
13 minute read
Manutenzione predittiva, una strategia proattiva
di Davide Biancorosso Evoluzione Manutenzione predittiva, una strategia proattiva
Utilizzato per la prima volta alla Fiera di Hannover nel 2011, da Henning Kagermann, Wolf-Dieter Lukas e Wolfgang Wahlster, il termine “Industria 4.0” indica la rivoluzione, trainata dalla digitalizzazione dei processi, che si sta compiendo nell’attuale panorama industriale. L’Industria 4.0 si realizza attraverso il concetto di “smart factory” basato su tre elementi: · Smart production: tecnologie produttive per la connessione tra operatore, macchina e strumenti; · Smart service: tecnologie informatiche per l’integrazione di sistemi, strutture e organizzazioni; · Smart energy: efficientamento dei consumi, crescita delle prestazioni e riduzione degli sprechi. Ogni rivoluzione industriale è caratterizzata da radicali cambiamenti delle tecnologie produttive che generano un considerevole aumento di produttività; rispetto alle prime tre rivoluzioni industriali, prima avvenute e successivamente studiate, la quarta rivoluzione è invece annunciata, descritta e commentata mentre avviene, se non addirittura prima che si compia. Sicuramente questo nuovo approccio può portare a previsioni errate ma d’altro canto consente anche di prendere decisioni ponderate e di operare da protagonisti del cambiamento in atto.
Quando si rompe, si aggiusta. I guasti possono causare problemi di qualità, fermi di produzione, danni collaterali. Manutenzione a intervalli regolari per la sostituzione programmata di componenti critiche sulla base delle statistiche di durata. - Le parti critiche identificate sono solo una parte del problema. - Spesso vengono sostituiti componenti ancora in grado di funzionare. Identificazione dei possibili guasti imminenti attraverso il monitoraggio delle grandezze fisiche d’interesse, prevedendo fermi, effetti collaterali e problemi di qualità.
La manutenzione predittiva di un impianto si basa sul monitoraggio del suo stato reale e delle sue condizioni di funzionamento tramite la misurazione e l’analisi di caratteristiche fisiche come suono, temperatura, vibrazioni, assorbimento elettrico e sui risultati di specifiche ispezioni visive.
Strategie manutentive
Le aziende, per competere oggi, devono non solo lavorare “just in time” ma anche in modo più efficiente, con maggiore flessibilità, in maniera più sicura e nel rispetto dell’ambiente. Le tecnologie e i servizi sviluppati per l’internet delle cose (Internet of Things - IoT) che sono alla base dell’Industria 4.0 stanno spingendo le aziende verso soluzioni sempre più efficienti, automatizzate, integrate e sicure. Garantire nel tempo prestazioni e risultati richiede, però, un nuovo approccio al “mantenimento” degli impianti e delle attrezzature che inevitabilmente richiederanno assistenza e riparazioni per evitare cali prestazionali o fermi. Al pari dell’industria, anche le strategie manutentive, nel tempo, si sono modificate ed evolute; dall’iniziale reattiva, attraverso la preventiva, arrivando all’attuale predittiva. 33
Manutenzione reattiva
La prima, e più semplice, attività manutentiva è quella effettuata solo a seguito di un guasto; la riparazione avviene solo quando il macchinario è fuori uso e non opera più correttamente. Questa strategia massimizza lo sfruttamento dell’impianto, ma ne riduce la vita utile totale. La manutenzione ordinaria, in questo scenario, è del tutto assente così come i sono assenti i costi a essa associati. Un approccio che mostra tutti i suoi limiti nei casi complessi o di emergenza. Le riparazioni effettuate in tali condizioni possono assorbire ingenti risorse, sia umane sia economiche. Ottenere i ricambi necessari in tempi rapidi può costare significativamente di più che ordinarli per tempo, così come reperire operatori qualificati per effettuare le riparazioni necessarie rischia di essere molto dispendioso in termini di rimborsi e straordinari. In aggiunta, un guasto di notevole entità può comportare anche lunghi fermi della produzione in momenti o contesti di mercato che generano perdite economiche notevoli, oltre a un significativo danno di immagine: non rispettare le consegne fa crollare la fiducia dei clienti! Spesso per ovviare ai limiti del modello reattivo, le aziende finiscono per creare strutture di manutenzione interne e magazzini di ricambi spesso sovradimensionati e costosi che, il più delle volte, non evitano i fermi e che finiscono per rimanere, in parte, non utilizzati. Oltretutto quasi sempre non vengono venduti o dismessi con l’impianto cui sono destinati finendo per diventare, anni dopo, rifiuti (ricambi nuovi non utilizzati, nel tempo, diventano obsoleti e quindi non più utilizzabili). Il costo di un simile approccio comprende il costo di acquisto, il costo di immagazzinamento e il costo di smaltimento; tutti costi in realtà evitabili con un approccio manutentivo più strutturato. La manutenzione reattiva appare quindi adatta solo a realtà molto piccole o per macchine semplici e di facile riparazione. In alcuni casi può anche servire per “guadagnare tempo”, in attesa di una manutenzione programmata ma, in ogni caso, non deve mai essere considerata come una strategia di medio/lungo periodo. Il modello reattivo inoltre non è adatto alle manutenzioni di apparati di sicurezza; un guasto che può compromettere la sicurezza dell’operatore non è mai accettabile perché può provocare danni, anche molto seri, a chi lavora sull’impianto stesso.
Manutenzione preventiva
Proprio per superare i limiti della manutenzione reattiva si sviluppa il modello preventivo. Gli impianti e le macchine vengono manutenuti con una cadenza temporale predefinita che ne assicura il corretto e continuo funzionamento a fronte di previsti e pianificati fermi. Il modello preventivo è inizialmente visto con sospetto, in quanto prevede di fermare un impianto che sta regolarmente funzionando, togliendolo dalla produzione senza un motivo apparente. Tuttavia, il conseguente aumento della durata della vista utile dell’impianto, e la possibilità di pianificare i fermi nei momenti più corretti (es. calo di produzione stagionale), ne fanno nel tempo apprezzare i vantaggi. Il modello preventivo si impone rapidamente sugli impianti che operano in continuo e sui dispositivi di sicurezza. Ancora oggi, infatti, molta manutenzione di sicurezza è effettuata secondo rigide cadenze temporali, spesso stabilite da leggi o norme, che pongono al primo posto la sicurezza di chi opera a fronte di interventi, anche molto anticipati, il cui scopo è evitare ogni possibile malfunzionamento o guasto. La manutenzione preventiva basa il calcolo dei tempi di intervento su modelli teorici e statistici senza pertanto riflettere la realtà dell’impianto. Per semplicità si pensi alla sostituzione del filtro dell’olio di un’automobile che avviene ogni 20.000 Km indipendentemente dal suo stato reale. Questo approccio comporta la sostituzione di parti non ancora usurate, che potrebbero ancora funzionare correttamente, se non fino al successivo intervento programmato, magari per altre settimane o mesi. Il limite di questo modello preventivo, detto appunto “ciclico”, è rappresentato dal costo che si deve pagare per avere una continuità di funzionamento dell’impianto; si pianifica e si spende prima per avere meno fermi e ridotti costi totali rispetto al modello reattivo. Oltre al modello ciclico, la manutenzione preventiva può essere effettuata anche al presentarsi di predeterminate condizioni. In questo caso si osservano le prestazioni di una macchina e/o lo stato di alcuni suoi parametri di funzionamento o di sue parti. La manutenzione viene quindi eseguita al solo raggiungimento di un valore limite predefinito che rappresenta lo stato di usura della macchina o di una sua parte specifica. Come ad esempio la sostituzione delle pastiglie dei freni delle automobili per i quali un modello ciclico non sarebbe applicabile; le pastiglie saranno sostituite al raggiungimento di un valore soglia che anticipa quello di esaurimento per consentirle la sostituzione. Questo approccio, detto “su condizione”, permette di superare alcuni limiti del modello “ciclico” evitando inutili interventi manutentivi e portandoli al numero minimo necessario a garantire l’affidabilità della macchina o dell’impianto.
Manutenzione predittivaIl modello preventivo, quindi, nel tempo si evolve, affiancando il ciclico a quello su condizione; entrambi però questi approcci sono statici e, anche se inferiori, hanno ancora costi elevati di gestione e comportano comunque la sostituzione anticipata di parti o elementi ancora lontani dal guastarsi. Il superamento di questi limiti avviene con l’introduzione della più recente manutenzione predittiva; approccio, evoluzione di quello su condizione, che si pone l’obiettivo dichiarato di anticipare e prevenire i guasti. La manutenzione avviene a seguito dell’individuazione e della misura di uno o più segnali elaborati da uno specifico software di calcolo che determina il tempo residuo atteso prima che si verifichi un guasto. In questo modo si potrà pianificare l’intervento al momento più appropriato, ovvero prima che il guasto si verifichi ma solo dopo che l’unità ha realmente iniziato a manifestare usura. La manutenzione predittiva è stata resa possibile dall’evoluzione dei sistemi informativi e dalla nascita dell’IoT (Internet of Things) e per questo è considerata uno degli strumenti necessari per l’attuazione dell’industria 4.0. Il concetto è di per sé semplice e ovvio: si misurano, ad esempio, le vibrazioni e la temperatura dell’olio di una macchina rotante e in base al variare di questa misura rispetto alle condizioni normali si può stabilire, tramite specifici modelli di calcolo, lo stato reale di usura della macchina e stabilire l’esatto tempo in cui intervenire.
Il modello manutentivo ideale
La manutenzione predittiva, nonostante tutti i sui vantaggi, ha comunque alcuni limiti rappresentati dai costi di implementazione e dalla sua complessità. Il suo utilizzo va quindi correttamente ponderato all’interno di un piano di manutenzione generale che, il più delle volte, vede un utilizzo razionale di tutte le strategie manutentive viste. La predittiva la si può riservare agli impianti principali e a quelli che non si devono mai fermare lasciando, ad esempio, quella di piccole macchine accessorie e facili da riparare, alla manutenzione reattiva lasciando alla preventiva ciclica le manutenzioni dei dispositivi di sicurezza. Non esiste un unico modello manutentivo vincente sugli altri, ogni azienda deve valutare quale approccio impiegare ed elaborare una sua strategia manutentiva. Il risultato sarà una maggiore disponibilità degli impianti a fronte di una riduzione dei costi globali di manutenzione. La manutenzione predittiva diventa quindi un fattore chiave per l’industria 4.0 e le tecnologie per implementarla sono già disponibili e sempre più accessibili.

>>
Come funziona la manutenzione predittiva
La manutenzione predittiva di un impianto o di una macchina si basa quindi sul monitoraggio del suo stato reale e delle sue condizioni di funzionamento tramite la misurazione e l’analisi di alcune caratteristiche fisiche come suono, temperatura, vibrazioni, assorbimento elettrico oltre che sui risultati di specifiche ispezioni visive. Prendiamo ad esempio il funzionamento di un motore elettrico che passa da condizioni normali ad anomale tramite i seguenti passaggi: emissione di ultrasuoni; vibrazioni; maggior assorbimento elettrico; rumore; surriscaldamento; fumo; rottura. Andando quindi a misurare in continuo alcune di queste grandezze come le vibrazioni, l’assorbimento e la temperatura, i sistemi di manutenzione predittiva possono prevedere quale elemento si stia deteriorando e calcolare il momento ottimale per la sua sostituzione o riparazione. In linea di principio, prima si identifica il nesso tra i diversi segnali registrati e l’insorgere del guasto, minori saranno i costi d’intervento e i fermi connessi alla riparazione.
Implementare la manutenzione predittiva
L’implementazione del modello predittivo non è però altrettanto semplice: richiede specifiche competenze multidisciplinari e una profonda e radicale revisione della gestione degli impianti, oltre a significativi investimenti iniziali. Senza entrare nel merito dei singoli passaggi, per attuare una manutenzione predittiva sono necessarie le fasi di: data acquisition (acquisizione dei dati, digitalizzazione e trasmissione); signal processing (pulizia dei segnali dalle distorsioni); feature rappresentation (rappresentazione del segnale sotto forma di funzione e sua visualizzazione grafica); feature extraction/feature selection (estrazioni e poi selezione delle funzioni vettoriali da utilizzare per il sistema di diagnosi e prognosi dei guasti); diagnostics (esame di sintomi e delle sindromi per stabilire la natura di guasti e difetti); monitoring (ricerca e raccolta di informazioni e dati che rappresentano lo stato della macchina); prognostics (prognosi della vita utile dell’impianto o di una sua parte).
I vantaggi della manutenzione predittiva
Semplificando potremmo dire che una volta installati i sensori questi inviano i dati al sistema di calcolo che li utilizza per ottimizzare i tempi di manutenzione. Tutto ciò garantisce che le attività correlate a un intervento manutentivo come l’ordine di ricambi, la disponibilità di risorse e la pianificazione del fermo, siano intraprese solo se effettivamente necessarie. Il tecnico manutentivo può quindi monitorare lo stato di singole parti di un macchinario in qualsiasi momento se non addirittura automatizzare il processo, tramite l’impiego di sistemi di intelligenza artificiale, eliminando così ogni tempo di inattività. La manutenzione predittiva si dimostra quindi, da un lato, più economica di altri modelli e, dall’altro, più efficiente ed efficace. Riparazioni inutili o non necessarie diventano un semplice ricordo in quanto conta solo lo stato effettivo dell’impianto e delle sue parti. Secondo uno studio americano (McKinsey), la manutenzione predittiva consente alle aziende di ridurre i tempi di fermo degli impianti del 50% con un risparmio, a fronte dell’iniziale investimento, compreso tra il10 e il 40% dei costi complessivi di manutenzione degli impianti.
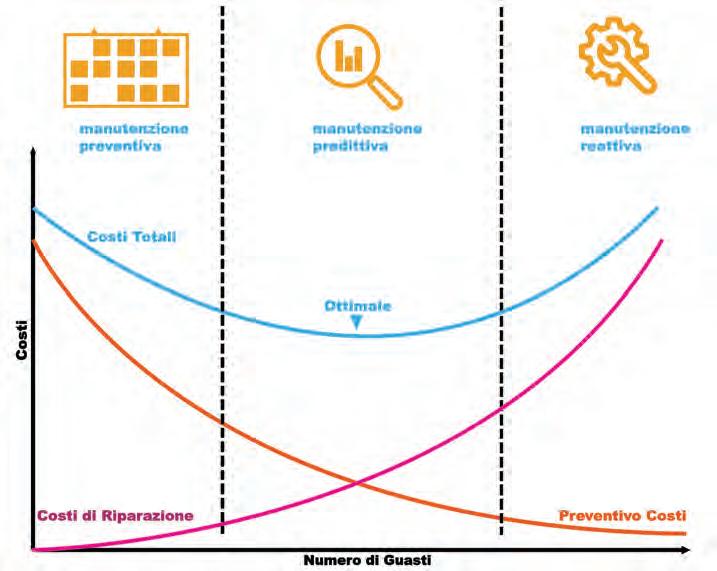
Stampa su legno ed effetti glossy realizzati con l’inchiostro clear: applicazioni prodotte da Beepag con Ricoh Pro T7210.
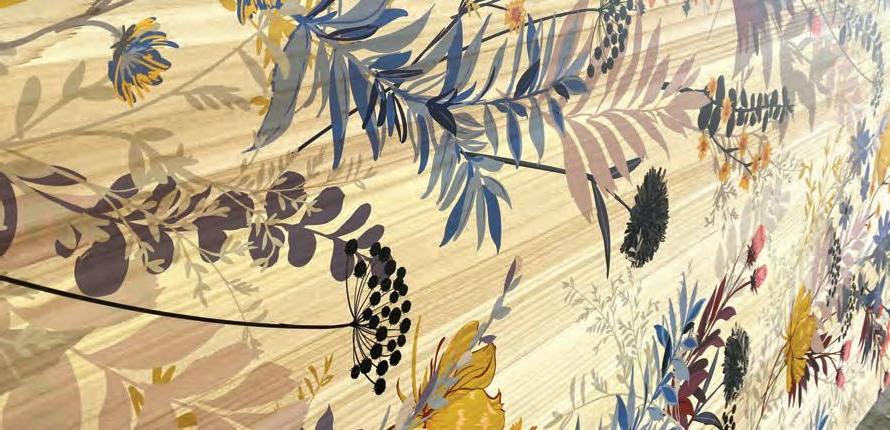
Ricoh Pro T7210,
se la provi… ne vuoi un’altra!
Beepag raddoppia la produttività e installa una seconda Ricoh Pro T7210 riuscendo così ad entrare in nuovi mercati come quelli del fashion e del lusso.
Fornitore di servizi di stampa fondato nel 2014, Beepag rappresenta in Toscana un punto di riferimento del settore anche grazie all’offerta di prodotti personalizzati. L’azienda negli ultimi anni ha registrato una crescita costante, supportata tra l’altro da una piattaforma di e-commerce che le ha consentito di ampliare il proprio mercato di riferimento in Italia e non solo. Innovazione e qualità sono due aspetti fondamentali per riuscire a rispondere alle crescenti esigenze dei brand, obiettivo che Beepag raggiunge anche grazie all’impiego di tecnologie Ricoh e ai servizi che questo partner è in grado di offrire a supporto dei propri clienti. L’ambiente di stampa dell’azienda include differenti tecnologie che spaziano dalle soluzioni a foglio singolo (Ricoh Pro C7200X) per applicazioni con colori speciali, al mondo industrial.
Innovazione a tutto campo
Da diversi anni Beepag utilizza la soluzione latex Ricoh Pro L4100 per offrire ai propri clienti applicazioni indoor e outdoor quali carta da parati – anche in fibra di vetro – roll-up, affissioni, vetrofanie e cartellonistica. “Qualche anno fa abbiamo deciso di andare oltre il mondo roll-to-roll e di gestire anche supporti rigidi” spiega Matteo Pinzauti, fondatore dell’azienda. “Abbiamo introdotto Ricoh Pro T7210, innovativa soluzione di stampa flatbed che ci consente di utilizzare materiali di diversa tipologia come legno, alluminio, vetro, plexiglas e cartone, fino a 11 cm di spessore. Porte, arredi per interni, materiali espositivi per punti vendita realizzati in cartone… sono solo alcuni degli esempi dei lavori che realizziamo e che hanno un unico minimo comun denominatore: la personalizzazione”. Beepag non si è fermata qui e ha deciso di “raddoppiare” la produttività introducendo una seconda Ricoh Pro T7210 con l’obiettivo di incrementare il just-intime ma anche per supportare la crescita del proprio business aprendosi all’offerta di applicazioni a valore aggiunto per i mercati del lusso e del fashion.
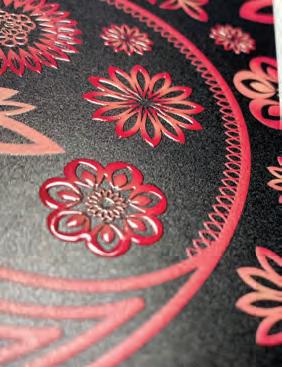
Verso nuovi orizzonti
“La prima Ricoh Pro T7210 – aggiunge Matteo Pinzauti – continua a essere utilizzata per applicazioni Sign and Display e Visual Communication, mentre con il nuovo sistema realizziamo lavori particolari che includono ad esempio il trasparente e il bianco oppure di tipo serigrafico che necessitano di lucidatura. Grazie a queste possibilità, abbiamo iniziato a rivolgerci ai settori del Fashion e del Lusso che hanno necessità di innovare il modo di relazionarsi con i consumatori e di coinvolgerli”. Flessibilità, produttività e qualità elevata sono tra i principali vantaggi garantiti dalla soluzione, senza dimenticare la sostenibilità dal momento che gli inchiostri Ricoh sono certificati ‘Greenguard Gold’. Matteo Pinzauti conclude: “Aiutiamo i nostri clienti a concretizzare le idee, mettendo a loro disposizione le migliori tecnologie di stampa, unite alla nostra esperienza e professionalità. Grazie alle soluzioni Ricoh, siamo un prezioso alleato per le aziende che si rivolgono a noi per differenziarsi sul mercato e comunicare al meglio la propria identità”.
COMUNICAZIONE D’IMPRESA 37