Page September10 Issue worldwide-engineering.com Titan CapacityFlowExpandsenterprisesitsLiquidMeterCalibration Page 16 Page 24 Making 3D printing models easy Quickpartscost-effectiveandwith NORD systemsefficiencyincreasecomponentstheenergyofdrive
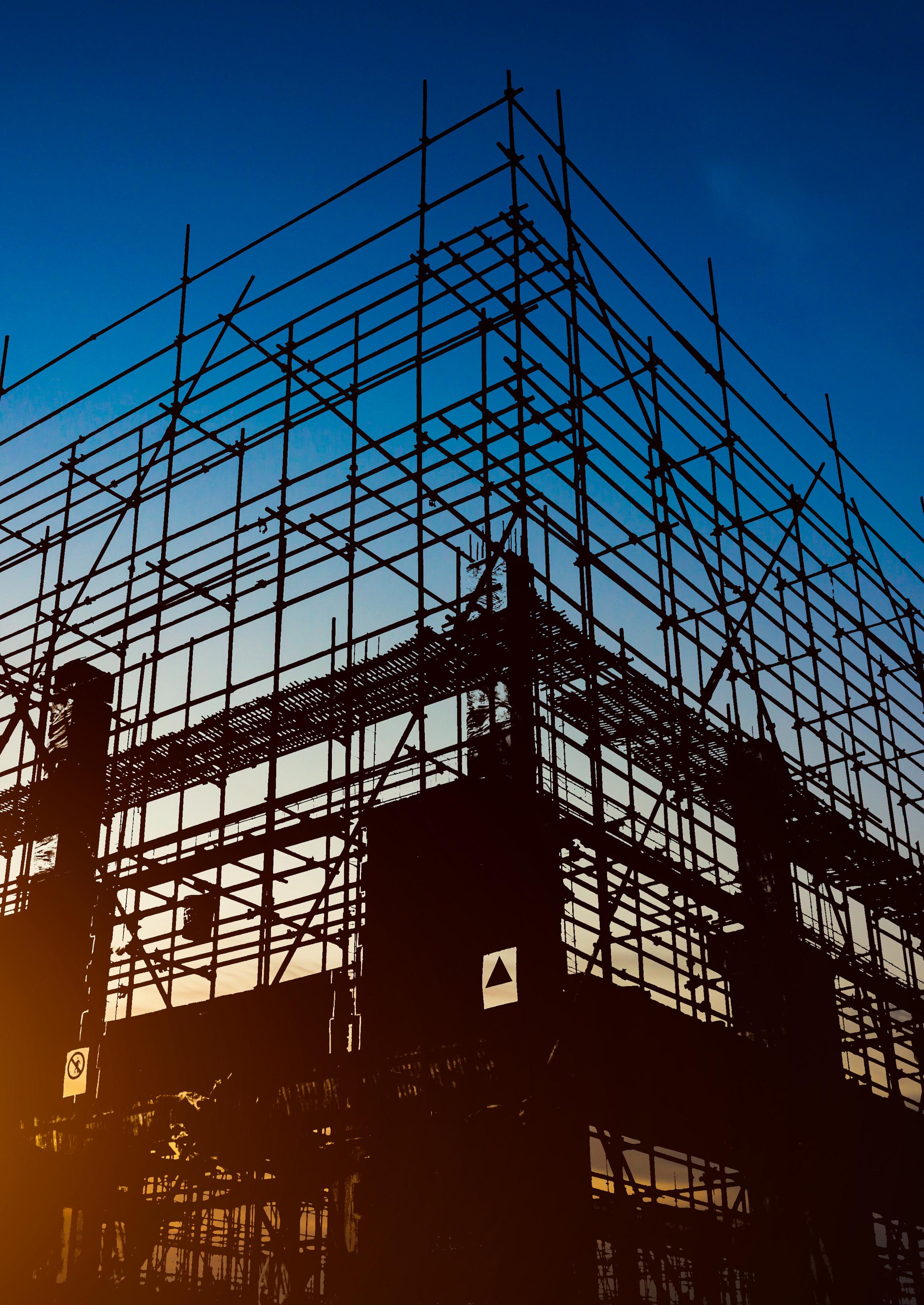
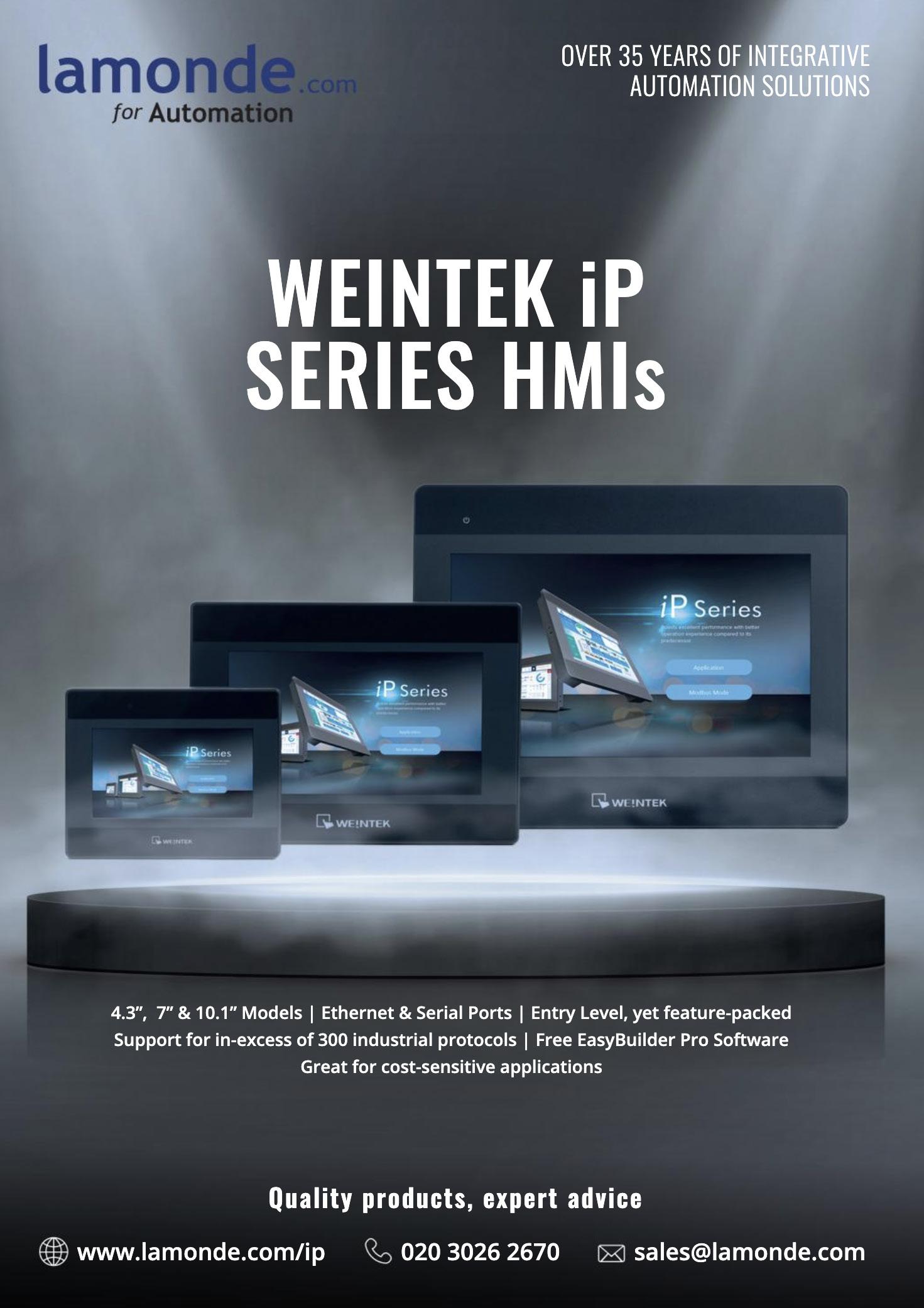
Electronics6 business receives £200k funding boost for space developmenttechnology Heat8 carrothelpsexchangerproducepowder Titan10 CalibrationLiquidExpandsenterprisesitsFlowMeterCapacity 3D-MID12 – minimized sensing high-tech within the patient Fanuc20 CNCS help electron engineering breathe new life info legacy equipment Adopting26 technology to fill the experience gap and do more with less. SICK’s32 Roller Sensor Bar Ends HeadachesConveyor Contents Providing timely industry news, exclusive features on advancing technology, equipment, materials, show previews, content marketing services for our valued clients and much more! Adam AdvertisingLing Enquiries: adam@worldwide-engineering.com Jonathan Adams Editorial Assistant: jonathan@worldwide-engineering.com Kyle SalesAdamsCoordinator: kyle@worldwide-engineering.com Worldwide Engineering Magazine Commercial22 off the shelf motors can decrease time and cost for defence projects
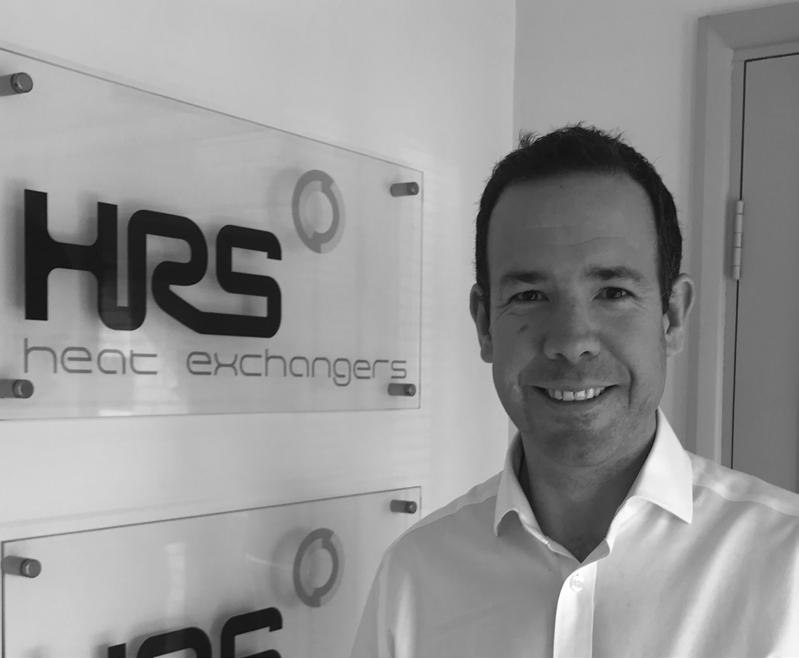
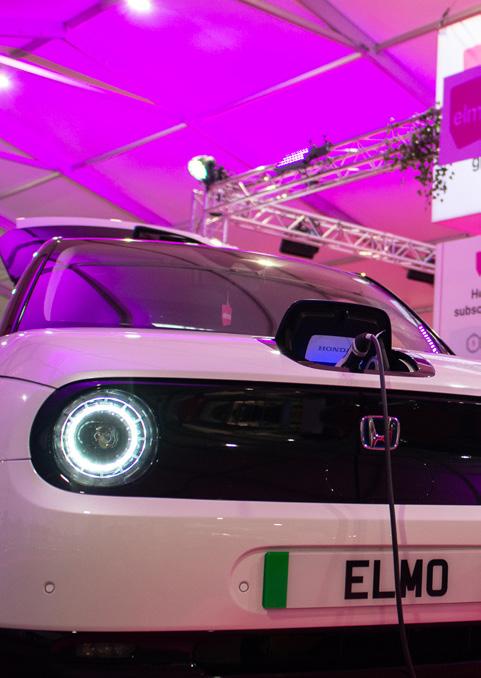
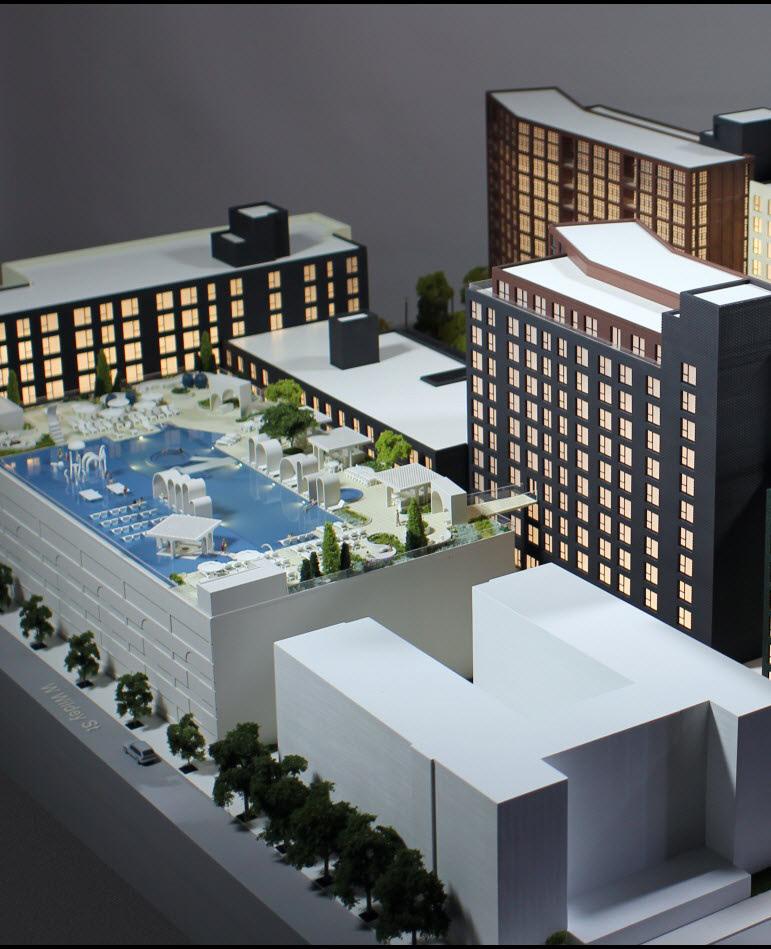

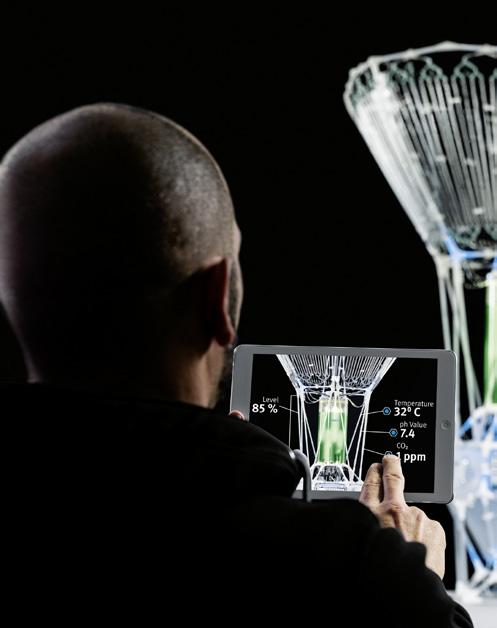
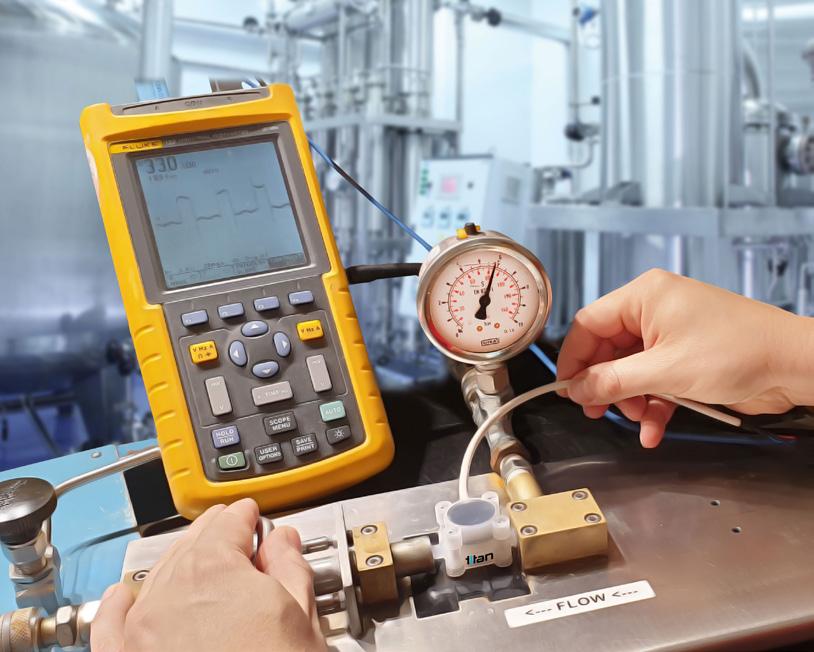
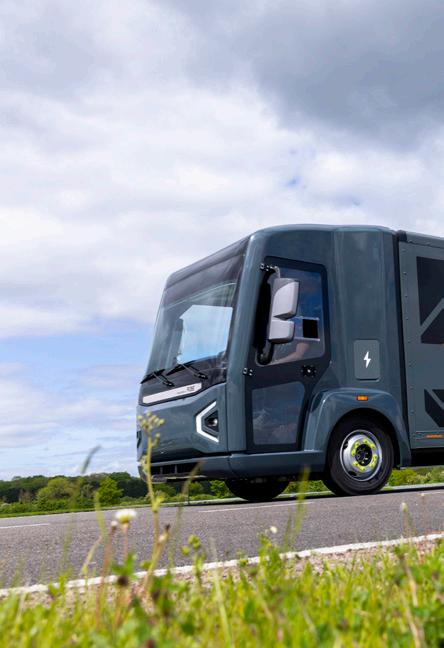
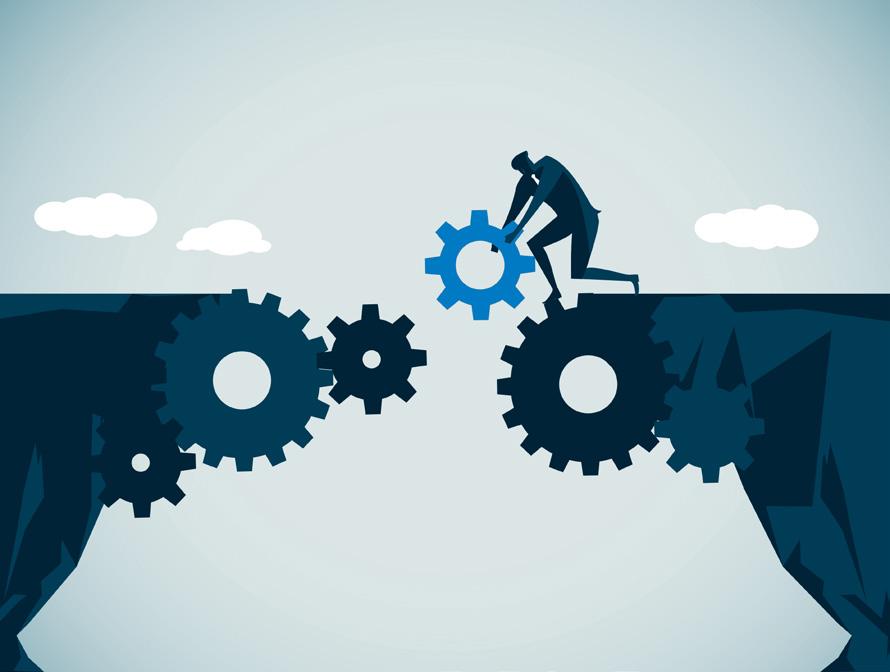
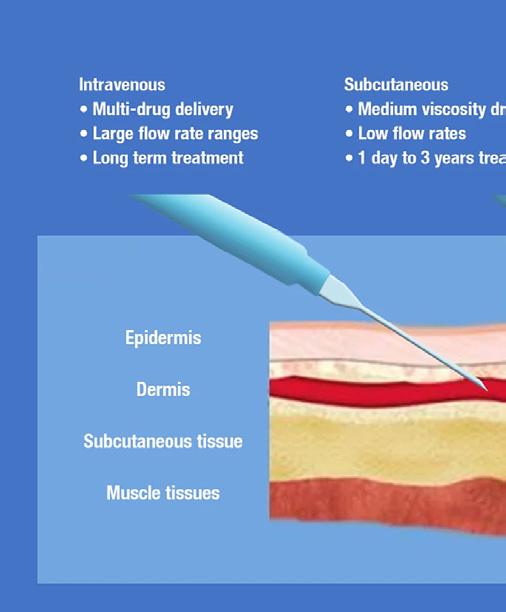

4
Now fully established as one of the UK’s must-attend motoring events, The British Motor Show 2022 saw over 21,000 people attend on the busiest day of its four-day calendar, with guests being treated to an array of live and interactive events, live stunt shows, the National Geographic Car SOS Live Stage, drift demonstrations from Shred Shed and Petrolheadonism Live (which were hugely wellreceived) and an incredible display of supercars from Premier GT.
The British Motor Show 2023 takes place at Farnborough International from August 17-20. Tickets are available at www.thebritishmotorshow.live
Record crowds attend The British Motor Show 2022 as bigger, better and busier event re-engages public with the love of cars
There was plenty for potential car buyers, too, as proven by one of the major new car retailers attending, which reported a sales lead every 52 Featuringseconds.everything from the latest high-tech electric cars to a glorious display of classics celebrating our unique motoring heritage, The British Motor Show developed its unique concept of being the most interactive car show in the world, with a 30% bigger site and more than twice as many exhibitors as the show enjoyed in 2021.
Bigger, better and busier than ever, The British Motor Show 2022 broke its own attendance record –along with some GUINNESS WORLD RECORDS – as nearly 60,000 visitors flocked to Farnborough for the most exciting car show in the calendar.
“From the very outset, one of our core aims was to re-engage the younger generation in a love of cars and the automotive industry. Seeing so many beaming young faces as we put on so much more than just a car show was my personal highlight of an incredible few days, and we can’t wait to do it all again next year.”
With motoring celebrities including Mike Brewer, Fuzz Townshend, Tim Shaw, Vicki Butler-Henderson, Tiff Needell, Mike Rutherford, Yianna, Abi Stephens, Ewan Thomas, Scott Ratarozza, Sam Hard and The Stig, there was lots of excitement and engagement from the guests, along with a family-friendly feel that remains truly unique in the car show environment.
The British Motor Show CEO, Andy Entwistle, said: “One thing that really came out from both visitors and exhibitors this year was that many of them were overwhelmed by the diversity of the event, and moreover of the people that attended. Families, in particular, were extremely visible, taking advantage of a truly exciting and terrific value day out.
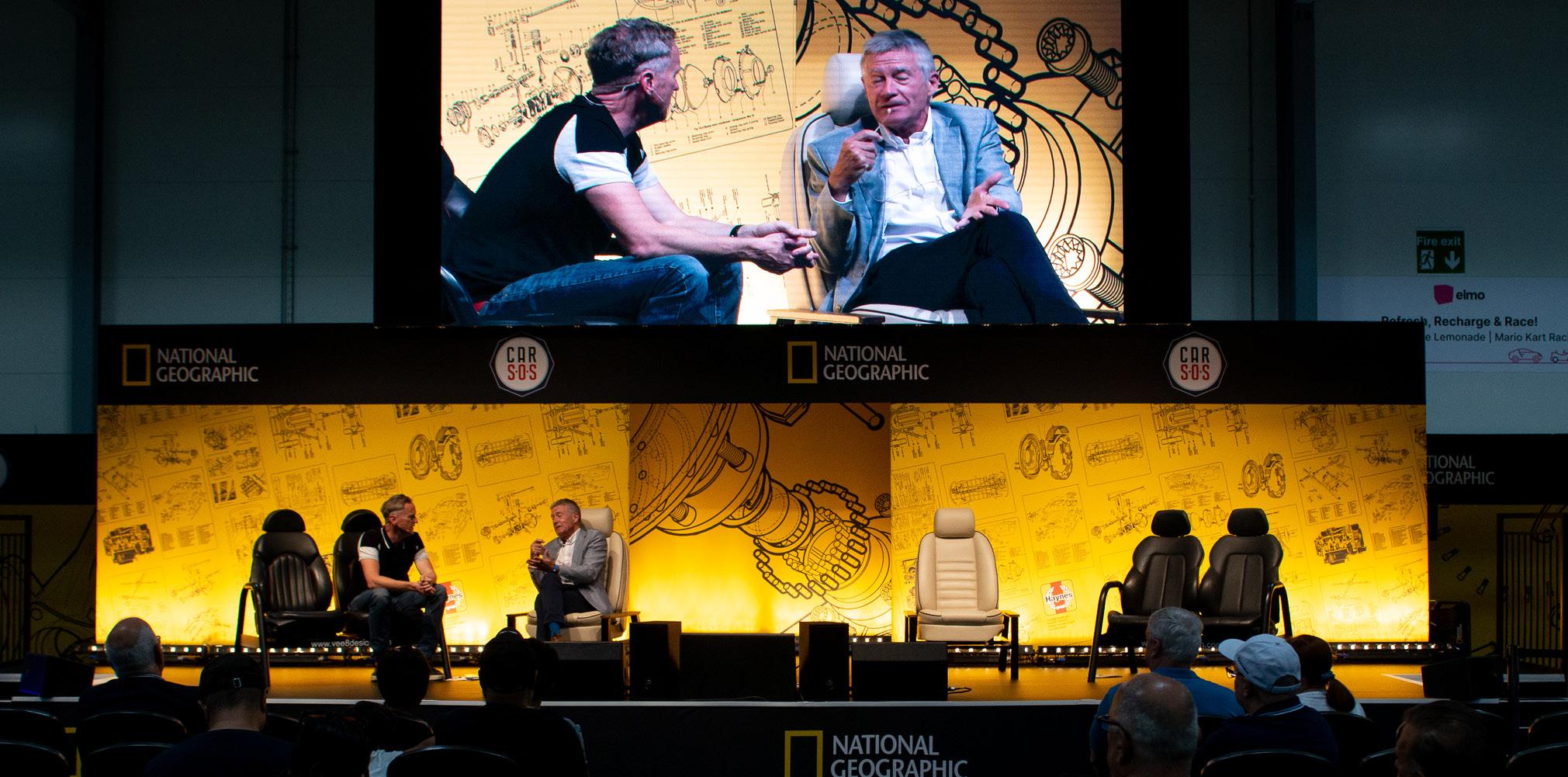
5
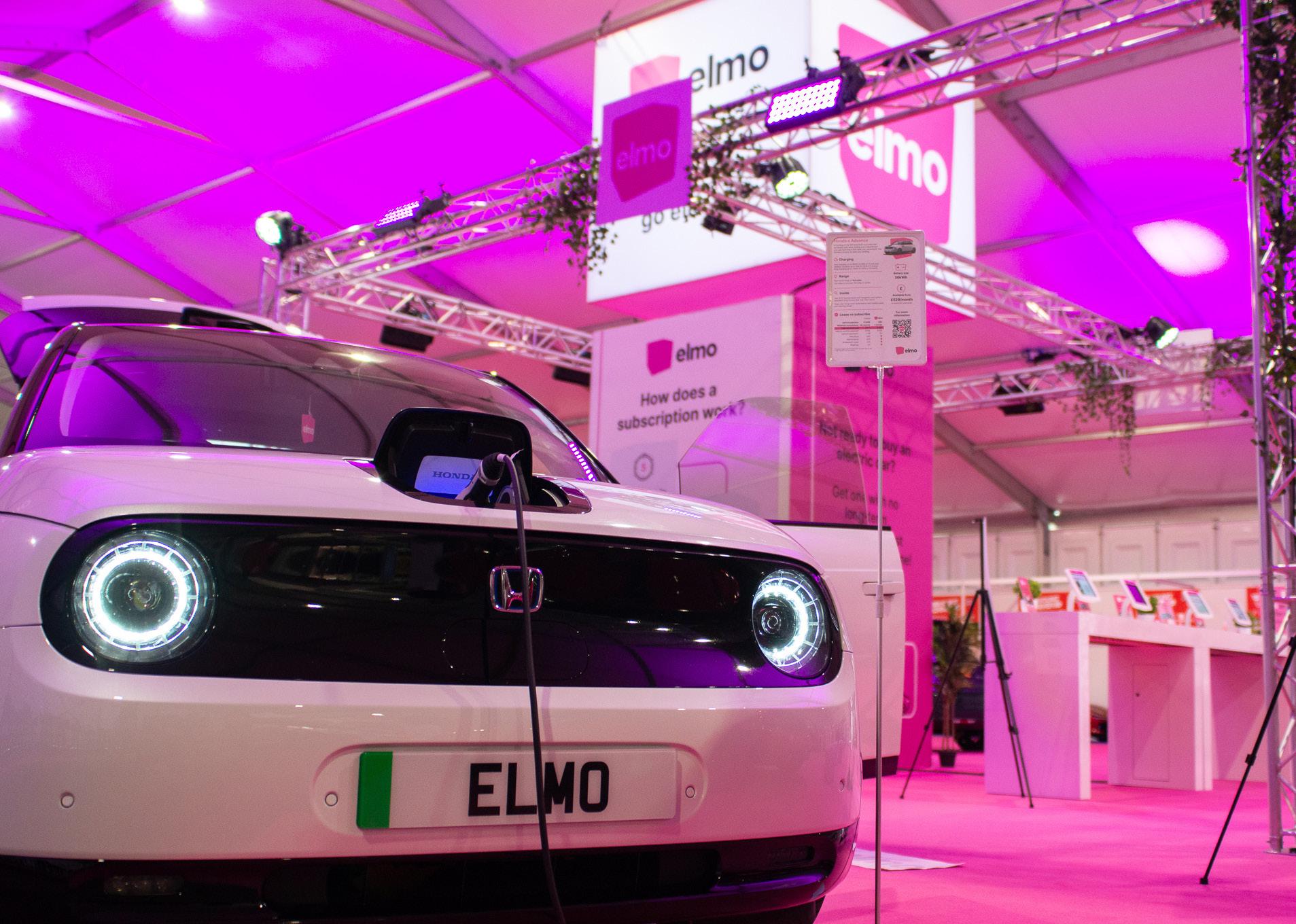
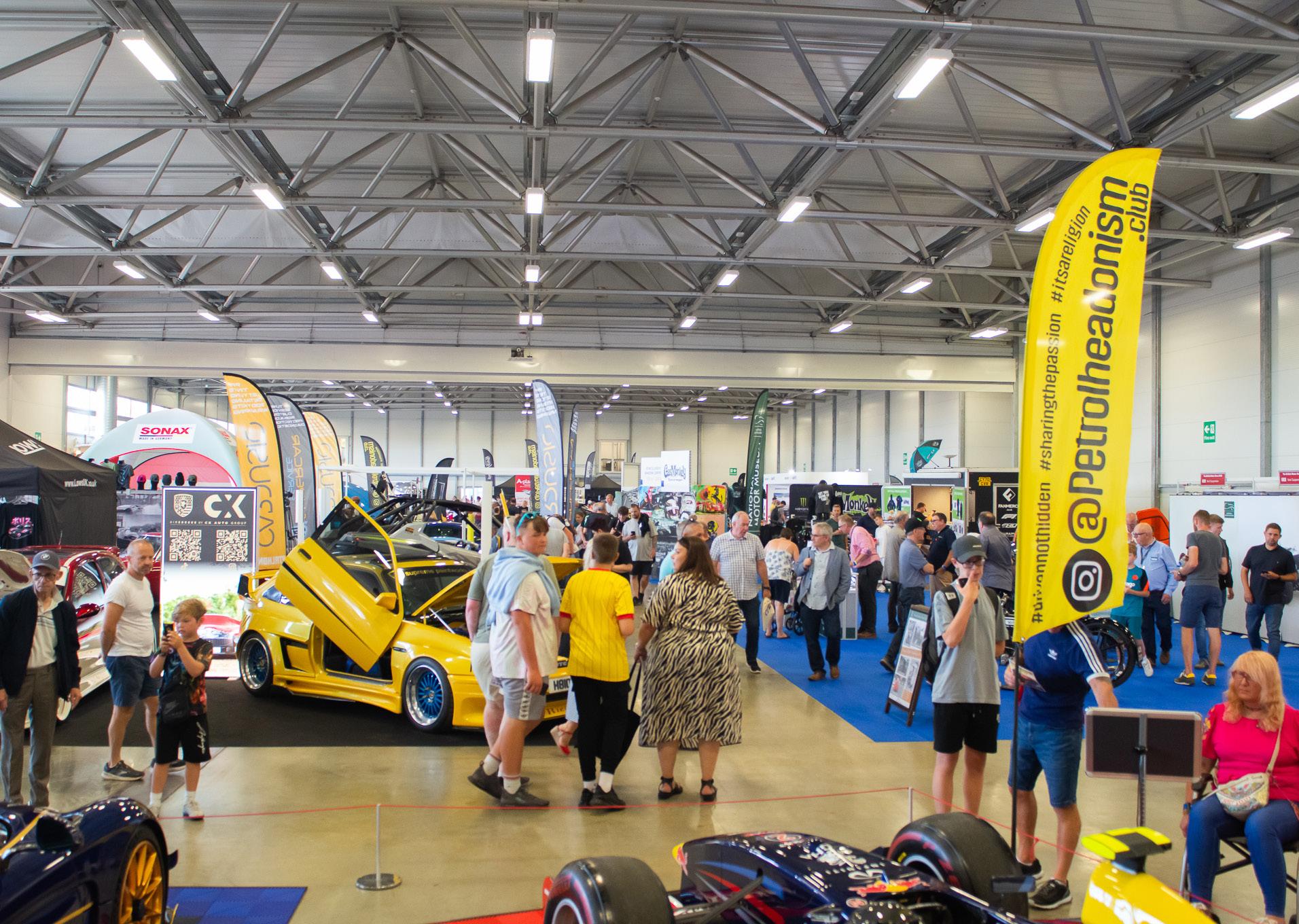
6
Slipstream Engineering Design has been awarded £199,054 for a project that aims to produce adaptable radio hardware for space applications. The funding was awarded through the Space to Innovate Campaign – Bravo Drop, a collaboration between the Defence Science and Technology Laboratory (Dstl), the UK Space Agency and the Defence and Security Accelerator (DASA).
Sarah says the Bravo Drop funding has come at an extremely exciting time for the company: “Being part of the Future Combat Air System development programme is an absolute privilege, and to have our expertise recognised by the Space to Innovate Campaign is another huge win for the business.
Currently, radio hardware is specifically designed to carry out a limited range of operations. On CubeSats, where payload space is at a premium, having hardware that can carry out multiple communication and sensing operations would be a major advantage. Our aim is to produce an adaptable radio platform which is software configurable and can switch between different types of wideband radio waveforms.”
“A core part of both these initiatives is to bring on the next generation of technologists and innovators. Both programmes require us to drive the development of new skills and expertise. We are deeply committed to nurturing talent in our field of digital radio frequency, and we have a proven model for accelerating career development.
Dr. Mike Roberts, Slipstream Engineering Design technical director and co-founder, says: “The Space to Innovate Campaign aims to find and fund solutions to major space hurdles to promote space resilience and operational effectiveness. Bravo Drop is the second ‘challenge drop’, which invited innovators to submit technologies and solutions to help overcome specified challenges.
Electronics business receives £200k funding boost for space technology development
Fast-growing technology business, Slipstream Engineering Design, has become one of just five organisations in the UK to receive a share of £1million funding through the Space to Innovate Campaign – Bravo Drop, to develop technologies that enhance the UK’s ability to safely operate in space.
“Our solution is designed to improve the signal-to-noise performance of space-related communications and sensing capabilities.
The Bravo Drop funding follows hot on the heels of the company’s attendance at the Farnborough International Air Show last month, as a partner of Team Tempest, the enterprise working to create the UK’s Future Combat Air System (FCAS).
The Bravo Drop funding and our involvement in the Future Air Combat System programme are giving us the confidence to grow and invest, and we are on track to create many highly skilled jobs in our sector.”
“Through our work with Leonardo UK, we are contributing specialised digital radio frequency expertise to the project, allowing cutting edge technologies to be developed at speed. The business has a proven heritage in accelerated product research and development that will help to realise this next generation capability for the UK.”
Commercial director Sarah Gregory explains: “Team Tempest is a technology initiative aimed at advancing combat air technology, involving the Ministry of Defence and UK industry partners including BAE Systems, Rolls-Royce, Leonardo UK and MBDA UK. It is a highly ambitious programme requiring the design and development of many ‘world firsts’ in aviation, with a flying demonstrator on track for delivery in five years’ time.
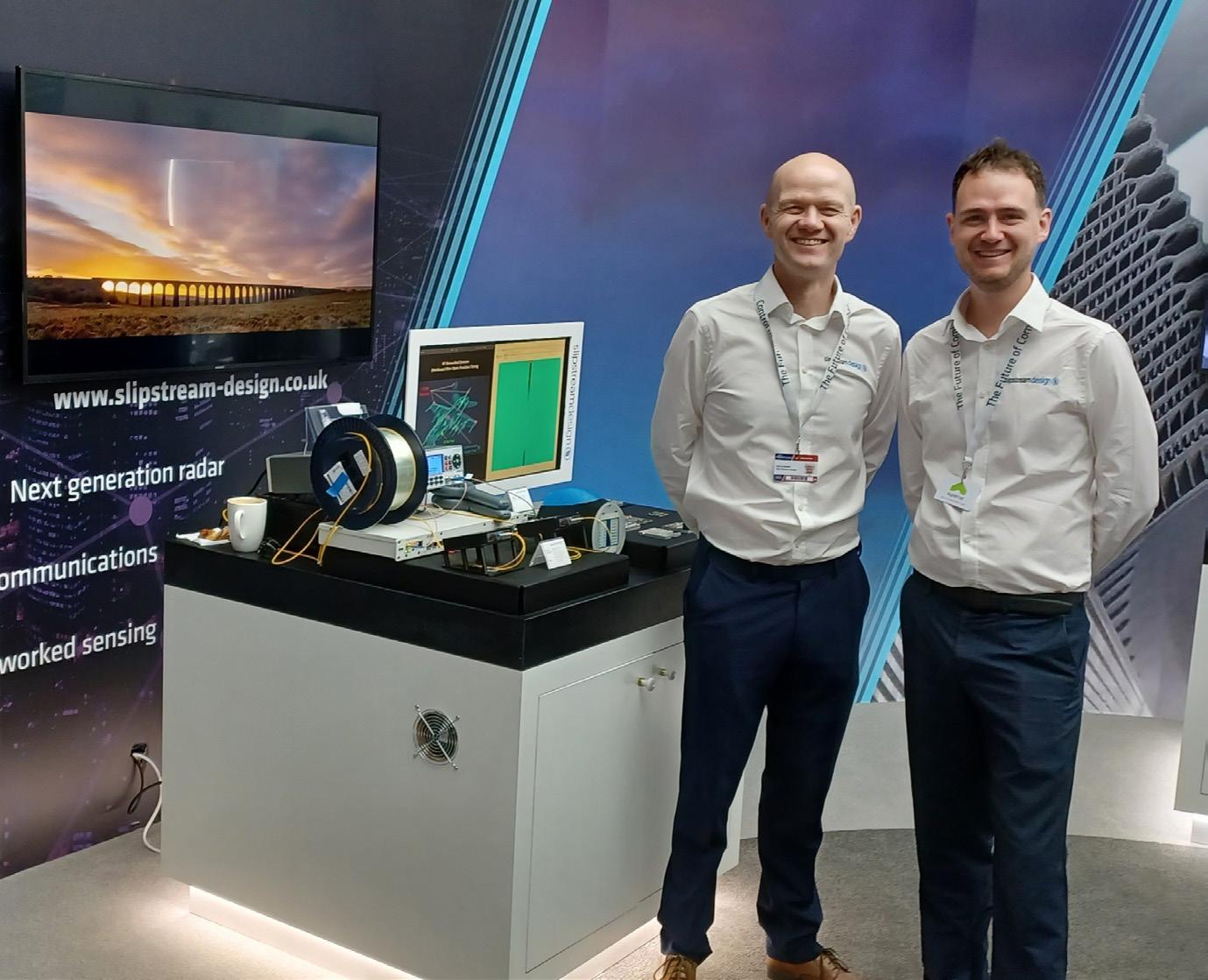
“A crucial distinction is that Fine Controls not only supplies a complete range of components, but that the team has a great deal of experience that enables them to specify applications for OEMs and end users,” says Clive.
Development also takes place inhouse at Fine Controls, as Gareth explains: “The Siemens PS2 positioner is one of the most common designs used in industry and it’s often specified.
While Fine Controls’ capabilities includes large-scale OEM projects for customers UK-wide, the distributor caters for customers of all sizes.
A recent combined project for the development of a pharmaceutical skid was specified from scratch.
Bürkert extends process control capabilities with fine controls partnership
With a relationship spanning 25 years, the level of trust means that Bürkert also develops customised solutions in support of important projects.
“We each provide products and services that compliment one another and on shared projects, we operate like one supplier. This is a significant advantage for the customer.”
“An OEM manufacturing display fountains needed a valve with IP68 rating, enabling it to be fully immersed,” explains Clive. “In partnership with Bürkert, an IP68equivilent valve was created, a customised version of a production valve, developed specially for Fine Controls’ project.”
7
“In reality, Fine Controls is an extension of Bürkert,” explains Clive Halliday, responsible for Bürkert’s north west of England projects.
“Fine Controls has expertise across the complete Bürkert range of valves, sensors, transmitters, and controllers, and can also specify the whole range of components required for complete process control applications, such as temperature or pressure regulators, or high-capacity flow meters. From the customer’s perspective, this gives them the benefit of just one company to deal with.”
For the best of both worlds, a distributor who can supply all the parts necessary to build a complete process system, as well as offering design and specification support is ideal. This is the advantage of the key distribution partner agreement between Bürkert and Fine Controls.
To provide the customer with the benefits in reliability of a Bürkert valve, we developed a customised solution that integrated the Siemens positioner, giving the customer the best possible outcome.”
For an OEM or end user in process control, a partnership between a manufacturer and distributor can mean an extended range of products and services available from a single source.
“Withsector.”Fine Controls and Bürkert, it’s a real team effort,” says Clive.
OEMs and end users often want the benefit of partnering with a single supplier, and it’s no different for fluid and gas control applications.Thisapproach simplifies project development, helps ensure compatibility and accountability for system performance, and makes supply more efficient.
While Fine Controls operates across a wide variety of process applications, major projects between Bürkert and Fine Controls have focussed on the energy market, pharmaceutical production, and process control solutions for fisheries.
In addition to specifying and supplying components, Fine Controls can also build and commission bespoke systems, including the assembly of subcomponents for main systems. This ranges from manufacturing regulator manifolds, through to fitting special seals for use with specific chemicals. If the application has special requirements, like ATEX Zone 1 panel build, Fine Controls can lead the project and work with Bürkert who can design and build a fully certified unit.
“We support low production OEMs as well, and end users of all sizes,” says Gareth. “We’ll provide end users with single units, with no minimum order quantity or value, and this is a reflection of the diversity of customer types we support across the process control
“They knew what they wanted to achieve, but they didn’t know how to achieve it,” says Gareth Hall, Fine Controls. “Together with Bürkert, we provided guidance and training on the type of valves they needed, explaining the advantages and suitability of the designs appropriate to each area of the application. For example, to increase operational efficiency, they wanted to know how to automatically control valves, so we introduced them to valve positioners, automated with electrical signals.”
Distributor, Fine Controls, provides the full range of Bürkert flow control products, as well as complimentary components that enables it to specify complete process systems. This capability is matched with in-house design and build facilities for large process projects.
“Five per cent may not sound like a lot, but when you are washing up to 400 tonnes of carrots a day, it soon adds up,” comments Huntapac’s Commercial Director Steven Kay.
8
Established near Preston by William Hunter in 1942, Huntapac initially grew a range of crops for fruit and vegetable markets in the North West, before starting to supply leading supermarkets almost fifty-years ago. The company was a major producer of root crops (carrots and parsnips), salads and brassicas (such as cauliflower and broccoli) until a few years ago, when it decided to rationalise its operations and concentrate solely on the root crops.
“We researched a few methods because there are lots of different drying techniques available, and we felt that the process that was right for use was to puree the carrots, put them over a drying drum and then mill the flake that results into a powder.”
Family-owned for four generations, Huntapac is a leading grower and supplier of root crops such as carrots and parsnips. Following a reorganisation of the business in 2019, the company wanted to develop new value-led product options and so installed a stateof-the-art line to produce carrot powder, with a heat exchanger from HRS Heat Exchangers forming a key part of the new process.
The process begins when the carrots are diced and then pureed, after which they are fed into the heat exchanger. This consists of two
The business grows more than 1,300 hectares of carrots and parsnips across the UK, from Suffolk to Scotland, all of which are taken to the company’s factory at Holmes near Preston for washing and packing. With the increased focus on root crops, the company was keen to add value to the five per cent of the crop which is not suitable for its packing customers and looked at a number of options before deciding on the production of carrot powder.
In early 2020 plans began in earnest for the powder production line. As the first of its kind in the country, this took a lot of consultation between all the parties involved, including equipment suppliers such as HRS Heat Exchangers.
Heat exchanger helps produce carrot powder

9
HRS R Series rotary scraped surface heat exchangers placed in series, which raise the temperature of the carrot puree from 10 °C to 60 °C. As well as the heat exchangers themselves, HRS supplied two feed hoppers and an HRS BP Series positive displacement pump to feed the puree into the heat exchanger. The heat for the process is supplied from a dedicated steam boiler and the line has a capacity of 500 kg of puree per hour. The warmed puree is then passed over a drying drum where it is dried to create a flaked product which is milled down into the finished powder.
“With the tight margins involved in fresh produce, it is important to maximise the value of the crop which has cost you money to grow, and this line allows us to utilise the entire crop,” adds Steven Kay. “The line has been designed to be able to handle other crops, but we have initially chosen to focus on carrots and although we have had to make tweaks as you do with any new process, we are now very happy with the quality and of the product that we are producing.”
“Pre-heating the puree before the drier performs two main functions,” explains HRS UK Sales Manager, Andy Ensor. “Warming the puree makes it easier to move through the line as it has less resistance, but the biggest benefit is that it reduces the amount of energy needed to dry the puree making the overall process more efficient.”
Production of carrot powder began in the first half of 2021 and the line now produces around 60kg of dried finished product an hour. The carrot powder is produced under Feed Materials Assurance Scheme (FEMAS) accreditation and is used as an ingredient in animal feed.
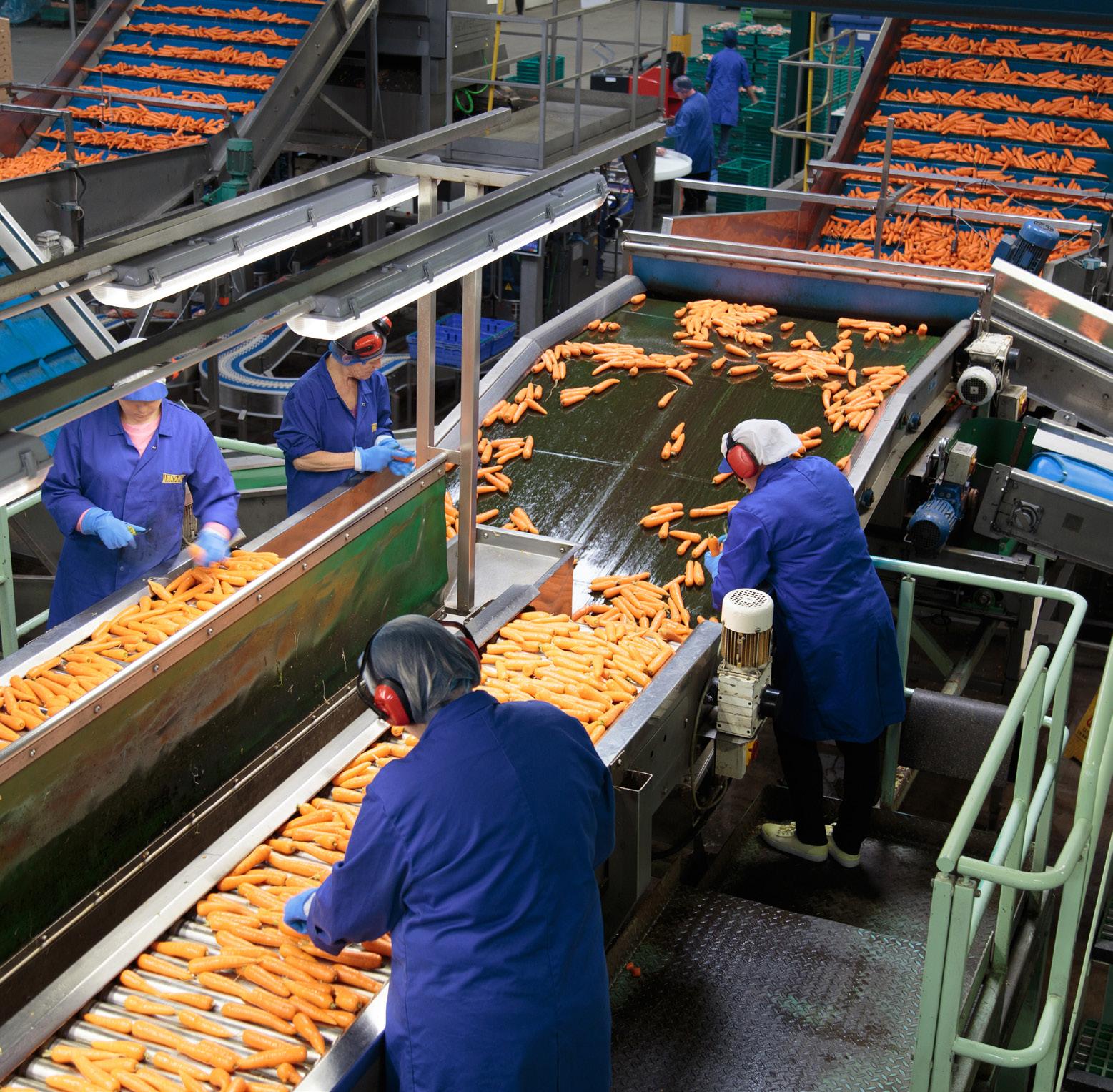
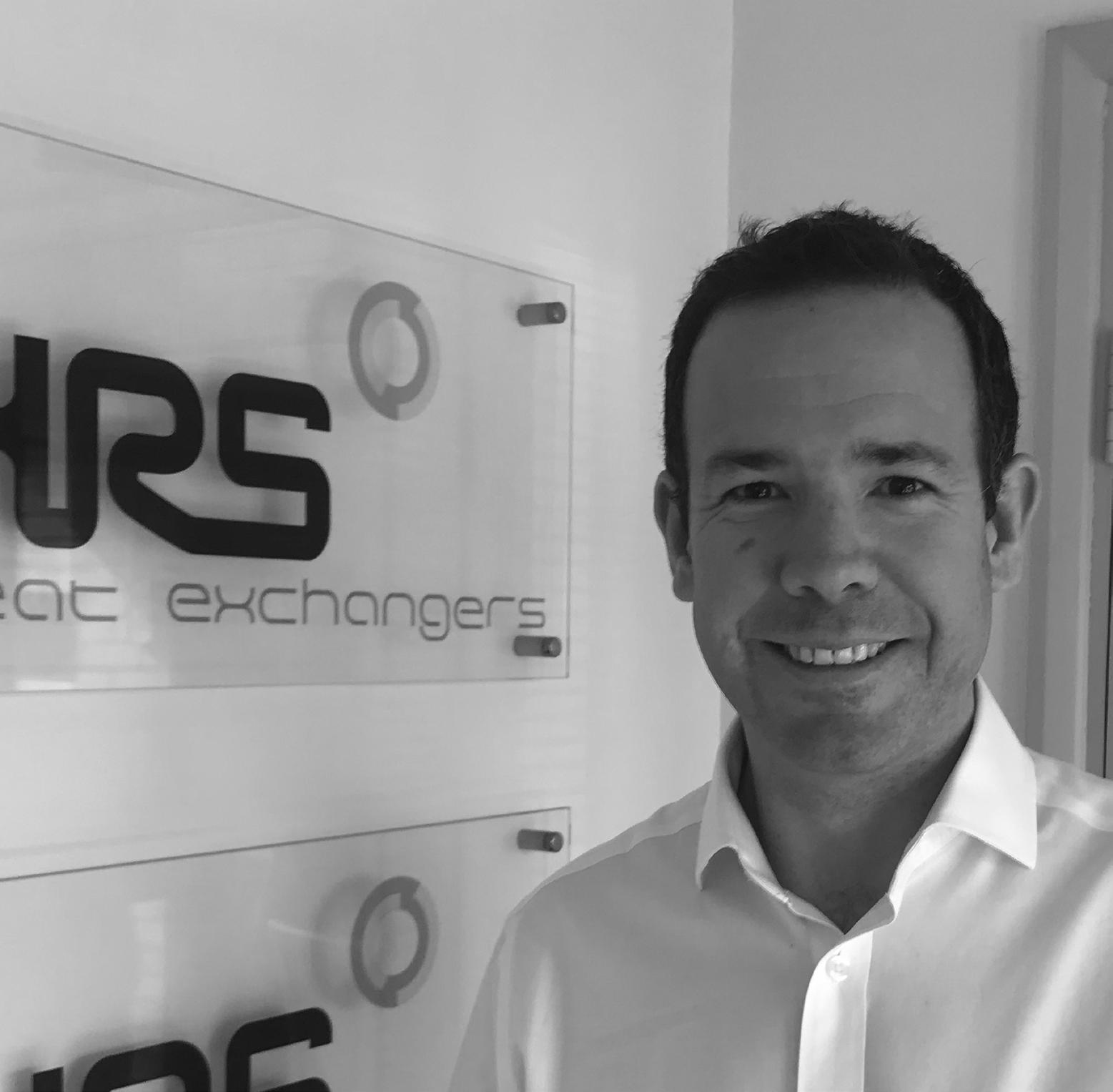
For further information on flow measurement devices to suit specific applications, please contact Titan Enterprises on +44 (0)1935 812790 or email: sales@flowmeters.co.uk.
Twelve months ago, Titan decided to make the significant investment in a new calibration rig which would both increase their capacity and improve their capability to calibrate their liquid flow measurement devices. Having just received delivery of this new rig, it is being commissioned, calibration software installed, and will be ready to be put to use within the month.
Titan Enterprises use piston provers for flow meter calibration, our primary rigs rated from 0.002-40 L/ min and 0.05-160 L/min. With the new rig our low-end flow calibration can be reduced to 0.05 ml/min. The calibrators use a piston within a smooth bore tube to act as a moving barrier between the pressurising gas and the displaced test fluid. All Titan flow calibrations are traceable to national standards and have real time temperature compensation to accommodate changes in the fluid properties. Our piston prover systems are calibrated annually against certified weigh scales and are pneumatically or hydraulically driven to ensure a constant flow rate. Like the main flow rigs the volumetric throughput for Titan’s new calibration rig is traceable to national standards via a water draw test. Flows as low as 0.05 ml/min may be calibrated using this rig, which has a repeatability value of ±0.02% and operates at an uncertainty of 0.03%.
Jeremy Thorne, Operations Manager at Titan Enterprises, commented: “Historically the production of our flowmeters has been limited by the flowmeter calibration capability. The new flow rig will increase our calibration capacity at the lower flow rates below 4 L/min. This will enable us to increase our production throughput as well as expanding Titan’s total range of flow calibration.”
Expands its Liquid Flow Meter Calibration Capacity
Flow Meter MethodologyCalibration
Titan Enterprises has been performing all its calibration requirements inhouse since 1994 using their positive displacement oil or water flow rigs. All flowmeters manufactured by Titan (except for the small beverage meters) are calibrated against traceable standards, tested and issued with a calibration certificate.
Why should flow meters be calibrated? Engineers, scientists and measurement specialists rely on a flow meter’s accuracy to maintain or improve the financial viability, quality and safety of a product or process. Used within a wide variety of applications, including pharmaceuticals, aerospace, food and beverage, energy, and agro/ petrochemical, where accurate flow measurement is critical, regular calibration ensures these measuring devices continue to operate within acceptable limits.
Jeremy concludes: “Titan will also be increasing its production staffing levels to meet increasing demand, optimise our production rates and functionality that the new rig will give us.”
Jeremy added: “As well as calibrating our flow meters during production, we also offer a re-calibration service to our customers. The performance and accuracy of flowmeters, even the most rugged ones, will degrade over time. Mechanical meters will wear, and electronic ones can suffer minor degradation in the electronics or mechanical damage from impact or corrosion.”
Titan Enterprises
10
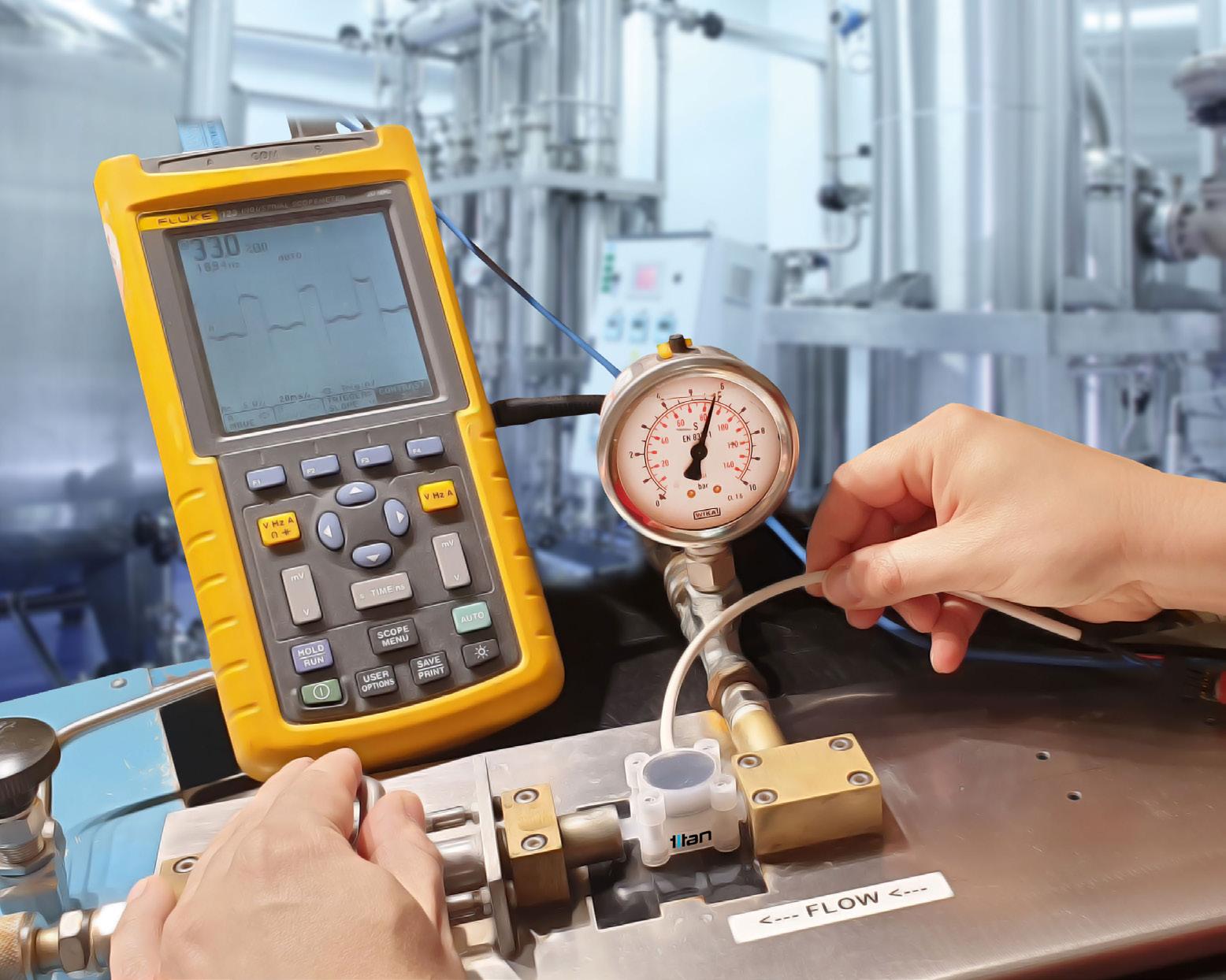

3D-MID – minimized sensing high-tech within the patient
Today, medical devices are a major focus of mechatronics. One of its breakthrough innovations are Mechatronic Integrated Devices (3D-MID). It’s a technology that allows higher density integration of electronic components into the smallest possible space. When it comes to miniaturization, the ideal partner is the leading 3D-MID supplier HARTING. The company is located in the innovative heart of the Swiss watch industry in Biel, which is also a growing hub for medical device technologies. This location was chosen with care, because in this region people have grown up in a world of micromechanics - generation after 3D-MIDgeneration.or3D-Circuits, has the potential to transform medical industry as we know it. As medical devices such as hearing aids and dental instruments become smaller and smaller, the manufacture of their most important elements - traditionally printed circuit boards (PCB’s with wires and other electrical parts) require much more delicacy and precision. High-end miniaturization is facilitated by 3D-Circuits: a fantastic combination of mechanical and electronic Thisintegration.articlebreaks down everything you need to know about 3D-MID technology, its many benefits, and its applications in the medical device industry.
12
Yaskawa coined the term “mechatronics” in 1969 by combining “mechanical” and “electronics.” Since then, steady developments in technology— notably at drives systems and wireless significantlyconnectivity—haveexpandeditsusage.
All About 3D-MID Technology HARTING’s 3D-Circuits technology makes it possible to combine mechanical and electronic What would our world look like in 1D or 2D? Well, 3D is our natural human visual reality and it is impossible to imagine life without it. In recent years, 3D has also become more and more a reality in modern high tech. How do designers and engineers in medical device technology use this new design freedom of three- dimensionality? By integrating functions and the three-dimensional routing of circuit tracks, the design space for the electronics of hearing aids can be optimally Japaneseutilised.corporation
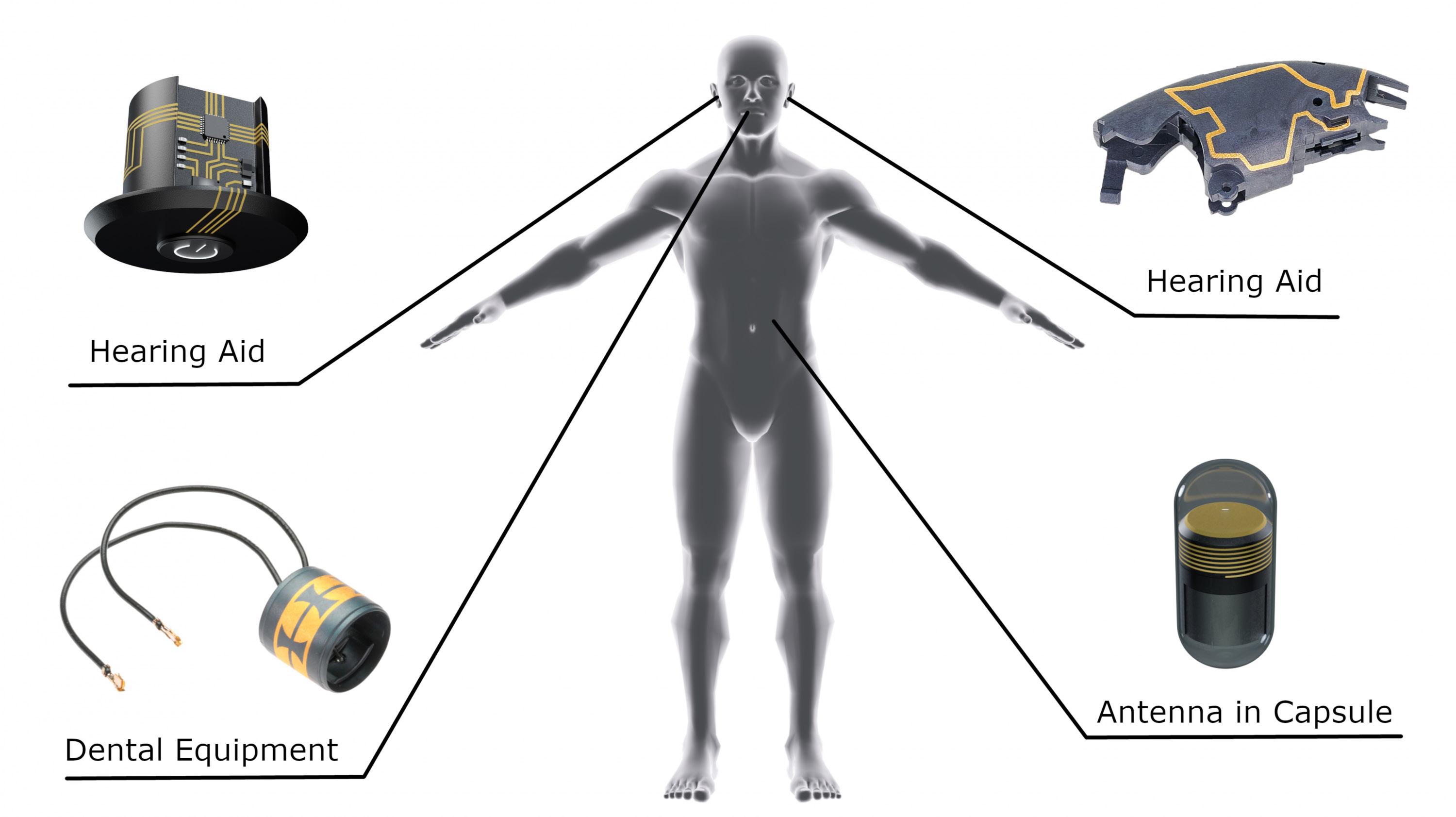
3D-MID Technology in the Medical Field
Injection molding is perfect for mass production of products with complex geometries and in miniature sizes, such as the components of high-end medical devices. A process called laser direct structuring (LDS), developed by LPKF Laser & Electronics in 1996, can then draw the needed electrical trace layout to these components, which will be made conductive in a subsequent chemical plating process.
As HARTING unifies all these process steps under one roof, customers benefit from quality “Made in Switzerland”.
3D-MID technology has become incredibly useful in many industries, especially so in the world of medical devices, where it drives miniaturization.
How 3D-MID Technology works Device designers can go above and beyond the limits of traditional manufacturing with the help of 3D- Circuits. The sky’s the limit when electrical and mechanical functions can be unified in a single three- dimensional component.
13
In the last few years, 3D printing has accelerated many advancements in the world of medicine, with millions of people benefiting from components and devices created with ease. And now, 3D-MID is poised to change the face of medicine forever. This technology takes all these advancements one giant step further by using mechatronics to create devices with an even wider range of electronic functions that fit in the smallest of spaces. Mechatronics allows for the extreme downsizing or miniaturizing of medical applications, enabling examination, sensing, and monitoring from within the patient. With such technology, medical devices can be designed to be much less invasive, leading to a significant improvement in patient care. With its many years of experience - HARTING started its activities in this field in 2003 – the team is familiar with the requirements of the medical market. The numerous series production projects confirm this. Taking large medical machines functions into a single component to fit into the smallest spaces. The electronic circuit can be built into the device itself, making it more compact and functionally dense. By using injection-molded circuit boards, the number of process steps, assembly times, and parts can all be drastically cut down.
With 3D-MID technology, there are virtually no limitations for designers. This opens up a world of possibilities and potentially huge savings for manufacturers and consumers alike. By combining mechanical and electrical hardware, the design and creation of electronic devices with very complex functions become easier and much more affordable. Because of its adaptability, mechatronics can be used in an ever-expanding variety of medical applications, ranging from bed positioning systems to robotic surgical equipment.
These components are constructed using very malleable bits of plastic through injection molding. This process makes it possible to create anything with precise measurements according to the requirements laid down by final customer usage.
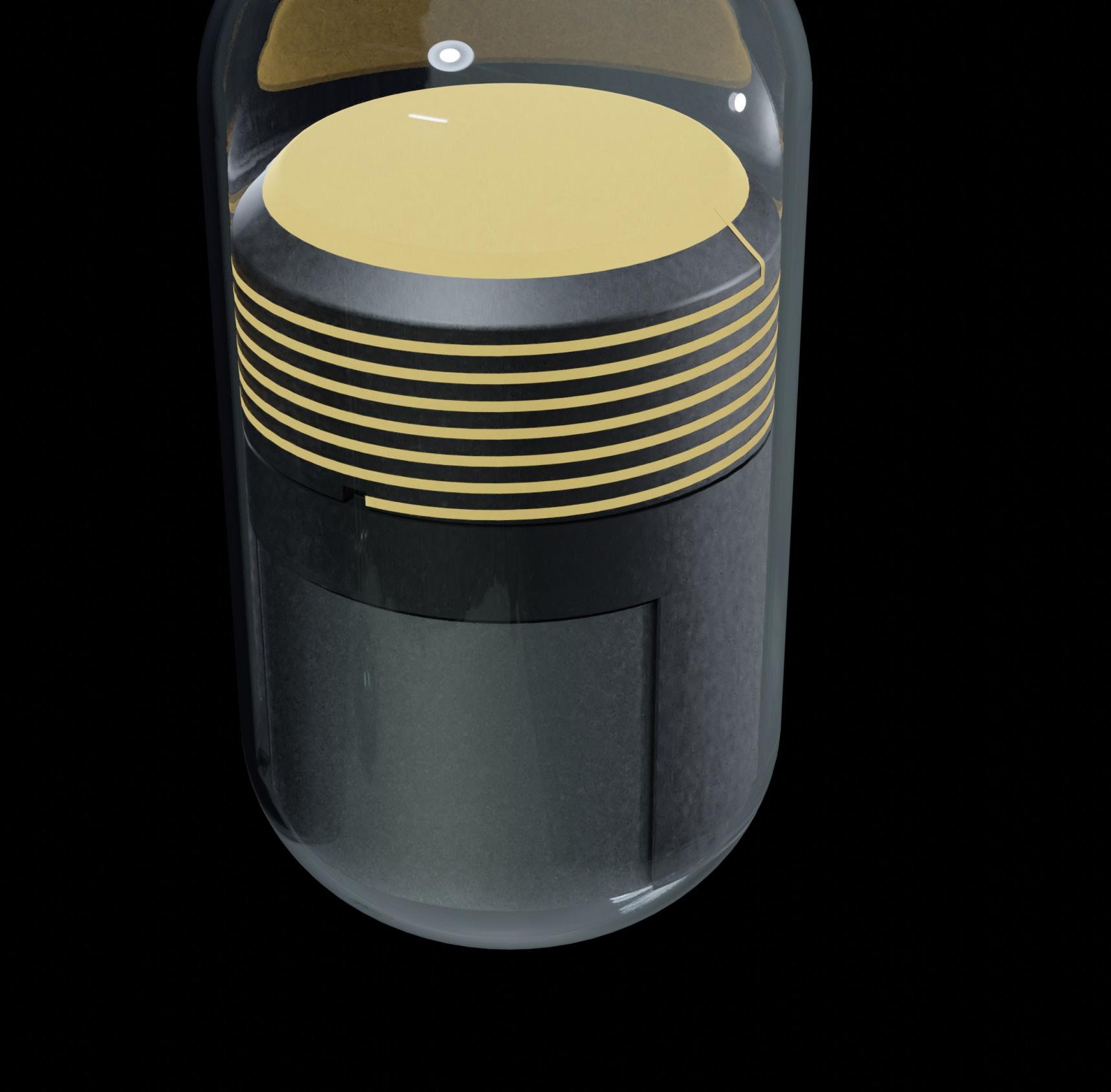
www.3D-Circuits.com and devices and putting them into a more compact package is a big part of what 3D-Circuits brings to the table. It offers significant improvements to changing how medical devices are used today.
The Benefits and Uses of 3D-MID
Some of the value-added benefits that medical organizations can gain from using mechatronics in place of more conventional manufacturing methods:
Redesign efforts for medical equipment aim to make them easier and more convenient for patients to use and manage in the long run.
14
Technology Miniaturization is one of the most critical trends in healthcare that affects how mechatronics technology is used. The development of ever-smaller instruments, devices, and equipment enables less invasive treatment methods, allowing faster recovery times and much-improved patient care. These micro actuators and miniature sensors also propel the development of small mechatronics systems for the following -Handheldapplications:diagnostics for use at the point of care, including ultrasound and blood testing -Scientific instruments for flow cytometry, DNA identification, pathogen detection, and DNA sequencing -Medical imaging using small, precise modules for lens control and laser tuning -Implantable devices that can be dynamically adjusted in-place -Mobile miniature robots -Micropumps and auto-injectors for drug delivery products (Source: Jabil)
Even conventional hydraulics are being phased out and replaced with mechatronics as the method of choice for controlling motion. Mechatronics systems are much simpler to operate, create less noise, weigh less, and are more compact.
There has also been a shift toward placing a greater emphasis on the convenience and aesthetics of medical technology as well as the level of comfort experienced by a patient. This is because more treatments are shifting from hospitals to outpatient settings, and today’s discerning customers now expect a more positive experience as a patient.
-The miniaturization of medical -Developmentdevices of low-cost disposable gadgets, which has become a pressing requirement -Device portability -High levels of accuracy and precision -Improved performance in all aspects -Design freedom -Weight -Simplificationreductionofproducts
In fact, as 3D-Circuits continues to grow in popularity, it will only get better, opening up new options for even smaller and more effective medical devices, from hearing aids and implants to surgical and dental instruments.
Conclusion The most important developments in mechatronics lead to new technologies that will shape the healthcare of the future so that devices are safer, more portable, and, most importantly, painless.
One of the most important benefits of this technology is that it makes these advances possible without sacrificing quality. You may think that shrinking a medical device down would make it less powerful or effective, but with 3D-MID, that isn’t the case at all.
HARTING’s 3D-Circuits technology is changing how medical devices are made, especially complex equipment with integrated electronics that must fit into increasingly miniscule spaces.
15

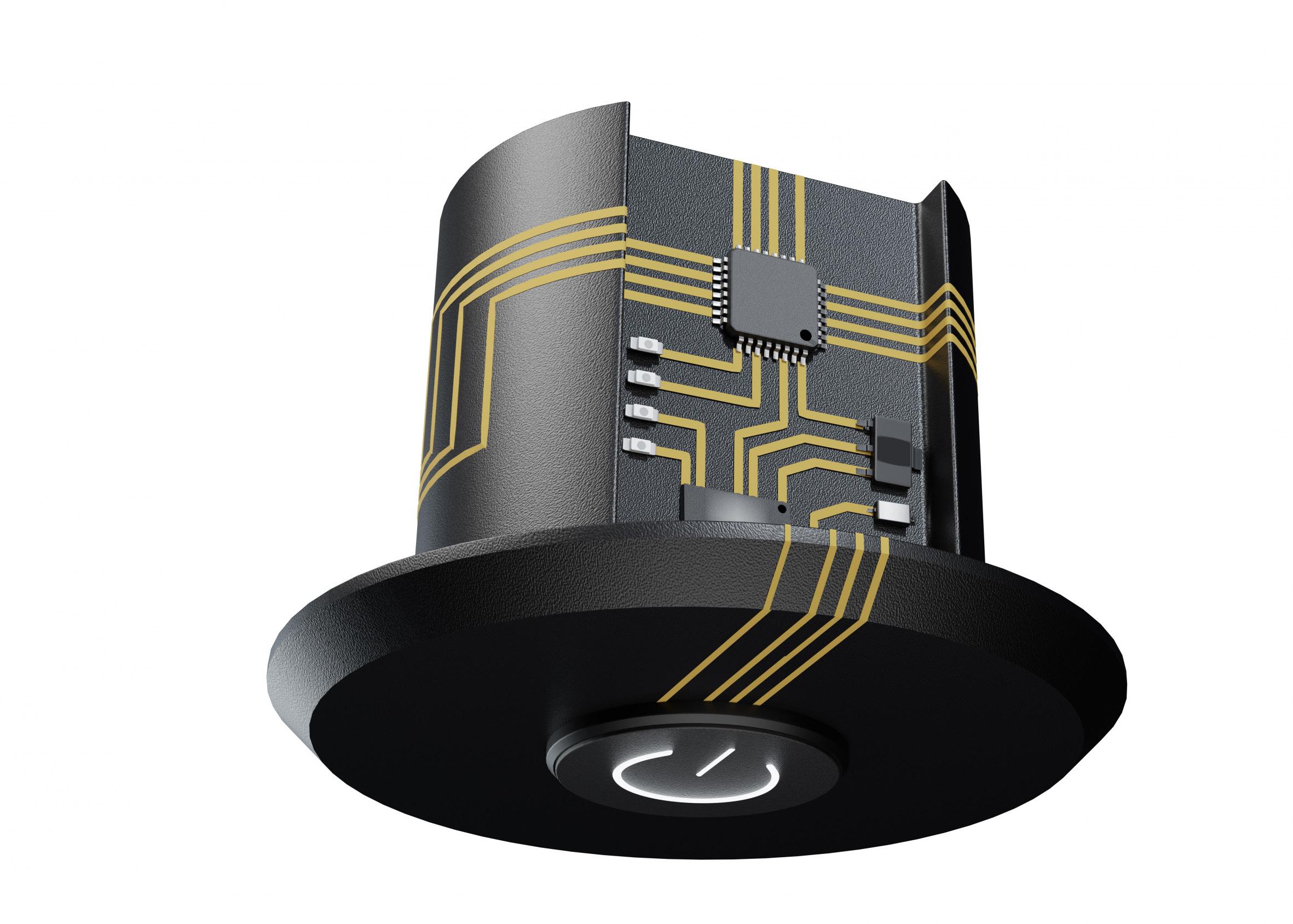
For more than 25 years, LGM has provided architectural models primarily for high-end residential and resort areas. LGM marries 3D printing to the fields of architecture, engineering, and development to provide state- ofthe-art visualisation and modelling, enabling their clients to efficiently design, build, and market products.
“I’m glad I don’t have to worry about build orientation and support structure,” said Jason. “It’s been great to not worry about that or pulling all the supports off to clean a part and get it ready. I can use my time within our own production to focus on other things.”
To see the final apartment complex these 3D prints became, visit The Piazza’s website. If you are looking to produce your own architectural models or start any kind of 3D printing project – begin a quote now or contact a manufacturing expert.
Industrial SLA 3D printing provides the right combination of large print size, detail, cost, and speed. However, because LGM’s SLA printing needs are intermittent, they needed a partner that could provide them with a lot of capacity for high-quality parts without the capital and hiring necessary to bring the process in-house.
When comparing Quickparts to other 3D printing companies he’s done business with, Jason noted accuracy as a deciding factor. “We have a higher degree of accuracy with Quickparts,” he said. “We come back because it’s easy, and the cost is there.”
16
Making 3D printing models easy and cost-effective with Quickparts
Speed and Accuracy on Demand
Challenge LGM is highly skilled at making architectural CAD files, like REVIT, ready for 3D printing and has been 3D printing in-house since 2000. LGM’s biggest and most high-profile projects need quick turnaround time on large prints and high level of accuracy, detail, and surface finish to achieve the look their clients have come to expect.
“We can send our 3D, print-ready files and know what we get back will be accurate, ready-to-go parts.”
“We can send our 3D, print-ready files and know what we get back is going to be accurate, ready-to-go parts that plug directly into our process every time,” Jason said. Saving time and costs by streamlining the 3D printing process for clients allows them, in turn, to streamline time and costs on projects for their clients.
Solution With Quickparts’ online, instantquote system, LGM could customise options for their architectural modelling needs and get initial project cost estimates quickly. LGM creates simple mass models for the project and uploads the 3D CAD file to obtain a quote. “Once the quote is approved and the final file is ready to go, Quickparts just runs with it and gets the part to us,” said Jason Berghauer, Senior Project Manager for LGM. Charles Overy, Director at LGM, concurs. “We have been using Quickparts for over 14 years. We have benchmarked parts with other vendors, but the quality is just not there. Quickparts is a vital partner we can rely on to deliver excellent SLA parts.”
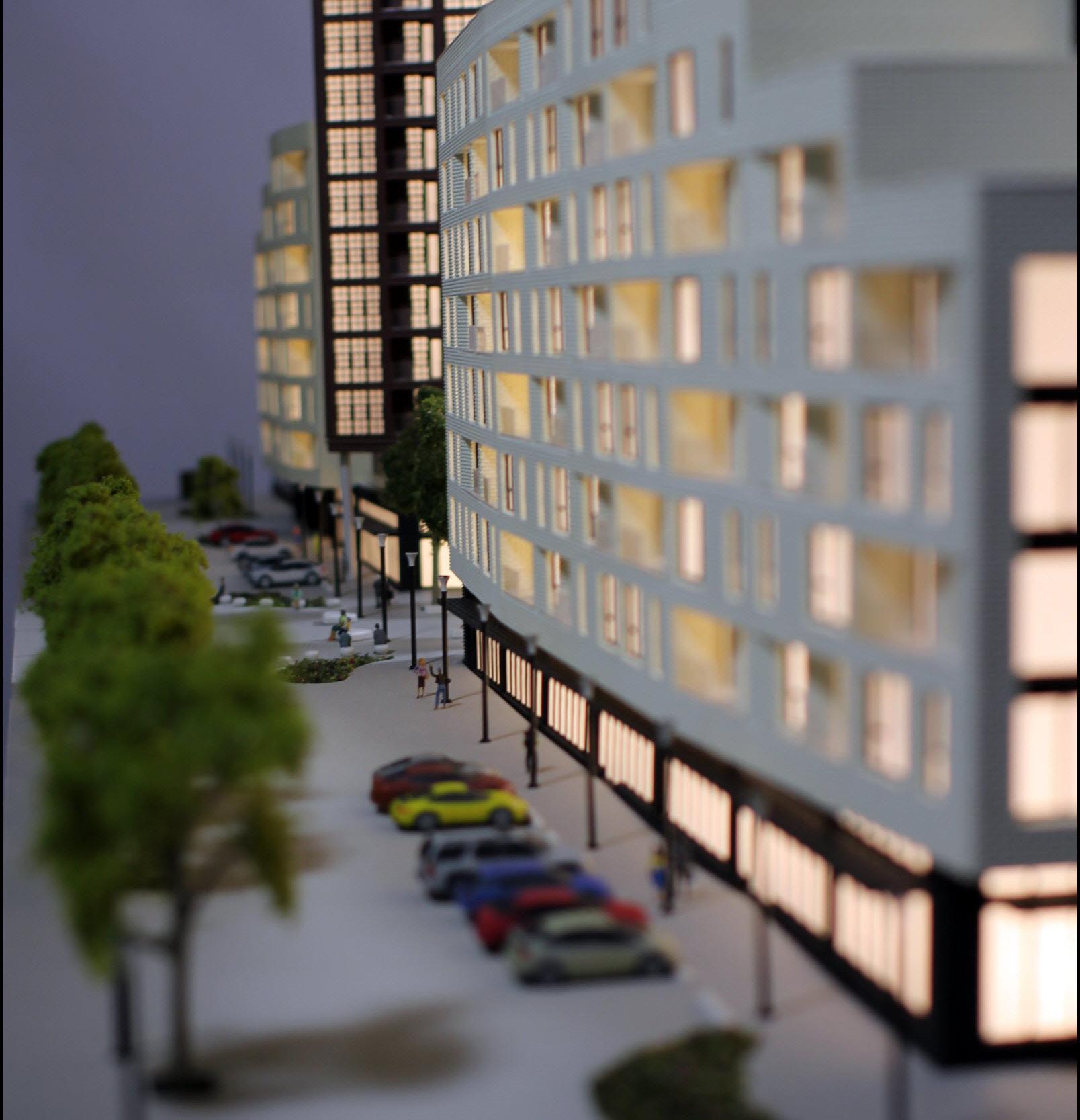
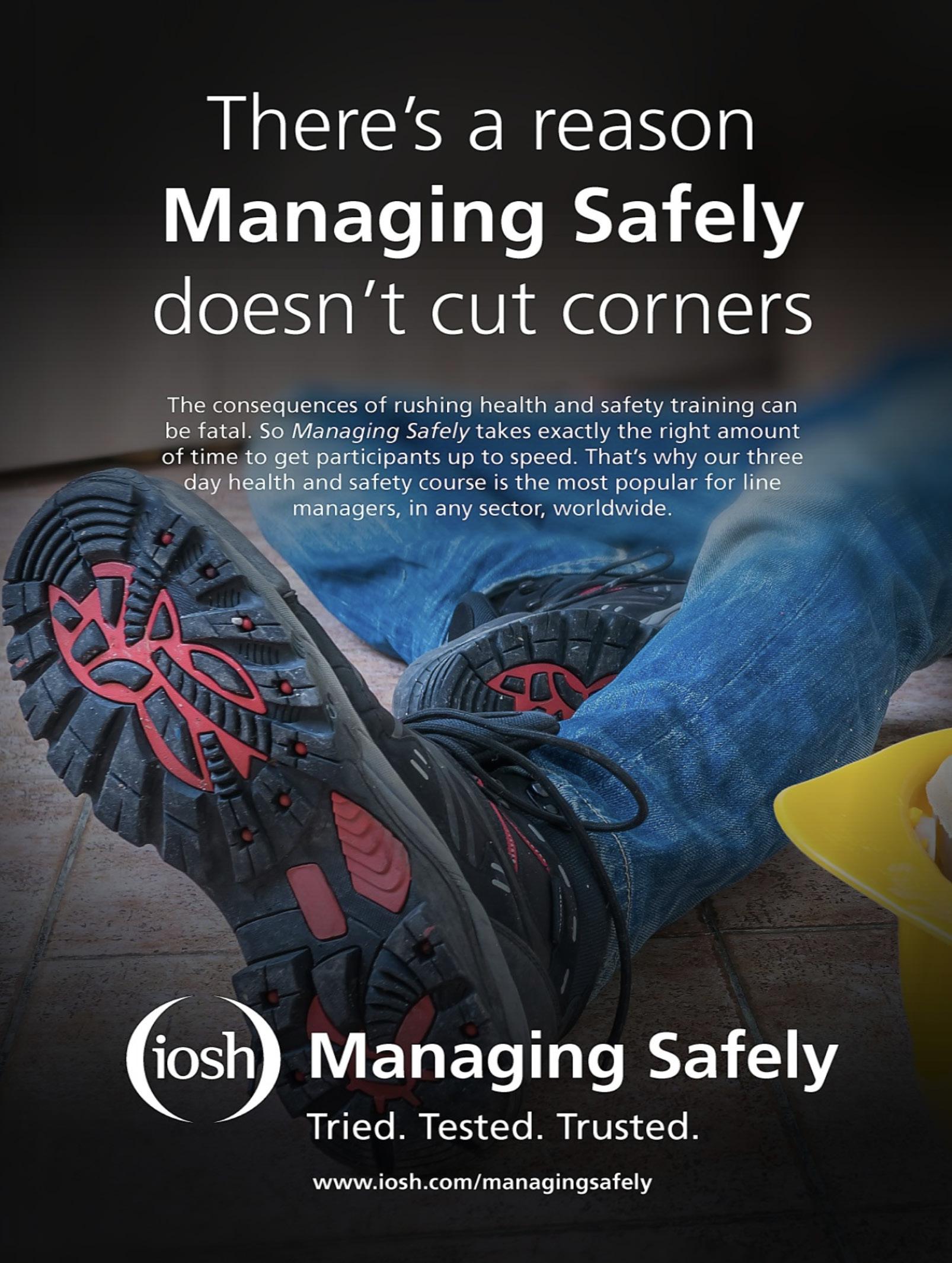
Biology as inspiration
“Our world is changing at an unprecedented rate. World population is growing and the consequences of climate change are already being felt. We will have a liveable future only if people, animals and the plant world live in harmony. This is why at Festo we consider the bioeconomy to be the economic system of the future. Our aim is to make a significant contribution to improving the quality of life for current and future generations through the large-scale cultivation of biomass using our automatic technology,” says Dr. Elias Knubben, Vice President Corporate Research and Innovation.
Efficient photosynthesis in the high-tech bioreactor
Festo demonstrates an automated bioreactor for photosynthesislarge-scaleofalgae Festo presented the PhotoBionicCell research project at the Hannover Fair – a bioreactor that enables the efficient and large-scale photosynthesis of Algaealgae. are small climate savers. Even in their natural state they are extremely efficient photosynthesizers and absorb ten times more carbon dioxide (CO) than land plants. In bioreactors equipped with appropriate sensors, control technology and automation, the efficiency of algae can be increased to one hundred times that of land plants. This shows that they have significant potential for a climate-neutral circular economy. Festo’s
The PhotoBionicCell features an innovative photobioreactor, where algae can be automatically cultivated, and their growth controlled. The algae cells, through photosynthesis in their chloroplasts, convert sunlight, carbon dioxide and water into oxygen and chemical energy carriers or organic recyclable materials. With automation technology from Festo, e.g., for optimal gassing and mixing, algae can absorb one hundred times more carbon dioxide than land plants such as trees or maize. Biological recyclables for climateneutral end products
What’s it all about… Algae?
The researchers focused on the cultivation of the blue- green algae Synechocystis, which produces colour pigments, omega-3 fatty acids and polyhydroxybutyrate (PHB). When this PHB has been extracted, it can be processed by adding other substances, and used for example in 3D printing.
PhotoBionicCell research project demonstrates a potential approach for the industrialisation of algae cultivation of tomorrow.
18
As part of their metabolic processes, algae produce fatty acids, colour pigments and surfactants. These can be used as the raw materials for the production of medicines, food, plastics or cosmetics. Unlike petroleum-based products, the biobased end products can usually be biodegraded and, in keeping with an overall circular economy, always recycled in a climate-neutral manner. For example, the production of a shampoo container requires about one litre of petroleum. If the shampoo bottle is incinerated after use, it releases an additional three kilogrammes of CO and thus has a negative CO balance. If bio-plastic based on algae is used instead, three kilogrammes of CO are absorbed, which are released again when the bottle is disposed of. Thus, the cycle is in balance.
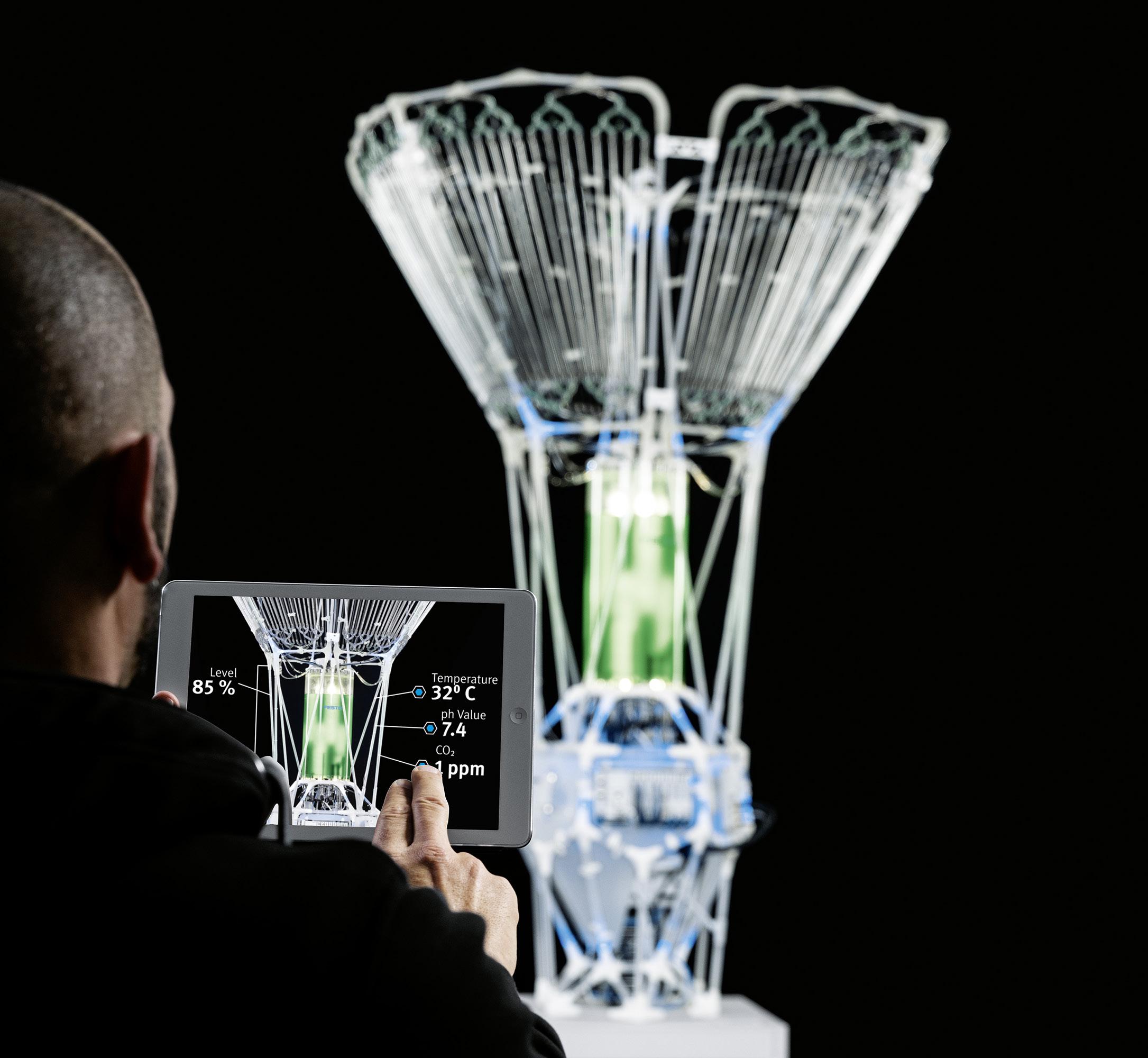
A major challenge for bioreactors is how to precisely determine the volume of biomass. Festo relies on a quantum technology sensor supplied by the startup Q.ANT to do this. It returns accurate information on the growth of the organisms in real time. Using microfluidics such as pumps to precisely control minute volumes of liquid, the algae are automatically and continuously monitored by the quantum sensor. The quantum sensor can optically analyse individual cells so that the amount of biomass can be precisely determined. In addition, it uses artificial intelligence (AI) to examine the cells for their vitality. Only then is it possible to anticipate and react to process events and to intervene in a controlled way.
Software solutions for a digitalised laboratory Many laboratory analyses have been done manually up to now. This is slow and can result in errors. The automation of such laboratory systems in the future will enable all required data to be read directly and in real time. To achieve this, in-house developed software is used for the PhotoBionicCell. The dashboard allows multiple photobioreactors to be displayed with the current data situation and live images. Changes to parameters and the corresponding evaluations can be made around the clock and even remotely. Users can thus respond to changes in the bioreactor at any time and, for example, start harvesting the product at the optimum time.
Artificial Intelligence for further optimisation
The developers at Festo are also using AI to evaluate the data. This allows the bioreactor to be optimised for propagation of the algae cultures or to maintain specified growth parameters with minimal energy input.
www.festo.com/gb
19
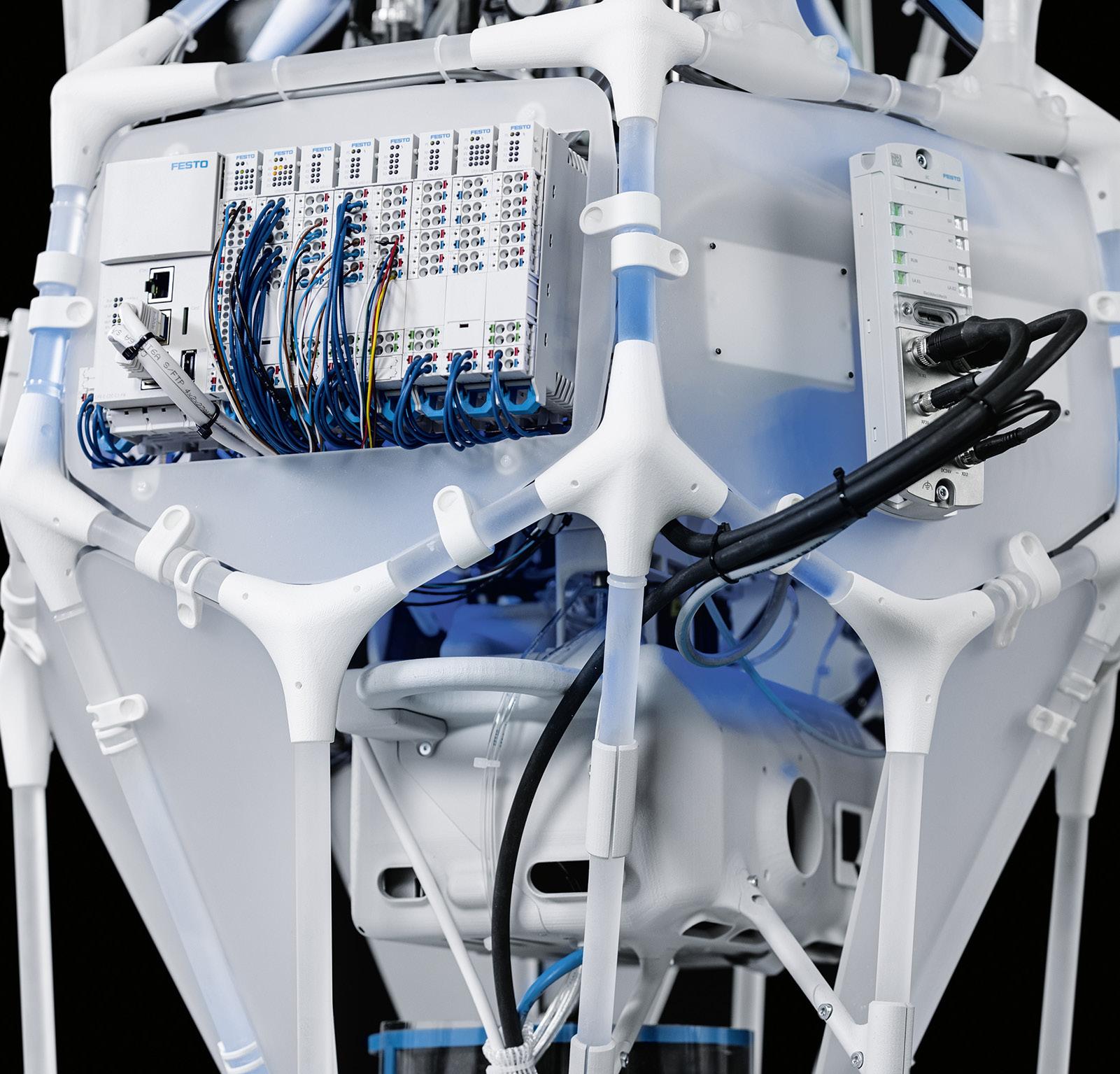
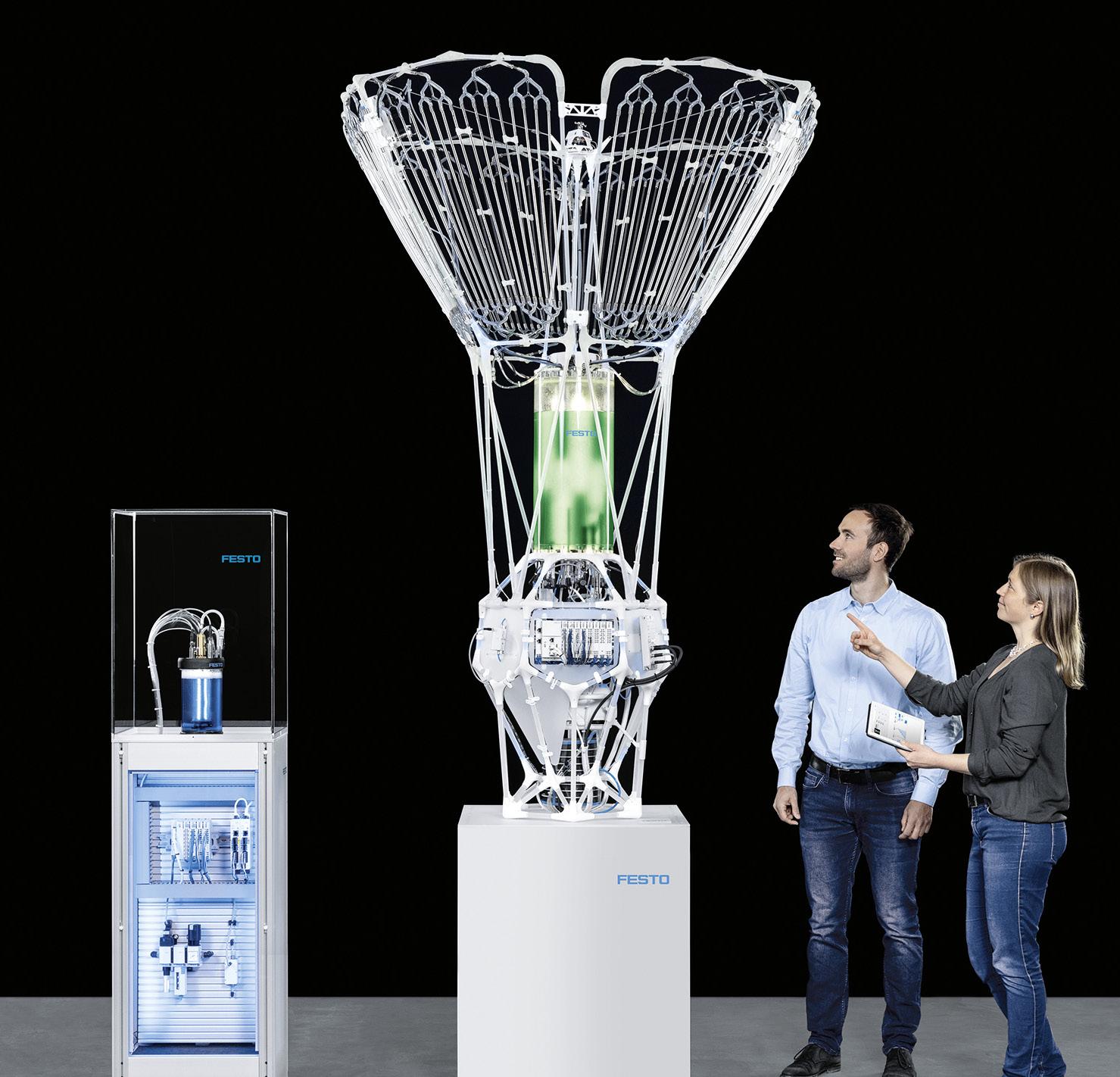
“When it comes to selecting the CNC, there are a number of factors to be considered, such as whether it will provide the required functionality and whether it will seamlessly integrate with the client’s existing manufacturing processes and requirements,” explains Richard. “In this case, the
A reputation for quality
Fanuc CNCS help electron engineering breathe new life info legacy equipment
Based in Halifax, West Yorkshire, Electron Engineering Services Ltd (EES) has been refurbishing machinery for over 30 years.
As part of its latest project, EES is completely stripping down and rebuilding a Binns & Berry Data 90 CNC Lathe, for a customer with a subcontract machine shop. By retrofitting it with a new FANUC 0i-TF CNC, as well as a FANUC digital spindle motor and drive, FANUC digital axis servo drives, and a completely new electrical interface, this legacy machine will be completely remanufactured and ready for the digital age.
“Thecommissioned.refurbishment service we provide brings these machines in line with modern day requirements, whilst ensuring that the brilliant engineering that went into them in the first place isn’t discarded. This includes making sure they are compliant with modern standards and regulations, as well as incorporating the latest software, motors and control technology to maximise efficiency.”
Superior digital control
20
“The majority of the machines we refurbish – that we essentially remanufacture – are actually of a higher build quality than many of their more modern counterparts,” explains Richard Vogel, EES Sales Director. “They are of robust, predominantly high integrity cast iron construction, and would have been at the cuttingedge of technology when first
Sustainability is at the heart of a partnership between robotics and automation specialist FANUC UK and machinery refurbishers Electron Engineering Services. By retrofitting a cutting-edge FANUC CNC into a lathe for a subcontract machinist, as well as a FANUC digital spindle motor and drive, servo drives and new electrical interface, this legacy machine has been upgraded ready for the digital age. As well as boosting productivity by delivering improved functionality, faster programming and enhanced reliability, the partnership is helping to cut waste by breathing new life into old machines, repurposing them for today’s smart manufacturing needs.
An important part of the machine refurbishment process is retrofitting a new CNC. Short for Computerised Numerical Control, CNC is an electronic process for controlling machine tools. From improved functionality and faster programming, through to enhanced reliability, CNCs play a vital role in boosting productivity in a manufacturing facility.

Benefitting planet and pocket Alongside the environmental benefits of machine refurbishment, there are also significant costsaving implications, as EES’ projects typically involve high-capital machinery. Richard continues: “A full remanufacture solution usually delivers around a 50% costsaving compared with a customer buying an equivalent, brand-new machine. That means the potential productivity gains can be accessed by a wider range of manufacturers, as well as improving our customers’ ROI.” As a result, EES is starting to see an increased demand for its services, both for retrofitting as well as for new, bespoke machine solutions. “We are definitely seeing signs of confidence from customers looking to invest in equipment and from our perspective, it’s great to know we can count on FANUC’s ongoing support to help meet this demand,” says Richard. “There are still a significant number of high-quality, older machines with great potential, provided they are updated to ensure compliance with the latest regulations and given modern CNCs, motors and drives to get the most out of their inherent mechanical capabilities.”
21 client was already using FANUC controls, which made this a straightforward decision. But even when this is not the case, FANUC CNCs are often the client’s control of choice. FANUC is a globally recognised name, and its products – both firmware and software – are reliable and userfriendly, which are absolutely key in the type of projects that we undertake.”
Ray Timberlake, Sales Manager at FANUC UK, adds: “The work that EES do is brilliant in terms of providing premium manufacturing equipment at a competitive price point. We’ve been working in partnership with them for over a decade, and every single project is an exciting opportunity to breathe new life into old machinery.”
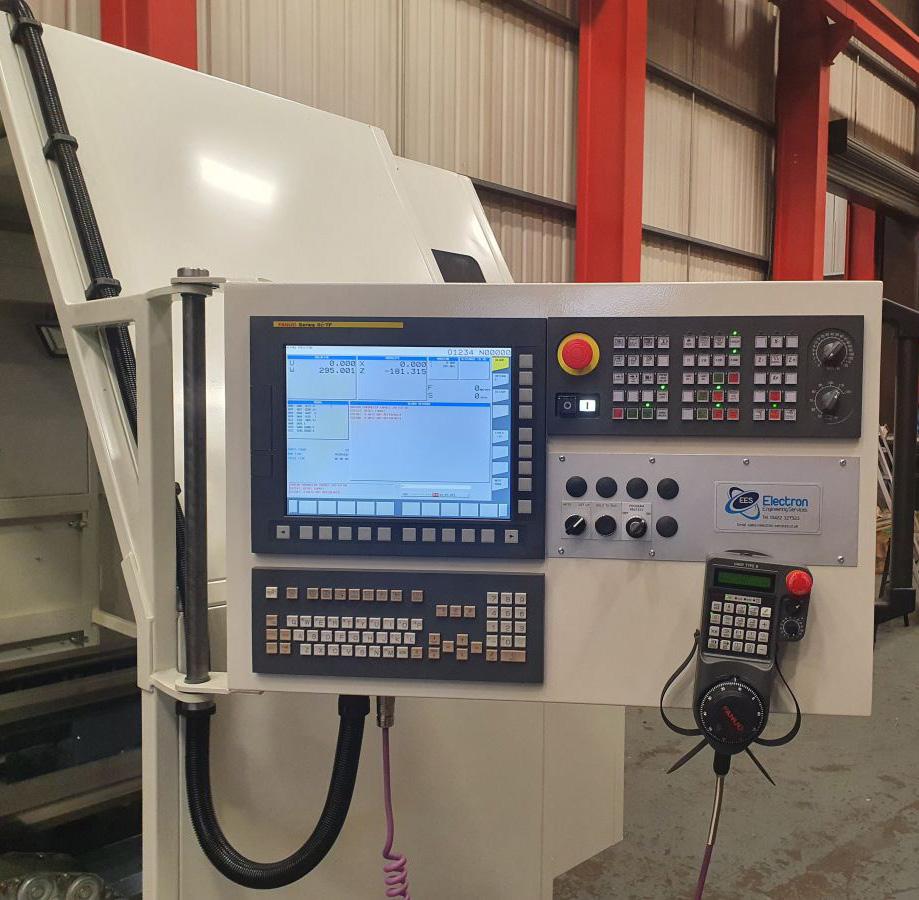

Louis Mongin, BLDC Product Strategy Manager, and Antonio Herrera, Business Development Manager, Portescap, explain how off-the-shelf miniaturised motors can be quickly converted to use in aerospace and defence projects.
Military grade equipment often demands the highest specifications to meet specialised requirements. To fulfil these criteria, aerospace and defence OEMs regularly stipulate the need for dedicated designs, developed specifically for the specific task. Miniature motion systems, typically involving motors, gearboxes, and encoders, are often used on critical military applications, from autonomous robotic vehicles through to radar systems. Field failure, error or inaccuracy isn’t an option, so it’s easy to see why a design-from-scratchdedicated,approach is Thetaken.main drawback however, with a design-from-scratch approach, is time. Requiring the development of a new design, plus testing, the manufacturing process then demands production-ready drawings, the creation of tooling, as well as process documentation. The tooling associated with a new motor design alone might take more than 12 months to complete, meaning the total duration of a bespoke development adds years to a project’s timescale. This kind of development also comes at a premium. Customising available designs
Commercial off the shelf motors can decrease time and cost for defence projects
22
The alternative process is to use a commercial, off the shelf motor solution as the basis for prototype development. Motors must be selected that achieve the necessary levels of performance (speed, power, precision etc.) and durability at the outset. It is also critical that a motor manufacturer such as Portescap is selected, who can demonstrate a comprehensive customisation service that provides the specific attributes required for the aerospace and defence Designindustry.criteria for military applications usually includes the ability to withstand shock and vibration. These extreme forces are particularly evident in applications such as missile fin actuation. Optimising resistance can be achieved by upgrading the bearing system, the focus of greatest shock loads. Feedback elements too must be ruggedised by replacing glass encoder discs with durable solutions such as resolvers or magnetic scales.
Military specifications also have to accommodate wide temperature ranges, enabling operation in extreme conditions. An aircraft fuel valve actuator, for example, is subject to temperature extremes as it transitions to high altitude flight. Temperature change can cause materials to expand or contract at different rates, potentially damaging the motor. Special bearing lubrication could be used, or the winding and insulation system materials could be modified to handle the extremes.
A common expectation for military spec OEM projects is that each and every component will need to be bespoke designed and manufactured to meet the strict standard and certifications. But, if a manufacturer can demonstrate that their off-the-shelf product range is already designed to meet the rigours of the industry, this can help reduce the prototyping phase and speed up delivery to the market.
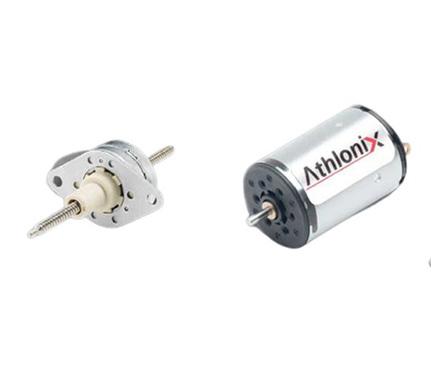
Meanwhile, vacuum conditions, particularly impacting high altitude aircraft and space vehicles, can affect the ability of the motor to dissipate heat. As a result, the standard brush materials in DC brush motors can fail. In addition, the outgassing of bearing lubrication can affect bearing life or harm the vacuum environment with unwanted particulates. Customised options such as substituting brush and commutator materials, as well as incorporating additional heat dissipation methods and mil-spec lubricants, can resolve these issues.
However, customising an existing motion solution for mil-spec use can only be achieved with a manufacturer like Portescap that has the required experience and capability.
In addition to working in the military sector, Portescap has cross-sector experience with other demanding industries, so is able to suggest new innovations to military contractors. This way, advances in materials, design, manufacturing and documentation can benefit the project.
23
When it comes to production of customised designs, motor manufacturers must also respond to critical manufacturing process needs tied to ISO and quality control. The motor manufacturer should also be able to produce several iterations in small batches, enabling a complete testing and validation process.
The advantages of customisation Customising off the shelf designs removes the time delay in initial development. Instead of creating a completely new design from scratch, a lightly modified version of the standard motor can be used as a proof of concept. Further modifications can then be made to the prototype according to requirements. This stage can include several iterations, as well as the extensive testing and validation required for military use.
The speed of development enables the designer to spend more time on the aspects that really matter: the specific modifications required to meet critical specifications.
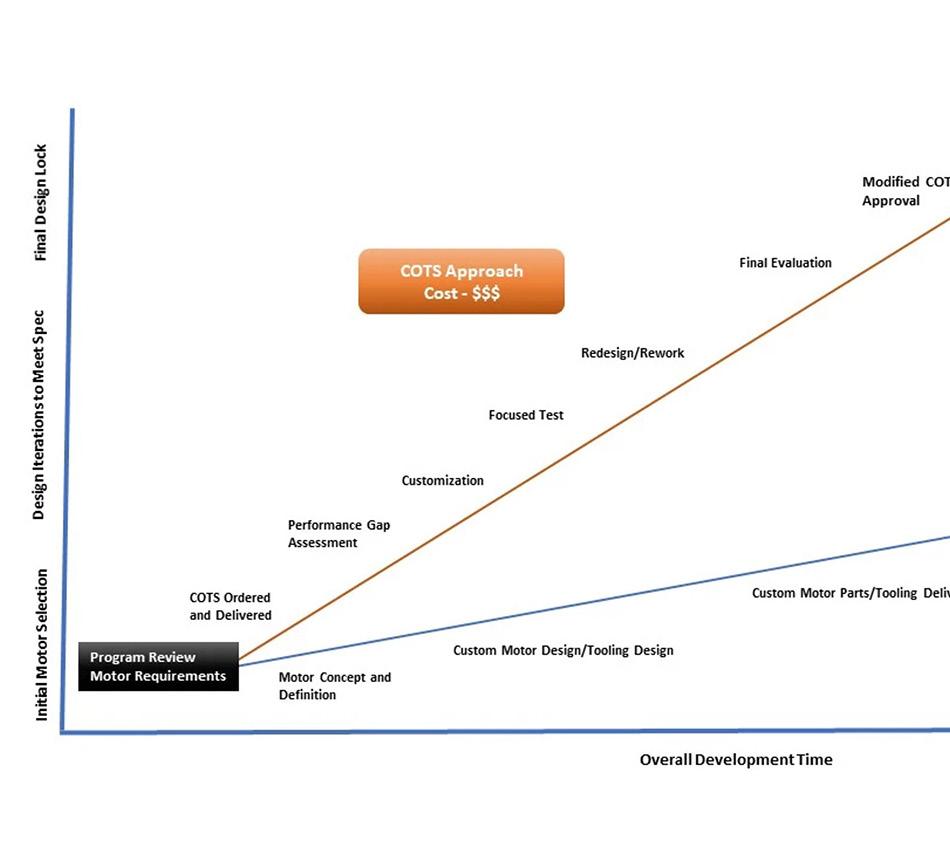
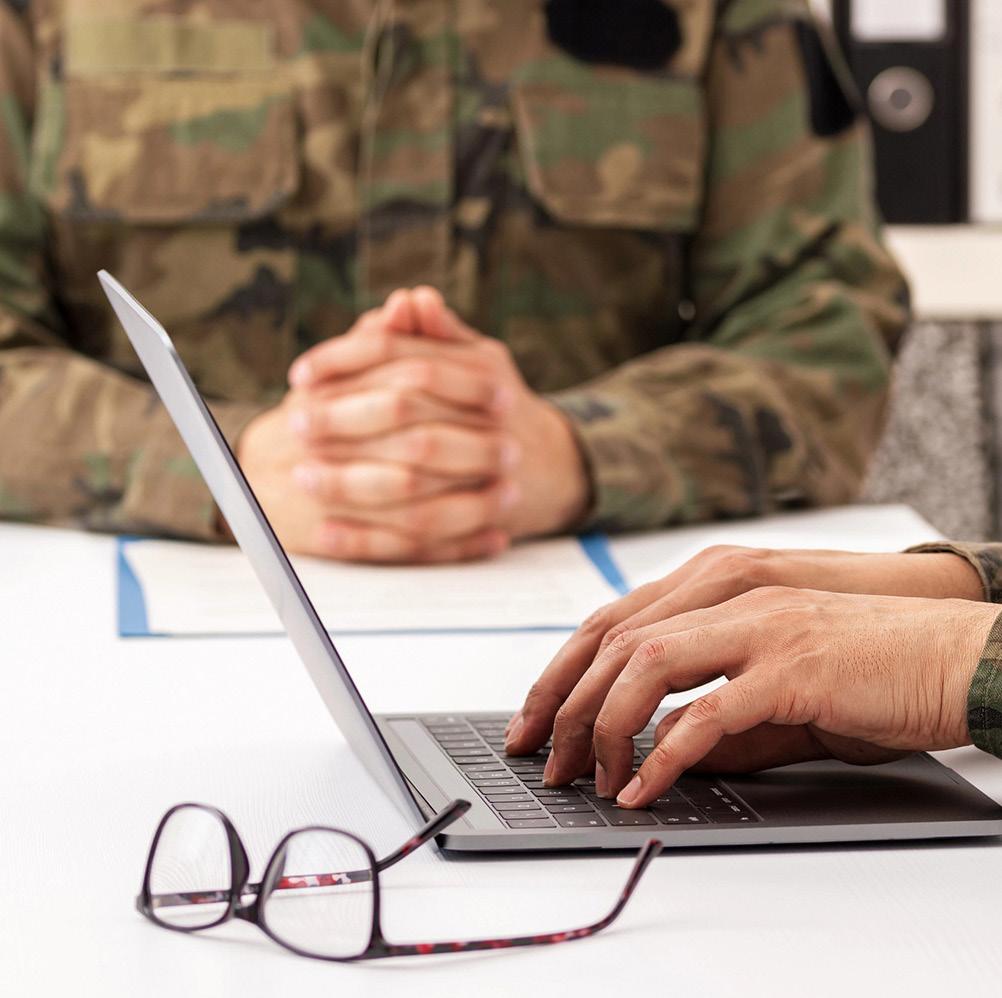
Energy efficiency – unused potential!
Reducing the carbon footprint
NORD DRIVESYSTEMS not only helps its customers to discover and achieve such a savings potential with its efficient components but also with a special service.
24
Highly efficient IE5+ synchronous motor NORD sets new standards with regard to energy efficiency with the IE5+ synchronous motor, which achieves an efficiency of up to 95 percent. Thanks to permanent magnet synchronous motor technology (PMSM), it achieves this high efficiency relatively constantly over a wide speed and torque range and also provides very good energy consumption performance in partial load and partial speed ranges. This means that it even surpasses the highest defined energy efficiency class IE5. Due to its wide power range, the IE5+ also contributes to reducing the Total Cost of Ownership (TCO) beyond the energy efficiency by enabling version reduction in an overall system. “Especially for systems with numerous drives, for example in intralogistics, there is a significant savings potential here”, Niermann says.
NORD components increase the energy efficiency of drive systems
“In times of rising energy prices, increasing energy efficiency is becoming more and more relevant”, Jörg Niermann emphasises. As a committed family business, NORD DRIVESYSTEMS also attaches great importance to reducing its ecological footprint in the interests of intergenerational justice and the fight against climate change.
Patented DuoDrive geared motor The IE5+ synchronous motor is also part of the patented DuoDrive geared motor, where it has been integrated into a single-stage helical gear unit. Calculated via the system, the geared motor achieves up to 92 percent, one of the highest efficiencies on the market in this power class. “The fewer interfaces, the higher the system efficiency”, Jörg Niermann explains. The integration of the drive into the gear unit housing reduces the installation space, the number of wear-prone parts and thus also the maintenance effort. The elimination of component joints also greatly minimises the risk of liquid ingress and bacterial contamination.
Not only in times of rising energy prices is energy efficiency one of the most important goals of industry. Highly efficient components from NORD DRIVESYSTEMS help to reduce the energy consumption of drive systems. Additionally, the drive specialist offers its customers energy-related advice. We help our customers to save energy”, is how Jörg Niermann, Head of Marketing, sums up one of the major guidelines of NORD DRIVESYSTEMS. The company’s drive components are increasingly optimised towards the factor of energy efficiency. A study by the Mechanical Engineering Industry Association VDMA and the management consultancy Boston Consulting Group has shown that innovative technologies in mechanical engineering and plant construction can help to reduce CO2 emissions in the entire industry by up to 86 percent. “And we want to support our customers in using their savings potential”, Niermann says.
The NORD ECO service checks the customer’s installed drives with regard to energy efficiency, dimensioning and number of versions. From this, NORD creates an energy efficiency concept that identifies possible savings potentials and is tailored to the customer’s requirements.
The DuoDrive was specifically developed for intralogistics and the food industry. In an application for the beverage industry, NORD also conducted an energy efficiency investigation. In an exhibition model, where bottles are conveyed in two circular systems, the drive specialist compared the power consumption of two drive configurations: first, a DuoDrive including a NORDAC PRO SK 500E control cabinet frequency inverter and the other a customary IE3 asynchronous motor with bevel gear unit and decentralised frequency inverter. The result: The DuoDrive consumes up to 50 percent less energy.
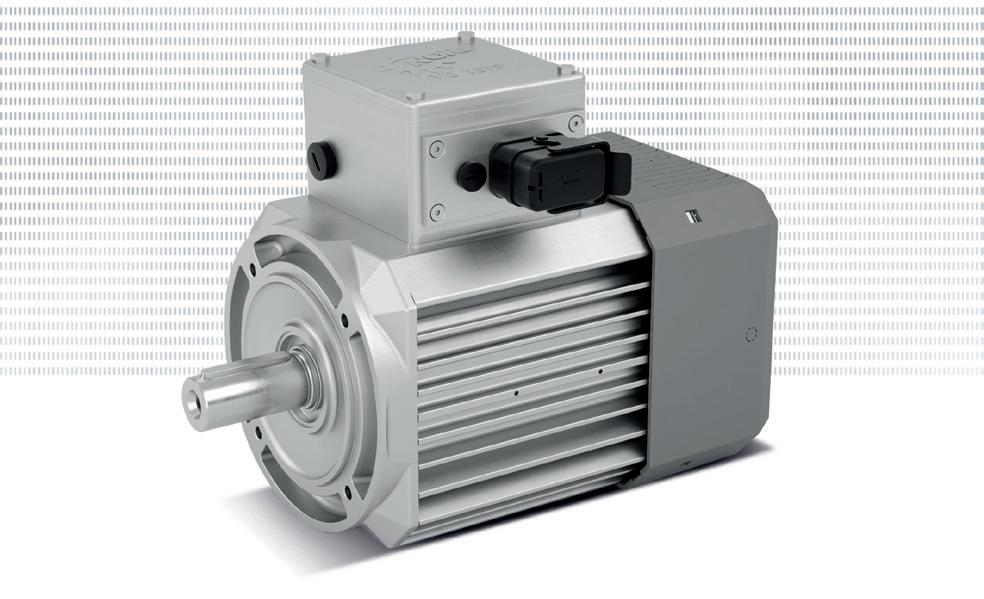
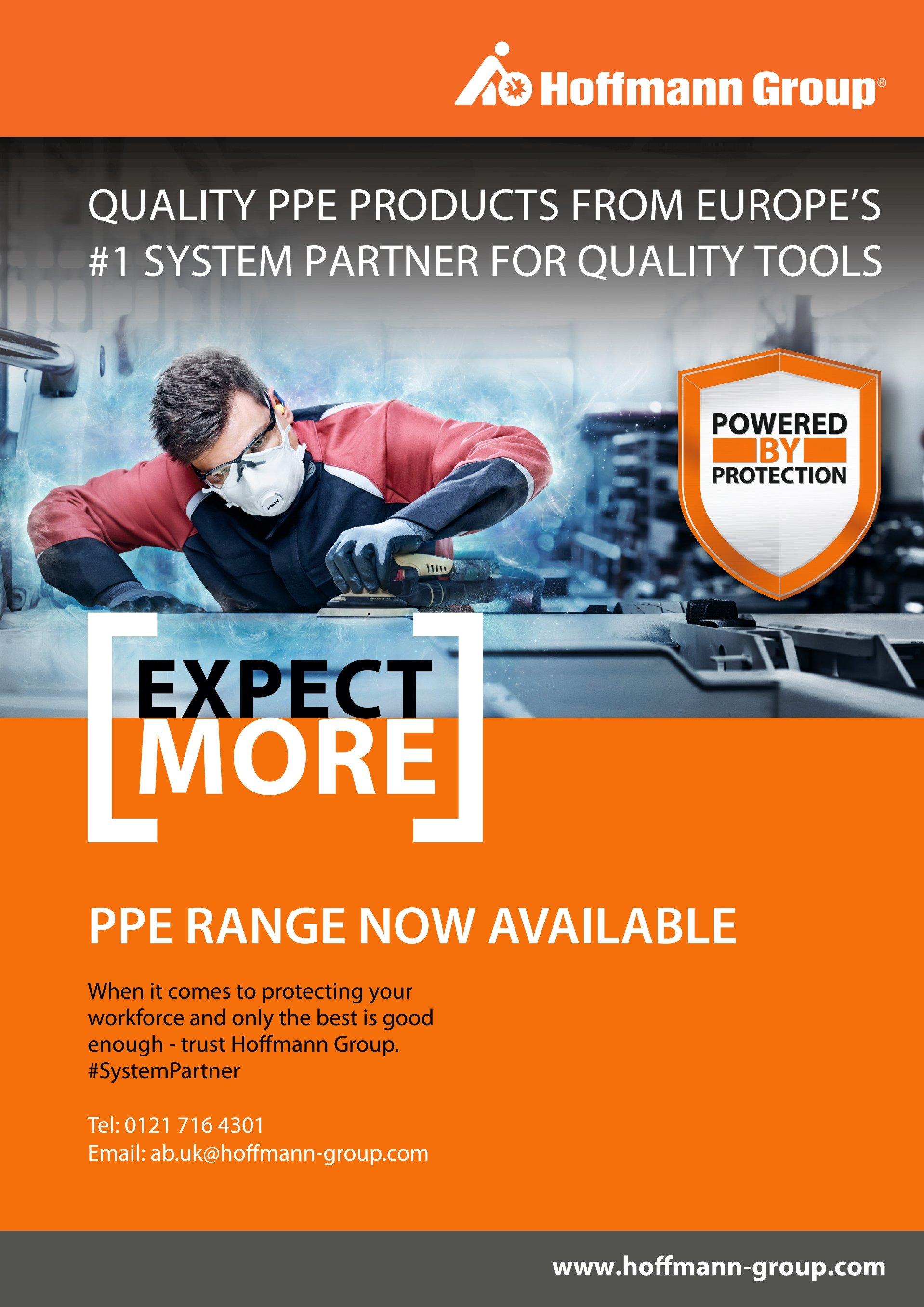
26
Smarter software and technology Software can provide a large amount of data and information that can be used to improve the manufacturing workflow and free up a skilled machinist’s time.
There is no denying that skilled machinists are hard to come by. With a large percentage of the current workforce of NC programmers and machinists getting ready to retire and a shortage of newly qualified engineering talent, finding people to work in this industry and fill the void is becoming increasingly more difficult.
VERICUT CNC simulation software can verify, simulate and optimise programs before they reach the shop floor. With these proven, optimised programs released to the shop floor, the need to have somebody monitoring the machine as it operates is eliminated. It also empowers newer machinists, helping them to learn quickly on the job, enabling greater automation and allowing operation of more machines with fewer people.
Adopting technology to fill the experience gap and do more with less.
Last year’s reports from the Institution of Engineering and Technology estimated a shortfall of over 173,000 workers in the STEM sector: an average of 10 unfilled roles per business in the UK. What is more, the Institution’s Skills Survey identifies that half (49%) of engineering businesses are experiencing difficulties in the skills available to them when trying to recruit. Long-term pipelines of talent have been established by creating pathways and opportunities for students to enter manufacturing, such as apprenticeships, UTC programs and higher education. Of course, this doesn’t happen overnight – bridging the skills gap will take time and requires an ongoing, continuous effort. So how can we deal with a skills shortage now? We learn to do more with less and this is where software can make a difference.
The VERICUT digital twin uses a control and machine to process the NC code exactly like the real machine does. Taking information from the real control, the virtual VERICUT machine is set up identically to the real machine –it is a true replica and seamless digital twin. Virtual machine kinematics simulate the machine movements throughout an NC program and VERICUT ensures that the parameters and limits on the virtual machine match the real operation on the shopfloor. Overtravel, collisions and other issues can be identified ahead of time; versus the machinist stopping the machine, trying to figure out what went wrong and then what is required to get the machine going VERICUTagain. can also connect with multiple sources of software including CAD/CAM and tool management systems. Stock models, design or finished parts and fixtures can be selected using direct interfaces and imported into VERICUT ready to run a simulation. A skilled machinist’s knowledge can be replaced by data from the tool manufacturer and tool databases. VERICUT further verifies the accuracy of a part by comparing the cut part to the design model and identifies any gouges, undercuts or excess material conditions. All of this ensures that the part being produced will be as intended and that machining will be safe, and will require minimal manual intervention.
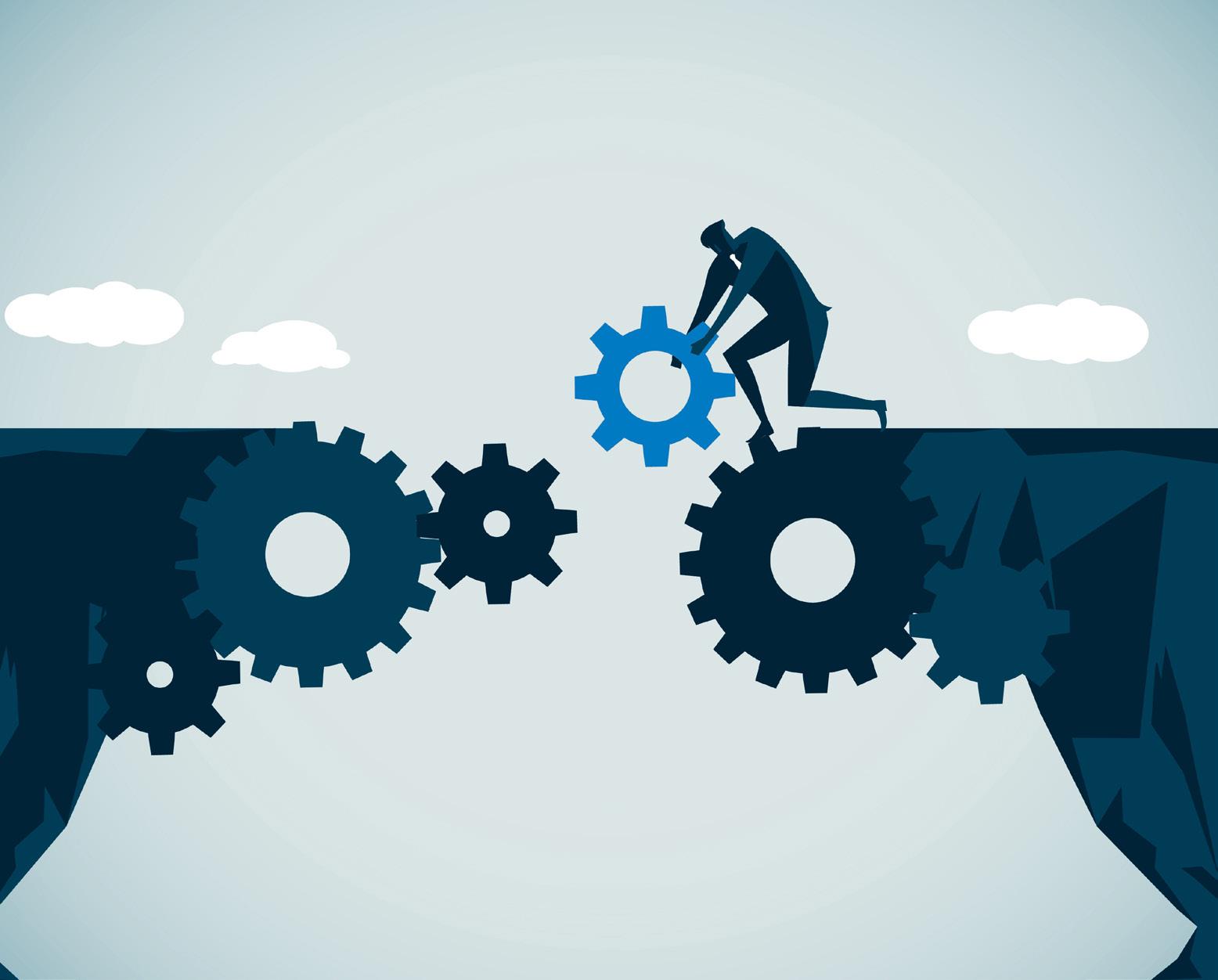
27
Once the part is verified dimensionally; set up documentation, inspection reports, and tool lists can be generated. In VERICUT everything is collated into one report, regardless of which CAD/CAM system it originated from, and a complete Reviewer file allows any personnel to view and interact with the full simulation away from the programming office. This provides machinists with data for easy set-up, as well as information for new machinists and programmers to learn. Now time to optimise The program is then ready to be optimised to create a more efficient program. VERICUT Force NC optimisation module identifies opportunities for faster feeds and speeds, or areas to reduce force loads, resulting in faster cycle times, reduced tool wear and better part finish. Doing this ahead of time, before the program reaches the shop floor, ensures that the program runs more efficiently and eliminates the need for a machinist to adjust the feedrates and spindle speed at the machine. Doing more with less Engineering companies are now facing the challenge of meeting increased demands and staying competitive with fewer programmers and machinists. Working smarter with software reduces the need to fill all those voids. VERICUT can verify a part, simulate the machining and optimise the NC code before any real machining has started. Therefore making unattended or lights out machining, and the ability to operate with less machinists, a reality. In addition, taking less time to make the parts by using the available machines, reduces the need to acquire additional equipment and machinists. When new machinists are recruited, the historic data that has been gathered and stored by VERICUT, will empower them to learn quickly and without the fear of damaging productivity.
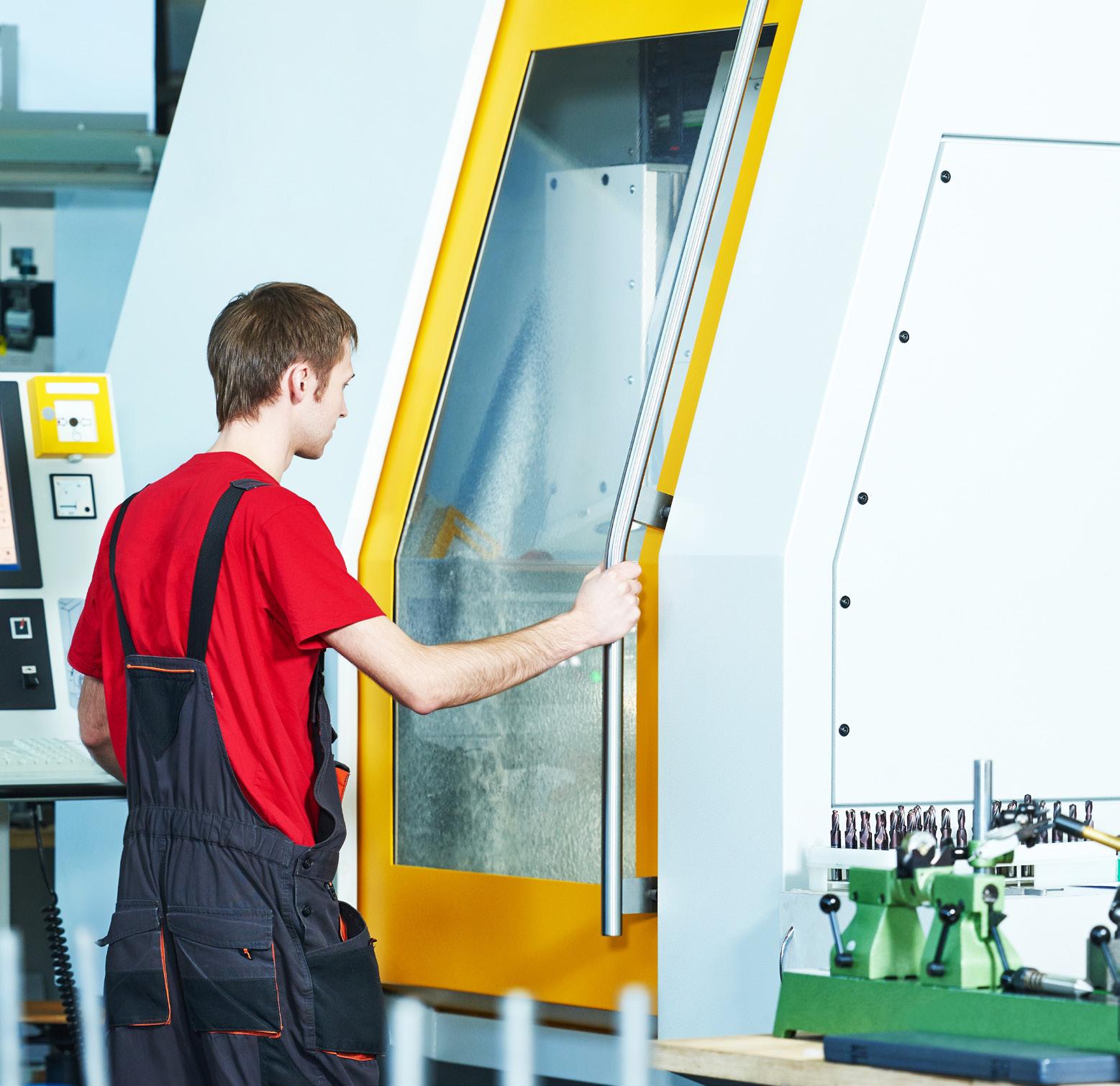
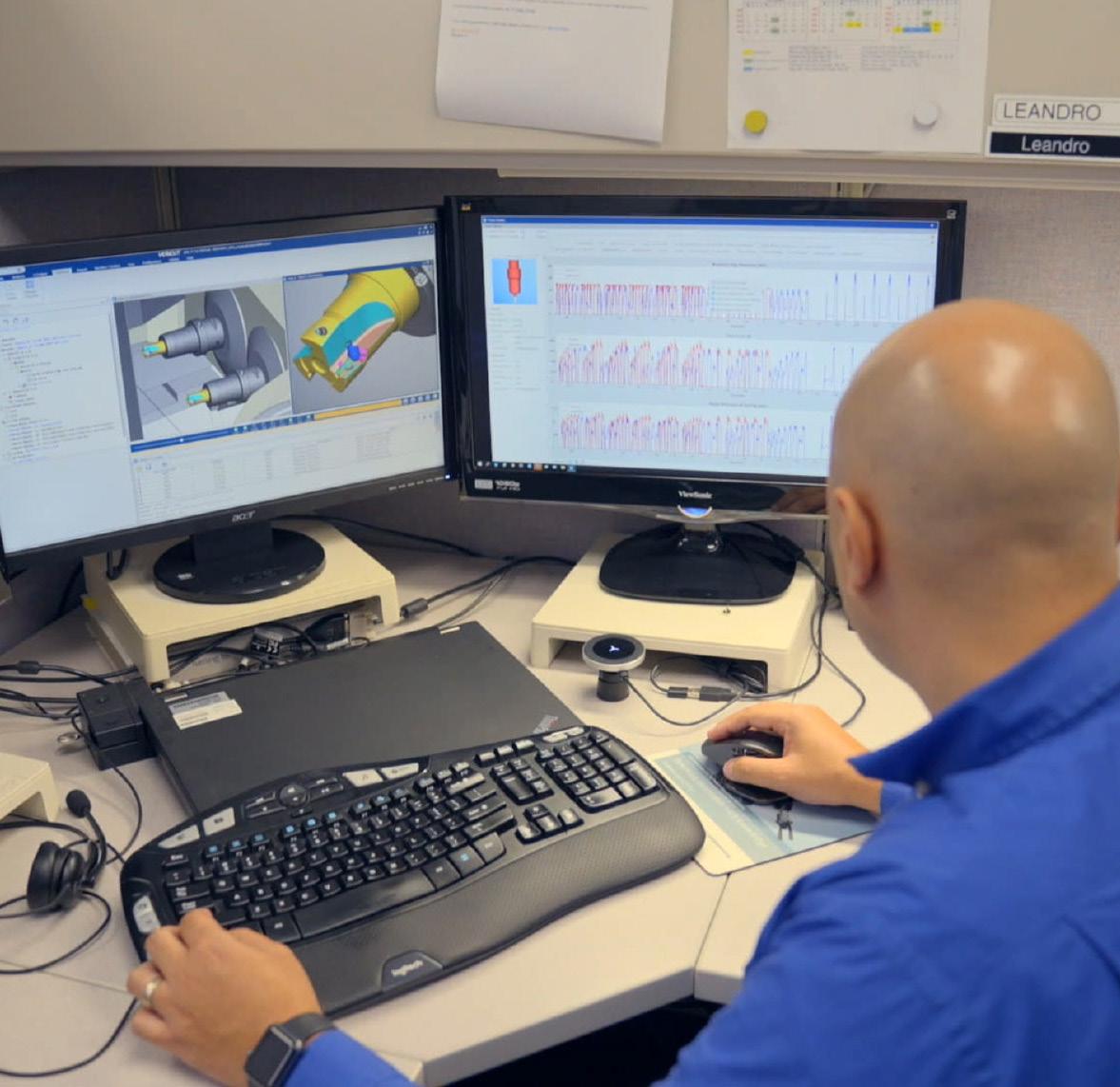
“The on-track testing of the P7-B and extensive customer evaluations are another crucial step on the road to commercialization and deployment of test fleets followed by scale adaptation in fleets,” said Tali Miller, chief business officer at REE. “Feedback from our customers has been that this is the truck they have been waiting for – a drivercentric work truck that drives like a saloon car but is built to deliver under the harshest commercial duty cycle. Our modular P7 chassis allows us to design vehicles tailored to our customers’ needs and we are excited to be showing them what our unique technology affords their fleets as we support them on their path towards electrification and carbon neutrality.”
To date, evaluations by prospective customers including global delivery, logistics, and e-commerce companies have been positive and encouraging. The prospective customers, to date, experienced firsthand the low step-in height designed for faster delivery times as well as reduced energy consumption due to better aerodynamics and highly efficient power management system of the P7 chassis architecture. Customers also experienced the agility and maneuverability afforded by REE’s all-wheel drive and all-wheel steer for unparalleled vehicle control, leading to better handling and safety in adverse conditions. The driver-focused cabin is designed for optimal ergonomics and human-machine interface for maximum driver comfort, safety, and productivity. The P7-B aims to reduce total cost of ownership (TCO) to help facilitate fleets’ transition to EVs.
New powered by REE EV to begin real-world customer evaluations this winter REE Automotive Ltd. (NASDAQ: REE), an automotive technology company and provider of electric vehicle (EV) platforms, today announced P7-B, a class 3 delivery truck built on a P7 cab chassis, following intensive customer evaluations at REE’s UK Engineering Center. The new P7-B is part of a fleet of vehicles available to prospective customers to evaluate, test, and experience the unique agility, performance, and design enabled by REE’s novel REEcorner x-by-wire technology.
REE Automotive Debuts P7-B, an Electric Class 3 Delivery Truck
28
The class 3, all-by-wire electric truck, designed and built by REE based on its P7 modular chassis, targets the important and growing commercial EV mid- and last-mile delivery market, with applications such as 16-foot vans and delivery trucks. It was built in response to market needs and represents a potential opportunity for REE to present fleets with complete vehicles. It also follows the recently announced Proxima Powered by REE, which is P7’s debut on a walk-in van and features JB Poindexter’s Morgan Olson and EAVX Proxima body paired with REE’s P7 stripped Thischassis.P7delivery truck configuration offers increased interior space for passengers and cargo and a low step-in height while targeting a maximum speed of 75 mph (120 km/h), max range of 150 miles (241 km), up to 4,400 lbs (2,000 kg) payload, and vehicle weight ratings (GVWR) of up to 14,000 lbs (6,350 kg). The configuration can be modified to best suit customer needs. The full x-by-wire architecture supports all-wheel steer, all-wheel drive, adaptive regenerative breaking, creep control, hill start assist, and torque vectoring as standard as well as over-the-air updates.
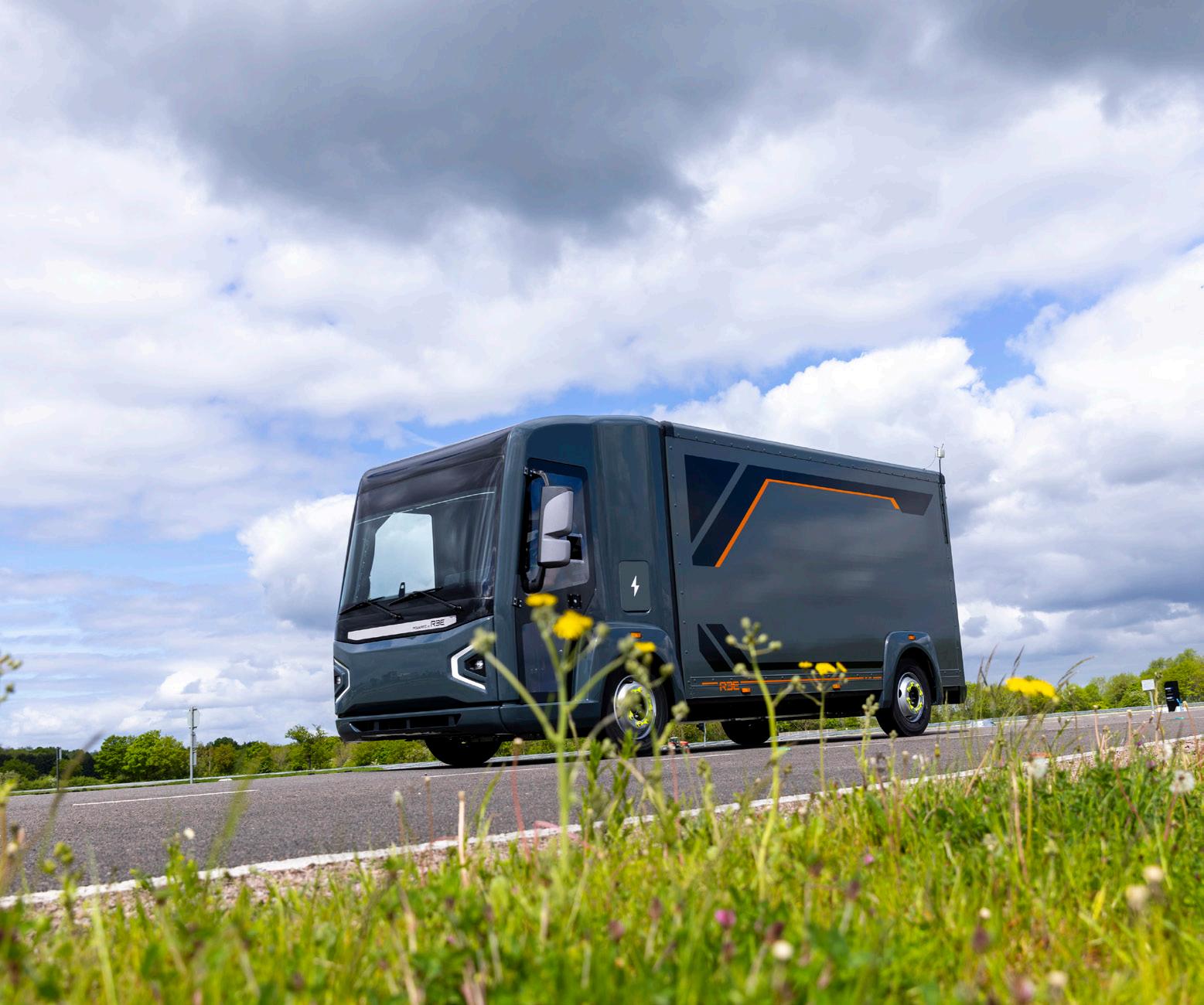
29
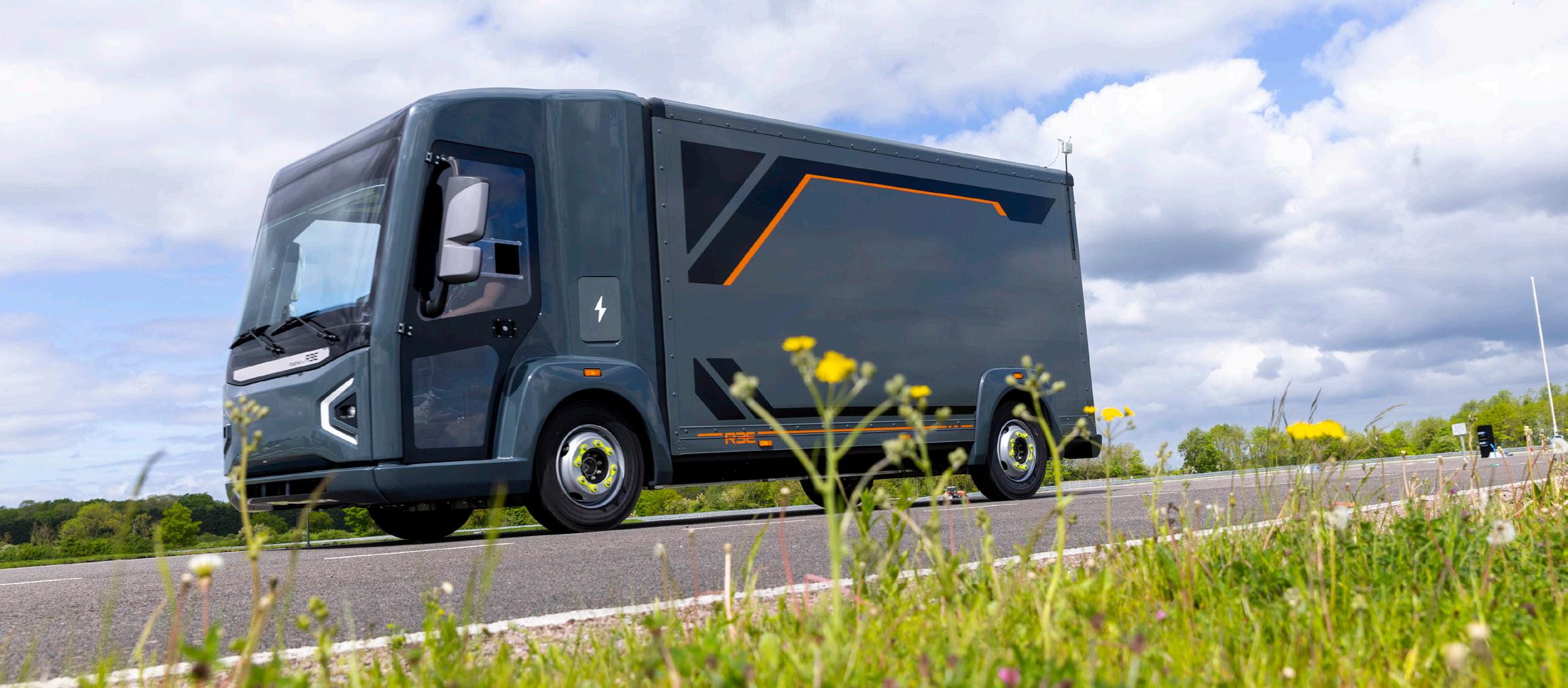
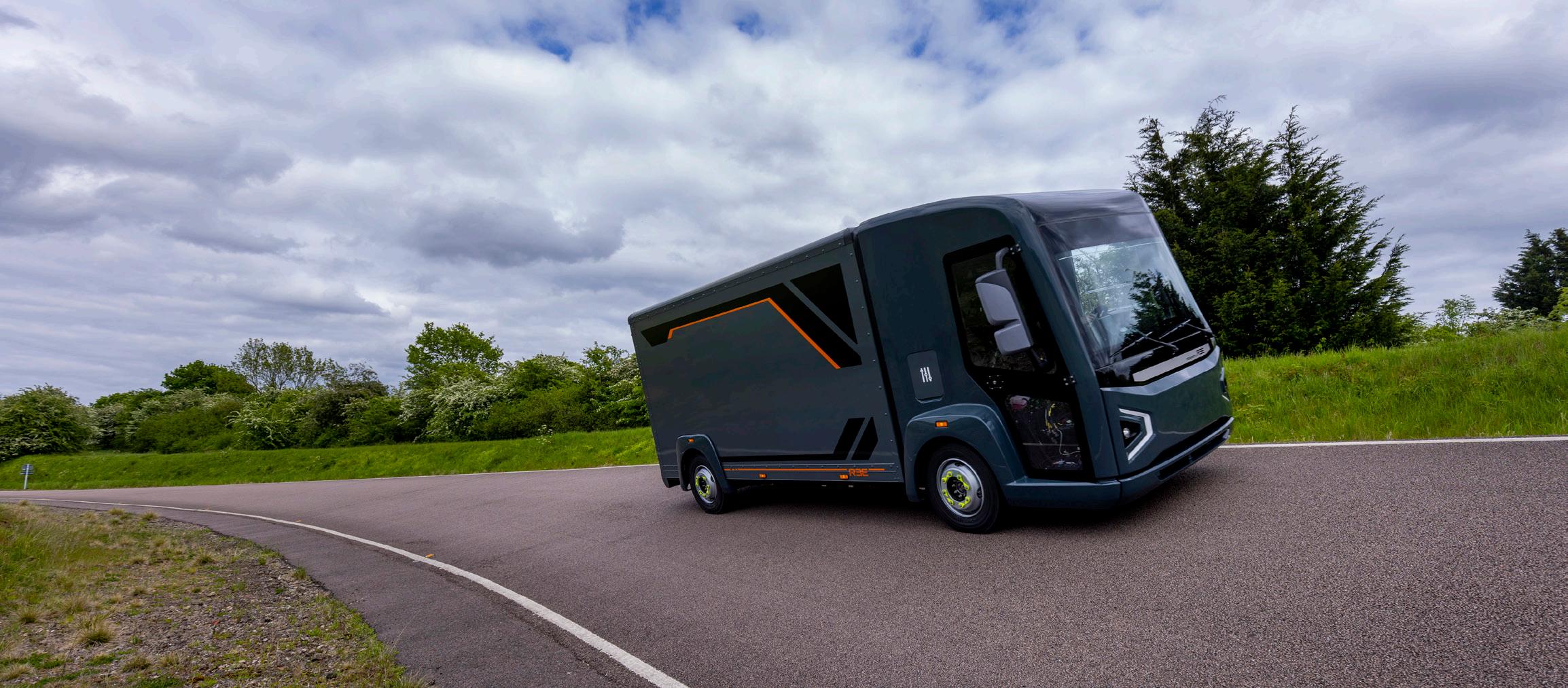
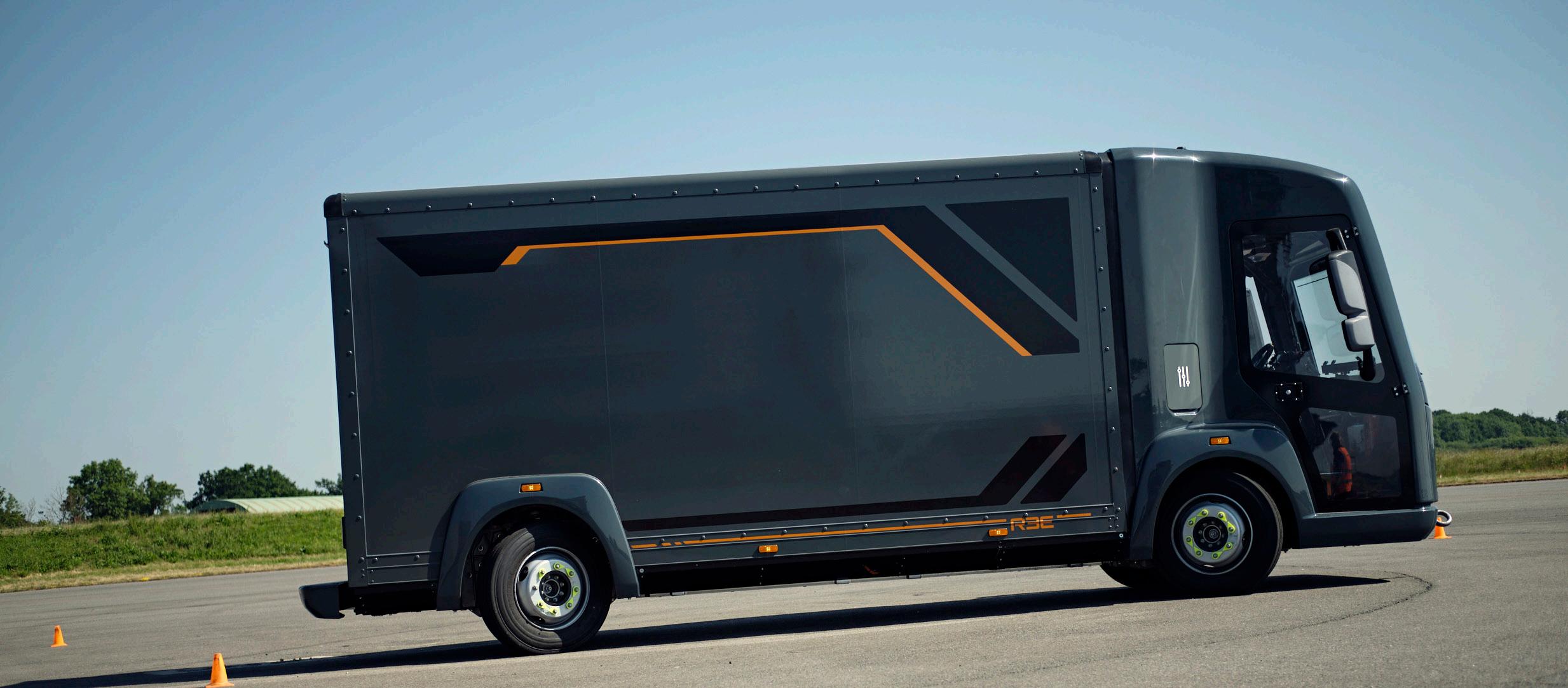
Advanced Energy’s LCC1200 Series of
The LCC1200 series also supports active current sharing, allowing parallel connection of up to three units for high current Allapplications.modelsinthe LCC1200 series come with a three-year warranty, are fully approved to the IEC 62368-1 ITE safety standard, and carry cUL, CE, UKCA, and CCC certifications. The built-in PMBus™ interface provides flexible and comprehensive digital communication with control and monitoring functions for voltage, current, and temperature, as well as reporting of fault conditions.
horticulturalissignage.consoles,basetelecommunicationstheTheofoverandincorporateefficiency,Ratedsuppliesconduction-cooledfully-enclosed,AC-DCpowerfromAdvancedEnergy.at1200Wandboasting93.5%thesepowersuppliesathermalbaseplatecandeliverfulloutputpowerawideoperatingtemperature-40°Cto+85°Cwithoutderating.targetapplicationsforpowersuppliesincludeantennaandstationequipment,controlandoutdoor/indoorAconstantcurrentmodealsoavailableforLEDlightingandlightingapplications.
TTI, Inc. – Europe, a leading specialty distributor of electronic components, is now stocking the LCC1200 series of
“With Advanced Energy’s LLC1200 series of conduction-cooled ACDC power supplies, We’ve got the Power!” said Oskar Czechowski, Technical Development Manager for Power, TTI Europe. “While other power supplies require output derating above 55°C, the LCC1200 can maintain its full 1200W load capacity across a wide baseplate temperature at up to +85°C without forced air, reducing overall system cost. In addition, with its high power density of 15W/in3, engineers save space in their endapplication.”
For more information about the LCC1200 conduction-cooled AC-DC power supplies, please visit the TTI Europe website: www.ttieurope.com
30
Maintains full 1200W load capacity across a wide -40°C to +85°C baseplate temperature without forced air cooling
Standard features include AC OK and DC OK signals, remote inhibit, and differential remote sense on the main output. The power supplies feature overtemperature and output overcurrent protection circuitry, with latching overvoltage protection of both the main and standby outputs.
Housed in a robust metal case, the LCC1200 series is available with standard input/output connectors or in fully sealed versions with integral cables that carry an IP65 rating against water or dust ingress. Their fanless operation also makes them suitable for environments where acoustic noise or dust disturbance would be an issue, such as in offices or medical Operatingfacilities. from a universal 90Vac to 264Vac input, the series can be used anywhere in the world without adjustment. Comprising four models, the LCC1200 series offers main output voltages of 24Vdc, 28Vdc, 36Vdc, and 48Vdc. The main output is adjustable across all models for maximum design flexibility, except the 28Vdc model. Each model also provides an additional 5Vdc standby output.
Fanless AC-DC Power Supplies Available from TTI Europe
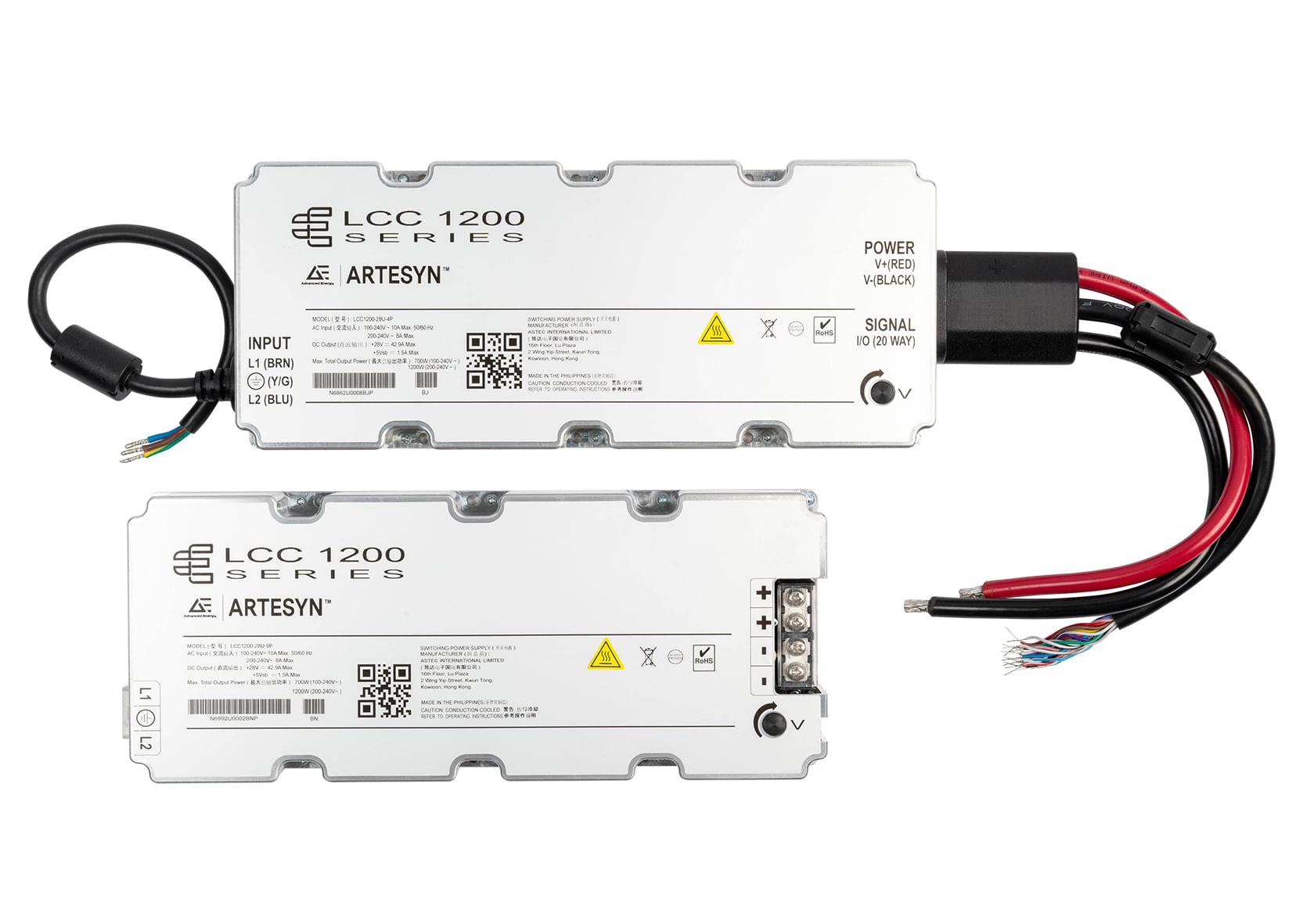
Limited use, motorised solutions separate a disposable drug unit from the reusable pump system and enable the infusion of multiple biologic drug cartridges over the course of the therapy. A new trend in the pharmaceutical industry, the advantage of a limited-use device provides a balance of performance and lifetime against the price.
These devices take the form of mechanical injectors and disposable patch pumps, worn directly on the body with a reservoir, pump and infusion set inside a small case worn on the body. Can-stack stepper and brush DC motors are commonly suited technologies because of their reliability, especially compared to actuation varieties that require more complex drive electronics.
From cancer to rheumatoid arthritis, biopharmaceuticals have revolutionised treatments, in some cases providing hope for patients who previously had no further options. Integral to their success are the delivery devices, which are driven by accurate, reliable motion systems. Whether intended for disposable, limited use, or long-term administration, a tailored motion system will help the OEM best meet patient needs.
A brushless DC motor or coreless brush DC motor with precious metal commutators are the ideal selection to achieve these requirements. For biologics applications, as efficiency and size are important parameters, BLDC slotless designs are comparatively more efficient, lower vibration, and easier to manufacture for smaller frame sizes such as 10mm, 12mm and 16mm, compared to slotted motors. The motors should also be combined with a spur or custom-designed gearhead to optimise torque density. To ensure optimum delivery accuracy, an absolute or incremental encoder with a special arrangement can be combined to provide feedback and additional repeatability.
As reusable pump systems could be used for three to five years, the motion solution has to be robust, and this could also include the need to withstand storage conditions, including cold temperatures and humidity. Brushless DC and stepper motors have electrical commutation, which provides longer motor life potential compared to the mechanical wear inherent to a brush DC motor. Motor life is also dependent on bearings, with ball bearings providing longer life than sleeve bearings. Long-term patient health is related to the accuracy, repeatability, and reliability of the delivery system’s motor package, so a tailored approach to motion system design will most closely deliver the requirements for the specific biologics involved. This will also help the OEM deliver the most cost-effective solution.
Motion solution requirements for biologic delivery devices
31
Commonly known as biologics, these drugs are manufactured in or from a biological source, unlike typical medication which is developed through chemical synthesis. The advantage is that biologics change the way the human immune system reacts, down-regulating the inflammatory response or supporting tumour-specific defence. Biologics are delivered by injection and as they have a much higher molecular weight than traditional, small-molecule chemical drugs, they are far more viscous. This makes accuracy injecting the drugs increasingly critical. The drugs are typically administered at regular intervals over a set time frame. Reliance for this task is placed on the delivery mechanism, which is driven by a miniaturised motion solution. The type of biologic determines several factors including the frequency and type of injection, as well as selection of the tissue type to be injected. These factors also impact the selection of the biologics injection device, and in turn, the required attributes of its motion system.
As limited use devices may be required to administer more than one type of biologic, each with its own viscosity and injection requirements, flexibility in injection force is advantageous. This means that a motion solution that can deliver a range between 50N and 80N is useful.
Optimising motion system design
Biologic delivery device technology
Disposable devices are intended for one-time use of a specific drug, delivered in the range of seconds to hours, and are a low-cost solution.
Limited use devices are batterydriven, so efficiency also has to be considered in pump design. Coreless brush DC motors with precious metal commutators are suited to higher battery life requirements, offering high power density and reliability. A spur compound gearbox or custom gearhead pairing can also enhance performance and efficiency. Accuracy and power density
Portescap’s Jigar Fulia and Kanti Vala, consider the selection criteria for biologics system motion solutions.
A primary advantage for disposable applications is that can stack stepper and brush DC motors are very cost effective.
Fully reusable pump systems are designed to be longer lasting and can also handle various viscosities, making them more flexible in therapy delivery, and means they can require a force output exceeding 100N. The device must also be worn by the patient, so the motion solution has to be small and lightweight, fitting into an outside diameter of 10-12mm. Higher power density also means the system can accommodate larger drug volumes up to 50ml.
SICK has developed a versatile and easy to install Roller Sensor Bar to tackle common conveyor downtime headaches for operators in wide-ranging materials handling, parcel sorting or logistics hubs. The SICK Roller Sensor Bar has been perfected to deliver high sensing performance when detecting the leading edges of varied, flat or irregular shaped packages on conveyors. Mounted between rollers or belted sections, the SICK Roller Sensor Bar’s flexible concept dispenses with the need to prequalify and stock multiple sensor Quicklytypes. mounted using springloaded end caps, a pre-configured SICK Roller Sensor Bar is ready to start work without needing to be aligned. Whether mounted during conveyor manufacture or fitted to an existing production line, the time taken to install and set up a Roller Sensor Bar is minimal.
SICK’s Roller Sensor Bar Ends Conveyor Headaches
Rapid Specification
32
Eliminate Conveyor Jams
Positioned to detect from below, the SICK Roller Sensor Bar has excellent ambient light immunity so false trips and triggers, e.g. by reflections from high visibility clothing, are avoided. A choice of ten different connector types and nine standard cable lengths ensure quick and easy installation, not just into all kinds of roller conveyors, but for belted conveyor sections and flexible Theconveyors.IO-Link variant of SICK’s Roller Sensor bar enables operators to access diagnostic information to reduce conveyor downtime. Using IO-Link, individual beam breaks can be identified for product alignment checks, e.g. to confirm a divert has happened, or to alert when objects are skewed or in the wrong position on the conveyor. It can also track each sensor’s operating status and alert to service or maintenance Withrequirements.anIP67-rated housing, the SICK Roller Sensor bar is resilient to the ingress of dust or water during cleaning procedures.
SICK has made it quick and easy to customise the Roller Sensor Bar so it can detect a wide range of shapes and sizes of packages simultaneously, in any orientation, and even when they have irregular or thin leading edges. It can therefore be quickly adapted for a broad range of detection needs from, non-transparent poly bags and jiffy packs through to totes or Userspallets.specify the sensor bar length ranging from 200mm to 1.2 metres, then set between two and eight sensing points spaced 50mm to 200mm apart. As a result, they achieve alignment precision and avoid detection blind zones.
“Conveyor jams are a common headache for all sorts of logistics and materials handling environments. The Roller Sensor Bar eliminates the unplanned downtime caused when conventional sensor set-ups cause jamming, package build-ups or misdirects.,” says David Hannaby, SICK’s UK Product Manager for Presence Detection. “Jams can happen when packages catch on sensing holes in the conveyor walls, or on the sensor themselves. The Roller Sensor Bar can also be configured without blind zones at the sides of the conveyor. Installation and alignment time is reduced, and there is no need to purchase extra mounting brackets or reflectors.”
For more information please contact Andrea Hornby on 01727 831121 or email andrea.hornby@sick.co.uk.
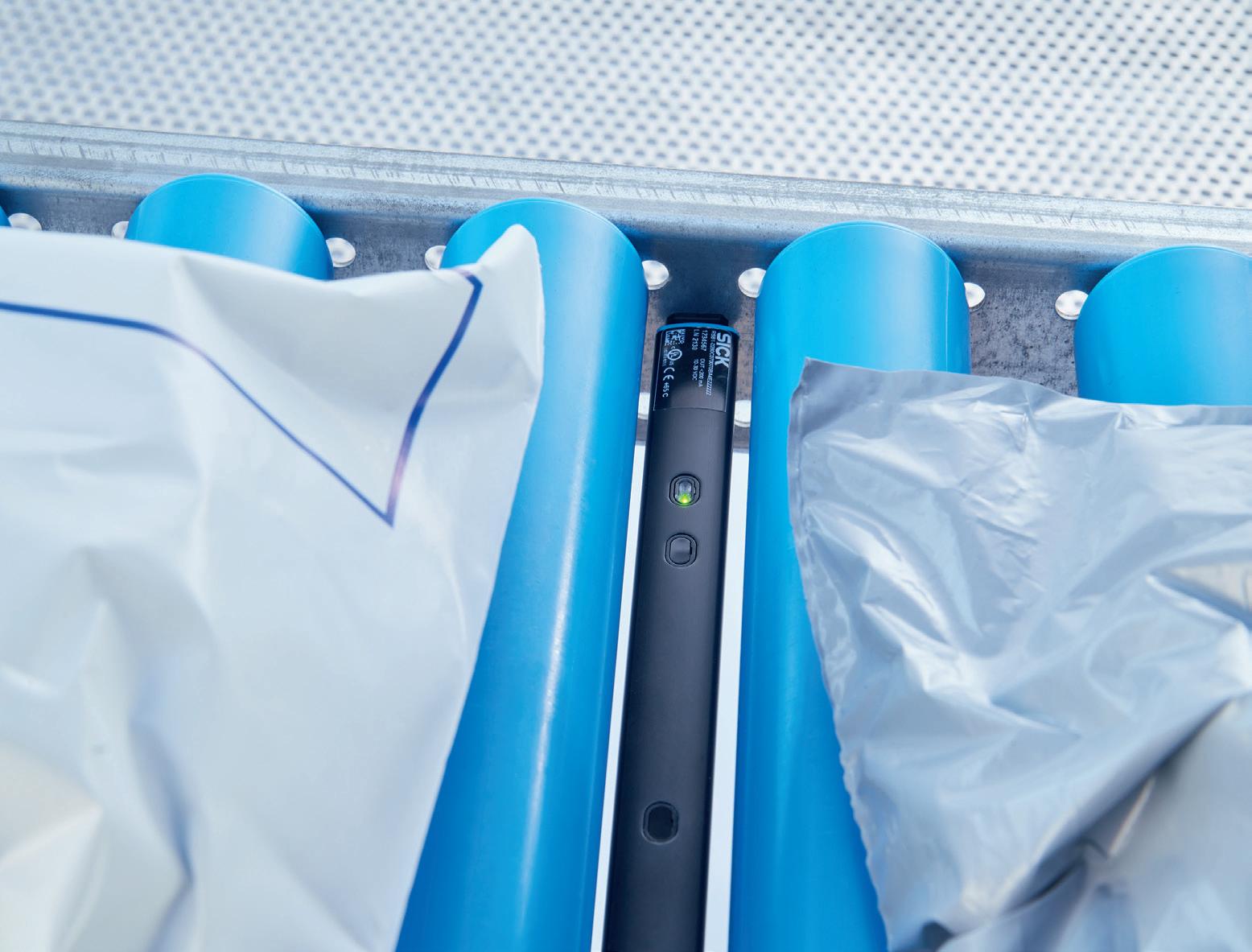
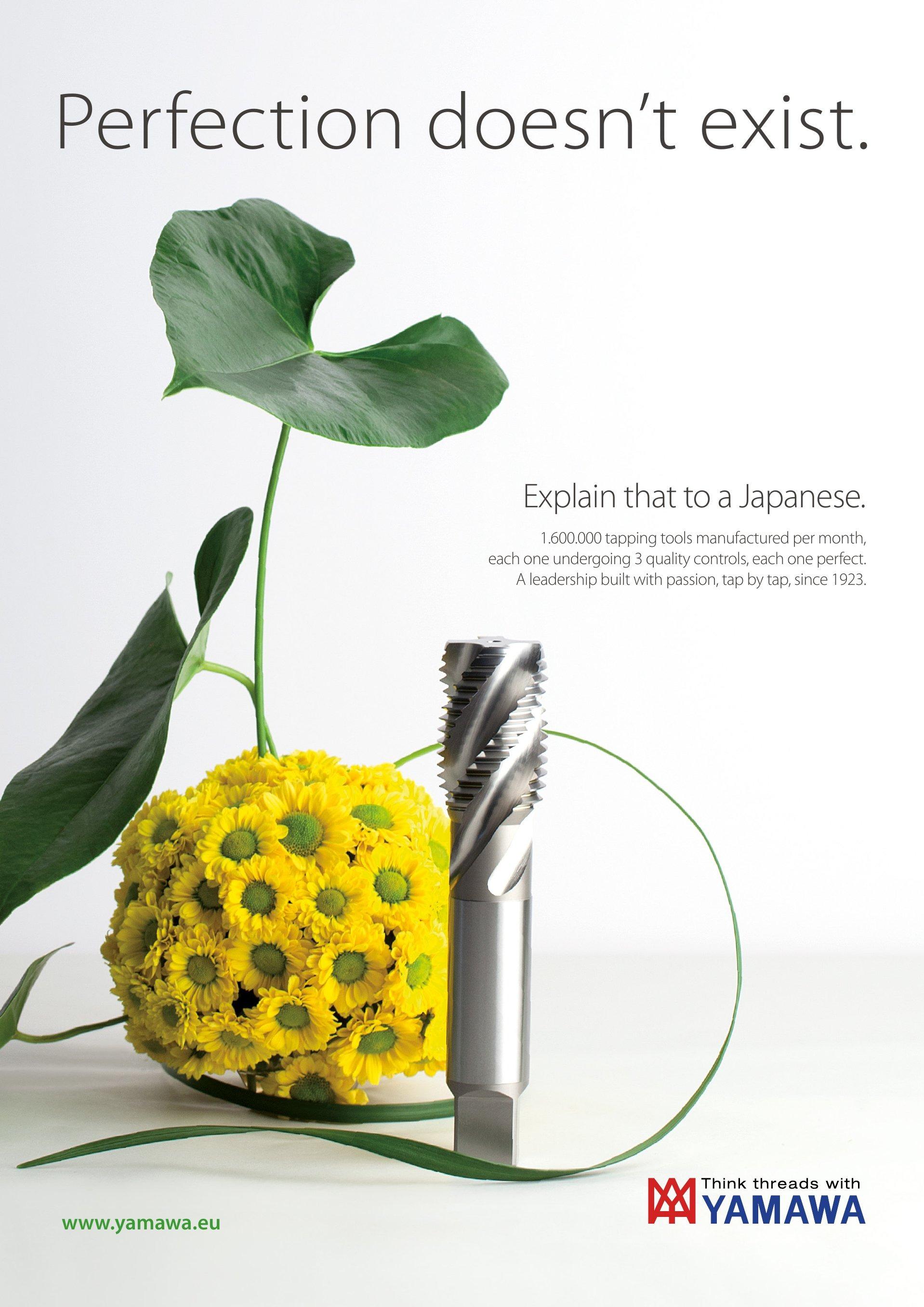
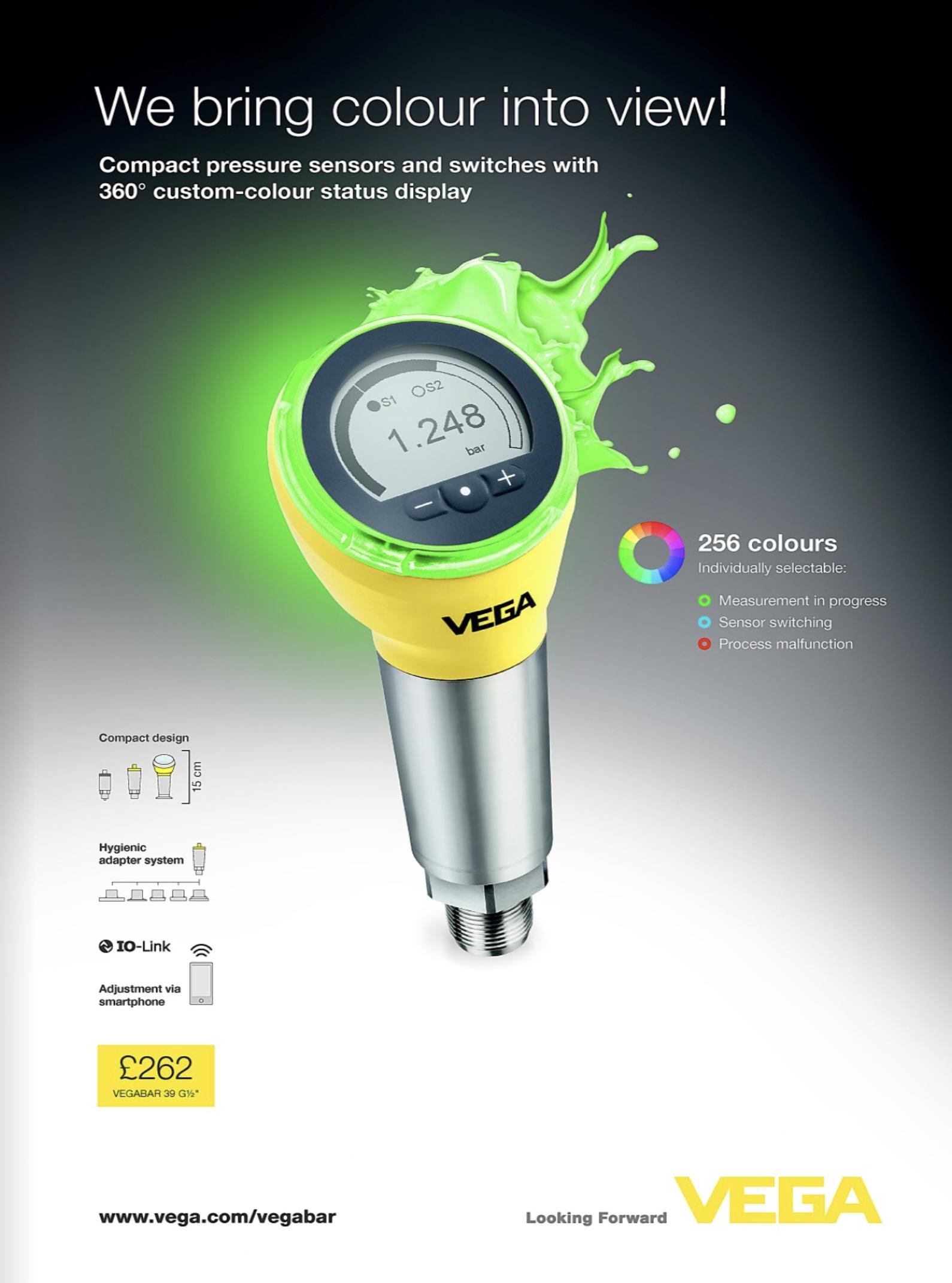