TALL BUILDINGS
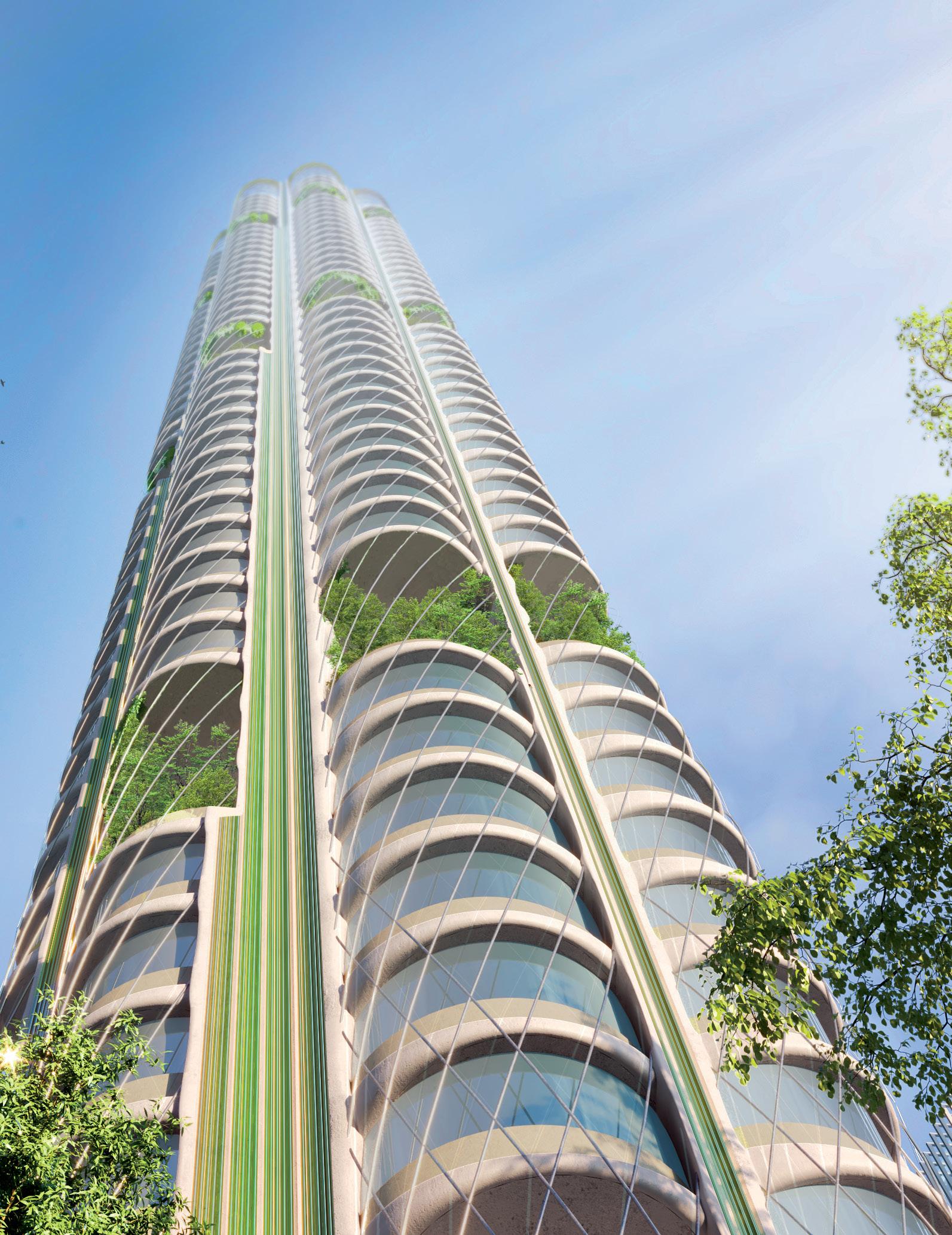
CAST CONNEX ® High Integrity Blocks ® (HIB) are specially engineered and manufactured solid structural steel sections which simplify design, streamline fabrication, and improve the performance of heavily loaded connections.
HIBs surpass traditional construction methods with simplification of fabrication and unmatched quality of material. Unlike laminated plate sections, HIBs are insusceptible to lamellar tearing. Cast Connex’s proprietary manufacturing process eliminates the problematic discontinuities inherent in conventional forgings.
Precise. Efficient. Uncompromising.
30 Hudson Yards — a 90-story, 1,296-foot -tall steel-framed skys craper is the second tallest office building in New York City. Cast Connex ® High Integrity Blocks ® provide an innovative solution for the most heavily stressed, geometrically complex outrigger connections in this super-tall tower.
The result: Unparalleled performance and reliability for modern construction.
30 Hudson Yards, NY
HIBs are engineered, ultra-heavy, weldable steel sections with consistent mechanical properties in all three directions. Performance under arduous loads is validated by Cast Connex engineers with a custom analysis calibrated by results of project-specific destructive and non-destructive testing.
• Simplifies design and fabrication
• Improves performance and reliability
• Achieves up to 65 ksi yield strength and elevated CVN toughness in all directions
Atlas Tube
AWI Panels
Cast Connex
Champion Fiberglass
Computers & Structures, Inc.
CTS Cement Manufacturing Corp
DCI Engineers
Degenkolb Engineers
ENERCALC
Integrated Engineering Software, Inc.
Keller - North America
KPFF
Magnusson Klemencic Associates
Magnusson Klemencic Associates Profile
Martin/Martin
Max USA Corp
New Millennium Building Systems
Nucor Vulcraft Group - Redicor
PCS-Structural
Schock North America
Simpson Strong-Tie
Trimble
Wood Products Council
Director for Sales, Marketing & Business Development
Monica Shripka
Tel: 773-974-6561 monica.shripka@STRUCTUREmag.org
Executive Editor Alfred Spada aspada@ncsea.com
Publisher Christine M. Sloat, P.E. csloat@STRUCTUREmag.org
Associate Publisher Nikki Alger nalger@STRUCTUREmag.org
Creative Director Tara Smith graphics@STRUCTUREmag.org
Chair John A. Dal Pino, S.E. FTF Engineering, Inc., San Francisco, CA chair@STRUCTUREmag.org
Jeremy L. Achter, S.E., LEED AP ARW Engineers, Ogden, UT
Erin Conaway, P.E. AISC, Littleton, CO
Linda M. Kaplan, P.E. Pennoni, Pittsburgh, PA
Charles “Chuck” F. King, P.E. Urban Engineers of New York, New York, NY Nicholas Lang, P.E. Masonry Industry Representative
Jessica Mandrick, P.E., S.E., LEED AP Gilsanz Murray Steficek, LLP, New York, NY
Jason McCool, P.E. Robbins Engineering Consultants, Little Rock, AR Brian W. Miller Davis, CA
Evans Mountzouris, P.E. Retired, Milford, CT
John “Buddy” Showalter, P.E. International Code Council, Washington, DC
Eytan Solomon, P.E., LEED AP Silman, New York, NY
Jeannette M. Torrents, P.E., S.E., LEED AP JVA, Inc., Boulder, CO
STRUCTURE ® magazine (ISSN 1536 4283) is published monthly by The National Council of Structural Engineers Associations (a nonprofit Association), 20 N. Wacker Drive, Suite 750, Chicago, IL 60606 312.649.4600. Periodical postage paid at Chicago, Il, and at additional mailing offices. STRUCTURE magazine, Volume 29, Number 6, © 2022 by The National Council of Structural Engineers Associations, all rights reserved. Subscription services, back issues and subscription information tel: 312-649-4600, or write to STRUCTURE magazine Circulation, 20 N. Wacker Drive, Suite 750, Chicago, IL 60606.The publication is distributed to members of The National Council of Structural Engineers Associations through a resolution to its bylaws, and to members of CASE and SEI paid by each organization as nominal price subscription for its members as a benefit of their membership. Yearly Subscription in USA $75; $40 For Students; Canada $90; $60 for Canadian Students; Foreign $135, $90 for foreign students. Editorial Office: Send editorial mail to: STRUCTURE magazine, Attn: Editorial, 20 N. Wacker Drive, Suite 750, Chicago, IL 60606. POSTMASTER: Send Address changes to STRUCTURE magazine, 20 N. Wacker Drive, Suite 750, Chicago, IL 60606.
STRUCTURE is a registered trademark of the National Council of Structural Engineers Associations (NCSEA). Articles may not be reproduced in whole or in part without the written permission of the publisher.
Jumbo HSS are now available and ready to order.
What makes for good times? Getting your hands on Jumbo HSS. Between our Blytheville mill rolling American-made, 100% EAF recycled steel HSS and manufacturing the largest HSS sizes in the industry, it doesn’t get much better than that.
The Urban Sequoia concept combines a broad range of sustainable design thinking, including emerging technologies. The structure is organized into eight petals around a tubular core. With an optimized structural design resulting in minimal materials and integrating biomaterials, biomass concepts, and carbon-capturing technologies into an integrated system, the building can achieve substantially more carbon reductions than using these techniques separately.
Project engineers and construction specialists were tasked with picking up and moving the magnificent 5-story structure. The project began by rotating the original section of the old hotel 50 degrees. Then, it was moved 350 feet as part of a redevelopment project. At 1,750 tons, it was a phenomenal achievement.
This mixed-use building sits above the Seattle Fault Zone, vulnerable to shallow earthquakes. The foundation and shoring system faced problematic conditions with a building just a few inches away and the tectonic sheered façade created different residential floor plates with variable cantilevers, posing an intriguing balancing act.
This project features a 50-story ultra-luxury mixed-use residential tower on top of a three-story podium. Elements of the project required unique solutions – from foundations and tight site parameters to occupant comfort and lateral systems, concrete strength, and the need for “walking columns” to capture additional floor area.
on once-in-a-lifetime projects, every day.
By Scott Stewart, S.E., et al.
This project includes an eleven-story Long Beach City Hall tower, eleven-story Port of Long Beach Headquarters tower, and single-story City Hall Council Chambers. All three buildings sit on top of a standard two-story subterranean parking garage. Desiring sustainability and resilience, the City adopted the Resilience-based Earthquake Design Initiative rating system.
The 19-story-tall facility will be Boston University’s tallest and largest 100 percent fossil-fuel-free building. Targeted to attain LEED Platinum, the building incorporates several high-performance sustainability features. This project yielded relatively significant reductions in the structural system’s embodied carbon. Many lessons learned will be employed in future projects.
Editorial From Caterpillar to Butterfly: If the Butterfly Could Talk...
By Carol Martsolf, P.E.
Building Blocks Sustainability and Beyond
By Laura Micheli, Ph.D., Bruce Brothersen, P.E., S.E., P.Eng, and Scott Russell, P.E., S.E., P.Eng
Structural Systems Reciprocal Frame Structures
By Jens Hübertz Larsen and Olga Popovic Larsen, Ph.D.
InSights Look (Way) Up By Thomas Wu, Ph.D., P.Eng, P.E., S.E., Daria Khachi, B.Eng, M.Eng, P.Eng, and Craig Applegath, Architect AIBC, AIA
Guest Column Bending and Shear Properties of Structural Glued Laminated Timber By BJ Yeh, Ph.D., P.E.
Structural Design Designing with Force-Transfer Shear Walls
By Michael Deigert, P.E., S.E., and John Lawson, P.E., S.E.
InFocus Automation and the Future of Structural Engineering –Installment 3 Eytan Solomon, P.E.
Advertiser Index
Resource Guide – Tall Buildings
NCSEA News
SEI Update
CASE in Point
Publication
CASE Business Practices Grade-Level Floors over Expansive Soils By Shruti Sharma, P.E.
CASE Spotlight Rainier Square’s History-Making Engineering
By Ron Klemencic, P.E., S.E., Hon. AIA
Organizations that promote and foster diversity, equity, and inclusion (DEI) are, according to recent studies, more successful and have higher retention rates. According to McKinsey &Company, leaders in ASCE who “walk the talk” of diversity, equity, inclusion, and justice also financially outperformed competition and have stronger boards. Performance, in general, is enhanced. These companies create safe spaces for their employees to discuss issues.
Conversations surrounding diversity, equity, and inclusion often lay the foundation by emphasizing a safe space. But, when you read the word safe , what do you think? Typically, it means no harm However, being safe does not mean being comfortable. In fact, most conversations that pave the way toward building truly inclusive and equitable environments are far from comfortable. Just like the cat erpillar growing wings and emerging as a butterfly – it takes time, energy, and support. It may be uncomfortable and even painful to crack through the cocoon protecting it, but eventually, the butterfly emerges stronger than before.
How can we work together to help people have the kinds of conver sations that may be uncomfortable while maintaining a safe space?
1) Lay ground rules ahead of time, so people know what is expected of them when discussing DEI. These rules can be called Group Agreements. Everyone in the group will be expected to suspend judgment and maintain an open mind.
2) Create an atmosphere that promotes trust: Build and main tain a trusting environment. DEI conversations can often become personal, and people need to know that what they say will be kept only within the group and that the group members can feel safe to share honestly. People will not be transparent and share their true feelings if they think they will be shared later with a broader audience.
3) Foster Active Listening: Say what? We are all guilty of doing it – someone is talking, and you are thinking about your response, what to eat for dinner, or the email you still need to send out. Be present. It is important to put in a conscious effort to hear the words someone is speaking and the complete message that is being conveyed. Listen to understand by paying careful attention to the person speaking. Instead of allowing distractions in thought or extraneous things going on around you, practice active listening and listening with the intent to understand. It is also easy to fall into the habit of forming counter-arguments in your head or creating a defense to what is being shared. Again, active listening is a skill that needs to be practiced, especially in difficult or uncomfortable conversations.
4) Use “I” statements when describing an issue surrounding DEI. Be sure to say how you feel using “I” statements instead of “You did…”. Starting the statement with “I” can reduce
defensiveness, whereas starting with “you” may unintention ally place blame on the other person. This also helps the recipient(s) hear what you are saying more openly and will ingly. Try it out a few times – it is also a valuable tool to use in non-DEI-related conversations.
5) Assume Best Intentions: When you have hard discussions around DEI, sometimes statements can appear to come from a place of bad intent. Avoid this assumption. Set your default to – assume what is being discussed is through the very best intent by the person speaking. So, if someone accidentally says, “You did…,” try not to jump to your defensive position immediately.
6) Lean Into Vulnerability: DEI discussions can often make you aware of previously overlooked things and may uncover some sensitivities. If we build up defenses against our vulner abilities by avoiding or minimizing those feelings, we are not being honest with ourselves. If we expect others to be open with us, we must first be honest and open with ourselves. Lean into the discussions.
These discussions are hard, painful, and sometimes they do not make sense. But they are important and necessary, and they help lay the groundwork for growth. So many people have built their own cocoons as a layer of protection, but it is time to all work together to create an environment where we all feel safe to break free.
Here is a challenge for you: go to https://bit.ly/3w2VrKd and choose ONE element of the guide to implement. Then, please write to me at ccmartsolf@urbanengineers.com and let me know what one you selected to implement! And remember…lean into any vulnerability or discomfort. You will discover the posi tive change that you may not have imagined.
■
Carol Martsolf is Vice President and Chief Learning Officer for Urban Engineers, Inc. (Urban Training Institute). She is a former President of the ASCE Philadelphia Section, past ASCE Region 2 Governor, and Chair of ASCE MOSAIC – Members of Society Advancing an Inclusive Culture.
The concept of Urban Sequoia (Figure 1) combines optimized structural design with low embodied carbon materials, efficient construction, and carbon-capturing technologies. These carboncapturing approaches allow buildings to start their service life with an ultra-low embodied carbon and sequester additional carbon over time, becoming net carbon negative. The structural approach to Urban Sequoia incorporates nature-based, living materials that embody far less carbon than conventional structural solutions while absorbing additional carbon over time. When combined with non-structural systems such as exterior wall systems that incorporate biomass and algae and technologies including Direct Air Capture (DAC), tall buildings could absorb three to five times the amount of carbon emitted at the time of construction. Urban Sequoia includes ideas that can be applied to buildings at all scales and uses. The floor framing system, for example, could be used in a building with only a few floors or one that has a hundred floors. The strength of the concept is enhanced when buildings that make up a city combine to become a source of biofuel that can be used to power heating systems, automobiles, and aircrafts and create bioprotein. An even broader impact could include using carbon byproducts for infrastructure.
The initial embodied carbon in a structure must be driven to abso lute minimums to go beyond carbon neutrality. Materials and construction are vital components in a building’s initial embodied carbon assessment. Materials must have low embodied carbon, high strength-to-weight ratios, components with injected carbon, and components that have already sequestered carbon. The construction process must require minimal time to build and include alternative processes such as robotics. Before conceptualizing the structural design of Urban Sequoia, available low-carbon materials and emerging technologies needed to be understood and a construc tion process curated for them.
High-strength materials combined with optimization analyses that carefully assess the placement of materials for given loadings are an essential initial basis for design to reduce embodied carbon. However, this approach alone is not nearly enough. Advancing existing materials to lower their embodied carbon and developing new building materials which absorb carbon is also essential to success.
Portland cement is currently responsible for more than 5% of global CO2 emissions. Therefore, low embodied carbon products used to replace part or all of the portland cement content in concrete like fly ash or slag can directly impact and significantly reduce global carbon emissions. An alternative Supplementary Cementitious Material (SCM) is recycled ground glass.
Low-carbon concrete made with carbon-neutral portland cement and other cementitious materials could become an environmentally friendly material that yields similar or superior performance characteristics to traditional portland cement and has a low carbon impact. Unlike ordi nary portland cement that is made by thermally decomposing limestone (CaCO3) into lime (CaO) and CO2, a process that emits 0.7 to 1.3 tons of CO2 per ton of cement, an emerging technology allows for the extraction of lime (CaO) from any calcium bearing-rock or minerals. This method can use an acid (e.g., H2SO4) or a combination of acids plus a calcium bearing-rock or mineral to produce a calcium salt (e.g., CaSO4) then hydrate or thermally decompose this salt to produce lime (CaO) while eliminating the CO2 emission compared to traditional lime extraction. Furthermore, as a waste byproduct of this process, magnesium hydroxide (Mg(OH)2) can absorb CO2 from the air result ing in magnesium carbonate (CMgO3) that permanently sequesters CO2. The overall process reduces the CO2 emissions associated with portland cement production by up to 60%, which, combined with the sequestration from magnesium hydroxide, renders the final produced cement net-zero or even net negative carbon.
High-strength recycled steel typically contains up to 70% recycled content. Strengths of available structural steel and reinforcing steel for concrete continue to increase along with increasing fire and cor rosion resistance. Ultra-high-strength reinforcing materials such as
carbon fiber offer an excellent alternative to conventional reinforcing in concrete and can also replace high-strength reinforcing steel com monly used for prestressing.
Structural materials which sequester and store carbon over their life include algae-based concrete, hempcrete, timber, Mycelium, and carbon sequestering fillers and aggregate. Algae-based concrete, developed at the University of Colorado Boulder, is a Living Building Material (LBM) created by combining a sand-hydrogel scaffold with Synechococcus sp. PCC 7002, a photosynthetic cyanobacterium. The algae-based concrete is essentially made of food-based products and uses biology to provide a structural binder to any aggregate type. When using fine sand without coarse aggregate, the structural material strength of the algae-based concrete is comparable to common concrete masonry units, with the advantage that the tensile strength of the material is considerably higher, offering a potentially wide range of applications where some tension demands exist.
Hempcrete is a biocomposite material that is a mixture of hemp shives (the woody inner portion of the hemp stalk broken into pieces), water, lime, and sand or cement binder. The strength of the material is limited, so the use is typically appropriate for nonstructural components.
Carbon sequestration of timber-based products occurs when atmo spheric CO2 is sequestered in the production of biomass through photosynthesis. The trees emit oxygen in return and permanently store the carbon until the material is combusted for fuel or decays in a landfill. Bamboo and other fast-growing grasses, including straw, are considered one of the best carbon-sequestering materials because of the rate at which they grow. For example, Guadua Angustifolia bamboo sequesters as much carbon in 6 years as Douglas fir does in 34 years.
Mycelium consists of a mass of thread-like branching fungus and is typically combined with natural fibers to increase its strength characteristics, and are used in non-structural components (e.g.,
insulation). Although overall material strengths are low, Mycelium has an excellent strength-to-weight characteristic.
Finally, emerging technologies have resulted in carbon sequester ing aggregates that can sequester carbon from the atmosphere. For example, through the process of mineralization, carbon is captured from natural gas-fired or similar fossil fuel-generated energy facilities and permanently stored in synthetic limestone.
A significant amount of carbon is emitted during the construction process, in some cases accounting for up to 25% of a building’s embodied carbon. The carbon associated with site construction includes emissions from machinery required to build, materials shipped from disparate locations, transportation of personnel required, and the like. Given the known properties of low carbon materials, how do we design for construction differently? What properties does low portland cement or even low-carbon concrete have, and how do we address them via the construction process, such as setting time? What type and size of steel are available from electric arc furnaces fueled with renewable energy? The answers to these questions should inform structural design.
As a widely used material for building structures, concrete has known embodied carbon associated with the construction process primarily centered around formwork and the number of days per floor in the construction cycle. Optimizing cores and columns for ease of vertical forming systems and floor plate geometry for ease of horizontal form ing systems can help reduce floor-to-floor cycles from 7 days to 5 days to even 3 days. A common characteristic of low portland cement and low-carbon concrete is low early strength and extended time to gain higher design strengths. While this seems at odds with the desire to achieve fast floor-to-floor cycles, the construction process could involve
precast to allow the material to reach necessary strength off-site and be quickly erected on-site, still achieving fast floor-to-floor cycles. Another approach is to provide formwork systems that are part of the permanent structural design, such as algae-based concrete or similar carbon-neutral materials from emerging technologies. These formwork systems are not removed, allowing the low-carbon concrete to have extended time to reach design strength. These approaches to the construction process lead to the pre-assembly of major building components to minimize construction time, waste, and associated carbon.
The Urban Sequoia Tower is conceptually organized around a tubular geometry integrating systems of vertical circulation, movement of air to the Direct Air Capture system, and movement of biomass and algae around the perimeter of the program space. The programmatic space is organized into eight petals around the tubular core (Figure 2, page 11). The structural system is directly integrated into this tubular geometry. It is articulated in a central structural core, perimeter gravity columns, and a floor framing system spanning between the core and the perimeter columns.
The low-carbon concrete core is considered a circular tube divided into four quadrants. Each quadrant contains two circular shafts forming the basis of the precast concrete module. Elevators can occupy a circular shaft, or two shafts could be combined to create a stair shaft. The shafts are lined with a recycled steel liner that extends above the top of the precast, serving as a shear key between precast units. The precast units are vertically tied together with vertical post-tensioned recycled steel strands and linked horizontally with a link beam element (Figure 3). Perimeter precast columns with low-carbon concrete are located in the inner concave portions of the petals’ geometry. The horizontal framing system is similarly organized around the eight programmatic floor spaces directly connecting the perimeter columns to the center
core. The low-carbon precast beam framing is curved in plan around each petal, leaving an open circular floor space in the center of each petal (Figure 3). The precast beams incorporate prefabricated ducts for post-tensioned strands and large diameter air ducts to directly capture outside air from the perimeter and channel it to the central tubes inside the core using the naturally occurring positive and negative air pressures from wind. The precast columns are also laced together with post-tensioned strands made with recycled steel.
The circular floor space between post-tensioned precast beams is infilled with leave-in-place algae-based concrete masonry formwork cast into eight pie-shaped elements and an octagonal (or circular) centerpiece. The pie-shaped segments are vaulted to keep the mate rial in pure compression and minimize the thickness required. The flooring system is completed with a low-carbon concrete topping slab that works compositely with the formwork (Figure 3).
The continuously growing industry of residential high-rise construction provides a meaningful basis to evaluate the carbon emission reduction potential of the Urban Sequoia Tower. The Benchmark Tower project is a high-performing 42-story, 420-foot-tall, 450,000-square-foot reinforced concrete residential tower recently designed and constructed in San Francisco (Figure 4a, page 14 ). The structural system for the tower includes a core-only lateral load-resisting system and perimeter gravity columns with post-tensioned flat slabs for the gravity system.
The typical tower floor plan and size of structural elements are illus trated in Figure 5a (page 15). This project is located in a high seismic hazard zone and was designed with particular attention to seismic resilience and environmental sustainability.
The tower considered was designed using a performance-based design process and was highly optimized in terms of structural material utilization compared to other structures of similar height,
Now you can specify a single connector for several jobs.
New from Simpson Strong-Tie, the code-listed LTTP2 light tension tie securely attaches wood joists to concrete or masonry walls. With allowable loads 25% higher than previous models, it enables greater design flexibility. This versatile connector has two distinct nailing patterns for horizontal installation as a tension tie with I-joist purlins or 2x solid sawn purlins. Also suitable for vertical installation as a holdown, it has an extruded anchor bolt hole that accommodates multiple bolt diameters. The LTTP2 can be fastened with nails or Strong-Drive ® SD Connector screws. Select the LTTP2 and Simpson Strong-Tie fasteners for your next project. To learn more, visit go.strongtie.com/lttp2 or call (800) 999-5099.
geometry, and site characteristics. is approach led to a reduction in structural embodied carbon by more than 20% compared to a similar building.
e total embodied carbon equivalent intensities associated with A1-A3 (Cradle-to-Gate) Life-cycle stages, according to the EN 15804 standard for the primary structural components for the Benchmark Tower, are reported in Table 1 (page 12) for reference.
e Urban Sequoia Tower represents the next generation of residential buildings with excellent opportunities to reduce embodied carbon and become net negative carbon over its operational life. For example, considering an Urban Sequoia Tower of equivalent floor and total area to the Benchmark Tower results in an overall tower diameter of 126 feet (Figure 5b) with the same typical 10-foot floorto-floor height, number of stories, and total tower height.
e precast cellular core has wall thicknesses varying from 24 inches at the base to 14 inches at the top and utilizes low-carbon concrete with a strength of 8,000 psi at the bottom two-thirds of the tower and 6,000 psi in the top one-third of the tower. e crescent-shaped precast columns vary from 170 by 30 inches at the base to 170 by 20 inches at the top. e columns utilize low-carbon concrete with a strength of 8,000 psi in the bottom two-thirds of the tower and 6,000 psi in the top one-third of the tower.
Figure 4. Axonometric view of the Benchmark Tower (a) and Urban Sequoia Tower (b).
e total embodied carbon equivalent intensities associated with the primary structural components for the Urban Sequoia Tower are summarized in Table 2.
e total A1-A3 structural embodied carbon of the Benchmark Tower adds 9,500 to11,700 tons of CO 2e, while the Urban Sequoia
Tower contains only 2,800 to 3,400 tons, representing more than 70% reduction in CO 2e. is extremely low starting point for structural embodied carbon is achieved by employing technologies available today or otherwise close to commercialization. Further embodied carbon reduction will be achieved by replacing low
Table 2.
Structural Element
Precast shear wall core
lb.CO
lb.CO
Tendon
Reinforcement
lb.CO
1.2~1.4 1.7~1.9 1.4~1.7
Precast columns 0.3~0.4 0.7~0.9 0.7~1.0
Precast beams and girders
Algae-based
carbon metrics
1.2~1.4 0.9~1.1 0.2~0.4
Plate
lb.CO
the miscellaneous
elements
not listed in the
carbon metrics are taken as 106~139 lb.CO2e/cy based on the NRMCA, Member Industry-Average EPD for Ready Mixed Concrete and modified for Low-Carbon Concrete emerging technologies.
3Embodied carbon metrics are taken as 2.27 lb.CO2e/lb based on the ICE, Industry average: Steel, Wire rod.
4Embodied carbon metrics are taken as 0.49 lb.CO2e/lb based on the Nucor Recycled Steel Rebar EPD.
5Embodied carbon metrics are taken as 1.26 lb.CO2e/lb based on the CLF, 2021 Material Baselines.
alone yields net carbon absorption (net-zero with the current assembly process).
carbon concrete with biogenic materials, opening up avenues to structural embodied carbon neutrality. For example, with the current developments of the algae-based concrete material, it is anticipated that the material and related assembly process will yield net carbon absorption. Nevertheless, the low embodied carbon based on today’s technologies combined with the additional carbon absorption enabled by the algae façade and the Direct Air Capture technologies renders Urban Sequoia a net-negative carbon emission Tower over its lifetime. It is estimated that the Urban
Sequoia Tower in Figure 4b can absorb 39,000 tons of CO 2e over a 60-year life span, where 25% of operational carbon sequestration comes from the algae façade and Direct Air Capture technologies sequester the remaining 75%.
The Urban Sequoia concept combines a broad range of sustainable design thinking, including emerging technologies, and applies them at scale in a tower. By combining optimized structural design resulting in minimal materials and integrating biomaterials, biomass concepts, and carbon-capturing technologies into an integrated system, the Urban Sequoia can achieve substantially more carbon reductions than using these techniques separately. Combining these systems in a typical residential tower based on today’s technologies can result in the sequestration of as much as 650 tons of carbon per year, equivalent to 31,500 full-grown trees each year.
The authors would like to acknowledge Professors Srubar, Cameron, Cook, and Hubler at the University of Colorado, Boulder, and L. Burnett at Prometheus Materials for provid ing insight into their research on Living Building Materials and the algae-based concrete’s structural material properties. They would also like to acknowledge the Skidmore, Owings & Merrill (SOM) Architecture Group and the SOM Research + Innovation (R+I) Group for collaborating on developing the Urban Sequoia concept.
■
References are included in the PDF version of the online article at STRUCTUREmag.org
All authors are with Skidmore, Owings & Merrill.
Mark Sarkisian is a Partner (mark.sarkisian@som.com).
Eric Long is a Principal (eric.long@som.com).
Alessandro Beghini is an Associate Principal (alessandro.beghini@som.com).
Karl Micallef is an Associate (karl.micallef@som.com).
Shahab Jaberansari is a Structural Designer (shahab.jaberansari@som.com).
The attributes of open web steel joists are well known to the structural engineering and construction community. Their efficiency, high strength-to-weight ratio, versatility, ease of erec tion, high durability, and cost-effectiveness make steel joists and joist girders a common consideration for today’s roofing and flooring systems. However, the manufacturing of open web steel joists and joist girders is often left out of the discussion, leaving engineers and decision-makers wondering what kind of processes occur behind the curtains of the manufacturing plant. This article aims to shed light on the typical life-cycle stages of steel joists, from steel production to building decommissioning, leading the readers into the realm of open web steel joist and joist girder manufacturing and sustainability.
The life cycle of a steel joist starts in the steel mill, where angles, rods, and bars are manufactured. In the mill, steel can be produced with two types of furnaces: 1) a combination of integrated blast furnace (BF) and basic oxygen furnace (BOF), or 2) an electric arc furnace (EAF). BF/BOF produces steel from mined materials, such as iron ore, coal, and limestone. First, purified coal, limestone, and iron ore are heated in the BF. The resulting product is then passed to the BOF, where oxygen is injected to reduce carbon content and impurities. From there, the liquid steel is cast and created into various steel products.
On the other hand, EAFs produce steel from recycled scrap material by melting the scrap with an electrical current. A small percentage of direct-reduced iron (DRI) and other material inputs can be added to the liquid steel to achieve the desired steel grade. EAFs are remarkably environmentally friendly relative to BF/BOFs, given their electricity usage as an energy source and recycled steel as the primary input.
It is estimated that EAFs produce 85% less greenhouse gas (GHG) emissions per ton of steel than BF/BOFs. While BF/BOF are widely spread in other parts of the world, in the United States, steel is mainly produced with EAFs. Specifically, 2019 data estimates that 70% of the total steel produced in the United States was by the EAF route. Products used in steel joist manufacturing are almost exclusively cre ated by the EAF process. The authors limited discussion to processes and products used for steel joists for this article.
Figure 1 schematically depicts the steel production process with an EAF. After the scrap is melted in the EAF, the furnace is de-energized and the liquid steel is poured into a ladle. The ladle transports the liquid steel to a stir station, where it is fed into a tundish through a ceramic tube. Subsequently, the tundish distributes the liquid steel to the caster, where continuous casting occurs, as shown in Figure 1 Next, each strand of the caster flows into a mold of the desired semifinished shape, which is typically cooled with cold water. At this stage, the liquid steel starts to solidify. There are three main types of semifinished products: blooms, billets, and slabs, which differ in shape and dimensions. Semi-finished products are then passed through a
reheat or normalizing furnace, where the steel is brought to the proper temperature before entering the rolling mill. Finally, in the rolling phase, billets are rolled to achieve the selected product shape (e.g., angle, rod, bar, plate) and cut to the desired length.
Angles, rods, plates, and bars produced at the steel mill are trans ported to the joist manufacturing facility, where they are assembled to form the selected joist series configuration. Joist series include K-series, typically employed for spans up to 60 feet, LH-series for longer spans well over 100 feet, and joist girders. Composite and special joists (e.g., single-pitched, multi-pitched, curved joists) are also regularly used. The steel joist’s chord, web, and bearing seat com ponents are carefully designed to achieve the required load-bearing capacity and meet specified design requirements. Joist components are then welded together, as shown in Figure 2. Finally, joists are coated with a primer to protect them from weather and corrosive substances during transportation to the site.
The above-described manufacturing processes produce GHG emissions. Information on the carbon footprint of the steel joist manufacturing process can be found in the Environmental Product Declaration (EPD), a report summarizing a product’s environmental impact. EPDs can be obtained by conducting a life-cycle assessment (LCA) that considers three main life stages: raw material supply (stage A1), transportation (stage A2), and manufacturing (stage A3). The results of the LCA are expressed in terms of six impact category indicators: global warming potential (GWP), ozone depletion potential (ODP), acidification potential (AP), eutrophication potential (EP), smog formation potential (SFP), and abiotic depletion potential (ADP). Out of these six impact category metrics, the GWP is the metric most commonly used to represent the carbon footprint of a given product. The Table reports the industry average values of the six impact category indicators for steel joists, derived from the EPD available on the Steel Joist Institute website (https://bit.ly/3Fc31qn). Such values refer to the production of one metric ton of joists and reflect the weighted industry average of different companies that manufacture steel joists. The EPD also reports that the industry average recycled content of open web steel joists and joist girders is 85%. On the other hand, the impact category indicator and recycled content values for a selected joist manufacturer can be found in the manufacturer-specific EPD, which contains information regarding their exact manufacturing process. The EPD also includes a description of the joist production process and the boundaries con sidered in the LCA.
The background LCA conducted to obtain the EPD of a given product typically spans only the raw material supply, transportation, and manufacturing life stages, referred to as “cradle-to-gate.” Selecting the construction material with the lowest GWP in the EPD does not necessarily correspond to the most sustainable solution for the whole building. In civil structures, other life stages (e.g., maintenance, repair, energy use, demolition, recycling) need to be considered to evaluate
the global carbon footprint of a building throughout its life cycle. This can be accomplished by performing a whole-building life-cycle analysis (WBLCA). Furthermore, EPDs of diverse construction mate rials (e.g., wood, steel, concrete) may be derived following different regulations and assumptions and considering different units of a given product. For example, steel EPDs usually refer to one metric ton of product, while wood products refer to one cubic meter of product. Therefore, a direct comparison between the GWP reported in EPDs of different construction materials may lead to incorrect results. The strength-to-weight ratio of steel is greater than wood and concrete, making the comparison based on weight even more complex.
From the values reported in the Table, it is evident that the life-cycle stage contributing most to the GWP is stage A1, which for steel joists is represented by the manufacturing process of the joist components. One strategy to reduce the carbon footprint of steel manufacturing could be to employ renewable sources to energize the electric grid and, thus, EAF mills. The use of solar, hydroelectric, geothermal, and wind power could significantly reduce greenhouse gas production associ ated with electricity generation, which would lower the GWP values of steel production. However, the usage of renewable energy sources might depend on regional availability. Some steel manufacturing companies in the United States are investing in and promoting the
Figure 3. End-of-life of a steel joist: after usage, the joist components can be dismantled and recycled.
creation of solar and wind farms to fuel their manufacturing plants with renewable energy locally.
Another decarbonization strategy is through the use of carbon offset credits. A carbon offset represents a reduction of CO2 (carbon diox ide) or other GHG in the atmosphere to compensate for emissions created by the manufacturing or transportation process. Typically, carbon offset credits fund projects aimed at decreasing GHG in both the short and long terms, such as constructing wind farms, hydro electric dams, destruction of landfill methane, and forestry projects. In the steel industry, Nucor pioneered the use of carbon offsets with the Econiq™ trademark. Econiq enables achieving net-zero emission targets by balancing scope 1 emissions with carbon offsets and scope 2 emissions with renewable energy credits via virtual power purchase agreements (VPPA). In this context, scope 1 emissions refer to the direct GHG emissions generated during manufacturing. In contrast, scope 2 emissions refer to the indirect emissions related to energy sources, such as electricity, steam, or cooling.
Lastly, ongoing research is investigating the potential of green hydro gen-based DRI production, where fossil fuels are replaced by hydrogen generated via renewable energy. In combination with EAFs energized with renewable power sources, hydrogen-based DRI can lead to the manufacturing of high-quality steel with a significant reduction in environmental impacts. However, hydrogen-based DRI is still in its infancy and far from widespread implementation due to high costs and low production efficiency.
Open-web steel joists are 100% recyclable at the end of their useful life. After the building is decommissioned, steel joists can be removed, transported to a scrap collection facility, and recycled to produce new steel, as schematically shown in Figure 3. This circular process of steel production and recycling truly makes steel a “cradle-to-cradle” mate rial. Steel components can be continuously recycled into new steel, which can be used for new products with no loss of metallurgical properties. This feature makes steel joists and all other steel products ideal for a circular economy. Note that a circular economy supports reusing and recycling a product, avoiding waste, and preventing the material from being discarded after its first use. In a circular economy, resources are kept in a circulatory system, and the materials are returned over and over in the recycling cycle.
In December 2021, the Biden Administration released a new federal sustainability executive order. Although quantifiable targets have not been set yet, the sustainability order explicitly supports a transition to a circular economy, aiming to drastically reduce the construction and demolition waste disposed of in landfills by 2030. Assessing the environmental impact of construction materials from a circular economy perspective could lay the foundation for a more sustainable future. Producing a product housed within a circulatory system may be more sustainable than singular-use products highlighting sustainable
attributes and manufacturing practices only from cradle-to-grave, particularly when the grave is a landfill.
Moreover, open web steel joists and joist girders have high durability. They are not sensitive to time-dependent phenomena like wear, creep, or strength loss. In the United States, joist manufacturing dates back to the 1920s. However, steel joists are still in place and functioning as originally intended, regardless of their manufacturing date.
When a building becomes obsolete, either a retrofit is needed, or the building is demolished. Existing joists can be retrofitted and/or reinforced to satisfy design requirements under some conditions for buildings that are being retrofitted. Tools and documented procedures to evaluate existing joists are available on the Steel Joist Institute web site (www.steeljoist.org). As discussed above, all the steel components can be captured and recycled into new steel products when a building is demolished. Many other construction products “can” be recycled, but the cost is more expensive than just creating new products. This is not the case with steel. Steel scrap is needed in many industries, has a monetary value, and is a commodity traded worldwide.
Not only can steel joists be infinitely recycled, but they may be dis mantled for reuse. For example, 446 open-web steel joists were reused to construct the Roy Stibbs School, an elementary school in West Coquitlam, British Columbia. A fire damaged a portion of the original school building, and it needed to be rebuilt. In the same period, a nearby school, the Cassiar, had been decommissioned and needed to be demolished. The steel joists from the Cassiar were dismantled and reused in the new Roy Stibbs School facility to expedite the construc tion process, leading to remarkable cost savings. Another example of open web steel joists reuse is the Mountain Equipment Co-op in Ottawa, Ontario. The facility was built on a site previously occupied by a 40-year-old two-story grocery store. The existing structure was carefully disassembled, and the majority of the steel components were reused in the new Mountain Equipment Co-op retail store. Among those components, 50% of the total roof joists in the new building were reused joists, supplemented with new open web steel joists to accommodate the rooftop equipment loads.
Open web steel joists are in a promising position to support a circular economy and zero waste policies, given their high recy cled content, reuse potential, and cradle-to-cradle properties.■
References are included in the PDF version of the online article at STRUCTUREmag.org
Laura Micheli is a Research Engineer in the Innovation Services Group, Nucor, St. Joe, Indiana (laura.micheli@nucor.com).
Bruce Brothersen is a Senior Innovator in the Innovation Services Group, Nucor, Brigham City, Utah (bbrothersen@vulcraft-ut.com).
Scott Russell is the Manager of the Innovation Services Group, Nucor, Norfolk, Nebraska (scott.russell@nucor.com).
You may know Vulcraft for its high-quality steel joists, deck and grating. But did you know that more than 70 percent of all our products are produced from recycled scrap steel?
And our eco-friendly responsibilities don’t end there. All of our divisions are committed to being “good neighbors”
and take seriously their role of protecting the environment in and around the communities they operate.
It’s not only good for the environment and good for our neighbors, it’s just good business.
Reciprocal frames (RF) are a family of structures that increasingly are attract ing interest from many participants in the construction industry. They offer architec tural opportunities through their expressive form and structural advantages due to their specific configuration. This article describes what makes this type of structure so differ ent from other systems.
A possible definition of a reciprocal frame is a grid of linear members where each member simultaneously supports and is supported by its neighboring members. Therefore, the members are structurally interdependent and in a structural hierarchy of equal importance. Although the basic RF configurations are typically used to enclose a regular rectangular/polygonal plan form, current built cases have also presented reciprocal frames with irregular shapes. Up-to-date digital design tools enable a broad spectrum of opportunities for RFs, facilitating the design and fabrication of complex RF geometries and building typologies for diverse purposes.
Figure 1. Sebastiano Serlio: flat beam grillage for a 15-foot span floor. Drawing by Cheng Sin Ariel Lim.
Historically they were used in flat beam systems for forming floors in covered spaces where the span exceeded the avail able timber lengths, spanning over circular or rectangular spaces, as illustrated by Sebastiano Serlio (Figure 1). Leonardo da Vinci sketched reciprocal frames as tempo rary bridges using a system of timber beams to create a simple structure with relatively short timber members and simple con nections, which would have been easy to construct (Figure 2). The timber members are used as they are, without any cuttings/ notches, and are simply held together through friction.
Reciprocal frames have been known for centuries, and there are numerous examples from the Middle Ages, Renaissance, and later periods from studies/drawings and built examples. Traditionally these frames were made of wood, the most readily available linear building material. They were used in buildings and bridges for permanent and temporary structures. Reciprocal frames are also known under the term nexorades in some literature. The British inventor Graham Brown built a number of reciprocal frames and coined the term reciprocal frames in the 1980s. However, it was only much later that the structures were researched and analyzed in depth.
The RF has also been used for curved structures such as vaults or domes. The Zollinger frame, developed by the German engineer Friedrich Zollinger and patented in 1926, is also a type of RF structure. The Zollinger frame can form a vault by using short lengths of timber that are connected at the half-points with equal elements forming rhombic (diamond) shapes. The connection of RF beams occurs at the same level, unlike a typical RF structure where the beams are sitting on top of each other after transferring the loads through notched carpentry connections. As a result, the load path in the Zollinger frame is more direct than in ordinary RFs because the members are at the same level due to the connections. Therefore, compression is dominant. Figure 3 is a drawing of a built Zollinger Frame, Alvaro Siza’s pavilion for the Serpentine Gallery in London constructed in 2005. The structure uses a common type of connection detail where all members are connected in the same plane, thus avoid ing eccentricity and ensuring an efficient load transfer. However, the
Figure 2. Leonardo da Vinci’s proposals for temporary bridges. Drawings by Cheng Sin Ariel Lim.
Figure 3. Zollinger frame type of reciprocal frame. Serpentine Gallery Pavilion, London, 2005. Architect: Alvaro Siza. Engineer: Cecil Balmond. Drawing by Cheng Sin Ariel Lim.
Figure 4. Zollinger frame. Left: principle of configuration. Right: example of the type of connection detail. Drawings by Cheng Sin Ariel Lim.
members are connected with a small offset in the plane, simplifying the execution of the connection (Figure 4 ).
In recent years RF structures have been used relatively frequently in Japan, building on a long tradition that has utilized timber and traditional connections. A prominent example is the Seiwa Puppet Theatre, Kumamoto, Japan, by architect Kazuhiro Ishii (Figure 5 ). The puppet theatre forms part of a cultural center with several buildings consisting of various reciprocal frame types.
The simplest reciprocal frame consists of at least three linear mem bers connected in a circular way to form a flat or pitched structure spanning a triangular or round plan space (Figure 6 ). The simple three-member structure can be expanded with more beams to form a roof over rectangular or polygonal spaces. When the members are connected, a multifaceted area is formed. For the simple threemember frame, this is a triangular area; for a six-member frame, the space forms a hexagon.
The simple frames described above can be connected to create com plex structures, such as domes, vaults, or free-form structures. For example, a small team erected a complex reciprocal frame structure in Copenhagen in 2017 using only handcraft and no machinery (Figure 7, page 22). The structure was erected in just 15 minutes. Note that the relatively low friction between the timber members and the paved street surface is sufficient to stabilize the structure.
In principle, all materials such as concrete, timber, or steel can be used in RFs. However, in practice, timber is best suited to the structural type because of its natu ral linear form. Thus, unsurprisingly, the majority of RF-built examples are in timber. In addition, especially at present, RF research focuses on timber because it is versatile and sustainable. Current RF research explores the possibilities of using short-length, re-used timbers to construct reciprocal frames, which further reduces the already low carbon footprints of RF structures.
An unusual example of an RF structure where steel instead of timber was the primary construction mate rial is the Rokko-Shidare observatory near Kobe, Japan (https://bit.ly/3vTcvUs). The observatory is
positioned at the top of a mountain, and the structure consists of tubu lar steel members with connections using thin and flexible steel ties.
RFs are a family of beam grid structures. Fundamentally, the reciprocal frame members are supported at each end and carry the load from one or more neighboring members along the length. Compared with better-known types of structures such as grid shells, grid domes, or trusses, forces in these structures are mainly transferred via normal forces, compression and tension, and forces are transferred at the ends
of members. The forces in reciprocal frames are transferred mainly via bending and shear in the members and are transferred both at intermediate points and endpoints of members.
If a load is applied to the structure at any point, all the other members contribute to transferring the load to the supports. This is a unique aspect of reciprocal frames: all the members have structurally equal importance (i.e., there is no hierarchy of primary and secondary ele ments as in most other structural frame systems). All elements in an RF rely equally on the neighboring elements for support and provide support to the same elements in return. In this type of structure, robustness and progressive collapse are essential issues to be dealt with. In very simple reciprocal frames arranged in a closed circuit (for example, forming a structure with one RF closed polygon with 3, 4, or more beams), removing one member would typically lead to a col lapse because all members are structurally interdependent. However, this problem can be overcome by using multiple, interconnected frame systems with inherent redundancy because they have multiple alternative load paths. There is also the possibility of designing the joints with a degree of rigidity (i.e., bending capacity), which adds redundancy and, therefore, robustness to the structure.
In RFs, bending is dominant, especially in the region of the beams where they support neighboring members. The relationship between the engagement lengths (distance between inner supports in relation to outer beam supports; lengths x1 and x2 in Figure 6 ) determines the relative size of shear force and bending. In frames with a curved shape, there are also normal forces in the members; the greater the curvature, the greater the normal forces in relation to the dominant bending and
shear. However, the size of the normal forces also depends on other factors, such as the eccentricity of the connections.
The eccentricity (e) is defined as the vertical (orthogonal) distance between centerlines between two connecting members (Figure 6 ). RFs start to behave like regular beam grid structures when e is made smaller. Load paths in RFs cannot always be intuitively understood. The beam depth and the eccentricity at the connections are essential parameters in the form-finding, and structural design cannot be separated from detailing.
Form-finding in three dimensions requires advanced computational tools for larger and more complex RF structures. The complexity of RF design is successfully handled through current parametric design tools, offering possibilities of optimization and reduced material use. For example, Rhinoceros 3D and Grasshopper are parametric design tools used to define overall geometry and superimpose an RF pattern over the main geometry. The analysis tool Caramba is an example of an analysis tool that has been used for RF frame systems.
Effects of creep in timber are important and need to be considered in the analysis. Deformations in RF structures are generally larger than in similar span regular structures. This is mainly due to the relatively large number of connections, which in timber are less rigid than in other materials.
One of the main challenges of designing large, complex RF structures is defining geometry. In addition, the interdependence of the structural parameters increases the challenge. Advanced form-finding tools are therefore required. The experience hitherto has been that parametric design tools offer the best possibilities in defining, fine-tuning, and optimizing the overall geometry.
The following stages follow a typical design process:
1) Define the overall geometry, including beam sizes.
2) Apply a mesh to the overall geometry.
3) Define an RF pattern with the help of the mesh. (An iterative process can follow where the overall geometry and the RF frame are changed).
4) Develop the structural model.
5) Model and design the connections.
Connections in RF structures are formed by joining only two members at one point, making the connection assembly straightforward. When using timber, to reduce the number of connections, joints can be simple contact bearings (one on top of the other) or use a cutout (notching)
or a build-up (addition). Members can also be positioned in the same plane, for example, the clamp connection in Figure 8. The clamp connection was used in an experimental structure erected temporarily at the School of Architecture in Copenhagen. All the timber used in the RF members and for forming the connections was second-hand reclaimed timber (Figure 9).
Notches in timber members are often difficult to avoid depending on the connection type. A general aim is to reduce the eccentricity, as previously mentioned. In addition, notches reduce the section capacity, which needs to be considered in the design, as shear forces are often dominant and can be critical.
In timber, direct contact pressure, which can transfer shear force via compression perpendicular to the grain, is most efficient. This requires a good contact area with precise notches, which can be accomplished using advanced 3-D cutting tools (Figure 8).
Small torsional moments occur due to the geometry of the connections. The analysis can eliminate these by setting the torsional bending capacity to near zero in the FEM software. Actual torsional moments are typically much smaller than the torsional moment capacity.
The structure often requires simple temporary supports during erection that can be moved up as the construction progresses.
A recently constructed reciprocal frame with complex geometry is the Franz Masereel Centre in Kasterlee, Belgium. The project is a collaboration between LIST Architects, Bureau Bouwtechniek, and Bollinger+Grohmann Engineers and consists of an extension to the existing Franz Masereel Centre. The structure is comprised of a truncated cone forming the walls and a timber structure of interconnected 4-member reciprocal frames. The overall complex geometry has a number of cutouts, showing the full potential of RFs in creating roof enclosures through up-to-date computational design and fabrication tools (refer to the aerial view of the build ing and roof detail in Figure 10).
Reciprocal frames (RF) are structures with novel geometries and form language, attracting increasing interest among architects, engineers, and clients. The advantages are, among others, that they offer opportunities to use relatively short members and that timber is often the most suitable building material, thereby lending itself favorably to the sustainability agenda. However, multiple RFs are typically geometrically complex, and the load paths cannot be intuitively determined. Therefore, it requires parametric design tools to reach an optimal form and to make it possible to analyze the structures.
Hopefully, in the future, further research and built examples will increase the theoretical and practical knowledge of designing and constructing these still relatively unknown types of structures.
■
References are included in the PDF version of the online article at STRUCTUREmag.org
Jens Hübertz Larsen is Senior Project Manager at COWI Consulting Engineers (jsln@cowi.com).
Olga Popovic Larsen is a Professor at the Royal Danish Academy and the author of Reciprocal Frame Architecture (olga.larsen@kglakademi.dk).
Sustainably harvested mass timber significantly reduces embodied carbon. And yet it remains a niche technology in the global con struction industry. Given the rather urgent timeline of the climate crisis, how can we make mass timber mass-market…and fast?
In response to this challenge, an interdisciplinary team of engineers and architects at DIALOG designed a 105-story supertall Hybrid Timber Tower (HTT) prototype that features a patent-pending, pre fabricated, composite Hybrid Timber Floor System (HTFS). Designed as a series of building types stacked one atop the other (commercial, office, residential, and hotel), the HTT shows it is possible, techni cally and economically, to incorporate significant quantities of mass timber into any building type – irrespective of size or function – using a hybrid floor system.
Without a doubt, floor systems in buildings represent the most significant opportunity for mass timber. A life cycle analysis showed that floor systems contribute as much as 73 percent of the envi ronmental impact of a high-rise building’s structure. However, Cross-Laminated Timber (CLT) panels are currently restricted to about 26 feet due to strength and vibration issues. This restriction makes it challenging to deliver the long, column-free floor spans required for Class-A office commercial space and represents a sig nificant barrier to mass-market acceptance.
The DIALOG team designed the HTFS to overcome this limita tion. The composite system leverages the structural properties of concrete and steel to reinforce the engineered wood; post-tensioning cables and steel cages are encased in a concrete band and recessed into a CLT panel, allowing for the greater column-free spans of up to 40 feet. In addition, the HTFS is designed to improve fire safety; exposed wood chars to form a protective layer while the
non-combustible concrete and steel band continues to support the panel (leaving the wood exposed reduces costs and offers the biophilic appeal of timber). Finally, an analysis by Canadian construction firm EllisDon shows the HTFS is cost-com petitive with conventional all-concrete or hybrid-steel and concrete structures. At the same time, prefabrication allows competitive floor cycles in tall building construction.
The DIALOG team designed a super tall prototype to put the floor system into practice, leveraging a hybrid approach for the structure. A survey by the Council on Tall Buildings and Urban Habitat showed 79 percent of buildings 10 stories or less were alltimber versus just 33 percent of those above 10 stories; a hybrid approach makes more sense for taller buildings.
e HTT structure comprises a concrete core with an external steel diagrid, wide at the base and narrow at the top, and designed to mimic a tree’s shape. e core is tied to the diagrid through outrigger trusses at each mechanical fl oor. RWDI’s collaborative partnership for wind studies confi rmed that openings on some of the mechanical fl oors for wind bypass help break up wind turbulence. ey also recommended placing a tuned mass damper at the top of the structure to reduce wind-induced building acceleration.
e design team incorporated the HTFS into the tower prototype to reduce structural embodied carbon by 46% versus a conventional fl oor system. e HTT incorporates 1,294,247 cubic feet of mass timber, 14 times more than the current tallest wood building, Mjøstårnet, in Norway. According to a 21-study review, mass timber sequesters an average of 119 pounds of carbon-dioxide equivalent emissions for each cubic foot of wood product, so the HTT locks up a signifi cant amount of carbon.
e HTT prototype was awarded Fast Company’s 2021 World Changing Idea in Architecture, yet the HTFS is more incremental than radical in terms of structural innovation; it is based on existing, proven structural engineering concepts. e HTFS design has gone through multiple internal peer reviews and independent external peer reviews. In addition, the team has received Investments in Forest Industry Transformation (IFIT) and Green Construction through Wood (GCWood) grants. Both grants are through the National Research Council Canada for testing that includes but is not limited to full-scale structural strength testing, long-term creep, defl ection, vibration, and small-scale fi re testing. e team is confi dent the design will stand the rigors of testing and off er a new tool for architects and engineers looking to reduce the impact of their buildings.
Structural engineers have a vast opportunity to help address the climate crisis. According to e Institution of Structural Engineers, the embodied carbon of building materials represents 11% of global emissions, and a building’s structure can represent the majority of its embodied carbon. It is conceivable that halving embodied carbon in our building structures (recall the 46% reduction in the HTT) could have a more signifi cant impact than if everyone on the planet stopped fl ying.
at is a massive impact. And if we all work together, we can achieve it. So, let’s get going.
References are included in the PDF version of the online article at
All
Insulate concrete-to-concrete,
g Prevent condensation and mold
Improve effective R-value of the building envelope by up to 50%
Increase floor temperature by up to 34°F/19°C adjacent to balcony
Reduce heat loss by up to 90%
Meet code requirements for continuous insulation with maximum effectiveness
Isokorb® Structural Thermal Breaks prevent condensation and mold, and reduce energy consumption by insulating balconies, canopies, beams, slab edges, parapets and rooftop equipment where they penetrate the building envelope.
Proud to offer Passive House, UL and ICC approved products.
125years ago, Henry Plant built the Belleview Biltmore Hotel in Belleair, FL, located just south of Clearwater on the state’s west coast. Chances are, Mr. Plant would never believe that someday someone would pick up and move his magnificent 5-story hotel, but that is precisely what happened. Working with engineers
from Pennoni Associates Inc., the structural engineer of record (SEOR), Wolfe House & Building Movers rotated the original section of the old hotel 50 degrees. en, they moved it about 350 feet as part of a significant redevelopment project. According to Wolfe, the structure weighed 1,750 tons, making it one of the heaviest framed buildings ever moved. e old hotel was then renovated into the Belleview Inn and is now the center point of a $125 million development that consists of four 8-story condominium buildings and 2-story carriage homes developed by JMC Communities of St. Petersburg, FL.
e hotel was constructed with rough sawn timber framing, including roof rafters, floor joists, planking, and loadbearing stud walls. e structure is supported on timber beams that span over a basement and bear on brick piers and exterior brick walls. ree 5-story-deep trusses span 65 feet over the lobby and support the structure above, creating a large column-free space. e trusses were built with
heavy timber chords and compression members notched and bolted together. e tension members are iron rods with bolted ends.
Henry Plant opened the hotel in 1897 as a winter destination for northern visitors seeking to escape the cold and snow. It was no coincidence that many people traveled to Florida by train in those days, and Mr. Plant owned the railroads. e hotel underwent major expansions in 1905, 1914, and 1925, increasing the total size to over 400 rooms and 820,000 square feet. It was one of the largest occupied wood structures in the world at that time. Over the years, the hotel guest list included omas Edison, Henry Ford, e Brooklyn Dodgers, Bob Hope, Gerald Ford, Jimmy Carter, George HW Bush, and many other dignitaries. It was added to the U.S. National Register of Historic Places in 1979 but then removed from the National Register in 2017.
Lobby truss deflected shape.
As time went on, however, the old building started to decline. Modern-day travelers were looking for beachfront access, a golf course, larger rooms – and other amenities that the Biltmore did not offer. e hotel went through a series of ownership changes until it was finally closed in 2009.
In 2010, e Town of Belleair hired Pennoni to conduct annual assessments of the building and document the structural system’s condition. When JMC acquired the property in 2015, it was in bad shape. e wood framing had deteriorated mainly from water intrusion beginning at the roof and progressing downward to the floors below.
After purchasing the property, JMC retained Pennoni to conduct a preliminary analysis of the structural system to help them determine what to do with the old structure. JMC eventually decided to “deconstruct” most of the existing building, preserving the original 1897 lobby portion, which, interestingly, was in the best condition. e deconstruction took much longer to complete than a standard demolition because many of the original building components were salvaged for reuse. For example, the heart pine timber framing went to a wood mill in North Carolina, and doors and windows went to a restoration company in Tampa. In addition, many original building components, like the Tiffany glass in the ballroom, were preserved for use in the new inn, along with much of the artwork.
Wolfe evaluated the existing structure before the move to identify the lifting load points and add temporary steel framing where needed to stabilize the building during the move. Next, they
installed temporary steel beams under each load point along with 45 Buckingham wheeled dollies. Finally, the entire structure was lifted, rotated, and moved via remote control to its new location, where a new concrete mat foundation, cast-in-place concrete walls, and concrete piers were built. is presented an unusual phasing challenge because the new walls and piers needed to be positioned under the load-bearing points that were being supported by the temporary steel beams during the move. To resolve that problem, the SEOR modifi ed the design of the piers and walls to allow for the phased removal of the beams without losing support under the building.
After the hotel was relocated and safely supported on its permanent foundation, Pennoni completed an in-depth structural analysis to make it safe for occupancy. As a result, the existing plaster on the walls and ceilings and the roof shingles were removed to allow visual access to the framing system. An added benefit is that the replace ment drywall and new roof materials weighed considerably less.
The most significant structural damage occurred at one end of the middle lobby truss, where the short timber beam that supported it had failed and deflected. This failure resulted in noticeable deflection of the floors above. Structural steel columns and beams were designed to repair the failed beam, and the truss members were cover-plated with bolted steel plates to restore their integrity. The engineering team initially considered jacking up the deflected floors to level them but quickly rejected that idea because it would
have caused more damage to the wood framing. Instead, it was decided to use a combination of shimming and a lightweight leveling compound to level the floors.
Other less critical damages, including deteriora tion from water intrusion, old improper repairs, excessive splitting and checks in the timber, and insect damage, were found throughout the build ing. The SEOR worked closely with the framing subcontractor, who was very experienced at histori cal renovation, to develop repair details in the field. This was made possible because Pennoni was on site frequently as the Florida Threshold Inspector.
The lobby trusses were analyzed using STAAD Pro software with assumed worst-case material properties, approximated member end condi tions, actual dead loads, and full live loads from the Florida Building Code. The trusses were found to be acceptable. A separate load case was run to confirm assumptions, representing the historic live and dead loads with an added long-term creep factor. The resulting deflection was reasonably close to the measured truss deflection, confirming the design approach.
JMC Communities is well known for developing high-quality resi dential projects. Although they spent a lot more time and money than anticipated to save, relocate, and renovate the old Belleview Biltmore Hotel, JMC said preserving a piece of history was the right thing to do. The team is sure Henry Plant would be pleased.■
Choose Champion Bridge Drain™ for your bridge environmental filtering strategy. The Champion Fiberglass Bridge Drain system is strong, durable and safely diverts accumulated rainwater and contaminants from bridge decking.
Made from strong fiberglass using epoxy resins for further strength, the Champion Fiberglass Bridge Drain system consists of straight lengths, fittings, non-metallic accessories and hangers that withstand harsh, corrosion-filled environments including gas, oil and salt.
bridge projects benefit from:
The Emerald City has its share of hidden passages and mysterious dark alleyways, but it is no secret that Seattle, Washington, is a metropolis on the move. According to census data released in August 2021, the city’s population grew by 21 percent over the previous decade to 737,015 people, with tech giants like Amazon, Google, and Microsoft bringing people to the area by the tens of thousands. While tech may be one of the city’s biggest draws, its 200 miles of shoreline and breathtaking views of Mt. Rainier make the area a truly magnificent place to settle down, but the region’s unique topography has a darker side, as well. Seattle sits atop a basin of sedimentary soil directly above the Seattle Fault Zone. The zone, which extends from east to west through the middle of the city, is vulnerable to shallow earthquakes that can cause devastating effects near the earth’s surface. These unique tectonics challenge structural engineers to pioneer new techniques to ensure that tall building designs meet the demands of forces at work down below.
To augment the city’s revered Cornish College of the Arts and meet the growing demand for upscale urban living in 2018, devel oper Holland Partner Group purchased the school’s former Centennial Labs building, a 14,400-square-foot site at the corner of Virginia Street and Terry Avenue. The firm then assembled a team to design and construct The Ayer, a 45-story mixed-use building on the prime corner lot at 1000 Virginia Street. The team leaders included Seattle architects Weber Thompson and Bellevue, Washingtonbased CKC Structural Engineers. Once completed in Spring 2023, the Ayer will fea ture 454 residential units, three above-grade parking levels, and six below-grade parking levels to accommodate 242 motorized vehicles and 397 bicycles.
Inspired by the unique tectonics of the Pacific Northwest, The Ayer’s visual energy derives from its façade of fractured sheer concrete blocks and geometric patterning. In addition to a year-round rooftop deck and other community-focused amenities, the tower design boasts a non-traditional porch at grade to encourage communal connectiv ity and activation. With The Ayer set far back from the street, the resulting reimagined “porch” provides ample space and encourages interaction amongst the residents and people in the community who are just passing by.
Even with a solid plan and team of seasoned experts, constructing a 480-foot tower with best-in-class seismic considerations is no small feat. The design and construction team faced several challenges, not the least of which was trying to fit a 600,000-square-foot tower into the confines of a sloped postage stamp site. The site measured 120 feet by 120 feet and featured a near 20-foot drop over a 120-foot run from its northeast corner to its southeast corner. In addition, the foundation and shoring system at the north property line faced problematic condi tions with an occupied mid-rise residential building just a few inches away. With a typical tower floor plate of 11,000 square feet, the Ayer’s limited floor area created a challenge for engineers to equip the tower with a structural lateral system that would adequately resist seismic
and wind forces and maximize the architectural program efficiency. Finally, the tectonic sheered façade created different residential floor plates with variable cantilevers. These cantilevers, combined with the stringent deflection requirements for the window wall system, posed an interesting balancing act between the ceiling height and control ling deflections. The design team met this challenge by designing an innovative slab column layout.
In The Ayer tower, a centrally located concrete core that wraps around the elevators and stairs helps meet interstory drift, strength, and serviceability requirements. CKC structural engineers performed sensitivity studies on wall thickness, concrete compressive strength, and concrete modulus of elasticity to enhance the concrete core performance. They also thoroughly analyzed the coupling beam locations, sizes, and frequencies to maximize ductility. This resulted in a core aspect ratio of roughly 14 to 1 and a coupling beams aspect ratio of 3 to 1. The concrete core wall thickness telescopes throughout the tower height to improve the architectural layout, increase leasable space and reduce concrete material and mass. The wall thicknesses vary between 33 and 21 inches and occur at levels 24, 30, and 40.
The team analyzed this lateral system using a three-dimensional Performance-Based Design (PBD) analysis model. The model integrated the nonlinear properties of critical elements in the concrete core, such as coupling beams and the yielding of wall vertical reinforcement. Structural engineers subjected the lateral model to two sets of 11 pairs of conditional mean spectrum-scaled ground motions. They scaled for the short and the long period of the target spectrum per ASCE 7-16, Minimum Design Loads and Associated Criteria for Buildings and Other Structures, Section16.2.1.2. This approach generally results in more realistic loading and a more efficient structural design. In addition to the nonlinear modeling, parametric studies on the foundations led to the use of soil springs to better represent the soil-structure interaction. This helped mitigate the moment demands on the tower’s foundation mat.
One of the unique features of The Ayer’s concrete core is its use of high-strength steel fiber-reinforced concrete (SFRC) coupling beams. The beam design featured a lower dosage of steel fiber rein forcement than previous tower applications like the Kiara tower (STRUCTURE, June 2019). While Kiara used 200 pounds per cubic yard of steel fiber dosage, The Ayer used 170. The team achieved this reduction in fiber reinforcement application by using the latest SFRC testing conducted by the University of Wisconsin and published in the Pankow Foundation Report (December 2016). CKC engineers calibrated the backbone curve of the SFRC coupling beam used in the PBD model using the test data for coupling beams with Bekaert Dramix 3D 55/30 steel fibers at 170 pounds per cubic yard. This lower dosage fiber beam helped improve cost and concrete work ability. Moreover, the SFRC coupling beams were optimized and placed them only at floors above the dynamic base up to the main roof slab. For below-grade coupling beams and rooftop penthouse coupling beams where shear/rotational demands are low, the design
used conventionally reinforced coupling beams to allow the use of the concrete wall mix design in the beam.
Used in combination, lower dosage SFRC coupling beams and the introduction of conventionally reinforced coupling beams where high shear and rotation demands are not present helped create cost efficiencies and sped up The Ayer’s core construction.
The Ayer’s state-of-the-art structure consists of cast-in-place concrete with post-tensioned floor slabs and a shear wall core for seismic and wind resistance. The gravity system utilizes long-span, 8-inch-thick post-tensioned flat plate slabs with perimeter cantilevers that extend up to 12 feet on the east side of the building. This resulted in 16 columns and zero transfer conditions, making way for fewer columns, optimized slab-bending moments, and reduced floor-to-floor height with thin ner slabs.
The column placement strategically limits the number of columns per floor, eliminates the need for deep transfer beams above the dynamic base, and uses gravity to help resist overturning lateral forces. Close collaboration with the architectural team and strategic column walks and rota tions along the building height helped thread 16 columns over the 480-foot height of the tower. This approach also eliminated the need for transfer beams that would otherwise have been required to shift column locations at levels where occupancies change. In addition, columns stand a distance away from the concrete core to increase the floor tributary area supported by the concentric core. Thus, most of the building’s dead load is transferred to the core, minimizing net tension in the walls from overturning due to wind and seismic forces.
The Ayer features post-tensioned, 8-inch-thick flat-plate slabs at typical residential levels, including the subterranean parking, creat ing flexible interior space with open layouts. At subterranean levels, shotcrete perimeter basement walls follow the construction of the slabs. This allowed slab shortening to occur before shotcrete wall construction. The team also poured subterranean levels against the shoring piles to provide bracing and allow the de-tensioning of tie backs prior to placing shotcrete walls. This approach eliminated the need for tieback blockouts in the basement wall, which are a constant water penetration problem.
The Ayer is a prime example of how the strategic, targeted use of highstrength materials can significantly improve structural efficiency as well as the architectural layout and the construction schedule. Column loads for a building the size of The Ayer can be in the order of 3,500 kips of allowable axial loads. A concrete compression strength of 15,000 psi was specified for the tower columns at the lower levels. The ability to specify high-strength concrete reflects steady advances in concrete materials technology. This “super concrete” allows for fewer and smaller columns per floor plate, maximizing interior unit layout and formwork productivity. The column concrete strength reduces from 15,000 psi at the base to 8,000 psi at the upper levels. This allows column sizes to remain constant almost to the top of the tower, maximizing formwork productivity and helping maintain a rapid construction pace.
In addition to the high-strength concrete mix, The Ayer takes full advantage of the latest ACI 318-19, Building Code Requirements for Structural Concrete and Commentary, high-strength reinforcement as outlined in Table 20.2.2.4(a) of the code. The team used A706 Grade 80 rebar in the foundations and all shear wall reinforcement. This resulted in significant cost savings since the 10 percent price premium for Grade 80 versus Grade 60 was offset by the 20 to 25 percent reduction in foundation and shear wall rebar tonnage. The design also used Grade 80 for all column ties to satisfy the stringent seismic confinement reinforcing requirements for ultra-high-strength concrete. The synergistic combination of high-strength reinforcement, high-strength concrete in the columns, and high-strength steel fibers in the coupling beams resulted in construction and cost efficiencies throughout the project.
Constructability thinking is a mindset that complements every deci sion, from the conceptual layout to the selection of the structural system to construction. The Ayer embodies the impact of constructa bility in improving construction productivity and structural efficiency. The successful implementation of constructability ideas was made possible with close communication between the design and construc tion team members.
The team worked closely from the early design phase to create a one-of-a-kind building that expresses the architectural intent and is also poised to achieve the project budget and construction schedule. Early buildability meetings between CKC and Conco, the concrete subcontractor responsible for the structural frame construction, focused on subterranean construction from mat foundation rein forcement placement to sequencing basement walls and elevated slabs. Those early discussions also made it possible to streamline the reinforcement of the core wall detailing to ensure compatibility with the self-climbing formwork system. Moreover, working closely with the architect to thread columns throughout 45 stories without introducing deep transfer beams had a significant positive impact on improving structural efficiency. Another example of construc tability was the elimination of puddling at high-strength concrete columns. Prior to pouring slab concrete, the team wrapped Stayform around the column tie perimeter through the depth of the slab. A cost-effective concrete forming system that does not require stripping after the concrete form, the Stay-form prevented slab concrete from flowing into the column core during the slab pour. When the column pours followed, column concrete flowed into these penetrations. The addition of shear-friction rebar through the slab/column joints in both directions supplemented the connection strength. This emphasis on constructability and its central role in the tower’s structural design and detailing created synergy between the design and construction team.
Once it is complete, The Ayer will be a significant addition to the expanding downtown Seattle landscape, one that will stand up to whatever the city’s growth and Mother Nature have in store. Its suc cess was made possible by the latest advancements in seismic design and the implementation of constructability through collaborative work between all the team members involved.■
Joe Ferzli is a Senior Principal at Cary Kopczynski & Company. He is the President of the American Concrete Institute’s Washington Chapter and a member of ACI Committee 374 on performance-based seismic design of concrete buildings, the 318T Committee on post-tensioned concrete, and the ASCE 7 concrete subcommittee (joef@ckcps.com).
Jerry Lee is a Senior Design Engineer and Associate at Cary Kopczynski & Company (jerryl@ckcps.com).
Owner: Holland Partners
Structural Engineer: CKC Structural Engineers
Architect: Weber Thompson
Contractor: Holland Construction
Concrete Subcontractor: Conco
The Laurel Rittenhouse Square is a 50-story, 583,000-square-foot residential tower currently under construction in Philadelphia. Located on the last undeveloped parcel on Philadelphia’s prestigious Rittenhouse Square, the project features an ultra-luxury mixed-use tower consisting of 65 condominiums and 184 apartments on top of a threestory podium with 44,000 square feet of retail and dining spaces. Once complete, e Laurel will rise 604 feet, making it the tallest residential building in Center City.
e 50-story tower is constructed of a cast-in-place concrete flat plate system with concrete shear walls. A portion of the podium outside the tower’s footprint is a steel-framed structure. Two concrete below-grade levels accommodate mechanical equipment space and parking.
With cost estimating assistance from the Construction Manager, Hunter Roberts, a concrete mat foundation was chosen as the most cost-effective solution. e mat thickness varies from 15 feet under the building core to 7 feet outside of the core and extends throughout the footprint of the main tower. is allows the engagement of all tower columns and the requisite dead loads to resist the overturning forces on the foundation. It further spreads the tower loads out over the entire footprint. Studies determined that differential settlement was approximately ½ inch and total building settlement was 1½ inches, which was deemed to be within serviceable limits for the project.
A 6,000 psi concrete was chosen, using a 70% slag cementitious substitute mix to slow the heat of hydration and, therefore, heat gain in the concrete. In addition, a compacted stone-filled space, 2.5 feet thick, was left between the basement floor and the top of the mat foundation to accommodate installation and future access to utilities under the slab on grade floor slab at the lowest basement level.
Because existing buildings and public streets surround the site, and the project occupies nearly all the site, construction methodologies needed to be considered in the structural design from street level down.
e entire structure below grade was concrete construction. To allow for the tower’s construction, the grade level fl oor outside the tower footprint was designed for construction material storage and construction equipment loads, including a mobile crane.
Foundation walls were designed to be constructed using a one-sided form system. e exterior side of the wall would be placed against the blind side waterproofing applied to the support of the excavation
(SOE) structure. This required accom modation of more liberal tolerances consistent with SOE systems, includ ing accommodating variations in the thickness of the wall and coordinating the interior spaces to accommodate that variation. The foundation wall's inside face was located such that any variation in the SOE system would be accommodated on the outside face of the foundation wall while maintaining minimum wall design thickness.
The mat foundation was placed directly against the SOE on all four sides. This also required that reinforc ing steel accommodate the potential variations in SOE location.
Once the excavation was complete, the mat foundation construc tion began. The most practical solution was to place the entire mat in one continuous pour. This required the placement of 400 tons of reinforcing steel, the design and installation of a “standee” system to support the top reinforcing steel mat (that remains in the concrete permanently), and the placement of 4,360 cubic yards of concrete using 440 concrete trucks.
To access the project site with this many concrete trucks required concrete placement through the night and on the weekend to accom modate street closures. Due to the mass concrete placement having the potential to generate heat and differential temperatures within the mat, special considerations were implemented in the design and testing of the concrete mix. In addition, insulated curing blankets were placed on top of the mat to reduce temperature loss at the top surface and avoid potentially damaging temperature differential through the concrete. Sensors were placed throughout the mat and were connected to a central monitoring computer to confirm that the temperatures throughout the depth of the mat during curing were
below recommended limits per the American Concrete Institute’s ACI 207.1R, Guide to Mass Concrete
The concrete placement began at 1:30 AM on a Saturday and was completed in 12 hours. The process resulted in temperatures within tolerance per ACI 207.1R, and all concrete was placed without delayed wait times in trucks.
Studies were undertaken to assess the best system to address windinduced motion in this tall tower. RWDI performed preliminary wind analysis and the final wind tunnel testing. The results were used to develop structural loads and to assess wind-induced motion for occupant comfort. An iterative process was applied to optimize the structure, balancing wind-induced accelerations against struc tural size and cost.
The use of a supplemental damping system to reduce windinduced motion was studied. The reduced cost of the structure
and an increase in program space did not justify the cost of the supplemental damp ing system. The team turned to “tuning” the lateral struc tural system to meet the one-year return period (8 milli-g) and 10-year return period (15 to 18 milli-g) resi dential building motion limits while optimizing the struc ture. Ultimately, an outrigger system was introduced at the 25th floor, engaging exterior columns to improve the behavior of the building and to help avoid supplemental damping.
The main lateral load-resist ing system is a central shear wall core. As is normally the case, shear walls around an elevator core require open ings to allow for the elevator lobby at nearly all floors. Residential towers tend to maintain the least floor-to-floor height possible, and the underside of slabs is finished to create the ceiling in the apartment below. At the same time, links above the elevator core openings are necessary for the core to act as closely as possible to a tubular spine extending up the building. The conflict of limited depth available for the link beams and the very high loads passing through those link beams presents a challenge. In addition, the beams obstruct mechanical systems that normally require access into the core area.
Outrigger beams at the 25th floor.
in the beam design to accommodate the MEP systems that pass through the beams.
Balancing these challenges led the design team to use steel beams embedded in the concrete link beams to resist high shear and moment loads imposed on those beams in some shear walls. This involves considering the transfer of forces from one wall, across the opening through the beam, and back to the wall on the other side of the opening. While the governing loads for these link beams are wind-induced, the American Institute of Steel Construction’s (AISC) Seismic Design Manual section on composite coupling beams and other research was useful in guiding the design of these beams. Complex details were required. Careful coordination down to each individual pipe sleeve was required and considered
A walking column is a term used to describe the condition where the column above is not located directly above the column below. This creates an offset and eccentric load on both columns, resulting in horizontal forces at each end of the column that must be resolved into the floors above and below.
For this project, there were conflicting desires. The local community desired a limit to the height of the building. The developer wanted to maximize the FAR (floor-to-site-area ratio) to that permitted by Code, yet a portion of the site was occupied by a three-story historic building that would be preserved. The floors above the height of the historic structure were expanded to the west to capture additional floor area, requiring the edge columns to be located outboard of the locations below. A transfer beam was considered, but the added depth of structure would “grow” the building taller. The team settled on walking the columns in four successive floors to achieve the transferred column location in the more than 40 floors above.
There are considerable horizontal loads at the top of the uppermost and bottom of the lowermost columns. This is particularly an issue where there are more than 40 floors of structure above. These horizontal forces must be resolved in the design of the floor diaphragms and drag struts to provide a load path to the concrete core. In tension strut locations, mechanically terminated tension drag strutsShear wall link beams with embedded steel.
were designed to drag these forces into the core. In areas outboard of the core, similar drag struts were designed, and then supplemental diaphragm reinforcing transferred the forces into the core.
High-strength concrete was required to accommodate the design of this structure. Based on experience, available data in the local supplier market, and extensive laboratory testing, these strengths were pre-validated early in the design process. Laboratory testing submissions were specified to demonstrate strength and a prescribed modulus of elasticity for concrete to be used in columns and shear walls. Shear wall and column concrete ranged from 14,000 psi at lower levels in the building to 8,000 psi at upper levels. Floor slabs required 8,000 psi at the lower fl oors to meet ACI 318 Building Code Requirements for Structural Concrete , requirements for load transmission through fl oors, and avoid placing higher strength concrete at the column/slab interface to control puddling . Puddling requires placing high-strength column concrete within a two-foot zone beyond the column/slab interface. is can be diffi cult to control during concrete slab placement. Floor slabs required 6,000 psi concrete at upper fl oors where column concrete strengths were lower. A 56-day strength testing procedure was specifi ed to accommodate the slow rate of hydration.
e cooperation between all members of the design and construction team is critical to the success of any project. Understanding the local concrete subcontractor and the material market proved a valuable asset for the design team, resulting in a smooth and efficient construction process.■
D. Kirk Harman is a Managing Principal and Client Executive with The Harman Group, now IMEG. He is an active participant in several industry organizations and has served on ACI Committee 318, Building Code Requirements for Structural Concrete.
Todd Campbell is a Senior Engineer with The Harman Group, now IMEG. He has served as Project Manager for several of the firm’s tall building projects, including The Laurel. He is a member of the American Institute of Steel Construction and the Structural Engineers Association of Pennsylvania.
Southern Land Company, Nashville, TN
Structural Engineer: e Harman Group
(now IMEG ), Philadelphia, PA
Architect of Record: Solomon Cordwell
Buenz, Chicago, IL
MEP Engineer:
Bala Consulting Engineers, King of Prussia, PA
Geotechnical Engineer: GeoStructures, Inc.,
King of Prussia, PA
Wind Consultant: RWDI, Guelph, ON (Canada)
Construction Manager: Hunter Roberts
Construction Group, Philadelphia, PA
The $350 million Long Beach Civic Center is a state-of-the-art facility that provides the City and Port of Long Beach, California, with performance-based infrastructure commensurate with its size and status as a world-class shipping and logistics hub. e City wanted a revitalized civic core that was environmentally sustainable and resilient. e project was developed under a public-private partnership (PPP) with developer Plenary-Edgemoor Civic Partners and general contractor Clark Construction. e design was led by Skidmore, Owings, and Merrill (SOM) as the architect, and structural engineering was shared by Nabih Youssef Associates Structural Engineers (NYASE) and SOM. e project includes a new eleven-story 247,000-square-foot City Hall tower, eleven-story 238,300-square-foot Port Headquarters tower, and single-story elliptical-shaped City Hall Council Chambers. All three buildings sit on top of a standard two-story 217,400-square-foot subterranean parking garage.
e City Hall and Port Headquarters towers are rectangular with an approximate overall dimension of 275 feet by 85 feet at the typical floor. e floors have flat-plate 10-inch-thick post-tensioned concrete slabs with exposed soffits. Due to architectural constraints, portions of the floor slabs at both towers have large cantilevers that required
creative design solutions to maintain the aesthetic of the flat slab. is condition occurred at all corners of the building above the third floor and in the middle of the building, where the second-floor slab was recessed off the column line to create a two-story-tall entry. e 16.5-foot cantilevers at the corners of the building were addressed by utilizing upturned post-tensioned beams within the depth of the access flooring system to keep the beams hidden and maintain the architectural integrity. e second floor recessed floor slab at the entry, which would have resulted in a 17.5-foot-long cantilever, was addressed by adding hanger columns supporting the edge of slab from beams located at the third floor, which successfully achieved the desired architectural aesthetic.
Re-occupancy
Expected
Acceptance
to
of building
A standard code-based design approach uses prescriptive design requirements that protect the building’s occu pants during a design-level seismic event. However, it does not ensure that the building can be re-occupied after a seismic event or even that repairs to the building are economical.
Resilient building design goes beyond the prescriptive objectives in the building code and focuses on the ability to recover from a large seismic event quickly. The Federal Emergency Management Agency (FEMA) developed a methodology and approach to assessing the probable seismic performance of a building, published in 2012 as FEMA P-58, Seismic Performance Assessment of Buildings, Methodology, and Implementation. FEMA P-58 provides a foundation for the ongoing evolution of resilient building design.
The City of Long Beach adopted the Resilience-based Earthquake Design Initiative (REDi™) rating system developed by Arup and speci fied REDi Gold as a project performance objective. In addition to life safety, the objectives include a 50% probability that the re-occupancy time will not exceed seven days, the functional recovery time will not exceed thirty days, and the repair costs will be less than five percent of the replacement cost of the building after a design level earthquake.
The SP3 software based on FEMA P-58 and developed by Haselton Baker Risk Group was used throughout the design process to assess conformance with project performance objectives. In addition, the final design was peer-reviewed by Arup for compliance with REDi Gold.
The seismic design was performed using linear dynamic analysis following the requirements of ASCE 7, Minimum Design Loads and Associated Criteria for Buildings and Other Structures. In addition to the code-based design analysis, a nonlinear time history analysis was performed to demonstrate compliance with the resilient-based design objective. Unlike performance-based design approaches commonly used in high-rise design, the approach outlined in the REDi rating system focuses on a life safety objective at the design level earthquake. It does not explicitly evaluate performance at the maximum considered design earthquake.
The conventional approach of using stacked wall openings in the shear walls was initially utilized to create coupling beams at every floor. However, even under a modest inter-story drift, the rotational demand on these beams resulted in extensive cracking and spalling, leading to long repair times.
Through extensive collaboration with SOM architects and engineers, staggering the wall openings at each floor was developed to eliminate the coupling beams that were susceptible to damage. However, this created new design challenges, with wall piers changing length at every floor. A portion of the wall shear force needed to be dragged between the openings using additional horizontal reinforcement in the walls that were concentrated between the openings. This unusual load path was seen in the wall shear stress results from the nonlinear analysis and verified using strut and tie models.
Results from the nonlinear time history analysis also indicated much higher shear demands in the walls, due to higher mode effects, than what was indicated by the linear analysis. Although currently codified in ACI 318-19, this phenomenon was, at the time, not commonly accounted for in midrise building design.
Special detailing was utilized at the base of the C-shaped core walls (i.e., two stories above grade), where hinging is most likely to occur due to flexural yielding in the wall. This included providing seismic ties at all vertical reinforcement throughout the length of the wall to prevent bar buckling due to large peak strains in the reinforcement. Diagonal shear reinforcement was also provided in the shear wall piers at the base of the wall, similar to the diagonal reinforcement commonly used in coupling beams, to supplement the standard hori zontal shear reinforcement. This unique approach was developed and tested by Paulay, Priestley, and Synge and shown to be effec tive in resisting diagonal tension and compression stresses due to shear demands in concrete shear walls. The horizontal shear rein forcement was designed to resist the code-level shear forces, and the diagonal shear reinforcement was designed to resist the shear forces from higher mode effects. Due to the higher Risk Category III designation, the City Hall Council Chambers building was seismically separated from the City Hall tower. Early in the design, steel moment frames wereDiagonal reinforcement at shearwall piers.
Both the City Hall and Port Headquarters towers have two C-shaped special reinforced concrete shear walls at opposite ends of the building.
considered for use as the lateral force-resisting system; however, due to large residual drifts, it was deemed unsuitable for achieving REDi Gold. Ultimately, steel braced frames were selected and designed to remain elastic in the design level earthquake to limit residual drifts.
A defining aspect of resilience-based design is the emphasis on assessing the seismic performance of nonstructural components. These components are influenced by the response of a building during an earthquake (inter-story drifts and floor accelerations). For example, a building that is too stiff increases seismic floor accelerations and forces on bracing and anchorage of mechanical and electrical components. At the same time, a building that is too flexible leaves partition walls, exterior façade elements, and stairs vulnerable to damage. An iterative design process found that a one percent inter-story drift target provided the right balance between
limiting bracing and anchorage forces while also protecting partition walls, exterior façades, and stairs.
Anchorage and bracing mechanical and electrical components with large lead times were designed using a maximum component response modification factor (Rp) of 2 to keep these components “essentially elastic.” Mission-critical components were required to be tested on a shake table to demonstrate operability after a design-level seismic event. One elevator per building was designed with an Rp of 1 to remain operational after a seismic event. Guide rail supports and retainer plates were designed using California Office of Statewide Health Planning and Development requirements.
The exterior façade was designed and tested in a lab to ensure the system would remain effective at preventing air and water intrusion at the design seismic drift and that no catastrophic failures would occur at twice the design seismic drift. In addition, egress stairs were detailed with a sliding connection at one end to accommodate twice the design seismic drift to ensure life safety after a large seismic event.
The Long Beach Civic Center was com pleted in the summer of 2019 and stands as a visual representation of resilient building design. Innovative engineering solutions and invaluable collabo ration led to the ultimate success of the project.■
Scott Stewart is Senior Project Engineer at Nabih Youssef Associates (sstewart@nyase.com).
Owen Hata is a Principal at Nabih Youssef Associates (ohata@nyase.com).
Nabih Youssef is Chief Executive Officer at Nabih Youssef Associates (nabih@nyase.com).
Marios Panagiotou is Senior Consultant at Nabih Youssef Associates (mpanagiotou@nyase.com).
Sliding connection at stairs.
The Center for Computing & Data Sciences is a dynamic new vertical campus building at Boston University. e design maximizes opportunities for interaction and interconnectivity and carefully integrates every element to establish Data Sciences as Boston University’s new iconic heart.
e 19-stories-tall, 345,000-square-foot facility will be the University’s tallest and the largest 100 percent fossil-fuel-free building in Boston, Massachusetts. Targeted to attain LEED Platinum, the building incorporates several high-performance sustainability features. e state-of-the-art building, designed by KPMB Architects of Toronto, Canada, will be home to the departments of Mathematics & Statistics, Computer Science, Computing and Data Sciences, and Computing and Computational Science & Engineering.
Located in the heart of the campus at the corner of Commonwealth Avenue and Granby Street, along the Charles River, the building is designed to be socially sustainable, putting the people it serves first. It is an open, welcoming building that encourages interaction, collaboration, and movement to enhance the student’s experience.
e building design provides a walkable vertical campus with the tower organized by a series of vertically stacked and staggered research “neighborhoods,” each with access to an outdoor green-roofed terrace, linked by an interconnecting feature stair encouraging faculty and students to walk the building.
The building will be a hub for the campus and a model for future building design, sustainability, and resiliency. It sets the direction for meeting Boston University’s Climate Action Plan goals for new con struction and achieving net-zero carbon emissions for the University by 2040. A key component of BU’s strategy is switching from fossil fuels and relying primarily on electricity generated from renewable sources. The building and systems are designed to minimize energy consumption and use ground-source heat pump “geothermal” for heating and cooling. Efficiency begins with the building enclosure incorporating, in this case, a triple glazed curtainwall to keep heat in during the winter and external sun shading to reduce solar heat gain in the summer. Mechanical systems designed by BR+A utilize highefficiency systems, including active chilled beams, dedicated outside air systems, and heat recovery. The geothermal system, designed by Haley and Aldrich, consists of thirty-one 1,500-foot-deep bores connected to the heat pump chillers. The closed-loop system will draw heat from the ground in the winter and expel heat in the summer and is the primary source for heating and cooling. The result of these efforts is zero operating carbon. The Center for Computing & Data Sciences aligns with the American Institute of Architects 2030 Challenge goals for new buildings to be operationally carbon-neutral by 2030. Embodied carbon is the other critically important component of the carbon equation representing the carbon associated with infra structure development. Embodied carbon includes the carbon dioxide equivalent for all phases of a building’s life cycle, starting from initial material extraction and building product fabrication, construction, repair, and refurbishment during the building’s use, and, finally, endof-building life, like demolition or product reuse and recycling. For a typical new building, structural and enclosure systems represent more than half of the total embodied carbon, with the structural system being dominant. This is primarily due to the materials those systems employ, which require a tremendous amount of energy and resources to produce. For operational carbon efficient buildings, the embodied carbon rep resents a significant portion of carbon associated with the building.
Embodied carbon in buildings is not a new concept, but attention has increased in recent years. With the urgency of addressing climate change and the rec ognized need to reduce total carbon drastically, it is imperative that the education, advocacy, and innova tions associated with embodied carbon advance rapidly. A movement is happening around addressing embod ied carbon and finding ways to reduce it that is gaining momentum. One challenge structural engineers face is the assumption that the structure cannot contribute to achieving sustainability goals and embodied carbon reductions. However, that has begun to change as a new focus and understanding of embodied carbon of structural and enclosure systems has begun. A strong signal of this change is the SE 2050 Commitment Program (SE 2050), launched in November 2020 by the Structural Engineering Institute (SEI) of the American Society of Civil Engineers (ASCE). Developed in response to the SE 2050 Challenge issued by the Carbon Leadership Forum (CLF), the goal is that “All structural engineers shall understand, reduce, and ultimately eliminate embodied carbon in their projects by 2050.” The SEI Board of Governors unanimously endorsed the vision of SE 2050 in December 2019. As of March 2022, over 75 structural engineering firms have signed up for the Program. One of the project’s sustainability goals was to achieve a USGBC LEED Platinum rating status. LEED BD+C: New Construction v4.1
(LEED v4.1) presents opportunities to address embodied carbon from a structural and enclosure standpoint that directly contribute to the rating point total. Using the LEED v4.1 through the Materials and Resources Credit (MR Credit): Building Impact Life-Cycle Impact Reduction Option 2, the project can achieve four points by performing a Whole Building Life-Cycle Assessment (WBLCA) that demonstrates at least a 20% reduction in embodied carbon (also known as Global Warming Potential) when compared to a typical baseline building. This path requires a minimum of 10% improvement in two additional environmental impact categories. The WBLCA requires a cradle-tograve life-cycle assessment of the project’s structure and enclosure systems; therefore, the total reduction from baseline includes the summation impacts of both systems.
In considering options for addressing embodied carbon of both the structure and enclosure, the design team determined that, since the design of the enclosure system was for optimal operational carbon, gains in embodied carbon efficiency would not outweigh potential losses in operational carbon efficiency by making design changes to the enclosure. Therefore, the design team concluded that the struc ture would be the primary system of focus for embodied carbon reductions. They presented options during early design sustainability charrettes, including adjustments to the structural system related to both structural material quantity reduction and material design and specification. Approximate embodied carbon reductions of the various options were outlined in conjunction with corresponding cost, schedule, and availability topics. Working with KPMB and The Green Engineer, the project’s sustainability consultant, an evaluation
of potential MR Credit points was reviewed. With strong support from Boston University, the design team was challenged to continue to explore and implement embodied carbon reductions wherever pos sible. This effort went for embodied carbon beyond what is tracked in LEED v4.1, with the design team specifying, for example, some of the lowest embodied carbon flooring materials available on the market, attention to the embodied carbon of the chosen furniture elements, and a wood biophilic design approach using FSC certified products.
For the steel portion of the structural system, the design team worked closely with the general contractor, Suffolk, and the steel provider, Canatal, which was engaged early as a design-assist partner, to minimize
Structural
60”
Tower
Tower
Podium
Foundation
Columns
the system’s environmental impact. Minimum truss connection material, optimal splice locations, minimizing crane picks and field welding, and optimizing member sizes while considering availability and shipping distances were evaluated. This process removed several tons of structural steel from the project beyond the typical efficiencies expected from a conventionally steel-framed system. The design team evaluated the use of higher grades of steel for columns, up to Grade 70, to further reduce steel tonnage. However, for various project constraints, the decision was made not to use the higher steel grades. Finally, consideration of the steel production, a significant contributor to embodied carbon of steel products, was evaluated and options outlined to source the steel from the least impact production sites in North America. For the concrete portion of the structural system, two primary areas of focus were explored – minimizing total portland cement content in the concrete mixes and minimizing the use of lightweight concrete. The production of portland cement is responsible for approximately 5%-10% of the world’s CO2 emissions and makes up 80-90% of con crete’s total embodied carbon impact. Minimizing the use of portland cement is critical in making substantive reductions in embodied carbon.
In Boston, concrete mixes have an average portland cement replacement rate of approximately 20%, pri marily replacing portland cement with supplemen tary cementitious materials (SCM) of fly ash, slag cement, silica fume, or a combination of the three. In general, replacing port land cement reduces the heat of hydration of the mix and thus can modestly increase set times; therefore, extensive discussions related to construction sequence took place early on. With support from Boston University, the design team explored options to replace all concrete on the project except concrete for flatwork at much higher rates than typically seen in the area. Working with Suffolk, the design team presented preliminary concrete mix design goals to two local concrete suppliers. The data shown in Table 1 was used primarily for conversational purposes with each supplier to describe the replacement rate goals and allow for a fruitful discussion around availability, available test data, anticipated set times, shrink age, and other considerations. A derivative of this table, following these initial discussions, was included in the Contract Documents. Another option would have been to specify the embodied carbon limits for each component instead of using the percent SCM as a proxy for reduced embodied carbon. Unfortunately, available third-party verified Environmental Product Declarations (EPDs) documenting embodied carbon of mixes were limited at the time of design. The team proceeded with using percentage SCM as the method of specification. Each supplier brought to the conversation important available test data, a plan for running project-specific trial batch mixes, a review of set time, mix constituent availability, and cost. Through the early collaboration with local suppliers, the design and construction teams were able to identify achievable goals for each structural component of the project and evaluate against the total embod ied carbon of the WBLCA to further inform the Owner. These early conversations allowed the design team and contractor to review impacts on the overall project schedule and evaluate options for where to make adjustments Extensive discussions revolving around the timing of form stripping and application of temporary construction loads factored into selecting appro priate mix designs. Through early engagement and subsequent dialogue throughout the procurement and installation process, the project employed concrete with portland cement replace ment rates of up to 70%, the highest ever used in Boston for this type of application. This yielded some mixes with a nearly 30% reduction in embodied carbon.
Nominal
LeMessurier performed the WBLCA usingTally and worked with The Green Engineer for incorporation into the LEED certification application process. With the design modifications to the steel and concrete products, a 9% reduction in structural and approximately 6% of total embodied carbon was achieved compared to the baseline structural and enclosure systems, equating to an approximate savings of over 1.14x10^6 kg of CO2e or approximately 1,300 tons. If accepted by the USGBC LEED reviewers, this will provide the project with 2 additional points through the MR Credit.
should be noted here that the portland cement replacement
study typically uses the published regional averages
National Ready Mix Concrete Association (NRMCA),
Minimize floor depth and maximize project performance. Deep-Dek® Composite enables open spans up to 36 feet, and low-profile slabs as thin as 7.635 inches. With Panelized Delivery Method™ floor panels are assembled on the ground, increasing worker safety, and decreasing assembly time.
in this case approximately 20% for baseline concrete in Boston. This was done for most of the concrete elements; however, for the large concrete mat foundation, it was not felt that using 20% would have been appropriate. For this element, designers used 40% for a baseline portland cement replacement given that is what is typi cally done for mat foundations of similar geometry in the Boston market, primarily to keep the heat of hydration down for constructibility, etc. Had a 20% baseline number be used, the improvement shown would have been higher than 9% which, in the designer’s opinion, did not appropri ately reflect the intent of the LEED credit. Figure 1 shows the breakdown of total embodied carbon for the substructure and superstructure. Over two-thirds of the contribution is in the superstruc ture, given the amount of structural steel and lightweight concrete. However, the primary reductions focused on concrete components of the substructure. Figure 2 further breaks down the concrete compo nents identifying where specific reductions were achieved.
Figure 1. Embodied carbon values for the substructure and superstructure.
The construction schedule required removing the formwork on some elements earlier than anticipated during initial planning and slightly reduced the amount of embodied carbon savings. The request resulted in a modest amount of concrete that required a lower replacement rate than previously assumed. Understanding the importance of embodied carbon reduction, Suffolk requested a review of the WBLCA before proceeding with the change to ensure at least a 5% reduction was maintained, which was only possible with early all-inclusive planning discus sions. Ultimately, the total savings was not reduced below 5%.
Figure 2. Embodied carbon contribution and reductions of the concrete components.
Although not required for certification, there were several reasons for performing a post-construction WBLCA analysis. First, it allowed the design team to compare the impacts of the designed and documented quantities versus the ‘real’ delivered-to-site quantities. Second, it allowed the design team to validate design assumptions and generally continue improvement in evaluating environmental impacts. For example, steel tonnages were assumed to increase by 5% to account for standard connection material and 10% for the large truss connections. Third, it provided valuable information on what impacts might exist but are not required to be assessed by LEED based on means and methods of constructing the structural and enclosure systems or nonstructural components like concrete site walls and landscape elements. The differ ences shown in Table 2 are a straight comparison between what the team modeled in Revit versus what was delivered to the site, with differences ranging between 12.6% and 14.9%. These differences were adjusted to account for actual delivery quantities but were not part of the base building structural system, such as the tower crane mat foundation or the temporary steel shoring columns used to support the trusses during erection. The adjusted values of concrete, concrete reinforcement, and structural steel dropped to 8.3% to 10.8%. Having such numbers will
help better inform design assumptions and, if tracked on subsequent projects, will continue to improve the accuracy of future WBCLAs towards understanding actual impacts.
This project yielded relatively significant reductions in the structural system’s embodied carbon, which would only have been possible with solid support and a challenge from the Owner. Boston University leadership was the key to success and allowed the design consultants to engage in essential and frequent dialogue with the sustainability consultant, contractors, and product suppliers. Throughout this process, there were many lessons that all parties learned from and will successfully employ on future projects.
■
Michael Gryniuk is a Principal with LeMessurier in Boston, MA. He is Chair of the SE 2050 Commitment subcommittee and serves on the steering committee of the SEI Sustainability Committee.
Paola Rocha is a Partner at KPMB Architects and served as the Design Architect for the project.
Dennis Carlberg is Boston University’s first Sustainability Director, joining Boston University in 2009. Dennis co-chairs the Climate Resilience Committee at the Urban Land Institute – Boston.
Figure
of holes
Structural glued laminated timber (glulam) beams are highly engineered components manufactured from specially selected and positioned lumber laminations of varying strength and stiffness. As most glulam beams are designed for and used in applications where they are highly stressed under design loads, drilling or notching of glulam should be avoided and never done without a thorough under standing of the effects on the structural integrity of a member. This is specifically addressed in Section R502.8.2 of the 2021 International Residential Code (IRC) as follows (the same wording also appears in Section R802.7.2 of the 2021 IRC): R502.8.2 Engineered wood products. Cuts, notches, and holes bored in trusses, structural composite lumber, structural glue-lam inated members, cross-laminated timber members, or I-joists are prohibited except where permitted by the manufacturer’s recom mendations or where the effects of such alterations are specifically considered in the design of the member by a registered design professional.
APA Technical Note, Field Notching and Drilling of Glued Laminated Timber Beams, Form S560, provides guidance for notching and drilling on glulam when the end notching and drilling of horizontal throughthickness holes cannot be avoided. For the latter, the guidelines are intended to prescribe the size, number, and location of holes to alle viate the reduction in the structural capacities of the glulam. Those prescriptive requirements are helpful for contractors and builders to minimize the need to re-engineer the glulam structural members due to some small horizontal holes.
However, it is not unusual in the structural design phase or in the field that some horizontal holes exceeding the guidance provided in S560 may become a necessity. This document is intended to provide an analytical tool for those conditions through engineering equations and supplemental hole placement requirements. It should be noted that this document is not intended to supersede the recommenda tions provided by the manufacturer of the glulam used in the specific construction project.
between holes.
a) The analytical equations provided in this document are limited to horizontal round holes. Rectangular holes are outside the scope of this document.
b) The diameter of any holes shall not exceed 2d/3, where d is the glulam depth with d ≤ 24 inches. When d > 24 inches, the maximum hole diameter (D) shall be limited to 16 inches.
c) The hole placement requirements specified in Section 6 of this document are integral to the analytical equations and must be satisfied to maintain the validity of Equations 1 through 3
d) Equations 1 through 3 apply to simple-span or multiple-span members that carry uniform and/or concentrated loads.
e) The glulam shall meet all requirements of ANSI A190.1, Standard for Wood Products – Structural Glued Laminated Timber, and ANSI 117, Standard Specification for Structural Glued Laminated Timber of Softwood Species, or shall be recognized in a code evaluation report or an APA Product Report®.
The bending capacity of a glulam member with horizontal holes can be estimated at each hole location using Equation 1 . The bending capacity shall meet or exceed the applied moment at each hole location.
M
where,
M
C
M
S
Figure
S
M
bending capacity with holes, lbf-ft
(Eqn. 1)
effect factor on bending capacity = Snet Sgross
bending capacity without holes, lbf-ft
section modulus with holes, in.3
section modulus without holes, in.3
Figure 3. Minimum distance along the length of the member between the nearest edge of a hole and the face of a top-load object.
The bending stiffness of a glulam member with horizontal holes can be estimated using Equation 2. When there are multiple holes in the member, the diameter of the largest hole should be used in Equation 2. The bending stiffness of the glulam member with holes shall satisfy the deflection limit specified in the building code.
(EI)net = Chole,EI (EI)gross = (1- 1.6 N D L )(EI)gross (Eqn. 2) where,
(EI)net = Net bending stiffness with holes, lbf-in.2
Chole,EI = Hole effect factor on bending stiffness = (1- 1.6 N D L )
(EI)gross = Gross bending stiffness without holes, lbf-in.2 N = Number of holes (see Note b in Section 6 below)
D = Hole diameter (the largest diameter for multiple holes) ≤ 2d/3, in. or 16 in., whichever is smaller L = Member span, in.
The shear capacity of a glulam member with horizontal holes can be estimated at each hole location using Equation 3. The shear capacity shall meet or exceed the applied shear at each hole location.
Vnet = Chole,V Vgross = ( d–D d )2 Vgross (Eqn. 3) where,
Vnet = Net shear capacity with holes, lbf
Chole,V = Hole effect factor on shear capacity = ( d–D d )2 Vgross = Gross shear capacity without holes, lbf d = Glulam depth, in.
D = Hole diameter ≤ 2d/3, in. or 16 in., whichever is smaller
Figure 4. Minimum distance along the length of the member between the nearest edge of a hole and the edge of a side-load object.
For the application of Equations 1 through 3, the following restric tions apply:
a) Holes shall be round and neatly cut with a hole saw or a router and template. Holes cut by other means, such as a reciprocating saw, are prohibited.
b) The number of holes in a given span shall be limited to three or less if the diameters of those holes are all greater than d/3. Otherwise, the maximum number of holes in a given span shall not be more than eight, provided that the other require ments of this section are all met.
c) A cluster of small holes may be analyzed as a single round hole that circumscribes the cluster and meets all other requirements prescribed in this section, as shown in Figure 1 (page 46).
d) Holes shall not be cut in cantilevers.
e) The minimum distance along the length of the member between the face of a support and the edge of a hole shall be 6 inches, as shown in Figure 2 (page 46)
f) At concentrated loads, the minimum distance along the length of the member between the nearest edge of a hole and the face of a top-load object (e.g., column above), as shown in Figure 3, or the edge of a side-load object (e.g., face of the glulam member, or hanger), as shown in Figure 4, and multiple concentrated loads, as shown in Figure 5, shall be 6 inches except for a single concentrated load (Figure 4 ) or a summa tion of multiple concentrated loads (Figure 5) that are 2,000 lbf or less. All concentrated loads combined within or above
Figure 5. Minimum distance along the length of the member between the nearest edge of a hole and multiple concentrated loads.
Figure 6. Combined concentrated loads above or near a hole.
the shaded area shown in Figure 6 shall not exceed 2,000 lbf. The concentrated loads shall not result in a compressive stress that exceeds the allowable edgewise compressive stress perpendicular to grain of the glulam member.
g) For taper or notch cuts at the end of the member, the minimum distance along the length of the member from the end of the taper or notch cut to the nearest edge of a hole shall be 12 inches, as shown in Figure 7.
h) For adjacent holes, the clear distance between holes shall be two hole diameters or larger based on the diameter of the larger hole, as shown in Figure 1. The clear distance shall be measured along the member length, as opposed to diagonally across the member depth if holes are staggered.
i) The hole diameter shall not exceed 2d/3, and the clear distance between the edge of the hole and either edge of the beam shall be at least 0.15d or 1¾ inches, whichever is greater, as shown in Figure 1 ■
References are included in the PDF version of the online article at STRUCTUREmag.org.
is article was previously published in APA Technical Note, Form V700, February 2019. It is reprinted with permission.
Sandy
Figure 7. Minimum distance from the end of the taper or notch cuts to the nearest edge of a hole.
A multi-use, multi-awardwinning structural project, next to Coors Field in Lower Downtown Denver. McGregor Square features parking, retail, office, hotel, and residential spaces in nearly 1 million square feet of structure.
Bruce and spouse Lindsay Structural Engineer | Lakewood, Colorado Ruby (age 3)
Wood-framed structural panel shear walls designed using the Force Transfer Around Openings (FTAO) method have become a very popular option for engineers, espe cially in areas with high lateral force requirements. The need for more affordable housing in metropolitan areas is leading to larger and taller multi-family residential buildings, and these typically wood-framed structures can benefit from the innovative approach behind FTAO design methodology. But do engi neers have all the tools they need to accurately determine the stiffness of these walls and the associated lateral force required for their design. Force-transfer is one of three types of shear walls discussed in the American Wood Council’s Special Design Provisions for Wind and Seismic (SDPWS). The FTAO method considers the strength and stiffness contributed by the wall segments between the window and door openings and the added strength and stiffness contribution from the continuously sheathed wall portions above and below the openings. Whether using the FTAO method or not, builders often opt to provide continuous wood structural panel sheathing across the exterior walls to provide a continuous nail base for cladding materials and eliminate sudden transitions in stucco thicknesses. FTAO shear walls use this continuous sheathing in conjunction with flat steel straps and blocking located at the corners, both above and below, to transfer tension and compression forces around openings ( Figure 1 ).
When the exterior walls of multi-story residential buildings have numerous window penetrations and narrow wall piers between, engineers can be severely challenged to find an adequate amount of shear walls with proper height-to-width aspect ratios capable of resisting code level lateral and overturning demands. FTAO shear walls can provide compliant shear walls using narrow pier lengths to reduce overturning demands (STRUCTURE, January 2018, Hensley).
Additionally, this engineering challenge of accommodating numerous window penetrations in exterior wall elevations leads to another trend in multi-family residential construction: using rigid diaphragm analy ses in conjunction with engaging long corridor shear walls (Figure 2). This idea intends to shift much of the shear load away from the weaker, more flexible exterior shear walls inward to the stronger, stiffer interior corridor walls. With a rigid diaphragm model, lateral forces seek out wall elements with larger in-plane stiffnesses, and those typically are longer walls capable of resisting higher forces. In comparison, most engineers use a flexible diaphragm model that simply divides the lateral forces by tributary areas without regard to wall stiffness or strength potential. A flexible diaphragm model is simpler to imple ment numerically but often is incapable of providing the required resistance associated with conventional wood structural panel shear walls. Therefore, other more costly design options are required.
Figure 2. Typical high-density residential wall layout.
The ability to classify a wood diaphragm idealized as either rigid or flexible is found in ASCE 7-16, Minimum Design Loads and Associated Criteria for Buildings and Other Structures, Section 12.3.1, or SDPWS Section 4.2.5. When wood diaphragms are used in conjunction with wood shear walls, the diaphragm’s classification and its proper distri bution of forces require the shear wall stiffness to be computed unless the building is only a one- or two-family dwelling. Errors in comput ing shear wall stiffness lead to errors in the design loads to the walls.
Another sometimes appealing alternative is to remove all exterior shear walls in one direction and use only the interior corridor walls in an open-front structure with a rigid diaphragm model; however, numerous code restrictions and significant computational complexity are involved.
The inverse of the computed shear wall deflection (or drift) is used to compute the relative stiffnesses of the various in-plane shear wall lines. The 4-term equation (Equation 1) to compute deflection of segmented shear walls has its origins in published materials since the 1950s and consists of evaluating separate con tributions from bending due to chord strains, panel shear deformation, panel nail slip, and wall anchorage slip. The 2001 SDPWS nonlinear 4-term equation was replaced in the 2005 SDPWS with a more straightforward linear 3-term equation (Equation 2), with the 4-term equation moved back into the Commentary.
bending shear nail-slip anchor
for the first time, a rational method to determine the estimated deflec tion in FTAO walls that is applicable to symmetric and asymmetric piers and walls with multiple openings supported by full-scale testing (APA Publication M410).
δsw = + + 0.75hen + ∆a (Eqn. 1)
δ
8vh 3 EAb vh Gvtv h b
= + + ∆a (Eqn. 2)
8vh 3 EAb vh 1000Ga h b
One of the challenges of designing with FTAO walls is accurately determining their stiffness for diaphragm classification and force distri bution purposes. Even though currently adopted standards provide no direct guidance on computing FTAO shear wall shears or deflections, the SDPWS does require that these wall types be designed based on a rational analysis. One tool that is now available was developed by APA – The Engineered Wood Association after conducting full-scale experimental research on these wall systems. This research provided,
The numeric model assumes the deflection is controlled by full-height piers away from the loaded edge and half-height piers toward the loaded edge (Figure 3), using the conventional shear wall deflection equations. For asymmetrical pier conditions, a deflection is calculated for the load applied in each direction and then averaged to achieve an equivalent deflection and stiffness. Practitioners can consult APA Tech Note T555A, with its companion spreadsheet-based FTAO calculator, to simplify the computations necessary to design these shear wall systems.
Recognizing the importance of FTAO shear wall stiffness, several full-scale tests were undertaken between 2019 and 2021 at Cal Poly, San Luis Obispo’s Architectural Engineering Department High Bay Lab, under dry-use conditions. The main objective was to evaluate the appropriateness of APA deflection calculation and methodology with several FTAO configurations. Single opening, symmetric FTAO shear walls with 15 32-inch Structural I plywood, Douglas-fir framing (moisture content less than 19%, not kiln dried), 10-penny common nailing, and Simpson Strong-Tie steel strapping and hold-downs were utilized. Other variables such as sensitivity to construction tolerances, imperfec tions, and conventional wall heights (9-12 feet) were included in the testing. Testing is still ongoing, and dissemination of the results will be provided at some point.
The FTAO walls were designed, built, and tested under faculty supervision by undergraduate and graduate students to supplement their wood design laboratory course, providing a hands-on experience enabling a better understanding of the workings, performance, and constructability issues associated with these wall types (Figure 4 ). A backbone curve was established from cyclic testing using a hydraulic actuator to apply the lateral force to the wall. AsFigure 4. Full-scale experimental FTAO shear wall test specimen.
Figure
shown in Figure 5, the experimental displacement of this FTAO wall tracked well with the APA calculated deflections using the 4-part equation. It showed that the wall was slightly stiffer than predicted by both the 4-part and 3-part deflection equations.
When developing empirical-based design equations from experimental data, researchers and engineers often tend towards the conservative side when data points are somewhat scattered. However, a conservative (over) estimation of deflection results in an unconservative underesti mation of distributed force to that element. Similarly, inaccuracies in shear wall stiffness estimations can also occur due to using the 3-term equation instead of the 4-term equation, ignoring cladding or plaster wall finishes, effects of lumber shrinkage, and construction issues. An additional issue is that the segmented shear wall deflection equations were validated with monotonic loading data. In contrast, the FTAO
shear wall deflection computation method is validated with cyclic loading data. How concerned should an engineer be regarding the accuracy of computing wood shear wall stiffnesses in rigid diaphragm systems?
When evaluating these concerns, an important factor to consider is the benefits of non-linear behavior and positive postyield stiffness of the shear wall systems. The non-linear “softening” of shear wall stiffness seen in Figure 6 will mitigate errors in the engineer’s estimation of shear wall stiffness. For example, consider several shear walls col lectively resisting the story shear below a rigid diaphragm. If one wall has more real stiffness than was estimated in the rigid diaphragm model, it will initially attract more load than considered initially. However, this additional wall load may cause the wall to soften to the point that it is less rigid than initially expected and thus redistribute a portion of the load back to the other shear walls. This redistribution of loads associated with non-linear wall behavior below a rigid diaphragm is an excellent asset in the inherent ability of these systems to help resist overloads.
But this reliance on a wall to soften and redirect loads to stiffer elements is only appropriate if there is adequate positive post-yield stiffness for the wall. In other words, once the wall has reached its design capacity and is softening, does it still continue to require more load to get more deflection? This characteristic is closely related to ductility, and wood-framed wood structural panel shear walls obtain significant ductility from the wood-to-wood nailing. As evident in Figure 6, despite the softening of the shear wall, which would allow overloads to be redirected through a rigid diaphragm, the wall con tinues to have the ability to carry more loads without a sudden loss in strength or stiffness.
In conclusion, wood-framed wood structural panel FTAO shear walls used in conjunction with rigid diaphragms and interior individual full-height wall segments are a popular system that depends upon the proper computation of stiffnesses and strengths. Recent testing and published guidance have given engineers tools to more easily adopt this system into their projects. While it is still important to properly estimate shear wall stiffnesses in a rigid diaphragm model, inadvertent errors in this estimation can be partially mitigated by the non-linearity and ductility of the complete system. Better performance and cost savings can be achieved with a solid understanding of FTAO shear walls.■
References are included in the PDF version of the online article at STRUCTUREmag.org.
Michael Deigert is an Assistant Professor in Architectural Engineer at Cal Poly, San Luis Obispo (mdeigert@calpoly.edu).
John Lawson is a Professor in Architectural Engineering at Cal Poly, San Luis Obispo (jwlawson@calpoly.edu).
Add simplicity, performance and sustainability to your low-slope roofing projects with OneDek® from All Weather Insulated Panels. Fewer layers equals a simplified design plus a faster, more convenient installation. For quality, performance and value, leverage the Power of OneDek
more
Continuing our series on automation (Installment 1, December 2021, Installment 2, March 2022), I sat down (virtually) in January 2022 with two more industry experts in digital design: Matt Sweeney, Production Technology Manager at PES Structural Engineers, and Derek Pedersen, Principal at JVA Consulting Engineers. Both serve on the SEI Digital Design Committee. Below are highlights from our discussion.
In the previous session of this series, we heard a lot about auto mating the repetitive tasks in an engineer’s day. Where have you seen automation of repetitive tasks work well? Or where is there room for improvement right now?
Sweeney: One example is that we have been able to get automa tion working well with dimensioning. On detailed drawings where we dimension elements a number of times, we’ve been able to get some tools to work really well. In the past, we used interns or engi neers to spend a lot of time, and they would just click, click, click. And you still never knew whether they hit the right reference plane. These tools work well because they do the same thing and hit the same line every single time, and they can do it over, say, 200 or 300 wall panels identically. Where that doesn’t work is that the computer sometimes cannot figure out when things overlap, so you still spend some time massaging things, but it does save an amazing amount of that mundane clicking.
Pedersen: We have had some success assisting PMs in getting their projects started with master content. We’ve got content organized by building systems. We bring it into the project file so everything is set up and ready for the engineer. We concentrate on that heavily so that the engineer is not reinventing the wheel. Similarly, we have leveraged our database of past projects so they can be recalled based on various combinations of project facets (material type, size, loca tion, building type), allowing for accessible ‘go-by’ content. This is
a great way to get new staff up to speed on how we do things. We have also dabbled into Clarity [an automated task server program by Imaginit]. We use that internally to update our content rou tinely because we do not have a BIM manager. We wear different hats, so pushing it out to staff is a hurdle when making updates. Clarity helps bridge that gap and automates communication. We can schedule pulling the model off the architect’s BIM 360 site and posting PDFs. There are a lot of possibilities there.
You both have broad experience with project types. Do you find that there is a specific structural material or project type that lends itself best to automation methods or advanced digital tools in general?
Pedersen: Obviously, steel and concrete have a lot of potential. I think in the last AutoCAD University, somebody had some genera tive design automation of floor plates for wood-framed houses. But we are already so fast at wood houses in our office. We turn around a single-family residence in one or two days, so there’s not a whole lot of fat to trim there.
Sweeney: But it can vary a bit based on your size and approach. JVA and PES are similar-sized and scaled firms. We don’t have development teams to get things like generative design or higher-level parametric tools. However, areas of repetition and automation ahead of time, like with dimensioning that I mentioned or detailed drawings on industrial warehouse buildings with hundreds of wall panels, that kind of repetition lends itself to automation at a scale that we can do, compared to bigger firms with development teams.
That’s why
are always plugged into conferences and committees. You learn where things take root and where they see success: what’s worth our time to invest in and to check out.
Derek PedersenPedersen: Yes, I agree. We sort of stand on the shoulders of giants, if you will, and let them go through the hard knocks to sort out what works. That’s why we are always plugged into conferences and committees. You learn where things take root and where they see success: what’s worth our time to invest in and to check out. We understand this works best as we do not have the bandwidth to be the earliest adopters.
Digital tools may appear on the surface to be more logical for the design of new construction projects than for existing structures. But where have you seen digital tools used well or creatively on existing structures?
Sweeney: Reality capture, whether it is a laser scan or even just decent photogrammetry solutions. 360degree walk-through situations where you can capture a building wholly in one visit. Then go back to the office,
and you don’t have to worry about whether you took a specific picture or where you were standing when you took a particular picture, or even, did I see that thing? You can revisit all of that simply. You used to need a laser scan, but now some of the tools are getting so common that you can use a relatively inexpensive 360-degree camera, walk around the site, and have a pretty good representation of what’s there.
Pedersen: Yes, absolutely. We have a historical preservation division and a forensic team, and they rely on laser scans and other imagery tools. In addition, one of our forensic team members is a licensed drone pilot; we use the drone to capture difficult-to-reach facets of buildings.
Where do you see opportunities for improvement in the relationship between structural design engineers and structural software developers?
Sweeney: One of the biggest things still missing with the analytical software is any interoperability with the design tools. ere are different ways to go about it, but we still primarily create and maintain two different models. Some firms I know do it slightly better than others as far as getting them to talk to each other. But I would say most structural engineers out there, without creating custom tools, make two very different models and keep them separate. And then, it’s up to an engineer to manually convert the two.
Pedersen: You struck a chord there, Matt. We are still going to have two models. At best, you pull the grids over or do something rudimentary that starts in one and goes to the other. I would love to see that grow. When Autodesk purchased Robot, we thought, well, they are onto something here. But we still have a good number of hoops to jump through to get the connection to go back and forth. Or compare the customer service presence to Hilti and Simpson. ose folks go around to firms, talk about their product, and interact with our staff. I would like to see more of that from the software companies and ask us: What are you working on? What are you up against? What would you like to see? A presence from someone who’s not purely sales. ere could be some ground gained there, and I think it would serve them well.
In the last series session, we talked a lot about explaining to architects our workflow because we need time outside of the BIM model to do our analysis. In contrast, the architects are continually designing within the BIM model. Have you also seen this as a challenge in communication between engineers and architects?
Pedersen: Yes, it is a challenge, but really, it’s just absolutely critical for our consultant position. I enjoyed reading that last article, and I commiserated with it quite a bit. Our team needs to be constantly touching base to figure out where the evolution of the design is in the various parts of the building. e model cannot be taken as gospel as is; you need confirmation from the authors. Sweeney: And you cannot just assume that somebody is constantly searching your model for things that are different. Because, as they mentioned in the previous discussion, there are times we
spend away from the BIM model, and we are not necessarily referencing it daily to see whether a whole bunch of openings got shifted. Or that they finally added that thing to the roof that they were talking about at one point.
Pedersen: ese days, there is so much emphasis placed on the model but, for most projects, the deliverables are the drawings. You can get caught by just looking at the architect model and not looking at what they are producing and what ends up on the sheets. In addition, the client might not be as savvy with their use of BIM. At the very least, at the end of each major milestone, it is essential to print out a set and go through what your client and the other disciplines are showing on the drawings. en bring that back to what you are seeing in the model, and start working through the discrepancies.■
e author would like to thank Matt and Derek for this discussion. You both have great insights that I hope can assist and inspire our fellow engineers in the industry.
You used to need a laser scan, but now some of the tools are getting so common that you can use a relatively inexpensive 360-degree camera, walk around the site, and have a pretty good representation of what’s there.
Eytan Solomon is a Senior Associate at Silman and a member of STRUCTURE’s Editorial Board (solomon@silman.com).
In expansive soil regions, the Geotechnical Engineer for a project usually provides recommendations for grade-level floor con struction – structural slab on void forms or conventional slab on grade – based on the existing subgrade properties, excavation depth, and compaction of select fill. The Structural Engineer of Record (SER) then provides a comparative study of both options. Conventional slab on grade is generally a thinner, lightly reinforced slab requiring exca vation and replacement of subgrade with a select fill but is subjected to movements as the existing subgrade heaves. In contrast, the structural slab on void form option often requires a thicker, heavily reinforced slab spanning between larger column foundations and other intermediate foundations but with out undercutting or removing the existing soil. The void forms allow for placement of wet weight of concrete during construction but absorb ground moisture gradually and lose strength after the concrete has set, thus creating a gap under the slab to allow for soil movements. The final decision by the owners is usually based on the comparison of the initial construction cost of each option without fully understanding the short- and long-term consequences.
This article attempts to take a holistic approach to this comparison between a con ventional slab on grade and a structural slab on void form to help the SER educate owners,
architects, contractors, and other disciplines to enable them to make an informed decision. Additional considerations beyond construc tion costs are outlined below and should be discussed with all stakeholders in the project:
• Potential Vertical Rise (PVR): A baseline for PVR, a measure of the swell poten tial of the soil, needs to be established for the project based on the current and future building occupancy in consulta tion with the owners. This is important in determining the depth of excavation of the existing subgrade and replace ment with select fill and determining the duration of compaction of subgrade under the conventional slab on grade. In addition, a baseline PVR could play a role in the choice of a flooring less sensitive to movements on slab on grade, relocating equipment sensitive to movements away from slab on grade, or choosing a structural slab on void form option for a portion or all the grade level floor construction.
• Differential movement: Expansive soil-related movements are essentially eliminated when using a structural slab on void form if a sufficient gap is maintained under the first floor, but, in a conventional slab on grade, differen tial movement is possible and should be expected. The owners should be edu cated about the cracks that are likely
to occur in a floor slab and potential distress to floor-supported finishes and interior walls due to the differential movement in slab on grade despite mitigating efforts such as thickening the slab under the interior walls.
• Landscaping: The presence of trees and vegetation adjacent to the building exacerbates the formation of cracks in slab on grade due to moisture loss in the subgrade from transpiration to the root systems of the vegetation. On the other hand, large trees with extensive root systems do not pose a significant risk to a project with a structural slab on the void form. Landscaping around and adjacent to the structure, existing or future, should be carefully selected to prevent roots from migrating beneath the structure and changing the soil moisture content.
• Crawl Space: If a crawl space is intro duced under the structural slab at the grade-level floor, owners should be advised that proper ventilation, perimeter closure, lighting, and crawl space access need to be provided and maintained throughout the life of the building to reduce moisture accumulation and humidity within the crawl space.
• Early Coordination: Slab on grade construction is more forgiving towards accommodation of trenches, slab
Example slab on grade construction.
Example
on on void form construction.
depressions, or openings coordinated after the foundation placement, provided that they do not conflict with column foundations. Conversely, slab openings significantly affect the punching shear capacity of a structural slab on void form. erefore, the trenches and depressions in the slab need to be coordinated around additional intermediate piers. e importance of accelerated coordination at the grade level floor should be emphasized to all the disciplines, the contractors, and the owners.
• Future modifications: Owners should be made aware of the limitations of future modifications to the grade level floor, if any, with each type of construction. e slab on grade construction tends to provide flexibility to the owners when it comes to adding openings or trenches in the future. At the same time, structural slabs on void forms require closer attention to detailing and identification of permissible areas where future openings could be added.
• Under-slab utilities: In the case of structural slab on void forms, the under-slab utilities are hung from the structural slab. A sufficient gap is maintained underneath so that the utilities are not affected by the movements in the expansive soils. e utilities typically have an expansion joint at the building perimeter to account for the differential movement between the building slab and the surroundings. In the case of slab on grade, if not protected correctly, the utility trench serves as a conduit that permits moisture migration under the slab. e utility trenches are typically backfilled with properly compacted clay fill and capped with a bentonite clay plug at the building perimeter to restrict moisture from migrating under the slab. e owners should be educated on the proper placement and maintenance of each option’s existing and future utility trenches.
• Flood Zone: In high or frequent flood zones, where the scouring of the top layer of soil is expected, a structural slab can provide a viable and, in some cases, the only alternative. e cost of additional
foundations or a thicker structural slab on void forms should be weighed against the cost of flood mitigation options, such as flood walls, otherwise required around the building with a conventional soil-supported slab on grade.
In conclusion, by discussing the advantages and disadvantages of a conventional slab on grade and a structural slab on void form, the SER can help all stakeholders understand the risks associated with each option and prepare
a risk mitigation plan critical for the success of long-term durability and performance of the building.
■
Shruti Sharma is a Principal in the Houston office of Walter P Moore. She is a member of the Coalition of American Structural Engineers (CASE), the leading provider of risk management and business practice education and information for structural engineering firms.
Phone: 407-284-9202
Email: support@asdipsoft.com
Web: www.asdipsoft.com
Product: ASDIP Steel
Description: An advanced software for the design of steel members and connections, such as composite/ non-composite beams, steel columns, base plates, anchoring to concrete, shear connections, and moment connections, per the latest design codes.
ASDIP STEEL comes with 5 intuitive modules that will substantially simplify time-consuming calculations for your structural designs.
Atlas Tube
Phone: 800-733-5683
Email: bradlee.fletcher@atlastube.com Web: www.atlastube.com
Product: Hollow Structural Sections
Description: Atlas Tube produces the largest hollow structural sections (HSS) in the world. Square and round shapes in sizes ranging from 8-inch square by 0.750-inch wall to 22-inch square by 1-inch wall. e largest rectangular section produced are up to 30- by 14- by 1-inch wall.
Cast Connex
Phone: 888-681-8786 Email: info@castconnex.com Web: www.castconnex.com
Product: High Integrity Block
Description: e industry leader in the architectural and structural use of cast steel components in the design and construction of building and bridge structures. Our products include pre-engineered connectors that simplify the design and enhance the performance of structures. We also offer design-build services for custom cast steel nodes and components.
Phone: 267-702-2815
Email: info-us@dlubal.com
Web: www.dlubal.com
Product: RFEM 6
Description: Complete with USA/International Standards for steel, concrete, mass timber, and aluminum, the user-friendly software allows for efficient modeling, powerful non-linear analysis, and highly detailed design results for multi-material tall buildings. New Building Model add-on outputs detailed story results like story shear, center of mass and rigidity, and shear wall forces.
Phone: 800-424-2252
Email: info@enercalc.com
Web: https://enercalc.com?utm source=SM2205
Product: ENERCALC Structural Engineering Library / ENERCALC 3D / ENERCALC for Revit
Description: Steel design is easy/fast with ENERCALC’s Structural Engineering Library (SEL). Beams, columns, 2-D frames, force distribution in bolt groups… SEL handles it all. Revit users: SEL + ENERCALC for Revit builds calculations directly from your Revit models. Fast, direct API means no messy, repetitive import/ export – just fast, intuitive design.
IES, Inc.
Phone: 800-707-0816 Email: info@iesweb.com Web: www.iesweb.com
Product: ShapeBuilder
Description: Efficient tall structures benefit from optimized design and economy of scale. Get the most out of structural members by using ShapeBuilder to tailor shapes to specific purposes. Handle custom architectural forms. ShapeBuilder provides fast results for designer questions about geometric or structural properties of cross sections. Get your free trial.
Phone: 260-969-3500
Email: joe.voigt@newmill.com
Web: www.newmill.com
Product: Structural Steel Joists and Decking
Description: A nationwide supplier of custom engineered and manufactured structural steel joist and deck building systems. Call us early in the design-build process. We can assist in right-system specification from our extensive portfolio of building system options. For multi-story projects, we offer the broadest range of long-span, “thinslab” composite floor systems.
Phone: 949-951-5815
Email: benf@risa.com
Web: risa.com
Product: RISA-3D/RISAFloor
Description: An unrivaled multistory building analysis and design package. Modeling has never been easier, whether you are doing a graphical layout, importing a BIM model (from Autodesk Revit), or prefer spreadsheets. Full code checks and optimization for six different material types makes RISA your first choice in buildings.
Phone: 855-572-4625
Email: info-na@schoeck.com
Web: www.schoeck.com
Product: Schöck Isokorb® T Type CK Structural ermal Break
Description: A load-bearing thermal insulation element for cantilever concrete slabs such as balconies. It transfers bending moments and shear forces. e structural components of the Isokorb T Type CK include upper tension bars, bent shear bars, and the lower HTE compression modules.
Trimble
Phone: 678-737-7379
Email: jodi.hendrixson@trimble.com Web: www.tekla.com/us
Product: Tekla Tedds
Description: A powerful software that will speed up your daily structural and civil calculations, Tekla Tedds automates repetitive structural calculations. Perform 2-D frame analysis, utilize a large library of automated calculations to U.S. codes, or write your own calculations while creating high-quality and transparent documentation.
Product: Tekla Structures
Description: Move from design-oriented to construction-oriented engineering and enable structural engineers improved additional services. With an open and collaborative environment, you can easily work with other disciplines and reduce RFIs for complete control from concept to project completion.
Williams Form Engineering Corp.
Phone: 616-866-0815
Email: williams@williamsform.com Web: www.williamsform.com
Product: All- read-Bar
Description: Williams Form Engineering Corporation has been providing threaded steel bars and accessories for rock anchors, soil anchors, high capacity concrete anchors, micropiles, tie rods, tiebacks, strand anchors, hollow bar anchors, post tensioning systems, and concrete forming hardware systems in the construction industry for over 100 years.
Listings are provided as a courtesy, STRUCTURE is not responsible for errors.
Sign up now for this valuable resourcein the October edition of STRUCTURE
• Free listings in categorized product guides
(Deadline - Sept. 9, 2022)
• STRUCTUREsolutions Company Profiles created from supplied editorial copy and graphics
• Special reducedrate packages are available
For details contact monica.shripka@STRUCTUREmag.org
Mark your calendars for November 1-4 in Chicago, and meet us in the “windy city” to network and learn with those who know “wind loads” best! The NCSEA Structural Engineering Summit offers unrivaled educational opportunities with leading experts, unique networking opportunities in the exhibit hall, inspirational keynote speakers, and a celebration of structural engineering ingenuity and service like no other. Visit www.ncseasummit.com to learn more.
Success begins and ends with self-confidence. Your belief in yourself is the foundation for thriving, achieving your dreams, and unlocking your potential. With self-confidence, you live the happy, inspired, connected life you deeply desire. As an award-winning coach and PhD sports psychologist, Dr. Ivan Joseph has focused on understanding the skill of self-confidence. He has developed, applied, and refined dozens of techniques that lead to high performance and excellence. In this energizing and motivational talk, you will learn the secrets Joseph used to help individuals and teams reach goals they never thought possible.
Submit your firm’s prized project to the 2022 Structural Engineering Excellence (SEE) Awards program. Visit bit.ly/2022SEEAwardsSubmit to enter your project before the July 12th deadline. The SEE Awards annually highlight some of the best examples of structural engineering ingenuity throughout the world. Projects are judged on innovative design, engineering achievement, and creativity. Winners will be announced and applauded at the Awards Celebration at the Structural Engineering Summit November 3, 2022, in downtown Chicago, IL. Winning projects will also receive significant promotional benefits including a poster board presentation at the Awards Celebration, coverage in STRUCTURE magazine and NCSEA media outlets, the opportunity to present in the annual awards webinar series, and more.
Join
a special free NCSEA webinar
Outstanding Project winners
NCSEA’s 2021 Excellence in Structural Engineering Awards. Thank you to Atlas Tube for sponsoring this series, making it freely available to all! This series will be held on six Thursdays – May 26 and June 2, 9, 16, 23, and 30; starting at 12 p.m. CST each day – and includes up to 8.5 hours of education. The award-winning structural engineers will present on their projects – highlights and successes, challenges and innovations, all from the structural engineer perspective. Learn more and register at bit.ly/2021SEEAwardsWebinar
Do you know a fellow engineer who has contributed exemplary service and commitment to the betterment of the structural engineering profession? NCSEA is now accepting nominations for the 2022 Special Awards including the Service Award, Robert Cornforth Award, Susan M. Frey Educator Award, and Susan Ann “Susie” Jorgensen Presidential Leadership Award. Submit your nomination at bit.ly/2022SpecialAwardsNominate before the July 12th deadline. Special Award honorees will be announced in advance of the Summit via NCSEA and STRUCTURE media outlets and celebrated at the Awards Celebration at the Structural Engineering Summit November 3, 2022, in downtown Chicago, IL.
It was great to get together again at Structures in Atlanta, meet colleagues, make new friends, and take in the latest learning and resources. Thank you to the many presenters and participants, sponsors, exhibitors, and special congrats to the over 30 SEI Futures Fund scholarship recipients!
May 3-6, 2023, in New Orleans
• Submit session proposals by June 15
• Students (B.S., M.S., Ph.D.) and Young Professionals (35 and younger): Apply for the SEI Futures Fund scholarship www.structurescongress.org
Review ASCE 7-22, changes from ASCE 7-16, the Digital Products/Hazard Tool, and join the discussion with the expert standard developers. 1.5 PDHs per session.
June 9, 2022: ASCE 7-22 Wind & Tornado
Join host Cherylyn Henry, P.E., F.SEI, M.ASCE with guest Donald Scott, P.E., F.SEI, F.ASCE, and Marc L. Levitan, Ph.D., A.M.ASCE
July 14, 2022: ASCE 7-22 Snow/Rain
Join host John Duntemann, P.E., S.E., M.ASCE with guest Sean M. Homem, P.E., S.E., P.Eng, M.ASCE
Learn more and register at: https://collaborate.asce.org/integratedstructures/sei-standards
I had the pleasure of receiving an SEI Futures Fund student scholarship to the Structures Congress in Atlanta, attended by leading academics, industry professionals, and other experts. As a thirdyear undergraduate, I found the conference a fantastic gateway into a vast and diverse industry. Commonly, undergraduate programs only expose students to buildings and bridges. However, at Structures Congress, these are covered in great detail along with less recognized segments of struc tural engineering. This exposure is invaluable for someone about to launch a professional career. I attended sessions on establishing the next iteration of the structural building code that I will be utilizing in the near future. With this insight, the standards hold deeper reasoning and logic than just numbers on a page, and I have a much stronger understanding of the new seismic and tornado provisions in ASCE 7-22.
Beyond the technical sessions and keynotes, there were plenty of opportunities to network with other students, young professionals, and established experts. At the evening receptions, I met everyone from a high-rise design startup founder in Chicago to a construction-oriented hydrologic structure engineer from rural Ohio. I am ecstatic to re-enter my professional life back home, having these people as friends.
Structures Congress is an opportunity to see the industry as it stands and where it is going. Only at Structures Congress can you listen to a board of world-leading experts discuss the seismic properties of laminated timber buildings, the 3-D printing concrete revolution, or how climate change impacts the sufficiency of standard wind loads. Structures Congress can serve as a catch up to current industry practices. It can also serve as an eyeopener, exposing everyone to the problems of tomorrow and the solutions being developed.
I am incredibly glad to have participated in this year’s Structures Congress. As a result, I feel more prepared to start a career in structural engineering, and I look forward to my involvement with SEI/ASCE throughout my career.
By Caleb Stevenson, S.M.ASCE, Iowa State University
SEI Standards
submit errata,
Errata
ASCE
www.asce.org/SEI
Your SEI Membership must be current (dues fully paid) in order to vote in the SEI online election for the SEI Board of Governors in July. So make sure to renew and ensure your email is up to date by June 15. Members above the student grade are eligible to vote, so if you are graduating, make sure to upgrade. Renew at www.asce.org or contact ASCE Customer Service at memrec@asce.org or 1-703-295-6300.
• Add SEI with your ASCE mem bership to receive SEI benefits, opportunities, and resources
• Update your contact info and member profile at www.asce.org
• Connect with your SEI Chapter or Grad Student Chapter www.asce.org/SEILocal
Get involved to advance your career and the profession, learn valuable skills, and broaden your network by joining SEI technical committees! Applications from Young Professionals and Graduate Students are especially encouraged. Whet your appetite with the committee activities highlighted below; indulge in the complete list at: www.asce.org/SEICommittees
• Bridge and Tunnel Management, Inspection, and Rehabilitation – webinar series development, investigation of topics such as structural inspection including robotics and advanced sensing, climate impacts
• Fire Protection – looking for the balance between academia and industry for a wide range of knowledge to provide education on fire protection engineering and on the development of a model to calculate fuel loads in buildings
• Innovative Modular, Rapidly Erectable, and Deployable Structures – creating an interview series on accelerated construc tion, rapid repair and rehabilitation, and existing manufacturing of relevant structures
• Bridge Security – develop educational materials to implement bridge security in design practices
• Steel Bridges – fill gaps within the bridge industry
• Seismic Effects for Non-Building Structures and Foundations – champion efforts related to non-building structures such as dams, nuclear, petrochemical, coast offshore, and new sustainable energy systems such as wind and solar
• Cold-Formed Steel Member – developing a technical report
• Concrete Shell Design and Construction – developing design guide
• Task Group 2: Reliability-Based Structural System Performance Indicators – working on a funded Special Project focused on climate change
SEI Committees need you – learn more and apply at https://bit.ly/3FzAafu If you have any questions, reach out to SEI Technical Activities staff; contact Bianca Augustin at baugustin@asce.org
August 3-4, 2022, Salt Lake City, Utah
This year’s CASE Summer Meeting will offer the opportunity to connect and network while earning some PDH credits too!
The 2022 Meeting includes:
• CASE Roundtable addressing trending industry topics.
• In-depth presentation on the Salt Lake Temple seismic upgrade and construction project, which includes new additions, revamped grounds, seismic upgrades and steel additions, along with an updated mechanical and electrical system. The presentation will give an overview of the project and its purpose, and a review of the base isolation system. It will discuss the unique design and construction efforts for this extraordinary project. Learning Objectives:
1. Learn how base isolation systems protect buildings.
2. Learn ways to minimize building movement during load transfer.
3. Learn the importance of proper shoring to meet project needs. This project will utilize massive concrete footings and transfer girders to support the temple on the base isolators. The presentation will discuss the measures taken to meet the ACI code requirements for mass concrete, bending, shear, and torsion.
• Education sessions will focus on Green Energy trends and how engineers can identify projects and opportunities for their firms.
Registration opening the last week in May. Visit www.acec.org for more details.
The CASE Coalition has several committees that meet regularly to develop documents that help guide engineers in their business practice. The work of these committees is an essential part of what coalitions do and is one of the most significant values in the CASE membership. The Programs and Communications Committee is responsible for developing program themes for conferences and sessions that enhance and highlight the structural engineering profession.
THIS MONTH , the Programs and Communications Committee has been working on preparations for the 2022 CASE/NCSEA Business of Structural Engineering event in Chicago, IL, in November; the 2022 ACEC Fall Conference in October in Colorado Springs, CO; and the Coalitions Summer Meeting in August in Salt Lake City, UT. We are currently seeking two to four new members to join the Programs and Communications Committee. Do you know some one in your firm looking for ways to expand and strengthen their business skillset, gain experience serving on a committee, sharpen their leadership skills, and travel to interesting places? Please consider applying for a position on the committee. Committee member commitments include a monthly virtual meeting, a few hours a month working on relevant documents, and travel to the Coalition's winter and summer meetings!
To apply, your firm should:
• Be a current member of ACEC
• Be a member of the Coalition of American Structural Engineers (CASE); or be willing to join the Coalition
• Be able to attend the groups’ regular face-to-face meetings each year: August, February (hotel, travel partially reimbursable)
• Be available to engage with the committees via email and video/conference call
• Have some specific experience and/or expertise to contribute to the group
Please submit the following information to (mkroeger@acec.org), subject line, CASE Committee:
• Letter of interest indicating which committee
• Brief bio (no more than a page)
CASE has tools and practice guidelines to help firms deal with a wide variety of business scenarios that structural engineering firms face daily. So whether your firm needs to establish a new Quality Assurance Program, update its risk management program, keep track of the skills engineers are learning at each level of experience, or need a sample contract document – CASE has the tools you need!
CASE 962-D – A Guideline Addressing Coordination and Completeness of Structural Construction Documents (2020)
Since the mid-1990s, owners, contractors, and design professionals have expressed concern about the level of quality of structural construction documents. They have observed that the quality of these documents has deteriorated, resulting, at times, in poorly coordinated and incomplete design drawings. Inadequate and/or incomplete design drawings often result in inaccurate competitive bids; delays in schedule; a multiplicity of requests for information (RFIs), change orders, revision costs; increased project costs; and general dissatisfaction with the project. The Council of American Structural Engineers (CASE) has prepared this Guideline to address these concerns. This book discusses the purpose of the guideline, the background behind the issue, the important aspects of design relationships, communication, coordination and completeness, guidance for dimensioning of structural drawings, effects of various project delivery systems, document revisions, and closes with recommendations for development and application of quality management procedures. A Drawing Review Checklist is attached.
CASE #6 – An Agreement Between Client and Structural Engineer for a Structural Condition Assessment. This document aims to provide a sample Agreement for structural engineers to use when providing a structural condition assessment directly to a client. For example, the assessment may be required for upgrading the structure for an increase in imposed loads; for damage from fire, wind, or earthquake; for seismic retrofitting; for historic preservation or change in occupancy; or for adding new structures upon or adjacent to an existing structure.
CASE #2 – An Agreement Between Client and Structural Engineer of Record for Professional Services. This agreement form may be used when the client, e.g., owner, contractor developer, etc., wishes to retain the Structural Engineer of Record directly. The contract contains an easy-to-understand matrix of services that simplify the “what’s included and what’s not” questions in negotiations with a prospective client. This agreement may also be used with a client who is an architect when the architect-owner agreement is not an AIA agreement.
can purchase these and other Risk Management Tools at www.acec.org/bookstore
Downtown Seattle’s 58-story, 850-foottall Rainier Square made history when it was completed in November 2020. The $600 million development did more than transform the site of an outdated indoor shop ping center into a vibrant, vertically stacked, mixed-use destination offering 1.4 million square feet of space for offices, luxury apart ment homes, and retail. It also represented the world’s first high-rise tower successfully built using safe, efficient, and highly innovative SpeedCore as its structural system.
Historically, a high-rise building’s structural system consisted of a central core made of reinforced concrete walls – to resist wind and earthquake forces – surrounded by structural steel floor beams and exterior steel columns. SpeedCore completely reimagines this conven tional approach by taking the basic structural components of the traditional concrete corewall system and turning them inside-out.
Instead of concrete walls with steel rein forcing bars inside, SpeedCore uses steel Concrete-Filled, Composite-Plate Shear Wall (CF-CPSW) modules to eliminate installing rebar and placing and stripping formwork.
Developers can build entire structures at the rapid pace of steel construction because SpeedCore’s modular CF-CPSW panels do three jobs at once – support the steel frame above until the concrete is placed, function as the concrete’s formwork, and provide all the concrete reinforcement typically pro vided by rebar.
Put more simply, SpeedCore’s structural system is akin to an ice cream sandwich, with steel plates serving as the cookies and the concrete serving as the filling.
Magnusson Klemencic Associates (MKA) was selected as Rainier Square’s Structural Engineer of Record two years before the project broke ground in 2017. Although backed by more than a decade of research and development championed by MKA and conducted by a variety of reputable industry organizations – the American Institute of Steel Construction, Charles Pankow Foundation, MKA Foundation, Purdue University, Steel Institute of New York, and the University at Buffalo – SpeedCore had yet to be incorpo rated into a high-rise building. If it were to be
used at Rainier Square, the proj ect would serve as SpeedCore’s proof-of-concept.
Fortunately, developer Wright Runstad & Company under stood SpeedCore’s sui generis value proposition – namely, how its assembly-line-like efficiency would allow a tower to be erected dramatically faster than if using a traditional structural core system. The developer trusted the project team to deliver this novel struc tural system successfully, and their decision paid off.
SpeedCore cut 10 months off a potential 32-month sched ule if Rainier Square had been constructed with a traditional structural system. The high-rise was erected 43% faster, with four floors completed weekly, resulting in a topping-out milestone just 10 months after the first steel arrived onsite. The savings in general conditions, construction financing interest, and earlier rental revenue streams were significant. In addition, the pre fabrication of SpeedCore’s modular panels meant less waste, fewer onsite workers, and fewer truck trips, which all generated positive environmental benefits.
The Rainier Square project is currently in the running for the prestigious Grand Award in the ACEC 2022 Engineering Excellence Awards competition to be announced at the end of May. Magnusson Klemencic Associates was an Outstanding Award winner for Rainier Square in NCSEA’s 2021 Excellence in Structural Engineering Awards program in the Category – New Buildings over $200 Million.
a 100-foot-deep excavation extending 50 feet below the mat foundation of the neighboring 40-story Rainier Tower, built in the late 1970s. Geotechnical engineer Hart Crowser provided an impressive temporary earth retention system that allowed Rainier Tower to remain fully occupied during Rainier Square’s excavation despite both towers’ snug proximities.
In the end, SpeedCore exceeded the devel oper’s expectations, with one Wright Runstad & Company executive describing SpeedCore as “my hero core” and adding, “I thank my lucky stars we [did not build with] a concrete core.”
But SpeedCore was not Rainier Square’s only innovation. The project’s engineering also included a Performance-Based Seismic Design and two bi-directional 35,700-gallon water tanks, which serve as dampers on the roof to reduce wind motion.
In addition, MKA incorporated the innovative use of two-story-deep outrigger belt trusses on the 38th floor on two sides of the core to engage six exterior columns for economic increases in overturning resistance. Buckling-Restrained Braces were used in a unique application for the diagonal truss members to provide superior performance during seismic events.
Adding to the complexity, Rainier Square’s seven levels of below-grade parking required
Today, Rainier Square is a shimmering, sweeping presence and the second-tallest building on downtown Seattle’s increasingly crowded skyline. It offers more than 730,000 square feet of office space, nearly 200 highrise apartment homes, a retail podium, and a below-grade parking garage on six levels accommodating nearly 800 vehicles. But one could argue that the engineering inside this lofty structure is equally impressive. Rainier Square’s use of SpeedCore is an industry-advancing trifecta of creativity, technical innovation, and design ingenuity that has captured the AEC industry’s imagina tion and reinvented the rules of high-rise steel construction. The project’s success has led to constructing a 19-story office building in San José, California, using SpeedCore, while other applications are slated for Boston and Oakland.
■
Ron Klemencic is Chairman and CEO of Magnusson Klemencic Associates (MKA), headquartered in Seattle, WA.