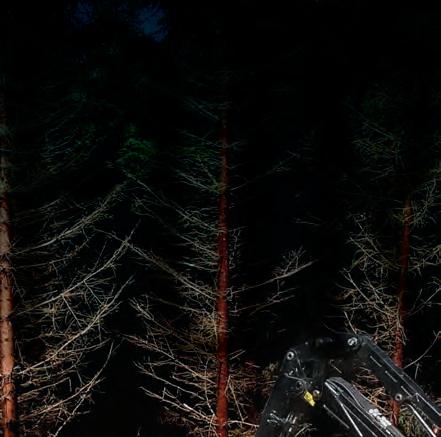
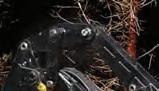
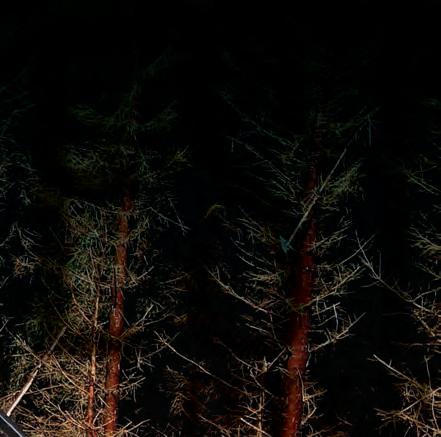
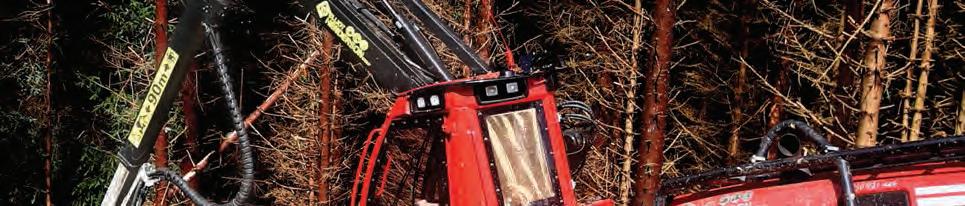
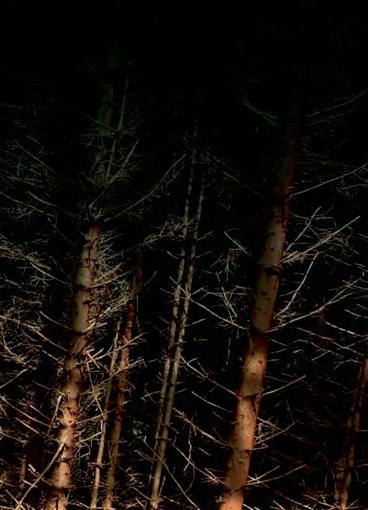



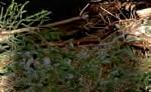
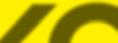
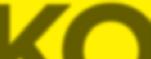
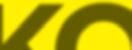




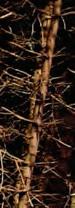
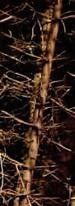
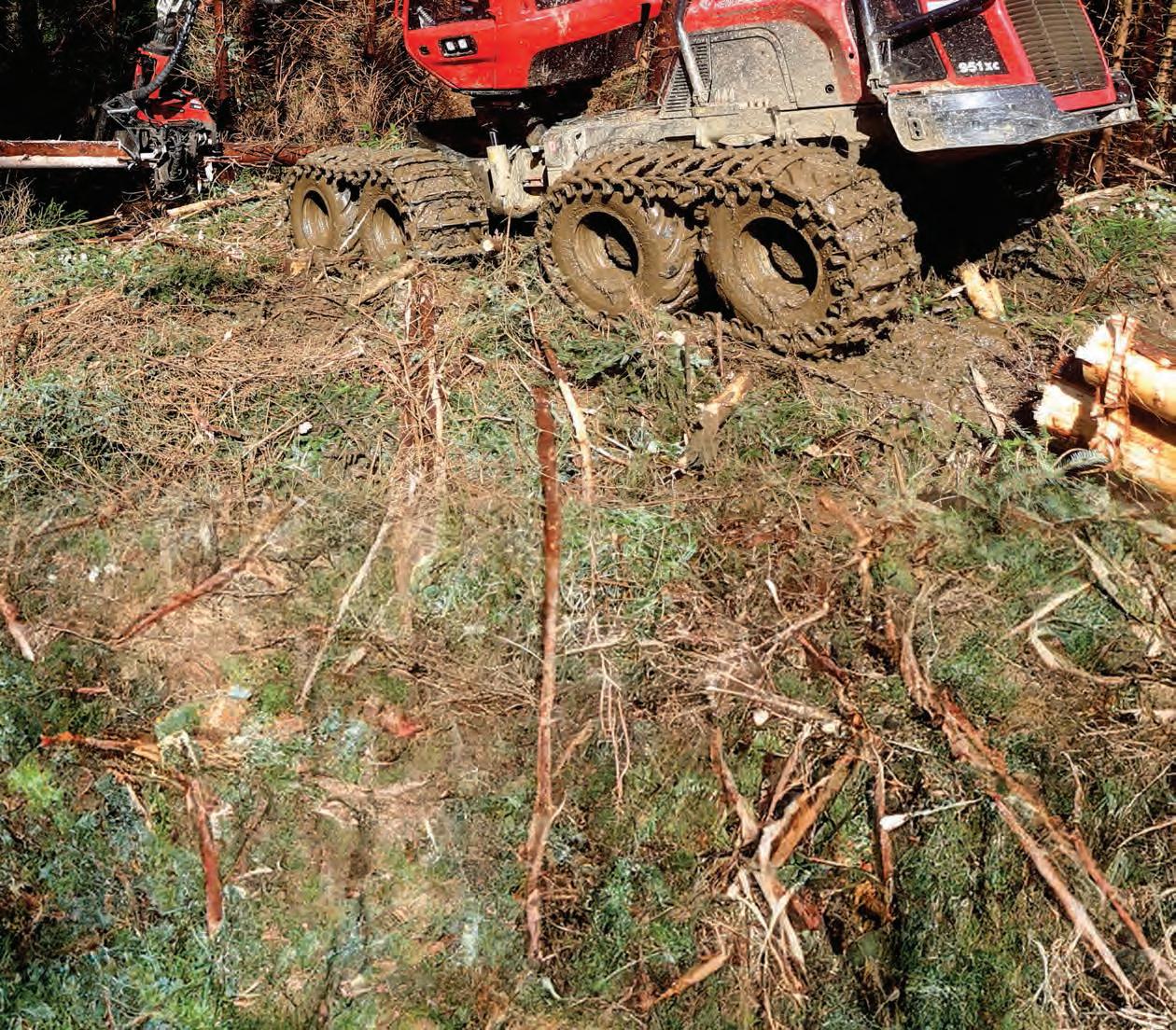
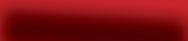
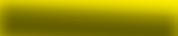
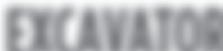
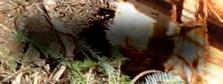


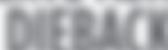
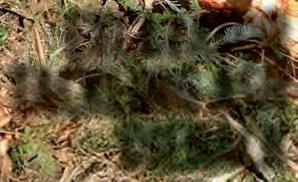

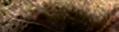



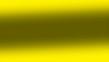

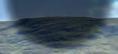



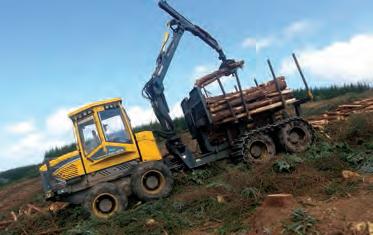
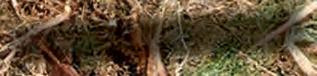



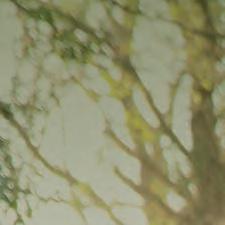

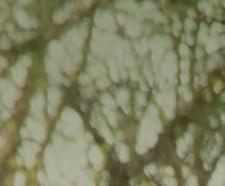
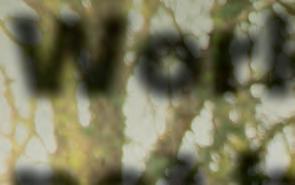
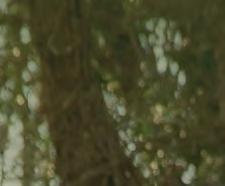

Learn more at avant.co.uk Avant 530
Discover unparalleled versatility and strength with Avant Loaders. From lifting heavy loads to maneuvering with precision, our machines excel in forestry tasks. Explore our diverse range of over 200 attachments and unleash the full potential of Avant on your business.
Optidrive™ drive circuit gives more power for the drive and hydraulic attachments.
Greater reach with Avant’s signature telescopic boom
EDITOR Jim Gerrard editor@forestrymachinerymagazine.co.uk
ART DIRECTOR David ‘Spike’ McCormack
ADVERTISEMENT SALES
020 8639 4406
ADMINISTRATOR Martin Attis 020 8639 4409
PUBLISHING DIRECTOR Paul Cosgrove 020 8639 4401
CONTRIBUTING WRITERS AND PHOTOGRAPHERS
Eoghan Daly, David Wylie and Paul Argent
Forestry Machinery is published by Sundial Magazines Ltd, Sundial House, 17 Wickham Road, Beckenham, Kent, BR3 5JS
TEL 020 8639 4400 FAX 020 8639 4411
EMAIL info@forestrymachinerymagazine.co.uk
WEB www.forestrymachinerymagazine.co.uk
SUBSCRIPTIONS
Earthmovers subscriptions, Trinity House, Sculpins Lane, Wethersfield, Essex, CM7 4AY
TEL +44 (0)1371 853632
EMAIL earthmovers@escosubs.co.uk
Farm Machinery Journal subscriptions, Trinity House, Sculpins Lane, Wethersfield, Essex, CM7 4AY
TEL +44 (0)1371 853634
EMAIL farmmachineryjournal@escosubs.co.uk
NEWSTRADE
Seymour Distribution, 2 East Poultry Avenue London, EC1A 9PT TEL 020 7429 4000
REPRO
Design & Printing Solutions Ltd, The Coach House 101 Northwood Road, Whitstable, Kent CT5 2HE
TEL 01227 770034
PRINTING
William Gibbons & Sons Ltd, 26 Planetary Road, Willenhall, West Midlands, WV13 3XB
COPYRIGHT
Sundial Magazines Ltd 2024. All rights reserved. Reproduction in whole or in part is forbidden without the express permission of the publishers. Sundial Magazines Ltd. Registered in England no. 4134490.
CONDITIONS FOR ADVERTISING
All advertisements are accepted subject to the publisher’s standard conditions of insertion. For a copy of advertising terms & conditions, please write to Paul Cosgrove at Sundial Magazines Ltd, Sundial House, 17 Wickham Road, Beckenham, Kent, BR3 5JS
The weather and UK politics have both had a major impact on many industries over the last few months, with forestry being one of them. The fallout of winter storms and the wet and more extreme weather experienced over the so-called summer has certainly created challenges all round. Some drier and calmer conditions as I write this have hopefully offered some form of respite to contractors and operators. Following a general election and change of government in the UK, it will be interesting to see what the implications are for the forestry sector. Let us hope it is not neglected and under-appreciated during ongoing nancial pressures.
Thinking more positively, David Wylie’s feature in this issue on the John Deere 1210G forwarder, that is both HVO-fuelled and using biodegradable uids, is one that is of great interest and maybe gives an impression of future fuel and oil usage in forestry machines. Working in very remote woodland on the edge of Loch Arkaig in the West Highlands of Scotland, a landing craft has been created specially to transport the forwarder and its collected timber. Demonstrating how there are no limitations to some jobs!
For those heading to APF very soon, there is no shortage of live demonstrations and competitions lined up, as well as a whole host of exhibitors, suppliers and other stands. A preview can be found in this issue.
Jim Gerrard, Editor
The FARMA LF8 is a compact 8-wheel forwarder with good manoeuvrability in rough terrain and dense forests. The forwarder has a load index of 1:1 with a load capacity of 8.5 tons. FARMA LF8 has a width of only 2.2 meters equipped with 600 tires.
A low centre of gravity and very good weight distribution contribute to the FARMA LF8 being stable and safe during crane work and when driving in difficult terrain, despite a high ground clearance. Through the transmission, where we optimize the speed of each wheel in the forest, damage to the ground and the environment is minimized. The diesel engine from Caterpillar is a modern and reliable engine that fulfils all present emissions standards.
The choice of cranes comes from our own FARMA range. For the LF8, we offer cranes from 6.7 up to 8.5 meters.
Back in June, Finnish manufacturer Sampo Rosenlew unveiled its brand new six-wheeled HR56 forestry harvester. The HR56 is based on Sampo’s successful HR46x four-wheeled harvester which incorporates new features that are claimed to ‘improve both ef ciency and productivity’ and will maintain ‘low operating and maintenance costs’.
The new model is tted with a 10-metrelong reach Logmer crane and a front bogie to increase stability and spread the ground pressure of the machine. They also claim that the machine is ‘environmentally friendly’. The new HR56 joins Sampo Rosenlew’s existing harvesters; the already mentioned and smaller HR46x and the eight-wheeled HR86.
A new crane option has been made available on the Komatsu 965 forwarder known as the 205F. It has a lifting torque of 205 kNM and a slewing torque of 51.9 kNm, and has been developed to increase productivity in final felling and plantation forestry. There is a choice between a reach of 7.5-8.5m with a single telescope, or 10m with double telescope. In addition to this, Komatsu are also o ering a new and larger grapple, the G88H, with a tip-to-tip area of 0.55m2 and a new rotator.
The 895 has also been upgraded with new load space, which consists of a telescopic gate and new hard-wearing bunks with a telescopic widening function. The entire gate can be raised and lowered hydraulically, and the foldable wideners can be locked in the retracted or extended position. There is also an option to make the gate movable along the rear frame direction. The forwarder’s frame, including the articulating frame and bearings, have been redesigned to handle the increased crane capacity and the new load space.
The latest mulcher from Prinoth is the Grizzly M350e, designed for excavators in the 3.5 to 7-tonne class. It is aimed for use for forestry work in narrow or di cult spaces such as residential areas, riverbanks and roadsides. It is equipped with a 60cm3 motor that covers the flow range of smaller excavators and features a flexible mounting plate to enable use on di erent machines.
It is claimed that its rotor diameter of 14inches, and a working width of 29.5inches, can shred bushes, shrubs and tree trunks. The integrated blades result in a finer mulch and the closed housing also prevents wood from being thrown out, particularly important when working on roadsides and near residential buildings.
Earlier in 2024, tyre manufacturer BKT released two new types of tyre aimed at machines employed for agroforestry work. With mixed use in mind for both farm and forestry work, the FORESTMAX tyres are of a radial construction and the FORESTLAND tyres are of cross-ply construction. FORESTMAX tyres feature a specially developed tread compound and a steel-belted structure to reduce the risk of punctures in woodland environments. Whilst BKT claim that on rough and uneven terrain, the tyres will ensure excellent traction and stability thanks to its strong open shoulder. They
also say that the new tyre range’s self-cleaning properties mean they can be used for some agricultural work such as soil tillage.
FORESTLAND tyres are being sold as a strong and resistant product that can cope in the most challenging conditions due to a special polyester casing and a strong sidewall, which should ensure a long tyre life. BKT claim the open shoulder design should provide excellent traction on soft soils, while the reinforced tread lugs will give good grip on any terrain along with its high self-cleaning properties.
On July 2024, the 75th anniversary of the founding of what is now the Liebherr Group, the 100,000th machine left the founding site at Kirchdorf an der Iller. It took the form of a LH 22 M ‘Industry’ material handling machine finished in white. This livery allowed for a very special commemoration with every Liebherr employee putting their signature on the landmark machine.
Ponsse has released its new Ponsse Scale crane system and Ponsse High-Precision Positioning solution to further aid and support operators of their forestry machines. The Scale system weighs, sorts, saves and manages load data during all stages of the operation. Ponsse says that the collected weighing data will make load handling routines easier and its precise weight measurements will ensure an optimal load at all times. The system also features full weighing automation during loading and unloading. Load details, load logbooks and measuring accuracy data are then available in ‘easy-to-read’ reports. Ponsse Scale can be installed in all PONSSE forwarder loader models.
The Ponsse High-Precision Positioning system is a solution that is aimed to help the operator know the exact location of the machine and the harvester head, enabling consistent and e ective logging operations to be maintained, even in changing conditions the company says. By defining the exact location of the harvester head and presenting it on a map, High-Precision Positioning is said to improve harvesting productivity. The set-up shows where the operator should harvest and the areas that should be avoided. Every stump location is saved in the production file, and then the path the harvester creates is clearly visible to the forwarder. The positioning system is available in Finland, Sweden and Germany for all Ponsse harvesters equipped with Active Crane and can be retrofitted. Its availability for other markets will be listed at a later date.
Wood chipper manufacturer ARBMAX have announced a new partnership with DJB Machinery based in Ashbourne. The Derbyshirebased dealership will make ARBMAX chippers available to customers throughout England, Scotland and Wales, along with their services and support backup. The partnership will allow machines made by the Northern Ireland-based manufacturer far more accessible to customers across the rest of the UK.
There are only a couple of weeks to go until the 2024 APF Show at the Ragley Estate in Warwickshire, which will be held over 19-21 September. It is the UK’s largest trade show specialising in the forestry, woodland, arboriculture, rewood and other timber-related industries. The event will feature a 1900m demonstration circuit where machines will be working in an ‘authentic’ setting. Exhibitors will be present on both sides of the circuit, resulting in 2.5 miles of working machinery.
The UK forwarder driving competition makes a welcome return to the event in 2024 which will take place in a much larger arena compared to previous occasions. The competition is courtesy of Richard Court Forestry Engineering and Coombes Forestry Ltd. Competitors will need to tackle a series of tasks and obstacles which will test their crane and machine control against the clock. John Deere G series forwarders will be used. Competitors may be able to enter on the day, subject to availability, and must hold the relevant Forest Machine Operator certi cation. Daily prizes will be awarded for the fastest time, less time penalties, and the UK trophy for the best overall time over the three days will also be presented.
The A.W. Jenkinson and Tilhill European Chainsaw Carving Championships will see 25 of Europe’s top carvers compete, some will be coming from as far a eld as Lithuania, Romania and Poland. The carvers will be using large dimension Redwood from the
Longleat Estate and there will be speed carving events twice daily as well as the main carve. All the carvings will be auctioned off on the Saturday of the event from 2pm.
The Husqvarna World 25m Pole Climbing Championships and UK Lumberjack Competition will also take place as per normal along with two British fencing championships and new this year is the Teufelberger and Pfanner APF Team Tree Climbing Challenge.
Over 300 exhibitors are expected, with many already listed on the APF website. Names familiar to Forestry Machinery readers who will be in attendance include Clark Engineering, Komastu Forest UK, Manitou UK and Merlo UK.
Another is Avant Tecno UK, who have released what machines will be in attendance, which includes a variety of compact loaders and attachments some of which will be giving live demonstrations and others that will be static. The Avant 650, e527 and 860i miniloaders will be providing live demonstrations along with various attachments and a range of Leguan platforms.
Other attractions at this years APF Show will include traditional woodland crafts, horse logging, seminars, the Forest Worker Zone and the opportunity to interact with various industry associations. Discounted tickets can be purchased in advance, or tickets can be bought on the gate priced at £25 per person, children under 16 are free. On-site camping with catering and other facilities is also available. For more information, please visit www.apfexhibition. co.uk or ring 01428 723545.
STAGE
As the Elliot Henderson Group gain an early impression of their Komatsu 951XC timber harvester, Eoghan Daly visited the machine on a challenging clear fell site to observe this all new eight-wheeler in action
IMAGES EOGHAN DALY
Generally, the more scenic the location, the more challenging it will be to harvest timber in such a location. This was the case at the current harvesting site of the Elliot Henderson Group’s new Komatsu 951XC harvester. Working on a steep clear fell site at Muirlaggan, near Balquhidder, Perthshire, the area is best known as the burial place of renowned Scottish outlaw, Rob Roy MacGregor. Perched on a hillside that forms the Braes of Balquhidder, the site comprises of a privately owned clear fell contract of 10,000 cubic metres with a 0.5 cubic metre average tree size, overlooking Lough Voil, for saw-millers
A.&J. Scott Ltd.
With the Elliot Henderson Group having taken delivery of the UK’s
At the time of FM’s visit the 951XC had already recorded over 550 trouble free hours leaving a very good early impression by the latest addition to the
rst Komatsu 951XC eight wheeled harvester, this machine was classed as the ideal unit to tackle this extensive and intricate clear fell contract. Working in tandem with a Komatsu 875 forwarder, the operator team of Colin Jackson and Steven
MacVicar are working together to tackle the challenging job. As one of Scotland’s largest and still privately owned timber harvesting contractors they have been serving the industry for over 35 years. With other business interests including construction and scaffolding services, the Elliot Henderson Group are by no means alien to signi cant and landmark machines joining their timber harvesting eet.
Coincidentally, they were also the rst to add the six-wheel drive variant of the Komatsu 951 to their eet and took delivery of a Ponsse Scorpion Giant harvester back in February 2023 which was the 19,000th machine built by the Finnish manufacturer. Running a mixed eet of forest machines, which exceeds 40, the line-up comprises of units from John Deere, Komatsu, Tigercat and Ponsse with harvesting jobs
completed all over the UK, but mainly in Scotland and the north of England. Continually striving to remain at the forefront of the industries they serve, a regular replacement policy applies as director and son of company founder Elliot Henderson, Gavin Henderson explained, “We usually nance our forest machines aggressively over three years and with the harvesters we run them for a fourth year before upgrading. Forwarders are usually held a bit longer and they commonly remain in the eet for up to ve years. It is important to keep the eet refreshed as there is no room for downtime and we need to keep the equipment as productive as possible.”
As the most recent machine upgrade, the purchase of the UK’s rst Komatsu 951XC is certainly not surprising. With Komastu already making up a substantial part of the eet, including 931XC and 951 harvesters along with 855 and 875 forwarders, the addition of the latest 951XC was seen as an inevitable move as Gavin continues, “Level harvesting sites are few and far between in the areas we mainly serve and will remain that way until the more level farmland that has been established as forest plantations in recent years comes on stream in the future. Because of this, the need for machines capable of working in steep terrain has never been greater. When Komatsu made their largest harvester available as an eight-wheel machine, the new 951XC, we immediately saw the potential it offered and moved quickly to order one for the eet.”
Having been presented publically as a prototype in 2023 at the Swedish Forest Machine Expo, the new model was greeted positively with its availability soon translating to sales.”
Combining the bene ts of the existing six-wheeled 951, Komatsu Forest have acted to successfully blend these elements with the unique design features of the XC series eight-wheeled harvester. In addition to this approach, a wealth of new generation features in Komatsu harvester base machines, crane design and capacity as well as with the latest harvesting head innovations and technological features have been incorporated in the new harvester.
Even though the complete concept ticked all the right boxes, the only true measure of the new machine would come once it went to work. This machine is operated by Colin Jackson who has been working as a forest machine operator following the transition from a career as an excavator operator. As a competent and highly con dent harvester operator when it comes to working in
Such is the stability of the 951XC, that it can fell trees at the maximum reach of the crane, 10.3 metres, whilst working on acute slopes without a ecting its firm stance.
challenging and adverse terrain, Colin operated forwarders before advancing to harvester operation utilising Komatsu 931, 951 and 931XC machines. Savouring the challenge of being at one with his new mount he explains how it is a machine with many advantages, “Eight-wheel harvesters have an automatic advantage over six-wheel machines on steep sites since they are so much better balanced and stable. The 951XC continues this trend but combines it with unbelievable harvesting capacity since the head and crane are getting the oil ow needed to get through the job regardless of how tough the challenge may be.”
Obviously in a different league to the 931XC previously operated by Colin, the new 951XC delivers much
greater performance and capacity, especially since it has been comprehensively loaded with a broad range of optional extras. Despite the comprehensive options catalogue incorporated, the base line unit still offers a high standard which is re ected in its durability and many novel design features and specialist innovations. Weighing in excess of 23,275kg, this 951XC runs on 710 mm wide tyres giving it a rm stance which has been enhanced by the wheels on this unit being set out by 100mm. Despite being longer than a six-wheeled 951, its steering angle of 37 degrees makes it particularly
“FEATURING KOMATSU’S COMFORT BOGIE CONCEPT, ALL FOUR BOGIES INCORPORATE PORTALS WITH AN
BALANCING FUNCTION”
manoeuvrable. The machine climbs well due to the 242kN of tractive force provided. Featuring Komatsu’s Comfort Bogie concept, all four bogies incorporate portals with an integrated balancing function ensuring they maintain constant ground contact when ascending slopes. In addition, the rear bogies also bene t from the unique Komatsu Forest feature which centres on a double oscillating system. This is achieved
maintained at all times. Providing plenty of opportunity to evaluate the system and the machine’s climbing and terrain traversing ability, the Muirlaggan clear fell on the Balquhidder Braes continually showed the machine’s worth.
With intensive harvesting in adverse conditions in mind, the machine features an AGCO Power 74LFTN-D5 six-cylinder engine which meets Stage V emissions
While the 951XC is seen to be consuming noticeably more fuel than the 931XC Colin previously operated, this is immaterial given the increase in productivity even in challenging conditions. This increased output is assisted greatly by the machine’s 3PS con guration which equates to three hydraulic pumps and ensures consistent performance even at times of simultaneous operation of different elements. Delivering
The C164 head is the largest member of the C series range and features four movable and one fixed delimbing knife together with three feed rollers.
The head’s rotator has benefitted from refinement to make it more durable and achieve greater performance.
While extending the eight-wheeled format to Komatsu’s largest harvester may be an important step forward, the new machine also draws on some very well proven design concepts which have stood the test of time since they were initiated on previous generation machines. This is especially true of the cabin and crane mounting position on a common slewing base with the origins of this system traceable back to 1984 when Komatsu Forest’s predecessor Valmet took timber harvester forward by a giant leap by introducing such a system on their visionary 901 thinning harvester.
The design has been re ned with the AutoLev automatic levelling feature with the cabin having longitudinal levelling capability of 20 and 22 degrees with 16 degrees lateral levelling possible. This is whilst being one of the few harvesters that can rotate the cabin and crane all the way around to the rear which makes it possible to process a tree behind the machine and, should the need arise, to replenish the brash mat in an inadequate area when reversing back to the start of the line.
“THE HIGH CAPACITY C164 HARVESTING HEAD IS THE JEWEL IN THE 951XC’S CROWN”
By positioning the crane and cabin in this position, and in tandem with the stability of the base machine design, it is possible to run longer reach cranes and larger harvesting heads on the 951XC. This has been proven by the Elliot Henderson Group’s machine which incorporates the longest reach crane and largest head option. This sees the machine equipped with the 270H parallel crane which delivers a reach of 10.3 metres, marking a substantial increase over the shorter 8.7 metre reach alternative. The harvesting head of choice is the Komatsu C
series’ largest model in the form of the C164, whilst a range of smaller C series and other S series alternatives are also available on this new agship harvester range.
From the point of view of the Henderson machine, selecting a crane with this reach and a high capacity harvesting head gives great con dence in the machine’s capability to work effectively with this combination in the most adverse conditions.
Obviously a crane with a generous reach is only as good as its lifting and slewing power allows it to be with the 270H delivering well in these vital areas as its 275kNm of lifting torque and 60 kNm slewing torque rating suggest.
Working at maximum reach, often to the side of the machine, the crane’s power and the machine’s stability ensure the maximum width can be harvested in a single pass, as Colin explained, “It is no problem to reach right out and fell a one-tonne tree and slew it back without noticing any loss of power or speed in the crane. The machine also has the Smart Crane control system which allows for crane tip control and makes a major difference to the amount of movements I need to make over the course of the day. It is just another feature that shows how much the modern timber harvester has evolved in recent times especially when it comes to taking some of the strain off the operator.” However, the user friendliness, crane power and reach is just the beginning, the high capacity C164 harvesting head is the jewel in the 951XC’s crown.
Upon witnessing the C164 in operation, it has shown it can work with a wide variety of material sizes, with the Balquhidder Braes clear fell serving to demonstrate this. As an unthinned stand, the upper reaches of the clear fell presented material with a broad diameter variation and branch density with Colin commendable of its capabilities, “We were a little worried about the C164 head before it arrived and expected it to be a big slow and powerful head, but it has proven us completely wrong as it is equally as fast as the C144 on the previous 931XC. It has the feeding power to delimb really hairy trees and the rst site proved this as it processed all the rough edge trees without any help from hand cutters with the machine handling everything.”
Looking closer at the formation of the C164, it is clearly a powerhouse of feeding power and speed as it deftly powers the coarsest material through without hesitation. Whilst larger average tree sizes were encountered closer to the forest road, in the section being harvested close to the uppermost extremes at the time of our visit, the average tree size was .44 cubic metres. With many stems presenting dense coarse limbs, this stand would clearly soon nd the inadequacies of any machine. No pre-brashing with a chain took place, and it was the task of the harvester to achieve an acceptable delimbing result which it clearly did with distinction. This comes as a true endorsement of the head design and knife arrangement which sees the tment of a sensibly pro led xed top knife and the full set of four movable knives which ensure affective branch removal even when low branches are present. Feeding takes place via three feed rollers, the usual two angular outer rollers and the third embedded in the rear of the head frame. The angular pro le of the outer rollers accounts for the C164’s designation as a ‘carry head’ as they grip the stem from beneath and therefore take the strain off the delimbing knives. A good grip is achieved by the chosen roller type which provides these gripping characteristics without biting in and damaging the log with the feed speed and force.
Nevertheless, the C164 has many more features in its favour which include its more robust rotator design. Along with the rotator, the saw box pro le and positioning of the saw motor and bar ensure favourable abilities in larger diameter trees or stems with ared butts, which is especially bene cial when harvesting on steep slopes allowing stump heights to be kept low. The Constant Cut saw motor delivers excellent sawing performance while the new ‘Find End’ feature is a welcome addition, as Colin
The Komatsu 951XC operator’s cabin o ers very good visibility and the layout of the controls works well.
says, “The ‘Find End’ system works with two lasers above the saw box and immediately senses the end of the log as it is fed through which means there is no longer a need to cut off ‘clogs’ to zero the measurement after delimbing the whole stem before cross cutting or processing pre lled trees from hand cutters or in wind blow. It saves on fuel as there is no unnecessary sawing which is demanding and it also saves on chain and bar wear as well as chain oil use.” The C164 has good access for greasing whilst the changing of saw chains can be performed without the need for tools through the Automatic Release function.
Even though delimbing and cross cutting performance are important traits, the ultimate measure of the head’s success is its accuracy when it comes to measuring as Colin insists, “Measurement accuracy is more important than ever and the C164 has proven to be really accurate and there is a new calibration system which is very easy to use.” In conclusion, the early impression of the new Komatsu 951XC is incredibly positive as it sets a high benchmark for operation in challenging clear fell harvesting operations. Endorsed from all perspectives, Colin cannot fault the new 951XC and when pushed to highlight any areas that could bene t from improvement, he could only
“RATED AS A 16-TONNE
PAYLOAD
CAPACITY MACHINE, THE 875 IS A CAPABLE MATCH FOR THE LONG HAUL DISTANCES”
highlight the need for storage capacity for larger items such as replacement hoses with a drawer in the rear of the machine no longer present on this model.
Even though an effective harvester which can climb well is a welcome asset in any challenging harvesting site, it is of little bene t without a forwarder with equal operating prowess. With Colin Jackson working as a team with his colleague Steven MacVicar for the past ve years, extraction of the Muirlaggan clear fell was obviously tasked to this experienced operator using a one-year old Komatsu 875 forwarder. As a long serving operator of Komatsu forwarders, Steven fully appreciates how they have evolved over the years.
Rated as a 16-tonne payload capacity machine, the 875 is a capable match for the long haul distances. To enhance the 875’s traction, it received a new set of Clark climbing band tracks on all four bogies
which enhanced its grip considerably. Viewing the 875 as a premium level machine, Steven is commendable of the many bene cial features it presents, “I’ve always been a big fan of Komatsu forwarders since I used them rst in my father’s timber harvesting business. They have advanced a
lot since then and this latest 875 is really user friendly. Features like Smart Flow and Smart Crane make a major difference in how well it handles and how smooth it is to operate. It also has great power, traction and load capacity making it an ideal forwarder for sites like this.”
David Wylie reports on award-winning Creel Maritime, and their John Deere 1210G forwarder running on HVO fuels and fully biodegradable fluids, along with JST Services inland water bespoke landing craft both working together at Loch Arkaig in Lochaber, Scotland
IMAGES KENNETH CALDWELL AND CREEL MARITIME LTD
Creel Maritime Ltd (Creel) director and founder, Neil Stoddart, has worked for over 30 years in (private sector) round timber harvesting, haulage and shipping. Creel, who are based in Inverness, specialise in brokerage, agency and logistics operations in ports and oating piers, this allows timber to be extracted from inaccessible locations. Before Creel Maritime Ltd, Neil held a senior position as general manager at Ayrshire-based JST Services where he added experience of port handling to his forestry portfolio. Neil also recently chaired the FISA Forest Haulage Working group, and he previously sat as chair of the Highlands & Islands Forest Industry Cluster for 2013-17.
“THE LOCH ARKAIG FOREST PROJECT STARTED AS FAR BACK AS 2011 WHEN NEIL WAS WORKING AS A CONSULTANT FOR THE THEN LANDOWNER, FORESTRY COMMISSION SCOTLAND”
challenging project at The Woodland Trust’s Loch Arkaig historic forest.
As a mark of his commitment to Net Zero, in February 2023 Neil was the winner of the ‘Net Zero Award’ at the Confor Awards 2023. As the rst winner of this award, Neil is delighted to receive recognition for the work he puts into ensuring that forestry remains sustainable and pro table whilst meeting net zero goals.
The team at Creel are said to have a passion for innovation. Neil has assisted in the creation and delivery of CPC +F driver training courses and training videos. Both are a solution-focused approach, to simply and easily integrate into customers’ existing management structure. Creel is about reviewing options and solutions rather than an emphasis on the problem, with a strong focus on providing a road map towards a positive outcome. None more so than the
Loch Arkaig is a large body of freshwater approximately 12 miles in length, and over 85 metres deep, which is located near Spean Bridge, about 10 miles from Fort William. The adjacent Loch Arkaig forest has some 4900 ha of nationally important ancient Caledonian pinewood and about 1000 hectares – with two areas known as Glen Mallie & Gusach - which are to be fully restored with the removal and harvesting of non-native species of trees.
“THE NEW CRAFT NAMED ‘WATER HORSE’, WAS DEPLOYED TO SUPPORT TIMBER MOVEMENTS FOR THE WOODLAND TRUST AT THEIR LOCH ARKAIG HISTORIC FOREST”
The Loch Arkaig forest project started as far back as 2011 when Neil was working as a consultant for the then landowner, Forestry Commission Scotland (now known as Forestry Land Scotland). This was to look at the most environmentally friendly way to remove non-native species of trees, as the 1000 hectares of forest is not accessible by any road.
For various reasons, Forestry Land Scotland put the land up for sale, and it was bought by Woodland Trust Scotland and by members of the community of Achnacarry, Bunarkaig and Clunes in Lochaber to form the Arkaig Community Forest in 2014. It is of special interest to the new owners as rare species of plants are associated with the trees. This is along with wildlife such as osprey, black grouse, sea eagles, pine marten, red deer and wild boar, which means the area is considered a priority habitat, and is on the Scottish Biodiversity list.
In the 1970s, much of the site was planted with non-native trees including Sitka Spruce and Japanese Larch in line
with the government objective of the time, resulting in approximately 30,000 tonnes of non-native timber which now needs removing as part of the restoration project. It is worth noting that this is not a commercial harvesting project as such, but more about improving and maintaining the biodiversity of one of Scotland’s most important forests with a strong drive to move forward with important rewilding and habitat restoration work.
Working alongside the main contractor JST Services (Scotland) Ltd, Creel Maritime Ltd, and its machinery ownership division Creel Maskina, is operating a pre-owned John Deere 1210G forwarder running on HVO and other biodegradable products to transport the felled timber. This has been cut by local rm Munro Harvesting, based at Munro Sawmills in Dingwall and their sub-contractor Black Isle Timber Harvesting using a mix of Ponsse machinery, speci cally Ergo and Scorpion harvesters and an Elephant forwarder. This is extracted out of the forest and on to a modular Roll-on-Roll-off (RORO) ferry owned and operated by JST Services.
The brief from The Woodland Trust was to move felled timber from the north side of the loch, where there are no roads, to a road connection on the southern bank, operating throughout the winter in a highly sensitive ecological area. JST’s craft is so shallow that it is able to use temporary gravel slips to operate from, which can be totally and easily removed at the end of the works.
During 2022 and 2023, Ayrshire based JST Services created a unique sectional landing craft for use on inland waters where access was restricted. The new craft named ‘Water Horse’, was deployed to support timber movements for The Woodland Trust at their Loch Arkaig historic forest. JST built the unique craft in Troon, taking existing basic NATO pontoons and then adapting them to the task in partnership with local companies Troon Tug Company and JC Laing Engineering.
The Water Horse RORO ferry has been a resounding success as the timber is felled and extraction has gone to plan, when the bird nesting and rearing season is not in session, moving the timber across the loch to a main public access road. Hence, this negates the need to put in a new timber road line, with all the associated costs and environmental impact.
The extracted timber is mainly pine and will make a relatively short road trip to Inverness and it will be processed into OSB boards for house building, thereby locking in the stored carbon in much needed homes for a very long time.
With Neil’s 30 plus years in the forestry sector, when he was looking to add a forwarder to his business his rst port of call was to contact Jock Mckie, country manager at John Deere Forestry Ltd Carlisle, to source a low-hours and very clean pre-owned 1210G model. As a result, their ‘Maskina’ 1210G forwarder was purchased with a service agreement. As an aside, Creel’s 1210G livery includes the wording ‘an talamh uaine’, Gaelic for ‘the green forwarder’.
The John Deere 1210G forwarder with its groundbreaking Intelligent Boom Control (IBC) is designed to signi cantly cut the operators workload
The main benefit of HVO fuels (Hydrotreated Vegetable Oil) is that it is a 100% renewable diesel that is helping the UK achieve its net zero carbon target. HVO fuels are a member of the para nic family of fuels, and as such HVO is virtually chemically identical to regular diesel, allowing it to be used as a pragmatic and e ective alternative to red and white diesel and is designed to reduce up to 90% of net CO2 emissions. HVO has a wide range of OEM approvals, and can easily be used within existing fleets (HGV and mobile plant), and machinery with no changes to infrastructure or capital expenditure. This removes cost barriers and enables companies to decarbonise quickly and e ciently. Experience from users find that HVO fuel is a clean-burning diesel alternative and is said to be one of the cleanest fuels on the market.
Neil says, “Our companies Creel Maritime and Creel Maskina work with clients such as JST and progressive supply partners such as John Deere, Oilfast and TYGRIS as they share our vision for innovation and decarbonised solutions. It is not a subject for everyone due to the economic and lifestyle changes required, but we all have to put our shoulders to the wheel as no change equals no change.”
To produce HVO fuel, feedstocks are saturated with hydrogen at high temperatures and pressures which removes any esters and oxygen, making it resistant to the dreaded ‘diesel bug’.
HVO fuel has a storage life of up to ten years which is much longer than the one-year shelf life of regular diesel. The clear advantage of HVO fuel is that it is made from 100% renewable raw materials. It is therefore sustainable and biodegradable, making it an ideal fuel for eliminating potential spillage issues when working in very sensitive areas such as forestry, peatland restoration and public water supply projects, etc. It eliminates up to 90% of net CO2 emissions and hugely reduces NOX by up to 30%, Particulate Material (PM) by up to 86% and CO emissions, as Green D+ HVO generates up to 90% fewer greenhouse gases.
However, the price of white diesel, as forestry and farming can still run on rebated red diesel, is also a factor in this application as it is circa 50p litre more (white vs. red), plus 15p extra for HVO as a premium product. But Neil is working with his fuel supplier Oilfast to obatin HVO as red diesel going forward to obtain the fuel duty benefit. As part of their green logistic services, through partnership with other companies, Creel Maritime Ltd also manage a demonstrator project with two 44-tonne Volvo electric vehicles operated by James Jones and Scotlog with the HGV trucks transporting timber products with no tailpipe CO2 emissions which has been taking place over the last 12 months.
Creel’s JD 1210G is running on HVO fuels which it claims cuts CO2 emissions by up to 90%.
For over 50 years, TYGRIS has been a global leader in industrial cleaning, lubrication, and protection solutions. From its headquarters on the Firth of Clyde in Scotland, TYGRIS has expanded its operations to become a global force, reducing downtime and increasing e ciency across diverse sectors and applications.
TYGRIS has recently announced the launch of its ONOS line, the company’s first-ever range of biodegradable lubricants. This innovative development marks a significant milestone in TYGRIS’ commitment to sustainability and signifies a major leap forward for the industrial lubrication industry.
“For over 50 years, TYGRIS has been a driving force in industrial progress through its commitment to reducing downtime and increasing e ciency,” says director, Jed Simpson. “We are thrilled to introduce ONOS, a revolutionary product line that prioritises environmental responsibility for ground and marine applications whilst maintaining the same performance as users have come to expect.”
After thousands of hours of development, the ONOS range is currently undergoing rigorous testing by forestry companies in northern and western Scotland. The line boasts two flagship products: ONOS Hydraulic Oil and ONOS Water Resistant Grease. The ONOS range o ers exceptional performance that rivals conventional lubricants. They deliver outstanding anti-wear and extreme pressure protection, ensuring smooth operation and reduced downtime. Most importantly, ONOS breaks down naturally, minimising environmental impact, making it a suitable choice for a wide range of industrial applications, including forestry, marine, agriculture, and more.
“ONOS represents a credible alternative for industries actively seeking to reduce their environmental impact,” continues Darren Pughe, technical director. “This innovative solution allows businesses to operate sustainably without sacrificing equipment performance or e ciency. In most cases, we are seeing extended lifetime and service cycles which means huge cost savings.” The launch of ONOS underscores TYGRIS’ ongoing commitment to revolutionising the industrial lubrication sector through continuous innovation and a dedication to environmental responsibility.
Neil Stoddart says, “We are delighted to be working closely with another Scottish company to help develop biodegradable products that work in the toughest conditions, particularly with grease that can stand the wet climate found on the west coast of Scotland, and Creel Maskina look forward to developing other products with TYGRIS.”
Above: Loch Arkaig’s forest is one of the most notable restoration projects and the largest ancient woodland restoration undertaken by the Woodland Trust on land under its direct care.
Right: The 1210G has a comfortable cab and easy to use controls.
“THE 1210G IS A FANTASTIC PIECE OF KIT PARTICULARLY FOR NEW OPERATORS WITH ITS EASYTO-USE IBC SYSTEM”
which proved to be an instant success for both Neil and his operators. The machine was initially operated by a 74-year young veteran and now by Neil’s son Jed who has sought to get into the machinery side of the forestry industry.
Neil explained that with the nal retirement of the forwarder’s initial operator, his son, 23-year-old Jed, stepped forward and asked to switch roles and take over the operation of the John Deere 1210G forwarder. Jed has an HNC in forestry management, and from a very young age Jed had spent many hours at the controls of the 1210G forwarder, albeit on Farming Simulator!
Below: Loch Arkaig is a large body of freshwater approximately 12 miles in length, and over 85metres deep, located near Spean Bridge.
This would come in handy, as to get his ‘realworld’ ticket for this machine, Jed took a test using a state-of-the-art simulator, and as an aside, the instructor set up a few logs to be picked up and transported during the test. However, he popped out for a few minutes and when he had returned, he found Jed had successfully loaded, transported and stacked a huge amount of timber! Jed had completed the initial task so quickly, that he jumped into the
programme settings, switched to the John Deere harvester and cut and felled some more timber, and loaded that into the simulated forwarder in record time. Suf ce to say the instructor was impressed and he passed the real-world competency test with ying colours!
In regard to John Deere sales and service, Neil comments, “In my 30 years working in the harvesting sector, I followed the technical development of John Deere machines and had a close working relationship with John Deere forestry, so it was an obvious choice to contact them when we needed a forwarder. Jock Mckie was very keen to embrace and support what I was wanting to do by coming up with a green forwarder, so we worked closely with John Deere in terms of the oils we could get to support this. It was a kind of slow burn, over four to eight months and Jock went out of his way to nd a clean machine that was four years old with around 6000hrs on the clock. That said, for the rst time ever, Jock agreed to repaint the rear chassis and bunk, as I knew our green initiative was going to attract some media and TV coverage, so I was grateful that they went above and beyond to meet the speci cation that we required for our client.
“The 1210G is a fantastic piece of kit particularly for new operators with its easy-to-use IBC system, and this machine is also very versatile as the bunk can be enlarged for extra carrying capacity for large timber on clearfell work and then made narrower if we ever needed to tackle thinning operations. With a service package from the John Deere dealer, this low-hours forestry machine not only looks like new, but runs like new on the HVO fuels and fully biodegradable uids and grease.”
Jed Stoddart comments, “This John Deere 1210G forwarder is very easy to operate with the IBC system, as it is so intuitive to use, it is
almost like one less thing to think about when you are operating the machine all day long. This is my rst forwarder experience, so I can’t really compare it to anything else, but the 1210G cab has all the creature comforts you would ever want, including a heated and vented seat, electric oven to heat food and tonnes of storage space. It is simply a brilliant machine to operate.”
“THE 1210G CAB HAS ALL THE CREATURE COMFORTS YOU WOULD EVER WANT, INCLUDING A HEATED AND VENTED SEAT, ELECTRIC OVEN TO HEAT FOOD AND TONNES OF STORAGE SPACE”
As part of the service agreement, John Deere supply Neil’s 1210G with a PLANTO MOT SAE 10W-40 engine oil from FUCHS that is low ash, and designed for modern diesel engines, which is biodegradable and is especially recommended for use with alternative diesel fuels. All other uids from hydraulic to transmission are also biodegradable.
Clearly, Creel Maritime Ltd have a huge amount of experience in project management and planning, decarbonisation, brokerage and ship agency for round wood timber, as well as leading the way with one of the greenest John Deere forwarders in the world. They have a successful track record in delivering a package of services for their varied customers by providing a value added service and bespoke solutions.
If you wish to nd out more about Creel Maritime Ltd, they will be attending APF 2024 taking place at the Ragley Estate, Warwickshire, over 19-21 September. They also have another new alternative fuel project to unveil, so catch up with Neil and his team at their booth.
Join us at the APF 2024 forestry show demo stand 1840 Sept 19th-21st Ragley Hall, Warwickshire.
Hydrostatic drive machine, with a 3t payload and full ROPS FOPS OPS cabin.
More hydraulic power due to its variable displacement hydraulic pump. Can cut pre programmable lengths in the forest
A combination forwarding and harvesting machine, which can be fitted with a stroke harvester head to fell trees of up to 30cm in diameter
Increased levels of sound proofing in the cabin
The good condition of this EcoLog 564D Blue forwarder, with a known history from its original Irish owner, made it a sensible purchase for P. & G. Forestry Ltd.
Eoghan Daly reports on a Co. Laois-based timber harvesting contractor who has built up a successful business while operating a number of preowned machines including two EcoLog harvesters and a rare EcoLog forwarder
IMAGES EOGHAN DALY
Modern timber harvesting and extraction equipment may be very productive, but this obviously comes at a price and it can often be dif cult to justify these new machines. As a result, many operators favour the purchase of used machines in the interests of minimising their investment costs. One such operator is P. & G. Forestry Ltd of Camross, Co. Laois, who run a eet based
completely around pre-owned harvesting and extraction machines.
Having shown how effective this route can be, when the right approach to machine selection is taken, preowned machines can still be very productive and reliable. Nevertheless, monitoring the age of the machine against a set threshold is central to the success of operating used forest machines. Also, their purchase from reputable sources
with a known history is always a great reassurance. In addition, resisting the temptation to hold on to a machine for too long is also an important consideration. P.& G. Forestry Ltd view this as being vital in maintaining good standards and avoiding high repair or replacement costs.
Specialising in harvesting on privately owned plantations, the company is based around a model in that they can, where
required, provide a complete package from consultation to timber purchasing and marketing to harvesting. Harvesting of these private forests is completed for a range of clients including Euro Forest Ireland and a number of the major sawmills. As well as harvesting timber, P. & G. Forestry Ltd have also purchased standing themselves.
With over 35 years of experience in the Irish forestry industry, the company is run by father and son team Pat and Gearoid Burke with Pat having considerable past experience of harvesting with his own contracting business in the 1990s. This was before he concentrated on a successful hurley making operation and later working as a timber buyer with major forestry contractors. As a quali ed forester, Gearoid brings distinct bene ts to serving the needs of privately owned forest owners and in addition to P. & G. Forestry Ltd he also works with Sar Caman Teo who are a forestry consultancy and rewood production business, set up by the later Peter Alley of Dundrum Nurseries.
Recognising the increased harvesting
activity in private forestry and the need for a dedicated harvesting service to cater for both thinning and clear fell operations, P.& G. Forestry Ltd commenced serving private sector timber growers in 2015. With the initial focus being largely on thinning operations, the early machine choices re ected this with a Gremo 950F forwarder operated together with a Gremo 1050H harvester. However, a need to cater for clear fell harvesting and extraction has led to more of an all-round machine structure for subsequent machine choices, which is a model dictated by industry demands as Gearoid explained, “It was never possible to beat a Gremo harvester and forwarder as the ideal thinning team and we completed a lot of work very successfully with
them. A working model where a contractor would focus exclusively on thinning may work well in Scandinavian countries like Sweden. But in Ireland it is different and machines that are equally suited to thinning and clear fell are the only way to succeed long term in the industry based on the rate structure and the need to be exible in the work that can be taken on. As a result of this and the increasing amount of clear fell activity in the privately owned forest sector, we have based our more recent machine choices on all-round units.”
“THE CURRENT HARVESTER LINE-UP INCORPORATES TWO ECOLOG 688 EIGHTWHEELED HARVESTERS WITH EXTRACTION CATERED FOR BY AN ECOLOG 564D BLUE FORWARDER”
Based on this, the current harvester line-up incorporates two EcoLog 688 eight-wheeled harvesters with extraction catered for by an EcoLog 564D Blue forwarder. A Komatsu 835 still forms a vital part of the operation with the original Gremo 950F also retained as a back-up machine. All purchased used, the four machines making up the core eet vary in age and service. Despite being
manufactured in 2015 and 2016, both EcoLog 688 harvesters are still very much up to the task and are a real tribute to the longevity and reliability of the machines from the manufacturer. Both machines have the same overall speci cation when it comes to tyre con guration, crane reach and harvesting head model, with this standard seen to present the greatest level of all-round harvesting capability. Originally, the newer of the two machines, which originated in Sweden and utilised an 11-metre reach crane with a Logmax 5000 harvesting head, was soon exchanged for a shorter reach unit in the interests of being able to host a larger Logmax 6000 Twin harvesting head.
While the original Logmax 5000 was a very impressive performer in typical thinnings, the abilities of the Logmax 6000 Twin made it seem a much more attractive prospect, as Gearoid explained, “LB Gremo had the used Logmax 6000 Twin available just at the right time which allowed an upscaling of the harvesting head on the 2016 EcoLog. It has made perfect sense and has allowed the machine to be far more capable in clear fell harvesting whilst the head is still compact enough to work in thinnings.” Nevertheless, while content with the performance of the Logmax units, the increased prevalence of heads of the angled roller design may lead to a change in the future as he explained. “I am satis ed with the performance of the Logmax heads. Their design handles rough and crooked timber very well, which is important since we harvest both softwood and hardwood. The developments in harvesting heads is something I am looking very closely at and if in the future I believe there is a better t for our operation, then I would be open to change. But for now, Logmax is meeting our needs with good performance and measurement accuracy.”
Among the attributes of the Logmax heads are the level of accessibility they provide to all main components. This is especially in the area of the valve chest assembly which is easily reached and particularly easy to work on in the event of a problem, with the entire area revealed by opening the main cover. However, the number of times that the heads have
Machine stability is maintained by the centre joint stabilising lock while machine manoeuvrability is delivered by a tight steering angle on the 688E harvester.
required attention remain low as they prove particularly reliable with this also applying to their EcoLog 688 hosts.
Not only do the machines work extremely well based on their proven design concept, which delivers equal suitability to thinning and clear felling on low weight bearing sensitive sites and steep terrain, but they have also met with approval by their operators. Operating P. & G. Forestry’s most recent EcoLog 688 harvester, Isle of Man native Paul Swales has now spent 18 months on the machine and despite being a self-confessed John Deere fan
“I WOULD CONSIDER FITTING A NEW HEAD TO THE 2016 ECOLOG 688 AFTER A YEAR TO 18 MONTHS TO MAKE SURE IT REMAINS AT PEAK OUTPUT”
through his forestry career, he does not hesitate to endorse the EcoLog, “I ran my own timber harvesting business and have operated machines for other contractors in Scotland and Ireland, but up to 18 months ago it has always been John Deere as well as the Timberjack and OSA variants of them that came before. I have no hesitation in saying that the EcoLog is an excellent machine.
It is stable and very light on the ground with decent crane power and is also very economical to run. This one may be a 2016 machine with over 14,000 hours, but it does not give any problems, with the exception of the occasional hose which shows how good a machine they are over long term service.”
Powered by Volvo Penta engines, generous oil ow from the hydraulics, their main elements culminate to form the ideal harvesting base machine. Fitted with an Ecolog built crane, the design of the crane’s inner boom is such that it does not obstruct the offside view, despite being mounted on a common slewing and levelling base with the cabin. Adopting a gooseneck pro le of the inner boom section, it offers offside visibility whilst also making the crane compact for manoeuvring through the remaining trees in thinnings. At the same time, there is still plenty of lifting and slewing power for heavier trees in clear fell.
Even though the EcoLog 688 harvesters are renowned among Irish users for their unique ability to function in all stages of thinning and clear felling operations, their forwarder counterparts are far less common among Irish users. However, this did not detract from the appeal of a 2019 built EcoLog 564D Blue
forwarder when it became available for sale recently. Taken as a trade-in against a new forwarder by Irish EcoLog dealer LB Gremo, the machine’s known history and the attention to detail in its upkeep by its previous owner, meant it was a very appealing choice. Gearoid says, “As a one owner Irish machine from new, having known the history of this EcoLog forwarder was a big plus in its favour. It had just over 10,000 genuine hours and based on its condition, it de nitely appeared to be capable of completing lots more work which made buying it an easy decision. It is a good solid and simple
forwarder and following over six months service it hasn’t given us any problems, with the exception of injectors which were resolved without delay by Liam Bergin of LB Gremo.” Fitting into the P. & G. Forestry eet particularly well, this 12-tonne payload capacity machine was con gured by its original owner to be a true all-round forwarder based on the combination of compact dimensions, manoeuvrability for thinning and a worthwhile load capacity for clear fell extraction.
Examining the machine’s speci cation more closely from the ground up, the 564D offers good oatation and excellent clearance. This is made possible by the tment of 710/40-26.5 tyres which give excellent ground contact for minimal ground pressure while their higher pro le, compared to other machines in the same size class, is a very useful feature. Nevertheless, of even greater signi cance is the machine’s ability to host wide oatation tyres without making the machine excessively wide. This is proven by its width of 2.84 metres while its tight steering angle of 43 degrees ensures good manoeuvrability in thinnings with the centre of gravity remaining essentially low to deliver favourable stability. Away from the machine’s terrain friendliness for thinning operations, the 564D Blue still has the necessary capacity for clear fell extraction even when a high percentage of sawlog material is present thanks to its 12-tonne payload. The machine’s
The load capacity of the 564D Blue makes it the ideal pairing for working with the 688 harvesters in either thinning or clear fell, even over longer haul distances.
powerful Mercedes OM934 four-cylinder engine delivers a 153kW power rating while tractive force from the hydrostatic transmission is rated at an impressive 174kN. All the machine’s elements, including its Cranab FC12 crane, are controlled by the IQAN control computer like the 688 harvester base machines.
While the use of preowned machines is certainly a model that works for P. & G. Forestry Ltd, their choice of machines is also a major part of this success, as Gearoid concludes, “Our four main machines are serving us well. The Komatsu 835 has just passed 10,500 hours with the only problem being a computer module replacement and a new grapple which is obviously a wearing part. The EcoLog machines have been really successful and in the case of the harvester base machines, they rarely give trouble once they are looked after and serviced regularly. Harvesting heads have a shorter life and this is where the majority of problems come from which is why I would consider tting a new head to the 2016 EcoLog 688 after a year to 18 months to make sure it remains at peak output. It is a major reassurance to have the kind of service available from Liam Bergin at LB Gremo who is always able to be contacted on the phone and gives a fast callout response to any problems we have which proves any machine is only as good as the dealer service.”
David Wylie traveled north to see the latest JCB 437HT wheel loader in action at Gordon Timber, Nairn
GThe JCB 437HT’s experienced operator is Artur Dobruk who has over eight years experience with wheel loaders.
ordon Timber is based in Nairn in the Highlands of Scotland and the company has a long history of supplying high-quality softwood timber. Founded in 1862, and since the late 1880s, they have been managed by four generations of the same family, the company is now recognised as one of the top sawmilling companies in the UK.
This sawmill has been processing locally grown softwood logs on the Nairn site for 85 years, and their core business is converting roundwood, grown in the North of Scotland, into a comprehensive range of high-quality sawn timber products for the construction, fencing and packaging markets.
Approximately 40% of their core business is producing sawn fencing for the UK, with a range of premium quality posts, rails, boards and sleepers that are ideal for agricultural and landscaping projects.
They also offer high-pressure preservative treatment in green or brown, Use Class 4, to ensure optimum performance and longevity, in particular for timber that will be exposed to ground contact. Due to a combination of
Main image: The high-lift arms of the JCB 437HT model and its tilting bucket work well here producing a highly e ective stockpile of ‘peelings’ at Gordon Timber’s premises.
Above: Logs are sorted by length and size before being processed into various timber products.
Right: The wood chip is loaded on to a constant stream of HGVs.
“WE EXPERIENCED SEVERAL COSTLY ENGINE ISSUES ON A COMPETITOR WHEEL LOADER, AND THEN DECIDED TO LOOK AT THE BRITISH-BUILT JCB 437HT”
the highest production and preservative treatment standards, they now offer customers a ‘no-nonsense’ 15-year warranty on all premium round posts and strainers.
For the construction market, their unseasoned softwood carcassing is also used across the UK, with lengths ranging from 2.4-6.0 metres, with high-pressure preservative treatment - C16 Stress Grading and Heat Treatment ISPM-15 (56/30) – also available on demand.
They also serve the UK pallet wood market all year-round, with pallets for both national and international sectors. They
report that sleepers have become an ever more popular choice for garden renovations in recent times, and have a multitude of applications such as landscaping features, raised beds, walkways, bordering and decks to name but a few.
Primary processing is carried out using the latest Scandinavian equipment and techniques which include 3D scanning, curve sawing and remote processing control. Logs are sorted by means of a 3D scanner which measures each log’s ‘true shape’ then batches them by form and diameter for primary conversion. Batched logs are converted into sawn timber prior to sorting and stacking in readiness for secondary processing.
With a signi cant re-investment programme for secondary processing, Gordon Timber utilises well the off-saw
timber produced in the primary process for fencing products or the timber can be kiln dried, crosscut, resawn and pointed prior to pressure treatment. Products destined for the construction market will typically be kiln dried in the company’s new biomass red kilning facility, before being strength graded and machined to a nal dimension in the semi-automatic planing line. The new kilns also provide welcome capacity for the growing heat-treated pallet and packaging market.
Johnny Dean is the harvesting manager who is responsible for buying timber and managing the sawmill’s mobile plant and special projects. Johnny explained that the market for co-products/wood chips has developed signi cantly in recent times, and therefore they need a highly productive and reliable large wheel loader, with great dealer service support, in order to carry out material handling duties across the entire operation. This is being carried out by a new JCB 437HT (High Torque loading arms) model.
Johnny also explained that the sawmill has, for many years now, produced chips that meet the stringent quality standards demanded by the Scandinavian export market. Regular monthly cargoes are shipped to Norway from the nearby port of Inverness. Produced to a strict uniformity in size and with minimal bark and sawdust, the betterquality whitewood chips are destined for magazine and newsprint production, while redwood chips are destined for other uses such as Tetra Pak juice cartons.
The balance of chip production is sold to the domestic market for both board manufacture and biomass energy generation. Of the other co-products - sawdust, bark and shavings – this is marketed within the UK for a variety of end uses ranging from horticulture, playgrounds and pathways, animal bedding and again, board and biomass industries.
At the time of FM’s visit, the JCB 437HT was busy stockpiling and loading trucks with various types of co-products in this busy operation, as the sawmill relies on the JCB 437HT to move sawdust, bark and shavings to keep the production process free- owing.
Johnny Dean says, “We experienced several costly engine issues on a competitor wheel loader, and then decided to look at the British-built JCB 437HT, and I’m pleased to report we made the right decision to switch brands. As the JCB 437HT has not missed a beat since it has arrived and we know the service support provided by Scot JCB is one of the best in the business and we have a good service agreement and warranty package from Scot JCB for piece-of-mind and xed costs over the next ve years.”
Right: Looking in the cab we can observe the joystick, one of the two LCD screens and the steering wheel and its controls.
Below right: One of the cabs colour LCD screens doubles up as a monitor for the rear-view camera.
Below far right: An additional safety feature added is a front-view camera system for a good view over the tipping bucket when working around the yard.
“THE CAB OF THE JCB 437HT IS ONE OF THE BEST I’VE OPERATED, AS IT HAS PLENTY OF SPACE AND STORAGE FOR PERSONAL ITEMS AND THE VISIBILITY IS VERY GOOD FROM THE LARGE WINDOWS”
Before Johnny placed the order for the JCB 437HT, he extensively researched the market and was supplied with anonymised fuel burn data from four other users by Scot JCB and a demonstrator machine to try out. Johnny comments, “I’m pleased to report the fuel gures JCB supplied are proving to be very accurate with our own experience and we are enjoying a signi cant reduction in the amount of fuel we burn compared to running a competitor machine. We can check the JCB LiveLink telematic monitoring data at anytime and Scot JCB send us weekly performance reports on all aspects of the machine.
“With over 120,000 tonnes of timber per annum running through the mill, and 50%
of that being residues, we need a wheel loader that we can rely on to handle this amount of residue, as we only have capacity for one day of storage for the residue materials. So if this prime mover were to go down, then our contingency plans kick in, but it still impacts on production, and so far so good, as the JCB 437HT has been a strong and reliable performer.”
With 1400hrs now racked up on the 437HT, their experience to date with the JCB wheel loader and Scot JCB’s service has been so good that management of Gordon Timber will be looking to grow the JCB eet going forward. During the visit we also saw one of the company’s other special projects in action. This was to design and
JCB 437HT
ENGINE: CUMMINS 6.7 LITRE
ENGINE 195HP 881 NM; EU
STAGE V, US EPA TIER 4F
EMISSION COMPLIANT
TRANSMISSION: ZF FIVE FORWARD AND THREE REVERSE
OPERATING WEIGHT: 15,496KG
FULL TURN TIPPING LOAD: 9625KG
STANDARD SHOVEL CAPACITY: 2.7M 3
HIGH LIFT ARMS PIN HEIGHT: 4306MM
HYDRAULIC SYSTEM: 210 LITRES
FUEL TANK: 270 LITRES
DEF TANK: 75 LITRES
commission a bespoke state-of-the-art high-speed robotic timber post stacker for a fast and safer operation.
The JCB 437HT’s experienced operator is Artur Dobruk, who has over eight years of experience on wheel loaders. Artur says, “The JCB 437HT is a very nice machine and has lots of power, especially in dynamic mode, to handle all the loading, stockpiling and material handling duties. Most of the time we run it in eco-mode, but when pushing large volumes of wood chips, the power boost is great. The fuel ef ciency is outstanding, compared to my last machine, as the JCB 437HT is using around seven to eight litres per hour, that is about 70 litres per day, whereas my last competitor machine was burning 90 litres per day! This means less downtime refueling with just two fueling stops per week from the 270-litre fuel tank
Having produced wheeled loaders for 50 years, the latest JCB 437 Stage V wheel loader incorporates many new and innovative features. It has 6% more power from its e cient and clean burning Stage V Cummins engine and improved fuel e ciency with a new auto engine shutdown feature. The 16-tonne JCB 437 is suited to for heavy-duty applications, for example, the articulation joint on the JCB 437 has a heavy-duty box section that is much stronger than a single plate with a boss. Steering rams are positioned high up and are well protected from possible impact and site damage.
This model has high torque (HT) for parallel lifting and multi-attachment work and is suited for tasks with high loading heights. It also has the JCB quick hitch system for swapping between the highcapacity tipping bucket and a hydraulic sweeping brush to help keep the yard tidy. The JCB wheel loaders have been designed with integral steel fluid tanks to prevent leaks; which are said to be a far superior solution to the plastic tanks favoured by other manufacturers.
JCB claim the all-new command plus cab was the result of a radical rethink and a rigorous research programme to provide maximum comfort, visibility, ergonomics and quietness. All of the main controls are seat-mounted, even going as far as to move with the seat’s suspension. This JCB has a single lever joystick, or multi-lever configurations can be specified, both of which are lever types that use electrohydraulics for precision.
The steering wheel position has a ‘set and forget’ feature, which makes operator access even easier, as the operator’s preferred steering wheel position is stored and can be instantly returned to the set position, even
after it has been folded away. The rear-view mirrors are mounted in front of the A-pillars for improved all-round visibility. Interior mirrors, heated exterior mirrors and bonnet mirrors combine to o er excellent visibility to every corner of the machine.
At the heart of the JCB 437 beats a Stage V Cummins B6.7-litre engine which produces 195hp, up on the previous Stage IV model, and 881Nm of torque at low revs for an incredibly responsive operating experience in dynamic mode (171hp in comfort mode). A variable geometry turbocharger provides increased performance at low engine speed for improved cycle times and tractive e ort. A cyclonic engine fan scavenge filter provides four times the filtering capacity of a standard air filter for longer service lifeparticularly useful in a sawmill environment.
The JCB 437’s variable displacement pumps feed a load-sensing valve block which only consumes power on demand, providing precise and e cient loader control. A hydraulic cooling fan automatically reacts to ambient temperature and adjusts the 437’s fan speed to optimise cooling and reduce fuel consumption and lower noise emissions. There are two full colour LCD screens to navigate the machine’s operating menus with one doubling as a monitor for the rear-view camera. The electronic handbrake is also quick and easy to operate. Accessing the diesel and AdBlue (Diesel Exhaust Fluid) tanks is straightforward via the lockable grille at the rear of the machine. The operator can check the washer fluid level, engine oil and coolant from inside the cab, with all other routine checks and grease points located at ground level. Full hydraulic dual circuit braking with multiple oil immersed discs is said to give the braking system a virtually maintenance-free lifespan.
and the AdBlue usage is very low too.”
“I also like the exhaust regeneration system on the JCB 437HT, as it regens on the go, whereas my last machine had to be parked up during this process, which resulted in a loss of productivity. The cab of the JCB 437HT is one of the best I’ve operated, as it has plenty of space and storage for personal items and the visibility is very good from the large windows, which is essential for such a busy yard and high traf c ows. It is also very quiet, comfortable and smooth to operate.”
In addition to the good front and side visibility from the large glass area, the JCB 437HT comes with a rear-view camera as standard and the rm’s management have added additional safety features by tting a front-view camera system high up on the cab for a good view over the large capacity tipping bucket when on loading and carrying work around the yard. The JCB 437HT has also been tted with transponders, so that visitors and ground workers can carry vibrating alarms on a lanyard to provide early warning of the machine’s approach. The site also has extensive use of segregated pedestrian walkways and traf c lights at main crossing points for site safety.
“THE LOADMASTER LCD MONITOR WILL DISPLAY THE TARGET PAYLOAD, AND NOTIFY THE OPERATOR WHEN THE LOAD CAPACITY HAS BEEN REACHED”
For accurate payload management, and on-road eet compliance, this JCB 437HT has been tted with a third-party weighing system by RDS. The RDS Loadmaster alpha 100 system is accurate to + or – 100kg so it can accurately load and track the total amount of weight that the HGV can carry. This onboard system provides on-the-go weighing and assistance to the loader
operator to achieve the exact load targets. These on-board payload systems are designed to improve site ef ciency.
The Loadmaster LCD monitor will display the target payload, and notify the operator when the load capacity has been reached. With this type of system, information can be easily transferred and monitored, allowing for easy analysis of productivity. Gordon Timber’s management team can then identify trends, issues and take steps to reduce fuel consumption. The nal vehicle weight check is conducted on the site’s weigh bridge. Fire suppression facilities have also been added to the JCB 437HT.
With outstanding reliability, low running costs and excellent sales and service from their local Scot JCB dealer, Gordon Timber are enjoying great performance from their rst JCB 437HT wheel loader to help offer their customers a highly professional, modern, fast and ef cient service for all of their timber product needs.
The JCB 437HT handling ‘peelings’ once the timber has been shaved to the correct size.
Indeco, founded in 1976, are an italian manufacturer of demolition attachments. They set their sights on predicting and reacting quickly to the needs of the marketplace, allowing them to develop into the international market and thus, becoming a leading brand. What ever your industry sector, demolition, construction, quarrying, civil engineer-
ing or landscaping, Indeco, backed up with a large UK-based stock holding, allows for speedy delivery and readily available parts supplied to you.
Reeds sales and service will provide all the support you and your attachment need.
As pictured, Indeco’s IMH series of hydraulically-driven, boom-mounted Mulching Heads were designed to turn your excavator or miniloader into a pow-
erful land-clearing tool. Tailored to fit a wide range of carriers from 3 to 36 tons, there will be an attachment suitable for your excavator. Their specific design allows for a vast range of applications including land clearing, site preparation, invasive vegetation, species management, storm damage removal and clean-up application.
Few companies can claim to have such a diverse range of interests in the forestry sector as Tottenham Timber, who operate a value added area of their operation utilising many forestry byproducts, as Eoghan Daly reports
Striving to develop the animal bedding and forest residue areas of their business, this niche activity continues to grow and runs successfully in tandem with the forestry consultancy, timber harvesting and marketing interests of Tottenham Timber. Committed to investing in the business, this has resulted in continual development and has culminated in the company reaching a deserving position among the leading providers of animal bedding and forest residue products in Ireland.
Operating from a dedicated facility in the centre of Ireland, outside Tullamore, Co. Offaly, the operation has bene tted from the installation of state of the art high capacity drying, screening and baling equipment coupled with considerable
storage capacity for bulk and baled products. Among the products produced and supplied are sawdust, wood shavings, woodchip, bark mulch and rewood.
Each of these products are supplied in a range of consistencies which satis es the speci c requirements of the end user. Recognising the unique demands of customers from a range of sectors, Tottenham Timber have taken these needs on board which accounts for the diversity of their product range, which is continually evolving as managing director and founder Robin Tottenham explained, “We are always acting on the requirements of customers and developing new products in response to their needs and even though we currently
have a comprehensive range, I still see potential for developing new products going forward which is crucial for the future development of the company.”
Nevertheless, producing such a diverse product range to the most speci c standards does not occur by coincidence and requires a depth of knowledge in how to achieve the desired results, along with signi cant investment in the latest state of the art drying and production equipment. This has seen Tottenham Timber invest considerably in making their operation as productive and ef cient as possible with the design of the plant being mindful of present demands and future growth opportunities. While all products have different production cycles, that of dried sawdust and wood shavings used as animal bedding necessitates by far the
most comprehensive process. Supplying both bulk and baled products, the production process ensures great uniformity of moisture content and material consistency with the capacity of the facility allowing material to be produced in volume without compromising on the necessary standards.
Raw material for animal bedding and forest residue products are obtained from a range of trusted and consistent sources, and so supply is clearly never an issue. Providing the volumes necessary to ful l the production demands of this sizeable operation, this can be linked to the building up of dependable contacts in the industry of which Robin has been serving all his working life. However, it is not just the necessary forest and sawmill residues that are required to feed the operation as a demand for a biomass product
also exists to fuel the operation’s dedicated drying equipment.
A consistent supply of boiler fuel comes from a number of different production streams and includes woodchip from local sawmills as well as chipped harvesting residues obtained through the timber harvesting wing of Tottenham Timber. An increasing number of clear fell site owners are now clearing brash in the interests of easing the reinstatement process while also allowing full restocking through the absence of brash windrows through the cleared area. This is a manifestation of how everything from the timber production cycle can be used while adding to the sustainability of the whole production chain. Utilising a combination of
Below: The screening system for dried material features an infeed hopper and transfer conveyor which works with a Bruks reciprocating screen. This segregates material to produce dried sawdust and wood shavings.
woodchip and chipped timber harvesting residues and shredded green waste, these sources culminate to feed the considerable appetite of the biomass boiler at the heart of the operation, as Robin emphasised, “We upgraded to a much larger biomass boiler during 2023 from the Fliegl unit we were running previously. The current 1.75 megawatt Danstoker typically uses three 120 cubic metre loads of woodchip or chipped forest residues per week which may seem a lot but is compensated for by the signi cant drying capability the system yields.”
However, ahead of feeding woodchip to the boiler, some preparation is needed including pre-screening to ensure there is no oversize material present. This is achieved by putting the woodchip through an Ultra Screen trommel screener with screened material WHILE ALL PRODUCTS HAVE DIFFERENT PRODUCTION CYCLES, THAT OF DRIED SAWDUST AND WOOD SHAVINGS USED AS ANIMAL BEDDING NECESSITATES BY FAR THE MOST COMPREHENSIVE PROCESS”
held in a dedicated holding bay inside the main storage building until it is needed at the nearby biomass boiler infeed. As a highly impressive installation, the biomass boiler is just a small part of the dedicated equipment and facility constructed to facilitate the drying process. At one end of the facility, an infeed hopper is lled with woodchip by one of the operation’s loaders with the capacity of this in-feed hopper being suf cient to ensure it does not require regular replenishment, allowing the loaders to concentrate on the many other handling duties around the facility. Infrequent lling is also necessitated by the fact that the biomass boiler and drying process runs continuously through the night seven days per week and means the system can operate autonomously while having the bene t of remote monitoring.
As woodchip is fed through from the in-feed holding hopper to the Danstoker biomass boiler, the intense heat generated acts to heat water which in turn heats the air that is directed to the drying bays. This action leads to a reduction to 10% moisture content following an 18 hour drying cycle. With about 30,000 litres of water in the system, the heated water heats the air which is drawn in through two large radiator units in a dedicated machine room at the rear of the
“VERSATILITY OF THE FACILITY ALLOWS IT TO BE USED TO EFFECTIVELY DRY A WIDE RANGE OF BULK WOOD PRODUCTS”
facility, with the heated air funnelled through two large concrete tunnels by two high capacity fans. With the tunnels running between two pairs of drying bays, the hot air passes through slots at the base of the tunnels which feed into the drying bay oors and rises up through the material through the slatted oor structure. To ensure uniform drying across the complete bay, the material is spread evenly to a prescribed depth by the loaders.
Versatility of the facility allows it to be used to effectively dry a wide range of bulk wood products as well as many other bulk products and in the case of sawdust, it is dried in its original form without pre-screening. As the dried sawdust is removed from the drying bay, it is transferred to an adjacent building where it is screened leading to the creation of two material classi cations: dried wood shavings and dried sawdust. This process is completed by a dedicated static screener unit with its in-feed bin fed by a loader while material then travels up an elevating conveyor before it passes over a Swedish-manufactured Bruks
screen. This ensures a sawdust product from three millimetres down is segregated and discharged to a holding bay below the screen while any oversize material is discharged by a conveyor to the left side with the wood shaving product emerging from a dedicated discharge to the right side of the screening unit. Typical material yields a ratio of 70% sawdust and 30% wood shavings with the dust free properties of the wood shavings giving the product a distinct advantage over other production approaches, as Robin added, “A major bene t of our wood shavings is that they are dust free which is not possible when using some other production approaches. Having a dust free product is vital when it is being used as bedding in the bloodstock industry where customers expect a premium product.”
While the production process for bulk product is completed following screening, there are still a number of other processes that need to be completed when wood shavings and sawdust are being directed to the baling and packaging facility. Alternatively, when they are going to a dedicated mixing station, sawdust is blended with lime to produce a dedicated product for dairy farmer customers. Here, the dried sawdust is fed into a converted Keenan Mech Fiber 360 diet feeder unit where 15% hydrated lime is added. This leads to the creation of bedding material with antibacterial properties to be used as cubicle bedding for dairy cows which has become an increasingly bene cial product for Tottenham Timber. Like standard dried sawdust and wood shavings, this can be obtained in bulk or baled format with the same baling line facilitating all products which are produced in batches according to the need to restock the reserves awaiting dispatch. Equipment used in the baling process depends on a UK-manufactured Bale Pack unit producing 20kg bales which are created and packaged in an automated process capable of three bales per minute.
While the complete production process has
Baling of sawdust and wood shavings is completed by a dedicated unit which produces high density bales at a rate of three per
All loading operations of dried bedding products are conducted indoors to ensure the material reaches the customer at the prescribed moisture content.
been designed and built around an ef cient working model, it obviously still generates considerable material handling requirements. This sees the use of three machines which includes a Volvo L70F wheeled loader with dedicated Pro Dig high tip large capacity bucket. The rest of the eet consists of a strong JCB in uence in the form of a 536-70 telescopic loader commonly paired with a dedicated log grab for feeding the rewood production line, where
hardwood and softwood is processed using a Posch 360 rewood processor. The most recent loader at the facility is a 2021-built JCB 560-80 telescopic handler purchased used from UK based dealer Gunn-JCB.
When it comes to loader procurement, buying used machines is usually favoured with the Volvo L70F being an example of how an effective machine can be obtained when the right avenues are pursued. Sourced in Sweden, this 2009 model has recorded 14,000 hours and based on the good upkeep by its previous owner, it offers the same performance and reliability as a new machine. Delivering a full speci cation with high lift long loader arms over a standard con guration, the machine has a dedicated weighing system and automatic greaser with Robin tting it with a ProDig high tip bucket. This gives a capacity of ve cubic metres which reaches a six cubic metres heaped capacity with the aid of the rear spill guard. Commenting on his choice of loaders, Robin sees the line-up as being ideal for the present needs of the facility, “All three loaders play a vital role in the running of the operation. I
favour purchasing quality used machines with a high speci cation with the Volvo L70F being a good example of this. As a Swedish import it is as tight as a new machine in every way and with the long loader arms it allows us to load walking oor trailers without a loading ramp.
Our JCB machines also rise to the challenge with the newer 2021 560-80 being a prime example of the standard of machines that are available on the used market.”
Applying an in-house approach to product deliveries and raw material haulage as far as possible, Tottenham Timber run a number of dedicated trucks and also use a number of subcontractors. As a consequence of the need for great exibility and an ability to overcome often constrained access to some customers’ yards and buildings, in-house trucks have a range of features to allow ease of access. This includes lower than normal body height and while this obviously reduces capacity, it is necessary to give the ability to conduct deliveries to the more challenging areas. Running four trucks
in-house, two are Volvo three axle rigid units with walking oors with the most recent 2022 registered FM 430 re ecting a high level of speci cation not least of which is the dedicated BMI walking oor body. The BMI in uence is also evident in the Volvo FH500 6x2 tag axle articulated truck’s dedicated trailer, which comprises of a 120 cubic metre capacity walking oor unit with a rear lift axle feature for greater ease of access.
Busy preparing for the increased demand for the company’s products with the approaching onset of winter, Robin and his team of employees are reaping the rewards of the level of investment directed to their dedicated facility. Looking to the future, other avenues to develop the product range are being explored, as part of Tottenham Timber’s strategy as Robin concludes, “There are a number of new product ideas and projects we would like to pursue in the future and it is all part of achieving the position of presenting the most comprehensive range of animal bedding and forest residue products alongside our forestry consultancy as well as timber marketing and harvesting activities.”
Paul Argent reports on the successes of a Cat 309CR midi-excavator, and its various forestry attachments, being used by a team of Norwichbased arboriculturists
IMAGES PAUL ARGENT
Currently having a devastating impact on the British landscape is ash dieback, a chronic fungal disease that will kill most native ash trees. This has resulted in a huge volume of work for the nation’s tree surgeons, such as Norwich-based arboriculturists Broadland Tree Services. In addition to regular domestic and commercial work across East Anglia, Cambridgeshire and beyond, the family rm has a steady stream of ash clearance jobs on its books. To deal with this workload more appropriately, the rm has further mechanised its operation, most recently with a Caterpillar midi-excavator.
The rm is headed by Phil Anderson, together with his sons Rory and Tom. Like many modern-day arboriculturists, Broadland has taken the step away from just using climbing gear and chainsaws. In a bid to make their operations more productive and safer, an increasing part of their job now centres round machine work.
It started with a Cat 302.7 mini-excavator tted with a Steelwrist tilt-rotator that, despite its small size, was a revelation. With specialist attachments, it provided a valuable insight into the advantages that mechanisation could bring to such an operation. It was followed by an access platform to perform work at height. This is a particular challenge on ash trees, as a diseased, dangerous example can look very similar to a healthy tree.
Phil Anderson said, “The trees seem ne, but have deteriorated so much inside they become extremely brittle, snapping under the slightest pressure. Climbing the larger trees is out of the question, hence the addition of the cherry picker into the eet, adding a level of safety to our operations. And while this is a great tool for the big trees, smaller specimens require a different approach.”
Already operating a small Cat mini, discussions started with salesman Chris Beavan from local dealer Bennie, the result was an order for a 9.6-tonne, compact-radius Cat 309CR midi-excavator. Tom Anderson was to become its regular operator and said, “We have been speaking with Chris for a long time over the spec of this machine. His attention to detail has matched our expectations and throughout the process he has been good at keeping us informed of what was going on.
“The dealings we have had so far with Bennie on the 302.7 mini have been few and far between, showing we’ve bought a reliable and well-made machine. In the few dealings we have had, they have been responsive and very helpful. If this is the same for the Cat 309CR, we are going to be very happy.
“We wanted a machine that was small enough to allow us to work in some of the more challenging locations. Some of the roads we work on are tight enough as they are, never mind introducing larger machines with increased weight and tailswing into the mix.
“The 309CR gave us a great combination of size and power, along with operator re nements. One of the most important
THE 309CR’S CURRENT ATTACHMENT OF CHOICE IS A COMBINATION OF AN INTERMERCATO GRAB EQUIPPED WITH A HULTDINS 550S EC10 SUPER SAW”
factors for us was that the Cat came as standard with a twin pump hydraulic system, allowing us to spec attachments without any fear of poor performance.”
The standard slewing boom and dipper on the 309CR provides a pin height of around 6m, which will be a bit more if, as planned, it also receives a Steelwrist tilt-rotator. The
The 9.6-tonne Cat 309CR provides a pin height of around 6m. At just 2.47m wide and with a reduced radius rear end, it is a powerful package with a small footprint.
working equipment is adorned with a full suite of hydraulic lines, served by a pump dedicated to the 75hp excavator’s auxiliary hydraulic services. Pushing out oil at 131 litres per minute at 285bar allows powerhungry forestry attachments to be used with ease.
The 309CR’s current attachment of choice is a combination of an Intermercato grab equipped with a Hultdins 550S EC10 Super saw. The 238kg GRX25 Intermercato grab features a body manufactured from Strenx 700 steel, while Hardox 450 is used for its ve-tine jaw assembly, which is capable of opening to almost 1.5m.
Tom continued, “We looked at a range of options for the attachment before buying this set-up. It is relatively light and very strong and, should we need to step up a weight size for any particular job, this combination can be carried by a larger machine.”
Broadland also speci ed a Marguard protective screen mounted in front of the standard windscreen, to stop any errant branches or even chainsaw blades coming through. At just 2.47m wide, this is a compact machine, but one that comes with a decent cab, with Tom commenting, “It
is a really comfortable machine to operate. Everything is laid out well and is easy to nd and use. The feedback on the levers is just enough and it’s also so smooth.”
We met the Broadland’s team on a road a few miles outside of Norwich, taking down a line of diseased ash trees. As they were in a well-developed hedgerow, it was impractical to remove the trees at their stumps on this visit. Instead, the plan was to cut them down to the height of the existing hedge, which would remove the risk to road users, while the whole stretch of hedgerow was due to be properly cut back next season.
In conjunction with the local council, it was decided that traf c would be held at both ends of the road while the team were cutting and chipping. Although these ash trees were small specimens, unlikely to explode when cut into, Tom says that they always like to ‘play it safe’.
However, only a short section of traf c management arrangements were allowed to be in place at any one time, sometimes covering only two or three trees. They would be dealt with and the road brushed clear, before the operation moved along to the next section.
Rory Anderson rst walked the line
THE 309CR SQUEEZES A LOT INTO A COMPACT PACKAGE, IN THIS CASE PROVIDING A SAFE AND PRODUCTIVE WAY TO TACKLE THE SCOURGE OF ASH DIEBACK”
trimming the wayward hedgerow, to provide his brother Tom in the new midi a clear view of the trees in question. With the traf c stopped, Tom quickly cut the trees into manageable sections and fed them into a chipper.
Like many modern 10-tonne class reduced radius excavators, the 309CR squeezes a lot into a compact package, in this case providing a safe and productive way to tackle the scourge of ash dieback.
Sitting on rubber tracks, the undercarriage also sports a dozer blade, which Tom says is ideal for stabilising the excavator when handling large limbs, not that this was needed on this job. Even so, there is a risk to life and limb when dealing with diseased ash trees, which is also a slow process if undertaken by traditional means. Broadland Tree Services has taken another big step in mechanising its operation against the menace that is ash dieback.
HSM’s 208F forwarder can be obtained in a wide range of load capacities with numerous options of engine power, crane model and reach, together with various bunk options.
Eoghan Daly takes a detailed look over the various forwarder options in the 8 to 12-tonne payload class and what machine could be best suited for your specific forestry needs
IMAGES EOGHAN DALY & MANUFACTURERS
Much has changed in recent years regarding the selection of forwarders that are offered in lower payload capacity size classes with many manufacturers discontinuing models below the 12-tonne payload threshold. Whilst this has come as dissatisfaction to many timber harvesting contractors, it perhaps serves as realisation of where the forest machine market has evolved towards through falling demand for lower payload capacity machines. This can be viewed by many as a consequence of the pressure on contractors to increase productivity in the interests of making their operations more viable. Together with the growing requirement for harvester and forwarder teams capable of performing all-round harvesting and extraction and not just thinning and some
premature clear-felling operations.
Whilst this may make perfect sense on economic grounds, it of course raises the question of the suitability of larger machines working in thinning applications. This is due to their higher laden weight through to their larger form and greater payload capacity being far from ideal for the extraction of logs from the thinning of the more sensitive forests
Nevertheless, in defence of the concept of larger machines extracting from thinnings stands, a greater payload machine will require fewer passes to extract a given thinned rack which puts up a legitimate argument in favour of opting for more of an all-round forwarder. However, a larger forwarder’s ability to function in thinnings is very much dependent on the overall speci cation and design measures. This is to
ensure the machine remains sympathetic to the terrain delivered by low ground pressure and responsibly compact dimensions to ensure damage free operation to the nal crop of trees.
Despite the advantages of all-round machines, there is also a trend towards the reintroduction of smaller payload capacity forwarders by some manufacturers while others have recon gured their ranges and no longer present 8-10 tonne capacity machines. For those involved in the industry long enough will recollect a time when the distinctive tones of a Bruunett 678 echoed through the trees, or more recently the Valmet 820 which seemed to oat over even the most challenging ground conditions, therefore the bene ts of using eight to ten tonne machines in thinnings may seem more acceptable. However, we will probably
never return to a time where smaller capacity forwarders are standard in thinning applications. Forcing the change is something that will need a combined approach and can only happen if forest owners command more ‘forest friendly’ machines and are willing to offer sustainable rates thereby making them a viable and attractive prospect for timber harvesting contractors. In the meantime, we have lost thinning greats such as the Gremo range which once absorbed into the EcoLog organisation were said to be no longer viable to produce from a research and development perspective. The manufacturer now offers a 14-tonne forwarder as their smallest unit in the form of the EcoLog 574F. Nevertheless, not all manufacturers have reneged on smaller machines, with Komatsu now offering their smallest 825TX as an interesting option despite their move away from machines in this size class some years ago.
When making a choice, machines in the 8-12 tonne class can have equal working capabilities in thinnings of all stages and clear fell operations. The options presented by manufacturers ensures it is possible to specify a machine exactly as a speci c contractor commands, with plenty of choices available such as tyres, crane reach and bunk proportions. Most manufacturers now offer a wealth of possible options to enhance operator comfort which extends to cabin suspension as well as crane tip control systems to ease the working demands placed on the operator and reduce fatigue over the course of a long working shift.
While at rst it may seem the German forestry machine manufacturer just offers a single eight-wheeled forwarder model, on closer evaluation it soon becomes clear that their 208F can be obtained in a wide range of formats with load capacities from 7-20 tonnes. At the lower end of load capacity classi cations, the 208F is available in 7-, 9-, 11- and 12-tonne variants with each having a wide range of options. Each variant is assigned a standard Volvo Stage V compliant engine with the option of upgrading to a more powerful higher torque variant from the same source. The 7- and 9-tonne machines utilise a four-cylinder engine whilst six-cylinder engines are tted above this threshold.
Based on the use of many HSM machines on steep slopes, they have always been associated with high tractive forces. The machine’s transmission is sourced from NAF with all machine settings and operator pre-selections under the command of the HSM Ecommand system which interacts with the operator through a generously proportioned colour monitor. As an option,
the cabin can be speci ed with the HCS cabin suspension system for added comfort. Other bene cial options include XY Control which is a dedicated crane tip control operating system with its use restricted to pairing with Epsilon crane models which are standard tment across the range, while Mesera cranes can be speci ed if the customer prefers this alternative.
To meet speci c customer requirements to deliver compatibility with speci c application demands over the working life of the machine, it can be speci ed with a broad range of bunk con gurations ensuring a shorter wheelbase or longer bunk to facilitate extraction of multiple bays of shorter log lengths. Irrespective of the options speci ed, the same reassuring level of build strength is re ected throughout the machines with HSM combining traditional engineering values with modern features particularly well.
Above: John Deere’s 1010G is available with the traditional fixed cabin or a slewing and levelling option. The fixed mount option is seen as a more simplistic and a ordable choice while still giving adequate comfort and visibility.
Left: The John Deere 1010G is viewed as one of the most capable all-round forwarders and remains one of the few machines in its size class that can be specified with a slewing and levelling cabin.
While the upgrade to the new H series will ultimately extend to all forwarders in the John Deere range, for now the two offerings in the 8-11 tonne payload category continue to be the 910G and 1010G models. Offered with a broad catalogue of options, which allows the machines to be tailored to individual user preferences and jobs, the machines can either be chosen with the xed or rotating and levelling cabin options. As the only forwarders in these size classes to offer a tilting and rotating cabin, the 910G and 1010G offer unrivalled comfort with the design now perfected over earlier variants meaning it is extremely reliable longer term.
In the case of the 910G, which succeeded the respected 810 which was produced in a number of model designations over the decades, a John Deere engine is at the heart of the machine which delivers high power and torque at low revs, thereby achieving
“MOST MANUFACTURERS NOW OFFER A WEALTH OF POSSIBLE OPTIONS TO ENHANCE OPERATOR COMFORT WHICH EXTENDS TO CABIN SUSPENSION AS WELL AS CRANE TIP CONTROL SYSTEMS”
The Komatsu 845 forwarder benefitted from a substantial upgrade in 2021 and since then has become one of the most popular models from the manufacturer in the thinning and clear fell size class.
acceptable fuel economy. It is possible to select the machine with 22.5 pro le tyres, with the 24.5 variants, increasing tractive force and clearance making them an attractive prospect for many users. A wide range of bunk and crane options are offered as well as balanced and unbalanced bogies. Similarly, a broad range of choices prevail for the larger 1010G which can be obtained in 10-11 tonne payload capacity variants. Technologically, the 910G and 1010G are very sophisticated. The machine’s TimberMatic system has a wide range of capabilities in regard to machine control and setup together with data transfer capabilities. The TimberMatic Maps element is recognised as a vital tool in managing timber extraction operations and places a wealth of data in the hands of the machine operator.
Logset may have changed their machine colour scheme to a distinctive black from the previous silver, but in the case of the 5F GT EVO, it is much more than just a colour change with the machine benefitting from substantial upgrades.
As a result of their most recent machine introductions, the Komatsu forwarder range ranks amongst one of the industry’s most comprehensive, which is especially true due to the choice re ected in the 8-12 tonne payload classes. The smallest model available is the 825TX which presents a nine-tonne payload capacity as well as the larger 835TX and 845TX forwarders which offer 11- and 12-tonne capacities respectively. Even though the machines differ in proportion and capacity, they share many common design features with the 824TX and 835TX, aimed at thinning and premature clear fell with many features to enhance their use for thinning. The larger capacity 845 represents a true all-round timber extraction machine and delivers greater build strength in many areas since it
shares common design elements with the larger capacity models from the range. Bene tting from a substantial upgrade in 2021, the 845 features a new chassis, engine and steering system among other enhancements.
Looking more closely at the 825RX and 835TX, their use for thinning work is enhanced by the narrower headboard and load bar design which angle inwards by ve degrees at the top to prevent accidental contact with remaining trees as the machine passes through the stand. Effective stand penetration is also ensured by the machine’s width of 2.6 metres when running on 600
“LOOKING MORE CLOSELY AT THE 825RX AND 835TX, THEIR USE FOR THINNING WORK IS ENHANCED BY THE NARROWER HEADBOARD AND LOAD BAR DESIGN”
mm wide tyres. In contrast, the 835TX offers a larger load capacity and higher clearance via higher pro le 24.5 tyres. The 835TX’s tractive force is also greater at 163 kN over the 150 kN of the 825TX.
While all three models have individual characteristics, they all share common aspects synonymous with Komatsu forwarders. This includes the stability enhancement system which aids the machine’s ability to travel over adverse terrain in a safe and surefooted manner. Another feature is the Komatsu Comfort Ride cabin suspension system which increases operator comfort while convenience is furthered by the availability of the optional Smart Crane crane tip control feature. Other common features include other proven control systems as well as the Agco Power engines used throughout.
Finnish manufacturer Logset offer their 4F GT and 5F GT EVO in the 10- and 12-tonne payload classes respectively. The 4F GT is aimed principally at thinning and like its larger counterparts draws power from an Agco Power engine which is well respected for power and economy. Weighing from 13,500kg, the 4F GT runs on 710/40-22.5 tyres as standard and remains essentially narrow to ensure ease of travel through thinning stands. Like the entire Logset forwarder range, the machine’s transmission and crane are governed by the TOC 2 control system which allows for the tailoring of settings according to user preferences. The crane is sourced from recognised manufacturer Mesera in the form of their 83 model which can be
speci ed in two reach variants.
For those who command a larger capacity machine with higher clearance and greater tractive force, Logset offer the 5FGT EVO model which has a 12-tonne load rating and bene tted from a major revamp in 2022. This has resulted in the restyling of the front hood which is now shorter and narrower in the interests of further improving visibility. The cabin has also had a major facelift while engine power and torque exerted by the 5FGT EVO are very suitable. Logset also offer the 5FP GT model which utilises a more powerful six-cylinder AGCO Power diesel engine. Yielding much greater performance over the standard unit, power increases from 140 kW to 169 kW while torque sees a massive leap to 1000 Nm from the 800 Nm of the 5F GT EVO model.
Streamlining of their forwarder offerings in the smaller payload capacity of the Ponsse range has resulted in the availability of a single option in the 8-12 tonne class which is the 12-tonne payload Wisent model. Forming part of the Ponsse range for many years, the Wisent has been re ned further through the company’s continual product development philosophy. Despite its progressive evolution, many features remain the same such as the allegiance to MercedesBenz when it comes to the power source. This sees the Wisent tted with a MercedesBenz OM934 engine with Stage V emissions compliance while delivering a power output of 150 kW and torque of 850 Nm reached at low revs.
Featuring what is arguably the most spacious forwarder cabin on the market, not only does it provide generous space, but also a good eld of vision in all crucial directions. All controls are within easy reach while all the machine’s functions are governed by the Ponsse Opti Control system. In line with current modern forwarder trends, Ponsse offer their Active Crane crane tip control system on the Wisent which delivers greater ease of use and alleviates the strain of repetitive crane movements by the operator. Presenting an in-house built crane, the Wisent is equipped with the K70+ model which can be speci ed in either 7.9 or 10 metre reach variants.
Swedish manufacturer Rottne have upgraded their forwarder range to the latest E series models with the 8-12 tonne payload models represented by their F10E and F11E units. Even though these latest E series machines may bear a visual resemblance to their previous variants, they have bene tted from a range of enhancements in many crucial areas.
Among these improvements are
The Ponsse Wisent forwarder o ers a 12-tonne payload capacity and draws power from a Mercedes-Benz engine which has been the engine supplier of choice for the Finnish manufacturer for many years.
re nements to the cabin suspension system ‘Comfort Line’ as well as the introduction of the latest machine control and management systems. With the forwarder’s control computer working with GPS/Geoinfo, the system allows for data transfer of classi cation volumes and locations within the forest. This can be used to coordinate
“THIS SEES THE WISENT FITTED WITH A MERCEDESBENZ OM934 ENGINE WITH STAGE V EMISSIONS COMPLIANCE WHILE DELIVERING A POWER OUTPUT OF 150 KW”
The Rottne H11E forwarder may have many visual similarities to the previous D model, but it still o ers substantial upgrades in areas such as the ‘Comfort Line’ cabin suspension system.
Rottne
haulage trucks and ensure log stacking space is made available to the forwarder through awareness of log stocks by management or sawmill truck dispatch personnel.
In addition, to the standard features which Rottne share with most other manufacturers, there are a number of elements and options that remain exclusive to the Swedish-built machines in many cases. These include bogie lift which is a welcome aid to shortening the turning radius of this nimble machine even further as well as improving its performance when climbing over steep banks. Another interesting option is the tilting crane kingpost which presents real advantages when working on slopes and alleviates the strain from the crane base when slewing uphill. Rottne continue to be one of the
few forest machinery manufacturers to design and build their own cranes in-house which means the cranes are a precise match for each speci c model.
Coming from a background where thinning and premature clear fell machines were previously their sole offering, Sampo Rosenlew present much appeal to those in the market for an 8-12 tonne class forwarder despite their present full-line range. With particular experience of thinning and all-round forwarder design and production, their FR28 and FR48 models have a range of
“SAMPO ROSENLEW’S SMALLEST FORWARDER, THE FR28 IS WELL PROVEN IN THINNING AND PREMATURE CLEAR FELL EXTRACTION OPERATIONS ”
features tailored to these applications while retaining simplicity without compromising the essential speci cation.
Sampo Rosenlew’s smallest forwarder, the FR28 is well proven in thinning and
premature clear fell extraction operations. It is particularly well-suited to sensitive sites due to its overall weight which can be as low as 13,000kg depending on the chosen options while its overall width is quoted at 2.7 metres. This Finnish harvesting specialist has sourced well proven components for its machines which are common to many other leading forest machine manufacturers such as AGCO Power engines. Three different bunk lengths can be selected for the FR28 while loading is catered for by either Mesera or Kesla cranes with a wide range of reach capabilities and grapple capacities.
With the FR28 representing Sampo Rosenlew’s original entry to forwarder design and production, the larger capacity FR48 soon followed in response to customer demand for a higher capacity machine to cater for later thinning and clear fell extraction. Utilising many of the FR28 features and components, the design may be similar in most respects, but the FR48 offers greater strength and performance in the areas that matter most to a higher capacity 12-tonne forwarder. Using larger NAF bogies more commonly associated with 14-tonne capacity forwarders, over specifying this aspect of the design is seen to give a greater reassurance of strength and longevity. Enhanced clearance is offered over the FR28 in that the FR48 runs on 26.5 pro le tyres while the ergonomics remain the same in terms of the cabin design coupled with ease of service access which still prevail on this higher capacity unit.
Forest machines that are loved by farmers and valued by professionals:
• Grapples 0.15-0.37 m2
• Cranes 4.3-10 m
• Trailers 6-18 t
• Hidden hydraulic hoses
• Made of especially tough steel: My Inner Strenx® and Hardox® In My Body
• Protected oil pump
• Protected cylinders
• Tough turning house
• Powder-coated surface
• Lowered centre of gravity
• Accessible greasing points
• M. Large Tree Services Ltd. “Coolewell”, Church Road Newtownabbey, BT36 6DH +44 (0)28 9034 2838 sales@mlarge.com www.mlarge.com
The Bruunett Mini 578F was responsible for introducing many new features to the forwarder concept, many of which feature on the modern machines of today.
“LARS WAS NEVER ONE TO ACCEPT ANYTHING AS BEING THE ULTIMATE SOLUTION”
Bruunett Mini 578F with 7.5-tonne load capacity; unladen weight was seven tonnes meaning a gentle footprint on the forest floor.
Sweden of the 1960s was, like other nations, reliant on primitive working methods to conduct harvesting, with horse extraction still widely practiced and some agricultural tractors employed as skidders and sometimes paired with timber trailers. However, the forward-thinking Lars Bruun believed there was a better way.
Born in Västra Götaland in west Sweden in 1934, the young engineer rst came to prominence during the early 60s when working with Värmlands skogsarbetsstudier (VSA). He developed the rst articulated frame timber forwarder and set a new standard for manoeuvrability and functionality. Utilising a BM 350 Boxer tractor, which was married to a rear trailer via the articulation joint, the tractor’s front axle had been removed with steering now ful lled by the centre joint.
Called Bruunett, the name translated from Swedish as ‘Bruun one’. It had a 41kW power rating, all-wheel drive and employed a Hiab 177 crane with log grapple more commonly used on trucks of the time. A prototype of the machine was demonstrated in 1962 and the Bruunett went on to be quite successful with 350 machines manufactured.
Few in the industry have made such a significant contribution to the mechanisation of timber harvesting as the late Lars Bruun. Eoghan Daly chronicles the achievements of this devoted Swedish innovator
IMAGES EOGHAN DALY & BRUUN
Often, it is only when an individual has passed on that we truly appreciate their achievements. However, this was not the case with the late Lars Bruun, with forestry professionals across the world hailing his immense contributions to the development of forestry equipment during his long career and 87 years. Lars remained actively engaged in his design work up to his sudden death on 3 December 2021, and was poised to introduce another revolutionary timber extraction solution at the time of his passing. Although unseen in 2021, details of this new machine have circulated in recent years.
Despite reaching the pinnacle of forest machine development early in his career through the designing of the rst articulated frame timber forwarder, Lars was never one to accept anything as being the ultimate solution and always strived for more productive and
terrain-friendly timber extraction. Having designed early machines that respected these values, Lars believed the modern forest machine had deviated from his original concept, which was light and compact, and capable of conducting timber extraction with minimal ground disturbance.
With regards to Lars’ new concept, one of the rumoured design aspects was a departure from bogies. It is reported that Lars considered bogies a chief contributor to terrain damage and this belief inspired him to create an electrically-powered forwarder with a 10-tonne load capacity and wheels suspended on pendulum arms that kept the load bunk level irrespective of terrain, while improving the machine’s centre of gravity and reducing the potential for ground damage. It still remains to be seen whether this ambitious design comes to fruition, but we certainly hope it does. What a sign-off it would be from the great man…
A change to Ford-based machines in 1965 led to the development of the Bruunett 5000 using a Ford 5000 tractor base, plus the larger Bruunett 9000 based on a Ford County. It is reported that between 1966 and 1968 production of these machines reached 200 units per year. This period of his career also saw the development of harvesters with what is claimed to be the rst timber harvester in the world built in 1966. As an eight-wheel drive machine, it was offered with optional bogie lift which, like the gear driven bogies it employed, were subsequently copied by many other manufacturers in the industry.
Fast developing a name for himself, Lars Bruun started Bruun System AB in 1969 and collaborated with Volvo BM until 1976, at which point Volvo BM withdrew from the forest machine business. During this partnership, machines such as the 880 and 980 harvesters were developed, as well as the Bruunett Maxi forwarder. What came next though, was even more impressive. Through his company Bruun System AB, Lars launched the Bruunett Mini 578F – a machine that revolutionised timber extraction and sold extremely well
alongside a larger Maxi 858F model.
Bruun System AB was sold to OSA in 1980, but production of the Bruunett Mini 578F continued and evolved into the more recent upgraded model – the Bruunett Mini 678F which, together with its earlier variant, collectively represents one of the most produced timber forwarders ever, sending mechanisation mainstream in the process. Production of the 678F continued up to the early 1990s and at this point OSA had become part of the FMG Group and later renamed Timberjack, which is now John Deere with the 678F nally giving way to a successor called the 810A.
“ANOTHER IMPORTANT MILESTONE WAS THE SECOND COLLABORATION WITH FORD”
larger, 8WD 7620F. Harvesters comprised the 7610H and 7620H both of which were available in 6WD or 8WD and like the forwarders were sold to markets such as Canada, Great Britain, Germany, Sweden, the Netherlands and Portugal. Based on Series 10 Ford tractors, the range was offered until 1992 when Ford withdrew from the forest machine sector.
At that point, Lars began a new chapter of machine design and manufacture, developing a new range of forwarders in 1994 (F10, F12 and F14) before adding two harvesters to the line-up (H10 and H14) two years later. As eight-wheeled machines they were powered by Iveco engines and utilised an electronically-controlled hydrostatic transmission coupled with an effective load sensing hydraulic system, while a range of Loglift parallel cranes and Keto harvesting head options were presented.
Refocusing on the career of Lars Bruun, following the sale of his company he formed a new operation called Firma Lars Bruun and continued on his path of innovation. With a modest 15 employees, the operation produced up to 30 machines per year and most of these were exported.
New product development efforts of the time brought mixed fortunes and while some ventures were graced with his Midas touch, some others proved less successful. Among the few failures was an attempt to develop a forwarder utilising wheel-encased band tracks known as the Bruun TwOO. Other machine
developments included the Bruun King, which was available as a forwarder and also in harvester con guration. Differing greatly from the earlier concepts, the Bruun King saw the cabin attain a frontal position with the engine bay positioned to the rear of the front section immediately forward of the articulation joint.
Another important milestone was the second collaboration with Ford, which ran from 1986 to 1992 and resulted in a forwarder range complemented by two harvester models. These units comprised the 7610F (6WD or 8WD) and the
The forwarders also had a few noteworthy features. The F12 model was hailed as the only forwarder with a narrow width of 2.62m while running on 800mm-wide, 26.5-high clearance tyres. The machine offered a 12-tonne payload and a massive tractive effort of 17 tonnes. Like all this later range of machines, the F12 was offered with the R-Mate levelling seat system and S-Mate grapple damping system as standard.
As patented systems developed personally by Lars Bruun, these features were yet more proof of his appetite for progression.
Ef ciency-boosting concepts such as the 1995 Eco-Mate energy recovery system further demonstrated the brilliant and unique ability of this true innovator, whose in uence on forest machine development will live on long into the future.
8-15 t 54 cm
TECHNICAL FEATURES:
•Powerful gripper
•Automatic chain tensioner
•Endless rotating tiltator
•Spring mounted saw box
APPLICATION:
•Safe removal of trees in sections
•Maintenance work along traffic roads and paths
•Felling of dangerous trees
•Fast processing of fallen trees