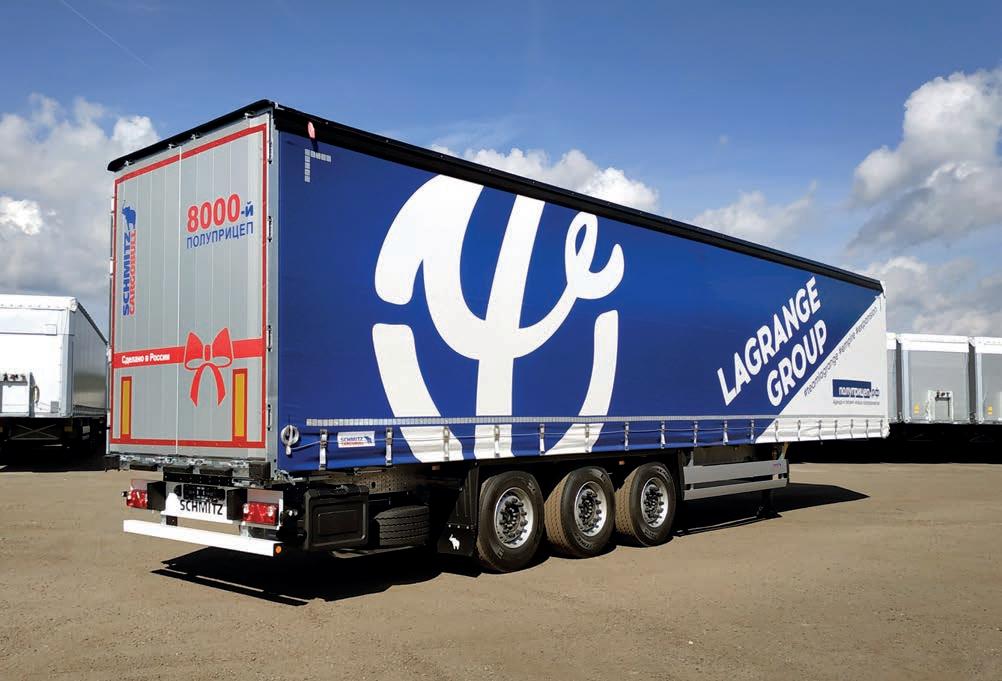
4 minute read
Schmitz Cargobull. Восьмая российская тысяча
Восьмая российская тысяча
Advertisement
Комп ания Schmitz Cargobull, многолетний лидер российского рынка новой прицепной техники, приступила к производству своих полуприцепов в нашей стране семь лет назад. Первоначально сборочный завод находился в Ленинградской области, а с 2016 года их выпуск осуществляется в Истринском районе Подмосковья. Производственная мощность работающего в деревне Духанино завода – 12 полуприцепов в день, площадь его сборочного цеха – 1200 м2. Сборочные кит-комплекты тентованных и самосвальных полуприцепов поставляются из Германии. Также на территории предприятия расположен склад запасных частей.
Изготовленным в России 8-тысячным полуприцепом Schmitz Cargobull стал трехосный «шторник» семейства S.CS со сдвигаемым боковым тентом, с осями собственного производства Schmitz Cargobull, с пневматической подвеской и односкатной ошиновкой всех колес. По конструкции и габаритной длине 13,62 м он полностью соответствует стандартам Евросоюза. Это одна из наиболее востребованных моделей компании, приспособленная для всех способов фиксации груза, среди отличительных черт которой можно отметить ускоряющую погрузочно-разгрузочные операции и снижающую усилия со стороны водителя продуманную конструкцию раскрытия кузова.
Покупателем 8-тысячного полуприцепа Schmitz Cargobull стало ООО «Полуприцеп» – молодая, быстро растущая компания, занимающаяся долгосрочной и краткосрочной арендой прицепной техники. А эксплуатировать юбилейный полуприцеп станет ООО «Лагранж» – компания, специализирующаяся на грузовых автомобильных перевозках.
В завершение – немного статистики. Согласно данным Russian Automotive Market Research, компания Schmitz Cargobull завершила июль на привычной позиции лидера российского рынка новой прицепной техники: заказчикам реализовано порядка 0,31 тыс. полуприцепов, что на 3,1% меньше к аналогичному периоду 2019 года. На втором месте – Нефтекамский автозавод (0,27 тыс. ед., –3,6%), на третьем – машиностроительный завод «ТОНАР» (0,24 тыс. ед., +26,3%). В пятерку лидеров также вошли KRONE (0,15 тыс. ед., –37,5%) и Grunwald (0,12 тыс. ед., +50%).
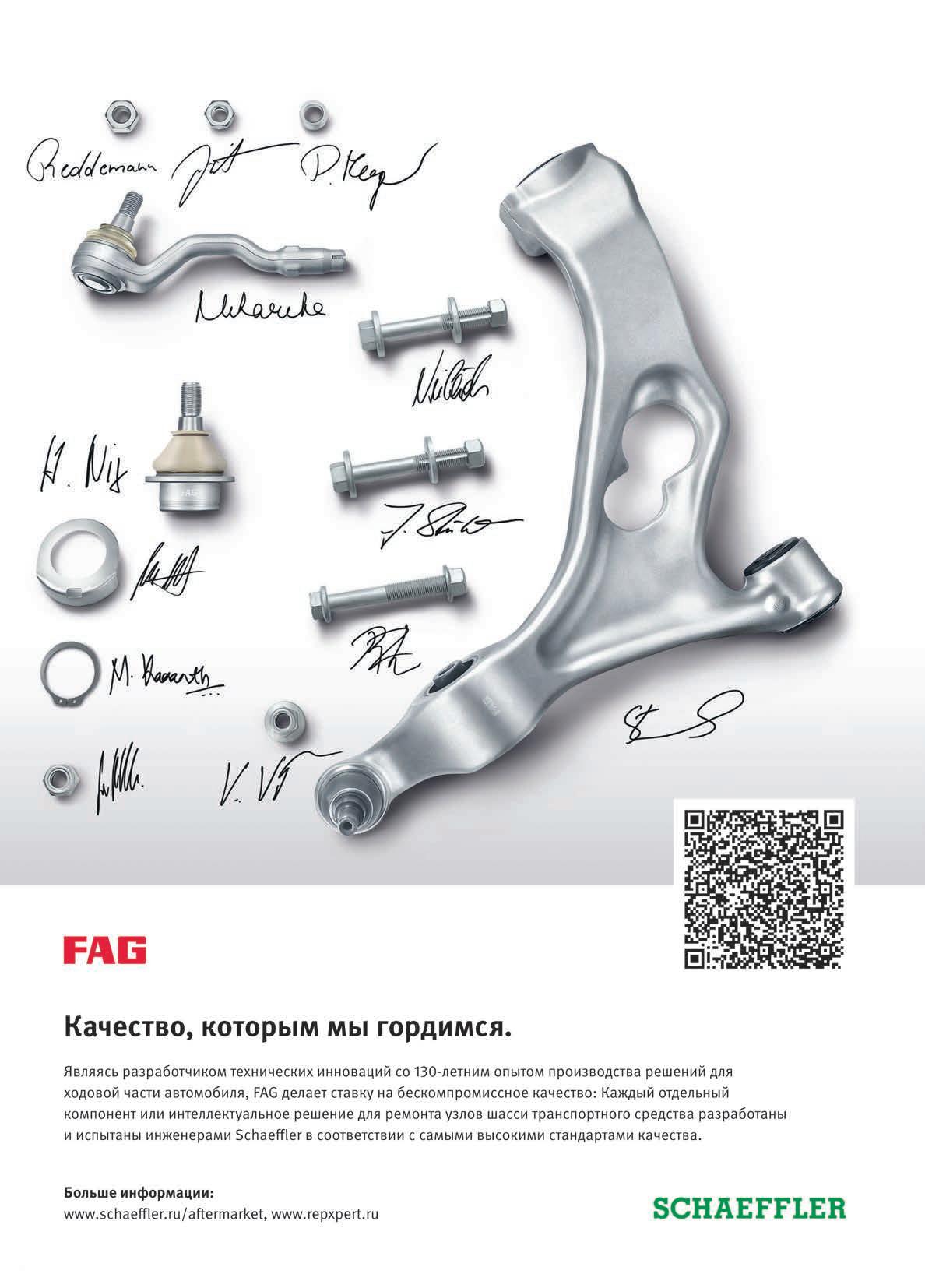
Компания HJ была основана в 2002 году, на данный момент является одним из самых больших предприятий, производящих и реализующих запасные части и детали для прицепов и полуприцепов в Азии. В группу компаний входит два завода, общая площадь которых составляет более 400 000 м2, на предприятиях работают более 800 сотрудников. За все время развития компания стала одним из главных производителей в своей области на внутреннем рынке. Основная деятельность компании направлена на исследование, разработку и производство ходовой части для прицепной техники, основная продукция включает: оси в сборе (европейского и американского стандартов), опорные устройства, рессорные подвески, пневматические подвески, рессорно-балансирные подвески и другие детали. При полной загрузке производства мощности компании составляют 400 000 осей в год.
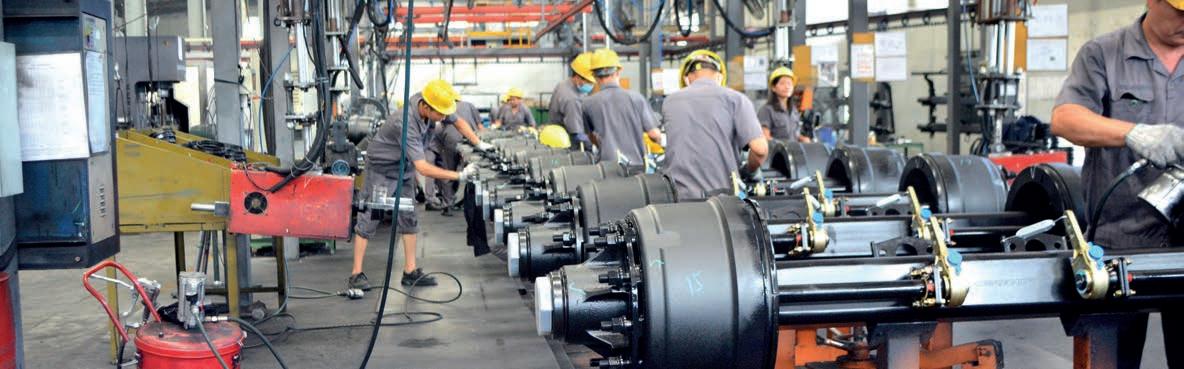
HJ – гарантия качества и международный стандарт
Мы производим оси для прицепной техники с нагрузкой от 8 до 20 тонн, с балкой круглого и квадратного сечения.
HJ – одна из первых компаний, кто начал производить цельнокованую балку оси, применяя метод горячего обжима с двух сторон заготовки, при этом увеличивается толщина стенки в ступичном узле, в том месте, на которое приходится основная нагрузка. Технология решает проблему опасности разрушения в результате усталости металла, происходящих при процессе работы и нагрева деталей и возникающих при этом скручиваний и деформаций.
Цельная балка оси полностью изготавливается из легированной стали, проходит процессы закалки и отпуска. Имеет более легкий вес и улучшенные показатели прочности. Цапфа оси проходит высокочастотную закалку, что увеличивает прочность поверхности в ступичном узле в несколько раз и улучшает механические свойства. Расточка выполняется роботом и обрабатывается на токарном станке с цифровым управлением, который обеспечивает допуск соосности отверстий менее 0,2 мм.
Каждая балка оси получает индивидуальный код, мы даем гарантию как минимум три года с момента ввода в эксплуатацию.
С расчетом на большие динамические нагрузки, идущие от дорог невысокого качества, балка оси успешно прошла усталостное испытание в 2 000 000 повторений при нагрузке, превышающей номинальную в 2,5 раза, при этом стандартом для таких испытаний является количество в 800 000 повторений.
Цапфа оси и сама ось изготавливаются из одного материала. Отсутствие сварных соединений исключает возможность излома из-за дефекта сварки, а также из-за отсутствия концентраций напряжения, полая балка оси, толщина которой увеличивается к концам, имеет лучшие показатели гибкости. Процесс обжима также позволяет сохранить продольные волокна материала, что положительно сказывается на механических свойствах.
Квадратная балка производится по технологии горячего деформирования, заготовка круглого сечения подвергается значительному нагреву, после этого металл приобретает требуемую пластичность, заготовка поступает на прошивочный пресс. Такая технология позволяет добиться одинакового размера балки по всей длине профиля, поддерживая высокую точность от партии к партии.
Соблюдение строгих требований по сборке гарантирует высокую надежность и максимальный ресурс подшипникового узла. Используемая при сборке смазка немецкого производителя предусматривает более длительный срок использования, что снижает расходы на обслуживание. Конструкция ступичного узла обеспечивает легкодоступность при выполнении операций по обслуживанию тормозных механизмов или замены подшипников.
Полностью автоматическая покрасочная линия обеспечивает высокие стандарты окрашивания. Образцы успешно прошли испытания в соляном тумане более 900 часов. Наша компания уделяет большое внимание вопросам качества, продукция также проходит испытания на упругость металлов, металлографический анализ, испытания на растяжение и текучесть, относительное удлинение при разрыве, ультразвуковой контроль, трёхкоординатный контроль допусков, макроскопический анализ металлов. Весь производственный процесс, начиная от сырья и до выхода готовой продукции, проходит строгий контроль, добиваясь гарантии качества и соответствия международным стандартам.
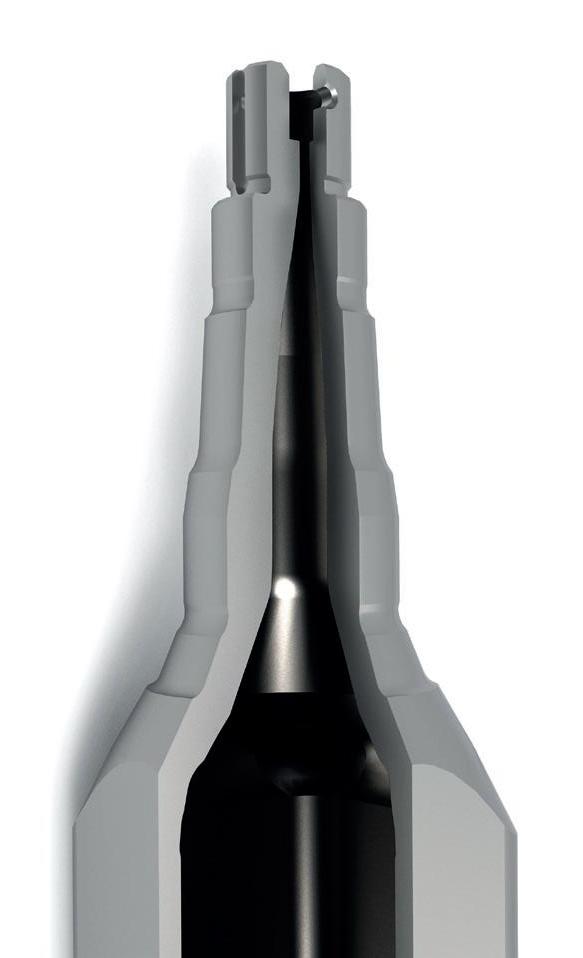
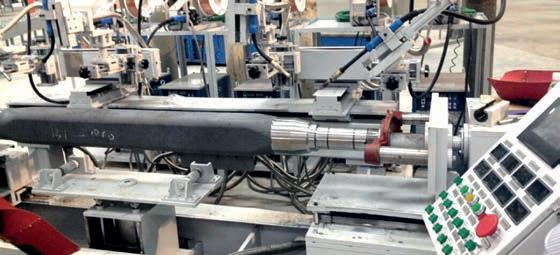
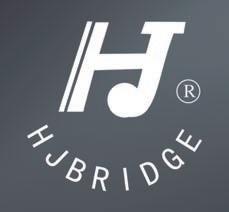
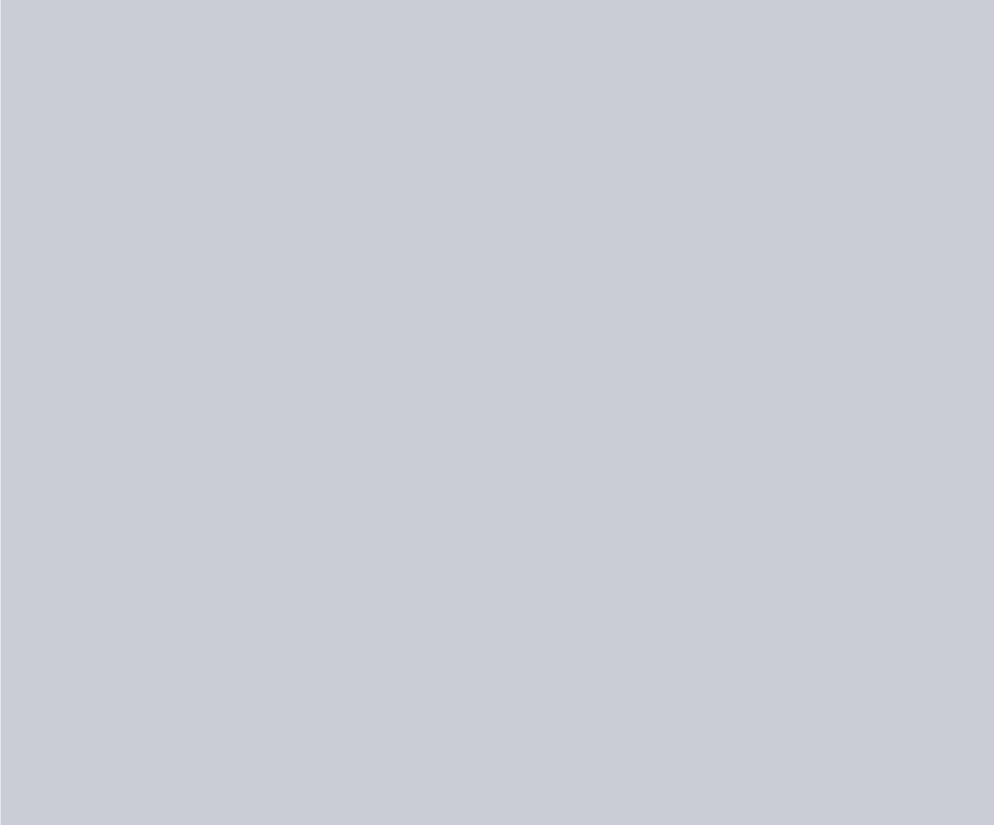
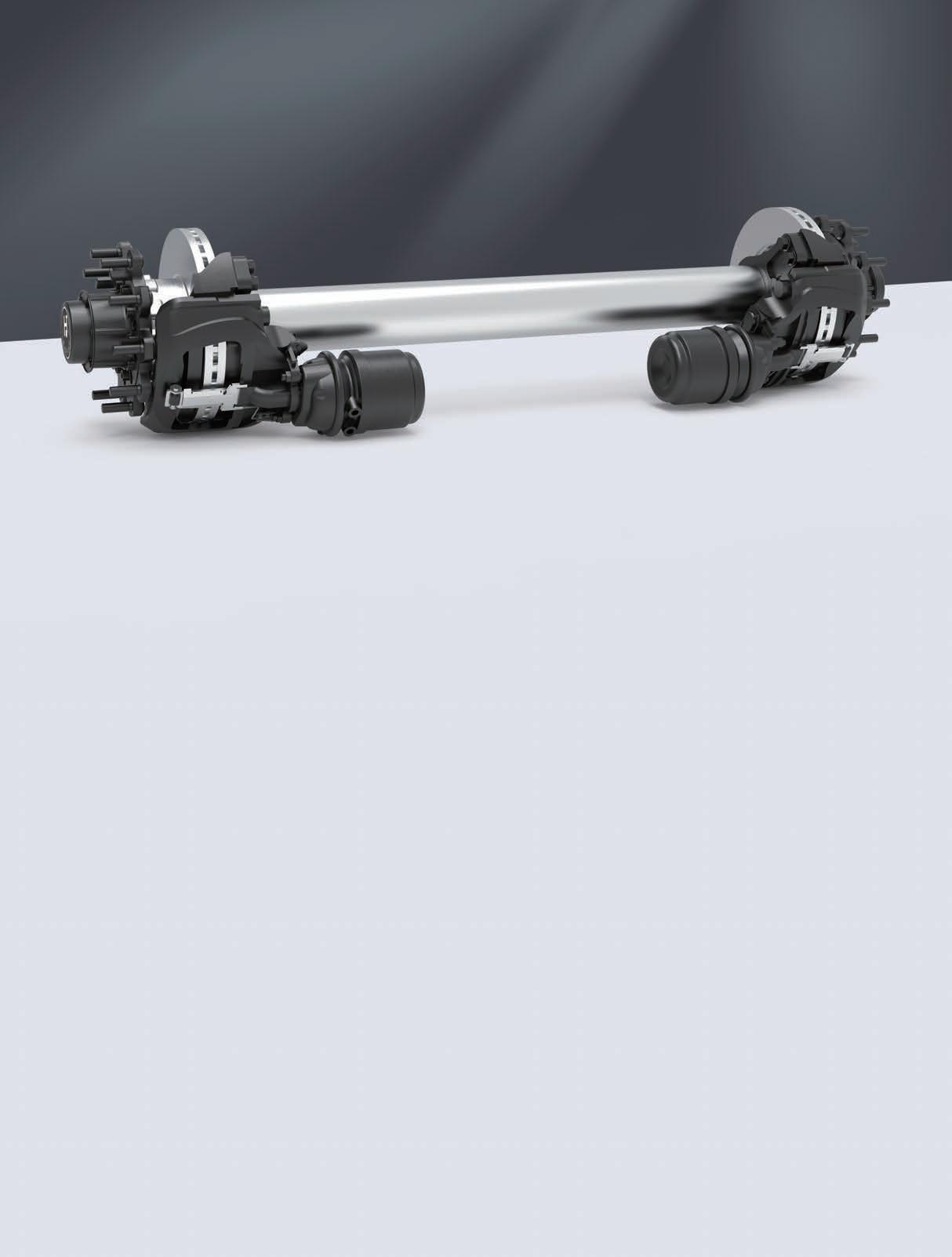
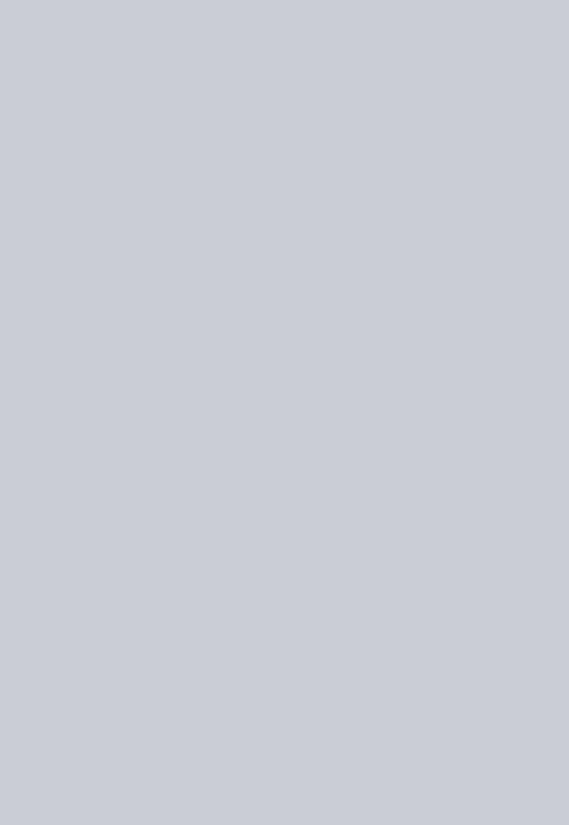
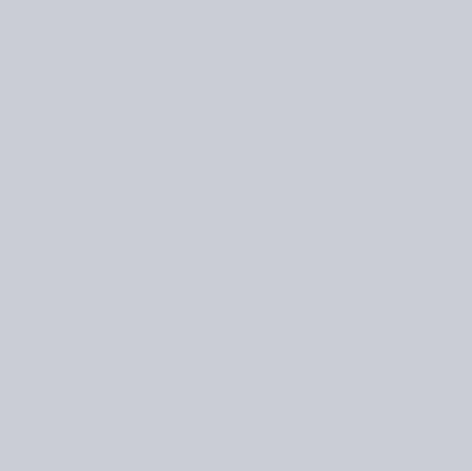
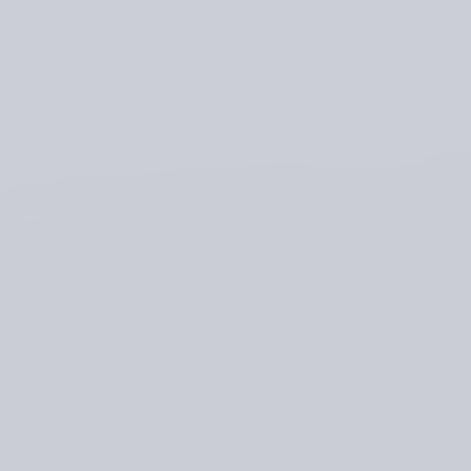
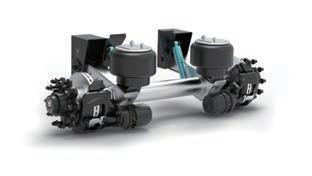
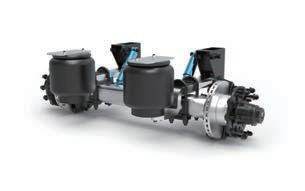
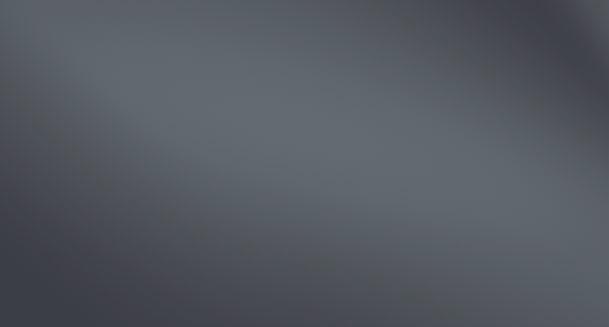

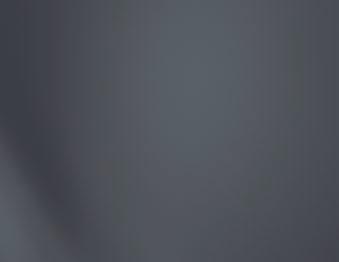