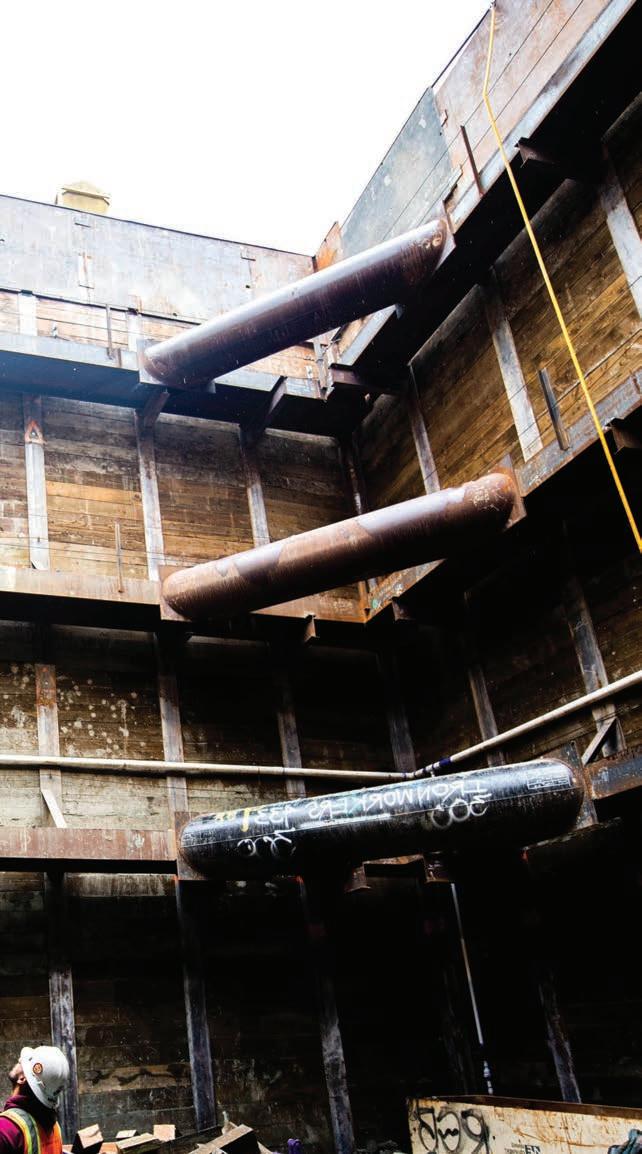
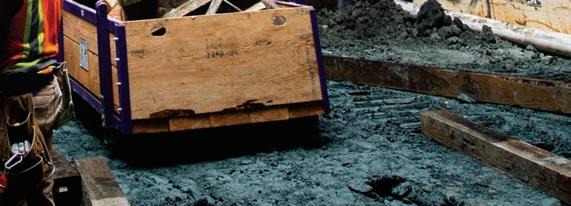


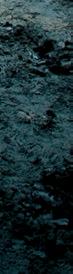

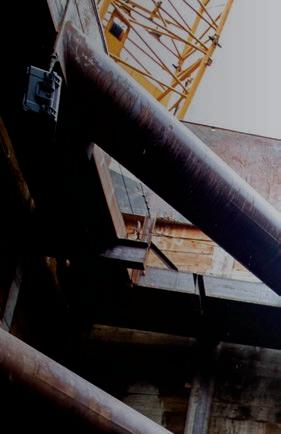
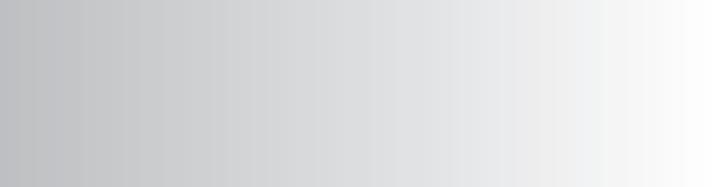
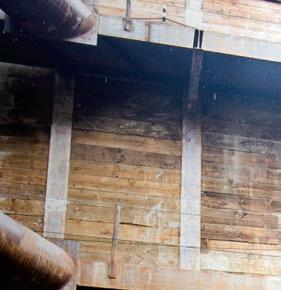

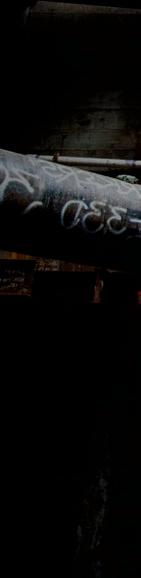
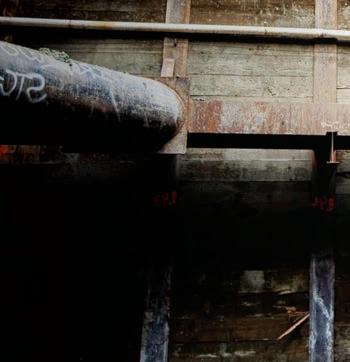
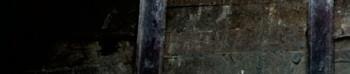
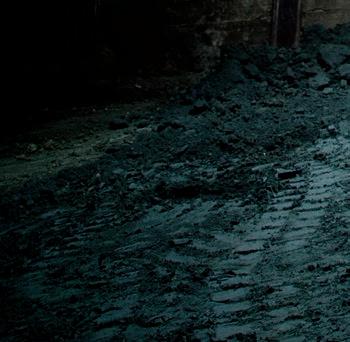
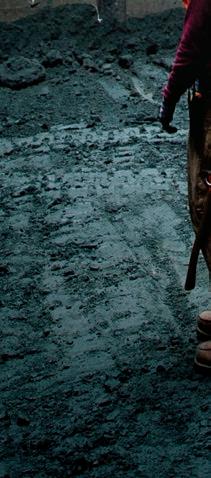
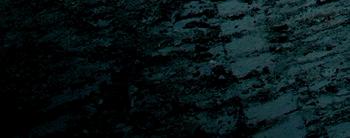


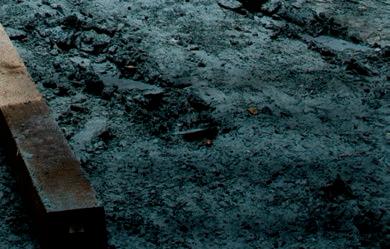
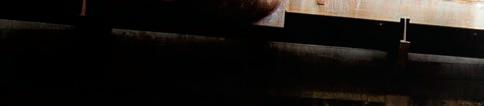

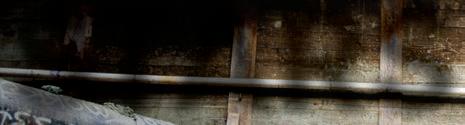
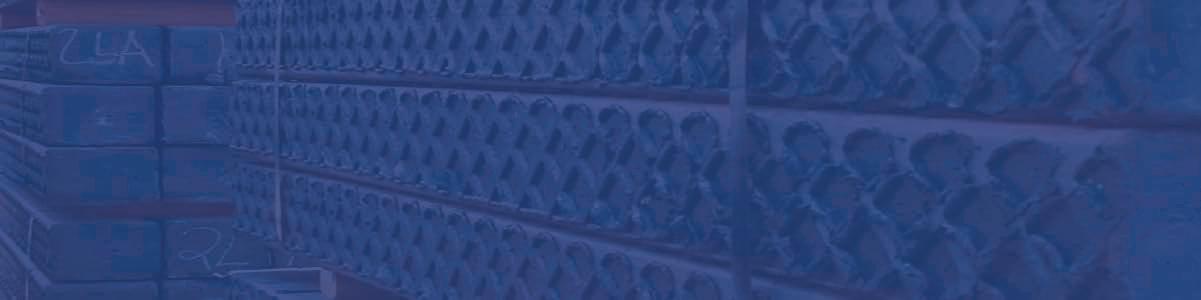
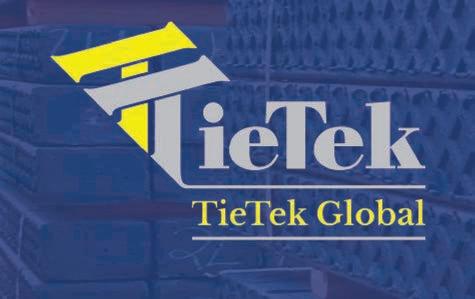


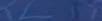

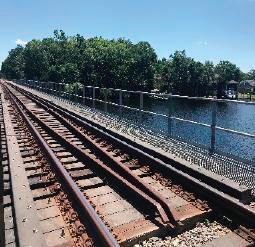
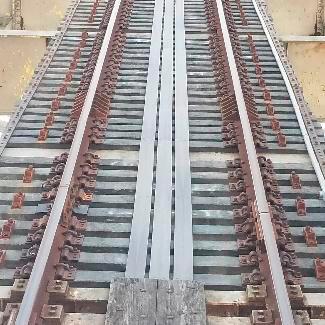
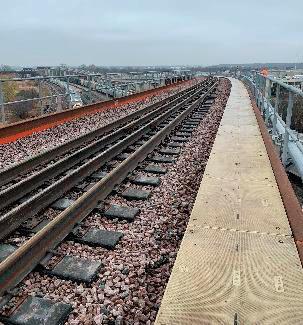
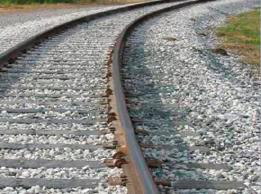
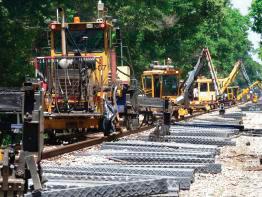
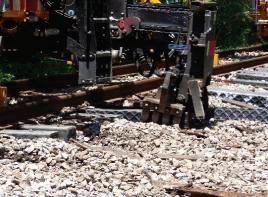






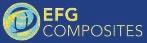
COLUMNS
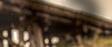
On Track Money and rainbows
36
Last Stop Rope-access bridge inspections
On the Cover
A worker inspects a section of tunnel on the Purple Line Extension. For story, see p 10.
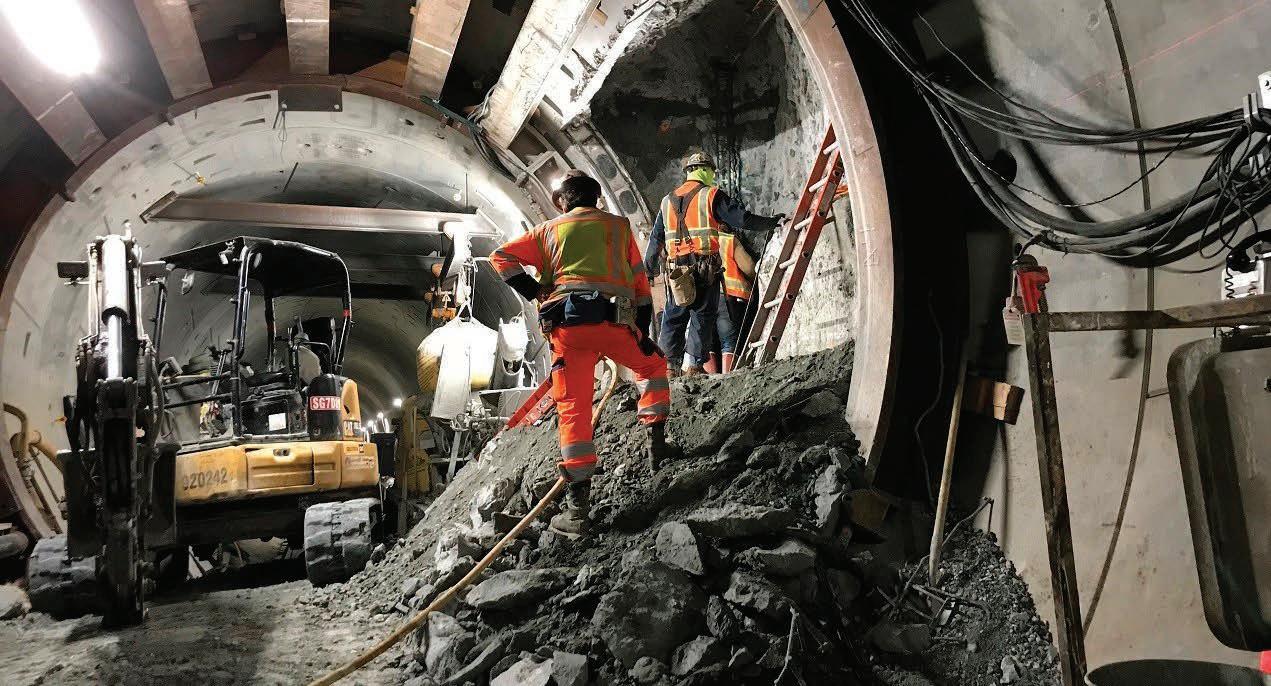
On Track Money and rainbows
36
Last Stop Rope-access bridge inspections
A worker inspects a section of tunnel on the Purple Line Extension. For story, see p 10.
Image of Way MBTA’s Orange Line project
The effects of shoulder ballast cleaning on ballast degradation
31
AREMA News
Message from the President, William H. Hay award winner, and more
One of the best products of Los Angeles is happening below the surface
The Civil War, a rail bridge, and dogs How specially trained canines kept a historic bridge project on budget after an unexpected environmental complication
Starting to sweat Crosstie market is experiencing a cycle of heavy activity
Follow Us On Social Media @RTSMag
26
The battle against moisture Fight against water in the roadbed never ends
A crew uses the help of an excavator bucket to place rail during MBTA’s Orange Line project in September. Photo courtesy of MBTA.
FOR THE LATEST INDUSTRY NEWS, GO TO WWW.RTANDS.COM.
If you would like to contribute a photo to the Image-of-Way section please send a high-res version to Bill Wilson at wwilson@sbpub.com. Photos must be no more than a month old.
degradation rate increases with the increas ing fine level, suggesting fine-filled ballast will degrade more quickly than clean ballast. In addition, analysis of two 15-mile segments of revenue service track showed that ballast shoulder cleaning reduced the ballast degra dation rate compared to track that had no shoulder maintenance performed.
SBC creates a shorter path through the center ballast resulting in quicker drainage. This clearing process may even wash center fines (fine migration) into the shoulders. Figure 1 shows both ballast drainage methods.
MxV Rail (formerly TTCI) analyzed the effects of shoulder ballast cleaning (SBC) on ballast degradation levels in revenue service. SBC is a production ballast mainte nance technique used by North American railroads to improve the drainage in finefilled ballasted track. Results from this study, performed under the Association of Ameri can Railroads’ (AAR) Strategic Research Initiatives (SRI) Program, found that ballast
Unlike undercutting (UC), which replaces the entire ballast section in the track, SBC removes and replaces only the shoulder ballast with reclaimed or clean ballast. By focusing on the shoulders, SBC has a higher production rate than UC; thus, either more track length can be cleaned or less track time is expended during the cleaning process. However, the specific benefits of SBC are not well quantified and may vary widely based on the condition of the ballast.
Theoretically, SBC can improve ballast drainage in a number of ways. First, SBC allows surface moisture to run off onto the clean shoulder instead of trapping the mois ture in the low permeability, fine-filled shoul der ballast. This runoff should reduce mud pumping from surface rainwater. Second,
A ballast section with improved drainage should experience less surface mud pumping and less track settlement, thereby reducing track geometry degradation and track compo nent damage. In the long term, the fine migra tion from the center of the track may reduce ballast degradation and extend the ballast life.
To quantify the benefits of shoulder cleaning on ballast fine levels in revenue service track, especially in the track center, MxV Rail used three years’ worth of ground penetrating radar (GPR) data collected by a Class 1 railroad from two 15-mile segments of track. This study was conducted in coordination with field tests and laboratory testing done by the University of South Carolina. The various testing methods are used to ensure testing occurs from a wide range of perspectives to allow for cross vali dations of findings between the fundamen tals (laboratory testing) and revenue service results (track inspection testing).
Figure 1. Conceptual diagram of fine-filled and shoulder ballast cleaned track.1The project used GPR data gathered from 2015 to 2017 at two 15-mile segments of revenue service track running through the same subdivision. The subdivision is a highly trafficked route in the midwestern U.S., and the track contained fines from ballast degra dation. Segment 1 is located on single track. No production ballast maintenance was conducted between the 2015 and 2016 GPR data collections, but SBC operations were conducted for the entire 15 miles between the 2016 and 2017 GPR data collections. Segment 2 is located in double-track territory and had GPR runs in 2015 and 2017 only. Between those two data collection runs, no mainte nance was implemented on 4 miles of track, and SBC and surfacing were performed on
the remaining 11 miles.
The GPR output analyzed for the study is called the Ballast Fouling Index (BFI). The BFI is calculated using the GPR measured signal for the ballast, and the data is typically grouped into five categories based on Selig’s Fouling Index (FI).
The categories include clean (FI = 0-4), moderately clean (FI = 5-9), moderately fouled (FI = 10-19), fouled (FI = 20-39), and highly fouled (FI = 40+). The GPR generates BFI values at the track center and both shoul ders every 15 ft, however, only the center BFI was used for this analysis.
Data analysis included four main steps to ensure data quality. The first step involved
cleaning and aligning the data. The second step involved removing data within 0.1 miles (528 ft) of any fixed asset (bridges, road crossings, and turnouts) because production SBC will avoid fixed assets. Initially, the fixed assets were identified from the track charts, and then the exact location was refined using the BFI data. The 0.1-mile buffer ensures the data representing the fixed asset and any transition effects were removed.
The third step involved removing any obvious spot maintenance locations through various methods (e.g., spot undercutting) to isolate the effect of production SBC. There were a few locations in each data set where a track section measuring track 45 ft or longer with a BFI above 15 (moderately fouled cate gory or higher) was reduced to a BFI of 5 or
Figure 2. Average change in center BFI for (a) Segment 1 and (b) Segment 2 plotted against various initial BFI categories.below (clean ballast category). This reduc tion in BFI likely indicates spot undercut ting, and the inclusion of these undercut locations would lower the average BFI and not truly represent the benefits of SBC. Therefore, regions that were judged to be undercut were removed from the data set.
Similar criteria were used for data removal, and the amount of data removed from each 15-mile track section was similar.
The fourth step involved aggregating the data into 0.05-mile (264-ft) block intervals. This involved averaging about 17 sets of 15-ft GPR data over each 0.05-mile section. This aggregation was done for the follow ing reasons. Railroads often aggregate GPR data for production maintenance planning, which considers long stretches of track instead of isolated locations that can be fixed by spot maintenance. Previous GPR calibra tion efforts suggest that GPR accuracy can vary for a single data point (15 ft), but, due to averaging, the accuracy improves when
considering longer stretches of track. 2 Both aggregated and non-aggregated methods were examined, and the general results and trends were similar.
This task involved comparing the changes in the center BFI over either a one-year period (Segment 1) or a two-year period (Segment 2). These segments were sepa rated for comparison based on whether they did or did not use SBC. The data was broken down according to Selig’s FI levels, which determined how the center BFI changed from the initial BFI levels.
Figure 2 shows the change in the average BFI for Segment 1 (a) and Segment 2 (b). The x-axis categorization was based on the initial BFI data (e.g., 2015), and the change in BFI indicates the difference between the two years (e.g., 2015 subtracted from 2016).
The results for both sections and all FI categories showed that the SBC sections had
a lower increase in BFI than the non-SBC sections. These results suggest that SBC does not necessarily “clean” the center ballast section but does reduce ballast degradation, leading to reduced ballast degradation in the track, likely due to improved drainage and fine migration paths as a result of clean shoulder ballast. In addition, the change in BFI increases with the increase in initial BFI, meaning ballast degradation rates will likely accelerate with time (or tonnage) and ballast will degrade more quickly for finefilled ballast compared to clean ballast.
Figure 3 shows the same data set as Figure 2 using a box-and-whisker plot where the bottom and top of the box plot represent the first and third quartiles (25% of data passing and 75% of data passing), the middle line represents the median, and the top and bottom whiskers represent the maximum and minimum, respectively. The results show similar trends to Figure 2 but emphasize the distribution of the data. The results also suggest the distribution range increases with increasing BFI. It is unclear how much of this distribution is physical and how much is an artifact of the accuracy of the GPR inspection system.
As more data is collected and analyzed, the results from this study will be refined. The key findings from this study include:
• The ballast degradation rate increases with the increasing fine level. This suggests fine-filled ballast will degrade more quickly than clean ballast; and
• An analysis of two 15-mile segments of revenue service track showed that ballast shoulder cleaning reduced the ballast degradation rate compared to track that had no shoulder maintenance performed.
Future work will include developing a forecasting model that will help project ballast degradation and future ballast condi tions for various types of production main tenance interventions (e.g., no interventions, shoulder cleaning, or undercutting).
1. Wilk, S. and D. Li, October 2019, “Ballast Rainy Section at FAST: Phase 1 Report,” Technology Digest TD19022, AAR/TTCI, Pueblo, Colo.
2. Bankston, A., M. Wnek, and S. Wilk, September 2019, “Implemen tation of BNSF Railway’s Geome try Car-Based Ground Penetrating Radar Program,” Proceedings 2019 AREMA Conference, Minneapo lis, Minn.
Figure 3. Box and Whisker plot showing changes in center BFI for (a) Segment 1 and (b) Segment 2 distributed by BFI category.Railway Age, Railway Track & Structures and International Railway Journal have teamed to offer our Rail Group On Air podcast series. The podcasts, available on Apple Music, Google Play and SoundCloud, tackle the latest issues and important projects in the rail industry. Listen to the railway leaders who make the news.
Not all of Los Angeles is Tinseltown USA, where they still try to polish the glitter every so often.
The city as a whole, however, still represents the trendy side of the nation at street level. Stars of the movie canvas and the sports arena often jump out and take over conversations, and the social media explo sion has only enriched L.A.’s influence over the masses.
Not all of Los Angeles is in perfect view.
Sure, there are the Hollywood secrets and skeletons gossip hounds churn out from the depths of rumors, but spotlights are painting the land a few hundred feet below; if only people could look to the subhorizon and get a feel that something big is happening.
It would certainly stir curiosity, which is not the purpose of the L.A. Metro Westside Subway (Purple Line) Extension project. No, this job is not about drawing the attention of any onlooker. The goal is to be stealth, unobtrusive, and free of any wonder while constructing a tunnel system that will help move Los Angeles for years to come.
Parsons is the prime designer of the Section 1 segment, which calls for extending the exist ing Purple Line from the current terminus at Wilshire/Western to Beverly Hills. Section 1 work involves boring 3.4-mile-long twin subway tunnels that have an inside diameter of 18 ft 10 in. and the construction of 23 cross passages. Three underground stations, each about 1,000 ft long, 70 ft wide and 80 ft deep, also will be created.
The entire 9-mile corridor has been broken down into three construction sections, and crews were still finishing up the opening portion at press time.
One of the biggest challenges cannot be seen at all.
The project is located in a hazard zone established by the city of Los Angeles for elevated gas conditions.
The entire length of the tunnel does not sit in this zone. Rather, it is along the west end of the La Brea Station and continues to the end of the project.
According to Parsons Project Manager Danson Kelii, the elevated gas condition zone affected the design of the underground tunnel
and the cross passages that connect the tunnel approximately every 800 linear ft. The precast tunnel segments needed to incorporate the design of a gasketed system that could seal the tunnel from any intrusion of gas or water.
“So that is the mechanism that is used along the tunnel and then at each cross passage,” Kelii told RT&S. “There’s a joint to connect those segments every 5 ft, and there is a gasket between those 5-ft-long segments.”
The segments are actually bolted together, creating a clamping force between the segments. The compression against the gasket creates the seal.
The concrete cross passages connect the twin bore tunnels, and they are cast in place and have an HDPE liner that ties into the tunnel segments and becomes
the waterproofing/gas-proofing transition between the cross passage construction and the tunnel construction. The station struc tures also are wrapped in the liner before any concrete is placed to provide a support for excavation.
There also is a venting system below the invert slab of each station. Gas vent pipes extend about 8 ft high and serve as an exhaust for any gas buildup.
“[The venting system] is for any gas that may build up below the station or to the sides of the station,” said Kelii. “The venting design allows the gas a way of getting up from under the station.”
Tar sands can be seen, but they were not originally expected to be in view. During the early stages of construction crews discovered the tar sands, which are not common in the underbelly of the region. The problem arose during the excavation of the Fairfax Station, which is adjacent to the Le Brea tar pits.
“As they excavated to the bottom and they reached the bottom it seemed like the mate rial was actually swelling,” remarked Kelii. “It’s really something we did not design for ... it’s just trying to understand how to deal with this material that is new to everybody.”
Kelii does have a theory behind the swell ing. He believes it was temperature-sensitive material. When it is cool, the material is relatively stable, but when you have warm conditions in the summer and created by hot equipment and work it becomes more fluid, which makes it hard to meet the compaction requirement.
Tar sands also were found at some of the cross passages, and crews used jet grouting as a solution.
Controlling the ground Removing dirt and everything else that is generated by using twin boring tunnel machines came with a certain process. Can mining techniques were used at the crosspas sages. Support was installed and then excavat ing commenced. The sequential excavating method was carried out.
“You don’t excavate the entire cross passage,” Kelii explained. “You do a top heading. So you just excavate the top, and then you excavate down below in sequence.
“It’s controlling the ground rather than having one big excavation and having the ground come at you from ground loading. You’re limiting the amount of exposure to the ground.”
Two tunnel boring machines are being used and are always separated by a minimum of 800 to 1,000 ft. So one would take off from
a station and the other would not start work until the minimum distance was achieved. Again, improper settlement is trying to be avoided.
“As the first tunnel machine proceeds it does take in material which creates potential settlement at the surface. So you don’t want those two machines working side by side where they are taking soil at the same time and potentially creating larger settlements.
“It’s better to move one forward and see what kind of settlement you are getting up top at the surface rather than boring both through and just hoping you don’t see much settlement.”
At every 5 ft of tunnel boring, a 5-ft-wide precast concrete section is installed.
However, before the tunnel boring machines are in play more excavation needs to be done. Support for the excavation is installed for each of the stations and then station excavation begins. Temporary traffic decking is placed over the station digs. Invert concrete is poured leading up to the tunnel boring machine launch.
An L.A. first?
Technology also is on full display during this project. Parsons is using Building Informa tion Modeling (BIM), which could be a first for an L.A. Metro project.
“We used the BIM model to produce all of our design drawings and our deliv erables,” Kelii described. “It created a 3-D model that makes it easier for the designers to collaborate.”
Kelii added with BIM the designer is working in a 3-D environment and then creating a 2-D design drawing based on the 3-D model. The model is then reviewed for
One of the best products of Los Angeles is happening below the surface
any obstructions or conflicts that may not be seen through 2-D technology.
“I think there have been some challenges [with the project],” said Kelii. “There have been
a lot of challenges on the electrical and systems work. I think you need to make sure that the right people are in the room when we are collab orating and finalizing designs. Sometimes that
communication is not the best with so many people involved.”
In addition to the tunnel, the station shafts range from about 75 ft to 80 ft below the ground surface and were designed with soldier pile lagging and a series of struts to support excavation with the challenging geology.
Western Station met the design subgrade elevation and the TBM slab was poured in October 2018. The interior walls, concourse slabs, and roof of La Brea Station were poured in 2021. The tar sands impacted Fairfax Station the most, but crews success fully reached design subgrade elevation in March 2019 and the invert slab was poured in August 2019. Fairfax Station interior walls were poured in 2021. Excavation of La Cienega Station was finished in October 2019 and the pouring of the invert slab was done in Febru ary 2020. Pouring of interior walls of La Cienega Station took place in 2021.
The entrance structure excavation started in January 2020 and was completed in May 2020.
Photo Credit: L.A. Metro“I think there have been some challenges. I think you need to make sure the right people are in the room when we are collaborating and finalizing designs.”
Ahistoric timber bridge over the Bonnet Carré Spillway near Norco, La., is approaching the end of its service life. Built in 1935, the bridge has seen several spillway openings as well as many severe weather events, and it is no longer economical to continue repairing it. Canadian National Railway (CN) and its subsidiary Illinois Central Railroad (ICRR) decided in 2018 on a new 8,000-ft-long precast concrete replacement, which would leave the track alignment and base of the rail profile unchanged.
The problem: At a preliminary permit ting meeting, the U.S. Army Corps of
Engineers (USACE) revealed a tenuous oral history from the 1980s, which placed a potential Civil War-era cemetery on the site.
Typically, this would require the excava tion of large swaths of the site, a process that would be extremely expensive and could add months of delay to the $70 million project. The project team, environmental specialists from CN, and engineering firm HDR, got to work on finding a solution.
To solve the mystery of the possi ble Union soldier cemetery, the team landed on a cutting-edge innovation: Historical Human Remains Detec tion dogs paired with a gradiometer and
ground-penetrating radar.
These specially trained dogs can detect the odor of human decomposition hundreds to thousands of years old, and they can distinguish between humans and other animals. This technique has been growing increasingly common in archaeo logical work. It’s been employed in archeo logical projects across the U.S. and Europe, but its use for cultural resources investiga tions during project development remains a novel application.
The team first convinced state and federal authorities that this methodol ogy was viable, and then with approvals in hand, mobilized for the investigation.
THE CIVIL WAR, A R AIL BRIDGE,
On a sunny, bone-chillingly cold day in January, two Labradors, two border collies, gradiometer and ground-penetrating radar handlers, and the rest of the team went to work searching the 1.5-acre site for poten tial remains.
The Baton Rouge Bridge 431 over the Bonnet Carré Spillway is an integral part of CN’s current freight operations and projected future freight growth along the east-west freight route to Geismar. The proposed project would replace a bridge at the end of its service life to improve the safety and reliability of the structure, minimize track closures from spillway operations and maintenance activities, and reduce longterm operational and maintenance costs.
The plan was to replace the existing 8,000ft-long, 601-span ballasted timber trestle bridge with prestressed, precast concrete double voided box girders supported on new, precast concrete piers and abutment caps on steel H-piles. In-line construction of the new bridge allows for an unchanged track alignment and base of rail profile, minimizing impacts to the existing rightof-way uses. The USACE had supported an abbreviated permitting review, but the
revelation of the oral history about a ceme tery in the area complicated matters.
Several cultural resource surveys had exam ined the entire spillway area and had found no cultural resources on what is now the bridge project site.
However, in 1986, one of those surveys uncovered an 89-year-old local resident whose grandfather had told him of a ceme tery in the area, separate from the three previously documented cemeteries nearby. The man did not remember marked graves but said his grandfather described the soldiers as having fought “for Uncle Sam.”
Additionally, a photograph from the Marshall Dunham Photograph Album at the Louisiana State University Library in Baton Rouge corroborated the oral history. The image showed graves with wooden markers in the foreground and a sugarhouse in the background. The reverse side of the photograph had an inscription which read “Soldiers Cem Bonnet Carré Bend.” This notation placed the cemetery on the east bank of the river encompassing the location specified by the resident in the 1980s.
This was a tenuous connection to a cemetery that might not even exist, but a
development that could create a major cost for the project.
It would be difficult to find answers. The wet conditions meant that bodies would likely have decomposed quickly. During the Civil War, many soldiers were buried without caskets and in unmarked graves, making any cemetery even more elusive.
Since the Civil War, the site also has changed drastically. The rail line was constructed. Then the spillway was built, and the rail line turned into a rail bridge at the spot in question. The spillway has been opened more than a dozen times, includ ing four in the past five years, sending water rushing under the bridge and around the project site. Maintenance on the bridge also has been conducted on the site over the years with no evidence of human remains.
An extensive historical study found some clues, but no answers. Union soldiers had been stationed nearby, specifically, the New York 177th Regiment. Many died of disease and a handful died in battle. Some Civil War soldiers had been buried in the area; Many were disinterred and relocated, but not necessarily all. There are three known cemeteries nearby, but the local resident was clear that the potential cemetery in ques tion was separate from the others.
Under Section 106 of the National Historic Preservation Act, and in accordance with the Advisory Council on Historic Preserva tion regulations pertaining to the protec tion of historic properties, federal agencies are required to locate, evaluate, and assess the effects of their undertaking on historic properties. In addition, due to the poten tial cemetery, the proposed effort required compliance with the Louisiana Unmarked Human Burial Sites Preservation Act.
The Louisiana Division of Archaeology (LDOA) initially required the excavation of the entire site—a time-consuming process that could have cost nearly $1 million. It also presented a safety challenge to operate heavy excavation machinery under the nearly 100-year-old timber bridge to depths of 6 ft. The site includes a high-water table that rises to fill holes and would have created extremely muddy conditions. Sand and clay mining in the areas adjacent to the right-ofway, where sediment has been placed and excavated, added to the complexity.
The team considered using a backhoe and pumping water out of the site or waiting until summer to see if possibly the water table would be lower. Neither was a good option due to the cost and delay. Instead, HDR and CN proposed bringing in human remains detection canines.
The USACE and LDOA approved the technique, provided that the dogs be used in conjunction with gradiometry and groundpenetrating radar. One selling point was that handler Karen Parquette was from Louisiana and border collie Polly had been trained in the spillway area, so they were familiar with local conditions.
The investigation was conducted in January 2022.
The team gathered on the site on Jan. 7 and 8. It included:
• Kari Harris, Environmental Impact Manager for CN’s U.S. Operations and chair of AREMA Committee 13;
• Raymond Baker, CN Project Manager;
• Gary Durbin, CN Employee-in-Charge;
• Zack Overfield, HDR’s South-Central Cultural Resources Leader;
• Ann Keen, HDR Senior Historian;
• Abby, a Labrador retriever, along with handler Paul Martin, RPA, of Martin Archaeology Consulting;
• Rip, a border collie, and handler Ben Alex ander, Ph.D., of FIRST Detection K9;
• Penny, a Labrador retriever, along with
handler Lisa Higgins; and
• Polly and Parquette.
USACE and LDOA officials also observed the investigation.
First, the dogs were deployed to sweep the area. They gave alerts in standing water that continually fills the depressions in the middle of the trestle area, as well as in stockpiled debris in soil that was previously in that area. However, that groundwater was flowing in from the area of a previ ously documented historical cemetery to the west, therefore, the detection of human remains odor was not conclusive.
The next step was to deploy the gradi ometer. The existing piles contained large metal bolts, so the team determined that gradiometry would not be effective there. In the other areas, the gradiometer detected several pits in the area as well as metallic objects. None was consistent with human burial.
Finally, the team had the standing water pumped and used ground-penetrating radar to survey between the pilings. Again, the team detected a variety of disturbances, but none that indicated human burial.
At the end of the investigation, the handlers took the dogs to the nearby Kenner cemetery to establish a control for their alert responses. The dogs showed intense alerts at the cemetery, even at unmarked but previously documented grave sites. In contrast, the alerts shown at the project site were much milder, which was clear to even
untrained observers.
From the two-day investigation, the team determined—and the USACE and LDOA later concurred—that no human remains had been identified and the results indicated no burial site was present at the project site.
The investigation indicated that there is likely a cemetery nearby but outside the project site, and outside CN right-of-way. Although it did not impact the project, the potential cemetery appears likely to be in the area as described in 1980s oral history— though more work would be needed to determine the final answer.
The project was allowed to move forward—disturbing no human remains— and completed the permitting process on budget with minimal schedule delays.
The entire investigation cost roughly $100,000, one-tenth of the estimated cost of excavating the site.
State and tribal historic preservation offices are managing a record number of proj ects, and that figure is only likely to grow. Between expanding regulations regarding cultural resources management and an influx of federal funding for infrastructure, more and more project sites are likely to include the possibility of unmarked human remains.
In this case, the soldiers might have been from a Black regiment. Marshall Dunham served as a first lieutenant in the 77th United States Colored Troops. That,
From the two-day investigation, the team determined that no human remains had been identified and the results indicated no burial site was present.
CN was able to avoid manual excavation of the entire site. This approach of using canines and technology can greatly narrow down the area of potential remains.
combined with the fact that these soldiers did not have a local connection, could explain why the potential cemetery was not maintained. More broadly, unmarked graves are likely to belong to a historically disadvantaged group including enslaved people and Native Americans. Burial sites for these groups are less likely to have been cared for and in some instances may have even been willfully neglected.
This new tool in the cultural resources management toolbox offers an opportu nity to restore what may have been lost. This approach can identify these unmarked graves and guide project development to avoid them.
In this instance, CN was able to avoid manual excavation of the entire site. But even in other cases where human remains are known to be on a project site, this approach can greatly narrow down the area of the potential remains, considerably reducing costs and delays that come along with excavation.
The use of the canines, paired with remote-sensing technology, is fast, incred ibly accurate, and can ensure that burials don’t get disturbed—a win for project owners, for regulatory agencies and, ulti mately, the best way to respect the deceased.
About the authors Harris is the Environmental Impact Manager and Project Manager for Cana dian National and the chair for AREMA’s Technical Committee 13 - Environmental.
Overfield is HDR’s Cultural Resources
Practice Leader for the south-central region and a senior archaeologist/princi pal investigator.
Robinson was HDR’s project manager for this project and is an environmental scientist.
Photo Credit: HDRWhen you own a small sawmill there are more days when you have to roll up your sleeves to meet demand. It is now officially t-shirt weather, as for the next 12 to 18 months crosstie production could be well above peak activ ity. It’s going to require a lot of work, so owners might as well dress for it.
Workforce sustainability, however, is at its worst, forcing those in power to pitch in for those who have permanently punched out. It has led some to venture into the world of automation. Before interest rates
started creeping up to flatten inflation a few months ago, the technology was start ing to catch on. According to the Railway Tie Association, sawmillers, especially those with lighter manpower, were begin ning to take a hard look at automation to fill the gap. Work at roller tables and anything that involves sorting can be handled by a machine, and with the price of the computer assistance becoming more affordable over the last few years automa tion had become more of a reality.
The true story of the current market place for crossties is that it has caught on
fire and could be ready for a slow burn. During the COVID-19 pandemic and the housing craze, sawmillers were focused on high-grade lumber for flooring and cabine try, with crosstie production dropping in importance. The market now has flipped, and it could not come any sooner. RTA data shows crosstie inventories are down to about 13.5 million when they are usually up close to 18 to 19 million.
If the upcoming winter keeps the forests relatively dry, crossties could be spitting out of the mills at a hefty pace. Putting more revolutions in the demand is President
WVCO’s CTR-100.
Biden’s infrastructure bill, which is getting short line railroad companies excited with the funding possibilities. Specialty tie work also is expected to rise over the next year or so.
RT&S reached out to a variety of crosstie suppliers, and most have been feeling the uptick in demand and believe it will carry into 2023. Vossloh’s Bear, Del., production facility has been running at capacity and will continue to run at capacity through the end of the year. The main contribu tors are capital projects in both the U.S. and Canada finally coming to fruition after COVID-related delays.
“We also are seeing a slight uptick from Class 1s through the end of the year as well,” Vossloh told RT&S . “There is slight increased demand going into 2023.”
“Our Class 1 customers continue to harden their networks to take on more business,” Stella-Jones told RT&S . “Preplated demand is strong, which indicates new projects for expansion.
“We expect this strong demand to continue into 2023.”
TieTek Global TieTek Global was recently acquired by
EFG Composites, a subsidiary of EF Global. Under EFG’s leadership, TTG will increase capacity at the Marshall, Texas, plant by year end, with additional facilities planned to assure adequate, timely supply of TieTek composite ties to meet market demand. Related services including special fabrica tion, pre-plating, and options for wood tie
grade crossings. TieTek ties are resistant to insects, fungi, moisture, harsh environ mental conditions, and rail-seat abrasion.
TieTek ties performed without failure between 2000 and 2015 at TTCI’s FAST high-tonnage loop track, accumulating over 2 billion gross tons. In more recent testing, TieTek ties installed in 2015 at FAST continue to perform well.
TieTek ties can be interspersed with treated wood ties or installed in new construction to reduce and eventually elim inate ongoing tie replacement and disposal costs. TieTek ties are manufactured using more than 80% recycled materials and are recyclable if mechanically damaged or at the end of life, helping customers address internal sustainability goals.
disposal will be an integral part of TTG’s complete sustainable bundle going forward.
TTG utilizes quality recycled materials in its proven TieTek formulation to produce composite ties that provide high perfor mance and extended service life in highdecay areas and severe environments such as tunnels, bridges, bridge approaches, and
Koppers Koppers offers the Crosstie Lifecycle Management Program as the environmen tally responsible solution for the entire lifecycle of crossties. From raw timber and dual-pressure treatment of new crossties to scrap tie collection, transportation, and recycling, this program will optimize your crosstie performance, risk management,
“ OUR CLASS 1 CUSTOMERS CONTINUE TO HARDEN THEIR NETWORKS TO TAKE ON MORE BUSINESS.
Hold gauge with EnduraPlug, our proven tie plugging compound - ready to ship.
Apply EnduraPlug with our wide range of applicators and equipment - available for purchase or lease.
Ensure maximum equipment uptime with our experienced field service team.
Get Pluggin’ with the best compound, equipment and service in the industry.
Encore Rail Systems, Inc. 2300 West Midway Boulevard, Broomfield, CO 80020
Find more at encorers.com
and environmental compliance with effec tive cost control.
Koppers implements environmentally responsible timber processing and dualpressure treating to maximize the perfor mance of the crosstie investment. The patented Tru-Cor dual-treatment process ensures accurate, measurable, and repeat able preservative retention levels of borate and creosote to meet the exact specifica tions for every decay zone.
After years of quality performance, crossties must be replaced and scrap crossties disposed of in accordance with environmental regulations. Koppers Life cycle Management Program provides timely collection and transportation of scrap ties to reduce liability, safety, and environmental risks of stockpiling scrap ties. Scrap ties are delivered to a process ing facility for energy recycling as a fuel source. This provides cost control since energy recycling typically costs less than disposal in landfills. To meet environ mental regulatory compliance, the entire recycling/fuel processing procedure is documented and submitted in proper report format.
Willamette Valley Company Spikefast is specifically designed to
remediate wood ties. Performance tests commissioned by Class 1 railroads indi cated that SpikeFast was a better option compared to wood plugs and foam in both lateral resistance and pullout resistance.
Results have indicated that SpikeFast’s withdrawal force is equivalent to that of un-spiked hardwood ties. Testing also has shown a proven resistance of 20% higher than that of previously un-spiked hard wood ties. One gallon can fill about 150 spike holes.
WVCO’s CTR-100 is able to seal and protect both moderately abraded and
non-abraded surfaces. The non-foaming, 100% solid polyurethane is designed to adhere to concrete surfaces in a variety of conditions. CTR-100 is engineered to provide durability and resistance to wear, prolonging the effective life of a rail seat. It also is appropriate for surface sealing or the repair of nominal seat abrasion. One gallon of the product is able to repair about 38 rail seats.
Omaha Track
Omaha Track’s latest release is a No. 4 grade “rustic tie.” The repurposed ties are
Photo Credit: Omaha Track, Willamette Valley Co. WVCO’s SpikeFast is designed to remediate wood ties. Omaha Track’s No. 4 grade “rustic tie.”ideal for landscape applications like prop erty line fences at a lower price point. The No. 4s are packaged with dual polyester banding with wood runners to increase safety as well as mobility for the end user.
Nisus Corporation’s Cellutreat liquid diso dium octaborate tetrahydrate (DOT) can help bridge ties and crossties. Cellutreat protects ties from decay fungi and wooddestroying insects. Its formulation allows for a higher concentration of borate and a single dip is sufficient to reach AWPA and AREMA retention standards.
The borate diffuses deep into the tie, protecting the heartwood from white and brown rot decay and reducing the risk of spike kill, termite infestation, and creo sote-tolerant fungi. Cellutreat can be used as a dip treatment prior to air seasoning to prevent incipient decay or as a remedial treatment in ties that have already been laid.
It also can be used as part of the BTX Tie Extender System for the dual treatment of green bridge ties. In this system, reservoirs are drilled into ties, filled with Cellutreat, and then sealed with BTX plugs prior to pressure treatment. When a vacuum is
pulled during the Boulton cycle, the borate in the reservoirs is pulled through the inte rior of the wood.
Railroad Solutions Sure Spike is a patented single component powder-based tie plug ging compound. It is both economical and effective for spike hole coverage. Sure Spike is a free-flowing powder designed to compact when the spike is driven into the filled hole. Sure Spike is recommended for rail gangs, rattle spike gangs, re-gauging work, and routine maintenance.
Benefits include:
• Works in all temperatures (especially cold weather, down to -40°), wet or dry;
• Reduces labor intensity—less manpower and hours;
• Environmentally safe;
• Stronger than wood plugs;
• Resealable containers;
• 600 tie holes per 40-lb container;
• Can be applied with a hand applicator, powder pac, or powder sling; and
• Can be applied by PAM (Powder Application Machine).
The newest applicator, PAM, makes
applying Sure Spike easy and efficient. The operator is seated in a safe position, adjust ing the eight heads to be in the correct posi tion for each spike hole on each tie.
EnduraPlug is a 1-to-1 ration tie plug ging compound. EnduraPlug densities are designed to match hard wood and compos ite ties. The compounds are extraction force tested and proven to ensure a tight spike hold, even in the most extreme situa tions. Used by Class 1s, short lines, transits, and contractors, EnduraPlug is used to help crossties live longer and hold spikes tighter.
Stella-Jones provides bridge prefab capa bilities. The company offers very detailed framing capabilities as well as the borate drill-and-fill option for both creosote and QNAP treatment. Stella-Jones also provides pre-plated bridge timbers that speed up installation and provides a higher level of safety during the installation.
There has been an increased demand for bridge timbers over the last year and StellaJones expects this demand to be strong into 2023.
Photo Credit: Railroad Solutions’ Sure Spike is a free-flowing powder designed to compact when the spike is driven into the filled hole.The Wheeling & Lake Erie Railway Company (W&LE), privately owned, is the largest Ohiobased railroad and among the largest regional railroads in the country. W&LE continues to move approximately 140,000 carloads annually along their service area of nearly 840 miles of track. Many of their existing tracks include wrought-iron trestles.
Along a portion of the W&LE track line located in Media, Ohio, an original trestle needed repair or replacement. Engineers determined that whatever type of bridge structure was selected, its installation could not disrupt the normal rail traffic on the line. The railway wanted to maintain the line above and avoid extended track closure. Therefore, excavation, removal of the exist ing trestle and track, and replacement was not the preferred solution.
Bridge and culvert replacements are a
common reality for all owners of drain age infrastructure and a routine part of maintenance and expansion projects on federal lands, roadways, and railroads; state department of transportation (DOT) road ways; and at the local level with county-, township-, and municipality-owned trans portation corridors. Fortunately, culvert rehabilitation via relining has gained momentum as a viable alternative to culvert replacement when dealing with aging drainage infrastructure. Whether an owner of a culvert wants to take a traditional design and delivery approach or conduct the work themselves, the construction methods of many reline options are avail able to parties whose normal work activities don’t include reline construction. In-house maintenance teams or entities who do most traditional open-cut drainage work can use these methods.
W&LE engineers evaluated the site and
concluded that a large-diameter DuroMaxx steel reinforced polyethylene (SRPE) liner pipe manufactured by Contech Engineered Solutions LLC would be ideal. DuroMaxx meets standards approved by the American Railway Engineering and Maintenance-ofWay Association (AREMA) for direct-bury and reline applications. It utilizes 80-ksi steel reinforcement ribs to provide struc tural strength, while the pressure-rated polyethylene pipe wall and rib encapsula tion provide durability. These materials result in a solid and durable pipe. Engineers determined that the reline of the existing trestle could occur over a single weekend.
A local contractor, Cocklin Trenching Inc., was chosen to facilitate the on-site installation. Contech Engineered Solutions also was on-site to provide assistance and oversee the project. Due to the SRPE pipe’s design, the contractor could use a small track hoe to transport it to the site. The
pipe was carried along the rail above the installation location and then set below and pulled into place under the existing bridge. Three 20-linear-ft segments of 120 in Duro Maxx were needed to reline the existing train trestle. After placing each segment, workers properly honed the bell and spigot joints to ensure a tight fit. Per the project requirements, the SRPE liner pipe adhered to ASTM F2562 standards, while the highperformance bell and spigot-gasketed joints met the requirements of ASTM D3212. All three segments were placed and installed in just one day.
After the successful installation of the new liner pipe, backfill material was placed around the pipe and then properly compacted to the finished grade. From this point, the timbers and older girders were removed, and the new rails and ties were set in place to reinforce the train tracks for an additional estimated service life of 100+ years. This particular project was a unique reline in that no grout was necessary. Given the hydraulic efficiencies provided by the SRPE liner pipe, capable of Manning’s “n” of 0.012, a 120-in.-diam. pipe was perfectly
sized and easily fit beneath the existing girders. Converting the original trestle to a buried culvert brought even greater effi ciencies to the railway, including minimal maintenance, which lowers overall lifecycle cost and increased safety with no freeze concerns and deck maintenance.
This SRPE pipe is considered a flexible pipe type with a profile wall. However, with the incorporation of steel, it is no longer a traditional flexible thermoplastic pipe. Instead, it acts more like a steel or metal flexible pipe when buried. W&LE has begun converting many of these older train trestle bridges to buried culverts to ensure the lines operate at optimal performance levels while maintaining structural integrity.
Loram provides a full range of products to ensure track structures effectively drain water. All drainage maintenance should start with a sound understanding of the root cause of the track’s symptoms. Loram’s GPR & LiDAR inspections take a holistic look at the track to identify if water presents issues due to ballast fouling, poor subgrade
conditions, or compromised ditches. Once engineers identify the root causes, Loram’s fleet of equipment can be utilized to remedy the issue correctly.
Loram continues to work with custom ers to improve drainage. By pairing the ditching machine, the Badger Ditcher, with a slot train, cut ditches can be created by removing any obstructions in the drain age path. The Badger Ditcher can easily clear clogged ditches and cut new ditches at up to 1,000 tons of material removal per hour. The excavator inside the slot machine is equipped with a roto tilt attachment and can grasp and remove oversized objects in ditches that prevent drainage. The slot machine can store material in areas where excavated material cannot be discharged directly to the right-of-way. The excavated material can then be offloaded at a location of the customer’s choosing.
Pairing the Loram LRV Excavator with one or more MHC60 Material Handling Cars allows customers to better utilize track windows for ditching and excavation projects. With 5,000 lb of nozzle tip force, the LRV removes compacted ballast and
mud from undertrack and opens drainage pathways to allow moisture to leave the track. The added material-carrying capac ity of the MHC60 speeds operating on
ballast deck bridges and tunnels where discharging material to the right-of-way is impossible and maximum material storage is required. Once at a suitable
offload location, the MHC60 can selfoffload quickly.
Ballast Tools Equipment (BTE) has devel oped a series of attachments to tackle tough drainage issues with a wide array of ditch ing and drainage buckets, culvert clean ers, undercutters, and vegetation and snow attachments.
The wide selection of BTE high-perfor mance undercutter attachments can be operated with nearly every machine in the BTE fleet, including the BTE-450 Hi-Rail Backhoe, the BTE-313 Hi-Rail Excavator, the BTE-326 Hi-Rail Excavator, and the BTE-329 Hi-Rail Excavator. Ranging from 9 ft to 18 ft in length, the BTE Undercutters can tackle any mud spot quickly and effec tively. Paired with BTE’s Hi-Rail Dump Trailer, moving large amounts of material and debris from problem areas is effectively done.
BTE’s Mulcher and Cold Air Snow Blower provide high-performance clearing of vegetation and snow from the track and right-of-way.
substructure,
mechanics, design, construction, measurements, and management.
environment,
professionals and graduate
primarily
Signals is an excellent guide for training signal personnel especially railway cross-function managers, supervisors, and support personnel. High-quality graphics and diagrams have been used throughout. Complies with all standards and commonly used practices.
Guide to Railway Signals
most comprehensive collection of definitions relating to track. Over 1500 terms from antiquated forgotten slang to today's jargon. Clearly illustrated line art enhances the text.
Railway Track
rugged, indestructible, composite
track inspectors, maintenance and welders
compact gauge measures the flangeway gap and checks proper spacing for guardrails.
10 or more and get
20%
Completed installation of Contech DuroMaxx pipe. PhotoRAIL GROUP NEWS brings you a daily round-up of news stories from Railway Age, RT&S, and IRJ. This email newsletter offers North American and global news and analysis of the freight and passenger markets. From developments in rail technology, operations, and strategic planning to legislative issues and engineering news, we’ve got you covered.
September 15 | 2:00 - 3:30 PM ET
1.5 PDH | Presenter: Dr. Mo Ehsani
September 20 | 2:00 - 3:00 PM ET
1.0 PDH | Presenter: Mark Austin, John Hilborn, PE, and Kyle Medick, PE
Rail Industry Update with Tony Hatch - Industry Consultant
October 26 | 2:00 - 3:00 PM ET
1.0 PDH | Presenter: Anthony “Tony” Hatch
To REGISTER or for more information, scan the QR code OR visit www.arema.org
Additionally, each chapter is provided $1,000 annually for chapter expenses and $1,000 annually reimbursed for expenses from attending the Annual Conference & Expo.
TRENT M. HUDAK AREMA President 2022-23With universities back in session this is an opportune time to discuss AREMA Student Chapters. They are an essential part of AREMA’s connection to the next generation of railway industry professionals. Committee 24 - Education and Training is responsible for supporting them with leadership guidance, resources, and industry speakers. The main goal is to bring students interested in railroading together in a setting where their interests can be directed toward activities that advance their academic curiosity in railway engineering. The hope is these chapters increase inter action and cooperation between railway professionals and students. Over the past 16 years, 25 chapters have been estab lished. The list of chapters can be found on AREMA’s homepage under the Students tab in the upper right corner.
AREMA provides many student benefits to help ensure the chapters are successful in reaching the goals for the association and the needs of the student. These include:
• Access to industry professionals;
• Participation in the mentoring program;
• Use of the Railway Careers Network Job Postings on the AREMA website;
• Free subscription to Railway Track & Structures (RT&S), Progressive Railroad ing and Mass Transit magazines;
• Free Student Membership (upon qualification);
• Free Annual Conference & Expo atten dance (requires free Student Member ship); and
• 50% discount on seminars and webinars.
Three members of Committee 24 provide the primary support for the chapters. Aaron Dean, a design engineer with Pettibone, is the lead Student Chapter Coordinator and Nick Kern, P.E., a rail project manager with Kimley-Horn, provides additional help. Daniel Rappoport, a track designer with Gannett Fleming, is the Student Chapter Mentor. The coordinators hold quarterly calls with the chapter leaders to provide guidance and support, help address issues and chal lenges, and assist with activity ideas and guest speakers. The Student Chapter Mentor is a new role started in 2021 that works with the coordinators to provide a little extra help to the chapters that need it. The universities have provided positive feedback on the coordina tion efforts—a big thanks to Aaron, Nick, and Daniel for your great work with the chapters. For those of you who were able to attend the Annual Conference & Expo in Denver, you may have had the opportunity to participate in Sunday’s student activities. The Student Chapter Coordinators and others from Committee 24 are responsible for all these additional student opportunities.
For an active and effective chapter there needs to be a university faculty advisor, such as a professor or other staff from the engineer ing school who is an AREMA member, one or more industry liaisons (preferably alumni), and students willing to take leadership roles to run the chapter. And, of course, AREMA members need to share railway engineering expertise with the students as chapter meeting guest speakers and/or by providing a handson experience visiting railway infrastructure. The Student Chapter Coordinators function as a clearing house for the industry profes sionals willing to help and the chapters who need industry support.
AREMA leadership meets with Commit tee 24 and the Student Chapter Coordina tors on a routine basis (almost monthly) to monitor that our goals are being achieved. Each chapter completes an annual report which provides an assessment of their activ ity and membership. The program is continu ously being reviewed to find opportunities for improvement. A Student Chapter Handbook in development should be helpful for forming new chapters and assisting existing chapters.
Another item in development is the Student Chapter Best Practices, where experiences from more established chapters will be made available for newer chapters. If you have ideas on how to enhance the Student Chapter expe rience, please contact the coordinators.
The pandemic has been detrimental to the student chapters because meetings and other activities were limited to virtual events or just not practical. As our world gets back to normal, some chapters are thriving, but others continue to struggle. The best value for students, and ultimately our industry, is for in-person meet ings with speakers and activities that facilitate hands-on learning. We need to re-engage with the chapters and help them revitalize. Students have limited time and unlimited competing opportunities so we as an industry need to help make the chapters engaging and worthwhile for the students who may have an interest in railway engineering.
I challenge the AREMA membership to look at the list of student chapters and see which one(s) you can support by becoming a liaison, by reaching out to attend a meeting in-person, and/or host an event that provides insight to our industry. You might consider reaching out to your human resources depart ment and they might be interested in making this an informal recruiting event. Some of the feedback we have received is that the students and young professionals are often intimi dated by the many highly experienced railway engineers in our industry and are reluctant to approach them for advice. How can we breakdown this barrier and remove the fear? One thought is for committees to reach out to students with invitations to have them sit in on a committee meeting. Maybe we can discuss with them how we started our careers, our experiences in the industry, and potential opportunities that may be available to them? Maybe we can provide an informal network ing opportunity? Everyone must start some where—we need to consider how we can make them feel welcome with our actions. Commit tee 24 will provide support with presentation material and match you up with a chapter that needs engagement from the industry, particu larly those that are struggling. Please contact the Student Chapter Coordinators at scc@ arema.org if you are willing to help. Enjoy your journey until next month.
TRENT M. HUDAK AREMA PresidentFor those of us who want a conference rewind, AREMA 2022 Annual Conference attendees have complimentary access to the On Demand version now available. You’ll be able to watch any session at your leisure and gain your Professional Development Hours (subject to your state’s approval). If you could not make the trip to Denver, it is available for purchase. Please visit www.conference.arema.org for more information and to purchase.
Don’t miss out on the conversation happening in AR EM A’s M ember Forum. The Member Forum connects you with other members allowing you to send messages, start conversations, and more. See what everyone is talking about today: https://community.arema.org/home.
S ave the date for the AR EM A Railway Roadbed & Ballast S ymposium, Feb. 6-8, in Kansas C ity, M o. For the latest information about speakers, presentations, sponsorship, and more, visit www.arema.org.
I f you’re looking for a new podcast to binge, listen to AR EM A’s P latform C hats. It features guests from every aspect of the railway industry. Come “roll with AREMA” on your favorite streaming platform.
2023 C all for P apers: P apers are now being accepted for the AR EM A 2023 Annual C onference in conjunction with Railway I nterchange to be held in I ndianapolis, I nd., O ct. 1-4, 2023. The deadline is Dec. 9. Please visit www.
arema.org for more information and to submit a paper online
O rder the new 2022 edition of the Portfolio of Trackwork P lans. This edition features new plans and specifications that relate to the design, details, materials, and workmanship for switches, frogs, turnouts and crossovers, crossings, rails, and other special trackwork. Order online now at www. arema.org or contact publications@ arema.org for more details.
N OT AN AR EMA M EM BER? JOIN TO DAY AT WWW. AR EMA .O RG
CONNECT WITH AREMA ON SOCIAL MEDIA:
OCT. 18-19
Committee 15 - Steel Structures Orlando, Fla.
OCT. 25-26
Committee 36 - Highway-Rail Grade Crossing Warning Systems St. Louis, Mo.
JAN. 31-FEB. 1
Committee 15 - Steel Structures Atlanta, Ga.
MAY 16-17
Committee 15 - Steel Structures Pueblo, Colo.
OCT. 26-27
Committee 37 - Signal Systems St. Louis, Mo.
Joining a technical committee is the starting point for involvement in the association and an opportunity for lifelong growth in the industry. AREMA has 30 technical committees covering a broad spectrum of railway engineering specialties. Build your network of contacts, sharpen your leadership skills, learn from other members, and maximize your membership investment. You can also earn necessary PDH hours by attending committee meetings. If you’re interested in joining a technical committee or sitting in on a meeting as a guest, please contact Alayne Bell at abell@arema.org. For a complete list of all committee meetings, visit www.arema.org.
Each year, the Dr. William W. Hay Award for Excellence is awarded to a project that represents an outstanding achievement in railway engineering and to honor the memory and accomplishments of one of their members and leaders: William Walter Hay. Dr. Hay was a professional railroader in both the military trans portation service and the private railway industry. He was a consultant on design, construction, and operations of railroads and, for over 25 years, he was a professor of Railway Civil Engineering at the Univer sity of Illinois at Urbana-Champaign. He also was a teacher, motivator, and mentor for dozens of men and women who chose to enter the transportation industry.
The 2022 Dr. William W. Hay Award for Excellence was awarded to CSX
and the North Carolina Department of Transportation (NCDOT) for the Caro lina Connector Intermodal Project. The project created the 310-acre Carolina Connector Intermodal Terminal (CCX) located in Rocky Mount, N.C., which is the newest and most advanced state-ofthe-art intermodal terminal on CSX’s system. The terminal serves as a vital link connecting rail cars and trucks to trans port products and goods across North Carolina and the country and represents a true public-private partnership success. Both CSX and North Carolina provided funding and support to the project. CSX contributed $40 million, which included certain engineering costs, purchasing the property, and the crane equipment. In addition, CSX also provided engineer ing and construction oversight. North
Carolina funded $118 million towards the design and construction of the termi nal in addition to supporting important roadway improvements.
The new facility went live in October 2021, has experienced strong early volumes, and has created intermodal link ages between the Carolinas, the Midwest, and the West.
Please join AREMA in congratulating CSX and the NCDOT on their achieve ment. The 2022 award was announced during the AREMA 2022 Annual Conference & Expo in Denver, Colo., on Monday, Aug. 29, in the General Session and was presented by Michael Franke, chair of the Hay Award Selection Committee. Also attending was Dr. Hay’s son, Dr. William W. Hay, Jr. (pictured on stage with the winners)
COMPANY
AREMA Marketing Department
Encore
Hougen Manufacturing, Inc.
Loram
Racine Railroad Products, Inc.
Railway Educational Bureau RELAM
Stella-Jone Corp
TieTek Global voestalpine Nortrak Inc
WVCO Railroad Solutions
PHONE # 301-459-3200 303-956-3776 866-245-3745 763-478-6014 262-637-9681 402-346-4300 770-335-9273 800-272-8437 281-444-3494 307-778-8700 541-484-9621
E-MAIL ADDRESS marketing@arema.org gs@encorers.com info@trak-star.com sales@loram.com custserv@racinerailroad.com bbrundige@sb-reb.com jroberts@relaminc.com kdulski@stella-jones.com sales@tietekglobal.com gord.weatherly@voestalpine.com wvcorailroadsolutions@wilvaco.com
AME RICAS, EU ROPE , ASI A, A FRICA, AU STR AL ASI A NO R TH AME RICA - CT, DE , DC, FL, GA , ME , MD, MA , NH, NJ, NY, NC, OH, PA , RI, SC, VT, VA , WV, AND EAS TE R N CANADA. EU ROPE E XC EPT GER MANY, AUSTRI A, GERMAN S PEAK I NG SWITZE R LAND, EAS TE R N EUROPE, ITALY, AND ITALIAN-S PEAK I NG SWITZE RLAND. ASI A E XC EPT JAPAN AND CH I NA.
JE ROME MAR ULLO (212) 620-7260 jmarullo@sbpub.com
Corte Lambruschini Corso Buenos Aires
V Piano, Genoa, Italy 16129 +39-10-570-4948
Fax: +39-10-553-0088 info@mediapointsrl.it
Media
OFFIC E) (312) 683-5026
EATHE
hdisabato@sbpub.com
GER MANY, AUSTRI A, GER MAN-S PEAK I NG SWITZE RL AND, L ATV IA, LITHUAN IA, ES TO NIA, P OLAND, CZEC H REPUBLIC, SLOVAK IA, H UNGA RY, SLOVEN IA, CROATIA AND SE RBIA Simone and Simon Fahr Breitenbergstr. 17 Füssen 87629 Germany Tel: +49 8362 5074996 sfahr@railjournal.com
This section has been created solely for the convenience of our readers to facilitate immediate contact with the RAILWAY TRACK & STRUCTURES advertisers in this issue.
The Advertisers Index is an editorial feature maintained for the convenience of readers. It is not part of the advertiser contract and RTS assumes no responsibility for the correctness.
Inc. 12-6 4-Chome, Nishiiko, Adachi-Ku
Tokyo 121-0824 Japan +81-3-5691-3335 Fax: +81-3-5691-3336 amkatsu@dream.com
JE
(212) 620-7260 jmarullo@sbpub.com
Every time a train comes to a stop represents a potential loss in revenue for a railroad. That can make annual bridge inspections, which are vital to safety and operations, an unpredictable and unreliable expense.
Traditional rail bridge inspections are often the culprit, as they require that a “snooper” truck occupy the tracks for the duration of the inspection. The necessity of clearing inspection team members and equipment results in costly delays for both railroad owners and the inspection team.
Rope-access inspections are becoming increasingly popular as a safe, less intrusive and more cost-effective way to inspect, without sacrificing the quality of the inspection. Anchored to the truss, a properly trained and SPRAT/IRATA-certi fied rope-access team can quickly rig up and go to work while main taining their positions on the bridge when a train needs to pass, causing little delay in the inspection process.
An owner, therefore, is both saving money and maximizing the usefulness of inspections while ensuring the safety of those people who depend on the bridge.
Rope access can be particularly effec tive in high-traffic locations while main taining—even enhancing—the safety of inspection teams. For example, in an industrial area of southeast Texas, inspec tors were able to work beneath a vertical lift bridge even as 20-plus trains passed over the bridge each day. That would have been an incredibly difficult task with a traditional snooper inspection.
In fact, there’s little down time at all for both the trains and the inspection team. When alerted that a train needs to pass through the Form B track protection, the
rope-access inspection team maneuvers to a safe position on the outboard side of the truss so as to not foul the track, usually in less than five minutes. The team secures equipment and rope tails, and comes to a set position, while continuing to record data, take photographs, etc. They can even check the train for loose loads or other unsafe conditions as it passes. Once they’ve ensured that everything is safe, the inspec tion team immediately gets back to work.
A four-person inspection team is typically needed at most sites, accompanied by one or two rope-access supervisors. Inspectors usually work in pairs, and they continuously communicate and share information as they go along to improve func tionality. It’s a system of checks and balances that enables the team to examine the bridge with increasing efficiency throughout the day.
Using a two-rope system consisting of working and safety lines, the inspectors can set up in less than 30 minutes. Once the equipment is in place, they can complete most single span trusses in a day or less. With this process, they’re gathering invaluable, and often more comprehensive, data since they’re always within an arm’s reach of all components. That can save additional time later should the inspection company be chosen to design and coordinate repair plans.
In many situations, therefore, ropeaccess inspections are a viable choice for a rail owner as a safe, low-tech, high-results method for inspecting bridges.
Dickens is the bridge inspection practice builder with HNTB’s Central States Office, based in Kansas City, Mo.
“ ROPE-ACCESS INSPECTIONS ARE A VIABLE CHOICE FOR A RAIL OWNER.
Loram delivers comprehensive solutions for ballast optimization and drainage maintenance. Inspection with Loram’s Ground Penetrating Radar and LiDAR technologies ensure targeted ditch and drainage maintenance that will maintain the stability of your ballast and subgrade. Ditch and shoulder ballast cleaning deliver the benefits of increased cycle time between surfacing and lining programs, while preventing premature tie deterioration and loss of stability in track infrastructure.
From inspection and geotechnical services that precisely identify drainage and ballast conditions, to our industry-leading array of maintenance equipment and remediation solutions, Loram is equipped to maximize and protect your infrastructure investment. Learn more at Loram.com