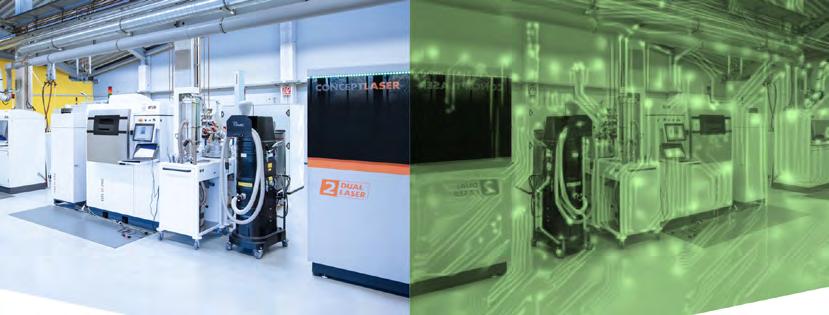
9 minute read
ADDITIVE FERTIGUNG
Das Virtual Lab macht den gesamten AM-Prozess transparent und spiegelt ihn digital.
Fraunhofer-Leitprojekt futureAM
Advertisement
3D-Druck mit Metallpulver vor dem Durchbruch
Mindestens um den Faktor 10 will ein Zusammenschluss von sechs Fraunhofer-Instituten im Fraunhofer-Leitprojekt «futureAM – Next Generation Additive Manufacturing» den 3D-Druck mit Metallpulver beschleunigen. Dass es sich nicht um Zukunftsmusik handelt, beweisen erste handfeste Ergebnisse, die das futureAM-Team auf der formnext im November 2019 in Frankfurt am Main vorstellte.
Petra Nolis¹
Eine wichtige Rolle im Fraunhofer-Leitpro jekt futureAM spielt das Virtual Lab, das in enger Zusammenarbeit der beteiligten Institute entsteht. Das Virtual Lab soll künftig über ein Netzwerk und eine Datenbank alle Bereiche und Institute in Sachen metallisches Additive Manufacturing (Metall AM) digital miteinander verknüpfen. Fritz Lange von der Fraunhofer-Einrichtung für Additive Produktionstechnologien IAPT in Hamburg, bei der die Fäden des virtuellen Labors zusammenlaufen, sagt dazu: «Die Institute werden über das Virtual Lab die verteilte Fertigung abwickeln und nachvollziehen.» Geplant ist dazu die geschlossene digitale Abbildung der Kompetenzen und Ausstattung aller beteiligten Institute.
Am digitalen Zwilling Prozesse optimieren Das Virtual Lab macht den gesamten AMProzess transparent und spiegelt ihn digi
tal: Digital Twins ermöglichen den Projektteilnehmern, Prozesse zu modellieren und zu simulieren, um so reale Systeme in allen Bereichen zu optimieren. Das Virtual Lab ist funktionsbereit und wird bereits mit sogenannten Dummy-Daten evaluiert. Aktuell verbinden sich die beteiligten Institute über ihre Datenbank mit dem Virtual Lab, damit es in Kürze seinen virtuellen Betrieb aufnehmen kann. Dazu zählt zum Beispiel das FraunhoferInstitut für Werkstoff- und Strahltechnik IWS aus Dresden, das den Part der Werkstoffe betreut. Im Mittelpunkt stehen die Erweiterung des einsetzbaren Spektrums von additiv verarbeitungsfähigen Werkstoffen und ausserdem die Multimaterial-Bauweise. Hier entsteht massgeschneidert mithilfe des Laserauftragschweissens (LMD) ein Bauteil aus verschiedenen Werkstoffen ohne nachgelagerte Fügeprozesse. «Das Verfahren beschleunigt die Materialentwicklungen enorm», sagt IWSWissenschaftler Michael Müller. «Wir erforschen im Verbundprojekt, welche Materialien sich miteinander kombinieren lassen und welche Probleme dabei auftreten.» Aktuell untersuchen die Dresdener Wis senschaftler, wie sich beispielsweise aus verschiedenen Superlegierungen ein Multimaterial-Bauteil herstellen lässt. Besonders wichtig ist beim Fügen von zwei Werkstoffen die Analyse der Übergangszone zwischen den Materialien. Den Materialübergang der Legierung Inconel 718 zu Merl 72 haben die Forscher mittlerweile optimiert, um Herausforderungen wie Rissbildung oder Versprödung zu minimieren.

Werkstoffexperten des Fraunhofer IWS entwickeln Multimaterial-Bauteile, an denen sie den Materialübergang analysieren. Die Farben zeigen den Übergang: Gelb: Kobalt, blau: Nickel, orange: Aluminium. Bild: Fraunhofer IWS
«futureAM – Next Generation Additive Manufacturing» Im November 2017 startete das Fraunhofer-Leitprojekt futureAM mit dem Ziel, die Additive Fertigung von Metallbauteilen mindestens um den Faktor 10 zu beschleunigen. Im Mittelpunkt der Aktivitäten steht zum einen die ganzheitliche Sicht auf die digitale und physische Wertschöpfung vom Auftragseingang bis zum fertigen metallischen 3D-Druck-Bauteil, zum anderen der Sprung in eine neue Technologie-Generation der Additiven Fertigung. An diesem Projekt beteiligen sich die folgenden FraunhoferInstitute:
–Fraunhofer-Institut für Lasertechnik ILT, Aachen (Projekt-Koordination) –Fraunhofer-Einrichtung für Additive Produktionstechnologien IAPT, Hamburg –Fraunhofer-Institut für Fertigungs technik und Angewandte Materialforschung IFAM, Bremen –Fraunhofer-Institut für Graphische Datenverarbeitung IGD, Darmstadt –Fraunhofer-Institut für Werkstoffund Strahltechnik IWS, Dresden –Fraunhofer-Institut für Werkzeug maschinen und Umformtechnik IWU, Chemnitz
Für den Sprung in eine neue Techno logie-Generation des AM definierten die Projektpartner die vier Handlungsfelder Industrie 4.0 und digitale Prozesskette, Skalierbare und robuste AM-Prozesse, Werkstoffe sowie Sys temtechnik und Automatisierung.
Neue skalierbare Metall AM-Prozesse und -Anlagen sind das Thema des FraunhoferInstituts für Lasertechnik ILT: Den Aachener gelang beim Extremen Hochgeschwindigkeits-Laserauftragschweissen (EHLA) der Schritt von der Beschichtung zur echten Additiven Fertigung. Gemeinsam mit Industriepartnern entstand eine 3D-EHLAAnlage, bei welcher die Bauplattform extrem schnell parallelkinematisch von drei Linearantrieben mit stillstehendem LaserBearbeitungskopf bewegt wird.
Beim Extremen Hochgeschwinigkeits-Laserauftragschweissen EHLA gelang mit einer neuen Anlage der Schritt von der Beschichtung zur echten additiven, dreidimensionalen Fertigung. Bild: Fraunhofer ILT

Für das Laser Powder Bed Fusion (LPBF) wurde ein neues, kompaktes Optiksystem entwickelt. Es kommt zum Einsatz im ersten Prototyp, der dank seines Bauraums (1000mm × 800mm × 500mm) auch grosse Metallbauteile bis zu zehnmal schneller als übliche LPBF-Anlagen additiv herstellen kann. Ein weiteres Highlight ist ein Software-Modell zum Steuern des Energieeintrags beim Umschmelzen des pulverförmigen Werkstoffs. Christian Tenbrock, wissenschaftlicher Mitarbeiter am Fraunhofer ILT und futureAM-Projektkoordinator: «Die Prozessparameter können dabei für jede einzelne Schmelzspur individuell eingestellt werden, um sowohl die Bauteilqualität als auch die Baugeschwin digkeit zu steigern.»
Automatisierte Nachbearbeitung senkt die Prozesskosten Besonders hoch ist beim Metall AM der Aufwand für die meist manuelle Nachbearbeitung, denn sie macht bis zu 70 Prozent der gesamten Prozesskosten aus. Dr. Ines Dani vom Fraunhofer-Institut für Werkzeugmaschinen und Umformtechnik IWU in Chemnitz: «Nachgelagerte Bearbeitungsschritte wurden unter anderem aufgrund der unterschiedlichen Geometrien bisher nicht automatisiert. Dies soll sich nun ändern.» Für die einzelnen Prozesse entwickelt das Fraunhofer IWU verschiedene autonom arbeitende TechnologieModule. Ein Roboter übernimmt das Werkstück-Handling und die spanende Nachbearbeitung. Die anspruchsvollen Ziele der FraunhoferPartner haben bislang zu einer Reihe von Innovationen geführt, von denen einige auf der formnext 2019 präsentiert wurden. Ausgestellt wurde unter anderem ein bionischer Hebel als Beispiel eines grossen additiv gefertigten Bauteils, hergestellt mit einer speziell ausgelegten LPBF-Maschine. Eine Multimaterial-Turbinenschaufel und eine Raketendüse mit Drallinjektoren sind weitere Innovationen aus Branchen, die von AM erobert werden. Gezeigt wurden ausserdem eine Software-Demo des Virtual Labs und das Modell einer Anlage zur Automatisierung der bisher händischen und daher zeitaufwändigen Nachbearbeitung.
Kontakt Fraunhofer-Institut für Lasertechnik ILT Christian Tenbrock M.Sc. Steinbachstrasse 15 D-52074 Aachen +49 241 8906-8350 christian.tenbrock@ilt.fraunhofer.de www.futuream.fraunhofer.de n
3D-Drucker Digital Anatomy
OP-Vorbereitung an realitätsgetreuen Organen
Stratasys verstärkt sein Engagement im medizinischen Bereich mit dem neuen 3D-Drucker J750 Digital Anatomy. Das System wurde entwickelt, um die Haptik, die Empfindlichkeit und die biomechanischen Eigenschaften der menschlichen Anatomie in medizinischen Modellen zu reproduzieren. Gleichzeitig werden OP-Vorbereitungen sowie die Ausbildung von Medizinern optimiert und neue medizintechnische Geräte schneller auf den Markt gebracht.
Mediziner können heute zwischen Leichen, Tieren, traditionellen Modellen oder VR-Modellen wählen, die allerdings alle erhebliche Einschränkungen aufweisen. Tiermodelle geben nur einen ungefähren Eindruck von der menschlichen Anatomie und können ethische Bedenken aufrufen. Leichen bieten kein lebendiges Gewebe und erfordern eine kontrollierte Umgebung. Der 3D-Drucker Digital Anatomy hingegen bildet die Reaktion von echtem Gewebe nach – und kann überall ohne spezielle Vorkehrungen genutzt werden. Darüber hinaus können sich die Anwender auf bestimmte Pathologien konzentrieren. «Wir denken, dass die Gesundheitsversorgung mithilfe von 3D-Druck verbessert werden kann. Hier bietet der 3D-Drucker Digital Anatomy einen grossen Fortschritt», sagt Eyal Miller, Healthcare Business Unit Head bei Stratasys. «Wir bieten Chirurgen die Möglichkeit einer Ausbildung in realis tischerer Umgebung ohne Risiken. Zudem erwarten wir, dass die Hersteller medizintechnischer Geräte die Markteinführung ihrer Produkte verbessern können, indem sie mit diesen neuen Modellen Designve rifikationen und -validierungen, Prüfungen der Gebrauchstauglichkeit und Fehleranalysen durchführen.» Mehrere Einrichtungen haben den neuen 3D-Drucker bereits getestet. Das Jacobs Institute, ein medizinisches Innovations zentrum mit Sitz in Buffalo, N.Y., das sich auf die Beschleunigung der Geräteentwicklung in der Gefässmedizin konzentriert, hat den 3D-Drucker getestet, um wichtige Gefässkomponenten für fortgeschrittene Tests und Schulungen neu zu erstellen. «3D-Druck war im Vergleich zu Leichen- oder Tiermodellen grossartig für die patientenspezifische anatomische
3D-gedrucktes Modell eines Herzens, hergestellt mit dem neuen 3D-Drucker J750 Digital Anatomy, der die Haptik, die Empfindlichkeit und die biomechanischen Eigenschaften der menschlichen Anatomie reproduzieren kann. Bild: Stratasys

Nachbildung. Der entscheidende Schritt auf dem Weg zu realitätsgetreuen Organmodellen war jedoch die Haptik sowie die realistischen biomechanischen Eigenschaften wie bei echtem Gewebe», sagt Dr. Adnan Siddiqui, Chief Medical Officer am Jacobs Institute. «Diese Modelle bieten uns unserer Ansicht nach die beste Möglichkeit, physiologische Bedingungen des Menschen auf struktureller Basis nachzubilden, um reale klinische Situationen zu simulieren und neue Hilfsmittel auf Wirksamkeit zu untersuchen, bevor sie am Patienten angewendet werden.» In Verbindung mit dem 3D-Drucker stellt Stratasys auch drei neue Materialien – TissueMatrix, GelMatrix und BoneMatrix – für 3D-Druckanwendungen in den Bereichen Kardiologie, Gefässmedizin und Orthopädie vor. Darüber hinaus kommt ein Reinigungsgerät für Blutgefässe auf den Markt, das Stützmaterial aus 3D-gedruckten Blutgefässen entfernt. Der neue 3D-Drucker von Stratasys wird voraussichtlich in erster Linie von Herstellern medizintechnischer Geräte genutzt werden, die nach neuen Möglichkeiten suchen, um Technologien und Verfahren schneller einzuführen. Zudem ist die Nutzung auch in akademischen medizinischen Einrichtungen, die unter zunehmendem Druck stehen und Schulungen ausserhalb des Operationssaals durchführen müssen, um das Risiko für Patienten zu minimieren, hilfreich. Die Lösung unterstützt auch die Bemühungen, vom zeitbasierten chirurgischen Training zur leistungsbasierten Auswertung überzugehen.
Kontakt Stratasys-Vertretung in der Schweiz: Alphacam Suisse GmbH Bahnhofstrasse 5 CH-9443 Widnau +41 71 775 82 40 info@alphacam.ch, www.alphacam.ch
Wirtschaftliche Lösung für Additive Fertigung
Stützstrukturen vollautomatisch entfernen
Dem Sondermaschinenbauer MartinMechanic ist es zusammen mit dem Institut IPMT der Technischen Universität Hamburg gelungen, in einem Pilotprojekt eine wirtschaftliche Lösung für das additive Fertigen von Bauteilen mit Stützstrukturen zu realisieren. Mit hochmoderner Robotertechnologie soll es erstmals möglich sein, einen im 3D-Druck produzierten Baukörper vollautomatisch von seinen Stützstrukturen zu trennen. Das Projekt wird vom Bundesministerium für Wirtschaft und Energie gefördert.
Die Branche der Additiven Fertigung verbucht aktuell Wachstumsraten mit bis zu 30 Prozent pro Jahr. Schicht für Schicht entstehen aus metallischen Pulvern Baukörper. Diese erhalten, um die geforderte Mass- und Formgenauigkeit zu erreichen, Stützen, die nach dem Produktionsvorgang bislang manuell vom Baukörper getrennt werden. Doch was bei Unikaten und Prototypen machbar ist, lässt sich kaum auf die Serienfertigung übertragen. Vor allem dann nicht, wenn es sich um komplexe Baugruppen in grosser Stückzahl handelt. Die werden immer häufiger von der Auto mobilindustrie sowie der Luft- und Raumfahrttechnik abgerufen. Bislang gibt es weltweit keine prozesssichere und wirtschaftliche Lösung, mit der man derartige Strukturen vollautomatisch entfernen kann. Deshalb lautet die Anforderung an MartinMechanic, eine Anlage zu bauen, deren Roboter mit entsprechenden Werkzeugen und hoher Bewegungsfreiheit an den richtigen Stellen ansetzt. Erschwerend kommt hinzu, dass oft jedes AMRohteil ein Unikat ist. Also muss die Technologie in der Lage sein, sich der individuellen Rohteilgeometrie anzupas sen, die sich aufgrund freigesetzter Eigenspannungen sogar verändern kann. Das Förderprojekt läuft unter dem Arbeitstitel «FASE», was für «Flexible Automatisierte Stützstruktur Entfernung» steht. Gemeinsam mit dem Team um Professor Wolfgang Hintze vom Institut für Produktionsmanagement und -technik der Technischen Universität Hamburg (IPMT) werden die mechanischen Grundlagen und passenden Technologien erarbeitet. Die Nagolder Ingenieure setzen sie dann in die Praxis um. Weitere Partner wie Rolf Lenk Werkzeug- und Maschinenbau oder Loll
Die Stützstrukturen dieses additiv gefertigten Bauteils werden mit modernster Robotertechnologie auf einer Anlage von MartinMechanic entfernt. Bilder: Loll
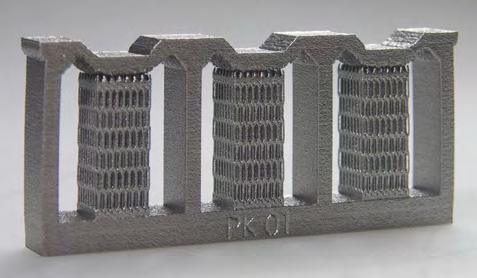
Feinmechanik liefern die Erprobungsteile. «Für uns ist dieses Pilotprojekt nicht nur eine grosse Herausforderung», sagt Claus Martin, geschäftsführender Gesellschafter von MartinMechanic. «Das Vertrauen in unsere Projekterfahrung erfüllt uns auch mit Stolz.» Einer der «Stolpersteine» ist in den Augen von Dr. Bernhard Bock, der das Pilotprojekt für MartinMechanic begleitet, die Frage der Technologie, die für das Trennen in Frage kommt. Ausserdem handle es sich häufig um komplizierte Bauformen, bei denen die Trennstellen nicht immer genau definiert seien. «Deshalb brauchen wir nicht nur eine Schnittstelle zum CAD-System, sondern auch eine entsprechende Sensorik, die den genauen Verlauf der Nahtstelle zwischen Stützstruktur und Bauteil erfasst.»

Kontakt MartinMechanic Friedrich Martin GmbH & Co. KG Heinrich-Hertz-Strasse 2 D-72202 Nagold +49 7452 8466-0 info@MartinMechanic.com www.MartinMechanic.com