
19 minute read
STADLER produce il separatore balistico numero 1000
STADLER ha raggiunto un importante traguardo con la produzione del suo separatore balistico numero 1000. La macchina STT5000_6_1 è stata acquistata da Vaersa, un’azienda spagnola, e consegnata al loro impianto di selezione di imballaggi leggeri a Castellón, dove ora è al lavoro con piena soddisfazione del cliente.
Advertisement
Innovazione continua che anticipa le esigenze del cliente
Leader mondiale nel mercato dei separatori balistici, STADLER è stato il pioniere di questa soluzione altamente efficiente ed economica. Sviluppato agli inizi degli anni ‘90, il prodotto è stato costantemente migliorato a livello di prestazioni ed efficienza. Al 2000 risalgono due importanti innovazioni: il telaio inclinabile brevettato, che ha eliminato la necessità di inclinare l’intera macchina e di regolare i nastri trasportatori, e le pale con griglie di vagliatura forate. Nel 2002, STADLER ha ampliato la sua offerta di separatori balistici STT2000 con un nuovo modello sviluppato appositamente per la separazione di carta e cartone, con pale a Z brevettate. Nello stesso anno, individuata una nuova esigenza del mercato, STADLER ha lanciato l’STT5000 per materiali pesanti, come RSU e rifiuti industriali. Più di recente, STADLER ha identificato una nuova richiesta del mercato relativa al riciclo di materiali molto pesanti, un settore in rapida crescita. Per rispondere a questa esigenza, ha sviluppato l’STT6000 per la selezione dei rifiuti da costruzione e demolizione, per l’estrazione in discarica e persino per i rifiuti solidi urbani con elevate impurità. Il Vice-responsabile Ricerca e Sviluppo di STADLER, Christian Nordmann, sottolinea i vantaggi principali della macchina: “Non c’è bisogno di pre-selezionare o pre-sminuzzare il materiale in ingresso. Inoltre, a differenza dei tamburi di
vagliatura, che separano il materiale solo in due frazioni, l’uscita a tre frazioni dell’STT6000 consente di rimuovere facilmente le impurità, poiché sono ancora nella loro dimensione originale”. I separatori balistici STADLER sono estremamente flessibili e possono essere adattati per soddisfare requisiti molto specifici. Ad esempio, l’azienda ha progettato separatori balistici con meno pale per adattarsi ai piccoli spazi degli impianti di selezione del Giappone. Ha inoltre creato macchine con pale più lunghe o più corte per soddisfare esigenze specifiche. È anche possibile assemblare fino a tre moduli di separatori balistici uno sopra l’altro o in serie per ottenere migliori frazioni.
STADLER Italia Srl Tel +39 0523 17277-68 pietro.navarotto@w-stadler.de www.w-stadler.de/it

STADLER celebrates history of pioneering innovation with milestone of 1,000th ballistic separator
STADLER has reached an impressive milestone with the production of its 1,000th ballistic separator. The machine STT5000_6_1 was purchased by a Spanish company, for their light packaging sorting plant, where it is now operating to the customer’s full satisfaction. A global market leader in ballistic separators, STADLER has pioneered this highly efficient solution. Development started in the early 1990s and since then important innovations, like the patented pivoting frame, paddles with screened perforation and new models developed for specific materials, were introduced to the market. STADLER ballistic separators are extremely flexible and can be adapted to match specific requirements, like fewer, longer or shorter paddles to address very particular needs. It can also assemble up to three ballistic separator modules on top of each other or serially to achieve better output fractions.

La nuova AUTOSORT di TOMRA: il futuro della selezione a sensori
TOMRA Sorting Recycling progetta e realizza tecnologie per la selezione a sensori per il settore del riciclo e della gestione dei rifiuti. Ad oggi, sono oltre 6.000 i sistemi TOMRA installati in 100 paesi del mondo. Il 9 giugno, durante un lancio globale online, TOMRA ha presentato due ultimissime tecnologie di selezione: la nuova generazione di AUTOSORT® e AUTO-
SORT® SPEEDAIR.
Questo sistema di selezione a sensori, compatto, altamente flessibile e aggiornabile, riunisce in sé le più recenti tecnologie di TOMRA per fornire una selezione precisa e a velocità elevata, anche con i materiali più complessi, addirittura impossibili da individuare con le tecnologie convenzionali. Questo grazie all’utilizzo della più ampia gamma di sensori di TOMRA e dei dati ricavati durante il

processo per classificare gli oggetti in maniera corretta. Grazie all’integrazione della tecnologia SHARP EYE e FLYING BEAM®, oggi di serie, AUTOSORT® offre prestazioni qualitativamente costanti in termini di precisione di selezione di tutte le frazioni target, anche nelle applicazioni più difficili. Disponibile su richiesta il nuovo DEEP
LAISER, un sistema di deep learning
(AI) integrabile nell’AUTOSORT® con funzione di riconoscimento degli oggetti in 3D. AUTOSORT® SPEEDAIR è la seconda novità lanciata da TOMRA: si tratta di un componente aggiuntivo della gamma AUTOSORT® progettato per stabilizzare materiali leggeri come pellicole plastiche o carta sul nastro d’accelerazione (grazie a ventole con getti d’aria a velocità controllata che generano un flusso
d’aria costante sul nastro trasportatore, aumentando la stabilità del materiale). Raddoppiando la velocità dei nastri d’accelerazione fino a 6 metri al secondo, la produttività è molto più alta e la qualità del materiale in uscita è costantemente elevata. I clienti beneficiano così di un migliore ritorno dell’investimento, oltre che di minori costi di installazione e di gestione. Fabrizio Radice, Vice President e Responsabile Sales & Marketing Global di TOMRA Sorting Recycling, commenta: “Lavoriamo a stretto contatto con i nostri clienti per garantire che i nostri prodotti soddisfino costantemente le loro esigenze e quelle dei loro clienti finali. Il nostro sistema AUTOSORT® di nuova generazione è un’innovazione entusiasmante, in quanto il suo utilizzo di sensori versatili e di software intelligente permetterà di soddisfare le richieste di tutta una serie di applicazioni di selezione attuali e future”.
TOMRA Sorting Recycling Tel +39 0521 681082 www.tomra.com/recycling

The new AUTOSORT by TOMRA: the future of sensor-based sorting
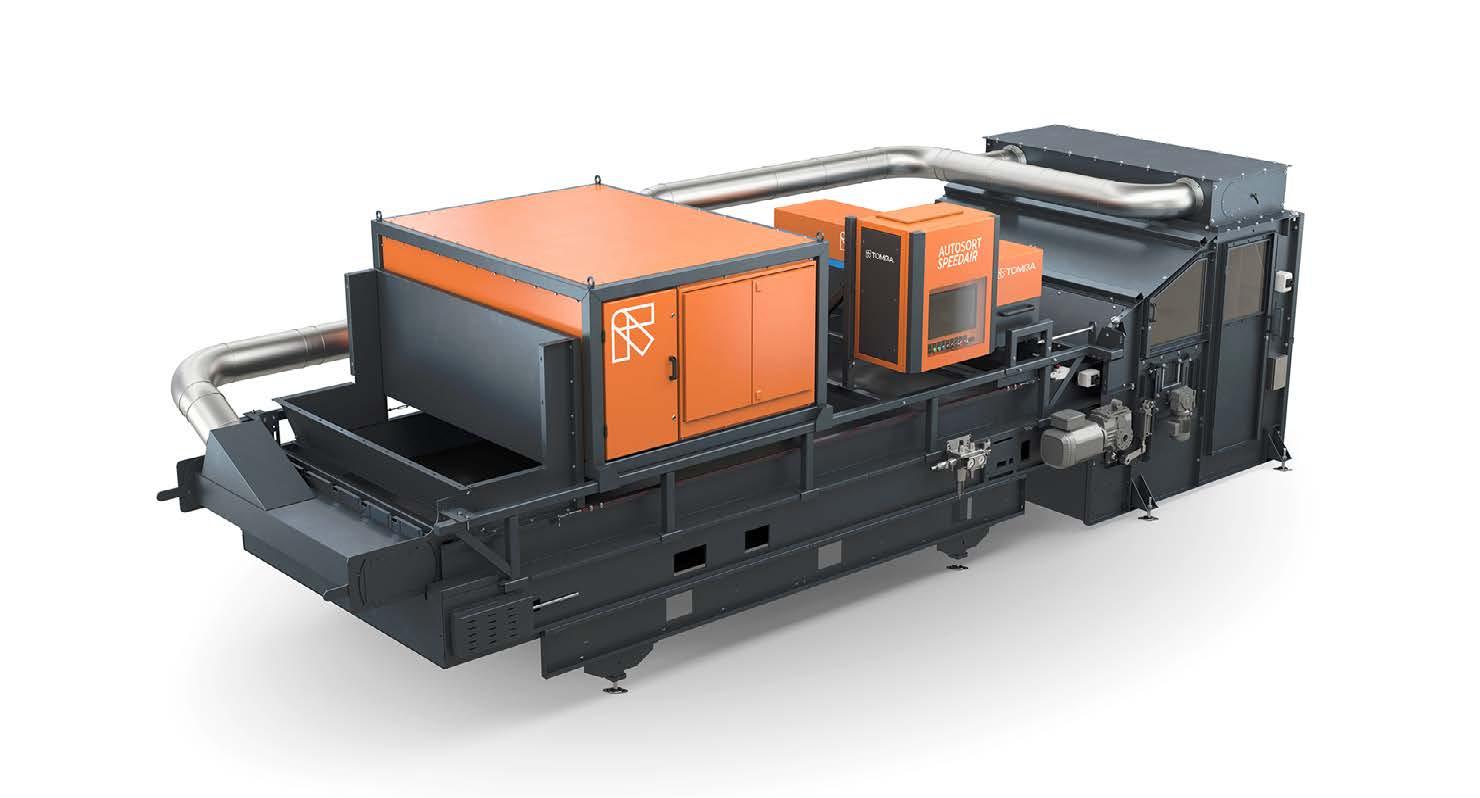
TOMRA Sorting Recycling designs and manufactures sensor-based sorting technologies for the global recycling and waste management industry. To date, more than 6,000 TOMRA systems are installed in 100 countries around the world. On June 9th, during a global online launch, TOMRA presented two latest sorting technologies: the new generation of AUTOSORT® and AUTOSORT® SPEEDAIR. This compact, highly flexible and upgradeable sensor-based sorting system combines TOMRA’s latest technologies to provide precise, high-speed sorting, even with the most complex materials that are impossible to detect with conventional technologies. This is thanks to the use of the widest range of TOMRA sensors and data obtained during the process to classify objects correctly. AUTOSORT® SPEEDAIR is the second product launched by TOMRA: it is an add-on to the AUTOSORT® range designed to stabilize lightweight materials such as plastic film or paper on the acceleration belt.
Camec: the new concept of technology
Fortemente orientata allo sviluppo del prodotto, oggi Camec riesce a garantire una continua innovazione tecnica, che da sempre rappresenta uno dei principali punti di forza dell’azienda. Da questa innovazione continua nascono 3 divisioni di successo: recycling, handling ed industrial, dove Camec gestisce un portafoglio clienti di elevato prestigio in tutto il mondo. Oltre alla progettazione e alla costruzione fino alla fornitura “chiavi in mano” dei suddetti impianti, Camec offre un servizio personalizzato a 360° con studi di fattibilità, simulazione 3D, revamping, manutenzione ordinaria e straordinaria e assistenza post-vendita, anche da remoto. Nella divisione recycling, in particolare, Camec si occupa di sviluppo e progettazione di macchine e impianti di riciclaggio per il trattamento di rifiuti industriali e urbani. Grazie ad un know-how sviluppato negli anni e sostenuto da una continua ricer-

ca tecnologica, siamo in grado di operare in quasi tutti i settori di riciclaggio e trattamento rifiuti interfacciandoci con le più svariate problematiche. La sintesi dell’esperienza Camec nella costruzione delle macchine per riciclaggio la ritroviamo in particolare in una delle nostre ultime realizzazioni denominata LCM520/20. Il doppio rotore si incontra in questa particolare configurazione con l’uso di utensili intercambiabili e l’applicazione di griglie di selezione che permettono di ottenere una pezzatura costante e controllata: in questa linea sono applicati tutti gli accorgimenti e le caratteristiche delle macchine finora prodotte per avere un processo affidabile e tecnologico. Lo spostamento su gomma che la rende semovente in autonomia mediante motore elettrico e il sistema di deferrizzazione montato sui nastri di evacuazione del materiale triturato, evidenziano la cura per il dettaglio e la professionalità con le quali Camec analizza e soddisfa costantemente le esigenze del cliente. Più che un semplice fornitore, ci consideriamo pertanto un partner strategico per soddisfare le necessità del Cliente, ecco perché più che macchine noi offriamo soluzioni. Per noi il cliente è sempre al centro dell’attenzione e la persona riveste il ruolo più importante nel grande processo di ascolto che si deve creare tra fornitore e
cliente. Con uno sguardo al futuro, la recente costituzione della nuova sede Camec Iberica, nel poligono industriale di Barcellona e le alleanze strategiche in Canada, Stati Uniti, Regno Unito e Bulgaria, evidenziano la forte spinta espansionistica verso l’estero che Camec ha deciso di intraprendere. Oggi siamo lieti di presentarvi un nuovo concetto di triturazione: ecco a voi CAMEC, la storia di un’azienda tutta italiana, proiettata in un panorama internazionale.
Camec Srl Tel +39 049 552115 info@camec.net www.camec.net


Strongly oriented to product development, today Camec is able to guarantee continuous technical innovation, from where are born 3 successful divisions: recycling, handling and industrial. As a recycling division, in particular, we deal with the development and design of machines and recycling plants for the treatment of industrial and urban waste. We also offer a 360° personalized service with feasibility studies, 3D simulation, revamping and after-sales assistance. We therefore consider ourselves a strategic partner to satisfy the Customer’s needs, that’s why more than machines we offer solutions. The summary of Camec’s experience in the construction of recycling machines is also found in one of our latest creations called LCM520 / 20: here all the precautions and characteristics of the machines produced so far for have a reliable and technological process. The movement on rubber that makes it self-propelled by an electric motor and the deferrization system mounted on the evacuation belts of the shredded material, highlight the attention to detail and professionalism with which Camec constantly analyzes and satisfies the customer’s needs. Recently, the establishment of a new headquarters, Camec Iberica, in the industrial area of Barcelona, as well as the strategic alliances in Canada, the United States and Bulgaria, highlight the strong expansion drive Camec has decided to follow. Today we are glad to present a new concept of shredding: this is CAMEC, the story of an all-Italian company, projected into an international panorama.
Stepper Screen: il nuovo brevetto di PAL per vagliare il rifiuto senza intasamenti
Questo particolare sistema di Vagliatura, secondo il brevetto EP2552606, permette di trattare materiali difficili abbattendo drasticamente i fermi macchina superando le problematiche dei tradizionali vagli a dischi, i quali soffrono tremendamente l’impigliamento e l’attorcigliamento di corpi lunghi e filamentosi presenti sempre in buona quantità nel rifiuto. Lo Stepper Screen sviluppato da PAL è la risposta a chi cerca una soluzione vagliante con la logica del vaglio a dischi ma senza fermi macchina e sistematici interventi di pulizia. Innovativo nel Sistema di scuotimento e avanzamento del flusso, il sistema di palette a moto alternato, impedisce ai materiali filamentosi di attorcigliarsi (non ci sono organi in completa rotazione) e separa il materiale in più frazioni. Ideale per trattare diversi tipi di rifiuto, nel settore industriale con presenza di metalli e materiali filamentosi di notevoli dimensioni, negli impianti di compostaggio, nel settore della selezione delle plastiche in alternativa al vaglio Balistico. Le numerose esperienze finora fatte sul campo hanno già dimostrato l’ultima evoluzione di questa macchina è in grado di lavorare su materiali notoriamente difficili con rese assimilabili o spesso migliorative rispetto ai tradizionali vagli a dischi o a tamburo, si tratti di materiale organico (FORSU), compostato misto dopo biocella, plasmix, legno riciclato o addirittura rottami metallici o da demolizione auto. I profili sono definiti in modo da consentire nei movimenti contrappo-
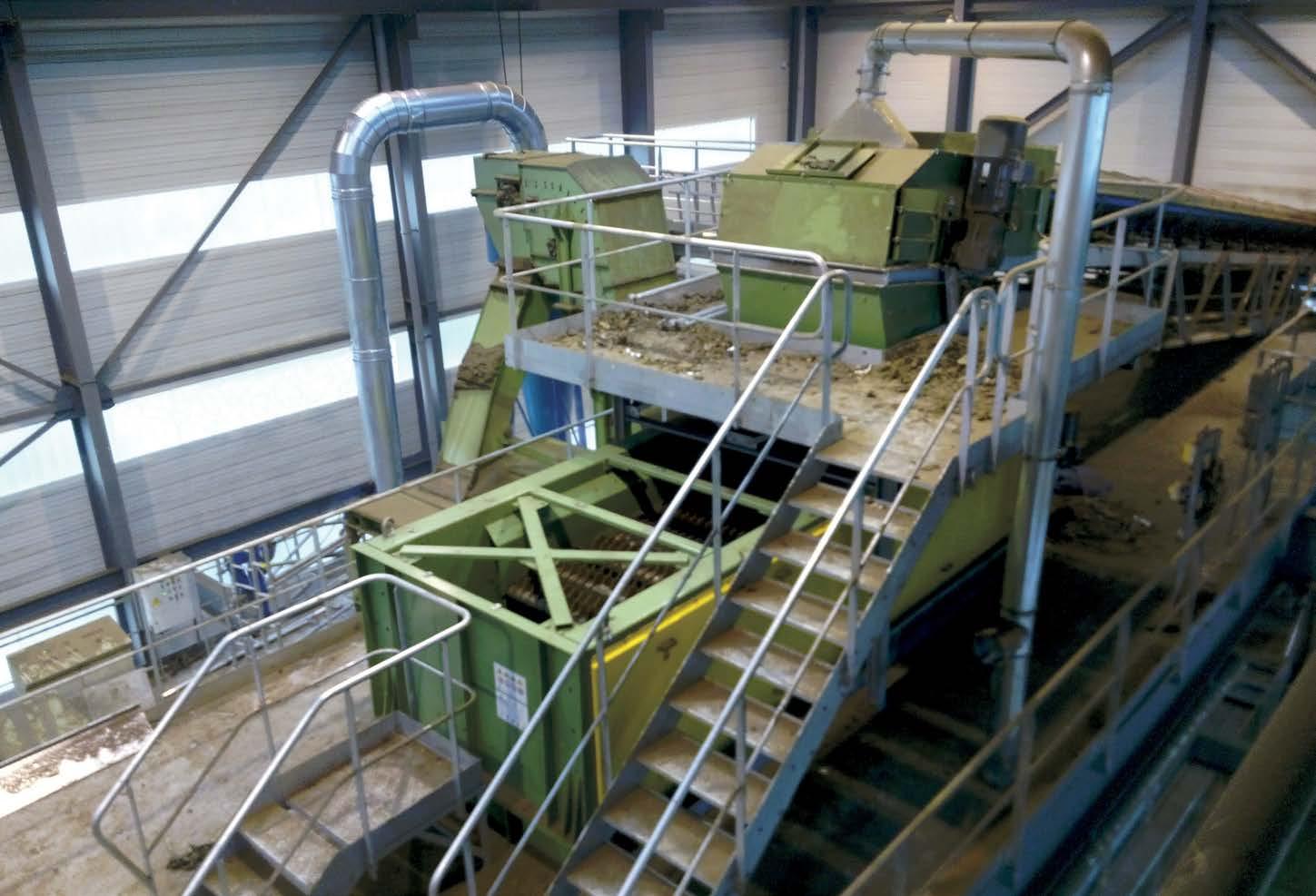
sti di due lame adiacenti l’avanzamento del flusso di materiale lungo il treno di alberi. Il piano di vagliatura, potrà lavorare orizzontale o leggermente in discesa (-3,5°) a seconda della tipologia e quantità di materiale ed è formato da una serie di alberi oscillanti (nessuna rotazione) che supportano speciali palette di lunghezza minima circa 230 mm e distanza minima tra gli alberi porta-palette di circa 190mm. I rulli dispari operano con moto oscillante in opposizione di fase rispetto ai rulli pari, in modo da garantire l’avanzamento del materiale. Il sottovaglio passa attraverso la luce (sezione di Vagliatura) tra le palette, la sezione di Vagliatura può essere regolata entro limiti di ±20%.

PAL Srl Tel +39 0422 852 300 info@pal.it www.pal-greendivision.it Stepper Screen: the new PAL’s patent for a clog free screening of waste
Thanks to the innovative flow shaking and forwarding system, the alternate motion paddle system prevents filamentous materials from wrapping around (no completely rotating parts) and separates the material into different fractions. This special screening system perfectly processes difficult-to-handle material allowing to drastically cut machinery downtimes and routine cleaning, thus overcoming the issues of traditional disc screens. The Stepper Screen developed by PAL is the answer to those looking for a screening solution based on the disc screen logic. Stepper Screen is the ideal solution for processing various types of waste, either in the industrial field with large size metals and filamentous materials, or in composting plants, or in the plastics sorting field as an alternative to the Ballistic screen. Our great deal of experience already gained in the field has proven that the recent evolution of the machine is capable of handling difficult-to-process materials with performances that are comparable or even better than those of traditional disc or drum screens, regardless of whether processing organic material (OFMSW), mixed compost after biocell, plasmix, recycled wood or even metal scrap and metal from car wreck.
Tiger Depack, indispensabile nel riciclo
Tiger Depack è un sistema brevettato per la separazione solido liquido; ideale per diverse tipologie di prodotto in ingresso. Negli ultimi dieci anni le esigenze del mercato hanno portato alla creazione di una gamma di prodotti che offre tre macchine con caratteristiche molto diverse per dimensioni e capacità di produzione: • Tiger HS 10, prodotto di partenza che fino al 2017 era conosciuta con il nome Tiger HS 640: è la macchina da cui è iniziato tutto e che ora conta oltre 80 modelli in tutto il mondo. • Tiger HS 20, progettata per affrontare capacità di trattamento più elevate fino a 20t/h in base al materiale trattato. • Tiger HS 5, la più piccola, per volumi di produzione contenuti fino a 5 t/h in funzione della matrice inserita. La gamma prodotti Tiger Depack si compone inoltre di allestimenti specifici per la lavorazione di particolari tipologie di materiali come il pulper, i sovvalli: • Tiger Depack PPS (Paper Pulp Solution), è progettato specificamente per l’uso in cartiera per il trattamento del pulper. • Tiger Depack OSC è ottimizzato per il trattamento dei sovvalli derivanti dal trattamento dell’organico da raccolta differenziata. I campi di applicazione della linea Tiger Depack si ampliano di anno in anno con la richiesta di macchinari dedicati allo specifico trattamento di materiali. Tutto è partito dalla “semplice” separazione del contenuto dall’imballaggio che lo riveste per ottenere matrici pulite e separate adatte al riutilizzo. Allo stato attuale, i campi di applicazione dei macchinari Tiger Depack sono divisi in tre settori. - Il settore principale è il depackaging. Questa è la necessità di separare l’imballaggio e il suo contenuto in matrici riutilizzabili pulite, come, ad esempio, l’imballaggio degli alimenti scaduti o gli scarti di mense o alimentari della grande distribuzione. In questo caso, il vantaggio per il cliente è quello di ottenere due matrici che sono riutilizzabili: organico e imballaggio che possono essere così introdotti in cicli successivi di lavorazione come biogas e mangimi per l’organico e produzione di materia prima seconda per gli imballaggi. - Il secondo campo di applicazione è il trattamento del rifiuto organico proveniente da raccolta differenziata. Tiger Depack applicata al trattamento dei rifiuti organici (FORSU) esprime la sua massima efficienza sia con trattamento

a secco che a umido sia del rifiuto tal quale che del sovvallo da ricircolo. Grazie a Tiger Depack, la frazione organica viene pulita dai materiali plastici (sacchetti e impurità) e al contempo viene omogeneizzata per i successivi trattamenti di digestione o compostaggio. Dall’esperienza acquisita con l’applicazione di Tiger Depack, da un peso del 27% di plastica e organico avviato a smaltimento si passa al solo 7% di plastiche pulite con un recupero totale dell’organico. - Il terzo campo di applicazione è all’interno dei cicli di produzione. Data la sua capacità di inserimento in catene di produzione che sono già operative il modello più piccolo è quello più indicato. La produzione industriale genera rifiuti per il controllo di qualità: ad esempio, etichette storte sugli imballaggi e prove a campione su lotti di prodotti. Inserendo Tiger Depack nel processo di produzione, è possibile dividere il prodotto, recuperare imballaggi e contenuto evitando la produzione di rifiuti alla fonte.
Cesaro Mac Import Srl Tel +39 0421 231101 cesaro@cesaromacimport.com www.cesaromacimport.com Tiger Depack is an indispensable machine for recycling
Tiger Depack line is represented by three machines very different from each other in terms of size and of production capacity: • Tiger HS 10, the starting point. Untill 2017 was known as Tiger HS 640. At the moment 80 models of this version are worlwide. • Tiger HS 20, developed to cope with a major capacity of treate-ment: up to 20 tonn/h depending on the materials treated. • Tiger HS 5Tiger HS 5, the smallest, produces up to 5 tonn/h according to the input material. Specific equipments to work particular materials, like pulper or scraps, are part of the Tiger Depack line of products. • Tiger Depack PPS (Paper Pulp Solution), the model especially-designed for paper mill and for the treatment of pulper. • Tiger Depack OSCTiger Depack OSC built up to work the scraps deriving from the treatment of the organic part of waste collection. The uses of Tiger Depack line increases year by year thanks to the demand of machines able to offer specific treatment for specific materials.
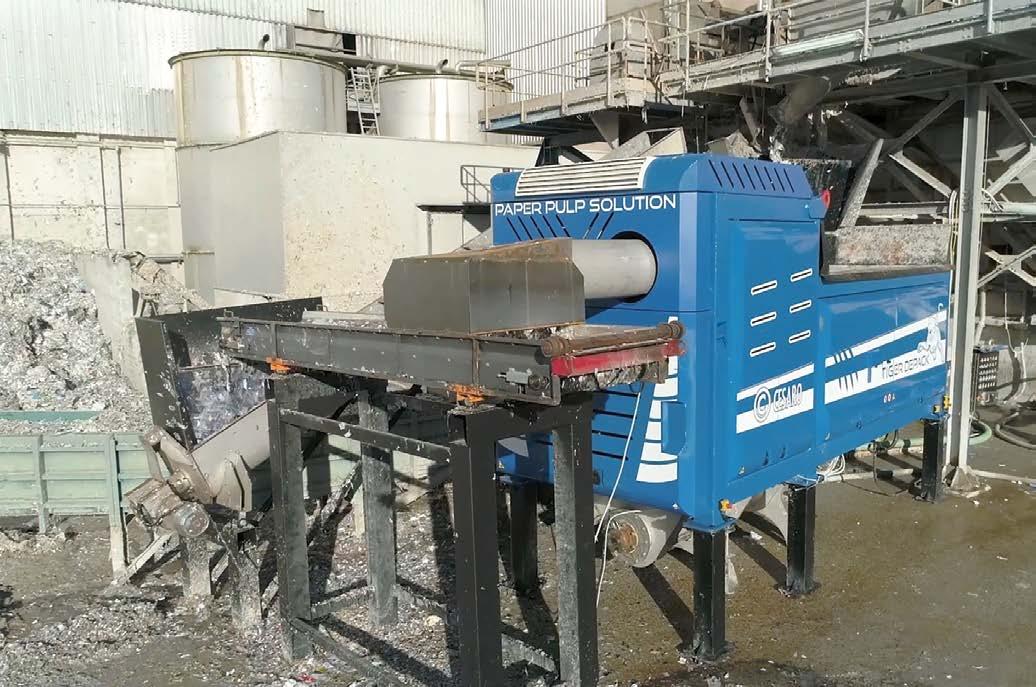
A Ferrara avviato il nuovo impianto pilota di riciclo molecolare, MoReTec
LyondellBasell, una delle più grandi aziende al mondo nel settore delle materie plastiche, della chimica e della raffinazione, ha annunciato l’avvio dell’impianto di riciclo molecolare MoReTec nel sito di Ferrara. LyondellBasell è proprietaria della tecnologia d’avanguardia di riciclo MoReTec il cui obiettivo è quello di riportare i rifiuti di plastica post-consumo alla loro forma molecolare da utilizzare come materia prima per la produzione di nuovi prodotti di plastica. “Eliminare i rifiuti plastici dall’ambiente e far progredire l’economia circolare sono i punti cardine della nostra società per quanto riguarda la sostenibilità” ha dichiarato Jim Seward, LyondellBasell Senior Vice President Ricerca e Sviluppo, Tecnologia e Sostenibilità. “Con la nostra avanzata tecnologia di riciclo, restituiamo alla catena del valore volumi maggiori di rifiuti (di plastica) destinati a produrre nuovi materiali per applicazio-

ni di alta qualità, assicurando così il loro valore il più a lungo possibile nel tempo.” I nuovi materiali plastici creati con la tecnologia MoReTec di LyondellBasell possono essere utilizzati anche per settori merceologici vincolati da severi requisiti normativi, come quello dell’imballaggio alimentare e dei dispositivi medici per il settore medicale. LyodellBasell conduce ricerca di base per portare l’industria dei polimeri verso il riciclo all’avanguardia per le plastiche. A luglio 2018, l’azienda ha annunciato una fattiva collaborazione con l’Istituto di Tecnologia Karlsruhe in Germania per portare avanti il proprio impegno nel riciclo molecolare che ha provato l’efficienza della tecnologia MoReTec su scala nei laboratori; a Ottobre 2019, la società ha annunciato la costruzione di un impianto pilota a Ferrara. Oggi, grazie alla ricerca e sviluppo dei gruppi di lavori in Germania, Italia e Stati Uniti, la società sta lavorando attivamente per esplorare le potenziali applicazioni su scala commerciale. “Il nuovo impianto di riciclo molecolare MoReTec prosegue la tradizione di innovazione, ricerca e sviluppo di nuove tecnologie a Ferrara” ha dichiarato Antonio Mazzucco, Direttore Centro di Ricerca Giulio Natta di Ferrara, LyondellBasell. “Insieme ai nostri colleghi in Germania e negli
Stati Uniti, siamo orgogliosi di contribuire a una tecnologia che è proiettata al futuro con l’obiettivo di affrontare concretamente il problema dei rifiuti plastici facendo progredire la circolarità dei prodotti in plastica. L’aver scelto il sito di Ferrara per la costruzione dell’impianto pilota MoReTec” conclude Mazzucco “è un grande riconoscimento per tutti i colleghi del Centro Ricerche Giulio Natta per il loro profondo impegno e la loro conoscenza. Dopo aver speso alcuni decenni a sviluppare nuovi processi e nuovi catalizzatori per polimerizzare, il sito studia soluzioni per invertire il processo (de-polimerizzare) grazie all’enorme know-how dei suoi ricercatori, ingegneri e tecnici.” L’impianto pilota è in grado di processare tra 5 e 10 chilogrammi (kg) all’ora di rifiuti di plastica domestici e si basa sulla nostra ricerca finora. Tale impianto (pilota) ha lo scopo di comprendere l’interazione tra i vari tipi di rifiuti nel processo di riciclo molecolare, di fare test di differenti catalizzatori e di confermare la temperatura di processo e il tempo necessario per decomporre il rifiuto di plastica in molecole. L’obiettivo è quello di completare tutti questi test nei prossimi anni per poter pianificare un impianto su scala industriale. Lo sviluppo della tecnologia MoReTec rientra nell’impegno di LyondellBasell della conversione delle plastiche in nuove plastiche ed è complementare alle altre soluzioni circolari messe in atto dalla società al fine di ridurre i rifiuti di plastica e far progredire l’economica circolare, tra cui: • Sviluppo di nuovi modelli di business per il riciclo meccanico: nel marzo 2018, LyondellBasell ha preso il controllo del 50% di Quality Circular Polymers (QCP), una joint-venture con SUEZ. QCP utilizza il processo di riciclo meccanico per produrre dai rifiuti di plastica pellet di qualità superiore per applicazioni che spaziano da elettrodomestici, flaconi di bottiglie per detergenti e valigie. Utilizzo di materie prime rinnovabili per la produzione delle plastiche: nell’aprile 2019, LyondellBasell ha prodotto plastiche partendo da materie prime rinnovabili, come oli esausti di cottura e oli vegetali, dalle quali è stato possibile realizzare nuovi articoli di plastica utilizzabili nei settori dell’imballaggio alimentare, dei giocattoli e degli articoli di arredamento.
Il lavoro di questa tecnologia è iniziato nel Centro Tecnologico di Houston (HTC) negli Stati Uniti quando sono stati testati diversi tipi di catalizzatori potenzialmente adatti per la tecnologia di riciclo molecolare. Lo sviluppo di questa tecnologa su scala pilota è proseguito in Germania, unendo i sistemi catalitici di LyondellBasell nel centro di Ricerca di Francoforte e il reattore dell’Istituto di Tecnologia Karlsruhe (KIT). L’impianto pilota di Ferrara si basa su questa ricerca e sta testando i catalizzatori più promettenti. Il Centro Tecnologico di Houston continua a lavorare sui catalizzatori, sta effettuando test sui rifiuti di plastica all’olio di pirolisi che serviranno come materia prima, sviluppando nuove tecniche analitiche per la caratterizzazione dei rifiuti di plastica e dell’olio di pirolisi, e ricercando tecniche di post-trattamento sull’olio di pirolisi per migliorarne la qualità.
LyondellBasell www.lyondellbasell.com
