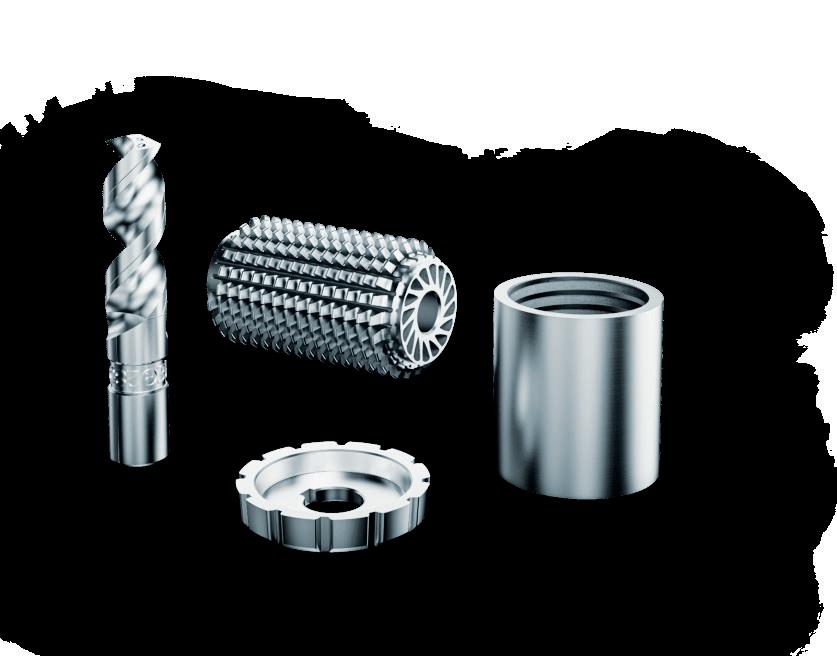
7 minute read
IN WITH THE NEW
Sam Davies speaks to several AM experts on the need for new and novel materials formulations.
If you could have any material, what would it be? If you could do anything with materials and 3D printing, what would you do?”
These are the questions metal additive manufacturing (AM) alloy developer Elementum 3D has been asking. Not as a fun hypothetical during the lunch hour, but in hundreds of conversations with its customers.
It is music to the ears of Eliana Fu and Melanie Lang, two recent Additive Insight podcast guests.
“My question is, why are we using materials that were developed 70+ years ago, when we could be using new materials developed specifically for AM?” the former told TCT after her appearance on the podcast.
“I think we are limiting ourselves right now to a set of materials that have been around for decades if not centuries,” offered the latter.
Fu and Lang aren’t alone in yearning for such developments, and neither is Elementum 3D in working to provide them. INTO THE WILD In Uppsala, Sweden, VBN Components has developed a so-far five-strong portfolio of Vibenite metals, all of which exhibit high carbon content to achieve extreme wear resistance. Because of this high carbon content, the materials are difficult to machine, forge and roll. They are, however, 3D printable and the Vibenite 290 material is believed to be the world’s hardest steel with a Rockwell hardness measurement of 72.
Over in Chaska, Minnesota, Jabil this year commercialised its patentpending PK 5000 material, based on a polyketone resin that is made from carbon monoxide and is said to boast high impact strength, high abrasion resistance and improved elongation compared to existing Nylon materials.
Back in the metals sphere, NASA has developed the high-conductivity and high-strength GRCop 42 copperchrome-niobium alloy, developed for harsh environments specific to regeneratively-cooled combustion chambers and nozzles with good oxidation resistance.
Here lies one of the key motivations for developing new materials formulations. To design the material and its characteristics for a specific process and a specific application. “We’re seeing people that now move to the concept of ‘what if we looked at an alloy that was designed for 3D printing, not just to make it printable, but to make it widely available and better than you could possibly do without printing,” says Jacob Nuechterlein, CEO of Elementum 3D, who supported NASA in the development of GRCop 42. “That’s exciting, as a metallurgist, to be able to go into the wild of brand-new materials and brand-new alloys.”
“Let’s get to a point where we can talk about what the part needs to do and what the part needs to perform and then go backwards and make that your requirement,” Lang noted.
For those tinkering with chemical formulations, these are important considerations to make. As Fu explained, the materials formulations that make it out of the lab and into the real world have several things in common: a manufacturing technique that can process it, an application that demands its properties, and an idea of what you do with the part after it’s been used.
“If you don’t have a process to make it, you can have a Noble Prize-winning chemistry but if it can’t be made in real life, it’s not going to go anywhere,” she said. “I’ve seen so many great ideas just come to a halt because there’s no end use, there’s no secondary market, there’s no way to handle the turning scrap, and there’s no recycling method.”
Fu believes it takes a community-led effort to bring new materials to fruition, citing some of the work being carried out by the ASTM F42 Committee as a positive. There may also be a requirement for risk and revenue sharing, whereby potential end-users team with the material developers to qualify new formulations against
SHOWN:
PARTS MADE WITH VBN COMPONENTS' VIBENITE METALS
SHOWN:
ELEMENTUM 3D HAS BEEN AWARDED NASA SBIR PHASE 1 FUNDING TO DEVELOP SOFT MAGNETIC MATERIALS FOR AM
existing or new applications in exchange for discounted rates or a cut of the profits.
Covestro Additive Manufacturing has several models in place for how such an arrangement might work. After its merger with Stratasys is closed, the company will be able to have instant access to the hardware it has previously had to strike partnership agreements for, while the company will also make deals whereby commitments are made to buy material upfront, as well as others where the manufacturer can decide at a later date whether the project is worth pursuing further after laying down a monetary deposit. There are also many instances where exclusivity is given to a single manufacturer.
TELL ME WHAT YOU WANT Whatever the journey for a new formulation, most agree it is paramount that an application is top of mind when it is being developed. You need to be solving a problem somewhere for someone, and ideally you know where and for who. Hugo da Silva, the VP of Covestro Additive Manufacturing, noted that the dental and medical markets will bring much opportunity for new chemistries, because of the demand for personalised goods. He also noted that entirely new applications will open the door for novel formulations, again citing an example in dental.
“Dental aligners didn’t exist in the past, and then they start making moulds to do dental aligners, but that mould in that process was new,” he said. “Now, all the companies are trying to print a direct printed dental aligner. It’s also a new application – there are no references out there. When you get applications [where] there are no references, it makes it much easier.”
Covestro AM, da Silva told TCT, is currently working on multiple materials that are tailored to applications in the medical, dental, and industrial sectors, with commercial launches anticipated in the not-too-distant future. It is likely that these are being brought to market via one of the risk and revenue sharing models detailed above. Yet, while having applications and customers in mind go a long way to overcoming the many hurdles involved with new materials development, there are still plenty of other elements to consider.
These include identifying potential secondary products where the material properties can be applied – in cases where there is no exclusivity – and also developing supply chains that make economic and environmental sense. Manufacturers that are moving away from familiar materials might also need to be educated and persuaded that this new grade can match or better the performance of the existing one, while also matching or bettering the cost, which raises another consideration. This becomes complex because with 3D printing there is likely to be less material used to make the part, there are no tooling costs, the engineering time that is factored in is different, and, in theory, the way spare parts might be handled will also change – hence, the cost modelling, in addition to the material, may be new to the end user.
The introduction of new materials, then, is not without its challenges. There is also the fact that materials are, in essence, brands that are trusted to carry out the job and there is decades’ worth of data points to back up their capabilities. To compete with a tried and trusted PEEK or 316L takes a lot of testing, a lot of data and a lot of time. But it all comes back to solving problems. If you can do that, the manufacturers will be interested, and there are benefits to be had all round.
“We are trying to take problems in additive, materials and production parts, and come up with solutions,” Matt Torosian, Director of Product Management at Jabil Additive, said at RAPID + TCT. “When you do that, it’s not hard to switch people at all. It’s much harder to take something out there and say, ‘here’s a me too, why don’t you use this?’ Then you’re in a price game that downward spirals to nothing.”
The best approach, for Jabil and others, is to address market problems – of which there are many – with novel solutions. Yes, there is an extensive workload required to bring those solutions to fruition, but the end results are worth it. What’s more, 3D printing technology is perhaps best placed to provide many of the answers.
“AM is re-inventing material development,” Ulrik Beste, CTO at VBN Components, said. “When you’re using additive manufacturing, you don’t have this production constraint that we talk about, and you also have a very high yield in your process, and you can print it near net shape. When you have a high yield, then you can also choose much more expensive elements that hopefully will result in a fantastic property. You have an enormous opportunity here by thinking outside of the box.”
“Instead of looking at what’s possible to make by, say, casting or forging, it is becoming possible to look at what you would like to have, which is not something people have been able to do before,” Pär Arumskog, Field Application and Development Engineer at VBN Components, finished. “Now, you can imagine your ideal material and you can probably find a way to produce it. And that really wasn’t possible.”
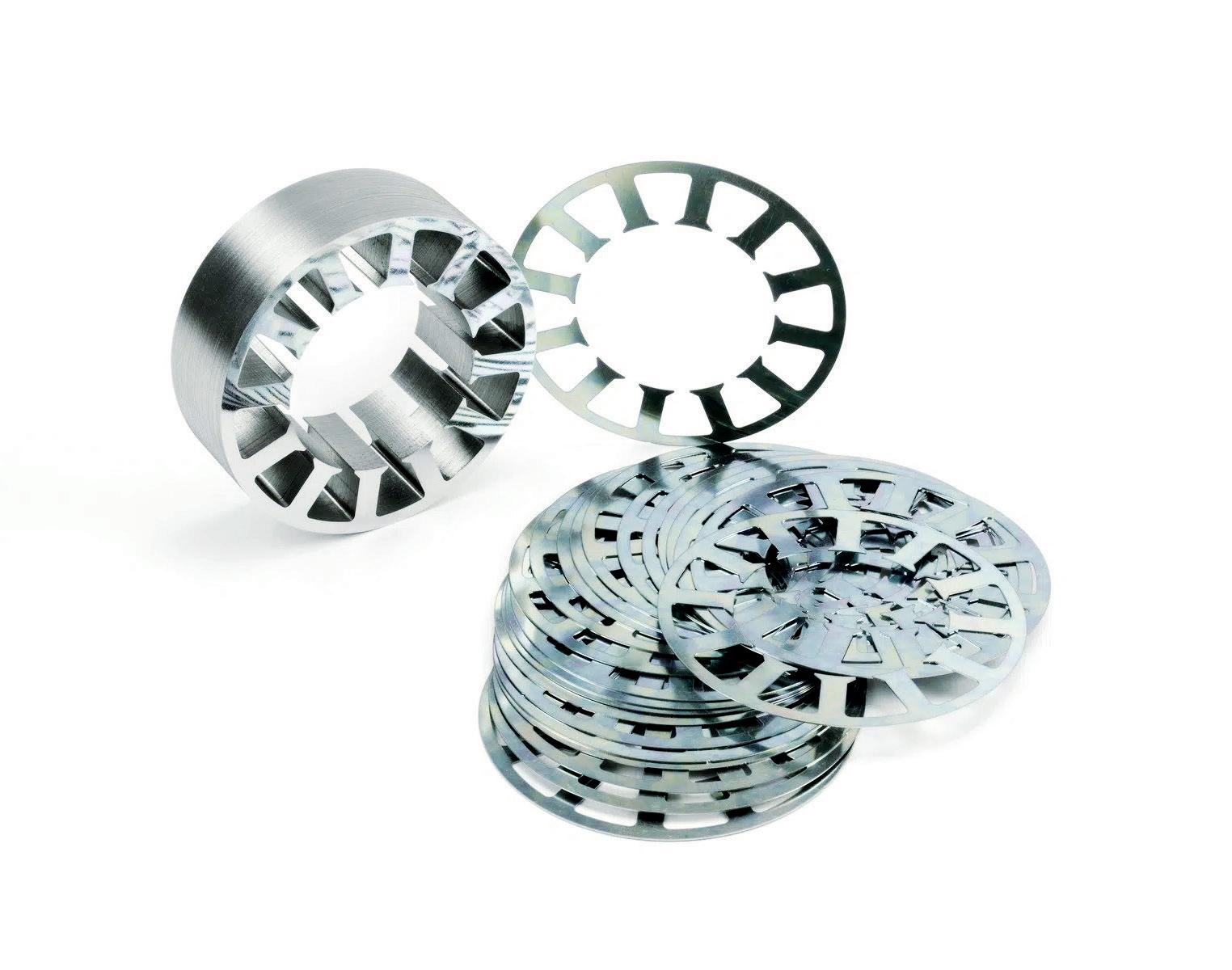