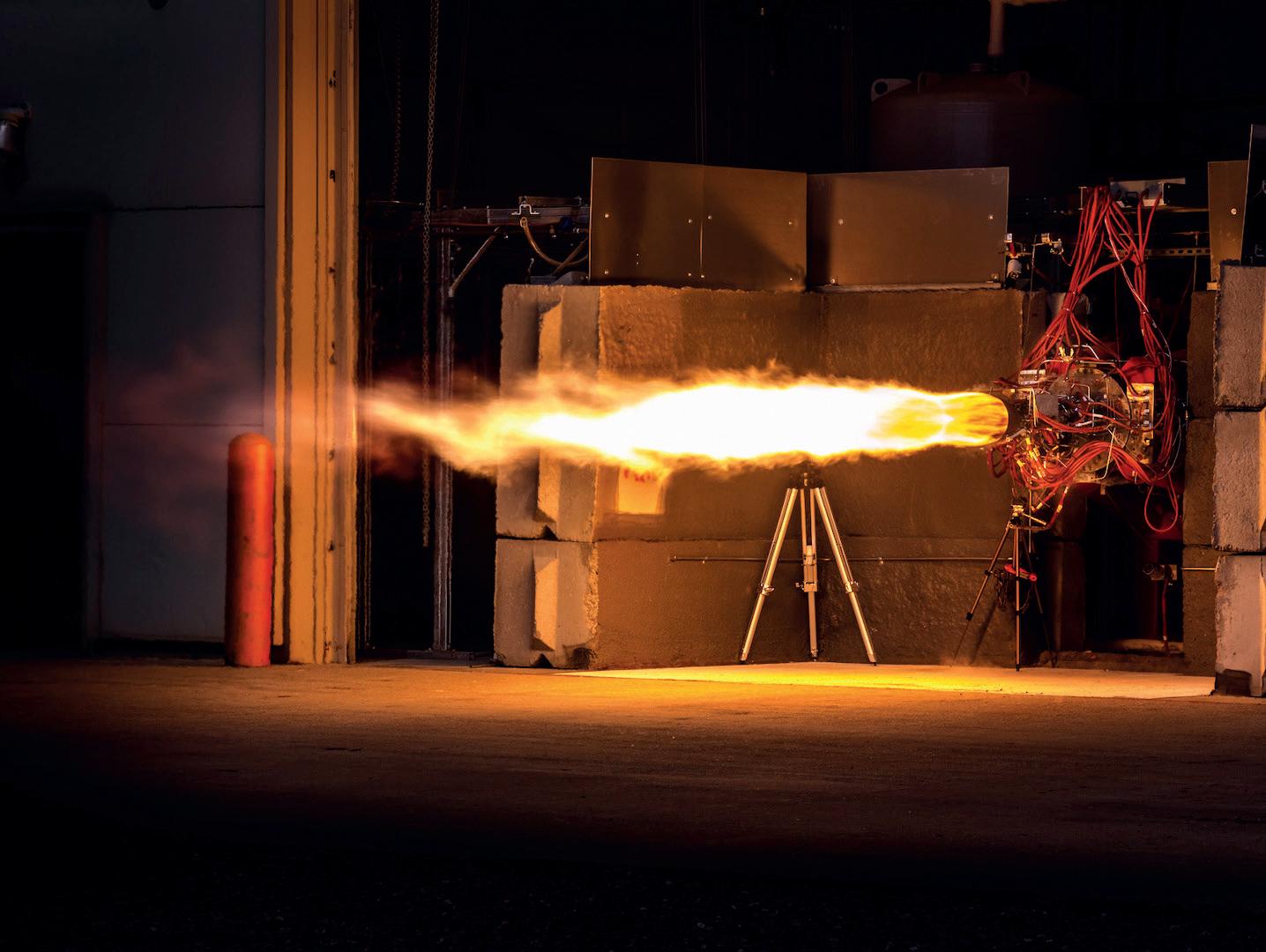
3 minute read
BLAST OFF
Ursa Major recently delivered its first copper-based 3D printed engine components. The combustion chambers were created in the company’s Advanced Manufacturing Lab in Youngstown, Ohio, which began producing and delivering various other rocket engine parts in May of this year.
Speaking to TCT, Thomas Pomorski, Additive Manufacturing Development Engineer for Ursa Major, said: “Our additive manufacturing team is tasked with advancing 3D printing processes for working with metal alloys like copper. They use a large format laser powder bed fusion 3D printer that is designed to work with metal alloys.
“The builds using copper powder feedstock can take up to a week to complete. After some additional processing, including heat treatment and bead blasting, the part is shipped out to our Berthoud, Colorado facility for final machining, inspection, and proof testing. Finally, the chamber is installed on an engine and tested for space launch and hypersonic applications.”
Copper traditionally presents difficulties when used in additive manufacturing due to its highly conductive nature. Pomorski spoke about how Ursa Major attempted to tackle such challenges: “The learnings from our research and development facility are helping to mature the knowledge in the industry around this type of 3D printing. We work with a specific copper alloy that is optimised for additive manufacturing.”
Elaborating on some of the issues Ursa Major is tackling in the industry through its developments in copper, Pomorski said: “The existing copper alloy supply chain is limited, which leads to long lead times for turning around a needed revision when producing and procuring parts by traditional manufacturing methods. Thanks to 3D printing, Ursa Major is able to compress the production and delivery cycle for its copper-based 3D printed rocket engine combustion chambers to one month, compared to a minimum of six months using traditional manufacturing processes.” Emphasising the importance of additive manufacturing to Ursa Major, Pomorski continued: “3D printing is one of the reasons why Ursa Major exists as a company today because it allows us to iterate designs quickly and cost effectively. In the early days of Ursa Major, 3D printing allowed a handful of engineers to design, build, and test a pump-fed oxygen-rich staged combustion engine.”
Ursa Major is the only privately funded company in the US that has a sole focus on rocket propulsion. The company has ambitions to speed up the rocket engine production process in an attempt to relieve restricted access to space and hypersonics testing in the US.
Pomorski shared how he envisions AM will impact the space exploration supply chain: “There is a new hardware rich mentality in the aerospace industry, and this is only possible due to additive manufacturing. It allows Ursa Major to speed up engine production and apply improvements gleaned from testing in real time, lowering costs and speeding through the development cycle.”
Additive manufacturing is used in all three Ursa Major rocket engine programmes: the Hadley, a 5,000 pound thrust, oxygen-rich staged combustion engine used in small launch and hypersonics; Ripley, a 50,000 pound thrust engine; and the recently announced Arroway, a 200,000 pound thrust engine designed for medium and heavy launch.
Ursa Major is scheduled to deliver 30 rocket engines in total by the end of the year. Speaking about the frequency with which Ursa Major can deliver for its customers, Pomorski concluded: “3D printing lets Ursa Major bring highperforming rocket propulsion to market for its customers in months, not years. Once in production, Ursa Major can build about two engines in a week. In fact, we were recently able to deliver three engines in one week.”
Oliver Johnson speaks to Ursa Major about the application of copper for rocket engines.
SHOWN:
URSA MAJOR ENGINE DURING TESTING
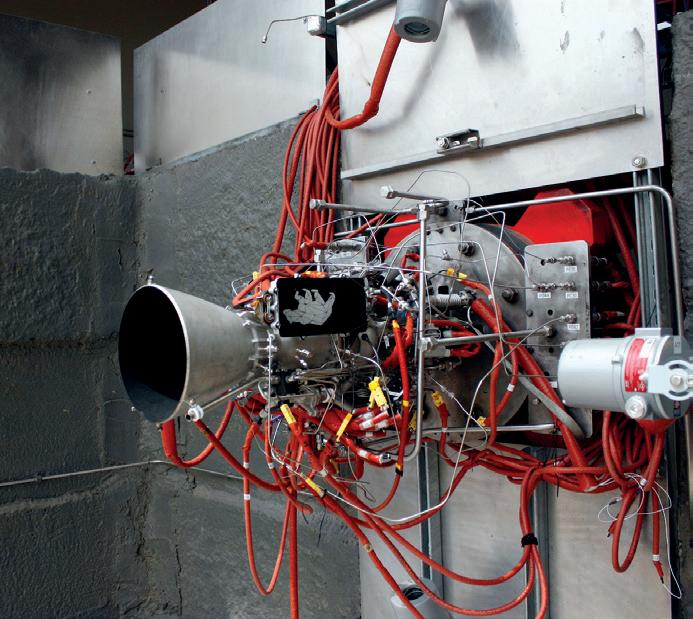
SHOWN:
THE FACILITY IS BASED IN THE YOUNGSTOWN BUSINESS INCUBATOR