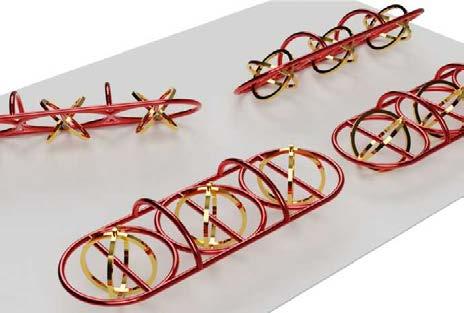
4 minute read
MEDIZINTECHNIK
Hightech Herstellungstechnik
Winzige Roboter aus Metall und Kunststoff
Advertisement
Forschende der ETH Zürich haben eine Methode entwickelt, mit der sie Mikrometer kleine Maschinen herstellen können, in denen mehrere Materialien auf komplexe Weise miteinander verwoben sind. Solche Mikroroboter sollen dereinst die Medizin revolutionieren.
Roboter, so winzig, dass sie sich durch unsere Blutgefässe bewegen und Medikamente im Körper an bestimmte Stellen bringen – dies ist ein Forschungsziel, das Wissenschaftler seit Jahren verfolgen. Forschenden der ETH Zürich ist es nun gelungen, erstmals solche «Mikromaschinen» zu bauen, die aus Metall und Kunststoff bestehen, und bei denen diese beiden Materialien so miteinander verknüpft sind, wie beispielsweise die Glieder einer Kette. Möglich ist dies dank einer von ihnen entwickelten neuen Herstellungstechnik. «Metalle und Polymere haben unterschiedliche Eigenschaften, und beide Materialien bieten Vorzüge beim Bau von Mikromaschinen. Um alle diese Eigenschaften gleichzeitig nutzen zu können, wollten wir die beiden Materialien kombinieren», erklärt Carlos Alcântara, ehemaliger Doktorand in der Gruppe von Salvador Pané am Institut für Robotik und Intelligente Systeme und einer der beiden Erstautoren der Arbeit. In der Regel werden Mikromaschinen von ausserhalb des Körpers mit Magnetfeldern angetrieben. Dazu müssen in die Mikromaschinen magnetische Metallteile eingebaut werden. Polymere wiederum haben den Vorteil, dass sich damit weiche und bewegliche Teile konstruieren lassen oder solche, die sich im Körperinnern auflösen. Werden Medikamente in solche auflösbaren Polymere eingebettet, lassen sich an bestimmten Körperstellen gezielt Wirkstoffe freisetzen.
Hightech-Herstellungsmethode
Die neue Herstellungsmethode basiert auf der Expertise von ETH-Professor Salvador Pané. Er arbeitet schon seit Jahren mit einer hochpräzisen 3D-Drucktechnik, mit der sich komplexe Gegenstände im Mikrometermassstab herstellen lassen: der 3D-
Computergrafik eines Mikrovehikels mit Eisenrädern (goldfarben) und einem Polymer-Chassis (rot). Das Vehikel ist 0,25 Millimeter lang.
Lithographie. Die ETH-Wissenschaftler haben mit dieser Technik für ihre Mikromaschinen eine Art Gussformen hergestellt. Letztere haben dünne Kanäle, die als Negativ dienen und mit dem entsprechenden Material gefüllt werden. Mittels elektrochemischer Abscheidung füllen die Ingenieure die einen Kanäle mit Metall, andere füllen sie mit Polymeren aus. Zum Schluss wird die Gussform mit Lösungsmitteln aufgelöst. «Wir konnten diese Methode entwickeln, weil in unserer interdisziplinären Gruppe Elektroingenieure, Maschineningenieure, Chemiker und Materialwissenschaftler eng zusammenarbeiten», sagt Fabian Landers. Er ist Doktorand in Panés Gruppe und ebenfalls Erstautor der Arbeit, die in der Fachzeitschrift Nature Communications veröffentlicht wurde.
Vehikel mit magnetischen Rädchen
Als Machbarkeitsnachweis von ineinander verwobenen Mikromaschinen stellten die ETH-Ingenieure verschiedene winzige Vehikel mit Kunststoff-Chassis und magnetischen Metallrädern her, die sich über ein rotierendes Magnetfeld antreiben lassen. Darunter sind solche, die sich auf einer Glasoberfläche fortbewegen lassen, und

Bilder: ETH Zürich Mikroskopiebilder weiterer Beispiele von Zwei-Komponenten-Mikromaschinen.
andere, die – je nach verwendetem Polymer – in Flüssigkeit oder an einer Flüssigkeitsoberfläche schwimmen können. Die Wissenschaftler werden ihre ZweiKomponenten-Mikromaschinen nun weiterentwickeln und mit weiteren Materialien experimentieren. Ausserdem werden sie versuchen, komplexere Formen und Maschinen herzustellen, auch solche, die sich zusammenfalten und auffalten können. Neben wirkstoffausschüttenden Fähren gehören zu künftigen Anwendungsmöglichkeiten Mikromaschinen, mit denen Aneurysmen (Blutgefässausbuchtungen) behandelt oder andere Operationen durchgeführt werden können. Ein weiteres Forschungsziel sind auffaltbare Stents (röhrenförmige Gefässstützen), welche mit Magnetfeldern an den gewünschten Ort gebracht im Körper werden können.
Kontakt ETH Zürich Fabio Bergamin Rämistrasse 101 CH-8092 Zürich +41 44 632 42 44 www.hk.ethz.ch
Simulationstechnologien in der Medizintechnik
Prothesen in Zukunft individuell berechnen
Circa 90 % der Prothesen werden in der Medizintechnik noch herkömmlich von Orthopädie-Technikern von Hand gefertigt. Über Simulationsberechnungen liessen sich Belastungen, Spannungen oder Druckstellen von Prothesen schon im Vorfeld erkennen.
Bei rund 10% moderner Prothesen kommen 3D-Drucker zum Einsatz. Die Konstruktion erfolgt dabei jedoch nicht anhand von Simulationstechnologien, sondern rein geometrisch anhand von gescannten Daten des Stumpfes. Wanddicken und Verrippungen werden nach Gefühl designt. Brechen Prothesen, wird aus der Erfahrung heraus verstärkt. Ein teurer Spass für die Krankenkassen, ganz zu schweigen für den Besitzer der Prothese, der auf die ordentliche Funktion angewiesen ist. Heutige Technologien können längst die Prothese für einen im MRT vermessenen Stumpf mit Knochen, Muskeln und Gewebe optimieren, bis der Kontaktdruck über mehrere Belastungsszenarien (Stehen, Gehen, Springen, Beugen, etc.) ein Minimum erreicht. Leider sind diese Fälle für die breite Anwendung in der Medizintechnik noch zu teuer. Über Näherungswerte über FEM-Verfahren jedoch können kritische Zonen bewertet und verstärkt werden. So werden Prothesen ingenieursmässig präziser ausgelegt. Dieser Prozess liesse sich nach Merkle & Partner sogar weitgehend automatisieren, gegebenenfalls auch über die Kombination mit KI-Verfahren. Allein die Kosteneinsparung durch die verlängerte Lebensdauer sollte bei grösseren Stückzahlen den erforderlichen Aufwand amortisieren. Das macht Simulationstechnologien so wertvoll – nicht nur für die Medizintechnik.
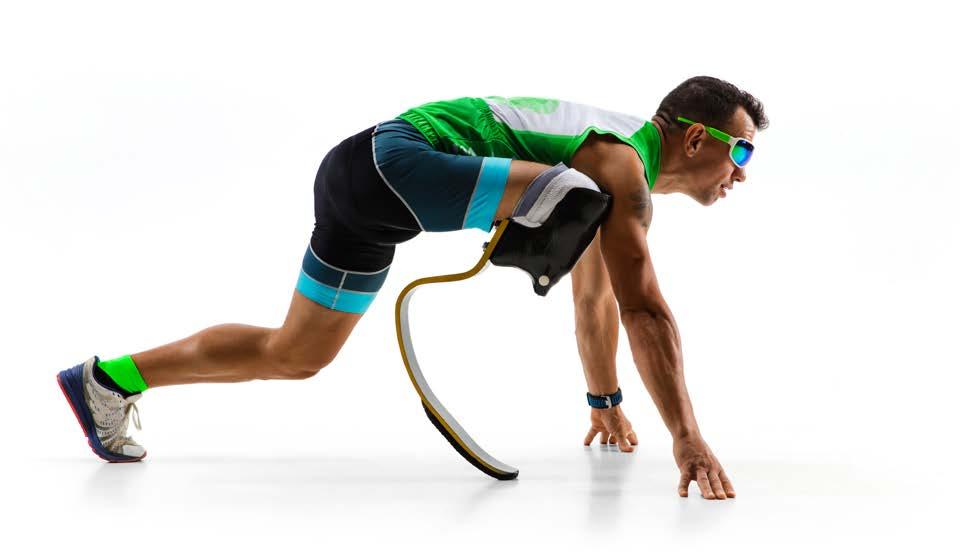
Moderne Hochleistungsprothesen leisten bereits Beachtliches.
«Mit einem unserer Forschungsprojekte, ROAD3D, beschäftigen wir uns mit den ertragbaren Spannungen von 3D-gedruckten Bauteilen. In einem weiteren Forschungsthema beschäftigen wir uns mit der Simulation des menschlichen Körpers oder von Teilen davon. Optimale Voraussetzungen also für das richtige Knowhow», so Dipl.-Ing. (TU) Stefan Merkle, Geschäftsführer der Merkle & Partner GbR. «Aktuell werden bereits Projekte im Bereich Medizintechnik umgesetzt. Ich bin überzeugt davon, dass wir hier in Zukunft vermehrt wertvolle Unterstützung leisten können.»
Kontakt Merkle & Partner GbR Ingenieurbüro für Simulation und Entwicklung Friedrichstrasse 1 D-89518 Heidenheim +49 7321 9343-0 kontakt@merkle-partner.de www.merkle-partner.de

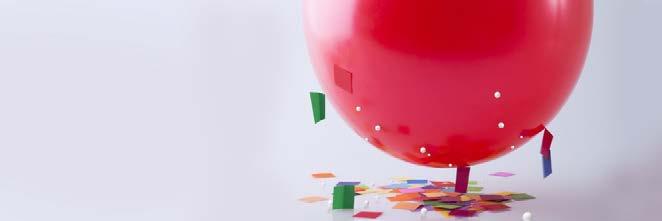
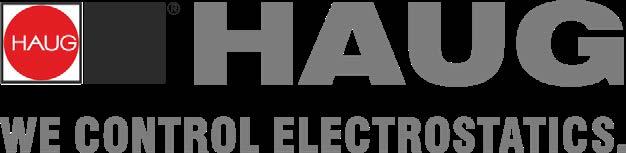
HAUG BIEL AG
Johann-Renfer-Str. 60
Postfach CH-2500 Biel/Bienne 6 Tel.: +41 (0) 32 344 96 96 Fax: +41 (0) 32 344 96 97 info@haug.swiss www.haug.swiss