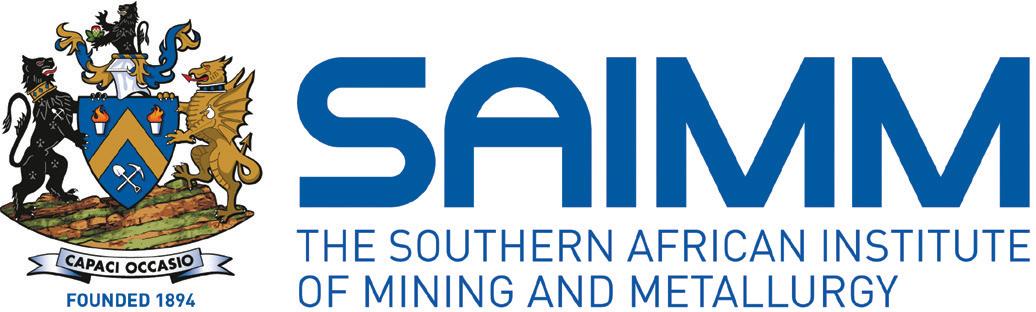
MINERALS AND EXTRACTIVE
AT THE UNIVERSITY OF PRETORIA
Faculty of
Fakulteit Ingenieurswese, Bou-omgewing en Inligtingtegnologie / Lefapha la Boetšenere, Tikologo ya Kago le Theknolotši ya Tshedimošo
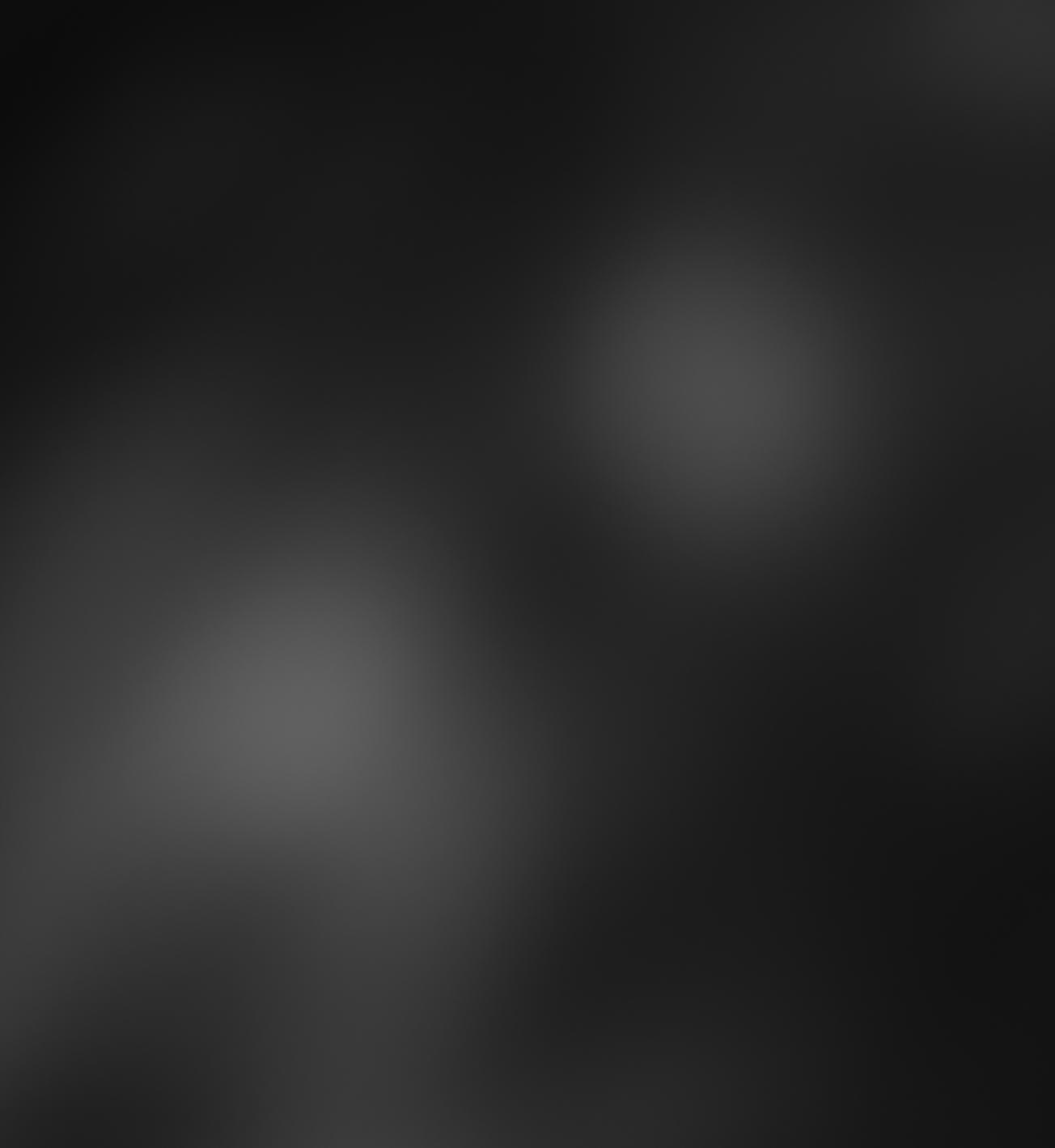

Faculty of
Fakulteit Ingenieurswese, Bou-omgewing en Inligtingtegnologie / Lefapha la Boetšenere, Tikologo ya Kago le Theknolotši ya Tshedimošo
The University of Pretoria has become a centre for mining and metallurgical research, focusing on issues relevant to South Africa’s mining industry. The University understands the importance of maintaining close working relationships with the local industry to pursue truly impactful research.
DEPARTMENT OF MINING ENGINEERING mechanisation and automation management and leadership rock engineering extended reality technology
DEPARTMENT OF MATERIALS SCIENCE AND METALLURGICAL ENGINEERING minerals processing pyrometallurgy hydrometallurgy physical metallurgy welding engineering corrosion engineering
FOR MINERALS AND MINING ENGINEERING WORLDWIDE IN THE LATEST QS UNIVERSITY RANKINGS BY SUBJECT
www.up.ac.za/ebit
Faculty of Engineering, Built Environment and Information Technology Fakulteit Ingenieurswese, Bou-omgewing en Inligtingtegnologie / Lefapha la Boetšenere, Tikologo ya Kago le Theknolotši ya Tshedimošo
OFFICE BEARERS AND COUNCIL FOR THE 2024/2025 SESSION
Honorary President
N. Tsengwa
President, Minerals Council South Africa
Honorary Vice Presidents
Gwede Mantashe
Minister of Mineral Resources and Energy, South Africa
P. Tau
Minister of Trade, Industry and Competition, South Africa
Blade Nzimande
Minister of Higher Education, Science and Technology, South Africa
President E. Matinde
President Elect
G.R. Lane
Senior Vice President
T.M. Mmola
Junior Vice President
M.H. Solomon
Incoming Junior Vice President
S.J. Ntsoelengoe
Immediate Past President
W.C. Joughin
Honorary Treasurer
W.C. Joughin
Ordinary Members on Council
W. Broodryk
Z. Fakhraei
B. Genc
K.M. Letsoalo
S.B. Madolo
M.A. Mello
K. Mosebi
Co-opted Council Members
A.D. Coetzee
L.T. Masutha
M.C. Munroe
S.M. Naik
G. Njowa
S.M. Rupprecht
A.T. van Zyl
E.J. Walls
Past Presidents Serving on Council
N.A. Barcza C. Musingwini
R.D. Beck S. Ndlovu
Z. Botha J.L. Porter
V.G. Duke M.H. Rogers
I.J. Geldenhuys G.L. Smith
R.T. Jones
G.R. Lane – TP Mining Chairperson
Z. Botha – TP Metallurgy Chairperson
K.W. Banda – YPC Chairperson
C.T. Chijara – YPC Vice Chairperson
Branch Chairpersons
Botswana K. Mosebi
DRC K.T. Kekana (Interim Chairperson)
Johannesburg N. Rampersad
Limpopo M.S. Zulu
Namibia T. Aipanda
Northern Cape Vacant
North West Vacant
Pretoria P.G.H. Pistorius
Western Cape Vacant
Zambia N.M. Kazembe
Zimbabwe L. Shamu
Zululand Vacant
*Deceased
* W. Bettel (1894–1895)
* A.F. Crosse (1895–1896)
* W.R. Feldtmann (1896–1897)
* C. Butters (1897–1898)
* J. Loevy (1898–1899)
* J.R. Williams (1899–1903)
* S.H. Pearce (1903–1904)
* W.A. Caldecott (1904–1905)
* W. Cullen (1905–1906)
* E.H. Johnson (1906–1907)
* J. Yates (1907–1908)
* R.G. Bevington (1908–1909)
* A. McA. Johnston (1909–1910)
* J. Moir (1910–1911)
* C.B. Saner (1911–1912)
* W.R. Dowling (1912–1913)
* A. Richardson (1913–1914)
* G.H. Stanley (1914–1915)
* J.E. Thomas (1915–1916)
* J.A. Wilkinson (1916–1917)
* G. Hildick-Smith (1917–1918)
* H.S. Meyer (1918–1919)
* J. Gray (1919–1920)
* J. Chilton (1920–1921)
* F. Wartenweiler (1921–1922)
* G.A. Watermeyer (1922–1923)
* F.W. Watson (1923–1924)
* C.J. Gray (1924–1925)
* H.A. White (1925–1926)
* H.R. Adam (1926–1927)
* Sir Robert Kotze (1927–1928)
* J.A. Woodburn (1928–1929)
* H. Pirow (1929–1930)
* J. Henderson (1930–1931)
* A. King (1931–1932)
* V. Nimmo-Dewar (1932–1933)
* P.N. Lategan (1933–1934)
* E.C. Ranson (1934–1935)
* R.A. Flugge-De-Smidt (1935–1936)
* T.K. Prentice (1936–1937)
* R.S.G. Stokes (1937–1938)
* P.E. Hall (1938–1939)
* E.H.A. Joseph (1939–1940)
* J.H. Dobson (1940–1941)
* Theo Meyer (1941–1942)
* John V. Muller (1942–1943)
* C. Biccard Jeppe (1943–1944)
* P.J. Louis Bok (1944–1945)
* J.T. McIntyre (1945–1946)
* M. Falcon (1946–1947)
* A. Clemens (1947–1948)
* F.G. Hill (1948–1949)
* O.A.E. Jackson (1949–1950)
* W.E. Gooday (1950–1951)
* C.J. Irving (1951–1952)
* D.D. Stitt (1952–1953)
* M.C.G. Meyer (1953–1954)
* L.A. Bushell (1954–1955)
* H. Britten (1955–1956)
* Wm. Bleloch (1956–1957)
* H. Simon (1957–1958)
* M. Barcza (1958–1959)
* R.J. Adamson (1959–1960)
* W.S. Findlay (1960–1961)
* D.G. Maxwell (1961–1962)
* J. de V. Lambrechts (1962–1963)
* J.F. Reid (1963–1964)
* D.M. Jamieson (1964–1965)
* H.E. Cross (1965–1966)
* D. Gordon Jones (1966–1967)
* P. Lambooy (1967–1968)
* R.C.J. Goode (1968–1969)
* J.K.E. Douglas (1969–1970)
* V.C. Robinson (1970–1971)
* D.D. Howat (1971–1972)
* J.P. Hugo (1972–1973)
* P.W.J. van Rensburg (1973–1974)
* R.P. Plewman (1974–1975)
* R.E. Robinson (1975–1976)
* M.D.G. Salamon (1976–1977)
* P.A. Von Wielligh (1977–1978)
* M.G. Atmore (1978–1979)
* D.A. Viljoen (1979–1980)
* P.R. Jochens (1980–1981)
* G.Y. Nisbet (1981–1982)
A.N. Brown (1982–1983)
* R.P. King (1983–1984)
J.D. Austin (1984–1985)
* H.E. James (1985–1986)
H. Wagner (1986–1987)
* B.C. Alberts (1987–1988)
* C.E. Fivaz (1988–1989)
* O.K.H. Steffen (1989–1990)
* H.G. Mosenthal (1990–1991)
R.D. Beck (1991–1992)
* J.P. Hoffman (1992–1993)
* H. Scott-Russell (1993–1994)
J.A. Cruise (1994–1995)
D.A.J. Ross-Watt (1995–1996)
N.A. Barcza (1996–1997)
* R.P. Mohring (1997–1998)
J.R. Dixon (1998–1999)
M.H. Rogers (1999–2000)
L.A. Cramer (2000–2001)
* A.A.B. Douglas (2001–2002)
* S.J. Ramokgopa (2002-2003)
T.R. Stacey (2003–2004)
F.M.G. Egerton (2004–2005)
W.H. van Niekerk (2005–2006)
R.P.H. Willis (2006–2007)
R.G.B. Pickering (2007–2008)
A.M. Garbers-Craig (2008–2009)
J.C. Ngoma (2009–2010)
G.V.R. Landman (2010–2011)
J.N. van der Merwe (2011–2012)
G.L. Smith (2012–2013)
M. Dworzanowski (2013–2014)
J.L. Porter (2014–2015)
R.T. Jones (2015–2016)
C. Musingwini (2016–2017)
S. Ndlovu (2017–2018)
A.S. Macfarlane (2018–2019)
M.I. Mthenjane (2019–2020)
V.G. Duke (2020–2021)
I.J. Geldenhuys (2021–2022)
Z. Botha (2022-2023)
W.C. Joughin (2023-2024)
S.O. Bada
R.D. Beck
P. den Hoed
I.M. Dikgwatlhe
M. Erwee
B. Genc
R Hassanalizadeh
R.T. Jones
W.C. Joughin
A.J. Kinghorn
D.E.P. Klenam
D.F. Malan
D. Morris
C. Musingwini
S. Ndlovu
P.N. Neingo
A. Nengovhela
S.S. Nyoni
M. Phasha
P. Pistorius
P. Radcliffe
N. Rampersad
Q.G. Reynolds
I. Robinson
S.M. Rupprecht
K.C. Sole
T.R. Stacey
D. Vogt
F. Uahengo
International Advisory Board members
R. Dimitrakopolous
R. Mitra
A.J.S. Spearing
E. Topal
D. Tudor
Editor /Chairperson of the Editorial Board
R.M.S. Falcon
Typeset and Published by
The Southern African Institute of Mining and Metallurgy
PostNet Suite #212 Private Bag X31
Saxonwold, 2132
E-mail: journal@saimm.co.za
Printed by Camera Press, Johannesburg
Advertising Representative
Barbara Spence
Avenue Advertising
Journal Comment: The Sustainability of Mining Engineering Education in South Africa by D.F.
Malan
President’s Corner: Reflections and Lessons Learnt From the 17th International Ferroalloys Congress (INFACON XVII) by E.
Matinde
THE INSTITUTE, AS A BODY, IS NOT RESPONSIBLE FOR THE STATEMENTS AND OPINIONS ADVANCED IN ANY OF ITS PUBLICATIONS.
Copyright© 2024 by The Southern African Institute of Mining and Metallurgy. All rights reserved. Multiple copying of the contents of this publication or parts thereof without permission is in breach of copyright, but permission is hereby given for the copying of titles and abstracts of papers and names of authors. Permission to copy illustrations and short extracts from the text of individual contributions is usually given upon written application to the Institute, provided that the source (and where appropriate, the copyright) is acknowledged. Apart from any fair dealing for the purposes of review or criticism under The Copyright Act no. 98, 1978, Section 12, of the Republic of South Africa, a single copy of an article may be supplied by a library for the purposes of research or private study. No part of this publication may be reproduced, stored in a retrieval system, or transmitted in any form or by any means without the prior permission of the publishers. Multiple copying of the contents of the publication without permission is always illegal. U.S. Copyright Law applicable to users In the U.S.A. The appearance of the statement of copyright at the bottom of the first page of an article appearing in this journal indicates that the copyright holder consents to the making of copies of the article for personal or internal use. This consent is given on condition that the copier pays the stated fee for each copy of a paper beyond that permitted by Section 107 or 108 of the U.S. Copyright Law. The fee is to be paid through the Copyright Clearance Center, Inc., Operations Center, P.O. Box 765, Schenectady, New York 12301, U.S.A. This consent does not extend to other kinds of copying, such as copying for general distribution, for advertising or promotional purposes, for creating new collective works, or for resale.
Honorary Legal Advisers
M H Attorneys Auditors
Genesis Chartered Accountants Secretaries
The Southern African Institute of Mining and Metallurgy 7th Floor, Rosebank Towers, 19 Biermann Avenue, Rosebank, 2196
PostNet Suite #212, Private Bag X31, Saxonwold, 2132 E-mail: journal@saimm.co.za
Telephone (011) 463-7940 . E-mail: barbara@avenue.co.za
ISSN 2225-6253 (print) . ISSN 2411-9717 (online)
v
Back analysis of LG6/LG6A chromitite pillar strength using displacement discontinuity modelling by P.J. Le
Roux
and D.F. Malan ..................................................................................
This paper explores the alternative approach of the back-analysis of actual LG6/LG6A mining layouts, using displacement discontinuity codes to simulate the average pillar stresses on a mine-wide scale. From this, a ‘minimum’ pillar strength (K-value in the pillar strength formula) can be estimated. The results are encouraging as the two codes produced similar APS values for a complex pillar geometry. The effect of element sizes and explicitly simulating the effect of the surface for shallow pillars is illustrated using both codes. The need for actual pillar observations and an iterative design process is also emphasized.
605
The role of leadership in technology adoption in the South African mining industry by P.J. Mokganya, R.C.W. Webber-Youngman, J. Uys, and J. Olwagen 617
This article discusses the critical role of leadership in the technology adoption process within organizations, particularly in industries like mining, where innovation is essential for maintaining competitiveness and operational efficiency. It highlights the limitations of traditional technology adoption models. The study proposes the ambidextrous leadership-technology adoption (ALTA) model, which integrates leadership styles such as transformational, transactional, adaptive, and ambidextrous leadership into the technology adoption process. The model emphasizes the balance between exploration (fostering innovation) and exploitation (ensuring operational efficiency). The findings suggest that transformational leadership fosters innovation by encouraging risk-taking and creativity, while transactional leadership ensures efficient technology integration. The study concludes by offering practical recommendations for leaders to foster a culture of innovation, manage resistance, and balance short-term efficiency with long-term technological advancement.
Pillar design and the associated mining engineering constraints in hard rock bord-and-pillar mines by
W.J. Theron and D.F. Malan
Practical mining aspects should be considered when conducting pillar designs for bord-and-pillar layouts. The current methodology for pillar design will result in increasing pillar sizes with depth, which affects the extraction ratio and will result in onerous ventilation requirements. A holistic approach is required to ensure that the rock engineering designs are optimized to ensure efficient mining operations and sustainable production. The use of a ‘squat pillar’ formula for hard rock is discussed, and the formula based on the exponents of the Hedley and Grant pillar formula is explored. The effect of abutments and geological losses on average pillar stress is also explored. These factors must be considered when designing layouts at increasing depths.
Re-evaluation of the PlatMine chromitite pillar strength database by B.P. Watson, M.I. Mabala, and M.J. Kanda
A failed and stable Upper Group 2 chromitite pillar database was collected in 2007 as part of the PlatMine 1.2 pillar strength project. This paper describes re-evaluations of the database, using a linear formula and several variations of the power formula. The formula providing the lowest standard deviation to the data in the database was considered as the best representation of the pillars in the database. Through this rigorous process, a new formula for peak pillar strength was developed for Upper Group 2 chromitite pillars, which is unaffected by volume. The small standard deviation provided by this formula suggests a reliable relationship between strength and w/h ratio, in the w/h ratio range between 1.5 and 4.7. Accuracy, precision, and recall analysis confirmed the efficacy of this equation to the data in the database
Fracturing of rock ahead of the face of an excavation and its relevance to mechanized excavation by M.
Mokgohloa and T.R. Stacey
Boring of tunnels and shafts in hard rock under high stress conditions is becoming more common as mines and tunnels are developed at greater depths. Under the high stress conditions, fracturing of the often brittle rock occurs in the walls, backs, and ahead of advancing faces of excavations. The focus of this paper is on fracturing in the face of the excavation. Examples of such fracturing behaviour are described briefly in the paper. Numerical analyses were carried out to predict the initiation of extension fractures and their orientations ahead of excavation surfaces, and the resulting formation of rock slabs/plates, and the stability of these plates. The results should be beneficial for the evaluation of the conditions prior to, and during boring operations.
Identifying the prone zones to initiation of unstable failure by numerical simulation of mining pillars under compression by A. Doroudgar and H. Noferesti
In this study, the numerical simulation of unstable rock failure was carried out using the three-dimensional explicit Lagranian finite-volume finite difference method to identify the onset and location of unstable failure events in the model. On this basis, a numerical simulation of mine pillars with width to height ratios of 0.5, 2, and 3 was performed. A criterion was developed, based on the calculation of the elastic strain energy. The results of this study showed that, in softer loading systems, due to large amounts of stored elastic strain energy, an unstable equilibrium is established, which leads to the rapid transfer of strain energy to the rock in the form of violent failure. It was also found that the unstable failure starts at the corners and free surface of the model. The new criterion developed in this study may help predict the occurrence of rock bursts in slender pillars and the design of pillars to control human and financial losses caused by this phenomenon.
645
653
661
The development of a linear cutting machine used to characterize Fem modelling parameters for cutting UG2 Reef by U. Du Preez, P.S.Heyns, and D.F. Malan
South Africa has two main platinum reef deposits, namely the Merensky reef and the UG2 reef. These reefs are currently mined using traditional drilling and blasting methods. Mechanized cutting could potentially enable continuous mining, which would offer significant advantages. This would require a thorough understanding of the cutability of the rock. To explore this, a linear cutting machine was developed to conduct laboratory scale cutting tests. This work describes the development and commissioning of the cutting machine using sandstone, as well as subsequent characterization tests on UG2 reef samples
Tracking the degradation of carbon steel mechanical properties due to high-temperature hydrogen attack through strain gauge monitoring by A. van Zyl, C.C.E. Pretorius, V.M. Mathoho, and R.J. Mostert .....................................................
The in-service degradation of the mechanical properties of steel components through the damage mechanism of high temperature hydrogen attack (HTHA), is a topic of concern in the refining and green hydrogen industry. The current investigation deals with the indirect monitoring of mechanical degradation via tracking of the swelling strain in affected structures. It was found that the degradation of carbon steel mechanical properties can be correlated to the swelling strain measured during exposure. The critical point for mechanical property degradation in the plate through-thickness orientation was found to be in the order of 1% of the total swelling strain measured during exposure, equivalent to 65 microstrain. This threshold was found to be significantly lower than that expected from the literature, where limits of 400 to 1000 microstrain were postulated.
Owing to increasing pressure on land use, mine operators do not have any other option other than to place the waste dumps from large-scale opencast mining for coal very near to the surface edge of the pit, which may lead to failure of the topsoil benches of the working pit. This study identified major controlling parameters that influence a stable but economic combination of height and slope angle of external dumps located close to the edge of an open coal pit.
Investigating the effect of different loading scenarios on the performance of wheel loaders: A case study on Can Lignite Enterprises by A. Çelik ...................................................................................................
Wheel loaders are widely used in many sectors due to their mobility, operational flexibility, and low costs. In this study, the effects of the loader operator and different working conditions on the loading performance were investigated. The study was carried out at the Can Lignite Enterprise (CLI), which is a major coal producer in Turkey. In this study, the effect of a single parameter on loading performance was investigated. The results showed that the biggest impact on loading performance (63.4%) was caused by the operator’s experience. PROFESSIONAL
673
683
Instability of topsoil benches of a pit caused by dumping of waste rock outside an opencast coal mine by A. Golder, S.P. Dandapat, and I. Roy 693
703
he mining engineering departments at the various South African tertiary institutes are responsible for producing the next generation of tech-savvy mining engineers. It is well known that it is an ongoing battle for these departments to attract top students. The problem is not unique to South Africa, however. Mining Digital reported earlier this year that mining is no longer seen as a popular career choice and enrolment in mining engineering courses decreased by 63% in Australia since 2014. The Mining Industry Human Resources Council of Canada found in a survey that 70% of the younger generation said they would not consider a career in mining and this was the highest proportion of all the industries included in the survey. This problem is even more complex in South Africa and addressing it will require a multi-pronged approach.
A major difficulty is that the basic education system is not training enough students in the science, technology, engineering, and mathematics (STEM) subjects. Numbers presented to parliament’s Portfolio Committee on Basic Education revealed that enrolment for STEM subjects decreased substantially from 2016 to 2020. During this period, mathematics decreased by 40 385, physical sciences decreased by 18 461 and life sciences decreased by 21 940. It is alarming that the various medical, computer science, engineering and pure science faculties at the tertiary institutes now compete to attract the best from this shrinking pool of STEM matriculants. Mining departments typically fall last in line as the best talent is grabbed by the offerings perceived to be more glamorous by the students. Although exceedingly difficult to implement, STEM subjects should assume a central role in the nation’s public and private education system. Diane Sengati from the African Institute of Mathematical Science (AIMS) noted “Most students don’t pursue STEM subjects because they think it is very difficult, but the perceived difficulties root from how they have been taught those subjects. If you teach the subject in a friendlier way, it becomes easier and attracts more students”. Training the teachers is therefore an important initiative for AIMS and it should be aggressively pursued by the government. James Lees of the Mail & Guardian wrote that the number of schools not offering science subjects increased from 512 in 2013 to 781 in 2021. This trend must be reversed to increase the pool of young talent.
The mining industry can also assist in making mining studies a more attractive option for students. This includes advocating for mining education and the marketing of its importance in schools and universities. Mining can improve its image and make itself a more desirable choice for students by focusing on the adoption of advanced mining equipment and technologies. Of concern is that the number of bursaries awarded by some mining groups has decreased in recent years. Approximately only 30% of the final year class at our university is currently studying with a bursary and this trend must be reversed.
The third aspect affecting the sustainability of mining departments is the sourcing of skilled staff. The requirements to fill lecturing positions at the universities are perhaps unnecessarily strict, and typically a PhD degree is a minimum requirement for a senior lecturer position. Sourcing mining graduates with a PhD, some teaching experience and a good publications record is exceedingly difficult. Finding a suitable professor candidate is the proverbial hen’s teeth. The universities need to be more innovative in this regard and career paths need to be more flexible. The development of younger staff into these roles is becoming more important. Industry can play a supportive role and aspects, such as secondments to industry for practical experience, can be of great assistance. Appointment of senior industry staff in part-time ‘extraordinary’ lecturer and professor positions has also been successfully used in the past and this should be supported by both industry and the tertiary institutes
D.F. Malan
he 17th edition of the International Ferroalloys Congress (INFACON XVII), jointly organized and hosted by the University of Science and Technology Beijing (USTB), Chinese Society for Metals, and the China Ferroalloy Industry Association, took place from 18 to 22 September 2024 in Beijing, People’s Republic of China. The INFACON series, often dubbed the ‘Olympics of Ferroalloy Research’, is held once every three years, and provides a platform for the global ferroalloys industry to meet and showcase knowledge and technologies driving the industry. The congress series is organized by the International Committee on Ferroalloys (ICFA) and is supported by a team of dedicated international experts representing industry, applied research, and academia. The conference papers published as part of the congress proceedings contribute to a rich and authoritative peer-reviewed body of knowledge in fundamental and applied ferroalloys research. This year’s congress comprised a variety of topics designed to address industry challenges and was centred around strategic themes such as:
➤ Fundamental knowledge and basic theory of ferroalloys production (e.g. thermodynamics, thermochemistry and process challenges).
➤ Climate change, environmental, sustainability, and social licence to operate, addressing the drive to decarbonization, climate neutrality and green transition (e.g. hydrogen/ hydrogen plasma reduction, use of biocarbons and other non-fossil reductants, carbon capture and utilization, and the like).
➤ Intelligent systems, incorporating computational modelling, automation, process control, and machine learning.
➤ Productivity and competitiveness (e.g. ability to utilize low grade ores and fines, stable furnace operation, prereduction, preheating, recycling and recovery of by-products, energy utilization and recovery).
➤ Markets and competitiveness, focusing on demand and supply, including in-depth analysis of growth drivers.
➤ Product quality control and its impact on downstream stainless steel production.
➤ Key technological and operational issues highlighted through case studies (e.g. slag properties, electrical controls, tap hole design, and optimized furnace operation).
The history of the INFACON series is especially fascinating and uniquely important to South Africa. The first edition, jointly organized by SAIMM, Mintek (formerly the National Institute of Metallurgy) and the Ferroalloys Producers’ Association (FAPA), was held in Johannesburg, South Africa in 1974. The chairperson of the first INFACON was none other than Dr R.E. ‘Robbie’ Robinson (1929-2016, MHDSRIP). Dr Robbinson was the President of SAIMM (1975-1976), Director of the (South African) Government Metallurgical Laboratory (GML) from 1961-1966, and Director General of the National Institute for Metallurgy (NIM) from 1966−1976. During this period, Dr Robinson was also instrumental in initiating university research group schemes involving the various university departments and Mintek. This year’s INFACON XVII edition marked the 50th anniversary of the conference series and it is by no coincidence that the conference was chaired by Prof. Rodney Trevor Jones, whose career and rich contribution to ferroalloys research is unparalleled globally. Ironically, Prof. Jones is a Past President of the SAIMM (2015−2016), an avid academic, a well respected mentor, and advisor in the industry. It is also important to note that, courtesy of the industry giants, South Africa, through Mintek, provides permanent secretariat to the international committee that arranges the INFACON events.
The INFACON XVII provided a nostalgic moment to reflect on both the demise and future of the ferroalloys industry in South Africa. The timing of the congress coincided with a period associated with fluctuations in the global prices of ferroalloys, leading to a decline in economic viability and competitiveness of most producers, including those in South Africa. Despite the availability of ores and long-term favourable international market conditions for stainless steel (with a compound annual growth rate of 5.3% since 1980), one would expect the installed capacity and capacity utilization of the South African ferroalloys producers to grow in line with the growth in the global stainless-steel market. However, the South African bulk ferroalloys industry gradually lost global competitiveness due to several factors, including the poor availability and increasing cost of electricity, ageing technologies, and a significant increase in the pricing of premium ores. These factors, among several others, have contributed to the precipitous decline of the ferroalloys industry in the past decade, resulting in the closure and mothballing of numerous smelters. The export of unbeneficiated raw ores, precipitated by the growth in demand from China, resulted in the emergence of a thriving export industry for raw or unbeneficiated ores at the demise of local value addition and beneficiation. To South Africa and the region, the 17th edition of the International Ferroalloys Congress thus coincides with the emergence of robust debate on how to revive and resuscitate the ferroalloys industry. The current state of the ferroalloys industry invariably presents both challenges and opportunities.
The vibrant discussions during the course of INFACON XVII were extremely fulfilling but naturally raised a number of open questions:
➤ Was China’s growth in the ferroalloys a result of deliberate investment in state-of-the-art technologies or simply state support as often alluded to in international media?
➤ Was the growth in Chinese ferroalloys production at the demise of the South African industry despite the former relying on imported ores from South Africa?
➤ What can the South African ferroalloys industry learn from their Chinese counterparts? Would the industry players from both sides be open to participating in jointly funded collaboration projects and programmes?
➤ Would a joint South Africa-China dialogue on ferroalloys research be a feasible vehicle to share knowledge, ideas, and technical expertise?
➤ Industry stoics, such as Prof. Robbie Robinson, were strong believers in collaborative research involving industry, academia, research councils, and other stakeholders. Would the conception and implementation of strategic research programmes help to alleviate the further demise of the local ferroalloys industry?
➤ Given the fragmentation of the local ferroalloys industry, is it a far-fetched dream to think of resuscitating Professor Robinson’s thinking and strategy towards building and sustaining scientific expertise in the industry?
➤ What role can research and industry organizations, such as Mintek and Ferro Alloy Producers Association (FAPA), respectively, play in developing a long-term research and development strategy leading to the revival of the ferroalloys industry in South Africa?
Obviously, these open-ended questions are not conclusive but are meant to stimulate debate and new thinking that could result in the revival of the local ferroalloys industry. The various INFACON editions provide a knowledge exchange platform and mechanism through which bilateral and multilateral collaborations are developed and sustained with the goal of developing and deepening human capital capabilities for South Africa. The collaboration and partnerships with international research institutions and industry also ensure that fit-forpurpose technologies and flowsheets are developed, leading to localization and adoption of global technologies in the local industry.
The next INFACON takes place in the scenic city of Reykjavik in Iceland in June/July 2027.
E. Matinde President, SAIMM
During closure planning there are usually four parties involved, being the mining house, external stakeholders, consultants and the authorities who are responsible for closure plan and eventual relinquishment approval. There are subsequently numerous conflicting ideals between the parties during the evolution of mine planning to post-closure. This leads to unrealistic closure expectations and vague obligations that result in the lack of setting or accepting specific closure and relinquishment criteria. Without clear direction, achieving a closure certificate in South Africa remains uncertain. This leads industry to adopt very different positions around closure planning that ranges between best practice, compliance to legislation to minimal planning.
Successful relinquishment has been achieved internationally by creating a value chain for sustainable post-mining economies as early as possible. In South Africa relinquishment could possibly be achieved successfully by complying to the current legislative closure approach or alternatively by creating third party value by means of parallel economies. This could potentially be supplemented with a regional closure approach between mining houses. It is therefore imperative that the third party needs to be part of the value chain development and execution through meaningful community engagement to ensure the benefits of local knowledge and achieve social acceptance. Once the long-term value chain is in place it lays the foundation for closure- and relinquishment criteria and social integration. ESG compliance adds another layer to closure planning but can be very useful to add specific criteria and expedite closure actions. Regardless of the approach taken, engagement with regulators is required for overall alignment and changes to policies.
To assist interested parties, industry and regulators to better understand the closure challenges within the current uncertain and fragmented closure space. This is underpinned by Environmental Social and Governance (ESG) compliance, reducing closure liabilities and risks, just transition and the ultimate goal of relinquishment. The conference will aim to present, workshop and identify the pressing focus areas for further research and engagement with the regulators.
• Current challenges towards relinquishment
• Alternative closure solutions
• Socio economics and just transitions
• ESG compliance and considerations to closure
• Conference proceedings
• Conference panel discussion to identify focus areas, needs and future actions
• Planned breakaway after the conference for academics and after interested parties to discuss future research topics flowing from the conference
• Identify relevant challenges and research topics
• Identifying areas for future engagement with the regulator to influence policy and legislation to address the challenges
• To promote and understand the appetite of the industry to consider alternative closure solutions
Gugu Charlie, Conferences and Events Co-ordinator
FOR FURTHER INFORMATION, CONTACT: E-mail: gugu@saimm.co.za Tel: +27 11 530 0238
Affiliation:
1Department of Mining Engineering, University of Pretoria, South Africa
Correspondence to:
P.J. Le Roux
Email: Jaco.LeRoux@samancorcr.com
Dates:
Received: 22 Aug. 2022
Revised: 20 Oct. 2024
Accepted: 22 Oct. 2024
Published: November 2024
How to cite:
Le Roux. P.J. and Malan D.F. 2024. Back analysis of LG6/LG6A chromitite pillar strength using. displacement discontinuity modelling. Journal of the Southern African Institute of Mining and Metallurgy, vol. 124, no.11 pp. 605–616
DOI:
http://dx.doi.org/10.17159/24119717/3548/2024
ORCiD:
P.J. Le Roux
http://orcid.org/0009-0004-4459-5875
by P.J. Le Roux1 and D.F. Malan1
Abstract
Almost no work has been published on the strength of pillars in mines exploiting the LG6/LG6A chromitite bands in the Western Bushveld Complex. The strength of these pillars is unknown, and the hard rock industry still uses the Hedley and Grant formula. Numerical modelling, using inelastic constitutive models, may be of some value in estimating the pillar strength, but this approach is difficult and prone to errors as many assumptions are made. This paper explores the alternative approach of the back-analysis of actual LG6/LG6A mining layouts, using displacement discontinuity codes to simulate the average pillar stresses on a mine-wide scale. From this, and underground observations, a ‘minimum’ pillar strength (K-value in the pillar strength formula) can be estimated. The codes TEXAN and Map3D are both used in the paper to simulate the actual pillar shapes and sizes in an LG6/LG6A mine. The results are encouraging as the two codes produced similar APS values for a complex pillar geometry. An estimated K-value of 77 MPa was determined for the LG6/LG6A pillars in this particular area. This is more or less similar to earlier work done for the UG2 chromitite seam, but higher than the K-value of 39 MPa for a linear formula obtained by other workers for LG6/LG6A pillars. Caution should therefore be exercised before using this higher value for all areas. The effect of element sizes and explicitly simulating the effect of the surface for shallow pillars is illustrated in the manuscript using both codes. The need for actual pillar observations and an iterative design process, which cycles between modelling and observations, is also emphasized.
Keywords
LG6 pillars, strength formula, chromitite pillars, back-analysis, pillar design
Introduction
Several publications were recently published on the strength of hard rock pillars in the Bushveld Complex (e.g., Watson et al, 2021; Couto and Malan, 2023; Oates and Malan, 2023). These studies focussed mostly on the UG2 reef and only to a limited extent on other hard rock reef types such as the Merensky Reef or the manganese pillars in the Northern Cape (Watson et al, 2008; Wessels and Malan, 2023). Almost no work has been published on the strength of pillars in excavations exploiting the other chromitite bands such as the MG1, MG2, and the LG6/LG6A package. The strength of these pillars is unknown and the hard rock industry still uses the Hedley and Grant (1972) formula for the design of bord and pillar layouts (Malan and Napier, 2011). The so-called K-value in this power-law strength formula was historically assumed to be a third of the uniaxial compressive strength (UCS) of the pillar material (K= ⅓UCS). The difficulty with the LG6/LG6A pillars is that these pillars are comprised of different rock materials as illustrated in Figure 1. The LG6A chromite is the upper layer and the LG6 is against the footwall. The two chromitite bands are separated by an internal waste band of pyroxenite. These rock types have different UCS values. The contacts between the chromitite may be frozen or consist of weak layers as demonstrated in Figure 1. These weak contacts are known to play a dominant role in the pillar failure mechanisms (Couto and Malan, 2023; Els and Malan, 2023). It is therefore meaningless to use the historic assumption of K= ⅓UCS for these pillars.
A case study of LG6 pillar strength is described by Wesseloo and Swart (2000). They calculated the factor of safety for two sections in an LG6 mine. The one section was subjected to a large collapse in 1960. They analysed 203 pillars in total, of which 90 were failed. This is a valuable database, but the authors of this paper unfortunately did not have access to this specific data. Wesseloo and Swart (2000) concluded from a statistical analysis that the conventional pillar design methodology is not acceptable. As an alternative, they suggested the use of the ‘critical factor of safety’ concept used by Salamon and Munro (1967). From their back analysis, they indicated that the pillar strength is better approximated by a linear formula with a K-value of 39 MPa.
Numerical modelling, using inelastic constitutive models, may be of some value in estimating the pillar strength, but this approach is problematic and risky. It is not clear what constitutive model will best describe the pillar material, as these models are extremely difficult to calibrate and the partings and joints can often not be accurately represented in the continuum codes. Calibration of the discontinuum inelastic codes is also extremely difficult. Malan and Napier (2011) already raised some concerns regarding the use of numerical modelling with appropriate failure criteria to determine pillar strength. For LG6 pillars, Joughin et al (2000) adopted a risk-based approach and two-dimensional modelling using the code PHASE2. The advantage of using the finite element approach was that the two chrome layers and the pyroxenite middling could be explicitly modelled. The authors used a Hoek-Brown strength model and the pyroxenite was simulated to be more competent than the chromitite. A historical area of a large collapse and a new mining area were simulated. The modelling indicated that the chromitite controlled the failure of the pillars and the results agreed well with the actual pillar failures observed in the different areas underground. It should be noted, however, that the models used to simulate the failure were two-dimensional and ideally threedimensional models of the actual pillar layout and geometries should be studied.
A recent example illustrating the risk of inelastic modelling was published by Le Bron et al (2024). The authors proposed the concept of ‘pillar load inversion’ and FLAC3D modelling was done. Elastic modelling will predict high stress at the pillar edges and less in the centre of the pillar. When the edges of the pillar fail, the pillar load is transferred to the confined core. With progressive failure, the stress profile changes from being higher near the pillar edge to a peak in the centre. This defines the ‘pillar load inversion’. The strain at failure for laboratory specimens was then used by the authors to determine if a pillar is failed or not. The difficulty is that a Mohr-Coulomb constitutive model without strain softening was used and the reason given in the paper is that: ‘For strain-softening to be attempted applying this approach, one would need post-peak residual strength properties. The associated friction angle and cohesion at the residual strength would have to be determined by running sensitivity analyses until representative residual strength parameters are obtained. This information is not available, which is why the Mohr-Coulomb Constitutive model was run.’ This approach may be questioned. A case study presented in the paper was pillars in the LG6 chromitite seam at depths of 370 m to 500 m below the surface. It is concluded that at a depth of 370 m below the surface, the 8 m × 8 m pillars will remain stable, whereas pillars at 500 m depth are predicted to experience full pillar load inversion and potential failure. These conclusions are based on a Mohr-Coulomb model with no strain softening, which may not be appropriate. The effect of possible
weak contacts, as illustrated in Figure 1, was also not simulated. The constitutive model is therefore possibly poorly defined and the modelling results need to be confirmed using underground observations.
This current manuscript explores the alternative approach of the back-analysis of actual LG6/LG6A mining layouts using displacement discontinuity codes to simulate the average pillar stresses on a mine-wide scale. Observations of the actual pillar behaviour are a critical component of this methodology. This allows for the building of a database of actual pillar behaviour and it attempts to mimic the benefit Salamon and Munro (1967) had with a good pillar database. From the modelling, if the simulated pillars are still intact, a ‘minimum’ K-value can be estimated. In 2009, the second author conducted a study of LG6/LG6A pillar strength at a mine close to Rustenburg. No pillar spalling was observed at a depth of 200 m, even for these very small pillars. From the numerical back-analysis, it was found that the conservative estimate is K > 57.5 MPa. The mine subsequently adopted a K-value of 57.5 MPa and the mining to date indicated a stable pillar environment. Following a similar approach, additional strength data for LG6/LG6A pillars are presented in the paper. This modelling approach was also used by Oates and Malan (2023) for UG2 pillars. The displacement discontinuity method can nevertheless lead to erroneous pillar stress simulations if the user does not have a good understanding of the numerical codes (Napier and Malan, 2011). A secondary objective of the paper is to give some guidelines to inexperienced users who attempt to use this methodology to estimate pillar strength. The effect of element sizes and simulating the effect of the surface for shallow pillars are illustrated using two different boundary element codes. The need for actual pillar observations and an iterative design process, which cycles between modelling and observations, is also emphasized.
Owing to the uncertainty in pillar strength and the spatial variability of rock mass strength, several aspects need to be considered. The section below was compiled to assist rock engineering practitioners in this regard.
➤ The empirical Salamon and Munro (1967) approach for coal strength has been very successful and this simple equation is still used five decades later. Calibrating the power-law strength equation was possible as they collected a good database of intact and failed coal pillar cases. Unfortunately, similar databases are currently not available in the hard rock mining industry for all the different reef types. Efforts should therefore be made to collect as much pillar data as possible.
➤ The researchers advocating numerical modelling as a muchimproved method to determine pillar strength need to consider the historic success of empirical methods. Examples are the empirical data used to determine stable spans and the coal pillar strength formula. Furthermore, inelastic numerical models can be difficult to calibrate owing to the large number of parameters. Selection of an appropriate constitutive model is difficult and an accurate representation of the discontinuities and their strength in the pillar can be problematic. A further problem is the high costs for the licenses and the difficulty of becoming an experienced user of some of the complex codes. For these modellers, a risk is that it may result in a cognitive bias that involves an over-reliance on a familiar modelling tool (Maslow, 1966). This is often quoted as ‘If the only tool you have is a hammer, it is tempting to treat everything as if it were a nail.’ Although displacement discontinuity boundary element codes are used below, it should be emphasized that other modelling codes should also be considered if the particular pillar problem requires alternative modelling techniques.
➤ The limitations of the various numerical modelling codes should be considered. Displacement discontinuity codes are well suited to simulate large-scale mining layouts containing a large number of irregular pillars. The effect of the surface for shallow excavations can be easily simulated. The drawback of these codes is that it cannot simulate the detailed pillar failure mechanisms. In contrast, finite difference and finite element codes can simulate the pillar failure mechanism in detail (provided an appropriate constitutive model is selected). The drawback of these codes is that it cannot simulate a large assembly of irregular pillars. Calibration of the complex constitutive models is also exceedingly difficult as it often includes a large number of parameters. The models are typically restricted to a single pillar only. Furthermore, for all types of codes, numerical modelling aspects, such as element size, may affect the simulated results and the modeller must be familiar with the limitations of the solution method and the particular code. The effect of element size for average pillar stress (APS) calculations in displacement discontinuity codes is demonstrated in the following.
➤ Malan and Napier (2011) concluded that neither empirical techniques nor numerical modelling can be used in isolation to provide a solid basis to predict pillar strength. Both these techniques should therefore be used when addressing pillar design problems to obtain the best possible insights. This was recently also advocated by Le Bron et al (2024) and they
proposed a hybrid methodology, which includes both the empirical method and numerical modelling (although the empirical method is not discussed in their paper).
➤ Owing to the uncertainty in pillar strength and the possible variability of rock mass strength in different areas of the mine, an iterative design process needs to be adopted. This is illustrated in Figure 2. As an illustration, if pillar sizes are reduced after conducting a numerical back-analysis study of the existing pillars and estimating a different K-value, a trial section needs to be established. Observations and possibly monitoring should be conducted in this section. Further numerical modelling is then required to determine if additional optimisation of the pillars is possible.
➤ For empirical pillar design, there is uncertainty about whether to adopt a power-law strength formula or a linear strength formula (Ryder and Jager, 2002). Salamon and Munro (1967) noted: ‘The volume and shape of square pillars are completely defined by their width (w) and height (h). The most commonlyoccurring pillar strength formula in the literature is a simple power function composed of these variables.’ The last sentence in the quote is of particular importance. The equation selected by Salamon and Munro (1967) was therefore ‘the most commonly-occurring pillar strength formula in literature’. For the hard rock strength formula, Hedley and Grant (1972) used the same references of the 1940s and 1950s, as well as Salamon’s work, to motivate the use of a power-law equation. The exponents of the Hedley and Grant formula appear to be a reasonable approximation to account for variations in pillar width and height and it is recommended that this be retained for now, unless good laboratory and underground data can be obtained to indicate otherwise. This equation is also adopted in this paper.
➤ When conducting a back-analysis of pillar strength, it may be difficult to find failed pillars in the existing bord-and-pillar layouts. As a useful alternative, it is recommended to search for the smallest pillars in the deeper sections of these layouts. The average pillar values will be the largest on these pillars. If the Hedley and Grant equation is adopted, the unknown value is the rock mass strength K in the equation below.
A good estimation of the ‘minimum’ K-value can be obtained by using the simulated APS value in the previous section as the ‘minimum’ pillar strength. If it is assumed that σs=APS and K = Kmin, Equation [2] can be written as:
This equation is used in the following in the back-analysis of the pillar stresses.
Numerical modelling aspects when estimating average pillar stress
The displacement discontinuity boundary element method to simulate tabular layouts has been popular in South Africa since the early 1970s (Plewman et al., 1969; Deist et al., 1972; Ryder and Napier, 1985; Napier and Stephansen, 1987). Unfortunately, the expertise to develop these codes in South Africa has now almost disappeared. A good understanding of the limitations of the method is currently limited to a handful of individuals and only limited numerical modelling is conducted on the mines. Two different boundary element codes were used for this study, namely MAP3D and TEXAN. This paper is a useful verification of the two codes and it was expected that similar pillar stresses would be simulated by these codes. TEXAN is a displacement discontinuity code and it has been described in many earlier papers (Malan and Napier, 2006; Napier and Malan, 2007). In MAP3D, the user can use both displacement discontinuity elements for tabular excavations and fictitious force elements to simulate large excavations (Wiles, 2024). The simulations for this study were nevertheless limited to displacement discontinuity elements to simulate bord-and-pillar layouts. Of particular interest was the effect of element size on average pillar stress (APS) and simulating the effect of the surface when analysing shallow excavations.
When adopting the displacement discontinuity method, the surface of the problem space needs to be divided into several sub-regions or elements. A simplified functional form of the displacement discontinuity distribution within each element needs to be adopted. In the early applications of the method, such as in MINSIM-D, this function was assumed to be a constant within each element and a square element shape was adopted. Ryder and Napier (1985) noted that the magnitudes of the solved displacement discontinuity values are affected by the element size when using this approach. The proposed solution was to use ‘partially mined elements’ and the excavation outlines were shifted by the ‘quarter grid correction’. This allowed for accurate far-field stress distributions to be computed, that are independent of element size. A major shortcoming of this approach was that it became difficult to estimate average pillar stresses as the pillar outlines were now approximated. The approach was nevertheless adopted as the early displacement discontinuity codes were developed for the gold mines, and the important parameters to compute were stope convergence and energy release rate (ERR). The need to simulate the average pillar stress of a large number of small pillars in bord and pillar layouts only became a requirement in later years. This resulted in the development of the TEXAN code that included higher-order triangular and quadrilateral elements (Napier and Malan, 2007). MAP3D also allows for the use of higher-order elements. The code allows for the selection of ‘linear’ or ‘quad’ in the analysis options, otherwise, the displacement discontinuities are treated as constant values. As stated in Wiles (2024), for the linear option, the stress or displacement discontinuity is distributed over the boundary
elements using a linear order polynomial distribution. For the ‘quad’ option the stress or displacement discontinuity is distributed over the boundary elements using a quadratic order polynomial distribution. All simulations in this paper were performed by using constant displacement discontinuity elements.
For the TEXAN code, Napier and Malan (2011) conducted a study on the effect of element size on APS. Errors can arise depending on the choice of element size and the element shape in a geometrically complicated layout. Typically, coarse constant strength displacement discontinuity elements underestimate the correct APS value. Interestingly, for a two-dimensional pillar problem, the simulated APS is very close to the analytical solution if the element size approaches zero. This was also illustrated for a circular pillar. The authors proposed extrapolation techniques and simulations with different element sizes to obtain better approximations of the correct APS values. They nevertheless recommended that this approach must be treated with caution for tabular excavations and noted: ‘Unfortunately, there are no simple numerical solutions to this problem.’ In practice, a pragmatic solution is simply to use the smallest possible element sizes that will not be too computationally arduous. Unfortunately, when reviewing previous papers where the APS values of pillars were computed, it is typically not known what element sizes the authors used in the simulations. For example, Wesseloo and Swart (2000) describe a case study of a large pillar collapse in a LG6 mine in 1960. The APS values of these pillars were calculated using BESOL/MS (a displacement discontinuity code), but the authors do not specify the element sizes used.
The effect of element size on APS has never been demonstrated for the MAP3D code and this could have led to an underestimation of pillar stress in many previous pillar simulations in South Africa. For this study, a number of simulations were therefore conducted to investigate this effect. It was found that the selected ‘element length’ and the overall size of the excavation (‘mining span’) will affect the simulated APS. To investigate the effect of element size on the simulation of bord-and-pillar layouts and how the simulated APS relates to tributary area theory (TAT), several simulations were conducted. Different bord-and-pillar layouts were constructed in Map3D using square 10 m × 10 m pillars. The bord widths and holings between the pillars were 10 m and the simulated depth was 1000 m. The density of the overburden was assumed to be 3100 kg/m3. During the setup of the numerical models, fixed element widths (AL) of 1, 2, 5, and 10 were used for the pillar and the bords. The resulting number of elements and the element lengths are given in Table I. Note that these were the actual element lengths and, for the smaller elements, it was different to the specified AL parameter. It is not clear how the meshing algorithm uses the various parameters. Several geometries of increasing total span were simulated. This is illustrated in Figure 3. The number of pillars in each geometry increased as the overall span increased. The pillar APS value of interest was that for the pillar in the centre of the layout.
Table I
Element length and the number of elements for each 10 m × 10 m pillar
Care should be exercised when computing the average pillar stress in Map3D. The author found that to obtain the correct value, the normal stress on the displacement discontinuity for each element should be exported to Excel and the average should then be computed. The calculated values for the centre pillar for various spans and element sizes are shown in Figure 4. It is clear from these results that large spans and many pillars are required for the APS value to approximate the tributary area value (TAT). If it is required that the difference in average pillar stress at the centre pillar be less than 1% of the TAT value as illistrated in Table II, the element length should be equal to or less than 1/2 of the smallest width of the pillar and the minimum half-span required was found to be 300 m. As a crude rule of thumb, the minimum mining half-span should be 30 times the pillar width for regular bord-and-pillar layouts for Map3D simulations.
It should be noted that MAP3D uses quadrilateral elements to accurately mesh irregular pillars. The meshing of a square pillar and an irregular pillar is shown in Figure 5. In TEXAN, triangular elements are used to accurately mesh irregular pillars.
A further important aspect to consider is shallow conditions. Many of the hard rock bord and pillar layouts are located close to the surface and the average pillar stress will be underestimated if the effect of close proximity to the surface is not accounted for. As
Table II
Difference between the simulated APS for the centre pillar and TAT
described in Napier and Malan (2007), shallow conditions can be simulated by an artificial ‘excavation’ at the surface position and included in the simulation with the ‘real’ underground mining excavation. The drawback is long run times and selecting the appropriate extent of the surface excavation is difficult. If large element sizes are used on the surface, this may lead to iterative solution difficulties if the underground excavations are in close proximity. As a more efficient approach, it is possible to use appropriate influence functions that allow for the effect of the
surface to be included automatically without requiring the inclusion of the explicit surface. These influence functions were developed for TEXAN and are given in Napier and Malan (2007). In MAP3D a displacement discontinuity plane is typically placed on the surface to simulate the effect of the free surface and this was also done for the Map3D simulations below. The effect of simulating the average pillar stress with and without the free surface is illustrated below for both codes.
Back analysis case study to determine the K-value
The mine used as a case study is situated in the western Bushveld Complex and is mining the LG6/LG6A chromitite seams. As shown in Figure 1, the LG6 is on average 1.0 m in thickness and overlain by the LG6A, averaging 30 cm in thickness. The internal waste comprising the pyroxenite has an average thickness of 50 cm. As shown in Figure 6, the selected areas for back analysis were Area 1 (last mined in 1991) and Area 2 (mined in 2009). The small pillars
in both areas are shown in Figures 7 and 8 and are highlighted in red. A total of 29 pillars were identified that had a width-to-height ratio ranging from smaller than 1 to larger than 3. The mining spans around these pillars were also typically larger than expected. Especially the small pillars in Area 1 are surrounded by large mining spans. It is expected that the stresses acting on these pillars would be larger than for the other pillars at these depths. Area 1 is situated at a mining depth ranging from 75 m to 121 m and in Area 2 the mining depths vary from 190 m to 201 m.
Numerical modelling results
Numerical modelling of Area 1 was done by using both the TEXAN and Map3D codes. A direct comparison of these two codes when simulating average pillar stresses in bord-and-pillar layouts has never before been published. These results are therefore also valuable as a verification of the codes. Area 2 was only simulated with the Map3D code to obtain additional pillar stress data. Note
that, for the areas simulated, the pillars of interest are typically small and these are surrounded by larger pillars. The question can be posed if there is any load ‘bridging’ to the larger pillars and if the numerical modelling results possibly overestimate the load on the smaller pillars. Napier (2023) conducted preliminary numerical modelling results, in which he used special traction discontinuity influence functions that were combined with the displacement discontinuity elements to represent thin beam flexure effects for stiff material layers above the pillars. From this study it was evident that the APS values are lower when there is a stiff overlying layer compared to the case where there is no layer. The modulus of the rock was 70 GPa and 90 GPa for the stiff beam. This modelling illustrated the so-called ‘stress bridging’ effect in which the stiff layer reduces the average pillar stress values. The example highlights that the presence of significant material property contrasts requires careful assessment when computing average pillar stress values and pillar stability. Ideally, stress measurements are needed in the small pillars to confirm that no stress bridging occurs. For the cases illustrated in Figures 7 and 8, such a modulus contrast was not present in the hanging wall and the rock was a uniform pyroxenite. It was therefore assumed that the simulated stress in this case is a good approximation of the average pillar stress.
Figure 9 illustrates the area simulated by TEXAN and the pillar shapes are approximated by straight-line polygons. The pillar of interest is highlighted by the red circle. Note that it is a small pillar
surrounded by very large spans and it is therefore expected to carry a large stress. The depth is 101 m and the overburden density is assumed to be 3100 kg/m3.
The simulated results for the pillar of interest (P92) are shown in Figure 10. The pillar size was 5.38 m2. Triangular elements were used, so the element size is the average size of the elements in the pillar of interest. Various element sizes and both the finite depth (simulating the free surface) and infinite depth (no free surface) solutions in TEXAN were used. As expected, the APS increases as the element size decreases. This is discussed in detail in Section 3.
The APS is the y-intercept (zero element size) and for the infinite depth solution it is APS = 76.5 MPa and for the finite depth solution, it is 81.8 MPa. Note that the APS value is approximately 7% higher when simulating the surface and it highlights the importance of considering this for shallow excavations. Also note the effect of element size and the importance to use extrapolation, or at least the smallest practical element sizes, to get a good approximation of the APS value.
The pillar still appears to be in good condition, but some spalling of the chromitite can be seen (Figure 11). Based on its condition, it is assumed that the factor of safety on this pillar is still higher than unity.
Map3D models of this area were also built and the stress on the same pillar was simulated using different element sizes. The element sizes were smaller than that used for the TEXAN simulations. Different simulations were conducted with a sheet of elements simulating the surface explicitly, and also without simulating the surface. The simulated pillar area was also 5.38 m2. The results are given in Figures 12 and 13. These results are encouraging as essentially similar results were obtained for the two codes. For
12—Simulated
in
for
as a function of element sizes. Linear trend lines are fitted to the data in this plot. This was
13—Similar data to that presented in Figure 12 (simulated APS in Map3D for pillar P92), but now polynomial trend lines are fitted to the data in this plot
a linear trend line (Figure 12), the infinite depth solution at the y-intercept is APS = 76.6 MPa and for the finite depth solution, it is 81.9 MPa. For a polynomial trend line (Figure 13), the infinite depth solution at the y-intercept is APS = 77.7 MPa and for the finite depth solution, it is 83 MPa. It seems as if Map3D is simulating marginally higher APS values, but this may be caused by the very small elements used.
Map3D was used to simulate the stress acting on the other 28 pillars of interest (both Areas 1 and 2). The surface was explicitly simulated for these runs. These pillars are situated at depths ranging from 75 m to 201 m and the overburden density is assumed to be 3100 kg/m3. The Map3D mesh parameter ‘element length’ (AL) for these pillars was fixed and was set to 0.5, 0.25 and 0.125 for the different models (these values gave the different element sizes in Figure 12). Figures 14 and 15 indicate the pillar conditions underground for some of the pillars used in the back analysis. In some areas, it was difficult to photograph these pillars due to dust and scalping (sorted waste rock) stored in the back areas.
It should be noted that the pillars shown in Figures 14 and 15 are in remarkably good condition for an area that was mined
in 1991, taking into consideration possible time-dependent deterioration, jointing, and poor mining. As mentioned, a total of 29 pillars were selected and 28 of these pillars had a width-to-height ratio ranging from larger than 1 to larger than 3. One pillar had a width-to-height ratio of smaller than 1 (Figure 16). In Area 1, the mining spans are larger than expected, with mining spans in some areas greater than 20 m.
The numerical results are summarized in Figure 17. Based on the underground observations of the pillars and the numerical modelling, three pillars were selected to estimate a Kmin value. These pillars are shown in Table III. Note the small w:h ratio, small pillar areas, and large APS values. It can therefore be speculated that these pillars are loaded close to failure.
Using the data in Table III and Equation [3], the Kmin value for the three identified pillars was calculated. The results are given in Table IV and K = 77 MPa may be a good approximation to determine the pillar strength. Interestingly, this is almost similar to that obtained by Oats and Malan (2023) for the UG2 pillars (K = 75 MPa). This value nevertheless needs to be tested in controlled trial mining sections before it is adopted on a larger scale.
Table III
Summary of data for the three pillars selected for further analysis
Table IV
Calculation of Kmin
of 1.8 m
The data collected as well as the pillar strength envelopes for a Hedley and Grant equation with a K-value of 35 MPa and 77 MPa are plotted in Figure 18. The historic assumption of K = 35 MPa was far too conservative. Only one failed pillar is in the database, however, and additional data needs to be collected.
Conclusions
This case study indicates that the current used K-value for the LG6/ LG6A pillars of 35 MPa may be too conservative in some areas. This is adversely affecting the extraction ratio in the western Bushveld Complex. From the back analysis done on small pillars, a K-value of 77 MPa for LG6/LG6A seems to be more appropriate for the area studied. This needs to be tested in a trial mining section before it can be implemented on a larger scale. Careful observations and further modelling of this trial section must be done to validate the new K-value. This is particularly important considering that previous workers estimated a K-value of 39 MPa for a linear formula for LG6 pillars at an unknown mine. The value of displacement discontinuity modelling to obtain better estimates of pillar strength is nevertheless clear from the study. Users should be careful with the selection of element sizes, however, and the surface must be explicitly simulated if the excavations are close to the surface.
Acknowledgements
The authors would like to thank Samancor Chrome Ltd. for permission to publish this data and for the opportunity to use Samancor equipment and numerical modelling software.
References
Couto, P.M., Malan, D.F. 2023. A limit equilibrium model to simulate thwe large-scale pillar collapse at the Everest Platinum Mine. Rock Mechanics and Rock Engineering, vol. 56, pp. 183–197.
Deist, F.H., Georgiadis, E., Moris, J.P.E. 1972. Computer applications in rock mechanics. Application of Computer Methods in the Mineral Industry. Proceedings of the 10th International Symposium, Johannesburg. pp.259-266. https://www.saimm. co.za/Conferences/Apcom72/000b-Contents.pdf
Els, R.P., Malan, D.F. 2023. Calibration of the limit equilibrium pillar failure model using physical models. Journal of the Southern African Institute of Mining and Metallurgy, vol. 124, no. 5, pp. 253–263.
Hedley, D.G.F., Grant, F. 1972. Stope-and-pillar design for the Elliot Lake Uranium Mines. Bulletin of the Canadian Institute of Mining and Metallurgy, vol. 65, pp. 37–44.
Joughin, W.C., Swart, A.H., Wesseloo, J. 2000. Risk based chromitite pillar design. SANIRE 2000 Symposium, “Keeping it up in the Bushveld”. https://www.researchgate.net/ publication/262767130_Risk_based_chromitite_pillar_ design_-_Part_II_Non-linear_modelling
Le Bron, K.B., Gardner, L.J., Van Zyl, J. 2024. Beyond the empirical pillar design method: The strain criterion and the pillar load inversion concepts. Journal of the Southern African Institute of Mining and Metallurgy, vol. 124, no. 5, pp. 293–302.
Malan D.F., Napier, J.A.L. 2006. Practical Application of the Texan Code to Solve Pillar Design Problems in Tabular Excavations, SANIRE Symposium “Facing the challenges”, Rustenburg, pp. 55–74.
Malan, D.F., Napier, J.A.L. 2011. The design of stable pillars in the Bushveld mines: A problem solved? Journal of the Southern African Institute of Mining and Metallurgy, vol. 111, pp. 821–836.
Maslow, A.H. 1966. The Psychology of Science: A Reconnaissance. Harper & Row. pp. 15. https://fumaca.pt/ wp-content/uploads/2022/12/The-Psychology-of-Science_-AReconnaissance-PDFDrive-.pdf
Napier, J.A.L. 2023. Unpublished numerical modelling.
Napier, J.A.L., Malan, D.F. 2011. Numerical computation of average pillar stress and implications for pillar design. Journal of the Southern African Institute of Mining and Metallurgy, pp. 837–846.
Napier, J.A.L., Malan, D.F. 2007. The computational analysis of shallow depth tabular mining problems, Journal of the Southern African Institute of Mining and Metallurgy, vol. 107, pp. 725–742.
Napier, J.A.L., Stephansen, S.J. 1987. Analysis of Deep-level Mine Design Problems Using the MINSIM-D Boundary Element Program, APCOM 87. Proceedings of the Twentieth International Symposium on the Applications of Computers and Mathematics in the Mineral Industries, vol. 1: Mining. Johannesburg, SAIMM. pp. 3–19.
Oates, T.E., Malan, D.F. 2023. A study of UG2 pillar strength using a new pillar database. Journal of the South African Institute of Mining and Metallurgy, vol. 123, no. 5, pp. 265–273.
Plewman, R.P., Deist, F.H., Ortlepp, W.D. 1969. The development and application of a digital computer method for the solution of strata control problems. Journal of the Southern African Institute of Mining and Metallurgy, vol. 70, pp. 33–44.
Ryder, J.A., Jager, A.J. 2002. A Textbook on Rock Mechanics for Tabular Hard Rock Mines. Safety in Mines Research Advisory Committee, Johannesburg, pp. 397–440.
Ryder, J.A., Napier, J.A.L. 1985. Error analysis and design of a large-scale tabular mining stress analyser. The 5th International Conference on Numerical Methods in Geomechanics, Nagoya, Japan. pp. 1549–1555.
Salamon, M., Munro, A. 1967. A study of the strength of coal pillars. Journal of the South African Institute of Mining and Metallurgy, vol. 67, pp. 56–67.
Watson, B., Ryder, J.A., Kataka, M.O., Kuijpers, J.S., Leteane, F.P. 2008. Merensky pillar strength formulae based on back-analysis of pillar failures at Impala Platinum. Journal of the Southern African Institute of Mining and Metallurgy, vol. 108, pp. 449–456.
Watson, B.P., Theron, W., Fernandes, N., Kekana, W.O., Mahlangu, M.P., Betz, G., Carpede, A. 2021. UG2 pillar strength: Verification of the PlatMine formula. Journal of the Southern African Institute of Mining and Metallurgy, vol. 121, pp. 449–456.
Wessels, D.G., Malan, D.F. 2023. A limit equilibrium model to simulate time-dependent pillar scaling, Rock Mechanics and Rock Engineering, vol. 56, pp. 3773–3786.
Wesseloo, J., Swart, A.H. 2000. Risk based chromitite pillar design – application of the locally empirically derived pillar formula, SANIRE 2000 Symposium, “Keeping it up in the Bushveld”.
Wiles, T.D. 2024. Map3D User’s Manual – Version 68. u
Affiliation:
1Department of Mining Engineering, University of Pretoria, South Africa
2Johan Olwagen and Associates, South Africa
*Deceased
Correspondence to: R.C.W. Webber-Youngman
Email: ronny.webber@up.ac.za
Dates:
Received: 14 July 2022
Revised: 4 Oct. 2023
Accepted: 18 October 2024
Published: November 2024
How to cite:
Mokganya, P.J., Webber-Youngman, R.C.W., Uys, J., and Olwagen, J. 2024. The role of leadership in technology adoption in the South African mining industry. Journal of the Southern African Institute of Mining and Metallurgy, vol. 124, no.11 pp. 617–630
DOI:
http://dx.doi.org/10.17159/24119717/2220/2024
ORCiD:
R.C.W. Webber-Youngman
http://orcid.org/0000-0002-0101-7125
by P.J. Mokganya1, R.C.W. Webber-Youngman1, J. Uys1*, and J. Olwagen2
Abstract
This article discusses the critical role of leadership in the technology adoption process within organizations, particularly in industries like mining, where innovation is essential for maintaining competitiveness and operational efficiency. It highlights the limitations of traditional technology adoption models, such as the Technology Acceptance Model (TAM), Diffusion of Innovations (DOI), and Unified Theory of Acceptance and Use of Technology (UTAUT), which focus on individual factors and overlook the strategic and organizational roles of leadership.
The study proposes the Ambidextrous Leadership-Technology Adoption (ALTA) model, which integrates leadership styles such as transformational, transactional, adaptive, and ambidextrous leadership into the technology adoption process. The model emphasizes the balance between exploration (fostering innovation) and exploitation (ensuring operational efficiency). The findings suggest that transformational leadership fosters innovation by encouraging risk-taking and creativity, while transactional leadership ensures efficient technology integration.
The article also identifies key barriers to technology adoption, such as organizational resistance to change, which can be mitigated through adaptive leadership that addresses employee concerns. The research emphasizes the importance of a supportive organizational culture and cross-functional collaboration, which are essential for successful technology adoption. The study concludes by offering practical recommendations for leaders to foster a culture of innovation, manage resistance, and balance short-term efficiency with long-term technological advancement.
Keywords leadership, technology adoption, innovation, ambidextrous leadership, transformational leadership, transactional leadership, organizational culture, mining industry
Introduction
Innovation is the process of developing new ideas, products, or processes, or the significant improvement of existing ones (Lopes-Claros, 2010; Tidd, 2001). In the South African mining industry, innovation is critical for transforming operational and strategic practices through processes such as digitization, realtime monitoring, data analytics, and automation, which are key drivers of the Fourth Industrial Revolution (Deloitte, 2018).
The industry faces significant challenges, including declining mineral grades, deeper deposits, and highpressure work environments. Consequently, there is an imperative need for increased production efficiency, reduced unit costs, improved ore quality, enhanced safety measures, and compliance with environmental regulations to ensure sustainability (Alem et al., 2012), underscoring the necessity of innovation and adopting new technologies for the industry’s viability.
Technology adoption encompasses the acceptance and utilization of innovations within organizations. It refers to a process through which individuals, organizations, or entire markets embrace and begin using new technologies. Rogers (2003) delineates the technology adoption process into three distinct stages, namely development of the innovation, trial testing by early adopters, and wider implementation of the innovation, respectively, interpolated as development, implementation and application by the authors.
➤ There are various technology adoption models in literature, derived with the purpose of providing a structured framework for understanding how individuals, groups and organizations adopt and integrate new technologies. These models help describe the factors that influence the adoption process, predict user behaviour and guide decision making for successful introduction of new technologies.
➤ The current existing models have limited focus on the influence of leadership. Most technology adoption models (e.g., Technology Acceptance Model (TAM), Diffusion of Innovation (DOI)), primarily emphasize individual-level factors, like perceived usefulness and ease of use, but they downplay or ignore the role of leadership in setting strategic direction, creating a vision for technology, or driving adoption initiatives. Leadership’s role in fostering a technologyfriendly culture and motivating employees to embrace new technologies is often underrepresented. Leadership styles such as transformational, transactional, or servant leadership significantly impact how technology is adopted within organizations (Bossink, 2007; Gilley et al., 2008, Rossing et al., 2011). Current models do not adequately capture how different leadership approaches influence adoption rates. For instance, transformational leaders who inspire and encourage innovation may accelerate adoption, while transactional leaders focused on short-term performance may slow it down (Bass, 1990).
➤ Adoption models rarely address how leadership aligns new technologies with the broader organizational strategy (Tornatsky et al., 1990). Leaders often evaluate whether a new technology fits with long-term business goals, and their decision to adopt may depend on whether it supports strategic objectives, such as digital transformation or operational efficiency (Westerman et al., 2014).
Aim of the article
Research into leadership and technology adoption has become a critical topic in the current volatile, uncertain, complex and ambiguous (VUCA) environment the world is currently experiencing. This article aims to address benefits and the limitations of current technology adoption models by emphasising the critical role of leadership in shaping the adoption of new technologies within organizations. It seeks to explore how various leadership styles - transformational, transactional, and ambidextrous leadershipimpact technology adoption rates and foster a culture conducive to embracing innovation. To address the central research question of what role leadership plays in technology adoption, this article will propose a comprehensive framework that directly integrates leadership dynamics with the technology adoption processes. This framework will illustrate how leadership influences technology alignment with organizational strategies, ultimately enhancing understanding of the interplay between leadership, innovation, and strategic objectives. The main purpose of the research is to establish the relevance of the ambidextrous leadership-technology adoption (ALTA) model, which seeks to address gaps such as the direct role of leadership in technology adoption.
➤ Technology adoption refers to the process by which people or organizations accept and use new technologies. The technology adoption process can be described in three phases, namely development phase, implementation phase and application phase. The development phase focuses on the creation and design of technology. During this stage, activities such as research and development (R&D), idea generation, and prototyping take place. This phase is characterized by high uncertainty and involvement of innovators and early adopters, who test and refine the technology for broader use (Rogers, 2003).
➤ In the implementation phase, organizations adopt and integrate the developed technology into their workflows or processes. This stage involves configuring infrastructure, training personnel, and making operational changes (Cresswell and Sheikh, 2013). A key challenge during this phase is overcoming resistance to change and manage unforeseen technical challenges. The quality of implementation often determines the eventual success or failure of technology adoption (Venkatesh et al., 2003).
➤ The application phase refers to the routine use of technology in daily operations. After successful implementation, organizations focus on optimizing the use of technology to achieve desired outcomes, such as improved productivity or cost efficiency (Davis, 1989).
➤ Technology adoption models aim to explain how individuals and organizations accept and use new technologies. Over time, various models have been developed to understand the factors that influence technology adoption. In this review, we explore four prominent technology adoption models: the Technology Acceptance Model (TAM), the Diffusion of Innovations (DOI) theory, the Unified Theory of Acceptance and Use of Technology (UTAUT), and the TechnologyOrganization-Environment (TOE) framework. We will also examine the limitations of each model, particularly in relation to leadership's role in technology adoption.
➤ The Technology Acceptance Model (TAM) is one of the most widely applied models in technology adoption research. Developed by Davis (1989), TAM is grounded in the Theory of Reasoned action (TRA) and posits that two key factors, Perceived usefulness (PU) and Perceived Ease of Use (PEOU), determine an individual's decision to adopt a new technology, as shown in Figure 1. PU refers to the extent to which a person believes that using a technology will improve their performance, while PEOU refers to the effort required to use the technology.
➤ Shortcomings of TAM in relation to leadership:
• Limited focus on external factors: TAM emphasizes individual perceptions but does not account for external leadership-driven factors such as organizational culture, vision, and strategic direction.
• Lack of focus on collective decision-making: Leadership often plays a significant role in shaping the collective decision to adopt new technologies (Yukl, 2013), but TAM primarily examines individual user behaviour.
• Does not consider organizational resistance or change management: Leaders must manage resistance to change and facilitate smooth transitions to new technologies (Burnes, 2004). TAM does not offer a framework for understanding how leadership can overcome organizational resistance during the technology adoption process.
➤ The Diffusion of Innovations (DOI) theory, developed by Rogers (2003), explains how an innovation is communicated and spread over time within a social system. Rogers identified five categories of adopters: Innovators, early adopters, early majority, late majority, and laggards as shown in Figure 2. The adoption process is influenced by five main factors: Relative advantage, compatibility, complexity, trialability, and observability.
➤ Shortcomings of DOI in relation to leadership:
• Inadequate consideration of leadership influence: DOI focuses on social systems and communication networks, largely ignoring the active role that leadership plays in driving adoption.
• Overemphasis on individual choices: DOI emphasizes individual adoption behaviors without considering how leadership can influence collective organizational decisions and enforce strategic priorities.
• Does not address the dynamic role of leadership in facilitating adoption: Leadership must actively guide the organization through phases of adoption, but DOI does not account for how leaders manage change or align technology with business objectives.
➤ The Unified Theory of Acceptance and Use of Technology (UTAUT), developed by Venkatesh et al. (2003), integrates elements from various technology adoption models, including TAM, DOI, and the theory of planned behaviour (TPB), which explains how the behaviors of individuals are influenced by their intentions as well as the factors that shape those intentions (Ajzen, 1991). UTAUT identifies four key constructs: Performance expectancy, effort expectancy, social influence, and facilitating conditions. These constructs explain user intentions to adopt technology and subsequent usage behaviour.
➤ Shortcomings of UTAUT in relation to leadership:
• Minimal focus on leadership's strategic role: UTAUT acknowledges social influence, but focuses mainly on peer pressure rather than the top-down influence of leadership on technology adoption.
• Limited insight into leadership’s role in change management: While facilitating conditions are considered in UTAUT, the model does not delve deeply into how leaders can proactively shape these conditions to drive technology adoption.
• Narrow focus on individual user behaviour: Similar to TAM, UTAUT primarily targets individual-level factors, with little consideration for leadership-driven organizational strategy or how leaders create an environment conducive to adoption.
➤ The Technology-Organization-Environment (TOE) framework, proposed by Tornatsky and Fleischer (1990), suggests that technology adoption is influenced by three interrelated factors: technological, organizational, and environmental contexts. The organizational context includes internal processes, organizational size, and managerial structure, while the environmental context encompasses external forces such as competition and regulation.
➤ Shortcomings of TOE in relation to leadership:
• Lacks a strong focus on leadership as a driving force: While TOE considers organizational factors, it does not explicitly highlight the role of leadership in shaping organizational readiness or strategy for technology adoption.
• Static view of organizational dynamics: TOE assumes that organizational and environmental factors are relatively stable, but in practice, leadership plays a crucial role in dynamically responding to shifts in these factors (Yulk, 2013).
• Limited guidance on leadership’s role in fostering a culture of innovation: Leaders often need to foster a culture of innovation and adaptability to facilitate technology adoption (Schein, 2010), but TOE does not provide a clear framework for how leaders can cultivate such a culture.
➤ The four technology adoption models reviewed, TAM, DOI, UTAUT, and TOE, offer valuable insights into the factors that influence the adoption of technology in organizations. However, each model has its shortcomings, particularly in relation to leadership. TAM and UTAUT emphasize individual behaviour, but overlook the organizational and strategic roles of leadership. DOI and TOE recognize broader organizational and environmental factors, but do not sufficiently explore the dynamic and pivotal role of leadership in driving and sustaining technology adoption.
Leadership
This research focused on integrating these leadership frameworks and models, to provide a more comprehensive understanding of technology adoption processes. To do so, a literature study
of leadership styles was conducted. Different leadership styles can either foster or hinder innovation and the implementation of technological advancements. This review examines four key leadership styles namely: Transformational leadership, transactional leadership, servant leadership, and adaptive leadership, and their influence on innovation and technology adoption, highlighting relevant studies and their conclusions. The choice of the leadership styles was influenced by considering leadership styles that tend to foster innovation. The styles discussed in this article are those that have support from multiple authors based on the work that they have done to prove their correlations to innovation, and/or denote their shortcomings thereof. The article combines the traits from each leadership style based on what is required per the technology adoption phase, because there is not just one leadership style that caters for the process of technology adoption.
➤ Transformational leadership: is one of the most studied leadership styles in relation to innovation. Introduced by Burns (1978) and further developed by Bass (1985), transformational leaders inspire and motivate their followers to achieve higher levels of performance and embrace change. These leaders focus on four key components: idealized influence, inspirational motivation, intellectual stimulation, and individualized consideration.
➤ Influence on innovation and technology adoption: intellectual stimulation encourages creativity and out-of-the-box thinking, which is essential for innovation and technology adoption. Leaders who promote intellectual stimulation challenge the status quo and encourage experimentation (Bass, 1985).
➤ Inspirational motivation fosters a vision of the future that includes the adoption of new technologies, helping to align the organization’s goals with innovative pursuits. Transformational leaders often act as change agents, creating a culture that embraces new technologies (Jung, Chow, and Wu, 2003). Their focus on vision and long-term strategic planning can make the transition to new technologies smoother and more aligned with organizational objectives. However, transformational leadership can face challenges in environments resistant to change, where employees or systems are rigid, as this style assumes openness to innovation.
➤ Transactional leadership: is characterized by a focus on clear structures, tasks, and rewards. Leaders using this style typically engage in an exchange process with followers: rewards for performance or penalties for underperformance.
Burns (1978) described it as a more managerial approach, where leaders maintain the status quo rather than encourage innovation.
➤ Influence on innovation and technology adoption: transactional leaders may be effective in ensuring efficient implementation of technology by offering clear guidelines and expectations, but they are less likely to drive the creative aspects of innovation.
➤ While transactional leadership promotes adherence to procedures and policies, it can stifle creativity and risk-taking, which are necessary for breakthrough innovations (Howell and Avolio, 1993). This leadership style may be suitable for managing incremental innovations but is less effective in fostering the adoption of disruptive technologies. The rewardpunishment framework may create short-term gains in terms of technology adoption, e.g., meeting deadlines, but it often lacks the visionary approach needed to drive long-term, transformative innovation.
➤ Servant leadership, introduced by Greenleaf (1970), emphasizes the leader’s role in serving their team and facilitating the growth and well-being of their followers. This leadership style focuses on empowering employees, encouraging collaboration, and prioritizing the needs of the team over the leader’s personal ambitions.
➤ Influence on innovation and technology adoption: servant leaders tend to empower employees by fostering a participatory culture where all members are encouraged to contribute ideas. This empowerment creates an environment where innovation can thrive, as employees feel supported in proposing new technologies or approaches (Van Dierendonck, 2011).
➤ By promoting collaborative decision-making, servant leaders can drive the collective adoption of technology. This inclusive approach aligns with the concept of shared leadership, where innovation emerges from multiple sources within the organization rather than being directed solely by top management.
➤ When requiring adoption of innovation, servant leaders may find it challenging in enforcing this adoption. At times they may have difficulty in establishing their authority in the different phases of adoption of innovation (Mautz, 2021).
➤ Adaptive leadership, developed by Heifetz (1994), focuses on the ability of leaders to help organizations and individuals adapt to complex, changing environments. Adaptive leaders emphasize the importance of flexibility, learning, and adjusting strategies based on evolving circumstances. This style is particularly relevant to technology adoption, where ongoing change and adaptation are critical (Heifats, 2009).
➤ Influence on innovation and technology adoption: adaptive leadership encourages learning and experimentation, which are essential for technology adoption and innovation in dynamic industries. These leaders focus on the organization’s ability to continuously evolve, thus creating an environment where technology is seen as a tool for long-term survival and competitiveness (Heifetz and Laurie, 1997). Adaptive leaders also promote a culture of resilience, helping teams navigate the uncertainties and complexities that often accompany the introduction of new technologies.
➤ One of the challenges for adaptive leaders is balancing short-term performance pressures with the need for long-
term adaptation. In organizations where immediate results are prioritized, adaptive leadership might struggle to gain traction.
➤ Ambidextrous leadership is a relatively recent but important concept in leadership theory, particularly in relation to innovation and technology adoption. It refers to the ability of a leader to balance exploration (fostering innovation and creativity) and exploitation (maximising efficiency and optimizing existing processes) within an organization (Rosing et al., 2011). This dual capability is essential in environments characterized by rapid technological change, where both adaptability and operational excellence are required for success.
The term 'ambidexterity' in leadership derives from organizational ambidexterity, which was initially introduced by Duncan (1976) and later refined by scholars such as Tushman and O'Reilly (1996). Ambidextrous leadership involves the capacity to switch between two distinct leadership behaviours:
➤ Exploration-oriented leadership focuses on encouraging risktaking, experimentation, and the search for new knowledge and innovation.
➤ Exploitation-oriented leadership emphasizes refining existing knowledge, improving efficiency, and maintaining consistent performance.
Ambidextrous leaders are expected to dynamically alternate between these behaviours depending on the context, ensuring that the organization is both innovative and efficient.
➤ Exploration: ambidextrous leaders encourage creative problem-solving, the exploration of new opportunities, and innovative thinking. They create environments that reward experimentation and tolerate failure as part of the innovation process (Raisch and Birkinshaw, 2008).
➤ Exploitation: at the same time, these leaders also promote the optimization of existing processes, cost-cutting, and performance improvement, helping the organization execute strategies more efficiently.
Ambidextrous leadership is particularly relevant for organizations seeking to adopt new technologies, as technology adoption often requires both exploration (to identify, develop, and pilot new technologies) and exploitation (to implement, scale, and optimize those technologies effectively). The value of this leadership approach lies in the following:
➤ Ambidextrous leaders support radical innovation by promoting a culture of exploration. They encourage employees to challenge the status quo, experiment with new ideas, and pursue novel technologies that can create competitive advantages (Jansen et al., 2008).
➤ Leaders who excel at exploration are more likely to recognize disruptive technologies early and create cross-functional teams that collaborate on developing innovative solutions.
➤ Once new technologies are identified or developed, ambidextrous leaders must shift toward exploitation, focusing on the systematic implementation and integration of these technologies. This involves process optimization, resource allocation, and training to ensure smooth technology adoption.
Exploitation-oriented leadership ensures that the organization does not lose sight of operational goals while experimenting with new technologies. It allows leaders to balance short-term performance with long-term innovation.
➤ These leaders reduce uncertainty by implementing structures that help employees effectively integrate new technologies into their daily operations, thus enhancing the technology adoption process.
Several studies have provided empirical support for the effectiveness of ambidextrous leadership in promoting innovation and technology adoption:
➤ Rosing, Frese, and Bausch (2011) conducted a meta-analysis of leadership behaviors and innovation and found that ambidextrous leadership significantly improved innovation outcomes. The ability to foster both exploration and exploitation was linked to higher levels of organizational adaptability and success in technology adoption.
➤ Jansen et al. (2008) found that organizations led by ambidextrous leaders were better able to achieve incremental and radical innovations, enabling them to stay competitive in dynamic markets.
➤ Tushman and O'Reilly (1996) highlighted the importance of ambidextrous leadership in managing organizational ambidexterity and maintaining alignment between innovation and operational efficiency. They emphasized the role of senior leaders in orchestrating both short-term efficiency and longterm innovation.
Ambidextrous leadership is a highly effective style for organizations seeking to innovate and adopt new technologies. By balancing the need for exploration (innovation, risk-taking, and creativity) with exploitation (efficiency, control, and process optimization), ambidextrous leaders create an environment where new technologies can be both developed and implemented effectively.
Despite these strengths there are also certain shortcomings and challenges linked to this approach:
➤ Balancing conflicting priorities: leaders must be adept at managing the tension between exploration and exploitation to fully capitalize on the benefits of ambidextrous leadership. The ability to switch between these two leadership behaviors requires a high level of flexibility, contextual awareness, and organizational support, which can pose challenges for leaders and organizations alike. One of the main challenges for ambidextrous leaders is managing the tension between exploration and exploitation. Exploration involves risk-taking and uncertainty, while exploitation emphasizes efficiency and control. These two objectives can often be in conflict, making it difficult for leaders to balance them effectively (O'Reilly and Tushman, 2013).
➤ Organizational structure: ambidextrous leadership requires an organizational structure that supports both exploration and exploitation. Some organizations may find it difficult to implement the dual structures needed to support innovation while maintaining operational efficiency.
➤ Leadership flexibility and adaptability: ambidextrous leaders need to be highly adaptive and flexible, as they must switch between different leadership behaviors based on changing organizational needs and environmental conditions. Not all leaders possess the skill or agility to navigate this dynamic leadership style effectively (Rosing et al., 2011). Additionally,
ambidextrous leadership requires contextual awareness, meaning that leaders must be able to read signals from their environment and know when to emphasize exploration versus exploitation.
Conceptual model (Theoretical framework developed from literature)
The conceptual model that follows, aims to integrate the principles of technology adoption and leadership styles, addressing the shortcomings identified in both areas. The model builds on the strengths of existing technology adoption frameworks (TAM, DOI, UTAUT, TOE) and incorporates leadership styles (transformational, transactional, servant, adaptive, and ambidextrous leadership) to enhance the effectiveness of innovation and technology adoption within organizations.
This integrated model, called the Ambidextrous LeadershipTechnology Adoption (ALTA) model therefore seeks to address gaps such as the direct role of leadership in technology adoption, the role of leadership in overcoming resistance, and the need for dynamic leadership styles that balance innovation with efficiency, consideration of all factors that influence the technology adoption (TA) process: external (societal factors and individual behaviour), and internal (organizational readiness), as shown in Table I.
The ALTA model is composed of three interconnected layers: leadership drivers, technology adoption phases, and organizational outcomes. Each layer interacts with the others, creating a comprehensive framework for guiding technology adoption.
Leadership drivers: at the core of this model is leadership, as leaders play a pivotal role in both fostering innovation and facilitating the adoption of technology. The ALTA model integrates key leadership styles that are most relevant to technology adoption, with a focus on balancing exploration and exploitation through ambidextrous leadership.
➤ Exploration-oriented behaviours (innovation and adaptability): based on transformational, adaptive, and ambidextrous leadership styles, leaders are tasked with promoting creativity, encouraging risk-taking, and fostering innovation within the organization.
• Vision setting: transformational leaders articulate a compelling vision of the future, including the strategic importance of adopting new technologies.
• Intellectual stimulation: leaders encourage innovation and out-of-the-box thinking to identify new technologies and potential disruptive changes.
• Organizational learning: adaptive leaders ensure that the organization remains flexible, fostering continuous learning and experimentation in rapidly evolving technological landscapes.
➤ Exploitation-oriented behaviours (efficiency and implementation): this includes transactional, servant, and ambidextrous leadership elements, focused on ensuring efficient implementation and operational excellence.
• Process optimization: transactional leaders enforce structure and guidelines to ensure the smooth integration of new technologies into existing workflows.
• Empowerment and support: servant leaders support employees by providing the necessary resources and training for them to adopt new technologies confidently.
Table I
Ambidextrous leadership-technology adoption conceptual Mmodel
Technology adoption phase Development (Exploration)
Leadership style
• Transformational
• Charismatic
• Visionary
Leadership characteristics
• Courageous
• Persuasive
• Good communicator
• Organization learning and determining readiness
• Set strategic vision
• Intellectual stimulation
• Create innovation task forces
• Identify new technologies
Leadership actions
• Consider the perceived use of the technology
• Consider the characteristics of the adopter
• Evaluate the feasibility of the innovation
• Facilitating conditions: leadership ensures that adequate support structures (such as IT infrastructure, funding, and organizational alignment) are in place to facilitate the use and scaling of new technologies.
The ALTA model integrates a dynamic, multi-phase technology adoption process. Each phase is influenced by leadership drivers that are aligned with different styles and behaviors to overcome the shortcomings of traditional technology adoption models.
➤ Leadership role: transformational and adaptive leadership styles dominate in this phase, as leaders foster a culture of innovation and exploration. Leaders encourage employees to identify emerging technologies and evaluate their potential for driving competitive advantage.
• Leadership action: set strategic visions for technology, create innovation task forces, and encourage employees to take calculated risks.
• Outcome: organizations generate creative ideas, identify new technologies, and explore how these innovations align with the organization's future goals.
➤ Leadership role: here, ambidextrous leadership becomes critical as leaders must balance exploration and exploitation. Leaders facilitate discussions across organizational levels to achieve consensus on which technologies to adopt.
• Leadership action: facilitate cross-functional collaboration, ensure that all relevant stakeholders are involved in
Implementation (Transition) Application (Exploitation)
• Ambidextrous
• Flexible
• Adaptable
• Contextual awareness
• Collaborative
• Facilitate cross-functional collaboration
• Stakeholder engagement
• Obtain buy in from stakeholders
• Reduce resistances toward the technology
• Change management
• Resource allocation
• Transactional
• Less experimental
• Focus on clear structures
• Prioritizes routines
• Prioritizes meeting deadlines
• Provide training
• Optimize resource allocation
• Establish monitoring systems
• Monitor for continuous improvement
• Establish reward systems for successful adoption
• Ensure organizational efficiency
decision-making, and provide evidence of how new technologies align with organizational strategy.
• Outcome: consensus is built around which technologies to adopt, with buy-in from key stakeholders at all levels of the organization.
➤ Leadership role: exploitation-oriented leadership styles such as transactional and servant leadership dominate. Leaders ensure that technology is seamlessly integrated into operational processes, with minimal disruption to the day-today functioning of the organization.
• Leadership action: provide training, establish monitoring systems, and reward employees who successfully adopt and use new technologies. Leaders focus on optimizing resource allocation and ensuring organizational efficiency during the adoption phase.
• Outcome: the organization successfully integrates the new technology into its operational framework, minimizing resistance and maximizing efficiency.
➤ Successful technology adoption is measured by several key outcomes, which are influenced by leadership behaviour throughout the adoption process:
• Innovation performance: the organization is more innovative, consistently identifying and adopting new technologies that drive competitive advantage.
• Operational efficiency: the organization is efficient in implementing technologies, with optimized processes and minimal disruption during technology integration.
• Employee engagement and empowerment: employees feel empowered and supported throughout the technology adoption process, contributing to a culture of continuous improvement and innovation.
• Adaptability and resilience: the organization becomes more adaptable to future technological changes and market shifts, able to pivot quickly when necessary.
➤ The ambidextrous leadership-technology adoption (ALTA) model integrates leadership styles with the technology adoption process to create a holistic approach to managing innovation and technological change. By focusing on both exploration and exploitation, and emphasizing the strategic role of leadership, this model addresses the key shortcomings of traditional technology adoption frameworks. It ensures that organizations are well-positioned to adopt new technologies efficiently, while fostering a culture of innovation and adaptability.
Methodological approach of ALTA Model ‘Testing’ (Relevance)
➤ A qualitative research design was selected to explore and test the conceptual model. This approach enables a detailed description of participants’ experiences, providing a deeper understanding of the subject matter, which is crucial for empirical research. To gather data, qualitative interviews were conducted with officials from the mining industry who had worked on or led innovation projects. This empirical method of data collection is based on observation and experience rather than theory or pure logic (Jasti, 2014). This approach was essential to the study, as valuable insights into the research topic could only be gained through direct communication with experienced individuals in the field.
➤ The interviews were semi-structured, with most questions prearranged, while allowing flexibility for new ideas to emerge during the conversations. On average, the interviews lasted 45 minutes, and responses were recorded via notetaking, voice recording, and/or video recording on Google Meet, with participants’ consent.
➤ An interview guide was developed and used to conduct interviews in a manner that addressed the main research
question and sub-research questions. The questions were derived from the literature review. The guide began with an introduction of the interviewer and an explanation of the purpose of the interviews in relation to the research topic. Participants were then asked about their occupation, current roles in the mining industry or at their respective mines, the type of operation they work in (either underground or open cast), and their experience with innovation projects. These initial questions helped assess their level of competency and ability to provide insightful information regarding the research topic.
➤ Participants who had worked on an innovation project were asked to select one successful project as the basis for further questions. The project's success was determined by the full adoption of the technology across the organization. Participants who met these criteria proceeded to the next stage.
➤ Twenty individuals were approached to take part in the study, which included mine managers, general managers, technical services managers, relationship managers, chief executive officers, and managing directors from selected mines. Of these, nine responded, meeting the requirements for a phenomenological study, which typically calls for 5 to 25 interviews (Cresswell, 1998; Morse, 1994). Table II shows the various roles of the participants and the innovation projects they have driven.
The results of this study were analysed using thematic analysis, a qualitative method used to identify, analyse, and report patterns or themes within data, applicable to data such as interviews, focus groups, or written material (Braun, 2012). In this case, the data consisted of interview transcriptions.
A theme, in this context, refers to elements of the data that are relevant to the research question or show patterns across the dataset. However, a theme is not necessarily defined by how often it appears in the data. Instead, the researcher exercises judgment in determining what constitutes a theme (Braun, 2012). A theme was selected if it captured something significant related to the overall research question or sub-questions.
Roles of participants and innovation projects Driven
Participant Role
Innovation project
1 Mechanical Engineer (Glencore) Implementation of collision avoidance system
2 Head of Engineering (Glencore Coal) Installation of proximity detection system
3 Vice President (SASOL Mining) Digitization of the organization
4 Technical Manager (Glencore Coal) Business optimization and improvement
5 M&R CEO (Underground Mining Division) Digital technology implementation
6 Director of Marketing and Supply Chain Autonomous blasting system
7 Production Manager Introduction of remotely operated bolters
8 Project Manager Introduction of remotely operated roof bolters
9 Mechanical Engineer Installation of proximity detection system
This study emphasizes qualitative descriptions over quantifiable measures, using terms such as 'many participants,' 'most respondents,' or 'several participants' to convey the prevalence of certain themes. The authors used the thematic analysis process stipulated by Chap et al. (2012) and Braun (2012) described in the following phases:
Phases of the thematic analysis
1. Familiarization: The researcher immersed in the data through repeated reading and transcription of interviews.
2. Generating Initial codes: an initial list of codes was developed to identify features in the data relevant to the research questions.
3. Searching for themes: themes were identified by clustering related codes and recognizing patterns.
4. Reviewing potential themes: themes were reviewed for quality and coherence, ensuring they accurately represented the dataset.
5. Defining and naming themes: each theme was clearly defined, ensuring they collectively told a coherent story about the data.
6. Producing a report: the final phase involved compiling the results of the thematic analysis into a comprehensive report.
Qualitative findings for testing the ALTA Model: Results
The findings for this qualitative research study testing the ambidextrous leadership-technology adoption (ALTA) model, indicate how leadership behaviors influence various phases of the technology adoption process, how organizations manage innovation, and how ambidextrous leadership plays a role in balancing exploration and exploitation. These findings are based on themes that emerged from the thematic analysis of the interviews conducted, and are discussed as follows (includes quotes of the people interviewed as recorded):
Leadership influence on exploration and innovation
➤ Theme 1: Transformational Leadership Encouraging Exploration and Risk-taking
• Finding: Interviewees often described leaders with transformational qualities—visionary, charismatic, and able to inspire innovation. They speak of how leaders encourage creative problem-solving and taking risks in identifying new technologies, creating an environment where employees feel empowered to suggest bold, innovative solutions.
➤ Quote: ‘‘I’ll give you a few keys that I think normally helps get to a new idea of innovation and to then move on with the project. The first one is vision. You need visionary leaders that will have a very clear picture and envisage the future. Vision is at the top of the list you know, without leaders that’s got vision none of this [innovation] will ever happen.’’
➤ Quote: ‘‘Leadership needs to be flexible and agile and courageous. You must be decisive in what you want to do, you must think on your feet and prepare for failure. When it fails, show agility, do something, and fix it. If you try to work out the perfect execution plan you will take too long. Procrastination will never get you anywhere.’’
➤ Theme 2: Ambidextrous Leadership Balancing Innovation with Operational Needs
• Finding: Case studies highlight that ambidextrous leaders excel at maintaining a balance between exploration and exploitation. Employees note that these leaders not only encourage innovation but also set boundaries to ensure operational processes are efficient, preventing the chaos that can arise from too much focus on new technologies.
➤
Quote: ‘‘Look I think flexibility should be high, I mean probably a four [out of 5], but you got to be careful. If you let the flexibility, get too high, you lose the effectiveness of the project. So, the system has to run, but when things come up that are better, unique, or different, you need to be quite flexible to accept them and adapt. You don't want to be completely flexible because if you do that, they're going to lose control of the process.’’
Leadership influence on implementation and efficiency
➤ Theme 3: Transactional Leadership Promoting Structured Implementation
• Finding: In interviews and focus groups, participants describe transactional leaders as vital during the implementation phase of technology adoption. These leaders focus on setting clear goals, timelines, and expectations, which helps ensure that technology is integrated smoothly into the organization.
➤
➤
Quote: ‘‘Once they have gotten all the parties together, put an implementation plan together that needs to include all the details about the collaboration, including the non-technical side of it. Ensure that the plan covers everything that it needs.’’
Quote: ‘‘The other important part of the implementation process is the management of change. As you start implementing, things do not necessarily go to plan. As you start implementing your plan, be flexible enough to change.’’
➤ Theme 4: Overcoming Resistance to Change through Leadership
• Finding: Participants highlighted the role of adaptive and transformational leadership in managing resistance to new technologies. These leaders communicate the long-term benefits of adoption, making employees feel more comfortable with the transition. Leaders must be transparent with the stakeholders about the technology's intentions and its potential benefits. This approach can help build trust and facilitate collaboration, ensuring that the concerns and needs of all stakeholders are addressed. Leadership must also invest in reskilling to expand employment opportunities and reduce the fear of job loss, which can contribute to resistance.
➤ Quote: ‘‘The way you overcome it [resistance] is to explain that what we're doing is to become more efficient. The reason why we are automating machines is to get more productive. When you automate machines, you can keep them working during normal times and when you wouldn't normally have people on underground, i.e., after a blast. Automation will make the mining process more efficient by reducing costs and making the mining industry more viable. This will lead to the increase in the profitable life of mine, and employment. The introduction of new technology can and will have the ability to have a positive impact on mining operations.’’
➤ Quote: ‘‘No, you have to put a lot of effort through automation, create transferable skills that will be transferable elsewhere in the job space, in the world outside of mining, and you have to do so as an organization; create jobs much bigger and better to offset the impact of automation to such an extent that you almost first have to eradicate unemployment before you are successful with this [automation] I can see how you're going to get automation into mining environment and how you are going to exacerbate the issue of unemployment.’’
Leadership's Role in decision-making and consensus building
➤ Theme 5: Cross-functional Collaboration Encouraged by Ambidextrous Leaders
• Finding: Employees frequently mention that ambidextrous leaders facilitate cross-functional collaboration, ensuring that stakeholders from different parts of the organization are involved in decisions related to technology adoption. This leadership style helps build consensus, especially in the decision-making phase.
➤ Quote: ‘‘The first thing that leaders need to do is to develop the vision around this implementation. Then they need to engage with the stakeholders involved, the people that must implement this, such as original equipment manufacturers, suppliers of technology, the employees who develop the application process, etc. Leaders need to engage with all stakeholders to ensure that they are all on board. This is important so that they all can understand how they can contribute in delivering the outcome that leaders have articulated in their vision.’’
➤ Theme 6: Dual Leadership Behaviours in Ambidextrous Leaders
• Finding: Case studies and interviews reveal that ambidextrous leaders can switch between behaviors depending on the phase of the technology adoption process. During exploration, they exhibit transformational behaviours, fostering creativity and risk-taking. During exploitation, they shift toward transactional or servant leadership behaviours, focusing on execution, efficiency, and process optimization.
➤ Quote: ‘‘On the level of flexibility in leadership; there is time to be flexible and there is time to be inflexible. In an idea generation stage, you must be at a five [out of five] but as you progress, evaluate until you come up with a proper concept, I mean once a concept is cast in stone I don't expect flexibility, otherwise you will never finish. Depending on where you are on the implementation of the innovation you start being flexible in the beginning. As you move towards finalizing the actual idea or the business case, the flexibility must come down to a three. However, you can never be inflexible because better ideas can come up during implementation so you should never get to a one flexibility. Lowest flexibility that can be achieved is a two because if an idea is proved to yield benefits the only difference is a new idea, which can yield more benefits, but it doesn't mean the original idea stops yielding benefits. At least capture the benefits that you started with, and you can take the new idea as an improvement on the original idea after the benefits of the original idea have been realised.’’
➤ Theme 7: Organizational Culture as a Mediator
• Finding: In some organizations, the existing culture either facilitates or hinders the success of leadership’s efforts to adopt new technologies. Companies with cultures of openness and collaboration are more successful in adopting technologies when leadership behaviors align
with these values. Additionally, the characteristics and readiness of the workforce to adopt new technologies must be carefully considered as a critical factor in the process.
➤ Quote: ‘‘The involvement of leadership varies from company to company and the reason it varies from company to company is that the maturity of that specific company in terms of just technology in general. I have worked in companies where most of the people, in general, are relatively technology driven. They want to be on the leading edge. This is a general culture in the company of cutting edge, they want to be the first. In companies like that, technology is driven by people. They want to do that [innovate], they are kind of pushing the envelope all the time, but I’ve also seen companies where they are relatively immature in terms of what I've said and if this is the case, having the right leaders in place to push the technology agenda is extremely important.’’
➤
Quote: ‘‘The younger generation tends to adopt new technologies more easily, especially when it comes to using smartphones. They quickly grasp the basics with minimal explanation and adapt swiftly. In contrast, the older generation often struggles with technology, requiring more extensive training, guidance, and support. When designing applications, it's important to keep them simple and user-friendly to prevent frustration, especially for older users. This highlights a generational difference, where younger individuals find technology adoption easier, while older individuals face more challenges.’’
➤ Theme 8: Resistance to Change and Leadership Strategies
• Finding: Resistance to change is a common barrier identified by participants. However, it can be noted that adaptive and transformational leaders are most effective at addressing this resistance, using communication, empathy, and vision to help employees understand the value of the new technology.
➤ Quote: ‘‘The way you overcome it is to try to explain that what we're trying to do is become more efficient. Why we are automating machines is to try to get more work out of the machine. When you automate machines, you can keep them working during normal times and when you wouldn't normally have people on underground, i.e., after a blast, automation would make the mining process more efficient to reduce costs and the mining industry becomes more viable. Therefore, because you can reduce costs, you can keep some mines open that under normal working practices wouldn't be able to work. Therefore, more mines in operation safeguard employment rather than destroy it by introducing technology.’’
➤ Quote: ‘‘To drive innovation within a company, it's essential to actively involve employees from the start. This can be done by organizing focus groups and brainstorming sessions, where employees across departments can share their work challenges and suggest how technology could improve their roles. This collaborative approach helps identify potential technologies and projects that align with business needs. Once a suitable technology is chosen, it's important to manage the change effectively. Early communication about the impact of the technology on employees' day-to-day tasks is crucial, along with
providing necessary training. Throughout the implementation process, it's vital to keep all stakeholders informed of progress. This ongoing communication and support ensure that, by the time the project is complete, employees are ready to accept and adopt the new technology.’’
Outcomes of Technology Adoption Driven by Leadership
➤ Theme 9: Operational Efficiency
• Finding: Participants describe how leadership, particularly transactional and servant leaders, ensures that new technologies are integrated efficiently, minimising disruptions to existing workflows.
➤ Quote: ‘‘One of the key challenges when introducing new projects or trials is overcoming resistance from the workforce, such as operators or labourers. They can hinder or even sabotage the project, especially if they feel their jobs are at risk, regardless of whether the project might have succeeded otherwise. From a leadership perspective, this is particularly difficult. Large mining companies must ensure that mine management, supervisors, and all levels of leadership fully grasp the importance of their role in fostering innovation. If leadership focuses too heavily on controlling costs, as often reflected in KPIs, it becomes difficult to engage these teams in new initiatives. Employees may struggle to meet their KPIs, while also supporting innovation. Therefore, it's crucial for senior leadership to align incentives in a way that encourages innovation. A failure to do so has often been a barrier to progress in the industry.’’
The findings from the interviews conducted, provided significant insights into how different leadership styles influence various stages of the technology adoption process within organizations, particularly in the mining industry. Transformational leaders play a crucial role in fostering innovation and encouraging risk-taking, while ambidextrous leaders are highly effective in balancing exploration (innovation) and exploitation (operational efficiency). Transactional and servant leaders are critical during the implementation and application phase, ensuring that technology is adopted efficiently. Ultimately, the findings suggest that leadership not only shapes the technology adoption process, but also directly influences the organization's innovation performance and operational efficiency.
The adoption of new technologies is highly dependent on the organizational culture, the flexibility of leadership, and the ability of leaders to foster collaboration and consensus-building among stakeholders. Leadership’s role in addressing barriers such as resistance to change, structural limitations, and resource constraints is vital for the successful integration of innovative technologies.
This section discusses the findings in relation to the study’s objectives and the ALTA model proposed earlier. The results are interpreted in the context of the literature and conceptual framework, addressing how leadership styles can influence technology adoption, innovation performance, and operational efficiency within organizations.
Leadership’s role in fostering innovation
The findings reveal that transformational leadership is instrumental in the exploration phase of technology adoption. Leaders with transformational qualities—visionary, charismatic, and risktaking—were found to create an environment where innovation could thrive.
This is consistent with the literature, which emphasizes that transformational leaders foster creativity and open-mindedness, key ingredients for breakthrough innovations (Bass, 1985).
However, the findings also suggest that innovation cannot occur in isolation from operational needs. Ambidextrous leadership was found to be crucial in balancing exploration with exploitation, ensuring that organizations do not over-prioritize experimentation at the expense of efficiency. This finding aligns with the work of O'Reilly and Tushman (2013), who highlight the importance of balancing exploration and exploitation to ensure the long-term success of an innovation.
Leadership’s role in implementing technology
Transactional leadership was found to be essential in the exploitation phase of technology adoption. This leadership style focuses on clear goal setting, establishing timelines, and managing the process to ensure that new technologies are seamlessly integrated into the organization. The interviews suggest that without structured leadership during implementation, projects can face challenges such as disorganization or scope creep, confirming the need for strong transactional leadership to maintain operational focus (Burns, 1978).
The importance of adaptive leadership was also highlighted, especially in managing resistance to change. This finding is consistent with Heifetz’s (1994) work, which emphasizes the need for leaders to guide organizations through periods of uncertainty and change by adapting to new circumstances and addressing employee concerns.
Overcoming barriers to technology adoption
The study identified several barriers to technology adoption, including resistance to change, and structural constraints. The study confirmed that organizational culture plays a critical role in determining the success of leadership efforts in technology adoption. Companies with cultures of collaboration and openness are likely to be more successful in adopting new technologies, which supports previous research that links organizational culture with innovation (Schein, 2010). Leaders in such environments can align their behaviors with the existing cultural values, facilitating smoother technology integration.
The role of cross-functional collaboration
Ambidextrous leadership also emerged as a facilitator of crossfunctional collaboration, an important factor in technology adoption. Leaders who could effectively bring together diverse teams and encourage collaboration across departments are able to build consensus, especially in the decision-making phase. This is consistent with the findings of Raisch and Birkinshaw (2008), who argue that ambidextrous leaders play a key role in promoting collaboration and coordination within organizations, especially when adopting new technologies.
Leadership’s impact on innovation performance and operational efficiency
The findings underscore the impact of ambidextrous and transformational leadership styles on innovation performance. Organizations led by these types of leaders are consistently at the forefront of innovation, introducing new products and processes faster than their competitors. This finding supports the broader literature, which emphasizes the role of transformational leaders in creating a culture of innovation and driving organizational change (Jung et al., 2003).
In contrast, operational efficiency was found to be heavily influenced by transactional and servant leadership styles. These leaders focus on ensuring that new technologies are integrated smoothly, without disrupting existing workflows, which is crucial for maintaining operational stability. The findings align with Burns’ (1978) distinction between transformational and transactional leadership, where the latter is more focused on maintaining efficiency and achieving short-term goals.
The findings largely support the ambidextrous leadershiptechnology adoption (ALTA) model proposed in this study. The model's emphasis on balancing exploration and exploitation was confirmed by the participants, who consistently highlighted the need for leaders to foster innovation while maintaining operational focus. The dual behaviors exhibited by ambidextrous leaders— switching between transformational and transactional styles depending on the phase of technology adoption—were found to be particularly effective.
This study set out to explore the role of leadership in the technology adoption process, particularly within the context of mining organizations. The research focused on the integration of various leadership styles and their influence on fostering innovation, managing resistance, and ensuring efficient implementation. The development and testing of the ambidextrous leadership-technology doption (ALTA) model provided a framework for understanding how leaders can balance the dual demands of exploration (driving innovation) and exploitation (maintaining operational efficiency) in a complex and technology-driven environment. From the main aim of the study the relevance of the ambidextrous leadershiptechnology adoption (ALTA) model in addressing gaps in the direct role of leadership in technology adoption has been shown.
The findings from the qualitative interviews affirmed that leadership is an indispensable factor in the successful adoption of new technologies. Transformational leadership was identified as critical for inspiring innovation and encouraging risk-taking, while transactional leadership played a key role in ensuring that technology was integrated efficiently during the implementation phase. Moreover, ambidextrous leadership emerged as essential for balancing the need to explore new technologies while also ensuring that current operational processes are optimized.
What is further evident is that there is no one leadership style that will effectively deal with the successful adoption of new technology, but that the ALTA model points us in the right direction, which was also highlighted by participants in the survey conducted. One therefore needs to look at leadership actions and behaviors that will enhance or are needed in a successful approach towards new technology adoption.
The study also highlighted the importance of adaptive leadership, particularly in managing resistance to change, which is often a significant barrier to technology adoption. Leaders who demonstrated flexibility, empathy, and clear communication are better able to address concerns related to job security and other anxieties associated with technological disruption.
Organizational culture is revealed as a critical mediator in the relationship between leadership and technology adoption success. Companies with a culture of openness, collaboration, and innovation are more likely to succeed in adopting new technologies, as leadership behaviors aligned with these values facilitate smoother transitions.
Finally, the study demonstrates that leadership plays a pivotal role in driving technology adoption, fostering innovation, and managing the challenges associated with technological change. The ambidextrous leadership-technology adoption (ALTA) model provides a robust framework for understanding how leaders can navigate the complexities of technology adoption, balancing the need for exploration and exploitation, while addressing resistance and fostering a culture of collaboration and innovation. As industries continue to evolve in response to technological advancements, the role of leadership will remain critical in ensuring that organizations not only adopt new technologies but thrive in an increasingly digital future.
This study makes several important contributions to the field of leadership and technology adoption. First, it expands the understanding of ambidextrous leadership, providing empirical support for the ALTA model. The study demonstrates that ambidextrous leaders are uniquely positioned to switch between transformational and transactional leadership behaviors depending on the phase of the technology adoption process. Second, the study highlights the importance of adaptive leadership in overcoming resistance to change and addressing the human elements of technology adoption, particularly in industries facing rapid technological shifts, such as mining.
Additionally, the study provides practical insights for leaders in technology-intensive industries, offering strategies for balancing innovation with operational efficiency, managing cross-functional collaboration, and fostering a culture conducive to technology adoption.
While this study provides valuable insights, it is not without limitations. The research was primarily qualitative and focused on a specific industry (mining), which may limit the generalizability of the findings to other industries or contexts. Additionally, the study did not explore the long-term effects of leadership on technology adoption, which could be a potential avenue for future research. Further studies could quantitively validate and refine the ALTA model by applying the model in a real-life innovation project.
The study offers several practical recommendations for leaders in organizations adopting new technologies:
1. Foster a culture of innovation: leaders should actively promote a culture where innovation is encouraged at all levels of the organization. This includes creating environments where employees feel safe to propose new ideas and take calculated risks.
2. Balance exploration and exploitation: leaders must balance the pursuit of new technological innovations with the need to maintain and optimize existing processes. Ambidextrous leadership, which enables leaders to switch between exploratory and exploitative behaviors, is essential in achieving this balance.
3. Manage resistance through communication and reskilling: leaders must proactively manage resistance by clearly communicating the benefits of new technologies and offering reskilling opportunities for employees whose roles may be affected by automation or other technological advancements.
4. Encourage cross-functional collaboration: successful technology adoption requires leaders to facilitate collaboration between different departments and stakeholders, ensuring alignment across the organization.
Future research could also explore the role of emerging leadership styles, such as digital leadership, which may play an increasingly important role as industries continue to adopt advanced technologies, such as artificial intelligence and machine learning. The feedback on the literature, in some cases seems to be outdated, but is still applicable. We are in the cusp of the Fourth Industrial Revolution, which relates significantly to an escalated new technology availability and the related adoption challenges associated with it. New research relating to leadership and technology adoption will in future become even more relevant, including the subsequent research interventions related to it.
I would like to extend my gratitude to the following people for their contributions towards this study, namely Dr Johann Uys and Prof. Ronny Webber-Youngman of the University of Pretoria, and the people who took part in the interviews, namely Johan Smit, Henk Pienaar, Kobus Louw, Mike da Costa, Sbu Buthelesi, Jaco Gouws, Kennedy Sengani, Mike Teke, and Allan Butcher. I would also like to extend my deepest gratitude to Murray & Roberts for their generous sponsorship and support, which made this project possible.
References
Ajzen, I. 1991. The Theory of Planned Behavior. Organizational Behavior and Human Decision Processes, vol. 50 no. 2, pp. 179–211. doi:10.1016/0749-5978(91)90020-T
Alem, L., Caris, C., Einicke, G.A., Gipps, I., Haustein, K., Hoehn, K., Huang, W., James, C. Malos, J.T., Munday, L., Poropat, G., Ralston, J.C., Stepanas, K., Strange, A., Eleonora, W.-C. 2012. Overview of the future mine. Australasian Mine Safety Journal, vol. 4, pp. 14–21. https://www.researchgate.net/ publication/324653920_Overview_of_the_future_mine
Bass, B.M. 1985. Leadership and performance beyond expectations. Free Press. https://doi.org/10.1002/hrm.3930250310
Bossink, B. 2007. Leadership for sustainable innovation. International Journal of Technology Management and Sustainable Development, vol. 6, pp.135–149. doi: 10.1386/ijtm.6.2.135_1
Braun, V., Clarke, V. 2012. Thematic analysis. In Cooper, H., et al. (Eds.), APA Handbook of Research Methods in Psychology (Vol. 2). American Psychological Association. https://www. researchgate.net/publication/269930410_Thematic_analysis
Burnes, B. 2004. Kurt Lewin and the planned approach to change: A re-appraisal. Journal of Management Studies, vol. 41, no. 6, pp. 977–1002. https://doi.org/10.1111/j.1467-6486.2004.00463.x
Burns, J.M. 1978. Leadership. Harper & Row. https://psycnet.apa. org/record/1980-03173-000
Creswell, J.W. 1998. Qualitative inquiry and research design: Choosing among five traditions. Thousand Oaks, CA: Sage Publications. https://www.researchgate.net/ publication/318757065_Book_Review_Creswell_John_1997_ Qualitative_inquiry_and_research_design_Choosing_among_ five_traditions
Cresswell, K., Sheikh, A. 2013. Organizational issues in the implementation and adoption of health information technology innovations: An interpretative review. International Journal of Medical Informatics, vol. 82, no. 5, pp. e73–e86. https://doi. org/10.1016/j.ijmedinf.2012.10.007
Davis, F.D. 1989. Perceived usefulness, perceived ease of use, and user acceptance of information technology. Management Information Systems Quarterly, vol. 13, no. 3, pp. 319–340. DOI: 10.2307/249008
Deloitte. 2020. The future of mining in Africa. Deloitte. https://www2.deloitte.com/content/dam/Deloitte/cn/ Documents/energy-resources/deloitte-cn-tracking-the-trends2020-en-200527.pdf
Duncan, R.B. 1976. The ambidextrous organization: Designing dual structures for innovation. R. Kilmann, L. Pondy, & D. Slevin (Eds.). The Management of Organization, pp. 167-188. North-Holland. https://www.scirp.org/reference/ referencespapers?referenceid=3596065
Fichman, R.G., Kemerer, C. F. 1997. The assimilation of software process innovations: An organizational learning perspective. Management Science, vol. 43, no. 10, pp. 1345–1363. doi: 10.1287/mnsc.43.10.1345
Gilley, A., Dixon, P., Gilley, J.W., 2008. Characteristics of leadership effectiveness: Implementing change and driving innovation in organizations. Human Resource Development Quarterly, vol. 19, no. 2, pp. 153–169. Greenleaf, R.K. 1970. The servant as leader. Paulist Press. https://digitalcommons.unf.edu/cgi/viewcontent. cgi?article=1816&context=etd
Greenleaf, R.K. 1970. The servant as leader. Paulist Press. http://www.ediguys.net/Robert_K_Greenleaf_The_Servant_as_ Leader.pdf
Heifetz, R.A. 1994. Leadership Without Easy Answers. Harvard University Press. https://www.degruyter.com/document/ doi/10.4159/9780674038479/html
Heifetz, R.A., Laurie, D.L. 1997. The work of leadership. Harvard Business Review, vol. 75, no. 1, pp. 124–134. https://www.scirp. org/reference/referencespapers?referenceid=1207380
Heifetz, R.A., Grashow, A., Linsky, M. 2009. The practice of adaptive leadership: Tools and tactics for changing your organization and the world. Harvard Business Press.
Howell, J.M., Avolio, B. J. 1993. Transformational leadership, transactional leadership, locus of control, and support for innovation: Key predictors of consolidated-business-unit performance. Journal of Applied Psychology, vol. 78, no. 6, pp. 891–902. DOI: 10.1037/0021-9010.78.6.891
Jansen, J.J.P., George, G., Van den Bosch, F.A.J., Volberda, H.W. 2008. Senior team attributes and organizational ambidexterity: The moderating role of transformational leadership. Journal of Management Studies, vol. 45, no. 5, pp. 982–1007. DOI: 10.1111/j.1467-6486.2008.00775.x
Jasti, N., Kodali, R. 2014. A literature review of empirical research methodology in lean manufacturing. International Journal of Operations & Production Management. 34. 10.1108/ IJOPM-04-2012-0169
Jung, D.I., Chow, C., Wu, A. 2003. The role of transformational leadership in enhancing organizational innovation: Hypotheses and some preliminary findings. The Leadership Quarterly, vol. 14 no. 4, pp. 525–544. DOI: 10.1016/S10489843(03)00050-X
Lopes-Claros, A. 2011. The Innovation For Development Report 2010–2011: Innovation as a Driver of Productivity and Economic Growth. Palgrave Macmillan. https://books.google. co.za/books/about/The_Innovation_for_Development_ Report_20.html?id=S-428omxpD8C&redir_esc=y
Lyytinen, K., Damsgaard, J. 2011. Inter-organizational information systems adoption: A Configuration Analysis Approach. European Journal of Information Systems, vol. 20, no. 5, pp. 496–509.
Mautz, S. 2021. The problem with servant leadership (and how to lead instead). Available at: https://bit.ly/2MLe5Do
Morse, J.M. 1994. Designing funded qualitative research. In Denizin, N. K. & Lincoln, Y. S., Handbook of qualitative research (2nd Ed). Thousand Oaks, CA: Sage. https://methods. sagepub.com/book/designing-qualitative-research
O'Reilly, C.A., Tushman, M.L. 2013. Organizational ambidexterity: Past, present, and future. Academy of Management Perspectives, vol. 27, no. 4, pp. 324–338. https://www.jstor.org/ stable/43822033
Raisch, S., Birkinshaw, J. 2008. Organizational ambidexterity: Antecedents, outcomes, and moderators. Journal of Management, vol. 34, no. 3, pp. 375–409. https://www. researchgate.net/publication/247570120_Organizational_ Ambidexterity_Antecedents_Outcomes_and_Moderators
Rogers, E.M. 2003. Diffusion of innovations (5th ed.). Free Press. https://www.researchgate.net/publication/257624104_
Diffusion_of_Innovations_5th_edition_Everett_M_Rogers_ Free_Press_New_York_NY_2003_551_pages
Rosing, K., Frese, M., Bausch, A. 2011. Explaining the heterogeneity of the leadership-innovation relationship: Ambidextrous leadership. The Leadership Quarterly, vol. 22, no. 5, pp. 956–974.
Schein, E. H. 2010. Organizational Culture and Leadership (4th ed.). Wiley. https://ia800809.us.archive.org/14/items/ EdgarHScheinOrganizationalCultureAndLeadership/Edgar_H_ Tornatzky, L.G., Fleischer, M. 1990. The processes of technological innovation. Lexington Books. https://www.researchgate.net/ publication/291824703_Technological_Innovation_as_a_ Process
Tushman, M.L., O'Reilly, C.A. 1996. Ambidextrous organizations: Managing evolutionary and revolutionary change. California Management Review, vol. 38, no. 4, pp. 8–30. https://web. mit.edu/curhan/www/docs/Articles/15341_Readings/ Organizational_Learning_and_Change/Tushman_&_ OReilly_1996_Ambidextrous_Organizations.pdf
Van Dierendonck, D. 2011. Servant leadership: A review and synthesis. Journal of Management, vol. 37, no. 4, pp. 1228–1261. https://www.researchgate.net/publication/254121257_Servant_ Leadership_A_Review_and_Synthesis
Venkatesh, V., Morris, M.G., Davis, G.B., Davis, F.D. 2003. User acceptance of information technology: Toward a unified view. Management Information Systems Quarterly, vol. 27 no. 3, pp. 425–478.
Yukl, G. 2013. Leadership in Organizations (8th ed.). Pearson Education. https://www.researchgate.net/ publication/323294985_Leadership_in_Organizations_8th_ edition u
Affiliation:
1Department of Mining Engineering, University of Pretoria, South Africa
Correspondence to: D.F. Malan
Email: francois.malan@up.ac.za
Dates:
Received: May 2024
Revised: 4 Oct. 2024
Accepted: 20 Oct. 2024
Published: November 2024
How to cite:
Theron, W.J. and Malan, D.F. 2024. Pillar design and the associated mining engineering constraints in hard rock bord-andpillar mines. Journal of the Southern African Institute of Mining and Metallurgy, vol. 124, no.11, pp. 631–644
DOI:
http://dx.doi.org/10.17159/24119717/3413/2024
ORCiD:
D.F. Malan
http://orcid.org/0000-0002-9861-8735
by W.J. Theron1 and D.F. Malan1
Abstract
Practical mining aspects should be considered when conducting pillar designs for bord-and-pillar layouts. The current methodology for pillar design will result in increasing pillar sizes with depth. This affects the extraction ratio and will result in onerous ventilation requirements when cutting large pillars. A holistic approach, including all mining engineering requirements, is required to ensure that the rock engineering designs are optimized to ensure efficient mining operations and sustainable production. Bord widths should not only be a function of the rock mass ratings, but should also be selected to fit the specifications of the mechanized equipment. The use of a ‘squat pillar’ formula for hard rock is discussed in the paper and the formula based on the exponents of the Hedley and Grant pillar formula, is explored. The effect of abutments and geological losses on average pillar stress is also explored. These factors must be considered when designing layouts at increasing depths.
Keywords
pillar design, bord-and-pillar mine, mining engineering constraints, squat pillar formula
Introduction
Extensive research on the strength of hard rock pillars have been conducted and recent examples can be found in Malan and Napier, 2011; Watson et al, 2021; Napier and Malan, 2021; Oates and Malan, 2023; and Wessels and Malan, 2023. The objective of these studies is to obtain improved estimates of pillar strength to ensure stable excavations and to optimize extraction ratios. A drawback of rock engineering designs is that it is often done in isolation without including the constraints imposed by practical mining considerations. As a result, rock engineers may inadvertently design pillar sizes and layouts that may slow down production rates, decrease extraction ratios, and negatively affect productivity. An important requirement in industry is to create an awareness amongst the specialist rock engineers of the possible conflicting requirements when designing bord-and-pillar layouts. Some level of compromise is required in the final layout designs.
In general, most practical mining engineering problems require the achievement of several objectives. These may be conflicting objectives and it can therefore not be solved in isolation. For any design optimization, it is important to consider the entire mining sequence. Design is a cyclic process of evaluation, asset optimization, and system engineering. A key requirement is that a mining operation is a business with financial goals to ensure a return on investment for its shareholders. The mining value chain requires the input from various departments, namely engineering (mechanical, electrical, metallurgical), rock engineering, geology, ventilation, safety and health, environmental, human resources, procurement, and finances. When technical departments introduce a change in isolation because of immediate perceived needs, the inter-dependency of the various elements is sometimes overlooked.
Although the focus in this paper is on pillar design, a real-life practical example experienced by the authors is described below to highlight the conflicting requirements occasionally encountered. This occurred at a shallow platinum mine in the Bushveld Complex where two types of advance strike drives (ASDs) are used namely strike ASDs and normal ASDs. The width of the strike ASDs is designed to accommodate a conveyor belt and a traveling way for personnel and equipment. The normal ASDs only accommodate the travelling of personnel and equipment. A complicating factor for the excavation shape is the steep 18° dip of the strata and the hangingwall of the strike drives is profiled along the dip of the
strata for stability. During development blasting, the Strike ASD dimensions result in approximately 174 tons of broken rock per blast. This is calculated for a density of 4.17 t/m³ and 3.39 t/m³ for reef and waste, respectively, and an advance of 3 m per blast. A normal ASD results in approximately 110 tons of broken rock per blast. The dimensions of both these excavations were increased, based on an instruction from the engineering department to have greater clearances for the mechanized equipment (Figure 1). This increased the tonnage in strike ASDs to 210 tons per blast and in the normal ASD’s to 125 tons per blast. A small change in dimensions therefore resulted in a significant increase in the volume of rock mined. The mine also suffered significant production losses. An activity simulation was conducted to determine the load out rate and mining cycle times with the new dimensions. Based on the input parameters in the simulation, the drilling pattern in strike ASDs could not be completed within the allowed parameters of the mining cycle. The unintended consequence of the change in clearance was a significant decrease in production.
In terms of pillar design in bord-and-pillar layouts, similar conflicting requirements can arise, owing to the current industry methodology used to design pillars. A power-law pillar strength formula of the following form is typically adopted:
where σs is the pillar strength, K is the strength of the rock material in the pillar, w is the pillar width and h is the pillar height. In South Africa hard rock mines, the values 0.5 and 0.75 are typically used for the exponents α and β respectively. These values were initially adopted by Hedley and Grant (1972). A problem arises when the depth of the mines increases. The strength of the pillars as given by Equation [1] is independent of depth, but a further requirement for the design is that a minimum factor of safety, SF, needs to be maintained. This is given by:
The average pillar stress, σp, increases with depth for a constant extraction ratio and the factor of safety therefore decreases (Ile and Malan, 2023). Practicing rock engineers counter this by increasing the pillar width w to increase the pillar strength σs.
This not only decreases the extraction ratio, but can also have an adverse effect on other mining engineering requirements, such as those for ventilation. Some of the mining engineering requirements are described in the following section and an interactive pillar design approach is required. Similar to the ASD example already mentioned, the unintended consequences of strictly applying Equations [1] and (2) at great depths may result in an operation not being profitable anymore. Also not considered, is that the so-called ‘squat’ pillar behaviour may already occur at a smaller w:h ratio for hard rock compared to coal (Ryder and Jager, 2002). Equation [1] may therefore not be applicable at the larger width to height stipulated by this traditional pillar design approach at the greater depths. Furthermore, mining engineering requirements and the need to mine profitably should also be considered at these greater mining depths. A similar conflict arises in terms of the need to introduce barrier pillars.
The sections that follow describe some important mining engineering considerations when designing bord-and-pillar layouts, namely, constraints imposed by the equipment and ventilation considerations. The paper is also used to illustrate that some of the traditional empirical rock engineering equations may not be applicable, as the original assumptions used when deriving the equations may not be valid. An important contribution of this study is the derivation of a new squat pillar formula for hard rock based on the exponents of the Hedley and Grant equation. Many practicing rock engineers in the hard rock mines do not know that the commonly used squat pillar formula is based on the Salamon coal pillar formula (Salamon, 1982).
An important mining engineering constraint when designing bordand-pillar layouts is bord widths. Rock engineering considerations and the use of empirical design charts based on rock mass ratings will dictate a particular span (Barton, 1989; Hutchinson and Diederichs, 1996; Brady et al. 2004). The selected bord span may not be practical owing to the specifications of the available mechanized equipment. Some of the parameters used for the selection of mechanized mining equipment are mining height, required advance per blast, tons load out rates, ventilation requirements, dip of the orebody, dip of the excavations relative to the orebody, and equipment matching.
Table I
Typical generic operating dimensions for drill rigs
An equipment manufacturer will give a specification sheet based on the generic dimensions its equipment can operate in. Figure 2 and Table I give an example of the possible bord dimensions for three different types of drill rigs. Rock engineers that design layouts
must be familiar with these typical constraints and the fleet of equipment available on the mine.
According to these specifications, the optimal bord width for drill rig A and B, with its auto parallel coverage function, is a maximum of 6.8 m and 6.18 m, respectively (Table I). Drill rig C is less at 5.5 m. This implies that a drill rig in a bord width with a larger dimension needs to be re-adjusted with manual override if extra coverage is required. This can typically be done in bord widths up to 8.15 m. Bord spans larger than 8.15 m will require that the rig be moved from one stationary position in the bord to another to drill all the required holes. This will adversely affect the machine efficiency and the mining cycle may not be completed in the required time. Similarly, equipment used for installing support are also specified with minimum and maximum operating dimensions, as illustrated in Figures 3 to 5.
Typical bord widths and other parameters used in the South African mining industry obtained from a survey in 2020
Commodity
Based on these considerations, practical bord widths are not only a function of rock engineering considerations, but the dimensions should be matched to the capabilities of the equipment available as far as possible. An industry survey was conducted in 2020 for the SAMERDI WP4.3.1 project (Rock engineering principles affecting the mechanization of the South African mines) The bord widths for the various mines are shown in Table II. These dimensions vary from 6 m to 10 m and many of the mines use widths of 8 m. The efficiency of some of these mining operations can possibly be improved if the widths are better matched to the capabilities of the equipment, as discussed in the aforementioned.
Pillar widths based on rock engineering requirements
A routine problem encountered by rock engineers in the bordand-pillar mines is to determine the optimum pillar width for an assumed factor of safety and a specified bord width. To illustrate the increase in pillar width with depth, consider the equation presented
by Oates and Malan (2023). This was a calibration of the Hedley and Grant formula (Equation[ 1]) at a mine in the eastern Bushveld based on underground observations and numerical modelling and the equation is given by:
An iterative process is required to determine the width of the pillars for a specified factor of safety and bord width, and the general methodology is described in Wessels (2022). The relevant equation to solve for the calibrated formula in Equation [3] is derived in the following, and a practical method of solution is described. The equation derived is a useful equation as it gives the precise width of the pillars required at increasing depths. Again, it should be emphasized that practical mining engineering considerations will dictate the pillar width and it is not practical to attempt to cut a pillar with a width that includes a fraction of a
meter, such as 7.341 m, although these precise dimensions can be determined by using the following equation.
The factor of safety SF for the layout is given by Equation [2].
Tributary area theory (TAT) is commonly used to determine the average pillar stress σp and is given by:
where
ρ = overburden density
g = gravitational acceleration
H = depth below surface
For square pillars and a bord-and-pillar regular layout, the extraction ratio is given by:
where w is the pillar width and l is the bord and holing width (assumed to be of identical dimension). For a specified SF, an iterative approach is required to solve for the pillar width as changes in w will affect the pillar strength in Equation [3], but also the extraction ratio in Equation [5], and therefore the average pillar stress in Equation [4]. To obtain a solution, Equation [5] can be inserted in [4]:
This can be inserted in Equation [2]:
This can be rearranged to give the pillar strength.
This can be set equal to Equation [3]
After rearranging:
This can be simplified to:
Equation [11] was used to solve w for increasing depths. The parameters l = 8 m, SF = 1.5, ρ = 2900 kg/m3, g = 9.81 m/s2 and h = 2.5 m. An interactive process is required to solve for w and a simple method to do is to use the function ‘Goal Seek’ in Excel. This function automatically modifies the value of w, until the left-hand side of Equation [11] is equal to the right-hand side. The calculated pillar widths for an increase in depth is given in Figure 6. Note the calculated 12 m wide pillars at a depth of a 1000 m. This can, however, be misleading and is probably not the optimum pillar design, as the large w:h ratio is not considered. Also plotted in Figure 6 is the w:h ratio. For example, for a 2.5 m mining height, a 10 m wide pillar at a depth of 800 m has a w:h ratio of 4 and the so-called ‘squat’ pillar behaviour needs to be considered. A squat pillar formula has never been derived for hard rock pillars in the Bushveld Complex and this is presented in Appendix A based on an approach similar to that adopted by the coal mines. Also note that the pillar design given in Figure 6 may be conservative, as tributary area theory is used and this will typically overestimate the stress acting on the pillars.
Productivity aspects related to very large pillars at depth
The analysis provided in Figure 6 indicates that the specified pillar width at depths greater than a 1000 m will exceed 12 m. These large pillars have an adverse effect on production and other mining engineering aspects. These aspects include activities such as entry examination, ventilation layout requirements, and mine production scheduling. It may be difficult to maintain a mining cycle within a shift period for very large pillars. The Mine Health and Safety Act (Act 29 of 1996) and Minerals Act (Act 50 of 1991) are prescriptive in terms of the legislative requirements imposed on mine operators and owners in South Africa. Workplaces must be safe for employees to work in and not adversely affect their health. Employers must ensure that all risks are identified and measures must be implemented to eliminate or reduce exposure to risk.
Trackless mobile machinery currently used in low profile tabular hard rock mines are mostly diesel units producing significant heat, diesel particulate matter, and carbon dioxide. To ameliorate the risks associated with the heat, gasses, dust, and diesel particulate matter, the ventilation needs to be sufficient in
quantity, quality, and be directed towards the working ends. This is governed through standards and the mandatory codes of practices required by the Department of Mineral Resource and Energy in South Africa. The engine kilowatt (kW) capacity and the number of trackless mobile machinery in a mine determine the ventilation required. As an example, in one particular bord-and-pillar mine, the air volume required per rig section is 50 m3/s, with a velocity of 0.5 m/s at the last through road from the working face. It is also required that mine personnel can only re-enter an underground workplace when the volume of air in the area has been replaced 8 times to ensure that all harmful gases are removed. This period is termed the re-entry time. Entry examination occurs after the reentry period and it is a critical procedure prior to any other mining activities to ensure that all risks are addressed in a working place and the area is declared safe. The entry examination starts with measuring all ventilation requirements as no work can commence if the environmental conditions are sub-standard and hence, unsafe for employees. Larger pillars require larger distances to be mined before the pillars can be cut to establish the next ventilation holing. This has implications in terms of maintaining adequate ventilation conditions in the workplaces and will require ventilation controls in
the form of scoop brattices, ventilation seals, and other mechanical means of ventilating. Examples from one particular mine is illustrated in Figures 7 and 8. This illustrates the more onerous requirement for 10 m (or larger) pillars versus 8 m wide pillars.
Figure 7 illustrates that, when an advancing working face progress beyond 16 m from the last through ventilation roadway (indicated by ‘A’), a ventilation control named a ‘scoop brattice’ will be required. This direct ventilation flows towards the working face to maintain the required ventilation conditions. This additional control will be adequate for up to 24 m. This allows for the next pillar holing to be holed through, reducing the need for additional ventilation controls.
Figure 8 illustrates that, as the advancing faces progress beyond a distance of 24 m because of increased pillar sizes, additional ventilation controls such as 11 kW air jet fans, will be required to meet the ventilation requirements. Pillar sizes beyond 10 m will require ventilation controls similar to those used in mining development ends consisting of a combination of 75-kW, 45kW,and 22.5-kW booster fans with a range of different diameter ventilation columns for each, with various delivery and pick-up positions to prevent recirculation. This means additional employees
Table III
Drill rig operator critical path-based activities and duties per shift Task
Pre-shift machine inspection.
Refuel machine at underground refueling location.
Tram to the nearest electrical point for electrical connection needed.
Park machine safely and connect machine to electrical point.
Tram to face / bord planned for drilling.
Park and position machine safely and correctly for drilling.
Suspend 70 m electrical cable to hanging wall as required.
Connect drilling water and establish water pumping arrangements.
Actual drilling time per bord based on bord width – An operator is required to complete two faces / bords per shift.
Tram machine to wash bay after drilling activity complete.
Wash machine and report at end of shift.
per stoping crew resulting in reduced efficiencies. The larger the pillars are, the more onerous the ventilation controls become and the more time it will take to complete a full mining cycle. This will lead to reduced productivity levels.
Mining operations consist of an activity sequence that works in series and an activity can only start when the preceding activity is fully completed. For example, the workers can only drill a working face when all required support in that workplace has been completed. They can only charge up that face with explosives when the drilling is completed. To illustrate the typical times, a drill rig operator’s daily duties are given in Table III.
The average times are derived from using a Sandvik DD210L single-boom electro-hydraulic development drill rig designed for underground mining. Key specifications include a coverage area of 36 m², a hole length of up to 3.5 m, and a hole diameter range of 43 to 64 mm. An operator needs 5.2 hours to drill just one working face that is 6 m wide, 5.6 hours for an 8 m wide excavation and 6.2 hours for a 10 m wide excavation. An operator is required to complete two working faces in a shift duration of 10 hours to meet productivity output parameters. Any additional requirements
6 m – 2h08 min
8 m – 2h42 min
10 m – 3h19 min
min
min
inhibiting the operator from utilizing the full shift hours available will result in the second end not to be completed in time.
Smaller pillars imply reduced meters advance required to affect holings, reducing additional ventilation control requirements and reduced time to declare working areas safe. This result in improved productivity efficiencies and cost benefits. A further benefit of using the smallest possible pillar size is that a larger overall extraction rate can be achieved (see Figure 9). Substantial additional revenue can be generated as the orebody is more efficiently mined. Some mines may argue that they have large reserves and therefore reducing the pillar sizes are not important. This approach is not acceptable as the onus is on the mining industry to exploit the orebodies optimally. The highest possible extraction ratio, which will still ensure stable excavations, needs to be adopted.
Smaller pillars and a higher extraction ratio reduce the required advance rate in the strike direction. It therefore takes longer to mine to the boundaries (see Figure 9). This is beneficial to the engineering department as there is less pressure to advance the conveyors on strike with associated labour and cost benefits. The conveyors can be kept close to the mining faces, reducing tramming time and
resulting in less wear and tear on the mining equipment. Smaller pillars also increase the life of mine, as one maximizes the available resource that can be economically extracted, providing significant benefits for communities and society at large.
Considering the mining engineering preference for smaller pillars discussed in the aforementioned, a careful study of the pillar design methodology is required. As shown in Section 3, the application of the Hedley and Grant formula in mines in the Bushveld Complex may result in a too conservative design if consideration is not given to the width to height (w:h) ratio of the pillars.
Regarding the strength of squat pillars, the original coal pillar database used by Salamon and Munro (1967) contained no pillar with a width to height ratio greater than 3.8. Evidence collected in the field suggested that, beyond a critical width to height ratio, the pillar strength exceeds that suggested by the simple power-law formula given in Equation [1]. Salamon (1982) therefore proposed that, when the width to height ratio exceeds a critical ratio, the pillar strength formula should be replaced by the following squat formula for coal pillars:
where
K = the strength of a unit cube of coal
V = the pillar volume (m3)
R = the pillar width to height ratio
R0 = the critical width to height ratio
ε = rate of pillar strength increase
From field data, no evidence was available of a collapse of a pillar with a width to height ratio greater than 4. Therefore, the critical width to height ratio was arbitrarily selected as 5. A value of 2.5 was chosen for ε as it was considerably lower than that obtained from laboratory tests on sandstone.
Interestingly, if R = R0, Equation [12] can be simplified as
[13]
and this is equivalent to the Salamon and Munro (1967) equation (Equation [A1], Appendix A) with values α = 0.46 and β = 0.66. At the critical width to height ratio (R0), the strength predicted by the coal squat pillar is therefore similar to that predicted by the Salamon power-law equation.
In the absence of any other equation, rock engineers in the hard rock mines of the Bushveld Complex often use Equation [12]. It should be considered that this equation was derived for coal pillars and its application to hard rock pillars can be questioned, as it was based on the coal pillar strength formula.
A further difficulty with this equation is that several assumptions need to be made and it is onerous to determine the rate of pillar strength increase (ε) and the critical width to height ratio (R0). Over the years, some criticism has been raised about the complexity of the need to combine the power-law equation and the squat pillar equations at an almost arbitrary w:h ratio. Ryder and Jager (2002) described it as follows: ‘‘Virtually all laboratory and field evidence indicates that the w:h strengthening curve actually has zero or positive upward curvature throughout – Figure 10. Yet, by its very structure, the power formula forces downward curvature on the fitted characteristic – dashed curve, Figure 10. This in turn forces the inelegant form of the ‘squat pillar formula’’.’
Figure 10—Laboratory and in-situ strengths of pillars for increasing w:h ratios (after Ryder and Jager, 2002)
If the same approach is followed for the Hedley and Grant equation, the equivalent squat pillar formula for hard rock using the Hedley and Grant exponents can be derived as (see Appendix A):
[14]
The same rate of pillar strength increase is assumed for hard rock (ε = 2.5) as for coal, which may be too conservative, but a smaller critical width to height ratio of 3 is deemed more appropriate for the onset of squat pillar behaviour. The motivation for this is as follows: Ryder and Jager (2002) noted that the onset of squat behaviour is significantly earlier for hard rock pillars than the w:h ratio of 5 adopted for coal pillars. Zipf (2001) also noted that the w:h ratios of pillars are always less than 3 for coal mine failures, usually much less than 1 in metal-mine failures, and less than about 2 for non-metal mine failures. An assumption of R0 = 3 for the UG2 pillars may therefore still be conservative. Based on these assumptions, Equation [14] can be used to estimate the strength of a 10 m wide UG2 pillar with a height of 2.5 m as:
For the Hedley and Grant equation with K = 75 MPa, the
[15]
Figure 11—Predicted strength of UG2 pillars using the combined Hedley and Grant formula and the squat formula for K = 75 MPa. The strength was calculated for a pillar height of 2.5 m. This is plotted for R0 = 3
predicted strength for a 10 m wide pillar is 119 MPa and the squat pillar formula therefore predicts that the 10 m wide pillar will be approximately 5% stronger. This is, however, based on the unverified assumptions and is only a first order estimate.
The combined Hedley and Grant and squat pillar strength for the UG2 is illustrated in Figure 11. Note that the upward curve in strength may start earlier than shown. This is for the adopted value of R0 = 3. Figure 12 illustrate the curves for of R0 = 2.5. Clearly the predicted strength will be significantly affected by the choice of R0.
There is not a significant difference between the coal and hard rock equations given in Equations [12] and [14]. This is to be expected as the exponents in the Salamon and Munro coal and Hedley and Grant hard rock formulae are not significantly different. These two squat pillar equations are compared in Figure 13 for w:h ratios between 3 and 5. Identical parameters are used in both equations namely K = 75 MPa, R0 = 3, ε = 2.5 and h = 2.5 m. Note that the coal squat pillar formula predicts a slightly lower strength. The predicted pillar strength will be more affected by the choice of R0.
Figures 11 and 12 highlight a very important aspect in terms of pillar design as part of the mining value chain. The uncertainty in the onset of squat pillar behaviour (R0 = 2.5 or R0 = 3.0) can result in significantly different pillar sizes. Faced with this uncertainty, rock engineers will invariably choose the conservative design and this may have an adverse effect on other aspects, such as the need for onerous ventilation requirements when cutting large pillars. There is therefore a need to critically examine the design criteria and the necessary studies and experimentation need to be done to obtain improved design methodologies. As an important cautionary note, Equation [14] needs to be tested using appropriate underground trial sites and monitoring. Furthermore, the uncertainty regarding the application of the coal squat pillar formula was highlighted by Mathey and Van der Merwe (2016), and these formulae should be used with caution.
Barrier pillars result in similar production constraints caused by large in-panel pillars. Use of these barrier pillars detrimentally affects the extraction ratio and time required to open new mining blocks. Some general rules for the introduction of barrier pillars
are given by Ryder and Jager (2002). There is not a good technical motivation for these pillars if the factor of safety is high on the in-panel pillars. It is stated in Ryder and Jager (2002): ‘It follows that the old ‘1/4 depth’ rule of thumb (that is, that the regional span:depth ratio should not exceed 1/4) is overly conservative if in-panel pillars are in place, and indeed regional pillars may not be necessary at all in the presence of strong in-panel pillars. Nevertheless, it is recommended that regional pillars be maintained as ‘barriers’, but at S/H ratios up to about ½.’. Interestingly, it is stated the ‘regional pillars may not be necessary at all’, but then it is recommended that it should be used anyway. This may result in an unjustified reduction in extraction ratio. Furthermore, potholes already cause substantial losses in some areas, especially when mining the UG2 reef. No attempt has been made to include these geological losses as part of regional pillar design. The in-pillar designs for the UG2 reef may possibly be rather conservative as a result.
Some understanding of the spatial distribution of potholes will be required to consider their possible use as part of a barrier pillar system for a new layout design. Chitiyo et al. (2008) describe the predictability of pothole characteristics and their spatial distribution at the Rustenburg Platinum Mine. They note that: ‘Prediction of pothole characteristics is a challenging task, confronting production geologists at the platinum mines of the Bushveld Complex. The frequency, distribution, size, shape, severity and relationship (FDS3R) of potholes has a huge impact on mine planning and scheduling, and consequently cost.’ Their quantitative analysis of potholes indicates that pothole size can be described by two partly overlapping lognormal distributions. They referred to these as Populations A (< 20 m diameter) and B (20-500m diameter). A third size range of very large potholes can be found and these were referred to as Population C (> 1 km in diameter). They state that for the UG2, Population A potholes are generally randomly distributed and clustered, whereas Population B potholes are randomly distributed with less clustering. The authors do not describe how they defined ‘clustering’ of the potholes, however. They also note that potholes are quasi- circular with a minor tendency of elongation. In the UG2, potholes with elongated forms are more prevalent in the size range 20 m – 500 m diameter. In summary, this previous study indicates that in both the UG2 and the Merensky Reef, the potholes are randomly distributed, with a tendency towards clustering. Clustering appears to be more prevalent in the smaller Population A potholes. No suitable proxy could be found for the prediction of UG2 pothole density and, according to the authors, these are best predicted by extrapolation of the known pothole density.
The distribution of potholes and other geological structures on the UG2 reef horizon at a mine in the eastern Bushveld are illustrated in Figure 14. Note the high density of these structures and it is clear that a tributary area theory assumption for the inpanel pillar stress will overestimate the average pillar stress (σp) values. Also, of significance is the light green dykes traversing the orebody. Only strategic development ends are mined through the dykes and potholes and these include important roadways, strike belts, and ventilation ends. The dykes will therefore also reduce the extraction ratio and reduce the stress on some of the in-panel pillars. The actual layout and the many regional pillars are shown in Figure 15.
The total pothole area for Figure 14 was calculated as 191 480 m2 and the total mine area, including the pillars and geology, as shown in Figure 15 is 2 629 761 m2. This implies that the extraction ratio is a maximum of 92.7%. It should be noted, however, that this is a conservative calculation of the extraction
ratio as all the other large pillars (e.g., the decline pillars and the dykes) were not considered. Recent figures obtained from the mine provided a worse extraction ratio. The total mine area, including pillars, is 3 150 589 m2, while the mined area is only 2 169 789 m2. This provides an overall extraction ratio of only 68.9%. It will therefore not be beneficial to introduce an additional barrier pillar system, as the average pillar stress (σp) values will be lower than that predicted by tributary area theory (TAT).
Although it is known that TAT is a conservative approach to estimate σp values and that abutments will reduce σp, the effect of different spans on σp has never been quantified. A number of modelling runs on square layouts with different mining spans were therefore conducted for this study using the TEXAN code (Napier and Malan, 2007). A layout of 7 m wide pillars and 8 m wide bords were used for all the simulations. The key objective was to determine if the proximity of abutments will affect the peak and average pillar stress in the mining areas.
Table IV
Square geometries simulated
Table V
APS values predicted by TAT for the depths simulated
The geometries simulated are illustrated in Figures 16 and 17. The parameters of the various layout sizes are also summarized in Table IV. All geometries were simulated at depths of 200 m, 400 m, and 600 m. The simulations were also conducted with the TEXAN code. The parameters used were Young’s modulus = 70 GPa, Poisson’s ratio = 0.2, and an overburden density = 3100 kg/m3. The TAT values at the three depths simulated are provided in Table V. Square elements with a size of 1 m were used. Each pillar therefore consisted of 49 elements and the largest model span required the use of 209 764 elements. For each of the simulations, the peak APS as
well as the average APS of all the pillars (except for the three largest spans) were computed. As expected, both the peak and average APS values increased as the span increased.
A study of the simulated data indicated that the peak APS and average APS as a function of the mining area can be simulated with the following empirical equations (these were derived for this study):
where
σpeak = peak σp in the centre of the square mining area
σave = average σp of all the pillars in the square mining area
TAT = σp predicted by tributary area theory
A = total area mined
A0 = tributary area (unit cell of the geometry)
γ,δ,ω,η = constants
Table VI
Calibrated parameters for the empirical stress equations for the ‘infinite’ depth simulations
The TAT value is given by Equation [4] and this can be inserted to give: [18] [19]
Note that in the limit if A → ∞, the values correctly tend to the TAT value: [20] [21]
The results for the different areas and the three depths are illustrated in Figures 18 to 20. Note that the newly derived empirical models in Equations [18] and [19] provide a very good fit with the numerical models. The simulated values are less than the TAT value in each case. It correctly predicts that as the area increases in sizes, the values tend to the TAT value. The peak APS value for all three depths is 98% of the TAT value for the largest mined area of 209 764 m2. In comparison, the σave of all pillars in the simulated area is substantially lower than the TAT value. The question should be posed if the pillar designs should not be rather done by using this σave value. Note that the σave values were not calculated for the largest two geometries owing to the lack of an automated post
processor for TEXAN and the onerous task of finding and averaging the correct pillar elements for 900 pillars in a data dump of 209 764 elements.
The calibrated parameters for Equations [18] and [19] are given in Table VI. The method of least squares was used to find the calibrated values of γ, δ, ω, and η. This can be easily done by using the ‘Solver’ add-in utility in Excel. Interestingly, the calibrated values are essentially similar for the various depths.
In summary, it is clear from this modelling that abutments and geological losses will result in average pillar stresses that can be substantially smaller than that predicted by TAT. Designs not considering these effects will likely be too conservative and will result in an unnecessary additional reduction in extraction ratio and an increase in pillar sizes. Numerical modelling can assist with these designs to estimate more realistic stress magnitudes acting on the pillars. It is important in future that rock engineering designs are not only based on historic methodologies and empirical equations that may not always be applicable. Rock engineers should question the methodologies, establish trial sites, and monitor the rock mass behaviour to search for methods to optimize designs. The sentiment expressed by Franklin (1977) is still applicable today:
‘One solution for design based on uncertain data is to adopt a conservative approach with correspondingly high factors of safety. A better alternative is to recognize that much of the design work must be done in the course of execution of the project based on observations of actual rock conditions and on the records obtained by monitoring.’
This study highlighted the importance to include practical mining considerations when conducting pillars designs for bord-and pillarlayouts. Mechanized equipment, such as drill rigs, are designed to function best when bord widths are restricted to a particular dimension and, if possible, the rock engineering designs should accommodate this. Large pillars should preferably be avoided at great depths, as this will result in onerous ventilation requirements and poor efficiencies when cutting these pillars. Extremely large pillars may in fact not be required at great depth owing to the squat pillar behaviour of these pillars. A squat pillar formula for hard rock pillars based on the exponents of the Hedley and Grant formula, is discussed in the paper. This work needs to be verified in future using experimental studies. Estimating pillar stress is a further important aspect of pillar design. It is clear from the modelling conducted in the study that abutments and geological losses will result in average pillar stresses that can be substantially smaller than that predicted by TAT. Numerical modelling should be used to estimate more realistic stress magnitudes acting on the in-panel pillars. Stress measurements should also be conducted to verify these modelling results.
Acknowledgements
This work forms part of the M Eng (Mining Engineering) study of Mr Willie Theron at the University of Pretoria. The authors would like to thank Northam Platinum for their permission to publish this information. The assistance provided by Noel Fernandes is greatly acknowledged.
References
Barton, N. 1989. Cavern design for Hong Kong rocks, In AW Malone & PGD Whiteside (eds), Rock cavern –Hong Kong. The Australasian Institute of Mining and Metallurgy, Melbourne, pp. 179–202.
Brady, T., Martin, L., Pakalnis, R. 2004. Empirical approaches for opening design in weak rock masses. National Institute of Occupational Safety and Health, United states of America. https://stacks.cdc.gov/view/cdc/8691
Chitiyo, G., Schweitzer, J., De Waal, S., Lambert, P., Olgilvie, P. 2008. Predictability of pothole characteristics and their spatial
distribution at Rustenburg Platinum Mine. Journal of the Southern African Institute of Mining and Metallurgy, vol. 108, no. 12, pp. 733–740.
Franklin, J.A. 1977. The monitoring of structures in rock. International Journal of Rock Mechanics and Mining Sciences & Geomechanics Abstracts, vol. 14, no. 4, pp. 163–192. https://doi.org/10.1016/0148-9062(77)90947-0
Hedley, D.G.F., Grant, F. 1972. Stope-and-pillar design for the Elliot Lake Uranium Mines. Canadian Institute of Mining and Metallurgy vol. 65, pp. 37–44.
Hutchinson, D.J., Diederichs, M.S. 1996. Cable Bolting in Underground Mines. Richmond: BiTech Publishers.
Ile, D., Malan, D.F. 2023. A study of backfill confinement to reinforce pillars in bord and pillar layouts. Journal of the Southern African Institute of Mining and Metallurgy, vol. 123, no. 5, pp. 223–234. http://dx.doi.org/10.17159/24119717/2452/2023
Malan, D.F., Napier, J.A.L. 2011. The design of stable pillars in the Bushveld mines: A problem solved? Journal of the Southern African Institute of Mining and Metallurgy, vol. 111, pp. 821–836.
Mathey, M., Van der Merwe, J.N. 2016. Critique of the South African squat coal pillar strength formula. Journal of the Southern African Institute of Mining and Metallurgy, vol. 116, pp 291–299. https://dx.doi.org/10.17159/2411-9717/2016/ v116n3a11
Napier, J.A.L. and Malan, D.F. 2007. The computational analysis of shallow depth tabular mining problems. Journal of the Southern African Institute of Mining and Metallurgy, vol. 107, pp. 725–742.
Napier, J.A.L., Malan D.F. 2021. A limit equilibrium model of tabular mine pillar failure. Rock Mechanics and Rock Engineering, vol. 54, pp. 71–89. https://dx.doi.org/ 10.1007/s00603-02002265-2
Oates, T., Malan, D.F. 2023. A study of UG2 pillar strength using a new pillar database. Journal of the Southern African Institute of Mining and Metallurgy, vol. 123, no. 5, pp. 265–274. http://dx.doi.org/10.17159/2411-9717/2656/2023
Ryder, J.A., Jager, A.J. 2002. A textbook on rock mechanics for tabular hard rock mines. Johannesburg: SIMRAC
Salamon, M.D.G., Munro, A.H. 1967. A study of the strength of coal pillars. Journal of the South African Institute of Mining and Metallurgy, vol. 68, pp. 56–67.
Salamon, M.D.G. 1982. Unpublished Report to Wankie Colliery. Sandvik. 2024. Underground Drill Rigs. Retrieved from www.rocktechnology.sandvik
Watson, B.P., Theron, W., Fernandes, N., Kekana, W.O., Mahlangu, M.P., Betz, G., Carpede, A. 2021. UG2 pillar strength: Verification of the PlatMine formula. Journal of the Southern African Institute of Mining and Metallurgy, pp. 449–456. http://dx.doi.org/10.17159/2411-9717/1491/2021
Wessels, D.G. 2022. A review of the pillar design methodology for manganese mining operations in South Africa, M Eng dissertation, University of Pretoria.
Wessels, D.G., Malan, D.F. 2023. A limit equilibrium model to simulate time-dependent pillar scaling, Rock Mechanics and Rock Engineering, vol. 56, pp. 3773–3786. http://dx.doi. org/10.1007/s00603-023-03239-w
Zipf, R.K. 2001. Toward pillar design to prevent collapse in roomand-pillar mines. 108th Annual Exhibit and Meeting, Society for Mining, Metallurgy and Exploration, Krakow, Poland, Jun 2001. u
Derivation of a squat pillar formula for hard rock
The power-law strength formula is given by:
where K reflects the ‘strength’ of the in-situ rock, w is the width of the (square) pillar and h is the height in meters. The pillar volume V is given by
The width:height ratio is given by R:
Rewrite Equation [A2]:
Rewrite Equation [A3]:
Insert [A4] in [A5] and rearrange
Insert [A6] in [A4] and rearrange
When inserting [A6] and [A7] in [A1]:
This can be simplified as
and further as
which is similar to Equation [12] in the text
For Hedley and Grant, α = 0.5 and β = 0.75 and Equation [A11] becomes:
This form of the equation was extended by Salamon (1982) by adding a simple power law function of the ratio of the pillar width to height ratio (R) to the critical width to height ratio (R0). The exponent is the rate of pillar strength increase (ε). Salamon selected the following constant as the width of the scaling relationship of the power law:
If these assumptions are also made for a hard rock squat pillar equation with the Hedley and Grant exponents, the resulting squat pillar formula is given as
And if the calibrated K-value for UG2 is adopted (Oates and Malan, 2023):
Affiliation:
1University of the Witwatersrand, Johannesburg, South Africa
Correspondence to: B.P. Watson
Email: bryan.watson@wits.ac.za
Dates:
Received: 25 Apr. 2024
Revised: 9 Aug. 2024
Accepted: 12 Sept. 2024
Published: November 2024
How to cite: Watson, B.P., Mabala, M.I., and Kanda, M.J. 2024. Re-evaluation of the PlatMine chromitite pillar strength database. Journal of the Southern African Institute of Mining and Metallurgy, vol. 124, no.11 pp. 645–652
DOI:
http://dx.doi.org/10.17159/24119717/3382/2024
ORCiD:
B.P. Watson
http://orcid.org/0000-0003-0787-8767
M.I. Mabala
http://orcid.org/0009-0002-1486-3715
M.J. Kanda
http://orcid.org/0000-0002-1220-855X
by B.P. Watson1, M.I. Mabala1, and M.J. Kanda1
Abstract
A failed and stable Upper Group 2 chromitite pillar database was collected in 2007 as part of the PlatMine 1.2 pillar strength project. The database consisted of 177 pillars, of which 33 had failed. Most of the data were collected from various intermediate-depth mines near the town of Thabazimbi. Spans between rows of chain pillars were about 30 m. Pillar loads were estimated using pseudo-3D, elastic, boundary element modelling software. The pillar-load data were evaluated using a maximum likelihood regression analysis to determine strength parameters, following a similar approach to historically acceptable practice. The original formula was named the PlatMine Formula. This paper describes re-evaluations of the database, using a linear formula and several variations of the power formula. The formula providing the lowest standard deviation to the data in the database was considered the best representation of the pillars in the database. Through this rigorous process, a new formula for peak pillar strength was developed for Upper Group 2 chromitite pillars, which is unaffected by volume. The small standard deviation provided by this formula suggests a reliable relationship between strength and w/h ratio, in the w/h ratio range between 1.5 and 4.7. Accuracy, precision, and recall analysis confirmed the efficacy of this equation to the data in the database. Importantly, the new formula provided in the paper does not predict a significantly different strength to the current PlatMine formula, within the confines of the database.
Keywords
UG2 pillars, strength formula, chromitite pillars, back-analysis, pillar design
Introduction
The South African Bushveld Complex is a large layered igneous intrusion in the northern part of the country (Figure 1). The platinum group metals are mined from two tabular orebodies that dip at about 8° to 15° towards the centre of the complex and are known as the Merensky and Upper Group 2 (UG2) Reefs. This paper will deal with the pillar strength of the UG2 Reef, which comprises one or more chromitite seams of about 0.7 m to 1.4 m in thickness (Watson, et al., 2008). Mining is extensive in the western part of the complex, and generally, the Merensky Reef was mined out first, without having considered subsequent mining on the UG2 Reef. The depth of mining extends down to about 1 400 m, which can be considered as ‘Intermediate (medium) mining depth’ (Jager and Ryder, 1999), and is susceptible to stope collapses, or colloquially known as ‘backbreaks’ (Roberts, et al., 1997). A high-resistance support system is therefore required, and this is achieved using in-stope pillars. Most of the mining on the western side of the Bushveld was done using a conventional method that makes use of crush chain pillars, which are between 30 m wide panels (Figure 2). The pillar lines are oriented either on strike for breast mining (Figure 2), or dip for upand down-dip mining. For a breast mining configuration, the in-panel pillars are often located 1.5 m to 2.0 m below a gully (Figure 3). (The gully is used to assist with ore removal to the boxholes or local orepasses.) The zone between the gully and the pillar is termed a siding (Figure 3). Many of the shallower operations did not make use of sidings, meaning that the in-panel pillars were higher on the gully side than on the panel side. Gully heights varied between 1.8 m and 2.5 m. Thus, typical pillars under these conditions could have a height of about 2.3 m on the up-dip side and 1.5 m on the down-dip side, respectively.
Mechanization has increased bord-and-pillar mining, particularly in the newer, shallow-depth workings of the UG2 reef. The Hedley and Grant formula (Hedley and Grant, 1972), developed for Canadian uranium mines, was adopted for pillar design. This formula's rock mass strength component was generally reduced to about a third of the laboratory-determined uniaxial compressive strength (UCS) of UG2 chromitite. A value of 35 MPa was widely used (Malan and Napier, 2011). Many assumptions used in the formulation of this equation are unproven, and therefore the use in the design of UG2 pillars is questionable (Malan and
Napier, 2011). A potential consequence of using this uncertain methodology is to cut oversized pillars, which lowers the extraction ratio.
In the Rustenburg area, the two reefs are far apart vertically, so there is little stress interaction between the two reefs. However, in the Thabazimbi area, the reefs are much closer to each other. In this environment, it was possible to observe UG2 pillars cut in a destressed environment and under high-stress conditions. The high stresses occurred where the UG2 Reef was mined under or near stability pillars left on the Merensky Reef. In such instances, pillars often ranged from solid and stable to failed or crushed in a single panel. A database of 167 pillars was collected in this area as part of the PlatMine 1.2 pillar strength project (Watson et al., 2007). The PlatMine database and initial evaluation of a formula for UG2 pillar strength are described in Watson et al. (2021).
The PlatMine database consisted of 134 stable pillars where the modelled stresses were below the best-fit strengths and 33 pillars provided stresses somewhat higher than the strengths. Most of the pillar width-to-height (w/h) ratios were between 1.5 and 4, with the largest proportion being between 2.0 and 3.0. The condition of the pillars was assessed visually and the possible stress on each pillar, at the date of observation, was determined using MinSim (COMRO, 1981), a pseudo-3D elastic displacement-discontinuity, boundary element model. Validation of the modelling results was done using analytical solutions (where possible), and by comparing the MinSim results to MINF (Spottiswoode and Milev, 2002). The analysis suggested an error of less than 10% in the average pillar stress (APS). Since the failure date of the pillars was not known, the strengths of many of the failed pillars in the database were overestimated by the models, and vice versa for stable pillars. It was, therefore, necessary to use a similar analysis approach as Salamon and Munro (1967) to determine a suitable equation. A maximum likelihood regression analysis was used to find the best fit to the available data by assuming a power formula and varying the values of the unknown exponents (α and β) and ‘k’, as shown in Equation [1]. The research described in this paper focuses on a re-evaluation of the PlatMine database.
Literature review
Various empirical formulae have been derived to design pillar dimensions based on pillar strength demand in coal and hard rock mines. Most of these formulae use the power-law and linear functions with various derivatives. Notable contributions have
[1]
been made by authors such as Salamon and Munro (1967), Hedley and Grant (1972), Bieniawski and Van Heerden (1975), Von Kimmelmann et al. (1984), Lunder and Pakalnis (1997), York and Canbulat (1998), Van der Merwe and Mathey (2013), Watson et al. (2021), Oates and Malan (2023), and many others. Despite the vast amount of research that has been done over almost five decades, most of these formulae lack sufficient data to provide confident statistical evaluations (Oates and Malan, 2023). There remains considerable uncertainty about the contributions of various strength parameters, and the current empirical formulae are only applicable to specific reef formations characterized by specific geological and geomechanical conditions. While the PlatMine formula (Watson et al., 2021) has demonstrated a notable increase in predicted UG2 pillar strength compared to traditional formulae, it has faced criticism for its tendency to forecast strength increase with an increase in volume.
The pursuit of a ‘universal’ strength equation remains elusive, primarily due to the challenge of reconciling many strength parameters into a single, simplistic equation. Since most of the simplistic equations are empirical, it stands to reason that a separate formula should be determined for each reef type. A further complication was described by Esterhuizen (2006) when the pillar w/h ratio fell below 1.5 (Figure 4). The results of his investigation suggest that a significant increase in variability occurs where the w/h ratio drops below 1.5. Oke and Esterhuizen (2017) showed that the influence of structure has a major influence on the stability of slender pillars. Zipf (2001), recorded that slender pillars have little load-bearing capacity. It was therefore decided that one of the reevaluations of the PlatMine database should exclude all pillars with a w/h ratio of less than 1.5.
Geomechanical laboratory tests were conducted on UG2 chromitite material (Maphosa, 2022). The results showed strong non-linear tendencies at low confinements (Figure 5). The laboratory results suggested that the UG2 pillars may also behave in a non-linear fashion and a power formula may therefore be more applicable than a linear formula to these pillars.
PlatMine database re-evaluation
Very little research has been conducted to develop reef-type specific pillar strength formulae for the hard rock mines in South Africa.
Considering the importance of designing UG2 pillars confidently, and the difficulties of collecting reliable data due to the ductile nature of chromitite, a decision was made to re-evaluate the existing PlatMine database. The published PlatMine formula (Watson et al., 2021) suggested a power relationship. Combinations of the unknown parameters in the formula (α, β and k) were varied iteratively until the lowest deviation coefficient was achieved. None of the parameters were manipulated. However, the final formula provided by Watson et al. (2021) suggested an increased strength with volume, which required further investigation. The re-evaluations described in this report include a linear formula and various forms of the power formula. The chosen linear formula (Scenario 1) was originally suggested by Bieniawski and Van Heerden (1975), and confirmed by York and Canbulat (1998). A modification for pillar length was added for rectangular pillars, as described by Watson et al. (2008):
Where: ki is the large-scale in situ cube strength, ‘a’ and ‘b’ are empirically determined factors for evaluating the strengthening effects of pillar length (for rectangular pillars) and w/h ratio, respectively.
Three different circumstances were considered for the power formula analyses:
➤ The β-exponent was fixed and varied manually until the α, and β-values were equal (Scenario 2). This analysis was adopted to understand the implication of eliminating of the volumetric effect.
➤ The α and β exponents proposed by Hedley and Grant (1972) were fixed and only the k-value was varied in the analysis (Scenario 3) to determine the efficacy of using this widely applied formula on the data in the database.
➤ All pillars with a w/h ratio of less than 1.5 were removed from the database (Scenario 4). The α and β-exponents were fixed at the same values as the PlatMine formula, and the k-value was determined by the analysis.
The standard deviation from a lognormal distribution (deviation coefficient) was calculated in every evaluation and used to determine the equation's effectiveness. This standard deviation (10±s) was evaluated regarding unity (Ryder et al., 2005). A lower deviation coefficient was considered to provide a more reliable strength law. The pillar conditions scale was coded as ‘stable’ or ‘failed’. Safety factors (SF) greater than unity were classified and
coded as ‘Stable’ and those values less than unity as ‘failed’. The original PlatMine formula for UG2 pillar strength (Watson et al., 2021) is: [3]
Where σp is the pillar strength, and we and he refer to the effective pillar width and height, respectively. The we parameter was determined using the Wagner (1974) formula for rectangular pillars: [4]
Where L is the pillar length
An ‘effective height’ (he) was calculated to allow for the presence of gullies adjacent to pillars. It was only used in the absence of a siding (Sd). The correction is based on numerical modelling by Roberts et al. (2002): [5]
Results
Scenario 1 involved the application of the linear formula as shown in Equation [1]. The back-fitted parameters from the database are shown in Table I.
The parameters of Scenario 2 are for the power formula (Equation [1]), where the volumetric effects on pillar strength were eliminated by assuming equal values for α and β. The results are provided in Table II and Equation [6]. [6]
In Scenario 3, the database was evaluated using the exponents suggested by Hedley and Grant (1972) and the analysis was only allowed to determine the k-value from the database. The k-value parameter resulting from the investigation and the input values are provided in Table III. Table III only shows the input parameters and not the results. Note that the k-value was the result.
The consideration in Scenario 4 was for a database with all pillar w/h ratios of less than 1.5 removed. The exponents (α and β)
Table I
Scenario 1 Back-fit values for linear Equation [1]
Parameter
ki (in situ cube strength)
a (Length parameter)
b (Linear w/he parameter) 0.43
Table II
Back-fit values for a power formula (Scenario 2) with equivalent exponents for w and h
Parameter
k
α (Effective width parameter)
β (Effective height parameter)
Table III
Back-fit values for a power formula (Scenario 3) with the exponents provided by Hedley and Grant (1972). Only the k-value was varied by the maximum likelihood analysis
Parameter
k
Value
MPa
α (Effective width parameter) 0.5
β (Effective height parameter) 0.75
Table IV
Back-fit values for a power formula (Scenario 4) with the slender pillars removed and α and β-values fixed to be the same as the PlatMine formula
Parameter
α (Effective width parameter) 0.67 β (Effective height parameter) 0.32
were fixed to be the same as the PlatMine formula, and the analysis evaluated the k-value. The k-value parameter resulting from the investigation and the input values are provided in Table IV. Comparisons were made between the various scenarios, the original PlatMine formula (Equation [3]) and the formula currently in use in the industry (Malan and Napier, 2011). The deviation coefficient was assumed to be a measure of the fit to the data in the database. A lower value indicates a better fit. The results showed that Scenario 2 provided the best solution and a better formula than the original PlatMine expression (Table V). The fact that Scenario 2 is slightly better than the linear formula, agrees with the non-linear behaviour of the laboratory test results in Figure 5. The removal of the slender pillars from the database had little effect on the strength results within the confines of the database (Figure 6). However, the deviation coefficient was significantly less for the original PlatMine formula, suggesting that the slender pillars did not have a negative effect on the database. The formula currently in use by the industry (Scenario 5 in Table V) shows the highest deviation coefficient (worst fit) to the data in the database.
of the results in Table V
Further analyses were carried out by comparing the predicted SF of each scenario described in Table V to the actual observed pillar conditions in the database. The aim was to identify the scenario/s that best predicted the observed conditions. To facilitate the comparison, predicted SF and pillar condition codes were transformed into two classes, representing ‘stable’ and ‘failed’ conditions:
SF > 1 = ‘stable’
SF < 1 = ‘failed’
The pillar conditions scale as illustrated by Watson et al. (2021) was also re-classified and coded as follows: ‘stable’ if the pillar condition code is less than 3, and ‘failed’ if the pillar conditions code is greater than 3. The result of the data re-coding was such that the database and the scenarios had a new data field with two classes, i.e. ‘stable’ or ‘failed’.
Table V
Comparison between the formulae
Scenario Equation S (Deviation coefficient)
Original PlatMine formula 0.0679
Scenario 1
Linear Formula 0.0676
Scenario 2
Power Formula with equal exponents for width and height 0.0671
Scenario 3
Exponents suggested by Hedley & Grant (1972) 0.0710
Scenario 4
Slender pillars removed 0.0691
Scenario 5
The formula currently in use by the industry. Exponents suggested by Hedley & Grant (1972). 1.309
The observed pillar conditions data (‘stable’ or ‘failed’) from the database were compared to the estimated data from the scenarios. The comparison allowed for the determination of the performance of all the variations of the pillar formulae (i.e., scenarios) used in classifying whether a pillar would ‘fail’ or be ‘stable’, based on the input parameters of its width and height. The analysis of the performance of the formulae and the varying parameters was evaluated, based on established metrics for classification models, i.e., accuracy, precision, and recall. The terms are described as:
➤ Accuracy: a measurement of how the model correctly predicted the failure of pillars. In other words, the rate at which the model predicts a pillar to be ‘stable’ and the pillar is indeed stable (or has been observed to be stable). It also measured the rate at which a pillar was predicted to have failed and is found to be failing. It is the overall correctness of the predictions. Careful consideration must be taken when using accuracy to evaluate the performance of a model. This is especially true when dealing with unbalanced data, as is the case in this database. Only 25% of the samples in the database
showed instances of failure while 75% illustrated stable conditions. It was therefore important to evaluate accuracy together with other measures, such as precision and recall.
➤ Precision is the ratio of true positive predictions to the total number of positive predictions (true positives + false positives). Note that in this case, a positive prediction was set to be the ‘stability’ classification. Precision asks: What proportion of ‘stability’ estimates was correct? That is, it reported how many of the pillars that were predicted to be stable, are stable. Precision is useful in the cases where a false positive (i.e., a pillar being predicted to be ‘stable’, and it is found not to be stable) is of higher concern than a false negative (i.e., a pillar predicted to have ‘failed’ and found rather to be ‘stable’). The cost of the false positives is that the pillars would be under-designed, and the consequence could cost lives, which is a higher price to pay than an overdesign that could be merely regarded as a more conservative design. Thus, when choosing a performance metric, precision was considered the most crucial in this study, however, it should be carefully studied along with other metrics.
➤ Recall (sensitivity) explained how many of the actual positive (i.e., ‘stable’ predictions) cases were predicted correctly. It is the ratio of true positives predicted divided by the total number of actual positives.
Table VI indicates that Scenario 1 (linear formula) and Scenario 2 (α = β = 0.71) achieve the same levels of accuracy, precision, and recall. In contrast, Scenario 5 (Hedley and Grant, 1972) demonstrates the poorest performance in accuracy and recall. While precision is the most critical metric in this study, it is important to note that Scenario 5, despite exhibiting ‘perfect precision,’ has very low recall. This high precision/low recall combination arises when a model is overly cautious in predicting stable pillars. Although Scenario 5 is always correct when it labels a pillar as stable, it misses many stable pillars, labelling them as unstable. For instance,
and Grant (1972)
Scenario 5 incorrectly classifies 88 stable pillars as unstable. Using Scenario 5 would lead to pillar overdesign due to its extreme conservatism. Considering all metrics, Scenario 1 and Scenario 2 show superior performance with a better balance between precision and recall.
Figure 7 provides a confusion matrix, showing the true positives (TP), false positives (FP), true negatives (TN), and false negatives (FN) found in all the scenarios:
➤ TP: When the model predicted the ‘stability’ of a pillar, and it was true.
➤ TN: When the model predicted a ‘failed’ pillar and it was true.
➤ FP (Type 1 error): When the model predicted the ‘stability’ of a pillar, but it was false (i.e., the pillar had failed).
➤ FN (Type 2 error): When the model predicted a ‘failed’ pillar, but it was false (i.e., the pillar was stable).
The performance matrices of Scenario 1 (linear formula), and Scenario 2 (α = β = 0.71) showed similar results in correctly classifying the pillars' stability and failure. Moreover, the models
All risk of false positives in the database when using Scenario 2 (Equation [6]) can be mitigated by a safety factor of 1.17. For uncertainty quantification using the deviation coefficient associated with Scenario 2, a probabilistic approach suggests that a safety factor of 1.6 would provide a confidence of stability of 99.9% for the data in the database (Figure 8). Table VI
from these scenarios outperformed the alternatives. Out of 167 predictions, the pillars were classified accurately 161 times. However, it is concerning that there were three instances where the pillars were classified as stable when they were not (i.e., false positives), which could pose a risk to human lives due to the potential pillar designs having been based on false positives. This occurred 2.24% of the time for Scenarios 1 and 2. FP rates for Scenario 3 (Hedley and Grant, 1972) - exponents only, Scenario 4 (slender pillars) and Scenario 5 (formula currently used by the industry) were 2.99%, 2.36%, and 0.00% respectively. Conversely, the false negative rates (FNR) for Scenarios 1 and 2 are the lowest at 9.09%, while FNR for Scenarios 3, 4, and 5 are 12.12%, 9.68% and 72.73%, respectively.
Discussion
All the analyses performed on the database suggest that Scenario 2 (Equation [6]) provides the best solution to the data in the database, followed closely by Scenario 1 (linear formula). These findings imply that there may not be a volume-strengthening effect as predicted by the original PlatMine Formula. However, it should be noted that the original PlatMine formula only shows a slightly poorer deviation coefficient (Table V), and the prediction performance metrics suggest a similar performance for both equations. In general, the results suggest a non-linear strengthening effect with a w/h ratio, in agreement with the behaviour of the laboratory tests. The results of all the equations are plotted against the w/h ratio for the range of data in the database in Figure 9. The analyses show that similar curves are provided by all the formulae, except the ‘commonly used’ method (Scenario 5), within the w/h ratio boundaries of the database. Of note is the small difference between the strength results of the original formula and the ‘equal α and β’ (Equation [6]) in the figure.
Figure 10 provides a comparison between the average pillar stress (APS) provided by Equation [6] (Scenario 2) and the APS that was determined by the elastic model. The small deviation coefficient (‘s’ in Table V) suggests that the formula provides a reliable relationship between strength and (w/h)e ratio for the range of pillar we and he in the database. It also indicates a high-quality database. However, it should be noted that there was a limited variation of pillar height in the database, ranging between 1.5 m and 2.0 m.
The distribution of 1.5 m high pillars in Figure 10 is illustrated by the green-coloured triangles and squares. The formula provided in Scenario 2 (Equation [6]) may be used for pillars with conditions like those in the database (Esterhuizen, 2014). These conditions are:
➤ The immediate foundation materials are pyroxenite and anorthosite.
➤ The pillars should not be weakened by thrust structures or weathering.
➤ The height should be restricted to between 1.5 m and about 2 m.
➤ The w/h ratio should be between 1.2 and 4.7.
One of the worst-performing scenarios in all the applied evaluations was Scenario 3 (Hedley and Grant, 1972). The calculated k-value was also significantly higher than the laboratory-determined UCS shown in Figure 5. The evaluations suggest that each rock type may require unique exponents (α and β) and k-value.
Conclusions and recommendations
The PlatMine database for UG2 pillar strength determination is shown to be of high quality. All the analyses of the database (including the prediction performance metrics) suggest that the most appropriate formula for the pillar strength data in the database is Equation [6]. The investigation suggests that the volumetric strengthening effect of pillars shown by the original PlatMine formula may not be true. The analysis implies that unique exponents (α and β) and k may be needed for every rock type. It should be noted that the prediction of pillar strength by Equation [6] is not significantly different to the original PlatMine formula, within the range of w/h ratios in the database. Equation [6] may be used cautiously on all Bushveld platinum mines with similar geotechnical, geometrical, and geomechanical conditions to the pillars in the database. It should be noted that there was a limited range of pillar heights in the database and therefore the formula should not be used on pillars higher than about 2 m. It is recommended that further work be done to verify Equation [6] in terms of underground measurements, laboratory tests, and numerical modelling. Further research should be done to improve confidence when extrapolating the formula to pillar heights above approximately 2 m.
Acknowledgements
PlatMine is acknowledged for facilitating the collection of data and the original data analysis. The Mandela Precinct is thanked for funding the re-evaluation of the PlatMine database. Dr John Ryder is thanked for his assistance in developing statistical software to evaluate the database.
References
Bieniawski, Z.T., Van Heerden, W.L. 1975. The significance of in situ tests on large rock specimens. International Journal of Rock Mechanics and Mining Sciences & Geomechanical Abstracts vol. 12, pp. 101–113. https://doi.org/10.1016/01489062(75)90004-2
COMRO. 1981. MINSIM-D User’s Manual. Chamber of Mines of South Africa, Johannesburg.
Esterhuizen, G.S. 2006. An evaluation of the strength of slender pillars. SME Annual Meeting, St. Louis, Missouri.
Esterhuizen, G.S. 2014. Extending Empirical Evidence through Numerical Modelling in Rock Engineering Design. The Southern African Institute of Mining and Metallurgy 6th South African Rock Engineering Symposium, vol. 114, pp 251–267.
Hedley, D.G.F., Grant, F. 1972. Stope pillar design for the Elliot Lake uranium mines. Bulletin of the Canadian Institute of Mining and Metallurgy, vol. 65, pp. 37.
Jager, A.J., Ryder, J.A. (Eds.), 1999. A Handbook on Rock Engineering Practise for tabular hard rock mines. The Safety in Mines Research Advisory Committee (SIMRAC), Johannesburg.
Lunder, P.J. 1994. Hard rock pillar strength estimation, an applied approach. MSc thesis, University of British Columbia.
Lunder, P.J., Pakalnis, R. 1997. Determination of the strength of hard-rock mine pillars. Bulletin of the Canadian Institute of Mining and Metallurgy. vol. 90, pp. 51–55.
Malan, D.F., Napier, J.A.L. 2011. The design of stable pillars in the Bushveld Complex mines: a problem solved? Journal of the South African Institute of Mining and Metallurgy, vol. 111, no. 12, pp. 821–836.
Maphosa, T.J. 2022. Optimum depth for the introduction of crush pillars at Impala platinum mine. MSc dissertation, School of Mining Engineering, University of Witwatersrand, Johannesburg, RSA.
Northam Platinum Limited. 2018. Annual Integrated Report 2018. Available at: https://www.northam.co.za/procurement/127investors-and-media/publications/719-annual-report [Accessed: 7 February 2020].
Oates, T.E., Malan, D.F. 2023. A study of UG2 pillar strength using a new pillar database. Journal of the South African Institute of Mining and Metallurgy. vol. 123, no. 5, pp. 265–274. http://dx.doi.org/10.17159/2411-9717/2656/2023
Oke, J., Esterhuizen G.S. 2017. Improving Hard Rock Pillar Design by Including Rock Mass Classification and Failure Mechanisms. Proceedings of 51st US Rock Mechanics/Geomechanics Symposium held in San Francisco, California, USA.
Potvin, Y., Hudyma, M., Miller, H.D.S. 1989. Rib pillar design in open stoping. Bulletin of the Canadian Institute of Mining and Metallurgy, vol. 82, pp. 31–36.
Roberts, D.P., Canbulat, I., Ryder, J.A. 2002. Design parameters for mine pillars: strength of pillars adjacent to gullies; design of stable pillars with w/h ratio greater than 6; optimum depth for
crush pillars. SIMRAC GAP617 Final Report. Safety in Mines Research Advisory Committee. Johannesburg.
Roberts, M.K.C., Grave, D.M.H., Jager, A.J., Klokow, J. 1997. Rock Mass Behaviour of the Merensky Reef at Northam Platinum Mine. SARES, Johannesburg, 1997.
Ryder, J.A., Watson, B.P., Kataka, M.O. 2005. Pillar strength backanalyses. PlatMine 1.2, Johannesburg.
Salamon, M.D.G., Munro, A.H. 1967. A study of the strength of coal pillars. Journal of the South African Institute of Mining and Metallurgy. vol. 68, pp. 55–67.
Spottiswoode, S.M., Milev, A.M. 2002. A methodology and computer program for applying improved, inelastic ERR for the design of mine layouts on planar reefs. SIMRAC GAP722 Final Report. SIMRAC. Johannesburg, pp 85.
Van der Merwe, J.N., Mathey, M. 2013. Update of coal pillar strength formulae for South African coal using two methods of analysis. Journal of the Southern African Institute of Mining and Metallurgy, vol. 113, no. 11, pp. 841–847.
Von Kimmelman, M.R., Hyde, B., Madgwick, R.J. 1984. The use of computer applications at BCL Limited in planning pillar extraction and the design of mining layouts. In Design and Performance of Underground Excavations. International Society of Rock Mechanics Symposium, Brown and Hudson, eds., British Geotechnical Society, London, pp. 53–63.
Wagner, H. 1974. Determination of the complete load-deformation characteristics of coal pillars. Proceedings of 3rd International Congress on Rock Mechanics, International Society of Rock Mechanics, Denver, vol. 2B, pp 1076–1082.
Watson, B.P., Kataka, M.O., Leteane, F.P., Kuijpers, J.S. 2007. Merensky and UG2 pillar strength back analyses. PlatMine 1.2, Johannesburg.
Watson, B.P., Lamos, R.A., Roberts, D.P. 2021. PlatMine pillar strength formula for the UG2 Reef. Journal of the Southern African Institute of Mining and Metallurgy, vol. 121, no. 8, pp. 437. http://dx.doi.org/10.17159/2411-9717/1387/2021
Watson, B.P., Ryder, J.A., Kataka, M.O., Kuijpers, J.S., and Leteane, F.P. 2008. Merensky pillar strength formulae based on back analysis of pillar failures at Impala Platinum. Journal of the Southern African Institute of Mining and Metallurgy, vol. 108, no. 8, pp. 449–461.
York, G., Canbulat, I. 1998. The scale effect, critical rock mass strength and pillar system design. Journal of the Southern African Institute of Mining and Metallurgy, vol. 98, no. 1, pp 23–37. http://dx.doi.org/0038-223X/3.00/0.00
Zipf, R.K. 2001. Toward pillar design to prevent collapse in roomand-pillar mines. 108th Annual Exhibit and Meeting, Society for Mining, Metallurgy and Exploration, Denver. u
Affiliation:
1Department of Mineral Resources and Energy, University of the Witwatersrand, South Africa
2School of Mining Engineering, University of the Witwatersrand, South Africa
Correspondence to: T.R. Stacey
Email: Thomas.Stacey@wits.ac.za
Dates:
Received: 17 July 2023
Revised: 7 Nov. 2023
Accepted: 17 Sept. 2024
Published: November 2024
How to cite:
Mokgohola, M. and Stacey, T.R.
2024. Fracturing of rock ahead of the face of an excavation and its relevance to mechanized excavation.
Journal of the Southern African Institute of Mining and Metallurgy, vol. 124, no.11 pp. 653–660
DOI:
http://dx.doi.org/10.17159/24119717/2966/2024
ORCiD:
T.R. Stacey
http://orcid.org/0000-0003-3763-9193
M. Mokgohola
http://orcid.org/0009-0006-6932-008X
by M. Mokgohloa1 and T.R. Stacey2
Abstract
Boring of tunnels and shafts in hard rock under high stress conditions is becoming more common as mines and tunnels are developed at greater depths. Under the high stress conditions, fracturing of the often-brittle rock occurs in the walls, backs, and ahead of advancing faces of excavations. Fracturing can have a significant impact on boring activities: sidewall spalling, which affects machine gripper capacity, and fractures can also develop in the rock ahead of the face, leading to blocky rock conditions, which may have a significant effect on machine excavation. Fracturing may develop dynamically, leading to rock bursts manifesting in the form of strain bursts, which can be hazardous and destructive. In brittle rock, fracturing is commonly extensional in nature. The focus of this paper is on fracturing in the face of the excavation. Examples of such fracturing behaviour are described briefly in the paper. Numerical analyses were carried out to predict the initiation of extension fractures and their orientations ahead of excavation surfaces, and the resulting formation of rock slabs/plates, and the stability of these plates. The results should be beneficial for the evaluation of the conditions prior to, and during boring operations.
Keywords
rock fracture, extension strain, tunnel boring, raise boring, strain burst
Introduction
Mines are operating at ever greater depths and therefore, access tunnels, shafts, and other excavations must be developed under very high stress conditions. In the civil engineering industry, tunnels are now also being developed under very deep cover for transport and hydroelectric purposes. As a result, the rock surrounding the excavations is subjected to very high stresses, leading to fracturing, spalling and, in some cases, rock bursting. Owing to the hazardous conditions, mechanized excavation methods are increasingly being used in the mining environment, and tunnel boring is commonly used for civil tunnels. The fracturing, spalling, and rock bursting that occur pose significant challenges to these mechanized excavation methods. In this paper, cases published in the literature are summarized to indicate the typical rock fracturing that mechanized equipment, in particular boring machines, will encounter under high stress conditions.
There are numerous publications dealing with spalling and its prediction under high stress conditions (Martin et al., 1997; Steffanizzi et al., 2007; Barla, 2014; Vazaios et al., 2019a; Vazaios et al., 2019b; Feng et al., 2018). In this section, brief descriptions reported in the literature will be given of cases of fracturing of brittle rock associated with boring under high stress conditions.
In the 1970s an open face 3.36 m diameter tunnel boring machine was introduced into a gold mine in South Africa, for the purpose of tunnel development at a depth of 2000 m (Graham, 1976). Shortly after the boring operation commenced, problems were encountered that severely limited the progress of the boring machine. These included ‘spalling of rock from the sidewalls, which in some cases was so extensive that the machine grippers could not reach the sidewalls; fall-out of blocks of rock from the face; abnormally high cutter wear, which resulted from inadequate gripping owing to fracturing of the sidewalls; damage to the belt conveyor caused by sharp pieces of fractured rock; accumulation alongside the machine of rock debris, which was hand lashed and resulted in delays.’ (Stacey and De Jongh, 1977). An investigation and analysis of the problems were carried out, involving mapping of the extent and orientation of stress-induced fractures around the tunnel and ahead of the face. This showed that all fractures observed were tensile, with clean surfaces, and there was no evidence of crushed material that would indicate shearing. Barring of the face
rock ahead of the face of an excavation and its relevance to mechanized excavation
revealed slabs 10 to 30 mm in thickness that were curved with the same radius as the cutter head. This confirmed the observation by borehole periscope of a fracture ahead of the face.
Problems were also experienced with another tunnel boring trial in a different gold mine (Taylor et al., 1978; Burgess and Taylor, 1980). This was a 3.4 m open face machine with two grippers on each side. After seven months of boring over a length of 196 m, major machine alterations were required, owing to the occurrence of rock fracturing (Taylor et al., 1978). The tunnel face came away in relatively large blocks, which measured around 0.6 m by 0.4 m by 0.3 m. These caused the head to jam, continually damaging the front transfer chute. Word of mouth also indicated that, to replace cutters (from the front), the machine had to be retracted several metres, since rocks popped somewhat violently from the face, causing hazardous conditions.
Fracturing at the face of a bored Alpine tunnel, which appears to be similar to the one described by Taylor et al. (1978), which was further described by Kaiser (2006), referring to Weh and Bertholet (2005). Experiences in other Alpine tunnels are described by Loew et al. (2010). During the construction of the Lötschberg base TBM tunnel with a cover of approximately 2000 m, spalling and bursting were experienced, mainly in front of the machine. In some instances, this involved the violent ejection of rock blocks, to the extent that the TBM cutter head vibrated for several minutes. Substantial energy release in the form of a strain burst was experienced (Kaiser et al., 1996).
Descriptions of rock burst, spalling and slabbing failures during construction of a hydropower station are given by Gong et al. (2012) and Feng et al. (2018). The overburden cover along the headrace tunnels is greater than 1500 m over much of its length, with a maximum cover of 2525 m. Rockbursts were experienced during excavation of the tunnels. Gong et al. (2012) refer to tunnel boring machine (TBM) cutterhead seizure due to rock bursting at the face, and the substantial time taken to clear rock debris in such a case. They also deal with the effects of rock bursting on cutter wear and cutterhead failure: the slabbing and rock bursting leading to an uneven face, impact loading, and cutterhead vibrations. The slabbing and irregular blocks resulting from rock bursting also caused problems with muck removal and damaged the belt conveyor. Zhang et al. (2012) also described major problems associated with rock bursting during tunnel development. However, these were associated with drill and blast excavation, not TBM excavation.
During raise boring at depth, many problems associated with rock fracturing have been experienced and large slabs of rock, with side lengths exceeding a metre, were frequently seen at the cutter head (Stacey and Harte, 1989). Hern and Engelsman (1988) reported problems associated with raise boring: ‘The bit body lost penetration. The bit body was lowered and found to be completely compacted. Large boulders fell from the cutting face and became trapped between the cutter wings and the stabilizer wings.’ Almost identical behaviour was described more recently by Rojat et al. (2009): ‘The boulders which led to packing problems also caused great concern for the miners’ safety when servicing the equipment… A large boulder fell and bent one of the pipes… This canopy was also damaged when a large boulder fell… Bit body was put back into service and reamed an additional 50 metres at which time the first stabilizer failed, allowing the bit body to fall 125 metres.’
Small diameter raise boring as a method of mechanized mining has been trialled in gold mines in South Africa. Early trials experienced fracturing of the rock at the face, as illustrated in Figure
1. More recent trials with this method are described by Roberts (2017). However, he focuses on the sidewall breakouts in the holes and does not mention fracturing of the face of the bore.
During experimental mechanized mining of gold reef by stope coring (Stacey, 1982b), shown in Figure 2, it was found that the rock being cored ‘burst’ spontaneously within the 600 mm diameter core barrel.
Figure 3 shows the face of a Stopecorer hole after face bursting, exhibiting a clean extension fracture surface. During one of the phases of the experimental coring programme, about an hour after coring in the first hole to be drilled, a ‘disc’, involving the full diameter, suddenly ‘burst’ very audibly off the face. This occurrence correlates with the observation of a fracture occurring ahead of the face of the Atomic Energy of Canada Limited (AECL) tunnel described by Martin (1997).
On a much smaller scale than the stope coring, drilling of borehole core under high stress conditions often results in discing of the core, examples being shown in Figure 4.
The fractures in the core are almost certainly extension fractures and extremely unlikely to be shear fractures. Stress analyses of coring, assuming axisymmetric conditions (Stacey, 1982a), showed a zone of extension strain ahead of the coring (Figure 5), which corresponds with the fracturing in Figure 4.
A relevant case, although not of a bored tunnel, involved the development of a drill and blast tunnel in a gold mine at a depth of 2800 m below surface (Ortlepp, 2001). After a blast to advance the tunnel, the tunnel self-mined a length of 16 m. This length formed along the line of a geological fault. The rock fragments resulting from the advance were similarly sized platelets 150 to 300 mm in size with a thickness of 0.1 to 0.2 times the diameter. The tunnel was partly filled with these fragments to a depth of 1.5 m, for a distance of 50 m from the blasted face. Release of occluded gas was associated with the event. Ortlepp (2001) suggested the following mechanism: ‘Extension fractures developed in the rock immediately ahead of the face. These would be sub-parallel to the face, forming thin slabs’; ‘The thin slabs or plates buckled under the high stress and burst outwards (ejection). In buckling, the slabs/plates broke into smaller fragments, which explains the size of platelets and the fines observed.’ Simple numerical stress analyses, using an extension strain failure criterion, indicated that a zone of extension strain occurred ahead of the tunnel face, and that the formation of the ‘cavity’ would follow the fault line.
It is apparent that the prediction of rock fracturing is critical for the evaluation of failure around excavations. The examples given indicate that extension fracture and failure are predominant in the high stress, brittle rock conditions encountered at deep levels. Van Aswegen (2013) states that, regarding fracturing of rock in a deep level gold mining environment, ‘The most commonly observed mining induced structures are extension fractures’. Barton and Shen (2017a) and Barton and Shen (2017b) describe extension failure in many competent rock conditions. The extension strain criterion (Stacey, 1981; Wesseloo and Stacey, 2016) for predicting fracturing and failure appears to be beneficial in this regard. The criterion predicts failure, even in areas of low stress magnitudes (Stacey and Yathavan, 2003), which occurs when total extension strain in the rock exceeds a critical value characterizing the rock type. The examples described in the afore-mentioned give a clear indication of the impact of extension fractures on the boring operations, ranging from spalling to buckling and even to bursting. Knowledge of the extent of potential fracturing will be beneficial to the boring projects, in particular when using tunnel boring machines, which may be susceptible to rock fracturing and rock bursting.
The above case studies demonstrate the detrimental effects that spalling of rock from the face and sidewalls of bored tunnels, shafts, and raises can have on the boring process. The implications are that the cutter head may encounter slabs and blocks of rock in the face that could be large. This will lead to uneven rotation, high cutter wear and irregular torque demand, all of which will affect the efficiency of the boring. Large blocks may also clog the cutter head and cause damage to the transfer chute and conveyor belt. In extreme conditions, strain bursting from the bored face may occur, with potentially destructive consequences. Fracturing and breakouts in the walls of the bore will be locations of impact on, and therefore wear and damage to gauge cutters. They will also result in uneven and loosened surfaces for machine grippers.
It is clear from many of the cases described that fracturing in a hard rock environment is extensile. Many descriptions of the fracturing involved refer to extension fractures. As a result, in this paper, the focus is on the face of the bore, and on the prediction of extension fracturing and spalling from the face that could occur in strong, brittle rock under high stress conditions. Wesseloo and Stacey (2000) evaluated zones of extension strain exceeding a typical critical magnitude surrounding, and ahead of, the face of a tunnel for a range of three dimensional in situ stress conditions (Figure 6). Such zones could certainly influence the performance of tunnel and raise boring, the further development of instability in the rock, and hence, the rock support requirements in the tunnel.
rock
of the face of an excavation and its relevance to mechanized excavation
A further example is the well-published AECL tunnel in Canada (Martin et al, 1997), which, although not a bored tunnel, did not involve excavation by blasting. This is a high-quality case study since the parameters are well known: the rock strength parameters and the in situ stresses, as well as the history of fracture and failure development. Breakout development was modelled using alternative failure criteria. The observed breakout geometry was matched well using the cohesion weakening friction strengthening criterion (Hadjiabdolmajid et al., 2002), as shown in Figure 7, but this also indicated failure on the sub-horizontal axis, which did not occur. The Mohr-Coulomb prediction was completely incorrect. Wesseloo (2000) modelled the development of the breakout, using a finite difference numerical analysis stepwise approach, applying an extension strain criterion (Wesseloo and Stacey, 2000). Zones adjacent to the surface, indicated as failed after each step, using the criterion, were nulled to simulate fallout of spalling rock. The predicted development of the breakout eventually stabilized, and its final geometry matched the observed geometry, as shown in Figure 7.
Criticism of this stepwise process could be levelled because of the ‘manual’ interaction, and because of the assumption of planestrain conditions. However, it is important to consider the threedimensional stresses. The axial stress magnitude, which may be different from that in the plane-strain assumption, has a significant influence on breakout formation (Xiang et al., 2023). However, the results of the analyses indicate the validity of the extension strain criterion, and further support in this regard is provided by Steffanizzi et al. (2007). This AECL example demonstrates the importance of using an appropriate failure criterion that corresponds with the expected failure mechanism. It is also important to note that, during development of this tunnel (Martin, 1997), microseismic events were recorded ahead of the tunnel face, indicating fracture development. In addition, it was noted that, after the drilling of the perimeter holes around the tunnel for mechanical excavation, a fracture formed ahead of the tunnel face (ISRM, 2012). Discrete fractures also occurred ahead of the face of the bored tunnel described by Stacey and De Jongh (1977).
In the stope coring example referred to, the bursting of the core was an obvious advantage from the point of view of production progress, since the rock was fragmented in the bursting process, allowing coring to be continuous. However, the problem that arose was one of the predictions of the conditions under which such bursting would, or would not, occur. This was dependent on the span of the stope created (the number of overlapping holes cored), which determined the stresses acting on the rock at the coring face. Some success was achieved with a simple analysis using an
extension strain criterion (Stacey, 1982b). Figure 8 shows a series of diagrams in which the black shading indicates that the critical extension strain has been exceeded.
At a span of 4.6 m, equivalent to 9 Stopecorer holes, it is only the circumferential area in which the extension strain criterion is not exceeded. The encountered condition showed that bursting occurred from the 8th hole onwards, indicating a satisfactory agreement between prediction and practice.
As a result of the widespread observations of extension fracturing associated with tunnel boring and the spalling from the face, the focus of stress analyses described in the next section will involve the face region and the use of an extension strain failure criterion (Wesseloo and Stacey, 2016). This criterion is summarized as follows:
ε3 = [σ3 – υ(σ1 + σ2)]/E [1]
For failure, the criterion is: ε3 ≥ εcr Where εcr is the critical value of extension strain. Applicable values can be determined from the uniaxial compressive strength, the modulus of elasticity and the Poisson's ratio of the rock, using the Equation [2]:
εcr = f. UCS. υ/E [2]
For fracture initiation strain, it is suggested that the value of ‘f ’ should be 0.3 and, for crack damage strain, the value of ‘f ’ should be 0.7. The orientation of the fracture (failure) surface will be normal to the direction of σ3.
It is postulated that, owing to the three-dimensional stress field acting on the tunnel face geometry, extension fractures will be formed in the rock ahead of the face as the tunnel boring progresses. It is also postulated that fractures will coalesce to form slabs or shells immediately ahead of the face, and that their thickness will be determined by the thickness critical for buckling. Thus, the extent of fracturing and the orientation of the fractures will be determined using an extension strain criterion, and the potential thickness of the slabs/blocks formed due to the high stresses will be determined using buckling criteria.
Stress analyses around a bored excavation in rock with the assumed properties of quartzite, and for several in situ stress ratios and magnitudes, were carried out using RocScience’s Examine3D program. The use of elastic analysis is justified, since the objective is to determine the potential failure extent at the onset of failure, and not to attempt to model actual failure, which will be in the nonlinear mode. In addition, excavation involves unloading, normal to the surface of the excavation, which is likely to be initially elastic, or at least linear. The input parameters used for the analyses are summarized in Tables I and II.
Principal stress and extension strain distributions were evaluated. In these analyses, critical extension strain values, ranging from 180 to 270 microstrain for crack initiation, and from 504 to 864 microstrain for the crack damage (failure), were considered for the quartzite (Wesseloo and Stacey, 2016). To identify the geometry of potential slabs resulting from the fracturing, fracture orientations were determined from the analyses. Potential buckling of the
Table I
Table II
Alternative in situ stress fields considered. (x-axial; y-vertical
σz
faces will be advanced into fractured rock, potentially causing problems with the head and cutters, and fracturing in the walls could lead to their instability, and gripping problems. The distance of predicted fracture development ahead of the face of the tunnel is dependent on the relative magnitudes of the principal stresses, and on the value of Poisson’s ratio.
slabs was then evaluated, based on fracture extents predicted for a critical extension strain of 200 microstrain. The results indicated similar principal stress distributions, under the same in situ stress conditions, around tunnels of different diameters. As would be expected, the predicted extents of failure vary for different tunnel sizes.
The relationships between the predicted maximum failure depths around an 8 m diameter tunnel and the critical extension strains are shown in Figure 9. This indicates the sensitivity of the in situ stress ratios and the critical extension strains. Both crack initiation and crack damage points are indicated on the graphs. As can be expected, since the analyses were elastic, there is a linear relationship between predicted depths of fracturing and values of the critical extension strain, and the tunnel size. This implies, confirming experience, that a smaller diameter tunnel is less likely to cause boring problems than a larger diameter tunnel.
For one of the in situ stress conditions, the potential extent of fracturing around and ahead of an 8 m diameter tunnel is shown as isosurfaces in Figure 10. From this figure, it can be seen that the tunnel face area is within a ‘cocoon’ of fractured rock. There are substantial zones of extension ahead of the tunnel face and in the tunnel walls, which are expected zones of fracturing that could lead to boring problems. These fractured zones will mean that tunnel
The orientations of extension fractures are normal to the minor principal stress orientation, that is, in the σ1-σ2 plane. Using the trajectory ribbon facility in Examine 3D, these orientations can be displayed, as shown in Figure 11. These ribbons illustrate the potential for the formation of ‘plates’ with flat slab, curved plate, and shell geometries ahead of the face. Buckling of such geometries will result in the release of the energy stored in the ‘plate’ due to the high stress levels. This release of energy could manifest as spalling and rock bursting, such as reported by Zhang et al. (2012) and Feng et al. (2018). Cutter pressures and their cutting action will also contribute to the break-up of the ‘plates’ in the absence of stresses sufficiently high to cause buckling.
As indicated in Figure 11, the rock ahead of the tunnel face will be substantially fractured and thus contain many incipient ‘plates’. To illustrate the extent of such zones, isosurfaces were generated, assuming a critical extension strain of 200 microstrain, which may be considered to be typical for brittle quartzite (Wesseloo and Stacey, 2000). It is suggested that the observed thickness of such ‘plates’ may be dictated by their buckling potential, which was thus investigated using three approaches.
rock ahead of the face of an excavation and its relevance to mechanized excavation
McGarr (1997) analysed slab buckling in excavation sidewalls, with dimension L, taking the maximum stress in the excavation sidewall (σ) to be close enough to the magnitude of the uniaxial compressive strength (UCS) of the rock, to generate cracks parallel to the free surface. The equation that follows, was used to analyse the generated slabs, with thickness of h, using a UCS of 180 MPa (E: elastic modulus; ν: Poisson’s ratio):
= {2√3√(1-0.22)√(180/50000)}/π
[3] = 0.0648
Therefore, the slenderness ratio L/h = 15.43. This is equivalent to l/t in Kazakidis (2002), who used Euler’s formula to calculate buckling stress (σb):
σb = π2E/{12(l/t)2}
= 172.8 MPa
[4]
These values are indications of the critical stress at which slab buckling would take place, and the slenderness ratio of 15.43, below which buckling failure will occur. The amplitude of flexure is given by:
C1 = (2/h)(L/π)2{(1-ν2)/E}σ1 [5] = 0.000664L2/h
Where:
L: Diameter
σ1: Applied stress
h: Slab thickness
L/h: Slenderness ratio
C1: Amplitude of flexure
The amplitude of flexure determines the point at which a tensile crack would propagate, causing the slab to break into two parts. It is apparent from the results obtained, that for the specified mechanical properties of rock, the amplitude of flexure will be dependent on the ratio of the square of the slab length to the slab thickness for noncircular excavations.
Similar models to that of McGarr (1997), were generated from the results obtained in Examine 3D, as indicated in Figures 12
III
and 13. It can be seen that, at the point where possible buckling is expected, the σ1/σ3 ratios range from 3.5 to 3.8 for a 6 m diameter tunnel and 3 to 5 for an 8 m diameter tunnel. The afore-mentioned equations were used to calculate some of the important parameters for the analysis of slab buckling. The results are summarized in Tables III and IV. For these values, graphs of generated stress versus slenderness ratio were plotted, shown in Figures 12 and 13, where an average slenderness ratio of 13 is predicted for 180 MPa, as indicated by red arrows on the graphs. It is apparent that the buckling stress is dependent on the slenderness ratio and elastic modulus.
It is evident that the smaller the slenderness ratio, the larger the buckling stress needed for buckling. When comparing the applied stress (σ1) and the buckling stress (σb), it can be seen that buckling is predicted. It is worth noting that the slab thicknesses determine the extent of the stability problem, in this case, the boring difficulty. For instance, comparing a 4 m diameter tunnel with an 8 m diameter tunnel, the slab thicknesses predicted are 150 mm and 340 mm, respectively. This implies that, owing to the much greater volume of rock involved, an eight-metre diameter tunnel would cause more boring problems than a four-metre tunnel at the same depth.
Contrary to this, when considering the buckling stress, considering the UCS of the rock, buckling is not predicted. According to Kazakidis (2002), the disadvantage of using Euler’s approach is the fact that, as the slenderness ratio increases, the presence of imperfections is likely to increase. Therefore, buckling can still occur, even under low critical loads (Pcr). In order to overcome this, the eccentricity of the applied load is considered, where the strength of the material is not taken into consideration. Therefore, the criterion of failure is based on the magnitude of the compressive (σcmax) and tensile (σtmax) stresses in the material. The following Equations [6]−[7] are used to calculate these parameters:
σcmax = σ + 6(σ/t)[e/cos(l√(3σ/E)/t)] [6]
σtmax = σ - 6(σ/t)[e/cos(l√(3σ/E)/t)] [7]
Application of these formulae yields the results in Tables V and VI, and Figures 14 and 15, assuming eccentricity (e) of t/4. It can be seen that potential buckling can be predicted when the slenderness
Summary of slab thickness, slenderness ratios and buckling stresses
Table IV
Summary of slab thickness, slenderness ratios, buckling stresses
Buckling Stress vs Slenderness Ratio (sx = 35, sy = 35, sz = 70)
Figure 13—Buckling stress versus slenderness ratio for buckling failure
Table V
Results for eccentric load approach for the determining maximum compressive and tensile stresses for σx=35 MPa, σy = 35 MPa, σz = 70 MPa D (m) t (m) σ (MPa) l/t σ max (MPa) compr σ
2
4
6
8
Figure 14—Determination of critical slenderness ratio for buckling analysis under eccentric load ratio is 26.2 or less, indicating that the compressive strength has been exceeded. This area is indicated as an unstable zone. The zone within the limits of UCS and uniaxial tensile strength (UTS) denotes stability, as can be seen in both Figures 14 and 15.
Conclusions
Observation of rock fracturing behaviour around the face of bored excavations under high stresses indicates the formation of extension fractures in the rock ahead of the face. A series of stress analyses was carried out to determine stress and strain distributions around
Table VI
Results for eccentric load approach for the determining maximum compressive and tensile stresses for σx = 70 MPa, σy = 35 MPa, σz = 70 MPa
Ratio
Figure 15—Determination of critical slenderness ratio for buckling analysis under eccentric load
and ahead of the faces of circular tunnels of various dimensions. Using an extension strain fracture criterion, the potential extents of fracturing ahead of the faces were determined, as well as the orientations of the extension fractures. The results of these analyses confirmed the observed fracturing behaviour. Using plate buckling theory, slab thicknesses, and their potential for failure were assessed. Stability was assessed by applying several plate buckling approaches to assess the buckling loads, and minimum and maximum compressive and tensile stresses. As can be expected, the results indicate that tunnels with larger diameters are more prone to significant failures than smaller diameter tunnels.
It is concluded that extension fracturing ahead of bored excavations can lead to the formation of rock slabs, and these can result in two failure mechanisms: slabs can suddenly detach with some violence from the face, and slabs formed may subsequently buckle with violence. Both mechanisms may result in rock bursts. The breaking up of the rock slabs by the cutters or by the bursting will result in blocky rock conditions, which can cause damage to the cutters and head, and lead to poor boring conditions. Damage to borers owing to severe bursting has also been reported.
References
Barla, G. 2014. TBM Tunneling in Deep Underground Excavation in Hard Rock with Spalling Behaviour. Proc GeomechanikKolloquium, Universitat Freiberg, pp. 25–39.
Barton, N., Shen, B. 2017a. Risk of shear failure and extensional failure around over-stressed excavations in brittle rock. Journal of Rock Mechanics and Geotechnical Engineering, (9), pp. 210–225. https://doi.org/10.1016/j.jrmge.2016.11.004
Barton, N., Shen, B. 2017b. Extension failure mechanisms explain failure initiation in deep tunnels and critical heights of cliff faces and near-vertical mountain walls. American Rock Mechanics Association, ARMA, vol. 17, no. 686, 20p.
Burgess, H., Taylor, J G. 1980. Tunnel boring in a deep South African gold mine. Trans. I.M.M., Section A, April 1980, pp. A84–A98.
Fracturing of rock ahead of the face of an excavation and its relevance to mechanized excavation
Feng, X-T., Xu, H., Qui, S-L., Li, S-J., Yang, C-X., Guo, H-S., Cheng, Y., Gao, Y-H. 2018. In situ observation of rock spalling in the deep tunnels of the China Jinping Underground Laboratory (2400m depth). Rock Mechanics and Rock Engineering, vol. 51, pp. 1193–1213.
Gong, Q. M., Yin, L. J., Wu, S. Y., Zhao, J., Ting, Y. 2012. Rock burst and slabbing failure and its influence on TBM excavation at headrace tunnel in Jinping II hydropower station. Engineering Geology, vol. 124, pp. 98–108.
Graham, P.C. 1976. Some problems associated with the use of a tunnel boring machine in deep-level mines, in Tunnelling ’76, ed. M.J. Jones, IMM London, pp. 397–403.
Hadjiabdolmajid, V., Kaiser, P. K., Martin, D. C. 2002. Modelling brittle failure of rock. International Journal of Rock Mechanics and Mining Sciences, vol. 39, pp. 731–741.
Hern, G.L., Engelsman, K.I. 1988. Two pass drilling a 6.1-meter diameter ventilation shaft. Proceedings of the 5th AustraliaNew Zealand Conference on Geomechanics. The Institution of Engineering and Technology, Australia, pp. 224–228.
ISRM. 2012. Why does it crack?, ISRM News Journal.
Kaiser, P.K. 2006. Rock mechanics considerations for the construction of deep tunnels in brittle ground, Keynote Lecture, Asia Rock Mechanics Symposium, Singapore, 12p
Kaiser, P. K., McCreath, D., Tannant, D. 1996. Canadian Rock burst Support Handbook, Sudbury: Geomechanics Research Centre and CAMIRO.
Kazakidis, V.N. 2002. Confinement effect and energy balance analyses for buckling failure under eccentric loading condition. Rock Mechanics and Rock Engineering, vol. 35, no. 2, pp. 115–126.
Loew, S., Barla, G., Diederichs, M. 2010. Engineering geology of Alpine tunnels: Past, present and future. Geologically active— Proceedings of the 11th IAEG Congress, pp. 201–253.
Martin, C.D. 1997. Seventeenth Canadian Geotechnical Colloquium: The effect of cohesion loss and stress path on brittle rock strength. Canadian Geotechnical Journal, vol. 34, no. 5, pp. 698–725.
Martin, C.D., Read, R.S., Martino, J.B. 1997. Observations of brittle failure around a circular test tunnel. International Journal of Rock Mechanics and Mining Sciences, vol. 34 no. 7, pp. 1065–1073.
McGarr, A. 1997. A mechanism for high wall-rock velocities in rockbursts. Pure and Applied Geophysics, vol. 150, pp. 381–391.
Ortlepp, W. D. 2001. The mechanism of a rock outburst in a quartzite tunnel in a deep mine. RaSiM5, South African Institute of Mining and Metallurgy, 5p.
Roberts, D. 2017. Calibration of a numerical model for bore-and-fill mining. Journal of the Southern African Institute of Mining and Metallurgy, vol. 117, no. 7, pp. 705–718.
Rojat, F., Labiouse, V., Kaiser, P.K., Descoeudres, F. 2009. Brittle rock failure in the Steg Lateral Adit of the Lotschberg Base Tunnel. Rock Mechanics and Rock Engineering, vol. 42, pp. 341–359.
Stacey, T.R. 1982a. Contribution to the mechanism of core discing, Journal of the Southern African Institute of Mining and Metallurgy, vol. 82, no. 9, pp. 269–274.
Stacey, T.R. 1982b. Mechanical mining of strong brittle rock by large diameter "Stopecoring" - rock mechanics investigations, Proceedings of the 14th Canadian Rock Mechanics Symposium, Vancouver, pp 96–99.
Stacey, T.R. 1981 A simple extension strain criterion for fracture of brittle rock. International Journal of Rock Mechanics and Mining Sciences, vol. 18, pp. 469–474.
Stacey, T.R., De Jongh, C.L. 1977. Stress fracturing around a deep level bored tunnel. Journal of the Southern African Institute of Mining and Metallurgy, vol. 78, no. 5, pp. 124–133.
Stacey, T.R., Harte, N.D. 1989. Deep level raise boring - prediction of rock problems. Proceedings of the International Symposium, Rock at Great Depth. Rock at Great Depth, ed V. Maury & D. Fourmaintraux, A A Balkema, vol. 2, pp. 583–588.
Stacey, T.R., Yathavan, K. 2003. Examples of fracturing of rock at very low stress levels. Proceedings of the 10th International Society for Rock Mechanics, ISRM 2003 – Technology Roadmap for Rock Mechanics. The Southern African Institute of Mining and Metallurgy, pp. 1155–1159.
Steffanizzi, S., Barla, G., Kaiser, P.K. 2007. Numerical modelling of strain driven fractures around tunnels in layered rock masses. Proceedings of the 11th International Congress of the International Society for Rock Mechanics, Ribeiro, Olalla and Grossmann (eds), Taylor and Francis Group, London, pp. 971–974.
Taylor, J.G., Taylor, R.N., Hall, A.E. 1978. The introduction of a tunnel borer into a South African gold mine. Journal of the Southern African Institute of Mining and Metallurgy, vol. 78, pp. 188–198.
Van Aswegen, G. 2013. Forensic rock mechanics, Ortlepp shears and other mining induced structures. Proceedings of RaSIM 2013, 8th International Symposium on Rockbursts and Seismicity in Mines, St Petersburg, Russia.
Vazaios, I., Diederichs, M.S., Vlachopoulos, N. 2019a. Assessment of strain bursting in deep tunnelling by using the finite-discrete element method. Journal of Rock Mechanics and Geotechnical Engineering, vol. 11, pp. 22–37.
Vazaios, I., Vlachopoulos, N., Diederichs, M.S. 2019b. Assessing fracturing mechanisms and evolution of excavation damaged zone of tunnels in interlocked rock masses at high stresses using a finite-discrete element approach. Journal of Rock Mechanics and Geotechnical Engineering, vol. 11, pp. 701–722.
Weh, M., Bertholet, F. 2005. TBM_Vortrieb und spannungsinduzierte Abschalungen im Vortrieb Raron/Steg, Presentation at GEAT’05 Symposium, Zurich, Switzerland, 9p.
Wesseloo, J. 2000. Predicting the extent of fracturing around underground excavations in brittle rock. Proceedings of the South African Young Geotechnical Engineers Conference, Stellenbosch. South African Institute of Civil Engineers, 12p.
Wesseloo, J., Stacey, T.R. 2016. Reconsideration of the extension strain criterion. Rock Mechanics and Rock Engineering, vol. 49, no. 12, pp. 4667–4679.
Wesseloo, J., Stacey, T.R. 2000. Face and sidewall fracturing in circular excavations and effects on excavation and support. Proceedings of the ITA World Tunnel Congress, “Tunnels Under Pressure”, Durban, South Africa, May 2000. The Southern African Institute of Mining and Metallurgy, pp. 553–558.
Xiang, Z., Moon, T., Si, G., Oh, J., Canbulat, I. 2023. Numerical analysis of V-shaped borehole breakout using three-dimensional discrete-element method. Rock Mechanics and Rock Engineering, vol. 56, pp. 3197–3214.
Zhang, C., Feng, X-T., Zhou, H., Qiu, S., Wu, W. 2012. Case histories of four extremely intense rockbursts in deep tunnels. Rock Mechanics and Rock Engineering, vol. 45, pp. 275–288. u
Affiliation:
1Faculty of Engineering, University of Birjand, Iran
Correspondence to:
H. Noferesti
Email: hnoferesty@birjand.ac.ir
Dates:
Received: 10 Aug. 2022
Revised: 5 Feb. 2024
Accepted: Aug. 2024
Published: November 2024
How to cite:
Doroudgar, A. and Noferrsti, H. 2024. Identifying the prone zones to initiation of unstable failure by numerical simulation of mining pillars under compression. Journal of the Southern African Institute of Mining and Metallurgy, vol. 124, no.11, pp. 661–672
DOI:
http://dx.doi.org/10.17159/24119717/2265/2024
ORCiD: H. Noferesti
http://orcid.org/0000-0003-0178-8429
A. Doroudgar
http://orcid.org/0009-0003-5213-0763
by A. Doroudgar1 and H. Noferesti1
Abstract
Unstable rock failure or rock bursting is one of the most dangerous problems in deep hard rock mines. This type of failure, that occurs uncontrollably, is associated with a significant release of strain energy from the surrounding rock. In this study, the numerical simulation of unstable rock failure was carried out using the three-dimensional explicit Lagranian finite-volume finite difference method to identify the onset and location of unstable failure events in the model. On this basis, a numerical simulation of mine pillars with width-to-height ratios of 0.5, 2 and 3 was performed. A criterion was developed, based on the calculation of the elastic strain energy, to determine the prone areas for the initiation of rockburst in the models. The results of this study showed that, in softer loading systems, due to large amounts of stored elastic strain energy, an unstable equilibrium is established, which leads to the rapid transfer of strain energy to the rock in the form of violent failure. It was also found that the unstable failure starts at the corners and free surface of the model. The new criterion developed in this study may help predict the occurrence of rockbursts in slender pillars and the design of pillars to control human and financial losses caused by this phenomenon.
Keywords mining pillars; rockburst; elastic strain energy; finite difference method
Introduction
Traditionally, in mathematical and numerical analyses for the design of surface or underground excavations, the stress-strength approach or safety factor has been given the main attention. If the safety factor is less than one or the permissible value, it is considered a failure, and then the design parameters are changed to prevent it. However, in actual deep mining practice, and based on many experiences, not all rock failures are considered dangerous. In some situations, deep underground miners deliberately create fractures in excavation walls or rock pillars to control ground stresses. By this logic, rock failures are divided into stable, which are safe and controllable, and unstable failures, which are uncontrollable and especially dangerous on a large scale. Based on the scale of this event, various names are given to the unstable failure phenomenon, including flaking, splitting, slabbing, and rock bursting.
As the mine depth increases, the in situ field stresses build up in the rocks. The mining activities cause the concentration of field stresses to increase to higher levels in the vicinity of underground excavations. As a result, in certain locations, the induced stress values are much higher than the stress level in situ. Very high-stress levels can cause sudden failure and a release of strain energy in a short period of time by throwing out rock fragments, or the so-called unstable rock failure or rockburst.
In the history of mining, various reports of unstable rock failure have been recorded at the mining pillars and stopes, which leads to the sudden outflow of debris and broken pieces into the work environment (Osterwald, 1962; Peperakis, 1958). So far, unstable rock failure has led to the instability of underground cavities, the total collapse of mining panels, and numerous physical and financial losses (Chase et al., 1995; Zingano et al., 2004).
Salamon (1970) conducted pioneering research that resulted in a stability criterion. This criterion determines whether the failure process occurs in a stable and non-violent manner or an unstable and violent manner. Since then, there has been a considerable amount of research conducted on the possibility of unstable failure, and several criteria have been proposed to classify and predict the severity of rockbursts (i.e., Barton et al., 1974; Russenes, 1974; Hoek and Brown, 1980; Kidybinski, 1981). While several criteria have been proposed for classifying and predicting rockburst intensity to provide a basis for the design of
excavation support, in practice, it has been found that applications of these criteria lead to inconsistent prediction results (Zhao et al., 2017). In addition, the suggested criteria have considered only the overall chance of this event at a particular mine site and cannot determine the exact location of rockburst in an underground excavation. In this paper, after reviewing the unstable failure theory, a new criterion is proposed that can be easily integrated into numerical models of underground excavations and has the potential to assist in the prediction of the location of rockbursts in mining pillars.
The unstable failure of the rock is closely related to the definitions of brittle and progressive failure. Brittle failure is a common failure of rock during which the strain energy of the material is greatly reduced. In this type of failure, there is usually very little plastic strain. Progressive failure is a type of failure in which the fracture and damage continue until the new geometry of the material reaches equilibrium. As a result, this type of failure is time dependent.
The unstable failure of rock occurs in underground mines when brittle rock is subjected to high stress by relatively soft loading systems (Cook, 1965; Salamon, 1970). This instability will be accompanied by the transfer of the potential energy stored in the loading system to the volume of crushed rock until the entire system reaches a static equilibrium. The energy required to propagate and develop the unstable failure is derived from the excess energy
released from the loading system during the failure process, which can neither be stored nor lost.
Rock failure typically occurs in a controlled quasi-static mode. However, if the stored strain energy of the external loading system is further applied to the failing rock, the failure can also acquire dynamic properties. If the loading system is shown to release more strain energy than can be stored or dissipated by the failing rock, then the system is said to be in unstable equilibrium (Garvey, 2013).
A new representation of the interaction between a rock specimen and the loading system in uniaxial compression is presented in Figure 1, based on Salamon's (1970) work. The rock sample and the loading system are demonstrated by elastic springs. The loading system is a linear spring with constant stiffness Ks, and the rock sample is considered a nonlinear spring with variable stiffness Kir Before the maximum rock strength, the rock sample is in static equilibrium with the loading system, i.e., the load F is applied to the rock by the loading system and vice versa.
Any small displacement, Δx, applied to the end of the rock specimen past the point of failure results in two changes: 1. a change of force on rock, ks×Δx, where ks represents the stiffness of the loading system, 2. a change of force on the loading system, Kfr×Δx, where Kfr represents the local slope of the post-failure force-displacement curve of the rock (Figure 2). If the loading system is softer than the rock specimen, i.e., ks < Kfr, then the total load applied on rock is greater than the load applied on the system and a net unstable load on failing rock exists that causes a violently unstable failure.
As mentioned earlier, the phenomenon of unstable rock failure has also been studied in terms of energy balance. Once the failing process starts, both the rock system and loading system will release the stored strain energy, but the rate of release is different and dependent on their stiffness values. Unstable equilibria exist when brittle rock is loaded past the point of failure by a comparatively soft loading system. If the loading system stiffness is less than the postfailure stiffness of a rock sample and the peak strength of the rock is exceeded, then potential energy stored in the loading system will be transferred rapidly into the failing rock in the form of an unstable failure.
Based on theoretical and experimental studies on rockburst events in the laboratory and field, several criteria have been proposed to classify and predict the intensity of rockbursts. New comprehensive reviews of these criteria are provided by Bacha et al. (2020) and Askaripour et al. (2022). In a broad sense, these criteria can be divided into two categories: 1. based on energy, 2. based on stress. Various indexes are used in these criteria, out of which one energy index, i.e., Wet, and three stress indexes, i.e., σθ/σc, σc/σ1, and σc/σv, are better known or accepted. The elastic strain energy index, Wet, was first proposed by Neyman et al. (1972) to categorize the intensity of the rockburst. The dimensionless value of this index is calculated as
Where Ee is the retained strain energy (elastic strain energy), and Ep is the dissipated strain energy. Both values are determined from elastic hysteresis loop parameters found in uniaxial compression loading and unloading tests.
The stress/strength index, σθ/σc, was first introduced by Russenes (1974) for classifying the intensity of rockburst events. This is where σθ and σc denote the tangential stress at the rockburst location and the uniaxial compressive strength of rock, respectively. Barton et al. (1974) introduced a strength/stress index, σc/σ1, for the classification of rockburst severity. Here σ1 denotes the major principal stress at the rockburst location. Another strength/stress index, σc/σv, was used by Hoek and Brown (1980) to estimate the damage potential of rockburst in underground mines. Here σv denotes the vertical stress at the mine location. Based on these four
Table I
Comparison between several criteria for rockburst classification
Figure 3—Stress-strain curves from loading-unloading uniaxial compression and the corresponding energy
indicators, many attempts have been made to classify the severity of rockbursts, usually into five categories: no, light, medium, heavy, and serious. Table I summarizes the different ranges proposed in this context. Subsequently, various other factors, including movement characteristics, sound characteristics, phenomenological characteristics, incision shape characteristics, time characteristics, and the degree of damage are employed to identify appropriate prevention strategies. Size of ejected fragments (d) is a factor that may be used as a rockburst descriptor: d < 10 cm for no rockburst, d = 10-30 cm for light rockburst, d = 30-80 cm for medium rockburst, d = 80-150 cm for heavy rockburst, and d > 150 cm for serious rockburst (Zhou et al., 2024).
Methodology
Developing a new criterion for identifying regions prone to unstable failure
As mentioned in the previous section, two approaches are followed in the study of unstable failure, i.e., the stress-strength approach and the energy balance approach. The stress-strength practice has been extensively developed in rock mechanics and used in various fields, such as experimental studies on rock, slope stability, and underground excavations. If the stresses on the rock overcome its strength, the rock fails.
Although the rock failure could be predicted using the stressstrength approach, the type of failure, i.e., stable, or unstable, is better predicted by using the energy balance approach. Therefore, the energy approach is adopted in this paper, and an unstable failure index (UFI) is proposed as the ratio of elastic work performed on a rock unit (W) to the maximum stored (retained) elastic energy in the rock (Ee):
In the uniaxial compression test of a rock sample, the area below the stress-strain curve up to the peak point is equal to the maximum density of the elastic strain energy stored in the rock, and is obtained from Equation [3] (Brady and Brown, 2013).
ee = ½σε
As mentioned, the unstable failure of the rock is closely related to the definition of brittle failure. Therefore, the behaviour of the rock, under unstable failure conditions up to the point of failure, can be assumed to be elastic. Also, given the maximum principal stress at the moment of failure, the elastic strain energy stored in the rock sample is:
Where V is the sample volume and E is Young's modulus. In triaxial compression, maximum storable elastic energy (Ee) in a rock sample is calculated using Equation [5] or [6]:
Substituting the normal strains from Equations [7−9] in Equation [6]:
According to Mohr-Coulomb failure criterion, at failure point:
Where c is the cohesion and ϕ is the angle of internal friction. By applying the Mohr-Coulomb behaviour model to the rock sample, the maximum elastic strain energy that could be stored in the rock, is calculated using the relation [12] or [13] for 3D or 2D simulations, respectively:
On the other hand, the elastic work performed on the rock (W) in 3D and 2D can be calculated from the relations [14−15] using shear and normal stresses (Brady and Brown, 2013).
Substituting Ee and W from Equations [12−15] in Equation [2], a new criterion, Equations [16−17] is obtained, which indicates the areas susceptible to the onset of unstable failure in rock.
According to Equation [2], UFI > 1 means that the work done on a rock unit is greater than the elastic strain energy stored in the rock. The excess energy can cause some kind of unstable failure unless it is absorbed by the plastic behaviour of the rock. Therefore, in a brittle rock that does not show plastic behaviour, UFI > 1 means the onset of unstable failure. As UFI increases from one, the severity of unstable failure increases. In general, UFI can be related to the widely studied Wet index to better estimate the onset of unstable failure. The minimum value of UFI above which unstable failure occurs is when the work done on a unit of rock is just equal to the maximum stored elastic energy plus the maximum strain energy dissipated in the rock:
There is an inverse relationship between UFImin and Wet values. Rocks that are more brittle and have a higher Wet exhibit unstable failure at lower UFImin values. Referring to Table I, and after using Equation [18], the minimum UFI for the onset of unstable failure are calculated as shown in Table II.
Previous criteria have been proposed only to classify and predict the intensity of rockbursts. However, the UFI index could be used in a numerical model to predict the rockburst's location (and intensity) around mining excavations. The next section presents an example of a UFI application in an FLAC3D model.
Table II The relation between the Wet index of rock and minimum UFI for the onset of unstable failure
In this study, a finite difference numerical method, based on continuum mechanics, was used to simulate unstable failure and to evaluate the post-failure behaviour of a brittle rock at the mine scale, similar to the work of Garvey (2013). Then, the criterion that was developed in this paper was applied to the numerical models to evaluate its efficiency.
Numerical methods based on continuum theory provide powerful tools to predict rock mass failure. The finite difference method is widely and successfully used in the field of rock mechanics (Itasca, 2018). One of the main reasons for studying unstable failure by the finite difference is the explicit numerical formulation of this method by calculating the dynamic motion as a response to the physical instability in the model. Unlike finite element and boundary element methods, the explicit numerical formulation of the finite difference method can calculate the equilibrium of unstable forces by applying motion equations to determine the potential of large strain displacements in a continuous environment.
A mine pillar was simulated in a 2D plane strain condition to represent a coal pillar with its roof and floor rock masses. The height of the coal layer is set at 2.4 m, but the pillar width takes values from 1.2 m to 7.2 m in different simulations. Therefore, the pillar width-to-height ratio varied from 1:2 to 3:1. Two entries, 3 m wide, were created in the model on both sides of the pillar. On the outer sides of the entries, elastic sidewalls were modelled outward at about 40 m and were given elastic properties identical to pillar properties. A height of 80 m was given to the roof and floor rocks. The final model is shown in Figure 4. On the left and right sides of the model, roller boundary conditions were applied.
The primary aim of this paper was to develop a new identifier for unstable failure in mining (coal) pillars. The characteristics of the surrounding rock mass and rock-coal interface affect the pillar behaviour, but considering the aim of this paper, the failure was not allowed to progress in the surrounding elastic mass, and no slipping was allowed at the rock-coal interface. Also, for a proper comparison, the analyses were conducted using the same bord span of 3 m.
Previous studies on simulating brittle rocks in a continuous medium have used the Mohr-Coulomb strain softening behaviour model to represent the deformation and strength properties of the coal seams (Badr 2004; Hobbs and Ord 1989; Garvey 2013). Therefore, in this study, the Mohr-Coulomb strain softening law is applied to the pillar model. Another reason for using this behavioural model is to reveal the natural strength reduction of brittle rocks. For this study, the model developed by Garvey (2013), which had been calibrated using the empirical Mark-Bieniawski and Salamon-Munro formulas for pillar strength, was modified to perform UFI calculations and then used to reflect the behaviour of coal pillars. The initial coal cohesion was set to 1.45 MPa, while the initial friction angle was assumed to be 23 degrees. With the introduction of a 0.0005 plastic strain, cohesion was varied with a drop rate of −60 MPa/strain. The assumption was made that the friction and dilation angles would increase when plastic deformation is introduced. Young's modulus and Poisson's ratio as the basic elastic properties are considered, 2.7 GPa and 0.12, respectively. The elastic properties of the roof and floor rocks are also adjusted based on the variable stiffness of the loading system during the tests. A square mesh with a unit size of 0.1 m x 0.1 m was used in the pillar area. In the rest of the models, a larger rectangular mesh was used to increase the calculation speed. A list of input parameters for the calibrated model is presented in Table III.
The stress-strain curves of the pillars with the width-to-height ratios of 1:2, 2:1, and 3:1, along with their post-peak behaviour, are shown in Figure 5. To plot these curves, the stresses were recorded at the base zones of the pillars. The pillar with W/H=0.5 is weaker than other pillars. Pillars with W/H=2 and 3 are stronger and show strain hardening with localized failures before the complete collapse.
The testing process is performed by applying velocity over the upper and lower boundaries of the pillar model to increase the stress in the pillar. Note that the effect of gravity is ignored and plays no role in pillar failure. The incremental loading process via boundary
Table III
Input parameters for the calibrated Garvey model
Coal properties
Density (kg/m3)
Young Modulus (GPa)
Initial cohesion value (Pa)
Cohesion drop initiating at 0.0005 plastic strain (Pa/strain)
Residual cohesion value at 0.0213 plastic strain (Pa)
Initial friction angle (°)
angle from 0.0005 to 0.0213 plastic strain (°)
angle at 0.0218 plastic strain (°)
dilation angle (°)
strength (Pa)
Rock mass properties
Density of rock mass (kg/m3)
Young Modulus of rockmass (GPa)
Figure 5—Stress-strain curves of coal pillars with 0.5 GPa stiffness of surrounding rock mass
displacement reduces the unstable equilibrium in the model, due to the energy released from the loading system. The velocity applied to the boundaries during each test is constant, but its value is chosen based on Young's modulus. The softer rock masses are loaded faster to reduce the time the test runs. The list of velocities applied to the model boundaries, based on Young's modulus mass values, is provided in Table IV.
x 106
x 106
x 106
x 106
Table IV
Boundary velocities relative to Young's modulus values Rockmass E (GPa)
The testing process is performed by applying velocity over the upper and lower boundaries of the pillar models up to the failure point. For each model, the UFI were estimated according to Equation [17]. Results of applying the proposed criterion to the pillar model with a width-to-height ratio of 1:2 for three different rock mass stiffness values are shown in the Figures 6 to 8.
In Figures 6 to 8, the UFI are higher at the corners, and lower at the top and bottom. In Figure 6, where the loading stiffness is lower than the pillar stiffness, the UFI are higher than one. This occurs in the corners and the pilar surface up to mid-height. These zones show the potential for unstable failure to occur suddenly with the release of high elastic strain energy. In Figures 7 and 8, where the loading stiffness is greater than the pillar stiffness, the UFI do not exceed one, which means that no unstable failure occurs in the pillars. For these pillars, keeping the width-to-height ratio at 1:2, the
maximum UFI value decreases with increasing Young's modulus of the surrounding rock mass, indicating the occurrence of more severe unstable failures in pillars with lower loading stiffness. By comparing Figures 6 to 8, it can be seen that, as the loading stiffness increases, the strain energy is distributed uniformly in the pillars. On the other hand, if the loading stiffness becomes less than the pillar stiffness, the strain energy is concentrated on the surface and corners of the pillar.
Figures 9 to 11 show the results of applying the proposed criterion to a pillar model with a width-to-height ratio of 2:1 for three different stiffness values of the rock mass. The UFI are higher at the corners and sidewalls, and lower at the top and bottom. Although similar results are obtained with the 1:2 pillar models, the maximum UFI decrease, which means the potential for unstable failure decreases as the width-to-height ratio increases. There is a clear difference in how strain energy is distributed in the pillar
models. It is concentrated in the walls and corners, while the centres of the pillars are less loaded. Results for the 2:1 pillar model provide a good comparison of the fracture concentration in the pillar walls. The elastic strain energy is concentrated closer to the pillar surface in Figure 9, with 0.5 GPa loading stiffness, than the pillars with 5 GPa and 20 GPa loading stiffness. In Figures 10 to 11, the energy levels are lower and are more dispersed throughout the pillar zones, and as a result, these conditions will not lead to unstable failure in the given pillar models.
Figures 12 to 14 show the results of applying the proposed criterion to the pillar model with a width-to-height ratio of 3:1 for three different rock mass stiffness values. Similar to the previous results, the concentration of elastic energy is greater at the corners and near the edges. If a failure occurred, the overall shape of the failed pillar would be similar. It is also observed that the elastic strain energy is more concentrated at the pillar ribs in the case of the 0.5 GPa rock mass. With the increase of rock mass stiffness, the energy distribution is more dispersed at the pillar.
Figure 15 shows the maximum UFI observed in each pillar against the loading stiffness and pillar width-to-height ratio. It is seen that UFI greater than one are developed only in the coal pillars with a loading stiffness of 0.5 GPa. When the surrounding rock mass or loading stiffness increases to 5 GPa, the maximum UFI decrease to less than one for all coal pillars. From 5 to 20GPa, no further decrease in maximum UFI is observed, but a slight increase of maximum UFI is recorded, which is strange at first glance. Regarding the local failures in the stress-strain curve of coal
pillars, an explanation for this issue is provided in Figure 5. Lower energy levels remain in the 2:1 coal pillar because more elastic strain energy is released compared to the 3:1 pillar. There are subtle differences in the mechanism of unstable failures in wide mining pillars.
The difference between the maximum and minimum UFI for each pillar versus loading stiffness is shown in Figure 16. How uniformly the strain energy is distributed throughout the coal pillars is revealed by the differential UFI. As the loading stiffness
increases, the strain energy is more dispersed in the coal pillars. A drastic change in energy distribution occurs when the loading stiffness changes from stiffness values lower than the pillar stiffness values to higher than the pillar stiffness values.
In Figure 17, the maximum UFI observed in each pillar are plotted against the ratio of pillar width-to-height. It is seen that the maximum UFI decrease with an increase in the width-to-height ratio. As this ratio increases, the potential for unstable failure decreases.
Based on the mining pillar models, the criterion proposed in this paper indicates that stress is concentrated in the upper and lower corners. This stress distribution pattern is also supported by a study conducted by Kabwe and Wang (2015) on the unstable failure of rock formations.
The excess energy values near the pillar edges are high, but they decrease from the surface to the depth of the model. This suggests that vertical fractures may extend layer by layer from the edges to the depth of the pillar. This result is consistent with definitions associated with unstable failure phenomena, such as spalling, slabbing, flaking, and splitting. Furthermore, this result is consistent with the experiments of Read and Martin (1996) and Hajiabdulmajid et al. (2002) in the Mine-by project regarding the simulation of the rock splitting process.
In addition, according to the above results, it is inferred that during the process of unstable failure, the rock pieces on the surface of the underground excavations may be thrown out at high speeds, and then the rock pieces behind them are thrown out at slower speeds. These results show that the instability of free surfaces of
Loading stiffness: 0.5 GPa
Loading stiffness: 5 GPa
Loading stiffness: 20 GPa
underground excavations leads to the initiation of unstable failure. Therefore, it is suggested to quickly reinforce all exposed surfaces with shotcrete and bolts after excavating the rock. These results are consistent with the numerical studies of Sun et al. (2007) on the simulation of rock bursting in circular tunnels under unloading conditions.
So far, many efforts have been made to reduce the probability of unstable failure events by modern mining operations. It is hard to completely prevent the phenomenon of unstable failure in mining practice, due to the uncertain stresses, strains, and micromechanical characteristics of the surrounding rocks. The application of numerical methods is essential in reducing the destructive effects of unstable failure in underground excavations, although the existing procedures for analysing this type of failure in numerical models also have limitations.
A method was developed to identify the location and intensity of unstable rock failure resulting from unstable equilibrium in continuous numerical models. Static energy balance was used to calculate the values of elastic strain energy and to develop a criterion to determine the areas prone to unstable failure initiation in mining pillars. The procedure of energy calculation as a direct method in the analysis of unstable failure compared to other presented approaches, has more physical relevance in the field of rock mechanics, providing a better understanding of the phenomenon of unstable fracture. In general, the proposed criterion performed well in identifying the fracture initiation regions and was consistent with previous studies on unstable rock failure.
The technique developed in this study can be used as a tool to assist future research on the design of mining pillars under unstable failure conditions, the selection of support systems, the evaluation of cutting sequences in retreat mining, the study of stress relaxation techniques, and the back analysis of unstable rock failures. This technique can help predict the occurrence of such incidents and control the resulting physical and financial damage.
References
Askaripour, M., Saeidi, A., Rouleau, A., Mercier-Langevin, P. 2022. Rockburst in underground excavations: A review of mechanism, classification, and prediction methods, Underground Space, vol. 7, no. 4, pp. 577–607. https://doi.org/10.1016/j. undsp.2021.11.008
Bacha, S., Mu, Z., Javed, A., Al Faisal, Sh. 2020. A review of rock burst’s experimental progress, warning, prediction, control and damage potential measures. Journal of Mining and Environment (JME), vol. 11, no. 1, pp. 31–48. https://dx.doi.org/10.22044/ jme.2019.9092.1797
Badr, S.A.E. 2004. Numerical analysis of coal yield pillars at deep longwall mines. PhD Thesis, Colorado School of Mines, Golden, CO, USA.
Barton, N., Lien, R., Lunde, J. 1974. Engineering classification of rock masses for the design of tunnel support. Rock Mechanics and Rock Engineering, vol. 6, no.4, pp. 189–236.
Brady, B.H.G., Brown, E.T. 2007. Rock mechanics: for underground mining. 3rd ed. Springer.
Chase, F.E., Zipf, R.K., Mark, C. 1994. The massive collapse of coal pillars: case histories from the United States. 13th International Conference on Ground Control in Mining. West Virginia University, Morgantown, pp. 69–80.
Cook, N.G.W. 1965. The failure of rock. International Journal of Rock Mechanics and Mining Sciences & Geomechanics Abstracts, vol. 2, no. 4, pp. 389–403.
Garvey, R.J. 2013. A study of unstable rock failure using finite difference and discrete element methods. PhD Thesis, Colorado School of Mines. Golden, CO, USA.
Hajiabdolmajid, V., Kaiser, P.K., Martin, C.D. 2002. Modelling brittle failure of rock. International Journal of Rock Mechanics and Mining Sciences, vol. 39, no. 6, pp. 731–741.
Hobbs, B.E., Ord, A. 1989. Numerical simulation of shear band formation in a frictional-dilational material. Archive of Applied Mechanics, vol. 59, no. 3, pp. 209–220.
Hoek, E., Brown, E.T. 1980. Underground excavation in rock. The Institute of Mining and Metallurgy, London, UK.
Itasca Consulting Group Inc. 2018. FLAC3D (Fast Lagrangian Analysis of Continua in 3 Dimensions), Version 6.00. Minneapolis, MN, USA.
Kabwe, E., Wang, Y. 2015. Review on Rockburst Theory and Types of Rock Support in Rockburst Prone Mines. Open Journal of Safety Science and Technology, vol. 5, no. 04, pp. 104–121. http://dx.doi.org/10.4236/ojsst.2015.54013
Kidybinski, A. 1981. Bursting liability indices of coal. Journal of Rock Mechanics and Mining Sciences, vol. 18, pp. 295–304.
Neyman, B., Szecowka, Z., Zuberek, W. 1972. Effective methods for fighting rock burst in Polish collieries. 5th International Strata Control Conference. London, pp. 1–9.
Osterwald, F.W. 1962. USGS relates geologic structures to bumps and deformation in coal mine workings. Mining Engineering, vol. 14, pp. 63–68.
Peperakis, J. 1958. Mountain bumps at the sunnyside mines. Mining Engineering, vol. 211, pp. 982–986.
Read, R.S., Martin, C.D. 1996. Technical summary of AECL’s Mineby Experiment phase I: Excavation response. Report no. AECL–11311, Atomic Energy of Canada Ltd. Pinawa, MB, Canada. Russenes, B.F. 1974. Analysis of rock spalling for tunnels in steep valley sides. M.Sc. thesis, Norwegian Institute of Technology, Trondheim, Department of Geology, 247p. (in Norwegian).
Salamon, M.D.G. 1970. Stability, instability and design of pillar workings. International Journal of Rock Mechanics and Mining Sciences & Geomechanics Abstracts, vol. 7, no. 6, pp. 613–631.
Sun, J., Zhu, Q., Lu, W. 2007. Numerical simulation of rock burst in circular tunnels under unloading conditions. Journal of China University of Mining and Technology, vol. 17, no. 4, pp. 552–556. https://doi.org/10.1016/S1006-1266(07)60144-8
Tao, Z.Y. 1988. Support design of tunnels subjected to rockbursting. ISRM International Symposium, Rock Mechanics and Power Plants, A.A. Balkema, pp. 407–411.
Wang, X.M., Dong, L.J., Fu, Y.H. 2009. Prediction of possibility and the level of rockburst based on uncertain average graded analysis method. Scientific Technical Review, vol. 27 no. 18, pp. 78–81. http://www.kjdb.org/EN/Y2009/V27/I0918/78
Zhang, G., Chen, J.X., Hu, B. 2003. Prediction and control of rockburst during deep excavation of a gold mine in China. Chinese Journal of Rock Mechanics and Engineering vol. 22, no. 10, pp. 1607–1612. https://wenku.baidu.com/ view/4e92c4d076a20029bd642d10.html
Zhao, G., Wang, D., Gao, B., Wang, S. 2017. Modifying rock burst criteria based on observations in a division tunnel. Engineering Geology. vol. 216, pp. 153–160. https://doi.org/10.1016/j. enggeo.2016.11.014
Zhou, J., Li, X.B., Mitri, H.S. 2017. A critical survey of empirical methods for evaluating rockburst potential. 15th IACMAG, Wuhan, China.
Zhou, J., Zhang, Y., Li, C., He, H., Li, X. 2024. Rockburst prediction and prevention in underground space excavation. Underground Space. vol. 14, pp. 70–98. https://doi.org/10.1016/j. undsp.2023.05.009
Zingano, A.C., Koppe, J.C., Costa, J. 2004. Violent coal pillar collapse–a case study. 23rd International Conference on Ground Control in Mining, Peng, Khair and Heasley Ed., West Virginia University, Morgantown, USA. u
The mining and minerals industry contributes 50% of South Africa’s exports and is one of the largest employers in the country. As such, it remains a key contributor to economic prosperity. The University of Pretoria takes its role in contributing to the sustainability of this vital economic sector seriously – with focused research and training opportunities emanating from both its Department of Mining Engineering and its Department of Materials Science and Metallurgical Engineering.
The Department of Mining Engineering focuses on conducting world-class research to meet the unique challenges of the South African mining industry. Through its research and teaching activities, the Department works towards expanding its role as a key player to rebuild and grow the country’s mining research capacity and find solutions to problems at grassroots level. Topics such as increased productivity and mine safety are crucial to the success of this endeavor. The Department of Mining Engineering at the University of Pretoria is guided by the principal of finding homegrown solutions for South Africa’s unique challenges.
The Department of Materials Science and Metallurgical Engineering prides itself on the valuable impact it makes on the minerals industry, both in terms of knowledge advancement and producing skilled professionals. With the support of its state-ofthe-art facilities, the Department ensures that its graduates are well prepared to meet the challenges of the modern world. The Department of Materials Science and Metallurgical Engineering at the University of Pretoria occupies a unique position in South Africa as the only academic department entirely dedicated to metallurgical engineering – allowing it to focus on issues relevant to the country’s unique metallurgy needs.
These two departments offer degree programmes at both undergraduate and postgraduate levels in their dedicated streams.
CONTACT MINING ENGIEERING
Abea Kgatshe: abea.kgatshe@up.ac.za
CONTACT MATERIALS SCIENCE AND METALLURGICAL ENGIEERING
Gabi Ngema: gabi.ngema@up.ac.za
www.up.ac.za/ebit
Faculty of Engineering, Built Environment and Information Technology
Fakulteit Ingenieurswese, Bou-omgewing en Inligtingtegnologie / Lefapha la Boetšenere, Tikologo ya Kago le Theknolotši ya Tshedimošo
Affiliation:
1University of Pretoria, South Africa
Correspondence to: U. Du Preez
Email: ulla.dup@gmail.com
Dates:
Received: May 2024
Revised: 28 Oct. 2024
Accepted: 29 Oct. 2024
Published: November 2024
How to cite:
Du Preez, U., Heyns, P.S. and Malan, D.F. 2024. The development of a linear cutting machine used to characterize FEM modelling parameters for cutting UG2 Reef.
Journal of the Southern African Institute of Mining and Metallurgy, vol. 124, no.11 pp. 673–682
DOI:
http://dx.doi.org/10.17159/24119717/3394/2024
ORCiD:
P.S. Heyns
http://orcid.org/0000-0002-6164-9490
D.F. Malan
http://orcid.org/0000-0002-9861-8735
by U. Du Preez1, P.S.Heyns1, and D.F. Malan1
Abstract
South Africa has two main platinum reef deposits, namely the Merensky reef and the UG2 reef. These reefs are currently mined using traditional drilling and blasting methods. Mechanized cutting could potentially enable continuous mining, which would offer significant advantages. This would require thorough understanding of the cutability of the rock. To explore this, a linear cutting machine was developed to conduct laboratory scale cutting tests. This work describes the development and commissioning of the cutting machine using sandstone, as well as subsequent characterization tests on UG2 reef samples.
UG2 reef has large variability in strength on a millimeter scale. This introduces uncertainty in the test results due to added variance from one cut to the next for the same UG2 reef sample. Another problem is the variability in rock properties of the UG2 reef, when testing samples from different mines. The cutting tests led to fine fragmentation, which is known to be a significant problem for cleaning operations in underground stopes and warrants further research.
A finite element method simulation of the rock cutting was conducted using ANSYS LS-DYNA and the continuous surface cap model to simulate rock cutting in the UG2 reef. It was found that it is possible to use LS-DYNA with the continuous surface cap model to model rock cutting of UG2 reef and get acceptable results, but the user must calibrate the model parameters using the experimental results. Therefore, the model is only fit for one set of cutting parameters and further work is required to generalize results.
Keywords
conical pick, continuous surface cap model, finite element method, linear cutting machine, specific energy, UG2 reef
Introduction
Traditional mining methods, involving drilling and blasting, have steadily been replaced by mechanized mining methods, to the extent that mechanized mining has become the predominant mode of mining for new mine developments in softer rock (Moxham, 2004). This is, however, not the case for gold mines, platinum mines and other hard rock mining operations in the South African Bushveld Complex.
South African gold and platinum mines have narrow tabular reefs, typically less than 1 m in height (Pickering, 2007). Equipment currently used for mechanized mining in soft rock are not suitable for narrow reef hard rock environments. The traditional drilling and blasting mining process is cyclic in nature. This constrains the rate of face advance and leads to poor utilization of the invested capital (Moxham, 2004).
Mechanized cutting offers the potential for continuous mining, which may lead to significantly improved rates of face advance (Vogt, 2016). Mechanized cutting does not cause instability of the rock due to explosions, there is no need to ventilate toxic gases before people can access the mine again after blasting, and it has the potential to reduce waste dilution (Moxham, 2004; Pickering, 2007). The cutting characteristics of South African hard rock narrow reef environments are not well understood, and this impedes the introduction of mechanical rock cutting in these mines.
Various researchers have used linear cutting machines (LCMs) to conduct laboratory scale cutting tests on different rock samples, using different cutting methods (Bilgin, et al., 2013; Copur, et al., 2017; Dehkhoda and Detournay, 2019; Hekimoglu, 2018; Kang, et al., 2016; Li, et al., 2022; Mendyka, 2017; Park, et al., 2018). In these tests, the cutting parameters were changed to determine the effect on the performance of the cutting method for a specific rock sample. Most of these tests were conducted using artificial rock samples, such as cement mortars and sandstones. There is, however, a dearth of research on South African hard rock types, such as UG2 reef.
Cutting parameters and cutting forces determined from laboratory scale experiments can be used to numerically simulate rock cutting using the finite-element method (FEM) (Huang, et al., 2016; Jaime, et al., 2015; Wicaksana, et al., 2021). Most of the numerical modelling for rock cutting are either for conical picks or symmetrical disk cutting used by tunnel boring machines (TBMs) (Stopka, 2021). The level of complexity of numerically modelling rock cutting using FEM is based on the selection of an appropriate rock failure model. The basic model frequently used is the MohrCoulomb failure criterion, whereas more advanced models include the concrete damage model, the Johnson Holmquist concrete model, and the continuous surface cap model (CSCM). Jaime (2015) compared these more advanced models and found that the CSCM gives the most realistic cutting forces and fragmentation patterns (Jaime, et al., 2015). This model was therefore used in this study.
Huang et al. (2016) used FEM for modelling of rock cutting using a conical pick. They compared the mean cutting forces and the peak cutting forces obtained from the simulation to theoretical values that were determined by using the equations given by Evans (1962) and Goktan (1997), as well as experimental values. The numerical simulations showed that there are various model parameters that influence the results and others have little effect. Previous research showed that there are many choices that need to be made about model parameters, such as element size, element type, boundary conditions, contact parameters and model parameters. Some are based on material properties and other are obtained through trial and error.
This work describes the development of a linear cutting machine (LCM) to determine the cutability of UG2 on laboratory scale samples. The first part of the work describes the development of the LCM, which was commissioned using sandstone with little to no variance in strength on a millimeter scale. Once the LCM was commissioned, various laboratory scale cutting tests with different cutting parameters were conducted on UG2 samples. The objective was to determine the impact of the different cutting parameters, to determine rock characteristics, and to investigate if the results follow the same trends as for other rock types. These UG2 rock characteristics are currently not available and represent an important new contribution.
The experimental results were used to calibrate the continuous surface cap model (CSCM) parameters, for one set of cutting parameters. The CSCM was selected because it was found by previous researchers to give good results for simulating rock cutting (Jaime, 2011; Huang, et al., 2016). The FEM results showed that it is possible to model rock cutting of UG2 reef using conical pick. The
present model requires calibration of the model using a specific set of cutting parameters and experimental results. Further work is required to ensure applicability of the model over a range of cutting conditions.
Development of a linear cutting machine for the UG2 experiments
A linear rock cutting machine was developed for this investigation. This LCM had to meet various design requirements. The LCM had to be sufficiently robust and stable when subjected to the cutting forces experienced along all three orthogonal directions (Kang, et al., 2016). Additionally, it had to allow linear motion of the conical pick, thus simulating the cutting process. This could be accomplished by either pushing the rock or pushing the conical pick (Bilgin, et al., 2013; Copur, et al., 2017; Park, et al., 2018).
Furthermore, the machine required the capability to measure three orthogonal cutting forces, namely drag force, normal force, and side force, as shown in Figure 1. Using the drag force, density, distance cut and mass of cut material, the specific energy could be determined for each cut. The specific energy is the amount of energy required to cut one cubic meter of material. The LCM should allow for accurate adjustments of the depth of cut, attack angle, skew angle, and cut spacing, as shown in Figure 1.
For this study, a radial arm drilling machine was modified to provide the translational degree-of-freedom requirements of the LCM. Figure 2 shows the different components of the LCM and the associated degrees-of-freedom.
A linear actuator moves horizontally, as shown by the red arrow. This horizontal movement simulates the cutting motion by pressing the pick through the rock. The linear actuator has a maximum horizontal movement of 240 mm. The speed at which it cuts can be adjusted. The radial arm drilling machine table allows for both horizontal and vertical movement. The vertical movement is shown by the yellow arrows. The table allows the cross-sliding table to move horizontally, as shown by the magenta arrow. Both the horizontal and vertical movement are used to move the rock specimen into the correct position. The cross-sliding table allows for accurate changes in cut spacing, shown by the light blue arrow. The spindle can move vertically, which allows for accurate changes to the cutting depth, shown by the green arrow. There are slots in the lower flange of the load cell assembly, which allow for change in the skew angle. The skew angle can be adjusted to a maximum of 30°. The attack angle can be changed by changing the bottom flange and pick holder. The bucket can hold a rock specimen with maximum dimensions of 500 mm wide, 250 mm long and 200 mm high. The bucket has a clamp that holds the rock specimen in place. The base
of the LCM is bolted to the ground. Because the LCM works as a press, all the forces act on the machine and not on the base. The base only gives stability. Figure 3 illustrates the dimensions of the conical pick used in the laboratory scale cutting tests.
A load cell was required to measure the cutting forces. This load cell was constructed by cementing four strain gauges to a cylindrical tube, as shown in Figure 4, and was calibrated by measuring strain while applying known forces. A combination of orthogonal forces was applied to emulate conditions during actual rock cutting.
The application of a combination of orthogonal forces for calibration purposes was done by pressing the point of the conical pick with a hydraulic jack and measuring the applied force. Two different combinations of forces were applied. The first was a combination of drag force and normal force, and the second was normal force and side force. The load cell outputs four values as measured by the half bridge strain gauges. These values were used in the linear equations as shown in Equations [1] to [3].
0°, and 10°. The attack angle was kept constant at 50°. The cutting speed was the same for all the tests at 50 mm/s and a sampling rate of 300 Hz was used for strain gauge measurements on all the tests. A cutting sequence comprized of firstly pre-cutting the surface to simulate a rock face (Park et al., 2018) and then nineteen subsequent cuts. The first cut was an initial cut. Then three of each cut spacing to cutting depth, s/d, ratios were cut. After each cut the cut material was collected and weighed. The weighed mass and the density of the material were used to determine the specific energy. Figure 5 shows the cutting sequence for a cutting depth of 2 mm. In the cutting sequence the single black line at the bottom of the figure is the initial cut, the magenta represents the first three cuts at a cut spacing of 2 mm, the cyan lines are at a cut spacing of
where FNormal is the predicted normal force, FDrag is the predicted drag force, FSide is the predicted side force, and SG1 to SG4 are the four strain gauge values. SG1 is the value of the front strain gauge, which is in line with the cutting direction, as shown in Figure 4. The rest of the strain gauges are numbered anti-clockwize when looking from the top of the load cell.
A1 to A13 are coefficients that were determined by minimizing the mean squared error for the calibration data. For the minimizing, Python scipy.optimize.minimize was used with the Broyden–Fletcher–Goldfarb–Shanno (BFGS) method. Table I shows the mean and standard deviation (std) of the absolute error of predicted values to actual values of the applied force.
For commissioning of the LCM, various cutting tests were conducted with different parameters on the sandstone sample. The drag force, normal force, and the side force, as shown in Figure 1, were measured for each cut and the cut material was gathered. The tests were performed at cutting depths of 2 mm and 4 mm. The cut spacing was changed so that the cut spacing to cutting depth ratio, s/d, was 1, 2, 3, 4, 5, and 6. The skew angle was changed from -10°,
Table I
Absolute error of predicted values to actual values of the load cell
4 mm, the yellow lines are at a cut spacing of 6 mm, the green lines are at a cut spacing of 8 mm, the blue lines are at a cut spacing of 10 mm, and the three red lines at the top of the figure are at a cut spacing of 12 mm. This is a total of 19 cuts.
The sandstone used for the commissioning had little to no variability in strength on a millimeter scale and was locally sourced from a building materials supplier. For the commissioning of the LCM, detailed measurements were obtained of the mean and peak drag force, normal force, and side force, as well as the specific energy for the different cut spacing to cutting depth ratios, s/d. These results were compared to results reported by Park et al. (2018). The results showed similarities in terms of magnitude of force values and the trends that occurred as the s/d ratio increased. For all the skew angles, the magnitude of the force increased linearly with the increase in s/d ratio. The negative skew angle experienced a higher magnitude in force at the same cutting depth and cut spacing and is similar to observations by Park et al. (2018). The specific energy had an optimum s/d ratio between 3 and 4.
A colour map was made of the mean force for all 19 cuts to show the variance in strength on a millimeter scale. Figure 6 illustrates one of these colour maps, where the map represents the surface of the sample as shown in Figure 5, and the x-axis is the cutting distance. The colour map shows how the cutting forces change as the s/d ratio changes and where more force was required to make a cut on the surface of the rock sample. The cutting distance is 150 mm. The cut is from left to right. The s/d ratio of one either starts at the top or at the bottom, depending on the direction of the cut sequence. To map the force the data of the 150 mm is divided into 12 sections. The mean of each section is then mapped. The
mapping uses a bi-linear interpolation between runs. The following cutting parameter was used: a cutting depth of 2 mm with skew angle 0°. Figure 6 shows the drag force map for cutting sandstone at 2 mm cutting depth.
Figure 6 shows that the color remains fairly consistent for each run. Thus, showing the little to no variability in strength on a millimeter scale of the sandstone. The figure also shows how the mean drag force increases from run 2 to run 19, from bottom to top. For the first 10 mm of the cut the mean drag force is low, which is due to the cut initiation.
The previous sections demonstrate the use and some results that were obtained during the commissioning of the LCM. From these results it was concluded that the LCM was suitable to continue with the characterization tests on the UG2 reef samples. The following sections present detailed results obtained from cutting UG2 reef rock samples.
For this study, a UG2 reef sample was obtained from the Siyanda Bakgatla Platinum Mine, located at Swartklip, in Limpopo, South Africa. The rock sample was taken out of the underground mine and brought to the University of Pretoria laboratories. The sample was not affected by weathering. The sample was subsequently cut into manageable sized samples that were used in the laboratory scale cutting tests.
The cutting sequence and method shown in Figure 5, was again used for cutting UG2 reef samples. The results of the laboratory scale cutting tests show the mean cutting forces, peak cutting forces, and the specific energy versus the cut spacing to cutting depth ratio, s/d. The cut spacing to cutting depth ratio was used to represent the data, because it is a dimensionless quantity. Thus, different cutting depths can be compared to one another (Park, et al., 2018). The graphs show the average value as well as the maximum and minimum values. This demonstrates the uncertainty in the data.
Figure 7 to Figure 15 show the results obtained when cutting UG2 samples with the different cutting parameters. For a cutting depth of 2 mm both the mean normal force and mean drag force follow the same trend, where the mean force increases linearly with the cut spacing to cutting depth ratio, s/d. Also, the mean forces for a negative skew angle are higher than that of zero skew angle and
positive skew angle. The mean forces for zero skew angle and positive skew angle are similar to one another. The increase in force for negative skew angle is due to increase in contact area when a negative skew angle is applied.
The peak normal force and peak drag force follow a different trend than expected when compared with findings from previous researchers (Kang, et al., 2016; Park, et al., 2018). It was expected that, at all the skew angles, the peak forces increased linearly with the s/d. For the UG2 reef sample this linear relationship only occurred at a positive skew angle. For negative skew angle and zero skew angle, the peak forces level out at s/d values of 3 and 2, respectively. This is an interesting observation for the UG2 reef sample. This can be due to the large variability in strength on a millimeter scale in the rock sample, or due to the contact area between the pick and the UG2 at different skew angles, which will be discussed later.
For a cutting depth of 4 mm, both the mean normal force and mean drag force level out at an s/d of 4. This implies that at an s/d value of 4 and more, the previous cut does not have an influence on the next cut. Owing to this, increasing the s/d will not influence the cutting force results. This does not follow the same trend as the UG2 reef sample at 2 mm cutting depth. The plateaus show that the depth of cut has a larger influence on the cutting performance. This behaviour needs to be considered when designing cutting machines for deep hard rock environments.
When looking at the results of the side forces, it must be noted that at large s/d depth ratios the mean is close to zero. Thus, the maximum and minimum value will either be positive or negative and when examining the side force results, the magnitude is the important value and not the sign. Also, the sign of the side force is dependent on the direction of the cutting sequence. For positive and negative skew angles, the sign differs as expected because the cutting sequence is executed in different directions. Thus, the direction of the side force will differ. This is something that must be considered when examining the results of the side forces.
The skew angle influences the mean side force. For a negative skew angle, the magnitude in force values is the highest and a positive skew angle has the lowest magnitude in force values when compared at different s/d values. For the positive skew angle, the side force is close to zero at an s/d value of 5.
The reason is due to the change in the frontal area that is in contact with the rock when cutting. Figure 10 shows the frontal area when cutting an initial cut, with a skew angle of 10°. The yellowcoloured area on the left, represents the area of the pick where the rock will apply a force to the right on the pick. The area on the right (blue), represents the area of the pick where the rock will apply a force to the left on the pick. The grey area represents the rock that is being cut. The blue area is larger than the yellow area. Thus, the force to the left is larger for an initial cut.
For a small s/d cut with a positive skew angle there is only an area on the left (yellow), that will apply a force to the right on the pick. Thus, for the small s/d the force will be to the right. For a large s/d cut with a positive skew angle, there are both a yellow and a blue area, that have about the same area. Thus, the forces to the left and the right will cancel one another, and the force will be close to zero. For a small s/d cut with a negative skew angle there is only an area on the right (blue), where the rock will apply a force to the left on the pick. Thus, for the small s/d, the force will be to the left. For a large s/d cut with a negative skew angle there are both a yellow and a blue area, but the blue area is larger. Thus, the forces to the left are larger than the forces to the right, thus the force applied on the pick will be to the left.
The specific energy of the UG2 reef samples, at a cutting depth of 2 mm, follow the expected trend. When examining the optimal s/d value for the different skew angles, a higher s/d value of approximately 4 is optimal for a -10°. A lower s/d value is optimal for a skew angle of +10°. Thus, a value of either 2 or 3. For 0° skew angle a s/d value of either 3 or 4 will be optimal. One difference is that, for almost all the s/d values the specific energy is lower at a skew angle of 0° than a skew angle of +10°. This is not the same for
material used by previous researchers (Kang, et al., 2016; Park, et al., 2018). The specific energy plateaus for a skew angle of 0° at an s/d value of 5. Figure 11 shows that there is a difference in the trend of the specific energy at different cutting depths. It was expected that the deeper the cut, the lower the specific energy for the different s/d values will be.
Both cutting depths show that an optimal s/d value is 3 when the skew angle is zero. At a cutting depth of 4 mm, the specific energy plateaus at an s/d of 4 when cutting UG2. This was the same for the normal forces and the drag forces. This implies that the deeper the cut the less influence the previous cut has at the same s/d.
Figure 12 and Figure 13 show the measured force signals at an s/d of 3, with cutting depths of 2 mm and 4 mm, respectively, when cutting UG2 reef samples. The skew angle is 0°.
The force signals are not regular in shape and amplitude, as shown in Figure 12 and Figure 13. In Figure 12 the amplitude is lower between a cutting distance of 60 mm to 80 mm. This shows inconsistency in strength of the sample being cut. A fast Fourier transform (FFT) analysis was done on the cutting force signals. The FFT showed that the drag force signal, when cutting UG2, is not periodic. This is consistent with the fact that UG2 does not display uniform chip formation. The fact that the UG2 has large variability in strength on a millimeter scale causes the cutting force to vary. Therefore, causing the cutting force to be non-periodic. Calculation
of the FFT confirms the observation that the chip forming is irregular. Figure 14 shows the cut material that was gathered for a 4 mm cutting depth. This fine material was also observed for a cutting depth of 2 mm.
The fine material shown in Figure 14 will be a significant problem for cleaning operations in underground stopes. Further work on this needs to be conducted and the reason for the fine fragmentation needs to be better understood.
As discussed in the commissioning of the LCM, the variance in strength on a millimeter scale of the material can be revealed by plotting a colour map of the cutting forces. A similar approach was employed here to investigate the variance in strength on a millimeter scale of the UG2 reef samples. The plot, for the UG2 sample, was normalized by dividing the mean force of each section by the mean force of the run. This shows where in each run there were low and high forces, compared to the mean of the run. Figure 15 shows the normalized drag force map for cutting UG2 at a 2 mm cutting depth with skew angle 0°.
The normalized maps show that there is an inconsistency in the lower middle of the rock sample identified by the green box. This inconsistency was present in all three cutting sequences. It is assumed that the rock is weaker at this point, due to the lower force required to cut the rock. There are two other similar inconsistencies where it may be assumed that the rock is weaker. One is at the start of the cut, between 0 mm to 40 mm, shown by the orange box. The other is shown by the yellow box. The lower right corner is assumed to be stronger than the rest, due to the required force being higher than the mean, shown by the blue box. The normalized colour
maps clearly show that the UG2 rock sample has large variability in strength on a millimeter scale. One can expect that such a sample with large variability in strength on a millimeter scale will cause more variance in the cutting data. This can be seen in the cutting data shown in Figure 12.
Wider adoption of cutting solutions for the extraction of UG2 would require the ability to better simulate these cutting processes. This section discusses the numerical model developed for simulating rock cutting using conical picks. Ansys LS-DYNA was used for the modelling. As was motivated in the introduction, the continuous surface cap model (CSCM) was used as the failure model, because it allows for element erosion, which allows modelling of the fragmentation process. This model is typically not used in rock engineering studies and further work needs to be done to verify this model, and to determine the most applicable constitutive failure model for UG2 when mined using mechanical methods.
There are various parameters that have to be selected and calibrated for the model. This includes mesh type, element size, contact properties, and boundary conditions. All these parameters have an influence on the computational time, efficiency, and simulation results.
A tetrahedron mesh was selected, following a recommendation by Jaime (2011) that a tetrahedron mesh gives a more realistic fracture pattern. Figure 16 illustrates the 3D view of the model set-up. An element size of 1.6 mm was used for the rock. The conical pick was modelled after the conical pick that was used in the experimental laboratory scale cutting tests. The pick has an element size of 1.2 mm. A vertex sizing with spherical influence at the tip of the pick was used, with a radius of 5 mm and an element size 0.4 mm. This ensures that the resolution of the pick shape at the tip is modelled accurately, but still saves computational time and resources. The pick is modelled as a rigid body.
For the numerical simulation, both side faces, the bottom face, and the back face were fixed. The front face, which will be in contact with the pick, was fixed in the z direction. For the ERODING_ SURFACE_TO_SURFACE, a parameter of the LS-DYNA, all three parameters, the viscous damping coefficient, contact penalty scale factor, and the target penalty scale factor were selected as 5 (Livermore Software Technology (LST), an ANSYS company, 2021). The friction coefficient and the dynamic coefficient had an influence
on the ratio of normal force to drag force. Through trial and error, a friction coefficient of 0.004, a dynamic coefficient of 0.001, and a decay constant of 1 was used.
Höll (2009) reported data on the density, Young's modulus, and Poisson's ratio of UG2 from different areas in the South African Bushveld complex. This data was used as initial values of the rock properties to calibrate the CSCM. The parameters for the CSCM were updated by changing the material properties, used in the equations presented by Novozhilov et al. (2022). The parameters were selected to accurately predict the cutting forces at a cutting depth of 2 mm, then the same model with the same parameters were used at a cutting depth of 4 mm to determine if the model extrapolates accurately.
The Novozhilov et al. (2022) equations for the CSCM parameters require the specification of specific material properties. These properties were determined through trial and error. The specific material properties that were used are: Young's modulus 83.2 GPa, Poisson's ratio 0.152, density 4.19 g/cm3, uniaxial compressive strength 70 MPa, and aggregate size 19 mm. These values of the material parameters fall in the range of values of UG2 reef samples. The aggregate size was chosen as the default value used by the CSCM. Determining the rock properties of UG2 reef rock is difficult due to the very large variability of this rock type. The only property that was known, of the sample that was used in the experimental cutting tests, is the density of the UG2 reef sample.
Numerical simulation results
In this section the numerical simulation results are compared to the experimental cutting results, when cutting UG2 samples, for the three initial cuts, no influence of previous cuts, at 2 mm cutting depth and 4 mm cutting depth with a skew angle of zero. Table II shows the data that was used to compare the experimental results to the numerical simulation results.
In this table FN is the normal force, FD is the drag force, FN’ is the peak normal force and FD’ is the peak drag force.
Table III shows the maximum error value and the maximum percentage error for the results of the experimental cutting forces compared to the mean of the three runs, at 2mm cutting depth.
Table IV and Table V show the results obtained for the numerical simulations at a cutting depth of 2 mm and 4 mm. The tables also show the percentage error between the numerical simulation results and the experimental results.
Experimental cutting data for UG2 at 2 mm and 4 mm cutting depth
Table III
error for experimental runs at 2 mm cutting depth
Table IV
Numerical simulation force results for UG2 reef
Table V
Numerical simulation ratio results for UG2 reef
The results in the tables show that the model parameters can be updated through trial and error to give similar results as the experimental results. But this only works when updating the model parameters so that the numerical simulation results are similar to the results for one particular set of experimental cutting parameters, in this case, a cutting depth of 2 mm. For the 2 mm cutting depth the percentage error for the force values is acceptable when compared to the percentage error in table Table III. Thus, the numerical simulation set-up can be updated so that acceptable results are obtained. When using the same model set-up for a cutting depth of 4 mm, as used for the 2 mm cutting depth, the results are less than ideal as indicated by the percentage errors shown in table Table IV.
This inability to generate the model parameters to be applicable to a large range of cutting parameters has also been observed by other researchers in previous work (Huang, et al., 2016; Jaime, et al., 2015). It was assumed that the error when changing cutting depth was due to poor modelling of the cutting tool. However, after the results of the numerical simulations were obtained it is clear that the error is due to other factors.
The results in Table V show that the ratios of peak force to mean force for both the normal force and the drag force, are close to 3, which is the same as the experimental results. This ratio was obtained by changing the element size. The material properties were updated so that the peak forces are similar, after which the element size was edited to get the correct ratio. The peak force to mean force ratio is acceptable for both cutting depths. Lastly, this study considers the ratio of the mean normal force to the mean drag force. Previous researchers also experienced a difficulty to get this ratio correct (Huang, et al., 2016; Su and Akcin, 2011; Van Wyk, et al., 2014). The contact parameters are important factors that change the ratio as well as element size. This ratio does not have an acceptable accuracy.
This section showed that it is possible to use Ansys LS-DYNA with the CSCM to model rock cutting of UG2 reef samples and get acceptable results, but the user must calibrate the model parameters using the experimental results. Thus, the model is only fit for one set of cutting parameters. The section showed that the model does not extrapolate accurately when the cutting parameters are changed.
Conclusion
Rock cutting using conical picks is a common method of mining that enables continuous mining operations. Various research projects have been conducted on different design aspects using
conical picks. None of these studies considered rock samples found in South African hard rock environments, such as the UG2 reef samples.
The main observation when cutting UG2 reef sample, is that it has large variance in strength on a millimeter scale. This introduces uncertainty in the results due to added variance from one cutting experiment to another for the same UG2 reef sample. Another problem is the inconsistency in rock properties of the UG2 reef, when examining the rock properties from one mine to another.
The results indicated that the optimal s/d ratio for the different cutting parameters follow the expected trends. But the normal force, drag force, and specific energy plateaus at a cutting depth of 4 mm for larger s/d values when cutting UG2. This implies that the depth of cut has a larger influence on the cutting force results of UG2 reef samples. Clearly, using optimized cutting parameters form cutting test performed on other material than UG2 might not be appropriate to use to make design decisions for mining equipment intended for UG2.
At 2 mm cutting depth the force signals were impulsive, and the material collected was of fine fragmentation. At a cutting depth of 4 mm the force signals had a saw tooth shape. This implies that larger chips are formed. However, the UG2 produced fine fragmentation. This is undesirable in underground mining conditions owing to the difficulty of cleaning this fine fragmentations from the stopes.
Using the fast Fourier transform (FFT) analysis is a useful method to discuss and compare rock cutting data. Valuable information can be obtained when looking at the FFT analysis, such as if the cutting force signal is periodic and the size of the fragmentation. This was true for material with little to no variance in strength on a millimeter scale, such as sandstone. The results for the UG2 however showed that the conclusions are not clear. Owing to the UG2 not being periodic, because of the UG2 having large variance in strength on a millimeter scale, the FFT analysis did, in this case, not give useful information about the size of the fragmentation.
The numerical simulations illustrated that there are various model parameters that influence the results and some that do not influence the results. Some parameters are based on material properties and other are updated through trial and error. The parameters are updated by changing model parameters and the material properties used in the equations given by (Novozhilov, et al., 2022), until an acceptable accuracy is obtained between the numerical simulation cutting results and the experimental cutting results for a constant set of cutting parameters.
It is possible to model rock cutting of UG2 reef samples using LS-DYNA and the CSCM. But this is only possible by updating the model parameters through trial and error for one set of cutting parameters. When the cutting parameters are changed, such as the cutting depth, the model does not produce acceptable results. Thus, the model is not capable of extrapolation.
In conclusion, it is unclear at this stage if conical picks can be used for mechanized mining in the UG2 hard rock environment, as the fine fragmentation will make the mining process impossible. This observation is based on a laboratory scale cutting test conducted on actual rock samples and further work is clearly necessary.
It was also shown that it is possible to simulate the cutting process using FEM software. Previous researchers have also successfully used FEM to simulate rock cutting, but not for rock found in deep hard rock environments in South Africa. The model, however, does not produce good results when extrapolating beyond the specific conditions considered to obtain the rock characteristics, for example, for different cut depths. Further research will be required to address the generalization of modelling.
Acknowledgements
The authors gratefully acknowledge the support that was received from the Mandela Mining Precinct through their SAMERDI programme.
References
Bilgin, N., Copur, and H., Balci, C. 2013. Mechanical excavation in mining and civil industries. Boca Raton: CRC Press.
Copur, H., Bilgin, N., Balci, C., Tumac, D. Avunduk, E. Effects of different cutting patterns and experimental conditions on the performance of a conical drag tool. Rock Mechanics and Rock Engineering, vol. 50, no. 6, pp. 1585–1609.
Dehkhoda, S., Detournay, E. 2019. Rock cutting experiments with an actuated disc. Rock Mechanics and Rock Engineering, vol. 52, no. 9, pp. 3443–3458.
Evans, I. 1962. A theory of the basic mechanics of coal ploughing.. Proceedings of the International Symposium on Mining Research, vol. 2, no. 1, pp. 761–768.
Goktan, R., Goktan, H.G., Goktan, M.H. 1997. A suggested improvement on Evans cutting theory for conical bits.. Proceedings of the fourth international symposium on mine mechanization and automation, vol. 1, no. 1, pp. 57–61.
Hekimoglu, O.Z. 2018. Investigations into tilt angles and order of cutting sequences for cutting head design of roadheaders. Tunnelling and Underground Space Technology, vol. 76, pp. 160–171.
Höll, H. 2009. Pillar design and cutting at Everest platinum mine, South Africa: Aquarius Platinum (South Africa) (Pty) Ltd..
Huang, J., Zhang, Y., Zhu, L., Wang, T. 2016. Numerical simulation of rock cutting in deep mining conditions. International Journal of Rock Mechanics and Mining Sciences, vol. 84, pp. 80–86.
Jaime, M.C. 2011. Numerical modeling of rock cutting and its associated fragmentation process using the finite element method, s.l.: University of Pittsburgh Swanson School of Engineering.
Jaime, M.C., Zhou, Y., Lin, J.-S. and Gamw, I.K. 2015. Finite element modeling of rock cutting and its fragmentation process, Pittsburgh, PA, USA: Department of Civil and Environmental Engineering, University of Pittsburgh.
Kalogeropoulos, A., Michalakopoulos, T. 2021. Numerical simulation of rock cutting using YADE. s.l., s.n.
Kang, H., Cho, J.-W., Park, J.-Y., Jang, J.-S., Kim, J.-H., Kim, K.-W., Rostami, J., Lee,J.-W. A new linear cutting machine for assessing the rock-cutting performance of a pick cutter. International Journal of Rock Mechanics and Mining Sciences, vol. 88, pp. 129–136.
Li, B., Zhang, B., Hu, M., Liu, B., Cao, W. Xu, B. 2022. Full-scale linear cutting tests to study the influence of pre-groove depth on rock-cutting performance by {TBM} disc cutter. Tunnelling and Underground Space Technology incorporating Trenchless Technology Research, vol. 122, no. 104366.
Livermore Software Technology (LST), an ANSYS company, 2021. LS-DYNA Keyword user's manual volume III. Livermore, California: Livermore Software Technology.
Mendyka, P. 2017. Laboratory stand tests of mining asymmetrical disc tools. s.l., s.n.
Moxham, K. 2004. A narrow reef mining machine - ARM1100. s.l., The South African Institute of Mining and Metallurgy, pp. 207–214.
Novozhilov, Y.V., Dmitriev, A.N., Mikhaluk, D.S. 2022. Precise calibration of the continuous surface cap model for concrete simulation., s.l.: Buildings.
Park, J.Y., Kang, H., Lee, J.-W., Kim, J.-H., Oh, J.-Y., Cho, J.-W., Rostami, J., Kim, H.D. 2018. A study on rock cutting efficiency and structural stability of a point attack pick cutter by lab-scale linear cutting machine testing and finite element analysis. International Journal of Rock Mechanics and Mining Sciences, vol. 103, no. 13651609, pp. 215–229.
Pickering, R.G.B. 2007. Has the South African narrow reef mining industry learnt how to change?. The Journal of The Southern African Institute of Mining and Metallurgy, vol. 107, pp. 557–565.
Stopka, G. 2021. Modelling of rock cutting with asymmetrical disc tool using discrete-element method (DEM). Rock Mechanics and Rock Engineering, vol. 54, no. 12, pp. 6265–6279.
Su, O., Akcin, N.A. 2011. Numerical simulation of rock cutting using the discrete element method. International Journal of Rock Mechanics and Mining Sciences, vol 48, no. 3, pp. 434–442.
Van Wyk, G., Els, D.N.J., Akdogan, G., Bradshaw, S.M., Sacks, N. 2014. Discrete element simulation of tribological interactions in rock cutting. International Journal of Rock Mechanics and Mining Sciences, vol. 65, pp. 8–19.
Vogt, D. 2016. A review of rock cutting for underground mining: Past, present, and future. South African Institute of Mining and Metallurgy, vol. 116, no. 11, pp. 1011–1026.
Wicaksana, Y., Jeong, H., Jeon, S. 2021. Numerical simulation of rock cutting process induced by a pick cutter considering dynamic properties of rock at intermediate strain rate. Bulletin of Engineering Geology and the Environment, vol. 80, no. 12, pp. 9049–9069.
Zárate, F., Oñate, E. 2015. A simple FEM–DEM technique for fracture prediction in materials and structures. Computational Particle Mechanics, vol. 2, no. 3, pp. 301–314.
Zou, J., Yang, W.,h Han, J. 2020. Discrete element modeling of the effects of cutting parameters and rock properties on rock fragmentation. IEEE Access, vol. 8, pp. 136393–136408. u
Affiliation:
1Department of Materials Science and Metallurgical Engineering, University of Pretoria, South Africa
2Sasol Synfuels (Pty) Ltd, Secunda
Correspondence to:
R. Mostert
Email:
roelf.mostert@up.ac.za
Dates:
Received: 30 Nov. 2022
Revised: 20 Sept. 2023
Accepted: 29 Oct. 2024
Published: November 2024
How to cite:
Van Zyl, A., Pretorius, C.C.E., Mathoho, V.M., and Mostert, R.J. 2024. Tracking the degradation of carbon steel mechanical properties due to high-temperature hydrogen attack through strain gauge monitoring. Journal of the Southern African Institute of Mining and Metallurgy, vol. 124, no.11, pp. 683–692
DOI:
http://dx.doi.org/10.17159/24119717/2486/2024
ORCiD: R.J. Mostert
http://orcid.org/0000-0002-8592-1313
by A. van Zyl1, C.C.E. Pretorius1, V.M. Mathoho1,2, and R.J. Mostert1
Abstract
The in-service degradation of the mechanical properties of steel components through the damage mechanism of high temperature hydrogen attack (HTHA), is a topic of concern in the refining and green hydrogen industry. This damage mechanism occurs in susceptible steels operating in environments at high temperatures and hydrogen pressures. The current investigation deals with the indirect monitoring of mechanical degradation via tracking of the swelling strain in affected structures. An autoclave with an AISI 316 shell was utilized to simulate accelerated HTHA damage at 550 °C and 46 bar for exposure times ranging from zero to 700 hours. The progress of the HTHA damage was tracked using encapsulated high-temperature strain gauges. The correlation between the swelling strain and mechanical property degradation was studied to develop a methodology for the continuous monitoring of embrittlement. The tensile sample orientation of the carbon steel plate was included as a variable, i.e., samples parallel, transverse, or perpendicular to the plate rolling direction were included, since it has been shown that the sample orientation influences the HTHA damage features.
For the through-thickness orientation, and upon exceeding a threshold value of exposure time, all tensile properties were severely degraded, with values in the order of a 90 per cent reduction being observed.
It was found that the degradation of carbon steel mechanical properties can be correlated to the swelling strain measured during exposure. The critical point for mechanical property degradation in the plate through-thickness orientation, whereafter a severe decrease in the ductility of the material occurs, was found to be in the order of 1% of the total swelling strain measured during exposure, equivalent to 65 microstrain. This threshold was found to be significantly lower than that expected from the literature, where limits of 400 to 1000 microstrain were postulated.
Keywords
high temperature hydrogen attack, mechanical properties, strain gauge monitoring, degradation
Introduction
High-temperature hydrogen attack, or HTHA, is a damage mechanism whereby susceptible steel alloys that are exposed to hydrogen-containing environments at elevated temperatures can see a marked degradation in their mechanical properties (Poorhaydari, 2021). The mechanism involves the diffusion of elemental hydrogen from the environment into the steel, where it reacts with carbon to form methane gas (CH4) according to Equation [1]:
Benac and McAndrew stated that the buildup of methane gas at locations such as grain boundaries, is due to the inability of the methane to diffuse out of the steel and may lead to an increase in the pressure exerted by the gas on the surrounding material (Benac and McAndrew, 2012). This results in microvoids that, over time, link up to form microcracks and lead to fissuring of the steel and subsequent failure at low applied loads. The fact that the reaction of Equation [1] will progress towards the right with increasing time, temperature, and hydrogen pressure, makes HTHA strongly dependent on process and plant variables. With the sharpened global focus on the development of the hydrogen economy, the HTHA damage mechanism is currently very topical. In South Africa, with ageing process plants still being used to produce fuels, HTHA is also a concerning phenomenon. Due to the severe consequence of failure associated with this damage mechanism, the timely identification of damage, along with knowledge regarding the associated
mechanical property degradation, are of crucial importance. Globally, procedures for the monitoring of structural health and the fitness for service of such affected components are currently in development (Welding Research Council, Inc., 2022). Previous work by Mostert et al. (2022), has also shown that the progression of HTHA can be monitored using strain-life curves, which expresses the amount of accumulated strain experienced by a sample due to swelling during its exposure to hydrogen environments at elevated temperatures and pressures as a function of time. Uncertainty however exists regarding the progression of swelling strain and its relationship to the decrease in a material’s mechanical properties. The influence of material orientation, relative to the plate rolling direction, on the severity of mechanical degradation has also not been fully researched to date. The current article therefore deals with research aimed at the degradation of components’ mechanical properties as swelling strain due to HTHA damage progresses. The influence of sample orientations on the mechanical property degradation is also investigated.
A useful tool for the determination of a specific steel’s susceptibility to HTHA is the so-called Nelson curves (API, 2016). According to these curves, which were first published in 1949, the susceptibility of a steel to HTHA is a function of hydrogen partial pressure (in MPa) and exposure temperature (in ˚C). Exposure combinations in which both the temperature and hydrogen partial pressure fall above the plotted curve of a specific material, indicate operating conditions that could result in HTHA of the material. These curves have been constructed and updated using plant exposure data to establish safe operating conditions, while taking the safety factor into account (API 941, 2016). Due to the new cases of damage being reported with the progression of time, some of these curves have recently been adjusted downwards to reflect the cumulative experience over the years. Some older process units may therefore currently operate under conditions that originally had been deemed safe, but are currently regarded as being at risk of attack. An example of these changes is that some units that were constructed using C-0.5 Mo and operated in ‘safe regions’ according to older Nelson curves, have subsequently been identified as suffering from HTHA degradation and, as a result, this alloy is not currently placed on the Nelson curves found in the current versions of API 941 (Mostert et al, 2022).
HTHA is associated with decarburization, which may manifest itself in one of two ways, surface decarburization or internal decarburization. In both cases, carbon in the material reacts with atomic hydrogen to form methane gas. The main difference between these two mechanisms is the location at which the methane reaction occurs. Regarding the former mechanism, the methane reaction occurs at the steel surface, resulting in a softened surface layer due to the depletion of carbon within the metal matrix. Internal decarburization, however, involves atomic hydrogen diffusing into the steel matrix, where it reacts with carbon to form methane gas bubbles at grain boundaries. As the methane reaction continues, the methane voids may grow and coalesce to form extended fissures and cracks, resulting in mechanical property degradation. Internal decarburization occurs in environments with larger hydrogen partial pressures.
Baker (1999) postulated that the degradation in the mechanical properties of a steel as a function of HTHA exposure time would take place in stages and represented this degradation by schematic diagrams, such as that shown in Figure 1.
According to this hypothesis, the percentage decrease in the mechanical properties would follow sigmoidal type behavior over time, from which three stages of damage could be distinguished. During the first stage of damage, an incubation period was postulated, in which the voids formed through methane gas production is small and have yet to coalesce and grow into microcracks. Stage 2 was postulated as the region in which the mechanical properties deteriorate at a high rate. This was ascribed to the continued growth of voids resulting from internal methane gas formation, until they coalesce to create the large cavities that may lead to fissuring and cracking, thereby resulting in a decrease in mechanical properties. Stage 3 is indicative of a damage plateau, where the rate of material property degradation decreases due to the depletion of carbon available for methane gas formation (Baker, 1999). The hypothesized relationships between microstructural and mechanical property degradation, and the corresponding microstructural transitions, were however not proven experimentally.
Liu investigated the impact of HTHA on the mechanical properties of C-0.5Mo steel as a function of time (Liu, 2001). For their study, Liu conducted tensile tests at ambient temperatures after high temperature hydrogen exposure. The operating conditions were defined using a Pw factor, which was defined using exposure time, temperature, and hydrogen partial pressure (Liu, 2001). Ductility degradation was then assessed by considering the reduction of area measured upon failure of the tensile samples. A threshold Pw factor was identified and, when exceeded, severe ductility degradation was expected to commence. Liu’s work proved useful, since the expected progression from Stage 1 to Stage 2 HTHA damage can be calculated for given process conditions. However, a shortcoming in this study was that the threshold Pwvalue will vary, depending on a number of process and metallurgical variables, including the specification of steel used.
The formation of HTHA voids and fissures is known to cause swelling-induced strain in steel and offers a possible way in which the progress of damage and, theoretically, embrittlement can therefore be continuously tracked in service. A threshold strain value could then be identified, corresponding to the critical Pw-value, to identify the start of severe mechanical property degradation. The formation and growth of methane-containing cavities exert a force on the steel matrix, causing it to expand. In laboratory work, it has been shown that the progression of HTHA
Table I
Chemical composition of the carbon steel plate, determined by spectrometric analysis
damage can be tracked over time by measuring the accumulated strain experienced by the steel, using high-temperature, encapsulated strain gauges (Mostert et al, 2022). A time-damage fraction plot for carbon steel at a temperature of 545 °C and an H2 partial pressure of 98 bar was produced by the authors and had a similar sigmoidal shape to that of the mechanical property degradation curves postulated by Baker. The measured strain values initially increased at a slow rate. Thereafter, the strain values progressed rapidly, before eventually reaching a maximum value when the carbon became depleted, preventing further straining of the material by new methane gas formation.
The directionality of the degradation is an important factor to consider due to the hot-rolled microstructure of carbon steel plate. Earlier work showed that significant segregation bands form due to hot rolling operations in C-0.5Mo steels, with HTHA fissuring and decarburization taking place in planes parallel to these segregation bands (Pretorius et al, 2021), leading to directional variability of the HTHA strain that developed. It can be expected that forces applied at different angles to these degraded planes – either parallel to the fissure orientation or perpendicular to the fissure orientation – will result in different degrees of ductility degradation. There is, however, little published work that investigated the influence of this variable on ductility degradation.
The aim of this study is, therefore, to investigate the magnitude of HTHA swelling strain that corresponds to significant mechanical property degradation in carbon steel plate material. Early research proposed that the strain that corresponds with the point of incubation for HTHA damage in carbon steels ranges from 400 and 1000 microstrain (Panda and Shewmon, 1984). At this point, it was believed that the individual methane bubbles on a particular grain boundary join to form a continuous grain boundary bubble, which then constitutes a microcrack. The proposed hypothesis for this work is, therefore, that the threshold of HTHA strain that will correspond to a significant ductility degradation can be measured using an encapsulated strain gauge and ranges from 400 to 1000 microstrain.
The influence of transverse (T), through-thickness (Z), and longitudinal (L) sample orientations on the degree of HTHA ductility degradation was also investigated, due to the presence of segregation bands and the directionality of fissuring identified by other authors (Pretorius et al, 2021), with the expectation that the degradation of tensile properties can vary with sample orientation and will be most severe in the through-thickness direction.
Methodology
Tensile samples used in the present study were machined from a 40 mm thick, hot-rolled carbon steel plate, which corresponded to the requirements of the ASTM A 516 Gr 70 specification. Table I summarizes the chemical composition of the plate material as determined by an independent accredited laboratory via spectrometric analysis.
Figure 2—Carbon steel plate with orientation directions for sample machining, relative to the longitudinal plate rolling direction
Table II
Dimensions of tensile test samples for longitudinal and transverse direction
Radius of fillet 8
– Length of reduced parallel section 45
Table III
Dimensions of tensile test samples for the through-thickness direction
Dimension Value (mm)
Plate thickness (t) 25 < = t < = 45 (Plate thickness of 40 mm)
Diameter (D) 6.25 + - 0.1
Radius (R) Optional ( 3 mm chosen)
Length of reduced section 16
Tensile samples were machined in three directions relative to the rolling direction of the plate. A total of 19 samples were used, with 4 machined in the longitudinal and transverse directions, respectively, and 15 machined in the through-thickness (normal) direction. A larger number of through-thickness samples were used during this study to investigate the impact of perpendicular forces applied to the HTHA degraded planes, expected to be parallel to the rolling direction. Figure 2 shows the relevant orientations: Rolling of the plate was in the longitudinal direction. Table II and Table III show the dimensions of the samples used.
The longitudinal and transverse samples were machined according to ASTM E8 specimen 2, while the through-thickness samples were machined according to ASTM A770 specimen type D with M12 thread. The thickness of the plate limited the size of the through-thickness samples and, therefore, an appropriate standard was selected for the machining of these specimens.
Temperature controller
Samples were then exposed to accelerated HTHA conditions in an autoclave at conditions of 550°C and 46 bar H2. A schematic representation of the autoclave setup containing the strain-gauged sample is shown in Figure 3.
During exposure, the swelling strain was monitored using a KHCM-10-120-G15-11 C2MV high-temperature, encapsulated strain gauge supplied by Kyowa Electronic Instruments. The sensing part of the strain gauge is depicted schematically in Figure 4, which is comprised of an active element (for strain measurement) and dummy element (for temperature correction). These elements are housed, along with refractory material, inside a sheath-tube made from highly heat-resistant Inconel 600. The sensing part is also mounted to a flange with dimensions of 3 mm x 20 mm x 0.1 mm, which provides the means for mounting the specimen to metallic components via precision capacitance discharge spot welding. Regarding the monitoring of swelling-strain during the current investigation, the strain gauge was mounted to a 34 mm x 4 mm x 10 mm carbon steel plate sample machined along the throughthickness direction, by capacitance discharge welding of the flanges to the sample. The sample/strain-gauge assembly was then fixed to a specialized mount to minimize the strain fluctuations during the exposure.
Samples in all three orientations were tested in the as-received (or unexposed) condition, providing baseline values with which to compare the mechanical property degradation of exposed samples. Due to the expectation that degradation of mechanical properties would be most severe in the through-thickness direction, specific focus was placed on these samples, which were exposed for intermittent time periods. This would allow a more accurate insight into the progression of HTHA through the steel. The longitudinal and transverse samples were only tested in the as received and maximum exposure stages. Cooling of all samples retrieved after
Strain gauge data acquisition
Oven
Strain gauge/ sample
Sample mount
Refractory brick
Table IV
HTHA Exposure times for tensile test samples
the times indicated in Table IV, was done in the autoclave and at slow cooling rates, by switching off the autoclave heaters to avoid distortion and thermal shock effects. Table IV summarizes the exposure time for the tensile test samples.
Upon completion of the specific HTHA exposure times, tensile testing was implemented at a rate of 2 mm / min to determine the mechanical properties of each sample. Conventional tensile testing of the through-thickness samples was found to be unpractical, due to the small head size caused by the 40 mm thick plate. The thread machined in the sample head was thus used to screw the samples into grips, which were placed in the tensile testing machine.
Results and discussion
Progress of HTHA damage against time
The progress of the HTHA damage mechanism, as measured by the swelling strain of the through-thickness sample during HTHA exposure, is shown in Figure 5.
The graph shows the swelling strain experienced by the instrumented sample, both in microstrain and as a percentage progression. The strain experienced a small increase during the initial stages of the test, followed by accelerated swelling before reaching a maximum strain value, and has the same sigmoidal shape as that proposed by Baker for degradation percentage versus time (see Figure 1). The red dots indicate instances in time where tensile samples were removed from the autoclave and tested for ductility degradation, with the sample that received the longest exposure to HTHA removed after 425 hours. The curve depicting the damage fraction versus time in this figure shows a similar progression to
that obtained by Munstermann (et al, 2010), who used a laboratory LVDT setup (see Figure 6). In both curves, measured swelling strain initially increased at a slow rate, before progressing rapidly and eventually reaching a maximum value.
Tensile test results
Tensile testing of samples exposed at different times to the HTHA conditions produced the UTS and yield strength results for the three sample orientations as shown in Figures 7 and 8.
The figures show that, in the as-received state, all three sample orientations had similar yield strengths and UTS values. However, for the exposure times of 350 hours and 425 hours, the throughthickness samples exhibited a severe degradation of strength. For the long exposure times, the z-samples also showed significantly larger reduction in the yield strength and UTS, compared to the longitudinal and transverse samples. Due to the limited number of samples tested from the longitudinal and transverse orientations, a comparison cannot be made regarding the relative degradation at shorter exposure times. The yield strength and UTS of the z-samples did not decrease at a constant rate, but rather reduced by a small degree during initial exposure times, before the severe degradation observed after exposure times of 285 and 350 hours. For both the unexposed and 425-hour exposed data sets, a minimal difference between both the yield and UT strength
values measured for the longitudinal and transverse samples was observed. At long exposure periods, the severe through-thickness direction degradation, as opposed to the longitudinal and transverse directions, was very prominent. It is probable that longer exposure periods for longitudinal and transverse samples will result in similar degradation, but more effort is needed to confirm this.
Following testing of the samples to failure, the reduction in area and elongation to failure of the samples were determined, as illustrated in Figure 9 and Figure 10, respectively.
Figure 9 shows that the reduction in area was between approximately 73% and 75% for all three orientations in the as-received state. The reduction in area of the through-thickness samples varied between 75% and 80% as the HTHA exposure time increased to 285 hours, then decreased to approximately zero percent at 350 hours and 425 hours HTHA exposure. The transverse and longitudinal samples, however, saw a decrease in the reduction in area to between 36% and 38%. Figure 10 indicates that the elongation of the three orientations in the as-received state was similar, at approximately 45%. The elongation of the throughthickness samples varied between 45% and 50% as the HTHA exposure time increased to 285 hours, when it also decreased to approximately zero percent at 350 hours and 425 hours. The elongation of longitudinal and transverse samples at 425 hours only saw a decrease to approximately 38%.
Similar trends were observed in the impact that HTHA exposure had on the elongation to fracture, reduction in area of the samples, yield strength, and UTS. The through-thickness samples showed larger decreases in yield strength and UTS values at the maximum exposure times. Similarly, significantly smaller elongation and reduction in areas values were observed in the through-thickness samples at maximum exposure as compared to
the longitudinal and transverse samples, also indicating a larger decrease in ductility and extensive HTHA degradation. These results confirm that the HTHA-induced degradation of all tensile properties is most severe in the through-thickness direction. HTHA microstructural degradation has earlier been observed to dominate in planes that are parallel to the plate rolling direction (Pretorius et al, 2021), and it is therefore probable that the observed severe
10—Elongation to fracture as a function of time and sample orientation following exposure at 550 °C and 46 bar H2
Figure 11—Ductility degradation of through-thickness samples as a function of swelling strain progression
z-direction ductility degradation is due to the HTHA defects in the plane, normal to the applied tensile force joining up and resulting in fracture without the matrix playing a significant role. At these combinations of high levels of internal microstructural defects and loading normal to the degraded planes, fracture cannot be explained through ductile bulk overload and microvoid coalescence, but rather through brittle fracture at low loads from sharp internal crack tips, employing fracture mechanics principles.
A plot of ductility degradation as a function of HTHA swelling strain was produced for the z-direction samples and is shown in Figure 11. The exclusive focus on z-direction degradation in this plot is due to the dominance of the degradation in this orientation.
The total ductility degradation parameter plotted on the y-axis, PD, follows the principle of the ΦR -parameter used by Liu (2001), but was calculated as an average of DRA and Del:
The DRA and Del parameters are given for each exposure time as
Where
RA0 = Reduction in area of the as-received sample
RAt = Reduction in area of the sample after exposure for t hours
∆l0 = Elongation of the as-received sample
∆lt = Elongation of the sample after exposure for t hours
The percentage swelling strain progression, as used by Mostert et al (2022), which is defined as [5]
where
et = Strain measured at a specific time instant
et = Total swelling strain measured.
wherein maximum ductility degradation was observed at approximately 2% of the total swelling strain, while the point of initiation for severe ductility degradation fell between swelling strains of 1 and 2 per cent of the total strain. The corresponding microstrain range is between 70 and 130 με. This result shows that a severe decrease in the ductility of the material takes place at very small values of experienced strain, which is lower than that proposed to be the point of incubation for HTHA damage by the earlier mentioned authors (compared to the 400 – 1000 με of Panda and Shewmon, 1984).
The degradation plot was recreated using the yield strength values to investigate the correlation between swelling strain and the degradation of the material’s strength, again for the z-direction samples only. This relationship is shown in Figure 12:
The mechanical property degradation was defined as: [6]
where (σy)0 = Yield strength of the as-received sample (σy)t = Yield strength of samples after exposure for t hours and t indicates a certain exposure time, while 0 indicates the as received properties.
The sigmoidal shape of the degradation-strain graphs in Figure 11 and Figure 12 shows trends similar to that postulated by (Baker, 1999) in Figure 1 for the decrease of material mechanical properties due to HTHA damage. However, the extent of ductility degradation was found to be much more severe than what one would describe as ‘incubation of HTHA damage’. Maximum ductility degradation was observed at approximately 2% of the total swelling strain, while the critical point is between 1% and 2% of total swelling strain. This indicates that the mechanism of HTHA will cause severe enough damage for the component to fail significantly before the carbon in the material is depleted through methane gas formation, provided that the loading direction is appropriate.
Optical micrographs were taken of samples at different exposure stages to investigate the progression of HTHA damage through decarburization and fissuring, and the impact this will have on the sample microstructure. For these evaluations, the following microscope was utilized: an Olympus BX51M optical microscope (OM) connected to calibrated Olympus Stream Essentials software via an Olympus U-TV0.63XC camera. The microstructural investigation was performed to investigate microstructural linkages to the observed changes in the HTHA strain and mechanical properties of the samples. Figure 13 shows the through-thickness sample in the as-received state.
Figure 13 also illustrates the banded structure consisting of alternating layers of darker pearlite phase and lighter ferrite phase present within the sample. The microstructures after 285 hours HTHA exposure are shown in Figure 14.
Figure 14(a) and Figure 14(b) illustrate that the banded pearlite and ferrite structure is still present within the sample. However, Figure 14(b) appears to show that some of the darker pearlite phase was broken up. This is possibly due to the decarburization mechanism through which HTHA damage occurs, as the atomic hydrogen from the environment diffuses into the sample and reacts with the carbon to form methane gas. The carbon will then be supplied from the pearlite, (which is a combination of ferrite and cementite or Fe3C), thus reducing the size of the pearlite phase. This phenomenon was also observed in previous work (Pretorius et al, 2021). However, there were no signs of any microvoids, fissuring or cracking, which were observed at these magnifications. This indicates that, after this extent of exposure, HTHA tensile degradation is not yet at an advanced stage, as is evident from Figures 7 to 11, due to insufficient methane gas developing in accordance with Equation [1], and collecting on the grain boundaries to result in voids and fissures.
Figure 15(a) and Figure 15(b) show the microstructures after 350 hours of exposure:
Figure 15(a) illustrates evidence of micro-cracking at a magnification of 200X. The cracking occurs parallel to the banded microstructure on the grain boundaries between the darker pearlite and lighter ferrite phase. Figure 15(b) shows the progression of the crack tip and evidence of more severe decarburization, as the darker pearlite phase has become more depleted. At 350 hours, a significant decrease in the yield strength, tensile strength, elongation to fracture, and reduction in area parameters were observed and thus probably corresponds to the presence of the cracks observed in the micrographs in the aforementioned illustrations. The application of load in the through-thickness direction (normal to the cracks noted
above) may lead to premature fracture from crack tips and thus, the rapid degradation of the through-thickness mechanical properties observed.
The microstructure demonstrates the outcome of the HTHA mechanism discussed earlier. The effect of the reaction of Equation [1] is shown, where the carbon contained in the carbon-rich cementite has been locally consumed due to the reaction with the dissociated hydrogen gas. The methane molecules that formed could not escape, due to its size, and the localized pressure that resulted caused the microcracking of the ferritic matrix that was observed. The concentration of the microcracks in planes parallel to the plate rolling direction is apparent. A comparison of this microstructure to that of the unexposed material, shown in Figure 13, explains the near complete loss of tensile ductility, as measured by reduction of area, compared to the excellent ductility (77.5%) of the unexposed ferrite and pearlite microstructure.
The microstructures after 425 hours are shown in Figure 16. Similar to the 350-hour exposed sample, there is significant evidence of damage even at lower magnification. The cracking occurs parallel to the pearlite phases on the grain boundaries. However, in this case, an even larger degree of decarburization has taken place. The fraction of dark pearlite phase in Figure 16(b) is observed to be severely reduced, compared to that in Figure 15(b). These findings support the tensile test results and indicate that severe degradation of the material occurred between 285 and 350 hours of exposure.
Monitoring of damage using encapsulated high-temperature strain gauges
Figures 11 and 12 demonstrate that the critical threshold of exposure time that corresponds to tensile property degradation can be identified by monitoring the HTHA swelling strain. Once the HTHA strain detected by the encapsulated high-temperature strain gauges exceeded a value of 65 με after an exposure time of 285 hours, corresponding to 1.1% of the maximum strain measured after 700 hours exposure, both the tensile strength and ductility of z-direction samples were irrevocably degraded. For these samples, the degradation process was completed after an HTHA strain of 124 με, corresponding to 2.1% of the total value measured after 350 hours of exposure. The investigation therefore showed that the encapsulated high-temperature strain gauging technique was sufficiently sensitive to identify the threshold time for HTHA damage, which was found to be in the region of 65 με. This value is significantly smaller than the 400 to 1000 microstrain value postulated by previous authors. Due to the variability of strain measurements during the early stages of the strain-time curve, the use of a threshold strain rate, rather than an absolute strain value or a percentage of maximum strain, can be effective. Even though the microcracks present at this stage of the HTHA process showed few signs of opening up, i.e., small levels of crack face separation were present, the presence of the cracks was sufficient to result in large levels of ductility and strength degradation. Contrary to the
previous thought, the point of incubation of HTHA damage results in very significant levels of embrittlement in the through-thickness direction.
Conclusions
➤ The degradation of carbon steel mechanical properties due to HTHA can be correlated to swelling-induced strain using high-temperature strain gauges.
➤ For the carbon steel studied and in the through-thickness direction, the threshold strain for HTHA tensile property degradation is in the order of 1 per cent of the total measured swelling strain, or 65 microstrain, significantly lower than the 400 to 1000 microstrain postulated by previous authors.
➤ Significant degradation of through-thickness tensile properties occurs at low amounts of measured swelling strain and is associated with a small degree of HTHA microstructural damage.
➤ For the plate material investigated, the HTHA degradation of carbon steel tensile properties is more severe and develops more rapidly in the through-thickness direction compared to that in the transverse and longitudinal directions. This difference is due to the preferential development of microstructural damage on planes parallel to the plate rolling direction.
➤ In order to prevent premature failures, the progress of HTHA of at-risk structures can be monitored using encapsulated high-temperature strain gauges. Using this technique, exceeding the threshold exposure conditions for HTHA mechanical property degradation and premature failure can be avoided.
Arno van Zyl carried out the study and wrote the manuscript. Christiaan Pretorius co-supervised the study and performed the HTHA exposure, strain gauging and mechanical testing. Moses Mathoho was the industrial collaborator, proofread the manuscript and co-conceived the project. Roelf Mostert co-conceived the project, assisted with the writing of the manuscript, and supervised the project. Sasol Synfuels (Pty) Ltd. supported the execution of the project.
References
API Recommended Practice 941. 2016. Steels for Hydrogen Service at Elevated Temperatures and Pressures in Petroleum Refineries and Petrochemical Plants. API Technical Report 941. (2008). The Technical Basis Document for API RP 941.
Baker, A. J. 1999. Combined creep and hydrogen attack of petro refinery steel. www.bl.uk
Benac, D. J., Paul, M. 2012. Reducing the risk of high temperature hydrogen attack (HTHA) failures. Journal of Failure Analysis and Prevention, vol. 12, no. 6, pp. 624–627. https://doi. org/10.1007/s11668-012-9605-x
Kyowa. 2011. Encapsulated Weldable Strain Gages, pp. 1–16.
Liu, P. 2001. Fundamental Studies of Hydrogen Attack in C-0.5Mo Steel and Weldments Applied in Petroleum and Petrochemical Industries. ui.adsabs.harvard.edu
Mostert, R.J., Mukarati, T.W., Pretorius, C.C.E., Mathoho, V.M. 2022. A constitutive equation for the kinetics of high temperature hydrogen attack and its use for structural life prediction. Procedia Structural Integrity, vol. 37(C), pp. 763–770. https://doi.org/10.1016/j.prostr.2022.02.007
Munsterman, Tim, Antonio, S., Dana, G.W. 2010. High Temperature Hydrogen Attack Resistance Using Autoclave Testing of Scoop Samples. IPEIA 14th Annual Conference in Banff. Alberta
Panda, B., Shewmon, P. 1984. Kinetics of Methane Bubble Growth in a 1020 Steel. Metallurgical Transactions, vol. 15A, pp. 487–494.
Poorhaydari, K. 2021. A Comprehensive Examination of HighTemperature Hydrogen Attack—A Review of over a Century of Investigations. Journal of Materials Engineering and Performance, vol. 30, no. 11, pp. 7875–7908. Springer. https://doi.org/10.1007/s11665-021-06045-z
Pretorius, C., Mostert, R., Mukarati, T., Mathoho, V. 2021. Microstructural influences on the damage evolution and kinetics of high temperature hydrogen attack in a C-0.5 Mo welded joint. Suid-Afrikaanse Tydskrif Vir Natuurwetenskap En Tegnologie, vol. 40, no. 1, pp. 212–223. https://doi.org/10.36303/ satnt.2021cosaami.40
Welding Research Council. 2021a. WRC Bulletin 585: The α-Ω HTHA Model and the Time Dependent Prager Curves, ISSN 2372-1057. 2021b. WRC Bulletin 586: The α-Ω Loss of Containment Model for HTHA with Guidelines for FFS, ISSN 2372–1057. u
Affiliation:
1Department of Civil Engineering, Haldia Institute of Technology, India
2Department of Civil and Environmental Engineering, Birla Institute of Technology, India
Correspondence to: A. Golder
Email: phdcee10054.17@bitmesra.ac.in
Dates:
Received: 4 Jan. 2022
Revised: 31 Oct. 2022
Accepted: 15 Sept. 2024
Published: November 2024
How to cite: Golder, A., Dandapat, S.P., and Roy, I. 2024. Instability of topsoil benches of a pit caused by dumping of waste rock outside an opencast coal mine. Journal of the Southern African Institute of Mining and Metallurgy, vol. 124, no.11, pp. 693–702
DOI:
http://dx.doi.org/10.17159/24119717/1973/2024
ORCiD:
A. Golder
http://orcid.org/0000-0002-5078-1613
S.P. Dandapat
http://orcid.org/0009-0005-6883-2780
I. Roy
http://orcid.org/0000-0003-2895-5135
by A. Golder1, S.P. Dandapat1, and I. Roy2
Abstract
One of the consequences of large-scale opencast mining for coal is the disposal of an enormous volume of overburden material that needs to be removed. With the enlargement of opencast mines and associated high stripping ratios, the volume of overburden extraction is rising. Overburden from the initial mine cut has to be necessarily dumped outside the mining area until enough void is created inside the mine for back-filling operations. The quantity of overburden placed outside the mining area normally varies from 10% to 30% of the total overburden removal. The stability of these dumps placed outside the mining area is of prime importance from the point of view of smooth operations of the mines and safety of persons in and around the dumping area. Owing to increasing pressure on land use, mine operators do not have any other option other than to place the waste dumps very near to the surface edge of the pit, which may lead to failure of the topsoil benches of the working pit. This study identified major controlling parameters that influence a stable but economic combination of height and slope angle of external dumps located close to the edge of an open coal pit.
Keywords
slope stability, circular failure, opencast mining, shear strength parameters, overburden dump
Introduction
In India, some 45% of total opencast coal production is by dragline-operated mining, which is considered the most efficient way of winning coal for opencast mines linked to power plants. In dragline-operated opencast mines, the overburden comprises both dragline dump and shovel-dumper dump. The dragline dump comes from parting between the bottom-most seam and just above to bottom-most seam; the shoveldump material originates comes from parting between intermediate seams and the top overburden above the upper seams. This complex process of dump formation by the combination of dragline and shoveldumper creates difficulty in positioning of the shovel-dumper dump with respect to the dragline dump due to following reasons:
➤ Dragline dump is often of low cohesive strength and is placed without compaction. The re-handled dump material is allowed to pile up at its natural angle of repose, i.e., at limiting equilibrium.
➤ If the shovel-dumper material is dumped just above fresh dragline dump that is not compacted and is standing at an factor of safety (FoS) of 1.00–1.05, this will lead to failure of both dragline and shoveldumper dumps.
➤ Dumping the shovel-dumper contents away from fresh dragline dump allows sufficient time for consolidation and development of cohesion and angle of internal friction within dragline dump mass, but will result in a substantial decrease in space for dumping.
➤ A reduction of space for dumping will lead to increase in height of both internal shovel-dumper and external dumps, thereby endangering the dump stabilities.
➤ The position of the shovel-dumper dump with respect to the toe of the fresh dragline dump is therefore a difficult decision for mine operators. This motivated an extensive study of this topic.
In opencast mining, the coal is mined after removing the overburden, which is placed either outside the open-pit area, known as external dumping, or in the void after de-coaling, i.e., within the open-pit area, known as internal dumping. Attempts are made to minimize external dumping to reduce the land use; however, the quantity of material to be placed as external or internal dumps depends on following geomining criteria (Sengupta and Roy, 2015; Zaitseva and Zaitsev, 2009):
➤ In case of multi-seam occurrences, especially in the Damodar Valley coalfield near Jharia and Raniganj (India), internal dumping over the de-coaled area of the upper seams will sterilize opencast mining of the lower seams. In such cases, it should be made certain that lower seams will not be workable in future by opencast methods. If there is a possibility of later opencast working of the lower seams, then the overburden removed from the top seams has to be placed as external dumps.
➤ In case of steep seam occurrence, simultaneous mine working and back-filling with the help of draglines is difficult. In such cases, back-filling may be performed in adjoining voids, if these exist; otherwise, overburden removal has to be placed as external dumps
➤ The location of external dumps requires selection of suitable sites. External dumping may be avoided, if possible, in the following site conditions, shown in Figure 1: (i) dumping over alluvium or soft-soil strata very close to the open-pit edge, (ii) dumping over a fault plane (Pit Slope Manual, 1976) that is exposed and dipping towards the quarry batter.
External dumping can be placed either close to or away from the pit crest. The following factors are considered in case of external dumping close to the pit crest:
➤ External dumps are normally placed close to the open-pit area to reduce the traverse distance of the overburden haul trucks, which in turn reduces the total complement of trucks operating in the mine;
➤ It is environmentally harmful to move overburden materials away from the pit area;
➤ Mining and dumping are in close proximity to the pit, which can facilitate management;
➤ Acquisition of large areas of land is required, with the concurrent problem of depletion of forest area.
Considering these factors, mine operators are often forced to place waste materials very near the edge of the working pit, which may lead to failure of the top benches of the pit batter due to surcharge loading of the external dump material. Determination of the optimum distance of the external dump from the edge of the nearest working-pit crest is necessary for both safety and land use management considerations.
The main objective of this study was to elucidate, using a computerized model, the influence of distance (B1) between the toe of the dump and the nearest surface edge of the open pit on the slope geometry of an external dump, i.e., slope and height of the dump (Figure 2) (Pit Slope Manual, 1976; Roy, 1998), depending on various geotechnical parameters (Roy, 2008).
Here, some parameters were kept constant and others were considered variable to show their influence on distance B1 Parameters that were kept constant are as follows (Sengupta and Roy, 2015; Sengupta et al., 2016):
B1: distance of toe of external dump from surface edge of the open pit crest; H: height of dump; DW2: depth of water table below external dump; DW1: height of accumulated water table within quarry
➤ Cohesion and angle of internal friction of dump material (C2, f2);
➤ Unit weight of dump material (g2);
➤ Ground acceleration due to blasting (Ag) (Indian Standard 1893 (Part 1), 2002);
➤ Capacity of dumper plying above dump-capacity and its surcharge load on the failure surface, shown in Figure 2.
The parameters that were considered variable are as follows (Sengupta and Roy, 2015; Sengupta et al., 2016) (Figures 2 and 3):
➤ Distance of toe of external dump from the edge of the openpit crest (B1);
➤ Height (H) and slope angle (b) of dump;
➤ Cohesion and angle of internal friction of foundation material (C1, f1);
Unit weight of foundation material (g1); Depth of water table below external dump (DW2); Height of accumulated water table within the open pit (DW1).
Back-analysis methodology
The following steps were employed for the back analysis (Roy et al., 2013):
1st step - FoS of the first trial surface was determined by the Fellenius method (Sengupta and Roy, 2015) with assumed values of cohesion and angle of internal friction of the dump material (close to the laboratory-determined value) and other geo-engineering parameters stated above.
2nd step - An iterative method was carried out to determine the most critical failure mode and corresponding absolute minimum FoS using the Fellenius method (considering that the FoS determined by Fellenius method is not absolute and can be underestimated).
3rd step - The FoS was modified using Bishop's Simplified method (Sengupta and Roy, 2015), which produced results that were more or less equivalent to those obtained by other complex methods, such as those of Janbu, Morgenstern–Price, and Spencer.
4th step - The above method was repeated until the most favourable combination of cohesion and angle of internal friction of dump mass was obtained for which the FoS was equal to 1.0.
To determine the site-specific shear strength parameters; namely, cohesion (C1) and angle of internal friction (ϕ1) (despite using laboratory-obtained values, due to the difficulty in accurately simulating site conditions), back analyses were conducted for overburden slopes along problematic sections in the study. These were slopes that had failed and/or were considered to be standing at limiting equilibrium, i.e., with an FoS equal to 1, or were on the verge of failure. The most frequently used approaches for assessing slope stability and constructing engineered slopes are limit equilibrium (LE) methods (Oh and Lu, 2015). One of the most accurate methods for determining the shear strength of slope material at the moment of failure is to conduct an LE back analysis of a collapsed slope, i.e., circular slope failure (Sancio, 1981; Topal and Akin, 2009; US Army Corps, 2003). For design, the shear strength parameters acquired by back analysis of slopes are recognized as being more consistent than those obtained by laboratory or in situ testing (Popescu and Schaefer, 2016). All feasible representative cohesive interpretations (nearer to the laboratory-defined value) of dump material are analysed and values of the angle of internal friction of the dump mass are achieved
for which the FoS is about 1.0 are compared by stability analysis. Similarly, all probable representative values of angle of internal friction (nearer to the laboratory-defined value) are analysed and similar cohesive values of the dump are obtained for which the FoS is about 1.0 (Zhang et al., 2010).
Back analysis was performed for failed overburden slopes and those considered to be standing at limiting equilibrium along problematic sections in the study area to identify the site-specific shear strength parameters; namely, C1 and ϕ1. The back-analysis results are tabulated in Table I.
Analysis, results, and discussion
Fellenius method used to calculate the safety factor
To determine FoS using the Fellenius method for a circular mode of failure, a trial surface was considered for an assumed part of the overburden slope (Figure 2). This was divided into a number of slices as necessary for subsequent calculations by randomly picking the centre for the iteration technique. The various forces acting on each slice are (Figures 3 and 4):
a) Force caused by the dead load, i.e., self-weight;
b) Effect of seismicity;
c) Blasting in the open pit for mining operations generates forces on the slice and, as a result, on the slope;
d) Upward thrust of water on each slice due to the presence of a water table within the overburden slope;
e) Water seepage force on each slice caused by water flowing through the overburden and highwall slope.
[1]
where S is the seismic co-efficient. [2]
Table I
Back-analysis results
Slope
1
2
3
= −19.33
XX1 = −10
Y1 =
XX1 = −5
*FM – Fellenius method and BM – Bishop’s Simplified Method
FS1 of the chosen trial surface was the ratio of cumulative resisting forces to cumulative disturbing forces.
Bishop’s simplified method to determine factor of safety
The FoS (FS1) calculated by the Fellenius method (Equation [5]) has some inaccuracy because inter-slice forces are ignored, Bishop's simplified method was used to obtain more precise findings using Equation [6:]
Values obtained were as follows:
➤ FoS using Fellenius method = 1.182, ➤ 1st FoS using Bishop’s Simplified method = 1.325, ➤ 2nd FoS using Bishop’s Simplified method = 1.397.
After considering all the recommended factor of safety suggested by different agencies such as National Coal Board U.K, United States D'Appolonia consulting engineers, Mines branch Canada, and Stability of pit slopes and dumps by G.L. Fiesenko, Russia for surface mine slope design, a factor of safety of more than 1.30-1.35 is envisaged here for the design of coal mines in Indian conditions which considers maximum seismic acceleration.
The optimum combination of height and slope of dump corresponding to a stipulated FoS of 1.30–1.35 (Roy, 1998) was selected and compared with the FoS determined by Bishop’s Simplified method. If the calculated FoS is less than 1.30, then a milder slope is to be considered to match the stipulated FoS; if the calculated FoS exceeds the stipulated range, then a steeper slope should be considered.
FoS considering seismicity and seepage force by Fellenius method is 1.182; that by Bishop’s Simplified method is 1.325.
For a dump on weak foundations, there is a steady increase in height or steepening of slope angle for an increase in the value of B1 (Figure 5); however, this is only true up to a particular value of B1, which differs for different combinations of input parameters.
Figure 5 shows no increase in stable height of dump for change in value of B1 from 5 m to 10 m when the angle of internal friction of the foundation material (f1) is ≥ 25°; whereas there is a steady increase in the stable height of the dump (Table III) for a change in value of B1 from 0 to 10 m when f1 = 20°.
With increase in shear strength of foundation materials (C1, f1), there is a steady increase in the stable height of the dump for a particular value of slope angle and particular value of Bh (Figures 5 and 6) (Sengupta et al., 2014).
For Figure 2, variations of slope geometry with different values of angle of internal friction of foundation material (f1) are presented in Table III.
In Table II, variations of slope geometry with different values of cohesion of foundation material (C1) are presented in Tables IV and V.
The angle of internal friction of the foundation is already below 20°, so the external dump is unsafe within 10 m of the pit crest when cohesion of the foundation is less than or equal to 30 kN/m2 (Figure 6).
Table II
Variation of slope geometry for different values of angle of internal friction (Φ1) of foundation material and B1 = 5 m distance between toe of external dump and surface edge of the pit slope batter with seepage
Angle of internal friction (Φ1 (°)
stable angle (β) (°)
Table III
Variation of height of dump with B1 = 5 m, slope angle (b) = 25°, and FOS = 1.325
of internal friction (f1) (°)
of dump (H) (m)
The effect of unit weight of foundation material (g1) is not significant in comparison with cohesion (C1) and angle of internal friction (f1) (Figure 6).
Comparing Figures 5–7 with Figures 8–10, it can be concluded that there is a steady decrease in the stable height for seepage of ground water through the foundation of the dump, as shown in
Figure 5—Influence of face angle of external dump on its stable height in high-risk zone (FoS: 1.30–1.35) for different values of angle of internal friction (Φ1) of foundation material and B1 distance between toe of external dump and surface edge of the pit slope batter. Φ2 = 40º, C2 = 15 kN/m2, C1 = 35 kN/m2, DW2 = −2 m, DW1 = −20 m, Unit weight of foundation material (Υ1) = 19 kN/m3, Unit weight of dump material (Υ2 ) = 21 kN/m3, Ag = 0, capacity = 50 t
Figure 6—Influence of face angle of external dump on its stable height in high-risk zone (FoS: 1.30–1.35) for different values of cohesion of foundation material (C1) and B1 distance between toe of external dump and surface edge of pit crest batter. Φ2 = 40º, Φ1 = 20º, C2 = 15 kN/m2, DW2 = −2 m, DW1 = − 20 m, Υ1 = 19 kN/m3, Υ2 = 21 kN/m3, Ag = 0, capacity = 50 t
Table IV
Variation of slope geometry for different values of cohesion of foundation material (C1) of foundation material and B1 = 10 m distance between toe of external dump and surface edge of the pit slope batter with seepage
Cohesion (C1) kN/m2
Table V
Variation of height of dump B1 = 10 m, slope angle (b) = 25°, and FOS = 1.261
Cohesion of foundation material (C1) (kN/m2)
Height of dump (H) (m)
20 25 30 35
20 35 40 55
Table VI. Depth of the water table (DW2) is −2m in Figures 5–7), i.e., there is seepage of ground water through the foundation of the dump; whereas DW2 is − 20 m in Figures 8–10), i.e., there is no seepage of ground water through the foundation. Hence, there is a decrease in safe height of dump due to seepage through the foundation of the dump in comparison with no seepage.
Table VI
Comparison of heights of dump with seepage condition and without seepage condition B1 = 5 m, slope angle (b) = 21°, angle of internal friction of foundation material (f1) = 20°, and FOS = 1.351
With seepage With seepage
Depth of water table (DW2) (m) −2 −20
Depth of water table (DW1) (m) −20 −20 Height of dump (H) (m) 70
Precautionary measures
In addition to maintaining the recommended geo-engineering parameters of shear parameters (C and ϕ) of dump and foundation material, dynamic forces (seismicity of the area and vibration due to blasting), hydrogeological parameters (upward thrust and seepage force), and mine floor inclination, the following measures are recommended:
1. Floor gradient of the mine should be maintained to ensure consistent natural gravitational flow of water towards the sump, thereby ensuring minimum accumulation of water in the de-coaled floor of the pit.
2. If a coal rib is left against the toe of the dump, its dimension should not exceed the recommendations of 7–7.5 m at the base and 1 m at the roof with full coal-seam thickness of 16–18 m and 4 m at the roof and 7 m at the base with half coal-seam thickness of 9–10 m (Sharma and Roy, 2015) (Figure 11).
3. No low-bearing capacity soil should be allowed to be dumped on the floor of the de-coaled area to form the base of the dump.
= 15kNm3
Slope geometry on density (Υ1) with seepage
Maximum stable angle (b) in degree Maximum stable height (H) of dump in m
Figure 7—Influence of face angle of external dump on its stable height in high-risk zone (FoS: 1.30–1.35) for different values of unit weight of foundation material (Υ1) and B1 distance between toe of external dump and surface edge of pit crest batter. Φ2 = 40º, Φ1 = 20º, C2 = 15 kN/m2, C1 = 35 kN/m2, DW2 = −2 m, DW1 = −20 m, Υ2 = 21 kN/m3, Ag = 0, capacity = 50 t
Variation of slope geometry on frictional angle (ϕ1) without seepage
Maximum stable height (H) of dump in m
Figure 8—Influence of face angle of external dump on its stable height in high-risk zone (FoS: 1.30–1.35) for different values of angle of internal friction of foundation material (Φ1) and B1 distance between toe of external dump and surface edge of pit crest batter, without seepage through foundation of dump. Φ1 = 20º, C2 = 15 kN/m2, C1 = 35 kN/m2, DW1 = −20 m, DW2 = −20 m, Υ1 = 19 kN/m3, Υ2 = 21 kN/m3, Ag = 0, capacity = 50 t
4. Topsoil should be separately dumped. as far as possible away from the site of active internal dumping.
5. The valley in the dragline dump may be filled up by dozing to the maximum possible volume of overburden.
6. The coal rib left at the toe of dump contributes little to the stability of the internal dump, but is prone to spontaneous heating and should be covered by dump material to the extent possible.
7. The interface layer, i.e., debris of coal dust, fragmented rock, and soil mixed with water, should be cleared as far as possible from the de-coaled floor before dumping by dragline.
8. The interface layer should be cleaned from areas where coal has been mined before being dumped by dragline (Singh et al., 2012). If possible, crushed overburden rock should be dropped in its place to cover the slushy ground at the dragline dump's base to increase the friction angle.
9. Minor blasting facilitates passage of water through the pit floor to the competent sandstone strata, thus preventing accumulation of water at the base of the dump.
10. The toe of the shovel dump should be formed at least 110–180 m away from the toe of the dragline dump to allow adequate time to stabilize before fresh dumping by the haul trucks.
stable height (H)
Maximum stable angle (b) in degree
Figure 9—Influence of face angle of external dump on its stable height in high-risk zone (FoS: 1.30–1.35) for different values of cohesion of foundation material (C1) and B1 distance between toe of external dump and surface edge of pit-crest batter, without seepage through foundation of dump. Φ1 = 20º, Φ2 = 40º, C2 = 15 kN/m2, DW1 = −20 m, DW2 = −20 m, Υ1 = 19 kN/m3, Υ2 = 21 kN/m3, Ag = 0, capacity = 50 t
Figure 10—Influence of face angle of external dump on its stable height in high-risk zone (FoS: 1.30–1.35) for different values of unit weight of foundation material (Υ1) and B1 distance between toe of external dump and surface edge of pit crest batter, without seepage through foundation of dump. Φ1 = 20º, Φ2 = 40º, C1 = 35 kN/m2, C2 = 15 kN/m2, DW1 = −20 m, DW2 = −20 m, Υ2 = 21 kN/m3, Ag = 0, capacity = 50 t
Table VII
Variation of slope geometry for different values of angle of internal Friction (Φ1) of foundation material and B1 = 5 m distance between toe of external dump and surface edge of the pit slope batter without seepage Angle of internal
(Φ1) (°)
Table VIII
Variation of slope geometry for different values of cohesion of foundation material (C1) of foundation material and B1 = 10 m distance between toe of external dump and surface edge of the pit slope batter without seepage Cohesion (C1) (kN/m2)
Table IX
Variation of slope geometry for different values of unit weight of foundation material (Υ1) of foundation material and B1 = 5 m distance between toe of external dump and surface edge of the pit slope batter without seepage
Unit weight (Υ1) (kN/m3)
(β) (°)
11. A dump-monitoring cell may be established to monitor movements within the dump slopes.
12. Monitoring of toe, crest, slope angle below the dragline operating level, berm at the dragline level, and coal rib roof level should be regularly carried out and recorded (two to three times a week). In case of any movement in these areas, the working zone near the dragline dump should be declared a high-risk zone: mining activity should be stopped until further action in stabilizing the dump slope is taken.
13. Advanced slope-monitoring instruments, such as threedimensional laser scanner or slope stability radar, are recommended for dragline dump monitoring.
Conclusion
This paper identifies major controlling parameters that influence a stable but economic combination of height and slope angle of external dumps located close to an open pit. Depending on parting thickness between the lowest coal seam and just above it and dragline capacity, these parameters can be applied for dragline dump design. An average water table height was considered.
A safe and economic distance of an external dump from the nearest open-pit batter depends on the total height of dragline and shovel dump; overall slope of dragline and shovel dump (as per the regulations (DGMS, 2017)); angle of internal friction, cohesion, and bulk unit weight of the dump material; angle of internal friction and cohesion of interface/foundation material, i.e., slushy material at the base of the dragline dump or foundation material; water table height inside the dragline dump; dump (mine) floor inclination; seismic
zone of that particular area. Other than geometrical dimensions, i.e., height and slope angle, the influence of internal friction is found to be more pronounced than cohesion. Mine floor inclination is also a major influencing factor.
A dragline dump profile based on the combination of these factors can be designed by adjusting the berm width at the dragline operating level and that at coal rib roof level.
The contributors are grateful to the administration of Birla Institute of Technology and Haldia Institute of Technology for providing the necessary permission to publish this paper. This research work was financially supported by Coal India Limited.
References
DGMS. 2017. The Coal Mine Regulations, Dhanbad. Golder, A., Roy, I. 2021. Investigation for safety of final quarry bench during mine closure stage: a case study. Journal of The Institution of Engineers (India): Series D. https://doi. org/10.1007/s40033-021-00298-7
Golder, A., Roy, I. 2022. Safety aspects of large dragline- operated opencast mines – an overview. The Journal of the Southern African Institute of Mining and Metallurgy, 122, 15–19. https:// doi.org/http://dx.doi.org/10.17159/2411- 9717/1452/2022
IS 1893 (Part 1). 2002. Criteria for earthquake resistant design of structures. Indian Standard, New Delhi. Available at: http:// rahat.up.nic.in/sdmplan/Earthquake/AnnexureI-V/AnnexureI_ Bldg. Earthquake.pdf
Oh, S., Lu, N. 2015. Slope stability analysis under unsaturated conditions: case studies of rainfall-induced failure of cut slopes. Engineering Geology https://doi.org/10.1016/j. enggeo.2014.11.007
Pit Slope Manual. 1976. Mining Research Laboratories Canada Centre for Mineral and Energy Technology Department of Energy, Mines and Resources Canada.
Popescu, M. E., Schaefer, V. R. 2016. Back analysis of slope failures to design landslide stabilizing piles. Forensic Geotechnical Engineering, pp. 119–130. https://doi.org/10.1007/978-81-3222377-1
Roy, I. 1998. Influence of geo-engineering parameters on the stability of dump. Indian Institute of Technology, Kharagpur (IIT-KGP).
Roy, I. (2008) ‘Slope stability study of external dump of SonepurBazari pencast Coal Mine , India — A Case Study’. International Conference on Case Histories in Geotechnical Engineering
Roy, I., Sharma, S., Shrivastava, A. K. 2013. Development of Guidelines for Safe Dragline Dump Profile under Geo-Engineering Conditions of Coal Mines in Coal India, vol. 13, no. 3, pp. 65–70.
Sancio, R.T. 1981. The use of back-calculations to obtain the shear and tensile strength of weathered rocks. ISRM International Symposium. [Preprint]
Sengupta, S., Roy, I. 2015. Study of internal dump stability of Dudhichua Open Cast Project, Northern Coalfields Limited, India. Journal of The Institution of Engineers (India): Series D, vol. 96, no. 1, pp. 67–75. https://doi.org/10.1007/s40033-0140061-5
Sengupta, S., Sharma, S., Roy, I. 2014. Investigation of shear strength parameters of highwall rock slopes and overburden dump mass in Opencast Coal Mines. 07(01), pp. 1–6.
Sengupta, S., Sharma, S., Roy, I. 2016. Stability analysis of overburden internal dump material of Amlohri opencast coal mine, India. ARPN Journal of Earth Sciences, vol. 5, no. 1, pp. 50–57.
Sharma, S., Roy, I. 2015. Slope failure of waste rock dump at Jayant opencast mine, India: A case study. International Journal of Applied Engineering Research, vol. 10, no. 13, pp. 33006–33012.
Sharma, S., Sengupta, S., Roy, I. 2015. Identification of failure surfaces in dragline dumps of opencast coal mines. ARPN Journal of Earth Sciences, vol. 4, no. 2, pp. 43–53.
Singh, P.K., Roy, M.P., Paswan, R.K., Sinha, A. 2012. Effect of production blasts on waste dump stability. Rock Fragmentation by Blasting (FRAGBLAST-10), November.
Topal, T., Akin, M. 2009. Geotechnical assessment of a landslide along a natural gas pipeline for possible remediations ( Karacabey-Turkey ). Environmental Earth Sciences, vol. 57, no. 03, pp. 611–620. https://doi.org/10.1007/s00254-008-1330-0
US Army Corps. (2003). Slope Stability.
Zaitseva, A. A., Zaitsev, G. D. 2009. Influence of geological and technological factors on the internal dump capacity in flat deposits. Journal of Mining Science, vol. 45, no. 4, pp. 380–389. https://doi.org/https://doi.org/10.1007/s10913-009-0048-z
Zhang, J., Tang, W. H., Zhang, L. M. 2010. Efficient probabilistic back-analysis of slope stability model parameters. Journal of Geotechnical and Geoenvironmental Engineering, vol. 136, no. 1, pp. 99–109. https://doi.org/https://doi.org/10.1061/ (ASCE)GT.1943-5606.0000205 u
Affiliation: Turkey
Correspondence to: A. Çelik
Email: arif_Rester@hotmail.com
Dates:
Received: 6 June 2023
Revised: 10 May 2024
Accepted: 12 Sep. 2024
Published: November 2024
How to cite:
Çelik, A. 2024. Investigating the effect of different loading scenarios on the performance of wheel loaders: A case study on Can Lignite Enterprises. Journal of the Southern African Institute of Mining and Metallurgy, vol. 124, no.11, pp. 703–710
DOI:
http://dx.doi.org/10.17159/24119717/2840/2024
ORCiD:
A. Çelik
http://orcid.org/0000-0002-2914-3369
by A. Çelik
Abstract
Wheel loaders are widely used in many sectors due to their mobility, operational flexibility, and low costs. The literature is mainly focused on improving the hydraulic, mechanical, and electronic subsystems of these machines in terms of efficiency or developing strategies for controlling these systems. In this study, the effects of the loader operator and different working conditions on the loading performance were investigated. The study was carried out at the Can Lignite Enterprise (CLI), which is a major coal producer in Turkey. In the study, which lasted approximately four months, a total of 808 measurements were performed to investigate seven different scenarios. The effect of a single parameter on loading performance was investigated in the first six scenarios. The results showed that the biggest impact on loading performance was caused by the operator's experience with 63.4%. On the other hand, the worst and most ideal working conditions determined from the first six scenarios were tested in the seventh scenario. It was tested as a script. The test results showed that the loading performance was 285.5% more effective under the most ideal operating conditions compared to the worst operating conditions. In addition, in the study, the loading performances of five loaders with four different capacities were examined in terms of energy efficiency and it was determined that the Kawasaki 115 work machine, which has a higher model and lower engine operating hours, was more advantageous. In the study, various suggestions were developed in parallel with the research results. The most prominent and easiest to implement of these suggestions is related to the selection of the loader operator.
Keywords different loading scenario, loader operator, loading performance, short loading cycle, wheel loader
Introduction
The most popular machines that are preferred to transport a material from one place to another or load it on a suitable vehicle are wheel loaders (Zauner et al. 2020). The popularity of these machines is based on their mobility, operational flexibility, and relatively low capital costs (Hartman, 1992). Wheel loaders have loader attachments (buckets, grapples, forks, material handling arms, cutting aggregates) that make it possible to load materials with different properties (Filla, 2008). These attachments have made the use of loaders widespread in many sectors such as mining, quarrying, construction, substructure development, and agriculture, etc. (Dadhich, 2018).
Due to its versatility, differences in operating conditions and operator behaviour makes it difficult to optimize fuel efficiency and productivity when designing a wheel loader (Frank et al. 2018). Nezhadali et al. (2016) stated that among experienced operators, the change due to operator behaviour can reach 150% in fuel efficiency and 300% in productivity.
Wheel loaders can be thought of as an integrated system consisting of hydraulic, mechanical, and electronic subsystems (Roux, 2011). Strategies applied for the control of different subsystems include lifting and carrying tasks that affect the fuel consumption and production rates of the main system (Frank et al. 2018). Many researchers have carried out technical studies on subsystems and strategies for controlling subsystems for fuel efficiency and production efficiency (Blake et al. 2006; Filla, 2011; Nilsson et al. 2014; Oh et al. 2016; Liu et al. 2017; Chen et al. 2022; Cao et al. 2023; Eriksson and Ghabcheloo, 2023).
Another important issue in terms of fuel and production efficiency is the operating cycle of wheel loaders. This cycle, which is called the short loading cycle in the literature (Huang et al. 2021), refers to the cycle that a wheel loader follows to load a vehicle in the shortest time possible. As can be seen from Figure 1, in this cycle consisting of 6 moves; In the first move, the wheel loader moves towards the loading area, and in the second move, it fills the material to be loaded into the bucket. In the third and fourth moves, it moves with the full load towards the vehicle to be loaded. In the fifth move, it unloads the
load into the vehicle and in the last move, it returns to its initial position. This cycle, which seems quite simple, is an important factor that separates experienced and inexperienced operators. Wrong cycle selections cause production to slow down and energy consumption to increase. Regarding the short loading cycle, Filla (2013) conducted a study on alternative routes for wheel loaders operating in short loading cycles and determined that alternative routes could be beneficial depending on the working conditions.
Nezhadali et al. (2013), conducted a study on the optimal control of a wheel loader in the lift-handling portion of the short loading cycle. Nezhadali et al. (2016), analyzed the effect of the operator's steering ability in a short loading cycle and revealed that the development of autonomous vehicles can be envisaged, especially for repeated cycles.
In recent years, studies on energy efficiency in all engineering disciplines have focused on designing existing systems/machines more efficiently in terms of energy and productivity with simulation methods (Filla, 2012, 2017; Yao et al. 2012; Oh et al. 2015; Xiong et al. 2019). This study focused on the operator and working conditions of the machine, rather than the machine’s energy efficiency. In the study, the loading performance of a wheel loader operator working with a bucket was investigated under the following conditions:
➤ Monitoring/not monitoring the loader operator
➤ Experienced/inexperienced operator
➤ Daytime and night studies
➤ Sunny and rainy weather conditions
➤ Loading with and without bucket scale
➤ Compressed and free material loading
➤ The most ideal and worst working conditions.
In addition to the scenarios mentioned, the loading performances of wheel loaders with 4 different capacities under similar conditions were investigated.
Method
Field studies were evaluated in five parts. In the first part, the effect of monitoring/not monitoring the loader operator on loading performance is evaluated. In the second part, the loading performances of 7 different loader operators are examined. In the third part, the effects of different operating conditions on the
loading performance of wheel loaders are investigated. In the fourth part, the effect of the ideal and worst working conditions on the loading performance is examined. In the fifth and last part, the loading performances of the loaders of different capacities used in CLI were evaluated.
In the study, performance data of wheel loaders were determined from field measurements. Field measurements were done in a classical V-cycle with equal orientation on both sides.
Loading time was taken into account as the main criterion in the performance analysis of wheel loaders. However, in the section where the effect of the loader bucket scale is examined, the amount of material loaded was also taken into account in addition to the loading time.
Furthermore, in the section where wheel loaders in CLI are compared in terms of energy efficiency, fuel consumption of wheel loaders was also taken into account in addition to loading times).
In the study, 40 measurements were made to determine the impact of each scenario. In each measurement, the loading of a single vehicle (approximately 26 tons-28 tons) was evaluated. The loading period started with the wheel loader moving to the loading area and stopped when the wheel loader reached the starting position after the material was loaded into the vehicle. Measurement times are expressed in seconds.
In the measurements where the effect of not monitoring the operator and the effect of the operators' experience on the results were investigated, the operator's short loading cycle was not intervened. In other measurements, the operator's short loading cycle was followed and measurements outside the cycle were cancelled.
In the section where the effect of the loader bucket scale on the loading performance is evaluated, the amount of material loaded as well as the loading times are taken into account. In the measurements made here, the amount of loaded material was found by weighing the loaded vehicles on vehicle scales.
In the section where wheel loaders in CLI are compared with each other, the amount of fuel consumed was also taken into account in addition to loading times. Diesel fuel consumption (ADF) of wheel loaders was calculated by Equation [1].
In Equation [1], TDM refers to the total duration of all measurements performed for a scenario. AADF is the hourly diesel fuel consumption of wheel loaders. This value was found by dividing the total amount of fuel consumed by the wheel loaders during their work in CLI in 2022 by their total working time. AADF values of wheel loaders are presented in Table I. The value 3,600 is a coefficient added to express TDM in hours.
Performance measurements of the wheel loaders specified in Table I were made at Can Lignite Enterprise in Turkey (Figure 2).
In the study, attention was paid not to interrupt coal sales activities while providing working conditions. For this reason, field studies lasted for approximately 4 months, and a total of 808 measurements were taken, including 720 valid and 88 invalid
*In the calculation of the AADF, the total working hours and total diesel consumption data of the loaders for the year 2022 are taken into account (Figure 3)
measurements. In the study, the loaded trucks were weighed to determine the amount of coal loaded in each measurement. When the truck weights determined from each measurement are evaluated, the difference between the lowest weighing amount (26.5 tons) and the highest weighing (27.3 tons) amount was determined as 2.9%. Since the difference in weighing amounts is low, performance evaluations were made only on loading times. However, in the tests where the loader bucket scale was evaluated, the amount of material loaded was also taken into account.
One of the important parameters in loading performance is the loading trajectory applied by the loader operator. Although the operators were instructed to use a classical V-cycle before the study, it is known from field experience that the operators will not fully comply with this cycle. For this reason, before starting the tests, the test was carried out to check whether the operators complied with the short loading cycle and the results were evaluated. In the conducted study, the loader operator's loading cycle (loading
cycle is associated with loading time) was first measured by remote monitoring without the operator's knowledge. The loading performance of the operator, who was then informed that the measurement would be made, was measured closely. A Kawasaki 115 wheel loader was used in the measurements. The operator with 7 years of experience in CLI used the loader. Measurements were made in sunny weather and compressed material. The bucket scale of the loader was not used in the loading process. A total of 80 measurements were made during the measurements that lasted 8 days. The measurement results are given in Figure 4.
When Figure 4 is examined, the following important conclusions/observations are made.
➤ When the operator did not know he was being monitored (initial case), the operator's time to load a truck was measured between 85 to147 seconds (Data: 40; Mean: 116.7; Standard deviation: 17.1; Variance: 290,4). The main reason for the significant 65-second difference here is the variability of the operator's loading cycle
➤ When the operator knew he was being monitored (second case), the operator's time to load a truck was measured between 82 to100 seconds (Data: 40; Mean: 93.0; Standard deviation: 4.9; Variance: 24.6). The main reason for the 18-second difference here is the variation in the loading difficulty of the compressed material
➤ When the two conditions are evaluated, it is determined that if the operator knows that he is being monitored, he can improve the average loading time by 20.3%.
After it was determined that the monitoring of the operator caused a significant difference in the results, measurements were carried out by closely monitoring the operators in all other scenario and measurements outside the short loading cycle were cancelled.
In the energy efficiency of the loader, the experience and ability of the operator who uses the machine are as important as the machine design. Within the scope of the study, the loading performances of 7 different wheel loader operators working in the enterprise were monitored. A Kawasaki 115 loader was used in performance measurements. Measurements were made in sunny weather and compressed material. The bucket scale of the loader was not used in the loading process. For each operator, 40 measurements were made. The results of the measurements completed in 26 days are presented in Table II.
When Table II is examined, the following important conclusions/observations were made.
➤ In the measurements, the highest loading time was determined from operator number 7. This operator has 3 months of experience in CLI and his total operator experience is 2 years
➤ In the measurements, the lowest loading time was determined from operator number 1. This operator started his career as an operator at CLI and has 8 years of operator experience
➤ It has been determined that, as the experience of the operators increases, the distribution of loading times becomes more balanced, in other words, the standard deviation values of the measurements decrease
➤ A difference of 63.4% was detected between the operators with the highest and lowest loading time. This difference showed that operator experience has a very significant effect on loading performance. In addition, the difference between the loading times of operators who have been working at CLI for
more than 6 years was determined to be 4.3%. This difference showed that similar experiences had little impact on loading performance.
The effect of different operating conditions on loading performance
In field experiences, it has been observed that weather conditions, loading zone, and loader bucket scale have an effect on loading performance and the degree of influence of these parameters has been measured within the scope of the study. In the performance measurements, the Kawasaki 115 loader was used by operator number 2, indicated in Table II. Measurements were completed in 16 days. Measurement results are given in Figure 5 and statistical analyses are given in Table III.
When Figure 5 and Table III are examined, the following important conclusions/observations are made.
➤ The average loading time of the wheel loader is 93 seconds in sunny weather and 99.3 seconds in rainy weather. Based on these values, it was calculated that the loading time of the wheel loader increased by 6.74% in rainy weather compared to sunny weather. The main reason for the difference here is that the operator increases the maneuver time in order to reduce the risk of work accidents that may occur due to slippery ground and reduced visibility. In other words, the operator works safer by reducing the machine speed. The loading in this scenario was carried out during the daytime and without
using the loader bucket scale
➤ The average loading time of the wheel loader is determined as 93 and 96 seconds, respectively, during daytime and night operations. Based on these values, it was calculated that the loading time of the wheel loader increased by 3.41% at night compared to daytime. The loading in this scenario was carried out in compacted material and without the use of a loader bucket scale
➤ The mine-out coal in the CLI stock areas are stacked in layers and during this process, the coal stacks filled in each floor are compressed by machines (dozer, grader, cylinder). In order to determine the effect of this situation on the loading performance, some of the coal coming to the stock area was poured freely on the stock floor and was not compressed. In the performance measurements, the average loading time of the wheel loader was determined as 93 and 78 seconds in compressed and free material, respectively. Based on these values, it was determined that the loading time of the wheel loader increased by 19.3% in the compressed material compared to the free material. The loading in this scenario was carried out during the daytime and without using the loader bucket scale
➤ Bucket scales are used to load the desired quantities of coal to trucks. In the field observations, it was observed that the loading performance of the loader operators decreased considerably when bucket scales were used. In
Table III
Statistical analysis of measurement results
*Indicated in Figure 5
the performance measurements made on this situation, the average loading time determined in the case of using the bucket scale is 111.7 seconds, while the average loading time determined in the case of not using the bucket scale is 93 seconds. Based on these values, it was calculated that the use of bucket scales in the loading process increased the loading time by 18.92%. In addition, in the measurements carried out, the amount of loaded material is 5.28% less in the case of using a bucket scale. When evaluated in terms of energy efficiency, less material (5.28%) was loaded in a longer time (18.92%). The energy loss here is calculated as 25.2%. The loading process in this study was carried out during the daytime and in compressed material
➤ When the 40 measurements for each parameter were evaluated, the most consistent measurements (standard deviation: 3.01) were determined from scenario No. 4, where free material was loaded. On the other hand, the most inconsistent measurements (standard deviation: 12.9) were detected from scenario number 5, where the loader bucket scale was used. The results of the study show that as loading conditions become easier, operators' loading times become more consistent
➤ When the study results were evaluated in terms of loading times and the consistency of these times, the ranking of the scenarios from best to worst was evaluated as 4-1-3-2-5.
The effect of the best and worst working conditions on loading performance
In this section, the effect of the best and worst operating conditions determined from the study and specified in Table IV on the loading performance is evaluated.
Table IV
The best and worst working conditions
Parameters The best The worst
Operator Experienced (Operator no. 1) Inexperienced (Operator no. 7)
Monitoring of the operator The operator knows The operator does not know
Weather conditions Sunny Rainy and night
Material Free Compressed
Bucket scale Not being used Being used
Measurements carried out with the working conditions specified in Table IV were completed on 2 different days. The results of the study, in which a total of 80 measurements were carried out, are given in Figure 6.
When Figure 6 is examined, the following important conclusions/observations were made.
➤ Loading time was found to be between 69-80 seconds in the best conditions and 169-249 seconds in the worst conditions
➤ When the averages of the measurement results were evaluated, it was determined that the loading time in the worst working conditions was 285.5% longer than in the best working conditions
➤ It has been observed that in the worst conditions, the operator with little experience has difficulty in using the loader bucket scale. This is the most important reason for the inconsistency of measurement times, in other words, the high standard deviation amount.
Evaluation of loading performances of loaders of different capacities
A total of 200 measurements were carried out to determine the most advantageous wheel loader used in CLI in terms of energy efficiency. In the measurements, the loaders specified in Table I were used by operator number 2 specified in Table II. Measurements were carried out on compressed material in sunny weather. Bucket scales of the loaders were not used in the measurements. The results of the measurements, which took 18 days in total, are given in Figure 7.
When Figure 7 is examined, the following important conclusions/observations were made.
➤ Among the loaders, Komatsu WA500 loaders with the lowest bucket capacity have the longest loading times depending on bucket capacity
➤ The lowest average loading times for loading a truck belong to Komatsu WA800 (70.6 seconds) and Cat 992K (70.9 seconds) loaders
➤ Komatsu loaders have the highest energy consumption (>1.3 L/truck), while the Kawasaki 115 has the lowest (0.91 L/ truck)
➤ Komatsu WA500s have the most ideal fuel consumption in terms of average diesel consumption per unit time (32−34 lt/h) as shown Table I. However, when the fuel consumption is evaluated together with the material loaded (1.3−1.4 L/ truck), it is determined that the machines have high energy consumption
➤ The Cat 992K and Komatsu WA800 have similar power, bucket capacity, and machine weight as shown in Table I. Considering the energy consumption of these machines, of which the average loading times are very close to each other, Cat 992K is 22.7% more advantageous than Kawasaki WA800. Although the Kawasaki 115 loader is preferably used in CLI due to energy efficiency, Cat 992 and Komatsu WA800 wheel loaders are needed due to the loading time advantage and increased workload. Additionally, Komatsu WA500 wheel loaders are generally operated at facility feed points due to their low fuel consumption per unit time. The comparison performed in this section involves the loaders used in the CLI. For example, it would be misleading to generalize that the Cat 992K loader is a more advantageous machine than the Komatsu WA800 loader as a result of this study. The main reason for this is that the models, technologies, engine hours, and maintenance and repair processes of the compared machines are quite different from each other.
The important conclusions drawn from the study, which investigated the effects of different operating conditions and operator differences on wheel loader loading performance, are listed below.
➤ It has been found that when loader operators realize that they are being monitored or their performance is being monitored by an observer/researcher/manager, they can reduce the loading time of a truck by 20.3%
➤ It has been determined that the most important effect on the loading performance of the wheel loader is the experience of the operator. In the study, the loading efficiency of 7 operators, 6 of whom are experienced and 1 of them inexperienced, were investigated. As a result, it was determined that the loading time of the inexperienced operator was 63.4% more than the experienced operators
➤ It has been observed that operators move more carefully and therefore slower, due to the slipperiness of the loading zone in rainy weather. As a result of the study carried out to determine the effect of this situation on the loading time, it was determined that the loading time increases by 6.74% in rainy weather
➤ As in rainy weather, the loading performance of the operator decreases depending on the clarity of vision during night work. During the measurements carried out to determine the effect of the decrease in loading performance, it was determined that the loading time increased by 3.41% in night studies compared to daytime studies
➤ In field observations, it was observed that the operators had difficulty in loading the compacted material. In the measurements carried out to determine the loading difficulty between the compressed material and the free material, it was determined that the loading time increased by 19.3% when the compressed material was loaded
➤ Another scenario measured detected that, in field observations the use of bucket scales for wheel loaders is implemented. Bucket scales for wheel loaders are used in order not to exceed the legal load allowed for trucks in coal sales. On-site observations determined that the efforts of the operators to adjust the desired load reduced the loading efficiency. In the measurements carried out to reveal the effect of this situation, it was revealed that the use of the loader bucket scale increased the loading time by 18.92%
➤ The measurements carried out to determine the effect of the best and worst working conditions on the loading performance, showed that the loading time of the inexperienced operator tested under the worst conditions was 285.5% longer than the experienced operator tested under the best conditions.
Within the scope of the study, the performances of 5 wheel loaders in CLI were also investigated. Research results showed that the most advantageous loader in terms of energy consumption is the Kawasaki 115 (0.91 L/truck). Kawasaki 115 has more advantages than other loaders in terms of model, engine hours, technology and maintenance-repair processes. When all these processes were evaluated, it was expected that the Kawasaki 115 would be the most advantageous loader. This result of the study actually showed how important machine renewal is in terms of fuel consumption and loading performance.
In parallel with the study results, the following recommendations were developed:
➤ The loader operator has the most significant impact on loading performance. It is recommended to implement social and economic improvements to increase the job commitment of experienced operators
➤ The use of a loader bucket scale increases loading time and the inconsistency of loading times. For this reason, it is recommended to investigate alternative options to the loader bucket scale along with cost analysis
➤ In CLI, it is recommended that wheel loaders that have reached the end of their useful life are replaced with new ones for energy efficiency.
Acknowledgement
The authors would like to thank the staff of Can Lignite Enterprises.
Credit Author Statement
AC: Conceptualization, methodology, investigation, validation, formal analysis, resources, writing.
Declaration of Competing Interest
The author declares that there is no conflict of interest.
References
Blake, C., Ivantysynova, M., Williams, K. 2006. Comparison of operational characteristics in power split continuously variable transmissions. Proceedings of the SAE 2006 Commercial Vehicle Engineering Congress & Exhibition, Rosemont/Chicago, IL, USA. Available at: https://doi.org/10.4271/2006-01-3468
Cao, B., Liu, X., Chen, W., Li, H., Wang, X. 2023. Intelligentization of wheel loader shovelling system based on multi-source data acquisition. Automation in Construction, vol. 147, no. 104733. Available at: https://doi.org/10.1016/j.autcon.2022.104733
Chen, Y., Jiang, H., Shi, G., Zheng, T. 2022. Research on the trajectory and operational performance of wheel loader automatic shovelling. Applied Science, vol. 12, no. 24. Available at: https://doi.org/10.3390/app122412919
Dadhich, S. 2018. Automation of Wheel-loaders. PhD Thesis, Lulea University, Sweden.
Eriksson, D., Ghabcheloo, R. 2023. Comparison of machine learning methods for automatic bucket filling: An imitation learning approach. Automation in Construction, vol.150, no. 104843. Available at: https://doi.org/10.1016/j.autcon.2023.104843
Filla, R. 2008. Alternative system solutions for Wheel loaders and other construction equipment. 1st International CTI Forum Alternative, Electric and Hybrid Drive Trains, Berlin, Almanya. DOI:10.13140/RG.2.1.3391.2801
Filla, R. 2011. Quantifying operability of working machines. PhD Thesis, Linkoping University, Sweden.
Filla, R. 2012. Simulating operability of wheel loaders: operator models and quantification on control effort. Proceeding of the 2nd Commercial Vehicle Technology Symposium, Kaiserslautern, Germany. DOI:10.13140/RG.2.1.2080.5606
Filla, R. 2013. Optimizing the trajectory of a wheel loader working in short loading cycles. 13th Scandinavian International Conference on Fluid Power, Linkoping, Sweden. 2013. DOI:10.3384/ ecp1392a30
Filla, R. 2017. Towards finding the optimal bucket filling strategy through simulation. 15th Scandinavian International Conference on Fluid Power, Linkoping, Sweden. DOI:10.3384/ecp17144402
Frank, B., Kleinert, J., Filla, R. 2018. Optimal control of wheel loader actuators in gravel applications. Automation in Construction, vol. 91, pp.1–14. Available at: https://doi.org/10.1016/j. autcon.2018.03.005
Hartman, H. 1992. SME Mining Engineering Handbook. Society for Mining, Metallurgy, and Exploration, Littleton, CO, USA, pp. 1327–1330.
Huang, J., Cheng, X., Shen, Y., Kong, D., Wang, J. 2021. Deep learning-based prediction of throttle value and state for wheel loaders. Energies, vol. 14, no. 21. Available at: https://doi.org/10.3390/en14217202
Liu, X., Sun, D., Qin, D., Liu, J. 2017. Achievement of fuel savings in wheel loader by applying hydrodynamic mechanical power split transmissions. Energies, vol. 10, no. 9. Available at: https://doi.org/10.3390/en10091267
Nezhadali, V., Eriksson, L., Fröberg, A. 2013. Modeling and optimal control of a wheel loader in the lift-transport section of the short loading cycle. IFAC Proceedings vol. 46, no. 21 pp. 195–200. Available at: https://doi.org/10.3182/20130904-4-JP-2042.00083
Nezhadali, V., Frank, B., Eriksson, L. 2016. Wheel loader operationoptimal control compared to real drive experience, Control Engineering Practice, vol. 48 pp. 1–9. Available at: https://doi.org/10.1016/j.conengprac.2015.12.015
Nilsson, T., Fröberg, A., and Aslund, J. 2014. Using Stochastic dynamic programming for look-ahead control of a wheel loader diesel electric transmission. IFAC Proceedings, vol. 47, no. 3, pp. 6630–6635. Available at: https://doi.org/10.3182/20140824-6-ZA-1003.01937
Oh, K., Kim, H., Ko, K., Kim, P., Yi, K. 2015. Integrated Wheel loader simulation model for improving performance and energy flow. Automation in Construction, vol. 58, pp. 129–143. Available at: https://doi.org/10.1016/j.autcon.2015.07.021
Oh, K., Yun, S., Ko, K., Ha, S., Kim, P., Seo, J., Yi, K. 2016. Gear ratio and shift Schedule optimization of wheel loader transmission for performance and energy efficiency. Automation in Construction, vol. 69, pp. 89–101.Available at: https://doi.org/10.1016/j. autcon.2016.06.004.
Roux, C. 2011. Crafting a reliability strategy to improve equipment uptime. Engineering and Mining Journal, vol. 11, pp. 129–131.
Shi, J., Güneş, D., Qin, D., Hu, M.H., Kan, Y., Ma, K., Chen, R. 2020. Planning the trajectory of an autonomous wheel loader and tracking its trajectory via adaptive model predictive control. Robotics and Autonomous Systems, vol. 131, no. 103570. Available at: https://doi.org/10.1016/j.robot.2020.103570
Xiong, S., Wilfong, G., Lumkes, J. 2019. Components sizing and performance analysis of hydro-mechanical power split transmission applied to a wheel loader. Energies, vol. 12, pp. 9. Available at: https://doi.org/10.3390/en12091613
Yao, K., Hou, Z.M., Yang, L.H. 2012. Performance simulation research on the conversion track wheel loader. Advanced Material Research, vol. 622–623, pp. 1253–1257. Available at: https://doi.org/10.4028/www.scientific.net/AMR.622-623.1253
Zauner, M., Altenberger, F., Knapp, H., Kozek, M. 2020. Phase independent finding and classification of wheel-loader workcycles. Automation in Construction, vol. 109, no. 102962. Available at: https://doi.org/10.1016/j.autcon.2019.102962. u
21-23 January 2025 — 14TH South African Conference on Computational and Applied Mechanics
Wits Science Stadium, South Africa
Website: https://sacam.co.za/
19-20 February 2025 — Mine Closure Conference 2025
Maslow Hotel, Sandton, South Africa
Contact: Gugu Charlie Tel: 011 538-0238
E-mail: gugu@saimm.co.za
Website: http://www.saimm.co.za
7-8 April 2025 — 2ND Southern African Hydrogen and Fuel Cell Conference 2025
Southern Sun Rosebank, Johannesburg
Contact: Gugu Charlie
Tel: 011 538-0238
E-mail: gugu@saimm.co.za
Website: http://www.saimm.co.za
8-10 April 2025 — 27TH International Conference on Paste, Thickened and Filtered Tailings
Swakopmund, Namibia
Website: https://acgpaste.com/2025/
26-29 May 2025 — 9TH Sulphur and Sulphuric Acid Conference 2025
Protea Hotel Stellenbosch and Conference Centre, Stellenbosch
Contact: Gugu Charlie
Tel: 011 538-0238
E-mail: gugu@saimm.co.za
Website: http://www.saimm.co.za
25-26 June 2025 — 4TH Digital Transformation in Mining Conference 2025
Glenburn Lodge and Spa, Muldersdrift
Contact: Camielah Jardine
Tel: 011 538-0237
E-mail: camielah@saimm.co.za
Website: http://www.saimm.co.za
21-25 July 2025 — AfriRock Conference 2025
Sun City, South Africa
Contact: Camielah Jardine
Tel: 011 538-0237
E-mail: camielah@saimm.co.za
Website: http://www.saimm.co.za
18-20 August 2025 — 13TH International Heavy Minerals Conference 2025
Sun City, South Africa
Contact: Gugu Charlie
Tel: 011 538-0238
E-mail: gugu@saimm.co.za
Website: http://www.saimm.co.za
13-15 October 2025 — 9TH International PGM Conference 2025
Sun City, South Africa
Contact: Camielah Jardine
Tel: 011 538-0237
E-mail: camielah@saimm.co.za
Website: http://www.saimm.co.za
16-22 November 2025 — The 12TH International Copper Conference (Copper 2025)
Phoenix, Arizona, USA
Website: https://www.extractionmeeting.org/ Extraction2025/Extraction2025/Copper2025/default.aspx
The following organizations have been admitted to the Institute as Company Affiliates
A and B Global Mining (Pty) Ltd
acQuire Technology Solutions
AECI Mining Chemicals, a division of AECI Mining Ltd
African Pegmatite
Allied Furnace Consultants
AMIRA International Africa (Pty) Ltd
Anglogold Ashanti Ltd
Anton Paar Southern Africa
Arcus Gibb (Pty) Ltd
Becker Mining (Pty) Ltd
Bluhm Burton Engineering Pty Ltd
Caledonia Mining South Africa
Castle Lead Works
DDP Specialty Products South Africa (Pty) Ltd
De-Tect Unit Inspection (Pty) Ltd
Digby Wells and Associates
EHL Consulting Engineers (Pty) Ltd
Elbroc Mining Products (Pty) Ltd
Epiroc South Africa (Pty) Ltd
Ex Mente Technologies (Pty) Ltd
Exxaro Resources Limited
FLSmidth Minerals (Pty) Ltd
G H H Mining Machines (Pty) Ltd
Geobrugg Southern Africa (Pty) Ltd
Glencore
Gravitas Minerals (Pty) Ltd
Hatch (Pty) Ltd
Herrenknecht AG
Impala Platinum Holdings Limited
IMS Engineering (Pty) Ltd
Ingwenya Mineral Processing
Ivanhoe Mines SA
Longyear South Africa (Pty) Ltd
Malvern Panalytical (Pty) Ltd
Maptek (Pty) Ltd
Mech-Industries
Micromine Africa (Pty) Ltd
Minearc South Africa (Pty) Ltd
Minerals Council of South Africa
MineRP Holding (Pty) Ltd
Mining Projection Concepts (Pty) Ltd
Mintek
MLB Investments CC
Modular Mining Systems Africa (Pty) Ltd
Murray & Roberts Cementation (Pty) Ltd
OPTRON
Paterson & Cooke Consulting Engineers (Pty) Ltd
Redpath Mining (South Africa) (Pty) Ltd
Rosond (Pty) Ltd
Roytec Global (Pty) Ltd
Rustenburg Platinum Mines Limited - Union
Salene Mining (Pty) Ltd
Schauenburg (Pty) Ltd
SENET (Pty) Ltd
Sibanye Gold Limited
Sound Mining Solution (Pty) Ltd
SRK Consulting SA (Pty) Ltd
Tomra (Pty) Ltd
Trans-Caledon Tunnel Authority
Ukwazi Mining Solutions (Pty) Ltd
VBKOM Consulting Engineers
Weir Minerals Africa
ZUTARI (Pty) Ltd
Pathway to industrialisation
The primary purpose of the 2ND Hydrogen and Fuel Cells conference is the advancement of green hydrogen technologies in Southern Africa and the global community, by highlighting the power of renewable and sustainable technologies and addressing the emerging challenges—through the exploration of hydrogen production, storage and utilization using fuel cells by way of engagement with industry, academia and government. The conference will provide a platform for high level exchange and networking opportunities with various experts in the field. The two-day conference will feature high-level scientific talks and posters, complemented with keynote and plenary presentations on country overviews, status of leading and major players in the Southern African and global arena.
Hydrogen: Production and storage
Fuel cell: Technologies, applications, and integration
Hydrogen mobility - strategies, safety, roadmaps, transitioning to hydrogen refueling stations (HRS)
Technology status in industry.
Will include inspiring technical talks, poster section as well as social networking events
Participants will have the opportunity to directly engage with conference attendees to discuss their research
FOR FURTHER
Gugu Charlie,
The conference presents an attractive programme for researchers, industry players, academic institutions, government, investors, policy makers and potential users of fuel cell and hydrogen technologies. The focus is on building collective know-how and fostering engagement between business, government, science and academic institutions. Participants from all countries are invited and welcome to attend the event.
Conferences and Events
Co-ordinator
following deadline dates.
• Submission of abstracts deadline 31 January 2025
• Submission of papers deadline: 28 February 2025
The conference is organized by the Southern African Institute of Mining and Metallurgy, and individuals are invited to submit papers or presentations or posters for the Conference. Titles and short abstracts (no more than 500 words) on any relevant subject should be submitted in English to:
Conferences and Events
Co-ordinator
Gugu Charlie
Enquiries may be made at: Tel: +27 011 538-0238
E-mail:gugu@saimm.co.za website: www.saimm.co.za
E-mail: gugu@saimm.co.za Tel: +27 11 538-0238 Web: www.saimm.co.za
25-26 JUNE 2025
Jardine, Head of Conferences and Events
Whatever terminology you wish to use, it is obvious the world of work is changing rapidly.
The Mining Industry, along the Mining Value Chain, is a part of this; seeking to take advantage of digital opportunities in the quest for competitiveness, sustainability and Zero Harm.
Mining businesses in Africa, as globally, are on this journey purposefully or by default. This event adds to purpose by being a showcase and learning experience for everyone associated with the Mining Industry. We will learn about Global Best Practices, network with global leaders in mining and other businesses, and do so in an exciting and interactive format.
Be prepared to be challenged and informed and to leave excited and better equipped for today’s digital journey.