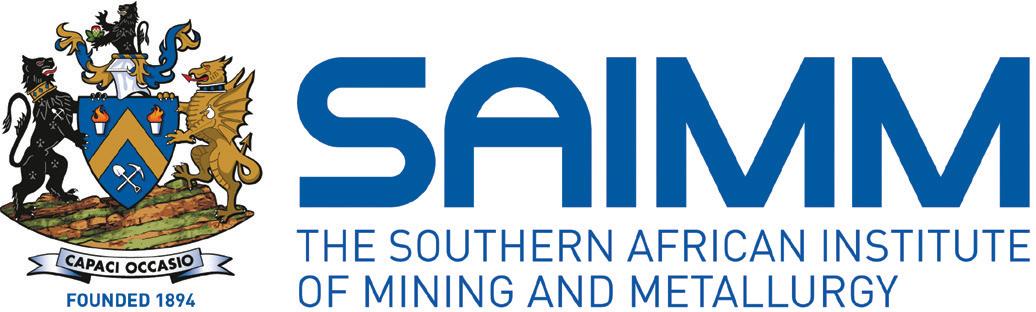
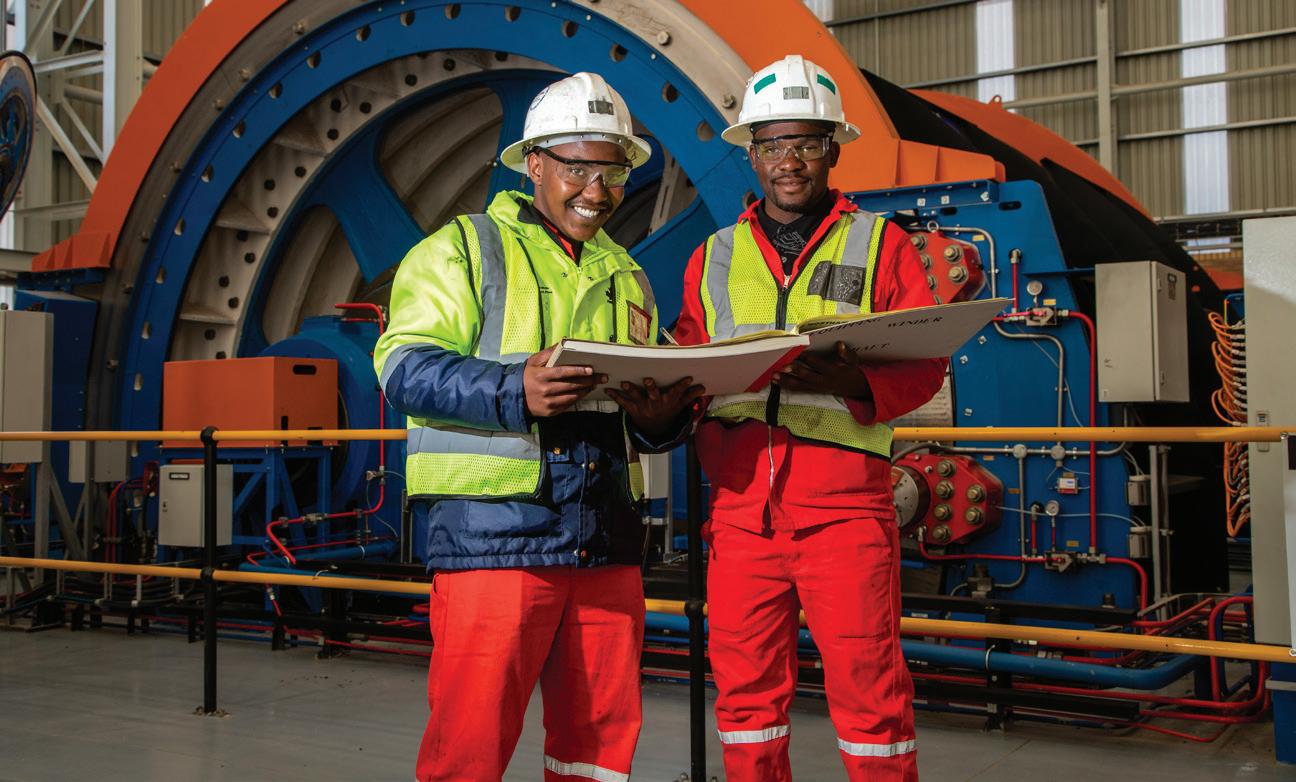
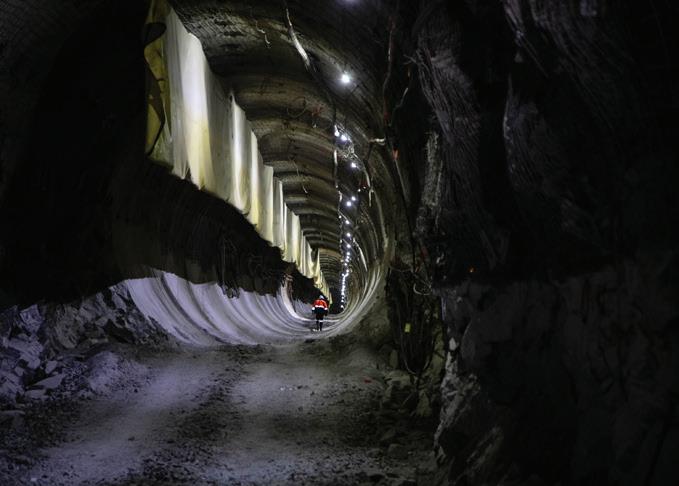
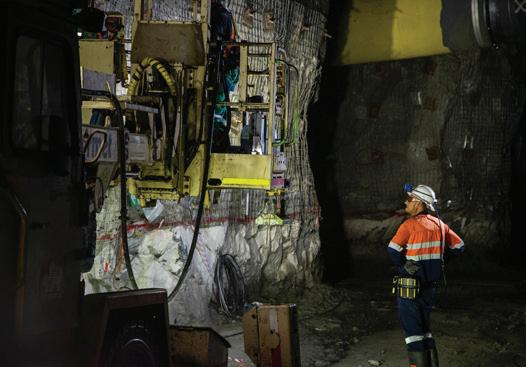
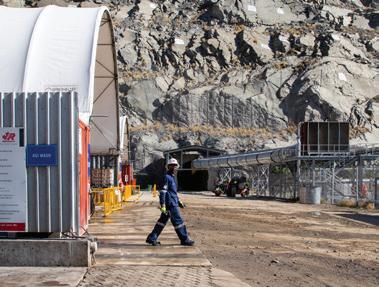
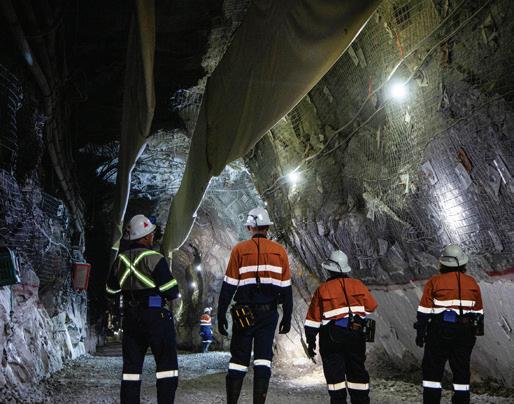
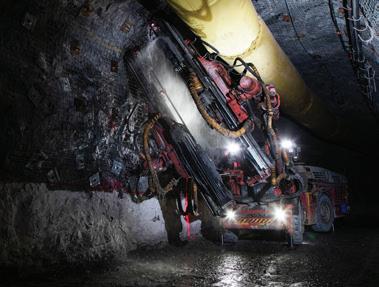
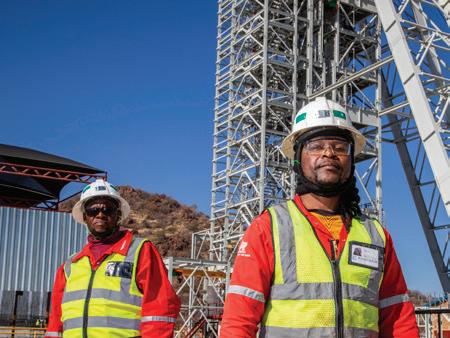

World’s largest raisebore hole achieved at Obuasi Gold Mine
OFFICE BEARERS AND COUNCIL FOR THE 2024/2025 SESSION
Honorary President
N. Tsengwa
President, Minerals Council South Africa
Honorary Vice Presidents
Gwede Mantashe
Minister of Mineral Resources and Energy, South Africa
P. Tau
Minister of Trade, Industry and Competition, South Africa
Blade Nzimande
Minister of Higher Education, Science and Technology, South Africa
President E. Matinde
President Elect
G.R. Lane
Senior Vice President
T.M. Mmola
Junior Vice President
M.H. Solomon
Incoming Junior Vice President
S.J. Ntsoelengoe
Immediate Past President
W.C. Joughin
Honorary Treasurer
W.C. Joughin
Ordinary Members on Council
W. Broodryk
Z. Fakhraei
B. Genc
K.M. Letsoalo
S.B. Madolo
M.A. Mello
K. Mosebi
Co-opted Council Members
A.D. Coetzee
L.T. Masutha
M.C. Munroe
S.M. Naik
G. Njowa
S.M. Rupprecht
A.T. van Zyl
E.J. Walls
Past Presidents Serving on Council
N.A. Barcza C. Musingwini
R.D. Beck S. Ndlovu
Z. Botha J.L. Porter
V.G. Duke M.H. Rogers
I.J. Geldenhuys G.L. Smith
R.T. Jones
G.R. Lane – TP Mining Chairperson
Z. Botha – TP Metallurgy Chairperson
K.W. Banda – YPC Chairperson
C.T. Chijara – YPC Vice Chairperson
Branch Chairpersons
Botswana K. Mosebi
DRC K.T. Kekana (Interim Chairperson)
Johannesburg N. Rampersad
Limpopo M.S. Zulu
Namibia T. Aipanda
Northern Cape Vacant
North West Vacant
Pretoria P.G.H. Pistorius
Western Cape Vacant
Zambia N.M. Kazembe
Zimbabwe L. Shamu
Zululand Vacant
*Deceased
* W. Bettel (1894–1895)
* A.F. Crosse (1895–1896)
* W.R. Feldtmann (1896–1897)
* C. Butters (1897–1898)
* J. Loevy (1898–1899)
* J.R. Williams (1899–1903)
* S.H. Pearce (1903–1904)
* W.A. Caldecott (1904–1905)
* W. Cullen (1905–1906)
* E.H. Johnson (1906–1907)
* J. Yates (1907–1908)
* R.G. Bevington (1908–1909)
* A. McA. Johnston (1909–1910)
* J. Moir (1910–1911)
* C.B. Saner (1911–1912)
* W.R. Dowling (1912–1913)
* A. Richardson (1913–1914)
* G.H. Stanley (1914–1915)
* J.E. Thomas (1915–1916)
* J.A. Wilkinson (1916–1917)
* G. Hildick-Smith (1917–1918)
* H.S. Meyer (1918–1919)
* J. Gray (1919–1920)
* J. Chilton (1920–1921)
* F. Wartenweiler (1921–1922)
* G.A. Watermeyer (1922–1923)
* F.W. Watson (1923–1924)
* C.J. Gray (1924–1925)
* H.A. White (1925–1926)
* H.R. Adam (1926–1927)
* Sir Robert Kotze (1927–1928)
* J.A. Woodburn (1928–1929)
* H. Pirow (1929–1930)
* J. Henderson (1930–1931)
* A. King (1931–1932)
* V. Nimmo-Dewar (1932–1933)
* P.N. Lategan (1933–1934)
* E.C. Ranson (1934–1935)
* R.A. Flugge-De-Smidt (1935–1936)
* T.K. Prentice (1936–1937)
* R.S.G. Stokes (1937–1938)
* P.E. Hall (1938–1939)
* E.H.A. Joseph (1939–1940)
* J.H. Dobson (1940–1941)
* Theo Meyer (1941–1942)
* John V. Muller (1942–1943)
* C. Biccard Jeppe (1943–1944)
* P.J. Louis Bok (1944–1945)
* J.T. McIntyre (1945–1946)
* M. Falcon (1946–1947)
* A. Clemens (1947–1948)
* F.G. Hill (1948–1949)
* O.A.E. Jackson (1949–1950)
* W.E. Gooday (1950–1951)
* C.J. Irving (1951–1952)
* D.D. Stitt (1952–1953)
* M.C.G. Meyer (1953–1954)
* L.A. Bushell (1954–1955)
* H. Britten (1955–1956)
* Wm. Bleloch (1956–1957)
* H. Simon (1957–1958)
* M. Barcza (1958–1959)
* R.J. Adamson (1959–1960)
* W.S. Findlay (1960–1961)
* D.G. Maxwell (1961–1962)
* J. de V. Lambrechts (1962–1963)
* J.F. Reid (1963–1964)
* D.M. Jamieson (1964–1965)
* H.E. Cross (1965–1966)
* D. Gordon Jones (1966–1967)
* P. Lambooy (1967–1968)
* R.C.J. Goode (1968–1969)
* J.K.E. Douglas (1969–1970)
* V.C. Robinson (1970–1971)
* D.D. Howat (1971–1972)
* J.P. Hugo (1972–1973)
* P.W.J. van Rensburg (1973–1974)
* R.P. Plewman (1974–1975)
* R.E. Robinson (1975–1976)
* M.D.G. Salamon (1976–1977)
* P.A. Von Wielligh (1977–1978)
* M.G. Atmore (1978–1979)
* D.A. Viljoen (1979–1980)
* P.R. Jochens (1980–1981)
* G.Y. Nisbet (1981–1982)
A.N. Brown (1982–1983)
* R.P. King (1983–1984)
J.D. Austin (1984–1985)
* H.E. James (1985–1986)
H. Wagner (1986–1987)
* B.C. Alberts (1987–1988)
* C.E. Fivaz (1988–1989)
* O.K.H. Steffen (1989–1990)
* H.G. Mosenthal (1990–1991)
R.D. Beck (1991–1992)
* J.P. Hoffman (1992–1993)
* H. Scott-Russell (1993–1994)
J.A. Cruise (1994–1995)
D.A.J. Ross-Watt (1995–1996)
N.A. Barcza (1996–1997)
* R.P. Mohring (1997–1998)
J.R. Dixon (1998–1999)
M.H. Rogers (1999–2000)
L.A. Cramer (2000–2001)
* A.A.B. Douglas (2001–2002)
* S.J. Ramokgopa (2002-2003)
T.R. Stacey (2003–2004)
F.M.G. Egerton (2004–2005)
W.H. van Niekerk (2005–2006)
R.P.H. Willis (2006–2007)
R.G.B. Pickering (2007–2008)
A.M. Garbers-Craig (2008–2009)
J.C. Ngoma (2009–2010)
G.V.R. Landman (2010–2011)
J.N. van der Merwe (2011–2012)
G.L. Smith (2012–2013)
M. Dworzanowski (2013–2014)
J.L. Porter (2014–2015)
R.T. Jones (2015–2016)
C. Musingwini (2016–2017)
S. Ndlovu (2017–2018)
A.S. Macfarlane (2018–2019)
M.I. Mthenjane (2019–2020)
V.G. Duke (2020–2021)
I.J. Geldenhuys (2021–2022)
Z. Botha (2022-2023)
W.C. Joughin (2023-2024)
Editorial Board
S.O. Bada
R.D. Beck
P. den Hoed
I.M. Dikgwatlhe
M. Erwee
B. Genc
R Hassanalizadeh
R.T. Jones
W.C. Joughin
A.J. Kinghorn
D.E.P. Klenam
D.F. Malan
D. Morris
C. Musingwini
S. Ndlovu
P.N. Neingo
A. Nengovhela
S.S. Nyoni
M. Phasha
P. Pistorius
P. Radcliffe
N. Rampersad
Q.G. Reynolds
I. Robinson
S.M. Rupprecht
K.C. Sole
T.R. Stacey
D. Vogt
F. Uahengo
International Advisory Board members
R. Dimitrakopolous
R. Mitra
A.J.S. Spearing
E. Topal
D. Tudor
Editor /Chairperson of the Editorial Board
R.M.S. Falcon
Typeset and Published by
The Southern African Institute of Mining and Metallurgy
PostNet Suite #212 Private Bag X31 Saxonwold, 2132
E-mail: journal@saimm.co.za
Printed by Camera Press, Johannesburg
Advertising Representative
Barbara Spence
Avenue Advertising
Journal Comment: Developing social capital to enhance mining community relations by D. Morris v
President’s Corner: Reflections on 2024: Resilience and hope by E. Matinde vi
THE INSTITUTE, AS A BODY, IS NOT RESPONSIBLE FOR THE STATEMENTS AND OPINIONS ADVANCED IN ANY OF ITS PUBLICATIONS.
Copyright© 2024 by The Southern African Institute of Mining and Metallurgy. All rights reserved. Multiple copying of the contents of this publication or parts thereof without permission is in breach of copyright, but permission is hereby given for the copying of titles and abstracts of papers and names of authors. Permission to copy illustrations and short extracts from the text of individual contributions is usually given upon written application to the Institute, provided that the source (and where appropriate, the copyright) is acknowledged. Apart from any fair dealing for the purposes of review or criticism under The Copyright Act no. 98, 1978, Section 12, of the Republic of South Africa, a single copy of an article may be supplied by a library for the purposes of research or private study. No part of this publication may be reproduced, stored in a retrieval system, or transmitted in any form or by any means without the prior permission of the publishers. Multiple copying of the contents of the publication without permission is always illegal. U.S. Copyright Law applicable to users In the U.S.A. The appearance of the statement of copyright at the bottom of the first page of an article appearing in this journal indicates that the copyright holder consents to the making of copies of the article for personal or internal use. This consent is given on condition that the copier pays the stated fee for each copy of a paper beyond that permitted by Section 107 or 108 of the U.S. Copyright Law. The fee is to be paid through the Copyright Clearance Center, Inc., Operations Center, P.O. Box 765, Schenectady, New York 12301, U.S.A. This consent does not extend to other kinds of copying, such as copying for general distribution, for advertising or promotional purposes, for creating new collective works, or for resale.
Honorary Legal Advisers
M H Attorneys Auditors
Genesis Chartered Accountants Secretaries
The Southern African Institute of Mining and Metallurgy 7th Floor, Rosebank Towers, 19 Biermann Avenue, Rosebank, 2196
PostNet Suite #212, Private Bag X31, Saxonwold, 2132 E-mail: journal@saimm.co.za
Telephone (011) 463-7940 . E-mail: barbara@avenue.co.za ISSN 2225-6253 (print) . ISSN 2411-9717 (online)
Ammonium thiosulfate leaching of gold from electronic printed circuit boards – effect of solution copper concentration by
D. Maharaj, T. Moyo, and J. Petersen
This study investigates the effect of ammonium thiosulfate on the leaching of gold from the contacts of unpopulated cut electronic printed circuit boards (PCB). Analysis of the data shows that the kinetic rate of gold leaching is correlated in a first-order dependence with the actual copper concentration in the solution. A lower threshold of 0.017M and an upper threshold of 0.15M copper in solution were determined. The findings of this study suggest that, in an industrial recovery operation of gold from waste PCB using the thiosulfate method, copper concentrations need to be carefully monitored, and the process should preferably operate with uncut or coarsely cut untreated boards to minimize exposure to copper circuits.
The free ligand model to describe and design cobalt extraction and nickel scrubbing in a base metal refinery by M.J. Matsela, O.S.L. Bruinsma, and D.J. van der Westhuizen
In this work, the free ligand (FL) model is validated to account for co-extraction of Ni and for designing the extraction and scrubbing sections of Co/Ni separation in a base metal refinery. Experimental and FL modelling results show that four equilibrium stages are required to purify the 99% Ni feed to a 99.97% Ni raffinate. The FL model as well as the Co/Ni/Naanalysis of the aqueous phase confirm that, in the scrubbing section, Ni in the extract is mainly replaced by Co. In the one stage stripper the Co concentration is increased from 5.6 g Co/L in the extract to 30.5 g Co/L.
Optimization of chromium precipitation from ferrochrome leach solutions by T.V. Nyangadzayi1 and F. Ntuli
Chromium green is an essential metal with applications in the paints, construction, electronics, and aerospace industries. The main source of chromium green is the carbo-thermic reduction of chromite ores, which are being heavily depleted on a global scale. To meet the global demand for chromium there is a need to keep chromium within the material loop. Ferrochrome slag and stainless steel slags are secondary resources that are potential sources of chromium. In this work, recovery of chromium from ferrochrome slag was investigated. The chromium recovery was found to be 93.3%.
711
719
725
Modelling unsaturated dual-phase flow through crushed ores for heap leaching by S.W. Robertson and J. Petersen 731
A large number of low-grade copper, gold, and uranium ore samples that were considered for heap leaching were physically and hydraulically tested. The data were reviewed to investigate the effect of physical properties such as particle size distribution (PSD) and bulk density on the hydrology. The author found the flow to be governed by capillary flow throughout. It was proposed that this is the result of unconnected or poorly connected pores. The point of discontinuity was also found to correspond with the air entry point. On average, the air entry point corresponds to the experiential rule that the void saturation should remain below 65% for aerated heaps.
Comparing the recovery of rare earth elements from ion-adsorption clay leach solutions using various precipitants by J. Chivavava, J. Petersen, and A.E. Lewis .......................................................................
The aim of this study was to understand the recovery of rare earth elements (REE) from IAC leach solutions using various reagents for precipitation. In the first part of the study, recoveries of REE were predicted via thermodynamic modeling. Simulation results showed that high yields of REE were possible using each of the reagents, but large quantities of C2H 5OH were required. Experimental results confirmed the high yields predicted from simulations.
Removal of iron from vanadium redox flow battery electrolyte using ion exchange by M. Makonese and K.C. Sole ..................................................................................
A plant for the production of electrolyte used in vanadium redox flow batteries is being commissioned but this is contaminated with Fe, which negatively affects battery performance. This study examined the use of ion exchange to reduce the Fe concentration to the target value of < 100 mg/L. Four resins with possible application were identified. Puromet MTS9570 outperformed the other three resins in all batch experiments. Based on these data, preliminary sizing and design of a full-scale column was undertaken.
Evaluation of surface tension of mold fluxes containing fluoride by J.F. Xu, P.W. Gu, L.J. Su, and J.Y. Zhang
A thermodynamic model was developed to determine the surface tension of mold flux containing fluoride based on the ion and molecule coexistence theory of slag structure and Butler’s equation. The relationship between composition and surface tension was investigated by this model. Results indicated that the calculated values showed good agreement with literature data. The surface tension value of the CaO–Al2O3-based mold flux was larger than that of the CaO–SiO2-based mold flux.
755
Evaluation of solar thermal pretreatment of carbonate-rich manganese ores in high-carbon ferromanganese production through dynamic process modelling by L. Hockaday, F. Dinter, Q.G. Reynolds, and C. McGregor 763
This paper reports on the results from a dynamic process model developed to investigate the feasibility of concentrating solar thermal pretreatment of manganese ores to pretreat carbonate-rich manganese ores for increased ferromanganese smelter productivity and reduced greenhouse gas emissions. The results indicate that pretreated ores reduce the energy requirement for smelting significantly for some ores and lowers total carbon dioxide emissions by 13 to 19% compared to the traditional smelting route.
Assessing the socio-economic impact of a zinc mine in South Africa through the application of digital tools: A case study by V.J. Mahadeo, U. Govender, S. Ramparsad4, and B. Genc 777
The study was intent on assessing the socio-economic impact of a zinc mine in South Africa through the application of people-centric digital tools using a case study research methodology. The study was conducted across five host communities surrounding the zinc mine in the Northern Cape region. Results indicated that the digital ESG tools could be used for data gathering for the mine’s informed decision-making as it provided real-time information of the needs of a community, both socially and economically. This allowed for securing insights into community needs in near real-time, and further proved practical for community use.
One of the more difficult challenges facing mining companies is the complex issue of local community engagement and partnership. Often large amounts of financial capital are invested in social projects with outcomes, which can be, to say the least, disappointing and unsustainable. On occasion the expenditure of resources and effort can result in community fragmentation, which compounds the problem. Low levels of trust, and fractious and failed relationships often characterize the interaction between the mine and surrounding community. Mining companies and business in general understand well the deployment of natural, economic, and human capital in the pursuit of their objectives, and performance is often assessed against the effective and efficient use of these three capitals. However, a fourth type of capital, that is social capital, can be neglected and not seen as an important business imperative through the lack of understanding of its value and a natural discomfort with the work that is needed to develop it.
Social capital is developed through the interactions between people whose lives intersect within and outside a business or community. These interactions foster relationships, shared norms, values, and understandings that collectively shape behaviour, actions, and outcomes. Factors such as trust, belonging, social identity, sense of self, networks, confidence, and community self-reliance all form part of the multi-dimensional nature of social capital. In a setting where social capital has been consciously developed there is a lower probability of friction and discontent and a higher probability of constructive, prosperous co-operation. In the context of a mining community, investing in the growth of social capital in an organized and structured way can lead to resilient, long-term trusting relationships, greater self-reliance, reduced dependencies, and a more effective use of other forms of capital, resulting in improved business and societal outcomes. The development of social capital is a long-term programme, which requires sustained effort and commitment, and a constancy of vision and leadership, which understands that social capital is a valuable and essential part of the business effort and not an elective or discretionary element. The work can be viewed as disquieting, uncomfortable, and traditionally ‘non-core’ and thus requires senior leaders to take a bold step out of their familiar environment, adapt new leadership styles and make a personal commitment towards civic and community engagement. Leaders who are transparent, reliable, and empathetic will excel at growing their organization’s social capital.
From small initial efforts, social capital can grow exponentially and deliver impact beyond original expectations. Such a programme could be focused on work in one of the critical needs of the community such as education, health services or security, where in-principle common ground is easily found. Practical and tested programmes of this nature exist, which with the support of expert knowledge and facilitation are easy to implement provided that the commitment exists. A particularly successful initiative partners key community members—in this case, school principals—with senior leaders and decision-makers from the business sector (the mine). Through a professionally coached and structured journey that builds social capital, these partnerships create meaningful impact, benefiting the individuals involved and fostering innovative leadership skills. The work enhances the school principals’ ability to find their own solutions to their unique challenges, through the growth of their personal social capital, resulting in, among other things, collateral benefit to school performance and a positive impact on the wider community. The business leaders develop an awareness and understanding of the social complexity of the community, learn new transformational leadership skills in situations where they lack expertise or authority, and gain exposure to and insight of a sector of society they would not normally interact with.
Most importantly, this work fosters close, trusting, and lasting personal relationships between key individuals who develop shared values and beliefs, leading to a stronger connection between the business and the community. This connection creates a tangible shift in both perceived and actual power dynamics and lowers barriers towards generating the common goal of mutual prosperity. These types of programmes generate agency, growth of confidence and independence, and a reduced sense of isolation and hopelessness in difficult circumstances, all of which contribute towards better mutual socio-economic outcomes.
The conscious and deliberate development of social capital is a valuable tool, which should warrant more formal consideration in the social and community programmes of mining companies.
D. Morris
ver the past few weeks, I have asked a number of my colleagues in the mining industry about their sentiments on the current and future status of the mining industry in South Africa and the region. Although this exploratory exercise was not based on any specific scientific design, the responses were extremely diverse, ranging from extreme pessimism and despondency to excitement and hope. Obviously, the responses depended on specific factors such as geographical location, stage in one’s career and commodity of interest. Of course, I totally understand the sentiments of those who felt overwhelmed, despondent, and even despair in 2024. Despite the optimism at the beginning of the year, 2024 was a tough year for most mining companies, especially those affected by falling basket prices of commodities such as PGM, lithium, and nickel. I also understand the positive sentiment for those whose operations were backed by star commodity performers such as gold, copper, rare earths, and graphite.
The huge supply/demand deficit arising from supply outpacing demand for most, had a significant impact on the producer market prices. Despite commodities such as PGM (in particular, palladium), lithium, and nickel playing a critical role in the clean energy transition, overcapacity and oversupply in the market depressed the commodity prices, leading to mothballed mining projects, mine closures, and retrenchments. The industry also had to contend with capital scarcity, inflation-induced increase in operating costs, resources and reserve depletion, technological disruptions, geopolitics, and protectionism. The fractured geopolitical environment not only creates challenges to raising capital and acquiring cutting edge technologies, but also presents security of tenure and operation in the various mining jurisdictions. At first glance, the outlook in the Southern African mining industry appears grim. The depressed prices of major commodities paint a picture of an industry in decline, a sunset industry with limited growth opportunities. Although disturbing, these challenges provide opportunities for a mindset shift in the industry. All we need is a growth mindset that can turn the current obstacles into an opportunity to build resilience in our beloved industry.
We have a lot of reasons to celebrate. We are talking about an industry that is capable of reinventing itself, an industry that is capable of mobilizing the resources and stamina needed to spur sustainable economic growth. For optimists like me, who view the world through the glass half full lenses, our industry is just going through a metamorphic change and will emerge stronger and better, like the mythical phoenix bird. According to Greek mythology and analogues in many other cultures, a phoenix is an immortal bird that cyclically regenerates itself. Associated with the sun, the phoenix obtains new life by rising from the ashes of its predecessor, symbolizing hope, resurrection and renewal. Our mining once went through many devastating economic cycles and yet emerged stronger and more resilient, thanks to the clean energy transition that has presented numerous opportunities to the mining industry. The mining industry is at the core of the clean transition as a supplier of the raw materials needed to transition to a net-zero economy. In my October commentary, I highlighted how the emerging economic epoch, driven by critical metals and minerals, is an opportunity for industrialization through high value exports and localization of manufacturing value chains for clean energy technologies. These opportunities can only be realized if we are intentional about the desired impact.
As the year comes to an end, we find ourselves reflecting. The key message for 2024 is that it is not all doom and gloom. Like the mythical phoenix bird, our industry will rise and shine again. As we take time off to break for a much deserved holiday, we need to remain hopeful and reflect on how we can continue to grow our industry.
I wish everyone happy and safe holidays.
E. Matinde President, SAIMM
Affiliation:
1Hydrometallurgy Research Group, Department of Chemical Engineering, University of Cape Town, South Africa
2Department of Energy and Mineral Engineering, College of Earth and Mineral Sciences, Penn State University, USA
Correspondence to: J. Petersen
Email: jochen.petersen@uct.ac.za
Dates:
Received: 14 Aug. 2024
Published: December 2024
How to cite:
Maharaj, D., Moyo, T., and Petersen, J. 2024. Ammonium thiosulfate leaching of gold from electronic printed circuit boards – effect of solution copper concentration. Journal of the Southern African Institute of Mining and Metallurgy, vol. 124,no. 12, pp. 711–718
DOI:
http://dx.doi.org/10.17159/24119717/724/2024
ORCiD:
D. Maharaj
http://orcid.org/0000-0002-3807-0878
T. Moyo
http://orcid.org/0000-0002-7211-9508
J. Petersen
http://orcid.org/0000-0003-2976-308X
This paper is based on a presentation given at the Hydrometallurgy Conference 2024, 1-3 September 2024, Hazendal Wine Estate, Stellenbosch, Western Cape, South Africa
by D. Maharaj1, T. Moyo², and J. Petersen1
Abstract
This study investigates the effect of ammonium thiosulfate on the leaching of gold from the contacts of unpopulated cut electronic printed circuit boards (PCBs). Studies in the literature show ammonium thiosulfate to be a viable option in comparison to the commonly used but hazardous cyanide leaching route. However, the simultaneous dissolution of Cu interferes with the Au leaching reaction, often limiting the extraction to moderate levels. To optimize the system, an ammoniumthiosulfate system containing 0.5M ammonia, 0.5M ammonium thiosulfate, and Cu(II) sulfate at varying concentrations was studied as an alternative hydrometallurgical option for the recovery of gold from PCB. Tests were done with unpopulated standardized model PCBs (cut to 15 x 30mm pieces). Gold extraction of 47.3% was achieved after a 24-hour leaching experiment with a 0.02M copper background concentration. Further experiments focused using different initial background Cu concentrations (0M – 0.1M) to determine its effect on both gold and copper extractions. An initial Cu concentration of 0.045M resulted in the highest gold extraction, with 93.7% extraction after 6 hours of leaching. Further analysis of the data shows that the kinetic rate of gold leaching is correlated in a first-order dependence with the actual copper concentration in the solution, which increases with the concomitant dissolution of copper and gold from the PCBs. A lower threshold of 0.017M and an upper threshold of 0.15M copper in solution were determined, in between which gold extraction shows this first-order rate increase. The upper threshold is potentially linked to the onset of copper precipitation, which blinds the metal surfaces, slowing further leaching. The findings of this study suggest that in an industrial recovery operation of gold from waste PCB using the thiosulfate method, copper concentrations need to be carefully monitored, and the process should preferably operate with uncut or coarsely cut untreated boards to minimize exposure to copper circuits.
Keywords leaching, gold, copper, printed circuit boards, thiosulfate
Introduction
Due to rapid advancements in electronic technology and its applications, there is an increase in the demand for new products resulting in an increasingly shorter life span of older models with much of this being disposed of as waste. The technology industry has been estimated to generate 53.6 million metric tonnes of waste electrical and electronic equipment (WEEE) globally per year (Forti et al., 2020). Consequently, the environmental burden due to this ‘ecological baggage’ has also increased alarmingly causing unsafe and improper waste management (Schwarzer et al., 2005). Printed circuit boards (PCB) make up an estimated 6% of the overall WEEE burden. There are a variety of recycling opportunities to lessen the waste burden; these especially target gold on PCB due to its relatively high value.
PCB contain a large variety of precious and base metals. Base metals, such as copper and tin are found underneath the protective coatings of the board, and precious metals, such as gold and silver are present on the surface of the board. On PCBs, gold is typically found in high concentrations, with some studies reporting figures as high as 903 g/t (Petter et al., 2014), while typical primary gold ores contain only between 10 to 90 g/t (Jeffrey et al., 2003; Arslan and Sayiner, 2018). Although there is a trend to use less precious metal in the manufacturing of PCBs, the waste stream still outmatches primary ores, of which the grades are decreasing, the mineralogy has become more complex, and which are much more difficult to mine.
There are many challenges to the processing of PCBs. Some of these challenges include their complexity and heterogeneity. Industrially, metal recovery of e-waste is carried out mainly via pyrometallurgical routes (Cui and Anderson, 2016), mostly by using PCBs as co-feed to a copper smelter. Although these routes
do have disadvantages, mainly stemming from the large energy requirements for processing and the shipping of collected WEEE over long distances, the precious metals can be recovered separately from the produced copper through the processing of anode slimes from electrorefining. The overall recovery of gold through this route from the original feed is unclear as there will be gold losses to flue dust, slag, or incorporation into the cathode copper product.
Active research in the past 20 years has been carried out to find direct hydrometallurgical routes as a viable alternative for operation at a small scale. Hydrometallurgy is perceived to have a lower environmental impact and is easier to manage (Cui and Zhang, 2008). The ammonium thiosulfate system is one such hydrometallurgical option. The system is non-toxic as opposed to its competitor, the cyanide system, and has been shown to extract gold at much faster rates in the processing of primary ores (Sullivan and Kohl, 1997; Aylmore and Muir, 2001; Jeffrey et al., 2001).
The gold-thiosulfate complex is formed via two reactions in the ammonium thiosulfate system as per Equations [1] and [2]. Initially, the gold-ammonia complex is formed on the gold surface [1] with cupric acting as the oxidant, before converting into the goldthiosulfate complex [2]. The overall dissolution reaction of gold in an ammonium thiosulfate solution in the presence of cupric ions is represented in Equation [3] (Xia et al., 2003).
The heterogeneous redox reaction between oxygen and copper is shown in Equation [4] (Fleming et al., 2003). Here the cupric ion (Cu2+) concentration eventually reaches steady state and at this point the rate of reduction of the cupric ions through gold dissolution is matched by the rate of oxidation of the cuprous (Cu+) ions by oxygen. Thus, the cuprous ions serve as a redox catalyst in the leaching process and are not consumed.
[4]
The overall redox reaction forming the gold-thiosulfate complex is shown in Equation [5]. The cupric-amine complex and the ammonia within the system are recycled and therefore need not appear in the overall Equation [5] (Xia et al., 2003).
[5]
However, cupric is also known to interfere in this reaction by slowly catalysing the oxidation of thiosulfate to higher oxidation products, such as tetrathionate as per Equation [6], thus effectively destroying the leaching reagent (Fleming et al., 2003):
[6]
The leaching of high-grade gold ore by ammoniacal solutions of ammonium thiosulfate was investigated by Abruzzese et al. (1995). They found the dissolution was favourable at ambient temperature, moderate copper concentration (0.1M) at elevated concentrations of (NH4)2S2O3 (2M) and NH3 (4M). The system has also been used for the leaching of gold from waste cell phone PCBs (Ha et al., 2014; Tripathy et al., 2012). In these studies, initial copper concentrations were varied, being from 0 to 0.048M, with increasing initial Cu concentrations resulting in an increased initial rate of leaching, but in all cases the Au extraction eventually levelled around 30%. Substantially better gold dissolution was achieved by leaching from whole boards compared to shredded boards, postulated to be due to the interference of copper, which preferentially dissolved from the shredded material.
A more systematic study of the effect of the Cu concentration on Au extraction as it increases in the course of PCB leaching remains outstanding. In the present study, the role of copper in the thiosulfate leaching of gold was investigated further with the custom-made cut PCBs.
Materials and methods
Materials
Printed circuit boards are complex and heterogeneous and require thorough analysis before being incorporated into experiments. A considerable drawback of studies with waste PCBs is that the gold grade is highly variable from board to board, and it is therefore nearly impossible to determine a consistent head grade for leaching experiments. It was therefore decided to conduct all experiments with a consistent design of the boards of the same composition, dimension and framework, manufactured from the same type of materials, thus ensuring that accurate comparison and reproducibility of the experiments could be accomplished. The PCBs used in all experiments were manufactured custom-made by Trax Interconnect (Pty) Ltd., based in Cape Town, South Africa. The dimension of the boards was 142 x 105 x 1.55 mm. Figure 1 shows both the top-side and the bottom-side of the model board. For the purposes of this paper, only unpopulated boards, as in Figure 1, were used. The single boards were cut into 15 x 30 mm pieces using a bandsaw, to allow a defined and uniform geometry and surface. All pieces of one PCB were used in each leaching trial to ensure a consistent feed throughout.
The PCBs are comprised of four distinct layers, which aid in the function of the board. The average weight per board was 52.24 g (Prestele, 2020). The four layers constitute the unpopulated PCB with an outer layer on the top and bottom of the PCB covered by the solder mask. The solder mask is a combination of solvents and polymers that make up the ink mask, which has the typical green colour shown in Figure 1. On the inside of the solder mask layer lies a copper layer. A large amount of the copper is found within the inner PCB layers whilst the remaining copper is within the top and bottom layers, as per Table I.
The gold-coloured areas in Figure 1 indicate the layers of gold and nickel that have been plated onto the board as contacts. These contacts are copper not covered by the solder mask which is electroplated with nickel and the nickel is subsequently electroplated with gold in the manufacturing process. The contacts are thus exposed to allow any interaction between the gold and the leach solution.
The mass of gold on the board was quantified utilizing the thickness of the gold plating on the board as well as the area of the gold-plated contacts on the top and bottom layers. The gold plating thickness was 0.07 μm as provided by the manufacturer. Incorporating the gold density, in addition to the gold area and thickness, produced the mass of gold for a single board. Table II contains both the area and mass of gold on the top and bottom outer layers.
The mass of gold was thus determined as 4.22 mg per board, which was taken as the initial gold concentration of the samples (this value was verified through acid digestion of the PCB followed by ICP). The mass of copper present on a single board was determined to be 11.77 g (Table I).
The equipment utilized in the leaching and dissolution experimentation consisted of a set of 3 jacketed 1L batch stirred tank reactors (BSTR) for the PCB leaching experiments (Figure 2). Each BSTR was fitted with an overhead stirrer running a 2-blade metal stirrer at 400 rpm for agitation. Temperature (25 ºC) was controlled by circulating water between the reactor jacket and a water bath. In addition, air as an oxidant was bubbled through the reactor at a rate of 70 mL/min, monitored by the flow meter shown on the right of Figure 2b).
Table I
Copper distribution in mass between each layer of a single PCB
Table II
Gold distribution in area and mass on the top and bottom layer of a single PCB
In the leaching experiments, ammonia and ammonium thiosulfate were used and copper(II) sulfate pentahydrate was added in small amounts to catalyse the reaction. A standard solution consisting of 0.5M ammonium thiosulfate, 0.5M ammonia, and 0.02M copper(II) sulfate pentahydrate was prepared for an initial 24-hour leaching experiment. All chemicals were supplied by Merck. The concentration of the added copper(II) sulfate pentahydrate was varied between 0.008M and 0.1M in later experiments, as reflected in Table III. Furthermore, 500 mL of the lixiviant solution was used in each reactor.
Sampling of 6 mL leachate through a 0.2 μm nylon syringe filter occurred at 15-minute intervals for the first hour, 30-minute intervals in the second hour and every hour up until the 6-hour mark. The reactors were left to run overnight with samples taken
Table III
Lixiviants and conditions for ammonia-ammonium thiosulfate leaching
Lixiviants/Conditions
again every hour from the 21-hour mark up until 24 hours. The solution samples were further diluted at a 1:1 ratio using a fresh solution of 0.5M ammonium thiosulfate and 0.5M ammonia before being refrigerated until analysis. Refrigeration was found to be essential to stabilize the solution over sufficiently long periods prior to analysis. To ensure a constant 500 mL volume in the reactor, 6 mL of the initial standard solution consisting of ammonium thiosulfate, ammonia, and copper(II) sulfate pentahydrate was added back into the reactor at each sampling time. The pH was determined at the start and the end of the 24-hour experiment. Solutions samples were then analysed for both gold and copper using inductively coupled plasma atomic emission spectroscopy (ICP-AES). At the end of each leach experiment the solutions were filtered using a 0.2 μm micro filter to recover any residues. Experimental gold extractions and recoveries were determined based on the initial gold and copper on the board, in relation to the extracted metal in the pregnant leaching solution.
The 6-hour experiments followed a similar procedure to the 24-hour experiment. Four tests were run at the various copper concentrations shown in Table III. Sampling occurred at the same intervals as the 24-hour experiment up until 6 hours, at which point the experiment was complete. In both the 24-hour and 6-hour experiments, one board, cut into 15 x 30 mm pieces, was leached in each reactor, resulting in a solid to liquid ratio of approximately 1:10. The blade of the overhead stirrer was immersed into the solution allowing for it to be slightly above the cut PCB pieces whilst at the same time allowing continuous mixing of the solution. However, the PCB board pieces itself were not brought into suspension by this. Once the experiment was completed, the solution and PCB were separated via a vacuum filter using a compressor, a Buchner funnel, and filter paper. The mass of the residual PCB pieces was recorded once they were completed dried.
Results and discussion
Gold and copper extraction over 24 hours
Figure 3 depicts the gold extraction over 24 hours for PCB
dissolution using the ammonia-ammonium thiosulfate system in the presence of 0.5M ammonia and ammonium thiosulfate and 0.02M background copper(II) sulfate. Additional conditions were stated in Table III. There was an increase in extraction up to 47.9% at 6 hours after an initial delay. Further sampling at 21 hours suggests that the concentrations exhibited only a slight increase and thereafter started to decrease. The experiment reached a maximum amount of gold in solution at 52% at 21 hours, indicating that only half of the gold had been extracted from the PCB. Between 6 and 21 hours, there was a slower increase in gold extraction and at 24 hours the gold in solution had declined to an equivalent of 47% extraction. Analysis of the residue confirmed approximately 50% of the gold had dissolved.
The dissolution rate of the PCB leaching experiment during the rapid phase between 4 and 6 hours was 0.77 mg/h. Additional copper leached from the PCB is likely to have hindered the gold leaching process as copper is known to compete with gold in forming a thiosulfate complex (Ha et al., 2014). The decline in the concentration after 21 hours of leaching was unexpected and is thought to be due to thiosulfate decomposition within the system, therefore hindering gold from staying in solution. This is in line
with observations made by Senanayake (2004) and Birich (2020), who found that over time gold losses increase due to the oxidation of thiosulfate into polythionates.
Figure 3 also shows the dissolution of copper in parallel with that of gold expressed in terms of measured solution concentrations. This clearly indicates that copper is released much more rapidly than gold and at much higher concentrations. The rapid leaching of copper, especially in the early stages of the experiment, may explain the initial delay in gold extraction. Furthermore, the PCBs contained other metals such as nickel and zinc, which also compete with gold ions for complexation with the thiosulfate ion. It was also noted that around 21 hours, the PCB experiment appeared to have attained its highest gold extraction. The increase in gold extraction between 6 and 21 hours for the PCB leaching experiment were 47.9% to 52%, respectively. Although the maximum extraction was at 21 hours, the increase between 6 and 21 hours was marginal and this experiment could have been terminated at 6 hours. The trend for the PCB leach curve could also indicate that a higher peak might have been reached between 6 and 21 hours. Nonetheless, it was assumed that maximum gold extraction in solution was achieved after 6 hours at the conditions of 0.5M NH3, 0.5M (NH4)2S2O3, and 0.02M background CuSO4.5H2O.
The decline in extractions after 21 hours may be due to the consumption of thiosulfate as well as the loss of ammonia in the solution. Consumption of thiosulfate is attributed to the ion being meta-stable in addition to potentially becoming oxidized to tetrathionate by cupric (Equation [6]). Both Molleman and Dreisinger (2002) and Xu et al. (2017) reported that thiosulfate consumption was a cause for lower gold extractions over time. Loss of ammonia due to evaporation and complexation with cupric in solution could also be a contributor to low gold extractions, as this disrupts the ratio of thiosulfate to ammonia, thereby inhibiting the regeneration of the cuprous ion and causing a decrease in pH due to a shift of the ammonium/ammonia buffer in solution (Equation (7), Xia et al., 2003). [7]
Indeed, the pH of the solution decreased from the initial 9.51 to 9.16 for PCB leaching over 24 hours. Thus, it is possible that low gold extractions can be attributed to ammonia loss in the PCB leaching experiment.
Gold and copper extraction over 6 hours
A further set of experiments investigated the effect of background copper(II) sulfate concentration on gold extraction in the PCB leaching experiment. Four different background copper concentrations (0.008M, 0.02M, 0.045M, and 0.1 M) were introduced into the system and the leaching experiment was conducted over 6 hours. Additionally, a 0M background copper concentration test was introduced to determine the effect on the gold extraction rate with the copper catalyst being extracted from the PCB material only. The results are demonstrated in Figure 4.
The lowest extraction after 6 hours was achieved in the 0M copper experiment. It was clear that an initial amount of copper in the solution was necessary to initiate the gold dissolution reaction via the formation of the Cu(II) amine complexes. With the absence of background copper in the solution, the gold oxidation reaction needed to be facilitated through the direct reduction of oxygen, which has poor kinetics, whereas in the presence of copper the cupric/cuprous couple can act as a redox mediator. In the system without initial copper there will be a lag until sufficient copper
has dissolved from the PCB to allow the cupric/cuprous couple to become active and act as the redox mediator. This was confirmed by the low gold extraction of a mere 1.66% after 6 hours for the 0M background copper experiment (Table IV). Gold extraction was found to increase up to 93.7% after 6 hours with the addition of 0.045M background copper. This value was much higher than the 25% gold extraction at 0.04M background copper in the copper leaching experiments conducted by Tripathy et al. (2012) in 0.1M ammonium thiosulfate after 6 hours. The authors attributed the low extraction value of 25% to the slow agitation rate of 250 rpm used in their investigation. Although a higher agitation rate was used in the present study (400 rpm), their study used shredded material, which was easier to suspend. The lower gold extraction reported by these researchers may need to be attributed to the lower thiosulfate background or stronger interference from copper dissolving from the material.
It is interesting to note that gold dissolution appears to reach an equilibrium at the 0.1M and 0M background copper concentrations after 6 hours, whereas the other reactions are continuing. A background copper concentration of 0.1M was expected to have a similar gold extraction to 0.045M, similar to the results reported in Abruzzese et al. (1995) at ambient temperature and 4M NH3; however, this was not demonstrated by the present experiments. Therefore, it can be said that at very high background copper concentrations, the gold extraction becomes independent of, or even impeded by the copper concentration in the context of PCB leaching. These results were consistent with those reported by Ha et al. (2010) who found that after 2 hours at concentrations higher
Gold extraction rates determined for the rapid leaching phase in each of the leach experiments as well as the average copper concentration in solution during these phases
than 0.015M background copper, the ultimate leaching of gold remained around 30% gold extraction. There was a significant difference in gold extraction between 0.02M and 0.045M copper from the start of the experiment up to 2 hours. After 2 hours, gold extraction in the 0.045M copper experiment occurred at a much faster rate than in the 0.02M copper experiment. This was similar to the results reported by Tripathi et al. (2012), where the gold extraction increased at a faster rate from 10% to 30% after 8 hours. Even lower gold extractions were observed for the 0.008M copper experiment due to the limited amount of copper in the system in comparison to the other experiments.
Analysing the effect of copper concentration on the gold leaching rate
Given the gold extraction results from Figure 4, there possibly is a threshold background copper concentration required for the reaction to proceed. Concentrations below this threshold result in sluggish kinetics, and thus minimal gold recovery. At the same time, there may be an upper threshold beyond which excessive thiosulfate degradation takes place. The previous study (Ha et al. , 2010) found that at background copper concentrations between 0.032M and 0.048M similar gold extractions of around 30% - 35% after 8 hours of leaching were achieved. They noted that at 0.005M, gold extraction was excessively slow, attaining below 5% gold extraction with a 0.2M thiosulfate concentration. The same study also confirmed that at a background copper concentration above 0.015M, no enhancing effect on gold extraction was observed. This was attributed to high cupric-ammonia complex concentrations causing higher losses of thiosulfate through its degradation into tetrathionate.
However, none of these studies measured the actual copper concentration in the solution, considering that in a cupric ammonia solution a considerable amount of metallic copper is dissolved simultaneously to Au from the PCB as per Equation [8]:
[8]
In this sense, Figure 5 shows the total copper concentration accumulating in the solution as leaching progresses over the 6 hours at the different initial copper concentrations. In all experiments, this concentration increases steadily, quite independent of the gold leaching shown in Figure 4. In all experiments the total copper concentration increases 2- to 3-fold for the 6 hours. It must also be understood that the molar concentration levels of copper in solution (0.005M to 0.22M) exceed the maximum molar concentration of gold in the present case (0.043mM) by 2−4 orders of magnitude and therefore entirely dominate the system.
Comparing Figures 4 and 5 allows one to draw some conclusions about the effect of copper solution concentration on the kinetics of gold extraction. It appears that a rapid increase in the dissolution of copper is linked to a certain background concentration of copper in solution. Thus, for example, the onset of more rapid leaching in the 0.02M experiment after 3 hours coincides with a copper concentration of 0.04M.
A possible correlation between gold leaching kinetics and actual copper concentration in solution was therefore investigated further, as illustrated in Figure 6. Here the phases during which gold leached most rapidly in the course of the various experiments were analysed by linear regression in order to determine an average leaching kinetic rate in each case. The results are shown in Table IV.
Also included in Table IV are the average copper concentrations determined in each experiment during the rapid leach phase. This analysis was also done for the rapid leach phase in the 24-hour
Figure 5—Total copper in solution from PCB leaching at various initial copper concentrations (0M, 0.008M, 0.02M, 0.045M, and 0.1M)
Figure 6—Gold extraction data at various initial copper concentrations (0M, 0.008M, 0.02M, 0.045M, and 0.1M) with the dashed lines marking phases of rapid increases used in the linear regression analysis
Figure 7—Gold average extraction rates plotted again average copper concentration in the leach solution for the rapid leach phases in various 6-hour leach experiments as well as the initial 24-hour run
experiment between 3 and 6 hours (Figure 3). From this data, the correlation between Au leaching rate and copper concentration is plotted in Figure 7.
The data suggests a linear correlation of the Au extraction rate to the copper concentration within the context of the present experiment (1 PCB with 4.22 mg of gold in 0.5 L of a solution 0.5M in (NH4)2S2O3 and 0.5M in NH3), i.e., the reaction is first order with respect to Cu(II) in solution.
It is now of interest to evaluate this result in the context of the leaching thresholds mentioned earlier. Taking the linear correlation shown in Figure 4, the line would intersect the x-axis at a copper
concentration of 0.017M, i.e., gold leaching would become inhibited at concentrations below this level. This is plausible when looking at the 0M and 0.008M gold and copper curves in Figures 4 and 5, respectively. Gold leaching accelerates for the 0.008M curve only once the copper concentration in solution exceeds 0.02M after about 3.5 hours, but the 0M copper curve stays well below this threshold throughout, and consequently gold leaching never accelerates in this experiment.
However, there also appears to be a maximum threshold beyond which gold leaching becomes inhibited. This is evident in both the 0.1M copper curve beyond the first hour, where the copper concentration exceeds 0.15M, and in the 24-hour leach experiment, where inhibition can be observed during the overnight period (between 6 and 21 hours) and the copper concentration exceeds 0.12M (Figure 6). Copper ions form strong complexes with both ammonia and the thiosulfate ion as was shown in Equations [1] to [3]. As Senanayake (2004) has shown, the Cu(NH3)42+ complex strongly prevails in the region pH 8-10 over other complexes at high ratios of ammonia to copper(II) concentrations (105) and mixed NH3 and OH-complexes at lower excess ratios.
With an increasing Cu(II) concentration in solution, an increasing shift away from the dominance of Cu(NH3)42+ occurs, which is the complex that drives Equations [1] to [3]. Likewise, the stability regions also of the Au-NH3 and Au-S2O3 complexes are shifted, resulting in decreased availability of total ammonia. In the current experiments the total initial ammonia/ammonium concentration was 1.5M and thus only around 10 times higher than the observed upper threshold copper concentration of 0.15M. Nonetheless, the abrupt cessation of gold leaching at the upper threshold points to a sudden onset of other mechanisms inhibiting the reaction, such as precipitation of CuS on the surface of the PCB, thus restricting further gold leaching. This is supported by the erratic nature of the copper in solution curve for the 0.1M copper experiment in Figure 6, once the 0.15M threshold has been exceeded.
This study investigated the ammonium-thiosulfate system for the leaching of gold from PCB. It was found that the ammoniumthiosulfate system was promising for PCB leaching experiments, which achieved gold extractions of as much as 93.7% using 0.045M background copper.
However, the Cu-NH3-S2O3-system is also conducive to the leaching of copper directly from PCBs in parallel with gold, thus resulting in a continued increase of the background copper concentration. Closer analysis of the data has shown that the rate of gold dissolution is in fact increased with copper concentrations in a first-order dependence up to 0.15M, but that once this threshold is exceeded, both gold and copper dissolution become more inhibited and erratic. This inhibition is likely caused by the onset of copper precipitation on the surface of the PCB rather than the gradual decomposition of thiosulfate.
In summary, the ammonium-thiosulfate system can be effective in removing gold from PCBs in solution, providing that the background concentration of copper is carefully managed to stay well below the potential inhibition threshold. In the ideal case, this should occur with the copper on the board minimally exposed during gold leaching, i.e., the feed should be boards that have been de-populated but not been size reduced, or it should be done on boards/residues where the copper has already been completely leached before thiosulfate leaching.
This research was supported through the following grants:
➤ German-African Innovation Incentive Awards (GAIIA) 2019;
➤ Council for Scientific and Industrial Research (CSIR), South Africa under Grant Number CSIR/BEI/WRUI/2019/026; and
➤ The South African National Research Foundation (NRF) through the Community of Practice ‘Waste to Value’ under grant UID 128149.
Ms Maharaj received a scholarship associated with the NRF SARChI Chair in Mineral Beneficiation (Grant UID 64829). The NRF accepts no liability for the findings presented in this paper.
Abbruzzese, C., Fornari, P., Massidda, R., Vegliò, F., Ubaldini, S. 1995. Thiosulfate leaching for gold hydrometallurgy. Hydrometallurgy, vol. 39, no. 1–3, pp. 265–276. DOI: 10.1016/0304-386X(95)00035-F
Arslan, F., Sayiner, B. 2018. Ammoniacal thiosulfate leaching of Ovacik gold ore. Mineral Processing on the Verge of the 21st Century. vol. 3, no. 3. pp. 517–522. DOI: 10.1201/9780203747117-90
Aylmore, M.G., Muir, D.M. 2001. Thiosulfate leaching of golda review. Minerals Engineering, vol. 14, no. 2, pp. 135–174. DOI: 10.1016/S0892-6875(00)00172-2
Birich, A. 2020. Early Stage Gold Recovery from Printed Circuit Boards via Thiosulfate Leaching; Shaker Verlag: Herzogenrath, Germany; ISBN 978-3-8440-7695-0.
Cui, H., Anderson, C.G. 2016. Literature Review of Hydrometallurgical Recycling of Printed Circuit Boards (PCBs). Journal of Advanced Chemical Engineering, vol. 6, no. 1. DOI: 10.4172/2090-4568.1000142
Cui, J., Zhang, L. 2008.Metallurgical recovery of metals from electronic waste: A review. Journal of Hazardous Materials, vol. 158, no. 2–3. pp. 228–256. DOI: 10.1016/j. jhazmat.2008.02.001
Fleming, C., McMullen, J., Thomas, G.K., Wells, J. 2003. Recent advances in the development of an alternative to the cyanidation process: Thiosulfate leaching and resin in pulp. Minerals and Metallurgical Processing, pp. 1–9. DOI: 10.1007/ BF03403107
Forti, V., Baldé, C.P., Kuehr, R., Bel, G. 2020. The Global E-waste Monitor 2020. Available: http://ewastemonitor.info/ .
Ha, H.V., Lee, J., Jeong, J., Trung Hai, H., Jha, M.K. 2010. Thiosulfate leaching of gold from waste mobile phones. Journal of Hazardous Materials, vol. 178, pp. 1115–1119. DOI: 10.1016/j. jhazmat.2010.01.099
Ha, V.H., Lee, J.C., Huynh, T.H., Jeong, J., Pandey, B.D. 2014. Optimizing the thiosulfate leaching of gold from printed circuit boards of discarded mobile phone. Hydrometallurgy, vol. 149, pp. 118–126. DOI: 10.1016/j.hydromet.2014.07.007
Jeffrey, M.I., Breuer, P.L., Choo, W.L. 2001. A kinetic study that compares the leaching of gold in the cyanide, thiosulfate, and chloride systems. Metallurgical and Materials Transactions B: Process Metallurgy and Materials Processing Science vol. 32, no. 6, pp. 979–986. DOI: 10.1007/s11663-001-0086-7
Jeffrey, M.I., Breuer, P.L., Chu, C.K. 2003. The importance of controlling oxygen addition during the thiosulfate leaching of gold ores. International Journal of Mineral Processing, vol. 72, nos 1–4, pp. 323–330. DOI: 10.1016/S03017516(03)00108-X
Molleman, E., Dreisinger, D. 2002. The treatment of copper-gold ores by ammonium thiosulfate leaching. Hydrometallurgy, vol. 66, nos.1–3, pp. 1–21. DOI: 10.1016/S0304-386X(02)00080-4
Petter, P.M.H., Veit, H.M., Bernardes, A.M. 2014. Evaluation of gold and silver leaching from printed circuit board of cellphones. Waste Management, vol. 34, no. 2, pp. 475–482. DOI: 10.1016/j. wasman.2013.10.032
Prestele, M.P. 2020. Assessment of a Shredding Technology of Waste Printed Circuit Boards in preparation for Ammo-nia-based Copper leaching. University of Cape Town.
Schwarzer, S., Bono, A., Peduzzi, P., Giuliani, G., Kluser, S. 2005. E-waste, the hidden side of IT equipment’s manufacturing and use UNEP Early Warning on Emerging Environmental Threats. United Nations Environmental Programme. Available: https:// archive-ouverte.unige.ch/unige:23132
Senanayake, G. 2004. Analysis of reaction kinetics, speciation and mechanism of gold leaching and thiosulfate oxidation by ammoniacal copper(II) solutions. Hydrometallurgy, vol. 75, nos. 1–4, pp. 55–75. DOI: 10.1016/j.hydromet.2004.06.004
Sullivan, A.M., Kohl, P.A. 1997. Electrochemical Study of the Gold Thiosulfate Reduction. Journal of The Electrochemical Society, vol. 144, no. 5, pp. 1686–1690. DOI: 10.1149/1.1837660
Tripathi, A., Kumar, M., Sau, C.D., Agrawal, A., Chakravarty, S., R. Mankhand, T. 2012. Leaching of Gold from the Waste Mobile Phone Printed Circuit Boards (PCBs) with Ammonium Thiosulfate. International Journal of Metallurgical Engineering, vol. 1, no. 2, pp. 17–21. DOI: 10.5923/j.ijmee.20120102.02
Xia, C., Yen, W.T., Deschenes, G. 2003. Improvement of thiosulfate stability in gold leaching. Mining, Metallurgy & Exploration vol. 20, pp. 68–72. https://doi.org/10.1007/BF03403135
Xu, B., Kong, W., Li, Q., Yang, Y., Jiang, T., Liu, X. 2017. A review of thiosulfate leaching of gold: Focus on thiosulfate consumption and gold recovery from pregnant solution. Metals, vol. 7, no. 6. DOI: 10.3390/met7060222 u
26 MAY 2025 - WORKSHOP
Sulfuric Acid Catalysis - Key Parameters to Increase Efficiency and Lower Costs
27-28 MAY 2025 - CONFERENCE
29 MAY 2025 - TECHNICAL VISIT
PROTEA HOTEL STELLENBOSCH AND CONFERENCE CENTRE, STELLENBOSCH OBJECTIVES
•
• To expose delegates to issues relating to the generation and handling of sulphur, sulphuric acid, and SO2 abatement in the metallurgical and other industries
•
• Provide an opportunity to producers and consumers of sulphur and sulphuric acid and related products to be introduced to new technologies and equipment in the field
•
• Enable participants to share information about and experience in the application of such technologies
•
• Provide an opportunity for role players in the industry to discuss common problems and their solutions. CONFERENCE | 2025 9TH
EXHIBITION AND SPONSORSHIP
There are a number of sponsorship opportunities available. Companies wishing to sponsor or exhibit should contact the Conferences and Events Co- Ordinator.
ECSA Validated CPD Activity, Credits = 0.1 points per hour attended
FOR FURTHER INFORMATION, CONTACT: Gugu Charlie, Conferences and Events Co-Ordinator, E-mail: gugu@saimm.co.za
Affiliation:
1School for Chemical and Minerals Engineering, Hydrometallurgy Group, Faculty of Engineering, North-West University, Potchefstroom, South Africa
2Bruinsma Solutions (Pty) Ltd, Potchefstroom, South Africa
3Chemical Resource Beneficiation, Hydrometallurgy Group, Faculty of Natural and Agricultural Sciences, North-West University, Potchefstroom, South Africa
Correspondence to:
D.J. van der Westhuizen
Email: derik.vanderwesthuizen@nwu.ac.za
Dates:
Received: 13 Sept. 2024
Published: December 2024
How to cite:
Matsela, M.J., Bruinsma, O.S.L. and van der Westhuizen, D.J. 2024
The free ligand model to describe and design cobalt extraction and nickel scrubbing in a base metal refinery.
Journal of the Southern African Institute of Mining and Metallurgy, vol. 124, no.12 pp. 719–724
DOI:
http://dx.doi.org/10.17159/24119717/714/2024
ORCiD:
M.J. Matsela
http://orcid.org/0000-0002-3144-1074
O.S.L. Bruinsma
http://orcid.org/0000-0001-8428-4909
D.J. van der Westhuizen
http://orcid.org/0000-0001-6764-4132
This paper is based on a presentation given at the Hydrometallurgy Conference 2024, 1-3 September 2024, Hazendal Wine Estate, Stellenbosch, Western Cape, South Africa
by M.J. Matsela1, O.S.L. Bruinsma2, and D.J. van der Westhuizen1
Abstract
Solvent extraction (SX) is a widely used separation and purification technique in hydrometallurgy, enabling the selective transfer of target metal ions between aqueous and organic phases. The process relies on chemical equilibrium and the interaction between metal ions and extractants in the organic phase. The free ligand (FL) model enhances the understanding of SX by focusing on the availability of free ligands in the organic phase, a critical factor influencing extraction efficiency and purity. The FL model to calculate the equilibrium concentrations in solvent extraction (SX) based on the distribution coefficient (Kd) at infinite dilution and the fraction of free ligand available for extraction. In this work, the FL model is validated to account for co-extraction of Ni and for designing the extraction and scrubbing sections of Co/Ni separation in a base metal refinery. Cyanex 272 is employed as a selective Co extractant in the process to yield high purity Ni. To enhance the loading capacity of the extractant, 50 mol% of NaOH is pre-loaded into it. Experimental and FL modelling results show that four equilibrium stages are required to purify the 99% Ni feed to a 99.97% Ni raffinate. The 53.59% co-extract with 26.76% free ligand is purified with a reflux scrub of 30 g Co/L in one equilibrium stage to 99.01%, Co in the scrubbed extract. The FL model as well as the Co/Ni/Na-analysis of the aqueous phase confirm that in the scrubbing section, Ni in the extract is mainly replaced by Co. Finally, in the one stage stripper the Co concentration in the scrubbed extract is increased from 5.6 g Co/L in the extract to 30.5 g Co/L that is partially used as reflux scrub liquor.
Keywords free ligand model, cobalt, nickel, Cyanex 272, extraction, scrubbing
Introduction
The primary objective of the free ligand (FL) model is to optimize the solvent extraction (SX) process by predicting the concentration of free ligands, which governs the equilibrium conditions. By understanding these dynamics, the model enables better control of the process, including the purity of the extracted product and the design of the scrubbing section. Conventionally the McCabe-Thiele graphical method has been the standard in designing the extraction section of SX plants. This approach is effective in determining the number of stages required to achieve the desired separation, however, it cannot predict the purity of the extract or aid in the design of the scrubbing section, which are both critical in achieving high quality outputs of the SX process. The free ligand model therefore addresses these limitations by determining the fraction of free ligands, which aids in determining the extract purity and consequently facilitates the design of the scrubbing section of the SX process.
Solvent extraction (SX) is a separation process that is used in hydrometallurgical plants to obtain one or more components of the aqueous solution into an immiscible organic phase, followed by stripping back into an aqueous solution (Nicol, 2008). This is done to obtain metals at the required purity levels or increase the concentration of the required metals (Kihlblom, 2021). A typical SX process has several stages of extraction, whereby the aqueous solution that contains the metals of interest is brought into contact with the organic solvent that contains the extractant. After extraction, the loaded organic also contains the other metals due to co-extraction. Consequently, a scrubbing section is required to eliminate the undesirable metals from the loaded organic (Kihlblom, 2021).
The conventional way to design the extraction section of an SX plant is by means of the McCabe-Thiele graphical method (Seader et al., 2011). However, this method is not able to predict the purity of the extract or to design the scrubbing section. In this paper a numerical method is demonstrated for the design of both the extraction and the scrubbing section with a limited number of parameters that all have a physical background.
The system that was selected for this was cobalt/nickel (Co/ Ni) purification using 50 mol% NaOH-preloaded Cyanex 272 (C272) as extractant (Mans, 2019). Metals are extracted by C272 via cation exchange mechanism (Rodrigues et al., 2022). The synthetic feed that was used contained 1 g Co/L and 100 g Ni/L corresponding with a composition of 99% Ni, as it occurs in a base metals refinery. Due to confidentiality restrictions, the aqueous feed solution from the industry was not accessible, therefore the use of the synthetic feed was employed for this study. The commercial purity of the raffinate is 99.95% Ni, and that of the scrubbed extract is 99% Co. Despite the high selectivity for Co, also Ni is co-extracted, both requiring the same stoichiometry of two C272 ligands per metal ion, however due to slightly larger ionic radius and higher electronegativity for Ni it can accommodate additional water molecules in its coordination sphere, as shown in Figure 1 (Santanilla et al., 2021).
The extraction reactions are shown by Equations [1] and [2], where (aq) and (org) represent the aqueous and the organic phases, respectively.
The FL model assumes that there is a limited number of ligands in the solvent that are available for extraction, and this is the loading capacity of the solvent. The model provides the equilibrium concentration of component i in the solvent as follows:
[3]
In this equation, xi (mol/L) is the concentration of metal i in the aqueous phase, Kdo,i (-) is the distribution coefficient of metal i at infinite dilution, and α (-) is the free ligand fraction still available for extraction and defined by:
[4]
Table I
List of chemicals used for the experiments
Chemical Purity Supplier
NiSO4.6H2O 95% Anyang General Chemical Company, Ltd
CoSO4.7H2O 99% Sigma-Aldrich
H2SO4 98% Labchem
NaOH 99.75% Promark
Cyanex 272 85% Solvay
1-Octanol >99% Sigma-Aldrich Shellsol D70 SNF Chemicals
where y0 (mol/L) is the maximum loading capacity of the solvent. It should be noted that in the FL model all concentrations are in mol/L. In the FL model the selectivity for a pair of metals, βij, is constant and equal to the ratio of the distribution coefficients at infinite dilution:
Synthetic solutions were prepared using the chemicals in Table I. The solvent used in the experiments was 22 wt.% C272 (Mans et al., 2020), with 5% v/v of 1-Octanol as modifier and Shellsol D70 as the diluent. Prior to extraction the solvent was pre-neutralized with 50% mol/mol of NaOH. The aqueous and the organic phases were thoroughly mixed at room temperature in an orbital shaking incubator (Labcon) for 1 hour at a frequency of 150 rpm to guarantee equilibrium. By determining the concentrations of the metals in the aqueous solutions, it was observed that after an hour of mixing and settling, the distribution of metals between the two phases did not change with time, therefore this confirmed that equilibrium had been achieved within an hour.
[5]
Analyses
Metal concentrations (Co, Ni and Na) of aqueous solutions were determined by ICP-OES (Agilent 5110). Metal concentrations in the solvent were calculated by mass balance. The pH was measured using a Metrohm 744 pH-meter with a calibrated 6.0258.010 electrode (Hanna instruments).
Application of the FL model in Co/Ni purification
The Co/Ni/C272 refinery
The block flow diagram (BFD) of a Co/Ni/C272 refinery is shown in Figure 2.
The 99% Ni feed is extracted counter currently with 22wt.%, C272 producing a 99.95% Ni raffinate. In the extraction section Co and Ni are exchanged with Na in the solvent. This composition includes only the metals of interest, specifically Co and Ni. The Co-extract that contains substantial amounts of Ni is scrubbed using a concentrated Co reflux from the stripper. In the scrubber, Ni in the solvent is exchanged with Co in the aqueous phase. The scrubbed extract is stripped with concentrated H2SO4 to produce a 99% Co at a typical concentration of 30 g Co/L. In this process all metals (Co, Ni and Na) are exchanged to bring the C272 back in the protonated form. Finally, the C272 is pre-loaded with 50 mol% using concentrated NaOH and the pre-loaded solvent enters the extraction section at the raffinate side. The aqueous return scrub streams are relatively small compared to the main streams as will be shown in the design paragraph.
FL model parameters for Co/Ni/C272
In a series of experiments with varying organic /aqueous (O/A)-ratios, the three FL model parameters were determined, as demonstrated in Table II. In these experiments, the pH of the aqueous solutions was maintained in the range of 5.0−5.5 and the (O/A)-ratios tested were in the range of 0.2−3.0, at room temperature (Mans, 2019). After mixing and settling, the concentration of metals in the aqueous solutions was determined
Table II
Free ligand parameters for Co/Ni/C272 (22 wt.%)
y0 (mol Me/L) 0.119 Kdo,Co 15 Kdo,Ni 0.089
by ICP-OES and that, in the organic phase, was determined by mass balance. Subsequently, Kd, Co and Kd, Ni were calculated as the ratios of the concentration of Co and Ni in organic phase over aqueous phase, respectively, and plotted as shown in Figure 3.
The maximum loading of 0.119 mol Me/L corresponds with a total metal concentration of approximately 7 g/L (Co and Ni have about the same molecular weight). The Co/Ni selectivity calculated from the distribution coefficients at infinite dilution is βCo/Ni = 169. The consistency of the model is shown in Figure 3, where for each experiment the distribution coefficients of Co and Ni were plotted for extraction conditions, that is 100 g Ni/L. As will be shown in the design, the Ni concentration in the extraction section only slightly reduced from feed to raffinate side. However, the co-extracted Ni results in an extract well below the 99% Co specification.
As illustrated in Figure 3, the maximum values of the distribution coefficients correspond with the values at infinite dilution and the slope is the inverse of the Co/Ni-selectivity. The observation that the experimental trend is not passing through the origin seems to suggest that Ni is also extracted by the other two components in the solvent. In the design sections this will be ignored. The competition between Co and Ni for free ligand is presented in Figure 4.
In Figure 4 the following can be observed. For the pure Co system, with increasing Co concentration in the aqueous phase, the Co concentration asymptotically approaches the maximum loading of y0=0.119 mol Co/L. Adding 100 g Ni/L, reduces the maximum concentration in the solvent to 0.052 mol Co/L. This is the maximum loading using the real Co/Ni feed. For the design
of n equilibrium stages and a binary system, this results in 2n mass balance and 1n equilibria. This set of 3n equations was conveniently solved using Excel-Solver. In Figure 5, for pure Ni system with increasing Ni concentration in the aqueous phase, the Ni concentration also approaches the maximum loading capacity of y0 = 0.119 mol Ni/L. Adding 1 g Co/L reduces the loading capacity and the graph approaches a maximum of 0.005 mol Ni/L in the solvent. This is below that of Co and this is consistent as C272 has more affinity for Co over Ni.
Design of the co-extraction section
The basis of design is a feed containing 1 g Co/L and 100 g Ni/L that needs to be purified to 99.95% Ni and 99.0% Co, respectively. The conventional method (Seader et al., 2011) is used for the flash calculations to determine the number of equilibrium stages to purify 99% Ni to 99.95% Ni in the raffinate. In a flash calculation it is assumed that both streams leaving the stage are in equilibrium, as described by the FL model in Equation [3]. This is combined with the mass balance over the equilibrium stage:
The minimum (O/A) ratio is calculated by assuming that: a) the solvent is in equilibrium with the feed, and b) all Ni is extracted. For this case, it is (O/A) min= 0.294. Details of the calculation, using the FL model, are shown in Table III.
The minimum O/A ratio required to achieve the desired metal separation is 0.294, with a free ligand fraction of 22.7% and the Co
extract purity of 62.8%. To achieve equilibrium between solvent and feed, an infinite number of stages would be required. In the conceptual design phase, a 20% higher value is used to reduce the number of stages to an acceptable level:
The method outlined in the following was used to predict the purity of the calculated stages. Firstly, estimate the concentrations of Co and Ni in the aqueous phase (xi). Next, use these estimates to determine the organic phase composition (yi) through mass balance calculations. Subsequently, calculate the free ligand fraction (α) using Equation [4] and the parameters in Table II. Following that, determine xi at equilibrium using Equation [3] and compare
Table III
Minimum O/A ratio
it with the xi from the mass balance. Finally, use a Solver in Excel to adjust xi until yi matches both the mass balance and equilibrium composition. When the Solver converges it will accurately determine yi, and yield the correct α
At this O/A ratio, the number of stages, the purity, and the free ligand fraction in the extract to obtain pure Ni raffinate are four (4) equilibrium stages to produce raffinate with Ni purity of 99.97%. This leads to Co purity of 53.59% in the extract and the free ligand fraction of 26.8%. The detailed results per stage are presented in Table IV.
Design of the Ni-scrubbing section
The basis of design for the scrubbing section is the extract, which is to be scrubbed from 53.59% Co to 99.0% Co with the scrubbing liquor of 30 g Co/L at 99.0% purity (reflux from the stripper). The design results from the scrubber showed that the O/A ratio needed to scrub all Ni from the extract is 13.48 using 20% excess. One (1) equilibrium stage is required to increase the extract purity from 53.59% to 99.01% and the free ligand fraction in the extract decreases further from 20.76% due to high Co affinity at the concentration of 30 g Co/L. The scrub return to the extraction section contains 37.2% Co. The Ni-rich scrub return is only 2.5% of the feed. Therefore, it can be conveniently added to the feed as shown in the BFD (Figure 2). A more detailed mass balance of the 1-stage scrubber is presented in Table V.
It should be noted that, with the available data, the H2SO4stripper cannot be designed with the FL model. For this, the H+ exchange with Co2+ should be included in shakeout tests. The same is true for the pre-loading, where H+ is exchanged with Na+
Validation of the method
The method was validated by shakeout tests that correspond with the design O/A ratios of extraction, scrubbing, and stripping. The Co-Ni-Na ICP data were used to verify if only Na was exchanged with Co and Ni. This was done by comparing the total ionic values of the aqueous phase, ∑zi xi, before and after shakeout, as well as the pH, where i is the summation over Co, Ni and Na. In Table VI, the Ni purity increases from 98.99% to 99.78% in a single stage. The Co purity in the extract increases from 1% in the feed to 38% in the extract. Additionally, the free ligand fraction decreases from 100% in the fresh solvent to 20.22% in the extract. These results validate the FL model, as they closely align with the results from Table IV, stage 1. The slight difference in the available free ligand fraction for extraction is likely due to a slight variation in the feed purity. In the scrubbing section, the free ligand fraction further decreases from 20.22% in the extract to 18.75% in the scrubbed
extract, with results that are closely aligned with the scrubber design in Table V. The minor differences in the results may be attributed to variations in the composition of the scrubbed extract.
The results are demonstrated in Table VI.
In the extraction shakeout at O/A=1.2x(O/A) min=0.352, the ∑zi xi, changes slightly from 3.121 mol/L in the feed to 3.262 mol/L in the raffinate. Since also the pH hardly changes, the assumption that Co and Ni only exchange with Na is valid. The observation that the nickel concentration in the raffinate is slightly higher than in the feed shows that some water is absorbed by the solvent. The nickel purity increases from 98.99% to 99.78% in one stage. The cobalt purity of the extract increases from 1% in the feed to 38% in the extract. The free ligand fraction reduces from 100% in the fresh solvent to 20.22% in the extract.
In the scrubbing shakeout at O/A=1.2x(O/A) min=8.63, the ∑zi xi, changes slightly from 1.086 mol/L in the scrub liquor to 1.077 mol/L in the scrub reflux. Since also the pH hardly changes, the assumption that Co and Ni only exchange with Na is valid. The free ligand fraction decreases from 20.22% in the extract to 18.75% in the scrubbed extract, indicating that some of the Na in the extract is replaced with Co from the scrub liquor.
In the stripping shakeout at O/A=6.00, the objective is to produce a 30 g Co/L solution that can partially be refluxed to the scrubber. The results for the rich liquor show that it contains 30.33 g Co/L and thus can be used for reflux scrubbing. The∑zi xi, = 3.269 mol Me/L, which is essentially equal to the feed, shows that the ion balance is correct. The pH=-0.30, which makes it less useful for reflux scrubbing. This problem can be bypassed by using less concentrated acid and two stripping stages. The first stripping stage is operated with a low O/A ratio to produce reflux scrub liquor at a higher pH, and the second with the rest of the acid to recover all Co and to produce metal-free solvent for pre-loading.
Table VI
Validation of the method
Solvent concentrations were calculated by mass balance and are given in Italics
The FL model provides a powerful numerical method for the design of the extraction and scrubbing section for cases that produce extracts that do not meet the product specifications. Given the high cost of the extractants, optimizing their use is important in minimizing the economic impact of the extraction processes. It is therefore crucial that the free ligands are utilized as efficiently as possible as more extractant will be required to achieve the desired separation if they are not utilized efficiently. The model therefore helps to determine how much of the free ligands are still available for extraction as inefficient use of the ligands can result in higher production costs.
This conclusion is based on a minimum number of physical parameters: maximum loading capacity of the solvent and distribution coefficients at infinite dilution for each relevant metal.
The FL model can be used for single metal as well as multicomponent and multi-species industrial solutions. In the latter, the graphical McCabe Thiele method is not applicable. While the FL model has not been verified for other metals, it can work in multi-species industrial solutions that contain Co and Ni, as the composition of the synthetic feed used in this study is as it occurs in a base metals refinery. The FL model only accounts for the interaction between free ligands and metals and cannot account for the interaction between metals where multi-metal complexes might be present in the system. Another limitation is that the model focuses only on the equilibrium conditions and does not consider the kinetics of the process.
This was demonstrated and validated for the design of a Co/Ni refinery using a 22 wt.% C272 solvent, showing that the same three FL parameters can be used for the extraction and the scrubbing section. The Co-Ni-Na ion balance was used in the method validation tests at conditions that were similar to the designed plant. In principle, the FL model is also able to design the stripping and pre-loading sections by including H-C272 exchange data.
References
Kihlblom, C. 2021. Separation of Cobalt and Nickel using CYANEX 272 for Solvent Extraction in the presence of other contaminates in sulphate based leaching solution. Master’s Thesis. Boliden Mineral AB, Finland.
Mans, N. 2019. The cobalt-nickel pertraction refinery to process recycled spent catalysts leach solutions. MSc Thesis. North-West University, South Africa.
Mans, N., Van Der Westhuizen, D., Bruinsma, D., Cole, P., Du Toit, J., Munnik, E., Coates, A., Coetzee, V., Krieg, H. 2020. Cobalt–Nickel Pertraction Refinery to Process Pregnant Leach Solution from Recycled Spent Catalysts Part 1: Cobalt Extraction from a Binary System. Solvent Extraction and Ion Exchange, vol. 38, no. 4, pp. 441–454. https://doi.org/10.1080/07366299.2020.1729328
Nicol, M. 2008. Hydrometallurgy Theory and Practice, UCT Masters programme: presented by Emeritus Professor Mike Nicol. Rodrigues, I.R., Deferm, C., Binnemans, K., Riaño, S. 2022. Separation of cobalt and nickel via solvent extraction with Cyanex-272: Batch experiments and comparison of mixer-settlers and an agitated column as contactors for continuous countercurrent extraction. Separation and Purification Technology, vol. 296. https://doi.org/10.1016/j.seppur.2022.121326
Santanilla, A.J.M., Aliprandini, P., Benvenuti, J., Tenorio, J.A.S., Espinosa, D.C.R. 2021. Structure investigation for nickel and cobalt complexes formed during solvent extraction with the extractants Cyanex 272, Versatic 10 and their mixtures. Minerals Engineering, vol. 160. https://doi.org/10.1016/j. mineng.2020.106691
Seader, J.D., Henley, E.J., Roper, D.K. 2011. Separation Process Principles: Chemical and Biochemical Operations 3rd Edition. John Wiley & Sons, Inc., 2011. (ISBN 978-0-470-48183-7) u
Affiliation:
1Botswana International University of Science and Technology, Botswana
Correspondence to: F. Ntuli
Email: ntulif@biust.ac.bw
Dates:
Received: 19 Aug. 2024
Published: December 2024
How to cite: Nyangadzayi, T.V. and Ntuli, F. 2024. Optimization of chromium precipitation from ferrochrome leach solutions. Journal of the Southern African Institute of Mining and Metallurgy, vol. 124, no.12 pp. 725–730
DOI:
http://dx.doi.org/10.17159/24119717/702/2024
ORCiD:
T.V. Nyangadzayi
http://orcid.org/0009-0005-9698-9611
F. Ntuli
http://orcid.org/0000-0003-4045-902X
This paper is based on a presentation given at the Hydrometallurgy Conference 2024, 1-3 September 2024, Hazendal Wine Estate, Stellenbosch, Western Cape, South Africa
by T.V. Nyangadzayi1 and F. Ntuli1
Abstract
Chromium green is an essential metal with various applications in the paints, construction, electronics, and aerospace industries. The main source of chromium green is the carbo-thermic reduction of chromite ores, however, chromite ores are being heavily depleted on a global scale, hence the need to find alternative or secondary sources for the chromium. In order to meet the global demand for chromium there is a need to implement principles of the sustainable circular economy to keep chromium within the material loop. Ferrochrome slag and stainless steel slags are secondary resources that are potential sources of chromium. In this work, recovery of chromium from ferrochrome slag was investigated. The ferrochrome slag was alkaline leached using sodium hydroxide- sodium hypochlorite solution to reduce the use of potent reagents that have a potential negative environmental impact.
The leachate produced by oxidative alkaline leaching of ferrochrome slag contained hexavalent chromium, which was used to recover the extracted chromium through a two-stage process involving reduction and precipitation. Reduction of hexavalent Cr to trivalent Cr was investigated using anhydrous FeSO4 at concentrations of 5 g/L, 10 g/L, and 15 g/L. Precipitation was conducted by dosing the reduced leach solution with 1 M sodium hydroxide at dosages of 5 ml/L, 10 ml/L, and 15 ml/L. The experiments were designed using the Taguchi (L9) orthogonal array and analysed according to the ANOVA, general linear model. The optimized conditions for the reduction step were ferrous sulfate dosage of 5 g/L with a pH of 12, and for the precipitation step, 1 M sodium hydroxide at a dosage of 15 ml/L with a setting time of 90 minutes and pH of 7. Physical changes were observed during the two-step chromium recovery, with solution changing from a yellowish colour to dark green colour indicating completion of the reaction. The chromium recovery was found to be 93.3%.
Keywords ferrochrome slag, precipitation, reduction, chromium recovery, alkaline leaching
Introduction
Chromium green is an essential element with various applications in the paints, food, and tanneries industries (Table I). Its market share in 2022 was 50.7% or USD631 million, which was projected to increase by 5.2% to USD864.9 million in 2028, as the chromium green market demand rises (Horckmans et al., 2019; Pacific, America and Forecasts, 2020; Pfaff, 2022). The primary source of chromium is the carbothermic reduction of the chromite ores (Holappa and Xiao, 2004; Sahu, Biswas and Kapure, 2016). The ferrochrome slag and stainless steel slags are secondary sources, with a potential to be further processed to recover chromium. This is of benefit to the environment as waste valorization of the slags will eliminate the release of hexavalent chromium, which is carcinogenic, mutagenic, and toxic. Hexavalent chromium has been recovered as chromium hydroxide, which is then calcined to chromium green. The ferrochrome slag residue after alkaline leaching can then be utilized in the road and construction industry (Erdem et al., 2005; Hariharan and Murali Krishna, 2013; Acharya and Patro, 2016).
The ferrochrome slag was alkaline leached and the main challenges are the presence of iron and aluminium, which co-dissolute and co-precipitate with the chromium (Kocaoba and Akcin, 2004; Kim et al., 2016). There are many solution concentration, purification, and metal recovery methods that may be implemented, however, not all methods are applicable for liquors produced from the oxidative alkaline leaching process. The commonly used methods are solvent extraction, ion exchange, and precipitation (Kanari et al., 2020). Studies to recover chromium(III) and chromium(VI) have been done mainly for recovering chromium from waste waters from industries like tanneries (Mane et al., 2016, Kocaoba and Akcin, 2004). Precipitation as a method of recovery does produce high recoveries of chromium due to its
Table I
Uses of chromium green
Application
End-use industry
· Pigments · Paints
· Refractories · Coatings
· Abrasives · Construction
· Catalysts · Electronics
· Ceramics · Aerospace
· Rubber · Glass
high selectivity in creating a pure and homogeneous product whilst retaining iron and aluminium in the ferrochrome leach solution (Gheju, 2018).
Precipitation is selected as the metal recovery step, as it focuses mainly on recovering the aqueous chromium into a purified solid phase of chromium, with the exception that in some cases, solution purification will be required since precipitation is a nonselective technique, thus other components may co-precipitate from the solution. Alkaline leaching of ferrochrome slag favours the formation of Cr(VI), which is toxic and mutagenic and a major threat to the environment due to its mobility. Many precipitating agents may be considered for Cr(VI) ions, namely: barium chloride, lead sulfate, sodium hydroxide, calcium hydroxide, calcium carbonate, sodium carbonate, sodium hydrosulfide, iron sulfide, and sodium borohydride. However, some compounds like barium chloride precipitate chromium in its hexavalent form, which is a major problem (Ramakrishnaiah and Prathima, 2012). Kim et al., (2016), investigated the precipitation of chromium by barium chloride to form BaCrO4 after oxidative alkaline leaching of stainless steel slag to recover chromium. The method achieved recoveries of above 90% with the following Equation [1].
[1]
To recover chromium in its most stable form, which is environmentally friendly, a conversion step from Cr(VI) to Cr(III) should be undertaken and followed by precipitation to hydroxyl species Cr (OH)3. This method has high recoveries of chromium and is an environmentally friendly method. The conversion step is known as the reduction step where various reducing agents may be used (Fang et al., 2012). These reducing agents are hydrogen sulfide, hydrogen peroxide, sulphur dioxide, sodium metabisulphite, and ferrous sulfate (Ramakrishnaiah and Prathima, 2012). The commonly used reducing agents are sulphur dioxide and sodium metabisulphite at pH = 2 with a retention time of 30-40 min. Ferrous sulfate, however, is used in alkaline/neutral conditions. H2S and SO2 are very toxic reagents and come with environmental problems (Shen and Forssberg, 2003). Ferrous(II) sulfate is abundant, cost-effective, and has no complicated chemistry in the reduction of Cr(VI) and the reaction is presented in Equation [2] (Lokothwayo, 2007):
[2]
After the reduction step, precipitation is the last step in chromium recovery. There are various hydroxide precipitating agents, mainly sodium hydroxide and calcium hydroxide (Baijnath
Product type
· Chromium trioxide
· Chromic acid (mainly used for electroplating and corrosion inhibitor)
· To form chromium compounds like chromates and dichromate
et al., 2014). The factors that affect precipitating reaction kinetics that were considered in this study are pH, chromium(VI) concentration, precipitant dosage, and settling time. For high recoveries of chromium(III), pH values during the chemical precipitation step should be in the neutral value of pH = 7 (Fang et al., 2012). Chemical precipitation cannot be conducted at low concentrations of Cr(III) as it is not economic due to the high costs of chemicals and reagents used for precipitations and also the removal of the precipitates after the process (Falagán, Grail and Johnson, 2017). The Cr(III) produced during alkaline leaching is concentrated and therefore will have high recoveries of chromium(III) hydroxide (Ramakrishnaiah and Prathima, 2012). The precipitant dosage affects the recovery efficiency of Cr(III), and an optimum dosage should be used. For NaOH low dosages are required for high recoveries compared to Ca(OH)2. NaOH is more soluble than Ca(OH)2, which is a weak base, and reacts rapidly with Cr(III) (Baijnath et al., 2014). The precipitate yield increases with an increase in settling time, as this allows for coagulation of small precipitate particles (Baijnath et al., 2014). The major advantage of this precipitation method is that Cr(OH)3 has limited mobility and is safe for the environment as it is an essential nutrient in the human diet (Beukes, Pienaar and Lachmann, 2000). In selecting the precipitating agent, the costs and effectiveness of the precipitating agent were considered. NaOH is readily available and cost-effective at USD0.30/kg of NaOH, with high recoveries of above 99% and solubility in water of 111g/100ml at 25°C (Ramakrishnaiah and Prathima., 2011), whereas Ca(OH)2 is readily available at USD0.45/ kg and operates at low pH values of 2 with solubility in water at 0.173g/100ml at 25°C (Baijnath et al., 2014). Sodium hydroxide was selected as the precipitating agent. The overall equation (Equation [3]) for chemical precipitation using NaOH as the precipitant is:
The aim of the study was to optimize the reduction and precipitation of Cr from ferrochrome leach solutions using ferrous sulfate as a reducing agent and sodium hydroxide as a precipitating agent.
Materials and methods
Materials
5.0 g Fe-Cr slag was weighed and premixed with 20 ml of NaOH for homogeneity and 20 ml of NaOCl. The slurry formed was reacted isothermally in an alumina crucible in a temperature-controlled heating oven without stirring for 6 hours. After cooling the slurry was water-leached with distilled water for 1 hour at 25°C. The
Table IVa
Taguchi design results for the precipitation step
pregnant liquor was collected by filtration and analysed for Cr, Al, and Fe to check for Cr leachability through the use of a Thermo Fisher inductively coupled plasma atomic emission spectroscopy (ICP- AES), of which the results are shown in Table II
Ferrous sulfate was used for the reduction step in reducing Cr6+ to Cr3+ oxidation state. The sodium hydroxide at 1M was used for the precipitation step to precipitate the Cr3+ to chromium hydroxide. Chromium hydroxide was to be calcined to produce chromium green.
Experimental method
Ferrous sulfate was added to the pregnant liquor to reduce Cr(VI) to Cr(III). Ferrous sulfate was added at different concentrations (5 g/l, 10 g/l, and 15 g/l) to ensure complete reduction of the Cr(VI). The Cr(VI) was determined using diphenyl-carbazide as a reagent at a pH of 1 and analysed by a spectrophotometer at a maximum wavelength of 540 nm (Wiryawan et al., 2018). The reduced Cr was analysed by ICP-AES to determine the Cr recovered. The Cr(III) in the solution was then precipitated by NaOH at 1 M. The precipitate was left to settle at the bottom and separated from the solution. The spent solution was analysed by ICP-AES for the remaining Cr in the solution in order to determine Cr recovery (Gheju, 2018; Weng et al., 1994).
Table III
(a) Reduction step design of experiments according to Taguchi L9
array
Precipitation step design of experiments according to Taguchi L9
Table IVb
Taguchi design (L9) for the reduction step
The reduction step (9 experiments) and precipitation step (9 experiments) for Cr recovery experiments were designed according to the Taguchi L9 orthogonal array with the effect of the following factors: reductant dosage, Cr6+ content in solution, precipitant dosage, pH, and settling time were investigated. Table III illistrates the Taguchi L9 orthogonal array design of experiments. The terms neutral mean pH range of 7‒8, alkaline 8‒10, and very alkaline 10‒14.
Results and discussion
The recovery was divided into two stages namely reduction (hexavalent Cr to trivalent Cr) using anhydrous FeSO4 at different dosages, and precipitation using NaOH as the precipitant. The
Table V
Response
chromium, iron, and aluminium content (Table IVa and Table IV2b) was analysed using atomic absorption spectroscopy, AAS, and Thermo Scientific ICE 3000. The initial amount of chromium in the ferrochrome leach solution was found to be 30 mg/L. The Cr6+ was determined colourimetrically using diphenylcarbazide in an acid solution with a red to violet colour change as a positive test.
Reduction stage: The chromium ions in solution were found to be Cr6+, which are favourable in alkaline conditions. The Cr6+ ions were reduced to Cr3+ ions in the presence of anhydrous ferrous(II) sulfate with the colour changing from yellow-greenish to dark green (positive colour change for Cr3+ ions), as shown in Figure 1.
The Taguchi design was analysed using the Minitab 19 software, and the S/N ratios were calculated with the Delta being the difference between the highest response value from the lowest response values. The important factor was the ferrous sulfate dosage. The pH was in the range of 7.5‒12.0 and it showed less significance as shown in Table V.
According to the main effects plot in Figure 2, the optimum conditions to effectively reduce the Cr6+ to Cr3+ were determined. The colour change was seen from yellow-greenish to dark green indicating completion of the reaction. The Cr6+ ions were analysed and the smaller the better approach was selected. The ferrous sulfate dosage of 5 g/L was observed as the optimum conditions at a pH of 7.5.
Table VI
ANOVA-analysis of variance for the reduction step
Source DF Adj SS Adj MS F-Value P-Value
2 334,462 167,231 359,65 0 pH 2 0,171 0,086 0,18 0,838 Error 4 1,86 0,465
Total 8 336,493
Table VII
Response table for means for the reduction step
effects for means plot for the reduction step
The ANOVA (in Table VI) identifies the significance and importance of each factor and ferrous sulfate p-value was 0.000, in which the Null hypothesis of p=0.05 confidence proves that the parameter is very significant in the reduction step reaction (Gülcan, Karahan and Gürmen, 2020). The response table for means was used to determine the importance of the individual parameter and it is in agreement with the S/N ratios values, which is that ferrous sulfate is the important factor with a Delta of 12.981 versus that of pH of 0.333 in Table VII. In Figure 3, the main effects plot does show that the pH is almost constant in the range of 7.5 to 12.0.
The experiments were designed according to Taguchi and analysed using ANOVA, and the Level 9 (33) orthogonal array was selected. The response table for signal to noise ratios (Table VIII), employing the optimization approach of smaller is better, shows the largest Delta as 5.073, thereby indicating precipitant dosage as the main important effect. The precipitant used was 1 M sodium hydroxide at room temperature. The settling time was the second factor, which has an effect on the precipitation step as small colloids were formed and required a lot of time to settle.
The response table for means (Table IX, agrees with the Table VIII for S/N ratios, with sodium hydroxide dosage as the main factor that affects the precipitation step.
Table VIII
Response table for signal to noise ratios for precipitation step
Level
Table IX
Response table for means for precipitation step
for precipitation step
Table X
ANOVA for the precipitation step
dosage 2 3,091 15,457 0,92 0,521
time 2 1,975 0,9877 0,59 0,63
Figure 4 shows the main effects plot for the precipitation step, and the optimum conditions to effectively recover the chromium as chromium hydroxide are NaOH dosage of 15 ml/L at 1 M, the pH of 7, and settling time of 90 mins. As the reaction progresses, the increase in NaOH dosage results in Cr being reduced and precipitated into chromium hydroxide. The longer the settling period, the more the chromium is removed from the solution.
The Taguchi design was analysed according to the ANOVA, general linear model in Table X, and the p-values were very significant for NaOH dosage, pH, and settling time at 0.521, 0.761, and 0.630, respectively. The lower the value of p-value (near to zero) of the parameters, the more successful the precipitation step (Essa et al., 2022).
Chromium in solution was reduced, precipitated, and investigated according to Taguchi L9 (33) orthogonal arrays. The chromium concentration was measured at different intervals of 10, 20, 30, 40, 50, 60, 70, 80, and 90 minutes, using the AAS. The chromium recovery was found to be 93.3% from the solution. In the first 10 minutes, there was a rapid increase in chromium removed in solution, which is due to the fact that the reaction is very fast, and anhydrous ferrous sulfate and sodium hydroxide at 1 M were used.
5—Graph for % chromium recovered over a period of time
These conditions were strongly alkaline and thereby improving the chromium removed from the solution. Figure 5 shows the recovery graph of chromium from the leachate solution. As the reaction progresses, the percentage recoveries of chromium started to stabilize and become almost constant at 93.3%, which was the highest recorded.
The hydroxide precipitation of chromium by the alkali-precipitating agent sodium hydroxide has proven to be effective. With chromium being amphoteric (soluble at both acidic and alkaline conditions) at a pH of 6-9, precipitation is favourable. The Fe3+ and Al3+ ions however, are effectively precipitated at a pH of 2 and 3, respectively. Due to Cr3+ ions being precipitated at a pH range of 6-9, the sodium hydroxide effectively precipitated chromium with minimal interference to co-precipitation from Fe3+ and Al3+ ions.
The recovery of chromium from the leachate was designed and analysed using Taguchi (L9 orthogonal array) and ANOVA respectively. The recovery of chromium from the leachate was calculated and found to be 93.3% at optimum conditions for the reduction step of ferrous sulfate dosage – 5 g/L and pH-7.5, and for the precipitation step: sodium hydroxide (1 M) dosage - 15 ml/L, pH - 7, and settling time – 90 minutes. These optimum conditions allowed for recoveries of the chromium from the solution at 93.3%. The chromium extracted was roughly 4.55 mg/g of slag.
References
Acharya, P.K., Patro, S.K. 2016. Utilization of ferrochrome wastes such as ferrochrome ash and ferrochrome slag in concrete manufacturing, Waste Management and Research, vol. 34, no. 8, pp. 764–774. doi: 10.1177/0734242X16654751
Baijnath, L.L., Gautam, V., Yadav, V.L. 2014. A Comparative Study of the Removal Efficiency of Calcium Hydroxide and Sodium Hydroxide as Precipitating Agents for Chromium (III). Journal of Civil Engineering and Environmental Technology, vol. 1, no. 1, pp. 17–20. https://krishisanskriti.org/vol_ image/03Jul20151207216.pdf
Beukes, J.P., Pienaar, J.J., Lachmann, G. 2000. The reduction of hexavalent chromium by sulphite in wastewater - An explanation of the observed reactivity pattern. Water SA, vol. 26, no. 3, pp. 393–395.
Erdem, M. 2005. Hexavalent chromium removal by ferrochromium slag. Journal of Hazardous Materials, vol. 126, no. 1–3, pp. 176–182. doi: 10.1016/j.jhazmat.2005.06.017
Essa, W. K. 2022. Polyethylene Terephthalate Nanofiber-MultiWalled Carbon Nanotube Composite, vol. 25. doi: 10.3390/w14081242
Falagán, C., Grail, B.M., Johnson, D.B. 2017. New approaches for extracting and recovering metals from mine tailings. Minerals Engineering, vol. 106, pp. 71–78. doi: 10.1016/j. mineng.2016.10.008
Fang, H.X., Li, H.Y., Xie, B. 2012. ‘Effective chromium extraction from chromium-containing vanadium slag by sodium roasting and water leaching’. ISIJ International, vol. 52, no. 11, pp. 1958–1965. doi: 10.2355/isijinternational.52.1958
Gheju, M. 2018. Progress in understanding the mechanism of CrVI Removal in Fe0-based filtration systems. Water (Switzerland), vol. 10, no. 5. doi: 10.3390/w10050651
Gülcan, M.F., Karahan, B.D., Gürmen, S. 2020. Leaching of iron and chromium from an indigenous ferro chromium alloy via a rotary evaporator: optimum conditions determination and kinetic analysis. Journal of Materials Research and Technology, vol. 9, no. 6, pp. 14103–14115. doi: 10.1016/j.jmrt.2020.09.133
Hariharan, A.V.L.N.S.H., Murali Krishna, D. 2013. Recovery of chromium from ferrochrome slag. Journal of Chemical and Pharmaceutical Research, vol. 5, no. 5, pp. 250–252. doi: 10.15680/ijirset.2015.0405041
Holappa, L., Xiao, Y. 2004. Slags in ferroalloys production—review of present knowledge Chromium–oxygen system, (January), pp. 25–28. https://hdl.handle.net/10520/AJA0038223X-2944
Horckmans, L. 2019. Multi-analytical characterization of slags to determine the chromium concentration for a possible reextraction. Minerals, vol. 9, no. 10, pp. 1–14. doi: 10.3390/ min9100646
Kanari, N. 2020. Reactivity of low-grade chromite concentrates towards chlorinating atmospheres. Materials, vol. 13, no. 20, pp. 1–18. doi: 10.3390/ma13204470
Kim, E. 2016. New method for selective Cr recovery from stainless steel slag by NaOCl assisted alkaline leaching and consecutive
BaCrO4 precipitation. Chemical Engineering Journal Elsevier B.V., vol. 295, no. 2016, pp. 542–551. doi: 10.1016/j. cej.2016.03.073
Kocaoba, S., Akcin, G. 2004. Chromium (III) removal from wastewaters by a weakly acidic resin containing carboxylic groups. Adsorption Science and Technology, vol. 22, no. 5, pp. 401–410. doi: 10.1260/0263617042863020
Lokothwayo, R.B. 2007. Hexavalent chromium analysis, reduction and stabilization in cement and concrete, p. 142. http://hdl. handle.net/10539/4649
Mane, C.P. 2016. Hexavalent chromium recovery by liquid–liquid extraction with 2-octylaminopyridine from acidic chloride media and its sequential separation from other heavy toxic metal ions. Arabian Journal of Chemistry, vol. 9, pp. S1420–S1427. King Saud University. doi: 10.1016/j.arabjc.2012.03.021
Pacific, A., America, S., Forecasts, S. 2020. Regional Insights, (Cr VI), pp. 2020–2025. RI_43079 www.reportinsights. com/industry-forecasts/chromium-salt-marketresearchreport_43079
Pfaff, G. 2022. Chromium oxide pigments. Physical Sciences Reviews, vol. 7, no. 2, pp. 103–108. doi: 10.1515/psr-2020-0159
Ramakrishnaiah, C.R., PrathimaB. 2011. Hexavalent Chromium Removal by Chemical Precipitation Method: A Comparative Study. International Journal of Environmental Research and Development, pp. 41–49.
Ramakrishnaiah, C.R., Prathima, B. 2012. Hexavalent Chromium Removal From Industrial Watsewater By Chemical Precipitation Method. International Journal of Engineering Research and Applications, vol. 2, no. 2, pp. 599–603.
Sahu, N., Biswas, A., Kapure, G.U. 2016. A Short Review on Utilization of Ferrochromium Slag. Mineral Processing and Extractive Metallurgy Review, vol. 37, no. 4, pp. 211–219. doi: 10.1080/08827508.2016.1168415
Shen, H., Forssberg, E. 2003. An overview of recovery of metals from slags. Waste Management, vol. 23, no. 10, pp. 933–949. doi: 10.1016/S0956-053X(02)00164-2
Weng, C.H. 1994. Chromium leaching behavior in soil derived from chromite ore processing waste. Science of The Total Environment Elsevier, vol. 154, no. 1, pp. 71–86. doi: 10.1016/00489697(94)90615-7
Wiryawan, A. 2018. ‘120-499-2-Pb’. Journal of Environmental Engineering and Sustainable Technology, vol. 5, no. 01, pp. 37–46.
Zhao, Q. 2014. Sulfuric acid leaching of South African chromite. Part 1: Study on leaching behavior. International Journal of Mineral Processing, vol. 130, pp. 95–101. Elsevier B.V. doi: 10.1016/j.minpro.2014.04.002 u
Affiliation:
1Mintek, Randburg, South Africa, 2Department of Chemical Engineering, University of Cape Town, South Africa
Correspondence to:
S.W. Robertson
Email: Stefanr@Mintek.co.za
Dates:
Received: 16 Aug. 2024
Published: December 2024
How to cite: Robertson, S.W. and Petersen, J. 2024. Modelling unsaturated dualphase flowthrough crushed ores for heap leaching. Journal of the Southern African Institute of Mining and Metallurgy, vol. 124, no.12 pp. 731–736
DOI:
http://dx.doi.org/10.17159/24119717/697/2024
ORCiD:
J. Petersen
http://orcid.org/0000-0003-2976-308X
by S.W. Robertson1 and J. Petersen2
Abstract
Heap leaching is used extensively for the processing of low-grade copper, gold, and uranium ores. The hydrodynamics is often the most important factor that limits the rate of metal recovery. Over the past decades the author has performed physical and hydraulic testing of a large number of ore samples considered for heap leaching. The data were reviewed to investigate the effect of physical properties such as particle size distribution (PSD) and bulk density on the hydrology. The unsaturated flow through the bed is traditionally modelled with soil science models such as Brooks-Corey (BC) and Van Genuchten-Mualem (VGM), which relate the hydraulic conductivity to the degree of saturation, also known as the hydraulic conductivity function (HCF). However, most authors found a disconnect between the saturated hydraulic conductivity (KS) and the rest of the HCF, which is explained as resulting from a transition from capillary-to gravity-controlled flow. However, the author found no such transition, and found the flow to be governed by capillary flow throughout. Traditional BC or VGM fits were found to be appropriate, however it was necessary to modify the model to include a point of inflection, above which the hydraulic conductivity remains constant while the moisture content keeps on increasing. It was proposed that this is the result of unconnected or poorly connected pores, which fill with solution but do not create additional flow channels. The point of discontinuity was also found to correspond with the air entry point, measured independently from the air conductivity curves. On average, the air entry point corresponds to the experiential rule that the void saturation should remain below 65% for aerated heaps.
Keywords
heap leaching, modelling, solution flow, air conductivity
This paper is based on a presentation given at the Hydrometallurgy Conference 2024, 1-3 September 2024, Hazendal Wine Estate, Stellenbosch, Western Cape, South Africa Introduction
Heap leaching accounts for approximately 17% of global gold production and 21% of global copper production (Marsden et al., 2017; Basov, 2015). Heap hydraulics are often the limiting factor, which determine the rate of metal dissolution. Poor solution permeability may limit the rate at which valuable metals can be flushed from the heap, whereas poor solution contact may result in uneven wetting and incomplete extraction. Over the years a number of operations have experienced problems with solution permeability, e.g., Benkala (Whiterow, 2013), Cerro Verde (Galdos et al., 2013), and Chuquicamata (Ramírez et al., 2019). Prior to heap leach design it is therefore necessary to perform physical and hydraulic testing of the crushed ores and agglomerates. This typically include compression tests to determine the bulk density profiles during compaction, as well as hydrodynamic column tests (Cherkaev, 2019; Pyper et al., 2015; Guzman et al., 2013; Milczarek et al., 2013; Robertson et al., 2013; Ilankoon and Neethling, 2012; Lupo, 2011; Afewu, 2009; Guzman et al., 2008). A number of benchmarks have been established by experience, for example, the bulk density should not exceed 1.9 t/m3 (equivalent to 30% porosity) (Robertson et al., 2013; Guzman et al., 2013). Higher compactions will result in insufficient voidage available for solution flow, resulting in ponding or channeling. Furthermore, it was established that the degree of void saturation during percolation should not exceed 65% for aerated heaps, above which the heaps will not conduct air. For non-aerated heaps, the degree of saturation should not exceed 85% to maintain slope stability (Robertson et al., 2013; Milczarek et al., 2012). The saturated hydraulic conductivity (Ks) should be at least 100 × the target ‘unsaturated’ application rate (Pyper et al., 2015; Milczarek et al., 2013; Robertson et al., 2013).
Summary of correlations used
Brooks-Corey (BC) Van Genuchten-Mualem (VGM)
The water retention curve (WRC) and the hydraulic conductivity function (HCF), which are rooted in pore-scale capillary and viscous flows, often form part of analytical and numerical models for flow and transport in unsaturated porous media. The WRC describes the relationship between soil matric potential (capillary head), h (m), and the soil water content, θ (m3/m3). The soil water content is typically represented as dimensionless effective saturation, Se (Equation [1]), where θs and θr are the soil saturated and residual volumetric contents, respectively (Assouline and Or, 2013). The HCF is often expressed in terms of the relative hydraulic conductivity (Kr), which is scaled by dividing the hydraulic conductivity (Kw) of the solution by the saturated hydraulic conductivity, Ks (Equation [2]).
Hydraulic properties of unsaturated soils have been modelled by authors such as Burdine (1953) and Mualem (1976), who attribute to the soil a single unimodal pore size distribution governed by capillary action. Burdine’s model (1953) defines the relative solution conductivity (Kr) in terms of the ratio between the square of the mean hydraulic radius (rH) of the unsaturated soil at effective saturation (Se) to the square of the mean hydraulic radius of the soil at full saturation (Se = 1). Applying the capillary law (rH = C / h), Burdine derived Equation [3] (Table I), where h is the capillary pressure, γ is the pore-size interaction term, and b and q are constants. For the Burdine model, γ = 2, b = 2 and q = 1. Mualem (1976) replaced the pore configuration with a pair of capillary elements whose lengths are proportional to their respective radii, and, by comparison of 45 soils, he found γ = 0.5 to provide the best fit when using measured Ks values as matching point. The Mualem model, also described by Equation [3], has γ = 0.5, b = 1 and q = 2. Brooks and Corey (BC) (1964) observed that for a large number of experimental data sets, the WRC can be represented by Equation [4] (Table I), where λ is referred to as the pore-size distribution index and is usually in the range of 0.3 to 10 (Kosugi et al., 2002). The BC function is discontinuous, and has a distinct air-entry head,
Hydrodynamic column tests (HCT) are performed in a 15 or 20 cm diameter column (75 cm tall), loaded with agglomerates at a uniform target bulk density and irrigated at incremental solution application rates (Figure 1). From the solution balance tracked throughout the duration of the test follows the hydraulic conductivity, moisture content and degree of saturation. Also obtained from the HCT test are the air conductivity, the drainTable I
hc, above which the soil is assumed to be saturated. Substituting the BC (Equation [4]) into Mualem’s formula (Equation [3]) yields the HCF (Equation [5]), where np is a fitting parameter (np = (2 + 3λ) / λ).
A continuous WRC function (Equation [7]) was also proposed by Van Genuchten (1980), where m and n are fitting parameters, and a corresponds approximately to the inverse of the air entry value. Van Genuchten (1980) further proposed the relationship of m = 1 – 1 / n (n > 1, 0 < m < 1) and substituted Equation [7] into Mualem’s formula (Equation [3]) to derive the Van GenuchtenMualem (VGM) HCF (Equation [8]). The VGM model has found widespread application and has been applied to heap leaching. However, in most cases authors have only measured the WRC and Ks, and calculated the HCF from Equation [8]. Several authors have found a discontinuity between the HCF and the measured Ks value, which is attributed to a transition between capillary- and gravitycontrolled flow regimes (Afewu, 2009; Mohanty et al., 1997; Luckner et al., 1989; Guzman et al., 2008, and Gerke and Van Genuchten, 1993).
The VGM model was further adapted by Parker et al. (1987) to describe the air conductivity function (ACF) (Equation [9]), where Kg is the air conductivity, and Kg max is the air conductivity when only residual moisture is present (corresponding to Sg = 0). Sg is the relative degree of gaseous saturation, as defined by Equation [10], and θaep is the air entry point, or the maximum solution moisture content (corresponding to Sg = 1) at which the air conductivity drops off completely as the bed becomes saturated.
Experimental
down curve, and the total, micro- and macro-porosity. Once ponding occurs, the column is allowed to saturate, and the saturated hydraulic conductivity is measured by passing solution upwards through the column from a constant-head reservoir. Finally, the column is allowed to drain for 2 to 3 days to generate a drain-down curve. The air permeability is determined according to the method described by Milczarek et al. (2013) by measuring the pressure drop as a function of flux at each moisture content. Experience shows that for copper oxide leaching the maximum liquid saturation should be kept below 85% for geotechnical stability. For aerated heaps the bed should have an air permeability of at least 100 darcys and the degree of void saturation during percolation should not exceed 60% to 65% (Robertson et al., 2013).
Results and discussion
The unsaturated flow in the bed, measured in the hydrodynamic column tests, is modelled with traditional soil capillary models such as the Van Genuchten-Mualem (VGM) and Brooks Corey (BC), in order to derive the hydraulic conductivity function (HCF), which represents the relative hydraulic conductivity (Kr) against the dimensionless effective saturation (Se), and the air conductivity function (ACF) (Equations [5], [8] and [9], and Table I). The hydraulic conductivity functions generated for the hydrodynamic column tests are mostly S-shaped curves if the measured Ks data
point is included in the data set. This type of curve cannot be modelled by the conventional BC or VGM functions, except if Ks is made a fitting parameter (Mohanty et al., 1997; Luckner et al., 1989). However, instead of modelling the data as a continuous S- or J-curve, the author proposes a discontinuous J-curve to be the most realistic. The J-curve includes an inflection point, (Se max), above which Kr remains equal to 1 (Equations [11] and [12]). Two examples of this approach are plotted in Figure 2. Also plotted in Figure 3 are the air conductivity curves. The modified VGM model (Equation [9]) was used to fit the air conductivity function (ACF), where Kg max (air conductivity when only residual moisture is present) and θaep (the air entry point) are derived from the data. The fact that the moisture content keeps increasing above the point of discontinuity was ascribed to the presence of ‘dead voids’ or poorly connected pores, which fill up but do then generate additional flow channels.
Figures 4 and 5 are plotted in order of increasing fines (-4.75 mm) content over the x-axis. The distribution of volumetric void fractions in the ore bed is plotted on the y-axis in Figure 4. The bed volume is divided into residual moisture (θr), the mobile moisture (defined as the increased moisture over and above the residual moisture) during irrigation governed by BC or VGM capillary flow (θmax - θr), the volume fraction comprising ‘dead voids’ (θs - θmax), and the volume fraction occupied by solids (1 - θs).
Also plotted on the y-axis is the air entry point (θaep) derived from the gas conductivity curves (Equation [9]). The close agreement between θaep and θmax suggests that the air entry point occurs close to the point of discontinuity in the HCF. This may be explained by the fact that no new solution flow channels are expected to form once all the air flow channels are filled up with
solution (one would expect air flow channels to be converted into solution flow channels as the moisture content increases).
The normalized void fractions (i.e., excluding the volume fraction occupied by solids) are plotted in Figure 5, as this allows visual comparison with some of the design targets used in geomechanical (hydrology and physical) testing, which are also plotted on the same graph. The design targets include the requirement that 65% void saturation (S ≤ 0.65) should not be exceeded in order to achieve proper aeration, and 85% void saturation (S ≤ 0.85) should not be exceeded in order to maintain geotechnical stability (Robertson et al., 2013; Milczarek et al., 2012). The 65% saturation rule appears to provide a good design target for heap aeration, as it agrees visually with the air entry point on average. The average air entry point occurs at S = 0.66. In other words, 65% void saturation provides on average a good estimate of the air entry point (θaep) above which gas does not pass through the bed and above which the heap cannot be aerated.
An air entry point substantially below 65% may be indicative of poor pore interconnectivity, whereas an air entry point above 65% suggests pores with good interconnectivity. It can also be seen from Figure 5 that coarser samples generally have a lower air entry point and that the proportion of ‘dead voids’ (θs -θmax) generally decreases as the fines content increases (from left to right over the x-axis). Coarser particles therefore contribute more to the formation of ‘dead voids’, which is counter-intuitive, as one would expect coarser rocks to generate larger macro-voids and hence larger flow channels. However, the formation of larger voids may not necessarily translate into larger flow channels, as the pores may not be well connected or may be blocked with finer material such as silt and clay.
The target for geotechnical stability (S ≤ 0.85) occurs above the air entry point and the point of discontinuity in most cases. Hence the bed will become geotechnically unstable during the filling up of the ‘dead voids’ and starts to break apart since further increase in moisture cannot be directed towards creating new flow channels.
High saturation may occur in non-aerated heaps (e.g., copper oxides) at very high bulk densities or due to non-homogeneity, or if the bed contains a high silt and clay content, which increases the compressibility of the bed. Increased water content can reduce the stability of the rock slope by increasing the unit weight of the soil. The increased water pressure may cause instability if the increased load exceeds the shear strength of the slope. At low moisture contents, for example, the pore pressure is negative (suction), but this is converted into positive pore pressure at higher moisture contents, resulting in increased pressure exerted by the water downwards and sideways in the heap. If the material is dry or nonsaturated, an increase in load compresses and compacts the mass and increases shear strength as grains and rock fragments come in closer contact with each other. However, increasing pore pressure with increased moisture content has a buoying effect, reducing the friction and shear strength.
Conclusions and recommendations
Whereas unsaturated flow models have been applied almost exclusively to material containing lower particle sizes (e.g., clay -0.002 mm, silt 0.002-0.075 mm, and sand 0.075-2 mm), typical heap leach material spans a wider range, with top sizes typically between 6 mm and 25 mm. It was shown that traditional capillary models, such as BC and VGM, may be applied to coarser heap leach samples at lower flowrates. The hydraulic conductivity function was however best described as a discontinuous J-curve, which allows the measured saturated hydraulic conductivity to be incorporated. The point of discontinuity coincided with the air entry point, measured independently. Hence it was proposed that at higher moisture content, ‘unconnected’ pores are filled up with moisture, without generating more flow paths. On average, the rule of thumb of <60% to 65% saturation required for forced aeration appears correct, however, the air entry point varied with fines content.
The VGM fit is popular since it provides a closed-form, continuous function suitable for mathematical models. Furthermore, most of the work publicised to date has been done on sand, where the effect of ‘dead voids’ will be less important.
However, the results obtained in the laboratory do not suggest dual-porosity flow and indicate that flow is governed by capillary forces up to the air entry point (a single discontinuous VGM curve). However, the conventional approach to heap leach data, which comprises measuring the WRC and Ks, and then using the VGM model to predict the HCF curve, is unsatisfactory. The benefit of measuring both the HCF and the Ks was demonstrated in this work as well as the importance of performing hydrodynamic column tests.
References
Afewu, K.I. 2009. Development and testing of a 2D axisymmetric water flow and solute transport model for heap leaching, PhD thesis, The University of British Columbia.
Assouline, S, Or, D. 2013. Conceptual and parametric representation of soil hydraulic properties: A Review. doi:10.2136/ vzj2013.07.0121, www.VadoseZoneJournal.org
Basov, V. 2015. Heap Leach: Mining’s breakthrough technology, https://www.mining.com/ heap-leach-minings-breakthroughtechnology [accessed on 9 June 2020].
Brooks, R.H., Corey, A.T. 1964. Hydraulic properties of porous media, Hydrology Papers No. 3, Colorado State University, Fort Collins, Colorado.
Burdine, N.T. 1953. Relative permeability calculations from poresize distribution data. Transactions of the American Institute of Mining and Metallurgical Engineers, vol. 198, pp. 71–77. https://onepetro.org/JPT/article/5/03/71/162358/RelativePermeability-Calculations-From-Pore-Size
Cherkaev, A. 2019. The art of soaking rocks: systematic study of liquid and solute flow in packed rock beds in the context of heap leaching, PhD thesis, University of Cape Town, pp. 100–110.
Galdos, H., Guevara, J., Saavedra, A. 2013. Geotechnical Lessons Learned from the Operation of Cerro Verde’s Crush Leach Pad 4-A. 5th International Seminar on Process Hydrometallurgy, Santiago, Chile. https://www.scribd.com/document/486219698/ Geotechnical-lessons-learned-from-the-operation-of-CerroVerde-s-Crush-Leach-Pad-4-A
Gerke, H.H., Van Genuchten, M.T. 1993. A Dual-Porosity Model for Simulating the Preferential Movement of Water and Solutes in Structured Porous Media. Water Resources Research, vol. 29, pp. 305–319.
Guzman, A., Scheffel, R., Flaherty, S. 2008. The Fundamentals of Physical Characterisation of Ore for Heap Leach. Sixth International Symposium on Hydrometallurgy, Y.A. Courtney et al., eds., Phoenix, AZ, Society for Mining, Metallurgy and Exploration Inc., Englewood, CO.
Ilankoon, I.M.S., Neethling, S.J. 2012. Hysteresis in unsaturated flow in packed beds and heaps Minerals Engineering, vol. 35, pp. 1–8.
Luckner, L., Van Genucten, M. T., Nielsen, D.R. 1989. A consistent set of parametric models for the two-phase flow of immiscible fluids in the subsurface. Water Resources Research, vol. 25, pp. 2187–2193.
Lupo, J.F. 2011. Sustainability issues related to heap leaching operations, Percolation leaching: The status globally and in Southern Africa. The Southern African Institute of Mining and Metallurgy, Misty Hills, Muldersdrift, South Africa.
Marsden, J., Botz, M.M. 2017. Heap leach modelling: A review of approaches to metal production forecasting. Minerals and Mineral Processing, vol. 34, no. 2, pp. 53–64.
Milczarek, M., Banerjee, M., Yao, T., Keller, J., Shrestha, P. 2012. Ore permeability methods of evaluation and application to heap leach optimisation, Geomet 2012. International Seminar on Geometallurgy, Santiago, Chile.
Milczarek, M., Yao, T., Banerjee, M., Keller, J. 2013. Ore permeability methods of evaluation and application to heap leach optimisation, Heap Leach Solutions, Vancouver, Canada. https://www. geosystemsanalysis.com/publications/Milczarek_et_al_Heap_ Leach_2013_Ore_Permeability.pdf
Mohanty, M.P., Bowman, R.S., Hendrickx, J.M.H., Van Genuchten, M.T. 1997. New piecewise-continuous hydraulic functions for modelling preferential flow in an intermittent-flood-irrigation field. Water Resources Research, vol. 33, no. 9, pp. 2049–2063.
Mualem, Y. 1976. A new model for predicting the hydraulic conductivity of unsaturated porous media. Water Resources Research, vol. 12, no. 3, pp. 513–522.
Parker, J.C., Lenhard, R.J., Kuppusamy, T. 1987. A parametric model for constitutive properties governing multiphase flow in porous media. Water Resources Research, vol. 23, no. 4, pp. 618–627.
Pyper, R., Kappes, D.W., Albert, T. 2015. Evaluation of agglomerates using the Kappes Percolation Test, Heap Leach Solutions, Reno Nevada, pp. 319–325.
Ramírez, L., Font, J., Saldaña, M. 2019. Chuquicamata Improvements for Low Permeability Heap Leaching Dump. 11th International Seminar on Process Hydrometallurgy, Santiago, Chile.
Robertson, S.W., Guzman, A., Miller, G. 2013. Implications of hydraulic behaviour testing for heap leach modelling. Hydroprocess: 5th International Seminar on Process Hydrometallurgy, Santiago, Chile.
Robertson, S.W., Basson, P., Van Staden, P.J., Petersen, J. 2023. Properties governing the flow of solution and air through crushed ore for heap leaching: Part II: Unsaturated dual-phase flow. Hydrometallurgy, vol. 215, p. 105990.
Van Genuchten, M. T. 1980. A closed-form equation for predicting the hydraulic conductivity of unsaturated soils. Soil Science Society of America, vol. 44, no. 5.
Whiterow, P. 2013. Update – Frontier Mining says Benkala now generating cash for the first time in its history. https://www. proactiveinvestors.com.au/companies/news/54061/updatefrontier-mining-says-benkala-now-generating-cash-for-firsttime-in-its-history-64083.html [accessed on 9 June 2020]. u
Nomenclature
A constant
Ai
a constant
Β constant
Bo Bond number
C constant
h m capillary head
hc m air entry head
Kw cm/s hydraulic conductivity of solution
Ks cm/s saturated hydraulic conductivity
Kr relative solution conductivity
Kg cm/s air conductivity
Kg max cm/s maximum air conductivity, air conductivity at residual moisture
b, q, m, n, np, ng fitting constants
rH m hydraulic radius
S m3/m3 degree of saturation
Se effective saturation
Se max effective saturation at air entry point
Sg relative degree of gaseous saturation
γ fitting constant
δ kPa stress
ε m3/m3 bed porosity, voidage
λ fitting constants
θ m3/m3 moisture content
θr
θs
θaep
θmax
m3/m3 residual moisture content
m3/m3 saturated moisture content
m3/m3 air entry point
m3/m3 moisture content at Se max
µ kg/m/s viscosity
ρ kg/m3 density
Affiliation:
1Crystallization and Precipitation Unit, Department of Chemical Engineering, University of Cape Town, South Africa
2Hydrometallurgy Research Group, Department of Chemical Engineering, University of Cape Town, South Africa
Correspondence to: J. Chivavava
Email: jemitias.chivavava@uct.ac.za
Dates:
Received: 23 Aug. 2024
Published: December 2024
How to cite:
Chivavava, J., Petersen, J., and Lewis, A.E. 2024. Comparing the recovery of rare earth elements from ion-adsorption clay leach solutions using various precipitants. Journal of the Southern African Institute of Mining and Metallurgy, vol. 124, no.12 pp. 737–746
DOI:
http://dx.doi.org/10.17159/24119717/730/2024
ORCID:
J. Chivavava
http://orcid.org/0000-0002-4640-9640
J. Petersen
http://orcid.org/0000-0003-2976-308X
A.E. Lewis
http://orcid.org/0000-0001-6544-1227
This paper is based on a presentation given at the Hydrometallurgy Conference 2024, 1-3 September 2024, Hazendal Wine Estate, Stellenbosch, Western Cape, South Africa
by J. Chivavava1, J. Petersen2, and A.E. Lewis1
Abstract
Rare earth elements (REEs) have special properties that prompted their extensive use in high-tech applications. The demand for REE has, therefore, increased over the past years, resulting in the supply risk of the materials. Extraction from non-conventional low-grade ores, like easy-to-mine ion-adsorption clays (IACs), by hydrometallurgical methods is being explored to supplement the supply of REEs. The extraction of REEs from low tenor IAC leach solutions requires enrichment using cost-effective methods such as precipitation. Therefore, the aim of this study was to understand the recovery of REEs from IAC leach solutions using various reagents for precipitation. In the first part of the study, recoveries of REEs from IAC leach solutions through direct precipitation using H2C2O4 and NH4HCO3, as well as antisolvent crystallization using C2H5OH, were predicted via thermodynamic modelling using OLI Stream Analyzer. Verification experiments were then conducted through the use of an agitated reactor. Simulation results showed that high yields of REEs were possible using each of the reagents, but large quantities of C2H5OH were required. Experimental results confirmed the high yields predicted from simulations. Precipitation with H2C2O4 was found to selectively recover REEs while rejecting Al. However, utilization of NH4HCO3 and C2H5OH resulted in the co-precipitation of Al. Furthermore, the yield of Y from antisolvent crystallization was significantly lower than the theoretical value. The product recovered from antisolvent crystallization consisted of well-faceted, large crystalline particles, which filtered faster than the fine, amorphous REE carbonates recovered using NH4HCO3. REE oxalates were crystalline, larger than the REE carbonates and, overall, showed the highest filtration rate.
Keywords rare earth elements, antisolvent crystallization, precipitation, ion adsorption clays
Introduction
Rare earth elements (REEs) are 17 metallic elements consisting of 15 lanthanides, scandium, and yttrium. The materials have special physico-chemical properties due to their screened 4f electrons and have several applications in the electronics, renewable energy, automobile, telecommunication, aerospace and security industry (Xie et al., 2014). The demand for REEs has increased substantially over recent years due to new applications in the energy transition economy (Korkmaz et al., 2020). Furthermore, geo-political factors have resulted in the global supply risk of REEs such as Nd and Dy, which are regarded as critical materials in the USA and Europe (Grohol and Veeh, 2023). In order to avoid shortages in the supply of REEs, different economies have been implementing strategies such as circular economy, stockpiling, and diversification of REE sources (Salim et al., 2022).
Although production from high-grade primary ores such as bastnaesite (Ce,La,Nd)(CO3)F, monazite (Ce,La,Nd)PO4, xenotime (YPO4), and loparite (Soltani et al., 2019; Wu et al., 2018) could be increased where the ores are available, the extraction of REEs from such ores is still faced with process and economic viability challenges. Harsh processing conditions and strict hazard management against radioactivity in the processing of monazite restricts its exploitation (Ahmed, 2017). Therefore, to supplement the current supply from conventional primary ores, there are attempts to recover REEs from spent products, tailings, and other non-conventional ores. However, the recycling of REEs from spent permanent magnets, nickel-metal hydride batteries, and catalysts can only partially resolve the supply risk of REEs. Thus, extraction of REEs from tailings like phosphogypsum and red mud, from the processing of phosphate minerals and bauxite, respectively, is necessary to secure and diversify the supply chains.
The supply of heavy REEs (HREEs), i.e., Sm (62) to Lu (71) and Y(39), remains insecure and even primary ores, such as bastnaesite, have low HREE content (Gupta and Krishnamurthy, 2005; Schulze et
al., 2017). Although ion-adsorption clays (IACs) have low grades of REEs, the ores are important sources of HREEs (Schulze et al., 2017). Thus, the extraction of REEs from IACs in China has contributed significantly to the global supply of HREEs. The recovery of REEs from IACs does not require extensive physical beneficiation, which offsets their low REE grades, making the extraction of REEs from such ores cost-effective (Huang et al., 2015; Xiao et al., 2015; Yin et al., 2020). Furthermore, IACs are less hazardous due to very low concentrations of radioactive Th and U (Schulze et al., 2017; Burcher-Jones et al., 2018). However, the mineralogy of IACs varies widely and the leaching of REEs from the ores results in dilute pregnant leach solutions (PLS) containing Fe, Al, Si, Ca, Na, Mg, NH4+, and SO42- impurities (Chi and Tian, 2008; Schulze et al., 2017). Outside China, IAC ores have been found in several African countries and South America (Nyakairu and Koeberl, 2001; Burcher-Jones et al., 2018; Ram et al., 2019; Temga et al., 2021).
The extraction of REEs from IAC ores involves either excavation followed by heap leaching, or drilling of boreholes and in situ leaching using aqueous (NH4)2SO4 or MgSO4 as lixiviants. During leaching, the ion-exchangeable REE fraction is desorbed from the surfaces of clay particles into the aqueous phase and is replaced by cations (NH4+ or Mg2+) from the lixiviants. This generates low-tenor PLS of REEs containing impurities such as Fe, Al, and Si, which, together with lixiviant species, influence the aqueous chemistry. Thus, selective extraction of REEs from such impurityladen and low-tenor leach solutions is necessary to upgrade REEs before downstream separation and refining processes. Although ion exchange, solvent extraction, and adsorption can recover REEs from PLS, precipitation is conventionally used to extract REEs from IAC leach solutions because it is cost-effective and relatively simpler than other methods. Precipitation occurs when the concentration of sparingly soluble compounds from the chemical reaction between REEs and anions, such as hydroxides, fluorides, phosphates, oxalates, and carbonates, exceed their solubility. Thus, concentrates of REEs are produced from low-tenor leach solutions of IACs primarily through bulk precipitation. Typically, Fe3+ and Al3+ are rejected from the PLS via precipitation at pHs of ~3.5 and ~5, respectively, using alkalis such as NaOH, Ca(OH)2, NH3, and NH4HCO3 (Chi and Xu, 1999; Chi and Tian, 2008; Zhou et al., 2017; da Silva et al., 2018; Silva et al., 2019; Judge and Azimi, 2020).
REEs are conventionally recovered from IAC pregnant leach solutions via precipitation with oxalic acid (H2C2O4) and ammonium bicarbonate (NH4HCO3)(Chi and Tian, 2008). Precipitation with H2C2O4 occurs at acidic pH via the reaction in Equation [1] (Chi and Tian, 2008; Schulze et al., 2017):
[1]
The use of H2C2O4 achieves selective precipitation of REEs from impurity-laden pregnant leach solutions in a single stage and produces large REE oxalate particles, which are easy to dewater (Chi and Tian, 2008). However, H2C2O4 is expensive, forms complexes with impurity species and generates acidic wastewaters from the operations. These challenges motivated the adoption of NH4HCO3 for precipitation of REEs from PLS of IAC ores. This occurs at pH between 5 and 8, often after prior rejection of metal impurities at lower pH, and proceeds according to the reaction in Equation [2] (Chi and Tian, 2008; Anawati and Azimi, 2022);
NH4HCO3 is cheaper, relatively safer, neutralizes leach solutions, and replenishes (NH4)2SO4 for recycling of the supernatant back to the leaching stage as a lixiviant. Furthermore, REE carbonates can be easily redissolved in acids for further processing. However, REE carbonates precipitate as fine amorphous particles, which are voluminous and difficult to dewater (Yin et al., 2020; Yu et al., 2020; Wang et al., 2021).
Recently, studies have shown that antisolvent crystallization can recover REEs from pregnant leach solutions of spent products and bauxite residue, as salt crystals with tunable physical properties (Kaya et al., 2018; Korkmaz et al., 2020; Pawar et al., 2024). Unlike oxalates and carbonates, sulphates of REEs are moderately soluble in water (Cunningham et al., 2024). Therefore, in antisolvent crystallization, water-miscible organic compounds with low dielectric constants reduce the solubility of dissolved REE salts in the resultant solution and induce crystallization of the salts when supersaturation is attained (Pawar et al., 2024). While high yields and recycling of antisolvents are possible, antisolvent crystallization is still being developed for industrial application in the recovery of metals. The method has been applied for the recovery of REEs from leach solutions with moderate tenors of REEs (Korkmaz et al., 2020), but has not been utilized for direct recovery of REEs from low tenor solutions, such as PLS' of IACs.
Overall, the recovery of REEs as carbonates is commonly practised and H2C2O4 is still applied for the recovery of REEs where high purity is required, while antisolvent crystallization has shown huge potential as an alternative method of recovering REEs (Schulze et al., 2017; da Silva et al., 2018). H2C2O4 and NH4HCO3 have different properties, react with REEs and impurity species differently, and produce particles with different physico-chemical characteristics resulting in process flowsheets with different levels of complexity. Antisolvents have different properties and their mechanism of action, i.e., polarization and dehydration of solutes, differs from that of classical precipitants (Korkmaz et al., 2020). Furthermore, the reagent demands, and the nature of the residual effluents differ. These aspects and operating conditions can be determined via thermodynamic simulation of aqueous chemistry.
Thermodynamic modelling of aqueous chemistry to predict equilibria and determine yields of REEs from PLS has been conducted using software such as PHREEQC, Visual MinteQ, and OLI Stream Analyzer (Judge et al., 2023). OLI Stream Analyzer uses the Helgeson-Kirkham-Flower equation of state while Visual MinteQ uses the Debye-Huckel and Davies equations to predict activities of the solutes in aqueous solutions. The solubility of respective REE compounds ultimately influences their precipitation behaviour. It is noted that solubility product constants (Ksp) of individual REE carbonates range from 10-35.8 to 10-28 and the data vary widely amongst different studies (Firsching and Mohammadzadei, 1986; Runde et al., 1992; Spahiu and Bruno, 1995; Chi and Tian, 2008). REE oxalates are slightly more soluble than carbonates and their Ksps vary between 10-32 and 10-25 (Chi and Tian, 2008; Xiong, 2011; Josso et al., 2018). The solubilities of Y2(SO4)3.8H2O in different H2O alcohol mixtures have been measured by Sussens et al. (2024), while solubility of various REE sulphates in H2O have been determined by Judge et al. (2023) and Moldoveanu et al. (2024).
[2]
The overall aim of this study was therefore to determine the recovery of REEs from PLS’ of IACs using bulk precipitation and antisolvent crystallization. The objective of the investigation was to study and compare the performance of different precipitants and antisolvents in the enrichment of REEs from IAC leach solutions.
Methods and materials
The extraction of REEs from PLS of IACs using NH4HCO3, H2C2O4, CH3OH, and C2H5OH was studied. A PLS obtained from the leaching of an IAC ore from Madagascar using 0.5M (NH4)2SO4 was used as the basis of synthetic PLS’ used in the experimental tests.
Thermodynamic modelling
The recovery of REEs from the IAC leach solution using precipitation was simulated using OLI Stream Analyzer to predict the yields of REEs, quantities of reagents, and precipitation conditions. The mixed solvent electrolyte (MSE) framework was used and extraction of REEs from the PLS using H2C2O4, NH4HCO3, CH3OH, and C2H5OH was simulated. Although thermodynamic data and models were available for a very limited number of REE carbonates and oxalates in OLI Stream Analyzer, the software was selected for simulations because it contained thermodynamic data and models for REE sulphates (Nd, Y, and Dy) in the C2H5OH-H2O system. The models were developed by OLI Systems Inc. for the University of Cape Town and included Y2(SO4)3 in the CH3OH-H2O system (Sussens et al., 2024). The software contained thermodynamic data and models for Nd carbonate and oxalate, as well as Yb oxalate. Thermodynamic data and a model for Dy2(CO3)3 in water were developed by OLI Systems Inc. for the University of Cape Town as part of this study. Although Visual MinteQ and PHREEQC databases contain thermodynamic data for several carbonates and oxalates, OLI Stream Analyzer was used for all simulations in this study for consistency.
The recovery of Nd from 1 L of the IAC leach solution containing 433 ppm of Nd3+ and 300 ppm of Al3+ in aqueous (NH4)2SO4 solution using precipitation/crystallization with H2C2O4, NH4HCO3, and C2H5OH was simulated. The crystallization of Y2(SO4)3 from the same aqueous matrix using CH3OH and C2H5OH was also simulated since its thermodynamic data and models in both systems were available.
Laboratory experimental tests
Laboratory experiments were carried out to compare the recovery of REEs from IAC leach solutions using H2C2O4, NH4HCO3, CH3OH, and C2H5OH. Although preliminary experiments were conducted using the PLS obtained from the leaching of IAC ore from Madagascar, the quantity of the solution was limited, hence
Table I
Concentrations of REEs, Al3+, NH4+ and SO42- in the model PLS Species
simplified, synthetic leach solutions were prepared and used for further investigations. The simplified model PLS’ contained only major REEs, Al3+, and lixiviant species as shown in Table I.
Reagent grade La2(SO4)3, Pr2(SO4)3.8H2O, Nd2(SO4)3.8H2O, Y2(SO4)3.8H2O (ThermoFisher, Germany), (NH4)2SO4 (Merck, South Africa), and Al2(SO4)3.xH2O (Sigma-Aldrich, South Africa) were dissolved in deionized water to prepare synthetic PLS'. Precipitant aqueous solutions were prepared by dissolving 4.3 g of H2C2O4 (Sigma Aldrich) and 10 g of NH4HCO3 (Merck and Sigma Aldrich) in 1 L of deionized water, but both CH3OH and C2H5OH (Kimix, South Africa) were utilized without modification. Laboratory tests were conducted to determine the yields of REEs when each of the four reagents was used, separately, to recover REEs from the IAC leach solution. In the experiments, 200 mL of 0.43 wt.% H2C2O4 and 1 wt.% NH4HCO3 aqueous solutions were individually added to 200 mL of synthetic PLS to precipitate REE oxalates and carbonates, respectively. In order to crystallize REE sulphates, 171 mL of C2H5OH and 200 mL of CH3OH were added to 200 mL of synthetic PLS in different experiments. These resulted in organic to aqueous (O/A) ratios of 0.86 for C2H5OH and 1.0 for CH3OH, which were selected to avoid co-crystallization of (NH4)2SO4 while achieving theoretical yields of total rare earth elements (TREEs) higher than 95%. In a separate experiment (AS3), the C2H5OH quantity was increased to 230 mL in an attempt to improve the recovery of REEs. A summary of the experiments is provided in Table II.
All experimental tests were conducted using an agitated 0.5 L glass reactor, fitted with three baffles, as illustrated in Figure 1. An overhead stirrer (IKA RW20), connected to a 6-blade Rushton turbine (0.033 m), was used for agitation and a Mettler Toledo pH electrode was used to measure the pH of the reactor contents. A peristaltic pump (Watson Marlow, 520S) was used to add precipitants and antisolvents into the reactor.
Experimental procedure
Two hundred (200) mL of the PLS was initially added into the reactor and the agitator was started. The precipitant/antisolvent was then pumped into the reactor using a peristaltic pump. In the case of C2H5OH, 171 mL and 230 mL were added to 200 mL and 181 mL
Table II
Details of conducted experiments and utilized reagents
of PLS, respectively. The agitator rotational speed was 500 rpm, and this was selected to avoid the settling of product particles during antisolvent crystallization. Each experiment was run for 2 hours to allow time for antisolvent crystallization of REEs, which was relatively slower at the selected O/A ratios, while keeping the duration relatively shorter to suit industrial operations (Silva et al., 2019). All experiments were repeated at least twice.
After each experiment, samples of the slurry were collected for size analysis using laser diffraction (Malvern Mastersizer 2000, UK). The remainder of the product slurry was harvested and vacuumfiltered using 0.22 mm nylon membrane filters, Merck Millipore flask and funnel, as well as an oil-less piston vacuum pump (Vacutec, South Africa). The filtration was monitored to determine the performance of the different products. Samples of the filtrate were collected for metal analysis, using inductively coupled plasma mass spectrometry (ICP-MS) (Agilent 7900, USA), to quantify the yields of REEs. The yields were estimated from Equation [3]:
Co and Cs are concentrations of the metal ions in the PLS and in the supernatant (ppm), respectively; Vo and Vs are the respective volumes (mL). After drying in the desiccator for at least 24 hours, samples of the products were collected for imaging and elemental analysis using the scanning electron microscope (Tescan Mira 3 RISE, Czech Republic) and energy dispersive X-ray spectroscopy (EDS). Samples of products from antisolvent crystallization were also analysed using powder X-ray diffraction (XRD).
Results and discussion
Thermodynamic Modelling: Recovery of Nd from an IAC leach solution using different reagents
The recovery of Nd from 1 L of the simplified IAC pregnant leach solution using H2C2O4, NH4HCO3 and C2H5OH was simulated using OLI Stream Analyzer (see Figure 2). The results showed that, further to conventional precipitation using H2C2O4 and NH4HCO3, antisolvent crystallization using C2H5OH can recover high yields of REEs from IAC leach solutions. The recovery of Nd using CH3OH could not be modelled because thermodynamic data for the Nd2(SO4)3-H2O-CH3OH system was unavailable at this stage. The yields of Nd from the IAC leach solution containing 433 ppm of Nd3+ are shown in Figure 2 as a function of the amounts of reagents utilized for recovery.
It was predicted that the amount of H2C2O4 required to recover >90% of Nd from 1 L of PLS was the least, but comparable to that of NH4HCO3, while the amount of C2H5OH required to recover the same amount of Nd was almost two orders of magnitude higher.
The marked difference in the reagent demand can be attributed to the differences in the mechanisms of action of the reagents and solubility behaviour of the recovered products.
While H2C2O4 and NH4HCO3 provide C2O42- and HCO3anions for reactive precipitation of Nd2(C2O4)3.10H2O and NdOHCO3, respectively, C2H5OH induces the crystallization of Nd2(SO4)3.8H2O via a different mechanism. C2H5OH reduces both the activity of water and the dielectric constant of the solution, which dehydrates and reduces polarization of the ions, respectively, thus facilitating the crystallization of REE sulphates (Korkmaz et al., 2020). It is noted that NdOHCO3, which is more soluble than Nd2(CO3)3, was predicted as the thermodynamically stable phase. Nd2(SO4)3.8H2O, was predicted to crystallize from the Nd2(SO4)3H2O-C2H5OH system and this was confirmed experimentally through XRD analysis by Pawar et al. (2024). The same compound was found to be the stable phase that crystallizes from Nd2(SO4)3H2O solutions at room temperature (Das et al., 2019; Judge et al., 2023; Moldoveanu et al., 2024).
Al3+ was predicted to remain in the aqueous phase when H2C2O4 was used to precipitate REEs from the IAC leach solution. This is due to the formation of soluble Al oxalate complexes, such as AlH3[C2O4]22+, which remain in aqueous phase as REE oxalates precipitate. Contrary to this, the utilization of NH4HCO3 was predicted to co-precipitate Al(OH)3 and Nd(OH)CO3. However, the Al(OH)3 was predicted to precipitate at a lower pH than Nd(OH)CO3, thus presenting an opportunity for sequential precipitation (Chi et al., 2003). Lastly, it was predicted that adding more than 670 g of C2H5OH to 1 L of PLS would result in the coprecipitation of (NH4)2SO4 with Nd2(SO4)3.8H2O. Operationally, the crystallization of the lixiviant limits the amount of antisolvent that can be utilized, although the antisolvent can be recovered.
Experimental: Precipitation of REEs from PLS of IACs using different reagents
Yields of REEs and rejection of Al by different precipitants/ antisolvents
The yields of the metals were evaluated using Equation [3] and the residual metal content in the supernatants, with results presented in Figure 3. The yields of TREEs were generally high when each of the four reagents was used to recover REEs from synthetic IAC leach solutions.
The highest recovery of TREEs (>99%) was achieved by using 1 wt.% NH4HCO3 aqueous solution for bulk precipitation and a similar yield (>98%) was achieved by using 0.43 wt.% H2C2O4 aqueous solution. Crystallization of REEs using CH3OH(OA=1) resulted in a 92% yield of TREEs, while crystallization using C2H5OH, at O/A=0.86 and 1.27, recovered 88% and 93%,
respectively. As shown in Figure 3, Al was virtually rejected when H2C2O4 was utilized to recover REEs from the IAC leach solutions, but was co-extracted with REEs when NH4HCO3, CH3OH and C2H5OH were used to precipitate REEs in a single stage. Although CH3OH rejected Al slightly better than C2H5OH (O/A=0.86) during crystallization of REE sulphates from IAC leach solutions, both antisolvents were less selective at the conditions employed in this study. The higher rejection of Al by CH3OH was probably due to its higher dielectric constant than that of C2H5OH (Korkmaz et al., 2020; Sussens et al., 2024).
The high yields of TREEs obtained from precipitation using NH4HCO3 and H2C2O4 were expected due to the extremely low solubilities of REE carbonates and oxalates, which resulted in high supersaturations and fast precipitation of REEs (Firsching and Mohammadzadei, 1986; Chi and Tian, 2008; Josso et al., 2018). Thus, instantaneous formation of particles occurred upon addition of the precipitants during experiments. The individual yields of La, Pr, and Nd recovered using CH3OH(O/A=1) and C2H5OH, at both O/A= 0.86 and 1.27, were generally high (>96%) and similar for all the reagents after 2 hours of crystallization. Therefore, the relatively lower yields of TREEs obtained in antisolvent crystallization were attributed to the yields of Y, which was significantly lower than the rest of the REEs, as demonstrated in Figure 4. The lower yield suggests that the crystallization of Y using C2H5OH at O/A=0.86 was slower than that of other REEs.
Increasing the amount of C2H5OH to O/A=1.27 and utilizing CH3OH(O/A=1) for crystallization enhanced the yield of Y significantly, but the recovery still remained below the theoretical values predicted from thermodynamic simulation, as demonstrated in Figure 5. The slow crystallization of Y could not be explained fully, but the behaviour could be attributed to the solubility of Y2(SO4)3.8H2O, which is higher than that of light REEs and similar to other HREEs. Analysis of the scaling tendency (S) using OLI Stream Analyzer showed that the supersaturation of Y2(SO4)3.8H2O (S=555) was significantly lower than that of Nd2(SO4)3.8H2O (S=3010) at C2H5OH (O/A=0.86). This possibly explains the associated slower crystallization kinetics at O/A=0.86, as shown
Figure 5—Experimental versus theoretical yields of Nd and Y after 2 h of crystallization at O/A(v/v) of 0.86 and 1.27
by lower yields. Although increasing the amount of C2H5OH to O/A=1.27 enhanced the supersaturation of the anhydrous Y2(SO4)3 by two orders of magnitude, S=6.5x104, the Y yield remained significantly lower than the theoretical value. The slow crystallization of Y was also observed by Korkmaz et al. (2020) in the recovery of REEs from leach solutions of NiMH batteries. Further studies to understand the crystallization behaviour of Y2(SO4)3 during antisolvent crystallization are recommended.
The selective precipitation of REEs from IAC leach solution achieved using 0.43 wt.% H2C2O4 aqueous solution was attributed to the formation of the soluble AlH3[C2O4]22+ complex at acidic pH, which remained in the aqueous phase during precipitation of REE oxalates, as suggested by thermodynamic simulation results (OLI Systems Inc, 2021). Elemental analysis of the REE oxalates product using EDS affirmed the rejection of Al during precipitation, as demonstrated in Figure 6a. The small amount of Al shown in Figure 3 was attributed to adsorption, which was also low. The high Al rejection efficiency in the recovery of REEs using H2C2O4 was also reported by Silva et al. (2019).
The least rejection of Al observed using NH4HCO3 was due to co-precipitation of Al(OH)3 with REE carbonates. This lowered the purity of the REE concentrates and was predicted from thermodynamic simulation. The comparably low rejection of Al achieved during crystallization of REE sulphates from IAC leach solution using C2H5OH and CH3OH was attributed to cocrystallization of Al. This was supported by EDS of the product recovered using CH3OH, which showed that the darker phase in Figure 6b (trigonal pyramid particles) contained Al. This was not predicted from simulation of aqueous chemistry and the identity of the Al compound that co-crystallized with REE sulphates during crystallization with both CH3OH and C2H5OH could not be established at this stage, as XRD analysis of the product was still inconclusive. However, the crystallization of an Al sulphate salt during antisolvent crystallization with C2H5OH is possible and has been reported by Kang et al. (1995). Ma et al. (2023) further showed that Al co-crystallized during antisolvent crystallization of metals from PLS of Li-ion batteries.
The filtration performance of the products generated using the different reagents was monitored and filtration rates are presented in Figure 7.
REE oxalates filtered at the fastest rate while REE carbonates filtered at the slowest rate. The filter cake of the REE carbonates also developed micro- and macro-fissures during filtration, which showed poor dewatering behaviour. The filtration of the product recovered using CH3OH(O/A=1) was faster, but comparable to
7—Filtration performance of the slurry produced using 0.43 wt.% H2C2O4, 1 wt.% NH4HCO3, CH3OH(O/A=1) and C2H5 OH(O/A=0.86&1.27) at N=500 rpm after 2h
that of the product recovered using C2H5OH(O/A=0.86). Utilising higher quantities of C2H5OH(O/A=1.27) produced a suspension that filtered at a slower rate. The difference in filtration performance was attributed to the differences in particle sizes, lattice structure, and habit of the products recovered using the different reagents. These properties determine the packing of the particles and the subsequent permeability of the filter cakes. Particle size distributions (PSDs) of the precipitates obtained from the experimental tests conducted for average batch times of 2 hours are shown in Figure 8.
The highest filtration rate of REE oxalates was attributed to crystalline particles, a narrow PSD and extensive particle clustering, which is evident in Figure 9(d-f). The crystalline prismatic particles had a mixture of sharp and rounded edges. On the contrary, the
poor filterability of REE carbonates was due to both smaller particle sizes and amorphous structure. As shown in SEM micrographs in Figure 9 (a-c), small spherical and amorphous particles were produced when NH4HCO3 was utilized for precipitation. The fast filtration of the suspensions obtained using C2H5OH(O/A=0.86) and CH3OH(O/A=1) can be attributed to the large, well-faceted, and predominantly crystalline product particles as shown in Figure 8 and Figure 9.
Although the product recovered using C2H5OH(O/A=0.86) consisted of slightly bigger particles than from CH3OH(O/A=1), as presented in Figure 8, the product from the latter filtered slightly better, possibly due to lower viscosity of the residual CH3OH-PLS solution. The product from crystallization using C2H5OH consisted of a mixture of prismatic and bipyramidal particles, with instances of sharp edges, broken corners, and intergrowth as illustrated in Figure 9(g-h). A phase with no clearly defined morphology was observed on the surfaces of bigger particles at higher magnifications (Figure 9i). Crystallization with CH3OH produced a similar mixture of particle morphologies as shown in Figure 9(j-k). However, sheaves were also produced as shown in Figure 9j.
Although more than just REE compounds crystallized when NH4HCO3, CH3OH, and C2H5OH were used to recover REEs, it was clear that crystal growth was dominant during antisolvent crystallization, hence the clearly defined product morphology. However, the poorly structured material that attached to the
for 2 h
surfaces of bigger particles suggests that the crystallization pathways were less obvious. An intensely white suspension formed after addition of the antisolvents, and this became progressively less with time. The formation of amorphous REE carbonates is extensively reported in previous studies and was therefore expected (Chi and Tian, 2008; Yin et al., 2020; Yu et al., 2020; Wang et al., 2021). Contrarily, crystalline REE oxalates formed at similar yields. Thus, the role of anions in the precipitation of REEs is clearly shown by the differences in the quality of the products recovered using the different reagents, in as much as antisolvent molecules and counterions influence the crystallization process.
The recovery of REEs from PLS of ion-adsorption clay ores was investigated in this study to understand the technical efficacy of each reagent to enrich the REEs from low-tenor solutions. Thermodynamic simulation was conducted using OLI Stream Analyzer and it revealed that high yields of REEs could be achieved with reactive precipitation using either H2C2O4 or NH4HCO3 and antisolvent crystallization with either CH3OH or C2H5OH. The highest yields were obtained from precipitation using H2C2O4 and NH4HCO3, but significantly large quantities of CH3OH and C2H5OH were necessary to achieve similar yields.
Experimental results confirmed the high REE yields predicted from thermodynamic simulations, especially for H2C2O4 and NH4HCO3. However, the recovery of Y from crystallization using both alcohols was significantly lower than the rest of the REEs and was below the thermodynamically predicted yield.
The utilization of NH4HCO3, CH3OH and C2H5OH for singlestage crystallization resulted in the co-precipitation of Al, which was predicted in the use of NH4HCO3, but not in the case of alcohols. This meant that REE concentrates of low purity were recovered when each of these three reagents was utilized.
The utilization of H2C2O4 in a single stage resulted in selective recovery of REEs (La, Nd, Pr, and Y), while Al remained in the spent solution, and resulted in a product with the best dewatering performance, i.e., highest filtration rate among the tested reagents. The product was crystalline and slightly larger than REE carbonates. Interestingly, the product recovered using alcohols was characterized by mostly well-faceted, large prismatic and crystalline particles that dewatered quite easily, as shown by good filtration performance. Thus, crystal growth appeared to be dominant in antisolvent crystallization of REEs at the O/A ratios employed in this study, as shown by the well-formed large and crystalline particles. The fine, amorphous product recovered using NH4HCO3 filtered at the slowest rate, and the process appeared to be dominated by nucleation and agglomeration.
Overall, it was concluded that the utilization of H2C2O4 as a precipitant achieved the best results in a single stage compared to other reagents. However, the precipitation/crystallization conditions for other reagents were not optimized and this conclusion is based on the technical performance in a single precipitation stage. Consideration of economic, environmental safety and other external factors is necessary to further compare the reagents and guide the selection of suitable precipitants.
Acknowledgements
The authors would like to thank Mr Eddy Miiro for generating PLS’ used in preliminary experiments, Ms Miranda Waldron of the Electron Microscope Unit for imaging services, colleagues in the Analytical Laboratory at the University of Cape Town and Ms Charney Anderson-Small of the Central Analytical Facilities at Stellenbosch for the analytical work.
References
Ahmed, U.A.Q. 2017. A Hydrometallurgical Comparison between the Caustic and Sulphuric Acid Cracking of Steenkampskraal (SKK) Monazite. MSc University of Cape Town.
Anawati, J., Azimi, G. 2022. Separation of rare earth elements from a South American ionic clay lixivium by sequential precipitation. Hydrometallurgy, 213, 105946.
Burcher-Jones, C., Mkhize, S., Becker, M., Ram, R., Petersen, J. Study of the deportment of REEs in ion adsorption clays towards the development of an in situ leaching strategy. Extraction 2018: Proceedings of the First Global Conference on Extractive Metallurgy, 2018. Springer, pp. 2429–2439.
Chi, R.A., Xu, Z.G. 1999. A solution chemistry approach to the study of rare earth element precipitation by oxalic acid. Metallurgical and Materials Transactions B, vol. 30, pp. 189–195.
Chi, R.A., Zhou, Z., Xu, Z., Hu, Y., Zhu, G., Xu, S. 2003. Solutionchemistry analysis of ammonium bicarbonate consumption in rare-earth-element precipitation. Metallurgical and Materials Transactions B, vol. 34, pp. 611–617.
Chi, R., Tian, J. 2008. Weathered crust elution-deposited rare earth ores, Nova Science Publishers.
Cunningham, S., Etherington-Rivas, M., Azimi, G. 2024. Solubility of neodymium and dysprosium sulfates at different pH and temperature and the effect of yttrium sulfate, sodium sulfate, and ammonium sulfate mixtures: Strengthening the predictive capacities of the OLI software. Hydrometallurgy, vol. 224, 106253.
Da Silva, R.G., De Morais, C.A., Teixeira, L.V., De Oliveira, É.D. 2018. Selective removal of impurities from rare earth sulphuric liquor using different reagents. Minerals Engineering, vol. 127, pp. 238–246.
Das, G., Lencka, M.M., Eslamimanesh, A., Wang, P., Anderko, A., Riman, R.E., Navrotsky, A. 2019. Rare earth sulfates in aqueous systems: Thermodynamic modeling of binary and multicomponent systems over wide concentration and temperature ranges. The Journal of Chemical Thermodynamics, vol. 131, pp. 49–79.
Firsching, F.H., Mohammadzadei, J. 1986. Solubility products of the rare-earth carbonates. Journal of Chemical and Engineering Data, vol. 31, pp. 40–42.
Grohol, M., Veeh, C. 2023. European Commission, Study on the Critical Raw Materials for the EU 2023 – Final Report. Brussels: DG Grow, European Commission.
Gupta, C., Krishnamurthy, N. 2005. Extractive Metallurgy of Rare Earths. London, New York, Washington: CRC Press.
Huang, X.W., Long, Z.Q., Wang, L.S., Feng, Z.Y. 2015. Technology development for rare earth cleaner hydrometallurgy in China. Rare Metals, vol. 34, pp. 215–222.
Josso, P., Roberts, S., Teagle, D.A., Pourret, O., Herrington, R., De Leon Albarran, C.P. 2018. Extraction and separation of rare earth elements from hydrothermal metalliferous sediments. Minerals Engineering, vol. 118, pp. 106–121.
Judge, W., Azimi, G. 2020. Recent progress in impurity removal during rare earth element processing: A review. Hydrometallurgy, vol. 196, 105435.
Judge, W., Ng, K., Moldoveanu, G., Kolliopoulos, G., Papangelakis, V., Azimi, G. 2023. Solubilities of heavy rare earth sulfates in water (gadolinium to lutetium) and H2SO4 solutions (dysprosium). Hydrometallurgy, vol. 218, 106054.
Kang, H.K., Park, H.C., Kim, K.H. 1995. Crystallite size control of aluminium sulphate precipitated in ethanol from kaolin-derived leach liquor. Journal of materials science letters, vol. 14, pp. 1338–1339.
Kaya, Ş., Peters, E.M., Forsberg, K., Dittrich, C., Stopic, S., Friedrich, B. 2018. Scandium recovery from an ammonium fluoride strip liquor by anti-solvent crystallization. Metals, vol. 8, p. 767.
Korkmaz, K., Alemrajabi, M., Rasmuson, Å.C., Forsberg, K.M. 2020. Separation of valuable elements from NiMH battery leach liquor via antisolvent precipitation. Separation and Purification Technology, vol. 234, 115812.
Ma, C., Gamarra, J. D., Younesi, R., Forsberg, K., Svärd, M. 2023.
Antisolvent crystallization from deep eutectic solvent leachates of LiNi1/3Mn1/3Co1/3O2 for recycling and direct synthesis of battery cathodes. Resources, Conservation and Recycling, vol. 198, 107210.
Moldoveanu, G., Kolliopoulos, G., Judge, W., Ng, K., Azimi, G., Papangelakis, V. 2024. Solubilities of individual light rare earth sulfates (lanthanum to europium) in water and H2SO4 solutions (neodymium sulfate). Hydrometallurgy, vol. 223, 106194.
Nyakairu, G.W., Koeberl, C. 2001. Mineralogical and chemical composition and distribution of rare earth elements in clay-rich sediments from central Uganda. Geochemical Journal, vol. 35, pp. 13–28.
OLI Systems Inc 2021. OLI Studio Stream Analyzer, vol. 11. Morris Plains, New Jersey.
Pawar, N., Svärd, M., Forsberg, K. 2024. Recovery of Rare Earth Sulfate Hydrates Using Antisolvent Crystallization. TMS Annual Meeting and Exhibition. Springer, pp. 55–62.
Ram, R., Becker, M., Brugger, J., Etschmann, B., Burcher-Jones, C., Howard, D., Kooyman, P.J., Petersen, J. 2019. Characterisation of a rare earth element-and zirconium-bearing ion-adsorption clay deposit in Madagascar. Chemical Geology, vol. 522, pp. 93–107.
Runde, W., Meinrath, G., Kim, J. 1992. A study of solid-liquid phase equilibria of trivalent lanthanide and actinide ions in carbonate systems. Radiochimica Acta, vol. 58, pp. 93–100.
Salim, H., Sahin, O., Elsawah, S., Turan, H., Stewart, R. A. 2022. A critical review on tackling complex rare earth supply security problem. Resources Policy, vol. 77, 102697.
Schulze, R., Lartigue-Peyrou, F., Ding, J., Schebek, L., Buchert, M. 2017. Developing a life cycle inventory for rare earth oxides from ion-adsorption deposits: key impacts and further research needs. Journal of Sustainable Metallurgy, vol. 3, pp. 753–771.
Silva, R.G., Morais, C.A., Teixeira, L.V., Oliveira, É.D. 2019. Selective precipitation of high-quality rare earth oxalates or carbonates from a purified sulfuric liquor containing soluble impurities.
Mining, Metallurgy & Exploration, vol. 36, pp. 967–977.
Spahiu, K., Bruno, J. 1995. A selected thermodynamic database for REE to be used in HLNW performance assessment exercises. Swedish Nuclear Fuel and Waste Management Co.
Sussens, J., Chivavava, J., Lewis, A.E. 2024. The recovery of yttrium sulfate through antisolvent crystallization using alcohols. Separation and Purification Technology, vol. 346, 127459.
Temga, J.P., Sababa, E., Mamdem, L.E., Bijeck, M.L.N., Azinwi, P.T., Tehna, N., Zame, P. Z.O., Onana, V.L., Nguetnkam, J.P., Bitom, L.D. 2021. Rare earth elements in tropical soils, Cameroon soils (Central Africa). Geoderma Regional, vol. 25, e00369.
Wang, M., Huang, X., Feng, Z., Xia, C., Meng, D., Yu, Z. 2021. Behavior of sulfate in preparation of single light rare earth carbonate by Mg (HCO3)2 precipitation method. Journal of Rare Earths, vol. 39, pp. 850–857.
Xiao, Y.F., Feng, Z.Y., Hu, G.H., Huang, L., Huang, X.W., Chen, Y.Y., Li, M.L. 2015. Leaching and mass transfer characteristics of elements from ion-adsorption type rare earth ore. Rare Metals, vol. 34, pp. 357–365.
Xiong, Y. 2011. Organic species of lanthanum in natural environments: Implications to mobility of rare earth elements in low temperature environments. Applied geochemistry, vol. 26, pp. 1130–1137.
Yin, J.Q., Zou, Z.Q., Tian, J. 2020. Preparation of crystalline rare earth carbonates with large particle size from the lixivium of weathered crust elution-deposited rare earth ores. International Journal of Minerals, Metallurgy and Materials, vol. 27, pp. 1482–1488.
Yu, Z., Wang, M., Wang, L., Zhao, L., Feng, Z., Sun, X., Huang, X. 2020. Preparation of crystalline mixed rare earth carbonates by Mg (HCO3)2 precipitation method. Journal of Rare Earths, vol. 38, pp. 292–298.
Zhou, F., Feng, J., Wang, Z., Xu, Y., Zhang, Z., Chi, R. 2017. One step purification of impurities in the leachate of weathered crust elution-deposited rare earth ores. Physicochemical Problems of Mineral Processing, vol. 53, no. 2, pp. 1188–1199. u
MASLOW HOTEL, SANDTON, JOHANNESBURG
During closure planning there are usually four parties involved, being the mining house, external stakeholders, consultants and the authorities who are responsible for closure plan and eventual relinquishment approval. There are subsequently numerous conflicting ideals between the parties during the evolution of mine planning to post-closure. This leads to unrealistic closure expectations and vague obligations that result in the lack of setting or accepting specific closure and relinquishment criteria. Without clear direction, achieving a closure certificate in South Africa remains uncertain. This leads industry to adopt very different positions around closure planning that ranges between best practice, compliance to legislation to minimal planning.
Successful relinquishment has been achieved internationally by creating a value chain for sustainable post-mining economies as early as possible. In South Africa relinquishment could possibly be achieved successfully by complying to the current legislative closure approach or alternatively by creating third party value by means of parallel economies. This could potentially be supplemented with a regional closure approach between mining houses. It is therefore imperative that the third party needs to be part of the value chain development and execution through meaningful community engagement to ensure the benefits of local knowledge and achieve social acceptance. Once the long-term value chain is in place it lays the foundation for closure- and relinquishment criteria and social integration. ESG compliance adds another layer to closure planning but can be very useful to add specific criteria and expedite closure actions. Regardless of the approach taken, engagement with regulators is required for overall alignment and changes to policies.
To assist interested parties, industry and regulators to better understand the closure challenges within the current uncertain and fragmented closure space. This is underpinned by Environmental Social and Governance (ESG) compliance, reducing closure liabilities and risks, just transition and the ultimate goal of relinquishment. The conference will aim to present, workshop and identify the pressing focus areas for further research and engagement with the regulators.
• Current challenges towards relinquishment
• Alternative closure solutions
• Socio economics and just transitions
• ESG compliance and considerations to closure
• Conference proceedings
• Conference panel discussion to identify focus areas, needs and future actions
• Planned breakaway after the conference for academics and after interested parties to discuss future research topics flowing from the conference
• Identify relevant challenges and research topics
• Identifying areas for future engagement with the regulator to influence policy and legislation to address the challenges
• To promote and understand the appetite of the industry to consider alternative closure solutions
FOR FURTHER INFORMATION, CONTACT:
Gugu Charlie, Conferences and Events Co-ordinator
E-mail: gugu@saimm.co.za
Tel: +27 11 530 0238 Web: www.saimm.co.za
Affiliation:
1Department of Materials Science and Metallurgical Engineering, University of Pretoria, South Africa
Correspondence to:
K.C. Sole
Email: kathy.sole@up.ac.za
Dates:
Received: 15 Feb. 2024
Published: December 2024
How to cite:
Makonese, M. and Sole, K.C. 2024. Removal of iron from vanadium redox flow battery electrolyte using ion exchange. Journal of the Southern African Institute of Mining and Metallurgy, vol. 124, no. 12, pp. 747–754
DOI:
http://dx.doi.org/10.17159/2411-9717/ BM20/2024
ORCiD:
K.C. Sole
http://orcid.org/0000-0003-4707-1060
M. Makonese
http://orcid.org/0000-0002-9210-7352
This paper is based on a presentation given at the Battery Materials 2024 Conference, 6-7 August 2024, Mbombela, South Africa
by M. Makonese1 and K.C. Sole1
Abstract
Bushveld Belco is commissioning a plant for production of electrolyte used in vanadium redox flow batteries. Owing to the source material, the electrolyte is contaminated with Fe, at concentrations up to 140 mg/L, which negatively affects battery performance. This study examined the use of ion exchange to reduce the Fe concentration to the target value of < 100 mg/L from a feed solution containing 100 g/L V in 4 M H2SO4. Four resins with possible application were identified: Puromet MTS9570, Puromet MTX7010, Puromet MTS9500, and Puromet MTC1600H. Puromet MTS9570 outperformed the other three resins in all batch experiments with respect to loading capacity and selectivity over V, and was evaluated for Fe removal in fixed-bed column loading tests. Based on these data, preliminary sizing and design of a full-scale column was undertaken. Owing to the difficulty of eluting this resin, a philosophy of discarding the resin on loading to full capacity was considered. These data revealed that, despite the high selectivity of this resin for Fe over V, it would be too expensive and impractical to use this resin for full-scale operation under such conditions. It is recommended to remove iron earlier in the flowsheet prior to generation of the 4 M H2SO4 electrolyte.
Keywords
Vanadium redox flow battery, iron, ion exchange, Puromet MTS9570
Introduction
Vanadium redox flow batteries (VRFB) are currently the world’s most promising technology for stationary energy storage. These batteries are widely used for solar energy applications, and can assist in providing a renewable energy solution that is crucial for reducing the global carbon footprint (Wang et al., 2023). As fossil fuels drive global warming, countries around the world, including South Africa, are advancing research in renewable energy. This will not only help combat climate change, but could assist in ensuring reliable electricity supply for the people of South Africa (Akinbami et al., 2021). South Africa is currently the third-largest vanadium producer in the world (Bushveld Minerals, 2024). Value addition by production of VRFB electrolyte from primary V products can contribute to a carbon-free future. It is therefore imperative that VRFB technology be given more attention in this country.
The most common VRFB system is based on the VO2+/VO2+ and V2+/V3+ systems (Chace et al., 2020). The catholyte and anolyte are fed through two separate half-cells within the battery. Each half-cell has an electrode and a bipolar plate. The two half-cells are separated by a membrane that serves two functions: firstly, it allows for selective exchange of ions between the two electrolytes, which completes the cell in the battery and allows for the passage of current; secondly, the membrane prevents cross-contamination, i.e., mixing of the two electrolytes, which prevents short-circuiting in the battery that would otherwise lead to current overload in the battery, with resulting overheating and malfunction (Prifti et al., 2012).
The following reduction and oxidation reactions occur at the cathode and anode, respectively:
The overall electrochemical reaction is given by:
This reaction produces the potential difference in the battery that generates electricity that can be sent to a power grid or used to turn wind turbines for electricity production. Multiple VRFB stacks can be electrically connected to form a large array for applications that require more energy (Kim et al., 2015).
Bushveld Energy, under their subsidiary Bushveld Belco, is the only South African producer of electrolyte used in VRFB. The starting raw material for this electrolyte is magnetite ore, which contains 0.3% V (Bushveld Minerals, 2024). The main impurity in the electrolyte is Fe, which has certain detrimental effects on the function and performance of VRFB. The electrolyte comprised 100 g/L V, 140 mg/L Fe in 4 M H2SO4. The Bushveld specification prescribes a maximum of 100 mg/L Fe per 100 g/L V for optimal battery performance.
Ion exchange (IX) is extensively used in hydrometallurgy to purify aqueous solutions at low concentrations of impurities (< 500 mg/L) (Sole et al., 2017), so this technology was evaluated for removal of Fe from the Bushveld electrolyte.
Effects of iron in vanadium electrolyte
Effect of Fe on electrolyte resistance
Ding et al. (2019) investigated the effect of Fe3+ concentration on the resistance of a VRFB catholyte (Figure 1). The presence of small amounts of Fe3+ (500 mg/L) resulted in a threefold increase in the electrical resistance of the electrolyte from 0.63 Ω cm2 to 1.66 Ω cm2. The resistance did, however, decrease between 500 mg/L Fe to 1100 mg/L Fe, reaching approximately 0.75 Ω m2 at 1100 mg/L Fe. Although this decrease in resistance was recorded, it should be noted that all resistances measured with Fe3+ in the electrolyte were higher than when no Fe3+ was present. A higher electrolyte resistance means that the V ions are restricted in their transport to the cathode to participate in the cathodic electrochemical reactions: a resistive force hinders the movement of the ions, which inhibits the electrochemical reaction and compromises battery performance and efficiency.
Effect of Fe3+ on diffusivity of V4+ ions
Ding et al. (2019) also investigated the effect of Fe3+ concentration on the diffusivity of V4+ ions in the electrolyte (Figure 2). Concentrations below 900 mg/L Fe3+ had a positive effect on the diffusivity of V4+ ions. The diffusion coefficient of the V4+ ions increased from 2.06 cm2/s at 0 mg/L Fe3+ to 2.72 cm2/s at 900 mg/L Fe3+. This result indicates that a small addition of Fe3+ ions in the electrolyte allowed the V4+ ions to rapidly diffuse to the cathode
to participate in the cathodic electrochemical reaction shown in Equation [1] (Ding et al., 2019). However, as the Fe3+ concentration increased above 900 mg/L, a decrease in diffusivity of the V4+ ions was observed: at 1300 mg/L Fe3+, the diffusion coefficient was 1.78 cm2/s, which is much lower than when there was no Fe in the electrolyte. This finding means that V4+ ions diffused slowly to the cathode to participate in the cathodic reaction, which would compromise efficiency of a battery. The Fe3+ concentration should therefore be kept low enough such that the presence of the Fe3+ ions is helpful to V ion diffusivity
Iron side-reactions
The presence of Fe as Fe3+ in the electrolyte can also have a direct effect on the cathodic electrochemical reaction. Fe3+ ions can participate in side-reactions and be reduced to Fe2+ (Ding et al., 2019). There is competition for electrons between the Fe3/ Fe2+ reduction and the cathodic reaction (Equation [1]), thereby reducing current efficiency of the battery.
Experimental
Electrolyte generation
The electrolyte was generated as per Bushveld specifications by mixing 300 mL of 4 M H2SO4 (CP grade) and 50 g of Vametcoproduced V2O3 in a 1 L beaker. The following reaction occurs:
[4]
The mixture was agitated using an overhead stirrer and 50% H2O2 was added dropwise until all V2O3 had dissolved, according to the following reaction:
[5]
On average, a 1.6× stoichiometric excess of H2O2 was required to dissolve all V2O3. Addition of H2O2 caused a highly exothermic reaction, so the electrolyte was cooled before use. The electrolyte typically assayed 100 g/L V, 140 mg/L Fe, and 15 mg/L Cr, with the impurities originating from the V2O3.
Construction of electrolyte E–pH diagrams
To determine the speciation of Fe and V in the electrolyte, E–pH diagrams were constructed using The Geochemist’s Workbench software (The Geochemist’s Workbench, 2023).
Resin screening batch test methodology
Four resins were identified that are used for removal of Fe in various hydrometallurgical applications:
➤ Puromet MTS9570: A polystyrenic chelating resin containing phosphonic- and sulfonic-acid groups (R–SO2(OH)PO(OH)2; capacity 0.97 eq/L Fe);
➤ Puromet MTX7010: A polystyrenic macroporous resin solvent-impregnated with di(2-ethyl-hexyl)phosphonic acid functionality (P(OR)2OOH; capacity 0.40 eq/L Zn);
➤ Puromet MTC1600H: A polystyrenic macroporous strongacid cationic resin (R–SO2(OH); capacity 2.3 eq/L);
➤ Puromet MTS9500: A polystyrenic macroporous aminomethylphosphonic-acid chelating resin (R–CH2–N–CH2–P(ONa)2; capacity 1.3 eq/L Ca).
Screening batch tests were carried out to evaluate the relative performance of these resins. The ideal resin would selectively extract most Fe from the electrolyte, leaving V in solution. The screening batch tests were carried out by adding 20 mL of the electrolyte and 1 mL of wet-tapped resin to a 100 mL conical flask. The flask was agitated for 24 h using a shaking table. The electrolyte was then filtered to separate it from the resin beads. The barren solution was assayed in duplicate, and the metal loadings calculated by difference. All aqueous analyses were carried out using inductively coupled plasma optical emission spectroscopy.
Isotherm loading test methodology
The two most promising resins identified from the screening tests, Puromet MTS9570 and Puromet MTX7010, were subjected to isotherm loading tests to determine their capacities for Fe under these aqueous conditions. The tests were performed at 25°C and 40°C, which is the maximum recommended operating temperature of these resins. Various volumes of electrolyte (10 mL to 600 mL) were added to eight conical flasks, each with 1 mL of resin. The solution:resin ratio (S/R) varied from 10:1 to 600:1. The flasks were shaken at 800 rpm for 24 h, after which the electrolyte was filtered to remove the resin beads and then assayed.
Column test methodology
Based on the isotherm test results, Puromet MTS9570 was identified as the most suitable resin for this application. Fixed-bed column loading tests were conducted in a glass column with a height of 258 mm and inner diameter of 22.2 mm. A wet-tapped resin volume of 50 mL was employed, corresponding to a bed height of 140 mm and aspect ratio of 6.3. The electrolyte was fed downflow through the resin bed. The flowrate was manually controlled according to the output volume collected with time. Operating conditions are shown in Table I.
Table I
Operating conditions for column tests
Electrolyte E–pH diagrams
Figures 3 and 4, respectively, show the E–pH diagrams for V and Fe under the conditions of the electrolyte. The activities of Fe, V, and the sulfate anion were taken as approximately 0.0003, 0.2, and 0.04, respectively, considering the high ionic strength of 4 M H2SO4 electrolyte. These values are derived from their molar concentrations and activity coefficients estimated at 0.1 due to significant interaction of the ions.
The average potential of the electrolyte was measured using an Ohaus ST20R ORP electrode as 0.8 V (SHE). The first proton of H2SO4 is fully dissociated (Ka1 = 1 × 103); the second is weakly dissociated (Ka2 = 1.2 × 10−2) (LibreTexts Chemistry, 2020). The proton concentration was hence calculated as [H+] = 1.012 mol/L. This means that 4 M H2SO4 has an approximate pH of −0.6. At these values of potential and pH (red dotted lines in Figures 3 and 4), V exists as the neutral VOSO4 species in the electrolyte. This accords with the expected reaction given in Equation [5]. Li et al. (2023) also concluded that the neutral VOSO4 species forms at high SO42− concentrations. Fe is expected to exist as the FeH(SO4)2+ cation under these high-acidity conditions. These speciation data suggested that use of a cation-exchange resin may offer the opportunity to load the cationic Fe species in preference to the neutral V species.
Resin loading results
Screening batch tests
Figure 5 shows the average extractions of Fe and V for the four resins. Puromet MTS9570 offered the highest Fe extraction of 65% under the experimental conditions employed; however, this resin, together with Puromet MTS9500, also gave the highest V extraction of 13%. Puromet MTX7010 exhibited only 38% Fe extraction, but gave the lowest V extraction of 7%. Puromet MTC1600H showed the lowest Fe extraction of 19% and coextracted 12% V. Puromet
MTS9500 performed similarly to Puromet MTX7010, extracting 38% of the Fe in the electrolyte, but also gave high V extraction. The two resins that showed most promise in the batch screening tests were therefore Puromet MTS9570 and Puromet MTX7010. Both resins reduced the Fe concentration to below the target of 100 mg/L (55 mg/L and 96 mg/L, respectively) using an S/R of 20:1. The co-extraction of V by these cation-exchangers suggested the presence of V in the cationic form as well as the neutral species. El Hage et al. (2019) studied the dissolution of VOSO4 in aqueous sulfuric acid solution, and concluded that this neutral species can dissociate into VO2+ and SO42−. It is likely that VO2+ competes with
FeH(SO4)2+ for cation sites on these resins, but the iron species is more strongly complexed. This result suggested that it may be possible to displace V by Fe under capacity-constrained conditions.
Both resins were then subjected to isotherm batch tests to determine their loading characteristics and relative selectivity under maximum loading conditions.
Isotherm batch tests
Figure 6 shows the Fe loading isotherms for Puromet MTS9570 and Puromet MTC1600H at 25°C and 40°C. The maximum Fe loading on Puromet MTS9570 at 25°C was considerably higher (6 g/L Fe) than that of Puromet MTX7010 (1.2 g/L Fe), as expected from capacity data provided by the manufacturer. There was no significant difference on loading of Fe based on temperature. At 40°C, Puromet MTX7010 reached a maximum loading of 1.2 g/L Fe, which was the same value as at 25°C. Loading of Fe on Puromet MTS9570 reached a maximum of 6 g/L at 25°C and 6.3 g/L at 40°C, representing an improvement of only 5% at the higher temperature. It should be noted that the shapes of these isotherms are distinctly unfavourable. A favourable shape would have a steep incline at low aqueous concentrations, indicating that the resin can reduce the target ion to low levels in the barren solution. Isotherms that have low loading at low solution concentrations, such as these, indicate sorption systems that only complex with the target metal ion at high aqueous concentrations and are more stable in the acid form (Naja and Volesky, 2006). In this case, strong extraction
occurred at > 120 mg/L Fe in the aqueous phase. This system may therefore be appropriate for bulk reduction of Fe concentration in the electrolyte to meet the target specification, but will not achieve low Fe concentrations in the V-containing barren solution.
Results from the isotherm tests were used to calculate separation factors, KFe/V, to determine the relative selectivity for Fe loading over V. The selectivity factor, KMt/Mi, which denotes the selectivity of a target ion in solution, Mt, over any other ion in solution, Mi, is given by Equation [6] (Adhikari et al., 2011):
where DMt is the distribution ratio of the target ion in solution and DMi is the distribution ratio of any other ion in solution. The distribution ratio, D, for an ion x in solution in solution is calculated using Equation [7] (Adhikari et al., 2011):
where qe is the amount of metal ion exchanged at equilibrium (g/L) and Ce is the aqueous concentration of that ion at equilibrium (g/L).
Figure 7 shows separation factors KFe/V plotted against S/R for Puromet MTS9570 and Puromet MTX7010. The Puromet MTS9570 data exceeded those for Puromet MTX7010 for all separation factors, except at S/R of 300. This result shows that Puromet MTS9570 has a higher Fe/V selectivity for these experimental conditions. The separation factors for Puromet MTS9570 increased with S/R, reaching a value of 6.1 at S/R = 600. It was therefore concluded that the selectivity of Puromet MTS9570 for Fe over V was higher at higher S/R. This would be especially beneficial in an IX column: the results suggested that if the electrolyte was continuously fed into a column with Puromet MTS9570, Fe would displace V that co-loaded onto the resin, within the relative selectivity constraints of the system. In the case of Puromet MTX7010, it appears that selectivity reversed at higher S/R ratios, with V displacing Fe on the extractant.
From the batch test results, it was concluded that Puromet MTS9570 was the best resin of those considered for application to this highly acidic liquor. This resin extracted more Fe than the other resins in the screening batch tests, gave much higher Fe loading than Puromet MTX7010 in the isotherm tests at both 25°C and 40°C, and showed the highest selectivity for Fe over V. This resin functionality is unique in its ability to complex Fe under highacidity conditions and has been commercially employed for removal of iron from copper electrolytes containing ~ 1.8 M H2SO4 (Izadi et al., 2017; Xue et al., 2001).
Column tests using Puromet MTS9570 were conducted at room temperature (25°C), because there was no significant difference in loading at 25°C and 40°C. This is beneficial because it reduces the energy demands associated with heating of the electrolyte and column equipment. Figure 8 shows breakthrough curves obtained from fixed-bed downflow loading of this resin at 2 BV/h and 4 BV/h. These tests confirmed the selectivity of this resin for Fe over V: Fe loaded onto the resin and the V concentration remained at the feed concentration C0 throughout both experiments, i.e., no V loaded onto the resin. However, it should be noted that breakthrough of Fe occurred almost immediately, which accords with the unfavourable isotherm shape (Figure 6).
Table II shows the mass-transfer zone length (MTZL) calculations obtained from the breakthrough curves (Crittenden et al., 2012). This calculation assumed that breakthrough occurs when the exit concentration is equal to 10% of C0 and resin saturation occurs when the exit concentration is equal to 90% of C0. As an example, the red dotted lines in Figure 8 show the volumes of feed passed when the discharge Fe concentration was 0.1C0 (14 mg/L Fe; 2 BV) and 0.9C0 concentration (126 mg/L Fe; 33 BV) for 2 BV/h flowrate. Equation [8] was used to calculate the MTZL (McCabe et al., 2018):
. [8]
The MTZL occupied a significant portion of the resin bed height, indicating inefficient adsorption. The MTZL calculations suggest that it would be more beneficial to operate the column at a flowrate of 2 BV/h, owing to the slightly shorter MTZL. This means that less resin is required to achieve the same results for specific conditions. A shorter MTZL also suggests faster mass transfer. As shown in Table I, however, the linear flowrate (superficial velocity) through the resin bed was very low under these conditions, which may have caused a stagnant film diffusion layer around the resin beads that inhibited mass transfer. Furthermore, to reach 90% resin capacity (the assumed resin saturation in this case), a flowrate of 2 BV/h allowed treatment of 33 BV of electrolyte compared with 4 BV/h, which only allowed treatment of 23 BV (Figure 8). This means that a higher volume of electrolyte could be treated for Fe removal prior to reaching saturation if the column is operated at 2 BV/h.
Preliminary full-scale column sizing
Table III shows selected full-scale column sizing variables calculated using the design equations provided by Crittenden et al. (2012) to treat an annual electrolyte volume of 8000 m3 (Bushveld specification) at 2 BV/h.
Table II
Calculation of mass-transfer zone length
Feed flowrate (BV/h)
in feed (mg/L) Resin bed height (mm)
The sizing calculations in Table III show that for a design flow rate Q of 1.01 m3/h, 500 L resin is required. This volume of resin would reach saturation after passing 43 BV electrolyte with an initial Fe concentration of 140 mg/L at 2 BV/h. However, it would not be possible to load all Fe from solution using a single column owing to the unfavourable isotherm shape.
To ensure that full resin loading is achieved without leakage of Fe to the V-containing barren solution exceeding the target specification, it would be necessary to employ two (or more) columns in series in a lead–lag(–lag) configuration. Figure 8 shows that the barren concentration exceeded 100 mg/L Fe when the resin capacity had only reached 70% (2 BV/h) at ~ 20 BV. Passing this eluate through a second (and possibly third) column in series would ensure that the discharge of the final column would remain below 100 mg/L Fe. Once maximum capacity is reached in the first column, the column can be taken off-line for unloading and loading of fresh resin. When the discharge from the second column exceeds 100 mg/L, this is directed into a third column, if necessary, or alternatively the first column, now loaded with fresh resin, is again brought online. The main advantage of such a system is the significant reduction in downtime. If a setup with only one column is used, the column would be offline at least once a day for unloading and loading of fresh resin (required every 21 h), during which time no processing would occur. If two (or three) columns were used, at least one column would continue to run whilst the saturated resin was unloaded and the column reloaded with fresh resin.
Because the electrolyte is highly acidic, it is very difficult to strip this resin with acid. Commercial applications of this resin to a copper electrolyte employ a reductive strip with Cu+ (Xue et al.,
2001). An approach was therefore considered in which the resin would be discarded after reaching saturation. Table IV summarizes the cost analysis of this approach using a flowrate of 2 BV/h. Assuming quantitative Fe removal from the electrolyte, the cost for the resin alone exceeds ZAR 127 million/a.
Conclusions and recommendations
IX was evaluated as a technology to remove 140 mg/L Fe from an electrolyte containing 100 g/L V at 4 M H2SO4, for application to a VRFB electrolyte produced from Bushveld Complex magnetite. From the test work conducted, Puromet MTS9570 proved to be the best of the resins assessed, noting that most commercial IX resins are unable to load metal ions at the high acidity of the electrolyte. This resin gave the best performance in screening, isotherm, and selectivity batch tests, and was selected for column loading tests. Under these conditions, the resin selectively extracted Fe from the electrolyte, leaving V in solution. Maximum loading capacity of the resin was 6 g/L Fe3+ and the resin loaded 90% of the feed concentration after 33 BV at a flowrate of 2 BV/h.
A critical drawback of Puromet MTS9570 is the difficulty in stripping using conventional eluants. Design and sizing of a fullscale column therefore assumed discard of the resin (rather than elution) on reaching full loading capacity. Preliminary sizing of a system to treat 8000 m3/a electrolyte showed that the resin would require replacement every 21 h, with a resin replacement cost exceeding ZAR 127 million/a. This frequency of resin change-out can be extended by using a larger resin volume, but at the cost of higher capital cost. Furthermore, owing to the unfavourable isotherm of this resin, at least two columns in series would be
Table III
Column sizing parameters Parameter
Table IV
Resin cost analysis based on single-pass loading of 140 mg/L Fe at 2 BV/h
(ZAR)**
*Purolite, personal communication, June 2024 **Assume USD 1.00 = ZAR 19.00
required to ensure that the target specification of the barren solution is consistently attained. This is a significant shortcoming of this technology, because the product value cannot justify such a high processing cost.
To progress this concept, future work is required to develop an elution technique for Puromet MTS9570 that would not be detrimental to the V product if any cross-contamination from the
elution step occurred. Large volumes of rinse waters between the loading and elution steps will likely be required. However, it would be preferable to consider a different process technology to achieve the target Fe specification of the electrolyte, in which Fe is separated from V earlier in the primary flowsheet (before generation of the 4 M H2SO4 electrolyte) and IX is merely used for scavenging trace residual Fe to meet the target specification.
Acknowledgements
Bushveld Vametco supplied V2O3 and background information for this testwork: Alicia Enslin is thanked for assistance and advice. All resins were kindly donated by Purolite: we thank Johanna van Deventer for assisting with training, advice, and experimental procedures. CM Solutions generously sponsored all chemical analyses for this work and provided laboratory equipment for some tests. Sincere appreciation is also extended to Johanna van Deventer (Purolite) and Olga Bazkho (Mintek), whose helpful comments considerably improved the quality of this manuscript.
CRediT author statement
MM: Investigation, Writing - Original draft preparation; KCS: Conceptualization, Supervision, Methodology, Funding, Writing- Reviewing and Editing.
References
Adhikari, C.R., Kumano, H., Tanaka, M. 2011. Selective removal of zinc from an electroless nickel plating bath by solvent impregnated resin using 2-ethylhexylphosphonic acid mono2-ethylhexyl ester as the extractant. Solvent Extraction and Ion Exchange, vol. 29, no. 3, pp. 323–336.
Akinbami, O.M., Oke, S.R., Bodunrin, M.O. 2021. The state of renewable energy development in South Africa: An overview. Alexandria Engineering Journal, vol. 60, no. 6, pp. 5077–5093. Bushveld Minerals. 2024. About vanadium. Retrieved from https://www.bushveldminerals.com/ about-vanadium/ [accessed 14 Apr. 2024].
Chace, W.S., Tiano, S.M., Arruda, T.M., Lawton, J.S. 2020. Effects of state of charge on the physical characteristics of V(IV)/V(V) electrolytes and membrane for the all vanadium flow battery. Batteries, vol. 6, no. 4, p. 49.
Crittenden, J.C., Trussell, R.R., Hand, D.W., Howe, K.J., Tchobanoglous, G. 2012. MWH's Water Treatment: Principles and Design. John Wiley & Sons.
Ding, M., Liu, T., Zhang, Y., Cai, Z., Yang, Y., Yuan, Y. 2019. Effect of Fe(III) on the positive electrolyte for vanadium redox flow battery. Royal Society Open Science, vol. 6, no. 1, p. 181309.
El Hage, R., Chauvet, F., Biscans, B., Cassayre, L., Maurice, L., Tzedakis, T. 2019. Kinetic study of the dissolution of vanadyl sulfate and vanadium pentoxide in sulfuric acid aqueous solution. Chemical Engineering Science, 199, 123–136.
Izadi, A., Mohebbi, A., Amiri, M., Izadi, N. 2017. Removal of iron ions from industrial copper raffinate and electrowinning electrolyte solutions by chemical precipitation and ion exchange. Minerals Engineering, vol. 113, pp. 23–35.
Kim, K.J., Park, M.S., Kim, Y.J., Kim, J.H., Dou, S.X., SkyllasKazacos, M. 2015. A technology review of electrodes and reaction mechanisms in vanadium redox flow batteries. Journal of Materials Chemistry A, vol. 3, no. 33, pp. 16913–16933.
LibreTexts Chemistry. 2020. Acid strength and the acid dissociation constant (Ka). Retrieved from https://chem.libretexts.org/ Bookshelves/General_Chemistry/Map%3A_A_Molecular_ Approach_(Tro)/16%3A_Acids_and_Bases/16.04%3A_Acid_ Strength_and_the_Acid_Dissociation_Constant_(Ka)
McCabe, W.L., Smith, J.C., Harriott, P. 2018. Unit Operations of Chemical Engineering. McGraw-Hill.
Naja, G., Volesky, B. 2006. Behaviour of the mass transfer zone in a biosorption column. Environmental Science & Technology, vol. 40, no. 12, pp. 3996–4003.
Prifti, H., Parasuraman, A., Winardi, S., Lim, T.M., Skyllas-Kazacos, M. 2012. Membranes for redox flow battery applications. Membranes, vol. 2, no. 2, pp. 275–306.
Sole, K.C., Mooiman, M.B., Hardwick, E. 2018. Ion exchange in hydrometallurgical processing: an overview and selected applications. Separation & Purification Reviews, vol. 47, no. 2, pp. 159–178.
The Geochemist’s Workbench. 2023. Retrieved from https://www.gwb.com/ [accessed 14 Apr. 2024].
Wang, H., Pourmousavi, S.A., Soong, W.L., Zhang, X., Ertugrul, N. 2023. Battery and energy management system for vanadium redox flow battery: A critical review and recommendations. Journal of Energy Storage, vol. 58, p. 106384.
Xue, S.S., Gula, M.J., Harvey, J.T., Horwitz, E.P. 2001. Control of iron in copper electrolyte streams with a new monophosphonic/ sulphonic acid resin. Minerals and Metallurgical Processing, vol. 18, no. 3, pp. 133–137. u
Affiliation:
1School of Iron and Steel, Soochow University, Suzhou, China
2State Key Laboratory of Advanced Special Steel, Shanghai University, Shanghai, China
Correspondence to: J.F. Xu
Email: xujifangsuda@163.com
Dates:
Received: 5 Aug. 2020
Revised: 10 Feb. 2024
Accepted: 15 May 2024
Published: December 2024
How to cite:
Xu, J.F., Gu, P.W., Su, L.J., and Zhang, J.Y. 2024. Evaluation of surface tension of mold fluxes containing fluoride. Journal of the Southern African Institute of Mining and Metallurgy, vol. 124, no.12, pp. 755–762
DOI:
http://dx.doi.org/10.17159/24119717/1313/2024
ORCiD:
J.F. Xu
http://orcid.org/0000-0002-5753-4041
P.W. Gu
http://orcid.org/0009-0002-6394-1062
L.J. Su
http://orcid.org/0009-0009-1226-2642
J.Y. Zhang
http://orcid.org/0009-0007-5393-1983
by J.F. Xu1, P.W. Gu1, L.J. Su1, and J.Y. Zhang²
Abstract
Surface tension of mold flux is a key factor affecting optimum casting conditions. A thermodynamic model was developed to determine the surface tension of mold flux containing fluoride based on the ion and molecule coexistence theory of slag structure and Butler’s equation. The relationship between composition and surface tension was investigated by this model. Results indicated that the calculated values showed good agreement with literature data, and the average error was 8.19%. The surface tension value of the CaO–Al2O3-based mold flux was larger than that of the CaO–SiO2-based mold flux. The surface tension in a multi-component system decreased with increasing contents of SiO2, CaF2, and Na2O, which are considered surface-active components. This trend was more significant in the CaO–Al2O3-based mold flux.
Keywords
surface tension, mold flux, fluoride, coexistence theory, model
Introduction
During the continuous casting of steel, the mold flux plays an important role in process performance and product defects, which directly determine the final slab quality (Mills et al., 2005). Typical mold fluxes belong to the conventional CaO–SiO2-based system and the newly developed CaO–Al2O3-based system. CaF2, MgO, and Na2O are added to mold flux to modify its properties (Wang et al., 2016). Although the presence of fluoride in mold flux has been identified as a health hazard and correlated to incidences of cancer, it is still widely used because of its remarkable effect on increasing melting point, viscosity, and surface tension. Knowledge of the surface tension of molten slag is useful for understanding various surface or interfacial phenomena in high-temperature processes. Many metallurgical phenomena are closely related to surface tension (Wang et al., 2016). The surface tension of mold flux is a key factor in achieving optimum casting conditions in a continuous casting process, because it affects the interfacial reaction between the mold flux and steel, the absorption of inclusions, and corrosion of the mold nozzle.
The main interest of this work concerns the surface tension of mold flux containing fluoride. Several prior experimental studies were carried out to determine surface tension data for mold fluxes (Mills et al., 2011; Slag Atlas, 1995); however, due to inherent problems and difficulties associated with measurements at high temperature, calculated results have become increasingly important for acquiring such data. It is necessary to have access to reliable models for estimating surface tension. There are many models for estimating surface tension of molten slag (Aune et al., 2002; Cheng and Liao, 1999; Chou and Zhang, 2009; Dong et al., 2014; Mills et al., 2011; Qiao et al., 2001; Xu et al., 2016; Zhang et al., 2003), most of which are proposed based on the structure of atoms and molecules with a physical picture of the practical solution, or combine theoretical considerations with practical thermodynamics. In the present work, based on the ion and molecule coexistence theory of slag structure and Butler’s equation, a new thermodynamic model was developed for determining the surface tension of mold flux containing fluoride. The relationship between the composition and surface tension was also investigated, which helps to understand its performance and provide candidates for the design of new mold fluxes.
A model derived for the estimation of surface tension of ionic mixtures was applied to a six-component molten slag in the CaO–MgO–Al2O3–SiO2–CaF2–Na2O system, which is a typical mold flux containing fluoride for continuous casting. Based on Butler’s equation, the surface tension (σ) of a mold flux containing fluoride is calculated as follows (Butler, 1932):
where subscript i refers to CaO, MgO, Al2O3, SiO2, CaF2, or Na2O in the present work. R is the gas constant, T is the absolute temperature, and Ai = N01/3∙Vi2/3 corresponds to the molar surface area in a monolayer of pure molten component i (N0 is Avogadro’s number, Vi is the molar volume of the pure molten component i). NiSurf and NiBulk are the mass action concentrations (activities) of component i in the surface and bulk, respectively.
For surface tension of the CaO–MgO–Al2O3–SiO2–CaF2–Na2O system, Equation [1] can be expressed as Equations [2]–[7]:
where the molar volumes of the pure molten components (Vi) recommended by Mills et al. (2011) are used in the present model, as listed in Table I. The surface tension of pure component i is given by σiPure, and the equations for determining the temperature dependences of surface tension are listed in Table II (Mills et al., 2011; National Institute of Standards and Technology, 1987).
Based on the above description, the key points of the model for surface tension calculation are established from the mass action concentrations in the surface (NiSurf) and bulk (NiBulk) for the CaO–MgO–Al2O3–SiO2–CaF2–Na2O system. The mass action concentrations of the structures in the surface and bulk were calculated by the ion and molecule coexistence theory of slag structure and related diagrams (Slag Atlas, 1995; Zhang, 2001; Zhang, 2003) as follows:
➤ The structural units of the surface phase of the CaO–MgO–Al2O3–SiO2–CaF2–Na2O system are the same as in the bulk phase of the molten slag, and composed of simple ions (Ca2+, Mg2+, Na2+, O2−, F ), simple molecules (Al2O3, SiO2), and complex molecules. At metallurgical temperatures, components such as CaO, MgO, CaF2, and Na2O in molten slag can dissociate to form simple ions. Components such as SiO2 and Al2O3 in molten slag cannot be dissociated due to the predominance of covalent bonds, and thus exist in a molecular state or in the form of complex compounds. The structural units of this system are listed in Table III.
➤ There are dynamic equilibrium chemical reactions between simple ions, simple molecules, and complex molecules both in the surface and bulk layers.
Taking calcium silicate formation as an example:
Table I
Molar volumes of pure component (m3/mol)
Component Temperature (K) dependence of molar volume (m3/mol)
CaO 20.7 × [1 + 1 × 10−4 × (T − 1773)] × 10−6
MgO 16.1 × [1 + 1×10−4 × (T − 1773)] × 10−6
Al2O3 28.3 × [1 + 1 × 10−4 × (T − 1773)] × 10−6
SiO2 27.516 × [1 + 1 × 10−4 × (T − 1773)] × 10−6
CaF2 31.3 × [1 + 1 × 10−4 × (T − 1773)] × 10−6
Na2O 33.0 × [1 + 1 × 10−4 × (T − 1773)] × 10−6
Table II
Temperature dependences of surface tensions of pure components
Component Temperature (K) dependence of surface tension (mN/m)
CaO 791 − 0.0935T
MgO 1770 − 0.636T
Al2O3 1024 − 0.177T
SiO2
[8]
243 + 0.031T
CaF2 1604.6 − 0.72T
Na2O 438 − 0.116T
➤ There are dynamic equilibria between ions and molecules both in the surface and bulk layers. The chemical reactions and their thermodynamic parameters are given in Table III (Bale et al., 2002; Turkdogan, 1980; Wu et al., 2014).
➤ Chemical reactions in molten slags obey the Law of Mass Action in both the surface and bulk layers. Equation [9] can be applied: [9]
where Kθ 2CaO SiO2 is the chemical reaction equilibrium constant of Equation [9], and can be calculated from ΔGθ. The surface mass action concentrations depicted by NSulf , NSulf , and NSulf are those of 2CaO SiO2, ion couples (Ca2++ O2−), and SiO2, respectively; the respective corresponding bulk mass action concentrations are given by NBulk , NBulk , and NBulk
The mass action concentrations of the structural unit are defined as the ratio of the equilibrium mole number of structural unit i to the total equilibrium mole numbers of all structural units, calculated by Ni = ni ⁄ ∑ni. The mole numbers of CaO, MgO, Al2O3, SiO2, CaF2, and Na2O in 100 g of total slag mass are defined as b1 = nCaO, b2 = nMgO, b3 = nCaF2, b4 = nNa2O, a1 = nAl2O3, and a2 = nSiO2, respectively. The symbols of the mass action concentrations for all structural units are listed as follows: N1 = NCaO, N2 = NMgO, N3 = NAl2O3, N4 = NSiO2, N5 = NCaF2, N6 = NNa2O. Mass equilibria formulae for the CaO–MgO–Al2O3–SiO2–CaF2–Na2O system are given by Equations [10]–[16]:
Table III
Expression of structural units, standard Gibbs free energies chemical reactions of complex molecules, their standard Gibbs free energies, and mass action concentrations of CaO–MgO–Al2O3–SiO2–CaF2–Na2O slag system
Structural unit Reaction ΔGθ (J·mol−1) Mass action concentration
Simple ions
Simple molecules
Complex molecules
Therefore, Equations [10]–[16] are the governing equations of the developed thermodynamic model for calculating mass action concentrations Ni of structural units or ion couples in the CaO–MgO–Al2O3–SiO2–CaF2–Na2O system for a certain temperature and components, where N7–N53 can be represented by N1–N6
➤ The relationship between surface tension of a melt system and mass action concentrations of surface and bulk components conforms to Butler’s equation. The process to estimate the surface tension model is shown in Figure 1; detailed discussions of this method are given by Cheng and Liao (1999) and Xu et al. (2017). For a given slag chemical composition xi and temperature T, the Kiθ reaction equilibrium constant can be calculated, and then the mass action concentrations in the bulk (NiBulk) can be calculated
from the mole fractions of the components and the chemical reaction equilibria constants of complex molecules based on the ion and molecule coexistence theory. Surface tension (σ) and the mass action concentrations in the surface (NiSur ) can be calculated from NiBulk, σiPure, and Ai based on this theory and Butler’s equation.
Results and discussion
Comparison between estimated values and experimental data
Comparison between the estimated surface tension values and those measured, as reported from the literature, for the CaO–MgO– Al2O3–SiO2–CaF2–Na2O related system is shown in Figure 2. The average error (Δ) of all calculated values can be assessed using Equation [17], where the Δ(%) value is calculated by taking the summation of the percentage differences of the calculated and measured values and dividing by the number of data points:
The estimated values using this model were compared with experimental data to verify the model. The result indicated that the estimated values agree with the experimental data (Dou et al., 2009; Slag Atlas, 1995). For all calculated values, the average error Δ(%) is 8.19%. The detailed average errors for related experimental systems are also shown in Table IV. The average error Δ(%) for the MgO–Al2O3–SiO2–CaF2 system is about 12.67%, which could be related to the slag composition, which has high CaF2 content and no CaO. The deviation of individual points is also relatively large in the CaO–Al2O3–SiO2–CaF2–Na2O system. The larger experimental measurements may be related to the fact that the slag may be in a non-homogeneous region due to its lower basicity (~ 0.45) owing to low CaF2 and Al2O3 contents. The model prediction achieved reasonable accuracy of surface tension variation in the fully liquid phase of the CaO–MgO–Al2O3–SiO2–CaF2–Na2O system and its sub-systems.
Traditional mold flux is based on the CaO–SiO2 system, which has low basicity (CaO/SiO2 mass ratio) and low viscosity, to which fluxing agents such as CaF2, Na2O, and B2O3 are added to optimize
Table IV
Composition, temperature, and relative average errors for related experimental systems System
CaO–MgO–Al2O3–SiO2–CaF2
the properties. The surface tension of the CaO–SiO2–CaF2 system was evaluated, and the calculated results are shown in Figure 3. The four lines in this figure indicate the calculated results for the iso-surface tensions at 330, 360, 390, and 420 mN/m. Figure 3 also shows the boundary of the homogeneous region at 1773 K, calculated using the thermodynamic software FACTSAGE. The result indicates that both CaF2 content and basicity influence the surface tension. When the CaF2 content was lower than 20%, the effects of basicity and CaF2 addition on the surface tension were similar; when the CaF2 content was higher than 20%, the basicity had a more significant effect. Figure 4(a) shows the effect of basicity with different Al2O3 contents on the surface tension at 1773 K. The results indicate that the surface tension increased with increase of basicity. The trends of surface tension effected by the Al2O3 content and basicity were the same. Figure 4(b) shows the effect of the CaF2 content with different Na2O contents on the surface tension at 1773 K. The surface tension decreased with increase of CaF2 content. The trends of surface tension effected by Na2O content and CaF2 content were also the same, although Na2O had a more significant effect.
Surface tension of CaO–Al2O3-based mold flux
The newly developed CaO–Al2O3-based mold flux has a high Al2O3 content and relatively low SiO2 content. This flux shows strong potential for application to continuous casting (Wang et al., 2016). Surface tension of the CaO–Al2O3–CaF2 system was also evaluated, and the calculated results are shown in Figure 5. The five
lines in this figure indicate the calculated results for the iso-surface tensions at 360, 390, 420, 450, and 480 mN/m. The boundary of the homogenous phase region at 1773 K, calculated using the thermodynamic software FACTSAGE, is also shown. The surface tension value of the CaO–Al2O3-based mold flux is larger than that of the CaO–SiO2-based mold flux. The result also indicates that the surface tension significantly decreased with increase of CaF2 content. The effects of CaO and Al2O3 contents on surface tension
4—Relationships between surface tension of CaO–SiO2-based mold flux with composition. (a) Basicity and Al2O3 content, (b) CaF2 content and Na2O content
are not significant for a given CaF2 content. CaF2 addition has a more significant effect on surface tension than the mass ratio of CaO/Al2O3. Figure 6(a) shows the effect of the CaO/Al2O3 mass ratio for different SiO2 contents on the surface tension at 1773 K. With increase of the CaO/Al2O3 mass ratio, the surface tension decreased with increase of SiO2 content. For the same SiO2 content, the surface tension slowly increased with increase in the CaO/Al2O3 mass ratio. Figure 6(b) shows the effect of CaF2 content for different Na2O contents on the surface tension at 1773 K. The surface tension significantly decreased with CaF2 content, more strongly than that in the CaO–SiO2-based mold flux. The trend of change of surface tension with Na2O content was the same as that of CaF2 content, but CaF2 had a more significant effect.
These results confirm other reports (Mills et al., 2011) that the surface-active components (SiO2, CaF2, and Na2O) preferentially migrate to the surface and cause a sharp decrease in surface tension. In general, on the basis of the additive method widely used for alloys and slags, surface tension of slag depends on the surface tension of the oxides (Mills, 1993). The surface tensions of CaO, MgO, Al2O3, SiO2, CaF2, and Na2O pure components are 625, 642, 710, 298, 32,8 and 232 mN/m at 1773 K, respectively (Hanao et al., 2007). Because the surface tensions of pure SiO2, CaF2, and Na2O are much lower than those of CaO, MgO, and Al2O3, surface tension of mold flux will decrease with small increases in SiO2, CaF2, and
Na2O contents. For instance, with increasing basicity of the CaO–SiO2-based mold flux, the SiO2 content will reduce, which could lead to an increase in the slag surface tension. With increasing CaO/ Al2O3 mass ratio in the CaO–Al2O3-based mold flux, the content of surface-active components is only slightly reduced and surface tension slowly increases.
Conclusions
➤ A thermodynamic model for determining the surface tension of mold flux slag containing fluoride was developed based on the ion and molecule coexistence theory of slag structure and Butler’s equation. The results indicated that the surface tension model could fit the experimental data well.
➤ Surface tension of the CaO–Al2O3-based mold flux is larger than that of the CaO–SiO2-based mold flux. The surface tension in a multi-component system decreased with increasing content of surface-active components: SiO2, CaF2, and Na2O. This effect was more significant in the CaO–Al2O3based mold flux.
➤ In the CaO–SiO2-based system, the surface tension increased with increasing basicity and Al2O3 content. In the CaO–Al2O3-based system, the surface tension slowly increased with increasing CaO/Al2O3 mass ratio and decreased with increasing SiO2 content.
Acknowledgements
This work was supported by Project no. 51704201, sponsored by the National Natural Science Foundation of China. English editing of this manuscript was carried by Kathryn C. Sole (PhD).
References
Aune, R., Hayashi, M., Nakajima, K., Seetharaman, S. 2002. Thermophysical properties of silicate slags. JOM, vol. 54, no. 11, pp. 62–69.
Bale, C.W., Chamand, P., Degterov, S.A., Erkseon, G., Hack, K., Ben Mehfoud, R., Melancan, J., Pelton, A.D., Petetaen, S. 2002. FactSage thermochemical software and databases. Calphad, vol, 26, no. 2, pp.189–228.
Butler, J.A.V. 1932. The thermodynamics of the surfaces of solutions. Proceedings of the Royal Society of London Series A, vol. 135, pp. 348–375.
Cheng, G.G., Liao, N.B. 1999. Calculation model for surface tension of slag melt. Journal of Iron and Steel Research International, vol. 6, no. 2, pp. 17–20.
Chou, K.C., Zhang, G.H. 2009. Calculation of physicochemical properties with limited discrete data in multicomponent systems. Materials Transactions B, vol. 40, no. 2, pp. 223–232.
Dong, Y.W., Jiang, Z.H., Cao, Y.Y., Zhang, H.K., Shen, H.J. 2014. Effect of MgO and SiO2 on surface tension of fluoride containing slag. Journal of Central South University, vol. 21, no. 11, pp. 4104–4108.
Dou, Z.H., Zhang, T.A., Yao, J.M., Niu, L.P., Jiang, X.L., He, J.C. 2009. Research on properties of CaF2–CaO–Al2O3–MgO–SiO2 refining slag. Chinese Journal of Process Engineering, vol. 9, no. S1, pp. 132–136 [in Chinese].
Hanao, M., Tanaka, T., Kawamoto, M., Takatani, K. 2007. Evaluation of surface tension of molten slag in multi-component systems. ISIJ International, vol. 47, no. 7, pp. 935–939.
Mills, K.C. 1993. The influence of structure on the physico-chemical properties of slags. ISIJ Inernational, vol. 33, no. 1, pp. 148–155.
Mills, K.C., Fox, A.B., Li, Z., Thackray, R.P. 2005. Performance and properties of mould fluxes. Ironmaking and Steelmaking, vol. 32, no. 1, pp. 26–34.
Mills, K.C., Yuan, L., Jones, R.T. 2011, Estimating the physical properties of slags. Journal of the Southern African Institute of Mining and Metallurgy, vol. 111, no. 10, pp. 649–658.
National Institute of Standards and Technology. 1987. NIST Molten Salt Database. National Institute of Standards and Technology, New York.
Qiao, Z.Y., Yan, L.J., Cao, Z.M., Xie, Y.N. 2001. Surface tension prediction of high-temperature melts. Journal of Alloys and Compounds, vol. 325, no. 1–2, pp. 180–189.
Slag Atlas. 1995. 2nd edn., Verlag Stahleisen, Düsseldorf. p. 425, p. 437, p. 445, p. 446, p. 455, p. 456.
Turkdogan, E.T. 1980. Physical Chemistry of High Temperature Technology. Academic Press Inc, New York.
Wang, W.L., Li, J.G., Zhou, L.U., Yang, J. 2016. Effect of MnO content on the interfacial property of mold flux and steel. Metals and Materials International, vol. 22, no. 4, pp. 700–706.
Wang, W.L., Lu B.X., Xiao, D. 2016. A review of mold flux development for the casting of high-Al steels. Materials Transactions B, vol. 47, no. 1, pp. 384–389.
Wu, C.C., Cheng, G.G., Ma, Q.Q. 2014. Calculating model on the surface tension of CaF2–CaO–Al2O3–MgO–SiO2 slag system. Shanghai Metals, vol. 36, no. 3, pp. 33–36 [in Chinese].
Xu, J.F., Zhang, J.Y., Chen, D., Sheng, M.Q., Weng, W.P. 2016. Effects of MgO content and CaO/Al2O3 ratio on surface tension of calcium aluminate refining slag. Journal of Central South University, vol. 23, no. 12, pp. 3079–3084.
Xu, J.F., Li, J.C., Weng, W.P., Sheng, M.Q., Chen, D., Zhang, J.Y., Chen, Y. 2017. Calculation of surface tension for MgO–B2O3–SiO2–CaO–Al2O3 molten boron-rich slag system. Chinese Journal of Nonferrous Metals, vol. 27, no. 1, pp. 206–214 [in Chinese].
Zhang, J. 2001. The application of the law of mass action in combination with the coexistence theory of slag structure to the multicomponent slag systems. Acta Metallurgica Sinica (English Edition), vol. 14, no. 3, pp. 177–190.
Zhang, J. 2003. Coexistence theory of slag structure and its application to calculation of oxidizing capability of slag melts. Journal of Iron and Steel Research, International, vol. 10, no. 1, pp. 1–10.
Zhang, J.Y., Shu, Q.F., Wei, S.K. 2003, Prediction of surface tension in molten metallic and ionic systems. High Temperature Materials and Processes, vol. 22, no. 5–6, pp. 395–400. u
In 2024, Redpath Mining South Africa (RMSA) celebrated its 30th anniversary, marking three decades of delivering world-class mining solutions. While RMSA focuses on operations within South Africa, Redpath’s broader African footprint currently extends to key countries such as Ghana, Zambia and Botswana and has historically extended to several other African countries. Redpath is currently exploring a number of opportunities across the continent, both in regions where it has worked previously and in new jurisdictions.
As part of the global Redpath Group, established in 1962, these entities work collaboratively to uphold the group’s reputation for excellence in underground mining maintaining its goal to serve its clients well. Globally, the Redpath Group employs over 6000 people, continuing to innovate and set benchmarks in underground mining.
Safety is a core value for Redpath, guided by its motto: Safety – First, Last and Always This commitment is evident in recent milestones such as 1047 Lost Time Injury (LTI) free days at Mogalakwena, 1141 LTIfree days achieved by the Northam Boxfront project crew and an exceptional 2698 LTIfree days at RMSA’s Alberton Raiseboring and Engineering Workshop. Numerous projects, including those at Obuasi Gold Mine, Tshepong Mine and Thubelisha West Mine, have remained accident-free since their inception. These milestones underscore Redpath’s unwavering dedication to safety.
A defining feature of Redpath’s success has been its ability to execute flagship projects that combine technical expertise with innovative solutions, such as Anglo American Platinum’s (AAP) Mogalakwena Underground Exploration Decline project (Phase B at present). Mogalakwena is a strategic capital project for AAP, supporting the future addition of underground mining at the mine. Redpath is collaborating with AAP to deliver this world-class project, leveraging global expertise and innovation. Two key objectives of the project are high-speed lateral development and skills transfer. To this end, Redpath’s Australian secondees
are executing high-speed development methodologies, while implementing a skills transfer programme which focuses on imparting these skills to local operators. The project is progressing on schedule, and most importantly, is being executed safely. In 2024, the team achieved a major milestone of three years without a LTI. The Mogalakwena project follows a similar model to the project presently being executed at Venetia Mine for De Beers. At Venetia, Redpath, in collaboration with Venetia management, have significantly improved development rates using Redpath Australian expatriates to upskill local Venetia employees. The fruits of these efforts have been realised over the last period where record development metres have been sustainably achieved.
Northam Zondereinde 3 Shaft is another significant project for Redpath’s South African operations. At Zondereinde, Redpath is equipping a raisebore shaft and executing ancillary construction works. The project is complex and has had its challenges which Redpath and Northam have worked collaboratively to solve. This continues a long-standing relationship with Northam and Redpath are proud to be entrusted with this critical capital work as part of Northam’s overall expansion.
Redpath’s Raiseboring Division has also delivered notable achievements. At Obuasi Gold Mine in Ghana, the Redpath Thonket Joint Venture set a world record by completing the largest raisebore hole to date – the Kwesi Mensah Ventilation Shaft. Measuring 944m in depth and 6.5m in diameter, the project demonstrated exceptional technical execution while incorporating sustainability measures such as water recycling and energy-efficient technologies. The Redpath Thonket team is currently reaming an additional underground hole with a diameter of 6.1m and a depth of 300m.
In South Africa, projects like the Zibulo Colliery ventilation shafts and the Thubelisha West ventilation shaft (both in Mpumalanga) further highlight the division’s ability to deliver high-quality results ahead of schedule. A key success
this year has been RMSA securing a raiseboring contract at AAP’s Der Brochen Project in Limpopo – a significant growth project for AAP. RMSA’s machinery is already in place and crew mobilisation is underway, with work scheduled to commence in 2025. This contract demonstrates Redpath’s ability to build on its strong relationships with key clients and expand its portfolio of high-impact projects. This underlines Redpath’s Guidelines for Success, including acting in the long-term interest of the company and its clients.
With its extensive footprint, technical expertise and strong focus on collaboration, Redpath continues to set new benchmarks in the industry. As RMSA reflects on its 30-year milestone, the organisation remains steadfast in its commitment to delivering excellence, driving innovation and upholding the highest safety and performance standards in the mining sector across Sub-Saharan Africa.
Affiliation:
1Curtin University, Western Australia School of Mines, Kent Street, Bentley, WA, Australia
2Stellenbosch University, Department of Mechanical and Mechatronic Engineering, Stellenbosch, South Africa
3Stellenbosch University, Department of Process Engineering, Stellenbosch, South Africa
4Mintek, Pyrometallurgy Division, 200 Malibongwe Drive, Randburg, South Africa
Correspondence to: L.Hockaday
Email: lina.hockaday@curtin.edu.au
Dates:
Received: 18 Feb. 2024
Revised: 14 Sept. 2024
Accepted: Nov. 20241
Published: December 2024
How to cite:
Hockaday, L., Dinter, F., Reynolds, Q.G., and MaGregor, C. 2024. Evaluation of solar thermal pretreatment of carbonate-rich manganese ores in high-carbon ferromanganese production through dynamic process modelling. Journal of the Southern African Institute of Mining and Metallurgy, vol. 124, no.12 pp. 763–776
DOI:
http://dx.doi.org/10.17159/24119717/3296/2024
ORCiD: L. Hockaday http://orcid.org/0000-0003-2597-9756
by L. Hockaday1,2, F. Dinter2, Q.G. Reynolds3,4, and C. McGregor2
Abstract
The necessity of reducing greenhouse gas emissions to limit the impact of anthropogenic climate change means that all industrial processes should investigate their options towards decarbonization. Iron, steelmaking, aluminium, and cement production produce the most industrial emissions. Although most research focuses on decarbonizing these industries, minerals processing industries must be decarbonized to achieve net zero emissions goals by 2050. Incorporating renewable energy sources and avoiding the combustion of fossil fuels are two ways to reduce greenhouse gas emissions. This paper reports on the results from a dynamic process model developed to investigate the feasibility of concentrating solar thermal pretreatment of manganese ores to pretreat carbonate-rich manganese ores for increased ferromanganese smelter productivity and reduced greenhouse gas emissions. The results indicate that pretreated ores reduce the energy requirement for smelting significantly for some ores and lowers total carbon dioxide emissions by 13 to 19% compared to the traditional smelting route. A high-level economic evaluation shows that solar thermal treatment is financially viable for low cryptomelane, high braunite ore that is common in the Kalahari Manganese Field.
Keywords
solar thermal, manganese ore, dynamic modelling, benefit assessment
Introduction
Globally, pressure has mounted on the mining and minerals processing sector to show commitment to fighting climate change by enacting sustainable governmental practices – one of which is lowering greenhouse gas (GHG) emissions. Concerns about the emission of GHG and their contribution to climate change have led to South Africa implementing a carbon tax on carbon dioxide emissions (South African Government, 2019). Despite the carbon tax having been introduced with large emission allowances, it is generally accepted that these allowances will be reduced over time to align with European regulations. Awareness of the impact of climate change has become more prevalent and having a social license to operate has become crucial in metal production (International Resource Panel, 2020; Mills, 2021).
This paper aims to investigate concentrating solar thermal pretreatment of manganese ores for ferroalloy production. This technology can be seen as a process energy efficiency initiative for smelters, replacing fossil fuel and reductant with solar energy. The use of carbon capture and sequestration of carbon dioxide emissions emitted during solar thermal pretreatment may be investigated in future but fall outside the scope of this study.
Current manganese ore pretreatment technologies (Olsen, Tangstad and Lindstad, 2007; Gasik, 2013; Gordon Y., 2013; Gordon, Nell and Yaroshenko, 2018) may be classified as preheating, calcination or sintering. Preheated materials are charged directly to smelters at 600–700°C after heating in rotary kilns with coal or furnace off-gas combustion and lower electric energy consumption by more than 20% (Tanabe, 1968; Ishak and Tangstad, 2007; Tangstad, Ichihara and Ringdalen, 2015). The calcination of manganese ores is mainly used as a preparation step for electrolytic processes in the production of highpurity manganese metal and manganese dioxide. Manganese ores mixed with ground coal are heated at temperatures between 850°C and 900°C to achieve the reduction of manganese to Mn2+ as well as carbonate decomposition (Harris, Meyer and Auerswald, 1977; Biswal et al., 2015). Sintering of manganese ores mixed with coal occurs at temperatures above 1200°C, decomposing all carbonates and reducing manganese oxides to MnO. Sinter operations are well described in the literature (Gericke, 1989; Pienaar and Smith, 1992; Daavittila et al., 2001; Malan, Barthel and Dippenaar, 2004; Zhang et al., 2013).
Table I
Reaction rate equations and activation energies and pre-exponential factors determined from experimental data (Hockaday, Dinter and Reynolds, In print)
Reaction Rate equation Ea, kJ/mol A
CaMg(CO3 )2 →CaO + MgO + 2CO2(g)
MgO + CO2 (g)
4MnO2 → 2Mn2 O3 + O2(g)
6Mn2O3 → 4Mn3 O4 + O2(g)
reactions with solid carbon
Pretreatment of manganese ores is currently practised only in reducing atmospheres. A novel concentrating solar thermal pretreatment in air has been proposed to offer the advantages of carbonate decomposition while limiting the reduction of manganese oxides to Mn3O4 (Hockaday, Dinter and Reynolds, In print). Materials treatment with concentrating solar technologies is still a developing field of research, but much progress has been made in the last decade (Ekman, Brooks and Rhamdhani, 2014; Koepf et al., 2017). Solar particle reactor technology has been researched for various applications, including solar processing of composite iron ore pellets (Purohit et al., 2018), particles as a heat transfer medium (Amsbeck et al., 2014), and the calcination of lime (Flamant et al., 2018). Several desktop studies have also been published regarding indirect solar heating in fuel-saving applications for manganese ore pretreatment (Hockaday, Dinter and Harms, 2018; Lubkoll, Hockaday and Harms, 2018). Desktop studies for indirect solar preheating of manganese ores up to 600°C using air as heat transfer medium and including thermal storage have also been shown as more cost effective that electrification of preheating (Hockaday et al., 2020; Mckechnie, McGregor and Venter, 2020, 2022).
The current study focuses on direct solar heating of manganese ores in air as a pretreatment for high-carbon ferromanganese production. The direct solar treatment of manganese ores has been performed on small scale and showed promising decomposition of carbonate minerals (Hockaday et al., 2021). The scaling of direct solar thermal treatment of manganese ores was evaluated based on several models describing the solar resource, the manganese ore reaction kinetics, and a solar particle reactor. These models were linked in HSC SIM (Roine and Bjorklund, 2002; Outotec, 2019) to estimate the annual production and composition of solar thermal pretreated manganese ores. The energy demand of solar-treated
–(1 – Xi)⅓
– Xi)⅓
material in a high-carbon ferromanganese furnace was then investigated based on an HSC Sim distribution model.
The reduction and calcination reactions that occur in high-calcite manganese ore pretreatment have been described by Hockaday, Dinter and Reynolds (In print). Thermal treatment in non-reducing conditions allows the decomposition of carbonate minerals, pyrolusite and bixbyite decomposed to hausmannite, and partial decomposition of braunite to hausmannite. The kinetic models describing the ore behaviour are summarized in Table I.
Mass and energy balances
Mass and energy balances were performed with HSC SIM software. The reactor energy balance was based on the solar energy entering the reactor being split between three reactor zones: Tank 1, Tank 2, and Tank 3. Each tank was assumed to act as an ideal mixer or continuously stirred tank reactor (CSTR), with all materials inside reaching the same temperature. The flows of gas and solid materials were counter-current. Tank 1 received untreated materials and served as an outlet for the process off-gas. Tank 3 received the solar flux and an air inflow and served as the kiln discharge for treated materials. The stream flows and operations of the dynamic process model are shown in Figure 1.
The control philosophies, and calculations for each time step, are described below:
➤ The receiver was charged with a batch of material to protect the receiver from solar flux. The batch size may vary from 120 kg to 500 kg based on the material density.
➤ Feed material was added to Tank 1 based on the feed rate setpoint if the temperatures in the receiver were high enough. For solar irradiance levels below 1000 kW the feed rate setpoint was halved.
➤ The solar irradiance was taken from the dynamic SET sheet and used in the radiation model, together with the current temperatures of the tanks, to determine the irradiance into each tank and the radiation losses from the receiver.
➤ An energy balance was performed on each tank based on the energy flows determined in the previous step to determine the new temperature of each zone.
➤ Materials in each tank were converted according to the reaction rate model and used to calculate the new composition of the tank. Product gasses flow to the previous tank number counter-current to the flow of solid materials.
➤ Solid materials were batched to the next tank or discharged to the product pile if the tank was too full.
➤ When the discharge zone temperature dropped below 950°C the addition of feed material was stopped. The receiver discharged until it reached the maximum capacity and then held the rest of the material inside the receiver. The mass and energy balances, and the reaction rate model, were still applied.
Assumptions for the dimensions and operation of the receiver are based on published data of the CentRec® receiver (Ebert et al., 2016, 2018, 2019; Amsbeck et al., 2018) and are given in Table II.
The CentRec® demonstration unit was tested with ceramic particles of 1 mm diameter. Similar behaviour was assumed for manganese ore particles. Manganese ore fines (< 6 mm) are readily available for processing at mines and smelters and are currently treated as waste or agglomerated through sintering or briquetting (Olsen, Tangstad and Lindstad, 2007), and can be the source for manganese ore particles of approximately 1 mm.
When the particle volume in the tank exceeds the maximum volume calculated for the layer thickness, particles in the tank are batched to the next tank or discharged, depending on the tank number. The dynamic module automatically calculates the volume of the solids in each tank, based on density values contained in the thermodynamic database. Each tank was specified to run in the energy input mode in the simulation, where the energy balance was solved to determine the new temperature of the tank at the end of each timestep.
A crucial aspect of the receiver is its ability to hold the particles in the receiver at high rotational speeds and then discharge the
Table II
Receiver model parameters (Ebert et al., 2016, 2018, 2019; Amsbeck et al., 2018)
Description Value Unit
Aperture,
Particle
particles by reducing rotational speed. This enables fine control over the temperature of the discharge material. The feed material control temperatures from 750°C to 1000°C were chosen, as this allows for the thermal decomposition of calcite. This temperature range is also close to the documented outlet temperatures for the CentRec® receiver but below the ore's sintering temperature (1100°C to 1300°C). The control temperature is used to control the feed rate to the receiver reactor and does not determine the discharge temperature. The discharge temperature is a result of the energy balance.
In the HSC process model, the off-gas was treated as an infinite-volume tank that captured all process emissions. This approach allowed easy evaluation of the carbon dioxide produced by the process for a specific scenario. Similarly, the product pile was an infinite-volume container reporting each chemical species by weight. The full derivation of the view factor-based energy distribution model and its validation is given as (Hockaday, 2023).
The residence time of particles in the rotary receiver can be difficult to quantify (Gallo et al., 2016). The process model assumption in this study is that the rotary receiver may be described as a series of continuous stirred tank reactors (CSTR) in series. This assumption has implications for the particle residence time distribution in the reactor. Some particles may theoretically never leave the perfectly mixed reactors, while others rush through without reacting. The mean residence time for a reactor can always be calculated from the reactor mass holdup divided by the steadystate inlet or outlet mass flow rate. In this process model, the mean residence time, τ, represents the average time for a particle to move through the receiver reactor.
It may appear at first glance that the assumption of a wellmixed tank does not describe the behaviour of the rotary receiver. However, the receiver has a 10 mm high holding rim, damming part of the particle mass and preventing plug flow behaviour. In addition, particles in a rotary receiver are expected to behave or vibrate in all directions and change positions within the particle layer.
The two ore samples used to construct the kinetic reaction rate models were also used as feed materials for the process evaluation. The measured compositions of the feed materials are given in Table III, with high braunite manganese ore abbreviated as braunite manganese (BMN) and high crypromelane manganese ore abbreviated as cryptomelane manganese (CMN)
The performance of the solar plant was modeled to provide a dataset of hourly solar flux values that can serve as input to the dynamic HSC model. The methodology of modeling the solar thermal plant is based on the previously proposed methods (Amsbeck et al., 2014; Lubkoll, Hockaday and Harms, 2018). The solar thermal plant is based on the Centrec® receiver and heliostats of equivalent size to Heliopod® technology (Mckechnie, McGregor and Venter, 2022). The Centrec® receiver (i) is suitable for handling of solid material, so can be used for the pretreatment of manganese ore particles, (ii) it enables direct irradiation of the ore without the need to go via a heat transfer medium (this matches the experimental onsun testing approach), (iii) has been extensively demonstrated at semi-commercial scale at the DLR's Juelich facility, and finally, (iv)
Table III Composition
Al2O3.3H2O
it can be scaled up to larger sizes understood by the solar thermal and mineral's processing industry. The Centrec® receiver operation and design are well documented (Amsbeck et al., 2018; Ebert et al., 2019) and may possibility be scaled further in the future (Gallo et al., 2016). This technology is being tested for commercialization in the HiFlex project (Santamarta, 2020; Sayles, 2020).
The design point for the solar thermal plant was taken as the DNI at midday on the solar equinox. The location assessed was the mining town of Hotazel in the Northern Cape province of South Africa. Hotazel is in the Kalahari Manganese Field, with large manganese mines belonging to different companies surrounding the town. The heliostat field design was done using SolarPILOT Version 1.3.2 software (Wagner, 2017, 2019) and is shown in Figure 2.
Table IV
Specifications for heliostats, receiver, and site
Specification value unit
Heliostat facet optical aperture area 1.83×1.22=2.23 m2
Heliostat facet focal length At slant m
Receiver aperture 1 m2
Receiver tilt angle -45 °
Solar field design power 2.5 MWt
Tower height 40 m
Site latitude (true) -27.2 °N
Site longitude 22.9 °E
Design point DNI 1040 W/m2
Solar field size 3760 m2
Average solar field efficiency at the design point 62.6 %
Incident flux reaching the receiver 5503 MWh/a Capacity factor (CF) based on incident flux 25 %
Hourly azimuth and elevation angles for the equinox, summer solstice, and winter solstice were calculated in Excel based on the equations for observer-sun angles (Stine and Geyer, 2011). These angles were then used in SolarPILOT as parametric input to determine the heliostat field efficiency curves. The output was interpolated to provide the heliostat field efficiency for each hour of the year. The land requirement for a 2.5 MW tower and solar field is approximately 160 m x 110 m or 1.76 ha.
Specifications for the SolarPILOT program are given in Table IV. Mirror performance parameters were set to 0.97 reflective surface ratio, 0.95 mirror reflectivity, and a soiling factor of 0.95. The receiver's horizontal acceptance angle was set to 80° and the vertical acceptance angle to 90°.
Results and discussions
The process model allowed for the investigation of a solar thermal process operation on different time scales. The residence time of the particles in the solar receiver, the temperatures in distinct parts of the receiver and the off-gas composition were estimated. Since the solar resource is variable, there is a concern that products from direct solar treatment may be erratic and inconsistent in quality.
This perception was investigated by running daily and monthly scenarios at the design specifications (ideal conditions) and nonideal conditions (cloudy or rainy days). Due to the short residence time of the particles in the reactor, the simulations were done with 1-minute timesteps.
Product quality and throughput per day
A day with patchy sunshine was selected and modeled to compare the throughput and quality to a day of bright uninterrupted sunshine. January 18th was chosen from the typical meteorological year (TMY) as a high irradiance day, and June 26th as a day with interrupted sunshine. The hourly power to the receiver is shown in Figure 2. The BMN ore was used for illustrative purposes.
The operation of the pretreatment plant should consistently produce a product below 1200°C to prevent the melting or sintering of the particles. If the particles should sinter, they may destabilize the particle layer and initiate the dumping of the material. In addition, molten material may stick to the receiver walls and solidify, leading to solid material build-up that can prevent the free flow of the particles.
The extent of calcination is positively influenced by higher temperatures and negatively by higher feed rates. Higher feed rates reduce the residence time of the material in the receiver and increase untreated material that gets passed through to the product. Several simulations at different feed rates were run for the ores to investigate the operating window where the temperatures were below 1200°C, while the product achieved a calcination target of 80% or more for both the design case and the low solar irradiation case. A limit to the solar irradiance incident on the receiver was imposed to achieve the required calcination while maintaining a temperature below 1200°C. The limit of 1700 kW irradiance combined with the feed rate setpoint of 3200 kg/h reached the operational targets for the BMN ore, while the CMN ore had a feed rate setpoint of 6400 kg/h. The difference in feed rate is due to the different compositions of the ores, and the different reaction kinetics for the calcination of the ores. Due to the unreactive nature of the BMN ore compared to the CMN ore, the BMN ore simulations operated on feeding only when the discharge zone temperature was above 980°C. In contrast, the CMN ore achieved calcination above 80% even with feeding when the discharge zone temperature was 780°C.
The irradiance limit also has practical advantages. Since the solar field has extra design capacity it lengthens the steady-state operational time achieved daily. The solar multiple, defined as the
solar plant design power divided by process energy demand, was 1.47 for this study.
The BMN ore at a feed rate of 3200 kg/h illustrates how the receiver operates for a high solar irradiance day (the design case), and a low irradiance day (a deviation). The energy flows for the solar receiver are provided in Figure 3.
While zone temperatures fluctuated at sunrise and sunset, each tank operated at a constant temperature for most of a sunny day, as shown in Figure 4 (a). Figure 4 (b) shows temperatures are erratic for a cloudy day, fluctuating by 200°C to 300°C.
The extent of reactions is discussed next, based on the oxidation state and calcination degree of the material as it moves through the reactor.
The oxidation state of the manganese ore may be expressed as a non-stoichiometric compound, MnOx, where x represents the amount of oxygen bound to manganese. For example, a highly oxidized ore would have a value of x close to 2, indicating that it contains mainly pyrolusite, MnO2. A reduced hausmannite ore would have a value of x of 1.33 or 4/3 as it contains mainly Mn3O4. Similarly, one can express the amount of oxygen bound to Fe in the sample with FeOy. Here, y will be equal to 1.5 for hematite, 1.33 for magnetite and 1 for wustite. For braunite, Mn7SiO12, we treat the oxygen to manganese ratio is treated to 10/7 or 1.43, and the remaining two oxygens are assumed to be bound to the silicon. The value of x reduces as thermal decomposition and reduction of manganese ores progress. The amount of organic carbon present in the feed material, the material's temperature, and the material's residence time in the high-temperature zone all limit the extent of reduction. During days with interrupted sunshine or low solar irradiance, more reduction may occur as feed rates are slower and residence times longer, as shown in Figure 6.
Figure 4—Energy flows for the solar receiver on an (a) high solar irradiance day and b) on a low solar irradiance day as calculated at a feed rate setpoint of 3200 kg/h BMN ore with a control temperature of 980 °C. At an irradiance of 1700 kW, radiation losses were 413 kW (24%). The kiln thermal efficiency, defined as the heat absorbed by the tanks over the incident power, was 76%
The extent of calcination reactions achieved is presented in Figure 6. Calcination occurred when temperatures were above 700°C. The final product maintained a calcination degree of >80% due to the selection of a high control temperature (980°C) and halving of the feed rate when irradiance to the receiver was below 1000 kW. Calcination continued in the tanks after sunset while tank temperatures remained high enough. Variability in the product composition may be lessened by heat recovery from the product to preheat the feed, by using indirect solar heating with thermal storage (Hockaday et al., 2020), or by raising the solar multiple in the heliostat field design. These options all have implications for the cost of solar thermal treatment as more space and capital are needed for heat exchangers or heliostats. Another way to smooth variability in product quality would be to implement more sophisticated feed rate control or to set an irradiance limit below which material is not treated. These strategies incur no plant modifications but will reduce the production rate of the solar thermal pretreatment plant.
The evaluations showed that products of similar grade could be obtained for both high and low solar irradiance conditions. During periods of interrupted solar irradiance, the product may vary in the level of calcination and reduction due to variances in temperature and residence time. However, the quantities produced are small, reducing the overall effect on product quality.
Monthly and annual throughput of a solar pretreatment facility
The annual production of a solar thermal pretreatment plant was estimated by evaluating the summer and winter solstice months and an equinox month for each ore. The summer and winter solstice months' production was then multiplied by three and added to
6 times the equinox month's production, and this total was then divided by 369 and multiplied by 365 to scale to the number of days in a year.
Each scenario was analysed according to the product quality, measured by the extent of reduction and calcination achieved. The throughput and average product temperature were evaluated over one-minute timesteps. The results for each ore are given in Table V. Each scenario took about 2 hours to simulate and contains much more data (Hockaday, 2023) than can be displayed, so only summaries are provided here.
The composition of the products from solar thermal pretreatment is given in Table VI.
Table VI shows the mass reduction of the treated product compared to the untreated ore is 10.3% for the CMN ore and 11.9% for the BMN ore. This reduction in mass will translate directly to reduced transport costs as ores are usually moved by rail on a per-ton basis. Scope 1 CO2 emissions were 0.09 t CO2/t product for CMN ore and 0.16 t CO2/t product for BMN ore. The emission factor specified for sinter production is 0.2 t CO2/ t product.
The mean residence time was calculated as the material in the reactor divided by the feed rate setpoints.
For the CMN ore, a 20 mm particle layer led to 561 kg material in the reactor. For a feed rate of 3200 kg/h, the mean residence time was 10.5 minutes, and for 6400 kg/h, the mean residence time was 5.3 minutes. Note that the residence time in the high-temperature zone, Tank 3, was only a third of this residence time, hence means particles will remain in the high-temperature zone for 1.75 to 3.5 minutes during sunny operating conditions.
For the BMN ore, a 20 mm particle layer led to 577 kg material in the reactor. For a feed rate of 1600 kg/h, the mean residence time
Table V
Composition of solar pretreated manganese ores in wt.%
was 21.6 minutes, and for 3200 kg/h, the mean residence time was 10.8 minutes. Particles remained in the high-temperature zone for 3.6 to 7.2 minutes during high irradiance conditions. Given the twofeed rate setpoints depending on the solar irradiance to the reactor, the particles experience heating rates of 125°C/min to 500 °C/min
To achieve calcination rates above 80% for both ores, the BMN ore required much higher temperatures (above 1000°C) and lower feed rates than the CMN ore (around 800°C) due to the different reaction kinetics found for each ore. In future studies, the process model may be used to investigate the relationship between the chosen operating temperature, the throughput of materials, and the product composition in greater detail to maximize the reduction in greenhouse gas emissions and electrical energy demand.
This study treated the solar pretreatment of manganese ores as a simple one-unit process. The pretreatment could also be done as part of a more integrated and energy-optimized process, with carbon capture and sequestration or heat recovery being possible process improvements.
benefits of solar pretreated material
Since the most significant use of manganese ores is ferroalloy production, the possible impact of products from the solar thermal treatment of manganese ores was investigated on a high-carbon
ferromanganese (HCFeMn) smelter. In South Africa, smelting is done in alternating-current submerged arc furnaces (AC SAF). Manganese ores are fed to the smelters with silica as flux and coal as reductant. The reductant requirement is determined by the amount of bonded oxygen that must be removed from the ore to reduce the iron and manganese to the metal, plus the carbon that reports to the alloy. The electricity demand is based on the latent energy required to heat all the materials to the smelting temperature and the net enthalpy demand from the reactions. This study considers the benefits of feeding pretreated material to the smelter at ambient temperatures. The benefits of feeding hot material is not evaluated and the solar pretreatment process is not coupled to the smelting process.
The stoichiometric carbon requirement for smelting is defined as the amount of carbon necessary to reduce all manganese to metallic manganese and all iron to metallic iron (the study does not consider the formation of carbides). Carbon reporting to the alloy is assumed dissolved rather than bound for modelling purposes. The specific energy requirement (SER) to produce a high-the carbon ferromanganese alloy (78% Mn, 7.5 %C remainder Fe) at 1300°C, slag at 1500°C and off-gas at 700°C, was estimated based on an HSC distribution model with carbon addition of twice the stoichiometric requirement in the smelting process shown in Figure 7. Silica flux was added to maintain the furnace basicity at 1.28 (Broekman and
Table VI
Monthly and annual production summaries for solar-pretreated carbonaceous ores
CMN ore
7—Calcination extent in Tank 1, Tank 2, Tank 3, and the product pile for an (a) high solar irradiance day and a (b) low solar irradiance day
Ford, 2004). The furnace off-gas was assumed to have a CO/CO2 ratio of 70/30. CO2 emissions were calculated based on the complete combustion of the furnace off-gas stream with air in a combustion chamber. The mass and energy balances were solved iteratively in the HSC Simulation module.
The annual production of pretreated material in a solar thermal plant with a 2.5 MWt design point is summarized for the two ores in Table V. These materials, and the untreated ores, were considered inputs to the smelting process. The smelting characteristics of the treated materials were named for their ores with subscript ‘s’ indicating solar thermal pretreatment.
The results for the smelting simulations for the BMN and CMN ores are given in Table VII.
Using solar-pretreated material lowers the SER per ton alloy produced by 38.7% for the BMNs ore compared to untreated BMN ore. Total CO2 emissions per ton alloy are lowered by 19.3% for BMNs material compared to untreated ore. Solar pretreatment
Table VII
Smelting production, consumption and CO2 emissions of BMN and CMN ores compared to solar pretreated ores (indicated by subscript s)
CO2 emissions, t/(t alloy)
reduces the SER per ton alloy produced by 0.6% for the CMNs ore compared to untreated CMN ore, and no significant reduction in electricity consumption was achieved by solar thermal pretreatment of the CMN ore. Compared to untreated ore, CO2 emission per ton alloy is lowered by 13% for CMNs material.
The total CO2 emissions were calculated to include the CO2 emissions during the solar thermal pretreatment and CO2 emissions from grid-connected electricity use, as shown in Figure 8. Scope 2 emissions from electricity consumption were determined from a grid electricity emission factor of 0.95 t CO2eq/MWh (Takahashi and Louhisuo, 2022), and all electricity was assumed to be sourced from the national grid.
For a smelting operation that maintains production of 160 tons of metal per day (Broekman and Ford, 2004), the amount of treated ore required to replace untreated ore is roughly 170 000 tons annually for the BMN ore and 160 000 tons annually for the CMN ore. The annual production of a 2.5 MWt solar pretreatment plant is around 8000 tons/year for the BMN ore, therefore 21 of these plants will be required to meet this demand. The estimated footprint
of such a solar pretreatment plant would be 37 ha. For the CMN ore, the annual production of a 2.5 MWt solar pretreatment plant is around 12 500 tons/year for BMN ore, hence, 13 of these plants will be required to meet this demand. The estimated footprint of such a solar pretreatment farm would be 23 ha. However, this can be built gradually as solar-pretreated material can be blended with untreated material to realize incremental benefits.
Financial modeling of levelized cost of heat from a solar plant
To evaluate the viability of using CST to directly pretreat manganese ores, it was necessary to estimate the cost of the energy provided and to compare it to alternative energy supplies. The CST plant process flow is shown in Figure 10.
The levelized cost of heat, LCOH_ST, can be described as the ratio of the discounted annual expenses over the discounted energy supplied (Short, Packey and Holt, 1995):
Table VIII
Cost assumptions for CAPEX of CST plant per 2.5 MWth tower
Item Cost, R1000
Heliostat field @ 100 €/m2
Receiver @ 123 k$
Vertical transport of feed materials (ores/reductant)
Reference
7829 (Buck and Giuliano, 2019)
2204 (Lubkoll, Hockaday and Harms, 2018)
2249 (Lubkoll, Hockaday and Harms, 2018)
Tower 835 (Lubkoll, Hockaday and Harms, 2018)
Land cost (3500 R/ha)
6 (property24, 2022)
Total investment (Capital expenditure or CAPEX) 13123
where n is the number of years in the lifetime of the project, Cn is the total expenses in year n and Qn is the total amount of energy supplied in year n, and r is the discount rate considering the time value of money (or opportunity cost). The meaning of the LCOHST is the price making the production of process energy break even at the end of the payback period. To be financially viable, one can compare the cost to alternatives and then show that the benefit (product produced) can make it worth doing.
The cost assumptions for the solar thermal process solution were based on a modular system consisting of a heliostat field surrounding a tower with a peak power delivery of 2.5 MWt. All costs were converted to South African rand (R) in the year of publication and adjusted for inflation to 2022. Inflation rates were found online (Inflationtool, 2022). Financial costs were converted back to USD at a conversion rate of R17.19/USD. It is estimated that the cost of undeveloped land in the Hotazel area is around USD204/ha based on advertised farms for sale (property24, 2022). In addition to the capital outlay described in Table VIII, operating and maintenance costs (O&M) are estimated at 3.9% of the CAPEX annually, and insurance costs at 1% of the CAPEX annually. Indirect costs are estimated at 22% of CAPEX annually
The levelized cost of heat from the solar thermal plant (LCOHST) was calculated over a project lifetime of 20 years, assuming the total investment is paid off over 20 years at a debt interest rate of 7%, as USD22/MWh. The plant produces a minimum of 8000 tons of treated ore BMN and 12 000 tons of treated CMN ore, making the cost of solar pretreatment USD5.6 per ton of BMN ore and USD4.0 per ton of treated CMN ore. The
cost of electricity, coke breeze and diesel costs for process heating were estimated to compare as alternative sources of process heat. Grid electricity cost in South Africa, which may be calculated from published tariffs by ESKOM (ESKOM, 2022), is a seasonally adjusted average of USD58/MWh without considering transmission network charges, distribution network charges or ancillary services. The change in LCOH for different repayment periods and the cost of solar thermal treatment after repayment of capital expenditure compared to the grid electricity cost in Soutth Africa is shown in Figure 11.
The diesel price in South Africa is R24.16/litre (Fuel SA, 2022) at the time of writing. Since diesel has an energy value of 11.83 kWh/kg (Boyle, 2012) and a density of 0.846 kg/litre (Engineering Toolbox, 2003), the cost of heating with diesel is USD140/MWh.
Between 2010 and 2020, the price of coal traded between USD50 per metric ton and USD130 per ton. Due to the volatility in the coal price, it is challenging to estimate its current and future costs. The cost of coal has increased sharply since 2020 and, during October 2022, was as high as USD400 per metric ton (IndexMundi, 2022; Trading Economics, 2022). Knowing that the cost of CST process heat is R380/MWh and coal has a calorific value of 8.39 kWh/kg, a parity cost of coal with CST process heat can be calculated as USD178.5 per ton.
It is therefore clear that concentrating solar thermal heating is cost competitive with other energy sources and in particular with electric or indirectly fire kilns. The benefits for ferromanganese smelters need to be evaluated based on the effect of changing from smelting untreated ore to pretreated ore. This study evaluates the benefits realized in reduced electricity consumption and reduced carbon monoxide emissions (as reduction in carbon tax).
The carbon tax liability was based on a full tax of USD8/ton of carbon dioxide emitted. Current legislation (South African Government, 2019) provides for industry allowances of 60% to 95% of total emissions at no cost, resulting in much lower liabilities in the short term. The intention is to gradually reduce emission allowances until the full tax (USD20/ton carbon dioxide) is applied. Replacing untreated ores with solar thermal treated ores may reduce future carbon tax liabilities, as shown in Figure 12.
The financial impact of including solar pretreated ores in highcarbon ferromanganese production is summarized in Table IX, assuming carbon tax liability of USD20/t CO2 over both the smelter and the solar pretreatment plant. The electricity savings cover the cost of solar pretreatment of the BMN ore. The solar pretreatment of
Financial impact of using solar pretreatment on HCFeMn production, based on LCOHth of $22/MWhth for CST plant
BMN ore treatment BMNs CMNs
Solar treatment cost, $/(ton alloy) (16) (11)
Electricity savings, $/(ton alloy)
43 0.5
Carbon tax savings, $/(ton alloy) 8 5
Project savings, $/(ton alloy) 35 (6)
the CMN ore cannot be offset by the electricity savings and possible carbon tax avoidance unless carbon tax liabilities double or the cost of solar thermal pretreatment halves. The savings in pretreating BMN ore, as shown in Table IX, amounts to USD2 million annually (assuming 160 ton/ day alloy production from BMNs ore).
Pretreatment of manganese ores with solar thermal energy may become an attractive project to avoid emissions and qualify for rebates, especially for braunite and calcite-rich ores. Such projects may also be eligible for certified emissions reductions tradable in the international carbon market.
This study investigated the solar thermal pretreatment of two carbonate-rich manganese ores and evaluated the performance of a rotating particle receiver to achieve 80% calcination of the ores. The solar thermal plant used typical meteorological year data and a heliostat field model to determine the hourly input of solar flux to the rotating receiver. A validated view factor-based energy distribution model was used to attribute the solar irradiance to three reactor zones and to determine radiation losses from the receiver. The products from the rotary solar receiver were based on reaction kinetics explicitly determined for each ore. It was found that the braunite-rich ore with a high activation energy of calcite decomposition benefits most from the solar thermal treatment, even though the high energy demand for calcination reduced the throughput of the solar thermal treatment plant.
The high braunite, calcite-rich ore (BMN) showed a reduced specific energy consumption for high carbon ferromanganese production of 39% and reduced CO2 emissions of 19%. The high cryptomelane, and high calcite ore (CMN) showed reduced specific energy consumption of only 0.6% and reduced total CO2 emissions of 13%.
Although the solar thermal treatment cost of the CMN ore is lower than for the BMN ore, the financial case for solar thermal treatment of the BMN ore is more favourable due to the electricity savings afforded by the solar thermal pretreatment. In contrast, the economic case for the solar thermal pretreatment of CMN ore is weak, as no significant reduction in electricity demand was realized. The study shows that the benefit of concentrating solar thermal treatment (or other oxidative calcination processes) is highly dependent on the reaction kinetics of the materials to be treated. Two superficially similar ores in manganese and carbonate content may exhibit vastly different decomposition and reduction behaviour.
Acknowledgements
This paper is published with permission of Mintek. The authors would like to acknowledge Transalloys for providing the ore samples studied.
Credit author statement
SACH: Conceptualization, Methodology, Validation, Visualization, Original draft preparation, Funding FD, QR, CM: Supervision, Review.
References
Amsbeck, L. 2014. ‘Particle tower system with direct absorption centrifugal receiver for high temperature process heat’, in Energy Procedia 00 (2015) 000–000. SolarPACES 2014, Beijing, China: Elsevier.
Amsbeck, L. 2018. First tests of a centrifugal particle receiver with a 1m2 aperture, in AIP Conference Proceedings. SolarPACES 2017: International Conference on Concentrating Solar Power and Chemical Energy Systems, Santiago, Chile: AIP Publishing. Available at: https://doi.org/10.1063/1.5067040
Biswal, A. 2015. Electrolytic manganese dioxide (EMD): a perspective on worldwide production, reserves and its role in electrochemistry. RSC Advances, vol. 5, no. 72, pp. 58255–58283. Available at: https://doi.org/10.1039/C5RA05892A
Boyle, G. (ed.) 2012 Renewable Energy, Power for a sustainable future. Oxford University Press.
Broekman, B.R., Ford, K.J.R. 2004. The Development and Application of a HCFeMn Furnace Simulation Model for Assmang Ltd, in Proceedings: Tenth International Ferroalloys Congress. INFACON X: ‘Transformation through Technology’, Cape Town, South Africa: SAIMM, pp. 194–205.
Buck, R., Giuliano, S. 2019. Solar tower system temperature range optimization for reduced LCOE, in. SOLARPACES 2018: International Conference on Concentrating Solar Power and Chemical Energy Systems, Casablanca, Morocco, p. 030010. Available at: https://doi.org/10.1063/1.5117522
Daavittila, J. 2001. Sintered Manganese Ore and Its Use in Ferromanganese Production, in The Ninth International Ferroalloy Congress. INFACON IX, Quebec City, Canada, pp. 212–222. Available at: https://www.pyrometallurgy.co.za/ InfaconIX/212-Jorma.pdf
Ebert, M. 2016. Upscaling, Manufacturing and Test of a Centrifugal Particle Receiver, in Volume 1: Biofuels, Hydrogen, Syngas, and Alternate Fuels; CHP and Hybrid Power and Energy Systems; Concentrating Solar Power; Energy Storage; Environmental, Economic, and Policy Considerations of Advanced Energy Systems; Geothermal, Ocean, and Emerging Energy Technologies; Photovoltaics; Posters; Solar Chemistry; Sustainable Building Energy Systems; Sustainable Infrastructure and Transportation; Thermodynamic Analysis of Energy Systems; Wind Energy Systems and Technologies. ASME 2016 10th International Conference on Energy Sustainability collocated with the ASME 2016 Power Conference and the ASME 2016 14th International Conference on Fuel Cell Science, Engineering and Technology, Charlotte, North Carolina, USA: American Society of Mechanical Engineers, p. V001T04A007. Available at: https://doi.org/10.1115/ES2016-59252
Ebert, M. 2018. First On-Sun Tests of a Centrifugal Particle Receiver System, in ASME 2018 12th International Conference on Energy Sustainability. ASME 2018 12th International Conference on Energy Sustainability collocated with the ASME 2018 Power Conference and the ASME 2018 Nuclear Forum, Lake Buena Vista, Florida, USA: American Society of Mechanical Engineers, p. V001T11A002. Available at: https://doi.org/10.1115/ES20187166
Ebert, M. 2019. Operational experience of a centrifugal particle receiver prototype, in. SOLARPACES 2018: International Conference on Concentrating Solar Power and Chemical Energy Systems, Casablanca, Morocco, p. 030018. Available at: https://doi.org/10.1063/1.5117530
Ekman, B.M., Brooks, G., Rhamdhani, M.A. 2014. A Review: Solar Thermal Reactors for Materials Production’, in C. Wang et al. (eds) Energy Technology 2014. Hoboken, NJ, USA: John Wiley & Sons, Inc., pp. 1–14. Available at: https://doi. org/10.1002/9781118888735.ch1
Engineering Toolbox 2003. Fuels - Densities and Specific Volumes Available at: https://www.engineeringtoolbox.com/fuelsdensities-specific-volumes-d_166.html (Accessed: 28 September 2022).
ESKOM. 2022. ESKOM Schedule-of-standard-prices-2022_23 Available at: https://www.eskom.co.za/distribution/wp-content/ uploads/2022/03/Schedule-of-standard-prices-2022_23.pdf (Accessed: 28 September 2022).
Flamant, G. 2018. Solar processing of reactive particles up to 900°C, the SOLPART project, in. SolarPACES 2017: International Conference on Concentrating Solar Power and Chemical Energy Systems, Santiago, Chile, p. 020004. Available at: https://doi. org/10.1063/1.5067013
Fuel SA. 2022. Fuel SA - South African Fuel - Petrol and Diesel Data. Available at: https://www.fuelsa.co.za/#current (Accessed: 28 September 2022).
Gallo, A. 2016. Considerations for Using Solar Rotary Kilns for High Temperature Industrial Processes with and Without Thermal Storage, in Proceedings of EuroSun2016. EuroSun2016, Palma de Mallorca, Spain: International Solar Energy
Society, pp. 1–10. Available at: https://doi.org/10.18086/ eurosun.2016.02.04
Gasik, M. (ed.) 2013. Handbook of ferroalloys: theory and technology Amsterdam: Elsevier/Butterworth-Heinemann.
Gericke, W.A. 1989. The establishment of a 500 000 t/a sinter plant at Samancor’s Mamatwan mine’, in Proceedings of 5th International Ferroalloys Congress. Infacon V, New Orleans, USA, pp. 24–33. Available at: https://www.pyrometallurgy.co.za/ InfaconV/ (Accessed: 5 February 2020).
Gordon Y.N.J. 2013. Methods of manganese ore thermal-treatment prior to smelting- what to choose?, in Efficient technologies in ferroalloy industry The thirteenth International Ferroalloys Congress, Almaty, Kazakhstan, pp. 05–16.
Gordon, Y., Nell, J., Yaroshenko, Y. 2018. Manganese Ore Thermal Treatment Prior to Smelting, KnE Engineering, vol. 3, no. 5, pp. 71–86. Available at: https://doi.org/10.18502/keg.v3i5.2656
Harris, K., Meyer, D.M., Auerswald. 1977. The production of electrolytic manganese in South Africa. Journal of South African Institute of Mining and Metallurgy, vol. 77, no. 7, pp. 137–149. Available at: https://hdl.handle.net/10520/AJA0038223X_738 (Accessed: 28 October 2020).
Hockaday, L. 2020. The Impact of Solar Resource Characteristics on Solar Thermal Pre-heating of Manganese Ores, in X. Chen et al. (eds). Energy Technology 2020: Recycling, Carbon Dioxide Management, and Other Technologies. Cham: Springer International Publishing (The Minerals, Metals & Materials Series), pp. 3–13. Available at: https://doi.org/10.1007/978-3030-36830-2_1
Hockaday, L. 2021. A comparison of direct concentrating solar thermal treatment of manganese ores to fossil fuel based thermal treatments, in Proceedings of INFACON XVI. International Ferro-alloys Congress, Trondheim, Norway: SINTEF/NTNU/FFF. Available at: Not published, under review.
Hockaday, S.A.C. 2023. Solar Thermal Treatment of Manganese Ores University of Stellenbosch.
Hockaday, S.A.C., Dinter, F., Harms, T.M. 2018. Introducing solar thermal heat into minerals processing: A case study on replacing a diesel burner at a sinter plant, in Proceedings of South African Solar Energy Conference. SASEC 2018, Durban: SASEC2018. Available at: https://www.sasec.org.za/full_papers/74.pdf (Accessed: 17 April 2019).
Hockaday, S.A.C., Dinter, F., Reynolds, Q.G. (In print) The thermal decomposition kinetics of carbonaceous and ferruginous manganese ores in atmospheric conditions, Journal of Southern African Institute of Mining and Metallurgy [Preprint].
IndexMundi. 2022. Coal, South African export price - Monthly Price - Commodity Prices - Price Charts, Data, and News. Available at: http://www.indexmundi.com/commodities/?commodity=coalsouth-african (Accessed: 26 October 2022).
Inflationtool. 2022. South Africa Inflation Rate - 2022. Available at: https://www.inflationtool.com/rates/south-africa (Accessed: 28 September 2022).
International Resource Panel. 2020. How minerals and metals companies can help achieve 2030 Agenda for Sustainable Development, UNEP. Available at: http://www.unep.org/newsand-stories/story/how-minerals-and-metals-companies-canhelp-achieve-2030-agenda-sustainable (Accessed: 17 January 2023).
Ishak, R., Tangstad, M. 2007. Degree of prereduction without coke consumption in industrial furnaces, in. INFACON XI, New Delhi, India: The Indian Ferro Alloy Producers’ Association, pp. 268–279. Available at: https://www.pyrometallurgy.co.za/ InfaconXI/ (Accessed: 16 November 2020).
Koepf, E. 2017. A review of high temperature solar driven reactor technology: 25years of experience in research and development at the Paul Scherrer Institute, Applied Energy, 188, pp. 620–651. Available at: https://doi.org/10.1016/j.apenergy.2016.11.088
Lubkoll, M., Hockaday, S.A.C., Harms, T.M. 2018. Integrating Solar Process Heat into Manganese Ore Pre-Heating’, in. SASEC 2018, Durban, p. 8. Available at: https://www.sasec.org.za/ full_papers/57.pdf (Accessed: 17 April 2019).
Malan, J., Barthel, W., Dippenaar, B.A. 2004. Optimizing manganese ore sinter plants: Process parameters and design implications, in Proceedings: Tenth International Ferroalloys Congress. INFACON X, Cape Town, South Africa: SAIMM, pp. 281–290. Available at: https://pyrometallurgy.co.za/InfaconX/057.pdf
Mckechnie, T., McGregor, C., Venter, G. 2020.Concentrating Solar Thermal Process Heat for Manganese Ferroalloy Production: Plant Modelling and Thermal Energy Storage Dispatch Optimization, in ASME 2020 14th International Conference on Energy Sustainability. ASME 2020 14th International Conference on Energy Sustainability, Virtual, Online: American Society of Mechanical Engineers, p. V001T14A001. Available at: https://doi.org/10.1115/ES2020-1635
Mckechnie, T., McGregor, C., Venter, G. 2022. Large HelioPodTM field layout design and optimisation, in. SOLARPACES 2020: 26th International Conference on Concentrating Solar Power and Chemical Energy Systems, Freiburg, Germany, p. 140008. Available at: https://doi.org/10.1063/5.0085721
Mills, R. 2021. ESG seen as biggest risk to mining industry, 13 April. Available at: https://aheadoftheherd.com/esg-seen-as-biggestrisk-to-mining-industry/ (Accessed: 17 January 2023).
Olsen, S.E., Tangstad, M., Lindstad, T. 2007. Production of manganese ferroalloys. Trondheim, Norway: Tapir Academic Press.
Outotec. 2019. HSC Sim – Process Simulation Module. Available at: https://www.outotec.com/products/digital-solutions/hscchemistry/hsc-sim-process-simulation-module/ (Accessed: 3 September 2019).
Pienaar, P.C., Smith, F.P. 1992. A Case Study of the Production of High-grade Manganese Sinter from Low-grade Mamatwan Manganese Ore, in Proceedings of the 6th International Ferroalloys Congress, Cape Town. INFACON 6, Johannesburg, South Africa: SAIMM, pp. 131–138. Available at: https://pyrometallurgy.co.za/InfaconVI/1131-Pienaar.pdf
Property24. 2022. Farms for sale in Hotazel. Available at: https://www.property24.com/farms-for-sale/hotazel/northerncape/2533 (Accessed: 6 October 2022).
Purohit, S. 2018. Solar processing of composite iron ore pellets: Preliminary assessments’, Journal of Cleaner Production, vol.
205, pp. 1017–1028. Available at: https://doi.org/10.1016/j. jclepro.2018.09.112
Roine, A., Bjorklund, P. 2002. Outokumpu HSC Chemistry for Windows. 02103-ORC-T. Finland: Outotec Research Oy. Santamarta, J. 2020. EU HiFlex project - Concentrated solar power for sustainable pasta, HELIOSCSP, 14 October. Available at: https://helioscsp.com/eu-hiflex-project-concentrated-solarpower-for-sustainable-pasta/ (Accessed: 6 January 2023).
Sayles, R. 2020. Solar tower at pasta plant spurs new generator design | Reuters Events | Renewables, Reuters Events | Renewables Available at: https://www.reutersevents.com/renewables/solarthermal/solar-tower-pasta-plant-spurs-new-generator-design (Accessed: 6 January 2023).
Short, W., Packey, D.J., Holt, T. 1995. A manual for the economic evaluation of energy efficiency and renewable energy technologies Manual NREL/TP--462-5173, 35391. Golden, Colorado: NREL, p. NREL/TP--462-5173, 35391. Available at: https://doi. org/10.2172/35391
South African Government. 2019. Carbon Tax Act 15 of 2019 Available at: https://www.gov.za/documents/carbon-tax-act15-2019-english-afrikaans-23-may-2019-0000 (Accessed: 2 September 2019).
Stine, W.B., Geyer, M. 2011. Power From The Sun. Available at: https://www.powerfromthesun.net/ (Accessed: 10 February 2021).
Takahashi, K., Louhisuo, M. 2022. IGES List of Grid Emission Factors. Institute for Global Environmental Strategies. Available at: https://doi.org/10.57405/iges-1215
Tanabe, I. 1968. Preheating of Ore for a Ferromanganese Furnace-a Recent Trend in Japan. Journal of Metals, vol. 20, pp. 81–87. Available at: https://doi.org/10.1007/BF03378711
Tangstad, M., Ichihara, K., Ringdalen, E. 2015. Pretreatment Unit in Ferromanganese Production, in The Fourteenth International Ferroalloys Congress. INFACON XIV, Kiev, Ukraine: INFACON, p. 8. Available at: https://www.pyrometallurgy.co.za/ InfaconXIV/099-Tangstad.pdf (Accessed: 4 October 2019).
Trading Economics. 2022. Coal - 2022 Data - 2008-2021 Historical2023 Forecast - Price - Quote - Chart. Available at: https://tradingeconomics.com/commodity/coal (Accessed: 26 October 2022).
Wagner, M.J. 2017. Optimization of stored energy dispatch for concentrating solar power systems. PhD. Colorado School of Mines. Available at: https://hdl.handle.net/11124/171000
Wagner, M.J. 2019. Solar Power Tower Integrated Layout and Optimization Tool | Concentrating Solar Power | NREL. Available at: https://www.nrel.gov/csp/solarpilot.html (Accessed: 3 September 2019).
Zhang, H. 2013. The Mechanism on Biomass Reduction of LowGrade Manganese Dioxide Ore, Metallurgical and Materials Transactions B, vol. 44, no. 4, pp. 889–896. Available at: https://doi.org/10.1007/s11663-013-9835-7 u
Pathway to industrialisation
ECSA VALIDATED CPD ACTIVITY, CREDITS = 0.1 POINTS PER HOUR ATTENDED
The primary purpose of the 2ND Hydrogen and Fuel Cells conference is the advancement of green hydrogen technologies in Southern Africa and the global community, by highlighting the power of renewable and sustainable technologies and addressing the emerging challenges—through the exploration of hydrogen production, storage and utilization using fuel cells by way of engagement with industry, academia and government. The conference will provide a platform for high level exchange and networking opportunities with various experts in the field.
Hydrogen: Production and storage
Fuel cell: Technologies, applications, and integration
Hydrogen mobility - strategies, safety, roadmaps, transitioning to hydrogen refueling stations (HRS)
Technology status in industry.
The two-day conference will feature high-level scientific talks and posters, complemented with keynote and plenary presentations on country overviews, status of leading and major players in the Southern African and global arena.
Will include inspiring technical talks, poster section as well as social networking events
Participants will have the opportunity to directly engage with conference attendees to discuss their research
The conference presents an attractive programme for researchers, industry players, academic institutions, government, investors, policy makers and potential users of fuel cell and hydrogen technologies. The focus is on building collective know-how and fostering engagement between business, government, science and academic institutions. Participants from all countries are invited and welcome to attend the event.
Gugu Charlie,
following deadline dates.
• Submission of abstracts deadline 31 January 2025
• Submission of papers deadline: 28 February 2025
The conference is organized by the Southern African Institute of Mining and Metallurgy, and individuals are invited to submit papers or presentations or posters for the Conference. Titles and short abstracts (no more than 500 words) on any relevant subject should be submitted in English to:
Conferences and Events
Co-ordinator
Gugu Charlie
Enquiries may be made at: Tel: +27 011 538-0238
E-mail:gugu@saimm.co.za website: www.saimm.co.za
Affiliation:
1The Research Institute for Innovation and Sustainability, South Africa
2School of Mining Engineering, University of the Witwatersrand, South Africa
3Vedanta Zinc International, South Africa
4Mandela Mining Precinct, South Africa
Correspondence to: B. Genc
Email: Bekir.Genc@wits.ac.za
Dates:
Received: 9 Oct. 2024
Revised: 24 Oct. 2024
Accepted: 5 Nov. 2024
Published: December 2024
How to cite:
Mahadeoa, V.J., Govender, U., Ramparsad, S., and Genc, B. 2024. Assessing the socio-economic impact of a zinc mine in South Africa through the application of digital tools: A case study. Journal of the Southern African Institute of Mining and Metallurgy, vol. 124, no.12 pp. 777–788
DOI:
http://dx.doi.org/10.17159/24119717/3580/2024
ORCiD: B. Genc
http://orcid.org/0000-0002-3943-5103
by V.J. Mahadeo1, U. Govender2,3, S. Ramparsad4, and B. Genc2
Abstract
The study was intent on assessing the socio-economic impact of a zinc mine in South Africa through the application of people-centric digital tools using a case study research methodology. The global mining industry is undergoing significant technological shifts to modernize, improve operational sustainability, and align with the environmental, social, and governance (ESG) agenda. While the case study mine is a more modernized mine, continuous improvement around the ‘social’ pillar becomes critical, and to this end application of people-centered digital tools presented as the vehicle to understand community needs and impacts. Despite considerable annual corporate social investment by mines annually, the overall impact or social return on investment is marginally understood. Towards contributing to addressing this gap, digital ESG ‘social-related’ data gathering tools for mines decision-making were developed, including the training-needs assessment tool, community-social needs assessment, small, micro, and medium enterprise (SMME) communications and engagement tool, digital leadership competencies gap assessment tool, and change management blueprint, which further allowed for customization to the mining context. Hence, the novelty of this paper relates to applying digital tools to provide real-time information of the needs of a community, both socially and economically. The findings suggested that these digital tools enabled gathering of information for the establishment of regional and operational baselines towards enabling of social investment returns in relation to socio-economic transformation development interventions. These tools have been applied to a zinc mine context, with lessons and experiences obtained through this study, invaluable to the application of these digital tool in other mines in South Africa.
The study was conducted in September 2023 across five host communities, surrounding the zinc mine, in the Northern Cape region, with 120 participants involved in the application of three relevant community-related digital tools, which included the training needs, community-social needs, and SMME communications and engagement tools. It was evident that the digital ESG tools could be used for data gathering for the mine’s informed decision-making and allowed for securing of insights on community needs in near real-time, and further proved practical for community use.
Keywords
ESG, digital tools, socio-economic transformation (SET), zinc mine, South African mining communities
Introduction
The ESG agenda has become an imperative across major industries worldwide, including the mining sector. The ‘social’ principle is highly relevant in mining as the sector is still a highly labour-intensive operation. The mining sector of South Africa contributed 7-8% of the national Gross Domestic Product and employed over 475,000 people, with a dependency ratio of 1:10 in 2022/3. Moreover, the mining sector supports more than 4.7 million livelihoods in the country, as per the Minerals Council South Africa's report (2023). Therefore, ensuring the socio-economic development and upliftment of host communities around regional mines are a national priority for economic growth. The subsequent section elaborates on the origins of ESG and its relevance to mining, why focusing on the ‘social’ narrative is important, and how implementing people-centric digital tools may improve an understanding of community needs and impact, and enable communication between mines and their host communities.
ESG agenda in the global and mining context
The ESG agenda was first used in the 2006 report of the United Nations (UN) Global Compact Initiative (Perrone, 2022), ‘Who Cares Wins.’ James Gifford devised the term in 2004 and described how investment decisions could contribute to a more stable and predictable market (Perrone, 2022).
‘A better inclusion of environmental, social, and corporate governance factors in investment decisions will ultimately contribute to more stable and predictable markets, which is in the interest of all market actors.’
ESG describes a set of factors to measure the non-financial impacts of the activities of corporations (Ingebretsen, 2023). At ESG's core are 22 metrics and an expanded 34 structured metrics to align with the UN’s 2030 sustainable development goals. As such, ESG grew out of investment philosophies clustered around sustainability and, after that, socially responsible investing. In turn, integration with strategy enables environmental stewardship, social responsibility, and governance quality (Fiscor, 2023):
➤ Environment (E): signifies improvements in energy efficiency, reduction in carbon footprints, mitigation of greenhouse gas emissions, prevention of deforestation, preservation of biodiversity, efforts to address climate change and pollution, effective waste management, and responsible water usage.
➤ Social (S): embodies standards for labour, compensation and benefits, diversity in the workplace and on boards, promoting racial justice, achieving pay equity, upholding human rights, managing talent, fostering community relations, ensuring privacy and data protection, prioritizing health and safety, overseeing supply-chain management, and addressing various human capital and social justice concerns.
➤ Governance (G): encompasses the oversight of environmental and social aspects, including the composition and structure of corporate boards, strategic supervision of sustainability practices and adherence, executive compensation, involvement in political contributions and lobbying, and measures against bribery and corruption.
ESG was influenced by a company's actions and, more specifically, how the public perceives those actions. The significant increase in ESG investments from 2018 indicates the value in aligning with ESG values. Investment inflows into sustainable funds rose from USD5 billion in 2018 to more than USD50 billion in 2020 and nearly USD70 billion in 2021 (NJCPA, 2021). Midway through 2022, the global sustainable assets were valued at approximately USD2.5 trillion (NJCPA, 2021). As a result, ESG market leaders showed better performances with higher profits and lower interest rates, while laggards displayed underperformance in these aspects (Kujala et al., 2022).
Regarding mining, prioritizing ESG values directly correlates to corporate responsibility, the socio-economic transformation of surrounding mining communities, the environmental impact of extraction, and the mine’s social license to operate within a region (Botts et al., 2023). While the focus of ESG may have been on the environment and governance in response to climate change, an
analysis has found that social-related shareholder proposals rose by 37% in 2021 compared to the previous year (Pérez et al., 2022), suggesting that mines are prioritizing action around the social pillar, which can further bolster socio-economic transformation from the years of implementing social and labour plans (SLP).
The Mineral and Petroleum Resource Development Act 28 of 2002 (MPRDA) ensures that companies holding mining rights give back and invest towards socio-economic development of host communities, and to accomplish this objective of the MPRDA, SLP guidelines are provided (DMR, 2010). However, one should take note that mines may attempt through the SLP to address community needs, only to find communities still remain disgruntled. What becomes critical for mines is to get a ‘real’ understanding of those needs, and the potential impacts that they are making in this regard, which could be considered through the development of key and relevant indicators and assessing for understanding and impacts. The people-centric digital tools applied through this case study seeks to enable this need.
Problem statement
Social-related considerations within the mining context are essential because these directly influence the mine’s ability to maintain a social license to operate within the region (Dikgwatlhe and Mulenga, 2023). The major mines in South Africa invested ZAR305 million in 2020/21 compared to ZAR1,278 million in 2021/22, representing a 76% increase. Figure 1 depicts the distribution of corporate social investment and social and economic development spending across the significant South African mining houses. The resultant socio-economic transformative impact of corporate social investment is unknown. Hence, companies cannot determine whether monetary inflows have resulted in socio-economic development within their mining communities.
*Note: This is a subsample as it does not represent the total mining industry investment in overall corporate social investment (CSI) and socio-economic development (SED) spending.
CSI is a concept that seeks to align society's interests and expectations with the mining industry's goals and practices (Seloa and Ngole-Jeme, 2022). One of the ways that the mine can demonstrate its CSI is by conducting an environmental impact assessment and producing a social labour plan (Seloa and NgoleJeme, 2022). These mechanisms help identify, evaluate, and mitigate mining activities' environmental and social impacts and ensure the fair and equitable distribution of benefits and opportunities for the affected communities. Notably, SLP need to contain direct obligations to contribute meaningfully to the economic and social development of mine-affected communities (DMR, 2010). They are meant to benefit mining communities to ensure that impacted areas are not left destitute and impoverished by mining.
It becomes evident from the above that mines need data gathering tools for their decision making, and to understand the impact made in their host communities through their social investments.
The Minerals Council South Africa is a mining-industry employer organization that supports and promotes the progression towards sustainable mining in South Africa. Through regular and continuous engagement with its members, it has identified the need to develop people-centric digital tools to improve the accuracy and consistency of data capture between regional mines and their host communities. The Minerals Council South Africa, through the SAMERDI Successful Application of Technology Centered Around People (SATCAP) programme has supported the development of people-centric digital tools. These digital tools include a Training Needs Assessment, NGO/Community Social Needs Assessment, Stakeholder Engagement and Communications Tool, and Digital Leadership Competency Gap Assessment Tool. These digital ESG tools were developed to gain a deeper understanding of the socioeconomic transformation needs of host communities and increase the accessibility to a broader target audience through the privacy of responding through mobile applications. For this study, the community-related ‘social’ tools are considered.
Research objective
The objective of this study was to determine if the ESG digital tools allow for data gathering for informed decision-making, using a zinc mine as a case study.
Research question
Mine closures are more detrimental than other industry closures because of the community's location. The geographically remote communities mean that the local community’s dependency on the mine increases as levels of education, internet access, and employment decrease within the community (Cole and Broadhurst, 2021). ‘With regulatory failure, the relationship between the livelihood of communities and mining activities is linked in a manner that creates a power imbalance where host communities become dependent on the mine for economic survival’ (Maloisane, 2023). Lack of consultation and community involvement has led to the debilitating circumstances of these local communities because, even when solutions are being brought forward, they are not aligned with what the people need (Maloisane, 2023).
These community-related digital tools, namely, a trainingneeds tool, a small, micro, and medium enterprises (SMME) communications tool and a social-needs tool, were developed to be ‘off-the-shelf' solutions for the South African mining industry.
This study aims to investigate the socio-economic impact of transformative investment from a zinc mine by applying these novel digital tools. The implementation of these digital tools within a zinc mining context in the Northern Cape employed a case study approach to validate, and ensure that each tool could provide insights into the following:
➤ Can the digital tools provide for gathering of information relating to the present and perceived future SMME needs?
➤ Can the relevant digital tool provide for an understanding of the host community’s current and future social needs?
➤ Can the relevant digital tool allow for evaluating the community and SMME's training needs?
➤ Can the relevant digital tool allow for identifying alternative economies and industrialists that meet the Broad-Based Black Economic Empowerment (B-BBEE) criteria within mine communities?
➤ Can the relevant digital tool allow for measuring the level of engagement between the community and the regional zinc mine?
Application of digital tools were needed for:
➤ An easier and quicker method to gather data – rather than mine staff gathering data through interviews with communities.
➤ Have a wider reach in host communities, more cost effectively – which could be possible through a digital medium.
➤ To obtain objective community views, for securing of community ‘real needs’ – rather than community leaders providing perceived community need.
➤ Mines could obtain quick data analysis for their informed decision-making and understanding of impacts in host communities.
➤ Applying digital tools to measure socio-economic transformation baselines from the onset may enable improvement of corporate social investment returns. Each digital ESG tool was designed to gather information, establish regional and operational baselines, and ensure the maximum return on social investment, specifically in socioeconomic transformation development interventions.
This paper introduces a novel approach by applying digital ESG tools to measure key factors contributing to socio-economic transformation in mining communities. These tools offer several advancements, including a deeper understanding of the community’s current and future social needs, which is essential for maintaining the mine's social license to operate. They allow for a rapid, near real-time assessment of material ESG issues, improving upon the traditional annual survey method. The tools also evaluate the training needs of both the community and SMME, measure the level of engagement between the community and the regional mine, and identify alternative economies and industrialists that meet B-BBEE criteria within mining communities. Additionally, they gather and respond to both present and future SMME needs, assess the digital capabilities of mine personnel in preparation for modernization, and provide a change management blueprint to guide the adoption of new technologies. This paper further contributes to the academic literature by validating these novel ESG tools and comparing their insights to traditional mining materiality assessments.
The study is relevant to the mining industry as it addresses critical aspects of socio-economic transformation, environmental responsibility, and the adoption of modern technologies, all of which are increasingly central to the industry's sustainability and growth. The mining industry often operates in remote regions, where communities face a variety of socio-economic challenges, such as poor infrastructure, environmental degradation, and economic vulnerability. This highlights how digital ESG tools can address these challenges by providing near real-time insights into community needs, engagement levels, and socio-economic conditions. Mining companies can more effectively align their operations with the long-term welfare of the communities they impact by measuring key indicators such as local training needs, community-business engagement, and alternative economic opportunities. This helps companies meet regulatory and social license-to-operate requirements, foster community resilience and support broader economic development goals. For the mining
industry, such tools enable proactive decision-making and strengthen relationships between mines and local stakeholders, which are crucial for maintaining operational stability and minimizing social risks.
Furthermore, the study delves into the practical application of digital ESG tools in the mining sector, focusing on their role in enhancing decision-making and preparing the workforce for modernization. These tools allow for faster, more dynamic assessments of ESG-related issues compared to traditional surveys, enabling mines to respond quickly to emerging community concerns. This is particularly relevant as the industry undergoes technological transformation, with digital tools playing a pivotal role in managing change. By identifying the digital readiness of workers, assessing alternative economies, and providing change management frameworks, mining companies can ensure smoother transitions to more modern, technology-driven operations. This relevance is underscored by the industry's push toward sustainability, modernization, and alignment with global ESG standards, which increasingly dictate access to investment and market competitiveness. Thus, adopting such tools is critical for mining companies to remain viable and responsible in today’s socioeconomic and environmental landscape.
Literature review
The literature review provides context on zinc mining from a global and African perspective, including examining the current socioeconomic challenges mining communities face, particularly around zinc mines. The people-centric digital tools will be explored.
Current socio-economic transformation challenges facing South African mining communities
Key socio-economic challenges include health and safety risks posed by exposure to mining-related hazards, such as dust and chemicals, which can lead to respiratory and other health problems (Maloisane, 2023). Environmental degradation caused by mining activities, including pollution, deforestation, and habitat destruction, adversely affects communities reliant on agriculture and natural resources (Forget and Rossi, 2021). Employment opportunities in mining are often coupled with insecurity, wage disputes, high-risk working conditions, and a lack of local skills development, which perpetuate reliance on external labour (Cole and Broadhurst, 2021). Furthermore, income inequality can be exacerbated, as only a segment of the population benefits from mining-related employment or business opportunities, while others experience minimal economic improvement (Maloisane, 2023).
The arrival of mining investments often strains local infrastructure, including housing, schools, healthcare, and transportation services, making it difficult to provide adequate support to both mining and non-mining communities (Maloisane, 2023). Mining can also lead to the displacement and resettlement of communities, causing social and economic upheaval (South African Human Rights Commission, 2019). Land rights conflicts, particularly when traditional agricultural lands are claimed by mining companies, are another common issue (South African Human Rights Commission, 2019). Additionally, mining disrupts communities' social and cultural fabric, leading to the loss of cultural heritage and cohesion (Dikgwatlhe and Mulenga, 2022). Economic vulnerability is prevalent in mining-dependent communities due to fluctuating global zinc prices or mine closures, hindering efforts toward economic diversification (The Assay, 2022). Legacy issues, such as abandoned or poorly managed mines, also leave long-lasting environmental and health impacts on communities (South African Human Rights Commission, 2019).
This case study explores how adopting and implementing specific digital tools can enhance social investment returns and improve decision-making in the zinc mining industry. The industry has committed to long-term environmental, social, and governance (ESG) targets requiring active engagement with local communities. However, current methods do not provide near real-time insight into community sentiment regarding ESG initiatives. The use of digital tools can bridge this gap, enabling mining companies to understand and respond to community concerns more effectively.
Zinc mining in South Africa is predominantly concentrated in the Northern Cape, with the Khai-Ma region being of particular interest. This region has a population of 14,574 people, which reflects the small size and limited resource allocation across the province. The lack of economic diversification in the Northern Cape, particularly in remote areas, presents significant risks and challenges (UNCTAD, 2022). Like other mining communities worldwide, zinc mining communities in South Africa are confronted with numerous socio-economic challenges. These challenges vary based on location, the scale of the mining operation, and the policies implemented.
This study focuses on three community related digital tools, which were deemed to be more relevant to the zinc, modern mining context. However, the five digital tools represented in Figure 2 were developed using design thinking principles (Mahadeo et al., 2022). These tools enable an understanding of the effects, impacts and challenges of mining modernization on people in the minerals sector. The tools focus on the ‘social’ or ‘benefits to
people in mining’ aspect. The tools were developed for the South African mining industry to adopt and embed in their operations freely. The purpose of each tool was to provide the mine with insightful information to assist in the decision-making process when considering development interventions for socio-economic transformation, digital training, and adoption of new technologies. From the five tools, only the three community related tools were piloted at the zinc mine for practical validation.
Based on the phase of modernization of the mine, deploying these tools was intended to ensure a new dimension of understanding for the mines and foster more inclusive decisionmaking proactively aligned to preparation for modernization and stakeholder relations. Hence, the digital tools sought to enable mines to gather data for informed decision-making, explicitly focused on community and employee needs, as per the developed tools.
The case study approach provides valuable in-depth and contextualized insights, particularly useful for exploring complex, real-world interactions in settings like socio-economic transformation in mining communities. By focusing on specific cases, researchers can gain a comprehensive understanding of nuanced dynamics, generating hypotheses and rich qualitative data that reveal stakeholder perspectives and motivations. This is especially beneficial in exploratory research where little prior work exists, as case studies can establish preliminary frameworks for future research. However, this approach has limitations, primarily in
terms of generalisability; findings from a single or limited number of cases may not apply to broader populations, as they are often influenced by specific contextual factors. Additionally, case studies carry a risk of researcher bias due to subjective interpretation, which can affect objectivity and validity.
This study employed a case study methodology. Yin (2009) defines a case study as an empirical inquiry investigating a phenomenon in its real-life context. As such, multiple data collection methods are used in case study research, which involves an in-depth study of a phenomenon.
The case study methodology is applied (Figure 3).
Design principles
Figure 4 shows the process flow for the data inputs, processing, and analytics to achieve the desired outputs for the paper. Central to the success of data collection was the designated involvement of a community liaison office from the regional mine. The community liaison office was a central point in implementing the digital tools, data collection, and analysis of the results. Once the data were analysed, it was ordered according to key themes related to improving the understanding of communities' current and future needs and improving communications between the regional mine and the host community.
The study collected research data from the host communities, which were then analysed and interpreted through a process flow map. Digital tools were developed, and relevant social metrics were considered for the zinc mine. The digital tools used in the host communities included those relevant for external mine use, such as training needs surveys, NGO/community social needs assessments, and SMME communications and engagement tools. Internal tools,
such as the digital leadership competency gap assessment tool and change management blueprint, will be applied to the zinc context in a follow-up study.
The digital tools were piloted at a zinc mine in the Northern Cape, Southern Africa's Khai-Ma region, for verification and practicality for operational use at an active mine.
To understand the context-specific socio-economic challenges, businesses need to undertake a materiality assessment (Thao, 2023). This materiality assessment identifies, refines, and assesses significant ESG issues that might impact the business and stakeholders (GRI, 2023). These are then prioritized into topics, metrics, and targets to guide the company’s ESG framework. Through an annual materiality assessment, the zinc business identified the social focus areas it needed to address as part of its ESG Framework. The metrics selected by the company are shown in Table I.
To seek community members' input into the ESG framework, the business currently uses manual approaches to survey completion and the Survey Monkey tool. The off-the-shelf digital tools allowed the company to improve its stakeholder engagement process and secure feedback from the community in a transparent and verifiable manner.
The digital tools developed aimed to improve the understanding between the mine and host communities and ensure an open and transparent line of communication between the parties. Subsequently, the digital tool focuses on enhancing data collection and is an additional feature in the engagement strategy with the mine and surrounding community. It is a means by which data can be collected from mining communities for further analysis and decision-making.
The tools were demonstrated to the internal mine subject matter experts in September 2023. All comments and inputs were utilized to improve the tools. These comments included modifying wording to remove ambiguity, translating the survey tools into the Afrikaans language, and including the purpose of the surveys. The digital tools were deployed within the zinc mine itself. The target population for the pilot study was randomly selected through participants entering a community liaison office in five mining regions. The foot traffic into the community liaison offices of Onseepkans, Witbank, Pella, Pofadder, and Aggeneys influenced the research sample. Notably, the selection of the participants was randomized and not according
Table I
to any specific criteria, apart from being a member of the targeted host communities. The importance of the community liaison officer was imperative in facilitating the completion of the assessments, whilst providing explanations to how to interpret the questions that were being asked on the survey tools. Without the community liaison officer, participation as well as the accuracy of the data collected would have been reduced.
The customized tools were presented internally to the organization and then launched externally for testing by the communities during October 2023. A public QR code was created to enable electronic completion of the assessments, and paper-based versions of each assessment were created for participants without internet access.
Challenges identified during this phase include too many input surveys for the community members to complete and the level of digital literacy required by older adults to complete the too-advanced survey. Table II shows the population size of the five targeted regions.
No comparative data sets exist as this is the digital tool's baseline dataset. The research team engaged in deductive and inductive interpretation to identify key themes represented by the data, which can inform future decision-making (Bingham and Witkowsky, 2022). These themes were then categorized to maintain alignment with the survey questions and make meaning of the survey inputs received. The data interpretation and analysis process (Figure 5) reflects the process a mine would use to understand the data collected.
Table II
Population size per target location
Region
Onseepkans
Witbank
Pella
Pofadder
Aggeneys
Total:
*Only census data from 2011 was available
Social-related metrics and targets for the mining company (Govender, 2023)
Metrics
Population size
*2 090
349 076
*1 681
3 524
*2 262
338 633
Target (2027)
Put safety first in the community. Elimination of safety-related fatalities.
Number of social incidents reported, investigated, and actioned. 100%
Human rights sssessment completed, and recommendations actioned. 100%
Local employment.
Local procurement.
>95%
>15%
Families impacted through skills development. Train and develop 1 500 community members. Community beneficiaries employed. For every one job on-site, support two jobs off-site.
Women and children are uplifted through education, nutrition, healthcare, and welfare.
Positively impact 17 500 lives.
Results
The survey assessment results were categorized according to the specific outcomes described in the process flow diagram (Figure 5). As such, the interpretation of the data is presented according to the themes that follow here..
Note: This pilot test did not implement the Change Management Blueprint and Digital Leadership Competencies Tool. However, considerations for application arehighlighted in Section 5.
Research sample
The sampled dataset per tool is shown in Table III, with the highest number of participants completing the training needs survey (59 participants). The feedback from the community liaison officers was that aiming to implement all three surveys simultaneously was a challenging and complicated task for the community members.
Findings from data analysis and interpretation
The results depicted in the subsequent headings are interpretations of the data collected during the research study. The interpretation of the results aims to align with the research objectives already mentioned.
Synthesis of insights
The assessment results reflect insights that can be used to determine the regional mine's future development inventions. The key insights received per focus area are described in the following (a synthesis is depicted in Figures 6 and 7).
Figure 6 provides key insights into the role of SMME within a host mining community, focusing on business-related training, post-mine closure sustainability, and economic activities tied to mining operations. It highlights that 69% of SMME have received
Table III
Sample size per digital tool Tool
Number
training in business planning (30%), finance (22%), and business management (19%), underscoring the importance of building core business competencies. To ensure sustainable income sources after mine closures, the top three industries identified are tourism and cultural attractions (19%), renewable energy (15%), and recycling or upcycling (15%), reflecting a shift towards diverse and environmentally conscious industries. Additionally, the primary economic activities that establish working relationships with the mine include agriculture, regenerative agro-processing, and re-forestry (30%), followed by catering (22%), and other activities (19%). These findings emphasize the significance of skill development, economic diversification, and collaborative efforts between the mining sector and local communities to drive longterm socio-economic transformation.
Figure 7 outlines the top five capacity development initiatives and alternative income sources relevant to post-mine closure planning in the host mining community. In terms of capacity development, the most readily available initiatives include
safety and risk management (10%), job readiness skills (8%), business management (7%), education and training (7%), and entrepreneurial skills (5%). These initiatives demonstrate a focus on building foundational skills and ensuring community readiness for employment opportunities within and beyond the mining sector. Furthermore, to ensure sustainable livelihoods post-mine closure, the top five alternative income sources identified are agriculture, farming and gardening (15%), sports and recreational facilities (15%), health facilities (15%), community halls (13%), and primary and secondary schools (11%). These findings highlight the importance of diversifying income sources and strengthening local infrastructure to support long-term socio-economic stability once mining activities cease. This approach encourages holistic development, preparing the community for a future without reliance on mining operations.
Gathering and actioning the present and perceived future SMME needs
The survey responses from SMME in mining communities provide critical insights into their access to financial support and their strategies for fostering socio-economic development beyond mining operations. Notably, 75% of SMME that applied for loans or grants were successful, with 66% using these funds to expand their businesses and 34% utilising them to hire additional employees. This demonstrates a strong focus on business growth and job creation. In alignment with broader community upliftment, SMME identified key alternative income sources post-mine closure, including agriculture, sports and recreational facilities, health services, community halls, and primary and secondary schools. These findings are consistent with previous data highlighting the importance of agriculture and local infrastructure in ensuring sustainable livelihoods post-mining. The results also underscore the community's drive to establish independent economic activities, addressing economic and social needs. Mining companies can
leverage these insights to shape their corporate social investment strategies, supporting industries that align with community priorities and long-term sustainability goals.
Understanding the community’s current and future social needs
To improve the effectiveness and impact of socio-economic development programmes, it is essential to have a deep understanding of the current and future social needs of the community being served. Figure 8 highlights the most pressing community challenges and the assets needed for community upliftment in a mining host community. The most urgent challenges identified by the community include economic inequality (17%), lack of infrastructure (16%), unemployment (15%), health services (15%), and education (14%). Correspondingly, the community identified key assets needed for upliftment, with priorities on employment opportunities (18%), improved infrastructure (18%), education facilities (17%), and healthcare services (17%).
When compared to previous insights, this data reinforces the themes of economic and social challenges, such as the need for job creation and better infrastructure, which were also highlighted by SMME. However, this new data emphasizes the immediate need for addressing unemployment and inequality, whereas the previous responses were more focused on leveraging financial support and alternative income sources post-mine closure, such as agriculture and education. Both sets of data underscore the importance of holistic socio-economic development, with the mining industry positioned to play a critical role in addressing these challenges through targeted community investments and support.
Evaluating the community and SMME training needs
To address the socio-economic needs of mining communities, it is essential to align training initiatives with the community’s
Assessing
impact of a zinc mine in South Africa through the application of digital tools
long-term development goals. The community has already engaged in several capacity-building initiatives, with the top five most accessible training programmes focusing on safety and risk management (10%), job readiness skills (8%), business management (7%), community education and training (7%), and entrepreneurial skills (5%). Additionally, 69% of SMMEs in the host community have received business-related training, primarily focused on business planning (30%), finance (22%), and business management (19%). These initiatives provide a solid foundation for further economic development.
Comparing these findings with the community’s identified needs for post-mine closure, such as job creation and infrastructure development, the mine can leverage existing skills to foster community-led economic activities. The mine can support sustainable business ventures by facilitating connections between individuals with complementary skills. This approach improves the mine’s relationship with the community and enhances the long-term viability of socio-economic activities beyond mining.
Identifying alternative economies and industrialists that meet the broad-based black economic empowerment (B-BBEE) criteria within mine communities
Industrialists play a crucial role in fostering economic growth in communities following the cessation of mining activities, potentially becoming the primary economic drivers in these regions. SMME stand to benefit from industrialist schemes but often lack awareness of these opportunities. The regional mine can assist in identifying and supporting SMME with the potential to evolve into industrialists. Survey data reveals that 67% of economically active community members were unaware of the Black Industrialist Scheme. The community, however, has identified industries such as tourism and cultural attractions (19%), renewable energy (15%), and recycling or upcycling (15%) as sustainable income sources post-mine closure. Additionally, 11% of respondents expressed no interest in these industries, suggesting a need for further engagement to identify their specific training and development needs. These findings highlight a communication gap between mining operations and the community regarding available support initiatives, indicating the need for a targeted and consistent promotional strategy to maximize community participation in industrialist schemes.
Measuring the level of engagement between the community and the regional zinc mine
Measuring the level of communication between regional mines and host communities is essential to ensure mutual understanding of each stakeholder's needs and how these can be addressed through available tools and resources. Survey data (Figure 9) indicate that a significant majority of SMME, specifically 71%, report a lack of understanding regarding tender requirements. Furthermore, 85%
of SMME find the process of uploading documents to the regional mine’s vendor/procurement portal to be challenging, a sentiment echoed by all participants who stated that the portal's instructions were difficult to follow. Additionally, 85% of respondents are not actively monitoring the status of their applications on the portal, likely due to a lack of knowledge about how to navigate it—100% of participants reported not knowing where to access the portal or how to operate it effectively. While over 86% of SMME are registered with the Companies and Intellectual Property Commission and possess a tax number, many are not registered with the Workman Compensation or the South African Revenue Service and struggle to comprehend tender requirements. Among those SMME that maintain working relationships with the mine, key economic activities include agriculture, regenerative agriculture, agro-processing, and re-forestry (21%), followed by catering (14%), and other activities (14%). These findings suggest that while SMME possess the foundational prerequisites for engaging in service exchanges with the regional zinc mine, they lack the technical expertise required to navigate the vendor platform effectively. The portal’s user-friendliness is a critical issue that needs addressing. Consequently, these insights indicate the necessity for the mine to enhance its mentoring efforts regarding the technical requirements of the vendor platform, facilitating the formation of mutually beneficial relationships.
The digital tools can provide a detailed perspective of most elements questioned within a mine’s materiality assessment (refer to Table IV. They can also enable more instantaneous and regular feedback with host communities.
In considering the application of digital ESG tools within mining contexts, several critical learnings emerge that can enhance their effectiveness and community engagement.
First and foremost, running campaigns in collaboration with community leaders is essential, ensuring that these efforts are wellpublicized and attended by a significant portion of the community. Such campaigns serve not only to explain the value of the tools but also to cultivate a compelling narrative around the potential benefits and outputs derived from their application.
Furthermore, community leadership plays a pivotal role in influencing and driving the uptake of surveys among local residents. By enlisting respected figures within the community, mines can foster a greater sense of trust and participation in the survey process.
Additionally, leveraging the technological assets available in community liaison offices is crucial for spurring further engagement. Providing access to computers and internet connections has proven essential, though it necessitates that
Table IV
Materiality comparison with digital tools
Mine Social Metric (Secured after annual materiality surveys) Identified using the Digital Tool (secured during November 2023)
Put safety first in the Community.
Number of social incidents reported, investigated, and actioned.
Human rights assessment completed, and recommendations actioned.
Local employment.
Local procurement.
Families impacted through skills development.
Community beneficiaries employed.
Women and children are uplifted through education, nutrition, healthcare, and welfare.
Justification for Response
Yes The community was keen to participate in safety and risk management training (10%) to prevent fatalities and injuries.
No
No
It is not included in the digital tools and is not highlighted by the Communities as an issue/concern based on the good relationship with the mines.
It is not included in the digital tools and is not highlighted by the Communities as an issue/concern based on the good relationship with the mines.
Yes Skills development for business-related capabilities was favoured by 69% of the host community, where skills to improve their ability to create a sustainable business were favoured and tended towards business planning (30%), finance (22%), and business management (19%).
Yes Through the SMME engagement tool, 100% of SMME in the host community expressed interest in providing services to the regional mine. However, 71% voiced difficulty understanding tender requirements. Those who were successful provided agricultural, agro-processing, catering, and other activities to the mine.
Yes The training needs assessment survey provides insight into the specific skills development requirements desired by the host community and indicates that job readiness (8%) and entrepreneurship (5%) are crucial in ensuring sustainable economic activities to improve the living conditions of families.
Yes The community social needs assessment tool indicates the success rate of SMME who applied for grant funding (75%) and the degree of awareness of Black industrialist schemes (33%) offered by the mine. The utilization of the specific funds tends towards expanding their business (66%) rather than providing immediate employment (33%).
Yes The community social needs assessment tool provides insight into the specific needs and challenges the host community faces and what specific industries can lead to community upliftment.
participants travel to these offices, which can be a barrier to participation. To mitigate this, mines should strive to create curiosity and excitement within the community to encourage regular visits to the community liaison offices.
The average completion time for the surveys was recorded at approximately 15 minutes, which highlights the need for consideration of participant concentration levels across different communities. In light of low response rates, there may be merit in merging surveys to streamline the process and enhance overall participation.
The zinc mine provided for capped data (approximately 500MB per person, per month). However, it should be noted that data usage is another vital consideration. Despite the provision of Wi-Fi to the community, issues regarding data consumption remain pertinent. Figures 10 and 11 provide a visual representation of the data utilized for completing assessments and accessing resources, further emphasizing the need for careful planning in this regard.
Consideration of the exact data usage to complete the assessments is imperative for other mines wishing to apply the digital tools as free available Wi-Fi may not be offered to host community members.
In summary, the application of digital ESG tools in mining communities requires a nuanced understanding of local dynamics and the importance of community involvement. By incorporating these learnings, mines can enhance the effectiveness of their
initiatives and foster more meaningful relationships with the communities they impact.
During the testing of the digital tools, several challenges were identified that affected participant engagement and survey completion rates. Firstly, the use of multiple separate surveys contributed to survey fatigue, resulting in decreased participation. To address this issue, it is recommended that the mine consolidate these into a single, integrated tool that encompasses all necessary surveys.
Additionally, participants reported a lack of motivation to complete the surveys, citing the excessive number of questions and concerns regarding data usage as significant barriers. To improve this, the mine could customize the tool by focusing on key questions that provide essential information, thus streamlining the process.
Furthermore, the implementation of the survey necessitated considerable physical presence, explanation, and micromanagement by mine representatives, highlighting the importance of active engagement and support to facilitate effective responses from community members. Many participants in the SMME communication and engagement survey also experienced fatigue Hence, regular forums could be established to foster ongoing community engagement, manage expectations, and minimize distractions.
The presence of nested questions and pop-ups was noted as a potential hindrance to completing the survey and fully absorbing the presented content.
Work sessions with pilot sites revealed stakeholders' need to understand the integration of the technology initiative into the overall strategy and operational structures. A company-wide digitization journey map is deemed necessary. Concerns were raised about the readiness of specific operations for technology adoption and the absence of assurance from the company regarding an integrated plan.
The progress of other initiatives and priorities affects the digitization journey, requiring a thorough understanding of contextual factors when the project team is established. Participants found that, what started as a beneficial project quickly became a burden, negatively impacting commitment. The larger organization requires reassurance about the specific project's intent and expected behaviour.
Projects consistently overlook a thorough review process, neglecting the plan, do, check, act (PDCA) cycle, which is necessary for quality improvement. Before launching new initiatives, projects need to facilitate knowledge-sharing to prevent repeating mistakes. The industry must disseminate insights, avoiding recurrent failures. Industry forums should promote learning and encourage participation. Reflecting on experiences is essential for averting future challenges and holding the organization accountable for the reasons behind project failures.
Past initiatives influence the perceived likelihood of success and establish the framework for gauging future success. Before embarking on the change process journey, it is essential to reassess the resource plan, acknowledging the distinction between current practices and desired actions. The recent change management approaches and methodologies are crucial in this phase to ensure cultural alignment.
In a follow-up study, the two other digital tools will be validated within the context of the zinc mine. These tools were intended to improve the understanding of the social and training needs of the external communities and the engagement between potential
suppliers. Additionally, the tools were meant to measure the digital capability of the workforce (i.e., digital leadership competency) and prescribe a roadmap for adopting modern technologies within the mining operation (i.e., change management).
The metrics and targets selected by the mining company for the social aspect of ESG criteria align closely with community expectations as highlighted in the survey, particularly regarding job creation and training to leverage the benefits of mining and foster local entrepreneurial opportunities. Based on the insights gathered from this study and the lessons learned from the pilot initiatives, several key considerations emerged to guide future development interventions and facilitate ongoing dialogue with the host community.
Firstly, the expansion of local SMME has the potential to significantly increase job availability, thereby enhancing the living conditions of community members through a multiplier effect. Secondly, enhancing the quality of primary and secondary education is essential to uplifting the community's skill base and addressing existing skill shortages.
Additionally, the community strongly desires access to fertile land for agricultural activities, recognizing that such endeavours could provide a vital source of income and sustenance following mine closure. Despite the awareness of agriculture's potential, current agricultural activities remain minimal. Furthermore, while there are established solid waste disposal and recycling depots, the overwhelming majority of community members (96%) do not view these as viable sustainable economic activities post-mining. A similar sentiment is reflected in the perception of tuckshops and spaza shops, which, despite their presence, are also not seen as sustainable economic options after mining ceases.
Notably, 14% of SMME reported having working relationships with the mine however, the survey results do not clarify what the ‘other’ category entails, indicating a need for follow-up discussions to explore how these relationships can be further developed and supported. Unanimously, community members reflected a misunderstanding of the tender application portal, which can motivate strategic intervention from the regional mine.
Importantly, these digital tools, though proven beneficial in gathering socio-economic insights, have not previously been applied to host communities in this manner. Recognizing that mining contexts vary significantly and that each mine is at a different stage of modernization, the lessons learned from the zinc mine may be applicable to other operations facing similar circumstances. A uniform approach is not advisable, rather, the digital tools should be adapted according to the unique context and specific needs of each mine. Continuous learning and adaptation remain essential, and organizations should leverage these insights to successfully implement digital tools that facilitate rapid impacts and advance social transformation within mining communities.
Acknowledgements
The work presented in this paper is part of a Postdoctoral research study in the School of Mining Engineering at the University of the Witwatersrand, Johannesburg, South Africa. The Minerals Council South Africa supported the development of digital ESG tools for application and distribution across mining operations in South Africa and beyond.
Sincere gratitude to contributors from Nadia Lawrence, the HSE-ESG, Social Enterprise Development and Training Teams (Vedanta Zinc International), Wessel Botha (Enterprise University of Pretoria), and Thiru Swettenham.
Abbreviations
B-BBEE Broad-based black economic empowerment
CIPC Companies and Intellectual Property Commission
CSI Corporate social investment
ESG Environmental, social, and governance
GDP Gross domestic product
MB Megabytes
MPRDA Mineral and Petroleum Resource Development Act
PDCA Plan, do, check, and act
SATCAP Successful application of technology centered around people
SED Socio-economic development
SET Socio-Economic transformation
SLP Social and labour plans
SMME Small, micro, and medium enterprises
UN United Nations
References
Bingham, J., Witkowsky, P. 2022. Deductive and inductive approaches to qualitative data analysis. In Vanover, C., Mihas, P., Saldaña, J. (eds.). Analyzing and interpreting qualitative data: After the interview. SAGE Publications, pp. 133–146.
Botts, R., Gilmer, Z., Samale, S. 2023. The mining industry should not ignore ESG. Engineering & Mining Journal, vol. 224, no. 6, pp. 55–57.
Cole, J.M., Broadhurst, L.J. 2021. Measuring the sustainable development goals (SDGs) in mining host communities: A South African case study. The Extractive Industries and Society, vol. 8, no. 1, pp. 233–243.
Department of Mineral Resources (DMR). 2010. Guidelines for the submission of a Social and Labour Plan. Pretoria, vol. 85. Dikgwatlhe, P., Mulenga, F. 2023. Perceptions of local communities regarding the impacts of mining on employment and economic activities in South Africa. Resources Policy, vol. 80, pp. 103138 https://doi.org/10.1016/j.resourpol.2022.103138
Fiscor, S. 2023. Putting ESG to work: successful programs provide benefits internally and externally while improving the mining industry’s image. Engineering & Mining Journal, vol. 224, no. 6, pp. 48–54.
Forget, M., Rossi, M. 2021. Mining region value and vulnerabilities: Evolutions over the mine life cycle. The Extractive Industries and Society, vol. 8, no. 1, pp. 176–187.
Ingebretsen, E. 2023. ESG as a key pillar of investment strategy. Journal of Securities Operations & Custody, vol. 16, no. 1, pp. 57–69.
Kujala, J., Sachs, S., Leinonen, H., Heikkinen, A., Laude, D. 2022. Stakeholder Engagement: Past, Present and Future. Business & Society, vol. 61, no. 5, pp. 1136–1196.
Mahadeo, V.J., Botha, P.W., Govindasamy, K., Swettenham, T., Ramparsad, S. 2022. Digital Leadership Competency Assessment Tool for SA Mining Operations. The South African Institute of Mining and Metallurgy.
Maloisane, P. 2023. The human cost of South Africa’s mining corporate riches. Available from https://mg.co.za/partnercontent/2023-03-27-the-human-cost-of-south-africas-miningand-corporate-riches/ [Accessed 23 Aug 2023].
Minerals Council South Africa. 2023. Facts and Figures Pocketbook 2022. Available from https://www.mineralscouncil.org.za/ downloads/send/18-facts-and-figures/1996-facts- and-figures2022-pocketbook [Accessed 15 Sep 2023].
NJCPA. 2021. ESG 101: The Benefits and Why It is Growing in Importance. Available from https://njcpa.org/ article/2021/09/15/esg-101-the-benefits-and-why-it-s-growingin- importance#:~:text=Proven%20effects%20include%20 smoother%20operations%2C%20 positive%20morale%20 and,can%20produce%20positive%20results%20beyond%20 solid%20financial%20performance [Accessed 7 Sep 2023].
Pérez, L., Hunt, V., Samandari, H., Nuttall, R., Biniek, K. 2022. Does ESG really matter— and why? McKinsey Quarterly. Available from https://www.mckinsey.com/~/media/mckinsey/ business%20functions/sustainability/our%20insights/does%20 esg%20really%20matter%20and%20why/does-esg-really-matterand-why-vf.pdf [Accessed 17 Jan 2024].
Perrone, G. 2022. The story behind the term ESG. Available from https://www.twentynow.com/sustainability-initiatives/people/thestory-behind-the-term-esg/ [Accessed 7 Sep 2023].
Seloa, P., Ngole-Jeme, V. 2022. Community perceptions on environmental and social impacts of mining in Limpopo South Africa and the implications on corporate social responsibility. Journal of Integrative Environmental Sciences, vol. 22, no. 1, pp. 189–207.
South African Human Rights Commission. 2019. National hearing on the underlying socio-economic challenges of mining-affected communities in South Africa. Available from https://view. officeapps.live.com/op/view.aspx?src=https%3A%2F%2Fstatic. pmg.org.za% 2F190220SAHRC.pptx&wdOrigin=BROWSELINK [Accessed 19 Sep 2023].
Thao, T.T. 2023. ESG Trend - The History of ESG Concept Formation and the Current Trends in the Goal of Business Sustainable Development. VNU Journal of Science: Policy and Management Studies, vol. 39, no. 2, pp. 56–62.
The Assay. 2022. Zinc mining and market outlook 2022-2025. Available from https://www.theassay.com/articles/the-assayinsights/zinc-market-analysis/ [Accessed 19 Sep 2023].
UNCTAD. 2022. Building resilience in small island developing States. Available from https://unctad.org/system/files/official-document/ aldcinf2022d2_en.pdf [Accessed 29 Nov 2023].
Yin, R. 2009. Case study research: Design and methods (4th ed.). Thousand Oaks, CA: Sage. https://doi.org/10.33524/cjar.v14i1.73 u
21-23 January 2025 — 14TH South African Conference on Computational and Applied Mechanics
Wits Science Stadium, South Africa
Website: https://sacam.co.za/
19-20 February 2025 — Mine Closure Conference 2025
Maslow Hotel, Sandton, South Africa
Contact: Gugu Charlie Tel: 011 538-0238
E-mail: gugu@saimm.co.za
Website: http://www.saimm.co.za
7-8 April 2025 — 2ND Southern African Hydrogen and Fuel Cell Conference 2025
Southern Sun Rosebank, Johannesburg
Contact: Gugu Charlie
Tel: 011 538-0238
E-mail: gugu@saimm.co.za
Website: http://www.saimm.co.za
8-10 April 2025 — 27TH International Conference on Paste, Thickened and Filtered Tailings
Swakopmund, Namibia
Website: https://acgpaste.com/2025/
26-29 May 2025 — 9TH Sulphur and Sulphuric Acid Conference 2025
Protea Hotel Stellenbosch and Conference Centre, Stellenbosch
Contact: Gugu Charlie
Tel: 011 538-0238
E-mail: gugu@saimm.co.za
Website: http://www.saimm.co.za
25-26 June 2025 — 4TH Digital Transformation in Mining Conference 2025
Glenburn Lodge and Spa, Muldersdrift
Contact: Camielah Jardine
Tel: 011 538-0237
E-mail: camielah@saimm.co.za
Website: http://www.saimm.co.za
21-25 July 2025 — AfriRock Pioneering Congress 2025
Sun City, South Africa
Contact: Camielah Jardine
Tel: 011 538-0237
E-mail: camielah@saimm.co.za
Website: http://www.saimm.co.za
18-19 August 2025 — 13TH International Heavy Minerals Conference 2025
Sun City, South Africa
Contact: Gugu Charlie
Tel: 011 538-0238
E-mail: gugu@saimm.co.za
Website: http://www.saimm.co.za
13-15 October 2025 — 9TH International PGM Conference 2025
Sun City, South Africa
Contact: Camielah Jardine
Tel: 011 538-0237
E-mail: camielah@saimm.co.za
Website: http://www.saimm.co.za
16-22 November 2025 — The 12TH International Copper Conference (Copper 2025)
Phoenix, Arizona, USA
Website: https://www.extractionmeeting.org/ Extraction2025/Extraction2025/Copper2025/default.aspx
The following organizations have been admitted to the Institute as Company Affiliates
A and B Global Mining (Pty) Ltd
acQuire Technology Solutions
AECI Mining Chemicals, a division of AECI Mining Ltd
African Pegmatite
Allied Furnace Consultants
AMIRA International Africa (Pty) Ltd
Anglogold Ashanti Ltd
Anton Paar Southern Africa
Arcus Gibb (Pty) Ltd
Becker Mining (Pty) Ltd
Bluhm Burton Engineering Pty Ltd
Caledonia Mining South Africa
Castle Lead Works
DDP Specialty Products South Africa (Pty) Ltd
De-Tect Unit Inspection (Pty) Ltd
Digby Wells and Associates
EHL Consulting Engineers (Pty) Ltd
Elbroc Mining Products (Pty) Ltd
Epiroc South Africa (Pty) Ltd
Ex Mente Technologies (Pty) Ltd
Exxaro Resources Limited
FLSmidth Minerals (Pty) Ltd
G H H Mining Machines (Pty) Ltd
Geobrugg Southern Africa (Pty) Ltd
Glencore
Gravitas Minerals (Pty) Ltd
Hatch (Pty) Ltd
Herrenknecht AG
Impala Platinum Holdings Limited
IMS Engineering (Pty) Ltd
Ingwenya Mineral Processing
Ivanhoe Mines SA
Longyear South Africa (Pty) Ltd
Malvern Panalytical (Pty) Ltd
Maptek (Pty) Ltd
Mech-Industries
Micromine Africa (Pty) Ltd
Minearc South Africa (Pty) Ltd
Minerals Council of South Africa
MineRP Holding (Pty) Ltd
Mining Projection Concepts (Pty) Ltd
Mintek
MLB Investments CC
Modular Mining Systems Africa (Pty) Ltd
Murray & Roberts Cementation (Pty) Ltd
OPTRON
Paterson & Cooke Consulting Engineers (Pty) Ltd
Redpath Mining (South Africa) (Pty) Ltd
Rosond (Pty) Ltd
Roytec Global (Pty) Ltd
Rustenburg Platinum Mines Limited - Union
Salene Mining (Pty) Ltd
Schauenburg (Pty) Ltd
SENET (Pty) Ltd
Sibanye Gold Limited
Sound Mining Solution (Pty) Ltd
SRK Consulting SA (Pty) Ltd
Tomra (Pty) Ltd
Trans-Caledon Tunnel Authority
Ukwazi Mining Solutions (Pty) Ltd
VBKOM Consulting Engineers
Weir Minerals Africa
ZUTARI (Pty) Ltd
The HMC series of conferences is traditionally focused on mining and processing of heavy minerals. Whilst this conference will still focus on these important aspects, new challenges and opportunities calls for the evolution of the industry.There is a shift in focus to move closer to some of the strategic downstream industries with a focus on improved integration and value chain optimisation. This conference will aim at involving these key downstream industry players to facilitate dialog and knowledge sharing around technical areas where these value chain improvements can be explored. Further to optimizing current value chains, with the recent changes in the global geopolitical landscape, a strong interest for strategic minerals including rare earth elements provide new opportunities for the industry. Development in these provide additional value from the current resources mined. It however requires evolution in how industry approaches geological characterization through to mining and processing to incorporate the rare earth element bearing mineral extraction alongside current value chain. To support the themes already highlighted for the conference, generational knowledge transfer needs to be effectively addressed to ensure the workforce of the future is enabled to lead the industry evolution. The development of technical professionals entering the industry workforce ranging from traditional training and exposure pathways to new approaches including Artificial Intelligence is seen as a key enabler for the future of the heavy minerals industry.
This series of conferences was started in 1997 and has run since that date. It provides a forum for an exchange of knowledge in all aspects of heavy minerals, from exploration through processing and product applications. This is a strictly technical conference, and efforts by the Organizing Committee are aimed at preserving its technical nature. The benefit of this focus is that it allows the operators of businesses within this sector to discuss topics not normally covered in such forums. The focus on heavy minerals includes the more obvious minerals such as ilmenite, rutile and zircon; and also other heavy minerals such as garnet, and alusite, and sillimanite.
FOR FURTHER INFORMATION, CONTACT:
Gugu Charlie, Conferences and events co-ordinator
ECSA Validated CPD Activity, Credits = 0.1 points per hour attended
Nestled in the rolling hills of the Pilanesberg, one of South Africa’s most scenic locations, Sun City is a world unto itself and has earned its reputation as Africa’s Kingdom of Pleasure. You will find whatever you want at Sun City, from sizzling entertainment, world class casinos and restaurants to cater for all tastes, to the more relaxed poolside venue, quiet places, lush gardens, and extensive sporting facilities including two world-class golf courses. These are just some of the elements that make Sun City unique among the world’s entertainment resorts. Finally re-discovered and now part of Sun City, the Lost City and the Valley of Waves, fabled to be the Ruins of a glorious ancient civilisation, celebrate and bring to life the legends of this mystical city. The Lost City is internationally applauded for its wonderfully imaginative theme and exquisite landscaping whilst the fantastic Valley of Waves is one of the world’s most exciting waterparks.
Professionals specialising or working in the areas of:
• Renewable energy
• Water purification
• Infrastructure
• Desalination plants
As well as the following industry professionals are invited to participate:
• Academics
• Business development managers
• Concentrator managers
• Consultants
• Engineers
Prospective authors are invited to submit abstracts of not more 500 words, in English. Please email abstracts and requests to be added to the conference mailing list to Gugu Charlie: Conferences and Events Co-ordinator, SAIMM at gugu@saimm.co.za
25 February 2025 – Abstract submissions
4 April 2025 - Paper submission 18-19 August 2025 – Conference 20 August 2025 – Technical Visit
E-mail: gugu@saimm.co.za Tel: +27 11 538-0238, Web: www.saimm.co.za
25-26 JUNE 2025
Jardine, Head of Conferences and Events
Whatever terminology you wish to use, it is obvious the world of work is changing rapidly.
The Mining Industry, along the Mining Value Chain, is a part of this; seeking to take advantage of digital opportunities in the quest for competitiveness, sustainability and Zero Harm.
Mining businesses in Africa, as globally, are on this journey purposefully or by default. This event adds to purpose by being a showcase and learning experience for everyone associated with the Mining Industry. We will learn about Global Best Practices, network with global leaders in mining and other businesses, and do so in an exciting and interactive format.
Be prepared to be challenged and informed and to leave excited and better equipped for today’s digital journey.