
12 minute read
COMPOSITES
Rinde und Flachs
Alternative zu Glasfaser, Öl und Chemie
Advertisement
Die Fahrzeug- und Luftfahrtindustrie steht unter Druck, umweltfreundlicher zu werden. Deshalb gibt es unter anderem Bedarf für ökologische Kunststoffalternativen. Forschung und Industrie arbeiten derzeit an feuerfesten Leichtbauteilen, die aus Holzresten und Flachs bestehen. Bei vergleichbaren Kosten und Produktionsaufwand sollen sie mindestens 30 Prozent CO 2 -Emissionen einsparen.
Prof. Dr. Gion Andrea Barandun¹
Ein Hauptargument für den Einsatz von Faserverbundkunststoffen ist ihr exzellentes Verhältnis von Steifigkeit oder Festigkeit und Dichte. Damit lassen sich Strukturen realisieren, die hohe Beanspruchungen ertragen, aber trotzdem ein niedriges Gewicht aufweisen. Nicht selten ist auch die eingesparte Energie – dank des geringen Gewichts – ein Grund, auf Composites zu setzen. Wird diese Energieeinsparung nun durch ein CO 2 -Äquivalent oder Global Warming Potential (GWP) ausgedrückt, muss natürlich der gesamte Lebenszyklus der verwendeten Materialien mit einberechnet werden. Häufig wird dadurch die eigentlich sehr gute Bilanz während der Einsatzzeit getrübt – die Erzeugung und Verarbeitung der Materialien ist mit hohem Energieaufwand verbunden, und insbesondere die Matrixsysteme basieren fast ausschliesslich auf Petrochemie. Der Ersatz von konventionellen Matrixund Harzsystemen durch biobasierte Produkte lohnt sich deshalb aus Umweltsicht in jedem Fall – die Erwartung ist, dass das hier untersuchte neue Material bei der Produktion mindestens 30 Prozent weniger CO 2 -Emissionen verursacht, als die bisher üblichen Faserverbundwerkstoffe. Andererseits müssen diese neuartigen Systeme immer noch die gleichen Anforderungen wie die substituierten Werkstoffe erfüllen. Dies betrifft nicht nur mechanische oder andere Anforderungen ans Bauteil, sondern auch die Verarbeitung in möglichst verbreiteten und bekannten Prozessen.
1 Prof. Dr. Gion Andrea Barandun, Fachbereich Faserverbundtechnik / Leichtbau, IWK, HSR Rapperswil Bild 1: Die neuartigen biobasierten Composites sollen u.a. künftig auch im Schienenverkehr zum Einsatz kommen, wie hier im Interieur in einer Metro. Bild: Faserplast Composites
Auch die Entsorgung oder – falls umsetz bar – Aufbereitung und Weiterverwendung von Composite-Bauteilen an deren Lebensdauerende muss für eine gesamtheitliche Betrachtung mit einbezogen werden.
Ein überraschend einfaches Konzept Das Rezept für die biobasierten Bauteile aus faserverstärkten Kunststoffen ist überraschend simpel: Die Baumrinde, aus der das Tannin für das Harzsystem gewonnen wird, fällt in der Holzindustrie als Abfall an. Flachsfasern als Verstärkung bieten eine nachwachsende Alternative zu Glasfasern, mit sehr ähnlichen Steifigkeitseigenschaften bei niedrigerer Dichte. Zusammen mit Projektpartnern aus Indus trie und Forschung arbeitet das IWK Institut für Werkstofftechnik und Kunststoffverarbeitung daran, die beiden natürlichen Rohstoffe in hoch belastbare, feuerfeste Komponenten zu verwandeln. Das Projekt wird durch die Schweizerische Agentur für Innovationsförderung Innosuisse unterstützt – beteiligt sind die Berner Fachhochschule BFH (Institut für Werkstoffe und Holztechnologie IWH) sowie die Unternehmen Gremolith, Bcomp, Faserplast Composites, Swiss CMT AG und Zeochem. Interessant sind in diesem Fall neben den ohnehin angestrebten guten mechanischen Eigenschaften vor allem die Möglichkeiten im Hinblick auf den Brandschutz. Wo heute unter anderem phenolbasierte Systeme zum Einsatz kommen, sollen die neuartigen Composites in Zukunft eine echte biobasierte Alternative dazu bieten. Dies eröffnet Anwendungen beispielsweise in der Schienenindustrie (Bild 1), wo sehr strenge Vorschriften bezüglich der Materialeigenschaften im Brandfall herrschen, gleichzeitig aber auch leichte Strukturbauteile gesucht sind.
Erfolgreiche Vorversuche Das Know-how zur Herstellung, Aufbereitung und Verarbeitung des neuen Harzsystems wurde schrittweise erarbeitet. Aus einer Zusammenarbeit zwischen IWH und IWK im Rahmen mehrere Studienarbeiten
Bild 2: Prozessversuch Bild: IWK

an beiden Standorten entstanden Materialrezepturen, Verarbeitungsrichtlinien und Erkenntnisse zu den Eigenschaften der hergestellten Verbundmaterialien (Bild 2). Diese Resultate weckten das Interesse der Industrie, sodass schliesslich ein breit abgestütztes Innosuisse-Forschungsprojekt gestartet werden konnte. Die nun durchgeführten ersten Versuche mit den neuen Materialien sind vielversprechend, aktuell erprobt das Team des IWK verschiedene Rezepturen und Produktionsprozesse. Bisher sind das lediglich kleine Test-Platten (Bild 3) für mechanische und andere Belastungstests. Zu einem späteren Zeitpunkt erfolgt dann die Umsetzung erster Realbauteile im Rahmen industrieüblicher Produktionsprozesse. Ziel ist es, ein möglichst serienfertiges FaserHarz-System anbieten zu können. Mittels verschiedener Bauteilprüfungen wird zudem während der Entwicklung darauf geachtet, dass ein gleichwertig produzierba
Bild 3: Test-Platten
res Ersatzprodukt mit potentiell besseren Eigenschaften entsteht.
Neue Materialien, unveränderte Produktionsverfahren Das Harzsystem ist der innovative Kern des Projektes. Statt herkömmlichen, erdölbasierten Harzen wird Tannin (aus Holzrinde) zusammen mit speziellen Alkoholen auf pflanzlicher Basis kombiniert. Im Verbund mit den Flachsfasern entsteht so ein fast vollständig aus nachwachsenden Rohstoffen bestehender, faserverstärkter Kunststoff. Zum Vergleich: Aktuelle biobasierte Alternativen kommen – immer noch selten - auf maximal ca. 50 Prozent Anteil an nachwachsenden Rohstoffen. Die Bauteile können in unterschiedlichen, industriell verbreiteten Verfahren wie Infusion, Injektion oder – für kleine Serien – Handlaminieren hergestellt werden. Die entsprechenden Verarbeitungsparameter
ARGO - IHRE STARKE GESCHÄFTSPARTNERIN • Tampondruck • Heissprägedruck • Ultraschallschweissen • Montagen • Laserbeschriftungen • Spanabhebende Bearbeitung Wir arbeiten unkompliziert, liefern termingerecht in hoher Qualität und genau so, wie es für Sie Sinn macht. Schildern Sie uns Ihre Bedürfnisse. Wir bieten Ihnen Lösungen. Tel. 081 257 15 57 | info@argo-gr.ch | www.argo.industries

wurden teilweise schon in Vorversuchen ermittelt und gestatten einen robusten und reproduzierbaren Herstellungsprozess. Damit das Produkt für die Zulieferer der Fahrzeug- und Luftfahrtindustrie eine echte Alternative wird, soll das Faser-HarzSystem zudem ohne Änderungen am Maschinenpark oder an Prozessen verarbeitet werden können. Im Hinblick auf eine spätere Serienfertigung stellt dies eine zentrale Forderung der Industrie dar. Das Projekt wurde im Sommer 2019 gestartet, die gemeinsamen Forschungs- und Entwicklungsarbeiten sollen im Sommer 2022 abgeschlossen sein.
Kontakt IWK Institut für Werkstofftechnik und Kunststoffverarbeitung Oberseestrasse 10 CH-8640 Rapperswil +41 55 222 47 70 iwk@hsr.ch, www.hsr.ch
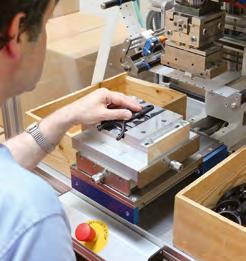
CFK-Bauteile wirtschaftlicher bearbeiten
Intelligente Nachbearbeitung und Versiegelung
Gemeinsam mit der Industrie haben Forscher vom Fraunhofer-Institut für Produktionstechnik und Automatisierung IPA eine Bearbeitungsmaschine entwickelt, die kohlenstofffaserverstärkte Kunststoffe (CFK) nicht nur hochpräzise fräst, sondern auch die gesamte Nachbearbeitung übernimmt. CFK-Werkstücke lassen sich damit um bis zu 50 Prozent wirtschaftlicher bearbeiten.
Hannes Weik¹
Ob Lastwagen, Busse, Autos, Fahrräder oder Roller: Sie alle werden in Zukunft mit Elektroantrieb unterwegs sein. Dabei gilt: Je leichter das Fahrzeug, desto länger reicht der Akku. Als Werkstoff für die Karosserie bieten sich deshalb kohlenstofffaserverstärkte Kunststoffe (CFK) an. Sie sind ähnlich stabil wie Stahl, aber rund achtmal leichter. Sogar Aluminium ist dreimal schwerer als CFK. Allerdings sind die Herstellungs- und Bearbeitungskosten von CFK-Bauteilen noch immer hoch. Vieles wird bis heute von Hand erledigt: Werker nehmen frisch gefräste Bauteile aus der Maschine, beseitigen überstehende Fasern und reinigen sie für die nachfolgende Versiegelung der Kanten. «Das ist nicht prozesssicher, weil Werker ein und dieselbe Kante subjektiv unterschiedlich bewerten», bemängelt Philipp Esch von der Abteilung Leichtbautechnologien am Fraunhofer IPA. Hinzu kommt: Die feinen CFK-Stäube, die beim Fräsen anfallen, sind gesundheitsschädigend und wirken abrasiv. Sie erhöhen also den Verschleiss bestimmter Maschinenkomponenten, wenn sie sich darauf absetzen.
Herstellung um bis zu 50 Prozent wirtschaftlicher Die Herstellung von CFK-Werkstücken wäre um 50 Prozent wirtschaftlicher, gäbe es eine Maschine, die die Leichtbauteile nicht nur bearbeitet, sondern auch automatisiert abmisst und versiegelt. Eine solche haben nun Esch und andere Forscher vom Fraunhofer IPA, die Firma Homag
¹ Hannes Weik, Presse- und Öffentlichkeitsarbeit, Fraunhofer IPA Führt ein Werker der Maschine ein endkonturnah hergestelltes CFK-Bauteil zu, fräst sie es zunächst hochpräzise. Bild: Fraunhofer IPA/Rainer Bez

Holzbearbeitungssysteme GmbH sowie weitere Partner aus der Industrie gemeinsam entwickelt. Die Bearbeitungsmaschine steht als betriebsbereiter Demonstrator in einer Halle auf dem Gelände des Fraunhofer IPA. Führt ein Werker der Maschine ein endkonturnah hergestelltes CFK-Bauteil zu, fräst sie es zunächst hochpräzise und verleiht ihm so die gewünschte Form. Eine Abrasivbürste entfernt danach alle überstehenden Fasern. Düsen blasen die feinen CFK-Stäube in eine Absauganlage. Diese filtert den Staub heraus, ehe sie die Luft an die Umgebung abgibt. Vorzeitiger Verschleiss an der Maschine wird so unterbunden. Per Streifenlichtprojektion tastet ein Sensor das CFK-Werkstück ab. So entsteht eine Punktwolke, in der spezielle Algorithmen eventuelle Abweichungen von der Idealkontur erkennen. Bewegen sich die Abweichungen innerhalb der Toleranz, versiegelt die Bearbeitungsmaschine die Kanten mit einem Flüssiglack. Dieser wird anschliessend mit ultraviolettem Licht bestrahlt und härtet umgehend aus – das Bauteil ist fertig.
Modulares Maschinenkonzept «Wir haben ein modulares, vollintegriertes Maschinenkonzept entwickelt», sagt Esch. Die einzelnen Prozessschritte können also in beliebiger Reihenfolge ablaufen, lassen sich mit anderen kombinieren und auf andere Bauteilgeometrien anpassen. Noch nicht einmal beim Werkstoff ist unsere Maschine CFKComplete festgelegt: «Sie könnte genauso gut Holz, Aluminium oder Metallkomponenten fräsen, nachbearbeiten und lackieren», so Esch weiter.
Kontakt Fraunhofer-Institut für Produktionstechnik und Automatisierung IPA Nobelstrasse 12, D-70569 Stuttgart +49 711 970-1557 philipp.esch@ipa.fraunhofer.de www.ipa.fraunhofer.de n
Brennstoffzellen-Elektrofahrzeuge
Hochdruck mit Leichtigkeit
Mit Wasserstoff angetriebene Brennstoffzellen-Elektrofahrzeuge (FCEV) sind batteriebetriebenen Autos in mehrfacher Hinsicht überlegen. In nur wenigen Minuten aufgetankt, haben sie eine grössere Reichweite und bieten dennoch alle Leistungsvorteile des Elektromotors. Aber die Technologie ist noch jung und muss einige Herausforderungen meistern.
Aus Sicht der Composite-Industrie sticht insbesondere die signifikante Menge an Fasermaterial hervor, die zur Herstellung der Wasserstofftanks benötigt wird. Die Ingenieure von Cevotec stellten sich dieser Herausforderung und entwickelten eine Lösung, die bei der Herstellung von Drucktanks auf Composite-Basis 20% Zeit, Material und Kosten spart. «Die Automobilindustrie hat Milliarden in die Entwicklung der Brennstoffzellen-Technologie investiert, aber derzeit sind nur sehr wenige solcher Fahrzeuge auf unseren Strassen unterwegs. Eines der Probleme ist die effiziente und sichere Speicherung von Wasserstoff im Fahrzeug», sagt Thorsten Groene, CEO des Münchener Fiber Patch Placement (FPP) Spezialisten Cevotec. «In den Tanks herrscht ein Arbeitsdruck von bis zu 700 bar, was ca. 10 kg Kohlefaser für 1 kg Wasserstoffspeicherung bedeutet – das ist sehr viel.» Dementsprechend sind Hersteller stark daran interessiert, weniger der teuren Fasern zu verarbeiten, um Gewicht und Kosten der Tanks zu reduzieren. «Endlosfasern um einen Kern zu wickeln, ist die beste Methode zur Produktion des zylindrischen Teils», sagt Dr. Neven Majic, Executive Vice President von Cevotec. «Aber eine solche direkte Filamentablage an den Kuppeln bedeutet redundantes Material auf dem zylindrischen Teil – welches das Gewicht und die Kosten des Endprodukts stark erhöht.» Cevotecs Lösung besteht darin, ma
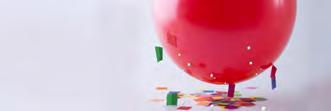
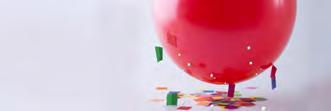

Drucktank auf Composite-Basis
terialgleiche Kohlefaser-Patches vor dem Wickelprozess in den Kuppelbereichen einzubringen. «Die Patches sind so konzipiert, dass sie genau die Bereiche abdecken, die Probleme beim Wickeln verursachen», erklärt Majic. In einem ersten Prozessschritt werden Kuppeln des Tankkerns mit Patches verstärkt, die so verstärkten Tankkerne werden dann dem verkürzten Wickelprozess zugeführt, der weniger Material und Produktionszeit für die Belegung der Kuppelbereiche benötigt. «Die Investition in die Patch-Technologie zahlt sich vom ersten Produktionstag an aus», berichtet Gröne. Eine einzige FPP Anlage kann Drucktanks für mehrere Wickelanlagen mit Patch-Verstärkungen versehen. Hersteller können so mindestens 20% Einsparungen an Material und Zykluszeit erreichen. «Wenn Wickel- und Patch-Technologie in der Serienproduktion kombiniert werden, amortisiert sich die FPP Investition bereits im ersten Jahr. Es
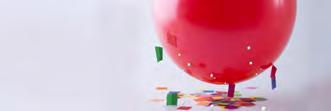
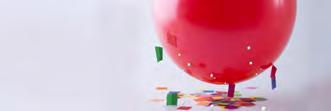


ist eine ziemlich einfache Rechnung, die wir unseren interessierten Kunden präsentieren können.» Durch die konsequente Anwendung der Fiber Patch Placement Technologie auf heutige Herausforderungen in der Herstellung von Composite-Bauteilen unterstützt Cevotec die Entwicklung von Verbundwerkstoffen für eine grüne Mobilitätsrevolution. Hersteller, die von manueller Produktion auf Fiber Patch Placement wechseln, profitieren gemäss eigenen Angaben von Materialeffizienz und Kosteneinsparungen von 20% bis 60%.
Kontakt Cevotec GmbH Daniela Klotz Willy-Messerschmitt-Strasse 1 D-82024 Taufkirchen b. München +49 89 2314 165-0 info@cevotec.com www.cevotec.com
HAUG BIEL AG
Johann-Renfer-Str. 60 Postfach CH-2500 Biel/Bienne 6 Tel.: +41 (0) 32 344 96 96 Fax: +41 (0) 32 344 96 97 info@haug.swiss www.haug.swiss
Revolution für den Leichtbau
Nägeli Swiss AG zeigte auf der Swiss Plastics Expo in Luzern einen Unterlegkeil aus Faserverbund für Flugzeuge bis 350 Tonnen. Der Chock Max von Alphachocks ist sehr leicht, absolut robust und lässt sich unter dem Rad zusammenklappen, bevor er mit wenig Kraftaufwand entfernt werden kann. Nägeli fertigt das patentierte Serienprodukt im neuen aCC-Verfahren. Dabei können Faserchips zu komplexen 3D-Formteilen mit nahezu jeder gewünschten Geometrie gepresst werden und dies auch in Serienstückzahlen.
«Mit dem neuen automated-CompositeCompression-Verfahren (aCC) können wir Faserchips in einem Werkzeug unter Druck und Temperatur automatisiert zu komplexen 3D-Formteilen pressen», berichtet Dominik Nägeli, jüngstes Familienmitglied in der Geschäftsleitung der Nägeli Swiss AG und verantwortlich für den Bereich Faser verbund. «Vor allem für den Leichtbau eröffnen sich dadurch bisher ungeahnte Möglichkeiten», ergänzt Christoph Nägeli, Geschäftsführer und Vater von Dominik. Auf der Swiss Plastics Expo zeigte das Schweizer Unternehmen den neu entwickelten Chock Max, einen faltbaren Unterlegkeil aus Polyamid-Faserchips für Flugzeuge. Hergestellt wird dieser mittels des neu entwickelten innovativen aCC-Verfahrens, das Nägeli gemeinsam mit Partnern entwickelt hat. Anlässlich der Swiss Plastics Expo wurde der Chock Max mit dem Swiss Plastics Award in der Kategorie Publikumsliebling ausgezeichnet (siehe auch S. 40/41).
Drei wesentliche Vorteile durch 3D-Faserverbund Der Chock Max aus PA6 mit Kohlefaserverstärkung hält Flugzeuge bis 350 Tonnen Startgewicht und Raddurchmesser bis 1050 mm sicher in Parkposition. Gegenüber herkömmlichen Chocks aus Metall oder Hartgummi weist der Chock Max drei wesentliche Vorteile auf. Mit nur 3,5 kg ist er erstens um vieles leichter als herkömmliche Unterlegkeile. Zweitens ist er nahezu unzerstörbar durch 3D-Formteile aus Carbon. Und drittens ist er faltbar. Durch das Zusammenklappen lässt sich der Chock Max mit wenig Kraftaufwand jederzeit unter dem Rad entfernen. Verspätungen im
Der faltbare Chock Max aus einem PA6/Carbon-Faserverbund für Flugzeuge bis 350 Tonnen. Bild: Nägeli
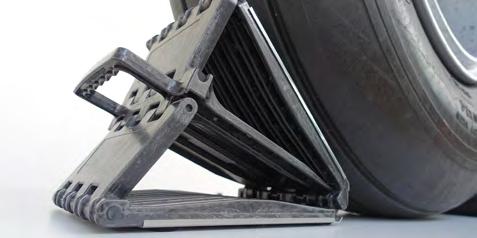
Flugverkehr durch verklemmte Chocks werden so vermieden.
Strukturbauteile automatisiert herstellen Nägeli fertigt die Chocks für die Schweizer Aerogenius AG, die das Produktpatent innehat. Mindestens genauso revolutionär wie das Produkt ist das innovative Verfahren, das Nägeli gemeinsam mit Partnern entwickelt hat. Die PA6/CF-Faserchips sind eine Kombination aus thermoplastischer Matrix und Verstärkungsfasern. Sie werden in definierter Länge in einem Formwerkzeug unter Druck und Temperatur zu komplexen 3D-Formteilen gepresst. Darüber hinaus können beispielsweise auch Gewindeabformungen, passgenaue Präzisionsbohrungen oder integrierte Verbindungelemente genauso wie unterschiedliche Wandstärken gefertigt werden. Das war bisher mit Faserverbundwerkstoffen kaum möglich. Durch die automatisierte, prozesssichere Fertigung mit hoher Wiederholgenauigkeit sind Serienstückzahlen bis 100000 Bauteile pro Jahr realisierbar. Das macht das aCC-Verfahren als alternatives Fertigungsverfahren für viele Leichtbauteile, vor allem auch für bewegte Teile, hochinteressant. «Konstrukteure und Maschinenbauer verfolgen unsere Arbeit sehr aufmerksam», berichtet Christoph Nägeli abschliessend.
Mit Carbon in die dritte Dimension Der aCC-Prozess eröffnet für Carbonteile völlig neue Denkweisen in der dritten Dimension. Dabei – und das ist das Neuartige – sind der Komplexität der Bauteilgeometrie nahezu keine Grenzen gesetzt. Kontakt Nägeli Swiss AG Seestrasse 4 CH-8594 Güttingen +41 71 694 50 10 mail@naegeli.ch www.naegeli.ch