI RAGA sensor allowed for increased data sampling frequency as well as improved signal-to-noiseratio performance. e new sensor achieved sustained data acquisition rates of at least 2,000 samples per second. e key ndings of the Phase IV research are as follows:
• Run-to-run testing demonstrated a high correlation among ve runs for the same and di erent speeds up to 15 mph, with runs within the same speed having the highest correlation.
• Pre- and post-grind crack depth trends were generally captured by the EMFI system, but an exact accuracy value is di cult to state due to the fundamental di erences in measurement techniques.
• EMFI crack depth values between 0 and 0.5 mm are considered insigni cant at the li -o where the sensor is currently being operated. ese crack depths can be a ected by grinding marks and are within the error band of the EMFI sensor.
MxV Rail recently completed work with
a revenue service trial of the productiontype EMFI system that will be reported in future publications. Athena is working with its commercial partners to bring this technology forward for deployment in the North American railroads.
References
1. Poudel, A., K. Morrison, and B. Lindeman. 2023. “Evaluating Electromagnetic Field Imaging for Use in RCF Crack Depth Analysis.” Technology Digest TD23-004. AAR/ MxV Rail. Pueblo, CO.
2. Poudel, A. and M. Witte. 2021. “Validation of In-Motion ECHO-Rail System for RCD Crack Depth Measurement.” Technology Digest TD21-012. AAR/Transportation Technology Center, Inc. (TTCI)/MxV Rail. Pueblo, CO..
3. Poudel, A. and M. Witte, M. 2020.
“Evaluation of In-Motion ECHO-Rail RCD Measurement System.” Technology Digest TD20-007, AAR/TTCI. Pueblo, CO.
4. Poudel, A. and M. Witte. 2020. 2020. “Evaluation of In-Motion ECHO-Rail RCD Measurement System.” Technology Digest TD20-006, AAR/TTCI. Pueblo, CO.
5. Poudel, A., M. Witte, and P. Gies. 2019. Rolling Contact Damage Characterization on Railroad Rails Using Electromagnetic Field Imaging (EMFI). Materials Evaluation 77 (7): 951-965. American Society for Nondestructive Testing. Columbus, OH.
6. Witte, M. and A. Poudel. 2018. “Measuring Rolling Contact Damage in Rails Using EMFI.” Technology Digest TD18-016. AAR/TTCI. Pueblo, CO.
The Educational Railroading Conference Leader Since 1994
The Rail Transit Seminar is devoted to examining wheel/rail, vehicle/ track interaction on rail transit systems. This cross-disciplinary seminar includes presentations from experts in vehicle/track dynamics, noise and vibration, vehicle/track design and maintenance, friction management, and State of Good Repair. Join a unique group of transit professionals, researchers and suppliers at this seminar to examine recent developments in research and technology, to participate in lively discussion and gain a better understanding of the complex interaction at the rail transit wheel/rail interface. Sample topics include:
•Rail Grinding/Rail Milling
•Wheel/Rail Interface Studies for Vehicle Procurement
•Practical Implementation of Friction Management Systems
The Principles of Wheel/ Rail Interaction Course is an intensive, full-day course that provides fundamental coverage of the primary aspects of wheel/ rail, vehicle/track interaction. Drawing from both theory and practical application, the course covers contact mechanics, track geometry, vehicle suspension systems, vehicle/track dynamics, wheel/rail profile design, friction management, measurement technologies and more—all the elements that are required to promote a more complete understanding of vehicle/track dynamics and wheel/rail interaction. Typical topics include:
•Wheel-Rail Contact Mechanics
•Track Structures, Components and Geometry
•Vehicle Types, Suspensions and Components
•Vehicle-Track Measurement Technologies
The Heavy Haul Seminar is devoted to examining wheel/rail, vehicle/track interaction on rail freight and sharedtrack passenger systems. The Seminar brings together track and mechanical users, researchers and suppliers in a positive, educational setting like no other in the industry. Information on where and how the latest technology is being used to improve wheel/rail interaction and overall performance on freight and passenger railways is presented by some of the best minds in railroading. Information is presented through a combination of seminar sessions, panel discussions, dedicated Q&A periods and “InfoZone” sessions. Sample Heavy Haul topics include:
•Lessons Learned from Derailment Investigations
•Reducing Rail Surface Defects through Rail Grinding
•Managing Longitudinal Forces Transmitted into the Rail
•Validating Effective Friction Management in Heavy Haul
Questions: Contact Brandon Koenig, Director of Operations 847-808-1818 or Brandon@wheel-rail-seminars.com
Successful young rail engineers will lead the way to the futureBy David C. Lester, Editor-in-Chief
As usual, we had approximately 50 nominations for the RT&S 2024 10 Under 40 engineering honors. Railroad engineering is very challenging, both mentally and physically. Mentally because of the highly technical nature of the work, physically because of the need to work in all types of weather, including scorching summers and harsh winters. While all professional railroaders work hard at their jobs, the engineering team faces special demands. e work is also very gratifying though. As many rail engineers have told me, it’s a great feeling when you nish a project on which you’ve worked with a team
for relatively short times or relatively long times to signi cantly improve or build new infrastructure. Rail engineering is a constant learning process as new technologies seem to become available every week. With articial intelligence, machine learning, and data analytics making its way into the industry, it will become a more critical part of the engineer’s tool kit. Also, while there has been a lot of mechanization for various types of MOW, there is still plenty of opportunity for handson work. While the rail industry competes on many fronts, without rst-class engineering capability, any road would be hard-pressed to operate safely.
KATE BARRY
Senior Manager S&E Engineering
Norfolk Southern
Kate Barry was an honoree in the RT&S 2023 Women in Railroad Engineering recognition, so her nomination for the 10 Under 40 honor must mean that she is widely respected for her work at Norfolk Southern. Indeed, her 2023 citation for Women in Railroad Engineering read as follows: “During her twelve-year career with Norfolk Southern, [Kate] has made signi cant contributions to promote a safer and more e cient railroad. She began her career at Norfolk Southern as a Management Trainee before becoming a signal engineer. roughout her career at the railroad, [Kate] has been responsible for leading signi cant and wide-reaching e orts that have improved the railroad’s ability to safely serve customers. Kate has shown that she is adept at navigating complexity and building e ective partnerships both within and outside the company.” For this year’s 10 Under 40 honors, the person who nominated her says it best. “Kate has advanced in position and taken on greater responsibility while striving for excellence and high quality work from her team. She has always shown tremendous dedication to high-quality work and attention to detail that is well above average. As she has continued to advance, I’ve seen no reduction in her enthusiasm for quality, and I see these same traits in her team. Whenever I nd an issue, she leverages the talent of her team in a demanding, yet constructive way. She is young and tough. She is also very smart. I wish we had more o cers like her.”
KATE HAS ALWAYS SHOWN TREMENDOUS DEDICATION TO HIGH-QUALITY WORK AND ATTENTION TO DETAIL THAT IS WELL ABOVE AVERAGE. SHE IS YOUNG AND TOUGH. SHE IS ALSO VERY SMART. I WISH WE HAD MORE OFFICERS LIKE HER.
Gary Bishop, CSX’s Director of Communications and Signals, excels in uniting and motivating team members and leveraging his innovative thinking to overcome diverse challenges. His cross-departmental collaborations have driven significant business and safety improvements across pivotal CSX projects. Notably, Gary led the upgrade of the Howard Street Tunnel’s ventilation system from manual fan to remote control, enhancing emergency response times and crew safety. He also modernized Curtis Bay operations by replacing a manual switch with a remotely controlled hydraulic mechanism, improving safety and efficiency. At Marley Neck Drawbridge/Bear Creek, his introduction of a proximity switch system ensured more reliable bridge operations. Gary’s strategic innovations have markedly advanced CSX’s safety and efficiency standards, highlighting his crucial role in the company’s success.
GARY’S CROSSDEPARTMENTAL COLLABORATIONS HAVE DRIVEN SIGNIFICANT BUSINESS AND SAFETY
IMPROVEMENTS ACROSS CSX PROJECTS. GARY’S STRATEGIC INNOVATIONS HAVE MARKEDLY ADVANCED CSX’S SAFETY AND EFFICIENCY
STANDARDS, HIGHLIGHTING HIS CRUCIAL ROLE IN THE COMPANY’S SUCCESS.
Congratulations, Katherine Barry for being recognized as one of Railway Track & Structures 10 Under 40
Leading our signal design team as Senior Manager, Signal and Electrical Engineering, Katherine has a key role in ensuring our trains run safely and efficiently. Over Katherine’s 12-year career with Norfolk Southern, she has been responsible for leading significant, wide-reaching efforts that have improved our ability to safely deliver for our customers and communities. We are proud to honor her for this recognition and thank her for the impact she has made to creating a railroad of the future.
RAIL GROUP NEWS brings you a daily round-up of news stories from Railway Age, RT&S, and IRJ. This email newsletter offers North American and global news and analysis of the freight and passenger markets. From developments in rail technology, operations, and strategic planning to legislative issues and engineering news, we’ve got you covered.
In the eleven years that Ramon has been employed in the railway industry, he has always held positions in the Engineering Department. His greatest contributions have been rail and track testing projects. Ramon was one of the rst Mexican Chief Operators, responsible for operating rail aw detector (RFD) cars at Ferromex. He rst joined Kansas City Southern de Mexico in the projects area, but when leaders recognized his expertise in ultrasonic testing, Ramon was tasked with creating a customized RFD car for Kansas City Southern de Mexico. In 2021, the RFD car was acquired, and the crew was hired. To date, this car has tested more than 12,000 miles across CPKC’s network. At CPKC, Ramon leads innovative initiatives in Mexico to enhance track testing, promote operational safety and reduce expenses. e most notable of these include implementing a nonstop system in Mexico. is technology has enabled increased testing frequency in the network, enhanced reliability in the detection of defects and reduced expenses. Since 2019, we have increased the total track mileage tested by 19 percent using ultrasound cars, while decreasing the cost per mile by 24 percent. At the end of 2023, the KCS 112378 ATGMS Boxcar entered Mexico. is is an autonomous test car that measures the geometric conditions of the track, allowing CPKC of Mexico to have its own equipment for the detection of geometric defects. is will increase the frequency of testing and reduce costs. Ramon is responsible for establishing the procedure for its entry into Mexico.
HE FIRST JOINED KANSAS CITY SOUTHERN DE MEXICO IN THE PROJECTS AREA, BUT WHEN LEADERS RECOGNIZED HIS EXPERTISE IN ULTRASONIC TESTING, RAMON WAS TASKED WITH CREATING A CUSTOMIZED RFD CAR FOR KANSAS CITY SOUTHERN DE MEXICO.
While in school, Andrew began working at Fort Worth & Western Railroad (FWWR), a part of the Davoil group of companies, in Maintenance of Way track gangs. After graduation, Andrew went from swinging spike mauls and welding to several other positions within FWWR. As a Roadmaster Apprentice in the Rail Inspections department of FWWR, Andrew spent hours analyzing the health of 276 miles of continuous welded and jointed rail. Andrew then moved to the mechanics department, servicing over 30 locomotives each year. At this point, Andrew had developed a firm grasp of rail mechanics and the manual labor required for the industry to function. In the contracts department of FWWR, Andrew first began to cultivate knowledge of dynamic business relationships within the industry and how they support those individuals who work to maintain and expand the rails. Then, as a Government Affairs Liaison, he applied for government grants and ensured FWWR abided by regulations. Andrew applies his knowledge by identifying manufacturers who can bring new efficiencies to the global rail market. His success in this venture is evident through Andrew’s exclusive distribution partnership with the McCulloch Group for the Western Hemisphere. By delivering innovative solutions at a fair price to countries around the globe, Andrews is set to change the world ––one railway at a time.
Lead Operational Safety Specialist
Amtrak
Aaron has constantly provided mentorship and guidance for less experienced members of engineering, and it has proved to be valuable because he takes his own experiences both positive and negative and turns it into a opportunity for learning and incorporating safety and risk management. Aaron is a “brothers keeper” type of employee where he is always looking out for every other person working so that they remain safe and healthy. Through his guidance, I’m sure he has helped mold hundreds of track and engineering workers.
AARON HAS CONSTANTLY PROVIDED MENTORSHIP AND GUIDANCE FOR LESS EXPERIENCED MEMBERS OF ENGINEERING.
Mr. Schafer’s work as a leader and technical expert for track and terminal design has been critical to the success of numerous fast-tracked Class I railroad capacity expansion projects. Mr. Schafer specializes in track and terminal design, utilizing his skills to contribute to the railroad industry in his career as a rail designer, a construction inspector, a project engineer, a project manager and currently as a group manager overseeing a nationwide sta of railway engineers. Mr. Schafer has personally contributed to the design of over 30 railroad intermodal and automotive terminals, both new facilities and upgrades and expansions to existing facilities. His rst project was as a track designer for Union Paci c’s Global IV Intermodal Terminal in Joliet, IL. Recently, Mr. Schafer has led the design team for the expansion of Norfolk Southern’s 47th St. Intermodal Facility to expand the existing facility footprint south of Gar eld Blvd. in Chicago, Ill. Mr. Schafer’s contributions to these projects included track, grading, stormwater, site, pavement and utility design. Mr. Schafer has also contributed to the design of numerous other highway-rail grade crossings, railroad yards and mainline capacity projects. In his current role as a group manager, he mentors and nurtures the upcoming generation of railroad engineers.
RT&S 2024 10 UNDER 40 HONOREE!
Thank you for embodying the core values of Modern Railway Systems, where customer satisfaction and project excellence take precedence above all else.
Your dedication and contributions play a crucial role in the success of our company, and we truly value your commitment.
Rodney’s e orts have made signi cant impacts on multiple rail projects in nearly every corner of the United States in his 9-year career. His contributions have led to the successful implementation of Positive Train Control (PTC) on 3 di erent railroad properties as well as the completion and startup of 4 light rail alignments. Rodney’s passion, tenacity, and positive outlook has given him a reputation as a project partner that will complete the toughest of tasks on time and with a smile on his face. e following provides an accounting of Rodney’s entry into the rail industry and his contributions to date. A er graduating from Utah Valley University, Rodney began his rail industry career in 2015 when he joined Stacy Witbeck (SW), a heavy civil contractor specializing in rail infrastructure projects. Within Rodney’s rst year at SW, he was asked to transfer to Modern Railway Systems (MRS), a fully owned subsidiary of SW specializing in train control, communication systems, and systems integration. Over the last 9-years, Rodney has held several positions on many di erent rail projects across the United States and helped the company win the multi-billion-dollar project.
With 11+ years of Class 1 Railroad experience specializing in Public Projects, Taylor Smith is a major industry contributor who has delivered rail projects, improved safety, and helped drive decision-making. His background in Public Projects consists of corridor safety improvements, grade separation and crossing elimination work, partnership with State DOTs and municipalities on Federal Section 130 projects, mining and organizing data to identify trends, leading on-site crossing assessments for both public and private crossings, and working on quiet zones. He also has experience in capital line and terminal railroad expansion, third-party utility permitting and oversight, so ware and project database management, and intermodal and auto facility expansion. From 2020 to 2022, Taylor managed a ~$120 million annual Capital Expansion Plan, which entailed working with Capacity Planning to identify the system bottlenecks, Capital Planning to identify when capital funds would be available, and Engineering to properly identify the scope, delivery schedule, and cost estimates. Prior to Public Projects, he served as a Project Engineer and oversaw coordination and safety aspects of third-party public projects on railroad property.
CSX congratulates Gary Bishop II for his well-deserved recognition as one of Railway Track and Structures’ esteemed Top 10 Under 40 honorees! Gary’s exceptional commitment to fostering unity and motivation among team members, coupled with his engineering ingenuity, has significantly contributed to enhancing CSX’s safety protocols and operational e ciency. His unwavering dedication underscores the immense value he brings to our organization.
Zach is actively involved in numerous rail professional organizations and is currently Vice Chair of APTA’s Passenger Rail Equipment Safety Standards Inspection and Maintenance Working Group and is also Secretary of APTA’s Rolling Stock Equipment Technical Forum. Zach and his wife are active foster parents and have (so far) adopted two children out of the Philadelphia foster care system. He is a Professional Engineer in Delaware, New Jersey, Pennsylvania Project Management Professional Leadership in Energy and Environmental Design (LEED) and holds an Accredited Professional Certi cate in Earned Value Management from University of Alabama. Zach’s long-term goal is to gain broad experience and expertise in executive engineering leadership to eventually drive the success of a progressive rail organization. Zach demonstrates strong leadership skills daily as he is currently responsible for directing ve rail vehicle capital asset acquisitions totaling over $2.6 billion across multiple transportation modes. He oversees SEPTA’s New Rail Vehicles group of 16 engineers, designers, and managers. He plans and leads the reorganization and recruiting process to expand the group to 29 and is responsible for group performance.
Ryan joined Mississippi Export Railroad (MSE) in 2021 as the Superintendent of the Maintenance of Way department. Ryan leads the maintenance and repair for all 42 miles of track that MSE owns, as well as the track operated by Alabama Export Railroad (ALE). Under Ryan’s management, MSE has installed close to 20,000 new crossties to support the increasing annual tonnage while promoting safety for its community and customers. Ryan has also made significant improvements within the compliance and safety department, completed over 10 rail grade crossing projects, and most importantly has kept an injury free record for his department.
Congratulations to Taylor Smith, Director of Public Projects, on being a 10 Under 40 honoree! Taylor forges collaborations between railroads and public agencies and has delivered rail projects and revolutionized safety operations. His passion for the industry is infectious, and his presentations have helped inspire young rail engineers.
We appreciate all you do, Taylor!
CRAIG JOHNSON
Director – Track &Structures
Thunder Bay Division, CPKCAs Director Track & Structures –under Bay, Craig is a recognized leader and innovator at CPKC. He recently led a team to design and implement a new patented technology called ‘Spring Drains’. e Spring Drain is a composite geo-synthetic installation that is installed vertically between track ties to stabilize the ground. Speci cally, the Spring Drain is used to repair ‘peat boils’, which cause surface defects beneath the track structure in swampy terrains in Northern Ontario. Peat boils can pose costly and unsafe consequences, including derailments. Spring Drains are both innovative and cost-e ective; they can be installed on existing rail lines between trains without taking essential rail links out of service and can be completed at a fraction of the cost of traditional solutions.
BEN MILLER
Director – TankCar Engineering
GreenbrierBen recently chaired the executive committee of the Railway Supply Institute Committee on Tank Cars. is was during a critical phase as the rail industry addressed the impact of the East Palestine derailment in 2023 as well as helping to promote new technologies and safer designs while on the committee. Ben is an active community member. He has volunteered as President of his Homeowners Association for the past two years. He is dedicated to giving back to his community and improving his neighbors’ living experience. Ben has a bachelor’s degree in mechanical engineering and was introduced as the Chairperson of the Railway Supply Institute Committee on Tank Cars (RSICTC) in 2023. Ben’s goals are to continue growing his career and building his relationships.
RT&S UNDER 40 ENGINEER AWARD
CONGRATULATIONS AND THANK YOU, AMTRAK®
Chris has worked for Holland since 2014, starting as one of its Product Engineers. rough his 10 years at Holland, he’s worked his way to represent the Holland Transportation Technology (HoTT) Business Unit, now as its Engineering Manager. Over his time, Chris has developed new rail car product solutions as well as tweaks to its products to keep them up to date with the ever-evolving rail car market. Speci cally with its auto rack rail car products, Chris has been working to ensure the Tri-Lo Chock’s new body will allow the chock to t into Group D clearance envelope. is new chock will replace its Model 2, currently in Group C, and allow its customers to have a wider range of use to keep vehicles traveling to their next destination in rail cars safe and secure.
OVER HIS TIME, CHRIS HAS DEVELOPED NEW RAIL CAR PRODUCT SOLUTIONS AS WELL AS TWEAKS TO ITS PRODUCTS TO KEEP THEM UP-TO-DATE WITH THE EVOLVING CAR MARKET.
There are many forces that work to deteriorate track geometry over time. These forces don’t begin and end at the wheel/ rail interface; they are transmitted to the vehicles and their components and into the track structure and its components. On ballasted track, ballast absorbs these forces, and its maintenance is critical to preserving and correcting several types of track geometry defects.
Maintaining track geometry is an ongoing process that affects both safety and ride quality. “It’s akin to fixing potholes on a roadway before they
become dangerous,” Fabian Hansmann, Deputy Director of Marketing at Plasser & Theurer/Plasser American told delegates at the 2023 Heavy Haul Wheel/Rail Interaction conference. “Small geometry deviations can grow exponentially worse if they’re not corrected early,” he added. Track geometry directly influences the condition and behavior of other components in the system such as the rail, fasteners, and ties. Through these components, forces are ultimately transmitted into the ballast, and as the ballast shifts, so too does the track.
“Tamping machines that combine
ballast-packing and track alignment functions are a universally-adopted technology for maintaining ballasted track,” Hansmann said. They vary in design and specification but generally function on the same principle. “Consider a track geometry surface defect that has been identified and measured,” he added; the process of correcting the defect with a tamper consists of the following steps:
• Centering: the tamping machinery is positioned at the defect site.
• Insertion: the tamping tools are inserted into the ballast on both sides of a tie.
• Squeeze/Oscillation: the tools lift the tie, perform a squeezing motion to fill the void beneath it, and oscillate to compact the ballast that fills the void.
The squeeze cycle typically occurs over 0.6 to 1.2 seconds. “This is where the magic happens,” Hansmann said. Depending on the characteristics and requirements of the rail system and the ballast conditions, there is nuance and variance in how the tamping parameters (like number of insertions and tamping cycle time) are applied. “Each part of this process is set by the operator, so the efficacy and quality of tamping is dependent on their experience,” he said. “Therein lies the potential for improving and optimizing the tamping process,” he added.
To better understand and to optimize the tamping process, Plasser & Theurer partnered with Penn State University to investigate tamper/ballast interaction at its most granular level, and take the first, early steps in developing a tamper that can assess and measure ballast characteristics, provide the operator with relevant data, and perform the work with precision and uniformity.
In order for a tamper to “know” ballast conditions and adjust its parameters, it requires a kind of tactile feedback. “It’s like a human hand gripping something. Your senses tell you the consistency of the material or the force you’re exerting,” said Yuliang Zhou, a
graduate research assistant in civil engineering, specializing in structure health monitoring of railroad infrastructure, at Penn State University. To replicate this tactile sense, Zhou and Plasser & Theurer instrumented a tamper with a suite of measurement devices including accelerometers, strain gauges, pressure sensors, and angle encoders. Combined, these sensors allowed them to precisely monitor the input forces of each part of the tamping cycle. To measure the output — the ballast response — the team developed and deployed a number of “smart rocks” — wireless devices that are roughly the size of a ballast stone and contain an accelerometer, gyrometer, and a stress cell. “When placed at a tamping site, the sensors can directly measure the translation, acceleration, rotation, and
SMART ROCKS” ARE WIRELESS DEVICES THAT ARE ROUGHLY THE SIZE OF A BALLAST STONE AND CONTAIN AN ACCELEROMETER, GYROMETER, AND A STRESS CELL
stress [of the ballast] during tamping,” Zhou said.
With these tools, the research concept was to measure tamping input parameters (number of insertions, oscillation cycles, squeezing time and force), measure the ballast performance during tamping, and measure ballast performance after tamping. “This allows us to establish a direct link between input and performance,” he said.
Field testing was conducted at two sites representing two ballast conditions: one site with clean ballast, and one with fouled ballast. At each site, tests were conducted with varying squeeze time and number of insertions, while the lifting value (25mm) and squeeze pressure (35Hz) remained constant. Smart rock sensors in groups of six were placed beneath four ties, spaced 20 ties apart.
These measured ballast reaction during and post-tamping.
Figure 1 shows an ideal reaction force and displacement curve for a single squeezing cycle (on the left). The cycle is broken into three phases: loading, unloading, and withdrawal. This cycle is repeated multiple times during the tamping process. In practice, these values fluctuate slightly from cycle to cycle (as shown on the right). “The maximum values as measured across multiple cycles set the boundaries of reaction force and displacement for the sake of data analysis,” Zhou said. Figure 2 shows these maximum reaction forces in kilonewtons over the course of multiple squeezing cycles at the fouled ballast site for squeeze time values of 0.6 seconds and 0.8 seconds. “The maximum reaction force starts low and increases until it hits the maximum value and stabilizes at around the 12th cycle, or about 0.35 seconds,” Zhou said. This means that a longer squeeze time equates to more time spent at maximum force values.
From the perspective of the ballast, there are two primary ballast acceleration events: tamper tine insertion and the squeeze cycle. At the clean ballast site, these events followed a pattern of a smaller, shorter acceleration during insertion, and a longer, higher acceleration during the squeezing cycle. The
fouled ballast site results were less clear, in some cases showing an opposite acceleration pattern with higher g-forces during insertion, and lower during the squeeze time. “Our guess is that fouled ballast has more fine particles and mud that absorb energy imparted by tine insertion and squeezing,” Zhou said.
Figure 3 shows a comparison of ballast acceleration forces in clean ballast (above) and fouled (below) ballast at multiple numbers of insertions and squeeze cycle lengths. “Another way to frame this nding is that clean ballast appears to be more sensitive to tamping parameters in general,” he said.
The smart rocks also measured ballast rotation during tamping. Here the data showed that clean ballast exhibited a relatively high rate of rotational change compared to the fouled ballast, which averaged less than half the clean ballast values. When particle rotation is correlated to acceleration data, the overall picture is one in which clean ballast generally shows higher rotation for higher acceleration, while fouled ballast shows less rotation for all acceleration values.
Figure 4 shows a comparison of tamping force (input) and ballast bulk stress (output) for different cycle lengths.
“The data shows that as tamping force increases, bulk stress increases quickly, and then tends to stabilize even as tool force stays constant,” Zhou said. This pattern is also apparent in the comparison of ballast bulk stress to tamping tool displacement – both increase rapidly, then (relatively) slowly level off over the course of a tamping cycle.
Although testing at these two sites is ongoing, there are some preliminary results on post-tamping ballast performance. To measure overall ballast stability, the team measured normalized ballast bulk stress over time. “If the smart
TrackSafetyStandards Subparts A-F
TrackSafetyStandards, containstheTrackSafety Standards,SubpartsA-F,forClassesoftrack1-5.The standardscovergeneralinformation,Roadbed,Track Geometry,TrackStructure,TrackAppliancesand Track-RelatedDevices,andInspection.IncludesDefectCodes. Updated December28,2023
BKTSSAF TrackSafetyStandards,SubpartsA-F $11.95
Only$10.75forordersof50ormore!
FRAPart237establishesFederalsafetyrequirements forrailroadbridges.Thisrulerequirestrackownersto implementbridgemanagementprograms,whichinclude annualinspectionsofrailroadbridges,andtoauditthe programs. Part237 alsorequirestrackownerstoknow thesafeloadcapacityofbridgesandtoconductspecialinspectionsif theweatherorotherconditionswarrantsuchinspections. Updated December28,2023
BKBRIDGE BridgeSafetyStandards $8.95
Only$8.00forordersof50ormore!
ThisreprintincludestheFRA's RailroadWorkplaceSafety Standards addressingroadwayworkersandtheirwork environments.Theselawscoversuchthingsas:personal protectiveequipment,fallprotection,andscaffoldingfor bridgeworkers;andtrainingissues.Alsoincludessafetystandardsfor on-trackroadwayvehicles. UpdatedDecember28,2023
BKWRK RailroadWorkplaceSafety
Only$10.35forordersof50ormore!
$11.50
The TrackSafetyStandardsCalculator isamustfor anyonewhoworksontrack.Thisslideruletype calculatorcontainsmanyofthedetailsforClassesof track1-5.Deviationfromuniformprofileandfromzero crosslevel.Differenceincrosslevel.Compliantwithpart213.
BKTCAL TrackCalculator
Only$10.75forordersof50ormore!
$11.50
UpdatesfromtheFederalRegistermaybesuppliedin supplementform.
rock stabilizes over time, it indicates the ballast has stabilized,” Zhou said.
Results at the clean ballast site show roughly similar stability for all test variables, except the combination of 1 insertion/0.6 seconds squeeze time. Results at the fouled ballast site are more divergent. Here, the ballast shows more consistent stability at 1 insertion/0.8 seconds, and 1 insertion/1.2 seconds squeeze time. “We believe that the ne particles and mud [in the fouled ballast] provide some dampening and stability that is disturbed by multiple insertions or more
LOOKING FURTHER TO THE FUTURE, TAMPERS MAY BE ABLE TO ADJUST THEIR PARAMETERS AND OPERATE AUTONOMOUSLY.
rapid cycles,” Zhou said. “However, this data represents a small sample over a fairly short period, and more testing and data analysis is required,” he added.
“For the time being, this investigation has yielded some general conclusions,” Zhou said. e rst is that from the ballast’s perspective, the squeezing phase can broadly be divided into two phases – the initial disruption of the ballast structure as it is swept into the void le by the tie, and the compaction or interlocking of that ballast.
e second is that clean ballast is generally more responsive to tamping parameters and variables, and that longer cycles (1 second vs 0.6 seconds) tend to yield better results in terms of ballast stability. It also appears that the de ciencies of short squeeze times in clean ballast can be improved by multiple insertions. “From a tamping production standpoint, this means slowing the process down may result in slightly fewer feet per hour but will leave the ballast in a more stable condition that requires less frequent tamping,” Plasser & eurer’s Hansmann said.
Penn State and Plasser & eurer plan to conduct further eld tests at these sites and perform additional data analyses on the tamping and post-tamping results. “Ultimately,” Hansmann said, “the goal
is to reach a level of con dence in these measurements that tampers can be out tted with feedback mechanisms that indicate to the operator the quality of the ballast, the ideal squeeze cycle, and whether an additional insertion is required.” Looking further to the future, tampers may be able to adjust their parameters and operate autonomously, leaving behind ballast that is
stable and consistent, and track that is free of geometry defects.
Je Tuzik is Managing Editor of Interface Journal ( www.interfacejournal.com )
is article is based on a presentation made at the 2023 Heavy Haul Wheel/Rail Interaction conference. Premier Rail Industry Events and Education - Wheel Rail Seminars (wheel-rail-seminars.com
or our April issue, I sat down with John Kasel, CEO of L.B. Foster, to get a better sense of the executive behind the rail supplier. O en, c-suite executives remain these picture-less names who are o en heard of but remain squarely behind the desk. I did not get that sense from Kasel. As I interviewed Kasel, the word “connection” came up numerous times. In speaking directly with employees to foster a sense of camaraderie within the company, John Kasel strikes a person as someone who genuinely wants to get
down to the root of a challenge and gure out the best way to solve it.
Jennifer McLawhorn: Can you give us a background of yourself to give our readers some information about who you are?
John Kasel: I was born and raised in St. Paul. At that time, the largest employer there was Burlington Northern railroad, so the neighbors where I grew up were executives of the railroads. at was my rst segue into what a railroad is. BN at that time was headquartered in St. Paul. So, I spent quite a bit of
time there for my career [and] I moved around the Midwest quite a bit. Back in 2002, I was in Minneapolis at the time, and I got a call from L.B. Foster. It looked like a wonderful opportunity to work for a company that really wanted to do something related to LEAN operational e ectiveness and become a world-class manufacturing operation but really had no leadership or ability to make that happen across all of North America. So, that was the thing that excited me because I did much of that working for other companies in the past. L.B.
was a small enough company where I felt there was an opportunity that I could do something and not be just a number, but where I had an opportunity to build a career. At that time, we had young kids, and it was an opportunity to go to a place where they could go through grade school, and we could settle down.
McLawhorn: What attracted you to the supplier industry? What made you want to stay and grow here?
Kasel: It’s a small, publicly traded company. I rst met with people who were running the company, [speci cally] Lee Foster and Stan Hasselbusch. ey were running it more like a family, and you could see that they had good, strong values and culture system. It looked like a great place to work [where] you could do things today, and you could see the results tomorrow. So, I liked that. ey wanted help and really didn’t know how to get there, and I felt I could help them as well. It wasn’t a huge company by any stretch of the imagination, but I could see where we could grow substantially, and we have over the last twenty years. I thought I could be a part of that. It’s worked out well.
McLawhorn: It sounds like you really focused on the longevity of it and how much growth and potential there is. I read that you had introduced LEAN manufacturing in your rst role, which seemed quite customercentered. Is that something you’re still doing years later?
Kasel: We do it from two angles. We do it from the customer as well as the employee. Because the employee is the one that feels the pain. So, you really want to drive the behaviors and really help them get through their day and be more e ective and e cient in what they do. at’s how you get the buy-in. And they know where and what the waste is. So, they feel empowered and engaged, and then it becomes part of the process moving forward. But you need to connect it to something. e easiest thing to do is to connect it to the customer. So, if you’re working with an admin group, you connect it to an internal customer such as another department. Much of what I did was in manufacturing operations, so you’d connect it to the end customer. In this case, it was the rail industry, the transit authorities, Class Is, Class IIs, or regional railroads. So, you have a better appreciation of what their pain is and how you a ect them and how you’re what I call an extension of them. en, you just connect the dots quickly. You don’t want to spend a lot of money on this stu . You want to think your way through this stu and get people really excited and motivated about making a change and doing it as soon as you possibly can.
McLawhorn: Stemming from that, what about your thought process? Whenever you’re developing anything new, is it collaborative right from get-go? Or do you take time to think your way through it?
Kasel: Well, I try to do what I can to think through it rst, so I can formulate my ideas. I do try to drive the vision for the company, but the people who work for me are much smarter and more intelligent than I am. My role is to facilitate. So, I’ll throw a new idea like we did with the new brand (our centrifuge), but then I’ll get other people engaged in what we want to do. So, it’s all about facilitation. Keep it simple.
McLawhorn: Looking at L.B. Foster’s history going into the present and the future, what are you really excited about?
Kasel: We’ve been around for 121 years now. We’ve come a long way but at the end of
WE USE THE WORD ‘FOSTER’ A LOT, BUT IT’S TRUE. OUR SECRET SAUCE IS OUR PEOPLE AND CONNECTING EMPLOYEES WITH THE CUSTOMER. THAT’S THE MAGIC.
the day, much of what we did was still making steel components. I wanted to do more than just make steel components. I want to bring technology and innovation into it. So, now we’re giving the end customer the ability to do something di erent, like when I was talking about LEAN. You’re working on safety and reliability in the railroad, but that’s a lot more than just components. In the last 15 years, we’ve branched o doing other things in the company. And we bought a company back in 2010 called Portec, which made us a global company literally overnight. And then, we did some acquisitions in the UK and Europe back in 2015 which brought in more technology. So, where we’re really starting to help the industry more than ever is with our condition monitoring. at’s designed to really help them understand how to make sure passengers and freight get to locations with reliability and repeatability. So, they understand if there’s an issue on the track. ey understand if there’s an issue related to something going on with the train and manage it before it becomes a possible
derailment or a slow order. So, that’s where the company is really transforming into a technology and innovation company, an e ort that has been building over the past 15 years.
McLawhorn: Is there anything you can tell our readers that L.B. Foster is currently working on?
Kasel: So many of the things that we have are now becoming more and more important to the FRA, especially with what happened in East Palestine, Ohio. It’s really understanding what’s going on related to the trains moving on the track. So much of the stu we’ve had is becoming noticed and more widely adopted by the markets today on the transit and freight side. At the end of the day, it’s the suppliers and the end customer that need to gure this out together. I think over the coming years, things are going to change for the better in the rail space. Rail is only 2.7% of the emissions of all of the transportation market. So, I think it is the answer of moving things o of airplanes and trucks and onto the rail space. It’s about getting better at LEAN and getting those products and services to the end market and doing it on time. It’s making it as easy for the trucking carrier as it is working with the rail. Today, that’s not the case. ere are many things that are happening in the rail space today that should help it be more competitive as well as start to move freight o roads and onto the rail systems. And people too. I think we’re going to start seeing Brightline and others come to fruition. I think we’re going to start seeing major cities being connected by rail systems.
McLawhorn: Like Brightline West.
Kasel: Oh yeah, that’s a great start. I spent a lot of travel around the world on transit systems that are fantastic. en, you come to North America, and you can’t get anywhere unless you get on a plane or drive across the country. at needs to change. I was just in the UK last week, and I got around the country all on rail. I didn’t spend any time in a car. It was so nice. e other thing about the company is not that we just have products we want to sell, but we provide innovation in engineering to the end market. I think that’s how we di erentiate ourselves. Customers come to us with a problem. One of the greatest things we can do is bring them a solution. And I think that’s what separates us from people just trying to sell what they have. We like to help them but do it with something that maybe doesn’t exist today or make modi cations to something we currently have. We use the word ‘foster’ a lot, but it’s true. Our secret sauce is our people and connecting the employees with the customer. at’s the magic. And when you can do that, you’re in a really special place.
McLawhorn: Is there a sector at L.B. Foster that you’re really drawn to?
Kasel: e company’s history has always been rail, so I gravitate toward that more than anything else. I do have that rail mindset, both transit and freight. It’s something that needs to continue to evolve. We’re moving people. We’re moving freight. So, at the end of the day, I gravitate towards that more than anything else. And, we’re doing our part to bring rail to the next generation. We need to get better. It’s like LEAN. You’ve got to keep evolving.
McLawhorn: You mentioned evolving. Is there anything you would change or add to LEAN?
Kasel: Well, LEAN is all about common sense unfortunately [laughs], which isn’t that common. e thing with LEAN is that we do a lot of good things, but you have to sustain what you do. It’s all about getting the right things, but you’ve got to keep at it each and every day, or you lose what you gained. It’s not a project. It’s a journey. It is about evolving. It’s tough because you never get to the end. at’s the most frustrating but fun thing about it because you’re never at a destination. What I get excited about is when the job is easier for the people who make the products and services. It’s very rewarding to see come together. And today in a post-covid, virtual world, it’s not easy on the admin side. It’s much more di cult to connect than it was in the past. So, these LEAN principles are more important than ever. Behind all this, you want to have good KPIs (key performance indicators) and goals and measures, and you want to challenge yourself to get better. And then, you bring in the tools, and you work on one thing at a time.
McLawhorn: So, that’s really the secret sauce. You have your goals, your KPIs, your tools, skills, and the right people?
Kasel: e key is the people. Most of the time, 95% of the problem when you have an issue is never people. People really want to do a good job. It’s the process, so you want to keep working on the process. But if you have a person who doesn’t want to be part of the solution and is against what you’re doing, you have to make the change. But that’s the exception, not the rule. Most people want to see something get better and improve.
McLawhorn: So, if that challenge came up, how would you go about solving that problem?
Kasel: First, clearly identify what the issue is. You glean information from your KPIs and data and say, “What does this really mean?” From there, what I’ve done is bring in a group of people together. And, then you talk about it. You start with the ve ‘Whys’. “Why is this happening?” You go down about ve levels where you start to understand, “Wow, maybe
“I try to be very engaging. . . When you’re talking to people, it’s about making them feel comfortable.”
this is really cause and e ect.” en, you can get your tools into place and talk about action plans. It becomes a project where you go out and make something happen. You get people energized about it. I just facilitate. People have roles, responsibilities, action items, and I let them foster their activities and get things done. Whenever possible, I try to do things within 90 days. Because many of the problems we have we can x just by talking and communicating and working on the process. You follow up and learn where you can take it to other parts in the organization. at organizational learning is where it gets kind of fun.
McLawhorn: Going from a smaller steel company to one on a global scale, do you nd any challenges with maintaining a smaller, connective feel?
Kasel: ere were two issues. One was getting our customers to understand we’re a di erent company today. Because they saw us as someone who just sold rail and track components. at was a whole pivot to a technology and innovation company than one that just sold components. And then, the connective part being global. As far as geography, it’s very di cult. What I do to help is travel a lot, but I also do town hall meetings o en where we meet with the entire company at one time. And then, I’ll have other people speak to what’s going on with the company. I nd that to be the best thing. And then, we have visual communication boards that we do. So, we have messaging to try to connect the employees which is very di cult to do when you’re working in di erent time zones. But, you have to really work at it. And there’s nothing like being in front of
people. at’s why I try to do as much as I can to get out to visit our employees and customers. Sta , too. It’s never just me. You want to set that positive tone from the top. e best way to do that is face-to-face.
McLawhorn: “Foster” seems to be the best word here. How is it when you’re in these town hall meetings or any virtual space with employees? How do you help foster and maintain very open communication? With CEOs, people can be intimidated and may not want to bring something up.
Kasel: What you see is what you get with me. I know exactly what you’re talking about. I did a graduate program at Harvard Business School with big CEOs from all over the world. I know how some people act. I’m not that way. I act completely di erently. I try to be very engaging. ere can be the other side of me too that’s very serious and to the point. But when you’re talking to people, it’s about making them feel comfortable. So, I’ll talk to anyone at any time about anything and make myself accessible. Our job at L.B. Foster is to protect that culture. I said it before, but that is our secret sauce.
e importance of communication became the running theme throughout the interview.
Kasel stressed that “Communication can end at one level, and then it just dies. When I visit, I grab small groups together, 12-15 people, and I just talk to them. ey work in all facets of the company, and we just talk. ere’s no agenda.
ey can ask me any question they like. Just like today. We just have a chat. ey learn about me and what’s going on in the company. I nd the most rewarding thing I do in the company is just to talk.”
Thisneweditionencompassescurrentdesignmethodsused forsteelrailwaybridgesinbothSIandImperial(US Customary)units.Itdiscussestheplanningofrailwaybridges andtheappropriatetypesofbridgesbasedonplanningconsiderations.
BKDMSRB2 Design&Const.ofMod.RailwayBridges
DictionaryofRailway TrackTerms
Themostcomprehensivecollectionofdefinitionsrelatingto track.Over1500termsfromantiquatedforgottenslangto today'sjargon.Clearlyillustratedlineartenhancesthetext.
Railgrindingsavesmillionsofdollarseveryyear!TheArt andScienceofRailGrindingisthefirstbookdedicated exclusivelytothesubject.
BKGRIND RailGrinding
History does repeatitself.Manyoftheseissuesarebrought tolifebyexploringexampleslearnedfrommitigatingvarious issuesandtacticsusedwhentheNYCTAassumedcontrol oftheBMTandIRTlines.
BKNYIRT Dev.&Op.ofNY’sIRTandBMT
TheTrackDataHandbook
Reprintedbypopulardemand,thisbookisavaluable referenceforroadmasters,tracksupervisors,trackforeman, surveyorsandothersinvolvedintheplanningandexecution oftrackmaintenanceandconstructionwork. Fold-outdiagrams.Softcover.301pages.
BKTDH TrackDataHandbook
TheTrackSafetyStandardsCalculatorisamustfor anyonewhoworksontrack.Thisslideruletype calculatorcontainsmanyofthedetailsforClassesof track1through5.Updatedasof July11,2013.
BKTCAL TrackCalculator $11.50
Only$10.75forordersof50ormore!
Railroads&Economic Regulation (AnInsidersAccount)
Railroads&EconomicRegulation tracesthedevelopment, failuresandsuccessesofrailroadeconomicregulationbyan insiderwhowasaWhiteHouseappointedchiefofstaffat theSurfaceTransportationBoardandaseniorofficeratthe AssociationofAmericanRailroads.Hardcover,414pages.
BKRER Railroads&EconomicRegulation $69.00
RailwayGeotechnics
RailwayGeotechnics coverstrack,tracksubstructure,load environment,materials,mechanics,design,construction, measurements,andmanagement.Itiswrittenprimarilyfor professionalsandgraduatestudents. BKGEOTECH
ClassesofTrack1-5;General;Roadbed;TrackGeometry;Track Structure;AppliancesandDevices;TrackInspection;andDefect codes.IncludesGaugerestraintMeasuringSystem(GRMS.).
BKTSSAF TrackSafety,SubpartA-F $11.95 Order50ormoreandpayonly$10.75each
YourGuidetoRailwaySignals isanexcellentguidefor trainingsignalpersonnelespeciallyrailwaycross-function managers,supervisors,andsupportpersonnel.Highqualitygraphicsanddiagramshavebeenusedthroughout. Complieswithallstandardsandcommonlyusedpractices.
BKYGRS YourGuidetoRailwaySignals
Gainadeeperunderstandingoftheevolutionoftrack technology.Thisbookpresentstheknowledgeneededfor rationaldesignandmaintenanceofpassenger,freight,and transittrack.
BKFRTE FundamentalsofRailwayTrackEngineering
Thefiftheditionof TheRailroad:WhatItIs,WhatitDoes is evenmorevaluablethanbefore.Insideyou’llfinda comprehensivelookathowtoday’srailroadsfunction—from equipmenttoproceduresandmarketingtomaintenance.
BKRRNN WhatitisWhatitdoes
$49.95 $220.00* $150.00Perhaps an overlooked area of track infrastructure maintenance, railroad hand tools still provide crews with what they need to complete tasks that are le to manual labor. From pullers and spike mauls to track wrenches to rail pullers to power tools, there is a vast array of railroad hand tools that can t and ll every maintenance equipment gap. What follows is a sampling of this area in the rail supplier industry.
Pandrol’s Light-Weight Battery-Operated Weld Shear provides a safe solution to zero-emission shearing of eld welds in track. e Weld Shear incorporates battery technology delivering the proven power for
removal of the welds that Pandrol has consistently brought to the rail industry. Designed to operate with the included battery-operated non-impacting drill, the simple chuck attachment allows easy installation of the shear, so it is quickly operational on track. is self-contained battery-operated weld shear eliminates that need for external power hose connections and permits for a clean emission free shearing method. Utilized from the heavy haul lines in Australia to the London underground along with domestic contractors and railroaders, its lightweight design is important in today’s decisions for choosing safe, reliable equipment. e Pandrol HRT100 Head Riser Removal Tool
allows for the safe removal of the welded riser without the need to use a hammer. e hand-held device works on any weld and weld shear for the safe removal process by the shear. A er shearing through the weld, retract the weld shear and hold the HRT100 in position for a secondary shear operation which clears the welded riser material safely o the weld. Use of this tool for the eld weld process now makes for a safer method in the day-to-day operation.
As part of the Goldschmidt Group, PortaCo Goldschmidt o ers a complete range of hydraulic tools and power units for the railroad industry. PortaCo is particularly proud of the tools it manufactures to support
the ermit® welding process. ese tools o er unbeatable power in all weather conditions with no detriment from either the heat or cold. Leveraging the knowledge and expertise of the Goldschmidt group’s global experts in ermit® welding, PortaCo is focused on how to continuously improve its products to drive e ciency as well as supporting the needs of our customers. With its focus on continuous improvement, PortaCo has been working closely with many customers including several Class I Railroads to enhance their tools to meet the requirements of working on the railroad. A number of subtle updates to the tools improved their performance and ergonomics, and the results have been well received by all customers who have used them. ese updated tools include pro le grinders – both heavy and lightweight based on the user preference, weld shear, rail notcher, and rail puller which complement its suite of proven maintenance of way tools. PortaCo tells RT&S it is “proud of the developments that we have made as well as new tools that we are working on that we look forward to sharing in the near future.”
If material handling systems sounds like a broad topic, that’s because it is. What can encompass specialized equipment to serve one purpose or handle a multitude of maintenance tasks, these machines allow contractors to nish a range of jobs across the globe, as seen in DavRail’s project story on Panel Li s in the Yucatán Peninsula. From loading and unloading material to machines that can be combined with or without material carts, suppliers o er their best in material handling systems for 2024.
Construction work on the railway involves shi ing enormous quantities of
By Jennifer McLawhorn, Managing Editormaterial in a short time. ousands of cubic yards of excavated material and new material have to be loaded into wagons and transported. Material conveyor and hopper units of Plasser American’s MFS series demonstrate how state-ofthe-art material logistics function and in uence the e ciency of the sequences, the duration of the construction work and ultimately on the cost-e ectiveness of the projects. ese machines come in four variations: MFS40, MFS60, MFS100, and MFS100 S. e units are capable of conveying, storing, and unloading up to 41 (MFS40), 61 (MFS60), and 90 (MFS100 and
MFS100 S) cubic yards of ballast, spoils, or other material in train formation to and from various work sites. e MFS100 S also sports an additional transfer conveyor belt and ballast distributing devices, which allows an exact dosage of the ballast onto the track or onto the ballast shoulder. e hoppers are suitable for all kinds of loose material. All conveyor belts are powered hydraulically, and a diesel engine supplies the power. Material conveyor and hopper units can make an important contribution towards raising the overall annual outputs of ballast cleaning machines. All storage, transporting, loading, and unloading can
DavRail, Inc.’s Panel Lifter’s size and maneuverability can remove and install any type of rail panel measuring up to 60 meters long and pre-position up to 12 concrete ties at once.
be performed in completely mechanized processes using the material conveyor and hopper units. And the adjacent track remains open for tra c. For single-track lines, this method is the only possible way to e ectively take away material.
Pettibone o ers the Speed Swing 445F2, the newest version of the industry’s original do-it-all rail crane. Developed with customer feedback in mind, the 445F2 is compatible with more than a dozen attachments for laying rails, setting ties and numerous other maintenanceof-way tasks. Powered by a fuel-e cient 163-horsepower Cummins QSB4.5 Tier 4 diesel engine, the Speed Swing 445F2 o ers a 49-gallon fuel tank, a 29-percent increase over the previous model’s tank, allowing for extended working intervals. e
445F2 o ers a maximum front load capacity of 10,000 pounds and maximum side load capacity of 8,000 pounds. Providing 180-degree boom rotation, the machine is primarily used to thread out old rail and thread in new rail. An optional magnet package quickly cleans up old plates, spikes and small pieces of rail. e unit can also tow rail carts, move railcars and supply air or hydraulics for hand tools. Featuring a Dana T20000 3-speed transmission with twist-grip electric shi control that delivers exceptional torque, the Speed Swing quickly transitions between jobsites, traveling at 25 mph on hi-rail and 20 mph with all-terrain rubber tires. e tires – along with 4-wheel-drive with a rear wheel disconnect – a ord greater maneuverability o the rails. Durably built for challenging railroad applications, the 445F2 o ers planetary front and rear axles with front di erential lock. Four-wheel outboard drydisc service brakes provide sure stopping power. A standard feature for the 445F2 is X-Command®, a Pettibone telematics program that o ers real-time access to machine data.
Industry-Railway Suppliers is the exclusive US distributor of Rosenqvist machines and attachments, and a leading North America distributor of AREMA track tools, abrasives, heavy railroad equipment, work equipment wear parts and mechanical shop tools. Rosenqvist has been designing, developing, and manufacturing rail handling solutions for over 30 years, and their equipment has assisted in the development of rail infrastructure in over 25 countries. e Rosenqvist SB60 Tie
Replacer is designed to provide safe and e cient replacement of concrete or wood ties. is single attachment will all-in-one remove and/or replace the ballast and dig out and replace the tie. e SB60 has a tilt and rotate function, so ties can be replaced from the side of track or between the rails in close clearance areas such as tunnels and station platform areas. e SB60 ts most tie types, both wood and concrete, and a wide variety of track gauges. In addition, the Tie Replacer can be out tted with an optional Automaster attachment for automatic clipping of Pandrol Fast Clip fasteners. e SB60 reduces labor time and manpower on track, lowering cost and worker risk.
e Vancer CTC08 Tie Crane was designed speci cally for railroad material handling maintenance and transport projects. With the ability to couple with a variety of attachments, the machine combines agility and strength to tackle the most demanding tie handling jobs. It is ideal for jobs that require both on-track accessibility and transport. e tie crane is highly maneuverable and quickly couples with a Hi-Rail maintenance scrap cart. is allows operators to safely handle and transport material on track. With bene ts such as powerful li capacity & precise tool control, it enhances tie handling agility. With an operating weight of 25,000 lbs. and speeds up to 25 mph, it allows for e cient concrete or wood tie work and other material handling applications. e tie placer can move multiple ties, and the grapple can hold multiple ties at once. e visibility o ered in the in-cab rear camera
allows for enhanced tie placement accuracy. Quadrant stop protection allows the operator to work on one side of the track (approximately 180 degrees), while protecting the machine and operator from swinging the boom to the adjacent rail line while working. ere is also a pre- ll system for hydraulic oil that ensures contaminants are not introduced into the hydraulic system. Additionally, a high-pressure lter ensures the hydraulic system stays clean to keep the machine components safe.
In the realm of rail infrastructure, a signi cant paradigm shi has transpired over the past decade, driven by the innovative technology of the McCulloch Group’s Panel Li ers. Patented and masterfully engineered, these specialized machines have optimized rail track maintenance and construction projects while substantially mitigating operational expenditures and safety concerns. DavRail, Inc. has made these machines available to the Americas through an exclusive partnership with the McCulloch Group. Operating via remote control, Panel Li ers have become synonymous with heightened e ciency and enhanced safety protocols in material handling and maintenance of way endeavors. By promptly establishing exclusion zones and neutralizing safety concerns regarding manual handling, these machines have signi cantly bolstered
the precision and productivity of panel installations. is innovation assumes paramount signi cance, particularly in scenarios where expeditious panel removal is imperative within restricted possession timelines, facilitating the swi reworking of track foundations in anticipation of replacement. e capability of Panel Li ers extends beyond their enhanced safety metrics. Panel Li ers have emerged successful in navigating logistical obstacles that historically challenged rail projects due to its modest footprint and omnidirectional movement. ese attributes enable easy transportation, rapid deployment, and demobilization. e Panel Li er’s compact size and maneuverability are compounded by the ability to remove and install any type of rail panel measuring up to 60 meters long and pre-position up to 12 concrete ties at once - well beyond American standards.
One notable application of Panel Li ers is discernible in the Tren Maya project, a 1,554-kilometer intercity railway in Mexico that traverses the Yucatán Peninsula. Herein, DavRail, Inc.’s o ering of Panel Li ers has helped to demonstrate unprecedented speed and precision along the length of track between Cancún and Tulum. e Panel Li er’s ability to navigate harsh terrain and densely populated areas while maintaining a compact footprint
underscores their e cacy and e ciency. As Tren Maya progresses, it serves as an archetype of the capabilities and sensibility of these Panel Li ers, available through DavRail, Inc. By substantially enhancing safety protocols, expediting project timelines, and reducing operational overheads, these machines have entrenched themselves as indispensable material handling assets within the rail industry. Looking ahead, Panel Li er technology accessible through DavRail, Inc. promises further improvement to rail infrastructure development. With its capacity to revolutionize conventional methodologies, accelerate project timelines, and uphold stringent safety standards, these machines represent the vanguard of a more e cient and secure future within the rail industry.
Loram’s material handling equipment eet continues to grow. In 2023, Loram delivered its 100th Material Handling Car (MHC) to the market. is came only 4 years a er the delivery of the 1st machine into its contract service eet as a new product. Customers cite the material throughput and o oading capabilities of the MHC product as improving the eciency of their ballast cleaning operations. Loram’s newest 7000 series self-powered slot trains (SPS 7000 series), pulled by a 3,600 HP 6 axle drive power unit, are bringing more e ciency to customer work sites. e increase in available horsepower and driven axles is giving customers new options regarding how much equipment and material can be towed during engineering projects. All of Loram’s slot trains bring an unmatched versatility to material handling by being able to load/unload any type of material that is within the reach of the excavator. ese machines pick up and o oad ballast, rip rap, rail, ties, and other material that either needs to be placed, or removed during maintenance operations. e DumpTrain and DumpTrain for Curves® ballast delivery trains continue to deliver more ballast faster than any other product on the market. Loram’s DumpTrains can deliver 1,500 tons of material to work sites, stockpiles, or washout locations and unload a full consist in under an hour. O oading is done up to 45 feet from track centerline. e DumpTrain for Curves® o ers all the same features as the traditional DumpTrain but can operate while in curves as well as tangent track.
Loram Technologies’ ballast maintenance solutions are designed to get the job done in the most e cient and reliable
way possible, minimizing the impact on your track time. Its GateSync utilizes two potential data streams that allow it to deliver ballast. e cars can be unloaded using manual surveys or data fed from ballast pro ling equipment. Once a survey is in place, the GateSync so ware synchronizes the opening, and closing of gates on the ballast cars to place ballast exactly where it’s needed. is is all done while avoiding crossings, switches, and other “no dump” zones. From 2 cars to 100, GateSync provides continuous ballast unloading at up to 10 miles per hour, making light work of even the longest stretches of ballast unloading.
Solaris improves the productivity and safety of existing ballast cars by converting their gates to remote operation. e conversion uses a reliable and rugged 24-volt electric hydraulic pump and hydraulic cylinders to produce the force needed to open and close the gates. Solar panels recharge the system when not in operation, creating a low-maintenance solution with no need for auxiliary air
lines. Solaris converted ballast cars can be unloaded by either operating joysticks on the sides of the cars or by using a handheld radio remote control that has a range of up to 300 feet. Solaris is particularly beneficial when combined with GateSync technology to automate ballast delivery. If one currently has cars that are manually operated, Solaris provides a quick and easy upgrade to make them GateSync compatible.
Omaha Track’s new equipment shop in Kansas City stands in the heart of the Midwest. Specializing in state-of-the-art knucklebooms, Omaha Track is a trusted e ciency partner. Its inventory boasts the latest in knuckleboom technology to o er unrivaled performance and versatility. From custom attachments to advanced safety features, its machines are engineered to exceed industry standards, ensuring maximum productivity and peace of mind on every job. Omaha Track focuses on solving problems through its equipment. Whether it’s custom building, fabrication, or maintenance, Omaha Track’s team of
experts has the skills and expertise to get the job done right.
RCE Equipment Solutions has a new series of Railavators (hi-rail excavators), John Deere models 85P, 135P, 210P, 245P, 250P and 350P High Rail Excavators. With its patented hydraulic powered retractable high rail, customers can take it anywhere they need, both on and o track. e new series 210P, 245P, 250P and 350P Railavators boast RCE’s new Ultra Life Axles.
ese drives are made of high strength alloy steel – two times more structural strength than existing cast iron nal drives. Many rail maintenance operations require severe duty applications with high point loading.
e Ultra Life Axles have overall increased axle bearing capacity and are rebuildable / repairable. e Ultra Life Axles have a three year / unlimited hours warranty. Railavators are the swiss army knife of MOW equipment and can be equipped with over 20 attachments and customizable carts to move material. In 2023, RCE also unveiled a new Series 5 P Swing Loader. e new series utilizes a John Deere 544 P-Tier
model machine with enhanced performance, e ciency, and comfort so customers can hit the heavy jobs harder. e new P-Tier wheel loaders provide spacious operator stations including customizable ergonomic electrohydraulic (EH) controls, and streamlined electrical and hydraulic routing, making these versatile and productive mid-size models the perfect match to take rail maintenance operation to the next level. e standard loader boom and housing has been replaced with a 200-degree turntable that allows the operator to accomplish swing crane functions. e main boom assembly retains it structural integrity, allowing the Series 5 to accomplish wheel loader functions with 14,500 lbs. of li capacity. Equipped with the high traction axles, the Series 5 Swing Loader has enough drawbar pull to handle the positioning of continuous rail. Whether working on or o rail, the Series 5 Swing Loader provides a powerful, safe machine that o ers the reliability of John Deere wheel loaders and the ultimate in swing crane technology.
It’s hard to believe that my term is more than half over. So far, it’s been a great experience working with AREMA Sta and collaborating with Trent Hudak, Past President and Bill Riehl, Senior Vice President. Since taking on the President’s role at AREMA, I have been involved in many committees to address the speci c needs of AREMA to better serve our members.
One such committee is the Strategic Planning Committee, formed in November of 2022, to ensure that AREMA’s Governing Documents are reviewed regularly and that changes are developed for the Association’s continued health.
There are several charges of the Strategic Planning Committee:
1. Maintain AREMA as a strong presence in the railroad industry.
2. Ensure AREMA’s practices, governing documents, and educational materials remain relevant in this ever-changing industry.
3. Encourage participation within this volunteer organization from its diverse group of industry experts.
4. Provide value to our membership and the railroad industry.
e Committee started with two signicant projects. e rst was to review and suggest edits to the AREMA Technical Committee Regulations and Procedures. e second task was to review and revamp AREMA’s Strategic Plan.
e most recent Strategic Plan was approved by the Board of Governors in 2018 and reafrmed in 2019. is Plan lays out AREMA’s Vision, Mission, provides goals, near and
long-term initiatives, and identi es operational needs. It is imperative that AREMA regularly evaluates and adapts its Strategic Plan to meet the changing needs of the railway industry.
Over this past year, the AREMA Strategic Planning Committee has met regularly to develop a new Plan guiding AREMA through the next few years. I’m happy to announce that the Board of Governors just approved it in February, and it will be released in the next few months, o ering a refreshing new direction from AREMA.
e Vision and Mission statements highlighted in the new Plan still represent our core ber and will guide us as we continue to evolve with the industry. AREMA’s vision “to be the pre-eminent railway engineering association for North American and international railway and transit organizations” and our mission to focus on “the development and advancement of both technical and practical knowledge and recommended practices pertaining to the design, construction, and maintenance of railway infrastructure,” will help us develop new initiatives that will support these statements.
Our Strategic Plan has been honed and re ned to cover four major focus areas. ese areas include:
In this area, we will strive to provide education to our membership and the industry through conferences, symposiums, webinars, and our publications. We intend to provide the highest quality materials, events, and platforms, and be responsive, timely and adaptable to the industry’s changing needs. We will evaluate our delivery methods regularly to assure that we remain current with technology and the needs of our members and continue to leverage the best forums and formats to provide the most e ective ways to reach our industry.
e primary charge of every technical organization is providing technical materials. AREMA has always been focused on developing technical materials to support the design, construction, and maintenance of railways. We will ensure we have the appropriate expertise to support our recommended practices. We will leverage that strength to provide top technical content and ensure that this material meets the needs of the industry. It is important that we continue to work with our functional
groups to leverage e ciencies and that we take a “systems approach” to tie the technical material together appropriately.
AREMA leadership has fully recognized the need to deliver programs to attract, develop, and retain talent in our industry. We will continue to support our educational foundation and foster new programs for career, skills, and leadership development for our frontline and professional members. We further pledge to tailor these programs to be inclusive and to attract and support a diverse membership.
A big part of our industry is the connections and the relationships developed from those connections. AREMA understands the importance of these relationships and supports facilitating opportunities to connect and engage members. We look to create and grow strategic partnerships with industry-related organizations that will enhance collaboration in our areas of expertise.
AREMA Leadership and Sta are committed to execute this Plan to meet the needs of the railway industry. We will adapt our strategy as necessary, as the industry and its needs may change. We will measure ourselves against the Plan and ensure that our goals and initiatives are keeping us on the right track.
As mentioned, the Plan will be available shortly, however, I felt it important to advise our Membership and Stakeholders that this is coming. Our Leadership is invested in AREMA’s future, and this document will tell AREMA’s story.
Keep an eye out for this important message on the AREMA 365 App and by visiting our website.
Secure your recognition for the AREMA 2024 Annual Conference & Expo by purchasing your booth and sponsorship. Contact us today at marketing@arema.org for the best available options for the event in Louisville, KY, September 15-18. Registration opens in May. Stay tuned for details.
Is your Library up to date? Order the 2024 Communications & Signals Manual today. With over 95 new, revised, reaffirmed, or extended Manual Parts, including over 800 pages of updates, it’s the perfect time to get your copy of the 2024 Manual. Order online now at www.arema.org.
Did you know we have a wide variety of
On Demand education for learning on your time? Browse our most popular webinars, seminars, and Annual Conferences to earn your PDH credits on the go. Visit www.arema.org to start your On Demand learning today.
Don’t miss out on the conversation in AREMA’s Member Forum. The Member Forum connects you with other Members, allowing you to send messages, start conversations, and more. See what everyone is talking about today: https:// community.arema.org/home.
If you’re looking for a podcast to binge, listen to AREMA’s Platform Chats. It features
APRIL 14
Committee 11 - Commuter & Intercity Rail Systems Orlando, FL
APRIL 14-16
Committee 12 - Rail Transit Orlando, FL
APRIL 14-16
guests from every aspect of the railway industry. Catch up on all four seasons available on all your favorite listening services today.
Leverage the power of your trusted association’s Railway Careers Network to tap into a talent pool of job candidates with the training and education needed for longterm success. Visit www.arema.org/careers to post your job today.
NOT AN AREMA MEMBER? JOIN TODAY AT WWW.AREMA.ORG
CONNECT WITH AREMA ON SOCIAL MEDIA:
JUNE 5
Committee 6 - Rail Facilities, Utilities and Buildings Virtual Meeting
JUNE 6
Committee 30 - Ties and Fasteners Urbana - Champaign, IL
JUNE 8
Committee 17 - High Speed Rail Systems Orlando, FL
APRIL 17
Committee 13 - Environmental Vancouver, BC
MAY 1
Committee 6 - Rail Facilities, Utilities and Buildings Virtual Meeting
MAY 13-15
Committee 5 - Track Pueblo, CO
MAY 14-15
Committee 15 - Steel Structures Newark, NJ
Committee 33 - Electrical Energy Utilization Greenville, SC
JULY 31 - AUGUST 1
Committee 7 - Timber Structures Kansas City, MO
SEPTEMBER 15
Committee 17 - High Speed Rail Systems
Louisville, KY
OCTOBER 24 - 25
Committee 2 - Track Measurement and Assessment Systems
San Francisco, CA
Join a technical committee
Joining a technical committee is the starting point for involvement in the Association and an opportunity for lifelong growth in the industry. AREMA has 30 technical committees covering a broad spectrum of railway engineering specialties. Build your network of contacts, sharpen your leadership skills, learn from other members and maximize your membership investment. If you’re interested in joining a technical committee or sitting in on a meeting as a guest, please contact Alayne Bell at abell@arema.org.
For a complete list of all committee meetings, visit www.arema.org.
The world is focusing its attention on how to create a society that is both sustainable and economically viable. That balance can be challenging, but achieving it is vital to creating a better future for our children.
The lifeblood of our world is commerce – from getting raw materials into production to supplying finished products to our neighbors. While there are various modes of transportation to make this possible, the railroads have been moving what we need for over a hundred years in an inherently sustainable way by maximizing fuel use per pound of freight. But all of us can
improve, including the railroads, which is why the American Railway Engineering and Maintenance-of-Way Association (AREMA) started a research effort in 2023 to focus on sustainability.
AREMA Technical Committee 13 – Environmental developed a Sustainability and Resilience Position Paper to focus on these efforts and lay the groundwork for AREMA to update their internal processes. The industry can begin to build resiliency into its infrastructure while developing a more sustainable approach to our transportation dependent economy. The good news is that
the railroad industry has already incorporated some sustainability and resilience methods into their processes, and this increased interest through AREMA’s efforts will continue to help navigate better ways to be sustainable and resilient.
This focus led to the AREMA 2024 Sustainability & Resiliency Symposium held February 5-7 in Tampa, Florida. The groundbreaking event was AREMA’s first-ever symposium dedicated to this increasingly important theme in the railway industry. The take-home lesson was that this is more than just a matter of using less fuel to move freight. The
Get PDHs At Your Own Pace With Arema’s On Demand Education
Access to important professional development content is just a few clicks away with AREMA Education. Our On Demand content spans many disciplines of PDH accredited courses that allow you to get your PDHs by learning from experts online without leaving your office.
1. LEARN MORE
Studies show that participants learn more while taking On Demand courses as you can skim through the material you understand and take more time in the more challenging areas.
2. GET INSTANT ACCESS
With AREMA On Demand courses, you don’t have to wait to learn and get your PDHs as they’re available instantly after purchase.
3. CONVENIENT AND FLEXIBLE
Above all things, On Demand education is meant to take at your own pace and on your time. Study from anywhere in the world, whether from your office or the convenience of your sofa.
4. COURSE VARIETY
AREMA On Demand education offers a wide variety of topics for all studies of the railway engineering community.
Register and Start Learning today at www.arema.org.
BECOME A MEMBER AND SAVE
Not an AREMA member? Join today at www.arema.org and get discounts on all AREMA Educational Offerings, from Virtual Conferences to our Webinars.
presentations helped attendees appreciate the bigger picture of how we move people, things, and the environment into the future.
The event started with a visit to the Florida Conservation and Technology Center, a 500-acre campus showcasing stewardship, research, habitat restoration, help for endangered species, and education about the fragile wetland ecosystems that help protect the Florida coastline from the effects of climate change. During our visit, we also got to view the Tom Hernandez Clean Energy Center, powered by a combination of solar, wind, and the grid, with an on-site laboratory monitoring the energy collected and distributed from the center’s solar and wind generation stations. This tour gave participants a look at how other industries can use renewable energy and its impact on sustainability and resiliency efforts.
On Tuesday morning, the Symposium started with keynote speaker Dr. Cris B. Liban, PE, NAC, Chief Sustainability Officer for the Los Angeles County Metropolitan Transportation Agency. Dr. Liban noted that railroads are a part of the larger sustainable economy and that we can grow those lessons into sustainable projects benefiting minority and environmental justice communities, from bus and transit projects to environmental restoration and education.
The day continued with a sustainability partnership panel. The rest of the morning saw discussions of nature-based solutions for supporting railroad remediation and restoration projects, decarbonizing port and intermodal facilities through electrification, and how railroads can use properties in their holdings to build a more sustainable system.
On Tuesday afternoon, the group heard from Class 1 leaders committed to incorporating sustainable solutions and ways to protect the environment. The afternoon wrapped up with a better understanding of how railroads can plan around implementing the Taskforce for Climate Related Financial Disclosures and two examples of implementing sustainable measures at intermodal and infrastructure projects were discussed.
The keynote speaker for the second day of the conference was Adam Roy Gordon, Executive Director at Global Compact Network USA, the US Chapter of the United Nations Global Compact, the largest corporate sustainability initiative
in the world. Mr. Gordon helped the group understand the basis and benefit of the United Nations’ 17 sustainable development goals (SDGs) and how they can be implemented in transportation and transit. Following that was a panel discussion highlighting examples of incorporating resilient design into infrastructure projects, additional reviews of climate change impacts on railroads, and discussing their initiative for a climate physical risk assessment.
Showing that the same resiliency issues that challenge the freight rail industry are also a concern when moving people, Wednesday afternoon kicked off with a final panel discussion that included key leaders in the transit industry who not only demonstrated their commitment to incorporating sustainability but also how their agencies are building more resilient infrastructure that will last into the future.
What did we learn from the 2024 Sustainability & Resiliency Symposium?
• The Symposium focused on the freight rail industry and introduced solutions that can benefit other modes of transportation, making us leaders in implementing resilient infrastructure solutions.
• In the transit world, we can find common sustainable elements and partner on projects to benefit communities most impacted by climate change.
• There is a lot of room for innovation, but there is no need to reinvent the wheel as the U.N. and other organizations have provided a structure we as an industry can gather around and collaborate on.
Was any of this shocking or new? Not really. e concepts presented in this forum are probably terms and ideas we have o en heard. But what the AREMA 2024 Sustainability & Resiliency Symposium did was keep this topic in the forefront of our minds and demonstrated our industry’s commitment to building a better world. In the end, we are all in this e ort together, and forums like this provide opportunities for us to share ideas that will carry us all into the future.
If you want to catch up on what you missed, the AREMA 2024 Sustainability & Resiliency Symposium is now available On Demand. Earn up to 14 Professional Development Hours (based on your state’s approval) by watching the innovative presentations at your leisure.
Those who read and follow Railway Track and Structures and Railway Age know that both publications focus a great deal on the role of women in railroading. From RT&S ’s annual “Women in Railroad Engineering” feature, RA’s annual “Women in Rail” feature, to the annual RA/RT&S , “Women in Rail” in-person conference, our organization recognizes and promotes the contributions made by women to one of North America’s most critical industries.
We are not alone in this endeavor. As an example, one lady, Ms. Shirley Burman, has spent a considerable portion of her life writing about and photographing women working in the rail industry. She recently published her first book on the topic, Sisters of the Iron Road , which should command wide interest.
Shirley graduated from the University of California, Davis and began her professional photography career working for a weekly newspaper. After a couple of photography jobs, she was hired in 1978 to photograph the construction and opening of the California State Railroad Museum in Sacramento. Shirley writes: “It was at the Railroad Museum that my interest in women’s history was kindled, especially after seeing the orientation film then under development inside the Shops where I worked. It was a scene right out of World War II with women at work on a locomotive. I inquired as to why they were filming the scene and was told that women had been employed by railroads during World War II.”
chronological, with each chapter focusing on women’s role on the railroad during a particular time or in a particular role. Shirley has an easy writing style and the book is heavily illustrated with photographs of women on the job in many roles. Among the more interesting chapters is the final one, entitled “First Barriers & Then Change –– 1970s through the 2000s.” Shirley leads off this
discriminate against any individual because of race, color, religion, sex or national origin.”
Shirley adds that even with this law on the books, there was still pushback against hiring women on the railroad, and various excuses were made. Finally, in the 1970s, the U.S. Government got serious about enforcing this law and told the railroads it was time for them to get serious, too. This chapter also profiles the careers of several women in a variety of railroad jobs.
For anyone interested in the topic of women in railroading, this book is a must. It provides historical perspective, presents challenges many women faced during their rail careers, and profiles Cindy Sanborn, who was an executive with CSX, Union Pacific, and Norfolk Southern before she retired a couple of years ago. Shirley also discusses the career of Katie Farmer, the current President and CEO of BNSF.
It’s worth noting that Shirley Burman was married to well-known rail photographer Richard Steinheimer, who died from Alzheimer’s disease in 2011.
Shirley tells the story of her work in ten chapters and 235 pages. The story is
chapter with the following: “Concerns over women invading the ‘male only bastions’ did not just begin in the 20th century, but rather in a 19th century magazine that ‘sounded the alarm.’ The warning came first in Fireman’s Magazine . It took another 72 years and Title VII of the Civil Rights Act of 1964 to make it unlawful for an employer to
Richard published countless books of rail photography and was often called “the Ansel Adams of railroad photography. Richard and Shirley worked together on rail photography for many years, until Richard’s health deteriorated. Their collective body of work documents the twentieth-century rail environment like few others, and their books continue to be widely available, primarily through used book stores and dealers.