
13 minute read
VERARBEITUNG
Hightech auf Holmlos-Maschinen
Advertisement
Die SFS intec, seit Januar 2020 tritt sie als SFS im Markt auf, ist mit Kaltmassivumformung gross geworden. Das Kunststoffwerk in Altstätten konzentriert sich allerdings ausschliesslich auf die Verarbeitung von Kunststoff. Standardprozesse verbindet man gemeinhin nicht mit dem Werkplatz Schweiz. Doch es sind genau diese und die damit erreichten Skaleneffekte, die das Werk auszeichnen und erst wettbewerbsfähig machen.
Marianne Flury
«Wenn immer möglich, versuchen wir mit Standard zu fahren», weist André Schmid, Standortleiter bei der SFS Kunststoffwerk AG in Altstätten, auf die Strategie hin, die offenbar aufgeht. 90 Prozent der Aufträge, die der Schweizer Lohnfertiger ausführt, basieren auf Standardlösungen. Doch auch die restlichen 10 Prozent spezifischer Einzellösungen tragen zum Erfolg bei. Das Kunststoffwerk, ursprünglich Teil des Elektrowatt-Konzerns, wurde 1996 als erstes Kunststoffwerk der SFS intec in die Gruppe integriert. Bereits damals erkannte man das Potenzial, das Kunststoff-/Metallverbindungen in sich bergen. Heute ist das Werk in Altstätten das Kompetenzzentrum für Kunststoff und beschäftigt rund 130 Mitarbeitende, 20 davon im hauseigenen Werkzeugbau. «Wir waren das erste Kunststoffwerk in der Schweiz, das nach IATF 16949 zertifiziert wurde und haben seit fünf Jahren die Zertifizierung ISO 13485. Dies geschah auf Kundenwunsch, weil wir auch für die Medizintechnik produzieren», erklärt Schmid. 60 Spritzgiessmaschinen laufen im Dreischichtbetrieb, teilweise sieben Tage die Woche und fertigen auf einer Produktionsfläche von 6000 m 2 Komponenten und komplette Baugruppen für die Bereiche Automotive, Aircraft, Medizin, Industrie und Weisse Ware. Obwohl das Unternehmen von seiner Kompetenzbreite her dem Kunden alles anbieten könnte, liegt ein Fokus klar auf der Herstellung filigraner Strukturen. «Wir machen zum Beispiel ABS-Bremsfilter, die eine Maschenöffnung von 70µm aufweisen und 100% optisch geprüft werden – dafür sind wir bekannt am Markt», weist Rolf Locher, Leiter Verkauf, auf eine Stärke hin. Kunststoff-Metall-Kombinationen,
Blick in die Produktion im Kunststoffwerk Altstätten.
Mehrkomponenten spritzgiessen, das Umspritzen von Formteilen und die Fertigung von Hochtemperaturteilen sind weitere Schwerpunkte im SFS-Programm. Ein Highlight ist die im Haus entwickelte CardaFlex-Technologie. Nicht das präzise und kontinuierliche Aufspritzen von Funktionselementen auf ein Trägermaterial macht das Alleinstellungsmerkmal aus, sondern der hohe Engineeringsgrad, den SFS in die verschiedenen Trägermaterialien steckt. Im vorliegenden Fall geht es um eine Polyesterkordel, die für den Türgewichtsausgleich bei einer Geschirrspülmaschine sorgt. Die Kordel wird thermisch im Werkzeug fixiert, so dass in der Anwendung die Dehnung genau den Anforderungen des Kunden entspricht. Speziell ist auch, dass die Funktionselemente auf die unter Spannung stehende Kordel aufgespritzt werden. Damit ist gewährleistet, dass die Längendehnungen genau übereinstimmen. «Der Prozess ist sehr konstant. Serienbegleitend messen wir jede Stunde die Dehnung und auch die Abzugskräfte», betont Schmid.

Zwei dieser CardaFlex-Elemente werden jeweils in einem Geschirrspülautomaten verbaut, wo sie für den Türgewichtsausgleich sorgen. Bild: Engel
Holmlos, was denn sonst
Für die CardaFlex-Anwendungen kommen typischerweise nur Engel Holmlos-Maschinen zum Zug. Die ersten Maschinen waren Vertikalanlagen, auf denen die Kordeln mittels Heissschnitt abgelängt und die Enden verschmolzen wurden oder die Kordeln wurden nach dem Aufspritzen aufgewickelt und der Kunde erhielt die Rollenware und konfektionierte sie nach seinen Bedürfnissen. Da es sich bei den Vertikal anlagen um eine Universalmaschine handelt – «sie kann verschiedene Längen spritzen, schneiden, wickeln, sie kann einfach alles», so Schmid dazu – die sich für eine Einzweckanwendung wie die Geschirrspülmaschinenkordel nicht auszahlt, musste eine innovative Lösung her. SFS fand sie in der holmlosen e-victory Horizontalspritzgiessmaschine. Mit der Horizontallösung war es nicht mehr möglich, den Heissschnitt zu realisieren. Hier funktioniert die thermische Fixierung, das Aufspritzen verschiedener Funktionselemente und der Kaltschnitt in einem Durchgang. «Dieser Innovationsschritt hat uns auch den Wettbewerbsvorteil verschafft, für einen Kunden, der diverse Marken bedient, sehr grosse Stückzahlen fertigen zu können. Ich spreche da von 6 Mio. Teilen im Jahr», verrät Schmid. Das Werkzeug ist in diesem Fall ein 8fach Werkzeug.
In diesem 8fach-Werkzeug auf einer Engel e-victory 140 werden die Polyesterkordeln unter Spannung umspritzt, vom integrierten Handling entnommen, auf eine Kühlstrecke abgelegt und anschliessend verpackt. Bild: SFS
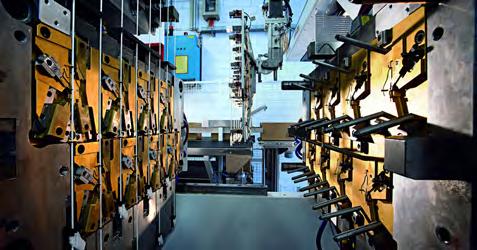
Für diese Anwendung ist die Holmlostechnik von Engel wie geschaffen. «Hätten wir das Projekt mit einer konventionellen Holmmaschine realisiert, würden wir ungefähr eine zweieinhalb Mal höhere Schliesskraft benötigen», stellt Schmid fest. «Selbst die Schliesskraft von 140 Tonnen, der aktuell im Einsatz stehenden holmlos Horizontalmaschine, ist höher als eigentlich benötigt wird. Sie ist aber nach Rahmenverbreiterung und Rahmenverlängerung die kleinst mögliche Maschine, auf der das riesige Werkzeug aufgespannt werden kann.» Abgesehen davon, dass die 140-Tonnen-Holmlosmaschine wesentlich günstiger ist als eine 350- oder gar 400-Tonnen-Holmmaschine, benötigt sie auch eine wesentlich kleinere Stellfläche und geringere Hallenhöhe. Zudem haben Handlinggeräte und Roboter ungehinderten Zugang zum Werkzeugbereich.
Standard – ein strategischer Entscheid Wenn immer möglich setzt SFS Standardlösungen ein. Das ist augenfällig in der Produktion: Praktisch überall findet sich das gleiche Konzept: Spritzgiessmaschine mit Standardhandling und Ablage nach hinten.
Stets im Zentrum, die Kleine
Agathon Mini-Feinzentrierung
Preis-Leistungs-Standard im Spritzguss-Formenbau
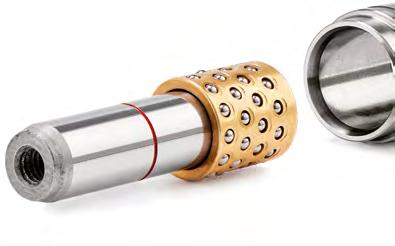

Spielfrei | ruckfrei abwälzend Universell | statische und dynamische Anwendung
«Wir legen grossen Wert darauf, Skaleneffekte nutzen zu können. Wir haben zwei Maschinenlieferanten, zwei Temperiergeräte-Lieferanten, zwei Handlinglieferanten usw. Das bedeutet gleiche Steuerungen, gleiche Logik in der Bedienung. Da sind wir uns über Jahrzehnte treu geblieben. Das ermöglicht es uns auch, im Dreischichtbetrieb, sieben Tage in der Woche zu arbeiten», so Schmid. Und Markus Schertler, Geschäftsführer von Engel Schweiz bestätigt: «Auch bei der 140-Tonnen-Holmlosmaschine handelt es sich um eine Standardmaschine, mit einem auf das Kundenbedürfnis zugeschnittenen verbreiterten Maschinenbett, das aber auch aus dem «modularen Baukasten» erhältlich ist.»
Eine ausgezeichnete Zusammenarbeit Eine gute und enge Zusammenarbeit zwischen Lieferanten und Kunden ist die Basis für eine langjährige und nachhaltige Geschäftsbeziehung. «Mit dem Kauf der Maschine ist das Geschäft bei weitem nicht abgeschlossen. Es braucht die schnelle Inbetriebnahme, die kompetenten Leute vor Ort, auch im Verkauf. Ich kaufe ja keine Katalogware, sondern für jede Maschine geht man die Einzelpositionen durch – auch wenn es um Standard geht. Jede Maschine ist zugeschnitten auf uns. Wir haben auf sehr vielen Maschinen eine Automation integriert – das bedeutet eine sehr enge Zusammenarbeit mit den Technikern von Engel», sagt Schmid. Und dies, obwohl SFS eine Produktionszelle nicht komplett als Paket kauft, sondern selber als Integrator auftritt. «Die Prozessintegration erfolgt mit den eigenen Ingenieuren und den Ingenieuren von Engel hier vor Ort. Das muss funktionieren, ebenso der Service, die Reparaturen, die Verfügbarkeit von Ersatzteilen, die kompetente Beratung und Betreuung – auch wenn mal etwas schiefläuft», sagt Schmid zum Anforderungskatalog. «Da kann ich sagen, haben wir eine ausgezeichnete Zusammenarbeit.»
Breites Know-how
Das Werk in Altstätten verfügt über einen eigenen Werkzeugbau, der 20 Mitarbeiter beschäftigt. Bauteile können kunststoffgerecht ausgelegt werden. Zur Verfügung
Die Zusammenarbeit funktioniert (v.l.): Franz Pressl, Produktmanager für Holmlose, Engel Austria, Markus Schertler, Geschäftsführer Engel Schweiz, Rolf Locher und André Schmid, beide SFS Kunststoffwerk, René Okle, Vertriebsingenieur, Engel Schweiz. Bild: Marianne Flury

stehen Verfahren wie Ultraschallschweissen, Tampondruck, Heissprägen, Gleitschleifen, Mikrostrahlen, Montagearbeiten werden automatisiert, halbautomatisiert oder mittels Handarbeit ausgeführt. «Innovationstreiber ist vor allem die Automobilindustrie», weiss Schmid, und Rolf Locher ergänzt: «Teile, die vor fünf bis sechs Jah ren noch klassisch aus Metall gemacht wurden, werden heute aus Kunststoff gespritzt, Centerless geschliffen, feinst gereinigt, 100% geprüft und verpackt. Der Gewichts- und Preisvorteil ist enorm.» Stolz ist das Unternehmen auch auf das bestens ausgerüstete physikalische Labor. Hier werden Bauteile untersucht, Empfehlungen an den Kunden abgegeben und mögliche Massnahmen erarbeitet, dies oft auch in enger Zusammenarbeit mit der Interstaatlichen Hochschule für Technik Buchs (NTB).
Mit Fachkräften gut bedient
Um das breite Anwendungsspektrum und die verschiedenen Verfahren im Griff zu haben, braucht es die nötigen Fachkräfte und die findet man offenbar auch im Dreiländereck. «Wir sind gut bedient mit Fachleuten, aber ein wichtiger Grund ist, denke ich, dass wir selber Leute ausbilden und entsprechend einen guten Ruf im Rheintal geniessen», ist Schmid überzeugt. SFS bildet Kunststofftechnologen – in der Regel ein bis zwei pro Lehrjahr – Polymechaniker, Konstrukteure und Logistiker aus. Mit dem Geschäftsverlauf ist André Schmid sehr zufrieden. «Das Wachstum in den Jahren 2017 und 2018 war sehr gut. Auch das laufende Jahr (2019/2020) ist überdurchschnittlich, wobei die Aufwertung des Frankens uns weiterhin stark fordert. Nach wie vor sind wir gut eingedeckt mit Arbeit. Beim Stahl im Bereich Automobil ist allerdings eine extreme Zurückhaltung zu spüren. Das wird Auswirkungen auf die Industrie haben. Das Kunststoff werk ist davon noch nicht tangiert. Wir haben noch einige Projekte in der Pipeline. Die Neuprojekte, die wir in den letzten drei Jahren gewonnen haben, werden den Umsatz in den nächsten zwei Jahren weiter steigen lassen. Wichtig ist, dass auch in diesem Jahr investiert wird. Anzeichen dafür sind vorhanden. Wir haben im Automobilbereich bereits Kunststoff/Metall-Kombinationen für die e-Mobilität liefern können. Interessant dabei ist, dass hier der Kunde kein Automobiler, sondern ein Elektriker ist. Die Volumina sind vergleichsweise noch klein, aber man erkennt die Veränderungen, die in der Automobilindustrie stattfinden.»
Kontakt SFS Kunststoffwerk AG André Schmid Schöntalstrasse 2a CH-9450 Altstätten +41 71 757 12 64 andre.schmid@sfs.biz www.sfsintec.biz/ksw
Kennzeichnung hochwertiger Kunststoff-Motorkomponenten
Kettenspanner mit Datamatrix-Code
Der Wunsch nach Rückverfolgbarkeit und individueller Codierung von Automobilkomponenten lässt sich nicht immer einfach umsetzen. Die Ingenieure der Weiss Kunststoffverarbeitung GmbH & Co. KG mussten intensive Detailarbeit leisten, um die Kettenspanner eines Premiumfahrzeugs mit einem sehr gut lesbaren DatamatrixCode zu versehen. Mehrere Druckvorgänge sind dafür nötig – und eine abschliessende Qualitätskontrolle.
Aus Sicht der Automobilhersteller wird das Änderungs- und Versionsmanagement immer komplexer. Die steigende Variantenvielfalt sowie häufigere Modellwechselund Modellpflegezyklen haben zur Folge, dass z.B. Ersatzteile in Reparaturfällen oft nur mit einigem Aufwand eindeutig zu identifizieren sind. Der Wunsch eines Premium-Herstellers an die Produktionsexperten der Weiss Kunststoffverarbeitung war daher nachvollziehbar: Spannschienen für NockenwellenSteuerketten sollten mit einer individuellen Codierung versehen werden. Stefan Martini, Projektleiter bei Weiss: «Damit lässt sich eine eindeutige Zuordnung der Bauteile realisieren. Das vereinfacht die Ersatzteilbeschaffung und die Rückverfolgbarkeit erheblich.» Der Autohersteller wünschte eine Datamatrix-Codierung (DMC) nach DIN EN ISO/ IEC 15415, die neben der Teile-Identnummer auch das Produktionsdatum und eine fortlaufende, d.h. individuelle Nummer, enthält. Grundsätzlich lässt sich eine solche Anforderung problemlos umsetzen, entsprechende Kennzeichnungssysteme stehen zur Verfügung.
Nur auf den ersten Blick einfach Im Falle der Spannschienen – die Weiss in grosser Stückzahl für diverse Motorenhersteller fertigt – gab es jedoch eine Herausforderung. Dipl.-Ing. Robert Heller, bei Weiss u.a. verantwortlich für die Konstruktion der Produktions- und Automatisierungstechnik: «Die hoch verschleissfesten und dauerhaft unter Öl laufenden Bauteile werden aus einem Polyamid mit gelblicher Eigenfarbe gefertigt. Eine Lasermarkierung kommt hier nicht in Frage, weil die Farbdifferenz zu ge
Ein Knickarmroboter positioniert die Spannschiene nach der Montage vor einem ZweifarbenInkjetmarkiersystem, wo sie im Farbton schwarz codiert und anschliessend optisch geprüft wird. Bild: Weiss

ring wäre. Das gleiche gilt für eine konventionelle Inkjetmarkierung: Sie ist ebenfalls nicht kontrastreich genug, um den hohen Qualitätsstandard nach DIN EN ISO/IEC 15415 für die DMC-Codierung zu erfüllen.» Nach Versuchen mit verschiedenen Druckverfahren haben die Weiss-Ingenieure die geeignete Technik gefunden und bereits in eine Montagestation integriert. Ein Knickarmroboter positioniert die Spannschiene nach der Montage vor einem ZweifarbenInkjetmarkiersystem. Nach einer Grundie rung mit dem Farbton «weiss» erfolgt die eigentliche Codierung im Farbton «schwarz». Als Abschluss des Kennzeichnungsprozesses fährt der Roboter das soeben codierte Bauteil vor das Objektiv einer Kamera, die das Ergebnis prüft und im Falle eines Falles «N.i.O»-Spannschienen ausschleust. Nach DIN EN ISO/IEC 15415 muss hierbei mindestens die zweithöchste Qualitätsstufe B erreicht werden, so fordert es der Anwender. Bei der Montage des leistungsstarken Motors wird der Code gelesen und in der Fahrzeugdokumentation gespeichert. Nach der Auslieferung des Fahrzeugs ist der Code sehr schnell nicht mehr lesbar, weil er auf die Kettenlauffläche gedruckt werden muss. Die erste Anlage dieser Art – die in eine Einrichtung für die automatisierte Montage einer Feder integriert wurde – ist inzwischen bei Weiss in Betrieb und bewährt sich bestens. Die umfassenden Entwicklungs- und Optimierungsarbeiten, die in dieses Projekt investiert wurden, werden sich nach Einschätzung der Beteiligten schnell auszahlen. Robert Heller: «Von anderen Motorherstellern haben wir inzwischen ebenfalls Anfragen für codierte Kettenspannelemente erhalten.»
Kontakt Weiss Kunststoffverarbeitung GmbH&Co.KG Rudolf-Diesel-Strasse 2-4 D-89257 Illertissen +49 7303 96 99-0 info@weiss-kunststoff.de www.weiss-kunststoff.de n
Anspruchsvolles Tiefziehen
Einzigartige Höhe bei Tiefziehteilen
Die Kunststoffverarbeitung von Polymerformteilen wird immer anspruchsvoller: Einerseits verkürzt sich der Lebenszyklus von Produkten aufgrund von Individualisierung, andererseits muss kostengünstig und trotzdem qualitativ hochwertig produziert werden. Hier stellt besonders das Tiefziehen für viele Lohnfertiger immer wieder eine Herausforderung dar, denn dabei können schnell Risse oder Falten im Formteil entstehen.
Die nordform Max Storch GmbH & Co. KG feierte 2019 ihr 100-Jahr-Jubiläum und kann aufgrund dieser langjährigen Erfahrung im Kunststoffbereich Formteile mit einer Höhe von 820 mm gleichmässig und fehlerfrei produzieren – dies ist gemäss eigenen Angaben bisher einzigartig in der Branche. Bei sämtlichen Prozessen setzt das Traditionsunternehmen stets auf eine enge Abstimmung mit seinen Kunden und stellt anspruchsvolle Sonderformen her, bei denen auch eine individuelle Einbindung von Optiken oder Leuchtmitteln möglich ist. Dies gelingt durch eine hohe Fertigungstiefe, da alles in-house entsteht – sowohl die Werkzeuge zur Herstellung als auch das Produkt selbst.
Lohnfertiger sind gefordert
Der Kunststoff für grosse Stadtlaternen oder Leuchtreklamen muss beispielsweise tiefgezogen werden – ein anspruchsvolles Verfahren. «Früher wurden vorrangig einzelne Leuchtkörper oder Dichtungen bestellt, doch heutzutage müssen diese Elemente oftmals in Metallgehäuse oder komplizierte Strukturen eingebunden werden», berichtet Rainer Knobloch, Geschäftsführer von nordform. «Dank unserer hohen Fertigungstiefe und unserer jahrelangen Erfahrung können wir aber individuell gestaltete Sonderformteile oder ganze Baugruppen optimal auf das jeweilige Anwendungsgebiet abstimmen.»
Bilder: nordform

Mit dem Tiefziehen ist die Herstellung von hohen und schlanken Formteilen mit einer hochwertigen Oberfläche möglich.
Mit dem Tiefziehen ist die Herstellung von hohen und schlanken Formteilen mit einer hochwertigen Oberfläche möglich – beispielsweise für Leuchtenabdeckungen, Maschinenschutz oder Deckenverkleidungen im Waggonbau. «Für dieses Verfahren wird das Werkmaterial zunächst in einem Ofen vorgetrocknet und dann in die Maschine eingespannt», erläutert Knobloch den Vorgang. «Eine Ober- und Unterhei zung fährt nun an den Kunststoff heran und bringt ihn auf die erforderliche Umformtemperatur. Anschliessend werden die Heizungen wieder zurückgefahren, damit das Werkzeug von unten in den leicht vorgeblasenen Kunststoff zum Fertigungsprozess eindringen kann. Das Material wird dabei mithilfe eines Vakuums angesaugt.» Nach einer kurzen Abkühlphase, die sich nach der Materialart- und stärke richtet, kann das Werkzeug aus dem Formteil entfernt und das Werkstück entnommen werden. Um eine optimale Materialverteilung zu gewährleisten, temperiert nordform seine Werkzeuge mithilfe von Wasser auf die jeweils erforderliche Wärme. So wird vermieden, dass der Kunststoff falsch fliesst und beispielsweise Materialfalten entstehen oder die Oberfläche einreisst. «Während des gesamten Prozesses muss ausserdem bedacht werden, dass sich der Kunststoff immer statisch auflädt», fügt Knobloch hinzu. «Gerade bei grossen Oberflächen müssen daher sämtliche Prozessschritte optimal aufeinander abgestimmt sein, da ansonsten beispielsweise Stäube aus der Luft eingearbeitet werden.» Dies verhindert nordform durch Luftwäscher in der Produktion.
Traditionsunternehmen mit intensiver Kundenbetreuung Bei sämtlichen Verarbeitungsverfahren stehen die Polymerexperten aus Norderstedt im Vorfeld beratend zur Verfügung. «Wir
Durch die Bauteilanalyse wird die Bemusterungsphase verkürzt. Die Messdaten werden mit den CAD Daten verglichen und invertiert in das Werkzeug übertragen.

interpack PROCESSING & PACKAGING
Damit beim Tiefziehen die Farbe nicht abplatzt, sind hochflexible Farbsysteme entwickelt worden. Dies ist beispielsweise für hochwertige Messestände mit anspruchsvollen Formen wichtig.
verstehen uns als Problemlöser, weshalb wir auch bei einem kompletten Re-Design eines Artikels unterstützen oder effizientere Alternativen vorschlagen», so Knobloch. «Üblicherweise kommen unsere Kunden mit den notwendigen 3D-Daten zu uns und erläutern uns ihre Anforderungen. Nachdem alle wichtigen Parameter abgesprochen wurden, gehen wir an die Umsetzung.» Da nordform die Werkzeuge für alle Fertigungsprozesse selbst herstellt, sind sämtliche Aluminiumformen immer optimal auf das jeweilige Formteil abgestimmt. Diese hohe Produktionstiefe ermöglicht massgeschneiderte Individuallösungen aus einer Hand – vom Werkzeug über das Material bis hin zum finalen Produkt. Das Unternehmen feierte Anfang 2019 sein 100-Jahr-Jubiläum und blickt zuversichtlich in die Zukunft. «Zwar sind viele Prozesse noch vom Erdöl abhängig, aber ein Umbruch mit alternativen Rohstoffen für Polymere steht bevor – beispielsweise für ökologische Produkte», resümiert Knobloch. «Wir freuen uns auf den Trend zu grüneren Kunststoffen und unterstützen ihn gerne durch unsere Umsetzung.» So sind die Produkte von nordform keine Wegwerfartikel, sondern besonders widerstandsfähig konstruiert und damit nachhaltig: Das Material der Produkte wird immer an sämtliche Anforderungen angepasst, um seine Lebenszeit zu er höhen und auf diese Weise den Kunststoffverbrauch zu reduzieren.
Kontakt nordform Max Storch GmbH & Co. KG Schützenwall 16-20 D-22844 Norderstedt +49 40 521973-0 info@nordform-kunststoffe.de www.nordform-kunststoffe.de