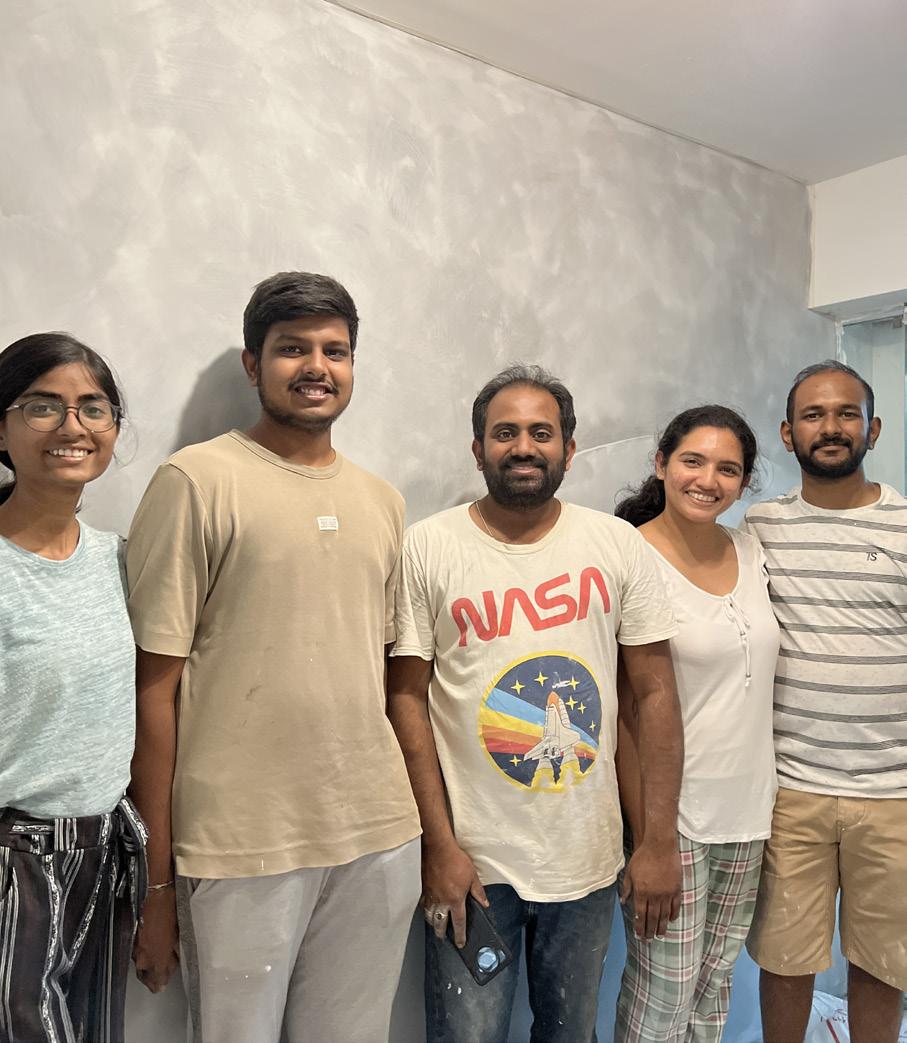
2 minute read
05 natural paints exploration


Advertisement
Malleshwaram | Bengaluru about the workshop
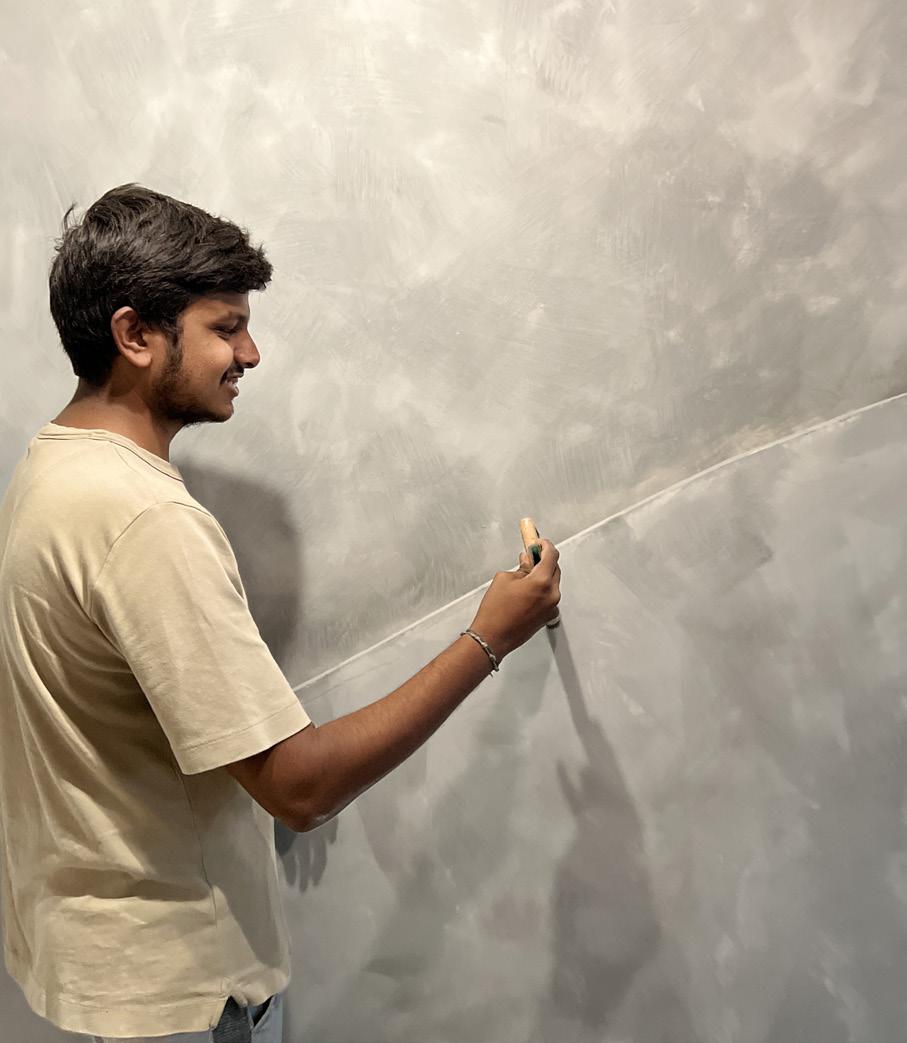
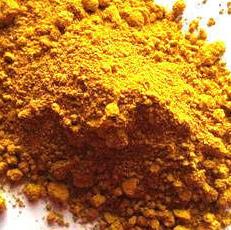
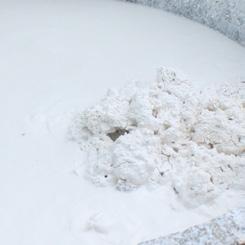

This was an experiment conducted for a client who wanted to explore natural options for paint like finishes for an office interior project. The site predominantly had dry walls. Hence we had to work out a mix that was suitable to dry wall and also end up paint like. We had gotten a few sample references from the client as of to the shades and color tones that we needed to achieve. To make it more naturally percieving we decided to use natural oxides as pigments. This was a 2 phase project - first, a studio experimentation and second, the onsite execution of the achieved mixes. I have discussed the experiences as well as learnings and challenges faced during the process.
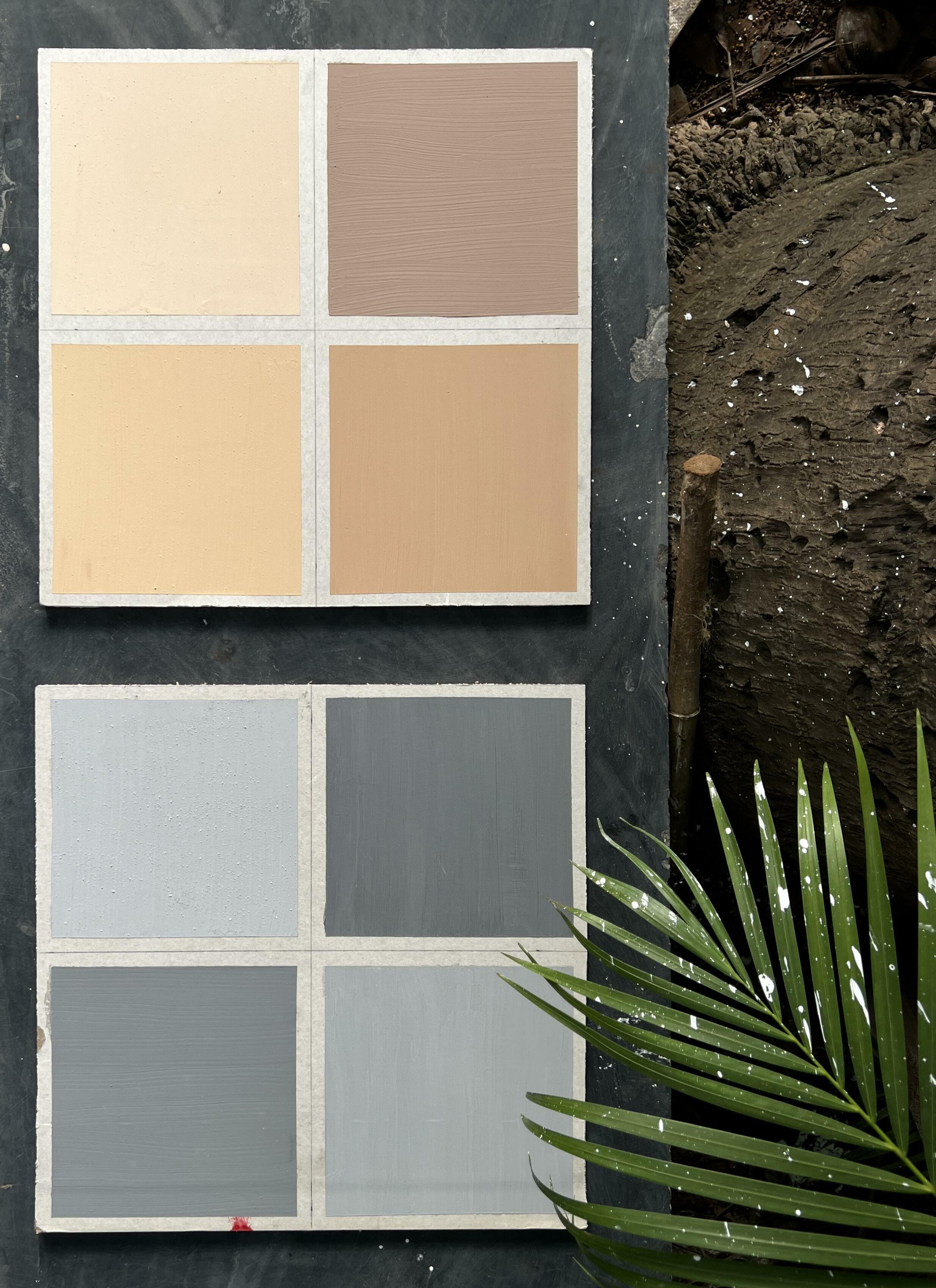
Experimenting At The Studio
When we had recieved the brief for coming up with paint like natural finish with the suggested color tones and shades, the main factor was that it should not be a trovel finish. It should be brush applied, like a paint finish. So we needed a liquidy mix. We then arrived at the previously mentioned materials. Over experimenting, it was realized that we needed a proper binding material for the finish to be applied on a ‘dry wall’. Hence we tried out white cement and later added fevicol too.
The concept of granulometry played a crucial role in ensuring the intermixing of these materials with one another. The basic proportions were restricted to ‘lime’, ‘dolomite’, ‘white cement’ & ‘fevicol’. The studio experimentation focused on getting the consistency right predominantly. We achieved the color roughly based on trail and error.
The client wanted variations in 2 dominant shades - ochre & greys. Hence we had used natural oxides as pigments. The red and yellow oxides worked perfectly as they blended in with the lime dolomite mix seamelessly. But the black oxide in powdered form didn’t work out. This was the lime mix having a finer granulometry than the oxide which didn’t allow it to blend in. Hence we ended up using an asian paints stainer to achieve the greys.
Another important learning was that, because the mix contains white cement and fevicol, it lightens as far as twice the color of the wet mix as it dries. This caused a lot of trial and errors as we were not able to be clear as of to how much should the pigment concentration be. But we did find a solution on site for this problem.
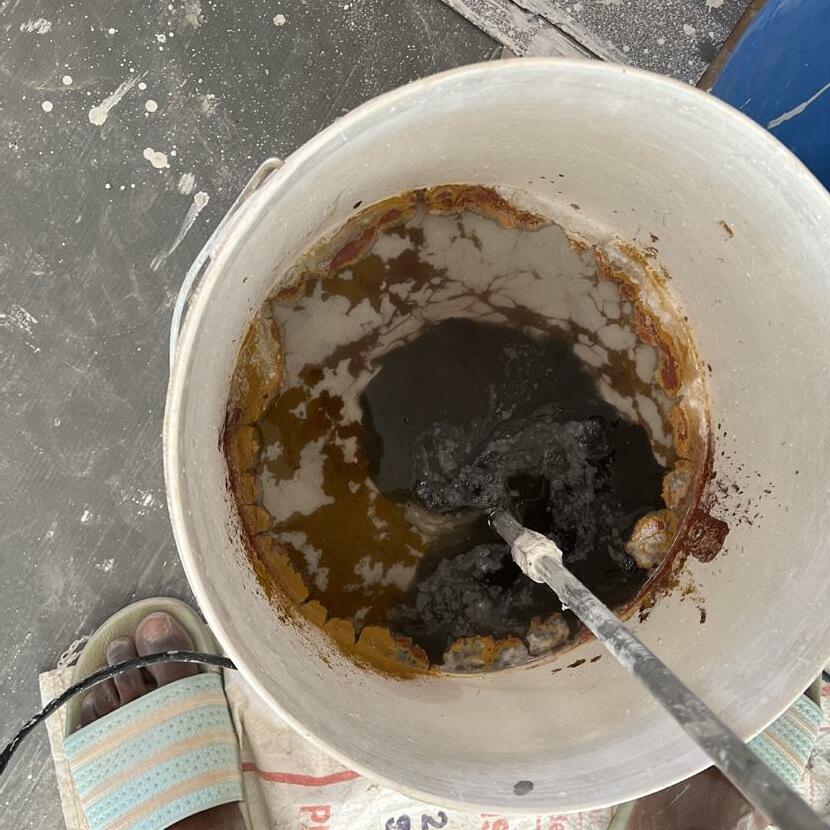
on-site execution
The execution part was large in scale compared to the studio experimentation. Hence, we had to do some pre-visit prepearations such as slaking and seiving the lime in large batches. We took all the necessary oxides and pigments to the site and decided to achieve the right mix there, as we could not arrive at a proportion for the pigmentation. The solution for the pigment’s proportion was to make a waterbased solution with oxides and add it gradually to small batches of the lime mixture in mililitres, until the desired mix was achieved. The proportions for the same were calculated for a larger batch later.
The first step was to make samples on the wall so that the client could choose the desired shades. The samples varied in concentration of the pigment alone, keeping the base mixture of lime, dolomite, fevicol and white cement as the same. Once the samples were finalized, we had to mix the same proportions in a large drum using a paint mixer.


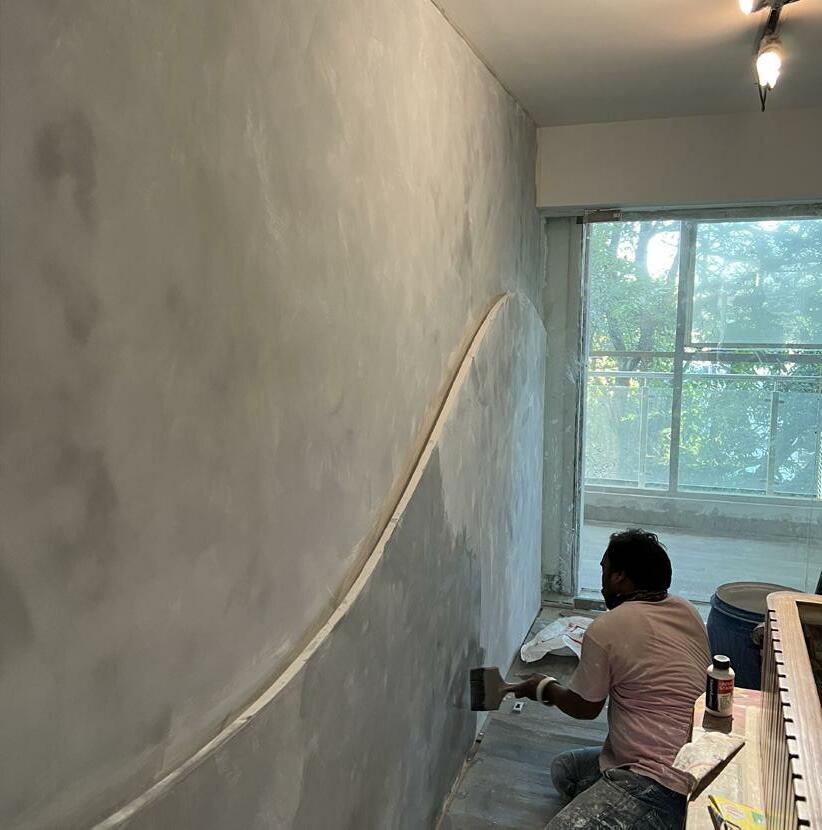
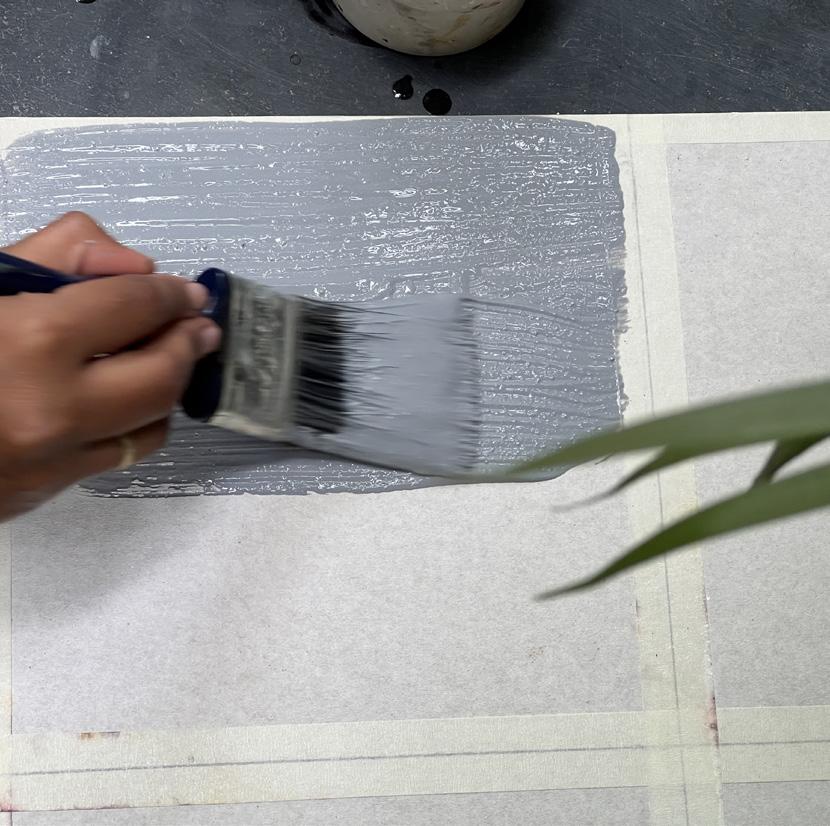

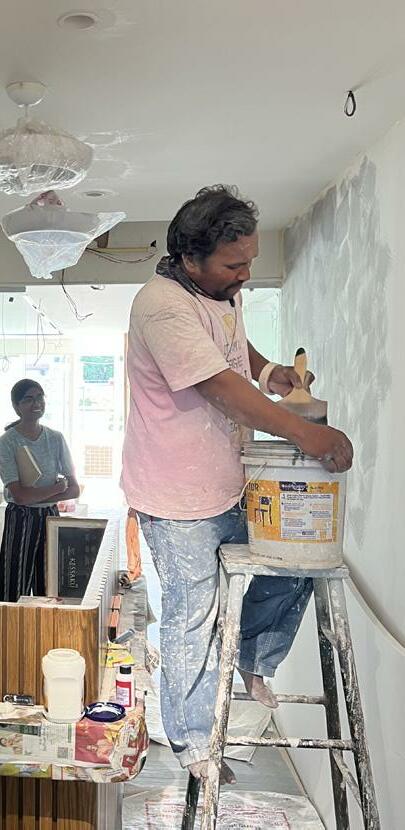

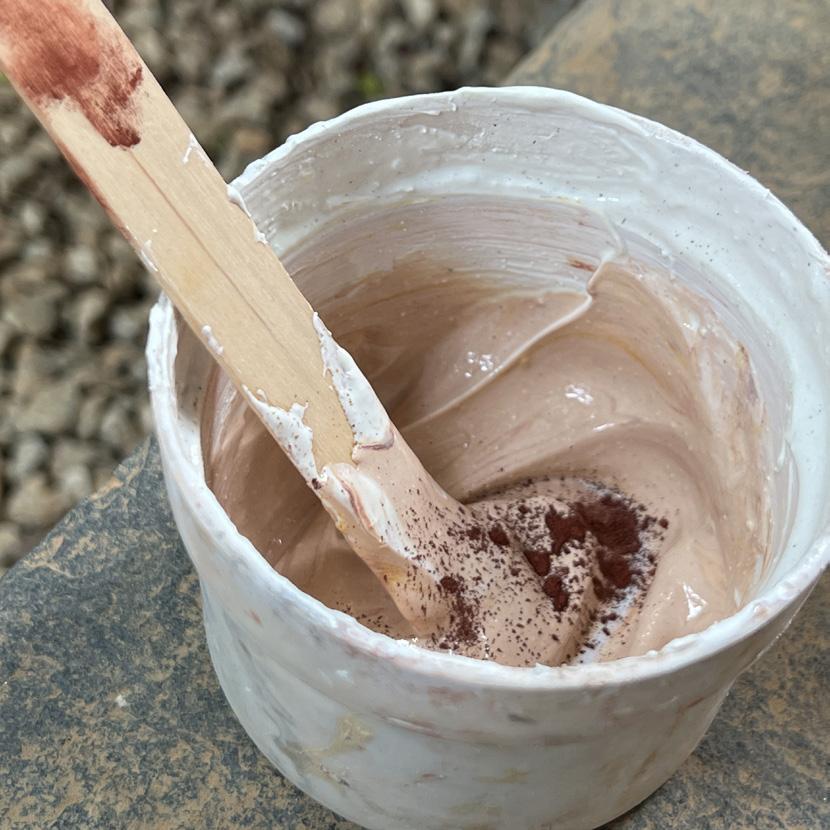


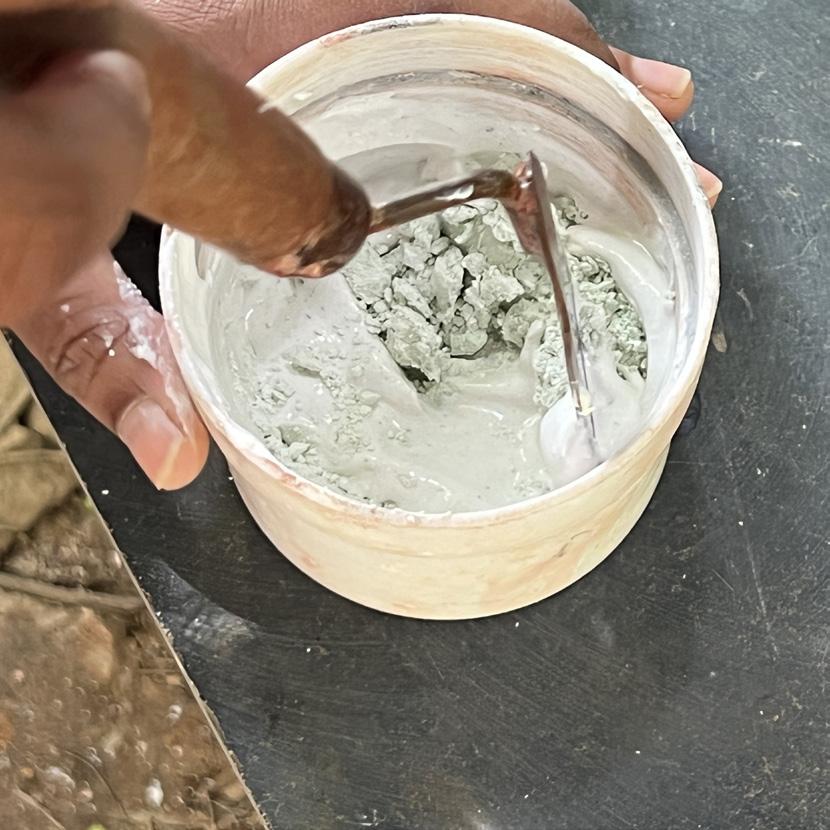
There was a requirement of a visual texture (cloud like) to be achieved. Hence we had to follow a two coat approach with broken brush strokes so that the patchy overlap of boath the coats would result in a cloud like visual texture. The painter had to be guided for the type of brush strokes we needed and he grasped it quickly.
One major learning from site was that a dry wall doesnt absorb or accept this kind of a natural paint finish beyond 2 coats. We had realized this when we tried to fix a few areas with an additional coat but it backfired by resulting in white patches. It then had to be sanded out to blend the finishes on the wall.