Inductees: Alvin Spence and Corey Claussen
Susan

PAGE 30
RESPONSIBLY AND ETHICALLY FOR BOTH BETTER QUALITY AND PRODUCTIVITY
PAGE 48
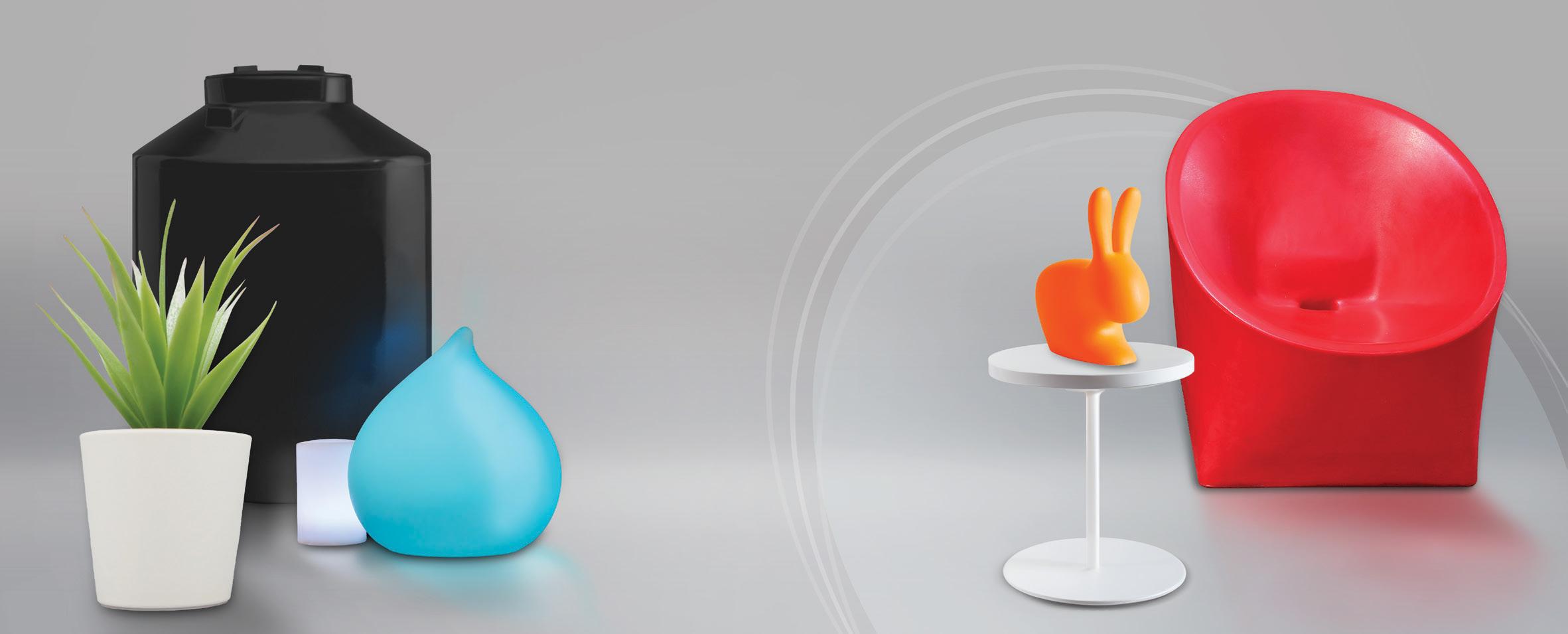

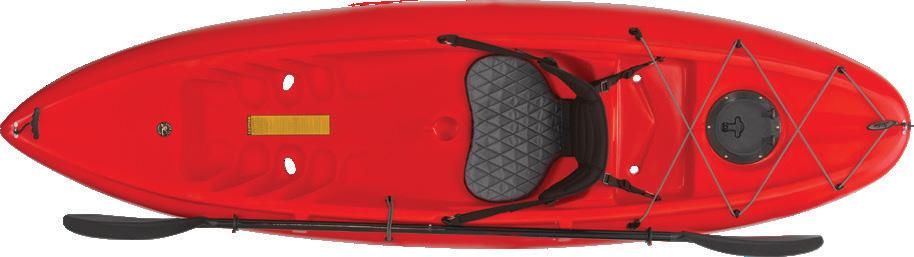
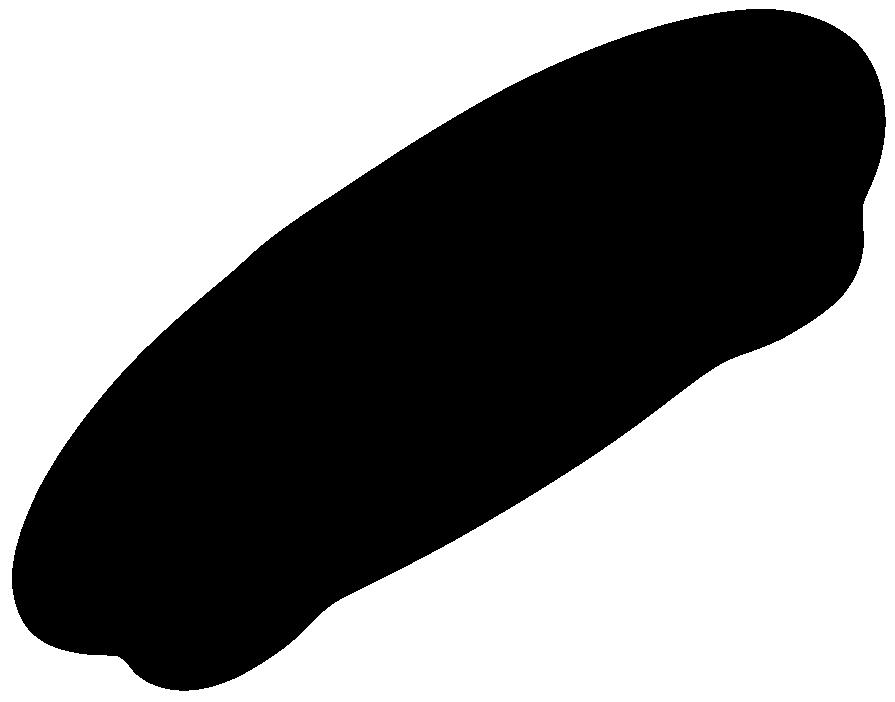
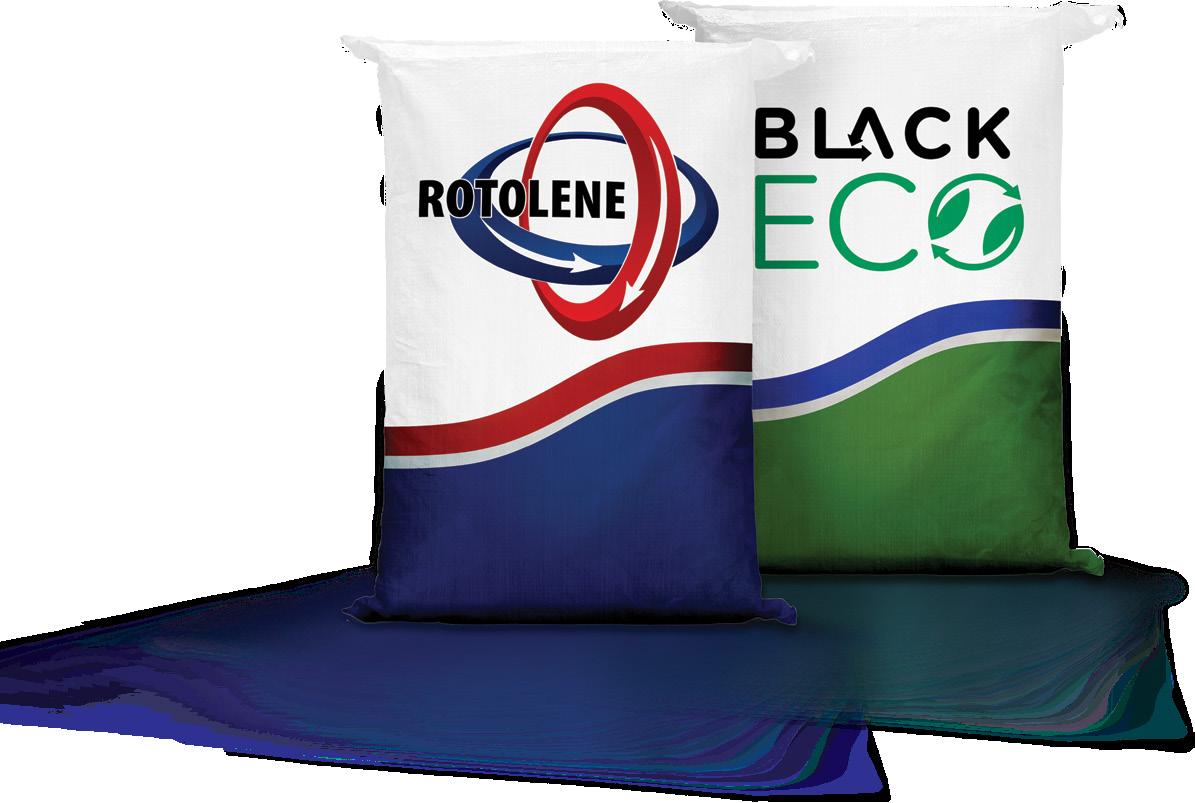

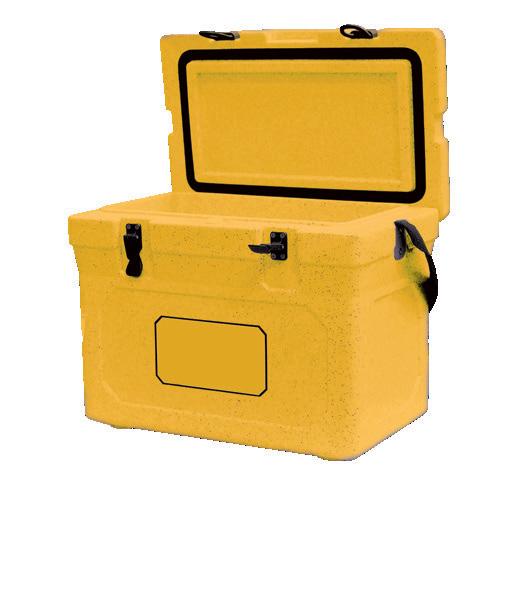
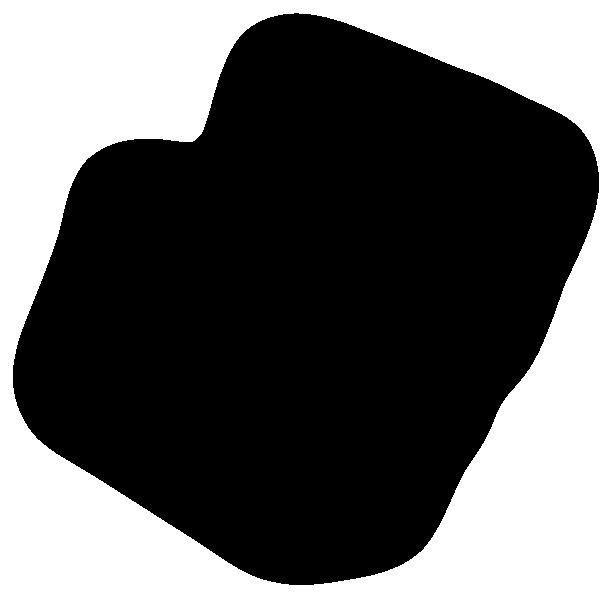
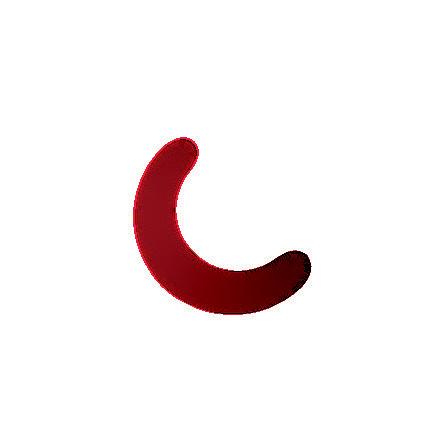
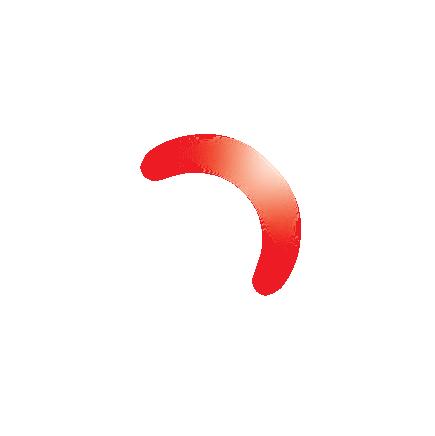

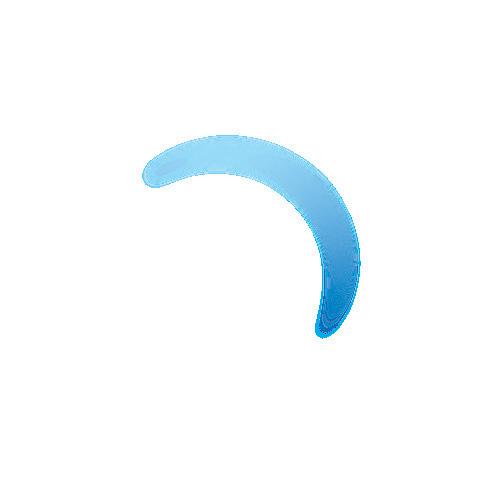
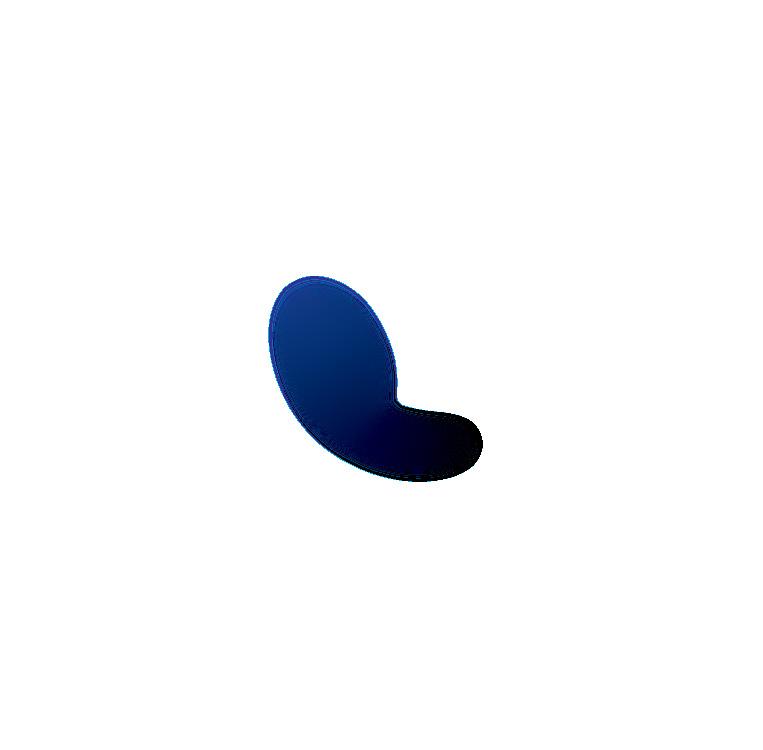
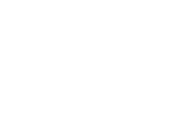
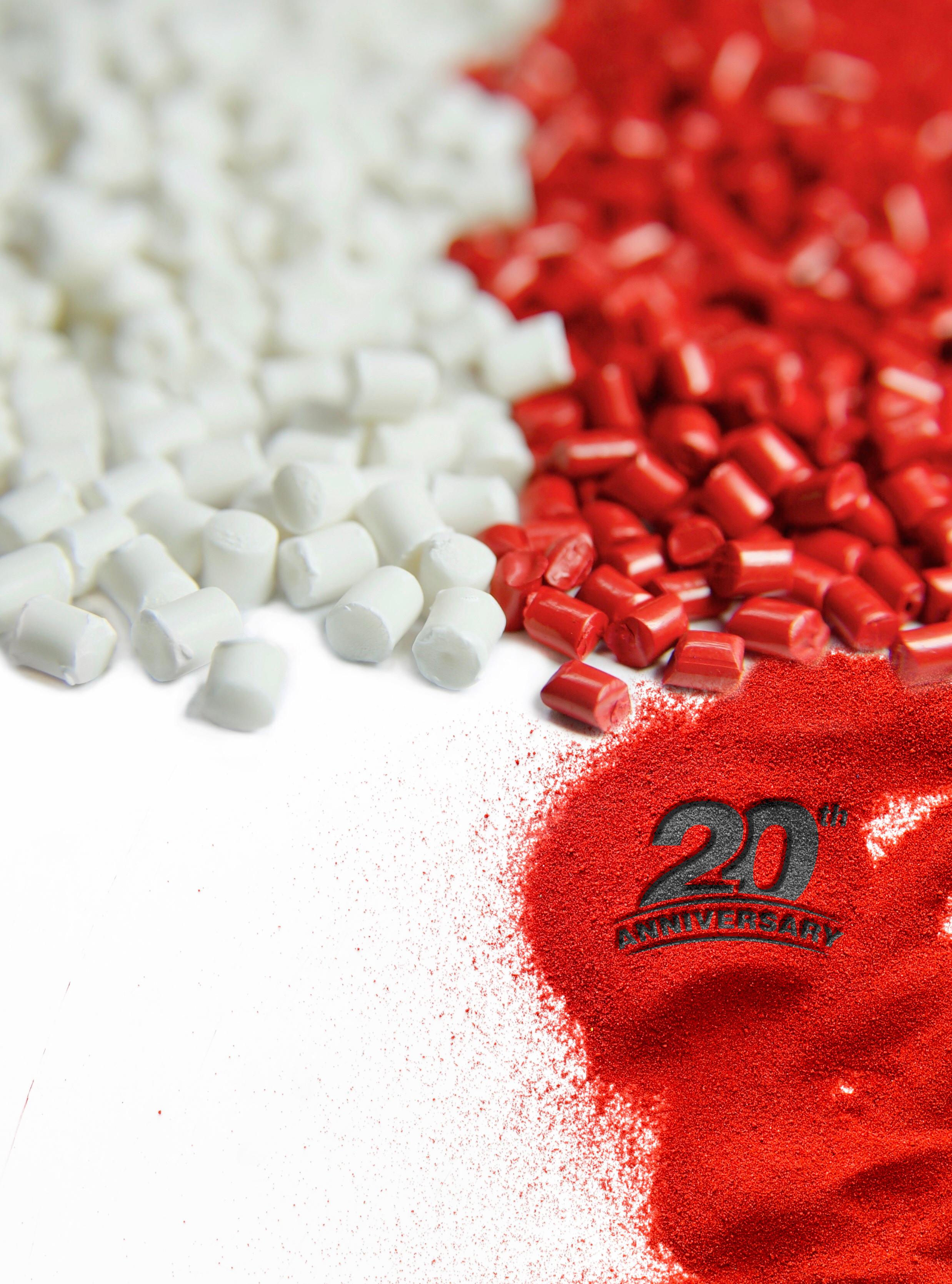
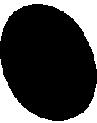
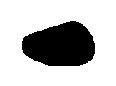



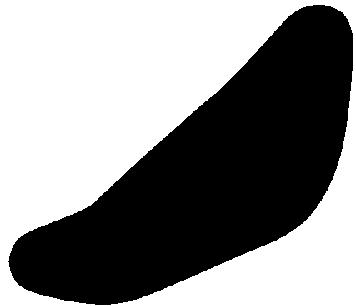
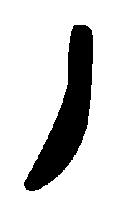
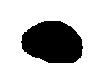
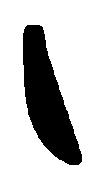

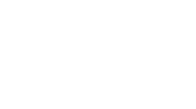
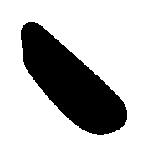
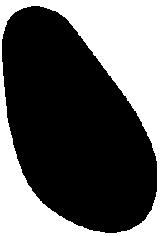
Inductees: Alvin Spence and Corey Claussen
Susan
PAGE 30
RESPONSIBLY AND ETHICALLY FOR BOTH BETTER QUALITY AND PRODUCTIVITY
PAGE 48
Upfront: Plastics Industry Association Announces Future Dates for NPE: The Plastics Show
ARM Report: 2024 ARM’s Spring Meeting and Tour In Northern Italy
ARMA: The Year Ahead with ARMA! Roto
08. FROM THE PUBLISHER
The Discussion
Susan Gibson, JSJ Productions, Inc.
10. CREDITS
12. GLOBAL CONTRIBUTING EDITORS
Global Contributors, Department Contributors, and Issue Contributors
15. UPFRONT
Industry News, Trends, and Products
25. AT ISSUE
44. ARM REPORT
What a great year we have in store.
It all started in 1638...
Rob Miller, Whittmann Battenfeld / Rotoload Canada
60. ROTO AROUND THE WORLD
53. INTERSECTION INDUSTRY 4.0 & SUBSCRIPTION BASED BUSINESS MODEL VANUATU Sustainable Rotomoulding Ian Hansen, RotaConsult
64. ARMO NEWS
The Year Ahead with ARMA!
Big Advances in Rotomoulding Technology are Coming Martin Coles, Matrix Polymers
26. X-FACTOR
Investiment in Employer Engagement Yields
Competitive Advantage
Tom Innis, Xcelerant Growth Partners
34. PRACTICAL ROTO TIPS
Quality Testing our Powders
Dru Laws, Brigham Young University, Idaho
68. GLOBAL CALENDAR
Prominent Roto Industry Dates!
70. ADVERTISERS’ INDEX
RotoWorld® advertiser contact information
There are discussions everywhere. Whether it is with colleagues, friends, family, or on social media, discussions ramp up daily on the issues that interest us and further our development, both in business and personally.
Social media is a great example: Facebook, Instagram, YouTube ... all support the discussion of the day. Maybe the discussion is just meant to be informative, but maybe it is meant to be persuasive. A mere question can start a conversation that grows into a discussion involving people’s insights and ideas, a building on those ideas, and opinions are given on any topic.
It is the behind the scenes work that frames a meaningful discussion—it is the work of a committee, a board, a group of people striving to have a united voice. This can be years in the making. It can also be spontaneous. The one thing that is for sure; change is inevitable, and we see discussions driving innovation and development taking place increments at a time until change has arrived.
The discussion inside highlights some important innovations taking place in the Rotomolding Industry. While AI is at the forefront of all sectors of industry, it has been evolving over the past years behind the scenes and it is now applicable in our everyday businesses and personal lives.
Our task is to learn how to use it responsibly and ethically. Kim Harrison of Cutting Edge PR, one of our trusted communications partners, discusses the art of using AI in communication inside this issue. We are all tasked with being communication professionals. We all want to increase our effectiveness in the workplace. Harrison says this will require our learning about the various AI tools, but not losing sight that humans are still needed. “Fundamental human traits like empathy, trust, humor, and relationship building are not represented by AI,” Harrison says. This article will work as a guide to get you started on your adventure of communicating utilizing AI. In doing so, you’ll free up some of your valuable time to develop more innovative processes, etc. There is a chart included for making sure the job is well done.
Other important discussions inside this issue include Driving Business Success through New Materials. Authors Brian Gooding, Saeplast Americas, and Dustin Turgeon, NOVA Chemicals, layout their collaboration to achieve a circular economy for plastics. New Impact Modifier Copolymer Acetals Solving the Problem of Creating a Single Layer Fuel Tank, authored by Dan Grinsteinner, Celanese, details the development of one important polymer solution development being carried out by Celanese for the rotomolding industry.
It is my honor to cover the induction of Alvin Spence, Centro Inc., and Corey Claussen, Custom Roto-Mold, into the 2023 ARM Hall of Fame. The high honor is well deserved by both. Alvin and Corey each presented moving remarks about their journey in rotational molding and how it has been instrumental in their career and personally. A huge congratulations to Alvin and Corey.
Keeping in mind “The Discussion”, inside our department editors are really stepping up this year to bring you highly educational and insightful articles. Welcome to Rob Miller, Whittmann Rotoload, as he tackles a new concept aligned with Industry 4.0, the idea of a “subscription” model for purchasing machinery and other equipment. Tom Innis, Xcelerant, addresses the yields of investing in employee engagement. Martin Coles, Matrix Polymers, talks about new advances in rotomolding technology that are on the forefront. Dru Laws lays out the importance of quality testing powders. Ian Hansen showcases how one company on the remote South Pacific Island of Vanuatu is working to increase sustainability in plastics.
I hope you will enjoy this issue, and that we’ll continue the discussion. R
Susan D. Gibson President - JSJ Productions, Inc. susan@jsjproductionsinc.com
Alvin Spence PhD MEng aspence@centroinc.com
Paul Nugent PhD MEng paul@paulnugent.com
Michael Paloian President - Integrated Design Systems, Inc. paloian@idsys.com
Celal Beysel Chairman - Floteks Plastik beysel@superonline.com
Tom Innis Excelerant Growth Partners w@xcelerantgrowthpartners.com
Martin Coles Matrix Polymers martin.coles@matrixpolymers.com
Adam Covington Ferry Industries acovington@ferryindustries.com
Mark Kearns Moulding Research Manager m.kearns@qub.ac.uk
Ravi Mehra Managing Director - Norstar International LLC maramehra@aol.com
Marketing/Advertising Director Jennifer Gibson Hebert Vice President, JSJ Productions, Inc. jennifer@jsjproductions,inc.com
Chief Art Director
Anya Wilcox JSJ Productions, Inc. awilcox@designintersection.com
Sheryl Bjorn JSJ Productions, Inc. sheryl@jsjproductionsinc.com
Suzanne Ketron | Oliver Wandres | Sheryl Bjorn
Jason Cooper JSJ Productions, Inc. jason@bound.by
RotoWorld® is a JSJ Productions, Inc. Trade Publication JSJ Productions, Inc. 625 West Market Street, Salinas, CA 93901
Phone: (512) 894.4106; Fax (512) 858.0486
Email: rotoworldmag@rotoworldmag.com and Website: www.rotoworldmag.com
Subscriptions One-year subscription (six issues), print or digital, $80 US, $100 Canada/Mexico, $155 All Other Countries. To subscribe or to submit change of address information, call us at (512) 894.4106; fax us at (512) 858.0486; visit us online at www.rotoworldmag.com; or email us at sheryl@jsjproductionsinc.com.
You may also write to RotoWorld® Subscriptions, JSJ Productions, Inc., 625 West Market Street, Salinas, CA 93901
Advertising For information on advertising, please contact Advertising Director Jennifer Gibson Hebert, JSJ Productions, Inc. Email Jennifer Gibson at jennifer@jsjproductionsinc.com
Letters We welcome letters about our contents. Write Letters to the Editor, JSJ Productions, Inc., 625 West Market Street, Salinas, CA 93901 512.894.4106 phone 512.858.0486 fax, or Email susan@jsjproductionsinc.com.
Editorial Queries We consider unsolicited contributions. Send manuscript submissions as email attachment to Susan Gibson at susan@jsjproductionsinc.com.
JSJ Productions, Inc. bears no responsibility for claim or factual data represented in contributed articles.
Postmaster Send changes of address to RotoWorld®, JSJ Productions, Inc., 625 West Market Street, Salinas, CA 93901 RotoWorld® is a JSJ Productions, Inc. independently owned, bi-monthly trade magazine for the international rotational molding and plastics design industries. JSJ Productions, Inc. owns all copyrights on articles published herein unless ownership is otherwise stated. Reproduction of this magazine, in whole or in part, without the express written permission of the publisher is not permitted.
Polyethylene Granules & Powders
Crosslink Polyethylene
Polypropylene Granules & Powders
Polyamide Powders
Ancillary Products
6
Designed for Roto® a dedicated range of materials to be used in rotational moulding applications.
Dedicated Technical Services Support Team
Multi-lingual Customer Service
Alvin Spence is Vice President Engineering at Centro, Inc., North Liberty, Iowa. He provides leadership for Centro’s product development team and quality resources. Alvin received his Bachelor’s degree in Mechanical & Industrial Engineering and PhD from Queen’s University Belfast. aspence@centroinc.com
Michael is President of Integrated Design Systems, Inc., Great Neck, New York. Over the past 25 years, Mike has developed a broad range of plastic products utilizing various processing methods including rotational molding. Mike’s B.S. degree in Plastics Engineering and Masters in Industrial Design, combined with his extensive experience, has formed the basis for his branded and unique insights into the field of plastics part design. paloian@idsys.com
Paul is a consultant who travels extensively across six continents assisting clients in many roles from training to expert witnessing. He received his Eng. degree in Aeronautical Engineering and Ph.D. in Mechanical Engineering from Queen’s University of Belfast. Paul developed the Rotolog system, the first complete computer simulation (RotoSim), and authored a book entitled Rotational Molding: A Practical Guide.
paul@paulnugent.com
Ravi Mehra has been associated with the rotational molding industry since the early 1970’s. He is a Past President of ARM – Association of Rotational Molders, and has been inducted into the ARM Hall of Fame. He is the Founding Chairman of StAR – the rotational moulding Trade Association of India. He was the Chairman of ARMO – Affiliation of Rotational Moulding Organizations from 2012 to 2014. Ravi consults internationally with companies in the rotational moulding arena to help their global strategy, facilitate technology tie-ups, and business alliances. maramehra@aol.com
Martin Coles, CEO of Matrix Polymers co-founded the business 30 years ago and is the company’s largest shareholder. Shortly after graduating from London University, he began his career in the plastics industry working for a major Italian petrochemical and soon became passionate about the unique world of rotomoulding. Matrix Polymers are experts in rotomoulding materials and have become a global supplier with compounding and grinding plants in the UK, Poland, Australia, New Zealand, and Malaysia. The company sells more than $150 million of rotomoulding materials each year and has 230 employees. martin.coles@matrixpolymers.com
Celal is Chairman of Floteks Plastik, the pioneer and innovative leader of the rotational molding industry in Turkey and a Global Contributing Editor for RotoWorld® magazine. Being an ARM member for more than 20 years, he has made many presentations at ARM meetings in various countries. He is also active in business and political organizations in his country. Celal has authored numerous articles published in various newspapers and magazines about politics, plastics, rotomolding, and innovation.
beysel@superonline.com
Tom Innis is owner and Principal CEO of Xcelerant Growth Partners, LLC (Madison, WI), a multi-discipline consulting firm with specific focus in the global plastics sector. Leveraging industry experience and relationships built over 25+ years in the international manufacturing realm, Xcelerant connects the links in the industry supply chain to accelerate speedto-market and deliver turnkey personnel, product development and manufacturing solutions to an international audience. tinnis@ xcelerantgrowthpartners.com
Rob Miller is Owner/President, Wittmann Battenfeld Canada Inc. Rotoload. Rob started in the plastics pneumatic conveying industry in 1986. He has spent his entire career developing, engineering, and designing all types of catalog, standard, and custom pneumatic conveying systems for the plastics industry. He started in the rotational molding industry in 2013, has enjoyed learning the idiosyncrasies of the industry and market, and most of all meeting the people and building relationships for the future.
Rob.Miller@wittmann-group.ca
Adam Covington is President of Ferry Industries, Inc. in Akron, Ohio U.S.A. Covington has been with Ferry Industries for over 11 years, advanced through the manufacturing, engineering, sales, and service positions within the company and was appointed President in 2019. Adam strives to find solutions for customer’s needs and advance machine technology for the rotomolding industry. He is a graduate of Ohio University’s Russ College of Engineering and Technology with a Bachelor’s degree in Industrial Technology. acovington@ferryindustries.com
Ian Hansen has over 30 years of experience in the rotational moulding industry and has presented to conferences around the world on the subject of quality, safety, and tank design standards. Rotomoulders around the globe have problems from time to time.
Rota Consult delivers production solutions so rotomoulders can improve productivity and profitability, without wasting more of their valuable time.
ianhansenconsult@gmail.com, www.ianhansenconsult.com
Mark Kearns is the Rotational Moulding Research Manager of the Polymer Processing Research Centre at Queen’s University of Belfast. He is a Chartered Chemical Engineer with a M. Phil Degree in Rotational Moulding. Mark manages rotational moulding research and development projects for companies across Europe, Australasia, and North America. M.Kearns@qub.ac.uk
R. Dru Laws, educator and rotomolding expert, graduated from Brigham Young University in 2003 with a BS in Mechanical Engineering and a minor in Mathematics. In 2005, he graduated top of his class with distinction (honors) from the Queens University Belfast in Northern Ireland with an MSc in Polymer Engineering from their school of Mechanical & Manufacturing Engineering. He has several rotomoulding-related patents. Laws is currently a fulltime Manufacturing Engineering professor at BYU-Idaho, as well as CEO of Halltech Systems and High Pointe Plastics.
Brian has over 35 yeawrs of relevant industry experience. Brian has served as the Managing Director of Sæplast Americas since 2011 where he has led the business through a period of significant growth. Prior to that, he held Vice President and Sales Manager positions at Pliant Corp., owned and operated a sales agency, Technical Pkg. Mgt., Canadian Sales and Marketing Manager at Mobil Chemical Canada, and various other positions of progressive responsibility. Brian holds an Honours Bachelor of Commerce from Queen’s University in Kingston, Ontario.
Dustin is registered Professional Engineer in Canada with a Bachelor of Science in Mechanical Engineering from the University of Saskatchewan and an MBA from the Australian Institute of Business. Currently, Dustin is a technical specialist for NOVA Chemicals’ rotational molding team where he leads a portfolio of technical projects that supports efforts in building a circular economy for plastics. Previously, Dustin was the driving force behind commercial projects focused on sustainability through GHG reduction and carbon capture, asset optimization, and new global commercial strategy development oil and gas industry.
Darin Grinsteinner has been designing processes and products in polymers for close to 30 years. Darin earned his Bachelors in Composite Materials Engineering from Winona State University in 1999. Darin is a Six Sigma Master Black Belt and has held several managerial and non-managerial positions in the composite materials industry since 1994. Darin currently works in Product Development and Process Excellence for Celanese at their Florence, Kentucky facility and focuses on bringing new polymer formulations and processes to the plastics industries.
• Technology-Enabled JV Increases LYB Access to Advantaged Feedstocks and Attractive Markets.
• Transaction Encompasses Existing Assets and Planned Growth Projects.
HOUSTON, TX AND RIYADH, SAUDI ARABIA, USA –LyondellBasell (LYB) today announced it entered into an agreement to acquire a 35% interest in Saudi Arabia–based National Petrochemical Industrial Company (NATPET) from Alujain Corporation (Alujain) for approximately $500 million. Enabled by its Spheripol polypropylene (PP) technology, the joint venture positions LYB to grow and upgrade its core PP business through access to advantaged feedstocks, plus additional product marketing capacity, in a strategic region.
Closing of the transaction is subject to regulatory and other customary closing conditions. Alujain and LYB are also assessing together potential construction of a new propylene via propane dehydrogenation (PDH) and PP facility at the NATPET site, subject to a final investment decision. The project is being studied with a shared goal to implement solutions that align with the Kingdom of Saudi Arabia’s 2060 carbon reduction strategy.
Alujain is a petrochemicals, energy, mining, and
metals company in the Kingdom of Saudi Arabia. As majority owner of NATPET, the company is a longtime licensee of LYB Spheripol PP technology, one of the solutions it uses to operate a propylene and PP complex in Yanbu Industrial City. NATPET currently has an annual PP production capacity of approximately 400,000 tons.
“This investment in NATPET reflects our strategy of growing and upgrading our core around assets and businesses with lasting advantages,” said LYB CEO Peter Vanacker. “We are pleased to invest in this joint venture, which leverages LYB’s technology, leading global market positions and Alujain’s proven operational excellence. We expect the joint venture will add value both through our ownership interest, as well as marketing of the products in key regions.”
“We welcome the opportunity to deepen our ties with LYB, first as licensee and now as joint venture partner,” said Alujain Chairman Mohammed Bin Saleh AlKhalil. “We look forward to advancing our collective efforts to produce and market essential materials that serve our customers’ needs across the globe. This new investment is a great step forward for developing the downstream sector in the Kingdom of Saudi Arabia, and Alujain has plans to drive these developments further.” LyondellBasell.com R
DALLAS, TX, USA – Celanese Corporation (NYSE: CE), a global specialty materials and chemical company, announced it has been approved by the U.S. Department of Energy (DOE)’s Office of Fossil Energy and Carbon Management as a Utilization Procurement Grants (UPGrants) vendor. Celanese is now the only producer offering low-carbon acetic acid under the ECO-CC product name, which positions the company to help municipalities meet the growing demand for more sustainable and circular solutions.
As the U.S. economy moves toward a lower carbon future, the DOE is seeking to support states, local governments, public utilities, and agencies to
procure commercial or industrial products derived from anthropogenic carbon emissions. This includes Celanese low carbon acetic acid, which uses the ECO-CC product name because it is manufactured using carbon capture and utilization (CCU) technology. These product offerings have demonstrated significant net reductions in life cycle greenhouse gas emissions and passed a critical DOE review of the product’s life cycle analysis. As an UPGrants vendor, Celanese has already begun working with our valuechain partners to extend product usage opportunities to eligible U.S. government entities nationwide. celanese.com R
The SPE Foundation and the Girl Scouts of Northeast Texas have created an exciting new program to help girls understand the importance of plastics in our modern lifestyle. We hope to inspire them to become engineers and scientists and to join us to solve problems and create innovative materials and products to make the world a better place. Color Your World with Science, a science and engineering event, took place at the Girl Scouts of Northeast Texas STEM Center of Excellence in Dallas, TX.
Data shows that girls who are scouts are more likely than girls who are not scouts to become science, technology, engineering, math (STEM) professionals with leadership aspirations. The plastics industry will greatly benefit from women who understand the benefits we enjoy and challenges we face.
This kick-off event provided more than 200 Girl Scouts the opportunity to earn the newly released SPE Polymer Science Patch (www.4spe.org/scoutpatch), achieving a STEM seal of approval. During the event, Girl Scouts and their families saw first-hand how polymer scientists and engineers are improving the world around us by developing new materials to make items like shoes, medical equipment, bike helmets, car parts, and more. Scouts also molded their own plastic items as they learn about basic color theory and how it is integrated into plastics.
The event also featured Keynote Speaker and plastics professional, Mercedes Landazuri, IDSA, CMG, Director of Technology & Innovation at Peacock Colors & Vortex Liquid Color, who presented in both Spanish and English to help celebrate Hispanic Heritage Month. R
The Plastics Industry Association (PLASTICS) Gears Up to Host Its Triennial Show on May 6-10, 2024, Encourages Attendees to Start Planning for 2027 and Beyond
WASHINGTON, D.C., USA – The Plastics Industry Association (PLASTICS) announced the upcoming dates for three subsequent show cycles of the global trade show for innovations in plastics. NPE2027, NPE2030 and NPE2033 will all be held in May of their respective years at the Orange County Convention Center (OCCC) in Orlando, Florida.
PLASTICS invites NPE2024 attendees and those who plan to attend in the future to save the following dates for upcoming shows:
• NPE2027: May 3 – 7, 2027
• NPE2030: May 6 – 10, 2030
• NPE2033: May 2 – 6, 2033
“As we look forward and prepare for NPE2024, we want our members, exhibitors, attendees, and stakeholders to know that we’re committed to planning for the future of this show and an exceptional quality experience,” said PLASTICS’ Senior Director of Trade Show Operations, Maureen Cudahy Cameron. “The industry’s future is bright, and we’re looking forward to hosting more bold leaders, creative thinkers, and visionaries from every industry in the world at future NPE shows for years to come.”
NPE2024, the most anticipated plastics exposition in the Americas, will open on Wednesday, May 6, 2024,
at the Orange County Convention Center with 2,000+ exhibiting companies and more than 55,000 expected attendees from all sectors of the global supply chain.
For more information about NPE2024: The Plastics Show, visit: NPE.org. Registration prices for NPE2024 increase Friday, December 15.
Connect with NPE2024 through LinkedIn, Instagram, Facebook, and Twitter, for the latest #NPE2024 show news and insights. The Plastics Industry Association (PLASTICS) is the only organization that supports the entire plastics supply chain, including Equipment Suppliers, Material Suppliers, Processors, and Recyclers, representing over one million workers in our $468 billion U.S. industry. PLASTICS advances the priorities of our members who are dedicated to investing in technologies that improve capabilities and advances in recycling and sustainability and providing essential products that allow for the protection and safety of our lives. Since 1937, PLASTICS has been working to make its members, and the sixth largest U.S. manufacturing industry, more globally competitive while supporting circularity through educational initiatives, industry-leading insights, and events, convening opportunities and policy advocacy, including the largest plastics trade show in the Americas, NPE2024: The Plastics Show. plasticsindustry.org R
DALLAS, TX, USA – Celanese Corporation (NYSE: CE), a global specialty materials and chemical company, announced it has begun running a carbon capture and utilization (CCU) project at its Clear Lake, Texas, site as part of its Fairway Methanol joint venture with Mitsui & Co., Ltd. The project is expected to capture 180,000 metric tons of CO2 industrial emissions and produce 130,000 metric tons of low-carbon methanol per year.
Celanese is actively leveraging CCU to offer low-carbon options across its Acetyl Chain and Engineered Materials products to help global customers meet the growing demand for more sustainable and circular solutions. The products will be launched under the ECO-CC name and be transparently supported through mass balance tracking and life cycle assessment processes.
“With this project, our Celanese value chain can convert CO2 waste into products for a wide array
of end-markets, including consumer goods like adhesives, packaging, toys, paints, coatings, and more.” said Mark Murray, senior vice president, Acetyls at Celanese. “Our globally-integrated value chain positions us to provide a wide range of solutions with carbon capture content across both our integrated Acetyl Chain as well as other methanol derived products like acetal copolymers (POM).”
CCU takes CO2 industrial emissions that would otherwise be emitted into the atmosphere from both Celanese and third-party sources and applies reduced-carbon-intensity hydrogen to chemically convert the captured CO2 into a methanol building block used for downstream production. This lowcarbon input is then used to reduce traditional fossil fuel-based raw materials and can help produce a wide range of end products across most major industries. Third-party sources account for 80% of the captured CO2 waste. celanese.com R
The project is led by Professor Ted Sargent and Dr. Ke Xie, among the world’s preeminent scientists in the field of electrocatalysis and contributes to Braskem’s strategy of combating climate change.
The project is led by Professor Ted Sargent and Dr. Ke Xie, among the world’s preeminent scientists in the field of electrocatalysis and contributes to Braskem’s strategy of combating climate change.
Braskem and Northwestern University (USA) have announced a partnership to develop a technology platform for converting the CO2 generated by industrial operations. It is based on co-electrolysis, a technology that makes full use of electricity to convert CO2 into products of interest.
In typical electrochemical devices, apart from CO2 conversion, water is converted into oxygen, which has no high commercial value. However, in this new strategy, two reactions of interest occur at the same time, resulting in greater productivity of the system, which creates intermediate chemicals and/or final products for commercial interest applications.
The project is led by Professor Ted Sargent and Dr. Ke Xie at Northwestern University, global experts in the field of electrocatalysis for CO2 conversion. The project, currently in the development stage, aims to build a versatile and modular system with high energy efficiency. In addition to efficiency gains, this approach enables the transformation of a higher volume of CO2, substantially contributing to the reduction of greenhouse gases. The laboratory-scale development stage, which began one year ago, is expected to advance considerably in the three years of the cooperation agreement, with the potential for scaling up and use in industrial applications after the technology is validated.
For Braskem, the investment in this partnership should help it to achieve its sustainable development targets, especially regarding reaching carbon neutrality and combating climate change. The company plans to reduce its greenhouse gas emissions by 15% by 2030 and attain carbon neutrality by 2050.
“In recent years, Braskem has signed several partnerships to study the possibilities and alternatives for using the CO2 generated by its operations. Through this partnership with Northwestern University, using the cutting-edge infrastructure of its laboratories and Prof. Sargent’s and Prof. Xie’s expertise, we will undoubtedly deploy an innovative technology – CO2 conversion through co-electrolysis. Therefore, we will efficiently reduce our greenhouse gas emissions and open new conversion possibilities through this pioneering and disruptive initiative,” explained Gus Hutras, Global Process Technology Director, Braskem.
According to Northwestern’s Dr. Ke Xie, a Research Assistant Professor leading the effort, “This partnership with Braskem is very exciting: it allows the team to explore new and adoption-accelerating concepts for the electrification of chemicals production.” Sargent added, “Brilliant post-doctoral fellows and PhD students, attracted from other leading universities globally, are as a result poised to make key contributions to decarbonizing chemicals and materials thanks to Braskem’s investment in the partnership.” Sargent is the Lynn Hopton Davis and Greg Davis Professor in the Department of Chemistry and in the Department of Electrical and Computer Engineering at Northwestern. braskem@cdn.com.br R
AB CANADA – NOVA Chemicals Corporation (“NOVA Chemicals”) is honoured to be named a 2024 Top Employer in Alberta for its leadership in talent recruitment and retention within the petrochemical industry.
The annual list, organized by Canada’s Top 100 Employers, annually recognizes select companies across the country as exceptional places to work based on criteria including workplace environment, social atmosphere, benefits, skills training, performance management, and community involvement.
“We are humbled to be recognized as a top employer in Alberta. Our vision at NOVA is to foster an agile, high-performing, and engaged team of employees and this recognition underscores this commitment to our people,” said Mona Jasinski, NOVA Chemicals SVP of HR and Communications. “Investing in our employees’ growth and development, creating a positive and supportive work environment, and building a modern and thriving learning culture all have direct impacts on
our incredible organization, as well as our partners up and down the value chain.”
Jasinski continued, “Alberta employers have always stepped forward to compete for the best and brightest talent that lives right here in our province. We’re proud to have operated in the region for nearly 50 years and to have created an environment where employees feel engaged, valued, and like they make positive impacts through their work.”
With its global headquarters in Calgary and approximately 2,200 of its 2,500 employees located across Canada, NOVA Chemicals encourages its people to use a human-centered and value-driven approach, upholding the pillars of passion, collaboration, responsibility, and innovation. The company boasts:
• Low voluntary turnover: averaging ~3% over the last five years.
• High job applicant submissions: nearly 9,000 applications received in 2023.
• Flexible work options: including earned days off and alternative work arrangements. novachem.com R
» ROTOLOAD™ is the ONLY solution to ALL of your powder resin handling needs.
» ROTOLOAD™ is the ONLY comprehensive line of powder resin conveying and weighing equipment, specifically designed to meet the demands of the Rotational Molding Industry.
» ROTOLOAD™ uses vacuum to load your material, hold it above your process machine, and dispense, quickly and accurately. In addition it is the ONLY solution to the question of how to reduce under and overweight parts, mess, downtime and resin loss.
CPChem received the results of its assessment in November.
“Sustainability is integral to CPChem and is embedded in its company strategy and across the organization to address its impacts as CPChem advances toward a more sustainable future,” said Benny Mermans, CPChem’s Vice President of Sustainability.
“CPChem is committed to continuously improving and progressing toward our sustainability goals,” Mermans said. “This year’s increased ratings in ethics and sustainable procurement highlight our team’s efforts to advance CPChem’s sustainable practices, and we will endeavor to further enhance our performance in the new year.”
The 12-month assessment rates companies on their progress in four key areas: the environment, labor and human rights, ethics, and sustainable procurement. The ratings are valid for 12 months.
CPChem’s EcoVadis score increased from 57% to 60% over the past year, placing it in the top quarter of companies assessed by EcoVadis during this period, according to the assessment.
CPChem’s scores in Ethics and Sustainable Procurement improved. In both subjects, the company’s scores increased from 60% to 70%. These ratings place CPChem in the top 10% within the industry for ethics, and the top 5% within the industry for Sustainable Procurement.
CPChem’s comprehensive and detailed ethics and compliance policies and related practices were specifically commended in the assessment.
CPChem maintained a score of 70% for Labor & Human Rights, which places CPChem in the top 14% within our industry for this subject. Enhanced information found in reports, such as CPChem’s Chemisphere at Work, as well as an alignment with the Index significantly contributed to CPChem’s score.
The Paris-based EcoVadis, a global provider of business sustainability ratings, operates as a collaborative performance improvement tool for global supply chains. Completing the EcoVadis Sustainability Assessment has become a common practice within the petrochemical industry, driven by a global call for suppliers to achieve standards and report metrics related to sustainability performance. cpchem.com R
AKRON, OHIO, USA – Myers Industries, Inc. (NYSE: MYE) (“Myers” or the “Company”), a leading manufacturer and distributor of industrial products, recently announced that it has completed its acquisition of Signature Systems (“Signature”), which was previously announced on January 2, 2024.
“We are excited to welcome the Signature team to Myers with the closing of this transaction,” said Mike McGaugh, Chief Executive Officer of Myers Industries. “This acquisition strengthens our growing portfolio of market leading brands, enhances our profitability profile, and demonstrates Myers’ capability as a platform for acquisitive growth. With a strong runway of future growth, due to increasing infrastructure investments over the next decade, we believe Signature’s sustainable competitive advantage, strong earnings growth, and free cashflow profile will help us accelerate EPS growth and achieve our long-term strategic objectives.”
The cash transaction of $350 million was funded through an amendment and restatement of Myers’ existing loan agreement, which maintained a $250 million revolving credit facility and added a new $400 million 5-year senior secured term loan A (collectively, the “Loan Agreement”). The term loan A was increased by $50 million from the amount initially contemplated. These combined senior secured loan agreements enhance Myers’ overall liquidity profile and capacity for future potential acquisitions. Pro forma for the acquisition, the Company’s net leverage ratio is approximately 3.0x, which is within management’s target range. The financial results of Signature Systems are expected to be included within Myers’ Material Handling segment.
Chief Financial Officer Grant Fitz commented, “As mentioned in January, this transaction is expected to be neutral to slightly dilutive to US GAAP EPS in fiscal year 2024, and we anticipate Signature will deliver EPS accretion of $0.20 to $0.30 in 2025 and $0.40 to $0.50 in 2026 with additional meaningful EPS accretion beyond 2026. We also expect annualized run-rate operational and cost synergies of $8 million to be fully captured by 2025 with additional synergies to be realized once Signature has an opportunity to leverage the Myers Business System. Excluding other potential opportunities that may come forward, we
anticipate using the free cash flow generated from the combined Myers and Signature company to allow Myers to reduce the net leverage ratio below 2.0x within two years of closing of this transaction.”
Moelis & Company LLC served as the exclusive financial advisor to Myers with respect to the transaction, while Vorys, Sater, Seymour and Pease LLP, and Davis Polk & Wardwell LLP provided legal counsel. William Blair & Company LLC served as exclusive financial advisor and Honigman LLP served as legal counsel to Signature. The Loan Agreement was led by J.P. Morgan Chase, U.S. Bank National, Wells Fargo Bank, and KeyBank National. myersindustries.com R
Obituary published on Legacy.com by Mallory-DeHaven-Carlson Funeral Home & Cremation Services - Garrettsville on Feb. 14, 2024.
Martin J. “Marty” Toth, 81, of Garrettsville, passed away Monday, February 12, 2024. He was born April 16, 1942, in Cleveland, to the late Joseph and Congetta (Cosentino) Toth.
Professionally, Marty consulted around the world in the plastics industry and was a long-time member of the Association of Rotational Molders (ARM). He also served honorably in the US Navy. Personally, he loved shooting sports, such as, competition rifle shooting and spending time with his family.
Marty will be deeply missed by his loving wife, Judy (Davison) Toth, who was blessed to share over 55 years of marriage; daughter, Amanda (Mitch) McAllister; grandson Ryan; brother, David (Marian) Toth; sister, Rose Lynn “Tina” (Tim) Dye, and many beloved family members and friends.
He was preceded in death by his brother, Anthony Toth. There was a memorial visitation held on February 20, to be followed by a private burial in Park Cemetery in Garrettsville at another date. R
Redline Plastics is thrilled to announce its nomination for the Manitowoc Chamber Awards of Distinction in the category of Large Business of the Year.
MANITOWOC, WI USA – This prestigious nomination reflects Redline’s unwavering commitment to excellence, innovation, and community engagement. As a cornerstone of the Manitowoc business community, Redline takes pride in its contributions to the local economy and the positive impact it has on the lives of its employees and stakeholders.
Redline Plastics has been named one of 10 other nominees for the Large Business/Industry of the Year: Recognizes a Manitowoc County business (26+ Employees) for its growth, success, innovation, and contribution to the community during 2023.
The anticipation is insurmountable,” says Chamber Executive Director Abbey Quistorf. “This event is truly a grand celebration of the non-profit organizations, businesses, and the people that make Manitowoc County a great place to live. We’ve received so many wonderful nominations and we can’t wait to find out who the winners will be.”
Chuck Webster, Redline Plastics CEO commented “It is truly an honor to be considered for the Manitowoc Chamber Awards of Distinction, particularly in the Large Business of the Year category. This nomination reflects the collective efforts and dedication of every member of the
Redline team.” Nick Murray, President of Redline Plastics noted “We are proud of our achievements and remain dedicated to fostering growth, creating opportunities, and contributing to the prosperity.”
The Manitowoc Chamber Awards of Distinction ceremony, was held in February, 2024, at the Capitol Civic Centre, Manitowoc. This event brought together leaders and influencers from the business community to celebrate excellence and innovation.
The Large Business/Industry of the Year Award nominees were:
• Americollect
• Aurora Health Care Manitowoc County
• Bank First
• Briess Malt & Ingredients Co.
• Burger Boat Company
• Eck Industries Inc
• Manitowoc Marina
• Manitowoc Tool & Manufacturing, LLC
• Redline Plastics
• Robinson Inc.
• Wisconsin Aluminum Foundry R
As I approach my 60th birthday I’ve been reflecting on my 37 years in the rotomoulding industry. I marvel at how it has changed and grown.
In the 1980’s the common phrase used by many was “Rotomoulding is an Art, not a Science”, and in many ways they were right. Often people guess what to do and trial and error is the name of the game.
Whilst the process remains fiendishly complicated owing to the massive range of variables involved in a zero-pressure casting process, the fact is that these days Rotomoulding is much more of a science.
Perhaps the founding father of this revolution was Professor Roy Crawford back in the late 1980’s and early 1990’s. With his team at Queen’s University in Belfast, he developed the Rotolog internal temperature measuring device.
This opened a whole new world of understanding of what is occurring with the powder inside the mould. It introduced us to novel concepts such as Peak Internal Air Temperature (PIAT) and real-time monitoring of the exact temperature inside the mould throughout the cycle.
This enhanced level of process control, combined with the much higher precision and repeatability we have with CNC moulds and the greatly improved polymers we have these days, means that we are a world away from how the
THE “HOLY GRAIL” IS A LOW-COST SYSTEM OF DIRECT HEATING OF MOULDS WITH ELECTRICITY THAT CAN ENABLE THE USE OF EXISTING TOOLING OF ANY SIZE.
industry was 40 years ago.
The overall quality, tight tolerances, aesthetic appearance, and physical performance of many mouldings made today would seem impossible only a relatively short time ago. These advances have led to the extremely diverse and evergrowing list of products made with this process.
There are some significant and exciting upcoming developments about to hit the market. Our industry has woken up to many challenges, particularly sustainability and poor energy efficiency in the process. In my view, the future will be electrically heated moulds requiring no ovens. These moulds will enable us to massively cut energy usage and have even increased process control. They will also provide us with more flexibility in the materials that can be used.
The “holy grail” is a low-cost system of direct heating of moulds with electricity that can enable the use of existing tooling of any size. From what I have been privileged to see, I don’t think that this is far away, and I believe that when fully commercialised the Rotomoulding industry will fully adopt this new technology and make another big leap-forward. Watch this space! R
As I re-entered the rotomolding realm in 2022 after a threeyear hiatus, I was struck by the significant changes that had occurred in a relatively short period of time. Fueled by several dynamics, including the pandemic, industry consolidation, and resultant heightened demand in roto-intensive market sectors, this growth surge placed significant pressure on rotomolders to quickly increase production capacity in the face of an intensely challenging labor market.
This was a similar dynamic to the one I faced during my three-year roto hiatus, in which my employer, a custom manufacturer of metal components engineered primarily for the household furniture sector, experienced 40%+ revenue growth as the meteoric rise in pandemicrelated remote work intensified demand for the household desks, lamps, and accessories which the company manufactured. Concurrent with pandemic-related work-at-home mandates, demand for household office products
surged, necessitating a rapid escalation of production capacity amid the challenging labor market mentioned above.
With the launch of Xcelerant Growth Partners and re-engagement with the rotomolding industry, it was evident that despite the increased integration of automation, robotics, and advancements in equipment efficiency, rotomolding remains a relatively labor-intensive manufacturing process, reliant on various levels of skilled labor
and largely typified by “high-mix, low-volume” production, and subsequently remains challenged to effectively manage this workforce labor-related predicament.
The challenges of employee retention
The inescapable reality is that irrespective of capital investment made in facilities, machinery, tools, and production efficiency, workers in the rotomolding operation have a dramatic and direct impact on business performance indicators, including product quality, production efficiency, profitability, on-time delivery, and customer satisfaction. Simply put, the success or failure of a rotomolding business is inextricably linked with the effectiveness and engagement of its workforce.
Exacerbated by the pandemic, access to and retention of manufacturing employees remains a significant challenge to the continued growth and success of our industry. And while production personnel in manufacturing
settings, including rotomolding, typically receive hands-on skills training to build proficiency with manual tasks, employee turnover across all manufacturing sectors remains high (currently 22%, according to Bureau of Labor Statistics). In other words, for every 10 new employees hired, two will leave the business, the majority of whom will exit within the first six months of their start date.
Not only is this turnover disruptive to a business, but it’s also very costly, as it’s estimated that the company’s cost per employee resignation is 33%+ of the worker’s salary, which includes reduced workplace productivity, recruiting costs, hiring temporary workers, etc. Thus, if skills training, in-and-of-itself, isn’t enough to retain employees, what can be done to retain employees and keep our rotomolding facilities operating at full capacity?
What is employee onboarding, and why should we do it?
Onboarding is a practice that
many organizations are now deploying, with a growing body of evidence underscoring its effectiveness in engaging and retaining new employees, and in driving organizational performance. In contrast to orientation (office policies, job duties, etc.) or training (developing specific skills to perform specific tasks), onboarding refers to the process through which new employees acquire the necessary knowledge, skills, and behaviors to become effective members of an organization.
Further, onboarding seeks to integrate employees into the workplace, help them understand the company culture, feel welcomed and valued in their team, and accelerate their development so they can achieve full productivity faster. Simply put, onboarding gets new hires “up-to-speed” faster while optimizing the probability of their enhanced tenure and longterm contribution to organizational success.
As mentioned earlier, the statistics clearly demonstrate that
deploying effective onboarding initiatives (or the opposite thereof) has a direct and significant impact on employee retention and organizational performance. Let’s consider the following data point samples as provided by Zippia Research and Exploding Topics, career resources organizations headquartered in San Francisco, CA:
• Organizations with strong onboarding processes increase new hire retention by 82%
• Organizations with strong onboarding processes improve employee productivity by 70%.
• 88% of employees believe that their company doesn’t do a great job when it comes to onboarding new employees.
• 12% of employees say their organization has a good onboarding process.
• Employees who attend a
structured orientation program are 69% more likely to remain at the company for at least three years.
• 64% of organizations deploying formalized onboarding initiatives report tangible improvements in Key Performance Metrics (KPI’s).
Though the above data are not rotomolding industry-specific, they do underscore the correlation between effective onboarding and employee engagement, retention, and organizational performance. Knowing this, and understanding the reality of staffing and budgetary constraints which make employee engagement initiatives difficult to actualize, what can we do that’s effective, low-cost, and readily deployable?
• 54% of organizations deploying formalized onboarding initiatives report measurable improvement
in employee engagement and retention metrics.
• 33% of employees leave their positions within six months primarily due to not receiving clear guidelines relative to job responsibilities and expectations.
Anecdotally, I’ve been closely involved with creating and deploying onboarding initiatives at my last two corporate leadership positions, both within and outside the rotomolding industry. Despite the different manufacturing focuses of these respective organizations, there were similarities in the challenges we sought to address: improve competitiveness for available labor, enhance employee engagement, reduce employee turnover, and leverage all of the above to drive
EVEN RELATIVELY SIMPLE, LOWCOST ONBOARDING INITIATIVES CAN EFFECTIVELY ENGAGE EMPLOYEES AND CATALYZE IMPROVEMENTS IN KEY PERFORMANCE INDICATORS.
improved KPI performance. And in both cases, we saw similarly positive results through effective deployment of onboarding and engagement processes.
Essentially, the onboarding process we developed was a two-pronged approach, with one module consisting of information and orientation required for all employees, and a second module tailored for the individual hire, and specific to his/her position and department. In each case, new hires participated in presentations, sessions, and interactions with current employees, with documented onboarding booklets prepared given to each new employee (and as necessary, translated into Spanish). These modules were presented by a cross-section of current employees, managers, and in some cases, company owners, creating a sense of shared ownership and accountability for the success of the onboarding initiative by all employees – both tenured employees and new hires.
Generally, described, the onboarding initiative included the following components:
All-Employee Module:
• Company background and history.
• Overview of customer base, markets, and industries served.
• Overview of company’s manufacturing capabilities, including in-depth tour of facilities.
• Corporate mission statement, vision statement, and values and introduction to Values committee.
• Overview of corporate safety policy and introduction to Safety committee.
• Review of employee manual.
• Review of performance objectives & KPI’s (Key Performance Indicators), including methodology and communication.
• Review of corporate strategic vision.
• Introduction to Leadership Team.
• Participation in quarterly all-employee meetings, etc.
Individual Employee Module (in addition to above):
• Introduction to area manager & immediate team members.
• Skills training program tailored to specific company role.
• Review of performance review process.
• Development of specific individual performance expectations.
• Review of departmentspecific KPI’s.
• Introduction to company action committees: Values, Safety, Internal Events, Employee Engagement, Employee Recognition, Customer Service, etc.
• On-site visits to key customers & suppliers within “x” days of start date, etc.
As we implemented the above components of a formalized onboarding program, and as a direct result of more engaged, informed, and participative employees, we reduced turnover to drive improvements in all the aforementioned areas, while realizing significant top-line growth and fortification of net profitability, aligning with the 64% figure (companies with formalized onboarding processes who realized tangible improvements in KPI performance) reported above.
Create an environment conducive to great performance.
The data presented above clearly demonstrates the benefits of formalized onboarding initiatives, but perhaps oversimplifies the challenges of establishing an effective onboarding strategy. Faced with the very real constraints of limited budget and available bandwidth, creating, implementing, and sustaining employee onboarding programs poses an intense challenge for smaller, more resourceconstrained organizations that tend to exemplify the rotomolding industry.
However, data also shows that literally any attempt to implement onboarding yields a positive impact on employee engagement, tenure, and organizational performance. Not accounting for the time invested by participating employees (i.e. those presenting material to new hires, participating on committees, etc.), the cost of implementing the components in the above examples was relatively low; further, since it entailed cross-functional participation, no single functional area was disproportionately burdened by onboarding responsibility.
As Simon Sinek, the expert, author, and inspirational speaker on business leadership stated, “An employee’s job is to give his or her best work every day. An employer’s job is to make sure we provide an environment in which they can do their best work every day.” As the data demonstrates, implementing an effective employee onboarding strategy is a meaningful starting point in creating the environment in which both employer and employee can thrive. R
Alvin Spence’s 30+ year career in rotational molding begin in 1991 at Queen’s University Belfast where he completed his PhD under the late Professor Roy Crawford. He then managed the Rotational Moulding Research Centre, overseeing industrysponsored research projects. In 1997, Alvin joined Centro Inc., where he has been instrumental in R&D, including the development of the patented ROTOLOPERMTM technology, used by Centro and licensed to rotomolders for CARB/EPA-compliant fuel tanks, and reactive Nylon 6 processing (known as anionic polymerization). Alvin is now the VP of Engineering at Centro, overseeing product development, quality, and three manufacturing sites. Beyond Centro, Alvin has been an ARM Board member for the last seven years and is the current ARM President. He has presented at ARM meetings, and serves as the Technical Editor of RotoWorld® magazine.
“I’m thrilled and honored to join this fine group of people who have given so much to our industry. I am also thrilled to be inducted with Corey Claussen,” Alvin said as he accepted the high award during
the 2023 ARM Awards Gala in Kansas City, MO.
Alvin acknowledged his parents. “I was blessed to have loving, Christian parents who were dairy farmers in Ireland. They were both of great character and terrific examples of hard-working people who strived to create a better life for themselves and their four children,” he said. Alvin also acknowledged his wife Denise who has been his greatest supporter over the years. “Denise has given me the freedom to do whatever my job has required, while taking on the vast majority of the responsibility of raising our three children,” he said.
Recalling early days when he was a young engineer, Alvin
worked for a small fabrication company in Northern Ireland. This job was not a particularly good experience and before long he was on the hunt for a new position. This was when he purchased the Thursday night edition of the Belfast Telegraph newspaper. After scanning the job market ads, one jumped out at him …. Queens University, PhD research project, into something called Rotational Molding, and for some guy called Roy Crawford. “What a life changing moment that was for me,” Alvin said.
Alvin joined Professor Crawford’s program at Queen’s University in March 1991 just as Paul Nugent was finishing up his research and starting to
manufacture Rotologs. Roy was building a strong reputation within the industry and attracting a lot of research funding. Alvin had a project funded by the material supplier Borealis and a molder in the UK called Lin Pac. During that time the research team grew to include Joe Butterfield and Gareth McDowell.
After Roy introduced several of the research students to the Association Rotational Molders (ARM) in Munich in 1993, one of Alvin’s lasting memories of that conference was the warm welcome they received from the ARM community. He recalled meeting Pat Long, Dave Mulligan, and Glenn Beall there for the first time. Roy, being a very gifted speaker, talked about the importance of internal air temperature measurement. He said: “It’s like going to the doctor’s office, and the doctor needs to determine if you have a fever or not, so the doctor takes a thermometer and doesn’t wave it around your head, but rather puts it in your mouth”. It was a simple but brilliant analogy that got the point across.
In the mid 1990’s, Roy established the Rotational Moulding Research Centre at Queens and the department’s capital equipment grew to include a state-of-theart Ferry 160 independent cart machine, a Wedco grinder, and Caccia high speed blender. One of Alvin’s fondest memories of those days was starting the Rotational Moulding Training Courses at Queens, which were 2-day handson using the molding and test equipment available. It was equally important to the Queens team that the attendees had a great time socially, he noted.
In 1997, both Centro and Alvin
took a “leap-of-faith” when he left the University and moved to Iowa, USA. Before joining Centro, Alvin had visited Iowa the previous year and found it to be similar to Ireland, with its farming communities and warm friendly people. His intent was to gain some industrial experience and probably return home again after a few years. However, that didn’t quite go to plan. Centro was a
growing, thriving business led by Gary Rozek at the time. In those early days he was befriended by the Sales leader, Brian Olesen. “Brian must have felt sorry for me for either being so far from home or being stuck in Iowa, as he graciously included me in many of his family events on the weekends and invited me to lunch with some of the sales team during the week,” he said. Alvin, being a bit shy, was a soft target during the lunch hour for some light-hearted abuse by the sales team. “This was when I decided offense was the best form of defense, and I put my slightly sarcastic humor to good use,” he said.
Alvin has grown to appreciate more and more the people that he works with and the environment that makes Centro a great place to work. “Covey Habits are very much at the core of our culture, along with an expectation of doing your best, keep getting better, and treating others how you would like to be treated,” he said. After working at Centro for over 26 years, “I could not have dreamed of working for a better organization, with abundant opportunities to grow and develop a career, working with a fantastic team of people,” he said.
“I was fortunate to have Roy Crawford as a leader, then Gary Rozek, but Brian Olesen has been the best of all for the last 18 years or so,” Alvin said. Brian is not just a terrific leader, but also a great friend, a therapist for life’s challenges, a financial advisor, and much more. Unfortunately, Brian could not attend the ceremony as he had tested positive for COVID the day before.
For 30 years Alvin has been attending ARM meetings and he has met some wonderful people. “Thank you for all of your support and technical expertise over the years. I know that I personally, along with many other molders, have benefitted greatly from the knowledge shared by our members. Sharing information and learning from others is an important part of what we do at ARM,” he said.
In conclusion, Alvin recalled someone once asking him the question as they looked back on their life’s accomplishments and wondered … is it all about the destination or is it all about the journey …. and the answer given was its neither … it’s the company,
and the people that we chose to surround ourselves with every day. “Well, I feel blessed to have worked with some wonderful people and organizations, that have brought great fulfillment to my life, and I have no doubt that will continue to be the case under Tank Holding,” he said.
Corey has been involved in rotomolding for more than 25 years, growing up in the family business started by his father. He rose through many positions in the company and is currently the President of Custom RotoMold (CRM), which has continued to expand and develop a global presence. Corey has been a strong proponent of ARM, serving twice on the Board, including two separate terms as President of the Association. He has been instrumental to the organization during challenging times. Corey has served on many committees and is always willing to share his knowledge and contribute at workshops, committee meetings, and regional meetings. He has attended practically every ARM Annual Meeting in the last two decades. Corey received the Charles D. Frederick Award for Distinguished Service in 2009.
Accepting the coveted award, Corey congratulated Alvin Spence and thanked him for all his service in promoting and building the Association. He thanked the Nominating Committee for granting him the incredible honor of being inducted into the ARM Hall of Fame. “It is truly humbling to be included with the pioneers of our industry and equally humbling to be selected by my peers,” he said.
Corey’s described his journey
in ARM, which started in 1994, as a tapestry of both trials and triumphs, yet he said the overarching narrative that underscores his time as an ARM member has been one of profound gratitude. He was deeply grateful for the countless opportunities that ARM has graciously given him, to CRM, and to his family.
While still in college in 1994, Corey remembered sitting in his father’s company conference room listening to some salesman selling a rotomolding oven. In that room was his father Steve Claussen, Uncle Bob, Harry Covington, and Denny Brazelton. It was after that meeting his father and uncle decided to move forward and buy a Ferry 280 oven, which set in motion a life-altering career journey.
into rotomolding. This not only accelerated the business, but it also set the stage for Corey’s involvement. Invited by Steve and Bob to join the company in the late 90s, Corey left his cubicle job at Prudential Insurance to explore the untapped potential of “custom” molding. He embarked on a career path he initially knew little about but was eager to pursue.
After a couple of years running the Ferry 280, they decided to join ARM in the late 90s. Corey’s initial experience with ARM was at the Disney Resort Swan in Orlando, FL, which he remembers vividly. That meeting quickly revealed ARM’s strength as a hub for meaningful connections. Adding a layer of enjoyment to the professional atmosphere was a golf outing. As a former college golfer, the prospect
The company’s existing partnership with Monsanto in the agricultural spray business was booming, fueled by high demand for plastic hooded sprayers among farmers.
Corey’s father Steve recognized the potential for diversification, drove the investment, and went
of playing golf in Orlando was irresistible. “It was an ideal blend of business and pleasure, making me feel right at home in this new community,” he said.
Corey recalled the 1996 Maui meeting when he brought his then bride-to-be Darcy and won the golf tournament alongside Tom Long
from Formed Plastics. “I began forging substantial relationships with professionals who shared similar goals. The openness within the ARM community didn’t just enhance the experience; it also became a driving force behind both my personal and professional growth,” he said.
Corey was invited to join the ARM board in the early 2000s. Board meetings at that time were time intense stretching over three long days and requiring meticulous preparation. His first assignment as a committee chair was to lead the Special Materials Committee, which was a daunting task as the committee included over 20 engineers and resin experts. He had never even attended a special materials meeting, and suddenly he was in charge. Thanks to Bob Swain for inviting him to visit Chroma in McHenry, IL, Corey was able to discuss the committee’s agenda and prepare for the upcoming meeting in Phoenix. This was another pivotal learning experience for Corey.
After several years serving on the ARM Board, Corey was chosen to run through the chairs. “While the prospect of public speaking and leadership responsibilities was intimidating, the allure of building new relationships and expanding my horizons was too compelling to resist,” he said.
Fast forward to around 2007, Corey assumed the presidency role, and life threw a succession of curveballs at him in just a sixmonth span of time. He faced challenges in the family business, experienced personal losses, and he and his wife discovered construction flaws in their newly built home. At the same time, they welcomed the birth of their second child, Julia. Corey was
faced with leading an association in financial straits. ARM was out of cash. Therefore, while managing all the issues back home, Corey was also tasked with navigating ARM through a challenging financial landscape. With need for immediate action, they found it was time for substantial organizational changes. Consulting with Joe Strzygowski, Mike Dorsey, Daven Claerbout, and Bill Ives, the group explored various pathways, including Bill Ives suggestion of
leveraging management groups. It was after many rigorous discussions and the full support from the Executive Committee, they took the significant step of transitioning ARM’s management to CM Services during the 2008 Spring Meeting in Las Vegas. With this move, ARM’s mission was set to primarily serve North American molders, providing more in-depth value and education opportunities. ARM’s international partnerships were maintained through their association with ARMO.
Corey recalled that this action did not come without its share of surprises and scrutiny. ARM Past President Chuck Carlsen (from Corey’s largest competitor Solar
Plastics), called him and this call led to what felt like a Senate-style hearing at the Chicago O’Hare Hilton. “Picture this: 7-10 past presidents sitting in horseshoe formation, while Daven Claerbout, Joe Strzygowski, Mike Dorsey, and Corey found themselves at the head table tasked with defending their new course of action,” he said. They navigated through the grilling, fortified their resolve, and moved forward. “Thanks to the concerted efforts of Dorsey, Strzygowski, Claerbout, and the whole ARM family, our bold choices to refocus ARM and shift our management strategy paid off, culminating in ARM now boasting a healthy financial reserve,” he said.
Corey thanked a number of people who have played pivotal roles in his journey including Bill Spenceley, Daven Claerbout, fellow ARM board members, and the Past Presidents, for putting the fear of God into him. He thanked Anna and Adam of Webb Evans for their leadership and guiding the Association. He thanked the team at CRM for their dedication, hard work, and support for him as he worked on behalf of ARM.
To his family, Darcy, Alex, and Julia, Corey said: “Darcy, your unwavering support has made this unique journey incredibly fulfilling. Your love has been my constant, and I am profoundly thankful for your presence in my life. To my kids, Alex, and Julia, thank you so much for being great students and great kids.
“ARM has been so much more than a mere professional network; it’s a haven of unwavering support and shared achievements. It is a gift beyond measure, one that I can never truly repay and for that I thank you a thousand times over,” Corey said. R
The Past
2 decades ago as an assistant engineer, one of my assignments was to perform incoming quality tests on our powders. The goal was to ensure the material was going to produce good parts before using them at the machine. If the material passed the tests, we would release it to the production floor. If it failed, we would communicate the issue with the supplier and seek a suitable resolution (which was sometimes a deviation and sometimes an outright rejection).
One common QC test conducted with the dry flow test. 100 grams of powder was placed in a funnel and the time it took to flow through the funnel was timed. Any material flowing faster than 30 seconds was approved. Any powder flowing slower than 30 seconds was quarantined and a call was made to the supplier. To my surprise, the supplier quickly rejected our rejection and claimed that the powder passed the dry flow test on their end before they ever shipped the material. Their testing suggested it was good powder, and my testing showed that it was bad powder. Now what?
It was apparent that we were both confident in our testing procedures, so we agreed to do a funnel comparison study. Small powder samples were shipped back and forth, and we quickly confirmed who was right …. we both were! The same 100 grams of material was passing their funnel and failing our funnel. So, where was the problem? Measurements were taken of both funnels, and although they both satisfied the standard being used at the time, they were drastically different. The exit orifice tolerance of the funnel standard was 10mm +/- 1mm. That may seem small, but that +/- 1mm allowance represents a 10% swing in each direction. Thus, a funnel with a 9mm exit orifice and a funnel with an 11mm exit orifice both fell within the allowable limits defined in the standard being used at the time (ASTM D 189596). Figure 1 shows a generic schematic of this original funnel design.
I wondered why such a large tolerance was
allowed, so I made a few phone calls to the ASTM offices, and soon got in touch with Dr. Dave Riley from ASTM section D20. He was part of the team that wrote the standard. He quickly explained that the original intent of the D 1895-96 standard was to measure bulk density, not dry flow. They included a simple funnel in the standard to introduce falling powders into a cup. The funnel design was only there to mimic hoppers used in industry. Its importance to the test was minimal, so the tolerances associated with the funnel weren’t that significant. This explained the large funnel tolerances (and other missing criteria) called out in the standard.
No wonder there was so much discrepancy in the industry. The funnel we were all depending on was the problem! This 2004 discovery led to a multi-year ARM project that resulted in a new dry flow standard published in late 2011. It was the first globally recognized standard in the rotational molding industry.
In this new standard, the funnel finally got the recognition it deserved. Figure 2 shows an image of this new and improved funnel, courtesy of Roto Solutions.
• Sampling and conditioning was outlined
• Procedures were clarified
Properly produced powder should flow quickly and uninhibited. The presence of particle tails or a poor particle size distribution will result in a slower flowing powder. Actual flow times should be published by your material supplier and should also be tested internally by all molders.
Though the test is not perfect, it is indeed an indicator of the quality of the powder you are about to mold. Poor flowing powders typically yield poorly detailed text, logos, threads, and/or tight radii. Powders that flow quickly through the funnel will mold much better details.
One molder called me with concerns of unacceptable bridging. It was more problematic
THIS 2004 DISCOVERY LED TO A MULTI-YEAR ARM PROJECT THAT RESULTED IN A NEW DRY FLOW STANDARD PUBLISHED IN LATE 2011. IT WAS THE FIRST GLOBALLY RECOGNIZED STANDARD IN THE ROTATIONAL MOLDING INDUSTRY.
• The exit orifice tolerance was appropriately tightened to 10mm +/- 0.01mm
• Funnel material and interior surface finish was defined
Several companies currently supply dry flow funnels for rotomolders throughout the world. Every rotomolder and material supplier should own at least one. Just make sure the one you get follows the standard. The exit orifice needs to be 10m +/0.01mm. It needs to be made from aluminum. The inside of the funnel needs to be sulfuric anodized. See the ARM website to read the entire standard. If the funnel you already have (or are looking at getting) does not follow the standard, consider looking elsewhere to get one that does.
The dry flow test is simple … 100 +/- 1 grams of room temperature powder is loaded into the funnel with the bottom closed off. The bottom is then opened, and the material should freely flow out. The application of taps or other such vibrations to initiate flow is not in accordance with this standard and the need for such assistance should be viewed as an indicator of unacceptable powder properties. The time it takes for all the material to flow through the funnel is an indication of the powder quality.
many molders have chosen not to spend the money on a funnel.
To help bridge this gap, ARM’s Education Committee launched a dry flow funnel project a couple years ago with the hopes of raising awareness by developing an entry level funnel of some sort. The aim of the project was NOT to develop yet another new dry flow standard. But rather, to develop a “quick reference funnel” using the existing 2011 global standard.
The molders and suppliers on the committee are well on their way to accomplishing their goal. After some promising tests from a few 3D printed funnels, an injection mold was made and a preliminary batch of funnels have been circulated to a strategically selected group of molders and suppliers. Comparison tests are being conducted as we speak to ensure the new quick reference plastic funnel is compatible enough with the official aluminum funnel. The hope is to give away these quick reference funnels to all ARM members. Figure 3 shows an image of a funnel from this preliminary batch.
Can you envision it with me? Every molder and every supplier having one (or more) of these in
IF DONE CORRECTLY, ANY POWDER THAT PASSES THE QUICK REFERENCE FUNNEL SHOULD ALSO PASS THE OFFICIAL FUNNEL.
from one supplier, and never an issue from another supplier. A simple dry flow test was conducted, and it confirmed the difference between suppliers. A phone call was made, some grinding parameters were changed, new powder was supplied that passed the dry flow test, and the bridging problem was permanently resolved. This simple test takes less than a minute and can prevent problems that you won’t discover until after you have molded a part.
I have always suggested to molders that if you are only going to do 1 incoming quality procedure, make sure it is the dry flow test. And yet, very few molders are doing it. Despite the quick advantages it offers,
the near future. Everyone using the same quick reference funnel at each machine, with an official funnel in their temperature-controlled lab. It will be a tremendous victory for our industry when that happens. Help me make it happen.
If done correctly, any powder that passes the quick reference funnel should also pass the official funnel. But if the powder fails the quick reference funnel, that doesn’t mean it will fail the official funnel. You’ll simply take the material to the aluminum funnel for the official test and result. R
NOVA Chemicals and Saeplast Americas have collaborated on rotomolding projects for several years. Both companies strive to develop more sustainable packaging and achieve a circular economy for plastics. Through their synergistic and innovative projects, their goals of sustainability are becoming a reality.
NOVA Chemicals, a producer of polyethylene and recycled polyethylene recently began a new endeavor with Saeplast to increase operational efficiency and sustainability. Saeplast, a subsidiary of Rotovia, has a strong history in Atlantic Canada dating back over 40 years, providing rotomolded solutions to the fish and meat markets in the form of insulated containers. The company has been under the leadership of Brian Gooding (Managing Director) since July 2011 supported by his all-star team. Rotovia was formed by a
management led purchase of the rotational molding business from a large international packaging firm. Rotovia has a large global presence in the rotational molding industry with ten manufacturing facilities in 7 countries. They utilize their expertise in the rotomolding process to produce sustainable plastic products that are used globally across the agriculture, commercial vehicles, renewable energy, leisure, chemical and food markets.
“Our rotomolded products are already inherently sustainable but as an organization we are striving to do more development in the circular economy and building a sustainable business model” says Gooding. “We believe in collaborative partnerships and that’s what we get when working with NOVA Chemicals”.
A good example of sustainability at Saeplast is the iTUB rental in Northern Europe.
iTUB rents Saeplast equipment in a circular pooling system. This business unit epitomizes the very essence of sustainability. The products are durable and last for many years if not decades. Additionally, iTUB controls the product through multiple rental depots, creating the opportunity to inspect inventory. Retaining this control puts the company in a position to conduct product maintenance as container degradation from normal wear and tear is seen, thus extending the product life expectancy. iTUB´s Saeplast products are used countless times during their lifetime, and it’s unfathomable to think about the amount of disposable packaging iTUB containers would replace.
At its current stage, Saeplast is developing a take-back service to reprocess bins and generate a next-generation product. It will use post-consumer reprocessed polyethylene and feed it back into
the core of new containers for iTUB. This is circularity as it’s intended and something Rotovia and Saeplast are very proud of.
NOVA Chemicals and Saeplast have always enjoyed a collaborative technical relationship that was originally fostered by retired Rotomolding Technical Service expert, Henry Hay, who has since passed the torch to Dustin Turgeon, Professional Engineer and Technical Service Specialist. “I was really eager to work with the Saeplast team,” says Turgeon. “Saeplast already had been using TRx0338 when I came in, but I knew that if Brian took advantage of its exceptional performance, it could not only improve their
bottom line but also help them down their sustainability path.”
The relationship began gaining momentum when NOVA Chemicals commercialized its new portfolio of hexene rotational molding polyethylene, NOVAPOL® TRx resin. Hay collaborated with Saeplast and began discussions on how to optimize the physical properties of their insulated containers and explore the processing benefits of the NOVAPOL® TRx0338-U(UG) resin.
As a material supplier, it is critical that NOVA Chemicals understands what customers need to be successful. Through many engagements with expert rotomolders, such as Gooding and his team at Saeplast, it was clear that all the key business drivers support the larger picture of improving
sustainability in products that are already inherently sustainable. Namely, improving cycle time, operational flexibility, energy savings, and the potential to lightweight.
The NOVAPOL® TRx0338-U(UG) resin is a hexene linear low polyethylene that was designed to have unprecedented productivity, part performance, and designed to support the key business drivers in the roto industry. NOVA Chemicals and Saeplast explored the practical benefits of the TRx0338-U(UG) material from a rotomolding process and part lightweighting potential.
NOVA Chemicals and Saeplast teams developed a testing plan to quantify and expand the benefits that Saeplast had already been
experiencing with the TRx material. The team decided to use the D660 double walled stackable insulated container as the part for the testing. This is a Saeplast legacy core product that is strong, dependable, and well suited for the seafood industry.
A series of in-field and lab testing was conducted to compare the NOVAPOL® TRx0338-U(UG) resin against a conventional 3 MI hexene roto resin. The primary quantitative test conducted was the cold temperature ARM impact test, with the pass criteria of ductile failures occurring in greater than 50% of the samples at a temperature of -40°C. The impact testing was conducted on the inside and outside walls of the container. Additionally, when examining lightweighting potential, side-wall stiffness deflection testing was completed, and qualitative testing was conducted to examine the level of cure (side wall bubbles present or signs of overcuring) and physical appearance.
The first processing benefit explored was to improve cycle time. The approach was simple. Using parts made from NOVAPOL® TRx0338 resin, the Saeplast team reduced the cycle time by 1 minute at a time until a 12% reduction was achieved, after which the parts were tested. The results spoke for themselves, as the parts had a perfect level of cure and equivalent physical appearance, and all parts passed the impact testing. These results proved that there was room for further reductions in cycle time.
Operational flexibility is the
• More throughput per machine (unlocking capacity without capital spends)
• More stable parts with higher impact & less scrap from improved cure
• Operational flexibility and resin consolidation from a broader process window
• Less energy consumption and reduced carbon footprint from lower oven temperatures
• Lightweighting potential from improved impacts
ability to run different, new, and/ or unique tooling combinations on the same machine arm using the same process conditions while still producing quality parts. One notable example of Saeplast’s success is their ability to run the D660 insulated container with their D1000 container. There is a 76% difference in part weight, preventing Saeplast from previously running this tooling combination. By running unique tooling combinations, Saeplast has been able to unlock capital free capacity and reduce energy usage by optimizing production runs to fit their orders.
What makes this operational
flexibility possible? The answer is the material’s (like the TRx0338) ability to achieve an optimal level of cure at a wide range of oven times and temperatures, which we call the process window. When molding parts of varied sizes, shapes, or thicknesses, molders can find the process window for each part and then compare them to find where they overlap – see Figure 1 . By using a material that has a broad processing window, there is more opportunity for overlap, increasing operational flexibility.
The final processing benefit explored was lowering the oven temperatures to reduce
• Standard weight: 48kg / 106 lb.
• Volume: 643.5 L / 170 gallons
energy consumption. D660 containers were molded using NOVAPOL® TRx0338 resin and with a conventional 3 MI hexene roto resin while reducing oven temperatures. The average impact energy for each part was found from the cold temperature ARM impact testing. As we lowered the oven temperature (as much as 14%), the TRx0338 was able to maintain the average impact toughness without changing cook time, as illustrated in Figure 2 on the next page. Our testing showed that even after a 14% reduction there was still room to continue decreasing the oven temperatures even further. When we start looking at combinations of the TRx material and working in a collaborative fashion, Saeplast is finding new and unique ways to optimize operations and deliver value to customers. A direct link can be made between the processing benefits and the goal of making rigid durable parts even more sustainable.
Lightweighting means a lot to Saeplast as there are obvious benefits, but there is no “one size fits all”. The insulated containers are built to last, and the ability to withstand the impacts of a physically demanding industry is paramount. Therefore, we used cold temperature ARM impact testing as our failure criteria. Saeplast has years of field experience and experimental data that we used to determine our required impact energy for our lightweighting experiment. The team at Saeplast molded the D660 containers using the
NOVAPOL® TRx0338 resin and reduced the shot weight in stages until there was a 15% reduction. The inside and outside walls were shipped to the labs at NOVA Chemicals’ Centre for Performance Application (CPA) for testing. The results in Figure 3 show that Saeplast could light weight up to 10% while staying
above the threshold impact toughness.
Whenever undertaking a lightweighting initiative, it is important to understand the trade-off between wall thickness (shot weight) and side wall stiffness. The initial lab testing focused only on the polyethylene solid side walls and not on the
composite sandwich structure (side wall plus foam insulation). Therefore, further collaboration is needed to perform in-field and lab stiffness testing on the full part and composite sandwich structure. The following testing was conducted at NOVA Chemicals’ CPA to understand the effect reducing the shot
weight has on the individual inside and outside wall stiffness. Each side wall was bent on an Instron testing machine and the force required to deflect the side wall by one inch was measured. The teams at NOVA Chemicals and Saeplast believe that the reduction in stiffness will be significantly less when testing the whole composite sandwich structure and part. Initial calculations by the Rotovia team suggest when lightweighting the polyethylene side walls the stiffness reduction in the composite will be significantly
Trademarks: ITUB
less when compared to only testing the individual side walls. Therefore, further testing will be conducted to verify if this reduction of stiffness will be a challenge in practice.
When we start to think broadly and put the benefits together, the teams at Saeplast and NOVA Chemicals are looking at new and innovative ways to improve the efficiency and sustainability of Saeplast’s operations. We are looking beyond the obvious
benefits of reducing the environmental footprint in products that are already inherently sustainable and essential to the value chain of our global meat and seafood industries. We strive to explore new ways of building a sustainable and circular business model by utilizing strategic opportunities where we can employ NOVAPOL® TRx0338-U resins to further optimize the production of insulated containers. R
We commence this year with our Association in a very strong position. Membership is growing steadily due to the value provided through our conferences, webinars, Intro & Advanced Rotomolding seminars …. and our recently introduced Online Operator Training Program. ARM staff continue to provide great services to our membership, helping to coordinate these various activities seamlessly. Also, board members and committee members are working hard to bring value to our industry by sharing knowledge and helping to guide our future. This really is an exciting time to be part of the industry!
As we look forward, our hope is that it’s going to be one of our best years ever! We are all committed to continuing to provide the programs and services that ARM members have come to expect. 2024 is going to be a special year, with ARM partnering with the Italian Association (IT-RO) to provide a unique tour of six factories in Northern Italy from June 10 to June 12, followed by an Executive Forum in Bardolino, Italy with our Italian colleagues on June 13 and 14. This will be an incredible opportunity to learn from some of the best in our industry and to share knowledge and ideas in the conference to follow. Please consider attending this event and register now at bit.ly/rotoitaly.
In September, we look forward to hosting another Rotoplas in Chicago. This is our most important event on the calendar for 2024 as so many from our industry come together for our annual fall conference. We aspire to make this an exceptional
event for all who attend! Rotoplas is typically held every three years in the US and prioritizes supplierattendee interactions, extending the exhibition hall time for enhanced networking opportunities.
As of January, there are 60 companies planning to exhibit at Rotoplas and we are still more than seven months away. Rotoplas brings manufacturers, suppliers, designers, engineers, and researchers together from around the world to advance the rotational molding process and learn from one another. At Rotoplas 2017 (pre-COVID), there were attendees from as many as 42 different countries.
Another important objective for ARM this year is to increase participation and value through our ARM Training Academy. We introduced the Online Certificate Program in August with our Operator Training series. By March, we plan to offer certificates in our Health and Safety series, with more new programs targeted for 2024. We will also continue presenting the Intro to Rotomolding and Advanced Rotomolding seminars throughout the year, along with valuable webinars and troubleshooting discussions online.
That’s a quick look at what lies ahead in 2024. Join us at any of our events you can–there’s something to learn from each one. If I personally can be of any service, please don’t hesitate to reach out to me.
Thank you for your continued support of our Association! R
Alvin Spence 2024 ARM President Centro, Inc. aspence@centroinc.comRotoplas, the premier global exposition for rotational molding, showcases cutting-edge technology, products, and services tailored for the industry. It unites manufacturers, suppliers, designers,
engineers, and researchers worldwide to discuss on rotational molding advancements. Plan to join us September 24-26 in Rosemont, IL. Registration opens in Spring of 2024.
• 493K Limited
• Anchor Inserts
• Avantech
• Bergen International LLC
• Brunk, LLC
• Chevron Phillips Chemical Company
• Cole Industries
• Custom Plastics Inc
• Custom Resins
• Diversified Mold and Castings
• Dow
• Drader Manufacturing
• ENTEC Polymers
• ExxonMobil Chemical Canada
• FABFOUR
• Ferry Industries, Inc.
• FSI
• Ingenia Polymers
• Jerico Plastic
• Kemflo Canada Inc.
• Lone Star Chemical
• LyondellBasell
• Lyten
• Matrix Polymers
• McCann
• M. Holland
• Midwest Patterns
• Mosaic Color & Additives, LLC
• Muehlstein
• N.A. Roto Machines & Moulds India
• Nexeo Plastics, LLC
• Nix Screw Machine Products Inc.
• NOVA Chemicals
• Orenda Automation Technologies Inc
• Optimax Plastic LLC
• Persico SpA
• Piyush Rotomac
• POWDER KING, LLC
• Precision Products Enterprises LLC
• PSI Brand
• Quantum Polymers
• Rock Lake Robotics
• Rota Design Limited
• Rotoline
• RotoEdge Pro/SmaK Plastics Inc.
• Rotaloc International
• RotoPolymers
• RotoWorld®
• Shanghai Young Mould Co., Ltd
• Shaw Polymers
• Shell Polymers
• Shree Momai Rotocast Containers Pvt Ltd
• Solvay
• Step2 Custom
• STP Rotomachinery
• Stoner, Inc.
• Teknor Apex Company
• Trademark Plastics Corporation
• Vinmar Polymers America
• Wenling Rising Sun Rotomolding Technology Co., Ltd
• Wittmann-RotoLoad
This list is up to date as of late January 2024. Sign up to exhibit at www.rotoplas.org R
Join ARM for a unique opportunity to tour six factories in Northern Italy before meeting with Italian rotomolders at the Executive Forum in Bardolino, Italy in the Lake Garda region.
TOUR DATES (JUNE 10 - JUNE 12)
• Rototech
• Cornaglia
• Persico
• Ve.Ca.
• Moulding Service
• Verzellesi
CONFERENCE DATES (JUNE 13 & JUNE 14)
Network and learn with rotomolders and suppliers from North America and Italy at the beautiful Caesius Spa in Bardolino. The conference runs all day Thursday and through mid-day on Friday.
Member registration for the tour, conference, and five nights hotel (Sunday night - Thursday night) is $2,000. More information at bit.ly/rotoitaly R
Since the fall launch of ARM’s Training Academy, we’ve awarded 50 certificates for completing our Operator Training series. Join your accomplished colleagues who have completed this training.
The ARM Training Academy is a new online benefit that provides certification programs to ARM members, free of charge. The first course available is The Operator Training Program which consists
of more than 20 videos and short quizzes that once completed, present the user with a certificate to recognize their proficiency in rotomolding. We expect to have more courses available soon. Members have shared praise for the Training Academy saying that colleagues, from new hires to seasoned rotomolders, have found it very beneficial. R
Train your employees, reduce scrap, connect with customers, learn from experts and peers. This is what comes with membership and the return on your investment is tremendous.
Complimentary Registration for the 2024 Annual Meeting
Provided for one employee for each new member company. This is your free entry to the world’s preeminent rotomolding meeting, held once every three years.
We review sales leads typically from companies seeking molders – and email them to our member companies. We actively advertise for leads on behalf of our members.
Sample Operator Instructions
An 80+ page document calling out the highlights of nine company’s operator instructions. Also more than 700 documents and presentations from past Annual Meetings.
Immediate Free Access to more than 125+ on-demand webinars
Topics range from Determining Your True Cost to Proper Sampling Techniques. Ten new titles were added in 2023.
Immediate Free Access to ARM’s classic training video library
Includes programs on curing, venting, and good manufacturing practices. All videos include Spanish subtitles.
Free Access to Troubleshooting Calls
These moderated teleconferences are conducted every six weeks (eight per year) and allow you to troubleshoot your process and discuss HR issues with other molders, suppliers, and rotomolding experts.
Networking with Industry Peers
The greatest ARM benefit: Informal learning at a coffee break could revolutionize your process or reduce your expenses by tens of thousands of dollars. We hear it from members again and again.
Awards and Awareness
Showcase your company in our online member directory and through awards including Safety Award, Product Competition, and more.
Discounted Registration to all ARM Meetings
Includes regional meetings, the in-depth Hands-On Rotomolding Workshop at Penn College, and our Executive Forum which will be held in Italy.
Rotolink
Our twice weekly e-newsletter shares important industry news.
The premier event for rotomolders, their suppliers, designers, and educators. Programming includes professional and industry speakers, valuable networking, group workshops, and exhibition. R
As communication professionals, we need to become more aware of the ways in which we can use AI to increase our effectiveness – both for better quality and productivity. This will require practitioners to keep up with the dramatic increases in sophistication and variety of AI tools. It also underlines the need to adopt an ethical approach to all things AI.
“Fundamental human traits such as emphathy, trust, humor, and relationship building can’t be automated.”
— Jean Valin
Benefits communicators gain from using AI
Using AI can strengthen PR and communication professionals’ future prospects rather than being an occupational threat. This is recognized by industry professionals. Canadian Jean Valin, international PR awardwinner who contributed to a major 2018 report on PR & AI, “AI: Humans still needed”, concluded that fundamental human traits such as empathy, trust, humor, and relationship building, which are central to the PR role, can’t be automated.
Valin also predicted that the proportion of a professional’s total skills (out of 52 skills) that could be complemented or replaced by AI would rise from 12% in 2018 to 38% in 2023 –an increase of more than 300% from the 2018 figure! Worth checking the extent to which this has changed now by 2023.
An important role for public relations practitioners in the future also will be to counsel organizations on how to interpret the impact of AI use on organizational reputation.
Navigating this new environment will involve an expansion of the public relations practitioner’s current skill and knowledge. In some ways, there has never been a greater need for public relations practitioners who can provide the insight and guidance relating for AI use that will be needed to guide top organizational management.
PR and communication managers are likely to benefit from these changes. A comforting article about ChatGPT by Sensorium states
that several jobs in our sector are safe. Under the heading, “What jobs AI can’t replace?” It lists 5 of the top 10 such jobs:
• PR managers
• Event planners
• Marketing managers
• Writers and authors
However, our good standing depends on PR/comms pros making the most of the advantages that AI brings. The best approach is to jump in and start experimenting with AI in a current project to explore the potential of the technology and how easy it could be integrated into your workflow. The experts say you can benefit by considering AI as a form of automation that can help you develop more effective processes, freeing up resources to work in a more innovative way.
Three great sources for AI ethical standards information Maintaining good ethical standards when using AI is an essential requirement for PR people. Ethical use of AI will become important to organizational reputation and culture, so PR pros have the opportunity of becoming trusted AI counsellors within organizations – from top to bottom.
The Public Relations Society of America released a new set of ethics guidelines in November 2023 to help PR/ communication professionals make informed, responsible choices in the fast-moving world of artificial intelligence. The PRSA’s ethics report, “Promise & Pitfalls: The
Ethical Use of AI for Public Relations Practitioners,” builds on the issues covered in the organization’s Code of Ethics.
The PRSA sees opportunity for communication professionals to act as an “ethical conscience” and combat disinformation related to AI development and applications. The PRSA considers we can communicate and educate people throughout our organizations about the challenges raised by AI, and how to confront those challenges.
In addition, the #AIinPR panel of the UK’s Chartered Institute of Public Relations (CIPR) has established a web page, “Artificial intelligence in public relations,” which it claims contains “the most comprehensive review of AI tools in public relations” in 2023. Worth reading.
Finally, Muck Rack offers a practical AI for PR checklists you can print and display near your laptop for your reference. This checklist provides key reminders when you’re working with generative AI. Really helpful!
The PDF document contains key info in 5 sections
• Before you get started, don’t forget …
• Words to get you started
• Research prompts
• Social media prompts
• Writing enhancement prompts
Key principles to guide you
The key to ethical decision making is to identify which principles are involved. Once identified, a decision-making tree can guide professionals through a process that helps to arrive at an ethical decision. This includes principles of using AI. The ethical principles adopted by the Global Alliance (GA)
are a valuable reference. Here are the 16 principles that the GA believe are universal and fundamental to the practice of public relations and communication management:
Guiding principles
1. Working in the public interest
2. Obeying laws and respect diversity and local customs
3. Freedom of speech
4. Freedom of assembly
5. Freedom of media
6. Honesty, truth, and fact-based communication
7. Integrity
8. Transparency and disclosure
9. Privacy
KIM HARRISON
Kim Harrison, Founder and Principal of Cutting Edge PR, loves sharing actionable ideas and information about professional communication and business management. He has wide experience as a corporate affairs manager, consultant, author, lecturer, and CEO of a non-profit organization. Kim is a Fellow and former national board member of the Public Relations Institute of Australia, and he ran his State’s professional development program for 7 years, helping many practitioners to strengthen their communication skills.
1. Commitment to continuous learning and training
2. Avoiding conflict of interest
3. Advocating for the profession
4. Respect and fairness in dealing with publics
5. Expertise without guarantee of results beyond capacity
6. Behaviors that enhance the profession
7. Professional conduct
After identifying the issues and confirming the principles are in place, communication professionals are ready to go through the CIPR decision-making process on the next page. R
continued from page 51
Will it break any law or regulation in the relevant jurisdiction
DON’T DO IT.
Should you report it (internally or externally?
YES NO
Will it breach the CIPR Code of Conduct?
DON’T DO IT.
Should you report it (internally or externally?
YES NO
Could it damage your reputation?
Do you have the power to say no?
YES NO
OK. It’s your decision
YES NO
Can you talk openly to your colleagues or managers?
YES NO
Have managers accepted your proposed course of action?
YES NO
OK. JOB IS DONE.
DON’T KNOW
Seek legal opinion Ring the CIPR free legal helpline 0844 561 8133 ref 33380
DON’T KNOW
Re-examine the CIPR Code of Conduct
Ring the CIPR ethics hotline +44 (0)207 631 6969
Do you need more advice? Talk to HR, ring the CIPR ethics hotline or the CIPR free legal helpline or see advice and guidance at www.acas.org.uk
Pardon? That might be a fairly common question related to clarification of this title. “What did?” might be equally as popular. The answer is “Subscription Based Business Models”.
Now you may ask …” So What?” or “What does that even mean?”
Stick with me, and over the next several issues, I will examine one of the emerging business models that has become possible with Industry 4.0.
I will start with a brief history of “SUBSCRIPTIONS” with the intent to explore the failures and successes of this type of business model. I would like to explain how Industry 4.0 principles and connectivity can contribute and facilitate successful growth to all parties involved. Show how the dollars and cents work, and why in many cases there can be a very strong business case.
The fact is that our day-to-day businesses primarily thrive on individual transactions. We receive an order, we fulfill the order, and we invoice for the order with the intent of collecting on our invoices.
Sure, there are reputational forces and responsibilities for all of us (as suppliers) that we would like to think ensure that as “customers” that we are getting the best value and support for the price paid. Picture what it might look like if there was a significant mind shift, where all of us as suppliers began the process of looking at
our products, and our customers, more like a service, a service that was developed more on the basis of a very long term, even lifetime relationship, rather than a single transactional function.
I realize that many relationships within our industry already may be based (vaguely) on this type of relationship, however, most of our business models are Purchase Order based with ONE TIME quantifiable performance requirements. We all have pride in our products in such a way that we make every effort to perform to the customer’s expectation and deliver what the customer purchased, always in the hope of repeat business.
From my initial research, there really isn’t anything today that you cannot get by subscription. You can literally pay on a periodic basis for every possible need in our private and personal lives, and for
many things in our professional/ business lives.
In fact, most of us are already deeply rooted in “SUBSCRIPTION” based consumption of multiple things in our lives. It has become so common place, invading almost every moment of our lives that we don’t even really think much about it.
However, what I would like to explore much deeper is how this emerging business model can change the way we think about our suppliers, our customers, and how we pay for the things that we use and consume in our day-to-day business models.
I can’t honestly say all the direction that this may lead as I get started, but I am intrigued to see what I can find, what I can learn, and hopefully, what I can communicate successfully to all of you. Until next time R
Celanese has developed a new generation of impact modified Polyoxymethylene (POM) copolymers. These polymers have been designed to deliver the lowest fuel permeability in a single layer balanced with the impact modification needs of rotomolding. This balance of properties has been achieved through the optimization of polymer stabilization with a new generation of impact modification systems. The new grades of POM, known as Hostaform® POM RF, have been designed with processing ease in mind. The material releases easily from tooling without the need for release sprays or coatings. The material also utilizes standard rotomolding and pulverization equipment. Neither drying the materials nor use of inert gas is needed.
Challenge: Multilayer Rotomolded Tanks
Plastic fuel tanks have long established themselves as a preferred alternative to metals in most industries and markets. Plastics provide the advantages of corrosion resistance, flexible design, lightweight, and lower cost. Rotomolding of thermoplastic fuel tanks has proven to be an excellent alternative to blow molding and injection molding. Rotomolding provides flexibility in design using low cost tooling. A part’s wall thickness can be easily varied in
rotomolding, and molded-in inserts are easily incorporated into tank designs. Although cycle times are higher in rotomolding than blow molding or injection molding, many applications in fuel tanks have volume requirements that are low enough to make rotomolding the process of choice.
As the workhorse of the rotomolding industry, polyethylene is usually the first polymer family considered for rotomolding applications. Manufacturers of fuel tanks, in particular, have migrated to the use of crosslinked polyethylene (XLPE). With excellent impact resistance, it has become the default material chosen for most fuel tanks for many years. However, all types of polyethylene, no matter the density or degree of crosslinking, are not suitable as a single layer gasoline fuel container. The fuel vapor readily permeates through even very thick layers of polyethylene, leading to fuel loss. Manufacturers must augment polyethylene with other polymers to prevent gasoline fuel vapor permeation.
There are three multilayer material technologies that have been deployed to modify polyethylene to improve its effectiveness against fuel permeation. The first is to fluorinate the inside of the tank. After containers are molded, tanks need to be shipped to specialized
companies that expose the insides of the containers to fluorine atoms that bond to the polyethylene. The resulting fluorinated inner layer has a very low pore size that results in low permeation of the fuel. Obvious drawbacks include supply chain complexity and cost, excessive transportation, and lead time. Less obvious issues include a new opportunity for defects to occur. It is nearly impossible to determine the effectiveness of this inner coating around every part feature on a part-to-part basis. Also, the future of fluorination is at best uncertain and likely coming to an end, as the U.S. Environmental Protection Agency has ordered the use of fluorination coating processes on plastics containers to cease, saying that it produces three highly toxic PFAS chemicals that can contaminate drinking water.
The second multilayer material technology uses an inner layer of polyamide. Polyamide has lower permeability to the fuel vapors than XLPE, and when the two are used in concert, an acceptable level of fuel permeation is possible. When using this method, a minimum thickness of the polyamide will be necessary to conform to regulations. A typical way to perform this type of molding uses a hopper called a drop box which is attached to the mold[1]
The initial charge of XLPE is loaded into the mold prior to closing, and the charge of polyamide will be
loaded into the insulated hopper that sits above the mold. This is essentially a 2-cycle process. The first oven cycle fully lays down the first layer of XLPE, then the mold rotation must stop so that the drop box can be activated and the second charge of material, the polyamide, can be dropped into the mold. A second rotational molding cycle must then lay down this second layer of polyamide. There are several drawbacks to this method. One is the need to optimize not just one oven cycle for time, temperature, and rotation, but two. The two different polymers require two different thicknesses as well as differing oven profiles. Another concern is the reliability of the mechanism used to drop the second layer of material. The added mechanistic complexity to the mold reduces the reliability of the process as a whole and adds a layer of equipment maintenance that the molding shop must manage. Multiple materials, multiple process steps, and extra equipment create extra opportunities for more defects and more failures.
The 3rd multilayer material technology for thermoplastic rotomolded fuel tanks is a 3-layer process known as RotoLoPerm®[2] This is a licensable technology that uses XLPE as the outer layer and the inner layer, with a barrier layer in the middle. This 3-step oven process lays Ethylene Vinyl Alcohol (EVOH) in the middle of the XLPE layers, with a minimum wall thickness of 0.5mm[3], which is relatively thin. EVOH is a specialty polymer that is known for its barrier properties against chemistries such as those used for fuels. This technology has been on the market for more than 10 years and has found applications
where it has worked. Drawbacks here include an even more complex 3-step oven process. Also, it is difficult, if not impossible, to validate that each part produced has an even distribution of the thin EVOH layer sandwiched between the two thick layers of XLPE. Additionally, cost complexity increases as there are licensing costs to consider with this technology.
The three multilayer technologies have each found a place in the market without any one of them dominating. Molders have chosen to pick which compromises are easiest for them to manage. Of course, this has created the demand for a one material solution that can ease the burdens these other solutions presented. The Hostaform® Copolymer Acetals RF bring a single layer solution option to molders and OEMs.
Copolymer Acetal as a One
Copolymer Acetals are also known as Polyoxymethylene (POM). Hostaform® POM RF is a specific type of POM that has been created
for the rotomolding process. POM is a semi-crystalline polymer that has been well established in the plastics industry for many years. Like the EVOH mentioned earlier, it is known for its excellent barrier properties with regard to hydrocarbon fuels and liquids. Manufacturers of fuel systems of all kinds (auto, marine, lawn & garden) have relied on POM for decades for many of their components. In fact, the gas caps on fuel tanks are most often made of POM. POM is known for its good stiffness, low wear, and dimensional stability. There are homopolymer and copolymer versions of POM, but the copolymer version of acetal works best in rotomolding applications due to its improved heat resistance during processing and in end-use applications. Unmodified, POM has inherently less notched impact strength than other polymers. However, during the last decade or so, impact modification systems applied to POM have continued to improve. Additionally, process stabilization technology has improved with POM to allow it to survive the long and
hot cycle times of rotomolding. The goal has been to obtain a polymer that has improved impact strength but still retains the inherent low fuel permeability. An internal test conducted by Celanese to determine permeability to fuel (see Figure 1 on the page prior) showed very low values for Hostaform® POM compared with those for Polyamide 6 (PA6) and High Density Polyethylene (PE-HD). The tests were carried out on 1 mm thick sheets at 40°C using M15 fuel.
Acetals have long been known for excellent mold release properties for demolding ease. They have also been known for being stiff and dimensionally stable at a wide range of temperatures. Additives used to enhance the impact resistance and heat stability in the POM Hostaform® RF grades have proven to retain both the release properties, dimensional stability, and stiffness. Generally speaking, POM’s mechanical and thermal properties sit in between XLPE and PA6 homopolymers, as illustrated in Figure 2. PA6 has a higher melting temperature, making it difficult to process, but
it has good stiffness and high usage temperatures. XLPE has a lower melting temperature, making it easy to process, but low stiffness and usage temperature. Hostaform® POM RF’s melting temperature and stiffness position it between these other two primary options. Rotomolding part designs typically must balance the tradeoffs of XLPE and PA6. Hostaform® POM RF gives part designers a balanced option when designing products for rotomolding.
Another significant advantage of a single layer Hostaform® POM RF solution is its environmental friendliness. POM is unique in the polymer world in that it is the only single carbon based polymer. This gives it the advantage of having a low carbon footprint potential. Additionally, a 1-layer system is much easier to recycle. Multilayer systems such as those mentioned earlier take away their ability to be recycled.
The new grades of POM, known as Hostaform® POM RF, have been designed with processing ease
in mind. Hostaform® POM RF has a melting temperature of 330ºF and an ideal melt temperature for flow of 375ºF. At this temperature, Hostaform® POM RF will be near a melt flow index of 3-5 g/10min when measured on standard instrumentation and conditions. Typical gas-fired ovens will often be set to around 480ºF to achieve a good cycle time at thicknesses such as 0.200”. When running POM for the first time in a gas-fired oven, it is important to monitor the Internal Air Temperature (IAT) with a wireless thermocouple. Figure 3 shows a typical IAT curve an operator would want to achieve when setting up the oven parameters during molding.
In addition to the internal temperature, it is also important to check the outer temperature of the tool, given a certain oven temperature. You will want to be sure the outer wall of the POM does not exceed 450ºF; the polymer will release excessive volatiles, and excessive pinholes may be formed on the outer wall if the tool gets too hot. Like all materials, you will also want to have generous levels of venting as the part design allows you, to control pinholes at the surface.
To maximize the quality of the outer surface and venting, you should consider as heavy of a surface tool texture as the part design allows.
POM is a highly crystalline material which makes its melting point quite sharp. This also means that it recrystallizes quite quickly. More specifically, POM Hostaform® POM RF grades recrystallize at about 290ºF. Good flow and seal around inserts and into corners have been demonstrated on various geometries.
To ensure good flow, Hostaform® POM RF will mold best when you pull the material from the oven at the target IAT shown in Figure 3 (about 375ºF) and rotate in the air outside the oven for about 5 to 10 minutes. After such time, you can apply whatever cooling technique optimizes your oven utilization (forced air or water). Shrink rates of polymers in rotomolding tend to all be similar, given the lack of directionality of flow in the mold. This means that Hostaform® POM RF grades in many cases will be able to utilize existing tooling. It should be mentioned, however, that you would want to avoid crosscontamination with other materials, so molds should be thoroughly cleaned and blasted to the bare metal condition to avoid any crosscontamination potential. POM, in general, will have a higher degree of crystallinity than polymers such as XLPE and PA6, so some tooling designs may need minor adjustments to accommodate these fine differences. However, a trial would be recommended on current tooling before jumping to conclusions on retooling.
Powder preparation of Hostaform® POM RF is with standard equipment. POM uses attrition mills at high throughputs and high yields without needing cryogenics. Screening to 35 mesh has worked best. Figure 4 shows a typical particle size distribution of a milled and screened Hostaform® POM RF grade.
A final mention in processing with Hostaform® POM RF regards a new technology being introduced by Gemstar, a manufacturer headquartered in Cannon Falls, MN. Gemstar is the first in the United States to offer an ovenless rotomolding technology called
Robomold® (Robomold® is a registered trademark of Gemstar. Celanese and these materials are not affiliated with or sponsored by Gemstar). It delivers high precision temperature control within the mold itself, without the use of ovens. The sharply defined melting and recrystallization temperature of POM makes for an ideal material for this type of molding. The material and process give the ability to create unique geometries such as high definition threads, unique design features
in parts and varied thickness walls. It has resulted in reduced process time and lower scrap rates in applications where the two technologies, Robomold® and Hostaform® POM RF, are utilized together[4]. These two technologies were recently recognized in September of 2023 when Gemstar won the 2023 ARM Product of the Year award at the annual meeting of the Association of Rotomolders. More information on the award winning application can be found at TECH NOTE:
Robomold® + Hostaform® POM RF - Gemstar Protective Hard Cases (gemstarmfg.com).
Hostaform® POM RF was designed to deliver low fuel permeation and the toughness necessary to pass industry standards. Two grades of Hostaform® POM RF, RF2162 and RF2464, have been verified by outside laboratories to pass low fuel permeation standards for both the US Environmental Protection Agency (EPA) and California Air Resources Board (CARB) regulations. Typical permeation rates of these two grades using CE10 or CARB-defined fuels at 28ºC are between 0.5 and 0.6 g/m2/day.
An example of industry based impact testing that POM Hostaform® POM RF has passed includes ANSI/OPEI N71.10-2018. In this requirement, a 2 inch diameter ball is dropped from a 51 inch height after the molded article has been soaked at -4ºF. This multi-hit test has an energy requirement of approximately 2.6ft-lb using a 2 inch diameter tup traveling at a velocity of 8.9 ft/sec. Although this particular test is considered to be more modest than other impact tests that rotomolded articles may experience, it illustrates how all 3 options are able to pass such a requirement (POM, XLPE, PA6). This leaves designers with a choice to take advantage of a single layer solution such as POM. XLPE and PA6 do indeed have higher levels of impact than Hostaform® POM RF, but these higher levels of impact come at the sacrifice of reduced fuel permeation or difficulty in processing. For demanding high impact applications, XLPE and PA6 will continue to be selected for applications that suit their
property profile. However, this new generation of POM Hostaform® POM RF polymers has helped close the gap as they have 2-4 times higher impact abilities than previous grades of commercially available POM polymers.
Beyond fuel permeation and impact testing, Hostaform® POM RF products have been shown to pass HY24 testing by the American Boat and Yacht Club (ABYC) for flammability, shock and slosh testing. Additionally, Hostaform® POM RF grades typically come with UV stabilization for outdoor use requirements. Hostaform® POM RF grades have good temperature resistance for applications such as hydraulic tanks that require fluid handling >100ºC. Lastly, POM is well known for its opacity, which makes it a good base resin to have colored. It should be noted that it is best to get the resin pre-colored versus trying to dry-blend it with other powder color concentrates.
POM, or acetal, has been commercially successful for decades. Its well balanced property profile has long been known to plastics producers. It wasn’t until recently, however, that Celanese was able to create Hostaform® POM RF grades of acetal that bring the right balance of impact modification and processing ease to carve out a solid place in the rotomolding industry.
These grades of resin have been primarily positioned to offer a single layer solution to the fuel tank rotomolding industry. With its ability to pass EPA and CARB standards without the need for secondary processing steps, Hostaform® POM RF offers a unique solution to rotomolders trying to lower
production costs and gain market share in the fuel tank market. With an impact resistance 2-4 times higher than historical acetals utilized in rotomolding, these new solutions close design gaps and offer part designers a more balanced property profile than had previously existed. Hostaform® POM RF shows potential to be in a sustainable position for many years to come, given its compatibility with new equipment technologies such as Robomold® and its low carbon footprint potential.
Hostaform® POM RF is one of many polymer solution developments being carried out by Celanese for the rotomolding industry. Information on these developments for rotomolding and other growth segments of the polymers industries can be found at www.celanese.com.
1) US7273364B2 - Drop box with thermal isolation: https:// patents.google.com/patent/ US7273364B2/en
2) Rotomolded fuel tank meets upcoming emissions standards: https://www.plasticstoday.com/ sustainability/rotomolded-fueltank-meets-upcoming-emissionsstandards
3) Centro’s Executive Order: https:// www.centroinc.com/Handler. ashx?Item_ID=8C2EB393-858E4F46-91C9-4BFA9D5CB78E
4) Robomold® + Hostaform® POM –Gemstar Protective Hard Cases: https://www.gemstarmfg.com/ education/technote_ hostaform/
• Robomold® is owned by Gemstar
• RotoLoPerm® is owned by Centro R
Jerico’s complete line of aesthetic compounded materials brings a bright and dazzling look to your rotational molded products. Our Stone Effect specialty color compounds are designed for many outdoor applications like hot tubs, lawn/garden accessories, flower pots, and patio furniture, and they’re now FDA compliant for use in coolers.
Stone Effect can be produced in any color and with varying color intensities by using our line of Stone Effect color concentrates. We work with you to acheive your optimum color and design goals every time!
As we grow, we look for ways to exceed your expectations and help you achieve even greater success! Our mission is to be the go-to resource for resins and compounds that meet your specifications, arrive on time, and provide the consistent level of quality you’ve come to expect from Jerico! You’ll always receive the kind of personal service that we like to call the Jerico Effect!
Our commitment and flexibility show in everything we do!
info@jericoplastic.com
Everyone involved in plastic processing will know there has been an increasing awareness of the need to protect our world for future generations. In 2022 ARMA set a goal for the rotational moulding industry in Australia and New Zealand to be using 3,600Mt of recycled material by 2025. The ARMO 2023
conference program focused on sustainability while the StAR 2024 conference was focused on sustainability and the industry navigating the future.
Vanuatu is a South Pacific Ocean nation comprised of more than 80 islands, stretching north to south across 1,300km (800miles). The islands have a
population estimated around 300,000, approximately 75% of which live in rural villages. It only became an independent nation in 1980. The name Vanuatu means “Our Land Forever” in many of the locally used Melanesian languages.
In countries such as Vanuatu, collecting plastic waste for
recycling and export is hampered by the long distances between islands, the high cost of transporting waste, and the low economic value of plastics. One of the approaches to managing plastic waste is to REDUCE the volume of plastic entering the waste stream by preventing plastic from becoming waste. Recycling is an important step towards this goal.
Pacific Poly Tanks (PPT) was established in 2001, located in Port Vila, the capital and largest city in Vanuatu. It is a family owned and operated business rotomoulding polyethylene water tanks up to 10,000L, bins, buckets, troughs, and many other products.
PPT understood the need to manufacture good quality, long lasting products which could cope with the harsh operating conditions in the Pacific. To reinforce their reputation & claims of quality to both customers and government authorities, PPT set out to become the first Vanuatu rotomoulder to be certified to the globally recognised Tank Standard AS/ NZS4766, which they achieved in 2016.
In 2018, the Vanuatu government introduced phase 1 of the country’s National Sustainable Development Plan (NSDP). Vanuatu made history by becoming the first nation in the world to ban some single use plastics which were known to make their way into Vanuatu’s pristine ocean. Some of this plastic waste travels the ocean currents from far away, but some of it arises from Vanuatu’s our own consumption patterns, improper waste management, and
dumping and littering behaviours.
While the NSDP did not affect rotomoulded products PPT made the decision to invest in a plastic granulator and other equipment, with the objective to commence
a recycling program to grind rotomoulded scrap parts into chips (flakes). It took some years to accumulate enough granulated chips to fill a shipping container. The first container of granulated
plastic was shipped to New Zealand in December 2020 to be recycled back into rotomoulded products within New Zealand.
Matrix Polymers partnered with PPT to pay for the shipping and local New Zealand freight costs to deliver the 6,730kg (14,800lbs) of chips to a New Zealand rotomoulder who uses the chips, combined with powder, to rotomould products like culvert pipes. Culvert pipes are used in agricultural applications within New Zealand.
While PPT would like to rotomould their recycled plastic within Vanuatu, it is simply too expensive to do this. The economic barriers of recycling plastics within Vanuatu just do not add up, except without external funding. The same economic barriers prevent the recycled plastic being reprocessed in New Zealand (or Australia) and return recycled powder to Vanuatu.
In the past the scrap plastic from the rotomoulding process was dumped in landfill. As a NiVanuatu company (a company owned by people of Vanuatu) PPT decided they needed to take responsibility for their own waste after the announcement of the National Sustainable Development Plan.
PPT has an obligation to their island paradise, to keep it as clean and free of waste, while at the same time providing their customers with quality & cost effective water storage products.
The achievement of this small rotomoulding business is impressive when you compare this to the plastic packaging industry who only exported their first container of plastic bottles from Vanuatu in 2021, which
were to be recycled into plastic bottles in Australia.
PPT are committed to recycling their rotomoulded scrap, although it has suffered some set-backs which are particular to the Pacific. Their recycling shed was damaged in a tropical storm in early 2023 and the granulation activity was temporarily put on hold as they waited for contractors to repair it. Vanuatu, like many other countries around the world, is experiencing a
widespread labour shortage. PPT will ship their next container of chips in 2024 to Vision Plastics, also in New Zealand.
While PPT are reducing the volume of waste plastic entering the waste stream, there is a new Oceania sustainability initiative due to commence in 2024 to improve the sustainability of plastics. The Plastic and Rubber Technical Education Centre (PARTEC) located in Brisbane, Queensland will
begin undertaking research & development into the recycling of single-use plastic waste using the rotomoulding process. To make this happen PARTEC are commissioning a 1m (39”) diameter fully electric Rising Sun shuttle oven in 1st quarter 2024.
The rotomoulding machine will also boost PARTEC’s ability to train highly skilled Rotomoulding apprentices, helping to ease the skills gap in Oceania plastics manufacturing.
Rotationally moulded polyethylene products are a longlasting resource and recyclable. Pacific Poly Tanks demonstrate that geographic isolation and transport distance can be overcome with commitment to ensure plastic waste does not go to landfill and that it achieves a new life.
Rotational moulding continues to be a process, that offers the possibility to make almost anything you can imagine, sustainably, wherever in the world you are. R
ARMA’s 2024 Board of Directors and CEO met in December last year for a full day of planning. They made some significant decisions and mapped out the Association’s year ahead allowing us to hit the ground running this year. Along with the usual work ARMA does for the industry, members and supporters, projects on the horizon for 2024 include:
• Overhaul & redesign of www.rotationalmoulding.com which will consolidate all things ARMA .
• Development of Online Training Program on rotational moulding basics.
• Rotomould24 Trade Exhibition & Conference: Gold Coast, 1719 June.
• Best Product Design Award @ Rotomould24
• Rototour Brazil, 13-26 September including Rotoplas, Chicago
• Master Class Technical Road Show
• ARMA Student Design Award 2024
In October last year, members had the opportunity to elect their 2024 Board of Directors. With four Moulder Member and two Supplier Member positions available, many nominations were received.
PRESIDENT: Chris Glenn
Bushmans Group (Australia)
PAST PRESIDENT: Trudi Duncan Gyro Plastics (New Zealand)
VICE PRESIDENT: Ian Gough Gough Plastics (Australia)
TREASURER: Mark Medew
Plastic Fabrications (Australia)
BOARD MEMBER: Paul Ayers
Galloway Group (New Zealand)
BOARD MEMBER: Varun Chand
Rotomould Group of Companies (Fiji)
BOARD MEMBER: Ben Hopley
Viscount Rotational Moulding (Australia)
BOARD MEMBER: Brad Smyth
Barron & Rawson (Australia)
SUPPLIER BOARD MEMBER: Kate McKie Qenos (Australia)
SUPPLIER BOARD MEMBER: Andrew Currie Price Plastics (Australia)
We are pleased to welcome Paul Ayers from Galloway Group, New Zealand as a new addition to the current board.
Paul’s professional expertise spans several critical areas of business, including sales and marketing, production and capacity management, innovation, compliance, risk management, governance, and strategy. Additionally, he excels in board process management, contributing to the development and
implementation of effective strategies for organisational growth and success. Paul’s introduction to the rotational moulding industry, through his acquisition of Galloway International New Zealand, has further advanced his twenty years of experience in the manufacturing sector. He is confident that his robust skill set, combined with his industry knowledge, positions him as an asset to the ARMA Board. R
Interested in being a Presenter, Panelist, or Program Influencer? We invite you to be a part of this dynamic event by contributing your insights, experiences, and innovative ideas. We’re eager to hear your unique stories, be involved in a panel session or one of our interview-style presentations. If you’ve always wanted to tell your story but are a little wary of public speaking, please reach out as we have some new ways of managing that so attendees can hear your story.
Rotational moulders worldwide, this is your chance to showcase a case study and, if accepted, enjoy a complimentary conference registration! R
Recycleye
Wins Fanuc Award for innovation and extends exclusive
FANUC UK has underlined its commitment to AI-powered robotic waste picking company Recycleye by extending its exclusive UK deal with the tech innovator, as well as internationally recognising its achievements at the FANUC Global Partner Awards.
The event, which took place in Japan in November 2023, saw Recycleye win one of seven Global Partner Awards for Innovation. In further evidence of FANUC’s faith in Recycleye’s technology, the two companies have recently extended their exclusivity agreement, meaning that Recycleye remains the only UK company that FANUC UK supply to for recycling applications. Recycleye will also continue to benefit from a commercial and technical partnership with FANUC throughout its current phase of growth and development.
Founded in London in 2019 with just four members of staff, Recycleye now employs over 50 people and is the European leader in AI/robotic waste picking technology. It has an installed base of more than 25 systems across the UK, Ireland, France, Italy, Spain, and Germany, where its technology is helping to revolutionise the waste sector by automating the detection and sorting of mixed recyclables. FANUC has been instrumental to the company’s rapid success since day one, working closely as a strategic partner to de-risk Recycleye’s offering to the market.
business to a recognised leader in AI waste sortation in just four years. The judging panel also praised the ability of the Recycleye system to be rapidly retrofitted into existing waste facilities.
The Global Partner Award for Innovation was presented to Peter Hedley, Chief Technical Officer, and co-founder of Recycleye, by FANUC’s Dr. Kiyonori Inaba, Executive Vice President & General Manager, Robot Business Division. “We are extremely proud of this recognition, especially as the award was open to FANUC partners from right across the globe,” comments Peter. “FANUC has been by our side since the start of our journey and we look forward to growing further together, offering materials recycling facilities an automated alternative to traditional sorting methods and helping to futureproof their business.”
“FOUNDED IN LONDON IN 2019 WITH JUST FOUR MEMBERS OF STAFF, RECYCLEYE NOW EMPLOYS OVER 50 PEOPLE AND IS THE EUROPEAN LEADER IN AI/ROBOTIC WASTE PICKING TECHNOLOGY.”
Combining its proprietary AI vision technology with FANUC 6-axis LR Mate robots, the Recycleye Robotics system increases sorting accuracy by up to 12% and improves line output by up to 10%, helping waste operators to boost their bottom line and providing a solution to ongoing labour shortages in the waste management industry. At the FANUC Global Partner Awards ceremony, the company was praised for its commitment to innovation, moving from a start-up
Oliver Selby is FANUC UK’s Head of Sales and has seen firsthand the impact that Recycleye is making on the waste industry.
“By combining FANUC’s LR Mate robots and iRPickTool visual line tracking technology with their proprietary AI-driven vision system, the Recycleye Robotics system improves sorting accuracy and increases purity, also helping to alleviate labour shortages in the waste sector,” states Oliver. “Our commitment to this partnership is as strong as it’s ever been, which is why FANUC is delighted to re-sign an exclusivity deal with Recycleye.”
For more information, contact: British Plastics Federation, BPF House, 6 Bath Place, Rivington Street, EC2A 3JE, Tel: +44 (0)20 74575000, Email: reception@ bpf.co.uk, Web: www.bpf.co.uk R
At the last British Plastics Federation’s (BPF) Sustainability Committee Meeting of 2023, it was announced that the committee’s widely respected chairman, Jason Leadbitter (Inovyn ChlorVinyls), will be retiring at the end of the year. Jason has been instrumental in guiding the BPF’s Sustainability Committee over the past eight years, always sharing his passion, knowledge, and commitment to bettering the plastics industry along the path of sustainability.
Moving forward, the committee has selected Jamie Riley as its new chairman. Jamie is currently the divisional sustainability manager of Berry Superfos (part of Berry Global). His role involves driving the sustainability agenda across the Superfos division in line with the Berry Global ESG objectives. Jamie believes education and effective, persuasive communication is key to engaging people on sustainability issues and to emphasise why sustainable development is increasingly vital for any business to thrive.
The BPF’s Sustainability Committee is made up of specialists from across the trade association’s membership. It aims to work proactively with industry, stakeholders, and legislators to contribute to the circular economy and global sustainability agenda.
Topics such as Net Zero, eco-design, the UN Global Treaty for Plastic Pollution, recycling, re-use, and Operation Clean Sweep are part of typical meeting agendas. In addition, the annual BPF Sustainability Seminar is a highlight for the committee, as it welcomes BPF members and non-members for an in-depth overview of current sustainability issues and initiatives.
Outgoing Sustainability Chairman Jason Leadbitter states: “I am sure that I leave the BPF’s Sustainability Committee in good hands with Jamie. Over the years, we have seen real progress, as this industry proves it is not only vital to a modern economy but also can be a shining beacon of how to adapt business practices so that sustainability is at the core of all key business decisions. I am very proud of what the committee has achieved so far and am confident it can still achieve much more.” R
ASSOCIATION OF ROTATIONAL MOULDERS AUSTRALASIA LTD
Michelle Rose, CAE Chief Executive Officer
PO Box 237 Moonee Ponds VIC 3039 Australia
Phone: + 61 (0)404 265 887 michellerose@ rotationalmoulding.com www.rotationalmoulding.com
ASSOCIATION OF ROTATIONAL MOULDERS SOUTHERN AFRICA PO Box 6966
Birchleigh 1621
Gauteng, South Africa
Phone: +27 82 772 3769
Fax: +27 12 541 1738
Chairman: Gary Wiid info@armsa.co.za www.armsa.co.za
IT-RO ITALIA ROTAZIONALE
Katia Zoppetti Via E. Brigatti 12 20152 Milano (MI) Italy
Phone: +039 348 7652560 www.it-ro.it
SOCIETY OF ASIAN ROTOMOULDERS (STAR)
40/145, Ground Floor, Chittaranjan Park New Delhi 110019
Phone: + 91-11-41630157
Fax: +91-11-41634952 Cell: + 91- 9810305356 sb.zaman@staraisa.org arnacz@satyam.net.in www.starasia.org
ASSOCIATION OF ROTATIONAL MOULDING
(Central Europe) e.V. (ARM-CE)
MAUS GmbHRotationsgießformen
Am Viehweg 9 - D-76229
Karlsruhe
Amtsgericht Mannheim, HRB 103433
Phone: +49 (0) 7 21 / 9 48 74 12
Fax: +49 (0) 7 21 / 9 48 74 44
Mr. Oliver Wandres, ARM-CE Chairman info@rotational-moulding.de www.rotational-moulding.de
British Plastics Federation
Rotational Moulding Group
6 Bath Place
Rivington Street
London EC2A 3JE
United Kingdom
Phone: 020 7457 5000
Fax: 020 7457 5045
Chairman: Mr. Philip Maddox PhilipM@LeafieldEnv.com
THE NORDIC ASSOCIATION OF ROTATIONAL MOULDERS
Executive Board Chairman: Mr. Ronny Ervik
ul. Zielona 8, 61-851 Poznań, Poland
Phone: +48 607-126-004
Fax: +48 61-858-8611
info@rotomoulding-europe.org www.nordicarm.org
Rotomould 2024 Conference & Trade Exhibition Gold Coast, Australia rotomouldconference.com.au
16 Diversified Mold & Castings 19800 Miles Road Warrensville Hts., OH 44128-4118 USA
216.663.1814 | 888.642.1222 info@diversifiedmolds.com www.diversifiedmolds.com
72 ExxonMobil Chemical Co. PO Box 96126 West Springs Calgary, Alberta Canada, T3H 0L3 800.668.0177
kevin.c.jamieson@exxonmobil.com https://www.exxonmobilchemical. com
/en/products-and-services/ polyethylene
5 Ferry Industries, Inc. 4445 Allen Road Stow, OH 44224-1093 USA 330.920.9200
sales@ferryindustries.com www.ferryindustries.com
9, 59 Jerico Plastic Industries, Inc.
7970 Boneta Road Wadsworth, OH 44281 USA 330.334.5244
Minerva Plant: 330.868.4600 steve@jericoplastic.com www.jericoplastic.com
63 JSJ Productions, Inc. 625 West Market Street Salinas, CA 93901 USA 512.894.4106
susan@jsjproductionsinc.com www.jsjproductionsinc.com
11 Matrix Polymers
The Priory Orchard Hill Little Billing Northhampton, NN9 9AG United Kingdom
+44.1604.789100
sales@matrixpolymers.com www.matrixpolymers.com
7 Orenda
165 Steelcase Rd. East Markham, Ontario L3R 1G1, Canada
905.513.8043
sales@orenda-automation.com www.orenda-automation.com
17 OREX Rotomoulding Sp. z o.o. Cieszyńska 6, 43-520 Chybie Poland
+48 32 440 83 15 magda.wantola@orex.pl www.orex-rotomoulding.com
43 Poliplast S.p.A.
Via Carrali, 8 24020 Casnigo (BG) Italy +39.035.724145 info@poliplastspa.com www.poliplastspa.com
3 Powder King, LLC
41780 N. Vision Way Unit 120 Bldg. 2 Anthem, AZ 85086 USA 623.551.9897
sales@powder-king.com www.powder-king.com
37 Rock Lake Robotics
100 S. CP. Avenue Lake Mills, WI 53551 USA 920.648.3402
sales@rocklakerobotics.com www.rocklakerobotics.com
19 Rotaloc
100 S. CP. Avenue Lake Mills, WI 53551 USA 303.948.5434
sales@rotaloc.com www.rotaloc.com
2 Roto Polymers 26210 Emery Road, Suite 202 Cleveland, OH 44128 USA 1.844.POLIMER (1.844.765.4637) info@rotopolymers.com www.rotopolymers.com
71 Rotomachinery Group
Via Crosa, 53 28065 Cerano (NO) Italy +39.0321.772021 polivinil@polivinil.com www.rotomachinerygroup.com
14 VMP, Inc.
24830 Avenue Tibbitts Valencia, CA 91355-3404 USA 888.4.VMP.INC 661.294.9934 info@vmpinc.com www.vmpinc.com
21 Wittmann Battenfeld Canada Inc. / ROTOLOADTM
35 Leek Crescent Richmond Hill, ON L4B 4C2, Canada 905.887.5355
Toll Free: 1.888.466.8266 info@wittmann-group.ca www.wittmann-group.ca
23 Xcelerant Growth Partners
624 W. Washington Avenue, #411 Madison, WI 53703 440.384.7654
info@xcelerantgrowthpartners.com xcelerantgrowthpartners.com