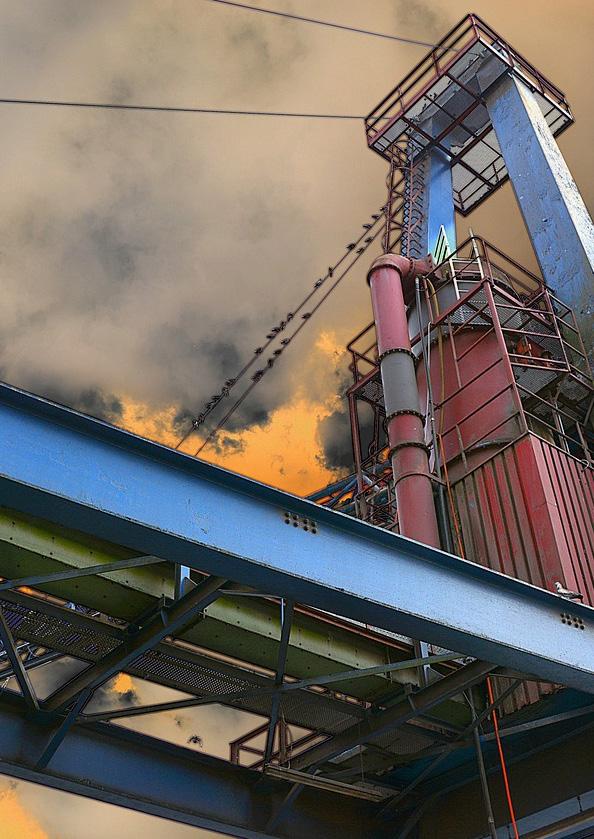
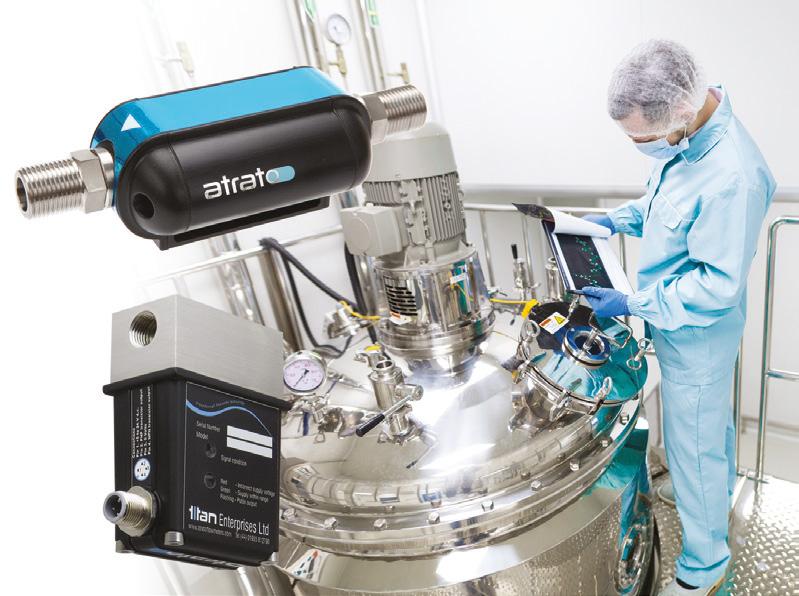
Turbine Flowmeters
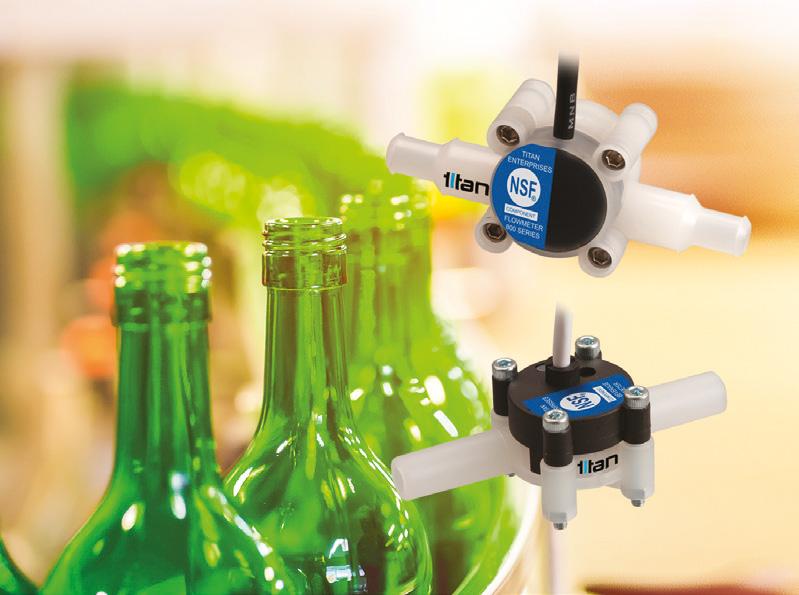
Oval Gear Flowmeters
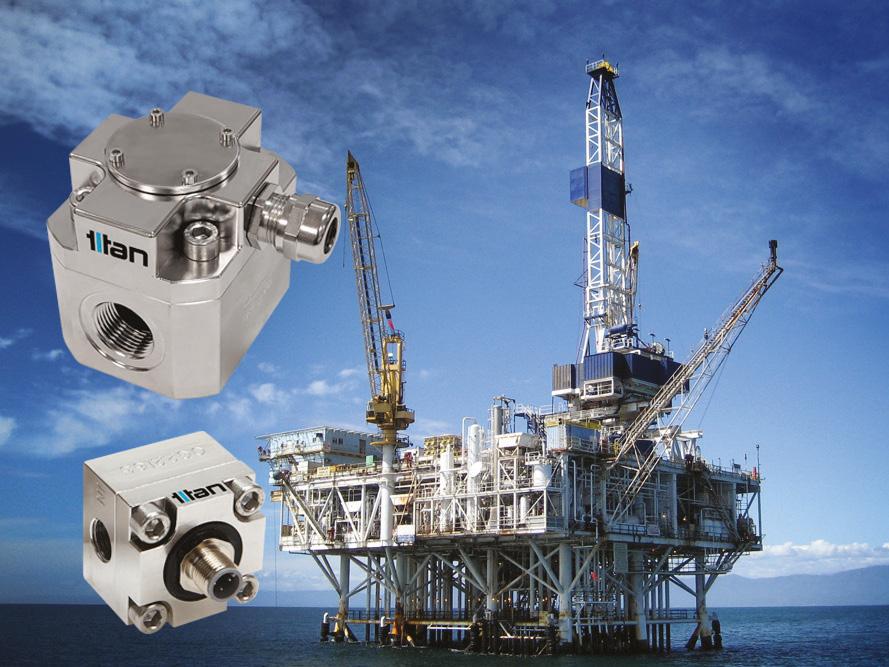
Instrumentation
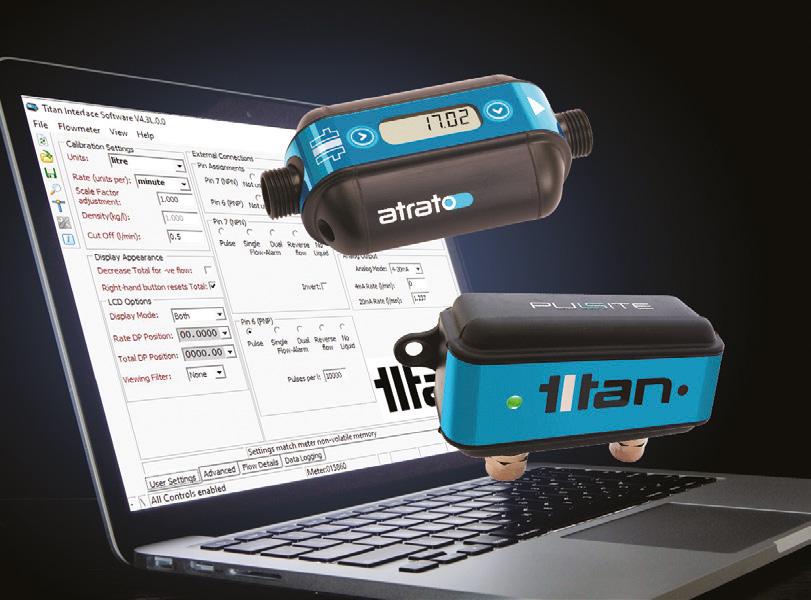
Titan Enterprises is a leading design and manufacturer of innovative end user and OEM high-performance flowmeters and flow measurement instrumentation, used within a wide range of processes, environments and applications.
• Compact, robust, reliable
• Excellent accuracy and repeatability
• Measure low to high flow ranges
• High chemical resistance
• NSF-Approved mini turbine flowmeters
• ATEX-compliant and high pressure Oval Gear models
• OEM bespoke design capability Titan’s liquid flowmeters are designed and manufactured to ISO 9001 with traceable calibrations.
+44 (0)1935 812790 sales@flowmeters.co.uk www.flowmeters.co.uk
Providing timely industry news, exclusive features on advancing technology, equipment, materials, show previews, content marketing services for our valued clients and much more!
4
Why it’s important we all renew our site safety passports
12
Atlas Copco oxygen generator helps Iona Management Services make biogas production even more sustainable
16
Designer EV charging brand Andersen launches 13 new colours inspired by the new electric Porsche Macan
8
Bunting Magnetising Innovation at The Magnetics Show Europe
14
Andersen named ‘Chargepoint Manufacturer of the Year’ at EVIEs
21
Festo AX: simple industrial AI solutions for maximum productivity
Stephen Thompson - 01227 314 329 Publication Manager | steve@worldwide-enegineering.com
Katie Sirdefield - 01227 314 329 Editorial Assistant | katie@worldwide-enegineering.com
Orla McGill - 01227 314 329 Newsletter/Editorial Assistant | orla@worldwide-enegineering.com
Daisy Shingles - 01227 314 329 Graphic Designer | design@worldwide-engineering.com
An experienced supervisor has urged workers in the engineering construction industry (ECI) to keep their safety passports up to date to ensure everyone stays safe on site
Daniel Williamson, 35, who works for Ledwood Mechanical Engineering, has been a CCNSG Safety Passport holder for 13 years and says making sure health and safety knowledge is kept current and relevant is vital when working in hazardous environments.
The fabrication supervisor (pictured) has worked in the industry 18 years, a decade with Ledwood in Pembrokeshire, Wales, and believes renewing safety cards helps prevent complacency.
The CCNSG Safety Passport is the nationally recognised safety card for the ECI and often a pre-requisite for workers to enter UK sites. The Engineering Construction Industry Training Board’s (ECITB) qualityassured CCNSG course is suitable for all members of the workforce, providing enhanced health and safety awareness to help reduce accidents.
“It’s a really good programme,” said Daniel. “It’s like guidance for how you should be working within these environments.
“It’s important because it keeps myself and people around me safe. When you come to work you want to go home in the same state, nobody wants to go to work to get hurt.”
Ledwood is an engineering, fabrication, coating and construction company specialising in energy production and processing industries.
As an ECITB-approved training provider, Ledwood delivers in-house courses to its workers, such as the CCNSG Safety Passport. It has delivered the safety scheme since 2013, which helps it plan courses around contract work and tailor content to mechanical engineering.
CCNSG safety cards are valid for three years after completion and can be renewed up to six months before the expiry date through a one-day renewal course or test-only route. If card holders fail to renew before the expiry date, they must re-do the two-day course to secure a new passport.
Daniel has been through the renewal process several times and insists it is about much more than ensuring workers can access sites.
“Renewing your CCNSG Safety Passport keeps things relevant, keeps your awareness high and stops complacency as the regulations are constantly changing,” he added.
“I’ve learnt something new sitting the renewal course each time, so I find it helpful. It definitely keeps things current and relevant to what we are doing.
“There’s reassurance that everyone’s been through it, everyone should share the same knowledge and follow the same practices.”
Find out more about CCNSG renewal at: www.ecitb.org.uk/professionaldevelopment/ccnsg/ccnsg-renewal/
3.7 million days lost annually due to accidents at work*
The CCNSG Safety Passport has been a trailblazer for quality-assured safety training across the UK engineering construction industry and many other sectors for 30 years, helping reduce accidents and lost time incidents on sites.
“As one of the largest employers in the engineering construction industry, Altrad completely supports the principles of the CCNSG and the benefits it brings to the workforce. It gives a baseline level of safety knowledge across all our projects and sites.”
Mark Poole, Learning and Competence Manager for UK and Ireland, Altrad
With projects ramping up, be confident workers on your sites at all levels have a common awareness of health and safety to keep themselves and their colleagues safe.
Find out more about the ECITB’s nationally recognised safety card
Bunting has developed a new Electromagnetic Wet Filter with an ultra-high-intensity, background magnetic field (from 3,500 up to 10,000 Gauss)
The magnetic separation technology separates fine iron and paramagnetic minerals from liquids and slurries and is used in the ceramics, mineral processing, and recycling industries, as well as cleaning wastewater in steel production and power stations.
The high-intensity magnetic field of the Electromagnetic Wet Filter enables the separation of very weakly magnetic particles untouched by other magnetic separation technology. In the ceramics industry, the Electromagnetic Wet Filter removes problematic magnetic particles, both free iron and magnetic minerals, from slips and glazes. In mineral processing, more powerful Electromagnetic Wet Filters remove fine grinding iron and some paramagnetic minerals (e.g. hematite) found in nonmetallic minerals. Electromagnetic Wet Filters are also used to remove free iron and scale from water in power stations, steelworks and water recycling plants.
The Electromagnetic Wet Filter provides one of the most effective methods of
continually removing problematic fine iron and paramagnetic minerals from ceramic slips and glazes, as well as industrial mineral slurries (e.g. kaolin, calcium carbonate, silica sand and feldspar). The technology produces a higher separation efficiency than permanent magnetic and smaller electromagnetic separators by generating a significant background magnetic field strength in the canister (2,500 Gauss, 5,000 Gauss or 10,000 Gauss) and high magnetic field gradient on the matrix surface. The enhancement of the magnetic field on the matrix surface is between 2 and 3 times the background field – e.g. a 5,000 Gauss background filed will generate between 10,000 and 15,000 Gauss on the matrix.
An Electromagnetic Wet Filters consists of an electromagnetic coil positioned around a central hollow core containing a magnetic (400 series) stainlesssteel matrix of various designs. The highly-efficient computer designed coil generates a high intensity magnetic field
that becomes intensified on the points of the matrix creating the magnetic force needed to separate paramagnetic particles from the slurry.
The magnetic coil is either enclosed in a circular or rectangular steel casing designed to intensify the magnetic field into the hollow centre of the coil. The design of the oil-cooled electromagnetic coils maintains thermal stability whilst generating high Gauss values. The coil designs are energy efficient and maintain low operating temperatures.
Valves trees (for the product feed and exit as well as cleaning water and air) are mounted on the top and bottom to suit the application and installation.
Removal of the captured magnetics inside the Electromagnetic Wet Filter is either undertaken manually or automatically. For fully automated operation, the Electromagnetic Wet Filter and process is managed through a separate control. The control has a Siemens S7-1200 PLC incorporating Siemens HMI. Via the control, operators are able to set the frequency and parameters of the matrix cleaning regime.
The directional flushing system ensures the maximum removal of captured magnetics and para magnetics from the matrix, maximizing magnetic separation from the next batch of product.
The Electromagnetic Wet Filter is fitted with a built-in jig to enable easy removal of the matrix, poles, and complete canister for maintenance and additional cleaning. The jig keeps production downtime to a minimum, whilst making matrix handling safer and easier. A separate transformer rectifier is used to deliver power.
“The new Electromagnetic Wet Filter solves a high-intensity magnetic separation problem for liquids and slurries,” explained Adrian Coleman, Bunting’s European Technical Director. “In ceramics, successfully removing any magnetic particle significantly reduces reject rates and rework costs. Having the ability to process non-metallic minerals in a wet state saves on drying costs and enables higher removal levels
of magnetics. The new Electromagnetic Wet Filter answers many wet magnetic separation questions.”
For further information, please contact us on: redditch@buntingmagnetics.com or visit our website to find out more about this product: www.bunting-redditch.com/product/ electromagnetic-filters-wet/
Bunting, one of the world’s leading designers and manufacturers of magnets, magnet assemblies and magnetising equipment, is exhibiting magnetic solutions and innovations in magnetising technology on stand 408 at The Magnetics Show Europe (December 3-4, 2024, RAI, Amsterdam, The Netherlands)
The inaugural The Magnetics Show Europe (December 3-4, 2024, RAI, Amsterdam, The Netherlands) brings together designers, producers, and users of magnets and magnetic products.
The Magnetics Show has been previously been held in the USA, with the 2025 event taking place in The Pasadena Convention Centre in California. The Magnetics Show Europe brings the popular magnetic conference and expo to Europe, where industrial experts will deliver a comprehensive programme of technical presentations. The conference is supported by an extensive supply chain exhibition featuring leading companies in the magnetics world.
On stand 408, Bunting’s technical team will provide advice on a wide range of magnetic issues, from the design of magnet assemblies through to industrial magnetisation. This includes postassembly magnetisation, a process which is changing the production and design process of magnet assemblies, maximising the finished assembly magnetic performance whilst improving manufacturing safety.
Bunting’s European Technical Product Manager and former Chairman of the UK Magnetics Society, Matthew Swallow was on the founding advisory board and explained the importance of The Magnetics Show Europe:
“Bringing The Magnetics Show to Europe is a great opportunity to bring together what can be a disparate group of industries who all rely on the fantastic properties of Rare Earth Magnets. The Magnetics Show will seek to advance
the scientific, technical and practical development and application of magnetics technology and as Chair of the UK Magnetics Society I am happy to support any event that aligns with our core values. By being at the event, the UK Magnetics Society will add members
to our continually growing communities, where more people means more connections and more activity to drive the magnetics community forward.”
For further information, please visit: www.bunting-berkhamsted.com
With the engineering skills crisis worsening year on year, Morson Group has once again shown a proactive approach to tackling the problem by inspiring a new generation of engineers to become leaders in their field with their annual Early Careers Development Programme(ECDP) conference in Manchester
Coinciding with Career Development Month in November, the conference brought together almost 150 engineers, architects, and project managers from across the Group’s Morson Projects, Waldeck and Ematics engineering businesses to challenge, inspire and encourage them as they progress on the award-winning ECDP. New recruits came together with those already advancing through the programme and mentors and senior colleagues from across the organisation, taking on problem solving and engineering challenges to encourage collaborative working, as well hearing talks about where their career could take them.
The conference comes as the Public Accounts Committee (PAC) warns that the UK lacks the technical and engineering skills to deliver major infrastructure projects. It also follows comments by IMechE president Dr Clive Hickman OBE about the essential need to invest in the development of engineers to deliver the government’s plan for a new Industrial Strategy by aligning skills programmes with industry needs to nurture the right talent to meet future demands.
“Our ECDP is totally focused on aligning the skills we’re developing to the talent that key industries need,” explains Executive Director, Chris Burke, “because these early careers professionals are given the opportunity and responsibility to work on live projects from day one. They do that with the full support and guidance of experienced senior engineers who are fully committed to helping our ECDP colleagues be the best version of themselves and reach their full potential.
“We are consistently and continuously developing the engineering skills the UK needs across the full range of engineering disciplines, with cross-disciplinary competences where possible. With our ECDP, we’re taking positive and proactive steps to resolve the skills gap with ambitious, homegrown talent, and our annual ECDP conference is a celebra-
tion of that, as well as a call to arms to the current cohort to embrace the challenges and opportunities it offers.”
To date, more than 125 engineers have progressed their career through Morson’s Early Careers Development Programme, which involves completing a competency framework based on engineering disciplines and workplace skills to ensure they have all the skills needed to successfully lead projects and deliver against client requirements. There is no set period for completing the programme and early careers engineers can opt to tackle each module in their own preferred sequence and timeframe, enabling each individual to work in a way that suits them.
“Engineering is a broad church,” Chris continues, “and our goal is to attract the best talent and encourage each individual to map their own path to career success and achievement. We’ve crafted our ECDP to support each engineer every step of the way, with trained mentors and collaborative project teams, but this is their programme and their career; it’s up to them to make it their own.”
The evidence suggests that Morson’s ECDP engineers are doing exactly that. The programme has been running for 4 years with 95 engineers currently developing their careers with the support of the ECDP. It has helped Morson’s engineering businesses to achieve an incredibly low 5 per cent staff turnover rate and engineers currently involved in the programme or who have completed it are currently involved in projects as diverse as the new Tempest Aircraft and Network Rail’s UK-wide Asset Management programme.
“The conference is just one of the ways in which we’re bringing early careers engineers together to enable them to connect and see the bigger picture,” Chris adds. “We all know that the UK needs more engineers, but we also need people who can lead in their field, manage projects and take bold deci-
sions. Our ECDP and the conference we held for the current cohort are an invitation to be part of a transformative approach to building on the UK’s engineering legacy and leading its future.”
Atlas Copco is supporting Iona Management Services in the production of high-quality biogas for general consumption by ensuring a reliable supply of pure oxygen at the Leeming Biogas facility in North Yorkshire
Atlas Copco supplied the original oxygen generation equipment via the EPC contractor when the biogas facility was originally built, and has since also supplied two additional air compressors. Atlas Copco now provides ongoing support to maintain equipment on-site to manufacturer specifications, including third-party equipment as well as its own oxygen generator and air compressors.
Iona Management Services (IMS) is one of the UK’s leading independent service providers within the low carbon renewables sector. Alongside other disruptive technologies, they provide operations and maintenance services on-demand to anaerobic digestion, combined heat and power (CHP) and biomass projects. Leeming Biogas became part of its portfolio in 2014. It generates over five million cubic metres of biomethane annually, which is directly injected into the local gas grid. It also produces PAS110 accredited digestate that is used on nearby farmlands.
The Leeming Biogas plant uses food waste products as its feedstock and deploys anaerobic digestion techniques to generate biomethane. Anaerobic digestion comprises a series of biological processes that use microorganisms to break down biodegradable material in the absence of oxygen. So why is the Atlas Copco oxygen generator so crucial for success?
James Smith, IMS General Manager for the Leeming Biogas plant, explains: “It may seem counterintuitive, but oxygen
is fundamental to the generation of gridquality biogas. It stabilises the biological activity inside the fermenters, which promotes efficient gas generation and helps to reduce unwanted by-products such as hydrogen sulphide.”
Hydrogen sulphide (H2S) is a particular concern because the food waste processed at the Leeming facility has a potentially high sulphur content. H2S is a highly flammable and corrosive gas, so it presents a potential safety risk and damages downstream equipment. Hydrogen sulphide also has a distinctive ‘bad eggs’ odour, so IMS aims to eliminate it from the process for the sake of site operatives and the local community.
“The Atlas Copco oxygen generator enables us to use pure oxygen to regulate and control biological activity in the fermenters. This reduces the need for expensive and potentially hazardous chemicals, which is better environmentally and reduces total cost of ownership.” continues James.
As a gas-to-grid site, the amount of oxygen allowed in the final gas stream (less than 1%) is also strictly limited. The reliable source of high-purity oxygen from Atlas Copco’s OGP10 oxygen generator makes controlling the levels easier, although the process requires regular manual intervention rather than automated dosing.
Reliable on-site O2 generation
An Atlas Copco OGP10 oxygen generator offers 90% to 95% oxygen purity at ISO 8573-1 Class 1.2.1 standard to meet customer quality requirements. It uses proven Pressure Swing Adsorption technology (PSA) to
isolate oxygen molecules from other molecules in compressed air, resulting in high-purity oxygen at the outlet of the generator. This enables the OGP10 to deliver a reliable supply of oxygen 24/7, at the exact purity required for the application and with its low operating cost and minimal maintenance requirements. Feeding the OGP10 with air is an Atlas Copco GA15FF rotary screw compressor. Iona also has a G15L FF compressor for instrument air and as a back-up, associated filtration and oil-water treatment equipment, plus an air receiver and an oxygen receiver. It also has a small piston compressor for plant duties.
Having completed over 62,000 hours of running, the OGP10 and compressor installation have provided Iona with a reliable and economical alternative to using alternative oxygen generators or third-party oxygen suppliers. Onsite oxygen generation also contributes to more sustainable operations by eliminating the carbon footprint associated with multiple oxygen cylinder deliveries.
In addition to the reliability and performance of its OGP10 oxygen generator and compressors, IMS is very pleased with the service it receives from Atlas Copco. Integration with the on-site team, good response times and detailed reporting save IMS time, enabling them to focus on optimising biogas production.
In conclusion, James says: “At IMS, we believe that low carbon energy projects are one of the fastest ways for consumers to embrace the necessary
transition to a sustainable economy. However, renewable energy generation is a dynamic industry, and innovations are being made all the time. Atlas Copco keeps me and my team abreast of new technological developments that could add further value to our operations, such as improving efficiency, and are committed to supporting our sustainability goals.”
For more information about Atlas Copco oxygen generators, please visit: www.atlascopco.com
Testing the sulphur content of the feedstock. The amount of sulphur present in the feedstock dictates how much oxygen is needed to stabilise the biological activity inside the fermenter
for
• UK firm wins brace of accolades at prestigious ‘Electric Vehicle Innovation & Excellence Awards’
• Compact new Andersen A3 charger comes top in hotly contested ‘Best New Product’ category
Leading UK-based EV charge point provider, Andersen EV, has secured two top accolades at the fifth annual Electric Vehicle Innovation & Excellence Awards (EVIEs).
In a ceremony held in London late last week, the company was named ‘Chargepoint Manufacturer of the Year (Domestic)’, while its compact new A3 charge point fought off a host of rivals to be named ‘Best New Product (Domestic)’.
Andersen introduced its advanced new A3 charger in May with a market-leading 7-year warranty – the longest available with any home charge point – covering the charger and all ancillary parts.
Reinforcing Andersen’s position as the UK’s leading premium home charging company, the EVIEs jurors commented on the “leading design” of Andersen’s products, and commended the brand for its “very high levels of customer satisfaction.” Andersen is the only charge point provider to receive 4.9 stars out of 5 on Trustpilot.
The Andersen A3 and the company’s acclaimed A2 are the only home chargers to feature a cable and plug that can be fully hidden away within the unit when not in use. In further contrast to the utilitarian look of most rivals, the look of each Andersen unit can be tailored to the preferences and requirements of each user. The company offers over 240 different colour and finish combinations for the fascia and side panels, including four premium Accoya wood options for a natural aesthetic.
The new A3 offers charging speeds up to 7kW and is equipped with an intuitive LED status indication, a presence sensor, a convenience light located on the underside of the unit, and ‘theatre lighting’ to help store the cable after dusk. It also comes with an advanced app that makes it easy to make the most of cost-effective new ‘smart’ EV-specific tariffs and track ongoing expenditure.
David Martell, Chief Executive of Andersen, said: “The UK is now home to an intensely competitive domestic charge point market, so to secure two EVIE awards underscores the efforts and progress made by the whole Andersen team to ensure we remain at the forefront in terms of design and technology. The EV market is evolving at a remarkable pace and we’re already working hard on a number of innovations to ensure we retain our top spot in the charge point segment.”
A number of special-edition finishes are now available for new Andersen units, including a carbon fascia and Andersen’s unique CALLUM fascia designed by renowned car designer Ian Callum CBE. Last month Andersen also partnered with luxury eco-sustainable paint brand COAT, with the two brands working together to curate a palette of six new fascias which are now available to order.
Andersen is building a remarkable tally of accolades. Just three months after its launch, the Andersen A3 was recognised as the best home EV charger for quality in the What Car? review of home EV chargers. The A3 received a score of four stars out of five, scoring highest overall for ‘installation satisfaction’ and joint highest for ‘ease of use’. In June, it won a ‘Platinum’ award in the 2024 London Design Awards ‘Product Design’ category. The London Design Awards is an international competition that recognises exceptional designs and outstanding creative projects worldwide.
Anyone with a non-Andersen charge point can upgrade to a new A2 or A3 for a reduced price.
To order an Andersen unit or to find out more about the upgrade scheme, visit: www.andersen-ev.com/pages/upgrade-your-charge-point
Andersen has introduced 13 new colours to match the full palette of standard exterior paint options being offered with the all-new car, all-electric Porsche Macan.
The new colours allow customers of the all-electric Macan to customise their designer EV charge point to their vehicle. Andersen is the only home charge point provider to offer a fully customisable choice of colour and finish for their unit, and customers can opt for different colours for the side panels and fascia.
To order their new fascia, customers must select the Custom Palette service on Andersen’s online configurator, which allows customers to match their charge point to any colour. Once the order has been placed, a member of Andersen’s design team will be in touch to specify the specific colour for the charge point.
Customers will have the choice of all 13 colours for both the A2 and A3 charge points, which are the only chargers in the UK to offer a 7-year warranty.
David Martell, Chief Executive of Andersen, said: “The launch of the Porsche
Macan is a significant milestone for Porsche and the EV industry. These new colours will allow all electric and hybrid Porsche customers to match their charge point to their new car, a service that is unique to the domestic charge point market. We are excited to introduce this new range which celebrates the launch of the Macan.”
Andersen offers a range of 13 aluminium fascias as standard for the price of £995, with four premium Accoya wood fascias also available. A number of special-edition finishes are also available, including a carbon fascia and Andersen’s CALLUM front, designed by renowned car designer Ian Callum CBE. Andersen also partnered with luxury eco-sustainable paint brand COAT last month, with the two brands working together to curate a palette of six new fascias which are now available to order.
The Andersen A3 and the company’s acclaimed A2 are the only home chargers to feature a cable and plug that is hidden away when not in use. The A3 offers charging speeds up to 7kW, is equipped with an intuitive LED status indication, as well as a presence sensor, a convenience light located on
the underside of the unit, and ‘theatre lighting’ activated when lifting the lid to highlight the cable location and Andersen EV branding.
Earlier this year Andersen launched its A3 charge point with a market-leading 7-year warranty, the longest available with any home charge point, covering the charger and all ancillary parts.
Just three months after its launch, the Andersen A3 was recognised as the best home EV charger for quality in the What Car? home EV charging review for 2024. The A3 received a score of four stars out of five, ranking fourth overall, but scoring the highest overall for installation satisfaction and joint highest for ease of use. In June, it won a Platinum award in the 2024 London Design Awards ‘Product Design’ category. The London Design Awards is an international competition that recognises exceptional designs and outstanding creative projects worldwide.
For more information on Andersen, please visit: www.andersen-ev.com/
Lantek v44, an enhanced version designed to revolutionize manufacturing processes with the concept of “Connected. Live. Smart.”
Lantek, the global leader in sheet metal software solutions, is proud to announce the release of Lantek v44, an enhanced version designed to revolutionize manufacturing processes with the concept of “Connected. Live. Smart.” This latest update is a comprehensive suite of innovations across its CAD/CAM, MES, and ERP software, aimed at maximizing production efficiency, connectivity and decision-making.
With v44, manufacturers gain unprecedented control over their production environments, leveraging new capabilities that integrate machines, streamline workflows, and enhance data-driven insights. This update marks a major leap forward for businesses looking to optimize their operations with cutting-edge software technology.
Lantek Expert v44 brings a host of enhancements designed to optimize CAD/ CAM 2D workflows. At the forefront is the Properties-Based Nesting feature, which allows users to group parts by attributes like delivery date, customer, or other data, resulting in improved efficiency throughout the production process. This new capability not only organizes parts for better packaging and assembly but also offers flexibility to separate or mix groups, with options to insert remnant lines to facilitate cutting. The new Import Assistant allows filtering of layers in DXF/DWG files, as well as deleting unnecessary geometry during file importation, significantly reducing manual cleanup and accelerating the preparation phase. Additionally, the Punch Swap in Turret Configuration solves the challenge of turret limitations by enabling users to use rectangular and
square punches on operations made with tools of different sizes, even when they are loaded at other angles, ensuring smoother operations without the need for time-consuming workarounds.
Lantek Flex3D v44 introduces significant enhancements that increase performance, usability, and productivity in tube and profile cutting. Both the part import process and the management/ saving of jobs have been reengineered, drastically improving performance, offering more agility in the system. For steelwork manufacturing, the introduction of new Split Parts Techniques allows users to choose from Straight, Angle, or Z Shape splits, incorporating welding preparations and gaps to maintain precise dimensions after welding. Additionally, support for robotic cutting heads extends the compatibility of Flex3D to machines with more than five axes, including robotic devices, delivering optimized cutting paths for complex steelwork projects.
Lantek MES v44 brings transformative upgrades to enhance shop floor efficiency and flexibility. The introduction of Lantek MES Intralogistics optimizes the flow of raw materials from the warehouse to work centers, reducing downtime and ensuring that materials are promptly available for manufacturing machines. This improvement enhances material traceability and minimizes errors, leading to more efficient operations. The new 3D Operations Finishing feature allows operators to register completed parts directly into the system without complex graphical nesting, simplifying remnant management, es-
pecially for manual processes. Additionally, the Advanced Management of Lost Parts provides operators with the ability to quickly rework or recover lost or damaged parts without restarting entire workflows, significantly reducing delays and boosting overall productivity.
Lantek Integra v44 introduces enhancements aimed at improving usability, cost management accuracy, and workflow efficiency. The new Files Drag & Drop feature streamlines file management, enabling users to quickly add geometry files or documents directly into Quotes, Sale Orders, or Tracking Numbers, with the system automatically identifying file types and taking the appropriate action significantly improving the speed and ease of commercial processes. Additionally, Material Scrap Price Definition offers more precise control over material cost calculations by allowing users to set specific scrap prices for different materials. This added flexibility ensures accurate, competitive quoting and cost estimation, with the system automatically factoring in scrap costs for each nesting while maintaining full traceability.
Lantek Bend v44 introduces powerful features aimed at enhancing automation, integration, and efficiency in the bending process. The Enhanced CAD Import Module now supports a wide range of native CAD file formats and uses the Hoops library to automatically recognize materials, thicknesses, and bending lines, significantly reducing manual input and accelerating the import process. Additionally, the new Starmatik Export Functionality expands
Lantek Bend’s capabilities for robotic programming by exporting bend line data into a DXF format for use with Lantek Expert, ensuring precise and automated programming based on specific material properties. Furthermore, deeper Integration with Lantek Expert, MES, and Integra transforms Lantek Bend into a fully interconnected solution, allowing users to open, modify, and sync 3D files seamlessly across all systems. This integration simplifies data management, provides real-time updates, and improves efficiency across quoting and production, reducing complexity for users of all skill levels while enhancing operational agility.
Lantek v44 is not just another software update; it redefines how modern manufacturing should operate. The new “Connected. Live. Smart.” concept, combined with Lantek Analytics, offers manufacturers real-time insights and smarter decision-making by connecting machines, operators, and data sources. This powerful tool enhances production efficiency, allowing users to optimize scheduling, monitor performance, and gain complete visibility over their lines.
“Our goal with v44 is to empower factories to become more connected, more efficient, and more intelligent,” says Raúl Chopitea, Head of Product for Lantek.
For further information, visit: www.lantek.com
Altus Group, a leading distributor of capital equipment in the UK and Ireland, in partnership with Fuji Corp, recently held its second ‘Factory of the Future’ event at the Advanced Manufacturing Technology Centre (AMTC) in Coventry
The two-day symposium marked a significant milestone as the largest event ever organised by Altus, showcasing the latest advancements in electronics manufacturing.
Building on the success of its inaugural event in 2022, this year’s ‘Factory of the Future’ attracted over 200 participants and featured nearly 30 suppliers, offering hands-on experiences with nearly 40 unique processes. This expanded scale allowed attendees to explore a comprehensive range of technologies essential for SMT, NPI, and through-hole production lines, as well as component management and peripheral production.
The event introduced several innovations to the UK market for the first time, including the Scienscope Xspection 3000 Batch Xray, the Inertec Cube 460 selective soldering unit, the Koh Young Neptune Conformal Coating Inspection System, actnano’s disruptive coating materials, and the YJ Link vision inspection buffer.
Joe Booth, CEO of Altus Group, said: “What an incredible few days! Organising an event of this scale is a monumental effort, and the Altus team truly outdid themselves this time. The positive feedback from our customers and partners has been exceptional, and having over 200 participants is a clear indicator of our growing presence in the UK and Ireland. We’re excited to build on this momentum and turn the interest from the event into successful projects in the months ahead.”
Artur Tobolski, Fuji Regional Account Manager, said: “The Factory of the Future event was a tremendous success, bringing together top industry leaders and showcasing the latest
innovations. It gave UK manufacturers a unique opportunity to engage with cutting-edge technology and gain insights into future trends. Fuji is proud to have partnered with Altus for this landmark event and looks forward to continuing our collaboration with the industry.”
The comprehensive program included 16 presentations from industry leaders, addressing several topics, including the future of electronics manufacturing and current industry trends and challenges. The timing of the event was particularly opportune, coinciding with a notable increase in capital equipment investment following the new government’s election, which has contributed to enhanced stability and growing manufacturing demand.
For more information, please visit: www.altusgroup.co.uk
Industrial automation specialist Festo is making it easier for manufacturers to harness the power of digital automation and artificial intelligence (AI) to optimise process efficiency. Festo AX is a suite of AI-based software solutions enabling customers to increase efficiency in their production processes
Festo AX makes digitalisation scalable and supports the advancement of Industry 4.0 in production. This means that manufacturing companies of all sizes can benefit from innovative technologies, while original equipment manufacturers can set up new business models immediately without the need for years of development work.
Steve Sands of Festo said: “We are excited to offer our customers this rapidly expanding range of solutions that make them more efficient and more productive. By using AI-supported tools, our customers can increase their competitiveness and take their production to a new level. Our AX latest Motion Insight Apps offer exactly that: easy-to-install, scalable solutions that enable effective implementation of predictive maintenance.”
The Festo AX suite currently comprises AX Industrial Intelligence, AX Solutions, AX Industrial Apps and AX Smartenance.
Festo AX Industrial Intelligence is a project based industrial software solution that uses artificial intelligence to turn plant data into actionable intelligence. It enables users to increase productivity, reduce energy costs, avoid quality losses and — in coordination with machine builders — establish new business models. Festo AX Industrial Intelligence thus enables optimisation in three typical fields of application: Predictive Maintenance, Predictive Energy and Predictive Quality. Customer experience shows optimisation rates
of over 20 percent, a clear indication of how much potential there is in deploying AI-driven data and algorithms.
With Festo AX Industrial Apps, the company is utilising its application knowledge to focus in on subsystems such as welding, glueing, riveting or packaging creating scalable solutions that allow customers to install standardised AI applications themselves without needing any AI expertise. They overcome the oftenencountered gap in the application of AI that lies between the computer scientists who can model and detect anomalies in data and the real-life interpretation of the output into actionable alerts.
The latest release is the AX Motion Insights Pneumatic App. It uses machine learning AI to detect anomalies in the behaviour of pneumatic drives early and reliably, without the need for additional, complex sensor technology. This enables companies to execute preventive maintenance measures and minimise unplanned downtimes. The Festo AX Motion Insights Pneumatic App offers a user-friendly interface within the containerised app and simple integration into existing systems. It enables companies to implement the monitoring of application critical pneumatic components independently and without the need for data science specialists.
The AX Smartenance package is the ideal companion to Industrial Apps or Motion Insight packages as it offers a solution for customers’ maintenance management to digitalise and simplify maintenance and servicing processes in a consistent and intuitive way. AX Smartenance closes the loop by using notification data from the AX Apps to deliver condition-based recommendations for action to the right addressee in the maintenance process at the right time. It also provides a platform for the management of routine maintenance tasks with the ability to
store all machinery documentation, drawings and multi-media information such as ‘how-to’ videos, photographs of previous fixes and links to supplier support portals.
Industrial apps also on Siemens Industrial Edge
Festo is also part of the Siemens Industrial Edge ecosystem. The Festo AX Data Insights App, available on the Siemens marketplace, feeds data from Festo components into Siemens Industrial Edge to supply analysis applications with data. Based on this data, customers can set up monitoring within the Siemens environment to improve maintenance processes, reduce their energy consumption and improve quality. More industrial apps from Festo will soon be available via this route, including versions for AI-based monitoring of pneumatic and electric drives.