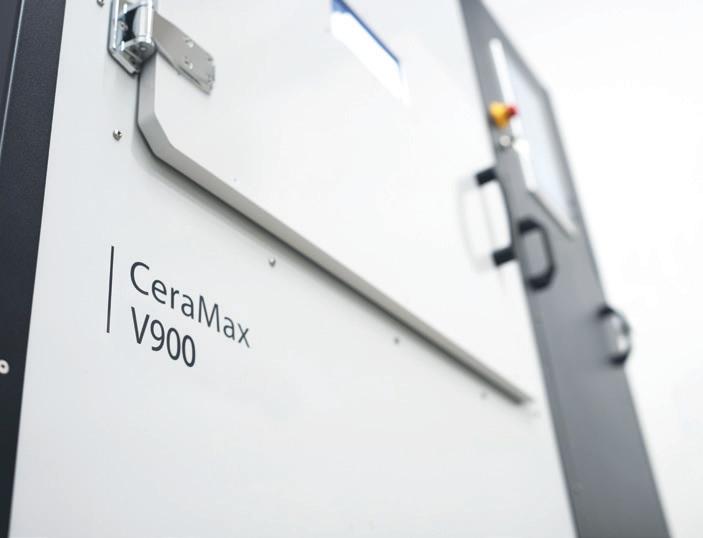
3 minute read
LIS DARK MATERIALS
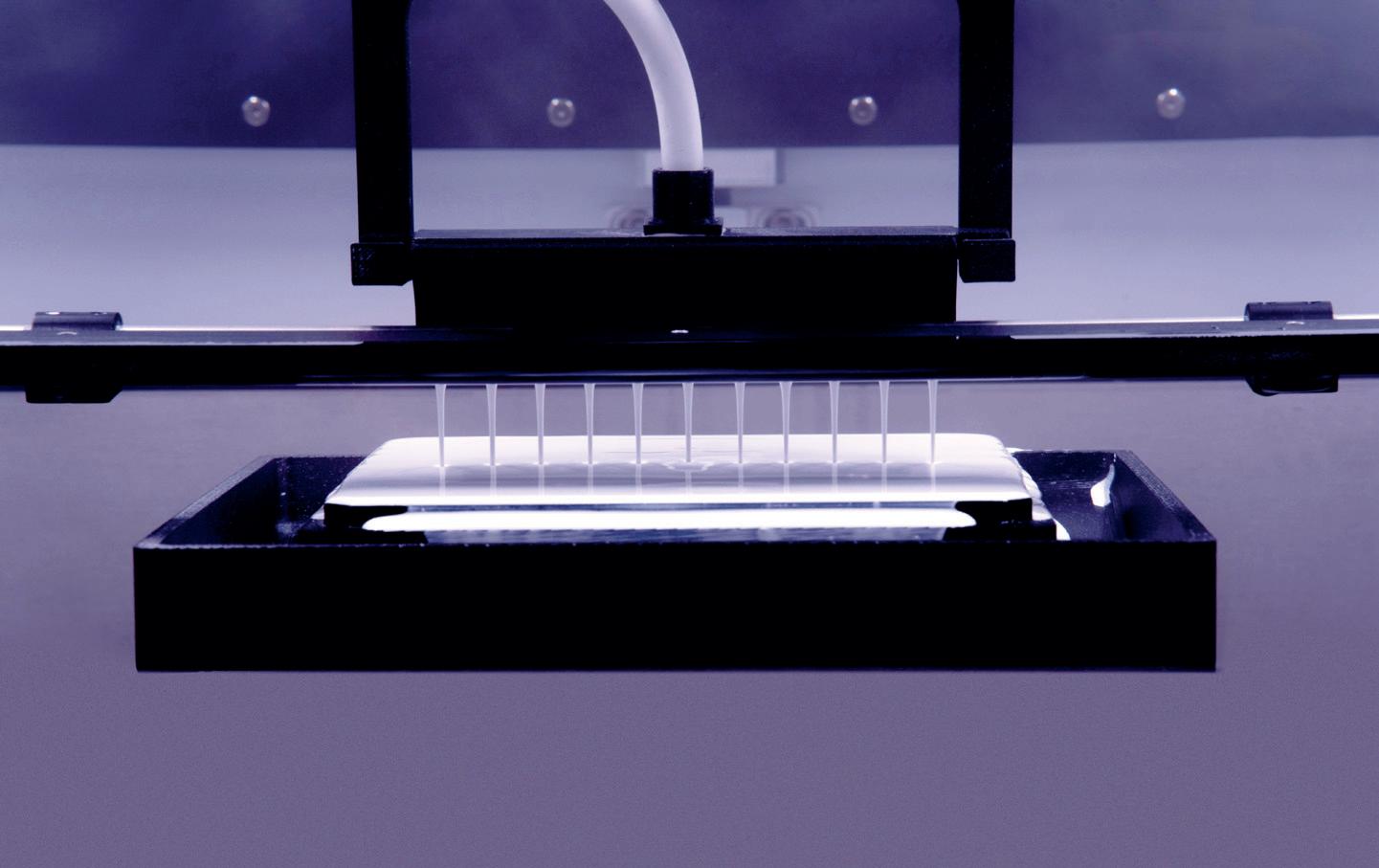
WORDS: LAURA GRIFFITHS
LIS DARK MATERIALS
When TCT met with Dr Johannes Homa to mark the 10th anniversary of Lithoz, the CEO recalled the ceramics 3D printing company’s early days. Homa, along with Lithoz CTO Dr. Johannes Benedikt, both university students at the time, had a gut feeling that there would be similar demand for additive manufacturing (AM) production capabilities in ceramics as there was for plastics and metals, if they could just develop the right solution.
Over that decade, Lithoz has successfully built and commercialised its Lithography-based Ceramic Manufacturing technology, and earned customers across demanding sectors from aerospace to medical, many of which have adopted multiple of its CeraFab systems – the biggest customer fleet will soon consist of 25 machines. Now, with the launch of its latest technology, Lithoz is once again going with its gut having established itself as a leader with its LCM technology as a tool for digital mass production, and listening to the market to step into an, as yet, underserved area.
“It was clear for us that there was this opportunity in the ceramic field, and the opportunity was simply having bigger parts and full densities,” Isabel Potestio, Director Sales & Marketing at Lithoz, told TCT. “Binder jetting is interesting for bigger parts but not when it comes to high density, and those densities really make a big difference in the kinds of applications you can access.”
The answer, Lithoz believes, is LaserInduced Slipcasting (LIS), a new process that specifically addresses those needs through a larger build volume and water-based suspensions with very low organic binder contents to manufacture thick-walled, fully dense parts in oxide and non-oxide ceramics with no debinding needed.
“The reason you can use different kinds of materials is at the heart of the LIS technology,” Potestio explained. “The technology uses a laser to evaporate water from a water-based slurry. As LIS is a heat-based process rather than light-based, the colour of the ceramic material makes no difference to the results.”
SHOWN:
LITHOZ LASER-INDUCED SLIPCASTING
SHOWN:
CERAMAX V900
ceramics including silicone carbide, “the king of ceramic materials,” as Potestio describes, due to its rapid cooling, high strength, heat, oxidation and wear resistance, and weight efficiency. But, it is notoriously difficult to additively manufacture. These properties, in addition to virtually no thermal expansion, have caught the eye of users in aerospace, semiconductor and heavy industries where dark ceramics can be used to meet demands for high hardness, density and chemical resistance and are able to withstand extreme temperatures above 3,000°C.
LOWERING THE BARRIER The LIS technology onboard the CeraMax Vario V900, with its 250 x 250 x 290 mm build area and ability to apply up to 1,000μm slurry per layer in under a minute, has been described as an ‘ideal technological entry point’ to ceramic 3D printing. Slipcasting is already widely used and understood in ceramics but limited in design complexity, while Lithoz says LIS parts, made using a wide range of familiar materials, can be easily reintroduced into the traditional ceramic workflow.
“The development of materials is very easy because there is no real chemistry knowledge needed,” said Potestio on LIS ability to process standard ceramic mateials already used by industry today due to the lack of binder content. “An industry that is used to working with its own powder can basically take the material they were already using, put it in the machine and work with it. This really helps lower the barrier.”
Having formally unveiled the machine at ceramitec in June, it’s still early days but Lithoz confirms several LIS systems are already being installed and operated by partners such as QEP3D and Alumina Systems.
“We’re constantly getting requests from the industry because there is no other solution right now on the market [for creating] thick-walled, fully dense ceramic parts, and at the same time, processing dark ceramics,” Potestio concluded. “We were expecting this kind of response but it’s been really nice to see your expectations paid off. Everything looks quite simple sometimes but there’s hard work behind it and that’s really satisfying to see the market react positively to it.”