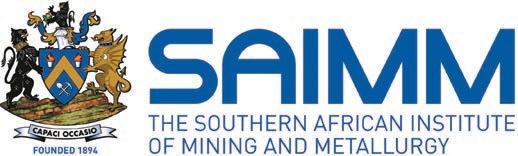
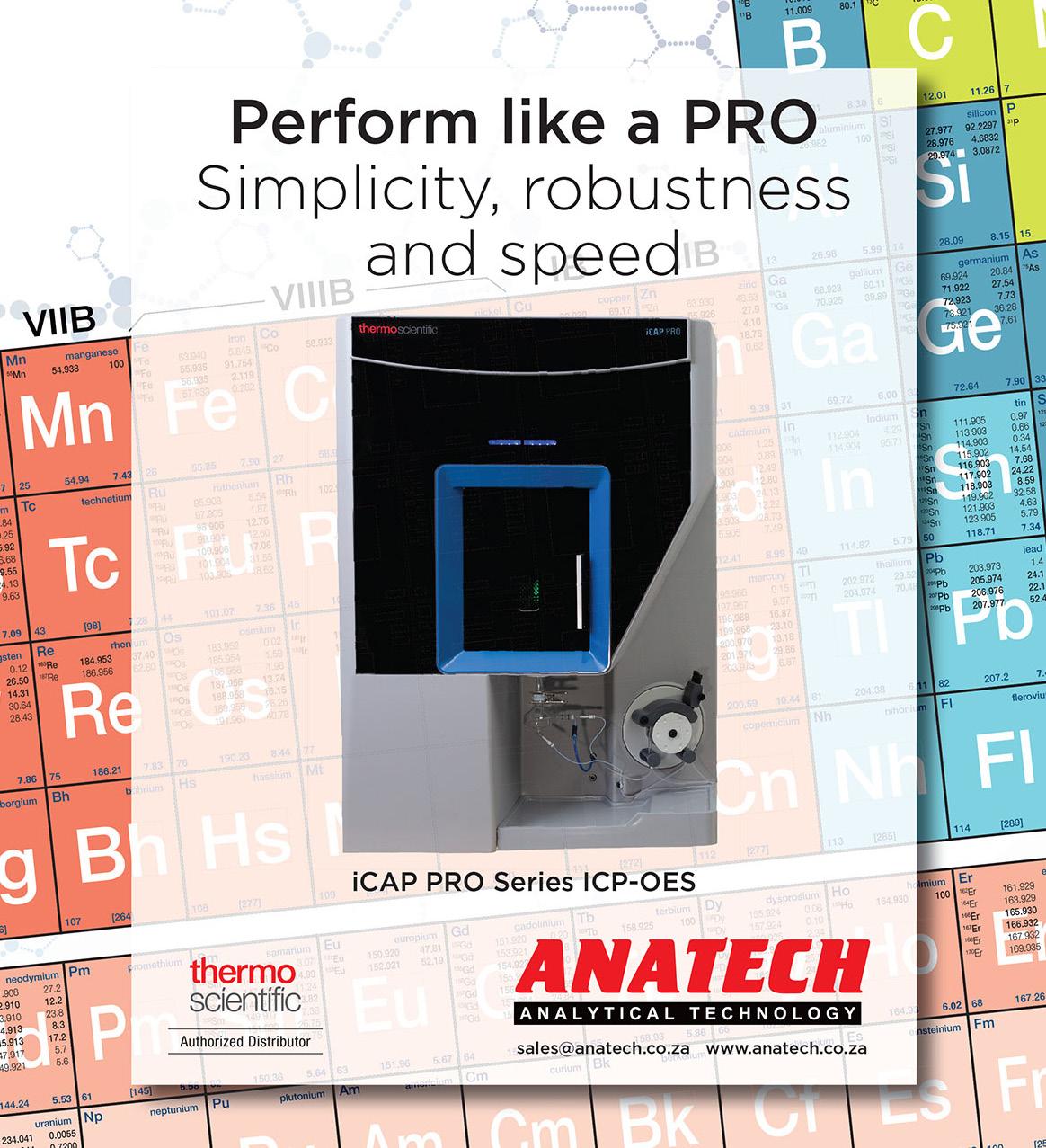
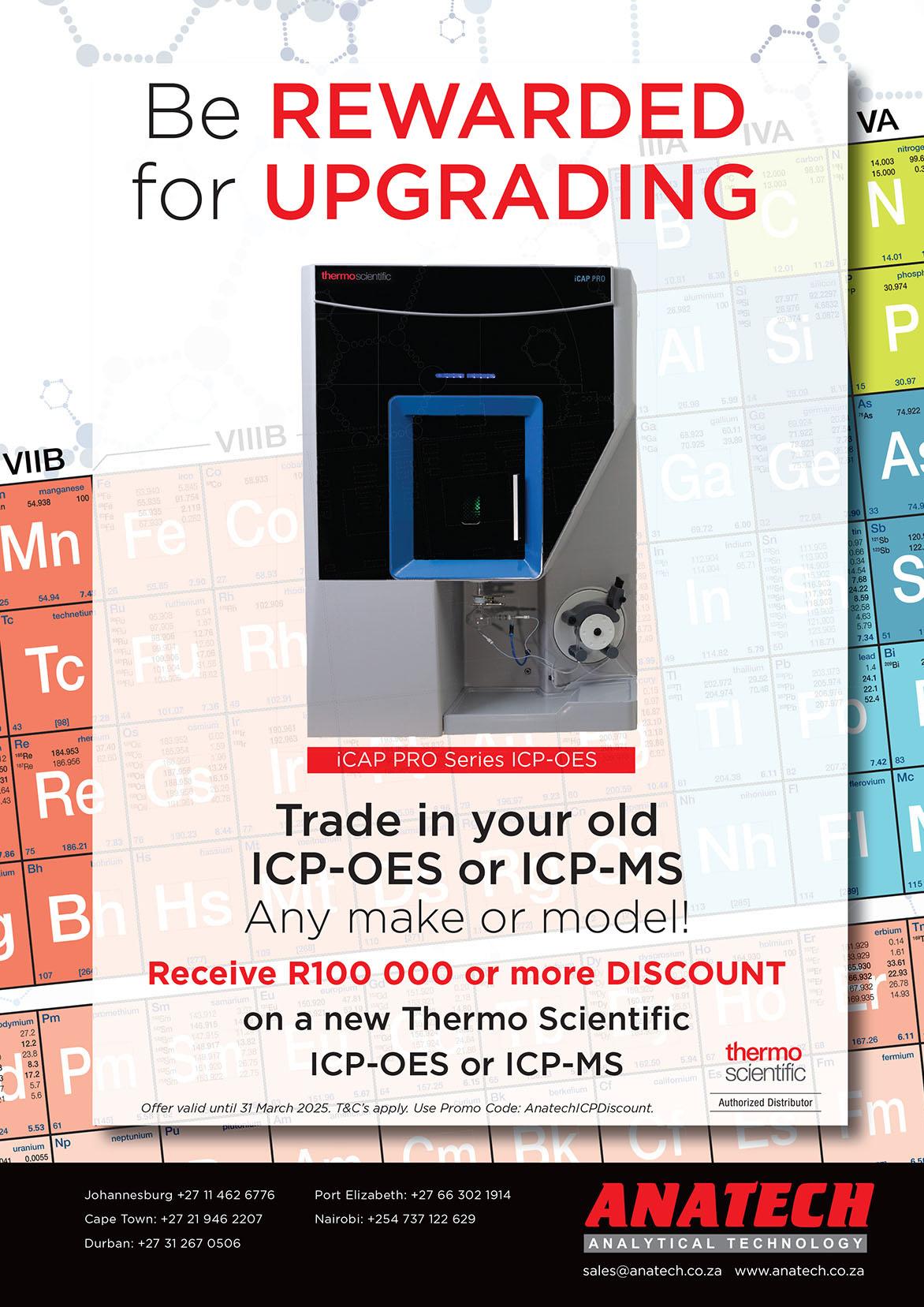
OFFICE BEARERS AND COUNCIL FOR THE 2024/2025 SESSION
Honorary President
N. Tsengwa
President, Minerals Council South Africa
Honorary Vice Presidents
Gwede Mantashe
Minister of Mineral Resources and Energy, South Africa
P. Tau
Minister of Trade, Industry and Competition, South Africa
Blade Nzimande
Minister of Higher Education, Science and Technology, South Africa
President E. Matinde
President Elect
G.R. Lane
Senior Vice President
T.M. Mmola
Junior Vice President
M.H. Solomon
Incoming Junior Vice President
S.J. Ntsoelengoe
Immediate Past President
W.C. Joughin
Honorary Treasurer
W.C. Joughin
Ordinary Members on Council
W. Broodryk
Z. Fakhraei
B. Genc
K.M. Letsoalo
S.B. Madolo
M.A. Mello
K. Mosebi
Co-opted Council Members
A.D. Coetzee
L.T. Masutha
M.C. Munroe
S.M. Naik
G. Njowa
S.M. Rupprecht
A.T. van Zyl
E.J. Walls
Past Presidents Serving on Council
N.A. Barcza C. Musingwini
R.D. Beck S. Ndlovu
Z. Botha J.L. Porter
V.G. Duke M.H. Rogers
I.J. Geldenhuys G.L. Smith
R.T. Jones
G.R. Lane – TP Mining Chairperson
Z. Botha – TP Metallurgy Chairperson
K.W. Banda – YPC Chairperson
C.T. Chijara – YPC Vice Chairperson
Branch Chairpersons
Botswana K. Mosebi
DRC K.T. Kekana (Interim Chairperson)
Johannesburg N. Rampersad
Limpopo M.S. Zulu
Namibia T. Aipanda
Northern Cape Vacant
North West Vacant
Pretoria P.G.H. Pistorius
Western Cape Vacant
Zambia N.M. Kazembe
Zimbabwe L. Shamu
Zululand Vacant
*Deceased
* W. Bettel (1894–1895)
* A.F. Crosse (1895–1896)
* W.R. Feldtmann (1896–1897)
* C. Butters (1897–1898)
* J. Loevy (1898–1899)
* J.R. Williams (1899–1903)
* S.H. Pearce (1903–1904)
* W.A. Caldecott (1904–1905)
* W. Cullen (1905–1906)
* E.H. Johnson (1906–1907)
* J. Yates (1907–1908)
* R.G. Bevington (1908–1909)
* A. McA. Johnston (1909–1910)
* J. Moir (1910–1911)
* C.B. Saner (1911–1912)
* W.R. Dowling (1912–1913)
* A. Richardson (1913–1914)
* G.H. Stanley (1914–1915)
* J.E. Thomas (1915–1916)
* J.A. Wilkinson (1916–1917)
* G. Hildick-Smith (1917–1918)
* H.S. Meyer (1918–1919)
* J. Gray (1919–1920)
* J. Chilton (1920–1921)
* F. Wartenweiler (1921–1922)
* G.A. Watermeyer (1922–1923)
* F.W. Watson (1923–1924)
* C.J. Gray (1924–1925)
* H.A. White (1925–1926)
* H.R. Adam (1926–1927)
* Sir Robert Kotze (1927–1928)
* J.A. Woodburn (1928–1929)
* H. Pirow (1929–1930)
* J. Henderson (1930–1931)
* A. King (1931–1932)
* V. Nimmo-Dewar (1932–1933)
* P.N. Lategan (1933–1934)
* E.C. Ranson (1934–1935)
* R .A. Flugge-De-Smidt (1935–1936)
* T.K. Prentice (1936–1937)
* R.S.G. Stokes (1937–1938)
* P.E. Hall (1938–1939)
* E.H.A. Joseph (1939–1940)
* J.H. Dobson (1940–1941)
* Theo Meyer (1941–1942)
* John V. Muller (1942–1943)
* C. Biccard Jeppe (1943–1944)
* P.J. Louis Bok (1944–1945)
* J.T. McIntyre (1945–1946)
* M. Falcon (1946–1947)
* A. Clemens (1947–1948)
* F.G. Hill (1948–1949)
* O.A.E. Jackson (1949–1950)
* W.E. Gooday (1950–1951)
* C.J. Irving (1951–1952)
* D.D. Stitt (1952–1953)
* M.C.G. Meyer (1953–1954)
* L.A. Bushell (1954–1955)
* H. Britten (1955–1956)
* Wm. Bleloch (1956–1957)
* H. Simon (1957–1958)
* M. Barcza (1958–1959)
* R.J. Adamson (1959–1960)
* W.S. Findlay (1960–1961)
* D.G. Maxwell (1961–1962)
* J. de V. Lambrechts (1962–1963)
* J.F. Reid (1963–1964)
* D.M. Jamieson (1964–1965)
* H.E. Cross (1965–1966)
* D. Gordon Jones (1966–1967)
* P. Lambooy (1967–1968)
* R.C.J. Goode (1968–1969)
* J.K.E. Douglas (1969–1970)
* V.C. Robinson (1970–1971)
* D.D. Howat (1971–1972)
* J.P. Hugo (1972–1973)
* P.W.J. van Rensburg (1973–1974)
* R.P. Plewman (1974–1975)
* R.E. Robinson (1975–1976)
* M.D.G. Salamon (1976–1977)
* P.A. Von Wielligh (1977–1978)
* M.G. Atmore (1978–1979)
* D.A. Viljoen (1979–1980)
* P.R. Jochens (1980–1981)
* G.Y. Nisbet (1981–1982)
A.N. Brown (1982–1983)
* R.P. King (1983–1984)
J.D. Austin (1984–1985)
* H.E. James (1985–1986)
H. Wagner (1986–1987)
* B.C. Alberts (1987–1988)
* C.E. Fivaz (1988–1989)
* O.K.H. Steffen (1989–1990)
* H.G. Mosenthal (1990–1991)
R.D. Beck (1991–1992)
* J.P. Hoffman (1992–1993)
* H. Scott-Russell (1993–1994)
J.A. Cruise (1994–1995)
D.A.J. Ross-Watt (1995–1996)
N.A. Barcza (1996–1997)
* R.P. Mohring (1997–1998)
J.R. Dixon (1998–1999)
M.H. Rogers (1999–2000)
L.A. Cramer (2000–2001)
* A.A.B. Douglas (2001–2002)
* S.J. Ramokgopa (2002-2003)
T.R. Stacey (2003–2004)
F.M.G. Egerton (2004–2005)
W.H. van Niekerk (2005–2006)
R.P.H. Willis (2006–2007)
R.G.B. Pickering (2007–2008)
A.M. Garbers-Craig (2008–2009)
J.C. Ngoma (2009–2010)
G.V.R. Landman (2010–2011)
J.N. van der Merwe (2011–2012)
G.L. Smith (2012–2013)
M. Dworzanowski (2013–2014)
J.L. Porter (2014–2015)
R.T. Jones (2015–2016)
C. Musingwini (2016–2017)
S. Ndlovu (2017–2018)
A.S. Macfarlane (2018–2019)
M.I. Mthenjane (2019–2020)
V.G. Duke (2020–2021)
I.J. Geldenhuys (2021–2022)
Z. Botha (2022-2023)
W.C. Joughin (2023-2024)
Editorial Board
S.O. Bada
R.D. Beck
P. den Hoed
I.M. Dikgwatlhe
M. Erwee
B. Genc
R Hassanalizadeh
R.T. Jones
W.C. Joughin
A.J. Kinghorn
D.E.P. Klenam
D.F. Malan
D. Morris
C. Musingwini
S. Ndlovu
P.N. Neingo
A. Nengovhela
S.S. Nyoni
M. Phasha
P. Pistorius
P. Radcliffe
N. Rampersad
Q.G. Reynolds
I. Robinson
S.M. Rupprecht
K.C. Sole
T.R. Stacey
D. Vogt
F. Uahengo
International Advisory Board members
R. Dimitrakopolous
R. Mitra
A.J.S. Spearing
E. Topal
D. Tudor
Editor /Chairperson of the Editorial Board
R.M.S. Falcon
Typeset and Published by
The Southern African Institute of Mining and Metallurgy
PostNet Suite #212 Private Bag X31
Saxonwold, 2132
E-mail: journal@saimm.co.za
Printed by Camera Press, Johannesburg
Advertising Representative
Barbara Spence
Avenue Advertising
Journal Comment: Special Edition of the Southern African Rare Earths Conference 2024 by E. Matinde
President’s Corner: Critical raw materials result in substantive technological and economic catch-up for the global south: Setting the scene for a deeper Socratic dialogue by E.
Matinde
THE INSTITUTE, AS A BODY, IS NOT RESPONSIBLE FOR THE STATEMENTS AND OPINIONS ADVANCED IN ANY OF ITS PUBLICATIONS.
Copyright© 2024 by The Southern African Institute of Mining and Metallurgy. All rights reserved. Multiple copying of the contents of this publication or parts thereof without permission is in breach of copyright, but permission is hereby given for the copying of titles and abstracts of papers and names of authors. Permission to copy illustrations and short extracts from the text of individual contributions is usually given upon written application to the Institute, provided that the source (and where appropriate, the copyright) is acknowledged. Apart from any fair dealing for the purposes of review or criticism under The Copyright Act no. 98, 1978, Section 12, of the Republic of South Africa, a single copy of an article may be supplied by a library for the purposes of research or private study. No part of this publication may be reproduced, stored in a retrieval system, or transmitted in any form or by any means without the prior permission of the publishers. Multiple copying of the contents of the publication without permission is always illegal. U.S. Copyright Law applicable to users In the U.S.A. The appearance of the statement of copyright at the bottom of the first page of an article appearing in this journal indicates that the copyright holder consents to the making of copies of the article for personal or internal use. This consent is given on condition that the copier pays the stated fee for each copy of a paper beyond that permitted by Section 107 or 108 of the U.S. Copyright Law. The fee is to be paid through the Copyright Clearance Center, Inc., Operations Center, P.O. Box 765, Schenectady, New York 12301, U.S.A. This consent does not extend to other kinds of copying, such as copying for general distribution, for advertising or promotional purposes, for creating new collective works, or for resale.
Honorary Legal Advisers
M H Attorneys Auditors
Genesis Chartered Accountants Secretaries
The Southern African Institute of Mining and Metallurgy 7th Floor, Rosebank Towers, 19 Biermann Avenue, Rosebank, 2196
PostNet Suite #212, Private Bag X31, Saxonwold, 2132 E-mail: journal@saimm.co.za
Telephone (011) 463-7940 . E-mail: barbara@avenue.co.za ISSN 2225-6253 (print) . ISSN 2411-9717 (online)
Rare Earth Extraction with Ionquest® 801 initial modelling development by C.F. Carrozza, F. Dutoy, and M.B. Stella 555
This study explored approaches to rare earth element extraction using IONQUEST® 801 and it integrated predictive modelling to enhance process understanding and optimization. A screening test to evaluate the best extraction efficiency was conducted. The data obtained were used to develop empirical and mechanistic models to predict rare earth extraction yields and flowsheets. The experimental results demonstrated the effectiveness of the proposed extraction methods, highlighting improvements in both yield and selectivity.
An assessment of Rare Earth Elements in borehole cores from the Ermelo, Witbank and Waterberg Coalfields, South Africa: Focus on mode of occurrence by D.G. Modiba and N.J. Wagner
This project aimed to determine the concentration of REE, including yttrium and scandium (REY+Sc) in various coal seams and adjacent sediments in borehole cores from the Ermelo, Witbank, and Waterberg coalfields in South Africa. The ICP-MS results following SCEP indicated that both coal and the associated sediments were light REY+Sc dominant. The Waterberg samples had the lowest REY+Sc from both the coal and associated sediments. MLA determined that monazite and xenotime in all the coal samples were the REY+Sc-bearing mineral.
Development of a physical separation pre-concentration process for the extraction of Rare Earth bearing ore by T. Mokgomola, G. Marape, A. Singh, and K. Bisaka
This paper investigated the pre-concentration amenability of sovite (carbonatite) ore to enhance the grade of rare earth elements (REE) bearing minerals by rejecting calcite, and to improve total rare earth elements (TREE) recovery using gravity and magnetic separation. Mineralogy liberation data at 2 mm top size indicated poor liberation of TREE. Grain size distribution data showed that the majority of REE minerals are fine grained and report to the <20 µm size class. A combination of a single-stage shaking table with a wet high intensity magnetic separator at a magnetic intensity of 7520 Gauss was found to be the optimum flowsheet. Due to the fine-grained nature of TREE, no flowsheet improved their grade.
Extraction of Rare Earth Elements from Phalaborwa phosphogypsum by R.A. Wildenboer and R.F. Sandenbergh
This paper presents the results of investigations into the leaching behaviour of rare earth elements and other impurities from phosphogypsum using aqueous sulfuric acid. The effects of acid concentration, temperature, residence time, and the influence of impurities were evaluated for their impact on the solubility of rare earth elements in a sulfate medium. It was found that a significant fraction of the REE can be leached from the phosphogypsum in a range of conditions much less severe than traditional hard rock rare earth processing conditions.
Rare Earth Elements enrichment in Triassic coals deposits and associated argillaceous rocks in Lesotho by S. Hlajoane and L.S. Mokhahlane
This study aims to characterize and evaluate the potential of rare earth elements and yttrium in the Taung coal deposit, southwest of Lesotho. Coal and associated argillaceous samples from the Taung coal deposit were analysed using microscopic petrography and an inductively coupled plasma mass spectrometry. The average critical rare earth elements and yttrium concentration of samples from the Taung coal deposit is 189.4 ppm, which is three times higher than that of the Chinese Bayan Obo deposit. Samples classified as very promising and promising because of their outlook coefficients, are found to contain up to 77% of critical rare earth elements and yttrium. It is envisioned that the area could be a prime deposit for these rare earth elements and yttrium.
Leaching characteristics of cerium and yttrium from non-magnetic coal fly ash after silicate digestion using acetic acid by H. Manurung, I.M. Bendiayasa, F. Anggara, K.C. Wanta, W. Astuti, and H.T.B.M. Petrus
The leaching kinetics of cerium (Ce) and yttrium (Y) in sodium-hydroxide-digested non-magnetic coal fly ash using acetic acid were investigated. The variables analysed were pH, solid-to-liquid ratio (S/L), and temperature. The results show that cerium and yttrium’s maximum recovery was 57.33% and 58.36%, respectively. The kinetic leaching models of cerium and yttrium all fit Dickinson’s new shrinking core model. The calculation results show that the leaching reaction is controlled by combining interface transfer and diffusion across the product layer.
567
575
583
595
Rare earths elements (REE), often dubbed the ‘vitamins driving the 21st century industrial epoch and clean energy transitions’, have been a subject of debate and are at the centre of the geopolitical and supply-side tensions between China and the West. With everyone scrambling for de-risk of their supply chains, the attention is now increasingly being focused on seeking alternative sources of these critical raw materials. This is where Southern Africa, as a geopolitically neutral region rich in these irreplaceable raw materials, comes in to ensure the sustainable supply of the critical raw materials needed to drive the clean energy transition.
Although the Institute is historically known for its acumen for organizing thought provoking and interesting conferences, nothing would have prepared any reader for the perfect timing to release the special October edition. The special edition of the Journal is unique in that it showcases the Institute’s contribution to the global conundrum on the debate about these critical and strategic raw materials. This special edition contains seven papers that were selected from the 2nd International Conference on Southern African Rare Earths 2024 held in Swakopmund, Namibia. With the theme ‘Global Impact and Sustainable Supply’, the conference focused on fostering dialogue, leveraging on global diversity and innovation in the rare earths sector. The selected papers enhance an understanding of the occurrence and extraction of these vital elements from both conventional, and non-conventional resources, ranging from exploration and geology, characterization and concentration, right up to leaching behaviour, extraction, and recovery from solutions. The diverse nature and scope of the topical issues discussed in the papers included in this special edition highlights both the challenges and opportunities in harnessing the feasibility and economies of scale associated with the recovery of REEs from such complex, and low-grade resources.
E. Matinde President, SAIMM
TCritical raw materials result in substantive technological and economic catch-up for the global south: Setting the scene for a deeper Socratic dialogue
he debate on sustainable economic development is increasingly focused on the widescale deployment of carbon neutral energy sources to drive the future energy systems. Renewable energy technologies such as hydropower, solar, wind, geothermal, fuel cells and bioenergy, among others, are indispensable to mitigating the impact of anthropogenic global warming while concurrently addressing the energy poverty faced by many countries in the global south. The transition to clean energy generation and storage systems is metal and mineral intensive and will require a substantive but sustainable supply of many of these critical metals and minerals. For example, metals and minerals such as lithium (Li), nickel (Ni), cobalt (Co), manganese (Mn), and graphite are irreplaceable in battery energy storage systems while rare earth metals are critical in the manufacture of high-performance magnets needed for wind turbines and electric vehicles. Likewise, industrial metals such as aluminium (Al) and copper (Cu) are irreplaceable in electricity generation and distribution systems. According to the International Energy Association (2021), electric vehicles require approximately 53 kg Cu, 9 kg Li, 40 kg, 25 kg Mn, 13k g Co, and 66 kg graphite per vehicle, compared to 22 kg Cu and 11 kg Mn in conventional vehicles. In the Minerals for Climate Action report (Hund et al. 2020) compiled by the World Bank Group, it is estimated that the production of critical raw materials (CRMs), such as graphite, lithium and cobalt, will increase by 500% by 2050 to meet the growing demand for clean energy technologies. This giganteum increase in demand in CRMs will create unprecedent opportunities for industrialization to resource-rich countries through exports and localization of value-added manufacturing activities.
Similar to a lot of other countries in the global south, Southern African states are either least developed or middle-income countries with ambitions to escape the poverty trap and catch up with more advanced economies. Contrary to these long-held ambitions to upgrade their economies, the GDP for most countries in sub-Saharan Africa has contracted over a protracted period of time and continue to face unprecedented challenges in transitioning from an economy driven by the exports of low value mineral commodities to manufacturing and knowledge driven economies. Being high value and high impact, clean energy technologies naturally present windows of opportunity for technological and economic upgrading to resource-rich countries such as South Africa. Although often associated with high risk and a high degree of uncertainty, clean energy technologies are characterized by high radical novelty, fast growth, and relatively high economic impact, with significant potential in creating new industries and/or transforming existing ones (Rotolo et al. 2015). There is indisputable evidence that, if managed properly, emerging technologies can indeed result in sustained technological and economic growth, and ultimately, lead to economic catch-up by the countries in the global south.
Economic scholars define ‘catch-up’ as a process by which a developing country narrows the income gap (‘economic catch-up’) and increases its technological capabilities (‘technological catch-up’) relative to frontier countries (Lee, 2013; Lee, 2019). When combined, technological and economic catch-up thus refers to the ability of a developing economy to grow faster compared to frontier economies and eventually reaching similar levels of technological capabilities and per capita income. Thus, in order to reduce the technological and income gaps relative to frontier economies, developing economies must attain and sustain both technological capabilities and income growth more rapidly than the advanced economies. Technological catch-up, which itself is a function of the specific technological strategies adopted as part of the growth strategy, logically precedes economic catch-up. Although ‘technological catch-up’ and ‘economic catch-up’ are not identical, they are closely related to each other in such a way that technological catch-up precedes or leads to market or economic catch-up (Lee, 2013).
Two main models have been proposed to explain catch-up trajectories, namely, path-following (also known as flying geese) catch-up, and leapfrogging catch-up, with the latter form occurring following a stage-skipping or path-creating strategy (Lee, 2013; Lee, 2019). The path following catch-up is a linear and cumulative process whereby the latecomer follows the same technological trajectories taken by frontrunners. In this case, the latecomer moves along the same path, but faster by taking advantage of historical factors such as the maturity, declining costs, and ubiquity of technologies and technical knowledge (Lee, 2013). The leapfrogging model is more complex and occurs when a latecomer bypasses traditional stages of development to either jump directly to the latest technologies (stage-skipping) or explore an alternative path of technological development involving emerging technologies with new benefits and opportunities (path-creating) (Lee, 2019; Yayboke et al. 2020). This form of catch-up often occurs when technologies are shifting towards new technological trajectories, which allow the latecomers to reduce the technological gaps by skipping the older generations to adopt the next generation and cost-efficient technologies. This may, however, depend on a number of factors, such as market availability, cost of next generation of technologies, and/or the willingness of incumbents to share their proprietary technologies (Lee, 2013; Lee, 2019; Yayboke et al. 2020).
Regardless of the leapfrogging model adopted, the ability to catch up is dependent on the windows of opportunity arising from the emergence of new technoeconomic paradigms (Perez and Soete, 1988; Lee and Malerba, 2017). The emergence of radically new technologies, for example, offers latecomers the window of opportunity to leapfrog the incumbents whose technological capabilities and investments are locked into older technologies, limiting their agility to mitigate against the destructive potential of new technologies and products. In contrast, latecomers are able to leapfrog older technologies, bypass sunk investments in previous technology systems, and adapt new and emerging technologies to assume control of markets and thus outcompete the incumbents (Lee and Malerba, 2017). Shorter cycle technologies also present windows of opportunity to latecomers by reducing reliance on old and existing knowledge bases characteristic of longer cycle, often capital-intensive technologies, often dominated by incumbents (Lee, 2013). Complimentary to emerging and shorter cycle technologies, radical changes in demand conditions, business cycles, and/or abrupt changes in markets, such as those presented by the clean energy transition, also increase the ability of agile latecomers to enter new markets, catch up, and leapfrog the incumbents (Lee and Malerba, 2017). The success to catch-up by leapfrogging also depends on the regulatory and institutional framework. Most importantly, deliberate government policies through strategic mission-oriented industrial policies and R&D programs can shape the rate of innovations and accumulation of technological capabilities by domestic firms (Mazzucato, 2018).
Obviously, the ability to catch up is not a free ride, but rather, depends on a number of deliberate efforts and strategic interventions. The answer to sustained catch-up and growth lies in the ability to build technological capabilities, which in this context, can be defined as the ability to effectively assimilate, use new and existing knowledge to create new technologies, products and processes, and to acquire and commercially exploit new knowledge and skills (Lee, 2013). Purposive efforts to build technological capabilities at macroscale can thus significantly increase the national absorptive capacity to assimilate technologies and knowledge developed by frontier economies (Kinoshita, 2000). Although the importance of national absorptive capacity in technology transfer is widely accepted, very few case studies are available to demonstrate its linkage to sustained technological and economic upgrading in most resource-based economies.
To conclude, the vast majority of literature and policy statements clearly articulate the high technological and economic importance of critical raw materials to the clean energy transition. Most notably, the emerging discourse on net zero transition has mostly focused on the critical roles of resource-rich countries from the global south derisking supply chains for these critical raw materials, which in my view, would only function to exacerbate the current ‘pit to port extractivist’ strategies being employed by most developing economies. In my mind, there is no doubt that the clean energy transition presents windows of opportunity for technological upgrading and industrialization through localization of value-added manufacturing activities. These issues definitely warrant further debate, and it is prudent to explore the macro-level linkages and challenges, and most importantly, the potential industrial policy tools available to increase the localization of manufacturing capabilities by resource-rich countries.
References
Hund, K., La Porta, D., Fabregas, T.P., Laing, T., Drexhage J. 2020. Minerals for Climate Action: The Mineral Intensity of the Clean Energy Transition. The World Bank. https://pubdocs.worldbank.org/ en/961711588875536384/Minerals-for-Climate-Action-The-Mineral-Intensity-of-the-Clean-Energy-Transition.pdf
International Energy Association. 2021. The Role of Critical Minerals in Clean Energy Transition. https://www.iea. org/reports/the-role-of-critical-minerals-in-clean-energy-transitions/executive-summary
Kinoshita, Y. 2000. R&D and technology spillovers via FDI: Innovation and absorptive capacity. CERGE-EI Working Paper Series No. 163. https://papers.ssrn.com/sol3/papers.cfm?abstract_id=258194
Lee, K. 2013. Schumpeterian analysis of economic catch-up: Knowledge, path-creation, and the middle-income trap. Cambridge University Press, UK, pp 3-37.
Lee, K., Malerba, F. 2017. Catch-up cycles and changes in industrial leadership: Windows of opportunity and responses of firms and countries in the evolution of sectoral systems. Research Policy, vol. 46, no. 2, pp. 338-351.
Lee, K. 2019. The economics of technological leapfrogging. UNIDO Department of Policy Research and Statistics Working Paper Series WP 17/2019, United Nations Industrial Development Organisation. https://papers.ssrn.com/ sol3/papers.cfm?abstract_id=3549420
Mazzucato, M. 2018. Mission-oriented innovation policies: Challenges and opportunities. Industrial and Corporate Change, vol. 27, no.5, pp. 803-815.
Perez, C., Soete, L. 1988. Catching up in technology: entry barriers and windows of opportunity. Dosi, G., Freeman, C., Nelson, R., Silverberg, G. & Soete, L. (Editors), Technical Change and Economic Theory, Pinter Publishers, London, pp 458-479.
Rotolo, D., Hicks, D., Martin B.R. 2015. What is an emerging technology? Research Policy vol. 44, no. 10, pp. 1827-1843.
Yayboke, E., Crumpler, W., Carter, W.A. 2020. The promise of leapfrogging. Center for Strategic and International Studies https://www.csis.org/analysis/need-leapfrog-strategy
E.Matinde President, SAIMM
Affiliation:
1Italmatch Chemicals Spa, Italy
2Italmatch Belgium Sprl, Belgium
Correspondence to: C.F. Carrozza
Email: c.carrozza@italmatch.com
Dates:
Received: 29 May 2024
Published: October 2024
How to cite:
Carrozza, C.F., Dutoy, F., Stella, M.B. 2024. Rare Earth Extraction with Ionquest® 801 initial modelling development. Journal of the Southern African Institute of Mining and Metallurgy, vol. 124, no.10 pp. 555–558
DOI ID:
http://dx.doi.org/10.17159/24119717/689/2024
ORCID:
C.F. Carrozza http://orcid.org/ 0000-0002-4692-3332
This paper is based on a presentation given at the Southern African Rare Earths 2nd International Conference 2024, 19-20 June 2024, Swakopmund Hotel and Entertainment Centre, Swakopmund, Namibia
by C.F. Carrozza1, F. Dutoy2, and M.B. Stella1
Abstract
Rare earth elements (REEs) are indispensable components in the manufacturing of high-tech devices, renewable energy technologies, and defence applications. As global demand for these elements continues to rise, there is a pressing need to optimize extraction processes for both efficiency and environmental sustainability. This study explores approaches to rare earth extraction using Ionquest® 801 and integrates a predictive modelling to enhance process understanding and optimization.
We conducted a screening test varying pH process to evaluate the best extraction efficiency. Starting pregnant leach solution (PLS), solution was prepared in the lab with the following rare earth elements: La, Ce, Gd, Dy, and Υ, at 0.02 M for each element. The data obtained were used to develop empirical and mechanistic models to predict rare earth extraction yields and flowsheet. Further tests were performed by mixing specific concentrations of different extractant and/ or phase modifier. Our experimental results demonstrated the effectiveness of the proposed extraction methods, highlighting improvements in both yield and selectivity. The developed models successfully captured the complex relationships between process parameters and extraction efficiency, providing valuable insights for process optimization.
Keywords rare earth elements, phosphinic acid-SX, distribution ratio, modeling development
Introduction
Rare earth elements (REEs) constitute a family of 15 elements crucial for various high-tech applications, including wind turbines, electric motors, catalysts, and batteries. The surge in REE prices in 2010, triggered by China's decision to reduce exports, underscored the need for countries to secure their own REE supplies. As a result, there has been a growing interest in exploiting REE resources domestically and through recycling.
The majority of REE production comes from mining ore bodies, where the elements are clustered in minerals like bastnasite and monazite. Extracting REE from these ores requires separating and precipitating them into individual rare earths, a process typically accomplished through solvent extraction (SX) in mixersettlers.
Unlike the more commonly used SX processes for metals like copper or uranium, REE extraction poses unique challenges due to the chemical similarities among the elements and the need for extensive separation steps. While conventional SX circuits may involve fewer than 10 units, REE separation circuits can require over 1 000 mixer-settlers, making piloting and plant design exceptionally complex.
For a common multi-component feed, the process configuration consists of sequentially arranged units, each of them well defined by specific inputs e.g., composition in g/L, pH, and mass balance between inlet and outlet. The outcomes should be able to solve the requirements of stage extraction efficiencies, considering all the experimental variables. The complexity of the system increases from bench to pilot scale and as a result, the output profile requires a large data set for obtaining an accurate representation. In addition, this challenge is directly linked to the optimization of design flowsheet, especially for industrial applications (Figure 1).
To improve the description of the extraction performances related to different scenarios, the experimental data need to be coupled with computing strategy. The simpler idea is starting from equilibrium parameters collected during the lab screening as input to develop a steady state model. The
equilibrium concentrations of the target REE are calculated under fixed conditions of temperature and pH. Those data are used to construct a curve fitting based on distribution ratio, this being the best choice to estimate the mass transfer between the phases and evaluate how the extraction profile is affected by pH.
The next level consists of extending this approach on a countercurrent separation model to include the description of multi-stage extraction. The D-ratios can be included in a set of equations, which define the mass balance for each REE in the mixer unit. The goal is to calculate the metal amount in every stage by setting some known parameters, such as the total number of stages, the organic and aqueous flow rate, and the selected equilibrium pH. This approach works under the assumption that the steady-state variables are reasonable for a good representation of reactions that rapidly proceed, not including kinetic or interfacial phenomenon.
A mid/heavy REE solution was chosen to evaluate Ionquest® 801 performance: 2-ethylhexyl phosphonic acid mono-2-ethylhexyl ester and 0.3 M in aliphatic diluent ESCAID 110 provided by Exxon Mobil. The primary purpose was to find the operating conditions in terms of pH, as REE recovery occurs at remarkable acidic range. The pregnant leach solution (PLS, Table I) was prepared in HCl media (0.02 M REE as chloride). The aqueous and organic phases were kept in contact at room temperature under magnetic stirring for 15 min. HCl 20% wt and NaOH 13% wt were used for pH adjustment. Ratio A/O was 1 for all the lab work. The Ionquest® 801 profile was compared published data obtained from commercial phosphonic acid-SX.
The metal ion concentration was determined by ICP-OES. The extraction efficiency can be calculated according to Equation [1]:
The distribution ratio and the separation factor are introduced to evaluate and quantify the performance of extractant. For the metals A and B, they are respectively expressed as Equations [2] and [3]:
Results
Solvent extraction results
The plots in Figure 2 exhibit a good trend of extraction for Ionquest® 801. As expected for Dy and Υ, the percentage of extraction is high already at low pH. For Gd the recovery gradually increases as pH increases. The light REE grouping La and Ce needs less acidic conditions to overcome the issue of co-extraction of other rare earth elements, but Ionquest® 801 can achieve far better results when compared with those obtained from a commercial phosphonic acid reagent, as demonstrated in Figure 3.
The good trend is evident when distribution ratios are calculated for each REE. Three values of pH are selected to achieve a description of extraction capability. As depicted in Figures 4 and 5, the Ionquest® 801 distributions are more efficient for Gd, Dy, and Υ when compared with commercial phosphonic acid extractants. Typically, it implies a high extractability of metal ions from the aqueous phase, in addition to separation factors (β) that reflect how selectively metal can be extracted. In Table II separation factors are listed for Ionquest® 801 and a commercial phosphonic
acid extractant. ionquest® 801 shows a remarkable selectivity for the heavy REE (Gd, Dy, Υ) at the investigated pH interval. For La and Ce Ionquest® 801 offers the same separation performances as commercial extractant but increases the percentage of extraction under the same conditions.
The distribution ratios that were experimentally determined were used to validate the fitting curves resulting from the simulations. The approach was to functionalize empirical correlations with parameters known to affect equilibrium distribution. An intuitive strategy is proposed in the Equations [4] and [5]: D-ratios can be expressed as a function of pH and then predicted from a polynomial fitting. Note that the polynomial grade is directly related to stoichiometric coefficients of proton in the equilibrium reaction and, consequently, to ionic state of metal in the aqueous phase.
5—Distribution ratio experimentally calculated for commercial phosphonic acid SX at three different pH values (0.00, 0.33, 1.00)
A programming tool was developed to estimate how the extraction profile was affected by pH. The objective was to fit the experimental D-ratio by minimizing the sum of the squares of the deviations of the data from the model (least-squares fit). The results are demonstrated in Table III. The correlations reveal a good agreement between the two data sets for the selected range of pH.
Separation factors experimentally calculated for Ionquest® 801 (left side) and a commercial phosphonic acid (right side) at three different pH values (0.00, 0.33, 1.00)
pH 0.00
pH 0.35
801
801
phosphonic acid
The threshold for the error estimation is below 5%, but some small discrepancies can be corrected by changing the grade of polynomial fitting. In other words, the model provides a good representation of which are the best conditions to achieve a target REE extraction.
Future development
The next challenge is to successfully implement the D-ratio model into a model for a counter-current extraction flowsheet. The first step consists of including the experimental data in the species mass balance equations (Equation [6] and [7]). In accordance with mass transfer, as schematized in Figure 6, the objective is determining the REE composition at stage n for each unit as present in the entire flowsheet.
The programming key will be simultaneously solving a set of equations to achieve the organic and aqueous metal profile in terms of percentage of extraction (Figure 7). Inlet and outlet flow are characterized by some input parameters, such as flow rates, volumetric ratios, and pH of the feed (See Table IV).
Acknowledegements
This work, in particular related to the modelling development, is supported by the IPCEI Eu-Batin project. We thank all people included for their hard work and collaboration.
References
Aguilar, M., Cortina, J.S. 2008 eds. Solvent extraction and liquid membranes: Fundamentals and applications in new materials CRC Press.
Iloeje, C.O. 2020. Modeling Liquid–Liquid Extraction for Critical Elements Separations: An Overview Multidisciplinary Advances
III
Figure 6—Mass balance diagram illustration for a single unit in a currentcurrent extraction process
Table IV
Parameters set up for counter-current simulation flowsheet
Input
Output
Experiment pH feed Distribution ratio for batch scale
Model
PLS composition Efficiency for single stage
Distribution ratio for (mass balance) flowsheet process
Flow rate Efficiency for n stages
in Efficient Separation Processes. ACS Symposium Series American Chemical Society. pp 335–365.
Lyon, K.L., Utgikar, V.P., Greenhalgh, M.R. 2017. Dynamic Modeling for the Separation of Rare Earth Elements Using Solvent Extraction: Predicting Separation Performance Using Laboratory Equilibrium Data Industrial & Engineering Chemistry Research.,vol. 56, no. 4, pp. 1048–1056 American Chemical Society.
Omelchuk, K., Chagnes, A. 2018. New cationic exchangers for the recovery of cobalt (II), nickel (II) and manganese (II) from acidic chloride solutions: Modelling of extraction curves. Hydrometallurgy vol. 180, pp. 96–103. u
Laboratory data and model predictions for REE distribution with Ionquest® 801
Affiliation:
1University of the Witwatersrand, South Africa
2DSI-NRF CIMERA, University of Johannesburg, South Africa
Correspondence to: D.G. Modiba
Email: Duduzile.Modiba@wits.ac.za
Dates:
Received: 29 May 2024
Accepted: 12 Jun. 2024
Published: October 2024
How to cite:
Modiba, D.G. and Wagner, N.J.
2024. An assessment of Rare Earth Elements in borehole cores from the Ermelo, Witbank and Waterberg Coalfields, South Africa: Focus on mode of cccurrence. Journal of the Southern African Institute of Mining and Metallurgy, vol. 124, no.10, pp. 559–566
DOI ID:
http://dx.doi.org/10.17159/24119717/692/2024
ORCID:
D.G. Modiba
http://orcid.org/0000-0002-2135-0769
N.J. Wagner
http://orcid.org/0000-0002-4046-4788
This paper is based on a presentation given at the Southern African Rare Earths 2nd International Conference 2024, 19-20 June 2024, Swakopmund Hotel and Entertainment Centre, Swakopmund, Namibia
by D.G. Modiba1,2 and N.J. Wagner2
Abstract
There is currently limited knowledge concerning South African coal deposits as hosts for rare earth elements (REE). This project aims to determine the concentration of REE, including yttrium and scandium (REY+Sc) in various coal seams and adjacent sediments in borehole cores from the Ermelo, Witbank, and Waterberg coalfields in South Africa. Coal petrography (maceral count and vitrinite reflectance), XRD, XRF, sequential chemical extraction procedure (SCEP) before ICPMS, and mineral liberation analysis (MLA) were conducted on the coal and associated sediment samples. The coals were inertinite-rich, medium-rank bituminous coal, with moderate to high ash content. The two dominant minerals in all the coalfields are kaolinite and quartz, except for sample ZBS2M, where dolomite was dominant. The dominant major oxides are Al2O3, SiO2, Fe2O3, and CaO, which concur with the XRD results. The ICP-MS results following SCEP indicated that both coal and the associated sediments were light REY+Sc dominant. There was also an elevation of medium REY+Sc in the Witbank coal’s associated sediment samples. Notably, the samples with the highest REY+Sc results were the sediment samples. The Waterberg samples had the lowest REY+Sc from both the coal (less than 2 µg/g to 7 µg/g) and associated sediments (2 µg/g to 15 µg/g). While the highest REY+Sc was yielded from the Witbank-associated sediments (500 µg/g to 2,500 µg/g). The carbonate fraction step proved to be the most successful leaching step, as most REY+Sc was recovered in that step for all coalfields. In addition to the carbonate fraction, the silicates and sulfide fraction in the Witbank samples, and the ion-exchangeable fraction for the Waterbergassociated sediments samples proved successful in leaching out the REY+Sc. MLA determined that monazite and xenotime in all the coal samples were the REY+Sc-bearing minerals.
Keywords REY+Sc, coal, South Africa, sequential chemical extraction procedure, ICP-MS
Introduction
There is an increase in the demand for critical elements such as lithium and rare earth elements globally with the advent of the fourth industrial revolution, green energy, and the need to reduce global greenhouse gas emissions (Bauer et al., 2022; Dai and Finkelman, 2018; Hower et al., 2018). Rare earth elements (REE) Sc, Y, La, Ce, Pr, Nd, Pm, Sm, Eu, Gd, Tb, Dy, Ho, Er, Tm, and Yb, including yttrium and scandium (REY+Sc), are relatively abundant in the upper continental crust, despite being referred to as rare, which is a misnomer. The challenge is the separation of the elements from each other. According to the International Union for Pure and Applied Chemistry (IUPAC), the REE are 17 elements found on the periodic table, comprising 15 elements in the lanthanide group, plus two transitions metal elements, namely yttrium and scandium, collectively referred to as REY+Sc for the purpose of this paper.
According to Zhou et al. (2017), there are 178 REY+Sc deposits globally and as of the year 2017, they were reported to amount to 478Mt REY+Sc, either from primary or secondary sources. Balaram (2019) further elaborated that the primary sources of REY+Sc are from magmatic, hydrothermal, and metamorphic processes, while the secondary source is from weathering and erosion of the primary sources. The global demand has led to a need to broaden extraction from both primary mineable ore deposits, and to expand extraction from alternative, non-conventional sources, such as coal and combustion ash (Dai and Finkelman, 2018; Seredin and Dai, 2012). The increased interest in investigating REY+Sc in coal bears its challenges, such as gaining a clear understanding of the element’s host minerals and potential extraction techniques.
To determine the best technique for REY+Sc extraction in coal, there needs to be an understanding of the modes of occurrence in which these elements occur. Internationally, many studies have been dedicated to this topic, including work conducted by Arnold (2023), Balaram (2019), Borzykowski (2019), Dai et al.
(2004), Dai et al. (2017), Fu et al. (2022), Hower et al. (2018), Li et al. (2008), Li et al. (2023), Serendin and Dai (2012), and Yang et al. (2023). These studies proposed that REY+Sc may be associated with either the organic or inorganic component of coal material. A stronger organic association is mainly observed in low-rank coals. REY+Sc may be associated with the inorganic i.e., mineral fractions of coal in authigenic and clastic minerals, for example, in phosphate minerals such as monazite and xenotime, carbonate minerals like bastnaesite, and accessory minerals such as zircon and apatite (Arnold, 2023; Bauer et al., 2022; Seredin and Dai, 2012). There are two classifications of REY+Sc associated with coal, according to Seredin and Dai (2012). In the first classification, the elements are classified geochemically into Light REE (La, Ce, Pr, Nd, Pm, Sm), Medium REE (Eu, Gd, Tb, Dy), and Heavy REE (Ho, Er, Tm, Tb, Lu). The second classification is based on their market or economic importance and is classified into whether they are critical (Nd, Eu, Tb, Dy, Y, Er), not critical (La, Pr, Sm, Gd), or excessive (Ce, Ho, Tb, Yb, Lu).
Despite the traction globally, there is limited knowledge regarding REY+Sc in South African coals. Wagner and Matiane (2018) focused on coal and coal ash from 3 power stations EterighoIkelegbe et al. (2021) reviewed the enrichment and mode of occurrence of REY+Sc in coal and coal discards. Mokoena et al. (2022) investigated the effects of acid concentration on the recovery of REE from coal fly ash. More recently, Chitlango et al. (2023) reported on REE in density-fractionated coal samples from the Waterberg coalfield. The knowledge gap in South Africa brought about the inception of the current research, intending to determine the concentration of REY+ Sc in a variety of South African coals and their associated sediments in borehole cores from the Ermelo, Witbank, and Waterberg coalfields. In this paper, we discuss coal characterization and the sequential analytical technique used for leaching, prior to the inductively coupled plasma mass spectrometry
Table I
Coal sample names per coalfield
Coalfield Sample name
Ermelo UNI2 A, UNI2 B, UNI2 C, UNI2 D, UNI2 E, UNI2 F, UNI2 G,UNI2 H, UNI2 I, UNI2 J, UNI2 K, UNI2 L, UNI2 M, UNI2 N, UNI2 O
Witbank ZBSDR1, ZBS5T, ZBS5M, ZBS5B, ZBSHF1,ZBSDR2, ZBS4T, ZBS4M, ZBS4B, ZBSYF1, ZBSDR3, ZBS3, ZBSYF2, ZBSDR4, ZBS2Y, ZBS2M, ZBS2B, ZBDIF
Waterberg 12A, 11A, 10A, 9B, 8A, 8B, 8H, 8J, 8K, 7B, 6A,5A,4A, 4B, 3A, 3B, 3C, 2A,2B
(ICP-MS) analysis to determine the association and concentration of REY+Sc in coal and associated sediment samples
Methodology
Sample collection
The Ermelo and Witbank coalfields are situated within the Mpumalanga province, over 200 km and 130 km east of Johannesburg, respectively. The Waterberg coalfield is in the Limpopo province, 297 km north of Johannesburg (Figure 1). We logged full borehole cores from the study areas and sampled both coal and lithologies found immediately above and below the coal seams. We obtained fifteen, eighteen and twenty coal and associated sediment samples from the Ermelo, Witbank, and Waterberg cores, respectively (Table I).
Sample preparation and characterization
All coal samples and associated sediments were crushed and milled at the University of Johannesburg (UJ), using the Retsch ZM200
ultra-centrifugal mill to achieve homogenous -1 mm samples. A riffler was used to split each sample into three sub-samples. Sub-sample one (-1 mm) was retained for petrography. Coal petrographic analysis is based on 500-point counts per sample, categorizing the components observed as either vitrinite, liptinite, inertinite, or one of five mineral groups (i.e., clay, quartz, sulfides, carbonates, and other minerals). This is based on the South African National Standard/International Organization for Standardization (SANS/ ISO) 7404-3 (2016).
Sub-sample 2 was milled to -212 μm for X-ray diffraction (XRD), X-ray fluorescence (XRF), proximate and total sulfur analyses. The proximate analysis was conducted following SANS/ ISO standard number 17246 (2011). The mineral content was determined using XRD and the bulk chemistry (as major element oxides) in the samples were determined using whole rock analysis by XRF. Sub-sample 3 was further milled, using a pestle and mortar, and passing a screen of 106 µm in preparation for the sequential chemical extraction procedure (SCEP), a chemical leaching process, prior to inductively coupled lasma mass spectrometry (ICP-MS) analysis. All the coal samples used in the SCEP and subsequently analysed using ICP-MS are fresh coal samples. Samples with the highest REY+Sc values, following ICP-MS analysis, were resampled and ashed for further analysis using elemental mapping measurement mode on the mineral liberation analyser (MLA).
X-ray diffraction analysis
XRD analysis was outsourced to XRD Analytical and Consulting, Pretoria, South Africa. Samples were prepared for XRD analysis using a backloading preparation method. Diffractograms were obtained using a Malvern Panalytical Aeris diffractometer with a PIXcel detector and fixed slits with Fe-filtered Co-Kα radiation. The phases were identified using X’Pert Highscore Plus software. The Rietveld refinement method estimated the relative phase amounts (weight %).
Whole rock geochemistry - X-ray Fluorescence (XRF)
XRF analysis was outsourced to Bureau Veritas Testing and Inspection South Africa, Centurion, South Africa. A 0.7 g of a pulverized sample was added to 7.0 g of 66:33 LiT, LiM (LiI) flux and fused using a Claisse M4 fusion instrument. The resulting fusion discs were measured on a PANalytical Epsilon 3-XL EDXRF spectrometer equipped with a 50 kW 3mA Ag-tube, 10 sample carousel, He-purge chamber, and silicon drift detector.
Sequential chemical extraction procedures (SCEP) and ICP-MS
SCEP was conducted at UJ, Spectra labs. This procedure has been adapted from Dai et al. (2004). SCEP entails the chemical leaching of samples by different lixiviants. One sample is leached in six steps depending on which lixiviant is used. The steps are watersoluble, ion-exchangeable, carbonates, organically bound, silicates, and sulfides. Each sample derived from the respective step is analysed in the ICP-MS to determine the REY+Sc concentration. A PerkinElmer NexION 300X ICP-MS, housed at UJ was used for element determination in the coal and associated rock samples. Mineral liberation analysis (MLA)
For MLA analysis, coal samples with the highest REY+Sc content were selected from each coalfield (UNI2M, ZBS2B, and 11A). The sample preparation for MLA was outsourced to SJT MetMin Services, South Africa. These samples were ashed at 450⁰C for eight hours, to remove all volatile matter, and then mounted in
30 mm diameter epoxy resin blocks and cured. The prepared resin blocks were analysed at the Spectrum MLA laboratory, UJ. A scanning electron microscope FEI QUANTA 650 FEG instrument was operated under a vacuum to ensure no interactions with air particles occurred. A back-scattered electron detector (BSE) was used at 25 kilovolts so that the elemental contrast could be used to locate the rare earth-containing carriers of interest. The BSE images were captured using MLA processing software. The results presented in this paper indicate which minerals host the respective REY+Sc. The results are presented as BSE images with their respective spectral plots.
General characterization
The coal samples consist mainly of coaly-shales, dull-banded coal, and bright coal. The associated sediments are mainly clastic material consisting of carbonaceous shale, mudstone, sandstone, siltstone, and diamictite. All coal samples have moderate to high ash content. Samples from the Witbank coalfield have the highest average volatile matter of 25%. All samples have low sulfur content, the highest value is from the Witbank coalfields, sample ZBS4T, with 5.9% sulfur content.
Petrographic results are shown in Figure 2 and Figure 3. Ermelo coal samples are classified as high inertinite, medium-rank D/C bituminous coal, while the Witbank and Waterberg coal samples are also high inertinite, medium-rank C bituminous coal. The dominant minerals, according to the petrographic analysis, are clay, quartz, calcite, and pyrite. These results agree with studies conducted by Mahooana (2022), Moroeng et al. (2024), and Wagner and Matiane (2018). Figure 3 illustrates the presence of calcite and clay in photomicrographs.
Mineralogy: XRD
The mineralogy results are represented in Figure 4a-c per coalfield. The two dominant minerals in all the coalfields are kaolinite and quartz, except sample ZBS2M where dolomite was dominant. These are followed by muscovite and microcline in the Ermelo and Witbank samples. Trace to minor amounts of calcite and pyrite were detected in samples from all three coalfields, while dolomite was only detected in samples from the Witbank and Waterberg coalfields. These findings were corroborated by the petrography results.
Whole rock geochemistry - X-ray Fluorescence (XRF)
The dominant major element oxides are Al2O3, SiO2, Fe2O3 and CaO, as indicated in Table II. These values reconcile with the mineralogy results discussed above and with work published by Bauer et al. (2022), Dai and Finkelman (2018), and Moroeng et al. (2024).
SCEP and ICP-MS analysis results
The SCEP results are indicated in Figures 5 to 7 a for the coal samples and b for the associated sediment samples). All the coal and associated sediment samples indicate that there is an enrichment in LREY+Sc. There is also an elevation of MREY+Sc for the Witbankassociated sediments (Figure 6b). Both coal and associated sediment samples display an affinity for the carbonate fraction. This agrees with the findings discussed by Moroeng et al. (2024). There is more REY+Sc recovered from the associated sentiments compared to the coal samples for all the study areas.
REY+Sc for the carbonate fraction in the Ermelo coal samples range from below 2 µg/g for the medium and heavy REE to ~16 µg/g and 7 µg/g for Ce and La, respectively (Figure 5a). While the associated sediments, indicated by Figure 5b, range from
~3 µg/g on average for the medium and heavy REE. Up to a maximum of ~35 µg/g and 18 µg/g for Ce and Nd, respectively. A similar pattern is observed in the Witbank coal samples, as indicated in Figure 6a. The medium and heavy REE are below 2 µg/g The light
Table II
Average major oxides per coalfield (Weight %)
REE displayed Ce amounting to 16 µg/g, followed by Nd and La at ~7 µg/g. The carbonates fraction yielded the most results in the Witbank coal samples. The carbonate, silicates, and sulfide fraction results from the Witbank coalfield-associated sediments yielded the highest REY+Sc from the SCEP process, ranging from ~200 µg/g to 600µg/g for HREE. Followed by ~500 µg/g to over ~1,000 µg/g for MREE. The LREE values ranged from ~500 µg/g to over ~2,500 µg/g for Ce, La, being the highest. Research conducted by Dai et al. (2004), Li et al. (2008), and Yang et al. (2023) also discussed REY+Sc associated with silicates and alumino-sillicates and clays.
The Waterberg coal and associated samples yielded the lowest concentration for all fractions and compared to the samples from the other two coalfields. The coal samples have the highest concentrations in the carbonates and silicates fractions. This ranges from less than ~ 2 µg/g to ~ 7 µg/g, indicated by Figure 7a. The Waterberg-associated samples indicated by Figure 7B have the highest concentration in both carbonates and ion-exchangeable fractions. This ranges from less than ~ 2 µg/g to ~ 15 µg/g. The REY+Sc associated with the ion-exchangeable fraction are also
discussed in the work conducted by Bauer et al. (2023). The SCEP results also imply that the highest concentrations of REY+Sc in a particular fraction indicate the highest leaching potential of the lixiviant used in that step.
MLA
Monazite and xenotime particles were detected in all three samples (Figures 8a and 9a). In one example, monazite is locked in kaolinite (Figure 8a). Figure 8b indicates that the main rare earth elements present are La, Ce, Pr, Nd and Gd. Figure 9a depicts a xenotime grain attached to kaolinite. The main rare earth elements detected in the xenotime grain are Y, Gd, Tb, Dy, Ho and Er.
The borehole core samples examined are medium-rank C bituminous coals with moderately high ash content, low volatile matter and low sulfur content. The minerals present in all coal samples were mainly kaolinite and quartz, followed by muscovite, microcline, dolomite and trace amounts of calcite and pyrite. Both coal and associated sediment samples are enriched with LREY+Sc, with an elevation of MREY+Sc in the Witbank associated sediment
samples. There is more REY+Sc recovered from the associated sediments compared to coals following the SCEP. The Waterberg has the lowest REY+Sc in both the coal and associated sediment samples, while the highest REY+Sc was yielded from the Witbank associated sediments. The carbonate fraction step proved to be the most successful leaching step, as most REY+Sc were recovered on that step. This may also indicate an affinity for the carbonate minerals present, indicated by dolomite and calcite. However, there is also an affinity for silicates, sulfide fraction in the Witbank samples, and the ion-exchangeable fraction for the Waterberg associated sediments samples. MLA determined that monazite and xenotime in all the coal samples were the REY+Sc-bearing minerals and most are locked in kaolinite.
The authors are grateful for the support from the Centre of Excellence for Integrated Mineral and Energy Resources Analysis (DSI-NRF CIMERA) at the University of Johannesburg and the University of Johannesburg Spectrum Analysis Facility. This work is based on research financially supported by the National Research Foundation (NRF) of South Africa under Grant Number 118564. Any opinion, findings, conclusions, or recommendations expressed in this material are those of the author(s) and therefore, the NRF does not accept any liability in regard thereto. The authors also thank Dr TV Makhubela for his support in conducting the study.
References
Arnold B.J. 2023. A review of element partitioning in coal preparation. International Journal of Coal Geology, issue 104296, https://doi.org/10.1016/j.coal.2023.104296
Balaram, V. 2019. Rare earth elements: A review of the application, occurrence, exploration, analysis, recycling and environmental impact. Geoscience Frontiers, vol. 10, pp. 1285–1303.
Bauer, S., Yang, J., Stuckman, M., Verba, C. 2022. Rare Earth Element (REE) and Critical Mineral Fractions of Central Appalachian Coal-Related Strata Determined by 7-Step Sequential. Minerals, vol. 12, no. 1350, pp. 1–17.
Borzykowski, B. 2019. Wyoming may hold the key to the rare earth minerals trade war with China. [Online] Available at: https://www.cnbc.com/2019/07/10/wyoming-may-hold-key-tothe-rare-earth-minerals-trade-war-with-china.html
Chitlango, Z.F., Wagner, N.J., Moroeng, O.M. 2023. Characterization and pre-concentration of rare earth elements in density fractionated samples from the Waterberg Coalfield, South. International Journal of Coal Geology, vol. 275, pp. 1–16
Dai, S., Li, D., Ren, D., Tang, Y., Shao, L., Song, H. 2004. Geochemistry of the late Permian No.30 coal seam, Zhijin Coalfield of Southwest China: influence of a siliceous lowtemperature hydrothermal fluid. Applied Geochemistry, vol. 19, pp. 1315–1330.
Dai, S., Xie, P., Ward, C.R., Yan, X., Guo, W., French, D., Graham, I.T. 2017. Anomalies of rare metals in Loping Ian super-highorganic-sulfur coals from the Yishan Coalfield, Guangxi, China. Ore Geology Reviews, vol. 88, pp. 235–250.
Dai, S., Finkelman, R.B. 2018. Coal as a promising source of critical elements: Progress and future prospects. International Journal of Coal Geology, vol. 186, pp. 155–164.
Eterigho-Ikelegbe, O., Harrar, H., Bada, S. 2021. Rare earth elements from coal and coal discard – A review. Minerals Engineering, vol. 173, pp. 17–187.
Fu, B., Hower, J.C., Zhang, W., Luo, G., Hu, H., Yao, H. 2022. A review of rare earth elements and yttrium in coal ash: Content, modes of occurrences, combustion behaviour, and extraction methods. Progress in Energy and Combustion Science, vol. 88, pp. 1–47.
Hancox, J.P., Götz, A.E. 2014. South Africa's Coalfields — A 2014 perspective. International Journal of Coal Geology, vol. 132, pp. 170–254.
Hower, J.C., Qian, D., Briot, N.J., Henke, K.R., Hood, M.M., Taggart, R.K., Hsu-Kim, H. 2018. Rare earth element associations in the Kentucky State University stoker ash. International Journal of Coal Geology, vol. 189, pp. 75–82.
Li, D., Tang, Y., Deng, T., Chen, K., Liu, D. 2008. Geochemistry of rare earth elements in coal—A case study from Chongqing, southwestern China. Energy Exploration & Exploitation, vol. 26, no. 6, pp. 355–362.
Li, X., Qiao, W., Chen, D.,Wu, P., Xie, P., Chen, X. 2023. Anomalous concentrations of rare earth elements in acid mine drainage and implications for rare earth resources from late Permian coal seams in northern Guizhou. Science of the Total Environment, vol. 879, pp. 1–10.
Mahooana, P.E. 2022. Assessment of the possible occurrence of torbanite in the Ermelo Coalfield, South Africa, MSc. Johannesburg: University of Johannesburg.
Mokoena, K., Mokhahlane, L.S., Clarke, S. 2022. Effects of acid concentration on the recovery of rare earth elements from coal fly ash. International Journal of Coal Geology, vol. 259, pp. 1–9.
Moroeng, O.M., Bridgette, M., Wagner, N.J. 2024. Enrichment of rare earth elements in epigenetic dolomite occurring in contact metamorphosed Witbank coals (South Africa). International Journal of Coal Geology, 282(104405), pp. 1–18.
Serendin, V.V., Dai, S. 2012. Coal deposits as potential alternative sources for lanthanides and yttrium. International Journal of Coal Geology, vol. 94, pp. 67–93.
South African National Standard (SANS) 11760, 2018. Coal Classification. ISO 11760:2005
South African National Standard (SANS) 17246, 2011. Coal –Proximate Analysis. ISO 17246:2010.
South African National Standard (SANS) 7404-3, 2016. Methods
for the Petrographic Analysis of Coals - Part 3: Method of Determining Maceral Group Composition. ISO 7404–3:2009.
Wagner, N.J., Matiane, A. 2018. Rare earth elements in select Main Karoo Basin (South Africa) coal and coal ash samples. International Journal of Coal Geology, vol. 196, pp. 82–92.
Yang, P., Dai, S., Nechaev, V.P., Song, X., Chekryzhov, I.Y., Tarasenko, I.A., Tian, X., Yao, M., Kang, S., Zheng, J. 2023. Modes of occurrence of critical metals (Nb-Ta-Zr-Hf-REY-Ga) in altered volcanic ashes in the Xuanwei Formation, eastern Yunnan Province, SW China: A quantitative evaluation based on sequential chemical extraction. Ore Geology Reviews, 160(105617), pp. 1–22.
Zhou, B., Li, Z., Chen, C. 2017. Global potential of rare earth resources and rare earth demand from clean technologies. Minerals, vol. 7(203), pp. 1–14. u
26 MAY 2025 - WORKSHOP
Sulfuric Acid Catalysis - Key Parameters to Increase Efficiency and Lower Costs
27-28 MAY 2025 - CONFERENCE
29 MAY 2025 - TECHNICAL VISIT
PROTEA HOTEL STELLENBOSCH AND CONFERENCE CENTRE, STELLENBOSCH
OBJECTIVES
•
• To expose delegates to issues relating to the generation and handling of sulphur, sulphuric acid, and SO2 abatement in the metallurgical and other industries
•
• Provide an opportunity to producers and consumers of sulphur and sulphuric acid and related products to be introduced to new technologies and equipment in the field
EXHIBITION AND SPONSORSHIP
• •
• Enable participants to share information about and experience in the application of such technologies
• Provide an opportunity for role players in the industry to discuss common problems and their solutions.
There are a number of sponsorship opportunities available. Companies wishing to sponsor or exhibit should contact the Conferences and Events Co- Ordinator.
ECSA Validated CPD Activity, Credits = 0.1 points per hour attended
FOR FURTHER INFORMATION, CONTACT: Gugu Charlie, Conferences and Events Co-Ordinator, E-mail: gugu@saimm.co.za
Affiliation:
1Mintek, Randburg, South Africa
2Broadmind Mining Pty Ltd, South Africa
Correspondence to:
T. Mokgomola
Email:
TebogoMo@mintek.co.za
Dates:
Received: 29 May 2024
Accepted: 2 July 2024
Published: October 2024
How to cite:
Mokgomola, T., Marape, G., Singh, A., and Bisaka, K. 2024. Development of a physical separation pre-concentration process for the extraction of Rare Earth bearing ore. Journal of the Southern African Institute of Mining and Metallurgy, vol. 124, no.10, pp. 567–574
DOI ID:
http://dx.doi.org/10.17159/24119717/695/2024
ORCID: T. Mokgomola http://orcid.org/0000-0002-4446-5390
This paper is based on a presentation given at the Southern African Rare Earths 2nd International Conference 2024, 19-20 June 2024, Swakopmund Hotel and Entertainment Centre, Swakopmund, Namibia
by T. Mokgomola1, G. Marape1, A. Singh1, and K. Bisaka2
Abstract
This paper investigated the pre-concentration amenability of sovite (carbonatite) ore to enhance the grade of rare earth elements (REE) bearing minerals by rejecting calcite, and to improve total rare earth elements (TREE) recovery using gravity and magnetic separation. A high proportion of calcite affects downstream processes like leaching due to high acid consumption. Multiple flowsheets combining gravity and magnetic separation were employed to target > 60% TREEs recovery to the final concentrate and > 60% calcite rejection to the tailings. Head analysis of the feed showed the sample’s main constituents as Fe (15.61%), Ca (16.04%), SiO2 (7.13%), and lastly TREEs (1.12%). Mineralogy liberation data at 2mm top size indicated poor liberation of TREEs, with the majority of minerals displaying < 30% mass greater than 80% liberated. Grain size distribution data showed that the majority of REE minerals are fine grained and report to the < 20 µm size class. Calcite liberation mineralogy showed < 60% mass greater than 80% liberation.A combination of a single-stage shaking table with a wet high intensity magnetic separator at a magnetic intensity of 7520 G was found to be the optimum flowsheet. For a shaking table feed with P80 of 150 μm followed by tails regrind to P80 of 45 μm as feed to wet high intensity magnetic separator, the overall mass balance results showed that 60.5% TREEs are recovered to the concentrate while 63.0% calcite is rejected to the tails. However, due to the fine-grained nature of TREEs, no flowsheet improved their grade.
Keywords
Sovite, total rare earth elements (TREEs), calcite, wet high intensity magnetic separation (WHIMS), low intensity magnetic separation (LIMS), shaking table (ST)
Introduction
In recent years, worldwide investment in the recovery of rare earth elements (REE) has been financed due to their increasing use in modern high technology industries. REEs are included in a growing list of critical raw materials (Berger et al., 2014; Sager and Wiche, 2024). REE’s primary recovery from value bearing ores is costly due to low concentrations within the ore. According to Sager and Wiche (2024), the concentration of REEs in the earth’s crust ranges from 66 mg/kg (Ce) to 0.3 mg/kg (Lu). For the extraction of REEs minerals for valuable and raw material to be feasible, various REEs beneficiation processes have been established and others are currently being explored to upgrade and recover REEs at optimum costs.
Rare earth elements (REEs) are comprised of seventeen chemical elements in the periodic table. Among the seventeen, fifteen of them are lanthanides and the other two are yttrium and scandium, which occur in the same ore deposits as lanthanides and exhibit the same chemical properties (Hoshino, et al., 2016; Sager and Wiche, 2024). Yttrium was the first REE discovered by chemist Johan Gadolin in 1794 and promethium was the last REE discovered approximately 150 years later in 1947. REEs are found within other minerals in the earth’s crust, as they do not occur individually (Hoshino et al., 2016). REEs are critical raw materials for modern technologies ranging from cellphones, magnets, and LED lights to wind turbines due to their properties like magnetic, catalytic, and phosphorescent properties (Frances, 2021).
In this paper, the mineral of interest is sovite ore originating from Southern Africa. The ore is carbonatite or calcite rich, thus making calcite the main gangue mineral. According to Frances (2021), the majority of operational REEs mines are carbonatite-related deposits. This paper thus focuses on the rejection of calcite to improve the recovery of REEs, which is important in the mining industry.
This paper aims to provide an economically viable route to recover REEs and reject calcite from sovite ore using gravity and magnetic separation techniques according to the properties of the valuable and the gangue minerals within the ore. To achieve this, ore characterization using elemental chemical analysis followed by bulk modal mineralogy using AutoSEM technology was conducted.
Gravity separation methods are the most commonly used beneficiation methods employed to exploit the density differences between valuable minerals and the gangue within a given ore. The method uses the differential settling velocity between particles. This settling velocity is governed by particle weight, buoyancy and drag force (Roy, 2009; Murthy and Tripathy, 2020). It is the oldest beneficiation technique and is widely used due to the associated low costs, simple operating procedures, and its eco-friendly nature. The most popular gravity separation units used for wet processes are shaking tables, jig, and spirals (Roy, 2009).
Gravity separation units are selected based on particle size and the capacity of the unit. Gravity separators provide peak performance when operated in optimum conditions and the right feed particle size range for a given material. The biggest challenge for most gravity separation methods has been fine and ultrafine particles (Murthy and Tripathy, 2020). For this paper, due to limitations in feed mass, a flowing film gravity concentrator such as the Wilfley shaking table was utilized. Tabling of ores is efficient when the differences in specific gravity between the minerals is high (Roy, 2009).
Magnetic separation methods are employed to exploit the differences in magnetic properties of minerals within a given ore. This technique uses magnetism to separate materials that respond more strongly to a magnetic force from materials that exhibit a weak response. It is a newer process when compared with gravity separation but old when compared with froth floatation methods. Selection of a magnetic separation unit or mechanism is based on the magnetic properties of the given mineral. Some materials are ferromagnetic, paramagnetic and others diamagnetic. Ferromagnetic materials require a low magnetic intensity for separation, whilst paramagnetic materials require a high magnetic intensity to be susceptible to the magnetic forces. According to Cohen (1986), only four elements namely cobalt, iron, gadolinium, and nickel are ferromagnetic but seven REEs are strongly paramagnetic.
Most minerals are weakly paramagnetic or diamagnetic and their magnetic susceptibilities are constant and show straightline relationships to the strength of the magnetic field exerted on them. Paramagnetic minerals have a higher magnetic permeability compared to their surrounding media making it easier for the particle to move in the direction of the field strength due to high field density within the particle. On the other hand, diamagnetic minerals have lower magnetic permeability than the surrounding
Head
mineralogy
media (Cohen, 1986). In this research, both low and high magnetic intensity (LIMS and WHIMS) separators were used to determine the optimum flowsheet for REE recovery whilst rejecting calcite.
Figures 1 to Figure 3 shows the schematic diagrams of flowsheets used for the procedures of characterization and the different possible combinations of magnetic and gravity separation flowsheets.
Sample receipt and preparation
Approximately 280kg of sovite feed sample was delivered for testwork purposes. The sample was at a top size of 1/4 core pieces, so roughly 10 mm x 10 cm pieces and dry upon receipt. The sample was weighed, blended, stage crushed using Jaw and cone to 100% passing 20 mm, and then subsampled using cross-cut method for coarser sizes for various tests according to the scope of the testwork. The subsamples were stage crushed to 100% passing 2 mm for mineralogy, 100% passing 1mm for particle size distribution and head analysis and 2 mm for ball milling to P80 = 300 µm, 150 µm, 106 µm, 53 µm and 45 µm. The finer fractions, that is, -2 mm, samples, were subsampled using the rotary splitter.
Elemental chemical analysis on the sovite ore was done using ICP base metal, and REE solid digestion methods to determine the grade of calcite, REE, and Fe. Mineralogical analysis on the sample was carried out using quantitative X-ray diffraction (qXRD), scanning electron microscopy (SEM), and automated scanning electron microscope (AutoSEM) analysis. The purpose of the
investigation was to establish the presence, identity, and relative abundance of minerals as well as to obtain information on REE minerals in terms of their mode of occurrence, relative abundance, REE deportment, and grain size, liberation at a top size of 100% passing 1.18 mm, mineral associations and bulk modal mineralogy.
Magnetic separation
Figure 2 shows a typical magnetic separation flowsheet comprising of Ball mill, LIMS and WHIMS.
Davis tube testwork
To determine the percentage of ferromagnetic material in the sample, magnetic separation was conducted using an electromagnet Davis tube as depicted in Figure 2. The separation occurs by exploiting the high susceptibility of ferrous material in the sample to magnetic forces. The sample was fed at P80 of 53 µm and tested at a magnetic field intensity of 1000 G. The non-magnetic products were sent to the WHIMS equipment.
Laboratory Wet LIMS and WHIMS Testwork
As per Figure 2, laboratory wet LIMS testwork, using a permanent magnet at a magnetic field intensity of 1000 G, was conducted on the feed at P80 of 150µm to recover ferrous material in the feed before WHIMS testwork.
The non-magnetic material was subjected to WHIMS at four intensities (2000 G, 4000 G, 6000 G, and 7520 G) to determine the intensity that will reject calcite and improve the grade of REE. This testwork was conducted five (5) times across multiple flowsheet combinations with shaking table tails and slimes as feed (Figure 3), and the Davis tube and LIMS non-magnetic streams as feed (Figure 2).
The roasted feed at a P80 of 150 µm was subjected to dry magnetic
Shaking Table Feed
Ball Mill
Rougher Shaking table
separation using laboratory high-intensity induced-roll lift type magnetic separator at seven magnetic intensities (800 G, 850 G, 870 G, 900 G, 920 G, 950 G, and 1000 G). The sample contained hematite, thus roasting of the sample at 1000°C increased the magnetic susceptibility for low intensity dry magnetic separation.
Combined gravity separation and magnetic separation testwork
Figure 3 shows the schematic diagram used for the combination of shaking table with magnetic separation.
Shaking table testwork
The shaking table test was conducted six times across multiple flowsheets for calcite rejection using the density difference between REE, Fe, and Ca. The shaking table consists of a slightly inclined deck that exposes particles to gravitational, vibrational, and flow water forces allowing the particles to separate due to their difference in density, shape, and size. The shaking table produced nine (9) products namely four concentrates, two middlings, two tails, and one slimes stream. Shaking table was conducted at P100 of 1.18 mm, P80 of 300 µm, 150 µm (three times) and 106µm (Scavenger in a flowsheet). The tails from shaking table at P100 = 1.18 mm, were subjected to WHIMS to form flowsheet 7 as shown in Table II. The slimes and tails of these tests were milled to P80 of 45 µm for magnetic separation using WHIMS, with the exception of WHIMS on shaking table tests tails at P100 = 1.18 mm.
Results and discussion
Head analysis and mineralogical evaluation
Table I shows the chemical composition of the sovite ore. It is observed that the REE collectively constitutes 1.12% of the sovite ore. The %Fe was higher than expected at 15.61% with %Ca at
Ball Mill
WHIMS Feed
P100 = 1.18 mm
P80 = 150 mm
P80 = 45 mm
Ball Mill Scavenger Shaking table WHIMS
16.04% (40.10% CaCO3). Bulk mineralogy of the samples (Figure 4) shows that the ore predominantly consists of ferruginous clay, calcite and kutnohorite.
REEs and calcite minerals liberation and grain size distribution
Liberation characteristics of cumulative REE and calcite minerals by free surface and particle composition are presented in Figure 5 to Figure 8. Liberation classification by particle composition is based on area percent of the mineral of interest (e.g., TREE) over the total area of a particle. Liberation classification by free surface is based on the degree to which valuable minerals within the ore have a free
surface after crushing, making them accessible for separation and concentration processes. Liberation classes are defined in 12 groups ranging from 0% to 100% area, in 10% intervals and reported by cumulative liberation by area. Results in each class are cumulated from 100% liberated to 0 % liberated.
With the exception of burbankite, the majority of REE minerals display poor liberation by both particle composition and free surface liberation with the majority of minerals displaying <30% mass greater than 80% liberated.
Calcite displayed <60% mass greater than 80% liberation by both particle composition and free surface liberation.
Grain size distribution
Size is reported in equivalent circle diameter (ECD), which is the diameter of a circle of equivalent area to that of the grain, in microns. Grain sizes are based on the average horizontal intercept through a grain and are measured on a two dimensional surface. The grain sizes of the minerals of interest are divided into size classes using ECD and presented in mass percentage. Grain size distribution is presented in Figure 9.
With the exception of bastnaesite (Ce), strontianite, and ancylite, the majority of REE minerals are finer grained and report to the <20 µm size class.
Overall comparison of flowsheet options
Due to multiple flowsheets used to generate an optimum flowsheet for calcite rejection and REEs recovery, the feed, concentrate, and tails of each flowsheet are presented in Table II and discussed in the following paragraphs.
Table II presents the Davis tube and WHIMS results at magnetic field intensities of 1000 G and 7520 G, respectively at a feed grind of P80 53 μm (Flowsheet 1). Davis tube was conducted to determine the fraction of ferrous material in the sample, and only 1.6% by mass reported to the magnetic stream suggesting the feed was predominantly paramagnetic. The overall mass balance results showed that at a WHIMS magnetic intensity of 7520 G, Ca rejection to the non-magnetic stream was 24.1% Ca not meeting target specification. At this intensity, about 12.3% TREE is lost to the waste stream at a grade of 1.00%. This flowsheet could not be optimized due to failure to reject Ca to the non-magnetic stream. A high proportion of calcite affects downstream processes such as leaching leading to high acid consumption (Thomas, 2021). To solve this problem gravity separation and roasting of the feed at at 1 000°C to increase the magnetic susceptibility for low intensity dry magnetic separation was recommended. According to Corte et al. (2019), roasting reduces a paramagnetic material such as hematite to ferromagnetic magnetite, allowing it to be recovered by wet low magnetic separation.
Flowsheets 2 to 4 in Table II shows the results of gravity separation on the shaking table for three size fractions. Ca rejection to the tails and slimes ranges from 79.7% to 84.1%. Rejection to the tails increased with decreasing feed particle size. Similar to the Ca trend, the TREE recovery to tails and slimes is observed to increase with decreasing particle size ranging from 64.3% to 68.7%. As a result, it was recommended to grind the tails and slimes to a P80 45 μm and process it through the WHIMS at 4 magnetic intensities to generate a gravity and magnetic separation flowsheet. The recommended shaking table feed grind for the combination flowsheet was P80 = 150 μm.
Flowsheets 5 and 6 show the results of gravity separation in conjunction with WHIMS. Flowsheet 6 has two gravity separation stages with the second shaking table (scavenger) fed at 80% passing 106μm (tails of rougher shaking table). The overall mass balance results of single stage shaking table and WHIMS (Flowsheet 5) showed that 60.5% TREEs are recovered to the concentrate while 63.0% Ca is rejected to the tails. In order to boost the rejection of Ca to the tails, a two-stage shaking table including the regrind of the rougher shaking table tails to 80% passing 106μm was recommended and the tails and slimes of the scavenger stage were fed through WHIMS magnetic separation. The overall recovery of Ca to the tails increased by 4% whilst the TREEs lost to the tails increased by 9%. Flowsheets 6 and 5 had slightly similar TREE
concentrate grades of 1.94% and 1.03% respectively. Since there is an increase in losses of TREEs to the tails in Flowsheet 6, Flowsheet 5 is recommended.
Flowsheet 7 combined shaking table and WHIMS using a coarse fraction, P100 = 1.18 mm, to observe if it will be different to the fine fraction Flowsheet. The results showed that 55.4% Ca can be rejected to the tails, which is lower than the rejection observed with a finer fraction. TREEs loss to the tails was 37.9%, lower than the losses observed with the finer fraction. From these combinations of gravity and WHIMS, a single stage gravity separation at a finer grind of P80 = 150 μm is recommended due to the highest rejection of Ca to the tails.
A roasted feed, at P80 = 150 μm, which increased the magnetic susceptibility of the feed was fed through LIMS +WHIMS (Flowsheet 8) and through a dry magnetic separator (Flowsheet 9) to observe if Ca can be rejected and if TREE recovery will be improved. For wet LIMS+WHIMS, the results showed that only 33.2% of Ca would be rejected to the non-magnetic stream. Compared to the non-roast feed, which rejected only 24% Ca at a finer fraction of P80 53 μm (Flowsheet 1) the roasted feed performed better.
Dry magnetic separation using laboratory high-intensity induced-roll lift type magnetic separator at seven magnetic intensities on demagnetized roasted feed at a grind of P80 150 μm achieved the lowest Ca rejection compared to all Flowsheets at 19.9% Ca to the tails. This process is therefore not feasible.
According to the mineralogy of the feed, the majority of REE minerals display poor liberation with the majority of minerals displaying <30% mass greater than 80% liberated and the majority of the grains lies in the <20 µm size fraction. This means that the REEs in the sample are fine-grained, indicating that the concentrate grade from gravity and magnetic separation methods could not be improved. Gravity and magnetic separation in combination were successful in pre-concentrating the feed by rejecting 60% Ca to the tails. According to Bidari and Aghazadeh (2017), the presence of calcite during leaching slows down the leaching rate by developing a surface layer. During leaching, calcite reacts quickly in acid and consequently, causing a decrease in pH and precipitation of secondary minerals (Thomas, 2021). Mineralogy indicated that the majority of the calcium bearing gangue is calcite, followed by kutnohorite and ankerite and therefore pre-concentration will thus reduce acid consumption during the leaching process.
Table II
Overall mass balance of multiple flowsheets tested
9
➤ Multiple flowsheets were investigated to determine the potential for calcite rejection whilst improving the TREE recovery.
➤ The mineralogy of the sample showed that the TREE bearing minerals are fine grained and reported to the <20 µm size class. Liberation showed that <30% by mass of the TREE bearing minerals are 80% liberated.
➤ A single stage gravity separation shaking table in conjunction with WHIMS at feed grind of P80 150 μm was found to be the optimum flowsheet amongst the flowsheets tested. The flowsheet showed that 60.5% TREE are recovered to the concentrate while 63.0% Ca is rejected to the tails.
➤ Removal of >60% of the calcite should improve the feasibility of downstream extraction of the REE.
➤ The flowsheets tested could not improve the grade of TREE because they are fine grained.
➤ At a pilot scale, we recommend the use of fine spiral processing technology or falcon concentrator to investigate gravity concentration of a finer feed at P80 < 150 µm.
➤ Due to the fine nature of the REE-bearing minerals, it is recommended to employ a multi-gravity separator. The benefits of multi-gravity over shaking table and spirals is that they tend to hone in on the -30 µm fraction, whilst shaking tables and spirals tend to misplace the slimes.
References
Berger, A., Janots, E., Gnos, E., Frei, R., Bernier, F., 2014. Rare earth element mineralogy and geochemistry in a laterite profile from Madagascar. Applied Geochemistry, pp. 218–228.
Bidari, E., Aghazadeh, V. 2017. Pyrite oxidation in the presence of calcite and dolomite: Alkaline leaching, chemical modeling and surface characterization. Transactions of Nonferrous Metals Society of China, vol. 28, no. 7, pp. 1433–1443.
Cohen, H.E. 1986. Magnetic Separation. Wills, B.A., Barley, R.W. (eds) Mineral Processing at a Crossroads. Dans: Mineral Processing at a Crossroads. London: Springer, pp. 287–286.
Corte, C.D., Bergmann, C., Woollacott, L. 2019. Improving the separation efficiency of Southern African haematite from slimes through selective flocculation coupled with magnetic separation. The Southern African Insitute of Mining and Metallurgy, pp. 963–972.
Frances, W. 2021. Encyclopedia of Geology (Second Edition). London: Elsevier.
Hoshino, M., Sanematsu, K., Watanabe, Y. 2016. Chapter 279REE Mineralogy and Resources. Handbook on the Physics and Chemistry of Rare Earths, pp. 129–291.
Murthy, Y.R., Tripathy, S. 2020. Process optimization of a chrome ore gravity concentration plant for sustainable development. Journal of the Southern African Institute of Mining and Metallurgy, pp. 261–268.
Roy, S. 2009. Recovery Improvement of Fine Iron Ore Particles by Multi Gravity. The Open Mineral Processing Journal, pp. 17–30.
Sager, M., Wiche, O. 2024. Rare Earth Elements (REE): Origins, Dispersion, and Environmental Implications—A Comprehensive Review. Environments, vol. 11, no. 2, pp. 1–3.
Thomas, M. 2021. Understanding gangue acid consumption in copper sulfide heap leaching: Predicting the impact of carbonates, silicates and secondary precipitates. Minerals Engineering, pp. 1–10. u
MASLOW HOTEL, SANDTON, JOHANNESBURG
During closure planning there are usually four parties involved, being the mining house, external stakeholders, consultants and the authorities who are responsible for closure plan and eventual relinquishment approval. There are subsequently numerous conflicting ideals between the parties during the evolution of mine planning to post-closure. This leads to unrealistic closure expectations and vague obligations that result in the lack of setting or accepting specific closure and relinquishment criteria. Without clear direction, achieving a closure certificate in South Africa remains uncertain. This leads industry to adopt very different positions around closure planning that ranges between best practice, compliance to legislation to minimal planning.
Successful relinquishment has been achieved internationally by creating a value chain for sustainable post-mining economies as early as possible. In South Africa relinquishment could possibly be achieved successfully by complying to the current legislative
closure approach or alternatively by creating third party value by means of parallel economies. This could potentially be supplemented with a regional closure approach between mining houses. It is therefore imperative that the third party needs to be part of the value chain development and execution through meaningful community engagement to ensure the benefits of local knowledge and achieve social acceptance. Once the longterm value chain is in place it lays the foundation for closure- and relinquishment criteria and social integration. ESG compliance adds another layer to closure planning but can be very useful to add specific criteria and expedite closure actions. Regardless of the approach taken, engagement with regulators is required for overall alignment and changes to policies.
FOR FURTHER INFORMATION, CONTACT:
Gugu Charlie, Conferences and Events Co-ordinator
E-mail: gugu@saimm.co.za Tel: +27 11 530 0238
Affiliation:
1Rainbow Rare Earths Pty. Ltd., South Africa
2University of Pretoria, South Africa
Correspondence to:
R.A. Wildenboer
Email: rouxwil@gmail.com
Dates:
Received: 29 May 2024
Accepted: 4 June 2024
Published: October 2024
How to cite:
Wildenboer, R.A. and Sandenbergh, R.F. 2024
Extraction of Rare Earth Elements from Phalaborwa phosphogypsum. Journal of the Southern African Institute of Mining and Metallurgy, vol. 124, no.10 pp. 575–582
DOI ID:
http://dx.doi.org/10.17159/2411-9717/ RE15/2024
ORCID:
R.A. Wildenboer
http://orcid.org/0009-0007-4685-7607
This paper is based on a presentation given at the Southern African Rare Earths 2nd International Conference 2024, 19-20 June 2024, Swakopmund Hotel and Entertainment Centre, Swakopmund, Namibia
by R.A. Wildenboer1,2 and R.F. Sandenbergh2
Abstract
Rare earth elements (REE) are present at concentrations of approximately 0.36 % in phosphogypsum stacks located in Phalaborwa, South Africa. The REE are present in the phosphogypsum in solid solution in the gypsum and as fluorine and aluminium rich precipitates. Recovery of the REE offers opportunities for valorization and reducing the environmental impact of the phosphogypsum waste. This paper presents the results of investigations into the leaching behaviour of rare earth elements and other impurities from phosphogypsum using aqueous sulfuric acid. The effects of acid concentration, temperature, residence time, and the influence of impurities were evaluated for their impact on the solubility of rare earth elements in a sulfate medium. It was found that a significant fraction of the REE can be leached from the phosphogypsum in a range of conditions much less severe than traditional hard rock rare earth processing conditions. The REE were leached at a sulfuric acid concentration of 110 g/l, temperature of 30°C – 40°C and a residence time of approximately 8 hours.
Keywords rare earth elements, phosphogypsum, Phalaborwa, extraction, sulfuric acid
Introduction
Demand for rare earth elements (REE) has increased in the last two decades, particularly those required in relatively large quantities for permanent magnets and other modern electronics. These elements include light rare earth elements (LREE) such as neodymium (Nd), praseodymium (Pr), and heavy rare earth elements (HREE) such as terbium (Tb), and dysprosium (Dy). The global drive particularly towards nonfossil fuel-based power generation and electrification of transport, has led to projections that between 2020 and 2030, annual demand will increase by 6.4% for Nd, 6.7% for Pr, 7.4% for Dy, and 33.4% for Tb. Argus Media estimates that by 2030, there will be a 25% supply deficit of critical rare earth elements, even if pipelined projects come online within schedule (Rainbow Rare Earths, 2022).
Typical hard-rock phosphate/carbonatite deposits require mining, comminution, concentration, hydrometallurgical extraction, purification, and separation to produce rare earth oxide products suitable for manufacture of magnets, etc. Ionic clay deposits are lower grade and may pose environmental risks by the way in which rare earths are leached, sometimes through the use of in-situ leaching, which can contaminate large areas of land. Recovery of rare earth elements from secondary sources and recycling of rare earths from electronic waste offers the opportunity to produce rare earth products without the need for mining or other costly, intensive, and hazardous extraction processes. The phosphogypsum (PG) residue stacks located near the town of Phalaborwa in South Africa contain approximately 0.43% total rare earth oxide (TREO) equivalent, one of the highest REE-grade phosphogypsum resources described in literature (Lambert et al., 2018; Li et al., 2021). PG produced from the treatment of sedimentary phosphate deposits typically contain 0.02% – 0.05% w/w REE, whilst PG from igneous sources such as those found in Poland, Russia, and Brazil may contain 0.43% – 0.73% w/w REE. Igneous sources are fewer however, and sedimentary sources such as those found in Florida, Spain, and Canada are far more abundant. The Phalaborwa PG contains high concentrations of REE due to the upgrading of REE in the igneous complex over long periods of time, and the subsequent concentration of phosphate rock for processing into phosphoric acid on site over the course of several decades from the 1960s to 2013. The rare earths are present in phosphate minerals in the area, apatite in particular, which is decomposed with sulfuric acid and heat to form gypsum and phosphoric acid. It is estimated that approximately 85% of the rare earths report to the phosphogypsum which is deposited as waste on unlined stacks.
The recovery of REE from PG at Phalaborwa presents several key benefits: The REE grade is high compared to other phosphogypsum residues around the world, processing costs can be kept comparatively low due to the resource being located above ground and not requiring blasting, mining, fine grinding, or concentration; recovery of REE can be achieved with less severe processing conditions and reagent consumption compared with traditional methods, the processing and rehabilitation of unlined, and acidic PG stacks will offer significant environmental benefits to the area that is known for its natural beauty and diversity.
The extraction of rare earths from phosphogypsum has been studied significantly by various investigators in the past. Phosphoric acid plants are widespread, and the phosphate mineral feed contains concentrations of rare earth elements, of which the majority reports to the PG waste. However, phosphate deposits vary in nature and origins, as well as in REE content: 0.03% – 2.78% on RE oxide basis (Wu et al., 2018). The composition of the feed phosphate rock, as well as the specific conditions in the various phosphoric acid processes produce PG with widely varying physical characteristics and chemical makeup. The result of these compounding variations is that there are no two PG sources that are identical and in fact, PG from different processes behave quite differently when subjected to hydrometallurgical treatment to extract REE. The manipulation of several key parameters has been shown to affect the leaching of REE from PG and are discussed below.
The mineral acids generally evaluated for the leaching of REE from PG are hydrochloric acid, nitric acid, and sulfuric acid. In work comparing the acids directly, nitric, and hydrochloric acid have been shown to be significantly more effective than sulfuric acid at leaching REE (Li et al., 2021; Lu and Liu., 2023; Walawalkar et al., 2016; Al-Thyabat and Zang, 2015; Ismail et al., 2015; Cánovas et al., 2019). The significantly lower leach efficiencies achieved by sulfuric acid have been ascribed to the suggested mechanism by which REE is leached from the PG, which is heavily dependent on the solubility of calcium sulfate in the various acids. Calcium sulfate is sparlingly soluble in solutions of sulfuric acid due to the common ion effect, but more soluble in solutions of nitric and hydrochloric acid (Azimi et al., 2007). However, sulfuric acid remains an economically attractive choice due to its lower cost, higher availability, generally lower corrosivity, and its comparative ease to store and handle. For example, Lu and Liu (2023) achieved 49.93% – 68.8% REE extraction from Indonesian PG with nitric and hydrochloric acid, and only 37.45% – 45.79% extraction with sulfuric acid under similar conditions. Lutke et al. (2022) found that sulfuric acid does, however, perform better than citric acid. Acids such as malic acid, boric acid, and citric acid have been tested to leach REE from Egyptian PG, but could only achieve <25% extraction and is considered less effective than mineral acids such as hydrochloric, nitric, and sulfuric (Gasser et al., 2019). Cánovas et al. achieved 46% – 58% REE extraction from Spanish PG (345 mg/kg REE) with 0.5 M H2SO4, and 82% – 86% REE extraction with 3 M HNO3.
Acid concentration
Sulfuric acid concentration has been found to have a positive effect on REE dissolution, but only up to a maximum of approximately 1.3 mol/l, after which an increase in acid concentration has a negative effect on REE dissolution (Li et al., 2022). Lokshin et al. (2010) found a positive correlation between REE leaching and sulfuric acid concentration in the range of 0.5% – 4% H2SO4 in
solution, which is lower than what has been observed to be the maximum beneficial acid concentration. The phenomenon has been observed with hydrochloric acid, where acid concentrations above 0.25 mol/l was found not to increase REE extraction (Lu et al., 2023). Rychkov et al. (2018) in contradiction found that REE leaching from Russian PG reached a maximum at an acid concentration of 5 mol/l, but it is worth noting that the total REE extraction only reached around 30%. It may be that this particular PG responds to a high acid concentration due to the specific nature of the REE precipitation or co-crystallization within the gypsum. Ismail et al. (2015) found that at sulfuric acid concentrations of up to 5 mol/l, there was a constant positive effect on REE leaching from Egyptian PG fertilizer. Gasser et al. (2019) used the same Egyptian PG and leached with boric, malic, and citric acid and found that a lower acid concentration is beneficial to REE extraction in the range of 0.1 mol/l – 3 mol/l. This suggests a similar mechanism to what is seen with particularly sulfuric acid, i.e., that higher acid concentrations do not necessarily translate into higher REE leaching.
Higher temperature has been found to benefit the leaching of REE (Lutke et al., 2022; Lambert et al., 2018), and also the solubility of calcium sulfate in the presence of sulfuric acid (Azimi et al., 2007). In water however, gypsum solubility increases up to a temperature of approximately 40°C, after which there is a decline in gypsum solubility. It is worthwhile noting that the presence of sulfuric acid affects this behavior, as at concentrations of up to 3 mol/l sulfuric acid, increasing temperature continues to have a positive effect on the solubility of gypsum. Ismail et al. (2015) found that leaching efficiency with nitric acid decreases as the temperature is increased beyond 55°C, and that leaching efficiency increases up to a temperature of 85°C with hydrochloric acid. Ismael’s work on sulfuric acid contradicted some other work done, showing that temperature did not influence the leach extraction significantly when using sulfuric acid.
Residence time
Leaching of REE from PG has been shown to have kinetics that are relatively fast, typically reaching equilibrium within an hour (Lu and Liu, 2023; Hammas-Nasri et al., 2019; Hammas-Nasri et al., 2016; Al-Thyabat and Zang, 2015; Lutke et al., 2022; Walawalker et al., 2016). However, there are contradicting references in literature, however. Ismail et al. (2015) leached Egyptian low-P2O5 PG with hydrochloric, nitric, and sulfuric acid, and found that leaching with nitric and hydrochloric reached completion within 2 hours, but REE continued leaching with sulfuric acid for up to 8 hours. Gasser et al. (2019) found that the time effect is dependent on the specific acid, having a negative effect with malic and citric (after approximately 30 min.), but that leaching increases with time with boric acid. Cánovas et al. (2019) found that with 0.5 M H2SO4 and with 3 M HNO3, leaching was ≈ 90% complete within 2 hours.
In most cases, a smaller solid/liquid ratio has proven to benefit the leaching of REE (Lu and Liu, 2023; Li et al., 2021; Lutke et al., 2022; Walawalker et al., 2016). Once again, better REE leaching at lower ratio of solids to solution suggests a solubility effect of calcium sulfate. A higher total mass of PG can dissolve if the solid/ liquid ratio is lower. However, decreasing the solid/liquid ratio has economic implications, leading to a higher volume of lixiviant to prepare and leach slurry to handle. Due to the concentration effect of acid, higher solution volumes also require higher quantities of acid.
Presence of resin in the leach
Due to their mostly trivalent cationic oxidation state in acidic solution, REE can be loaded onto cation exchange resin and thereby selectively removed from solution. Virolainen (2019) evaluated the use of resin-in-leach (RIL) techniques to extract REE from Finnish PG containing approximately 1686 mg/kg REE. Virolainen used two sulfonic strong acid cation exchange resins and an aminophosphonic chelating resin and achieved approximately 60% recovery of REE from the PG after only one stage of RIL leaching with sulfuric acid, and at considerably lower acid concentrations than was required without resin (5 g/l vs 20 g/l). This indicates that to some extent, there is a solubility effect which retards the leaching of additional REE from the PG, where there is already high REE in the solution. Continuously depleting the aqueous REE concentration with resin has a positive effect on the leaching of REE. However, calcium co-loaded to a significant extent onto the resin leads to the logical consequence of higher PG mass loss during the leach. It is not clear whether the increased REE leaching is caused by higher calcium sulfate solubility, or the depletion of REE from solution. It has further been shown that several strong acid cation exchange resins are selective for REE over Ca, and that in consecutive leaching stages, REE substitutes for Ca on the resin and loads almost to capacity in REE in 10 g/l of sulfuric acid (Kurkinen et al., 2021). Yahorava et al. (2016) showed that leaching of South African PG containing 3387 mg/kg REE in sulfuric acid without resin could achieve the same REE extraction (approximately 17%) as with RIL, but RIL achieved the extraction at a much lower acid concentration. The work also showed that at higher acid concentrations, both REE and Ca loading on the resin decreased, indicating that a higher acid concentration may not be optimal for RIL applications.
Table I
QEMSCAN analysis of PG Mineral
Bastnaesite (Ce,La,Nd)(CO3)F 0.001
Monazite-Ce (Ce,La,Nd,Th)PO4 0.06
REE minerals REE, Y, CO3, PO4, O 0.04
Ca,F precipitate phase Ca,(Ce,La,Nd)Al,S,O,F•X(H2O) 3.00
Others Various 0.03 Unclassified 0.80
Table III
Elemental analysis of PG
Table II
Rare earth deportment in PG phases
characterization
For the test work performed, several different samples of PG were used, gathered from the PG stacks located at Phalaborwa, South Africa. For each test or series of tests using the same feed sample, a feed sample chemical assay is given.
QEMSCAN and energy-dispersive X-ray spectroscopy (EDS) analyses were conducted on a composite PG sample at the Australian Nuclear Science and Technology Organization (ANSTO). The analysis (Table I) revealed that the PG comprised primarily of gypsum, as expected, but contained approximately 3% of what could be identified as a precipitated REE-rich Ca, Al, F phase. Only minor quantities of residual phosphate mineralization were detected, but a significant quantity of quartz was detected, presumably the residual from quartzitic mineral carryover into the primary upstream phosphate mineral concentration.
From the QEMSCAN results, REE deportment was calculated using known phase compositions in the QEMSCAN software database. The calculations suggest that the majority of REE is contained within the precipitated Ca, F phase, and that only minor quantities of REE is associated with gypsum, indicating a low degree of isomorphic substitution of Ca with REE in the calcium sulfate crystal lattice. EDS analyses of randomly selected calcium sulfate particles confirmed that REE is not contained within the calcium sulfate particles, as is the case with other PG sources (Lokshin et al., 2010; Wu et al., 2018). Results from REE deportment calculations are shown in Table II.
Elemental composition was determined via fuse-digest-ICP. As illustrated in Table III, the PG analysed had considerable quantities of fluorine, aluminium, silicon, and phosphorus residual from the fluorapatite mineral that is also the source of REE in the PG. Other base metals present in lower concentrations include magnesium and iron. The REE grade of the published resource statement is substantially higher than that of other PG sources described in literature at 0.43% TREO - equivalent to approximately 3500 mg/kg REE (Rainbow Rare Earths, 2022).
Experimental
Leaching test work campaigns were conducted at ANSTO and at Mintek in South Africa, using different PG samples. For each of the leaching tests described below, the feed PG assay is also given. For all leaching tests, solution samples were analysed for REE with ICP-MS, for base metals with ICP-OES, for fluorine and phosphate with an ion-selective electrode (ANSTO), and ion chromatography (Mintek). Solid samples were dried at 105°C before fusion with sodium hydroxide and sodium peroxide, followed by a nitric acid digest and ICP-MS/ICP-OES. Solid samples were dried at 105°C because at lower drying temperatures, it was found that gypsum was not fully dehydrated, and that varying degrees of hydration may influence the consistency of results. Leach residues were filtered under vacuum with a Buchner funnel, and then washed with gypsum saturated water before drying and analysis. Temperature control, where applicable, was achieved by measuring the reactor temperature with a thermometer and adjusting the temperature control set point on a water heater, which circulated water through a water bath in which the leaching vessels were placed. Leaching tests were performed under ambient pressure conditions in open reactor vessels.
Results and discussion
Effect of acid concentration and temperature on calcium sulfate solubility
The solubility behavior of calcium was observed from results of REE leaching tests. Temperature was found to have a positive effect on the solubility of calcium, which was also used as a proxy for the solubility of calcium sulfate, as shown in Figure 1. It is notable that calcium concentration in solution reaches a peak, after which the concentration decreases with time. One proposed explanation for this is that calcium sulfate hemihydrate is relatively more soluble than the dihydrate (gypsum), and therefore that any hemihydrate that is present and dissolves, increases the calcium concentration in the solution beyond the solubility of calcium sulfate dihydrate,
which drives the precipitation of gypsum. Literature references the competing calcium sulfate precipitation side reaction as a reaction that may decrease the final extraction of REE from PG. Further tests were conducted at 40°C but at varying acid concentrations. Calcium solubility was observed to increase with an increase in acid concentration up to 150 g/l H2SO4 (Figure 2). Figure 2 shows the calcium concentration with time for six different tests. For acid concentrations 25 – 45 g/l, the leach solids density was 25g % w/w. For 75 – 110 g/l the solids density was 30% w/w, and for 150 g/l the solids density was 34% w/w. The differing solids densities were not expected to affect the solubility of calcium sulfate. At low acid concentrations (25 – 45 g/l), calcium concentration increased with an increase in acid concentration. At higher acid concentrations (75 – 150 g/l), that behaviour is reversed, suggesting an inflection point somewhere between 45 and 75 g/l sulfuric acid, where calcium concentration starts decreasing with an increase in acid concentration, correlating well with findings presented by Azimi et al. (2007). There is, however, also a time-dependent change in calcium solubility. For all acid concentrations tested, calcium concentration in solution increased initially but decreased with time, suggesting re-precipitation of calcium. This phenomenon is more pronounced at higher acid concentrations, indicating a faster and higher degree of calcium mobility. For the 150 g/l test, a second increase in calcium concentration was observed between 8 and 10 hours.
The optimal residence time based only on the solubility of calcium sulfate is therefore a function of acid concentration. For high acid concentrations (75 – 150 g/l), a short residence time of 2 – 4 hours is suggested. For lower acid concentrations (25 – 45 g/l) a residence time of approximately 12 hours is suggested, after which the decrease in calcium concentration indicates a possible nett re-precipitation regime. This may translate into REE losses in a sulfuric acid leach due to co-precipitation of REE that was initially solubilised but are then precipitated as the calcium solubility decreases.
Table IV
Leach parameters for evaluating the impact of pulp density
Parameter
Residence time
Temperature
Feed Solids RE content
Feed Solids F content
Acid concentration
Lixiviant
Initial
Final RE extraction
Dry mass loss
Table V
Leach test summary with key conditions and results
Three leaches were done to evaluate the effect of pulp density on the kinetics and ultimate RE extraction when leaching at 110 g/l H2SO4 for 12 hours. Key leach parameters are given in Table IV.
Within the range of solids densities tested, there was no significant impact on the leaching of REE. Leach solution samples were taken throughout the leach to determine the reaction kinetics, which is shown in Figure 3. In all three tests, the leach reaction reached completion by 8 hours, which correlates well with the 8 to 10 hours suggested by the calcium sulfate solubility shown in Figure 2. Mass loss of PG during the leach does decrease with an increase in solids density, likely due to the lower dilution and potential for gypsum to dissolve.
Six leaching tests were conducted to evaluate the impact that acid concentration and temperature has on the extraction of REE at concentrations of 25 g/l – 45 g/l H2SO4. The key results are presented in Table V.
Figure 4 is a graphical representation of the extractions achieved with the leaching conditions given in Table V. Leach extractions are favoured by higher temperature and higher acid concentration. However, temperature has a significantly larger effect on the ultimate REE leaching. At 40°C, the difference in extraction from 25 g/l to 45 g/l sulfuric acid is small, whereas at 30°C, there is three times more
of REE at 45 g/l
than there is at 25 g/l.
Similar results were achieved when leaching at 40°C but varying the acid concentration between 75 g/l and 150 g/l H2SO4, shown in Figure 5. At 40°C, there is a relatively small difference between leach efficiency at 75 g/l and 150 g/l. This indicates that at any given acid concentration, the leaching of REE is more dependent on the temperature than on the acidity. This is consistent with what is reported in literature, being that for a given acid type, the acid concentration and temperature are the most influential factors. In the leaching tests performed, acid is seen to have an impact, but this impact becomes smaller and smaller as the temperature is increased. Based on this work, temperature is the most influential factor. This is consistent with what is reported in literature for calcium sulfate solubility, further reinforcing the hypothesis that REE dissolution is favored in conditions that also favor highest calcium sulfate solubility.
Four tests were conducted, testing two different resins. Resin 1 is a weakly acidic cation exchange resin with a chelating aminomethylphosphonic functional group and a theoretical capacity of 2.3 eq/l. Resin 2 is a strong acid cation exchange resin with a sulfonic functional group and a theoretical capacity of 2.3 eq/l. Resin concentration in the leach was 0.27 and 0.54 ml of resin per gram of dry solids respectively for Resin 1 and Resin 2. The final extraction of each of the four leaches is graphically presented in Figure 6. An exhaustive study on optimal RIL conditions was not conducted, due to the fact that the resin loading was low at approximately 8.1 and 4.6 g REE/l resin respectively for Resin 1 and Resin 2. Theoretically, resin with a capacity of 2.3 equivalents per litre could load approximately 100 grams of REE per litre of resin, which means that the total resin utilization for REE was low. This means that on commercial scale, the movement
of large resin volume due to poor loading will become problematic and loading and elution equipment will become very large. With large volumes of resin, resin replacement costs will escalate.
The economic implications of using resin for REE recovery aside, it is interesting to note the considerably higher REE extraction using resin, compared with leaching without resin in the same conditions. Due to the resin being a cationic exchange resin, it will most likely load large quantities of other dissolved cations including Ca. It is proposed that the continuous depletion of Ca from the solution allows for more dissolution of gypsum, in turn allowing for higher extractions of REE. The dry mass loss for the same four tests is shown in Figure 7.
The considerably higher mass loss for the tests using resin confirms that the presence of the resin enhances the dissolution of calcium sulfate due to the continuous depletion of Ca from the leach solution, and thereby maintaining a concentration gradient between the PG and the liquid phase and driving the dissolution of gypsum. The correlation between mass loss and REE extraction strongly suggests that the dissolution of gypsum also drives the dissolution of REE, even from a PG source where the majority of the REE is present as a precipitated phase as opposed to co-crystallized in the calcium sulfate matrix. This is consistent with the mechanism suggested by Li et al. (2022).
Due to the relatively high acid concentrations required to leach any quantity of REE from the PG, it is critical to be able to recycle leach solution several times. The recycling of leach solution facilitates the increase in concentration of REE, which favors any subsequent precipitation or other recovery process. It also allows acid to be reused, but leach solution can only be recycled if it does not adversely affect the leaching of REE.
Table VI
Leach parameters for PLS recycle tests
Parameter
Initial pulp density %w/w Solids
30
Residence time h per cycle 12
Feed solids RE content mg/kg 4358 – 4562
Feed solids F content %w/w
Temperature °C 40
Lixiviant
Five cycles of concentrated acid leaching were performed on PG. The first cycle used fresh phosphogypsum and acidified gypsum saturated water, whereafter the leach solution from the first cycle was used for the next cycle, and so forth. Leach residues from each cycle were analysed. Acid titrations were performed on the leach solution after each cycle, and acid was added to maintain 110 g/l acid per cycle.
Figure 8 shows how the leaching performance decreases cycle by cycle. It is seen that REE extraction in the first cycle is approximately 65% but decreases gradually to around 32% by the 5th cycle. REE concentration in the leach solution does build up and is still increasing by the 5th cycle, at which point the REE concentration reaches approximately 3250 mg/l.
The mechanism by which the leach solution’s ability to leach REE from fresh PG decreases with recycle is not yet understood in great detail. As shown in Table III, there are significant quantities of Si, F, Al, and P in the PG, residual from the phosphate concentrate and carried over to the PG during the phosphoric acid process. These elements may lead to the formation of other weak acids in solution alongside any sulfuric acid that is added.
Gypsum Sat. water for Cycle 1, then Recycled PLS
The phenomena that REE extraction from the PG decreases cycle by cycle, and that the REE extraction decrease correlates well with a buildup and eventual stabilization of Ca in solution, suggests that the capacity of the leach solution to accommodate soluble REE depends also on the leach solution’s capacity to accommodate calcium as well.
The PG at Phalaborwa is characterized by a high concentration of REE, present in the solid as a distinctly precipitated phase that is rich in REE, Ca, F, and Al, among others. The leaching of REE from the Phalaborwa PG has been shown to be favored by higher temperatures, and higher concentrations of sulfuric acid. In the range of temperatures tested (20°C – 40°C), temperature appears to have the highest impact on REE extraction. Approximately 65% REE extraction was achieved at 40°C and an acid concentration of 110 g/l H2SO4. The effect of pulp density was tested at 110 g/l and 40°C and was shown not to affect REE extraction.
Pulp density similarly also did not have a significant effect on the kinetics of leaching, as leach solution concentrations reached
a plateau after approximately 8 hours, but with no significantly steeper or flatter gradient, depending on the pulp density. The introduction of a cation exchange resin into the leach led to considerably higher dry mass loss during the leach, as well as higher REE extraction. An extraction of 65% could be achieved with RIL at 25 g/l H2SO4, substantially lower than what is otherwise required to achieve similar extractions without resin. Recycling of leach solution decreased REE extraction in subsequent leaching stages, and the suggested mechanism by which REE leaching decreases, is that calcium becomes saturated in solution and cannot facilitate dissolution or recrystallization of fresh PG.
Calcium was seen to reach steady state concentrations of approximately 1400 mg/l in the leach solution after the third solution recycle stage, after which there was no further observable increase. This correlated well with the decrease in REE extraction. The data provides strong evidence that leaching of REE is dependent on conditions that maximize calcium sulfate solubility.
References
Al-Thyabat, S., and Zhang, P. 2015. REE extraction from phosphoric acid, phosphoric acid sludge, and phosphogypsum, Mineral Processing and Extractive Metallurgy, vol. 124, no. 3, pp. 143–150.
Azimi, G., Papangelakis, V.G., Dutrizac, B. 2007. Modelling of calcium sulphate solubility in concentrated multi-component sulphate solutions. Fluid Phase Equilibria, vol. 260, pp. 300–315.
Cánovas, C.R., Chapron, S., Arrachart, G., Pellet-Rostaing, S. 2019. Leaching of rare earth elements (REEs) and impurities from phosphogypsum: A preliminary insight for further recovery of critical raw materials. Journal of Cleaner Production, vol. 219, pp. 225–235.
Gasser, M.S., Ismail, Z.H., Elgoud, E.A., Hai, F.A., Ali, O.I., Aly, H.F. 2019. Process for lanthanides-Y leaching from phosphogypsum fertilizers using weak acids. Journal of Hazardous Materials, vol. 378, 120762 p.
Hammas-Nasri, I., Horchani-Naifer, K., Férid, M., Barca, D. 2016. Rare earths concentration from phosphogypsum waste by twostep leaching method. International Journal of Mineral Processing, vol. 149, pp. 78–83.
Hammas-Nasri, I., Horchani-Naifer, K., Férid, M., Barca, D. 2019. Production of a rare earths concentrate after phosphogypsum treatment with dietary NaCl and Na2CO3 solutions. Minerals Engineering, vol. 132, pp. 169–174.
Ismail, Z., Abu Elgoud, E.M., Abdel Hai, F., Ali, I.O., Gasser, M.S., Aly, H.F. 2015. Leaching of some lanthanides from phosphogypsum fertilizers by mineral acids. Arab Journal of Nuclear Science and Applications, vol. 48, no. 2, pp. 37–50.
Kurkinen, S., Virolainen, S., Sainio, T. 2021. Recovery of rare earth elements from phosphogypsum waste in resin-in-leach process by eluting with biodegradable complexing agents. Hydrometallurgy, vol. 201, pp. 105569.
Lambert, A., Anawati, J., Walawalkar, M., Tam, J., Azimi, G. 2018. Innovative application of microwave treatment for recovering of rare earth elements from phosphogypsum. ACS sustainable chemistry & engineering, vol. 6, no. 12, pp. 16471–16481.
Li, S., Malik, M., Azimi, G. 2021. Extraction of rare earth elements from phosphogypsum using mineral acids: process development and mechanistic investigation. Industrial & Engineering Chemistry Research, vol. 61, no. 1, pp. 102–114.
Lokshin, E.P., Tareeva, O.A., Elizarova, I.P. 2010. A study of the sulfuric acid leaching of rare-earth elements, phosphorus, and alkali metals from phosphodihydrate. Russian Journal of Applied Chemistry, vol. 83, pp. 958–964.
Lu, S.B., Liu, J.C. 2023. Recovery of rare earth elements from phosphogypsum using subcritical water extraction. Chemical Engineering and Processing-Process Intensification, vol. 190, pp. 109433.
Lütke, S.F., Oliveira, M.L., Waechter, S.R., Silva, L.F., Cadaval Jr, T.R., Duarte, F.A., Dotto, G.L. 2022. Leaching of rare earth elements from phosphogypsum. Chemosphere, vol. 301, 134661 p.
Rainbow Rare Earths. 2022. Phalaborwa Rare Earths Project Preliminary Economic Assessment https://www.rainbowrareearths.com/wp-content/ uploads/2022/10/PHALABORWA-RARE-EARTHS-PROJECTPEA-FINAL.pdf
Rychkov, V.N., Kirillov, E.V., Kirillov, S.V., Semenishchev, V.S., Bunkov, G.M., Botalov, M.S., Smyshlyaev, D.V. and Malyshev, A.S. 2018. Recovery of rare earth elements from phosphogypsum. Journal of Cleaner Production, vol. 196. pp. 674–681.
Virolainen, S., Repo, E., Sainio, T. 2019. Recovering rare earth elements from phosphogypsum using a resin-in-leach process: Selection of resin, leaching agent, and eluent. Hydrometallurgy, vol. 189, 105125 p.
Walawalkar, M., Nichol, C.K., Azimi, G. 2016. Process investigation of the acid leaching of rare earth elements from phosphogypsum using HCl, HNO3, and H2SO4 Hydrometallurgy, vol. 166, pp. 195–204.
Wu, S., Wang, L., Zhao, L., Zhang, P., El-Shall, H., Moudgil, B., Huang, X., Zhang, L. 2018. Recovery of rare earth elements from phosphate rock by hydrometallurgical processes – A critical review. Chemical Engineering Journal, vol. 335, pp. 774–800.
Yahorava, V., Bazhko, V., Freeman, M. 2016. Viability of phosphogypsum as a secondary resource of rare earth elements Proceedings of the XXVIII International Mineral Processing Congress Proceedings, Quebec City, QC, Canada, pp. 11–15 u
Affiliation:
1University of the Witwatersrand, Geosciences, South Africa
2University of the Witwatersrand, School of Chemical and Metallurgical Engineering, South Africa
Correspondence to: S. Hlajoane
Email: sehai.mokhahlane@wits.ac.za
Dates:
Received: 14 Dec. 2023
Revised: 14 Jun. 2024
Accepted: 27 September 2024
Published: October 2024
How to cite:
Hlajoane, S., and Mokhahlane, L.S.
2024. Rare Earth Elements enrichment in Triassic coals deposits and associated argillaceous rocks in Lesotho. Journal of the Southern African Institute of Mining and Metallurgy, vol. 124, no.10, pp. 583–594
DOI ID:
http://dx.doi.org/10.17159/24119717/3217/2024
ORCiD:
S. Hlajoane
http://orcid.org/0000-0002-3618-4978
L.S. Mokhahlane
http://orcid.org/0000-0001-7833-042X
by S. Hlajoane1 and L.S. Mokhahlane2
Abstract
The demand for rare earth elements has increased around the world due to their application in a variety of technological advancements. Previous studies have evaluated the potential of the rare earth elements and yttrium (REY) hosted within the Permian coal deposits of the main Karoo Basin (MKB) in Southern Africa. However, not a lot of scientific research has gone into the Triassic coal deposits. The Triassic coals in South Africa were the first coals to be exploited for their thermal use in the 1880s, but the discovery of the higher rank and more abundant Ecca coal deposits led to the Triassic coals remaining largely unexplored. The demand for rare earth elements has sparked interest in these coal deposits as potential sources for valuable minerals. Late Triassic coal deposits in Lesotho have previously not been well documented and these low-rank coals can be a potential source of rare earth elements. This study aims to characterize and evaluate the potential of REY in the Taung coal deposit, southwest of Lesotho. Coal and associated argillaceous samples from the Taung coal deposit were analyzed using microscopic petrography for coal characterization and an inductively coupled plasma mass spectrometry (ICP-MS) to determine the amount of rare earth elements. Taung coal is classified as middle medium rank D bituminous coal. The total REY content in Taung coal and its associated rocks range from 162.9 ppm to 855.1 ppm, which is significantly higher than the upper continental crustal (UCC) average. The average critical REY concentration of samples from the Taung coal deposit is 189.4 ppm, which is three times higher than that of the Chinese Bayan Obo deposit. Samples classified as very promising and promising because of their outlook coefficients, are found to contain up to 77% of critical REY. It is envisioned that the area could be a prime deposit for these REY.
Keywords rare earth elements and yttrium (REY), low-grade coals, Triassic coals, Taung Lesotho
Introduction
The demand of rare earth elements and yttrium (hereafter referred to as REY) in the world has sharply increased because of their use in a variety of high technological applications (Seredin and Dai, 2012). They play a critical role for renewable energy as essential components of wind turbines and hybrid cars, which are essential as the world transitions to a more carbon neutral future (Balaram, 2019; Hower et al., 2016). Because of supply challenges, several countries and bodies have adopted policies in identifying REY as critical raw materials for which these policies intend to secure these materials through various geological sources (European Commission, 2023; U.S. Department of Energy, 2023). Naturally, rare earth elements are a group of 15 lanthanide elements identified by increasing atomic numbers from 57 (lanthanum) to 71 (lutetium); La, Ce, Pr, Nd, Sm, Eu, Gd, Tb, Dy, Ho, Er, Tm, Yb, and Lu (Damhus et al., 2005). Even though the atomic number of yttrium (Y) is 21, it is commonly added to the rare earth elements list and positioned between Dy and Ho on REY normalized plots (Bau, 1996). Geochemically, REY are classified as light REY (La, Ce, Pr, Nd, and Sm), medium REY (Eu, Gd, Tb, Dy, and Y), and heavy REY (Ho, Er, Tm, Yb, and Lu) (Seredin and Dai, 2012). Another significant classification of REY is associated with market considerations such as the ease or difficulty of supply and the demand of each element, where Nd, Eu, Tb, Dy, Y, and Er are recognized as critical REY, La, Pr, Sm, and Gd as uncritical REY, and Ce, Ho, Tm, Yb, and Lu as excessive REY (Kingsnorth, 2009).
The primary sources of REY ores are bastnasite, monazite, and xenotime minerals, for which viable deposits are associated with magmatic processes, and thus common in alkaline igneous rocks and carbonatites (Orris and Grauch, 2002). Secondary REY ores are found as placers, laterite deposits and the commonly economic ion-absorption in clay ore deposits (Suli et al., 2017). The challenge related to the availability of REY is based on mined conventional ore bodies not being able to meet the demand of
REY because their usage has been significantly increasing over the years (Scott et al., 2015). Another challenge is that most of these conventional deposits are in China, thus giving China leverage in terms of market considerations (Jowitt, 2022). The demand of REY, extraction efficiencies of REY from traditional ore bodies, and geo-politics have enabled unconventional sources like coal and coal derivatives such as fly ash to be considered as potential sources of these elements (Eterigho-Ikelegbe et al., 2021). Geological processes that are responsible for the accretion of REY in coal deposits include movement of natural leachates and volcanic ash (tuffaceous), interaction of hydrothermal fluids with coal, contact with aquifer waters (infiltration), and REY carried to coal depositional sites by surface waters (terrigenous) (Seredin and Dai, 2012).
Coal and coal fly ash have been explored extensively as alternative sources of REY (Chitlango et al., 2023; Dai et al., 2016; Finkelman, 1993; Mokoena et al., 2022; Wagner and Matiane, 2018). In coal fly ash, the REY are generally encapsulated in the glass matrix and extraction has proved to be a challenge with low yields recorded (Mokoena et al., 2022). In low-rank coals, REY can be hosted within the organic part (macerals) and are associated with various organometallic compounds, and side chain functional groups such as carboxylic acids (Dai et al., 2021). REY also occur within the inorganic component of coal as replacement minerals such as apatite, those absorbed by other minerals such as clays, the terrigenous primary REY minerals such as xenotime, and as ions being dissolved in pore fluids (Fu et al., 2022). To evaluate the potential of REY in coal, their dominance in either organic or inorganic components can have an impact on the success of their extraction using methods such as leaching (Finkelman et al., 2018). For example, studies have shown that methods such as sequential leaching have proven to be efficient (80% – 95%) in extracting REY from younger coals such as Fort Union lignite coal in North America, because these coals contain carboxylic acids, which are associated with the organic components of coal (Laudal et al., 2018). On the contrary, some studies have shown that extracting REY by sequential leaching method from the inorganic components of coal fly ash can be very challenging, as the majority of REY (70%) are locked within the structures of aluminosilicate glasses (Querol et al., 1996; Wang et al., 2019). Even though the volumes of fly ash produced in most coal-fired power stations are significant, extraction challenges have positioned low quality coals as an alternative source of REY. Using coal as a source of REY will always result in competing interests, where the temptation for thermal use will always outweigh REY extraction. However, poor quality coal can diminish this contradiction as there is less appetite for lowrank coal in the world market due to the associated high cost of beneficiation needed to meet the requirements of the end user.
The average sum of REY of the world-low-rank coals is 65 ppm, which necessitates enrichment of REY for these coals to be considered economic (Finkelman, 1993). There is substantial evidence that coals can be enriched in REY, such as the Pavlova lignite deposits of Russian Far East coal and Luizhi bituminous deposit in Guizhou China, with REY concentrations of 5952 ppm and 2491 ppm, respectively (Seredin and Dai, 2012). In South Africa, most of the coalfields being exploited are of a Permian age because they host good quality coal, leaving the generally lowquality Triassic coalfields under-utilized. Wagner and Matiane (2018) reported that the total REY range from 121 ppm to 150 ppm for the Permian coals, which are lower than the upper continental crustal (UCC) abundances, as determined by Taylor and McLennan (1985), but higher than the hard coals reported by Ketris and Yudovich (2009). A study by (Chitlango et al., 2023) on bituminous coal samples from the Waterberg Coalfield (Permian)
reported concentration of REY ranging from 45.1 ppm to 389.2 ppm. Nonetheless, very little is known regarding the potential of REY in younger Triassic coals in South Africa, and more specifically in Lesotho. In this regard, the Triassic coals in South Africa and Lesotho are available in significant quantities because they are hosted within the Molteno Coalfield, which is the largest single coalfield in South Africa (Hancox and Götz, 2014). The quality of coal from the Molteno Coalfield is generally considered to be low quality (Hancox and Götz, 2014).
The aim of this study is to evaluate the REY concentrations in Triassic coals from the mountainous Kingdom of Lesotho. Coal deposits in this part of Southern Africa have not been reported previously and hence this study will add new insights into the coal deposits and their associated rocks in a new geographical area. Current Lesotho mining activity is primarily dominated by diamonds, which account for almost 98% of mining activities in the mountain kingdom (Lesotho Chamber of Mines, 2022). Exploring coal deposits could help Lesotho diversify their minerals industry.
Geological setting and background
The Molteno Coalfield is of a Triassic age (Figure 1) and is predominantly positioned in the Eastern Cape Province with an estimated surface area of 13 million hectares covering an extensive area in South Africa (Christie, 1986; Macdonald, 1993). This coalfield also extends northward into the southwestern parts of Lesotho, outcropping largely at Taung village (Nixon, 1971). Coal in South Africa was first discovered in the Molteno Coalfield with production beginning in the 1860s and ceasing during the late 1940s due to the relatively poor-quality coal and the discovery of good quality Permian coals in Mpumalanga Province (Hancox and Götz, 2014). There is a general increase of coal rank from the west (high volatile bituminous coal) to the east (low volatile bituminous to anthracite coals) of the Molteno Coalfield, with local variations in coal quality occurring because of the presence of nearby igneous intrusions (Saggerson, 1991).
The Molteno Coalfield is hosted within the sediments of the main Karoo Basin, which is an asymmetrical basin filled with mainly clastic sediments of the Karoo Supergroup (Johnson et al., 2006). The study area (Taung Coal) is situated in the southwestern corner of Lesotho on the southern boundary of the Kaapvaal Craton (Figure 2) and is part of the greater Molteno Coalfield, with intermittent coal seams hosted within the sediments of the Molteno Formation (Figure 3) (Hancox and Götz, 2014).
The Bamboesberg Member is thickest in the southern parts of the basin and is characterized by five stacked cycles of upward fining successions with sandstones at the base, followed by siltstones, mudstones, and coal (Christie, 1981). In addition, the Bamboesberg Member pinches out to the north, being absent in the northern parts of the Molteno Formation (Figure 2). The Bamboesberg Member hosts the economically significant Indwe and Guba coal seams, which occur as partitions of dull and bright bands of coal (Figure 3), interchanging with carbonaceous rocks (Hancox and Götz, 2014). The top of the Indwe and Guba seams consists of sandstone while the floor is characterized by the presence of shale/ mudstone (Hancox and Götz, 2014). Analyses on the properties of the Indwe and Guba coals indicate high ash content (31%–51%), high inherent moisture (7%-11%), low volatile matter (7%–12%) according to Prevost (2002), a fixed carbon content between 30–41% (Macdonald, 1993), and a calorific value (CV) ranging from 23.9 MJ/kg to 25.9 MJ/kg (De Jager, 1983). These coals are of a poor quality when comparing them with other coalfields in South Africa, such as the Ermelo Coalfield (Vryheid Formation) with an average ash content (26.74%), inherent moisture (3.11%), volatile matter
0o0'0"
10o0'0"S
20o0'0"S
30o0'0"S
(23.64%), fixed carbon (46.72%), and a CV of 22.57MJ/kg (Wagner et al., 2018). The thicknesses of the Indwe and Guba seams fluctuate in relatively small distances, attaining maximum thicknesses of 4.5 m and 3 m, respectively (Christie, 1981, 1986). When reference is made to the name ‘Indwe’ when discussing Molteno Formation literature, it is worth mentioning that the Indwe Seam is not associated with the Indwe Member, as the former is hosted within the Bamboesberg Member (Christie, 1986).
The coal seams found within the upper stratigraphic units (Figure 3) identified by Christie (1981) are therefore important for this study because there is no evidence of coal occurrence in the lower Indwe Member. The Cala Pass/Molteno Seam is 2–3 m thick impersistent with poor-quality coal hosted within the argillaceous
rocks at the top of the Mayaputi Member and comprises of carbonaceous shales with thin bands of bright coal (Christie, 1981; Turner, 1975). Gubenxa/Ulin Seam is made up of laterally intermittent bands about 1.7 m thick lenses of bright coal with coaly siltstones, mudstones, and shale, which are found within the sediments of the Qiba Member (Christie, 1981). The Umnachean and Offa Seams of the Loskop Member are the youngest seams of the Molteno Coalfield and have similar characteristics with Ulin coal, although they are thinner than the Ulin Seam (Christie, 1981). All these coal seams in the upper stratigraphic units are not well recorded in the northern parts of the Molteno Coalfield and this study will provide an insight on some coal properties, including REY potential, within these units.
Methodology
Sampling, preparation, and coal characterization
The sampling area comprises of coal outcrops with fissile, carbonaceous, dark grey rocks interlayered with argillaceous rocks, which are associated with the Cala Pass/Molteno Seams of the Molteno Coalfield (Christie, 1981). The coal and its associated argillaceous rock samples were collected from the outcrops exposed by weathering and erosion forming deep dongas (Figure 4). The geographical positions of all the sampling points are located within the Taung geological map (Figure 5). Well-labelled polystyrene bags were used to collect a total of 10 samples with an average weight
of 2 kg per sample. The sample names were abbreviated as CPL denoting Coal Project Lesotho (CPL01 to CPL10). All descriptions of the properties of the samples and the sampling site were carried out in accordance with the best practices following the Australian Standard AS2916-1986. Sample preparation/handling was also done according to the SANS 18283 (2007).
Table I summarizes the methods and standards that were applied for coal characterization, which are all important in evaluating coal utilization capabilities. For example, calorific value (CV) is an important parameter as it measures the amount of heat per kilogram that coal can produce (a proxy of coal quality), which is critical for utilizing coal for producing thermal electricity. Besides thermal applications, coal can also be used as a potential source of REY through assessing the ash content in coal, as these minerals can be locked in the inorganic part of coal (ash) (Seredin et al., 2013). Proximate analysis (ash, moisture, volatile matter, fixed carbon) including CV and total sulphur (TS) were carried out at Eskom’s central coal laboratory, which is accredited for all these methods. All the results for these methods were reported on an air-dry basis (a.r.).
Samples were sent to the University of Johannesburg for petrographic analysis. Here, the organic (maceral groups) and inorganic (mineral groups) components of coal were analysed through a technique as stipulated by SANS ISO 7407-2 (2015). This is important as low-rank coals are associated with REY concentrated within the organic component of coal (macerals) (Dai et al., 2021). Coal rank analysis reporting the random vitrinite reflectance (%RoV) was determined through a Zeiss Axio Imager microscope (reflected light) according to SABS ISO 7404-3 (2016).
Table I
Coal analysis and corresponding standards
Analysis
Procedure/ Method
Sample preparation SANS 18283:2007 / ISO 18283:2006
Proximate analysis - Ash content (mass%) SABS ISO 1171:1997
Proximate analysis - Volatile matter content (mass%) SABS ISO 562:1998
Proximate analysisMoisture content (mass%) SANS 5925:2007
Proximate analysis - Fixed carbon content (mass%) By difference
Gross calorific value (MJ/kg) SABS ISO 1928:1995
Total sulphur (mass%) ISO 19579
Table II
Proximate analysis of the coal and argillaceous rocks samples (mass%)
SAMPLE ID
Rare earth elements and yttrium (REY) analysis
Inductively coupled plasma mass spectrometry (ICP-MS) analysis is efficient in determining the concentration of trace elements, which include rare earth elements and yttrium. About 50 mg sample is weighed and digested in the microwave digester (MARS from CEM). The 50 mg sample is added to a Teflon vessel containing 6 ml of ultra-high Purity 2:1 HF: HNO3 forming a mixture. The mixture is transferred inside a microvan that is set to a temperature of 180°C and pressure of 400 psi for 40 minutes. The sample is moved into a 15 ml savilex beaker, which is followed by thorough rinsing of the Teflon vessel. The savilex beaker containing the sample is closed and transferred to a hot plate set at 70°C for a duration of 24 hours to evaporate the acid. Approximately 2 ml of HNO3 is added to the sample in in savilex beaker and returned to the same settings of the hot plate for another 24 hours. The same process of acid addition (HNO3) and heating of the sample is repeated. The sample is removed from the hot plate and an additional 300 µl of HNO3 is added to the sample that is ready for analysis. The sample is then transferred to the ICP-MS on a Thermo Scientific iCAP RQ, which is based at the University of the Witwatersrand, Earth laboratory.
Results and discussion
Sample characterization
Table II lists the results of proximate analysis of all the samples. The ash content in the samples range from 56.8 mass% to 93.9 mass%, which clearly indicates very high ash content (minerals) in these samples. Samples CPL09 and CPL10 have fixed carbon values at 17 mass% and 13.6%, respectively, while the rest of the samples have fixed carbon content lower than 6.5%, which is significantly lower than the Indwe and Guba Seams. The calorific values of these two samples (CPL09 and CPL10) are just above 13 MJ/kg while the other samples record CVs lower than 3 MJ/kg. The results indicate that all the samples have very low CVs compared to those of Indwe and Guba Seams, which range from 23.9 MJ/kg to 25.9 MJ/kg, respectively. (Rice, 1993).
Maceral analysis supports the proximate data, showing only sample CPL09 to contain less than 18 vol% of minerals while all samples, including CPL10, contain minerals more than 70 vol% (Figure 5). Because of the data presented by proximate analysis,
mineralogy, and maceral analysis, only sample CPL09 is classified as medium rank D bituminous coal borderline medium rank C, with a random reflectance (%RoV) of 0.6 (Figure 6A-F). This is a low-rank coal because it is very close to being lignite (%RoV of 0.5), which provides evidence of the overall low-quality nature of the coals from the Molteno Coalfield. All the other nine samples are argillaceous rocks, which are very common in proximity of Cala Pass/Molteno Coal Seam of the Mayaputi Member (Christie, 1981).
The mineralogical composition determined by petrography indicates that the inorganic component in coal for sample CPL09 is quartz (14.4 mass%), clay (2.8 mass%), and carbonate (0.4 mass%), with no presence of pyrite. In addition, CPL09 is dominated by the liptinite maceral group, especially cutinite (about 45 vol%), followed by vitrinite (~25 vol%) and inertinite (~12%) (Figure 6). This observation is unusual because Gondwana coals have been found to contain relatively small amounts of liptinite compared to the Northern Hemisphere coals (Wagner et al., 2018). Palynological studies for the high content of liptinite can provide more depth in terms of the original plant make-up of this coal, but they were not the scope of this study. The liptinite in this sample is associated with quartz included within it (Figure 7A-A). Petrography shows that sample CPL09 is a banded (humic) coal with dark bands made up of liptinite, medium grey bands as vitrinite, and lighter grey as
inertinite (Figure 7C-D) (Hutton and Hower, 1999). Humic coals have fractures that are orientated parallel to the cleats (O’Keefe et al., 2013). This can be seen where calcite cleats are cutting through the vitrinite (Figure 7F). The quartz present within the structures of liptinite in the sample and the occurrence of calcite cleats on vitrinite is a clear indication that this coal has both syngenetic and epigenetic minerals.
The results for rare earth elements and yttrium (REY) distribution in all the samples are from the ICP-MS analysis. The total content of REY in sample CPL09 (Taung coal) is 485.0 ppm, higher than the 472.3 ppm total average concentration of REY in the other argillaceous samples. The range of the argillaceous samples is from 162.9 ppm up to 855.1 ppm. The total REY concentration in all the samples, except CPL03 is above that of the UCC, with samples CPL02, CPL05, CPL06, CPL07, CPL09, and CPL10 above 400 ppm (Figure 8). Moreover, sample CPL05 is enriched with the LREY while both MREY and HREY are mostly enriched in samples CPL06, CPL07, CPL09, and CPL10. According to Ketris and Yudovich (2009), the average sum of the concentration of total REY in the world coals is roughly 68.5 ppm, while data from
Finkelman (1993) and Seredin and Dai (2012) for USA and China coals are 62.1 ppm and 137.9 ppm, respectively. The concentration of REY within the Taung coal is greater than the world coals, USA, and Chinese coals. Chitlango et al. (2023) reported a range from 45.1 ppm to 389.2 ppm of the total REY concentration within the Waterberg Coalfield samples, which is lower than the 485.0 ppm total REY content of the Taung coal.
The ICP-MS results of the Taung coal and argillaceous samples further present the distribution of REY within all the samples relative to the values of the upper continental crust (UCC) by Taylor and McLennan (1985), which normalizes the REY data (Figure 9A-B). The distribution patterns of REY in samples CPL03 and CPL01 show depletion of heavy REY and some weak enrichment in light REY (Figure 9A). All the other eight samples, including CPL09 (Taung coal), show patterns of enrichment of the heavy REY. Anomaly ratios of Ce, Eu, and Gd are significant in delineating depositional environments, fluid conditions, and sediment sourceregion of coal strata (Dai et al., 2016). The equations for calculating anomalies of these REY are presented in Equations [1] to [3]. For each equation, the ratio that equates to 1 indicates no anomaly, while greater or less than 1 is indicative of positive or negative anomalies, respectively. The calculations are summarized in Table III.
China shows negative Ce anomaly, and its sediment source-region is attributed to the felsic-intermediate rocks (Dai et al., 2015).
The CeN/CeN ratio for Taung coal (CPL09) is 0.95, which suggests a weakly negative anomaly. This observation is common for most coals although host rocks can sometimes display positive anomalies (Dai et al., 2016). The positive Ce anomalies are displayed by some Taung coal host rocks, such as samples CPL05 with CeN/ CeN ratio of 1.19 and CPL05 at 1.07. The other argillaceous samples exhibit weakly negative to no anomalies of cerium, with ratios ranging from 0.92 to 1.01. Negative Ce anomalies are usually associated with a sediment source-region that is dominated by felsic to felsic-intermediate rocks (Dai et al., 2016). For example, the Guxu Coalfield, seam No. 25 from the Sichuan Province in
Europium is a redox-sensitive element, and this enables it to decouple from other REY, which generates Eu anomalies in coal and its associated rocks (Elderfield, 1988). The EuN/EuN ratio for Taung coal is 1.00, indicating no Eu anomalies, which is also observed in Chinese coals and world low-rank coals (Figure 9B). The No Eu anomaly for Taung coal can be associated with possible interaction of high-temperature hydrothermal fluids, which shadow negative Eu anomalies sourced from felsic rich rocks (Dai et al., 2016). The EuN/EuN ratios for all the argillaceous samples range from 0.55 to 1.06 with an average of 0.94, indicating a range from a very strong negative anomaly to weakly positive anomaly. Strong negative Eu anomalies for host rocks such as CPL08, have been largely associated with rocks that have evolved through the fractional crystallization of feldspars, and therefore a felsic to intermediatefelsic sediment source-region (Cullers, 2000). High temperature hydrothermal fluids when interacting with coal strata can elevate the concentration of Eu and display weakly positive Eu anomalies such as sample CPL05, with EuN/EuN ratio of 1.06 (Bau, 1991). Gadolinium is another REY of which its anomalies are used to determine the influence of various forms of fluids and/water in coal and its host rocks because of its ability to dissociate itself from other REY (Bau and Dulski, 1996). The GdN/GdN ratio for Taung coal is 1.11, while the rest of the argillaceous samples range from 1.09 to 1.19 with an average of 1.13, showing positive anomalies. A similar trend is observed in other coals such as the main Karoo Basin (MKB)-PS1 coal, Chinese coals, and world low-rank coals (Figure 9B). Injection of hydrothermal fluids is suspect to positive anomalies of Gd in Taung coal as evidence of interaction of these fluids can be inferred from the behavior of Eu anomalies in Taung coal. The ratio of YN/HoN is also useful in determining the yttrium anomalies, which provide insight into sediment-source region rock make-up (Dai et al., 2016). Taung coal YN/HoN ratio is 0.89, showing negative anomaly of Y while the argillaceous samples range from 0.85 to 1.33 with an average of 1.01, suggesting negative to strong positive Y anomalies. Sample CPL06 shows a YN/HoN ratio of 1.33, which indicates a strong positive anomaly that can be associated with a sediments-source region enriched with phosphate minerals (Dai et al., 2016). The high concentration of total REY (855.1 ppm) and the high proportion of medium REY (Eu, Gd, Tb, Dy, and Y) in sample CPL06 (Figure 8), could be the result of strong
positive Y anomaly in the sample. The provenance of Molteno Formation sediments is a south-east granitic region and the overall anomaly signature of Taung coal and some of its associated rocks does display a similar felsic type of sediment-source region (Eriksson, 1984; Turner, 1975).
Comparisons of the REY distribution pattern of the Taung coal with the world low-rank coals, Chinese coals, and main Karoo Basin (MKB) coal sample PS1 (South Africa), normalized by UCC as per Taylor and McLennan (1985) are presented in Figure 9B. The results show that the content of REY in CPL09 is significantly larger than the average REY content of the world low-rank coals and the Chinese coals, including the total REY content of the MKB (PS1) coal sample. Both the Chinese and MKB (PS1) coal samples are particularly enriched with the LREY and depleted in HREY.
Table III shows that Taung coal and most argillaceous samples have a higher concentration of the light REY than the heavy REY (HREY/LREY ratio less than 1.0) except sample CPL07 with HREY/ LREY ratio of 1.3. There is a very weak/poor correlation between the HREY/LREY ratio of the samples and their ash content (Figure 10). Similarly, there is a very weak to no correlation between the ash content and the total REY content in the samples. This suggests that the distribution of REY in the samples is not necessarily associated with only the inorganic part of Taung coal and its associated rocks as observed in many coals. A strong negative correlation is displayed between the ash content and the calorific value, which is consistent with thermal characteristics of most coals.
It is also important to determine the enrichment types in coal relative to REY (Table III). There are three enrichment types
and are normalized (N) to the upper continental crust by Taylor and McLennan (1985), which include the L-type (light-REY), the M-type (medium-REY), and H-type (heavy-REY) (Seredin and Dai, 2012). These enrichment types (Table III) are based on the ratios between La/Lu, La/Sm, and Gd/Lu with the following thresholds for each type: L-type (LaN/LuN > 1), M-type (LaN/SmN < 1, GdN/ LuN > 1), and H-type (LaN/LuN < 1) (Seredin and Dai, 2012). The data clearly show that the enrichment type associated with sample CPL09 (Taung coal), is an H-type enrichment and therefore the coal is enriched mainly in heavy REY such as Ho, Er, Tm, Yb, and Lu. This observation is consistent with the UCC normalized distribution pattern of REY content in Figure 9A. The argillaceous samples CPL01 and CPL03 have L-type enrichment meaning that they are particularly depleted in HREEs, which is also evident from their REY distribution patterns. These samples contain the least total REY content (Figure 8) even though maceral analysis indicate ash concentrations above 90 mass% (Figure 6). Therefore, these samples represent the lowest grade of REY within the resource. The rest of the argillaceous samples belong to the M-type enrichment, which implies they are mostly enriched in the medium REY compared to other types.
Economic considerations
The coals around the world have variable concentrations of REY within the coal seams and their associated host rocks. Some coals have significantly high content of REY such as the Cenozoic Russian Far East coal deposit with REY content reaching as high as 1 000 ppm (Seredin, 1996) while considering that the world coal
Table III
REY enrichment trends and types in Taung coal and associated argillaceous rocks
average sum REY concentration is considerably low (68.6 ppm) (Finkelman, 1993). Due to this REY disparity in coal resources, there is a need to estimate the economic potential of coal deposits if they are to be utilized as alternative sources of REY. There are a variety of tools that can be applied to evaluate the economic viability of coal deposits. Firstly, the concentration of critical REY (Nd, Eu, Tb, Dy, Y, Er) in coal deposits can be used as a proxy in understanding the economic importance of such deposits. This is because critical REY such as dysprosium (Dy) and neodymium (Nd) are very crucial for the development of permanent magnets used in wind turbines and many other industrial applications for which their demand is projected to grow by 2600% for Dy and 700% for Nd in the next two decades (Alonso et al., 2012). The results show that the total critical REY in samples CPL06, CPL07, CPL09, CPL10 is above 200 ppm and range from 208.6 ppm to 425.4 ppm (Figure 11). In addition, these samples have significantly higher (4 to 9 times) content of critical REY than the UCC, Chinese coals, and world low-rank coals. Moreover, the amount of critical REY on all the Taung coal deposits are still higher than some known operating mines, for example, the Bayan Obo mine located in northern China is the largest commercial mine in the world where REY are extracted from LREY-rich carbonatite hydrothermal related rocks (Lehmann, 2014). A geochemical background and dispersion study in the Bayan Obo region shows that the average sum of critical REY is 61.57 ppm (Zhou et al., 2020). The average sum content of critical REY in all the Taung coal deposit samples is 189.4 ppm, which is three times more enriched than those from the Bayan Obo region. Another example is that the average sum of critical REY in the Harmon-Hanson coal zone of the North Dakota lignite is almost half of that of the Taung coal (CPL09). The results also show that samples CPL06, CPL07, CPL09, CPL10 are enriched in Y, Dy, and Er (HREY) and Nd (LREY) and depleted in Tb (HREY) and Eu (LREY) of their critical REY. Overall, these results indicate that Taung coal and its associated argillaceous rocks can be a potential source of critical REY.
The outlook coefficient (Coutl) is one of the tools that is commonly used to appraise the economic potential of coal deposits. It calculates the ratio of critical REY in total REY and excessive REY in total REY in each sample (Seredin and Dai, 2012). This ratio is calculated by, (Coutl) = (Nd + Eu + Tb + Dy + Er + Y/Total REY)/ (Ce + Ho + Tm + Yb + Lu/Total REY) where elevated values (Coutl) represent a promising potential source of REY (Dai et al., 2017). According to this evaluation scheme, the (Coutl) values greater than 2.4 are considered highly promising, (Coutl)) values between 0.7 and 1.9 are regarded as promising, and those less than 0.7 as unpromising
Figure 10—Correlation between ash content and HREY/LREY, calorific value, and total REY within the samples
(Dai et al., 2017). The results for the outlook coefficient and the percentage of critical REY in total REY of the samples are presented in Figure 12. They show CPL07 as highly promising because of its (Coutl) being above 2.4 while all the other samples are indicated as promising, as they range from 0.7 to 1.9. The corresponding percentage of critical REY in total REY in the highly promising samples is 57% and ranges between 30% – 50% in the promising samples, followed by less than 31% locked within the unpromising samples. The results indicate that many of the samples including Taung coal, plot within the very promising and promising categories and contain up to almost 77% of the critical REY in total REY.
To determine the industrial potential of recovering REY from coal resources, a cut-off grade of ≥ 1 000 ppm (0.1%) of REY oxide (REO) is required (Seredin, 2004). This cut-off grade evaluates various coal resources’ potential of being an alternative source of extractable REY. The total REY in each sample is compared with the outlook coefficient of the corresponding samples in Figure 13. Here, the cut-off grade of REY ≥ 1 000 ppm influences if the samples plot on either the unpromising areas, or the very promising/promising areas of the plot. The results show that all the samples plot within the unpromising area, despite some having very high Coutl values because their individual total REY are below the 1 000 ppm threshold. Nevertheless, an increase in REY prices (supply and demand) and other geological considerations can
reduce the cut-off grade between 800 ppm to 900 ppm as the 1 000 ppm cut-off grade was determined a while ago (Seredin and Dai, 2012). This will render samples such as CPL07 plotting within the promising area of the total REY outlook coefficient diagrams and therefore a potential source of extractive REY.
Conclusions
This study provides an insight into the enrichment of REY in Triassic Taung coal and associated argillaceous rocks within the Molteno Coalfield. The following conclusions were drawn from this study:
A total of ten samples (coal and argillaceous material), were collected from the Taung coal deposit of the Molteno Coalfield. Taung coal is a low-quality coal and is categorized as medium rank D bituminous coal with a total REY content of 485.0 ppm. The average sum of REY in all the samples is 472.3 ppm, ranging from 162.9 ppm to 855.1 ppm. Most of the samples are enriched with critical REY, especially yttrium (Y) and neodymium (Nd). Market considerations for critical REY such as Nd, show a projected high future demand and therefore the Taung coal deposit can be a potential for these elements. The potential of the Taung coal deposit is also supported by the outlook coefficient trends, which place
many of the samples within the promising area range from 0.7 –1.9. The Ce, Eu, and Y anomalies for Taung coal and some samples suggest a felsic-intermediate source rock for the sediments that formed this deposit. To further understand the economic potential of this deposit, it is recommended that sequential leaching be used to determine the mode of occurrence of REY in all samples.
Authors’ contribution
This research was conducted as part of a PhD degree in the Department of Geosciences at the University of the Witwatersrand under the supervision of Dr Lehlohonolo Mokhahlane. The research forms part of a broad study intended to evaluate the potential of rare earth elements and suitable extraction techniques within the Molteno Coalfield.
Hlajoane: Conducted sampling, analysis and interpreted the results, and wrote the manuscript.
Mokhahlane: Supervisor, defined and gave direction on the research, edited the manuscript.
The authors acknowledge the Ministry of Mining in Lesotho for access to the study site and financial support of the research.
Figure 13—The total REY content with fields indicating the economic viability of Taung coal and argillaceous samples (Dai et al., 2017)
We would like to thank Mr Ngakane Ngakane, the Director of Geosciences, Lesotho, for providing us with logistics during sampling. Prof. Nicola J. Wagner also played a great role in petrography of the samples and therefore we appreciate her involvement. We also thank the reviewers for their wealth of knowledge in the field and being able to make this manuscript well organized.
References
Alonso, E., Sherman, A.M., Wallington, T.J., Everson, M.P., Field, F.R., Roth, R., Kirchain, R.E. 2012. Evaluating Rare Earth Element Availability: A Case with Revolutionary Demand from Clean Technologies. Environmental Science & Technology, vol. 46, no. 6, pp. 3406–3414. https://doi.org/10.1021/es203518d
Balaram, V. 2019. Rare earth elements: A review of applications, occurrence, exploration, analysis, recycling, and environmental impact. Geoscience Frontiers, vol. 10, no. 4, pp. 1285–1303. Available at: https://doi.org/10.1016/J.GSF.2018.12.005
Bau, M. 1991. Rare-earth element mobility during hydrothermal and metamorphic fluid-rock interaction and the significance of the oxidation state of europium. Chemical Geology, vol. 93, no. 3, pp. 219–230. https://doi.org/https://doi.org/10.1016/00092541(91)90115-8
Bau, M. 1996. Controls on the fractionation of isovalent trace elements in magmatic and aqueous systems: evidence from Y/Ho, Zr/Hf, and lanthanide tetrad effect. Contributions to Mineralogy and Petrology, vol. 123, no. 3, pp. 323–333.
Bau, M., Dulski, P. 1996. Anthropogenic origin of positive gadolinium anomalies in river waters. Earth and Planetary Science Letters, vol. 143, no. 1–4, pp. 245–255.
Chitlango, F.Z., Wagner, N.J., Moroeng, O.M. 2023. Characterization and pre-concentration of rare earth elements in density fractionated samples from the Waterberg Coalfield, South Africa. International Journal of Coal Geology, vol. 275, 104299 p. https://doi.org/https://doi.org/10.1016/j.coal.2023.104299
Christie, A.D.M. 1981. Stratigraphy and sedimentology of the Molteno Formation in the Elliot and Indwe area, Cape Province [M.Sc. Thesis (unpubl.)]. Univ. Natal.
Christie, A.D.M. 1986. Molteno coalfield. Mineral Deposits of Southern Africa, pp. 2063–2069.
Cullers, R.L. 2000. The geochemistry of shales, siltstones and sandstones of Pennsylvanian–Permian age, Colorado, USA: implications for provenance and metamorphic studies. Lithos, vol. 5, no. 3, pp. 181–203. https://doi.org/10.1016/S00244937(99)00063-8
Dai, S., Finkelman, R.B., French, D., Hower, J.C., Graham, I.T., Zhao, F. 2021. Modes of occurrence of elements in coal: A critical evaluation. Earth-Science Reviews (Vol. 222). Elsevier B.V. Available at: https://doi.org/10.1016/j.earscirev.2021.103815
Dai, S., Graham, I.T., Ward, C.R. 2016. A review of anomalous rare earth elements and yttrium in coal. International Journal of Coal Geology, vol. 159, pp. 82–95. https://doi.org/10.1016/J. COAL.2016.04.005
Dai, S., Xie, P., Ward, C.R., Yan, X., Guo, W., French, D., Graham, I.T. 2017. Anomalies of rare metals in Lopingian super-high-organicsulfur coals from the Yishan Coalfield, Guangxi, China. Ore Geology Reviews, vol. 88, pp. 235–250. https://doi.org/10.1016/j. oregeorev.2017.05.007
Dai, S., Yang, J., Ward, C.R., Hower, J.C., Liu, H., Garrison, T.M., French, D., O’Keefe, J.M.K. 2015. Geochemical and mineralogical evidence for a coal-hosted uranium deposit in the Yili Basin, Xinjiang, northwestern China. Ore Geology Reviews, vol. 70, pp. 1–30. https://doi.org/10.1016/J.OREGEOREV.2015.03.010
Damhus, T., Hartshorn, R.M., Hutton, A.T. 2005. Nomenclature of inorganic chemistry: IUPAC recommendations 2005. Chemistry International
De Jager, F. S. J. 1983. Coal reserves of the Republic of South Africa: An evaluation at the end of 1982.
Elderfield, H. 1988. The oceanic chemistry of the rare-earth elements. Philosophical Transactions of the Royal Society of London. Series A, Mathematical and Physical Sciences, vol. 325, no. 1583, pp. 105–126.
Eriksson, P.G. 1984. A palaeoenvironmental analysis of the Molteno Formation in the Natal Drakensberg. South African Journal of Geology, vol. 87, pp. 237–244.
Eterigho-Ikelegbe, O., Harrar, H., Bada, S. 2021. Rare earth elements from coal and coal discard – A review. Minerals Engineering, vol. 173, pp. 107187. https://doi.org/10.1016/J. MINENG.2021.107187
European Commission. 2023. Study on the Critical Raw Materials for the EU 2023 Final Report https://doi.org/10.2873/725585
Finkelman, R.B. 1993. Trace and Minor Elements in Coal. In M. H. Engel & S. A. Macko (Eds.), Organic Geochemistry: Principles and Applications, pp. 593–607. Springer US. https://doi. org/10.1007/978-1-4615-2890-6_28
Finkelman, R.B., Palmer, C.A., Wang, P. 2018. Quantification of the modes of occurrence of 42 elements in coal. International Journal of Coal Geology, vol. 185, pp. 138–160. https://doi.org/10.1016/J. COAL.2017.09.005
Fu, B., Hower, J.C., Zhang, W., Luo, G., Hu, H., Yao, H. 2022. A review of rare earth elements and yttrium in coal ash: content, modes of occurrences, combustion behavior, and extraction methods. Progress in Energy and Combustion Science, vol. 88. Elsevier Ltd. https://doi.org/10.1016/j.pecs.2021.100954
Hancox, P. J., Götz, A.E. 2014. South Africa’s coalfields — A 2014 perspective. International Journal of Coal Geology, vol. 132, pp. 170–254. https://doi.org/10.1016/J.COAL.2014.06.019
Hancox, P.J., Rubidge, B.S. 2023. The Beaufort-Stormberg Group contact – Implications for Karoo Basin development in the Triassic. Journal of African Earth Sciences, vol. 198, 104767p. https://doi.org/10.1016/J.JAFREARSCI.2022.104767
Hower, J.C., Elbe, C.F., Dai, S., Belkin, H.E. 2016. Distribution of rare earth elements in eastern Kentucky coals: Indicators of multiple modes of enrichment. International Journal of Coal Geology, vol. 160, pp. 73–81.
Hutton, A.C., Hower, J.C. 1999. Cannel coals: implications for classification and terminology. International Journal of Coal Geology, vol. 41, no. 1–2, pp. 157–188.
Johnson, M.R., van Vuuren, C.J., Visser, J.N.J., Cole, D.I., Wickens, H.D.V., Christie, A.D.M., Roberts. D.L, Brandl, G. 2006. Sedimentary rocks of the Karoo Supergroup. The Geological Society of South Africa. Geological Society of South Africa and Council for Geoscience, pp. 461–499.
Jowitt, S.M. 2022. Mineral economics of the rare-earth elements. In MRS Bulletin (Vol. 47, Issue 3, pp. 276–282). Springer Nature. https://doi.org/10.1557/s43577-022-00289-3
Ketris, M.P., Yudovich, Ya. E. 2009. Estimations of Clarkes for Carbonaceous biolithes: World averages for trace element contents in black shales and coals. International Journal of Coal Geology, vol. 78, no. 2, pp. 135–148. https://doi.org/https://doi. org/10.1016/j.coal.2009.01.002
Kingsnorth, D. J. 2009. An Overview of the Rare Earth Markets. IMCOA.
Laudal, D. A., Benson, S. A., Palo, D., Addleman, R. S. 2018. Rare earth elements in North Dakota lignite coal and lignite-related materials. Journal of Energy Resources Technology, vol. 140, no. 6, 062205p. Lehmann, B. 2014. Economic geology of rare-earth elements in 2014: a global perspective Topical-Metallic Minerals http://www. techmetalsresearch.com
Lesotho Chamber of Mines. 2022. Lesotho Diamond Mining Industry Performance Report.
Macdonald, A.J. 1993. A reassessment of coal resources in the western part of the Molteno Coal Province. Bulletin - Geological Survey South Africa, 116p.
Merril, M.D., Tewalt, S.J. 2008. GIS representation of coal-bearing areas in Africa https://pubs.usgs.gov/of/2008/1258/ Mokoena, B.K., Mokhahlane, L.S., Clarke, S. 2022. Effects of acid concentration on the recovery of rare earth elements from coal fly ash. International Journal of Coal Geology, vol. 259, 104037p. https://doi.org/10.1016/J.COAL.2022.104037
Nixon, P.H. 1971. The Coal Deposits of Taung, Mohale’s Hoek District. O’Keefe, J.M.K., Bechtel, A., Christanis, K., Dai, S., DiMichele, W.A., Eble, C.F., Esterle, J.S., Mastalerz, M., Raymond, A.L., Valentim, B.V., Wagner, N.J., Ward, C.R., Hower, J.C. 2013. On the fundamental difference between coal rank and coal type.
International Journal of Coal Geology, vol. 118, pp. 58–87. https://doi.org/10.1016/j.coal.2013.08.007
Orris, G. J., Grauch, R. I. 2002. Rare Earth Element Mines, Deposits, and Occurrences
Prevost, X. 2002. South African Mineral’s Industry 2001/2002
Querol, X., Juan, R., Lopez-Soler, A., Fernandez-Turiel, JoséL., Ruiz, C.R. 1996. Mobility of trace elements from coal and combustion wastes. Fuel, vol. 75, no. 7, pp. 821–838. https://doi.org/https://doi.org/10.1016/0016-2361(96)00027-0
Saggerson, E.P. 1991. Distribution of coal rank in South Africa. Conference on South Africa’s Coal Resources
Scott, C., Deonarine, A., Kolker, A., Adams, M. 2015. Size distribution of rare earth elements in coal ash. World of Coal Ash (WOCA) Conference
Seredin, V.V. 1996. Rare earth element-bearing coals from the Russian Far East deposits. International Journal of ELSEVIER International Journal of Coal Geology, vol. 30.
Seredin, V.V. 2004. Metalliferous coals: formation conditions and outlooks for development. Coal Resources of Russia, vol. 6, pp. 452–519.
Seredin, V.V., Dai, S. 2012. Coal deposits as potential alternative sources for lanthanides and yttrium. International Journal of Coal Geology, vol. 94, pp. 67–93. https://doi.org/10.1016/j. coal.2011.11.001
Seredin, V.V., Dai, S., Sun, Y., Chekryzhov, I.Y. 2013. Coal deposits as promising sources of rare metals for alternative power and energy-efficient technologies. Applied Geochemistry, vol. 31, pp. 1–11. https://doi.org/10.1016/J.APGEOCHEM.2013.01.009
Suli, L.M., Ibrahim, W.H.W., Aziz, B.A., Deraman, M.R., and Ismail, N.A. 2017. A Review of rare earth mineral processing technology. Chemical Engineering Research Bulletin, pp. 20–35.
Taylor, S.R., McLennan, S.M. 1985. The Continental Crust: its Composition and Evolution. Blackwell (312th ed.). Geoscience Texts.
Turner, B.R. 1975. The stratigraphy and sedimentary history of the Molteno Formation in the main Karoo Basin of South Africa and Lesotho [Ph.D. thesis (Unpubl.)]. Univ. Witwatersrand.
U.S. Department of Energy. (2023). Critical Materials Assessment. Wagner, N.J., Malumbazo, N., Falcon, R. 2018. Southern African Coals and Carbons: Definitions and Applications of Organic Petrology. Struik Nature South Africa.
Wagner, N.J., Matiane, A. 2018. Rare earth elements in select Main Karoo Basin (South Africa) coal and coal ash samples. International Journal of Coal Geology, vol. 196, pp. 82–92. Available at: https://doi.org/10.1016/J.COAL.2018.06.020
Wang, Z., Dai, S., Zou, J., French, D., Graham, I. T. 2019. Rare earth elements and yttrium in coal ash from the Luzhou power plant in Sichuan, Southwest China: Concentration, characterization and optimized extraction. International Journal of Coal Geology, vol. 203, pp. 1–14. https://doi.org/https://doi.org/10.1016/j. coal.2019.01.001
Zhou, J., Wang, X., Nie, L., McKinley, J.M., Liu, H., Zhang, B., Han, Z. 2020. Geochemical background and dispersion pattern of the world’s largest REE deposit of Bayan Obo, China. Journal of Geochemical Exploration, vol. 215. https://doi.org/10.1016/j. gexplo.2020.106545 u
Affiliation:
1Department of Chemical Engineering
(Sustainable Mineral Processing Research Group), Faculty of Engineering, Universitas Gadjah Mada, Indonesia
2Department of Geological Engineering, Faculty of Engineering, Universitas Gadjah Mada, Indonesia
3Unconventional Geo-resources Research Center, Faculty of Engineering, Indonesia
4Department of Chemical Engineering, Faculty of Industrial Technology, Parahyangan Catholic University, Indonesia
5Research Center for Mineral Processing, National Research and Innovation Agency (BRIN), Indonesia
Correspondence to:
H.T.B.M. Petrus
Email: bayupetrus@ugm.ac.id
Dates:
Received: 25 Feb. 20222
Accepted: 15 October 2024
Published: October 2024
How to cite:
Manurung, H., Bendiayasa, I.M., Anggara, F., Wanta, K.C., Astuti, W., and Petrus, H.T.B.M. 2024
Leaching characteristics of cerium and yttrium from non-magnetic coal fly ash after silicate digestion using acetic acid. Journal of the Southern African Institute of Mining and Metallurgy, vol. 124, no.10, pp. 595–604
DOI ID:
http://dx.doi.org/10.17159/24119717/2034/2024
ORCiD:
H.T.B.M. Petrus
http://orcid.org/0000-0001-9372-0784
by H. Manurung1, I.M. Bendiayasa1, F. Anggara2,3, K.C. Wanta4, W. Astuti5, and H.T.B.M. Petrus1,3
Abstract
The leaching kinetics of cerium (Ce) and yttrium (Y) in sodium-hydroxide-digested non-magnetic coal fly ash using acetic acid were investigated. The variables analysed were pH, solid-to-liquid ratio (S/L), and temperature. The results show that cerium and yttrium's maximum recovery was 57.33% and 58.36%, respectively, under leaching temperature of 90°C for Ce and 60°C for Y at pH of 1,74 and 10 g/mL solid-liquid ratio in 240 minutes. Increasing the leaching time to more than 120 minutes did not significantly improve the results. After the magnetic separation process, the ICP-OES analysis shows a slight increase in the concentration of cerium and yttrium on nonmagnetic components. The XRD and ICP-OES analysis for the sample before and after silicate digestion shows that 40% silicate was dissolved. The calculation of apparent activation energies of leaching using the Arrhenius law for the leaching of cerium and yttrium gives 22.72 kJ/mol and 35.84 kJ/mol, respectively. The kinetic leaching model of cerium and yttrium all fit Dickinson's new shrinking core model. The calculation results show that the leaching reaction is controlled by combining interface transfer and diffusion across the product layer.
Keywords coal fly ash, cerium, yttrium, kinetics, recovery
Introduction
In recent years, rare earth elements (REE) have become essential due to increasing demand in many industries. The exploration of alternative sources of rare earth elements has been conducted on materials such as red mud, coal, spent catalyst, tailing zircon, and coal fly ash (Aung and Ting, 2005; Abhilash et al., 2014; Borra et al., 2015; Anggara et al., 2018; Prameswara et al., 2020; Rosita et al., 2020).
The importance of recovering rare earth elements (REE), such as cerium and yttrium, from coal fly ash lies in their growing demand across various high-tech industries, including renewable energy, electronics, and defense. Traditional sources of REE are becoming increasingly scarce and challenging to mine, making alternative sources, such as industrial waste, essential. Coal fly ash, a by-product of coal combustion, offers a promising opportunity for REE extraction. Zhou et al. (2017) predicted that the demand for lanthanum, cerium, neodymium, europium, terbium, yttrium, and dysprosium oxide will rise to 33,600 ton by 2025 and reach 51,900 ton in 2030. The global demand for rare earth oxides is projected to increase from 208,250 metric tons in 2019 to 304,678 metric tons by 2025 (Zhou et al., 2017). This surge in demand underscores the need for sustainable extraction methods. However, current literature often focus on inorganic acids for REE recovery, leaving a gap in exploring the efficiency of organic acids such as acetic acid. This study addresses that gap by investigating the leaching kinetics of cerium and yttrium from non-magnetic coal fly ash using acetic acid, contributing to sustainable resource management. The findings are expected to offer new insights into optimizing extraction processes, reducing chemical waste, and improving the viability of coal fly ash as a secondary source of critical REE.
Coal fly ash is one of the alternative sources of rare earth elements (REE), listed as solid waste from coal power plants (Peramaki, 2014; Anggara et al., 2018). In Indonesia, 50% of energy is produced by coal-fired power plants (Edi, 2017). According to data from 2019, the demand for coal increased annually. The byproduct of coal combustion, fly ash and bottom ash, reached production of 19.92 million tons in 2019 (Energy and Mineral Resources Ministry, 2016). Anggara et al. (2018) recently reported that fly ash and bottom ash (FABA) from the coal power plant in Java are promising raw materials for rare earth element extraction. Kashiwakura et al. (2013) also reported that the rare earth elements and yttrium (REY) concentration increased by ten times after the combustion process in coal fly ash in amorphous phases, such as quartz (SiO2) and mullite (Al2O3). Because REE were accumulated in amorphous silicate, it can be enriched in the non-magnetic component of coal fly ash (Blissett et al., 2014; Rosita et al., 2020).
Rare earth elements include lanthanides and scandium groups, with atomic numbers ranging from 57 to 71. The components of the rare earth elements include La, Ce, Pr, Nd, Pm, Sm, Eu, Gd, Tb, Dy, Ho, Er, Tm, Yb, Lu, Sc, and Y. These elements are highly electropositive and have good conductivity, making them valuable for various industrial applications, including renewable and clean energy technologies (Nagaiyar and Gupta, 2016; Rosita et al., 2024).
There are some requirements to estimate the prospect of REE extraction from coal fly ash, such as the possibility of beneficiation, metal resources, simplicity, and hydrometallurgical recovery (Seredin and Dai, 2012). Seredin (2010) reported that the minimum cut of REE grade should be higher than 1,000 ppm, such as in monazite, xenotime, and bastnasite. However, due to the increasing price, this criterion is not the main requirement for REE extraction. The present criterion for REE extractions from coal fly ash is based on the individual concentration of the elements. They have been divided into three classifications: critical (Nd, Eu, Tb, Dy, Y, and Er), uncritical (La, Pr, Sm, and Gd), and excessive (Ce, Ho, Tm, Yb, and Lu)(Seredin, 2010). The amount of critical is essential to identify the viability of REE extraction. Mathematically, the equation is presented as
The Coutlook is the index used to identify the viability of REE extraction, in which the minimum Coutlook should be higher than 0.7 (Cout > 0.7) - the more promising material for extracting REE, the higher the Cout value.
Hydrometallurgy is one of the most efficient extraction methods for extracting metal in low concentrations because this method consumes little energy but has high recovery. Leaching is a hydrometallurgy method where acid is used as a solvent to leach the valuable metal from a solid to a liquid. Inorganic acid is widely used as a leaching agent, including fluoride, hydrochloric, sulfuric, and nitric acids (Kashiwakura et al., 2013). However, inorganic acid produces harmful byproducts in gas and liquid form. In recent years, organic acids such as acetic, oxalic, nitric, and citric acid as leaching agents have been investigated to substitute inorganic acids. (Behera and Parhi, 2016; Lazo et al., 2017; Sari et al., 2018; Sekar et al., 2018; Anggraeni et al., 2023; Prameswara et al., 2024).
This study investigates acetic acid as a leaching agent for extracting rare earth elements from non-magnetic coal fly ash. Two elements are the focus of this study: cerium and yttrium, where cerium is in the excessive group, and yttrium is in the critical group. The usage of acetic acid as a leaching agent has been demonstrated by Parhi for leaching neodymium from the scrub magnet and Setiawan et al. for leaching lithium and cobalt from spent lithiumion batteries (Behera and Parhi, 2016). The magnetic separator wet method was applied to obtain the non-magnetic coal fly ash. Silicate digestion was conducted to decrease and break the amorphous silicate content. The effect of pH levels, solid-to-liquid ratio, and temperature on the leaching process of cerium and yttrium was investigated in this study. The leaching kinetic models of cerium and yttrium are formulized by analysing the influence of temperature using the existing model, whereafter the apparent activation energies were calculated.
The focus on rare earth elements (REE) extraction from coal fly ash in Indonesia holds significant global relevance due to the increasing demand for REE in various industries worldwide. While the samples for this study were collected in Indonesia, the methodologies and findings are applicable across different
geographical regions, including South Africa, which also has substantial coal power production. The techniques and results presented in this paper contribute to the broader understanding and potential applications of REE recovery, making the research valuable for a global audience. This research addresses universally pertinent issues in mining and metallurgy, providing insights that can be adapted and utilized by researchers and industries in Africa and beyond (Cornelius et al., 2021; Uysal, 2022).
The characterization of coal fly ash
Coal fly ash (CFA) samples were collected from the Tuban coal powered plant (PLTU-Tuban) in East Java province, Indonesia. The samples were collected continuously during regular operating hours over one week to ensure a representative sample of typical operations. The power plant operates under standard conditions for coal-fired facilities with combustion temperatures typically ranging from 1,200°C to 1,500°C. The plant has a capacity of 2 x 330 MW and primarily uses sub-bituminous coal, influencing the composition of the fly ash produced. The fly ash is collected from electrostatic precipitators, ensuring the consistency and quality of the samples used in this study.
The samples were then separated based on particle size using a sieve, with raw material particles smaller than 38 µm (-400 mesh) being selected for further analysis. To obtain the magnetic and nonmagnetic components of coal fly ash, a wet magnetic separator was applied at the Centre for Research and Technology Development of Mineral and Coal (PUSLITBANG Teknologi Mineral dan Batubara) in Bandung, West Java province, Indonesia. The XRD analysis of raw material and magnetic and non-magnetic coal fly ash, was performed using the XRD X'Pert 3 Powder instrument (Figure 1). XRF analyses were conducted to determine the raw material's primary and minor components and magnetic and non-magnetic coal fly ash. Additionally, the non-magnetic coal fly ash was analysed using ICP-OES at the ALS Global-Geochemistry Analytical Laboratory in North Vancouver, British Columbia, to quantify the concentration of rare earth elements and yttrium. All measurements were conducted in triplicate to ensure data accuracy and reproducibility.
Coal fly ash was characterized using XRF, XRD, and the ICPOES instrument. Material characterization aims to identify the raw material composition, phase (crystalline or amorphous), and concentration of rare earth elements. The XRF analysis results show that non-magnetic components of coal fly ash contain SiO2, Al2O3, Fe2O3, CaO, and MgO as major minerals, and K2O, Cr2O3, TiO2, MnO, P2O5, SrO, and BaO as minor minerals (Figure 2). Generally, SiO2 is the main mineral in non-magnetic coal fly ash (Figure 1).
The benefit of the magnetic separation step is that it concentrates rare earth elements (REE) by segregating magnetic and non-magnetic components. Although REE are present in both fractions, magnetic separation can simplify subsequent chemical processes by reducing the volume of material to be processed and potentially increasing the concentration of REE in the non-magnetic fraction. This step is beneficial when processing large quantities of fly ash. However, the data indicates that REE are hosted in magnetic and non-magnetic components, and their concentration is not significantly different from the raw fly ash, suggesting that further refinement in the separation process or additional steps may be necessary to enhance the REE recovery.
The separation process of the magnetic and non-magnetic components using a wet magnetic separator was conducted based on literature, which indicate that rare earth elements accumulate and enrich in the glass phase after melting during the combustion process (Jorjani and Shahbazi, 2016). Kashiwakura et al. reported that, due to the high temperature of the combustion process, rare earth elements melted, distributed, and slightly enriched the amorph phase, such as quartz and mullite (Kashiwakura et al., 2013).
Figure 1—XRD analysis pattern for coal fly ash (Sample A: raw material, Sample B: after silicate digestion, Sample C: acid leaching at 90°C, Sample D: acid leaching at 60°C, and Sample E: acid leaching at 30°C (Note: A: SiO2, B: 3Al2O3.2SiO2, C: Fe2O3, D: (Fe2+, Mg)5Al(AlSi3O10)(OH)8, E: Ca(OH)2, F: SiO2.(Na2O.K2O), G: Ca(Al2Si14O12).12H2O, H: CaCO3, I: Fe3O4, K: Al2O3)
Figure 3 shows that a wet magnetic separator slightly enriches rare earth elements and yttrium after physical separation. It presents the concentration of each rare earth element in raw material, magnetic, and non-magnetic components. Equation [1] is used to compute the Coutlook, a metric determining the feasibility of rare earth element extraction. The Coutlook value is 1.08 (> 0.7), indicating that rare earth elements in non-magnetic coal fly ash are promising for extraction.
The non-magnetic coal fly ash was digested using 8M sodium hydroxide (NaOH, pro-analysis grade, Merck Inc.) to break down the silicate structures. The digestion was conducted in a 500 mL three-necked flask fitted with a reflux condenser, temperature probe, and mechanical stirrer (500 rpm). The setup was placed in a water bath, maintained at a constant temperature of 90°C using a PID temperature controller.
A fixed mass of 62.5 mg CFA was combined with 250 mL NaOH solution (8M), resulting in a 25% mass-to-liquid ratio to maximize the reaction. Digestion was performed for 120 minutes under atmospheric pressure, with continuous stirring to prevent sedimentation and ensure homogeneous contact between solid and liquid phases. After digestion, the resulting solids were filtered using Whatman filter paper (pore size: 0.45 µm) and washed with distilled water until a constant dry sample weight was achieved, indicating the complete removal of sodium silicate residues (NaSiO3). The solids were then dried at 110°C for 5 hours in an oven. XRD analysis was performed post-digestion to assess structural changes and confirm the dissolution of amorphous silicates.
Acid selection
The acid selection process was conducted to assess the efficiency and selectivity of various acids in extracting rare earth elements (REE). Two organic acids (acetic and oxalic acids) and one inorganic acid (sulfuric acid) were tested. Each acid was prepared to a pH of 1.7 and used under identical conditions: a temperature of 90°C, agitation speed of 500 rpm, and a leaching duration of 120 minutes.
Condition Parameters
Solid-to-liquid ratio (w/v) 5%, 10%, 15%
Temperature 30°C, 70°C, 90°C
pH Levels 1.72, 2.4, 2.9
Equipment
Agitation
Leaching duration
Three-necked flask, reflux condenser, thermometer, heating mantle with temperature controller
External agitator, stirring rate of 500 rpm
4 hours
Sample collection intervals 0, 1, 2, 3, 5, 8, 15, 30, 60, 180, 240 minutes
After leaching, 2 mL of the sample was collected at 10-minute intervals using a pipette fitted with a microfilter (0.22 µm) to avoid contamination from suspended solids. The collected samples were analysed using ICP-OES (Perkin Elmer Optima 8000) to determine the concentration of critical metals (e.g., Y) and excessive group metals (e.g., Ce). Selectivity for each acid was calculated based on the Y/Ce ratio to assess which acid provided optimal separation.
Leaching
The leaching reagent was acetic acid (100% vol) pro-analytical produced by Merck Inc. The metal leaching experiment was carried out under various conditions, summarized in Table I.
The leaching process was conducted in a three-necked flask equipped with a reflux condenser and thermometer on a heating mantle with a temperature controller. The solution was agitated using an external agitator with a stirring rate of 500 rpm. The solution was leached over 4 hours to dissolve the rare earth elements and yttrium from non-magnetic coal fly ash. Samples of 2 mL were collected at specified intervals during the experiment to examine the kinetics of the leaching reaction.
The samples for ICP-OES analysis were prepared by diluting 1 mL of each leached sample into 20 mL using deionized water (20 x dilution) to achieve optimal detection. The diluted samples were filtered through a microfilter (0.22 µm) to remove suspended particles that could interfere with the optical emission spectrometry. All measurements were performed in triplicate, and the standard deviation was reported to ensure data accuracy.
The prepared filtrate was analysed using inductive coupled plasma-optical emission spectrometry (ICP-OES, Perkin Elmer Optima 8000) at the Instrumental Analyst Laboratory, Department of Chemical Engineering, Faculty of Engineering, Universitas Gadjah Mada, Special Region of Yogyakarta province, Indonesia. The instrument was calibrated using certified standards to ensure reliable quantification of rare earth elements, with the detection limit set at 0.01 ppm.
Results and discussion
Silicate digestion
The characterization of coal fly ash shows that silicious and glass minerals were the most abundant. The dissolving silicious component becomes a critical material to remove. Generally, silicious removal can be achieved using alkaline fusion or alkaline leaching. This study used sodium hydroxide (NaOH) 8 M as a reagent to dissolve and break the silicious bounding. The XRF results show that 20% - 40% of silicious components were dissolved. The general reaction for silicate digestion can be described as the equation below.
SiO2REY, as a silicious component, is transformed into sodium silicate salt based on Equation [2]. Besides that, sodium hydroxide also changes the REY bound to form REY(OH)3, where the silicate component replaced O.H.- from sodium hydroxide (Nagaiyar and Gupta, 2016). After silicate digestion, some filtrates were analysed
using ICP-OES to identify the amount of rare earth and yttrium (REY) in the solution. The ICP results show that only a tiny amount of REY was leached, and the recovery was not more than 5.6% for all elements of REY. Gupta et al. (2016) also reported that alkaline fusion is applied to recover rare earth elements from monazite (CePO4) to remove phosphate as a pretreatment before acid leaching.
Acid selection
The acid selection was conducted to determine the impact of various organic and inorganic acids at pH 1.7, at a temperature of 90°C for 120 minutes. They were oxalic acid and acetic acid as organic acids, and sulfuric acid as inorganic acid. Four elements were selected for comparison to determine the impact of various acids (Figure 4a).
Figure 4(a) illustrates that sulfuric acid has a higher recovery than other organic acids, oxalic acid, and acetic acid. The recoveries were 74.51% and 33.07%, respectively, for cerium and yttrium for sulfuric acid, and 44.44% and 57.01% for acetic acid. However, acetic acid can dissolve higher than sulfuric acid for metals like La and Yb. Of the four elements, oxalic acid has the lowest recovery. The general reaction for each acid with rare earth elements is shown in Equations [2]−[4] (Feng et al., 2013; Jorjani and Shahbazi, 2016):
acid, and it is also biodegradable and safer to handle in industrial applications. This statement makes it an appealing choice for processes that minimize environmental impact.
Furthermore, acetic acid offers comparable selectivity for critical elements such as yttrium, achieving a selectivity ratio (Y/ Ce) of 0.96. As essential in renewable energy technologies, yttrium makes the use of acetic acid particularly beneficial in applications related to sustainable industries. These findings highlight the potential for integrating acetic acid into eco-friendly industrial processes, especially with strict environmental regulations. Additionally, achieving high recovery rates without relying on aggressive inorganic acids opens new possibilities for future REE recovery processes, potentially reducing operational costs and simplifying waste management. The mildness of acetic acid also reduces equipment corrosion, which can prolong the operational lifespan of processing plants, leading to further cost savings. Future studies could explore scaling up the process and integrating acetic acid leaching with other beneficiation methods to enhance overall recovery efficiency.
The influence of pH on metal recovery
Figure 4(b) indicates that acetic acid has the highest ratio for metal selectivity. Based on this data, we can conclude that acetic acid has a high selectivity for rare earth elements. Thus, acetic acid was selected as a reagent for rare earth leaching.
Acid leaching using acetic acid
Acid leaching was conducted using acetic acid to leach at various leaching conditions. As explained in the aforementioned, acetic acid was selected as a leaching reagent based on the high selectivity of acetic acid compared to oxalic acid and sulfuric acid. The results indicate that acetic acid efficiently extracts rare earth elements (REE) from non-magnetic coal fly ash, achieving a recovery rate of 44.44% for cerium and 57.01% for yttrium, respectively. While sulfuric acid exhibits higher recovery for some elements, such as cerium, with a recovery rate of 74.51%, acetic acid presents distinct advantages. Acetic acid is more environmentally friendly, producing fewer hazardous byproducts than inorganic acids like sulfuric
Acid-leaching experiments were carried out by varying the pH level at the same temperature and solid-to-liquid ratio, as presented in Figure 5. Figure 5a shows that the pH levels influenced the extraction of cerium. The potential of hydrogen (pH) had a significant effect on the one-minute leaching of cerium. The recovery of cerium was 21.16%, 35.75%, and 41.30%, respectively, for pH 2.90, 2.40, and 1.72. The recovery of cerium steadily increases during the first 60 minutes of leaching, but beyond this point, the rate of increase becomes minimal.
Figure 5b shows that pH levels strongly influence the yttrium extraction, increasing yttrium recovery. The equilibrium of yttrium was achieved at 5 minutes of leaching for each pH level. After 5 minutes, Yttrium recovery was relatively constant, as shown in Figure 5b. The final recovery of yttrium after leaching of 240 minutes was 38.29%, 51.00%, and 57.63%, respectively, for pH 2.90, pH 2.40, and pH 1.72. The complexation of Ce3+ and Y3+ can be explained as REE3+. More H+ ions will be released with a lower pH level, generating a complex REE(CH3COO)3 ion. This complexation has a significant effect on REE leaching.
The influence of temperature on REE recovery
The experiments regarding the effect of temperature on rare earth elements recovery were conducted at various temperatures, as shown in Figure 6, with a pH of 1.72. The extraction of cerium
increased gradually for all temperatures from 1 to 60 minutes of leaching. The high reaction temperature increases the cerium recovery. When the temperature increases from 30°C to 60°C and 90°C, the extracted cerium rises from 40% to 48% and 52%, respectively (Figure 6a). After 60 minutes of leaching, the leaching rate becomes almost constant. This phenomenon is consistent with the Arrhenius rate law, which states that increasing the reaction temperature by 10°C will increase the reaction rate twice (Levenspiel, 1999; Fogler, 2005).
The extraction of yttrium increases significantly after oneminute leaching at all temperatures (Figure 6b). They are 53.60%, 54.70%, and 54.30%, respectively, for 30°C, 60°C, and 90°C. Increasing the temperature from 30°C to 90°C only increases the recovery slightly. Increasing the leaching time to 240 minutes does not increase the recovery. It can be inferred that Y3+ quickly diffuses to the liquid body. Therefore, the temperature does not influence the yttrium extraction but significantly influences the cerium extraction. The ion radius of both elements could influence this. The ion radius of yttrium is smaller than cerium, with an ion radius of 0.9 Å and 1.01 Å, respectively (Hartman and Chan, 1993).
The influence of solid-to-liquid ratio on metal recovery
The experiments were conducted by varying the solid-to-liquid ratio at the same condition (pH 1.72 and temperature 90°C), as shown in Figure 7. The recovery of cerium (Figure 7a) achieved 59% after 180 minutes for a solid-to-liquid ratio of 10% (w/v). The decreasing solid-to-liquid ratio from 15% to 5% slightly increased the recovery. The recoveries were 54.25%, 57.33%, and 59.59% for solid-to-liquid ratios of 15%, 10% and 5%, respectively. It is well known that, the
lower the liquid ratio, the more surface contact between particle and reagent. Besides that, a higher solid-to-liquid ratio can increase the viscosity of the slurry. From the result of cerium extraction, it can be inferred that the cerium leaching process is controlled by diffusion. The extraction of yttrium (Figure 7b) achieved 57.60% after 15 minutes for a solid-to-liquid ratio of 10%. There was no significant effect of varying solid-to-liquid ratios.
Leaching kinetics study
The leaching kinetics study of rare earth elements from nonmagnetic coal fly ash was analysed by using the shrinking core model for spherical particles of constant size (Levenspiel, 1999). The selection of the shrinking core model in this application is driven by its effectiveness in describing the reaction kinetics of solid-fluid systems. This model is particularly suitable for processes involving the leaching or dissolution of solid particles, where the reaction occurs at the interface between the solid and the fluid (Maulidia et al., 2023). The shrinking core model simplifies the complex process by assuming that the unreacted core of the solid shrinks over time while the product layer grows outward. This model allows for a clear and quantifiable description of the reaction rate and extent, making it easier to predict the system's behaviour under various conditions. Moreover, the model aligns well with the physical and chemical characteristics of the rare earth elements extraction process from coal fly ash, where the reactants and products exhibit distinct phases and interfaces. Its ability to account for factors such as diffusion through the product layer and chemical reaction at the surface, makes the shrinking core model a robust choice for this application, facilitating accurate and reliable analysis (Supriadi et al., 2023). The
existing model was validated against the experiment data using the linearization method to determine the kinetic parameters. The existing model is described in Equations [5]−[7].
Chemical reaction control
Inner diffusion control
Ash diffusion control
where α is rare earth elements conversion (cerium and yttrium), k is equilibrium reaction constant (min-1), and t is time (minute/s). The kinetic equation can be determined by fitting all the experimental data in different temperatures with different kinetics models in various rate-controlling mechanisms.
The experimental data shown in Figure 6 was substituted into Equations [5], [6], and [7] and then plotted as model vs. time. After plotting model vs. time, the straight line's correlation coefficient (R2) values were calculated after linearization using the regression method, as shown in Tables II and III. The result indicates that the leaching process did not agree with a chemical reaction or ash diffusion control due to the R2 value being below 0.95 for cerium and 0.85 for yttrium. Subsequently, the new modification model for the shrinking core model suggested by Dickinson and Heal was tested to fit the kinetic data. The equation was expressed as Equation [8] below.
The result of this model was presented in Table I for cerium and Table II for yttrium. The results show that the R2 for both metals was higher using the last model by Dickinson and Heal. The correlation coefficient for cerium were 0.74, 0.96, and 0.95, respectively, for temperatures 30°C, 60°C, and 90°C. As for cerium, Dickinson and Heal's models were also fitted to test the experimental data, as shown in Table II. The results show that the last model presented a higher correlation coefficient (R2) than other models, although the correlation coefficient was not higher than 0.95. These kinetic models indicate that the leaching of rare earth elements from non-magnetic coal fly is controlled by chemical reaction and diffusion control. However, the correlation coefficient at a temperature of 30°C in cerium and yttrium kinetic models was very low. They were 0.74 and 0.49, for cerium and yttrium, respectively. The experimental data in Figure 6 shows that it only slightly increases the recovery of cerium and yttrium.
Activation energy must be provided to a chemical reaction or phenomenon. The activation energy is often calculated using the Arrhenius equation. The equation of Arrhenius is represented as: [9]
where k is the reaction rate constant, A is the pre-exponential factor, E is the apparent activation energy, R is the mole gas constant, and T is the reaction temperature (K). Model vs. time was plotted to calculate the activation energy to obtain the intercept and slope (as a k-value) using the regression method (y=a+bx). This plot should be straight to get the slope, as presented in Figure 8. After the k-value is obtained, Equation [9] is modified to become a linear trendline as:
Linear fitting parameter equations for various leaching kinetic models of cerium
Table IIII
Linear fitting parameter equations for various leaching kinetic models of yttrium
where ln k is ordinate, and 1/T is absis. From Figure 8, the k-value was obtained as a slope. The ln k vs. 1/T should be plotted as a straight line to calculate the apparent activation energy, as presented in Figure 9.
Figure 9 shows a correlation between ln k vs. 1/T. This figure indicates that the apparent rate constant (k) can be calculated. Thus, the apparent activation energy of the overall reaction for cerium and yttrium is 22.72 kJ/mole and 35.84 kJ/mole, respectively. These energy activation values indicate that the leaching of cerium and yttrium from non-magnetic coal fly ash after silicate digestion using acetic acid is controlled by combining interface transfer and diffusion across the product layer. The silicate digestion step involved treating the non-magnetic coal fly ash with sodium hydroxide to break down and dissolve siliceous components, which was crucial in preparing the sample for effective leaching. The same digested sample was used for subsequent leaching experiments to ensure consistency. Feng et al. (2013) reported that the activation energy of the diffusion-controlled process is less than 13 kJ/mol,
while for the chemical reaction-controlled process, it is usually greater than 43 kJ/mol. The activation energy in the 13 kJ/mol43 kJ/mol range is controlled by mixed processes such as chemical reaction and ash diffusion-controlled, and/or chemical reaction control and inner diffusion. This statement is also similar to Huang et al. (2017), which reported that leaching rare earth elements and fluoride from mixed rare earth element concentrate after roasting with calcium hydroxide, was controlled by both interfacial transfer and diffusion through the product layer affected by the reaction with activation energy in the range of 13 kJ/mol − 43 kJ/ mol. Therefore, the results from this study align with existing literature, further validating the mechanism of leaching involving a combination of interface transfer and diffusion processes.
Conclusion
This study shows that physical separation using a magnetic separator slightly increases the cerium and yttrium concentration in non-magnetic coal fly ash. Acetic acid has a higher selectivity
for Ce/Y than oxalic acid and sulfuric acid. The main factors influencing the leaching of cerium and yttrium were temperature and pH levels. Increasing the S/L ratio did not provide any significant improvement. The highest recovery of cerium and yttrium was 57.33% and 58.36%, respectively, under different temperatures, i.e., 90°C for Ce and 60°C for Y at pH 1.74 and 10 g/mL solid-liquid ratio in 240 minutes. However, extending the leaching time to 240 minutes does not appear to be necessary as the recovery becomes relatively constant after 60 minutes.
The apparent activation energies were 22.72 kJ/mol and 35.84 kJ/mol for cerium and yttrium, respectively. The kinetic data of leaching cerium and yttrium were fitted using a new shrinking core model by Dickinson and Heal. The calculation results show that the leaching reaction is controlled by combining interface transfer and diffusion across the product layer. This understanding can be applied in optimizing industrial processes for rare earth elements extraction from coal fly ash, reducing energy consumption, and improving efficiency by focusing on the most effective leaching conditions identified, such as appropriate temperatures, pH levels, and shorter leaching durations.
Acknowledgements
The Ministry of Research, Technology, and Higher Education of the Republic of Indonesia supported this research financially.
Conflict of Interest
The corresponding author states that there is no conflict of interest on behalf of all authors.
References
Abhilash, Sinha, S., Manish, K.S., Banshi, D.P. 2014. Extraction of lanthanum and cerium from Indian red mud. International Journal of Mineral Processing, vol. 127, pp. 70–73.
Anggara, F., Ayu, B.D.A., Widya, R., Petrus, H.T.B.M. 2018. The Composition and mode of occurrence of rare earth elements and yttrium in fly ash and bottom ash from coal-fired plants in Java, Indonesia. The Society for Organic Petrology Annual Meeting https://archives.datapages.com/data/tsop/ tsop-v35-2018/abstracts/anggara.htm
Anggraeni, V.M.P., Supriyatna, Y.I., Astuti, W., Sumardi, S., Prasetya, A., Petrus, H.T.B.M., Purnomo, C.W. 2023. Ilmenite Sand Direct Leaching Kinetics in Hydrochloric Acid Solution. Journal of Sustainable Metallurgy. vol. 9, no. 4, pp. 1578–1588. http://dx.doi.org/10.1007/s40831-023-00749-3
Aung, K.M.M., Ting, Y.P. 2005. Bioleaching of spent fluid catalytic cracking catalyst using Aspergillus niger. Journal of Biotechnology. vol. 116, no. 2, pp. 159–170. http://dx.doi.org/10.1016/j.jbiotec.2004.10.008
Behera, S.S., Parhi, P.K. 2016. Leaching kinetics study of neodymium from the scrap magnet using acetic acid. Separation and Purification Technology. vol. 160, pp. 59–66. http://dx.doi.org/10.1016/j.seppur.2016.01.014
Blissett, R.S., Smalley, N., Rowson, N.A. 2014. An investigation into six coal fly ashes from the United Kingdom and Poland to evaluate rare earth element content. Fuel, vol. 119, pp. 236–239. Available at: http://dx.doi.org/10.1016/j.fuel.2013.11.053
Borra, C.R., Pontikes, Y., Binnemans, K., Gerven, T. Van. 2015. Leaching of rare earths from bauxite residue (red mud). Minerals Engineering, vol. 76, pp. 20–27. http://dx.doi. org/10.1016/j.mineng.2015.01.005
Cornelius, M.L.U., Ameh, A.E., Eze, C.P., Fatoba, O., Sartbaeva, A., Petrik, L.F. 2021. The Behaviour of Rare Earth Elements from South African Coal Fly Ash during Enrichment Processes: Wet, Magnetic Separation and Zeolitisation. Minerals, vol. 11, no. 9, 950p. http://dx.doi.org/10.3390/min11090950
Edi, S. 2017. Handbook of Energy and Economic Statistic of Indonesia. Jakarta: Ministry of Energy and Mineral Resources Republic of Indonesia. https://www.esdm.go.id/assets/media/ content/content-handbook-of-energy-economic-statistics-ofindonesia-2017-.pdf.
Energy and Mineral Resources Ministry. 2016. Indonesia Electricity Development Plan and Indonesia Coal-Ash Management Implementation. International Coal Based Power Conference New Delhi, pp. 4–8.
Feng, X.L., Long, Z.Q., Cui, D.L., Wang, L.S., Huang, X.W., Zhang, G.C. 2013. Kinetics of rare earth leaching from roasted ore of bastnaesite with sulfuric acid. Transactions of Nonferrous Metals Society of China (English Edition), vol. 23, no. 3, pp. 849–854. http://dx.doi.org/10.1016/S1003-6326(13)62538-8
Fogler, H.S. 2005. Elements of Chemical Reaction Engineering Fourth Edi. Andreas, A., John, D., Thomas, Ha. J., and E, S. L. eds. Michigan United States America: Prentice Hall Professional Technical Reference.
Hartman, P., Chan, H.K. 1993. Application of the Periodic Bond Chain (PBC) Theory and Attachment Energy Consideration to Derive the Crystal Morphology of Hexamethylmelamine. Pharmaceutical Research: An Official Journal of the American Association of Pharmaceutical Scientists, vol. 10, no. 7, pp. 1052–1058. http://dx.doi.org/10.1023/A:1018927109487
Huang, Y., Dou, Z., Zhang, T., Liu, J. 2017. Hydrometallurgy Leaching kinetics of rare earth elements and fl uoride from mixed rare earth concentrate after roasting with calcium hydroxide and sodium hydroxide. Hydrometallurgy, vol. 173, (July), pp. 15–21. http://dx.doi.org/10.1016/j. hydromet.2017.07.004
Jorjani, E., Shahbazi, M. 2016. The production of rare earth elements group via tributyl phosphate extraction and precipitation stripping using oxalic acid. Arabian Journal of Chemistry, vol. 9, pp. S1532–S1539. http://dx.doi.org/10.1016/j. arabjc.2012.04.002
Kashiwakura, S., Kumagai, Y., Kubo, H., Wagatsuma, K. 2013. Dissolution of Rare Earth Elements from Coal Fly Ash Particles in a Dilute H2SO4 Solvent. 2013 (May), pp. 69–75.
Lazo, D.E., Dyer, L.G., Alorro, R.D., Browner, R. 2017. Hydrometallurgy Treatment of monazite by organic acids I: Solution conversion of rare earths. Hydrometallurgy, vol. 174, (October), pp. 202–209. http://dx.doi.org/10.1016/j. hydromet.2017.10.003
Levenspiel, O. 1999. Chemical Reaction Engineering. United States of America: John Wiley & Sons.
Maulidia, A. et al. 2023. Kinetic Study of Lithium Leaching from Sidoarjo Mud Using Sulfuric Acid. Mining, Metallurgy and Exploration, vol. 40, no. 4, pp. 1279–1288. http://dx.doi. org/10.1007/s42461-023-00812-3
Nagaiyar, K., Gupta, C.K. 2016. Extractive Metallurgy of Rare Earth Second Edi. CRC Press Taylor & Francis Group Boca Raton London New York. https://doi.org/10.1201/b19055
Peramaki, S. 2014. Method Development for Determination and Recovery of Rare Earth Elements from Industrial Fly Ash https://jyx.jyu.fi/handle/123456789/45043
Leaching characteristics of cerium and yttrium from non-magnetic coal fly ash after silicate digestion using acetic acid
Prameswara, G., Amin, I., Ulfah, A.N., Trisnawati, I., Petrus, H.T.B.M., Puspita, F. 2024. Atmospheric Leaching Behavior and Kinetics Study of Roasted Laterite Ore. Mining, Metallurgy and Exploration, vol. 41, no. 2, pp. 1025–1033. http://dx.doi. org/10.1007/s42461-024-00947-x
Prameswara, G., Trisnawati, I., Poernomo, H., Mulyono, P., Prasetya, A., Petrus, H.T.B.M. 2020. Kinetics of Yttrium Dissolution from Alkaline Fusion on Zircon Tailings. Mining, Metallurgy and Exploration, vol. 37, no. 4, pp. 1297–1305. http://dx.doi. org/10.1007/s42461-020-00220-x
Rosita, W., Bendiyasa, I.M., Perdana, I., Anggara, F. 2020. Sequential particle-size and magnetic separation for enrichment of rareearth elements and yttrium in Indonesia coal fly ash. Journal of Environmental Chemical Engineering, vol. 8, no.1, 103575p. http://dx.doi.org/10.1016/j.jece.2019.103575
Rosita, W., Perdana, I., Bendiyasa, I.M., Anggara, F., Petrus, H.T.B.M., Prasetya, A., Rodliyah, I. 2024. Sequential alkalineorganic acid leaching process to enhance the recovery of rare earth elements from Indonesian coal fly ash. Journal of Rare Earths, vol. 42, no. 7, pp. 1366–1374. http://dx.doi.org/10.1016/j. jre.2023.09.001
Sari, D.P., Tawfiequrahman, A., Petrus, H.T.B.M., Mufakir, F.R., Astuti, W., Iskandar, Y., Bratakusuma, D. 2018. Valuable Metals Extraction From Hydrocracking Spent Catalyst Using Citric Acid. Seminar Nasional Teknik Kimia “Kejuangan” : Pengembangan Teknologi Kimia untuk Pengolahan Sumber Daya Alam Indonesia, (April), pp. 1–5.
Sekar, H., Ayu, E., Bendiyasa, I.M., Petrus, H.T.B.M., Murti, B., Rofiek, F., Astuti, W. 2018. Pelindian Nikel dari Bijih Limonit Low-Grade Pomalaa Menggunakan Pelarut Asam Asetat. (April), pp. 1–7.
Seredin, V.V. 2010. A New Method for Primary Evaluation of the Outlook for Rare Earth Element Ores. Geology of Ore Deposits, vol. 52, no. 5, pp. 5–6. http://dx.doi.org/10.1134/ S1075701510050077
Seredin, V.V., Dai, S. 2012. International Journal of Coal Geology Coal deposits as potential alternative sources for lanthanides and yttrium. International Journal of Coal Geology, vol. 94, pp. 67–93. http://dx.doi.org/10.1016/j.coal.2011.11.001
Supriadi, H., Trisnawati, I., Handini, T., Susilowati, S.R., Sujoto, V.S.H., Mulyono, P., Petrus, H.T.B.M. 2023. Kinetics Study of Yttrium Leaching from Zircon Tailings Using Sulfuric Acid. Indonesian Journal of Chemistry https://doi.org/10.22146/ ijc.79966.
Uysal, T. 2022. Economic analysis of rare earth element processing methods for Mountain Pass ore. Journal of the Southern African Institute of Mining and Metallurgy, vol. 122, no. 7, pp. 1–6. http://dx.doi.org/10.17159/2411-9717/1989/2022
Zhou, B., Li, Z., Chen, C. 2017. Global potential of rare earth resources and rare earth demand from clean technologies. Minerals, vol. 7, no. 11. http://dx.doi.org/10.3390/ min7110203
7 - 8 APRIL 2025
CSIR International Convention Centre, Pretoria
The primary purpose of the 2ND Hydrogen and Fuel Cells conference is the advancement of green hydrogen technologies in Southern Africa and the global community, by highlighting the power of renewable and sustainable technologies and addressing the emerging challenges— through the exploration of hydrogen production, storage and utilization using fuel cells by way of engagement with industry, academia and government.
FOR FURTHER INFORMATION, CONTACT:
Gugu Charlie, Conferences and Events Co-ordinator
E-mail: gugu@saimm.co.za
Tel: +27 11 538-0238
Web: www.saimm.co.za
The conference will provide a platform for high level exchange and networking opportunities with various experts in the field.
The two-day conference will feature high-level scientific talks and posters, complemented with keynote and plenary presentations on country overviews, status of leading and major players in the Southern African and global arena.
6-8 November 2024 — MineSafe Conference 2024
Emperors Palace Convention Centre, South Africa
Contact: Camielah Jardine
Tel: 011 538-0237
E-mail: camielah@saimm.co.za
Website: http://www.saimm.co.za
11-12 November 2024 — Mintek@90 Conference 2024
Sandton Convention Centre, South Africa
Contact: Camielah Jardine
Tel: 011 538-0237
E-mail: camielah@saimm.co.za
Website: http://www.saimm.co.za
2025
21-23 January 2025 — 14TH South African Conference on Computational and Applied Mechanics
Wits Science Stadium, South Africa
Website: https://sacam.co.za/
19-20 February 2025 — Mine Closure Conference 2025
Maslow Hotel, Sandton, South Africa
Contact: Gugu Charlie
Tel: 011 538-0238
E-mail: gugu@saimm.co.za
Website: http://www.saimm.co.za
7-8 April 2025 — 2ND Southern African Hydrogen and Fuel Cell Conference 2025
CSIR International Convention Centre, Pretoria
Contact: Camielah Jardine
Tel: 011 538-0237
E-mail: camielah@saimm.co.za
Website: http://www.saimm.co.za
8-10 April 2025 — 27TH Conference on Paste, Thickened and Filtered Tailings
Swakopmund, Namibia
Website: https://acgpaste.com/2025/
26-29 May 2025 — 9TH Sulphur and Sulphuric Acid Conference 2025
Protea Hotel Stellenbosch and Conference Centre, Stellenbosch
Contact: Gugu Charlie
Tel: 011 538-0238
E-mail: gugu@saimm.co.za
Website: http://www.saimm.co.za
25-26 June 2025 — 4TH Digital Transformation in Mining Conference 2025
Glenburn Lodge and Spa, Muldersdrift
Contact: Camielah Jardine
Tel: 011 538-0237
E-mail: camielah@saimm.co.za
Website: http://www.saimm.co.za
21-25 July 2025 — AfriRock Conference 2025
Sun City, South Africa
Contact: Camielah Jardine
Tel: 011 538-0237
E-mail: camielah@saimm.co.za
Website: http://www.saimm.co.za
16-22 November 2025 — The 12TH International Copper Conference (Copper 2025)
Phoenix, Arizona, USA
Website: https://www.extractionmeeting.org/ Extraction2025/Extraction2025/Copper2025/default.aspx
The following organizations have been admitted to the Institute as Company Affiliates
A and B Global Mining (Pty) Ltd
acQuire Technology Solutions
AECI Mining Chemicals, a division of AECI Mining Ltd
African Pegmatite
Allied Furnace Consultants
AMIRA International Africa (Pty) Ltd
Anglogold Ashanti Ltd
Anton Paar Southern Africa
Arcus Gibb (Pty) Ltd
Becker Mining (Pty) Ltd
Bluhm Burton Engineering Pty Ltd
Caledonia Mining South Africa
Castle Lead Works
DDP Specialty Products South Africa (Pty) Ltd
De-Tect Unit Inspection (Pty) Ltd
Digby Wells and Associates
EHL Consulting Engineers (Pty) Ltd
Elbroc Mining Products (Pty) Ltd
Epiroc South Africa (Pty) Ltd
Ex Mente Technologies (Pty) Ltd
Exxaro Resources Limited
FLSmidth Minerals (Pty) Ltd
G H H Mining Machines (Pty) Ltd
Geobrugg Southern Africa (Pty) Ltd
Glencore
Gravitas Minerals (Pty) Ltd
Hatch (Pty) Ltd
Herrenknecht AG
Impala Platinum Holdings Limited
IMS Engineering (Pty) Ltd
Ingwenya Mineral Processing
Ivanhoe Mines SA
Longyear South Africa (Pty) Ltd
Malvern Panalytical (Pty) Ltd
Maptek (Pty) Ltd
Mech-Industries
Micromine Africa (Pty) Ltd
Minearc South Africa (Pty) Ltd
Minerals Council of South Africa
MineRP Holding (Pty) Ltd
Mining Projection Concepts (Pty) Ltd
Mintek
MLB Investments CC
Modular Mining Systems Africa (Pty) Ltd
Murray & Roberts Cementation (Pty) Ltd
OPTRON
Paterson & Cooke Consulting Engineers (Pty) Ltd
Redpath Mining (South Africa) (Pty) Ltd
Rosond (Pty) Ltd
Roytec Global (Pty) Ltd
Rustenburg Platinum Mines Limited - Union
Salene Mining (Pty) Ltd
Schauenburg (Pty) Ltd
SENET (Pty) Ltd
Sibanye Gold Limited
Sound Mining Solution (Pty) Ltd
SRK Consulting SA (Pty) Ltd
Tomra (Pty) Ltd
Trans-Caledon Tunnel Authority
Ukwazi Mining Solutions (Pty) Ltd
VBKOM Consulting Engineers
Weir Minerals Africa
ZUTARI (Pty) Ltd
Perform like a PRO with the iCAP PRO Series ICP-OES
Simplicity, robustness and speed
When your day ends, you want to have produced results that you know are right and on time. The Thermo Scientific™ iCAP™ PRO Series ICPOES provides analysis in the fastest possible time with the assurance that your trace analyses will always be of the highest calibre for accuracy and productivity. How? We’ve reduced barriers to multi-element analysis while auto-configuring for long term stability and matrix endurance. The robust detection capabilities of the iCAP™ PRO Series ICP-OES are matched only by the effort-free maintenance and the fastest known start up times (less than 5 minutes) of any ICPOES instrument. On top of all that, this verticaltorch-based instrument features the smallest bench footprint known today.
The iCAP™ PRO Series ICP-OES combines powerful multi-element capability with flexibility, so your lab is ready for any challenge. Produce consistent, reliable data quickly and easily. Experience enhanced sample throughput, matrix tolerance, and flexibility to produce results you can trust. With four models to choose from, our instruments can solve your trace elemental analytical challenges.
Ignite your ICP-MS analysis with simplicity
Transform workflows with right-first-time analysis, ensuring your laboratory is fully optimized from sample to result. Thermo Scientific™ iCAP™ MX Series ICP-MS systems are the innovative solution for outstanding productivity with simplicity. These systems enable analytical testing laboratories to maximize output with accuracy and confidence in data quality, regardless of the sample matrix.
The Thermo Scientific™ iCAP™ MX Series ICP-MS comprises both single and triple quadrupole ICPMS systems and is ideal for applications ranging from high-throughput environmental monitoring to ultra-trace elemental analysis of industrial chemicals.
Ignite your productivity
Ignite your confidence
The Thermo Scientific™ iCAP™ MTX ICP-MS is designed to exceed the requirements of research laboratories demanding cutting edge interference removal and flexibility to challenge the boundaries of known and novel applications. At the same time, the instrument offers the performance and flexibility needed to perform cutting-edge applications in research-oriented and testing laboratories. Combined with unmatched ease of use, the iCAP™ MTX ICP-MS sets a new standard for triple quadrupole inductively coupled plasma mass spectrometry.
The Thermo Scientific™ iCAP™ MSX ICP-MS is designed to exceed the requirements of analytical testing laboratories demanding maximum uptake and productivity for a wide range of sample types. At the same time, the instrument offers the simplicity and productivity required in analytical testing laboratories. Combined with unmatched ease of use, the iCAP™ MSX ICP-MS sets a new standard for inductively coupled plasma mass spectrometry.
Thermo Scientific™ iCAP™ MX Series ICP-MS systems combine innovative hardware and software tools to provide a unique balance of matrix robustness and sensitivity. Both our single and triple quadrupole ICP-MS systems are suited to the analysis of a wide range of sample types and they incorporate productivity tools, including:
• Reliable and robust sample handling with Easy Argon Gas Dilution (AGD) and Integrated Argon Humidifier - The pre-defined argon gas dilution (AGD) factors help to ensure the optimal AGD mode is applied to your sample, allowing even the most challenging samples to be introduced directly into the system.
• Intellilens™ for optimal performance - optimizes the optical lens settings per analyte to provide maximum sensitivity across the mass range
• Intelligent matrix handling - reduces exposure of the instrument to the sample when sample detection is not taking place, helping to ensure long-term stability and preventing interruptions to your productivity by significantly extending the time intervals between cone-cleaning cycles.
• Interference removal - The Thermo Scientific™ iCAP™ MSX Single Quadrupole ICP-MS utilizes QCell technology to effectively remove interferences. The QCell combines helium as cell gas with kinetic energy discrimination in a time-saving single analysis mode to remove interferences across the entire mass range. For more challenging interferences, the Thermo Scientific™ iCAP™ MTX Triple Quadrupole ICPMS leverages the unique Reaction Finder method development tool combined with the QCell for use with on-mass or mass-shift reactions to deliver interference-free analysis.
• Hawk Consumables and Maintenance Assistant - keeps track of and displays reminders for important maintenance activities to maximize instrument uptime.
Weir is a global leader in mining technology. We recognise that our planet’s future depends on the transition to renewable energy, and that transition can only happen with the metals and minerals our mining customers deliver.
With signature brands including ESCO®, WARMAN®, ENDURON®, GEHO®, CAVEX®, LINATEX®, and MOTION METRICSTM, we combine our deep customer insights, world class engineering, materials science expertise and intelligent automation to deliver innovative end-toend mining technology solutions that help our customers move less rock, use less energy, use water wisely and create less waste — accelerating the path to smart, e cient and sustainable mining.
global.weir