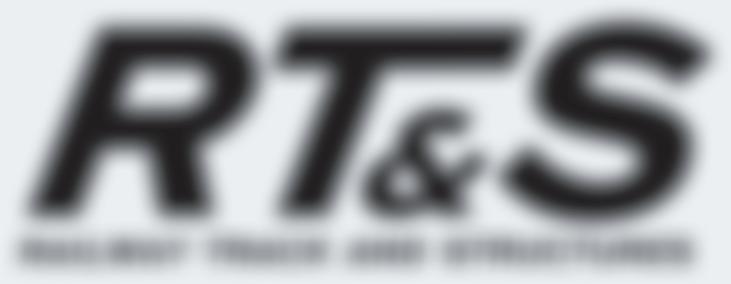
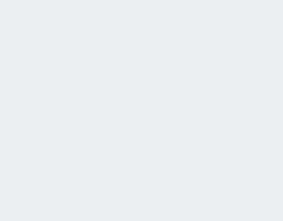
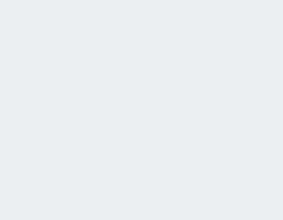
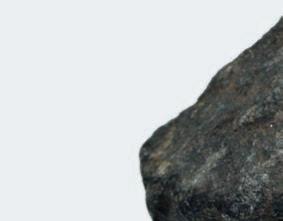
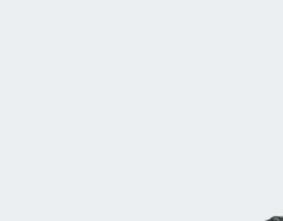
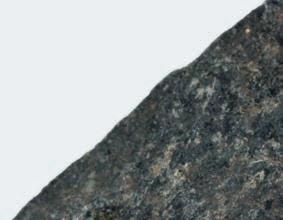

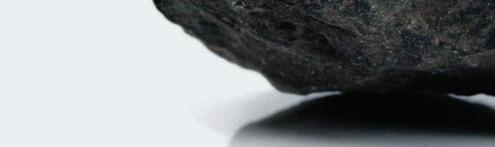
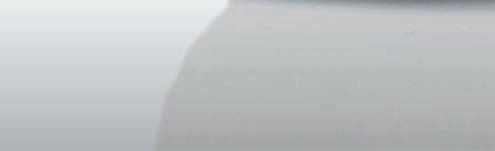
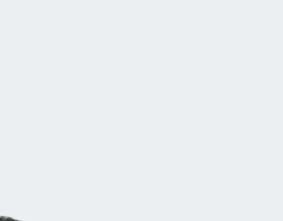
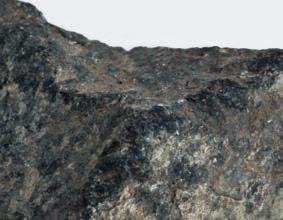

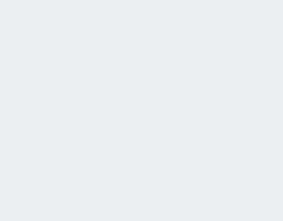

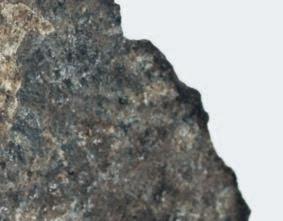
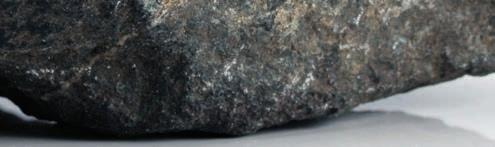
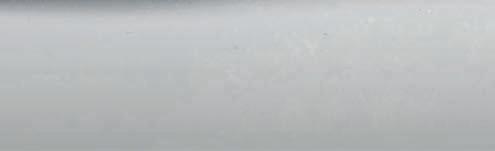
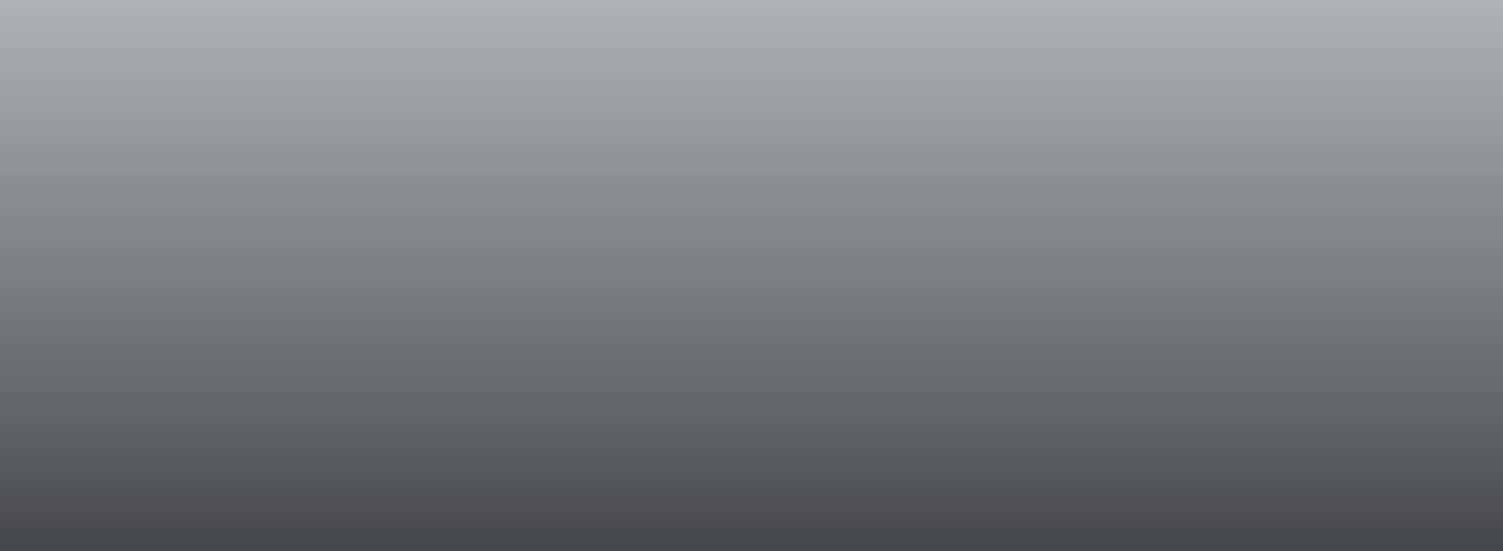
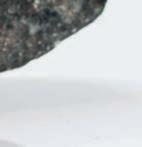
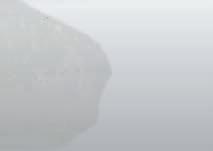
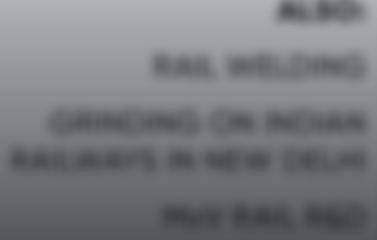


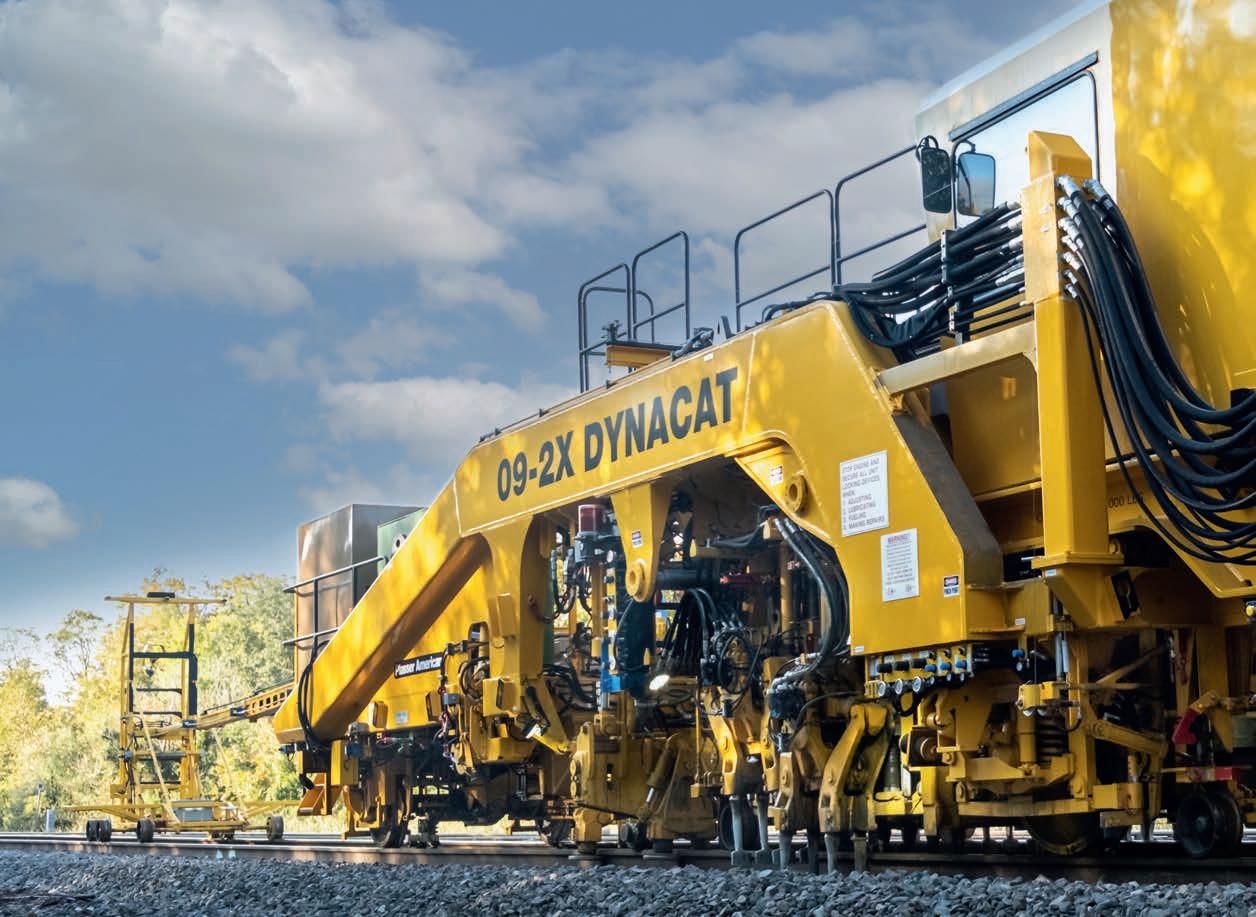
The Pl as ser h e avy-duty, high speed, continuous action switch and p ro d uct iontrackta mpingmachine 09-2X DYNACAT is capable of ta mping oneortwo ti esat a time with an inte g rate d dynamic track stabi lize r.Ta mping andl ifting units are mounted on a separate satellite fra me attached to the main frame. While the satellite indexes two ties duri ng theactualworkp roc ess (l ifting, lining, cross-leveling, and ta mping ),the machine ’s main frame with stabilizer system moves s moothly and continuously. Equipped with AGGS, ATLAS, PLC CANbus control sy ste m, an dit s un iq ue design and construction allows the 09-2 XD YNAC AT to achieve production rates of up to 4,200 feet per hou r.
Vol. 120, No. 8
Print ISSN # 0033-9016, Digital ISSN # 2160-2514
EDITORIAL OFFICES
1025 Rose Creek Drive Suite 620-121 Woodstock, GA 30189
Telephone (470) 865-0933 Website www.rtands.com
DAVID C. LESTER Editor-in-Chief dlester@sbpub.com
JENNIFER M c LAWHORN Managing Editor jmclawhorn@sbpub.com
EDITORIAL BOARD
David Clarke, University of Tennessee
Brad Kerchof, formerly Norfolk Southern William Riehl, Genesee & Wyoming/AREMA
Scott Sandoval, Genesee & Wyoming
Robert Tuzik, Talus Associates Gary Wolf, Wolf Railway Consulting
CORPORATE OFFICES
1809 Capitol Avenue Omaha, NE 68102
Telephone (212) 620-7200 Fax (212) 633-1165
ARTHUR J. MCGINNIS, JR. President and Chairman
JONATHAN CHALON Publisher
MARY CONYERS Production Director
NICOLE D’ANTONA Art Director
HILLARY COLEMAN Graphic Designer
JO ANN BINZ Circulation Director
MICHELLE ZOLKOS Conference Director
CUSTOMER SERVICE: 847-559-7372
Reprints: PARS International Corp. 253 West 35th Street 7th Floor New York, NY 10001
212-221-9595; fax 212-221-9195 curt.ciesinski@parsintl.com
The Association of American Railroads (AAR) says that all Class I railroads must have winter plans. ese plans exist to assure rail employees, shippers, the public, and regulators that the railroad has done everything it can to prepare for whatever an upcoming winter can throw at it and remain in operation to keep supply chains and the economy moving. ese plans are particularly robust for Canadian railroads. For example, in the 2023-2024 Canadian National winter plan, President and CEO Tracy Robinson said “ . . . the challenges of each winter’s extreme cold, snow, ice and rain remain unpredictable for us all. e severity, frequency and geographic range of these impacts change year to year. eir reality is also felt on other parts of the supply chain, creating a domino e ect on our operations.”
As this is being written in mid-July, the U.S. is experiencing a signi cant heatwave, with temperatures near and above 100 degrees in various parts of the country, including the northeast, where America’s railroad racetrack, the Northeast Corridor, operates every day.
When rail is laid for the rst time, engineers must be sensitive to the fact that steel expands when it’s hot and contracts when it’s cool. According to the Association of American Railroads, establishing the correct rail temperature during installation is essential to ensure the rail does not later expand and become misaligned on the next hot summer day. is is achieved by laying the rail at a temperature where compressive (pushing toward the center) and tensile forces (pulling away from the center) are zero. is is also called the rail neutral temperature. For example, if the focus is to minimize sun kinks, and rail is laid in cooler weather, engineers would likely heat the rail to roughly 95 degrees for most parts of the country. is will reduce the likelihood that rail will kink on hot days. If the rail temperature rises roughly 40-50 degrees over the rail neutral temperature the risk of a sun kink rises, depending on track conditions. On a hot
sunny day, with an ambient temperature in the high 90s, the rail temperature can rise to over 135 degrees, or 40 degrees above the rail neutral temperature. Of course, rail laid at such a high rail neutral temperature is more likely to have a pull-apart in the winter, which, while serious, poses a lower safety risk than sun kinks. ere is a lot of engineering science behind laying new rail, but this is the essential process from the standpoint of temperature.
Something similar happens with overhead catenary. In colder weather, the catenary wire tends to contract, while it expands in hotter weather. If the catenary begins to sag too much in the heat, it can interfere with the power collection device on top of the rail vehicle. In older systems, according to the ,
“Contraction and expansion with temperature changes sometimes causes wire breaks in the winter or sagging catenary in the summer that interfered with smooth pantograph operation at high speeds. Modern electri cation practice employs a xed-tension system, in which sections of catenary –– usually up to a mile in length –– are tensioned by suspended weights at each end, providing equal tension in the wire and providing a smooth contactwire pro le under all weather conditions.” (Page 405) In addition, high wind associated with the increasing ferocity of storms and hurricanes is not a friend of catenary. e point of this essay is to underscore the impact of climate change, particularly hotter than normal summers, on the operation of railroads. While railroads do keep a close eye on how infrastructure is impacted in hot weather, as the impact of climate change grows and summers become hotter, they may want to consider strengthening their spring/ summer plans.
DAVID C. LESTER Editor-in-Chief
Evidence of outward fine migration in SBC track under a variety of testing conditions
Stephen Wilk, Principal Investigator I MxV Rail, Pueblo, CO
Yu
Qian, Professor
of Civil Engineering University of South Carolina, Columbia, SC
MxV Rail partnered with the University of South Carolina (UofSC) to investigate ne migration in shoulder ballast cleaned (SBC) track. In 2021 and 2022, UofSC conducted laboratory “ ume tests” that allowed UofSC to quantify ne migration in a variety of maintenance and ne- lled ballast conditions. Laboratory test results were compared with the results from an actual test track “Rainy Section” at the Facility for Accelerated Service Testing (FAST) in Pueblo, Colo., along with revenue service testing in the central United States.
In addition to improved drainage,1 a second possible bene t of SBC is ne migration or the “cleaning out” of nes from the center of the track. With this cleaning mechanism, SBC can extend the ballast life by reducing the nes in the center track and increasing the amount of
time before undercutting or track renewal is required. In the long term, SBC may also reduce track geometry degradation. Historically, there has been some debate about this “cleaning” process, so it is possible that it happens in certain situations and not others.
is publication documents evidence of outward ne migration in SBC track under a variety of testing conditions. In addition, it explores how di erent ballast conditions can a ect this ne migration. is work will help in developing ballast degradation models and, eventually, aid in SBC maintenance planning. is article presents a summary of TD22-018,2 and more test details can be found there.
Fine Migration
Fine migration can occur through multiple processes. In one process, the downward “shaking” or vibration that happens during
train operations moves nes in the upper ballast to the lower ballast and creates a gradient of nes. Another process involves the upward migration of nes toward the surface. In certain cases, this can be a result of surface mud pumping that may occur when a section oods or has a ballast pocket with a water table.
A third process, and the one relevant to this work, involves the fine migration from the center of the track outward to the shoulders that typically occurs after SBC. This migration can either happen internally through voids in the ballast or as a result of surface runoff. Figure 1 illustrates various proposed fine migration processes. However, few studies have quantified fine migration or investigated the parameters that may affect the fine migration processes.
Hardly any historical testing has focused on the mechanism of outward ne migration. Previous studies using ground penetrating radar (GPR) did show a reduction in center ne degradation in locations where SBC occurred, as compared to non-SBC track.3 However, the exact reason for this reduction could not be deduced from the particular dataset.
In an effort to directly test the outward fine mechanism, UofSC in 2020 developed the laboratory “flume” tests. Since then, UofSC has completed multiple testing iterations that investigated different fine levels, fine types, and ballast maintenance methods (SBC or none).4 The setup includes a full track cross-section and has a symmetric separation in the middle so two different conditions can be compared simultaneously. A sprinkler system replicates rainfall; however, thus far, the test setup can only replicate the “cleaning” mechanism and not ballast degradation from loading.
Four tests were conducted for this study, and two types of nes were tested: granular and cohesive. e granular nes consisted of sand that was donated by a supplier. e cohesive nes were provided by MxV Rail from the Rainy Section at FAST. Using both types of nes, UofSC developed two di erent Fouling Index (FI) levels to simulate “moderately fouled” and “fouled” situations. e results for all tests were monitored a er 6 and 30 hours of continual wetting. e wetting intensity was 4 inches per hour, corresponding to 24 and 120 inches of cumulative rainfall.
Fine Migration
Figure 2 summarizes the change in center FI (fine migration) due to wetting as a function of initial FI. The downward y-axis shows a reduction in center fines after wetting, and the two lines represent the two different fine types. The results show a significant difference between
the two fine types. The granular material shows greater outward fine migration (up to a reduction of a third of fines). This migration is likely due to granular sand particles having the capability of being washed internally through the ballast voids. In addition, the amount of fine reduction increases with increasing FI. There was also fine reduction for the
cohesive fines; however, the amount of reduction was almost six times less than for the granular fines due to the inability of water to move internally through the ballast. Most of the fine migration occurred through surface runoff and the erosion of the side walls. These results strongly indicate that while fine migration occurs for both fine types, the fine type and gradation can have a significant impact on both the amount and location of “cleaning” that occurs.
A second assessment of the change in center FI was made by plotting the fine reduction with cumulative rainfall, as shown in Figure 3. The results show a non-linear trend where there is a sudden migration (a reduction in FI) followed by a reduction in the migration rate. This non-linear trend indicates that initial wetting “washes away” most of the loose fines, leaving only the fines that are more difficult to wash away. The remaining fines are likely near the bottom and center of the ballast section or are trapped by ballast grains and/or fines.
The laboratory test results were compared with the field Rainy Section test results. Despite the fact that the Rainy Section inherently experiences both tonnage and rainfall, the results and observations made during wetting tests largely agreed with the UofSC laboratory results. Visual observations showed that the moisture did not penetrate deeply into the
section, but mostly ran off the surface. The photograph in Figure 4 depicts the excavated shoulder after 61 MGT. The photograph shows the “scarifier” region being filled with fines and the sidewall angle expanding, suggesting gradual fine buildup over time.
The change of center fines in SBC track will be dictated either by the competing mechanisms of increasing fines from ballast degradation due to tonnage3 or by external sources versus reducing fines due to cleaning (either internally or through surface runoff). Both the laboratory and Rainy Section test results indicate that fine migration occurs, which has multiple implications for SBC maintenance.
First, it appears that SBC “cleans” the track center by washing away loose nes, and periodic cleaning should extend useable ballast life. SBC will likely be most e ective at “moderately fouled” levels (FI from 15 to 30). And while SBC can have drainage bene ts for “highly fouled” sections (FI > 30), it will probably not wash away any nes except those from surface runo , unless the nes are purely sand.
Second, increasing ne levels most likely occur in tracks that are located in wet climates, or in tracks with high tonnage/axle loads, more rapidly degradable ballast (e.g., limestone), or windblown sand. ese tracks would be better suited for regular SBC as it can continually wash away recently introduced loose nes. At
this time, it is unclear if “regular” means using SBC every year, every two years, or every ve years, because other factors such as tonnage, ballast degradation, rainfall, type of ne material, and introduction rate of external nes must also be considered. Unless the area experiences extensive windblown sand, using SBC on low tonnage/axle load lines will likely not be as e ective a er the rst cleaning due to the lack of new nes from ballast degradation.
References
1. Wilk, S., R. Chaparro, D. Li, and D. DeVencenty. (2022). “Shoulder Ballast Cleaning in Mud Spot Location.” TD22-017. Association of American Railroads (AAR)/ MxV Rail, Pueblo, Colo.
2. Qian, Y. and S. Wilk. (2022). “Laboratory Assessment of Fine Migration in Shoulder Cleaned Track.” TD22-018. AAR/MxV Rail, Pueblo, Colo.
3. Wilk, S., S. Galvan-Nunez, and D. Li. (2021). “Benefits of Ballast Shoulder Cleaning.” TD21016. AAR/Transportation Technology Center, Inc., Pueblo, Colo.
4. Qian, Y., Y. Wang, H. Kashani, and F. Fanucci. (2021). “Effect of Ballast Shoulder Cleaning on Fouling Particles Migration within Ballast Matrix.” September 2021.
William C. Vantuono
Railway Age
David C. Lester
Railway Track & Structures
Kevin Smith International Railway Journal
Railway Age, Railway Track & Structures and International Railway Journal have teamed to offer our Rail Group On Air podcast series. The podcasts, available on Apple Music, Google Play and SoundCloud, tackle the latest issues and important projects in the rail industry. Listen to the railway leaders who make the news.
by Je Tuzik
Rail transit properties around the world all contend with the same general issues. The corrugation on track in San Francisco is the same as corrugation on track in New Delhi. There may be a few different details, but the physics is constant. When it comes to addressing surface defects like corrugation, rolling contact fatigue (RCF), spalling, and more, rail grinding is another constant. The Delhi Metro Rail Corporation, a relatively young transit system in India, has found recent success implementing a rail grinding program with both corrective and preventive elements.
Delhi Metro Rail Corporation (DMRC) operates 390 km of track in and around New Delhi. A joint venture between the Government India and the State of Delhi, construction began in 1998, and revenue service began in 2002. The DMRC operates 12 lines of track, four of which are broad-gage (5 ft 6 in or 1.676 m) and
eight of which are standard gage. With an annual ridership of 2.37 billion, DMRC is the fourth most heavily trafficked rail transit system in the world. As is the case in many transit systems in densely populated cities (particularly older cities), DMRC track has a lot of curvature. “Across all lines, sharp curves [500 meter radius ( > 3.5 degree) or less] make up 40% to 60% of the system,” Ashwani Kumar, DMRC’s Executive Director of Track, told delegates at the WRI 2023 Rail Transit conference.
The DMRC’s 12 lines were all laid with premium head-hardened rail (UIC 60, 1080 grade) sourced globally — notably through Evraz, Voestalpine, and Nippon Steel. “Despite the quality of the steel, DMRC noticed rapid accrual of surface defects including corrugation, RCF, studs, pitting, and spalling in the first two years of operation,” Kumar said. “Based on our projections, we estimated that the rail in curves would have to be replaced within
12 years if conditions didn’t improve.” The prospect of replacing so much premium rail so early was financially and logistically untenable. To avoid this, the DMRC had to quickly develop and implement an aggressive corrective and preventive rail grinding regime.
India’s rail traffic generally operates on broad gage; (this is, coincidentally, the same track gage used on San Francisco’s Bay Area Rapid Transit) and expertise from that field influenced the design and construction of the earliest DMRC lines. These lines, in fact, once connected to freight lines at some interlockings but no longer do. “Ease of procurement and wide international support for standard gage led DMRC to switch to standard for the rest of the metro construction,” Kumar said.
Because they operate both broad and standard gage lines, the DMRC needed a grinder that could move between the two with relative ease. This led them to
Executive Director of Track
Loram Maintenance of Way, from whom they purchased a 16-stone grinder and a four-year operations and maintenance support contract (provided by Loram’s partner Vandhana International Pvt Ltd, India). “This operations and maintenance partnership has been extended several times and exists in this configuration today,” he said.
The DMRC also worked with Loram to determine optimal grinding frequency for their tangent track and mild/sharp curves, based on MGT. This worked out to every 27 months on tangent, 18
months on mild curves, and 9 months on sharp curves for lines with less than 25 MGT annually. “For lines with higher MGT, the determined frequency was 18 months tangent, 12 months on mild curves, and six months on sharp curves,” Kumar said.
Like most transit systems, the DMRC has very limited maintenance windows — typically four hours per night — which, due to travel time and logistics, can often mean a grinder only gets only 60 to 100 minutes of actual spark time. Rather than focus on heavy corrective
spot grinding, the DMRC initially aimed to use their maintenance windows to cover the system broadly, with a focus on corrugation and RCF removal, trusting that subsequent cycles would bring the rail profile closer to the target. Kumar also noted that the broad-gage lines tended to have generally more wear and surface defects, but that the root causes for this are not fully understood at this time.
The grinding program that DMRC and Loram developed also included a measurement component; they selected
multiple representative track locations in tangent and curved track to take pre- and post-grind profile measurements. These measurements, which indicate the amount of metal removed by the grinder and the differences between the pre-grind, postgrind, and target profiles, form the basis of a Grind Quality Index (GQI).
“At first, we saw the GQI steadily improve after each grinding cycle, before becoming flatter as the rail profile was corrected,” said Venket Rao, Senior Vice President of Vandhana International PVT. LTD. This is also an indication of moving from a corrective grinding mode to a preventive grinding mode. “The DMRC saw immediate improvements in wear rates and defect growth rates after only the first cycle,” Rao said. The DMRC continues to operate this grinding program today.
Owing to the positive results of the program, the DMRC purchased another 16-stone Loram grinder in 2017. This machine is now dedicated to broadgage lines, while the other handles standard gage. The doubling of grind capacity has also enabled the DMRC to get closer to their target grind frequencies, although narrow maintenance windows continue to be the limiting factor in the operation.
The DMRC is currently working with the data they’ve collected to determine the quantitative rail life increase they’ve achieved since the grinding program was implemented in 2009. Preliminary data obtained from MiniProf measurements indicate that natural wear on tangent track and mild and sharp curves has been reduced since the grinding program was initiated.
“We know that the rail has improved
Venket Rao, Senior Vice President of Vandhana International PVT. LTD.
The same industry-leading equipment as a traditional MobileWelder® with a battery-powered welder head
greatly in terms of surface condition, but we need more data still to be confident about rail life results,” Rao said.
Measurements and GQI data also indicate that shape of both right and left rail profiles are better matched and closer to the desired profile, which has led to better wheel/rail dynamics, which has reduced wheel wear.
While the current rail grinding strategy is yielding positive results, DMRC realizes that due to its limited maintenance windows, more innovative efforts will have to be implemented to maximize the potential of its grinding program. As DMRC continues to accrue rail grinding data and experience, they expect to see further year-over-year improvement in grinding production, rail wear, and surface defect growth.
Jeff Tuzik is Managing Editor of Interface Journal.
is article is based on a presentation made at the 2023 WRI Rail Transit Conference.
4. A graph showing wear rates on high and low rails in a sharp curve; note the shallower wear slope after grinding intervention at 08-2022.
Themostcomprehensivecollectionofdefinitionsrelatingto track.Over1500termsfromantiquatedforgottenslangto today'sjargon.Clearlyillustratedlineartenhancesthetext.
Reprintedbypopulardemand,thisbookisavaluablereference forroadmasters,tracksupervisors,trackforeman,surveyors andothersinvolvedintheplanningandexecution oftrackmaintenanceandconstructionwork. Fold-outdiagrams.Softcover.301pages.
Railgrindingsavesmillionsofdollarseveryyear!TheArt andScienceofRailGrindingisthefirstbookdedicated exclusivelytothesubject.
coverstrack,tracksubstructure,load environment,materials,mechanics,design,construction, measurements,andmanagement.Itiswrittenprimarilyfor professionalsandgraduatestudents.
Thisneweditionencompassescurrentdesignmethodsusedfor steelrailwaybridgesinbothSIandImperial(USCustomary)units. Itdiscussestheplanningofrailwaybridgesandtheappropriate typesofbridgesbasedonplanningconsiderations.
BasicPrinciplesofTrackMaintenance progressesfroman overviewofthebasictrackstructuretoexaminationsofits componentsandendswithacomprehensivelookat turnoutsandright-of-way.
Nov. 5 & 6, 2024 Chicago, IL
We’re returning to Chicago with an expanded event!
Railway Age and RT&S are proud to recognize the growth in leadership roles for women in the railway industry. Our second annual Women in Rail Conference is now a two-day event, filled with instructive panels, an awards luncheon, and a local transit tour.
Join a diverse group of railroaders with a shared commitment to our industry’s future.
PROGRAM HIGHLIGHTS:
•Furthering industry inclusivity and showing allyship
• Advancing your career—from asking for a raise to developing new skills
•Understanding the latest regulatory and legislative happenings
•New tech innovations and the latest applications
SUPPORTING ORGANIZATIONS
•How mentorship can change your journey
•Building a safety culture
•Railway Age’s Women in Rail / RT&S’ Women in Railroad Engineering awards luncheon
•Tour of Metra’s rebuild shop and training center
By Jennifer McLawhorn, Managing Editor
Materials like crushed stone need to be properly maintained in order to hold the track in line.
n keeping up with the roadbed, materials like crushed stone need to be properly maintained in order to hold the track in line. From ballast cleaning to regulators and sweepers, consider the following a “greatest hits” track list of what companies o er in this particular sector.
e Midwest has been hit with excessive rain and storms over the last month, leading to widespread ooding. BNSF and Union Paci c (UP) recently deployed Herzog’s Automated Conveyor Trains (ACT) and Multi-Purpose Machines (MPM), which were on lease, to address track washouts caused by this severe weather. e equipment is working around the clock to unload ballast and clean up debris, supporting the railroads’ e orts to
restore a ected subdivisions.
ese circumstances also called for Herzog to step up and provide additional on demand equipment including its newest specialized MOW equipment – the Track Li er, which made its rst debut in a ood situation last week. e Track Li er is being used in conjunction with equipment from another supplier to ll in washouts from ooding. is new machine is capable of li ing track and dumping ballast before placing the track back down. is has made it perfect for restabilizing the track bed throughout parts of Iowa and South Dakota.
“We take great pride in delivering excellent customer service and support to our partners. In times like these, when
stress levels are high, we aim to alleviate concerns with the reliability of our equipment and trained personnel,” Vice President of Ballast Operations Ryan Crawford said. “When we get a call for more equipment and it is available, we respond right away – just like we did with our new track li er, plus the additional MPM to aid the eet in Iowa. Our collaboration with other suppliers was also crucial; everyone came together to help restore the a ected tracks.” Ballast is a vital component of rail track foundation. It bears the load of the track, helps with drainage and reduces vegetation’s interference with the track. When ballast functions properly, rail tra c moves safely. As cars have gotten heavier, ballast works to disperse this weight over
With 25,000+ ballast gates sold worldwide, Miner AggreGate® sets the standard, delivering proven reliability and innovative flexibility. Our new Stand-Alone Solar Powered Electric AggreGate—complete with its own car-mounted work lights for night ballasting—enables independent operation of individual cars anywhere within the ballast train. This boosts MOW agility and efficiency by eliminating the need for grouping manual and automatic cars. An optional remote wireless control system allows for specific car and gate selection for up to 1000 cars. Standard electric, air-powered and manual models are also available.
LEFT: Accessible gate controllers and battery banks ensure smooth operations and efficient maintenance.
MIDDLE: Car-mounted solar panels keep the battery banks charged and ready for stand-alone ballast operations.
RIGHT: Miner’s stand-alone LED lighting system enables safer night operations.
larger areas. Without proper ballast, the ties would sink unevenly into the subgrade. Making sure ballast is properly maintained is a vital component to ensuring the safety and e ectiveness of rail movement. Vancer equipment o ers a comprehensive approach to ballast maintenance, including:
• Ballast and roadbed drainage
• Ballast strengthening and stabilizing
• Track support, including reducing abasement
• Extension of ballast lifecycle
e Vancer team is focused on developing equipment for comprehensive maintenance of way needs. With high horsepower, Vancer’s Hi-Rail Excavators can be coupled
with attachments such as the Vancer Undercutter, Ballast Cribber, and Ballast Tamper featuring 360-degree rotation. Excavators include hydraulically powered Hi-Rail gear undercarriage with train air brakes, multiple tool carrier functionality, and dual pivoting railcar couplers.
In addition, Vancer also o ers a 35 Yard Ballast Cart designed for distributing and spreading ballast. e cart can be towed at speeds up to 25 mph and includes brakes on all wheels, li points and chains. Vancer told , “With rental, used and new equipment available – as well as service and support – Vancer helps railroads focus on what it is they do best: getting the job
done within deadlines, within budget, safely, and e ciently.”
Miner’s AggreGate® line of ballast outlet gates, control systems and accessories is available in electric, air-powered and manual operating models. AggreGate outlet gates are suitable for both retro t and new car systems. e newest model, the solar-powered stand-alone electric AggreGate, enables railroads to bring more e ciency and exibility to their maintenance-of-way operations. By integrating solar power into each railcar, it enables independent operation of every car from anywhere within the ballast train. is eliminates the need for grouping manual and automatic cars. Operators can e ectively ballast inside, outside or both sides of the rail simultaneously. e dual cylinder air-powered AggreGate is also available for either push button or remote-control operation. e operator can select a speci c car and gate as well as control ballast ow, ensuring more accurate ballast discharge from distances as great as 300 feet. e manual AggreGate is available with transition sheets designed to enable new or retro t application to any open top hopper car. It features a three-position handle for easy opening and closing of doors. Spring tension holds the large, guillotine door in position at any opening for controlled ow of ballast. More than 7200 carsets of Miner AggreGates have been sold into service
Without proper ballast, the ties would sink unevenly into the subgrade.
since it rst received AAR certi cation over four decades ago.
Pettibone’s Speed Swing 445F2 is a do-it-all rail crane designed to accept numerous rail maintenance attachments, including three attachments that assist with ballast maintenance. A track cleaning bucket is available to e ciently clear excess ballast from the tracks while the machine steadily travels on rail. e Speed Swing can also use a switch broom to clean switches and clear unwanted ballast and debris. When maintaining a rail crossing area, the Speed Swing is o en used with rail mat tongs to set mats. at attachment is then swapped out for a general purpose bucket, which allows the machine to scoop up ballast and lay it down where required.
Additionally, a Speed Swing equipped with an AAR car coupler can pull heavy rail cars that are loaded with ballast.
e Speed Swing 445F2 is powered by a 163-horsepower Cummins Tier 4 diesel engine and includes a 49-gallon fuel tank, a 29% increase over the previous model’s tank capacity. Providing a maximum front load capacity of 10,000 pounds and maximum side load capacity of 8,000 pounds, the 445F2 features 180-degree boom rotation. e Speed Swing can travel up to 25 mph on hi-rail and 20 mph with all-terrain rubber tires.
Robert Grant from NxGen told “When it comes to ballast maintenance planning, cost is always a major factor. With limited means, where and what can be done to optimize ballast performance is the issue.
is is where Ground Penetrating Radar comes into play.” NxGen uses advanced multi-frequency GPR technology available, with specially designed antennas to optimize performance on rail infrastructure.
ese can pinpoint where to use undercutting, shoulder cleaning, drainage maintenance or subgrade maintenance. Knowing exactly where, and where not to employ each of these costly maintenance procedures, ensures that the available budget is focused where it is most needed.
For larger railroads, NxGen can install GPR systems on manned or autonomous inspection vehicles. For special work or on smaller railroads, NxGen has developed a “plug-and-play” GPR that can be mounted on any track inspector’s Hi-Rail with a hitch receiver, and start testing in as little as 15 minutes. NxGen has also developed its own automated processing algorithms that substantially reduce the cost of GPR testing, making it affordable and efficient. Over recent years, NxGen has recorded well over 100,000 miles of GPR on rail tracks, both on Class 1 and on other railroads.
NxGen also has its own rail-bound track inspection car built on an Amtrak sleeper unit. e car has a full track and rail geometry measuring system, machine vision and GPR capability at line speed. Combining geometry and GPR data helps clients understand the root cause of defects, and quickly deploy the correct maintenance strategy. is is particularly useful for resolving recurring geometry defects.
Loram continues its standards for productivity, quality, reliability and overall cost e ectiveness when it comes to ballast maintenance. Forward looking customers pursuing preventive maintenance utilize Loram’s shoulder ballast cleaners and ditchers to get ahead of drainage related issues. A clean shoulder pro le ensures that water can dissipate from the ballast section quickly so track sti ness returns as fast as possible a er rainfall events. A clean and consistent ditch diverts runo away from the track quickly, ensuring soils do not become saturated and less stable. e Badger Ditcher and DC Max Ditchers are the industry standard for high-speed ditch clearing and creation. e high e ciency machines can excavate material at up to 800 tons per hour to quickly restore drainage and direct water away from the track.
Loram o ers advanced and productive shoulder ballast cleaning services, equipment and technologies, resulting in increased e ciencies and reduced costs. By consistently excavating at 8 inches below the tie and restoring the ballast shoulder structure, nes can migrate through the shoulder with dramatically improved seepage time. eir equipment is specically designed to break open mud pockets, compacted nes, and ballast voids in the cribs and under the ties to release damaging trapped water.
When corrective maintenance is required, Loram’s LRV vacuum excavators and undercutters o er industry leading performance. Spot work is executed with
TrackSafetyStandards Subparts A-F
TrackSafetyStandards, containstheTrackSafety Standards,SubpartsA-F,forClassesoftrack1-5.The standardscovergeneralinformation,Roadbed,Track Geometry,TrackStructure,TrackAppliancesand Track-RelatedDevices,andInspection.IncludesDefectCodes. Updated December28,2023
BKTSSAF TrackSafetyStandards,SubpartsA-F $11.95 Only$10.75forordersof50ormore!
FRAPart237establishesFederalsafetyrequirements forrailroadbridges.Thisrulerequirestrackownersto implementbridgemanagementprograms,whichinclude annualinspectionsofrailroadbridges,andtoauditthe programs. Part237 alsorequirestrackownerstoknow thesafeloadcapacityofbridgesandtoconductspecialinspectionsif theweatherorotherconditionswarrantsuchinspections. Updated December28,2023.
BKBRIDGE BridgeSafetyStandards $8.95
Only$8.00forordersof50ormore!
the LRV. ese machines pair vacuum power with a manipulator that can apply 5,000 pounds of force at the tip of the nozzle. e LRV is able to excavate even the most fouled and cemented ballast in hardto-reach locations. In addition to excavating in tight clearances on ballast deck bridges, in tunnels, and around switches and crossings, the LRV can perform mud spot undercutting and removal, cross drain or trench digging, and drain cleaning. Because there are no moving parts associated with vacuum excavation, ballast can be removed from critical (and typically expensive) components without any damage.
Tamping is essential for maintaining railroad track geometry. An ongoing research project with Pennsylvania State University has shown that incorrect tamping a ects ballast stability and increases maintenance demand. Plasser American acknowledges current market challenges including a shortage of skilled workers and a rising demand for capacity. Continuous innovation enhances machine capabilities. e 09-2X DYNACAT, featuring a dynamic track stabilizer and two-tie tamping,
ThisreprintincludestheFRA's RailroadWorkplaceSafety Standards addressingroadwayworkersandtheirwork environments.Theselawscoversuchthingsas:personal protectiveequipment,fallprotection,andscaffoldingfor bridgeworkers;andtrainingissues.Alsoincludessafetystandardsfor on-trackroadwayvehicles. UpdatedDecember28,2023.
BKWRK RailroadWorkplaceSafety $11.50 Only$10.35forordersof50ormore!
The TrackSafetyStandardsCalculator isamustfor anyonewhoworksontrack.Thisslideruletype calculatorcontainsmanyofthedetailsforClassesof track1-5.Deviationfromuniformprofileandfromzero crosslevel.Differenceincrosslevel.Compliantwithpart213.
BKTCAL TrackCalculator $11.50 Only$10.75forordersof50ormore!
UpdatesfromtheFederalRegistermaybesuppliedin supplementform.
A clean shoulder profile ensures that water can dissipate from the
addresses these challenges by improving e ciency. Equipped with the Tamping Assistant system, this machine represents a step towards tamping machine automation.
The Tamping Assistant utilizes sensors, AI, and neural networks to create a digital twin of tracks and turnouts. Obstacles on the track are detected in real time and consequently the tamping unit and the lifting and lining unit are automatically positioned accordingly. The operator is supervising and approves the final suggestions provided by the machine. This ensures consistently high tamping quality, improving usability and operating convenience of the machines. With advancements like the Tamping Assistant setting new standards in track maintenance, Plasser American continues to innovate. Last year, Plasser American introduced the GRM4000, the latest model in the GRM tamping machine line. This new machine includes a redesigned two-tie tamping unit that greatly increases production rates and has improved weight distribution, making it suitable for transport by road trucks or flat cars.
Plug & Play Ground Penetrating Radar (GPR) for Hi-Rail vehicles
• Use your own Hi-Rail Vehicle
• Simple one-man DIY man operation
• Advanced antenna technology for higher definition
• Fast turnaround using automated AI processing algorithms
• Low cost
• High availability
• Train mounted and autonomous systems also available. Contact Robert Grant for more information at 630 254 5350 robert.grant@nxgenrail.com
e GRM4000 can be linked to the Plasser Dynamic Track Stabilizer PTS90C using the Autonomous Remote Stabilizer Upgrade Kit. is kit, installed on both the stabilizer and the tamping machine, allows the stabilizer to be controlled by the lead machine operator, eliminating the need for an additional operator. Field tests con rmed its safety and e ectiveness, enhancing e ciency and versatility during track maintenance.
Industry-Railway Suppliers , founded in 1966, is a leading North American distributor of ballast maintenance tools, work equipment wear parts, AREMA hand tools, battery and gas tools, abrasives, heavy railroad equipment, and mechanical shop tools. The heavy-duty construction of its solid-rubber ballast broom elements are constructed for durability and longevity and fit all standard ballast regulator machines. It offers both standard and club-style broom elements, designed to quickly sweep excess ballast without damaging the ties.
e high-performance, club-designed broom elements feature a broader, more
durable construction that enhances ballast leveling and clearing by increasing broom-to-ballast contact area. Developed for busy surfacing gangs, these club-style broom elements save time and reduce costs associated with both ballast and broom maintenance. ey last 15 to 20 percent longer than standard brooms and are also ideal for clearing snow and debris from tracks during winter. e double-broom clamps enable the secure attachment of two elements simultaneously, reducing replacement time. Made from forged alloy steel, these clamps enhance element support during brooming and are reusable, further extending the lifespan of the broom elements.
Mitchell’s Rail Gear Hydraulic Drive Rail Gear is a component of railroad ballast maintenance, designed to enhance the functionality of hydraulic excavators. By equipping a standard hydraulic excavator with Mitchell’s Hydraulic Drive Rail Gear, it is transformed into a highly e ective railroad track maintenance system.
This system enables a variety of hydraulic excavator models to be outfitted with
RAIL GROUP NEWS brings you a daily round-up of news stories from Railway Age, RT&S, and IRJ. This email newsletter offers North American and global news and analysis of the freight and passenger markets. From developments in rail technology, operations, and strategic planning to legislative issues and engineering news, we’ve got you covered.
quick-connect attachments via a tiltrotator, facilitating efficient execution of various ballast maintenance tasks. The excavator can swiftly travel to the work site and then either operate on the rails or use its tracks to move along railroad ties for added stability. This is particularly useful when using attachments such as an undercutter or a large clam shell bucket for distributing ballast. The tiltrotator allows for rapid switching between different buckets, such as digging, grading, and clam buckets. After distributing new ballast, Mitchell’s single or double Tamper is employed to pack (or tamp) the ballast beneath the railway tracks, enhancing the durability and levelness of the tracks and roadbed.
Following the tamping process, Mitchell’s Ballast Regulator attachment is used to shape and distribute the gravel track ballast, which supports the ties in rail tracks. With Mitchell’s Hydraulic Drive Rail Gear, a standard hydraulic excavator becomes a versatile, efficient, and cost-effective solution for railroad track ballast maintenance.
E ciency, quality, and endurance are the name of the game.
By Jennifer McLawhorn, Managing Editor
Run annually, focuses on the rail welding work of suppliers in the industry. To ensure lasting rail alignment, Class Is and Short Lines need to be able to keep up with rail maintenance needs, underscoring the demand for high-quality products and services. While this area of infrastructure maintenance is vast, we have assembled but a sampling of what the industry currently offers.
With over fifty years of experience, Holland continues its legacy of mobile flash-butt welding, while also making enhancements to their existing trucks, pullers and control systems.
Newer to Holland’s flash-butt welding portfolio is their low-density repair welding service, which provides railways with higher quality and more costeffective defect remediation compared to the traditional thermite process. This reduces the gang size along with fewer trucks to be more nimble when performing these maintenance of way services. The “4.1” truck model is a four-person
fully contained rail welding gang in one truck that is able to carry “seed rail” to replace defects or joints as well as longer sections for curve replacements. This single four-person crew can match the efficiency of three thermite crews as well as the superior strength and durability of flash-butt compared to thermite welding.
Another way they are looking toward the future of welding is with their first battery-operated battery welder (Hybrid welder™) which uses a smaller, lighter battery to perform flash-butt welds rather than a diesel generator.
The Hybrid Welder puts sustainable flash-butt welding forward and can perform approximately 20 to 25 welds currently with a prototype battery system. This truck reduces noise and emissions to give clean consistent power to welding operations. The design also eliminates mechanical systems that have known failure points and increases Holland’s already robust uptime. In the future, Holland’s “version 2” Hybrid Welder will allow for faster charging to
give the unit the ability to easily do 40-45 welds per shift.
Orgo-Thermit® manufactures both its molds and its Thermit® at a facility in New Jersey which makes it fully compliant with all Buy America requirements.
Orgo-Thermit®’s innovations include its patented Safe Start Crucible, eliminating the need for ignitors which makes the welding process safer. The Thermit® 2.0 portion is the only Thermit® portion specifically developed to work with head hardened rail. The Railstraight Dual is used to measure both the running surface and the gage face of a weld and has been used on a number of projects within North America to guarantee the finished quality of the weld.
At the AREMA 2024 exhibition, OrgoThermit® says it is excited to reveal a number of new products to support the Thermit® welding process which it has developed and has undergone significant testing with its customers. With Technical Sales and Services Representatives based in Canada, America and
The Hybrid Welder puts sustainable flashbutt welding forward and can perform approximately 20 to 25 welds currently with a prototype battery system.
Mexico, Orgo-Thermit® says it is able to support its customers in all of their Thermit® welding needs with its team’s 120+ years of practical Thermit® welding experience.
With the PortaCo tools, Orgo-Thermit® offers a complete range of tools to perform a Thermit® weld. This capability enables full support in all aspects of the execution of a Thermit® weld.
RailWorks , a successful rail infrastructure solutions provider in North America, delivers best-in-class track services with award-winning safety performance standards. The multifaceted suite of track services includes track inspections, track maintenance, large scale track rehabilitation, emergency repairs, track construction, rail grinding, undercutting, thermite welding, flash-butt welding, narrow gauge, and cog railways.
These track services are provided throughout North America to all segments, which include freight, transit, streetcar, military, commercial
and industrial.
RailWorks has an expanding fleet of Narrow Head Flash Butt trucks equipped
TO ENSURE LASTING
ALIGNMENT, CLASS I ROADS AND SHORT LINES MUST KEEP UP WITH RAIL MAINTENANCE NEEDS.
with a 70-ton weld head to add to the existing fleet of standard mobile welders. This head only requires 8.0” of clearance to perform a weld. This unique design
allows RailWorks to safely make close clearance welds around the frog and switch points, which are usually done with thermite welds.
The trucks are equipped with a 25’ Hiab crane that maximizes reach, allowing welding both adjacent to or on track with less moves. These units operate with a standard Chemetron Control System and remote monitoring, which allows for observation of real time weld data. When utilizing right conditions, RailWorks is seeing extremely high production rates, which is lowering the capital expenditure for special track work.
Properly functioning track infrastructure is the sum of many parts, and even a small issue can cause a failure. These failures can impact safety, increase cost, reduce efficiency, and impact system reliability. By partnering with the track experts at RailWorks, customers can be ensured they are receiving quality track work and protecting the performance of their track infrastructure.
RAY VERRELLE
AREMA President 2023-2024
And just like that.…I’m on my last article. It’s hard to believe how fast this year went by. It seems like only yesterday when I was at the Conference waiting to go on stage and give my acceptance speech. When I took over last October, I had some big shoes to ll when Trent moved on to the Past President role. Since the role of President lasts only a year, there are o en tasks that get passed from President to President. A big responsibility of the AREMA President is to maintain continuity in the organization and continue to move those initiatives along with the hopes of getting some of them over the nish line. is allows the AREMA Sta Team the ability to do what they do best and for some great achievements that they can be proud of.
is year, for starters, AREMA has created the strongest position of nancial stability it has had in many years. With this position of strength came the need to update the nancial philosophy from one of survival to one of growth and investment in the organization. e team has almost nalized a new reserve policy to ensure the organization is covered should a rainy day arise. We are also evaluating and enhancing our nancial policies surrounding the AREMA Educational Foundation to guarantee a solid future in providing educational support for the continued growth of our industry.
In addition, we started discussions on ways to put our surplus funds to work to add more value to our Members. Some of these initiatives include a database upgrade that
will create a better and more secure user experience and a refresh to our website. We have also contracted a technical editor to improve Manual material, and these e orts will continue to invest in our educational content to be the best in the industry.
Another notable accomplishment was the completion of AREMA’s new Strategic Plan. I mentioned this great accomplishment in my April article with a full reveal coming at the Annual Conference & Expo. is plan was quite a few years in the making, and I have the honor of helping get it across the nish line. is plan is the foundation for achieving our vision “to be the pre-eminent railway engineering association for North American and international railway and transit organizations” by executing our mission to focus on “the development and advancement of both technical and practical knowledge and recommended practices pertaining to the design, construction, and maintenance of railway infrastructure.”
Let’s not forget my digital debut on the Podcast scene on the #9 globally ranked railway podcast, “Platform Chats.” I had a lot of fun doing that and would consider an encore performance in Season 4 to help move the ranking up a few positions.
All in all, I really enjoyed my time serving the organization as Senior Vice President, President and look forward to transitioning into the Past President role. It truly was an honor when I was approached to serve AREMA in these roles. Serving as President of AREMA has been an eye-opening experience. Working with the AREMA Sta and the volunteer leaders of the association has been extremely rewarding. e hard work, passion, and professionalism displayed by all involved in the organization
is indescribable. I was amazed at the level of e ort required to put on the Annual Conference & Expo each year and in awe of the way they make it look e ortless. Now that they’ve broken me in, I hope the Sta keeps me involved even a er my term is up.
I’m also eternally grateful to the volunteer leaders of AREMA and the AREMA Sta for helping to focus on the greater good of the organization and moving the needle of success. I o er a special thanks to Trent Hudak, my predecessor, for his guidance continuing to be a driving force behind the many AREMA initiatives, and to Beth Caruso for leadership and dedication to the organization. anks to Bill Riehl for his support as Senior Vice President, and I wish him all the best as he takes over the reins of the organization. I’m excited to pass the baton to him and to continue to work with him and the team in my new role. I would also like to thank HNTB for their support during my term as AREMA President.
I would be remiss if I failed to thank my wife Stacy and my daughters Jillian and Hailey for all the support they have given me during my term as President and in my transition from the railroad to HNTB. ey have always supported me throughout my career, as well as the crazy ideas I have had outside of my career. ey are the main reason I get up in the morning and they make my life full. I really couldn’t be where I am today without their support.
I hope those who followed my articles found the topics interesting, and hopefully, they cracked a smile on occasion. I look forward to seeing everyone at the Annual Conference & Expo in Louisville next month. Feel free to come up and introduce yourself if we have not met before.
“ A BIG RESPONSIBILITY OF THE AREMA PRESIDENT IS TO MAINTAIN CONTINUITY IN THE ORGANIZATION AND CONTINUE TO MOVE THOSE INITIATIVES ALONG WITH THE HOPES OF GETTING SOME OF THEM OVER THE FINISH LINE.
Register before August 9 to save money for the AREMA 2024 Annual Conference & Expo in Louisville, KY, September 15-18. Save your seat for the best education, speakers, networking events, Expo, and more, all in one event at www.conference. arema.org.
Discover the ultimate guide for railway engineering professionals in the 2024 Manual for Railway Engineering. With over 6,100 pages of essential practices and detailed specifications, this comprehensive resource offers everything needed to design and build efficient, safe, cost-effective railway systems. It is available in print or PDF formats for immediate use. Order online now at www.arema.org.
Did you know we offer a wide variety
AUGUST 13-14
Committee 1 - Roadbed & Ballast Chicago, IL
SEPTEMBER 10-11
Committee 15 - Steel Structures Virtual Meeting
of on demand education for learning on your time? Browse our most popular webinars, seminars, and Annual Conferences to earn your PDH credits on the go. Visit www.arema.org to start your On Demand education today.
Download the AREMA 365 App for essential rail resources and networking opportunities. Easy access to news, events, and educational materials lets you stay informed and connected to the industry. Download it today by searching for AREMA in your phone’s app store.
Don’t miss out on the conversation in AREMA’s Member Forum. The Member Forum connects you with other Members, allowing you to send messages, start conversations, and more. See what everyone is talking about today: https://
community.arema.org/home.
If you’re looking for a podcast to binge, listen to AREMA’s Platform Chats. It features guests from every aspect of the railway industry. Catch up on all four seasons available on all your favorite listening services today.
Leverage the power of your trusted association’s Railway Careers Network to tap into a talent pool of job candidates with the training and education needed for long-term success. Visit www.arema. org/careers to post your job today.
CONNECT WITH AREMA ON SOCIAL MEDIA: NOT AN AREMA MEMBER? JOIN TODAY AT WWW.AREMA.ORG
Committee 16 - Economics of Railway Engineering Operations
Committee 17 - High Speed Rail Systems
Committee 18 - Light Density & Short Line Railways
Committee 33 - Electric Energy Utilization
*Louisville, KY, in conjunction with the AREMA 2024 Annual Conference & Expo
SEPTEMBER 14-15
Committee 05 - Track
SEPTEMBER 14-15
Committee 24 - Education & Professional Development
SEPTEMBER 15
Committee 10 - Structures
Maintenance & Construction
Committee 11 - Commuter & Intercity Rail Systems
Committees 11/17 Joint Meeting
Committee 12 - Rail Transit
Committee 13 - Environmental
Committee 14 - Yards & Terminals
Committee 40 - Engineering Safety & Training
SEPTEMBER 16-17
Committee 35 - Information Technology
SEPTEMBER 15
Committee 41 - Track Maintenance
SEPTEMBER 17-19
Committee 04 - Rail
SEPTEMBER 18-19
Committee 38 - Information, Defect Detection & Energy Systems
SEPTEMBER 18-19
Committee 39 - Positive Train Control
SEPTEMBER 19
Committee 27 - Maintenance of Way Work Equipment
OCTOBER 24-25
Committee 2 - Track Measurement and Assessment Systems
San Francisco, CA
Joining a technical committee is the starting point for involvement in the Association and an opportunity for lifelong growth in the industry. AREMA has 30 technical committees covering a broad spectrum of railway engineering specialties. Build your network of contacts, sharpen your leadership skills, learn from other members and maximize your membership investment. If you’re interested in joining a technical committee or sitting in on a meeting as a guest, please contact Alayne Bell at abell@arema.org.
For a complete list of all committee meetings, visit www.arema.org.
By Committee 14 – Yards and Terminals
The AREMA Committee 14 – Yards and Terminals (C14) is part of the Engineering Services Functional Group. C14 comprises ten subcommittees aligning with the six parts of the Yard and Terminal chapter of the Manual for Railway Engineering (MRE), references, webinars, recommendations for further investigation and research, and general manual revisions. e subcommittees are responsible for manual revisions and progressing the committee forward respective of the non-manual subcommittees.
C14 meets three times per year – a fall meeting on Sunday at the AREMA Annual Conference, a winter meeting virtually in January, and a spring meeting in April or May at varying locations, usually highlighting a yard and terminal eld trip alongside the standard business meeting. e spring meeting in 2022 was held in conjunction with a tour of the Mason Mega Rail
Facility in Savannah, Georgia, and the spring meeting in 2023 was in conjunction with a tour of the Watco Greens Port Facility in Houston, Texas.
In 2024, C14 was able to participate in a spring meeting where we toured the Belt Railway of Chicago (BRC) Clearing Yard which is a pivotal transition point in rerouting eastbound and westbound rail cars that meet in Chicago and redistributing to the U.S. Rail Network through the major Class I Railroads (UPRR, BNSF, NS, CSX). is rail yard is unique as it “humps” rail cars in two directions east and westbound. Michael Martinez, Director Business Development for BRC, gave a presentation highlighting that the yard was established in 1882, employs over 430 sta , and works with 41 customers. e yard handles over 8,400 cars per day and encompasses 28 mainline track miles, 78 bridges, 25 crossings, and 300-yard track miles. Clearing Yard is owned by the
six Class I Railroads and serves 14 roads. Committee members were given a tour of the control room, hump, and perimeter of the yard via bus. We extend our thanks to Mr. Martinez for taking time out of his incredibly busy day and to the BRC for hosting us at this incredible facility.
In addition to the site tour, committee members enjoyed a kicko reception at Lou Malnati’s and participated in our committee meeting at the Chicago Marriott Midway.
ank you to our event sponsors: e Nolan Company, SEMA Construction, Ames Construction, Alameda Corridor Transportation Authority, Michael Baker International, Benesch, Via Rail Engineering, BNSF, Burns & McDonnell, and TKDA.
If anyone has an interest in becoming an active participant in AREMA Committee 14, please reach out to the o cers here:
AREMA is committed to your education and advancement in the railway industry by providing Professional Development Hours (PDH) through our Seminars. These Seminars serve your educational needs and offer an opportunity to network with peers in the industry. Attendees can gain valuable insights into railway engineering and maintenance, featuring cutting-edge technologies, best practices, and industry trends. Whether a seasoned professional or newcomer, participants will leave equipped with practical tools and strategies for success and a network of industry professionals to support their journey.
INTRODUCTION TO PRACTICAL RAILWAY ENGINEERING SEMINAR
DATE: Saturday, September 14Sunday, September 15
LOCATION: Louisville, KY - in conjunction with the AREMA 2024 Annual Conference & Expo PDH: 16
TRACK ALIGNMENT DESIGN, PART I SEMINAR
DATE: Wednesday, September 18 - Friday, September 20 Track Alignment Design, Part I Seminar
LOCATION: Louisville, KY - in conjunction with the AREMA 2024 Annual Conference & Expo PDH: 16
TRACK ALIGNMENT DESIGN, PART II SEMINAR
DATE: Wednesday, September 18 - Friday, September 20
LOCATION: Louisville, KY - in conjunction with the AREMA 2024 Annual Conference & Expo PDH: 16
These courses comprise recommended practices and relevant accumulated knowledge from subject matter experts in the railroad industry. They are not intended as a regulatory qualification.
To register for these Seminars, please visit www.conference. arema.org.
RAIL GROUP NEWS brings you a daily round-up of news stories from Railway Age, RT&S, and IRJ. This email newsletter offers North American and global news and analysis of the freight and passenger markets. From developments in rail technology, operations, and strategic planning to legislative issues and engineering news, we’ve got you covered.
AREMA
Brandt Road Rail
Danella Rental Systems
DavRail
Herzog
Holland Co
Hougen Manufacturing, Inc.
Knox Kershaw Inc
Miner
Mitchell Rail Gears
NxGen Rail Services Inc.
Plasser American Corp
Railway Educational Bureau
RELAM Inc
Women In Rail
PHONE #
301-459-3200
306-791-7541
561-743- 7373
817-201-0157
816-901-4038
708-672-2300
866-245-3745
334-387-5669
708-220-7137
734-529-3400
630 254 5350
757-543-3526
402-346-4300
770-335-9273
212-620-7200
E-MAIL ADDRESS
marketing@arema.org MHaliwyz@brandt.ca SBolte@danella.com jalopez@davmarketing.com amcclain@hrsi.com sales@hollandco.com info@trak-star.com knox@knoxkershaw.com john.arends@arends-inc.com lovitt@mitchell-railgear.com Robert.grant@nxgenrail.com plasseramerican@plausa.com bbrundige@sb-reb.com jroberts@relaminc.com www.railwayage.com/womeninrail
This section has been created solely for the convenience of our readers to facilitate immediate contact with the RAILWAY TRACK & STRUCTURES advertisers in this issue. The Advertisers Index is an editorial feature maintained for the convenience of readers. It is not part of the advertiser contract and RTS assumes no responsibility for the correctness.
By David C. Lester, Editor-in-Chief
One of the most thorough and worthwhile analyses on the outlook for railroads to achieve zero emissions within the next 25 years was published on the website news feed on July 16 The title is “The Clock is Ticking: Railroads and the Net-Zero 2050 Goal,” and was prepared by Jason Kuehn, a Vice President at Oliver Wyman, one of the world’s leading management consulting firms. I’m not generally given to praise consulting firms, but Oliver Wyman is a good one. In Jason Kuehn’s case, he is a former railroader, has deep industry knowledge, and is an excellent analyst of the current rail environment.
One of Kuehn’s key messages is the opening sentence of his piece: “The Class I railroads set ambitious goals to reduce greenhouse gas (GHG) emissions in the past 5-10 years, but a review of recent data shows mixed progress at best.” Kuehn says that railroads’ goals were set, most likely, on a continuing trend of fuel efficiency to improve by 1% per year, along with more rapid development of bio-based diesel fuels, neither of which have occurred.
Kuehn points out that this lack of progress puts a black cloud over expectations of net zero emissions by 2050, giving advantage to the trucking industry, which has a much shorter replacement cycle for trucks (3-5 years) compared to 20-25 years for railroads. For various reasons, railroads have been rebuilding locomotives instead of buying new ones, and Kuehn shares the startling fact that only 137 new locomotives have been built during the past five years. He adds that things which drove increasing fuel efficiency and reduced emissions in the last decade have essentially maxed out.
The Association of American Railroads (AAR), Kuehn says, favors hydrogen as the fuel of the future to meet net-zero standards by 2050. One thing that you don’t often see in discussions about zeroemissions is emphasis on what it will require to build a network of storage,
distribution, and point of delivery for an alternative fuel like hydrogen. Kuehn aptly compares the work required to do this with the effort required to transition from steam locomotives to diesels in the late 1940s-50s. When folks address new network needs, they lament the cost and time required to do this yet may forget that the same effort was required when railroads moved away from steam.
Kuehn urges railroads to get going now because of all the trial and error that will be required. He likens the process to the moon shot, in the sense that each step from sending satellites in space to orbit the Earth to a crewed landing on the moon in 1969 was required to learn and build on.
THE CLASS I ROADS SET AMBITIOUS GOALS TO REDUCE EMISSIONS IN THE PAST 5-10 YEARS, BUT PROGRESS IS MIXED
Using the implementation of PTC as an example, Kuehn says “Initially, in the early 2000s, federally mandated PTC implementation was going nowhere fast until railroad CEO leadership got involved and built consensus; then, things started to happen . . .” He adds that “we believe something similar must happen with hydrogen, or any other alternative fuel choice, for the industry to meet a netzero 2050 goal.”
However, since the PTC mandate was passed in 2008 and was essentially “done” in 2020 (with the mandated dated of 2015), did the industry require 12 years to develop and implement the technology or could they have done it in seven? I don’t know for sure, but Kuehn implies that if CEO leadership had gotten involved initially, it could have been done in seven or something close. Nevertheless, one can
argue that the railroads got a slow start because they needed some time to ponder a project that seemed as lofty as figuring out a way to change the direction of Earth’s orbit around the sun.
As the 2015 deadline approached, the U.S. Government and the railroad industry geared up for a big game of chicken. The Federal Railroad Administration held firm in its position that the industry must meet the 12/31/15 deadline or they would levy heavy daily fines on the railroads for every day they operated without PTC starting in 2016. The railroads came back with the response of “OK, PTC is not ready, so if you’re going to fine us, we simply won’t run trains over the lines and segments of the railroad that require PTC.” The government finally blinked and extended the deadline to December 31, 2018 with the stipulation that if a railroad could demonstrate that it had made good, measurable progress toward implementation, it could have until December 31, 2020 to complete implementation. In effect, this gave the railroads an additional five years to install PTC. Most railroads implemented PTC on December 31, 2020.
As Kuehn implies, we shouldn’t have a “last few years” rush to meet emissions goals. One reason is that regulations are likely to tighten as time goes by and tension between railroads and regulators will grow. Another is that most everyone agrees that climate change is real and we’re already seeing some spooky issues occurring, like polar ice melt, and sea levels to rise. e prevalence and ferocity of storms throughout the year seem to be increasing.
While the rails may need to pick up the pace of alternate fuel implementation, remember that it is di cult to set realistic goals without detailed planning of what needs to be done. And some work ow details or obstacles may not be known at the time of planning. I believe railroads and regulators must closely communicate so that everyone is one the same page throughout the transition. While achieving zero emissions is not yet a federal mandate, the government shouldn’t throw a hot potato in the railroads’ hands and say “deal with it” without skin in the game.