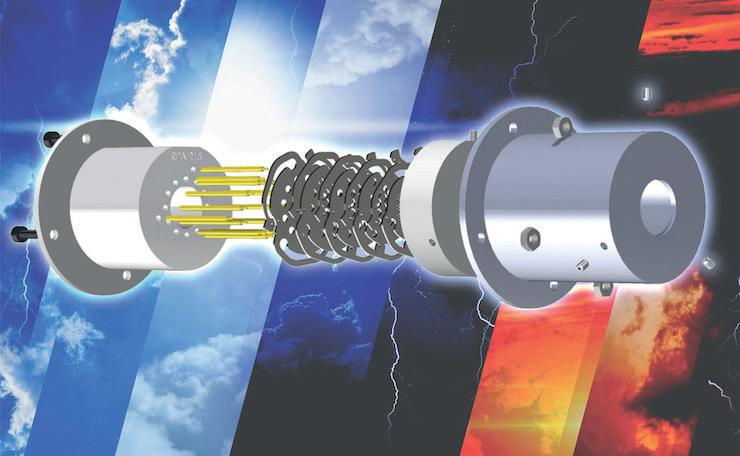
3 minute read
RESEARCH ROUND-UP
3D PRINTING RESEARCH ROUND-UP
Oliver Johnson collects standout 3D printing developments from four American universities.
MASSACHUSETTS INSTITUTE OF TECHNOLOGY - SATELLITE SENSORS AND AI ADDITIVE MANUFACTURING PROCESS
MIT alone has seen a handful of 3D printing developments over the last few months. A new programmable 3D printed material that can sense its surroundings, 3D printed sensors for satellites, and using artificial intelligence to correct AM errors in real time.
In late July, MIT announced that a team of researchers had created the “first completely digitally manufactured plasma sensors” for orbiting spacecraft. The sensors are known as retarding potential analysers (RPAs) and are used by satellites to determine the chemical composition and ion energy distribution of the atmosphere.
Researchers at MIT also trained a machine-learning model to monitor and adjust the 3D printing process to correct errors in real time. The scientists used artificial intelligence to develop a system which uses computer vision to watch the manufacturing process and correct the errors in how it handles the material. UMASS AMHERST AND GEORGIA TECH – 3D PRINTED ULTRASTRONG AND DUCTILE ALLOY
Researchers at Universty of Massachusetts Amherst (UMass) and Georgia Tech developed a 3D printed, dual-phase, nanostructured, highentropy alloy that they say exceeds the strength and ductility of other AM materials.
High entropy alloys (HEAs) are comprised of five or more elements and allow for the creation of near unlimited numbers of combinations for alloy design. The researchers combined an HEA with laser powder bed fusion technology during the development of the new material.
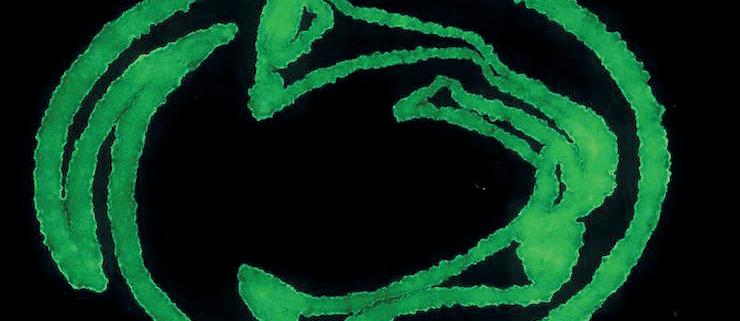
PENN STATE - GRANULAR HYDROGEL FOR TISSUE BIOPRINTING
Researchers at Pennsylvania State University have made a potential breakthrough in biomaterials. A team developed a novel nanoengineered granular hydrogel bioink that makes use of self-assembling nanoparticles and hydrogel microparticles, or microgels.
Wen Chen, Assistant Professor of Mechanical and Industrial Engineering at UMass, stated that the atomic rearrangement of the microstructure the team created gives rise to ultrahigh strength and enhanced ductility, which is uncommon.
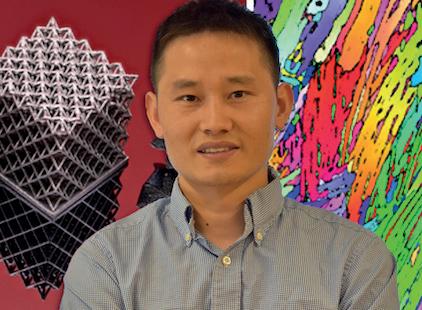
A big problem that has been present in the past when developing bioinks is having high fidelity whilst not compromising porosity. Penn State researchers approached this by increasing the stickiness of microgels to each other. The way the microgels cling together removes the need for them to be tightly packed, preserving microscale pores.
The researchers plan to explore how the newly nanoengineered bioink can be further applied for tissue engineering and regeneration, models of organs and possibly insitu 3D bioprinting of organs (the direct printing of bioinks to create or repair at a defect site).
WASHINGTON STATE – MARTIAN ROCK-METAL COMPOSITE FOR 3D PRINTING ON MARS
Researchers at Washington State University have combined a small amount of simulated crushed Martian rock with a titanium alloy, to create a strong highperformance material. The team who took part in the research hope that the process could one day be used on Mars to produce tools or rocket parts.
The team created parts with as little as 5% Martian regolith, a black powdery substance that mimics the material found on the surface of the red planet, all the way up to 100%. The 5% regolith parts were strong, and even had better properties than just the titanium alloy, but the 100% parts were brittle and cracked easily. However, researchers did determine that high-Martian content materials would be useful for making coatings to protect equipment from rust or radiation damage.
The main benefits that could be achieved from using this 3D printing process would be found in weight and cost savings. The authors of the study noted that it costs NASA 54,000 USD for a space shuttle to put just one kilogramme of payload into Earth orbit.
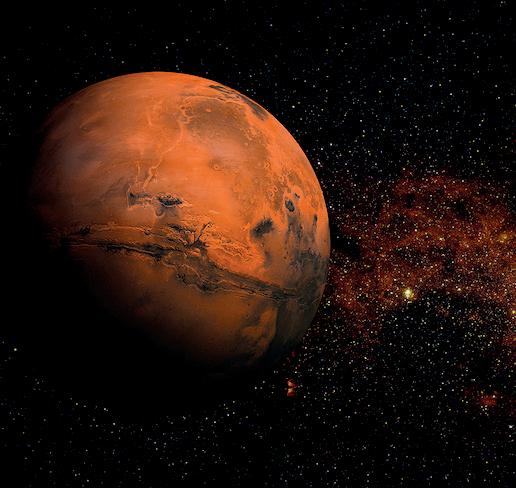