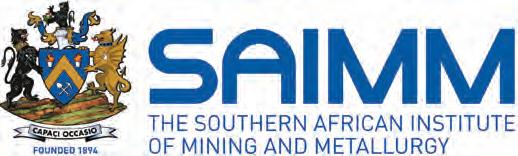
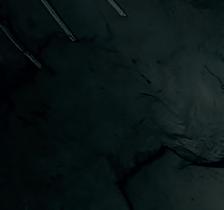
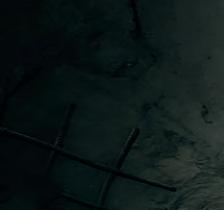
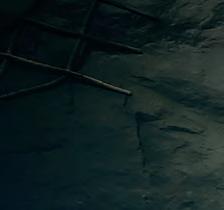
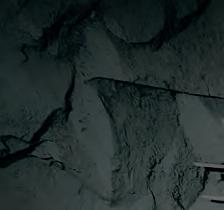
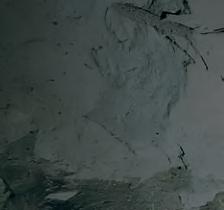
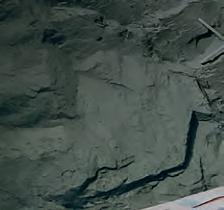
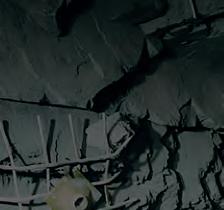
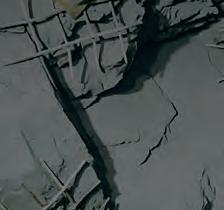
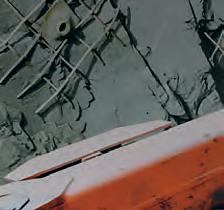
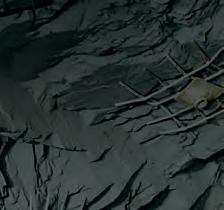
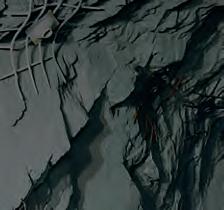
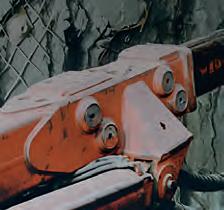
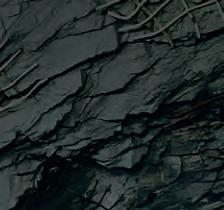
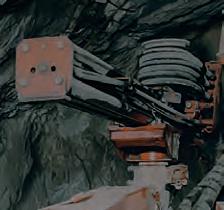
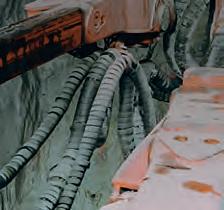

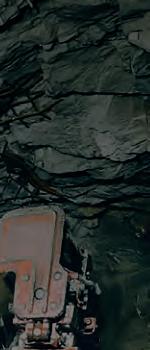
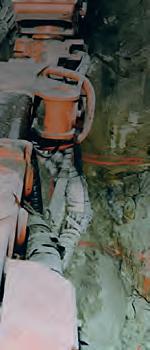
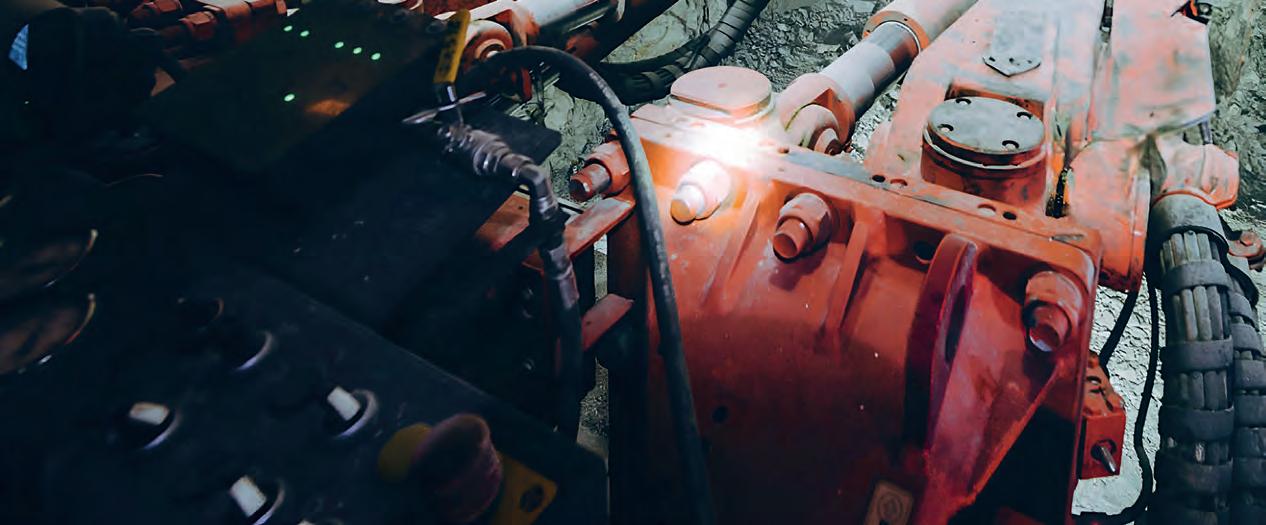
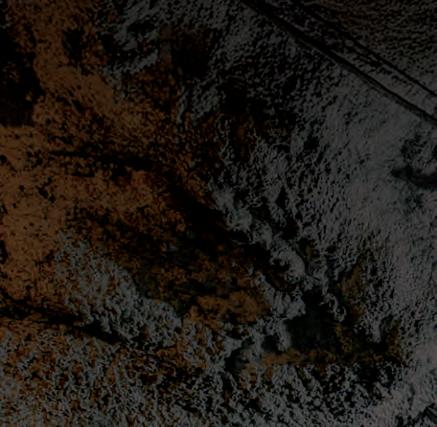
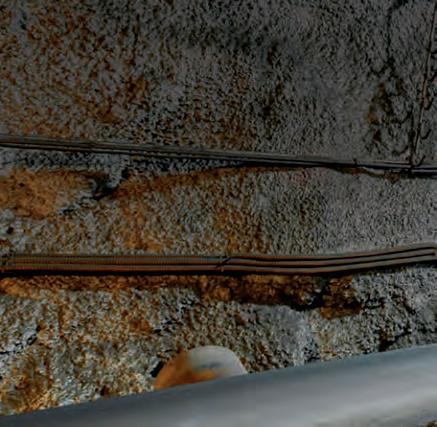
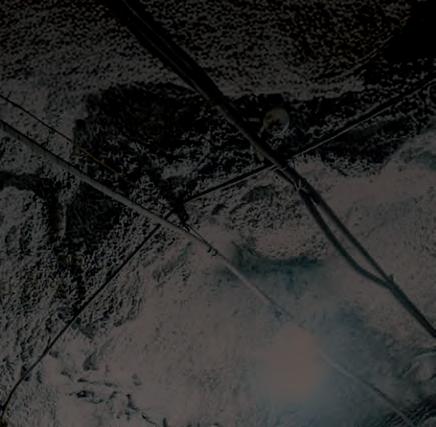
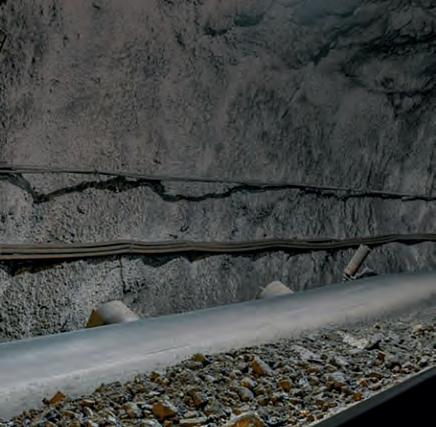
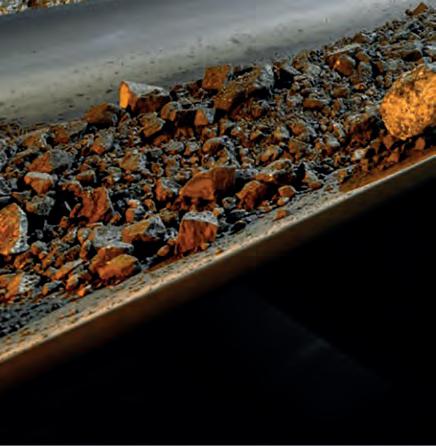
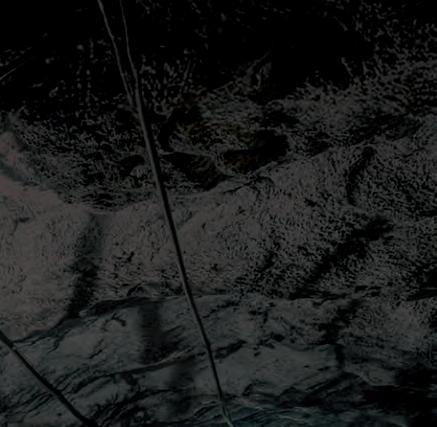
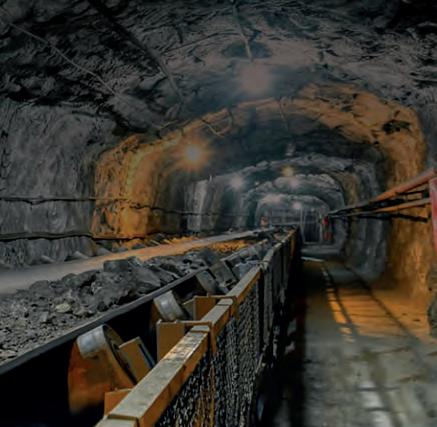
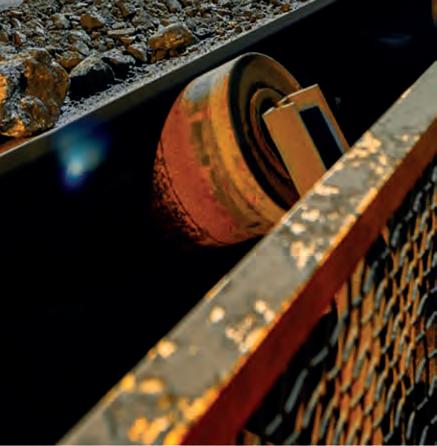
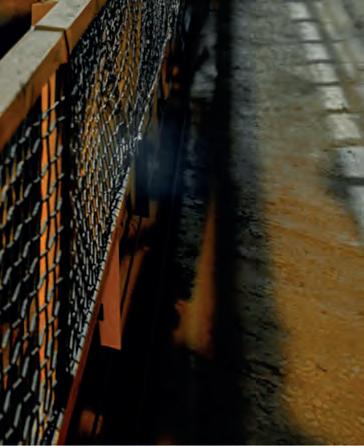
OFFICE BEARERS AND COUNCIL FOR THE 2024/2025 SESSION
President E. Matinde
President Elect
G.R. Lane
Senior Vice President
T.M. Mmola
Junior Vice President
M.H. Solomon
Incoming Junior Vice President
S.J. Ntsoelengoe
Immediate Past President
W.C. Joughin
Honorary Treasurer
W.C. Joughin
Ordinary Members on Council
W. Broodryk M.C. Munroe
Z. Fakhraei S.M. Naik
B. Genc G. Njowa
K.M. Letsoalo S.M. Rupprecht
S.B. Madolo A.T. van Zyl
M.A. Mello E.J. Walls
K. Mosebi
Co-opted Council Members
A.D. Coetzee
L.T. Masutha
Past Presidents Serving on Council
N.A. Barcza C. Musingwini
R.D. Beck S. Ndlovu
Z. Botha J.L. Porter
V.G. Duke M.H. Rogers
I.J. Geldenhuys G.L. Smith
R.T. Jones
G.R. Lane – TP Mining Chairperson
Z. Botha – TP Metallurgy Chairperson
K.W. Banda – YPC Chairperson
C.T. Chijara – YPC Vice Chairperson
Branch Chairpersons
Botswana K. Mosebi
DRC K.T. Kekana (Interim Chairperson)
Johannesburg N. Rampersad
Limpopo M.S. Zulu
Namibia T. Aipanda
Northern Cape Vacant
North West Vacant
Pretoria P.G.H. Pistorius
Western Cape Vacant
Zambia N.M. Kazembe
Zimbabwe L. Shamu
Zululand Vacant
*Deceased
* W. Bettel (1894–1895)
* A.F. Crosse (1895–1896)
* W.R. Feldtmann (1896–1897)
* C. Butters (1897–1898)
* J. Loevy (1898–1899)
* J.R. Williams (1899–1903)
* S.H. Pearce (1903–1904)
* W.A. Caldecott (1904–1905)
* W. Cullen (1905–1906)
* E.H. Johnson (1906–1907)
* J. Yates (1907–1908)
* R.G. Bevington (1908–1909)
* A. McA. Johnston (1909–1910)
* J. Moir (1910–1911)
* C.B. Saner (1911–1912)
* W.R. Dowling (1912–1913)
* A. Richardson (1913–1914)
* G.H. Stanley (1914–1915)
* J.E. Thomas (1915–1916)
* J.A. Wilkinson (1916–1917)
* G. Hildick-Smith (1917–1918)
* H.S. Meyer (1918–1919)
* J. Gray (1919–1920)
* J. Chilton (1920–1921)
* F. Wartenweiler (1921–1922)
* G.A. Watermeyer (1922–1923)
* F.W. Watson (1923–1924)
* C.J. Gray (1924–1925)
* H.A. White (1925–1926)
* H.R. Adam (1926–1927)
* Sir Robert Kotze (1927–1928)
* J.A. Woodburn (1928–1929)
* H. Pirow (1929–1930)
* J. Henderson (1930–1931)
* A. King (1931–1932)
* V. Nimmo-Dewar (1932–1933)
* P.N. Lategan (1933–1934)
* E.C. Ranson (1934–1935)
* R.A. Flugge-De-Smidt (1935–1936)
* T.K. Prentice (1936–1937)
* R.S.G. Stokes (1937–1938)
* P.E. Hall (1938–1939)
* E.H.A. Joseph (1939–1940)
* J.H. Dobson (1940–1941)
* Theo Meyer (1941–1942)
* John V. Muller (1942–1943)
* C. Biccard Jeppe (1943–1944)
* P.J. Louis Bok (1944–1945)
* J.T. McIntyre (1945–1946)
* M. Falcon (1946–1947)
* A. Clemens (1947–1948)
* F.G. Hill (1948–1949)
* O.A.E. Jackson (1949–1950)
* W.E. Gooday (1950–1951)
* C.J. Irving (1951–1952)
* D.D. Stitt (1952–1953)
* M.C.G. Meyer (1953–1954)
* L.A. Bushell (1954–1955)
* H. Britten (1955–1956)
* Wm. Bleloch (1956–1957)
* H. Simon (1957–1958)
* M. Barcza (1958–1959)
* R.J. Adamson (1959–1960)
* W.S. Findlay (1960–1961)
* D.G. Maxwell (1961–1962)
* J. de V. Lambrechts (1962–1963)
* J.F. Reid (1963–1964)
* D.M. Jamieson (1964–1965)
* H.E. Cross (1965–1966)
* D. Gordon Jones (1966–1967)
* P. Lambooy (1967–1968)
* R.C.J. Goode (1968–1969)
* J.K.E. Douglas (1969–1970)
* V.C. Robinson (1970–1971)
* D.D. Howat (1971–1972)
* J.P. Hugo (1972–1973)
* P.W.J. van Rensburg (1973–1974)
* R.P. Plewman (1974–1975)
* R.E. Robinson (1975–1976)
* M.D.G. Salamon (1976–1977)
* P.A. Von Wielligh (1977–1978)
* M.G. Atmore (1978–1979)
* D.A. Viljoen (1979–1980)
* P.R. Jochens (1980–1981)
* G.Y. Nisbet (1981–1982)
A.N. Brown (1982–1983)
* R.P. King (1983–1984)
J.D. Austin (1984–1985)
* H.E. James (1985–1986)
H. Wagner (1986–1987)
* B.C. Alberts (1987–1988)
* C.E. Fivaz (1988–1989)
* O.K.H. Steffen (1989–1990)
* H.G. Mosenthal (1990–1991)
R.D. Beck (1991–1992)
* J.P. Hoffman (1992–1993)
* H. Scott-Russell (1993–1994)
J.A. Cruise (1994–1995)
D.A.J. Ross-Watt (1995–1996)
N.A. Barcza (1996–1997)
* R.P. Mohring (1997–1998)
J.R. Dixon (1998–1999)
M.H. Rogers (1999–2000)
L.A. Cramer (2000–2001)
* A.A.B. Douglas (2001–2002)
* S.J. Ramokgopa (2002-2003)
T.R. Stacey (2003–2004)
F.M.G. Egerton (2004–2005)
W.H. van Niekerk (2005–2006)
R.P.H. Willis (2006–2007)
R.G.B. Pickering (2007–2008)
A.M. Garbers-Craig (2008–2009)
J.C. Ngoma (2009–2010)
G.V.R. Landman (2010–2011)
J.N. van der Merwe (2011–2012)
G.L. Smith (2012–2013)
M. Dworzanowski (2013–2014)
J.L. Porter (2014–2015)
R.T. Jones (2015–2016)
C. Musingwini (2016–2017)
S. Ndlovu (2017–2018)
A.S. Macfarlane (2018–2019)
M.I. Mthenjane (2019–2020)
V.G. Duke (2020–2021)
I.J. Geldenhuys (2021–2022)
Z. Botha (2022-2023)
W.C. Joughin (2023-2024)
S.O. Bada
R.D. Beck
P. den Hoed
I.M. Dikgwatlhe
M. Erwee
B. Genc
R.T. Jones
W.C. Joughin
A.J. Kinghorn
D.E.P. Klenam
D.F. Malan
D. Morris
C. Musingwini
P.N. Neingo
A. Nengovhela
S.S. Nyoni
M. Phasha
P. Pistorius
P. Radcliffe
N. Rampersad
Q.G. Reynolds
I. Robinson
S.M. Rupprecht
K.C. Sole
T.R. Stacey
International Advisory Board members
R. Dimitrakopolous
R. Mitra
S. Ndlovu
A.J.S. Spearing
E. Topal
D. Tudor
F. Uahengo
D. Vogt
Editor /Chairperson of the Editorial Board
R.M.S. Falcon
Typeset and Published by
The Southern African Institute of Mining and Metallurgy
PostNet Suite #212 Private Bag X31
Saxonwold, 2132
E-mail: journal@saimm.co.za
Printed by Camera Press, Johannesburg
Advertising Representative
Barbara Spence
Avenue Advertising
Journal Comment: To act or not act (timeously), that is the question for the future by A.
Nengovhela
...............................................................
President’s Corner: Industrial policy: Key to unlocking beneficiation potential? by E. Matinde ..................................................................
SAMCODES Quarterly Snaps vii by J. Mainama
THE INSTITUTE, AS A BODY, IS NOT RESPONSIBLE FOR THE STATEMENTS AND OPINIONS ADVANCED IN ANY OF ITS PUBLICATIONS.
Copyright© 2025 by The Southern African Institute of Mining and Metallurgy. All rights reserved. Multiple copying of the contents of this publication or parts thereof without permission is in breach of copyright, but permission is hereby given for the copying of titles and abstracts of papers and names of authors. Permission to copy illustrations and short extracts from the text of individual contributions is usually given upon written application to the Institute, provided that the source (and where appropriate, the copyright) is acknowledged. Apart from any fair dealing for the purposes of review or criticism under The Copyright Act no. 98, 1978, Section 12, of the Republic of South Africa, a single copy of an article may be supplied by a library for the purposes of research or private study. No part of this publication may be reproduced, stored in a retrieval system, or transmitted in any form or by any means without the prior permission of the publishers. Multiple copying of the contents of the publication without permission is always illegal. U.S. Copyright Law applicable to users In the U.S.A. The appearance of the statement of copyright at the bottom of the first page of an article appearing in this journal indicates that the copyright holder consents to the making of copies of the article for personal or internal use. This consent is given on condition that the copier pays the stated fee for each copy of a paper beyond that permitted by Section 107 or 108 of the U.S. Copyright Law. The fee is to be paid through the Copyright Clearance Center, Inc., Operations Center, P.O. Box 765, Schenectady, New York 12301, U.S.A. This consent does not extend to other kinds of copying, such as copying for general distribution, for advertising or promotional purposes, for creating new collective works, or for resale.
Honorary Legal Advisers
M H Attorneys Auditors
Genesis Chartered Accountants Secretaries
The Southern African Institute of Mining and Metallurgy 7th Floor, Rosebank Towers, 19 Biermann Avenue, Rosebank, 2196
PostNet Suite #212, Private Bag X31, Saxonwold, 2132 E-mail: journal@saimm.co.za
Telephone (011) 463-7940 . E-mail: barbara@avenue.co.za
ISSN 2225-6253 (print) . ISSN 2411-9717 (online)
South Africa’s mineral resource availability as a potential driver for transitioning to a circular economy by S. Khan, B. Maphalala, Z. Nontso, F. Magweregwede, L. Godfrey
The aim of this paper was to establish if mineral resource scarcity is a driver for South Africa to transition to a circular economy. At least 18 minerals were classified indicatively (for the purpose of this study) as critical or strategic. The findings suggest that the scarcity of mineral resources is a critical driver for the country. Minerals are non-renewable resources and at-risk of depletion, therefore sustainable extraction and use are critical. There is an opportunity for South Africa to transition from a minerals export-based model to one that promotes local mineral beneficiation and manufacturing of end products.
Refinery effluent water reduction and treatment by Z. Ndabezimbi, S. Pule, E. Cupido, A. Hefer
This paper outlines projects implemented at Rand Refinery to reduce effluent generation and freshwater consumption. The refinery has initiated projects such as granulation water recycle and silver leach optimisation to address these issues. The granulation water recycle project has successfully reduced effluent volumes, while the silver leach optimisation has further decreased effluent. The vibratory shear enhanced processing (VSEP) trial showed promising results for gold recovery from wastewater with further trials recommended.
MINESAFE CONFERENCE PAPER
Preventing another health tragedy: A framework to manage diesel particulate matter in underground mines by C.J. Badenhorst, J.D. Swanepoel, S. Horn
Diesel particulate matter (DPM) is a significant health hazard in underground mining operations, where the use of diesel-powered equipment in confined spaces can lead to high levels of exposure among people working in these environments. Classified as a carcinogen, DPM has been linked to severe health effects. Effective management of DPM is essential, not only to protect people’s health but also to ensure regulatory compliance, maintaining operational efficiency, and safeguarding the long-term viability of mining companies.
PROFESSIONAL TECHNICAL AND SCIENTIFIC PAPERS
Application of an empirical method and numerical modelling to the Merensky Reef crush pillar stability by K.B. Le Bron, T. van Aard
When it comes to pillar stability analyses for mines in the Bushveld Igneous Complex (BIC), this paper presents the case for combining the empirical method with numerical modelling. The benefits include an understanding of potential failure mechanisms, which may then be accounted for in the designs. In addition, a number of other factors may be studied using numerical modelling as these are not accounted for in the empirical method.
Simulation of kinetic joint forces in a nutating grinding mill by J.J. van Tonder, J.R. Bredell, C. Coetzee, J. Branehog
A nutating grinding mill achieves efficient particle size reduction through the accelerated motion of the material charge within the nutating chamber. This design offers a compact solution compared to tumbling mills. Recognising the need to model internal forces in such a mill, this study focuses on the uncoupled simulation using multibody dynamics and the discrete element method. The combined simulation approach predicted the resultant forces in the critical kinematic joint within a 20% margin.
Investigation of physical and mechanical properties of polymer based composite material using volcanic tuff dust in Cappadocia, Turkey
by I. Çinar
Quarries in Cappadocia release large amounts of tuff into the environment as waste. Such material can be of use in the building sector. In this study it was observed that, as the percentage of volcanic tuff dust in the mixture increased, the water absorption rate of the material increased, uniaxial compression strength and point load strength decreased, and uniaxial compressive strength and point load strength decreased.
Prediction and measurement of blast induced rock fragmentation − A case study of Kajiado County quarries, Kenya by E.K. Mutinda, B.O. Alunda, I.O. Ondicho, E. Agyekum
Driven by the necessity to improve blast performance regarding fragment size distribution in limestone mines, this paper introduces the prediction and measurement thereof through the modified Kuz-Ram (MKR) and Kuznetsov-Cunningham-Ouchterlony (KCO) models. The MKR and KCO models were utilised to identify the most appropriate model for application in Bisil and Simba quarries situated in Kajiado County, Kenya. The study concluded that KCO outperformed MKR in accurately predicting blast fragment sizes in the examined quarries. ESG CONFERENCE PAPERS
113
MTo act or not act (timeously), that is the question for the future
ining has always been about more than just extracting minerals from the earth. It is about securing the future, balancing economic imperatives with environmental responsibility, technological innovation, and the well-being of those who power this industry. As we move forward, we must ask ourselves: are we truly mining with the future in mind?
The challenge of resource scarcity is real, and it is reshaping how we think about mining. The days of endless reserves are behind us, and the industry must shift from a model of extraction and export to one that embraces beneficiation, circularity, and long-term resource stewardship. The push towards a circular economy is no longer a theoretical discussion, it is a business imperative. If we fail to maximise the value of our minerals beyond extraction, we risk losing economic opportunities that could drive sustainable development across the continent.
Operational excellence remains key. New technologies are transforming mining, allowing us to extract resources with greater efficiency while reducing waste and energy consumption. But efficiency cannot come at the cost of health and safety. The risks of occupational diseases, particularly in underground mining, are well known, yet we often move too slowly in addressing them. Have we learned enough from past health crises, or are we waiting for another preventable tragedy before we take decisive action? Mining cannot afford to be reactive, it must be proactive in protecting its workforce.
The environment is another frontier where mining must do better. The industry is under greater scrutiny than ever, with water use, emissions, and rehabilitation practices facing intense public and regulatory pressure. Companies that do not prioritise sustainability will find themselves struggling to maintain their license to operate. Those that embrace environmental responsibility as a core business principle will be the ones that thrive in the years ahead.
Mining has the potential to be a driver of economic and social progress, but only if we rise to meet the challenges before us. The research in this edition highlights both the risks and the opportunities that lie ahead. It reminds us that the choices we make today will define the legacy of our industry. Will we be remembered as the generation that mined responsibly, using innovation and sustainability to build a lasting future? That is the challenge and the opportunity before us.
n one of my previous articles, I floated the idea that critical minerals can be key levers to industrial development, leading to substantive technological and economic catch-up. Although the role of mineral endowment in the technological and economic catch-up framework is vague and still poorly understood, there is no doubt that value addition and localisation of manufacturing value chains can have a long term impact on the economic well-being of resource-rich countries. The emphasis on industrial development means that the concept of technological and economic catch-up should not be viewed narrowly within the context of clean energy or just energy transition, but rather, from a broader industrialisation and technology upgrading point of view. The nexus between value-added manufacturing capabilities and industrial development has precipitated urgent calls for resource-rich countries to increase the level of beneficiation of mineral resources in host communities.
The view that Africa should focus on exporting processed products rather than raw commodities were echoed in various discussion forums at the recently concluded Mining Indaba 2025 held in Cape Town. The theme of this year’s indaba had an interesting vibe to it, with key discussions focusing on the requisite actions to secure the future of African mining, with specific emphasis on increasing investment confidence, policy stability, and on building collaborative partnerships that can lead to shared and tangible economic value. Judging by the intensity of messaging, there is obvious convergence among politicians, academia, and industry on the need to increase the levels of value addition and beneficiation in host communities. Public announcements by key industry and public figures also highlighted the need to promulgate policies that incentivises local beneficiation, with specific emphasis on fostering innovation and sustainability in the minerals industry. Despite the strong convergence on the need to maximise the value addition and beneficiation of mineral products, both industry and the public seem to hold diverging views on the implementation framework and way forward. For example, the focus by industry on the need for more incentives, tax breaks, infrastructure availability (such as electricity, rail, and port), and quality of skills, may be dichotomous to government priorities of focusing on industrialisation, socio-economic development, and employment creation for historically disadvantaged members of society. These diverging views and priorities naturally create challenges to the implementation of a holistic value addition and beneficiation strategy unless protracted effort is directed at developing and implementing an industrial policy and implementation strategy that caters for the needs of all the stakeholders in the industry.
Industrial policy can be defined in many ways. In principle, industrial policy refers to a deliberate government strategy to actively support and shape specific industries in economic sectors deemed crucial for competitiveness in the global arena. Depending on economic capacity and need, a government can use industrial policy tools and levers such as subsidies, tax breaks, trade protection, dedicated R&D funding, and preferential procurement, among others, to promote a sector-specific technological advancement and, ultimately, the overall industrial development and economic development. Using industrial policies and its levers to stimulate growth in a specific industry is not new and can be traced back to influential economists. One such example was Friedrich List (1789-1846), a German economist who, through his seminal nationalist theory of political economy, advocated for the need to use tariffs as a tool to protect fledgling industries. Recent examples of targeted industrial policies levers include China’s Made in China 2025 strategy, the United States’ CHIPS and Science Act 2022, Japan’s Monozukuri economic blueprint,
and Germany’s Industrie 4.0, among others. For the African continent, the African Minerals Development Strategy promulgated by the African Union is a bold and ambitious strategy that has significant potential to promote the sustainable extraction, production, beneficiation, and commercialisation of Africa’s mineral resources.
While industrial policies and other statutory instruments can act as effective tools and levers to increase the local content of value-added manufacturing and services in the mining sector, their effectiveness is strongly dependent on a myriad of economic, social, technological, and political factors. If value-addition and beneficiation is a mission, then the industry needs mission-oriented industrial policies to drive innovation and technological upgrading in that specific industry. Instead of protectionism and tariffs as tools and policy levers, a clear strategic framework supported by bold strategies and incentive levers to encourage new players to integrate into the downstream beneficiation of mineral products is required.
Similar to China’s deliberate support of new and strategic industries through the Made in China 2025 strategy, tangible results and impact can be achieved by supporting and incubating agile SMEs and SMMEs to drive the downstream industries. By supporting the so-called “little giants” in strategic industries (see details here https://thediplomat.com/2024/08/china-is-betting-big-on-its-little-giants/), the Chinese government deliberately considers smaller firms as valuable sources of innovation and basic force for improving the competitiveness of the value addition and beneficiation supply chain. Through strategic support, the state plays dual entrepreneurial and accelerator roles (an interesting analysis is available here: https://merics.org/en/report/accelerator-state-how-china-fosters-little-giant-companies), akin to building and supporting an Olympic sports team.
In conclusion, the dissonance arising from the current export of raw and unbeneficiated mineral commodities is understandable. However, there is a need for practical steps to increase the levels of value addition and beneficiation in host communities. A clear strategic framework supported by bold policies and incentive levers is required to integrate new entrants into the downstream beneficiation of mineral products. Akin to craftmanship, building a solid base of skills through high quality STEM graduates and industry PhDs is crucial to unlock the entrepreneurial potential of SMMEs and SMEs active in the downstream industries. R&D incentive levers and collaborations (local, regional, and international) are also required to unlock value from complex value chains.
In line with my quest for a deeper Socratic engagement, I am looking forward to further engagement on this complex subject.
E. Matinde President, SAIMM
March 2025 marks the 25th anniversary of the initial SAMREC Code. A series of celebratory events are planned throughout the year and will be announced in due course.
March 2025 marks the 25th anniversary of the initial SAMREC Code. A series of celebratory events are planned throughout the year and will be announced in due course.
A SAMCODES profile has been established on LinkedIn, pay a visit to get up to speed with current developments. https://www.linkedin.com/company/samcodessa/
A SAMCODES profile has been established on LinkedIn, pay a visit to get up to speed with current developments. https://www.linkedin.com/company/samcodessa/ SAMCODES App
SAMCODES App
The App is alive and updated and offers a useful platform to access current SAMCODES information.
The App is alive and updated and offers a useful platform to access current SAMCODES information.
The new quiz has been uploaded. Test your proficiency and know-how on the SAMCODES by doing the effective and informative quiz. It will take only a few minutes to complete. Check out the SAMCODES App User Guide for step-by-step instructions: https://lnkd.in/emT8976z
The new quiz has been uploaded. Test your proficiency and know-how on the SAMCODES by doing the effective and informative quiz. It will take only a few minutes to complete. Check out the SAMCODES App User Guide for step-by-step instructions: https://lnkd.in/emT8976z
Training programmes
Training programmes
The Young Professionals course is planned to be offered as part of the of the celebrations of the 25th anniversary of the SAMREC Code.
The Young Professionals course is planned to be offered as part of the of the celebrations of the 25th anniversary of the SAMREC Code.
Additional training and awareness campaigns will be announced in due course. In the meantime, look out for the Launch of Industrial Minerals Guideline in March 2025.
Additional training and awareness campaigns will be announced in due course. In the meantime, look out for the Launch of Industrial Minerals Guideline in March 2025.
Committee updates
Committee updates
Continuation of incorporation of ESG Factors into SAMCODES and recommendations for additions January and feedback is expected by 15 January 2025
Continuation of incorporation of ESG F into SAMCODES and ecommendations for additions updates to the is expected by 15th January 2025
to SAMCODES course was also held successfully in October 2023 for
Progress is being made on the update of the Industrial Minerals Guidelines and a draft working document has been circulated for comment and feedback is expected by 15 January 2025. Link to updates
Progress is being made on the update of the Industrial Minerals Guidelines and a draft working document has been circulated for comment and feedback is expected by 15 January 2025. Link to updates
SAMCODES ESG Working Group Activities
The committee has been driving the use of the SAMCODES App and running quizzes successfully in October 2023 for will focus on what the UNFC is, Minerals Act, AMREC, and brief Africa, as well as an update on https://www.gssa.org.za/uploads/newsletters/Events/UNFC_Workshop.pdf of the SAMCODES App and
Draft documents from the SAMCODES ESG Working Group have been released for comments. The documents provide reviews of the disclosure requirements for incorporation into the SAMCODES. Andy McDonald, Chairperson of the SAMCODES ESG Working Group presented at the ESGS conference. The recording and presentation is available on the following link.
20 February 2024, to be hosted by GSSA, will focus on what the UNFC is, studies of how it is applied, the Critical Raw Minerals Act, AMREC, and brief PARC, and then what the situation is in South Africa, as well as an update on CRISCO bridging document: https://www.gssa.org.za/uploads/newsletters/Events/UNFC_Workshop.pdf
Draft documents from the SAMCODES ESG Working Group have been released for comments. The documents provide reviews of the disclosure requirements for incorporation into the SAMCODES. Andy McDonald, Chairperson of the SAMCODES ESG Working Group presented at the ESGS conference. The recording and presentation is available on the following link.
International Liaison
International Liaison
The JORC Code update is in progress and consultation with stakeholders has been completed. The JORC Committee will advise of the anticipated adoption of the updated Code in due course.
The JORC Code update is in progress and consultation with stakeholders has been completed. The JORC Committee will advise of the anticipated adoption of the updated Code in due course.
J. Mainama
Vice Chairperson of the SSC (SAMCODES Standards Committee)
Mining operators are seeing an increased demand for minerals and ores. Operators must now consider the costs of pump maintenance and replacement as well as the cost-benefit of utilizing fewer larger pumps versus several smaller pumps to perform the same work.
Mining operators are seeing an increased demand for minerals and ores. Operators must now consider the costs of pump maintenance and replacement as well as the cost -benefit of utilizing fewer larger pumps versus several smaller pumps to perform the same work.
The KSB GIW® MDX pump line delivers proven results in the harshest hard rock mining applications.
The KSB GIW® MDX pump line delivers proven results in the harshest hard rock mining applications.
Affiliation:
1Council for Scientific and Industrial Research (CSIR), South Africa
2Mine Health and Safety Council (MHSC), South Africa
Correspondence to:
S. Khan
Email: SKhan2@csir.co.za
Dates:
Received: 1 Oct. 2024
Published: February 2025
How to cite: Khan, S., Maphalala, B., Nontso, Z., Magweregwede, F., Godfrey, L. 2025
South Africa’s mineral resource availability as a potential driver for transitioning to a circular economy. Journal of the Southern African Institute of Mining and Metallurgy, vol. 125, no. 2, pp. 61–68
DOI ID:
https://doi.org/10.17159/2411-9717/742/2025
ORCiD:
S. Khan
https://orcid.org/0000-0002-6362-5361
B. Maphalala
https://orcid.org/0000-0002-4152-472X
Z. Nontso
https://orcid.org/0009-0004-5464-4108
F. Magweregwede
https://orcid.org/0000-0002-4824-2266
L. Godfrey
https://orcid.org/0000-0003-1616-6921
This paper is based on a presentation given at the Southern African ESG in the Minerals Industry Challenges and Oppportunities Conference 2024, 16-17 October 2024, Glenburn Lodge and Spa, Muldersdrift
by S. Khan1, B. Maphalala1, Z. Nontso1, F. Magweregwede2, L. Godfrey1
Abstract
The aim of this paper was to establish if mineral resource scarcity is a driver for South Africa to transition to a circular economy. The project objectives were achieved by investigating economically viable, and critical or strategic minerals remaining in South Africa, as well as resource scarcity, as a driver for South Africa to transition to a circular economy. The study found that some minerals in South Africa, such as iron ore, lead, manganese, gold, and cobalt have less than 50 years of economically viable mining remaining. At least 18 minerals can be classified indicatively as critical or strategic: aggregates, bauxite, chromite, cobalt, copper, gold, graphite, iron, limestone, lithium, manganese, nickel, phosphorous, platinum group metals, rare earth elements, silver, titanium, and vanadium. The classification was based on the minerals’ economic importance, supply risk, and potential use in the development and manufacturing of emerging technologies.
The findings suggest that the scarcity of mineral resources is a critical driver for the country to transition to a circular economy. Other identified drivers include socio-economic factors, climate change commitments, and business objectives. All minerals are non-renewable resources and at risk of depletion, therefore sustainable extraction and use are critical. Priority should be directed at investigating circular economy opportunities and substitutes for commodities at risk of being depleted within the next 50 years. There is an opportunity for South Africa to transition from a minerals export-based model to one that promotes local mineral beneficiation and manufacturing of end products.
Keywords circular economy, critical minerals, critical raw materials, resource scarcity, strategic minerals
Circular economy (CE) is defined by the Ellen MacArthur Foundation as a systematic approach to economic development designed to benefit businesses, society, and the environment (EMF, 2017). In the South African mining sector, the popular economic model is a ‘take-make-dispose’ model where resources are extracted, used for a short period, and then discarded back into the environment. This generates large amounts of waste materials, water, and energy (Nahman, et al., 2021). Contrary to the ‘take-make-dispose’ economic model, a circular economy entails ‘keeping materials and products in circulation for as long as possible through practices such as reuse and repurposing of products, sharing of underused assets, repairing, recycling and remanufacturing’ (Schroder, 2020).
Mining can simply be defined as the extraction of mineral deposits from the surface or subsurface of the earth. The methods that are used to extract mineral deposits can be generally classified into underground and surface mining (Hartman, 1987). Surface mining methods are used to extract nearsurface mineral deposits, while underground mining methods are used to extract deep orebodies that cannot be economically mined using surface mining methods (Hartman, 1987). Mining was historically left outside the CE loop; however, recent studies show that CE may present many opportunities to the mining sector through the sustainable use of natural resources (Lebre, et al., 2017) (Figure 1).
This paper explores CE from a resource perspective and in the context of the South African mining sector.
The objective of the study detailed in this paper was to determine whether South Africa’s (SA) resource availability is a potential driver to transition to a CE in the South African mining sector. The approach taken to achieve these objectives was by answering the following research questions:
➤ How many years of economically viable minerals and metals does SA have?
➤ What are potentially SA’s critical/strategic minerals?
➤ Is resource scarcity a driver for SA to transition to a more CE?
Literature review
South African mineral landscape
SA is rich in natural resources, particularly minerals. The mining and metals sector (MMS) comprises nine subsectors: cement, lime, aggregates, and sand (CLAS); coal mining; diamond mining; diamond processing; gold mining; jewellery manufacturing; platinum group metals (PGM); services incidental to mining; and other mining, which includes the mining of iron ore, chrome, manganese, copper, and phosphates (MQA, 2021).
The MMS has contributed greatly to the South African economy and provides both direct, and indirect employment. The MMS employs more than 450 000 workers, whereby the majority are employed in the PGM (163 538), gold (93 682), and coal (91 459) subsectors (Statista, 2021).
Some of the commodities that the country hosts include gold, PGM, coal, diamond, copper, chrome, iron, lead, manganese, nickel, titanium, vanadium, zinc, andalusite, fluorspar, phosphate, vermiculite, asbestos, and uranium. In terms of its mining contribution to the country’s GDP, SA ranks as fifth in the world (Wits Mining Institute, 2020). Of the total global reserves, SA hosts 88% PGM, 80% manganese, 75% chromite, and 13% gold reserves (Wits Mining Institute, 2020).
The South African mining industry is unique and gradually evolving in that complex ore bodies are being mined at greater depths. Consequently, challenges, such as increasing operating costs, aging infrastructure, and severe health and safety concerns become apparent (Mitchell, 2016). Additionally, there is an increased demand for access to reliable energy, better quality of resources exploited, and interventions for transitioning to carbon neutrality (OreFlow, 2020).
Critical raw materials (CRM), as defined by the European Union (EU), are raw materials that are economically and strategically important to the European economy and have a supply that is subjected to high risk (Ferro and Bonollo, 2019), whereas strategic minerals are minerals/metals that are also essential to the economy, modern technology and industry, have a limited supply, and are subject to disruption (Bharat, n.d.). In SA, the concept of CRM is relatively new, and the term ‘strategic minerals’ is generally accepted as CRM, as both are economically important and their supply is associated with high risk, therefore these terms may be
used interchangeably in SA. These minerals could be critical to a variety of sectors for commercial and governmental applications, for example, green technology, telecommunication, space explorations, aerial imaging, aviation, medical devices, micro-electronics, transportation, defense, and other high-tech products (Critical Raw Materials Alliance, 2020). Additionally, the lack of viable substitutes for these essential minerals, because of their unique and reliable properties, further adds to their critical nature.
The existing EU formula for determining CRM could not be adopted in the South African context due to its complexity and the lack of data in SA. Therefore, the technology landscape was assessed to identify emerging technologies that will drive the demand for specific minerals and metals rendering them critical.
Globally, countries are steadily transitioning to renewable energy (RE) to sustain energy requirements and meet increasing energy demands whilst also trying to reduce their carbon footprint. This has given rise to the use of electric vehicles (EV), batteries, wind turbines, solar, and hydropower, which all contribute greatly to the reduction of greenhouse gas emissions (GHG) (Buschke, et al., 2021). Furthermore, the digital transformation of the twenty-first century has led to the development of cutting-edge technologies that are critically dependent on several minerals, thus any resourcerich country needs to have an informed understanding of the correlation between RE and digital technologies respective to the required minerals/metals.
The rapid adoption of EV coupled with low carbon future targets has placed minerals/metals like rare earth elements (REE), PGM, lithium, and cobalt, among others, in high demand. The automotive industry is the leading driver of platinum demand, and the use of platinum as a substitute for palladium has amplified its demand (Creamer, 2021). Notably, some of these potential CRM are not actively mined in SA. One example of a mineral not currently mined in SA is bauxite for aluminium production, which has properties critical to CE in that it can be infinitely recycled and thus has been dubbed as ‘a metal of the future’ (Kapur, 2020).
Clean energy technologies, the military, and consumer electronics have increasingly been associated with REE, and growth in these sectors is directly proportional to the demand for REE (Massachusetts Institute of Technology, 2016). Although SA hosts only about 0.7% of the world’s REE reserves and no active mining has occurred, reserves are reported to be of very high grade (Steenkampskraal, 2022).
Current trends in technology development and adoption indicate a transition toward sustainability in sectors such as mining being inevitable (Anglo American, 2019). For the mining industry in SA to be in the optimal position to exploit opportunities that will
arise from this transition and technology evolution, it is essential to understand the resources available, their applicability, technology trend adoption, and minerals properties such as recyclability, available substitutes, and quantity.
The methodology entailed collating secondary data through a literature review and gathering primary data through the use of qualitative research methods comprising stakeholder engagements and survey questionnaires. Stakeholder engagements were conducted through two workshops and interviews between January and February 2022. The stakeholder groups for the first workshop included geologists, mining engineers, mineral economists, and mineral resource management practitioners. The stakeholder groups for the second workshop included environmental management practitioners and professionals involved in issues related to sustainability and environmental, social and governance (ESG), and materials stewardship.
The information solicited enabled the project team to answer the research questions for this study.
Determining the remaining number of years of economically viable minerals in SA
A reserve is that part of an in situ demonstrated resource that can be economically extracted or produced at the time of estimation (SAMCODES, 2016). The years to depletion of minerals in SA was calculated using secondary mineral reserve and production data as shown in Equation 1 (Parry, 2021).
Mineral reserve and production data were obtained from different sources including the Minerals Council South Africa (MCSA), Statista, United States Geological Society (USGS), and the World Nuclear Association. The units of the data for reserves and production were standardised to million tonnes (Mt). The mineral reserve for each commodity was reported in terms of metal content and the annual production for each commodity was reported in terms of the tonnage of the saleable product.
Determining SA’s critical raw materials/strategic minerals
At the time this study was undertaken, there was no well-defined methodology for determining CRM in SA. Different countries have used various methods over time to determine the criticality of raw materials, which vary due to differences in mineral resource strategies based on a country's mineral endowment and mineral resource access. Martin et al. (2022) introduced a method in Spain that uses three quantifying indicators: overall supply, environmental impacts of sourcing material, and environmental justice threats at the sourcing location. In Germany, the Economic Product Importance method was introduced to evaluate the relevance and significance of a specific raw material for a particular product system (Lütkehaus, et al., 2022).
The EU methodology was selected as a reference for determining CRM in SA for several reasons. Firstly, it is an established methodology that has been used and refined over time, making it a reliable reference point. Secondly, the criticality of raw materials in the EU methodology is linked to demand driven by technological advancements, which aligns with the current global context of technological advancement and innovation. Thirdly, unlike other countries, SA has a substantial mineral endowment
that renders certain variables in the methodologies from other countries less significant. Therefore, the EU methodology's adaptability to different contexts makes it a suitable reference for SA’s criticality evaluation. However, it should be noted that data availability, accessibility, and accuracy are critical in any methodology. Since there may be challenges with the availability and accessibility of data relating to mineral resources in SA, a ‘hybrid’ methodology that adapts elements of the EU approach was selected.
The EU uses two key parameters for determining the criticality of materials, which are: economic importance (EI) and supply risk (SR), as shown in Equation 2 and Equation 3.
Where:
EI
= Economic importance
As = The share of an end use of a raw material in an NACE Rev 2 (2-digit level) sector
Qs = The sector’s VA at the NACE Rev (2-digit level)
SIEI = The substitution index of a raw material related to economic importance
S = denotes sector
Where:
SR = Supply risk
HHI = Herfindahl Hirschman index
WGI = scaled World Governance index
IR = Import reliance
EoLRIR = End-of-life recycling input rate
SI = Substitution index (in supply risk)
It was found that the EU methodology could not be used as-is in the South African context due to the complexity of the variables it uses in its formulae and the lack of appropriate local data. To address this, CRM in SA were determined by linking minerals to emerging technologies, which links to the ‘economic importance’ parameter in the EU methodology. This was done by taking cognisance of the fact that the world has been in a steady transition of adopting many disruptive technologies, such as clean-energy and Fourth Industrial Revolution (4IR) technologies. The intention of linking minerals with technologies was to understand which minerals will be in demand in the future in terms of parameters such as offering opportunities for socio-economic growth, gross domestic product (GDP) contribution, employment, and reducing the environmental impact of mining.
As of November 2024, a critical minerals strategy, including a critical minerals list for SA, is in the process of being developed by the South African government. The list provided in this paper was defined only for the purpose of achieving the objectives of this study and was primarily focused on energy transition minerals, which have an export significance in the context of SA. Once the strategy is finalised, the critical minerals list for SA will be officially adopted.
This research question was addressed based on the results of the preceding research questions and through the collection of qualitative data from engagements with stakeholders.
Results and discussion
South African economically viable minerals and years to depletion
The results showing the remaining years to depletion of mineral commodities are reported in ranges and summarised in Table 1.
The detailed reserve and production data used in the calculations for each mineral commodity is shown in Table 2.
The limitation of the equation used was that the years to depletion determined in this study were based on current knowledge of parameters such as current reserves, current production rates, and demand and supply and are therefore indicative figures. However, it is acknowledged that various technical and economic factors could affect the reserves and
Table 1
Summary of remaining years to depletion of mineral commodities
Range of years to depletion Mineral commodities
< 20 Iron ore, lead, manganese
20 – 50 Gold, cobalt
50 – 100 Zinc
100 – 500 Coal, copper, PGM, vanadium
> 500 Chromium, fluorspar, nickel, phosphate, titanium, uranium, vermiculite, zirconium, diamonds
Table 2
production values, such as the dynamic nature of reserves, geological factors, demand, and commodity prices.
The results indicate that three (3) minerals (iron ore, lead, and manganese) could potentially be depleted in less than twenty (20) years of mining, two (2) minerals (gold and cobalt) in twenty to fifty (20 -50 years), one (1) mineral (zinc) in fifty to one-hundred (50100) years, four (4) minerals (coal, copper, PGM, and vanadium) in 100 - 500 years, and nine (9) minerals (chromium, fluorspar, nickel, phosphate, titanium, uranium, vermiculite, zirconium, and diamonds) could potentially be depleted after five-hundred (500) years. Even though SA hosts large reserves of graphite and REE, there is currently no production – despite positive growth in demand for these minerals globally. Both have an expected compound annual growth rate (CAGR) greater than 4%.
As per the project scope, the years to depletion calculations considered in situ underground reserves only. However, recommendations for future work include investigating reserves in tailings storage facilities and/or waste dumps, as mining of tailings and waste dumps may prove to be economically viable. The results indicating that some minerals have less than 50 years of economically viable mining remaining raises concerns regarding mineral scarcity and the impacts thereof.
From the selected approach, eighteen (18) minerals were identified as potentially critical or strategic in SA, based on their applicability and importance to emerging technologies and in their respective sectors. A summary of the minerals corresponding to emerging technologies is shown in Table 3.
Input data and years to depletion for mineral commodities
Commodity
*Source: IBM, (2020); MCSA, (2021); Statista, (2020); USGS, (2021); World Nuclear Association, (2021)
Table 3
Summary of emerging technologies with corresponding minerals required for technology development
Emerging technology Corresponding minerals required to develop the technology
Hydrogen fuel cells
Platinum, rare-earth elements (REE), PGM, cobalt, vanadium, manganese
3D printing Titanium, magnesium, REE, lithium
Solar photovoltaic cells REE, copper, aluminium, indium, gallium, selenium, silver, tellurium
Robotics
Cobalt, chrome, lithium, vanadium, PGM
E-mobility (electric vehicles) Manganese, nickel, copper, PGM, vanadium, cobalt, natural graphite, lithium
Drones and UAV Manganese, chromium, nickel, copper, tellurium
Cloud and remote computing Copper, REE, indium, tungsten
Energy storage Copper, cobalt, nickel, lithium, REE
Table 4
South Africa’s strategic minerals
Critical/strategic minerals in SA
Justification for criticality status
Aggregates Essential in the construction sector
The identified critical or strategic minerals in SA are shown in Table 4 and Figure 2.
From the literature review and the hybrid methodology selected, findings regarding the CRM identified are aligned to findings from later research that was conducted by VBKOM (VBKOM, 2023), apart from coal that was not listed in the authors’ results. The reason for the exclusion of coal was that coal is not linked to an emerging technology, even though it is economically important. Furthermore, coal is not part of the green energy transition, it is however, recognised as a key mineral since SA is still heavily reliant on coal for power generation.
The stakeholders that were engaged were of similar views in terms of CRM that were identified, with the addition of minerals from the construction and agriculture sectors. The stakeholders concurred with the general observation that local beneficiation of these resources is lacking, such that growth is limited in local industries like manufacturing, and it must thus be improved, as quoted, ‘We would like to mine minerals and use them within SA rather than export them’.
Key comments and suggestions from stakeholders regarding CRM are summarised below:
➤ An understanding of the quantity of minerals and commodities will improve understanding of the requirements
Bauxite Essential in aluminium production, metallurgy, chemical industry, and use as a catalyst. SA does not have bauxite reserves.
Chromite Essential in robotics, UAV; steel production in SA accounts for about 70% of the world’s chrome reserves.
Cobalt (Co) Essential in energy storage technology and EV economy, however, SA was ranked 10th in world production in 2020.
Copper (Cu) Essential in solar photovoltaic (PV) cell production, electric mobility (e-mobility) industry, drones and unmanned aerial vehicles (UAV), remote computing, and energy storage.
Gold (Au)
Gold is important to the SA economy for its vital contribution to the GDP, employment, and for attracting foreign capital. Scarcity of gold resources and difficulty in mining are being experienced. SA was ranked 7th in production with 100 tonnes in 2021.
Graphite Essential in the e-mobility industry, however, SA has no graphite operations.
Iron (Fe) Essential in steel making; steel is highly recyclable, reusable, and can be used for renewable energy infrastructure and transportation networks.
Limestone Essential in steel manufacturing, mining, paper production, water treatment and purification, and plastic production.
Lithium (Li) Essential in green energy technologies, electric vehicles (EV), and electronics. SA has no lithium extraction or processing, however, can play a role in the refining and processing stage (Stage 3) as a key supply chain stage. SA does not have significant lithium reserves.
Manganese (Mn) Essential in the steel industry, hydrogen fuel cells, e-mobility, and UAV. SA possesses the largest manganese reserves at 5.5 million tons and is the leading producer. However, production has decreased in 2020.
Nickel (Ni) Essential in e-mobility, drones and UAV, and energy storage.
PGM (individual elements listed below): Often used as catalysts. SA holds 88% of the world’s PGM reserves.
Iridium (Ir) Essential in use as a hardening agent for platinum, also used in spin electronic devices.0
Osmium (Os) Essential in producing very hard alloys for fountain tips, instrument pivots, needles, and electrical contacts. Also used in the chemical industry as a catalyst.
Palladium (Pd) Essential in catalytic convertors. Can also be used in jewelry, medicine, and recently started being used in fuel cells to power cars.
Table 4 (continued)
Critical/strategic minerals in SA
Platinum (Pt)
Rhodium (Rh)
Justification for criticality status
Essential in the motor industry with use as a catalytic converter, also used in laboratory equipment, electrical contact, and electrodes.
Essential in use as a catalytic converter for cars, jewelry chemical, and electrical trades.
Ruthenium (Ru) Essential in the chemical industry for coating anodes of electrochemical cells for chlorine production, can also be used in solar cells.
Phosphorous Essential in the agriculture sector for fertilising purposes.
REE (individual elements listed below):
Essential in clean energy, defense technologies, high-tech devices, and LED lighting. SA only holds about 0.7% of the world’s REE reserves.
Cerium (Ce) Used in electronics like lights, TVs, and ovens.
Dysprosium (Dy) Used in wind turbines, EV, and nuclear reactors when mixed within alloys.
Erbium (Er) Used in lasers and fibre optics cables.
Europium (Eu) Used in light bulbs, nuclear reactors, and lasers.
Gadolinium (Gd) Used in magnets, nuclear reactors, and magnetic resonance.
Holmium (Ho) Used in magnets and nuclear reactors.
Lanthanum (La) Mixed within alloys that are used in batteries and hydrogen vehicles.
Lutetium (Lu) Used as a catalyst in refineries.
Neodymium (Nd) Used in magnets and lasers.
Praseodymium (Pr) Used in aircraft engines, fiber optic cables, and magnets.
Promethium (Pm) Used in pacemakers and guided missiles.
Samarium (Sm) Used in microwave devices and and other electronic devices such as stereos and headphones devices.
Scandium (Sc) Used for fuel cells and alloys used in jet planes.
Terbium (Tb) Used in light bulbs, memory devices, and X-rays.
Thulium (Tm) Used in lasers.
Ytterbium (Yb) Used in displays, x-ray machines, and fibre-optic cables.
Yttrium (Y) Used in radars and as an additive within allows used in high-tech devices.
Silver Essential in alloys, batteries, light emitting diode (LED) chips, PV energy, electronics, and jewellery.
Titanium Essential in rechargeable batteries, electronics, medicine industry, and EV.
Vanadium Essential in hydrogen fuel cells, robotics, and e-mobility.
*Source: Arcelormittal (2019); Anglo American (2015); Anglo American (2019); Basov (2022); Britannica (2021); BYju’s (2022); DMR (2014); Geology.com (2022); Geology News and Information (2014); Goodenough et al. (2021); Minerals Education Coalition (2016); Nickel Institute (2022); Passels (n.d.); Pistili (2021); Royal Society of Chemistry (2022); US Energy Information Administration (2022); Yuksel (2021)
Figure 2—Summary of SA’s potentially CRMs or strategic minerals
for the transition towards CE and can also put SA in an optimal position to manufacture and maintain technologies locally.
➤ Localisation and local beneficiation should be further assessed.
➤ Beneficiation to leverage mineral demand through the manufacturing industry to reduce the heavy reliance on exports is important.
➤ The importance of drawing the link between manufacturing and metals since the demand for certain minerals will be driven by the technologies regardless of whether certain minerals are produced locally or exported.
➤ Although SA remains in support of greater local beneficiation, one participant stated, “It is likely we will remain a net exporter of a lot of our new resources”.
➤ Investigate alternative or replacement materials for those minerals that are at high risk of depletion.
➤ REE and PGM must be looked at individually to determine the criticality and application of each element to contribute to further economic growth. Although the relevance of REE to SA has been recognised, the challenges associated with the mining of REE include supply chain, processing, environmental and geopolitical issues (Jellicoe, 2019). Investigate alternative economies that might arise with these emerging technologies, which may, in turn, unlock new employment opportunities.
As the results suggest, some minerals that were classified as critical in SA have less than 50 years of economically viable mining remaining (cobalt, gold, iron ore, lead, and manganese). It is therefore crucial that they be extracted and utilised in a sustainable manner to ensure that current and future minerals and metals demands are met. Although adopting circularity within the mineral value chain may be a potential solution for sustainable resource use, these minerals are mostly exported, suggesting that SA may have little control over their downstream circularity. This in turn shows the importance of local beneficiation and local manufacturing in SA so that the country may benefit from its own resources. Additionally, the idea of resource leasing as opposed to resource sales to trading partners may be further explored as a potential means to encourage responsible and sustainable resource use.
Resource availability (or scarcity) as a driver for a circular economy in South Africa
Coupled with several factors, resource scarcity is indeed the driver for CE in SA, although it is not the primary driver. The finite nature of resources, coupled with the excessive use that results from the global adoption of the ‘take-make-waste’ economy, ultimately result in constant resource shortage risk and inevitable depletion (Govindan, et al., 2015). With this reality in sight, CE may offer alternative solutions that will ensure economic and environmental sustainability, and the responsible consumption of natural resources. A CE may offer an alternative option that will optimise materials by aiming to keep them in use for as long as possible (PwC, 2019).
Certain international companies have already started using recycled materials for their electronic applications (e.g., Apple uses aluminum, copper, tin, and tungsten). Research conducted by the Organisation for Economic Co-operation and Development (OECD) showed drivers for the transition to a more CE, and in addition to resource scarcity, they include economic development, climate change, global agendas, private sector initiatives,
potential driver for transitioning to a circular
technological developments, and others (OECD iLibrary, 2022). Moreover, certain minerals have less than 50 years of economic viability, with some of these classified as strategic or critical in SA. The remaining years of economic viability of minerals, coupled with the finite nature of natural resources, which will eventually be depleted further, emphasise the availability and the supply constraints.
Key comments from stakeholder engagements pertaining to resource scarcity being a potential driver for the transition to a more circular economy are summarised in the following:
➤ Consider presenting CE from a growth and job creation standpoint in SA.
➤ Although SA is a resource-rich country, the answer to the driver for the transition has been challenging to specify because CE emerged from a resource scarcity context, however, the focus has now shifted.
➤ In instances where there are thousands of years of resources remaining, resource scarcity cannot be the driver for the transition. It then becomes essential to quantify jobs and new businesses that could be unlocked through CE.
➤ Some opportunities that could be derived from CE from mining operations could benefit mining communities socially, economically, and environmentally, however, understanding communities' skills is key in exploiting these opportunities.
➤ Drivers for CE transition are not limited to one factor but several, like the need for optimised processes, materials, and waste valorisation, limited supply of critical resources, climate change, global initiatives, economic growth, employment opportunities, population growth, and energy demands.
This paper details the methodology and findings of a study undertaken to determine if resource scarcity is a potential driver for SA to transition to a CE. Three key research questions were addressed in this paper, relating to remaining economically viable minerals in SA, critical or strategic minerals in SA, and resource scarcity as a driver for transitioning to a CE.
The findings revealed that there are less than 50 years of economically viable mining of certain minerals in the country, suggesting the risk of mineral depletion and its consequences.
Adopting circularity may mitigate this risk, however, these minerals are mainly exported and thereby limits the country to implement interventions to control the use of these minerals to benefit the economy and the people.
Eighteen minerals were identified as potentially critical or strategic in SA due to their economic importance and supply risk. The critical minerals in SA include aggregate, bauxite, chromite, cobalt, copper, gold, graphite, iron, limestone, lithium, manganese, nickel, PGM, phosphorous, REE, silver, titanium, and vanadium. Based on the findings, it was concluded that resource scarcity may in fact be a driver for SA to transition to a CE. Other drivers include the need for job creation, socio-economic factors, climate change commitments, and business objectives. All mineral commodities are scarce and should be used sparingly, sustainably, and responsibly for the benefit of present and future generations. Urgent priority should be aimed at those commodities that may potentially be depleted within the next 50 years of extraction, i.e., cobalt, gold, iron ore, lead, and manganese, by identifying and investing in CE opportunities for these commodities. These minerals, however, are mostly exported, suggesting that SA may
have little control over their downstream circularity. The importance of local beneficiation and manufacturing was emphasised in the study, especially as the demand for critical or strategic minerals increases. It is recommended that local beneficiation and local manufacturing should be prioritised so that SA may have control over its resources and potentially realise its long-term benefits.
Acknowledgements
We would like to thank the Department of Science and Innovation for funding this project, through the Waste Research Development and Innovation (RDI) Roadmap Implementation Unit hosted by the CSIR. We would like to acknowledge Prof. Linda Godfrey, Manager of the Waste RDI Roadmap Implementation Unit, for her guidance. We also thank all the stakeholders for their participation in this research.
References
Anglo American, 2019. Anglo American. [Online] https://www.angloamerican.com/futuresmart/stories/ourindustry/technology/trends-in-modern-mining-technology [Accessed 12 January 2022].
Bharat, S., n.d. Strategic & Critical Metals. [Online] https://nml.res. in/strategic-critical-metals [Accessed 19 April 2023].
Buschke, F., Estreguil, C., Mancini, L., Mathieux, F., Battistella, L., Weynants, E. 2021. Digital Storytelling Through the European Commission’s Africa Knowledge Platform to Bridge the Science-Policy Interface for Raw Materials. Circular Economy and Sustainability, vol. 3, pp. 1141–1154. Creamer, M. 2021. Platinum demand strengthening. Mining Weekly, 9 September. Critical Raw Materials Alliance. 2020. Critical Raw Materials. [Online] https://www.crmalliance.eu/critical-raw-materials [Accessed 04 August 2022]
EMF. 2017. Circular Economy in Detail, s.l.: s.n. Ferro, P., Bonollo, F. 2019. Materials selection in a critical raw materials perspective. Elsevier, pp. 1–9.
Geoscience Australia. 2022. Critical Minerals at Geoscience Australia. [Online] https://www.ga.gov.au/scientific-topics/ minerals/critical-minerals [Accessed 28 February 2023].
Hartman, H.L. 1987. Introductory Mining Engineering. United States of America: John Wiley & Sons Inc. IBM. 2020. Vermiculite, India: Government of India Ministry of Mines - Indian Bureau of Mines.
ICCM. 2016. Mining and metals and the circular economy, s.l.: International Council on Mining and Metals. IET. 2018. IET Raw MAterials, s.l.: IET( European Institute ofInnovation and Technology).
Jellicoe, B.C. 2019. The relevance of rare earths to South Africa. [Online] http://www.nstf.org.za/wp-content/uploads/2019/09/ Mr-Brent-Jellico-NSTF-Presentation-13-09-2019-v3-cut.pdf [Accessed 28 March 2022].
Kapur, A. 2020. The Green Metal, Aluminium, is the Metal of the Future. EPC World, 4 October.
Lebre, E., Corder, G.D., Golev, A. 2017. The Role of the Mining Industry in a Circular Economy - A Framework for Resource Management at the Mine Site Level. Journal Of Industrial, Issue 21.
Lütkehaus, H., Pade, C., Oswald, M., Brand, U., Naegler, T., Vogt, T. 2022. Measuring raw material criticality of product systems through an economic product importance indicator: a case study of battery electric vehicles. The International Journal of Life Cycle Assessment, vol. 27, pp. 122–137.
Massachusetts Institute of Technology. 2016. Rare Earth Elements Supply and Demand, Massachusetts: MIT.
MCSA. 2021. Facts and Figures 2020, Johannesburg: Minerals Council South Africa.
Mitchell, G. 2016. Challenges facing the emerging miners sector in South Africa, Johannesburg: Chamber of Mines.
MQA. 2021. Mining Company Registration. [Online] https://mqa.org.za/mining-company-registration/ [Accessed 05 January 2022].
Nahman, A., Godfrey, L., Oelofse, S., Trotter, D. 2021. Driving economic growth in South Africa through a low carbon, sustainable and inclusive circular economy. In: L. Godfrey, ed. The circular economy as development opportunity. Pretoria: CSIR, pp. 1–8.
OreFlow. 2020. OreFlow. [Online] https://oreflow.com.au/5challenges-the-mining-industry-is-currently-facing/ [Accessed 10 August 2021].
Outlook, W.E. 2021. The Role of Critical Minerals in Clean Energy Minerals in Clean Energy, s.l.: IEA.
Parry, R. 2021. Data on the remaining years of economically viable minerals in South Africa . [Interview] (19 October 2021).
Pistili, M. 2023. Cobalt uses: batteries and more. [Online] https://investingnews.com/daily/resource-investing/batterymetals-investing/cobalt-investing/cobalt-applications/ [Accessed 19 April 2023]. SAMCODES. 2016. The South African Code For The Reporting of Exploration Results, Mineral Resources and Mineral Reserves, s.l.: SAMCODES.
Plant and Soil Sciences e-Library (PASSel), n.d. Importance of Phosphorus to Plants. [Online] https://passel2.unl.edu/view/ lesson/0718261a1c9d/2 [Accessed 16 February 2022] Schroder, P. 2020. Promoting a Just Transition to an Inclusive Circular Economy, London: Chantam House.
Statista. 2020. Flourspar Mine Production Worldwide in 2020 By Country. [Online] https://www.statista.com/statistics/1051717/global-fluorsparproduction-by-country/ [Accessed 25 November 2021].
Statista. 2021. Number of People Employed by South Africa's Mining Industry in 2020 by Commodity. [Online] https://www.statista.com/statistics/241420/south-africanmining-key-facts/ [Accessed 22 November 2021].
Steenkampskraal. 2022. Steenkampskraal. [Online] https://www. steenkampskraal.com/ [Accessed 28 March 2022].
USGS. 2021. Mineral Commodity Summaries 2021, Reston, Virginia: United States Geological Survey.
VBKOM. 2023. Critical Minerals: A South African Perspective, Pretoria: VBKOM.
WEF. 2016. Can the circular economy transform the world's number one consumer of raw materials? [Online] https://www.weforum.org/agenda/2016/05/can-the-circulareconomy-transform-the-world-s-number-one-consumer-ofraw-materials/ [Accessed 10 February 2022].
Wits Mining Institute. 2020. The South African Mining Sector. [Online] https://www.wits.ac.za/wmi/about-us/the-south-africanmining-sector/ [Accessed 22 November 2021].
World Nuclear Association. 2021. World Uranium Mining Production. [Online] http://www.world-nuclear.org/ information-library/nuclear-fuel-cycle/mining-of-uranium/ world-uranium-mining-production.aspx [Accessed 05 January 2022].
Yuksel, A. 2021. What are tech metals and rare earth elements, and how are they used? [Online] https://www.cummins. com/news/2021/04/19/what-are-tech-metals-and-rare-earthelements-and-how-are-they-used#:~:text=How%20rare%20 earth%20elements%20and,electric%20vehicles%20and%20 nuclear%20reactors. [Accessed 17 February 2022].
Affiliation: Rand Refinery (Pty) Ltd, South Africa
Correspondence to: Z. Ndabezimbi
Email: ZintleN@gold.co.za
Dates:
Received: 25 Sept. 2024
Accepted: 13 Jan. 2025
Published: February 2025
How to cite:
Ndabezimbi, Z., Pule, S., Cupido, E., Hefer, A. 2025. Refinery effluent water reduction and treatment. Journal of the Southern African Institute of Mining and Metallurgy, vol. 125, no. 2 pp. 69–76
DOI ID: https://doi.org/10.17159/2411-9717/767/2025
This paper is based on a presentation given at the Southern African ESG in the Minerals Industry Challenges and Oppportunities Conference 2024, 16-17 October 2024, Glenburn Lodge and Spa, Muldersdrift
by Z. Ndabezimbi, S. Pule, E. Cupido, A. Hefer
Abstract
This article outlines various projects implemented at Rand Refinery to reduce effluent generation and freshwater consumption. The refinery generates about 2800 m³ of effluent annually and has initiated projects such as granulation water recycle and silver leach optimisation to address these issues. The granulation water recycle project has successfully reduced effluent volumes, while the silver leach optimisation has further decreased effluent by implementing stoichiometric addition of HCl and NaClO3. The vibratory shear enhanced processing (VSEP) trial showed promising results for gold recovery from wastewater, though further trials are recommended. The water savings of the effluent reduction projects are monitored by measuring the amount of effluent pumped to service yard effluent storage facilities with the use of flow meters connected on SCADA. Since the effluent reduction initiative of granulation effluent recycle in FY23, the effluent reduced to 2676 m³. In FY24, the stoichiometric addition of HCl and NaClO3 was implemented in the silver leach process, further reducing the effluent to 2083 m³.
Keywords
refinery effluent, granulation water recycle, vibratory shear enhanced processing (VSEP), silver leach optimisation, gold recovery, effluent management, resource conservation, environmental, social, and governance (ESG), fresh water consumption reduction
Introduction
Rand Refinery (Pty) Limited, established in 1920, is the world's largest integrated single-site precious metals refining and smelting complex. It refines gold within South Africa, handling mine dore’ deposits, jewellery scrap, and alluvial deposits with gold content ranging from 10% to 99%. The refinery employs three main technologies for refining gold and silver: Miller chlorination, gold electrolysis, and silver electrolysis, focusing on achieving 99.99% purity for gold (Au), and silver (Ag) and producing platinum group metals (PGMs), mainly Pt and Pd, containing sludge for sale (Figure 1).
Effluent is generated from silver leach, gold refining, offgas fumes scrubbing processes, and general processes such as granulation, quenching, and housekeeping. Between 2019 and 2023, the refinery generated about 2800 m³ of effluent per year on average, with limited recycling options, leading to high freshwater consumption. The target product quality of 99.99% on most products limits recycling options, as any trace element can lead to quality failure. The effluent is filtered for solids collection, passed through ion exchange resin for further polishing, and sent to an external company for treatment and disposal (Figure 2).
Several projects have been initiated to reduce effluent and freshwater use, contributing to environmental, social, and governance (ESG) compliance, focusing on natural resource conservation and waste management.
Rand Refinery, with its 103-year heritage, has refined over 56,000 metric tons of gold, accounting for 26% of the gold produced to date on earth. As a member of the London Bullion Market Association (LBMA) and with international accreditations, Rand Refinery adheres to best practices in ESG compliance.
Rand Refinery's ESG strategy aims to meet existing and upcoming regulations and demands, responding to climate change, societal risks and challenges while ensuring sustainable business practices. The journey to ESG maturity involves connecting various frameworks such as the UN Sustainable Development Goals (SDGs), LBMA Responsible Gold Guidance (RGG), and OECD Due Diligence Guidance, guiding the company's strategy in aligning business operations with global ESG objectives.
Rand Refinery has set clear deliverables for the next five years, focusing on decarbonisation and energy projects, waste and effluent reduction, water recycling and reuse, sourcing integrity platform – Gold Bar Integrity, community development, and skills development.
The ESG strategy offers several strategic benefits, including improved reputation and brand value, long-term sustainability and resilience, innovation and efficiency, regulatory compliance, and
enhanced stakeholder engagements. These benefits contribute to the company's overall goal of maintaining its legitimacy, credibility, and trust in the marketplace.
Firstly, the ESG strategy significantly improves Rand Refinery's reputation and brand value, enhancing customer loyalty and trust. Secondly, it encourages long-term sustainability and resilience by focusing on resource management and waste reduction. Innovation and efficiency are also key benefits, with the adoption of best-inclass operating efficiency standards and the development of new technologies and procedures. Regulatory compliance is another important aspect, with dedicated personnel examining required changes and offering appropriate advice. Lastly, the ESG strategy emphasises stakeholder engagement, building positive relationships with all key stakeholders through openness and transparent communication.
These strategic benefits collectively contribute to Rand Refinery's legitimacy, credibility, and trust in the marketplace, ensuring the company's long-term success and sustainability. Rand Refinery's commitment to ESG is not just about compliance but about creating value and ensuring a sustainable future. The company's efforts in safety, health, environment, governance, and community engagement are integral to its business operations and reputation.
Rand Refinery launched multiple projects, including evaluating the potential to extract additional gold and silver from various sources and devising techniques for water recycling to cut down on Rand Water costs. These activities primarily consisted of internal initiatives and testwork, although some involved assessing both existing and new technologies from suppliers. Here is a summary of these efforts.
A filtration testwork was conducted to determine the filtration
characteristics of the scrubber solution under pressure filtration conditions to enable possibilities of recirculation of the effluent back to the scrubber. Scrubber solution samples were collected to conduct analysis on the following:
➤ Slurry density
➤ Feed solids
➤ pH
➤ PSD
➤ Temperature.
The test was conducted using the following methodology: The agitated slurry was fed into the filter press using a diaphragm pump, with a predetermined slurry feed pressure applied. A timer was started simultaneously with the pressure application. The cake formation time was recorded when the last of the liquid passed through the surface of the cake, making it visible. The filtrate flow rate was reduced to approximately 10% of the initial flow rate. During filtration, the cumulative mass of discharged filtrate was recorded. After formation, the cake was subjected to a membrane squeeze, with the cumulative mass of discharged filtrate recorded over time. The cake was then collected, and its wet mass and thickness were measured before being oven-dried to determine its moisture content.
Granulation water recycling testwork
A feasibility study was carried out to quantify the effluent produced during the refinery process. Following this, an effluent sampling test was performed, where samples from various effluent streams were collected to examine their properties and pH levels. The pH analysis was conducted using a pH probe meter, while ICP-OES and titration methods were employed to determine the trace elements present in the effluent.
Silver leach stoichiometric addition
Testing was carried out to examine the feasibility and impact of total oxidation in silver leach operations by incorporating the necessary stoichiometric amounts of HCl and NaClO3 during the oxidation phase. To ensure complete oxidation and decrease the number of
HCl wash stages, an optimal copper concentration was established before the silver leach process. This was done to safely introduce the required stoichiometric quantities of HCl and NaClO3 into the silver leach reactors without risking overly vigorous reactions.
Vibratory shear enhanced processing techniques
The pilot study at Rand Refinery in Germiston involved running the VSEP pilot plant in batch mode on three waste streams: silver, primary scrubber, and fine gold. Samples were collected in 1000 L flow bins, and a smaller quantity was fed to the VSEP feed flow bin tank. A line out was conducted at 50psi to condition the membranes, followed by a pressure study at various pressures to determine the optimum operating pressure. The batch test run aimed to concentrate gold and other minerals for recovery by separating particulate materials into two streams. The concentrate stream had a high total suspended solids (TSS) value, while the permeate stream had a much lower suspended solids content.
The permeate stream was removed and fed to a permeate storage tank, while the concentrate was recycled back to the feed tank. This process continued until the membrane could no longer process the stream, and the flux began to decline. After each run or day, the system was cleaned using cleaning chemicals and water flushes. The pilot plant setup included the feed flow bin, VSEP skid with membrane pack, CIP tank, and permeate flow bin. The membrane pack, piping, feed pump, and vibratory motor were essential components of the system. During the trial, 19 membrane and diverter trays were used, but due to malfunctioning, a damaged membrane tray and one diverter tray were removed after processing the silver stream effluent, leaving 17 trays for the remaining runs.
For context, Tables 1 and 2 provide a summary of the effluent data for both the gold and silver effluent streams. The effluent output data for the fiscal years 2022 to 2024 show a general trend of reduction, with some fluctuations. In FY 2022, the effluent output was relatively high across all quarters. In FY 2023, there was a
Table 2
noticeable reduction, particularly in Quarter 4 (161.10 kl), which coincides with the start of the granulation recycling work on 29 July 2023. This trend continued into FY 2024, with significant reductions in Quarter 1 (173.62 kl), Quarter 2 (181.61 kl), and Quarter 4 (129.90 kl). However, there was an increase observed in Quarter 3 of FY 2024 (281.37 kl), indicating some variability in the effluent output over the years, which was caused a floor repairs project conducted on the granulation water recycle circuit area.
The effluent output data for the silver streams over the fiscal years 2022 to 2024 shows a general trend of reduction, with some fluctuations. In FY 2022, the effluent output was relatively high across all quarters, with Quarter 1 having the highest output at 313.96 kl. In FY 2023, there was a noticeable reduction in effluent output, particularly in Quarter 1 (236.02 kl) and Quarter 2 (194.36 kl), which coincides with the start of the silver leach stoichiometric testwork on 1 December 2022. This trend continued into FY 2024, with further reductions in Quarter 2 (195.78 kl) and Quarter 4 (172.19 kl). However, there were some increases observed in FY 2024, specifically in Quarter 1 (264.76 kl) and Quarter 3 (229.68 kl), indicating some variability in the effluent output over the years, this which was caused by floor repairs in the fine gold area, the effluent recycle area was off to allow the floor repair project to be completed. During this period all the high-pressure wash activities were conducted in the silver plant with clean water.
The Miller chlorination process generates chlorine fumes that contain trace amounts of gold and silver in the dust. These fumes are processed through a chlorine scrubber system, which uses caustic soda to neutralise the gaseous chlorine and capture the metal particles. The system consists of two sequential scrubbers—a primary and a secondary. The primary scrubber captures most of the metal particles in a caustic solution, while the secondary scrubber ensures complete neutralisation before the gases are released into the environment. The collected metal particulates in the scrubber solution are filtered monthly using a central filter press for metal accounting.
Due to limited recycling options, filtering the scrubber solution resulted in approximately 20 m³ of effluent being disposed of monthly via an external company, necessitating freshwater additions to the scrubber. To resolve this, a project was initiated in 2019 and completed in 2020 to install a dedicated filter press for the primary scrubber, allowing the scrubber filtrate solution to be recycled back into the primary scrubber. The advantages of this initiative include:
➤ Reduced handling and treatment of effluent since the filtrate will be recirculated.
➤ Continuous filtration and recovery of metal particles, improving daily metal accounting.
➤ Enhanced scrubber efficiency with ongoing removal of metal particles, increasing the solid loading capacity of the scrubber solution.
Currently, the main scrubber is drained every three months for metal accounting, saving about 160 m3 annually, which reduces treatment costs by roughly half a million rands. Figure 3 presents a 3D model of the primary scrubber filter press, illustrating the layout of the filter press in relation to the primary scrubber.
Effluent generated from various processes, such as silver and gold granulation, scrap cleaning, ducting washing, and melthouse sump, is first gathered in a fine gold effluent tank for preliminary filtration. It is then transported to a central effluent plant for further filtration and polishing disposal (see Figure 4).
The primary factor behind the increase in refinery output was the implementation of high-pressure wash cleaning for scrap in the fine gold area, along with the granulation process that involved daily production of gold granules. To minimise effluent generated by the fine gold plant, an initiative was introduced to reuse process water from the plants, thereby reducing the consumption of clean water and the effluent produced (Reeves, 2000).
Granulation effluent, identified as a clean effluent with a pH above 6.5, presents minimal risk of material corrosion and is thus suitable for use as process water, especially in scrap metal cleaning,
Silver Granulation Gold Granulation
ducting washing, and silver chloride quenching. Cleaning scrap metal is crucial for ensuring gold contaminants adhere to the scrap, so only clean scrap exits the refinery. Ducting washing is essential for stocktaking, as it removes material buildup in the ducts, which can then be collected through a filter press and treated as part of the recycle stream. Silver chloride quenching involves cooling molten chlorides in water, producing a slurry containing silver chloride that
is subsequently processed in a silver leach plant. Historically, these washing processes utilised potable water, resulting in significant effluent generation within the refinery.
A 5000-litre tank was installed to segregate and store the granulation effluent for reuse in less critical areas. This tank features instrumentation controls, including a level transmitter and a highlevel switch, to prevent overflows. Two filter housings were fitted
in series on the tank's outlet streams, equipped with 25-micron polypropylene Sentinel ring filter bags. These filters ensure efficient removal of solids, protecting sensitive equipment in areas where the effluent will be reused. Figure 5 illustrates the modification in the process flow, highlighting the newly added equipment within the shaded regions.
The refinery has effectively installed and commissioned a granulation water recycling system, which includes a 5000 L tank, a pump, and distribution pipes that supply various areas for tasks such as washing scrap and fine gold fumes ducting (refer to Figure 6). The project was fully operational by 29 July 2023, marking significant milestones like the successful cleaning of fine gold fumes ducting, efficient scrap metal management, silver chloride quenching, Ducon scrubber top and housekeeping improvements.
By August 2024, the amount of effluent released from the fine gold effluent tank to the central effluent plant had dropped by 205 m³ compared to FY22 (see Figure 7). This decrease represents a cost saving of about half a million rands in effluent treatment expenses.
Silver leach stoichiometric addition
The process of refining gold with chlorine in Miller furnaces generates byproducts like silver and base metal chlorides (Auerswald & Radcliffe, 2005). The molten chlorides produced are transferred using a ladle into a water-filled tank for quenching. This chloride slurry is then directed to the silver leach reactors, which mostly contain copper chloride and other soluble base metal chlorides. Based on the copper content in the feed solution, hydrochloric acid and sodium chlorate are added to the leach reactors. Within these reactors, the slurry undergoes a leaching reaction that converts slightly soluble copper(I)chloride (CuCl) into soluble copper (II)chloride (CuCl2). The reaction is described in Equations 1 and 2. [1]
The reaction mentioned in the aforementioned is exothermic, releasing energy and increasing the solution's temperature. This heat enables a side reaction between HCl and NaClO3, described below.
[2]
The previously mentioned reaction is endothermic, indicating that it absorbs energy and only proceeds after Reaction 1 has begun in the presence of excess HCl or NaClO3. This reaction is notably intense and can result in a violent release of energy, potentially causing reactor overflow. Efforts to minimise this overflow have
led to an increase in effluent production and higher potable water consumption. The ensuing adjustments were identified as the reasons for the elevated use of potable water:
For Reaction 1, HCl and NaClO3 must be added in precise stoichiometric amounts to transform copper(I)chloride (CuCl) into soluble copper (II)chloride (CuCl2). Since accurately measuring CuCl in the chloride feed solution is difficult, it is assumed that all copper is present as CuCl, raising the likelihood of adding excess reagents. To mitigate the risk of runaway reactions due to over-addition, potentially triggering Reaction 2, the team devised an empirical method for the addition of HCl and NaClO3. The empirical approach used several water washes, consistently adding HCl with each wash and monitoring copper levels in the solution. Usually, four washes were needed to reach acceptable copper concentrations, leading to excess effluent.
An additional issue was the inadequate drainage of solution in the reactor. During draining, around 600 L of solution and silvercontaining solids remain in the cone of the silver leach reactor. This leftover solution contains copper, which is diluted and removed when fresh, warm potable water is added during the copper leaching and washing stage.
Generally, the reactor is loaded with 1050 liters of solution (450 litres of chlorides and 600 litres of water), resulting in the consumption of 2400 litres of fresh water for four washes per batch. Post-leaching, the effluent is discharged, getting the reactor ready for the zinc reduction phase, which necessitates 600 liters of fresh water.
Each batch uses 3600 litres of water, and with 20 batches processed monthly, the total water usage reaches 72,000 litres per month. To reduce water consumption in the silver leach process, a stoichiometric addition of HCl and NaClO3 will be implemented in a controlled environment designed to prevent Reaction 2 and ensure minimal leftover solution by draining the reactor.
The operational approach has been optimised to enable the stoichiometric addition of HCl and NaClO3 in discrete batches, ensuring precise regulation of pH and temperature. These control measures are designed to minimise the risk of intense reactions associated with Reaction 2. Moreover, supplementary effluent drainage from the cone is utilised to further extract copper from the solution.
At present, a manual drain decreases the volume to around 400 litres, making sure that no silver solids are removed. Adding HCl and NaClO3 stoichiometrically would cut water usage by 1800 litres per batch, translating to a monthly decrease of 36,000 litres. As shown in Figure 7 this solution has led to an effluent reduction of 266 cubic metres between FY22 and FY24.
Vibratory shear enhanced processing techniques
The aim of the trial, guided by bench top trials conducted by New Logic Research, was to further assess the potential for removing and concentrating solid mineral particles of gold and silver using the VSEP in batch operation. The pilot trial processed three waste streams from the smelting refinery: silver, primary scrubber, and fine gold. Visual inspection revealed almost no solid particles in the silver stream and fine gold run 2, while the primary scrubber streams and fine gold run 1 were slurry streams.
Pressure studies were conducted by starting the system in recirculation mode at 50 psi (3.5 bar) and increasing the pressure in 10 psi (0.7 bar) increments up to 110 psi (7.6 bar). The flux was recorded at each pressure, with the results indicating a flattening of the curve at 80−100 psi. The trial was run at 110 psi to optimise recovery, although it is recommended to run future trials or fullscale VSEP plants at 100 psi (~6.9 bar) to avoid the potential inverse effect of 'tightening' membrane pores.
The Silver Stream Concentration Study began with the system in recirculation mode at 100 psi (6.9 bar). The permeate line was diverted to the permeate tank, and the batch concentration study commenced. The permeate flow rate was measured at timed intervals, and as permeate was removed, the sample became more concentrated. The test concluded when the flow rate dropped to 10 GFD/17 LMH, achieving 41.7% water recovery at 100 psi. However, due to a malfunction caused by a damaged membrane tray and a diverter tray, the results were inconclusive. It was recommended to not process this stream with the VSEP, as the potential for solid mineral recovery is minimal.
The Primary Scrubber Concentration Study processed two effluent samples from the primary scrubber using the VSEP system in batch mode. The runs were stopped when the effluent level became too low to continue without damaging the feed pump. The results were promising, with good flux and potential for continued processing in a different equipment arrangement for full-scale design.
For Primary Scrubber Run 1, the average flux was 62.1 LMH, achieving 95.0% water recovery at 100 psi (6.9 bar). For Run 2, the average flux was 39.7 LMH, achieving 90.9% water recovery at 100 psi. The flux remained steady during Run 1, while Run 2 saw an increase in flux, possibly due to increased pressures or settling solids in the concentrated feed, resulting in reduced resistance to separation.
The Fine Gold Concentration Study processed fine gold stream samples using the VSEP system in batch mode. Run 1 ended when the feed pump had to be stopped to prevent it from running dry, indicating potential for continued processing in a different setup. Run 2 stopped when the limiting flux was reached.
For Run 1, the average flux was 37.1 LMH, achieving 97.5% water recovery at 100 psi (6.9 bar). For Run 2, the average flux was 13.8 LMH, achieving 95% water recovery at 100 psi. Both runs showed decreasing flux trends, with Run 2 showing less decrease. Differences in permeate flux values were due to varying properties of the fine gold streams, such as pH and total suspended solids (TSS) content.
The trial involved processing three waste streams: silver, primary scrubber, and fine gold. The silver stream trials yielded inconclusive results due to a membrane malfunction. It was
recommended not processing this stream due to low total suspended solids (TSS) of less than 348 ppm and subsequently low gold recovery potential. However, the primary scrubber stream showed viability for gold recovery via VSEP, with 3.5 and 2.4 times gold concentration for runs 1 and 2, respectively. Similarly, the fine gold stream run 1 concentrated gold up to 11 times, indicating potential for gold recovery using VSEP.
It was highly recommended to do additional trials for a longer period on the primary scrubber and fine gold streams to provide VSEP design data and cleaning information. Additional trials with pH correction may also be considered at the lab scale level to determine if precious metal total dissolved solids (TDS) can be precipitated and recovered by VSEP. If positive results are obtained, the waste streams can be pH corrected before processing in the VSEP plant.
Further testing and exploration of cleaning regimens should be conducted in future pilot testing to determine if a baseline flux has been established, how this affects throughput on feed material, and if other cleaners could be more effective. From the analytical information tested, the permeate had extremely high chlorides, dissolved solids, and conductivity in multiple runs, making it difficult to further treat the permeate for both mineral and water recovery. Recovery from the permeate stream for dissolved gold, silver, copper, and water is not possible with conventional reverse osmosis or advanced techniques such as VSEP with reverse osmosis membranes due to the high TDS content requiring unreasonably high osmotic pressures. Other techniques such as thermal processing, eutectic freeze crystallisation, or advanced softening should be investigated to determine their feasibility.
Based on these and mineral recovery estimates, the plant should be paid off within less than three years. The feasibility of implementing the VSEP unit should consider the performance of the existing filter presses and the quantity of recoverable minerals being disposed of.
These findings from the VSEP trial provide valuable insights into the potential for gold recovery from wastewater at Rand Refinery and highlight the need for further trials and exploration of alternative treatment techniques.
To conclude, the effluent reduction and treatment initiatives at Rand Refinery have achieved notable advancements in decreasing freshwater usage and effluent generation. The successful launch of the granulation water recycle plant and improvements to the silver leach process have significantly lowered effluent volumes and treatment expenses. The Vibratory Shear Enhanced Processing (VSEP) trial has yielded encouraging outcomes for gold recovery from wastewater, but additional trials and the investigation of other treatment methods are suggested.
The water savings from the effluent reduction initiatives are tracked by measuring the volume of effluent transferred to service yard storage facilities using flow meters integrated with SCADA. Since the FY23 introduction of the granulation effluent recycling initiative, effluent has been reduced to 2676 m³. In FY24, the addition of HCl and NaClO3 to the silver leach process was introduced, further reducing the effluent to 2083 m³. The cumulative improvements in effluent management between FY23 and FY24 have resulted in a reduction of 590 m³, achieving savings of R560,500.
These initiatives support Rand Refinery's commitment to ESG compliance, emphasising resource conservation and waste management. The projects not only promote environmental sustainability but also offer staff valuable training in process engineering and effluent management.
In summary, the refinery’s proactive stance on reducing and treating effluent highlights its commitment to sustainable practices and responsibility as a corporate entity. By consistently pursuing innovation and process optimisation, Rand Refinery strives for long-term sustainability and resilience, securing its ongoing success and beneficial influence on both the environment and society.
I would like to express my gratitude to the Rand Refinery Management for granting me the opportunity to present the effluent reduction advancements. My appreciation extends to the Production team for their support and help in commissioning the granulation effluent recycle initiative, the Project team for overseeing the installation and commissioning process of the granulation recycle plant, and the Silver team for managing and assisting with the execution of the stoichiometric addition tests involving HCL and NaClO3
References
Auerswald, D.A., Radcliffe, P. H. 2005. Process technology development at Rand Refinery. Minerals Engineering, vol. 18, no. 8, pp. 748–753.
Reeves, G.G. 2000. Wastewater minimization with chemical-free water treating. Environmental Progress, vol. 19, no. 4, pp. 292–298.
Teodosiu, C.C., Kennedy, M.D., Van Straten, H.A., Schippers, J.C. 1999. Evaluation of secondary refinery effluent treatment using ultrafiltration membranes. Water Research, vol. 33, no. 9, pp. 2172–2180.
Affiliation:
1Occupational Hygiene and Health Research Initiative, North-West University, Potchefstroom, South Africa
2University of Wollongong, Wollongong, Australia
3D’Sayensi Occupational Hygiene
Correspondence to: C.J. Badenhorst
Email: Cas@occhygienist.com
Dates:
Received: 30 Oct. 2024
Accepted: 10 Dec. 2024
Published: February 2025
How to cite:
Badenhorst, C.J., Swanepoel, J.D., Horn, S. 2025. Preventing another health tradegy: A framework to manage diesel particulate matter in underground mines. Journal of the Southern African Institute of Mining and Metallurgy, vol. 125, no. 2, pp. 77–86
DOI ID:
https://doi.org/10.17159/2411-9717/785/2025
This paper is based on a presentation given at the Southern African MineSafe Conference 2024, 6-8 November 2024, Emperors Palace Convention Centre
by C.J. Badenhorst1,2, J.D. Swanepoel2, S. Horn1
Abstract
Diesel particulate matter (DPM) is the particulate component of diesel exhaust, which includes diesel soot and aerosols. When released into the atmosphere, DPM can take the form of individual particles or chain aggregates, with most in the invisible sub-micrometer range of 100 nanometres. The main particulate fraction of diesel exhaust consists of fine particles and because of their small size, inhaled particles may easily penetrate deep into the lungs. The rough surfaces of these particles make it easy for them to bind with other toxins in the environment, thus increasing the hazards of particle inhalation.
DPM is a significant health hazard in underground mining operations, where the use of dieselpowered equipment in confined spaces can lead to high levels of exposure among people working in these environments. Classified as a carcinogen by the International Agency for Research on Cancer (IARC), DPM has been linked to severe health effects, including respiratory and cardiovascular diseases, as well as an increased risk of lung cancer. Effective management of DPM is essential not only for protecting people’s health but also for ensuring regulatory compliance, maintaining operational efficiency, and safeguarding the long-term viability of mining companies.
Keywords
diesel particulate matter, carcinogen, control, management plan
Silicosis litigation in South Africa has been a significant legal battle involving thousands of miners who contracted the disease while working in the mines. In 2011, the South African Constitutional Court ruled that affected mineworkers could claim damages from mining companies under the Occupational Diseases in Mines and Works Act (ODIMWA), leading to the certification of class-action lawsuits. In 2023 a motion was filed in the High Court of South Africa requesting class certification for thousands of prospective class members. The litigation alleges that the responding coal mining companies were aware of the dangers posed to coal miners by coal dust, but failed to protect its workers from high levels of exposure.
Whilst over the last number of years the South African Mining Industry (SAMI) made good progress in reducing exposures in the workplace and achieved a year-on-year reduction in the number of reported cases of occupational disease, the SAMI is still some distance away from achieving ‘zero harm’ in occupational health. In 2012 the International Agency for Research on Cancer (IARC), declared diesel engine exhaust (DEE) as a human carcinogen, with diesel particulate matter (DPM) being identified as a key contributor to its harmful effects. Twelve years later, the South African Mining Industry still has no occupational exposure limit (OEL) set for DPM and, whilst we have seen some isolated pockets of events to manage harmful exposure to DPM, we have not yet seen a consolidated response to this significant threat to the health of underground miners in SAMI. Could DPM become the next class action or can we as stakeholders prevent another health tragedy in our industry? How can we, as opposed to getting ourselves stuck in endless clinical debates over diagnosis criteria, occupational hygiene measurement methodologies, feasible OELs, and ongoing research projects, move to action?
Effective management of DPM is crucial for ensuring the health and safety of everyone working in underground mining operations. Following an understanding of the unique challenges posed by confined spaces in these environments, it is essential to establish a robust framework for assessing and controlling DPM exposure. This paper outlines a framework of the critical steps required for effectively managing DPM and diesel exhaust emissions overall in the workplace within SAMI.
Underground mining is particularly complicated as mines can be kilometres deep, with high temperatures, confined spaces and ventilation challenges. Operating traditional mining vehicles underground creates even further challenges – the creation of airborne particulates which, when breathed in, can impact the health of people working in these mines for many years.
Background
What is diesel engine exhaust?
Diesel engine exhaust comes from engines burning diesel fuel. It is a complex mixture of gases, vapours, liquid aerosols, and particulate substances. These substances are the products of combustion. The main chemical components of diesel exhaust emissions are:
➤ Gases and vapours – these are mostly the gases found in atmospheric air like nitrogen, oxygen, water vapour, and carbon dioxide. There are also hazardous chemicals like nitrous oxide, nitrogen dioxide, sulphur dioxide, and carbon monoxide.
➤ Ultrafine particles known as DPM are elemental carbon (EC) particles that typically have additional hazardous chemicals, such as poly aromatic hydrocarbons (PAHs), or heavy metals adhered to the surface of carbon particles. DPM, specifically elemental carbon (EC), is often used as a surrogate to evaluate diesel emission exposure (Birch, 2014).
DPM can act like a gas and stay airborne for long periods of time. Furthermore, it can penetrate deep into the lungs because of its small size.
DPM is the particulate component of diesel exhaust, which includes diesel soot and aerosols. When released into the atmosphere, DPM can take the form of individual particles or chain aggregates, with most in the invisible submicrometre range of 100 nanometres. The main particulate fraction of diesel exhaust consists of fine particles and because of their small size, inhaled particles may easily penetrate deep into the lungs. The rough surfaces of these particles make it easy for them to bind with other toxins in the environment, thus increasing the hazards of particle inhalation.
Exposures have been linked with acute symptoms, such as headache, dizziness, lightheadedness, nausea, coughing, difficult or laboured breathing, tightness of the chest, and irritation of the eyes, nose, and throat. Long-term exposures can lead to chronic, more serious health problems such as cardiovascular disease, cardiopulmonary disease, and lung cancer.
It is important to note that the IARC classification is based on diesel engine exhaust, which includes DPM. The classification as confirmed carcinogen does not specify DPM as the carcinogen.
Health impacts of DPM
DPM is a significant health threat that people working underground may face daily(Chang and Xu, 2017). The ultra-fine particles in DPM penetrate deep into the respiratory system, bypassing natural defences and reaching the lungs and bloodstream. In the confined, poorly ventilated spaces typical of underground mining, the exposure levels are much higher compared to surface mining, increasing the risks substantially.
DPM containing DEE is classified by the International Agency for Research on Cancer (IARC) as a Group 1 carcinogen (IARC, 2012), linking it directly to lung cancer. DPM presents a real and present risk for people who are exposed to high concentrations of DPM over long periods. Moreover, DPM exposure is associated with severe cardiovascular risks. The fine particles can cause systemic inflammation and oxidative stress, exacerbating conditions like hypertension, and increasing the risk of heart attacks and strokes. For people working underground with physically demanding jobs, these additional health burdens can lead to sudden and potentially fatal health crises.
Other business risks to consider
In addition to the health impacts, DPM exposure presents a range
of significant business risks that can threaten a company's longterm viability. These risks extend beyond regulatory compliance and encompass reputational damage, financial implications, and potential legal liabilities. For companies operating in industries with high DPM exposure, such as underground mining, it is crucial to recognise and proactively manage these risks. Addressing these risks through comprehensive DPM management strategies is essential for safeguarding both people and the business.
Regulatory compliance challenges
To protect people’s health, some countries have established occupational exposure limits (OELs) for DPM, typically measured as EC. These OELs are becoming increasingly stringent as countries recognise the serious health risks associated with DPM exposure, whilst some countries, like South Africa, have yet to implement OELs aimed at controlling DPM exposure. Globally, regulations mandate regular monitoring of air quality and worker exposure to ensure compliance with these OELs. When an exceedance of the exposure standard occurs, mine operators are required to notify relevant regulatory bodies, take corrective actions, conduct investigations, resample after corrective measures, and review their principal hazard management plans. Maintaining records of monitoring and corrective actions is also required, with retention periods varying by jurisdiction.
Failure to comply with these regulations can lead to legal and financial consequences, including fines, sanctions, and operational shutdowns. Many regulatory bodies are continuously lowering permissible exposure limits for DPM, compelling companies to invest in advanced monitoring and control technologies. For example, the Organisation for Economic Cooperation and Development (OECD) emphasises the need for clear and enforceable OELs that are protective of worker health and feasible to implement, based on scientific, technical and socio-economic considerations.
Non-compliance (Organisation for Economic Co-operation and Development. 2023) not only exposes companies to legal risks, but also damages their credibility and relationships with regulators. To avoid these pitfalls, companies must remain current with regulatory updates and proactively enhance their DPM management practices. This includes implementing effective control strategies, regular monitoring, and adopting available best practices in DPM management to meet or exceed regulatory standards. By doing so, industries can ensure a safer work environment, protect health, and maintain operational continuity.
Unmanaged exposure to DPM can pose financial risks for companies, particularly over the long term. While direct links between DPM exposure and immediate absenteeism or turnover may not be as strong, the long-term health impacts of chronic exposure can lead to increased costs related to health surveillance, case management, and potential compensation or legal claims from affected people. Investing in preventive measures and effective DPM management strategies can help mitigate these long-term financial risks by ensuring compliance with health regulations and reducing the likelihood of chronic health issues that could result in costly legal actions or compensation claims.
As DPM is a recognised respiratory irritant and causative agent of lung cancer, people who are exposed and then develop these
conditions could have a basis for compensation claims. Depending on jurisdiction, these claims may extend to civil lawsuits based on a failure to maintain a safe and healthy work environment. Class action lawsuits can serve as a means for affected parties to seek justice but also present potential reputational damage and increased regulatory scrutiny for businesses (Jones and Musk, 2021).
The threat of health-related class action suits is significant in industries with high DPM exposure, such as underground mining. Companies that fail to manage DPM risks effectively may face substantial legal repercussions. These lawsuits not only lead to significant financial liabilities but also damage the reputation and trustworthiness of the companies and ultimately, the industry as a whole, which affects long-term business viability.
To mitigate these risks, it is crucial for companies to implement robust DPM management practices, ensuring compliance with health and safety standards and thereby reducing the likelihood of legal claims and associated financial liabilities.
The primary concern associated with DPM exposure is the safety and health of employees. Protecting people from the harmful effects of DPM is not only a moral and legal obligation, but also essential for maintaining a healthy and productive workforce. Beyond this, effective DPM management also helps to mitigate significant business risks, including reputational damage, regulatory compliance challenges, financial implications, and potential compensation and legal claims. By prioritising health through robust DPM management and strict adherence to health and safety regulations, companies can safeguard their employees while also ensuring their long-term viability.
The major source of workplace exposure to diesel exhaust is from heavy vehicles that use diesel fuel, such as trucks, buses, trains, tractors, ships, bulldozers, and forklift trucks. Other sources include equipment in mines such as bucket lifts and excavators. All vehicles that use diesel fuel generate diesel exhaust when running, including during workshop repair or servicing, in car parks, when passing security checkpoints, weighbridge control rooms, or in enclosed areas where vehicles operate to load or offload loads and trains.
Diesel exhaust may also be generated from stationary power sources like generators and winch motors, including those mounted to vehicles. These may be used in tunnels, alongside railway lines during maintenance work, and on construction sites.
Levels of exposure can be higher in enclosed, poorly ventilated areas where the concentration of exhaust can build up, like in vehicle repair workshops, tunnels, and partially covered roadways and walkways.
Workers who may be exposed to diesel exhaust include drive-in booth operators, miners, construction workers, oil and gas workers, airline ground workers, forklift drivers, loading dock workers, truck drivers, farm workers, and vehicle maintenance workers.
DPM occupational exposure limit
Currently, no OEL has been set for DPM under the South African Mine Health and Safety Act, Act 29 of 1998.
To ensure that mining operations are aligned with global best practices, it is important to reference international standards for DPM exposure in the absence of local standards. Guidelines set by prominent organisations provide a benchmark for OELs and offer insight into how different regions approach DPM management.
In 2021, the Minister of Employment and Labour promulgated the Regulations for Hazardous Chemical Agents (RHCA, 2021). As part of this update, diesel particulate matter (DPM), which is
emitted from diesel engines during combustion, was added to the RHCA with an occupational exposure limit (OEL) of 0.16 mg m3 for total carbon over an eight-hour time-weighted average (Regulations for Hazardous Chemical Agents (RHCA). 2021.) (TWA).
National Institute for Occupational Safety and Health (NIOSH)
NIOSH recommends an exposure limit of 0.1 mg/m³ for DPM measured as elemental carbon (EC) in underground metal and nonmetal mines (NIOSH 2003).
Australian Institute of Occupational Hygienists (AIOH)
AIOH recommends a guideline of 0.1 mg/m³ for DPM measured as EC, to reduce the incidence of ocular and respiratory irritation, with a more protective action level of 0.05 mg/m³ to trigger an investigation and improved controls. This action level is intended to ensure early detection of potential overexposures and prompt implementation of corrective measures to protect worker health. This level is intended to address irritation and not chronic exposure cancer risk. This exposure limit is based on a feasible control of emissions in mines, and not on all adverse health effects. SafeWork Australia will implement an EC exposure limit of 0.01 mg/m³, effective December 1, 2026 (Minerals Council of Australia, 2021).
Effective management of DPM is crucial for ensuring the health and safety of everyone working in underground mining operations. Following an understanding of the unique challenges posed by confined spaces in these environments, it is essential to establish a robust framework for assessing and controlling DPM exposure. DPM is unique in associated health hazards as it is generated by human activity and is not naturally occurring, such as respirable crystalline silica. DPM presents several challenges, including:
➤ Variability in its concentration, composition, and aerodynamic properties.
➤ Mobility of source (vehicles), as it is not static and can disperse over large areas.
➤ Requires continuous monitoring and management due to its dynamic nature.
➤ Influence by factors such as:
• The maintenance and efficiency of diesel engines.
• The type and design of equipment used.
• Efficiency of exhaust after-treatment employed.
• Fuel quality, particularly sulphur content.
DPM control strategies can be divided into three (3) main categories, namely:
a) Prevention of DPM generation: Focuses on optimising engine performance. This includes using cleaner-burning diesel, upgrading to higher-tier engines, and conducting regular engine maintenance to minimise emissions.
b) Prevention of DPM release: Involves capturing or destroying DPM before it is released into the ambient environment. This can be achieved through technologies like diesel particulate filters (DPF) and other exhaust aftertreatment systems.
c) Management of released DPM: Aims to reduce worker exposure through engineering and administrative controls, such as improving ventilation systems, restricting the use of diesel equipment, and providing enclosed operator cabins with appropriate filters.
d) Optimisation of control strategies: Focuses on gathering data through continuous monitoring and risk assessment to adjust and improve existing controls. This involves integrating real-time monitoring technologies to track DPM levels and verify the effectiveness of controls.
DPM control hierarchy
For each control, activities should be established to verify that the controls are operating effectively according to their design, and that processes are in place to ensure the control is effectively managing the risk (Figure 1). Exposure monitoring is not a control, but rather useful to understand the current situation with a risk-based focus. The integration of real-time monitoring technology into monitoring frameworks demonstrates an effective control verification method.
Risk assessment
A baseline risk assessment should be conducted to identify and quantify DPM exposure levels among employees. This process establishes whether a hazard exists and helps prioritise control measures based on the level of risk. Key steps include:
➤ Identifying and quantifying sources of DPM within the mine.
➤ Quantifying exposure levels for different areas and workers.
➤ Prioritising controls based on vehicle emissions profile, exposure duration and concentration.
➤ Implementing a control improvement plan based on the hierarchy of controls.
Maintaining a DPM source inventory is essential for tracking emission sources and ensuring targeted mitigation efforts. Mines should regularly update their source inventory and use it to inform their control strategies.
The controls and processes listed in the following have their primary goal in the prevention of the generation of DPM. These controls and processes are mainly engineering related, with the core aim of improving engine efficiency and the prevention of DPM generation. These include:
➤ The use of low sulphur content diesel with a maximum allowable concentration of 50 ppm. Diesel handling is an important component of control. Quarterly analyses of diesel should be done, and records kept confirming quality and sulphur content.
➤ Based on available technology, consideration will be given to the following:
• Replacement of diesel-powered equipment with electrically powered equipment.
• Replacement of lower tier engines with higher tier, more efficient engines.
➤ An emissions-based maintenance programme shall be implemented:
• Every vehicle should have a service/maintenance plan according to the specifications of the original manufacturer of the equipment (OEM).
• Maintenance plans should be extended after diesel particulate filters are fitted, including engine performance testing and diesel exhaust emissions measurements.
• Engine performance testing should include DPM generation, such as opacity, differential pressure across exhaust aftertreatment, and exhaust temperature testing.
• DPM testing should be used as an indication of overall engine health.
➤ Exhaust gas temperature should be measured to determine any engine combustion problems, and backpressure values should be used to assess the efficiency of filter regeneration.
➤ Only low ash lubricants should be used.
The controls listed above are all related to the operation and efficiency of the internal combustion unit utilising diesel as a fuel source, and records of these activities should be maintained.
The following list of controls and processes have their primary goal in the prevention of the release of DPM from a diesel-powered vehicle into the ambient environment. These controls and processes are mainly engineering related, with the core aim of destroying DPM prior to release into the ambient environment. These include:
➤ Installation of diesel particulate filters.
➤ Local extraction ventilation (LEV) systems.
These controls are related to the destruction of generated DPM after generation by the engine, usually in the exhaust system or by capturing the DPM directly from the exhaust system and preventing its release into the ambient atmosphere.
The following controls and processes have their primary goal of the management of the generated DPM in the ambient environment. These controls and processes are a mixture of engineering, administrative, PPE and related controls and processes to minimise workers' exposure to DPM. These include:
• Non-combustion powertrains Low-emission engines (T4&T5)
• Low-emission fuel Fuel additives
• Emission-based maintenance, diesel particulate filters
• Tailpipe after treatment, ventilation circuits
• Enclosed cabs with filters, engineered desing of roadways Operator behaviour (training)
• Remote control
• Fleet management (e.g., diesel tag board) Demarcated and barricaded areas
• Respiratory protective equipment
➤ Dilution ventilation
Ventilation should be optimised to dilute diesel particulate matter as much as feasible. Provision for an adequate volume flow rate of air is required with the following minimum ventilation design criteria:
• 0.06 m3/s/kW dilution rate to be used when complying with the diesel particulate matter management programme, including the use of higher tier engines such as Tier 3 and 4 engines, DPF catalytic converters, and 50 ppm sulphur in diesel.
• 0.12 m3/s/kW if ventilation dilution is the only control.
➤ Equipment driver enclosure (heating, ventilation, and air conditioning (HVAC) system).
➤ Equipment restrictions.
➤ The number of diesel equipment should be restricted based on the ventilation design.
➤ Segregation/separation of workforce from diesel equipment, including remote control options.
Personal protective equipment (PPE)
Due to the size and composition of DPM, respiratory protective equipment (RPE) should comply to the following specifications:
➤ Filtration media must be of an FFP3 (EN 14683) or Level 100 (NIOSH - 42 CFR* 84) efficient particulate filter for negative pressure respirators or high efficiency particulate air (HEPA) filter for powered air purifying respirators (PAPR).
➤ Filtration media must be rated as an R or P series due to the presence of oil in the DPM.
➤ R-series filters: These are filters intended for the removal of any particle including oil-based liquid aerosol. They may be used for any solid or liquid airborne particulate hazard. If the atmosphere contains oil, the R-series filter should be used only for a single shift (or for 8 hours of continuous or intermittent use). They are only recommended for disposable respirators that are changed every day.
➤ P-series filters: These are filters intended for removal of any particle including oil-based liquid aerosols. They may be used for any solid or liquid particulate airborne hazard. NIOSH requires that respirator manufacturers establish time-use limitations for all P-series filters. An international manufacturer of RPE recommends that, in atmospheres containing oil aerosols, P-series filters should be used and reused for no more than 40 hours or 30 days, whichever occurs first, unless the filter needs to be changed for hygiene reasons, is damaged, or becomes difficult to breathe through before the time limit is reached. P-series filters are recommended for all respirators except disposable respirators, as the increased breathing resistance could lead to increased leakage around the respirator.
It is important to note that personal protective equipment (PPE) is the lowest level of the Hierarchy of Controls. This is not because it is the last consideration or the least effective means of protecting people. Properly managed PPE is the difference between life and death in many safety critical industries. It is at the bottom of the Hierarchy of Controls because it is the last line of individual defence and ‘it fails to danger.’ If PPE is relied upon and does not work, then only the body's own natural protections are left. PPE failure therefore directly exposes a worker to a hazard.
Reviewing and maintaining control measures
Control measures should be reviewed regularly to make sure that
they are effective, for example, checking the airflow and filters in ventilation systems and ensuring DPF are effective in removing DPM from exhaust stream. Reviewing risk control measures may include inspecting the workplace, consulting workers, and testing and analysing records and data. It also involves considering whether the use of a higher order control measure is now reasonably practicable.
Control measures should be reviewed and, if necessary, revised:
➤ When the control measure is not effective in controlling risk.
➤ Before a change at the workplace that is likely to give rise to a new or different health and safety risk.
➤ If a new hazard or risk is identified.
➤ If the results of consultation indicate that a review is necessary.
➤ If a health and safety representative or worker requests a review.
Control measures must be reviewed on a continuous basis. If a person conducting a business or undertaking has concerns, they should refer back to the risk management steps, review the information, and make decisions about control measures.
A mine should ensure that all the measures provided to control exposure to DPM emitted as part of diesel exhaust emissions in the workplace are maintained in an effective state, kept in efficient working order, and in good repair. Where engineering controls are used, they should be thoroughly examined and tested at regular intervals.
Except for disposable filtering facepiece respirators intended for single shift use, RPE should not be used unless users has had face fit testing, and it has had a recent thorough examination and maintenance.
The process to reduce DPM emissions should follow some core steps. A mine should be able to streamline a data-driven approach that optimises efficiency. Through defining a solid benchmark, developing sound practices, and carefully analysing relevant data, mines can understand the needs of their machines, and develop a customised emission control system for underground equipment.
A well-structured strategy and diligent implementation are crucial for effectively controlling DPM emissions in mining operations. Establishing a comprehensive DPM management plan helps ensure worker health, regulatory compliance, and operational efficiency. By following the defined steps—define, measure, analyse, improve, control, and verify—mining operations can systematically reduce DPM emissions, enhance workplace safety, and maintain sustainable operational practices. The benefits include improved worker health and safety, reduced legal and financial risks, and enhanced operational performance.
A successful DPM management plan is built on a series of critical components, each of which plays a vital role in the overall strategy for reducing emissions. This subsection outlines the key elements of the plan, guiding mining operations through the define, measure, analyse, improve, control and verify process. By following these steps, companies can create a tailored approach to managing DPM emissions, ensuring that all aspects of their operations are optimised for safety, compliance, and efficiency.
This framework should be used in conjunction with other sections of this article to produce a management plan tailored to the company and operation (Figure 2).
Step
The Define step involves capturing the current situation, establishing clear project parameters, and ensuring that all relevant aspects of the operation are considered. This step is also where a dedicated committee is formed to oversee the project, and a compliance review is conducted to ensure that all regulatory requirements are being met.
Capture the current situation:
a) Conduct a comprehensive baseline risk assessment to understand the current levels of DPM emissions and worker exposure.
b) Document all existing control measures, equipment specifications, and operational practices.
Establish project parameters:
a) Define clear objectives and goals for DPM reduction, such as specific emission reduction targets and timelines.
b) Set key performance indicators (KPI) to measure progress and success.
Establish the scope:
a) Determine the full scope of the DPM management plan, including all relevant equipment, areas and processes within the mining operation.
b) Ensure that the plan addresses all sources of DPM and includes measures to control and reduce emissions.
Form a committee:
a) Assemble a dedicated committee with representatives from key stakeholder groups, including management, health and safety officers, maintenance personnel, and worker representatives.
b) Assign roles and responsibilities to ensure accountability and effective communication.
Compliance review:
a) Conduct a thorough review of current compliance with local, national, and international regulations and standards related to DPM emissions.
b) Identify any gaps in compliance and areas that require improvement.
Step 2 - Assess
The assess step involves systematically measuring and collecting data on current levels of DPM emissions and exposure. This phase focuses on gathering accurate and comprehensive information through various monitoring techniques, providing a foundation for identifying areas of concern, and ensuring compliance with exposure limits.
Measure manifold and tailpipe emissions:
a) Perform emissions testing on all diesel-powered equipment to quantify DPM emissions from each machine.
b) Use standardised methods to ensure accurate measurement.
Equipment utilisation:
a) Track utilisation rates of all diesel-powered equipment to identify high-use machines that may contribute significantly to DPM emissions.
b) Collect data on equipment operating hours, fuel consumption and maintenance schedules.
Personnel monitoring:
a) Implement personal monitoring devices to measure individual worker exposure to DPM.
b) Collect data on exposure levels during different tasks and in various work areas.
Area monitoring:
a) Deploy stationary monitoring devices to measure DPM concentrations in key areas of the mine.
b) Ensure continuous monitoring to capture real-time data and identify areas with high DPM levels.
Assess controls:
a) Use the afore-mentioned data that were gathered to assess control adequacy and improvement.
b) Identify areas of high exposure and prioritise controls.
This step involves evaluating the data collected during the assess phase to identify key sources of DPM emissions, prioritise risks, and develop targeted control strategies. This phase focuses on turning raw data into actionable insights that guide decision-making and improvements in DPM management.
Develop equipment emission profiles:
a) Analyse the collected emissions data to create a detailed profile for each piece of equipment.
b) Identify high-emission equipment and prioritise them for upgrades or replacements.
Prioritise equipment and work areas:
a) Rank equipment and work areas based on their contribution to overall DPM emissions and worker exposure.
b) Focus initial improvement efforts on the highest-priority items to achieve the greatest impact.
Identify patterns and trends:
a) Look for patterns and trends in the data to understand the factors contributing to high DPM levels.
b) Use this analysis to inform targeted DPM reduction strategies and optimise resource allocation.
Starting with the define, assess and analyse steps is crucial for the successful implementation of DPM reduction initiatives. By capturing the current situation, measuring emissions accurately and analysing the data, mines can develop targeted and effective DPM control systems. This approach ensures that resources are used efficiently, costs are minimised, and health and safety are prioritised. With a solid foundation in place, mines can move forward with confidence, implementing strategies that significantly reduce DPM emissions and improve overall operational performance.
The control step involves taking action to manage DPM. The hierarchy of control should be the foundation of any DPM management strategy, prioritising controls in the following order: Elimination: This is the most effective form of control and involves removing the source of DPM altogether. Strategies include replacing
diesel-powered equipment with electric vehicles or implementing automation and remote operation technologies to reduce the need for diesel equipment.
➤ Substitution: When elimination is not possible, substitution involves replacing high-emission diesel engines with lower emission options. This can include using engines that meet higher emission standards or switching to fuels like ultra-low sulphur diesel (ULSD) or biodiesel blends, which generate fewer particulates.
➤ Engineering controls: These controls are designed to isolate people from the DPM hazard. Effective engineering controls may include:
➤ Exhaust gas after-treatment: Implementing technologies like diesel particulate filters (DPF), diesel oxidation catalysts (DOC) and selective catalytic reduction (SCR) systems to capture or convert harmful emissions before they are released into the environment.
➤ Improving ventilation: Optimising mine ventilation systems, including designing efficient primary and auxiliary ventilation to remove or dilute DPM from work areas.
➤ Enclosed cabins: Using enclosed operator cabins with highefficiency particulate air (HEPA) filters to protect workers from direct exposure.
Administrative controls: These involve changing the way work is performed to reduce exposure. This may include:
➤ Work schedules: Rotating shifts to minimise individual exposure time in high-DPM areas.
➤ Training and awareness: Educating people on the risks of DPM and safe work practices.
➤ Monitoring and auditing: Regularly monitoring DPM levels with real-time and personal monitoring devices, conducting audits, and reviewing control measures for effectiveness.
➤ Personal protective equipment: This should be the last line of defence when other controls are not sufficient. This includes the provision of respirators with appropriate filters and ensuring people are fit tested and trained in its correct use and maintenance.
Step 5 - Verify
The verify step is important in ensuring the effectiveness of a DPM management plan. Once a DPM management plan is in place, it is important to monitor progress and verify that controls are working.
This should include the following steps:
a) Set cadence for periodic and systematic monitoring of emissions and controls.
b) Set up and use DPM emissions register or data warehouse/ data visualisation tools.
c) Set up workflow trigger automation, such as alarms and responses to real-time monitoring of emission levels in designated work areas as part of the trigger action response plans (TARP) (Zhang, et al. 2023 ).
To summarise, the steps to DPM reduction are:
1. Define – Capture the current situation, establish project parameters, establish the scope, committee, compliance review.
2. Assess – Measure the tailpipe emissions, equipment utilisation, personnel monitoring and area monitoring.
3. Analyse – Equipment emission profile, prioritise equipment and work areas.
4. Control – Implement standard operating procedures related to DPM exposure mitigation.
5. Verify – Set cadence for periodic and systematic review of emission by machinery, create equipment emissions register.
Where to start?
Without the first three steps, a mine cannot begin the process of implementing DPM reduction initiatives. Calculating and analysing emissions allows accurate and targeted DPM systems to be applied, which can save time and money.
Benchmark current diesel equipment
➤ Maintain an up-to-date equipment register, knowing which equipment is in service in which area - Carry out tailpipe emissions testing.
➤ Identify equipment with the greatest emissions output.
➤ Use collected data to calculate emissions outputs - Monitor equipment with high fuel usage and emissions outputs.
➤ Evaluate workplace exposure.
➤ Consider exposure/emitting time of equipment and location.
➤ Conduct NIOSH 5040 testing by work area - Assess worker concentration and exposure.
From there, enough data should be available to develop a plan and begin the process of implementing emissions reduction measures. This is highly dependent on the evaluation, and may include rearranging machine schedules, phasing-out certain equipment, or using diesel particular filters and selective catalytic reduction systems.
Lastly, it is imperative that standards are administrated, monitored, and periodically reviewed. Reducing emissions is not a one-off task and will need to be continuously reassessed as businesses and technology change.
To support the development of DPM control management plans the following guidance is provided.
Initial DPM controls
For all mines where workplace exposures are above the DPM OEL, the following control strategy could be considered in a DPM plan:
➤ Low emission fuel (if available).
➤ An emissions-based maintenance programme.
➤ Ventilation strategies consistent with the control of diesel emissions.
➤ A purchasing policy to buy low emission engines (where available).
➤ Controls on contractor or hire vehicles to minimise exhaust emissions.
➤ Workforce and driver education programme.
Secondary management plan
In cases where the initial controls management plan is not effective in reducing emissions to below the DPM OEL, mines could consider implementing one or more of the following:
➤ Low emission engines.
➤ Diesel exhaust filters.
➤ Disposable diesel exhaust filters.
➤ Air conditioned and filtered operator cabins.
➤ Alternative power systems (e.g., electric).
➤ Supply of appropriate respiratory protective equipment to affected workers (as a temporary control).
It should be feasible for the initial management plan to be fully implemented within 6 to 12 months. Secondary management plans (if applicable) will be dependent on equipment availability and thus should be progressed without delay.
Roles and responsibilities
Mine diesel management plan committee
The first step to implementing the mine’s DPM Management Programme is assembling a DPM management committee. The programme committee’s responsibilities would include monitoring the quality of implementation, effectiveness of the planned activities, and timely reporting to various stakeholders. Each member of the committee should have a defined role. Over time, the committee will be responsible for identifying opportunities for programme improvement.
Occupational hygiene team
The asset’s DPM Management Programme must provide fundamental information so that the occupational hygiene and occupational health teams can be assured of the integrity of data and confirm that the asset is not exposing workers to levels that may present a health risk. A DPM Management Programme will provide ongoing information on possible DPM exposures within the workplace.
To meet the mine’s DPM Management Programme objectives, the DPM monitoring programme must produce information of consistently high quality. The mine’s occupational hygiene team is responsible for assessing exposure risks and developing standard operating procedures for each component of the Occupational Hygiene DPM Programme. Quality control measures need to be in place at each step of the sampling program to allow assessment of data quality. The occupational hygiene team may also be responsible for initiating the incident management procedure based on DPM sampling results.
Ventilation plays a critical role in the management of DPM concentrations through dilution. The ventilation team is responsible, but not limited to, the following:
➤ Ensuring sufficient and suitable infrastructure to enable effective ventilation of working places.
➤ Ensuring sufficient ventilating air of suitable quality, is available to dilute generated DPM.
➤ Ensuring sufficient ventilating air is available to dilute generated DPM in areas where the DPM is generated.
➤ Ensuring air contaminated with DPM is removed from the working place in an efficient manner to reduce the number of workers possibly exposed.
➤ Ensuring that ventilation related infrastructure and airflow controls are maintained and kept operational as required.
Due to the nature of DPM being formed by the internal combustion engine, a large variety of factors can influence the amount of DPM generated. The engineering team is responsible, but not limited to, the following:
➤ Maintenance of vehicles.
➤ Maintenance of DPM control devices.
➤ Maintenance of LEV system components.
➤ Maintenance of vehicle cabins and filters.
The equipment producing DPM is generally utilised by the production teams to move material and equipment to achieve production related goals. The production team is responsible, but not limited to, the following:
➤ Ensure equipment is used as per OEM recommendations.
➤ Ensure adherence to operational standards and procedures.
➤ Identify and report any substandard engine operations to the engineering team.
DPM can be well managed in many underground mines through high-grade protective equipment and ventilation, use of low sulphur fuels, adequate maintenance practices, as well as transitioning to zero-emission equipment, however, failing to manage DPM can cause debilitating illness for people working underground. The moral imperative is clear: addressing DPM exposure prioritises the health and safety of workers and meets regulatory requirements. Protecting people from the harms of DPM means valuing their lives and wellbeing, ensuring they can work safely and return home healthy. Effective DPM management is not just good practice; it is a moral responsibility that reflects a commitment to human dignity and the welfare of our people.
Company leadership in creating a safe and healthy work environment is crucial for managing the risks associated with DPM and ensuring the well-being of all employees.
AIOH Australian Institute of Occupational Hygienists
DEE Diesel exhaust emissions
DOC Diesel oxidation catalysts
DPF Diesel particulate filters
DPM Diesel particulate matter
EC Elemental carbon
HEPA High efficiency particulate air
IARC International Agency for Research on Cancer
LEV Local extraction ventilation
NIOSH National Institute for Occupational Safety and Health
ODIMWA Occupational Diseases in Mines and Works Act
OECD Organisation for Economic Cooperation and Development
OEL Occupational exposure limit
OEM Original equipment manufacturer
PAH Poly aromatic hydrocarbons
PAPR Powered air purifying respirators
PPE Personal protective equipment
RHCA Regulations for hazardous chemical agents
RPE Respiratory protective equipment
SAMI South African Mining Industry
SCR Selective catalytic reduction
References
Chang, P., Xu, G. 2017. A review of the health effects and exposureresponsible relationship of diesel particulate matter for underground mines. International Journal of Mining Science and Technology, vol. 27, no. 5, pp. 831–838.
https://doi.org/10.1016/j.ijmst.2017.07.020
International Agency for Research on Cancer (IARC). 2012. “IARC Diesel Engine Exhaust Carcinogenic”2. Complete list of agents, mixtures and exposures evaluated and their classification, International Agency for Research on Cancer, Lyon. https://monographs.iarc.who.int/list-of-classifications
Organisation for Economic Co-operation and Development. 2023. Establishing Occupational Exposure Limits: Practices and Criteria (OECD, 2023), pp. 15–18. Available at: https://www.oecd-ilibrary.org/establishing-occupationalexposure-limits_901f4b5a-en.pdf?itemId=%2Fcontent%2Fpublic ation%2F901f4b5a-en&mimeType=pdf
Bunn, W.B., Pikelny, D.B., Slavin, T.J., Paralkar, S., Borden, M. 2016. "Health And Productivity as a Business Strategy." Health Affairs, vol. 35, no. 2, pp. 213–221. Available at: Health Affairs.
Jones, O., Musk, B. 2021. The Threat of Health-Related Class Action Suits Due to the Impacts on the Health of Underground Mine Workers. AusIMM Bulletin, October 25, 2021. Available at: Threat of Health-Related Class Action Suits Due to the Impacts on the Health of Underground Mine Workers. Regulations for Hazardous Chemical Agents (RHCA). 2021. Occupational Health and Safety Act (85 of 1993), GOVERNMENT GAZETTE, No. 44348, 29 March 2021.
NIOSH. 2003. Diesel Particulate Matter (as Elemental Carbon) 5040. National Institute for Occupational Safety and Health. Available at: https://www.cdc.gov/niosh/docs/2003-154/pdfs/5040.pdf
Australian Institute of Occupational Hygiene (AIOH). 2017. Diesel Particulate Matter and Occupational Health issues. Position Paper. Available at: https://www.aioh.org.au/product/diesel
Minerals Council of Australia. 2021. Submission on Safe Work Australia's Releases 2-14 Selected Substances WES. Available at: https://minerals.org.au/wp-content/uploads/2023/01/MCASubmission-on-SWA-Releases-2-14-selected-substances-WES12-Feb-2021-final.pdf
Zhang, H., Li, B., Karimi, M., Saydam, S., Hassan, M. 2023. Recent advancements in IoT implementation for environmental, safety, and production monitoring in underground mines. IEEE Internet of Things Journal, vol. 10, no. 16, pp.14507–14526. Available at: https://ieeexplore.ieee.org/document/10104078
Click
Pathway to industrialisation
ECSA VALIDATED CPD ACTIVITY, CREDITS = 0.1 POINTS PER HOUR ATTENDED
The primary purpose of the 2ND Hydrogen and Fuel Cells conference is the advancement of green hydrogen technologies in Southern Africa and the global community, by highlighting the power of renewable and sustainable technologies and addressing the emerging challenges—through the exploration of hydrogen production, storage and utilization using fuel cells by way of engagement with industry, academia and government. The conference will provide a platform for high level exchange and networking opportunities with various experts in the field.
Hydrogen: Production and storage
Fuel cell: Technologies, applications, and integration
Hydrogen mobility - strategies, safety, roadmaps, transitioning to hydrogen refueling stations (HRS)
Technology status in industry.
The two-day conference will feature high-level scientific talks and posters, complemented with keynote and plenary presentations on country overviews, status of leading and major players in the Southern African and global arena.
Will include inspiring technical talks, poster section as well as social networking events
Participants will have the opportunity to directly engage with conference attendees to discuss their research
The conference presents an attractive programme for researchers, industry players, academic institutions, government, investors, policy makers and potential users of fuel cell and hydrogen technologies. The focus is on building collective know-how and fostering engagement between business, government, science and academic institutions. Participants from all countries are invited and welcome to attend the event.
Gugu Charlie, Conferences and Events Co-ordinator
following deadline dates.
• Submission of abstracts deadline 31 January 2025
• Submission of papers deadline: 28 February 2025
The conference is organized by the Southern African Institute of Mining and Metallurgy, and individuals are invited to submit papers or presentations or posters for the Conference. Titles and short abstracts (no more than 500 words) on any relevant subject should be submitted in English to:
Conferences and Events
Co-ordinator
Gugu Charlie
Enquiries may be made at: Tel: +27 011 538-0238
E-mail:gugu@saimm.co.za website: www.saimm.co.za
Affiliation:
1MLB Consulting, Ballito, South Africa
2BHP, Australia
Correspondence to:
K.B. Le Bron
Email: kevin@mlbconsulting.co.za
Dates:
Received: 23 Aug. 2023
Revised: 14 Nov. 2024
Accepted: 13 Dec. 2024
Published: February 2025
How to cite:
Le Bron, K.B., van Aard, T. 2025
Application of an empirical method and numerical modelling to the Merensky Reef crush pillar stability. Journal of the Southern African Institute of Mining and Metallurgy, vol. 125, no. 2 pp. 87–98
DOI ID:
https://doi.org/10.17159/2411-9717/3060/2025
ORCiD:
K.B. Le Bron
https://orcid.org/0009-0008-9541-0016
by K.B. Le Bron1, T. van Aard2
Abstract
The empirical pillar strength formulae have been widely, and in most cases successfully, applied to design underground pillars for mines in the Bushveld Igneous Complex (BIC). This paper presents the case for combining the empirical method with numerical modelling when it comes to crush pillar stability analyses. The benefits include an understanding of potential failure mechanisms, which may then be accounted for in the designs. In addition, the impact of weak layers, such as shear zones, the impact of the dip of the orebody, differences in layouts, such as holing widths and the presence of advanced strike gulleys (ASGs) immediately adjacent to the crush pillars, and stress regime (k-ratio) may be studied using numerical modelling, as it is not accounted for in the empirical method.
Keywords
cube strength, numerical modelling, stress regime, empirical method, crush pillar stability
Introduction
The empirical pillar strength formulae have been widely, and in most cases successfully, applied to design underground pillars for mines in the Bushveld Igneous Complex (BIC). These formulae have limitations in the sense that it does not account for:
➤ (Site specific rock mass conditions in the formulae, i.e., weak layers such as the presence of shear zones at the top of the UG2 chromitite seam has such a persistent weak clay layer above or at the top contact, and bottom (the MG1 on the western limb of the BIC has such a persistent shear/fault at its bottom contact) of tabular orebodies,
➤ A stress regime in the formulae (the dip of the orebody impacts the normal and shear loading of the pillars),
➤ The complexity of layout in the formulae, i.e., the difference in heights on either side of the pillars, e.g., the presence of an advanced strike gully (ASG) next to the pillar,
➤ Any method for determining the cube strength. It was recommended to be a factor of the uniaxial compressive strength (UCS) of the pillar material; however a combination of different rock types may be present within the pillars, etc. Numerical models however allow for an investigation of site-specific rock mass conditions, complex layouts, different stress regimes, etc., which is useful in understanding the impact of these parameters on the pillar behaviour. The aim of the empirical pillar strength formulae is to ensure the design of stable pillars, which would not fail prematurely. However, there have been reports of crush pillar bursts on the Merensky Reef horizon, which is on the opposite end of the scale resulting in the following conundrum:
• if the pillars are too small, they may fail prematurely, and
• if they are too large, they may result in rock bursts.
This study was commissioned to study specific underground panel and pillar layouts, which have been based on the empirical pillar strength formulae, to determine the following:
1. The cube strength of Merensky Reef.
2. The impact of pillar height on crush pillar stability.
3. The impact of ASG versus siding on crush pillar stability.
4. The impact of pillar holing width on crush pillar stability.
Following here is a discussion about the learnings of this study.
Literature review
Pillar strength can be estimated from empirical equations that have been developed by observing both failed and stable pillar configurations. The design of stable pillars requires that both the strength and loading of the pillars be known. In addition, an appropriate safety factor should be selected to ensure that the variability and uncertainty of the pillar strength and loading is accounted for. In the case of regular arrays of flat lying pillars, the load can be estimated by the tributary area method (Salamon and Munro, 1967), or if the layout is more complex, estimates of average pillar loading can be obtained from numerical models (Brady and Brown, 1985). Following the Coalbrook North Colliery disaster in 1960, where the entire mine collapsed as a result of a cascading pillar failure, a study was commissioned to determine what the causes were of pillar failures, as well as to compile guidelines for future pillar designs. An empirical approach was followed, which involved studying data from a total of 125 pillars in South African coalfields, of which 27 constituted collapsed pillars. Based on a statistical appraisal of the data, Salamon and Munro (1967) developed a pillar strength formula, which is presented below: [1]
where:
s = strength of coal pillar
K = statistically determined strength of a unit cube of coal
w = pillar width
, = empirical constants
h = height of a pillar
A factor of safety (FOS) of 1.6 was recommended by Salamon and Munro (1967) (ratio of pillar strength to pillar stress). Several empirically based pillar strength equations have since been developed for hard rock mines (Hedley and Grant, 1972; Von Kimmelman et al. (1984); Lunder and Pakalnis, 1997). Hedley and Grant (1972) specifically applied the approach adopted by Salamon and Munro (1967) to hard rock mines. They monitored 28 pillars at uranium mines in Canada, of which only three were defined to have failed. Based on this, Hedley and Grant (1972) developed a pillar strength formula for hard rock mines, which is presented below:
where:
s = strength of hard rock pillar
K = statistically determined strength of a unit cube of rock
w = pillar width
, = empirical constants
h = height of a pillar
[2]
minimum recommended width-to-height ratio for crush pillars. The extent of brittle and shear failure in pillars with width-to-height ratios of 0.5, 1.0, and 2.0 are presented in Figure 2 (Esterhuizen, 2006), illustrating the increasing role of brittle failure as the widthto-height ratio decreases. Failure of the wider model pillars is initiated by brittle failure around the outside of the pillar, which commences when the stress in the outer skin of the pillar exceeds the brittle rock strength. The brittle failure process continues as the pillar load increases. Note that the progression of potential failure within the crush pillars is expected to follow that of the schematic for a width-to-height ratio of ~2 (Figure 2).
One of the main findings of this study was that the standard deviation of the strengths of slender pillars was 25.4%, while it was 7.8% for the wider pillars. The variability can be caused by several factors, which can include uncertainty of the actual rock strength, uncertainty of the pillar stress, variations in the degree and severity of jointing, a variation in the bedding characteristics, and the presence of weak layers in the pillars.
In the case of crush pillars, a factor of safety (FOS) of less than 1 is recommended as the pillars are designed to crush in a stable manner. Width-to-height ratios of crush pillars employed in the South African gold and platinum mines generally vary between ~1.3 to ~2.5. The schematic shown in Figure 1, highlights guidelines for pillar designs for mines located in the Bushveld Igneous Complex (Anon, 2006).
Esterhuizen (2006) studied the impact of width-to-height ratio on pillar stability, where he showed that for the presented case histories, the pillar strength becomes highly variable as the widthto-height ratio decreases (two pillars failed at width-to-height ratios of 2 and above). Esterhuizen (2006) defined pillars with width-toheight ratios of less than 1.0 as slender pillars, which is less than the
Malan (2010) surmised that two different methods to determine the strength of pillars are currently used namely, empirical equations derived from the back analyses of both failed and stable cases and numerical modelling tools with appropriate failure criteria. Both techniques have their limitations and additional work is required to obtain a better understanding of pillar strength. He concluded that neither empirical techniques nor numerical modelling currently provide a solid basis to conduct pillar design. He further recommended that both these techniques be utilised when confronted with pillar designs to obtain the best possible insight into the problem.
The vertical axial strain at failure may be used to predict potential failure in the rock mass where similar unconfined conditions may exist. The edges and corners of the underground pillars may experience similar unconfined compression, which means that
the vertical axial strain may be applied as a criterion in numerical simulations, to determine the onset of pillar fracturing, as a precursor to slabbing and spalling of the pillar sides. The best fit power law relationship is shown in Figure 3 for the 11 site-specific test samples tested, which has a coefficient of determination (R2) of ~0.91. Based on the analysis, the minimum axial strain value of ~ 0.9 mm/m may be used as a criterion to indicate in which zones the peak strength had been exceeded, i.e., which zones are in the postpeak strain-softening phase.
Elastic material properties were initially assigned to the rock mass simulated in the numerical models, in order to determine the minimum deformation levels predicted within the crush pillars. It is assumed that if the deformation levels predicted for the elastic material properties result in vertical strain exceeding the strain criterion of 0.9 mm/m (from Figure 3), the pillars would be considered crush pillars and would not pose a risk of bursting as the actual resultant in situ inelastic deformation would be greater than the elastic deformation.
In the non-linear numerical models, it was assumed that if the model does not converge (reach equilibrium), the crush pillars will
continue to deform and eventually disintegrate. The crush pillar dimensions that resulted in the models not converging were then defined as not suitable for the mining conditions. Furthermore, this method was also applied to quantify strain values for disintegration of the crush pillars. Unfortunately, there is no technical publication that could be cited as a benchmark against which this novel approach can be tested.
A back analysis of the insitu Merensky reef cube strength was conducted, using the Hedley and Grant (1972) formula, which has been used to design most of the Merensky Reef pillars of the Bushveld Igneous Complex. Detailed information on pillar dimensions and rock wall conditions was available after a comprehensive data gathering exercise in preparation for this back analysis had been conducted. The stoping layout incorporating the stope panels and crush pillars was modelled elastically to a fine discretised mesh of 0.5 m (vertical) x 0.5 m (strike) x 1 m (along dip). Figure 4 presents the crush pillar numbering convention and actual pillar heights measured at all four exposed sides (for ease of
reference, a plan view of the stope panel and annotated crush pillars are presented in Figure 1, together with the pillar dimensions). Pillar A had not yet been formed at the time of the study and was therefore not incorporated into the study. Pillar B was also not completely formed; however all four sides had been exposed and was therefore included in the study. Pillar E was significantly undersized and was also excluded from the back analysis. The average pillar heights were calculated by averaging the three sides of the pillars referred to as 1 (holing), 3 (holing) and 4 (panel). The value obtained from this calculation was then averaged with pillar side 2 (ASG side). This method assumes a pillar height, which is unlikely to overestimate the effective pillar height. The pillar widths and pillar lengths were taken at 3 locations across the pillars, based on the survey measurement data. The pillar widths were averaged based on three measurements across the pillar, which include the measurements at the pillar ends and one in the middle of the pillar.
1,80E+08
1,60E+08
1,40E+08
1,20E+08
1,00E+08
8,00E+07
6,00E+07
4,00E+07
2,00E+07
0,00E+00
Underground data collection and modelling results Figure 5 to Figure 11 present the modelled stress in the crush pillars, as well as photos showing the condition of the pillar walls. Photos are shown for the pillar closest to the face (Pillar B) and the pillar furthest from the face (Pillar G), for comparison. The results generally show that the pillar stress is highest where the pillar height is smallest, i.e., on the ASG side the pillar stresses are generally lower due to the increased height of the ASG. The photos indicate that most of the pillars are extensively fractured and may have crushed. Figure 11, which details a graph of the average modelled pillar stress (APS) for the crush pillars, shows that the stress on the pillars closer to the panel face is generally lower than the pillars in the back area. It must be noted that the stress on pillars D, F, and G tends towards an APS of approximately 120 MPa, whereas pillar C has an APS of ~110 MPa and pillar B, which has not yet been fully created, has an APS of ~ 80 MPa. As mentioned previously, pillar E
1,60E+08-1,80E+08
1,40E+08-1,60E+08
1,20E+08-1,40E+08
1,00E+08-1,20E+08
8,00E+07-1,00E+08
6,00E+07-8,00E+07
4,00E+07-6,00E+07
2,00E+07-4,00E+07
0,00E+00-2,00E+07
was significantly undersized and resulted in a significantly higher APS value of ~155 MPa (stress is calculated by dividing the load with the area, i.e., smaller area of Pillar E resulting in higher stress). The back analysis is based on the reasonable assumption that the crush pillars are either at an FOS of 1 or very close to it (the sides of the crush pillars have already fractured, whilst Pillar B has not been fully created on the face). It is therefore reasonable to assume that these pillars would have an FOS of ~1.s.
The strain and stress profiles across pillar B are shown in Figure 12. Figure 13 shows the locations in pillar B, where the stress and strain values were taken. The strain criterion of 0.9 mm/m (derived from Figure 3) is used to locate the critical stress in Figure 13. A critical stress of approximately 47 MPa is suggested for pillar B, based on the FLAC3D results.
The same approach has been applied to pillar C to pillar G. Figure 14 presents the relationship between stress and strain for pillar C to pillar G. Pillar E has not been included due to its irregular shape. It should be noted that the lowest strain values in pillar C to pillar G exceeded the strain criterion of 0.9 mm/m, however the relationship between stress and strain for each pillar was extended to the intersect the strain criterion of 0.9 mm/m, from which the critical stress was inferred. The critical stress level in pillar C is ~56 MPa. The critical stress level in pillar D is ~44 MPa. The critical stress level in pillar F is ~37 MPa. The critical stress level in pillar G is ~43 MPa.
Table I
Summary of back analysis of insitu cube strength (K-value)
Back analysis of the Merensky Reef cube strength (K-Value)
For this study, the Hedley Grant (1972) formula (Equation 2) was applied to back analyse the insitu cube strength (K) for the Merensky Reef. As explained previously, once the critical stress was determined for the critical vertical strain of 0.9 mm/m, the critical stress was then determined at those locations. When the FOS is equal to 1, the pillar stress would be equal to the pillar strength. These critical stress values were then used in the Hedley Grant formula by substituting the pillar strength (PS) to determine the cube strength (K-value). The heights were calculated by averaging three sides of the pillar including the holings and the down-dip panel. The average of the height obtained and the height in the ASG were used to calculate the pillar height. The calculated K-values based on the back analysis of each pillar are presented in Table 1
Summary of the Merensky cube strength back analysis results
The FOS for the pillars based on the APS and H-G formula using: (i) a minimum of 58 and (ii) the individual back-calculated K-values, is shown in Table 2 and Table 3 respectively.
The skin of the pillars for all cases are predicted to fracture by the modelling (also shown in the pictures), which is why the inferred critical stress at failure was used. The results indicate that the face area has a major effect in reducing the stress level on the pillars, which is why the FOS is greater than 1 for pillar B. The minimum K-value of 58 MPa seems realistic based on the FOS calculations, and the underground visual observations (especially for pillar B, which has not been fully created).
The impact of mining height on crush pillar behaviour
The following combinations of crush pillar dimensions were simulated in FLAC3D (note that no ASG was modelled next to the crush pillars):
➤ 6 m (length) x 2 m (width) x 1.0/1.5 m (height)
➤ 6 m (length) x 2.5 m (width) x 1.0/1.5 m (height)
➤ 6 m (length) x 3 m (width) x 1.0/1.5 m (height)
➤ 6 m (length) x 4 m (width) x 1.0/1.5 m (height)
➤ 6 m (length) x 5 m (width) x 1.0/1.5 m (height)
The decline protection pillars were included in these models to realistically determine resultant deformation and strain of crush pillar instability. Plots of the vertical strain block contours predicted within the simulated crush pillars are shown in Figure 15, also presented in graph format in Figure 16. The results show that the strain that is predicted to occur in the crush pillars, will
Table 2
FOS based on in situ cube strength (K-value) of 58 MPa
exceed the criterion of 0.9 mm/m, which is required for fracturing to occur. Nowhere within the simulated crush pillars will the strain at failure not be reached, which for all intents and purposes implied that pillar bursting, was unlikely to occur (provided that the actual underground mining layout comply with the design).
In order to reduce run-time, separate models were set up to carry out analyses on crush pillar widths. In these models, only two of the three regional pillars were simulated with a single belt drive, as the focus was on the crush pillars rather than the service excavations. It is therefore not directly comparable to the previous set of results. The strain criterion was used in this sensitivity analysis. The results show that the 2 m and 4.5 m wide crush pillars are predicted to crush at a pillar height of 1.5 m (see Figure 17 and Figure 18). However, if the regional pillars are excluded from the model, the 3 m wide crush pillar deforms significantly more. The models simulating the crush pillars at widths of less than 3 m
Table 3
FOS based on individual in situ cube strength (K-value) of each pillar as back calculated
-1.3731E-02 -1.3000E-02 -1.2000E-02 -1.1000E-02 -1.0000E-02 -9.0000E-03 -8.0000E-03 -7.0000E-03 -6.0000E-03 -5.0000E-03 -4.0000E-03 -3.0000E-03 -2.0000E-03 -1.0000E-03
Contour of ZZ Strain Increment Calculated by: Volumetric Averaging
-6.3384E-02 -6.2500E-02 -6.0000E-02
-5.7500E-02 -5.5000E-02
-5.2500E-02 -5.0000E-02
-4.7500E-02 -4.5000E-02 -4.2500E-02 -4.0000E-02 -3.7500E-02 -3.5000E-02 -3.2500E-02
-3.0000E-02 -3.0000E-02
Figure 17—Schematic showing the vertical strain contours predicted to occur in the crush pillars (6 m x 2 m x 1.5 m (height)) with regional pillar
Contour of ZZ Strain Increment Calculated by: Volumetric Averaging
-6.0000E-02 -5.5000E-02 -5.0000E-02 -4.5000E-02 -4.0000E-02 -3.5000E-02 -3.0000E-02 -2.5000E-02 -2.0000E-02 -1.5000E-02 -1.0000E-02
Figure 18—Schematic showing the vertical strain contours predicted to occur in the crush pillars (6 m x 4.5 m x 1.5 m (height) with regional pillars
Figure 19—Graph showing the relationship between vertical strain contours and pillar width for 1 m and 1.5 m pillar heights (stope widths), respectively
with no regional pillars included, do not converge, indicating that the crush pillars are predicted to continuously deform, leading to disintegration of the crush pillars.
Based on the results, when the strain in the core of the crush pillars exceeded a value of ~18 mm/m, the models did not converge, which was defined as the criterion indicating crush pillar failure/ collapse. The criterion of 0.9 mm/m (indicating brittle failure of the crush pillars), together with the strain criterion of ~18 mm/m
(indicating collapse of the crush pillars) was applied to determine lower and upper limits of crush pillar widths for pillar heights of 1 m and 1.5 m (Figure 19).
The derived upper and lower width dimensions for crush pillars of different mining heights are summarised in Table 4, which are: i) 1.7 m and 2.6 m for a 1 m stoping height, and ii) 3.2 m and 4.4 m for a 1.5 m stoping height.
Table 4
Derived upper and lower width dimensions for crush pillars of different mining heights of 1 m and 1.5 m
The effect of ASG versus siding on crush pillar behaviour
The impact of the ASG versus the siding on the down-dip side of the stope panel was investigated by simulation within the same model: (i) stope panel with an ASG but without a siding and (ii) stope panel with an ASG, but with a siding. Elastic material properties were assigned to the rock mass for this comparative assessment. An orebody dip of 12°was assumed. The height of the ASG was modelled at 2.4 m, with the stope width being 1.2 m.
The results show that where a siding is cut, the stresses that form within a crush pillar is symmetrical, whereas the stresses in a crush pillar where no siding is present, is not symmetrical (see plots of vertical stresses within crush pillars for the scenarios in Figure 20 and Figure 21).
The presence of an ASG with a modelled height of 2.4 m, results in a significant stress drop on the down-dip side of the crush pillar, resulting in the uneven stress profile along dip. The results of this uneven stress profile are:
➤ Differential movement in the dip direction (see plots in Figure 22 and Figure 23). The differential movement may lead to the formation of shear fractures, along which dilation may occur, which will ultimately reduce the crush pillar stability.
➤ The potential for fracture formation, which may lead to sidewall slabbing is highest on the up-dip side for the case where no siding is present. This may lead to pillar scaling, resulting in higher loads being carried by the remaining portion of the crush pillar. However, due to the height of the
Contour of X-Displacement
-6.0000E-04
-2.0000E-03 -1.8000E-03 -1.6000E-03 -1.4000E-03 -1.2000E-03 -1.0000E-03 -8.0000E-04 -4.0000E-04 -2.0000E-04 0.0000E+00 5.0000E-05
will reduce the crush pillar stability)
Contour of X-Displacement
-3.0000E-03 -2.8000E-03 -2.6000E-03 -2.4000E-03 -2.2000E-03 -2.0000E-03 -1.8000E-03 -1.6000E-03 -1.4000E-03 -1.2000E-03 -1.0000E-03
strike gully being ~2.4 m, the crush pillars will have a reduced capacity to absorb the additional load that is transferred due to scaling on the up-dip side of the pillar. This scenario may ultimately lead to disintegration of the crush pillars due to excessive slabbing and continuous scaling.
The impact of ventilation holing width on crush pillar behaviour
The impact of the ventilating holing width was investigated through numerical modelling as part of this study. Figure 24 presents the locations of vertical stress profiles through a 4 m (strike) x 3 m (dip) crush pillar with a 4 m holing at a vertical depth of 600 m below surface.
The results from these modelled stress profiles were used to determine the average pillar stress (APS). The models were run elastically to determine the maximum stress predicted in the crush pillars, which also allows a comparison between the tributary area theory (TAT) and the numerical modelling methods.
Figure 25 presents a graph showing the stress profile across the crush pillar, as well as the APS determined using both the TAT and numerical modelling (FLAC3D) methods. The results indicate that the APS applying the TAT method is calculated to be ~391 MPa, compared to a value of ~366 MPa predicted by the numerical modelling. The profiles indicate that the pillar corners and sides are predicted to experience significantly higher stresses than the pillar core.
Applying a K-value of 58 MPa (based on the back analysis results), the factor of safety is calculated at ~0.3 (using the modelled APS), which is less than 1. Therefore the 3 m (width) x 4 m (length) pillars are predicted to crush.
Figure 26 presents a strain profile through the core of the crush pillar, indicating that the core of the 4 m crush pillar would experience strain levels of ~6.5 mm/m, compared to the sidewalls, which are predicted to experience strain levels of up to ~9.5 mm/m. The corners are predicted to experience strain levels of up to ~15 mm/m. The strain in the core of the 6 m long crush pillar with
Profile Contour of ZZ-Stress Calculated by: Constant 0.0000E+00
-4.5293E+08 -4.5000E+08 -4.0000E+08 -3.5000E+08 -3.0000E+08 -2.5000E+08 -2.0000E+08 -1.5000E+08 -1.0000E+08 -5.0000E+07
Profile Contour of ZZ-Stress Calculated by: Constant
1 -3.6430E+08 -3.5000E+08 -3.0000E+08 -2.5000E+08 -2.0000E+08 -1.0000E+08 -5.0000E+07 0.0000E+00
Profile Contour of ZZ-Stress Calculated by: Constant
3 -1.0000E+08
2 -1.5000E+08 -3.4643E+08 -3.0000E+08 -2.5000E+08 -2.0000E+08 -1.5000E+08 -5.0000E+07 0.0000E+00
24—Schematic showing the locations of the vertical stress profiles across the crush pillar
Figure 25—Schematic showing the profiles of vertical compressive stress in the pillar at different locations through the pillar (red indicate APS based on TAT; purple indicates APS based on FLAC3D)
Figure 26—Schematic showing the vertical strain through the core of the crush pillar
a 2 m holing is ~4 mm/m, which is approximately a third less than the ~6.5 mm/m in the 4 m crush pillar with a 4 m holing. The strain criterion of 0.9 mm/m is however exceeded throughout the 4 m and 6 m long crush pillars, indicating that all the zones within the crush pillars will reach peak stress/strain.
Due to the high pillar stress resulting in a low factor of safety of ~0.3 and the high vertical strain of ~6.5 mm/m in the pillar core, significant fracturing of the crush pillars was predicted for a depth of 600 m below surface (photographs taken underground at a
depth of 500 m below surface support the prediction that fracturing will occur, which may lead to pillar scaling). The sidewalls and the corners, which are predicted to experience vertical strain ranging between ~10 and 15 mm/m will most definitely result in slabbing, which may lead to scaling. The holing width does not seem to affect the crush pillar performance but may impact roof stability between the pillars. The models predict that the stress overlap between the crush pillars will not result in the formation of a high tensile zone within the holing (analytical method suggests a tensile zone height
of less than 20 cm). However, experience has shown that a 2 m pillar holing at depths that may result in fracture formation in the roof, will tend towards a stable arch shape as a result of the compressive stress. The horizontal clamping stress from the adjacent crush pillars appears to be lower in a 4 m holing width, compared to a 2 m holing width. In addition, the potential for dilation along persistent reefparallel stringers, is more likely to occur in a 4 m holing compared to a 2 m holing.
Summary
This paper presents a method for back analysis of rock mass strength, and pillar stress strain behaviour using advanced inelastic numerical modelling. The study further illustrates how the different variables impact the stability of crush pillars, including the pillar dimensions (width, height, and length), the dip of the orebody, and differences in layouts (such as holing widths and the presence of ASGs immediately adjacent to the crush pillars). Based on the findings, it is suggested that an empirical method be used as a first step due to its many limitations, rather than the final step in the pillar design process. This should then be followed by an in-depth analysis using advanced inelastic numerical modelling to investigate all possible failure mechanism.
References
Anon. 2006. Schematic of pillar design guidelines. Anon. 2014. FLAC3D Version 5.01 Manual.
Brady, B.H.G., Brown, E.T. 1985. Rock Mechanics for Underground Mining, George Allen and Unwin, London, 527 pp.
Esterhuizen, G.S. 2006. An evaluation of the strength of slender pillars. SME Annual Meeting, St. Louis, Missouri.
Hedley, D.G.F., Grant, F. 1972. Stope and pillar design for the Elliot lake uranium mines. Canadian Institute of Mining and Metallurgy, vol. 65, pp. 37–44.
Jager, A.J., Ryder, J.A. 1999. A handbook on Rock Engineering Practice for tabular hard rock mines, SIMRAC, Johannesburg.
Lunder, P.J., Pakalnis, R. 1997. Determining the strength of hard rock mine pillars, Canadian Institute of Mining and Metallurgy, vol. 90, pp. 51-55.
Malan, D.F. 2010. Pillar Design in Hard Rock Mines – Can we do this with Confidence? Second Australasian Ground Control in Mining Conference. Sydney, NSW.
Ryder, J.A., Jager, A.J. 2002. A textbook on rock mechanics for tabular hard rock mines, SIMRAC, Johannesburg.
Salamon, M.D.G., Munro, A.H. 1967. A study of the strength of coal pillars, Journal of South African Institute of Mining and Metallurgy, vol. 68, pp. 55–67.
Von Kimmelman, M.R., Hyde, B., Madgwick, R.J. 1984. The use of computer applications at BCL Limited in planning pillar extraction and the design of mining layouts, In Design and Performance of Underground Excavations. International Society for Rock Mechanics. Symposium, Brown and Hudson, eds., Brit. Geotech. Soc., London, pp. 53–63.
THIRTEENTH INTERNATIONAL HEAVY MINERALS CONFERENCE
18-19 AUGUST 2025SUN CITY RESORT, RUSTENBURG, SOUTH AFRICA
This series of conferences was started in 1997 and has run since that date. It provides a forum for an exchange of knowledge in all aspects of heavy minerals, from exploration through processing and product applications. This is a strictly technical conference, and efforts by the Organizing Committee are aimed at preserving its technical nature. The benefit of this focus is that it allows the operators of businesses within this sector to discuss topics not normally covered in such forums. The focus on heavy minerals includes the more obvious minerals such as ilmenite, rutile and zircon; and also other heavy minerals such as garnet, and alusite, and sillimanite.
FOR FURTHER INFORMATION, CONTACT:
Gugu Charlie, Conferences and events co-ordinator
E-mail: gugu@saimm.co.za
Tel: +27 11 538-0238, Web: www.saimm.co.za
Affiliation:
1Department of Mechanical and Mechatronic Engineering, Stellenbosch Univeristy, South Africa
2De Beers Group, South Africa
Correspondence to:
J.R. Bredell
Email: jrbredell@sun.ac.za
Dates:
Received: 16 Apr. 2024
Revised: 5 Nov. 2024
Accepted: 10 Dec. 2024
Published: February 2025
How to cite:
van Tonder, J.J. Bredell, J.R., Coetzee, C., Branehog, J. 2025. Simulation of kinetic joint forces in a nutating grinding mill. Journal of the Southern African Institute of Mining and Metallurgy, vol. 125, no. 2 pp. 99–106
DOI ID:
https://doi.org/10.17159/2411-9717/3376/2025
ORCiD:
J.J. van Tonder
https://orcid.org/0009-0009-6290-2978
J.R. Bredell
https://orcid.org/0000-0002-0748-746X
C. Coetzee
https://orcid.org/0000-0002-9924-8123
J. Branehog
https://orcid.org/0009-0001-5625-8989
by J.J. van Tonder1, J.R. Bredell1, C. Coetzee1, J. Branehog2
Abstract
A nutating grinding mill, exemplified by the commercial HICOM mill, achieves efficient particle size reduction through the accelerated motion of the material charge within the nutating chamber. This design, characterised by high particle velocities and rapid charge circulation, offers a compact solution compared to tumbling mills. There have been concerns regarding the mechanical reliability of kinetic joints for certain specialised mining applications. Recognising the need to model internal forces in such systems, this study focuses on the uncoupled simulation using multibody dynamics and the discrete element method. The investigation employed a small-scale experimental test mill, referred to as the NuMILL, featuring a cylindrical chamber (140 mm internal diameter, 245 mm height, 6° nutation angle). Instrumented with an array of sensors, the NuMILL provided internal load data for validating the simulations. Experiments were conducted with an empty chamber or filled with charge material. Charge materials included coarse sand or steel pellets with a charge-to-chamber mass ratio of 0.25. The mill speed ranged between 100 to 700 RPM. Multibody dynamics modelled resultant inertial and frictional loads within 5%, while the discrete element method simulated the internal material contact loads with accuracies ranging from 1% to 19%. The combined simulation approach predicted the resultant forces in the critical kinetic joint within a 20% margin. Representing the charge using rigid lumped mass elements was also studied. The presented simulation techniques, validated against experimental data, offer a robust foundation for analysing larger systems, including the industrial-scale HICOM.
Keywords HICOM, nutating grinding mill, multibody dynamics, discrete element method
Introduction
Grinding is a particle size reduction process involving abrasion and impact forces, typically occurring in a rotating cylindrical chamber filled with screened mined material, termed the charge (Wills and Finch, 2016). Figure 1 illustrates a common grinding machine referred to as a tumbling mill. Figure 2 depicts various charge tumbling regimes, dependent on chamber rotation speed, gravitational acceleration, and internal diameter.
The cataracting regime proves most effective for grinding in a mill (Yulia et al., 2016), as it is characterised by high material impact and compression loads. However, achieving this regime requires a fine balance, since a slight increase in rotation speed beyond the optimum leads to centrifuging, resulting in significantly reduced grinding efficiency. To increase material throughput, large diameter mills are often required. However, practical limitations in operations with spatial constraints may prevent enlarging the mill diameter.
An alternative is the centrifugal mill (Bradley et al., 1974). A centrifugal mill includes multiple slender mill tubes, which contain the charge and rotate about their own axes. In addition to the own-axis rotation, the tubes also rotate about a centred primary axis, which is parallel to the mill tube axes. The drive mechanism is typically achieved using a planetary gear train. The primary axis is vertical with the feed-end located at the top and dischargeend located at the bottom to enable continuous throughput. This dual-axes rotation creates intense acceleration fields and charge motion conducive to grinding (Hoyer and Lee, 1997). Compared to a conventional horizontal tumbling mill of equivalent size, a centrifugal mill achieves superior material breakage rate and operating throughput. Liner wear has been identified as a drawback of such systems.
Nutating mills advance the idea of tumbling a charge within an induced centrifugal acceleration field through nutating motion (Nesbit and Moys, 1998). An example of such a nutating grinding mill is the HICOM, depicted in Figure 3. The HICOM's nutating movement resembles the dynamic motion of swirling a conical flask by the wrist, featuring rapid circular oscillations inducing varying centrifugal acceleration fields (Nesbit et al., 2001). These acceleration fields can achieve material breakage rates 50 to 100 times greater than conventional tumbling mills per unit volume (Hoyer, 1999).
The HICOM's appeal lies in its reduced chamber size, high acceleration fields, and rapid comminution rates. Although widely used in industry for stated reasons, shortcomings relating to mechanical reliability have been found for specific mining applications. Sensitivity to dimensional tolerances and load path characterisation are thought to be potential root causes, which may lead to bearing and component fatigue failure.
The cost, size, and availability of commercial machines often prohibit research using full-scale physical measurements. Simulation offers a more practical method to analyse grinding equipment and conduct virtual experiments.
This research aims to develop a verified simulation method for a generalised nutating mill to accurately predict the dynamic forces at selected kinetic joints. The simulations are based on the combination of multibody dynamics (MBD) and discrete element method (DEM) analyses. To facilitate this research, a small-scale laboratory model of a nutating mill, inspired by HICOM but with simplified component geometries, was designed and manufactured. This small-scale nutating mill will be referred to as the NuMILL. The NuMILL provided the experimental data necessary for validating the simulations and studying the internal forces and material motion. The insights gained from the experimental and simulated NuMILL analyses will aid in identifying which kinetic joint within the HICOM is subjected to the highest loads. Deeper understanding of the critical load paths and quantification of operational loads at kinetic joints can inform design decisions and operating practices. This in turn, will reduce the risk of component failure and improve system availability.
Figure 4 provides a cross-sectional view of the NuMILL CAD model, along with a photo of the fully assembled NuMILL with reference dimensions. The NuMILL serves as a kinetic equivalent laboratory model of the HICOM, playing a pivotal role in experimentally validating simulations. Its primary objective is to measure kinetic joint loads at critical locations, including the nutation point and torque arm crankpin. A more detailed description of the load paths and constraints, accompanied by a free body diagram of the nutating chamber, are presented in the following section covering the simulations. It is also capable of capturing video footage of the material motion within the grinding chamber.
The universal joint assembly, designed to serve as a force balance, incorporates load cells for measurement of forces and moments at the nutation point. The assembly is shown in Figure 4 and Figure 7. It is composed of a solid aluminium stationary yoke (196 mm × 216 mm × 40 mm) that interfaces with load cells, the universal cross-element, and an oscillating yoke connected into the top of the grinding chamber.
The rotating torque arm supports the eccentrically rotating crankpin, which in turn interfaces with the bottom of the chamber via a spherical bearing. The bearing was designed with axial float to avoid an over constrained and statically indeterminate system. The crankpin is mounted on radial guide rails and is connected to a wireless load cell (SG-link), allowing the measurement of the radial force acting on the crankpin. Detail of the torque arm assembly is shown in Figure 5.
The base frame houses the drivetrain, which includes the driveshafts, associated bearings, a 0.37 kW motor, and a torque transducer for measuring torque and inferring tangential loads on the crankpin. Masses of NuMILL components and assemblies are detailed in Table 1.
The experiments conducted using the NuMILL involved varying the rotational speed of the motor and the type of charge material inside the chamber. Photos of the different charge materials are shown in Figure 6. It is noted that Figure 6 displays plastic pellets not discussed in this article; the relevant materials are the coarse silica sand (dry) 3 mm to 5 mm grain size, 5 mm diameter steel pellets and rigid steel bars. The steel pellets and sand were chosen to reduce modelling uncertainty, since they have been wellcharacterised in previous work (Coetzee and Katterfeld, 2023a). All the rotation speed profiles had the same constant rotational
acceleration followed by a constant rotation speed of either 100, 400, or 700 RPM (except for the steel pellets, where the power limit of the motor was reached at 560 RPM). The constant rotational speed was maintained for at least 30 seconds before power to the motor was cut allowing free rotation until the chamber came to rest. Once the target speed was reached, the transient response in the experimental torque and force data was not significant and a steady state condition was reached shortly after the acceleration ramp. Steady state data for which the torque and forces amplitudes remained constant were selected for further processing. The dependent variables included kinetic joint forces, driveshaft torque, and charge motion. Only steady state results at different rotation speeds are presented. Table 2 summarises the NuMILL experiments discussed in this work.
The experiments adhered to the following procedure: For the empty case, no charge material or steel bars were used. The steel bars were rigidly mounted on the outside face of the chamber base for the case where the charge is represented by lumped mass. For the steel pellet and sand cases, the chamber was filled with charge masses listed in Table 2. Subsequently, the NuMILL was accelerated to a constant rotational speed required for testing and maintained at that speed throughout the test. To account for statistical variation in measurements, each test point was repeated three times, allowing for the averaging of measurement data. Only mean results are reported here.
Two distinct types of experiments were conducted. The first focused on load cell measurements of joint forces, while the second involved the video recording of the particle motion relative to the chamber. For the latter, additional structural supports for the camera assembly were introduced into the chamber. This addition altered the inertial loads of the nutating chamber due to the added mass. Consequently, no force data were recorded during the video recording experiments. Given the high degree of rigidity of the
support frames and chamber, the particle motion is not expected to be influenced by the additional mass of the camara and frame, since the only additional displacements would be the elastic deformation of metal components. This enabled visual comparison of the particle motion between the experimental video footage and DEM simulations. The force data of the experiments conducted without the camera, however, served the purpose of validating the modelled force response from MBD and DEM simulations.
The MBD model, developed in ANSYS Mechanical simulation software (ANSYS, 2022), is depicted in Figure 7 and Figure 8. Figure 7 shows the modelled components, highlighting key elements such as the six load cells in the universal assembly, the radial load cell (purple) in the torque arm assembly, and the transparent grinding chamber. Figure 8 shows a simplified free body diagram with kinetic parameters and system layout. Points 0, 1, and 2 refer to the nutation point inside the universal assembly, torque arm rotation point and crankpin position, respectively. The torque arm rotation axis corresponds to the global Z-axis, and the local chamber axis coincides with the line between points 0 and 2. The local radial and tangential axes at the crankpin are shown at point 2. The linear distance between points 0 and 1, and between points 1 and 2, are given by L01 (366 mm) and L12 (39 mm), respectively. The universal assembly is connected to the top frame using six rods with spherical rod ends. Three of the rods are aligned with the vertically z-axis, two with the y-axis, and one with the x-axis, as shown in Figure 7. This arrangement rigidly supports the stationary yoke. The cross-element and oscillating yoke are free to rotate about their respective axes. In the experiments, loads cells were fitted to certain rods to enable the measurement of the reaction forces and moments at the nutation point. The chamber is supported at point 0 using two cylindrical joints in the X- and Y-axes, representing the universal joint. In addition, a cylindrical joint is defined between the torque arm and the chamber at point 2, where the radial and tangential crankpin loads are calculated. The torque arm is rigidly connected to the driveshaft, which rotates with prescribed speed Ω), and the driveshaft torque (τ) is calculated. A friction coefficient of 0.03 was used at all kinetic joints to account for frictional losses in the system. The friction coefficient was obtained through a calibration process where the value was tuned in the simulation to match the experimental steady state torque for an empty chamber rotating at 400 RPM.
The DEM simulations were performed using PFC3D simulation software (ITASCA, 2023), based on the dimensions and force decomposition described in Figure 8. The DEM model, which refers to the massless facet walls, DEM particles, coordinate system, constraints, and torque arm rotation speed ω) is shown in Figure 9. To enable comparison to experimental steady state data, simulations were run for a long enough period to ensure steady state conditions in terms of reaction forces.
The simulated charge materials included 5 mm steel pellets and coarse sand. The steel pellet simulation was previously validated (Van Tonder, 2024), utilising literature data (Bian et al., 2017) and factorial analysis to determine parameter sensitivity. Calibration and validation work by Scheffer and Coetzee (2023a) and Scheffer and Coetzee (2023b), provided the foundation for modelling the coarse sand charge. In this research, magnified images of sand particles were used to characterise particle geometries and associated properties. Material parameters such as bulk density, normal stiffness, and shear stiffness, were experimentally determined. A linear contact model was used in both the steel particle and sand simulations (Coetzee and Katterfeld, 2023). Table 3 summarises the finalised DEM material parameters for both steel and sand simulations.
Both the coarse sand and steel pellet simulations where 1:1 scaled simulations of the experiments performed on the NuMILL. Apart from the material parameters, another modelling difference was that the steel pellet simulation made use of ball elements and the sand was modelled using clump elements. The modelled sand clump geometries were based on scanned geometrical data of ten different sand grains. Each of the grain geometry types were represented with a clump consisting of three spherical particles.
Table 3
Discrete element method material parameters
DEM simulation parameter
Particle type
Particle
Normal stiffness of linear model [kN/m]
Shear stiffness of linear model [kN/m]
Static friction coefficient (particle-particle)
Static friction coefficient (particle-facet)
Rolling friction coefficient (particle-particle) 0.01 -
Rolling friction coefficient (particle-facet) 0.01 -
Normal critical damping ratio (particle-particle)
Normal critical damping ratio (particle-facet) 0.28 0.212
The sizes and positions of the spherical particles in a clump were optimised to represent the associated scanned geometry. In addition, an experimentally determined size distribution was applied to each clump type. Details of the clump geometries and size distribution are reported in Scheffer and Coetzee (2023a).
Examples of the video footage from the camera attached to the nutating chamber are shown in Figure 10. The figure shows the steel pellet charge at various angular positions for a rotation speed of 400 RPM for visual comparison with DEM results. The fringe scale in the DEM results indicate the vertical (Z-coordinate) particle position relative to the origin located at the nutation point. Detailed analysis of video footage is covered by Van Tonder (2024), which includes a sensitivity analysis of the particle-to-particle and the particle-to-facet friction coefficients. These properties were found to significantly influence the shape of the charge. The primary purpose of the recorded video (240 frames per second) was for qualitative visual comparison of particle distribution. Approximate measurements of the material crest height and phase lag were taken using 10 mm (tangential) by 10 mm (axial) grid paper adhered to the outside face of the transparent cylindrical section of the chamber. This method relied on the visual estimation of particle positions in a video frame corresponding to the approximate
chamber angular position of interest. Significant uncertainty can therefore be expected in terms of measurement resolution and repeatability. Despite these limitations, the sensitivity analysis of material friction properties showed reasonably good qualitative comparison between simulation and experiment. However, since the purpose of the current research was to calculate internal component forces, load cell measurements were used as the primary validation metric.
and discussion
This section presents results of the uncoupled MBD and DEM simulations and subsequently, compares the results to experimental measurements. Several key points are highlighted to assist with the interpretation of the results, as well as to provide context and motivation for selected results presented here.
Firstly, the results are plotted against a non-dimensional centrifugal acceleration parameter (λ) on the primary x-axis of the graphs. During the preliminary analysis of experimental data, it was observed that the force data exhibited a more linear relationship with λ, compared to the rotation speed (Ω). However, for a more intuitive reference, the rotation speed in RPM is shown on the nonlinear secondary x-axis.
The non-dimensional centrifugal acceleration parameter (λ) is defined as,
and
where is the rotation speed in rad/s, Ω is the rotation speed in RPM, L12 is a linear dimension shown in Figure 8, and g is gravitational acceleration in m/s2
Secondly, the MBD simulations include the frictional and inertial loads of the empty nutating mill, while the DEM results account for the material contact loads acting on the chamber walls. To compare measured experimental forces to calculated DEM results for a specific material, forces for the empty nutating chamber at the corresponding speed must be subtracted from the experimental data, which included charge material. In so doing, the material loads are isolated and represent the contact loads that are modelled using DEM.
Thirdly, when MBD and DEM simulations are superimposed, they become comparable with experimental values since the results will include inertial, frictional, and material effects. In the presented graphs the combined simulation results are indicated as (MBD+DEM).
Moreover, the magnitude of the forces acting on the crankpin via the spherical bearing was found to be significantly higher than at the universal assembly (Van Tonder, 2024). Anecdotal evidence of field failures also identifies the bottom of the chamber as a critical location in industrial systems. Furthermore, the influence of the material contact loads on the drive shaft torque (and therefore power) was a particularly interesting aspect of the research. For these reasons, the reported results will focus on the forces at the crankpin and the torque in the drive shaft.
The MBD simulation for an empty chamber rotating at 100, 400, and 700 RPM is compared to experimental results for the same load cases and summarised in Table 4. Percentage differences, considering experimental values as the reference, reveal the highest difference for radial force is 6%, tangential is >20% and the resultant force, i.e., the vector sum of radial and tangential forces, is 5%, all at a speed of 100 RPM. The notable difference for the tangential force is attributed to the empty system's small torque magnitudes, magnifying any slight deviation and measurement error at low speeds and force values. It is observed that for steady state operation the tangential force component is <1% for the radial force component and therefore insignificant. Higher tangential forces can however be expected during startup or shutdown due to angular acceleration. Nevertheless, it is noteworthy that the resultant load, representing the resultant force acting on the crankpin, is simulated with good accuracy across all rotational velocities, with the highest error being 5%.
The radial, tangential, and resultant crankpin forces due to material interaction are shown in Figure 11, Figure 12 and Figure
Table 4
13, respectively. The corresponding driveshaft torque is plotted in Figure 14. In these figures, favourable correlation between experimental and simulated results is observed for both sand and steel pellet charges. Notable observations include the most significant deviations in radial force occurring at 560 RPM for steel and 400 RPM for sand. Similarly, tangential and torque loads exhibit their highest deviations at 400 RPM for both charge types.
Analysing the resultant force on the crankpin reveals speeddependent deviations for the steel charge of 7.8%, 12.7%, and 12.6% at 100, 400, and 560 RPM, respectively. For the sand charge, the speed-dependent deviation is 29.8%, 17.9%, and 0.4% at 100, 400, and 700 RPM, respectively. Importantly, for all simulation test points for both sand and steel simulations, the error is below 20% (except for sand at 100 RPM, where the error is 29.8%), aligning with the criteria set by Scheffer and Coetzee (2023a) for considering particle flow simulations as being accurate.
The superimposed results from DEM and MBD simulations in comparison to the equivalent experimental measurements are presented in Figure 15 and Figure 16. Notably, torque, radial, and tangential crankpin loads exhibit a strong correlation with experimental values, particularly evident when evaluating resultant crankpin forces.
Analysing the resultant force on the crankpin reveals speeddependent deviations for the steel charge of 19%, 6%, and 1% at 100, 400, and 560 RPM, respectively. For the sand charge, the deviations are found to be 36%, 1%, and 1% at 100, 400, and 700 RPM, respectively. As mentioned earlier, any error value below 20% is considered accurate.
The combined DEM and MBD simulations are reasonably accurate, except for sand at 100 RPM. This discrepancy can potentially be attributed to measurement error, especially given the small torque and radial force magnitudes, where the influence of transducer sensitivity and external effects, such as friction, are likely significant.
The DEM material parameters were adapted from research by Scheffer and Coetzee (2023a), who performed thorough characterisation of the specific coarse sand used in the experiments. The DEM parameters were applied to the NuMILL simulation model without extensive parameter iteration or simulation calibration, potentially contributing to the observed simulation error at 100 RPM. Despite this, the very low simulation errors at 400 and 700 RPM demonstrate that the characterisation done using a linear contact model, was effective. This suggests that with thorough material characterisation, simulations may achieve sufficient accuracy with minimal additional calibration.
Moreover, an observation from this evaluation is that the charge material does not equally influence torque and radial loads. In the case of radial load, the force resulting from charge contact force (DEM) contributes less to the overall experimental measurement compared to the contribution of the inertial and frictional loads of the rotating structure (MBD). However, for driveshaft torque, the contribution of material loads (DEM) is far more significant than inertial and friction loads (MBD) under constant speed operation.
Comparison between experimental and simulated (MBD) crankpin forces for an empty chamber
Furthermore, it is evident that identical charge masses, such as steel and sand, exhibit notable differences in resultant force and torque responses. The steel demonstrates a significantly higher resultant response compared to sand, i.e., 22% greater radial load and a 56% greater torque at 560 RPM. This difference is further magnified when equivalent rigid lumped masses replace the material charge. Table 5 presents results of an experimental investigation on the error incurred by representing the charge as a lumped mass (equal to the mass of the charge), neglecting all other material properties and charge motion. In general, it is shown that the lumped mass approximation overpredicts the radial force (indicated by ‘+’), and underpredicts the torque (indicated by ‘-’).
For the crankpin radial load, a lumped mass approximation is relatively accurate, with the highest error of 26.8% occurring at 700 RPM. However, significant inaccuracies are shown in the torque values, with the highest error reaching 1,000% for steel pellets at 560 RPM. Despite torque loads being of a lower scale than the radial component, the derived mill power is influenced by torque, introducing substantial error that can negatively impact mill operation and reliability. This underscores the limitations of lumped mass approximations and the necessity to include material load effects in simulations.
Table 5
Summary of experimental tests to quantify the errors when using a lumped mass approximation in calculating the radial crankpin force and driveshaft torque
Material
Conclusion
A nutating mill achieves particle size reduction by accelerating the charge inside a nutating chamber inducing high impact and abrasion forces. The mechanical design of the system requires an understanding of the complex internal loads. The critical region in terms of load magnitude was identified as the load transfer mechanism between the torque arm and chamber via the crankpin, which formed the focus of this investigation.
Two simulation techniques, namely multibody dynamics (MBD) and discrete element method (DEM), were used to model the kinetic joint forces of a small-scale experimental mill (NuMILL) for various charge materials and rotation speeds. The MBD models inertial and frictional loads of the moving structure, whereas the DEM models the material motion and calculates the contact forces acting on the grinding chamber. Crankpin forces from these uncoupled simulations are combined and compared with experimental measurements.
Simulated resultant crankpin forces showed errors of 19%, 6%, and 1% at 100, 400, and 560 RPM, respectively, for the steel pellet charge, and errors of 36%, 1%, and 1% at 100, 400, and 700 RPM, respectively, for the coarse sand charge. Presented simulation techniques can be used to analyse full-scale systems. Calculated forces at the kinetic joints can be used in detailed structural design, bearing selection and fatigue analysis. For these purposes the accuracies of the simulations are deemed sufficiently accurate.
Further experimental tests were performed to quantify the difference in force magnitude when using lumped masses to represent the moving charge inside the nutating chamber. The outcome of these tests indicated that the lumped mass assumption provides conservative estimates for radial crankpin loads but significantly underestimates the driveshaft torque. This underscores the necessity for accounting for charge material loads where the prediction of driveshaft torque and power is of interest.
The current investigation was limited to an essentially rigid support structure and dry homogeneous charge materials. Future work aims to explore the inclusion of flexible mountings and modelling of the transient dynamic response using coupled simulation methods and wet charge materials. The modelling of material breakage and non-autogenous grinding may also be investigated. In the presented work video footage and approximate visual measurements were used for qualitative validation of simulated particles distributions. Computer vision techniques can be explored to improve the measurement resolution and repeatability of this method.
Credit author statement
JJvT: Investigation, validation, formal analysis, writing, visualisation. JRB: Conceptualisation, methodology, writing, supervision. CJC: Conceptualisation, methodology, writing, supervision. JB: Conceptualisation, methodology.
References
Ansys®. 2022. Academic Research Mechanical - User's Guide
Bian, X., Wang, G., Wang, H., Wang, S., Lv, W. 2017. Effect of lifters and mill speed on particle behaviour, torque, and power consumption of a tumbling ball mill: Experimental study and DEM simulation. Minerals Engineering, vol. 105, pp. 22–35.
Bradley, A.A., Freemantle, A.J., Lloyd, P.J.D. 1974. Developments in centrifugal milling. Journal of the South African Institute of Mining and Metallurgy, vol. 11, pp. 379–387.
Coetzee, C., Katterfeld, A. 2023 April. Calibration of DEM Parameters. In: McGlinchey, D. (ed.), Simulations in Bulk Solids Handling, 1st ed, pp. 1–40. Wiley.
Hoyer, D., Lee, D. 1997. High-intensity autogenous liberation of diamonds from kimberlite in the HICOM mill. Minerals Engineering, vol. 10, no. 3, pp. 265–273.
Hoyer, D.I. 1999. The discrete element method for fine grinding scale-up in HICOM mills. Powder Technology, vol. 105, no. 1−3, pp. 250–256.
ITASCA®. 2023. PFC 6.0 User's Guide. https://docs.itascacg.com/ pfc600/pfc/docproject/index.html [accessed 5 March 2024].
Nesbit, P., Moys, M. 1998. Load behaviour in the HICOM nutating mill. Minerals Engineering, vol. 11, no. 10, pp. 979–988.
Nesbit, P., Du Toit, G., Mapasa, K., Feldman, C. 2001. Evaluation of the HICOM 120 mill at Venetia mine. Minerals Engineering, vol. 14, no. 7, pp. 711–721.
Owen, P., Cleary, P.W. 2016. Understanding performance variation of a HICOM mill with operating conditions and media attributes. International Journal of Mineral Processing, vol. 155, pp. 13–31.
Scheffler, O.C., Coetzee, C. 2023a. DEM calibration for simulating bulk cohesive materials. Computers and Geotechnics, vol. 161, 105476. https://doi.org/10.1016/j.compgeo.2023.105476
Scheffler, O.C., Coetzee, C. 2023b. Discrete element modelling of a bulk cohesive material discharging from a conveyor Belt onto an impact plate. Minerals, vol. 13, 1501. https://doi.org/10.3390/ min13121501
Van Tonder, J.J. 2024. Experimental testing and simulation of a nutating grinding mill. Master's thesis, Stellenbosch University, South Africa.
Wills, B.A., Finch, J.A. 2016. Wills’ Mineral Processing Technology: An Introduction to the Practical Aspects of Ore Treatment and Mineral Recovery. 8th ed. Elsevier/Butterworth-Heinemann, Amsterdam.
Yulia, Mardiansyah, Y., Khotimah, S.N., Suprijadi, Viridi, S. 2016. Characterization of motion modes of pseudo-two-dimensional granular materials in a vertical rotating drum. 6th Asian Physics Symposium - Journal of Physics: Conference Series, vol. 739, 012148. https://doi.org/-10.1088/1742-6596/739/1/012148
Affiliation:
Konya Technical University, Dept. of Mining Engineering, Konya, Turkey
Correspondence to: I. Çinar
Email: icinar@ktun.edu.tr
Dates:
Received: 24 Mar. 2021
Revised: 7 Jul. 2024
Accepted: 22 Nov. 2024
Published: February 2025
How to cite:
Çinar, I. 2025. Investigation of physical and mechnical properties of polymer based composite material using volcanic tuff dust in Cappadocia, Turkey Journal of the Southern African Institute of Mining and Metallurgy, vol. 125, n. 2 pp. 107–112
DOI ID:
https://doi.org/10.17159/2411-9717/1583/2025
ORCiD:
I. Çinar
https://orcid.org/0000-0002-3814-7273
by I. Çinar
Abstract
Cappadocia is not only a region of Turkey with historical and touristic importance. During the cutting and processing of volcanic tuff, quarries in this region release large amounts of tuff into the environment that is viewed as waste. The release of this waste constitutes an economic loss and contributes to environmental pollution.
However, through experimentation with deformation, weight per unit of volume, water absorption, uniaxial compression strength, modulus of elasticity, and point load strength index, volcanic tuff and marble dust composite materials can be produced for use in the building sector. In this study it was observed that, as the percentage of volcanic tuff dust in the mixture increased, the water absorption rate of the material increased, and uniaxial compression strength and point load strength decreased. The produced composite samples used in this study were kept for a predetermined number of times per day, and no deformation in the surface characteristics of the materials was observed. In a statistical parameter analysis, averages, variances, standard deviations, coefficients of variation, and skewness coefficients were calculated. Covariance changes between experimental parameters were also determined.
In this study, two types of volcanic tuff dust, that is, yellow and red, were produced during the production of tuff-marble dust composite material. When the percentage of either type of volcanic tuff dust was increased, an increase in water absorption was observed. It was also observed that when the percentage of volcanic tuff dust was increased, uniaxial compressive strength and point load strength decreased. Furthermore, the physical and mechanical properties of the materials obtained by mixing different colored tuff powders and marble powders in different proportions were evaluated using statistical parameter analysis.
Keywords composite material, marble dust, volcanic tuff dust, statistical parameter analysis
Introduction
Composite material is defined as the product formed by the combination of two or more materials and that has properties that differ from the original components (Şahin, 2000). Composite materials are not invented; rather, they are produced by the combining of materials in nature that have different properties. The purpose of combining materials is to produce mechanical (strength, toughness, etc.) and/ or physical (electrical conductivity, thermal conductivity, etc.) properties that cannot be obtained from a single material (Gibson, 1994; Balasubramanian, 2013).
Concrete is one of the most commonly used composite materials in modern construction. The material, comprised of cement and sand, is supported by a matrix of steel bars. Cob is another composite material, first used 2000 years ago in Ancient Egypt, and it is produced by combining mud and straw. Cob is a durable building material and may be the oldest building material used by humanity (Matthews et al., 1999).
Composite materials can be classified by the materials that they are made of, their properties, and the compounds they contain. Generally, composite materials can be classified into the following groups (Shwwartz, 1997; Strong, 2008):
➤ Polymer matrix composite materials
➤ Ceramic matrix composite materials
➤ Metal matrix composite materials.
Marble powder is often used as a filling material in polymer matrix composites, and it has been observed that, as the percentage of a filler increases, the mechanical properties of the composite material improves (Gürü et al., 2005). For example, one study found that waste marble powder can be used in the production of paving stones (Filiz et al., 2010). It has also been concluded that adding a certain amount of waste marble powder to the mixture in brick production has a positive effect on the phase in which
pores and crystals form, and the use of waste marble powder in industrial production has been seen to benefit the environment and the national economy (Bilgin et al., 2012; Sütçü et al., 2015). In addition, studies have found that adding a specific amount of waste marble dust improves the physical and mechanical properties of concrete (Aliabdo et al., 2014; Arel 2016). Other studies have noted that it is beneficial to use natural stone and marble waste as additives in ceramic tile production (Garcia et al., 2003; Erol and Pekdemir, 2018).
Underground cities carved into soft tuff rocks have hosted many civilisations throughout history. The most important of these are the underground cities in the Cappadocia region. Due to its binding nature, tuff is often used in the construction of lightweight concrete and wall elements and as an additive material in cement. The use of tuff in the consolidation of soil and construction projects requiring large fill volumes, such as highways and airports, has also been investigated (Ene and Okagbue, 2009; Saltan and Findik, 2008; Hossain, 2007; Kaya and Durukan, 2004). In some prior studies on tuff, a strong relationship was found between the elasticity modulus and porosity (Price 1983; Price and Bauer 1985; Price et al. 1994).
This study examined the reusability of yellow and red volcanic tuff waste produced in the Cappadocia region. The physical and mechanical properties of the materials obtained by mixing different colored tuff powders and marble powders in different proportions were evaluated using statistical parameter analysis.
Volcanic tuffs
Volcanic tuff is the name given to the melted magma particles thrown into the atmosphere as a result of volcanic eruptions. The Anatolian region is rich in volcanic tuff because of the large number of volcanic activity (Fisher et al., 2006). For this reason, the use of tuff in cement production is especially economical in the Middle Anatolian region.
While the chemical properties of tuffs are similar, they differ slightly depending on the region of origin (Liebig and Althaus, 1998). For example, Cakırca et al. (2016) found that the dense quartz (SiO2) content of tuff from the Cappadocia region delayed the weathering of tuff, and the high clay content (Al2O3) accelerated the alteration thereof. They also noted that the tuff with a high quartz content was lighter in color, while an increase in the magnetite (Fe2O3) content darkened the color of the rock.
Volcanic tuff can sometimes be observed as ground layers. This is the result of the deposition of materials in lakes and the sea or on the ground or hillsides after a volcanic eruption. Particles are sometimes found in tuff that are separated from volcano vents. Because of its porous structure, composite material containing tuff produces light, natural building stones (Arıcı, 1997).
Volcanic tuff can be found in many regions of Turkey and especially in the Central Anatolian region. Volcanic tuffs containing different kinds of minerals can be found in Ankara, Eskişehir, Kayseri, Konya, Niğde and Nevşehir. (Duran, 2009).
Production method of the tuffs in the Cappadocia region Cappadocia, Turkey, is an important region that produces volcanic tuff in the country. Natural stones that are produced in the quarries of the Cappadocia region, which produces volcanic tuffs, are used by the building sector for multistory buildings, mosques, separate houses, interior façade linings, exterior façade linings, and decorative additions to fire places and barbeques. There are waste particles in different sizes that come off during production at the quarries and in factories after cutting.
(a)
Deformations in quarries like faults, cracks, and fissures are causes of not handling blocks appropriately during block production and, as a result, there are large and small particles that come off as waste. In addition, the absence of deciding on an appropriate production method for the geological structure of the volcanic tuff quarries and crystal structures, is causing tuff waste production in quarries.
In the Cappadocia region, mining firms use similar methods for the production of volcanic tuff natural stones. Before production commences, excavation, land stripping, and cleaning works are done. After cleaning works are completed, the land is deemed ready for production. Production is made possible by double cut machines.
Production of the red colored volcanic tuffs in Cappadocia is shown in Figure 1a and piles of waste after mining is shown in Figure 1b.
Samples of applications for tuffs in Cappadocia
Volcanic tuffs are commonly used in buildings, load bearing walls, door and window frames, interior and exterior facade siding, stairs, pavements, base fillings, garden walls, and handrails, examples of which are illustrated in Figure 2a and Figure 2b.
The volcanic tuffs used in the experiments were taken from the quarries of the Saray Taş firm in Nevşehir. Two different colors of tuff, yellow and red, were extracted from these quarries.
The flow chart shown in Figure 3 illustrates the method followed for the production of composite samples using the Cappadocia region volcanic tuffs. (Siniksaran, 2012).
Yellow and red colored volcanic tuff waste that was used in the experiments were grinded in laboratories. Grinded volcanic tuff dust was classified by means of sieve analysis. Volcanic tuff dust that was used in the experiments has a particle size of -200 µm.
Materials, sample types, and amounts of materials in mixtures of produced composite samples are shown in Table 1.
Polyester was added to the agitation vessels in accordance with their formulations. After that, cobalt octoate with 0,5 percentage by volume was added to the mixture. The mixing procedure
was continued until the cobalt octoate was homogeneously distributed in the mixture. Then methyl ethyl ketone peroxide with 1 percentage by volume was added to the mixture. Once again, the mixing procedure was continued until it was homogeneously distributed in the mixture. Thereafter volcanic tuff dusts were added to the mixture in accordance with their formulations and the mixing procedure was continued. The mixing procedure was continued until volcanic tuff dusts were homogeneously distributed in the mixture. To conclude, marble powder was added to the mixture in accordance with its formulations and the mixing procedure was continued. Ultimately, the mixing procedure was continued until the mixture became homogeneously.
After the moulding was finished, the samples were left in the molds for 24 hours to harden. These samples, which were kept in the molds for 24 hours, were then removed from the moulds.
After the samples were removed, they were left to rest for 28 days, both to complete the reaction and to test the changes in their surface. The samples, of which the resting period had been completed, were made ready for experimental procedures.
Methods that are used for the determination of the physical properties (deformations, unit volume weight, amount of water absorption) and mechanical properties (uniaxial compressive stress, modulus of elasticity, point load stress index) of composite samples are indicated in the following.
Samples that were removed from molds with 125 x 80 x 20 mm sizes were left in clean and smooth surfaces at 18°C–22°C room temperature for 28 days. At the end of this procedure, there was no change or deformation observed in the surface and shapes of these samples.
When the samples completed the resting duration, they were weighed by a 0,01 grammes precision scaled weighing machine. The volumes of each of the samples were calculated by size. The sizes of the experiment samples were determined by measuring the sizes in two perpendicular directions and their arithmetic average was taken. Volumes of experiment samples was calculated in accordance with those sizes found.
In order to determine the water absorption ratio, experiment samples that were rested for 28 days (14 days in room temperature conditions and another 14 days in an external environment), were weighed by a 0,01 grammes precision scaled weighing machine. Following this, the samples were again rested in appropriately sized vessels, submerged in water at a depth of 25 mm for 24 hours, at a temperature of +20±2ºC. Experiment samples that were submerged in water for 24 hours at the beginning of the experiment were weighed with 0,01 sensitivity after all surface water (droplets) was removed by means of wet rags, and the sample mass in water was determined.
Materials, sample types, and amounts of materials in mixtures of produced composite samples Sample
The values are valid for samples that were
Unit volume weight values and percentage water absorption ratio of the samples are calculated and shown in Figure 4.
In accordance with the results of the unit weight experiment results, composite samples that are produced by the yellow volcanic tuffs have the highest unit weight value and 30 percent by volume of volcanic tuff dust is found in the Y-1 coded sample, which contains 50% marble powder. The highest unit weight value in composite samples that is produced by the red volcanic tuff dusts is the R-1 coded sample and that sample contains volcanic tuff dust with 30 percent by volume and contains 50% marble powder.
When the volcanic tuff dust ratio is increased in composite samples, the unit volume weight value decreases.
In accordance with the results of the water absorption by weight experiment, the Y-6 coded sample has the highest water absorption by weight value in composite samples, which is produced by the yellow volcanic tuff dust, containing 80% volcanic tuff dust. The R-6 coded sample has the highest water absorption by weight value in composite samples, which is produced by the red volcanic tuff dust, containing 80% volcanic tuff dust.
In accordance with the results of the water absorption by weight experiments, water absorption values are increased for both samples of yellow volcanic tuff dust and red volcanic tuff dust when volcanic tuff dust ratios are increased.
Mechanical properties
The uniaxial compressive strength of the samples is determined by the uniaxial press of the experiment samples that have been prepared as a cylindrical rectangular prism, which has two times the length of its diameter.
Results of uniaxial compressive stress, elasticity modulus, and point load strength of the samples are shown in Figure 5a, Figure 5b, and Figure 5c.
In accordance with the uniaxial compressive strength test results, the highest compressive strength value in composite samples that is produced by the yellow-coloured volcanic tuff dust was found to be the Y-2 coded sample, which contains 40% volcanic tuff dust and 40% marble powder. The highest compressive strength value in composite samples produced by the red colored volcanic tuff dusts was found to be the R-1 coded sample, which comprised 30% volcanic tuff dust and 50% marble powder.
In accordance with the uniaxial compressive strength test results, the lowest compressive strength value in composite samples that was produced by the yellow-colored volcanic tuff dust was determined to be the Y-6 coded sample, which contained volcanic tuff dust with 80% of volume. The lowest compressive strength value in composite samples that was produced by the red colored volcanic tuff dust was determined as being the R-6 coded sample, which contains volcanic tuff dust of 80% of volume.
The point load test is based upon the breaking of the rock that is located between two conical bits. The sample is located between those two conical bits and the load that is applied hydraulically raises the conical bit at the end. The top is fixed to the frame. This frame is designed for placement of the cylindrical or irregular samples. The applied load can be established from the press indicator on the device.
Table 2
Statistical parameter analysis results of all experiments
Uniaxial
Table 3
Results of covariance values between experiments
The point load strength of the samples is determined by loading the samples that have been prepared in a rectangular prism shape with a length of two times its diameter, between two conical bits.
In accordance with the results of the point load strength index experiments, the highest point load strength was determined to be the Y-4 coded sample, which is produced by yellow volcanic tuff dust, which contains 60% volcanic tuff dust by volume and 20% marble powder. The highest point load strength was determined to be the R-1 coded sample, which is produced by red volcanic tuff dust, which contains 30% volcanic tuff dust by volume and 50% marble powder.
In accordance with the point load strength index experiments, the lowest point load strength was found to be the Y-6 sample, which is produced by yellow volcanic tuff dust and contains 80% volcanic tuff dust by volume. The lowest point load strength for the composite samples was found to be the sample coded as R-6, which was produced by red coloured volcanic tuff and contains 80% volcanic tuff dust by volume.
Statistical parameter analysis
In accordance with the results of the uniaxial compressive strength experiments, the average uniaxial compressive strength value for the samples produced by yellow-coloured volcanic tuff is 291,83 kg/cm2. On the other hand, the average uniaxial compressive strength value for the samples produced by red coloured volcanic tuff is 237,17 kg/cm2.
In accordance with the results of the point load strength index experiments, the samples produced by the yellow tuff dust have an average point load strength index value of 27,33 kg/cm2, while the samples that were produced by using red volcanic tuff dust have an average point load strength index value of 23,83 kg/cm2
For statistical parameter analysis, the averages, variances, standard deviations, coefficients of variation, and skewness coefficients were calculated and are presented in Table 2.
Covariance reveals the increase-decrease relationship between the two data. The covariance values obtained as a result of the experiments are given in Table3 .
Here, only the water absorption test results were found to be negative. In other words, while one data increases, the other decreases. The other results being positive shows that the data are directly proportional to each other.
The use of a combination of volcanic tuff dust and marble powder in composite materials results in an increased volcanic tuff dust ratio and a decrease in strength and hardness. On the other hand, it has been determined that polyester resin, which is used to attach volcanic tuff dust and marble powder, must be applied in definite volumes. Using inadequate amounts of polyester causes problems in attaching the polyester reinforcement materials. Furthermore, using more than just sufficient amounts of polyester causes a weakness in the polyester due to the use of reinforcement material, which is reflected in the material.
However, samples that were rested in room temperature conditions first and afterwards in an exterior environment for 28 days in total exhibited no deformation. Composite materials that are produced in those ratios can be used in buildings for interior and exterior facades.
Previous studies on volcanic tuff rock have pointed out that natural volcanic stone has a water absorption ratio of approximately 23%. For composite materials that are produced by volcanic tuff dust, the water absorption ratio reduces to 0,14%. Thus, composite materials coded as Y-1, Y-2, Y-3, R-1, and R-2 can be used in wet floors, kitchen benches, washbasins, basements of buildings, and the inside of swimming pools.
In previous studies on natural volcanic tuff rocks, it was shown that their uniaxial compressive strength value is approximately 150 kg/cm2. For composite samples that are produced by volcanic
tuff dust, the Y-2 sample’s uniaxial compressive strength value is 358 kg/cm2. Composite materials that are produced with the volcanic tuff dust ratios determined in this study will be used in areas of natural volcanic tuff rock.
During the production of the composite materials, no press machine or vibrating bench is used. Thus, small air spaces are not closed or trapped in these samples. In order to close or eliminate these small air spaces, a vibrating bench or press machine that squeezes the material in mould can be utilised.
During composite material production there are two different colours of volcanic tuff dust taken from the quarries in the Cappadocia region and composite samples are used with those dusts. There are various coloured volcanic tuff dusts in that area. Different colours of volcanic dust can be used for the production of composite material, and composite materials with different colours and properties can be produced. Different colours of volcanic tuff dust increase the variety of the products.
Compliance with ethical standards
Conflict of interest: On behalf of all authors, the corresponding author states that there is no conflict of interest.
References
Aliabdo, A.A., Abd Elmoaty, M., Auda, E.M. 2014. Re-use of waste marble dust in the production of cement and concrete. Constructions and Building Materials, vol. 50, pp. 28–41.
Arel H.Ş. 2016. Recyclability of waste marble in concrete production. Journal of Cleaner Production, vol. 131, pp. 179–188.
Arıcı E. 1997. Investigation of the effect of the volcanic tuff in Van region and of its usabelty as lightweight concrete aggregate. The Graduate School of Naturel and Applied Sciences, Firat University, Turkey, p 77.
Balasubramanian, M. 2013. Composite Materials and Processing, CRC Press.
Bilgin, N., Yeprem, H.A., Arslan, S., Bilgin, A., Günay, E., Marşoğlu, M. 2012. Use of waste marble powder in brick industry. Construction and Building Materials, vol. 29, pp. 449–457.
Çakırca, D., Turan, N. 2016. Correlations Between Chemical Properties of Liquid Crystal Tuff Nevşehir, Tunceli University. Journal of Science and Youth, vol. 4, Issue 1, pp.1–7.
Duran, F. 2009. Formation of the Erciyes volcanism, stratigraphy around Koçcağız village (Kayseri) and usage of tuffs as building - facing stone. The Graduate School of Naturel and Applied Sciences, Cukurova University, Turkey, p 148.
Ene, E., Okagbue, C. 2009. Some basic geotechnical properties of expansive soil modified using pyroclastic dust. Engineering Geology, ISSN: 00137952, vol. 107, pp. 61–65.
Erol, G., Pekdemir, D. 2018. Investigation of thermal and mechanical behaviors of construction materials obtained from some natural stone waste. Journal of MTA, vol. 157, pp. 193–199.
Filiz, M., Özel, C., Soykan, O., Ekiz, Y. 2010. Usage of Waste Marble Dust at Paving Stones. Electronic Journal of Construction Technologies, vol. 6, no. 2, pp. 57–72.
Fisher, R.V., Heiken, G., Mazzoni, M. 2006. Where do tuffs fit into the framework of volcanoes? in Heiken, G., ed.Tuffs. Geological Society of America Special Paper, vol. 408, pp. 5–9.
Garcia, J., Mallol, C., Bou, E., Silva, G., Fernandez, J., Molina, A., Romera, J. 2003. Recycling Marble working wastes in manufacturing ceramic products. CFI Ceramic Forum International, vol. 80, pp. 84–90.
Gibson, R.F. 1994. Principles of composite material mechanics, Mc Graw Hill, Inc, Department Of Mechanical Engneering. Wayne State University, Detroit, Michigan, pp.135–139.
Gürü, M., Akyüz, Y., Akın, E. 2005. The effects of filling ratio on the mechanical properties of marble powder/polyester composites. Journal of Polytechnic, vol. 8, no. 3, pp. 271–274.
Hossain, K.M.A., Lachemi, M., Easa, S. 2007. Stabilized soils for construction applications incorporating natural resources of Papua new Guinea. Resources conservation & Recycling 51, pp. 711–731.
Kaya, A., Durukan, S. 2004. Utilization of bentonite-embedded zeolite as clay liner. Applied Clay Science, vol. 25, pp. 83–91.
Liebig, E., Althaus, E. 1998. Pozzolanic activity of volcanic tuff and suevite, effects of calcination. Cement and Concrete Research, vol. 28, pp. 567–575.
Matthews, F.L., Rawlings, R.D. 1999. Composite Materials: Engineering and Science, CRC Woodhead Publishing.
Saltan, M., Findik, F.C. 2008. Stabilization of subbase layer materials with waste pumice in flexible pavement. Building and Environment, vol. 43, pp. 415–421.
Shwwartz, M. 1997. Composite Materials, Prentice Hall PTR, New Jersey, pp1-15, pp. 170–171.
Siniksaran, M. 2012. Production of polymer based composite material using volcanic tuff dust, MsC Thesis, The Graduate School of Naturel and Applied Sciences, Selcuk University, Konya, p88.
Sütçü, M., Alptekin, H., Erdoğmuş, E., Er, Y., Gencel, O. 2015. Characteristics of fired clay bricks with waste marble powder addition as building materials. Constructions and Building Materials, vol. 82, pp. 1–8.
Şahin, Y. 2000. Introduction to composite materials, Gazi Publisher, Ankara, p327.
Price, R.H. 1983. Analysis of the Rock Mechanics Properties of Volcanic Tuff Units from Yucca Mountain, Nevada Test Site, Sandia Report SAND82-1315, Albuquerque, New Mexico: Sandia National Laboratories.
Price, R.H., Bauer, S.J. 1985. Analysis of the Elastic and Strength Properties of Yucca Mountain Tuff, Nevada, Research & Engineering Applications in Rock Masse. Proceedings of the 26th U.S. Symposium on Rock Mechanics, Rapid City, South Dakota, June 26‒28, 1985. pp. 89–96.
Price, R.H., Boyd, P.J., Noel, J.S., Martin, R.J. 1994. Relationship between Staticand Dynamic Rock Properties in Welded and Nonwelded Tuff, Rock Mechanics, ISBN 90-5410-380-8, Nelson & Laubach (eds), Balkme, Rotterdam, pp 505–512.
Strong, A.B. 2008 Fundamentals of Composites Manufacturing: Materials, Methods and Applications, SME.
Affiliation:
1School of Mines and Engineering, Taita Taveta University, Kenya
2School of Engineering, Dedan Kimathi University of Technology, Kenya
3University of Mines and Technology, Ghana
Correspondence to:
B.O. Alunda
Email: benard.ouma@ttu.ac.ke
Dates:
Received: 11 May 2023
Revised: 21 Nov. 2024
Accepted: 21 Nov. 2024
Published: February 2025
How to cite:
Mutinda, E.K., Alunda, B.O., Ondicho, I.O., Agyekum, E. 2025. Prediction and measurement of blast induced rock fragmentation − A case study of Kajiado County quarries, Kenya.
Journal of the Southern African Institute of Mining and Metallurgy, vol. 125, no. 2, pp. 113–120
DOI ID:
https://doi.org/10.17159/2411-9717/2803/2025
ORCiD:
E.K. Mutinda
https://orcid.org/0000-0002-1012-9655
B.O. Alunda
https://orcid.org/0000-0003-0283-6525
I.O. Ondicho
https://orcid.org/0000-0002-4488-5459
E. Agyekum
https://orcid.org/0009-0008-8485-3049
by E.K. Mutinda1, B.O. Alunda1, I.O. Ondicho2, E. Agyekum3
Abstract
Driven by the necessity to improve blast performance regarding fragment size distribution in limestone mines, this paper introduces the prediction and measurement of blast fragmentation distribution through the modified Kuz-Ram (MKR) and Kuznetsov-Cunningham-Ouchterlony (KCO) models. Precise prediction and measurement of rock fragmentation resulting from blasting play a critical role in hard rock ore extraction. This is due to the substantial influence of post-blast ore size distribution on the efficiency of all subsequent downstream rock handling and processing operations. Additionally, employing secondary breakage of boulders, when necessary, leads to an unjustified rise in production costs. In this paper, the MKR and KCO models were utilised to identify the most appropriate model for application in Bisil and Simba quarries situated in Kajiado County, Kenya. Split-Desktop was used for blast fragment measurement by processing digital images obtained after blasting and computing the fragment size distribution of the blasted rock. As per the investigation, the recorded percentages of boulders generated at the sites ranged from 7% to 12.3% for the Simba quarry and from 11.2% to 23.9% for the Bisil quarry, respectively. Regression, correlation, and root mean square error (RMSE) were employed as the primary performance indicators. The study concluded that KCO outperformed MKR in accurately predicting blast fragment sizes in the examined quarries.
Keywords blasting, rock fragmentation, fragmentation model, split-desktop, particle size distribution
Drilling and blasting in limestone mining act to minimise the size of rock to enable easy handling of the fragments in the downstream mining processes (Babaeian et al., 2019). Fragments of specific sizes are crucial in mining activities as they affect subsequent operations such as loading, hauling, and crushing. Precise measurement of rock fragmentation resulting from blasting, which is the initial stage of size reduction, is particularly significant in hard rock drilling and blasting (Gheibie et al., 2009). The distribution of rock sizes after blasting significantly impacts the effectiveness of all subsequent rock processing and comminution processes downstream (Abuhasel, 2019). In case there are too many fines or boulders, there is a direct economic liability to the mining company (Kanchibotla, Valery, and Morrell, 1999; Jahed Armaghani, 2018).
Several methods have been proposed for measuring blasted rock size distribution (Yusuf and Hashim, 2020). The sieve method provides a direct and precise method of measuring fragment sizes (Ouchterlony and Sanchidrián, 2019). However, the process is costly, time-consuming, and generally unrealistic for large-scale applications (Ouchterlony, 2005). Direct observation of the muck piles after blasting has also been used in the past but can only result in an approximation at best. The limitations of the sieve and observation methods can be overcome by the use of empirical models that have been developed by different researchers (Ouchterlony and Sanchidrián, 2019), as discussed in the theory section.
Kansake and other researchers in 2016, while studying fragmentation models in gold mines in Ghana, found that the distribution of the fines in a blast greatly influences the fragmentation models to be used (Kansake, Temeng, and Afum, 2016). Both Kuz-Ram and modified Kuz-Ram (MKR) provided a more accurate fragment size distribution prediction compared to Kuznetsov-Cunningham-Ouchterlony (KCO). The ability of these models to predict depends mainly on the geology of the rock and the blast design. Therefore, a more comprehensive study is needed to point out the most suitable empirical fragmentation model for sedimentary rocks. When planning hard rock mining using drilling and blasting methods, it is important to carry out fragmentation modelling for optimal material handling and informed control of blast output (Tosun and Konak, 2015).
An accurate model for predicting rock fragmentation is crucial for enhancing production efficiency during blasting operations. Factors such as geological conditions, geometric configurations, and explosive properties, including rock mass features, blast design, and explosive type, influence the distribution of blast fragment sizes (Hekmat, Munoz, and Gomez, 2019). Rock fragmentation influences the volumetric and packing properties of rocks (e.g., the fill factor and bulk volume) and therefore, the digging and hauling efficiency of the equipment utilised (Adebayo and Aladejare, 2013). Similarly, several studies have demonstrated the direct influence of the rock size distribution when fed into the crusher and mill processes on energy consumption, therefore, influencing the productivity of these processes (Latham and Lu, 1999; Tosun, 2018). Thus, blast fragmentation prediction and post-blast rock fragmentation measurements are identified as critical metrics in mining operation optimisation. With blasting affecting all the preceding downstream operations, including loading, hauling, and processing, there is a need for blasts to be designed and fragment sizes modelled to ensure that the selected blast parameters give the desired fragmentation.
The creation of fragmentation models arises from the necessity to offer engineering solutions to blasting challenges, including the optimisation of run-of-mine (ROM) fragmentation (Esen, 2013). Different models have been developed for fragment size distribution prediction from specific blast designs (Ouchterlony and Sanchidrián, 2019). Nevertheless, none of these models adeptly forecasts the size distribution resulting from a blast. The inputs for such models include explosive properties, the geometry of the blast design, and insitu rock properties.
Fragment size distribution prediction models are mainly classified into two broad groups, which consist of empirical and mechanistic models. Every model operates under its set of assumptions regarding the origins of fines production, whereas empirical models presume that finer fragmentation results from a heightened powder factor, characterised by increased input energy from explosives (Sanchidrián and Ouchterlony, 2017). On the contrary, mechanistic models attribute fines production to the physics and dynamics of detonation, as well as the transfer of blast energy during blasting. Consequently, their complexity and the requirement for intricate data render mechanistic models less favoured on mine sites (Cardu, Dompieri, and Seccatore, 2012).
Mechanistic models represent the pinnacle of modelling sophistication, showcasing progressive systems. They employ numerous numerical techniques and deliver blast predictions by accurately mimicking changes in conditions over time (Ouchterlony and Sanchidrián, 2019). By analysing stress or strain within the affected region, they have the capability to simulate the loading of bulk explosives and the movement of rocks around the blast area (Tosun and Konak, 2015). They are the most perplexing prediction models that are often used to describe the behaviour of complex system components, and some can take days or weeks to run even on powerful multi-centre or graphical user interface (GPU)-based computers (Raina, Murthy and Soni, 2015).
In contrast, empirical computer models rely on the direct fitting of scientific and computational expressions to data obtained from field measurements or potential estimation. Examples of these models incorporate the fracture forecast models and the scaled
separation equation for predicting vibration (Abuhasel, 2019). Among these models is Da Gama's 1970 model, which forecasts fragment size distribution by considering the required energy and explosives, as well as rock characteristics (Ouchterlony and Sanchidrián, 2019). This model had the disadvantage of neglecting the effects of stemming length, spacing, and bench height and did not have factors for predicting the uniformity of the fragmented rocks. In 1973, Larsson developed another model, which utilised burden, spacing, specific charge and characteristics of the rock’s discontinuities for prediction (Ouchterlony and Sanchidrián, 2019; Shehu, Yusuf and Hashim, 2020). This model was the earliest model to account for the uniformity index of blasted rock (Ouchterlony and Sanchidrián, 2019). In 1973, Kuznetsov introduced an empirical model that accounted for variables such as the type of explosives, rock mass classification, the impact of applied blast energy, and assessment of fragmentation uniformity. This model quantifies fragmentation in terms of mass percentage, powder factor (blast energy applied per unit volume of rock), and mean fragment size (Franklin and Maerz, 2018).
In 1983, Cunningham introduced the Kuz-Ram model, which could compute both the average fragment size and the uniformity index for the muck pile resulting from a bench blasting round. This model utilises the Rosin Rammler (RR) sieving curve function, which characterises fragmentation curves for equal mean size (Ouchterlony, 2019). In 1987, Kou and Rustan, working under the Swedish Detonic Research Foundation (SveDeFo) adjusted Larson’s model (Ouchterlony, 2019). The main parameters considered were the bench height, stemming length, discontinuity characteristics, and the rock’s nature. One of the drawbacks of the model was the approximation of the rocks’ parameters leading to a lower value of the predicted dimensions of the rocks fragmented. (Gheibie et al., 2009).
In 2000, Chung and Katsabanis used Otterness’ and other researchers' data collected in 1991 to verify the accuracy of the Kuz-Ram model (Ouchterlony, 2019). They proposed that the RR function gives a better representation of the fragment size distribution data (Ouchterlony and Sanchidrián, 2019). More advanced empirical models were developed with KuznetsovCunningham-Ouchterlony (KCO) in 2005 and modified Kuz-Ram in 2009 (Ouchterlony and Sanchidrián, 2019). These models can often be represented in a spreadsheet and run on a laptop in almost no time (Monjezi et al., 2010).
Modified Kuz-Ram model
This empirical model closely resembles the previous Kuz-Ram model, with the only alteration being the adjustment of the Kuznetsov equation through the application of a 0.073 multiplier. This modification aims to enhance the model's accuracy in predicting the mean fragmentation size (Gheibie et al., 2009).
The Kuz-Ram uniformity index is further refined with an enhanced version proposed by Cunningham, which takes into account the blastability index (BI) of the specific rock under consideration (Ouchterlony and Sanchidrián, 2019). The model is made up of two main functions, namely the average broken rock size (Xm), as shown in Equation 1 and the modified uniformity index (n’). The input parameters of the two functions (Xm and n’) are easy to obtain on-site, however, the model does not factor in the impact of blast timing, and the top size is also not well defined (Gheibie et al., 2009):
where Xm is the average broken rock size in cm, Qe is the explosive weight per drill hole in kg. The broken rock volume per blast hole, V0 (m3) is, SANFO is the relative weight strength of the explosive to ANFO, and BI is the blastability index as shown in Equation 2:
where HF is the hardness factor, JPS is the joint plane spacing, JPA is the joint plane angle, RDI is the rock density influence, and RMD is the rock mass description (Bieniawski, 1988). These parameters are computed based on the rock mass classification introduced by Bieniawski in 1988, as outlined in Table 1.
The broken rock volume per blast hole V0 (m3) can be found by using Equation 3:
where B is the blasting burden in m, S is the blast hole spacing in m, and H is the bench height in m. The uniformity index n is defined by Equation 4:
where B is the blasting burden in m, D is the blast hole diameter in mm, S is the blast hole spacing in m, W is the drilling accuracy in m, BCL is the bottom charge length in m, and CCL is the column charge length in m, and H is the bench height in m, and L is the total charge length in m. When employing a staggered pattern, Equation 4 needs to be be multiplied by 1.1 (Gheibie et al., 2009).
The modified uniformity index (n’) is shown in Equation 5.
Rock density influence (RDI) or specific gravity influence (SGI)
Hardness factor (HF) Young’s Modulus, E < 50 GPa
Young’s Modulus, E > 50 GPa
The Kuznetsov-Cunningham-Ouchterlony (KCO) fragmentation model extends the Kuz-Ram model by substituting the RosinRammler equation with the Swebrec function (Ouchterlony and Sanchidrián, 2019). It was proposed to address two significant weaknesses of the Kuz-Ram model: its limited ability to accurately predict fragments with high fines, and its upper limit cut-off of block sizes (Ouchterlony, 2005). The Swebrec function shown in Equation 6 includes three parameters, the 50% passing (X50), the maximum block size (XMax), and b, which is a curve undulation parameter that depends on the uniformity index of the Kuz-Ram model (Franklin, 1993; Babaeian et al., 2019; Ouchterlony and Sanchidrián, 2019).
where P(x) is the percentage fraction of fragments passing sieve size X, and b denotes the curve undulation parameter. XMax stands for the minimum (insitu block size; S or B). The equations comprising the KCO models are illustrated in Equations 7 to 11.
[7]
where A is the rock factor as shown in Equation 8, q is the specific charge/powder factor, kg/m3, Q is the explosive weight per drill hole in kg, and SANFO is the relative weight strength of the explosive to ANFO.
0.025ρ – 50 or 25SG – 50 (ρ is the density of the rock in kg/m3 and SG is the specific density of rock in tonnes/cubic meters)
(σc is the uniaxial compressive strength (UCS) in MPa)
Alternatively, the value of b can be determined by using Equation 10, as reported by Choudhary and Gupta (2012):
where DbMax is the least burden, spacing, or maximum insitu block size as suggested by Ouchterlony (2005) (Ouchterlony and Sanchidrián, 2019). The KCO model also gives an alternative equation for the X50 than originally proposed by the Kuz-Ram model as given in Equation 11.
However, Equation 11 reduces the fragment size distribution to smaller values, which leads to an increased percentage of fines. This drawback of Equation 11 led to the use of Equation 7 in this article for fragment size distribution.
Materials and method
This study was conducted at limestone quarries situated in Kajiado, as depicted in Figure 1. The management of these quarries falls under the purview of two companies: East African Portland Cement Company Ltd (EAPCC), which oversees operations in the Bisil quarries, while National Cement Company Limited (NCCL) operates the Simba Kajiado mine. Bisil quarry comprises four mining faces, whereas the Simba quarry consists of two mining faces, with extraction conducted in benches. Following the collection of bench data, blasting operations were conducted, and fragment images were captured for subsequent analysis using Split-Desktop software. In the Kajiado region, limestone and
quartzite formations are typically bordered by semi-calcareous gneisses. The primary crystalline limestone is followed by a series of pelitic gneisses with minor calcareous and semi-pelitic layers. The basement system in the Kajiado region might be arranged into the accompanying transformed calcareous sediments, which comprise crystalline limestones and calc-silicate gneisses (see Figure 2). Even in areas surrounded by intensely migmatised gneisses, there has been minimal introduction of pegmatitic material into the limestones. The research methodology comprised the following steps:
➤ Fragmentation prediction involved the utilisation of both the modified Kuz-Ram model and the KCO model. Geotechnical data collection encompassed parameters, such as joint plane angle, hardness factor, rock density, joint plane spacing, and rock mass description for rock mass classification. Following that, the prediction of fragment sizes was conducted by applying Python code to implement the modified KuzRam and KCO models. Quarry activities for data collection included identifying pushbacks, bench faces (as depicted in Figure 3), geological measurements, and capturing spatial and explosive parameters for each blast. Geological measurements were conducted to ascertain pre-existing fractures and their orientations. Additionally, joints on each bench face were identified, and distances between them were measured to determine the rock mass rating (RMR).
➤ Fragmentation analysis was conducted using image based particle tracking (IPT). Blast fragment images were captured using a digital camera and subsequently processed utilising Split-Desktop 4.0 software to ascertain fragment distribution.
➤ Comparative analyses of the prediction and measured results using statistical techniques. Regression, correlation, and root mean square error (RMSE) computations were applied to determine model performance indices. The performance indices helped identify the most suitable fragmentation model for the studied limestone mines.
Six blasts were examined for every quarry, and the process was repeated six times. The findings, which allow for the identification of blast performance at each quarry site in relation to the chosen empirical models, are provided in the results section.
Results and discussion
Blast fragment size prediction by empirical modelling
The data for blast fragmentation prediction using empirical formulae were obtained from both the Simba and Bisil quarries, which were acquired through field measurements. The data included the geometrical, explosive and rock parameters as shown in Table 2 to Table 4. The rock mass was classified based
on Bieniawski's geomechanical rock classification and the determination of the model’s particle distribution was done using a code written in Python programming language.
Fragment size analysis by image processing
Even though the size distribution analysis by sieving is a direct and more accurate method, it is time-consuming and costly (Mohamed et al., 2015). It is also not practical for large-scale blasts. The only practical quantitative method of large-scale blast fragmentation analysis currently available is digital image processing, where photographs or video images are analysed via computer image processing software (Shehu, Yusuf, and Hashim, 2020). Digital image processing is used popularly in the mining industry because it is affordable, produces useful results, does not interrupt the production cycle, and is time efficient (Maerz, 1996). However, the method has a few setbacks compared to sieve analysis as it can only process the visible part of the muck pile (Shehu, Yusuf and Hashim, 2020). The sampling strategy is carefully considered, as image analysis processing techniques cannot take into account the internal muck pile structure (Sanchidrián, Segarra and López, 2006).
There exist several computer software for image analysis. These include SPLIT (e.g., Split Desktop), Wip Frag, Gold Size (Maerz, Palangio and Franklin, 1996), Frag Scan, TUCIPS, CIAS, Power Sieve, IPACS, KTH, and WIEP (Esen, 2013). In this research work the Split Desktop was used because of its availability, ease of use, and ability to produce reliable results (Júlio et al., 2019). The software employs grayscale to ascertain the particle size distribution of blast rock fragments (Júlio et al., 2019). Digital images were obtained using either a digital camera or smartphone. Multiple images were captured using a smartphone equipped with the Split Camera application, with a scale object included, as depicted in Figure 4 (a). High-quality images were transferred to a computer and those with a resolution of 600 dpi were delineated as shown in Figure 4 (b), to help determine blasted rock fragment size distribution using Split
Table 2
Rock Parameters used in the studied blast rounds
Table 3
Geometrical Parameters used in the studied blast rounds
Table 4
Desktop 4.1 software. After delineation was done, fragment size distribution was generated representing the measured fragment size distribution.
Statistical analysis of results
Correlation, regression, and root mean square error (RMSE) computations of the results obtained from the prediction models and the fragmentation measurements were conducted per quarry.
They were presented in regression graphs measured against predicted results. Six blasts were considered for this research paper for both quarries. Simba quarry regression analysis showed KCO had a higher R2 value than MKR in the blasts considered at 99.08% against 96.7%, respectively as illustrated in Figure 5 (a). The correlation analysis showed that there is a stronger correlation of KCO prediction to the measured fragment sizes than MKR prediction with a correlation value of 99.5% and 99.0%, respectively
5—Regression graphs for (a) Bisil and (b) Simba quarries. KCO has a higher R2 value at 97.87% and 99.08% compared to MKR at 96.50% and 96.74% for both quarries, respectively
Figure 6—(a) Simba and (b) Bisil quarries material passing through crusher opening, boulder produced measurement and prediction analysis. It can be noted that the KCO graph almost resembles the Split Desktop graph, unlike the MKR graph. KCO also has the least error margin
for the same quarry. On the other hand, Bisil quarry regression analysis showed KCO had a higher R2 value than MKR in five out of the six blasts considered. The overall regression analysis showed that KCO performed better than MKR with 97.9% against 96.5%, respectively as illustrated by Figure 5 (b). The correlation analysis showed that there is a stronger correlation between KCO prediction and MKR prediction with correlation values of 98.9% and 98.2%, respectively for the six blasts considered.
The RMSE results for Simba showed that KCO had the lowest RMSE at 3.8% compared to MKR whose RMSE was at 7.1% for the overall six blasts considered. On the other hand, the RMSE results for Bisil showed that KCO had the lowest error margin between 4.8% and 22.5% against MKR at 5.9% and 24.3% for the six blasts. The high correlation values indicate that all the predictions from the models correlated well with the actual results from the blasts studied. The maximum crusher feed for both quarries is 50 cm, where all materials of size greater than 50 cm were considered boulders. In Simba quarry, the KCO model showed better boulder prediction with an error margin between 1.6% to 8.7%, compared to MKR whose error margin was between 2.5% to 11.3% as illustrated by Figure 6 (a).
There was a general trend of overpredicting boulders by the KCO, while MKR underpredicted the number of boulders produced per blast round at Simba quarry, as can be seen in Figure 4 (a). KCO had a better boulder prediction in four blasts while MKR performed better in two out of the six blasts studied. A varying trend of boulder prediction was observed with MKR tending to underpredict the percentage of boulders, while KCO tended to overpredict the percentage of boulders produced per blast. According to Split Desktop, the percentage of boulders produced at the site was between 7.1% to 12.3%. This percentage is quite
significant but not as much as the percentage of boulders produced at Bisil quarries. This could be attributed to the fact that Simba quarry has a better strategy for planning and executing blast rounds. However, the application of empirical fragment size modelling could reduce this percentage of boulders significantly. This can possibly be achieved by redesigning blast round parameters and simulating the new parameters using empirical models. Optimal parameters can thereafter be used in performing blasts for better fragmentation.
At Bisil quarry, the KCO model showed better boulder prediction with an error margin between 0.6% to 8.2% compared to MKR, of which the error margin was between 4.2% to 19.9% as illustrated by Figure 6 (b). However, there was a general trend of underpredicting boulders by the MKR while KCO overpredicted the percentage of boulders produced per blast round at Bisil quarry. According to Split Desktop, the percentage of boulders produced at the site was between 11.2% to 23.9%. The percentage of boulders is significant and thus has some negative impact on the overall mining cost as they will need to perform secondary blasting and also slow down the loading and hauling process. It was noted that KCO generally performed better in the prediction of boulders than MKR.
This research conducted a comparative analysis of two empirical blast fragmentation models in separate quarries in Kenya. The study highlights the superior predictive performance of the KuznetsovCunningham-Ouchterlony (KCO) model over the modified Kuz-Ram (MKR) model in both boulder and overall particle size predictions. Interestingly, the prediction trends varied between the Bisil and Simba formations, indicating geological influence on model performance. Despite these variations, both MKR and KCO models offer valuable guidance on blast fragment particle
size distribution, tailored to specific geological conditions and blast designs. This enables miners to assess different blast designs, explore the effects of altering blast variables, and predict resulting particle size distributions accurately. Mining operators can leverage empirical modelling as a tool to optimise blast round fragment size distribution. The observed tendency of boulder overestimation at Bisil quarry and underestimation at Simba quarry underscores the importance of accurate modelling. Notably, KCO exhibited stronger correlation, higher coefficient of determination, and lower error margins, reinforcing its reliability in predicting particle sizes. Moreover, variations in prediction trends across geological formations suggest that model performance is influenced by geological factors. Additionally, the relationship between powder factor and fragment sizes highlights the importance of considering blasting variables in fragmentation outcomes.
Acknowledgements
We express our sincere appreciation for the support provided by Split-Engineering for this project, particularly in granting the software license. Additionally, we extend our gratitude to the Exploration and Tertiary Material Department of East African Portland Cement Company (EAPCC) and the Mining Department of National Cement Company Ltd (NCCL) for their cooperation and for providing their personnel, equipment, and laboratory facilities for this research endeavour.
References
Abuhasel, K.A. 2019. A comparative study of regression model and the adaptive neuro-fuzzy conjecture systems for predicting energy consumption for jaw crusher. Applied Sciences, vol. 9, no. 18. doi: 10.3390/app9183916
Adebayo, B., Aladejare, A.E. 2013. Effect of Rock Properties on Excavation-Loading Operation in Selected Quarries. Advanced Materials Research, vol. 824, pp. 86–90. doi: 10.4028/www.scientific.net/AMR.824.86
Babaeian, M., Ataei, M., Sereshki, F., Sotoudeh, F., Mohammadi, S. 2019. A new framework for evaluation of rock fragmentation in open pit mines. Journal of Rock Mechanics and Geotechnical Engineering. Elsevier Ltd, vol. 11, no. 2, pp. 325–336. doi: 10.1016/j.jrmge.2018.11.006
Bieniawski, Z.T. 1988. The Rock Mass Rating (RMR) System (Geomechanics Classification) in Engineering Practice, in Kirkaldie, L. (ed.) Rock Classification Systems for Engineering Purposes. West Conshohocken, PA: ASTM International, pp. 17–34. doi: 10.1520/STP48461S
Cardu, M., Dompieri, M., Seccatore, J. 2012. Complexity analysis of blast-induced vibrations in underground mining: A case study. International Journal of Mining Science and Technology, vol. 22, no. 1, pp. 125–131.
Esen, S. 2013. Fragmentation modelling and the effects of ROM fragmentation on comminution circuits. 23rd International Mining Congress & exhibition of Turkey, pp. 252–260.
Franklin, J.A. 1993. 32 - Empirical Design and Rock Mass Characterization, in FAIRHURST, C. (ed.) Analysis and Design Methods. Oxford: Pergamon, pp. 795–806. doi: https://doi. org/10.1016/B978-0-08-040615-2.50038-1
Franklin, J.A., Maerz, N.H. 2018. Empirical design and rock mass characterization. Measurement of Blast Fragmentation. Routledge, pp. 193–201. doi: 10.1201/9780203747919-28
Gheibie, S., Aghababaei, H., Hoseinie, S.H., Pourrahimian, Y. 2009. Modified Kuz-Ram fragmentation model and its use at the Sungun Copper Mine. International Journal of Rock Mechanics and Mining Sciences. Elsevier, vol. 46, no. 6, pp. 967–973. doi: 10.1016/j.ijrmms.2009.05.003
Hekmat, A., Munoz, S., Gomez, R. 2019. Prediction of Rock Fragmentation Based on a Modified Kuz-Ram Model. Proceedings of the 27th International Symposium on Mine
Planning and Equipment Selection - MPES 2018. Cham: Springer International Publishing, pp. 69–79. doi: 10.1007/978-3-31999220-4_6
Jahed Armaghani, D. 2018. Rock Fragmentation Prediction through a New Hybrid Model Based on Imperial Competitive Algorithm and Neural Network. Smart Construction Research, vol. 2, no. 3. doi: 10.18063/scr.v2i3.397
Júlio, S., Andrêvhity, S., Silva, S. 2019. Analysis of Blasting Rocks Prediction and Rock Fragmentation Results Using Split-Desktop Software. Brazilian Association of Metallurgy, Materials and Mining, vol. 15, no. 1, pp. 22–30.
Kanchibotla, S.S., Valery, W., Morrell, S. 1999. Modelling fines in blast fragmentation and its impact on crushing and grinding. Explo 99–A conference on rock breaking, The Australasian Institute of Mining and Metallurgy, Kalgoorlie, Australia, pp. 137–144.
Kansake, B.A., Temeng, V.A., Afum, B.O. 2016. Comparative Analysis of Rock Fragmentation Models – A Case Study. 4th UMaT Biennial International Mining and Mineral Conference, no. September, pp. MP 1–11.
Latham, J.-P., Lu, P. 1999. Development of an assessment system for the blastability of rock masses. International Journal of Rock Mechanics and Mining Sciences, vol. 36, no. 1, pp. 41–55. doi: 10.1016/S0148-9062(98)00175-2
Maerz, N.H. 1996. Image sampling techniques and requirements for automated image analysis of rock fragmentation. Proceedings of the FRAGBLAST 5 Workshop on Measurement of Blast Fragmentation, Montreal, Quebec, Canada, pp. 115–120. doi: 10.1201/9780203747919-18
Maerz, N.H., Palangio, T.C., Franklin, J.A. 1996. WipFrag image based granulometry system. Proceedings of the FRAGBLAST 5 Workshop on Measurement of Blast Fragmentation, Montreal, Quebec, Canada, pp. 91–99. doi: 10.1201/9780203747919-15
Mohamed, F., Hafsaoui, A., Talhi, K., Menacer, K. 2015. Study of the Powder Factor in Surface Bench Blasting. Procedia Earth and Planetary Science, vol. 15, pp. 892–899. doi: 10.1016/j.proeps.2015.08.142
Monjezi, M., Amiri, H., Farrokhi, A., Goshtasbi, K. 2010. Prediction of Rock Fragmentation Due to Blasting in Sarcheshmeh Copper Mine Using Artificial Neural Networks. Geotechnical and Geological Engineering, vol. 28, no. 4, pp. 423–430. doi: 10.1007/ s10706-010-9302-z
Ouchterlony, F. 2005. The Swebrec © function : linking fragmentation by blasting and crushing, 114 (March), pp. 29–44. doi: 10.1179/037178405X44539
Ouchterlony, F., Sanchidrián, J.A. 2019. A review of development of better prediction equations for blast fragmentation. Journal of Rock Mechanics and Geotechnical Engineering. Elsevier Ltd, vol. 11, no. 5, pp. 1094–1109. doi: 10.1016/j.jrmge.2019.03.001
Raina, A.K., Murthy, V.M. S.R., Soni, A.K. 2015. Flyrock in surface mine blasting: Understanding the basics to develop a predictive regime. Current Science, vol. 108, no. 4, pp. 660–665. doi: 10.18520/cs/v108/i4/660-665
Sanchidrián, J.A., Ouchterlony, F. 2017. A Distribution-Free Description of Fragmentation by Blasting Based on Dimensional Analysis. Rock Mechanics and Rock Engineering. Springer-Verlag Wien, vol. 50, no. 4, pp. 781–806. doi: 10.1007/s00603-016-1131-9
Sanchidrián, J.A., Segarra, P., López, L.M. 2006. A Practical Procedure for the Measurement of Fragmentation by Blasting by Image Analysis. Rock Mechanics and Rock Engineering, vol. 39, no. 4, pp. 359–382. doi: 10.1007/s00603-005-0073-4
Shehu, S.A., Yusuf, K.O., Hashim, M.H.M. 2020. Comparative study of WipFrag image analysis and Kuz-Ram empirical model in granite aggregate quarry and their application for blast fragmentation rating. Geomechanics and Geoengineering, pp. 1–9. doi: 10.1080/17486025.2020.1720830
Tosun, A. 2018. A modified Wipfrag program for determining muckpile fragmentation. Journal of the Southern African Institute of Mining and Metallurgy, vol. 118, no. 10, pp. 1113–1119. doi: 10.17159/2411-9717/2018/v118n10a13
Tosun, A., Konak, G. 2015. Determination of specific charge minimizing total unit cost of open pit quarry blasting operations. Arabian Journal of Geosciences, vol. 8, no. 8, pp. 6409–6423. doi: 10.1007/s12517-014-1657-7
By Spencer Eckstein, Director, Ukwazi Mining
The recent Stillfontein disaster in which 88 people lost their lives challenges us to re-think mine closure.
The current orthodoxy is that mining operations once closed can be repurposed and the disturbed areas rehabilitated, with residual environmental impacts managed via post closure measures.
It assumes sufficient planning, execution capability and resources in a predictable regulatory framework, where mine infrastructure can be repurposed, and people and skills sets can “pivot” into new industries.
The reality is very different. Mine closures particularly in South Africa come with significant socio-economic dislocation, exacerbating high poverty, unemployment and legacy issues related to environmental damage, as well as illegal mining.
The underlying economic assumptions are flawed. By definition, you have a limited socio-economic base for development because of a lack of capital investment in non-miningrelated industries or activities located in the sphere of influence of the mine.
For post-closure economies to come into existence, we need to appreciate that:
• Mining is not a network industry – it crowds out other non-mining related industries, when investment in other industries is what is needed to enable the creation of a post mine closure economy
• Mining creates a skills mismatch between skills required in mining and skills required in other industries surrounding the mine. This implies that mines need to focus on a system of skills development that priorities capability, competence and employability not only over the life cycle of the mine but also over the life cycle of the employee’s development
• The location of the mine, imposed and dedicated by geology, creates structural constraints for a post-closure economy. This implies a shift in focus is required, which prioritises final land use and soil capability for agriculture and aquaculture particularly via the creation of pit lakes for nutritional solutions (where feasible), rather than on the demolition of existing infrastructure and backfill strategies, which constitutes the major component of closure costs.
The national closure strategy and the GNR1147 create more uncertainty than certainty. The recent Stillfontein tragedy should encourage the industry to be more proactive in providing betterengineered and integrated closure measures, as well as clearer policy direction for managing closure, more optimally. Closure objectives, which prioritises future land use capabilities and infrastructure development for food security, water security and energy security based on renewables, should be preferred as these industries will enable the creation of an eco-system, which can serve as a prerequisite for economic diversification and a more successful post-closure economy.
12-13 March 2025 — GMG-SAIMM In-Person Forum
Exploring the future of mining through innovation and sustainability
54 on Bath, Rosebank, Johannesburg
Contact: Gugu Charlie Tel: 011 538-0238
E-mail: gugu@saimm.co.za
Website: http://www.saimm.co.za
7-8 April 2025 — 2ND Southern African Hydrogen and Fuel Cell Conference 2025
Southern Sun Rosebank, Johannesburg
Contact: Gugu Charlie Tel: 011 538-0238
E-mail: gugu@saimm.co.za
Website: http://www.saimm.co.za
8-10 April 2025 — 27TH International Conference on Paste, Thickened and Filtered Tailings Swakopmund, Namibia
Website: https://acgpaste.com/2025/
26-29 May 2025 — 9TH Sulphur and Sulphuric Acid Conference 2025
Protea Hotel Stellenbosch and Conference Centre, Stellenbosch
Contact: Gugu Charlie Tel: 011 538-0238
E-mail: gugu@saimm.co.za
Website: http://www.saimm.co.za
3-5 June 2025 — Introduction to Mining Hydrology and Mine Dewatering Design Workshop
Indaba Hotel, Spa and Conference Centre, Fourways
Contact: Gugu Charlie Tel: 011 538-0238
E-mail: gugu@saimm.co.za
Website: http://www.saimm.co.za
22-25 June 2025 — European Metallurgical Conference 2025 (EMC) Hamburg, Germany
Website: https://gdmb.de/home/
25-26 June 2025 — 4TH Digital Transformation in Mining Conference 2025
Glenburn Lodge and Spa, Muldersdrift
Contact: Gugu Charlie
Tel: 011 538-0238
E-mail: gugu@saimm.co.za
Website: http://www.saimm.co.za
21-25 July 2025 — AfriRock 2025
Pioneering Progress: The Future of Rock Engineering
Sun City, South Africa
Contact: Camielah Jardine Tel: 011 538-0237
E-mail: camielah@saimm.co.za
Website: http://www.saimm.co.za
18-19 August 2025 — 13TH International Heavy Minerals Conference 2025
Sun City Resort, Rustenburg, South Africa
Contact: Gugu Charlie Tel: 011 538-0238
E-mail: gugu@saimm.co.za
Website: http://www.saimm.co.za
1-3 October 2025 — International Mineral Asset Valuation Conference 2025 Navigating Mineral Asset Valuations in an Uncertain Future
The Maslow Hotel, Sandton
Contact: Gugu Charlie Tel: 011 538-0238
E-mail: gugu@saimm.co.za
Website: http://www.saimm.co.za
13-16 October 2025 — Geometallurgy Conference 2025
Future-Ready Geometallurgy: Trusted Data, Advanced Tools, Smarter Decisions
Glenburn Lodge and Spa, Muldersdrift
Contact: Gugu Charlie Tel: 011 538-0238
E-mail: gugu@saimm.co.za
Website: http://www.saimm.co.za
27-29 October 2025 — 9TH International PGM Conference 2025
PGM - Enabling a cleaner world
Sun City, Rustenburg, South Africa
Contact: Gugu Charlie Tel: 011 538-0238
E-mail: gugu@saimm.co.za
Website: http://www.saimm.co.za
16-22 November 2025 — The 12TH International Copper Conference (Copper 2025) Phoenix, Arizona, USA
Website: https://www.extractionmeeting.org/ Extraction2025/Extraction2025/Copper2025/default.aspx
The following organizations have been admitted to the Institute as Company Affiliates
acQuire Technology Solutions
AECI Mining Chemicals, a division of AECI Mining Ltd
African Pegmatite
Allied Furnace Consultants
AMIRA International Africa (Pty) Ltd
Anglogold Ashanti Ltd
Anton Paar Southern Africa
Arcus Gibb (Pty) Ltd
Becker Mining (Pty) Ltd
Bluhm Burton Engineering Pty Ltd
Caledonia Mining South Africa
Castle Lead Works
DDP Specialty Products South Africa (Pty) Ltd
De-Tect Unit Inspection (Pty) Ltd
Digby Wells and Associates
EHL Consulting Engineers (Pty) Ltd
Elbroc Mining Products (Pty) Ltd
Epiroc South Africa (Pty) Ltd
Ex Mente Technologies (Pty) Ltd
Exxaro Resources Limited
FLSmidth Minerals (Pty) Ltd
G H H Mining Machines (Pty) Ltd
Geobrugg Southern Africa (Pty) Ltd
Glencore
Gravitas Minerals (Pty) Ltd
Hatch (Pty) Ltd
Herrenknecht AG
Impala Platinum Holdings Limited
IMS Engineering (Pty) Ltd
Ingwenya Mineral Processing
Ivanhoe Mines SA
Longyear South Africa (Pty) Ltd
Malvern Panalytical (Pty) Ltd
Maptek (Pty) Ltd
Mech-Industries
Micromine Africa (Pty) Ltd
Minearc South Africa (Pty) Ltd
Minerals Council of South Africa
MineRP Holding (Pty) Ltd
Mining Projection Concepts (Pty) Ltd
Mintek
MLB Investments CC
Modular Mining Systems Africa (Pty) Ltd
Murray & Roberts Cementation (Pty) Ltd
Paterson & Cooke Consulting Engineers (Pty) Ltd
Redpath Mining (South Africa) (Pty) Ltd
Rosond (Pty) Ltd
Roytec Global (Pty) Ltd
Rustenburg Platinum Mines Limited - Union
Schauenburg (Pty) Ltd
SENET (Pty) Ltd
Sibanye Gold Limited
Sound Mining Solution (Pty) Ltd
SRK Consulting SA (Pty) Ltd
Tomra (Pty) Ltd
Trans-Caledon Tunnel Authority
Ukwazi Mining Solutions (Pty) Ltd
VBKOM Consulting Engineers
Weir Minerals Africa
Zutari (Pty) Ltd
Pump and Abrasion Technologies (Pty) Ltd
CIGroup ACE Pty Ltd
Buraaq mining Services (Pty) Ltd
Sebotka (Pty) Ltd
The purpose of this Mineral Asset Valuation Conference is to bring together professionals from the international mining and finance sectors to discuss and debate mineral asset valuation methodologies and best practices in the context of an uncertain and rapidly changing landscape.
In a time of global transformation, the mineral resources sector faces unprecedented challenges and opportunities. From the increasing influence of Environmental and Social Governance (ESG) considerations to the shifting dynamics of the global economy and geopolitics, the valuation of mineral assets must adapt to navigate an uncertain future.
The International Mineral Asset Valuation Conference 2025 serves as a cornerstone for thought leadership, collaboration, and innovation in this evolving field globally. This event will bring together a diverse group of experts, practitioners, and decision-makers to explore solutions and strategies that ensure mineral asset valuations remain relevant, reliable, and responsive to the world’s rapidly changing landscape.
The conference will delve into key aspects shaping the mineral valuation process, offering attendees valuable insights into how the industry continues to tackle current and emerging challenges.
Join us as we engage in meaningful dialogue, share innovative practices, and build a path toward a sustainable and resilient future for the mineral valuation profession.
The conference in 2025 will be structured around the following Core Themes:
u The application of Best Practice when uncertain
u Value in the context of ESG requirements
u ‘Rules of the Game’ in today’s evolving world order
u The West/East Principles Divide
u The enhancement and destruction of value from technologies and valuation methodologies
u IMVAL as the driver for international alignment
TARGET AUDIENCE
u Mining Industry Professionals
u Valuation Experts and Consultants
u Investors and Financial Analysts
u Legal and Compliance Experts
u Academics and Researchers
u Environmental and ESG Professionals
u Technology Providers
u Account Practitioners Consultants
Prospective authors may choose to submit papers or presentations only.
In person presentations will be preferred, although virtual presentations may be streamed live or prerecorded.
Prospective authors are invited to submit titles and abstracts of their papers and/or presentations in English.
Authors must note whether they plan to attend in person or deliver a live-streamed or recorded virtual presentation.
Abstracts should be no longer than 500 words and should be submitted to: Gugu Charlie, Conferences and Events Coordinator, E-mail: gugu@saimm.co.za Tel: +27 11 538 0238
The complete Proceedings volume will be made available on the internet for public access after the conference.
Acceptance of papers for publication in the SAIMM Journal will be subject to peer review by the Conference Committee and SAIMM Publications Committee post-conference.
27 - 28 OCTOBER 2025 - CONFERENCE
29 OCTOBER 2025 - TECHNICAL VISIT
VENUE - SUN CITY, RUSTENBURG, SOUTH AFRICA
Building on the success of previous events since its inception in 2004, the Platinum Conference Series continues to address the opportunities and challenges facing the global platinum group metals (PGM) industry. As the sector faces increasing demand, from technological innovation and decarbonisation to cost management and market volatility, the 9th International PGM Conference offers a critical platform for addressing these challenges head-on.
Guided by an expert Organising Committee and informed by insights from the industry, this year’s conference will delve into various themes designed to spark meaningful dialogue to drive innovation at every level of the PGM value chain and maintain competitiveness in a rapidly changing global landscape. Attendees can expect high-quality technical papers and presentations, robust networking opportunities, and strategic insights that help shape the future of the industry.
Now more than ever, the platinum industry needs fresh ideas, collaborative partnerships, and forward-thinking strategies to remain relevant. Whether you’re an academic, industry professional, sponsor, or policy leader, your participation will contribute to a dynamic exchange of expertise and solutions that can safeguard the sector’s long-term success. Join us as we explore cutting-edge developments, address the industry’s most pressing issues, and shape a sustainable, competitive future for the PGM industry.
• Academics and Researchers
• Business Development Managers
• Concentrator Managers
• Consultants
• Engineers (Mining, Mechanical, Process, Ventilation)
• Exploration and Geology Professionals
• Fund and Investment Managers
• Innovation and Technology Managers
• Market Researchers and Strategy Analysts
• Metallurgists and Pyrometallurgists
• Planning Managers
• Production Managers (Mining and Metallurgy)
• Project Managers
• Scientists
• And anyone interested in shaping the future of the PGM industry
• Technology for Efficient Production
• Decarbonization and Sustainability
• Safety and Cost Management
27 June 2025 - Submission of abstracts
1 August 2025- Submission of papers
27-28 October 2025 - Conference
29 October 2025 - Technical Visit
• Market Outlook and Strategic Positioning
• Driving Competitiveness, Relevance, and Self-determination
Be part of this dynamic event and help shape the future of the platinum and PGM sector. We invite you to submit your abstracts, register as a delegate, or explore sponsorship opportunities to ensure that this conference continues to be the premier platform for exchanging knowledge, ideas, and best practices.
FOR FURTHER INFORMATION, CONTACT:
Gugu Charlie, Conferences and Events Coordinator
E-mail: gugu@saimm.co.za
Tel: +27 011 538 0238
Web: www.saimm.co.za