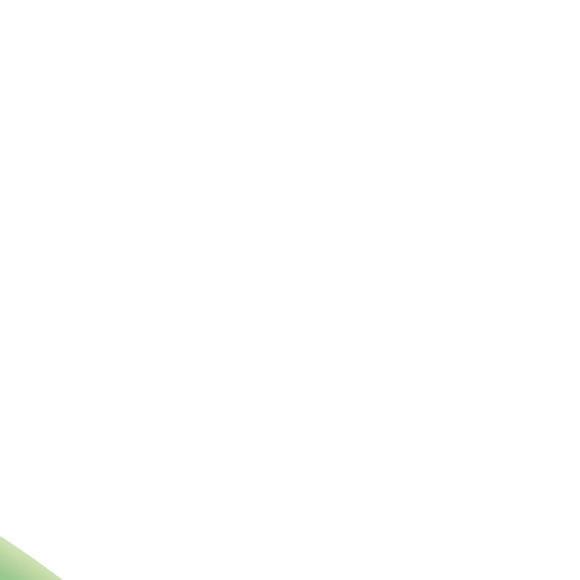
Dr. Nick Henwood, Rotomotive Limited



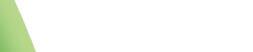
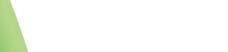
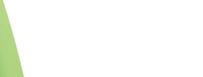
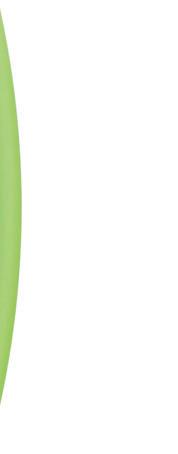

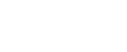
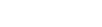




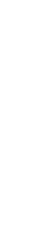
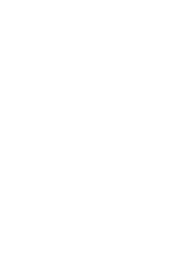


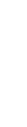
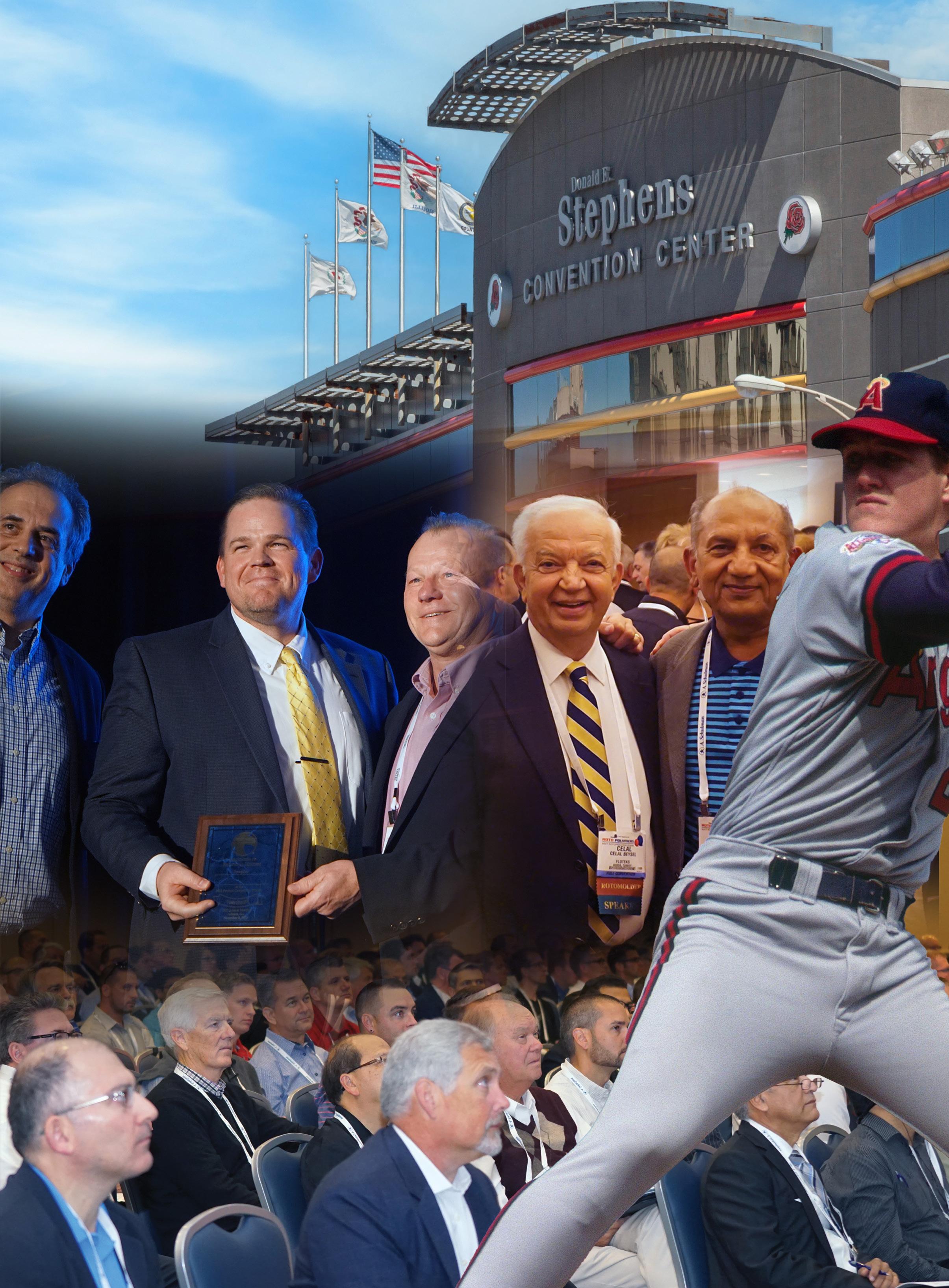
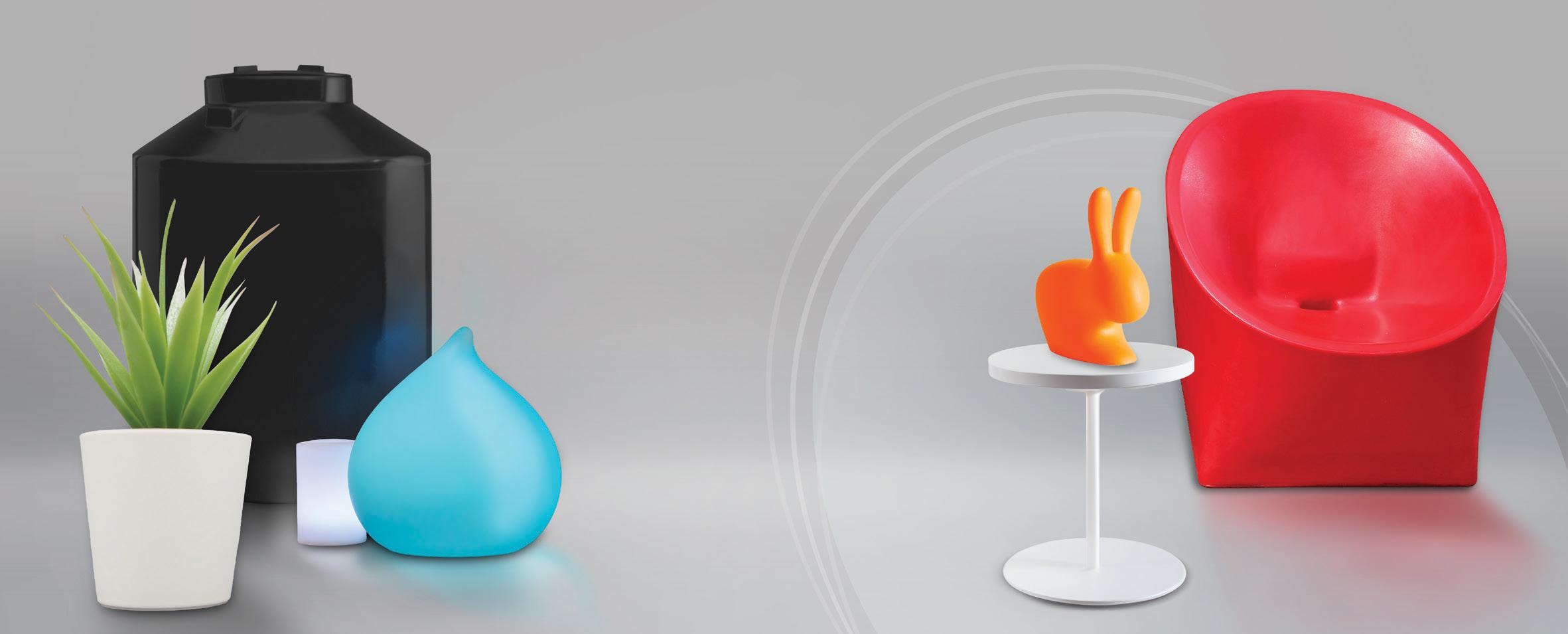
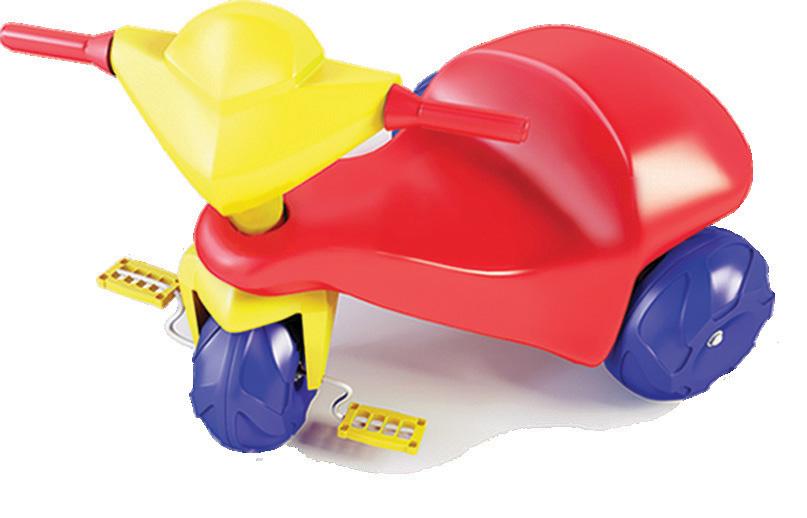
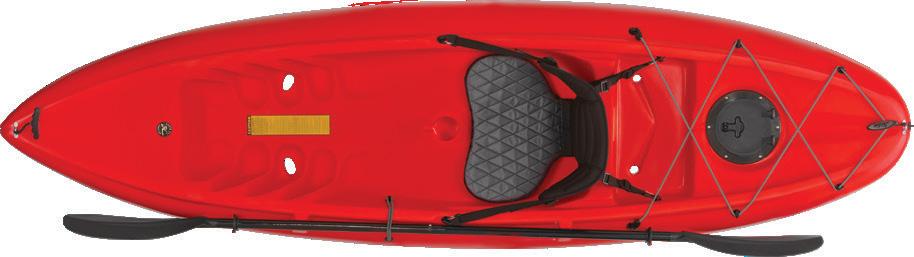
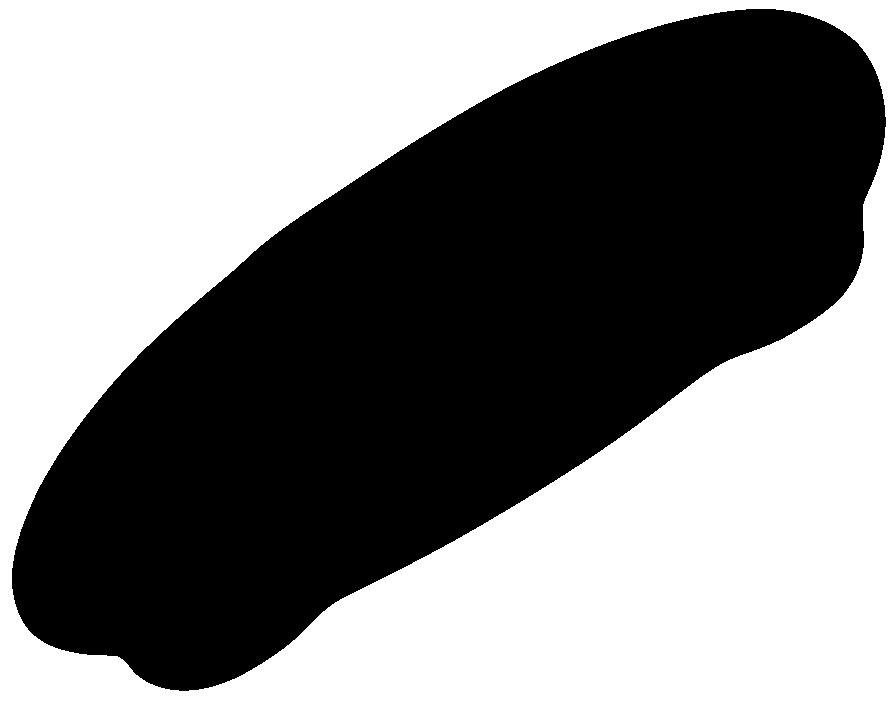
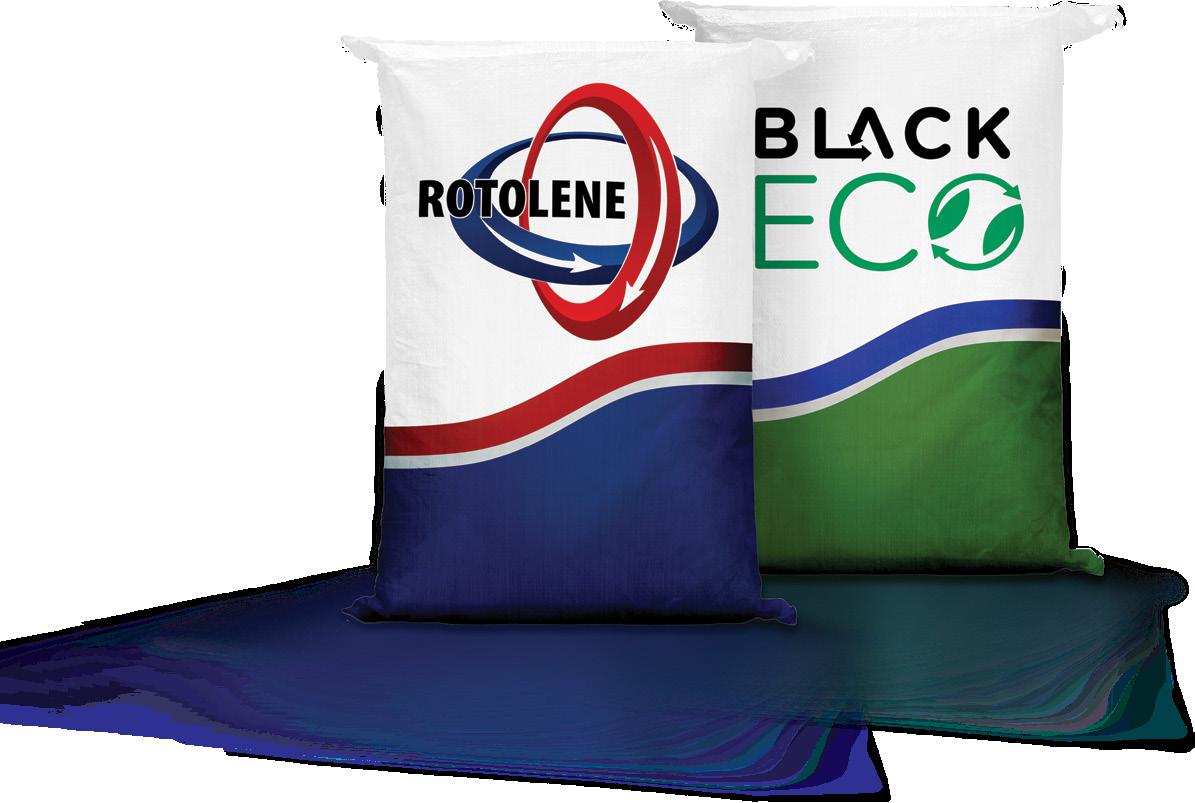
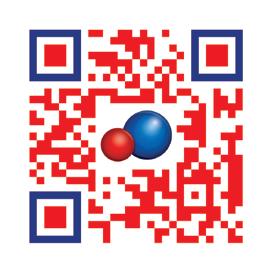
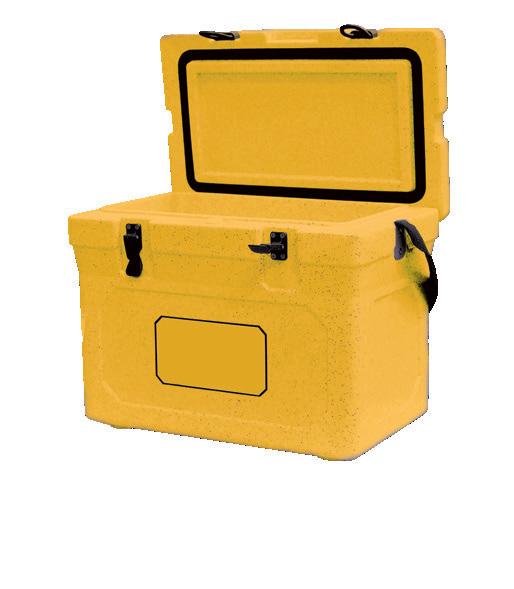
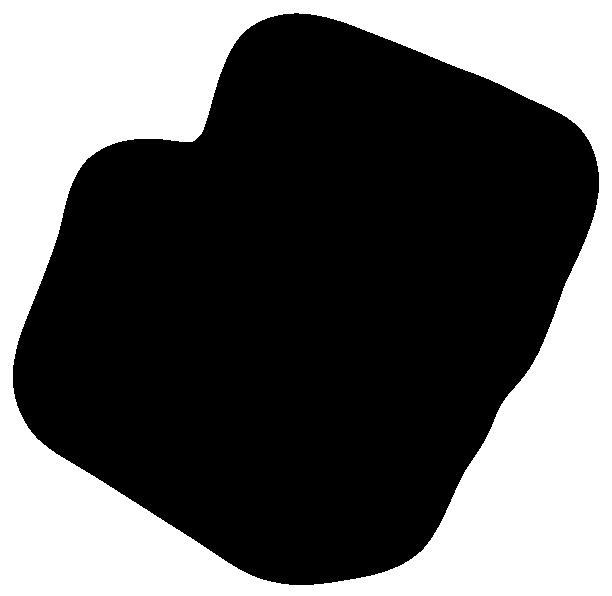
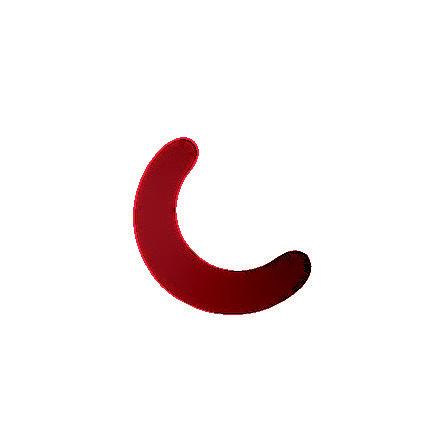
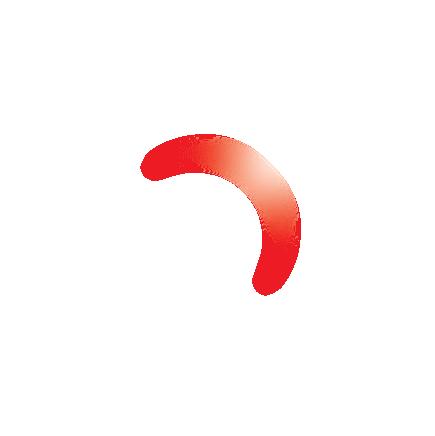
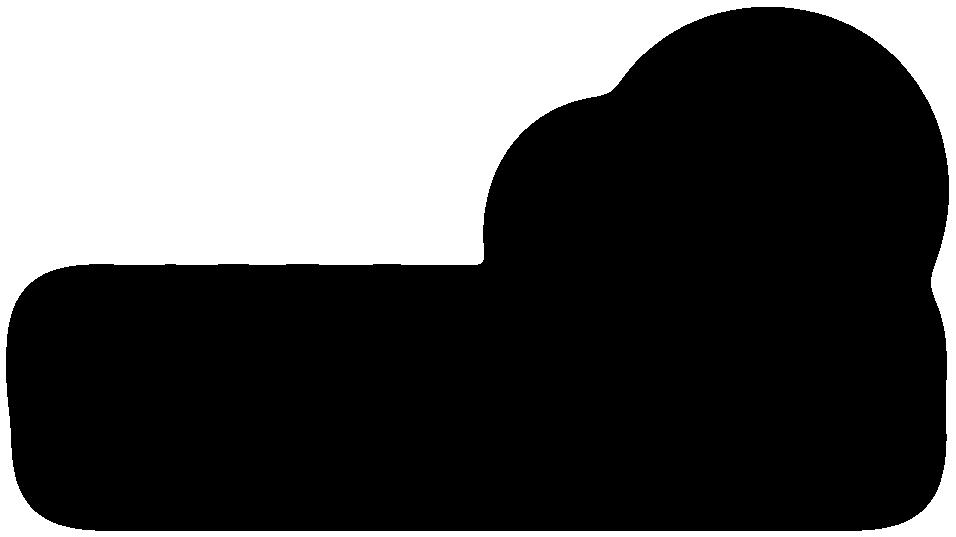
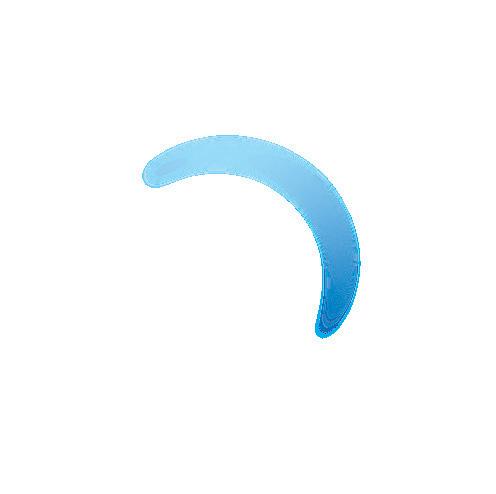
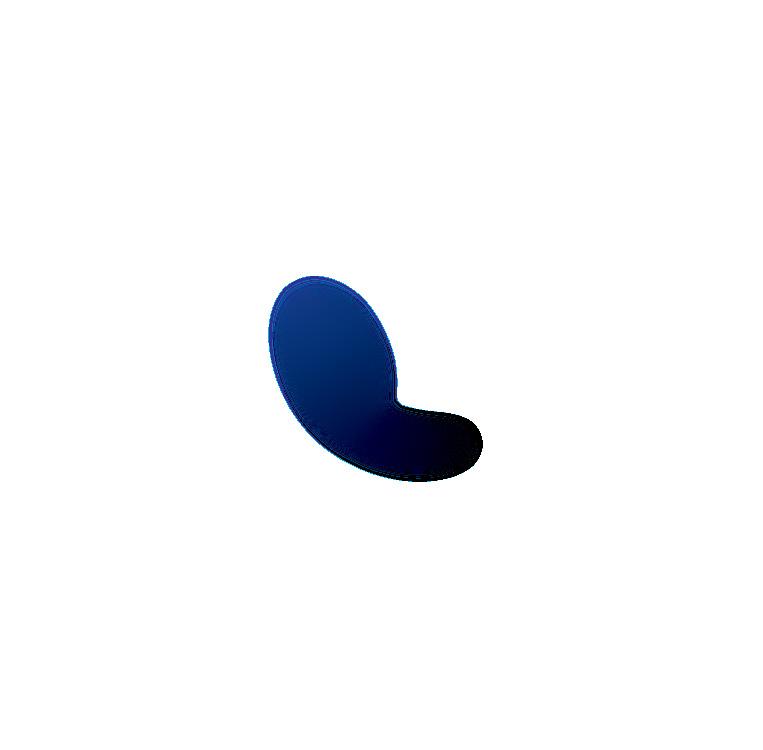
Dr. Nick Henwood, Rotomotive Limited
Powder King® is proud to say that we have been building pulverizers for over 20 years and is the most well known pulverizer manufacturing company worldwide. At Powder King®, we focus on design consistency with proof of performance from around the world. In fact, we believe our design is so unique and delivers exceptional results because of its original design. Here at Powder King®, we stick with what truly works. Our pulverizing systems are built with pride and all American-made parts from start to finish.
In addition to over exceeding our customers' expectations with our technical services and grinding rates, Powder King® offers a proprietary EC200 Operating System with full remote accessibility for the customer and by the supplier in order to keep your business running without having to stop production. At Powder King®, our mission is to turn ideas into value and transform pellets into powder for the rotational molding industry.
On the Cover
38 Rotoplas 2024
Every three years the Association Rotational Molders (ARM) hosts Rotoplas. This year Rotoplas 2024 will take place September 24-26 at the Donald E. Stephens Convention Center in Rosemont, IL. See the complete program inside. Association Rotational Molders (ARM)
50. What Rotomolders Need to Know about Polymer Chemistry “Knowledge is power,” — Dr. Nick Henwood, Rotomotive Limited Dr.
Upfront: Rotomolder Michiana expands for more production opportunities
XFactor: Remembering Underappreciated Rock Stars
Practical Roto Tips: Regrind vs Repro
Roto Around the World: China Rotomoulding Conference 2024 Lasting memories and relationships 永恒的回忆与联系 At Issue : Bridging the Skills Gap: Nurturing Tomorrow’s Talent in STEM
08. FROM THE PUBLISHER Why industry conferences matter Susan Gibson, JSJ Productions, Inc.
10. CREDITS
12. GLOBAL CONTRIBUTING EDITORS
Global Contributors, Department Contributors, and Issue Contributors
15. UPFRONT Industry News, Trends, and Products
26. X-FACTOR
Remembering Underappreciated Roto Rock Stars
Tom Innis, Xcelerant Growth Partners
38. ARM REPORT Rotoplas 2024
44. PRACTICAL ROTO TIPS
Regrind vs Repro
Dru Laws, Brigham Young University – Idaho
46. AT ISSUE
Bridging the Skills Gap: Nurturing Tomorrow’s Talent in STEM
Aldo Quaratino, Matrix Polymers
48. INTERSECTION INDUSTRY 4.0 & A
SUBSCRIPTION BASED BUSINESS MODEL
Rob Miller, Whittmann Battenfeld / Rotoload Canada
54. ROTO AROUND THE WORLD
China Rotomoulding Conference 2024!
Ian Hansen, RotaConsult Where does this all start?
59. ARMO NEWS
Rotomould24 brings in more than 160 attendees
64. GLOBAL CALENDAR
Prominent Roto Industry Dates!
66. ADVERTISERS’ INDEX
RotoWorld® advertiser contact information
I’ve been thinking about why we attend industry conferences. There are the many obvious reasons to attend conferences, but I think there are some that are not so obvious. Conferences are a great way to meet people and catch up with people you know already and whom you share similar interests and goals. Conferences are all about collaboration, and the faceto-face opportunity a conference provides you, even in this day and age of consuming online communication. There will always be the greatest impact when it comes to learning, growing brand awareness, and getting inspired and motivated when it is in person.
We have a lot of great options when it comes to conferences in the Rotational Molding industry. We have quality regional associations in most parts of the world that work hard to provide education and networking on both a local and international level. We also have the advantage of a once every three years Rotoplas, which is the largest trade exhibition for the Rotational Molding industry worldwide. We have the once every three years ARMO Show that takes place in Europe. They are all important, and for different reasons.
The takeaways you get from vital conference education sessions, the invaluable networking opportunities, the chance to open the door for new business opportunities, and the new perspectives you will gain are all credible reasons to not miss these
incredible opportunities provided by your industry associations. By regularly attending your industry conferences, you will build your own credibility and help shape thought leadership. You’ll have all kinds of opportunities to get involved in a meaningful way, offer your voice, and participate in a united voice for the industry.
When you return to your office, I suggest taking the time to de-brief with your staff that couldn’t attend, creating a mini conference for them. Then together you can pull out what seems to be the most beneficial of your take aways and create an actionable game plan.
One final thought: Remember, while the day-to-day business of your company happens primarily behind the computer screen, nothing beats a real-life meeting with your like-minded colleagues. This just leads to a win-win for everyone involved. With that said, I hope to see you at Rotoplas 2024, September 24-26, in Rosemont, IL. I can’t wait!
I hope you’ll gain some valuable information from this issue. There was a wealth of value-added content derived from the Joint 2024 ARM & IT-RO conference in the Lake Garda region of Italy. From the Italian plant tours to the education and thought sharing on things like worker retention, environmental footprint initiatives, new equipment technology updates, and hearing from noted industrial product designers that work closely with our process. It was clear to
me that as an industry, we are growing in not only our knowledge and technology, but we are also growing in our ability to share and grow together. I want to again congratulate ARM and IT-RO for such an outstanding event.
Inside, there is a lot of good information. Dru Laws, Brigham Young University, Idaho, writes an educational review on Regrind vs Repro. Aldo Quaratino, Matrix Polymers, writes about nurturing tomorrow’s talent in STEM. Rob Miller builds on his series about a thought-inspiring new business model of subscription purchasing. Ian Hansen writes a spectacular review of the China Rotomoulding Conference for 2024. And, a big Congratulations goes out to Andrew Currie for winning the ARM ICONS of the Industry award during Rotomould24 that took place in Queensland.
Lastly, I want to draw your attention to the RotoWorld® calendar of events on pages 64-65. This is the place where you can first learn what conferences are set for the year and years to come (as fast as we know them) and begin to make your decisions to attend! If you have important dates that should be included in the RotoWorld® Calendar, please send them to us! See you in Chicago! R
SUSAN GIBSON Publisher & Editor
Jerico is first in quality resins and compounds! We’ve made our name by providing vibrant colors, specialty blends, and recycled black, while focusing on being that one complete source for ALL your rotational molding compound needs. Now you can add natural PE to the list!
Time and again over the years, our team has responded to the changing times with resilience, ingenuity, resolve, and confidence. In true Jerico fashion, we developed sustainable and adhesion compounds, then
blended vibrant colors into both. Make no mistake, we are expanding and are focused on becoming your supplier of choice for rotational molding materials.
As we grow, we look for ways to improve so that we exceed your expectations and help you achieve success! Our mission is to be the go-to resource for resins and compounds that meet your precise specifications, arrive on time, and provide the consistent level of quality you have come to expect from Jerico!
PUBLISHER & EDITOR
Susan D. Gibson President - JSJ Productions, Inc. susan@jsjproductionsinc.com
TECHNICAL EDITOR
Alvin Spence PhD MEng aspence@centroinc.com
PROCESS EDITOR
Paul Nugent PhD MEng paul@paulnugent.com
DESIGN EDITOR
Michael Paloian President - Integrated Design Systems, Inc. paloian@idsys.com
GLOBAL CONTRIBUTING EDITORS
Celal Beysel Chairman - Floteks Plastik beysel@superonline.com
Tom Innis Xcelerant Growth Partners info@xcelerantgrowthpartners.com
Martin Coles Matrix Polymers martin.coles@matrixpolymers.com
Adam Covington Ferry Industries acovington@ferryindustries.com
Mark Kearns Moulding Research Manager m.kearns@qub.ac.uk
Ravi Mehra Managing Director - Norstar International LLC maramehra@aol.com
ADVERTISING AND ART PRODUCTION
Marketing/Advertising Director Jennifer Gibson Hebert Vice President, JSJ Productions, Inc. jennifer@jsjproductionsinc.com
Chief Art Director Anya Wilcox JSJ Productions, Inc. awilcox@designintersection.com
CIRCULATION & DISTRIBUTION ADMINISTRATION
Sheryl Bjorn JSJ Productions, Inc. sheryl@jsjproductionsinc.com
EDITING & TRANSLATIONS
Suzanne Ketron | Oliver Wandres | Sheryl Bjorn
WEBSITE & ONLINE TECHNOLOGY
Jason Cooper JSJ Productions, Inc. jason@bound.by
RotoWorld® is a JSJ Productions, Inc. Trade Publication JSJ Productions, Inc. 625 West Market Street, Salinas, CA 93901 Phone: (512) 894.4106; Fax (512) 858.0486 Email: rotoworldmag@rotoworldmag.com and Website: www.rotoworldmag.com
Subscriptions: One-year subscription (six issues), print or digital, $80 US, $100 Canada/Mexico, $155 All Other Countries. To subscribe or to submit change of address information, call us at (512) 894.4106 visit us online at www.rotoworldmag.com; or email us at sheryl@jsjproductionsinc.com. You may also write to RotoWorld® Subscriptions, JSJ Productions, Inc., 625 West Market Street, Salinas, CA 93901
Advertising: For information on advertising, please contact Advertising Director Jennifer Gibson Hebert, JSJ Productions, Inc. Email Jennifer Gibson at jennifer@jsjproductionsinc.com
Letters: We welcome letters about our contents. Write Letters to the Editor, JSJ Productions, Inc., 625 West Market Street, Salinas, CA 93901 512.894.4106 phone 512.858.0486 fax, or Email susan@jsjproductionsinc.com.
Editorial Queries: We consider unsolicited contributions. Send manuscript submissions as email attachment to Susan Gibson at susan@jsjproductionsinc.com.
JSJ Productions, Inc. bears no responsibility for claims or factual data represented in contributed articles.
Postmaster: Send changes of address to RotoWorld®, JSJ Productions, Inc., 625 West Market Street, Salinas, CA 93901
RotoWorld® is a JSJ Productions, Inc. independently owned, bi-monthly trade magazine for the international rotational molding and plastics design industries. JSJ Productions, Inc. owns all copyrights on articles published herein unless ownership is otherwise stated. Reproduction of this magazine, in whole or in part, without the express written permission of the publisher is not permitted.
Polyethylene Granules & Powders
Crosslink Polyethylene
Polypropylene Granules & Powders
Polyamide Powders
Designed for Roto® a dedicated range of materials to be used in rotational moulding applications.
Bio-Polymers
Ancillary Products
Dedicated Technical Services Support Team
Post-Consumer Recyle Materials
UK • Poland • Australia • New Zealand • Malaysia • Thailand
6 Manufacturing Sites across 3 Continents
To learn more about our products & material solutions get in touch at:
Alvin Spence is Vice President Engineering at Centro, Inc., North Liberty, Iowa. He provides leadership for Centro’s product development team and quality resources. Alvin received his Bachelor’s degree in Mechanical & Industrial Engineering and PhD from Queen’s University Belfast. aspence@centroinc.com
Michael is President of Integrated Design Systems, Inc., Great Neck, New York. Over the past 25 years, Mike has developed a broad range of plastic products utilizing various processing methods including rotational molding. Mike’s B.S. degree in Plastics Engineering and Masters in Industrial Design, combined with his extensive experience, has formed the basis for his branded and unique insights into the field of plastics part design. paloian@idsys.com
Paul is a consultant who travels extensively across six continents assisting clients in many roles from training to expert witnessing. He received his Eng. degree in Aeronautical Engineering and Ph.D. in Mechanical Engineering from Queen’s University of Belfast. Paul developed the Rotolog system, the first complete computer simulation (RotoSim), and authored a book entitled Rotational Molding: A Practical Guide.
paul@paulnugent.com
Ravi Mehra has been associated with the rotational molding industry since the early 1970’s. He is a Past President of ARM – Association of Rotational Molders, and has been inducted into the ARM Hall of Fame. He is the Founding Chairman of StAR – the rotational moulding Trade Association of India. He was the Chairman of ARMO – Affiliation of Rotational Moulding Organizations from 2012 to 2014. Ravi consults internationally with companies in the rotational moulding arena to help their global strategy, facilitate technology tie-ups, and business alliances. maramehra@aol.com
Martin Coles, CEO of Matrix Polymers co-founded the business 30 years ago and is the company’s largest shareholder. Shortly after graduating from London University, Martin began his career in the plastics industry working for a major Italian petrochemical company and soon became passionate about the unique world of rotomoulding. Matrix Polymers are experts in rotomoulding materials and have become a global supplier with compounding and grinding plants in the UK, Poland, Australia, Thailand, New Zealand and Malaysia. The company sells more than $150 million of rotomoulding materials each year and has 230 employees. martin.coles@matrixpolymers.com
Celal is Chairman of Floteks Plastik, the pioneer and innovative leader of the rotational molding industry in Turkey and is a Global Contributing Editor for RotoWorld® magazine. Being an ARM member for more than 20 years, Celal has made many presentations at ARM meetings in various countries. He is also active in business and political organizations in his country. Celal has authored numerous articles published in various newspapers and magazines about politics, plastics, rotomolding, and innovation. beysel@superonline.com
Tom Innis is owner and Principal CEO of Xcelerant Growth Partners, LLC (Madison, WI), a multi-discipline consulting firm with specific focus in the global plastics sector. Leveraging industry experience and relationships built over 25+ years in the international manufacturing realm, Xcelerant connects the links in the industry supply chain to accelerate speedto-market and deliver turnkey personnel, product development, and manufacturing solutions to an international audience. tinnis@ xcelerantgrowthpartners.com
Rob Miller is Owner/President, Wittmann Battenfeld Canada Inc./ Rotoload. Rob started in the plastics pneumatic conveying industry in 1986. He has spent his entire career developing, engineering, and designing all types of catalog, standard, and custom pneumatic conveying systems for the plastics industry. He started in the rotational molding industry in 2013, has enjoyed learning the idiosyncrasies of the industry and market, and most of all meeting the people and building relationships for the future. Rob.Miller@wittmann-group.ca
Adam Covington is President of Ferry Industries, Inc. in Akron, Ohio U.S.A. Covington has been with Ferry Industries for over 11 years, advanced through the manufacturing, engineering, sales, and service positions within the company and was appointed President in 2019. Adam strives to find solutions for customer’s needs and advance machine technology for the rotomolding industry. He is a graduate of Ohio University’s Russ College of Engineering and Technology with a Bachelor’s degree in Industrial Technology. acovington@ferryindustries.com
Ian Hansen has over 30 years of experience in the rotational moulding industry and has presented to conferences around the world on the subject of quality, safety, and tank design standards. Rotomoulders around the globe have problems from time to time. Rota Consult delivers production solutions so rotomoulders can improve productivity and profitability, without wasting more of their valuable time. ianhansenconsult@gmail.com
Mark Kearns is the Rotational Moulding Research Manager of the Polymer Processing Research Centre at Queen’s University of Belfast. He is a Chartered Chemical Engineer with a M. Phil Degree in Rotational Moulding. Mark manages rotational moulding research and development projects for companies across Europe, Australasia, and North America. M.Kearns@qub.ac.uk
R. Dru Laws, educator and rotomolding expert, graduated from Brigham Young University in 2003 with a BS in Mechanical Engineering and a minor in Mathematics. In 2005, he graduated top of his class with distinction (honors) from the Queens University Belfast in Northern Ireland with an MSc in Polymer Engineering from their school of Mechanical & Manufacturing Engineering. He has several rotomoulding-related patents. Laws is currently a fulltime Manufacturing Engineering professor at BYU-Idaho, as well as CEO of Halltech Systems and High Pointe Plastics. drulaws @gmail.com
Dr. Nick Henwood is well known to rotomoulding audiences, through his numerous contributions to international conferences and technical seminars. He has 30 years-plus experience in rotomoulding, specialising in the fields of materials development and process control. Nick operates as a consultant, researcher, and educator through his own company, Rotomotive Limited, based in UK. He is also the Technical Director of ARM – The Association of Rotational Molders. nick@rotomotive.net
As the Group Technical Director of Matrix Polymers, Aldo Quaratino spearheads the company’s research and development initiatives. He leads a dedicated team in identifying new opportunities and crafting innovative solutions to address the dynamic needs of their customers. Aldo’s deep expertise in polymer science has been the driving force behind many of Matrix Polymers groundbreaking advancements. Under his leadership, the company has developed a suite of high-performance polymers that have revolutionized the rotomoulding industry. Aldo is renowned for his technical acumen and forward-thinking approach, earning him a reputation as a leading expert in the field. His passion for innovation and unwavering commitment to excellence have been instrumental in Matrix Polymers’ continued success. Thanks to Aldo’s visionary leadership, the company remains at the forefront of the industry, delivering high-quality polymer solutions that set new standards. Aldo Quaratino’s contributions to Matrix Polymers and the broader rotomoulding industry are invaluable. His expertise and leadership not only bolster the company’s growth and evolution but also significantly impact the industry’s progress.
aldo.quaratino@MATRIXPOLYMERS.COM
– On June 5, ARM
President Alvin Spence, and ARM Past President Matt Bushman, visited the School of Mechanical & Aerospace Engineering at Queens University Belfast to meet with Dr. Joe Butterfield, Dr. Peter Martin, Mark Kearns, and Professor Adrian Murphy. The purpose of the meeting was to gain an understanding of current research activities at Queens related to rotational molding, and to discuss possible future collaborations between ARM and the University.
Queens remains committed to researching the rotational molding process and offers various options for collaboration depending on the nature of the work. For example, short-term exploratory work can be carried out by dedicated University staff, or longerterm investigations can take the form of a PhD or post-doctoral research program. For either scenario, intellectual property rights can be granted to the sponsor, provided most if not all the research costs are funded by the sponsor. Potential projects such as wall thickness simulation, AI control of the cooling process, and a possible material property comparison for new resins were discussed. Following the meeting there was a tour of the molding lab where both a conventional Ferry molding machine and an AMS RoboMould machine, with electrically heated molds were on display. Queens has been very actively researching the use of electrically heated molds to produce hydrogen gas containers in recent years. Other equipment in use at Queens included a Wedco pulverizer and a Caccia highspeed blender. R
Myers Industries officials said in a statement that they plan to consolidate the rotational molding business by phasing out its Atlantic facility. The Atlantic facility was formerly Elkhart Plastics, which was acquired by Myers Industries in 2020.
In a second quarter report, officials said they will be consolidating the Atlantic rotational facility into other rotational molding plants in Indiana. The report says while the company is “benefiting from worldwide investments in Infrastructure,” it also says the company is “taking actions to reduce costs and increase productivity,” and is consolidating three distribution centers in the Myers Tire Supply Business
as well consolidating Atlantic’s rotational molding facility into other rotational molding plants in Indiana. Officials said in the statement that production at the site will end in the fourth quarter of 2024, and the plant will close by Dec. 31, 2025. The plans were announced on July 31 to employees, customers, and suppliers. Approximately 60 full-time employees are based in Atlantic, and other reports said nearly all positions will be eliminated by the end of this year. Employees will have the option to apply for jobs at other Myers facilities, and customers in Atlantic will work with staff from other plants for their products. Those plants include Indiana, Ohio, Colorado, or Washington. R
Michiana Rotational Molding LLC., a Michiganbased rotational molding company in Constantine, has expanded its facility to create more production space and added a new Rotoline rotomolding machine. This is the company’s second expansion within the last five years.
The company has added 35,000 square feet, bringing its facility up to 135,000 square feet, and six rotational molding machines. “Some of the expansion is to prepare for business that we’ve just been awarded, and some of it is for future business that we’re working on — hoping to get — but not secured yet,” said Todd Outman, chief operating officer. The expansion will mostly be for material storage and flow due to the additional machine taking up existing space. Michiana Rotational Molding will hire 18 new employees to operate the new machine and secondary services.
“WE HAVE GOALS TO EXPAND ORGANICALLY, AND POTENTIALLY THROUGH ACQUISITIONS AS WELL, BUT OUR FIRST PRIORITY IS SUPPORTING OUR CURRENT CUSTOMER BASE.”
— Todd Outman, Chief Operating Officer, Michiana
The new machine is the Rotoline Carrossel CR 3.60 with four arms, an oven for heating plastic resin to be shaped and molded, pre-cooling and cooling stations, and standby to improve productivity. The company said the expansion will increase productivity by 35 percent.
“We have goals to expand organically, and potentially through acquisitions as well, but our first priority is supporting our current customer base,” said Outman. “We’re always looking for things that help diversify us. We’re pretty heavy in RV and marine right now and then we also have several new and pending customers that allow us to diversify our company.”
Michiana Rotational Molding also has customers in the material handling, home and garden, and agricultural sectors. Its secondary services include assembly, quality testing, mold repair, finishing, and delivery service for local customers. R
German Thermoforming and packaging systems supplier Illig has a new lease on life, with backing from Munich-based investor Orlando Capital GmbH.
Having faced financial strains over the past few years, Illig will continue operations as an independent entity starting in August but must cut 200 of its roughly 500 employees as part of the deal, in which Orlando Capital has acquired Illig’s entire portfolio.
“With the entry of a financially strong investor, Illig will once again invest more in the development of new technologies and innovations, the company said. At the same time the company will focus even more strongly on international growth and the further development of strategically important product areas and markets.
With two production sites and eight service subsidiaries worldwide, Illig is indeed looking ahead to new launches. In September, the company will present a now sustainable packaging product at the
Fachpack show in Nuremberg. Adding to its range of packaging machines, Illig will unveil a system for processing dry natural fibers.
“Illig is optimistic about the future: In a dynamic market situation, packaging will continue to be an essential component of brand products and will fulfill even more functionalities particularly around product protection, “the company said. Addressing sustainability trends, Illig “intends to contribute to these global trends with its existing expertise, technologies, and services and wants to set its own innovative trends for the packaging technology of the future.
Illig, which marked it 75th anniversary in 2021, initiated is restructuring at the end of 2023. While the purchase contract was signed July 17, full ownership transfer is expected at the beginning of August. R
INSIGHTS BLOG – In 2023, the market for rotational moulding machines is anticipated to reach US$ 918.7 million. By 2033, the market is anticipated to reach US$ 1,321 million, growing at a 3.7% CAGR. The global packaging machinery market, which was estimated to be worth US$ 60.91 billion in 2022, includes 1% to 2% of rotational moulding machines.
Roto molding, sometimes referred to as rotational moulding in the plastics industry, is a great way to create seamless and double-walled items. Although it is a casting technique, unlike many other plastic processing methods, it does not involve pressure. The method needs moulds that are relatively inexpensive because there isn’t much pressure. Demand from the number of end-use sectors is increasing as a result of the incredibly affordable production of relatively small production runs.
The last 50% of the twentieth century saw improvement in the items made, with center around checking the means of the cycle and their effect on consistency and quality. This prompted the making of the Rotolog, to screen and control the cooling perspective, giving guidance for the development of the business.
Rotational checking machines as they exist today are being viewed as an ideal arrangement, with additional applications for the cycle being thought about, the rotational moldings market is probably going to fill soon.
As a cycle, rotational embellishment, the utilization of which are profoundly flexible as are progressively being utilized in the assembling items across enterprises. Notwithstanding, the utilization of rotational embellishment machines for the production of holders, for example, tanks is probably going to stay high while the drums and containers and comparative items are additionally getting momentum.
In view of the sort of machine, rotational embellishment machines can be delegated rock and roll machine, clamshell machine, vertical or up and over rotational machine, transport machine, swing arm machine, and the merry go round machine. Of these machines, because of their functional proficiency, wild machines are set to observe appeal soon. However, vertical rotational embellishment
machines are set to see drowsy development over a similar period.
Inside assembling as an industry, the pattern of customization has impacted rotational embellishment machines. Makers are hoping to benefit from this pattern by adding the creation of tailor-made machines to take special care of the shopper’s necessity, to their portfolio. This is being executed as a methodology by central participants hoping to keep up with their strategic advantage in the market.
The overarching influence of advancement has led to the integration of programmable logic controller (PLC) with machine interfaces in order to simplify the process itself. With the introduction of PLC machines, along with overall operational efficiency, productivity rates also significantly improved, benefitting players in the business. Because every aspect can be monitored and controlled, including temperature, pressure, and even the thickness of the product itself, they are being considered as a viable alternative to non-PLC machines.
Players in the industry are slowly but steadily getting into rotational moulding machines that are equipped with PLC to hold their advantage in the landscape.
Integrating Tech in Rotational Moulding Machines
The advent of advanced technology has had a pervasive impact on rotational moulding machines, as with every major manufacturing process. The integration of technology has been highly beneficial to players in the industry as they focus on increasing operational efficiency without sacrificing the quality of the end product. Better control of various components such as temperature and time, has led to significant savings of time, energy resources, and costs. This is being used to increase the quality quotient of the
“ROTO MOLDING, SOMETIMES REFERRED TO AS ROTATIONAL MOLDING IN THE PLASTICS INDUSTRY, IS A GREAT WAY TO CREATE SEAMLESS AND DOUBLE WALLED ITEMS.”
process and the product itself. Manufacturers, to cater to growing demand from end users are focusing on shorter process time with high efficiency.
One specific innovation in recent years that has changed the face of the rotational moulding machines market is real-time temperature monitoring. Rotational moulding machines that have real-time temperature control allow for the raw material placed inside to be effectively melted and used, for the creation of products that are uniformly aesthetical, with improved performance of finished product,
With the influence of technology and advanced procedures being developed to ensure quality, the future of rotational moulding machines is set to lie in precision. The industry itself is moving towards smart machines and the industrial internet of things and the rotational moulding machines is also set to do the same, with PLC enabled machines quickly getting popular.
This is in line with ‘Industry 4.0’ that is focusing on wireless connectivity and sensors and is connected to a system that is capable of visualizing the process to make decisions themselves. And with aspects like customization and flexibility becoming a standard offer, manufacturing is set to get easier, safer, and more efficient than ever before. With cloud computing, block chain, and artificial intelligence
and advanced tech already being implemented, the future of rotational moulding machines is set to be in automation of processes.
Rotational Moulding Machines Market by Category
By Product Type:
• Carousel Rotational Moulding Machines
• Rock & Roll Rotational Moulding Machines
• Shuttle Rotational Moulding Machines
• Up & Over Rotational Moulding Machines
• Clamshell Rotational Moulding Machines
By Application:
• Tanks & Container
• Drums & Bins
• Carts & Carrier
• Toys & Kayaks
• Others
By End Use:
• Food & Beverage
• Agriculture
• Automotive & Marine
• Chemicals & Petrochemicals
• Pharmaceuticals
• Homecare
• Other Industrial
By Region:
• North America
• Latin America
• Europe
• South Asia
• East Asia
• Oceania
• MEA
Future Market Insights, Inc. (ESOMAR certified, Stevie Award – recipient market research organization and a member of Greater New York Chamber of Commerce) provides in-depth insights into governing factors elevating the demand in the market. It discloses opportunities that will favor the market growth in various segments on the basis of Source, Application, Sales Channel, and End Use over the next 10 years.
For more information, Contact Future Market Insights, Inc. Christiana Corporate, 200 Continental Drive, Suite 401, Newark, Delaware – 19713, USAT: +1.845.579.5705. R
ORLANDO, FL, USA – NPE2024: The Plastics Show, announced its final registration and paid exhibit space results data, totaling 51,396 registrants and 1,106,767 square feet respectively. NPE2024, held from May 6-10 in Orlando, Florida, saw a record-breaking number of international attendees, first-time attendees, and paid exhibit space.
“NPE2024 was truly a momentous event in plastics industry history,” said Matt Seaholm, PLASTICS’ Chief Executive Officer, “With an outstanding international turnout, NPE2024 is re-established as a global hub for the plastics industry, welcoming professionals and innovators from around the world. As we look ahead to our next show in 2027, we’re seeing incredible potential for more industry-shaping collaboration to establish a new standard for circularity and ground-breaking plastic applications.”
Additional NPE2024 numbers include:
plastics industry,” said Dr. Perc Pineda, PLASTICS’ Chief Economist. “As the US is the second largest importer of plastics machinery, accounting for 12% of global imports, European countries make up six of the top ten countries supplying the US in 2023, totaling $1.6 billion. Similarly, over the past five years, US exports of plastics machinery to Latin America have also grown by 6.5% annually, supporting the region’s expanding plastics industry.” In addition to the attendance results, NPE2024 marked the largest show in history with the following exhibit space statistics:
“WITH AN OUTSTANDING INTERNATIONAL TURNOUT, NPE2024 IS RE-ESTABLISHED AS A GLOBAL HUB FOR THE PLASTICS INDUSTRY.”
• 15,156 international registrants from 133 countries, establishing NPE2024 as the most global show in the event’s history.
• 36,123 domestic registrants, 70%of all registrants (this does not include 0.23% who did not respond).
• 20,378 first-time attendees, a nearly 9% increase over NPE2018. With the outstanding number of NPE2024 international registrations, the results also revealed a significant growth in attendance across different regions, including:
• 4,438 Latin American (LATAM) registrants, 29.3% of international registration and a 9.9% increase of LATAM registrations compared to NPE2018. Significant registration increases were seen from countries including Brazil, Colombia, and Guatemala.
• 2,801 European registrants, 18.5% of international registration, and a 23% increase of European registrations over NPE2018 with the largest registration increase from Italy. “This growing presence of European and LATAM registrants is indicative of the respective countries’ impact on the
• 1,106,767 total paid exhibit space, designating an additional 10,581 square feet over NPE2018
• 2,202 exhibitors, a 10.3% increase over NPE2018. NPE2027 is set to return to Orlando from May 3-7, 2027. The Plastics Industry Association (PLASTICS) is the only organization that supports the entire plastics supply chain, including Equipment Suppliers, Material Suppliers, Processors, and Recyclers, representing over one million workers in our $548 billion U.S. industry. PLASTICS advances the priorities of our members who are dedicated to investing in technologies that improve capabilities and advances in recycling and sustainability and providing essential products that allow for the protection and safety of our lives. Since 1937, PLASTICS has been working to make its members, and the seventh largest U.S. manufacturing industry, more globally competitive while supporting circularity through educational initiatives, industry-leading insights, and events, convening opportunities and policy advocacy, including the largest plastics trade show in the Americas, NPE2024: The Plastics Show.
For more information contact: Catherine Lockwood pr@npe.org or Camille Gallo cgallo@plasticsindustry.org. R
Yurma Maca feared for the lives of her daughter, Esteisy, and two sons, Joel and Celin. Her three children repeatedly became ill, missing classes at school in the remote Peruvian village of San Roque, and falling behind in their studies. “My children — all three of them — were close to dying, and I would get desperate,” Yurma, holding back tears, explains in Spanish in a YouTube video.
As it turned out, parasite-contaminated water from the Amazon rainforest’s Cumbaza River — then the village’s main source of drinking water — was sickening her kids. Today, though, Yurma’s three children are much healthier thanks to a newly installed solar-powered system that supplies clean drinking water to the 300 or so households in San Roque.
A positive and tangible impact
For this project, led by Water Mission, an engineering nonprofit, and Chevron Phillips Chemical’s
Performance Pipe division donated 3.7 miles of black high-density polyethylene (HDPE) pipe along with HDPE pipe fittings.
“Our collaboration with Water Mission is a perfect example of how we are using our social responsibility strategy to deliver positive and tangible impact to society through our products,” said Benny Mermans, vice president of sustainability at CPChem. “Working with Water Mission represents our dedication to contribute to the betterment of communities around the world.”
Water Mission completed the $485,000 water-tohomes project in December 2023, supplying filtered, chlorinated water from a nearby lake to San Roque’s roughly 1,500 residents. In addition to CPChem’s contributed equipment, other strategic partners of Water Mission — including Grundfos and Georg Fischer —donated money, technology and know-how for this project. R
MANITOWOC, WI, USA – For Redline Plastics LLC, being involved in the community is about more than being a good corporate citizen. It’s also about standing out as the best employer in the communities where it does business.
That includes both the headquarters plant in Manitowoc and the company’s factory in Hartwell, Ga., that it purchased a year ago. “Before Redline, our focus was on just filling jobs. It was recruitment constantly. Now turnover has dropped tremendously,” said Karen Beasley, human resources manager at the Hartwell plant.
The culture has changed under Redline’s ownership, she said. In the past year, the company has supported local charities including a food pantry and a coat and blanket drive. It’s also stepped up its participation in the local chamber of commerce.
“People here really want to be the best employer in Hartwell,” Beasley said. Many workers are getting involved. Being active in the community is a trait that
helped Redline Plastics repeat as a Processor of the Year finalist for 2023. This year, the rotational molder, heavy-gauge thermoformer, composite fabricator, and cut-and-sew company also won the PN Excellence Award for Industry and Public Service.
Redline and its employees are already well known for their support of community charities and projects in Manitowoc. One effort that gets a lot of attention is Redline’s support of Lighthouse Recovery Community Center, a local nonprofit that empowers those seeking recovery from addiction. Redline has 11 employees who are active in the Lighthouse program, and it also supports employees who volunteer as recovery coaches. In 2023, Redline received a Recovery Ally Employer Award from Lighthouse for the second year in a row.
Employees in Manitowoc also supported some new projects in 2023, including a Toys for Tots drive and a Salvation Army Adopt-a-Family effort. Redline also worked with a local anti-hunger organization, a local
nonprofit that supports expectant families, and Big Brothers Big Sisters Wisconsin Shoreline charity. “At Redline, we value our connection to our communities,” President Nick Murray said. The company stood out in other Processor of the Year criteria, too.
On financial performance, Redline posted strong growth in profit and sales for the fifth year in a row. The company moved up 20 spaces in PN ‘s 2023 ranking of North American rotomolders, rising to No. 19.
“We’ve had a very nice run of growth, both on the revenue side and the profitability side,” said Jennifer Brungraber, director of finance. “We’ve made some good investments over the years, and we have a little bit of capacity to fill up, and we’re looking for new opportunities at every turn.”
Keeping up that pace will be more difficult as the company keeps getting larger, but Murray feels he
has a strong team in place that will help the company continue to grow. “I think we’ve built a team here that is geared for growth. That’s been very important over the past five years,” Murray said.
“I think that growth makes this a very interesting place to be on a daily basis. There’s excitement here. I feel it around the new projects that we’ve done in the past year,” he said.
Looking at quality, Redline’s scrap percentage and cost of quality metrics have continued to improve even after the acquisition.
The company noted in its Processor of the Year application that making difficult-to-mold parts, including unusual materials, often requires Redline to develop new processes and inspection methods.
“I know Nick likes to say that we cut our teeth on challenging parts, which is true,” said John Shackleton, director of engineering. “We do a lot of different things today, including the one. R
Submit your photos to RotoWorld® magazine for inclusion in future issues.
CEDARBURG, WI, USA – Donald Alan Kohlwey, 74, of Cedarburg passed away on Monday, July 1, 2024, after a heroic nine-year journey with Parkinson’s disease. His loving family was by his side.
Don was born on November 5, 1949, to Benoit and Lillian (Growth) Kohlwey. He married Sandra Wollner on October 25, 1975. Don was a member at First Immanuel Lutheran Church where he was an usher and a member of Men’s Club. Don was an avid fan of the Green Bay Packers, Milwaukee Brewers, Milwaukee Bucks, and WI Badgers.
Don retired from Norstar Aluminum Molds in 2018 after 47 plus years of dedication and countless accomplishments. He left with extraordinary memories and friendships. Don was also a blood donor and became a 46-gallon donor helping patients in our community. Don enjoyed family vacations, yard work, biking, golfing, walking, camping with his son Kyle, listening to rock ‘n roll music, playing Sheepshead, and putting together jigsaw puzzles with his granddaughter Caitlyn. He also passed along his love of gardening to his children. Don was a loving husband and a wonderful father.
Don is survived by his wife Sandra; daughter Kimberly (Bill) and son Kyle (Lyndsey). He was a loving grandpa to Caitlyn, Graham, and Oliver. He will be missed by his brothers: Keith (Lois) and Kevin (Janet). He was cherished by his extended family: Nancy (Fred), David (Wendy), and Judy (Robert). Don will be remembered by his nieces, nephews, and cousins. Don was preceded in death by his parents, his son Eric who died unexpectedly at the age of 9 years of age, his sister Barbara and her husband Paul, and his brother-in-law Jim.
A memorial service was held on Thursday, July 11, 2024, at First Immanuel Lutheran Church in Cedarburg, WI. Memorials may be made to First Immanuel Lutheran or First Immanuel Men’s Club. Online condolences may be sent to the family by visiting www.muellerfuneralhome.com. The family would like to thank Horizon Hospice for their care and support. They also extended a big thank you to all their family and friends for their love and support. R
In Theodore Roosevelt’s famous “The man in the arena” speech, he extolls the quiet, overlooked hero who seeks not the attention of the spotlight or the adoration of the masses, but rather lets his deeds and contributions speak for themselves. The rotomolding industry recently lost two such men in the arena: unpretentious and underappreciated associates with whom I collaborated closely and who left a rich legacy through their immeasurable industry contributions.
Though having passed away in 2021 at the age of 81, Alan Heller, who channeled his mantra of “good design at affordable prices” into the development of plastic furniture and housewares, deserves the remembrance and respect from the rotomolding community.
Based in New York City, Heller was an early adapter of rotomolding as a means of transforming his creative mindset into numerous furniture pieces, including collaborations with renowned designers Massimo Vignelli, Frank Gehry and others that pushed the boundaries of the rotomolding process and helped define a niche where functionality and aesthetics could coexist in the consumer space.
This breakthrough design required a different rotomolding production mindset: due to the
complexity of the design, the unyielding focus on aesthetics and the product’s position as a consumer product, Heller’s rotomolded product line was not easy to manufacture. Highly polished, multi-piece molds required painstaking parting line configuration to conceal witness lines on finished product.
Specialized materials with enhanced UV stability and vibrant colors were a necessity. Large, flat surfaces – such as tabletops – needed to remain flat despite rotomolding’s propensity to the contrary. All these issues created challenges for the rotomolder, but also helped to push the process forward and deliver unique, creative, beautiful products to the market.
Heller was driven and famously stubborn, necessary attributes to break new ground in rotational molding, collaborate with high-powered designers and to fully deliver on his “good design at affordable prices” promise. He was also brilliant, kind, generous and had a terrific sense of humor. I was fortunate to know him well, and along with his long-time partner and owner of ErgoErgo (blowmolded active seating stools), Barbara Bluestone, earn his valued friendship through many years of close collaboration.
We also recently received word of the passing of Don Kohlwey on July 1st at the age of 74, who
retired from Norstar Aluminum Molds in 2018 after building a 47-year career with the company. Don held numerous positions with Norstar (previously Kelch Aluminum Molds) prior to settling into his long-time technical sales position with the business in the late-80’s. It is through this role that Don made an indelible impact on the success of his employer, his customers and the industry alike in helping tool-up rotomolding projects and product lines that have contributed countless millions of dollars to our industry’s output, and to the success of rotational molders throughout the world.
My first rotomolding industry role was as National Sales Manager with then-Kelch Aluminum Molds in Cedarburg, WI in 1996, after leaving the eyecare pharmaceutical realm and joining an industry about which I knew close to nothing. I’ll always remember Don, as a member of the sales team I inherited, and his willingness and desire to help me through what was a challenging learning curve – as we all
know, our industry has its own unique vernacular, is somewhat idiosyncratic and it takes time for outsiders to acclimate.
A few weeks into the job, and after I asked one-too-many stupid questions in a project review meeting, Don was kind enough to pull me aside, offer his guidance and mentoring, introduce me to key people in the company, and quickly schedule customer visits to accelerate my on-the-job training. What’s important to note is that Don didn’t HAVE to do this: he was simply being kind and considerate in helping his new manager get up-to-speed.
But this was the essence of Don. Clearly, he had amassed a very strong technical acumen of the mold-building and rotomolding processes and parlayed this vast knowledge into his role as a valued and respected solutions provider on an industry-wide basis. Aside from his professional attributes, he was also very kind, loyal, principled, committed to his team, his company, his family and community, and in our relationship first as coworkers and eventually as industry collaborators, I likely learned much more from Don than he did from me.
Both Alan Heller and Don Kohlwey forged successful and meaningful careers through their close affiliation with the rotomolding industry, while helping to move the industry forward, create new markets, and facilitate the success of so many, among whom I’m grateful and privileged to be a part.
Please join me in remembering these underappreciated roto rock stars and the indelible legacies they’ve bestowed on our industry. R
This year marked a first for the Association Rotational Molders (ARM) and the Italian Rotomoulding Association (IT-RO). The two associations worked together to present the 2024 Executive Forum and Italian Plant Tour this spring in Lake Garda (Bardonlino), Italy.
As a special part of the event, North American attendees were invited to tour Italian factories: Rototech, Cornaglia, Persico, VECA, Moulding Service, and Verzellesi. The North Americans were then joined by their Italian colleagues for the Executive Forum, which featured a multitude of hot topic education sessions, a tabletop trade show, networking, and social events.
David Smith, H. Muelhstein and ARMO liaison, kicked off the Executive Forum with a report on the North American rotomolding industry. “The industry in North America is strong, and the future looks great. ARM has expanded its membership substantially over the past year, and considerable consolidation has taken place,” Smith said. Tank Holding and Myers Industries have become North America’s two largest rotomolding companies. The average molding company achieved 15% annual growth in
2022. The top custom rotational molders in the US are Tank Holding, Myers Industries, Moeller Marine Products, Plasticraft Corp., Redline Plastics, Rhino, Hedstrom Plastics, Forte Products, and Horizon Manufacturing. The top proprietary rotational molders are Tank Holding, Toter, Step2 Discovery, Little Tykes, Pelican Products, Den Hartog Industries, Confluence Outdoor, Iowa Rotocast Plastics, Laerdal Medical, and Rhino. The top markets include Tanks: Agriculture and Industrial; Recreational and Sporting Goods; Non-Tank Industrial Applications; Lawn and Garden; and Consumer Products.
IT-RO President Katia Zoppetti reported the Italian industry is also strong. The Italian Rotomoulding Association (IT-
RO) has 60 members in 2024 including 27 suppliers and 33 rotomolders. “Italian Rotomolding factories are concentrated in the North and Central regions of the country, with very few in the South,” Zoppetti said. The top rotomolding companies in the Italian market are Nuova Simplast, Rototech, and Cornagia. The primary materials being used are PE; XLPE; PP, and Nylon. Extrusion technology is the dominant process, however, rotomolding claims 35% of all other processes utilized. According to Plastics Consult business insight, “The top market sectors for the Italian Rotomouding industry are Automotive, Agriculture, Water Treatment, Medical, Furniture, Building, Playgrounds, and Marine.”
Noted Italian designers Ricardo Giovanetti, Marco Serralunga, and Stefano Giovanonni were on hand to discuss product designs and possibilities for new product markets. Ricardo Giovanetti talked about opportunities in new and innovative product markets that look beyond conventional ones. He featured a Pedal Cargo Bike (urban mobility product) that
Continued on page 34
The ARM Executive conference tipped off with a visit to two of Italy’s technical molders, Rototech and Cornaglia. Rototech shared some information about the company, along with examples of the types of products they manufacture, which includes fuel tanks, DEF tanks, and other technical parts. They also had several examples of hydrogen tanks on display. During the facility tour, several SMART machines were in use along with conventional rotational molding equipment. The ARM group enjoyed a very nice lunch before moving on to Cornaglia. When touring Cornaglia, many blow molding machines were in use, typically manufacturing air ducts. Cornaglia had several conventional molding machine manufacturing fuel and DEF tanks. Day 2 started with a visit to Persico, which did not disappoint. Persico is not only one of our industry’s premier mold builders, but they are also Automotive and Marine industry leaders. During the tour all parts of their business were on display. The ARM group had the opportunity to see the manufacture of custom yachts, automotive compression mold equipment, SMART machine technology, and CNC rotational mold building. Following lunch at Persico, the group proceeded to VECA for the afternoon. VECA offers many of their products through a catalogue company, for consumer and commercial use. The tour started with a visit to their product display area, where a wide variety of their offerings were on display, such as many varieties of plant pots, furniture, lighting stands, bar tops etc. The production tour followed, which included both injection
molding and rotational molding.
Day 3 started with a visit to Moulding Service and ended with a visit to Verzellesi. Like the previous days, the hospitality experience by the ARM group at Moulding Services and Verzellesi was exceptional and the welcomes at each facility were very warm and friendly.
Both are excellent custom molders, manufacturing high quality products for a wide variety of industries. Their facilities were impressive, with well-organized and clean manufacturing environments. Their products were of the highest quality, with sharp vibrant colors manufactured from compounded materials. Both company’s take a lot of pride in the quality of their parts and have excellent finishing areas prior to final packaging and shipping.
During the Executive Forum, ARM Technical Director Dr. Nick Henwood, thanked the companies who participated in the tour for allowing the North American contingency to visit their factories. Henwood’s top takeaways from the tour highlighted the factories cleanliness and organization, their design creativity and visual impact, how they embrace new technology and have adopted automation, and ways they exhibited parallel process options. He gave high marks to the displays of quality of molds, finishing techniques and tools, multilayer parts, and clever use of shielding. Henwood noted some differences in the areas of safety priorities and systems, use of compound color vs dry blend, packaging of raw material inputs, use of crosslink (esp. fuel tanks), and in building design /loading bays. “Italy is famous for its design and functionality,” Henwood said. R
could be used to transport goods in hard-to-reach areas such as downtown areas with limited parking. This vehicle can also be used in the tourism sector to transfer goods.
Marco Serralunga, talked about his company’s history and passion for innovation. Founded in Biella in 1825, Serralunga has been the creative and entrepreneurial heart of the company for six generations, and now exports into 50 countries around the world. The company first experimented with rotomolding in the US and started making planters. It was a huge success, which provided the stimulus for them to go on and design products with beautiful shapes. “Design is intelligence made visible, and aesthetics are useful. In Italy people know what is beautiful,” he said.
Stefano Giovannoni founded and launched Qeeboo in 2016 in Milan. The company was founded with 80 cast molds. Giovannoni’s well-known Rabbit Chair design, which includes a variety of finishes, is a prime example of a Qeeboo product. Other products include King Kong, also designed by Giovannoni, which is the same size as a real gorilla but is also made in larger and smaller sizes. The Giraffe in Love, designed by Marcantonio is featured at Qeeboo in 4.5 meters. This along with the Fallen Chandelier is made for both indoors and outdoors. Matt Bushman, Plasticraft, presented a comparative look of two primary processes: Blow Molding and Rotational Molding. Blow molding is a high-pressure process while rotational molding a low-pressure process. Bushman covered how the two processes work and talked about their
differences. Rotomolding involves color compounding, pulverizing, mold filling and closing, and heating and cooling. The molds open and parts are removed manually. To select the right process for a part, Bushman recommended doing a thorough review of all the features of a given part, go through a process of elimination, determine if the part size is too large or too small, determine part geometry (the cores and irregular shape), examine the material to be used, and decide if the resin is available for the process. Finally go through the aesthetics and determine the quantity of parts required.
Work retention was the topic for Elisa Martini of Holzhoff. Holzhoff
produces products involved in the production of playgrounds for public and private areas. They also produce street furniture, offering solutions for furnishing squares, streets, and entire cities. Martini discussed Holzhoff’s corporate overview and objectives in achieving worker retention. She advised creating a welcoming work environment and building employee loyalty by involving them, keeping them enthusiastic about the work they perform, and making them an integral part of the organization.
Several equipment manufacturers were on hand to present updates on their companies and products. Oscar Orefice of Rotoplastic talked about
how his company placed in the panorama of rotational molding machine manufacturers. Adam Covington of Ferry Industries presented a close look at Ferry’s newest and most advanced technologies. James Hould of STP presented a look at the latest and most innovative products and services the company has to offer.
ML Engraving has been enhancing surfaces of plastic and rubber products by laser engraving on molds of all kinds for 25 years. Fabio Barcella reported the company utilizes a digital co-design and laser technology to enhance the surfaces of products and improve the management of projects. The company has 80 employees, 22 laser machines, 25,000 sm of production space, and they are members of the GG Global Laser Group. The company also has 3 patents and 9 projects granted by the European Commission.
Sergio Zillioli, Persico presented the evolution and growth of Persico, which started in 1976 along with the technology offered today including automated and traditional rotomolding machines. Rob Miller, Whittman/ROTOLOAD discussed success in automation highlighting the 3Ds (development, design, and discover). He went through the equations of both direct and indirect labor savings. Oliver Wandres presented an overview and history on German molding making company MAUS. The company has been a family run business since 1925. The company has a production area of 5000 sm, 8 CNC machining centers, and 62 years’ experience in manufacturing rotational aluminum rotational molding tools.
Carsten Erkel, Elkamet,
introduced his company’s Apprentice program, which has proved to be an enormous success with a recent retention rate of 75%. The two-year program involves three semesters of college and 3,000 work hours, in which the apprentice is paid. It is offered to recent high school graduates and adult learners, and it is free of charge. The program includes 13 credits total, and students earn a Certificate in Mechatronics Engineering Technology and a Journeyman Certificate. Class is one day per week, and they work four days a week at one of the partner companies. If they want to keep learning after the apprenticeship they can, and classes count toward an associate degree at Blue Ridge College.
Also on the topic of worker retention, Corey Eystad, Rhino, and Tony Short, Myers Industries, shared their insights. Rhino is a rotomolder in Central Minnesota with 140 employees whose whole focus is on proprietary products within the Marine, Tank, and Outdoor Recreation sectors. “Employees mainly leave due to insufficient wages, lack of advancement opportunity, poor leadership, absent communication/transparency, poor culture, inadequate training, and/or not being challenged in their roles,” Eystad said. The labor market is challenging with labor shifting away from manual labor jobs, and this puts rotomolding in a compromising position. Rhino places a lot of emphasis on understanding why employees leave and taking a continuous improvement approach.
Tony Short, Myers Industries, said Myers is a world leader
in materials handling. It is a 90-year-old company with 2400 employees and the 2nd largest rotomolder in the North America. They employ the processes of rotomolding, injection, blow, and thermoforming. “The pandemic created challenges in the labor market in the US. We are in a workers’ market, and we offer competitive wages,” he said. They listen to workers’ demands to work remotely and are seeing less desire among young workers to move into manufacturing. “We work to promote a career and not just a job,” he added. Myers offers stock options, advancement opportunities, and being part of something bigger. Myers values are promoting culture, integrity, optimism, customer focus servant leadership training, cross training, and the ARM Training Academy.
Alvin Spence talked about Centro and managing a growing business nationally and internationally. The company’s main products include Agriculture, Lawn and Garden, Construction, and a variety of others. Centro’s product development history includes a time (during the 80s) when tanks became more technical. “Now plastics is the primary material used in tanks,” Spence said. In the 2000s, Centro got involved in environmental products, during a time of environmental regulation, when they designed a 3-layer system. These tanks came to the fore in 2000. In 2023, Centro sold to Tank Holding and purchased CRM. Spence talked about the integral role of RotoLoPerm®, which is proprietary and a standard in the industry. Today, the company has 681,946 sf production space. “Our growth has been the result of our
strong bond with our customers and the success of RotoLoPerm®,” Spence said. International growth began in Northern Ireland (engineering only), and in Brazil, which has been the most challenging journey,” he added. He attributed their secret to success as being the people on their team, customer relationships, product development resources, RotoLoPerm®, and management operating systems ISO 9001 adopted in 2015.
On a more technical topic, Alvin Spence presented on multilayer rotational molding utilizing their skin-foam 2-layer system to provide insulation, stiffness (even though it reduces modulus) and floatation. They also utilize a 3-layer system to provide all the above with greater strength and stiffness. RotoLoPerm® XLPE/ Barrier/XLPE – 3-layer is used for gasoline fuel tanks requiring low emissions and high impact strength. Crosslink/PA11 (2 layer) in used for hydraulic tanks for temperatures exceeding XLPE capabilities and gasoline fuel tanks requiring low emissions. Crosslink/PA6 -2 layer is used for hydraulic fuel tanks for temperatures exceeding XLPE capabilities and gasoline fuel tanks requiring low emissions. Spence compared post mold PU foam and in-mold PE foam and cited some successful product examples. The RotoLoPerm® (3-layer) gasoline tank was developed by Centro and uses XLPE/Hydrocarbon Barrier/ XLPE combination (3 shot). RotoLoPerm® is trademarked and has 3 patents. It passed SAE J288 & J1241 impact tests, and B71.10, CARB, and EPA compliant. For more information see RotoWorld® Volume XX, Issue 2, 2024.
Gerbaldo Polimeri S.p.A. has been at the forefront of the plastics industry for over 40 years offering innovative and reliable solutions for the production and delivery of compounds for rotational molding and blow molding. Gianmario Maglian said they have a strong commitment to innovation and sustainability.
Davide Accornero, Rototech, presented a stimulating look Rototech’s ESG & Carbon Neutrality Path. He defined the scope of the project as: ‘Scope 1 emissions’ from sources that the organization owns or controls directly; ‘Scope 2 emissions’ from sources the company causes indirectly and come from where the energy is produced; and ‘Scope 3 emissions’ from sources not produced by the company itself and not the result of activities from assets owned or controlled, but by those that it’s indirectly responsible for up and down its value chain. As part of Rototech’s plan, Scope 1 & 2 priorities are projected to move from 25% in 2025 to 100% in 2040. The Rototech Carbon Neutrality
Path involves a 5-step process: Step 1, initial assessment; Step 2, use green energy; Step 3, use green materials; Step 4, electric or hybrid machines; and Step 5, re-use scrap. Rototech will install solar panels on its plant rooftop (initially in the Turin Plant, and later to be extended to other plants) to produce 1.5 MS of green solar energy. This will provide for the direct utilization at Rototech and the sale of excess energy to the grid. This is expected to cause a CO2 reduction of 430 ton of CO2/ year. Rototech is going to source electricity from providers that ensure such energy to be made for renewable sources, mainly hydroelectric units based in Piemonte region.
Finishing up the session Fabio Ferrarini, Boca, presented the company’s commitment to reduce the footprint of molds construction. Boca is based in San Pietro Mosezzo Novara and manufactures CNC Aluminum molds, Cast Aluminum molds, Steel molds, Patterns for composites materials, Thermoforming molds, and Thermosetting molds. “Boca’s
commitment to reducing energy consumption in rotational molding production is unwavering,” Ferrarini said. “We continually invest in advanced technologies and processes that minimize energy use without compromising quality by optimizing our manufacture techniques.
The industry event was an outstanding success. Attendees were full of enthusiasm for learning and networking. The event earned very high marks due to the quality of the information provided and the fostering of new relationships within the industry.
Here are just a couple important comments:
“Once again international cooperation led to excellent business and excellent enjoyment – smiles all round.”
Alison, McKeand, DRAM srl
“ARM put together a fantastic executive forum in conjunction with the IT-RO group resulting in an unforgettable experience for not
only myself but my sons as well.”
Vince Costello, Diversified Mold and Castings
A huge shoutout goes to Barbara Gonzini and Lyondell Basell and Rob Miller and Wittmann/ROTOLOAD for sponsoring the event helping to make it all possible. Also thank you to the companies who exhibited at the Executive
Forum Trade Show. There were many quality networking and socializing opportunities during the conference including a stellar Group Dinner event at Caesius Spa. Finally, a debt of gratitude goes out to ARM and IT-RO for putting together this successful and memorable event.
Stay tuned for upcoming events for both ARM and IT-RO! R
mission of the Association of Rotational Molders is to promote, educate, and inspire the rotomolding industry. For more information, visit ARM’s website at www.rotomolding.org or contact the Association at 630.942.6589 or info@rotomolding.org.
Join us September 24-26 at Rotoplas, ARM’s tradeshow, which gathers the largest audience from the world of rotomolding. This year’s event will be held at the Donald E. Stephens Convention Center in Rosemont, IL, just a few minutes from Chicago O’Hare International Airport.
Walk the show floor or attend one of the many workshops or seminars. If you’re from outside of North America, you can add on a tour of leading rotomolders, Plasticraft, andRoyal Basket Trucks on Monday, September 23. Learn more and review the list of 80 exhibitors at Rotoplas.org
TUESDAY, SEPTEMBER 24
Rotomolding 101
Dru Laws
Manufacturing Engineering Professor, Brigham Young University
This seminar covers the key elements of the rotomolding process. This includes available materials, the main types of equipment used, processing parameters, process control methods to optimize part properties, and key design guidelines. Attendees will have plenty of opportunities to ask questions and explore areas of particular interest.
Advanced Rotomolding
Dr. Nick Henwood, Rotomotive Limited
This seminar will cover how melt index and density relate to rotomolding, alternatives to PE, how to use data sheets, thickness control, correct cure, how cooling affects shrinkage, controlling your oven for efficiency, process monitoring, troubleshooting, the top causes of scrap, and more.
Outside Sales Mindset and Mastery
Michael Corcoran
As an Outside Salesperson, you are the frontline representative of your team and company, responsible for fostering relationships and driving business growth. Effective territory development and management, combined with sales skills and strategies, are essential for successfully expanding business within your area. This program will delve
into these aspects alongside the mindset needed to juggle multiple responsibilities, maximizing sales and opportunities across all product lines and services for existing customers and prospects. The program’s core lies in fostering interaction, generating ideas, and promoting participant collaboration. This highly interactive format ensures heightened engagement and a deeper commitment to applying discussed ideas and concepts, surpassing traditional training and workshop presentations.
Dr. Robin Kent, Tangram Technology Ltd
This seminar covers the detail of site (gate-togate) carbon footprint and the sources of reliable emissions factors for most activities. At the end of the seminar, most sites will be able to calculate
their carbon footprint within 4-8 hours (including gathering the data). This seminar will focus on site carbon footprinting but will also briefly cover ‘Scope 3’ emissions and product carbon footprinting to show the difference in approaches.
Inspiration, Creativity, and Basics: Designing Great Rotationally Molded Parts
Michael Paloian, Integrated Design Systems, Inc.
This four-hour seminar will provide you with an immersive experience in understanding the basic principles required to design rotationally molded parts. You will learn the fundamental guidelines associated with part design based on an explanation of why they are needed. This design seminar will discuss the importance of understanding material selection, part geometry, and mold design. In addition to these “basics”, you will also experience how these principles have been applied to several actual products with case studies. Mr. Paloian has designed hundreds of rotationally molded parts. His extensive experience during the past thirty years will be generously shared with all who attend. Drink lots of coffee to keep up with the fast-paced program. CAD files from numerous products will also be shared to delve deep into the details of parts, illustrating how the recommended guidelines have been successfully applied in actual applications.
WEDNESDAY, SEPTEMBER 25
ADAPT: Overcoming Adversity
Jim Abbott
As a one-handed athlete, some would say Jim Abbott overcame obstacles to become a standout major league baseball player. Abbott would beg to differ and say he was incredibly blessed. In order to continue to move towards our goals, Abbott shares we must be willing to adapt, change, and mold ourselves to meet the challenges in our own way. Using ADAPT as an acronym he will show audiences that by putting together a powerful set of words that stand alone in their significance, they also string together like a chain in an amazing way.
Enhance competitive advantage through smart product design
Tom Innis, Xcelerant Growth Partners
This session provides a case study of a newly developed consumer sports product to demonstrate effective product design process for a consumer product. This presentation includes the impetus for product designs, the product design process, involvement of key supply chain partners and, “In retrospect”: what did we learn that we can apply to future projects?
Extreme Applications, a series of case studies for unexpected and amazing rotomolded products
Ronny Ervik, Norner
With 28 years of experience, Ronny Ervik has witnessed and contributed to rotational molding’s evolution through various projects. The Norwegian rotomolding projects Ronny will highlight in this presentation exemplify the field’s innovative spirit, showcasing exceptional construction, material selection, and research and development. These projects reflect the technical prowess of Norwegian designers and the collaborative efforts in pushing the boundaries of rotational molding. This presentation aims to catalyze further innovation, encouraging professionals to explore new materials, designs, and applications to redefine the industry’s future.
Breakthrough Heating Technology for Rotomoulding
Bill Spenceley, Flexahopper Plastics Ltd
After 7 years of research a new heat process technology has been developed to provide solutions to energy challenges for our industry. Bill Spenceley (Flexahopper Plastics Ltd.) will discuss his experience with this revolutionary new technology and how it will provide solutions to convert all types of molds to electrical heating and open doors to many production efficiency opportunities.
Functional Automation Solutions
Oliver Wandres, Maus GmbH
With this presentation Oliver Wandres will introduce a variety of different available and functional
automation solutions – both for conventional and electrically heated moulds. From rather easy to high-end solutions, such systems can meet different demands from molders or market and can help to make rotomolding more repeatable, failproof, operator friendly, sustainable, and profitable. Different case studies will give a guide to best practice of adopting such solutions to both new or retrofit/upgraded molds.
SMART AUTOMATION: How to navigate the future
Sergio Zillioli, Persico
This presentation will provide an overview of automation systems for both Smart machinery and conventional oven machinery, focused to reduce manpower required, increase efficiency, productivity, and safety.
THURSDAY, SEPTEMBER 26
AI Unleashed: Disruptions & Opportunities
Patrick Schwerdtfeger
New AI technologies like ChatGPT are revolutionizing industries from healthcare to finance, and from manufacturing to education. In this groundbreaking keynote, updated almost daily, Patrick Schwerdtfeger explores the transformative impact AI is unleashing on business models across the economy, including some scary disruptions as well as massive opportunities. Gain insights into the productivity explosion available to those who strategically leverage these remarkable technologies.
Artificial Intelligence in Rotomolding
Marthijn Koorn & Sander Staal, Pentas
Join Marthijn Koorn and Sander Staal from Pentas
Moulding as they explore the forefront of AI in the rotational molding industry. Their talk will cover the practical applications of AI technologies that are integral to moving towards an autonomous production management. They will discuss the various tools currently in use at Pentas, including the latest advancements in vision AI, and outline their
roadmap for the future as they innovate towards fully autonomous factory operations. Don’t miss insights into how AI is reshaping traditional manufacturing processes at Pentas, paving the way for the next generation of industrial automation.
Challenges and Collaborative Solutions: Integrating Recycled Polyethylene into Rotomolded Parts
Dustin Turgeon, NOVA Chemicals & Matthew Bushman, Plasticraft
Incorporating recycled polyethylene into rotomolded parts has been a challenge for the industry, especially when most recycled polyethylene sources do not come from rotomolded parts. True rotomolding recycled sources are difficult to find due to the relatively small size of the industry and the long life of most rotomolding products. Plasticraft and NOVA Chemicals collaborated on a case study, incorporating EX-PCR-WR3 into a consumer rotomolded part in various colors meeting Plasticraft’s and their customer’s requirements. Plasticraft performed the rotomolding and customer testing supported by NOVA Chemicals Center for Performance Applications where the laboratory testing was conducted.
(WEDNESDAY & THURSDAY)
Rotovia’s Sustainability Journey
Dadi Valdimarsson, Rotovia
In this presentation Valdimarsson will to share with the roto industry Rotovia’s sustainability vision and actions. Rotovia has ambitious plans in place where their goal is to significantly reduce the environmental footprint of Rotovia. Some of those plans are around energy usage and how to move from fossil fuel energy over to greener alternatives. Other plans are around polymer usage and how we can reduce the usage of virgin materials with light weighing initiatives and increased recycling content.
of
Denis Rodrigue, Laval University
Crosslinked polyethylene is a major problem for the rotational molding industry as very limited information is available on its recyclability and waste management. In this presentation, some preliminary results will be presented on the possibilities to process/recycle crosslinked polyethylene with respect to materials and methods. Then, a study on the reintroduction of the
recycled materials into virgin resins will be discussed in terms of concentration and processing conditions. Finally, general conclusions will be made with proposal for future development on similar as well as other applications. As a first step, only single layers of the same resin is used to better understand the relationships and interactions between the processing conditions and the final parts properties.
Overview
Dr. Nick Henwood, Rotomotive Limited
This presentation provides an overview of many types of wall thickness including feedback from rotomolders with the pros and cons of each method including air amplifiers, air scoops, fins and heating pins, and painting exterior mold sections.
Melissa Derheim & Jeremy Williams, Advanced Pedestals Inc.
Introducing a training culture in the RotoMolding industry can be a challenging task. “Molding with confidence” is a phrase that represents a culture where every employee can take pride in their achievements and learn from their mistakes. Join us as we provide some insight into the advantages of establishing a platform that aims to enhance the skill set of roto molders.
Moderators: Jon Ratzlaff, Chevron Phillips Chemical Company; Sandy Scaccia, 4Roto; and Wayne Wiid, Pioneer Plastics
An ARM tradition: troubleshoot your problems with your colleagues and industry experts. This effective workshop can change your operation, help you reduce scrap, and reduce significant expenses.
Compare Advantages to Using 3-Arm Carousel vs. 4-Arm Carousel vs. Inline Shuttle Machines
Adam Covington, Ferry Industries
This presentation will review quantitative cycle outputs
of various machine styles using RotoCycle simulation software. It will also share insights into the advantages of different machine types. Audience participation is encouraged to discuss pros and cons, helping molders gain valuable knowledge and best practices for their businesses.
Dr. Robin Kent, Tangram Technology Ltd.
This workshop covers the highlights of energy management for rotational molders and covers the real basics about where energy is used. It gives the ‘Top Tips’ for rotational molders and is a call to action to reduce energy use using simple techniques.
Dave Sullivan & Carmine D’Agostino, NOVA Chemicals
This workshop explores key material evaluation and trial planning strategies, focusing on next-generation polyethylene (PE) resins. We’ll compare the subtle differences of qualifying traditional drop-in PE resins with advanced next-generation PE materials, emphasizing how the latter opens new production opportunities, potentially leading to cost savings, improved operational flexibility, higher machine production rates, and improved part performance. This session will delve into the latest methods and best practices for assessing material properties, ensuring compatibility, and integrating these next-generation PE resins into processes previously optimized for traditional resins. Through interactive discussions and practical examples, participants will gain both practical
knowledge and skills, preparing them to successfully incorporate advanced resin materials into their manufacturing operations.
Darin Grinsteinner, Celanese
In the last few years, new Copolymer Acetals have shown the ability to be a 1-layer solution for Fuel tanks due to its low fuel permeation and good mechanical property balance. These materials have recently been shown to also work well for Hydraulic fluid tanks. These new copolymer acetals provide good thermal stability, low swell and low permeation. This gives OEM and molders an option to polyamides that process at lower temperatures and have excellent mold release properties.
Steve Ma, Dow
Dow RESILITY ™ XUS58441.00 is a specialty rotomolding resin that combines a soft tactile
experience with exceptional impact, slip, and abrasion resistance. These attributes are further complimented by ease of processing, ambient pulverization capabilities, and outstanding color stability, making this resin the ideal choice for grips, non-slip surfaces, toys, furniture, and other applications that can benefit from enhanced haptics, tactility, and durability. This presentation aims to showcase the versatility and effectiveness of the RESILITY™ XUS54441.00 resin through the examination of its application in the grinding, processing, molding, and performance testing of rotomolded products.
Sam
Talbot, PSI Brand
In this presentation, we’ll explore how plastics can be branded with a wide range of graphics including branding, QR codes, barcodes, and RFID, and what some of the common challenges are when branding plastic. In this workshop rotomoulders will learn just how easy it is to create long-lasting branding solutions that will pop for decades ahead. Attendees will also have the chance to try both a post mold and an in-mould application themselves and will be provided with their own packs to trial at the workshop and to take away after the event.
Chantal Laflamme, Wittmann-ROTOLOAD
This session will explore the concept of a futuristic plant. We will delve into the potential benefits of automation, starting from the foundational level and covering how it can revolutionize plant operations.
Moderator: Daren Balderson, Myers Industries
Join this panel workshop for information and best practices on safety in a rotomolding shop. Topics include:
• De-Molding
• Oven fire prevention
• Oven fire response & suppression
• Temp employee and new hire safety orientation
• PPE
• Incident response and reporting / Incident communications
• Heat stress prevention R
In anticipation of a recycling webinar that Steve Ma from Dow and I are hosting later this fall, I’d like to share a practical comparison between two “recycled” materials commonly used in our industry: (1) regrind material and (2) repro material. But first, let’s discuss the basic components of the virgin polyethylene material we initially purchase.
You see, polyethylene (PE) is much more than just polyethylene. Without the right additives in the right quantities, PE wouldn’t be at all suitable for rotomolding. With the help of ARM’s technical director, Dr. Nick Henwood, I have compiled a simplified list of what polymer chemists add to polyethylene to make it viable for our Rotomolding process:
• Polyethylene (PE) – PE is obviously the first and main ingredient. But PE polymer chains are quite unstable and need some protection if they are to survive their intended purpose. Just like our skin needs lotion in dry environments and sunscreen in UV enhanced environments, PE needs some conditioning as well, in the form of stabilizing additives. When formulated correctly, different stabilizers in PE combine synergistically to provide the desired level of longlasting protection against both heat and UV.
• Anti-Oxidation (AO) Packages – Most materials, including PE, oxidize in the presence of oxygen, and this oxidation process is accelerated at elevated temperatures. The first thing that happens to PE is a short (but hot) extrusion process to create pellets. Then those pellets are pulverized into powder (the pulverizing process is a lower temperature than extrusion, but the material stays hot for longer). And then we send that powder through our slow hot Rotomolding process. To survive these hot processes, there is a strategic combination of primary and secondary AO additives in the PE intended to protect it against oxidation. These AO additives also help protect the part after molding during its end-use application. There is a widely held concept that the “primary” AO (usually a sterically hindered phenolic)
has the purpose of long-term protection of the PE and that the “secondary” AO (usually an organic phosphite or phosphonite) has the purpose of in-process protection. The reality is more complex in that these two types of AO work synergistically to provide both short-term and long-term protection. In the absence of primary AO, the secondary AO will take the burden. The reverse is also true. But relying on only one to do all the work is not an optimum way of formulating PE. It may interest you to know that by the time we have properly Rotomolded the PE, nearly half of the AO packages have been consumed (more if the part is overcooked).
• Ultraviolet (UV) Package – The mechanism that compromises polymers because of oxidation are different than those that compromise it because of ultraviolet light, thus a UV package is also added to the PE. The purpose of this additive is self-explanatory – it protects the parts from UV attack throughout its life. Unfortunately, it does not last forever and once this UV additive has been consumed, the PE polymer chain starts to degrade and fail. Thus, it is crucial to know the UV rating of your resin, as well as the final product’s end-use location. Note that the UV additive used in PE is compatible with the AO additives mentioned previously. When engineered correctly, these additives work synergistically to protect the PE. It’s also critical to realize that if a rotomolded part is overcooked, the UV stabilizer will also lend a hand in heat protection (but less efficiently than a properly formulated AO package). When this happens, it will drastically reduce the UV protection you think you have in your finished part.
Material
After most parts are Rotomolded, some sort of postprocess will remove unneeded areas of the part, for instance, a large opening will be trimmed away). This removed material is often referred to as “trim stock”. This trim stock, in combination with any scrap produced, is gathered and combined in hopes of being reused later. They are cut into small chunks prior to
being ground into smaller pieces, and later run through a pulverizer to produce powder. Molders typically take this powder and dry blend it with black pigment to create what is traditionally referred to as black REGRIND. Because this regrind came from parts that never left the facility, it is considered post-industrial recycled material (or sometimes sneakily called preconsumer recycled material). Now, take a few minutes and go back to the beginning of this article and re-read the purpose of each ingredient in the virgin material to see if you can identify the big issue with regrind. Do you see it? Here it is — if almost half of the AO packages are already consumed, then what additives are protecting our regrind material when we pass it through the Rotomolding process a second time? The answer is… unfortunately not enough. There will be some residual additives left in the regrind, but the quantity will be uncertain and unreliable. Rotomolding regrind will likely completely consume any residual AO that might still exist in the material, as well as start to use-up the UV package that should remain. And to add insult to injury, the carbon black pigment that was dry blended in isn’t really contributing much either, other than making the product black.
The molded result will be an initially nice-looking black part with no physical impact properties to speak of, because it has no short or long-term AO or UV protection. Ironically, other properties like tensile strength and stiffness will be largely retained, which gives a false sense of security, in terms of final part performance.
So then, how can we take advantage of the postindustrial material we have without all the problems associated with regrind materials? The answer lies in the same additives and processes used to make the virgin material. Let’s do the same thing polymer chemist do with virgin material but replace the PE ingredient with our post-industrial material. This time, after grinding the trim stock and scrap into small pieces, let’s send them through an extruder along with a fortification additive package (including black pigment) to restore the AO and UV protection we need. The pellets coming off the extruder are then pulverized into powder, leaving us with what is commonly known as reprocessed material, or “repro”.
Oh, and by the way, after reintroducing the correct
additives in the correct way, black repro materials will exhibit properties that exceed those of virgin materials that are dry blended with black pigment. Some molders have pulverizing equipment in house, so they are able to make their own regrind. However, molders rarely have their own extruder, so the pursuit of repro will require a relationship with a compounding company (not to mention the freight to get the material back and forth).
This topic is worthy of a much lengthier article. But until then, below are a few additional things to keep in mind:
• If your scrap contains PE from other processes (i.e. injection molding or blow molding), the concentration of stabilizers in these components will be much lower.
• These stabilizers will not perform their function properly if they are dry blended into the PE; they must be incorporated by melt extrusion. Even carbon black pigment has minimal effect as a UV stabilizer if it’s dry blended.
• The presence of other polymers in a PE recycle blend can be disastrous, even at low percentages. Commercially available “post-industrial HDPE” can often contain as much as 5% polypropylene (PP). Using this as a component for Rotomolding could easily reduce its ARM impact to virtually zero.
• It’s common practice to take roto trim stock, directly pulverize it into regrind and then dry blend it with virgin PE powder, as a way of reducing cost. This will invariably produce parts with high brittleness and low impact strength.
As a result of the additional out-of-house processing, you can expect that repro material will cost more than regrind material. But, as is usually the case, you get what you pay for. Other than initial cost, repro will always outperform regrind.
Though they both come from our own post-industrial scrap, regrind and repro follow very different journeys on their way to becoming moldable powder again. Understanding these differences is a must for every molder (and their customers). The only reliable way of recycling trim stock is to re-extrude it and boost the additives pack again to create repro.
Watch for more information from ARM about the recycling webinar coming your way later this Fall. R
One of the paramount challenges for today’s leaders is cultivating the talent of the future and shaping the leaders of tomorrow. In our rapidly evolving world, people remain the core assets of any organization, and the urgent need for fresh talent is particularly acute in STEM (Science, Technology, Engineering, and Maths) fields. However, the UK’s ongoing shortage of STEM skills continue to be a significant issue, costing the economy an estimated £1.5 billion annually.
The Decline in STEM Interest STEM (Science, Technology, Engineering, and Maths) subjects
have seen a waning interest among younger generations, who often gravitate towards more immediately appealing fields of study. This trend is further aggravated by a perceived reduction in investment in skills development by businesses, as individual companies do not always realize immediate returns from such investments.
In recent years, the uptake of apprenticeships in STEM areas, including engineering, manufacturing, and technology, has noticeably declined.
From 2016/17 to 2020/21,
apprenticeship enrollments in England fell by 35% across all subjects, with a specific 30% decline in engineeringrelated apprenticeships. Additionally, in 2020/21, women represented only 14.5% of new starts in engineering-related apprenticeships.
This lack of interest is compounded by challenging working conditions. A staggering 75,000 STEM graduates in 2016 saw only 24% working in STEM occupations within six months. Common misconceptions about STEM careers further exacerbate this issue. A survey by The Smallpeice Trust revealed that
nearly 40% of parents would not encourage their child to pursue a career in engineering, perceiving it as too ‘grimy’ and unsuitable for their ‘girly’ daughters.
Despite these challenges, there are promising developments. The United Kingdom Accreditation Service (UKAS) reported an almost 30% increase in girls starting STEM A-levels in England from 2009 to 2020, and a 50.1% increase in women accepted into full-time STEM undergraduate courses from 2011 to 2020. Yet, women still constituted only 29.4% of the STEM workforce in 2020. This upward trend is encouraging, as enhancing science education and increasing young people’s interest in STEM subjects are vital for addressing the skills shortage and bolstering the UK economy.
UK Research and Innovation (UKRI), a non-departmental public body, has been instrumental in attracting new talent to the industry.
Innovate UK, operating under UKRI, recently funded a project focused on developing a biopolymer for rotomoulding applications. This project, in collaboration with Queens University Belfast, CP Cases, and Matrix Polymers, resulted in a cutting-edge biopolymer case designed specifically for delicate equipment in rotomoulding applications.
At Matrix Polymers, we are dedicated to bridging the gap
between academia and our innovative rotational moulding process. As a creative and an innovative raw material supplier, we partner with numerous universities across the UK and Europe. For decades, we have actively sponsored university programs to cultivate the essential skills required for a seamless transition from academia to our dynamic industrial laboratory.
commitment to addressing the STEM skills shortage. By bridging the gap between academic knowledge and industrial application, we are fostering an environment where innovation thrives and new talent flourishes.
We invite educators, researchers, and aspiring professionals to join us on this journey. Whether you are a student seeking an exciting
We have also implemented a comprehensive Induction Programme to welcome new talent, laying the groundwork for a professional career within our organization. Our initiatives aim to connect the academic and industrial worlds, driving innovation and growth.
At Matrix Polymers, we believe in the power of collaboration and the importance of investing in future generations. Our partnerships with universities and research institutions, combined with our innovative projects and dedicated induction programs, exemplify our
career path, a researcher looking to apply your expertise in a dynamic industry, or a business leader interested in innovative collaborations, Matrix Polymers offers opportunities to make a meaningful impact.
Together, we can overcome the STEM skills shortage and cultivate the next generation of leaders and innovators. By investing in education, promoting STEM careers, and creating pathways for young talent, we can ensure a vibrant and prosperous future for our industry and society. Join us in shaping this future and be a part of the solution that drives progress and innovation forward. R
After some research, there are some physical real-world examples of where these types of billing models are being worked on and implemented.
In a 2022 report titled, “The Future of Food Production”, The Association of Equipment Manufacturers predicted that new business models will emerge in the Agriculture Machinery Industry.
“Equipment manufacturers in other industries are looking to equipment as a service, (a model used predominantly outside of North America until this point) as a possible payment model alongside subscription services. This would allow companies (Farmers in this example) to lease equipment for a specified period, with payment based on the output of that equipment, along with any other services that go along with it, such as data analytics and preventive maintenance, according to AEM’s
report. Equipment as a service is to be of benefit to companies as it allows for machinery to remain current and functional without the need of significant capital expense.”
As mentioned in my last article, we are used to selling and buying our machinery as a one-time business interaction. Instead of paying for the hardware entirely upfront, companies are starting to offer subscription agreements, providing a cheaper entry point, comparable to a cell phone plan.
To reiterate one of the benefits of this model is that it puts responsibility on the machinery company to ensure that their equipment is running beyond expectations. Forcing us to earn and maintain the business. These solutions, as a service, not only minimize upfront costs, but also allow for continually enhancing effectiveness, allowing them to pay only for what their process needs.
The process of collecting data and billing based on the data collected is not new. Therefore, there is a fair amount of market expectations from competitors and related industries driving price positioning. The technology to collect, organize, and categorize this data currently exists off-theshelf with current PLC technology, so the rest is up to the equipment manufacturers and the molding customers to work towards profitable solutions on both sides. Pricing strategy must be geared toward facilitating a rapid return on investment for molders to improve their profitability.
During the manufacturing process, any amount of downtime can affect a manufacturers bottom line. While most of these subscription-based services require a data connection for full
function, it isn’t always necessary for access.
The data is always logged in the PLC, display, or in the architecture onboard the piece of machinery or any connected piece.
Access to timely customer service is just as important. Establishing a robust infrastructure is critical in effectively overseeing the intricate facets of subscriptions. It’s an essential element in guaranteeing a favorable experience for all stakeholders involved.
Machinery manufacturers gain the real time ability to know how products are being used, and are therefore able to provide the latest and greatest insight for successful and efficient use. They also need to make sure that they are obtaining all the content
needed however you want to access it. It also adds a level of responsibility to the machinery manufacturer to be available and connected. Do you want to text somebody? Talk to somebody? All those options need to be available.
While equipment suppliers will always value selling new equipment, they additionally can also emphasize the sale of technology that enhances the intelligence and precision of existing machinery.
In the end, I guess it is up to us!
“Us” is Equipment Manufacturers and “Us” is Molding companies to develop the necessary SupplierCustomer relationships and develop the platform and costing models to make this work.
Speaking personally as an Equipment Manufacturer, there does need to be a certain appetite for this kind of business as it creates a paradigm shift in our receivables. The flip side is that it has the potential to increase overall sales and build long-lasting relationships with our customers.
Stay tuned for more on how it can benefit the Molders in the Audience, and what the billing models might look like.
As always, I would really like to hear any feedback. Please feel free to reach out at rob.miller@ wittmann-group.ca I would be happy to explore, research, examine, and expose any thoughts or concerns, as well as any pros or cons that may come from this topic. R
» ROTOLOAD™ is the ONLY solution to ALL of your powder resin handling needs.
» ROTOLOAD™ is the ONLY comprehensive line of powder resin conveying and weighing equipment, specifically designed to meet the demands of the Rotational Molding Industry.
» ROTOLOAD™ uses vacuum to load your material, hold it above your process machine, and dispense, quickly and accurately. In addition it is the ONLY solution to the question of how to reduce under and overweight parts, mess, downtime and resin loss.
DR. NICK HENWOOD, ROTOMOTIVE LIMITED
Rotomolders tend to be more mechanically minded than chemically minded and typically they do not have a deep understanding of polymer chemistry. Fortunately, the technical experts within polymer supply companies can often help with material selection decisions and with resolving performance issues. While this approach usually works from a practical standpoint, “knowledge is power” and molders will benefit from sufficient understanding of polymer chemistry to make the right choices, especially when they are receiving conflicting advice from different suppliers!
The Association of Rotational Molders (ARM) frequently receives queries from members who are trying to make the right choices, whilst navigating their way through a maze of information. As ARM’s Technical Director, most of these queries land on my desk. I always try to provide the most direct and straightforward answers that I can, but often a little background information is required to explain my comments and recommendations. In this series of articles, I will seek to provide useful insight, without getting readers too immersed in unnecessary detail, concentrating on some of the more common questions that I get asked.
A rotomolder’s go-to material is usually Polyethylene (PE) and a range of grades are available from commercial suppliers. The Technical Data Sheet for a roto grade PE will highlight two key properties: Density and Melt Index. This article will focus on what Melt Index means in a PE context, how it affects overall material physical properties and how it affects processing. Issues involved with density were covered in Parts 1 and 2 of this series.
Molecules of polyethylene consist of long chains of so-called “repeat units” with a structure C2H4 (see Figure 1), with each unit consisting of 2 carbon atoms and 4 hydrogen atoms. These chains can be made from many or thousands of repeat units. For typical grades used in
rotomolding, the “chain length” will consist of at least 1000 repeat units.
A nominal molecular mass, commonly referred to as “molecular weight” (MW), can be assigned to the repeat unit based on the atomic mass of its constituents. By convention, a hydrogen atom (the lightest element in the universe) has an atomic mass of 1 atomic mass unit (amu) and carbon (an atom approximately twelve times as heavy as hydrogen) has an atomic weight of 12 amu. Totaling the constituents gives us a molecular weight for a polyethylene repeat unit as:
(2 x 12) + (4 x 1) = 28 amu
If the number of repeat units is known, the molecular weight for the entire polyethylene chain can
then be calculated. For example, if the chain length is 1200 repeat units, the MW is:
(1200 x 28) = 33,600 amu
Why is chain length so important?
When polyethylene is fully molten (i.e. when its temperature is above approximately 250ºF), all of the polyethylene chains are randomly distributed in a disordered state. This condition is known as the amorphous state.
A good visual analogy would be a bowl of cooked spaghetti. Individual spaghetti strands become entangled with their neighbors, and it can be difficult to remove an individual strand from the bowl. If extra-long spaghetti is used, extraction of a single strand would become even more difficult. If the spaghetti strands are broken up before cooking them, the short strands would be easier to move about.
The behavior of polyethylene chains in the melt state is similar. The longer the chain (as exemplified by a higher molecular weight), the more resistance there will be to flow of the whole molten mass. Resistance to flow can be measured in a variety of ways, but the property being measured is called the viscosity of the melt.
Viscosity and Molecular Weight
It follows, from the previous section, that as the molecular weight of the polyethylene chains increases, so does its viscosity in the molten state. This is exactly what is found in practice, see Figure 2. The type of viscosity measured in this graph is called the “zero shear viscosity” (ZSV), which is a measure that is particularly relevant to rotational
molding. In Figure 2 the viscosity of the melt increases as the chain length increases (as exemplified by molecular weight). After a critical molecular weight is reached (around 3,000 amu in Figure 2), the viscosity increase with molecular weight becomes even more
apply a significant amount of shear to the polymer melt, which enables higher molecular weight grades to be utilized. In contrast, rotomolding applies no shear to the melt, and so the choice of PE grades with useable molecular weights is more limited.
pronounced. This is due to the influence of chain entanglements. It should be noted that polyethylene rotomolding grades tend to have molecular weights well above this level (see previous section), so chain entanglement is an important phenomenon for our process.
Unlike conventional fluids, the viscosity of melted polymers can be affected by how much shear is applied to the melt. Many polymers including polyethylene are prone to shear thinning i.e. increasing the amount of shear reduces (i.e. “thins”) the viscosity. Processes like injection molding, blow molding and extrusion
Viscosity measured at zero shear could be viewed as the “gold standard” for assessing the rotomoldability of a polyethylene melt. However, the equipment to make such a measurement would be prohibitively expensive for many users and the test protocols involved are complex. Mostly we use an alternative method of measurement called Melt Index. Melt Index (MI) measurements are simple to carry out and the equipment required is relatively inexpensive. The polymer melt is subjected to considerably less shear than typical injection molding systems, although significantly more shear than rotomolding.
Figure 3 shows a simple Melt Indexer and Figure 4 shows its component parts.
measurement of polyethylene this temperature is specified as 190°C, but for other polymers the set temperature may be higher. The lower end of the bore is terminated by a plug or “die” with a precise drilled hole through it.
After the material is inserted into the heated bore, it melts quite quickly, within a few minutes. A weighted plunger is then inserted into the bore above the melted material, which will exert a load on the material. This causes molten material to start to flow through the die and a thin strand of material starts to appear; this is called “extrudate”.
After a specified conditioning period, the extrudate strand is cut off at the base of the die and a timer is started. The next extrudate strand is allowed to develop for a set time interval, after which it is again cut off. This
process is repeated several times, to produce a number of extruded strand lengths. When the strands have cooled and solidifed, they are weighed. The average weight of the strands is used to calculate the quantity of extrudate that would have been formed in a 10 minute period. This value is known as the Melt Index (MI) for the material, with units of g/10min.
Figure 5 shows the relationship between Melt Index and Molecular Weight for one specific type of polyethylene. This illustrates an important point, that MI decreases as MW increases. This trend will remain true for all types of PE, although the precise values may vary. Similarly, a high MI will indicate the likelihood of a low zero shear viscosity, so high MI grades will be easier to rotomold than low MI grades.
A MI test is performed per ASTM D-1238. A small sample of test material is inserted into a vertical bore in a solid metal barrel. The sample can be in pellet or powder form. The barrel is maintained at a set temperature, by electrical heating. For the
A PE grade with a high MI will have relatively low zero shear viscosity, which infers that the polymer melt will flow more easily. All other factors being equal, this will result in improved aesthetics for the rotomolded part, with a glossier surface. In addition, surface pinholing should be less prevalent, and any air bubbles trapped in the wall of the part will disappear quickly during the heating cycle.
High MI grades are usually avoided when making thick wall parts. As well as the melt being less viscous, melt strength will be lower. This affects the ability of the melt to support itself on the mold wall when melted, as low melt strength may lead to the formation of drips and other surface defects on the inside walls.
As described earlier, the decrease in viscosity and improvement in flow of a high MI grade is due to less molecular entanglements. However, molecular entanglements have a positive effect on some important material properties, especially impact strength and long-term resistance to stress (e.g. Environmental Stress Crack Resistance, ESCR).
The information contained in this article combined with that in the previous articles of this series can be used to provide a practical basis for choosing the correct grade of PE for a particular application. This is illustrated in Figure 6.
Choosing the correct PE grade for an application involves
a basic trade-off between moldability (high MI is better) and physical properties (high MI may reduce these).
For the majority of small to medium sized rotomolded parts, a combination of medium MI and medium density will be most applicable. In North America, there are many such grades available with MI in the range 3.0-4.0 g/10 min and density in the range 0.935-0.939 g/cm3
may opt for a higher density grade. All other factors being equal, this higher density would result in increased brittleness, lower impact strength and significantly reduced ESCR. These negative effects can be countered by reducing MI, which will also increase melt strength and reduce the incidence of drips on the inside surface. In North America, “big tank” grades are available with lower MI in the range 1.5-2.0
For small to medium sized parts, where speed of processability and excellent aesthetics are paramount, molders may opt for a higher MI and a marginally lower density. In North America, there are a number of such grades available with MI in the range 5.07.0 g/10 min and density in the range 0.930-0.935 g/cm3
For larger sized parts with thicker wall sections, where extra stiffness is beneficial, molders
g/10 min and density in the range 0.942-0.945 g/cm3
Generally speaking, these three MI / density combinations will cover the requirements of approximately 80% of the rotomolding market. Some applications may require other combinations of properties, and in such cases, specialty grades and extruder blends may be needed to fully meet requirements. R
I recently returned from China having attended their annual rotomoulding conference, a supplier factory open day, a rotomoulding factory tour, and finally a visit to Chinaplas. My previous China conference was 2014. This 10 year interval highlighted the changes and improvements in their conference organisation and delivery of local and international speakers. This rotomoulding meeting was one which moulders attending ARMO conferences would recognise as familiar and would appreciate.
The China rotomoulding conference was collectively organised by the country’s rotomoulding association
永恒的回忆与联系
我最近刚从中国回来,参加了中国的滚塑年会、供应商 工厂开放日、滚塑工厂参观,最后还参观了中国国际橡 塑展。我上一次参加中国的滚塑会议是在 2014 年,这 10年的间隔凸显了他们在会议组织和国内外演讲者排程 方面的变化和改进。这次滚塑会议对于参加 ARMO 会 议的厂商来说再熟悉不过了,他们也会对这次会议表示 赞赏及认可。
中国滚塑年会由中国滚塑协会(RPC-CPPIA)及温 岭市旭日滚塑科技有限公司(Rising Sun Rotomoulding Technology)共同组织,旭日滚塑是当地的协调方。会 议于 4 月 17 日至 19 日在中国浙江省的沿海城市温岭 举行。这是我第三次参加中国滚塑会议。
中国滚塑年会由中国滚塑协会(RPC-CPPIA)及温 岭市旭日滚塑科技有限公司(Rising Sun Rotomoulding Technology)共同组织,旭日滚塑是当地的协调方。会
(RPC-CPPIA) and Rising Sun Rotomoulding Technology as the local coordinator. It took place from 17-19 April in the coastal city of Wenling, Zhejiang Province, China. This was my 3rd China conference.
The event was structured over three days. The first day featured a pre-conference technical seminar. The two conference days included 20 technical presentations, of which 12 were from Chinese companies and 8 were from foreign companies. The conference was held in Chinese and English languages, with simultaneous translation available for everyone during both the seminar and conference sessions.
There were networking breaks around the supplier tabletop exhibits throughout the conference days allowing for multiple opportunities to visit with suppliers and investigate new products and services. A formal networking gala dinner was held on the first night of the conference presentations.
RotaConsult delivered an all day seminar on Wednesday to around 60 people. This level of support indicating that there is a thirst for more practical technical information by local moulders. A good inclusion by organisers. I attended the conference presentations along with 220 people from 11 countries. Making this conference one of the largest ever since RPC-CPPIA was established in 2005.
Gareth McDowell, 493K, delivered 2 sessions on the importance of the cooling cycle Gareth McDowell 493K,就冷却循环的重要性发表了两场演讲
Presentations from the United Kingdom to New Zealand reminded me how global this industry is. These included 3 Chinese university professors, local Chinese suppliers, Matrix Polymers, PolymerLink, ExxonMobil, La Plastenica, Lysis, 493K and RotaConsult.
A wide range of subjects were covered including presentations on electrically heated moulds, venting, cooling, machine safety, sustainable materials, recycling XLPE , graphics, industrial tanks and the ever popular hydrogen fuel tanks.
[7180] Networking break time at suppliers exhibition area 在供应商展区的交流休息时间
议于 4 月 17 日至 19 日在中国浙江省的沿海城市温岭 举行。这是我第三次参加中国滚塑会议。
会议为期三天。第一天是会前技术研讨会。两天的会 议包括 20 个技术型演讲,其中 12 个来自中国公司,8 个来自外国公司。研讨会和会议期间均提供中英双语同 声传译。
整个会议期间,供应商桌面展品周围都设有交流休息 区,这为参观供应商和考察新产品及服务提供了许多机
Conference dinner, representing Malaysia, China, Jordan, New Zealand, United Kingdom & Australia. English being the common language spoken at this table of 10. 会议晚宴, 代表马来西亚、中国、约旦、新西兰、 英国和澳大利亚。英语是这 10 人餐桌上的共同语言。
The pre-conference seminar proved surprising to me because of the high level of engagement by the attendees. When delivering these seminars it is satisfying to find an audience willing to ask many questions as it indicates they are not just listening, they are also reacting and interacting with the information. I had a preconceived opinion that the Chinese audience would be hesitant to ask questions. How wrong was I.
While there is simultaneous translation during the formal parts of the conference it is more difficult to network during the breaks and dinner events if you only speak English. While there are increasing numbers of business people in China, especially the younger, who can speak some English, many of the moulders conduct business in China or the Asian region, and like me, only speak their native language. This does not make it impossible to communicate, just more challenging.
The networking gala diner event was a welcome reception for the 220 people. Entertainment included a Dragon dance and the fascinating Chinese dramatic art of face changing, where a performer changes their masks in lightning-fast speed. As if by magic. The quality of the dinner and entertainment program was certainly equal to those of other major rotomoulding associations around the world.
会。会议的第一天晚上还举行了正式的交流 晚宴。
RotaConsult 于周三举办了为期一天的研 讨会,约有 60 人参加。从参加人数可见当 地滚塑制造商渴望获得更多实用的技术信 息,组织者很好地融入了这一活动。我与 来自 11 个国家的 220 人一起参加了会议演 讲。此次会议是 RPC-CPPIA 自 2005 年成 立以来规模最大的会议之一。
从英国到新西兰,来自各个地区的演 讲体现了行业的全球化。其中包括 3 位 中国大学教授、中国本地供应商、Matrix Polymers、PolymerLink、ExxonMobil、La Plastenica、Lysis、493K 和 RotaConsult。
会议涵盖的主题很广泛,包括电加热模 具、通气、冷却、机器安全、可持续材料、XLPE 回 收、滚塑曲线、工业储罐和一直很受欢迎的氢燃料储 罐。
让我感到惊讶的是,会前研讨会与会者的参与度很 高。在举办此类研讨会时,我很高兴听众愿意提出许多 问题,因为这表明他们不仅在聆听,还在对信息做出反 应和互动。我曾先入为主地认为,中国听众会对提问犹 豫不决,但事实证明我是错的。
虽然在会议的正式部分有同声传译,但如果只讲英 语,就很难在休息时间和晚餐活动中进行交流。虽然中 国会说一些英语的商务人士,尤其是年轻人越来越多, 但许多在中国或亚洲地区开展业务的厂商们,我也一 样,只会说自己的母语。这并不意味着无法沟通,只是 更具挑战性。
交流晚宴是 220 人的欢迎招待会。娱乐节目包括舞龙 和引人入胜的中国戏剧艺术--变脸,表演者以迅雷不及
Robot in action during Rising Sun factory open day 旭日工厂开放日运行中的机器人
On Saturday many of the conference delegates attended the Rising Sun Rotomoulding Technology new factory open day and were invited to the Rising Sun dinner celebration for their 20 years business anniversary. The tour around the new 3 level factory was interesting, especially seeing the use of automation and robotics in their mould and machine fabrication operation. Labour costs in China are continuing to rise and discussions with conference attendees highlighted that many within the China rotomoulding industry are adopting advanced manufacturing technologies to improve their quality and competitiveness.
While the conference gala dinner was equal to other rotomoulding associations the Rising Sun anniversary dinner and entertainment evening was on another level. More closely related to a world class spectacular entertainment event. It was amazing for the more than 300 guests. The additional networking opportunity appealed to me as it allowed me to connect with some more new contacts whom I had not spoken with during the rotomoulding conference.
Saturday nights 20yr anniversary theme 周六晚的 20 周年主题
Another reason why some foreign moulders attended the China rotomoulding conference was Chinaplas, which was held the following week in Shangahai. This is the worlds 2nd largest plastic exhibition, which had over 4,000 exhibitors and received 321,879 visitors, of which 73,000 were from overseas, during the 4 day global event. I joined a bus load of moulders from
Face changing (Bian lian) performer. 变脸表
掩耳之势更换面具,就像变魔术一样。晚宴和娱乐节目 的质量与全球其他主要滚塑协会举办的不相上下。
周六,许多会议代表参加了旭日滚塑新工厂开放日活 动,并应邀参加了旭日20 周年庆典晚宴。参观新的三 层工厂非常有趣,尤其是看到他们 在模具和机械制造操作中应用了自 动化和机器人技术。中国的劳动力 成本正在持续上升,与会人员的讨 论突出表明,中国滚塑行业的许多 企业正在采用先进的制造技术来提 高质量和竞争力。
年会晚宴与其他滚塑协会的晚宴 不相上下,而旭日周年晚宴和娱乐 晚会则另有一番风味,它更像是一 场世界级的精彩娱乐活动。这对 300 多名来宾来说实在是太棒了。 额外的交流机会对我很有吸引力, 因为它让我与更多在滚塑会议期间 未曾交谈过的人们建立了联系
Konstantia Asteriadou(Lysis)和 Rory Jones(La Plastenica)
Oceania region travelling 400km (250mi) between Wenling and Shanghai, visiting Chinaplas and the city sights in the evenings.
Our tour group was organised by Grant Palling from FLEXr Solutions in Australia and included a rotomoulding factory tour at Kuer Group in Ningbo (near Shanghai). While you can travel around China independently it is definitely easier, and another great opportunity for networking, when you can join a group of like minded people on an organised business tour. Networking is one of the valuable benefits of attending conferences or joining tours. R
一些外国厂参加中国滚塑年会的另一个原因是下周将 在上海举办的中国国际橡塑展。这是全球第二大塑料展 览会,有 4000 多家参展商,在为期 4 天的全球活动中 接待了 321 879 名参观者,其中 73 000 人来自海外。
我和来自大洋洲地区的厂商一起,乘坐400km的大巴从 温岭到上海,参观了中国国际橡塑展和一些城市景点。
我们的旅行团是由澳大利亚 FLEXr Solutions 公司的 Grant Palling 组织的,其中包括参观位于宁波(上海附 近)的 酷尔集团的滚塑工厂。虽然您可以独立游览中国 各地,但如果您能加入一个由志同道合者组成的团队, 参加一次有组织的商务旅行,无疑会更加轻松,而且也 是建立联系的另一个绝佳机会。建立关系网是参加会议 或旅行团的宝贵好处之一。 R
What a whirlwind few days at our annual industry conference Rotomould24. We hosted 160 attendees from across the globe on the stunning Gold Coast, and current feedback is highlighting its success.
With keynote speakers Dan Gregory and Kieran Flanagan kicking things off, to Ian Hansen and Mark Kearns sharing invaluable technical knowledge, as well as a range of high-quality speakers providing compelling business presentations and case studies Rotomould24 was an engaging and informative event that covered a wide spectrum of topics. Kevin Humphreys DSC closed the event on a high note, leaving us all inspired.
Thank you to everyone who made our Welcome Dinner and first official ARMA Awards Dinner such a success.
A heartfelt thank you to my incredible team Zoe Perrington, Karly Gniel, Alyce Wood, and Kerrie Wise for their hard work and support—you made
everything smoother and more enjoyable.
A huge thank you to all our sponsors and trade exhibitors for your support.
Michelle Rose, ARMA CEO R
was an engaging and informative event that covered a wide spectrum of topics.”
—Michelle Rose at the end as it’s written in first person
ARMA proudly presented the Icons of Rotomoulding Award to this year’s honouree, Andrew Currie, Managing Director at Price Plastics.
With a long career in the rotational moulding industry, Andrew began his journey at ICI, followed by Huntsman Chemicals, before taking on his current role. His leadership is characterised by a proactive approach to both business and industry challenges.
Andrew has been pivotal in supporting Price Plastics and its customers through the industry’s fluctuations, often extending financial support during critical times. His leadership during stressful periods, particularly about 15 years ago, helped stabilise many of his company’s clients. Furthermore, Andrew has been an active member of
This year, the ARMA Board decided to relaunch the Best Product Award, and we extend our gratitude to all the companies that entered and showcased their innovative products. The categories for this award included rotational moulded consumer products, technical products, and conversion products.
the ARMA board, where he has significantly contributed to safety and operational standards across the industry.
Andrew’s commitment extends beyond corporate governance. He is a regular presenter at ARMA conferences, where he shares valuable insights on noncommercial topics like Workplace Health and Safety, which have been beneficial to the industry. His initiatives, especially in supporting the WHS related to tank unloading, demonstrate his dedication to enhancing industry practices and safety standards. Andrew Currie’s influential role in driving both business success and industrywide improvements marks him as a distinguished nominee for the Icons of Rotomoulding award.
Congratulations Andrew! R
Conference attendees had the opportunity to view these outstanding products and cast their votes using the conference app. The winner will receive a complimentary one-year ARMA membership and free registration for the next conference.
The products entered were:
• Tip & Run Coolant Recovery Tray by BR Plastics
• Lastro Solar – Solar Ballast by Fortlev Industria, Brazil
• Water Tank Base by KK Kingston, Papua New Guinea
• The Wash Tub by KK Kingston, Papua New Guinea
• Loof Watering Can by Melbourne Rotomould, Australia
• Train Carriage Crossover by Plastic Fabrications, Australia
• Noise Control Wall by Pact Group
The 2024 Best Product Award goes to the Noise Control Wall by Pact Group. A very close runner up was the Tip & Run Coolant Recovery Tray by BR Plastics.
For more information about the Best Product Awards, or to be put in contact with any of the entrants, please email ARMA: info@rotationalmoulding.com. R
The last Student Design Awards were held back in 2010, and re-establishing these awards has been a goal for ARMA. Although it wasn’t initially planned for this year, a fantastic opportunity arose when a New Zealand university reached out with a request to include rotational moulding in their curriculum for the first semester. The ARMA team eagerly seized this chance, and we relaunched the Student Design Awards this year.
Despite having minimal time to prepare and promote, we were delighted to receive 12 entries, mostly from 2nd-year students. This level of interest is promising, and we look forward to building on this momentum in the future.
For judging, ARMA CEO Michelle Rose selected a diverse group of experts from across the industry to ensure a fair and comprehensive evaluation. We extend our gratitude to them for their time and expertise.
The entries were:
• Showerease | Abigail Hall
• AquaLounge | Angelina Ashley
• Sofa King Seat | Charles Abalos
• EduDock | George Allen
• Anywhere Chair | George Haig
• Portable Gazeboda | Hannah Gaboda
• Oval | James Mitchell
• Team Manta Board | Janiqua McCarthy
• The EcoCrush | Liam Black
• O-Buoy | Samuel Clark
• Grow-With-Me-Bed | Wesley Quider
• Glow Worm | William Scheffe
The winners received their prizes, including certificates, after the conference. The total prize pool of $5000.00 was distributed among the top entries.
• 1st Prize was awarded to the O-Buoy designed by Samuel Clark
• 2nd Prize went to the Oval by James Mitchell
• 3rd Prize was awarded to Janiqua McCarthy for Team Manta Board.
Students always retain ownership of their own designs. For more information about the Student Design Awards, or to be put in contact with any of the entrants, please email ARMA: info@rotationalmoulding.com. R
BPF took part in the BPF Joint Meetings Day!
The Rotational Moulding Group of the British Plastics Federation (BPF) took part in the BPF Joint Group Meetings Day for its members – the first event of its kind that the trade association has run. The event (held on 4 June) was designed to be an informative mix of top-level industry updates, sub-sector updates, and cross-sector networking. As the BPF represents the entire plastics supply chain, the event covered everything from raw materials to processors and recyclers, to equipment suppliers. As a result, a few BPF groups were invited to host meetings at the joint Group Meetings Day to see if it helped people to network with others outside of their typical professional circles.
The event included a small industry exhibition, including stands from a few universities, many of which had recently joined the BPF’s University Network launched in 2024 to support and foster collaborative initiatives to enhance the evolution of plastics research and innovation throughout the UK. The UK is a hub of innovative excellence, with outstanding capabilities in the field of polymers research within a range of diverse research areas ranging from artificial intelligence, design, novel materials, green chemistry, polymer processing, advanced recycling, and much more.
Long-term Rotational Group member, Queens University Belfast is part of the BPF University Network and will be familial to moulders around the world as the world’s leading research facility in Rotational Moulding.
For the Rotational Moulding Group meeting, there were 15 delegates representing 9 companies in attendance. Members enjoyed a guest speaker that reported on Corporate Sustainability Due Diligence - sustainability measures being implemented in the EU at reporting level and that are already impacting supply chains in the UK. Stakeholders increasing shaping their procurement around environmental, social and governance (ESG) credentials, and more consumers are making ethical choices. Members agreed that is an area that should be addressed by
the BPF and plans are now in place to provide guidance to members.
Members also discussed plans for this year’s Annual Rotational Moulding Group Seminar (to be held on 3 December), and proposals for further Group factory tours, replicating the success of last year’s mission to Italy.
For more information contact gcraig@bpf.co.uk
This year’s Plastics and AI Online Seminar returns with a focus on the latest developments in machine learning and data science. Chaired by BPF’s current President, Nigel Flowers, the programme will include the implications of AI in industrial manufacturing, essential updates on AI legislation for UK businesses, and AI’s role in corporate governance.
THIS SEMINAR will focus on the latest developments in machine learning and data science.” “
The seminar will also explore new advancements from the past year and what they mean for the plastics industry. Topics will cover AI-driven solutions to measure and reduce the carbon footprint in plastics manufacturing and the transformative potential of AI in predicting polymer solubility for improved solvent recycling and chemical formulation.
This event promises valuable insights into the integration of AI in enhancing industrial processes and sustainability efforts in the plastics sector. R
ASSOCIATION OF ROTATIONAL MOULDERS AUSTRALASIA LTD Michelle Rose, CAE Chief Executive Officer PO Box 237 Moonee Ponds VIC 3039 Australia
Phone: + 61 (0)404 265 887 michellerose@ rotationalmoulding.com www.rotationalmoulding.com
ASSOCIATION OF ROTATIONAL MOULDERS SOUTHERN AFRICA PO Box 6966
Birchleigh 1621 Gauteng, South Africa
Phone: +27 82 772 3769
Fax: +27 12 541 1738
Chairman: Gary Wiid info@armsa.co.za www.armsa.co.za
IT-RO ITALIA ROTAZIONALE
Katia Zoppetti Via E. Brigatti 12 20152 Milano (MI) Italy
Phone: +039 348 7652560 www.it-ro.it
SOCIETY OF ASIAN ROTOMOULDERS (STAR) 40/145, Ground Floor, Chittaranjan Park New Delhi 110019
Phone: + 91-11-41630157
Fax: +91-11-41634952
Cell: + 91- 9810305356 sb.zaman@staraisa.org arnacz@satyam.net.in www.starasia.org
ASSOCIATION OF ROTATIONAL MOULDING
(Central Europe) e.V. (ARM-CE)
MAUS GmbHRotationsgießformen
Am Viehweg 9 - D-76229
Karlsruhe
Amtsgericht Mannheim, HRB 103433
Chairman info@rotational-moulding.de www.rotational-moulding.de
17 Diversified Mold & Castings
19800 Miles Road
Warrensville Hts., OH 44128-4118 USA 216.663.1814 | 888.642.1222 info@diversifiedmolds.com www.diversifiedmolds.com
5 Ferry Industries, Inc. 4445 Allen Road
Stow, OH 44224-1093 USA 330.920.9200 sales@ferryindustries.com www.ferryindustries.com
9, 68 Jerico Plastic Industries, Inc. 7970 Boneta Road Wadsworth, OH 44281 USA 330.334.5244
Minerva Plant: 330.868.4600 steve@jericoplastic.com www.jericoplastic.com
58 JSJ Productions, Inc.
625 West Market Street Salinas, CA 93901 USA 512.894.4106 susan@jsjproductionsinc.com www.jsjproductionsinc.com
11 Matrix Polymers
The Priory Orchard Hill Little Billing Northhampton, NN9 9AG United Kingdom
+44.1604.789100 sales@matrixpolymers.com www.matrixpolymers.com
7 Orenda
165 Steelcase Rd. East Markham, Ontario L3R 1G1, Canada 905.513.8043 sales@orenda-automation.com www.orenda-automation.com
29 OREX Rotomoulding Sp. z o.o. Cieszyńska 6, 43-520 Chybie Poland +48 32 440 83 15 magda.wantola@orex.pl www.orex-rotomoulding.com
23 Poliplast S.p.A. Via Carrali, 8 24020 Casnigo (BG) Italy +39.035.724145 info@poliplastspa.com www.poliplastspa.com
3 Powder King, LLC 41780 N. Vision Way Unit 120 Bldg. 2 Anthem, AZ 85086 USA 623.551.9897 sales@powder-king.com www.powder-king.com
21 Rotaloc 100 S. CP. Avenue Lake Mills, WI 53551 USA 303.948.5434 sales@rotaloc.com www.rotaloc.com
2 Roto Polymers 26210 Emery Road, Suite 202 Cleveland, OH 44128 USA 1.844.POLIMER (1.844.765.4637) info@rotopolymers.com www.rotopolymers.com
67 Rotomachinery Group Via Crosa, 53 28065 Cerano (NO) Italy +39.0321.772021 polivinil@polivinil.com www.rotomachinerygroup.com
14 VMP, Inc. 24830 Avenue Tibbitts Valencia, CA 91355-3404 USA 888.4.VMP.INC 661.294.9934 info@vmpinc.com www.vmpinc.com
49 Wittmann Battenfeld Canada Inc. / ROTOLOADTM 35 Leek Crescent Richmond Hill, ON L4B 4C2, Canada 905.887.5355 Toll Free: 1.888.466.8266 info@wittmann-group.ca www.wittmann-group.ca
25 Xcelerant Growth Partners
624 W. Washington Avenue, #411 Madison, WI 53703 440.384.7654 info@xcelerantgrowthpartners.com xcelerantgrowthpartners.com
625
Jerico’s experience in the rotational molding industry has uniquely positioned us to address the material challenges faced by molders today. We understand your compounded resin requirements and provide the quality, consistency, and support necessary to help you grow and achieve your production goals.
Jerico’s three North American plants are strategically located and we are poised to deliver on any size job, anywhere in North America!
It all matters—Stick with Jerico!