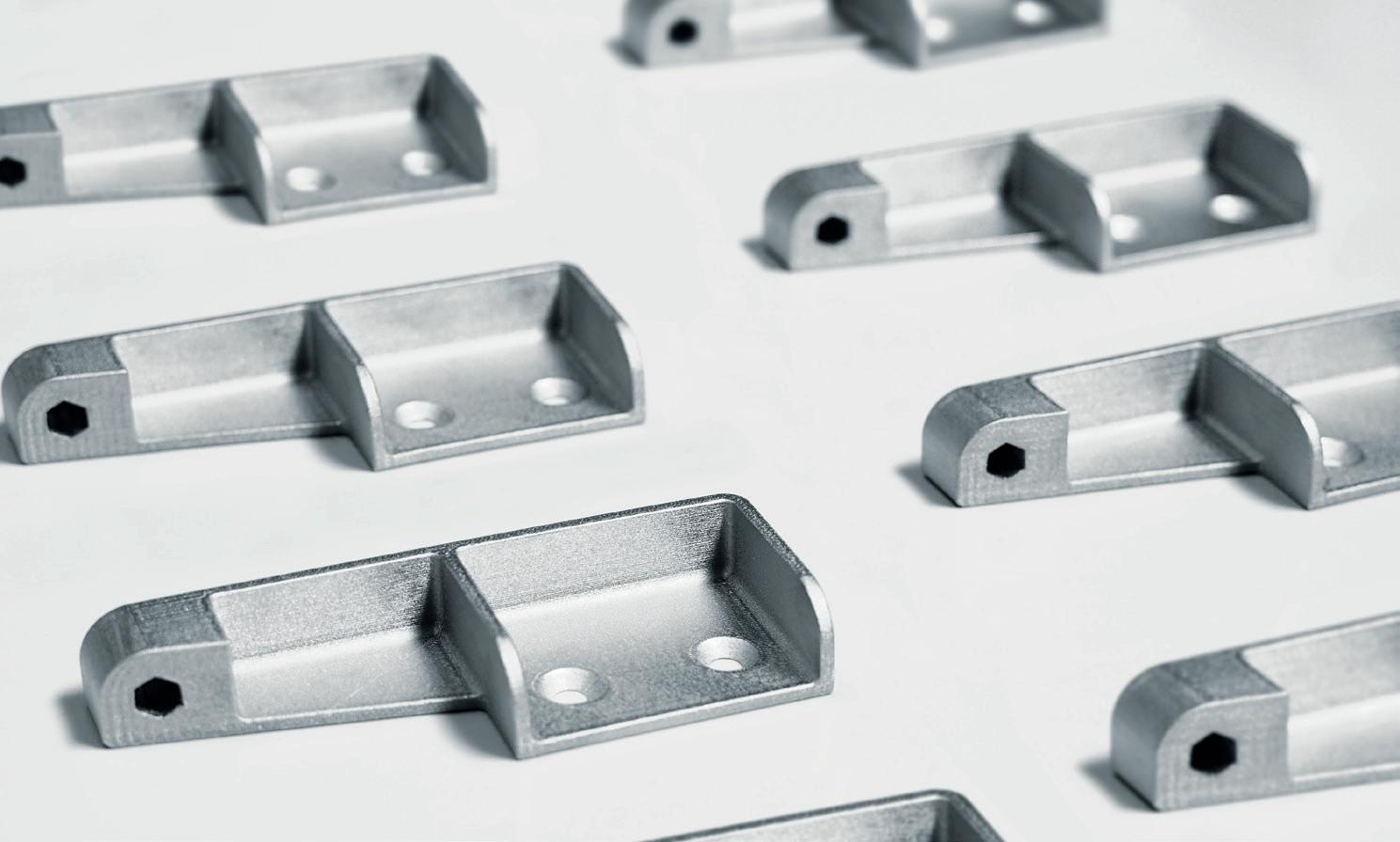
4 minute read
A FOOT IN THE DOOR
Alstom and Replique discuss their collaboration after the additive manufacture of a series of doorstopper components.
ten parts able to be printed per build. The parts were then sintered and debinded in a total postprocessing time of around five hours. Alstom then carried out the required qualification process, which included static testing, to assure themselves that the part was in line with its quality standards and could feasibly fulfil its function over the entire service life of the train. From beginning to end, the delivery of the parts was completed within six weeks.
Additive manufacturing (AM) is now a key part of our supply chain,” the 3D Printing Hub Manager of Alstom Transport Deutschland GmbH noted this summer.
After working with AM for several years, it was gratifying that Alstom could say that.
In June, Alstom revealed a series of doorstopper components had been produced with the BASF Ultrafuse 316L material on Ultimaker and BCN3D extrusion printers. It followed an earlier application of 3D printing by the French rolling stock manufacturer for spare parts, which included the 3D printing of a dozen rubber drainage plugs to seal the holes in tram headlights.
The doorstopper parts are deployed within the partition door between the first- and second-class carriages of a train and are required to be durable – to last the service life of the train – and to have aesthetic qualities – since it is visible to passengers. To deliver the parts, Alstom turned to Replique.
“This doorstopper was made of sheet metal in the past and we thought to buy sheet metal, to laser it, to bend it, to weld it, to shot blast it, and then to paint it, that’s a complex manufacturing [process],” explained Dr. Uwe Jurdeczka, Senior Expert, AM at Alstom. “What about 3D printing? We looked around at who will be able to provide quality, material, experience and all the service around [the part]. That’s [when] we made contact with Replique.” platform to deliver functional end-use parts. The venture of the internal incubator programme of BASF arised from BASF’s Digital Transformation initiative and has built a network of partners that gives its users access to polymer, metal and composite AM. Though Replique’s materials collaborators include more than just BASF, it deemed its Ultrafuse 316L the best material for the job when Alstom reached out.
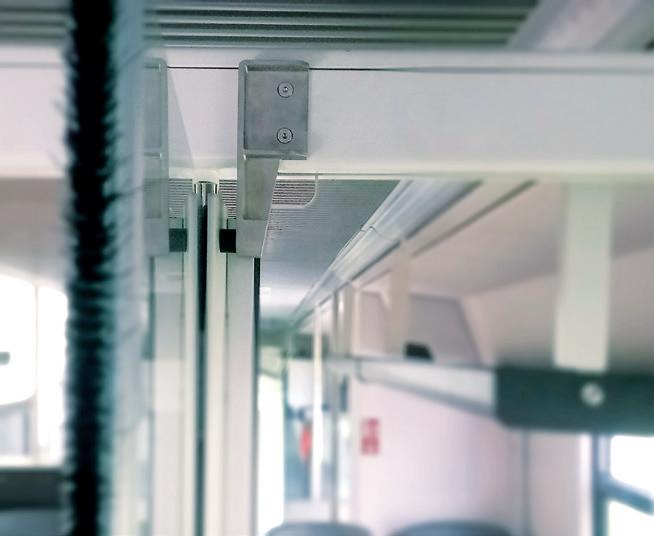
“We wanted to have the best price, performance and quality combination, so that was why we selected [FDM and the Ultrafuse 316L],” Replique CEO Max Siebert said. “[Using Ultrafuse 316L] was quite a nice solution, fitting very nicely because, sizewise, it’s still able to be manufactured in the filament process and, cost-wise, it turned out to be superior to an SLM process. In close collaboration with Alstom, we optimised a little bit the design and we found the right manufacturing parameters later on for the serial process. Then, the part has been produced, and we sent it over to Alstom for qualification and first article inspection.” But Alstom and Replique might not be done yet.
With Alstom’s international footprint and Replique’s growing decentralised manufacturing network, there may be scope for further collaboration. Decentralised manufacturing, per Alstom Additive Manufacturing Programme Manager Aurelien Fussel, is the ‘golden target’ for all industrial companies, though he believes this is more a long-term goal than a short-term one. As such, there is still work to do.
Alstom still wants to see improvements to AM before it rolls the technology out to the extent it believes it can, while factory audits on Replique partner factories would also need to be carried out. But, after the doorstopper success, there is a will to see it come to fruition.
“I propose an exercise of putting [Replique] in our shoes,” Fussel added. “Our customer could ask to audit or visit the place where the parts are manufactured. If we qualify a site of Replique, it should be followed, known and auditable. This will not be negotiable. It is because when you put yourself in the shoes of our customer, you understand that it’s quality first.”
“It is important to understand the meaning of quality from the customer’s perspective,” Siebert finished. “That is why we regularly visit our partners to ensure high quality of our print farm network, but also from a technical perspective we want to ensure repeatable quality. If some parts have to be replaced, we need to be able to achieve the same quality five years later, ten years later. We can ensure this by locking production parameters, technology and materials for parts produced anywhere worldwide. We also have a quality documentation module on the platform, recording quality parameters of the used machines and produced parts before sending it out, enabling tracing of single parts in all quality aspects.”