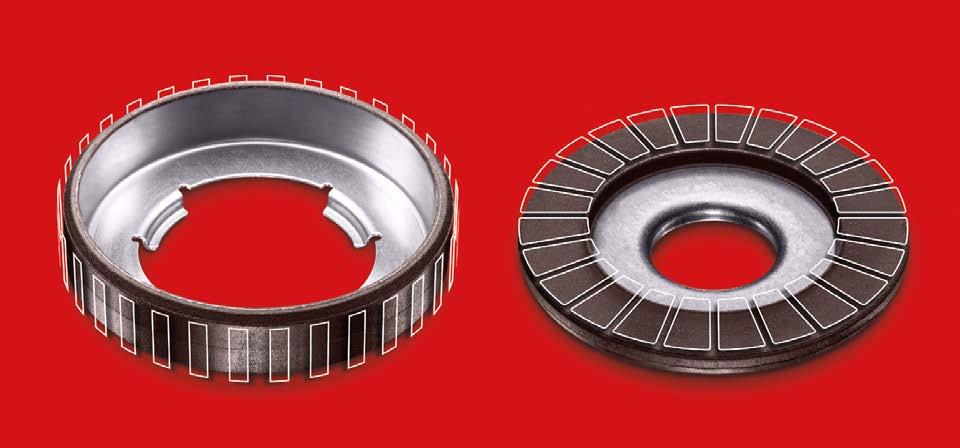
7 minute read
WERKSTOFFE
Elastomergebundene Magnete
Perfekt verbunden ohne Spannungen
Advertisement
Kunststoffgebundene Magnete, die im Spritzgussverfahren hergestellt und auf einen Träger aufgebracht werden, stossen bei verschiedenen Anwendungen an ihre Grenzen: Der Materialschwund beim Erstarren der Masse sowie unterschiedliche Ausdehnungskoeffizienten können innere Spannungen und sogar Risse verursachen. MS-Schramberg erweitert deshalb das Portfolio um elastomergebundene Magnete, die in solchen Fällen durch ihre hohe Elastizität deutliche Vorteile bieten.
Ob in Motorgetrieben und Nockenwellen in der Automobil- und Zulieferbranche, als Drehgeber in der Haustechnik und im Maschinenbau, in Polrädern und Kugellagern oder Pneumatik- und Hydraulikzylindern: Magnete übernehmen in zahlreichen industriellen Anwendungen wichtige Aufgaben. Sie helfen unter anderem dabei, Positionen, Geschwindigkeiten, Drehzahlen, Winkel und Lagen zu erkennen und zu erfassen. Oft kommen dafür kunststoffgebundene Magnete zum Einsatz, bei denen Magnetpulver in ein thermoplastisches Grundmaterial wie Polyamid (PA) oder Polyphenylensulfid (PPS) eingebracht wird. Dieses Compound wird anschliessend direkt auf den in der Regel metallischen Träger aufgespritzt. Dabei kann es jedoch in einigen Fällen zu Problemen kommen – denn der bei hohen Temperaturen aufgebrachte Kunststoff zieht sich beim Erkalten zusammen, und das führt zu einem Materialschwund. Dies ist wiederum die Ursache für innere Spannungen im Magneten und bedeutet, dass dieser nicht optimal am Träger haften bleibt. Auch unterschiedliche Ausdehnungskoeffizienten von Magnet- und Trägermaterial können die Verbindung und damit die Funktion der Baugruppe beeinträchtigen, insbesondere in Anwendungen mit grossen Temperaturschwankungen.
Hohe Elastizität und chemische Verbindung
Ein zusätzliches Verkleben des Magneten ist zwar eine naheliegende Lösung, bedeutet allerdings auch einen Mehraufwand und führt nicht immer zu einem optimalen Ergebnis.
Elastomergebundene Magnete bieten durch ihre hohe Elastizität deutliche Vorteile bei einer Vielzahl von Anwendungen.
Bei der Herstellung elastomergebundener Magnete wird ein Magnetpulver in ein synthetisches Elastomer wie etwa hydrierten oder nicht hydrierten Acrylnitril-ButadienKautschuk (HNBR, NBR) eingebracht.
Eine deutlich bessere Alternative sind in diesen Fällen elastomergebundene Magnete. Auch hier sorgt ein Magnetpulver für die gewünschte magnetische Wirkung. Dieses wird jedoch nicht in einen thermoplastischen Kunststoff, sondern in ein synthetisches Elastomer wie etwa hydrierten oder nicht hydrierten Acrylnitril-ButadienKautschuk (HNBR, NBR) eingebracht. Diese Materialien sind gegenüber thermoplastischem Kunststoff deutlich elastischer. Ausserdem geht das Elastomer beim Aufbringen auf das Trägermaterial mit diesem eine chemische Verbindung ein. Das ermöglicht einen besonders zuverlässigen und festen Halt ohne innere Spannungen im Magneten. Auch weisen Elastomere eine hohe Schlagzähigkeit auf und sind äusserst beständig gegenüber einer Vielzahl von Medien, etwa Schmierstoffen und Chemikalien. Die Temperaturbeständigkeit liegt je nach Material bei bis zu 180 Grad Celsius. Risse durch Aufweitung bei der Montage sind dank der hohen Elastizität so gut wie ausgeschlossen. Verschiedene Magnetisierungsarten möglich
Ein weiterer Vorteil elastomergebundener Magnete ist die hohe Homogenität des Grundmaterials. Dies erlaubt eine besonders genaue Magnetisierung – ideal für Anwendungen, in denen es auf Präzision ankommt. Anisotrope Magnete sind mit
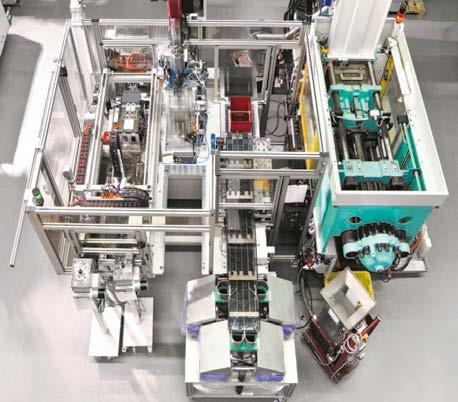
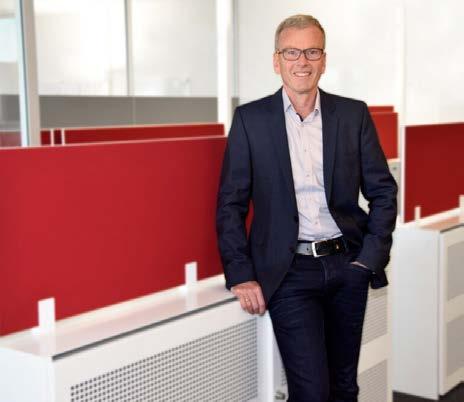
Heinz Schell, Key Account Manager bei MSSchramberg: «Anwender profitieren von unserem über Jahrzehnte angesammelten Know-how und unserer umfassenden Beratungskompetenz.» spiel, wenn Thermoplast-Magnete aufgrund des Schwunds nicht direkt in Hülsen gespritzt werden können oder wenn Ringmagnete aufgrund von Rissbildung nicht direkt auf das Trägermaterial aufgespritzt, sondern verklebt werden müssen. Auch wenn eine hohe Genauigkeit der Polteilung gefordert ist oder sich die Ausdehnungskoeffizienten von Trägermaterial und Magnet stark unterscheiden, sind Elastomere eine funktionale Lösung. In manchen Fällen können durch ihren Einsatz auch andere Trägermaterialien gewählt werden, die das Bauteil in der Herstellung günstiger machen. Damit bieten elastomergebundene Magnete in einer Vielzahl von Szenarien ein erhebliches Optimierungspotenzial.
Kontakt MS-Schramberg GmbH & Co. KG Max-Planck-Strasse 15 D-78713 Schramberg +49 7422 519-0 info@ms-schramberg.de www.ms-schramberg.de
einer typischen Remanenz von 230 Millitesla herstellbar. Die Magnetisierung erfolgt in der Regel vielpolig am Umfang oder sektorenförmig, weitere Magnetisierungsarten sind jedoch bei Bedarf ebenfalls möglich. Die minimale Polbreite liegt bei etwa einem Millimeter. Die MS-Schramberg GmbH & Co. KG, einer der europaweit führenden Hersteller von Permanentmagneten und Baugruppen, hat deshalb elastomergebundene Magnete in ihr Produktportfolio aufgenommen. Das Unternehmen entwickelt und realisiert kundenspezifische Artikel für Anwendungen in verschiedenen Branchen – etwa Automotive, Heizung und Klima, Elektro- und Automatisierungstechnik sowie im Maschinenbau. «Wir unterstützen unsere Kunden bei der mechanischen und magnetischen Auslegung ihrer Bauteile und verfügen über die Möglichkeiten der magnetischen, mechanischen und thermischen Simulation», erklärt Heinz Schell, Key Account Manager bei MS-Schramberg. «Auch die Herstellung der benötigten Magnetisierspulen und Werkzeuge sowie die für die Fertigung geeignete Automatisierung erfolgt bei uns im Haus. Anwender profitieren von unserem über Jahrzehnte angesammelten Know-how und unserer umfassenden Beratungskompetenz.»
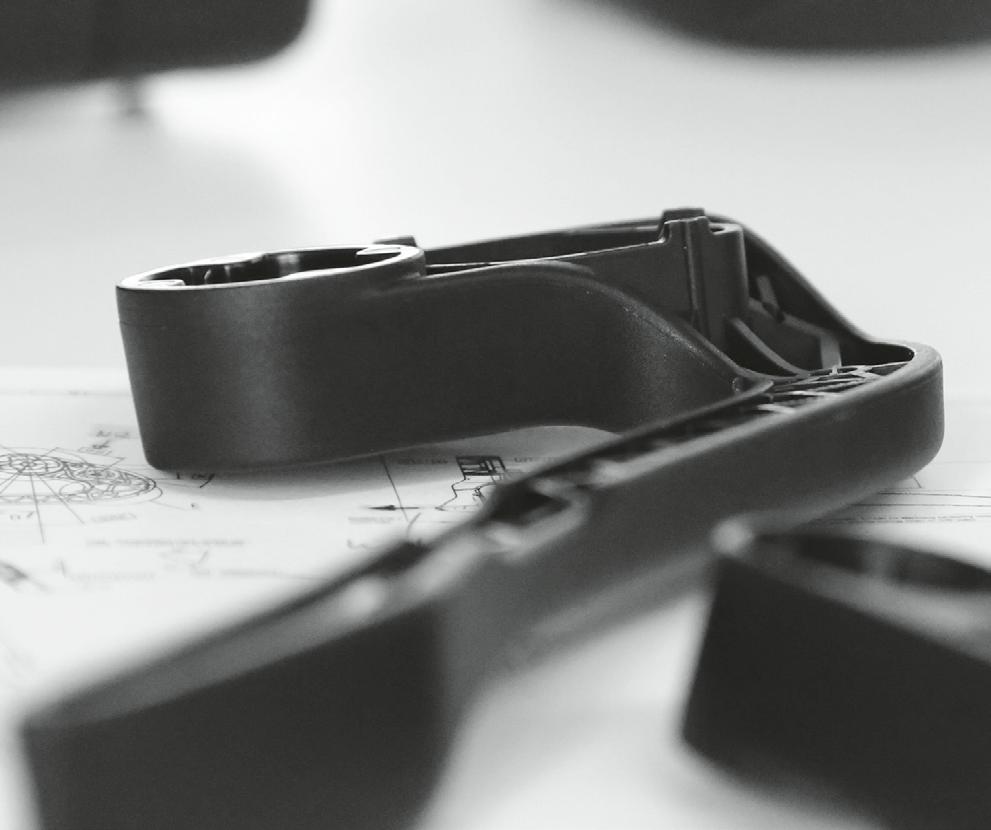
Neue Materialien für mehr Einsatzmöglichkeiten
Durch den Einsatz elastomergebundener Magnete kann MS-Schramberg das Anwendungsspektrum seiner Produkte deutlich erweitern. Sie eignen sich zum Bei-
units - Ihr Full-Service Partner in den Bereichen Simulation, Engineering und industrieller Messtechnik an drei Standorten für D-A-CH.
Von der Entwicklung bis zur Serienproduktion – mit unseren vernetzten Leistungen unterstützen wir die Umsetzung Ihrer Projekte, bieten ganzheitliche Lösungen und generieren langfristigen Mehrwert.
Ihr Erfolg liegt in unserem Fokus.
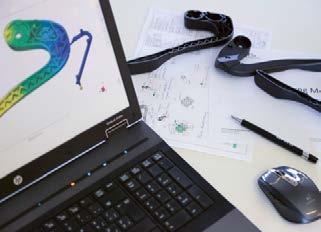


units OST AG Rosenbergs-Au-Strasse 1 CH-9434 Au (SG)
T: +41 71 242 42 00 info@units.ch units MITTELLAND AG Industriestrasse 14 Gebäude 212 CH-4528 Zuchwil
T: +41 32 671 60 70 mittelland@units.ch units IMT GmbH Millennium Park 4 A-6890 Lustenau
T: +43 5577 84 111 info@units.at
SIMULATION ENGINEERING INDUSTRIELLE MESSTECHNIK DIE EINHEIT FÜR ERFOLG
Die richtige Wahl der Werkstoffe
Aromaverschleppung – keine Chance
Trelleborg Sealing Solutions hat mit dem Abfüllspezialisten Krones die möglichen Gründe für die ungewollte Übertragung von Aromen bei der aufeinanderfolgenden Abfüllung von unterschiedlichen Getränken analysiert. Als ein massgeblicher Faktor erwies sich der für die verwendeten Dichtungen gewählte Elastomer-Werkstoff.
Wie in fast allen Konsumgütermärkten müssen auch Hersteller von Getränken immer flexibler produzieren. Produktionszeiten werden kürzer, Produktinnovationen erfolgen in immer höherem Takt. Auch die Produktlebenszyklen im Markt für Softdrinks verkürzen sich. Produkte werden schneller modifiziert oder durch Neuentwicklungen ersetzt. Entsprechend häufiger kommen Produktwechsel in den Abfüllanlagen vor. Mit ihrer Anzahl wächst das Risiko einer Aromaverschleppung. Also müssen komplizierte Produktionspläne erstellt oder die Anlagen aufwändig gereinigt werden – das erfordert grosse Mengen Wasser und Energie und verursacht kostspielige Stillstandzeiten. Krones und Trelleborg Sealing Solutions haben mögliche Gründe für die ungewollte Übertragung von Aromen in Abfüllanlagen analysiert und Möglichkeiten gefunden, diese zu verhindern. Als besonders relevanter Faktor erwiesen sich die für Komponenten mit Produktkontakt verwendeten Werkstoffe, speziell im Bereich der Dichtungen. Die Analyse der verschiedenen Dichtungswerkstoffe ergab, dass Ethylen-PropylenDien-Kautschuk (EPDM) in erheblichem Ausmass Aroma absorbierte, während sich Fluorkautschuk (FKM) deutlich resistenter zeigte und daher für die Verwendung bei der Abfüllung vieler Getränke geeignet ist. Tests führten auch zu dem Schluss, dass Dichtungen aus Perfluorelastomer (FFKM), wie beispielsweise die Isolast FoodPro Compounds von Trelleborg Sealing Solutions, eine effektive Lösung sein können. Die FFKM-Materialien absorbierten keinerlei Aromen und zeigten auch unter ungünstigen Bedingungen praktisch keinen nachweisbaren Einfluss auf den Geschmack der nachfolgenden Getränke. Dies macht diese Dichtungsmaterialien
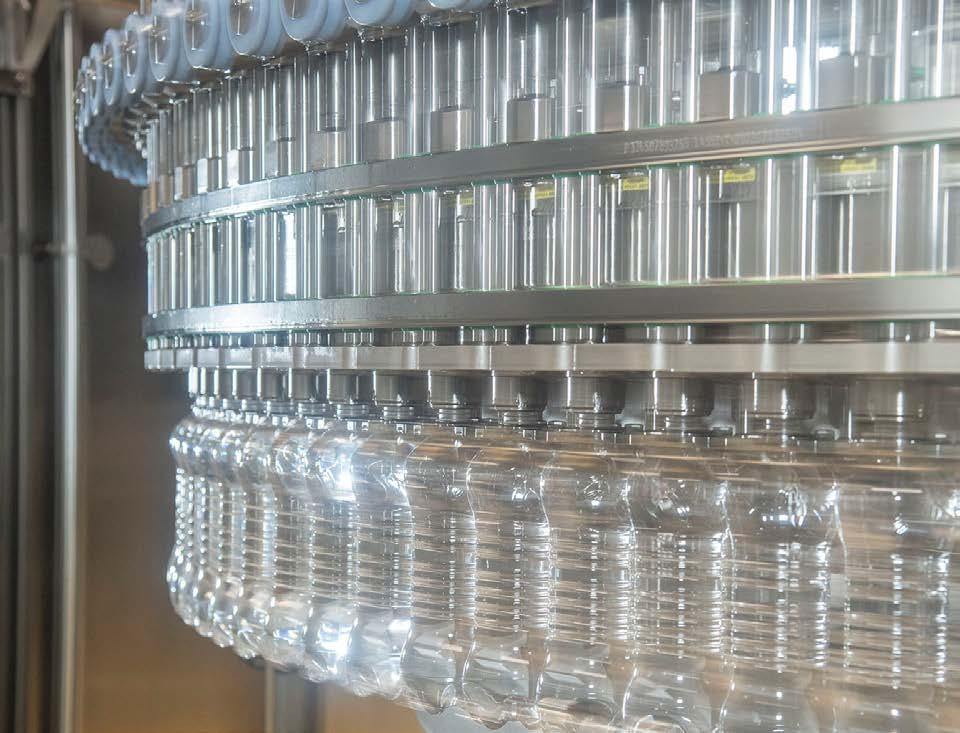
Bild: Krones Bei Produktwechseln in Abfüllanlagen für Getränke muss sichergestellt sein, dass es nicht zur ungewollten Übertragung von Aromastoffen kommen kann. Mit der richtigen Dichtung ist das garantiert.
ideal für den Einsatz in Abfüllanlagen, die Getränke mit intensiven Aromen verarbeiten.
Trend hin zu intensiveren Aromen
Dr. Eva Beierle Development Engineer Aseptic and Process Technology bei Krones kennt die Hintergründe aus Sicht der Abfüller: «Ein Trend bei modernen Getränken sind immer intensivere Aromen. Das stellt uns vor Herausforderungen, da Getränke mit hohen Konzentrationen von Aromen natürlich eher wahrnehmbare Spuren in den Abfüllanlagen hinterlassen als schwach aromatisierte. Die Zusammenarbeit mit Trelleborg Sealing Solutions hat uns ein tiefes Verständnis dafür vermittelt, wie die nicht zulässige Aromenverschleppung in der Abfüllung vermieden werden kann.» Martin Krüger, Area Sales Manager Industrial bei Trelleborg Sealing Solutions, ergänzt: «Unsere Kunden müssen sich auf eine uneingeschränkte Funktion der von ihnen verwendeten Dichtungslösungen verlassen können. Wir können unsere Dichtungssysteme in Geometrie und Material exakt an die jeweiligen Anforderungen anpassen. In Abfüllanlagen ist die Auswahl der optimalen Dichtung extrem wichtig, um Aromaverschleppung zu verhindern. Hier haben sich Werkstoffe auf Basis FKM oder FFKM wie beispielsweise unser Isolast FoodPro Compound bewährt. Diese Werkstoffklassen sind gegenüber den gängigen Reinigungsmitteln und Tem-
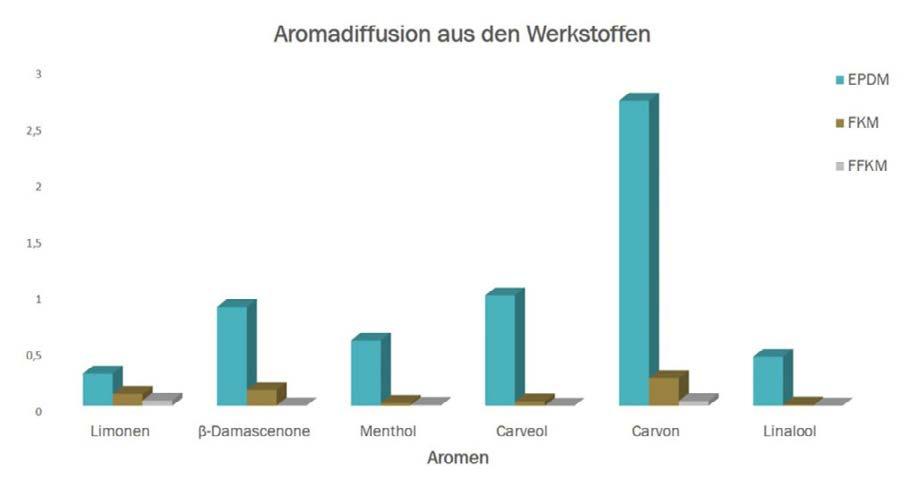
Die Aufnahme von Aromastoffen ist bei EPDM unter bestimmten Umständen erheblich. Bei FKM sind sie viel geringer, während FFKM so gut wie kein Aroma aufnahm.
peraturprofilen, welche in den CIP/SIP Prozessen der Abfüllindustrie vorkommen, beständig und verfügen weiterhin über die erforderlichen Zulassungen für den Kontakt mit Lebensmitteln.» Konrad Saur, Vice President Innovation & Technologie bei Trelleborg Sealing Solutions, sagt: «Die Vermeidung von Geschmacksverschleppung spielt eine bedeutende Rolle bei der Steigerung der Nachhaltigkeit in der Lebensmittel- und Getränkeindustrie. Durch unsere Forschungspartnerschaft mit Krones haben wir unser Know-how im Bereich der elastomeren Dichtungswerkstoffe mit der Expertise von Krones bei Getränketrends und -entwicklungen kombiniert. Im Ergebnis haben wir herausgefunden, dass die Auswahl des optimalen Dichtungswerkstoffs entscheidend für die Vermeidung von Aromaverschleppung ist. Davon profitieren sowohl unsere Kunden als auch die von Krones.»
Kontakt Trelleborg Sealing Solutions Business Area Head Office Schockenriedstrasse 1 D-70565 Stuttgart +49 711 7864 0 sealing.solutions@trelleborg.com www.trelleborg.com
Innovative Kunststoffe für Ihre Mobility-Anwendungen
