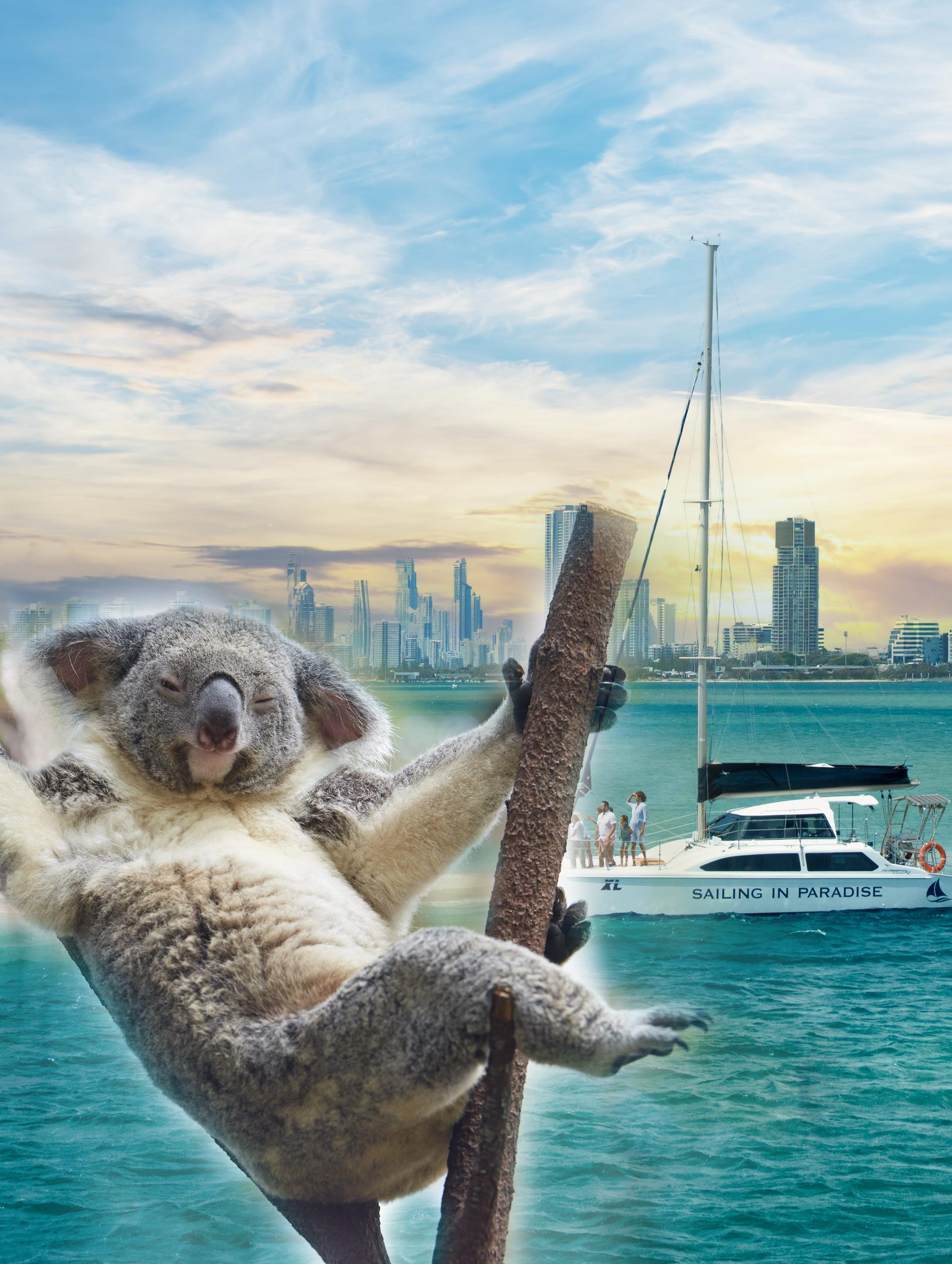
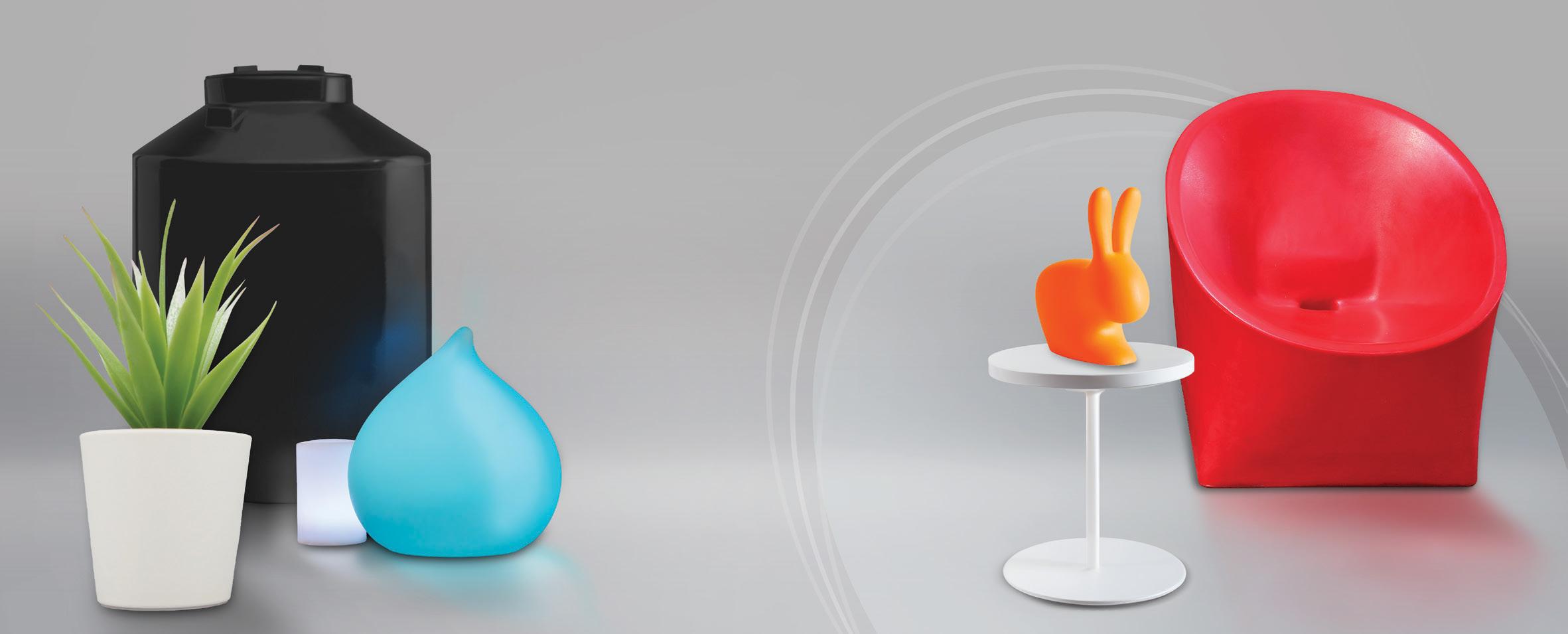

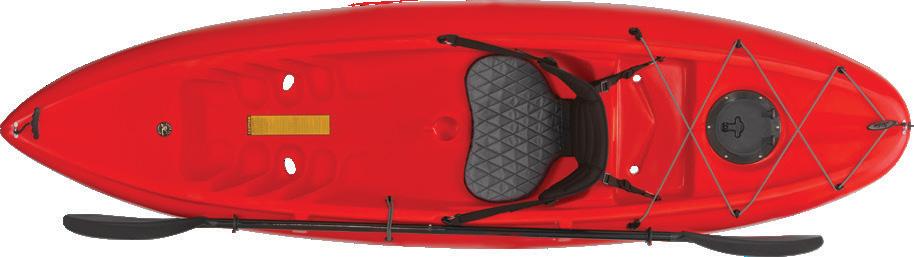
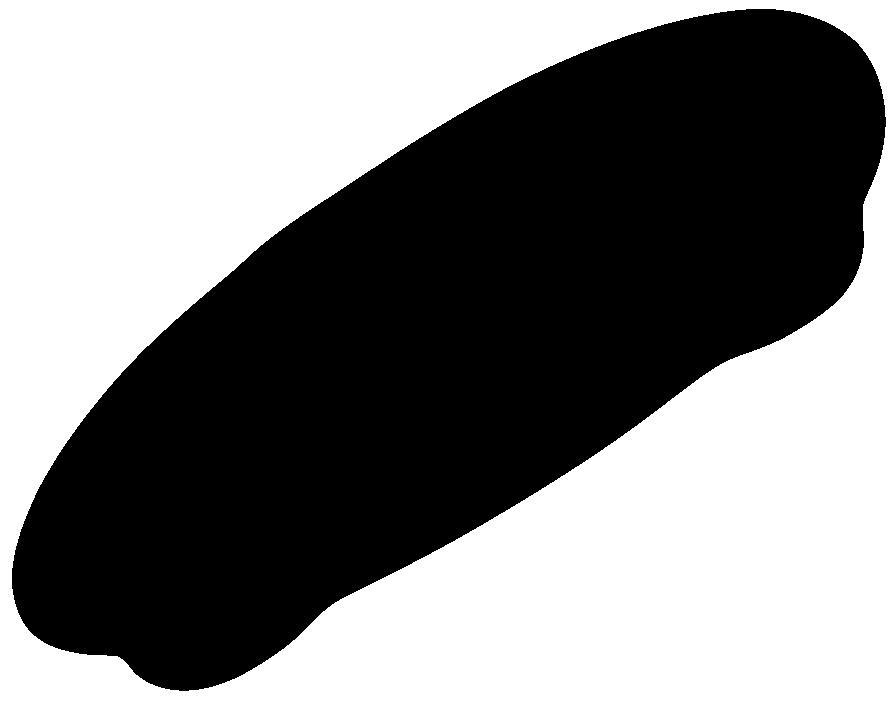
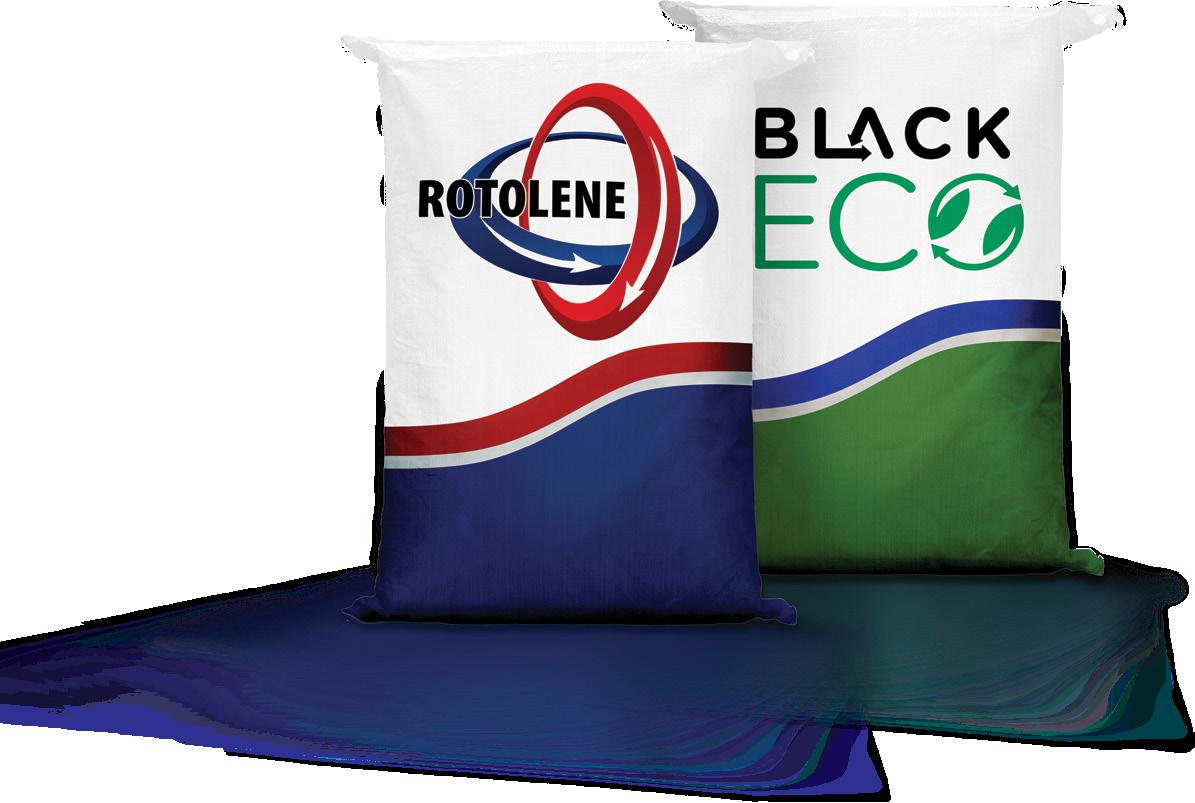
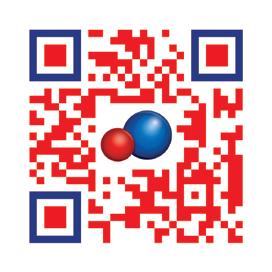
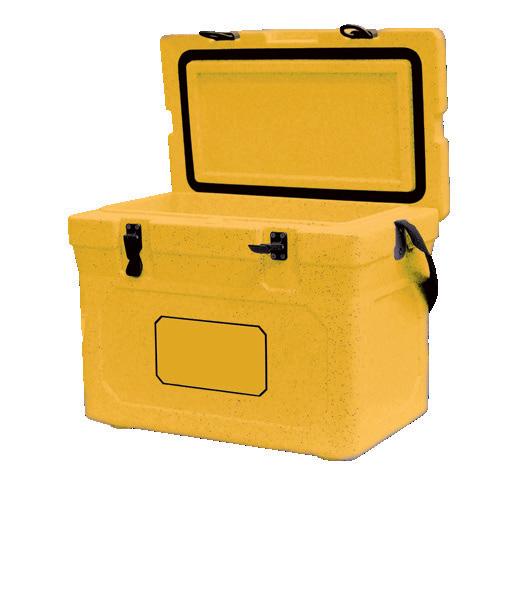


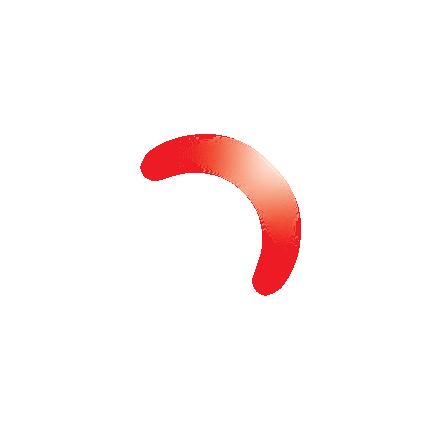
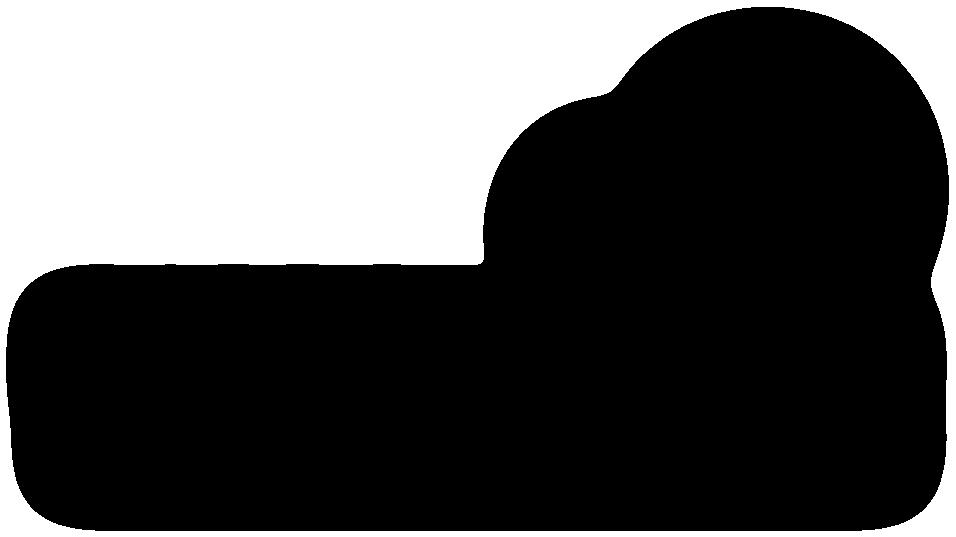

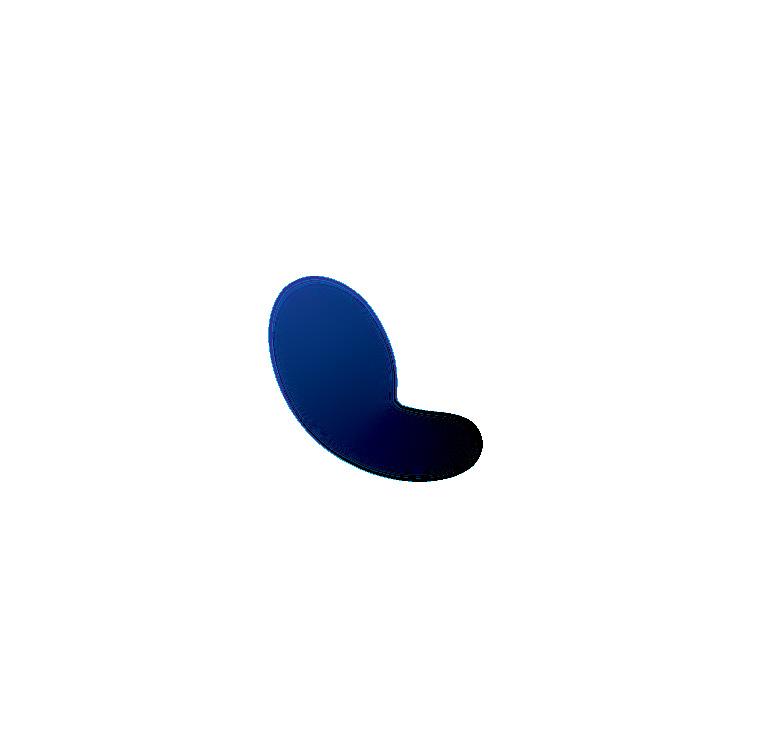
Powder King® is proud to say that we have been building pulverizers for over 20 years and is the most well known pulverizer manufacturing company worldwide. At Powder King®, we focus on design consistency with proof of performance from around the world. In fact, we believe our design is so unique and delivers exceptional results because of its original design. Here at Powder King®, we stick with what truly works. Our pulverizing systems are built with pride and all American-made parts from start to finish.
In addition to over exceeding our customers' expectations with our technical services and grinding rates, Powder King® offers a proprietary EC200 Operating System with full remote accessibility for the customer and by the supplier in order to keep your business running without having to stop production. At Powder King®, our mission is to turn ideas into value and transform pellets into powder for the rotational molding industry.
26. Iceland Delivers.
A remarkable blend of Iceland’s natural beauty and the latest advances in rotational moulding.
Ronnie Ervik, Norner 36
44. Welcome to Rotomould24: The Must-Attend Conference of the Year! ARMA once again raises the bar promising an exciting, valuable conference on the Gold Coast.
Michelle Rose, ARMA CEO 26
36. StAR 2024
A Success with Valuable Takeaways for Participants
S B Zaman, StAR Executive Director
56. Why RotoLoPerm® is the best solution to meet CARB/EPA Emission Requirements without having to sacrifice Impact Resistance
Dan Grimes & Alvin Spence Centro, Inc.
Upfront: Dow showcases circular and innovative materials science solutions and industry collaborations at Chinaplas 2024
08. FROM THE PUBLISHER Raising the Bar!
Susan Gibson, JSJ Productions, Inc.
10. CREDITS
ARM Report: ARM Technical Director - Key Points on Rotation
From the Mail’s Perspective
53. AT ISSUE
Investing In and Developing Young Talent is a Big Priority for Our Industry
Martin Coles, Matrix Polymers
54. INTERSECTION INDUSTRY 4.0 & A
12. GLOBAL CONTRIBUTING EDITORS
Global Contributors, Department Contributors, and Issue Contributors
15. UPFRONT Industry News, Trends, and Products
30. X-FACTOR
Five Things We Need to Stop Saying!
Tom Innis, Xcelerant Growth Partners
34. PRACTICAL ROTO TIPS
Finding Conditions of Failure
Dru Laws, Brigham Young University – Idaho
40. ARM REPORT Spring is in the Air!
SUBSCRIPTION BASED BUSINESS MODEL
What is the Big Question when it comes to Industrial and Machinery Needs?
Rob Miller, Whittmann Battenfeld / Rotoload Canada
64. ROTO AROUND THE WORLD
Moulding India’s Sustainable Future: A Rotomoulders Journey
Ian Hansen, RotaConsult
69. ARMO NEWS From the Mail’s Perspective
72. GLOBAL CALENDAR
Prominent Roto Industry Dates!
74. ADVERTISERS’ INDEX RotoWorld® advertiser contact information
Raising the Bar, by definition, means to set a high standard and raise expectations. It also means to set higher goals and expectations than you currently have, whether it is in your career, profession, avocation, or personal life. Raising the Bar mentally or as a part of a stated plan gives us a chance to look at our current situation, assess our part, and decide what is of value and what is of non-value. It gives us a chance to better see matters that are urgent as well as matters that are important. It gives us a chance to see where we really want to go and what we want to achieve. It allows us to determine our motivation to achieve a new standard. Welcome to RotoWorld® Issue 2!
The idiom “Raising the Bar’ came to mind as I read all the excellent content inside this issue. Our very talented and thoughtful editors are all right on track when it comes setting a higher standard for our industry. Starting with Tom Innis’ column Five Things We Need to Stop Saying! Tom’s words ring true for our industry. For far too long we have been hearing Rotational Molding is the whipping boy of the plastics manufacturing industry. But the truth is that we have come far in terms of manufacturing advances and the products produced through Rotational Molding all around the world. I think we can heed Tom’s wise advice when he says, “Let’s
confidently position Rotomolding with “Here’s what we can do that no other manufacturing process can do mindset, and let’s channel our collective energy and creativity to raise the profile and awareness of our unique and eminently capable industry”. Thank you, Tom! Dru Laws writes in his column about “defining the quality of a part or process by taking it to its extreme edge, and only then can you truly understand its acceptable limits”. Only if we push innovation to the very limit will we ever understand the limit we can reach. Martin Coles exemplifies this whole notion in his column on “Investing in and Developing Young Talent is a Big Priority for Our Industry”. If we are not training those experts to follow us, we are falling behind. Martin makes us think about how important (and maybe urgent) it is to Raise the Bar by re-defining the fabulous industry of Rotational Molding for young people so they can understand the opportunities. Rob Miller writes about taking our industry to a whole new level with “Subscription Based Business Models”. What an idea...maybe Rotational Molding is not that different from other industries that have found this kind of model highly successful, i.e. food delivery, Amazon online shopping...all the things we are doing in our regular lives. Ian Hansen, RotaConsult, talks about the initiatives Frontier in India has taken to Raise the Bar
regarding recycled plastics. “They have demonstrated that high value and high-quality recycled products can be successfully manufactured and marketed to end users.” And, how about Raising the Bar in design with ARMA’s reporting on noted photographer Des Crossley and rotomolder Mark Medew of Plastic Fabrications, who teamed up to produce some incredibly attractive custom mailboxes.
Ultimately, Raising the Bar whether it is for your company, your employees, or yourself means you care about growth and progress. You care about those exciting advances you can discover and achieve. We can set the bar low and tread along, or we can set the bar high and achieve greater heights than we ever expected. That is what I see happening in the Rotational Molding industry every day. And we want to do our part to get the word out, educate, and make designers, OEMs, and the world aware of what this process can do!
Wishing you a happy and successful summer! R
Jerico is first in quality resins and compounds! We’ve made our name by providing vibrant colors, specialty blends, and recycled black, while focusing on being that one complete source for ALL your rotational molding compound needs. Now you can add natural PE to the list!
Time and again over the years, our team has responded to the changing times with resilience, ingenuity, resolve, and confidence. In true Jerico fashion, we developed sustainable and adhesion compounds, then
blended vibrant colors into both. Make no mistake, we are expanding and are focused on becoming your supplier of choice for rotational molding materials.
As we grow, we look for ways to improve so that we exceed your expectations and help you achieve success! Our mission is to be the go-to resource for resins and compounds that meet your precise specifications, arrive on time, and provide the consistent level of quality you have come to expect from Jerico!
PUBLISHER & EDITOR
Susan D. Gibson President - JSJ Productions, Inc. susan@jsjproductionsinc.com
TECHNICAL EDITOR
Alvin Spence PhD MEng aspence@centroinc.com
PROCESS EDITOR
Paul Nugent PhD MEng paul@paulnugent.com
DESIGN EDITOR
Michael Paloian President - Integrated Design Systems, Inc. paloian@idsys.com
GLOBAL CONTRIBUTING EDITORS
Celal Beysel Chairman - Floteks Plastik beysel@superonline.com
Tom Innis Excelerant Growth Partners w@xcelerantgrowthpartners.com
Martin Coles Matrix Polymers martin.coles@matrixpolymers.com
Adam Covington Ferry Industries acovington@ferryindustries.com
Mark Kearns Moulding Research Manager m.kearns@qub.ac.uk
Ravi Mehra Managing Director - Norstar International LLC maramehra@aol.com
ADVERTISING AND ART PRODUCTION
Marketing/Advertising Director Jennifer Gibson Hebert Vice President, JSJ Productions, Inc. jennifer@jsjproductionsinc.com
Chief Art Director Anya Wilcox JSJ Productions, Inc. awilcox@designintersection.com
CIRCULATION & DISTRIBUTION ADMINISTRATION
Sheryl Bjorn JSJ Productions, Inc. sheryl@jsjproductionsinc.com
EDITING & TRANSLATIONS
Suzanne Ketron | Oliver Wandres | Sheryl Bjorn
WEBSITE & ONLINE TECHNOLOGY Jason Cooper JSJ Productions, Inc. jason@bound.by
RotoWorld® is a JSJ Productions, Inc. Trade Publication JSJ Productions, Inc. 625 West Market Street, Salinas, CA 93901 Phone: (512) 894.4106; Fax (512) 858.0486 Email: rotoworldmag@rotoworldmag.com and Website: www.rotoworldmag.com
Subscriptions: One-year subscription (six issues), print or digital, $80 US, $100 Canada/Mexico, $155 All Other Countries. To subscribe or to submit change of address information, call us at (512) 894.4106 visit us online at www.rotoworldmag.com; or email us at sheryl@jsjproductionsinc.com. You may also write to RotoWorld® Subscriptions, JSJ Productions, Inc., 625 West Market Street, Salinas, CA 93901
Advertising: For information on advertising, please contact Advertising Director Jennifer Gibson Hebert, JSJ Productions, Inc. Email Jennifer Gibson at jennifer@jsjproductionsinc.com
Letters: We welcome letters about our contents. Write Letters to the Editor, JSJ Productions, Inc., 625 West Market Street, Salinas, CA 93901 512.894.4106 phone 512.858.0486 fax, or Email susan@jsjproductionsinc.com.
Editorial Queries: We consider unsolicited contributions. Send manuscript submissions as email attachment to Susan Gibson at susan@jsjproductionsinc.com.
JSJ Productions, Inc. bears no responsibility for claim or factual data represented in contributed articles.
Postmaster: Send changes of address to RotoWorld®, JSJ Productions, Inc., 625 West Market Street, Salinas, CA 93901
RotoWorld® is a JSJ Productions, Inc. independently owned, bi-monthly trade magazine for the international rotational molding and plastics design industries. JSJ Productions, Inc. owns all copyrights on articles published herein unless ownership is otherwise stated. Reproduction of this magazine, in whole or in part, without the express written permission of the publisher is not permitted.
Polyethylene Granules & Powders
Crosslink Polyethylene
Polypropylene Granules & Powders
Polyamide Powders
Ancillary Products
Designed for Roto® a dedicated range of materials to be used in rotational moulding applications.
Dedicated Technical Services Support Team
Multi-lingual Customer Service
NEW for 2023 our latest investment in a purpose-built compounding and grinding plant in Rayong, Thailand.
6 Manufacturing Sites across 3 Continents
To learn more about our products & material solutions get in touch at:
Alvin Spence is Vice President Engineering at Centro, Inc., North Liberty, Iowa. He provides leadership for Centro’s product development team and quality resources. Alvin received his Bachelor’s degree in Mechanical & Industrial Engineering and PhD from Queen’s University Belfast. aspence@centroinc.com
Michael is President of Integrated Design Systems, Inc., Great Neck, New York. Over the past 25 years, Mike has developed a broad range of plastic products utilizing various processing methods including rotational molding. Mike’s B.S. degree in Plastics Engineering and Masters in Industrial Design, combined with his extensive experience, has formed the basis for his branded and unique insights into the field of plastics part design. paloian@idsys.com
Paul is a consultant who travels extensively across six continents assisting clients in many roles from training to expert witnessing. He received his Eng. degree in Aeronautical Engineering and Ph.D. in Mechanical Engineering from Queen’s University of Belfast. Paul developed the Rotolog system, the first complete computer simulation (RotoSim), and authored a book entitled Rotational Molding: A Practical Guide.
paul@paulnugent.com
Ravi Mehra has been associated with the rotational molding industry since the early 1970’s. He is a Past President of ARM – Association of Rotational Molders, and has been inducted into the ARM Hall of Fame. He is the Founding Chairman of StAR – the rotational moulding Trade Association of India. He was the Chairman of ARMO – Affiliation of Rotational Moulding Organizations from 2012 to 2014. Ravi consults internationally with companies in the rotational moulding arena to help their global strategy, facilitate technology tie-ups, and business alliances. maramehra@aol.com
Martin Coles, CEO of Matrix Polymers co-founded the business 30 years ago and is the company’s largest shareholder. Shortly after graduating from London University, Martin began his career in the plastics industry working for a major Italian petrochemical company and soon became passionate about the unique world of rotomoulding. Matrix Polymers are experts in rotomoulding materials and have become a global supplier with compounding and grinding plants in the UK, Poland, Australia, New Zealand, and Malaysia. The company sells more than $150 million of rotomoulding materials each year and has 230 employees. martin.coles@matrixpolymers.com
Celal is Chairman of Floteks Plastik, the pioneer and innovative leader of the rotational molding industry in Turkey and is a Global Contributing Editor for RotoWorld® magazine. Being an ARM member for more than 20 years, Celal has made many presentations at ARM meetings in various countries. He is also active in business and political organizations in his country. Celal has authored numerous articles published in various newspapers and magazines about politics, plastics, rotomolding, and innovation. beysel@superonline.com
Tom Innis is owner and Principal CEO of Xcelerant Growth Partners, LLC (Madison, WI), a multi-discipline consulting firm with specific focus in the global plastics sector. Leveraging industry experience and relationships built over 25+ years in the international manufacturing realm, Xcelerant connects the links in the industry supply chain to accelerate speedto-market and deliver turnkey personnel, product development, and manufacturing solutions to an international audience. tinnis@ xcelerantgrowthpartners.com
Rob Miller is Owner/President, Wittmann Battenfeld Canada Inc./ Rotoload. Rob started in the plastics pneumatic conveying industry in 1986. He has spent his entire career developing, engineering, and designing all types of catalog, standard, and custom pneumatic conveying systems for the plastics industry. He started in the rotational molding industry in 2013, has enjoyed learning the idiosyncrasies of the industry and market, and most of all meeting the people and building relationships for the future. Rob.Miller@wittmann-group.ca
Adam Covington is President of Ferry Industries, Inc. in Akron, Ohio U.S.A. Covington has been with Ferry Industries for over 11 years, advanced through the manufacturing, engineering, sales, and service positions within the company and was appointed President in 2019. Adam strives to find solutions for customer’s needs and advance machine technology for the rotomolding industry. He is a graduate of Ohio University’s Russ College of Engineering and Technology with a Bachelor’s degree in Industrial Technology. acovington@ferryindustries.com
Ian Hansen has over 30 years of experience in the rotational moulding industry and has presented to conferences around the world on the subject of quality, safety, and tank design standards. Rotomoulders around the globe have problems from time to time. Rota Consult delivers production solutions so rotomoulders can improve productivity and profitability, without wasting more of their valuable time. ianhansenconsult@gmail.com
Mark Kearns is the Rotational Moulding Research Manager of the Polymer Processing Research Centre at Queen’s University of Belfast. He is a Chartered Chemical Engineer with a M. Phil Degree in Rotational Moulding. Mark manages rotational moulding research and development projects for companies across Europe, Australasia, and North America. M.Kearns@qub.ac.uk
R. Dru Laws, educator and rotomolding expert, graduated from Brigham Young University in 2003 with a BS in Mechanical Engineering and a minor in Mathematics. In 2005, he graduated top of his class with distinction (honors) from the Queens University Belfast in Northern Ireland with an MSc in Polymer Engineering from their school of Mechanical & Manufacturing Engineering. He has several rotomoulding-related patents. Laws is currently a fulltime Manufacturing Engineering professor at BYU-Idaho, as well as CEO of Halltech Systems and High Pointe Plastics. drulaws @gmail.com
Michelle Rose brings a wealth of experience to her role at the Association of Rotational Moulders Australasia. With an impressive tenure spanning over 17 years, Michelle is well versed in advocating for the interests of the rotomoulding industry in Australasia. For over 3 years, she has held the position of CEO and as a certified and seasoned association and event manager, Michelle upholds unwavering dedication to the core principles of honesty, respect, and integrity. Throughout her career, she has had the privilege of touring hundreds of factories across the globe, creating solid international networks and friendships in the rotomoulding industry. michellerose@rotationalmoulding.com
S B Zaman has been an industry promotion professional in the Plastics sector for about two and a half decades; he has been executive head of StAR since inception of the association in 2004. As its Executive Director currently, he has played his role in the continuing success of StAR being a truly representative body of the Indian & South Asian rotomoulding industry, as well as proactive member of ARMO. Coming from a Media background, Zaman has been involved in several publication projects and frequent industry articles. sbzamnp@gmail.com
Dan Grimes graduated from the University of Iowa with a degree in Chemical Engineering. After spending 5 years in full time ministry, Dan began his career in rotational molding. At Centro, Dan has been involved in Research & Development since 2006, and currently serves as Advanced Technology and Resin Leader. He is responsible for both the technical and commercial aspects of resin materials as well as process related advancements.
DGrimes@centroinc.com
Pivotal fourth session of negotiations on a global plastics treaty opens in Ottawa.
CANADA – The fourth session of the Intergovernmental Negotiating Committee to develop an international legally binding instrument on plastic pollution, including in the marine environment (INC-4), recently in Canada’s capital, Ottawa. The session aims to advance negotiations so that the Committee can finalize, at its fifth session (INC-5) in November, the text of the instrument.
Members will also decide on intersessional work – informal INC sessions taking place between the official meetings – required between the INC-4 and INC-5, to support the further development of the text.
INC-4 is the penultimate stage of the negotiations; it follows three earlier rounds of negotiations: INC-1, which took place in Punta del Este, in November 2022; INC-2, which was held in Paris in June 2023; and INC-3; which happened in Nairobi in November 2023.
instrument – have a critical role to play in providing the effective and impactful solutions needed to end plastic pollution. The spirit of multilateralism is: “together, we are stronger”,” said Luis Vayas Valdivieso, Chair of the INC.
“Let us negotiate with accountability and integrity grounded in the scientific evidence and facts on the scale and urgency of ending plastic pollution. Let us also approach this task with optimism, that it is both necessary and possible for us to achieve this new treaty,” he added.
“WE WILL CONTINUE TO NEED PLASTIC FOR SPECIFIC USES, SUCH AS RENEWABLE ENERGY TECHNOLOGIES.”
“We are seeing convergence on eliminating the uses that are problematic and avoidable. We will continue to need plastic for specific uses, such as renewable energy technologies. But there is growing agreement that short-lived and single use can go,” said Inger Andersen, Executive Director of the UN Environment Programme.
“We can be proud of what we have achieved. But a job half-done is a job not done. Time is against us – both in terms of finalizing the instrument and how much more the planet can take. As we deliberate, plastic pollution continues to gush into ecosystems,” she added. “So, I ask for INC-4 to show energy, commitment, collaboration, and ambition. To make progress and set the stage for INC-5 to finalize an instrument that will end plastic pollution, once and for all.”
INC-5, to be held in Busan, the Republic of Korea, from 25 November to 1 December 2024, is intended as the end of the INC process. It will be followed by a Diplomatic Conference where Heads of State will sign the agreement.
“We are here seeking to advance these negotiations and deliver a treaty because collectively we have recognized that multilateral cooperation – this INC process, a new legally binding international
The start of INC-4 was preceded by regional consultations and a conversation with Observers, and Canada hosted a Partnerships Day and a Ministerial Day on the sidelines of the session.
“Agreeing to a global agreement on plastic pollution by the end of 2024 would mark one of the most significant environmental decisions and would be a first-of-its-kind agreement to unite the world around a shared goal to end plastic pollution,” said Steven Guilbeault, Canada’s Minister of Environment and Climate Change.
“Canada has put in place a number of measures to stem the tide of plastic pollution at home, and we are keen to keep up the momentum for a global agreement that aligns with our ambition. We welcome delegations, partners, and stakeholders from around the world to Ottawa for INC-4 to continue the ambitious work needed to achieve this united goal.”
At the sixth session of the United Nations Environment Assembly in February 2024, Canada convened the other host countries of the INC process – France, Kenya, the Republic of Korea, and Uruguay – for a Ministerial meeting, under the umbrella of the Host Country Alliance, to galvanize momentum toward the global instrument.
“Seize this opportunity, make these seven days count, deliver a text that is as close as possible to the final agreement that we all want to see,” said Jyoti Mathur-Filipp, Executive Secretary of the INC. “You delegates know the issues that need to be addressed at this session, and that flexibility will be needed to reach consensus. This is the only way forward.” R
– NOVA Chemicals Corporation (“NOVA Chemicals”) is honoured to be named a 2024 Top Employer in Alberta for its leadership in talent recruitment and retention within the petrochemical industry.
The annual list, organized by Canada’s Top 100 Employers, annually recognizes select companies across the country as exceptional places to work based on criteria including workplace environment, social atmosphere, benefits, skills training, performance management, and community involvement.
“We are humbled to be recognized as a top employer in Alberta. Our vision at NOVA is to foster an agile, highperforming, and engaged team of employees and this recognition underscores this commitment to our people,” said Mona Jasinski, NOVA Chemicals SVP of HR and Communications. “Investing in our employees’ growth and development, creating a positive and supportive work environment, and building a modern and thriving learning culture all have direct impacts on our incredible organization, as well as our partners up and down the value chain.”
“WE’RE PROUD TO HAVE OPERATED IN THE REGION FOR NEARLY 50 YEARS AND TO HAVE CREATED AN ENVIRONMENT WHERE EMPLOYEES FEEL ENGAGED, VALUED, AND LIKE THEY MAKE POSITIVE IMPACTS THROUGH THEIR WORK.”
Jasinski continued, “Alberta employers have always stepped forward to compete for the best and brightest talent that lives right here in our province. We’re proud to have operated in the region for nearly 50 years and to have created an environment where employees feel engaged, valued, and like they make positive impacts through their work.”
With its global headquarters in Calgary and approximately 2,200 of its 2,500 employees located across Canada, NOVA Chemicals encourages its people to use a human-centered and value-driven
approach, upholding the pillars of passion, collaboration, responsibility, and innovation.
The company boasts:
• Low voluntary turnover: averaging ~3% over the last five years
• High job applicant submissions: nearly 9,000 applications received in 2023
• Flexible work options: including earned days off and alternative work arrangements
• Desirable culture: focusing on safety, overall atmosphere, celebrations, and social events
• Comprehensive and competitive benefits package: including immediate eligibility upon hire and a total well-being program
The sustainable polyethylene company aspires to become the leading sustainable polyethylene producer in North America. In 2023, it launched its strategic plan for 2030, which includes environmental, social, and corporate governance (ESG) ambitions.
NOVA Chemicals, headquartered in Calgary, Alberta, Canada, has nearly 2,500 employees worldwide and is wholly owned by Mubadala Investment Company of the Emirate of Abu Dhabi, United Arab Emirates. Learn more at www.novachem.com or follow us on LinkedIn. R
HOUSTON, TX USA – LyondellBasell (NYSE: LYB), a leader in the chemical industry, is excited to include the stateof-the-art KARO® 5.0 laboratory stretching machine from Brückner Maschinenbau into our portfolio. This latest addition to the research and development capabilities offered at the LyondellBasell (LYB) Technical Center in Akron, Ohio will greatly enhance the company’s ability to develop and test masterbatch solutions for various oriented film applications. The advanced technology of the KARO® 5.0 will enable LYB to:
• Troubleshoot and test masterbatch solutions for diverse oriented film applications with greater accuracy and efficiency.
• Create a closer match to masterbatch materials in real-world production processes, significantly reducing the time it takes to bring new products to market.
• Improve the speed-to-market process by allowing customers to quickly identify and select the optimal masterbatch for their specific needs.
“The KARO® 5.0 represents a significant investment in our research and development capabilities,” said Tiago Piccoli, LYB director of APS PAD for Consumer & Industrial Markets in the Americas. “This advanced technology will allow us to accelerate the development of new and improved masterbatch solutions, ultimately helping our customers bring their products to market faster and with greater confidence.”
The KARO® 5.0 offers several cutting-edge features, including:
• Multi-cast film capabilities that enable the testing of a wider range of masterbatch materials.
• Stretch capabilities in both the machine direction (MD) and transverse direction (TD) to accurately simulate real-world production conditions.
• Monitoring of various material characteristics like tension, elongation, torque, temperature, and thickness to ensure optimal performance and quality control.
For more information go to lyondellbasell.com. R
• Partnership with Sealed Air aims to develop more e-commerce packaging with increased recycled content.
• Partnership with Changchun FAWSN will promote lightweight polyolefin elastomer (POE) artificial leather solution in automotive market.
SHANGHAI, CHINA – Dow (NYSE: DOW), announced two new partnerships at Chinaplas 2024 to develop solutions that meet both performance and circular demands.
In collaboration with Dow, Sealed Air has commercialized an e-commerce packaging with increased recycled content. With the partnership, both parties will work together to develop more e-commerce packaging using Dow’s REVOLOOP™ postconsumer recycled (PCR) resins, offering an effective way to protect products while also reducing carbon footprint through less use of virgin plastics.
Dow and Changchun FAWSN Automotive Technology Research and Development Co., Ltd. also announced a new collaboration to explore applications of polyolefin elastomer (POE) artificial leather and POE-based 3D Loop solutions in the automotive industry. POE artificial leather is 25% to 40% lighter in weight than PVC leather and offers performance benefits without the use of hazardous materials.
The announcements were made at Dow’s customer event held alongside Chinaplas 2024; the region’s largest plastics industry tradeshow held in Shanghai from 23 to 26 April. At this event, Dow also showcased its Asia Pacific portfolio of innovative materials science solutions that help enable circularity and low carbon.
Centered around Dow’s sustainability commitments to Protect the Climate, Transform the Waste, and Close the Loop, the showcase featured solutions that are both high-performing and designed for circularity.
“With many local and regional brands going global, Asia has taken centerstage as a dynamic growth hub,” said Bambang Candra, commercial vice president for Asia Pacific, Dow Packaging and Specialty Plastics. “Our commitment to innovation allows us to meet the evolving needs of customers seeking more sustainable and circular products. No single company can change the industry alone, and we continually drive collaboration with value chain partners to design for recyclability at the beginning of a product’s life cycle so that plastic waste can be transformed into a valuable resource to be reused.”
Other Dow solutions that were highlighted include: Flexible packaging designed for circularity: Monomaterial all-PE stand-up pouches which are designed for recyclability enable packaging to be more easily integrated into closed-loop recycling streams. Additionally, our vacuum metallized all-PE packaging solutions enable design for recyclability and high barrier performance to co-exist, delivering a balance of sustainability and performance.
REVOLOOP™ Recycled Plastics Resins: Several
grades of post-consumer recycled (PCR) resins available in China and across Asia enrich Dow’s portfolio of mechanically recycled products that can be used in personal care packaging, artificial turf, and other consumer product packaging.
Bio-based and circular feedstock solutions: LVMH Beauty is the first user of SURLYN™ REN and SURLYN™ CIR, two new sustainable ionomers grades which pioneer the use of renewable and circular feedstocks in cosmetics packaging. Dow also supplies Crocs footwear with bio-based polyolefin elastomers (POEs) produced with renewable energy and plant-based feedstocks such as used cooking oil, enabling the footwear industry to reduce carbon footprint without compromising on performance.
Polyolefin elastomer (POE)-based leather for automotive: Addressing the automotive industry’s shift towards animal-free products, while delivering benefits such as ultra-soft tactility, better color stability, good aging and low temperature resistance, elimination of hazardous materials as well as 25% to 40% lighter in weight than PVC leather.
As part of enhancing industry engagement, Dow experts also spoke at several Chinaplas fairground activities such as Tech Talks, Circular Economy
Conference, World Trends & Plastics & Rubber Technology Summit and the Applications in Focus forum, sharing insights on enabling flexible packaging for circularity as well as low-carbon solutions for automotive and photovoltaic applications.
As part of Dow’s Transform the Waste sustainability target, the company aims to transform plastic waste and other forms of alternative feedstock to commercialize 3 million metric tons of circular and renewable solutions annually by 2030. Dow also plans to make 100% of the packaging applications we sell into to be reusable or recyclable by 2035.
Dow will work with Procter & Gamble to develop a new proprietary recycling technology targeting hardto-recycle plastic waste. The technology aims to deliver high quality post-consumer recycled (PCR) polymer with a lower greenhouse gas emissions footprint than fossil-based polyethylene.
Additionally, Dow’s global investment to build the world’s first net zero ethylene and derivatives complex in Alberta, Canada is expected to decarbonize 20% of Dow’s global ethylene capacity, enabling Dow to become the industry’s first provider of zero-emissions products and solutions. R
HOUSTON, TEXAS, USA – Shell Mobility Company Operations LLC (Shell), has completed the acquisition of Brewer Oil Company’s (BOC) retail division, acquiring 45 fuel and convenience store sites in New Mexico.
• The acquisition is part of Shell’s strategy to strengthen its company-owned footprint within the U.S. as it continues to seek opportunities for retail growth in key markets.
• Shell has acquired 45 BOC sites in New Mexico, comprised of convenience stores, cardlocks for fleet vehicles, and traditional fueling stations.
• The acquisition complements Shell’s companyowned footprint in the U.S., where it owns and operates nearly 200 convenience retail sites.
• In the U.S., Shell serves around 8 million customers per day with a brand presence at approximately
12,000 fueling stations across 49 states.
• The U.S. is a key market for Shell, where it operates in 50 states across sectors such as oil, gas, refined products, petrochemicals, wind, and solar. Shell employs more than 12,000 people in the U.S., working to provide a secure supply of energy today, while tackling the energy challenges of the future.
• Globally, Shell serves around 32 million customers per day at its mobility sites, who visit for quality fuels, electric vehicle (EV) charging, and convenience and non-fuel products and services.
To submit an inquiry to Media Relations, visit https:// shell.us/media. R
The innovative scholarship from the SPE Foundation and Brightmark meets students’ prolonged interest in plastics sustainability and circularity while addressing the workforce shortage by supporting students seeking careers in the field.
The SPE Foundation is proud to announce the establishment of the Brightmark Scholarship in Plastics Circularity endowment. In collaboration with the SPE Foundation, Brightmark, a circular innovation company with a mission to Reimagine Waste®, has created an enduring legacy by establishing an endowed scholarship intended for students attending the Georgia Institute of Technology. The initiative underscores the Foundation and Brightmark’s dedication to fostering the next generation of talent while addressing the global waste challenge and workforce shortages in the circularity industry.
Brightmark seeks to inspire and empower future leaders to develop innovative solutions that address some of the world’s most pressing waste challenges while supplementing new talent in the industry. The Brightmark Scholarship in Plastics Circularity endowment will support exceptional undergraduate and graduate students committed to advancing sustainability within the plastics sector.
relevant to the plastics industry with a focus on sustainability and/or circularity. To qualify, candidates must maintain a minimum cumulative GPA of 3.0 and submit an essay showcasing their contributions to sustainability or circularity through research, projects, internships, or volunteer work. The deadline for applicants interested in applying is April 30, 2024.
“One of the most critical transitions of a sustainable chemical industry will be the ability to process solid feedstocks like pre- and post-consumer, mixed waste plastics and biomass,” says Professor Carsten Sievers of Georgia Institute of Technology’s School of Chemical and Biomolecular Engineering. “Developing new technologies to regulate landfill-bound plastics will require a fresh, educated generation of engineers to solve today’s most pressing environmental problems.”
“THE DEVELOPMENT OF THE SCHOLARSHIP IS A SIGNIFICANT MILESTONE IN BRIGHTMARK’S ENDURING DEDICATION TO CULTIVATING THE NEXT GENERATION OF THOSE WANTING TO DEVELOP SOLUTIONS.”
– Bob Powell, Brightmark Founder and CEO
“The development of the scholarship is a significant milestone in Brightmark’s enduring dedication to cultivating the next generation of those wanting to develop solutions to solve the world’s biggest waste challenges,” says Bob Powell, Brightmark founder and CEO. “By investing in the education and development of future leaders at the Georgia Institute of Technology, we are supporting a pipeline of talent equipped to tackle intricate sustainability issues and drive ingenuity.”
As a Georgia Institute of Technology graduate, Mr. Powell credits the university as one of his best decisions, galvanizing his confidence and passion to make a positive impact. Mr. Powell and Brightmark commit to funding one annual scholarship and providing financial assistance to deserving students. Applicants for the Brightmark Scholarship must be enrolled as undergraduate or graduate students pursuing degrees
In general, sustainability is a significant driver of student interest at the Georgia Institute of Technology, as student enrollment in Professor Sievers’ course “Fundamentals and Challenges for a Sustainable Chemical Enterprise” demonstrates. Today, the university recognizes an increased interest in sustainability, seen by an upswing in conversations from current and incoming students at the university.
“We are honored to partner with Brightmark in this transformative initiative,” said Eve Vitale, Chief Executive of the SPE Foundation. “The establishment of this scholarship reflects Brightmark’s commitment to nurturing future plastics professionals and underscores the positive impact that strategic partnerships can have on education and industry. By empowering students to explore the intersection of plastics, sustainability, and circularity, Brightmark is laying the foundation for a brighter, more resilient world.”
To learn more about the Brightmark Scholarship in Plastics Circularity or to apply, visit www.spefoundation.org/scholarships. R
In the ever-evolving landscape of automotive manufacturing, Nexeo Plastics is taking the lead in driving sustainability with our portfolio of sustainable materials that includes the latest innovations from our suppliers. We’re committed to revolutionizing the road, from encouraging customers to adopt biobased plastics to helping customers meet their net zero carbon goals. Let’s discuss the details of our sustainable solutions and their pivotal role in shaping the future of mobility.
The automotive industry is at a crossroads as it tries to respond to global environmental concerns and to adopt more sustainable practices. Original Equipment Manufacturers (OEMs) are now prioritizing the
reduction of their carbon footprints through Extended Producer Responsibility (“EPR”) programs and seeking to achieve end-of-life recyclability goals. Although legislation mandating EPR’s is being developed specifically for EV battery producers and packaging manufacturers, we expect this trend to spread to other automotive segments.
Our sustainable solutions aim to cover the entire spectrum of goals our customers are striving to achieve. We want to help customers minimize reliance on traditional plastics, reduce their own and their customers’ carbon emissions, and, in general, help everyone mitigate their environmental impact. Carbon mass balance, Circularity, or a combination of both have become the chief philosophies in the industry, and Nexeo Plastics has product solutions for each approach.
For more information, go to https://www. nexeoplastics.com/contact-us/ R
CALGARY, AB CANADA – NOVA Chemicals Corporation (“NOVA Chemicals”) recently announced the launch of its Centre of Excellence for Plastics Circularity (“Centre of Excellence”), a hub for knowledge exchange and technology development for the circular economy of plastics. The Centre of Excellence will serve as a network of industry innovators and Canadian research institutions who have a shared vision of furthering global efforts in sustainable plastics management.
NOVA Chemicals’ Centre of Excellence aims to further Canadian innovation, meet customer needs, and help achieve global plastics sustainability goals by focusing on two key objectives:
• R&D Collaboration – Addressing the complex challenges and opportunities of plastics circularity by fostering collaborative relationships and integrating expertise across disciplines, including material science, engineering, chemistry, environmental science, and public policy.
• Value Chain-Integrated Solutions – Ensuring solutions meet the needs of stakeholders across the value chain by actively working with strategic partners across industry, academia, and government to accelerate and deliver practical and scalable technologies.
“We welcome innovators from across Canada and beyond to join us in developing scalable solutions for the world’s most complex plastics challenges,” said Roger Kearns, President, and CEO at NOVA Chemicals. “NOVA has an established reputation for working with others to spearhead innovation, and we are excited to continue bridging gaps between leading-edge ideas and commercially viable technologies.”
Adds Rocky Vermani, SVP of Sustainability and Innovation with NOVA Chemicals “As the world looks to grow the circular economy, we are committed to investing in the technology and infrastructure needed to achieve global ambitions while ensuring Canada remains at the forefront of petrochemical and plastics innovation.”
Over five decades, NOVA Chemicals has grown from a small pipeline company on the prairies to a significant contributor to the Canadian economy and leading player in the North American petrochemical and plastics industry. The company’s scientists at
its Centres for Applied Research and Performance Applications continually drive innovation and make up western Canada’s largest private research entity. NOVA Chemicals is also a founding member of Responsible Care®, the global chemistry industry’s standard for health, safety, security, and environmental performance.
“We are pleased to see an Alberta-born-andbred company taking a leading role in accelerating Canada’s leadership in the plastics circular economy by encouraging interprovincial collaboration and innovation. It’s this kind of initiative that leads to real action in protecting the environment while encouraging a prosperous economy.” – Hon. Rebecca Schulz, Alberta Minister of Environment and Protected Areas
“This Centre of Excellence demonstrates a pragmatic approach to addressing the opportunities and challenges presented by plastic circularity. By fostering collaboration across sectors, the Centre of Excellence and its partners will be poised to deliver tangible solutions with real-world impact. We are pleased to support these efforts in advancing sustainability within our industry.” – Sam Bendavid, Chief Corporate Development and Procurement Officer, TC Transcontinental
“As a strategic partner, we fully recognize the value proposition that the Centre of Excellence represents for the betterment of the global circular economy. The COE’s commitment to continuous learning, interdisciplinary collaboration, and disruptive innovation resonates deeply with our own organizational values, and we are eager to support its mission.” – Mehdi Pakravan, Vice President, and Chief Technology Officer, Polykar
In addition to building on the 20+ years of education and science support that NOVA Chemicals’ genScience initiative has provided to young STEM innovators, the Centre of Excellence will play a pivotal role in supporting the company’s 2030 Roadmap as it looks to lead the development of and transition to circular plastics. In 2023, the company announced its aspiration to achieve 30 per cent recycled content as a share of its total polyethylene sales by 2030 as part of its work to become the leading sustainable polyethylene producer in North America. R
Dow’s new MobilityScience™ Studio in Correggio, Italy, will support and advance electric vehicle growth
MIDLAND, MICHIGAN, USA – DOW (NYSE: DOW) announced its expanded investment in MobilityScience™ capabilities today by opening the doors of its first European MobilityScience™ Studio in Correggio, Italy, marking its long-term commitment to the mobility industry as it continues to transform and grow.
The new studio will allow Dow to further collaborate with Tiers and OEMs on-site and beyond, growing its existing innovative solutions. In expanding its presence in Italy, the studio will support Dow’s Research & Development and Technical Services & Development engineers in focusing on new sustainable solutions within the mobility market and others, paving the way for new ecosystem collaborations in Europe.
“Dow is thrilled to commemorate the opening of the first MobilityScience™ innovation studio in Europe,” said Ryan Smith, global marketing director for Dow MobilityScience™. “This investment in Correggio, Italy will serve as a hub for Dow’s technical and commercial experts to connect with the European mobility industry and drive forward the necessary investments to ensure global success in the burgeoning EV market,” he continued. “Electrification is the future of mobility and Dow’s unique breath of chemistry knowledge
will provide much of the toolbox needed by our global partners in mobility.”
This weekend, Dow will open its studio’s doors for the first time to select customers in conjunction with the 2024 Misano E-Prix where technical partner Jaguar TCS Racing continues their pursuit for podiums as they compete in the ABB FIA Formula E World Championship.
The Correggio studio will be the third of Dow’s state-of-the-art MobilityScience™ facilities. The existing MobilityScience™ Studios, located in Midland, Michigan and Lake Jackson, Texas, offer collaborative workspaces for acoustic and powertrain testing capabilities for fast-moving automotive applications. Through these studios, Dow is able to create tailormade noise, vibration, and harshness (NVH) and sealing, powertrain, and fluid transfer system options unique to any specifications.
Dow builds on 100+ years of transportation experience and expertise in application development to deliver innovative, cutting-edge solutions that keep the world moving.
For more detailed information on Dow’s ongoing commitment to the mobility industry visit: https://www.dow.com/mobilityscience . R
Despite price increase nominations going into second quarter, it appeared there was potential for generally flat pricing with the exception of a major downward correction for PP.
Going into the first month of second quarter, prices of at least three if not four of the five commodity resins had a likelihood of rolling over, despite price increase nominations for all. PP was an exception, where a long-awaited downward correction appeared to be underway as propylene monomer supply shortages were coming to an end. While higher prices of key raw materials were behind the resin price hikes issued for PS, PET and PP, there was a downward trajectory forecast, barring any major production or
logistical disruptions. But, the overall ‘thread’ was that a recovery in demand for key markets was not yet evident.
These are the views of purchasing consultants from Resin Technology Inc.(RTi), senior analysts from Houston-based PetroChemWire (PCW), CEO Michael Greenberg of The Plastics Exchange, Scott Newell, executive v.p. polyolefins at distributor/compounder Spartan Polymers, Mike Burns of Plastic Resin Market Advisors, and resin pricing expert Robin Chesshier. R
The GENIUS lab aims to enhance generative AI methods
DELFT, NETHERLANDS – Delft University of Technology, Maastricht University, dsm-firmenich, Kickstart AI, and ICAI recently announced the launch of a new AI lab: GENIUS. The goal of the GENIUS lab is to make AI even more useful, trustworthy, and understandable for everyone for any question.
The GENIUS lab (Generative Enhanced NextGeneration Intelligent Understanding Systems lab) aims to improve generative AI methods to assist human experts in addressing scientific and operational questions. It thereby focuses on how humans and AI can collaborate in knowledge management and knowledge discovery within large organisations.
The lab will develop human-centred approaches that involve humans in extracting, organising, and accessing stored knowledge. This research aims to accelerate how AI is used in science, research, innovation, and operations, where knowledge management and decision-making through AI-based systems might have far-reaching implications for many industries. The lab plans to showcase these impacts through real-world use cases.
The lab will co-develop generative, human-AI collaborative knowledge engineering methods and techniques for distinct yet highly interweaved knowledge engineering steps: collaborative knowledge synthesis; integration and linking of distributed knowledge fragments; integration of structured knowledge in generative AI models; trustworthy conversational AI using FAIR data and services; and hybrid human-AI ethics. These methods and techniques are designed, developed, experimented with, evaluated, and validated in a variety of contexts.
Delft University of Technology, Maastricht University, dsm-firmenich, Kickstart AI, and ICAI share a longterm vision to improve human-AI collaboration to increase the scalability, trustworthiness, and efficiency of AI- supported content-creation and decision-making systems.
“Generative AI is transforming the innovation landscape in industry and society. Bringing together partners with tons of experience in AI research and innovation, the GENIUS lab aims to address urgent challenges in the development and usage of Generative
AI in large organisations.”
—Jie Yang (GENIUS Lab Manager)
At TU Delft, we are excited to partner with our academic colleagues from Maastricht University and our research colleagues from both dsm-firmenich and Kickstart AI in order to advance our knowledge and impact on society on this important topic of responsible and effective human-AI collaboration.”
—Geert-Jan Houben (TU Delft)
“Generative AI heralds exciting new possibilities for guided content creation, but it raises many questions with respect to data provenance, generative accuracy, and overall AI trustworthiness. At Maastricht University, we are thrilled to have this opportunity to work with our academic and industry partners to tackle social, scientific, and technical challenges pertaining to generative AI with our newly appointed PhD candidates.”
—Michel Dumontier (Maastricht University)
“At the forefront of innovation, the newly founded GENIUS lab embarks on a transformative journey, exploring how generative AI, FAIR data, and knowledge services can be introduced to accelerate the development of novel solutions and sustainable applications in Nutrition, Health, and Beauty.”
—Hans Roubos (dsm-firmenich)
“We are thrilled to contribute to this groundbreaking initiative, aimed at accelerating the adoption of AI in the Netherlands. Partnering with leading academic institutions and industry partners in the field of AI, we are committed with the GENIUS lab to improve the utility, reliability, and comprehensibility of AI, making it accessible to everyone for addressing any type of question.’’
—Sander Stomph, CEO and co-founder Kickstart R
OBERGLATT, SWITZERLAND – MAAG Group is a broadly diversified global solutions provider of Pump & Filtration Systems, Pelletizing & Pulverizing Systems, Recycling Systems, and digital solutions. The acquisition of Witte by the MAAG Group at the beginning of 2023 marks the start of a new path of cooperation. The two leading companies in the industry have merged to create a new generation of gear pumps, and strive to set new benchmarks for performance, dependability, and efficiency. This strategic move combines decades of experience and research.
The first joint product development will be presented at Achema in Frankfurt, Germany, from June 10 to 14, 2024 in Hall 8.0, Stand K78:
The new CHEM-X gear pump emerges as a symbol of this synergistic partnership, designed to meet the most demanding applications across various industries. With a focus on performance, durability, and efficiency.
The pump features an advanced gear tooth design, optimized for minimal hydraulic pulsation and maximum volumetric efficiency. The use of innovative materials ensures that the pump can withstand harsh chemicals and high temperatures without compromising its lifespan or performance.
The new product can be set with an intelligent control system. These systems enable real-time monitoring and adjustments, ensuring that the pump operates at peak efficiency under varying process conditions.
Take the opportunity to chat with our experts about our extensive portfolio of gear pumps, pelletizers, dryers, and filters for a broad range of applications in the chemical and plastics processing industry.
For more information on our products, visit www.maag.com. R
The Nordic ARM Conference 2024 in Reykjavik showcased a remarkable blend of Iceland’s natural beauty and the latest advancements in the field of rotational moulding. Prior to the conference some attended a breathtaking experience of Iceland’s geological wonders and culinary uniqueness on a cold but sunny day with an extraordinary clear blue sky.
Visiting Kerid, a 3000-year-old volcano crater, Geysir (hot spring), Gullfoss (Golden Waterfall), Thingvellir, where the two tectonic plates drift apart and Fridheimar, a tomato farm that serves tomato soup, pasta with homemade pasta sauce, fresh mussels cooked in a special tomato seafood sauce, tomato ice cream and served with a tomato beer, and more food and drinks originating from tomatoes...a fantastic tour that all visiting Iceland should make. The day was rounded out with a “Thorrablot” where we got served traditional Icelandic food, like blood pudding, boiled sheep head, sour ram’s testicles, and fermented shark served with “Black Death” also known as Brennivin.
The conference had a very good turnout with approx. 110 registrants. Due to illness and some extreme weather conditions (0,5 m snow at airport) approx. 95 persons attended the conference. The conference agenda contained many high valuable contents for the audience. Anna Walorek-Iwanowska was the host for the event and excellently guided the attendees through the 2-day conference.
It started with Dharana Jayawardane exploiting the broad offering of sustainable and renewable offerings from Matrix Polymers. Luca Zanni from Poliplast presented their latest research where Poliplast can produce polyethylene with up to 98% of recycled content. Ronny Ervik presented NPRs possibilities to collect and recycle end of life products and produce high quality rPE for rotomoulding. Gunnar Dofri Ólafsson presented the increased interest and use of biogas in Europe. And Arianna
correct glossary of sustainability. David Almroth from GS1 explained the Digital Product Passport –enabling the circular economy. Oliver Wandres from Maus, showed their latest innovations enabling the rotomoulders to mould more efficient.
The first day of the conference was rounded out by Gareth McDowell who told us how to establish sustainable rotomoulding through controlled cooling.
The Nordic ARM Dinner and quiz took place at Bryggjan Brugghus, a high-quality restaurant located by the old harbour with a brewery room, cocktail bar, and wine room. The restaurant first opened in 2015 and has since been a leader among craft breweries in Iceland. The famous Nordic ARM Quiz was won by FC Dallas followed by Rural Squirrel and Dex. FC Dallas consist of a team from Rotovia.
Day 2 of the Nordic ARM Conference started with Oscar Orefice from Rotoplastics
The famous Nordic ARM Quiz was won by FC Dallas (team from Rotovia) followed by Rural Squirrel and Dex.
De Lellis of Rotoplastic presented pros and cons of using biogas in rotational moulding. Dadi Valdimarsson shared with the audience Rotovias’ 11-12 years of experience running an electrical RM machine. Thomasz Czulek from Norner followed up with navigating the audience through the jungle of explaining the
explaining about their Hybrid and High performance machines, followed by Johan Portagent from AMS who told the audience how to use Robomould with artificial intelligence software. Niccolo Signorelli from Persico impressed the audience by how they have contributed to automatization in the industry. Eric Maziers from Total
Energies presented the different routes that Total Energies will pursue in the future to deliver sustainable materials to the industry. Konstantia Asteriadou presented Lysis Technologies solution for sustainable graphics and coating options for rotational moulding. Mark Kearns from Queens University of Belfast
enlightened the audience about the many possibilities there are for rotomoulders by replacing fossil fuel with hydrogen. This presentation was followed up by Daniela Watermann and Herman Diem from Ultrapolymers on some of their projects within hydrogen tanks. Lorenzo Colomobo from Boca Moulds talked about the many solutions they can offer, and the conference was rounded off with Ronny Ervik from Norner presenting a market study of the use of sustainable materials in the Nordics.
The night after the conference ended, a volcanic outburst happened close to the international airport.
This was very exiting for the conference attendees because seen from the airport, it looked like the outbreak was very close (it was not). The Icelandic people working at the airport were very relaxed and calm and no flights were delayed.
The next Nordic ARM Conference will be held in Stockholm, Sweden 2025
Next Nordic ARM Academy will be arranged in Copenhagen, Denmark 2025 and will be focussed on moulds, everything you will need to know about moulds from A-Z. Maus and Boca have volunteered to give some of the lectures. R
“Mark Kearns of Queens University of Belfast enlightened the audience about the many possibilities there are for rotomoulders by replacing fossil fuel with hydrogen.”
Full disclosure: much of the following copy appeared in a blog post I authored several years ago; looming deadlines combined with a taxing travel schedule and exacerbated by questionable time management necessitated lifting this from the archives. But still, upon review of the comments, I believe this content to be salient today.
As I recently re-visited the above mentioned blog post, I was reminded of the impetus for writing it: a month or so prior to publishing the post, I had represented the Association of Rotational Molders (ARM) “Roto Made Local” initiative at the Industrial Design Society of America’s (IDSA) international conference in Austin, Texas. The objective of “Roto Made Local” was to build a bridge between our industry and industrial designers, promoting the benefits of our process while enhancing their familiarity and knowledge with rotomolding as a means
of increasing their usage of rotomolding as a viable product design medium.
While manning the “Roto Made Local” booth at the event, a writer for a prominent plastics industry publication approached the booth and asked who we were. When I explained “we’re here on behalf of the rotomolding industry,” the writer snarkily remarked (please forgive my language) “we’ve always thought of rotomolding as the bi*ch of the plastics industry.” In addition to leaving me dumbfounded, I took this insult quite personally, and have since made it my mission to counter this
negative perception and promote rotomolding in the positive light it deserves, wherever and with whomever the topic arises. Thus, it is with the objective of enhancing our self-perception as well as outside opinions of the rotomolding industry, that I posit the following items that we need to stop saying:
1) “Rotomolding is cheap.” As an industry, we tend to lead with this line when competing against other manufacturing processes. Yes, rotomolding can be more cost-effective when assessing conversion
opportunities from metal, fiberglass, wood, complex assemblies, etc., but product designers and marketers are more impressed with features, benefits, and overall value of a rotomolded product as opposed
when confronted with challenges such as tight tolerances, high volumes, predictable/consistent outcomes, automation, and developing consumer-focused products. ALL these challenges have been successfully overcome
capable industry.
3) “Well, that’s just roto.” We recently connected an OEM customer with a rotational molder and brought the customer to the rotomolding facility to check
to producing a cheaper version of their existing products.
And let’s admit it: the neverending hunt for cheap design, cheap materials, cheap tools, and cheap labor results in (surprise!) products that look cheap and have very little perceived intrinsic value.
Instead of the “roto-is-cheap/ race to the bottom” mindset, let’s challenge ourselves to approach product development and conversion opportunities by leading with “rotomolding is a value-added and cost-effective manufacturing process.”
2) “We can’t do that.” Indeed, there are obvious manufacturing applications that aren’t viable fits for rotomolding; we certainly don’t want to misrepresent our capabilities and lead customers (nor ourselves) down the wrong path. At the same time, we shouldn’t succumb to our collective inferiority complex
“LET’S CONFIDENTLY POSITION ROTOMOLDING WITH A ‘HERE’S WHAT WE CAN DO THAT NO OTHER MANUFACTURING PROCESS CAN DO’ MINDSET, AND CHANNEL OUR COLLECTIVE ENERGY AND CREATIVITY TO RAISE THE PROFILE AND AWARENESS OF OUR UNIQUE AND EMINENTLY CAPABLE INDUSTRY.”
in our industry, and there’s no reason we should back down from them.
Instead, let’s confidently position rotomolding with a “here’s what we can do that no other manufacturing process can do” mindset, and channel our collective energy and creativity to raise the profile and awareness of our unique and eminently
progress of initial production of a relatively high-tech, value-added consumer product. This was the first visit to a rotomolding plant the customer had made, and (as it was for all of us) it was an eyeopening experience.
When the customer expressed concerns over sporadic materialfill results in a challenging part geometry, the rotomolder
defensively replied, “well, that’s just roto – get used to it!”
While we do need to understand our manufacturing limitations and position our capabilities accordingly, we can’t continue to exacerbate perceptions of rotomolding as a low-tech, “black art” that produces unpredictable results beyond our control. Today’s materials, machines, tools, automation, process-enhancing equipment, and lean manufacturing techniques allow us to control the rotomolding process and drive consistent and high-quality results to our customers. Let’s embrace the confidence and discipline necessary to drive improved outcomes and enhance perceptions of the viability of rotomolding.
4) “Roto is only suited for industrial applications.”
Yes, it’s true that rotomolding is terrific for industrial applications, such as liquid storage tanks, agricultural implements, materials handling containers, storage bins, etc. Attributes such as chemical resistance, durability, and indestructibility have made roto indispensable in heavy-duty industrial applications.
But for years, companies in the toy, outdoor recreation, kayak, furniture, cooler, etc. sectors have understood that rotomolding is terrific for consumer-facing products as well. Attributes such as durability, indestructibility, and sustainability are also marketable advantages for consumer products companies who have successfully leveraged the “you only get this with roto” characteristics to build powerhouse, global brands.
“TODAY’S MATERIALS, MACHINES, TOOLS, AUTOMATION, PROCESSENHANCING EQUIPMENT, AND LEAN MANUFACTURING TECHNIQUES ALLOW US TO CONTROL THE ROTOMOLDING PROCESS AND DRIVE CONSISTENT AND HIGH-QUALITY RESULTS TO OUR CUSTOMERS.”
As an industry, we’re making great strides in appealing to the consumer with these rotomolded product success stories. Still, there is much work to be done to raise the profile of rotomolding within the design community, who can then help us drive uniquely cool rotomolded products to the consumer.
5) “Marketing the industry is a waste of time.”
Collectively, we stink at promoting rotomolding to the audience beyond “preaching to choir,” and efforts to reach a broader audience through aggressive marketing are often dismissed by industry pundits as a waste of time.
But if you’re the owner of a laptop computer, there’s a very good chance your laptop sports an “Intel Inside ® ” sticker, indicating your computer is powered by an Intel processor. While Intel doesn’t manufacture the laptop, per se, its processor powers the computer and directly impacts the laptop user’s product experience. When I see that Intel Inside ® sticker, I’m confident I have well-built, dependable, fast
machine that will perform to my expectations.
Crazy thought, but maybe we could do something similar on every rotomolded product we build place a “Powered by Roto” image/graphic to assure the end-user that the product will be tough, durable, dependable, indestructible, sustainable, and value-added. Pretty soon, the world’s consumers will share our opinion of the awesomeness of roto and will demand more and more of what only WE can deliver.
As an industry, we tend to undervalue ourselves.
In closing, and roughly concurrent with the abovementioned experience at IDSA, a long-time industry all-star and past-President of ARM stated at an industry event that “as an industry, we tend to undervalue ourselves…” I agree and believe that if we can shift the perception of rotomolding from bi*tch to bad-as*, we’ll enhance consumer awareness of rotomolding and catalyze industry growth and proliferation on a global scale.” R
It is often easier to define the quality of a part or a process by first taking it to its extreme edge. Only then can you truly understand its acceptable limits. To this point, our ARM Low Temperature Impact Test is actually designed to find conditions of FAILURE. This is especially true for what is known as Bruceton analysis, the staircase method we use in our industry to manually test for impact strength. This Bruceton method is sometimes referred to as the “up and down test” and was originally utilized in 1948 to test explosive sensitivity. Any Bruceton analysis relies on two parameters: (1) a stimulus, and (2) a step size. A stimulus is provided to a sample and the result is recorded. If a favorable result is noted, the stimulus is decreased by the step size. If a negative
result occurs, then the stimulus is increased by the step size.
For our low temperature impact test, the stimulus is the falling dart and the step size is the change in drop height. Because the test is intended to define failure, a favorable test result is one that fails the test (you may need to think about that for a minute or two). Thus, per the explanation in the previous paragraph, we would decrease the drop height when a sample fails the test (a favorable result).
Per version 4 of ARM’s test procedure, published in 2003, Table 1 illustrates a summary of these two parameters. Typically the step size remains constant for all 4 different procedures, with only the weight of the falling dart changing (as well as the profile of the dart tip in the case of procedure D).
B 15 lb (6.804 kg) falling dart
A 10 lb (4.536 kg) falling dart 6 inches (152.4mm)
C 20 lb (9.072 kg) falling dart
D 30 lb (13.61 kg) falling dart
Table 1
For all 4 procedures, a weight is strategically dropped on a properly oriented and carefully prepared sample plaque, according to specifications found in Table 2
For each individual impact test, there are 3 possible outcomes. Each outcome determines the next test in the Bruceton sequence, as illustrated in Table 3. For rotomolding, the sample is not considered a failure if the detent created by the dart will still hold water.
For the Bruceton method, non-failure is considered a negative result because it didn’t fail, which means you
Sample
Size 5.0 x 5.0 ± 0.08” (127 x 127 ± 2mm)
Thickness 0.125” (3.17mm) ± 10%
0.250” (6.34mm) ± 5%
Temperature -40 ± 3.5°F (-40 ± 2°C) for 2+ hours
Orientation Impact the outside of the part
would increase the drop height on the next sample. Remember, we are trying to define the failure point. The test wants the sample to fail!
The test continues as you sequentially increase or decrease the drop height of the next test, until you have tested a statistically significant number of samples to provide enough data to calculate the average impact failure of the group of samples (typically about 20-24 samples). Ideally, you will reach a “toggle point” in the testing where a sample will non-fail, and the next sample at the increased height will fail, then the next sample will non-fail at the lower drop, then fail at the higher drop, etc.
For more detailed information, please consult your material supplier and the ARM Low Temperature Impact Test publication. Just remember, it is a test deliberately written to identify failure. Then, from those failure levels, you can easily calculate and publish acceptable quality standards for your material, process, or product. R
A
StAR significantly completed two decades of organising international rotomoulding conferences in India by holding the 20th annual conference in Kovalam, Kerala from January 28th to 30th. The 2024 conference took place at the beautiful beachside resort Uday Samudra. With a busy 3–day programme of high quality and variety, the forward looking theme was NAVIGATING THE FUTURE. The event included many valuable highlights including:
• 20 presentations covering key future aspects
• Attention catching Seminar “World Class Product Development” by four industry experts
• For the first time at a StAR conference, four very participative Panel Discussions
• A Roto Trade Show featuring Indian and International suppliers including Sponsor exhibitors who championed the conference
• Matrix Polymers, PolymerLink, and Greenage
Industries were Principal Sponsors
• Persico, NAROTO and Reinhardt Teknik were Diamond Sponsors
• Ingenia Polymers and Jaljog Rotomould were Platinum Sponsors
• A NOTABLE CALENDAR EVENT announced at the conference was the upcoming ARMO 2025 to be hosted by StAR
• Twenty speakers of international eminence from India and around the world shared knowledge and rotomoulding interest.
A snapshot of the programme and most of the speakers speaks volumes for the substance that was at the core of the takeaways:
SEMINAR
World-Class Product Development
Ravi Mehra, Satish Gokhale, Umakant Savadekar, and Akshay Saini
PRESENTATIONS
Charged for Success: Unleashing the Power of Rotomoulding
Martin Coles, Matrix Polymers – UK
A Business Odyssey
Ashish Baheti, Vectus Industries – India
Rotomoulding: Grow Sustainably Creating Value
Davide Accornero, Rototech – Italy
Navigating the Future
Ian Hansen, Consultant – Australia
New Materials – A Never Ending Demand
Venkit Mahadevan, PolymerLink – India
Importance of Creep Data for Designers
Umakant Savadekar, Phychem Technologies – India
Comparison of Bio-PE and Standard PE Rotomoulded Products
Marek Szostak, Poznan University – Poland
Icorene 1490: A Game-Changer for Rotomoulding?
John Steele, LyondellBasell – UK
Sustainable Materials Aproach to Rotomoulding
Aldo Quaratino, Matrix Polymers – UK
Developing Sustainable Rotomoulding Material –a case study in India
Ravi Kadiwar, Greenage Industries – India
Smart Manufacturing – stepping into the future
R Ravikumar, Roots Multiclean – India
Design and Modelling of Type IV Hydrogen Tanks
Jitendra Seregar – Queens University, Belfas – UK
Specialty Rotational Moulding Products and Uses Thereof
Emillio Chargoy, Ingenia Polymers – Canada
Role of Mould Design in Cost Saving
Prasad Deshpande, Jaljog Rotomould – India
Advances in Research towards a Sustainable Future for Rotomoulding
Dr. Peter Martin, Queens University, Belfast – UK
Speakers
Smart Automation – how to navigate the future
Matteo Cortesi, Persico SpA – Italy
NET ZERO – the end of rotational moulding?
Martin Spencer, UniqueRoto – UK
PANEL DISCUSSION: Navigating the future of rotomoulding for a Net-Zero world
Martin Spencer, Matteo Cortesi, Davide Accornero, Peter Martin, and Shivinder Chawla
Recyclability as a Pathway to New Horizons
Yuvraj Singh Ahuja, Frontier Polymers – India
Beyond Traditional: Outlook on Sustainable Product Development
Dominic Polayil, Rototech Welspun – India
R & D: As a long term survival strategy –from a 40 years experienced rotomoulder
Celal Beysel, Floteks – Turkey
PANEL DISCUSSION: R&D – basic science to innovative products
Celal Beysel, Dominic Polayil, Yuvraj Singh Ahuja, Satish Gokhale, and Dr. Sachin Waigaonkar Appreciation came in great measure not only for
Performers & Attendees
new knowledge that was in abundance, but also for the highly enjoyable social evenings, the Networking Dinner & Gala Dinner with Entertainment, which were wonderful opportunities for networking.
The musicians who enthralled the audience with traditional instrumental music, and the Kairali Fusion of South Indian dancers have left behind memories to be cherished for a long time.
There is much more to come as we look forward to the ARMO 2025 Conference to be hosted by StAR. Stay tuned! R
The mission of the Association of Rotational Molders is to promote, educate, and inspire the rotomolding industry. For more information, visit ARM’s website at www.rotomolding.org or contact the Association at 630-942-6589 or info@rotomolding.org.
Spring is in the air and our thoughts turn to the ARM Executive Forum, which is just a few weeks away. ARM Staff, in collaboration with Katia Zoppetti, have put together a wonderful opportunity to visit some of Europe’s premier rotomolders in Northern Italy followed by the Executive Forum meeting in Bardolino.
This year ARM will partner with the Italian Association (IT-RO) to co-host the Executive Forum, with each group sharing knowledge on topics of interest. This event will no doubt be an incredible opportunity to not only learn from some of the best in our industry but also to build international relationships and partnerships that could potentially grow your business. For those who have signed up for this wonderful opportunity, I know you won’t be disappointed in what’s to come. Of course, the cultural and culinary experience will be the icing on the cake!
Regarding ARM activities, it’s been a busy start to 2024. We hosted multiple webinars, one of which focused on wall thickness control and had great interactive participation that extended long after the webinar ended. ARM has also presented three well-attended training seminars.
Our planning for Rotoplas in Chicago later this year is in full swing. This will be a tremendous networking opportunity, with so many in our industry coming together to enjoy sharing information and meeting with the supply base. Also, membership continues to grow, a testament to what we offer to those in our industry.
To follow, please find more detailed information regarding ARM activities provided by ARM staff.
If I personally can be of any service, please don’t hesitate to reach out to me. Thank you for your continued support of our Association! R
Alvin Spence 2024 ARM President Centro, Inc. aspence@centroinc.comEducational Programs
• Our new Operator Training Certificate program – included for the whole company with your membership.
• Join our What’s Your Problem? calls every 6-8 weeks. Recently we’ve discussed product warpage, rotomolding with PCR, maintenance schedules, rotation ratio, and much more.
• Intro to Rotomolding and Advanced Rotomolding Seminars have been presented in person eight times over the past 12 months.
New Webinars
• Overview of Wall Thickness Control Methods
• Case Study of Molds with Baffle Plates and Heat Pipes
• Curing of Mold Release
• Icorene 1490 Case Studies
• Introduction to PFAS Concerns
• Navigating Global Plastics Policies
• Employee Engagement and Retention
• Using Graphics in Rotomolding
• Simulation Techniques to Model Shrinkage and Warpage
• The Impact of Impact Testing
These titles join our 125+ webinars available on demand
Blog Posts on Rotomolding Fundamentals and Technical Topics
• Fire-Rating Roto Materials
• LLDPE Failure Analysis
• Key Points on Rotation
• Bleed-Out of Pigment
• Guidelines for Vent Sizes
• Ignition Properties of Roto Powders
• Mold Pressurization
• Suggestions for an Overheating Hoist
• Unexpected Part Shrinkage
• Technical advice on Rotomolding TPE
Also, in the Last 12 Months
• ARM ended the year with 161 Rotomolder Company Members
• Shared dozens of rotomolded product case studies
• Organized an inter-laboratory study to evaluate the consistency of the Low-Temperature Impact Test
• Awarded five scholarships to high school seniors R
Recent ARM calls and committee meetings have sparked discussions on rotation ratios. As a result, we’re developing multiple items to share with members on the subject. Here are some key points for now.
• Size Sensitivity to Rotation Ratios: Small molds are less sensitive to rotation ratios than larger molds.
• Preference for Non-Integral Ratios: Non-integral ratios (e.g., 1:4.1 instead of 1:4) are favored as they significantly increase flow paths.
• Limited Impact of Rotation Ratio: The rotation ratio matters for only about 15% of the cycle; once the powder is laid up, it has no effect.
• Rotation Speeds: Some advocate for maximum rotation speeds to create more flow paths before powder lays up, but others argue against it citing potential issues like static build-up and mechanical/safety limits.
• RPM Theory and Evidence: While higher RPMs may theoretically lead to more even wall thickness distribution, there’s a lack of hard evidence. Counterarguments include static build-up and mechanical/safety limitations.
• Visual Checks: Visual measurements are preferred over relying solely on machinery manufacturers’ data. Modern machines often display RPMs directly, but manual checks, especially on older machines, are recommended due to wear and accuracy issues.
• Arm Balance: It’s crucial to balance arms to avoid excessive bearing wear mechanically.
• Mechanical Drag and Creep: Gearboxes may have mechanical drag or “creep,” where the plate may still turn slowly even when set to zero rotation. Negative RPMs may be needed to keep the plate fixed.
Dr. Nick Henwood, Technical Director of the Association of Rotational Molders, is a 30-year expert in materials and process control. He operates Rotomotive Limited as a consultant, researcher, and educator in the UK and was inducted into the Rotational Molding Hall of Fame in 2022. R
2024 Tour of Italian Rotomolding Factories & Executive Forum
June 9 - 12th: Factory Tour
June 13 - 14th: Conference Lake Garda, Italy
Rotoplas 2024: International Rotomolding Exposition
September 24 - 26, 2024 Rosemont, IL
2025 Annual Meeting
September 29 - October 1, 2025 Hilton Anatole Dallas, TX
The 2024 ARM Executive Forum takes place in Northern Italy, June 10-14. Join us for a tour of Italian rotomolding companies and a joint meeting in Bardolino with IT-RO. You will learn from the top Italian rotomolders what they do differently than North American rotomolders, how they think about the rotomolding process, and the industries they serve throughout Europe.
Register and learn more at: https://bit.ly/rotoitaly This is a great opportunity to improve your process, network with leaders across the globe, and have access to six amazing factories.
In particular, we expect you to learn about automation, molding complex parts, creating highaesthetic products for a shift to luxury, and much more.
• Assess technology and processes that are less common in North America
• Observe firsthand cost-saving measures that will help you optimize your process to be more efficient and reduce production costs.
Conference Topics to Include:
• Four Types of Growth for Rotomolding Companies
• Case Studies on Success in Automation
• Overviews of Rotomolding Markets in Italy and North America
• How Rotomolding Compares with and Competes with Other Processes
• Aesthetics on Surface Finishing
• Unique Characteristics of Different Rotomolding Machines and more!
• Use what you’ve seen to encourage continuous improvement at home.
• Learn about Italian quality standards and how they are achieved.
• Gain insights into market dynamics, consumer preferences, and regulatory requirements. This can inform strategies at home as their trends will influence North America and vice versa.
• Understand European eco-friendly practices as we expect similar regulations to become more prominent in North America.
Tour Dates (June 10 - June 12)
Rototech
Cornaglia
Persico
Ve.Ca.
Moulding Service
Verzellesi
Conference Dates (June 13 & June 14)
Network and learn with rotomolders and suppliers from North America and Italy at the beautiful Caesius Spa in Bardolino. The conference runs all day Thursday and through mid-day on Friday. R
In recent years, the ARMA team has consistently raised the bar for our annual conference, prioritising high-quality programs, effective networking opportunities for business development, and creating an enjoyable escape from the daily grind. Last year’s conference received rave reviews for its exceptional programming in a stunning location. At Rotomould24, we’re dedicated to surpassing those expectations, offering an experience unrivalled in the rotational moulding industry.
And what a place to host this year’s event…on the beautiful Gold Coast, Australia – our first return in 8 years, but this time right in the throbbing heart of it all. Ocean views, exquisite restaurants, vibrant bars, thrilling entertainment, and the most delightful winter weather imaginable.
Our venue, the QT Hotel stands out with its funky vibe, fun atmosphere, and a breakfast buffet that’s truly second to none, all complimented by breathtaking views from every room.
“The QT Gold Coast experience: Bask in the sun at the reimagined QT
where chic meets
beach
summer vibe. Dive into
Hotel
Gold
Coast,
in
an endless
luxury by the poolside, indulge in spa treatments, dine, dance, and revel in a designer playground. Discover Yamagen Japanese, explore the Bazaar Marketplace, and relax in rooms where golden hues echo the serenity of sun-kissed shores. This is your invitation to relaxation.”
We’ve secured a special accommodation rate at the QT, available for a limited number of rooms when you register for the conference.
| With a twist
This year, our trade exhibition breaks away from the traditional booth setup, adopting a modern, streamlined design that aligns with our growing commitment to sustainability. All signage and furniture is included, eliminating the need for pull-up banners and disposable materials. Unclaimed signage will be recycled, and for each booth booked, a tree is planted.
Highlights include the Rotomachinery Group Recharge Area and the Micropellets Australia Snack Bar, and maybe even a chance to get that professional headshot you’ve always wanted.
your adventure.
This year, Rotomould24 is thrilled to present two distinct workshops designed to enrich your professional skills and knowledge. Whether your interest lies in the realms of business acumen or technical prowess, our curated workshops offer invaluable insights tailored to the unique needs of our industry.
How to build & lead a high-performance business
Kieran Flanagan and Dan Gregory will guide you in a workshop session designed to give you actionable leadership strategies and practical “people tools” to ensure your team’s engagement lifts, individual performance increases, and that your business delivers the results required to turn customers into passionate advocates.
Designed for business owners, leaders, managers, and supervisors, this interactive and engaging presentation will include skills and tools that have practical application to leadership, persuasive communication, customer service, autonomous performance, and innovative problem solving.
This will be a working session, so come prepared to learn new skills, to apply them to your business and build a strategy for implementation for when you get back to work after the conference.
Dan & Kieran are the strategic and creative team behind the most successful new product launch in Australian history, have worked with the UN in Asia, created customer engagement systems for financial institutions, and developed communications and behavioural design strategies for high performance leaders and teams across six continents and look forward to doing the same for the rotational moulding industry.
Some of their proudest achievements include:
• Working with the UN and the Singapore government on strategies to reduce human trafficking.
• Serving as Partners and a Faculty Members at Thought Leaders Business School
• Developing a graduate curriculum on The Business of Human Behaviour with the Schools of Psychology & Business at Western Sydney University
• Co-authoring three books about: Behavioural trends | Our Fundamental Human Drives | The Future of Skills and Intelligence
• Developing leadership teams for multinational tech giants across multiple continents and cultures
• Developing the strategy behind for the most successful new product launch in Australian history
• Directing one of the most extraordinary brand resurrections achieved anywhere in the world.
Rotomoulding Workshop at PARTEC with Ian Hansen
Dive into the practical aspects of rotomoulding with our hands-on Technical Workshop at the Plastic & Rubber Technical Education Centre (PARTEC). This session will cover the intricacies of moulding parameters, the science behind shrinkage and warpage, and effective testing methods, including powder dry flow and low-temperature impact testing.
With PARTEC’s newly installed shuttle oven, attendees will gain firsthand experience in rotomoulding techniques and technologies. This workshop is a must-attend for anyone looking to build their technical skills in rotomoulding.
This 3-hour workshop will be presented by Ian Hansen who is a rotomoulding industry veteran, with over 40 years’ experience in the plastics industry. His background includes 15 years in colour compounding and grinding of powders plus over 25 years in rotational moulding operations.
Ian is an ARMA Icon of Rotomoulding, and he has previously served as President of ARMA, and on the ARMO Executive Board. He has
presented to rotomoulding audiences around the world about quality, safety, and tank design. Over the years he has written articles for Rotoworld®, the global industry magazine, plus has presentations available at the online Roy Crawford Library.
Ian has worked for both small and large manufacturing companies within Australia and New Zealand and is currently working as an independent consultant to the global rotational moulding industry.
This year’s Rotomould24 conference boasts a dynamic program that spans a broad spectrum of topics, including safety, sustainability, business practices, and the transformative power of artificial
intelligence. Each session is crafted to ensure that every participant, regardless of their specific interest, leaves with valuable insights and actionable strategies to apply back when they return to the office or factory.
We’re thrilled to announce Jyotsna Chand as our professional master of ceremonies. With her extensive experience in marketing and leadership within the rotational moulding industry, Jyotsna’s unique blend of clear communication, industry insight, storytelling, humour, and style promises to weave together our diverse program into a cohesive and engaging experience.
Our program will commence with an enlightening keynote presentation from Kieran Flanagan and Dan Gregory, who will delve into the “People Principles”. This session is designed to enhance your understanding of behavioural dynamics, fostering greater self-awareness, improving communication skills, navigating team dynamics, driving collaboration, and ultimately boosting both personal and team performance.
Rather than a conventional keynote, this promises to be an immersive experience that combines insightful learning with entertainment, offering a fresh perspective on teamwork, influence, and performance.
We’re also pleased to welcome back Mark Kearns from Queens University Belfast with the support of Vision Plastics, who will be sharing his expertise on several cutting-edge topics. These include the evolving hydrogen economy, recycling, biobased materials research & development in rotational moulding, and modelling and simulation techniques for addressing shrinkage and warpage. Mark’s sessions will provide a wealth of technical information that’s sure to enlighten delegates. Considering the ongoing importance of environmental and sustainability discussions in the plastics industry, our events will continue to feature vital sessions on these themes. Blake Witherow
from Loof will offer insights into the founding and growth of Precious Plastic Melbourne, discussing challenges, the value added for customers, and the vision for future circular economies. Heidi Tait from Tangaroa Blue will address the critical issue of Zero Feedstock Loss, highlighting new regulatory focuses on microplastic pollution and how the Operation Clean Sweep Program can assist businesses in meeting their environmental responsibilities.
A key component of our program is the panel session “Safe Today, Safer Tomorrow: Navigating the Future of Industry Safety”. This discussion will cover a wide range of current trends, issues, and innovations in safety practices, aimed at empowering
“A key component of our program is the panel session “Safe Today, Safer Tomorrow: Navigating the Future of Industry Safety”. This discussion will cover a wide range of current trends, issues, and innovations in safety practices.”
you with the knowledge and tools needed to enhance safety protocols in your workplace. This is a prime opportunity to engage with industry representatives, share experiences, and gain insights into implementing effective safety measures.
Rotomould24 will also showcase presentations from several industry leaders making their first appearance on the Rotomould conference stage.
Kerry Hall, Founder and Managing Director of Halgan Pty Ltd, will discuss overcoming regulation and market bias, sharing insights from his extensive career in manufacturing, plumbing, trade waste, and rotomoulding.
Paul Ayers, with his rich background in various sectors of business and his transition into the rotational moulding industry, will present “Lessons from the Frontline”, combining professional wisdom with engaging storytelling.
Additionally, Peter Turner and Gaylene Emett will take us through “The Story of ThinTanks and Their Journey into the Global Market”, detailing their path to international success through resilience, collaboration, and sustainable innovation.
Lastly, I, as ARMA’s CEO, will not only provide an ARMA Update: Progress and Pathways - A Mid-Year Review but also lead a session titled “Rise & Shine with AI: Discover the Future of Business”. Despite the challenge of presenting in the post-dinner morning slot, I promise an interactive and enlightening presentation on how AI can revolutionise productivity, sales, and opportunities in business, complete with ‘WOW’ moments about what’s on the AI horizon.
Rotoload drinks in the Trade Exhibition
Kick off Rotomould24 with a drink within the lively ambiance of the Trade Exhibition. This initial gathering provides a perfect platform for attendees to reconnect and network on day one, setting the stage for the collaborative spirit that defines our conference.
Price Plastics Winter Wonderland at the Beach Dinner Imagine a mystical evening just a brief walk away to a hidden rooftop oasis in the heart of the Gold Coast. As the excitement builds, join us by the warmth of a crackling fire to toast marshmallows, exchange stories, and enjoy the glow of good company. Venture into a cozy log cabin for a night of mingling with old friends and new amidst the backdrop of the ocean’s vast beauty.
Feast on a spread of exquisite food and drink, all while surrounded by stunning sea views and enveloped in the warmth of our winter wonderland. This unique welcome to Rotomould24 promises an unforgettable blend of warmth, wonder, and culinary delight.
Conference & Awards Night
Dive into an evening of relaxation and celebration at the ARMA Conference & Awards Dinner. As we transform our conference space into a haven of elegance, you’re invited to indulge in a gastronomic journey complemented by a curated selection of fine local wines. The night is dedicated to celebrating our industry’s achievements, with every dish, toast, and shared laughter marking the recognition of excellence and innovation. It’s more than a dinner; it’s an opportunity to forge lasting memories with peers, celebrate shared successes, and toast to the future of our vibrant industry.
ARMA AWARDS | Honouring innovation, design, and dedication Best Product Award
This year, we’re thrilled to bring back our Best Product Competition.
Exhibited within the trade show, this contest invites members to showcase their innovations, with attendees casting their votes for their favourite products. The culmination of this competition will see the winner announced during the conference’s finale, rewarded with a complimentary 12-month ARMA membership for 2025 and a full registration to Rotomould25, celebrating excellence in product innovation.
Student Design Award
In a renewed commitment to fostering the next generation of industry talent, ARMA has proudly reintroduced the Student Design Award for 2024. Reviving a tradition that began in 1999, this program has historically paved the way for students to transition their innovative designs from concept to production, and for many, into
rewarding careers. This year, entrants are challenged to conceive designs that harmonise with themes of environmental sustainability and innovation. Displayed at Rotomould24, these designs will compete for the spotlight, with winners unveiled at the Conference Dinner. This initiative represents our dedication to inspiring sustainable innovation in rotational moulding, encouraging students to envision designs that contribute to a greener future.
The Icons of Rotomoulding Award stands as a testament to those individuals whose unwavering dedication and remarkable achievements have significantly advanced our industry. This prestigious recognition is reserved for individuals embodying the spirit of innovation, leadership, and collaborative success, marking their enduring impact on the rotational moulding sector.
Nominees for this award are those who have not only dedicated a substantial portion of their careers to our industry but have also made significant personal contributions that have spurred growth, fostered innovation, and left a legacy within the community.
Finalists, selected through a rigorous review process by the ARMA CEO and Board, embody the pinnacle of professional excellence and commitment.
In homage to the sustained support and loyalty of our members, the 20 Years of Membership award celebrates companies that have stood with ARMA through decades of evolution. Recognising not just continuity but the depth of commitment to the association, this award acknowledges those who have significantly contributed to the industry’s strength and unity over the years. It’s a recognition that the foundation of our industry’s success is built on the enduring support and actions of our members, a principle we honour with this award.
For more information on any of these awards you can contact info@rotationalmoulding.com
As we celebrate excellence, innovation, and dedication within our industry, we extend our heartfelt thanks to our sponsors. Your unwavering support plays a crucial role in bringing our vision for Rotomould24 to life, enabling us to create a platform for learning, sharing, and advancing our industry.
Your contributions foster a spirit of collaboration and innovation that resonates throughout our event and beyond. Together, we are shaping the future of rotational moulding, inspired by your support and partnership. Thank you for being an integral part of our journey.
Along with all the amazing sponsorships mentioned, delegates will also receive conference items from Austworld, Matrix Polymers, Rising Sun Rotomolding Machinery, Chem-Trend Australia, and PolymerLink.
“The ARMA conference stands out as a mustattend event that is not just for professionals, but for those at all levels of rotomoulding knowledge. With its robust technical presentations, attendees gain invaluable insights into the latest innovations and best practices shaping the field. Furthermore, the conference fosters unparalleled networking opportunities, allowing moulders and suppliers to
exchange practical ideas, forge new partnerships, and stay at the forefront of this dynamic industry.”
(Shaun Nagy, Bushmans Group)
“ARMA’s Rotomould conference is a must attend for us. Each year we step away from the factory to focus on the topics that matter, catch up with rotomoulders and suppliers, and return to the factory recharged.”
(Steven Kyval, Melbourne Rotomould)
“ARMA has always provided the ideal learning and development experience for rotational moulders and suppliers at their conferences. Whatever your level of knowledge and experience you are guaranteed to find some great ideas and thoughts you can take back to your business. Rotomould is always straight in my calendar as a don’t miss event.” (Graeme Hall, Viscount Rotational Moulding)
“Attending the Rotomould conference was an eye-opening experience! The wealth of knowledge shared by industry experts, coupled with engaging networking opportunities, truly sets this event apart. Whether you’re a seasoned professional or new to the field, the conference offers invaluable insights and connections that can elevate your understanding and impact in the rotational moulding industry. I highly recommend it to anyone looking to stay ahead of the curve!” (Jason Kumetaitis, Micropellets Australia) R
Rotomoulding and indeed the whole plastics industry faces many challenges and one of the biggest is the recruitment, development, and retention of top young talent.
The general manufacturing sector is seen by many young people as old-fashioned, in decline, and unattractive and if you add onto this the term “plastic” then it’s doubly unappealing.
But delivering the growth and bright future that our industry surely has is dependent on bringing highly talented and entrepreneurial young people on board.
One of the striking things I see across the world when visiting Rotomoulders is the problem many founders are having passing on their businesses to the next generation. A very big proportion of Rotomoulders are family companies and more often than not the next generation seems to want to go into IT, finance, fashion, or some other “sexier” career. So what hope do we have when people who have grown up knowing about Rotomoulding are wanting to go into something else?
There are no simple answers, but I think it’s important that all of us who are advocates of Rotomoulding make sure that we talk positively about our industry and emphasize all the many benefits that are delivered. For one thing, our products are not throw-away single-use plastics, and instead are durable and are usually made to last 10, 20, or
even 30 years. And at the end of life, they can usually be recycled. We need to educate people about the wonderful range of products that can be made. One of the things we started to do about 18 months ago was to produce a magazine for Rotomoulders to share with their customers, which highlights some of the fantastic design flexibility and diversity of products being made. If you Google “Matrix Polymers Expanding Horizons” you will find the first two publications and a third one will be released soon. There are also ARMO publications called RotoTrends and ARMO Showcase highlighting new applications, which are also extremely useful tools to share with potential clients and even employees.
Another very important thing that we all must do when we have
succeeded in attracting someone talented into our organisation is to retain and develop them. This means that we need to invest and create a career path for them. As a general principle we like to develop people from within our organisation, and a recent example is Jake Kelly-Walley who is in our Technical team based in Liverpool in the UK. We are sponsoring him to do a PhD. titled “A Sustainable Approach to Materials for Advanced Rotational Moulding Applications” at the Polymer Processing Research Centre at Queen’s University in Belfast.
Jake is one of our stars of the future and I think it’s important that all of us in our industry do our bit to help develop the next generation and ensure its future success. R
Happy Spring. As of this writing the sun is shining, and spring is definitely here. Except for a couple of hold-out blasts of winter up here in the north, the grass, trees, and plants are all very excited about the coming warmth. Most of us from northern climates are looking to close out our snow plowing subscription services and looking to negotiate our Lawn Service subscriptions for the coming months.
The big question is, why are Industrial and Machinery needs any different?
While I am quite sure that none of us wishes to remember the Pandemic, regardless of our views or opinions, Covid 19 saw the challenge of business in some markets, and it saw rapid increase of businesses in others across
various subscription models. And, in our private lives, we have seen the growth of every kind of subscription offering.
For our entertainment, Netflix, Prime, Roku, etc., as well as any number of “E” game offerings such as “Hunt a Killer” (an immersive murder mystery box game that turns you into an armchair detective, paying close attention to all the clues in hopes of solving the mystery).
Subscription based online escape rooms became a great way to escape the reality of the Pandemic all from the comfort of your living room.
The big question is, why are Industrial and Machinery needs any different?
Apparently, through 2023, there were approximately 323
companies offering food delivery subscriptions across the USA. Alcohol, medication, Amazon, clothing, shoes, etc., etc., and an unending multitude of other options for subscription-based BOX programs.
The big question is, why are Industrial and Machinery needs any different?
While a lot of businesses, including many of ours, saw adverse impacts from the Pandemic, the subscription-based model of business saw the exact reverse in % of growth.
Previous generations, and perhaps OUR generation... valued and were focused on the importance of ownership. They/we bought houses, bought cars, purchased our business spaces, made capital purchases
of machinery, bought computers, TV’s, appliances, etc.
Newer generations are much more focused on flexibility and are actively considering other models to acquire what they want. They/we rent bicycles, e-scooters, cars, and Air B&B’s. We use Uber and Lyft.
The big question is, why are Industrial and Machinery needs any different?
Almost every possible requirement to run a business can be acquired from providers that are realizing this and focusing on recurring revenue models instead of onetime purchase revenue models.
Furniture can be upgraded, tech (computers tablets, cell phones) can be upgraded and replaced, rental space can be increased or decreased on demand with little
care for the amount of upfront investment due to the fact that essentially there is NO upfront investment. Software can have modules added or removed, and will receive constant updates, upgrades, and improvements as the software companies continue to build and improve their platform. Items can have unlimited warrantee periods, PM programs from the supplier can eliminate the need for in-house service and repair capabilities.
The big question is, why are Industrial and Machinery needs any different?
CAN this be the future of our EQUIPMENT and MACHINERY based needs?
Or...WILL this be the future of our EQUIPMENT and MACHINERY based needs?
Or...SHOULD this be the future of our EQUIPMENT and MACHINERY based needs?
Stay tuned as I examine the primary paradigm shift in thinking for suppliers and what needs to change in our business models? How do we transition from traditional single transaction to more of a long-term relationshipbased model, requiring ongoing performance and long-term support mechanisms and infrastructure, but potentially offering a significant revenue boost.
I would really like to hear any feedback. Please feel free to reach out. rob.miller@wittmann-gorup.ca I would be happy to examine and expose further any pros or cons that may come from this topic. R
» ROTOLOAD™ is the ONLY solution to ALL of your powder resin handling needs.
» ROTOLOAD™ is the ONLY comprehensive line of powder resin conveying and weighing equipment, specifically designed to meet the demands of the Rotational Molding Industry.
» ROTOLOAD™ uses vacuum to load your material, hold it above your process machine, and dispense, quickly and accurately. In addition it is the ONLY solution to the question of how to reduce under and overweight parts, mess, downtime and resin loss.
Over the past two decades
RotoLoPerm® has grown from a concept into the industry leading solution for rotationally molded fuel tanks subject to CARB and EPA emissions regulations. The RotoLoPerm® solution has now been successfully used to manufacture more than ten million gasoline fuel tanks for the Lawn & Garden and Marine industries as well as other market sectors. Developed over several years by Centro’s research and development team, this patented[1-3] technology was invented after an exhaustive analysis of many material combinations to yield the best balanced solution. Built with a molder’s perspective from the ground up, this multilayer technology has been rigorously tested to meet the challenges of safety, material handling, moldability, value, efficiency, aesthetics, permeation performance, mechanical performance, and durability. RotoLoPerm® resin, method to mold, and molded tanks are available from Centro or approved licensees.
Starting in the early 2000s, the California Air Resource Board (CARB) worked to develop and implement evaporative emissions regulations that resulted in
CARB CP-901/ TP-901
Small off-road/ marine
EPA 1060
Evaporative emissions
Small off-road/ marine
ANSI B71.10 Small off-road
ABYC H24/ USCG 33 CFR 183 Marine
Evaporative emissions
Cyclic pressure, low temp impact, hot soak
Design guidelines, Shock, impulse, slosh, fire tests
SAE J1241 Motorcycle (on/ off-road) Lateral impact
SAE J288 Snowmobile
gasoline fuel tanks produced from a single layer of crosslinked polyethylene (XLPE) being noncompliant. CARB implemented these regulations for small off-road engines in 2007 and for marine/watercraft in 2011. The Environmental Protection Agency (EPA) adopted similar regulations in 2009.
Beyond permeability, other standards and test procedures have been developed for several
Low temp impact
Needs to be 20x lower than single layer XLPE
Needs to be 20x lower than single layer XLPE
Strength, structural integrity, toughness, heat resistance
Strength, toughness, durability & fire resistance
Toughness, impact resistance
Low temp impact resistance, ductility
market sectors to ensure fuel tanks are safe for use in gasoline containment applications. ANSI B71.10, ABYC H24, USCG 33 CFR 183, SAE J288, and SAE J1241 are examples of regulations to be considered for various applications. Table 1 outlines a summary of some of the key aspects to each regulation and what makes it challenging for tanks manufactured from polymers to meet.
These various regulations have been a major driver to determine the most suitable rotomoldable materials for gasoline fuel tank applications used for small offroad equipment and watercraft. However, the optimal solution must also take into consideration the customer’s requirements for these applications. Original Equipment Manufacturers (OEMs) have stressed the importance of the design and performance of the fuel tank on their equipment, as it is considered a critical component for vehicle performance and more importantly, safety. Suitable technologies must do more than provide low permeability. Key characteristics to balance include processing safety, permeability, processability, aesthetics, material costs, processing costs/cycle time, impact (including low temperature impact properties), toughness (balance of stiffness and impact), finishing needs (including drilling holes and cut-outs), resistance to chemicals, resistance to UV, heat/fire resistance, insert torque resistance, and supply chain stability. Ultimately, RotoLoPerm® has met these key characteristics, providing tough, durable, compliant fuel tanks for many OEMs in the Lawn & Garden and Marine industries, and other market sectors.
Shortly after CARB announced plans to reduce the evaporative allowances for gasoline fuel tanks, Centro launched an intense research & development program to find a solution to meet the impending regulations. The objective was to find a solution that would allow Centro and
other molders (and the rotational molding process) to continue to be the supplier of choice for the affected products. Options such as modified XLPE, Nylon 6 (PA6), Acetal (which is known as Polyoxymethylene or POM), fluorination/sulfonation, Nylon 11 (PA11), XLPE/PA11, XLPE/ PA6, etc. were evaluated. XLPE had a long-standing history of being the material of choice for these gasoline fuel tank applications prior to the CARB/ EPA regulations. While XLPE had excellent low temperature impact properties and suitable fire test performance, it lacked permeability resistance. With 3-5mm XLPE tanks being common for small off-road fuel tanks prior to the regulations taking effect, Centro established a target impact strength of >40 ft-lbs, tested at low temperature, with >75% ductility. This test alone initially ruled out numerous material options that would not meet the functional requirements for these types of applications.
During the development phase, the Centro team decided that the best solution would likely incorporate a layer of Ethylene Vinyl Alcohol (EVOH), as this material was already the accepted material of choice in the blow molding process to provide a barrier to hydrocarbon molecule transmission. In blow molding, EVOH is co-extruded (Co-Ex) with Polyethylene (PE) to form multilayer fuel tanks, typically for automotive fuel tank applications. In the CoEx process, 5-7 layers are utilized, incorporating discrete adhesive layers to establish adhesion between PE and EVOH layers as illustrated in Figure 1
In order to effectively use
EVOH in rotational molding, some major challenges had to be overcome, which included how to best incorporate the material and which EVOH material should be used (Note: the EVOH material choice will not be discussed in the article, as it must remain confidential). The initial focus was how best to include EVOH in the rotomolding process. Unlike the blow molding process, establishing complete layers that represent just 2% of the overall shot weight is not feasible for rotational molding. Also, a 5-layer structure would further complicate the rotomolding process and would be undesirable. Therefore, efforts were focused on the
development of a 3-layer structure, encapsulating EVOH with XLPE either side, and with optimized layer adhesion. Initially, the development work tried to produce a 3-layer structure
without manually adding the 2nd or 3rd layers. At one point during the development process Centro did successfully rotationally mold a 3-layer fuel tank in a single shot. This was achieved by utilizing the properties of particle size, natural separation, and technology like that used in “batch inclusion bags”, which contain resin in a bag that later melts to deliver the inner most layer. However, the lack of process repeatability and the costs to achieve it meant that the process was not viable for production. Ultimately, the most efficient and cost-effective process involved molding a XLPE shell with the first shot of material, followed by indexing arms from the oven to load the 2nd (middle) layer of the barrier material, later followed by the 3rd (inner) layer of XLPE powder. This 3-layered product with layers of XLPE/EVOH/XLPE describes what RotoLoPerm® is.
Numerous methods were trialed to achieve adhesion between the XLPE layers and the EVOH layer, ranging from mechanical adhesion, controlled through addition temperatures enabling slight mixing of layers, to chemical bonding with functionalized polymers incorporated into one or more of the layers. Through this iterative process, an important discovery was made regarding the relationship between layer adhesion and impact strength/ ductility. With EVOH being a high density, highly crystalline polymer, a single layer of EVOH is very stiff and brittle. Therefore, too much adhesion could result in reduced impact properties. This was shown to be the case in Figure 2, which illustrates that as layer adhesion increased
(ftlbs) Mean Failure Energy (ft-lbs) Ductility (%)
between the EVOH layer and the XLPE layers, impact strength and especially ductility would drop off. Therefore, a balance in the formulation had to be established to yield both good impact
and good
During this development work, linear PE was evaluated as a potential cost reduction opportunity for both the outer and inner layers. Using PE on the
outside layer was challenging, as many of the applications required a high Melt Flow Index (MFI) material to be able to form thread detail. Another downside was the effect linear PE had on the mechanical properties. The impact data in Figure 3 illustrates that replacing either the outer or inner layer with linear PE (instead of XLPE) caused impact strength to fall off significantly.
Another challenge during development related to the optimization of the wall thickness for each of the three layers of material. To remain viable, the material content had to be sufficient to meet the structural needs and permeation requirements for the product. However, too much material content would negatively impact the molding cycle time and the cost of the product. During development, an optimal wall thickness for each layer was established, beginning with the outer XLPE layer. This initial layer typically had to be at least 2mm in thickness to provide a solid shell to build the additional layers on. Establishing an initial layer with uniform wall thickness was critically important, as the wall thickness distribution for the layers to follow closely replicate that of the first layer. It was observed during the development that the inner layer of XLPE had a significant influence on impact strength. The greater the inner wall thickness, the greater the impact strength (see Figure 4). Therefore, the overall structure of RotoLoPerm® was established as having a 2mm XLPE outer skin, with a 1 mm (minimum) EVOH middle layer and sufficient wall thickness of the inner XLPE
layer to meet the performance requirements of the application.
In addition to the permeation and mechanical performance aspects, the profitability of any solution was an important consideration. Some low permeation materials were not feasible because the overall cost was not competitive compared to competing processes. Key aspects of value are derived from material cost, cycle time, cavity placement, load/ unload time, and scrap rates. At first glance, a three-layer process sounds daunting and inefficient. In fact, many in the rotomolding industry still hold this misconception about the overall cycle time required to produce tanks in this way. Centro’s focus was not on finding reasons a three-layer process was problematic, but rather to develop a safe, efficient, and effective
process to deliver the most costeffective product which meets the requirements. To do this, various molding trials focused to develop the most efficient process by:
• Focusing on operator safety through the entire process
• Use of stepped cycles to balance careful heating of XLPE, while minimizing overall cycle time
• Minimizing time to load materials safely into hot molds
• Maximizing cavity placement to efficiently use arm space
• Use of internal air temperature measurement to establish optimal addition temperatures for the 2nd and 3rd layers, to provide the best combination of impact properties and layer adhesion
Rotational molding relies on gravity, heat, rotation, and powder flow properties and typically an empty mold and a
single load of powder. However, for RotoLoPerm®, an initial charge of XLPE powder is heated and allowed to lay up on the mold walls. This initial charge of material should be minimal but have enough powder to adequately cover all flat/curved surfaces, fill threads, encapsulate inserts, and cover features such as deep cores, which can be challenging. It is common in the rotational molding industry to add additional resin in order to overcome coverage or wall thickness challenges. However, using advanced techniques to balance the thermodynamic properties of the mold’s heat conduction, a more uniform wall thickness can be achieved with less variation. This is extremely important to establish for the initial layer, as the wall thickness distribution for the initial layer will typically be replicated in the 2nd and 3rd layers, which will ultimately result in the most costeffective 3-layer product.
Generally speaking, with the appropriate focus during prototyping, a 3-layer relatively complex RotoLoPerm® gasoline fuel tank can be produced with a standard mold. This is because XLPE offers a great benefit in being able to flow extremely well due to its high MFI prior to crosslinking. This allows the molder to replicate the surface of the mold with a relatively thin initial shell, approximately 2mm in thickness. The EVOH barrier layer only requires a thin coating to meet the permeation requirements. This 2nd layer can be easily achieved using an appropriate mesh size material, provided a uniform first layer has been established. The final layer of XLPE is a formality and provides the product with
Regulation Or Application Specific Testing
Pass/Fail
CARB/EPA Evaporative Permeation Regs PASS
ANSI B71.10 (impact, cyclic P/V, hot soak) PASS
USCG/ABYC H24 (impact, impulse, heptane burn) PASS
ANSI J288 (cold drop – in and out of frame) PASS
ANSI J1241 (cold pendulum impact) PASS
On-road Motorcyle customer tests (simulation of tire shred) PASS
Customer testing beyond B71.10 (burst test, extended P/V, additional cold drop of assembly) PASS
Permeation before and after durability testing (Centro designated) PASS
excellent low temperature impact strength, which is a highly desirable attribute for most if not all gasoline fuel tank applications. Figure 5 shows some examples of material wall thickness distribution produced by the RotoLoPerm® process.
Performance Capabilities
The commercial success of RotoLoPerm® speaks for itself,
with well over ten million gasoline fuel tanks in the field over the past 15 years. Table 2 illustrates how RotoLoPerm® has performed relative to the various regulatory standards these applications fall under. It should be noted that the permeation and durability testing performed by Centro was not an actual requirement, but it speaks to the durability of the RotoLoPerm® solution. During the
Centro designated testing, fuel tanks molded with RotoLoPerm® technology were initially tested for permeation rate using Flame Ionization Detection (FID) after an initial soak period with E10 fuel. Next, those same tanks were put through various tests including low temperature drop tests (conditioned to -18C with ethylene glycol, tank filled 50%, dropped from a height of 3 ft onto a concrete floor) and 10,000 cycle cyclic pressure/vacuum testing. Normally, verifying no leaks alone would dictate a passing result for this test. Centro understood that many of the OEM applications would have exposure to impact and/or other
functional conditions, therefore it was important to understand the effect of impact on permeation performance. Centro took further steps to put tanks back through permeation testing and validated that even after simulation of these severe events, fuel permeation performance was still far below the allowable limit of 1.5 g/m2/ day. A summary of these test results can be seen in Figure 6.
RotoLoPerm® has evolved into a highly successful method for Centro (see Figure 7) and several other licensed molders within the industry to produce low permeation gasoline fuel tanks since 2007 (see Figure 8). After obtaining the first patent related to the technology in 2013[1], with
two more following in 2014[2, 3] , the decision was made to pursue licensing the technology. Licensing enables greater access to this high-impact solution without the limitation of one molder’s capacity, market specialization, or geographic location. Centro now licenses the technology to multiple molders fulfilling needs in various industries including Marine fuel tanks, Lawn & Garden fuel tanks and portable fuel containers for off-road vehicles. It should be noted that the original granted licenses have been renewed and represent long-term mutually beneficial relationships. Centro welcomes parties interested in RotoLoPerm® technology to contact Ty Windy, Director of Sales (twindy@centroinc.com) for additional information.
References
1. US Patent #: 8,597,747 B2, Multi-Layer Rotationally Molded Low Permeation Vessels and Methods for Manufacture Thereof, Dec. 3rd, 2013, Alvin G. Spence, Jeremy R. Knepper, Daniel D. Grimes.
2. US Patent #: 8,721,951 B2, Multi-Layer Rotationally Molded Low Permeation Vessels and Methods for Manufacture Thereof, May 13th, 2014, Alvin G. Spence, Jeremy R. Knepper, Daniel D. Grimes.
3. US Patent #: 8,911,842 B2, Multi-Layer Rotationally Molded Low Permeation Vessels and Methods for Manufacture Thereof, Dec. 16th, 2014, Alvin G. Spence, Jeremy R. Knepper, Daniel D. Grimes. R
India’s economy has been of global importance for some time. When I visited India in 2016 to attend the StAR Goa rotomoulding conference, India had the world’s 3rd largest population and was ranked 7th in the world’s GDP rankings.
During my next visit 8 years later, to attend 2024 StAR Kovalam conference, India now has the world’s largest population. It is one of the world’s fastest growing economies, is ranked 5th in the GDP rankings, and remains a contributor to global economic growth.
India’s plastic consumption has grown faster than other developing and developed countries. India produces nearly 3.5 million tonnes of plastic waste per annum. In the past 5 years there has been a twofold increase in per capita plastic waste generation. With plastic usage expected to jump up to 4 times by 2050, the waste problem is also expected to jump 4 times, if a ‘business-asusual’ approach continues.
India recognises the scale and complexity of the plastic waste problem and its
interconnectedness with global ocean plastic pollution.
At an individual level many rotomoulders around the world are increasingly playing their part to reduce plastic waste by driving innovation and enabling new circular economy design and business models to achieve this.
Frontier Polymers are one such example. They have a rotomoulding facility located in Amrtisar, about 250 miles (400km) north east of New Delhi, India. Established in 1989, they manufacture a wide range of industrial, commercial, and household products such as
water tanks up to 10,000L, road safety products, material handling containers, planters, wheelie bins and waste bins.
Yuvraj Singh Ahuja, a director of Frontier Polymers, gave a presentation at the 2024 StAR Kovlam rotomoulding conference about his experience in recycling within India.
He outlined some of the problems associated with recycling of plastic, which actually apply to most countries:
Lack of standardisation in recycling process
High cost of recycling polymer
Supply chain is unreliable
Recycled products carry perception of inferiority
Traceability of recycled polymers
Lack of recycled polymer quality transparency
Yuvraj highlighted European companies such as Dragon Plastics (www.dragonplastics. nl/en) and Eco Birdy (www. ecobirdy.com) to demonstrate that high value, high quality, and sustainable recycled products can be successfully manufactured and marketed to end users.
Within the last couple of years we have seen Toter, (www.toter. com) a major rotomoulder in
the US, launch EVR-Green, the first 100% recycled cart body in North America. This demanding application will likely help build confidence in recycled products, with both industry peers and end users.
These companies demonstrate that high value and high quality recycled products can be successfully manufactured and marketed to end users.
Frontier Polymers saw the potential for recycled polymers in
multi-layer rotomoulded products some years ago. Yuvraj, along with lead designer Satish Gokhale (Design Directions), had designed a contemporary range of high value, high quality Sereno branded products, be it flower pots, large planters, outdoor seating, or lamps, (www.sereno.co.in)
They were aiming for high value, high quality, and sustainable products for the Indian market. The designs have been recognised with a European product Design Award and Confederation of Indian Industries Design Excellance Award,
Frontier also saw the value in manufacturing their mobile wheel bins and large waste bins with recycled polymers. The main cart bodies are offered in a 100% recycled polymer option.
A major component of plastic waste in India is single-use plastic items like Tetra Pak® cartons, which are 70% cardboard, 25% plastic, and 5% aluminium. Frontier began using recycled plastic from Tetra Pak some years ago for the inner layer of recycled material in their Sereno range, instead of just PIR-Post Industrial Recycled.
Good government, corporate, and community initiatives can be found within India and many countries around the world, as they attempt to overcome the bad press the plastics sector receives. Yuvraj highlighted commercial use is challenged by mixed streams of plastic waste, waste contamination, and poor segregation.
One of the major problems Frontier had as they started their Tetra Pak® waste recycling journey was the poor quality and consistency of the TetraPak Post Consumer Recycled plastic. Moulding the polymer was already
challenging, but they found it to be contaminated with small bits of cardboard and aluminium. Even when blending the PCR material with virgin rotomoulding material, and using it as a second inner layer, it was too problematic to mould acceptable products. They had to end this project.
However, another major component of single-use plastic waste in India is the milk pouch (bag). These bags are typically made using LDPE or HDPE. India is one of the few countries in the world selling milk in pouches, and on average dairies across India sell over 100 million milk pouches per day.
The current PCR project Frontier has been focused on is using recycled milk pouches as the inner layer, instead of recycled Tetra Pak plastic.
They have studied 100% recycled black (PIR) and compared this against 80% PIR and 20% milk pouches and 70% PIR and 30% milk pouches. For the specific product application targeted, the initial results are looking promising and Frontier are hoping to have some positive news about the inclusion of milk pouch PCR into their products later this year.
The essentially linear ‘takemake-waste’ packaging industry needs to be replaced with a circular economy that should use as little virgin plastic as possible and maximise the use of recycled material. All levels of Indian government are putting pressure on the manufacturers of milk pouches to come up with an effective waste collection and recycling system – sooner rather than later. Rotational moulding has an opportunity to help the packaging industry, our plastics industry.
“ROTATIONAL MOULDING CONTINUES TO BE A PROCESS THAT OFFERS THE POSSIBILITY TO MANUFACTURE AND RECYCLE ALMOST ANYTHING YOU CAN IMAGE.”
The incorporation of Post Industrial Recycled (PIR) PE is proudly marketed by Frontier Polymers in their use of the 3 R symbol - Reduce, Reuse, Recycle.
The use of recycled milk pouches (PCR) will strengthen the circular economy design aspect into their products, while allowing them to help make plastics sustainable in our environment.
Frontier Polymers are not
solving the plastic waste problem in India, but their corporate social responsibility actions at a micro level matter on a macro-level, the level of shifting mass perception. They also help generate demand for recycled plastic products.
Rotational moulding continues to be a process that offers the possibility to manufacture and recycle almost anything you can imagine. R
Des Crossley is a Melbourne based conceptual photographer who wanted to create a unique exhibition in Melbourne, Australia. He teamed up with Mark Medew, a rotational moulder from Plastic Fabrications, to produce some custom mail boxes that matched his artistic vision for one of the pieces to create. The mailboxes were not only functional, but also expressive of the emotions and themes that Des wanted to convey through his conceptual art. The exhibition was a success, and the mailboxes showcased the versatility and creativity of rotational moulding as a technique.
Artist Statement: Uprising
In a digital age, the absence of printed photographs in our mail system carries profound emotional weight. My work delves into the poignant reality of nostalgia and connection, exploring the wistfulness when the tactile charm of receiving photos in the post vanishes. The emotive power of physical photographs, once cherished mementos, becomes more apparent when we lose them to digital galleries. I aim to rekindle that sentiment through my art, reminding us of the irreplaceable joy of holding, sharing, and preserving tangible memories. It’s a testament to the profound emotions tied to our photographic history, inviting viewers to reflect on the beauty of a bygone era and be part of a future existence. R
PRESIDENT: Chris Glenn Bushmans Group (Australia)
PAST PRESIDENT: Trudi Duncan Gyro Plastics (New Zealand)
VICE PRESIDENT: Ian Gough Gough Plastics (Australia)
TREASURER: Mark Medew Plastic Fabrications (Australia)
BOARD MEMBER: Paul Ayers Galloway Group (New Zealand)
BOARD MEMBER: Varun Chand Rotomould Group of Companies (Fiji)
BOARD MEMBER: Ben Hopley Viscount Rotational Moulding (Australia)
BOARD MEMBER: Brad Smyth Barron & Rawson (Australia)
SUPPLIER BOARD MEMBER: Andrew Currie Price Plastics (Australia)
Rotomarket serves as the premier destination for purchasing and selling pre-owned machinery and tooling within the rotational moulding industry. This advertising platform is offered at no cost to our members and supporters, while a nominal fee applies to other companies. Listings remain active until the sale is completed and receive additional exposure through our newsletters and social media channels for enhanced visibility.
For more information or to view current listings visit www.rotationalmoulding.com/rotomarket R
Stay connected and up to date with us by following our social media channels! We’re excited to announce that we’ve now joined Instagram, bringing you closer to the latest in our industry with engaging visuals and instant updates. It’s a cool new way to stay informed and get a behind-the-scenes look at what we’re up to. Following us is easy – just scan the QR codes we’ve provided, and you’ll be linked directly to our profiles. Don’t miss out on this simple yet effective way to keep in touch and be part of our growing community online! R
Forward thinking and well trusted media brand, Eljays44, are continuing their recent period of growth following a highly successful 2023, with the launch of Recycling Expo at the London ExCeL!
The event will take place on the 15-16 October 2024 at the ExCeL in London, and will be free to attend for all visitors! Registration is now open. Visit BPF stand T40.
Eljays44 have spent over a decade building the most trusted media brands in the landscaping industry and earning a reputation for high quality, well attended exhibitions with their leading brand, FutureScape. Now, as they embark on this new venture, they have partnered with The Recycling Association to apply their expertise in the exciting world of recycling and responsible waste management, bringing a much desired recycling event to the capital.
Designed for the industry, by the industry, Recycling Expo has been launched to fill the gap in the market for a purely recycling focused exhibition that enables investment into the future of recycling, remanufacturing, and environmental innovation. With a seminar agenda
formulated in collaboration with The recycling Association Chief Executive, Paul Sanderson, and over 150 exciting exhibitors from across the sector, visitors can expect a highly comprehensive and educational B2B event.
Recycling Expo 2024 is the premier destination for private sector, public sector, recycling operators, and waste generating companies to source and purchase the latest in ‘green’ waste management products. Keep up to date with current and future trends, and network with like-minded peers from across the world of recycling and waste reduction.
“Recycling Expo is more than just an event” says Event Director, Eddy Lawrance. “It’s a marketplace dedicated to connecting industry providers with buyers and creating business relationships centred around responsible resource management, an increase in the reuse of materials, a reduction of consumption based Co2 production, and a shift away from wasteful linear economy models.”
Current exhibitors for the 2024 event include:
• Kaizen Recycling
• Everest Labs
• Thalia Waste Management
• Danu Robotics
• Recycle Eye
• Clearpoint Recycling
• Deep Tech recycling
• Presona
ASSOCIATION OF ROTATIONAL MOULDERS AUSTRALASIA LTD
Michelle Rose, CAE Chief Executive Officer PO Box 237 Moonee Ponds VIC 3039 Australia
Phone: + 61 (0)404 265 887 michellerose@ rotationalmoulding.com www.rotationalmoulding.com
With new companies being added weekly, the current exhibitor lineup can be found online, the first wave of speakers for the event includes leading figures from the likes of Biffa, Suez, and Thalia Waste Management.
Having already established partnerships with key industry associations and publications including the likes of the BPF, MRW, REB Market Intelligence, NAWDO, RECOUP, and UROC, Eljays44 are committed to growing, developing, and raising the profile of this important sector.
The event will take place on the 15-16 October 2024 at the ExCeL in London, and will be free to attend for all visitors! R
ASSOCIATION OF ROTATIONAL MOULDING
(Central Europe) e.V. (ARM-CE)
MAUS GmbHRotationsgießformen
Am Viehweg 9 - D-76229
Karlsruhe
Amtsgericht Mannheim, HRB 103433
ASSOCIATION OF ROTATIONAL MOULDERS SOUTHERN AFRICA PO Box 6966
Birchleigh 1621 Gauteng, South Africa
Phone: +27 82 772 3769
Fax: +27 12 541 1738
Chairman: Gary Wiid info@armsa.co.za www.armsa.co.za
IT-RO ITALIA ROTAZIONALE
Katia Zoppetti Via E. Brigatti 12 20152 Milano (MI) Italy
Phone: +039 348 7652560 www.it-ro.it
SOCIETY OF ASIAN ROTOMOULDERS (STAR)
40/145, Ground Floor, Chittaranjan Park New Delhi 110019
Phone: + 91-11-41630157
Fax: +91-11-41634952
Cell: + 91- 9810305356 sb.zaman@staraisa.org arnacz@satyam.net.in www.starasia.org
Mr. Oliver Wandres, ARM-CE Chairman
info@rotational-moulding.de www.rotational-moulding.de
British Plastics Federation Rotational Moulding Group
6 Bath Place
Rivington Street London EC2A 3JE
United Kingdom
Phone: 020 7457 5000 Fax: 020 7457 5045
Chairman: Mr. Philip Maddox PhilipM@LeafieldEnv.com THE NORDIC
17 Diversified Mold & Castings
19800 Miles Road Warrensville Hts., OH 44128-4118 USA
216.663.1814 | 888.642.1222 info@diversifiedmolds.com www.diversifiedmolds.com
76 ExxonMobil Chemical Co. PO Box 96126 West Springs Calgary, Alberta Canada, T3H 0L3 800.668.0177
kevin.c.jamieson@exxonmobil.com https://www.exxonmobilchemical. com/en/products-and-services/ polyethylene
5 Ferry Industries, Inc.
4445 Allen Road Stow, OH 44224-1093 USA 330.920.9200
sales@ferryindustries.com www.ferryindustries.com
9, 63 Jerico Plastic Industries, Inc.
7970 Boneta Road Wadsworth, OH 44281 USA 330.334.5244
Minerva Plant: 330.868.4600 steve@jericoplastic.com www.jericoplastic.com
11 Matrix Polymers
The Priory Orchard Hill Little Billing Northhampton, NN9 9AG United Kingdom
+44.1604.789100 sales@matrixpolymers.com www.matrixpolymers.com
7 Orenda
165 Steelcase Rd. East Markham, Ontario L3R 1G1, Canada 905.513.8043
sales@orenda-automation.com www.orenda-automation.com
33 OREX Rotomoulding Sp. z o.o. Cieszyńska 6, 43-520 Chybie Poland
+48 32 440 83 15 magda.wantola@orex.pl www.orex-rotomoulding.com
68 Poliplast S.p.A. Via Carrali, 8 24020 Casnigo (BG) Italy +39.035.724145 info@poliplastspa.com www.poliplastspa.com
3 Powder King, LLC
41780 N. Vision Way Unit 120 Bldg. 2 Anthem, AZ 85086 USA 623.551.9897 sales@powder-king.com www.powder-king.com
39 Rock Lake Robotics
100 S. CP. Avenue Lake Mills, WI 53551 USA 920.648.3402 sales@rocklakerobotics.com www.rocklakerobotics.com
21 Rotaloc
100 S. CP. Avenue Lake Mills, WI 53551 USA 303.948.5434 sales@rotaloc.com www.rotaloc.com
2 Roto Polymers 26210 Emery Road, Suite 202 Cleveland, OH 44128 USA
1.844.POLIMER (1.844.765.4637) info@rotopolymers.com www.rotopolymers.com
75 Rotomachinery Group Via Crosa, 53 28065 Cerano (NO) Italy +39.0321.772021 polivinil@polivinil.com www.rotomachinerygroup.com
14 VMP, Inc.
24830 Avenue Tibbitts Valencia, CA 91355-3404 USA 888.4.VMP.INC 661.294.9934 info@vmpinc.com www.vmpinc.com
55 Wittmann Battenfeld Canada Inc. / ROTOLOADTM 35 Leek Crescent Richmond Hill, ON L4B 4C2, Canada 905.887.5355 Toll Free: 1.888.466.8266 info@wittmann-group.ca www.wittmann-group.ca
25 Xcelerant Growth Partners
624 W. Washington Avenue, #411 Madison, WI 53703 440.384.7654 info@xcelerantgrowthpartners.com xcelerantgrowthpartners.com
625 West Market Street
Salinas, CA 93901 USA
Delivering proven performance so you can innovate with confidence.
Your rotational molding capabilities begin with the quality and dependability of your polyethylene resin supply. Start your day with PE products and process innovations that help leading rotomolders bring their most complex designs to reality. Accomplish more with our reliable supply network, responsive sales support and expert technology team